Lead Control Guide for Bridges and Steel Structures
Summary Statement
A guide for construction workers, and contractors who work on bridge rehabilitation jobs, describing lead controls and contractor responsibilities to provide a safe working environment.
1998
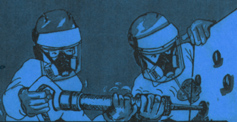
Acknowledgments
The Guide could not have been written without the cooperation and assistance of many people and organizations. We give special thanks to:
- Kevin Gorham, Director
- Marty Keane, Instructor, Local 361
- Harry Lynch, Instructor and Business Manager Local 361
- Jerry McCloskey, Instructor, Local 361
- Roy Mainelli, Instructor, Local 40
- Kevin O'Rourke, Instructor, Local 40
- Frank Tooze, Safety & Health Director Emeritus
- Pam Susi, MSPH,
Exposure Assessment Project Director
- Susan Klitzman, DrPH, Assistant Commissioner
- Liza Nicaj, MPH, Epidemiologist
- Deborah Nagin, MPH, Director of Public Health Partnership, Metro Region
- John Koloya, PE, Vice President
J. Bidosky, III
Tom Melvin
TABLE OF CONTENTSStephen M. Levin, MD, Medical Director
Jean Weiner, MS, Industrial Hygienist
Norm Zuckerman, MS, Industrial Hygienist
INTRODUCTION
- OSHA LEAD IN CONSTRUCTION
- INTERIM CONTROLS
- CONTRACT SPECIFICATIONS
- ROLES & RESPONSIBILITIES
- MODEL COMPLIANCE PROGRAM
ENGINEERING & WORK PRACTICE CONTROLS
- CLEANING
- PAINT REMOVAL: CHEMICAL STRIPPING
- PAINT REMOVAL: POWER TOOLS
- MECHANICAL REMOVAL OF STEEL
- ENCAPSULATION
- DISTANCING
In 1992, ten workers came to the Mount Sinai Center for Occupational and Environmental Medicine, a clinic specializing in the diagnosis and treatment of work-related disease in New York City. They were suffering from the acute effects of lead poisoning and two of the workers were hospitalized for chelation treatment.
The contractor had been hired to repaint the facade of a cast iron building in one of New York's historic districts. The workers had been using pneumatic needle guns to remove layers of paint and rust from the iron surface. The contractor and the building owner were unaware that the paint contained lead.
Lesson One: Assume
that the protective coatings on steel structures contain lead until appropriate
testing confirms otherwise.
.
The purpose of this guide is to assist construction professionals in developing and implementing engineering and work practice controls designed to protect workers from lead and other paint hazards during repair and demolition of bridges and other steel structures. The guide covers ironwork and spot paint removal phases of structural steel rehabilitation projects. Control methods for open abrasive blasting inside containment are beyond the scope and are not included in this publication.Contractors, owners, engineers, and industrial hygienists should find the guide useful in their efforts to comply with contract specifications and the OSHA Lead Exposure in Construction Standard. Building trades unions and employers can use the guide as a resource in training programs.
OSHA requires employers to implement feasible engineering and work practice controls to protect workers and to use worker rotation and respirators only as supplementary protection. However, the construction environment is complex and exposures can be difficult to evaluate and to control. Exposure conditions are effected by constant changes in work operations, crews, materials, equipment, and weather. Thus, control designers must often be creative and flexible so that exposure remedies are practical, safe and suitable for the site.
. "Integrating control measures with the plan of operation is critical throughout the life of the project."
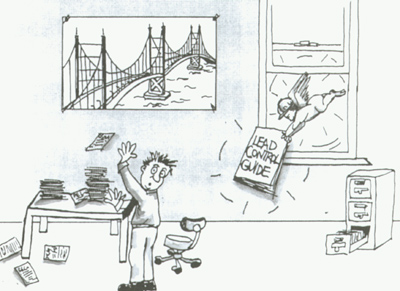
Selection and successful implementation of controls require skill, informed decision-making, and collaboration among management, engineers, industrial hygienists, suppliers, unions and workers. Construction employers are challenged to use engineering and work practice controls for job tasks that have traditionally been performed without any special consideration for worker protection. When the OSHA lead standard was issued in 1993, little was known about engineering strategies to control worker ex- posure to lead in construction. Since that time, much has been learned. Construction professionals have developed several successful approaches that have been assessed by Mount Sinai and other researchers. The results of these assessments are presented here as a practical guide for project personnel responsible for implementing lead health and safety programs.
While many of the "fixes" are straightforward, optimum results require serious commitment from design and project management and the active participation of workers. Integration of control measures with the work process throughout the life of the project is critical. Before controls are activated, both management and workers should be trained so that they understand the rationale behind the controls and proper operating procedures.
On many projects, engineering and work practice controls fail to reduce worker lead exposure below the OSHA permissible exposure limit. In these cases, respirators are required to fully protect workers. In other words, engineering controls may not be the final solution - but they may reduce exposure enough so that air purifying respirators can be used safely. Regular cleanup of the work area, personal hygiene facilities and blood lead testing are other major components of worker protection programs.
.
Rehabilitation of steel structures poses serious lead hazards not only to workers on the site, but also to nearby residents, children, and the environment. Because the engineering and work practice controls described in this guide aim to decrease worker exposure to lead by controlling dust emissions at the source, environmental contamination is reduced as well.
Departments of transportation and other owners of steel structures have been confronted by public demands to prevent community exposure to lead during repair activities. Placing containment structures around lead-emitting work operations has become the most commonly used and effective environmental control. Unfortunately, performing lead-emitting activities, such as abrasive blasting, torch cutting, rivet busting, and grinding, inside containment can greatly increase worker exposures.
Owners must avoid shifting the risk of lead exposure between workers and communities. Each project must develop a well-planned and coordinated control program so that both construction workers, the most exposed group, and community residents, the most vulnerable group, are protected. Communication with residents about the project is also very important.
. "... avoid shifting risk of lead exposure between workers and communities."
Lead enters the body when people breathe it or swallow it. Lead from paint does not go through the skin - but lead dust on the hands can be accidentally swallowed while eating, drinking, or smoking.
Lead is hazardous when it gets into the bloodstream where it can move around the body. High exposures over a short period of time or lower exposures spread out over time can cause lead poisoning. The early effects of lead poisoning resemble flu symptoms. Lead can damage the brain and nervous system, blood, kidneys, and reproductive systems. Lead in the body is eventually stored in the bones where it may stay for decades; under certain conditions, it may leach back into the bloodstream.
"Lead poisoning is preventable. Many health problems caused by lead are reversible if exposure is eliminated."
SHORT
TERM EFFECTS
|
|
fatigue/weakness
|
|
muscle/joint pain
|
|
irritability/anxiety
|
|
sleep problems
|
|
LONG
TERM EFFECTS
|
|
|
|
brain damage
|
|
reproductive damage
|
birth defects
|
PREVENT FAMILY EXPOSURES
Worker protection is the responsibility of the contractor. Protecting workers and their families from lead requires a systematic approach and daily attention to detail. OSHA regulations, owner specifications, and good management practices form the basis of effective lead health and safety programs. All site personnel must be well trained and aware of their roles and responsibilities regarding lead controls.
However, the most important elements of a worker protection program are a strong commitment from the employer and the management skills to implement controls effectively and practically. Good management means that decision makers are equipped with the right information - results of exposure assessments, blood lead levels, and daily inspection reports. Managers should continuously reevaluate the implementation and effectiveness of controls and make adjustments when needed.
This chapter describes OSHA requirements and the importance of worker protection specifications. Roles and responsibilities of owners, contractors, competent persons, foremen, and workers are summarized and an outline for a model compliance program is provided.
The Occupational Safety and Health Administration issued the Interim Final Rule: Lead Exposure in Construction in 1993. The standard requires construction employers to protect workers from lead exposure with engineering and work practice controls and respirators. The standard also requires air monitoring, blood lead testing, training, protective clothing, wash-up areas, housekeeping, and daily inspections.
THE PERMISSIBLE EXPOSURE LIMIT (PEL) is 50 micrograms of lead per cubic meter of air (50 mcg/m 3 ) averaged over an 8-hour shift. Worker exposures must be kept below this level.
THE ACTION LEVEL is 30 mcg/m 3 averaged over an 8-hour shift. Training, air monitoring, and blood test begin at this level.
WHEN
DOES THE STANDARD APPLY?
There are two
key factors that determine if the lead standard applies:
|
- Develop a written compliance program; implement engineering and work practice controls. Update the program at least every 6 months.
- Implement interim controls for lead disturbing tasks until air levels are determined.
- Perform air monitoring and inform workers of results. Repeat air monitoring every 3 months or sooner if conditions might increase exposure.
- Arrange for initial blood lead testing and repeat at least every two months. Set up a medical monitoring program.
- Provide hygiene facilities: change areas, clean eating areas, hand washing stations and showers.
- Use HEPA vacuums or wet methods to clean work areas.
- Establish a respiratory protection program.
- Provide protective clothing and equipment.
- Conduct site-specific training about lead hazards and controls. Post warning signs: no eating or smoking.
- Assign a competent person to inspect site daily and correct hazards.
- Reassign workers or provide medical removal benefits if blood lead levels exceed 50 mcg/dl (micrograms of lead per deciliter of blood).
- All of the requirements listed in the "Summary of the Standard" must be implemented, including wash-up facilities, decontamination procedures, HEPA vacuuming or wet cleanup, and protective clothing.
- Blood tests must be provided within 2 days of exposure.
- Respirators are selected based on the task as follows:
INTERIM RESPIRATOR SELECTION
TASK
CATEGORIES
|
PRESUMED
EXPOSURE mcg/m3 |
RESPIRATOR
|
1:
scraping, manual demolition, chemical stripping, using shrouded
tools with dust collectors
|
50-500
|
Half-face
APR with P-100 (HEPA)filters
|
2:
rivetbusting, power tool cleaning without shrouds, cleaning up abrasives,
moving containment
|
500-2500
|
(HEPA)filters
Full-face APR with P-100 (HEPA) filters, PAPR with HEPA filters,
or
|
3:
torch cutting, burning, welding, abrasive blasting
|
2500
+
|
Pressure
demand airline
|
APR: air purifying respirator |
Some owners of bridges and other steel structures, including state and city departments of transportation, have adopted worker protection specifications in their contracts to supplement the requirements of the OSHA standard. These specifications and engineering instructions assure owners that worker protection will not be overlooked on lead projects. Owner inspectors are responsible for enforcing contractor compliance.
Contract specifications "level the playing field" so that all bidders add in the costs for lead health and safety programs. Even the lowest bidders have line items for expenses related to worker protection from lead. CPWR – Center for Construction Research and Training has published model specifications for worker protection on lead projects. This publication is an important resource for owners and contractors. See "Resources" for ordering information.
Specifications may include:
- monthly blood lead testing
- review of program by industrial hygienist
- training for all site personnel
- documentation of lead exposure problems and solutions
- investigation of elevated blood lead levels and/or air levels by industrial hygienist
- decontamination units at the site
- worker health & safety specialists
- medical removal programs
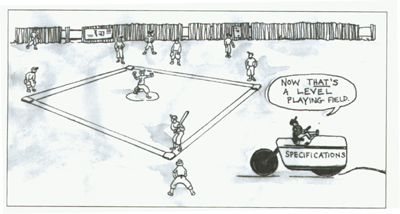
Coordination and cooperation of site personnel is crucial in assuring that the lead health and safety program is effectively implemented. Roles and responsibilities of owners, management, competent persons, and workers, should be clearly spelled out in the written compliance program and other site documents. Project management should also be prepared to work with occupational health providers, industrial hygienists, labor unions, public health agencies, trade associations, and equipment and material suppliers as needs arise.
OWNER
- Prequalify bidders; specify worker protection in contract.
- Coordinate protection of workers, environment,and community.
- Develop communication with community.
- Approve contractor lead health & safety (compliance) plan.
- Inspect site for compliance with contract and regulations.
- Provide protection for owner's employees.
CONTRACTOR
- Implement lead health and safety programs.
- Designate competent person.
- Develop compliance program: engineering &work practice controls.
- Arrange for blood lead testing and medical evaluations.
- Arrange for air monitoring.
- Set up respirator program - selection, fit testing, use, maintenance.
- Provide hygiene facilities and protective clothing.
- Train all site personnel about lead hazards and controls at the site.
- Enforce use of engineering and work practice controls.
COMPETENT PERSON
- Recognize lead hazards on the site and make daily inspections.
- Authorize corrective actions.
- Coordinate lead health and safety plan.
- Inform workers of blood lead and air monitoring results.
- Keep records of all lead related activities.
FOREMAN/PUSHER
- Assure that engineering and work practice controls are functional.
- Make sure that all control equipment is maintained in good condition and used properly.
- Enforce safety rules.
WORKER
- Follow all safe work rules and use controls properly.
- Attend training & safety meetings.
- Participate in blood testing.
- Wear respirator in lead areas; check face piece seal before each use.
- Don't smoke, drink or eat in lead areas.
- Wash up before lunch & leaving site; leave work clothes at site.
- Keep lunch box clean and isolate work equipment from family areas at home.
LEAD
TRAINING
Owners and contractors
must assure that all site personnel are fully trained in lead health
and safety procedures. EPA has proposed that all structural steel
supervisors and workers attend 2-4 days of special training. Some
states have training requirements currently in place. Many building
trade unions provide lead training for their members based on the
EPA proposal. Check with local and state agencies for training requirements
in your area. Some lead training providers include:
|
OSHA requires contractors to develop and implement a site specific compliance program if workers are exposed to lead at or above the PEL. The program describes the implementation of engineering and work practice controls and includes records of compliance activities. The written program should include:
- Introduction: Project description, scope & schedule of work, location.
- Personnel: Project manager, competent person, industrial hygienist.
- Lead-emitting activities: Describe tasks, equipment, materials, crews.
- Engineering and work practice controls: Describe type of control, equipment, use/maintenance procedures. Include rationale for selecting each control and alternative technologies considered.
- Personal air monitoring results: Provide industrial hygiene reports and air sampling results for lead-emitting activities.
- Schedule: Provide timetable for implementing compliance program.
- Interim controls: Describe respiratory protection and other controls that will be used for each task.
- Hygiene procedures: Describe protective clothing and equipment, housekeeping, clean areas, showers, and handwashing stations.
- Worker rotation schedule (if applicable).
- Notification procedures: Informing other employers on site.
Attach the following programs and records to the compliance program:
- Respirator Program: Provide written program and program administrator; include respirator selected for each task; records for training, fit testing, & medical clearance.
- Training & Information: Training schedule, topics & records; location of warning posters; procedures for providing air and blood test results to workers.
- Medical Surveillance Program: Include blood test schedule and results.
- Medical Removal Procedures: Include lead-free work assignments, medical evaluations and return to work criteria.
Contractors must review the project for potential lead-emitting tasks, arrange for exposure assessments, and select controls. This chapter briefly describes common lead-emitting activities on bridge and structural steel rehabilitation projects, and presents various control strategies. In the next chapter, each control option is described in more detail.
Over the years, lead based paint, (sometimes containing as much as 70% lead) has been used on thousands of bridges and steel structures to protect them from corrosion and the effects of weather. Because of normal wear or lapse in regular maintenance, many of these structures are in dire need of rehabilitation.
WORKERS AT RISK
During repair and demolition projects, ironworkers, laborers, painters and other construction workers are exposed to lead hazards. Anticipating exposures and planning ahead can greatly reduce these hazards. Dismantling and surface preparation operations can be especially hazardous. Exposure risks are greatly effected by tasks, tools, and proximity to the work operation. Assessing exposure of specific tasks provides information needed to select and implement controls.
SOURCES
OF EXPOSURE
|
TASK-BASED EXPOSURE ASSESSMENT
Task-based exposure assessment is an important tool for evaluating worker exposure on construction sites. Studies by Mount Sinai//Hunter College and other researchers have shown that monitoring single tasks provides a useful basis for selecting controls. Exposures to lead during rehabilitation projects can vary widely from week to week, day to day, and even hour to hour. Conditions - such as project phase, task, controls, enclosure, nearby operations, weather conditions, and work crew - can have a profound effect on exposure at any particular time. The traditional industrial hygiene approach of determining 8-hour time weighted average exposures (TWA) can mask peak concentrations and thus miss opportunities to control important sources of exposure.
OSHA recognizes the practicality of controlling exposures for specific tasks. In the Lead Exposure in Construction Standard, employers are required to use "interim controls" based on work tasks until exposure assessments are completed. OSHA presumes that certain tasks result in specific estimated exposures, and thus requires worker protection. For example, if workers are using scalers without vacuum attachments to remove lead paint, OSHA presumes that they are exposed up to 2500 mcg/m 3 ; respirators that protect up to 50 times the PEL must be used.
In the descriptions of lead-emitting tasks that follow, task-based exposure estimates are presented, so that contractors can target their control programs to the task - the most important determinant of exposure.
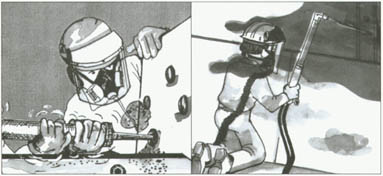
PERSONAL AIR MONITORING
Contractors usually hire an industrial hygiene firm or use a staff hygienist to perform exposure assessments. It is very important that the hygienist doing the monitoring be familiar with the construction environment and be well-informed about the scope and schedule of work.
Air monitoring should be targeted at "worst case" exposures so that the best controls can be selected. OSHA requires that all job classifications be monitored for a full shift. Monitoring should be repeated whenever there is a rise in blood lead levels, a change in conditions that could increase exposure, and every 3 months if exposures exceed the PEL.
TAKING SAMPLES
Air sampling is performed with a small vacuum pump equipped with flexible tubing and a filter cassette. The pump is attached to the worker's belt and the filter is positioned on the chest just below the shoulder. The filter may be changed if it gets loaded with dust or if the task changes. At the end of the shift, the filters are sent to an accredited lab for analysis.
INTERPRETING RESULTS
Results are given in mcg/m 3 for each sampling period. The results are then weighted by time and averaged to make up the full-shift result. This result, known as an 8-hour time weighted average (TWA), is compared with the PEL and the AL.
Sample results that represent specific task exposures are very important for choosing controls, even if they were taken for less than a full shift. These results should be used to select task controls.
"Monitoring should be repeated whenever there is a rise in blood lead levels or a change in conditions that could increase exposure..."
Four lead-emitting task groups - torch cutting, rivet busting, power tools, and installation - are described in the following pages of this chapter. An exposure rating has been assigned to each of the task categories. These ratings are based on the presumed exposure values that OSHA published in the preamble to the Lead Exposure in Construction; Final Interim Rule in 1993. Presumed exposure values are used to select respirators and other controls until personal air monitoring is completed. Once the air results are received, contractors can adjust respirator selections and other controls to fit the actual exposure conditions.
Since 1992, the Mount Sinai Construction Hygiene and Ergonomics Program along with Hunter College has been assessing worker exposures during the performance of various rehabilitation and demolition tasks in the New York City area. The results of these studies verify the exposure levels that OSHA presumes for these tasks. A listing of these articles appears in the reference section of this guide.
The exposure ratings used for each of the lead-emitting task groups represent a range of potential exposures. Site conditions, management of the controls, and individual work practices will determine the actual exposures. The ratings are estimates that contractors and owners can use for planning and implementing controls.
TASK | PRESUMED
EXPOSURE mcg/m 3 |
RATING |
Torch Cutting | 2,500 - 10,000 | High |
Rivet Busting | 50 - 500 | Moderate |
Surface Preparation | 100 - 2,500 | Moderate to High |
Installation | up to 280 | Low to Moderate |
TASK DESCRIPTION
Torch cutting is a common and quick method of dismantling steel structures. A torch fueled by acetylene or propane produces a hot narrow flame (5720°F) to cut through steel and to burn out rivets. An acetylene torch heats the steel to "cherry red" (about1500-1800°F) to start cutting. Thermolancing produces an even hotter flame by burning a lancing rod and is often used on very thick and large steel parts.
SOURCE OF LEAD EXPOSURE
The high temperature torch burns the lead paint producing vapors which quickly condense to form extremely small particles called " lead fumes". Lead boils releasing vapors at about 3000°F, well within the temperature of the torch flame.
EXPOSURE RATING - HIGH
Torch cutting results in very high exposure levels. Controls must be well coordinated and managed. Respirators will be needed. High exposures may result even when lead paint is removed due to residues on the steel.
ENGINEERING & WORK PRACTICE CONTROLS
MECHANICAL REMOVAL: ALTERNATIVE OPERATION
Steel members can be dissembled by reversing installation procedures removing rivets or bolts and then removing the steel. In some cases, steel members can be cut out using hydraulic shears or abrasive saws, also called chop saws.
PAINT REMOVAL
Lead-based paint can be removed prior to torch cutting by either chemical strippers or power tools. It is recommended that at least 4 inches of paint be removed from either side of the cut line, although there is little data to support this width.
DISTANCING
Increasing the distance between the source of lead emissions and the worker's breathing zone can theoretically reduce exposures, however, little data is available to substantiate the claim. Using longer, demolition torches (up to 6 feet long) rather than short-handle torches, and positioning the body upwind of the torch, when possible, are two common sense work practices that may result in reduced exposure.
OTHER HAZARDS
Using oxyacetylene or thermolance torches may require protection from other hazards such as:
- Skin contact with molten metal and hot parts.
- Eye exposure to harmful levels of ultraviolet and infrared radiation from flame, lance or molten metal.
- Fire.
- Toxic gases and fumes from other materials.
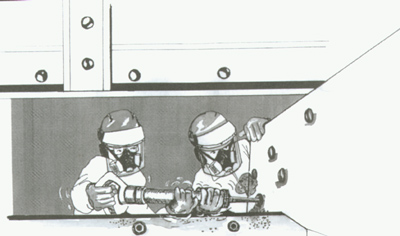
TASK DESCRIPTION
A rivet buster, also called a "hell dog", is a pneumatic chisel used to remove rivets from structural members. An ironworker uses the tool to knock off the rivet head and then punch the rivet shaft out of the steel. Sometimes a torch is used on hard to remove rivet heads.
SOURCE OF LEAD EXPOSURE
The impact of the hell dog on painted steel produces lead dust and chips. Settled dust and debris on flanges and adjacent steel gets stirred up in the air by tool vibrations and exhaust air from pneumatic tools.
EXPOSURE RATING - MODERATE
Rivet busting usually results in exposures less than 500 mcg/m 3 . Even with controls, exposures will most likely exceed the PEL so that air purifying respirators will be needed. Applying an encapsulant, such as "plastic dip", to rivet heads prior to removal has resulted in significant reductions in exposure. To be effective, encapsulation methods must be coupled with aggressive cleanup of lead debris on surrounding surfaces. If torches are used, exposures will greatly increase.
PRECLEANING
Horizontal surfaces, especially flanges, should be precleaned with a HEPA vacuum to prevent dispersal of settled lead-containing dust and debris.
PAINT REMOVAL
Lead-based paint can be removed from rivet heads and surrounding steel by shrouded power tools equipped with HEPA vacuums or with chemical strippers.
ENCAPSULATON
Rivet heads and surrounding areas can be covered with a flexible coating to reduce chipping and dust generation during rivet busting. Encapsulant may be brushed, rolled or sprayed on.
OTHER HAZARDS
Workers should be protected, to the extent possible, from other rivet busting hazards such as:
- Ergonomic stress caused by operating the tool in awkward positions, excessive force, vibrations, and heavy loads. Cold temperatures may compound dangers.
- Noise exposure caused by impact of tool on steel structures and sound from compressors. Noise levels of 110 dBA have been measured.
- Tool and compressed air hazards.
- Eye hazards from flying particles and chips.
- Traumatic injuries from flying rivets.
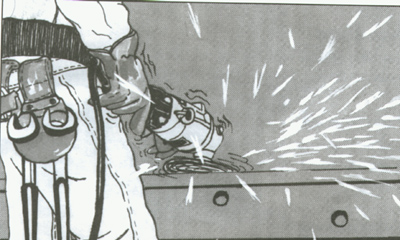
TASK DESCRIPTION
Surface preparation involves using power tools to remove spots of paint, rust, and scale from existing steel. Paint is removed so that new steel can be installed or old surfaces can be overcoated. This work is performed with pneumatic tools - grinders, needleguns, rotopeens, scalers, and chippers. Hand scrapers and chipping hammers are also sometimes used.
SOURCE OF LEAD EXPOSURE
Lead paint is pulverized mechanically by the tool action. Exhaust from pneumatic tools can reentrain settled dust and debris from surfaces.
EXPOSURE RATING - MODERATE TO HIGH
Exposure varies depending on the tool used. Grinders release fine particles that may result in high exposures. Scalers generate larger particles and exposures tend to be lower. Needleguns are somewhere in between. Without vacuum shroud and dust collector systems, exposures may be as high as 2500 mcg/m 3 . Chipping hammers, scrapers and other manual tools also result in exposures above the PEL.
ENGINEERING & WORK PRACTICE CONTROLS
PRECLEANING
Horizontal surfaces, especially flanges, should be precleaned with a HEPA vacuum to prevent dispersal of settled lead-containing dust and debris.
VACUUM BLASTING
An abrasive blasting nozzle equipped with a vacuum shroud can be used to remove paint and to prepare the surface instead of traditional power tools. This equipment can recycle the blast media by removing lead particles and reduce waste generation and disposal costs.
HEPA VACUUM ATTACHMENTS
Most power tools can be fitted with vacuum attached shrouds that capture lead dust as it is being generated. HEPA filters prevent exhausting the dust back into the work area. Unfortunately, larger paint particles are not always collected by the shrouds.
CHEMICAL PAINT REMOVAL
Lead-based paint can be removed with chemical strippers prior to power tool treatment.
OTHER HAZARDS
Workers assigned to power tool operations, to the extent possible, should be protected from other hazards, such as:
- Ergonomic stress caused by operating the tool in awkward positions, excessive force, vibrations, and heavy loads. Cold temperature may compound dangers.
- Noise exposure - as high as 104 dBA - caused by impact of tool on steel structures and sound from compressors.
- Tool and compressed air hazards.
- Eye hazards from flying particles and chips.
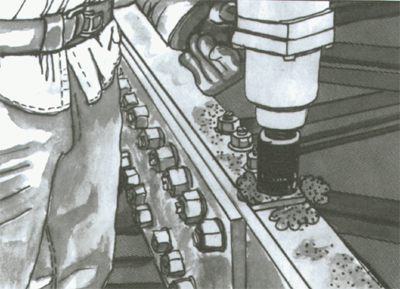
TASK DESCRIPTION
Most new and refurbished steel is installed onto old steel by bolting or welding in place. Bolt holes are drilled or enlarged with power drills and reamers. Steel members are bolted together with impact air guns and manual tools. Alternatively, adjacent steel components may be welded together.
SOURCE OF LEAD EXPOSURE
Exhaust from impact guns and other pneumatic tools can stir up settled lead dust and debris. Drills and reamers may release lead particles from residual paint. Welders that contact painted steel or debris may emit lead fume.
EXPOSURE RATING - LOW
Installation tasks generally cause low exposures unless area is contaminated with lead dust and debris. Aggressive cleanup prevents reentrainment caused by activity. Air purifying respirators are recommended unless site is well controlled with lead exposures low and stable.
ENGINEERING & WORK PRACTICE CONTROLS
PRECLEANING
Horizontal surfaces, especially flanges, should be precleaned with a HEPA vacuum to prevent dispersal of lead-containing dust and debris during installation activities.
PAINT REMOVAL
Lead-based paint should be completely removed from old steel before welding, drilling, reaming, or doing other activities that would disturb lead paint. Paint removal can be done with power tools equipped with HEPA vacuum attachments or chemical strippers.
OTHER HAZARDS Controlling other hazards associated with installation activities should be considered, such as:
- Welding hazards - toxic gases, metal fumes, light hazards to the eyes. Also see torch cutting hazards.
- Ergonomic stress caused by operating power tools in awkward positions, excessive force, vibrations, and heavy loads. Cold temperatures may compound dangers.
- Noise exposure caused by impact of tool on steel structures and compressors. Noise levels of 110 dBA have been measured.
- Tool and compressed air hazards.
- Eye hazards from
flying particles and chips.
Once lead emitting activities are identified, contractors and owners can select appropriate controls to reduce worker lead exposure. On most rehabilitation projects, a combination of controls will be necessary. It is important to carefully consider site specific factors and schedules so that the controls can be fully integrated into project. Many owners have found that designating controls in the planning phase and including them in the project specifications are very effective ways to assure that workers are protected during the job.
Before work begins, the contractor must describe the controls to be used in its lead compliance program which is often reviewed by the owner. Once the job starts, the employer must assign a competent person to oversee effective implementation and use of all lead controls.
OSHA requires employers to implement engineering and work practice controls first to minimize lead hazards. If these measures do not lower lead exposures below the PEL, worker rotation and/or respirators, as last resorts, are permitted.
ENGINEERING CONTROLS
Engineering controls change the work at the point of lead emissions by substituting one operation for another, or by modifying processes or equipment. These solutions offer the greatest opportunity to eliminate or substantially reduce exposure.
Design initiatives from the engineering community and sincere commitments from the construction industry to use new technology are needed so that workplace controls are incorporated into the work. Examples of engineering controls include: removing steel members with hydraulic shears or by mechanical dismantling rather than with torch cutting, substituting vacuum blasting for scaling or grinding operations, using HEPA vacuum attachments on power tools, and other ventilation methods.
WORK PRACTICE CONTROLS
Work practice controls reduce exposure by adding protective procedures to high risk activities. These controls rely on readily available materials and methods but, as with all controls, close attention to proper implementation is crucial. Common work practices that reduce exposure are: stripping paint before torch cutting, encapsulating lead paint, using HEPA vacuums to clean up work areas, and wet methods for dust suppression and cleaning. However, wet methods are not always recommended on steel structures. due to potential slip hazards, flash rust on cleaned steel, and frozen water lines in cold weather.
ADMINISTRATIVE CONTROLS
Worker rotation is an administrative control designed to restrict the time that workers spend performing lead-emitting tasks. The problem with this method is there is no reduction in lead emissions, so if work schedules are ignored or respirators are inadequate, workers will be at risk. To be effective, this control must be strictly enforced on the job site. Work assignments and time limits must be clearly described in the lead compliance program and carefully documented.
RESPIRATORY PROTECTION
Respiratory protection is a common adjunct to engineering and work practice controls when these preferred methods fail to reduce exposures below the PEL. Respirators should never be introduced at the site as a primary control.
Implementation of a respiratory protection program is crucial. Contractors must appoint a program administrator to be responsible for selecting respirators and assuring that they are properly used and maintained at the site. Studies have shown that merely providing respirators to exposed workers is no guarantee that exposure will be reduced. Improper selection, poor fit, faulty use, and inadequate cleaning and maintenance can result in little or no protection at all.
IMPLEMENTING AND MANAGING CONTROLS
Mount Sinai and Hunter College researchers have studied the effectiveness of many control methods commonly used on rehabilitation sites. The results of these studies show the importance of management's role in selecting and implementing engineering and work practice controls. The technology applied in these control operations is not complicated, however the site where the controls are employed can be very complex. Management responsible for protecting workers at the site must be aware of the obstacles that can impede effectiveness of controls and the jobsite factors that effect exposure.
CONTROL METHODS
In this section, six lead control methods for steel rehabilitation are described including appropriate uses, materials, and equipment.
- Cleanup & Waste Removal
- Mechanical Removal of Steel
- Paint Removal:Chemical Stripping
- Paint Removal:Power Tools
- Encapsulation
- Distancing
MAKING IT WORK
Selecting a control is the first step in protecting workers from lead - making it work is the second. Each control description includes tips and reminders to assist contractors and workers in using the control effectively.
- Exposure Factors
- Work Procedures & Productivity
- Supervision & Quality Control
- Personal Protective Equipment
- Health & Safety Factors
- Environmental Factors
"Selecting a control is the first important step in protecting workers from lead - making it work is the second."
TASK | CONTROLS | COMMENTS |
Torch Cutting | 2,3,4,6,7 | Combination of controlsand respirators required; most paint removal methods leave lead residues. |
Rivet Busting | 1,2,3,5,7 | Encapsulation can reduce exposures. Use of torches to remove rivets will increase exposure. Respirators are needed. |
Surface Preparation with power tools | 1,2,3,7 | Vacuum blasting can be substituted for scaling and grinding Respirators are needed. |
Installation | 1,2,3,7 | Cleanup of lead debris is most important control. Respirators are needed. |
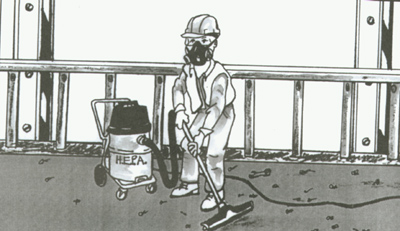
CONTROL: ESSENTIAL FOR ALL PROJECTS
Cleanup and removal of settled dust and paint debris from surfaces and floors eliminates reentrainment due to air exhaust, vibrations, and movement of people and materials in the area. Without aggressive cleanup, effectiveness of other controls will be undermined.
MATERIALS & EQUIPMENT
HEPA (high efficiency particle) vacuums or wet methods can be used for cleaning. HEPA vacuums are preferred because wet methods can cause slip hazards and flash rust on steel. Vacuums are equipped with prefilters, HEPA filters, hoses, attachments and suction capacity (cfm) for the job. Sealable, labelled drums and containers are used for waste storage.
EXPOSURE FACTORS
Workers doing cleanup should wear respirators and protective clothing. Dry sweeping and compressed air can cause high exposures and are prohibited by OSHA. Cleanup reduces exposure to other workers in the area.
"Without aggressive cleanup, effectiveness of other controls will be undermined."
WORK PROCEDURES & PRODUCTIVITY
- Operate vacuum as per manufacturer's instructions.
- Use wide mouthed attachments and rigid wands.
- Use vacuums only for small debris and paint chips to avoid clogging.
- Shovel or scrape large pieces. Use magnets to pick up loose steel.
- Maintain adequate vacuum capacity (cfm) for the job.
- Use prefilters to extend the service life of HEPA filters.
- Train personnel in proper operating and safety practices.
SUPERVISION & QUALITY CONTROL
- Assure proper use of attachments and hose assembly.
- Maintain equipment.
- Inspect areas for visible debris.
PERSONAL PROTECTIVE EQUIPMENT & INTERIM CONTROLS
- Use protective clothing, eye protection, and gloves.
- Use a half-face air purifying respirator with HEPA filters as a minimum.
- Put washup station near the work.
HEALTH & SAFETY FACTORS
- Prevent trip hazards caused by lengthy hoses and cords.
- Avoid "stooping postures" caused by short or non-rigid wands.
- Use proper personal protective equipment and disposal methods while emptying vacuum to avoid exposure.
ENVIRONMENTAL FACTORS
- Store, label and transport lead paint debris as hazardous waste.
- Control contamination with HEPA vacuums in the work area and in public access areas.
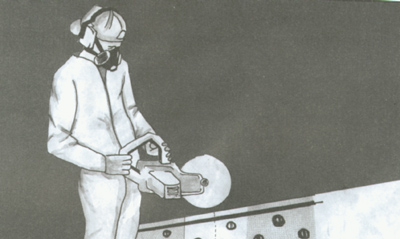
CONTROL: ALTERNATIVE TO TORCH CUTTING
Dissemble steel members by reversing installation procedures - removing rivets and bolts and then removing the steel, or by cutting out steel with abrasive/chop saws, hydraulic shears, or metal cutters.
MATERIALS & EQUIPMENT
Standard tools - rivet busters, air guns, hand tools - are used for dissembling operations. Special shears or saws are needed for cutting operations. Additional controls, such as paint removal or encapsulation, may be needed to reduce exposure.
EXPOSURE FACTORS
Mechanical dismantling methods create significantly lower lead exposures than torch cutting. Spot paint removal or encapsulation prior to rivet busting or saw cutting will further reduce exposure to workers.
"Mechanical cutting requires heavy equipment - works best on small, flat surfaces."
WORK PROCEDURES & PRODUCTIVITY
- Remove or encapsulate paint in areas where steel will be cut or unbolted.
- When cutting, stay in the center of cut lines that have been stripped or encapsulated with protective tape. Never cut along the edge of the stripped area.
- Saw cutting operations work best on flat surfaces with good access.
- Train personnel in proper operating and safety practices.
PERSONAL PROTECTIVE EQUIPMENT & INTERIM CONTROLS
- Use protective clothing, eye/face shield, gloves, hearing protection.
- Select a half-face air purifying respirator with HEPA filters as a minimum.
SUPERVISION AND QUALITY CONTROL
- Plan ahead and schedule prep work before dismantling activities.
- Ensure that surface preparation is completed properly before dissembling operations begin.
- Enforce safe work practices and use of personal protective equipment.
HEALTH & SAFETY FACTORS
- Avoid ergonomic stress from awkward tool position, vibrations, forceful exertion, and heavy load while operating abrasive chop saw.
- Prevent tool, cutting, and compressed air hazards.
- Expect high noise levels and use hearing protection.
- Cleanup lead debris with HEPA vacuums.
ENVIRONMENTAL FACTORS
- Store, label, and transport lead debris and contaminated steel as hazardous waste.
- Use containment barriers to protect community and environment.
- Consider impact of containment on worker exposure.
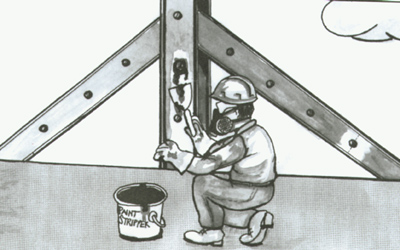
CONTROL: WORK PRACTICE FOR LEAD DISTURBANCE
Lead paint is removed prior to torch cutting, rivet busting, and surface preparation. Stripper is applied to steel surface and left in place for 1-24 hours. Paint and stripper are scraped off and residues are wiped away. Some strippers require neutralization.
MATERIALS & EQUIPMENT
There are three types of strippers: water-based caustic, water-based non-caustic, and petroleum-based (organic) solvent. Petroleum-based strippers may contain methylene chloride, a suspect human carcinogen. Equipment: sprayers, trowels, spatulas, scrapers, paper towels, rags, disposal containers and containment barriers.
EXPOSURE FACTORS
Exposure to lead is generally low for workers doing stripping. Exposure can be quite high for workers torch cutting or operating power tools after paint removal if stripping is incomplete or cut lines are too narrow. Torch cutters must be trained to cut in the middle of the cut line - not along the edge!
WORK PROCEDURES & PRODUCTIVITY
- Layout cut lines and areas to be stripped at least 4" on either side of the cut. Wider strips are even better.
- Coordinate location and stripping of cut lines with demolition cut requirements.
- Strip cut lines matching on the front and back of the steel.
- Train personnel in proper operating and safety practices.
SUPERVISION AND QUALITY CONTROL
- Allow enough time for stripper to work per weather conditions or stubborn paint layers.
- Assure adequate paint removal.
- Ensure safe work practices and use of personal protective equipment.
PERSONAL PROTECTIVE EQUIPMENT & INTERIM CONTROLS
- Use protective clothing, eye/face protection, gloves.
- Use a half-face air purifying respirator with HEPA filters and chemical cartridges.
- Review hazards of stripping compounds. Caustic strippers are corrosive to skin and eyes; organic strippers may cause nervous system effects and irritation, and contain cancer-causing chemicals.
- Protect other workers, who may be positioned nearby, from chemical splashes, vapors, and stripper residues.
- Use of containment barriers may increase worker exposure to solvents.
- Prevent contact with caustic residues.
ENVIRONMENTAL FACTORS
- Lead debris and stripping waste must be collected, labelled, stored and transported as hazardous waste.
- Use containment barriers to control environmental contamination.
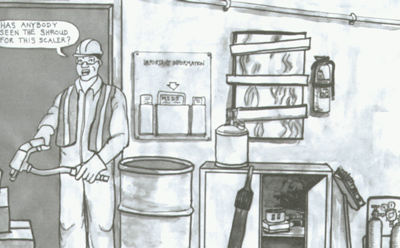
CONTROL: WORK PRACTICE FOR LEAD EMITTING TASKS
Lead paint is removed with power tools equipped with dust collectors prior to other lead-emitting activities. Small lead particles are collected by a HEPA vacuum system as they are released by the tools.
MATERIALS & EQUIPMENT
Rotopeens, piston scalers, and grinders work best on large flat areas. Vacuum blaster has a flexible shroud and performs well on irregular surfaces. Needle guns have various attachments for inside edges, outside edges, and flat areas.
EXPOSURE FACTORS
Expect high exposures for workers operating tools if shrouds are not held flush against the surface. Can be an effective control for torch cutting and other tasks if cut lines are laid out properly and paint is completely removed.
WORK PROCEDURES & PRODUCTIVITY
- Layout cut lines and areas to be treated at least 4" on all sides of the cut. Wider strips are even better.
- Select appropriate tool based on type of surface to be treated.
- Follow manufacturer's instructions for the tools.
- Keep tool shroud flush with the surface for effective results.
- Coordinate paint removal with demolition cut locations and other requirements of ironwork.
- Train personnel in operating and safety practices.
SUPERVISION AND QUALITY CONTROL
- Utilize technical assistance from equipment manufacturers.
- Ensure proper tool use.
- Enforce safe work practices and use of ppe.
PERSONAL PROTECTIVE EQUIPMENT & INTERIM CONTROLS
- Use protective clothing, eye/face protection, gloves.
- Use a half-face air purifying respirator with P-100 (HEPA) filters.
- Use hearing protection.
HEALTH & SAFETY FACTORS
- Avoid ergonomic stress from awkward tool position, vibrations, forceful exertion, and heavy loads. Overhead positions are hell!
- Prevent tool and compressed air hazards.
- Expect high noise levels - wear hearing protectors.
ENVIRONMENTAL FACTORS
- Store and transport lead debris as hazardous waste.
- Power tools with dust collectors prevent emission of smaller particles into environment; however larger particles are too heavy for the vacuum and will fall away from the work.
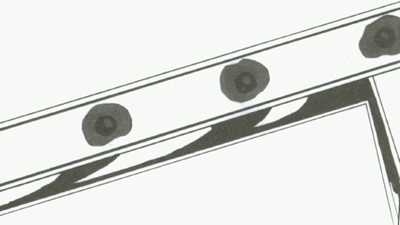
CONTROL: WORK PRACTICE FOR RIVET BUSTING
Rivet heads and steel members are treated with an elastomeric coating (plastic dip) prior to rivet busting. Duct tape has been used as an encapsulant for sawing. In either case, the coating or tape holds the paint together and reduces dust generation at point of impact.
MATERIALS & EQUIPMENT
Encapsulants are elastomeric coatings and are usually applied by brush
or spray. High quality duct tape is used for sawing operations. Materials
should be field tested before use.
EXPOSURE FACTORS
Workers who apply encapsulants have very low exposures to lead. Workers who do rivet busting on encapsulated steel may have significantly lowered exposure. Exposure will increase in presence of loose paint debris and contamination.
WORK PROCEDURES & PRODUCTIVITY
- Coordinate encapsulation with ironwork.
- Application of encapsulant may be weather dependent. Allow for drying time.
- Train personnel in application and safety practices.
SUPERVISION AND QUALITY CONTROL
- Ensure complete coverage of impacted and surrounding areas.
- Enforce safe work practices and use of ppe.
PERSONAL PROTECTIVE EQUIPMENT
- Use protective clothing, eye/face protection, gloves.
- Select respirator for encapsulant applicators according to hazard assessment. Consult material safety data sheets.
HEALTH & SAFETY FACTORS
- Review hazards of encapsulants and solvents.
- Control other hazards associated with lead disturbing tasks.
ENVIRONMENTAL FACTORS
- Lead debris and lead painted steel must be collected, labelled, stored and transported as hazardous waste.
WATCH OUT!
|
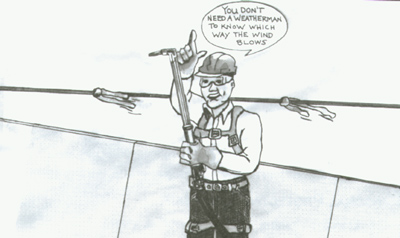
WORK PRACTICE CONTROL
Distancing is a work practice control where the worker "distances" the point of lead emissions from his/her breathing zone, for example, an ironworker standing upwind during torch cutting. Distancing is also achieved by using a long demolition torch (up to 6' in length) which positions the worker's breathing zone further away from the cut.
EXPOSURE FACTORS
Little data exist to substantiate lower exposures from this method. Because the effectiveness of this control is uncertain, it should only be used in stable wind conditions and in conjunction with respiratory protection. Be aware that other workers in the area may be exposed if working downwind of emissions.
WORK PROCEDURES & PRODUCTIVITY
- Maintain body position upwind of burning.
- Use demolition (long) torch whenever possible.
- Train personnel in operating and safety practices.
SUPERVISION & QUALITY CONTROL
- Monitor effectiveness of control and suspend in variable winds.
- Enforce safe work practices and use of ppe.
PERSONAL PROTECTIVE EQUIPMENT
- Use protective clothing, eye/face protection, gloves.
- Select appropriate air supplied respirator based on actual air monitoring data.
HEALTH & SAFETY FACTORS
- Review lead hazards.
ENVIRONMENTAL FACTORS
- Containment may be required to protect community. However containment may prevent dispersion of lead emissions and thus negate distancing as an effective control.
WATCH
OUT!
|
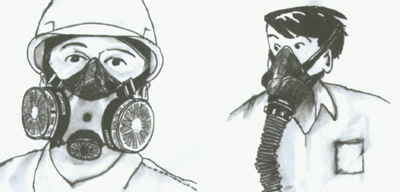
LAST RESORT PROTECTION
Although respirators are the least preferred control, they are often needed when engineering and work practice controls fail to lower lead exposures below the OSHA permissible exposure limit. Respirators are also required as "interim controls" while exposure assessment is being completed.
RESPIRATOR PROGRAM
To assure proper selection and use of respirators, OSHA requires a respirator program in accordance with the respirator standard (1910.134), which was revised in 1998, and the lead construction standard (1926.62).
TYPES OF RESPIRATORS
Respirator facepieces cover the nose and mouth with a half-face or full-face mask, or with a hood or helmet. There are two general types of respirators approved for lead exposure:
- air purifying respirators (APRs) with100-series (HEPA) filters
- supplied air respirators (SARs) equipped with continuous flow or pressure demand air delivery and a source of clean breathing air.
- Assures that the respirator program is fully implemented including: selection, training, fit testing, no facial hair policy, availability of replacement filters and parts, maintaining, cleaning, inspecting, and storing.
SELECTION
- Select respirators based on personal air monitoring at the job site or OSHA interim control requirements for specific lead-emitting tasks. Each type of respirator has an assigned protection factor that determines the maximum concentration in which it can be used.
- Powered air purifying respirators must be supplied to employees if requested as long as exposure is not greater than 2500 mcg/m 3
RESPIRATOR | Protection Factor | Maximum
Use Concentration MCG/M3 |
|
![]() |
APR - HEPA
filters |
10
50 50 |
500 |
![]() |
SAR CF: Half- or full-face PD: Half-face PD: Full-face |
50
1000 2000 |
2500
50,000 100,000 |
![]() |
Blasting
Helmet or Hood PAPR SAR |
25
25 |
1250
1250 |
|
"Select respirators based on personal air monitoring at the job site or OSHA interim control requirements for specific lead-emitting tasks."
FIT TESTING
- All workers who are assigned tight fitting, half-face or full-face, air purifying or supplied air respirators must be fit tested.
- Fit testing must be repeated every year using OSHA approved methods.
TRAINING
- Wearers must be trained every year in proper respirator use, including:
- How to check the facepiece seal (positive and negative pressure checks).
- How to inspect, maintain, clean and store respirator.
- Emergency procedures in case respirator fails.
USING AIR PURIFYING RESPIRATORS
- Use 100-Series (HEPA) filters for protection from lead. Change filters whenever they becomes dirty, damaged, or difficult to breathe through. P-100 filters are required if the airborne particulate include oily substances.
- Use chemical cartridges, or combination HEPA/chemical cartridges, for protection against paint removers and other solvents. Change cartridges on a regular schedule before smell, taste or irritation is detected.
- Replacement filters and spare parts, fit testing supplies, and cleaning facilities must be available at the site.
- Do not interchange parts from different manufacturers.
- Damaged filters, facepieces, straps, and valves should be replaced before use.
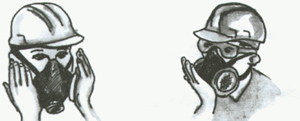
USING SUPPLIED AIR RESPIRATORS
- For air supplying respirators, total hose length must not exceed capacity of compressor as noted on NIOSH respirator approval label.
- Be sure that compressor is not feeding more respirators than recommended by the manufacturer.
- Breathing air must meet Grade D requirements. Compressor intake must be placed in a clean area away from lead emissions, engine exhaust, and other contaminants.
- Carbon monoxide alarms and air purifiers on compressors must be inspected and maintained.
- Facepiece and other components must be inspected, maintained, cleaned and stored properly.
GRADE D AIR
Contractors must have procedures to assure that respirator breathing air meets Grade D Specifications of the Compressed Gas Association.
- Oxygen content: 19.5% - 23.5%
- Condensed hydrocarbons: 5 milligrams per cubic meter of air (5 mg/m 3 )
- Carbon monoxide: 10 parts per million (ppm)
- Carbon dioxide: 1000 PPM
- No noticeable odors
CLEANING
- Respirators should be cleaned and inspected according to manufacturers' instructions.
- Most manufacturers recommend dissembling the respirator, washing in warm soap and water (not the filter!), disinfecting with a weak bleach solution, and air or hand drying.
- Moistened wipes can be used during the workday to keep respirator clean, but not as a regular cleaning method.
STORAGE
- Respirators must be stored when not in use.
- Use rigid containers
with tight lids, such as small plastic buckets, to protect respirator
from damage and contamination. Plastic bags don't hold up well on most
construction sites!
The case studies described below illustrate actual work site situations and emphasize the importance of coordinating and managing worker protection programs.
CASE I-II: TORCH CUTTING
Bridge Renovation:
Ironworkers were cutting out steel beams from a suspension bridge
with oxyacetylene torches. The paint contained 35% lead. The workers wore
half-face respirators with HEPA filters. A different contractor had used
shrouded needleguns to remove 8-inch strips of paint. It was intended
that cutting would be through the middle of these strips.
Lead exposure results: 1500 mcg/m 3 , well above the maximum use
concentration of the respirators.
Industrial Demolition: Ironworkers used oxyacetylene torches to
cut out steel sections of freight elevators in an industrial building.
All work was done indoors, inside containment, or in the enclosed space
of the elevator shaft. The ironworkers wore half-face respirators with
HEPA filters. Prior to cutting, a different contractor used chemical strippers
to remove 8-inch strips of paint on the front and back of the steel. As
in the bridge case, the paint was about 35% lead by weight.
Lead exposure results: More than 10,000 mcg/m 3 - more
than 20 times the maximum use concentration of the respirators being worn.
WHAT WENT WRONG?
- Paint removal was incomplete. Some surfaces were difficult to access and primer was imbedded in the steel.
- There was little coordination between paint removal and lay out of cut lines. Steel was sometimes cut on a diagonal, outside the vertical stripped areas, to accommodate lifting out the cut pieces. Cutting was also sometimes aimed in hard to reach areas where paint had not been stripped. Strip lines did not always match up front to back.
- Working inside containment increased exposures, but additional controls weren't implemented.
CASE III: RIVET BUSTING
On a steel suspension
bridge, workers used pneumatic rivet busters to remove rivets that had
been coated with a lead paint encapsulant. The original bridge paint contained
about 40% lead. Problem rivets were burned out with a thermolance. All
work was performed inside containment and workers wore half-face respirators
with HEPA filters.
Lead exposure results: 1200 mcg/m 3 - more than twice
the limits of the respirators. Blood lead levels became dangerously high
and two workers were medically removed.
WHAT WENT WRONG?
- Controls were not designed for lancing operations. Uncontrolled burning resulted in high exposures:
- Lead dust was stirred up by air exhausted from tools and vibrations from tool impact. Clean up activities were not aggressive.
- The particular encapsulant did not substantially reduce lead dust generation during rivet busting. Encapsulation is ineffective during lancing.
- Working inside containment increases exposure. Effects of containment on worker exposure were not assessed and protection was not increased.
In this case, workers
also removed rivets with a rivet buster on a steel suspension bridge.
Lead content of the paint was 35-40%. Rivets were coated with an elastomeric,
flexible encapsulant before rivet removal. Work was performed in the open
air and workers wore half face respirators with HEPA filters.
Lead exposure results: 400 mcg/m 3 - above the OSHA
permissible exposure limit (50 mcg/m 3 ) but within the protection provided
by the respirators.
- In this case, encapsulation combined with respiratory protection was an effective control.
CASE V: VACUUM-BLASTING PAINT REMOVAL
Workers used vacuum
blasting equipment to perform spot removal of lead paint prior to overcoating
on an elevated highway structure. The paint contained about 30% lead.
Work was done inside a containment and workers wore half-face respirators
with HEPA filters and chemical cartridges.
Blood lead monitoring results: By the end of the four month project,
several workers had blood lead levels above 35 mcg/dl.
WHAT WENT WRONG?
- Vacuum blast nozzle was not held flush against the painted surface allowing lead dust to escape into work place air.
- The vacuum blast nozzle did not work well in corners and on very uneven surfaces.
- The particular respirator model became distorted from the weight of the double filter/chemical cartridges. The distortion caused facepiece leakage.
- Paint removal controls must be planned, implemented, and evaluated so that paint is removed thoroughly and in the right place. The owner and all contractors should understand the purpose of the controls and how the control fits into the rest of the work. Inspection responsibilities should be clearly defined.
- Field test controls - especially encapsulation - to be sure that the methods suit work site conditions.
- Train workers in proper operation of control equipment. Equipment suppliers should provide technical assistance when needed.
- Don't assume controls work. Use personal air monitoring to assess effectiveness of controls and select respirators.
- Discuss paint removal controls and cutting procedures with workers in initial training, tool box talks and safety meetings.
- Competent persons should use site specific checklists to inspect work areas and respond to deficiencies as soon as they are identified. Special attention should be given to proper use of respirators and hygiene facilities.
- Contractor and owners should review blood lead levels and air monitoring results regularly and investigate the cause of elevated levels.
- Owners should assess the effects of working in containment on worker exposure. Exposures will increase when work is performed in enclosed spaces.
Goldberg, M, Levin, SM, Doucette, J, Griffin, G: A task-based approach to assessing lead exposure among ironworkers engaged in bridge rehabilitation. Am J Ind Med 31:310-318. (1997)
Levin, SM, Goldberg, M, Doucette, J: The effect of the OSHA lead exposure in construction standard on blood lead levels among iron workers employed in bridge rehabilitation. Am J Ind Med 31:303-309. (1997)
The Mount Sinai-Irving J. Selikoff Center for Occupational and Environmental Medicine, Construction Hygiene and Ergonomics Program: Working with lead on bridges. New York. (1998)
National Ironworkers and Employers Apprenticeship Training and Journeyman Upgrading Fund: Lead Hazard Training for Ironworkers. Washington, DC (1995).
NIOSH (National Institute for Occupational Safety and Health): NIOSH Hazard Alert: Request for Assistance in Preventing Lead Poisoning in Construction Workers. DHHS (NIOSH) Publ No. 91-116a. (1992)
Trimber, Kenneth A., Industrial Lead Paint Removal Handbook, 2nd ed., KTA-TATOR, Inc, SSPC 93-02, Pittsburgh, PA. (1993)
U.S. Department of Labor, Occupational Safety and Health Administration (OSHA), 29 CFR Part 1926: Lead Exposure in Construction; Interim Final Rule: Fed Reg, Vol. 58, No 84 - Tuesday, May 4, 1993.
US Department of Labor, Occupational Safety and Health Administration (OSHA), OSHA Instruction, Directive CPL 2.105: Special Emphasis Program: Lead in Construction: March 11, 1996
ORDERING INFORMATION Contact:
Mount Sinai CHEP
Box 1057
1 Gustave L. Levy Place
New York, NY 10029
212/241-7573
FAX: 212/987-6407
e-mail: nancy.clark@mountsinai.orgSingle copies: $6.00 each Bulk orders: 6-25: 5.50 each
26+: 5.00 each