New York FACE Report: Mechanic Electrocuted when a Mobile Light Tower Contacted Powerline
-
Fatality Assessment and Control Evaluation (FACE) Program Reports
The National Institute for Occupational Safety and Health’s (NIOSH) Fatality Assessment and Control Evaluation (FACE) Program and State FACE Programs study fatal workplace injuries and prepare reports with recommendations to prevent similar injuries. The following are links to all of the items in this collection:
Documents
- Kentucky FACE Report: Commercial Roofer Falls 30 Feet Through a Skylight While Installing Roof Insulation
- Fatal Occupational Injuries in Massachusetts 2008-2013
- Fatality Assessment & Control Evaluation (FACE) Program
- Washington FACE Report: Glazier Foreman Falls From Stepladder
- Preventing Construction Falls Toolkit
- Hazard Alert: Pedestrian Workers Killed by Forklifts
- Keep Employees in Motor Vehicles Safe
- New York FACE Brochure
- Washington FACE Report: Construction Laborer Falls When Ladder Breaks
- Washington FACE Report: Pipelayer Dies when Trench Wall Collapses
- Washington FACE Report: Carpenter Falls 60 Feet from Bridge Concrete Form
- Washington FACE Report: Foreman and Laborer Fall when Aerial Lift Struck by Vehicle
- Washington FACE Report: Framer Falls 18 Feet while Sheathing Roof
- New York FACE Report: Mechanic Electrocuted when a Mobile Light Tower Contacted Powerline
- New York FACE Report: Two Construction Workers Fatally Crushed when Cement Formwork Collapsed
- Kentucky FACE Report: Construction Laborer Killed in Trench Collapse while Taking Grade Measurements
- California FACE Report: A Heating, Ventilaton and Air Conditioning (HVAC) Contractor Dies when He Falls through a Skylight
- Massachusetts FACE Report: Carpenter Fatally Injured after Falling from an Extension Ladder
- Massachusetts FACE Report: Laborer Fatally Injured after Falling from a Home under Construction
- Oregon FACE Report: Worker Falls When Ladder Slips
- Michigan FACE Information Sheet: Look for Mobile Equipment Blind Spots
- Oregon FACE Report: Collapsed roof trusses kill carpenter foreman
- Washington FACE Report: Roofer Falls 19 Feet from Roof
- Hazard Alert: Plan. Provide. Train. Prevent Fall Injuries & Deaths
- Kentucky FACE Report: 19-Year-Old Construction Laborer Crushed in Trench Collapse While Laying Sewage Pipe
- Kentucky FACE Report: Construction Flagger Struck and Killed in Two-Lane Highway Work Zone
- Kentucky FACE Report:Temporary Electrician Helper Steps into Unguarded Elevator Shaft and Dies
- Fatality Narrative: Roofing Contractor Falls 25 Feet From Church Roof
- Kentucky FACE Report: Construction Siding Subcontractor Installer Killed when Oversized Scaffolding Platform Destabilized and Telescopic Forklift Overturned
- NIOSH FACE Report - Maintenance Worker Struck by Forklift Carriage—Tennessee
- Kentucky Hazard Alert: Roofing and Construction Workers Killed Due to High Winds
- Poster: Secure it to move it!
- Oregon FACE Report: Crane Operator Killed By Falling Steel Beam
- New Jersey FACE Report: Mechanic Dies After Being Crushed Under Electrical Cabinet
- New Jersey FACE Report: Plant Manager Crushed to Death Under Fallen Pile of Steel Beams
- NIOSH FACE Report: Hispanic worker falls from residential roof
- Oregon FACE Report: Construction worker died after falling 20-25 feet from a pump-jack scaffold
- FACE Fact Sheet: Prevent Construction Falls from Roofs, Ladders, and Scaffolds
- Construction Fatality Narrative: Roofer Falls 18 Feet from Wet House Roof
- Construction Worker Killed when Trench Collapsed, Oregon
- A Tree Trimmer is Electrocuted While Trimming a Palm Tree
- A Tree Feller Dies When Struck By a Tree Limb While Felling a Fire-Damaged Tree
- Concrete Finisher Electrocuted When Bull Float Contacted an Energized Power Line
- Warehouse Worker Crushed by Forks of Laser Guided Vehicle
Summary Statement
In May 2012, a 47-year-old maintenance mechanic of a paving company was electrocuted at a road construction site when a mobile light tower contacted a powerline.
December 8, 2017
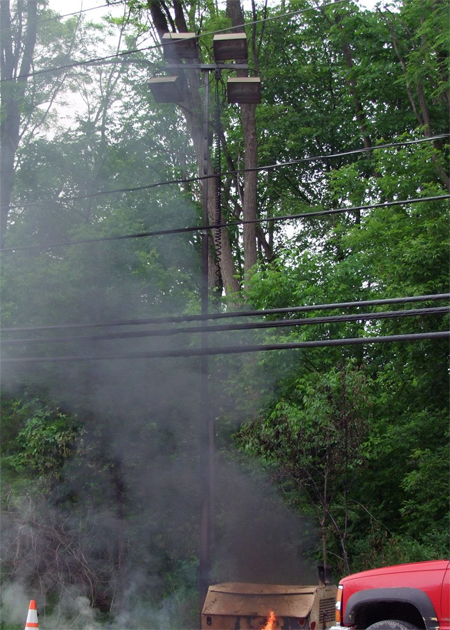
Photo 1. The mobile tower contacted a 7,620-volt powerline causing
a fire and an explosion
at the road construction site (photo courtesy
of the town police department)
Case Report 12NY018
CASE SUMMARY
In May 2012, a 47-year-old maintenance mechanic of a paving company was electrocuted at a road construction site when a mobile light tower contacted a powerline. The paving company was contracted by the New York State Department of Transportation (NYSDOT) to build a roundabout intersection and reconstruct the roads leading to the roundabout. On the day of the incident, the victim was assigned to take down ten mobile light towers at the site and return them to a local rental company one at a time in a company pickup. By 9:20 AM, he had returned three light towers and started taking down the fourth. The victim was working alone on the roadside while other employees were working at a staging area. The incident was not witnessed. The light tower was positioned off the pavement on grass under a 7,620-volt powerline that was approximately 24.6 feet above the ground. For an unknown reason, the victim apparently extended the telescopic mast and raised the tower instead of retracting and lowering it. The tower came into contact with the powerline and the victim was electrocuted. The electric current ignited the diesel in the tower’s fuel tank causing an explosion and setting the light tower on fire. The other workers heard the explosion and rushed to the site. They called 911 to summon emergency services. The police and fire department responded within minutes. The fire department had to wait for the power company to turn off electricity before fighting the fire. It took approximately an hour to extinguish the fire. The victim was pronounced dead at the scene.
CONTRIBUTING FACTORS
- Jobsite survey failed to identify the electrocution hazard associated with positioning a mobile light tower and or around powerlines.
- Victim was not trained on jobsite hazards and control measures.
- Victim may not have been familiar with the controls of the light tower.
- Victim worked alone while handling mobile light towers positioned under a powerline.
- The potential electrocution hazard of placing a mobile light tower under a powerline was not addressed in the Lighting Plan.
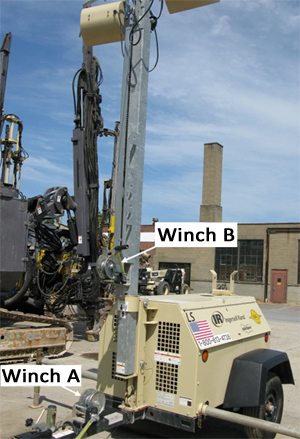
Photo 2. A Doosan mobile light tower Model
LightSource, the same model as
the one in the incident.
KEY RECOMMENDATIONS
- Employers should conduct a thorough jobsite survey to identify hazards including overhead powerlines and implement appropriate control measures prior to placing mobile light towers.
- Employers should ensure that all workers know the safety and health hazards and control measures specific to their job assignments.
- Employers should assign additional personnel to observe and maintain clearances when equipment is being operated or handled in the vicinity of powerlines.
- Agencies that manage road construction projects should require contractors to address overhead powerline hazards in the nighttime lighting plan.
- Agencies that manage road construction projects should train their field representatives on basic knowledge and skills to identify high hazard working conditions at road construction sites.
- Manufacturers should provide clear and specific instructions in operating manual on how to raise and lower a light tower.
INTRODUCTION
In May 2012, a 47-year-old maintenance mechanic of a paving company was electrocuted at a road construction site when a mobile light tower that he was handling contacted a 7,620-volt powerline. The New York State Fatality Assessment and Control Evaluation (NY FACE) staff learned of the incident from the news media and initiated an investigation. The Occupational Safety and Health Administration (OSHA), the town police, and state police also investigated the case. The NY FACE investigator visited the incident site to photograph and take measurements. The light tower that was involved in the incident was rented from a rental company. The NY FACE investigator met with the owner of the rental company and observed a light tower of the same model as the one involved in the incident. The case was discussed with the OSHA compliance officers. The OSHA report, the reports of police, and the death certificate were reviewed.
The paving company declined to participate in the NY FACE investigation. The paving company employed approximately 30 employees with 20 workers in the paving division. It provided asphalt paving, road repairing, and maintenance in New York, southern Vermont and western Massachusetts. The company had developed written safety and health programs as required by OSHA. A company safety coordinator oversaw the development and update of the written safety and health programs, provided worker training, maintained training records, and conducted job site inspections. The safety coordinator had inspected the incident site twice a week. A toolbox safety talk was held at the incident site every Monday morning by either the site superintendent or the safety coordinator.
The victim was a mechanic who normally worked at the company’s maintenance shop. He provided assistance as needed at road construction sites. This was the company’s first work-related fatality.
INVESTIGATION
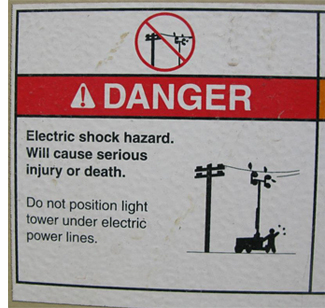
Photo 3. A manufacturer’s sticker on the Doosan light
tower warned of the electric shock
hazard associated
with positioning a light tower under powerlines.
The paving company was contracted by the New York State Department of Transportation (NYSDOT) to build a roundabout intersection and reconstruct the roads leading to the roundabout. The NYSDOT requires contractors to submit a Nighttime Lighting Plan for road construction projects involving nighttime operations. The purpose of the plan is to ensure a safe and properly illuminated work zone for both workers and motorists. The paving company submitted its Nighttime Lighting Plan prior to the commencement of the project. The plan specified the type of the lighting towers to be used and the layout of the lighting towers in the work zone including the location, spacing, and mounting height. The plan did not address overhead powerline hazards. The NYSDOT Construction Safety Engineering Department reviewed and approved the plan before the summer of 2011 when the project started.
The incident occurred at the final stage of the project, the day before the official opening of the roundabout. On the day before the incident, the paving company prepared the site for a subcontractor to stripe the road during the night. Ten mobile light towers were rented from a rental company who delivered them to the site. Three employees of the paving company including a superintendent set up the light towers according to the Nighttime Lighting Plan in the afternoon. According to the superintendent, she had a conversation with one of the workers about setting up the towers at least ten feet away from any powerlines. The superintendent performed a final “drive through” to inspect all of the light towers. She stated that all lights were placed a safe distance from the powerlines.
The safety coordinator, the owner of the paving company, and a NYSDOT engineer were all at the site the night before the incident. None of them observed that any of the light towers were in close proximity to the powerlines. The safety coordinator was at the site supervising four flaggers to direct the traffic. She worked under the light towers until 1 am. She stated that the light towers were properly placed according to the plan specification and provided adequate lighting for the flaggers.
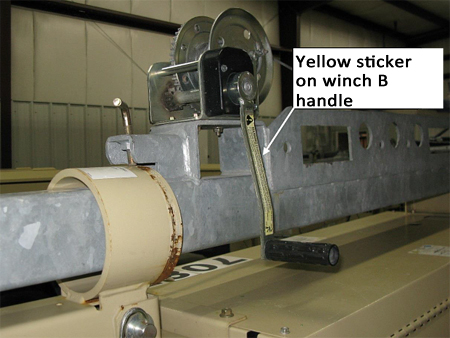
Photo 4. The yellow sticker on winch handles stated that "to raise load,
turn handle clockwise" and "to lower load, turn handle counter-clockwise."
On the morning of the incident, the owner of the paving company called the victim and asked him to return the light towers to the rental company. At approximately 7:30 am, the victim arrived at the site and started taking down the light towers and returning them one at a time in a company pickup. By 9:20 am, he had returned three light towers and started taking down the fourth.
The mobile light tower was manufactured by Doosan Ingersoll Rand (Model: LightSource) and powered by a 4.6L diesel engine (Photo 2). The fuel capacity of the engine was 27 gallons (102 liters) and would allow lighting to be maintained for up to 52 hours. The light tower had four 1,000-watt metal halide lamps mounted on a telescoping mast made of galvanized steel. The telescopic mast could extend to 30 feet high with a 360° rotation and could be locked in position. The manufacturer stated in the Operating & Maintenance Manual: “Danger: DO NOT raise or position light tower under electrical powerlines.” There was a sticker on the tower warning the users of the electric shock hazard associated with positioning the light tower under powerlines (Photo 3).
The position and height of the tower was controlled by two hand winches (A and B). Winch A raised the tower from a horizontal position to an upright position and winch B extended (or retracted) the light tower (Photo 2). There was a yellow sticker on both winch handles stating that turning the handle clockwise would raise the tower and turning handle counter-clockwise would lower the tower (Photos 4). However, the Tower Operating Instruction posted on the tower did not specify which direction to turn the winch to raise or extend the tower. It simply stated that “operate winch A to raise tower” and “operate winch B to extend tower” (Photo 4).
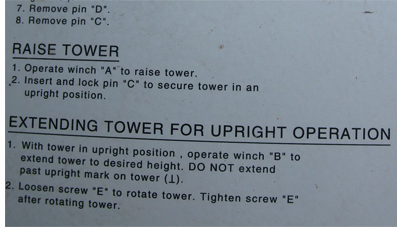
Photo 5. The Operating Instruction posted on the tower did not
specify
which direction to turn the winches to raise or extend the tower.
At the time of the incident, the victim was working alone on the roadside while other employees were working at a staging area. The incident was not witnessed. The light tower was positioned off the pavement on the grass under a 7,620-volt powerline that was approximately 25 feet above the ground. To lower the tower from its upright position, the victim first had to crank winch B to retract the telescopic mast and then crank winch A to fold the tower from upright to the horizontal storage position. For an unknown reason, the victim extended the mast instead of retracting it. The lights came in contact with the powerline and the victim was electrocuted. The electric current ignited the diesel fuel in the tank causing an explosion and setting the light tower on fire. The other workers heard the explosion and rushed to the site. They called 911 to summon emergency services. The police and fire department responded within minutes. The fire department had to wait for the power company to off the electricity before fighting the fire. It took approximately an hour to extinguish the fire. The victim was pronounced dead at 10:25am at the scene. The immediate cause of death was severe high voltage electrocution with thermal burns.
Both OSHA and Police reports indicated that there might be a locking mechanism on the light tower. The telescopic mast might have to be cranked up in order to unlock the mechanism before it can be retracted. Both reports speculated that this may be the reason that the victim raised the mast.
The NY FACE investigator visited the rental company after the incident and asked the owner of the company to demonstrate how to operate the Doosan Ingersoll Rand light tower. The telescopic mast can be retracted by simply turning winch B counter clockwise. There was no lock that needs to be released by extending the telescopic mast before retracting it. One thing that happened during the demonstration was that the owner did extend the tower first by mistake while he was trying to retract the mast. He first cranked the winch clockwise. He was underneath the tower looking straight up at the lights against the background sky. He could not tell whether the lights were being raised or lowered. After a while he realized that the lights were actually being raised, he then reversed the winch and lowered the lights.
RECOMMENDATIONS/DISCUSSION
Recommendation #1: Employers should conduct a thorough jobsite survey to identify hazards including overhead powerlines and implement appropriate control measures prior to placing mobile light towers.
Discussion: A jobsite hazard survey and evaluation should be performed by a competent person prior to placing mobile light towers at a construction site. Energized powerlines in proximity to a work area constitute a serious safety hazard. The hazard survey should identify: 1) the location and height of all overhead powerlines, 2) equipment to be placed under or near the powerline and the size (maximum height) of this equipment, 3) tasks to be performed underneath and in proximity to an overhead powerline, and 4) workers who are to perform those tasks. Once potential hazards are identified, appropriate control measures should be developed and implemented.
Control measures should be taken to maintain a minimum safe distance between powerlines and mobile lighting equipment. If the minimum safe distance cannot be maintained, the employer should make arrangements with the power company to de-energize the powerlines or otherwise protect the powerlines from contact.
The manufacturer in this case required an overhead clearance of 40 feet for setting up the light tower. The maximum height of the tower was 30 feet. Therefore, the minimum safe distance was ten feet. The minimum safe distance was not maintained since the height of the powerline was approximately 25 feet and the tower was placed directly underneath the powerline.
Recommendation #2: Employers should ensure that all workers know the safety and health hazards and control measures specific to their job assignments.
Discussion: Employers should ensure that all workers receive adequate safety training so that they are aware of the specific hazards they may encounter while performing their job assignments and the control measures. The victim in this case was a mechanic who usually worked at the maintenance shop. Occasionally he was called to assist in the field. He may not have been aware of the danger of the light tower contacting the overhead powerline.
Recommendation #3: Employers should assign additional personnel to observe and maintain clearances when equipment is being operated or handled in the vicinity of powerlines.
Discussion: The victim in this case worked alone taking down the mobile light tower. He had to operate the winches and assess the clearance between the tower and the powerline at the same time. It could have been difficult for him to assess the clearance when he was directly underneath the powerline. A spotter should be designated to observe the clearances and help guide the operation of the tower.
Recommendation #4: Agencies that manage road construction projects should require contractors to address overhead powerline hazards in the nighttime lighting plan.
Discussion: Mobile light towers are widely used as primary means of illumination for road construction projects. Electrocution hazards of overhead powerlines should be addressed in the guidelines for lighting plan submission. Agencies that manage road construction projects should require contractors to show the locations of the powerlines in relation to the locations of the light towers and state measures to prevent contact in the lighting plan.
Recommendation #5: Agencies that manage road construction projects should train their field representatives on basic knowledge and skills to identify high hazard working conditions at road construction sites.
Discussion: The agencies that manage road construction projects have field representatives including engineers to oversee and monitor the site activities to ensure that the work is conducted according to the criteria specified in the contract. These agencies should train their field staff so that they are able to identify high risk working conditions and serious safety hazards to prevent injuries at construction sites.
Recommendation #6: Manufacturers should provide clear and specific instructions in operating manual on how to raise and lower a light tower.
Discussion: The operating manual and the operating instruction posted on the tower in this case did not state the specific directions (clockwise or counter clockwise) to crank the winches for extending or retracting the light tower. Manufacturers should provide clear instructions on which direction raises or lowers the tower.
Keywords: electrocution, mobile light towers, powerlines, road construction
REFERENCES
- New York State Department of Transportation, 2008 Standard Specifications Section 600
Incidental Construction. Retrieved July 2, 2013 from https://www.dot.ny.gov/main/business-center/engineering/specifications/2008-standard-specs-us - CDC/NIOSH. Painter Electrocuted When Metal Ladder Contacts a Powerline. Retrieved July2, 2013 from http://www.cdc.gov/niosh/face/in-house/full9227.html
Andrew M. Cuomo
Governor
Howard A. Zucker, M.D., J.D.
Commissioner
Sally Dreslin, M.S., R.N.
Executive Deputy Commissioner
The New York State Fatality Assessment and Control Evaluation (NY FACE) program is funded by the National Institute for Occupational Safety and Health and administered by the New York State Department of Health. NY FACE is a research program designed to study the causes of workplace fatalities and develop practical and effective prevention measures. NY FACE investigators evaluate information from multiple sources and provide recommendations for prevention in summary reports. These recommendations are distributed to employers, workers, and other organizations interested in promoting workplace safety. The NY FACE does not determine fault or legal liability associated with a fatal incident. Names of employers, victims and/or witnesses are not included in written investigative reports or other databases to protect the confidentiality of those who voluntarily participate in the program.
Additional information regarding the NY FACE program can be obtained from:
New York State Department of Health FACE Program
Bureau of Occupational Health and Injury Prevention
Corning Tower, Room 1325
Empire State Plaza
Albany, NY 12237
866-807-2130
518-402-7900
boh@health.ny.gov
https://www.health.ny.gov/environmental/investigations/face/