Attempt to read property 'getID' from NULL value
PHPTAL_VariableNotFoundException Object
(
[srcFile] => /home/agsafe5/repositories/elcosh/live/templates/elcosh/record.html/collections
[srcLine] =>
[message:protected] => Attempt to read property 'getID' from NULL value
[string:Exception:private] =>
[code:protected] => 0
[file:protected] => /home/agsafe5/repositories/elcosh/live/templates/elcosh/record.html/collections
[line:protected] =>
[trace:Exception:private] => Array
(
[0] => Array
(
[file] => /home/agsafe5/repositories/elcosh/live/sblib/core/SB_PHPTAL/PHPTAL/PHPTAL/Context.php
[line] => 353
[function] => pathError
[class] => PHPTAL_Context
[type] => ::
[args] => Array
(
[0] =>
[1] => getID
[2] => getID
)
)
[1] => Array
(
[file] => /tmp/tpl_61515a6c_record_macros__gMFg5NvPLybiFfYjAv9Aag.php
[line] => 105
[function] => path
[class] => PHPTAL_Context
[type] => ::
[args] => Array
(
[0] =>
[1] => getID
)
)
[2] => Array
(
[file] => /home/agsafe5/repositories/elcosh/live/sblib/core/SB_PHPTAL/PHPTAL/PHPTAL.php
[line] => 772
[function] => tpl_61515a6c_record_macros__gMFg5NvPLybiFfYjAv9Aag_collections
[args] => Array
(
[0] => PHPTAL Object
(
[_prefilters:protected] => Array
(
)
[_prefilter:PHPTAL:private] => REMOVED: DO NOT USE
[_postfilter:protected] =>
[_repositories:protected] => Array
(
[0] => /home/agsafe5/repositories/elcosh/live/templates/elcosh
)
[_path:protected] => record_macros.html
[_resolvers:protected] => Array
(
)
[_source:protected] => PHPTAL_FileSource Object
(
[_path:PHPTAL_FileSource:private] => /home/agsafe5/repositories/elcosh/live/templates/elcosh/record_macros.html
)
[_codeFile:protected] => /tmp/tpl_61515a6c_record_macros__gMFg5NvPLybiFfYjAv9Aag.php
[_functionName:protected] => tpl_61515a6c_record_macros__gMFg5NvPLybiFfYjAv9Aag
[_prepared:protected] => 1
[_triggers:protected] => Array
(
)
[_translator:protected] =>
[_globalContext:protected] => stdClass Object
(
)
[_context:protected] => PHPTAL_Context Object
(
[_line] =>
[_file] => /home/agsafe5/repositories/elcosh/live/templates/elcosh/record.html
[repeat] => stdClass Object
(
)
[_xmlDeclaration] =>
[_docType] =>
[_nothrow:PHPTAL_Context:private] =>
[_slots:PHPTAL_Context:private] => Array
(
)
[_slotsStack:PHPTAL_Context:private] => Array
(
[0] => Array
(
)
[1] => Array
(
)
)
[_parentContext:PHPTAL_Context:private] => PHPTAL_Context Object
(
[_line] =>
[_file] => /home/agsafe5/repositories/elcosh/live/templates/elcosh/record.html
[repeat] => stdClass Object
(
)
[_xmlDeclaration] =>
[_docType] =>
[_nothrow:PHPTAL_Context:private] =>
[_slots:PHPTAL_Context:private] => Array
(
)
[_slotsStack:PHPTAL_Context:private] => Array
(
[0] => Array
(
)
[1] => Array
(
)
)
[_parentContext:PHPTAL_Context:private] =>
[_globalContext:PHPTAL_Context:private] => stdClass Object
(
)
[_echoDeclarations:PHPTAL_Context:private] =>
[referer] => http://www.elcosh.org/document/3827/d001298/Getting%2Bthe%2Bmost%2Bout%2Bof%2Bthe%2BIUOE%2BToolbox%2BTalks.html
[curr_module] => Record
[styles] => Array
(
)
[javascript] => Array
(
[0] => jquery.min.js
)
[metas] => Array
(
[language] => en
[robots] => index, follow
)
[user] =>
[curr_url] => https://www.elcosh.org/index.php?module=Record&id=3827&type=document
[base_url] => https://www.elcosh.org/index.php?module=Record
[title] => eLCOSH : Getting the most out of the IUOE Toolbox Talks
[language] => en
[search_query] =>
[module] => Record
[new_records] => Array
(
[0] => Search_Result Object
(
[title] => Toolbox Talk: Fixed Ladder
[image] => /record/images/notavailable-p.png
[blurb] => The CPWR Toolbox Talk on Fixed Ladders addresses the potential risks associated with using fixed ladders. The resource includes a brief case example,...
[category] => Array
(
[0] => 15
[1] => 47
[2] => 49
[3] => 51
[4] => 53
[5] => 55
[6] => 60
[7] => 64
[8] => 73
[9] => 76
[10] => 78
[11] => 80
[12] => 86
[13] => 87
[14] => 90
[15] => 92
[16] => 93
[17] => 94
[18] => 100
)
[labels] => Array
(
[0] => Falls
[1] => Work Environment
[2] => Hazards
[3] => Bricklayer
[4] => Trades
[5] => Carpenter
[7] => Cement Mason
[9] => Concrete Polisher
[11] => Electrical Worker
[13] => HVAC
[15] => Laborer
[17] => PCC/Restoration
[19] => Plumber/Pipefitter
[21] => Roofer/Waterproofer
[23] => Sheetmetal Worker
[25] => Welder
[27] => Commercial & Institutional
[28] => Jobsites
[29] => Industrial
[31] => LEED/Green Construction
[33] => Renovations
[35] => Residential
[37] => Toolbox Talks
[38] => Documents
[39] => Media & Documents
)
[type] => Toolbox Talks
[sub_category] =>
[url] => /document/4430/d001660/Toolbox%2BTalk%253A%2BFixed%2BLadder.html
[item:protected] => DocumentRecord Object
(
[records:protected] => Array
(
)
[recordId:protected] =>
[searchWordClass:protected] =>
[searchWordPeerClass:protected] =>
[bok_record:protected] =>
[authors:protected] =>
[organizations:protected] =>
[collections:protected] =>
[categories:protected] => Array
(
[15] => Category Object
(
[languages:protected] =>
[bok_resources:protected] =>
[bok_topics:protected] =>
[bok_keywords:protected] =>
[id:protected] => 15
[type:protected] => category
[parent:protected] => 7
[label:protected] => Falls
[alreadyInSave:protected] =>
[alreadyInValidation:protected] =>
[validationFailures:protected] => Array
(
)
[_new:BaseObject:private] =>
[_deleted:BaseObject:private] =>
[modifiedColumns:protected] => Array
(
)
)
[47] => Category Object
(
[languages:protected] =>
[bok_resources:protected] =>
[bok_topics:protected] =>
[bok_keywords:protected] =>
[id:protected] => 47
[type:protected] => category
[parent:protected] => 2
[label:protected] => Bricklayer
[alreadyInSave:protected] =>
[alreadyInValidation:protected] =>
[validationFailures:protected] => Array
(
)
[_new:BaseObject:private] =>
[_deleted:BaseObject:private] =>
[modifiedColumns:protected] => Array
(
)
)
[49] => Category Object
(
[languages:protected] =>
[bok_resources:protected] =>
[bok_topics:protected] =>
[bok_keywords:protected] =>
[id:protected] => 49
[type:protected] => category
[parent:protected] => 2
[label:protected] => Carpenter
[alreadyInSave:protected] =>
[alreadyInValidation:protected] =>
[validationFailures:protected] => Array
(
)
[_new:BaseObject:private] =>
[_deleted:BaseObject:private] =>
[modifiedColumns:protected] => Array
(
)
)
[51] => Category Object
(
[languages:protected] =>
[bok_resources:protected] =>
[bok_topics:protected] =>
[bok_keywords:protected] =>
[id:protected] => 51
[type:protected] => category
[parent:protected] => 2
[label:protected] => Cement Mason
[alreadyInSave:protected] =>
[alreadyInValidation:protected] =>
[validationFailures:protected] => Array
(
)
[_new:BaseObject:private] =>
[_deleted:BaseObject:private] =>
[modifiedColumns:protected] => Array
(
)
)
[53] => Category Object
(
[languages:protected] =>
[bok_resources:protected] =>
[bok_topics:protected] =>
[bok_keywords:protected] =>
[id:protected] => 53
[type:protected] => category
[parent:protected] => 2
[label:protected] => Concrete Polisher
[alreadyInSave:protected] =>
[alreadyInValidation:protected] =>
[validationFailures:protected] => Array
(
)
[_new:BaseObject:private] =>
[_deleted:BaseObject:private] =>
[modifiedColumns:protected] => Array
(
)
)
[55] => Category Object
(
[languages:protected] =>
[bok_resources:protected] =>
[bok_topics:protected] =>
[bok_keywords:protected] =>
[id:protected] => 55
[type:protected] => category
[parent:protected] => 2
[label:protected] => Electrical Worker
[alreadyInSave:protected] =>
[alreadyInValidation:protected] =>
[validationFailures:protected] => Array
(
)
[_new:BaseObject:private] =>
[_deleted:BaseObject:private] =>
[modifiedColumns:protected] => Array
(
)
)
[60] => Category Object
(
[languages:protected] =>
[bok_resources:protected] =>
[bok_topics:protected] =>
[bok_keywords:protected] =>
[id:protected] => 60
[type:protected] => category
[parent:protected] => 2
[label:protected] => HVAC
[alreadyInSave:protected] =>
[alreadyInValidation:protected] =>
[validationFailures:protected] => Array
(
)
[_new:BaseObject:private] =>
[_deleted:BaseObject:private] =>
[modifiedColumns:protected] => Array
(
)
)
[64] => Category Object
(
[languages:protected] =>
[bok_resources:protected] =>
[bok_topics:protected] =>
[bok_keywords:protected] =>
[id:protected] => 64
[type:protected] => category
[parent:protected] => 2
[label:protected] => Laborer
[alreadyInSave:protected] =>
[alreadyInValidation:protected] =>
[validationFailures:protected] => Array
(
)
[_new:BaseObject:private] =>
[_deleted:BaseObject:private] =>
[modifiedColumns:protected] => Array
(
)
)
[73] => Category Object
(
[languages:protected] =>
[bok_resources:protected] =>
[bok_topics:protected] =>
[bok_keywords:protected] =>
[id:protected] => 73
[type:protected] => category
[parent:protected] => 2
[label:protected] => PCC/Restoration
[alreadyInSave:protected] =>
[alreadyInValidation:protected] =>
[validationFailures:protected] => Array
(
)
[_new:BaseObject:private] =>
[_deleted:BaseObject:private] =>
[modifiedColumns:protected] => Array
(
)
)
[76] => Category Object
(
[languages:protected] =>
[bok_resources:protected] =>
[bok_topics:protected] =>
[bok_keywords:protected] =>
[id:protected] => 76
[type:protected] => category
[parent:protected] => 2
[label:protected] => Plumber/Pipefitter
[alreadyInSave:protected] =>
[alreadyInValidation:protected] =>
[validationFailures:protected] => Array
(
)
[_new:BaseObject:private] =>
[_deleted:BaseObject:private] =>
[modifiedColumns:protected] => Array
(
)
)
[78] => Category Object
(
[languages:protected] =>
[bok_resources:protected] =>
[bok_topics:protected] =>
[bok_keywords:protected] =>
[id:protected] => 78
[type:protected] => category
[parent:protected] => 2
[label:protected] => Roofer/Waterproofer
[alreadyInSave:protected] =>
[alreadyInValidation:protected] =>
[validationFailures:protected] => Array
(
)
[_new:BaseObject:private] =>
[_deleted:BaseObject:private] =>
[modifiedColumns:protected] => Array
(
)
)
[80] => Category Object
(
[languages:protected] =>
[bok_resources:protected] =>
[bok_topics:protected] =>
[bok_keywords:protected] =>
[id:protected] => 80
[type:protected] => category
[parent:protected] => 2
[label:protected] => Sheetmetal Worker
[alreadyInSave:protected] =>
[alreadyInValidation:protected] =>
[validationFailures:protected] => Array
(
)
[_new:BaseObject:private] =>
[_deleted:BaseObject:private] =>
[modifiedColumns:protected] => Array
(
)
)
[86] => Category Object
(
[languages:protected] =>
[bok_resources:protected] =>
[bok_topics:protected] =>
[bok_keywords:protected] =>
[id:protected] => 86
[type:protected] => category
[parent:protected] => 2
[label:protected] => Welder
[alreadyInSave:protected] =>
[alreadyInValidation:protected] =>
[validationFailures:protected] => Array
(
)
[_new:BaseObject:private] =>
[_deleted:BaseObject:private] =>
[modifiedColumns:protected] => Array
(
)
)
[87] => Category Object
(
[languages:protected] =>
[bok_resources:protected] =>
[bok_topics:protected] =>
[bok_keywords:protected] =>
[id:protected] => 87
[type:protected] => category
[parent:protected] => 3
[label:protected] => Commercial & Institutional
[alreadyInSave:protected] =>
[alreadyInValidation:protected] =>
[validationFailures:protected] => Array
(
)
[_new:BaseObject:private] =>
[_deleted:BaseObject:private] =>
[modifiedColumns:protected] => Array
(
)
)
[90] => Category Object
(
[languages:protected] =>
[bok_resources:protected] =>
[bok_topics:protected] =>
[bok_keywords:protected] =>
[id:protected] => 90
[type:protected] => category
[parent:protected] => 3
[label:protected] => Industrial
[alreadyInSave:protected] =>
[alreadyInValidation:protected] =>
[validationFailures:protected] => Array
(
)
[_new:BaseObject:private] =>
[_deleted:BaseObject:private] =>
[modifiedColumns:protected] => Array
(
)
)
[92] => Category Object
(
[languages:protected] =>
[bok_resources:protected] =>
[bok_topics:protected] =>
[bok_keywords:protected] =>
[id:protected] => 92
[type:protected] => category
[parent:protected] => 3
[label:protected] => LEED/Green Construction
[alreadyInSave:protected] =>
[alreadyInValidation:protected] =>
[validationFailures:protected] => Array
(
)
[_new:BaseObject:private] =>
[_deleted:BaseObject:private] =>
[modifiedColumns:protected] => Array
(
)
)
[93] => Category Object
(
[languages:protected] =>
[bok_resources:protected] =>
[bok_topics:protected] =>
[bok_keywords:protected] =>
[id:protected] => 93
[type:protected] => category
[parent:protected] => 3
[label:protected] => Renovations
[alreadyInSave:protected] =>
[alreadyInValidation:protected] =>
[validationFailures:protected] => Array
(
)
[_new:BaseObject:private] =>
[_deleted:BaseObject:private] =>
[modifiedColumns:protected] => Array
(
)
)
[94] => Category Object
(
[languages:protected] =>
[bok_resources:protected] =>
[bok_topics:protected] =>
[bok_keywords:protected] =>
[id:protected] => 94
[type:protected] => category
[parent:protected] => 3
[label:protected] => Residential
[alreadyInSave:protected] =>
[alreadyInValidation:protected] =>
[validationFailures:protected] => Array
(
)
[_new:BaseObject:private] =>
[_deleted:BaseObject:private] =>
[modifiedColumns:protected] => Array
(
)
)
[100] => Category Object
(
[languages:protected] =>
[bok_resources:protected] =>
[bok_topics:protected] =>
[bok_keywords:protected] =>
[id:protected] => 100
[type:protected] => category
[parent:protected] => 6
[label:protected] => Toolbox Talks
[alreadyInSave:protected] =>
[alreadyInValidation:protected] =>
[validationFailures:protected] => Array
(
)
[_new:BaseObject:private] =>
[_deleted:BaseObject:private] =>
[modifiedColumns:protected] => Array
(
)
)
)
[categories_initialized:protected] => 1
[mapped_items:protected] =>
[content:protected] =>
[files:protected] =>
[language:protected] => Language Object
(
[id:protected] => 1
[code:protected] => en
[name:protected] => English
[alreadyInSave:protected] =>
[alreadyInValidation:protected] =>
[validationFailures:protected] => Array
(
)
[_new:BaseObject:private] =>
[_deleted:BaseObject:private] =>
[modifiedColumns:protected] => Array
(
)
)
[old_record:protected] =>
[id:protected] => 4430
[old_id:protected] =>
[elcosh_id:protected] => d001660
[type:protected] => document
[display_type:protected] => HTML only (and links)
[user_id:protected] => 0
[language_id:protected] => 1
[tagging_id:protected] => Mike Aguilar
[priority_id:protected] => 1
[title:protected] => Toolbox Talk: Fixed Ladder
[total_pages:protected] => 0
[billed_pages:protected] => 0
[publication_number:protected] =>
[part_of:protected] =>
[keywords:protected] => Fixed Ladders, Fall Prevention, Falls
[comments:protected] =>
[summary:protected] => The CPWR Toolbox Talk on Fixed Ladders addresses the potential risks associated with using fixed ladders. The resource includes a brief case example, steps to prevent a related injury and questions for discussion. It includes an image that illustrates the hazard, which can be posted in a central location as a reminder of steps to work safely.
Available in English
and Spanish.
[transition_comments:protected] =>
[external_link:protected] =>
[consol_link:protected] =>
[more_like_this:protected] => d001257,d001254,d001255,d001256,d001258,d001262,d001279
[permission_given_by:protected] =>
[published:protected] => T
[billable:protected] => F
[img_name:protected] =>
[img_ext:protected] =>
[img_width:protected] =>
[img_height:protected] =>
[img_credit:protected] =>
[img_practice:protected] =>
[vid_source_id:protected] =>
[vid_running_time:protected] =>
[vid_intended_audience:protected] =>
[vid_acquisition_info:protected] =>
[vid_cost:protected] =>
[vid_producer:protected] =>
[vid_filename:protected] =>
[vid_filename_downloadable:protected] =>
[date_summary:protected] =>
[date_permission_requested:protected] =>
[date_permission_received:protected] =>
[date_review_needed:protected] =>
[date_received:protected] => 06/10/22
[date_completed:protected] => 06/10/22
[date_billed:protected] =>
[date_modified:protected] => 05/22/23
[collBokExports:protected] =>
[lastBokExportCriteria:BaseElcoshItem:private] =>
[alreadyInSave:protected] =>
[alreadyInValidation:protected] =>
[validationFailures:protected] => Array
(
)
[_new:BaseObject:private] =>
[_deleted:BaseObject:private] =>
[modifiedColumns:protected] => Array
(
)
)
)
[1] => Search_Result Object
(
[title] => Toolbox Talk: Challenges Preventing Falling Objects
[image] => /record/images/notavailable-p.png
[blurb] => The CPWR Toolbox Talk on Challenges Preventing Falling Objects addresses the hazards of being struck by falling objects on the job site. The resource...
[category] => Array
(
[0] => 12
[1] => 47
[2] => 49
[3] => 51
[4] => 55
[5] => 64
[6] => 68
[7] => 71
[8] => 75
[9] => 78
[10] => 79
[11] => 82
[12] => 62
[13] => 86
[14] => 87
[15] => 88
[16] => 89
[17] => 91
[18] => 90
[19] => 92
[20] => 93
[21] => 94
[22] => 95
[23] => 100
)
[labels] => Array
(
[0] => Crushed/Struck By
[1] => Work Environment
[2] => Hazards
[3] => Bricklayer
[4] => Trades
[5] => Carpenter
[7] => Cement Mason
[9] => Electrical Worker
[11] => Laborer
[13] => Maintenance Worker
[15] => Painter
[17] => Plasterer
[19] => Roofer/Waterproofer
[21] => Scaffold Erector
[23] => Stonemason
[25] => Structural Ironworker
[27] => Welder
[29] => Commercial & Institutional
[30] => Jobsites
[31] => Demolition
[33] => Disasters
[35] => Heavy & Highway
[37] => Industrial
[39] => LEED/Green Construction
[41] => Renovations
[43] => Residential
[45] => Underground
[47] => Toolbox Talks
[48] => Documents
[49] => Media & Documents
)
[type] => Toolbox Talks
[sub_category] =>
[url] => /document/4431/d001661/Toolbox%2BTalk%253A%2BChallenges%2BPreventing%2BFalling%2BObjects.html
[item:protected] => DocumentRecord Object
(
[records:protected] => Array
(
)
[recordId:protected] =>
[searchWordClass:protected] =>
[searchWordPeerClass:protected] =>
[bok_record:protected] =>
[authors:protected] =>
[organizations:protected] =>
[collections:protected] =>
[categories:protected] => Array
(
[12] => Category Object
(
[languages:protected] =>
[bok_resources:protected] =>
[bok_topics:protected] =>
[bok_keywords:protected] =>
[id:protected] => 12
[type:protected] => category
[parent:protected] => 7
[label:protected] => Crushed/Struck By
[alreadyInSave:protected] =>
[alreadyInValidation:protected] =>
[validationFailures:protected] => Array
(
)
[_new:BaseObject:private] =>
[_deleted:BaseObject:private] =>
[modifiedColumns:protected] => Array
(
)
)
[47] => Category Object
(
[languages:protected] =>
[bok_resources:protected] =>
[bok_topics:protected] =>
[bok_keywords:protected] =>
[id:protected] => 47
[type:protected] => category
[parent:protected] => 2
[label:protected] => Bricklayer
[alreadyInSave:protected] =>
[alreadyInValidation:protected] =>
[validationFailures:protected] => Array
(
)
[_new:BaseObject:private] =>
[_deleted:BaseObject:private] =>
[modifiedColumns:protected] => Array
(
)
)
[49] => Category Object
(
[languages:protected] =>
[bok_resources:protected] =>
[bok_topics:protected] =>
[bok_keywords:protected] =>
[id:protected] => 49
[type:protected] => category
[parent:protected] => 2
[label:protected] => Carpenter
[alreadyInSave:protected] =>
[alreadyInValidation:protected] =>
[validationFailures:protected] => Array
(
)
[_new:BaseObject:private] =>
[_deleted:BaseObject:private] =>
[modifiedColumns:protected] => Array
(
)
)
[51] => Category Object
(
[languages:protected] =>
[bok_resources:protected] =>
[bok_topics:protected] =>
[bok_keywords:protected] =>
[id:protected] => 51
[type:protected] => category
[parent:protected] => 2
[label:protected] => Cement Mason
[alreadyInSave:protected] =>
[alreadyInValidation:protected] =>
[validationFailures:protected] => Array
(
)
[_new:BaseObject:private] =>
[_deleted:BaseObject:private] =>
[modifiedColumns:protected] => Array
(
)
)
[55] => Category Object
(
[languages:protected] =>
[bok_resources:protected] =>
[bok_topics:protected] =>
[bok_keywords:protected] =>
[id:protected] => 55
[type:protected] => category
[parent:protected] => 2
[label:protected] => Electrical Worker
[alreadyInSave:protected] =>
[alreadyInValidation:protected] =>
[validationFailures:protected] => Array
(
)
[_new:BaseObject:private] =>
[_deleted:BaseObject:private] =>
[modifiedColumns:protected] => Array
(
)
)
[64] => Category Object
(
[languages:protected] =>
[bok_resources:protected] =>
[bok_topics:protected] =>
[bok_keywords:protected] =>
[id:protected] => 64
[type:protected] => category
[parent:protected] => 2
[label:protected] => Laborer
[alreadyInSave:protected] =>
[alreadyInValidation:protected] =>
[validationFailures:protected] => Array
(
)
[_new:BaseObject:private] =>
[_deleted:BaseObject:private] =>
[modifiedColumns:protected] => Array
(
)
)
[68] => Category Object
(
[languages:protected] =>
[bok_resources:protected] =>
[bok_topics:protected] =>
[bok_keywords:protected] =>
[id:protected] => 68
[type:protected] => category
[parent:protected] => 2
[label:protected] => Maintenance Worker
[alreadyInSave:protected] =>
[alreadyInValidation:protected] =>
[validationFailures:protected] => Array
(
)
[_new:BaseObject:private] =>
[_deleted:BaseObject:private] =>
[modifiedColumns:protected] => Array
(
)
)
[71] => Category Object
(
[languages:protected] =>
[bok_resources:protected] =>
[bok_topics:protected] =>
[bok_keywords:protected] =>
[id:protected] => 71
[type:protected] => category
[parent:protected] => 2
[label:protected] => Painter
[alreadyInSave:protected] =>
[alreadyInValidation:protected] =>
[validationFailures:protected] => Array
(
)
[_new:BaseObject:private] =>
[_deleted:BaseObject:private] =>
[modifiedColumns:protected] => Array
(
)
)
[75] => Category Object
(
[languages:protected] =>
[bok_resources:protected] =>
[bok_topics:protected] =>
[bok_keywords:protected] =>
[id:protected] => 75
[type:protected] => category
[parent:protected] => 2
[label:protected] => Plasterer
[alreadyInSave:protected] =>
[alreadyInValidation:protected] =>
[validationFailures:protected] => Array
(
)
[_new:BaseObject:private] =>
[_deleted:BaseObject:private] =>
[modifiedColumns:protected] => Array
(
)
)
[78] => Category Object
(
[languages:protected] =>
[bok_resources:protected] =>
[bok_topics:protected] =>
[bok_keywords:protected] =>
[id:protected] => 78
[type:protected] => category
[parent:protected] => 2
[label:protected] => Roofer/Waterproofer
[alreadyInSave:protected] =>
[alreadyInValidation:protected] =>
[validationFailures:protected] => Array
(
)
[_new:BaseObject:private] =>
[_deleted:BaseObject:private] =>
[modifiedColumns:protected] => Array
(
)
)
[79] => Category Object
(
[languages:protected] =>
[bok_resources:protected] =>
[bok_topics:protected] =>
[bok_keywords:protected] =>
[id:protected] => 79
[type:protected] => category
[parent:protected] => 2
[label:protected] => Scaffold Erector
[alreadyInSave:protected] =>
[alreadyInValidation:protected] =>
[validationFailures:protected] => Array
(
)
[_new:BaseObject:private] =>
[_deleted:BaseObject:private] =>
[modifiedColumns:protected] => Array
(
)
)
[82] => Category Object
(
[languages:protected] =>
[bok_resources:protected] =>
[bok_topics:protected] =>
[bok_keywords:protected] =>
[id:protected] => 82
[type:protected] => category
[parent:protected] => 2
[label:protected] => Stonemason
[alreadyInSave:protected] =>
[alreadyInValidation:protected] =>
[validationFailures:protected] => Array
(
)
[_new:BaseObject:private] =>
[_deleted:BaseObject:private] =>
[modifiedColumns:protected] => Array
(
)
)
[62] => Category Object
(
[languages:protected] =>
[bok_resources:protected] =>
[bok_topics:protected] =>
[bok_keywords:protected] =>
[id:protected] => 62
[type:protected] => category
[parent:protected] => 2
[label:protected] => Structural Ironworker
[alreadyInSave:protected] =>
[alreadyInValidation:protected] =>
[validationFailures:protected] => Array
(
)
[_new:BaseObject:private] =>
[_deleted:BaseObject:private] =>
[modifiedColumns:protected] => Array
(
)
)
[86] => Category Object
(
[languages:protected] =>
[bok_resources:protected] =>
[bok_topics:protected] =>
[bok_keywords:protected] =>
[id:protected] => 86
[type:protected] => category
[parent:protected] => 2
[label:protected] => Welder
[alreadyInSave:protected] =>
[alreadyInValidation:protected] =>
[validationFailures:protected] => Array
(
)
[_new:BaseObject:private] =>
[_deleted:BaseObject:private] =>
[modifiedColumns:protected] => Array
(
)
)
[87] => Category Object
(
[languages:protected] =>
[bok_resources:protected] =>
[bok_topics:protected] =>
[bok_keywords:protected] =>
[id:protected] => 87
[type:protected] => category
[parent:protected] => 3
[label:protected] => Commercial & Institutional
[alreadyInSave:protected] =>
[alreadyInValidation:protected] =>
[validationFailures:protected] => Array
(
)
[_new:BaseObject:private] =>
[_deleted:BaseObject:private] =>
[modifiedColumns:protected] => Array
(
)
)
[88] => Category Object
(
[languages:protected] =>
[bok_resources:protected] =>
[bok_topics:protected] =>
[bok_keywords:protected] =>
[id:protected] => 88
[type:protected] => category
[parent:protected] => 3
[label:protected] => Demolition
[alreadyInSave:protected] =>
[alreadyInValidation:protected] =>
[validationFailures:protected] => Array
(
)
[_new:BaseObject:private] =>
[_deleted:BaseObject:private] =>
[modifiedColumns:protected] => Array
(
)
)
[89] => Category Object
(
[languages:protected] =>
[bok_resources:protected] =>
[bok_topics:protected] =>
[bok_keywords:protected] =>
[id:protected] => 89
[type:protected] => category
[parent:protected] => 3
[label:protected] => Disasters
[alreadyInSave:protected] =>
[alreadyInValidation:protected] =>
[validationFailures:protected] => Array
(
)
[_new:BaseObject:private] =>
[_deleted:BaseObject:private] =>
[modifiedColumns:protected] => Array
(
)
)
[91] => Category Object
(
[languages:protected] =>
[bok_resources:protected] =>
[bok_topics:protected] =>
[bok_keywords:protected] =>
[id:protected] => 91
[type:protected] => category
[parent:protected] => 3
[label:protected] => Heavy & Highway
[alreadyInSave:protected] =>
[alreadyInValidation:protected] =>
[validationFailures:protected] => Array
(
)
[_new:BaseObject:private] =>
[_deleted:BaseObject:private] =>
[modifiedColumns:protected] => Array
(
)
)
[90] => Category Object
(
[languages:protected] =>
[bok_resources:protected] =>
[bok_topics:protected] =>
[bok_keywords:protected] =>
[id:protected] => 90
[type:protected] => category
[parent:protected] => 3
[label:protected] => Industrial
[alreadyInSave:protected] =>
[alreadyInValidation:protected] =>
[validationFailures:protected] => Array
(
)
[_new:BaseObject:private] =>
[_deleted:BaseObject:private] =>
[modifiedColumns:protected] => Array
(
)
)
[92] => Category Object
(
[languages:protected] =>
[bok_resources:protected] =>
[bok_topics:protected] =>
[bok_keywords:protected] =>
[id:protected] => 92
[type:protected] => category
[parent:protected] => 3
[label:protected] => LEED/Green Construction
[alreadyInSave:protected] =>
[alreadyInValidation:protected] =>
[validationFailures:protected] => Array
(
)
[_new:BaseObject:private] =>
[_deleted:BaseObject:private] =>
[modifiedColumns:protected] => Array
(
)
)
[93] => Category Object
(
[languages:protected] =>
[bok_resources:protected] =>
[bok_topics:protected] =>
[bok_keywords:protected] =>
[id:protected] => 93
[type:protected] => category
[parent:protected] => 3
[label:protected] => Renovations
[alreadyInSave:protected] =>
[alreadyInValidation:protected] =>
[validationFailures:protected] => Array
(
)
[_new:BaseObject:private] =>
[_deleted:BaseObject:private] =>
[modifiedColumns:protected] => Array
(
)
)
[94] => Category Object
(
[languages:protected] =>
[bok_resources:protected] =>
[bok_topics:protected] =>
[bok_keywords:protected] =>
[id:protected] => 94
[type:protected] => category
[parent:protected] => 3
[label:protected] => Residential
[alreadyInSave:protected] =>
[alreadyInValidation:protected] =>
[validationFailures:protected] => Array
(
)
[_new:BaseObject:private] =>
[_deleted:BaseObject:private] =>
[modifiedColumns:protected] => Array
(
)
)
[95] => Category Object
(
[languages:protected] =>
[bok_resources:protected] =>
[bok_topics:protected] =>
[bok_keywords:protected] =>
[id:protected] => 95
[type:protected] => category
[parent:protected] => 3
[label:protected] => Underground
[alreadyInSave:protected] =>
[alreadyInValidation:protected] =>
[validationFailures:protected] => Array
(
)
[_new:BaseObject:private] =>
[_deleted:BaseObject:private] =>
[modifiedColumns:protected] => Array
(
)
)
[100] => Category Object
(
[languages:protected] =>
[bok_resources:protected] =>
[bok_topics:protected] =>
[bok_keywords:protected] =>
[id:protected] => 100
[type:protected] => category
[parent:protected] => 6
[label:protected] => Toolbox Talks
[alreadyInSave:protected] =>
[alreadyInValidation:protected] =>
[validationFailures:protected] => Array
(
)
[_new:BaseObject:private] =>
[_deleted:BaseObject:private] =>
[modifiedColumns:protected] => Array
(
)
)
)
[categories_initialized:protected] => 1
[mapped_items:protected] =>
[content:protected] =>
[files:protected] =>
[language:protected] => Language Object
(
[id:protected] => 1
[code:protected] => en
[name:protected] => English
[alreadyInSave:protected] =>
[alreadyInValidation:protected] =>
[validationFailures:protected] => Array
(
)
[_new:BaseObject:private] =>
[_deleted:BaseObject:private] =>
[modifiedColumns:protected] => Array
(
)
)
[old_record:protected] =>
[id:protected] => 4431
[old_id:protected] =>
[elcosh_id:protected] => d001661
[type:protected] => document
[display_type:protected] => HTML only (and links)
[user_id:protected] => 0
[language_id:protected] => 1
[tagging_id:protected] => Mike Aguilar
[priority_id:protected] => 1
[title:protected] => Toolbox Talk: Challenges Preventing Falling Objects
[total_pages:protected] => 0
[billed_pages:protected] => 0
[publication_number:protected] =>
[part_of:protected] =>
[keywords:protected] => dropped objects, falling objects, struck by incidents, struck by fatalities
[comments:protected] =>
[summary:protected] => The CPWR Toolbox Talk on Challenges Preventing Falling Objects addresses the hazards of being struck by falling objects on the job site. The resource includes a brief example, steps to prevent a related injury, and questions for discussion. It includes a graphic that illustrates a group workers observing a scaffold free of debris during high winds, which can be posted in a central location as a reminder of steps to work safely.
Available in English and Spanish.
[transition_comments:protected] =>
[external_link:protected] =>
[consol_link:protected] =>
[more_like_this:protected] => d001234,d001238,d001244,d001251,d001253,d001260,d001268,d001278
[permission_given_by:protected] =>
[published:protected] => T
[billable:protected] => F
[img_name:protected] =>
[img_ext:protected] =>
[img_width:protected] =>
[img_height:protected] =>
[img_credit:protected] =>
[img_practice:protected] =>
[vid_source_id:protected] =>
[vid_running_time:protected] =>
[vid_intended_audience:protected] =>
[vid_acquisition_info:protected] =>
[vid_cost:protected] =>
[vid_producer:protected] =>
[vid_filename:protected] =>
[vid_filename_downloadable:protected] =>
[date_summary:protected] =>
[date_permission_requested:protected] =>
[date_permission_received:protected] =>
[date_review_needed:protected] =>
[date_received:protected] => 06/10/22
[date_completed:protected] => 06/10/22
[date_billed:protected] =>
[date_modified:protected] => 05/22/23
[collBokExports:protected] =>
[lastBokExportCriteria:BaseElcoshItem:private] =>
[alreadyInSave:protected] =>
[alreadyInValidation:protected] =>
[validationFailures:protected] => Array
(
)
[_new:BaseObject:private] =>
[_deleted:BaseObject:private] =>
[modifiedColumns:protected] => Array
(
)
)
)
[2] => Search_Result Object
(
[title] => Toolbox Talk: Tower Crane Safety
[image] => /record/images/notavailable-p.png
[blurb] => The CPWR Toolbox Talk on Tower Crane Safety addresses the potential hazards of Tower Cranes and the importance of following procedure before and durin...
[category] => Array
(
[0] => 11
[1] => 12
[2] => 18
[3] => 70
[4] => 87
[5] => 88
[6] => 91
[7] => 90
[8] => 92
[9] => 100
)
[labels] => Array
(
[0] => Cranes & Hoists
[1] => Work Environment
[2] => Hazards
[3] => Crushed/Struck By
[6] => Motor Vehicles/Heavy Equipment
[9] => Operating Engineer
[10] => Trades
[11] => Commercial & Institutional
[12] => Jobsites
[13] => Demolition
[15] => Heavy & Highway
[17] => Industrial
[19] => LEED/Green Construction
[21] => Toolbox Talks
[22] => Documents
[23] => Media & Documents
)
[type] => Toolbox Talks
[sub_category] =>
[url] => /document/4427/d001657/Toolbox%2BTalk%253A%2BTower%2BCrane%2BSafety.html
[item:protected] => DocumentRecord Object
(
[records:protected] => Array
(
)
[recordId:protected] =>
[searchWordClass:protected] =>
[searchWordPeerClass:protected] =>
[bok_record:protected] =>
[authors:protected] =>
[organizations:protected] =>
[collections:protected] =>
[categories:protected] => Array
(
[11] => Category Object
(
[languages:protected] =>
[bok_resources:protected] =>
[bok_topics:protected] =>
[bok_keywords:protected] =>
[id:protected] => 11
[type:protected] => category
[parent:protected] => 7
[label:protected] => Cranes & Hoists
[alreadyInSave:protected] =>
[alreadyInValidation:protected] =>
[validationFailures:protected] => Array
(
)
[_new:BaseObject:private] =>
[_deleted:BaseObject:private] =>
[modifiedColumns:protected] => Array
(
)
)
[12] => Category Object
(
[languages:protected] =>
[bok_resources:protected] =>
[bok_topics:protected] =>
[bok_keywords:protected] =>
[id:protected] => 12
[type:protected] => category
[parent:protected] => 7
[label:protected] => Crushed/Struck By
[alreadyInSave:protected] =>
[alreadyInValidation:protected] =>
[validationFailures:protected] => Array
(
)
[_new:BaseObject:private] =>
[_deleted:BaseObject:private] =>
[modifiedColumns:protected] => Array
(
)
)
[18] => Category Object
(
[languages:protected] =>
[bok_resources:protected] =>
[bok_topics:protected] =>
[bok_keywords:protected] =>
[id:protected] => 18
[type:protected] => category
[parent:protected] => 7
[label:protected] => Motor Vehicles/Heavy Equipment
[alreadyInSave:protected] =>
[alreadyInValidation:protected] =>
[validationFailures:protected] => Array
(
)
[_new:BaseObject:private] =>
[_deleted:BaseObject:private] =>
[modifiedColumns:protected] => Array
(
)
)
[70] => Category Object
(
[languages:protected] =>
[bok_resources:protected] =>
[bok_topics:protected] =>
[bok_keywords:protected] =>
[id:protected] => 70
[type:protected] => category
[parent:protected] => 2
[label:protected] => Operating Engineer
[alreadyInSave:protected] =>
[alreadyInValidation:protected] =>
[validationFailures:protected] => Array
(
)
[_new:BaseObject:private] =>
[_deleted:BaseObject:private] =>
[modifiedColumns:protected] => Array
(
)
)
[87] => Category Object
(
[languages:protected] =>
[bok_resources:protected] =>
[bok_topics:protected] =>
[bok_keywords:protected] =>
[id:protected] => 87
[type:protected] => category
[parent:protected] => 3
[label:protected] => Commercial & Institutional
[alreadyInSave:protected] =>
[alreadyInValidation:protected] =>
[validationFailures:protected] => Array
(
)
[_new:BaseObject:private] =>
[_deleted:BaseObject:private] =>
[modifiedColumns:protected] => Array
(
)
)
[88] => Category Object
(
[languages:protected] =>
[bok_resources:protected] =>
[bok_topics:protected] =>
[bok_keywords:protected] =>
[id:protected] => 88
[type:protected] => category
[parent:protected] => 3
[label:protected] => Demolition
[alreadyInSave:protected] =>
[alreadyInValidation:protected] =>
[validationFailures:protected] => Array
(
)
[_new:BaseObject:private] =>
[_deleted:BaseObject:private] =>
[modifiedColumns:protected] => Array
(
)
)
[91] => Category Object
(
[languages:protected] =>
[bok_resources:protected] =>
[bok_topics:protected] =>
[bok_keywords:protected] =>
[id:protected] => 91
[type:protected] => category
[parent:protected] => 3
[label:protected] => Heavy & Highway
[alreadyInSave:protected] =>
[alreadyInValidation:protected] =>
[validationFailures:protected] => Array
(
)
[_new:BaseObject:private] =>
[_deleted:BaseObject:private] =>
[modifiedColumns:protected] => Array
(
)
)
[90] => Category Object
(
[languages:protected] =>
[bok_resources:protected] =>
[bok_topics:protected] =>
[bok_keywords:protected] =>
[id:protected] => 90
[type:protected] => category
[parent:protected] => 3
[label:protected] => Industrial
[alreadyInSave:protected] =>
[alreadyInValidation:protected] =>
[validationFailures:protected] => Array
(
)
[_new:BaseObject:private] =>
[_deleted:BaseObject:private] =>
[modifiedColumns:protected] => Array
(
)
)
[92] => Category Object
(
[languages:protected] =>
[bok_resources:protected] =>
[bok_topics:protected] =>
[bok_keywords:protected] =>
[id:protected] => 92
[type:protected] => category
[parent:protected] => 3
[label:protected] => LEED/Green Construction
[alreadyInSave:protected] =>
[alreadyInValidation:protected] =>
[validationFailures:protected] => Array
(
)
[_new:BaseObject:private] =>
[_deleted:BaseObject:private] =>
[modifiedColumns:protected] => Array
(
)
)
[100] => Category Object
(
[languages:protected] =>
[bok_resources:protected] =>
[bok_topics:protected] =>
[bok_keywords:protected] =>
[id:protected] => 100
[type:protected] => category
[parent:protected] => 6
[label:protected] => Toolbox Talks
[alreadyInSave:protected] =>
[alreadyInValidation:protected] =>
[validationFailures:protected] => Array
(
)
[_new:BaseObject:private] =>
[_deleted:BaseObject:private] =>
[modifiedColumns:protected] => Array
(
)
)
)
[categories_initialized:protected] => 1
[mapped_items:protected] =>
[content:protected] =>
[files:protected] =>
[language:protected] => Language Object
(
[id:protected] => 1
[code:protected] => en
[name:protected] => English
[alreadyInSave:protected] =>
[alreadyInValidation:protected] =>
[validationFailures:protected] => Array
(
)
[_new:BaseObject:private] =>
[_deleted:BaseObject:private] =>
[modifiedColumns:protected] => Array
(
)
)
[old_record:protected] =>
[id:protected] => 4427
[old_id:protected] =>
[elcosh_id:protected] => d001657
[type:protected] => document
[display_type:protected] => HTML only (and links)
[user_id:protected] => 0
[language_id:protected] => 1
[tagging_id:protected] => Mike Aguilar
[priority_id:protected] => 1
[title:protected] => Toolbox Talk: Tower Crane Safety
[total_pages:protected] => 0
[billed_pages:protected] => 0
[publication_number:protected] =>
[part_of:protected] =>
[keywords:protected] => Tower Crane, Crane, Stability, Tipping, Lift Zone Safety, Lift, Zone, Safety, Struck by
[comments:protected] =>
[summary:protected] => The CPWR Toolbox Talk on Tower Crane Safety addresses the potential hazards of Tower Cranes and the importance of following procedure before and during Tower Crane operation. The resource includes a brief example, steps to prevent a related injury, and questions for discussion. It includes a graphic that illustrates a worker inspecting a Tower Crane before operation, which can be posted in a central location as a reminder of steps to work safely.
Available in English and Spanish.
[transition_comments:protected] =>
[external_link:protected] =>
[consol_link:protected] =>
[more_like_this:protected] => d001234,d001238,d001250,d001251,d001253,d001258,d001262,d001273
[permission_given_by:protected] =>
[published:protected] => T
[billable:protected] => F
[img_name:protected] =>
[img_ext:protected] => jpg
[img_width:protected] =>
[img_height:protected] =>
[img_credit:protected] =>
[img_practice:protected] =>
[vid_source_id:protected] =>
[vid_running_time:protected] =>
[vid_intended_audience:protected] =>
[vid_acquisition_info:protected] =>
[vid_cost:protected] =>
[vid_producer:protected] =>
[vid_filename:protected] =>
[vid_filename_downloadable:protected] =>
[date_summary:protected] =>
[date_permission_requested:protected] =>
[date_permission_received:protected] =>
[date_review_needed:protected] =>
[date_received:protected] => 12/23/21
[date_completed:protected] => 12/23/21
[date_billed:protected] =>
[date_modified:protected] => 05/19/23
[collBokExports:protected] =>
[lastBokExportCriteria:BaseElcoshItem:private] =>
[alreadyInSave:protected] =>
[alreadyInValidation:protected] =>
[validationFailures:protected] => Array
(
)
[_new:BaseObject:private] =>
[_deleted:BaseObject:private] =>
[modifiedColumns:protected] => Array
(
)
)
)
[3] => Search_Result Object
(
[title] => Toolbox Talk: Work Zone Safety: Working Around Vehicles
[image] => /record/images/notavailable-p.png
[blurb] => The CPWR Toolbox Talk on Working Around Vehicles in the Work Zone addresses methods to avoid being struck-by a vehicle on a construction site. The res...
[category] => Array
(
[0] => 12
[1] => 18
[2] => 52
[3] => 57
[4] => 70
[5] => 85
[6] => 87
[7] => 88
[8] => 89
[9] => 91
[10] => 90
[11] => 92
[12] => 93
[13] => 94
[14] => 95
[15] => 100
)
[labels] => Array
(
[0] => Crushed/Struck By
[1] => Work Environment
[2] => Hazards
[3] => Motor Vehicles/Heavy Equipment
[6] => Commercial Diver
[7] => Trades
[8] => Flagger
[10] => Operating Engineer
[12] => Truck Driver
[14] => Commercial & Institutional
[15] => Jobsites
[16] => Demolition
[18] => Disasters
[20] => Heavy & Highway
[22] => Industrial
[24] => LEED/Green Construction
[26] => Renovations
[28] => Residential
[30] => Underground
[32] => Toolbox Talks
[33] => Documents
[34] => Media & Documents
)
[type] => Toolbox Talks
[sub_category] =>
[url] => /document/4428/d001658/Toolbox%2BTalk%253A%2BWork%2BZone%2BSafety%253A%2BWorking%2BAround%2BVehicles.html
[item:protected] => DocumentRecord Object
(
[records:protected] => Array
(
)
[recordId:protected] =>
[searchWordClass:protected] =>
[searchWordPeerClass:protected] =>
[bok_record:protected] =>
[authors:protected] =>
[organizations:protected] =>
[collections:protected] =>
[categories:protected] => Array
(
[12] => Category Object
(
[languages:protected] =>
[bok_resources:protected] =>
[bok_topics:protected] =>
[bok_keywords:protected] =>
[id:protected] => 12
[type:protected] => category
[parent:protected] => 7
[label:protected] => Crushed/Struck By
[alreadyInSave:protected] =>
[alreadyInValidation:protected] =>
[validationFailures:protected] => Array
(
)
[_new:BaseObject:private] =>
[_deleted:BaseObject:private] =>
[modifiedColumns:protected] => Array
(
)
)
[18] => Category Object
(
[languages:protected] =>
[bok_resources:protected] =>
[bok_topics:protected] =>
[bok_keywords:protected] =>
[id:protected] => 18
[type:protected] => category
[parent:protected] => 7
[label:protected] => Motor Vehicles/Heavy Equipment
[alreadyInSave:protected] =>
[alreadyInValidation:protected] =>
[validationFailures:protected] => Array
(
)
[_new:BaseObject:private] =>
[_deleted:BaseObject:private] =>
[modifiedColumns:protected] => Array
(
)
)
[52] => Category Object
(
[languages:protected] =>
[bok_resources:protected] =>
[bok_topics:protected] =>
[bok_keywords:protected] =>
[id:protected] => 52
[type:protected] => category
[parent:protected] => 2
[label:protected] => Commercial Diver
[alreadyInSave:protected] =>
[alreadyInValidation:protected] =>
[validationFailures:protected] => Array
(
)
[_new:BaseObject:private] =>
[_deleted:BaseObject:private] =>
[modifiedColumns:protected] => Array
(
)
)
[57] => Category Object
(
[languages:protected] =>
[bok_resources:protected] =>
[bok_topics:protected] =>
[bok_keywords:protected] =>
[id:protected] => 57
[type:protected] => category
[parent:protected] => 2
[label:protected] => Flagger
[alreadyInSave:protected] =>
[alreadyInValidation:protected] =>
[validationFailures:protected] => Array
(
)
[_new:BaseObject:private] =>
[_deleted:BaseObject:private] =>
[modifiedColumns:protected] => Array
(
)
)
[70] => Category Object
(
[languages:protected] =>
[bok_resources:protected] =>
[bok_topics:protected] =>
[bok_keywords:protected] =>
[id:protected] => 70
[type:protected] => category
[parent:protected] => 2
[label:protected] => Operating Engineer
[alreadyInSave:protected] =>
[alreadyInValidation:protected] =>
[validationFailures:protected] => Array
(
)
[_new:BaseObject:private] =>
[_deleted:BaseObject:private] =>
[modifiedColumns:protected] => Array
(
)
)
[85] => Category Object
(
[languages:protected] =>
[bok_resources:protected] =>
[bok_topics:protected] =>
[bok_keywords:protected] =>
[id:protected] => 85
[type:protected] => category
[parent:protected] => 2
[label:protected] => Truck Driver
[alreadyInSave:protected] =>
[alreadyInValidation:protected] =>
[validationFailures:protected] => Array
(
)
[_new:BaseObject:private] =>
[_deleted:BaseObject:private] =>
[modifiedColumns:protected] => Array
(
)
)
[87] => Category Object
(
[languages:protected] =>
[bok_resources:protected] =>
[bok_topics:protected] =>
[bok_keywords:protected] =>
[id:protected] => 87
[type:protected] => category
[parent:protected] => 3
[label:protected] => Commercial & Institutional
[alreadyInSave:protected] =>
[alreadyInValidation:protected] =>
[validationFailures:protected] => Array
(
)
[_new:BaseObject:private] =>
[_deleted:BaseObject:private] =>
[modifiedColumns:protected] => Array
(
)
)
[88] => Category Object
(
[languages:protected] =>
[bok_resources:protected] =>
[bok_topics:protected] =>
[bok_keywords:protected] =>
[id:protected] => 88
[type:protected] => category
[parent:protected] => 3
[label:protected] => Demolition
[alreadyInSave:protected] =>
[alreadyInValidation:protected] =>
[validationFailures:protected] => Array
(
)
[_new:BaseObject:private] =>
[_deleted:BaseObject:private] =>
[modifiedColumns:protected] => Array
(
)
)
[89] => Category Object
(
[languages:protected] =>
[bok_resources:protected] =>
[bok_topics:protected] =>
[bok_keywords:protected] =>
[id:protected] => 89
[type:protected] => category
[parent:protected] => 3
[label:protected] => Disasters
[alreadyInSave:protected] =>
[alreadyInValidation:protected] =>
[validationFailures:protected] => Array
(
)
[_new:BaseObject:private] =>
[_deleted:BaseObject:private] =>
[modifiedColumns:protected] => Array
(
)
)
[91] => Category Object
(
[languages:protected] =>
[bok_resources:protected] =>
[bok_topics:protected] =>
[bok_keywords:protected] =>
[id:protected] => 91
[type:protected] => category
[parent:protected] => 3
[label:protected] => Heavy & Highway
[alreadyInSave:protected] =>
[alreadyInValidation:protected] =>
[validationFailures:protected] => Array
(
)
[_new:BaseObject:private] =>
[_deleted:BaseObject:private] =>
[modifiedColumns:protected] => Array
(
)
)
[90] => Category Object
(
[languages:protected] =>
[bok_resources:protected] =>
[bok_topics:protected] =>
[bok_keywords:protected] =>
[id:protected] => 90
[type:protected] => category
[parent:protected] => 3
[label:protected] => Industrial
[alreadyInSave:protected] =>
[alreadyInValidation:protected] =>
[validationFailures:protected] => Array
(
)
[_new:BaseObject:private] =>
[_deleted:BaseObject:private] =>
[modifiedColumns:protected] => Array
(
)
)
[92] => Category Object
(
[languages:protected] =>
[bok_resources:protected] =>
[bok_topics:protected] =>
[bok_keywords:protected] =>
[id:protected] => 92
[type:protected] => category
[parent:protected] => 3
[label:protected] => LEED/Green Construction
[alreadyInSave:protected] =>
[alreadyInValidation:protected] =>
[validationFailures:protected] => Array
(
)
[_new:BaseObject:private] =>
[_deleted:BaseObject:private] =>
[modifiedColumns:protected] => Array
(
)
)
[93] => Category Object
(
[languages:protected] =>
[bok_resources:protected] =>
[bok_topics:protected] =>
[bok_keywords:protected] =>
[id:protected] => 93
[type:protected] => category
[parent:protected] => 3
[label:protected] => Renovations
[alreadyInSave:protected] =>
[alreadyInValidation:protected] =>
[validationFailures:protected] => Array
(
)
[_new:BaseObject:private] =>
[_deleted:BaseObject:private] =>
[modifiedColumns:protected] => Array
(
)
)
[94] => Category Object
(
[languages:protected] =>
[bok_resources:protected] =>
[bok_topics:protected] =>
[bok_keywords:protected] =>
[id:protected] => 94
[type:protected] => category
[parent:protected] => 3
[label:protected] => Residential
[alreadyInSave:protected] =>
[alreadyInValidation:protected] =>
[validationFailures:protected] => Array
(
)
[_new:BaseObject:private] =>
[_deleted:BaseObject:private] =>
[modifiedColumns:protected] => Array
(
)
)
[95] => Category Object
(
[languages:protected] =>
[bok_resources:protected] =>
[bok_topics:protected] =>
[bok_keywords:protected] =>
[id:protected] => 95
[type:protected] => category
[parent:protected] => 3
[label:protected] => Underground
[alreadyInSave:protected] =>
[alreadyInValidation:protected] =>
[validationFailures:protected] => Array
(
)
[_new:BaseObject:private] =>
[_deleted:BaseObject:private] =>
[modifiedColumns:protected] => Array
(
)
)
[100] => Category Object
(
[languages:protected] =>
[bok_resources:protected] =>
[bok_topics:protected] =>
[bok_keywords:protected] =>
[id:protected] => 100
[type:protected] => category
[parent:protected] => 6
[label:protected] => Toolbox Talks
[alreadyInSave:protected] =>
[alreadyInValidation:protected] =>
[validationFailures:protected] => Array
(
)
[_new:BaseObject:private] =>
[_deleted:BaseObject:private] =>
[modifiedColumns:protected] => Array
(
)
)
)
[categories_initialized:protected] => 1
[mapped_items:protected] =>
[content:protected] =>
[files:protected] =>
[language:protected] => Language Object
(
[id:protected] => 1
[code:protected] => en
[name:protected] => English
[alreadyInSave:protected] =>
[alreadyInValidation:protected] =>
[validationFailures:protected] => Array
(
)
[_new:BaseObject:private] =>
[_deleted:BaseObject:private] =>
[modifiedColumns:protected] => Array
(
)
)
[old_record:protected] =>
[id:protected] => 4428
[old_id:protected] =>
[elcosh_id:protected] => d001658
[type:protected] => document
[display_type:protected] => HTML only (and links)
[user_id:protected] => 0
[language_id:protected] => 1
[tagging_id:protected] => Daniela Caceres
[priority_id:protected] => 1
[title:protected] => Toolbox Talk: Work Zone Safety: Working Around Vehicles
[total_pages:protected] => 0
[billed_pages:protected] => 0
[publication_number:protected] =>
[part_of:protected] =>
[keywords:protected] => Struck, Struck by, Vehicle, Work Zone Safety, Truck, Operator, Driver, Mobile Equipment
[comments:protected] =>
[summary:protected] => The CPWR Toolbox Talk on Working Around Vehicles in the Work Zone addresses methods to avoid being struck-by a vehicle on a construction site. The resource includes a case example, steps to prevent a related injury, and questions for discussion. It includes a graphic that illustrates the hazard, which can be posted in a central location as a reminder of steps to work safely. Available in English and Spanish.
[transition_comments:protected] =>
[external_link:protected] =>
[consol_link:protected] =>
[more_like_this:protected] => d001640
[permission_given_by:protected] =>
[published:protected] => T
[billable:protected] => F
[img_name:protected] =>
[img_ext:protected] =>
[img_width:protected] =>
[img_height:protected] =>
[img_credit:protected] =>
[img_practice:protected] =>
[vid_source_id:protected] =>
[vid_running_time:protected] =>
[vid_intended_audience:protected] =>
[vid_acquisition_info:protected] =>
[vid_cost:protected] =>
[vid_producer:protected] =>
[vid_filename:protected] =>
[vid_filename_downloadable:protected] =>
[date_summary:protected] =>
[date_permission_requested:protected] =>
[date_permission_received:protected] =>
[date_review_needed:protected] =>
[date_received:protected] => 12/23/21
[date_completed:protected] => 12/23/21
[date_billed:protected] =>
[date_modified:protected] => 05/19/23
[collBokExports:protected] =>
[lastBokExportCriteria:BaseElcoshItem:private] =>
[alreadyInSave:protected] =>
[alreadyInValidation:protected] =>
[validationFailures:protected] => Array
(
)
[_new:BaseObject:private] =>
[_deleted:BaseObject:private] =>
[modifiedColumns:protected] => Array
(
)
)
)
[4] => Search_Result Object
(
[title] => Construction Dive -- DeWalt's Jobsite Pro headphones recalled for fire hazards
[image] => /record/images/notavailable-p.png
[blurb] => A recall notice by the United States Consumer Product Safety Commission affects over 300,000 DeWalt Jobsite Pro Headphones. The recall is a result of...
[category] => Array
(
[0] => 16
[1] => 44
[2] => 45
[3] => 46
[4] => 47
[5] => 48
[6] => 49
[7] => 50
[8] => 51
[9] => 52
[10] => 53
[11] => 54
[12] => 55
[13] => 56
[14] => 57
[15] => 58
[16] => 59
[17] => 60
[18] => 61
[19] => 64
[20] => 65
[21] => 66
[22] => 67
[23] => 68
[24] => 69
[25] => 70
[26] => 71
[27] => 72
[28] => 73
[29] => 74
[30] => 75
[31] => 76
[32] => 77
[33] => 63
[34] => 78
[35] => 79
[36] => 80
[37] => 81
[38] => 82
[39] => 62
[40] => 83
[41] => 84
[42] => 85
[43] => 86
[44] => 87
[45] => 88
[46] => 89
[47] => 91
[48] => 90
[49] => 92
[50] => 93
[51] => 94
[52] => 95
)
[labels] => Array
(
[0] => Fire & Explosions
[1] => Work Environment
[2] => Hazards
[3] => Acoustical Ceiling Carpenter
[4] => Trades
[5] => Asbestos/Insulator
[7] => Boilermaker
[9] => Bricklayer
[11] => Cabinetmaker
[13] => Carpenter
[15] => Carpet Layer
[17] => Cement Mason
[19] => Commercial Diver
[21] => Concrete Polisher
[23] => Drywall Applicator Specialist
[25] => Electrical Worker
[27] => Elevator Constructor
[29] => Flagger
[31] => Glazier
[33] => Hazardous Waste Cleanup
[35] => HVAC
[37] => Interior Systems Carpenter
[39] => Laborer
[41] => Landscaper
[43] => Lather
[45] => Lead Abatement Worker
[47] => Maintenance Worker
[49] => Millwright
[51] => Operating Engineer
[53] => Painter
[55] => Paper Hanger
[57] => PCC/Restoration
[59] => Pile Driver
[61] => Plasterer
[63] => Plumber/Pipefitter
[65] => Refractory Worker
[67] => Reinforcing Ironworker
[69] => Roofer/Waterproofer
[71] => Scaffold Erector
[73] => Sheetmetal Worker
[75] => Sprinkler Fitter
[77] => Stonemason
[79] => Structural Ironworker
[81] => Terrazzo Worker
[83] => Tile Setter
[85] => Truck Driver
[87] => Welder
[89] => Commercial & Institutional
[90] => Jobsites
[91] => Demolition
[93] => Disasters
[95] => Heavy & Highway
[97] => Industrial
[99] => LEED/Green Construction
[101] => Renovations
[103] => Residential
[105] => Underground
)
[type] =>
[sub_category] =>
[url] => /document/4426/d001656/Construction%2BDive%2B--%2BDeWalt%2527s%2BJobsite%2BPro%2Bheadphones%2Brecalled%2Bfor%2Bfire%2Bhazards.html
[item:protected] => DocumentRecord Object
(
[records:protected] => Array
(
)
[recordId:protected] =>
[searchWordClass:protected] =>
[searchWordPeerClass:protected] =>
[bok_record:protected] =>
[authors:protected] =>
[organizations:protected] =>
[collections:protected] =>
[categories:protected] => Array
(
[16] => Category Object
(
[languages:protected] =>
[bok_resources:protected] =>
[bok_topics:protected] =>
[bok_keywords:protected] =>
[id:protected] => 16
[type:protected] => category
[parent:protected] => 7
[label:protected] => Fire & Explosions
[alreadyInSave:protected] =>
[alreadyInValidation:protected] =>
[validationFailures:protected] => Array
(
)
[_new:BaseObject:private] =>
[_deleted:BaseObject:private] =>
[modifiedColumns:protected] => Array
(
)
)
[44] => Category Object
(
[languages:protected] =>
[bok_resources:protected] =>
[bok_topics:protected] =>
[bok_keywords:protected] =>
[id:protected] => 44
[type:protected] => category
[parent:protected] => 2
[label:protected] => Acoustical Ceiling Carpenter
[alreadyInSave:protected] =>
[alreadyInValidation:protected] =>
[validationFailures:protected] => Array
(
)
[_new:BaseObject:private] =>
[_deleted:BaseObject:private] =>
[modifiedColumns:protected] => Array
(
)
)
[45] => Category Object
(
[languages:protected] =>
[bok_resources:protected] =>
[bok_topics:protected] =>
[bok_keywords:protected] =>
[id:protected] => 45
[type:protected] => category
[parent:protected] => 2
[label:protected] => Asbestos/Insulator
[alreadyInSave:protected] =>
[alreadyInValidation:protected] =>
[validationFailures:protected] => Array
(
)
[_new:BaseObject:private] =>
[_deleted:BaseObject:private] =>
[modifiedColumns:protected] => Array
(
)
)
[46] => Category Object
(
[languages:protected] =>
[bok_resources:protected] =>
[bok_topics:protected] =>
[bok_keywords:protected] =>
[id:protected] => 46
[type:protected] => category
[parent:protected] => 2
[label:protected] => Boilermaker
[alreadyInSave:protected] =>
[alreadyInValidation:protected] =>
[validationFailures:protected] => Array
(
)
[_new:BaseObject:private] =>
[_deleted:BaseObject:private] =>
[modifiedColumns:protected] => Array
(
)
)
[47] => Category Object
(
[languages:protected] =>
[bok_resources:protected] =>
[bok_topics:protected] =>
[bok_keywords:protected] =>
[id:protected] => 47
[type:protected] => category
[parent:protected] => 2
[label:protected] => Bricklayer
[alreadyInSave:protected] =>
[alreadyInValidation:protected] =>
[validationFailures:protected] => Array
(
)
[_new:BaseObject:private] =>
[_deleted:BaseObject:private] =>
[modifiedColumns:protected] => Array
(
)
)
[48] => Category Object
(
[languages:protected] =>
[bok_resources:protected] =>
[bok_topics:protected] =>
[bok_keywords:protected] =>
[id:protected] => 48
[type:protected] => category
[parent:protected] => 2
[label:protected] => Cabinetmaker
[alreadyInSave:protected] =>
[alreadyInValidation:protected] =>
[validationFailures:protected] => Array
(
)
[_new:BaseObject:private] =>
[_deleted:BaseObject:private] =>
[modifiedColumns:protected] => Array
(
)
)
[49] => Category Object
(
[languages:protected] =>
[bok_resources:protected] =>
[bok_topics:protected] =>
[bok_keywords:protected] =>
[id:protected] => 49
[type:protected] => category
[parent:protected] => 2
[label:protected] => Carpenter
[alreadyInSave:protected] =>
[alreadyInValidation:protected] =>
[validationFailures:protected] => Array
(
)
[_new:BaseObject:private] =>
[_deleted:BaseObject:private] =>
[modifiedColumns:protected] => Array
(
)
)
[50] => Category Object
(
[languages:protected] =>
[bok_resources:protected] =>
[bok_topics:protected] =>
[bok_keywords:protected] =>
[id:protected] => 50
[type:protected] => category
[parent:protected] => 2
[label:protected] => Carpet Layer
[alreadyInSave:protected] =>
[alreadyInValidation:protected] =>
[validationFailures:protected] => Array
(
)
[_new:BaseObject:private] =>
[_deleted:BaseObject:private] =>
[modifiedColumns:protected] => Array
(
)
)
[51] => Category Object
(
[languages:protected] =>
[bok_resources:protected] =>
[bok_topics:protected] =>
[bok_keywords:protected] =>
[id:protected] => 51
[type:protected] => category
[parent:protected] => 2
[label:protected] => Cement Mason
[alreadyInSave:protected] =>
[alreadyInValidation:protected] =>
[validationFailures:protected] => Array
(
)
[_new:BaseObject:private] =>
[_deleted:BaseObject:private] =>
[modifiedColumns:protected] => Array
(
)
)
[52] => Category Object
(
[languages:protected] =>
[bok_resources:protected] =>
[bok_topics:protected] =>
[bok_keywords:protected] =>
[id:protected] => 52
[type:protected] => category
[parent:protected] => 2
[label:protected] => Commercial Diver
[alreadyInSave:protected] =>
[alreadyInValidation:protected] =>
[validationFailures:protected] => Array
(
)
[_new:BaseObject:private] =>
[_deleted:BaseObject:private] =>
[modifiedColumns:protected] => Array
(
)
)
[53] => Category Object
(
[languages:protected] =>
[bok_resources:protected] =>
[bok_topics:protected] =>
[bok_keywords:protected] =>
[id:protected] => 53
[type:protected] => category
[parent:protected] => 2
[label:protected] => Concrete Polisher
[alreadyInSave:protected] =>
[alreadyInValidation:protected] =>
[validationFailures:protected] => Array
(
)
[_new:BaseObject:private] =>
[_deleted:BaseObject:private] =>
[modifiedColumns:protected] => Array
(
)
)
[54] => Category Object
(
[languages:protected] =>
[bok_resources:protected] =>
[bok_topics:protected] =>
[bok_keywords:protected] =>
[id:protected] => 54
[type:protected] => category
[parent:protected] => 2
[label:protected] => Drywall Applicator Specialist
[alreadyInSave:protected] =>
[alreadyInValidation:protected] =>
[validationFailures:protected] => Array
(
)
[_new:BaseObject:private] =>
[_deleted:BaseObject:private] =>
[modifiedColumns:protected] => Array
(
)
)
[55] => Category Object
(
[languages:protected] =>
[bok_resources:protected] =>
[bok_topics:protected] =>
[bok_keywords:protected] =>
[id:protected] => 55
[type:protected] => category
[parent:protected] => 2
[label:protected] => Electrical Worker
[alreadyInSave:protected] =>
[alreadyInValidation:protected] =>
[validationFailures:protected] => Array
(
)
[_new:BaseObject:private] =>
[_deleted:BaseObject:private] =>
[modifiedColumns:protected] => Array
(
)
)
[56] => Category Object
(
[languages:protected] =>
[bok_resources:protected] =>
[bok_topics:protected] =>
[bok_keywords:protected] =>
[id:protected] => 56
[type:protected] => category
[parent:protected] => 2
[label:protected] => Elevator Constructor
[alreadyInSave:protected] =>
[alreadyInValidation:protected] =>
[validationFailures:protected] => Array
(
)
[_new:BaseObject:private] =>
[_deleted:BaseObject:private] =>
[modifiedColumns:protected] => Array
(
)
)
[57] => Category Object
(
[languages:protected] =>
[bok_resources:protected] =>
[bok_topics:protected] =>
[bok_keywords:protected] =>
[id:protected] => 57
[type:protected] => category
[parent:protected] => 2
[label:protected] => Flagger
[alreadyInSave:protected] =>
[alreadyInValidation:protected] =>
[validationFailures:protected] => Array
(
)
[_new:BaseObject:private] =>
[_deleted:BaseObject:private] =>
[modifiedColumns:protected] => Array
(
)
)
[58] => Category Object
(
[languages:protected] =>
[bok_resources:protected] =>
[bok_topics:protected] =>
[bok_keywords:protected] =>
[id:protected] => 58
[type:protected] => category
[parent:protected] => 2
[label:protected] => Glazier
[alreadyInSave:protected] =>
[alreadyInValidation:protected] =>
[validationFailures:protected] => Array
(
)
[_new:BaseObject:private] =>
[_deleted:BaseObject:private] =>
[modifiedColumns:protected] => Array
(
)
)
[59] => Category Object
(
[languages:protected] =>
[bok_resources:protected] =>
[bok_topics:protected] =>
[bok_keywords:protected] =>
[id:protected] => 59
[type:protected] => category
[parent:protected] => 2
[label:protected] => Hazardous Waste Cleanup
[alreadyInSave:protected] =>
[alreadyInValidation:protected] =>
[validationFailures:protected] => Array
(
)
[_new:BaseObject:private] =>
[_deleted:BaseObject:private] =>
[modifiedColumns:protected] => Array
(
)
)
[60] => Category Object
(
[languages:protected] =>
[bok_resources:protected] =>
[bok_topics:protected] =>
[bok_keywords:protected] =>
[id:protected] => 60
[type:protected] => category
[parent:protected] => 2
[label:protected] => HVAC
[alreadyInSave:protected] =>
[alreadyInValidation:protected] =>
[validationFailures:protected] => Array
(
)
[_new:BaseObject:private] =>
[_deleted:BaseObject:private] =>
[modifiedColumns:protected] => Array
(
)
)
[61] => Category Object
(
[languages:protected] =>
[bok_resources:protected] =>
[bok_topics:protected] =>
[bok_keywords:protected] =>
[id:protected] => 61
[type:protected] => category
[parent:protected] => 2
[label:protected] => Interior Systems Carpenter
[alreadyInSave:protected] =>
[alreadyInValidation:protected] =>
[validationFailures:protected] => Array
(
)
[_new:BaseObject:private] =>
[_deleted:BaseObject:private] =>
[modifiedColumns:protected] => Array
(
)
)
[64] => Category Object
(
[languages:protected] =>
[bok_resources:protected] =>
[bok_topics:protected] =>
[bok_keywords:protected] =>
[id:protected] => 64
[type:protected] => category
[parent:protected] => 2
[label:protected] => Laborer
[alreadyInSave:protected] =>
[alreadyInValidation:protected] =>
[validationFailures:protected] => Array
(
)
[_new:BaseObject:private] =>
[_deleted:BaseObject:private] =>
[modifiedColumns:protected] => Array
(
)
)
[65] => Category Object
(
[languages:protected] =>
[bok_resources:protected] =>
[bok_topics:protected] =>
[bok_keywords:protected] =>
[id:protected] => 65
[type:protected] => category
[parent:protected] => 2
[label:protected] => Landscaper
[alreadyInSave:protected] =>
[alreadyInValidation:protected] =>
[validationFailures:protected] => Array
(
)
[_new:BaseObject:private] =>
[_deleted:BaseObject:private] =>
[modifiedColumns:protected] => Array
(
)
)
[66] => Category Object
(
[languages:protected] =>
[bok_resources:protected] =>
[bok_topics:protected] =>
[bok_keywords:protected] =>
[id:protected] => 66
[type:protected] => category
[parent:protected] => 2
[label:protected] => Lather
[alreadyInSave:protected] =>
[alreadyInValidation:protected] =>
[validationFailures:protected] => Array
(
)
[_new:BaseObject:private] =>
[_deleted:BaseObject:private] =>
[modifiedColumns:protected] => Array
(
)
)
[67] => Category Object
(
[languages:protected] =>
[bok_resources:protected] =>
[bok_topics:protected] =>
[bok_keywords:protected] =>
[id:protected] => 67
[type:protected] => category
[parent:protected] => 2
[label:protected] => Lead Abatement Worker
[alreadyInSave:protected] =>
[alreadyInValidation:protected] =>
[validationFailures:protected] => Array
(
)
[_new:BaseObject:private] =>
[_deleted:BaseObject:private] =>
[modifiedColumns:protected] => Array
(
)
)
[68] => Category Object
(
[languages:protected] =>
[bok_resources:protected] =>
[bok_topics:protected] =>
[bok_keywords:protected] =>
[id:protected] => 68
[type:protected] => category
[parent:protected] => 2
[label:protected] => Maintenance Worker
[alreadyInSave:protected] =>
[alreadyInValidation:protected] =>
[validationFailures:protected] => Array
(
)
[_new:BaseObject:private] =>
[_deleted:BaseObject:private] =>
[modifiedColumns:protected] => Array
(
)
)
[69] => Category Object
(
[languages:protected] =>
[bok_resources:protected] =>
[bok_topics:protected] =>
[bok_keywords:protected] =>
[id:protected] => 69
[type:protected] => category
[parent:protected] => 2
[label:protected] => Millwright
[alreadyInSave:protected] =>
[alreadyInValidation:protected] =>
[validationFailures:protected] => Array
(
)
[_new:BaseObject:private] =>
[_deleted:BaseObject:private] =>
[modifiedColumns:protected] => Array
(
)
)
[70] => Category Object
(
[languages:protected] =>
[bok_resources:protected] =>
[bok_topics:protected] =>
[bok_keywords:protected] =>
[id:protected] => 70
[type:protected] => category
[parent:protected] => 2
[label:protected] => Operating Engineer
[alreadyInSave:protected] =>
[alreadyInValidation:protected] =>
[validationFailures:protected] => Array
(
)
[_new:BaseObject:private] =>
[_deleted:BaseObject:private] =>
[modifiedColumns:protected] => Array
(
)
)
[71] => Category Object
(
[languages:protected] =>
[bok_resources:protected] =>
[bok_topics:protected] =>
[bok_keywords:protected] =>
[id:protected] => 71
[type:protected] => category
[parent:protected] => 2
[label:protected] => Painter
[alreadyInSave:protected] =>
[alreadyInValidation:protected] =>
[validationFailures:protected] => Array
(
)
[_new:BaseObject:private] =>
[_deleted:BaseObject:private] =>
[modifiedColumns:protected] => Array
(
)
)
[72] => Category Object
(
[languages:protected] =>
[bok_resources:protected] =>
[bok_topics:protected] =>
[bok_keywords:protected] =>
[id:protected] => 72
[type:protected] => category
[parent:protected] => 2
[label:protected] => Paper Hanger
[alreadyInSave:protected] =>
[alreadyInValidation:protected] =>
[validationFailures:protected] => Array
(
)
[_new:BaseObject:private] =>
[_deleted:BaseObject:private] =>
[modifiedColumns:protected] => Array
(
)
)
[73] => Category Object
(
[languages:protected] =>
[bok_resources:protected] =>
[bok_topics:protected] =>
[bok_keywords:protected] =>
[id:protected] => 73
[type:protected] => category
[parent:protected] => 2
[label:protected] => PCC/Restoration
[alreadyInSave:protected] =>
[alreadyInValidation:protected] =>
[validationFailures:protected] => Array
(
)
[_new:BaseObject:private] =>
[_deleted:BaseObject:private] =>
[modifiedColumns:protected] => Array
(
)
)
[74] => Category Object
(
[languages:protected] =>
[bok_resources:protected] =>
[bok_topics:protected] =>
[bok_keywords:protected] =>
[id:protected] => 74
[type:protected] => category
[parent:protected] => 2
[label:protected] => Pile Driver
[alreadyInSave:protected] =>
[alreadyInValidation:protected] =>
[validationFailures:protected] => Array
(
)
[_new:BaseObject:private] =>
[_deleted:BaseObject:private] =>
[modifiedColumns:protected] => Array
(
)
)
[75] => Category Object
(
[languages:protected] =>
[bok_resources:protected] =>
[bok_topics:protected] =>
[bok_keywords:protected] =>
[id:protected] => 75
[type:protected] => category
[parent:protected] => 2
[label:protected] => Plasterer
[alreadyInSave:protected] =>
[alreadyInValidation:protected] =>
[validationFailures:protected] => Array
(
)
[_new:BaseObject:private] =>
[_deleted:BaseObject:private] =>
[modifiedColumns:protected] => Array
(
)
)
[76] => Category Object
(
[languages:protected] =>
[bok_resources:protected] =>
[bok_topics:protected] =>
[bok_keywords:protected] =>
[id:protected] => 76
[type:protected] => category
[parent:protected] => 2
[label:protected] => Plumber/Pipefitter
[alreadyInSave:protected] =>
[alreadyInValidation:protected] =>
[validationFailures:protected] => Array
(
)
[_new:BaseObject:private] =>
[_deleted:BaseObject:private] =>
[modifiedColumns:protected] => Array
(
)
)
[77] => Category Object
(
[languages:protected] =>
[bok_resources:protected] =>
[bok_topics:protected] =>
[bok_keywords:protected] =>
[id:protected] => 77
[type:protected] => category
[parent:protected] => 2
[label:protected] => Refractory Worker
[alreadyInSave:protected] =>
[alreadyInValidation:protected] =>
[validationFailures:protected] => Array
(
)
[_new:BaseObject:private] =>
[_deleted:BaseObject:private] =>
[modifiedColumns:protected] => Array
(
)
)
[63] => Category Object
(
[languages:protected] =>
[bok_resources:protected] =>
[bok_topics:protected] =>
[bok_keywords:protected] =>
[id:protected] => 63
[type:protected] => category
[parent:protected] => 2
[label:protected] => Reinforcing Ironworker
[alreadyInSave:protected] =>
[alreadyInValidation:protected] =>
[validationFailures:protected] => Array
(
)
[_new:BaseObject:private] =>
[_deleted:BaseObject:private] =>
[modifiedColumns:protected] => Array
(
)
)
[78] => Category Object
(
[languages:protected] =>
[bok_resources:protected] =>
[bok_topics:protected] =>
[bok_keywords:protected] =>
[id:protected] => 78
[type:protected] => category
[parent:protected] => 2
[label:protected] => Roofer/Waterproofer
[alreadyInSave:protected] =>
[alreadyInValidation:protected] =>
[validationFailures:protected] => Array
(
)
[_new:BaseObject:private] =>
[_deleted:BaseObject:private] =>
[modifiedColumns:protected] => Array
(
)
)
[79] => Category Object
(
[languages:protected] =>
[bok_resources:protected] =>
[bok_topics:protected] =>
[bok_keywords:protected] =>
[id:protected] => 79
[type:protected] => category
[parent:protected] => 2
[label:protected] => Scaffold Erector
[alreadyInSave:protected] =>
[alreadyInValidation:protected] =>
[validationFailures:protected] => Array
(
)
[_new:BaseObject:private] =>
[_deleted:BaseObject:private] =>
[modifiedColumns:protected] => Array
(
)
)
[80] => Category Object
(
[languages:protected] =>
[bok_resources:protected] =>
[bok_topics:protected] =>
[bok_keywords:protected] =>
[id:protected] => 80
[type:protected] => category
[parent:protected] => 2
[label:protected] => Sheetmetal Worker
[alreadyInSave:protected] =>
[alreadyInValidation:protected] =>
[validationFailures:protected] => Array
(
)
[_new:BaseObject:private] =>
[_deleted:BaseObject:private] =>
[modifiedColumns:protected] => Array
(
)
)
[81] => Category Object
(
[languages:protected] =>
[bok_resources:protected] =>
[bok_topics:protected] =>
[bok_keywords:protected] =>
[id:protected] => 81
[type:protected] => category
[parent:protected] => 2
[label:protected] => Sprinkler Fitter
[alreadyInSave:protected] =>
[alreadyInValidation:protected] =>
[validationFailures:protected] => Array
(
)
[_new:BaseObject:private] =>
[_deleted:BaseObject:private] =>
[modifiedColumns:protected] => Array
(
)
)
[82] => Category Object
(
[languages:protected] =>
[bok_resources:protected] =>
[bok_topics:protected] =>
[bok_keywords:protected] =>
[id:protected] => 82
[type:protected] => category
[parent:protected] => 2
[label:protected] => Stonemason
[alreadyInSave:protected] =>
[alreadyInValidation:protected] =>
[validationFailures:protected] => Array
(
)
[_new:BaseObject:private] =>
[_deleted:BaseObject:private] =>
[modifiedColumns:protected] => Array
(
)
)
[62] => Category Object
(
[languages:protected] =>
[bok_resources:protected] =>
[bok_topics:protected] =>
[bok_keywords:protected] =>
[id:protected] => 62
[type:protected] => category
[parent:protected] => 2
[label:protected] => Structural Ironworker
[alreadyInSave:protected] =>
[alreadyInValidation:protected] =>
[validationFailures:protected] => Array
(
)
[_new:BaseObject:private] =>
[_deleted:BaseObject:private] =>
[modifiedColumns:protected] => Array
(
)
)
[83] => Category Object
(
[languages:protected] =>
[bok_resources:protected] =>
[bok_topics:protected] =>
[bok_keywords:protected] =>
[id:protected] => 83
[type:protected] => category
[parent:protected] => 2
[label:protected] => Terrazzo Worker
[alreadyInSave:protected] =>
[alreadyInValidation:protected] =>
[validationFailures:protected] => Array
(
)
[_new:BaseObject:private] =>
[_deleted:BaseObject:private] =>
[modifiedColumns:protected] => Array
(
)
)
[84] => Category Object
(
[languages:protected] =>
[bok_resources:protected] =>
[bok_topics:protected] =>
[bok_keywords:protected] =>
[id:protected] => 84
[type:protected] => category
[parent:protected] => 2
[label:protected] => Tile Setter
[alreadyInSave:protected] =>
[alreadyInValidation:protected] =>
[validationFailures:protected] => Array
(
)
[_new:BaseObject:private] =>
[_deleted:BaseObject:private] =>
[modifiedColumns:protected] => Array
(
)
)
[85] => Category Object
(
[languages:protected] =>
[bok_resources:protected] =>
[bok_topics:protected] =>
[bok_keywords:protected] =>
[id:protected] => 85
[type:protected] => category
[parent:protected] => 2
[label:protected] => Truck Driver
[alreadyInSave:protected] =>
[alreadyInValidation:protected] =>
[validationFailures:protected] => Array
(
)
[_new:BaseObject:private] =>
[_deleted:BaseObject:private] =>
[modifiedColumns:protected] => Array
(
)
)
[86] => Category Object
(
[languages:protected] =>
[bok_resources:protected] =>
[bok_topics:protected] =>
[bok_keywords:protected] =>
[id:protected] => 86
[type:protected] => category
[parent:protected] => 2
[label:protected] => Welder
[alreadyInSave:protected] =>
[alreadyInValidation:protected] =>
[validationFailures:protected] => Array
(
)
[_new:BaseObject:private] =>
[_deleted:BaseObject:private] =>
[modifiedColumns:protected] => Array
(
)
)
[87] => Category Object
(
[languages:protected] =>
[bok_resources:protected] =>
[bok_topics:protected] =>
[bok_keywords:protected] =>
[id:protected] => 87
[type:protected] => category
[parent:protected] => 3
[label:protected] => Commercial & Institutional
[alreadyInSave:protected] =>
[alreadyInValidation:protected] =>
[validationFailures:protected] => Array
(
)
[_new:BaseObject:private] =>
[_deleted:BaseObject:private] =>
[modifiedColumns:protected] => Array
(
)
)
[88] => Category Object
(
[languages:protected] =>
[bok_resources:protected] =>
[bok_topics:protected] =>
[bok_keywords:protected] =>
[id:protected] => 88
[type:protected] => category
[parent:protected] => 3
[label:protected] => Demolition
[alreadyInSave:protected] =>
[alreadyInValidation:protected] =>
[validationFailures:protected] => Array
(
)
[_new:BaseObject:private] =>
[_deleted:BaseObject:private] =>
[modifiedColumns:protected] => Array
(
)
)
[89] => Category Object
(
[languages:protected] =>
[bok_resources:protected] =>
[bok_topics:protected] =>
[bok_keywords:protected] =>
[id:protected] => 89
[type:protected] => category
[parent:protected] => 3
[label:protected] => Disasters
[alreadyInSave:protected] =>
[alreadyInValidation:protected] =>
[validationFailures:protected] => Array
(
)
[_new:BaseObject:private] =>
[_deleted:BaseObject:private] =>
[modifiedColumns:protected] => Array
(
)
)
[91] => Category Object
(
[languages:protected] =>
[bok_resources:protected] =>
[bok_topics:protected] =>
[bok_keywords:protected] =>
[id:protected] => 91
[type:protected] => category
[parent:protected] => 3
[label:protected] => Heavy & Highway
[alreadyInSave:protected] =>
[alreadyInValidation:protected] =>
[validationFailures:protected] => Array
(
)
[_new:BaseObject:private] =>
[_deleted:BaseObject:private] =>
[modifiedColumns:protected] => Array
(
)
)
[90] => Category Object
(
[languages:protected] =>
[bok_resources:protected] =>
[bok_topics:protected] =>
[bok_keywords:protected] =>
[id:protected] => 90
[type:protected] => category
[parent:protected] => 3
[label:protected] => Industrial
[alreadyInSave:protected] =>
[alreadyInValidation:protected] =>
[validationFailures:protected] => Array
(
)
[_new:BaseObject:private] =>
[_deleted:BaseObject:private] =>
[modifiedColumns:protected] => Array
(
)
)
[92] => Category Object
(
[languages:protected] =>
[bok_resources:protected] =>
[bok_topics:protected] =>
[bok_keywords:protected] =>
[id:protected] => 92
[type:protected] => category
[parent:protected] => 3
[label:protected] => LEED/Green Construction
[alreadyInSave:protected] =>
[alreadyInValidation:protected] =>
[validationFailures:protected] => Array
(
)
[_new:BaseObject:private] =>
[_deleted:BaseObject:private] =>
[modifiedColumns:protected] => Array
(
)
)
[93] => Category Object
(
[languages:protected] =>
[bok_resources:protected] =>
[bok_topics:protected] =>
[bok_keywords:protected] =>
[id:protected] => 93
[type:protected] => category
[parent:protected] => 3
[label:protected] => Renovations
[alreadyInSave:protected] =>
[alreadyInValidation:protected] =>
[validationFailures:protected] => Array
(
)
[_new:BaseObject:private] =>
[_deleted:BaseObject:private] =>
[modifiedColumns:protected] => Array
(
)
)
[94] => Category Object
(
[languages:protected] =>
[bok_resources:protected] =>
[bok_topics:protected] =>
[bok_keywords:protected] =>
[id:protected] => 94
[type:protected] => category
[parent:protected] => 3
[label:protected] => Residential
[alreadyInSave:protected] =>
[alreadyInValidation:protected] =>
[validationFailures:protected] => Array
(
)
[_new:BaseObject:private] =>
[_deleted:BaseObject:private] =>
[modifiedColumns:protected] => Array
(
)
)
[95] => Category Object
(
[languages:protected] =>
[bok_resources:protected] =>
[bok_topics:protected] =>
[bok_keywords:protected] =>
[id:protected] => 95
[type:protected] => category
[parent:protected] => 3
[label:protected] => Underground
[alreadyInSave:protected] =>
[alreadyInValidation:protected] =>
[validationFailures:protected] => Array
(
)
[_new:BaseObject:private] =>
[_deleted:BaseObject:private] =>
[modifiedColumns:protected] => Array
(
)
)
)
[categories_initialized:protected] => 1
[mapped_items:protected] =>
[content:protected] =>
[files:protected] =>
[language:protected] => Language Object
(
[id:protected] => 1
[code:protected] => en
[name:protected] => English
[alreadyInSave:protected] =>
[alreadyInValidation:protected] =>
[validationFailures:protected] => Array
(
)
[_new:BaseObject:private] =>
[_deleted:BaseObject:private] =>
[modifiedColumns:protected] => Array
(
)
)
[old_record:protected] =>
[id:protected] => 4426
[old_id:protected] =>
[elcosh_id:protected] => d001656
[type:protected] => document
[display_type:protected] => HTML only (and links)
[user_id:protected] => 0
[language_id:protected] => 1
[tagging_id:protected] => Mike Aguilar
[priority_id:protected] => 1
[title:protected] => Construction Dive -- DeWalt's Jobsite Pro headphones recalled for fire hazards
[total_pages:protected] => 1
[billed_pages:protected] => 1
[publication_number:protected] =>
[part_of:protected] =>
[keywords:protected] => DeWalt, Fire Hazards, recall, headphones
[comments:protected] =>
[summary:protected] => A recall notice by the United States Consumer Product Safety Commission affects over 300,000 DeWalt Jobsite Pro Headphones. The recall is a result of a malfunction that can cause earbuds to overheat while charging or during use, leading to fire and burn hazards.
[transition_comments:protected] =>
[external_link:protected] => https://www.constructiondive.com/news/dewalts-jobsite-pro-headphones-recalled-for-fire-hazards/611248/?utm_source=Sailthru&utm_medium=email&utm_campaign=Issue:%202021-12-10%20Construction%20Dive%20Newsletter%20%5Bissue:38532%5D&utm_term=Construction%20Dive
[consol_link:protected] =>
[more_like_this:protected] =>
[permission_given_by:protected] =>
[published:protected] => T
[billable:protected] => F
[img_name:protected] =>
[img_ext:protected] =>
[img_width:protected] =>
[img_height:protected] =>
[img_credit:protected] =>
[img_practice:protected] =>
[vid_source_id:protected] =>
[vid_running_time:protected] =>
[vid_intended_audience:protected] =>
[vid_acquisition_info:protected] =>
[vid_cost:protected] =>
[vid_producer:protected] =>
[vid_filename:protected] =>
[vid_filename_downloadable:protected] =>
[date_summary:protected] =>
[date_permission_requested:protected] =>
[date_permission_received:protected] =>
[date_review_needed:protected] =>
[date_received:protected] => 12/13/21
[date_completed:protected] => 12/13/21
[date_billed:protected] =>
[date_modified:protected] => 12/13/21
[collBokExports:protected] =>
[lastBokExportCriteria:BaseElcoshItem:private] =>
[alreadyInSave:protected] =>
[alreadyInValidation:protected] =>
[validationFailures:protected] => Array
(
)
[_new:BaseObject:private] =>
[_deleted:BaseObject:private] =>
[modifiedColumns:protected] => Array
(
)
)
)
)
[new_images] => Array
(
[0] => Search_Result Object
(
[title] => Morning Toolbox Talk
[image] => /record/images/4003-p.jpg
[blurb] => This photo is from an early morning toolbox talk on a construction job in Mclean, Virginia. It is being delivered in English and Spanish....
[category] => Array
(
[0] => 20
[1] => 51
[2] => 57
[3] => 64
[4] => 70
[5] => 63
[6] => 78
[7] => 82
[8] => 62
[9] => 87
[10] => 88
[11] => 89
[12] => 91
[13] => 90
[14] => 93
[15] => 94
[16] => 97
)
[labels] => Array
(
[0] => Safety Culture
[1] => Work Environment
[2] => Hazards
[3] => Cement Mason
[4] => Trades
[5] => Flagger
[7] => Laborer
[9] => Operating Engineer
[11] => Reinforcing Ironworker
[13] => Roofer/Waterproofer
[15] => Stonemason
[17] => Structural Ironworker
[19] => Commercial & Institutional
[20] => Jobsites
[21] => Demolition
[23] => Disasters
[25] => Heavy & Highway
[27] => Industrial
[29] => Renovations
[31] => Residential
[33] => Images
[34] => Media
[35] => Media & Documents
)
[type] => Images
[sub_category] =>
[url] => /image/4003/i002691/Morning%2BToolbox%2BTalk.html
[item:protected] => ImageRecord Object
(
[records:protected] => Array
(
)
[recordId:protected] =>
[searchWordClass:protected] =>
[searchWordPeerClass:protected] =>
[bok_record:protected] =>
[authors:protected] =>
[organizations:protected] =>
[collections:protected] =>
[categories:protected] => Array
(
[20] => Category Object
(
[languages:protected] =>
[bok_resources:protected] =>
[bok_topics:protected] =>
[bok_keywords:protected] =>
[id:protected] => 20
[type:protected] => category
[parent:protected] => 7
[label:protected] => Safety Culture
[alreadyInSave:protected] =>
[alreadyInValidation:protected] =>
[validationFailures:protected] => Array
(
)
[_new:BaseObject:private] =>
[_deleted:BaseObject:private] =>
[modifiedColumns:protected] => Array
(
)
)
[51] => Category Object
(
[languages:protected] =>
[bok_resources:protected] =>
[bok_topics:protected] =>
[bok_keywords:protected] =>
[id:protected] => 51
[type:protected] => category
[parent:protected] => 2
[label:protected] => Cement Mason
[alreadyInSave:protected] =>
[alreadyInValidation:protected] =>
[validationFailures:protected] => Array
(
)
[_new:BaseObject:private] =>
[_deleted:BaseObject:private] =>
[modifiedColumns:protected] => Array
(
)
)
[57] => Category Object
(
[languages:protected] =>
[bok_resources:protected] =>
[bok_topics:protected] =>
[bok_keywords:protected] =>
[id:protected] => 57
[type:protected] => category
[parent:protected] => 2
[label:protected] => Flagger
[alreadyInSave:protected] =>
[alreadyInValidation:protected] =>
[validationFailures:protected] => Array
(
)
[_new:BaseObject:private] =>
[_deleted:BaseObject:private] =>
[modifiedColumns:protected] => Array
(
)
)
[64] => Category Object
(
[languages:protected] =>
[bok_resources:protected] =>
[bok_topics:protected] =>
[bok_keywords:protected] =>
[id:protected] => 64
[type:protected] => category
[parent:protected] => 2
[label:protected] => Laborer
[alreadyInSave:protected] =>
[alreadyInValidation:protected] =>
[validationFailures:protected] => Array
(
)
[_new:BaseObject:private] =>
[_deleted:BaseObject:private] =>
[modifiedColumns:protected] => Array
(
)
)
[70] => Category Object
(
[languages:protected] =>
[bok_resources:protected] =>
[bok_topics:protected] =>
[bok_keywords:protected] =>
[id:protected] => 70
[type:protected] => category
[parent:protected] => 2
[label:protected] => Operating Engineer
[alreadyInSave:protected] =>
[alreadyInValidation:protected] =>
[validationFailures:protected] => Array
(
)
[_new:BaseObject:private] =>
[_deleted:BaseObject:private] =>
[modifiedColumns:protected] => Array
(
)
)
[63] => Category Object
(
[languages:protected] =>
[bok_resources:protected] =>
[bok_topics:protected] =>
[bok_keywords:protected] =>
[id:protected] => 63
[type:protected] => category
[parent:protected] => 2
[label:protected] => Reinforcing Ironworker
[alreadyInSave:protected] =>
[alreadyInValidation:protected] =>
[validationFailures:protected] => Array
(
)
[_new:BaseObject:private] =>
[_deleted:BaseObject:private] =>
[modifiedColumns:protected] => Array
(
)
)
[78] => Category Object
(
[languages:protected] =>
[bok_resources:protected] =>
[bok_topics:protected] =>
[bok_keywords:protected] =>
[id:protected] => 78
[type:protected] => category
[parent:protected] => 2
[label:protected] => Roofer/Waterproofer
[alreadyInSave:protected] =>
[alreadyInValidation:protected] =>
[validationFailures:protected] => Array
(
)
[_new:BaseObject:private] =>
[_deleted:BaseObject:private] =>
[modifiedColumns:protected] => Array
(
)
)
[82] => Category Object
(
[languages:protected] =>
[bok_resources:protected] =>
[bok_topics:protected] =>
[bok_keywords:protected] =>
[id:protected] => 82
[type:protected] => category
[parent:protected] => 2
[label:protected] => Stonemason
[alreadyInSave:protected] =>
[alreadyInValidation:protected] =>
[validationFailures:protected] => Array
(
)
[_new:BaseObject:private] =>
[_deleted:BaseObject:private] =>
[modifiedColumns:protected] => Array
(
)
)
[62] => Category Object
(
[languages:protected] =>
[bok_resources:protected] =>
[bok_topics:protected] =>
[bok_keywords:protected] =>
[id:protected] => 62
[type:protected] => category
[parent:protected] => 2
[label:protected] => Structural Ironworker
[alreadyInSave:protected] =>
[alreadyInValidation:protected] =>
[validationFailures:protected] => Array
(
)
[_new:BaseObject:private] =>
[_deleted:BaseObject:private] =>
[modifiedColumns:protected] => Array
(
)
)
[87] => Category Object
(
[languages:protected] =>
[bok_resources:protected] =>
[bok_topics:protected] =>
[bok_keywords:protected] =>
[id:protected] => 87
[type:protected] => category
[parent:protected] => 3
[label:protected] => Commercial & Institutional
[alreadyInSave:protected] =>
[alreadyInValidation:protected] =>
[validationFailures:protected] => Array
(
)
[_new:BaseObject:private] =>
[_deleted:BaseObject:private] =>
[modifiedColumns:protected] => Array
(
)
)
[88] => Category Object
(
[languages:protected] =>
[bok_resources:protected] =>
[bok_topics:protected] =>
[bok_keywords:protected] =>
[id:protected] => 88
[type:protected] => category
[parent:protected] => 3
[label:protected] => Demolition
[alreadyInSave:protected] =>
[alreadyInValidation:protected] =>
[validationFailures:protected] => Array
(
)
[_new:BaseObject:private] =>
[_deleted:BaseObject:private] =>
[modifiedColumns:protected] => Array
(
)
)
[89] => Category Object
(
[languages:protected] =>
[bok_resources:protected] =>
[bok_topics:protected] =>
[bok_keywords:protected] =>
[id:protected] => 89
[type:protected] => category
[parent:protected] => 3
[label:protected] => Disasters
[alreadyInSave:protected] =>
[alreadyInValidation:protected] =>
[validationFailures:protected] => Array
(
)
[_new:BaseObject:private] =>
[_deleted:BaseObject:private] =>
[modifiedColumns:protected] => Array
(
)
)
[91] => Category Object
(
[languages:protected] =>
[bok_resources:protected] =>
[bok_topics:protected] =>
[bok_keywords:protected] =>
[id:protected] => 91
[type:protected] => category
[parent:protected] => 3
[label:protected] => Heavy & Highway
[alreadyInSave:protected] =>
[alreadyInValidation:protected] =>
[validationFailures:protected] => Array
(
)
[_new:BaseObject:private] =>
[_deleted:BaseObject:private] =>
[modifiedColumns:protected] => Array
(
)
)
[90] => Category Object
(
[languages:protected] =>
[bok_resources:protected] =>
[bok_topics:protected] =>
[bok_keywords:protected] =>
[id:protected] => 90
[type:protected] => category
[parent:protected] => 3
[label:protected] => Industrial
[alreadyInSave:protected] =>
[alreadyInValidation:protected] =>
[validationFailures:protected] => Array
(
)
[_new:BaseObject:private] =>
[_deleted:BaseObject:private] =>
[modifiedColumns:protected] => Array
(
)
)
[93] => Category Object
(
[languages:protected] =>
[bok_resources:protected] =>
[bok_topics:protected] =>
[bok_keywords:protected] =>
[id:protected] => 93
[type:protected] => category
[parent:protected] => 3
[label:protected] => Renovations
[alreadyInSave:protected] =>
[alreadyInValidation:protected] =>
[validationFailures:protected] => Array
(
)
[_new:BaseObject:private] =>
[_deleted:BaseObject:private] =>
[modifiedColumns:protected] => Array
(
)
)
[94] => Category Object
(
[languages:protected] =>
[bok_resources:protected] =>
[bok_topics:protected] =>
[bok_keywords:protected] =>
[id:protected] => 94
[type:protected] => category
[parent:protected] => 3
[label:protected] => Residential
[alreadyInSave:protected] =>
[alreadyInValidation:protected] =>
[validationFailures:protected] => Array
(
)
[_new:BaseObject:private] =>
[_deleted:BaseObject:private] =>
[modifiedColumns:protected] => Array
(
)
)
[97] => Category Object
(
[languages:protected] =>
[bok_resources:protected] =>
[bok_topics:protected] =>
[bok_keywords:protected] =>
[id:protected] => 97
[type:protected] => category
[parent:protected] => 5
[label:protected] => Images
[alreadyInSave:protected] =>
[alreadyInValidation:protected] =>
[validationFailures:protected] => Array
(
)
[_new:BaseObject:private] =>
[_deleted:BaseObject:private] =>
[modifiedColumns:protected] => Array
(
)
)
)
[categories_initialized:protected] => 1
[mapped_items:protected] =>
[content:protected] =>
[files:protected] =>
[language:protected] => Language Object
(
[id:protected] => 1
[code:protected] => en
[name:protected] => English
[alreadyInSave:protected] =>
[alreadyInValidation:protected] =>
[validationFailures:protected] => Array
(
)
[_new:BaseObject:private] =>
[_deleted:BaseObject:private] =>
[modifiedColumns:protected] => Array
(
)
)
[old_record:protected] =>
[id:protected] => 4003
[old_id:protected] =>
[elcosh_id:protected] => i002691
[type:protected] => image
[display_type:protected] => Image
[user_id:protected] => 0
[language_id:protected] => 1
[tagging_id:protected] => Bruce Lippy
[priority_id:protected] => 1
[title:protected] => Morning Toolbox Talk
[total_pages:protected] => 0
[billed_pages:protected] => 0
[publication_number:protected] =>
[part_of:protected] =>
[keywords:protected] => toolbox talk, tailgate talk, Spanish, bilingual
[comments:protected] =>
[summary:protected] => This photo is from an early morning toolbox talk on a construction job in Mclean, Virginia. It is being delivered in English and Spanish.
[transition_comments:protected] =>
[external_link:protected] =>
[consol_link:protected] => http://www.cpwrconstructionsolutions.org/electrical/solution/662/worker-training.html
[more_like_this:protected] => d001285,d001304,c000079
[permission_given_by:protected] =>
[published:protected] => T
[billable:protected] => F
[img_name:protected] =>
[img_ext:protected] => jpg
[img_width:protected] =>
[img_height:protected] =>
[img_credit:protected] => Morgan Zavertnik and Hoar Construction
[img_practice:protected] => good
[vid_source_id:protected] =>
[vid_running_time:protected] =>
[vid_intended_audience:protected] =>
[vid_acquisition_info:protected] =>
[vid_cost:protected] =>
[vid_producer:protected] =>
[vid_filename:protected] =>
[vid_filename_downloadable:protected] =>
[date_summary:protected] => November 2015
[date_permission_requested:protected] =>
[date_permission_received:protected] =>
[date_review_needed:protected] =>
[date_received:protected] => 03/02/16
[date_completed:protected] => 03/02/16
[date_billed:protected] =>
[date_modified:protected] => 03/02/16
[collBokExports:protected] =>
[lastBokExportCriteria:BaseElcoshItem:private] =>
[alreadyInSave:protected] =>
[alreadyInValidation:protected] =>
[validationFailures:protected] => Array
(
)
[_new:BaseObject:private] =>
[_deleted:BaseObject:private] =>
[modifiedColumns:protected] => Array
(
)
)
)
[1] => Search_Result Object
(
[title] => Toolbox talk - crew view
[image] => /record/images/4005-p.jpg
[blurb] => Photo of crew listening to a toolbox safety talk before starting work....
[category] => Array
(
[0] => 97
[1] => 20
[2] => 47
[3] => 49
[4] => 51
[5] => 55
[6] => 61
[7] => 64
[8] => 71
[9] => 75
[10] => 63
[11] => 79
[12] => 62
[13] => 87
[14] => 88
[15] => 91
[16] => 90
[17] => 93
[18] => 94
[19] => 95
)
[labels] => Array
(
[0] => Images
[1] => Media
[2] => Media & Documents
[3] => Safety Culture
[4] => Work Environment
[5] => Hazards
[6] => Bricklayer
[7] => Trades
[8] => Carpenter
[10] => Cement Mason
[12] => Electrical Worker
[14] => Interior Systems Carpenter
[16] => Laborer
[18] => Painter
[20] => Plasterer
[22] => Reinforcing Ironworker
[24] => Scaffold Erector
[26] => Structural Ironworker
[28] => Commercial & Institutional
[29] => Jobsites
[30] => Demolition
[32] => Heavy & Highway
[34] => Industrial
[36] => Renovations
[38] => Residential
[40] => Underground
)
[type] => Images
[sub_category] =>
[url] => /image/4005/i002692/Toolbox%2Btalk%2B-%2Bcrew%2Bview.html
[item:protected] => ImageRecord Object
(
[records:protected] => Array
(
)
[recordId:protected] =>
[searchWordClass:protected] =>
[searchWordPeerClass:protected] =>
[bok_record:protected] =>
[authors:protected] =>
[organizations:protected] =>
[collections:protected] =>
[categories:protected] => Array
(
[97] => Category Object
(
[languages:protected] =>
[bok_resources:protected] =>
[bok_topics:protected] =>
[bok_keywords:protected] =>
[id:protected] => 97
[type:protected] => category
[parent:protected] => 5
[label:protected] => Images
[alreadyInSave:protected] =>
[alreadyInValidation:protected] =>
[validationFailures:protected] => Array
(
)
[_new:BaseObject:private] =>
[_deleted:BaseObject:private] =>
[modifiedColumns:protected] => Array
(
)
)
[20] => Category Object
(
[languages:protected] =>
[bok_resources:protected] =>
[bok_topics:protected] =>
[bok_keywords:protected] =>
[id:protected] => 20
[type:protected] => category
[parent:protected] => 7
[label:protected] => Safety Culture
[alreadyInSave:protected] =>
[alreadyInValidation:protected] =>
[validationFailures:protected] => Array
(
)
[_new:BaseObject:private] =>
[_deleted:BaseObject:private] =>
[modifiedColumns:protected] => Array
(
)
)
[47] => Category Object
(
[languages:protected] =>
[bok_resources:protected] =>
[bok_topics:protected] =>
[bok_keywords:protected] =>
[id:protected] => 47
[type:protected] => category
[parent:protected] => 2
[label:protected] => Bricklayer
[alreadyInSave:protected] =>
[alreadyInValidation:protected] =>
[validationFailures:protected] => Array
(
)
[_new:BaseObject:private] =>
[_deleted:BaseObject:private] =>
[modifiedColumns:protected] => Array
(
)
)
[49] => Category Object
(
[languages:protected] =>
[bok_resources:protected] =>
[bok_topics:protected] =>
[bok_keywords:protected] =>
[id:protected] => 49
[type:protected] => category
[parent:protected] => 2
[label:protected] => Carpenter
[alreadyInSave:protected] =>
[alreadyInValidation:protected] =>
[validationFailures:protected] => Array
(
)
[_new:BaseObject:private] =>
[_deleted:BaseObject:private] =>
[modifiedColumns:protected] => Array
(
)
)
[51] => Category Object
(
[languages:protected] =>
[bok_resources:protected] =>
[bok_topics:protected] =>
[bok_keywords:protected] =>
[id:protected] => 51
[type:protected] => category
[parent:protected] => 2
[label:protected] => Cement Mason
[alreadyInSave:protected] =>
[alreadyInValidation:protected] =>
[validationFailures:protected] => Array
(
)
[_new:BaseObject:private] =>
[_deleted:BaseObject:private] =>
[modifiedColumns:protected] => Array
(
)
)
[55] => Category Object
(
[languages:protected] =>
[bok_resources:protected] =>
[bok_topics:protected] =>
[bok_keywords:protected] =>
[id:protected] => 55
[type:protected] => category
[parent:protected] => 2
[label:protected] => Electrical Worker
[alreadyInSave:protected] =>
[alreadyInValidation:protected] =>
[validationFailures:protected] => Array
(
)
[_new:BaseObject:private] =>
[_deleted:BaseObject:private] =>
[modifiedColumns:protected] => Array
(
)
)
[61] => Category Object
(
[languages:protected] =>
[bok_resources:protected] =>
[bok_topics:protected] =>
[bok_keywords:protected] =>
[id:protected] => 61
[type:protected] => category
[parent:protected] => 2
[label:protected] => Interior Systems Carpenter
[alreadyInSave:protected] =>
[alreadyInValidation:protected] =>
[validationFailures:protected] => Array
(
)
[_new:BaseObject:private] =>
[_deleted:BaseObject:private] =>
[modifiedColumns:protected] => Array
(
)
)
[64] => Category Object
(
[languages:protected] =>
[bok_resources:protected] =>
[bok_topics:protected] =>
[bok_keywords:protected] =>
[id:protected] => 64
[type:protected] => category
[parent:protected] => 2
[label:protected] => Laborer
[alreadyInSave:protected] =>
[alreadyInValidation:protected] =>
[validationFailures:protected] => Array
(
)
[_new:BaseObject:private] =>
[_deleted:BaseObject:private] =>
[modifiedColumns:protected] => Array
(
)
)
[71] => Category Object
(
[languages:protected] =>
[bok_resources:protected] =>
[bok_topics:protected] =>
[bok_keywords:protected] =>
[id:protected] => 71
[type:protected] => category
[parent:protected] => 2
[label:protected] => Painter
[alreadyInSave:protected] =>
[alreadyInValidation:protected] =>
[validationFailures:protected] => Array
(
)
[_new:BaseObject:private] =>
[_deleted:BaseObject:private] =>
[modifiedColumns:protected] => Array
(
)
)
[75] => Category Object
(
[languages:protected] =>
[bok_resources:protected] =>
[bok_topics:protected] =>
[bok_keywords:protected] =>
[id:protected] => 75
[type:protected] => category
[parent:protected] => 2
[label:protected] => Plasterer
[alreadyInSave:protected] =>
[alreadyInValidation:protected] =>
[validationFailures:protected] => Array
(
)
[_new:BaseObject:private] =>
[_deleted:BaseObject:private] =>
[modifiedColumns:protected] => Array
(
)
)
[63] => Category Object
(
[languages:protected] =>
[bok_resources:protected] =>
[bok_topics:protected] =>
[bok_keywords:protected] =>
[id:protected] => 63
[type:protected] => category
[parent:protected] => 2
[label:protected] => Reinforcing Ironworker
[alreadyInSave:protected] =>
[alreadyInValidation:protected] =>
[validationFailures:protected] => Array
(
)
[_new:BaseObject:private] =>
[_deleted:BaseObject:private] =>
[modifiedColumns:protected] => Array
(
)
)
[79] => Category Object
(
[languages:protected] =>
[bok_resources:protected] =>
[bok_topics:protected] =>
[bok_keywords:protected] =>
[id:protected] => 79
[type:protected] => category
[parent:protected] => 2
[label:protected] => Scaffold Erector
[alreadyInSave:protected] =>
[alreadyInValidation:protected] =>
[validationFailures:protected] => Array
(
)
[_new:BaseObject:private] =>
[_deleted:BaseObject:private] =>
[modifiedColumns:protected] => Array
(
)
)
[62] => Category Object
(
[languages:protected] =>
[bok_resources:protected] =>
[bok_topics:protected] =>
[bok_keywords:protected] =>
[id:protected] => 62
[type:protected] => category
[parent:protected] => 2
[label:protected] => Structural Ironworker
[alreadyInSave:protected] =>
[alreadyInValidation:protected] =>
[validationFailures:protected] => Array
(
)
[_new:BaseObject:private] =>
[_deleted:BaseObject:private] =>
[modifiedColumns:protected] => Array
(
)
)
[87] => Category Object
(
[languages:protected] =>
[bok_resources:protected] =>
[bok_topics:protected] =>
[bok_keywords:protected] =>
[id:protected] => 87
[type:protected] => category
[parent:protected] => 3
[label:protected] => Commercial & Institutional
[alreadyInSave:protected] =>
[alreadyInValidation:protected] =>
[validationFailures:protected] => Array
(
)
[_new:BaseObject:private] =>
[_deleted:BaseObject:private] =>
[modifiedColumns:protected] => Array
(
)
)
[88] => Category Object
(
[languages:protected] =>
[bok_resources:protected] =>
[bok_topics:protected] =>
[bok_keywords:protected] =>
[id:protected] => 88
[type:protected] => category
[parent:protected] => 3
[label:protected] => Demolition
[alreadyInSave:protected] =>
[alreadyInValidation:protected] =>
[validationFailures:protected] => Array
(
)
[_new:BaseObject:private] =>
[_deleted:BaseObject:private] =>
[modifiedColumns:protected] => Array
(
)
)
[91] => Category Object
(
[languages:protected] =>
[bok_resources:protected] =>
[bok_topics:protected] =>
[bok_keywords:protected] =>
[id:protected] => 91
[type:protected] => category
[parent:protected] => 3
[label:protected] => Heavy & Highway
[alreadyInSave:protected] =>
[alreadyInValidation:protected] =>
[validationFailures:protected] => Array
(
)
[_new:BaseObject:private] =>
[_deleted:BaseObject:private] =>
[modifiedColumns:protected] => Array
(
)
)
[90] => Category Object
(
[languages:protected] =>
[bok_resources:protected] =>
[bok_topics:protected] =>
[bok_keywords:protected] =>
[id:protected] => 90
[type:protected] => category
[parent:protected] => 3
[label:protected] => Industrial
[alreadyInSave:protected] =>
[alreadyInValidation:protected] =>
[validationFailures:protected] => Array
(
)
[_new:BaseObject:private] =>
[_deleted:BaseObject:private] =>
[modifiedColumns:protected] => Array
(
)
)
[93] => Category Object
(
[languages:protected] =>
[bok_resources:protected] =>
[bok_topics:protected] =>
[bok_keywords:protected] =>
[id:protected] => 93
[type:protected] => category
[parent:protected] => 3
[label:protected] => Renovations
[alreadyInSave:protected] =>
[alreadyInValidation:protected] =>
[validationFailures:protected] => Array
(
)
[_new:BaseObject:private] =>
[_deleted:BaseObject:private] =>
[modifiedColumns:protected] => Array
(
)
)
[94] => Category Object
(
[languages:protected] =>
[bok_resources:protected] =>
[bok_topics:protected] =>
[bok_keywords:protected] =>
[id:protected] => 94
[type:protected] => category
[parent:protected] => 3
[label:protected] => Residential
[alreadyInSave:protected] =>
[alreadyInValidation:protected] =>
[validationFailures:protected] => Array
(
)
[_new:BaseObject:private] =>
[_deleted:BaseObject:private] =>
[modifiedColumns:protected] => Array
(
)
)
[95] => Category Object
(
[languages:protected] =>
[bok_resources:protected] =>
[bok_topics:protected] =>
[bok_keywords:protected] =>
[id:protected] => 95
[type:protected] => category
[parent:protected] => 3
[label:protected] => Underground
[alreadyInSave:protected] =>
[alreadyInValidation:protected] =>
[validationFailures:protected] => Array
(
)
[_new:BaseObject:private] =>
[_deleted:BaseObject:private] =>
[modifiedColumns:protected] => Array
(
)
)
)
[categories_initialized:protected] => 1
[mapped_items:protected] =>
[content:protected] =>
[files:protected] =>
[language:protected] => Language Object
(
[id:protected] => 1
[code:protected] => en
[name:protected] => English
[alreadyInSave:protected] =>
[alreadyInValidation:protected] =>
[validationFailures:protected] => Array
(
)
[_new:BaseObject:private] =>
[_deleted:BaseObject:private] =>
[modifiedColumns:protected] => Array
(
)
)
[old_record:protected] =>
[id:protected] => 4005
[old_id:protected] =>
[elcosh_id:protected] => i002692
[type:protected] => image
[display_type:protected] => Image
[user_id:protected] => 0
[language_id:protected] => 1
[tagging_id:protected] => Bruce Lippy
[priority_id:protected] => 1
[title:protected] => Toolbox talk - crew view
[total_pages:protected] => 0
[billed_pages:protected] => 0
[publication_number:protected] =>
[part_of:protected] =>
[keywords:protected] => toolbox talk, tailgate talk, safety talk, Spanish
[comments:protected] =>
[summary:protected] => Photo of crew listening to a toolbox safety talk before starting work.
[transition_comments:protected] =>
[external_link:protected] =>
[consol_link:protected] => http://www.cpwrconstructionsolutions.org/electrical/solution/662/worker-training.html
[more_like_this:protected] => i002691,d001269, c000079, d001285
[permission_given_by:protected] =>
[published:protected] => T
[billable:protected] => F
[img_name:protected] =>
[img_ext:protected] => jpg
[img_width:protected] =>
[img_height:protected] =>
[img_credit:protected] => Morgan Zavertnik and Hoar Construction
[img_practice:protected] => good
[vid_source_id:protected] =>
[vid_running_time:protected] =>
[vid_intended_audience:protected] =>
[vid_acquisition_info:protected] =>
[vid_cost:protected] =>
[vid_producer:protected] =>
[vid_filename:protected] =>
[vid_filename_downloadable:protected] =>
[date_summary:protected] => November 2015
[date_permission_requested:protected] =>
[date_permission_received:protected] =>
[date_review_needed:protected] =>
[date_received:protected] => 03/02/16
[date_completed:protected] => 03/02/16
[date_billed:protected] =>
[date_modified:protected] => 03/02/16
[collBokExports:protected] =>
[lastBokExportCriteria:BaseElcoshItem:private] =>
[alreadyInSave:protected] =>
[alreadyInValidation:protected] =>
[validationFailures:protected] => Array
(
)
[_new:BaseObject:private] =>
[_deleted:BaseObject:private] =>
[modifiedColumns:protected] => Array
(
)
)
)
[2] => Search_Result Object
(
[title] => Toolbox talk - long shot
[image] => /record/images/4006-p.jpg
[blurb] => This crew gathered every morning before starting work to discuss a new safety topic....
[category] => Array
(
[0] => 20
[1] => 47
[2] => 49
[3] => 51
[4] => 55
[5] => 64
[6] => 68
[7] => 75
[8] => 76
[9] => 63
[10] => 78
[11] => 79
[12] => 82
[13] => 62
[14] => 87
[15] => 88
[16] => 91
[17] => 90
[18] => 93
[19] => 94
[20] => 95
[21] => 97
)
[labels] => Array
(
[0] => Safety Culture
[1] => Work Environment
[2] => Hazards
[3] => Bricklayer
[4] => Trades
[5] => Carpenter
[7] => Cement Mason
[9] => Electrical Worker
[11] => Laborer
[13] => Maintenance Worker
[15] => Plasterer
[17] => Plumber/Pipefitter
[19] => Reinforcing Ironworker
[21] => Roofer/Waterproofer
[23] => Scaffold Erector
[25] => Stonemason
[27] => Structural Ironworker
[29] => Commercial & Institutional
[30] => Jobsites
[31] => Demolition
[33] => Heavy & Highway
[35] => Industrial
[37] => Renovations
[39] => Residential
[41] => Underground
[43] => Images
[44] => Media
[45] => Media & Documents
)
[type] => Images
[sub_category] =>
[url] => /image/4006/i002693/Toolbox%2Btalk%2B-%2Blong%2Bshot.html
[item:protected] => ImageRecord Object
(
[records:protected] => Array
(
)
[recordId:protected] =>
[searchWordClass:protected] =>
[searchWordPeerClass:protected] =>
[bok_record:protected] =>
[authors:protected] =>
[organizations:protected] =>
[collections:protected] =>
[categories:protected] => Array
(
[20] => Category Object
(
[languages:protected] =>
[bok_resources:protected] =>
[bok_topics:protected] =>
[bok_keywords:protected] =>
[id:protected] => 20
[type:protected] => category
[parent:protected] => 7
[label:protected] => Safety Culture
[alreadyInSave:protected] =>
[alreadyInValidation:protected] =>
[validationFailures:protected] => Array
(
)
[_new:BaseObject:private] =>
[_deleted:BaseObject:private] =>
[modifiedColumns:protected] => Array
(
)
)
[47] => Category Object
(
[languages:protected] =>
[bok_resources:protected] =>
[bok_topics:protected] =>
[bok_keywords:protected] =>
[id:protected] => 47
[type:protected] => category
[parent:protected] => 2
[label:protected] => Bricklayer
[alreadyInSave:protected] =>
[alreadyInValidation:protected] =>
[validationFailures:protected] => Array
(
)
[_new:BaseObject:private] =>
[_deleted:BaseObject:private] =>
[modifiedColumns:protected] => Array
(
)
)
[49] => Category Object
(
[languages:protected] =>
[bok_resources:protected] =>
[bok_topics:protected] =>
[bok_keywords:protected] =>
[id:protected] => 49
[type:protected] => category
[parent:protected] => 2
[label:protected] => Carpenter
[alreadyInSave:protected] =>
[alreadyInValidation:protected] =>
[validationFailures:protected] => Array
(
)
[_new:BaseObject:private] =>
[_deleted:BaseObject:private] =>
[modifiedColumns:protected] => Array
(
)
)
[51] => Category Object
(
[languages:protected] =>
[bok_resources:protected] =>
[bok_topics:protected] =>
[bok_keywords:protected] =>
[id:protected] => 51
[type:protected] => category
[parent:protected] => 2
[label:protected] => Cement Mason
[alreadyInSave:protected] =>
[alreadyInValidation:protected] =>
[validationFailures:protected] => Array
(
)
[_new:BaseObject:private] =>
[_deleted:BaseObject:private] =>
[modifiedColumns:protected] => Array
(
)
)
[55] => Category Object
(
[languages:protected] =>
[bok_resources:protected] =>
[bok_topics:protected] =>
[bok_keywords:protected] =>
[id:protected] => 55
[type:protected] => category
[parent:protected] => 2
[label:protected] => Electrical Worker
[alreadyInSave:protected] =>
[alreadyInValidation:protected] =>
[validationFailures:protected] => Array
(
)
[_new:BaseObject:private] =>
[_deleted:BaseObject:private] =>
[modifiedColumns:protected] => Array
(
)
)
[64] => Category Object
(
[languages:protected] =>
[bok_resources:protected] =>
[bok_topics:protected] =>
[bok_keywords:protected] =>
[id:protected] => 64
[type:protected] => category
[parent:protected] => 2
[label:protected] => Laborer
[alreadyInSave:protected] =>
[alreadyInValidation:protected] =>
[validationFailures:protected] => Array
(
)
[_new:BaseObject:private] =>
[_deleted:BaseObject:private] =>
[modifiedColumns:protected] => Array
(
)
)
[68] => Category Object
(
[languages:protected] =>
[bok_resources:protected] =>
[bok_topics:protected] =>
[bok_keywords:protected] =>
[id:protected] => 68
[type:protected] => category
[parent:protected] => 2
[label:protected] => Maintenance Worker
[alreadyInSave:protected] =>
[alreadyInValidation:protected] =>
[validationFailures:protected] => Array
(
)
[_new:BaseObject:private] =>
[_deleted:BaseObject:private] =>
[modifiedColumns:protected] => Array
(
)
)
[75] => Category Object
(
[languages:protected] =>
[bok_resources:protected] =>
[bok_topics:protected] =>
[bok_keywords:protected] =>
[id:protected] => 75
[type:protected] => category
[parent:protected] => 2
[label:protected] => Plasterer
[alreadyInSave:protected] =>
[alreadyInValidation:protected] =>
[validationFailures:protected] => Array
(
)
[_new:BaseObject:private] =>
[_deleted:BaseObject:private] =>
[modifiedColumns:protected] => Array
(
)
)
[76] => Category Object
(
[languages:protected] =>
[bok_resources:protected] =>
[bok_topics:protected] =>
[bok_keywords:protected] =>
[id:protected] => 76
[type:protected] => category
[parent:protected] => 2
[label:protected] => Plumber/Pipefitter
[alreadyInSave:protected] =>
[alreadyInValidation:protected] =>
[validationFailures:protected] => Array
(
)
[_new:BaseObject:private] =>
[_deleted:BaseObject:private] =>
[modifiedColumns:protected] => Array
(
)
)
[63] => Category Object
(
[languages:protected] =>
[bok_resources:protected] =>
[bok_topics:protected] =>
[bok_keywords:protected] =>
[id:protected] => 63
[type:protected] => category
[parent:protected] => 2
[label:protected] => Reinforcing Ironworker
[alreadyInSave:protected] =>
[alreadyInValidation:protected] =>
[validationFailures:protected] => Array
(
)
[_new:BaseObject:private] =>
[_deleted:BaseObject:private] =>
[modifiedColumns:protected] => Array
(
)
)
[78] => Category Object
(
[languages:protected] =>
[bok_resources:protected] =>
[bok_topics:protected] =>
[bok_keywords:protected] =>
[id:protected] => 78
[type:protected] => category
[parent:protected] => 2
[label:protected] => Roofer/Waterproofer
[alreadyInSave:protected] =>
[alreadyInValidation:protected] =>
[validationFailures:protected] => Array
(
)
[_new:BaseObject:private] =>
[_deleted:BaseObject:private] =>
[modifiedColumns:protected] => Array
(
)
)
[79] => Category Object
(
[languages:protected] =>
[bok_resources:protected] =>
[bok_topics:protected] =>
[bok_keywords:protected] =>
[id:protected] => 79
[type:protected] => category
[parent:protected] => 2
[label:protected] => Scaffold Erector
[alreadyInSave:protected] =>
[alreadyInValidation:protected] =>
[validationFailures:protected] => Array
(
)
[_new:BaseObject:private] =>
[_deleted:BaseObject:private] =>
[modifiedColumns:protected] => Array
(
)
)
[82] => Category Object
(
[languages:protected] =>
[bok_resources:protected] =>
[bok_topics:protected] =>
[bok_keywords:protected] =>
[id:protected] => 82
[type:protected] => category
[parent:protected] => 2
[label:protected] => Stonemason
[alreadyInSave:protected] =>
[alreadyInValidation:protected] =>
[validationFailures:protected] => Array
(
)
[_new:BaseObject:private] =>
[_deleted:BaseObject:private] =>
[modifiedColumns:protected] => Array
(
)
)
[62] => Category Object
(
[languages:protected] =>
[bok_resources:protected] =>
[bok_topics:protected] =>
[bok_keywords:protected] =>
[id:protected] => 62
[type:protected] => category
[parent:protected] => 2
[label:protected] => Structural Ironworker
[alreadyInSave:protected] =>
[alreadyInValidation:protected] =>
[validationFailures:protected] => Array
(
)
[_new:BaseObject:private] =>
[_deleted:BaseObject:private] =>
[modifiedColumns:protected] => Array
(
)
)
[87] => Category Object
(
[languages:protected] =>
[bok_resources:protected] =>
[bok_topics:protected] =>
[bok_keywords:protected] =>
[id:protected] => 87
[type:protected] => category
[parent:protected] => 3
[label:protected] => Commercial & Institutional
[alreadyInSave:protected] =>
[alreadyInValidation:protected] =>
[validationFailures:protected] => Array
(
)
[_new:BaseObject:private] =>
[_deleted:BaseObject:private] =>
[modifiedColumns:protected] => Array
(
)
)
[88] => Category Object
(
[languages:protected] =>
[bok_resources:protected] =>
[bok_topics:protected] =>
[bok_keywords:protected] =>
[id:protected] => 88
[type:protected] => category
[parent:protected] => 3
[label:protected] => Demolition
[alreadyInSave:protected] =>
[alreadyInValidation:protected] =>
[validationFailures:protected] => Array
(
)
[_new:BaseObject:private] =>
[_deleted:BaseObject:private] =>
[modifiedColumns:protected] => Array
(
)
)
[91] => Category Object
(
[languages:protected] =>
[bok_resources:protected] =>
[bok_topics:protected] =>
[bok_keywords:protected] =>
[id:protected] => 91
[type:protected] => category
[parent:protected] => 3
[label:protected] => Heavy & Highway
[alreadyInSave:protected] =>
[alreadyInValidation:protected] =>
[validationFailures:protected] => Array
(
)
[_new:BaseObject:private] =>
[_deleted:BaseObject:private] =>
[modifiedColumns:protected] => Array
(
)
)
[90] => Category Object
(
[languages:protected] =>
[bok_resources:protected] =>
[bok_topics:protected] =>
[bok_keywords:protected] =>
[id:protected] => 90
[type:protected] => category
[parent:protected] => 3
[label:protected] => Industrial
[alreadyInSave:protected] =>
[alreadyInValidation:protected] =>
[validationFailures:protected] => Array
(
)
[_new:BaseObject:private] =>
[_deleted:BaseObject:private] =>
[modifiedColumns:protected] => Array
(
)
)
[93] => Category Object
(
[languages:protected] =>
[bok_resources:protected] =>
[bok_topics:protected] =>
[bok_keywords:protected] =>
[id:protected] => 93
[type:protected] => category
[parent:protected] => 3
[label:protected] => Renovations
[alreadyInSave:protected] =>
[alreadyInValidation:protected] =>
[validationFailures:protected] => Array
(
)
[_new:BaseObject:private] =>
[_deleted:BaseObject:private] =>
[modifiedColumns:protected] => Array
(
)
)
[94] => Category Object
(
[languages:protected] =>
[bok_resources:protected] =>
[bok_topics:protected] =>
[bok_keywords:protected] =>
[id:protected] => 94
[type:protected] => category
[parent:protected] => 3
[label:protected] => Residential
[alreadyInSave:protected] =>
[alreadyInValidation:protected] =>
[validationFailures:protected] => Array
(
)
[_new:BaseObject:private] =>
[_deleted:BaseObject:private] =>
[modifiedColumns:protected] => Array
(
)
)
[95] => Category Object
(
[languages:protected] =>
[bok_resources:protected] =>
[bok_topics:protected] =>
[bok_keywords:protected] =>
[id:protected] => 95
[type:protected] => category
[parent:protected] => 3
[label:protected] => Underground
[alreadyInSave:protected] =>
[alreadyInValidation:protected] =>
[validationFailures:protected] => Array
(
)
[_new:BaseObject:private] =>
[_deleted:BaseObject:private] =>
[modifiedColumns:protected] => Array
(
)
)
[97] => Category Object
(
[languages:protected] =>
[bok_resources:protected] =>
[bok_topics:protected] =>
[bok_keywords:protected] =>
[id:protected] => 97
[type:protected] => category
[parent:protected] => 5
[label:protected] => Images
[alreadyInSave:protected] =>
[alreadyInValidation:protected] =>
[validationFailures:protected] => Array
(
)
[_new:BaseObject:private] =>
[_deleted:BaseObject:private] =>
[modifiedColumns:protected] => Array
(
)
)
)
[categories_initialized:protected] => 1
[mapped_items:protected] =>
[content:protected] =>
[files:protected] =>
[language:protected] => Language Object
(
[id:protected] => 1
[code:protected] => en
[name:protected] => English
[alreadyInSave:protected] =>
[alreadyInValidation:protected] =>
[validationFailures:protected] => Array
(
)
[_new:BaseObject:private] =>
[_deleted:BaseObject:private] =>
[modifiedColumns:protected] => Array
(
)
)
[old_record:protected] =>
[id:protected] => 4006
[old_id:protected] =>
[elcosh_id:protected] => i002693
[type:protected] => image
[display_type:protected] => Image
[user_id:protected] => 0
[language_id:protected] => 1
[tagging_id:protected] => Bruce Lippy
[priority_id:protected] => 1
[title:protected] => Toolbox talk - long shot
[total_pages:protected] => 0
[billed_pages:protected] => 0
[publication_number:protected] =>
[part_of:protected] =>
[keywords:protected] => toolbox talk, tailgate talk, safety minute
[comments:protected] =>
[summary:protected] => This crew gathered every morning before starting work to discuss a new safety topic.
[transition_comments:protected] =>
[external_link:protected] =>
[consol_link:protected] => http://www.cpwrconstructionsolutions.org/electrical/solution/662/worker-training.html
[more_like_this:protected] => i002691,i002692,d001269,d000527
[permission_given_by:protected] =>
[published:protected] => T
[billable:protected] => F
[img_name:protected] =>
[img_ext:protected] => jpg
[img_width:protected] =>
[img_height:protected] =>
[img_credit:protected] => Morgan Zavertnik and Hoar Construction
[img_practice:protected] => good
[vid_source_id:protected] =>
[vid_running_time:protected] =>
[vid_intended_audience:protected] =>
[vid_acquisition_info:protected] =>
[vid_cost:protected] =>
[vid_producer:protected] =>
[vid_filename:protected] =>
[vid_filename_downloadable:protected] =>
[date_summary:protected] => November 2015
[date_permission_requested:protected] =>
[date_permission_received:protected] =>
[date_review_needed:protected] =>
[date_received:protected] => 03/02/16
[date_completed:protected] => 03/02/16
[date_billed:protected] =>
[date_modified:protected] => 03/02/16
[collBokExports:protected] =>
[lastBokExportCriteria:BaseElcoshItem:private] =>
[alreadyInSave:protected] =>
[alreadyInValidation:protected] =>
[validationFailures:protected] => Array
(
)
[_new:BaseObject:private] =>
[_deleted:BaseObject:private] =>
[modifiedColumns:protected] => Array
(
)
)
)
[3] => Search_Result Object
(
[title] => Safety officer discussing ongoing project with marketing coordinator
[image] => /record/images/4014-p.jpg
[blurb] => The safety officer (left) points out the good safety practices on this project that reflect well on the firm and may influence future clients....
[category] => Array
(
[0] => 97
[1] => 20
[2] => 46
[3] => 47
[4] => 49
[5] => 50
[6] => 51
[7] => 54
[8] => 55
[9] => 58
[10] => 60
[11] => 61
[12] => 64
[13] => 71
[14] => 75
[15] => 76
[16] => 63
[17] => 79
[18] => 80
[19] => 82
[20] => 62
[21] => 83
[22] => 87
[23] => 91
[24] => 90
[25] => 93
[26] => 94
)
[labels] => Array
(
[0] => Images
[1] => Media
[2] => Media & Documents
[3] => Safety Culture
[4] => Work Environment
[5] => Hazards
[6] => Boilermaker
[7] => Trades
[8] => Bricklayer
[10] => Carpenter
[12] => Carpet Layer
[14] => Cement Mason
[16] => Drywall Applicator Specialist
[18] => Electrical Worker
[20] => Glazier
[22] => HVAC
[24] => Interior Systems Carpenter
[26] => Laborer
[28] => Painter
[30] => Plasterer
[32] => Plumber/Pipefitter
[34] => Reinforcing Ironworker
[36] => Scaffold Erector
[38] => Sheetmetal Worker
[40] => Stonemason
[42] => Structural Ironworker
[44] => Terrazzo Worker
[46] => Commercial & Institutional
[47] => Jobsites
[48] => Heavy & Highway
[50] => Industrial
[52] => Renovations
[54] => Residential
)
[type] => Images
[sub_category] =>
[url] => /image/4014/i002700/Safety%2Bofficer%2Bdiscussing%2Bongoing%2Bproject%2Bwith%2Bmarketing%2Bcoordinator.html
[item:protected] => ImageRecord Object
(
[records:protected] => Array
(
)
[recordId:protected] =>
[searchWordClass:protected] =>
[searchWordPeerClass:protected] =>
[bok_record:protected] =>
[authors:protected] =>
[organizations:protected] =>
[collections:protected] =>
[categories:protected] => Array
(
[97] => Category Object
(
[languages:protected] =>
[bok_resources:protected] =>
[bok_topics:protected] =>
[bok_keywords:protected] =>
[id:protected] => 97
[type:protected] => category
[parent:protected] => 5
[label:protected] => Images
[alreadyInSave:protected] =>
[alreadyInValidation:protected] =>
[validationFailures:protected] => Array
(
)
[_new:BaseObject:private] =>
[_deleted:BaseObject:private] =>
[modifiedColumns:protected] => Array
(
)
)
[20] => Category Object
(
[languages:protected] =>
[bok_resources:protected] =>
[bok_topics:protected] =>
[bok_keywords:protected] =>
[id:protected] => 20
[type:protected] => category
[parent:protected] => 7
[label:protected] => Safety Culture
[alreadyInSave:protected] =>
[alreadyInValidation:protected] =>
[validationFailures:protected] => Array
(
)
[_new:BaseObject:private] =>
[_deleted:BaseObject:private] =>
[modifiedColumns:protected] => Array
(
)
)
[46] => Category Object
(
[languages:protected] =>
[bok_resources:protected] =>
[bok_topics:protected] =>
[bok_keywords:protected] =>
[id:protected] => 46
[type:protected] => category
[parent:protected] => 2
[label:protected] => Boilermaker
[alreadyInSave:protected] =>
[alreadyInValidation:protected] =>
[validationFailures:protected] => Array
(
)
[_new:BaseObject:private] =>
[_deleted:BaseObject:private] =>
[modifiedColumns:protected] => Array
(
)
)
[47] => Category Object
(
[languages:protected] =>
[bok_resources:protected] =>
[bok_topics:protected] =>
[bok_keywords:protected] =>
[id:protected] => 47
[type:protected] => category
[parent:protected] => 2
[label:protected] => Bricklayer
[alreadyInSave:protected] =>
[alreadyInValidation:protected] =>
[validationFailures:protected] => Array
(
)
[_new:BaseObject:private] =>
[_deleted:BaseObject:private] =>
[modifiedColumns:protected] => Array
(
)
)
[49] => Category Object
(
[languages:protected] =>
[bok_resources:protected] =>
[bok_topics:protected] =>
[bok_keywords:protected] =>
[id:protected] => 49
[type:protected] => category
[parent:protected] => 2
[label:protected] => Carpenter
[alreadyInSave:protected] =>
[alreadyInValidation:protected] =>
[validationFailures:protected] => Array
(
)
[_new:BaseObject:private] =>
[_deleted:BaseObject:private] =>
[modifiedColumns:protected] => Array
(
)
)
[50] => Category Object
(
[languages:protected] =>
[bok_resources:protected] =>
[bok_topics:protected] =>
[bok_keywords:protected] =>
[id:protected] => 50
[type:protected] => category
[parent:protected] => 2
[label:protected] => Carpet Layer
[alreadyInSave:protected] =>
[alreadyInValidation:protected] =>
[validationFailures:protected] => Array
(
)
[_new:BaseObject:private] =>
[_deleted:BaseObject:private] =>
[modifiedColumns:protected] => Array
(
)
)
[51] => Category Object
(
[languages:protected] =>
[bok_resources:protected] =>
[bok_topics:protected] =>
[bok_keywords:protected] =>
[id:protected] => 51
[type:protected] => category
[parent:protected] => 2
[label:protected] => Cement Mason
[alreadyInSave:protected] =>
[alreadyInValidation:protected] =>
[validationFailures:protected] => Array
(
)
[_new:BaseObject:private] =>
[_deleted:BaseObject:private] =>
[modifiedColumns:protected] => Array
(
)
)
[54] => Category Object
(
[languages:protected] =>
[bok_resources:protected] =>
[bok_topics:protected] =>
[bok_keywords:protected] =>
[id:protected] => 54
[type:protected] => category
[parent:protected] => 2
[label:protected] => Drywall Applicator Specialist
[alreadyInSave:protected] =>
[alreadyInValidation:protected] =>
[validationFailures:protected] => Array
(
)
[_new:BaseObject:private] =>
[_deleted:BaseObject:private] =>
[modifiedColumns:protected] => Array
(
)
)
[55] => Category Object
(
[languages:protected] =>
[bok_resources:protected] =>
[bok_topics:protected] =>
[bok_keywords:protected] =>
[id:protected] => 55
[type:protected] => category
[parent:protected] => 2
[label:protected] => Electrical Worker
[alreadyInSave:protected] =>
[alreadyInValidation:protected] =>
[validationFailures:protected] => Array
(
)
[_new:BaseObject:private] =>
[_deleted:BaseObject:private] =>
[modifiedColumns:protected] => Array
(
)
)
[58] => Category Object
(
[languages:protected] =>
[bok_resources:protected] =>
[bok_topics:protected] =>
[bok_keywords:protected] =>
[id:protected] => 58
[type:protected] => category
[parent:protected] => 2
[label:protected] => Glazier
[alreadyInSave:protected] =>
[alreadyInValidation:protected] =>
[validationFailures:protected] => Array
(
)
[_new:BaseObject:private] =>
[_deleted:BaseObject:private] =>
[modifiedColumns:protected] => Array
(
)
)
[60] => Category Object
(
[languages:protected] =>
[bok_resources:protected] =>
[bok_topics:protected] =>
[bok_keywords:protected] =>
[id:protected] => 60
[type:protected] => category
[parent:protected] => 2
[label:protected] => HVAC
[alreadyInSave:protected] =>
[alreadyInValidation:protected] =>
[validationFailures:protected] => Array
(
)
[_new:BaseObject:private] =>
[_deleted:BaseObject:private] =>
[modifiedColumns:protected] => Array
(
)
)
[61] => Category Object
(
[languages:protected] =>
[bok_resources:protected] =>
[bok_topics:protected] =>
[bok_keywords:protected] =>
[id:protected] => 61
[type:protected] => category
[parent:protected] => 2
[label:protected] => Interior Systems Carpenter
[alreadyInSave:protected] =>
[alreadyInValidation:protected] =>
[validationFailures:protected] => Array
(
)
[_new:BaseObject:private] =>
[_deleted:BaseObject:private] =>
[modifiedColumns:protected] => Array
(
)
)
[64] => Category Object
(
[languages:protected] =>
[bok_resources:protected] =>
[bok_topics:protected] =>
[bok_keywords:protected] =>
[id:protected] => 64
[type:protected] => category
[parent:protected] => 2
[label:protected] => Laborer
[alreadyInSave:protected] =>
[alreadyInValidation:protected] =>
[validationFailures:protected] => Array
(
)
[_new:BaseObject:private] =>
[_deleted:BaseObject:private] =>
[modifiedColumns:protected] => Array
(
)
)
[71] => Category Object
(
[languages:protected] =>
[bok_resources:protected] =>
[bok_topics:protected] =>
[bok_keywords:protected] =>
[id:protected] => 71
[type:protected] => category
[parent:protected] => 2
[label:protected] => Painter
[alreadyInSave:protected] =>
[alreadyInValidation:protected] =>
[validationFailures:protected] => Array
(
)
[_new:BaseObject:private] =>
[_deleted:BaseObject:private] =>
[modifiedColumns:protected] => Array
(
)
)
[75] => Category Object
(
[languages:protected] =>
[bok_resources:protected] =>
[bok_topics:protected] =>
[bok_keywords:protected] =>
[id:protected] => 75
[type:protected] => category
[parent:protected] => 2
[label:protected] => Plasterer
[alreadyInSave:protected] =>
[alreadyInValidation:protected] =>
[validationFailures:protected] => Array
(
)
[_new:BaseObject:private] =>
[_deleted:BaseObject:private] =>
[modifiedColumns:protected] => Array
(
)
)
[76] => Category Object
(
[languages:protected] =>
[bok_resources:protected] =>
[bok_topics:protected] =>
[bok_keywords:protected] =>
[id:protected] => 76
[type:protected] => category
[parent:protected] => 2
[label:protected] => Plumber/Pipefitter
[alreadyInSave:protected] =>
[alreadyInValidation:protected] =>
[validationFailures:protected] => Array
(
)
[_new:BaseObject:private] =>
[_deleted:BaseObject:private] =>
[modifiedColumns:protected] => Array
(
)
)
[63] => Category Object
(
[languages:protected] =>
[bok_resources:protected] =>
[bok_topics:protected] =>
[bok_keywords:protected] =>
[id:protected] => 63
[type:protected] => category
[parent:protected] => 2
[label:protected] => Reinforcing Ironworker
[alreadyInSave:protected] =>
[alreadyInValidation:protected] =>
[validationFailures:protected] => Array
(
)
[_new:BaseObject:private] =>
[_deleted:BaseObject:private] =>
[modifiedColumns:protected] => Array
(
)
)
[79] => Category Object
(
[languages:protected] =>
[bok_resources:protected] =>
[bok_topics:protected] =>
[bok_keywords:protected] =>
[id:protected] => 79
[type:protected] => category
[parent:protected] => 2
[label:protected] => Scaffold Erector
[alreadyInSave:protected] =>
[alreadyInValidation:protected] =>
[validationFailures:protected] => Array
(
)
[_new:BaseObject:private] =>
[_deleted:BaseObject:private] =>
[modifiedColumns:protected] => Array
(
)
)
[80] => Category Object
(
[languages:protected] =>
[bok_resources:protected] =>
[bok_topics:protected] =>
[bok_keywords:protected] =>
[id:protected] => 80
[type:protected] => category
[parent:protected] => 2
[label:protected] => Sheetmetal Worker
[alreadyInSave:protected] =>
[alreadyInValidation:protected] =>
[validationFailures:protected] => Array
(
)
[_new:BaseObject:private] =>
[_deleted:BaseObject:private] =>
[modifiedColumns:protected] => Array
(
)
)
[82] => Category Object
(
[languages:protected] =>
[bok_resources:protected] =>
[bok_topics:protected] =>
[bok_keywords:protected] =>
[id:protected] => 82
[type:protected] => category
[parent:protected] => 2
[label:protected] => Stonemason
[alreadyInSave:protected] =>
[alreadyInValidation:protected] =>
[validationFailures:protected] => Array
(
)
[_new:BaseObject:private] =>
[_deleted:BaseObject:private] =>
[modifiedColumns:protected] => Array
(
)
)
[62] => Category Object
(
[languages:protected] =>
[bok_resources:protected] =>
[bok_topics:protected] =>
[bok_keywords:protected] =>
[id:protected] => 62
[type:protected] => category
[parent:protected] => 2
[label:protected] => Structural Ironworker
[alreadyInSave:protected] =>
[alreadyInValidation:protected] =>
[validationFailures:protected] => Array
(
)
[_new:BaseObject:private] =>
[_deleted:BaseObject:private] =>
[modifiedColumns:protected] => Array
(
)
)
[83] => Category Object
(
[languages:protected] =>
[bok_resources:protected] =>
[bok_topics:protected] =>
[bok_keywords:protected] =>
[id:protected] => 83
[type:protected] => category
[parent:protected] => 2
[label:protected] => Terrazzo Worker
[alreadyInSave:protected] =>
[alreadyInValidation:protected] =>
[validationFailures:protected] => Array
(
)
[_new:BaseObject:private] =>
[_deleted:BaseObject:private] =>
[modifiedColumns:protected] => Array
(
)
)
[87] => Category Object
(
[languages:protected] =>
[bok_resources:protected] =>
[bok_topics:protected] =>
[bok_keywords:protected] =>
[id:protected] => 87
[type:protected] => category
[parent:protected] => 3
[label:protected] => Commercial & Institutional
[alreadyInSave:protected] =>
[alreadyInValidation:protected] =>
[validationFailures:protected] => Array
(
)
[_new:BaseObject:private] =>
[_deleted:BaseObject:private] =>
[modifiedColumns:protected] => Array
(
)
)
[91] => Category Object
(
[languages:protected] =>
[bok_resources:protected] =>
[bok_topics:protected] =>
[bok_keywords:protected] =>
[id:protected] => 91
[type:protected] => category
[parent:protected] => 3
[label:protected] => Heavy & Highway
[alreadyInSave:protected] =>
[alreadyInValidation:protected] =>
[validationFailures:protected] => Array
(
)
[_new:BaseObject:private] =>
[_deleted:BaseObject:private] =>
[modifiedColumns:protected] => Array
(
)
)
[90] => Category Object
(
[languages:protected] =>
[bok_resources:protected] =>
[bok_topics:protected] =>
[bok_keywords:protected] =>
[id:protected] => 90
[type:protected] => category
[parent:protected] => 3
[label:protected] => Industrial
[alreadyInSave:protected] =>
[alreadyInValidation:protected] =>
[validationFailures:protected] => Array
(
)
[_new:BaseObject:private] =>
[_deleted:BaseObject:private] =>
[modifiedColumns:protected] => Array
(
)
)
[93] => Category Object
(
[languages:protected] =>
[bok_resources:protected] =>
[bok_topics:protected] =>
[bok_keywords:protected] =>
[id:protected] => 93
[type:protected] => category
[parent:protected] => 3
[label:protected] => Renovations
[alreadyInSave:protected] =>
[alreadyInValidation:protected] =>
[validationFailures:protected] => Array
(
)
[_new:BaseObject:private] =>
[_deleted:BaseObject:private] =>
[modifiedColumns:protected] => Array
(
)
)
[94] => Category Object
(
[languages:protected] =>
[bok_resources:protected] =>
[bok_topics:protected] =>
[bok_keywords:protected] =>
[id:protected] => 94
[type:protected] => category
[parent:protected] => 3
[label:protected] => Residential
[alreadyInSave:protected] =>
[alreadyInValidation:protected] =>
[validationFailures:protected] => Array
(
)
[_new:BaseObject:private] =>
[_deleted:BaseObject:private] =>
[modifiedColumns:protected] => Array
(
)
)
)
[categories_initialized:protected] => 1
[mapped_items:protected] =>
[content:protected] =>
[files:protected] =>
[language:protected] => Language Object
(
[id:protected] => 1
[code:protected] => en
[name:protected] => English
[alreadyInSave:protected] =>
[alreadyInValidation:protected] =>
[validationFailures:protected] => Array
(
)
[_new:BaseObject:private] =>
[_deleted:BaseObject:private] =>
[modifiedColumns:protected] => Array
(
)
)
[old_record:protected] =>
[id:protected] => 4014
[old_id:protected] =>
[elcosh_id:protected] => i002700
[type:protected] => image
[display_type:protected] => Image
[user_id:protected] => 0
[language_id:protected] => 1
[tagging_id:protected] => Bruce Lippy
[priority_id:protected] => 1
[title:protected] => Safety officer discussing ongoing project with marketing coordinator
[total_pages:protected] => 0
[billed_pages:protected] => 0
[publication_number:protected] =>
[part_of:protected] =>
[keywords:protected] => Latino, safety officer, safety culture
[comments:protected] =>
[summary:protected] => The safety officer (left) points out the good safety practices on this project that reflect well on the firm and may influence future clients.
[transition_comments:protected] =>
[external_link:protected] =>
[consol_link:protected] => http://www.cpwrconstructionsolutions.org/index.php
[more_like_this:protected] => d000989,d001351,d001362,d000652, d001101, d000931, d001395
[permission_given_by:protected] =>
[published:protected] => T
[billable:protected] => F
[img_name:protected] =>
[img_ext:protected] => jpg
[img_width:protected] =>
[img_height:protected] =>
[img_credit:protected] => Hoar Construction, Photo by Neil Lippy
[img_practice:protected] => good
[vid_source_id:protected] =>
[vid_running_time:protected] =>
[vid_intended_audience:protected] =>
[vid_acquisition_info:protected] =>
[vid_cost:protected] =>
[vid_producer:protected] =>
[vid_filename:protected] =>
[vid_filename_downloadable:protected] =>
[date_summary:protected] => November 2015
[date_permission_requested:protected] =>
[date_permission_received:protected] =>
[date_review_needed:protected] =>
[date_received:protected] => 03/02/16
[date_completed:protected] => 03/02/16
[date_billed:protected] =>
[date_modified:protected] => 01/30/23
[collBokExports:protected] =>
[lastBokExportCriteria:BaseElcoshItem:private] =>
[alreadyInSave:protected] =>
[alreadyInValidation:protected] =>
[validationFailures:protected] => Array
(
)
[_new:BaseObject:private] =>
[_deleted:BaseObject:private] =>
[modifiedColumns:protected] => Array
(
)
)
)
[4] => Search_Result Object
(
[title] => Scaffolding at top of large column
[image] => /record/images/3994-p.jpg
[blurb] => This shot shows innovative guarding around the top of a large concrete column in the base of a high rise structure going up....
[category] => Array
(
[0] => 15
[1] => 21
[2] => 47
[3] => 51
[4] => 63
[5] => 78
[6] => 79
[7] => 80
[8] => 62
[9] => 87
[10] => 97
[11] => 56
[12] => 64
[13] => 74
)
[labels] => Array
(
[0] => Falls
[1] => Work Environment
[2] => Hazards
[3] => Scaffolds
[6] => Bricklayer
[7] => Trades
[8] => Cement Mason
[10] => Reinforcing Ironworker
[12] => Roofer/Waterproofer
[14] => Scaffold Erector
[16] => Sheetmetal Worker
[18] => Structural Ironworker
[20] => Commercial & Institutional
[21] => Jobsites
[22] => Images
[23] => Media
[24] => Media & Documents
[25] => Elevator Constructor
[27] => Laborer
[29] => Pile Driver
)
[type] => Images
[sub_category] =>
[url] => /image/3994/i002689/Scaffolding%2Bat%2Btop%2Bof%2Blarge%2Bcolumn.html
[item:protected] => ImageRecord Object
(
[records:protected] => Array
(
)
[recordId:protected] =>
[searchWordClass:protected] =>
[searchWordPeerClass:protected] =>
[bok_record:protected] =>
[authors:protected] =>
[organizations:protected] =>
[collections:protected] =>
[categories:protected] => Array
(
[15] => Category Object
(
[languages:protected] =>
[bok_resources:protected] =>
[bok_topics:protected] =>
[bok_keywords:protected] =>
[id:protected] => 15
[type:protected] => category
[parent:protected] => 7
[label:protected] => Falls
[alreadyInSave:protected] =>
[alreadyInValidation:protected] =>
[validationFailures:protected] => Array
(
)
[_new:BaseObject:private] =>
[_deleted:BaseObject:private] =>
[modifiedColumns:protected] => Array
(
)
)
[21] => Category Object
(
[languages:protected] =>
[bok_resources:protected] =>
[bok_topics:protected] =>
[bok_keywords:protected] =>
[id:protected] => 21
[type:protected] => category
[parent:protected] => 7
[label:protected] => Scaffolds
[alreadyInSave:protected] =>
[alreadyInValidation:protected] =>
[validationFailures:protected] => Array
(
)
[_new:BaseObject:private] =>
[_deleted:BaseObject:private] =>
[modifiedColumns:protected] => Array
(
)
)
[47] => Category Object
(
[languages:protected] =>
[bok_resources:protected] =>
[bok_topics:protected] =>
[bok_keywords:protected] =>
[id:protected] => 47
[type:protected] => category
[parent:protected] => 2
[label:protected] => Bricklayer
[alreadyInSave:protected] =>
[alreadyInValidation:protected] =>
[validationFailures:protected] => Array
(
)
[_new:BaseObject:private] =>
[_deleted:BaseObject:private] =>
[modifiedColumns:protected] => Array
(
)
)
[51] => Category Object
(
[languages:protected] =>
[bok_resources:protected] =>
[bok_topics:protected] =>
[bok_keywords:protected] =>
[id:protected] => 51
[type:protected] => category
[parent:protected] => 2
[label:protected] => Cement Mason
[alreadyInSave:protected] =>
[alreadyInValidation:protected] =>
[validationFailures:protected] => Array
(
)
[_new:BaseObject:private] =>
[_deleted:BaseObject:private] =>
[modifiedColumns:protected] => Array
(
)
)
[63] => Category Object
(
[languages:protected] =>
[bok_resources:protected] =>
[bok_topics:protected] =>
[bok_keywords:protected] =>
[id:protected] => 63
[type:protected] => category
[parent:protected] => 2
[label:protected] => Reinforcing Ironworker
[alreadyInSave:protected] =>
[alreadyInValidation:protected] =>
[validationFailures:protected] => Array
(
)
[_new:BaseObject:private] =>
[_deleted:BaseObject:private] =>
[modifiedColumns:protected] => Array
(
)
)
[78] => Category Object
(
[languages:protected] =>
[bok_resources:protected] =>
[bok_topics:protected] =>
[bok_keywords:protected] =>
[id:protected] => 78
[type:protected] => category
[parent:protected] => 2
[label:protected] => Roofer/Waterproofer
[alreadyInSave:protected] =>
[alreadyInValidation:protected] =>
[validationFailures:protected] => Array
(
)
[_new:BaseObject:private] =>
[_deleted:BaseObject:private] =>
[modifiedColumns:protected] => Array
(
)
)
[79] => Category Object
(
[languages:protected] =>
[bok_resources:protected] =>
[bok_topics:protected] =>
[bok_keywords:protected] =>
[id:protected] => 79
[type:protected] => category
[parent:protected] => 2
[label:protected] => Scaffold Erector
[alreadyInSave:protected] =>
[alreadyInValidation:protected] =>
[validationFailures:protected] => Array
(
)
[_new:BaseObject:private] =>
[_deleted:BaseObject:private] =>
[modifiedColumns:protected] => Array
(
)
)
[80] => Category Object
(
[languages:protected] =>
[bok_resources:protected] =>
[bok_topics:protected] =>
[bok_keywords:protected] =>
[id:protected] => 80
[type:protected] => category
[parent:protected] => 2
[label:protected] => Sheetmetal Worker
[alreadyInSave:protected] =>
[alreadyInValidation:protected] =>
[validationFailures:protected] => Array
(
)
[_new:BaseObject:private] =>
[_deleted:BaseObject:private] =>
[modifiedColumns:protected] => Array
(
)
)
[62] => Category Object
(
[languages:protected] =>
[bok_resources:protected] =>
[bok_topics:protected] =>
[bok_keywords:protected] =>
[id:protected] => 62
[type:protected] => category
[parent:protected] => 2
[label:protected] => Structural Ironworker
[alreadyInSave:protected] =>
[alreadyInValidation:protected] =>
[validationFailures:protected] => Array
(
)
[_new:BaseObject:private] =>
[_deleted:BaseObject:private] =>
[modifiedColumns:protected] => Array
(
)
)
[87] => Category Object
(
[languages:protected] =>
[bok_resources:protected] =>
[bok_topics:protected] =>
[bok_keywords:protected] =>
[id:protected] => 87
[type:protected] => category
[parent:protected] => 3
[label:protected] => Commercial & Institutional
[alreadyInSave:protected] =>
[alreadyInValidation:protected] =>
[validationFailures:protected] => Array
(
)
[_new:BaseObject:private] =>
[_deleted:BaseObject:private] =>
[modifiedColumns:protected] => Array
(
)
)
[97] => Category Object
(
[languages:protected] =>
[bok_resources:protected] =>
[bok_topics:protected] =>
[bok_keywords:protected] =>
[id:protected] => 97
[type:protected] => category
[parent:protected] => 5
[label:protected] => Images
[alreadyInSave:protected] =>
[alreadyInValidation:protected] =>
[validationFailures:protected] => Array
(
)
[_new:BaseObject:private] =>
[_deleted:BaseObject:private] =>
[modifiedColumns:protected] => Array
(
)
)
[56] => Category Object
(
[languages:protected] =>
[bok_resources:protected] =>
[bok_topics:protected] =>
[bok_keywords:protected] =>
[id:protected] => 56
[type:protected] => category
[parent:protected] => 2
[label:protected] => Elevator Constructor
[alreadyInSave:protected] =>
[alreadyInValidation:protected] =>
[validationFailures:protected] => Array
(
)
[_new:BaseObject:private] =>
[_deleted:BaseObject:private] =>
[modifiedColumns:protected] => Array
(
)
)
[64] => Category Object
(
[languages:protected] =>
[bok_resources:protected] =>
[bok_topics:protected] =>
[bok_keywords:protected] =>
[id:protected] => 64
[type:protected] => category
[parent:protected] => 2
[label:protected] => Laborer
[alreadyInSave:protected] =>
[alreadyInValidation:protected] =>
[validationFailures:protected] => Array
(
)
[_new:BaseObject:private] =>
[_deleted:BaseObject:private] =>
[modifiedColumns:protected] => Array
(
)
)
[74] => Category Object
(
[languages:protected] =>
[bok_resources:protected] =>
[bok_topics:protected] =>
[bok_keywords:protected] =>
[id:protected] => 74
[type:protected] => category
[parent:protected] => 2
[label:protected] => Pile Driver
[alreadyInSave:protected] =>
[alreadyInValidation:protected] =>
[validationFailures:protected] => Array
(
)
[_new:BaseObject:private] =>
[_deleted:BaseObject:private] =>
[modifiedColumns:protected] => Array
(
)
)
)
[categories_initialized:protected] => 1
[mapped_items:protected] =>
[content:protected] =>
[files:protected] =>
[language:protected] => Language Object
(
[id:protected] => 1
[code:protected] => en
[name:protected] => English
[alreadyInSave:protected] =>
[alreadyInValidation:protected] =>
[validationFailures:protected] => Array
(
)
[_new:BaseObject:private] =>
[_deleted:BaseObject:private] =>
[modifiedColumns:protected] => Array
(
)
)
[old_record:protected] =>
[id:protected] => 3994
[old_id:protected] =>
[elcosh_id:protected] => i002689
[type:protected] => image
[display_type:protected] => Image
[user_id:protected] => 0
[language_id:protected] => 1
[tagging_id:protected] => Bruce Lippy
[priority_id:protected] => 1
[title:protected] => Scaffolding at top of large column
[total_pages:protected] => 0
[billed_pages:protected] => 0
[publication_number:protected] =>
[part_of:protected] =>
[keywords:protected] => Guardrail, railing, fall prevention, falls
[comments:protected] =>
[summary:protected] => This shot shows innovative guarding around the top of a large concrete column in the base of a high rise structure going up.
[transition_comments:protected] =>
[external_link:protected] =>
[consol_link:protected] => http://www.cpwrconstructionsolutions.org/masonry/solution/8/adjustable-tower-scaffold.html
[more_like_this:protected] => c1002680,i002662,d000608,d001255
[permission_given_by:protected] =>
[published:protected] => T
[billable:protected] => F
[img_name:protected] =>
[img_ext:protected] => jpg
[img_width:protected] =>
[img_height:protected] =>
[img_credit:protected] => Photo by Pam Susi
[img_practice:protected] => good
[vid_source_id:protected] =>
[vid_running_time:protected] =>
[vid_intended_audience:protected] =>
[vid_acquisition_info:protected] =>
[vid_cost:protected] =>
[vid_producer:protected] =>
[vid_filename:protected] =>
[vid_filename_downloadable:protected] =>
[date_summary:protected] => January 2016
[date_permission_requested:protected] =>
[date_permission_received:protected] =>
[date_review_needed:protected] =>
[date_received:protected] => 02/01/16
[date_completed:protected] => 02/01/16
[date_billed:protected] =>
[date_modified:protected] => 02/01/16
[collBokExports:protected] =>
[lastBokExportCriteria:BaseElcoshItem:private] =>
[alreadyInSave:protected] =>
[alreadyInValidation:protected] =>
[validationFailures:protected] => Array
(
)
[_new:BaseObject:private] =>
[_deleted:BaseObject:private] =>
[modifiedColumns:protected] => Array
(
)
)
)
[5] => Search_Result Object
(
[title] => Construction bracing
[image] => /record/images/3995-p.jpg
[blurb] => This shows structural support that prevents collapses during construction....
[category] => Array
(
[0] => 12
[1] => 15
[2] => 21
[3] => 49
[4] => 51
[5] => 55
[6] => 56
[7] => 60
[8] => 64
[9] => 68
[10] => 74
[11] => 63
[12] => 78
[13] => 79
[14] => 80
[15] => 62
[16] => 87
[17] => 90
[18] => 97
)
[labels] => Array
(
[0] => Crushed/Struck By
[1] => Work Environment
[2] => Hazards
[3] => Falls
[6] => Scaffolds
[9] => Carpenter
[10] => Trades
[11] => Cement Mason
[13] => Electrical Worker
[15] => Elevator Constructor
[17] => HVAC
[19] => Laborer
[21] => Maintenance Worker
[23] => Pile Driver
[25] => Reinforcing Ironworker
[27] => Roofer/Waterproofer
[29] => Scaffold Erector
[31] => Sheetmetal Worker
[33] => Structural Ironworker
[35] => Commercial & Institutional
[36] => Jobsites
[37] => Industrial
[39] => Images
[40] => Media
[41] => Media & Documents
)
[type] => Images
[sub_category] =>
[url] => /image/3995/i002690/Construction%2Bbracing.html
[item:protected] => ImageRecord Object
(
[records:protected] => Array
(
)
[recordId:protected] =>
[searchWordClass:protected] =>
[searchWordPeerClass:protected] =>
[bok_record:protected] =>
[authors:protected] =>
[organizations:protected] =>
[collections:protected] =>
[categories:protected] => Array
(
[12] => Category Object
(
[languages:protected] =>
[bok_resources:protected] =>
[bok_topics:protected] =>
[bok_keywords:protected] =>
[id:protected] => 12
[type:protected] => category
[parent:protected] => 7
[label:protected] => Crushed/Struck By
[alreadyInSave:protected] =>
[alreadyInValidation:protected] =>
[validationFailures:protected] => Array
(
)
[_new:BaseObject:private] =>
[_deleted:BaseObject:private] =>
[modifiedColumns:protected] => Array
(
)
)
[15] => Category Object
(
[languages:protected] =>
[bok_resources:protected] =>
[bok_topics:protected] =>
[bok_keywords:protected] =>
[id:protected] => 15
[type:protected] => category
[parent:protected] => 7
[label:protected] => Falls
[alreadyInSave:protected] =>
[alreadyInValidation:protected] =>
[validationFailures:protected] => Array
(
)
[_new:BaseObject:private] =>
[_deleted:BaseObject:private] =>
[modifiedColumns:protected] => Array
(
)
)
[21] => Category Object
(
[languages:protected] =>
[bok_resources:protected] =>
[bok_topics:protected] =>
[bok_keywords:protected] =>
[id:protected] => 21
[type:protected] => category
[parent:protected] => 7
[label:protected] => Scaffolds
[alreadyInSave:protected] =>
[alreadyInValidation:protected] =>
[validationFailures:protected] => Array
(
)
[_new:BaseObject:private] =>
[_deleted:BaseObject:private] =>
[modifiedColumns:protected] => Array
(
)
)
[49] => Category Object
(
[languages:protected] =>
[bok_resources:protected] =>
[bok_topics:protected] =>
[bok_keywords:protected] =>
[id:protected] => 49
[type:protected] => category
[parent:protected] => 2
[label:protected] => Carpenter
[alreadyInSave:protected] =>
[alreadyInValidation:protected] =>
[validationFailures:protected] => Array
(
)
[_new:BaseObject:private] =>
[_deleted:BaseObject:private] =>
[modifiedColumns:protected] => Array
(
)
)
[51] => Category Object
(
[languages:protected] =>
[bok_resources:protected] =>
[bok_topics:protected] =>
[bok_keywords:protected] =>
[id:protected] => 51
[type:protected] => category
[parent:protected] => 2
[label:protected] => Cement Mason
[alreadyInSave:protected] =>
[alreadyInValidation:protected] =>
[validationFailures:protected] => Array
(
)
[_new:BaseObject:private] =>
[_deleted:BaseObject:private] =>
[modifiedColumns:protected] => Array
(
)
)
[55] => Category Object
(
[languages:protected] =>
[bok_resources:protected] =>
[bok_topics:protected] =>
[bok_keywords:protected] =>
[id:protected] => 55
[type:protected] => category
[parent:protected] => 2
[label:protected] => Electrical Worker
[alreadyInSave:protected] =>
[alreadyInValidation:protected] =>
[validationFailures:protected] => Array
(
)
[_new:BaseObject:private] =>
[_deleted:BaseObject:private] =>
[modifiedColumns:protected] => Array
(
)
)
[56] => Category Object
(
[languages:protected] =>
[bok_resources:protected] =>
[bok_topics:protected] =>
[bok_keywords:protected] =>
[id:protected] => 56
[type:protected] => category
[parent:protected] => 2
[label:protected] => Elevator Constructor
[alreadyInSave:protected] =>
[alreadyInValidation:protected] =>
[validationFailures:protected] => Array
(
)
[_new:BaseObject:private] =>
[_deleted:BaseObject:private] =>
[modifiedColumns:protected] => Array
(
)
)
[60] => Category Object
(
[languages:protected] =>
[bok_resources:protected] =>
[bok_topics:protected] =>
[bok_keywords:protected] =>
[id:protected] => 60
[type:protected] => category
[parent:protected] => 2
[label:protected] => HVAC
[alreadyInSave:protected] =>
[alreadyInValidation:protected] =>
[validationFailures:protected] => Array
(
)
[_new:BaseObject:private] =>
[_deleted:BaseObject:private] =>
[modifiedColumns:protected] => Array
(
)
)
[64] => Category Object
(
[languages:protected] =>
[bok_resources:protected] =>
[bok_topics:protected] =>
[bok_keywords:protected] =>
[id:protected] => 64
[type:protected] => category
[parent:protected] => 2
[label:protected] => Laborer
[alreadyInSave:protected] =>
[alreadyInValidation:protected] =>
[validationFailures:protected] => Array
(
)
[_new:BaseObject:private] =>
[_deleted:BaseObject:private] =>
[modifiedColumns:protected] => Array
(
)
)
[68] => Category Object
(
[languages:protected] =>
[bok_resources:protected] =>
[bok_topics:protected] =>
[bok_keywords:protected] =>
[id:protected] => 68
[type:protected] => category
[parent:protected] => 2
[label:protected] => Maintenance Worker
[alreadyInSave:protected] =>
[alreadyInValidation:protected] =>
[validationFailures:protected] => Array
(
)
[_new:BaseObject:private] =>
[_deleted:BaseObject:private] =>
[modifiedColumns:protected] => Array
(
)
)
[74] => Category Object
(
[languages:protected] =>
[bok_resources:protected] =>
[bok_topics:protected] =>
[bok_keywords:protected] =>
[id:protected] => 74
[type:protected] => category
[parent:protected] => 2
[label:protected] => Pile Driver
[alreadyInSave:protected] =>
[alreadyInValidation:protected] =>
[validationFailures:protected] => Array
(
)
[_new:BaseObject:private] =>
[_deleted:BaseObject:private] =>
[modifiedColumns:protected] => Array
(
)
)
[63] => Category Object
(
[languages:protected] =>
[bok_resources:protected] =>
[bok_topics:protected] =>
[bok_keywords:protected] =>
[id:protected] => 63
[type:protected] => category
[parent:protected] => 2
[label:protected] => Reinforcing Ironworker
[alreadyInSave:protected] =>
[alreadyInValidation:protected] =>
[validationFailures:protected] => Array
(
)
[_new:BaseObject:private] =>
[_deleted:BaseObject:private] =>
[modifiedColumns:protected] => Array
(
)
)
[78] => Category Object
(
[languages:protected] =>
[bok_resources:protected] =>
[bok_topics:protected] =>
[bok_keywords:protected] =>
[id:protected] => 78
[type:protected] => category
[parent:protected] => 2
[label:protected] => Roofer/Waterproofer
[alreadyInSave:protected] =>
[alreadyInValidation:protected] =>
[validationFailures:protected] => Array
(
)
[_new:BaseObject:private] =>
[_deleted:BaseObject:private] =>
[modifiedColumns:protected] => Array
(
)
)
[79] => Category Object
(
[languages:protected] =>
[bok_resources:protected] =>
[bok_topics:protected] =>
[bok_keywords:protected] =>
[id:protected] => 79
[type:protected] => category
[parent:protected] => 2
[label:protected] => Scaffold Erector
[alreadyInSave:protected] =>
[alreadyInValidation:protected] =>
[validationFailures:protected] => Array
(
)
[_new:BaseObject:private] =>
[_deleted:BaseObject:private] =>
[modifiedColumns:protected] => Array
(
)
)
[80] => Category Object
(
[languages:protected] =>
[bok_resources:protected] =>
[bok_topics:protected] =>
[bok_keywords:protected] =>
[id:protected] => 80
[type:protected] => category
[parent:protected] => 2
[label:protected] => Sheetmetal Worker
[alreadyInSave:protected] =>
[alreadyInValidation:protected] =>
[validationFailures:protected] => Array
(
)
[_new:BaseObject:private] =>
[_deleted:BaseObject:private] =>
[modifiedColumns:protected] => Array
(
)
)
[62] => Category Object
(
[languages:protected] =>
[bok_resources:protected] =>
[bok_topics:protected] =>
[bok_keywords:protected] =>
[id:protected] => 62
[type:protected] => category
[parent:protected] => 2
[label:protected] => Structural Ironworker
[alreadyInSave:protected] =>
[alreadyInValidation:protected] =>
[validationFailures:protected] => Array
(
)
[_new:BaseObject:private] =>
[_deleted:BaseObject:private] =>
[modifiedColumns:protected] => Array
(
)
)
[87] => Category Object
(
[languages:protected] =>
[bok_resources:protected] =>
[bok_topics:protected] =>
[bok_keywords:protected] =>
[id:protected] => 87
[type:protected] => category
[parent:protected] => 3
[label:protected] => Commercial & Institutional
[alreadyInSave:protected] =>
[alreadyInValidation:protected] =>
[validationFailures:protected] => Array
(
)
[_new:BaseObject:private] =>
[_deleted:BaseObject:private] =>
[modifiedColumns:protected] => Array
(
)
)
[90] => Category Object
(
[languages:protected] =>
[bok_resources:protected] =>
[bok_topics:protected] =>
[bok_keywords:protected] =>
[id:protected] => 90
[type:protected] => category
[parent:protected] => 3
[label:protected] => Industrial
[alreadyInSave:protected] =>
[alreadyInValidation:protected] =>
[validationFailures:protected] => Array
(
)
[_new:BaseObject:private] =>
[_deleted:BaseObject:private] =>
[modifiedColumns:protected] => Array
(
)
)
[97] => Category Object
(
[languages:protected] =>
[bok_resources:protected] =>
[bok_topics:protected] =>
[bok_keywords:protected] =>
[id:protected] => 97
[type:protected] => category
[parent:protected] => 5
[label:protected] => Images
[alreadyInSave:protected] =>
[alreadyInValidation:protected] =>
[validationFailures:protected] => Array
(
)
[_new:BaseObject:private] =>
[_deleted:BaseObject:private] =>
[modifiedColumns:protected] => Array
(
)
)
)
[categories_initialized:protected] => 1
[mapped_items:protected] =>
[content:protected] =>
[files:protected] =>
[language:protected] => Language Object
(
[id:protected] => 1
[code:protected] => en
[name:protected] => English
[alreadyInSave:protected] =>
[alreadyInValidation:protected] =>
[validationFailures:protected] => Array
(
)
[_new:BaseObject:private] =>
[_deleted:BaseObject:private] =>
[modifiedColumns:protected] => Array
(
)
)
[old_record:protected] =>
[id:protected] => 3995
[old_id:protected] =>
[elcosh_id:protected] => i002690
[type:protected] => image
[display_type:protected] => Image
[user_id:protected] => 0
[language_id:protected] => 1
[tagging_id:protected] => Bruce Lippy
[priority_id:protected] => 1
[title:protected] => Construction bracing
[total_pages:protected] => 0
[billed_pages:protected] => 0
[publication_number:protected] =>
[part_of:protected] =>
[keywords:protected] => Bracing, support, scaffold
[comments:protected] =>
[summary:protected] => This shows structural support that prevents collapses during construction.
[transition_comments:protected] =>
[external_link:protected] =>
[consol_link:protected] => http://www.cpwrconstructionsolutions.org/masonry/solution/8/adjustable-tower-scaffold.html
[more_like_this:protected] => i002660
[permission_given_by:protected] =>
[published:protected] => T
[billable:protected] => F
[img_name:protected] =>
[img_ext:protected] => jpg
[img_width:protected] =>
[img_height:protected] =>
[img_credit:protected] => Photo by Pam Susi
[img_practice:protected] => good
[vid_source_id:protected] =>
[vid_running_time:protected] =>
[vid_intended_audience:protected] =>
[vid_acquisition_info:protected] =>
[vid_cost:protected] =>
[vid_producer:protected] =>
[vid_filename:protected] =>
[vid_filename_downloadable:protected] =>
[date_summary:protected] => January 2016
[date_permission_requested:protected] =>
[date_permission_received:protected] =>
[date_review_needed:protected] =>
[date_received:protected] => 02/01/16
[date_completed:protected] => 02/01/16
[date_billed:protected] =>
[date_modified:protected] => 02/01/16
[collBokExports:protected] =>
[lastBokExportCriteria:BaseElcoshItem:private] =>
[alreadyInSave:protected] =>
[alreadyInValidation:protected] =>
[validationFailures:protected] => Array
(
)
[_new:BaseObject:private] =>
[_deleted:BaseObject:private] =>
[modifiedColumns:protected] => Array
(
)
)
)
)
[preview_mode] =>
[description] => Toolbox talks have been the main tool for communicating safety information on construction jobs for decades.
Unfortunately, there has been little research on what makes for effective toolbox talks. The IUOE National
Training Fund worked with OSHA and NIOSH to make sure their series of 24 Focus Four toolbox talks were based on the best recommendations for effective design. These toolbox talks accompany an entire package of training materials, but can be used alone. This guide points out the key features of these toolbox talks and how best to deliver them.
[keywords] => toolbox talks, tailgate talks
[related_items] => Array
(
[Toolbox Talks] => Array
(
[0] => DocumentRecord Object
(
[records:protected] => Array
(
)
[recordId:protected] =>
[searchWordClass:protected] =>
[searchWordPeerClass:protected] =>
[bok_record:protected] =>
[authors:protected] =>
[organizations:protected] =>
[collections:protected] =>
[categories:protected] =>
[categories_initialized:protected] =>
[mapped_items:protected] =>
[content:protected] =>
[files:protected] =>
[language:protected] => Language Object
(
[id:protected] => 1
[code:protected] => en
[name:protected] => English
[alreadyInSave:protected] =>
[alreadyInValidation:protected] =>
[validationFailures:protected] => Array
(
)
[_new:BaseObject:private] =>
[_deleted:BaseObject:private] =>
[modifiedColumns:protected] => Array
(
)
)
[old_record:protected] =>
[id:protected] => 1605
[old_id:protected] => 1262
[elcosh_id:protected] => d001137
[type:protected] => document
[display_type:protected] => HTML w/ PDF
[user_id:protected] =>
[language_id:protected] => 1
[tagging_id:protected] => Garber
[priority_id:protected] => 1
[title:protected] => Focus Four Toolbox Talks, Module 1 – Falls, Talk #2 – Falls from debris piles?
[total_pages:protected] => 1
[billed_pages:protected] => 1
[publication_number:protected] =>
[part_of:protected] =>
[keywords:protected] => disaster response, hazard clean-up, uneven surface, disaster site, disaster clean-up
[comments:protected] =>
[summary:protected] => A toolbox talk on preventing falls from debris piles. Includes questions to ask, an incident to discuss with images, and a place to record questions the trainer would like to ask about the incident. Part of a collection. Click on the 'collection' button to access the other items.
[transition_comments:protected] =>
[external_link:protected] =>
[consol_link:protected] => http://www.cpwrconstructionsolutions.org/roofing/hazard/1463/install-asphalt-roofs-fall-from-heights.html
[more_like_this:protected] => a000081,d000478,d000530
[permission_given_by:protected] =>
[published:protected] => T
[billable:protected] => F
[img_name:protected] =>
[img_ext:protected] =>
[img_width:protected] =>
[img_height:protected] =>
[img_credit:protected] =>
[img_practice:protected] =>
[vid_source_id:protected] =>
[vid_running_time:protected] =>
[vid_intended_audience:protected] =>
[vid_acquisition_info:protected] =>
[vid_cost:protected] =>
[vid_producer:protected] =>
[vid_filename:protected] =>
[vid_filename_downloadable:protected] =>
[date_summary:protected] =>
[date_permission_requested:protected] =>
[date_permission_received:protected] =>
[date_review_needed:protected] =>
[date_received:protected] => 02/15/12
[date_completed:protected] => 03/19/12
[date_billed:protected] =>
[date_modified:protected] => 07/10/12
[collBokExports:protected] =>
[lastBokExportCriteria:BaseElcoshItem:private] =>
[alreadyInSave:protected] =>
[alreadyInValidation:protected] =>
[validationFailures:protected] => Array
(
)
[_new:BaseObject:private] =>
[_deleted:BaseObject:private] =>
[modifiedColumns:protected] => Array
(
)
)
[1] => DocumentRecord Object
(
[records:protected] => Array
(
)
[recordId:protected] =>
[searchWordClass:protected] =>
[searchWordPeerClass:protected] =>
[bok_record:protected] =>
[authors:protected] =>
[organizations:protected] =>
[collections:protected] =>
[categories:protected] =>
[categories_initialized:protected] =>
[mapped_items:protected] =>
[content:protected] =>
[files:protected] =>
[language:protected] => Language Object
(
[id:protected] => 1
[code:protected] => en
[name:protected] => English
[alreadyInSave:protected] =>
[alreadyInValidation:protected] =>
[validationFailures:protected] => Array
(
)
[_new:BaseObject:private] =>
[_deleted:BaseObject:private] =>
[modifiedColumns:protected] => Array
(
)
)
[old_record:protected] =>
[id:protected] => 1610
[old_id:protected] => 1271
[elcosh_id:protected] => d001146
[type:protected] => document
[display_type:protected] => HTML w/ PDF
[user_id:protected] => 0
[language_id:protected] => 1
[tagging_id:protected] => Garber
[priority_id:protected] => 1
[title:protected] => Focus Four Toolbox Talks, Module 2 – Struck-by, Talk #5 – Rigging and Securing Loads
[total_pages:protected] => 1
[billed_pages:protected] => 1
[publication_number:protected] =>
[part_of:protected] =>
[keywords:protected] => rigging, lift loads, loading areas, chains
[comments:protected] =>
[summary:protected] => A toolbox talk on preventing struck-by incidents caused by not securing loads properly. Includes questions to ask, an incident to discuss with images, and a place to record questions the trainer would like to ask about the incident. Part of a collection. Click on the 'collection' button to access the other items.
[transition_comments:protected] =>
[external_link:protected] =>
[consol_link:protected] => http://www.cpwrconstructionsolutions.org/heavy_equipment/hazard/1591/move-equipment-to-from-and-between-sites-work-zone-struck-by-injuries-and-fatalities.html
[more_like_this:protected] => d000144,d000360,d000873
[permission_given_by:protected] =>
[published:protected] => T
[billable:protected] => F
[img_name:protected] =>
[img_ext:protected] =>
[img_width:protected] =>
[img_height:protected] =>
[img_credit:protected] =>
[img_practice:protected] =>
[vid_source_id:protected] =>
[vid_running_time:protected] =>
[vid_intended_audience:protected] =>
[vid_acquisition_info:protected] =>
[vid_cost:protected] =>
[vid_producer:protected] =>
[vid_filename:protected] =>
[vid_filename_downloadable:protected] =>
[date_summary:protected] =>
[date_permission_requested:protected] =>
[date_permission_received:protected] =>
[date_review_needed:protected] =>
[date_received:protected] => 02/15/12
[date_completed:protected] => 03/28/12
[date_billed:protected] =>
[date_modified:protected] => 05/12/14
[collBokExports:protected] =>
[lastBokExportCriteria:BaseElcoshItem:private] =>
[alreadyInSave:protected] =>
[alreadyInValidation:protected] =>
[validationFailures:protected] => Array
(
)
[_new:BaseObject:private] =>
[_deleted:BaseObject:private] =>
[modifiedColumns:protected] => Array
(
)
)
[2] => DocumentRecord Object
(
[records:protected] => Array
(
)
[recordId:protected] =>
[searchWordClass:protected] =>
[searchWordPeerClass:protected] =>
[bok_record:protected] =>
[authors:protected] =>
[organizations:protected] =>
[collections:protected] =>
[categories:protected] =>
[categories_initialized:protected] =>
[mapped_items:protected] =>
[content:protected] =>
[files:protected] =>
[language:protected] => Language Object
(
[id:protected] => 1
[code:protected] => en
[name:protected] => English
[alreadyInSave:protected] =>
[alreadyInValidation:protected] =>
[validationFailures:protected] => Array
(
)
[_new:BaseObject:private] =>
[_deleted:BaseObject:private] =>
[modifiedColumns:protected] => Array
(
)
)
[old_record:protected] =>
[id:protected] => 1645
[old_id:protected] => 1274
[elcosh_id:protected] => d001149
[type:protected] => document
[display_type:protected] => HTML w/ PDF
[user_id:protected] => 0
[language_id:protected] => 1
[tagging_id:protected] => Garber
[priority_id:protected] => 1
[title:protected] => Focus Four Toolbox Talks, Module 3 – Caught-in/between, Talk #2 – Trenches & Heavy Equipment
[total_pages:protected] => 1
[billed_pages:protected] => 1
[publication_number:protected] =>
[part_of:protected] =>
[keywords:protected] => back-up alarms, spotter, soil cave-in, spoil pikes, ROPs, trenching, rain
[comments:protected] =>
[summary:protected] => A toolbox talk on preventing incidents involving trenches such as trench collapse. Includes questions to ask, an incident to discuss with images, and a place to record questions the trainer would like to ask about the incident. Part of a collection. Click on the 'collection' button to access the other items.
[transition_comments:protected] =>
[external_link:protected] =>
[consol_link:protected] =>
[more_like_this:protected] => d000019,d000035,d000168
[permission_given_by:protected] =>
[published:protected] => T
[billable:protected] => F
[img_name:protected] =>
[img_ext:protected] =>
[img_width:protected] =>
[img_height:protected] =>
[img_credit:protected] =>
[img_practice:protected] =>
[vid_source_id:protected] =>
[vid_running_time:protected] =>
[vid_intended_audience:protected] =>
[vid_acquisition_info:protected] =>
[vid_cost:protected] =>
[vid_producer:protected] =>
[vid_filename:protected] =>
[vid_filename_downloadable:protected] =>
[date_summary:protected] =>
[date_permission_requested:protected] =>
[date_permission_received:protected] =>
[date_review_needed:protected] =>
[date_received:protected] => 02/15/12
[date_completed:protected] => 04/02/12
[date_billed:protected] =>
[date_modified:protected] => 05/23/23
[collBokExports:protected] =>
[lastBokExportCriteria:BaseElcoshItem:private] =>
[alreadyInSave:protected] =>
[alreadyInValidation:protected] =>
[validationFailures:protected] => Array
(
)
[_new:BaseObject:private] =>
[_deleted:BaseObject:private] =>
[modifiedColumns:protected] => Array
(
)
)
[3] => DocumentRecord Object
(
[records:protected] => Array
(
)
[recordId:protected] =>
[searchWordClass:protected] =>
[searchWordPeerClass:protected] =>
[bok_record:protected] =>
[authors:protected] =>
[organizations:protected] =>
[collections:protected] =>
[categories:protected] =>
[categories_initialized:protected] =>
[mapped_items:protected] =>
[content:protected] =>
[files:protected] =>
[language:protected] => Language Object
(
[id:protected] => 1
[code:protected] => en
[name:protected] => English
[alreadyInSave:protected] =>
[alreadyInValidation:protected] =>
[validationFailures:protected] => Array
(
)
[_new:BaseObject:private] =>
[_deleted:BaseObject:private] =>
[modifiedColumns:protected] => Array
(
)
)
[old_record:protected] =>
[id:protected] => 1654
[old_id:protected] => 1284
[elcosh_id:protected] => d001159
[type:protected] => document
[display_type:protected] => HTML w/ PDF
[user_id:protected] => 0
[language_id:protected] => 1
[tagging_id:protected] => Garber
[priority_id:protected] => 1
[title:protected] => Focus Four Toolbox Talks, Module 4 – Electrocutions, Talk #6 – Hazards on Disaster Sites
[total_pages:protected] => 1
[billed_pages:protected] => 1
[publication_number:protected] =>
[part_of:protected] =>
[keywords:protected] => powerlines, underground, utilities, generators, wet conditions, GFCIs, energized lines, disasters, emergency response
[comments:protected] =>
[summary:protected] => A toolbox talk on how to avoid electrocution on a disaster site. Includes questions to ask, an incident to discuss with images, and a place to record questions the trainer would like to ask about the incident. Part of a collection. Click on the 'collection' button to access the other items.
[transition_comments:protected] =>
[external_link:protected] =>
[consol_link:protected] => http://www.cpwrconstructionsolutions.org/electrical/hazard/1138/install-and-repair-high-voltage-lines-transformers-switches-electrical-shocks-burns-and-or-electrocution.html
[more_like_this:protected] => d000135,d000361,d000437
[permission_given_by:protected] =>
[published:protected] => T
[billable:protected] => F
[img_name:protected] =>
[img_ext:protected] =>
[img_width:protected] =>
[img_height:protected] =>
[img_credit:protected] =>
[img_practice:protected] =>
[vid_source_id:protected] =>
[vid_running_time:protected] =>
[vid_intended_audience:protected] =>
[vid_acquisition_info:protected] =>
[vid_cost:protected] =>
[vid_producer:protected] =>
[vid_filename:protected] =>
[vid_filename_downloadable:protected] =>
[date_summary:protected] =>
[date_permission_requested:protected] =>
[date_permission_received:protected] =>
[date_review_needed:protected] =>
[date_received:protected] => 02/15/12
[date_completed:protected] => 04/02/12
[date_billed:protected] =>
[date_modified:protected] => 05/23/23
[collBokExports:protected] =>
[lastBokExportCriteria:BaseElcoshItem:private] =>
[alreadyInSave:protected] =>
[alreadyInValidation:protected] =>
[validationFailures:protected] => Array
(
)
[_new:BaseObject:private] =>
[_deleted:BaseObject:private] =>
[modifiedColumns:protected] => Array
(
)
)
)
)
[collections] => Array
(
[1294] =>
[1295] =>
[1292] =>
[1293] => CollectionRecord Object
(
[collection_items:protected] =>
[records:protected] => Array
(
)
[recordId:protected] =>
[searchWordClass:protected] =>
[searchWordPeerClass:protected] =>
[bok_record:protected] =>
[authors:protected] =>
[organizations:protected] =>
[collections:protected] =>
[categories:protected] =>
[categories_initialized:protected] =>
[mapped_items:protected] =>
[content:protected] =>
[files:protected] =>
[language:protected] =>
[old_record:protected] =>
[id:protected] => 1293
[old_id:protected] =>
[elcosh_id:protected] => c000026
[type:protected] => collection
[display_type:protected] => Collection
[user_id:protected] =>
[language_id:protected] =>
[tagging_id:protected] =>
[priority_id:protected] =>
[title:protected] => Focus Four-Struck By
[total_pages:protected] =>
[billed_pages:protected] =>
[publication_number:protected] =>
[part_of:protected] =>
[keywords:protected] =>
[comments:protected] =>
[summary:protected] => The following are links to all of the items in this collection:
[transition_comments:protected] =>
[external_link:protected] =>
[consol_link:protected] =>
[more_like_this:protected] =>
[permission_given_by:protected] =>
[published:protected] => T
[billable:protected] => F
[img_name:protected] =>
[img_ext:protected] =>
[img_width:protected] =>
[img_height:protected] =>
[img_credit:protected] =>
[img_practice:protected] =>
[vid_source_id:protected] =>
[vid_running_time:protected] =>
[vid_intended_audience:protected] =>
[vid_acquisition_info:protected] =>
[vid_cost:protected] =>
[vid_producer:protected] =>
[vid_filename:protected] =>
[vid_filename_downloadable:protected] =>
[date_summary:protected] =>
[date_permission_requested:protected] =>
[date_permission_received:protected] =>
[date_review_needed:protected] =>
[date_received:protected] => 05/08/12
[date_completed:protected] => 05/08/12
[date_billed:protected] =>
[date_modified:protected] => 05/08/12
[collBokExports:protected] =>
[lastBokExportCriteria:BaseElcoshItem:private] =>
[alreadyInSave:protected] =>
[alreadyInValidation:protected] =>
[validationFailures:protected] => Array
(
)
[_new:BaseObject:private] =>
[_deleted:BaseObject:private] =>
[modifiedColumns:protected] => Array
(
)
)
)
[record] => DocumentRecord Object
(
[records:protected] => Array
(
)
[recordId:protected] =>
[searchWordClass:protected] =>
[searchWordPeerClass:protected] =>
[bok_record:protected] =>
[authors:protected] => Array
(
)
[organizations:protected] => Array
(
[256] => Organization Object
(
[id:protected] => 256
[elcosh_id:protected] => o000276
[user_id:protected] => 14
[province_id:protected] => 0
[country_id:protected] => 0
[title:protected] => IUOE National Training Fund
[address:protected] =>
[postal_code:protected] =>
[city:protected] =>
[department:protected] =>
[phone:protected] => 304-253-8674
[fax:protected] =>
[email:protected] =>
[website:protected] => http://www.iuoeiettc.org
[filename:protected] =>
[about:protected] =>
[comments:protected] =>
[logo_available:protected] => T
[no_details:protected] => F
[date_received:protected] => 2012-02-13
[date_completed:protected] => 2012-02-13
[date_billed:protected] =>
[alreadyInSave:protected] =>
[alreadyInValidation:protected] =>
[validationFailures:protected] => Array
(
)
[_new:BaseObject:private] =>
[_deleted:BaseObject:private] =>
[modifiedColumns:protected] => Array
(
)
)
)
[collections:protected] => Array
(
[1294] =>
[1295] =>
[1292] =>
[1293] => CollectionRecord Object
(
[collection_items:protected] =>
[records:protected] => Array
(
)
[recordId:protected] =>
[searchWordClass:protected] =>
[searchWordPeerClass:protected] =>
[bok_record:protected] =>
[authors:protected] =>
[organizations:protected] =>
[collections:protected] =>
[categories:protected] =>
[categories_initialized:protected] =>
[mapped_items:protected] =>
[content:protected] =>
[files:protected] =>
[language:protected] =>
[old_record:protected] =>
[id:protected] => 1293
[old_id:protected] =>
[elcosh_id:protected] => c000026
[type:protected] => collection
[display_type:protected] => Collection
[user_id:protected] =>
[language_id:protected] =>
[tagging_id:protected] =>
[priority_id:protected] =>
[title:protected] => Focus Four-Struck By
[total_pages:protected] =>
[billed_pages:protected] =>
[publication_number:protected] =>
[part_of:protected] =>
[keywords:protected] =>
[comments:protected] =>
[summary:protected] => The following are links to all of the items in this collection:
[transition_comments:protected] =>
[external_link:protected] =>
[consol_link:protected] =>
[more_like_this:protected] =>
[permission_given_by:protected] =>
[published:protected] => T
[billable:protected] => F
[img_name:protected] =>
[img_ext:protected] =>
[img_width:protected] =>
[img_height:protected] =>
[img_credit:protected] =>
[img_practice:protected] =>
[vid_source_id:protected] =>
[vid_running_time:protected] =>
[vid_intended_audience:protected] =>
[vid_acquisition_info:protected] =>
[vid_cost:protected] =>
[vid_producer:protected] =>
[vid_filename:protected] =>
[vid_filename_downloadable:protected] =>
[date_summary:protected] =>
[date_permission_requested:protected] =>
[date_permission_received:protected] =>
[date_review_needed:protected] =>
[date_received:protected] => 05/08/12
[date_completed:protected] => 05/08/12
[date_billed:protected] =>
[date_modified:protected] => 05/08/12
[collBokExports:protected] =>
[lastBokExportCriteria:BaseElcoshItem:private] =>
[alreadyInSave:protected] =>
[alreadyInValidation:protected] =>
[validationFailures:protected] => Array
(
)
[_new:BaseObject:private] =>
[_deleted:BaseObject:private] =>
[modifiedColumns:protected] => Array
(
)
)
)
[categories:protected] =>
[categories_initialized:protected] =>
[mapped_items:protected] => Array
(
[1605] => DocumentRecord Object
(
[records:protected] => Array
(
)
[recordId:protected] =>
[searchWordClass:protected] =>
[searchWordPeerClass:protected] =>
[bok_record:protected] =>
[authors:protected] =>
[organizations:protected] =>
[collections:protected] =>
[categories:protected] =>
[categories_initialized:protected] =>
[mapped_items:protected] =>
[content:protected] =>
[files:protected] =>
[language:protected] =>
[old_record:protected] =>
[id:protected] => 1605
[old_id:protected] => 1262
[elcosh_id:protected] => d001137
[type:protected] => document
[display_type:protected] => HTML w/ PDF
[user_id:protected] =>
[language_id:protected] => 1
[tagging_id:protected] => Garber
[priority_id:protected] => 1
[title:protected] => Focus Four Toolbox Talks, Module 1 – Falls, Talk #2 – Falls from debris piles?
[total_pages:protected] => 1
[billed_pages:protected] => 1
[publication_number:protected] =>
[part_of:protected] =>
[keywords:protected] => disaster response, hazard clean-up, uneven surface, disaster site, disaster clean-up
[comments:protected] =>
[summary:protected] => A toolbox talk on preventing falls from debris piles. Includes questions to ask, an incident to discuss with images, and a place to record questions the trainer would like to ask about the incident. Part of a collection. Click on the 'collection' button to access the other items.
[transition_comments:protected] =>
[external_link:protected] =>
[consol_link:protected] => http://www.cpwrconstructionsolutions.org/roofing/hazard/1463/install-asphalt-roofs-fall-from-heights.html
[more_like_this:protected] => a000081,d000478,d000530
[permission_given_by:protected] =>
[published:protected] => T
[billable:protected] => F
[img_name:protected] =>
[img_ext:protected] =>
[img_width:protected] =>
[img_height:protected] =>
[img_credit:protected] =>
[img_practice:protected] =>
[vid_source_id:protected] =>
[vid_running_time:protected] =>
[vid_intended_audience:protected] =>
[vid_acquisition_info:protected] =>
[vid_cost:protected] =>
[vid_producer:protected] =>
[vid_filename:protected] =>
[vid_filename_downloadable:protected] =>
[date_summary:protected] =>
[date_permission_requested:protected] =>
[date_permission_received:protected] =>
[date_review_needed:protected] =>
[date_received:protected] => 02/15/12
[date_completed:protected] => 03/19/12
[date_billed:protected] =>
[date_modified:protected] => 07/10/12
[collBokExports:protected] =>
[lastBokExportCriteria:BaseElcoshItem:private] =>
[alreadyInSave:protected] =>
[alreadyInValidation:protected] =>
[validationFailures:protected] => Array
(
)
[_new:BaseObject:private] =>
[_deleted:BaseObject:private] =>
[modifiedColumns:protected] => Array
(
)
)
[1610] => DocumentRecord Object
(
[records:protected] => Array
(
)
[recordId:protected] =>
[searchWordClass:protected] =>
[searchWordPeerClass:protected] =>
[bok_record:protected] =>
[authors:protected] =>
[organizations:protected] =>
[collections:protected] =>
[categories:protected] =>
[categories_initialized:protected] =>
[mapped_items:protected] =>
[content:protected] =>
[files:protected] =>
[language:protected] =>
[old_record:protected] =>
[id:protected] => 1610
[old_id:protected] => 1271
[elcosh_id:protected] => d001146
[type:protected] => document
[display_type:protected] => HTML w/ PDF
[user_id:protected] => 0
[language_id:protected] => 1
[tagging_id:protected] => Garber
[priority_id:protected] => 1
[title:protected] => Focus Four Toolbox Talks, Module 2 – Struck-by, Talk #5 – Rigging and Securing Loads
[total_pages:protected] => 1
[billed_pages:protected] => 1
[publication_number:protected] =>
[part_of:protected] =>
[keywords:protected] => rigging, lift loads, loading areas, chains
[comments:protected] =>
[summary:protected] => A toolbox talk on preventing struck-by incidents caused by not securing loads properly. Includes questions to ask, an incident to discuss with images, and a place to record questions the trainer would like to ask about the incident. Part of a collection. Click on the 'collection' button to access the other items.
[transition_comments:protected] =>
[external_link:protected] =>
[consol_link:protected] => http://www.cpwrconstructionsolutions.org/heavy_equipment/hazard/1591/move-equipment-to-from-and-between-sites-work-zone-struck-by-injuries-and-fatalities.html
[more_like_this:protected] => d000144,d000360,d000873
[permission_given_by:protected] =>
[published:protected] => T
[billable:protected] => F
[img_name:protected] =>
[img_ext:protected] =>
[img_width:protected] =>
[img_height:protected] =>
[img_credit:protected] =>
[img_practice:protected] =>
[vid_source_id:protected] =>
[vid_running_time:protected] =>
[vid_intended_audience:protected] =>
[vid_acquisition_info:protected] =>
[vid_cost:protected] =>
[vid_producer:protected] =>
[vid_filename:protected] =>
[vid_filename_downloadable:protected] =>
[date_summary:protected] =>
[date_permission_requested:protected] =>
[date_permission_received:protected] =>
[date_review_needed:protected] =>
[date_received:protected] => 02/15/12
[date_completed:protected] => 03/28/12
[date_billed:protected] =>
[date_modified:protected] => 05/12/14
[collBokExports:protected] =>
[lastBokExportCriteria:BaseElcoshItem:private] =>
[alreadyInSave:protected] =>
[alreadyInValidation:protected] =>
[validationFailures:protected] => Array
(
)
[_new:BaseObject:private] =>
[_deleted:BaseObject:private] =>
[modifiedColumns:protected] => Array
(
)
)
[1645] => DocumentRecord Object
(
[records:protected] => Array
(
)
[recordId:protected] =>
[searchWordClass:protected] =>
[searchWordPeerClass:protected] =>
[bok_record:protected] =>
[authors:protected] =>
[organizations:protected] =>
[collections:protected] =>
[categories:protected] =>
[categories_initialized:protected] =>
[mapped_items:protected] =>
[content:protected] =>
[files:protected] =>
[language:protected] =>
[old_record:protected] =>
[id:protected] => 1645
[old_id:protected] => 1274
[elcosh_id:protected] => d001149
[type:protected] => document
[display_type:protected] => HTML w/ PDF
[user_id:protected] => 0
[language_id:protected] => 1
[tagging_id:protected] => Garber
[priority_id:protected] => 1
[title:protected] => Focus Four Toolbox Talks, Module 3 – Caught-in/between, Talk #2 – Trenches & Heavy Equipment
[total_pages:protected] => 1
[billed_pages:protected] => 1
[publication_number:protected] =>
[part_of:protected] =>
[keywords:protected] => back-up alarms, spotter, soil cave-in, spoil pikes, ROPs, trenching, rain
[comments:protected] =>
[summary:protected] => A toolbox talk on preventing incidents involving trenches such as trench collapse. Includes questions to ask, an incident to discuss with images, and a place to record questions the trainer would like to ask about the incident. Part of a collection. Click on the 'collection' button to access the other items.
[transition_comments:protected] =>
[external_link:protected] =>
[consol_link:protected] =>
[more_like_this:protected] => d000019,d000035,d000168
[permission_given_by:protected] =>
[published:protected] => T
[billable:protected] => F
[img_name:protected] =>
[img_ext:protected] =>
[img_width:protected] =>
[img_height:protected] =>
[img_credit:protected] =>
[img_practice:protected] =>
[vid_source_id:protected] =>
[vid_running_time:protected] =>
[vid_intended_audience:protected] =>
[vid_acquisition_info:protected] =>
[vid_cost:protected] =>
[vid_producer:protected] =>
[vid_filename:protected] =>
[vid_filename_downloadable:protected] =>
[date_summary:protected] =>
[date_permission_requested:protected] =>
[date_permission_received:protected] =>
[date_review_needed:protected] =>
[date_received:protected] => 02/15/12
[date_completed:protected] => 04/02/12
[date_billed:protected] =>
[date_modified:protected] => 05/23/23
[collBokExports:protected] =>
[lastBokExportCriteria:BaseElcoshItem:private] =>
[alreadyInSave:protected] =>
[alreadyInValidation:protected] =>
[validationFailures:protected] => Array
(
)
[_new:BaseObject:private] =>
[_deleted:BaseObject:private] =>
[modifiedColumns:protected] => Array
(
)
)
[1654] => DocumentRecord Object
(
[records:protected] => Array
(
)
[recordId:protected] =>
[searchWordClass:protected] =>
[searchWordPeerClass:protected] =>
[bok_record:protected] =>
[authors:protected] =>
[organizations:protected] =>
[collections:protected] =>
[categories:protected] =>
[categories_initialized:protected] =>
[mapped_items:protected] =>
[content:protected] =>
[files:protected] =>
[language:protected] =>
[old_record:protected] =>
[id:protected] => 1654
[old_id:protected] => 1284
[elcosh_id:protected] => d001159
[type:protected] => document
[display_type:protected] => HTML w/ PDF
[user_id:protected] => 0
[language_id:protected] => 1
[tagging_id:protected] => Garber
[priority_id:protected] => 1
[title:protected] => Focus Four Toolbox Talks, Module 4 – Electrocutions, Talk #6 – Hazards on Disaster Sites
[total_pages:protected] => 1
[billed_pages:protected] => 1
[publication_number:protected] =>
[part_of:protected] =>
[keywords:protected] => powerlines, underground, utilities, generators, wet conditions, GFCIs, energized lines, disasters, emergency response
[comments:protected] =>
[summary:protected] => A toolbox talk on how to avoid electrocution on a disaster site. Includes questions to ask, an incident to discuss with images, and a place to record questions the trainer would like to ask about the incident. Part of a collection. Click on the 'collection' button to access the other items.
[transition_comments:protected] =>
[external_link:protected] =>
[consol_link:protected] => http://www.cpwrconstructionsolutions.org/electrical/hazard/1138/install-and-repair-high-voltage-lines-transformers-switches-electrical-shocks-burns-and-or-electrocution.html
[more_like_this:protected] => d000135,d000361,d000437
[permission_given_by:protected] =>
[published:protected] => T
[billable:protected] => F
[img_name:protected] =>
[img_ext:protected] =>
[img_width:protected] =>
[img_height:protected] =>
[img_credit:protected] =>
[img_practice:protected] =>
[vid_source_id:protected] =>
[vid_running_time:protected] =>
[vid_intended_audience:protected] =>
[vid_acquisition_info:protected] =>
[vid_cost:protected] =>
[vid_producer:protected] =>
[vid_filename:protected] =>
[vid_filename_downloadable:protected] =>
[date_summary:protected] =>
[date_permission_requested:protected] =>
[date_permission_received:protected] =>
[date_review_needed:protected] =>
[date_received:protected] => 02/15/12
[date_completed:protected] => 04/02/12
[date_billed:protected] =>
[date_modified:protected] => 05/23/23
[collBokExports:protected] =>
[lastBokExportCriteria:BaseElcoshItem:private] =>
[alreadyInSave:protected] =>
[alreadyInValidation:protected] =>
[validationFailures:protected] => Array
(
)
[_new:BaseObject:private] =>
[_deleted:BaseObject:private] =>
[modifiedColumns:protected] => Array
(
)
)
)
[content:protected] =>
[files:protected] => Array
(
[9400] => File Object
(
[id:protected] => 9400
[filename:protected] => 1.jpg
[downloadable:protected] => F
[timestamp:protected] => 2014-05-08 15:05:37
[alreadyInSave:protected] =>
[alreadyInValidation:protected] =>
[validationFailures:protected] => Array
(
)
[_new:BaseObject:private] =>
[_deleted:BaseObject:private] =>
[modifiedColumns:protected] => Array
(
)
)
[9401] => File Object
(
[id:protected] => 9401
[filename:protected] => d001298.pdf
[downloadable:protected] => T
[timestamp:protected] => 2014-05-08 15:05:37
[alreadyInSave:protected] =>
[alreadyInValidation:protected] =>
[validationFailures:protected] => Array
(
)
[_new:BaseObject:private] =>
[_deleted:BaseObject:private] =>
[modifiedColumns:protected] => Array
(
)
)
)
[language:protected] => Language Object
(
[id:protected] => 1
[code:protected] => en
[name:protected] => English
[alreadyInSave:protected] =>
[alreadyInValidation:protected] =>
[validationFailures:protected] => Array
(
)
[_new:BaseObject:private] =>
[_deleted:BaseObject:private] =>
[modifiedColumns:protected] => Array
(
)
)
[old_record:protected] =>
[id:protected] => 3827
[old_id:protected] =>
[elcosh_id:protected] => d001298
[type:protected] => document
[display_type:protected] => HTML w/ PDF
[user_id:protected] => 23
[language_id:protected] => 1
[tagging_id:protected] => Bruce Lippy
[priority_id:protected] => 1
[title:protected] => Getting the most out of the IUOE Toolbox Talks
[total_pages:protected] => 2
[billed_pages:protected] => 2
[publication_number:protected] =>
[part_of:protected] =>
[keywords:protected] => toolbox talks, tailgate talks
[comments:protected] =>
[summary:protected] => Toolbox talks have been the main tool for communicating safety information on construction jobs for decades.
Unfortunately, there has been little research on what makes for effective toolbox talks. The IUOE National
Training Fund worked with OSHA and NIOSH to make sure their series of 24 Focus Four toolbox talks were based on the best recommendations for effective design. These toolbox talks accompany an entire package of training materials, but can be used alone. This guide points out the key features of these toolbox talks and how best to deliver them.
[transition_comments:protected] =>
[external_link:protected] =>
[consol_link:protected] =>
[more_like_this:protected] => d001137,d001146,d001149,d001159
[permission_given_by:protected] => IUOE National Hazmat Program
[published:protected] => T
[billable:protected] => F
[img_name:protected] =>
[img_ext:protected] => png
[img_width:protected] =>
[img_height:protected] =>
[img_credit:protected] =>
[img_practice:protected] =>
[vid_source_id:protected] =>
[vid_running_time:protected] =>
[vid_intended_audience:protected] =>
[vid_acquisition_info:protected] =>
[vid_cost:protected] =>
[vid_producer:protected] =>
[vid_filename:protected] =>
[vid_filename_downloadable:protected] =>
[date_summary:protected] => 2007
[date_permission_requested:protected] =>
[date_permission_received:protected] =>
[date_review_needed:protected] =>
[date_received:protected] => 05/08/14
[date_completed:protected] => 05/08/14
[date_billed:protected] =>
[date_modified:protected] => 05/08/14
[collBokExports:protected] =>
[lastBokExportCriteria:BaseElcoshItem:private] =>
[alreadyInSave:protected] =>
[alreadyInValidation:protected] =>
[validationFailures:protected] => Array
(
)
[_new:BaseObject:private] =>
[_deleted:BaseObject:private] =>
[modifiedColumns:protected] => Array
(
)
)
[show_text] =>
[document_content] => ElcoshItemDocumentContent Object
(
[id:protected] => 2896
[item_id:protected] => 3827
[type:protected] => main
[title:protected] =>
[content:protected] => Why were these talks developed?
Toolbox talks have been the main tool for communicating safety information on construction jobs for decades. Unfortunately, there has been almost no research on what makes for effective toolbox talks. The IUOE National Training Fund has worked with OSHA, the National Institute for Occupational Safety and Health and the Lippy Group, LLC to make sure these Focus Four toolbox talks are based on the latest fi ndings on the most effective design and tailored to the hazards operating engineers face daily. These toolbox talks accompany an entire package of training materials, but can be used alone. The way these are delivered is as important as how well they are designed.
What did NIOSH find out?
- Just handing out factsheets and toolbox talks to workers doesn’t work. Providing copies after toolbox talks doesn’t make much of an impact either.
- Using case studies (real life stories of accidents that ended in fatality or injury) in toolbox talks is effective.
- When toolbox talks containing case studies were accompanied by discussion questions to encourage group participation, they were more effective. Consequently, getting the workers to participate in the discussion about the case study is important. It’s not enough to tell the story, it is better to have the workers engage in problem solving that analyzes why the accident occurred and how it could have been prevented. Active learning is always better than passive.
How should you deliver these toolbox talks?
- Choose a topic that is related to work going on at the site.
- Hold the meeting on the job, preferably where everyone can sit and relax.
- Hold the meeting at the beginning of a shift or after a break. Folks are too tired at the end of a shift to carefully listen and they want to get home.
- Read the toolbox talk sheet on the topic prior to conducting the talk.
- Start at the top of the form and work right through to the end, which should take around 10 to 15 minutes. Guidance is provided in blue print to help you with each section.
- Use the questions provided to generate discussions. Always allow time for the crew to respond to your questions before you provide an answer. Some suggested responses are written in italics.
- Review the case study and emphasize that this was a real incident. Ask the crew for a case study before you review the one provided, however.
- Always end with a discussion of the particular worksite where you are conducting the talk. Tie the talk as closely to hazards on the site as possible and encourage the crew to constantly look for and immediately correct hazards. They should also know how to report any problems that can’t be immediately corrected.
- Provide copies to each person, if you like, but NIOSH has not found that to be particularly effective.
- Encourage workers to do similar talks on their sites and provide them with the IUOE phone number for ordering in bulk.
- Have everyone sign the back of the form to indicate they attended this session and point out it is a pledge to look out for the health and safety of everyone on the site.
What are the key features of these toolbox talks?

[content_transformed:protected] =>
Why were these talks developed?
Toolbox talks have been the main tool for communicating safety information on construction jobs for decades. Unfortunately, there has been almost no research on what makes for effective toolbox talks. The IUOE National Training Fund has worked with OSHA, the National Institute for Occupational Safety and Health and the Lippy Group, LLC to make sure these Focus Four toolbox talks are based on the latest fi ndings on the most effective design and tailored to the hazards operating engineers face daily. These toolbox talks accompany an entire package of training materials, but can be used alone. The way these are delivered is as important as how well they are designed.
What did NIOSH find out?
- Just handing out factsheets and toolbox talks to workers doesn’t work. Providing copies after toolbox talks doesn’t make much of an impact either.
- Using case studies (real life stories of accidents that ended in fatality or injury) in toolbox talks is effective.
- When toolbox talks containing case studies were accompanied by discussion questions to encourage group participation, they were more effective. Consequently, getting the workers to participate in the discussion about the case study is important. It’s not enough to tell the story, it is better to have the workers engage in problem solving that analyzes why the accident occurred and how it could have been prevented. Active learning is always better than passive.
How should you deliver these toolbox talks?
- Choose a topic that is related to work going on at the site.
- Hold the meeting on the job, preferably where everyone can sit and relax.
- Hold the meeting at the beginning of a shift or after a break. Folks are too tired at the end of a shift to carefully listen and they want to get home.
- Read the toolbox talk sheet on the topic prior to conducting the talk.
- Start at the top of the form and work right through to the end, which should take around 10 to 15 minutes. Guidance is provided in blue print to help you with each section.
- Use the questions provided to generate discussions. Always allow time for the crew to respond to your questions before you provide an answer. Some suggested responses are written in italics.
- Review the case study and emphasize that this was a real incident. Ask the crew for a case study before you review the one provided, however.
- Always end with a discussion of the particular worksite where you are conducting the talk. Tie the talk as closely to hazards on the site as possible and encourage the crew to constantly look for and immediately correct hazards. They should also know how to report any problems that can’t be immediately corrected.
- Provide copies to each person, if you like, but NIOSH has not found that to be particularly effective.
- Encourage workers to do similar talks on their sites and provide them with the IUOE phone number for ordering in bulk.
- Have everyone sign the back of the form to indicate they attended this session and point out it is a pledge to look out for the health and safety of everyone on the site.
What are the key features of these toolbox talks?
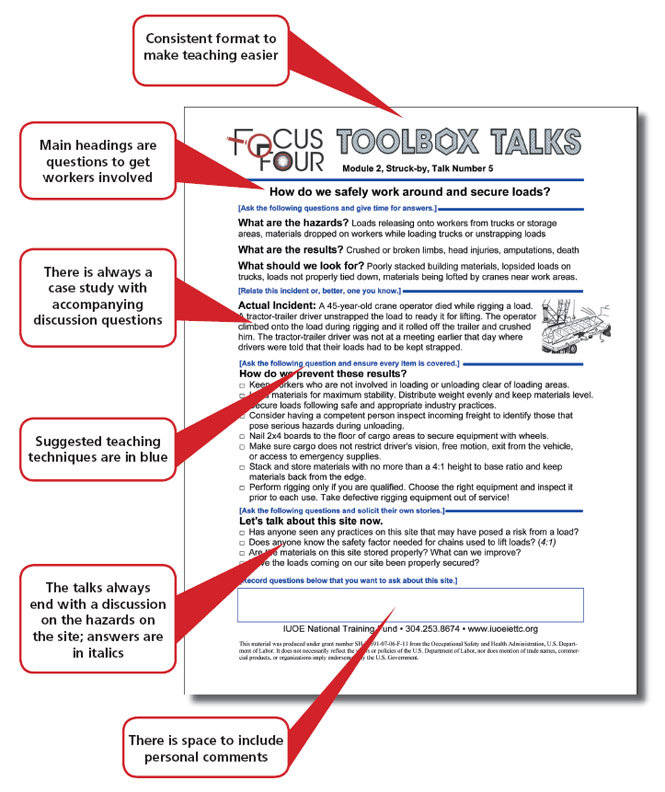
[disclaimer:protected] =>
[disclaimer_transformed:protected] =>
[alreadyInSave:protected] =>
[alreadyInValidation:protected] =>
[validationFailures:protected] => Array
(
)
[_new:BaseObject:private] =>
[_deleted:BaseObject:private] =>
[modifiedColumns:protected] => Array
(
)
)
[template] => record
)
[_globalContext:PHPTAL_Context:private] => stdClass Object
(
)
[_echoDeclarations:PHPTAL_Context:private] =>
[referer] => http://www.elcosh.org/document/3827/d001298/Getting%2Bthe%2Bmost%2Bout%2Bof%2Bthe%2BIUOE%2BToolbox%2BTalks.html
[curr_module] => Record
[styles] => Array
(
)
[javascript] => Array
(
[0] => jquery.min.js
)
[metas] => Array
(
[language] => en
[robots] => index, follow
)
[user] =>
[curr_url] => https://www.elcosh.org/index.php?module=Record&id=3827&type=document
[base_url] => https://www.elcosh.org/index.php?module=Record
[title] => eLCOSH : Getting the most out of the IUOE Toolbox Talks
[language] => en
[search_query] =>
[module] => Record
[new_records] => Array
(
[0] => Search_Result Object
(
[title] => Toolbox Talk: Fixed Ladder
[image] => /record/images/notavailable-p.png
[blurb] => The CPWR Toolbox Talk on Fixed Ladders addresses the potential risks associated with using fixed ladders. The resource includes a brief case example,...
[category] => Array
(
[0] => 15
[1] => 47
[2] => 49
[3] => 51
[4] => 53
[5] => 55
[6] => 60
[7] => 64
[8] => 73
[9] => 76
[10] => 78
[11] => 80
[12] => 86
[13] => 87
[14] => 90
[15] => 92
[16] => 93
[17] => 94
[18] => 100
)
[labels] => Array
(
[0] => Falls
[1] => Work Environment
[2] => Hazards
[3] => Bricklayer
[4] => Trades
[5] => Carpenter
[7] => Cement Mason
[9] => Concrete Polisher
[11] => Electrical Worker
[13] => HVAC
[15] => Laborer
[17] => PCC/Restoration
[19] => Plumber/Pipefitter
[21] => Roofer/Waterproofer
[23] => Sheetmetal Worker
[25] => Welder
[27] => Commercial & Institutional
[28] => Jobsites
[29] => Industrial
[31] => LEED/Green Construction
[33] => Renovations
[35] => Residential
[37] => Toolbox Talks
[38] => Documents
[39] => Media & Documents
)
[type] => Toolbox Talks
[sub_category] =>
[url] => /document/4430/d001660/Toolbox%2BTalk%253A%2BFixed%2BLadder.html
[item:protected] => DocumentRecord Object
(
[records:protected] => Array
(
)
[recordId:protected] =>
[searchWordClass:protected] =>
[searchWordPeerClass:protected] =>
[bok_record:protected] =>
[authors:protected] =>
[organizations:protected] =>
[collections:protected] =>
[categories:protected] => Array
(
[15] => Category Object
(
[languages:protected] =>
[bok_resources:protected] =>
[bok_topics:protected] =>
[bok_keywords:protected] =>
[id:protected] => 15
[type:protected] => category
[parent:protected] => 7
[label:protected] => Falls
[alreadyInSave:protected] =>
[alreadyInValidation:protected] =>
[validationFailures:protected] => Array
(
)
[_new:BaseObject:private] =>
[_deleted:BaseObject:private] =>
[modifiedColumns:protected] => Array
(
)
)
[47] => Category Object
(
[languages:protected] =>
[bok_resources:protected] =>
[bok_topics:protected] =>
[bok_keywords:protected] =>
[id:protected] => 47
[type:protected] => category
[parent:protected] => 2
[label:protected] => Bricklayer
[alreadyInSave:protected] =>
[alreadyInValidation:protected] =>
[validationFailures:protected] => Array
(
)
[_new:BaseObject:private] =>
[_deleted:BaseObject:private] =>
[modifiedColumns:protected] => Array
(
)
)
[49] => Category Object
(
[languages:protected] =>
[bok_resources:protected] =>
[bok_topics:protected] =>
[bok_keywords:protected] =>
[id:protected] => 49
[type:protected] => category
[parent:protected] => 2
[label:protected] => Carpenter
[alreadyInSave:protected] =>
[alreadyInValidation:protected] =>
[validationFailures:protected] => Array
(
)
[_new:BaseObject:private] =>
[_deleted:BaseObject:private] =>
[modifiedColumns:protected] => Array
(
)
)
[51] => Category Object
(
[languages:protected] =>
[bok_resources:protected] =>
[bok_topics:protected] =>
[bok_keywords:protected] =>
[id:protected] => 51
[type:protected] => category
[parent:protected] => 2
[label:protected] => Cement Mason
[alreadyInSave:protected] =>
[alreadyInValidation:protected] =>
[validationFailures:protected] => Array
(
)
[_new:BaseObject:private] =>
[_deleted:BaseObject:private] =>
[modifiedColumns:protected] => Array
(
)
)
[53] => Category Object
(
[languages:protected] =>
[bok_resources:protected] =>
[bok_topics:protected] =>
[bok_keywords:protected] =>
[id:protected] => 53
[type:protected] => category
[parent:protected] => 2
[label:protected] => Concrete Polisher
[alreadyInSave:protected] =>
[alreadyInValidation:protected] =>
[validationFailures:protected] => Array
(
)
[_new:BaseObject:private] =>
[_deleted:BaseObject:private] =>
[modifiedColumns:protected] => Array
(
)
)
[55] => Category Object
(
[languages:protected] =>
[bok_resources:protected] =>
[bok_topics:protected] =>
[bok_keywords:protected] =>
[id:protected] => 55
[type:protected] => category
[parent:protected] => 2
[label:protected] => Electrical Worker
[alreadyInSave:protected] =>
[alreadyInValidation:protected] =>
[validationFailures:protected] => Array
(
)
[_new:BaseObject:private] =>
[_deleted:BaseObject:private] =>
[modifiedColumns:protected] => Array
(
)
)
[60] => Category Object
(
[languages:protected] =>
[bok_resources:protected] =>
[bok_topics:protected] =>
[bok_keywords:protected] =>
[id:protected] => 60
[type:protected] => category
[parent:protected] => 2
[label:protected] => HVAC
[alreadyInSave:protected] =>
[alreadyInValidation:protected] =>
[validationFailures:protected] => Array
(
)
[_new:BaseObject:private] =>
[_deleted:BaseObject:private] =>
[modifiedColumns:protected] => Array
(
)
)
[64] => Category Object
(
[languages:protected] =>
[bok_resources:protected] =>
[bok_topics:protected] =>
[bok_keywords:protected] =>
[id:protected] => 64
[type:protected] => category
[parent:protected] => 2
[label:protected] => Laborer
[alreadyInSave:protected] =>
[alreadyInValidation:protected] =>
[validationFailures:protected] => Array
(
)
[_new:BaseObject:private] =>
[_deleted:BaseObject:private] =>
[modifiedColumns:protected] => Array
(
)
)
[73] => Category Object
(
[languages:protected] =>
[bok_resources:protected] =>
[bok_topics:protected] =>
[bok_keywords:protected] =>
[id:protected] => 73
[type:protected] => category
[parent:protected] => 2
[label:protected] => PCC/Restoration
[alreadyInSave:protected] =>
[alreadyInValidation:protected] =>
[validationFailures:protected] => Array
(
)
[_new:BaseObject:private] =>
[_deleted:BaseObject:private] =>
[modifiedColumns:protected] => Array
(
)
)
[76] => Category Object
(
[languages:protected] =>
[bok_resources:protected] =>
[bok_topics:protected] =>
[bok_keywords:protected] =>
[id:protected] => 76
[type:protected] => category
[parent:protected] => 2
[label:protected] => Plumber/Pipefitter
[alreadyInSave:protected] =>
[alreadyInValidation:protected] =>
[validationFailures:protected] => Array
(
)
[_new:BaseObject:private] =>
[_deleted:BaseObject:private] =>
[modifiedColumns:protected] => Array
(
)
)
[78] => Category Object
(
[languages:protected] =>
[bok_resources:protected] =>
[bok_topics:protected] =>
[bok_keywords:protected] =>
[id:protected] => 78
[type:protected] => category
[parent:protected] => 2
[label:protected] => Roofer/Waterproofer
[alreadyInSave:protected] =>
[alreadyInValidation:protected] =>
[validationFailures:protected] => Array
(
)
[_new:BaseObject:private] =>
[_deleted:BaseObject:private] =>
[modifiedColumns:protected] => Array
(
)
)
[80] => Category Object
(
[languages:protected] =>
[bok_resources:protected] =>
[bok_topics:protected] =>
[bok_keywords:protected] =>
[id:protected] => 80
[type:protected] => category
[parent:protected] => 2
[label:protected] => Sheetmetal Worker
[alreadyInSave:protected] =>
[alreadyInValidation:protected] =>
[validationFailures:protected] => Array
(
)
[_new:BaseObject:private] =>
[_deleted:BaseObject:private] =>
[modifiedColumns:protected] => Array
(
)
)
[86] => Category Object
(
[languages:protected] =>
[bok_resources:protected] =>
[bok_topics:protected] =>
[bok_keywords:protected] =>
[id:protected] => 86
[type:protected] => category
[parent:protected] => 2
[label:protected] => Welder
[alreadyInSave:protected] =>
[alreadyInValidation:protected] =>
[validationFailures:protected] => Array
(
)
[_new:BaseObject:private] =>
[_deleted:BaseObject:private] =>
[modifiedColumns:protected] => Array
(
)
)
[87] => Category Object
(
[languages:protected] =>
[bok_resources:protected] =>
[bok_topics:protected] =>
[bok_keywords:protected] =>
[id:protected] => 87
[type:protected] => category
[parent:protected] => 3
[label:protected] => Commercial & Institutional
[alreadyInSave:protected] =>
[alreadyInValidation:protected] =>
[validationFailures:protected] => Array
(
)
[_new:BaseObject:private] =>
[_deleted:BaseObject:private] =>
[modifiedColumns:protected] => Array
(
)
)
[90] => Category Object
(
[languages:protected] =>
[bok_resources:protected] =>
[bok_topics:protected] =>
[bok_keywords:protected] =>
[id:protected] => 90
[type:protected] => category
[parent:protected] => 3
[label:protected] => Industrial
[alreadyInSave:protected] =>
[alreadyInValidation:protected] =>
[validationFailures:protected] => Array
(
)
[_new:BaseObject:private] =>
[_deleted:BaseObject:private] =>
[modifiedColumns:protected] => Array
(
)
)
[92] => Category Object
(
[languages:protected] =>
[bok_resources:protected] =>
[bok_topics:protected] =>
[bok_keywords:protected] =>
[id:protected] => 92
[type:protected] => category
[parent:protected] => 3
[label:protected] => LEED/Green Construction
[alreadyInSave:protected] =>
[alreadyInValidation:protected] =>
[validationFailures:protected] => Array
(
)
[_new:BaseObject:private] =>
[_deleted:BaseObject:private] =>
[modifiedColumns:protected] => Array
(
)
)
[93] => Category Object
(
[languages:protected] =>
[bok_resources:protected] =>
[bok_topics:protected] =>
[bok_keywords:protected] =>
[id:protected] => 93
[type:protected] => category
[parent:protected] => 3
[label:protected] => Renovations
[alreadyInSave:protected] =>
[alreadyInValidation:protected] =>
[validationFailures:protected] => Array
(
)
[_new:BaseObject:private] =>
[_deleted:BaseObject:private] =>
[modifiedColumns:protected] => Array
(
)
)
[94] => Category Object
(
[languages:protected] =>
[bok_resources:protected] =>
[bok_topics:protected] =>
[bok_keywords:protected] =>
[id:protected] => 94
[type:protected] => category
[parent:protected] => 3
[label:protected] => Residential
[alreadyInSave:protected] =>
[alreadyInValidation:protected] =>
[validationFailures:protected] => Array
(
)
[_new:BaseObject:private] =>
[_deleted:BaseObject:private] =>
[modifiedColumns:protected] => Array
(
)
)
[100] => Category Object
(
[languages:protected] =>
[bok_resources:protected] =>
[bok_topics:protected] =>
[bok_keywords:protected] =>
[id:protected] => 100
[type:protected] => category
[parent:protected] => 6
[label:protected] => Toolbox Talks
[alreadyInSave:protected] =>
[alreadyInValidation:protected] =>
[validationFailures:protected] => Array
(
)
[_new:BaseObject:private] =>
[_deleted:BaseObject:private] =>
[modifiedColumns:protected] => Array
(
)
)
)
[categories_initialized:protected] => 1
[mapped_items:protected] =>
[content:protected] =>
[files:protected] =>
[language:protected] => Language Object
(
[id:protected] => 1
[code:protected] => en
[name:protected] => English
[alreadyInSave:protected] =>
[alreadyInValidation:protected] =>
[validationFailures:protected] => Array
(
)
[_new:BaseObject:private] =>
[_deleted:BaseObject:private] =>
[modifiedColumns:protected] => Array
(
)
)
[old_record:protected] =>
[id:protected] => 4430
[old_id:protected] =>
[elcosh_id:protected] => d001660
[type:protected] => document
[display_type:protected] => HTML only (and links)
[user_id:protected] => 0
[language_id:protected] => 1
[tagging_id:protected] => Mike Aguilar
[priority_id:protected] => 1
[title:protected] => Toolbox Talk: Fixed Ladder
[total_pages:protected] => 0
[billed_pages:protected] => 0
[publication_number:protected] =>
[part_of:protected] =>
[keywords:protected] => Fixed Ladders, Fall Prevention, Falls
[comments:protected] =>
[summary:protected] => The CPWR Toolbox Talk on Fixed Ladders addresses the potential risks associated with using fixed ladders. The resource includes a brief case example, steps to prevent a related injury and questions for discussion. It includes an image that illustrates the hazard, which can be posted in a central location as a reminder of steps to work safely.
Available in
English
and
Spanish.
[transition_comments:protected] =>
[external_link:protected] =>
[consol_link:protected] =>
[more_like_this:protected] => d001257,d001254,d001255,d001256,d001258,d001262,d001279
[permission_given_by:protected] =>
[published:protected] => T
[billable:protected] => F
[img_name:protected] =>
[img_ext:protected] =>
[img_width:protected] =>
[img_height:protected] =>
[img_credit:protected] =>
[img_practice:protected] =>
[vid_source_id:protected] =>
[vid_running_time:protected] =>
[vid_intended_audience:protected] =>
[vid_acquisition_info:protected] =>
[vid_cost:protected] =>
[vid_producer:protected] =>
[vid_filename:protected] =>
[vid_filename_downloadable:protected] =>
[date_summary:protected] =>
[date_permission_requested:protected] =>
[date_permission_received:protected] =>
[date_review_needed:protected] =>
[date_received:protected] => 06/10/22
[date_completed:protected] => 06/10/22
[date_billed:protected] =>
[date_modified:protected] => 05/22/23
[collBokExports:protected] =>
[lastBokExportCriteria:BaseElcoshItem:private] =>
[alreadyInSave:protected] =>
[alreadyInValidation:protected] =>
[validationFailures:protected] => Array
(
)
[_new:BaseObject:private] =>
[_deleted:BaseObject:private] =>
[modifiedColumns:protected] => Array
(
)
)
)
[1] => Search_Result Object
(
[title] => Toolbox Talk: Challenges Preventing Falling Objects
[image] => /record/images/notavailable-p.png
[blurb] => The CPWR Toolbox Talk on Challenges Preventing Falling Objects addresses the hazards of being struck by falling objects on the job site. The resource...
[category] => Array
(
[0] => 12
[1] => 47
[2] => 49
[3] => 51
[4] => 55
[5] => 64
[6] => 68
[7] => 71
[8] => 75
[9] => 78
[10] => 79
[11] => 82
[12] => 62
[13] => 86
[14] => 87
[15] => 88
[16] => 89
[17] => 91
[18] => 90
[19] => 92
[20] => 93
[21] => 94
[22] => 95
[23] => 100
)
[labels] => Array
(
[0] => Crushed/Struck By
[1] => Work Environment
[2] => Hazards
[3] => Bricklayer
[4] => Trades
[5] => Carpenter
[7] => Cement Mason
[9] => Electrical Worker
[11] => Laborer
[13] => Maintenance Worker
[15] => Painter
[17] => Plasterer
[19] => Roofer/Waterproofer
[21] => Scaffold Erector
[23] => Stonemason
[25] => Structural Ironworker
[27] => Welder
[29] => Commercial & Institutional
[30] => Jobsites
[31] => Demolition
[33] => Disasters
[35] => Heavy & Highway
[37] => Industrial
[39] => LEED/Green Construction
[41] => Renovations
[43] => Residential
[45] => Underground
[47] => Toolbox Talks
[48] => Documents
[49] => Media & Documents
)
[type] => Toolbox Talks
[sub_category] =>
[url] => /document/4431/d001661/Toolbox%2BTalk%253A%2BChallenges%2BPreventing%2BFalling%2BObjects.html
[item:protected] => DocumentRecord Object
(
[records:protected] => Array
(
)
[recordId:protected] =>
[searchWordClass:protected] =>
[searchWordPeerClass:protected] =>
[bok_record:protected] =>
[authors:protected] =>
[organizations:protected] =>
[collections:protected] =>
[categories:protected] => Array
(
[12] => Category Object
(
[languages:protected] =>
[bok_resources:protected] =>
[bok_topics:protected] =>
[bok_keywords:protected] =>
[id:protected] => 12
[type:protected] => category
[parent:protected] => 7
[label:protected] => Crushed/Struck By
[alreadyInSave:protected] =>
[alreadyInValidation:protected] =>
[validationFailures:protected] => Array
(
)
[_new:BaseObject:private] =>
[_deleted:BaseObject:private] =>
[modifiedColumns:protected] => Array
(
)
)
[47] => Category Object
(
[languages:protected] =>
[bok_resources:protected] =>
[bok_topics:protected] =>
[bok_keywords:protected] =>
[id:protected] => 47
[type:protected] => category
[parent:protected] => 2
[label:protected] => Bricklayer
[alreadyInSave:protected] =>
[alreadyInValidation:protected] =>
[validationFailures:protected] => Array
(
)
[_new:BaseObject:private] =>
[_deleted:BaseObject:private] =>
[modifiedColumns:protected] => Array
(
)
)
[49] => Category Object
(
[languages:protected] =>
[bok_resources:protected] =>
[bok_topics:protected] =>
[bok_keywords:protected] =>
[id:protected] => 49
[type:protected] => category
[parent:protected] => 2
[label:protected] => Carpenter
[alreadyInSave:protected] =>
[alreadyInValidation:protected] =>
[validationFailures:protected] => Array
(
)
[_new:BaseObject:private] =>
[_deleted:BaseObject:private] =>
[modifiedColumns:protected] => Array
(
)
)
[51] => Category Object
(
[languages:protected] =>
[bok_resources:protected] =>
[bok_topics:protected] =>
[bok_keywords:protected] =>
[id:protected] => 51
[type:protected] => category
[parent:protected] => 2
[label:protected] => Cement Mason
[alreadyInSave:protected] =>
[alreadyInValidation:protected] =>
[validationFailures:protected] => Array
(
)
[_new:BaseObject:private] =>
[_deleted:BaseObject:private] =>
[modifiedColumns:protected] => Array
(
)
)
[55] => Category Object
(
[languages:protected] =>
[bok_resources:protected] =>
[bok_topics:protected] =>
[bok_keywords:protected] =>
[id:protected] => 55
[type:protected] => category
[parent:protected] => 2
[label:protected] => Electrical Worker
[alreadyInSave:protected] =>
[alreadyInValidation:protected] =>
[validationFailures:protected] => Array
(
)
[_new:BaseObject:private] =>
[_deleted:BaseObject:private] =>
[modifiedColumns:protected] => Array
(
)
)
[64] => Category Object
(
[languages:protected] =>
[bok_resources:protected] =>
[bok_topics:protected] =>
[bok_keywords:protected] =>
[id:protected] => 64
[type:protected] => category
[parent:protected] => 2
[label:protected] => Laborer
[alreadyInSave:protected] =>
[alreadyInValidation:protected] =>
[validationFailures:protected] => Array
(
)
[_new:BaseObject:private] =>
[_deleted:BaseObject:private] =>
[modifiedColumns:protected] => Array
(
)
)
[68] => Category Object
(
[languages:protected] =>
[bok_resources:protected] =>
[bok_topics:protected] =>
[bok_keywords:protected] =>
[id:protected] => 68
[type:protected] => category
[parent:protected] => 2
[label:protected] => Maintenance Worker
[alreadyInSave:protected] =>
[alreadyInValidation:protected] =>
[validationFailures:protected] => Array
(
)
[_new:BaseObject:private] =>
[_deleted:BaseObject:private] =>
[modifiedColumns:protected] => Array
(
)
)
[71] => Category Object
(
[languages:protected] =>
[bok_resources:protected] =>
[bok_topics:protected] =>
[bok_keywords:protected] =>
[id:protected] => 71
[type:protected] => category
[parent:protected] => 2
[label:protected] => Painter
[alreadyInSave:protected] =>
[alreadyInValidation:protected] =>
[validationFailures:protected] => Array
(
)
[_new:BaseObject:private] =>
[_deleted:BaseObject:private] =>
[modifiedColumns:protected] => Array
(
)
)
[75] => Category Object
(
[languages:protected] =>
[bok_resources:protected] =>
[bok_topics:protected] =>
[bok_keywords:protected] =>
[id:protected] => 75
[type:protected] => category
[parent:protected] => 2
[label:protected] => Plasterer
[alreadyInSave:protected] =>
[alreadyInValidation:protected] =>
[validationFailures:protected] => Array
(
)
[_new:BaseObject:private] =>
[_deleted:BaseObject:private] =>
[modifiedColumns:protected] => Array
(
)
)
[78] => Category Object
(
[languages:protected] =>
[bok_resources:protected] =>
[bok_topics:protected] =>
[bok_keywords:protected] =>
[id:protected] => 78
[type:protected] => category
[parent:protected] => 2
[label:protected] => Roofer/Waterproofer
[alreadyInSave:protected] =>
[alreadyInValidation:protected] =>
[validationFailures:protected] => Array
(
)
[_new:BaseObject:private] =>
[_deleted:BaseObject:private] =>
[modifiedColumns:protected] => Array
(
)
)
[79] => Category Object
(
[languages:protected] =>
[bok_resources:protected] =>
[bok_topics:protected] =>
[bok_keywords:protected] =>
[id:protected] => 79
[type:protected] => category
[parent:protected] => 2
[label:protected] => Scaffold Erector
[alreadyInSave:protected] =>
[alreadyInValidation:protected] =>
[validationFailures:protected] => Array
(
)
[_new:BaseObject:private] =>
[_deleted:BaseObject:private] =>
[modifiedColumns:protected] => Array
(
)
)
[82] => Category Object
(
[languages:protected] =>
[bok_resources:protected] =>
[bok_topics:protected] =>
[bok_keywords:protected] =>
[id:protected] => 82
[type:protected] => category
[parent:protected] => 2
[label:protected] => Stonemason
[alreadyInSave:protected] =>
[alreadyInValidation:protected] =>
[validationFailures:protected] => Array
(
)
[_new:BaseObject:private] =>
[_deleted:BaseObject:private] =>
[modifiedColumns:protected] => Array
(
)
)
[62] => Category Object
(
[languages:protected] =>
[bok_resources:protected] =>
[bok_topics:protected] =>
[bok_keywords:protected] =>
[id:protected] => 62
[type:protected] => category
[parent:protected] => 2
[label:protected] => Structural Ironworker
[alreadyInSave:protected] =>
[alreadyInValidation:protected] =>
[validationFailures:protected] => Array
(
)
[_new:BaseObject:private] =>
[_deleted:BaseObject:private] =>
[modifiedColumns:protected] => Array
(
)
)
[86] => Category Object
(
[languages:protected] =>
[bok_resources:protected] =>
[bok_topics:protected] =>
[bok_keywords:protected] =>
[id:protected] => 86
[type:protected] => category
[parent:protected] => 2
[label:protected] => Welder
[alreadyInSave:protected] =>
[alreadyInValidation:protected] =>
[validationFailures:protected] => Array
(
)
[_new:BaseObject:private] =>
[_deleted:BaseObject:private] =>
[modifiedColumns:protected] => Array
(
)
)
[87] => Category Object
(
[languages:protected] =>
[bok_resources:protected] =>
[bok_topics:protected] =>
[bok_keywords:protected] =>
[id:protected] => 87
[type:protected] => category
[parent:protected] => 3
[label:protected] => Commercial & Institutional
[alreadyInSave:protected] =>
[alreadyInValidation:protected] =>
[validationFailures:protected] => Array
(
)
[_new:BaseObject:private] =>
[_deleted:BaseObject:private] =>
[modifiedColumns:protected] => Array
(
)
)
[88] => Category Object
(
[languages:protected] =>
[bok_resources:protected] =>
[bok_topics:protected] =>
[bok_keywords:protected] =>
[id:protected] => 88
[type:protected] => category
[parent:protected] => 3
[label:protected] => Demolition
[alreadyInSave:protected] =>
[alreadyInValidation:protected] =>
[validationFailures:protected] => Array
(
)
[_new:BaseObject:private] =>
[_deleted:BaseObject:private] =>
[modifiedColumns:protected] => Array
(
)
)
[89] => Category Object
(
[languages:protected] =>
[bok_resources:protected] =>
[bok_topics:protected] =>
[bok_keywords:protected] =>
[id:protected] => 89
[type:protected] => category
[parent:protected] => 3
[label:protected] => Disasters
[alreadyInSave:protected] =>
[alreadyInValidation:protected] =>
[validationFailures:protected] => Array
(
)
[_new:BaseObject:private] =>
[_deleted:BaseObject:private] =>
[modifiedColumns:protected] => Array
(
)
)
[91] => Category Object
(
[languages:protected] =>
[bok_resources:protected] =>
[bok_topics:protected] =>
[bok_keywords:protected] =>
[id:protected] => 91
[type:protected] => category
[parent:protected] => 3
[label:protected] => Heavy & Highway
[alreadyInSave:protected] =>
[alreadyInValidation:protected] =>
[validationFailures:protected] => Array
(
)
[_new:BaseObject:private] =>
[_deleted:BaseObject:private] =>
[modifiedColumns:protected] => Array
(
)
)
[90] => Category Object
(
[languages:protected] =>
[bok_resources:protected] =>
[bok_topics:protected] =>
[bok_keywords:protected] =>
[id:protected] => 90
[type:protected] => category
[parent:protected] => 3
[label:protected] => Industrial
[alreadyInSave:protected] =>
[alreadyInValidation:protected] =>
[validationFailures:protected] => Array
(
)
[_new:BaseObject:private] =>
[_deleted:BaseObject:private] =>
[modifiedColumns:protected] => Array
(
)
)
[92] => Category Object
(
[languages:protected] =>
[bok_resources:protected] =>
[bok_topics:protected] =>
[bok_keywords:protected] =>
[id:protected] => 92
[type:protected] => category
[parent:protected] => 3
[label:protected] => LEED/Green Construction
[alreadyInSave:protected] =>
[alreadyInValidation:protected] =>
[validationFailures:protected] => Array
(
)
[_new:BaseObject:private] =>
[_deleted:BaseObject:private] =>
[modifiedColumns:protected] => Array
(
)
)
[93] => Category Object
(
[languages:protected] =>
[bok_resources:protected] =>
[bok_topics:protected] =>
[bok_keywords:protected] =>
[id:protected] => 93
[type:protected] => category
[parent:protected] => 3
[label:protected] => Renovations
[alreadyInSave:protected] =>
[alreadyInValidation:protected] =>
[validationFailures:protected] => Array
(
)
[_new:BaseObject:private] =>
[_deleted:BaseObject:private] =>
[modifiedColumns:protected] => Array
(
)
)
[94] => Category Object
(
[languages:protected] =>
[bok_resources:protected] =>
[bok_topics:protected] =>
[bok_keywords:protected] =>
[id:protected] => 94
[type:protected] => category
[parent:protected] => 3
[label:protected] => Residential
[alreadyInSave:protected] =>
[alreadyInValidation:protected] =>
[validationFailures:protected] => Array
(
)
[_new:BaseObject:private] =>
[_deleted:BaseObject:private] =>
[modifiedColumns:protected] => Array
(
)
)
[95] => Category Object
(
[languages:protected] =>
[bok_resources:protected] =>
[bok_topics:protected] =>
[bok_keywords:protected] =>
[id:protected] => 95
[type:protected] => category
[parent:protected] => 3
[label:protected] => Underground
[alreadyInSave:protected] =>
[alreadyInValidation:protected] =>
[validationFailures:protected] => Array
(
)
[_new:BaseObject:private] =>
[_deleted:BaseObject:private] =>
[modifiedColumns:protected] => Array
(
)
)
[100] => Category Object
(
[languages:protected] =>
[bok_resources:protected] =>
[bok_topics:protected] =>
[bok_keywords:protected] =>
[id:protected] => 100
[type:protected] => category
[parent:protected] => 6
[label:protected] => Toolbox Talks
[alreadyInSave:protected] =>
[alreadyInValidation:protected] =>
[validationFailures:protected] => Array
(
)
[_new:BaseObject:private] =>
[_deleted:BaseObject:private] =>
[modifiedColumns:protected] => Array
(
)
)
)
[categories_initialized:protected] => 1
[mapped_items:protected] =>
[content:protected] =>
[files:protected] =>
[language:protected] => Language Object
(
[id:protected] => 1
[code:protected] => en
[name:protected] => English
[alreadyInSave:protected] =>
[alreadyInValidation:protected] =>
[validationFailures:protected] => Array
(
)
[_new:BaseObject:private] =>
[_deleted:BaseObject:private] =>
[modifiedColumns:protected] => Array
(
)
)
[old_record:protected] =>
[id:protected] => 4431
[old_id:protected] =>
[elcosh_id:protected] => d001661
[type:protected] => document
[display_type:protected] => HTML only (and links)
[user_id:protected] => 0
[language_id:protected] => 1
[tagging_id:protected] => Mike Aguilar
[priority_id:protected] => 1
[title:protected] => Toolbox Talk: Challenges Preventing Falling Objects
[total_pages:protected] => 0
[billed_pages:protected] => 0
[publication_number:protected] =>
[part_of:protected] =>
[keywords:protected] => dropped objects, falling objects, struck by incidents, struck by fatalities
[comments:protected] =>
[summary:protected] => The CPWR Toolbox Talk on Challenges Preventing Falling Objects addresses the hazards of being struck by falling objects on the job site. The resource includes a brief example, steps to prevent a related injury, and questions for discussion. It includes a graphic that illustrates a group workers observing a scaffold free of debris during high winds, which can be posted in a central location as a reminder of steps to work safely.
Available in
English and
Spanish.
[transition_comments:protected] =>
[external_link:protected] =>
[consol_link:protected] =>
[more_like_this:protected] => d001234,d001238,d001244,d001251,d001253,d001260,d001268,d001278
[permission_given_by:protected] =>
[published:protected] => T
[billable:protected] => F
[img_name:protected] =>
[img_ext:protected] =>
[img_width:protected] =>
[img_height:protected] =>
[img_credit:protected] =>
[img_practice:protected] =>
[vid_source_id:protected] =>
[vid_running_time:protected] =>
[vid_intended_audience:protected] =>
[vid_acquisition_info:protected] =>
[vid_cost:protected] =>
[vid_producer:protected] =>
[vid_filename:protected] =>
[vid_filename_downloadable:protected] =>
[date_summary:protected] =>
[date_permission_requested:protected] =>
[date_permission_received:protected] =>
[date_review_needed:protected] =>
[date_received:protected] => 06/10/22
[date_completed:protected] => 06/10/22
[date_billed:protected] =>
[date_modified:protected] => 05/22/23
[collBokExports:protected] =>
[lastBokExportCriteria:BaseElcoshItem:private] =>
[alreadyInSave:protected] =>
[alreadyInValidation:protected] =>
[validationFailures:protected] => Array
(
)
[_new:BaseObject:private] =>
[_deleted:BaseObject:private] =>
[modifiedColumns:protected] => Array
(
)
)
)
[2] => Search_Result Object
(
[title] => Toolbox Talk: Tower Crane Safety
[image] => /record/images/notavailable-p.png
[blurb] => The CPWR Toolbox Talk on Tower Crane Safety addresses the potential hazards of Tower Cranes and the importance of following procedure before and durin...
[category] => Array
(
[0] => 11
[1] => 12
[2] => 18
[3] => 70
[4] => 87
[5] => 88
[6] => 91
[7] => 90
[8] => 92
[9] => 100
)
[labels] => Array
(
[0] => Cranes & Hoists
[1] => Work Environment
[2] => Hazards
[3] => Crushed/Struck By
[6] => Motor Vehicles/Heavy Equipment
[9] => Operating Engineer
[10] => Trades
[11] => Commercial & Institutional
[12] => Jobsites
[13] => Demolition
[15] => Heavy & Highway
[17] => Industrial
[19] => LEED/Green Construction
[21] => Toolbox Talks
[22] => Documents
[23] => Media & Documents
)
[type] => Toolbox Talks
[sub_category] =>
[url] => /document/4427/d001657/Toolbox%2BTalk%253A%2BTower%2BCrane%2BSafety.html
[item:protected] => DocumentRecord Object
(
[records:protected] => Array
(
)
[recordId:protected] =>
[searchWordClass:protected] =>
[searchWordPeerClass:protected] =>
[bok_record:protected] =>
[authors:protected] =>
[organizations:protected] =>
[collections:protected] =>
[categories:protected] => Array
(
[11] => Category Object
(
[languages:protected] =>
[bok_resources:protected] =>
[bok_topics:protected] =>
[bok_keywords:protected] =>
[id:protected] => 11
[type:protected] => category
[parent:protected] => 7
[label:protected] => Cranes & Hoists
[alreadyInSave:protected] =>
[alreadyInValidation:protected] =>
[validationFailures:protected] => Array
(
)
[_new:BaseObject:private] =>
[_deleted:BaseObject:private] =>
[modifiedColumns:protected] => Array
(
)
)
[12] => Category Object
(
[languages:protected] =>
[bok_resources:protected] =>
[bok_topics:protected] =>
[bok_keywords:protected] =>
[id:protected] => 12
[type:protected] => category
[parent:protected] => 7
[label:protected] => Crushed/Struck By
[alreadyInSave:protected] =>
[alreadyInValidation:protected] =>
[validationFailures:protected] => Array
(
)
[_new:BaseObject:private] =>
[_deleted:BaseObject:private] =>
[modifiedColumns:protected] => Array
(
)
)
[18] => Category Object
(
[languages:protected] =>
[bok_resources:protected] =>
[bok_topics:protected] =>
[bok_keywords:protected] =>
[id:protected] => 18
[type:protected] => category
[parent:protected] => 7
[label:protected] => Motor Vehicles/Heavy Equipment
[alreadyInSave:protected] =>
[alreadyInValidation:protected] =>
[validationFailures:protected] => Array
(
)
[_new:BaseObject:private] =>
[_deleted:BaseObject:private] =>
[modifiedColumns:protected] => Array
(
)
)
[70] => Category Object
(
[languages:protected] =>
[bok_resources:protected] =>
[bok_topics:protected] =>
[bok_keywords:protected] =>
[id:protected] => 70
[type:protected] => category
[parent:protected] => 2
[label:protected] => Operating Engineer
[alreadyInSave:protected] =>
[alreadyInValidation:protected] =>
[validationFailures:protected] => Array
(
)
[_new:BaseObject:private] =>
[_deleted:BaseObject:private] =>
[modifiedColumns:protected] => Array
(
)
)
[87] => Category Object
(
[languages:protected] =>
[bok_resources:protected] =>
[bok_topics:protected] =>
[bok_keywords:protected] =>
[id:protected] => 87
[type:protected] => category
[parent:protected] => 3
[label:protected] => Commercial & Institutional
[alreadyInSave:protected] =>
[alreadyInValidation:protected] =>
[validationFailures:protected] => Array
(
)
[_new:BaseObject:private] =>
[_deleted:BaseObject:private] =>
[modifiedColumns:protected] => Array
(
)
)
[88] => Category Object
(
[languages:protected] =>
[bok_resources:protected] =>
[bok_topics:protected] =>
[bok_keywords:protected] =>
[id:protected] => 88
[type:protected] => category
[parent:protected] => 3
[label:protected] => Demolition
[alreadyInSave:protected] =>
[alreadyInValidation:protected] =>
[validationFailures:protected] => Array
(
)
[_new:BaseObject:private] =>
[_deleted:BaseObject:private] =>
[modifiedColumns:protected] => Array
(
)
)
[91] => Category Object
(
[languages:protected] =>
[bok_resources:protected] =>
[bok_topics:protected] =>
[bok_keywords:protected] =>
[id:protected] => 91
[type:protected] => category
[parent:protected] => 3
[label:protected] => Heavy & Highway
[alreadyInSave:protected] =>
[alreadyInValidation:protected] =>
[validationFailures:protected] => Array
(
)
[_new:BaseObject:private] =>
[_deleted:BaseObject:private] =>
[modifiedColumns:protected] => Array
(
)
)
[90] => Category Object
(
[languages:protected] =>
[bok_resources:protected] =>
[bok_topics:protected] =>
[bok_keywords:protected] =>
[id:protected] => 90
[type:protected] => category
[parent:protected] => 3
[label:protected] => Industrial
[alreadyInSave:protected] =>
[alreadyInValidation:protected] =>
[validationFailures:protected] => Array
(
)
[_new:BaseObject:private] =>
[_deleted:BaseObject:private] =>
[modifiedColumns:protected] => Array
(
)
)
[92] => Category Object
(
[languages:protected] =>
[bok_resources:protected] =>
[bok_topics:protected] =>
[bok_keywords:protected] =>
[id:protected] => 92
[type:protected] => category
[parent:protected] => 3
[label:protected] => LEED/Green Construction
[alreadyInSave:protected] =>
[alreadyInValidation:protected] =>
[validationFailures:protected] => Array
(
)
[_new:BaseObject:private] =>
[_deleted:BaseObject:private] =>
[modifiedColumns:protected] => Array
(
)
)
[100] => Category Object
(
[languages:protected] =>
[bok_resources:protected] =>
[bok_topics:protected] =>
[bok_keywords:protected] =>
[id:protected] => 100
[type:protected] => category
[parent:protected] => 6
[label:protected] => Toolbox Talks
[alreadyInSave:protected] =>
[alreadyInValidation:protected] =>
[validationFailures:protected] => Array
(
)
[_new:BaseObject:private] =>
[_deleted:BaseObject:private] =>
[modifiedColumns:protected] => Array
(
)
)
)
[categories_initialized:protected] => 1
[mapped_items:protected] =>
[content:protected] =>
[files:protected] =>
[language:protected] => Language Object
(
[id:protected] => 1
[code:protected] => en
[name:protected] => English
[alreadyInSave:protected] =>
[alreadyInValidation:protected] =>
[validationFailures:protected] => Array
(
)
[_new:BaseObject:private] =>
[_deleted:BaseObject:private] =>
[modifiedColumns:protected] => Array
(
)
)
[old_record:protected] =>
[id:protected] => 4427
[old_id:protected] =>
[elcosh_id:protected] => d001657
[type:protected] => document
[display_type:protected] => HTML only (and links)
[user_id:protected] => 0
[language_id:protected] => 1
[tagging_id:protected] => Mike Aguilar
[priority_id:protected] => 1
[title:protected] => Toolbox Talk: Tower Crane Safety
[total_pages:protected] => 0
[billed_pages:protected] => 0
[publication_number:protected] =>
[part_of:protected] =>
[keywords:protected] => Tower Crane, Crane, Stability, Tipping, Lift Zone Safety, Lift, Zone, Safety, Struck by
[comments:protected] =>
[summary:protected] => The CPWR Toolbox Talk on Tower Crane Safety addresses the potential hazards of Tower Cranes and the importance of following procedure before and during Tower Crane operation. The resource includes a brief example, steps to prevent a related injury, and questions for discussion. It includes a graphic that illustrates a worker inspecting a Tower Crane before operation, which can be posted in a central location as a reminder of steps to work safely.
Available in
English and
Spanish.
[transition_comments:protected] =>
[external_link:protected] =>
[consol_link:protected] =>
[more_like_this:protected] => d001234,d001238,d001250,d001251,d001253,d001258,d001262,d001273
[permission_given_by:protected] =>
[published:protected] => T
[billable:protected] => F
[img_name:protected] =>
[img_ext:protected] => jpg
[img_width:protected] =>
[img_height:protected] =>
[img_credit:protected] =>
[img_practice:protected] =>
[vid_source_id:protected] =>
[vid_running_time:protected] =>
[vid_intended_audience:protected] =>
[vid_acquisition_info:protected] =>
[vid_cost:protected] =>
[vid_producer:protected] =>
[vid_filename:protected] =>
[vid_filename_downloadable:protected] =>
[date_summary:protected] =>
[date_permission_requested:protected] =>
[date_permission_received:protected] =>
[date_review_needed:protected] =>
[date_received:protected] => 12/23/21
[date_completed:protected] => 12/23/21
[date_billed:protected] =>
[date_modified:protected] => 05/19/23
[collBokExports:protected] =>
[lastBokExportCriteria:BaseElcoshItem:private] =>
[alreadyInSave:protected] =>
[alreadyInValidation:protected] =>
[validationFailures:protected] => Array
(
)
[_new:BaseObject:private] =>
[_deleted:BaseObject:private] =>
[modifiedColumns:protected] => Array
(
)
)
)
[3] => Search_Result Object
(
[title] => Toolbox Talk: Work Zone Safety: Working Around Vehicles
[image] => /record/images/notavailable-p.png
[blurb] => The CPWR Toolbox Talk on Working Around Vehicles in the Work Zone addresses methods to avoid being struck-by a vehicle on a construction site. The res...
[category] => Array
(
[0] => 12
[1] => 18
[2] => 52
[3] => 57
[4] => 70
[5] => 85
[6] => 87
[7] => 88
[8] => 89
[9] => 91
[10] => 90
[11] => 92
[12] => 93
[13] => 94
[14] => 95
[15] => 100
)
[labels] => Array
(
[0] => Crushed/Struck By
[1] => Work Environment
[2] => Hazards
[3] => Motor Vehicles/Heavy Equipment
[6] => Commercial Diver
[7] => Trades
[8] => Flagger
[10] => Operating Engineer
[12] => Truck Driver
[14] => Commercial & Institutional
[15] => Jobsites
[16] => Demolition
[18] => Disasters
[20] => Heavy & Highway
[22] => Industrial
[24] => LEED/Green Construction
[26] => Renovations
[28] => Residential
[30] => Underground
[32] => Toolbox Talks
[33] => Documents
[34] => Media & Documents
)
[type] => Toolbox Talks
[sub_category] =>
[url] => /document/4428/d001658/Toolbox%2BTalk%253A%2BWork%2BZone%2BSafety%253A%2BWorking%2BAround%2BVehicles.html
[item:protected] => DocumentRecord Object
(
[records:protected] => Array
(
)
[recordId:protected] =>
[searchWordClass:protected] =>
[searchWordPeerClass:protected] =>
[bok_record:protected] =>
[authors:protected] =>
[organizations:protected] =>
[collections:protected] =>
[categories:protected] => Array
(
[12] => Category Object
(
[languages:protected] =>
[bok_resources:protected] =>
[bok_topics:protected] =>
[bok_keywords:protected] =>
[id:protected] => 12
[type:protected] => category
[parent:protected] => 7
[label:protected] => Crushed/Struck By
[alreadyInSave:protected] =>
[alreadyInValidation:protected] =>
[validationFailures:protected] => Array
(
)
[_new:BaseObject:private] =>
[_deleted:BaseObject:private] =>
[modifiedColumns:protected] => Array
(
)
)
[18] => Category Object
(
[languages:protected] =>
[bok_resources:protected] =>
[bok_topics:protected] =>
[bok_keywords:protected] =>
[id:protected] => 18
[type:protected] => category
[parent:protected] => 7
[label:protected] => Motor Vehicles/Heavy Equipment
[alreadyInSave:protected] =>
[alreadyInValidation:protected] =>
[validationFailures:protected] => Array
(
)
[_new:BaseObject:private] =>
[_deleted:BaseObject:private] =>
[modifiedColumns:protected] => Array
(
)
)
[52] => Category Object
(
[languages:protected] =>
[bok_resources:protected] =>
[bok_topics:protected] =>
[bok_keywords:protected] =>
[id:protected] => 52
[type:protected] => category
[parent:protected] => 2
[label:protected] => Commercial Diver
[alreadyInSave:protected] =>
[alreadyInValidation:protected] =>
[validationFailures:protected] => Array
(
)
[_new:BaseObject:private] =>
[_deleted:BaseObject:private] =>
[modifiedColumns:protected] => Array
(
)
)
[57] => Category Object
(
[languages:protected] =>
[bok_resources:protected] =>
[bok_topics:protected] =>
[bok_keywords:protected] =>
[id:protected] => 57
[type:protected] => category
[parent:protected] => 2
[label:protected] => Flagger
[alreadyInSave:protected] =>
[alreadyInValidation:protected] =>
[validationFailures:protected] => Array
(
)
[_new:BaseObject:private] =>
[_deleted:BaseObject:private] =>
[modifiedColumns:protected] => Array
(
)
)
[70] => Category Object
(
[languages:protected] =>
[bok_resources:protected] =>
[bok_topics:protected] =>
[bok_keywords:protected] =>
[id:protected] => 70
[type:protected] => category
[parent:protected] => 2
[label:protected] => Operating Engineer
[alreadyInSave:protected] =>
[alreadyInValidation:protected] =>
[validationFailures:protected] => Array
(
)
[_new:BaseObject:private] =>
[_deleted:BaseObject:private] =>
[modifiedColumns:protected] => Array
(
)
)
[85] => Category Object
(
[languages:protected] =>
[bok_resources:protected] =>
[bok_topics:protected] =>
[bok_keywords:protected] =>
[id:protected] => 85
[type:protected] => category
[parent:protected] => 2
[label:protected] => Truck Driver
[alreadyInSave:protected] =>
[alreadyInValidation:protected] =>
[validationFailures:protected] => Array
(
)
[_new:BaseObject:private] =>
[_deleted:BaseObject:private] =>
[modifiedColumns:protected] => Array
(
)
)
[87] => Category Object
(
[languages:protected] =>
[bok_resources:protected] =>
[bok_topics:protected] =>
[bok_keywords:protected] =>
[id:protected] => 87
[type:protected] => category
[parent:protected] => 3
[label:protected] => Commercial & Institutional
[alreadyInSave:protected] =>
[alreadyInValidation:protected] =>
[validationFailures:protected] => Array
(
)
[_new:BaseObject:private] =>
[_deleted:BaseObject:private] =>
[modifiedColumns:protected] => Array
(
)
)
[88] => Category Object
(
[languages:protected] =>
[bok_resources:protected] =>
[bok_topics:protected] =>
[bok_keywords:protected] =>
[id:protected] => 88
[type:protected] => category
[parent:protected] => 3
[label:protected] => Demolition
[alreadyInSave:protected] =>
[alreadyInValidation:protected] =>
[validationFailures:protected] => Array
(
)
[_new:BaseObject:private] =>
[_deleted:BaseObject:private] =>
[modifiedColumns:protected] => Array
(
)
)
[89] => Category Object
(
[languages:protected] =>
[bok_resources:protected] =>
[bok_topics:protected] =>
[bok_keywords:protected] =>
[id:protected] => 89
[type:protected] => category
[parent:protected] => 3
[label:protected] => Disasters
[alreadyInSave:protected] =>
[alreadyInValidation:protected] =>
[validationFailures:protected] => Array
(
)
[_new:BaseObject:private] =>
[_deleted:BaseObject:private] =>
[modifiedColumns:protected] => Array
(
)
)
[91] => Category Object
(
[languages:protected] =>
[bok_resources:protected] =>
[bok_topics:protected] =>
[bok_keywords:protected] =>
[id:protected] => 91
[type:protected] => category
[parent:protected] => 3
[label:protected] => Heavy & Highway
[alreadyInSave:protected] =>
[alreadyInValidation:protected] =>
[validationFailures:protected] => Array
(
)
[_new:BaseObject:private] =>
[_deleted:BaseObject:private] =>
[modifiedColumns:protected] => Array
(
)
)
[90] => Category Object
(
[languages:protected] =>
[bok_resources:protected] =>
[bok_topics:protected] =>
[bok_keywords:protected] =>
[id:protected] => 90
[type:protected] => category
[parent:protected] => 3
[label:protected] => Industrial
[alreadyInSave:protected] =>
[alreadyInValidation:protected] =>
[validationFailures:protected] => Array
(
)
[_new:BaseObject:private] =>
[_deleted:BaseObject:private] =>
[modifiedColumns:protected] => Array
(
)
)
[92] => Category Object
(
[languages:protected] =>
[bok_resources:protected] =>
[bok_topics:protected] =>
[bok_keywords:protected] =>
[id:protected] => 92
[type:protected] => category
[parent:protected] => 3
[label:protected] => LEED/Green Construction
[alreadyInSave:protected] =>
[alreadyInValidation:protected] =>
[validationFailures:protected] => Array
(
)
[_new:BaseObject:private] =>
[_deleted:BaseObject:private] =>
[modifiedColumns:protected] => Array
(
)
)
[93] => Category Object
(
[languages:protected] =>
[bok_resources:protected] =>
[bok_topics:protected] =>
[bok_keywords:protected] =>
[id:protected] => 93
[type:protected] => category
[parent:protected] => 3
[label:protected] => Renovations
[alreadyInSave:protected] =>
[alreadyInValidation:protected] =>
[validationFailures:protected] => Array
(
)
[_new:BaseObject:private] =>
[_deleted:BaseObject:private] =>
[modifiedColumns:protected] => Array
(
)
)
[94] => Category Object
(
[languages:protected] =>
[bok_resources:protected] =>
[bok_topics:protected] =>
[bok_keywords:protected] =>
[id:protected] => 94
[type:protected] => category
[parent:protected] => 3
[label:protected] => Residential
[alreadyInSave:protected] =>
[alreadyInValidation:protected] =>
[validationFailures:protected] => Array
(
)
[_new:BaseObject:private] =>
[_deleted:BaseObject:private] =>
[modifiedColumns:protected] => Array
(
)
)
[95] => Category Object
(
[languages:protected] =>
[bok_resources:protected] =>
[bok_topics:protected] =>
[bok_keywords:protected] =>
[id:protected] => 95
[type:protected] => category
[parent:protected] => 3
[label:protected] => Underground
[alreadyInSave:protected] =>
[alreadyInValidation:protected] =>
[validationFailures:protected] => Array
(
)
[_new:BaseObject:private] =>
[_deleted:BaseObject:private] =>
[modifiedColumns:protected] => Array
(
)
)
[100] => Category Object
(
[languages:protected] =>
[bok_resources:protected] =>
[bok_topics:protected] =>
[bok_keywords:protected] =>
[id:protected] => 100
[type:protected] => category
[parent:protected] => 6
[label:protected] => Toolbox Talks
[alreadyInSave:protected] =>
[alreadyInValidation:protected] =>
[validationFailures:protected] => Array
(
)
[_new:BaseObject:private] =>
[_deleted:BaseObject:private] =>
[modifiedColumns:protected] => Array
(
)
)
)
[categories_initialized:protected] => 1
[mapped_items:protected] =>
[content:protected] =>
[files:protected] =>
[language:protected] => Language Object
(
[id:protected] => 1
[code:protected] => en
[name:protected] => English
[alreadyInSave:protected] =>
[alreadyInValidation:protected] =>
[validationFailures:protected] => Array
(
)
[_new:BaseObject:private] =>
[_deleted:BaseObject:private] =>
[modifiedColumns:protected] => Array
(
)
)
[old_record:protected] =>
[id:protected] => 4428
[old_id:protected] =>
[elcosh_id:protected] => d001658
[type:protected] => document
[display_type:protected] => HTML only (and links)
[user_id:protected] => 0
[language_id:protected] => 1
[tagging_id:protected] => Daniela Caceres
[priority_id:protected] => 1
[title:protected] => Toolbox Talk: Work Zone Safety: Working Around Vehicles
[total_pages:protected] => 0
[billed_pages:protected] => 0
[publication_number:protected] =>
[part_of:protected] =>
[keywords:protected] => Struck, Struck by, Vehicle, Work Zone Safety, Truck, Operator, Driver, Mobile Equipment
[comments:protected] =>
[summary:protected] => The CPWR Toolbox Talk on Working Around Vehicles in the Work Zone addresses methods to avoid being struck-by a vehicle on a construction site. The resource includes a case example, steps to prevent a related injury, and questions for discussion. It includes a graphic that illustrates the hazard, which can be posted in a central location as a reminder of steps to work safely. Available in
English and
Spanish.
[transition_comments:protected] =>
[external_link:protected] =>
[consol_link:protected] =>
[more_like_this:protected] => d001640
[permission_given_by:protected] =>
[published:protected] => T
[billable:protected] => F
[img_name:protected] =>
[img_ext:protected] =>
[img_width:protected] =>
[img_height:protected] =>
[img_credit:protected] =>
[img_practice:protected] =>
[vid_source_id:protected] =>
[vid_running_time:protected] =>
[vid_intended_audience:protected] =>
[vid_acquisition_info:protected] =>
[vid_cost:protected] =>
[vid_producer:protected] =>
[vid_filename:protected] =>
[vid_filename_downloadable:protected] =>
[date_summary:protected] =>
[date_permission_requested:protected] =>
[date_permission_received:protected] =>
[date_review_needed:protected] =>
[date_received:protected] => 12/23/21
[date_completed:protected] => 12/23/21
[date_billed:protected] =>
[date_modified:protected] => 05/19/23
[collBokExports:protected] =>
[lastBokExportCriteria:BaseElcoshItem:private] =>
[alreadyInSave:protected] =>
[alreadyInValidation:protected] =>
[validationFailures:protected] => Array
(
)
[_new:BaseObject:private] =>
[_deleted:BaseObject:private] =>
[modifiedColumns:protected] => Array
(
)
)
)
[4] => Search_Result Object
(
[title] => Construction Dive -- DeWalt's Jobsite Pro headphones recalled for fire hazards
[image] => /record/images/notavailable-p.png
[blurb] => A recall notice by the United States Consumer Product Safety Commission affects over 300,000 DeWalt Jobsite Pro Headphones. The recall is a result of...
[category] => Array
(
[0] => 16
[1] => 44
[2] => 45
[3] => 46
[4] => 47
[5] => 48
[6] => 49
[7] => 50
[8] => 51
[9] => 52
[10] => 53
[11] => 54
[12] => 55
[13] => 56
[14] => 57
[15] => 58
[16] => 59
[17] => 60
[18] => 61
[19] => 64
[20] => 65
[21] => 66
[22] => 67
[23] => 68
[24] => 69
[25] => 70
[26] => 71
[27] => 72
[28] => 73
[29] => 74
[30] => 75
[31] => 76
[32] => 77
[33] => 63
[34] => 78
[35] => 79
[36] => 80
[37] => 81
[38] => 82
[39] => 62
[40] => 83
[41] => 84
[42] => 85
[43] => 86
[44] => 87
[45] => 88
[46] => 89
[47] => 91
[48] => 90
[49] => 92
[50] => 93
[51] => 94
[52] => 95
)
[labels] => Array
(
[0] => Fire & Explosions
[1] => Work Environment
[2] => Hazards
[3] => Acoustical Ceiling Carpenter
[4] => Trades
[5] => Asbestos/Insulator
[7] => Boilermaker
[9] => Bricklayer
[11] => Cabinetmaker
[13] => Carpenter
[15] => Carpet Layer
[17] => Cement Mason
[19] => Commercial Diver
[21] => Concrete Polisher
[23] => Drywall Applicator Specialist
[25] => Electrical Worker
[27] => Elevator Constructor
[29] => Flagger
[31] => Glazier
[33] => Hazardous Waste Cleanup
[35] => HVAC
[37] => Interior Systems Carpenter
[39] => Laborer
[41] => Landscaper
[43] => Lather
[45] => Lead Abatement Worker
[47] => Maintenance Worker
[49] => Millwright
[51] => Operating Engineer
[53] => Painter
[55] => Paper Hanger
[57] => PCC/Restoration
[59] => Pile Driver
[61] => Plasterer
[63] => Plumber/Pipefitter
[65] => Refractory Worker
[67] => Reinforcing Ironworker
[69] => Roofer/Waterproofer
[71] => Scaffold Erector
[73] => Sheetmetal Worker
[75] => Sprinkler Fitter
[77] => Stonemason
[79] => Structural Ironworker
[81] => Terrazzo Worker
[83] => Tile Setter
[85] => Truck Driver
[87] => Welder
[89] => Commercial & Institutional
[90] => Jobsites
[91] => Demolition
[93] => Disasters
[95] => Heavy & Highway
[97] => Industrial
[99] => LEED/Green Construction
[101] => Renovations
[103] => Residential
[105] => Underground
)
[type] =>
[sub_category] =>
[url] => /document/4426/d001656/Construction%2BDive%2B--%2BDeWalt%2527s%2BJobsite%2BPro%2Bheadphones%2Brecalled%2Bfor%2Bfire%2Bhazards.html
[item:protected] => DocumentRecord Object
(
[records:protected] => Array
(
)
[recordId:protected] =>
[searchWordClass:protected] =>
[searchWordPeerClass:protected] =>
[bok_record:protected] =>
[authors:protected] =>
[organizations:protected] =>
[collections:protected] =>
[categories:protected] => Array
(
[16] => Category Object
(
[languages:protected] =>
[bok_resources:protected] =>
[bok_topics:protected] =>
[bok_keywords:protected] =>
[id:protected] => 16
[type:protected] => category
[parent:protected] => 7
[label:protected] => Fire & Explosions
[alreadyInSave:protected] =>
[alreadyInValidation:protected] =>
[validationFailures:protected] => Array
(
)
[_new:BaseObject:private] =>
[_deleted:BaseObject:private] =>
[modifiedColumns:protected] => Array
(
)
)
[44] => Category Object
(
[languages:protected] =>
[bok_resources:protected] =>
[bok_topics:protected] =>
[bok_keywords:protected] =>
[id:protected] => 44
[type:protected] => category
[parent:protected] => 2
[label:protected] => Acoustical Ceiling Carpenter
[alreadyInSave:protected] =>
[alreadyInValidation:protected] =>
[validationFailures:protected] => Array
(
)
[_new:BaseObject:private] =>
[_deleted:BaseObject:private] =>
[modifiedColumns:protected] => Array
(
)
)
[45] => Category Object
(
[languages:protected] =>
[bok_resources:protected] =>
[bok_topics:protected] =>
[bok_keywords:protected] =>
[id:protected] => 45
[type:protected] => category
[parent:protected] => 2
[label:protected] => Asbestos/Insulator
[alreadyInSave:protected] =>
[alreadyInValidation:protected] =>
[validationFailures:protected] => Array
(
)
[_new:BaseObject:private] =>
[_deleted:BaseObject:private] =>
[modifiedColumns:protected] => Array
(
)
)
[46] => Category Object
(
[languages:protected] =>
[bok_resources:protected] =>
[bok_topics:protected] =>
[bok_keywords:protected] =>
[id:protected] => 46
[type:protected] => category
[parent:protected] => 2
[label:protected] => Boilermaker
[alreadyInSave:protected] =>
[alreadyInValidation:protected] =>
[validationFailures:protected] => Array
(
)
[_new:BaseObject:private] =>
[_deleted:BaseObject:private] =>
[modifiedColumns:protected] => Array
(
)
)
[47] => Category Object
(
[languages:protected] =>
[bok_resources:protected] =>
[bok_topics:protected] =>
[bok_keywords:protected] =>
[id:protected] => 47
[type:protected] => category
[parent:protected] => 2
[label:protected] => Bricklayer
[alreadyInSave:protected] =>
[alreadyInValidation:protected] =>
[validationFailures:protected] => Array
(
)
[_new:BaseObject:private] =>
[_deleted:BaseObject:private] =>
[modifiedColumns:protected] => Array
(
)
)
[48] => Category Object
(
[languages:protected] =>
[bok_resources:protected] =>
[bok_topics:protected] =>
[bok_keywords:protected] =>
[id:protected] => 48
[type:protected] => category
[parent:protected] => 2
[label:protected] => Cabinetmaker
[alreadyInSave:protected] =>
[alreadyInValidation:protected] =>
[validationFailures:protected] => Array
(
)
[_new:BaseObject:private] =>
[_deleted:BaseObject:private] =>
[modifiedColumns:protected] => Array
(
)
)
[49] => Category Object
(
[languages:protected] =>
[bok_resources:protected] =>
[bok_topics:protected] =>
[bok_keywords:protected] =>
[id:protected] => 49
[type:protected] => category
[parent:protected] => 2
[label:protected] => Carpenter
[alreadyInSave:protected] =>
[alreadyInValidation:protected] =>
[validationFailures:protected] => Array
(
)
[_new:BaseObject:private] =>
[_deleted:BaseObject:private] =>
[modifiedColumns:protected] => Array
(
)
)
[50] => Category Object
(
[languages:protected] =>
[bok_resources:protected] =>
[bok_topics:protected] =>
[bok_keywords:protected] =>
[id:protected] => 50
[type:protected] => category
[parent:protected] => 2
[label:protected] => Carpet Layer
[alreadyInSave:protected] =>
[alreadyInValidation:protected] =>
[validationFailures:protected] => Array
(
)
[_new:BaseObject:private] =>
[_deleted:BaseObject:private] =>
[modifiedColumns:protected] => Array
(
)
)
[51] => Category Object
(
[languages:protected] =>
[bok_resources:protected] =>
[bok_topics:protected] =>
[bok_keywords:protected] =>
[id:protected] => 51
[type:protected] => category
[parent:protected] => 2
[label:protected] => Cement Mason
[alreadyInSave:protected] =>
[alreadyInValidation:protected] =>
[validationFailures:protected] => Array
(
)
[_new:BaseObject:private] =>
[_deleted:BaseObject:private] =>
[modifiedColumns:protected] => Array
(
)
)
[52] => Category Object
(
[languages:protected] =>
[bok_resources:protected] =>
[bok_topics:protected] =>
[bok_keywords:protected] =>
[id:protected] => 52
[type:protected] => category
[parent:protected] => 2
[label:protected] => Commercial Diver
[alreadyInSave:protected] =>
[alreadyInValidation:protected] =>
[validationFailures:protected] => Array
(
)
[_new:BaseObject:private] =>
[_deleted:BaseObject:private] =>
[modifiedColumns:protected] => Array
(
)
)
[53] => Category Object
(
[languages:protected] =>
[bok_resources:protected] =>
[bok_topics:protected] =>
[bok_keywords:protected] =>
[id:protected] => 53
[type:protected] => category
[parent:protected] => 2
[label:protected] => Concrete Polisher
[alreadyInSave:protected] =>
[alreadyInValidation:protected] =>
[validationFailures:protected] => Array
(
)
[_new:BaseObject:private] =>
[_deleted:BaseObject:private] =>
[modifiedColumns:protected] => Array
(
)
)
[54] => Category Object
(
[languages:protected] =>
[bok_resources:protected] =>
[bok_topics:protected] =>
[bok_keywords:protected] =>
[id:protected] => 54
[type:protected] => category
[parent:protected] => 2
[label:protected] => Drywall Applicator Specialist
[alreadyInSave:protected] =>
[alreadyInValidation:protected] =>
[validationFailures:protected] => Array
(
)
[_new:BaseObject:private] =>
[_deleted:BaseObject:private] =>
[modifiedColumns:protected] => Array
(
)
)
[55] => Category Object
(
[languages:protected] =>
[bok_resources:protected] =>
[bok_topics:protected] =>
[bok_keywords:protected] =>
[id:protected] => 55
[type:protected] => category
[parent:protected] => 2
[label:protected] => Electrical Worker
[alreadyInSave:protected] =>
[alreadyInValidation:protected] =>
[validationFailures:protected] => Array
(
)
[_new:BaseObject:private] =>
[_deleted:BaseObject:private] =>
[modifiedColumns:protected] => Array
(
)
)
[56] => Category Object
(
[languages:protected] =>
[bok_resources:protected] =>
[bok_topics:protected] =>
[bok_keywords:protected] =>
[id:protected] => 56
[type:protected] => category
[parent:protected] => 2
[label:protected] => Elevator Constructor
[alreadyInSave:protected] =>
[alreadyInValidation:protected] =>
[validationFailures:protected] => Array
(
)
[_new:BaseObject:private] =>
[_deleted:BaseObject:private] =>
[modifiedColumns:protected] => Array
(
)
)
[57] => Category Object
(
[languages:protected] =>
[bok_resources:protected] =>
[bok_topics:protected] =>
[bok_keywords:protected] =>
[id:protected] => 57
[type:protected] => category
[parent:protected] => 2
[label:protected] => Flagger
[alreadyInSave:protected] =>
[alreadyInValidation:protected] =>
[validationFailures:protected] => Array
(
)
[_new:BaseObject:private] =>
[_deleted:BaseObject:private] =>
[modifiedColumns:protected] => Array
(
)
)
[58] => Category Object
(
[languages:protected] =>
[bok_resources:protected] =>
[bok_topics:protected] =>
[bok_keywords:protected] =>
[id:protected] => 58
[type:protected] => category
[parent:protected] => 2
[label:protected] => Glazier
[alreadyInSave:protected] =>
[alreadyInValidation:protected] =>
[validationFailures:protected] => Array
(
)
[_new:BaseObject:private] =>
[_deleted:BaseObject:private] =>
[modifiedColumns:protected] => Array
(
)
)
[59] => Category Object
(
[languages:protected] =>
[bok_resources:protected] =>
[bok_topics:protected] =>
[bok_keywords:protected] =>
[id:protected] => 59
[type:protected] => category
[parent:protected] => 2
[label:protected] => Hazardous Waste Cleanup
[alreadyInSave:protected] =>
[alreadyInValidation:protected] =>
[validationFailures:protected] => Array
(
)
[_new:BaseObject:private] =>
[_deleted:BaseObject:private] =>
[modifiedColumns:protected] => Array
(
)
)
[60] => Category Object
(
[languages:protected] =>
[bok_resources:protected] =>
[bok_topics:protected] =>
[bok_keywords:protected] =>
[id:protected] => 60
[type:protected] => category
[parent:protected] => 2
[label:protected] => HVAC
[alreadyInSave:protected] =>
[alreadyInValidation:protected] =>
[validationFailures:protected] => Array
(
)
[_new:BaseObject:private] =>
[_deleted:BaseObject:private] =>
[modifiedColumns:protected] => Array
(
)
)
[61] => Category Object
(
[languages:protected] =>
[bok_resources:protected] =>
[bok_topics:protected] =>
[bok_keywords:protected] =>
[id:protected] => 61
[type:protected] => category
[parent:protected] => 2
[label:protected] => Interior Systems Carpenter
[alreadyInSave:protected] =>
[alreadyInValidation:protected] =>
[validationFailures:protected] => Array
(
)
[_new:BaseObject:private] =>
[_deleted:BaseObject:private] =>
[modifiedColumns:protected] => Array
(
)
)
[64] => Category Object
(
[languages:protected] =>
[bok_resources:protected] =>
[bok_topics:protected] =>
[bok_keywords:protected] =>
[id:protected] => 64
[type:protected] => category
[parent:protected] => 2
[label:protected] => Laborer
[alreadyInSave:protected] =>
[alreadyInValidation:protected] =>
[validationFailures:protected] => Array
(
)
[_new:BaseObject:private] =>
[_deleted:BaseObject:private] =>
[modifiedColumns:protected] => Array
(
)
)
[65] => Category Object
(
[languages:protected] =>
[bok_resources:protected] =>
[bok_topics:protected] =>
[bok_keywords:protected] =>
[id:protected] => 65
[type:protected] => category
[parent:protected] => 2
[label:protected] => Landscaper
[alreadyInSave:protected] =>
[alreadyInValidation:protected] =>
[validationFailures:protected] => Array
(
)
[_new:BaseObject:private] =>
[_deleted:BaseObject:private] =>
[modifiedColumns:protected] => Array
(
)
)
[66] => Category Object
(
[languages:protected] =>
[bok_resources:protected] =>
[bok_topics:protected] =>
[bok_keywords:protected] =>
[id:protected] => 66
[type:protected] => category
[parent:protected] => 2
[label:protected] => Lather
[alreadyInSave:protected] =>
[alreadyInValidation:protected] =>
[validationFailures:protected] => Array
(
)
[_new:BaseObject:private] =>
[_deleted:BaseObject:private] =>
[modifiedColumns:protected] => Array
(
)
)
[67] => Category Object
(
[languages:protected] =>
[bok_resources:protected] =>
[bok_topics:protected] =>
[bok_keywords:protected] =>
[id:protected] => 67
[type:protected] => category
[parent:protected] => 2
[label:protected] => Lead Abatement Worker
[alreadyInSave:protected] =>
[alreadyInValidation:protected] =>
[validationFailures:protected] => Array
(
)
[_new:BaseObject:private] =>
[_deleted:BaseObject:private] =>
[modifiedColumns:protected] => Array
(
)
)
[68] => Category Object
(
[languages:protected] =>
[bok_resources:protected] =>
[bok_topics:protected] =>
[bok_keywords:protected] =>
[id:protected] => 68
[type:protected] => category
[parent:protected] => 2
[label:protected] => Maintenance Worker
[alreadyInSave:protected] =>
[alreadyInValidation:protected] =>
[validationFailures:protected] => Array
(
)
[_new:BaseObject:private] =>
[_deleted:BaseObject:private] =>
[modifiedColumns:protected] => Array
(
)
)
[69] => Category Object
(
[languages:protected] =>
[bok_resources:protected] =>
[bok_topics:protected] =>
[bok_keywords:protected] =>
[id:protected] => 69
[type:protected] => category
[parent:protected] => 2
[label:protected] => Millwright
[alreadyInSave:protected] =>
[alreadyInValidation:protected] =>
[validationFailures:protected] => Array
(
)
[_new:BaseObject:private] =>
[_deleted:BaseObject:private] =>
[modifiedColumns:protected] => Array
(
)
)
[70] => Category Object
(
[languages:protected] =>
[bok_resources:protected] =>
[bok_topics:protected] =>
[bok_keywords:protected] =>
[id:protected] => 70
[type:protected] => category
[parent:protected] => 2
[label:protected] => Operating Engineer
[alreadyInSave:protected] =>
[alreadyInValidation:protected] =>
[validationFailures:protected] => Array
(
)
[_new:BaseObject:private] =>
[_deleted:BaseObject:private] =>
[modifiedColumns:protected] => Array
(
)
)
[71] => Category Object
(
[languages:protected] =>
[bok_resources:protected] =>
[bok_topics:protected] =>
[bok_keywords:protected] =>
[id:protected] => 71
[type:protected] => category
[parent:protected] => 2
[label:protected] => Painter
[alreadyInSave:protected] =>
[alreadyInValidation:protected] =>
[validationFailures:protected] => Array
(
)
[_new:BaseObject:private] =>
[_deleted:BaseObject:private] =>
[modifiedColumns:protected] => Array
(
)
)
[72] => Category Object
(
[languages:protected] =>
[bok_resources:protected] =>
[bok_topics:protected] =>
[bok_keywords:protected] =>
[id:protected] => 72
[type:protected] => category
[parent:protected] => 2
[label:protected] => Paper Hanger
[alreadyInSave:protected] =>
[alreadyInValidation:protected] =>
[validationFailures:protected] => Array
(
)
[_new:BaseObject:private] =>
[_deleted:BaseObject:private] =>
[modifiedColumns:protected] => Array
(
)
)
[73] => Category Object
(
[languages:protected] =>
[bok_resources:protected] =>
[bok_topics:protected] =>
[bok_keywords:protected] =>
[id:protected] => 73
[type:protected] => category
[parent:protected] => 2
[label:protected] => PCC/Restoration
[alreadyInSave:protected] =>
[alreadyInValidation:protected] =>
[validationFailures:protected] => Array
(
)
[_new:BaseObject:private] =>
[_deleted:BaseObject:private] =>
[modifiedColumns:protected] => Array
(
)
)
[74] => Category Object
(
[languages:protected] =>
[bok_resources:protected] =>
[bok_topics:protected] =>
[bok_keywords:protected] =>
[id:protected] => 74
[type:protected] => category
[parent:protected] => 2
[label:protected] => Pile Driver
[alreadyInSave:protected] =>
[alreadyInValidation:protected] =>
[validationFailures:protected] => Array
(
)
[_new:BaseObject:private] =>
[_deleted:BaseObject:private] =>
[modifiedColumns:protected] => Array
(
)
)
[75] => Category Object
(
[languages:protected] =>
[bok_resources:protected] =>
[bok_topics:protected] =>
[bok_keywords:protected] =>
[id:protected] => 75
[type:protected] => category
[parent:protected] => 2
[label:protected] => Plasterer
[alreadyInSave:protected] =>
[alreadyInValidation:protected] =>
[validationFailures:protected] => Array
(
)
[_new:BaseObject:private] =>
[_deleted:BaseObject:private] =>
[modifiedColumns:protected] => Array
(
)
)
[76] => Category Object
(
[languages:protected] =>
[bok_resources:protected] =>
[bok_topics:protected] =>
[bok_keywords:protected] =>
[id:protected] => 76
[type:protected] => category
[parent:protected] => 2
[label:protected] => Plumber/Pipefitter
[alreadyInSave:protected] =>
[alreadyInValidation:protected] =>
[validationFailures:protected] => Array
(
)
[_new:BaseObject:private] =>
[_deleted:BaseObject:private] =>
[modifiedColumns:protected] => Array
(
)
)
[77] => Category Object
(
[languages:protected] =>
[bok_resources:protected] =>
[bok_topics:protected] =>
[bok_keywords:protected] =>
[id:protected] => 77
[type:protected] => category
[parent:protected] => 2
[label:protected] => Refractory Worker
[alreadyInSave:protected] =>
[alreadyInValidation:protected] =>
[validationFailures:protected] => Array
(
)
[_new:BaseObject:private] =>
[_deleted:BaseObject:private] =>
[modifiedColumns:protected] => Array
(
)
)
[63] => Category Object
(
[languages:protected] =>
[bok_resources:protected] =>
[bok_topics:protected] =>
[bok_keywords:protected] =>
[id:protected] => 63
[type:protected] => category
[parent:protected] => 2
[label:protected] => Reinforcing Ironworker
[alreadyInSave:protected] =>
[alreadyInValidation:protected] =>
[validationFailures:protected] => Array
(
)
[_new:BaseObject:private] =>
[_deleted:BaseObject:private] =>
[modifiedColumns:protected] => Array
(
)
)
[78] => Category Object
(
[languages:protected] =>
[bok_resources:protected] =>
[bok_topics:protected] =>
[bok_keywords:protected] =>
[id:protected] => 78
[type:protected] => category
[parent:protected] => 2
[label:protected] => Roofer/Waterproofer
[alreadyInSave:protected] =>
[alreadyInValidation:protected] =>
[validationFailures:protected] => Array
(
)
[_new:BaseObject:private] =>
[_deleted:BaseObject:private] =>
[modifiedColumns:protected] => Array
(
)
)
[79] => Category Object
(
[languages:protected] =>
[bok_resources:protected] =>
[bok_topics:protected] =>
[bok_keywords:protected] =>
[id:protected] => 79
[type:protected] => category
[parent:protected] => 2
[label:protected] => Scaffold Erector
[alreadyInSave:protected] =>
[alreadyInValidation:protected] =>
[validationFailures:protected] => Array
(
)
[_new:BaseObject:private] =>
[_deleted:BaseObject:private] =>
[modifiedColumns:protected] => Array
(
)
)
[80] => Category Object
(
[languages:protected] =>
[bok_resources:protected] =>
[bok_topics:protected] =>
[bok_keywords:protected] =>
[id:protected] => 80
[type:protected] => category
[parent:protected] => 2
[label:protected] => Sheetmetal Worker
[alreadyInSave:protected] =>
[alreadyInValidation:protected] =>
[validationFailures:protected] => Array
(
)
[_new:BaseObject:private] =>
[_deleted:BaseObject:private] =>
[modifiedColumns:protected] => Array
(
)
)
[81] => Category Object
(
[languages:protected] =>
[bok_resources:protected] =>
[bok_topics:protected] =>
[bok_keywords:protected] =>
[id:protected] => 81
[type:protected] => category
[parent:protected] => 2
[label:protected] => Sprinkler Fitter
[alreadyInSave:protected] =>
[alreadyInValidation:protected] =>
[validationFailures:protected] => Array
(
)
[_new:BaseObject:private] =>
[_deleted:BaseObject:private] =>
[modifiedColumns:protected] => Array
(
)
)
[82] => Category Object
(
[languages:protected] =>
[bok_resources:protected] =>
[bok_topics:protected] =>
[bok_keywords:protected] =>
[id:protected] => 82
[type:protected] => category
[parent:protected] => 2
[label:protected] => Stonemason
[alreadyInSave:protected] =>
[alreadyInValidation:protected] =>
[validationFailures:protected] => Array
(
)
[_new:BaseObject:private] =>
[_deleted:BaseObject:private] =>
[modifiedColumns:protected] => Array
(
)
)
[62] => Category Object
(
[languages:protected] =>
[bok_resources:protected] =>
[bok_topics:protected] =>
[bok_keywords:protected] =>
[id:protected] => 62
[type:protected] => category
[parent:protected] => 2
[label:protected] => Structural Ironworker
[alreadyInSave:protected] =>
[alreadyInValidation:protected] =>
[validationFailures:protected] => Array
(
)
[_new:BaseObject:private] =>
[_deleted:BaseObject:private] =>
[modifiedColumns:protected] => Array
(
)
)
[83] => Category Object
(
[languages:protected] =>
[bok_resources:protected] =>
[bok_topics:protected] =>
[bok_keywords:protected] =>
[id:protected] => 83
[type:protected] => category
[parent:protected] => 2
[label:protected] => Terrazzo Worker
[alreadyInSave:protected] =>
[alreadyInValidation:protected] =>
[validationFailures:protected] => Array
(
)
[_new:BaseObject:private] =>
[_deleted:BaseObject:private] =>
[modifiedColumns:protected] => Array
(
)
)
[84] => Category Object
(
[languages:protected] =>
[bok_resources:protected] =>
[bok_topics:protected] =>
[bok_keywords:protected] =>
[id:protected] => 84
[type:protected] => category
[parent:protected] => 2
[label:protected] => Tile Setter
[alreadyInSave:protected] =>
[alreadyInValidation:protected] =>
[validationFailures:protected] => Array
(
)
[_new:BaseObject:private] =>
[_deleted:BaseObject:private] =>
[modifiedColumns:protected] => Array
(
)
)
[85] => Category Object
(
[languages:protected] =>
[bok_resources:protected] =>
[bok_topics:protected] =>
[bok_keywords:protected] =>
[id:protected] => 85
[type:protected] => category
[parent:protected] => 2
[label:protected] => Truck Driver
[alreadyInSave:protected] =>
[alreadyInValidation:protected] =>
[validationFailures:protected] => Array
(
)
[_new:BaseObject:private] =>
[_deleted:BaseObject:private] =>
[modifiedColumns:protected] => Array
(
)
)
[86] => Category Object
(
[languages:protected] =>
[bok_resources:protected] =>
[bok_topics:protected] =>
[bok_keywords:protected] =>
[id:protected] => 86
[type:protected] => category
[parent:protected] => 2
[label:protected] => Welder
[alreadyInSave:protected] =>
[alreadyInValidation:protected] =>
[validationFailures:protected] => Array
(
)
[_new:BaseObject:private] =>
[_deleted:BaseObject:private] =>
[modifiedColumns:protected] => Array
(
)
)
[87] => Category Object
(
[languages:protected] =>
[bok_resources:protected] =>
[bok_topics:protected] =>
[bok_keywords:protected] =>
[id:protected] => 87
[type:protected] => category
[parent:protected] => 3
[label:protected] => Commercial & Institutional
[alreadyInSave:protected] =>
[alreadyInValidation:protected] =>
[validationFailures:protected] => Array
(
)
[_new:BaseObject:private] =>
[_deleted:BaseObject:private] =>
[modifiedColumns:protected] => Array
(
)
)
[88] => Category Object
(
[languages:protected] =>
[bok_resources:protected] =>
[bok_topics:protected] =>
[bok_keywords:protected] =>
[id:protected] => 88
[type:protected] => category
[parent:protected] => 3
[label:protected] => Demolition
[alreadyInSave:protected] =>
[alreadyInValidation:protected] =>
[validationFailures:protected] => Array
(
)
[_new:BaseObject:private] =>
[_deleted:BaseObject:private] =>
[modifiedColumns:protected] => Array
(
)
)
[89] => Category Object
(
[languages:protected] =>
[bok_resources:protected] =>
[bok_topics:protected] =>
[bok_keywords:protected] =>
[id:protected] => 89
[type:protected] => category
[parent:protected] => 3
[label:protected] => Disasters
[alreadyInSave:protected] =>
[alreadyInValidation:protected] =>
[validationFailures:protected] => Array
(
)
[_new:BaseObject:private] =>
[_deleted:BaseObject:private] =>
[modifiedColumns:protected] => Array
(
)
)
[91] => Category Object
(
[languages:protected] =>
[bok_resources:protected] =>
[bok_topics:protected] =>
[bok_keywords:protected] =>
[id:protected] => 91
[type:protected] => category
[parent:protected] => 3
[label:protected] => Heavy & Highway
[alreadyInSave:protected] =>
[alreadyInValidation:protected] =>
[validationFailures:protected] => Array
(
)
[_new:BaseObject:private] =>
[_deleted:BaseObject:private] =>
[modifiedColumns:protected] => Array
(
)
)
[90] => Category Object
(
[languages:protected] =>
[bok_resources:protected] =>
[bok_topics:protected] =>
[bok_keywords:protected] =>
[id:protected] => 90
[type:protected] => category
[parent:protected] => 3
[label:protected] => Industrial
[alreadyInSave:protected] =>
[alreadyInValidation:protected] =>
[validationFailures:protected] => Array
(
)
[_new:BaseObject:private] =>
[_deleted:BaseObject:private] =>
[modifiedColumns:protected] => Array
(
)
)
[92] => Category Object
(
[languages:protected] =>
[bok_resources:protected] =>
[bok_topics:protected] =>
[bok_keywords:protected] =>
[id:protected] => 92
[type:protected] => category
[parent:protected] => 3
[label:protected] => LEED/Green Construction
[alreadyInSave:protected] =>
[alreadyInValidation:protected] =>
[validationFailures:protected] => Array
(
)
[_new:BaseObject:private] =>
[_deleted:BaseObject:private] =>
[modifiedColumns:protected] => Array
(
)
)
[93] => Category Object
(
[languages:protected] =>
[bok_resources:protected] =>
[bok_topics:protected] =>
[bok_keywords:protected] =>
[id:protected] => 93
[type:protected] => category
[parent:protected] => 3
[label:protected] => Renovations
[alreadyInSave:protected] =>
[alreadyInValidation:protected] =>
[validationFailures:protected] => Array
(
)
[_new:BaseObject:private] =>
[_deleted:BaseObject:private] =>
[modifiedColumns:protected] => Array
(
)
)
[94] => Category Object
(
[languages:protected] =>
[bok_resources:protected] =>
[bok_topics:protected] =>
[bok_keywords:protected] =>
[id:protected] => 94
[type:protected] => category
[parent:protected] => 3
[label:protected] => Residential
[alreadyInSave:protected] =>
[alreadyInValidation:protected] =>
[validationFailures:protected] => Array
(
)
[_new:BaseObject:private] =>
[_deleted:BaseObject:private] =>
[modifiedColumns:protected] => Array
(
)
)
[95] => Category Object
(
[languages:protected] =>
[bok_resources:protected] =>
[bok_topics:protected] =>
[bok_keywords:protected] =>
[id:protected] => 95
[type:protected] => category
[parent:protected] => 3
[label:protected] => Underground
[alreadyInSave:protected] =>
[alreadyInValidation:protected] =>
[validationFailures:protected] => Array
(
)
[_new:BaseObject:private] =>
[_deleted:BaseObject:private] =>
[modifiedColumns:protected] => Array
(
)
)
)
[categories_initialized:protected] => 1
[mapped_items:protected] =>
[content:protected] =>
[files:protected] =>
[language:protected] => Language Object
(
[id:protected] => 1
[code:protected] => en
[name:protected] => English
[alreadyInSave:protected] =>
[alreadyInValidation:protected] =>
[validationFailures:protected] => Array
(
)
[_new:BaseObject:private] =>
[_deleted:BaseObject:private] =>
[modifiedColumns:protected] => Array
(
)
)
[old_record:protected] =>
[id:protected] => 4426
[old_id:protected] =>
[elcosh_id:protected] => d001656
[type:protected] => document
[display_type:protected] => HTML only (and links)
[user_id:protected] => 0
[language_id:protected] => 1
[tagging_id:protected] => Mike Aguilar
[priority_id:protected] => 1
[title:protected] => Construction Dive -- DeWalt's Jobsite Pro headphones recalled for fire hazards
[total_pages:protected] => 1
[billed_pages:protected] => 1
[publication_number:protected] =>
[part_of:protected] =>
[keywords:protected] => DeWalt, Fire Hazards, recall, headphones
[comments:protected] =>
[summary:protected] => A recall notice by the United States Consumer Product Safety Commission affects over 300,000 DeWalt Jobsite Pro Headphones. The recall is a result of a malfunction that can cause earbuds to overheat while charging or during use, leading to fire and burn hazards.
[transition_comments:protected] =>
[external_link:protected] => https://www.constructiondive.com/news/dewalts-jobsite-pro-headphones-recalled-for-fire-hazards/611248/?utm_source=Sailthru&utm_medium=email&utm_campaign=Issue:%202021-12-10%20Construction%20Dive%20Newsletter%20%5Bissue:38532%5D&utm_term=Construction%20Dive
[consol_link:protected] =>
[more_like_this:protected] =>
[permission_given_by:protected] =>
[published:protected] => T
[billable:protected] => F
[img_name:protected] =>
[img_ext:protected] =>
[img_width:protected] =>
[img_height:protected] =>
[img_credit:protected] =>
[img_practice:protected] =>
[vid_source_id:protected] =>
[vid_running_time:protected] =>
[vid_intended_audience:protected] =>
[vid_acquisition_info:protected] =>
[vid_cost:protected] =>
[vid_producer:protected] =>
[vid_filename:protected] =>
[vid_filename_downloadable:protected] =>
[date_summary:protected] =>
[date_permission_requested:protected] =>
[date_permission_received:protected] =>
[date_review_needed:protected] =>
[date_received:protected] => 12/13/21
[date_completed:protected] => 12/13/21
[date_billed:protected] =>
[date_modified:protected] => 12/13/21
[collBokExports:protected] =>
[lastBokExportCriteria:BaseElcoshItem:private] =>
[alreadyInSave:protected] =>
[alreadyInValidation:protected] =>
[validationFailures:protected] => Array
(
)
[_new:BaseObject:private] =>
[_deleted:BaseObject:private] =>
[modifiedColumns:protected] => Array
(
)
)
)
)
[new_images] => Array
(
[0] => Search_Result Object
(
[title] => Morning Toolbox Talk
[image] => /record/images/4003-p.jpg
[blurb] => This photo is from an early morning toolbox talk on a construction job in Mclean, Virginia. It is being delivered in English and Spanish....
[category] => Array
(
[0] => 20
[1] => 51
[2] => 57
[3] => 64
[4] => 70
[5] => 63
[6] => 78
[7] => 82
[8] => 62
[9] => 87
[10] => 88
[11] => 89
[12] => 91
[13] => 90
[14] => 93
[15] => 94
[16] => 97
)
[labels] => Array
(
[0] => Safety Culture
[1] => Work Environment
[2] => Hazards
[3] => Cement Mason
[4] => Trades
[5] => Flagger
[7] => Laborer
[9] => Operating Engineer
[11] => Reinforcing Ironworker
[13] => Roofer/Waterproofer
[15] => Stonemason
[17] => Structural Ironworker
[19] => Commercial & Institutional
[20] => Jobsites
[21] => Demolition
[23] => Disasters
[25] => Heavy & Highway
[27] => Industrial
[29] => Renovations
[31] => Residential
[33] => Images
[34] => Media
[35] => Media & Documents
)
[type] => Images
[sub_category] =>
[url] => /image/4003/i002691/Morning%2BToolbox%2BTalk.html
[item:protected] => ImageRecord Object
(
[records:protected] => Array
(
)
[recordId:protected] =>
[searchWordClass:protected] =>
[searchWordPeerClass:protected] =>
[bok_record:protected] =>
[authors:protected] =>
[organizations:protected] =>
[collections:protected] =>
[categories:protected] => Array
(
[20] => Category Object
(
[languages:protected] =>
[bok_resources:protected] =>
[bok_topics:protected] =>
[bok_keywords:protected] =>
[id:protected] => 20
[type:protected] => category
[parent:protected] => 7
[label:protected] => Safety Culture
[alreadyInSave:protected] =>
[alreadyInValidation:protected] =>
[validationFailures:protected] => Array
(
)
[_new:BaseObject:private] =>
[_deleted:BaseObject:private] =>
[modifiedColumns:protected] => Array
(
)
)
[51] => Category Object
(
[languages:protected] =>
[bok_resources:protected] =>
[bok_topics:protected] =>
[bok_keywords:protected] =>
[id:protected] => 51
[type:protected] => category
[parent:protected] => 2
[label:protected] => Cement Mason
[alreadyInSave:protected] =>
[alreadyInValidation:protected] =>
[validationFailures:protected] => Array
(
)
[_new:BaseObject:private] =>
[_deleted:BaseObject:private] =>
[modifiedColumns:protected] => Array
(
)
)
[57] => Category Object
(
[languages:protected] =>
[bok_resources:protected] =>
[bok_topics:protected] =>
[bok_keywords:protected] =>
[id:protected] => 57
[type:protected] => category
[parent:protected] => 2
[label:protected] => Flagger
[alreadyInSave:protected] =>
[alreadyInValidation:protected] =>
[validationFailures:protected] => Array
(
)
[_new:BaseObject:private] =>
[_deleted:BaseObject:private] =>
[modifiedColumns:protected] => Array
(
)
)
[64] => Category Object
(
[languages:protected] =>
[bok_resources:protected] =>
[bok_topics:protected] =>
[bok_keywords:protected] =>
[id:protected] => 64
[type:protected] => category
[parent:protected] => 2
[label:protected] => Laborer
[alreadyInSave:protected] =>
[alreadyInValidation:protected] =>
[validationFailures:protected] => Array
(
)
[_new:BaseObject:private] =>
[_deleted:BaseObject:private] =>
[modifiedColumns:protected] => Array
(
)
)
[70] => Category Object
(
[languages:protected] =>
[bok_resources:protected] =>
[bok_topics:protected] =>
[bok_keywords:protected] =>
[id:protected] => 70
[type:protected] => category
[parent:protected] => 2
[label:protected] => Operating Engineer
[alreadyInSave:protected] =>
[alreadyInValidation:protected] =>
[validationFailures:protected] => Array
(
)
[_new:BaseObject:private] =>
[_deleted:BaseObject:private] =>
[modifiedColumns:protected] => Array
(
)
)
[63] => Category Object
(
[languages:protected] =>
[bok_resources:protected] =>
[bok_topics:protected] =>
[bok_keywords:protected] =>
[id:protected] => 63
[type:protected] => category
[parent:protected] => 2
[label:protected] => Reinforcing Ironworker
[alreadyInSave:protected] =>
[alreadyInValidation:protected] =>
[validationFailures:protected] => Array
(
)
[_new:BaseObject:private] =>
[_deleted:BaseObject:private] =>
[modifiedColumns:protected] => Array
(
)
)
[78] => Category Object
(
[languages:protected] =>
[bok_resources:protected] =>
[bok_topics:protected] =>
[bok_keywords:protected] =>
[id:protected] => 78
[type:protected] => category
[parent:protected] => 2
[label:protected] => Roofer/Waterproofer
[alreadyInSave:protected] =>
[alreadyInValidation:protected] =>
[validationFailures:protected] => Array
(
)
[_new:BaseObject:private] =>
[_deleted:BaseObject:private] =>
[modifiedColumns:protected] => Array
(
)
)
[82] => Category Object
(
[languages:protected] =>
[bok_resources:protected] =>
[bok_topics:protected] =>
[bok_keywords:protected] =>
[id:protected] => 82
[type:protected] => category
[parent:protected] => 2
[label:protected] => Stonemason
[alreadyInSave:protected] =>
[alreadyInValidation:protected] =>
[validationFailures:protected] => Array
(
)
[_new:BaseObject:private] =>
[_deleted:BaseObject:private] =>
[modifiedColumns:protected] => Array
(
)
)
[62] => Category Object
(
[languages:protected] =>
[bok_resources:protected] =>
[bok_topics:protected] =>
[bok_keywords:protected] =>
[id:protected] => 62
[type:protected] => category
[parent:protected] => 2
[label:protected] => Structural Ironworker
[alreadyInSave:protected] =>
[alreadyInValidation:protected] =>
[validationFailures:protected] => Array
(
)
[_new:BaseObject:private] =>
[_deleted:BaseObject:private] =>
[modifiedColumns:protected] => Array
(
)
)
[87] => Category Object
(
[languages:protected] =>
[bok_resources:protected] =>
[bok_topics:protected] =>
[bok_keywords:protected] =>
[id:protected] => 87
[type:protected] => category
[parent:protected] => 3
[label:protected] => Commercial & Institutional
[alreadyInSave:protected] =>
[alreadyInValidation:protected] =>
[validationFailures:protected] => Array
(
)
[_new:BaseObject:private] =>
[_deleted:BaseObject:private] =>
[modifiedColumns:protected] => Array
(
)
)
[88] => Category Object
(
[languages:protected] =>
[bok_resources:protected] =>
[bok_topics:protected] =>
[bok_keywords:protected] =>
[id:protected] => 88
[type:protected] => category
[parent:protected] => 3
[label:protected] => Demolition
[alreadyInSave:protected] =>
[alreadyInValidation:protected] =>
[validationFailures:protected] => Array
(
)
[_new:BaseObject:private] =>
[_deleted:BaseObject:private] =>
[modifiedColumns:protected] => Array
(
)
)
[89] => Category Object
(
[languages:protected] =>
[bok_resources:protected] =>
[bok_topics:protected] =>
[bok_keywords:protected] =>
[id:protected] => 89
[type:protected] => category
[parent:protected] => 3
[label:protected] => Disasters
[alreadyInSave:protected] =>
[alreadyInValidation:protected] =>
[validationFailures:protected] => Array
(
)
[_new:BaseObject:private] =>
[_deleted:BaseObject:private] =>
[modifiedColumns:protected] => Array
(
)
)
[91] => Category Object
(
[languages:protected] =>
[bok_resources:protected] =>
[bok_topics:protected] =>
[bok_keywords:protected] =>
[id:protected] => 91
[type:protected] => category
[parent:protected] => 3
[label:protected] => Heavy & Highway
[alreadyInSave:protected] =>
[alreadyInValidation:protected] =>
[validationFailures:protected] => Array
(
)
[_new:BaseObject:private] =>
[_deleted:BaseObject:private] =>
[modifiedColumns:protected] => Array
(
)
)
[90] => Category Object
(
[languages:protected] =>
[bok_resources:protected] =>
[bok_topics:protected] =>
[bok_keywords:protected] =>
[id:protected] => 90
[type:protected] => category
[parent:protected] => 3
[label:protected] => Industrial
[alreadyInSave:protected] =>
[alreadyInValidation:protected] =>
[validationFailures:protected] => Array
(
)
[_new:BaseObject:private] =>
[_deleted:BaseObject:private] =>
[modifiedColumns:protected] => Array
(
)
)
[93] => Category Object
(
[languages:protected] =>
[bok_resources:protected] =>
[bok_topics:protected] =>
[bok_keywords:protected] =>
[id:protected] => 93
[type:protected] => category
[parent:protected] => 3
[label:protected] => Renovations
[alreadyInSave:protected] =>
[alreadyInValidation:protected] =>
[validationFailures:protected] => Array
(
)
[_new:BaseObject:private] =>
[_deleted:BaseObject:private] =>
[modifiedColumns:protected] => Array
(
)
)
[94] => Category Object
(
[languages:protected] =>
[bok_resources:protected] =>
[bok_topics:protected] =>
[bok_keywords:protected] =>
[id:protected] => 94
[type:protected] => category
[parent:protected] => 3
[label:protected] => Residential
[alreadyInSave:protected] =>
[alreadyInValidation:protected] =>
[validationFailures:protected] => Array
(
)
[_new:BaseObject:private] =>
[_deleted:BaseObject:private] =>
[modifiedColumns:protected] => Array
(
)
)
[97] => Category Object
(
[languages:protected] =>
[bok_resources:protected] =>
[bok_topics:protected] =>
[bok_keywords:protected] =>
[id:protected] => 97
[type:protected] => category
[parent:protected] => 5
[label:protected] => Images
[alreadyInSave:protected] =>
[alreadyInValidation:protected] =>
[validationFailures:protected] => Array
(
)
[_new:BaseObject:private] =>
[_deleted:BaseObject:private] =>
[modifiedColumns:protected] => Array
(
)
)
)
[categories_initialized:protected] => 1
[mapped_items:protected] =>
[content:protected] =>
[files:protected] =>
[language:protected] => Language Object
(
[id:protected] => 1
[code:protected] => en
[name:protected] => English
[alreadyInSave:protected] =>
[alreadyInValidation:protected] =>
[validationFailures:protected] => Array
(
)
[_new:BaseObject:private] =>
[_deleted:BaseObject:private] =>
[modifiedColumns:protected] => Array
(
)
)
[old_record:protected] =>
[id:protected] => 4003
[old_id:protected] =>
[elcosh_id:protected] => i002691
[type:protected] => image
[display_type:protected] => Image
[user_id:protected] => 0
[language_id:protected] => 1
[tagging_id:protected] => Bruce Lippy
[priority_id:protected] => 1
[title:protected] => Morning Toolbox Talk
[total_pages:protected] => 0
[billed_pages:protected] => 0
[publication_number:protected] =>
[part_of:protected] =>
[keywords:protected] => toolbox talk, tailgate talk, Spanish, bilingual
[comments:protected] =>
[summary:protected] => This photo is from an early morning toolbox talk on a construction job in Mclean, Virginia. It is being delivered in English and Spanish.
[transition_comments:protected] =>
[external_link:protected] =>
[consol_link:protected] => http://www.cpwrconstructionsolutions.org/electrical/solution/662/worker-training.html
[more_like_this:protected] => d001285,d001304,c000079
[permission_given_by:protected] =>
[published:protected] => T
[billable:protected] => F
[img_name:protected] =>
[img_ext:protected] => jpg
[img_width:protected] =>
[img_height:protected] =>
[img_credit:protected] => Morgan Zavertnik and Hoar Construction
[img_practice:protected] => good
[vid_source_id:protected] =>
[vid_running_time:protected] =>
[vid_intended_audience:protected] =>
[vid_acquisition_info:protected] =>
[vid_cost:protected] =>
[vid_producer:protected] =>
[vid_filename:protected] =>
[vid_filename_downloadable:protected] =>
[date_summary:protected] => November 2015
[date_permission_requested:protected] =>
[date_permission_received:protected] =>
[date_review_needed:protected] =>
[date_received:protected] => 03/02/16
[date_completed:protected] => 03/02/16
[date_billed:protected] =>
[date_modified:protected] => 03/02/16
[collBokExports:protected] =>
[lastBokExportCriteria:BaseElcoshItem:private] =>
[alreadyInSave:protected] =>
[alreadyInValidation:protected] =>
[validationFailures:protected] => Array
(
)
[_new:BaseObject:private] =>
[_deleted:BaseObject:private] =>
[modifiedColumns:protected] => Array
(
)
)
)
[1] => Search_Result Object
(
[title] => Toolbox talk - crew view
[image] => /record/images/4005-p.jpg
[blurb] => Photo of crew listening to a toolbox safety talk before starting work....
[category] => Array
(
[0] => 97
[1] => 20
[2] => 47
[3] => 49
[4] => 51
[5] => 55
[6] => 61
[7] => 64
[8] => 71
[9] => 75
[10] => 63
[11] => 79
[12] => 62
[13] => 87
[14] => 88
[15] => 91
[16] => 90
[17] => 93
[18] => 94
[19] => 95
)
[labels] => Array
(
[0] => Images
[1] => Media
[2] => Media & Documents
[3] => Safety Culture
[4] => Work Environment
[5] => Hazards
[6] => Bricklayer
[7] => Trades
[8] => Carpenter
[10] => Cement Mason
[12] => Electrical Worker
[14] => Interior Systems Carpenter
[16] => Laborer
[18] => Painter
[20] => Plasterer
[22] => Reinforcing Ironworker
[24] => Scaffold Erector
[26] => Structural Ironworker
[28] => Commercial & Institutional
[29] => Jobsites
[30] => Demolition
[32] => Heavy & Highway
[34] => Industrial
[36] => Renovations
[38] => Residential
[40] => Underground
)
[type] => Images
[sub_category] =>
[url] => /image/4005/i002692/Toolbox%2Btalk%2B-%2Bcrew%2Bview.html
[item:protected] => ImageRecord Object
(
[records:protected] => Array
(
)
[recordId:protected] =>
[searchWordClass:protected] =>
[searchWordPeerClass:protected] =>
[bok_record:protected] =>
[authors:protected] =>
[organizations:protected] =>
[collections:protected] =>
[categories:protected] => Array
(
[97] => Category Object
(
[languages:protected] =>
[bok_resources:protected] =>
[bok_topics:protected] =>
[bok_keywords:protected] =>
[id:protected] => 97
[type:protected] => category
[parent:protected] => 5
[label:protected] => Images
[alreadyInSave:protected] =>
[alreadyInValidation:protected] =>
[validationFailures:protected] => Array
(
)
[_new:BaseObject:private] =>
[_deleted:BaseObject:private] =>
[modifiedColumns:protected] => Array
(
)
)
[20] => Category Object
(
[languages:protected] =>
[bok_resources:protected] =>
[bok_topics:protected] =>
[bok_keywords:protected] =>
[id:protected] => 20
[type:protected] => category
[parent:protected] => 7
[label:protected] => Safety Culture
[alreadyInSave:protected] =>
[alreadyInValidation:protected] =>
[validationFailures:protected] => Array
(
)
[_new:BaseObject:private] =>
[_deleted:BaseObject:private] =>
[modifiedColumns:protected] => Array
(
)
)
[47] => Category Object
(
[languages:protected] =>
[bok_resources:protected] =>
[bok_topics:protected] =>
[bok_keywords:protected] =>
[id:protected] => 47
[type:protected] => category
[parent:protected] => 2
[label:protected] => Bricklayer
[alreadyInSave:protected] =>
[alreadyInValidation:protected] =>
[validationFailures:protected] => Array
(
)
[_new:BaseObject:private] =>
[_deleted:BaseObject:private] =>
[modifiedColumns:protected] => Array
(
)
)
[49] => Category Object
(
[languages:protected] =>
[bok_resources:protected] =>
[bok_topics:protected] =>
[bok_keywords:protected] =>
[id:protected] => 49
[type:protected] => category
[parent:protected] => 2
[label:protected] => Carpenter
[alreadyInSave:protected] =>
[alreadyInValidation:protected] =>
[validationFailures:protected] => Array
(
)
[_new:BaseObject:private] =>
[_deleted:BaseObject:private] =>
[modifiedColumns:protected] => Array
(
)
)
[51] => Category Object
(
[languages:protected] =>
[bok_resources:protected] =>
[bok_topics:protected] =>
[bok_keywords:protected] =>
[id:protected] => 51
[type:protected] => category
[parent:protected] => 2
[label:protected] => Cement Mason
[alreadyInSave:protected] =>
[alreadyInValidation:protected] =>
[validationFailures:protected] => Array
(
)
[_new:BaseObject:private] =>
[_deleted:BaseObject:private] =>
[modifiedColumns:protected] => Array
(
)
)
[55] => Category Object
(
[languages:protected] =>
[bok_resources:protected] =>
[bok_topics:protected] =>
[bok_keywords:protected] =>
[id:protected] => 55
[type:protected] => category
[parent:protected] => 2
[label:protected] => Electrical Worker
[alreadyInSave:protected] =>
[alreadyInValidation:protected] =>
[validationFailures:protected] => Array
(
)
[_new:BaseObject:private] =>
[_deleted:BaseObject:private] =>
[modifiedColumns:protected] => Array
(
)
)
[61] => Category Object
(
[languages:protected] =>
[bok_resources:protected] =>
[bok_topics:protected] =>
[bok_keywords:protected] =>
[id:protected] => 61
[type:protected] => category
[parent:protected] => 2
[label:protected] => Interior Systems Carpenter
[alreadyInSave:protected] =>
[alreadyInValidation:protected] =>
[validationFailures:protected] => Array
(
)
[_new:BaseObject:private] =>
[_deleted:BaseObject:private] =>
[modifiedColumns:protected] => Array
(
)
)
[64] => Category Object
(
[languages:protected] =>
[bok_resources:protected] =>
[bok_topics:protected] =>
[bok_keywords:protected] =>
[id:protected] => 64
[type:protected] => category
[parent:protected] => 2
[label:protected] => Laborer
[alreadyInSave:protected] =>
[alreadyInValidation:protected] =>
[validationFailures:protected] => Array
(
)
[_new:BaseObject:private] =>
[_deleted:BaseObject:private] =>
[modifiedColumns:protected] => Array
(
)
)
[71] => Category Object
(
[languages:protected] =>
[bok_resources:protected] =>
[bok_topics:protected] =>
[bok_keywords:protected] =>
[id:protected] => 71
[type:protected] => category
[parent:protected] => 2
[label:protected] => Painter
[alreadyInSave:protected] =>
[alreadyInValidation:protected] =>
[validationFailures:protected] => Array
(
)
[_new:BaseObject:private] =>
[_deleted:BaseObject:private] =>
[modifiedColumns:protected] => Array
(
)
)
[75] => Category Object
(
[languages:protected] =>
[bok_resources:protected] =>
[bok_topics:protected] =>
[bok_keywords:protected] =>
[id:protected] => 75
[type:protected] => category
[parent:protected] => 2
[label:protected] => Plasterer
[alreadyInSave:protected] =>
[alreadyInValidation:protected] =>
[validationFailures:protected] => Array
(
)
[_new:BaseObject:private] =>
[_deleted:BaseObject:private] =>
[modifiedColumns:protected] => Array
(
)
)
[63] => Category Object
(
[languages:protected] =>
[bok_resources:protected] =>
[bok_topics:protected] =>
[bok_keywords:protected] =>
[id:protected] => 63
[type:protected] => category
[parent:protected] => 2
[label:protected] => Reinforcing Ironworker
[alreadyInSave:protected] =>
[alreadyInValidation:protected] =>
[validationFailures:protected] => Array
(
)
[_new:BaseObject:private] =>
[_deleted:BaseObject:private] =>
[modifiedColumns:protected] => Array
(
)
)
[79] => Category Object
(
[languages:protected] =>
[bok_resources:protected] =>
[bok_topics:protected] =>
[bok_keywords:protected] =>
[id:protected] => 79
[type:protected] => category
[parent:protected] => 2
[label:protected] => Scaffold Erector
[alreadyInSave:protected] =>
[alreadyInValidation:protected] =>
[validationFailures:protected] => Array
(
)
[_new:BaseObject:private] =>
[_deleted:BaseObject:private] =>
[modifiedColumns:protected] => Array
(
)
)
[62] => Category Object
(
[languages:protected] =>
[bok_resources:protected] =>
[bok_topics:protected] =>
[bok_keywords:protected] =>
[id:protected] => 62
[type:protected] => category
[parent:protected] => 2
[label:protected] => Structural Ironworker
[alreadyInSave:protected] =>
[alreadyInValidation:protected] =>
[validationFailures:protected] => Array
(
)
[_new:BaseObject:private] =>
[_deleted:BaseObject:private] =>
[modifiedColumns:protected] => Array
(
)
)
[87] => Category Object
(
[languages:protected] =>
[bok_resources:protected] =>
[bok_topics:protected] =>
[bok_keywords:protected] =>
[id:protected] => 87
[type:protected] => category
[parent:protected] => 3
[label:protected] => Commercial & Institutional
[alreadyInSave:protected] =>
[alreadyInValidation:protected] =>
[validationFailures:protected] => Array
(
)
[_new:BaseObject:private] =>
[_deleted:BaseObject:private] =>
[modifiedColumns:protected] => Array
(
)
)
[88] => Category Object
(
[languages:protected] =>
[bok_resources:protected] =>
[bok_topics:protected] =>
[bok_keywords:protected] =>
[id:protected] => 88
[type:protected] => category
[parent:protected] => 3
[label:protected] => Demolition
[alreadyInSave:protected] =>
[alreadyInValidation:protected] =>
[validationFailures:protected] => Array
(
)
[_new:BaseObject:private] =>
[_deleted:BaseObject:private] =>
[modifiedColumns:protected] => Array
(
)
)
[91] => Category Object
(
[languages:protected] =>
[bok_resources:protected] =>
[bok_topics:protected] =>
[bok_keywords:protected] =>
[id:protected] => 91
[type:protected] => category
[parent:protected] => 3
[label:protected] => Heavy & Highway
[alreadyInSave:protected] =>
[alreadyInValidation:protected] =>
[validationFailures:protected] => Array
(
)
[_new:BaseObject:private] =>
[_deleted:BaseObject:private] =>
[modifiedColumns:protected] => Array
(
)
)
[90] => Category Object
(
[languages:protected] =>
[bok_resources:protected] =>
[bok_topics:protected] =>
[bok_keywords:protected] =>
[id:protected] => 90
[type:protected] => category
[parent:protected] => 3
[label:protected] => Industrial
[alreadyInSave:protected] =>
[alreadyInValidation:protected] =>
[validationFailures:protected] => Array
(
)
[_new:BaseObject:private] =>
[_deleted:BaseObject:private] =>
[modifiedColumns:protected] => Array
(
)
)
[93] => Category Object
(
[languages:protected] =>
[bok_resources:protected] =>
[bok_topics:protected] =>
[bok_keywords:protected] =>
[id:protected] => 93
[type:protected] => category
[parent:protected] => 3
[label:protected] => Renovations
[alreadyInSave:protected] =>
[alreadyInValidation:protected] =>
[validationFailures:protected] => Array
(
)
[_new:BaseObject:private] =>
[_deleted:BaseObject:private] =>
[modifiedColumns:protected] => Array
(
)
)
[94] => Category Object
(
[languages:protected] =>
[bok_resources:protected] =>
[bok_topics:protected] =>
[bok_keywords:protected] =>
[id:protected] => 94
[type:protected] => category
[parent:protected] => 3
[label:protected] => Residential
[alreadyInSave:protected] =>
[alreadyInValidation:protected] =>
[validationFailures:protected] => Array
(
)
[_new:BaseObject:private] =>
[_deleted:BaseObject:private] =>
[modifiedColumns:protected] => Array
(
)
)
[95] => Category Object
(
[languages:protected] =>
[bok_resources:protected] =>
[bok_topics:protected] =>
[bok_keywords:protected] =>
[id:protected] => 95
[type:protected] => category
[parent:protected] => 3
[label:protected] => Underground
[alreadyInSave:protected] =>
[alreadyInValidation:protected] =>
[validationFailures:protected] => Array
(
)
[_new:BaseObject:private] =>
[_deleted:BaseObject:private] =>
[modifiedColumns:protected] => Array
(
)
)
)
[categories_initialized:protected] => 1
[mapped_items:protected] =>
[content:protected] =>
[files:protected] =>
[language:protected] => Language Object
(
[id:protected] => 1
[code:protected] => en
[name:protected] => English
[alreadyInSave:protected] =>
[alreadyInValidation:protected] =>
[validationFailures:protected] => Array
(
)
[_new:BaseObject:private] =>
[_deleted:BaseObject:private] =>
[modifiedColumns:protected] => Array
(
)
)
[old_record:protected] =>
[id:protected] => 4005
[old_id:protected] =>
[elcosh_id:protected] => i002692
[type:protected] => image
[display_type:protected] => Image
[user_id:protected] => 0
[language_id:protected] => 1
[tagging_id:protected] => Bruce Lippy
[priority_id:protected] => 1
[title:protected] => Toolbox talk - crew view
[total_pages:protected] => 0
[billed_pages:protected] => 0
[publication_number:protected] =>
[part_of:protected] =>
[keywords:protected] => toolbox talk, tailgate talk, safety talk, Spanish
[comments:protected] =>
[summary:protected] => Photo of crew listening to a toolbox safety talk before starting work.
[transition_comments:protected] =>
[external_link:protected] =>
[consol_link:protected] => http://www.cpwrconstructionsolutions.org/electrical/solution/662/worker-training.html
[more_like_this:protected] => i002691,d001269, c000079, d001285
[permission_given_by:protected] =>
[published:protected] => T
[billable:protected] => F
[img_name:protected] =>
[img_ext:protected] => jpg
[img_width:protected] =>
[img_height:protected] =>
[img_credit:protected] => Morgan Zavertnik and Hoar Construction
[img_practice:protected] => good
[vid_source_id:protected] =>
[vid_running_time:protected] =>
[vid_intended_audience:protected] =>
[vid_acquisition_info:protected] =>
[vid_cost:protected] =>
[vid_producer:protected] =>
[vid_filename:protected] =>
[vid_filename_downloadable:protected] =>
[date_summary:protected] => November 2015
[date_permission_requested:protected] =>
[date_permission_received:protected] =>
[date_review_needed:protected] =>
[date_received:protected] => 03/02/16
[date_completed:protected] => 03/02/16
[date_billed:protected] =>
[date_modified:protected] => 03/02/16
[collBokExports:protected] =>
[lastBokExportCriteria:BaseElcoshItem:private] =>
[alreadyInSave:protected] =>
[alreadyInValidation:protected] =>
[validationFailures:protected] => Array
(
)
[_new:BaseObject:private] =>
[_deleted:BaseObject:private] =>
[modifiedColumns:protected] => Array
(
)
)
)
[2] => Search_Result Object
(
[title] => Toolbox talk - long shot
[image] => /record/images/4006-p.jpg
[blurb] => This crew gathered every morning before starting work to discuss a new safety topic....
[category] => Array
(
[0] => 20
[1] => 47
[2] => 49
[3] => 51
[4] => 55
[5] => 64
[6] => 68
[7] => 75
[8] => 76
[9] => 63
[10] => 78
[11] => 79
[12] => 82
[13] => 62
[14] => 87
[15] => 88
[16] => 91
[17] => 90
[18] => 93
[19] => 94
[20] => 95
[21] => 97
)
[labels] => Array
(
[0] => Safety Culture
[1] => Work Environment
[2] => Hazards
[3] => Bricklayer
[4] => Trades
[5] => Carpenter
[7] => Cement Mason
[9] => Electrical Worker
[11] => Laborer
[13] => Maintenance Worker
[15] => Plasterer
[17] => Plumber/Pipefitter
[19] => Reinforcing Ironworker
[21] => Roofer/Waterproofer
[23] => Scaffold Erector
[25] => Stonemason
[27] => Structural Ironworker
[29] => Commercial & Institutional
[30] => Jobsites
[31] => Demolition
[33] => Heavy & Highway
[35] => Industrial
[37] => Renovations
[39] => Residential
[41] => Underground
[43] => Images
[44] => Media
[45] => Media & Documents
)
[type] => Images
[sub_category] =>
[url] => /image/4006/i002693/Toolbox%2Btalk%2B-%2Blong%2Bshot.html
[item:protected] => ImageRecord Object
(
[records:protected] => Array
(
)
[recordId:protected] =>
[searchWordClass:protected] =>
[searchWordPeerClass:protected] =>
[bok_record:protected] =>
[authors:protected] =>
[organizations:protected] =>
[collections:protected] =>
[categories:protected] => Array
(
[20] => Category Object
(
[languages:protected] =>
[bok_resources:protected] =>
[bok_topics:protected] =>
[bok_keywords:protected] =>
[id:protected] => 20
[type:protected] => category
[parent:protected] => 7
[label:protected] => Safety Culture
[alreadyInSave:protected] =>
[alreadyInValidation:protected] =>
[validationFailures:protected] => Array
(
)
[_new:BaseObject:private] =>
[_deleted:BaseObject:private] =>
[modifiedColumns:protected] => Array
(
)
)
[47] => Category Object
(
[languages:protected] =>
[bok_resources:protected] =>
[bok_topics:protected] =>
[bok_keywords:protected] =>
[id:protected] => 47
[type:protected] => category
[parent:protected] => 2
[label:protected] => Bricklayer
[alreadyInSave:protected] =>
[alreadyInValidation:protected] =>
[validationFailures:protected] => Array
(
)
[_new:BaseObject:private] =>
[_deleted:BaseObject:private] =>
[modifiedColumns:protected] => Array
(
)
)
[49] => Category Object
(
[languages:protected] =>
[bok_resources:protected] =>
[bok_topics:protected] =>
[bok_keywords:protected] =>
[id:protected] => 49
[type:protected] => category
[parent:protected] => 2
[label:protected] => Carpenter
[alreadyInSave:protected] =>
[alreadyInValidation:protected] =>
[validationFailures:protected] => Array
(
)
[_new:BaseObject:private] =>
[_deleted:BaseObject:private] =>
[modifiedColumns:protected] => Array
(
)
)
[51] => Category Object
(
[languages:protected] =>
[bok_resources:protected] =>
[bok_topics:protected] =>
[bok_keywords:protected] =>
[id:protected] => 51
[type:protected] => category
[parent:protected] => 2
[label:protected] => Cement Mason
[alreadyInSave:protected] =>
[alreadyInValidation:protected] =>
[validationFailures:protected] => Array
(
)
[_new:BaseObject:private] =>
[_deleted:BaseObject:private] =>
[modifiedColumns:protected] => Array
(
)
)
[55] => Category Object
(
[languages:protected] =>
[bok_resources:protected] =>
[bok_topics:protected] =>
[bok_keywords:protected] =>
[id:protected] => 55
[type:protected] => category
[parent:protected] => 2
[label:protected] => Electrical Worker
[alreadyInSave:protected] =>
[alreadyInValidation:protected] =>
[validationFailures:protected] => Array
(
)
[_new:BaseObject:private] =>
[_deleted:BaseObject:private] =>
[modifiedColumns:protected] => Array
(
)
)
[64] => Category Object
(
[languages:protected] =>
[bok_resources:protected] =>
[bok_topics:protected] =>
[bok_keywords:protected] =>
[id:protected] => 64
[type:protected] => category
[parent:protected] => 2
[label:protected] => Laborer
[alreadyInSave:protected] =>
[alreadyInValidation:protected] =>
[validationFailures:protected] => Array
(
)
[_new:BaseObject:private] =>
[_deleted:BaseObject:private] =>
[modifiedColumns:protected] => Array
(
)
)
[68] => Category Object
(
[languages:protected] =>
[bok_resources:protected] =>
[bok_topics:protected] =>
[bok_keywords:protected] =>
[id:protected] => 68
[type:protected] => category
[parent:protected] => 2
[label:protected] => Maintenance Worker
[alreadyInSave:protected] =>
[alreadyInValidation:protected] =>
[validationFailures:protected] => Array
(
)
[_new:BaseObject:private] =>
[_deleted:BaseObject:private] =>
[modifiedColumns:protected] => Array
(
)
)
[75] => Category Object
(
[languages:protected] =>
[bok_resources:protected] =>
[bok_topics:protected] =>
[bok_keywords:protected] =>
[id:protected] => 75
[type:protected] => category
[parent:protected] => 2
[label:protected] => Plasterer
[alreadyInSave:protected] =>
[alreadyInValidation:protected] =>
[validationFailures:protected] => Array
(
)
[_new:BaseObject:private] =>
[_deleted:BaseObject:private] =>
[modifiedColumns:protected] => Array
(
)
)
[76] => Category Object
(
[languages:protected] =>
[bok_resources:protected] =>
[bok_topics:protected] =>
[bok_keywords:protected] =>
[id:protected] => 76
[type:protected] => category
[parent:protected] => 2
[label:protected] => Plumber/Pipefitter
[alreadyInSave:protected] =>
[alreadyInValidation:protected] =>
[validationFailures:protected] => Array
(
)
[_new:BaseObject:private] =>
[_deleted:BaseObject:private] =>
[modifiedColumns:protected] => Array
(
)
)
[63] => Category Object
(
[languages:protected] =>
[bok_resources:protected] =>
[bok_topics:protected] =>
[bok_keywords:protected] =>
[id:protected] => 63
[type:protected] => category
[parent:protected] => 2
[label:protected] => Reinforcing Ironworker
[alreadyInSave:protected] =>
[alreadyInValidation:protected] =>
[validationFailures:protected] => Array
(
)
[_new:BaseObject:private] =>
[_deleted:BaseObject:private] =>
[modifiedColumns:protected] => Array
(
)
)
[78] => Category Object
(
[languages:protected] =>
[bok_resources:protected] =>
[bok_topics:protected] =>
[bok_keywords:protected] =>
[id:protected] => 78
[type:protected] => category
[parent:protected] => 2
[label:protected] => Roofer/Waterproofer
[alreadyInSave:protected] =>
[alreadyInValidation:protected] =>
[validationFailures:protected] => Array
(
)
[_new:BaseObject:private] =>
[_deleted:BaseObject:private] =>
[modifiedColumns:protected] => Array
(
)
)
[79] => Category Object
(
[languages:protected] =>
[bok_resources:protected] =>
[bok_topics:protected] =>
[bok_keywords:protected] =>
[id:protected] => 79
[type:protected] => category
[parent:protected] => 2
[label:protected] => Scaffold Erector
[alreadyInSave:protected] =>
[alreadyInValidation:protected] =>
[validationFailures:protected] => Array
(
)
[_new:BaseObject:private] =>
[_deleted:BaseObject:private] =>
[modifiedColumns:protected] => Array
(
)
)
[82] => Category Object
(
[languages:protected] =>
[bok_resources:protected] =>
[bok_topics:protected] =>
[bok_keywords:protected] =>
[id:protected] => 82
[type:protected] => category
[parent:protected] => 2
[label:protected] => Stonemason
[alreadyInSave:protected] =>
[alreadyInValidation:protected] =>
[validationFailures:protected] => Array
(
)
[_new:BaseObject:private] =>
[_deleted:BaseObject:private] =>
[modifiedColumns:protected] => Array
(
)
)
[62] => Category Object
(
[languages:protected] =>
[bok_resources:protected] =>
[bok_topics:protected] =>
[bok_keywords:protected] =>
[id:protected] => 62
[type:protected] => category
[parent:protected] => 2
[label:protected] => Structural Ironworker
[alreadyInSave:protected] =>
[alreadyInValidation:protected] =>
[validationFailures:protected] => Array
(
)
[_new:BaseObject:private] =>
[_deleted:BaseObject:private] =>
[modifiedColumns:protected] => Array
(
)
)
[87] => Category Object
(
[languages:protected] =>
[bok_resources:protected] =>
[bok_topics:protected] =>
[bok_keywords:protected] =>
[id:protected] => 87
[type:protected] => category
[parent:protected] => 3
[label:protected] => Commercial & Institutional
[alreadyInSave:protected] =>
[alreadyInValidation:protected] =>
[validationFailures:protected] => Array
(
)
[_new:BaseObject:private] =>
[_deleted:BaseObject:private] =>
[modifiedColumns:protected] => Array
(
)
)
[88] => Category Object
(
[languages:protected] =>
[bok_resources:protected] =>
[bok_topics:protected] =>
[bok_keywords:protected] =>
[id:protected] => 88
[type:protected] => category
[parent:protected] => 3
[label:protected] => Demolition
[alreadyInSave:protected] =>
[alreadyInValidation:protected] =>
[validationFailures:protected] => Array
(
)
[_new:BaseObject:private] =>
[_deleted:BaseObject:private] =>
[modifiedColumns:protected] => Array
(
)
)
[91] => Category Object
(
[languages:protected] =>
[bok_resources:protected] =>
[bok_topics:protected] =>
[bok_keywords:protected] =>
[id:protected] => 91
[type:protected] => category
[parent:protected] => 3
[label:protected] => Heavy & Highway
[alreadyInSave:protected] =>
[alreadyInValidation:protected] =>
[validationFailures:protected] => Array
(
)
[_new:BaseObject:private] =>
[_deleted:BaseObject:private] =>
[modifiedColumns:protected] => Array
(
)
)
[90] => Category Object
(
[languages:protected] =>
[bok_resources:protected] =>
[bok_topics:protected] =>
[bok_keywords:protected] =>
[id:protected] => 90
[type:protected] => category
[parent:protected] => 3
[label:protected] => Industrial
[alreadyInSave:protected] =>
[alreadyInValidation:protected] =>
[validationFailures:protected] => Array
(
)
[_new:BaseObject:private] =>
[_deleted:BaseObject:private] =>
[modifiedColumns:protected] => Array
(
)
)
[93] => Category Object
(
[languages:protected] =>
[bok_resources:protected] =>
[bok_topics:protected] =>
[bok_keywords:protected] =>
[id:protected] => 93
[type:protected] => category
[parent:protected] => 3
[label:protected] => Renovations
[alreadyInSave:protected] =>
[alreadyInValidation:protected] =>
[validationFailures:protected] => Array
(
)
[_new:BaseObject:private] =>
[_deleted:BaseObject:private] =>
[modifiedColumns:protected] => Array
(
)
)
[94] => Category Object
(
[languages:protected] =>
[bok_resources:protected] =>
[bok_topics:protected] =>
[bok_keywords:protected] =>
[id:protected] => 94
[type:protected] => category
[parent:protected] => 3
[label:protected] => Residential
[alreadyInSave:protected] =>
[alreadyInValidation:protected] =>
[validationFailures:protected] => Array
(
)
[_new:BaseObject:private] =>
[_deleted:BaseObject:private] =>
[modifiedColumns:protected] => Array
(
)
)
[95] => Category Object
(
[languages:protected] =>
[bok_resources:protected] =>
[bok_topics:protected] =>
[bok_keywords:protected] =>
[id:protected] => 95
[type:protected] => category
[parent:protected] => 3
[label:protected] => Underground
[alreadyInSave:protected] =>
[alreadyInValidation:protected] =>
[validationFailures:protected] => Array
(
)
[_new:BaseObject:private] =>
[_deleted:BaseObject:private] =>
[modifiedColumns:protected] => Array
(
)
)
[97] => Category Object
(
[languages:protected] =>
[bok_resources:protected] =>
[bok_topics:protected] =>
[bok_keywords:protected] =>
[id:protected] => 97
[type:protected] => category
[parent:protected] => 5
[label:protected] => Images
[alreadyInSave:protected] =>
[alreadyInValidation:protected] =>
[validationFailures:protected] => Array
(
)
[_new:BaseObject:private] =>
[_deleted:BaseObject:private] =>
[modifiedColumns:protected] => Array
(
)
)
)
[categories_initialized:protected] => 1
[mapped_items:protected] =>
[content:protected] =>
[files:protected] =>
[language:protected] => Language Object
(
[id:protected] => 1
[code:protected] => en
[name:protected] => English
[alreadyInSave:protected] =>
[alreadyInValidation:protected] =>
[validationFailures:protected] => Array
(
)
[_new:BaseObject:private] =>
[_deleted:BaseObject:private] =>
[modifiedColumns:protected] => Array
(
)
)
[old_record:protected] =>
[id:protected] => 4006
[old_id:protected] =>
[elcosh_id:protected] => i002693
[type:protected] => image
[display_type:protected] => Image
[user_id:protected] => 0
[language_id:protected] => 1
[tagging_id:protected] => Bruce Lippy
[priority_id:protected] => 1
[title:protected] => Toolbox talk - long shot
[total_pages:protected] => 0
[billed_pages:protected] => 0
[publication_number:protected] =>
[part_of:protected] =>
[keywords:protected] => toolbox talk, tailgate talk, safety minute
[comments:protected] =>
[summary:protected] => This crew gathered every morning before starting work to discuss a new safety topic.
[transition_comments:protected] =>
[external_link:protected] =>
[consol_link:protected] => http://www.cpwrconstructionsolutions.org/electrical/solution/662/worker-training.html
[more_like_this:protected] => i002691,i002692,d001269,d000527
[permission_given_by:protected] =>
[published:protected] => T
[billable:protected] => F
[img_name:protected] =>
[img_ext:protected] => jpg
[img_width:protected] =>
[img_height:protected] =>
[img_credit:protected] => Morgan Zavertnik and Hoar Construction
[img_practice:protected] => good
[vid_source_id:protected] =>
[vid_running_time:protected] =>
[vid_intended_audience:protected] =>
[vid_acquisition_info:protected] =>
[vid_cost:protected] =>
[vid_producer:protected] =>
[vid_filename:protected] =>
[vid_filename_downloadable:protected] =>
[date_summary:protected] => November 2015
[date_permission_requested:protected] =>
[date_permission_received:protected] =>
[date_review_needed:protected] =>
[date_received:protected] => 03/02/16
[date_completed:protected] => 03/02/16
[date_billed:protected] =>
[date_modified:protected] => 03/02/16
[collBokExports:protected] =>
[lastBokExportCriteria:BaseElcoshItem:private] =>
[alreadyInSave:protected] =>
[alreadyInValidation:protected] =>
[validationFailures:protected] => Array
(
)
[_new:BaseObject:private] =>
[_deleted:BaseObject:private] =>
[modifiedColumns:protected] => Array
(
)
)
)
[3] => Search_Result Object
(
[title] => Safety officer discussing ongoing project with marketing coordinator
[image] => /record/images/4014-p.jpg
[blurb] => The safety officer (left) points out the good safety practices on this project that reflect well on the firm and may influence future clients....
[category] => Array
(
[0] => 97
[1] => 20
[2] => 46
[3] => 47
[4] => 49
[5] => 50
[6] => 51
[7] => 54
[8] => 55
[9] => 58
[10] => 60
[11] => 61
[12] => 64
[13] => 71
[14] => 75
[15] => 76
[16] => 63
[17] => 79
[18] => 80
[19] => 82
[20] => 62
[21] => 83
[22] => 87
[23] => 91
[24] => 90
[25] => 93
[26] => 94
)
[labels] => Array
(
[0] => Images
[1] => Media
[2] => Media & Documents
[3] => Safety Culture
[4] => Work Environment
[5] => Hazards
[6] => Boilermaker
[7] => Trades
[8] => Bricklayer
[10] => Carpenter
[12] => Carpet Layer
[14] => Cement Mason
[16] => Drywall Applicator Specialist
[18] => Electrical Worker
[20] => Glazier
[22] => HVAC
[24] => Interior Systems Carpenter
[26] => Laborer
[28] => Painter
[30] => Plasterer
[32] => Plumber/Pipefitter
[34] => Reinforcing Ironworker
[36] => Scaffold Erector
[38] => Sheetmetal Worker
[40] => Stonemason
[42] => Structural Ironworker
[44] => Terrazzo Worker
[46] => Commercial & Institutional
[47] => Jobsites
[48] => Heavy & Highway
[50] => Industrial
[52] => Renovations
[54] => Residential
)
[type] => Images
[sub_category] =>
[url] => /image/4014/i002700/Safety%2Bofficer%2Bdiscussing%2Bongoing%2Bproject%2Bwith%2Bmarketing%2Bcoordinator.html
[item:protected] => ImageRecord Object
(
[records:protected] => Array
(
)
[recordId:protected] =>
[searchWordClass:protected] =>
[searchWordPeerClass:protected] =>
[bok_record:protected] =>
[authors:protected] =>
[organizations:protected] =>
[collections:protected] =>
[categories:protected] => Array
(
[97] => Category Object
(
[languages:protected] =>
[bok_resources:protected] =>
[bok_topics:protected] =>
[bok_keywords:protected] =>
[id:protected] => 97
[type:protected] => category
[parent:protected] => 5
[label:protected] => Images
[alreadyInSave:protected] =>
[alreadyInValidation:protected] =>
[validationFailures:protected] => Array
(
)
[_new:BaseObject:private] =>
[_deleted:BaseObject:private] =>
[modifiedColumns:protected] => Array
(
)
)
[20] => Category Object
(
[languages:protected] =>
[bok_resources:protected] =>
[bok_topics:protected] =>
[bok_keywords:protected] =>
[id:protected] => 20
[type:protected] => category
[parent:protected] => 7
[label:protected] => Safety Culture
[alreadyInSave:protected] =>
[alreadyInValidation:protected] =>
[validationFailures:protected] => Array
(
)
[_new:BaseObject:private] =>
[_deleted:BaseObject:private] =>
[modifiedColumns:protected] => Array
(
)
)
[46] => Category Object
(
[languages:protected] =>
[bok_resources:protected] =>
[bok_topics:protected] =>
[bok_keywords:protected] =>
[id:protected] => 46
[type:protected] => category
[parent:protected] => 2
[label:protected] => Boilermaker
[alreadyInSave:protected] =>
[alreadyInValidation:protected] =>
[validationFailures:protected] => Array
(
)
[_new:BaseObject:private] =>
[_deleted:BaseObject:private] =>
[modifiedColumns:protected] => Array
(
)
)
[47] => Category Object
(
[languages:protected] =>
[bok_resources:protected] =>
[bok_topics:protected] =>
[bok_keywords:protected] =>
[id:protected] => 47
[type:protected] => category
[parent:protected] => 2
[label:protected] => Bricklayer
[alreadyInSave:protected] =>
[alreadyInValidation:protected] =>
[validationFailures:protected] => Array
(
)
[_new:BaseObject:private] =>
[_deleted:BaseObject:private] =>
[modifiedColumns:protected] => Array
(
)
)
[49] => Category Object
(
[languages:protected] =>
[bok_resources:protected] =>
[bok_topics:protected] =>
[bok_keywords:protected] =>
[id:protected] => 49
[type:protected] => category
[parent:protected] => 2
[label:protected] => Carpenter
[alreadyInSave:protected] =>
[alreadyInValidation:protected] =>
[validationFailures:protected] => Array
(
)
[_new:BaseObject:private] =>
[_deleted:BaseObject:private] =>
[modifiedColumns:protected] => Array
(
)
)
[50] => Category Object
(
[languages:protected] =>
[bok_resources:protected] =>
[bok_topics:protected] =>
[bok_keywords:protected] =>
[id:protected] => 50
[type:protected] => category
[parent:protected] => 2
[label:protected] => Carpet Layer
[alreadyInSave:protected] =>
[alreadyInValidation:protected] =>
[validationFailures:protected] => Array
(
)
[_new:BaseObject:private] =>
[_deleted:BaseObject:private] =>
[modifiedColumns:protected] => Array
(
)
)
[51] => Category Object
(
[languages:protected] =>
[bok_resources:protected] =>
[bok_topics:protected] =>
[bok_keywords:protected] =>
[id:protected] => 51
[type:protected] => category
[parent:protected] => 2
[label:protected] => Cement Mason
[alreadyInSave:protected] =>
[alreadyInValidation:protected] =>
[validationFailures:protected] => Array
(
)
[_new:BaseObject:private] =>
[_deleted:BaseObject:private] =>
[modifiedColumns:protected] => Array
(
)
)
[54] => Category Object
(
[languages:protected] =>
[bok_resources:protected] =>
[bok_topics:protected] =>
[bok_keywords:protected] =>
[id:protected] => 54
[type:protected] => category
[parent:protected] => 2
[label:protected] => Drywall Applicator Specialist
[alreadyInSave:protected] =>
[alreadyInValidation:protected] =>
[validationFailures:protected] => Array
(
)
[_new:BaseObject:private] =>
[_deleted:BaseObject:private] =>
[modifiedColumns:protected] => Array
(
)
)
[55] => Category Object
(
[languages:protected] =>
[bok_resources:protected] =>
[bok_topics:protected] =>
[bok_keywords:protected] =>
[id:protected] => 55
[type:protected] => category
[parent:protected] => 2
[label:protected] => Electrical Worker
[alreadyInSave:protected] =>
[alreadyInValidation:protected] =>
[validationFailures:protected] => Array
(
)
[_new:BaseObject:private] =>
[_deleted:BaseObject:private] =>
[modifiedColumns:protected] => Array
(
)
)
[58] => Category Object
(
[languages:protected] =>
[bok_resources:protected] =>
[bok_topics:protected] =>
[bok_keywords:protected] =>
[id:protected] => 58
[type:protected] => category
[parent:protected] => 2
[label:protected] => Glazier
[alreadyInSave:protected] =>
[alreadyInValidation:protected] =>
[validationFailures:protected] => Array
(
)
[_new:BaseObject:private] =>
[_deleted:BaseObject:private] =>
[modifiedColumns:protected] => Array
(
)
)
[60] => Category Object
(
[languages:protected] =>
[bok_resources:protected] =>
[bok_topics:protected] =>
[bok_keywords:protected] =>
[id:protected] => 60
[type:protected] => category
[parent:protected] => 2
[label:protected] => HVAC
[alreadyInSave:protected] =>
[alreadyInValidation:protected] =>
[validationFailures:protected] => Array
(
)
[_new:BaseObject:private] =>
[_deleted:BaseObject:private] =>
[modifiedColumns:protected] => Array
(
)
)
[61] => Category Object
(
[languages:protected] =>
[bok_resources:protected] =>
[bok_topics:protected] =>
[bok_keywords:protected] =>
[id:protected] => 61
[type:protected] => category
[parent:protected] => 2
[label:protected] => Interior Systems Carpenter
[alreadyInSave:protected] =>
[alreadyInValidation:protected] =>
[validationFailures:protected] => Array
(
)
[_new:BaseObject:private] =>
[_deleted:BaseObject:private] =>
[modifiedColumns:protected] => Array
(
)
)
[64] => Category Object
(
[languages:protected] =>
[bok_resources:protected] =>
[bok_topics:protected] =>
[bok_keywords:protected] =>
[id:protected] => 64
[type:protected] => category
[parent:protected] => 2
[label:protected] => Laborer
[alreadyInSave:protected] =>
[alreadyInValidation:protected] =>
[validationFailures:protected] => Array
(
)
[_new:BaseObject:private] =>
[_deleted:BaseObject:private] =>
[modifiedColumns:protected] => Array
(
)
)
[71] => Category Object
(
[languages:protected] =>
[bok_resources:protected] =>
[bok_topics:protected] =>
[bok_keywords:protected] =>
[id:protected] => 71
[type:protected] => category
[parent:protected] => 2
[label:protected] => Painter
[alreadyInSave:protected] =>
[alreadyInValidation:protected] =>
[validationFailures:protected] => Array
(
)
[_new:BaseObject:private] =>
[_deleted:BaseObject:private] =>
[modifiedColumns:protected] => Array
(
)
)
[75] => Category Object
(
[languages:protected] =>
[bok_resources:protected] =>
[bok_topics:protected] =>
[bok_keywords:protected] =>
[id:protected] => 75
[type:protected] => category
[parent:protected] => 2
[label:protected] => Plasterer
[alreadyInSave:protected] =>
[alreadyInValidation:protected] =>
[validationFailures:protected] => Array
(
)
[_new:BaseObject:private] =>
[_deleted:BaseObject:private] =>
[modifiedColumns:protected] => Array
(
)
)
[76] => Category Object
(
[languages:protected] =>
[bok_resources:protected] =>
[bok_topics:protected] =>
[bok_keywords:protected] =>
[id:protected] => 76
[type:protected] => category
[parent:protected] => 2
[label:protected] => Plumber/Pipefitter
[alreadyInSave:protected] =>
[alreadyInValidation:protected] =>
[validationFailures:protected] => Array
(
)
[_new:BaseObject:private] =>
[_deleted:BaseObject:private] =>
[modifiedColumns:protected] => Array
(
)
)
[63] => Category Object
(
[languages:protected] =>
[bok_resources:protected] =>
[bok_topics:protected] =>
[bok_keywords:protected] =>
[id:protected] => 63
[type:protected] => category
[parent:protected] => 2
[label:protected] => Reinforcing Ironworker
[alreadyInSave:protected] =>
[alreadyInValidation:protected] =>
[validationFailures:protected] => Array
(
)
[_new:BaseObject:private] =>
[_deleted:BaseObject:private] =>
[modifiedColumns:protected] => Array
(
)
)
[79] => Category Object
(
[languages:protected] =>
[bok_resources:protected] =>
[bok_topics:protected] =>
[bok_keywords:protected] =>
[id:protected] => 79
[type:protected] => category
[parent:protected] => 2
[label:protected] => Scaffold Erector
[alreadyInSave:protected] =>
[alreadyInValidation:protected] =>
[validationFailures:protected] => Array
(
)
[_new:BaseObject:private] =>
[_deleted:BaseObject:private] =>
[modifiedColumns:protected] => Array
(
)
)
[80] => Category Object
(
[languages:protected] =>
[bok_resources:protected] =>
[bok_topics:protected] =>
[bok_keywords:protected] =>
[id:protected] => 80
[type:protected] => category
[parent:protected] => 2
[label:protected] => Sheetmetal Worker
[alreadyInSave:protected] =>
[alreadyInValidation:protected] =>
[validationFailures:protected] => Array
(
)
[_new:BaseObject:private] =>
[_deleted:BaseObject:private] =>
[modifiedColumns:protected] => Array
(
)
)
[82] => Category Object
(
[languages:protected] =>
[bok_resources:protected] =>
[bok_topics:protected] =>
[bok_keywords:protected] =>
[id:protected] => 82
[type:protected] => category
[parent:protected] => 2
[label:protected] => Stonemason
[alreadyInSave:protected] =>
[alreadyInValidation:protected] =>
[validationFailures:protected] => Array
(
)
[_new:BaseObject:private] =>
[_deleted:BaseObject:private] =>
[modifiedColumns:protected] => Array
(
)
)
[62] => Category Object
(
[languages:protected] =>
[bok_resources:protected] =>
[bok_topics:protected] =>
[bok_keywords:protected] =>
[id:protected] => 62
[type:protected] => category
[parent:protected] => 2
[label:protected] => Structural Ironworker
[alreadyInSave:protected] =>
[alreadyInValidation:protected] =>
[validationFailures:protected] => Array
(
)
[_new:BaseObject:private] =>
[_deleted:BaseObject:private] =>
[modifiedColumns:protected] => Array
(
)
)
[83] => Category Object
(
[languages:protected] =>
[bok_resources:protected] =>
[bok_topics:protected] =>
[bok_keywords:protected] =>
[id:protected] => 83
[type:protected] => category
[parent:protected] => 2
[label:protected] => Terrazzo Worker
[alreadyInSave:protected] =>
[alreadyInValidation:protected] =>
[validationFailures:protected] => Array
(
)
[_new:BaseObject:private] =>
[_deleted:BaseObject:private] =>
[modifiedColumns:protected] => Array
(
)
)
[87] => Category Object
(
[languages:protected] =>
[bok_resources:protected] =>
[bok_topics:protected] =>
[bok_keywords:protected] =>
[id:protected] => 87
[type:protected] => category
[parent:protected] => 3
[label:protected] => Commercial & Institutional
[alreadyInSave:protected] =>
[alreadyInValidation:protected] =>
[validationFailures:protected] => Array
(
)
[_new:BaseObject:private] =>
[_deleted:BaseObject:private] =>
[modifiedColumns:protected] => Array
(
)
)
[91] => Category Object
(
[languages:protected] =>
[bok_resources:protected] =>
[bok_topics:protected] =>
[bok_keywords:protected] =>
[id:protected] => 91
[type:protected] => category
[parent:protected] => 3
[label:protected] => Heavy & Highway
[alreadyInSave:protected] =>
[alreadyInValidation:protected] =>
[validationFailures:protected] => Array
(
)
[_new:BaseObject:private] =>
[_deleted:BaseObject:private] =>
[modifiedColumns:protected] => Array
(
)
)
[90] => Category Object
(
[languages:protected] =>
[bok_resources:protected] =>
[bok_topics:protected] =>
[bok_keywords:protected] =>
[id:protected] => 90
[type:protected] => category
[parent:protected] => 3
[label:protected] => Industrial
[alreadyInSave:protected] =>
[alreadyInValidation:protected] =>
[validationFailures:protected] => Array
(
)
[_new:BaseObject:private] =>
[_deleted:BaseObject:private] =>
[modifiedColumns:protected] => Array
(
)
)
[93] => Category Object
(
[languages:protected] =>
[bok_resources:protected] =>
[bok_topics:protected] =>
[bok_keywords:protected] =>
[id:protected] => 93
[type:protected] => category
[parent:protected] => 3
[label:protected] => Renovations
[alreadyInSave:protected] =>
[alreadyInValidation:protected] =>
[validationFailures:protected] => Array
(
)
[_new:BaseObject:private] =>
[_deleted:BaseObject:private] =>
[modifiedColumns:protected] => Array
(
)
)
[94] => Category Object
(
[languages:protected] =>
[bok_resources:protected] =>
[bok_topics:protected] =>
[bok_keywords:protected] =>
[id:protected] => 94
[type:protected] => category
[parent:protected] => 3
[label:protected] => Residential
[alreadyInSave:protected] =>
[alreadyInValidation:protected] =>
[validationFailures:protected] => Array
(
)
[_new:BaseObject:private] =>
[_deleted:BaseObject:private] =>
[modifiedColumns:protected] => Array
(
)
)
)
[categories_initialized:protected] => 1
[mapped_items:protected] =>
[content:protected] =>
[files:protected] =>
[language:protected] => Language Object
(
[id:protected] => 1
[code:protected] => en
[name:protected] => English
[alreadyInSave:protected] =>
[alreadyInValidation:protected] =>
[validationFailures:protected] => Array
(
)
[_new:BaseObject:private] =>
[_deleted:BaseObject:private] =>
[modifiedColumns:protected] => Array
(
)
)
[old_record:protected] =>
[id:protected] => 4014
[old_id:protected] =>
[elcosh_id:protected] => i002700
[type:protected] => image
[display_type:protected] => Image
[user_id:protected] => 0
[language_id:protected] => 1
[tagging_id:protected] => Bruce Lippy
[priority_id:protected] => 1
[title:protected] => Safety officer discussing ongoing project with marketing coordinator
[total_pages:protected] => 0
[billed_pages:protected] => 0
[publication_number:protected] =>
[part_of:protected] =>
[keywords:protected] => Latino, safety officer, safety culture
[comments:protected] =>
[summary:protected] => The safety officer (left) points out the good safety practices on this project that reflect well on the firm and may influence future clients.
[transition_comments:protected] =>
[external_link:protected] =>
[consol_link:protected] => http://www.cpwrconstructionsolutions.org/index.php
[more_like_this:protected] => d000989,d001351,d001362,d000652, d001101, d000931, d001395
[permission_given_by:protected] =>
[published:protected] => T
[billable:protected] => F
[img_name:protected] =>
[img_ext:protected] => jpg
[img_width:protected] =>
[img_height:protected] =>
[img_credit:protected] => Hoar Construction, Photo by Neil Lippy
[img_practice:protected] => good
[vid_source_id:protected] =>
[vid_running_time:protected] =>
[vid_intended_audience:protected] =>
[vid_acquisition_info:protected] =>
[vid_cost:protected] =>
[vid_producer:protected] =>
[vid_filename:protected] =>
[vid_filename_downloadable:protected] =>
[date_summary:protected] => November 2015
[date_permission_requested:protected] =>
[date_permission_received:protected] =>
[date_review_needed:protected] =>
[date_received:protected] => 03/02/16
[date_completed:protected] => 03/02/16
[date_billed:protected] =>
[date_modified:protected] => 01/30/23
[collBokExports:protected] =>
[lastBokExportCriteria:BaseElcoshItem:private] =>
[alreadyInSave:protected] =>
[alreadyInValidation:protected] =>
[validationFailures:protected] => Array
(
)
[_new:BaseObject:private] =>
[_deleted:BaseObject:private] =>
[modifiedColumns:protected] => Array
(
)
)
)
[4] => Search_Result Object
(
[title] => Scaffolding at top of large column
[image] => /record/images/3994-p.jpg
[blurb] => This shot shows innovative guarding around the top of a large concrete column in the base of a high rise structure going up....
[category] => Array
(
[0] => 15
[1] => 21
[2] => 47
[3] => 51
[4] => 63
[5] => 78
[6] => 79
[7] => 80
[8] => 62
[9] => 87
[10] => 97
[11] => 56
[12] => 64
[13] => 74
)
[labels] => Array
(
[0] => Falls
[1] => Work Environment
[2] => Hazards
[3] => Scaffolds
[6] => Bricklayer
[7] => Trades
[8] => Cement Mason
[10] => Reinforcing Ironworker
[12] => Roofer/Waterproofer
[14] => Scaffold Erector
[16] => Sheetmetal Worker
[18] => Structural Ironworker
[20] => Commercial & Institutional
[21] => Jobsites
[22] => Images
[23] => Media
[24] => Media & Documents
[25] => Elevator Constructor
[27] => Laborer
[29] => Pile Driver
)
[type] => Images
[sub_category] =>
[url] => /image/3994/i002689/Scaffolding%2Bat%2Btop%2Bof%2Blarge%2Bcolumn.html
[item:protected] => ImageRecord Object
(
[records:protected] => Array
(
)
[recordId:protected] =>
[searchWordClass:protected] =>
[searchWordPeerClass:protected] =>
[bok_record:protected] =>
[authors:protected] =>
[organizations:protected] =>
[collections:protected] =>
[categories:protected] => Array
(
[15] => Category Object
(
[languages:protected] =>
[bok_resources:protected] =>
[bok_topics:protected] =>
[bok_keywords:protected] =>
[id:protected] => 15
[type:protected] => category
[parent:protected] => 7
[label:protected] => Falls
[alreadyInSave:protected] =>
[alreadyInValidation:protected] =>
[validationFailures:protected] => Array
(
)
[_new:BaseObject:private] =>
[_deleted:BaseObject:private] =>
[modifiedColumns:protected] => Array
(
)
)
[21] => Category Object
(
[languages:protected] =>
[bok_resources:protected] =>
[bok_topics:protected] =>
[bok_keywords:protected] =>
[id:protected] => 21
[type:protected] => category
[parent:protected] => 7
[label:protected] => Scaffolds
[alreadyInSave:protected] =>
[alreadyInValidation:protected] =>
[validationFailures:protected] => Array
(
)
[_new:BaseObject:private] =>
[_deleted:BaseObject:private] =>
[modifiedColumns:protected] => Array
(
)
)
[47] => Category Object
(
[languages:protected] =>
[bok_resources:protected] =>
[bok_topics:protected] =>
[bok_keywords:protected] =>
[id:protected] => 47
[type:protected] => category
[parent:protected] => 2
[label:protected] => Bricklayer
[alreadyInSave:protected] =>
[alreadyInValidation:protected] =>
[validationFailures:protected] => Array
(
)
[_new:BaseObject:private] =>
[_deleted:BaseObject:private] =>
[modifiedColumns:protected] => Array
(
)
)
[51] => Category Object
(
[languages:protected] =>
[bok_resources:protected] =>
[bok_topics:protected] =>
[bok_keywords:protected] =>
[id:protected] => 51
[type:protected] => category
[parent:protected] => 2
[label:protected] => Cement Mason
[alreadyInSave:protected] =>
[alreadyInValidation:protected] =>
[validationFailures:protected] => Array
(
)
[_new:BaseObject:private] =>
[_deleted:BaseObject:private] =>
[modifiedColumns:protected] => Array
(
)
)
[63] => Category Object
(
[languages:protected] =>
[bok_resources:protected] =>
[bok_topics:protected] =>
[bok_keywords:protected] =>
[id:protected] => 63
[type:protected] => category
[parent:protected] => 2
[label:protected] => Reinforcing Ironworker
[alreadyInSave:protected] =>
[alreadyInValidation:protected] =>
[validationFailures:protected] => Array
(
)
[_new:BaseObject:private] =>
[_deleted:BaseObject:private] =>
[modifiedColumns:protected] => Array
(
)
)
[78] => Category Object
(
[languages:protected] =>
[bok_resources:protected] =>
[bok_topics:protected] =>
[bok_keywords:protected] =>
[id:protected] => 78
[type:protected] => category
[parent:protected] => 2
[label:protected] => Roofer/Waterproofer
[alreadyInSave:protected] =>
[alreadyInValidation:protected] =>
[validationFailures:protected] => Array
(
)
[_new:BaseObject:private] =>
[_deleted:BaseObject:private] =>
[modifiedColumns:protected] => Array
(
)
)
[79] => Category Object
(
[languages:protected] =>
[bok_resources:protected] =>
[bok_topics:protected] =>
[bok_keywords:protected] =>
[id:protected] => 79
[type:protected] => category
[parent:protected] => 2
[label:protected] => Scaffold Erector
[alreadyInSave:protected] =>
[alreadyInValidation:protected] =>
[validationFailures:protected] => Array
(
)
[_new:BaseObject:private] =>
[_deleted:BaseObject:private] =>
[modifiedColumns:protected] => Array
(
)
)
[80] => Category Object
(
[languages:protected] =>
[bok_resources:protected] =>
[bok_topics:protected] =>
[bok_keywords:protected] =>
[id:protected] => 80
[type:protected] => category
[parent:protected] => 2
[label:protected] => Sheetmetal Worker
[alreadyInSave:protected] =>
[alreadyInValidation:protected] =>
[validationFailures:protected] => Array
(
)
[_new:BaseObject:private] =>
[_deleted:BaseObject:private] =>
[modifiedColumns:protected] => Array
(
)
)
[62] => Category Object
(
[languages:protected] =>
[bok_resources:protected] =>
[bok_topics:protected] =>
[bok_keywords:protected] =>
[id:protected] => 62
[type:protected] => category
[parent:protected] => 2
[label:protected] => Structural Ironworker
[alreadyInSave:protected] =>
[alreadyInValidation:protected] =>
[validationFailures:protected] => Array
(
)
[_new:BaseObject:private] =>
[_deleted:BaseObject:private] =>
[modifiedColumns:protected] => Array
(
)
)
[87] => Category Object
(
[languages:protected] =>
[bok_resources:protected] =>
[bok_topics:protected] =>
[bok_keywords:protected] =>
[id:protected] => 87
[type:protected] => category
[parent:protected] => 3
[label:protected] => Commercial & Institutional
[alreadyInSave:protected] =>
[alreadyInValidation:protected] =>
[validationFailures:protected] => Array
(
)
[_new:BaseObject:private] =>
[_deleted:BaseObject:private] =>
[modifiedColumns:protected] => Array
(
)
)
[97] => Category Object
(
[languages:protected] =>
[bok_resources:protected] =>
[bok_topics:protected] =>
[bok_keywords:protected] =>
[id:protected] => 97
[type:protected] => category
[parent:protected] => 5
[label:protected] => Images
[alreadyInSave:protected] =>
[alreadyInValidation:protected] =>
[validationFailures:protected] => Array
(
)
[_new:BaseObject:private] =>
[_deleted:BaseObject:private] =>
[modifiedColumns:protected] => Array
(
)
)
[56] => Category Object
(
[languages:protected] =>
[bok_resources:protected] =>
[bok_topics:protected] =>
[bok_keywords:protected] =>
[id:protected] => 56
[type:protected] => category
[parent:protected] => 2
[label:protected] => Elevator Constructor
[alreadyInSave:protected] =>
[alreadyInValidation:protected] =>
[validationFailures:protected] => Array
(
)
[_new:BaseObject:private] =>
[_deleted:BaseObject:private] =>
[modifiedColumns:protected] => Array
(
)
)
[64] => Category Object
(
[languages:protected] =>
[bok_resources:protected] =>
[bok_topics:protected] =>
[bok_keywords:protected] =>
[id:protected] => 64
[type:protected] => category
[parent:protected] => 2
[label:protected] => Laborer
[alreadyInSave:protected] =>
[alreadyInValidation:protected] =>
[validationFailures:protected] => Array
(
)
[_new:BaseObject:private] =>
[_deleted:BaseObject:private] =>
[modifiedColumns:protected] => Array
(
)
)
[74] => Category Object
(
[languages:protected] =>
[bok_resources:protected] =>
[bok_topics:protected] =>
[bok_keywords:protected] =>
[id:protected] => 74
[type:protected] => category
[parent:protected] => 2
[label:protected] => Pile Driver
[alreadyInSave:protected] =>
[alreadyInValidation:protected] =>
[validationFailures:protected] => Array
(
)
[_new:BaseObject:private] =>
[_deleted:BaseObject:private] =>
[modifiedColumns:protected] => Array
(
)
)
)
[categories_initialized:protected] => 1
[mapped_items:protected] =>
[content:protected] =>
[files:protected] =>
[language:protected] => Language Object
(
[id:protected] => 1
[code:protected] => en
[name:protected] => English
[alreadyInSave:protected] =>
[alreadyInValidation:protected] =>
[validationFailures:protected] => Array
(
)
[_new:BaseObject:private] =>
[_deleted:BaseObject:private] =>
[modifiedColumns:protected] => Array
(
)
)
[old_record:protected] =>
[id:protected] => 3994
[old_id:protected] =>
[elcosh_id:protected] => i002689
[type:protected] => image
[display_type:protected] => Image
[user_id:protected] => 0
[language_id:protected] => 1
[tagging_id:protected] => Bruce Lippy
[priority_id:protected] => 1
[title:protected] => Scaffolding at top of large column
[total_pages:protected] => 0
[billed_pages:protected] => 0
[publication_number:protected] =>
[part_of:protected] =>
[keywords:protected] => Guardrail, railing, fall prevention, falls
[comments:protected] =>
[summary:protected] => This shot shows innovative guarding around the top of a large concrete column in the base of a high rise structure going up.
[transition_comments:protected] =>
[external_link:protected] =>
[consol_link:protected] => http://www.cpwrconstructionsolutions.org/masonry/solution/8/adjustable-tower-scaffold.html
[more_like_this:protected] => c1002680,i002662,d000608,d001255
[permission_given_by:protected] =>
[published:protected] => T
[billable:protected] => F
[img_name:protected] =>
[img_ext:protected] => jpg
[img_width:protected] =>
[img_height:protected] =>
[img_credit:protected] => Photo by Pam Susi
[img_practice:protected] => good
[vid_source_id:protected] =>
[vid_running_time:protected] =>
[vid_intended_audience:protected] =>
[vid_acquisition_info:protected] =>
[vid_cost:protected] =>
[vid_producer:protected] =>
[vid_filename:protected] =>
[vid_filename_downloadable:protected] =>
[date_summary:protected] => January 2016
[date_permission_requested:protected] =>
[date_permission_received:protected] =>
[date_review_needed:protected] =>
[date_received:protected] => 02/01/16
[date_completed:protected] => 02/01/16
[date_billed:protected] =>
[date_modified:protected] => 02/01/16
[collBokExports:protected] =>
[lastBokExportCriteria:BaseElcoshItem:private] =>
[alreadyInSave:protected] =>
[alreadyInValidation:protected] =>
[validationFailures:protected] => Array
(
)
[_new:BaseObject:private] =>
[_deleted:BaseObject:private] =>
[modifiedColumns:protected] => Array
(
)
)
)
[5] => Search_Result Object
(
[title] => Construction bracing
[image] => /record/images/3995-p.jpg
[blurb] => This shows structural support that prevents collapses during construction....
[category] => Array
(
[0] => 12
[1] => 15
[2] => 21
[3] => 49
[4] => 51
[5] => 55
[6] => 56
[7] => 60
[8] => 64
[9] => 68
[10] => 74
[11] => 63
[12] => 78
[13] => 79
[14] => 80
[15] => 62
[16] => 87
[17] => 90
[18] => 97
)
[labels] => Array
(
[0] => Crushed/Struck By
[1] => Work Environment
[2] => Hazards
[3] => Falls
[6] => Scaffolds
[9] => Carpenter
[10] => Trades
[11] => Cement Mason
[13] => Electrical Worker
[15] => Elevator Constructor
[17] => HVAC
[19] => Laborer
[21] => Maintenance Worker
[23] => Pile Driver
[25] => Reinforcing Ironworker
[27] => Roofer/Waterproofer
[29] => Scaffold Erector
[31] => Sheetmetal Worker
[33] => Structural Ironworker
[35] => Commercial & Institutional
[36] => Jobsites
[37] => Industrial
[39] => Images
[40] => Media
[41] => Media & Documents
)
[type] => Images
[sub_category] =>
[url] => /image/3995/i002690/Construction%2Bbracing.html
[item:protected] => ImageRecord Object
(
[records:protected] => Array
(
)
[recordId:protected] =>
[searchWordClass:protected] =>
[searchWordPeerClass:protected] =>
[bok_record:protected] =>
[authors:protected] =>
[organizations:protected] =>
[collections:protected] =>
[categories:protected] => Array
(
[12] => Category Object
(
[languages:protected] =>
[bok_resources:protected] =>
[bok_topics:protected] =>
[bok_keywords:protected] =>
[id:protected] => 12
[type:protected] => category
[parent:protected] => 7
[label:protected] => Crushed/Struck By
[alreadyInSave:protected] =>
[alreadyInValidation:protected] =>
[validationFailures:protected] => Array
(
)
[_new:BaseObject:private] =>
[_deleted:BaseObject:private] =>
[modifiedColumns:protected] => Array
(
)
)
[15] => Category Object
(
[languages:protected] =>
[bok_resources:protected] =>
[bok_topics:protected] =>
[bok_keywords:protected] =>
[id:protected] => 15
[type:protected] => category
[parent:protected] => 7
[label:protected] => Falls
[alreadyInSave:protected] =>
[alreadyInValidation:protected] =>
[validationFailures:protected] => Array
(
)
[_new:BaseObject:private] =>
[_deleted:BaseObject:private] =>
[modifiedColumns:protected] => Array
(
)
)
[21] => Category Object
(
[languages:protected] =>
[bok_resources:protected] =>
[bok_topics:protected] =>
[bok_keywords:protected] =>
[id:protected] => 21
[type:protected] => category
[parent:protected] => 7
[label:protected] => Scaffolds
[alreadyInSave:protected] =>
[alreadyInValidation:protected] =>
[validationFailures:protected] => Array
(
)
[_new:BaseObject:private] =>
[_deleted:BaseObject:private] =>
[modifiedColumns:protected] => Array
(
)
)
[49] => Category Object
(
[languages:protected] =>
[bok_resources:protected] =>
[bok_topics:protected] =>
[bok_keywords:protected] =>
[id:protected] => 49
[type:protected] => category
[parent:protected] => 2
[label:protected] => Carpenter
[alreadyInSave:protected] =>
[alreadyInValidation:protected] =>
[validationFailures:protected] => Array
(
)
[_new:BaseObject:private] =>
[_deleted:BaseObject:private] =>
[modifiedColumns:protected] => Array
(
)
)
[51] => Category Object
(
[languages:protected] =>
[bok_resources:protected] =>
[bok_topics:protected] =>
[bok_keywords:protected] =>
[id:protected] => 51
[type:protected] => category
[parent:protected] => 2
[label:protected] => Cement Mason
[alreadyInSave:protected] =>
[alreadyInValidation:protected] =>
[validationFailures:protected] => Array
(
)
[_new:BaseObject:private] =>
[_deleted:BaseObject:private] =>
[modifiedColumns:protected] => Array
(
)
)
[55] => Category Object
(
[languages:protected] =>
[bok_resources:protected] =>
[bok_topics:protected] =>
[bok_keywords:protected] =>
[id:protected] => 55
[type:protected] => category
[parent:protected] => 2
[label:protected] => Electrical Worker
[alreadyInSave:protected] =>
[alreadyInValidation:protected] =>
[validationFailures:protected] => Array
(
)
[_new:BaseObject:private] =>
[_deleted:BaseObject:private] =>
[modifiedColumns:protected] => Array
(
)
)
[56] => Category Object
(
[languages:protected] =>
[bok_resources:protected] =>
[bok_topics:protected] =>
[bok_keywords:protected] =>
[id:protected] => 56
[type:protected] => category
[parent:protected] => 2
[label:protected] => Elevator Constructor
[alreadyInSave:protected] =>
[alreadyInValidation:protected] =>
[validationFailures:protected] => Array
(
)
[_new:BaseObject:private] =>
[_deleted:BaseObject:private] =>
[modifiedColumns:protected] => Array
(
)
)
[60] => Category Object
(
[languages:protected] =>
[bok_resources:protected] =>
[bok_topics:protected] =>
[bok_keywords:protected] =>
[id:protected] => 60
[type:protected] => category
[parent:protected] => 2
[label:protected] => HVAC
[alreadyInSave:protected] =>
[alreadyInValidation:protected] =>
[validationFailures:protected] => Array
(
)
[_new:BaseObject:private] =>
[_deleted:BaseObject:private] =>
[modifiedColumns:protected] => Array
(
)
)
[64] => Category Object
(
[languages:protected] =>
[bok_resources:protected] =>
[bok_topics:protected] =>
[bok_keywords:protected] =>
[id:protected] => 64
[type:protected] => category
[parent:protected] => 2
[label:protected] => Laborer
[alreadyInSave:protected] =>
[alreadyInValidation:protected] =>
[validationFailures:protected] => Array
(
)
[_new:BaseObject:private] =>
[_deleted:BaseObject:private] =>
[modifiedColumns:protected] => Array
(
)
)
[68] => Category Object
(
[languages:protected] =>
[bok_resources:protected] =>
[bok_topics:protected] =>
[bok_keywords:protected] =>
[id:protected] => 68
[type:protected] => category
[parent:protected] => 2
[label:protected] => Maintenance Worker
[alreadyInSave:protected] =>
[alreadyInValidation:protected] =>
[validationFailures:protected] => Array
(
)
[_new:BaseObject:private] =>
[_deleted:BaseObject:private] =>
[modifiedColumns:protected] => Array
(
)
)
[74] => Category Object
(
[languages:protected] =>
[bok_resources:protected] =>
[bok_topics:protected] =>
[bok_keywords:protected] =>
[id:protected] => 74
[type:protected] => category
[parent:protected] => 2
[label:protected] => Pile Driver
[alreadyInSave:protected] =>
[alreadyInValidation:protected] =>
[validationFailures:protected] => Array
(
)
[_new:BaseObject:private] =>
[_deleted:BaseObject:private] =>
[modifiedColumns:protected] => Array
(
)
)
[63] => Category Object
(
[languages:protected] =>
[bok_resources:protected] =>
[bok_topics:protected] =>
[bok_keywords:protected] =>
[id:protected] => 63
[type:protected] => category
[parent:protected] => 2
[label:protected] => Reinforcing Ironworker
[alreadyInSave:protected] =>
[alreadyInValidation:protected] =>
[validationFailures:protected] => Array
(
)
[_new:BaseObject:private] =>
[_deleted:BaseObject:private] =>
[modifiedColumns:protected] => Array
(
)
)
[78] => Category Object
(
[languages:protected] =>
[bok_resources:protected] =>
[bok_topics:protected] =>
[bok_keywords:protected] =>
[id:protected] => 78
[type:protected] => category
[parent:protected] => 2
[label:protected] => Roofer/Waterproofer
[alreadyInSave:protected] =>
[alreadyInValidation:protected] =>
[validationFailures:protected] => Array
(
)
[_new:BaseObject:private] =>
[_deleted:BaseObject:private] =>
[modifiedColumns:protected] => Array
(
)
)
[79] => Category Object
(
[languages:protected] =>
[bok_resources:protected] =>
[bok_topics:protected] =>
[bok_keywords:protected] =>
[id:protected] => 79
[type:protected] => category
[parent:protected] => 2
[label:protected] => Scaffold Erector
[alreadyInSave:protected] =>
[alreadyInValidation:protected] =>
[validationFailures:protected] => Array
(
)
[_new:BaseObject:private] =>
[_deleted:BaseObject:private] =>
[modifiedColumns:protected] => Array
(
)
)
[80] => Category Object
(
[languages:protected] =>
[bok_resources:protected] =>
[bok_topics:protected] =>
[bok_keywords:protected] =>
[id:protected] => 80
[type:protected] => category
[parent:protected] => 2
[label:protected] => Sheetmetal Worker
[alreadyInSave:protected] =>
[alreadyInValidation:protected] =>
[validationFailures:protected] => Array
(
)
[_new:BaseObject:private] =>
[_deleted:BaseObject:private] =>
[modifiedColumns:protected] => Array
(
)
)
[62] => Category Object
(
[languages:protected] =>
[bok_resources:protected] =>
[bok_topics:protected] =>
[bok_keywords:protected] =>
[id:protected] => 62
[type:protected] => category
[parent:protected] => 2
[label:protected] => Structural Ironworker
[alreadyInSave:protected] =>
[alreadyInValidation:protected] =>
[validationFailures:protected] => Array
(
)
[_new:BaseObject:private] =>
[_deleted:BaseObject:private] =>
[modifiedColumns:protected] => Array
(
)
)
[87] => Category Object
(
[languages:protected] =>
[bok_resources:protected] =>
[bok_topics:protected] =>
[bok_keywords:protected] =>
[id:protected] => 87
[type:protected] => category
[parent:protected] => 3
[label:protected] => Commercial & Institutional
[alreadyInSave:protected] =>
[alreadyInValidation:protected] =>
[validationFailures:protected] => Array
(
)
[_new:BaseObject:private] =>
[_deleted:BaseObject:private] =>
[modifiedColumns:protected] => Array
(
)
)
[90] => Category Object
(
[languages:protected] =>
[bok_resources:protected] =>
[bok_topics:protected] =>
[bok_keywords:protected] =>
[id:protected] => 90
[type:protected] => category
[parent:protected] => 3
[label:protected] => Industrial
[alreadyInSave:protected] =>
[alreadyInValidation:protected] =>
[validationFailures:protected] => Array
(
)
[_new:BaseObject:private] =>
[_deleted:BaseObject:private] =>
[modifiedColumns:protected] => Array
(
)
)
[97] => Category Object
(
[languages:protected] =>
[bok_resources:protected] =>
[bok_topics:protected] =>
[bok_keywords:protected] =>
[id:protected] => 97
[type:protected] => category
[parent:protected] => 5
[label:protected] => Images
[alreadyInSave:protected] =>
[alreadyInValidation:protected] =>
[validationFailures:protected] => Array
(
)
[_new:BaseObject:private] =>
[_deleted:BaseObject:private] =>
[modifiedColumns:protected] => Array
(
)
)
)
[categories_initialized:protected] => 1
[mapped_items:protected] =>
[content:protected] =>
[files:protected] =>
[language:protected] => Language Object
(
[id:protected] => 1
[code:protected] => en
[name:protected] => English
[alreadyInSave:protected] =>
[alreadyInValidation:protected] =>
[validationFailures:protected] => Array
(
)
[_new:BaseObject:private] =>
[_deleted:BaseObject:private] =>
[modifiedColumns:protected] => Array
(
)
)
[old_record:protected] =>
[id:protected] => 3995
[old_id:protected] =>
[elcosh_id:protected] => i002690
[type:protected] => image
[display_type:protected] => Image
[user_id:protected] => 0
[language_id:protected] => 1
[tagging_id:protected] => Bruce Lippy
[priority_id:protected] => 1
[title:protected] => Construction bracing
[total_pages:protected] => 0
[billed_pages:protected] => 0
[publication_number:protected] =>
[part_of:protected] =>
[keywords:protected] => Bracing, support, scaffold
[comments:protected] =>
[summary:protected] => This shows structural support that prevents collapses during construction.
[transition_comments:protected] =>
[external_link:protected] =>
[consol_link:protected] => http://www.cpwrconstructionsolutions.org/masonry/solution/8/adjustable-tower-scaffold.html
[more_like_this:protected] => i002660
[permission_given_by:protected] =>
[published:protected] => T
[billable:protected] => F
[img_name:protected] =>
[img_ext:protected] => jpg
[img_width:protected] =>
[img_height:protected] =>
[img_credit:protected] => Photo by Pam Susi
[img_practice:protected] => good
[vid_source_id:protected] =>
[vid_running_time:protected] =>
[vid_intended_audience:protected] =>
[vid_acquisition_info:protected] =>
[vid_cost:protected] =>
[vid_producer:protected] =>
[vid_filename:protected] =>
[vid_filename_downloadable:protected] =>
[date_summary:protected] => January 2016
[date_permission_requested:protected] =>
[date_permission_received:protected] =>
[date_review_needed:protected] =>
[date_received:protected] => 02/01/16
[date_completed:protected] => 02/01/16
[date_billed:protected] =>
[date_modified:protected] => 02/01/16
[collBokExports:protected] =>
[lastBokExportCriteria:BaseElcoshItem:private] =>
[alreadyInSave:protected] =>
[alreadyInValidation:protected] =>
[validationFailures:protected] => Array
(
)
[_new:BaseObject:private] =>
[_deleted:BaseObject:private] =>
[modifiedColumns:protected] => Array
(
)
)
)
)
[preview_mode] =>
[description] => Toolbox talks have been the main tool for communicating safety information on construction jobs for decades.
Unfortunately, there has been little research on what makes for effective toolbox talks. The IUOE National
Training Fund worked with OSHA and NIOSH to make sure their series of 24 Focus Four toolbox talks were based on the best recommendations for effective design. These toolbox talks accompany an entire package of training materials, but can be used alone. This guide points out the key features of these toolbox talks and how best to deliver them.
[keywords] => toolbox talks, tailgate talks
[related_items] => Array
(
[Toolbox Talks] => Array
(
[0] => DocumentRecord Object
(
[records:protected] => Array
(
)
[recordId:protected] =>
[searchWordClass:protected] =>
[searchWordPeerClass:protected] =>
[bok_record:protected] =>
[authors:protected] =>
[organizations:protected] =>
[collections:protected] =>
[categories:protected] =>
[categories_initialized:protected] =>
[mapped_items:protected] =>
[content:protected] =>
[files:protected] =>
[language:protected] => Language Object
(
[id:protected] => 1
[code:protected] => en
[name:protected] => English
[alreadyInSave:protected] =>
[alreadyInValidation:protected] =>
[validationFailures:protected] => Array
(
)
[_new:BaseObject:private] =>
[_deleted:BaseObject:private] =>
[modifiedColumns:protected] => Array
(
)
)
[old_record:protected] =>
[id:protected] => 1605
[old_id:protected] => 1262
[elcosh_id:protected] => d001137
[type:protected] => document
[display_type:protected] => HTML w/ PDF
[user_id:protected] =>
[language_id:protected] => 1
[tagging_id:protected] => Garber
[priority_id:protected] => 1
[title:protected] => Focus Four Toolbox Talks, Module 1 – Falls, Talk #2 – Falls from debris piles?
[total_pages:protected] => 1
[billed_pages:protected] => 1
[publication_number:protected] =>
[part_of:protected] =>
[keywords:protected] => disaster response, hazard clean-up, uneven surface, disaster site, disaster clean-up
[comments:protected] =>
[summary:protected] => A toolbox talk on preventing falls from debris piles. Includes questions to ask, an incident to discuss with images, and a place to record questions the trainer would like to ask about the incident. Part of a collection. Click on the 'collection' button to access the other items.
[transition_comments:protected] =>
[external_link:protected] =>
[consol_link:protected] => http://www.cpwrconstructionsolutions.org/roofing/hazard/1463/install-asphalt-roofs-fall-from-heights.html
[more_like_this:protected] => a000081,d000478,d000530
[permission_given_by:protected] =>
[published:protected] => T
[billable:protected] => F
[img_name:protected] =>
[img_ext:protected] =>
[img_width:protected] =>
[img_height:protected] =>
[img_credit:protected] =>
[img_practice:protected] =>
[vid_source_id:protected] =>
[vid_running_time:protected] =>
[vid_intended_audience:protected] =>
[vid_acquisition_info:protected] =>
[vid_cost:protected] =>
[vid_producer:protected] =>
[vid_filename:protected] =>
[vid_filename_downloadable:protected] =>
[date_summary:protected] =>
[date_permission_requested:protected] =>
[date_permission_received:protected] =>
[date_review_needed:protected] =>
[date_received:protected] => 02/15/12
[date_completed:protected] => 03/19/12
[date_billed:protected] =>
[date_modified:protected] => 07/10/12
[collBokExports:protected] =>
[lastBokExportCriteria:BaseElcoshItem:private] =>
[alreadyInSave:protected] =>
[alreadyInValidation:protected] =>
[validationFailures:protected] => Array
(
)
[_new:BaseObject:private] =>
[_deleted:BaseObject:private] =>
[modifiedColumns:protected] => Array
(
)
)
[1] => DocumentRecord Object
(
[records:protected] => Array
(
)
[recordId:protected] =>
[searchWordClass:protected] =>
[searchWordPeerClass:protected] =>
[bok_record:protected] =>
[authors:protected] =>
[organizations:protected] =>
[collections:protected] =>
[categories:protected] =>
[categories_initialized:protected] =>
[mapped_items:protected] =>
[content:protected] =>
[files:protected] =>
[language:protected] => Language Object
(
[id:protected] => 1
[code:protected] => en
[name:protected] => English
[alreadyInSave:protected] =>
[alreadyInValidation:protected] =>
[validationFailures:protected] => Array
(
)
[_new:BaseObject:private] =>
[_deleted:BaseObject:private] =>
[modifiedColumns:protected] => Array
(
)
)
[old_record:protected] =>
[id:protected] => 1610
[old_id:protected] => 1271
[elcosh_id:protected] => d001146
[type:protected] => document
[display_type:protected] => HTML w/ PDF
[user_id:protected] => 0
[language_id:protected] => 1
[tagging_id:protected] => Garber
[priority_id:protected] => 1
[title:protected] => Focus Four Toolbox Talks, Module 2 – Struck-by, Talk #5 – Rigging and Securing Loads
[total_pages:protected] => 1
[billed_pages:protected] => 1
[publication_number:protected] =>
[part_of:protected] =>
[keywords:protected] => rigging, lift loads, loading areas, chains
[comments:protected] =>
[summary:protected] => A toolbox talk on preventing struck-by incidents caused by not securing loads properly. Includes questions to ask, an incident to discuss with images, and a place to record questions the trainer would like to ask about the incident. Part of a collection. Click on the 'collection' button to access the other items.
[transition_comments:protected] =>
[external_link:protected] =>
[consol_link:protected] => http://www.cpwrconstructionsolutions.org/heavy_equipment/hazard/1591/move-equipment-to-from-and-between-sites-work-zone-struck-by-injuries-and-fatalities.html
[more_like_this:protected] => d000144,d000360,d000873
[permission_given_by:protected] =>
[published:protected] => T
[billable:protected] => F
[img_name:protected] =>
[img_ext:protected] =>
[img_width:protected] =>
[img_height:protected] =>
[img_credit:protected] =>
[img_practice:protected] =>
[vid_source_id:protected] =>
[vid_running_time:protected] =>
[vid_intended_audience:protected] =>
[vid_acquisition_info:protected] =>
[vid_cost:protected] =>
[vid_producer:protected] =>
[vid_filename:protected] =>
[vid_filename_downloadable:protected] =>
[date_summary:protected] =>
[date_permission_requested:protected] =>
[date_permission_received:protected] =>
[date_review_needed:protected] =>
[date_received:protected] => 02/15/12
[date_completed:protected] => 03/28/12
[date_billed:protected] =>
[date_modified:protected] => 05/12/14
[collBokExports:protected] =>
[lastBokExportCriteria:BaseElcoshItem:private] =>
[alreadyInSave:protected] =>
[alreadyInValidation:protected] =>
[validationFailures:protected] => Array
(
)
[_new:BaseObject:private] =>
[_deleted:BaseObject:private] =>
[modifiedColumns:protected] => Array
(
)
)
[2] => DocumentRecord Object
(
[records:protected] => Array
(
)
[recordId:protected] =>
[searchWordClass:protected] =>
[searchWordPeerClass:protected] =>
[bok_record:protected] =>
[authors:protected] =>
[organizations:protected] =>
[collections:protected] =>
[categories:protected] =>
[categories_initialized:protected] =>
[mapped_items:protected] =>
[content:protected] =>
[files:protected] =>
[language:protected] => Language Object
(
[id:protected] => 1
[code:protected] => en
[name:protected] => English
[alreadyInSave:protected] =>
[alreadyInValidation:protected] =>
[validationFailures:protected] => Array
(
)
[_new:BaseObject:private] =>
[_deleted:BaseObject:private] =>
[modifiedColumns:protected] => Array
(
)
)
[old_record:protected] =>
[id:protected] => 1645
[old_id:protected] => 1274
[elcosh_id:protected] => d001149
[type:protected] => document
[display_type:protected] => HTML w/ PDF
[user_id:protected] => 0
[language_id:protected] => 1
[tagging_id:protected] => Garber
[priority_id:protected] => 1
[title:protected] => Focus Four Toolbox Talks, Module 3 – Caught-in/between, Talk #2 – Trenches & Heavy Equipment
[total_pages:protected] => 1
[billed_pages:protected] => 1
[publication_number:protected] =>
[part_of:protected] =>
[keywords:protected] => back-up alarms, spotter, soil cave-in, spoil pikes, ROPs, trenching, rain
[comments:protected] =>
[summary:protected] => A toolbox talk on preventing incidents involving trenches such as trench collapse. Includes questions to ask, an incident to discuss with images, and a place to record questions the trainer would like to ask about the incident. Part of a collection. Click on the 'collection' button to access the other items.
[transition_comments:protected] =>
[external_link:protected] =>
[consol_link:protected] =>
[more_like_this:protected] => d000019,d000035,d000168
[permission_given_by:protected] =>
[published:protected] => T
[billable:protected] => F
[img_name:protected] =>
[img_ext:protected] =>
[img_width:protected] =>
[img_height:protected] =>
[img_credit:protected] =>
[img_practice:protected] =>
[vid_source_id:protected] =>
[vid_running_time:protected] =>
[vid_intended_audience:protected] =>
[vid_acquisition_info:protected] =>
[vid_cost:protected] =>
[vid_producer:protected] =>
[vid_filename:protected] =>
[vid_filename_downloadable:protected] =>
[date_summary:protected] =>
[date_permission_requested:protected] =>
[date_permission_received:protected] =>
[date_review_needed:protected] =>
[date_received:protected] => 02/15/12
[date_completed:protected] => 04/02/12
[date_billed:protected] =>
[date_modified:protected] => 05/23/23
[collBokExports:protected] =>
[lastBokExportCriteria:BaseElcoshItem:private] =>
[alreadyInSave:protected] =>
[alreadyInValidation:protected] =>
[validationFailures:protected] => Array
(
)
[_new:BaseObject:private] =>
[_deleted:BaseObject:private] =>
[modifiedColumns:protected] => Array
(
)
)
[3] => DocumentRecord Object
(
[records:protected] => Array
(
)
[recordId:protected] =>
[searchWordClass:protected] =>
[searchWordPeerClass:protected] =>
[bok_record:protected] =>
[authors:protected] =>
[organizations:protected] =>
[collections:protected] =>
[categories:protected] =>
[categories_initialized:protected] =>
[mapped_items:protected] =>
[content:protected] =>
[files:protected] =>
[language:protected] => Language Object
(
[id:protected] => 1
[code:protected] => en
[name:protected] => English
[alreadyInSave:protected] =>
[alreadyInValidation:protected] =>
[validationFailures:protected] => Array
(
)
[_new:BaseObject:private] =>
[_deleted:BaseObject:private] =>
[modifiedColumns:protected] => Array
(
)
)
[old_record:protected] =>
[id:protected] => 1654
[old_id:protected] => 1284
[elcosh_id:protected] => d001159
[type:protected] => document
[display_type:protected] => HTML w/ PDF
[user_id:protected] => 0
[language_id:protected] => 1
[tagging_id:protected] => Garber
[priority_id:protected] => 1
[title:protected] => Focus Four Toolbox Talks, Module 4 – Electrocutions, Talk #6 – Hazards on Disaster Sites
[total_pages:protected] => 1
[billed_pages:protected] => 1
[publication_number:protected] =>
[part_of:protected] =>
[keywords:protected] => powerlines, underground, utilities, generators, wet conditions, GFCIs, energized lines, disasters, emergency response
[comments:protected] =>
[summary:protected] => A toolbox talk on how to avoid electrocution on a disaster site. Includes questions to ask, an incident to discuss with images, and a place to record questions the trainer would like to ask about the incident. Part of a collection. Click on the 'collection' button to access the other items.
[transition_comments:protected] =>
[external_link:protected] =>
[consol_link:protected] => http://www.cpwrconstructionsolutions.org/electrical/hazard/1138/install-and-repair-high-voltage-lines-transformers-switches-electrical-shocks-burns-and-or-electrocution.html
[more_like_this:protected] => d000135,d000361,d000437
[permission_given_by:protected] =>
[published:protected] => T
[billable:protected] => F
[img_name:protected] =>
[img_ext:protected] =>
[img_width:protected] =>
[img_height:protected] =>
[img_credit:protected] =>
[img_practice:protected] =>
[vid_source_id:protected] =>
[vid_running_time:protected] =>
[vid_intended_audience:protected] =>
[vid_acquisition_info:protected] =>
[vid_cost:protected] =>
[vid_producer:protected] =>
[vid_filename:protected] =>
[vid_filename_downloadable:protected] =>
[date_summary:protected] =>
[date_permission_requested:protected] =>
[date_permission_received:protected] =>
[date_review_needed:protected] =>
[date_received:protected] => 02/15/12
[date_completed:protected] => 04/02/12
[date_billed:protected] =>
[date_modified:protected] => 05/23/23
[collBokExports:protected] =>
[lastBokExportCriteria:BaseElcoshItem:private] =>
[alreadyInSave:protected] =>
[alreadyInValidation:protected] =>
[validationFailures:protected] => Array
(
)
[_new:BaseObject:private] =>
[_deleted:BaseObject:private] =>
[modifiedColumns:protected] => Array
(
)
)
)
)
[collections] => Array
(
[1294] =>
[1295] =>
[1292] =>
[1293] => CollectionRecord Object
(
[collection_items:protected] =>
[records:protected] => Array
(
)
[recordId:protected] =>
[searchWordClass:protected] =>
[searchWordPeerClass:protected] =>
[bok_record:protected] =>
[authors:protected] =>
[organizations:protected] =>
[collections:protected] =>
[categories:protected] =>
[categories_initialized:protected] =>
[mapped_items:protected] =>
[content:protected] =>
[files:protected] =>
[language:protected] =>
[old_record:protected] =>
[id:protected] => 1293
[old_id:protected] =>
[elcosh_id:protected] => c000026
[type:protected] => collection
[display_type:protected] => Collection
[user_id:protected] =>
[language_id:protected] =>
[tagging_id:protected] =>
[priority_id:protected] =>
[title:protected] => Focus Four-Struck By
[total_pages:protected] =>
[billed_pages:protected] =>
[publication_number:protected] =>
[part_of:protected] =>
[keywords:protected] =>
[comments:protected] =>
[summary:protected] => The following are links to all of the items in this collection:
[transition_comments:protected] =>
[external_link:protected] =>
[consol_link:protected] =>
[more_like_this:protected] =>
[permission_given_by:protected] =>
[published:protected] => T
[billable:protected] => F
[img_name:protected] =>
[img_ext:protected] =>
[img_width:protected] =>
[img_height:protected] =>
[img_credit:protected] =>
[img_practice:protected] =>
[vid_source_id:protected] =>
[vid_running_time:protected] =>
[vid_intended_audience:protected] =>
[vid_acquisition_info:protected] =>
[vid_cost:protected] =>
[vid_producer:protected] =>
[vid_filename:protected] =>
[vid_filename_downloadable:protected] =>
[date_summary:protected] =>
[date_permission_requested:protected] =>
[date_permission_received:protected] =>
[date_review_needed:protected] =>
[date_received:protected] => 05/08/12
[date_completed:protected] => 05/08/12
[date_billed:protected] =>
[date_modified:protected] => 05/08/12
[collBokExports:protected] =>
[lastBokExportCriteria:BaseElcoshItem:private] =>
[alreadyInSave:protected] =>
[alreadyInValidation:protected] =>
[validationFailures:protected] => Array
(
)
[_new:BaseObject:private] =>
[_deleted:BaseObject:private] =>
[modifiedColumns:protected] => Array
(
)
)
)
[record] => DocumentRecord Object
(
[records:protected] => Array
(
)
[recordId:protected] =>
[searchWordClass:protected] =>
[searchWordPeerClass:protected] =>
[bok_record:protected] =>
[authors:protected] => Array
(
)
[organizations:protected] => Array
(
[256] => Organization Object
(
[id:protected] => 256
[elcosh_id:protected] => o000276
[user_id:protected] => 14
[province_id:protected] => 0
[country_id:protected] => 0
[title:protected] => IUOE National Training Fund
[address:protected] =>
[postal_code:protected] =>
[city:protected] =>
[department:protected] =>
[phone:protected] => 304-253-8674
[fax:protected] =>
[email:protected] =>
[website:protected] => http://www.iuoeiettc.org
[filename:protected] =>
[about:protected] =>
[comments:protected] =>
[logo_available:protected] => T
[no_details:protected] => F
[date_received:protected] => 2012-02-13
[date_completed:protected] => 2012-02-13
[date_billed:protected] =>
[alreadyInSave:protected] =>
[alreadyInValidation:protected] =>
[validationFailures:protected] => Array
(
)
[_new:BaseObject:private] =>
[_deleted:BaseObject:private] =>
[modifiedColumns:protected] => Array
(
)
)
)
[collections:protected] => Array
(
[1294] =>
[1295] =>
[1292] =>
[1293] => CollectionRecord Object
(
[collection_items:protected] =>
[records:protected] => Array
(
)
[recordId:protected] =>
[searchWordClass:protected] =>
[searchWordPeerClass:protected] =>
[bok_record:protected] =>
[authors:protected] =>
[organizations:protected] =>
[collections:protected] =>
[categories:protected] =>
[categories_initialized:protected] =>
[mapped_items:protected] =>
[content:protected] =>
[files:protected] =>
[language:protected] =>
[old_record:protected] =>
[id:protected] => 1293
[old_id:protected] =>
[elcosh_id:protected] => c000026
[type:protected] => collection
[display_type:protected] => Collection
[user_id:protected] =>
[language_id:protected] =>
[tagging_id:protected] =>
[priority_id:protected] =>
[title:protected] => Focus Four-Struck By
[total_pages:protected] =>
[billed_pages:protected] =>
[publication_number:protected] =>
[part_of:protected] =>
[keywords:protected] =>
[comments:protected] =>
[summary:protected] => The following are links to all of the items in this collection:
[transition_comments:protected] =>
[external_link:protected] =>
[consol_link:protected] =>
[more_like_this:protected] =>
[permission_given_by:protected] =>
[published:protected] => T
[billable:protected] => F
[img_name:protected] =>
[img_ext:protected] =>
[img_width:protected] =>
[img_height:protected] =>
[img_credit:protected] =>
[img_practice:protected] =>
[vid_source_id:protected] =>
[vid_running_time:protected] =>
[vid_intended_audience:protected] =>
[vid_acquisition_info:protected] =>
[vid_cost:protected] =>
[vid_producer:protected] =>
[vid_filename:protected] =>
[vid_filename_downloadable:protected] =>
[date_summary:protected] =>
[date_permission_requested:protected] =>
[date_permission_received:protected] =>
[date_review_needed:protected] =>
[date_received:protected] => 05/08/12
[date_completed:protected] => 05/08/12
[date_billed:protected] =>
[date_modified:protected] => 05/08/12
[collBokExports:protected] =>
[lastBokExportCriteria:BaseElcoshItem:private] =>
[alreadyInSave:protected] =>
[alreadyInValidation:protected] =>
[validationFailures:protected] => Array
(
)
[_new:BaseObject:private] =>
[_deleted:BaseObject:private] =>
[modifiedColumns:protected] => Array
(
)
)
)
[categories:protected] =>
[categories_initialized:protected] =>
[mapped_items:protected] => Array
(
[1605] => DocumentRecord Object
(
[records:protected] => Array
(
)
[recordId:protected] =>
[searchWordClass:protected] =>
[searchWordPeerClass:protected] =>
[bok_record:protected] =>
[authors:protected] =>
[organizations:protected] =>
[collections:protected] =>
[categories:protected] =>
[categories_initialized:protected] =>
[mapped_items:protected] =>
[content:protected] =>
[files:protected] =>
[language:protected] =>
[old_record:protected] =>
[id:protected] => 1605
[old_id:protected] => 1262
[elcosh_id:protected] => d001137
[type:protected] => document
[display_type:protected] => HTML w/ PDF
[user_id:protected] =>
[language_id:protected] => 1
[tagging_id:protected] => Garber
[priority_id:protected] => 1
[title:protected] => Focus Four Toolbox Talks, Module 1 – Falls, Talk #2 – Falls from debris piles?
[total_pages:protected] => 1
[billed_pages:protected] => 1
[publication_number:protected] =>
[part_of:protected] =>
[keywords:protected] => disaster response, hazard clean-up, uneven surface, disaster site, disaster clean-up
[comments:protected] =>
[summary:protected] => A toolbox talk on preventing falls from debris piles. Includes questions to ask, an incident to discuss with images, and a place to record questions the trainer would like to ask about the incident. Part of a collection. Click on the 'collection' button to access the other items.
[transition_comments:protected] =>
[external_link:protected] =>
[consol_link:protected] => http://www.cpwrconstructionsolutions.org/roofing/hazard/1463/install-asphalt-roofs-fall-from-heights.html
[more_like_this:protected] => a000081,d000478,d000530
[permission_given_by:protected] =>
[published:protected] => T
[billable:protected] => F
[img_name:protected] =>
[img_ext:protected] =>
[img_width:protected] =>
[img_height:protected] =>
[img_credit:protected] =>
[img_practice:protected] =>
[vid_source_id:protected] =>
[vid_running_time:protected] =>
[vid_intended_audience:protected] =>
[vid_acquisition_info:protected] =>
[vid_cost:protected] =>
[vid_producer:protected] =>
[vid_filename:protected] =>
[vid_filename_downloadable:protected] =>
[date_summary:protected] =>
[date_permission_requested:protected] =>
[date_permission_received:protected] =>
[date_review_needed:protected] =>
[date_received:protected] => 02/15/12
[date_completed:protected] => 03/19/12
[date_billed:protected] =>
[date_modified:protected] => 07/10/12
[collBokExports:protected] =>
[lastBokExportCriteria:BaseElcoshItem:private] =>
[alreadyInSave:protected] =>
[alreadyInValidation:protected] =>
[validationFailures:protected] => Array
(
)
[_new:BaseObject:private] =>
[_deleted:BaseObject:private] =>
[modifiedColumns:protected] => Array
(
)
)
[1610] => DocumentRecord Object
(
[records:protected] => Array
(
)
[recordId:protected] =>
[searchWordClass:protected] =>
[searchWordPeerClass:protected] =>
[bok_record:protected] =>
[authors:protected] =>
[organizations:protected] =>
[collections:protected] =>
[categories:protected] =>
[categories_initialized:protected] =>
[mapped_items:protected] =>
[content:protected] =>
[files:protected] =>
[language:protected] =>
[old_record:protected] =>
[id:protected] => 1610
[old_id:protected] => 1271
[elcosh_id:protected] => d001146
[type:protected] => document
[display_type:protected] => HTML w/ PDF
[user_id:protected] => 0
[language_id:protected] => 1
[tagging_id:protected] => Garber
[priority_id:protected] => 1
[title:protected] => Focus Four Toolbox Talks, Module 2 – Struck-by, Talk #5 – Rigging and Securing Loads
[total_pages:protected] => 1
[billed_pages:protected] => 1
[publication_number:protected] =>
[part_of:protected] =>
[keywords:protected] => rigging, lift loads, loading areas, chains
[comments:protected] =>
[summary:protected] => A toolbox talk on preventing struck-by incidents caused by not securing loads properly. Includes questions to ask, an incident to discuss with images, and a place to record questions the trainer would like to ask about the incident. Part of a collection. Click on the 'collection' button to access the other items.
[transition_comments:protected] =>
[external_link:protected] =>
[consol_link:protected] => http://www.cpwrconstructionsolutions.org/heavy_equipment/hazard/1591/move-equipment-to-from-and-between-sites-work-zone-struck-by-injuries-and-fatalities.html
[more_like_this:protected] => d000144,d000360,d000873
[permission_given_by:protected] =>
[published:protected] => T
[billable:protected] => F
[img_name:protected] =>
[img_ext:protected] =>
[img_width:protected] =>
[img_height:protected] =>
[img_credit:protected] =>
[img_practice:protected] =>
[vid_source_id:protected] =>
[vid_running_time:protected] =>
[vid_intended_audience:protected] =>
[vid_acquisition_info:protected] =>
[vid_cost:protected] =>
[vid_producer:protected] =>
[vid_filename:protected] =>
[vid_filename_downloadable:protected] =>
[date_summary:protected] =>
[date_permission_requested:protected] =>
[date_permission_received:protected] =>
[date_review_needed:protected] =>
[date_received:protected] => 02/15/12
[date_completed:protected] => 03/28/12
[date_billed:protected] =>
[date_modified:protected] => 05/12/14
[collBokExports:protected] =>
[lastBokExportCriteria:BaseElcoshItem:private] =>
[alreadyInSave:protected] =>
[alreadyInValidation:protected] =>
[validationFailures:protected] => Array
(
)
[_new:BaseObject:private] =>
[_deleted:BaseObject:private] =>
[modifiedColumns:protected] => Array
(
)
)
[1645] => DocumentRecord Object
(
[records:protected] => Array
(
)
[recordId:protected] =>
[searchWordClass:protected] =>
[searchWordPeerClass:protected] =>
[bok_record:protected] =>
[authors:protected] =>
[organizations:protected] =>
[collections:protected] =>
[categories:protected] =>
[categories_initialized:protected] =>
[mapped_items:protected] =>
[content:protected] =>
[files:protected] =>
[language:protected] =>
[old_record:protected] =>
[id:protected] => 1645
[old_id:protected] => 1274
[elcosh_id:protected] => d001149
[type:protected] => document
[display_type:protected] => HTML w/ PDF
[user_id:protected] => 0
[language_id:protected] => 1
[tagging_id:protected] => Garber
[priority_id:protected] => 1
[title:protected] => Focus Four Toolbox Talks, Module 3 – Caught-in/between, Talk #2 – Trenches & Heavy Equipment
[total_pages:protected] => 1
[billed_pages:protected] => 1
[publication_number:protected] =>
[part_of:protected] =>
[keywords:protected] => back-up alarms, spotter, soil cave-in, spoil pikes, ROPs, trenching, rain
[comments:protected] =>
[summary:protected] => A toolbox talk on preventing incidents involving trenches such as trench collapse. Includes questions to ask, an incident to discuss with images, and a place to record questions the trainer would like to ask about the incident. Part of a collection. Click on the 'collection' button to access the other items.
[transition_comments:protected] =>
[external_link:protected] =>
[consol_link:protected] =>
[more_like_this:protected] => d000019,d000035,d000168
[permission_given_by:protected] =>
[published:protected] => T
[billable:protected] => F
[img_name:protected] =>
[img_ext:protected] =>
[img_width:protected] =>
[img_height:protected] =>
[img_credit:protected] =>
[img_practice:protected] =>
[vid_source_id:protected] =>
[vid_running_time:protected] =>
[vid_intended_audience:protected] =>
[vid_acquisition_info:protected] =>
[vid_cost:protected] =>
[vid_producer:protected] =>
[vid_filename:protected] =>
[vid_filename_downloadable:protected] =>
[date_summary:protected] =>
[date_permission_requested:protected] =>
[date_permission_received:protected] =>
[date_review_needed:protected] =>
[date_received:protected] => 02/15/12
[date_completed:protected] => 04/02/12
[date_billed:protected] =>
[date_modified:protected] => 05/23/23
[collBokExports:protected] =>
[lastBokExportCriteria:BaseElcoshItem:private] =>
[alreadyInSave:protected] =>
[alreadyInValidation:protected] =>
[validationFailures:protected] => Array
(
)
[_new:BaseObject:private] =>
[_deleted:BaseObject:private] =>
[modifiedColumns:protected] => Array
(
)
)
[1654] => DocumentRecord Object
(
[records:protected] => Array
(
)
[recordId:protected] =>
[searchWordClass:protected] =>
[searchWordPeerClass:protected] =>
[bok_record:protected] =>
[authors:protected] =>
[organizations:protected] =>
[collections:protected] =>
[categories:protected] =>
[categories_initialized:protected] =>
[mapped_items:protected] =>
[content:protected] =>
[files:protected] =>
[language:protected] =>
[old_record:protected] =>
[id:protected] => 1654
[old_id:protected] => 1284
[elcosh_id:protected] => d001159
[type:protected] => document
[display_type:protected] => HTML w/ PDF
[user_id:protected] => 0
[language_id:protected] => 1
[tagging_id:protected] => Garber
[priority_id:protected] => 1
[title:protected] => Focus Four Toolbox Talks, Module 4 – Electrocutions, Talk #6 – Hazards on Disaster Sites
[total_pages:protected] => 1
[billed_pages:protected] => 1
[publication_number:protected] =>
[part_of:protected] =>
[keywords:protected] => powerlines, underground, utilities, generators, wet conditions, GFCIs, energized lines, disasters, emergency response
[comments:protected] =>
[summary:protected] => A toolbox talk on how to avoid electrocution on a disaster site. Includes questions to ask, an incident to discuss with images, and a place to record questions the trainer would like to ask about the incident. Part of a collection. Click on the 'collection' button to access the other items.
[transition_comments:protected] =>
[external_link:protected] =>
[consol_link:protected] => http://www.cpwrconstructionsolutions.org/electrical/hazard/1138/install-and-repair-high-voltage-lines-transformers-switches-electrical-shocks-burns-and-or-electrocution.html
[more_like_this:protected] => d000135,d000361,d000437
[permission_given_by:protected] =>
[published:protected] => T
[billable:protected] => F
[img_name:protected] =>
[img_ext:protected] =>
[img_width:protected] =>
[img_height:protected] =>
[img_credit:protected] =>
[img_practice:protected] =>
[vid_source_id:protected] =>
[vid_running_time:protected] =>
[vid_intended_audience:protected] =>
[vid_acquisition_info:protected] =>
[vid_cost:protected] =>
[vid_producer:protected] =>
[vid_filename:protected] =>
[vid_filename_downloadable:protected] =>
[date_summary:protected] =>
[date_permission_requested:protected] =>
[date_permission_received:protected] =>
[date_review_needed:protected] =>
[date_received:protected] => 02/15/12
[date_completed:protected] => 04/02/12
[date_billed:protected] =>
[date_modified:protected] => 05/23/23
[collBokExports:protected] =>
[lastBokExportCriteria:BaseElcoshItem:private] =>
[alreadyInSave:protected] =>
[alreadyInValidation:protected] =>
[validationFailures:protected] => Array
(
)
[_new:BaseObject:private] =>
[_deleted:BaseObject:private] =>
[modifiedColumns:protected] => Array
(
)
)
)
[content:protected] =>
[files:protected] => Array
(
[9400] => File Object
(
[id:protected] => 9400
[filename:protected] => 1.jpg
[downloadable:protected] => F
[timestamp:protected] => 2014-05-08 15:05:37
[alreadyInSave:protected] =>
[alreadyInValidation:protected] =>
[validationFailures:protected] => Array
(
)
[_new:BaseObject:private] =>
[_deleted:BaseObject:private] =>
[modifiedColumns:protected] => Array
(
)
)
[9401] => File Object
(
[id:protected] => 9401
[filename:protected] => d001298.pdf
[downloadable:protected] => T
[timestamp:protected] => 2014-05-08 15:05:37
[alreadyInSave:protected] =>
[alreadyInValidation:protected] =>
[validationFailures:protected] => Array
(
)
[_new:BaseObject:private] =>
[_deleted:BaseObject:private] =>
[modifiedColumns:protected] => Array
(
)
)
)
[language:protected] => Language Object
(
[id:protected] => 1
[code:protected] => en
[name:protected] => English
[alreadyInSave:protected] =>
[alreadyInValidation:protected] =>
[validationFailures:protected] => Array
(
)
[_new:BaseObject:private] =>
[_deleted:BaseObject:private] =>
[modifiedColumns:protected] => Array
(
)
)
[old_record:protected] =>
[id:protected] => 3827
[old_id:protected] =>
[elcosh_id:protected] => d001298
[type:protected] => document
[display_type:protected] => HTML w/ PDF
[user_id:protected] => 23
[language_id:protected] => 1
[tagging_id:protected] => Bruce Lippy
[priority_id:protected] => 1
[title:protected] => Getting the most out of the IUOE Toolbox Talks
[total_pages:protected] => 2
[billed_pages:protected] => 2
[publication_number:protected] =>
[part_of:protected] =>
[keywords:protected] => toolbox talks, tailgate talks
[comments:protected] =>
[summary:protected] => Toolbox talks have been the main tool for communicating safety information on construction jobs for decades.
Unfortunately, there has been little research on what makes for effective toolbox talks. The IUOE National
Training Fund worked with OSHA and NIOSH to make sure their series of 24 Focus Four toolbox talks were based on the best recommendations for effective design. These toolbox talks accompany an entire package of training materials, but can be used alone. This guide points out the key features of these toolbox talks and how best to deliver them.
[transition_comments:protected] =>
[external_link:protected] =>
[consol_link:protected] =>
[more_like_this:protected] => d001137,d001146,d001149,d001159
[permission_given_by:protected] => IUOE National Hazmat Program
[published:protected] => T
[billable:protected] => F
[img_name:protected] =>
[img_ext:protected] => png
[img_width:protected] =>
[img_height:protected] =>
[img_credit:protected] =>
[img_practice:protected] =>
[vid_source_id:protected] =>
[vid_running_time:protected] =>
[vid_intended_audience:protected] =>
[vid_acquisition_info:protected] =>
[vid_cost:protected] =>
[vid_producer:protected] =>
[vid_filename:protected] =>
[vid_filename_downloadable:protected] =>
[date_summary:protected] => 2007
[date_permission_requested:protected] =>
[date_permission_received:protected] =>
[date_review_needed:protected] =>
[date_received:protected] => 05/08/14
[date_completed:protected] => 05/08/14
[date_billed:protected] =>
[date_modified:protected] => 05/08/14
[collBokExports:protected] =>
[lastBokExportCriteria:BaseElcoshItem:private] =>
[alreadyInSave:protected] =>
[alreadyInValidation:protected] =>
[validationFailures:protected] => Array
(
)
[_new:BaseObject:private] =>
[_deleted:BaseObject:private] =>
[modifiedColumns:protected] => Array
(
)
)
[show_text] =>
[document_content] => ElcoshItemDocumentContent Object
(
[id:protected] => 2896
[item_id:protected] => 3827
[type:protected] => main
[title:protected] =>
[content:protected] =>
Why were these talks developed?
Toolbox talks have been the main tool for communicating safety information on construction jobs for decades. Unfortunately, there has been almost no research on what makes for effective toolbox talks. The IUOE National Training Fund has worked with OSHA, the National Institute for Occupational Safety and Health and the Lippy Group, LLC to make sure these Focus Four toolbox talks are based on the latest fi ndings on the most effective design and tailored to the hazards operating engineers face daily. These toolbox talks accompany an entire package of training materials, but can be used alone. The way these are delivered is as important as how well they are designed.
What did NIOSH find out?
- Just handing out factsheets and toolbox talks to workers doesn’t work. Providing copies after toolbox talks doesn’t make much of an impact either.
- Using case studies (real life stories of accidents that ended in fatality or injury) in toolbox talks is effective.
- When toolbox talks containing case studies were accompanied by discussion questions to encourage group participation, they were more effective. Consequently, getting the workers to participate in the discussion about the case study is important. It’s not enough to tell the story, it is better to have the workers engage in problem solving that analyzes why the accident occurred and how it could have been prevented. Active learning is always better than passive.
How should you deliver these toolbox talks?
- Choose a topic that is related to work going on at the site.
- Hold the meeting on the job, preferably where everyone can sit and relax.
- Hold the meeting at the beginning of a shift or after a break. Folks are too tired at the end of a shift to carefully listen and they want to get home.
- Read the toolbox talk sheet on the topic prior to conducting the talk.
- Start at the top of the form and work right through to the end, which should take around 10 to 15 minutes. Guidance is provided in blue print to help you with each section.
- Use the questions provided to generate discussions. Always allow time for the crew to respond to your questions before you provide an answer. Some suggested responses are written in italics.
- Review the case study and emphasize that this was a real incident. Ask the crew for a case study before you review the one provided, however.
- Always end with a discussion of the particular worksite where you are conducting the talk. Tie the talk as closely to hazards on the site as possible and encourage the crew to constantly look for and immediately correct hazards. They should also know how to report any problems that can’t be immediately corrected.
- Provide copies to each person, if you like, but NIOSH has not found that to be particularly effective.
- Encourage workers to do similar talks on their sites and provide them with the IUOE phone number for ordering in bulk.
- Have everyone sign the back of the form to indicate they attended this session and point out it is a pledge to look out for the health and safety of everyone on the site.
What are the key features of these toolbox talks?

[content_transformed:protected] =>
Why were these talks developed?
Toolbox talks have been the main tool for communicating safety information on construction jobs for decades. Unfortunately, there has been almost no research on what makes for effective toolbox talks. The IUOE National Training Fund has worked with OSHA, the National Institute for Occupational Safety and Health and the Lippy Group, LLC to make sure these Focus Four toolbox talks are based on the latest fi ndings on the most effective design and tailored to the hazards operating engineers face daily. These toolbox talks accompany an entire package of training materials, but can be used alone. The way these are delivered is as important as how well they are designed.
What did NIOSH find out?
- Just handing out factsheets and toolbox talks to workers doesn’t work. Providing copies after toolbox talks doesn’t make much of an impact either.
- Using case studies (real life stories of accidents that ended in fatality or injury) in toolbox talks is effective.
- When toolbox talks containing case studies were accompanied by discussion questions to encourage group participation, they were more effective. Consequently, getting the workers to participate in the discussion about the case study is important. It’s not enough to tell the story, it is better to have the workers engage in problem solving that analyzes why the accident occurred and how it could have been prevented. Active learning is always better than passive.
How should you deliver these toolbox talks?
- Choose a topic that is related to work going on at the site.
- Hold the meeting on the job, preferably where everyone can sit and relax.
- Hold the meeting at the beginning of a shift or after a break. Folks are too tired at the end of a shift to carefully listen and they want to get home.
- Read the toolbox talk sheet on the topic prior to conducting the talk.
- Start at the top of the form and work right through to the end, which should take around 10 to 15 minutes. Guidance is provided in blue print to help you with each section.
- Use the questions provided to generate discussions. Always allow time for the crew to respond to your questions before you provide an answer. Some suggested responses are written in italics.
- Review the case study and emphasize that this was a real incident. Ask the crew for a case study before you review the one provided, however.
- Always end with a discussion of the particular worksite where you are conducting the talk. Tie the talk as closely to hazards on the site as possible and encourage the crew to constantly look for and immediately correct hazards. They should also know how to report any problems that can’t be immediately corrected.
- Provide copies to each person, if you like, but NIOSH has not found that to be particularly effective.
- Encourage workers to do similar talks on their sites and provide them with the IUOE phone number for ordering in bulk.
- Have everyone sign the back of the form to indicate they attended this session and point out it is a pledge to look out for the health and safety of everyone on the site.
What are the key features of these toolbox talks?
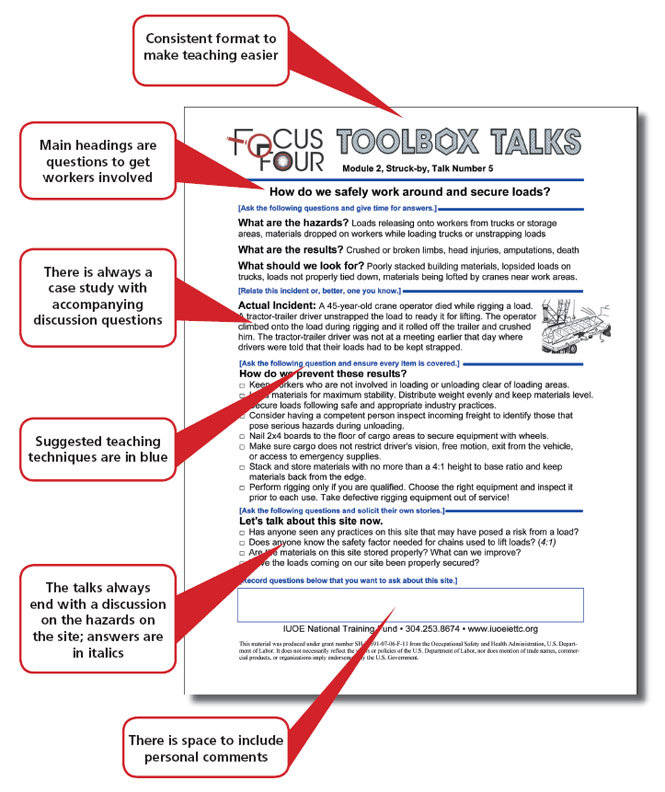
[disclaimer:protected] =>
[disclaimer_transformed:protected] =>
[alreadyInSave:protected] =>
[alreadyInValidation:protected] =>
[validationFailures:protected] => Array
(
)
[_new:BaseObject:private] =>
[_deleted:BaseObject:private] =>
[modifiedColumns:protected] => Array
(
)
)
[template] => record
)
[_file] => /home/agsafe5/repositories/elcosh/live/templates/elcosh/record_macros.html
[_errors:protected] => Array
(
)
[_encoding:protected] => UTF-8
[_outputMode:protected] => 11
[_forceReparse:protected] =>
[_phpCodeDestination:protected] => /tmp/
[_phpCodeExtension:protected] => php
[_cacheLifetime:protected] => 30
[_cachePurgeFrequency:protected] => 30
[externalMacroTemplatesCache:PHPTAL:private] => Array
(
)
)
[1] => PHPTAL Object
(
[_prefilters:protected] => Array
(
)
[_prefilter:PHPTAL:private] => REMOVED: DO NOT USE
[_postfilter:protected] =>
[_repositories:protected] => Array
(
)
[_path:protected] => /home/agsafe5/repositories/elcosh/live/templates/elcosh/record.html
[_resolvers:protected] => Array
(
)
[_source:protected] => PHPTAL_FileSource Object
(
[_path:PHPTAL_FileSource:private] => /home/agsafe5/repositories/elcosh/live/templates/elcosh/record.html
)
[_codeFile:protected] => /tmp/tpl_61515a6c_record__uvBJJSo8xT_sgOY5gjP7ug.php
[_functionName:protected] => tpl_61515a6c_record__uvBJJSo8xT_sgOY5gjP7ug
[_prepared:protected] => 1
[_triggers:protected] => Array
(
)
[_translator:protected] =>
[_globalContext:protected] => stdClass Object
(
)
[_context:protected] => PHPTAL_Context Object
(
[_line] =>
[_file] => /home/agsafe5/repositories/elcosh/live/templates/elcosh/record_macros.html
[repeat] => stdClass Object
(
[collection] => PHPTAL_RepeatController Object
(
[key] => 1294
[current:PHPTAL_RepeatController:private] =>
[valid:PHPTAL_RepeatController:private] => 1
[validOnNext:PHPTAL_RepeatController:private] => 1
[uses_groups:PHPTAL_RepeatController:private] =>
[iterator:protected] => ArrayIterator Object
(
[storage:ArrayIterator:private] => Array
(
[1294] =>
[1295] =>
[1292] =>
[1293] => CollectionRecord Object
(
[collection_items:protected] =>
[records:protected] => Array
(
)
[recordId:protected] =>
[searchWordClass:protected] =>
[searchWordPeerClass:protected] =>
[bok_record:protected] =>
[authors:protected] =>
[organizations:protected] =>
[collections:protected] =>
[categories:protected] =>
[categories_initialized:protected] =>
[mapped_items:protected] =>
[content:protected] =>
[files:protected] =>
[language:protected] =>
[old_record:protected] =>
[id:protected] => 1293
[old_id:protected] =>
[elcosh_id:protected] => c000026
[type:protected] => collection
[display_type:protected] => Collection
[user_id:protected] =>
[language_id:protected] =>
[tagging_id:protected] =>
[priority_id:protected] =>
[title:protected] => Focus Four-Struck By
[total_pages:protected] =>
[billed_pages:protected] =>
[publication_number:protected] =>
[part_of:protected] =>
[keywords:protected] =>
[comments:protected] =>
[summary:protected] => The following are links to all of the items in this collection:
[transition_comments:protected] =>
[external_link:protected] =>
[consol_link:protected] =>
[more_like_this:protected] =>
[permission_given_by:protected] =>
[published:protected] => T
[billable:protected] => F
[img_name:protected] =>
[img_ext:protected] =>
[img_width:protected] =>
[img_height:protected] =>
[img_credit:protected] =>
[img_practice:protected] =>
[vid_source_id:protected] =>
[vid_running_time:protected] =>
[vid_intended_audience:protected] =>
[vid_acquisition_info:protected] =>
[vid_cost:protected] =>
[vid_producer:protected] =>
[vid_filename:protected] =>
[vid_filename_downloadable:protected] =>
[date_summary:protected] =>
[date_permission_requested:protected] =>
[date_permission_received:protected] =>
[date_review_needed:protected] =>
[date_received:protected] => 05/08/12
[date_completed:protected] => 05/08/12
[date_billed:protected] =>
[date_modified:protected] => 05/08/12
[collBokExports:protected] =>
[lastBokExportCriteria:BaseElcoshItem:private] =>
[alreadyInSave:protected] =>
[alreadyInValidation:protected] =>
[validationFailures:protected] => Array
(
)
[_new:BaseObject:private] =>
[_deleted:BaseObject:private] =>
[modifiedColumns:protected] => Array
(
)
)
)
)
[index] => 0
[end] =>
[length:PHPTAL_RepeatController:private] =>
)
)
[_xmlDeclaration] =>
[_docType] =>
[_nothrow:PHPTAL_Context:private] =>
[_slots:PHPTAL_Context:private] => Array
(
)
[_slotsStack:PHPTAL_Context:private] => Array
(
[0] => Array
(
)
[1] => Array
(
)
)
[_parentContext:PHPTAL_Context:private] => PHPTAL_Context Object
(
[_line] =>
[_file] => /home/agsafe5/repositories/elcosh/live/templates/elcosh/record_macros.html
[repeat] => stdClass Object
(
[collection] => PHPTAL_RepeatController Object
(
[key] => 1294
[current:PHPTAL_RepeatController:private] =>
[valid:PHPTAL_RepeatController:private] => 1
[validOnNext:PHPTAL_RepeatController:private] => 1
[uses_groups:PHPTAL_RepeatController:private] =>
[iterator:protected] => ArrayIterator Object
(
[storage:ArrayIterator:private] => Array
(
[1294] =>
[1295] =>
[1292] =>
[1293] => CollectionRecord Object
(
[collection_items:protected] =>
[records:protected] => Array
(
)
[recordId:protected] =>
[searchWordClass:protected] =>
[searchWordPeerClass:protected] =>
[bok_record:protected] =>
[authors:protected] =>
[organizations:protected] =>
[collections:protected] =>
[categories:protected] =>
[categories_initialized:protected] =>
[mapped_items:protected] =>
[content:protected] =>
[files:protected] =>
[language:protected] =>
[old_record:protected] =>
[id:protected] => 1293
[old_id:protected] =>
[elcosh_id:protected] => c000026
[type:protected] => collection
[display_type:protected] => Collection
[user_id:protected] =>
[language_id:protected] =>
[tagging_id:protected] =>
[priority_id:protected] =>
[title:protected] => Focus Four-Struck By
[total_pages:protected] =>
[billed_pages:protected] =>
[publication_number:protected] =>
[part_of:protected] =>
[keywords:protected] =>
[comments:protected] =>
[summary:protected] => The following are links to all of the items in this collection:
[transition_comments:protected] =>
[external_link:protected] =>
[consol_link:protected] =>
[more_like_this:protected] =>
[permission_given_by:protected] =>
[published:protected] => T
[billable:protected] => F
[img_name:protected] =>
[img_ext:protected] =>
[img_width:protected] =>
[img_height:protected] =>
[img_credit:protected] =>
[img_practice:protected] =>
[vid_source_id:protected] =>
[vid_running_time:protected] =>
[vid_intended_audience:protected] =>
[vid_acquisition_info:protected] =>
[vid_cost:protected] =>
[vid_producer:protected] =>
[vid_filename:protected] =>
[vid_filename_downloadable:protected] =>
[date_summary:protected] =>
[date_permission_requested:protected] =>
[date_permission_received:protected] =>
[date_review_needed:protected] =>
[date_received:protected] => 05/08/12
[date_completed:protected] => 05/08/12
[date_billed:protected] =>
[date_modified:protected] => 05/08/12
[collBokExports:protected] =>
[lastBokExportCriteria:BaseElcoshItem:private] =>
[alreadyInSave:protected] =>
[alreadyInValidation:protected] =>
[validationFailures:protected] => Array
(
)
[_new:BaseObject:private] =>
[_deleted:BaseObject:private] =>
[modifiedColumns:protected] => Array
(
)
)
)
)
[index] => 0
[end] =>
[length:PHPTAL_RepeatController:private] =>
)
)
[_xmlDeclaration] =>
[_docType] =>
[_nothrow:PHPTAL_Context:private] =>
[_slots:PHPTAL_Context:private] => Array
(
)
[_slotsStack:PHPTAL_Context:private] => Array
(
[0] => Array
(
)
[1] => Array
(
)
)
[_parentContext:PHPTAL_Context:private] => PHPTAL_Context Object
(
[_line] =>
[_file] => /home/agsafe5/repositories/elcosh/live/templates/elcosh/record.html
[repeat] => stdClass Object
(
)
[_xmlDeclaration] =>
[_docType] =>
[_nothrow:PHPTAL_Context:private] =>
[_slots:PHPTAL_Context:private] => Array
(
)
[_slotsStack:PHPTAL_Context:private] => Array
(
[0] => Array
(
)
[1] => Array
(
)
)
[_parentContext:PHPTAL_Context:private] =>
[_globalContext:PHPTAL_Context:private] => stdClass Object
(
)
[_echoDeclarations:PHPTAL_Context:private] =>
[referer] => http://www.elcosh.org/document/3827/d001298/Getting%2Bthe%2Bmost%2Bout%2Bof%2Bthe%2BIUOE%2BToolbox%2BTalks.html
[curr_module] => Record
[styles] => Array
(
)
[javascript] => Array
(
[0] => jquery.min.js
)
[metas] => Array
(
[language] => en
[robots] => index, follow
)
[user] =>
[curr_url] => https://www.elcosh.org/index.php?module=Record&id=3827&type=document
[base_url] => https://www.elcosh.org/index.php?module=Record
[title] => eLCOSH : Getting the most out of the IUOE Toolbox Talks
[language] => en
[search_query] =>
[module] => Record
[new_records] => Array
(
[0] => Search_Result Object
(
[title] => Toolbox Talk: Fixed Ladder
[image] => /record/images/notavailable-p.png
[blurb] => The CPWR Toolbox Talk on Fixed Ladders addresses the potential risks associated with using fixed ladders. The resource includes a brief case example,...
[category] => Array
(
[0] => 15
[1] => 47
[2] => 49
[3] => 51
[4] => 53
[5] => 55
[6] => 60
[7] => 64
[8] => 73
[9] => 76
[10] => 78
[11] => 80
[12] => 86
[13] => 87
[14] => 90
[15] => 92
[16] => 93
[17] => 94
[18] => 100
)
[labels] => Array
(
[0] => Falls
[1] => Work Environment
[2] => Hazards
[3] => Bricklayer
[4] => Trades
[5] => Carpenter
[7] => Cement Mason
[9] => Concrete Polisher
[11] => Electrical Worker
[13] => HVAC
[15] => Laborer
[17] => PCC/Restoration
[19] => Plumber/Pipefitter
[21] => Roofer/Waterproofer
[23] => Sheetmetal Worker
[25] => Welder
[27] => Commercial & Institutional
[28] => Jobsites
[29] => Industrial
[31] => LEED/Green Construction
[33] => Renovations
[35] => Residential
[37] => Toolbox Talks
[38] => Documents
[39] => Media & Documents
)
[type] => Toolbox Talks
[sub_category] =>
[url] => /document/4430/d001660/Toolbox%2BTalk%253A%2BFixed%2BLadder.html
[item:protected] => DocumentRecord Object
(
[records:protected] => Array
(
)
[recordId:protected] =>
[searchWordClass:protected] =>
[searchWordPeerClass:protected] =>
[bok_record:protected] =>
[authors:protected] =>
[organizations:protected] =>
[collections:protected] =>
[categories:protected] => Array
(
[15] => Category Object
(
[languages:protected] =>
[bok_resources:protected] =>
[bok_topics:protected] =>
[bok_keywords:protected] =>
[id:protected] => 15
[type:protected] => category
[parent:protected] => 7
[label:protected] => Falls
[alreadyInSave:protected] =>
[alreadyInValidation:protected] =>
[validationFailures:protected] => Array
(
)
[_new:BaseObject:private] =>
[_deleted:BaseObject:private] =>
[modifiedColumns:protected] => Array
(
)
)
[47] => Category Object
(
[languages:protected] =>
[bok_resources:protected] =>
[bok_topics:protected] =>
[bok_keywords:protected] =>
[id:protected] => 47
[type:protected] => category
[parent:protected] => 2
[label:protected] => Bricklayer
[alreadyInSave:protected] =>
[alreadyInValidation:protected] =>
[validationFailures:protected] => Array
(
)
[_new:BaseObject:private] =>
[_deleted:BaseObject:private] =>
[modifiedColumns:protected] => Array
(
)
)
[49] => Category Object
(
[languages:protected] =>
[bok_resources:protected] =>
[bok_topics:protected] =>
[bok_keywords:protected] =>
[id:protected] => 49
[type:protected] => category
[parent:protected] => 2
[label:protected] => Carpenter
[alreadyInSave:protected] =>
[alreadyInValidation:protected] =>
[validationFailures:protected] => Array
(
)
[_new:BaseObject:private] =>
[_deleted:BaseObject:private] =>
[modifiedColumns:protected] => Array
(
)
)
[51] => Category Object
(
[languages:protected] =>
[bok_resources:protected] =>
[bok_topics:protected] =>
[bok_keywords:protected] =>
[id:protected] => 51
[type:protected] => category
[parent:protected] => 2
[label:protected] => Cement Mason
[alreadyInSave:protected] =>
[alreadyInValidation:protected] =>
[validationFailures:protected] => Array
(
)
[_new:BaseObject:private] =>
[_deleted:BaseObject:private] =>
[modifiedColumns:protected] => Array
(
)
)
[53] => Category Object
(
[languages:protected] =>
[bok_resources:protected] =>
[bok_topics:protected] =>
[bok_keywords:protected] =>
[id:protected] => 53
[type:protected] => category
[parent:protected] => 2
[label:protected] => Concrete Polisher
[alreadyInSave:protected] =>
[alreadyInValidation:protected] =>
[validationFailures:protected] => Array
(
)
[_new:BaseObject:private] =>
[_deleted:BaseObject:private] =>
[modifiedColumns:protected] => Array
(
)
)
[55] => Category Object
(
[languages:protected] =>
[bok_resources:protected] =>
[bok_topics:protected] =>
[bok_keywords:protected] =>
[id:protected] => 55
[type:protected] => category
[parent:protected] => 2
[label:protected] => Electrical Worker
[alreadyInSave:protected] =>
[alreadyInValidation:protected] =>
[validationFailures:protected] => Array
(
)
[_new:BaseObject:private] =>
[_deleted:BaseObject:private] =>
[modifiedColumns:protected] => Array
(
)
)
[60] => Category Object
(
[languages:protected] =>
[bok_resources:protected] =>
[bok_topics:protected] =>
[bok_keywords:protected] =>
[id:protected] => 60
[type:protected] => category
[parent:protected] => 2
[label:protected] => HVAC
[alreadyInSave:protected] =>
[alreadyInValidation:protected] =>
[validationFailures:protected] => Array
(
)
[_new:BaseObject:private] =>
[_deleted:BaseObject:private] =>
[modifiedColumns:protected] => Array
(
)
)
[64] => Category Object
(
[languages:protected] =>
[bok_resources:protected] =>
[bok_topics:protected] =>
[bok_keywords:protected] =>
[id:protected] => 64
[type:protected] => category
[parent:protected] => 2
[label:protected] => Laborer
[alreadyInSave:protected] =>
[alreadyInValidation:protected] =>
[validationFailures:protected] => Array
(
)
[_new:BaseObject:private] =>
[_deleted:BaseObject:private] =>
[modifiedColumns:protected] => Array
(
)
)
[73] => Category Object
(
[languages:protected] =>
[bok_resources:protected] =>
[bok_topics:protected] =>
[bok_keywords:protected] =>
[id:protected] => 73
[type:protected] => category
[parent:protected] => 2
[label:protected] => PCC/Restoration
[alreadyInSave:protected] =>
[alreadyInValidation:protected] =>
[validationFailures:protected] => Array
(
)
[_new:BaseObject:private] =>
[_deleted:BaseObject:private] =>
[modifiedColumns:protected] => Array
(
)
)
[76] => Category Object
(
[languages:protected] =>
[bok_resources:protected] =>
[bok_topics:protected] =>
[bok_keywords:protected] =>
[id:protected] => 76
[type:protected] => category
[parent:protected] => 2
[label:protected] => Plumber/Pipefitter
[alreadyInSave:protected] =>
[alreadyInValidation:protected] =>
[validationFailures:protected] => Array
(
)
[_new:BaseObject:private] =>
[_deleted:BaseObject:private] =>
[modifiedColumns:protected] => Array
(
)
)
[78] => Category Object
(
[languages:protected] =>
[bok_resources:protected] =>
[bok_topics:protected] =>
[bok_keywords:protected] =>
[id:protected] => 78
[type:protected] => category
[parent:protected] => 2
[label:protected] => Roofer/Waterproofer
[alreadyInSave:protected] =>
[alreadyInValidation:protected] =>
[validationFailures:protected] => Array
(
)
[_new:BaseObject:private] =>
[_deleted:BaseObject:private] =>
[modifiedColumns:protected] => Array
(
)
)
[80] => Category Object
(
[languages:protected] =>
[bok_resources:protected] =>
[bok_topics:protected] =>
[bok_keywords:protected] =>
[id:protected] => 80
[type:protected] => category
[parent:protected] => 2
[label:protected] => Sheetmetal Worker
[alreadyInSave:protected] =>
[alreadyInValidation:protected] =>
[validationFailures:protected] => Array
(
)
[_new:BaseObject:private] =>
[_deleted:BaseObject:private] =>
[modifiedColumns:protected] => Array
(
)
)
[86] => Category Object
(
[languages:protected] =>
[bok_resources:protected] =>
[bok_topics:protected] =>
[bok_keywords:protected] =>
[id:protected] => 86
[type:protected] => category
[parent:protected] => 2
[label:protected] => Welder
[alreadyInSave:protected] =>
[alreadyInValidation:protected] =>
[validationFailures:protected] => Array
(
)
[_new:BaseObject:private] =>
[_deleted:BaseObject:private] =>
[modifiedColumns:protected] => Array
(
)
)
[87] => Category Object
(
[languages:protected] =>
[bok_resources:protected] =>
[bok_topics:protected] =>
[bok_keywords:protected] =>
[id:protected] => 87
[type:protected] => category
[parent:protected] => 3
[label:protected] => Commercial & Institutional
[alreadyInSave:protected] =>
[alreadyInValidation:protected] =>
[validationFailures:protected] => Array
(
)
[_new:BaseObject:private] =>
[_deleted:BaseObject:private] =>
[modifiedColumns:protected] => Array
(
)
)
[90] => Category Object
(
[languages:protected] =>
[bok_resources:protected] =>
[bok_topics:protected] =>
[bok_keywords:protected] =>
[id:protected] => 90
[type:protected] => category
[parent:protected] => 3
[label:protected] => Industrial
[alreadyInSave:protected] =>
[alreadyInValidation:protected] =>
[validationFailures:protected] => Array
(
)
[_new:BaseObject:private] =>
[_deleted:BaseObject:private] =>
[modifiedColumns:protected] => Array
(
)
)
[92] => Category Object
(
[languages:protected] =>
[bok_resources:protected] =>
[bok_topics:protected] =>
[bok_keywords:protected] =>
[id:protected] => 92
[type:protected] => category
[parent:protected] => 3
[label:protected] => LEED/Green Construction
[alreadyInSave:protected] =>
[alreadyInValidation:protected] =>
[validationFailures:protected] => Array
(
)
[_new:BaseObject:private] =>
[_deleted:BaseObject:private] =>
[modifiedColumns:protected] => Array
(
)
)
[93] => Category Object
(
[languages:protected] =>
[bok_resources:protected] =>
[bok_topics:protected] =>
[bok_keywords:protected] =>
[id:protected] => 93
[type:protected] => category
[parent:protected] => 3
[label:protected] => Renovations
[alreadyInSave:protected] =>
[alreadyInValidation:protected] =>
[validationFailures:protected] => Array
(
)
[_new:BaseObject:private] =>
[_deleted:BaseObject:private] =>
[modifiedColumns:protected] => Array
(
)
)
[94] => Category Object
(
[languages:protected] =>
[bok_resources:protected] =>
[bok_topics:protected] =>
[bok_keywords:protected] =>
[id:protected] => 94
[type:protected] => category
[parent:protected] => 3
[label:protected] => Residential
[alreadyInSave:protected] =>
[alreadyInValidation:protected] =>
[validationFailures:protected] => Array
(
)
[_new:BaseObject:private] =>
[_deleted:BaseObject:private] =>
[modifiedColumns:protected] => Array
(
)
)
[100] => Category Object
(
[languages:protected] =>
[bok_resources:protected] =>
[bok_topics:protected] =>
[bok_keywords:protected] =>
[id:protected] => 100
[type:protected] => category
[parent:protected] => 6
[label:protected] => Toolbox Talks
[alreadyInSave:protected] =>
[alreadyInValidation:protected] =>
[validationFailures:protected] => Array
(
)
[_new:BaseObject:private] =>
[_deleted:BaseObject:private] =>
[modifiedColumns:protected] => Array
(
)
)
)
[categories_initialized:protected] => 1
[mapped_items:protected] =>
[content:protected] =>
[files:protected] =>
[language:protected] => Language Object
(
[id:protected] => 1
[code:protected] => en
[name:protected] => English
[alreadyInSave:protected] =>
[alreadyInValidation:protected] =>
[validationFailures:protected] => Array
(
)
[_new:BaseObject:private] =>
[_deleted:BaseObject:private] =>
[modifiedColumns:protected] => Array
(
)
)
[old_record:protected] =>
[id:protected] => 4430
[old_id:protected] =>
[elcosh_id:protected] => d001660
[type:protected] => document
[display_type:protected] => HTML only (and links)
[user_id:protected] => 0
[language_id:protected] => 1
[tagging_id:protected] => Mike Aguilar
[priority_id:protected] => 1
[title:protected] => Toolbox Talk: Fixed Ladder
[total_pages:protected] => 0
[billed_pages:protected] => 0
[publication_number:protected] =>
[part_of:protected] =>
[keywords:protected] => Fixed Ladders, Fall Prevention, Falls
[comments:protected] =>
[summary:protected] => The CPWR Toolbox Talk on Fixed Ladders addresses the potential risks associated with using fixed ladders. The resource includes a brief case example, steps to prevent a related injury and questions for discussion. It includes an image that illustrates the hazard, which can be posted in a central location as a reminder of steps to work safely.
Available in
English
and
Spanish.
[transition_comments:protected] =>
[external_link:protected] =>
[consol_link:protected] =>
[more_like_this:protected] => d001257,d001254,d001255,d001256,d001258,d001262,d001279
[permission_given_by:protected] =>
[published:protected] => T
[billable:protected] => F
[img_name:protected] =>
[img_ext:protected] =>
[img_width:protected] =>
[img_height:protected] =>
[img_credit:protected] =>
[img_practice:protected] =>
[vid_source_id:protected] =>
[vid_running_time:protected] =>
[vid_intended_audience:protected] =>
[vid_acquisition_info:protected] =>
[vid_cost:protected] =>
[vid_producer:protected] =>
[vid_filename:protected] =>
[vid_filename_downloadable:protected] =>
[date_summary:protected] =>
[date_permission_requested:protected] =>
[date_permission_received:protected] =>
[date_review_needed:protected] =>
[date_received:protected] => 06/10/22
[date_completed:protected] => 06/10/22
[date_billed:protected] =>
[date_modified:protected] => 05/22/23
[collBokExports:protected] =>
[lastBokExportCriteria:BaseElcoshItem:private] =>
[alreadyInSave:protected] =>
[alreadyInValidation:protected] =>
[validationFailures:protected] => Array
(
)
[_new:BaseObject:private] =>
[_deleted:BaseObject:private] =>
[modifiedColumns:protected] => Array
(
)
)
)
[1] => Search_Result Object
(
[title] => Toolbox Talk: Challenges Preventing Falling Objects
[image] => /record/images/notavailable-p.png
[blurb] => The CPWR Toolbox Talk on Challenges Preventing Falling Objects addresses the hazards of being struck by falling objects on the job site. The resource...
[category] => Array
(
[0] => 12
[1] => 47
[2] => 49
[3] => 51
[4] => 55
[5] => 64
[6] => 68
[7] => 71
[8] => 75
[9] => 78
[10] => 79
[11] => 82
[12] => 62
[13] => 86
[14] => 87
[15] => 88
[16] => 89
[17] => 91
[18] => 90
[19] => 92
[20] => 93
[21] => 94
[22] => 95
[23] => 100
)
[labels] => Array
(
[0] => Crushed/Struck By
[1] => Work Environment
[2] => Hazards
[3] => Bricklayer
[4] => Trades
[5] => Carpenter
[7] => Cement Mason
[9] => Electrical Worker
[11] => Laborer
[13] => Maintenance Worker
[15] => Painter
[17] => Plasterer
[19] => Roofer/Waterproofer
[21] => Scaffold Erector
[23] => Stonemason
[25] => Structural Ironworker
[27] => Welder
[29] => Commercial & Institutional
[30] => Jobsites
[31] => Demolition
[33] => Disasters
[35] => Heavy & Highway
[37] => Industrial
[39] => LEED/Green Construction
[41] => Renovations
[43] => Residential
[45] => Underground
[47] => Toolbox Talks
[48] => Documents
[49] => Media & Documents
)
[type] => Toolbox Talks
[sub_category] =>
[url] => /document/4431/d001661/Toolbox%2BTalk%253A%2BChallenges%2BPreventing%2BFalling%2BObjects.html
[item:protected] => DocumentRecord Object
(
[records:protected] => Array
(
)
[recordId:protected] =>
[searchWordClass:protected] =>
[searchWordPeerClass:protected] =>
[bok_record:protected] =>
[authors:protected] =>
[organizations:protected] =>
[collections:protected] =>
[categories:protected] => Array
(
[12] => Category Object
(
[languages:protected] =>
[bok_resources:protected] =>
[bok_topics:protected] =>
[bok_keywords:protected] =>
[id:protected] => 12
[type:protected] => category
[parent:protected] => 7
[label:protected] => Crushed/Struck By
[alreadyInSave:protected] =>
[alreadyInValidation:protected] =>
[validationFailures:protected] => Array
(
)
[_new:BaseObject:private] =>
[_deleted:BaseObject:private] =>
[modifiedColumns:protected] => Array
(
)
)
[47] => Category Object
(
[languages:protected] =>
[bok_resources:protected] =>
[bok_topics:protected] =>
[bok_keywords:protected] =>
[id:protected] => 47
[type:protected] => category
[parent:protected] => 2
[label:protected] => Bricklayer
[alreadyInSave:protected] =>
[alreadyInValidation:protected] =>
[validationFailures:protected] => Array
(
)
[_new:BaseObject:private] =>
[_deleted:BaseObject:private] =>
[modifiedColumns:protected] => Array
(
)
)
[49] => Category Object
(
[languages:protected] =>
[bok_resources:protected] =>
[bok_topics:protected] =>
[bok_keywords:protected] =>
[id:protected] => 49
[type:protected] => category
[parent:protected] => 2
[label:protected] => Carpenter
[alreadyInSave:protected] =>
[alreadyInValidation:protected] =>
[validationFailures:protected] => Array
(
)
[_new:BaseObject:private] =>
[_deleted:BaseObject:private] =>
[modifiedColumns:protected] => Array
(
)
)
[51] => Category Object
(
[languages:protected] =>
[bok_resources:protected] =>
[bok_topics:protected] =>
[bok_keywords:protected] =>
[id:protected] => 51
[type:protected] => category
[parent:protected] => 2
[label:protected] => Cement Mason
[alreadyInSave:protected] =>
[alreadyInValidation:protected] =>
[validationFailures:protected] => Array
(
)
[_new:BaseObject:private] =>
[_deleted:BaseObject:private] =>
[modifiedColumns:protected] => Array
(
)
)
[55] => Category Object
(
[languages:protected] =>
[bok_resources:protected] =>
[bok_topics:protected] =>
[bok_keywords:protected] =>
[id:protected] => 55
[type:protected] => category
[parent:protected] => 2
[label:protected] => Electrical Worker
[alreadyInSave:protected] =>
[alreadyInValidation:protected] =>
[validationFailures:protected] => Array
(
)
[_new:BaseObject:private] =>
[_deleted:BaseObject:private] =>
[modifiedColumns:protected] => Array
(
)
)
[64] => Category Object
(
[languages:protected] =>
[bok_resources:protected] =>
[bok_topics:protected] =>
[bok_keywords:protected] =>
[id:protected] => 64
[type:protected] => category
[parent:protected] => 2
[label:protected] => Laborer
[alreadyInSave:protected] =>
[alreadyInValidation:protected] =>
[validationFailures:protected] => Array
(
)
[_new:BaseObject:private] =>
[_deleted:BaseObject:private] =>
[modifiedColumns:protected] => Array
(
)
)
[68] => Category Object
(
[languages:protected] =>
[bok_resources:protected] =>
[bok_topics:protected] =>
[bok_keywords:protected] =>
[id:protected] => 68
[type:protected] => category
[parent:protected] => 2
[label:protected] => Maintenance Worker
[alreadyInSave:protected] =>
[alreadyInValidation:protected] =>
[validationFailures:protected] => Array
(
)
[_new:BaseObject:private] =>
[_deleted:BaseObject:private] =>
[modifiedColumns:protected] => Array
(
)
)
[71] => Category Object
(
[languages:protected] =>
[bok_resources:protected] =>
[bok_topics:protected] =>
[bok_keywords:protected] =>
[id:protected] => 71
[type:protected] => category
[parent:protected] => 2
[label:protected] => Painter
[alreadyInSave:protected] =>
[alreadyInValidation:protected] =>
[validationFailures:protected] => Array
(
)
[_new:BaseObject:private] =>
[_deleted:BaseObject:private] =>
[modifiedColumns:protected] => Array
(
)
)
[75] => Category Object
(
[languages:protected] =>
[bok_resources:protected] =>
[bok_topics:protected] =>
[bok_keywords:protected] =>
[id:protected] => 75
[type:protected] => category
[parent:protected] => 2
[label:protected] => Plasterer
[alreadyInSave:protected] =>
[alreadyInValidation:protected] =>
[validationFailures:protected] => Array
(
)
[_new:BaseObject:private] =>
[_deleted:BaseObject:private] =>
[modifiedColumns:protected] => Array
(
)
)
[78] => Category Object
(
[languages:protected] =>
[bok_resources:protected] =>
[bok_topics:protected] =>
[bok_keywords:protected] =>
[id:protected] => 78
[type:protected] => category
[parent:protected] => 2
[label:protected] => Roofer/Waterproofer
[alreadyInSave:protected] =>
[alreadyInValidation:protected] =>
[validationFailures:protected] => Array
(
)
[_new:BaseObject:private] =>
[_deleted:BaseObject:private] =>
[modifiedColumns:protected] => Array
(
)
)
[79] => Category Object
(
[languages:protected] =>
[bok_resources:protected] =>
[bok_topics:protected] =>
[bok_keywords:protected] =>
[id:protected] => 79
[type:protected] => category
[parent:protected] => 2
[label:protected] => Scaffold Erector
[alreadyInSave:protected] =>
[alreadyInValidation:protected] =>
[validationFailures:protected] => Array
(
)
[_new:BaseObject:private] =>
[_deleted:BaseObject:private] =>
[modifiedColumns:protected] => Array
(
)
)
[82] => Category Object
(
[languages:protected] =>
[bok_resources:protected] =>
[bok_topics:protected] =>
[bok_keywords:protected] =>
[id:protected] => 82
[type:protected] => category
[parent:protected] => 2
[label:protected] => Stonemason
[alreadyInSave:protected] =>
[alreadyInValidation:protected] =>
[validationFailures:protected] => Array
(
)
[_new:BaseObject:private] =>
[_deleted:BaseObject:private] =>
[modifiedColumns:protected] => Array
(
)
)
[62] => Category Object
(
[languages:protected] =>
[bok_resources:protected] =>
[bok_topics:protected] =>
[bok_keywords:protected] =>
[id:protected] => 62
[type:protected] => category
[parent:protected] => 2
[label:protected] => Structural Ironworker
[alreadyInSave:protected] =>
[alreadyInValidation:protected] =>
[validationFailures:protected] => Array
(
)
[_new:BaseObject:private] =>
[_deleted:BaseObject:private] =>
[modifiedColumns:protected] => Array
(
)
)
[86] => Category Object
(
[languages:protected] =>
[bok_resources:protected] =>
[bok_topics:protected] =>
[bok_keywords:protected] =>
[id:protected] => 86
[type:protected] => category
[parent:protected] => 2
[label:protected] => Welder
[alreadyInSave:protected] =>
[alreadyInValidation:protected] =>
[validationFailures:protected] => Array
(
)
[_new:BaseObject:private] =>
[_deleted:BaseObject:private] =>
[modifiedColumns:protected] => Array
(
)
)
[87] => Category Object
(
[languages:protected] =>
[bok_resources:protected] =>
[bok_topics:protected] =>
[bok_keywords:protected] =>
[id:protected] => 87
[type:protected] => category
[parent:protected] => 3
[label:protected] => Commercial & Institutional
[alreadyInSave:protected] =>
[alreadyInValidation:protected] =>
[validationFailures:protected] => Array
(
)
[_new:BaseObject:private] =>
[_deleted:BaseObject:private] =>
[modifiedColumns:protected] => Array
(
)
)
[88] => Category Object
(
[languages:protected] =>
[bok_resources:protected] =>
[bok_topics:protected] =>
[bok_keywords:protected] =>
[id:protected] => 88
[type:protected] => category
[parent:protected] => 3
[label:protected] => Demolition
[alreadyInSave:protected] =>
[alreadyInValidation:protected] =>
[validationFailures:protected] => Array
(
)
[_new:BaseObject:private] =>
[_deleted:BaseObject:private] =>
[modifiedColumns:protected] => Array
(
)
)
[89] => Category Object
(
[languages:protected] =>
[bok_resources:protected] =>
[bok_topics:protected] =>
[bok_keywords:protected] =>
[id:protected] => 89
[type:protected] => category
[parent:protected] => 3
[label:protected] => Disasters
[alreadyInSave:protected] =>
[alreadyInValidation:protected] =>
[validationFailures:protected] => Array
(
)
[_new:BaseObject:private] =>
[_deleted:BaseObject:private] =>
[modifiedColumns:protected] => Array
(
)
)
[91] => Category Object
(
[languages:protected] =>
[bok_resources:protected] =>
[bok_topics:protected] =>
[bok_keywords:protected] =>
[id:protected] => 91
[type:protected] => category
[parent:protected] => 3
[label:protected] => Heavy & Highway
[alreadyInSave:protected] =>
[alreadyInValidation:protected] =>
[validationFailures:protected] => Array
(
)
[_new:BaseObject:private] =>
[_deleted:BaseObject:private] =>
[modifiedColumns:protected] => Array
(
)
)
[90] => Category Object
(
[languages:protected] =>
[bok_resources:protected] =>
[bok_topics:protected] =>
[bok_keywords:protected] =>
[id:protected] => 90
[type:protected] => category
[parent:protected] => 3
[label:protected] => Industrial
[alreadyInSave:protected] =>
[alreadyInValidation:protected] =>
[validationFailures:protected] => Array
(
)
[_new:BaseObject:private] =>
[_deleted:BaseObject:private] =>
[modifiedColumns:protected] => Array
(
)
)
[92] => Category Object
(
[languages:protected] =>
[bok_resources:protected] =>
[bok_topics:protected] =>
[bok_keywords:protected] =>
[id:protected] => 92
[type:protected] => category
[parent:protected] => 3
[label:protected] => LEED/Green Construction
[alreadyInSave:protected] =>
[alreadyInValidation:protected] =>
[validationFailures:protected] => Array
(
)
[_new:BaseObject:private] =>
[_deleted:BaseObject:private] =>
[modifiedColumns:protected] => Array
(
)
)
[93] => Category Object
(
[languages:protected] =>
[bok_resources:protected] =>
[bok_topics:protected] =>
[bok_keywords:protected] =>
[id:protected] => 93
[type:protected] => category
[parent:protected] => 3
[label:protected] => Renovations
[alreadyInSave:protected] =>
[alreadyInValidation:protected] =>
[validationFailures:protected] => Array
(
)
[_new:BaseObject:private] =>
[_deleted:BaseObject:private] =>
[modifiedColumns:protected] => Array
(
)
)
[94] => Category Object
(
[languages:protected] =>
[bok_resources:protected] =>
[bok_topics:protected] =>
[bok_keywords:protected] =>
[id:protected] => 94
[type:protected] => category
[parent:protected] => 3
[label:protected] => Residential
[alreadyInSave:protected] =>
[alreadyInValidation:protected] =>
[validationFailures:protected] => Array
(
)
[_new:BaseObject:private] =>
[_deleted:BaseObject:private] =>
[modifiedColumns:protected] => Array
(
)
)
[95] => Category Object
(
[languages:protected] =>
[bok_resources:protected] =>
[bok_topics:protected] =>
[bok_keywords:protected] =>
[id:protected] => 95
[type:protected] => category
[parent:protected] => 3
[label:protected] => Underground
[alreadyInSave:protected] =>
[alreadyInValidation:protected] =>
[validationFailures:protected] => Array
(
)
[_new:BaseObject:private] =>
[_deleted:BaseObject:private] =>
[modifiedColumns:protected] => Array
(
)
)
[100] => Category Object
(
[languages:protected] =>
[bok_resources:protected] =>
[bok_topics:protected] =>
[bok_keywords:protected] =>
[id:protected] => 100
[type:protected] => category
[parent:protected] => 6
[label:protected] => Toolbox Talks
[alreadyInSave:protected] =>
[alreadyInValidation:protected] =>
[validationFailures:protected] => Array
(
)
[_new:BaseObject:private] =>
[_deleted:BaseObject:private] =>
[modifiedColumns:protected] => Array
(
)
)
)
[categories_initialized:protected] => 1
[mapped_items:protected] =>
[content:protected] =>
[files:protected] =>
[language:protected] => Language Object
(
[id:protected] => 1
[code:protected] => en
[name:protected] => English
[alreadyInSave:protected] =>
[alreadyInValidation:protected] =>
[validationFailures:protected] => Array
(
)
[_new:BaseObject:private] =>
[_deleted:BaseObject:private] =>
[modifiedColumns:protected] => Array
(
)
)
[old_record:protected] =>
[id:protected] => 4431
[old_id:protected] =>
[elcosh_id:protected] => d001661
[type:protected] => document
[display_type:protected] => HTML only (and links)
[user_id:protected] => 0
[language_id:protected] => 1
[tagging_id:protected] => Mike Aguilar
[priority_id:protected] => 1
[title:protected] => Toolbox Talk: Challenges Preventing Falling Objects
[total_pages:protected] => 0
[billed_pages:protected] => 0
[publication_number:protected] =>
[part_of:protected] =>
[keywords:protected] => dropped objects, falling objects, struck by incidents, struck by fatalities
[comments:protected] =>
[summary:protected] => The CPWR Toolbox Talk on Challenges Preventing Falling Objects addresses the hazards of being struck by falling objects on the job site. The resource includes a brief example, steps to prevent a related injury, and questions for discussion. It includes a graphic that illustrates a group workers observing a scaffold free of debris during high winds, which can be posted in a central location as a reminder of steps to work safely.
Available in
English and
Spanish.
[transition_comments:protected] =>
[external_link:protected] =>
[consol_link:protected] =>
[more_like_this:protected] => d001234,d001238,d001244,d001251,d001253,d001260,d001268,d001278
[permission_given_by:protected] =>
[published:protected] => T
[billable:protected] => F
[img_name:protected] =>
[img_ext:protected] =>
[img_width:protected] =>
[img_height:protected] =>
[img_credit:protected] =>
[img_practice:protected] =>
[vid_source_id:protected] =>
[vid_running_time:protected] =>
[vid_intended_audience:protected] =>
[vid_acquisition_info:protected] =>
[vid_cost:protected] =>
[vid_producer:protected] =>
[vid_filename:protected] =>
[vid_filename_downloadable:protected] =>
[date_summary:protected] =>
[date_permission_requested:protected] =>
[date_permission_received:protected] =>
[date_review_needed:protected] =>
[date_received:protected] => 06/10/22
[date_completed:protected] => 06/10/22
[date_billed:protected] =>
[date_modified:protected] => 05/22/23
[collBokExports:protected] =>
[lastBokExportCriteria:BaseElcoshItem:private] =>
[alreadyInSave:protected] =>
[alreadyInValidation:protected] =>
[validationFailures:protected] => Array
(
)
[_new:BaseObject:private] =>
[_deleted:BaseObject:private] =>
[modifiedColumns:protected] => Array
(
)
)
)
[2] => Search_Result Object
(
[title] => Toolbox Talk: Tower Crane Safety
[image] => /record/images/notavailable-p.png
[blurb] => The CPWR Toolbox Talk on Tower Crane Safety addresses the potential hazards of Tower Cranes and the importance of following procedure before and durin...
[category] => Array
(
[0] => 11
[1] => 12
[2] => 18
[3] => 70
[4] => 87
[5] => 88
[6] => 91
[7] => 90
[8] => 92
[9] => 100
)
[labels] => Array
(
[0] => Cranes & Hoists
[1] => Work Environment
[2] => Hazards
[3] => Crushed/Struck By
[6] => Motor Vehicles/Heavy Equipment
[9] => Operating Engineer
[10] => Trades
[11] => Commercial & Institutional
[12] => Jobsites
[13] => Demolition
[15] => Heavy & Highway
[17] => Industrial
[19] => LEED/Green Construction
[21] => Toolbox Talks
[22] => Documents
[23] => Media & Documents
)
[type] => Toolbox Talks
[sub_category] =>
[url] => /document/4427/d001657/Toolbox%2BTalk%253A%2BTower%2BCrane%2BSafety.html
[item:protected] => DocumentRecord Object
(
[records:protected] => Array
(
)
[recordId:protected] =>
[searchWordClass:protected] =>
[searchWordPeerClass:protected] =>
[bok_record:protected] =>
[authors:protected] =>
[organizations:protected] =>
[collections:protected] =>
[categories:protected] => Array
(
[11] => Category Object
(
[languages:protected] =>
[bok_resources:protected] =>
[bok_topics:protected] =>
[bok_keywords:protected] =>
[id:protected] => 11
[type:protected] => category
[parent:protected] => 7
[label:protected] => Cranes & Hoists
[alreadyInSave:protected] =>
[alreadyInValidation:protected] =>
[validationFailures:protected] => Array
(
)
[_new:BaseObject:private] =>
[_deleted:BaseObject:private] =>
[modifiedColumns:protected] => Array
(
)
)
[12] => Category Object
(
[languages:protected] =>
[bok_resources:protected] =>
[bok_topics:protected] =>
[bok_keywords:protected] =>
[id:protected] => 12
[type:protected] => category
[parent:protected] => 7
[label:protected] => Crushed/Struck By
[alreadyInSave:protected] =>
[alreadyInValidation:protected] =>
[validationFailures:protected] => Array
(
)
[_new:BaseObject:private] =>
[_deleted:BaseObject:private] =>
[modifiedColumns:protected] => Array
(
)
)
[18] => Category Object
(
[languages:protected] =>
[bok_resources:protected] =>
[bok_topics:protected] =>
[bok_keywords:protected] =>
[id:protected] => 18
[type:protected] => category
[parent:protected] => 7
[label:protected] => Motor Vehicles/Heavy Equipment
[alreadyInSave:protected] =>
[alreadyInValidation:protected] =>
[validationFailures:protected] => Array
(
)
[_new:BaseObject:private] =>
[_deleted:BaseObject:private] =>
[modifiedColumns:protected] => Array
(
)
)
[70] => Category Object
(
[languages:protected] =>
[bok_resources:protected] =>
[bok_topics:protected] =>
[bok_keywords:protected] =>
[id:protected] => 70
[type:protected] => category
[parent:protected] => 2
[label:protected] => Operating Engineer
[alreadyInSave:protected] =>
[alreadyInValidation:protected] =>
[validationFailures:protected] => Array
(
)
[_new:BaseObject:private] =>
[_deleted:BaseObject:private] =>
[modifiedColumns:protected] => Array
(
)
)
[87] => Category Object
(
[languages:protected] =>
[bok_resources:protected] =>
[bok_topics:protected] =>
[bok_keywords:protected] =>
[id:protected] => 87
[type:protected] => category
[parent:protected] => 3
[label:protected] => Commercial & Institutional
[alreadyInSave:protected] =>
[alreadyInValidation:protected] =>
[validationFailures:protected] => Array
(
)
[_new:BaseObject:private] =>
[_deleted:BaseObject:private] =>
[modifiedColumns:protected] => Array
(
)
)
[88] => Category Object
(
[languages:protected] =>
[bok_resources:protected] =>
[bok_topics:protected] =>
[bok_keywords:protected] =>
[id:protected] => 88
[type:protected] => category
[parent:protected] => 3
[label:protected] => Demolition
[alreadyInSave:protected] =>
[alreadyInValidation:protected] =>
[validationFailures:protected] => Array
(
)
[_new:BaseObject:private] =>
[_deleted:BaseObject:private] =>
[modifiedColumns:protected] => Array
(
)
)
[91] => Category Object
(
[languages:protected] =>
[bok_resources:protected] =>
[bok_topics:protected] =>
[bok_keywords:protected] =>
[id:protected] => 91
[type:protected] => category
[parent:protected] => 3
[label:protected] => Heavy & Highway
[alreadyInSave:protected] =>
[alreadyInValidation:protected] =>
[validationFailures:protected] => Array
(
)
[_new:BaseObject:private] =>
[_deleted:BaseObject:private] =>
[modifiedColumns:protected] => Array
(
)
)
[90] => Category Object
(
[languages:protected] =>
[bok_resources:protected] =>
[bok_topics:protected] =>
[bok_keywords:protected] =>
[id:protected] => 90
[type:protected] => category
[parent:protected] => 3
[label:protected] => Industrial
[alreadyInSave:protected] =>
[alreadyInValidation:protected] =>
[validationFailures:protected] => Array
(
)
[_new:BaseObject:private] =>
[_deleted:BaseObject:private] =>
[modifiedColumns:protected] => Array
(
)
)
[92] => Category Object
(
[languages:protected] =>
[bok_resources:protected] =>
[bok_topics:protected] =>
[bok_keywords:protected] =>
[id:protected] => 92
[type:protected] => category
[parent:protected] => 3
[label:protected] => LEED/Green Construction
[alreadyInSave:protected] =>
[alreadyInValidation:protected] =>
[validationFailures:protected] => Array
(
)
[_new:BaseObject:private] =>
[_deleted:BaseObject:private] =>
[modifiedColumns:protected] => Array
(
)
)
[100] => Category Object
(
[languages:protected] =>
[bok_resources:protected] =>
[bok_topics:protected] =>
[bok_keywords:protected] =>
[id:protected] => 100
[type:protected] => category
[parent:protected] => 6
[label:protected] => Toolbox Talks
[alreadyInSave:protected] =>
[alreadyInValidation:protected] =>
[validationFailures:protected] => Array
(
)
[_new:BaseObject:private] =>
[_deleted:BaseObject:private] =>
[modifiedColumns:protected] => Array
(
)
)
)
[categories_initialized:protected] => 1
[mapped_items:protected] =>
[content:protected] =>
[files:protected] =>
[language:protected] => Language Object
(
[id:protected] => 1
[code:protected] => en
[name:protected] => English
[alreadyInSave:protected] =>
[alreadyInValidation:protected] =>
[validationFailures:protected] => Array
(
)
[_new:BaseObject:private] =>
[_deleted:BaseObject:private] =>
[modifiedColumns:protected] => Array
(
)
)
[old_record:protected] =>
[id:protected] => 4427
[old_id:protected] =>
[elcosh_id:protected] => d001657
[type:protected] => document
[display_type:protected] => HTML only (and links)
[user_id:protected] => 0
[language_id:protected] => 1
[tagging_id:protected] => Mike Aguilar
[priority_id:protected] => 1
[title:protected] => Toolbox Talk: Tower Crane Safety
[total_pages:protected] => 0
[billed_pages:protected] => 0
[publication_number:protected] =>
[part_of:protected] =>
[keywords:protected] => Tower Crane, Crane, Stability, Tipping, Lift Zone Safety, Lift, Zone, Safety, Struck by
[comments:protected] =>
[summary:protected] => The CPWR Toolbox Talk on Tower Crane Safety addresses the potential hazards of Tower Cranes and the importance of following procedure before and during Tower Crane operation. The resource includes a brief example, steps to prevent a related injury, and questions for discussion. It includes a graphic that illustrates a worker inspecting a Tower Crane before operation, which can be posted in a central location as a reminder of steps to work safely.
Available in
English and
Spanish.
[transition_comments:protected] =>
[external_link:protected] =>
[consol_link:protected] =>
[more_like_this:protected] => d001234,d001238,d001250,d001251,d001253,d001258,d001262,d001273
[permission_given_by:protected] =>
[published:protected] => T
[billable:protected] => F
[img_name:protected] =>
[img_ext:protected] => jpg
[img_width:protected] =>
[img_height:protected] =>
[img_credit:protected] =>
[img_practice:protected] =>
[vid_source_id:protected] =>
[vid_running_time:protected] =>
[vid_intended_audience:protected] =>
[vid_acquisition_info:protected] =>
[vid_cost:protected] =>
[vid_producer:protected] =>
[vid_filename:protected] =>
[vid_filename_downloadable:protected] =>
[date_summary:protected] =>
[date_permission_requested:protected] =>
[date_permission_received:protected] =>
[date_review_needed:protected] =>
[date_received:protected] => 12/23/21
[date_completed:protected] => 12/23/21
[date_billed:protected] =>
[date_modified:protected] => 05/19/23
[collBokExports:protected] =>
[lastBokExportCriteria:BaseElcoshItem:private] =>
[alreadyInSave:protected] =>
[alreadyInValidation:protected] =>
[validationFailures:protected] => Array
(
)
[_new:BaseObject:private] =>
[_deleted:BaseObject:private] =>
[modifiedColumns:protected] => Array
(
)
)
)
[3] => Search_Result Object
(
[title] => Toolbox Talk: Work Zone Safety: Working Around Vehicles
[image] => /record/images/notavailable-p.png
[blurb] => The CPWR Toolbox Talk on Working Around Vehicles in the Work Zone addresses methods to avoid being struck-by a vehicle on a construction site. The res...
[category] => Array
(
[0] => 12
[1] => 18
[2] => 52
[3] => 57
[4] => 70
[5] => 85
[6] => 87
[7] => 88
[8] => 89
[9] => 91
[10] => 90
[11] => 92
[12] => 93
[13] => 94
[14] => 95
[15] => 100
)
[labels] => Array
(
[0] => Crushed/Struck By
[1] => Work Environment
[2] => Hazards
[3] => Motor Vehicles/Heavy Equipment
[6] => Commercial Diver
[7] => Trades
[8] => Flagger
[10] => Operating Engineer
[12] => Truck Driver
[14] => Commercial & Institutional
[15] => Jobsites
[16] => Demolition
[18] => Disasters
[20] => Heavy & Highway
[22] => Industrial
[24] => LEED/Green Construction
[26] => Renovations
[28] => Residential
[30] => Underground
[32] => Toolbox Talks
[33] => Documents
[34] => Media & Documents
)
[type] => Toolbox Talks
[sub_category] =>
[url] => /document/4428/d001658/Toolbox%2BTalk%253A%2BWork%2BZone%2BSafety%253A%2BWorking%2BAround%2BVehicles.html
[item:protected] => DocumentRecord Object
(
[records:protected] => Array
(
)
[recordId:protected] =>
[searchWordClass:protected] =>
[searchWordPeerClass:protected] =>
[bok_record:protected] =>
[authors:protected] =>
[organizations:protected] =>
[collections:protected] =>
[categories:protected] => Array
(
[12] => Category Object
(
[languages:protected] =>
[bok_resources:protected] =>
[bok_topics:protected] =>
[bok_keywords:protected] =>
[id:protected] => 12
[type:protected] => category
[parent:protected] => 7
[label:protected] => Crushed/Struck By
[alreadyInSave:protected] =>
[alreadyInValidation:protected] =>
[validationFailures:protected] => Array
(
)
[_new:BaseObject:private] =>
[_deleted:BaseObject:private] =>
[modifiedColumns:protected] => Array
(
)
)
[18] => Category Object
(
[languages:protected] =>
[bok_resources:protected] =>
[bok_topics:protected] =>
[bok_keywords:protected] =>
[id:protected] => 18
[type:protected] => category
[parent:protected] => 7
[label:protected] => Motor Vehicles/Heavy Equipment
[alreadyInSave:protected] =>
[alreadyInValidation:protected] =>
[validationFailures:protected] => Array
(
)
[_new:BaseObject:private] =>
[_deleted:BaseObject:private] =>
[modifiedColumns:protected] => Array
(
)
)
[52] => Category Object
(
[languages:protected] =>
[bok_resources:protected] =>
[bok_topics:protected] =>
[bok_keywords:protected] =>
[id:protected] => 52
[type:protected] => category
[parent:protected] => 2
[label:protected] => Commercial Diver
[alreadyInSave:protected] =>
[alreadyInValidation:protected] =>
[validationFailures:protected] => Array
(
)
[_new:BaseObject:private] =>
[_deleted:BaseObject:private] =>
[modifiedColumns:protected] => Array
(
)
)
[57] => Category Object
(
[languages:protected] =>
[bok_resources:protected] =>
[bok_topics:protected] =>
[bok_keywords:protected] =>
[id:protected] => 57
[type:protected] => category
[parent:protected] => 2
[label:protected] => Flagger
[alreadyInSave:protected] =>
[alreadyInValidation:protected] =>
[validationFailures:protected] => Array
(
)
[_new:BaseObject:private] =>
[_deleted:BaseObject:private] =>
[modifiedColumns:protected] => Array
(
)
)
[70] => Category Object
(
[languages:protected] =>
[bok_resources:protected] =>
[bok_topics:protected] =>
[bok_keywords:protected] =>
[id:protected] => 70
[type:protected] => category
[parent:protected] => 2
[label:protected] => Operating Engineer
[alreadyInSave:protected] =>
[alreadyInValidation:protected] =>
[validationFailures:protected] => Array
(
)
[_new:BaseObject:private] =>
[_deleted:BaseObject:private] =>
[modifiedColumns:protected] => Array
(
)
)
[85] => Category Object
(
[languages:protected] =>
[bok_resources:protected] =>
[bok_topics:protected] =>
[bok_keywords:protected] =>
[id:protected] => 85
[type:protected] => category
[parent:protected] => 2
[label:protected] => Truck Driver
[alreadyInSave:protected] =>
[alreadyInValidation:protected] =>
[validationFailures:protected] => Array
(
)
[_new:BaseObject:private] =>
[_deleted:BaseObject:private] =>
[modifiedColumns:protected] => Array
(
)
)
[87] => Category Object
(
[languages:protected] =>
[bok_resources:protected] =>
[bok_topics:protected] =>
[bok_keywords:protected] =>
[id:protected] => 87
[type:protected] => category
[parent:protected] => 3
[label:protected] => Commercial & Institutional
[alreadyInSave:protected] =>
[alreadyInValidation:protected] =>
[validationFailures:protected] => Array
(
)
[_new:BaseObject:private] =>
[_deleted:BaseObject:private] =>
[modifiedColumns:protected] => Array
(
)
)
[88] => Category Object
(
[languages:protected] =>
[bok_resources:protected] =>
[bok_topics:protected] =>
[bok_keywords:protected] =>
[id:protected] => 88
[type:protected] => category
[parent:protected] => 3
[label:protected] => Demolition
[alreadyInSave:protected] =>
[alreadyInValidation:protected] =>
[validationFailures:protected] => Array
(
)
[_new:BaseObject:private] =>
[_deleted:BaseObject:private] =>
[modifiedColumns:protected] => Array
(
)
)
[89] => Category Object
(
[languages:protected] =>
[bok_resources:protected] =>
[bok_topics:protected] =>
[bok_keywords:protected] =>
[id:protected] => 89
[type:protected] => category
[parent:protected] => 3
[label:protected] => Disasters
[alreadyInSave:protected] =>
[alreadyInValidation:protected] =>
[validationFailures:protected] => Array
(
)
[_new:BaseObject:private] =>
[_deleted:BaseObject:private] =>
[modifiedColumns:protected] => Array
(
)
)
[91] => Category Object
(
[languages:protected] =>
[bok_resources:protected] =>
[bok_topics:protected] =>
[bok_keywords:protected] =>
[id:protected] => 91
[type:protected] => category
[parent:protected] => 3
[label:protected] => Heavy & Highway
[alreadyInSave:protected] =>
[alreadyInValidation:protected] =>
[validationFailures:protected] => Array
(
)
[_new:BaseObject:private] =>
[_deleted:BaseObject:private] =>
[modifiedColumns:protected] => Array
(
)
)
[90] => Category Object
(
[languages:protected] =>
[bok_resources:protected] =>
[bok_topics:protected] =>
[bok_keywords:protected] =>
[id:protected] => 90
[type:protected] => category
[parent:protected] => 3
[label:protected] => Industrial
[alreadyInSave:protected] =>
[alreadyInValidation:protected] =>
[validationFailures:protected] => Array
(
)
[_new:BaseObject:private] =>
[_deleted:BaseObject:private] =>
[modifiedColumns:protected] => Array
(
)
)
[92] => Category Object
(
[languages:protected] =>
[bok_resources:protected] =>
[bok_topics:protected] =>
[bok_keywords:protected] =>
[id:protected] => 92
[type:protected] => category
[parent:protected] => 3
[label:protected] => LEED/Green Construction
[alreadyInSave:protected] =>
[alreadyInValidation:protected] =>
[validationFailures:protected] => Array
(
)
[_new:BaseObject:private] =>
[_deleted:BaseObject:private] =>
[modifiedColumns:protected] => Array
(
)
)
[93] => Category Object
(
[languages:protected] =>
[bok_resources:protected] =>
[bok_topics:protected] =>
[bok_keywords:protected] =>
[id:protected] => 93
[type:protected] => category
[parent:protected] => 3
[label:protected] => Renovations
[alreadyInSave:protected] =>
[alreadyInValidation:protected] =>
[validationFailures:protected] => Array
(
)
[_new:BaseObject:private] =>
[_deleted:BaseObject:private] =>
[modifiedColumns:protected] => Array
(
)
)
[94] => Category Object
(
[languages:protected] =>
[bok_resources:protected] =>
[bok_topics:protected] =>
[bok_keywords:protected] =>
[id:protected] => 94
[type:protected] => category
[parent:protected] => 3
[label:protected] => Residential
[alreadyInSave:protected] =>
[alreadyInValidation:protected] =>
[validationFailures:protected] => Array
(
)
[_new:BaseObject:private] =>
[_deleted:BaseObject:private] =>
[modifiedColumns:protected] => Array
(
)
)
[95] => Category Object
(
[languages:protected] =>
[bok_resources:protected] =>
[bok_topics:protected] =>
[bok_keywords:protected] =>
[id:protected] => 95
[type:protected] => category
[parent:protected] => 3
[label:protected] => Underground
[alreadyInSave:protected] =>
[alreadyInValidation:protected] =>
[validationFailures:protected] => Array
(
)
[_new:BaseObject:private] =>
[_deleted:BaseObject:private] =>
[modifiedColumns:protected] => Array
(
)
)
[100] => Category Object
(
[languages:protected] =>
[bok_resources:protected] =>
[bok_topics:protected] =>
[bok_keywords:protected] =>
[id:protected] => 100
[type:protected] => category
[parent:protected] => 6
[label:protected] => Toolbox Talks
[alreadyInSave:protected] =>
[alreadyInValidation:protected] =>
[validationFailures:protected] => Array
(
)
[_new:BaseObject:private] =>
[_deleted:BaseObject:private] =>
[modifiedColumns:protected] => Array
(
)
)
)
[categories_initialized:protected] => 1
[mapped_items:protected] =>
[content:protected] =>
[files:protected] =>
[language:protected] => Language Object
(
[id:protected] => 1
[code:protected] => en
[name:protected] => English
[alreadyInSave:protected] =>
[alreadyInValidation:protected] =>
[validationFailures:protected] => Array
(
)
[_new:BaseObject:private] =>
[_deleted:BaseObject:private] =>
[modifiedColumns:protected] => Array
(
)
)
[old_record:protected] =>
[id:protected] => 4428
[old_id:protected] =>
[elcosh_id:protected] => d001658
[type:protected] => document
[display_type:protected] => HTML only (and links)
[user_id:protected] => 0
[language_id:protected] => 1
[tagging_id:protected] => Daniela Caceres
[priority_id:protected] => 1
[title:protected] => Toolbox Talk: Work Zone Safety: Working Around Vehicles
[total_pages:protected] => 0
[billed_pages:protected] => 0
[publication_number:protected] =>
[part_of:protected] =>
[keywords:protected] => Struck, Struck by, Vehicle, Work Zone Safety, Truck, Operator, Driver, Mobile Equipment
[comments:protected] =>
[summary:protected] => The CPWR Toolbox Talk on Working Around Vehicles in the Work Zone addresses methods to avoid being struck-by a vehicle on a construction site. The resource includes a case example, steps to prevent a related injury, and questions for discussion. It includes a graphic that illustrates the hazard, which can be posted in a central location as a reminder of steps to work safely. Available in
English and
Spanish.
[transition_comments:protected] =>
[external_link:protected] =>
[consol_link:protected] =>
[more_like_this:protected] => d001640
[permission_given_by:protected] =>
[published:protected] => T
[billable:protected] => F
[img_name:protected] =>
[img_ext:protected] =>
[img_width:protected] =>
[img_height:protected] =>
[img_credit:protected] =>
[img_practice:protected] =>
[vid_source_id:protected] =>
[vid_running_time:protected] =>
[vid_intended_audience:protected] =>
[vid_acquisition_info:protected] =>
[vid_cost:protected] =>
[vid_producer:protected] =>
[vid_filename:protected] =>
[vid_filename_downloadable:protected] =>
[date_summary:protected] =>
[date_permission_requested:protected] =>
[date_permission_received:protected] =>
[date_review_needed:protected] =>
[date_received:protected] => 12/23/21
[date_completed:protected] => 12/23/21
[date_billed:protected] =>
[date_modified:protected] => 05/19/23
[collBokExports:protected] =>
[lastBokExportCriteria:BaseElcoshItem:private] =>
[alreadyInSave:protected] =>
[alreadyInValidation:protected] =>
[validationFailures:protected] => Array
(
)
[_new:BaseObject:private] =>
[_deleted:BaseObject:private] =>
[modifiedColumns:protected] => Array
(
)
)
)
[4] => Search_Result Object
(
[title] => Construction Dive -- DeWalt's Jobsite Pro headphones recalled for fire hazards
[image] => /record/images/notavailable-p.png
[blurb] => A recall notice by the United States Consumer Product Safety Commission affects over 300,000 DeWalt Jobsite Pro Headphones. The recall is a result of...
[category] => Array
(
[0] => 16
[1] => 44
[2] => 45
[3] => 46
[4] => 47
[5] => 48
[6] => 49
[7] => 50
[8] => 51
[9] => 52
[10] => 53
[11] => 54
[12] => 55
[13] => 56
[14] => 57
[15] => 58
[16] => 59
[17] => 60
[18] => 61
[19] => 64
[20] => 65
[21] => 66
[22] => 67
[23] => 68
[24] => 69
[25] => 70
[26] => 71
[27] => 72
[28] => 73
[29] => 74
[30] => 75
[31] => 76
[32] => 77
[33] => 63
[34] => 78
[35] => 79
[36] => 80
[37] => 81
[38] => 82
[39] => 62
[40] => 83
[41] => 84
[42] => 85
[43] => 86
[44] => 87
[45] => 88
[46] => 89
[47] => 91
[48] => 90
[49] => 92
[50] => 93
[51] => 94
[52] => 95
)
[labels] => Array
(
[0] => Fire & Explosions
[1] => Work Environment
[2] => Hazards
[3] => Acoustical Ceiling Carpenter
[4] => Trades
[5] => Asbestos/Insulator
[7] => Boilermaker
[9] => Bricklayer
[11] => Cabinetmaker
[13] => Carpenter
[15] => Carpet Layer
[17] => Cement Mason
[19] => Commercial Diver
[21] => Concrete Polisher
[23] => Drywall Applicator Specialist
[25] => Electrical Worker
[27] => Elevator Constructor
[29] => Flagger
[31] => Glazier
[33] => Hazardous Waste Cleanup
[35] => HVAC
[37] => Interior Systems Carpenter
[39] => Laborer
[41] => Landscaper
[43] => Lather
[45] => Lead Abatement Worker
[47] => Maintenance Worker
[49] => Millwright
[51] => Operating Engineer
[53] => Painter
[55] => Paper Hanger
[57] => PCC/Restoration
[59] => Pile Driver
[61] => Plasterer
[63] => Plumber/Pipefitter
[65] => Refractory Worker
[67] => Reinforcing Ironworker
[69] => Roofer/Waterproofer
[71] => Scaffold Erector
[73] => Sheetmetal Worker
[75] => Sprinkler Fitter
[77] => Stonemason
[79] => Structural Ironworker
[81] => Terrazzo Worker
[83] => Tile Setter
[85] => Truck Driver
[87] => Welder
[89] => Commercial & Institutional
[90] => Jobsites
[91] => Demolition
[93] => Disasters
[95] => Heavy & Highway
[97] => Industrial
[99] => LEED/Green Construction
[101] => Renovations
[103] => Residential
[105] => Underground
)
[type] =>
[sub_category] =>
[url] => /document/4426/d001656/Construction%2BDive%2B--%2BDeWalt%2527s%2BJobsite%2BPro%2Bheadphones%2Brecalled%2Bfor%2Bfire%2Bhazards.html
[item:protected] => DocumentRecord Object
(
[records:protected] => Array
(
)
[recordId:protected] =>
[searchWordClass:protected] =>
[searchWordPeerClass:protected] =>
[bok_record:protected] =>
[authors:protected] =>
[organizations:protected] =>
[collections:protected] =>
[categories:protected] => Array
(
[16] => Category Object
(
[languages:protected] =>
[bok_resources:protected] =>
[bok_topics:protected] =>
[bok_keywords:protected] =>
[id:protected] => 16
[type:protected] => category
[parent:protected] => 7
[label:protected] => Fire & Explosions
[alreadyInSave:protected] =>
[alreadyInValidation:protected] =>
[validationFailures:protected] => Array
(
)
[_new:BaseObject:private] =>
[_deleted:BaseObject:private] =>
[modifiedColumns:protected] => Array
(
)
)
[44] => Category Object
(
[languages:protected] =>
[bok_resources:protected] =>
[bok_topics:protected] =>
[bok_keywords:protected] =>
[id:protected] => 44
[type:protected] => category
[parent:protected] => 2
[label:protected] => Acoustical Ceiling Carpenter
[alreadyInSave:protected] =>
[alreadyInValidation:protected] =>
[validationFailures:protected] => Array
(
)
[_new:BaseObject:private] =>
[_deleted:BaseObject:private] =>
[modifiedColumns:protected] => Array
(
)
)
[45] => Category Object
(
[languages:protected] =>
[bok_resources:protected] =>
[bok_topics:protected] =>
[bok_keywords:protected] =>
[id:protected] => 45
[type:protected] => category
[parent:protected] => 2
[label:protected] => Asbestos/Insulator
[alreadyInSave:protected] =>
[alreadyInValidation:protected] =>
[validationFailures:protected] => Array
(
)
[_new:BaseObject:private] =>
[_deleted:BaseObject:private] =>
[modifiedColumns:protected] => Array
(
)
)
[46] => Category Object
(
[languages:protected] =>
[bok_resources:protected] =>
[bok_topics:protected] =>
[bok_keywords:protected] =>
[id:protected] => 46
[type:protected] => category
[parent:protected] => 2
[label:protected] => Boilermaker
[alreadyInSave:protected] =>
[alreadyInValidation:protected] =>
[validationFailures:protected] => Array
(
)
[_new:BaseObject:private] =>
[_deleted:BaseObject:private] =>
[modifiedColumns:protected] => Array
(
)
)
[47] => Category Object
(
[languages:protected] =>
[bok_resources:protected] =>
[bok_topics:protected] =>
[bok_keywords:protected] =>
[id:protected] => 47
[type:protected] => category
[parent:protected] => 2
[label:protected] => Bricklayer
[alreadyInSave:protected] =>
[alreadyInValidation:protected] =>
[validationFailures:protected] => Array
(
)
[_new:BaseObject:private] =>
[_deleted:BaseObject:private] =>
[modifiedColumns:protected] => Array
(
)
)
[48] => Category Object
(
[languages:protected] =>
[bok_resources:protected] =>
[bok_topics:protected] =>
[bok_keywords:protected] =>
[id:protected] => 48
[type:protected] => category
[parent:protected] => 2
[label:protected] => Cabinetmaker
[alreadyInSave:protected] =>
[alreadyInValidation:protected] =>
[validationFailures:protected] => Array
(
)
[_new:BaseObject:private] =>
[_deleted:BaseObject:private] =>
[modifiedColumns:protected] => Array
(
)
)
[49] => Category Object
(
[languages:protected] =>
[bok_resources:protected] =>
[bok_topics:protected] =>
[bok_keywords:protected] =>
[id:protected] => 49
[type:protected] => category
[parent:protected] => 2
[label:protected] => Carpenter
[alreadyInSave:protected] =>
[alreadyInValidation:protected] =>
[validationFailures:protected] => Array
(
)
[_new:BaseObject:private] =>
[_deleted:BaseObject:private] =>
[modifiedColumns:protected] => Array
(
)
)
[50] => Category Object
(
[languages:protected] =>
[bok_resources:protected] =>
[bok_topics:protected] =>
[bok_keywords:protected] =>
[id:protected] => 50
[type:protected] => category
[parent:protected] => 2
[label:protected] => Carpet Layer
[alreadyInSave:protected] =>
[alreadyInValidation:protected] =>
[validationFailures:protected] => Array
(
)
[_new:BaseObject:private] =>
[_deleted:BaseObject:private] =>
[modifiedColumns:protected] => Array
(
)
)
[51] => Category Object
(
[languages:protected] =>
[bok_resources:protected] =>
[bok_topics:protected] =>
[bok_keywords:protected] =>
[id:protected] => 51
[type:protected] => category
[parent:protected] => 2
[label:protected] => Cement Mason
[alreadyInSave:protected] =>
[alreadyInValidation:protected] =>
[validationFailures:protected] => Array
(
)
[_new:BaseObject:private] =>
[_deleted:BaseObject:private] =>
[modifiedColumns:protected] => Array
(
)
)
[52] => Category Object
(
[languages:protected] =>
[bok_resources:protected] =>
[bok_topics:protected] =>
[bok_keywords:protected] =>
[id:protected] => 52
[type:protected] => category
[parent:protected] => 2
[label:protected] => Commercial Diver
[alreadyInSave:protected] =>
[alreadyInValidation:protected] =>
[validationFailures:protected] => Array
(
)
[_new:BaseObject:private] =>
[_deleted:BaseObject:private] =>
[modifiedColumns:protected] => Array
(
)
)
[53] => Category Object
(
[languages:protected] =>
[bok_resources:protected] =>
[bok_topics:protected] =>
[bok_keywords:protected] =>
[id:protected] => 53
[type:protected] => category
[parent:protected] => 2
[label:protected] => Concrete Polisher
[alreadyInSave:protected] =>
[alreadyInValidation:protected] =>
[validationFailures:protected] => Array
(
)
[_new:BaseObject:private] =>
[_deleted:BaseObject:private] =>
[modifiedColumns:protected] => Array
(
)
)
[54] => Category Object
(
[languages:protected] =>
[bok_resources:protected] =>
[bok_topics:protected] =>
[bok_keywords:protected] =>
[id:protected] => 54
[type:protected] => category
[parent:protected] => 2
[label:protected] => Drywall Applicator Specialist
[alreadyInSave:protected] =>
[alreadyInValidation:protected] =>
[validationFailures:protected] => Array
(
)
[_new:BaseObject:private] =>
[_deleted:BaseObject:private] =>
[modifiedColumns:protected] => Array
(
)
)
[55] => Category Object
(
[languages:protected] =>
[bok_resources:protected] =>
[bok_topics:protected] =>
[bok_keywords:protected] =>
[id:protected] => 55
[type:protected] => category
[parent:protected] => 2
[label:protected] => Electrical Worker
[alreadyInSave:protected] =>
[alreadyInValidation:protected] =>
[validationFailures:protected] => Array
(
)
[_new:BaseObject:private] =>
[_deleted:BaseObject:private] =>
[modifiedColumns:protected] => Array
(
)
)
[56] => Category Object
(
[languages:protected] =>
[bok_resources:protected] =>
[bok_topics:protected] =>
[bok_keywords:protected] =>
[id:protected] => 56
[type:protected] => category
[parent:protected] => 2
[label:protected] => Elevator Constructor
[alreadyInSave:protected] =>
[alreadyInValidation:protected] =>
[validationFailures:protected] => Array
(
)
[_new:BaseObject:private] =>
[_deleted:BaseObject:private] =>
[modifiedColumns:protected] => Array
(
)
)
[57] => Category Object
(
[languages:protected] =>
[bok_resources:protected] =>
[bok_topics:protected] =>
[bok_keywords:protected] =>
[id:protected] => 57
[type:protected] => category
[parent:protected] => 2
[label:protected] => Flagger
[alreadyInSave:protected] =>
[alreadyInValidation:protected] =>
[validationFailures:protected] => Array
(
)
[_new:BaseObject:private] =>
[_deleted:BaseObject:private] =>
[modifiedColumns:protected] => Array
(
)
)
[58] => Category Object
(
[languages:protected] =>
[bok_resources:protected] =>
[bok_topics:protected] =>
[bok_keywords:protected] =>
[id:protected] => 58
[type:protected] => category
[parent:protected] => 2
[label:protected] => Glazier
[alreadyInSave:protected] =>
[alreadyInValidation:protected] =>
[validationFailures:protected] => Array
(
)
[_new:BaseObject:private] =>
[_deleted:BaseObject:private] =>
[modifiedColumns:protected] => Array
(
)
)
[59] => Category Object
(
[languages:protected] =>
[bok_resources:protected] =>
[bok_topics:protected] =>
[bok_keywords:protected] =>
[id:protected] => 59
[type:protected] => category
[parent:protected] => 2
[label:protected] => Hazardous Waste Cleanup
[alreadyInSave:protected] =>
[alreadyInValidation:protected] =>
[validationFailures:protected] => Array
(
)
[_new:BaseObject:private] =>
[_deleted:BaseObject:private] =>
[modifiedColumns:protected] => Array
(
)
)
[60] => Category Object
(
[languages:protected] =>
[bok_resources:protected] =>
[bok_topics:protected] =>
[bok_keywords:protected] =>
[id:protected] => 60
[type:protected] => category
[parent:protected] => 2
[label:protected] => HVAC
[alreadyInSave:protected] =>
[alreadyInValidation:protected] =>
[validationFailures:protected] => Array
(
)
[_new:BaseObject:private] =>
[_deleted:BaseObject:private] =>
[modifiedColumns:protected] => Array
(
)
)
[61] => Category Object
(
[languages:protected] =>
[bok_resources:protected] =>
[bok_topics:protected] =>
[bok_keywords:protected] =>
[id:protected] => 61
[type:protected] => category
[parent:protected] => 2
[label:protected] => Interior Systems Carpenter
[alreadyInSave:protected] =>
[alreadyInValidation:protected] =>
[validationFailures:protected] => Array
(
)
[_new:BaseObject:private] =>
[_deleted:BaseObject:private] =>
[modifiedColumns:protected] => Array
(
)
)
[64] => Category Object
(
[languages:protected] =>
[bok_resources:protected] =>
[bok_topics:protected] =>
[bok_keywords:protected] =>
[id:protected] => 64
[type:protected] => category
[parent:protected] => 2
[label:protected] => Laborer
[alreadyInSave:protected] =>
[alreadyInValidation:protected] =>
[validationFailures:protected] => Array
(
)
[_new:BaseObject:private] =>
[_deleted:BaseObject:private] =>
[modifiedColumns:protected] => Array
(
)
)
[65] => Category Object
(
[languages:protected] =>
[bok_resources:protected] =>
[bok_topics:protected] =>
[bok_keywords:protected] =>
[id:protected] => 65
[type:protected] => category
[parent:protected] => 2
[label:protected] => Landscaper
[alreadyInSave:protected] =>
[alreadyInValidation:protected] =>
[validationFailures:protected] => Array
(
)
[_new:BaseObject:private] =>
[_deleted:BaseObject:private] =>
[modifiedColumns:protected] => Array
(
)
)
[66] => Category Object
(
[languages:protected] =>
[bok_resources:protected] =>
[bok_topics:protected] =>
[bok_keywords:protected] =>
[id:protected] => 66
[type:protected] => category
[parent:protected] => 2
[label:protected] => Lather
[alreadyInSave:protected] =>
[alreadyInValidation:protected] =>
[validationFailures:protected] => Array
(
)
[_new:BaseObject:private] =>
[_deleted:BaseObject:private] =>
[modifiedColumns:protected] => Array
(
)
)
[67] => Category Object
(
[languages:protected] =>
[bok_resources:protected] =>
[bok_topics:protected] =>
[bok_keywords:protected] =>
[id:protected] => 67
[type:protected] => category
[parent:protected] => 2
[label:protected] => Lead Abatement Worker
[alreadyInSave:protected] =>
[alreadyInValidation:protected] =>
[validationFailures:protected] => Array
(
)
[_new:BaseObject:private] =>
[_deleted:BaseObject:private] =>
[modifiedColumns:protected] => Array
(
)
)
[68] => Category Object
(
[languages:protected] =>
[bok_resources:protected] =>
[bok_topics:protected] =>
[bok_keywords:protected] =>
[id:protected] => 68
[type:protected] => category
[parent:protected] => 2
[label:protected] => Maintenance Worker
[alreadyInSave:protected] =>
[alreadyInValidation:protected] =>
[validationFailures:protected] => Array
(
)
[_new:BaseObject:private] =>
[_deleted:BaseObject:private] =>
[modifiedColumns:protected] => Array
(
)
)
[69] => Category Object
(
[languages:protected] =>
[bok_resources:protected] =>
[bok_topics:protected] =>
[bok_keywords:protected] =>
[id:protected] => 69
[type:protected] => category
[parent:protected] => 2
[label:protected] => Millwright
[alreadyInSave:protected] =>
[alreadyInValidation:protected] =>
[validationFailures:protected] => Array
(
)
[_new:BaseObject:private] =>
[_deleted:BaseObject:private] =>
[modifiedColumns:protected] => Array
(
)
)
[70] => Category Object
(
[languages:protected] =>
[bok_resources:protected] =>
[bok_topics:protected] =>
[bok_keywords:protected] =>
[id:protected] => 70
[type:protected] => category
[parent:protected] => 2
[label:protected] => Operating Engineer
[alreadyInSave:protected] =>
[alreadyInValidation:protected] =>
[validationFailures:protected] => Array
(
)
[_new:BaseObject:private] =>
[_deleted:BaseObject:private] =>
[modifiedColumns:protected] => Array
(
)
)
[71] => Category Object
(
[languages:protected] =>
[bok_resources:protected] =>
[bok_topics:protected] =>
[bok_keywords:protected] =>
[id:protected] => 71
[type:protected] => category
[parent:protected] => 2
[label:protected] => Painter
[alreadyInSave:protected] =>
[alreadyInValidation:protected] =>
[validationFailures:protected] => Array
(
)
[_new:BaseObject:private] =>
[_deleted:BaseObject:private] =>
[modifiedColumns:protected] => Array
(
)
)
[72] => Category Object
(
[languages:protected] =>
[bok_resources:protected] =>
[bok_topics:protected] =>
[bok_keywords:protected] =>
[id:protected] => 72
[type:protected] => category
[parent:protected] => 2
[label:protected] => Paper Hanger
[alreadyInSave:protected] =>
[alreadyInValidation:protected] =>
[validationFailures:protected] => Array
(
)
[_new:BaseObject:private] =>
[_deleted:BaseObject:private] =>
[modifiedColumns:protected] => Array
(
)
)
[73] => Category Object
(
[languages:protected] =>
[bok_resources:protected] =>
[bok_topics:protected] =>
[bok_keywords:protected] =>
[id:protected] => 73
[type:protected] => category
[parent:protected] => 2
[label:protected] => PCC/Restoration
[alreadyInSave:protected] =>
[alreadyInValidation:protected] =>
[validationFailures:protected] => Array
(
)
[_new:BaseObject:private] =>
[_deleted:BaseObject:private] =>
[modifiedColumns:protected] => Array
(
)
)
[74] => Category Object
(
[languages:protected] =>
[bok_resources:protected] =>
[bok_topics:protected] =>
[bok_keywords:protected] =>
[id:protected] => 74
[type:protected] => category
[parent:protected] => 2
[label:protected] => Pile Driver
[alreadyInSave:protected] =>
[alreadyInValidation:protected] =>
[validationFailures:protected] => Array
(
)
[_new:BaseObject:private] =>
[_deleted:BaseObject:private] =>
[modifiedColumns:protected] => Array
(
)
)
[75] => Category Object
(
[languages:protected] =>
[bok_resources:protected] =>
[bok_topics:protected] =>
[bok_keywords:protected] =>
[id:protected] => 75
[type:protected] => category
[parent:protected] => 2
[label:protected] => Plasterer
[alreadyInSave:protected] =>
[alreadyInValidation:protected] =>
[validationFailures:protected] => Array
(
)
[_new:BaseObject:private] =>
[_deleted:BaseObject:private] =>
[modifiedColumns:protected] => Array
(
)
)
[76] => Category Object
(
[languages:protected] =>
[bok_resources:protected] =>
[bok_topics:protected] =>
[bok_keywords:protected] =>
[id:protected] => 76
[type:protected] => category
[parent:protected] => 2
[label:protected] => Plumber/Pipefitter
[alreadyInSave:protected] =>
[alreadyInValidation:protected] =>
[validationFailures:protected] => Array
(
)
[_new:BaseObject:private] =>
[_deleted:BaseObject:private] =>
[modifiedColumns:protected] => Array
(
)
)
[77] => Category Object
(
[languages:protected] =>
[bok_resources:protected] =>
[bok_topics:protected] =>
[bok_keywords:protected] =>
[id:protected] => 77
[type:protected] => category
[parent:protected] => 2
[label:protected] => Refractory Worker
[alreadyInSave:protected] =>
[alreadyInValidation:protected] =>
[validationFailures:protected] => Array
(
)
[_new:BaseObject:private] =>
[_deleted:BaseObject:private] =>
[modifiedColumns:protected] => Array
(
)
)
[63] => Category Object
(
[languages:protected] =>
[bok_resources:protected] =>
[bok_topics:protected] =>
[bok_keywords:protected] =>
[id:protected] => 63
[type:protected] => category
[parent:protected] => 2
[label:protected] => Reinforcing Ironworker
[alreadyInSave:protected] =>
[alreadyInValidation:protected] =>
[validationFailures:protected] => Array
(
)
[_new:BaseObject:private] =>
[_deleted:BaseObject:private] =>
[modifiedColumns:protected] => Array
(
)
)
[78] => Category Object
(
[languages:protected] =>
[bok_resources:protected] =>
[bok_topics:protected] =>
[bok_keywords:protected] =>
[id:protected] => 78
[type:protected] => category
[parent:protected] => 2
[label:protected] => Roofer/Waterproofer
[alreadyInSave:protected] =>
[alreadyInValidation:protected] =>
[validationFailures:protected] => Array
(
)
[_new:BaseObject:private] =>
[_deleted:BaseObject:private] =>
[modifiedColumns:protected] => Array
(
)
)
[79] => Category Object
(
[languages:protected] =>
[bok_resources:protected] =>
[bok_topics:protected] =>
[bok_keywords:protected] =>
[id:protected] => 79
[type:protected] => category
[parent:protected] => 2
[label:protected] => Scaffold Erector
[alreadyInSave:protected] =>
[alreadyInValidation:protected] =>
[validationFailures:protected] => Array
(
)
[_new:BaseObject:private] =>
[_deleted:BaseObject:private] =>
[modifiedColumns:protected] => Array
(
)
)
[80] => Category Object
(
[languages:protected] =>
[bok_resources:protected] =>
[bok_topics:protected] =>
[bok_keywords:protected] =>
[id:protected] => 80
[type:protected] => category
[parent:protected] => 2
[label:protected] => Sheetmetal Worker
[alreadyInSave:protected] =>
[alreadyInValidation:protected] =>
[validationFailures:protected] => Array
(
)
[_new:BaseObject:private] =>
[_deleted:BaseObject:private] =>
[modifiedColumns:protected] => Array
(
)
)
[81] => Category Object
(
[languages:protected] =>
[bok_resources:protected] =>
[bok_topics:protected] =>
[bok_keywords:protected] =>
[id:protected] => 81
[type:protected] => category
[parent:protected] => 2
[label:protected] => Sprinkler Fitter
[alreadyInSave:protected] =>
[alreadyInValidation:protected] =>
[validationFailures:protected] => Array
(
)
[_new:BaseObject:private] =>
[_deleted:BaseObject:private] =>
[modifiedColumns:protected] => Array
(
)
)
[82] => Category Object
(
[languages:protected] =>
[bok_resources:protected] =>
[bok_topics:protected] =>
[bok_keywords:protected] =>
[id:protected] => 82
[type:protected] => category
[parent:protected] => 2
[label:protected] => Stonemason
[alreadyInSave:protected] =>
[alreadyInValidation:protected] =>
[validationFailures:protected] => Array
(
)
[_new:BaseObject:private] =>
[_deleted:BaseObject:private] =>
[modifiedColumns:protected] => Array
(
)
)
[62] => Category Object
(
[languages:protected] =>
[bok_resources:protected] =>
[bok_topics:protected] =>
[bok_keywords:protected] =>
[id:protected] => 62
[type:protected] => category
[parent:protected] => 2
[label:protected] => Structural Ironworker
[alreadyInSave:protected] =>
[alreadyInValidation:protected] =>
[validationFailures:protected] => Array
(
)
[_new:BaseObject:private] =>
[_deleted:BaseObject:private] =>
[modifiedColumns:protected] => Array
(
)
)
[83] => Category Object
(
[languages:protected] =>
[bok_resources:protected] =>
[bok_topics:protected] =>
[bok_keywords:protected] =>
[id:protected] => 83
[type:protected] => category
[parent:protected] => 2
[label:protected] => Terrazzo Worker
[alreadyInSave:protected] =>
[alreadyInValidation:protected] =>
[validationFailures:protected] => Array
(
)
[_new:BaseObject:private] =>
[_deleted:BaseObject:private] =>
[modifiedColumns:protected] => Array
(
)
)
[84] => Category Object
(
[languages:protected] =>
[bok_resources:protected] =>
[bok_topics:protected] =>
[bok_keywords:protected] =>
[id:protected] => 84
[type:protected] => category
[parent:protected] => 2
[label:protected] => Tile Setter
[alreadyInSave:protected] =>
[alreadyInValidation:protected] =>
[validationFailures:protected] => Array
(
)
[_new:BaseObject:private] =>
[_deleted:BaseObject:private] =>
[modifiedColumns:protected] => Array
(
)
)
[85] => Category Object
(
[languages:protected] =>
[bok_resources:protected] =>
[bok_topics:protected] =>
[bok_keywords:protected] =>
[id:protected] => 85
[type:protected] => category
[parent:protected] => 2
[label:protected] => Truck Driver
[alreadyInSave:protected] =>
[alreadyInValidation:protected] =>
[validationFailures:protected] => Array
(
)
[_new:BaseObject:private] =>
[_deleted:BaseObject:private] =>
[modifiedColumns:protected] => Array
(
)
)
[86] => Category Object
(
[languages:protected] =>
[bok_resources:protected] =>
[bok_topics:protected] =>
[bok_keywords:protected] =>
[id:protected] => 86
[type:protected] => category
[parent:protected] => 2
[label:protected] => Welder
[alreadyInSave:protected] =>
[alreadyInValidation:protected] =>
[validationFailures:protected] => Array
(
)
[_new:BaseObject:private] =>
[_deleted:BaseObject:private] =>
[modifiedColumns:protected] => Array
(
)
)
[87] => Category Object
(
[languages:protected] =>
[bok_resources:protected] =>
[bok_topics:protected] =>
[bok_keywords:protected] =>
[id:protected] => 87
[type:protected] => category
[parent:protected] => 3
[label:protected] => Commercial & Institutional
[alreadyInSave:protected] =>
[alreadyInValidation:protected] =>
[validationFailures:protected] => Array
(
)
[_new:BaseObject:private] =>
[_deleted:BaseObject:private] =>
[modifiedColumns:protected] => Array
(
)
)
[88] => Category Object
(
[languages:protected] =>
[bok_resources:protected] =>
[bok_topics:protected] =>
[bok_keywords:protected] =>
[id:protected] => 88
[type:protected] => category
[parent:protected] => 3
[label:protected] => Demolition
[alreadyInSave:protected] =>
[alreadyInValidation:protected] =>
[validationFailures:protected] => Array
(
)
[_new:BaseObject:private] =>
[_deleted:BaseObject:private] =>
[modifiedColumns:protected] => Array
(
)
)
[89] => Category Object
(
[languages:protected] =>
[bok_resources:protected] =>
[bok_topics:protected] =>
[bok_keywords:protected] =>
[id:protected] => 89
[type:protected] => category
[parent:protected] => 3
[label:protected] => Disasters
[alreadyInSave:protected] =>
[alreadyInValidation:protected] =>
[validationFailures:protected] => Array
(
)
[_new:BaseObject:private] =>
[_deleted:BaseObject:private] =>
[modifiedColumns:protected] => Array
(
)
)
[91] => Category Object
(
[languages:protected] =>
[bok_resources:protected] =>
[bok_topics:protected] =>
[bok_keywords:protected] =>
[id:protected] => 91
[type:protected] => category
[parent:protected] => 3
[label:protected] => Heavy & Highway
[alreadyInSave:protected] =>
[alreadyInValidation:protected] =>
[validationFailures:protected] => Array
(
)
[_new:BaseObject:private] =>
[_deleted:BaseObject:private] =>
[modifiedColumns:protected] => Array
(
)
)
[90] => Category Object
(
[languages:protected] =>
[bok_resources:protected] =>
[bok_topics:protected] =>
[bok_keywords:protected] =>
[id:protected] => 90
[type:protected] => category
[parent:protected] => 3
[label:protected] => Industrial
[alreadyInSave:protected] =>
[alreadyInValidation:protected] =>
[validationFailures:protected] => Array
(
)
[_new:BaseObject:private] =>
[_deleted:BaseObject:private] =>
[modifiedColumns:protected] => Array
(
)
)
[92] => Category Object
(
[languages:protected] =>
[bok_resources:protected] =>
[bok_topics:protected] =>
[bok_keywords:protected] =>
[id:protected] => 92
[type:protected] => category
[parent:protected] => 3
[label:protected] => LEED/Green Construction
[alreadyInSave:protected] =>
[alreadyInValidation:protected] =>
[validationFailures:protected] => Array
(
)
[_new:BaseObject:private] =>
[_deleted:BaseObject:private] =>
[modifiedColumns:protected] => Array
(
)
)
[93] => Category Object
(
[languages:protected] =>
[bok_resources:protected] =>
[bok_topics:protected] =>
[bok_keywords:protected] =>
[id:protected] => 93
[type:protected] => category
[parent:protected] => 3
[label:protected] => Renovations
[alreadyInSave:protected] =>
[alreadyInValidation:protected] =>
[validationFailures:protected] => Array
(
)
[_new:BaseObject:private] =>
[_deleted:BaseObject:private] =>
[modifiedColumns:protected] => Array
(
)
)
[94] => Category Object
(
[languages:protected] =>
[bok_resources:protected] =>
[bok_topics:protected] =>
[bok_keywords:protected] =>
[id:protected] => 94
[type:protected] => category
[parent:protected] => 3
[label:protected] => Residential
[alreadyInSave:protected] =>
[alreadyInValidation:protected] =>
[validationFailures:protected] => Array
(
)
[_new:BaseObject:private] =>
[_deleted:BaseObject:private] =>
[modifiedColumns:protected] => Array
(
)
)
[95] => Category Object
(
[languages:protected] =>
[bok_resources:protected] =>
[bok_topics:protected] =>
[bok_keywords:protected] =>
[id:protected] => 95
[type:protected] => category
[parent:protected] => 3
[label:protected] => Underground
[alreadyInSave:protected] =>
[alreadyInValidation:protected] =>
[validationFailures:protected] => Array
(
)
[_new:BaseObject:private] =>
[_deleted:BaseObject:private] =>
[modifiedColumns:protected] => Array
(
)
)
)
[categories_initialized:protected] => 1
[mapped_items:protected] =>
[content:protected] =>
[files:protected] =>
[language:protected] => Language Object
(
[id:protected] => 1
[code:protected] => en
[name:protected] => English
[alreadyInSave:protected] =>
[alreadyInValidation:protected] =>
[validationFailures:protected] => Array
(
)
[_new:BaseObject:private] =>
[_deleted:BaseObject:private] =>
[modifiedColumns:protected] => Array
(
)
)
[old_record:protected] =>
[id:protected] => 4426
[old_id:protected] =>
[elcosh_id:protected] => d001656
[type:protected] => document
[display_type:protected] => HTML only (and links)
[user_id:protected] => 0
[language_id:protected] => 1
[tagging_id:protected] => Mike Aguilar
[priority_id:protected] => 1
[title:protected] => Construction Dive -- DeWalt's Jobsite Pro headphones recalled for fire hazards
[total_pages:protected] => 1
[billed_pages:protected] => 1
[publication_number:protected] =>
[part_of:protected] =>
[keywords:protected] => DeWalt, Fire Hazards, recall, headphones
[comments:protected] =>
[summary:protected] => A recall notice by the United States Consumer Product Safety Commission affects over 300,000 DeWalt Jobsite Pro Headphones. The recall is a result of a malfunction that can cause earbuds to overheat while charging or during use, leading to fire and burn hazards.
[transition_comments:protected] =>
[external_link:protected] => https://www.constructiondive.com/news/dewalts-jobsite-pro-headphones-recalled-for-fire-hazards/611248/?utm_source=Sailthru&utm_medium=email&utm_campaign=Issue:%202021-12-10%20Construction%20Dive%20Newsletter%20%5Bissue:38532%5D&utm_term=Construction%20Dive
[consol_link:protected] =>
[more_like_this:protected] =>
[permission_given_by:protected] =>
[published:protected] => T
[billable:protected] => F
[img_name:protected] =>
[img_ext:protected] =>
[img_width:protected] =>
[img_height:protected] =>
[img_credit:protected] =>
[img_practice:protected] =>
[vid_source_id:protected] =>
[vid_running_time:protected] =>
[vid_intended_audience:protected] =>
[vid_acquisition_info:protected] =>
[vid_cost:protected] =>
[vid_producer:protected] =>
[vid_filename:protected] =>
[vid_filename_downloadable:protected] =>
[date_summary:protected] =>
[date_permission_requested:protected] =>
[date_permission_received:protected] =>
[date_review_needed:protected] =>
[date_received:protected] => 12/13/21
[date_completed:protected] => 12/13/21
[date_billed:protected] =>
[date_modified:protected] => 12/13/21
[collBokExports:protected] =>
[lastBokExportCriteria:BaseElcoshItem:private] =>
[alreadyInSave:protected] =>
[alreadyInValidation:protected] =>
[validationFailures:protected] => Array
(
)
[_new:BaseObject:private] =>
[_deleted:BaseObject:private] =>
[modifiedColumns:protected] => Array
(
)
)
)
)
[new_images] => Array
(
[0] => Search_Result Object
(
[title] => Morning Toolbox Talk
[image] => /record/images/4003-p.jpg
[blurb] => This photo is from an early morning toolbox talk on a construction job in Mclean, Virginia. It is being delivered in English and Spanish....
[category] => Array
(
[0] => 20
[1] => 51
[2] => 57
[3] => 64
[4] => 70
[5] => 63
[6] => 78
[7] => 82
[8] => 62
[9] => 87
[10] => 88
[11] => 89
[12] => 91
[13] => 90
[14] => 93
[15] => 94
[16] => 97
)
[labels] => Array
(
[0] => Safety Culture
[1] => Work Environment
[2] => Hazards
[3] => Cement Mason
[4] => Trades
[5] => Flagger
[7] => Laborer
[9] => Operating Engineer
[11] => Reinforcing Ironworker
[13] => Roofer/Waterproofer
[15] => Stonemason
[17] => Structural Ironworker
[19] => Commercial & Institutional
[20] => Jobsites
[21] => Demolition
[23] => Disasters
[25] => Heavy & Highway
[27] => Industrial
[29] => Renovations
[31] => Residential
[33] => Images
[34] => Media
[35] => Media & Documents
)
[type] => Images
[sub_category] =>
[url] => /image/4003/i002691/Morning%2BToolbox%2BTalk.html
[item:protected] => ImageRecord Object
(
[records:protected] => Array
(
)
[recordId:protected] =>
[searchWordClass:protected] =>
[searchWordPeerClass:protected] =>
[bok_record:protected] =>
[authors:protected] =>
[organizations:protected] =>
[collections:protected] =>
[categories:protected] => Array
(
[20] => Category Object
(
[languages:protected] =>
[bok_resources:protected] =>
[bok_topics:protected] =>
[bok_keywords:protected] =>
[id:protected] => 20
[type:protected] => category
[parent:protected] => 7
[label:protected] => Safety Culture
[alreadyInSave:protected] =>
[alreadyInValidation:protected] =>
[validationFailures:protected] => Array
(
)
[_new:BaseObject:private] =>
[_deleted:BaseObject:private] =>
[modifiedColumns:protected] => Array
(
)
)
[51] => Category Object
(
[languages:protected] =>
[bok_resources:protected] =>
[bok_topics:protected] =>
[bok_keywords:protected] =>
[id:protected] => 51
[type:protected] => category
[parent:protected] => 2
[label:protected] => Cement Mason
[alreadyInSave:protected] =>
[alreadyInValidation:protected] =>
[validationFailures:protected] => Array
(
)
[_new:BaseObject:private] =>
[_deleted:BaseObject:private] =>
[modifiedColumns:protected] => Array
(
)
)
[57] => Category Object
(
[languages:protected] =>
[bok_resources:protected] =>
[bok_topics:protected] =>
[bok_keywords:protected] =>
[id:protected] => 57
[type:protected] => category
[parent:protected] => 2
[label:protected] => Flagger
[alreadyInSave:protected] =>
[alreadyInValidation:protected] =>
[validationFailures:protected] => Array
(
)
[_new:BaseObject:private] =>
[_deleted:BaseObject:private] =>
[modifiedColumns:protected] => Array
(
)
)
[64] => Category Object
(
[languages:protected] =>
[bok_resources:protected] =>
[bok_topics:protected] =>
[bok_keywords:protected] =>
[id:protected] => 64
[type:protected] => category
[parent:protected] => 2
[label:protected] => Laborer
[alreadyInSave:protected] =>
[alreadyInValidation:protected] =>
[validationFailures:protected] => Array
(
)
[_new:BaseObject:private] =>
[_deleted:BaseObject:private] =>
[modifiedColumns:protected] => Array
(
)
)
[70] => Category Object
(
[languages:protected] =>
[bok_resources:protected] =>
[bok_topics:protected] =>
[bok_keywords:protected] =>
[id:protected] => 70
[type:protected] => category
[parent:protected] => 2
[label:protected] => Operating Engineer
[alreadyInSave:protected] =>
[alreadyInValidation:protected] =>
[validationFailures:protected] => Array
(
)
[_new:BaseObject:private] =>
[_deleted:BaseObject:private] =>
[modifiedColumns:protected] => Array
(
)
)
[63] => Category Object
(
[languages:protected] =>
[bok_resources:protected] =>
[bok_topics:protected] =>
[bok_keywords:protected] =>
[id:protected] => 63
[type:protected] => category
[parent:protected] => 2
[label:protected] => Reinforcing Ironworker
[alreadyInSave:protected] =>
[alreadyInValidation:protected] =>
[validationFailures:protected] => Array
(
)
[_new:BaseObject:private] =>
[_deleted:BaseObject:private] =>
[modifiedColumns:protected] => Array
(
)
)
[78] => Category Object
(
[languages:protected] =>
[bok_resources:protected] =>
[bok_topics:protected] =>
[bok_keywords:protected] =>
[id:protected] => 78
[type:protected] => category
[parent:protected] => 2
[label:protected] => Roofer/Waterproofer
[alreadyInSave:protected] =>
[alreadyInValidation:protected] =>
[validationFailures:protected] => Array
(
)
[_new:BaseObject:private] =>
[_deleted:BaseObject:private] =>
[modifiedColumns:protected] => Array
(
)
)
[82] => Category Object
(
[languages:protected] =>
[bok_resources:protected] =>
[bok_topics:protected] =>
[bok_keywords:protected] =>
[id:protected] => 82
[type:protected] => category
[parent:protected] => 2
[label:protected] => Stonemason
[alreadyInSave:protected] =>
[alreadyInValidation:protected] =>
[validationFailures:protected] => Array
(
)
[_new:BaseObject:private] =>
[_deleted:BaseObject:private] =>
[modifiedColumns:protected] => Array
(
)
)
[62] => Category Object
(
[languages:protected] =>
[bok_resources:protected] =>
[bok_topics:protected] =>
[bok_keywords:protected] =>
[id:protected] => 62
[type:protected] => category
[parent:protected] => 2
[label:protected] => Structural Ironworker
[alreadyInSave:protected] =>
[alreadyInValidation:protected] =>
[validationFailures:protected] => Array
(
)
[_new:BaseObject:private] =>
[_deleted:BaseObject:private] =>
[modifiedColumns:protected] => Array
(
)
)
[87] => Category Object
(
[languages:protected] =>
[bok_resources:protected] =>
[bok_topics:protected] =>
[bok_keywords:protected] =>
[id:protected] => 87
[type:protected] => category
[parent:protected] => 3
[label:protected] => Commercial & Institutional
[alreadyInSave:protected] =>
[alreadyInValidation:protected] =>
[validationFailures:protected] => Array
(
)
[_new:BaseObject:private] =>
[_deleted:BaseObject:private] =>
[modifiedColumns:protected] => Array
(
)
)
[88] => Category Object
(
[languages:protected] =>
[bok_resources:protected] =>
[bok_topics:protected] =>
[bok_keywords:protected] =>
[id:protected] => 88
[type:protected] => category
[parent:protected] => 3
[label:protected] => Demolition
[alreadyInSave:protected] =>
[alreadyInValidation:protected] =>
[validationFailures:protected] => Array
(
)
[_new:BaseObject:private] =>
[_deleted:BaseObject:private] =>
[modifiedColumns:protected] => Array
(
)
)
[89] => Category Object
(
[languages:protected] =>
[bok_resources:protected] =>
[bok_topics:protected] =>
[bok_keywords:protected] =>
[id:protected] => 89
[type:protected] => category
[parent:protected] => 3
[label:protected] => Disasters
[alreadyInSave:protected] =>
[alreadyInValidation:protected] =>
[validationFailures:protected] => Array
(
)
[_new:BaseObject:private] =>
[_deleted:BaseObject:private] =>
[modifiedColumns:protected] => Array
(
)
)
[91] => Category Object
(
[languages:protected] =>
[bok_resources:protected] =>
[bok_topics:protected] =>
[bok_keywords:protected] =>
[id:protected] => 91
[type:protected] => category
[parent:protected] => 3
[label:protected] => Heavy & Highway
[alreadyInSave:protected] =>
[alreadyInValidation:protected] =>
[validationFailures:protected] => Array
(
)
[_new:BaseObject:private] =>
[_deleted:BaseObject:private] =>
[modifiedColumns:protected] => Array
(
)
)
[90] => Category Object
(
[languages:protected] =>
[bok_resources:protected] =>
[bok_topics:protected] =>
[bok_keywords:protected] =>
[id:protected] => 90
[type:protected] => category
[parent:protected] => 3
[label:protected] => Industrial
[alreadyInSave:protected] =>
[alreadyInValidation:protected] =>
[validationFailures:protected] => Array
(
)
[_new:BaseObject:private] =>
[_deleted:BaseObject:private] =>
[modifiedColumns:protected] => Array
(
)
)
[93] => Category Object
(
[languages:protected] =>
[bok_resources:protected] =>
[bok_topics:protected] =>
[bok_keywords:protected] =>
[id:protected] => 93
[type:protected] => category
[parent:protected] => 3
[label:protected] => Renovations
[alreadyInSave:protected] =>
[alreadyInValidation:protected] =>
[validationFailures:protected] => Array
(
)
[_new:BaseObject:private] =>
[_deleted:BaseObject:private] =>
[modifiedColumns:protected] => Array
(
)
)
[94] => Category Object
(
[languages:protected] =>
[bok_resources:protected] =>
[bok_topics:protected] =>
[bok_keywords:protected] =>
[id:protected] => 94
[type:protected] => category
[parent:protected] => 3
[label:protected] => Residential
[alreadyInSave:protected] =>
[alreadyInValidation:protected] =>
[validationFailures:protected] => Array
(
)
[_new:BaseObject:private] =>
[_deleted:BaseObject:private] =>
[modifiedColumns:protected] => Array
(
)
)
[97] => Category Object
(
[languages:protected] =>
[bok_resources:protected] =>
[bok_topics:protected] =>
[bok_keywords:protected] =>
[id:protected] => 97
[type:protected] => category
[parent:protected] => 5
[label:protected] => Images
[alreadyInSave:protected] =>
[alreadyInValidation:protected] =>
[validationFailures:protected] => Array
(
)
[_new:BaseObject:private] =>
[_deleted:BaseObject:private] =>
[modifiedColumns:protected] => Array
(
)
)
)
[categories_initialized:protected] => 1
[mapped_items:protected] =>
[content:protected] =>
[files:protected] =>
[language:protected] => Language Object
(
[id:protected] => 1
[code:protected] => en
[name:protected] => English
[alreadyInSave:protected] =>
[alreadyInValidation:protected] =>
[validationFailures:protected] => Array
(
)
[_new:BaseObject:private] =>
[_deleted:BaseObject:private] =>
[modifiedColumns:protected] => Array
(
)
)
[old_record:protected] =>
[id:protected] => 4003
[old_id:protected] =>
[elcosh_id:protected] => i002691
[type:protected] => image
[display_type:protected] => Image
[user_id:protected] => 0
[language_id:protected] => 1
[tagging_id:protected] => Bruce Lippy
[priority_id:protected] => 1
[title:protected] => Morning Toolbox Talk
[total_pages:protected] => 0
[billed_pages:protected] => 0
[publication_number:protected] =>
[part_of:protected] =>
[keywords:protected] => toolbox talk, tailgate talk, Spanish, bilingual
[comments:protected] =>
[summary:protected] => This photo is from an early morning toolbox talk on a construction job in Mclean, Virginia. It is being delivered in English and Spanish.
[transition_comments:protected] =>
[external_link:protected] =>
[consol_link:protected] => http://www.cpwrconstructionsolutions.org/electrical/solution/662/worker-training.html
[more_like_this:protected] => d001285,d001304,c000079
[permission_given_by:protected] =>
[published:protected] => T
[billable:protected] => F
[img_name:protected] =>
[img_ext:protected] => jpg
[img_width:protected] =>
[img_height:protected] =>
[img_credit:protected] => Morgan Zavertnik and Hoar Construction
[img_practice:protected] => good
[vid_source_id:protected] =>
[vid_running_time:protected] =>
[vid_intended_audience:protected] =>
[vid_acquisition_info:protected] =>
[vid_cost:protected] =>
[vid_producer:protected] =>
[vid_filename:protected] =>
[vid_filename_downloadable:protected] =>
[date_summary:protected] => November 2015
[date_permission_requested:protected] =>
[date_permission_received:protected] =>
[date_review_needed:protected] =>
[date_received:protected] => 03/02/16
[date_completed:protected] => 03/02/16
[date_billed:protected] =>
[date_modified:protected] => 03/02/16
[collBokExports:protected] =>
[lastBokExportCriteria:BaseElcoshItem:private] =>
[alreadyInSave:protected] =>
[alreadyInValidation:protected] =>
[validationFailures:protected] => Array
(
)
[_new:BaseObject:private] =>
[_deleted:BaseObject:private] =>
[modifiedColumns:protected] => Array
(
)
)
)
[1] => Search_Result Object
(
[title] => Toolbox talk - crew view
[image] => /record/images/4005-p.jpg
[blurb] => Photo of crew listening to a toolbox safety talk before starting work....
[category] => Array
(
[0] => 97
[1] => 20
[2] => 47
[3] => 49
[4] => 51
[5] => 55
[6] => 61
[7] => 64
[8] => 71
[9] => 75
[10] => 63
[11] => 79
[12] => 62
[13] => 87
[14] => 88
[15] => 91
[16] => 90
[17] => 93
[18] => 94
[19] => 95
)
[labels] => Array
(
[0] => Images
[1] => Media
[2] => Media & Documents
[3] => Safety Culture
[4] => Work Environment
[5] => Hazards
[6] => Bricklayer
[7] => Trades
[8] => Carpenter
[10] => Cement Mason
[12] => Electrical Worker
[14] => Interior Systems Carpenter
[16] => Laborer
[18] => Painter
[20] => Plasterer
[22] => Reinforcing Ironworker
[24] => Scaffold Erector
[26] => Structural Ironworker
[28] => Commercial & Institutional
[29] => Jobsites
[30] => Demolition
[32] => Heavy & Highway
[34] => Industrial
[36] => Renovations
[38] => Residential
[40] => Underground
)
[type] => Images
[sub_category] =>
[url] => /image/4005/i002692/Toolbox%2Btalk%2B-%2Bcrew%2Bview.html
[item:protected] => ImageRecord Object
(
[records:protected] => Array
(
)
[recordId:protected] =>
[searchWordClass:protected] =>
[searchWordPeerClass:protected] =>
[bok_record:protected] =>
[authors:protected] =>
[organizations:protected] =>
[collections:protected] =>
[categories:protected] => Array
(
[97] => Category Object
(
[languages:protected] =>
[bok_resources:protected] =>
[bok_topics:protected] =>
[bok_keywords:protected] =>
[id:protected] => 97
[type:protected] => category
[parent:protected] => 5
[label:protected] => Images
[alreadyInSave:protected] =>
[alreadyInValidation:protected] =>
[validationFailures:protected] => Array
(
)
[_new:BaseObject:private] =>
[_deleted:BaseObject:private] =>
[modifiedColumns:protected] => Array
(
)
)
[20] => Category Object
(
[languages:protected] =>
[bok_resources:protected] =>
[bok_topics:protected] =>
[bok_keywords:protected] =>
[id:protected] => 20
[type:protected] => category
[parent:protected] => 7
[label:protected] => Safety Culture
[alreadyInSave:protected] =>
[alreadyInValidation:protected] =>
[validationFailures:protected] => Array
(
)
[_new:BaseObject:private] =>
[_deleted:BaseObject:private] =>
[modifiedColumns:protected] => Array
(
)
)
[47] => Category Object
(
[languages:protected] =>
[bok_resources:protected] =>
[bok_topics:protected] =>
[bok_keywords:protected] =>
[id:protected] => 47
[type:protected] => category
[parent:protected] => 2
[label:protected] => Bricklayer
[alreadyInSave:protected] =>
[alreadyInValidation:protected] =>
[validationFailures:protected] => Array
(
)
[_new:BaseObject:private] =>
[_deleted:BaseObject:private] =>
[modifiedColumns:protected] => Array
(
)
)
[49] => Category Object
(
[languages:protected] =>
[bok_resources:protected] =>
[bok_topics:protected] =>
[bok_keywords:protected] =>
[id:protected] => 49
[type:protected] => category
[parent:protected] => 2
[label:protected] => Carpenter
[alreadyInSave:protected] =>
[alreadyInValidation:protected] =>
[validationFailures:protected] => Array
(
)
[_new:BaseObject:private] =>
[_deleted:BaseObject:private] =>
[modifiedColumns:protected] => Array
(
)
)
[51] => Category Object
(
[languages:protected] =>
[bok_resources:protected] =>
[bok_topics:protected] =>
[bok_keywords:protected] =>
[id:protected] => 51
[type:protected] => category
[parent:protected] => 2
[label:protected] => Cement Mason
[alreadyInSave:protected] =>
[alreadyInValidation:protected] =>
[validationFailures:protected] => Array
(
)
[_new:BaseObject:private] =>
[_deleted:BaseObject:private] =>
[modifiedColumns:protected] => Array
(
)
)
[55] => Category Object
(
[languages:protected] =>
[bok_resources:protected] =>
[bok_topics:protected] =>
[bok_keywords:protected] =>
[id:protected] => 55
[type:protected] => category
[parent:protected] => 2
[label:protected] => Electrical Worker
[alreadyInSave:protected] =>
[alreadyInValidation:protected] =>
[validationFailures:protected] => Array
(
)
[_new:BaseObject:private] =>
[_deleted:BaseObject:private] =>
[modifiedColumns:protected] => Array
(
)
)
[61] => Category Object
(
[languages:protected] =>
[bok_resources:protected] =>
[bok_topics:protected] =>
[bok_keywords:protected] =>
[id:protected] => 61
[type:protected] => category
[parent:protected] => 2
[label:protected] => Interior Systems Carpenter
[alreadyInSave:protected] =>
[alreadyInValidation:protected] =>
[validationFailures:protected] => Array
(
)
[_new:BaseObject:private] =>
[_deleted:BaseObject:private] =>
[modifiedColumns:protected] => Array
(
)
)
[64] => Category Object
(
[languages:protected] =>
[bok_resources:protected] =>
[bok_topics:protected] =>
[bok_keywords:protected] =>
[id:protected] => 64
[type:protected] => category
[parent:protected] => 2
[label:protected] => Laborer
[alreadyInSave:protected] =>
[alreadyInValidation:protected] =>
[validationFailures:protected] => Array
(
)
[_new:BaseObject:private] =>
[_deleted:BaseObject:private] =>
[modifiedColumns:protected] => Array
(
)
)
[71] => Category Object
(
[languages:protected] =>
[bok_resources:protected] =>
[bok_topics:protected] =>
[bok_keywords:protected] =>
[id:protected] => 71
[type:protected] => category
[parent:protected] => 2
[label:protected] => Painter
[alreadyInSave:protected] =>
[alreadyInValidation:protected] =>
[validationFailures:protected] => Array
(
)
[_new:BaseObject:private] =>
[_deleted:BaseObject:private] =>
[modifiedColumns:protected] => Array
(
)
)
[75] => Category Object
(
[languages:protected] =>
[bok_resources:protected] =>
[bok_topics:protected] =>
[bok_keywords:protected] =>
[id:protected] => 75
[type:protected] => category
[parent:protected] => 2
[label:protected] => Plasterer
[alreadyInSave:protected] =>
[alreadyInValidation:protected] =>
[validationFailures:protected] => Array
(
)
[_new:BaseObject:private] =>
[_deleted:BaseObject:private] =>
[modifiedColumns:protected] => Array
(
)
)
[63] => Category Object
(
[languages:protected] =>
[bok_resources:protected] =>
[bok_topics:protected] =>
[bok_keywords:protected] =>
[id:protected] => 63
[type:protected] => category
[parent:protected] => 2
[label:protected] => Reinforcing Ironworker
[alreadyInSave:protected] =>
[alreadyInValidation:protected] =>
[validationFailures:protected] => Array
(
)
[_new:BaseObject:private] =>
[_deleted:BaseObject:private] =>
[modifiedColumns:protected] => Array
(
)
)
[79] => Category Object
(
[languages:protected] =>
[bok_resources:protected] =>
[bok_topics:protected] =>
[bok_keywords:protected] =>
[id:protected] => 79
[type:protected] => category
[parent:protected] => 2
[label:protected] => Scaffold Erector
[alreadyInSave:protected] =>
[alreadyInValidation:protected] =>
[validationFailures:protected] => Array
(
)
[_new:BaseObject:private] =>
[_deleted:BaseObject:private] =>
[modifiedColumns:protected] => Array
(
)
)
[62] => Category Object
(
[languages:protected] =>
[bok_resources:protected] =>
[bok_topics:protected] =>
[bok_keywords:protected] =>
[id:protected] => 62
[type:protected] => category
[parent:protected] => 2
[label:protected] => Structural Ironworker
[alreadyInSave:protected] =>
[alreadyInValidation:protected] =>
[validationFailures:protected] => Array
(
)
[_new:BaseObject:private] =>
[_deleted:BaseObject:private] =>
[modifiedColumns:protected] => Array
(
)
)
[87] => Category Object
(
[languages:protected] =>
[bok_resources:protected] =>
[bok_topics:protected] =>
[bok_keywords:protected] =>
[id:protected] => 87
[type:protected] => category
[parent:protected] => 3
[label:protected] => Commercial & Institutional
[alreadyInSave:protected] =>
[alreadyInValidation:protected] =>
[validationFailures:protected] => Array
(
)
[_new:BaseObject:private] =>
[_deleted:BaseObject:private] =>
[modifiedColumns:protected] => Array
(
)
)
[88] => Category Object
(
[languages:protected] =>
[bok_resources:protected] =>
[bok_topics:protected] =>
[bok_keywords:protected] =>
[id:protected] => 88
[type:protected] => category
[parent:protected] => 3
[label:protected] => Demolition
[alreadyInSave:protected] =>
[alreadyInValidation:protected] =>
[validationFailures:protected] => Array
(
)
[_new:BaseObject:private] =>
[_deleted:BaseObject:private] =>
[modifiedColumns:protected] => Array
(
)
)
[91] => Category Object
(
[languages:protected] =>
[bok_resources:protected] =>
[bok_topics:protected] =>
[bok_keywords:protected] =>
[id:protected] => 91
[type:protected] => category
[parent:protected] => 3
[label:protected] => Heavy & Highway
[alreadyInSave:protected] =>
[alreadyInValidation:protected] =>
[validationFailures:protected] => Array
(
)
[_new:BaseObject:private] =>
[_deleted:BaseObject:private] =>
[modifiedColumns:protected] => Array
(
)
)
[90] => Category Object
(
[languages:protected] =>
[bok_resources:protected] =>
[bok_topics:protected] =>
[bok_keywords:protected] =>
[id:protected] => 90
[type:protected] => category
[parent:protected] => 3
[label:protected] => Industrial
[alreadyInSave:protected] =>
[alreadyInValidation:protected] =>
[validationFailures:protected] => Array
(
)
[_new:BaseObject:private] =>
[_deleted:BaseObject:private] =>
[modifiedColumns:protected] => Array
(
)
)
[93] => Category Object
(
[languages:protected] =>
[bok_resources:protected] =>
[bok_topics:protected] =>
[bok_keywords:protected] =>
[id:protected] => 93
[type:protected] => category
[parent:protected] => 3
[label:protected] => Renovations
[alreadyInSave:protected] =>
[alreadyInValidation:protected] =>
[validationFailures:protected] => Array
(
)
[_new:BaseObject:private] =>
[_deleted:BaseObject:private] =>
[modifiedColumns:protected] => Array
(
)
)
[94] => Category Object
(
[languages:protected] =>
[bok_resources:protected] =>
[bok_topics:protected] =>
[bok_keywords:protected] =>
[id:protected] => 94
[type:protected] => category
[parent:protected] => 3
[label:protected] => Residential
[alreadyInSave:protected] =>
[alreadyInValidation:protected] =>
[validationFailures:protected] => Array
(
)
[_new:BaseObject:private] =>
[_deleted:BaseObject:private] =>
[modifiedColumns:protected] => Array
(
)
)
[95] => Category Object
(
[languages:protected] =>
[bok_resources:protected] =>
[bok_topics:protected] =>
[bok_keywords:protected] =>
[id:protected] => 95
[type:protected] => category
[parent:protected] => 3
[label:protected] => Underground
[alreadyInSave:protected] =>
[alreadyInValidation:protected] =>
[validationFailures:protected] => Array
(
)
[_new:BaseObject:private] =>
[_deleted:BaseObject:private] =>
[modifiedColumns:protected] => Array
(
)
)
)
[categories_initialized:protected] => 1
[mapped_items:protected] =>
[content:protected] =>
[files:protected] =>
[language:protected] => Language Object
(
[id:protected] => 1
[code:protected] => en
[name:protected] => English
[alreadyInSave:protected] =>
[alreadyInValidation:protected] =>
[validationFailures:protected] => Array
(
)
[_new:BaseObject:private] =>
[_deleted:BaseObject:private] =>
[modifiedColumns:protected] => Array
(
)
)
[old_record:protected] =>
[id:protected] => 4005
[old_id:protected] =>
[elcosh_id:protected] => i002692
[type:protected] => image
[display_type:protected] => Image
[user_id:protected] => 0
[language_id:protected] => 1
[tagging_id:protected] => Bruce Lippy
[priority_id:protected] => 1
[title:protected] => Toolbox talk - crew view
[total_pages:protected] => 0
[billed_pages:protected] => 0
[publication_number:protected] =>
[part_of:protected] =>
[keywords:protected] => toolbox talk, tailgate talk, safety talk, Spanish
[comments:protected] =>
[summary:protected] => Photo of crew listening to a toolbox safety talk before starting work.
[transition_comments:protected] =>
[external_link:protected] =>
[consol_link:protected] => http://www.cpwrconstructionsolutions.org/electrical/solution/662/worker-training.html
[more_like_this:protected] => i002691,d001269, c000079, d001285
[permission_given_by:protected] =>
[published:protected] => T
[billable:protected] => F
[img_name:protected] =>
[img_ext:protected] => jpg
[img_width:protected] =>
[img_height:protected] =>
[img_credit:protected] => Morgan Zavertnik and Hoar Construction
[img_practice:protected] => good
[vid_source_id:protected] =>
[vid_running_time:protected] =>
[vid_intended_audience:protected] =>
[vid_acquisition_info:protected] =>
[vid_cost:protected] =>
[vid_producer:protected] =>
[vid_filename:protected] =>
[vid_filename_downloadable:protected] =>
[date_summary:protected] => November 2015
[date_permission_requested:protected] =>
[date_permission_received:protected] =>
[date_review_needed:protected] =>
[date_received:protected] => 03/02/16
[date_completed:protected] => 03/02/16
[date_billed:protected] =>
[date_modified:protected] => 03/02/16
[collBokExports:protected] =>
[lastBokExportCriteria:BaseElcoshItem:private] =>
[alreadyInSave:protected] =>
[alreadyInValidation:protected] =>
[validationFailures:protected] => Array
(
)
[_new:BaseObject:private] =>
[_deleted:BaseObject:private] =>
[modifiedColumns:protected] => Array
(
)
)
)
[2] => Search_Result Object
(
[title] => Toolbox talk - long shot
[image] => /record/images/4006-p.jpg
[blurb] => This crew gathered every morning before starting work to discuss a new safety topic....
[category] => Array
(
[0] => 20
[1] => 47
[2] => 49
[3] => 51
[4] => 55
[5] => 64
[6] => 68
[7] => 75
[8] => 76
[9] => 63
[10] => 78
[11] => 79
[12] => 82
[13] => 62
[14] => 87
[15] => 88
[16] => 91
[17] => 90
[18] => 93
[19] => 94
[20] => 95
[21] => 97
)
[labels] => Array
(
[0] => Safety Culture
[1] => Work Environment
[2] => Hazards
[3] => Bricklayer
[4] => Trades
[5] => Carpenter
[7] => Cement Mason
[9] => Electrical Worker
[11] => Laborer
[13] => Maintenance Worker
[15] => Plasterer
[17] => Plumber/Pipefitter
[19] => Reinforcing Ironworker
[21] => Roofer/Waterproofer
[23] => Scaffold Erector
[25] => Stonemason
[27] => Structural Ironworker
[29] => Commercial & Institutional
[30] => Jobsites
[31] => Demolition
[33] => Heavy & Highway
[35] => Industrial
[37] => Renovations
[39] => Residential
[41] => Underground
[43] => Images
[44] => Media
[45] => Media & Documents
)
[type] => Images
[sub_category] =>
[url] => /image/4006/i002693/Toolbox%2Btalk%2B-%2Blong%2Bshot.html
[item:protected] => ImageRecord Object
(
[records:protected] => Array
(
)
[recordId:protected] =>
[searchWordClass:protected] =>
[searchWordPeerClass:protected] =>
[bok_record:protected] =>
[authors:protected] =>
[organizations:protected] =>
[collections:protected] =>
[categories:protected] => Array
(
[20] => Category Object
(
[languages:protected] =>
[bok_resources:protected] =>
[bok_topics:protected] =>
[bok_keywords:protected] =>
[id:protected] => 20
[type:protected] => category
[parent:protected] => 7
[label:protected] => Safety Culture
[alreadyInSave:protected] =>
[alreadyInValidation:protected] =>
[validationFailures:protected] => Array
(
)
[_new:BaseObject:private] =>
[_deleted:BaseObject:private] =>
[modifiedColumns:protected] => Array
(
)
)
[47] => Category Object
(
[languages:protected] =>
[bok_resources:protected] =>
[bok_topics:protected] =>
[bok_keywords:protected] =>
[id:protected] => 47
[type:protected] => category
[parent:protected] => 2
[label:protected] => Bricklayer
[alreadyInSave:protected] =>
[alreadyInValidation:protected] =>
[validationFailures:protected] => Array
(
)
[_new:BaseObject:private] =>
[_deleted:BaseObject:private] =>
[modifiedColumns:protected] => Array
(
)
)
[49] => Category Object
(
[languages:protected] =>
[bok_resources:protected] =>
[bok_topics:protected] =>
[bok_keywords:protected] =>
[id:protected] => 49
[type:protected] => category
[parent:protected] => 2
[label:protected] => Carpenter
[alreadyInSave:protected] =>
[alreadyInValidation:protected] =>
[validationFailures:protected] => Array
(
)
[_new:BaseObject:private] =>
[_deleted:BaseObject:private] =>
[modifiedColumns:protected] => Array
(
)
)
[51] => Category Object
(
[languages:protected] =>
[bok_resources:protected] =>
[bok_topics:protected] =>
[bok_keywords:protected] =>
[id:protected] => 51
[type:protected] => category
[parent:protected] => 2
[label:protected] => Cement Mason
[alreadyInSave:protected] =>
[alreadyInValidation:protected] =>
[validationFailures:protected] => Array
(
)
[_new:BaseObject:private] =>
[_deleted:BaseObject:private] =>
[modifiedColumns:protected] => Array
(
)
)
[55] => Category Object
(
[languages:protected] =>
[bok_resources:protected] =>
[bok_topics:protected] =>
[bok_keywords:protected] =>
[id:protected] => 55
[type:protected] => category
[parent:protected] => 2
[label:protected] => Electrical Worker
[alreadyInSave:protected] =>
[alreadyInValidation:protected] =>
[validationFailures:protected] => Array
(
)
[_new:BaseObject:private] =>
[_deleted:BaseObject:private] =>
[modifiedColumns:protected] => Array
(
)
)
[64] => Category Object
(
[languages:protected] =>
[bok_resources:protected] =>
[bok_topics:protected] =>
[bok_keywords:protected] =>
[id:protected] => 64
[type:protected] => category
[parent:protected] => 2
[label:protected] => Laborer
[alreadyInSave:protected] =>
[alreadyInValidation:protected] =>
[validationFailures:protected] => Array
(
)
[_new:BaseObject:private] =>
[_deleted:BaseObject:private] =>
[modifiedColumns:protected] => Array
(
)
)
[68] => Category Object
(
[languages:protected] =>
[bok_resources:protected] =>
[bok_topics:protected] =>
[bok_keywords:protected] =>
[id:protected] => 68
[type:protected] => category
[parent:protected] => 2
[label:protected] => Maintenance Worker
[alreadyInSave:protected] =>
[alreadyInValidation:protected] =>
[validationFailures:protected] => Array
(
)
[_new:BaseObject:private] =>
[_deleted:BaseObject:private] =>
[modifiedColumns:protected] => Array
(
)
)
[75] => Category Object
(
[languages:protected] =>
[bok_resources:protected] =>
[bok_topics:protected] =>
[bok_keywords:protected] =>
[id:protected] => 75
[type:protected] => category
[parent:protected] => 2
[label:protected] => Plasterer
[alreadyInSave:protected] =>
[alreadyInValidation:protected] =>
[validationFailures:protected] => Array
(
)
[_new:BaseObject:private] =>
[_deleted:BaseObject:private] =>
[modifiedColumns:protected] => Array
(
)
)
[76] => Category Object
(
[languages:protected] =>
[bok_resources:protected] =>
[bok_topics:protected] =>
[bok_keywords:protected] =>
[id:protected] => 76
[type:protected] => category
[parent:protected] => 2
[label:protected] => Plumber/Pipefitter
[alreadyInSave:protected] =>
[alreadyInValidation:protected] =>
[validationFailures:protected] => Array
(
)
[_new:BaseObject:private] =>
[_deleted:BaseObject:private] =>
[modifiedColumns:protected] => Array
(
)
)
[63] => Category Object
(
[languages:protected] =>
[bok_resources:protected] =>
[bok_topics:protected] =>
[bok_keywords:protected] =>
[id:protected] => 63
[type:protected] => category
[parent:protected] => 2
[label:protected] => Reinforcing Ironworker
[alreadyInSave:protected] =>
[alreadyInValidation:protected] =>
[validationFailures:protected] => Array
(
)
[_new:BaseObject:private] =>
[_deleted:BaseObject:private] =>
[modifiedColumns:protected] => Array
(
)
)
[78] => Category Object
(
[languages:protected] =>
[bok_resources:protected] =>
[bok_topics:protected] =>
[bok_keywords:protected] =>
[id:protected] => 78
[type:protected] => category
[parent:protected] => 2
[label:protected] => Roofer/Waterproofer
[alreadyInSave:protected] =>
[alreadyInValidation:protected] =>
[validationFailures:protected] => Array
(
)
[_new:BaseObject:private] =>
[_deleted:BaseObject:private] =>
[modifiedColumns:protected] => Array
(
)
)
[79] => Category Object
(
[languages:protected] =>
[bok_resources:protected] =>
[bok_topics:protected] =>
[bok_keywords:protected] =>
[id:protected] => 79
[type:protected] => category
[parent:protected] => 2
[label:protected] => Scaffold Erector
[alreadyInSave:protected] =>
[alreadyInValidation:protected] =>
[validationFailures:protected] => Array
(
)
[_new:BaseObject:private] =>
[_deleted:BaseObject:private] =>
[modifiedColumns:protected] => Array
(
)
)
[82] => Category Object
(
[languages:protected] =>
[bok_resources:protected] =>
[bok_topics:protected] =>
[bok_keywords:protected] =>
[id:protected] => 82
[type:protected] => category
[parent:protected] => 2
[label:protected] => Stonemason
[alreadyInSave:protected] =>
[alreadyInValidation:protected] =>
[validationFailures:protected] => Array
(
)
[_new:BaseObject:private] =>
[_deleted:BaseObject:private] =>
[modifiedColumns:protected] => Array
(
)
)
[62] => Category Object
(
[languages:protected] =>
[bok_resources:protected] =>
[bok_topics:protected] =>
[bok_keywords:protected] =>
[id:protected] => 62
[type:protected] => category
[parent:protected] => 2
[label:protected] => Structural Ironworker
[alreadyInSave:protected] =>
[alreadyInValidation:protected] =>
[validationFailures:protected] => Array
(
)
[_new:BaseObject:private] =>
[_deleted:BaseObject:private] =>
[modifiedColumns:protected] => Array
(
)
)
[87] => Category Object
(
[languages:protected] =>
[bok_resources:protected] =>
[bok_topics:protected] =>
[bok_keywords:protected] =>
[id:protected] => 87
[type:protected] => category
[parent:protected] => 3
[label:protected] => Commercial & Institutional
[alreadyInSave:protected] =>
[alreadyInValidation:protected] =>
[validationFailures:protected] => Array
(
)
[_new:BaseObject:private] =>
[_deleted:BaseObject:private] =>
[modifiedColumns:protected] => Array
(
)
)
[88] => Category Object
(
[languages:protected] =>
[bok_resources:protected] =>
[bok_topics:protected] =>
[bok_keywords:protected] =>
[id:protected] => 88
[type:protected] => category
[parent:protected] => 3
[label:protected] => Demolition
[alreadyInSave:protected] =>
[alreadyInValidation:protected] =>
[validationFailures:protected] => Array
(
)
[_new:BaseObject:private] =>
[_deleted:BaseObject:private] =>
[modifiedColumns:protected] => Array
(
)
)
[91] => Category Object
(
[languages:protected] =>
[bok_resources:protected] =>
[bok_topics:protected] =>
[bok_keywords:protected] =>
[id:protected] => 91
[type:protected] => category
[parent:protected] => 3
[label:protected] => Heavy & Highway
[alreadyInSave:protected] =>
[alreadyInValidation:protected] =>
[validationFailures:protected] => Array
(
)
[_new:BaseObject:private] =>
[_deleted:BaseObject:private] =>
[modifiedColumns:protected] => Array
(
)
)
[90] => Category Object
(
[languages:protected] =>
[bok_resources:protected] =>
[bok_topics:protected] =>
[bok_keywords:protected] =>
[id:protected] => 90
[type:protected] => category
[parent:protected] => 3
[label:protected] => Industrial
[alreadyInSave:protected] =>
[alreadyInValidation:protected] =>
[validationFailures:protected] => Array
(
)
[_new:BaseObject:private] =>
[_deleted:BaseObject:private] =>
[modifiedColumns:protected] => Array
(
)
)
[93] => Category Object
(
[languages:protected] =>
[bok_resources:protected] =>
[bok_topics:protected] =>
[bok_keywords:protected] =>
[id:protected] => 93
[type:protected] => category
[parent:protected] => 3
[label:protected] => Renovations
[alreadyInSave:protected] =>
[alreadyInValidation:protected] =>
[validationFailures:protected] => Array
(
)
[_new:BaseObject:private] =>
[_deleted:BaseObject:private] =>
[modifiedColumns:protected] => Array
(
)
)
[94] => Category Object
(
[languages:protected] =>
[bok_resources:protected] =>
[bok_topics:protected] =>
[bok_keywords:protected] =>
[id:protected] => 94
[type:protected] => category
[parent:protected] => 3
[label:protected] => Residential
[alreadyInSave:protected] =>
[alreadyInValidation:protected] =>
[validationFailures:protected] => Array
(
)
[_new:BaseObject:private] =>
[_deleted:BaseObject:private] =>
[modifiedColumns:protected] => Array
(
)
)
[95] => Category Object
(
[languages:protected] =>
[bok_resources:protected] =>
[bok_topics:protected] =>
[bok_keywords:protected] =>
[id:protected] => 95
[type:protected] => category
[parent:protected] => 3
[label:protected] => Underground
[alreadyInSave:protected] =>
[alreadyInValidation:protected] =>
[validationFailures:protected] => Array
(
)
[_new:BaseObject:private] =>
[_deleted:BaseObject:private] =>
[modifiedColumns:protected] => Array
(
)
)
[97] => Category Object
(
[languages:protected] =>
[bok_resources:protected] =>
[bok_topics:protected] =>
[bok_keywords:protected] =>
[id:protected] => 97
[type:protected] => category
[parent:protected] => 5
[label:protected] => Images
[alreadyInSave:protected] =>
[alreadyInValidation:protected] =>
[validationFailures:protected] => Array
(
)
[_new:BaseObject:private] =>
[_deleted:BaseObject:private] =>
[modifiedColumns:protected] => Array
(
)
)
)
[categories_initialized:protected] => 1
[mapped_items:protected] =>
[content:protected] =>
[files:protected] =>
[language:protected] => Language Object
(
[id:protected] => 1
[code:protected] => en
[name:protected] => English
[alreadyInSave:protected] =>
[alreadyInValidation:protected] =>
[validationFailures:protected] => Array
(
)
[_new:BaseObject:private] =>
[_deleted:BaseObject:private] =>
[modifiedColumns:protected] => Array
(
)
)
[old_record:protected] =>
[id:protected] => 4006
[old_id:protected] =>
[elcosh_id:protected] => i002693
[type:protected] => image
[display_type:protected] => Image
[user_id:protected] => 0
[language_id:protected] => 1
[tagging_id:protected] => Bruce Lippy
[priority_id:protected] => 1
[title:protected] => Toolbox talk - long shot
[total_pages:protected] => 0
[billed_pages:protected] => 0
[publication_number:protected] =>
[part_of:protected] =>
[keywords:protected] => toolbox talk, tailgate talk, safety minute
[comments:protected] =>
[summary:protected] => This crew gathered every morning before starting work to discuss a new safety topic.
[transition_comments:protected] =>
[external_link:protected] =>
[consol_link:protected] => http://www.cpwrconstructionsolutions.org/electrical/solution/662/worker-training.html
[more_like_this:protected] => i002691,i002692,d001269,d000527
[permission_given_by:protected] =>
[published:protected] => T
[billable:protected] => F
[img_name:protected] =>
[img_ext:protected] => jpg
[img_width:protected] =>
[img_height:protected] =>
[img_credit:protected] => Morgan Zavertnik and Hoar Construction
[img_practice:protected] => good
[vid_source_id:protected] =>
[vid_running_time:protected] =>
[vid_intended_audience:protected] =>
[vid_acquisition_info:protected] =>
[vid_cost:protected] =>
[vid_producer:protected] =>
[vid_filename:protected] =>
[vid_filename_downloadable:protected] =>
[date_summary:protected] => November 2015
[date_permission_requested:protected] =>
[date_permission_received:protected] =>
[date_review_needed:protected] =>
[date_received:protected] => 03/02/16
[date_completed:protected] => 03/02/16
[date_billed:protected] =>
[date_modified:protected] => 03/02/16
[collBokExports:protected] =>
[lastBokExportCriteria:BaseElcoshItem:private] =>
[alreadyInSave:protected] =>
[alreadyInValidation:protected] =>
[validationFailures:protected] => Array
(
)
[_new:BaseObject:private] =>
[_deleted:BaseObject:private] =>
[modifiedColumns:protected] => Array
(
)
)
)
[3] => Search_Result Object
(
[title] => Safety officer discussing ongoing project with marketing coordinator
[image] => /record/images/4014-p.jpg
[blurb] => The safety officer (left) points out the good safety practices on this project that reflect well on the firm and may influence future clients....
[category] => Array
(
[0] => 97
[1] => 20
[2] => 46
[3] => 47
[4] => 49
[5] => 50
[6] => 51
[7] => 54
[8] => 55
[9] => 58
[10] => 60
[11] => 61
[12] => 64
[13] => 71
[14] => 75
[15] => 76
[16] => 63
[17] => 79
[18] => 80
[19] => 82
[20] => 62
[21] => 83
[22] => 87
[23] => 91
[24] => 90
[25] => 93
[26] => 94
)
[labels] => Array
(
[0] => Images
[1] => Media
[2] => Media & Documents
[3] => Safety Culture
[4] => Work Environment
[5] => Hazards
[6] => Boilermaker
[7] => Trades
[8] => Bricklayer
[10] => Carpenter
[12] => Carpet Layer
[14] => Cement Mason
[16] => Drywall Applicator Specialist
[18] => Electrical Worker
[20] => Glazier
[22] => HVAC
[24] => Interior Systems Carpenter
[26] => Laborer
[28] => Painter
[30] => Plasterer
[32] => Plumber/Pipefitter
[34] => Reinforcing Ironworker
[36] => Scaffold Erector
[38] => Sheetmetal Worker
[40] => Stonemason
[42] => Structural Ironworker
[44] => Terrazzo Worker
[46] => Commercial & Institutional
[47] => Jobsites
[48] => Heavy & Highway
[50] => Industrial
[52] => Renovations
[54] => Residential
)
[type] => Images
[sub_category] =>
[url] => /image/4014/i002700/Safety%2Bofficer%2Bdiscussing%2Bongoing%2Bproject%2Bwith%2Bmarketing%2Bcoordinator.html
[item:protected] => ImageRecord Object
(
[records:protected] => Array
(
)
[recordId:protected] =>
[searchWordClass:protected] =>
[searchWordPeerClass:protected] =>
[bok_record:protected] =>
[authors:protected] =>
[organizations:protected] =>
[collections:protected] =>
[categories:protected] => Array
(
[97] => Category Object
(
[languages:protected] =>
[bok_resources:protected] =>
[bok_topics:protected] =>
[bok_keywords:protected] =>
[id:protected] => 97
[type:protected] => category
[parent:protected] => 5
[label:protected] => Images
[alreadyInSave:protected] =>
[alreadyInValidation:protected] =>
[validationFailures:protected] => Array
(
)
[_new:BaseObject:private] =>
[_deleted:BaseObject:private] =>
[modifiedColumns:protected] => Array
(
)
)
[20] => Category Object
(
[languages:protected] =>
[bok_resources:protected] =>
[bok_topics:protected] =>
[bok_keywords:protected] =>
[id:protected] => 20
[type:protected] => category
[parent:protected] => 7
[label:protected] => Safety Culture
[alreadyInSave:protected] =>
[alreadyInValidation:protected] =>
[validationFailures:protected] => Array
(
)
[_new:BaseObject:private] =>
[_deleted:BaseObject:private] =>
[modifiedColumns:protected] => Array
(
)
)
[46] => Category Object
(
[languages:protected] =>
[bok_resources:protected] =>
[bok_topics:protected] =>
[bok_keywords:protected] =>
[id:protected] => 46
[type:protected] => category
[parent:protected] => 2
[label:protected] => Boilermaker
[alreadyInSave:protected] =>
[alreadyInValidation:protected] =>
[validationFailures:protected] => Array
(
)
[_new:BaseObject:private] =>
[_deleted:BaseObject:private] =>
[modifiedColumns:protected] => Array
(
)
)
[47] => Category Object
(
[languages:protected] =>
[bok_resources:protected] =>
[bok_topics:protected] =>
[bok_keywords:protected] =>
[id:protected] => 47
[type:protected] => category
[parent:protected] => 2
[label:protected] => Bricklayer
[alreadyInSave:protected] =>
[alreadyInValidation:protected] =>
[validationFailures:protected] => Array
(
)
[_new:BaseObject:private] =>
[_deleted:BaseObject:private] =>
[modifiedColumns:protected] => Array
(
)
)
[49] => Category Object
(
[languages:protected] =>
[bok_resources:protected] =>
[bok_topics:protected] =>
[bok_keywords:protected] =>
[id:protected] => 49
[type:protected] => category
[parent:protected] => 2
[label:protected] => Carpenter
[alreadyInSave:protected] =>
[alreadyInValidation:protected] =>
[validationFailures:protected] => Array
(
)
[_new:BaseObject:private] =>
[_deleted:BaseObject:private] =>
[modifiedColumns:protected] => Array
(
)
)
[50] => Category Object
(
[languages:protected] =>
[bok_resources:protected] =>
[bok_topics:protected] =>
[bok_keywords:protected] =>
[id:protected] => 50
[type:protected] => category
[parent:protected] => 2
[label:protected] => Carpet Layer
[alreadyInSave:protected] =>
[alreadyInValidation:protected] =>
[validationFailures:protected] => Array
(
)
[_new:BaseObject:private] =>
[_deleted:BaseObject:private] =>
[modifiedColumns:protected] => Array
(
)
)
[51] => Category Object
(
[languages:protected] =>
[bok_resources:protected] =>
[bok_topics:protected] =>
[bok_keywords:protected] =>
[id:protected] => 51
[type:protected] => category
[parent:protected] => 2
[label:protected] => Cement Mason
[alreadyInSave:protected] =>
[alreadyInValidation:protected] =>
[validationFailures:protected] => Array
(
)
[_new:BaseObject:private] =>
[_deleted:BaseObject:private] =>
[modifiedColumns:protected] => Array
(
)
)
[54] => Category Object
(
[languages:protected] =>
[bok_resources:protected] =>
[bok_topics:protected] =>
[bok_keywords:protected] =>
[id:protected] => 54
[type:protected] => category
[parent:protected] => 2
[label:protected] => Drywall Applicator Specialist
[alreadyInSave:protected] =>
[alreadyInValidation:protected] =>
[validationFailures:protected] => Array
(
)
[_new:BaseObject:private] =>
[_deleted:BaseObject:private] =>
[modifiedColumns:protected] => Array
(
)
)
[55] => Category Object
(
[languages:protected] =>
[bok_resources:protected] =>
[bok_topics:protected] =>
[bok_keywords:protected] =>
[id:protected] => 55
[type:protected] => category
[parent:protected] => 2
[label:protected] => Electrical Worker
[alreadyInSave:protected] =>
[alreadyInValidation:protected] =>
[validationFailures:protected] => Array
(
)
[_new:BaseObject:private] =>
[_deleted:BaseObject:private] =>
[modifiedColumns:protected] => Array
(
)
)
[58] => Category Object
(
[languages:protected] =>
[bok_resources:protected] =>
[bok_topics:protected] =>
[bok_keywords:protected] =>
[id:protected] => 58
[type:protected] => category
[parent:protected] => 2
[label:protected] => Glazier
[alreadyInSave:protected] =>
[alreadyInValidation:protected] =>
[validationFailures:protected] => Array
(
)
[_new:BaseObject:private] =>
[_deleted:BaseObject:private] =>
[modifiedColumns:protected] => Array
(
)
)
[60] => Category Object
(
[languages:protected] =>
[bok_resources:protected] =>
[bok_topics:protected] =>
[bok_keywords:protected] =>
[id:protected] => 60
[type:protected] => category
[parent:protected] => 2
[label:protected] => HVAC
[alreadyInSave:protected] =>
[alreadyInValidation:protected] =>
[validationFailures:protected] => Array
(
)
[_new:BaseObject:private] =>
[_deleted:BaseObject:private] =>
[modifiedColumns:protected] => Array
(
)
)
[61] => Category Object
(
[languages:protected] =>
[bok_resources:protected] =>
[bok_topics:protected] =>
[bok_keywords:protected] =>
[id:protected] => 61
[type:protected] => category
[parent:protected] => 2
[label:protected] => Interior Systems Carpenter
[alreadyInSave:protected] =>
[alreadyInValidation:protected] =>
[validationFailures:protected] => Array
(
)
[_new:BaseObject:private] =>
[_deleted:BaseObject:private] =>
[modifiedColumns:protected] => Array
(
)
)
[64] => Category Object
(
[languages:protected] =>
[bok_resources:protected] =>
[bok_topics:protected] =>
[bok_keywords:protected] =>
[id:protected] => 64
[type:protected] => category
[parent:protected] => 2
[label:protected] => Laborer
[alreadyInSave:protected] =>
[alreadyInValidation:protected] =>
[validationFailures:protected] => Array
(
)
[_new:BaseObject:private] =>
[_deleted:BaseObject:private] =>
[modifiedColumns:protected] => Array
(
)
)
[71] => Category Object
(
[languages:protected] =>
[bok_resources:protected] =>
[bok_topics:protected] =>
[bok_keywords:protected] =>
[id:protected] => 71
[type:protected] => category
[parent:protected] => 2
[label:protected] => Painter
[alreadyInSave:protected] =>
[alreadyInValidation:protected] =>
[validationFailures:protected] => Array
(
)
[_new:BaseObject:private] =>
[_deleted:BaseObject:private] =>
[modifiedColumns:protected] => Array
(
)
)
[75] => Category Object
(
[languages:protected] =>
[bok_resources:protected] =>
[bok_topics:protected] =>
[bok_keywords:protected] =>
[id:protected] => 75
[type:protected] => category
[parent:protected] => 2
[label:protected] => Plasterer
[alreadyInSave:protected] =>
[alreadyInValidation:protected] =>
[validationFailures:protected] => Array
(
)
[_new:BaseObject:private] =>
[_deleted:BaseObject:private] =>
[modifiedColumns:protected] => Array
(
)
)
[76] => Category Object
(
[languages:protected] =>
[bok_resources:protected] =>
[bok_topics:protected] =>
[bok_keywords:protected] =>
[id:protected] => 76
[type:protected] => category
[parent:protected] => 2
[label:protected] => Plumber/Pipefitter
[alreadyInSave:protected] =>
[alreadyInValidation:protected] =>
[validationFailures:protected] => Array
(
)
[_new:BaseObject:private] =>
[_deleted:BaseObject:private] =>
[modifiedColumns:protected] => Array
(
)
)
[63] => Category Object
(
[languages:protected] =>
[bok_resources:protected] =>
[bok_topics:protected] =>
[bok_keywords:protected] =>
[id:protected] => 63
[type:protected] => category
[parent:protected] => 2
[label:protected] => Reinforcing Ironworker
[alreadyInSave:protected] =>
[alreadyInValidation:protected] =>
[validationFailures:protected] => Array
(
)
[_new:BaseObject:private] =>
[_deleted:BaseObject:private] =>
[modifiedColumns:protected] => Array
(
)
)
[79] => Category Object
(
[languages:protected] =>
[bok_resources:protected] =>
[bok_topics:protected] =>
[bok_keywords:protected] =>
[id:protected] => 79
[type:protected] => category
[parent:protected] => 2
[label:protected] => Scaffold Erector
[alreadyInSave:protected] =>
[alreadyInValidation:protected] =>
[validationFailures:protected] => Array
(
)
[_new:BaseObject:private] =>
[_deleted:BaseObject:private] =>
[modifiedColumns:protected] => Array
(
)
)
[80] => Category Object
(
[languages:protected] =>
[bok_resources:protected] =>
[bok_topics:protected] =>
[bok_keywords:protected] =>
[id:protected] => 80
[type:protected] => category
[parent:protected] => 2
[label:protected] => Sheetmetal Worker
[alreadyInSave:protected] =>
[alreadyInValidation:protected] =>
[validationFailures:protected] => Array
(
)
[_new:BaseObject:private] =>
[_deleted:BaseObject:private] =>
[modifiedColumns:protected] => Array
(
)
)
[82] => Category Object
(
[languages:protected] =>
[bok_resources:protected] =>
[bok_topics:protected] =>
[bok_keywords:protected] =>
[id:protected] => 82
[type:protected] => category
[parent:protected] => 2
[label:protected] => Stonemason
[alreadyInSave:protected] =>
[alreadyInValidation:protected] =>
[validationFailures:protected] => Array
(
)
[_new:BaseObject:private] =>
[_deleted:BaseObject:private] =>
[modifiedColumns:protected] => Array
(
)
)
[62] => Category Object
(
[languages:protected] =>
[bok_resources:protected] =>
[bok_topics:protected] =>
[bok_keywords:protected] =>
[id:protected] => 62
[type:protected] => category
[parent:protected] => 2
[label:protected] => Structural Ironworker
[alreadyInSave:protected] =>
[alreadyInValidation:protected] =>
[validationFailures:protected] => Array
(
)
[_new:BaseObject:private] =>
[_deleted:BaseObject:private] =>
[modifiedColumns:protected] => Array
(
)
)
[83] => Category Object
(
[languages:protected] =>
[bok_resources:protected] =>
[bok_topics:protected] =>
[bok_keywords:protected] =>
[id:protected] => 83
[type:protected] => category
[parent:protected] => 2
[label:protected] => Terrazzo Worker
[alreadyInSave:protected] =>
[alreadyInValidation:protected] =>
[validationFailures:protected] => Array
(
)
[_new:BaseObject:private] =>
[_deleted:BaseObject:private] =>
[modifiedColumns:protected] => Array
(
)
)
[87] => Category Object
(
[languages:protected] =>
[bok_resources:protected] =>
[bok_topics:protected] =>
[bok_keywords:protected] =>
[id:protected] => 87
[type:protected] => category
[parent:protected] => 3
[label:protected] => Commercial & Institutional
[alreadyInSave:protected] =>
[alreadyInValidation:protected] =>
[validationFailures:protected] => Array
(
)
[_new:BaseObject:private] =>
[_deleted:BaseObject:private] =>
[modifiedColumns:protected] => Array
(
)
)
[91] => Category Object
(
[languages:protected] =>
[bok_resources:protected] =>
[bok_topics:protected] =>
[bok_keywords:protected] =>
[id:protected] => 91
[type:protected] => category
[parent:protected] => 3
[label:protected] => Heavy & Highway
[alreadyInSave:protected] =>
[alreadyInValidation:protected] =>
[validationFailures:protected] => Array
(
)
[_new:BaseObject:private] =>
[_deleted:BaseObject:private] =>
[modifiedColumns:protected] => Array
(
)
)
[90] => Category Object
(
[languages:protected] =>
[bok_resources:protected] =>
[bok_topics:protected] =>
[bok_keywords:protected] =>
[id:protected] => 90
[type:protected] => category
[parent:protected] => 3
[label:protected] => Industrial
[alreadyInSave:protected] =>
[alreadyInValidation:protected] =>
[validationFailures:protected] => Array
(
)
[_new:BaseObject:private] =>
[_deleted:BaseObject:private] =>
[modifiedColumns:protected] => Array
(
)
)
[93] => Category Object
(
[languages:protected] =>
[bok_resources:protected] =>
[bok_topics:protected] =>
[bok_keywords:protected] =>
[id:protected] => 93
[type:protected] => category
[parent:protected] => 3
[label:protected] => Renovations
[alreadyInSave:protected] =>
[alreadyInValidation:protected] =>
[validationFailures:protected] => Array
(
)
[_new:BaseObject:private] =>
[_deleted:BaseObject:private] =>
[modifiedColumns:protected] => Array
(
)
)
[94] => Category Object
(
[languages:protected] =>
[bok_resources:protected] =>
[bok_topics:protected] =>
[bok_keywords:protected] =>
[id:protected] => 94
[type:protected] => category
[parent:protected] => 3
[label:protected] => Residential
[alreadyInSave:protected] =>
[alreadyInValidation:protected] =>
[validationFailures:protected] => Array
(
)
[_new:BaseObject:private] =>
[_deleted:BaseObject:private] =>
[modifiedColumns:protected] => Array
(
)
)
)
[categories_initialized:protected] => 1
[mapped_items:protected] =>
[content:protected] =>
[files:protected] =>
[language:protected] => Language Object
(
[id:protected] => 1
[code:protected] => en
[name:protected] => English
[alreadyInSave:protected] =>
[alreadyInValidation:protected] =>
[validationFailures:protected] => Array
(
)
[_new:BaseObject:private] =>
[_deleted:BaseObject:private] =>
[modifiedColumns:protected] => Array
(
)
)
[old_record:protected] =>
[id:protected] => 4014
[old_id:protected] =>
[elcosh_id:protected] => i002700
[type:protected] => image
[display_type:protected] => Image
[user_id:protected] => 0
[language_id:protected] => 1
[tagging_id:protected] => Bruce Lippy
[priority_id:protected] => 1
[title:protected] => Safety officer discussing ongoing project with marketing coordinator
[total_pages:protected] => 0
[billed_pages:protected] => 0
[publication_number:protected] =>
[part_of:protected] =>
[keywords:protected] => Latino, safety officer, safety culture
[comments:protected] =>
[summary:protected] => The safety officer (left) points out the good safety practices on this project that reflect well on the firm and may influence future clients.
[transition_comments:protected] =>
[external_link:protected] =>
[consol_link:protected] => http://www.cpwrconstructionsolutions.org/index.php
[more_like_this:protected] => d000989,d001351,d001362,d000652, d001101, d000931, d001395
[permission_given_by:protected] =>
[published:protected] => T
[billable:protected] => F
[img_name:protected] =>
[img_ext:protected] => jpg
[img_width:protected] =>
[img_height:protected] =>
[img_credit:protected] => Hoar Construction, Photo by Neil Lippy
[img_practice:protected] => good
[vid_source_id:protected] =>
[vid_running_time:protected] =>
[vid_intended_audience:protected] =>
[vid_acquisition_info:protected] =>
[vid_cost:protected] =>
[vid_producer:protected] =>
[vid_filename:protected] =>
[vid_filename_downloadable:protected] =>
[date_summary:protected] => November 2015
[date_permission_requested:protected] =>
[date_permission_received:protected] =>
[date_review_needed:protected] =>
[date_received:protected] => 03/02/16
[date_completed:protected] => 03/02/16
[date_billed:protected] =>
[date_modified:protected] => 01/30/23
[collBokExports:protected] =>
[lastBokExportCriteria:BaseElcoshItem:private] =>
[alreadyInSave:protected] =>
[alreadyInValidation:protected] =>
[validationFailures:protected] => Array
(
)
[_new:BaseObject:private] =>
[_deleted:BaseObject:private] =>
[modifiedColumns:protected] => Array
(
)
)
)
[4] => Search_Result Object
(
[title] => Scaffolding at top of large column
[image] => /record/images/3994-p.jpg
[blurb] => This shot shows innovative guarding around the top of a large concrete column in the base of a high rise structure going up....
[category] => Array
(
[0] => 15
[1] => 21
[2] => 47
[3] => 51
[4] => 63
[5] => 78
[6] => 79
[7] => 80
[8] => 62
[9] => 87
[10] => 97
[11] => 56
[12] => 64
[13] => 74
)
[labels] => Array
(
[0] => Falls
[1] => Work Environment
[2] => Hazards
[3] => Scaffolds
[6] => Bricklayer
[7] => Trades
[8] => Cement Mason
[10] => Reinforcing Ironworker
[12] => Roofer/Waterproofer
[14] => Scaffold Erector
[16] => Sheetmetal Worker
[18] => Structural Ironworker
[20] => Commercial & Institutional
[21] => Jobsites
[22] => Images
[23] => Media
[24] => Media & Documents
[25] => Elevator Constructor
[27] => Laborer
[29] => Pile Driver
)
[type] => Images
[sub_category] =>
[url] => /image/3994/i002689/Scaffolding%2Bat%2Btop%2Bof%2Blarge%2Bcolumn.html
[item:protected] => ImageRecord Object
(
[records:protected] => Array
(
)
[recordId:protected] =>
[searchWordClass:protected] =>
[searchWordPeerClass:protected] =>
[bok_record:protected] =>
[authors:protected] =>
[organizations:protected] =>
[collections:protected] =>
[categories:protected] => Array
(
[15] => Category Object
(
[languages:protected] =>
[bok_resources:protected] =>
[bok_topics:protected] =>
[bok_keywords:protected] =>
[id:protected] => 15
[type:protected] => category
[parent:protected] => 7
[label:protected] => Falls
[alreadyInSave:protected] =>
[alreadyInValidation:protected] =>
[validationFailures:protected] => Array
(
)
[_new:BaseObject:private] =>
[_deleted:BaseObject:private] =>
[modifiedColumns:protected] => Array
(
)
)
[21] => Category Object
(
[languages:protected] =>
[bok_resources:protected] =>
[bok_topics:protected] =>
[bok_keywords:protected] =>
[id:protected] => 21
[type:protected] => category
[parent:protected] => 7
[label:protected] => Scaffolds
[alreadyInSave:protected] =>
[alreadyInValidation:protected] =>
[validationFailures:protected] => Array
(
)
[_new:BaseObject:private] =>
[_deleted:BaseObject:private] =>
[modifiedColumns:protected] => Array
(
)
)
[47] => Category Object
(
[languages:protected] =>
[bok_resources:protected] =>
[bok_topics:protected] =>
[bok_keywords:protected] =>
[id:protected] => 47
[type:protected] => category
[parent:protected] => 2
[label:protected] => Bricklayer
[alreadyInSave:protected] =>
[alreadyInValidation:protected] =>
[validationFailures:protected] => Array
(
)
[_new:BaseObject:private] =>
[_deleted:BaseObject:private] =>
[modifiedColumns:protected] => Array
(
)
)
[51] => Category Object
(
[languages:protected] =>
[bok_resources:protected] =>
[bok_topics:protected] =>
[bok_keywords:protected] =>
[id:protected] => 51
[type:protected] => category
[parent:protected] => 2
[label:protected] => Cement Mason
[alreadyInSave:protected] =>
[alreadyInValidation:protected] =>
[validationFailures:protected] => Array
(
)
[_new:BaseObject:private] =>
[_deleted:BaseObject:private] =>
[modifiedColumns:protected] => Array
(
)
)
[63] => Category Object
(
[languages:protected] =>
[bok_resources:protected] =>
[bok_topics:protected] =>
[bok_keywords:protected] =>
[id:protected] => 63
[type:protected] => category
[parent:protected] => 2
[label:protected] => Reinforcing Ironworker
[alreadyInSave:protected] =>
[alreadyInValidation:protected] =>
[validationFailures:protected] => Array
(
)
[_new:BaseObject:private] =>
[_deleted:BaseObject:private] =>
[modifiedColumns:protected] => Array
(
)
)
[78] => Category Object
(
[languages:protected] =>
[bok_resources:protected] =>
[bok_topics:protected] =>
[bok_keywords:protected] =>
[id:protected] => 78
[type:protected] => category
[parent:protected] => 2
[label:protected] => Roofer/Waterproofer
[alreadyInSave:protected] =>
[alreadyInValidation:protected] =>
[validationFailures:protected] => Array
(
)
[_new:BaseObject:private] =>
[_deleted:BaseObject:private] =>
[modifiedColumns:protected] => Array
(
)
)
[79] => Category Object
(
[languages:protected] =>
[bok_resources:protected] =>
[bok_topics:protected] =>
[bok_keywords:protected] =>
[id:protected] => 79
[type:protected] => category
[parent:protected] => 2
[label:protected] => Scaffold Erector
[alreadyInSave:protected] =>
[alreadyInValidation:protected] =>
[validationFailures:protected] => Array
(
)
[_new:BaseObject:private] =>
[_deleted:BaseObject:private] =>
[modifiedColumns:protected] => Array
(
)
)
[80] => Category Object
(
[languages:protected] =>
[bok_resources:protected] =>
[bok_topics:protected] =>
[bok_keywords:protected] =>
[id:protected] => 80
[type:protected] => category
[parent:protected] => 2
[label:protected] => Sheetmetal Worker
[alreadyInSave:protected] =>
[alreadyInValidation:protected] =>
[validationFailures:protected] => Array
(
)
[_new:BaseObject:private] =>
[_deleted:BaseObject:private] =>
[modifiedColumns:protected] => Array
(
)
)
[62] => Category Object
(
[languages:protected] =>
[bok_resources:protected] =>
[bok_topics:protected] =>
[bok_keywords:protected] =>
[id:protected] => 62
[type:protected] => category
[parent:protected] => 2
[label:protected] => Structural Ironworker
[alreadyInSave:protected] =>
[alreadyInValidation:protected] =>
[validationFailures:protected] => Array
(
)
[_new:BaseObject:private] =>
[_deleted:BaseObject:private] =>
[modifiedColumns:protected] => Array
(
)
)
[87] => Category Object
(
[languages:protected] =>
[bok_resources:protected] =>
[bok_topics:protected] =>
[bok_keywords:protected] =>
[id:protected] => 87
[type:protected] => category
[parent:protected] => 3
[label:protected] => Commercial & Institutional
[alreadyInSave:protected] =>
[alreadyInValidation:protected] =>
[validationFailures:protected] => Array
(
)
[_new:BaseObject:private] =>
[_deleted:BaseObject:private] =>
[modifiedColumns:protected] => Array
(
)
)
[97] => Category Object
(
[languages:protected] =>
[bok_resources:protected] =>
[bok_topics:protected] =>
[bok_keywords:protected] =>
[id:protected] => 97
[type:protected] => category
[parent:protected] => 5
[label:protected] => Images
[alreadyInSave:protected] =>
[alreadyInValidation:protected] =>
[validationFailures:protected] => Array
(
)
[_new:BaseObject:private] =>
[_deleted:BaseObject:private] =>
[modifiedColumns:protected] => Array
(
)
)
[56] => Category Object
(
[languages:protected] =>
[bok_resources:protected] =>
[bok_topics:protected] =>
[bok_keywords:protected] =>
[id:protected] => 56
[type:protected] => category
[parent:protected] => 2
[label:protected] => Elevator Constructor
[alreadyInSave:protected] =>
[alreadyInValidation:protected] =>
[validationFailures:protected] => Array
(
)
[_new:BaseObject:private] =>
[_deleted:BaseObject:private] =>
[modifiedColumns:protected] => Array
(
)
)
[64] => Category Object
(
[languages:protected] =>
[bok_resources:protected] =>
[bok_topics:protected] =>
[bok_keywords:protected] =>
[id:protected] => 64
[type:protected] => category
[parent:protected] => 2
[label:protected] => Laborer
[alreadyInSave:protected] =>
[alreadyInValidation:protected] =>
[validationFailures:protected] => Array
(
)
[_new:BaseObject:private] =>
[_deleted:BaseObject:private] =>
[modifiedColumns:protected] => Array
(
)
)
[74] => Category Object
(
[languages:protected] =>
[bok_resources:protected] =>
[bok_topics:protected] =>
[bok_keywords:protected] =>
[id:protected] => 74
[type:protected] => category
[parent:protected] => 2
[label:protected] => Pile Driver
[alreadyInSave:protected] =>
[alreadyInValidation:protected] =>
[validationFailures:protected] => Array
(
)
[_new:BaseObject:private] =>
[_deleted:BaseObject:private] =>
[modifiedColumns:protected] => Array
(
)
)
)
[categories_initialized:protected] => 1
[mapped_items:protected] =>
[content:protected] =>
[files:protected] =>
[language:protected] => Language Object
(
[id:protected] => 1
[code:protected] => en
[name:protected] => English
[alreadyInSave:protected] =>
[alreadyInValidation:protected] =>
[validationFailures:protected] => Array
(
)
[_new:BaseObject:private] =>
[_deleted:BaseObject:private] =>
[modifiedColumns:protected] => Array
(
)
)
[old_record:protected] =>
[id:protected] => 3994
[old_id:protected] =>
[elcosh_id:protected] => i002689
[type:protected] => image
[display_type:protected] => Image
[user_id:protected] => 0
[language_id:protected] => 1
[tagging_id:protected] => Bruce Lippy
[priority_id:protected] => 1
[title:protected] => Scaffolding at top of large column
[total_pages:protected] => 0
[billed_pages:protected] => 0
[publication_number:protected] =>
[part_of:protected] =>
[keywords:protected] => Guardrail, railing, fall prevention, falls
[comments:protected] =>
[summary:protected] => This shot shows innovative guarding around the top of a large concrete column in the base of a high rise structure going up.
[transition_comments:protected] =>
[external_link:protected] =>
[consol_link:protected] => http://www.cpwrconstructionsolutions.org/masonry/solution/8/adjustable-tower-scaffold.html
[more_like_this:protected] => c1002680,i002662,d000608,d001255
[permission_given_by:protected] =>
[published:protected] => T
[billable:protected] => F
[img_name:protected] =>
[img_ext:protected] => jpg
[img_width:protected] =>
[img_height:protected] =>
[img_credit:protected] => Photo by Pam Susi
[img_practice:protected] => good
[vid_source_id:protected] =>
[vid_running_time:protected] =>
[vid_intended_audience:protected] =>
[vid_acquisition_info:protected] =>
[vid_cost:protected] =>
[vid_producer:protected] =>
[vid_filename:protected] =>
[vid_filename_downloadable:protected] =>
[date_summary:protected] => January 2016
[date_permission_requested:protected] =>
[date_permission_received:protected] =>
[date_review_needed:protected] =>
[date_received:protected] => 02/01/16
[date_completed:protected] => 02/01/16
[date_billed:protected] =>
[date_modified:protected] => 02/01/16
[collBokExports:protected] =>
[lastBokExportCriteria:BaseElcoshItem:private] =>
[alreadyInSave:protected] =>
[alreadyInValidation:protected] =>
[validationFailures:protected] => Array
(
)
[_new:BaseObject:private] =>
[_deleted:BaseObject:private] =>
[modifiedColumns:protected] => Array
(
)
)
)
[5] => Search_Result Object
(
[title] => Construction bracing
[image] => /record/images/3995-p.jpg
[blurb] => This shows structural support that prevents collapses during construction....
[category] => Array
(
[0] => 12
[1] => 15
[2] => 21
[3] => 49
[4] => 51
[5] => 55
[6] => 56
[7] => 60
[8] => 64
[9] => 68
[10] => 74
[11] => 63
[12] => 78
[13] => 79
[14] => 80
[15] => 62
[16] => 87
[17] => 90
[18] => 97
)
[labels] => Array
(
[0] => Crushed/Struck By
[1] => Work Environment
[2] => Hazards
[3] => Falls
[6] => Scaffolds
[9] => Carpenter
[10] => Trades
[11] => Cement Mason
[13] => Electrical Worker
[15] => Elevator Constructor
[17] => HVAC
[19] => Laborer
[21] => Maintenance Worker
[23] => Pile Driver
[25] => Reinforcing Ironworker
[27] => Roofer/Waterproofer
[29] => Scaffold Erector
[31] => Sheetmetal Worker
[33] => Structural Ironworker
[35] => Commercial & Institutional
[36] => Jobsites
[37] => Industrial
[39] => Images
[40] => Media
[41] => Media & Documents
)
[type] => Images
[sub_category] =>
[url] => /image/3995/i002690/Construction%2Bbracing.html
[item:protected] => ImageRecord Object
(
[records:protected] => Array
(
)
[recordId:protected] =>
[searchWordClass:protected] =>
[searchWordPeerClass:protected] =>
[bok_record:protected] =>
[authors:protected] =>
[organizations:protected] =>
[collections:protected] =>
[categories:protected] => Array
(
[12] => Category Object
(
[languages:protected] =>
[bok_resources:protected] =>
[bok_topics:protected] =>
[bok_keywords:protected] =>
[id:protected] => 12
[type:protected] => category
[parent:protected] => 7
[label:protected] => Crushed/Struck By
[alreadyInSave:protected] =>
[alreadyInValidation:protected] =>
[validationFailures:protected] => Array
(
)
[_new:BaseObject:private] =>
[_deleted:BaseObject:private] =>
[modifiedColumns:protected] => Array
(
)
)
[15] => Category Object
(
[languages:protected] =>
[bok_resources:protected] =>
[bok_topics:protected] =>
[bok_keywords:protected] =>
[id:protected] => 15
[type:protected] => category
[parent:protected] => 7
[label:protected] => Falls
[alreadyInSave:protected] =>
[alreadyInValidation:protected] =>
[validationFailures:protected] => Array
(
)
[_new:BaseObject:private] =>
[_deleted:BaseObject:private] =>
[modifiedColumns:protected] => Array
(
)
)
[21] => Category Object
(
[languages:protected] =>
[bok_resources:protected] =>
[bok_topics:protected] =>
[bok_keywords:protected] =>
[id:protected] => 21
[type:protected] => category
[parent:protected] => 7
[label:protected] => Scaffolds
[alreadyInSave:protected] =>
[alreadyInValidation:protected] =>
[validationFailures:protected] => Array
(
)
[_new:BaseObject:private] =>
[_deleted:BaseObject:private] =>
[modifiedColumns:protected] => Array
(
)
)
[49] => Category Object
(
[languages:protected] =>
[bok_resources:protected] =>
[bok_topics:protected] =>
[bok_keywords:protected] =>
[id:protected] => 49
[type:protected] => category
[parent:protected] => 2
[label:protected] => Carpenter
[alreadyInSave:protected] =>
[alreadyInValidation:protected] =>
[validationFailures:protected] => Array
(
)
[_new:BaseObject:private] =>
[_deleted:BaseObject:private] =>
[modifiedColumns:protected] => Array
(
)
)
[51] => Category Object
(
[languages:protected] =>
[bok_resources:protected] =>
[bok_topics:protected] =>
[bok_keywords:protected] =>
[id:protected] => 51
[type:protected] => category
[parent:protected] => 2
[label:protected] => Cement Mason
[alreadyInSave:protected] =>
[alreadyInValidation:protected] =>
[validationFailures:protected] => Array
(
)
[_new:BaseObject:private] =>
[_deleted:BaseObject:private] =>
[modifiedColumns:protected] => Array
(
)
)
[55] => Category Object
(
[languages:protected] =>
[bok_resources:protected] =>
[bok_topics:protected] =>
[bok_keywords:protected] =>
[id:protected] => 55
[type:protected] => category
[parent:protected] => 2
[label:protected] => Electrical Worker
[alreadyInSave:protected] =>
[alreadyInValidation:protected] =>
[validationFailures:protected] => Array
(
)
[_new:BaseObject:private] =>
[_deleted:BaseObject:private] =>
[modifiedColumns:protected] => Array
(
)
)
[56] => Category Object
(
[languages:protected] =>
[bok_resources:protected] =>
[bok_topics:protected] =>
[bok_keywords:protected] =>
[id:protected] => 56
[type:protected] => category
[parent:protected] => 2
[label:protected] => Elevator Constructor
[alreadyInSave:protected] =>
[alreadyInValidation:protected] =>
[validationFailures:protected] => Array
(
)
[_new:BaseObject:private] =>
[_deleted:BaseObject:private] =>
[modifiedColumns:protected] => Array
(
)
)
[60] => Category Object
(
[languages:protected] =>
[bok_resources:protected] =>
[bok_topics:protected] =>
[bok_keywords:protected] =>
[id:protected] => 60
[type:protected] => category
[parent:protected] => 2
[label:protected] => HVAC
[alreadyInSave:protected] =>
[alreadyInValidation:protected] =>
[validationFailures:protected] => Array
(
)
[_new:BaseObject:private] =>
[_deleted:BaseObject:private] =>
[modifiedColumns:protected] => Array
(
)
)
[64] => Category Object
(
[languages:protected] =>
[bok_resources:protected] =>
[bok_topics:protected] =>
[bok_keywords:protected] =>
[id:protected] => 64
[type:protected] => category
[parent:protected] => 2
[label:protected] => Laborer
[alreadyInSave:protected] =>
[alreadyInValidation:protected] =>
[validationFailures:protected] => Array
(
)
[_new:BaseObject:private] =>
[_deleted:BaseObject:private] =>
[modifiedColumns:protected] => Array
(
)
)
[68] => Category Object
(
[languages:protected] =>
[bok_resources:protected] =>
[bok_topics:protected] =>
[bok_keywords:protected] =>
[id:protected] => 68
[type:protected] => category
[parent:protected] => 2
[label:protected] => Maintenance Worker
[alreadyInSave:protected] =>
[alreadyInValidation:protected] =>
[validationFailures:protected] => Array
(
)
[_new:BaseObject:private] =>
[_deleted:BaseObject:private] =>
[modifiedColumns:protected] => Array
(
)
)
[74] => Category Object
(
[languages:protected] =>
[bok_resources:protected] =>
[bok_topics:protected] =>
[bok_keywords:protected] =>
[id:protected] => 74
[type:protected] => category
[parent:protected] => 2
[label:protected] => Pile Driver
[alreadyInSave:protected] =>
[alreadyInValidation:protected] =>
[validationFailures:protected] => Array
(
)
[_new:BaseObject:private] =>
[_deleted:BaseObject:private] =>
[modifiedColumns:protected] => Array
(
)
)
[63] => Category Object
(
[languages:protected] =>
[bok_resources:protected] =>
[bok_topics:protected] =>
[bok_keywords:protected] =>
[id:protected] => 63
[type:protected] => category
[parent:protected] => 2
[label:protected] => Reinforcing Ironworker
[alreadyInSave:protected] =>
[alreadyInValidation:protected] =>
[validationFailures:protected] => Array
(
)
[_new:BaseObject:private] =>
[_deleted:BaseObject:private] =>
[modifiedColumns:protected] => Array
(
)
)
[78] => Category Object
(
[languages:protected] =>
[bok_resources:protected] =>
[bok_topics:protected] =>
[bok_keywords:protected] =>
[id:protected] => 78
[type:protected] => category
[parent:protected] => 2
[label:protected] => Roofer/Waterproofer
[alreadyInSave:protected] =>
[alreadyInValidation:protected] =>
[validationFailures:protected] => Array
(
)
[_new:BaseObject:private] =>
[_deleted:BaseObject:private] =>
[modifiedColumns:protected] => Array
(
)
)
[79] => Category Object
(
[languages:protected] =>
[bok_resources:protected] =>
[bok_topics:protected] =>
[bok_keywords:protected] =>
[id:protected] => 79
[type:protected] => category
[parent:protected] => 2
[label:protected] => Scaffold Erector
[alreadyInSave:protected] =>
[alreadyInValidation:protected] =>
[validationFailures:protected] => Array
(
)
[_new:BaseObject:private] =>
[_deleted:BaseObject:private] =>
[modifiedColumns:protected] => Array
(
)
)
[80] => Category Object
(
[languages:protected] =>
[bok_resources:protected] =>
[bok_topics:protected] =>
[bok_keywords:protected] =>
[id:protected] => 80
[type:protected] => category
[parent:protected] => 2
[label:protected] => Sheetmetal Worker
[alreadyInSave:protected] =>
[alreadyInValidation:protected] =>
[validationFailures:protected] => Array
(
)
[_new:BaseObject:private] =>
[_deleted:BaseObject:private] =>
[modifiedColumns:protected] => Array
(
)
)
[62] => Category Object
(
[languages:protected] =>
[bok_resources:protected] =>
[bok_topics:protected] =>
[bok_keywords:protected] =>
[id:protected] => 62
[type:protected] => category
[parent:protected] => 2
[label:protected] => Structural Ironworker
[alreadyInSave:protected] =>
[alreadyInValidation:protected] =>
[validationFailures:protected] => Array
(
)
[_new:BaseObject:private] =>
[_deleted:BaseObject:private] =>
[modifiedColumns:protected] => Array
(
)
)
[87] => Category Object
(
[languages:protected] =>
[bok_resources:protected] =>
[bok_topics:protected] =>
[bok_keywords:protected] =>
[id:protected] => 87
[type:protected] => category
[parent:protected] => 3
[label:protected] => Commercial & Institutional
[alreadyInSave:protected] =>
[alreadyInValidation:protected] =>
[validationFailures:protected] => Array
(
)
[_new:BaseObject:private] =>
[_deleted:BaseObject:private] =>
[modifiedColumns:protected] => Array
(
)
)
[90] => Category Object
(
[languages:protected] =>
[bok_resources:protected] =>
[bok_topics:protected] =>
[bok_keywords:protected] =>
[id:protected] => 90
[type:protected] => category
[parent:protected] => 3
[label:protected] => Industrial
[alreadyInSave:protected] =>
[alreadyInValidation:protected] =>
[validationFailures:protected] => Array
(
)
[_new:BaseObject:private] =>
[_deleted:BaseObject:private] =>
[modifiedColumns:protected] => Array
(
)
)
[97] => Category Object
(
[languages:protected] =>
[bok_resources:protected] =>
[bok_topics:protected] =>
[bok_keywords:protected] =>
[id:protected] => 97
[type:protected] => category
[parent:protected] => 5
[label:protected] => Images
[alreadyInSave:protected] =>
[alreadyInValidation:protected] =>
[validationFailures:protected] => Array
(
)
[_new:BaseObject:private] =>
[_deleted:BaseObject:private] =>
[modifiedColumns:protected] => Array
(
)
)
)
[categories_initialized:protected] => 1
[mapped_items:protected] =>
[content:protected] =>
[files:protected] =>
[language:protected] => Language Object
(
[id:protected] => 1
[code:protected] => en
[name:protected] => English
[alreadyInSave:protected] =>
[alreadyInValidation:protected] =>
[validationFailures:protected] => Array
(
)
[_new:BaseObject:private] =>
[_deleted:BaseObject:private] =>
[modifiedColumns:protected] => Array
(
)
)
[old_record:protected] =>
[id:protected] => 3995
[old_id:protected] =>
[elcosh_id:protected] => i002690
[type:protected] => image
[display_type:protected] => Image
[user_id:protected] => 0
[language_id:protected] => 1
[tagging_id:protected] => Bruce Lippy
[priority_id:protected] => 1
[title:protected] => Construction bracing
[total_pages:protected] => 0
[billed_pages:protected] => 0
[publication_number:protected] =>
[part_of:protected] =>
[keywords:protected] => Bracing, support, scaffold
[comments:protected] =>
[summary:protected] => This shows structural support that prevents collapses during construction.
[transition_comments:protected] =>
[external_link:protected] =>
[consol_link:protected] => http://www.cpwrconstructionsolutions.org/masonry/solution/8/adjustable-tower-scaffold.html
[more_like_this:protected] => i002660
[permission_given_by:protected] =>
[published:protected] => T
[billable:protected] => F
[img_name:protected] =>
[img_ext:protected] => jpg
[img_width:protected] =>
[img_height:protected] =>
[img_credit:protected] => Photo by Pam Susi
[img_practice:protected] => good
[vid_source_id:protected] =>
[vid_running_time:protected] =>
[vid_intended_audience:protected] =>
[vid_acquisition_info:protected] =>
[vid_cost:protected] =>
[vid_producer:protected] =>
[vid_filename:protected] =>
[vid_filename_downloadable:protected] =>
[date_summary:protected] => January 2016
[date_permission_requested:protected] =>
[date_permission_received:protected] =>
[date_review_needed:protected] =>
[date_received:protected] => 02/01/16
[date_completed:protected] => 02/01/16
[date_billed:protected] =>
[date_modified:protected] => 02/01/16
[collBokExports:protected] =>
[lastBokExportCriteria:BaseElcoshItem:private] =>
[alreadyInSave:protected] =>
[alreadyInValidation:protected] =>
[validationFailures:protected] => Array
(
)
[_new:BaseObject:private] =>
[_deleted:BaseObject:private] =>
[modifiedColumns:protected] => Array
(
)
)
)
)
[preview_mode] =>
[description] => Toolbox talks have been the main tool for communicating safety information on construction jobs for decades.
Unfortunately, there has been little research on what makes for effective toolbox talks. The IUOE National
Training Fund worked with OSHA and NIOSH to make sure their series of 24 Focus Four toolbox talks were based on the best recommendations for effective design. These toolbox talks accompany an entire package of training materials, but can be used alone. This guide points out the key features of these toolbox talks and how best to deliver them.
[keywords] => toolbox talks, tailgate talks
[related_items] => Array
(
[Toolbox Talks] => Array
(
[0] => DocumentRecord Object
(
[records:protected] => Array
(
)
[recordId:protected] =>
[searchWordClass:protected] =>
[searchWordPeerClass:protected] =>
[bok_record:protected] =>
[authors:protected] =>
[organizations:protected] =>
[collections:protected] =>
[categories:protected] =>
[categories_initialized:protected] =>
[mapped_items:protected] =>
[content:protected] =>
[files:protected] =>
[language:protected] => Language Object
(
[id:protected] => 1
[code:protected] => en
[name:protected] => English
[alreadyInSave:protected] =>
[alreadyInValidation:protected] =>
[validationFailures:protected] => Array
(
)
[_new:BaseObject:private] =>
[_deleted:BaseObject:private] =>
[modifiedColumns:protected] => Array
(
)
)
[old_record:protected] =>
[id:protected] => 1605
[old_id:protected] => 1262
[elcosh_id:protected] => d001137
[type:protected] => document
[display_type:protected] => HTML w/ PDF
[user_id:protected] =>
[language_id:protected] => 1
[tagging_id:protected] => Garber
[priority_id:protected] => 1
[title:protected] => Focus Four Toolbox Talks, Module 1 – Falls, Talk #2 – Falls from debris piles?
[total_pages:protected] => 1
[billed_pages:protected] => 1
[publication_number:protected] =>
[part_of:protected] =>
[keywords:protected] => disaster response, hazard clean-up, uneven surface, disaster site, disaster clean-up
[comments:protected] =>
[summary:protected] => A toolbox talk on preventing falls from debris piles. Includes questions to ask, an incident to discuss with images, and a place to record questions the trainer would like to ask about the incident. Part of a collection. Click on the 'collection' button to access the other items.
[transition_comments:protected] =>
[external_link:protected] =>
[consol_link:protected] => http://www.cpwrconstructionsolutions.org/roofing/hazard/1463/install-asphalt-roofs-fall-from-heights.html
[more_like_this:protected] => a000081,d000478,d000530
[permission_given_by:protected] =>
[published:protected] => T
[billable:protected] => F
[img_name:protected] =>
[img_ext:protected] =>
[img_width:protected] =>
[img_height:protected] =>
[img_credit:protected] =>
[img_practice:protected] =>
[vid_source_id:protected] =>
[vid_running_time:protected] =>
[vid_intended_audience:protected] =>
[vid_acquisition_info:protected] =>
[vid_cost:protected] =>
[vid_producer:protected] =>
[vid_filename:protected] =>
[vid_filename_downloadable:protected] =>
[date_summary:protected] =>
[date_permission_requested:protected] =>
[date_permission_received:protected] =>
[date_review_needed:protected] =>
[date_received:protected] => 02/15/12
[date_completed:protected] => 03/19/12
[date_billed:protected] =>
[date_modified:protected] => 07/10/12
[collBokExports:protected] =>
[lastBokExportCriteria:BaseElcoshItem:private] =>
[alreadyInSave:protected] =>
[alreadyInValidation:protected] =>
[validationFailures:protected] => Array
(
)
[_new:BaseObject:private] =>
[_deleted:BaseObject:private] =>
[modifiedColumns:protected] => Array
(
)
)
[1] => DocumentRecord Object
(
[records:protected] => Array
(
)
[recordId:protected] =>
[searchWordClass:protected] =>
[searchWordPeerClass:protected] =>
[bok_record:protected] =>
[authors:protected] =>
[organizations:protected] =>
[collections:protected] =>
[categories:protected] =>
[categories_initialized:protected] =>
[mapped_items:protected] =>
[content:protected] =>
[files:protected] =>
[language:protected] => Language Object
(
[id:protected] => 1
[code:protected] => en
[name:protected] => English
[alreadyInSave:protected] =>
[alreadyInValidation:protected] =>
[validationFailures:protected] => Array
(
)
[_new:BaseObject:private] =>
[_deleted:BaseObject:private] =>
[modifiedColumns:protected] => Array
(
)
)
[old_record:protected] =>
[id:protected] => 1610
[old_id:protected] => 1271
[elcosh_id:protected] => d001146
[type:protected] => document
[display_type:protected] => HTML w/ PDF
[user_id:protected] => 0
[language_id:protected] => 1
[tagging_id:protected] => Garber
[priority_id:protected] => 1
[title:protected] => Focus Four Toolbox Talks, Module 2 – Struck-by, Talk #5 – Rigging and Securing Loads
[total_pages:protected] => 1
[billed_pages:protected] => 1
[publication_number:protected] =>
[part_of:protected] =>
[keywords:protected] => rigging, lift loads, loading areas, chains
[comments:protected] =>
[summary:protected] => A toolbox talk on preventing struck-by incidents caused by not securing loads properly. Includes questions to ask, an incident to discuss with images, and a place to record questions the trainer would like to ask about the incident. Part of a collection. Click on the 'collection' button to access the other items.
[transition_comments:protected] =>
[external_link:protected] =>
[consol_link:protected] => http://www.cpwrconstructionsolutions.org/heavy_equipment/hazard/1591/move-equipment-to-from-and-between-sites-work-zone-struck-by-injuries-and-fatalities.html
[more_like_this:protected] => d000144,d000360,d000873
[permission_given_by:protected] =>
[published:protected] => T
[billable:protected] => F
[img_name:protected] =>
[img_ext:protected] =>
[img_width:protected] =>
[img_height:protected] =>
[img_credit:protected] =>
[img_practice:protected] =>
[vid_source_id:protected] =>
[vid_running_time:protected] =>
[vid_intended_audience:protected] =>
[vid_acquisition_info:protected] =>
[vid_cost:protected] =>
[vid_producer:protected] =>
[vid_filename:protected] =>
[vid_filename_downloadable:protected] =>
[date_summary:protected] =>
[date_permission_requested:protected] =>
[date_permission_received:protected] =>
[date_review_needed:protected] =>
[date_received:protected] => 02/15/12
[date_completed:protected] => 03/28/12
[date_billed:protected] =>
[date_modified:protected] => 05/12/14
[collBokExports:protected] =>
[lastBokExportCriteria:BaseElcoshItem:private] =>
[alreadyInSave:protected] =>
[alreadyInValidation:protected] =>
[validationFailures:protected] => Array
(
)
[_new:BaseObject:private] =>
[_deleted:BaseObject:private] =>
[modifiedColumns:protected] => Array
(
)
)
[2] => DocumentRecord Object
(
[records:protected] => Array
(
)
[recordId:protected] =>
[searchWordClass:protected] =>
[searchWordPeerClass:protected] =>
[bok_record:protected] =>
[authors:protected] =>
[organizations:protected] =>
[collections:protected] =>
[categories:protected] =>
[categories_initialized:protected] =>
[mapped_items:protected] =>
[content:protected] =>
[files:protected] =>
[language:protected] => Language Object
(
[id:protected] => 1
[code:protected] => en
[name:protected] => English
[alreadyInSave:protected] =>
[alreadyInValidation:protected] =>
[validationFailures:protected] => Array
(
)
[_new:BaseObject:private] =>
[_deleted:BaseObject:private] =>
[modifiedColumns:protected] => Array
(
)
)
[old_record:protected] =>
[id:protected] => 1645
[old_id:protected] => 1274
[elcosh_id:protected] => d001149
[type:protected] => document
[display_type:protected] => HTML w/ PDF
[user_id:protected] => 0
[language_id:protected] => 1
[tagging_id:protected] => Garber
[priority_id:protected] => 1
[title:protected] => Focus Four Toolbox Talks, Module 3 – Caught-in/between, Talk #2 – Trenches & Heavy Equipment
[total_pages:protected] => 1
[billed_pages:protected] => 1
[publication_number:protected] =>
[part_of:protected] =>
[keywords:protected] => back-up alarms, spotter, soil cave-in, spoil pikes, ROPs, trenching, rain
[comments:protected] =>
[summary:protected] => A toolbox talk on preventing incidents involving trenches such as trench collapse. Includes questions to ask, an incident to discuss with images, and a place to record questions the trainer would like to ask about the incident. Part of a collection. Click on the 'collection' button to access the other items.
[transition_comments:protected] =>
[external_link:protected] =>
[consol_link:protected] =>
[more_like_this:protected] => d000019,d000035,d000168
[permission_given_by:protected] =>
[published:protected] => T
[billable:protected] => F
[img_name:protected] =>
[img_ext:protected] =>
[img_width:protected] =>
[img_height:protected] =>
[img_credit:protected] =>
[img_practice:protected] =>
[vid_source_id:protected] =>
[vid_running_time:protected] =>
[vid_intended_audience:protected] =>
[vid_acquisition_info:protected] =>
[vid_cost:protected] =>
[vid_producer:protected] =>
[vid_filename:protected] =>
[vid_filename_downloadable:protected] =>
[date_summary:protected] =>
[date_permission_requested:protected] =>
[date_permission_received:protected] =>
[date_review_needed:protected] =>
[date_received:protected] => 02/15/12
[date_completed:protected] => 04/02/12
[date_billed:protected] =>
[date_modified:protected] => 05/23/23
[collBokExports:protected] =>
[lastBokExportCriteria:BaseElcoshItem:private] =>
[alreadyInSave:protected] =>
[alreadyInValidation:protected] =>
[validationFailures:protected] => Array
(
)
[_new:BaseObject:private] =>
[_deleted:BaseObject:private] =>
[modifiedColumns:protected] => Array
(
)
)
[3] => DocumentRecord Object
(
[records:protected] => Array
(
)
[recordId:protected] =>
[searchWordClass:protected] =>
[searchWordPeerClass:protected] =>
[bok_record:protected] =>
[authors:protected] =>
[organizations:protected] =>
[collections:protected] =>
[categories:protected] =>
[categories_initialized:protected] =>
[mapped_items:protected] =>
[content:protected] =>
[files:protected] =>
[language:protected] => Language Object
(
[id:protected] => 1
[code:protected] => en
[name:protected] => English
[alreadyInSave:protected] =>
[alreadyInValidation:protected] =>
[validationFailures:protected] => Array
(
)
[_new:BaseObject:private] =>
[_deleted:BaseObject:private] =>
[modifiedColumns:protected] => Array
(
)
)
[old_record:protected] =>
[id:protected] => 1654
[old_id:protected] => 1284
[elcosh_id:protected] => d001159
[type:protected] => document
[display_type:protected] => HTML w/ PDF
[user_id:protected] => 0
[language_id:protected] => 1
[tagging_id:protected] => Garber
[priority_id:protected] => 1
[title:protected] => Focus Four Toolbox Talks, Module 4 – Electrocutions, Talk #6 – Hazards on Disaster Sites
[total_pages:protected] => 1
[billed_pages:protected] => 1
[publication_number:protected] =>
[part_of:protected] =>
[keywords:protected] => powerlines, underground, utilities, generators, wet conditions, GFCIs, energized lines, disasters, emergency response
[comments:protected] =>
[summary:protected] => A toolbox talk on how to avoid electrocution on a disaster site. Includes questions to ask, an incident to discuss with images, and a place to record questions the trainer would like to ask about the incident. Part of a collection. Click on the 'collection' button to access the other items.
[transition_comments:protected] =>
[external_link:protected] =>
[consol_link:protected] => http://www.cpwrconstructionsolutions.org/electrical/hazard/1138/install-and-repair-high-voltage-lines-transformers-switches-electrical-shocks-burns-and-or-electrocution.html
[more_like_this:protected] => d000135,d000361,d000437
[permission_given_by:protected] =>
[published:protected] => T
[billable:protected] => F
[img_name:protected] =>
[img_ext:protected] =>
[img_width:protected] =>
[img_height:protected] =>
[img_credit:protected] =>
[img_practice:protected] =>
[vid_source_id:protected] =>
[vid_running_time:protected] =>
[vid_intended_audience:protected] =>
[vid_acquisition_info:protected] =>
[vid_cost:protected] =>
[vid_producer:protected] =>
[vid_filename:protected] =>
[vid_filename_downloadable:protected] =>
[date_summary:protected] =>
[date_permission_requested:protected] =>
[date_permission_received:protected] =>
[date_review_needed:protected] =>
[date_received:protected] => 02/15/12
[date_completed:protected] => 04/02/12
[date_billed:protected] =>
[date_modified:protected] => 05/23/23
[collBokExports:protected] =>
[lastBokExportCriteria:BaseElcoshItem:private] =>
[alreadyInSave:protected] =>
[alreadyInValidation:protected] =>
[validationFailures:protected] => Array
(
)
[_new:BaseObject:private] =>
[_deleted:BaseObject:private] =>
[modifiedColumns:protected] => Array
(
)
)
)
)
[collections] => Array
(
[1294] =>
[1295] =>
[1292] =>
[1293] => CollectionRecord Object
(
[collection_items:protected] =>
[records:protected] => Array
(
)
[recordId:protected] =>
[searchWordClass:protected] =>
[searchWordPeerClass:protected] =>
[bok_record:protected] =>
[authors:protected] =>
[organizations:protected] =>
[collections:protected] =>
[categories:protected] =>
[categories_initialized:protected] =>
[mapped_items:protected] =>
[content:protected] =>
[files:protected] =>
[language:protected] =>
[old_record:protected] =>
[id:protected] => 1293
[old_id:protected] =>
[elcosh_id:protected] => c000026
[type:protected] => collection
[display_type:protected] => Collection
[user_id:protected] =>
[language_id:protected] =>
[tagging_id:protected] =>
[priority_id:protected] =>
[title:protected] => Focus Four-Struck By
[total_pages:protected] =>
[billed_pages:protected] =>
[publication_number:protected] =>
[part_of:protected] =>
[keywords:protected] =>
[comments:protected] =>
[summary:protected] => The following are links to all of the items in this collection:
[transition_comments:protected] =>
[external_link:protected] =>
[consol_link:protected] =>
[more_like_this:protected] =>
[permission_given_by:protected] =>
[published:protected] => T
[billable:protected] => F
[img_name:protected] =>
[img_ext:protected] =>
[img_width:protected] =>
[img_height:protected] =>
[img_credit:protected] =>
[img_practice:protected] =>
[vid_source_id:protected] =>
[vid_running_time:protected] =>
[vid_intended_audience:protected] =>
[vid_acquisition_info:protected] =>
[vid_cost:protected] =>
[vid_producer:protected] =>
[vid_filename:protected] =>
[vid_filename_downloadable:protected] =>
[date_summary:protected] =>
[date_permission_requested:protected] =>
[date_permission_received:protected] =>
[date_review_needed:protected] =>
[date_received:protected] => 05/08/12
[date_completed:protected] => 05/08/12
[date_billed:protected] =>
[date_modified:protected] => 05/08/12
[collBokExports:protected] =>
[lastBokExportCriteria:BaseElcoshItem:private] =>
[alreadyInSave:protected] =>
[alreadyInValidation:protected] =>
[validationFailures:protected] => Array
(
)
[_new:BaseObject:private] =>
[_deleted:BaseObject:private] =>
[modifiedColumns:protected] => Array
(
)
)
)
[record] => DocumentRecord Object
(
[records:protected] => Array
(
)
[recordId:protected] =>
[searchWordClass:protected] =>
[searchWordPeerClass:protected] =>
[bok_record:protected] =>
[authors:protected] => Array
(
)
[organizations:protected] => Array
(
[256] => Organization Object
(
[id:protected] => 256
[elcosh_id:protected] => o000276
[user_id:protected] => 14
[province_id:protected] => 0
[country_id:protected] => 0
[title:protected] => IUOE National Training Fund
[address:protected] =>
[postal_code:protected] =>
[city:protected] =>
[department:protected] =>
[phone:protected] => 304-253-8674
[fax:protected] =>
[email:protected] =>
[website:protected] => http://www.iuoeiettc.org
[filename:protected] =>
[about:protected] =>
[comments:protected] =>
[logo_available:protected] => T
[no_details:protected] => F
[date_received:protected] => 2012-02-13
[date_completed:protected] => 2012-02-13
[date_billed:protected] =>
[alreadyInSave:protected] =>
[alreadyInValidation:protected] =>
[validationFailures:protected] => Array
(
)
[_new:BaseObject:private] =>
[_deleted:BaseObject:private] =>
[modifiedColumns:protected] => Array
(
)
)
)
[collections:protected] => Array
(
[1294] =>
[1295] =>
[1292] =>
[1293] => CollectionRecord Object
(
[collection_items:protected] =>
[records:protected] => Array
(
)
[recordId:protected] =>
[searchWordClass:protected] =>
[searchWordPeerClass:protected] =>
[bok_record:protected] =>
[authors:protected] =>
[organizations:protected] =>
[collections:protected] =>
[categories:protected] =>
[categories_initialized:protected] =>
[mapped_items:protected] =>
[content:protected] =>
[files:protected] =>
[language:protected] =>
[old_record:protected] =>
[id:protected] => 1293
[old_id:protected] =>
[elcosh_id:protected] => c000026
[type:protected] => collection
[display_type:protected] => Collection
[user_id:protected] =>
[language_id:protected] =>
[tagging_id:protected] =>
[priority_id:protected] =>
[title:protected] => Focus Four-Struck By
[total_pages:protected] =>
[billed_pages:protected] =>
[publication_number:protected] =>
[part_of:protected] =>
[keywords:protected] =>
[comments:protected] =>
[summary:protected] => The following are links to all of the items in this collection:
[transition_comments:protected] =>
[external_link:protected] =>
[consol_link:protected] =>
[more_like_this:protected] =>
[permission_given_by:protected] =>
[published:protected] => T
[billable:protected] => F
[img_name:protected] =>
[img_ext:protected] =>
[img_width:protected] =>
[img_height:protected] =>
[img_credit:protected] =>
[img_practice:protected] =>
[vid_source_id:protected] =>
[vid_running_time:protected] =>
[vid_intended_audience:protected] =>
[vid_acquisition_info:protected] =>
[vid_cost:protected] =>
[vid_producer:protected] =>
[vid_filename:protected] =>
[vid_filename_downloadable:protected] =>
[date_summary:protected] =>
[date_permission_requested:protected] =>
[date_permission_received:protected] =>
[date_review_needed:protected] =>
[date_received:protected] => 05/08/12
[date_completed:protected] => 05/08/12
[date_billed:protected] =>
[date_modified:protected] => 05/08/12
[collBokExports:protected] =>
[lastBokExportCriteria:BaseElcoshItem:private] =>
[alreadyInSave:protected] =>
[alreadyInValidation:protected] =>
[validationFailures:protected] => Array
(
)
[_new:BaseObject:private] =>
[_deleted:BaseObject:private] =>
[modifiedColumns:protected] => Array
(
)
)
)
[categories:protected] =>
[categories_initialized:protected] =>
[mapped_items:protected] => Array
(
[1605] => DocumentRecord Object
(
[records:protected] => Array
(
)
[recordId:protected] =>
[searchWordClass:protected] =>
[searchWordPeerClass:protected] =>
[bok_record:protected] =>
[authors:protected] =>
[organizations:protected] =>
[collections:protected] =>
[categories:protected] =>
[categories_initialized:protected] =>
[mapped_items:protected] =>
[content:protected] =>
[files:protected] =>
[language:protected] =>
[old_record:protected] =>
[id:protected] => 1605
[old_id:protected] => 1262
[elcosh_id:protected] => d001137
[type:protected] => document
[display_type:protected] => HTML w/ PDF
[user_id:protected] =>
[language_id:protected] => 1
[tagging_id:protected] => Garber
[priority_id:protected] => 1
[title:protected] => Focus Four Toolbox Talks, Module 1 – Falls, Talk #2 – Falls from debris piles?
[total_pages:protected] => 1
[billed_pages:protected] => 1
[publication_number:protected] =>
[part_of:protected] =>
[keywords:protected] => disaster response, hazard clean-up, uneven surface, disaster site, disaster clean-up
[comments:protected] =>
[summary:protected] => A toolbox talk on preventing falls from debris piles. Includes questions to ask, an incident to discuss with images, and a place to record questions the trainer would like to ask about the incident. Part of a collection. Click on the 'collection' button to access the other items.
[transition_comments:protected] =>
[external_link:protected] =>
[consol_link:protected] => http://www.cpwrconstructionsolutions.org/roofing/hazard/1463/install-asphalt-roofs-fall-from-heights.html
[more_like_this:protected] => a000081,d000478,d000530
[permission_given_by:protected] =>
[published:protected] => T
[billable:protected] => F
[img_name:protected] =>
[img_ext:protected] =>
[img_width:protected] =>
[img_height:protected] =>
[img_credit:protected] =>
[img_practice:protected] =>
[vid_source_id:protected] =>
[vid_running_time:protected] =>
[vid_intended_audience:protected] =>
[vid_acquisition_info:protected] =>
[vid_cost:protected] =>
[vid_producer:protected] =>
[vid_filename:protected] =>
[vid_filename_downloadable:protected] =>
[date_summary:protected] =>
[date_permission_requested:protected] =>
[date_permission_received:protected] =>
[date_review_needed:protected] =>
[date_received:protected] => 02/15/12
[date_completed:protected] => 03/19/12
[date_billed:protected] =>
[date_modified:protected] => 07/10/12
[collBokExports:protected] =>
[lastBokExportCriteria:BaseElcoshItem:private] =>
[alreadyInSave:protected] =>
[alreadyInValidation:protected] =>
[validationFailures:protected] => Array
(
)
[_new:BaseObject:private] =>
[_deleted:BaseObject:private] =>
[modifiedColumns:protected] => Array
(
)
)
[1610] => DocumentRecord Object
(
[records:protected] => Array
(
)
[recordId:protected] =>
[searchWordClass:protected] =>
[searchWordPeerClass:protected] =>
[bok_record:protected] =>
[authors:protected] =>
[organizations:protected] =>
[collections:protected] =>
[categories:protected] =>
[categories_initialized:protected] =>
[mapped_items:protected] =>
[content:protected] =>
[files:protected] =>
[language:protected] =>
[old_record:protected] =>
[id:protected] => 1610
[old_id:protected] => 1271
[elcosh_id:protected] => d001146
[type:protected] => document
[display_type:protected] => HTML w/ PDF
[user_id:protected] => 0
[language_id:protected] => 1
[tagging_id:protected] => Garber
[priority_id:protected] => 1
[title:protected] => Focus Four Toolbox Talks, Module 2 – Struck-by, Talk #5 – Rigging and Securing Loads
[total_pages:protected] => 1
[billed_pages:protected] => 1
[publication_number:protected] =>
[part_of:protected] =>
[keywords:protected] => rigging, lift loads, loading areas, chains
[comments:protected] =>
[summary:protected] => A toolbox talk on preventing struck-by incidents caused by not securing loads properly. Includes questions to ask, an incident to discuss with images, and a place to record questions the trainer would like to ask about the incident. Part of a collection. Click on the 'collection' button to access the other items.
[transition_comments:protected] =>
[external_link:protected] =>
[consol_link:protected] => http://www.cpwrconstructionsolutions.org/heavy_equipment/hazard/1591/move-equipment-to-from-and-between-sites-work-zone-struck-by-injuries-and-fatalities.html
[more_like_this:protected] => d000144,d000360,d000873
[permission_given_by:protected] =>
[published:protected] => T
[billable:protected] => F
[img_name:protected] =>
[img_ext:protected] =>
[img_width:protected] =>
[img_height:protected] =>
[img_credit:protected] =>
[img_practice:protected] =>
[vid_source_id:protected] =>
[vid_running_time:protected] =>
[vid_intended_audience:protected] =>
[vid_acquisition_info:protected] =>
[vid_cost:protected] =>
[vid_producer:protected] =>
[vid_filename:protected] =>
[vid_filename_downloadable:protected] =>
[date_summary:protected] =>
[date_permission_requested:protected] =>
[date_permission_received:protected] =>
[date_review_needed:protected] =>
[date_received:protected] => 02/15/12
[date_completed:protected] => 03/28/12
[date_billed:protected] =>
[date_modified:protected] => 05/12/14
[collBokExports:protected] =>
[lastBokExportCriteria:BaseElcoshItem:private] =>
[alreadyInSave:protected] =>
[alreadyInValidation:protected] =>
[validationFailures:protected] => Array
(
)
[_new:BaseObject:private] =>
[_deleted:BaseObject:private] =>
[modifiedColumns:protected] => Array
(
)
)
[1645] => DocumentRecord Object
(
[records:protected] => Array
(
)
[recordId:protected] =>
[searchWordClass:protected] =>
[searchWordPeerClass:protected] =>
[bok_record:protected] =>
[authors:protected] =>
[organizations:protected] =>
[collections:protected] =>
[categories:protected] =>
[categories_initialized:protected] =>
[mapped_items:protected] =>
[content:protected] =>
[files:protected] =>
[language:protected] =>
[old_record:protected] =>
[id:protected] => 1645
[old_id:protected] => 1274
[elcosh_id:protected] => d001149
[type:protected] => document
[display_type:protected] => HTML w/ PDF
[user_id:protected] => 0
[language_id:protected] => 1
[tagging_id:protected] => Garber
[priority_id:protected] => 1
[title:protected] => Focus Four Toolbox Talks, Module 3 – Caught-in/between, Talk #2 – Trenches & Heavy Equipment
[total_pages:protected] => 1
[billed_pages:protected] => 1
[publication_number:protected] =>
[part_of:protected] =>
[keywords:protected] => back-up alarms, spotter, soil cave-in, spoil pikes, ROPs, trenching, rain
[comments:protected] =>
[summary:protected] => A toolbox talk on preventing incidents involving trenches such as trench collapse. Includes questions to ask, an incident to discuss with images, and a place to record questions the trainer would like to ask about the incident. Part of a collection. Click on the 'collection' button to access the other items.
[transition_comments:protected] =>
[external_link:protected] =>
[consol_link:protected] =>
[more_like_this:protected] => d000019,d000035,d000168
[permission_given_by:protected] =>
[published:protected] => T
[billable:protected] => F
[img_name:protected] =>
[img_ext:protected] =>
[img_width:protected] =>
[img_height:protected] =>
[img_credit:protected] =>
[img_practice:protected] =>
[vid_source_id:protected] =>
[vid_running_time:protected] =>
[vid_intended_audience:protected] =>
[vid_acquisition_info:protected] =>
[vid_cost:protected] =>
[vid_producer:protected] =>
[vid_filename:protected] =>
[vid_filename_downloadable:protected] =>
[date_summary:protected] =>
[date_permission_requested:protected] =>
[date_permission_received:protected] =>
[date_review_needed:protected] =>
[date_received:protected] => 02/15/12
[date_completed:protected] => 04/02/12
[date_billed:protected] =>
[date_modified:protected] => 05/23/23
[collBokExports:protected] =>
[lastBokExportCriteria:BaseElcoshItem:private] =>
[alreadyInSave:protected] =>
[alreadyInValidation:protected] =>
[validationFailures:protected] => Array
(
)
[_new:BaseObject:private] =>
[_deleted:BaseObject:private] =>
[modifiedColumns:protected] => Array
(
)
)
[1654] => DocumentRecord Object
(
[records:protected] => Array
(
)
[recordId:protected] =>
[searchWordClass:protected] =>
[searchWordPeerClass:protected] =>
[bok_record:protected] =>
[authors:protected] =>
[organizations:protected] =>
[collections:protected] =>
[categories:protected] =>
[categories_initialized:protected] =>
[mapped_items:protected] =>
[content:protected] =>
[files:protected] =>
[language:protected] =>
[old_record:protected] =>
[id:protected] => 1654
[old_id:protected] => 1284
[elcosh_id:protected] => d001159
[type:protected] => document
[display_type:protected] => HTML w/ PDF
[user_id:protected] => 0
[language_id:protected] => 1
[tagging_id:protected] => Garber
[priority_id:protected] => 1
[title:protected] => Focus Four Toolbox Talks, Module 4 – Electrocutions, Talk #6 – Hazards on Disaster Sites
[total_pages:protected] => 1
[billed_pages:protected] => 1
[publication_number:protected] =>
[part_of:protected] =>
[keywords:protected] => powerlines, underground, utilities, generators, wet conditions, GFCIs, energized lines, disasters, emergency response
[comments:protected] =>
[summary:protected] => A toolbox talk on how to avoid electrocution on a disaster site. Includes questions to ask, an incident to discuss with images, and a place to record questions the trainer would like to ask about the incident. Part of a collection. Click on the 'collection' button to access the other items.
[transition_comments:protected] =>
[external_link:protected] =>
[consol_link:protected] => http://www.cpwrconstructionsolutions.org/electrical/hazard/1138/install-and-repair-high-voltage-lines-transformers-switches-electrical-shocks-burns-and-or-electrocution.html
[more_like_this:protected] => d000135,d000361,d000437
[permission_given_by:protected] =>
[published:protected] => T
[billable:protected] => F
[img_name:protected] =>
[img_ext:protected] =>
[img_width:protected] =>
[img_height:protected] =>
[img_credit:protected] =>
[img_practice:protected] =>
[vid_source_id:protected] =>
[vid_running_time:protected] =>
[vid_intended_audience:protected] =>
[vid_acquisition_info:protected] =>
[vid_cost:protected] =>
[vid_producer:protected] =>
[vid_filename:protected] =>
[vid_filename_downloadable:protected] =>
[date_summary:protected] =>
[date_permission_requested:protected] =>
[date_permission_received:protected] =>
[date_review_needed:protected] =>
[date_received:protected] => 02/15/12
[date_completed:protected] => 04/02/12
[date_billed:protected] =>
[date_modified:protected] => 05/23/23
[collBokExports:protected] =>
[lastBokExportCriteria:BaseElcoshItem:private] =>
[alreadyInSave:protected] =>
[alreadyInValidation:protected] =>
[validationFailures:protected] => Array
(
)
[_new:BaseObject:private] =>
[_deleted:BaseObject:private] =>
[modifiedColumns:protected] => Array
(
)
)
)
[content:protected] =>
[files:protected] => Array
(
[9400] => File Object
(
[id:protected] => 9400
[filename:protected] => 1.jpg
[downloadable:protected] => F
[timestamp:protected] => 2014-05-08 15:05:37
[alreadyInSave:protected] =>
[alreadyInValidation:protected] =>
[validationFailures:protected] => Array
(
)
[_new:BaseObject:private] =>
[_deleted:BaseObject:private] =>
[modifiedColumns:protected] => Array
(
)
)
[9401] => File Object
(
[id:protected] => 9401
[filename:protected] => d001298.pdf
[downloadable:protected] => T
[timestamp:protected] => 2014-05-08 15:05:37
[alreadyInSave:protected] =>
[alreadyInValidation:protected] =>
[validationFailures:protected] => Array
(
)
[_new:BaseObject:private] =>
[_deleted:BaseObject:private] =>
[modifiedColumns:protected] => Array
(
)
)
)
[language:protected] => Language Object
(
[id:protected] => 1
[code:protected] => en
[name:protected] => English
[alreadyInSave:protected] =>
[alreadyInValidation:protected] =>
[validationFailures:protected] => Array
(
)
[_new:BaseObject:private] =>
[_deleted:BaseObject:private] =>
[modifiedColumns:protected] => Array
(
)
)
[old_record:protected] =>
[id:protected] => 3827
[old_id:protected] =>
[elcosh_id:protected] => d001298
[type:protected] => document
[display_type:protected] => HTML w/ PDF
[user_id:protected] => 23
[language_id:protected] => 1
[tagging_id:protected] => Bruce Lippy
[priority_id:protected] => 1
[title:protected] => Getting the most out of the IUOE Toolbox Talks
[total_pages:protected] => 2
[billed_pages:protected] => 2
[publication_number:protected] =>
[part_of:protected] =>
[keywords:protected] => toolbox talks, tailgate talks
[comments:protected] =>
[summary:protected] => Toolbox talks have been the main tool for communicating safety information on construction jobs for decades.
Unfortunately, there has been little research on what makes for effective toolbox talks. The IUOE National
Training Fund worked with OSHA and NIOSH to make sure their series of 24 Focus Four toolbox talks were based on the best recommendations for effective design. These toolbox talks accompany an entire package of training materials, but can be used alone. This guide points out the key features of these toolbox talks and how best to deliver them.
[transition_comments:protected] =>
[external_link:protected] =>
[consol_link:protected] =>
[more_like_this:protected] => d001137,d001146,d001149,d001159
[permission_given_by:protected] => IUOE National Hazmat Program
[published:protected] => T
[billable:protected] => F
[img_name:protected] =>
[img_ext:protected] => png
[img_width:protected] =>
[img_height:protected] =>
[img_credit:protected] =>
[img_practice:protected] =>
[vid_source_id:protected] =>
[vid_running_time:protected] =>
[vid_intended_audience:protected] =>
[vid_acquisition_info:protected] =>
[vid_cost:protected] =>
[vid_producer:protected] =>
[vid_filename:protected] =>
[vid_filename_downloadable:protected] =>
[date_summary:protected] => 2007
[date_permission_requested:protected] =>
[date_permission_received:protected] =>
[date_review_needed:protected] =>
[date_received:protected] => 05/08/14
[date_completed:protected] => 05/08/14
[date_billed:protected] =>
[date_modified:protected] => 05/08/14
[collBokExports:protected] =>
[lastBokExportCriteria:BaseElcoshItem:private] =>
[alreadyInSave:protected] =>
[alreadyInValidation:protected] =>
[validationFailures:protected] => Array
(
)
[_new:BaseObject:private] =>
[_deleted:BaseObject:private] =>
[modifiedColumns:protected] => Array
(
)
)
[show_text] =>
[document_content] => ElcoshItemDocumentContent Object
(
[id:protected] => 2896
[item_id:protected] => 3827
[type:protected] => main
[title:protected] =>
[content:protected] =>
Why were these talks developed?
Toolbox talks have been the main tool for communicating safety information on construction jobs for decades. Unfortunately, there has been almost no research on what makes for effective toolbox talks. The IUOE National Training Fund has worked with OSHA, the National Institute for Occupational Safety and Health and the Lippy Group, LLC to make sure these Focus Four toolbox talks are based on the latest fi ndings on the most effective design and tailored to the hazards operating engineers face daily. These toolbox talks accompany an entire package of training materials, but can be used alone. The way these are delivered is as important as how well they are designed.
What did NIOSH find out?
- Just handing out factsheets and toolbox talks to workers doesn’t work. Providing copies after toolbox talks doesn’t make much of an impact either.
- Using case studies (real life stories of accidents that ended in fatality or injury) in toolbox talks is effective.
- When toolbox talks containing case studies were accompanied by discussion questions to encourage group participation, they were more effective. Consequently, getting the workers to participate in the discussion about the case study is important. It’s not enough to tell the story, it is better to have the workers engage in problem solving that analyzes why the accident occurred and how it could have been prevented. Active learning is always better than passive.
How should you deliver these toolbox talks?
- Choose a topic that is related to work going on at the site.
- Hold the meeting on the job, preferably where everyone can sit and relax.
- Hold the meeting at the beginning of a shift or after a break. Folks are too tired at the end of a shift to carefully listen and they want to get home.
- Read the toolbox talk sheet on the topic prior to conducting the talk.
- Start at the top of the form and work right through to the end, which should take around 10 to 15 minutes. Guidance is provided in blue print to help you with each section.
- Use the questions provided to generate discussions. Always allow time for the crew to respond to your questions before you provide an answer. Some suggested responses are written in italics.
- Review the case study and emphasize that this was a real incident. Ask the crew for a case study before you review the one provided, however.
- Always end with a discussion of the particular worksite where you are conducting the talk. Tie the talk as closely to hazards on the site as possible and encourage the crew to constantly look for and immediately correct hazards. They should also know how to report any problems that can’t be immediately corrected.
- Provide copies to each person, if you like, but NIOSH has not found that to be particularly effective.
- Encourage workers to do similar talks on their sites and provide them with the IUOE phone number for ordering in bulk.
- Have everyone sign the back of the form to indicate they attended this session and point out it is a pledge to look out for the health and safety of everyone on the site.
What are the key features of these toolbox talks?

[content_transformed:protected] =>
Why were these talks developed?
Toolbox talks have been the main tool for communicating safety information on construction jobs for decades. Unfortunately, there has been almost no research on what makes for effective toolbox talks. The IUOE National Training Fund has worked with OSHA, the National Institute for Occupational Safety and Health and the Lippy Group, LLC to make sure these Focus Four toolbox talks are based on the latest fi ndings on the most effective design and tailored to the hazards operating engineers face daily. These toolbox talks accompany an entire package of training materials, but can be used alone. The way these are delivered is as important as how well they are designed.
What did NIOSH find out?
- Just handing out factsheets and toolbox talks to workers doesn’t work. Providing copies after toolbox talks doesn’t make much of an impact either.
- Using case studies (real life stories of accidents that ended in fatality or injury) in toolbox talks is effective.
- When toolbox talks containing case studies were accompanied by discussion questions to encourage group participation, they were more effective. Consequently, getting the workers to participate in the discussion about the case study is important. It’s not enough to tell the story, it is better to have the workers engage in problem solving that analyzes why the accident occurred and how it could have been prevented. Active learning is always better than passive.
How should you deliver these toolbox talks?
- Choose a topic that is related to work going on at the site.
- Hold the meeting on the job, preferably where everyone can sit and relax.
- Hold the meeting at the beginning of a shift or after a break. Folks are too tired at the end of a shift to carefully listen and they want to get home.
- Read the toolbox talk sheet on the topic prior to conducting the talk.
- Start at the top of the form and work right through to the end, which should take around 10 to 15 minutes. Guidance is provided in blue print to help you with each section.
- Use the questions provided to generate discussions. Always allow time for the crew to respond to your questions before you provide an answer. Some suggested responses are written in italics.
- Review the case study and emphasize that this was a real incident. Ask the crew for a case study before you review the one provided, however.
- Always end with a discussion of the particular worksite where you are conducting the talk. Tie the talk as closely to hazards on the site as possible and encourage the crew to constantly look for and immediately correct hazards. They should also know how to report any problems that can’t be immediately corrected.
- Provide copies to each person, if you like, but NIOSH has not found that to be particularly effective.
- Encourage workers to do similar talks on their sites and provide them with the IUOE phone number for ordering in bulk.
- Have everyone sign the back of the form to indicate they attended this session and point out it is a pledge to look out for the health and safety of everyone on the site.
What are the key features of these toolbox talks?
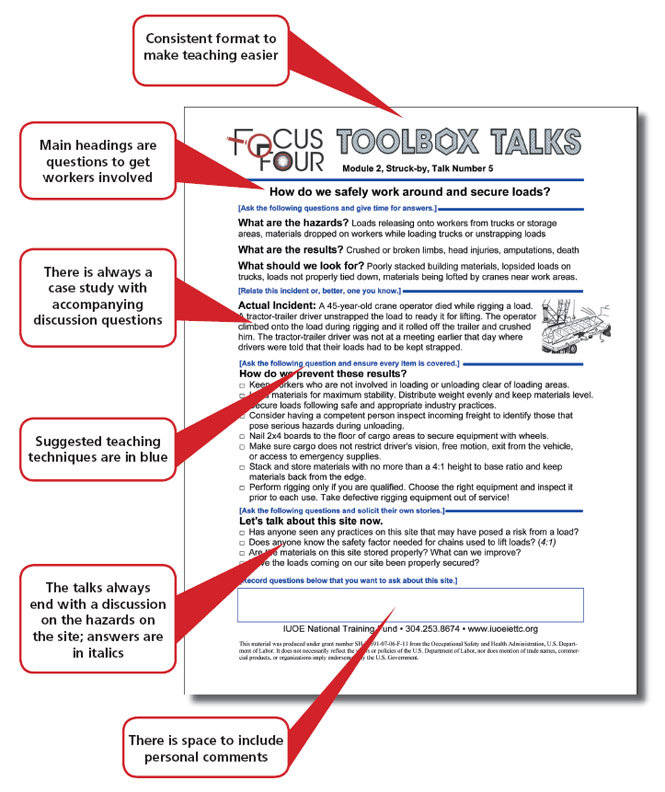
[disclaimer:protected] =>
[disclaimer_transformed:protected] =>
[alreadyInSave:protected] =>
[alreadyInValidation:protected] =>
[validationFailures:protected] => Array
(
)
[_new:BaseObject:private] =>
[_deleted:BaseObject:private] =>
[modifiedColumns:protected] => Array
(
)
)
[template] => record
)
[_globalContext:PHPTAL_Context:private] => stdClass Object
(
)
[_echoDeclarations:PHPTAL_Context:private] =>
[referer] => http://www.elcosh.org/document/3827/d001298/Getting%2Bthe%2Bmost%2Bout%2Bof%2Bthe%2BIUOE%2BToolbox%2BTalks.html
[curr_module] => Record
[styles] => Array
(
)
[javascript] => Array
(
[0] => jquery.min.js
)
[metas] => Array
(
[language] => en
[robots] => index, follow
)
[user] =>
[curr_url] => https://www.elcosh.org/index.php?module=Record&id=3827&type=document
[base_url] => https://www.elcosh.org/index.php?module=Record
[title] => eLCOSH : Getting the most out of the IUOE Toolbox Talks
[language] => en
[search_query] =>
[module] => Record
[new_records] => Array
(
[0] => Search_Result Object
(
[title] => Toolbox Talk: Fixed Ladder
[image] => /record/images/notavailable-p.png
[blurb] => The CPWR Toolbox Talk on Fixed Ladders addresses the potential risks associated with using fixed ladders. The resource includes a brief case example,...
[category] => Array
(
[0] => 15
[1] => 47
[2] => 49
[3] => 51
[4] => 53
[5] => 55
[6] => 60
[7] => 64
[8] => 73
[9] => 76
[10] => 78
[11] => 80
[12] => 86
[13] => 87
[14] => 90
[15] => 92
[16] => 93
[17] => 94
[18] => 100
)
[labels] => Array
(
[0] => Falls
[1] => Work Environment
[2] => Hazards
[3] => Bricklayer
[4] => Trades
[5] => Carpenter
[7] => Cement Mason
[9] => Concrete Polisher
[11] => Electrical Worker
[13] => HVAC
[15] => Laborer
[17] => PCC/Restoration
[19] => Plumber/Pipefitter
[21] => Roofer/Waterproofer
[23] => Sheetmetal Worker
[25] => Welder
[27] => Commercial & Institutional
[28] => Jobsites
[29] => Industrial
[31] => LEED/Green Construction
[33] => Renovations
[35] => Residential
[37] => Toolbox Talks
[38] => Documents
[39] => Media & Documents
)
[type] => Toolbox Talks
[sub_category] =>
[url] => /document/4430/d001660/Toolbox%2BTalk%253A%2BFixed%2BLadder.html
[item:protected] => DocumentRecord Object
(
[records:protected] => Array
(
)
[recordId:protected] =>
[searchWordClass:protected] =>
[searchWordPeerClass:protected] =>
[bok_record:protected] =>
[authors:protected] =>
[organizations:protected] =>
[collections:protected] =>
[categories:protected] => Array
(
[15] => Category Object
(
[languages:protected] =>
[bok_resources:protected] =>
[bok_topics:protected] =>
[bok_keywords:protected] =>
[id:protected] => 15
[type:protected] => category
[parent:protected] => 7
[label:protected] => Falls
[alreadyInSave:protected] =>
[alreadyInValidation:protected] =>
[validationFailures:protected] => Array
(
)
[_new:BaseObject:private] =>
[_deleted:BaseObject:private] =>
[modifiedColumns:protected] => Array
(
)
)
[47] => Category Object
(
[languages:protected] =>
[bok_resources:protected] =>
[bok_topics:protected] =>
[bok_keywords:protected] =>
[id:protected] => 47
[type:protected] => category
[parent:protected] => 2
[label:protected] => Bricklayer
[alreadyInSave:protected] =>
[alreadyInValidation:protected] =>
[validationFailures:protected] => Array
(
)
[_new:BaseObject:private] =>
[_deleted:BaseObject:private] =>
[modifiedColumns:protected] => Array
(
)
)
[49] => Category Object
(
[languages:protected] =>
[bok_resources:protected] =>
[bok_topics:protected] =>
[bok_keywords:protected] =>
[id:protected] => 49
[type:protected] => category
[parent:protected] => 2
[label:protected] => Carpenter
[alreadyInSave:protected] =>
[alreadyInValidation:protected] =>
[validationFailures:protected] => Array
(
)
[_new:BaseObject:private] =>
[_deleted:BaseObject:private] =>
[modifiedColumns:protected] => Array
(
)
)
[51] => Category Object
(
[languages:protected] =>
[bok_resources:protected] =>
[bok_topics:protected] =>
[bok_keywords:protected] =>
[id:protected] => 51
[type:protected] => category
[parent:protected] => 2
[label:protected] => Cement Mason
[alreadyInSave:protected] =>
[alreadyInValidation:protected] =>
[validationFailures:protected] => Array
(
)
[_new:BaseObject:private] =>
[_deleted:BaseObject:private] =>
[modifiedColumns:protected] => Array
(
)
)
[53] => Category Object
(
[languages:protected] =>
[bok_resources:protected] =>
[bok_topics:protected] =>
[bok_keywords:protected] =>
[id:protected] => 53
[type:protected] => category
[parent:protected] => 2
[label:protected] => Concrete Polisher
[alreadyInSave:protected] =>
[alreadyInValidation:protected] =>
[validationFailures:protected] => Array
(
)
[_new:BaseObject:private] =>
[_deleted:BaseObject:private] =>
[modifiedColumns:protected] => Array
(
)
)
[55] => Category Object
(
[languages:protected] =>
[bok_resources:protected] =>
[bok_topics:protected] =>
[bok_keywords:protected] =>
[id:protected] => 55
[type:protected] => category
[parent:protected] => 2
[label:protected] => Electrical Worker
[alreadyInSave:protected] =>
[alreadyInValidation:protected] =>
[validationFailures:protected] => Array
(
)
[_new:BaseObject:private] =>
[_deleted:BaseObject:private] =>
[modifiedColumns:protected] => Array
(
)
)
[60] => Category Object
(
[languages:protected] =>
[bok_resources:protected] =>
[bok_topics:protected] =>
[bok_keywords:protected] =>
[id:protected] => 60
[type:protected] => category
[parent:protected] => 2
[label:protected] => HVAC
[alreadyInSave:protected] =>
[alreadyInValidation:protected] =>
[validationFailures:protected] => Array
(
)
[_new:BaseObject:private] =>
[_deleted:BaseObject:private] =>
[modifiedColumns:protected] => Array
(
)
)
[64] => Category Object
(
[languages:protected] =>
[bok_resources:protected] =>
[bok_topics:protected] =>
[bok_keywords:protected] =>
[id:protected] => 64
[type:protected] => category
[parent:protected] => 2
[label:protected] => Laborer
[alreadyInSave:protected] =>
[alreadyInValidation:protected] =>
[validationFailures:protected] => Array
(
)
[_new:BaseObject:private] =>
[_deleted:BaseObject:private] =>
[modifiedColumns:protected] => Array
(
)
)
[73] => Category Object
(
[languages:protected] =>
[bok_resources:protected] =>
[bok_topics:protected] =>
[bok_keywords:protected] =>
[id:protected] => 73
[type:protected] => category
[parent:protected] => 2
[label:protected] => PCC/Restoration
[alreadyInSave:protected] =>
[alreadyInValidation:protected] =>
[validationFailures:protected] => Array
(
)
[_new:BaseObject:private] =>
[_deleted:BaseObject:private] =>
[modifiedColumns:protected] => Array
(
)
)
[76] => Category Object
(
[languages:protected] =>
[bok_resources:protected] =>
[bok_topics:protected] =>
[bok_keywords:protected] =>
[id:protected] => 76
[type:protected] => category
[parent:protected] => 2
[label:protected] => Plumber/Pipefitter
[alreadyInSave:protected] =>
[alreadyInValidation:protected] =>
[validationFailures:protected] => Array
(
)
[_new:BaseObject:private] =>
[_deleted:BaseObject:private] =>
[modifiedColumns:protected] => Array
(
)
)
[78] => Category Object
(
[languages:protected] =>
[bok_resources:protected] =>
[bok_topics:protected] =>
[bok_keywords:protected] =>
[id:protected] => 78
[type:protected] => category
[parent:protected] => 2
[label:protected] => Roofer/Waterproofer
[alreadyInSave:protected] =>
[alreadyInValidation:protected] =>
[validationFailures:protected] => Array
(
)
[_new:BaseObject:private] =>
[_deleted:BaseObject:private] =>
[modifiedColumns:protected] => Array
(
)
)
[80] => Category Object
(
[languages:protected] =>
[bok_resources:protected] =>
[bok_topics:protected] =>
[bok_keywords:protected] =>
[id:protected] => 80
[type:protected] => category
[parent:protected] => 2
[label:protected] => Sheetmetal Worker
[alreadyInSave:protected] =>
[alreadyInValidation:protected] =>
[validationFailures:protected] => Array
(
)
[_new:BaseObject:private] =>
[_deleted:BaseObject:private] =>
[modifiedColumns:protected] => Array
(
)
)
[86] => Category Object
(
[languages:protected] =>
[bok_resources:protected] =>
[bok_topics:protected] =>
[bok_keywords:protected] =>
[id:protected] => 86
[type:protected] => category
[parent:protected] => 2
[label:protected] => Welder
[alreadyInSave:protected] =>
[alreadyInValidation:protected] =>
[validationFailures:protected] => Array
(
)
[_new:BaseObject:private] =>
[_deleted:BaseObject:private] =>
[modifiedColumns:protected] => Array
(
)
)
[87] => Category Object
(
[languages:protected] =>
[bok_resources:protected] =>
[bok_topics:protected] =>
[bok_keywords:protected] =>
[id:protected] => 87
[type:protected] => category
[parent:protected] => 3
[label:protected] => Commercial & Institutional
[alreadyInSave:protected] =>
[alreadyInValidation:protected] =>
[validationFailures:protected] => Array
(
)
[_new:BaseObject:private] =>
[_deleted:BaseObject:private] =>
[modifiedColumns:protected] => Array
(
)
)
[90] => Category Object
(
[languages:protected] =>
[bok_resources:protected] =>
[bok_topics:protected] =>
[bok_keywords:protected] =>
[id:protected] => 90
[type:protected] => category
[parent:protected] => 3
[label:protected] => Industrial
[alreadyInSave:protected] =>
[alreadyInValidation:protected] =>
[validationFailures:protected] => Array
(
)
[_new:BaseObject:private] =>
[_deleted:BaseObject:private] =>
[modifiedColumns:protected] => Array
(
)
)
[92] => Category Object
(
[languages:protected] =>
[bok_resources:protected] =>
[bok_topics:protected] =>
[bok_keywords:protected] =>
[id:protected] => 92
[type:protected] => category
[parent:protected] => 3
[label:protected] => LEED/Green Construction
[alreadyInSave:protected] =>
[alreadyInValidation:protected] =>
[validationFailures:protected] => Array
(
)
[_new:BaseObject:private] =>
[_deleted:BaseObject:private] =>
[modifiedColumns:protected] => Array
(
)
)
[93] => Category Object
(
[languages:protected] =>
[bok_resources:protected] =>
[bok_topics:protected] =>
[bok_keywords:protected] =>
[id:protected] => 93
[type:protected] => category
[parent:protected] => 3
[label:protected] => Renovations
[alreadyInSave:protected] =>
[alreadyInValidation:protected] =>
[validationFailures:protected] => Array
(
)
[_new:BaseObject:private] =>
[_deleted:BaseObject:private] =>
[modifiedColumns:protected] => Array
(
)
)
[94] => Category Object
(
[languages:protected] =>
[bok_resources:protected] =>
[bok_topics:protected] =>
[bok_keywords:protected] =>
[id:protected] => 94
[type:protected] => category
[parent:protected] => 3
[label:protected] => Residential
[alreadyInSave:protected] =>
[alreadyInValidation:protected] =>
[validationFailures:protected] => Array
(
)
[_new:BaseObject:private] =>
[_deleted:BaseObject:private] =>
[modifiedColumns:protected] => Array
(
)
)
[100] => Category Object
(
[languages:protected] =>
[bok_resources:protected] =>
[bok_topics:protected] =>
[bok_keywords:protected] =>
[id:protected] => 100
[type:protected] => category
[parent:protected] => 6
[label:protected] => Toolbox Talks
[alreadyInSave:protected] =>
[alreadyInValidation:protected] =>
[validationFailures:protected] => Array
(
)
[_new:BaseObject:private] =>
[_deleted:BaseObject:private] =>
[modifiedColumns:protected] => Array
(
)
)
)
[categories_initialized:protected] => 1
[mapped_items:protected] =>
[content:protected] =>
[files:protected] =>
[language:protected] => Language Object
(
[id:protected] => 1
[code:protected] => en
[name:protected] => English
[alreadyInSave:protected] =>
[alreadyInValidation:protected] =>
[validationFailures:protected] => Array
(
)
[_new:BaseObject:private] =>
[_deleted:BaseObject:private] =>
[modifiedColumns:protected] => Array
(
)
)
[old_record:protected] =>
[id:protected] => 4430
[old_id:protected] =>
[elcosh_id:protected] => d001660
[type:protected] => document
[display_type:protected] => HTML only (and links)
[user_id:protected] => 0
[language_id:protected] => 1
[tagging_id:protected] => Mike Aguilar
[priority_id:protected] => 1
[title:protected] => Toolbox Talk: Fixed Ladder
[total_pages:protected] => 0
[billed_pages:protected] => 0
[publication_number:protected] =>
[part_of:protected] =>
[keywords:protected] => Fixed Ladders, Fall Prevention, Falls
[comments:protected] =>
[summary:protected] => The CPWR Toolbox Talk on Fixed Ladders addresses the potential risks associated with using fixed ladders. The resource includes a brief case example, steps to prevent a related injury and questions for discussion. It includes an image that illustrates the hazard, which can be posted in a central location as a reminder of steps to work safely.
Available in
English
and
Spanish.
[transition_comments:protected] =>
[external_link:protected] =>
[consol_link:protected] =>
[more_like_this:protected] => d001257,d001254,d001255,d001256,d001258,d001262,d001279
[permission_given_by:protected] =>
[published:protected] => T
[billable:protected] => F
[img_name:protected] =>
[img_ext:protected] =>
[img_width:protected] =>
[img_height:protected] =>
[img_credit:protected] =>
[img_practice:protected] =>
[vid_source_id:protected] =>
[vid_running_time:protected] =>
[vid_intended_audience:protected] =>
[vid_acquisition_info:protected] =>
[vid_cost:protected] =>
[vid_producer:protected] =>
[vid_filename:protected] =>
[vid_filename_downloadable:protected] =>
[date_summary:protected] =>
[date_permission_requested:protected] =>
[date_permission_received:protected] =>
[date_review_needed:protected] =>
[date_received:protected] => 06/10/22
[date_completed:protected] => 06/10/22
[date_billed:protected] =>
[date_modified:protected] => 05/22/23
[collBokExports:protected] =>
[lastBokExportCriteria:BaseElcoshItem:private] =>
[alreadyInSave:protected] =>
[alreadyInValidation:protected] =>
[validationFailures:protected] => Array
(
)
[_new:BaseObject:private] =>
[_deleted:BaseObject:private] =>
[modifiedColumns:protected] => Array
(
)
)
)
[1] => Search_Result Object
(
[title] => Toolbox Talk: Challenges Preventing Falling Objects
[image] => /record/images/notavailable-p.png
[blurb] => The CPWR Toolbox Talk on Challenges Preventing Falling Objects addresses the hazards of being struck by falling objects on the job site. The resource...
[category] => Array
(
[0] => 12
[1] => 47
[2] => 49
[3] => 51
[4] => 55
[5] => 64
[6] => 68
[7] => 71
[8] => 75
[9] => 78
[10] => 79
[11] => 82
[12] => 62
[13] => 86
[14] => 87
[15] => 88
[16] => 89
[17] => 91
[18] => 90
[19] => 92
[20] => 93
[21] => 94
[22] => 95
[23] => 100
)
[labels] => Array
(
[0] => Crushed/Struck By
[1] => Work Environment
[2] => Hazards
[3] => Bricklayer
[4] => Trades
[5] => Carpenter
[7] => Cement Mason
[9] => Electrical Worker
[11] => Laborer
[13] => Maintenance Worker
[15] => Painter
[17] => Plasterer
[19] => Roofer/Waterproofer
[21] => Scaffold Erector
[23] => Stonemason
[25] => Structural Ironworker
[27] => Welder
[29] => Commercial & Institutional
[30] => Jobsites
[31] => Demolition
[33] => Disasters
[35] => Heavy & Highway
[37] => Industrial
[39] => LEED/Green Construction
[41] => Renovations
[43] => Residential
[45] => Underground
[47] => Toolbox Talks
[48] => Documents
[49] => Media & Documents
)
[type] => Toolbox Talks
[sub_category] =>
[url] => /document/4431/d001661/Toolbox%2BTalk%253A%2BChallenges%2BPreventing%2BFalling%2BObjects.html
[item:protected] => DocumentRecord Object
(
[records:protected] => Array
(
)
[recordId:protected] =>
[searchWordClass:protected] =>
[searchWordPeerClass:protected] =>
[bok_record:protected] =>
[authors:protected] =>
[organizations:protected] =>
[collections:protected] =>
[categories:protected] => Array
(
[12] => Category Object
(
[languages:protected] =>
[bok_resources:protected] =>
[bok_topics:protected] =>
[bok_keywords:protected] =>
[id:protected] => 12
[type:protected] => category
[parent:protected] => 7
[label:protected] => Crushed/Struck By
[alreadyInSave:protected] =>
[alreadyInValidation:protected] =>
[validationFailures:protected] => Array
(
)
[_new:BaseObject:private] =>
[_deleted:BaseObject:private] =>
[modifiedColumns:protected] => Array
(
)
)
[47] => Category Object
(
[languages:protected] =>
[bok_resources:protected] =>
[bok_topics:protected] =>
[bok_keywords:protected] =>
[id:protected] => 47
[type:protected] => category
[parent:protected] => 2
[label:protected] => Bricklayer
[alreadyInSave:protected] =>
[alreadyInValidation:protected] =>
[validationFailures:protected] => Array
(
)
[_new:BaseObject:private] =>
[_deleted:BaseObject:private] =>
[modifiedColumns:protected] => Array
(
)
)
[49] => Category Object
(
[languages:protected] =>
[bok_resources:protected] =>
[bok_topics:protected] =>
[bok_keywords:protected] =>
[id:protected] => 49
[type:protected] => category
[parent:protected] => 2
[label:protected] => Carpenter
[alreadyInSave:protected] =>
[alreadyInValidation:protected] =>
[validationFailures:protected] => Array
(
)
[_new:BaseObject:private] =>
[_deleted:BaseObject:private] =>
[modifiedColumns:protected] => Array
(
)
)
[51] => Category Object
(
[languages:protected] =>
[bok_resources:protected] =>
[bok_topics:protected] =>
[bok_keywords:protected] =>
[id:protected] => 51
[type:protected] => category
[parent:protected] => 2
[label:protected] => Cement Mason
[alreadyInSave:protected] =>
[alreadyInValidation:protected] =>
[validationFailures:protected] => Array
(
)
[_new:BaseObject:private] =>
[_deleted:BaseObject:private] =>
[modifiedColumns:protected] => Array
(
)
)
[55] => Category Object
(
[languages:protected] =>
[bok_resources:protected] =>
[bok_topics:protected] =>
[bok_keywords:protected] =>
[id:protected] => 55
[type:protected] => category
[parent:protected] => 2
[label:protected] => Electrical Worker
[alreadyInSave:protected] =>
[alreadyInValidation:protected] =>
[validationFailures:protected] => Array
(
)
[_new:BaseObject:private] =>
[_deleted:BaseObject:private] =>
[modifiedColumns:protected] => Array
(
)
)
[64] => Category Object
(
[languages:protected] =>
[bok_resources:protected] =>
[bok_topics:protected] =>
[bok_keywords:protected] =>
[id:protected] => 64
[type:protected] => category
[parent:protected] => 2
[label:protected] => Laborer
[alreadyInSave:protected] =>
[alreadyInValidation:protected] =>
[validationFailures:protected] => Array
(
)
[_new:BaseObject:private] =>
[_deleted:BaseObject:private] =>
[modifiedColumns:protected] => Array
(
)
)
[68] => Category Object
(
[languages:protected] =>
[bok_resources:protected] =>
[bok_topics:protected] =>
[bok_keywords:protected] =>
[id:protected] => 68
[type:protected] => category
[parent:protected] => 2
[label:protected] => Maintenance Worker
[alreadyInSave:protected] =>
[alreadyInValidation:protected] =>
[validationFailures:protected] => Array
(
)
[_new:BaseObject:private] =>
[_deleted:BaseObject:private] =>
[modifiedColumns:protected] => Array
(
)
)
[71] => Category Object
(
[languages:protected] =>
[bok_resources:protected] =>
[bok_topics:protected] =>
[bok_keywords:protected] =>
[id:protected] => 71
[type:protected] => category
[parent:protected] => 2
[label:protected] => Painter
[alreadyInSave:protected] =>
[alreadyInValidation:protected] =>
[validationFailures:protected] => Array
(
)
[_new:BaseObject:private] =>
[_deleted:BaseObject:private] =>
[modifiedColumns:protected] => Array
(
)
)
[75] => Category Object
(
[languages:protected] =>
[bok_resources:protected] =>
[bok_topics:protected] =>
[bok_keywords:protected] =>
[id:protected] => 75
[type:protected] => category
[parent:protected] => 2
[label:protected] => Plasterer
[alreadyInSave:protected] =>
[alreadyInValidation:protected] =>
[validationFailures:protected] => Array
(
)
[_new:BaseObject:private] =>
[_deleted:BaseObject:private] =>
[modifiedColumns:protected] => Array
(
)
)
[78] => Category Object
(
[languages:protected] =>
[bok_resources:protected] =>
[bok_topics:protected] =>
[bok_keywords:protected] =>
[id:protected] => 78
[type:protected] => category
[parent:protected] => 2
[label:protected] => Roofer/Waterproofer
[alreadyInSave:protected] =>
[alreadyInValidation:protected] =>
[validationFailures:protected] => Array
(
)
[_new:BaseObject:private] =>
[_deleted:BaseObject:private] =>
[modifiedColumns:protected] => Array
(
)
)
[79] => Category Object
(
[languages:protected] =>
[bok_resources:protected] =>
[bok_topics:protected] =>
[bok_keywords:protected] =>
[id:protected] => 79
[type:protected] => category
[parent:protected] => 2
[label:protected] => Scaffold Erector
[alreadyInSave:protected] =>
[alreadyInValidation:protected] =>
[validationFailures:protected] => Array
(
)
[_new:BaseObject:private] =>
[_deleted:BaseObject:private] =>
[modifiedColumns:protected] => Array
(
)
)
[82] => Category Object
(
[languages:protected] =>
[bok_resources:protected] =>
[bok_topics:protected] =>
[bok_keywords:protected] =>
[id:protected] => 82
[type:protected] => category
[parent:protected] => 2
[label:protected] => Stonemason
[alreadyInSave:protected] =>
[alreadyInValidation:protected] =>
[validationFailures:protected] => Array
(
)
[_new:BaseObject:private] =>
[_deleted:BaseObject:private] =>
[modifiedColumns:protected] => Array
(
)
)
[62] => Category Object
(
[languages:protected] =>
[bok_resources:protected] =>
[bok_topics:protected] =>
[bok_keywords:protected] =>
[id:protected] => 62
[type:protected] => category
[parent:protected] => 2
[label:protected] => Structural Ironworker
[alreadyInSave:protected] =>
[alreadyInValidation:protected] =>
[validationFailures:protected] => Array
(
)
[_new:BaseObject:private] =>
[_deleted:BaseObject:private] =>
[modifiedColumns:protected] => Array
(
)
)
[86] => Category Object
(
[languages:protected] =>
[bok_resources:protected] =>
[bok_topics:protected] =>
[bok_keywords:protected] =>
[id:protected] => 86
[type:protected] => category
[parent:protected] => 2
[label:protected] => Welder
[alreadyInSave:protected] =>
[alreadyInValidation:protected] =>
[validationFailures:protected] => Array
(
)
[_new:BaseObject:private] =>
[_deleted:BaseObject:private] =>
[modifiedColumns:protected] => Array
(
)
)
[87] => Category Object
(
[languages:protected] =>
[bok_resources:protected] =>
[bok_topics:protected] =>
[bok_keywords:protected] =>
[id:protected] => 87
[type:protected] => category
[parent:protected] => 3
[label:protected] => Commercial & Institutional
[alreadyInSave:protected] =>
[alreadyInValidation:protected] =>
[validationFailures:protected] => Array
(
)
[_new:BaseObject:private] =>
[_deleted:BaseObject:private] =>
[modifiedColumns:protected] => Array
(
)
)
[88] => Category Object
(
[languages:protected] =>
[bok_resources:protected] =>
[bok_topics:protected] =>
[bok_keywords:protected] =>
[id:protected] => 88
[type:protected] => category
[parent:protected] => 3
[label:protected] => Demolition
[alreadyInSave:protected] =>
[alreadyInValidation:protected] =>
[validationFailures:protected] => Array
(
)
[_new:BaseObject:private] =>
[_deleted:BaseObject:private] =>
[modifiedColumns:protected] => Array
(
)
)
[89] => Category Object
(
[languages:protected] =>
[bok_resources:protected] =>
[bok_topics:protected] =>
[bok_keywords:protected] =>
[id:protected] => 89
[type:protected] => category
[parent:protected] => 3
[label:protected] => Disasters
[alreadyInSave:protected] =>
[alreadyInValidation:protected] =>
[validationFailures:protected] => Array
(
)
[_new:BaseObject:private] =>
[_deleted:BaseObject:private] =>
[modifiedColumns:protected] => Array
(
)
)
[91] => Category Object
(
[languages:protected] =>
[bok_resources:protected] =>
[bok_topics:protected] =>
[bok_keywords:protected] =>
[id:protected] => 91
[type:protected] => category
[parent:protected] => 3
[label:protected] => Heavy & Highway
[alreadyInSave:protected] =>
[alreadyInValidation:protected] =>
[validationFailures:protected] => Array
(
)
[_new:BaseObject:private] =>
[_deleted:BaseObject:private] =>
[modifiedColumns:protected] => Array
(
)
)
[90] => Category Object
(
[languages:protected] =>
[bok_resources:protected] =>
[bok_topics:protected] =>
[bok_keywords:protected] =>
[id:protected] => 90
[type:protected] => category
[parent:protected] => 3
[label:protected] => Industrial
[alreadyInSave:protected] =>
[alreadyInValidation:protected] =>
[validationFailures:protected] => Array
(
)
[_new:BaseObject:private] =>
[_deleted:BaseObject:private] =>
[modifiedColumns:protected] => Array
(
)
)
[92] => Category Object
(
[languages:protected] =>
[bok_resources:protected] =>
[bok_topics:protected] =>
[bok_keywords:protected] =>
[id:protected] => 92
[type:protected] => category
[parent:protected] => 3
[label:protected] => LEED/Green Construction
[alreadyInSave:protected] =>
[alreadyInValidation:protected] =>
[validationFailures:protected] => Array
(
)
[_new:BaseObject:private] =>
[_deleted:BaseObject:private] =>
[modifiedColumns:protected] => Array
(
)
)
[93] => Category Object
(
[languages:protected] =>
[bok_resources:protected] =>
[bok_topics:protected] =>
[bok_keywords:protected] =>
[id:protected] => 93
[type:protected] => category
[parent:protected] => 3
[label:protected] => Renovations
[alreadyInSave:protected] =>
[alreadyInValidation:protected] =>
[validationFailures:protected] => Array
(
)
[_new:BaseObject:private] =>
[_deleted:BaseObject:private] =>
[modifiedColumns:protected] => Array
(
)
)
[94] => Category Object
(
[languages:protected] =>
[bok_resources:protected] =>
[bok_topics:protected] =>
[bok_keywords:protected] =>
[id:protected] => 94
[type:protected] => category
[parent:protected] => 3
[label:protected] => Residential
[alreadyInSave:protected] =>
[alreadyInValidation:protected] =>
[validationFailures:protected] => Array
(
)
[_new:BaseObject:private] =>
[_deleted:BaseObject:private] =>
[modifiedColumns:protected] => Array
(
)
)
[95] => Category Object
(
[languages:protected] =>
[bok_resources:protected] =>
[bok_topics:protected] =>
[bok_keywords:protected] =>
[id:protected] => 95
[type:protected] => category
[parent:protected] => 3
[label:protected] => Underground
[alreadyInSave:protected] =>
[alreadyInValidation:protected] =>
[validationFailures:protected] => Array
(
)
[_new:BaseObject:private] =>
[_deleted:BaseObject:private] =>
[modifiedColumns:protected] => Array
(
)
)
[100] => Category Object
(
[languages:protected] =>
[bok_resources:protected] =>
[bok_topics:protected] =>
[bok_keywords:protected] =>
[id:protected] => 100
[type:protected] => category
[parent:protected] => 6
[label:protected] => Toolbox Talks
[alreadyInSave:protected] =>
[alreadyInValidation:protected] =>
[validationFailures:protected] => Array
(
)
[_new:BaseObject:private] =>
[_deleted:BaseObject:private] =>
[modifiedColumns:protected] => Array
(
)
)
)
[categories_initialized:protected] => 1
[mapped_items:protected] =>
[content:protected] =>
[files:protected] =>
[language:protected] => Language Object
(
[id:protected] => 1
[code:protected] => en
[name:protected] => English
[alreadyInSave:protected] =>
[alreadyInValidation:protected] =>
[validationFailures:protected] => Array
(
)
[_new:BaseObject:private] =>
[_deleted:BaseObject:private] =>
[modifiedColumns:protected] => Array
(
)
)
[old_record:protected] =>
[id:protected] => 4431
[old_id:protected] =>
[elcosh_id:protected] => d001661
[type:protected] => document
[display_type:protected] => HTML only (and links)
[user_id:protected] => 0
[language_id:protected] => 1
[tagging_id:protected] => Mike Aguilar
[priority_id:protected] => 1
[title:protected] => Toolbox Talk: Challenges Preventing Falling Objects
[total_pages:protected] => 0
[billed_pages:protected] => 0
[publication_number:protected] =>
[part_of:protected] =>
[keywords:protected] => dropped objects, falling objects, struck by incidents, struck by fatalities
[comments:protected] =>
[summary:protected] => The CPWR Toolbox Talk on Challenges Preventing Falling Objects addresses the hazards of being struck by falling objects on the job site. The resource includes a brief example, steps to prevent a related injury, and questions for discussion. It includes a graphic that illustrates a group workers observing a scaffold free of debris during high winds, which can be posted in a central location as a reminder of steps to work safely.
Available in
English and
Spanish.
[transition_comments:protected] =>
[external_link:protected] =>
[consol_link:protected] =>
[more_like_this:protected] => d001234,d001238,d001244,d001251,d001253,d001260,d001268,d001278
[permission_given_by:protected] =>
[published:protected] => T
[billable:protected] => F
[img_name:protected] =>
[img_ext:protected] =>
[img_width:protected] =>
[img_height:protected] =>
[img_credit:protected] =>
[img_practice:protected] =>
[vid_source_id:protected] =>
[vid_running_time:protected] =>
[vid_intended_audience:protected] =>
[vid_acquisition_info:protected] =>
[vid_cost:protected] =>
[vid_producer:protected] =>
[vid_filename:protected] =>
[vid_filename_downloadable:protected] =>
[date_summary:protected] =>
[date_permission_requested:protected] =>
[date_permission_received:protected] =>
[date_review_needed:protected] =>
[date_received:protected] => 06/10/22
[date_completed:protected] => 06/10/22
[date_billed:protected] =>
[date_modified:protected] => 05/22/23
[collBokExports:protected] =>
[lastBokExportCriteria:BaseElcoshItem:private] =>
[alreadyInSave:protected] =>
[alreadyInValidation:protected] =>
[validationFailures:protected] => Array
(
)
[_new:BaseObject:private] =>
[_deleted:BaseObject:private] =>
[modifiedColumns:protected] => Array
(
)
)
)
[2] => Search_Result Object
(
[title] => Toolbox Talk: Tower Crane Safety
[image] => /record/images/notavailable-p.png
[blurb] => The CPWR Toolbox Talk on Tower Crane Safety addresses the potential hazards of Tower Cranes and the importance of following procedure before and durin...
[category] => Array
(
[0] => 11
[1] => 12
[2] => 18
[3] => 70
[4] => 87
[5] => 88
[6] => 91
[7] => 90
[8] => 92
[9] => 100
)
[labels] => Array
(
[0] => Cranes & Hoists
[1] => Work Environment
[2] => Hazards
[3] => Crushed/Struck By
[6] => Motor Vehicles/Heavy Equipment
[9] => Operating Engineer
[10] => Trades
[11] => Commercial & Institutional
[12] => Jobsites
[13] => Demolition
[15] => Heavy & Highway
[17] => Industrial
[19] => LEED/Green Construction
[21] => Toolbox Talks
[22] => Documents
[23] => Media & Documents
)
[type] => Toolbox Talks
[sub_category] =>
[url] => /document/4427/d001657/Toolbox%2BTalk%253A%2BTower%2BCrane%2BSafety.html
[item:protected] => DocumentRecord Object
(
[records:protected] => Array
(
)
[recordId:protected] =>
[searchWordClass:protected] =>
[searchWordPeerClass:protected] =>
[bok_record:protected] =>
[authors:protected] =>
[organizations:protected] =>
[collections:protected] =>
[categories:protected] => Array
(
[11] => Category Object
(
[languages:protected] =>
[bok_resources:protected] =>
[bok_topics:protected] =>
[bok_keywords:protected] =>
[id:protected] => 11
[type:protected] => category
[parent:protected] => 7
[label:protected] => Cranes & Hoists
[alreadyInSave:protected] =>
[alreadyInValidation:protected] =>
[validationFailures:protected] => Array
(
)
[_new:BaseObject:private] =>
[_deleted:BaseObject:private] =>
[modifiedColumns:protected] => Array
(
)
)
[12] => Category Object
(
[languages:protected] =>
[bok_resources:protected] =>
[bok_topics:protected] =>
[bok_keywords:protected] =>
[id:protected] => 12
[type:protected] => category
[parent:protected] => 7
[label:protected] => Crushed/Struck By
[alreadyInSave:protected] =>
[alreadyInValidation:protected] =>
[validationFailures:protected] => Array
(
)
[_new:BaseObject:private] =>
[_deleted:BaseObject:private] =>
[modifiedColumns:protected] => Array
(
)
)
[18] => Category Object
(
[languages:protected] =>
[bok_resources:protected] =>
[bok_topics:protected] =>
[bok_keywords:protected] =>
[id:protected] => 18
[type:protected] => category
[parent:protected] => 7
[label:protected] => Motor Vehicles/Heavy Equipment
[alreadyInSave:protected] =>
[alreadyInValidation:protected] =>
[validationFailures:protected] => Array
(
)
[_new:BaseObject:private] =>
[_deleted:BaseObject:private] =>
[modifiedColumns:protected] => Array
(
)
)
[70] => Category Object
(
[languages:protected] =>
[bok_resources:protected] =>
[bok_topics:protected] =>
[bok_keywords:protected] =>
[id:protected] => 70
[type:protected] => category
[parent:protected] => 2
[label:protected] => Operating Engineer
[alreadyInSave:protected] =>
[alreadyInValidation:protected] =>
[validationFailures:protected] => Array
(
)
[_new:BaseObject:private] =>
[_deleted:BaseObject:private] =>
[modifiedColumns:protected] => Array
(
)
)
[87] => Category Object
(
[languages:protected] =>
[bok_resources:protected] =>
[bok_topics:protected] =>
[bok_keywords:protected] =>
[id:protected] => 87
[type:protected] => category
[parent:protected] => 3
[label:protected] => Commercial & Institutional
[alreadyInSave:protected] =>
[alreadyInValidation:protected] =>
[validationFailures:protected] => Array
(
)
[_new:BaseObject:private] =>
[_deleted:BaseObject:private] =>
[modifiedColumns:protected] => Array
(
)
)
[88] => Category Object
(
[languages:protected] =>
[bok_resources:protected] =>
[bok_topics:protected] =>
[bok_keywords:protected] =>
[id:protected] => 88
[type:protected] => category
[parent:protected] => 3
[label:protected] => Demolition
[alreadyInSave:protected] =>
[alreadyInValidation:protected] =>
[validationFailures:protected] => Array
(
)
[_new:BaseObject:private] =>
[_deleted:BaseObject:private] =>
[modifiedColumns:protected] => Array
(
)
)
[91] => Category Object
(
[languages:protected] =>
[bok_resources:protected] =>
[bok_topics:protected] =>
[bok_keywords:protected] =>
[id:protected] => 91
[type:protected] => category
[parent:protected] => 3
[label:protected] => Heavy & Highway
[alreadyInSave:protected] =>
[alreadyInValidation:protected] =>
[validationFailures:protected] => Array
(
)
[_new:BaseObject:private] =>
[_deleted:BaseObject:private] =>
[modifiedColumns:protected] => Array
(
)
)
[90] => Category Object
(
[languages:protected] =>
[bok_resources:protected] =>
[bok_topics:protected] =>
[bok_keywords:protected] =>
[id:protected] => 90
[type:protected] => category
[parent:protected] => 3
[label:protected] => Industrial
[alreadyInSave:protected] =>
[alreadyInValidation:protected] =>
[validationFailures:protected] => Array
(
)
[_new:BaseObject:private] =>
[_deleted:BaseObject:private] =>
[modifiedColumns:protected] => Array
(
)
)
[92] => Category Object
(
[languages:protected] =>
[bok_resources:protected] =>
[bok_topics:protected] =>
[bok_keywords:protected] =>
[id:protected] => 92
[type:protected] => category
[parent:protected] => 3
[label:protected] => LEED/Green Construction
[alreadyInSave:protected] =>
[alreadyInValidation:protected] =>
[validationFailures:protected] => Array
(
)
[_new:BaseObject:private] =>
[_deleted:BaseObject:private] =>
[modifiedColumns:protected] => Array
(
)
)
[100] => Category Object
(
[languages:protected] =>
[bok_resources:protected] =>
[bok_topics:protected] =>
[bok_keywords:protected] =>
[id:protected] => 100
[type:protected] => category
[parent:protected] => 6
[label:protected] => Toolbox Talks
[alreadyInSave:protected] =>
[alreadyInValidation:protected] =>
[validationFailures:protected] => Array
(
)
[_new:BaseObject:private] =>
[_deleted:BaseObject:private] =>
[modifiedColumns:protected] => Array
(
)
)
)
[categories_initialized:protected] => 1
[mapped_items:protected] =>
[content:protected] =>
[files:protected] =>
[language:protected] => Language Object
(
[id:protected] => 1
[code:protected] => en
[name:protected] => English
[alreadyInSave:protected] =>
[alreadyInValidation:protected] =>
[validationFailures:protected] => Array
(
)
[_new:BaseObject:private] =>
[_deleted:BaseObject:private] =>
[modifiedColumns:protected] => Array
(
)
)
[old_record:protected] =>
[id:protected] => 4427
[old_id:protected] =>
[elcosh_id:protected] => d001657
[type:protected] => document
[display_type:protected] => HTML only (and links)
[user_id:protected] => 0
[language_id:protected] => 1
[tagging_id:protected] => Mike Aguilar
[priority_id:protected] => 1
[title:protected] => Toolbox Talk: Tower Crane Safety
[total_pages:protected] => 0
[billed_pages:protected] => 0
[publication_number:protected] =>
[part_of:protected] =>
[keywords:protected] => Tower Crane, Crane, Stability, Tipping, Lift Zone Safety, Lift, Zone, Safety, Struck by
[comments:protected] =>
[summary:protected] => The CPWR Toolbox Talk on Tower Crane Safety addresses the potential hazards of Tower Cranes and the importance of following procedure before and during Tower Crane operation. The resource includes a brief example, steps to prevent a related injury, and questions for discussion. It includes a graphic that illustrates a worker inspecting a Tower Crane before operation, which can be posted in a central location as a reminder of steps to work safely.
Available in
English and
Spanish.
[transition_comments:protected] =>
[external_link:protected] =>
[consol_link:protected] =>
[more_like_this:protected] => d001234,d001238,d001250,d001251,d001253,d001258,d001262,d001273
[permission_given_by:protected] =>
[published:protected] => T
[billable:protected] => F
[img_name:protected] =>
[img_ext:protected] => jpg
[img_width:protected] =>
[img_height:protected] =>
[img_credit:protected] =>
[img_practice:protected] =>
[vid_source_id:protected] =>
[vid_running_time:protected] =>
[vid_intended_audience:protected] =>
[vid_acquisition_info:protected] =>
[vid_cost:protected] =>
[vid_producer:protected] =>
[vid_filename:protected] =>
[vid_filename_downloadable:protected] =>
[date_summary:protected] =>
[date_permission_requested:protected] =>
[date_permission_received:protected] =>
[date_review_needed:protected] =>
[date_received:protected] => 12/23/21
[date_completed:protected] => 12/23/21
[date_billed:protected] =>
[date_modified:protected] => 05/19/23
[collBokExports:protected] =>
[lastBokExportCriteria:BaseElcoshItem:private] =>
[alreadyInSave:protected] =>
[alreadyInValidation:protected] =>
[validationFailures:protected] => Array
(
)
[_new:BaseObject:private] =>
[_deleted:BaseObject:private] =>
[modifiedColumns:protected] => Array
(
)
)
)
[3] => Search_Result Object
(
[title] => Toolbox Talk: Work Zone Safety: Working Around Vehicles
[image] => /record/images/notavailable-p.png
[blurb] => The CPWR Toolbox Talk on Working Around Vehicles in the Work Zone addresses methods to avoid being struck-by a vehicle on a construction site. The res...
[category] => Array
(
[0] => 12
[1] => 18
[2] => 52
[3] => 57
[4] => 70
[5] => 85
[6] => 87
[7] => 88
[8] => 89
[9] => 91
[10] => 90
[11] => 92
[12] => 93
[13] => 94
[14] => 95
[15] => 100
)
[labels] => Array
(
[0] => Crushed/Struck By
[1] => Work Environment
[2] => Hazards
[3] => Motor Vehicles/Heavy Equipment
[6] => Commercial Diver
[7] => Trades
[8] => Flagger
[10] => Operating Engineer
[12] => Truck Driver
[14] => Commercial & Institutional
[15] => Jobsites
[16] => Demolition
[18] => Disasters
[20] => Heavy & Highway
[22] => Industrial
[24] => LEED/Green Construction
[26] => Renovations
[28] => Residential
[30] => Underground
[32] => Toolbox Talks
[33] => Documents
[34] => Media & Documents
)
[type] => Toolbox Talks
[sub_category] =>
[url] => /document/4428/d001658/Toolbox%2BTalk%253A%2BWork%2BZone%2BSafety%253A%2BWorking%2BAround%2BVehicles.html
[item:protected] => DocumentRecord Object
(
[records:protected] => Array
(
)
[recordId:protected] =>
[searchWordClass:protected] =>
[searchWordPeerClass:protected] =>
[bok_record:protected] =>
[authors:protected] =>
[organizations:protected] =>
[collections:protected] =>
[categories:protected] => Array
(
[12] => Category Object
(
[languages:protected] =>
[bok_resources:protected] =>
[bok_topics:protected] =>
[bok_keywords:protected] =>
[id:protected] => 12
[type:protected] => category
[parent:protected] => 7
[label:protected] => Crushed/Struck By
[alreadyInSave:protected] =>
[alreadyInValidation:protected] =>
[validationFailures:protected] => Array
(
)
[_new:BaseObject:private] =>
[_deleted:BaseObject:private] =>
[modifiedColumns:protected] => Array
(
)
)
[18] => Category Object
(
[languages:protected] =>
[bok_resources:protected] =>
[bok_topics:protected] =>
[bok_keywords:protected] =>
[id:protected] => 18
[type:protected] => category
[parent:protected] => 7
[label:protected] => Motor Vehicles/Heavy Equipment
[alreadyInSave:protected] =>
[alreadyInValidation:protected] =>
[validationFailures:protected] => Array
(
)
[_new:BaseObject:private] =>
[_deleted:BaseObject:private] =>
[modifiedColumns:protected] => Array
(
)
)
[52] => Category Object
(
[languages:protected] =>
[bok_resources:protected] =>
[bok_topics:protected] =>
[bok_keywords:protected] =>
[id:protected] => 52
[type:protected] => category
[parent:protected] => 2
[label:protected] => Commercial Diver
[alreadyInSave:protected] =>
[alreadyInValidation:protected] =>
[validationFailures:protected] => Array
(
)
[_new:BaseObject:private] =>
[_deleted:BaseObject:private] =>
[modifiedColumns:protected] => Array
(
)
)
[57] => Category Object
(
[languages:protected] =>
[bok_resources:protected] =>
[bok_topics:protected] =>
[bok_keywords:protected] =>
[id:protected] => 57
[type:protected] => category
[parent:protected] => 2
[label:protected] => Flagger
[alreadyInSave:protected] =>
[alreadyInValidation:protected] =>
[validationFailures:protected] => Array
(
)
[_new:BaseObject:private] =>
[_deleted:BaseObject:private] =>
[modifiedColumns:protected] => Array
(
)
)
[70] => Category Object
(
[languages:protected] =>
[bok_resources:protected] =>
[bok_topics:protected] =>
[bok_keywords:protected] =>
[id:protected] => 70
[type:protected] => category
[parent:protected] => 2
[label:protected] => Operating Engineer
[alreadyInSave:protected] =>
[alreadyInValidation:protected] =>
[validationFailures:protected] => Array
(
)
[_new:BaseObject:private] =>
[_deleted:BaseObject:private] =>
[modifiedColumns:protected] => Array
(
)
)
[85] => Category Object
(
[languages:protected] =>
[bok_resources:protected] =>
[bok_topics:protected] =>
[bok_keywords:protected] =>
[id:protected] => 85
[type:protected] => category
[parent:protected] => 2
[label:protected] => Truck Driver
[alreadyInSave:protected] =>
[alreadyInValidation:protected] =>
[validationFailures:protected] => Array
(
)
[_new:BaseObject:private] =>
[_deleted:BaseObject:private] =>
[modifiedColumns:protected] => Array
(
)
)
[87] => Category Object
(
[languages:protected] =>
[bok_resources:protected] =>
[bok_topics:protected] =>
[bok_keywords:protected] =>
[id:protected] => 87
[type:protected] => category
[parent:protected] => 3
[label:protected] => Commercial & Institutional
[alreadyInSave:protected] =>
[alreadyInValidation:protected] =>
[validationFailures:protected] => Array
(
)
[_new:BaseObject:private] =>
[_deleted:BaseObject:private] =>
[modifiedColumns:protected] => Array
(
)
)
[88] => Category Object
(
[languages:protected] =>
[bok_resources:protected] =>
[bok_topics:protected] =>
[bok_keywords:protected] =>
[id:protected] => 88
[type:protected] => category
[parent:protected] => 3
[label:protected] => Demolition
[alreadyInSave:protected] =>
[alreadyInValidation:protected] =>
[validationFailures:protected] => Array
(
)
[_new:BaseObject:private] =>
[_deleted:BaseObject:private] =>
[modifiedColumns:protected] => Array
(
)
)
[89] => Category Object
(
[languages:protected] =>
[bok_resources:protected] =>
[bok_topics:protected] =>
[bok_keywords:protected] =>
[id:protected] => 89
[type:protected] => category
[parent:protected] => 3
[label:protected] => Disasters
[alreadyInSave:protected] =>
[alreadyInValidation:protected] =>
[validationFailures:protected] => Array
(
)
[_new:BaseObject:private] =>
[_deleted:BaseObject:private] =>
[modifiedColumns:protected] => Array
(
)
)
[91] => Category Object
(
[languages:protected] =>
[bok_resources:protected] =>
[bok_topics:protected] =>
[bok_keywords:protected] =>
[id:protected] => 91
[type:protected] => category
[parent:protected] => 3
[label:protected] => Heavy & Highway
[alreadyInSave:protected] =>
[alreadyInValidation:protected] =>
[validationFailures:protected] => Array
(
)
[_new:BaseObject:private] =>
[_deleted:BaseObject:private] =>
[modifiedColumns:protected] => Array
(
)
)
[90] => Category Object
(
[languages:protected] =>
[bok_resources:protected] =>
[bok_topics:protected] =>
[bok_keywords:protected] =>
[id:protected] => 90
[type:protected] => category
[parent:protected] => 3
[label:protected] => Industrial
[alreadyInSave:protected] =>
[alreadyInValidation:protected] =>
[validationFailures:protected] => Array
(
)
[_new:BaseObject:private] =>
[_deleted:BaseObject:private] =>
[modifiedColumns:protected] => Array
(
)
)
[92] => Category Object
(
[languages:protected] =>
[bok_resources:protected] =>
[bok_topics:protected] =>
[bok_keywords:protected] =>
[id:protected] => 92
[type:protected] => category
[parent:protected] => 3
[label:protected] => LEED/Green Construction
[alreadyInSave:protected] =>
[alreadyInValidation:protected] =>
[validationFailures:protected] => Array
(
)
[_new:BaseObject:private] =>
[_deleted:BaseObject:private] =>
[modifiedColumns:protected] => Array
(
)
)
[93] => Category Object
(
[languages:protected] =>
[bok_resources:protected] =>
[bok_topics:protected] =>
[bok_keywords:protected] =>
[id:protected] => 93
[type:protected] => category
[parent:protected] => 3
[label:protected] => Renovations
[alreadyInSave:protected] =>
[alreadyInValidation:protected] =>
[validationFailures:protected] => Array
(
)
[_new:BaseObject:private] =>
[_deleted:BaseObject:private] =>
[modifiedColumns:protected] => Array
(
)
)
[94] => Category Object
(
[languages:protected] =>
[bok_resources:protected] =>
[bok_topics:protected] =>
[bok_keywords:protected] =>
[id:protected] => 94
[type:protected] => category
[parent:protected] => 3
[label:protected] => Residential
[alreadyInSave:protected] =>
[alreadyInValidation:protected] =>
[validationFailures:protected] => Array
(
)
[_new:BaseObject:private] =>
[_deleted:BaseObject:private] =>
[modifiedColumns:protected] => Array
(
)
)
[95] => Category Object
(
[languages:protected] =>
[bok_resources:protected] =>
[bok_topics:protected] =>
[bok_keywords:protected] =>
[id:protected] => 95
[type:protected] => category
[parent:protected] => 3
[label:protected] => Underground
[alreadyInSave:protected] =>
[alreadyInValidation:protected] =>
[validationFailures:protected] => Array
(
)
[_new:BaseObject:private] =>
[_deleted:BaseObject:private] =>
[modifiedColumns:protected] => Array
(
)
)
[100] => Category Object
(
[languages:protected] =>
[bok_resources:protected] =>
[bok_topics:protected] =>
[bok_keywords:protected] =>
[id:protected] => 100
[type:protected] => category
[parent:protected] => 6
[label:protected] => Toolbox Talks
[alreadyInSave:protected] =>
[alreadyInValidation:protected] =>
[validationFailures:protected] => Array
(
)
[_new:BaseObject:private] =>
[_deleted:BaseObject:private] =>
[modifiedColumns:protected] => Array
(
)
)
)
[categories_initialized:protected] => 1
[mapped_items:protected] =>
[content:protected] =>
[files:protected] =>
[language:protected] => Language Object
(
[id:protected] => 1
[code:protected] => en
[name:protected] => English
[alreadyInSave:protected] =>
[alreadyInValidation:protected] =>
[validationFailures:protected] => Array
(
)
[_new:BaseObject:private] =>
[_deleted:BaseObject:private] =>
[modifiedColumns:protected] => Array
(
)
)
[old_record:protected] =>
[id:protected] => 4428
[old_id:protected] =>
[elcosh_id:protected] => d001658
[type:protected] => document
[display_type:protected] => HTML only (and links)
[user_id:protected] => 0
[language_id:protected] => 1
[tagging_id:protected] => Daniela Caceres
[priority_id:protected] => 1
[title:protected] => Toolbox Talk: Work Zone Safety: Working Around Vehicles
[total_pages:protected] => 0
[billed_pages:protected] => 0
[publication_number:protected] =>
[part_of:protected] =>
[keywords:protected] => Struck, Struck by, Vehicle, Work Zone Safety, Truck, Operator, Driver, Mobile Equipment
[comments:protected] =>
[summary:protected] => The CPWR Toolbox Talk on Working Around Vehicles in the Work Zone addresses methods to avoid being struck-by a vehicle on a construction site. The resource includes a case example, steps to prevent a related injury, and questions for discussion. It includes a graphic that illustrates the hazard, which can be posted in a central location as a reminder of steps to work safely. Available in
English and
Spanish.
[transition_comments:protected] =>
[external_link:protected] =>
[consol_link:protected] =>
[more_like_this:protected] => d001640
[permission_given_by:protected] =>
[published:protected] => T
[billable:protected] => F
[img_name:protected] =>
[img_ext:protected] =>
[img_width:protected] =>
[img_height:protected] =>
[img_credit:protected] =>
[img_practice:protected] =>
[vid_source_id:protected] =>
[vid_running_time:protected] =>
[vid_intended_audience:protected] =>
[vid_acquisition_info:protected] =>
[vid_cost:protected] =>
[vid_producer:protected] =>
[vid_filename:protected] =>
[vid_filename_downloadable:protected] =>
[date_summary:protected] =>
[date_permission_requested:protected] =>
[date_permission_received:protected] =>
[date_review_needed:protected] =>
[date_received:protected] => 12/23/21
[date_completed:protected] => 12/23/21
[date_billed:protected] =>
[date_modified:protected] => 05/19/23
[collBokExports:protected] =>
[lastBokExportCriteria:BaseElcoshItem:private] =>
[alreadyInSave:protected] =>
[alreadyInValidation:protected] =>
[validationFailures:protected] => Array
(
)
[_new:BaseObject:private] =>
[_deleted:BaseObject:private] =>
[modifiedColumns:protected] => Array
(
)
)
)
[4] => Search_Result Object
(
[title] => Construction Dive -- DeWalt's Jobsite Pro headphones recalled for fire hazards
[image] => /record/images/notavailable-p.png
[blurb] => A recall notice by the United States Consumer Product Safety Commission affects over 300,000 DeWalt Jobsite Pro Headphones. The recall is a result of...
[category] => Array
(
[0] => 16
[1] => 44
[2] => 45
[3] => 46
[4] => 47
[5] => 48
[6] => 49
[7] => 50
[8] => 51
[9] => 52
[10] => 53
[11] => 54
[12] => 55
[13] => 56
[14] => 57
[15] => 58
[16] => 59
[17] => 60
[18] => 61
[19] => 64
[20] => 65
[21] => 66
[22] => 67
[23] => 68
[24] => 69
[25] => 70
[26] => 71
[27] => 72
[28] => 73
[29] => 74
[30] => 75
[31] => 76
[32] => 77
[33] => 63
[34] => 78
[35] => 79
[36] => 80
[37] => 81
[38] => 82
[39] => 62
[40] => 83
[41] => 84
[42] => 85
[43] => 86
[44] => 87
[45] => 88
[46] => 89
[47] => 91
[48] => 90
[49] => 92
[50] => 93
[51] => 94
[52] => 95
)
[labels] => Array
(
[0] => Fire & Explosions
[1] => Work Environment
[2] => Hazards
[3] => Acoustical Ceiling Carpenter
[4] => Trades
[5] => Asbestos/Insulator
[7] => Boilermaker
[9] => Bricklayer
[11] => Cabinetmaker
[13] => Carpenter
[15] => Carpet Layer
[17] => Cement Mason
[19] => Commercial Diver
[21] => Concrete Polisher
[23] => Drywall Applicator Specialist
[25] => Electrical Worker
[27] => Elevator Constructor
[29] => Flagger
[31] => Glazier
[33] => Hazardous Waste Cleanup
[35] => HVAC
[37] => Interior Systems Carpenter
[39] => Laborer
[41] => Landscaper
[43] => Lather
[45] => Lead Abatement Worker
[47] => Maintenance Worker
[49] => Millwright
[51] => Operating Engineer
[53] => Painter
[55] => Paper Hanger
[57] => PCC/Restoration
[59] => Pile Driver
[61] => Plasterer
[63] => Plumber/Pipefitter
[65] => Refractory Worker
[67] => Reinforcing Ironworker
[69] => Roofer/Waterproofer
[71] => Scaffold Erector
[73] => Sheetmetal Worker
[75] => Sprinkler Fitter
[77] => Stonemason
[79] => Structural Ironworker
[81] => Terrazzo Worker
[83] => Tile Setter
[85] => Truck Driver
[87] => Welder
[89] => Commercial & Institutional
[90] => Jobsites
[91] => Demolition
[93] => Disasters
[95] => Heavy & Highway
[97] => Industrial
[99] => LEED/Green Construction
[101] => Renovations
[103] => Residential
[105] => Underground
)
[type] =>
[sub_category] =>
[url] => /document/4426/d001656/Construction%2BDive%2B--%2BDeWalt%2527s%2BJobsite%2BPro%2Bheadphones%2Brecalled%2Bfor%2Bfire%2Bhazards.html
[item:protected] => DocumentRecord Object
(
[records:protected] => Array
(
)
[recordId:protected] =>
[searchWordClass:protected] =>
[searchWordPeerClass:protected] =>
[bok_record:protected] =>
[authors:protected] =>
[organizations:protected] =>
[collections:protected] =>
[categories:protected] => Array
(
[16] => Category Object
(
[languages:protected] =>
[bok_resources:protected] =>
[bok_topics:protected] =>
[bok_keywords:protected] =>
[id:protected] => 16
[type:protected] => category
[parent:protected] => 7
[label:protected] => Fire & Explosions
[alreadyInSave:protected] =>
[alreadyInValidation:protected] =>
[validationFailures:protected] => Array
(
)
[_new:BaseObject:private] =>
[_deleted:BaseObject:private] =>
[modifiedColumns:protected] => Array
(
)
)
[44] => Category Object
(
[languages:protected] =>
[bok_resources:protected] =>
[bok_topics:protected] =>
[bok_keywords:protected] =>
[id:protected] => 44
[type:protected] => category
[parent:protected] => 2
[label:protected] => Acoustical Ceiling Carpenter
[alreadyInSave:protected] =>
[alreadyInValidation:protected] =>
[validationFailures:protected] => Array
(
)
[_new:BaseObject:private] =>
[_deleted:BaseObject:private] =>
[modifiedColumns:protected] => Array
(
)
)
[45] => Category Object
(
[languages:protected] =>
[bok_resources:protected] =>
[bok_topics:protected] =>
[bok_keywords:protected] =>
[id:protected] => 45
[type:protected] => category
[parent:protected] => 2
[label:protected] => Asbestos/Insulator
[alreadyInSave:protected] =>
[alreadyInValidation:protected] =>
[validationFailures:protected] => Array
(
)
[_new:BaseObject:private] =>
[_deleted:BaseObject:private] =>
[modifiedColumns:protected] => Array
(
)
)
[46] => Category Object
(
[languages:protected] =>
[bok_resources:protected] =>
[bok_topics:protected] =>
[bok_keywords:protected] =>
[id:protected] => 46
[type:protected] => category
[parent:protected] => 2
[label:protected] => Boilermaker
[alreadyInSave:protected] =>
[alreadyInValidation:protected] =>
[validationFailures:protected] => Array
(
)
[_new:BaseObject:private] =>
[_deleted:BaseObject:private] =>
[modifiedColumns:protected] => Array
(
)
)
[47] => Category Object
(
[languages:protected] =>
[bok_resources:protected] =>
[bok_topics:protected] =>
[bok_keywords:protected] =>
[id:protected] => 47
[type:protected] => category
[parent:protected] => 2
[label:protected] => Bricklayer
[alreadyInSave:protected] =>
[alreadyInValidation:protected] =>
[validationFailures:protected] => Array
(
)
[_new:BaseObject:private] =>
[_deleted:BaseObject:private] =>
[modifiedColumns:protected] => Array
(
)
)
[48] => Category Object
(
[languages:protected] =>
[bok_resources:protected] =>
[bok_topics:protected] =>
[bok_keywords:protected] =>
[id:protected] => 48
[type:protected] => category
[parent:protected] => 2
[label:protected] => Cabinetmaker
[alreadyInSave:protected] =>
[alreadyInValidation:protected] =>
[validationFailures:protected] => Array
(
)
[_new:BaseObject:private] =>
[_deleted:BaseObject:private] =>
[modifiedColumns:protected] => Array
(
)
)
[49] => Category Object
(
[languages:protected] =>
[bok_resources:protected] =>
[bok_topics:protected] =>
[bok_keywords:protected] =>
[id:protected] => 49
[type:protected] => category
[parent:protected] => 2
[label:protected] => Carpenter
[alreadyInSave:protected] =>
[alreadyInValidation:protected] =>
[validationFailures:protected] => Array
(
)
[_new:BaseObject:private] =>
[_deleted:BaseObject:private] =>
[modifiedColumns:protected] => Array
(
)
)
[50] => Category Object
(
[languages:protected] =>
[bok_resources:protected] =>
[bok_topics:protected] =>
[bok_keywords:protected] =>
[id:protected] => 50
[type:protected] => category
[parent:protected] => 2
[label:protected] => Carpet Layer
[alreadyInSave:protected] =>
[alreadyInValidation:protected] =>
[validationFailures:protected] => Array
(
)
[_new:BaseObject:private] =>
[_deleted:BaseObject:private] =>
[modifiedColumns:protected] => Array
(
)
)
[51] => Category Object
(
[languages:protected] =>
[bok_resources:protected] =>
[bok_topics:protected] =>
[bok_keywords:protected] =>
[id:protected] => 51
[type:protected] => category
[parent:protected] => 2
[label:protected] => Cement Mason
[alreadyInSave:protected] =>
[alreadyInValidation:protected] =>
[validationFailures:protected] => Array
(
)
[_new:BaseObject:private] =>
[_deleted:BaseObject:private] =>
[modifiedColumns:protected] => Array
(
)
)
[52] => Category Object
(
[languages:protected] =>
[bok_resources:protected] =>
[bok_topics:protected] =>
[bok_keywords:protected] =>
[id:protected] => 52
[type:protected] => category
[parent:protected] => 2
[label:protected] => Commercial Diver
[alreadyInSave:protected] =>
[alreadyInValidation:protected] =>
[validationFailures:protected] => Array
(
)
[_new:BaseObject:private] =>
[_deleted:BaseObject:private] =>
[modifiedColumns:protected] => Array
(
)
)
[53] => Category Object
(
[languages:protected] =>
[bok_resources:protected] =>
[bok_topics:protected] =>
[bok_keywords:protected] =>
[id:protected] => 53
[type:protected] => category
[parent:protected] => 2
[label:protected] => Concrete Polisher
[alreadyInSave:protected] =>
[alreadyInValidation:protected] =>
[validationFailures:protected] => Array
(
)
[_new:BaseObject:private] =>
[_deleted:BaseObject:private] =>
[modifiedColumns:protected] => Array
(
)
)
[54] => Category Object
(
[languages:protected] =>
[bok_resources:protected] =>
[bok_topics:protected] =>
[bok_keywords:protected] =>
[id:protected] => 54
[type:protected] => category
[parent:protected] => 2
[label:protected] => Drywall Applicator Specialist
[alreadyInSave:protected] =>
[alreadyInValidation:protected] =>
[validationFailures:protected] => Array
(
)
[_new:BaseObject:private] =>
[_deleted:BaseObject:private] =>
[modifiedColumns:protected] => Array
(
)
)
[55] => Category Object
(
[languages:protected] =>
[bok_resources:protected] =>
[bok_topics:protected] =>
[bok_keywords:protected] =>
[id:protected] => 55
[type:protected] => category
[parent:protected] => 2
[label:protected] => Electrical Worker
[alreadyInSave:protected] =>
[alreadyInValidation:protected] =>
[validationFailures:protected] => Array
(
)
[_new:BaseObject:private] =>
[_deleted:BaseObject:private] =>
[modifiedColumns:protected] => Array
(
)
)
[56] => Category Object
(
[languages:protected] =>
[bok_resources:protected] =>
[bok_topics:protected] =>
[bok_keywords:protected] =>
[id:protected] => 56
[type:protected] => category
[parent:protected] => 2
[label:protected] => Elevator Constructor
[alreadyInSave:protected] =>
[alreadyInValidation:protected] =>
[validationFailures:protected] => Array
(
)
[_new:BaseObject:private] =>
[_deleted:BaseObject:private] =>
[modifiedColumns:protected] => Array
(
)
)
[57] => Category Object
(
[languages:protected] =>
[bok_resources:protected] =>
[bok_topics:protected] =>
[bok_keywords:protected] =>
[id:protected] => 57
[type:protected] => category
[parent:protected] => 2
[label:protected] => Flagger
[alreadyInSave:protected] =>
[alreadyInValidation:protected] =>
[validationFailures:protected] => Array
(
)
[_new:BaseObject:private] =>
[_deleted:BaseObject:private] =>
[modifiedColumns:protected] => Array
(
)
)
[58] => Category Object
(
[languages:protected] =>
[bok_resources:protected] =>
[bok_topics:protected] =>
[bok_keywords:protected] =>
[id:protected] => 58
[type:protected] => category
[parent:protected] => 2
[label:protected] => Glazier
[alreadyInSave:protected] =>
[alreadyInValidation:protected] =>
[validationFailures:protected] => Array
(
)
[_new:BaseObject:private] =>
[_deleted:BaseObject:private] =>
[modifiedColumns:protected] => Array
(
)
)
[59] => Category Object
(
[languages:protected] =>
[bok_resources:protected] =>
[bok_topics:protected] =>
[bok_keywords:protected] =>
[id:protected] => 59
[type:protected] => category
[parent:protected] => 2
[label:protected] => Hazardous Waste Cleanup
[alreadyInSave:protected] =>
[alreadyInValidation:protected] =>
[validationFailures:protected] => Array
(
)
[_new:BaseObject:private] =>
[_deleted:BaseObject:private] =>
[modifiedColumns:protected] => Array
(
)
)
[60] => Category Object
(
[languages:protected] =>
[bok_resources:protected] =>
[bok_topics:protected] =>
[bok_keywords:protected] =>
[id:protected] => 60
[type:protected] => category
[parent:protected] => 2
[label:protected] => HVAC
[alreadyInSave:protected] =>
[alreadyInValidation:protected] =>
[validationFailures:protected] => Array
(
)
[_new:BaseObject:private] =>
[_deleted:BaseObject:private] =>
[modifiedColumns:protected] => Array
(
)
)
[61] => Category Object
(
[languages:protected] =>
[bok_resources:protected] =>
[bok_topics:protected] =>
[bok_keywords:protected] =>
[id:protected] => 61
[type:protected] => category
[parent:protected] => 2
[label:protected] => Interior Systems Carpenter
[alreadyInSave:protected] =>
[alreadyInValidation:protected] =>
[validationFailures:protected] => Array
(
)
[_new:BaseObject:private] =>
[_deleted:BaseObject:private] =>
[modifiedColumns:protected] => Array
(
)
)
[64] => Category Object
(
[languages:protected] =>
[bok_resources:protected] =>
[bok_topics:protected] =>
[bok_keywords:protected] =>
[id:protected] => 64
[type:protected] => category
[parent:protected] => 2
[label:protected] => Laborer
[alreadyInSave:protected] =>
[alreadyInValidation:protected] =>
[validationFailures:protected] => Array
(
)
[_new:BaseObject:private] =>
[_deleted:BaseObject:private] =>
[modifiedColumns:protected] => Array
(
)
)
[65] => Category Object
(
[languages:protected] =>
[bok_resources:protected] =>
[bok_topics:protected] =>
[bok_keywords:protected] =>
[id:protected] => 65
[type:protected] => category
[parent:protected] => 2
[label:protected] => Landscaper
[alreadyInSave:protected] =>
[alreadyInValidation:protected] =>
[validationFailures:protected] => Array
(
)
[_new:BaseObject:private] =>
[_deleted:BaseObject:private] =>
[modifiedColumns:protected] => Array
(
)
)
[66] => Category Object
(
[languages:protected] =>
[bok_resources:protected] =>
[bok_topics:protected] =>
[bok_keywords:protected] =>
[id:protected] => 66
[type:protected] => category
[parent:protected] => 2
[label:protected] => Lather
[alreadyInSave:protected] =>
[alreadyInValidation:protected] =>
[validationFailures:protected] => Array
(
)
[_new:BaseObject:private] =>
[_deleted:BaseObject:private] =>
[modifiedColumns:protected] => Array
(
)
)
[67] => Category Object
(
[languages:protected] =>
[bok_resources:protected] =>
[bok_topics:protected] =>
[bok_keywords:protected] =>
[id:protected] => 67
[type:protected] => category
[parent:protected] => 2
[label:protected] => Lead Abatement Worker
[alreadyInSave:protected] =>
[alreadyInValidation:protected] =>
[validationFailures:protected] => Array
(
)
[_new:BaseObject:private] =>
[_deleted:BaseObject:private] =>
[modifiedColumns:protected] => Array
(
)
)
[68] => Category Object
(
[languages:protected] =>
[bok_resources:protected] =>
[bok_topics:protected] =>
[bok_keywords:protected] =>
[id:protected] => 68
[type:protected] => category
[parent:protected] => 2
[label:protected] => Maintenance Worker
[alreadyInSave:protected] =>
[alreadyInValidation:protected] =>
[validationFailures:protected] => Array
(
)
[_new:BaseObject:private] =>
[_deleted:BaseObject:private] =>
[modifiedColumns:protected] => Array
(
)
)
[69] => Category Object
(
[languages:protected] =>
[bok_resources:protected] =>
[bok_topics:protected] =>
[bok_keywords:protected] =>
[id:protected] => 69
[type:protected] => category
[parent:protected] => 2
[label:protected] => Millwright
[alreadyInSave:protected] =>
[alreadyInValidation:protected] =>
[validationFailures:protected] => Array
(
)
[_new:BaseObject:private] =>
[_deleted:BaseObject:private] =>
[modifiedColumns:protected] => Array
(
)
)
[70] => Category Object
(
[languages:protected] =>
[bok_resources:protected] =>
[bok_topics:protected] =>
[bok_keywords:protected] =>
[id:protected] => 70
[type:protected] => category
[parent:protected] => 2
[label:protected] => Operating Engineer
[alreadyInSave:protected] =>
[alreadyInValidation:protected] =>
[validationFailures:protected] => Array
(
)
[_new:BaseObject:private] =>
[_deleted:BaseObject:private] =>
[modifiedColumns:protected] => Array
(
)
)
[71] => Category Object
(
[languages:protected] =>
[bok_resources:protected] =>
[bok_topics:protected] =>
[bok_keywords:protected] =>
[id:protected] => 71
[type:protected] => category
[parent:protected] => 2
[label:protected] => Painter
[alreadyInSave:protected] =>
[alreadyInValidation:protected] =>
[validationFailures:protected] => Array
(
)
[_new:BaseObject:private] =>
[_deleted:BaseObject:private] =>
[modifiedColumns:protected] => Array
(
)
)
[72] => Category Object
(
[languages:protected] =>
[bok_resources:protected] =>
[bok_topics:protected] =>
[bok_keywords:protected] =>
[id:protected] => 72
[type:protected] => category
[parent:protected] => 2
[label:protected] => Paper Hanger
[alreadyInSave:protected] =>
[alreadyInValidation:protected] =>
[validationFailures:protected] => Array
(
)
[_new:BaseObject:private] =>
[_deleted:BaseObject:private] =>
[modifiedColumns:protected] => Array
(
)
)
[73] => Category Object
(
[languages:protected] =>
[bok_resources:protected] =>
[bok_topics:protected] =>
[bok_keywords:protected] =>
[id:protected] => 73
[type:protected] => category
[parent:protected] => 2
[label:protected] => PCC/Restoration
[alreadyInSave:protected] =>
[alreadyInValidation:protected] =>
[validationFailures:protected] => Array
(
)
[_new:BaseObject:private] =>
[_deleted:BaseObject:private] =>
[modifiedColumns:protected] => Array
(
)
)
[74] => Category Object
(
[languages:protected] =>
[bok_resources:protected] =>
[bok_topics:protected] =>
[bok_keywords:protected] =>
[id:protected] => 74
[type:protected] => category
[parent:protected] => 2
[label:protected] => Pile Driver
[alreadyInSave:protected] =>
[alreadyInValidation:protected] =>
[validationFailures:protected] => Array
(
)
[_new:BaseObject:private] =>
[_deleted:BaseObject:private] =>
[modifiedColumns:protected] => Array
(
)
)
[75] => Category Object
(
[languages:protected] =>
[bok_resources:protected] =>
[bok_topics:protected] =>
[bok_keywords:protected] =>
[id:protected] => 75
[type:protected] => category
[parent:protected] => 2
[label:protected] => Plasterer
[alreadyInSave:protected] =>
[alreadyInValidation:protected] =>
[validationFailures:protected] => Array
(
)
[_new:BaseObject:private] =>
[_deleted:BaseObject:private] =>
[modifiedColumns:protected] => Array
(
)
)
[76] => Category Object
(
[languages:protected] =>
[bok_resources:protected] =>
[bok_topics:protected] =>
[bok_keywords:protected] =>
[id:protected] => 76
[type:protected] => category
[parent:protected] => 2
[label:protected] => Plumber/Pipefitter
[alreadyInSave:protected] =>
[alreadyInValidation:protected] =>
[validationFailures:protected] => Array
(
)
[_new:BaseObject:private] =>
[_deleted:BaseObject:private] =>
[modifiedColumns:protected] => Array
(
)
)
[77] => Category Object
(
[languages:protected] =>
[bok_resources:protected] =>
[bok_topics:protected] =>
[bok_keywords:protected] =>
[id:protected] => 77
[type:protected] => category
[parent:protected] => 2
[label:protected] => Refractory Worker
[alreadyInSave:protected] =>
[alreadyInValidation:protected] =>
[validationFailures:protected] => Array
(
)
[_new:BaseObject:private] =>
[_deleted:BaseObject:private] =>
[modifiedColumns:protected] => Array
(
)
)
[63] => Category Object
(
[languages:protected] =>
[bok_resources:protected] =>
[bok_topics:protected] =>
[bok_keywords:protected] =>
[id:protected] => 63
[type:protected] => category
[parent:protected] => 2
[label:protected] => Reinforcing Ironworker
[alreadyInSave:protected] =>
[alreadyInValidation:protected] =>
[validationFailures:protected] => Array
(
)
[_new:BaseObject:private] =>
[_deleted:BaseObject:private] =>
[modifiedColumns:protected] => Array
(
)
)
[78] => Category Object
(
[languages:protected] =>
[bok_resources:protected] =>
[bok_topics:protected] =>
[bok_keywords:protected] =>
[id:protected] => 78
[type:protected] => category
[parent:protected] => 2
[label:protected] => Roofer/Waterproofer
[alreadyInSave:protected] =>
[alreadyInValidation:protected] =>
[validationFailures:protected] => Array
(
)
[_new:BaseObject:private] =>
[_deleted:BaseObject:private] =>
[modifiedColumns:protected] => Array
(
)
)
[79] => Category Object
(
[languages:protected] =>
[bok_resources:protected] =>
[bok_topics:protected] =>
[bok_keywords:protected] =>
[id:protected] => 79
[type:protected] => category
[parent:protected] => 2
[label:protected] => Scaffold Erector
[alreadyInSave:protected] =>
[alreadyInValidation:protected] =>
[validationFailures:protected] => Array
(
)
[_new:BaseObject:private] =>
[_deleted:BaseObject:private] =>
[modifiedColumns:protected] => Array
(
)
)
[80] => Category Object
(
[languages:protected] =>
[bok_resources:protected] =>
[bok_topics:protected] =>
[bok_keywords:protected] =>
[id:protected] => 80
[type:protected] => category
[parent:protected] => 2
[label:protected] => Sheetmetal Worker
[alreadyInSave:protected] =>
[alreadyInValidation:protected] =>
[validationFailures:protected] => Array
(
)
[_new:BaseObject:private] =>
[_deleted:BaseObject:private] =>
[modifiedColumns:protected] => Array
(
)
)
[81] => Category Object
(
[languages:protected] =>
[bok_resources:protected] =>
[bok_topics:protected] =>
[bok_keywords:protected] =>
[id:protected] => 81
[type:protected] => category
[parent:protected] => 2
[label:protected] => Sprinkler Fitter
[alreadyInSave:protected] =>
[alreadyInValidation:protected] =>
[validationFailures:protected] => Array
(
)
[_new:BaseObject:private] =>
[_deleted:BaseObject:private] =>
[modifiedColumns:protected] => Array
(
)
)
[82] => Category Object
(
[languages:protected] =>
[bok_resources:protected] =>
[bok_topics:protected] =>
[bok_keywords:protected] =>
[id:protected] => 82
[type:protected] => category
[parent:protected] => 2
[label:protected] => Stonemason
[alreadyInSave:protected] =>
[alreadyInValidation:protected] =>
[validationFailures:protected] => Array
(
)
[_new:BaseObject:private] =>
[_deleted:BaseObject:private] =>
[modifiedColumns:protected] => Array
(
)
)
[62] => Category Object
(
[languages:protected] =>
[bok_resources:protected] =>
[bok_topics:protected] =>
[bok_keywords:protected] =>
[id:protected] => 62
[type:protected] => category
[parent:protected] => 2
[label:protected] => Structural Ironworker
[alreadyInSave:protected] =>
[alreadyInValidation:protected] =>
[validationFailures:protected] => Array
(
)
[_new:BaseObject:private] =>
[_deleted:BaseObject:private] =>
[modifiedColumns:protected] => Array
(
)
)
[83] => Category Object
(
[languages:protected] =>
[bok_resources:protected] =>
[bok_topics:protected] =>
[bok_keywords:protected] =>
[id:protected] => 83
[type:protected] => category
[parent:protected] => 2
[label:protected] => Terrazzo Worker
[alreadyInSave:protected] =>
[alreadyInValidation:protected] =>
[validationFailures:protected] => Array
(
)
[_new:BaseObject:private] =>
[_deleted:BaseObject:private] =>
[modifiedColumns:protected] => Array
(
)
)
[84] => Category Object
(
[languages:protected] =>
[bok_resources:protected] =>
[bok_topics:protected] =>
[bok_keywords:protected] =>
[id:protected] => 84
[type:protected] => category
[parent:protected] => 2
[label:protected] => Tile Setter
[alreadyInSave:protected] =>
[alreadyInValidation:protected] =>
[validationFailures:protected] => Array
(
)
[_new:BaseObject:private] =>
[_deleted:BaseObject:private] =>
[modifiedColumns:protected] => Array
(
)
)
[85] => Category Object
(
[languages:protected] =>
[bok_resources:protected] =>
[bok_topics:protected] =>
[bok_keywords:protected] =>
[id:protected] => 85
[type:protected] => category
[parent:protected] => 2
[label:protected] => Truck Driver
[alreadyInSave:protected] =>
[alreadyInValidation:protected] =>
[validationFailures:protected] => Array
(
)
[_new:BaseObject:private] =>
[_deleted:BaseObject:private] =>
[modifiedColumns:protected] => Array
(
)
)
[86] => Category Object
(
[languages:protected] =>
[bok_resources:protected] =>
[bok_topics:protected] =>
[bok_keywords:protected] =>
[id:protected] => 86
[type:protected] => category
[parent:protected] => 2
[label:protected] => Welder
[alreadyInSave:protected] =>
[alreadyInValidation:protected] =>
[validationFailures:protected] => Array
(
)
[_new:BaseObject:private] =>
[_deleted:BaseObject:private] =>
[modifiedColumns:protected] => Array
(
)
)
[87] => Category Object
(
[languages:protected] =>
[bok_resources:protected] =>
[bok_topics:protected] =>
[bok_keywords:protected] =>
[id:protected] => 87
[type:protected] => category
[parent:protected] => 3
[label:protected] => Commercial & Institutional
[alreadyInSave:protected] =>
[alreadyInValidation:protected] =>
[validationFailures:protected] => Array
(
)
[_new:BaseObject:private] =>
[_deleted:BaseObject:private] =>
[modifiedColumns:protected] => Array
(
)
)
[88] => Category Object
(
[languages:protected] =>
[bok_resources:protected] =>
[bok_topics:protected] =>
[bok_keywords:protected] =>
[id:protected] => 88
[type:protected] => category
[parent:protected] => 3
[label:protected] => Demolition
[alreadyInSave:protected] =>
[alreadyInValidation:protected] =>
[validationFailures:protected] => Array
(
)
[_new:BaseObject:private] =>
[_deleted:BaseObject:private] =>
[modifiedColumns:protected] => Array
(
)
)
[89] => Category Object
(
[languages:protected] =>
[bok_resources:protected] =>
[bok_topics:protected] =>
[bok_keywords:protected] =>
[id:protected] => 89
[type:protected] => category
[parent:protected] => 3
[label:protected] => Disasters
[alreadyInSave:protected] =>
[alreadyInValidation:protected] =>
[validationFailures:protected] => Array
(
)
[_new:BaseObject:private] =>
[_deleted:BaseObject:private] =>
[modifiedColumns:protected] => Array
(
)
)
[91] => Category Object
(
[languages:protected] =>
[bok_resources:protected] =>
[bok_topics:protected] =>
[bok_keywords:protected] =>
[id:protected] => 91
[type:protected] => category
[parent:protected] => 3
[label:protected] => Heavy & Highway
[alreadyInSave:protected] =>
[alreadyInValidation:protected] =>
[validationFailures:protected] => Array
(
)
[_new:BaseObject:private] =>
[_deleted:BaseObject:private] =>
[modifiedColumns:protected] => Array
(
)
)
[90] => Category Object
(
[languages:protected] =>
[bok_resources:protected] =>
[bok_topics:protected] =>
[bok_keywords:protected] =>
[id:protected] => 90
[type:protected] => category
[parent:protected] => 3
[label:protected] => Industrial
[alreadyInSave:protected] =>
[alreadyInValidation:protected] =>
[validationFailures:protected] => Array
(
)
[_new:BaseObject:private] =>
[_deleted:BaseObject:private] =>
[modifiedColumns:protected] => Array
(
)
)
[92] => Category Object
(
[languages:protected] =>
[bok_resources:protected] =>
[bok_topics:protected] =>
[bok_keywords:protected] =>
[id:protected] => 92
[type:protected] => category
[parent:protected] => 3
[label:protected] => LEED/Green Construction
[alreadyInSave:protected] =>
[alreadyInValidation:protected] =>
[validationFailures:protected] => Array
(
)
[_new:BaseObject:private] =>
[_deleted:BaseObject:private] =>
[modifiedColumns:protected] => Array
(
)
)
[93] => Category Object
(
[languages:protected] =>
[bok_resources:protected] =>
[bok_topics:protected] =>
[bok_keywords:protected] =>
[id:protected] => 93
[type:protected] => category
[parent:protected] => 3
[label:protected] => Renovations
[alreadyInSave:protected] =>
[alreadyInValidation:protected] =>
[validationFailures:protected] => Array
(
)
[_new:BaseObject:private] =>
[_deleted:BaseObject:private] =>
[modifiedColumns:protected] => Array
(
)
)
[94] => Category Object
(
[languages:protected] =>
[bok_resources:protected] =>
[bok_topics:protected] =>
[bok_keywords:protected] =>
[id:protected] => 94
[type:protected] => category
[parent:protected] => 3
[label:protected] => Residential
[alreadyInSave:protected] =>
[alreadyInValidation:protected] =>
[validationFailures:protected] => Array
(
)
[_new:BaseObject:private] =>
[_deleted:BaseObject:private] =>
[modifiedColumns:protected] => Array
(
)
)
[95] => Category Object
(
[languages:protected] =>
[bok_resources:protected] =>
[bok_topics:protected] =>
[bok_keywords:protected] =>
[id:protected] => 95
[type:protected] => category
[parent:protected] => 3
[label:protected] => Underground
[alreadyInSave:protected] =>
[alreadyInValidation:protected] =>
[validationFailures:protected] => Array
(
)
[_new:BaseObject:private] =>
[_deleted:BaseObject:private] =>
[modifiedColumns:protected] => Array
(
)
)
)
[categories_initialized:protected] => 1
[mapped_items:protected] =>
[content:protected] =>
[files:protected] =>
[language:protected] => Language Object
(
[id:protected] => 1
[code:protected] => en
[name:protected] => English
[alreadyInSave:protected] =>
[alreadyInValidation:protected] =>
[validationFailures:protected] => Array
(
)
[_new:BaseObject:private] =>
[_deleted:BaseObject:private] =>
[modifiedColumns:protected] => Array
(
)
)
[old_record:protected] =>
[id:protected] => 4426
[old_id:protected] =>
[elcosh_id:protected] => d001656
[type:protected] => document
[display_type:protected] => HTML only (and links)
[user_id:protected] => 0
[language_id:protected] => 1
[tagging_id:protected] => Mike Aguilar
[priority_id:protected] => 1
[title:protected] => Construction Dive -- DeWalt's Jobsite Pro headphones recalled for fire hazards
[total_pages:protected] => 1
[billed_pages:protected] => 1
[publication_number:protected] =>
[part_of:protected] =>
[keywords:protected] => DeWalt, Fire Hazards, recall, headphones
[comments:protected] =>
[summary:protected] => A recall notice by the United States Consumer Product Safety Commission affects over 300,000 DeWalt Jobsite Pro Headphones. The recall is a result of a malfunction that can cause earbuds to overheat while charging or during use, leading to fire and burn hazards.
[transition_comments:protected] =>
[external_link:protected] => https://www.constructiondive.com/news/dewalts-jobsite-pro-headphones-recalled-for-fire-hazards/611248/?utm_source=Sailthru&utm_medium=email&utm_campaign=Issue:%202021-12-10%20Construction%20Dive%20Newsletter%20%5Bissue:38532%5D&utm_term=Construction%20Dive
[consol_link:protected] =>
[more_like_this:protected] =>
[permission_given_by:protected] =>
[published:protected] => T
[billable:protected] => F
[img_name:protected] =>
[img_ext:protected] =>
[img_width:protected] =>
[img_height:protected] =>
[img_credit:protected] =>
[img_practice:protected] =>
[vid_source_id:protected] =>
[vid_running_time:protected] =>
[vid_intended_audience:protected] =>
[vid_acquisition_info:protected] =>
[vid_cost:protected] =>
[vid_producer:protected] =>
[vid_filename:protected] =>
[vid_filename_downloadable:protected] =>
[date_summary:protected] =>
[date_permission_requested:protected] =>
[date_permission_received:protected] =>
[date_review_needed:protected] =>
[date_received:protected] => 12/13/21
[date_completed:protected] => 12/13/21
[date_billed:protected] =>
[date_modified:protected] => 12/13/21
[collBokExports:protected] =>
[lastBokExportCriteria:BaseElcoshItem:private] =>
[alreadyInSave:protected] =>
[alreadyInValidation:protected] =>
[validationFailures:protected] => Array
(
)
[_new:BaseObject:private] =>
[_deleted:BaseObject:private] =>
[modifiedColumns:protected] => Array
(
)
)
)
)
[new_images] => Array
(
[0] => Search_Result Object
(
[title] => Morning Toolbox Talk
[image] => /record/images/4003-p.jpg
[blurb] => This photo is from an early morning toolbox talk on a construction job in Mclean, Virginia. It is being delivered in English and Spanish....
[category] => Array
(
[0] => 20
[1] => 51
[2] => 57
[3] => 64
[4] => 70
[5] => 63
[6] => 78
[7] => 82
[8] => 62
[9] => 87
[10] => 88
[11] => 89
[12] => 91
[13] => 90
[14] => 93
[15] => 94
[16] => 97
)
[labels] => Array
(
[0] => Safety Culture
[1] => Work Environment
[2] => Hazards
[3] => Cement Mason
[4] => Trades
[5] => Flagger
[7] => Laborer
[9] => Operating Engineer
[11] => Reinforcing Ironworker
[13] => Roofer/Waterproofer
[15] => Stonemason
[17] => Structural Ironworker
[19] => Commercial & Institutional
[20] => Jobsites
[21] => Demolition
[23] => Disasters
[25] => Heavy & Highway
[27] => Industrial
[29] => Renovations
[31] => Residential
[33] => Images
[34] => Media
[35] => Media & Documents
)
[type] => Images
[sub_category] =>
[url] => /image/4003/i002691/Morning%2BToolbox%2BTalk.html
[item:protected] => ImageRecord Object
(
[records:protected] => Array
(
)
[recordId:protected] =>
[searchWordClass:protected] =>
[searchWordPeerClass:protected] =>
[bok_record:protected] =>
[authors:protected] =>
[organizations:protected] =>
[collections:protected] =>
[categories:protected] => Array
(
[20] => Category Object
(
[languages:protected] =>
[bok_resources:protected] =>
[bok_topics:protected] =>
[bok_keywords:protected] =>
[id:protected] => 20
[type:protected] => category
[parent:protected] => 7
[label:protected] => Safety Culture
[alreadyInSave:protected] =>
[alreadyInValidation:protected] =>
[validationFailures:protected] => Array
(
)
[_new:BaseObject:private] =>
[_deleted:BaseObject:private] =>
[modifiedColumns:protected] => Array
(
)
)
[51] => Category Object
(
[languages:protected] =>
[bok_resources:protected] =>
[bok_topics:protected] =>
[bok_keywords:protected] =>
[id:protected] => 51
[type:protected] => category
[parent:protected] => 2
[label:protected] => Cement Mason
[alreadyInSave:protected] =>
[alreadyInValidation:protected] =>
[validationFailures:protected] => Array
(
)
[_new:BaseObject:private] =>
[_deleted:BaseObject:private] =>
[modifiedColumns:protected] => Array
(
)
)
[57] => Category Object
(
[languages:protected] =>
[bok_resources:protected] =>
[bok_topics:protected] =>
[bok_keywords:protected] =>
[id:protected] => 57
[type:protected] => category
[parent:protected] => 2
[label:protected] => Flagger
[alreadyInSave:protected] =>
[alreadyInValidation:protected] =>
[validationFailures:protected] => Array
(
)
[_new:BaseObject:private] =>
[_deleted:BaseObject:private] =>
[modifiedColumns:protected] => Array
(
)
)
[64] => Category Object
(
[languages:protected] =>
[bok_resources:protected] =>
[bok_topics:protected] =>
[bok_keywords:protected] =>
[id:protected] => 64
[type:protected] => category
[parent:protected] => 2
[label:protected] => Laborer
[alreadyInSave:protected] =>
[alreadyInValidation:protected] =>
[validationFailures:protected] => Array
(
)
[_new:BaseObject:private] =>
[_deleted:BaseObject:private] =>
[modifiedColumns:protected] => Array
(
)
)
[70] => Category Object
(
[languages:protected] =>
[bok_resources:protected] =>
[bok_topics:protected] =>
[bok_keywords:protected] =>
[id:protected] => 70
[type:protected] => category
[parent:protected] => 2
[label:protected] => Operating Engineer
[alreadyInSave:protected] =>
[alreadyInValidation:protected] =>
[validationFailures:protected] => Array
(
)
[_new:BaseObject:private] =>
[_deleted:BaseObject:private] =>
[modifiedColumns:protected] => Array
(
)
)
[63] => Category Object
(
[languages:protected] =>
[bok_resources:protected] =>
[bok_topics:protected] =>
[bok_keywords:protected] =>
[id:protected] => 63
[type:protected] => category
[parent:protected] => 2
[label:protected] => Reinforcing Ironworker
[alreadyInSave:protected] =>
[alreadyInValidation:protected] =>
[validationFailures:protected] => Array
(
)
[_new:BaseObject:private] =>
[_deleted:BaseObject:private] =>
[modifiedColumns:protected] => Array
(
)
)
[78] => Category Object
(
[languages:protected] =>
[bok_resources:protected] =>
[bok_topics:protected] =>
[bok_keywords:protected] =>
[id:protected] => 78
[type:protected] => category
[parent:protected] => 2
[label:protected] => Roofer/Waterproofer
[alreadyInSave:protected] =>
[alreadyInValidation:protected] =>
[validationFailures:protected] => Array
(
)
[_new:BaseObject:private] =>
[_deleted:BaseObject:private] =>
[modifiedColumns:protected] => Array
(
)
)
[82] => Category Object
(
[languages:protected] =>
[bok_resources:protected] =>
[bok_topics:protected] =>
[bok_keywords:protected] =>
[id:protected] => 82
[type:protected] => category
[parent:protected] => 2
[label:protected] => Stonemason
[alreadyInSave:protected] =>
[alreadyInValidation:protected] =>
[validationFailures:protected] => Array
(
)
[_new:BaseObject:private] =>
[_deleted:BaseObject:private] =>
[modifiedColumns:protected] => Array
(
)
)
[62] => Category Object
(
[languages:protected] =>
[bok_resources:protected] =>
[bok_topics:protected] =>
[bok_keywords:protected] =>
[id:protected] => 62
[type:protected] => category
[parent:protected] => 2
[label:protected] => Structural Ironworker
[alreadyInSave:protected] =>
[alreadyInValidation:protected] =>
[validationFailures:protected] => Array
(
)
[_new:BaseObject:private] =>
[_deleted:BaseObject:private] =>
[modifiedColumns:protected] => Array
(
)
)
[87] => Category Object
(
[languages:protected] =>
[bok_resources:protected] =>
[bok_topics:protected] =>
[bok_keywords:protected] =>
[id:protected] => 87
[type:protected] => category
[parent:protected] => 3
[label:protected] => Commercial & Institutional
[alreadyInSave:protected] =>
[alreadyInValidation:protected] =>
[validationFailures:protected] => Array
(
)
[_new:BaseObject:private] =>
[_deleted:BaseObject:private] =>
[modifiedColumns:protected] => Array
(
)
)
[88] => Category Object
(
[languages:protected] =>
[bok_resources:protected] =>
[bok_topics:protected] =>
[bok_keywords:protected] =>
[id:protected] => 88
[type:protected] => category
[parent:protected] => 3
[label:protected] => Demolition
[alreadyInSave:protected] =>
[alreadyInValidation:protected] =>
[validationFailures:protected] => Array
(
)
[_new:BaseObject:private] =>
[_deleted:BaseObject:private] =>
[modifiedColumns:protected] => Array
(
)
)
[89] => Category Object
(
[languages:protected] =>
[bok_resources:protected] =>
[bok_topics:protected] =>
[bok_keywords:protected] =>
[id:protected] => 89
[type:protected] => category
[parent:protected] => 3
[label:protected] => Disasters
[alreadyInSave:protected] =>
[alreadyInValidation:protected] =>
[validationFailures:protected] => Array
(
)
[_new:BaseObject:private] =>
[_deleted:BaseObject:private] =>
[modifiedColumns:protected] => Array
(
)
)
[91] => Category Object
(
[languages:protected] =>
[bok_resources:protected] =>
[bok_topics:protected] =>
[bok_keywords:protected] =>
[id:protected] => 91
[type:protected] => category
[parent:protected] => 3
[label:protected] => Heavy & Highway
[alreadyInSave:protected] =>
[alreadyInValidation:protected] =>
[validationFailures:protected] => Array
(
)
[_new:BaseObject:private] =>
[_deleted:BaseObject:private] =>
[modifiedColumns:protected] => Array
(
)
)
[90] => Category Object
(
[languages:protected] =>
[bok_resources:protected] =>
[bok_topics:protected] =>
[bok_keywords:protected] =>
[id:protected] => 90
[type:protected] => category
[parent:protected] => 3
[label:protected] => Industrial
[alreadyInSave:protected] =>
[alreadyInValidation:protected] =>
[validationFailures:protected] => Array
(
)
[_new:BaseObject:private] =>
[_deleted:BaseObject:private] =>
[modifiedColumns:protected] => Array
(
)
)
[93] => Category Object
(
[languages:protected] =>
[bok_resources:protected] =>
[bok_topics:protected] =>
[bok_keywords:protected] =>
[id:protected] => 93
[type:protected] => category
[parent:protected] => 3
[label:protected] => Renovations
[alreadyInSave:protected] =>
[alreadyInValidation:protected] =>
[validationFailures:protected] => Array
(
)
[_new:BaseObject:private] =>
[_deleted:BaseObject:private] =>
[modifiedColumns:protected] => Array
(
)
)
[94] => Category Object
(
[languages:protected] =>
[bok_resources:protected] =>
[bok_topics:protected] =>
[bok_keywords:protected] =>
[id:protected] => 94
[type:protected] => category
[parent:protected] => 3
[label:protected] => Residential
[alreadyInSave:protected] =>
[alreadyInValidation:protected] =>
[validationFailures:protected] => Array
(
)
[_new:BaseObject:private] =>
[_deleted:BaseObject:private] =>
[modifiedColumns:protected] => Array
(
)
)
[97] => Category Object
(
[languages:protected] =>
[bok_resources:protected] =>
[bok_topics:protected] =>
[bok_keywords:protected] =>
[id:protected] => 97
[type:protected] => category
[parent:protected] => 5
[label:protected] => Images
[alreadyInSave:protected] =>
[alreadyInValidation:protected] =>
[validationFailures:protected] => Array
(
)
[_new:BaseObject:private] =>
[_deleted:BaseObject:private] =>
[modifiedColumns:protected] => Array
(
)
)
)
[categories_initialized:protected] => 1
[mapped_items:protected] =>
[content:protected] =>
[files:protected] =>
[language:protected] => Language Object
(
[id:protected] => 1
[code:protected] => en
[name:protected] => English
[alreadyInSave:protected] =>
[alreadyInValidation:protected] =>
[validationFailures:protected] => Array
(
)
[_new:BaseObject:private] =>
[_deleted:BaseObject:private] =>
[modifiedColumns:protected] => Array
(
)
)
[old_record:protected] =>
[id:protected] => 4003
[old_id:protected] =>
[elcosh_id:protected] => i002691
[type:protected] => image
[display_type:protected] => Image
[user_id:protected] => 0
[language_id:protected] => 1
[tagging_id:protected] => Bruce Lippy
[priority_id:protected] => 1
[title:protected] => Morning Toolbox Talk
[total_pages:protected] => 0
[billed_pages:protected] => 0
[publication_number:protected] =>
[part_of:protected] =>
[keywords:protected] => toolbox talk, tailgate talk, Spanish, bilingual
[comments:protected] =>
[summary:protected] => This photo is from an early morning toolbox talk on a construction job in Mclean, Virginia. It is being delivered in English and Spanish.
[transition_comments:protected] =>
[external_link:protected] =>
[consol_link:protected] => http://www.cpwrconstructionsolutions.org/electrical/solution/662/worker-training.html
[more_like_this:protected] => d001285,d001304,c000079
[permission_given_by:protected] =>
[published:protected] => T
[billable:protected] => F
[img_name:protected] =>
[img_ext:protected] => jpg
[img_width:protected] =>
[img_height:protected] =>
[img_credit:protected] => Morgan Zavertnik and Hoar Construction
[img_practice:protected] => good
[vid_source_id:protected] =>
[vid_running_time:protected] =>
[vid_intended_audience:protected] =>
[vid_acquisition_info:protected] =>
[vid_cost:protected] =>
[vid_producer:protected] =>
[vid_filename:protected] =>
[vid_filename_downloadable:protected] =>
[date_summary:protected] => November 2015
[date_permission_requested:protected] =>
[date_permission_received:protected] =>
[date_review_needed:protected] =>
[date_received:protected] => 03/02/16
[date_completed:protected] => 03/02/16
[date_billed:protected] =>
[date_modified:protected] => 03/02/16
[collBokExports:protected] =>
[lastBokExportCriteria:BaseElcoshItem:private] =>
[alreadyInSave:protected] =>
[alreadyInValidation:protected] =>
[validationFailures:protected] => Array
(
)
[_new:BaseObject:private] =>
[_deleted:BaseObject:private] =>
[modifiedColumns:protected] => Array
(
)
)
)
[1] => Search_Result Object
(
[title] => Toolbox talk - crew view
[image] => /record/images/4005-p.jpg
[blurb] => Photo of crew listening to a toolbox safety talk before starting work....
[category] => Array
(
[0] => 97
[1] => 20
[2] => 47
[3] => 49
[4] => 51
[5] => 55
[6] => 61
[7] => 64
[8] => 71
[9] => 75
[10] => 63
[11] => 79
[12] => 62
[13] => 87
[14] => 88
[15] => 91
[16] => 90
[17] => 93
[18] => 94
[19] => 95
)
[labels] => Array
(
[0] => Images
[1] => Media
[2] => Media & Documents
[3] => Safety Culture
[4] => Work Environment
[5] => Hazards
[6] => Bricklayer
[7] => Trades
[8] => Carpenter
[10] => Cement Mason
[12] => Electrical Worker
[14] => Interior Systems Carpenter
[16] => Laborer
[18] => Painter
[20] => Plasterer
[22] => Reinforcing Ironworker
[24] => Scaffold Erector
[26] => Structural Ironworker
[28] => Commercial & Institutional
[29] => Jobsites
[30] => Demolition
[32] => Heavy & Highway
[34] => Industrial
[36] => Renovations
[38] => Residential
[40] => Underground
)
[type] => Images
[sub_category] =>
[url] => /image/4005/i002692/Toolbox%2Btalk%2B-%2Bcrew%2Bview.html
[item:protected] => ImageRecord Object
(
[records:protected] => Array
(
)
[recordId:protected] =>
[searchWordClass:protected] =>
[searchWordPeerClass:protected] =>
[bok_record:protected] =>
[authors:protected] =>
[organizations:protected] =>
[collections:protected] =>
[categories:protected] => Array
(
[97] => Category Object
(
[languages:protected] =>
[bok_resources:protected] =>
[bok_topics:protected] =>
[bok_keywords:protected] =>
[id:protected] => 97
[type:protected] => category
[parent:protected] => 5
[label:protected] => Images
[alreadyInSave:protected] =>
[alreadyInValidation:protected] =>
[validationFailures:protected] => Array
(
)
[_new:BaseObject:private] =>
[_deleted:BaseObject:private] =>
[modifiedColumns:protected] => Array
(
)
)
[20] => Category Object
(
[languages:protected] =>
[bok_resources:protected] =>
[bok_topics:protected] =>
[bok_keywords:protected] =>
[id:protected] => 20
[type:protected] => category
[parent:protected] => 7
[label:protected] => Safety Culture
[alreadyInSave:protected] =>
[alreadyInValidation:protected] =>
[validationFailures:protected] => Array
(
)
[_new:BaseObject:private] =>
[_deleted:BaseObject:private] =>
[modifiedColumns:protected] => Array
(
)
)
[47] => Category Object
(
[languages:protected] =>
[bok_resources:protected] =>
[bok_topics:protected] =>
[bok_keywords:protected] =>
[id:protected] => 47
[type:protected] => category
[parent:protected] => 2
[label:protected] => Bricklayer
[alreadyInSave:protected] =>
[alreadyInValidation:protected] =>
[validationFailures:protected] => Array
(
)
[_new:BaseObject:private] =>
[_deleted:BaseObject:private] =>
[modifiedColumns:protected] => Array
(
)
)
[49] => Category Object
(
[languages:protected] =>
[bok_resources:protected] =>
[bok_topics:protected] =>
[bok_keywords:protected] =>
[id:protected] => 49
[type:protected] => category
[parent:protected] => 2
[label:protected] => Carpenter
[alreadyInSave:protected] =>
[alreadyInValidation:protected] =>
[validationFailures:protected] => Array
(
)
[_new:BaseObject:private] =>
[_deleted:BaseObject:private] =>
[modifiedColumns:protected] => Array
(
)
)
[51] => Category Object
(
[languages:protected] =>
[bok_resources:protected] =>
[bok_topics:protected] =>
[bok_keywords:protected] =>
[id:protected] => 51
[type:protected] => category
[parent:protected] => 2
[label:protected] => Cement Mason
[alreadyInSave:protected] =>
[alreadyInValidation:protected] =>
[validationFailures:protected] => Array
(
)
[_new:BaseObject:private] =>
[_deleted:BaseObject:private] =>
[modifiedColumns:protected] => Array
(
)
)
[55] => Category Object
(
[languages:protected] =>
[bok_resources:protected] =>
[bok_topics:protected] =>
[bok_keywords:protected] =>
[id:protected] => 55
[type:protected] => category
[parent:protected] => 2
[label:protected] => Electrical Worker
[alreadyInSave:protected] =>
[alreadyInValidation:protected] =>
[validationFailures:protected] => Array
(
)
[_new:BaseObject:private] =>
[_deleted:BaseObject:private] =>
[modifiedColumns:protected] => Array
(
)
)
[61] => Category Object
(
[languages:protected] =>
[bok_resources:protected] =>
[bok_topics:protected] =>
[bok_keywords:protected] =>
[id:protected] => 61
[type:protected] => category
[parent:protected] => 2
[label:protected] => Interior Systems Carpenter
[alreadyInSave:protected] =>
[alreadyInValidation:protected] =>
[validationFailures:protected] => Array
(
)
[_new:BaseObject:private] =>
[_deleted:BaseObject:private] =>
[modifiedColumns:protected] => Array
(
)
)
[64] => Category Object
(
[languages:protected] =>
[bok_resources:protected] =>
[bok_topics:protected] =>
[bok_keywords:protected] =>
[id:protected] => 64
[type:protected] => category
[parent:protected] => 2
[label:protected] => Laborer
[alreadyInSave:protected] =>
[alreadyInValidation:protected] =>
[validationFailures:protected] => Array
(
)
[_new:BaseObject:private] =>
[_deleted:BaseObject:private] =>
[modifiedColumns:protected] => Array
(
)
)
[71] => Category Object
(
[languages:protected] =>
[bok_resources:protected] =>
[bok_topics:protected] =>
[bok_keywords:protected] =>
[id:protected] => 71
[type:protected] => category
[parent:protected] => 2
[label:protected] => Painter
[alreadyInSave:protected] =>
[alreadyInValidation:protected] =>
[validationFailures:protected] => Array
(
)
[_new:BaseObject:private] =>
[_deleted:BaseObject:private] =>
[modifiedColumns:protected] => Array
(
)
)
[75] => Category Object
(
[languages:protected] =>
[bok_resources:protected] =>
[bok_topics:protected] =>
[bok_keywords:protected] =>
[id:protected] => 75
[type:protected] => category
[parent:protected] => 2
[label:protected] => Plasterer
[alreadyInSave:protected] =>
[alreadyInValidation:protected] =>
[validationFailures:protected] => Array
(
)
[_new:BaseObject:private] =>
[_deleted:BaseObject:private] =>
[modifiedColumns:protected] => Array
(
)
)
[63] => Category Object
(
[languages:protected] =>
[bok_resources:protected] =>
[bok_topics:protected] =>
[bok_keywords:protected] =>
[id:protected] => 63
[type:protected] => category
[parent:protected] => 2
[label:protected] => Reinforcing Ironworker
[alreadyInSave:protected] =>
[alreadyInValidation:protected] =>
[validationFailures:protected] => Array
(
)
[_new:BaseObject:private] =>
[_deleted:BaseObject:private] =>
[modifiedColumns:protected] => Array
(
)
)
[79] => Category Object
(
[languages:protected] =>
[bok_resources:protected] =>
[bok_topics:protected] =>
[bok_keywords:protected] =>
[id:protected] => 79
[type:protected] => category
[parent:protected] => 2
[label:protected] => Scaffold Erector
[alreadyInSave:protected] =>
[alreadyInValidation:protected] =>
[validationFailures:protected] => Array
(
)
[_new:BaseObject:private] =>
[_deleted:BaseObject:private] =>
[modifiedColumns:protected] => Array
(
)
)
[62] => Category Object
(
[languages:protected] =>
[bok_resources:protected] =>
[bok_topics:protected] =>
[bok_keywords:protected] =>
[id:protected] => 62
[type:protected] => category
[parent:protected] => 2
[label:protected] => Structural Ironworker
[alreadyInSave:protected] =>
[alreadyInValidation:protected] =>
[validationFailures:protected] => Array
(
)
[_new:BaseObject:private] =>
[_deleted:BaseObject:private] =>
[modifiedColumns:protected] => Array
(
)
)
[87] => Category Object
(
[languages:protected] =>
[bok_resources:protected] =>
[bok_topics:protected] =>
[bok_keywords:protected] =>
[id:protected] => 87
[type:protected] => category
[parent:protected] => 3
[label:protected] => Commercial & Institutional
[alreadyInSave:protected] =>
[alreadyInValidation:protected] =>
[validationFailures:protected] => Array
(
)
[_new:BaseObject:private] =>
[_deleted:BaseObject:private] =>
[modifiedColumns:protected] => Array
(
)
)
[88] => Category Object
(
[languages:protected] =>
[bok_resources:protected] =>
[bok_topics:protected] =>
[bok_keywords:protected] =>
[id:protected] => 88
[type:protected] => category
[parent:protected] => 3
[label:protected] => Demolition
[alreadyInSave:protected] =>
[alreadyInValidation:protected] =>
[validationFailures:protected] => Array
(
)
[_new:BaseObject:private] =>
[_deleted:BaseObject:private] =>
[modifiedColumns:protected] => Array
(
)
)
[91] => Category Object
(
[languages:protected] =>
[bok_resources:protected] =>
[bok_topics:protected] =>
[bok_keywords:protected] =>
[id:protected] => 91
[type:protected] => category
[parent:protected] => 3
[label:protected] => Heavy & Highway
[alreadyInSave:protected] =>
[alreadyInValidation:protected] =>
[validationFailures:protected] => Array
(
)
[_new:BaseObject:private] =>
[_deleted:BaseObject:private] =>
[modifiedColumns:protected] => Array
(
)
)
[90] => Category Object
(
[languages:protected] =>
[bok_resources:protected] =>
[bok_topics:protected] =>
[bok_keywords:protected] =>
[id:protected] => 90
[type:protected] => category
[parent:protected] => 3
[label:protected] => Industrial
[alreadyInSave:protected] =>
[alreadyInValidation:protected] =>
[validationFailures:protected] => Array
(
)
[_new:BaseObject:private] =>
[_deleted:BaseObject:private] =>
[modifiedColumns:protected] => Array
(
)
)
[93] => Category Object
(
[languages:protected] =>
[bok_resources:protected] =>
[bok_topics:protected] =>
[bok_keywords:protected] =>
[id:protected] => 93
[type:protected] => category
[parent:protected] => 3
[label:protected] => Renovations
[alreadyInSave:protected] =>
[alreadyInValidation:protected] =>
[validationFailures:protected] => Array
(
)
[_new:BaseObject:private] =>
[_deleted:BaseObject:private] =>
[modifiedColumns:protected] => Array
(
)
)
[94] => Category Object
(
[languages:protected] =>
[bok_resources:protected] =>
[bok_topics:protected] =>
[bok_keywords:protected] =>
[id:protected] => 94
[type:protected] => category
[parent:protected] => 3
[label:protected] => Residential
[alreadyInSave:protected] =>
[alreadyInValidation:protected] =>
[validationFailures:protected] => Array
(
)
[_new:BaseObject:private] =>
[_deleted:BaseObject:private] =>
[modifiedColumns:protected] => Array
(
)
)
[95] => Category Object
(
[languages:protected] =>
[bok_resources:protected] =>
[bok_topics:protected] =>
[bok_keywords:protected] =>
[id:protected] => 95
[type:protected] => category
[parent:protected] => 3
[label:protected] => Underground
[alreadyInSave:protected] =>
[alreadyInValidation:protected] =>
[validationFailures:protected] => Array
(
)
[_new:BaseObject:private] =>
[_deleted:BaseObject:private] =>
[modifiedColumns:protected] => Array
(
)
)
)
[categories_initialized:protected] => 1
[mapped_items:protected] =>
[content:protected] =>
[files:protected] =>
[language:protected] => Language Object
(
[id:protected] => 1
[code:protected] => en
[name:protected] => English
[alreadyInSave:protected] =>
[alreadyInValidation:protected] =>
[validationFailures:protected] => Array
(
)
[_new:BaseObject:private] =>
[_deleted:BaseObject:private] =>
[modifiedColumns:protected] => Array
(
)
)
[old_record:protected] =>
[id:protected] => 4005
[old_id:protected] =>
[elcosh_id:protected] => i002692
[type:protected] => image
[display_type:protected] => Image
[user_id:protected] => 0
[language_id:protected] => 1
[tagging_id:protected] => Bruce Lippy
[priority_id:protected] => 1
[title:protected] => Toolbox talk - crew view
[total_pages:protected] => 0
[billed_pages:protected] => 0
[publication_number:protected] =>
[part_of:protected] =>
[keywords:protected] => toolbox talk, tailgate talk, safety talk, Spanish
[comments:protected] =>
[summary:protected] => Photo of crew listening to a toolbox safety talk before starting work.
[transition_comments:protected] =>
[external_link:protected] =>
[consol_link:protected] => http://www.cpwrconstructionsolutions.org/electrical/solution/662/worker-training.html
[more_like_this:protected] => i002691,d001269, c000079, d001285
[permission_given_by:protected] =>
[published:protected] => T
[billable:protected] => F
[img_name:protected] =>
[img_ext:protected] => jpg
[img_width:protected] =>
[img_height:protected] =>
[img_credit:protected] => Morgan Zavertnik and Hoar Construction
[img_practice:protected] => good
[vid_source_id:protected] =>
[vid_running_time:protected] =>
[vid_intended_audience:protected] =>
[vid_acquisition_info:protected] =>
[vid_cost:protected] =>
[vid_producer:protected] =>
[vid_filename:protected] =>
[vid_filename_downloadable:protected] =>
[date_summary:protected] => November 2015
[date_permission_requested:protected] =>
[date_permission_received:protected] =>
[date_review_needed:protected] =>
[date_received:protected] => 03/02/16
[date_completed:protected] => 03/02/16
[date_billed:protected] =>
[date_modified:protected] => 03/02/16
[collBokExports:protected] =>
[lastBokExportCriteria:BaseElcoshItem:private] =>
[alreadyInSave:protected] =>
[alreadyInValidation:protected] =>
[validationFailures:protected] => Array
(
)
[_new:BaseObject:private] =>
[_deleted:BaseObject:private] =>
[modifiedColumns:protected] => Array
(
)
)
)
[2] => Search_Result Object
(
[title] => Toolbox talk - long shot
[image] => /record/images/4006-p.jpg
[blurb] => This crew gathered every morning before starting work to discuss a new safety topic....
[category] => Array
(
[0] => 20
[1] => 47
[2] => 49
[3] => 51
[4] => 55
[5] => 64
[6] => 68
[7] => 75
[8] => 76
[9] => 63
[10] => 78
[11] => 79
[12] => 82
[13] => 62
[14] => 87
[15] => 88
[16] => 91
[17] => 90
[18] => 93
[19] => 94
[20] => 95
[21] => 97
)
[labels] => Array
(
[0] => Safety Culture
[1] => Work Environment
[2] => Hazards
[3] => Bricklayer
[4] => Trades
[5] => Carpenter
[7] => Cement Mason
[9] => Electrical Worker
[11] => Laborer
[13] => Maintenance Worker
[15] => Plasterer
[17] => Plumber/Pipefitter
[19] => Reinforcing Ironworker
[21] => Roofer/Waterproofer
[23] => Scaffold Erector
[25] => Stonemason
[27] => Structural Ironworker
[29] => Commercial & Institutional
[30] => Jobsites
[31] => Demolition
[33] => Heavy & Highway
[35] => Industrial
[37] => Renovations
[39] => Residential
[41] => Underground
[43] => Images
[44] => Media
[45] => Media & Documents
)
[type] => Images
[sub_category] =>
[url] => /image/4006/i002693/Toolbox%2Btalk%2B-%2Blong%2Bshot.html
[item:protected] => ImageRecord Object
(
[records:protected] => Array
(
)
[recordId:protected] =>
[searchWordClass:protected] =>
[searchWordPeerClass:protected] =>
[bok_record:protected] =>
[authors:protected] =>
[organizations:protected] =>
[collections:protected] =>
[categories:protected] => Array
(
[20] => Category Object
(
[languages:protected] =>
[bok_resources:protected] =>
[bok_topics:protected] =>
[bok_keywords:protected] =>
[id:protected] => 20
[type:protected] => category
[parent:protected] => 7
[label:protected] => Safety Culture
[alreadyInSave:protected] =>
[alreadyInValidation:protected] =>
[validationFailures:protected] => Array
(
)
[_new:BaseObject:private] =>
[_deleted:BaseObject:private] =>
[modifiedColumns:protected] => Array
(
)
)
[47] => Category Object
(
[languages:protected] =>
[bok_resources:protected] =>
[bok_topics:protected] =>
[bok_keywords:protected] =>
[id:protected] => 47
[type:protected] => category
[parent:protected] => 2
[label:protected] => Bricklayer
[alreadyInSave:protected] =>
[alreadyInValidation:protected] =>
[validationFailures:protected] => Array
(
)
[_new:BaseObject:private] =>
[_deleted:BaseObject:private] =>
[modifiedColumns:protected] => Array
(
)
)
[49] => Category Object
(
[languages:protected] =>
[bok_resources:protected] =>
[bok_topics:protected] =>
[bok_keywords:protected] =>
[id:protected] => 49
[type:protected] => category
[parent:protected] => 2
[label:protected] => Carpenter
[alreadyInSave:protected] =>
[alreadyInValidation:protected] =>
[validationFailures:protected] => Array
(
)
[_new:BaseObject:private] =>
[_deleted:BaseObject:private] =>
[modifiedColumns:protected] => Array
(
)
)
[51] => Category Object
(
[languages:protected] =>
[bok_resources:protected] =>
[bok_topics:protected] =>
[bok_keywords:protected] =>
[id:protected] => 51
[type:protected] => category
[parent:protected] => 2
[label:protected] => Cement Mason
[alreadyInSave:protected] =>
[alreadyInValidation:protected] =>
[validationFailures:protected] => Array
(
)
[_new:BaseObject:private] =>
[_deleted:BaseObject:private] =>
[modifiedColumns:protected] => Array
(
)
)
[55] => Category Object
(
[languages:protected] =>
[bok_resources:protected] =>
[bok_topics:protected] =>
[bok_keywords:protected] =>
[id:protected] => 55
[type:protected] => category
[parent:protected] => 2
[label:protected] => Electrical Worker
[alreadyInSave:protected] =>
[alreadyInValidation:protected] =>
[validationFailures:protected] => Array
(
)
[_new:BaseObject:private] =>
[_deleted:BaseObject:private] =>
[modifiedColumns:protected] => Array
(
)
)
[64] => Category Object
(
[languages:protected] =>
[bok_resources:protected] =>
[bok_topics:protected] =>
[bok_keywords:protected] =>
[id:protected] => 64
[type:protected] => category
[parent:protected] => 2
[label:protected] => Laborer
[alreadyInSave:protected] =>
[alreadyInValidation:protected] =>
[validationFailures:protected] => Array
(
)
[_new:BaseObject:private] =>
[_deleted:BaseObject:private] =>
[modifiedColumns:protected] => Array
(
)
)
[68] => Category Object
(
[languages:protected] =>
[bok_resources:protected] =>
[bok_topics:protected] =>
[bok_keywords:protected] =>
[id:protected] => 68
[type:protected] => category
[parent:protected] => 2
[label:protected] => Maintenance Worker
[alreadyInSave:protected] =>
[alreadyInValidation:protected] =>
[validationFailures:protected] => Array
(
)
[_new:BaseObject:private] =>
[_deleted:BaseObject:private] =>
[modifiedColumns:protected] => Array
(
)
)
[75] => Category Object
(
[languages:protected] =>
[bok_resources:protected] =>
[bok_topics:protected] =>
[bok_keywords:protected] =>
[id:protected] => 75
[type:protected] => category
[parent:protected] => 2
[label:protected] => Plasterer
[alreadyInSave:protected] =>
[alreadyInValidation:protected] =>
[validationFailures:protected] => Array
(
)
[_new:BaseObject:private] =>
[_deleted:BaseObject:private] =>
[modifiedColumns:protected] => Array
(
)
)
[76] => Category Object
(
[languages:protected] =>
[bok_resources:protected] =>
[bok_topics:protected] =>
[bok_keywords:protected] =>
[id:protected] => 76
[type:protected] => category
[parent:protected] => 2
[label:protected] => Plumber/Pipefitter
[alreadyInSave:protected] =>
[alreadyInValidation:protected] =>
[validationFailures:protected] => Array
(
)
[_new:BaseObject:private] =>
[_deleted:BaseObject:private] =>
[modifiedColumns:protected] => Array
(
)
)
[63] => Category Object
(
[languages:protected] =>
[bok_resources:protected] =>
[bok_topics:protected] =>
[bok_keywords:protected] =>
[id:protected] => 63
[type:protected] => category
[parent:protected] => 2
[label:protected] => Reinforcing Ironworker
[alreadyInSave:protected] =>
[alreadyInValidation:protected] =>
[validationFailures:protected] => Array
(
)
[_new:BaseObject:private] =>
[_deleted:BaseObject:private] =>
[modifiedColumns:protected] => Array
(
)
)
[78] => Category Object
(
[languages:protected] =>
[bok_resources:protected] =>
[bok_topics:protected] =>
[bok_keywords:protected] =>
[id:protected] => 78
[type:protected] => category
[parent:protected] => 2
[label:protected] => Roofer/Waterproofer
[alreadyInSave:protected] =>
[alreadyInValidation:protected] =>
[validationFailures:protected] => Array
(
)
[_new:BaseObject:private] =>
[_deleted:BaseObject:private] =>
[modifiedColumns:protected] => Array
(
)
)
[79] => Category Object
(
[languages:protected] =>
[bok_resources:protected] =>
[bok_topics:protected] =>
[bok_keywords:protected] =>
[id:protected] => 79
[type:protected] => category
[parent:protected] => 2
[label:protected] => Scaffold Erector
[alreadyInSave:protected] =>
[alreadyInValidation:protected] =>
[validationFailures:protected] => Array
(
)
[_new:BaseObject:private] =>
[_deleted:BaseObject:private] =>
[modifiedColumns:protected] => Array
(
)
)
[82] => Category Object
(
[languages:protected] =>
[bok_resources:protected] =>
[bok_topics:protected] =>
[bok_keywords:protected] =>
[id:protected] => 82
[type:protected] => category
[parent:protected] => 2
[label:protected] => Stonemason
[alreadyInSave:protected] =>
[alreadyInValidation:protected] =>
[validationFailures:protected] => Array
(
)
[_new:BaseObject:private] =>
[_deleted:BaseObject:private] =>
[modifiedColumns:protected] => Array
(
)
)
[62] => Category Object
(
[languages:protected] =>
[bok_resources:protected] =>
[bok_topics:protected] =>
[bok_keywords:protected] =>
[id:protected] => 62
[type:protected] => category
[parent:protected] => 2
[label:protected] => Structural Ironworker
[alreadyInSave:protected] =>
[alreadyInValidation:protected] =>
[validationFailures:protected] => Array
(
)
[_new:BaseObject:private] =>
[_deleted:BaseObject:private] =>
[modifiedColumns:protected] => Array
(
)
)
[87] => Category Object
(
[languages:protected] =>
[bok_resources:protected] =>
[bok_topics:protected] =>
[bok_keywords:protected] =>
[id:protected] => 87
[type:protected] => category
[parent:protected] => 3
[label:protected] => Commercial & Institutional
[alreadyInSave:protected] =>
[alreadyInValidation:protected] =>
[validationFailures:protected] => Array
(
)
[_new:BaseObject:private] =>
[_deleted:BaseObject:private] =>
[modifiedColumns:protected] => Array
(
)
)
[88] => Category Object
(
[languages:protected] =>
[bok_resources:protected] =>
[bok_topics:protected] =>
[bok_keywords:protected] =>
[id:protected] => 88
[type:protected] => category
[parent:protected] => 3
[label:protected] => Demolition
[alreadyInSave:protected] =>
[alreadyInValidation:protected] =>
[validationFailures:protected] => Array
(
)
[_new:BaseObject:private] =>
[_deleted:BaseObject:private] =>
[modifiedColumns:protected] => Array
(
)
)
[91] => Category Object
(
[languages:protected] =>
[bok_resources:protected] =>
[bok_topics:protected] =>
[bok_keywords:protected] =>
[id:protected] => 91
[type:protected] => category
[parent:protected] => 3
[label:protected] => Heavy & Highway
[alreadyInSave:protected] =>
[alreadyInValidation:protected] =>
[validationFailures:protected] => Array
(
)
[_new:BaseObject:private] =>
[_deleted:BaseObject:private] =>
[modifiedColumns:protected] => Array
(
)
)
[90] => Category Object
(
[languages:protected] =>
[bok_resources:protected] =>
[bok_topics:protected] =>
[bok_keywords:protected] =>
[id:protected] => 90
[type:protected] => category
[parent:protected] => 3
[label:protected] => Industrial
[alreadyInSave:protected] =>
[alreadyInValidation:protected] =>
[validationFailures:protected] => Array
(
)
[_new:BaseObject:private] =>
[_deleted:BaseObject:private] =>
[modifiedColumns:protected] => Array
(
)
)
[93] => Category Object
(
[languages:protected] =>
[bok_resources:protected] =>
[bok_topics:protected] =>
[bok_keywords:protected] =>
[id:protected] => 93
[type:protected] => category
[parent:protected] => 3
[label:protected] => Renovations
[alreadyInSave:protected] =>
[alreadyInValidation:protected] =>
[validationFailures:protected] => Array
(
)
[_new:BaseObject:private] =>
[_deleted:BaseObject:private] =>
[modifiedColumns:protected] => Array
(
)
)
[94] => Category Object
(
[languages:protected] =>
[bok_resources:protected] =>
[bok_topics:protected] =>
[bok_keywords:protected] =>
[id:protected] => 94
[type:protected] => category
[parent:protected] => 3
[label:protected] => Residential
[alreadyInSave:protected] =>
[alreadyInValidation:protected] =>
[validationFailures:protected] => Array
(
)
[_new:BaseObject:private] =>
[_deleted:BaseObject:private] =>
[modifiedColumns:protected] => Array
(
)
)
[95] => Category Object
(
[languages:protected] =>
[bok_resources:protected] =>
[bok_topics:protected] =>
[bok_keywords:protected] =>
[id:protected] => 95
[type:protected] => category
[parent:protected] => 3
[label:protected] => Underground
[alreadyInSave:protected] =>
[alreadyInValidation:protected] =>
[validationFailures:protected] => Array
(
)
[_new:BaseObject:private] =>
[_deleted:BaseObject:private] =>
[modifiedColumns:protected] => Array
(
)
)
[97] => Category Object
(
[languages:protected] =>
[bok_resources:protected] =>
[bok_topics:protected] =>
[bok_keywords:protected] =>
[id:protected] => 97
[type:protected] => category
[parent:protected] => 5
[label:protected] => Images
[alreadyInSave:protected] =>
[alreadyInValidation:protected] =>
[validationFailures:protected] => Array
(
)
[_new:BaseObject:private] =>
[_deleted:BaseObject:private] =>
[modifiedColumns:protected] => Array
(
)
)
)
[categories_initialized:protected] => 1
[mapped_items:protected] =>
[content:protected] =>
[files:protected] =>
[language:protected] => Language Object
(
[id:protected] => 1
[code:protected] => en
[name:protected] => English
[alreadyInSave:protected] =>
[alreadyInValidation:protected] =>
[validationFailures:protected] => Array
(
)
[_new:BaseObject:private] =>
[_deleted:BaseObject:private] =>
[modifiedColumns:protected] => Array
(
)
)
[old_record:protected] =>
[id:protected] => 4006
[old_id:protected] =>
[elcosh_id:protected] => i002693
[type:protected] => image
[display_type:protected] => Image
[user_id:protected] => 0
[language_id:protected] => 1
[tagging_id:protected] => Bruce Lippy
[priority_id:protected] => 1
[title:protected] => Toolbox talk - long shot
[total_pages:protected] => 0
[billed_pages:protected] => 0
[publication_number:protected] =>
[part_of:protected] =>
[keywords:protected] => toolbox talk, tailgate talk, safety minute
[comments:protected] =>
[summary:protected] => This crew gathered every morning before starting work to discuss a new safety topic.
[transition_comments:protected] =>
[external_link:protected] =>
[consol_link:protected] => http://www.cpwrconstructionsolutions.org/electrical/solution/662/worker-training.html
[more_like_this:protected] => i002691,i002692,d001269,d000527
[permission_given_by:protected] =>
[published:protected] => T
[billable:protected] => F
[img_name:protected] =>
[img_ext:protected] => jpg
[img_width:protected] =>
[img_height:protected] =>
[img_credit:protected] => Morgan Zavertnik and Hoar Construction
[img_practice:protected] => good
[vid_source_id:protected] =>
[vid_running_time:protected] =>
[vid_intended_audience:protected] =>
[vid_acquisition_info:protected] =>
[vid_cost:protected] =>
[vid_producer:protected] =>
[vid_filename:protected] =>
[vid_filename_downloadable:protected] =>
[date_summary:protected] => November 2015
[date_permission_requested:protected] =>
[date_permission_received:protected] =>
[date_review_needed:protected] =>
[date_received:protected] => 03/02/16
[date_completed:protected] => 03/02/16
[date_billed:protected] =>
[date_modified:protected] => 03/02/16
[collBokExports:protected] =>
[lastBokExportCriteria:BaseElcoshItem:private] =>
[alreadyInSave:protected] =>
[alreadyInValidation:protected] =>
[validationFailures:protected] => Array
(
)
[_new:BaseObject:private] =>
[_deleted:BaseObject:private] =>
[modifiedColumns:protected] => Array
(
)
)
)
[3] => Search_Result Object
(
[title] => Safety officer discussing ongoing project with marketing coordinator
[image] => /record/images/4014-p.jpg
[blurb] => The safety officer (left) points out the good safety practices on this project that reflect well on the firm and may influence future clients....
[category] => Array
(
[0] => 97
[1] => 20
[2] => 46
[3] => 47
[4] => 49
[5] => 50
[6] => 51
[7] => 54
[8] => 55
[9] => 58
[10] => 60
[11] => 61
[12] => 64
[13] => 71
[14] => 75
[15] => 76
[16] => 63
[17] => 79
[18] => 80
[19] => 82
[20] => 62
[21] => 83
[22] => 87
[23] => 91
[24] => 90
[25] => 93
[26] => 94
)
[labels] => Array
(
[0] => Images
[1] => Media
[2] => Media & Documents
[3] => Safety Culture
[4] => Work Environment
[5] => Hazards
[6] => Boilermaker
[7] => Trades
[8] => Bricklayer
[10] => Carpenter
[12] => Carpet Layer
[14] => Cement Mason
[16] => Drywall Applicator Specialist
[18] => Electrical Worker
[20] => Glazier
[22] => HVAC
[24] => Interior Systems Carpenter
[26] => Laborer
[28] => Painter
[30] => Plasterer
[32] => Plumber/Pipefitter
[34] => Reinforcing Ironworker
[36] => Scaffold Erector
[38] => Sheetmetal Worker
[40] => Stonemason
[42] => Structural Ironworker
[44] => Terrazzo Worker
[46] => Commercial & Institutional
[47] => Jobsites
[48] => Heavy & Highway
[50] => Industrial
[52] => Renovations
[54] => Residential
)
[type] => Images
[sub_category] =>
[url] => /image/4014/i002700/Safety%2Bofficer%2Bdiscussing%2Bongoing%2Bproject%2Bwith%2Bmarketing%2Bcoordinator.html
[item:protected] => ImageRecord Object
(
[records:protected] => Array
(
)
[recordId:protected] =>
[searchWordClass:protected] =>
[searchWordPeerClass:protected] =>
[bok_record:protected] =>
[authors:protected] =>
[organizations:protected] =>
[collections:protected] =>
[categories:protected] => Array
(
[97] => Category Object
(
[languages:protected] =>
[bok_resources:protected] =>
[bok_topics:protected] =>
[bok_keywords:protected] =>
[id:protected] => 97
[type:protected] => category
[parent:protected] => 5
[label:protected] => Images
[alreadyInSave:protected] =>
[alreadyInValidation:protected] =>
[validationFailures:protected] => Array
(
)
[_new:BaseObject:private] =>
[_deleted:BaseObject:private] =>
[modifiedColumns:protected] => Array
(
)
)
[20] => Category Object
(
[languages:protected] =>
[bok_resources:protected] =>
[bok_topics:protected] =>
[bok_keywords:protected] =>
[id:protected] => 20
[type:protected] => category
[parent:protected] => 7
[label:protected] => Safety Culture
[alreadyInSave:protected] =>
[alreadyInValidation:protected] =>
[validationFailures:protected] => Array
(
)
[_new:BaseObject:private] =>
[_deleted:BaseObject:private] =>
[modifiedColumns:protected] => Array
(
)
)
[46] => Category Object
(
[languages:protected] =>
[bok_resources:protected] =>
[bok_topics:protected] =>
[bok_keywords:protected] =>
[id:protected] => 46
[type:protected] => category
[parent:protected] => 2
[label:protected] => Boilermaker
[alreadyInSave:protected] =>
[alreadyInValidation:protected] =>
[validationFailures:protected] => Array
(
)
[_new:BaseObject:private] =>
[_deleted:BaseObject:private] =>
[modifiedColumns:protected] => Array
(
)
)
[47] => Category Object
(
[languages:protected] =>
[bok_resources:protected] =>
[bok_topics:protected] =>
[bok_keywords:protected] =>
[id:protected] => 47
[type:protected] => category
[parent:protected] => 2
[label:protected] => Bricklayer
[alreadyInSave:protected] =>
[alreadyInValidation:protected] =>
[validationFailures:protected] => Array
(
)
[_new:BaseObject:private] =>
[_deleted:BaseObject:private] =>
[modifiedColumns:protected] => Array
(
)
)
[49] => Category Object
(
[languages:protected] =>
[bok_resources:protected] =>
[bok_topics:protected] =>
[bok_keywords:protected] =>
[id:protected] => 49
[type:protected] => category
[parent:protected] => 2
[label:protected] => Carpenter
[alreadyInSave:protected] =>
[alreadyInValidation:protected] =>
[validationFailures:protected] => Array
(
)
[_new:BaseObject:private] =>
[_deleted:BaseObject:private] =>
[modifiedColumns:protected] => Array
(
)
)
[50] => Category Object
(
[languages:protected] =>
[bok_resources:protected] =>
[bok_topics:protected] =>
[bok_keywords:protected] =>
[id:protected] => 50
[type:protected] => category
[parent:protected] => 2
[label:protected] => Carpet Layer
[alreadyInSave:protected] =>
[alreadyInValidation:protected] =>
[validationFailures:protected] => Array
(
)
[_new:BaseObject:private] =>
[_deleted:BaseObject:private] =>
[modifiedColumns:protected] => Array
(
)
)
[51] => Category Object
(
[languages:protected] =>
[bok_resources:protected] =>
[bok_topics:protected] =>
[bok_keywords:protected] =>
[id:protected] => 51
[type:protected] => category
[parent:protected] => 2
[label:protected] => Cement Mason
[alreadyInSave:protected] =>
[alreadyInValidation:protected] =>
[validationFailures:protected] => Array
(
)
[_new:BaseObject:private] =>
[_deleted:BaseObject:private] =>
[modifiedColumns:protected] => Array
(
)
)
[54] => Category Object
(
[languages:protected] =>
[bok_resources:protected] =>
[bok_topics:protected] =>
[bok_keywords:protected] =>
[id:protected] => 54
[type:protected] => category
[parent:protected] => 2
[label:protected] => Drywall Applicator Specialist
[alreadyInSave:protected] =>
[alreadyInValidation:protected] =>
[validationFailures:protected] => Array
(
)
[_new:BaseObject:private] =>
[_deleted:BaseObject:private] =>
[modifiedColumns:protected] => Array
(
)
)
[55] => Category Object
(
[languages:protected] =>
[bok_resources:protected] =>
[bok_topics:protected] =>
[bok_keywords:protected] =>
[id:protected] => 55
[type:protected] => category
[parent:protected] => 2
[label:protected] => Electrical Worker
[alreadyInSave:protected] =>
[alreadyInValidation:protected] =>
[validationFailures:protected] => Array
(
)
[_new:BaseObject:private] =>
[_deleted:BaseObject:private] =>
[modifiedColumns:protected] => Array
(
)
)
[58] => Category Object
(
[languages:protected] =>
[bok_resources:protected] =>
[bok_topics:protected] =>
[bok_keywords:protected] =>
[id:protected] => 58
[type:protected] => category
[parent:protected] => 2
[label:protected] => Glazier
[alreadyInSave:protected] =>
[alreadyInValidation:protected] =>
[validationFailures:protected] => Array
(
)
[_new:BaseObject:private] =>
[_deleted:BaseObject:private] =>
[modifiedColumns:protected] => Array
(
)
)
[60] => Category Object
(
[languages:protected] =>
[bok_resources:protected] =>
[bok_topics:protected] =>
[bok_keywords:protected] =>
[id:protected] => 60
[type:protected] => category
[parent:protected] => 2
[label:protected] => HVAC
[alreadyInSave:protected] =>
[alreadyInValidation:protected] =>
[validationFailures:protected] => Array
(
)
[_new:BaseObject:private] =>
[_deleted:BaseObject:private] =>
[modifiedColumns:protected] => Array
(
)
)
[61] => Category Object
(
[languages:protected] =>
[bok_resources:protected] =>
[bok_topics:protected] =>
[bok_keywords:protected] =>
[id:protected] => 61
[type:protected] => category
[parent:protected] => 2
[label:protected] => Interior Systems Carpenter
[alreadyInSave:protected] =>
[alreadyInValidation:protected] =>
[validationFailures:protected] => Array
(
)
[_new:BaseObject:private] =>
[_deleted:BaseObject:private] =>
[modifiedColumns:protected] => Array
(
)
)
[64] => Category Object
(
[languages:protected] =>
[bok_resources:protected] =>
[bok_topics:protected] =>
[bok_keywords:protected] =>
[id:protected] => 64
[type:protected] => category
[parent:protected] => 2
[label:protected] => Laborer
[alreadyInSave:protected] =>
[alreadyInValidation:protected] =>
[validationFailures:protected] => Array
(
)
[_new:BaseObject:private] =>
[_deleted:BaseObject:private] =>
[modifiedColumns:protected] => Array
(
)
)
[71] => Category Object
(
[languages:protected] =>
[bok_resources:protected] =>
[bok_topics:protected] =>
[bok_keywords:protected] =>
[id:protected] => 71
[type:protected] => category
[parent:protected] => 2
[label:protected] => Painter
[alreadyInSave:protected] =>
[alreadyInValidation:protected] =>
[validationFailures:protected] => Array
(
)
[_new:BaseObject:private] =>
[_deleted:BaseObject:private] =>
[modifiedColumns:protected] => Array
(
)
)
[75] => Category Object
(
[languages:protected] =>
[bok_resources:protected] =>
[bok_topics:protected] =>
[bok_keywords:protected] =>
[id:protected] => 75
[type:protected] => category
[parent:protected] => 2
[label:protected] => Plasterer
[alreadyInSave:protected] =>
[alreadyInValidation:protected] =>
[validationFailures:protected] => Array
(
)
[_new:BaseObject:private] =>
[_deleted:BaseObject:private] =>
[modifiedColumns:protected] => Array
(
)
)
[76] => Category Object
(
[languages:protected] =>
[bok_resources:protected] =>
[bok_topics:protected] =>
[bok_keywords:protected] =>
[id:protected] => 76
[type:protected] => category
[parent:protected] => 2
[label:protected] => Plumber/Pipefitter
[alreadyInSave:protected] =>
[alreadyInValidation:protected] =>
[validationFailures:protected] => Array
(
)
[_new:BaseObject:private] =>
[_deleted:BaseObject:private] =>
[modifiedColumns:protected] => Array
(
)
)
[63] => Category Object
(
[languages:protected] =>
[bok_resources:protected] =>
[bok_topics:protected] =>
[bok_keywords:protected] =>
[id:protected] => 63
[type:protected] => category
[parent:protected] => 2
[label:protected] => Reinforcing Ironworker
[alreadyInSave:protected] =>
[alreadyInValidation:protected] =>
[validationFailures:protected] => Array
(
)
[_new:BaseObject:private] =>
[_deleted:BaseObject:private] =>
[modifiedColumns:protected] => Array
(
)
)
[79] => Category Object
(
[languages:protected] =>
[bok_resources:protected] =>
[bok_topics:protected] =>
[bok_keywords:protected] =>
[id:protected] => 79
[type:protected] => category
[parent:protected] => 2
[label:protected] => Scaffold Erector
[alreadyInSave:protected] =>
[alreadyInValidation:protected] =>
[validationFailures:protected] => Array
(
)
[_new:BaseObject:private] =>
[_deleted:BaseObject:private] =>
[modifiedColumns:protected] => Array
(
)
)
[80] => Category Object
(
[languages:protected] =>
[bok_resources:protected] =>
[bok_topics:protected] =>
[bok_keywords:protected] =>
[id:protected] => 80
[type:protected] => category
[parent:protected] => 2
[label:protected] => Sheetmetal Worker
[alreadyInSave:protected] =>
[alreadyInValidation:protected] =>
[validationFailures:protected] => Array
(
)
[_new:BaseObject:private] =>
[_deleted:BaseObject:private] =>
[modifiedColumns:protected] => Array
(
)
)
[82] => Category Object
(
[languages:protected] =>
[bok_resources:protected] =>
[bok_topics:protected] =>
[bok_keywords:protected] =>
[id:protected] => 82
[type:protected] => category
[parent:protected] => 2
[label:protected] => Stonemason
[alreadyInSave:protected] =>
[alreadyInValidation:protected] =>
[validationFailures:protected] => Array
(
)
[_new:BaseObject:private] =>
[_deleted:BaseObject:private] =>
[modifiedColumns:protected] => Array
(
)
)
[62] => Category Object
(
[languages:protected] =>
[bok_resources:protected] =>
[bok_topics:protected] =>
[bok_keywords:protected] =>
[id:protected] => 62
[type:protected] => category
[parent:protected] => 2
[label:protected] => Structural Ironworker
[alreadyInSave:protected] =>
[alreadyInValidation:protected] =>
[validationFailures:protected] => Array
(
)
[_new:BaseObject:private] =>
[_deleted:BaseObject:private] =>
[modifiedColumns:protected] => Array
(
)
)
[83] => Category Object
(
[languages:protected] =>
[bok_resources:protected] =>
[bok_topics:protected] =>
[bok_keywords:protected] =>
[id:protected] => 83
[type:protected] => category
[parent:protected] => 2
[label:protected] => Terrazzo Worker
[alreadyInSave:protected] =>
[alreadyInValidation:protected] =>
[validationFailures:protected] => Array
(
)
[_new:BaseObject:private] =>
[_deleted:BaseObject:private] =>
[modifiedColumns:protected] => Array
(
)
)
[87] => Category Object
(
[languages:protected] =>
[bok_resources:protected] =>
[bok_topics:protected] =>
[bok_keywords:protected] =>
[id:protected] => 87
[type:protected] => category
[parent:protected] => 3
[label:protected] => Commercial & Institutional
[alreadyInSave:protected] =>
[alreadyInValidation:protected] =>
[validationFailures:protected] => Array
(
)
[_new:BaseObject:private] =>
[_deleted:BaseObject:private] =>
[modifiedColumns:protected] => Array
(
)
)
[91] => Category Object
(
[languages:protected] =>
[bok_resources:protected] =>
[bok_topics:protected] =>
[bok_keywords:protected] =>
[id:protected] => 91
[type:protected] => category
[parent:protected] => 3
[label:protected] => Heavy & Highway
[alreadyInSave:protected] =>
[alreadyInValidation:protected] =>
[validationFailures:protected] => Array
(
)
[_new:BaseObject:private] =>
[_deleted:BaseObject:private] =>
[modifiedColumns:protected] => Array
(
)
)
[90] => Category Object
(
[languages:protected] =>
[bok_resources:protected] =>
[bok_topics:protected] =>
[bok_keywords:protected] =>
[id:protected] => 90
[type:protected] => category
[parent:protected] => 3
[label:protected] => Industrial
[alreadyInSave:protected] =>
[alreadyInValidation:protected] =>
[validationFailures:protected] => Array
(
)
[_new:BaseObject:private] =>
[_deleted:BaseObject:private] =>
[modifiedColumns:protected] => Array
(
)
)
[93] => Category Object
(
[languages:protected] =>
[bok_resources:protected] =>
[bok_topics:protected] =>
[bok_keywords:protected] =>
[id:protected] => 93
[type:protected] => category
[parent:protected] => 3
[label:protected] => Renovations
[alreadyInSave:protected] =>
[alreadyInValidation:protected] =>
[validationFailures:protected] => Array
(
)
[_new:BaseObject:private] =>
[_deleted:BaseObject:private] =>
[modifiedColumns:protected] => Array
(
)
)
[94] => Category Object
(
[languages:protected] =>
[bok_resources:protected] =>
[bok_topics:protected] =>
[bok_keywords:protected] =>
[id:protected] => 94
[type:protected] => category
[parent:protected] => 3
[label:protected] => Residential
[alreadyInSave:protected] =>
[alreadyInValidation:protected] =>
[validationFailures:protected] => Array
(
)
[_new:BaseObject:private] =>
[_deleted:BaseObject:private] =>
[modifiedColumns:protected] => Array
(
)
)
)
[categories_initialized:protected] => 1
[mapped_items:protected] =>
[content:protected] =>
[files:protected] =>
[language:protected] => Language Object
(
[id:protected] => 1
[code:protected] => en
[name:protected] => English
[alreadyInSave:protected] =>
[alreadyInValidation:protected] =>
[validationFailures:protected] => Array
(
)
[_new:BaseObject:private] =>
[_deleted:BaseObject:private] =>
[modifiedColumns:protected] => Array
(
)
)
[old_record:protected] =>
[id:protected] => 4014
[old_id:protected] =>
[elcosh_id:protected] => i002700
[type:protected] => image
[display_type:protected] => Image
[user_id:protected] => 0
[language_id:protected] => 1
[tagging_id:protected] => Bruce Lippy
[priority_id:protected] => 1
[title:protected] => Safety officer discussing ongoing project with marketing coordinator
[total_pages:protected] => 0
[billed_pages:protected] => 0
[publication_number:protected] =>
[part_of:protected] =>
[keywords:protected] => Latino, safety officer, safety culture
[comments:protected] =>
[summary:protected] => The safety officer (left) points out the good safety practices on this project that reflect well on the firm and may influence future clients.
[transition_comments:protected] =>
[external_link:protected] =>
[consol_link:protected] => http://www.cpwrconstructionsolutions.org/index.php
[more_like_this:protected] => d000989,d001351,d001362,d000652, d001101, d000931, d001395
[permission_given_by:protected] =>
[published:protected] => T
[billable:protected] => F
[img_name:protected] =>
[img_ext:protected] => jpg
[img_width:protected] =>
[img_height:protected] =>
[img_credit:protected] => Hoar Construction, Photo by Neil Lippy
[img_practice:protected] => good
[vid_source_id:protected] =>
[vid_running_time:protected] =>
[vid_intended_audience:protected] =>
[vid_acquisition_info:protected] =>
[vid_cost:protected] =>
[vid_producer:protected] =>
[vid_filename:protected] =>
[vid_filename_downloadable:protected] =>
[date_summary:protected] => November 2015
[date_permission_requested:protected] =>
[date_permission_received:protected] =>
[date_review_needed:protected] =>
[date_received:protected] => 03/02/16
[date_completed:protected] => 03/02/16
[date_billed:protected] =>
[date_modified:protected] => 01/30/23
[collBokExports:protected] =>
[lastBokExportCriteria:BaseElcoshItem:private] =>
[alreadyInSave:protected] =>
[alreadyInValidation:protected] =>
[validationFailures:protected] => Array
(
)
[_new:BaseObject:private] =>
[_deleted:BaseObject:private] =>
[modifiedColumns:protected] => Array
(
)
)
)
[4] => Search_Result Object
(
[title] => Scaffolding at top of large column
[image] => /record/images/3994-p.jpg
[blurb] => This shot shows innovative guarding around the top of a large concrete column in the base of a high rise structure going up....
[category] => Array
(
[0] => 15
[1] => 21
[2] => 47
[3] => 51
[4] => 63
[5] => 78
[6] => 79
[7] => 80
[8] => 62
[9] => 87
[10] => 97
[11] => 56
[12] => 64
[13] => 74
)
[labels] => Array
(
[0] => Falls
[1] => Work Environment
[2] => Hazards
[3] => Scaffolds
[6] => Bricklayer
[7] => Trades
[8] => Cement Mason
[10] => Reinforcing Ironworker
[12] => Roofer/Waterproofer
[14] => Scaffold Erector
[16] => Sheetmetal Worker
[18] => Structural Ironworker
[20] => Commercial & Institutional
[21] => Jobsites
[22] => Images
[23] => Media
[24] => Media & Documents
[25] => Elevator Constructor
[27] => Laborer
[29] => Pile Driver
)
[type] => Images
[sub_category] =>
[url] => /image/3994/i002689/Scaffolding%2Bat%2Btop%2Bof%2Blarge%2Bcolumn.html
[item:protected] => ImageRecord Object
(
[records:protected] => Array
(
)
[recordId:protected] =>
[searchWordClass:protected] =>
[searchWordPeerClass:protected] =>
[bok_record:protected] =>
[authors:protected] =>
[organizations:protected] =>
[collections:protected] =>
[categories:protected] => Array
(
[15] => Category Object
(
[languages:protected] =>
[bok_resources:protected] =>
[bok_topics:protected] =>
[bok_keywords:protected] =>
[id:protected] => 15
[type:protected] => category
[parent:protected] => 7
[label:protected] => Falls
[alreadyInSave:protected] =>
[alreadyInValidation:protected] =>
[validationFailures:protected] => Array
(
)
[_new:BaseObject:private] =>
[_deleted:BaseObject:private] =>
[modifiedColumns:protected] => Array
(
)
)
[21] => Category Object
(
[languages:protected] =>
[bok_resources:protected] =>
[bok_topics:protected] =>
[bok_keywords:protected] =>
[id:protected] => 21
[type:protected] => category
[parent:protected] => 7
[label:protected] => Scaffolds
[alreadyInSave:protected] =>
[alreadyInValidation:protected] =>
[validationFailures:protected] => Array
(
)
[_new:BaseObject:private] =>
[_deleted:BaseObject:private] =>
[modifiedColumns:protected] => Array
(
)
)
[47] => Category Object
(
[languages:protected] =>
[bok_resources:protected] =>
[bok_topics:protected] =>
[bok_keywords:protected] =>
[id:protected] => 47
[type:protected] => category
[parent:protected] => 2
[label:protected] => Bricklayer
[alreadyInSave:protected] =>
[alreadyInValidation:protected] =>
[validationFailures:protected] => Array
(
)
[_new:BaseObject:private] =>
[_deleted:BaseObject:private] =>
[modifiedColumns:protected] => Array
(
)
)
[51] => Category Object
(
[languages:protected] =>
[bok_resources:protected] =>
[bok_topics:protected] =>
[bok_keywords:protected] =>
[id:protected] => 51
[type:protected] => category
[parent:protected] => 2
[label:protected] => Cement Mason
[alreadyInSave:protected] =>
[alreadyInValidation:protected] =>
[validationFailures:protected] => Array
(
)
[_new:BaseObject:private] =>
[_deleted:BaseObject:private] =>
[modifiedColumns:protected] => Array
(
)
)
[63] => Category Object
(
[languages:protected] =>
[bok_resources:protected] =>
[bok_topics:protected] =>
[bok_keywords:protected] =>
[id:protected] => 63
[type:protected] => category
[parent:protected] => 2
[label:protected] => Reinforcing Ironworker
[alreadyInSave:protected] =>
[alreadyInValidation:protected] =>
[validationFailures:protected] => Array
(
)
[_new:BaseObject:private] =>
[_deleted:BaseObject:private] =>
[modifiedColumns:protected] => Array
(
)
)
[78] => Category Object
(
[languages:protected] =>
[bok_resources:protected] =>
[bok_topics:protected] =>
[bok_keywords:protected] =>
[id:protected] => 78
[type:protected] => category
[parent:protected] => 2
[label:protected] => Roofer/Waterproofer
[alreadyInSave:protected] =>
[alreadyInValidation:protected] =>
[validationFailures:protected] => Array
(
)
[_new:BaseObject:private] =>
[_deleted:BaseObject:private] =>
[modifiedColumns:protected] => Array
(
)
)
[79] => Category Object
(
[languages:protected] =>
[bok_resources:protected] =>
[bok_topics:protected] =>
[bok_keywords:protected] =>
[id:protected] => 79
[type:protected] => category
[parent:protected] => 2
[label:protected] => Scaffold Erector
[alreadyInSave:protected] =>
[alreadyInValidation:protected] =>
[validationFailures:protected] => Array
(
)
[_new:BaseObject:private] =>
[_deleted:BaseObject:private] =>
[modifiedColumns:protected] => Array
(
)
)
[80] => Category Object
(
[languages:protected] =>
[bok_resources:protected] =>
[bok_topics:protected] =>
[bok_keywords:protected] =>
[id:protected] => 80
[type:protected] => category
[parent:protected] => 2
[label:protected] => Sheetmetal Worker
[alreadyInSave:protected] =>
[alreadyInValidation:protected] =>
[validationFailures:protected] => Array
(
)
[_new:BaseObject:private] =>
[_deleted:BaseObject:private] =>
[modifiedColumns:protected] => Array
(
)
)
[62] => Category Object
(
[languages:protected] =>
[bok_resources:protected] =>
[bok_topics:protected] =>
[bok_keywords:protected] =>
[id:protected] => 62
[type:protected] => category
[parent:protected] => 2
[label:protected] => Structural Ironworker
[alreadyInSave:protected] =>
[alreadyInValidation:protected] =>
[validationFailures:protected] => Array
(
)
[_new:BaseObject:private] =>
[_deleted:BaseObject:private] =>
[modifiedColumns:protected] => Array
(
)
)
[87] => Category Object
(
[languages:protected] =>
[bok_resources:protected] =>
[bok_topics:protected] =>
[bok_keywords:protected] =>
[id:protected] => 87
[type:protected] => category
[parent:protected] => 3
[label:protected] => Commercial & Institutional
[alreadyInSave:protected] =>
[alreadyInValidation:protected] =>
[validationFailures:protected] => Array
(
)
[_new:BaseObject:private] =>
[_deleted:BaseObject:private] =>
[modifiedColumns:protected] => Array
(
)
)
[97] => Category Object
(
[languages:protected] =>
[bok_resources:protected] =>
[bok_topics:protected] =>
[bok_keywords:protected] =>
[id:protected] => 97
[type:protected] => category
[parent:protected] => 5
[label:protected] => Images
[alreadyInSave:protected] =>
[alreadyInValidation:protected] =>
[validationFailures:protected] => Array
(
)
[_new:BaseObject:private] =>
[_deleted:BaseObject:private] =>
[modifiedColumns:protected] => Array
(
)
)
[56] => Category Object
(
[languages:protected] =>
[bok_resources:protected] =>
[bok_topics:protected] =>
[bok_keywords:protected] =>
[id:protected] => 56
[type:protected] => category
[parent:protected] => 2
[label:protected] => Elevator Constructor
[alreadyInSave:protected] =>
[alreadyInValidation:protected] =>
[validationFailures:protected] => Array
(
)
[_new:BaseObject:private] =>
[_deleted:BaseObject:private] =>
[modifiedColumns:protected] => Array
(
)
)
[64] => Category Object
(
[languages:protected] =>
[bok_resources:protected] =>
[bok_topics:protected] =>
[bok_keywords:protected] =>
[id:protected] => 64
[type:protected] => category
[parent:protected] => 2
[label:protected] => Laborer
[alreadyInSave:protected] =>
[alreadyInValidation:protected] =>
[validationFailures:protected] => Array
(
)
[_new:BaseObject:private] =>
[_deleted:BaseObject:private] =>
[modifiedColumns:protected] => Array
(
)
)
[74] => Category Object
(
[languages:protected] =>
[bok_resources:protected] =>
[bok_topics:protected] =>
[bok_keywords:protected] =>
[id:protected] => 74
[type:protected] => category
[parent:protected] => 2
[label:protected] => Pile Driver
[alreadyInSave:protected] =>
[alreadyInValidation:protected] =>
[validationFailures:protected] => Array
(
)
[_new:BaseObject:private] =>
[_deleted:BaseObject:private] =>
[modifiedColumns:protected] => Array
(
)
)
)
[categories_initialized:protected] => 1
[mapped_items:protected] =>
[content:protected] =>
[files:protected] =>
[language:protected] => Language Object
(
[id:protected] => 1
[code:protected] => en
[name:protected] => English
[alreadyInSave:protected] =>
[alreadyInValidation:protected] =>
[validationFailures:protected] => Array
(
)
[_new:BaseObject:private] =>
[_deleted:BaseObject:private] =>
[modifiedColumns:protected] => Array
(
)
)
[old_record:protected] =>
[id:protected] => 3994
[old_id:protected] =>
[elcosh_id:protected] => i002689
[type:protected] => image
[display_type:protected] => Image
[user_id:protected] => 0
[language_id:protected] => 1
[tagging_id:protected] => Bruce Lippy
[priority_id:protected] => 1
[title:protected] => Scaffolding at top of large column
[total_pages:protected] => 0
[billed_pages:protected] => 0
[publication_number:protected] =>
[part_of:protected] =>
[keywords:protected] => Guardrail, railing, fall prevention, falls
[comments:protected] =>
[summary:protected] => This shot shows innovative guarding around the top of a large concrete column in the base of a high rise structure going up.
[transition_comments:protected] =>
[external_link:protected] =>
[consol_link:protected] => http://www.cpwrconstructionsolutions.org/masonry/solution/8/adjustable-tower-scaffold.html
[more_like_this:protected] => c1002680,i002662,d000608,d001255
[permission_given_by:protected] =>
[published:protected] => T
[billable:protected] => F
[img_name:protected] =>
[img_ext:protected] => jpg
[img_width:protected] =>
[img_height:protected] =>
[img_credit:protected] => Photo by Pam Susi
[img_practice:protected] => good
[vid_source_id:protected] =>
[vid_running_time:protected] =>
[vid_intended_audience:protected] =>
[vid_acquisition_info:protected] =>
[vid_cost:protected] =>
[vid_producer:protected] =>
[vid_filename:protected] =>
[vid_filename_downloadable:protected] =>
[date_summary:protected] => January 2016
[date_permission_requested:protected] =>
[date_permission_received:protected] =>
[date_review_needed:protected] =>
[date_received:protected] => 02/01/16
[date_completed:protected] => 02/01/16
[date_billed:protected] =>
[date_modified:protected] => 02/01/16
[collBokExports:protected] =>
[lastBokExportCriteria:BaseElcoshItem:private] =>
[alreadyInSave:protected] =>
[alreadyInValidation:protected] =>
[validationFailures:protected] => Array
(
)
[_new:BaseObject:private] =>
[_deleted:BaseObject:private] =>
[modifiedColumns:protected] => Array
(
)
)
)
[5] => Search_Result Object
(
[title] => Construction bracing
[image] => /record/images/3995-p.jpg
[blurb] => This shows structural support that prevents collapses during construction....
[category] => Array
(
[0] => 12
[1] => 15
[2] => 21
[3] => 49
[4] => 51
[5] => 55
[6] => 56
[7] => 60
[8] => 64
[9] => 68
[10] => 74
[11] => 63
[12] => 78
[13] => 79
[14] => 80
[15] => 62
[16] => 87
[17] => 90
[18] => 97
)
[labels] => Array
(
[0] => Crushed/Struck By
[1] => Work Environment
[2] => Hazards
[3] => Falls
[6] => Scaffolds
[9] => Carpenter
[10] => Trades
[11] => Cement Mason
[13] => Electrical Worker
[15] => Elevator Constructor
[17] => HVAC
[19] => Laborer
[21] => Maintenance Worker
[23] => Pile Driver
[25] => Reinforcing Ironworker
[27] => Roofer/Waterproofer
[29] => Scaffold Erector
[31] => Sheetmetal Worker
[33] => Structural Ironworker
[35] => Commercial & Institutional
[36] => Jobsites
[37] => Industrial
[39] => Images
[40] => Media
[41] => Media & Documents
)
[type] => Images
[sub_category] =>
[url] => /image/3995/i002690/Construction%2Bbracing.html
[item:protected] => ImageRecord Object
(
[records:protected] => Array
(
)
[recordId:protected] =>
[searchWordClass:protected] =>
[searchWordPeerClass:protected] =>
[bok_record:protected] =>
[authors:protected] =>
[organizations:protected] =>
[collections:protected] =>
[categories:protected] => Array
(
[12] => Category Object
(
[languages:protected] =>
[bok_resources:protected] =>
[bok_topics:protected] =>
[bok_keywords:protected] =>
[id:protected] => 12
[type:protected] => category
[parent:protected] => 7
[label:protected] => Crushed/Struck By
[alreadyInSave:protected] =>
[alreadyInValidation:protected] =>
[validationFailures:protected] => Array
(
)
[_new:BaseObject:private] =>
[_deleted:BaseObject:private] =>
[modifiedColumns:protected] => Array
(
)
)
[15] => Category Object
(
[languages:protected] =>
[bok_resources:protected] =>
[bok_topics:protected] =>
[bok_keywords:protected] =>
[id:protected] => 15
[type:protected] => category
[parent:protected] => 7
[label:protected] => Falls
[alreadyInSave:protected] =>
[alreadyInValidation:protected] =>
[validationFailures:protected] => Array
(
)
[_new:BaseObject:private] =>
[_deleted:BaseObject:private] =>
[modifiedColumns:protected] => Array
(
)
)
[21] => Category Object
(
[languages:protected] =>
[bok_resources:protected] =>
[bok_topics:protected] =>
[bok_keywords:protected] =>
[id:protected] => 21
[type:protected] => category
[parent:protected] => 7
[label:protected] => Scaffolds
[alreadyInSave:protected] =>
[alreadyInValidation:protected] =>
[validationFailures:protected] => Array
(
)
[_new:BaseObject:private] =>
[_deleted:BaseObject:private] =>
[modifiedColumns:protected] => Array
(
)
)
[49] => Category Object
(
[languages:protected] =>
[bok_resources:protected] =>
[bok_topics:protected] =>
[bok_keywords:protected] =>
[id:protected] => 49
[type:protected] => category
[parent:protected] => 2
[label:protected] => Carpenter
[alreadyInSave:protected] =>
[alreadyInValidation:protected] =>
[validationFailures:protected] => Array
(
)
[_new:BaseObject:private] =>
[_deleted:BaseObject:private] =>
[modifiedColumns:protected] => Array
(
)
)
[51] => Category Object
(
[languages:protected] =>
[bok_resources:protected] =>
[bok_topics:protected] =>
[bok_keywords:protected] =>
[id:protected] => 51
[type:protected] => category
[parent:protected] => 2
[label:protected] => Cement Mason
[alreadyInSave:protected] =>
[alreadyInValidation:protected] =>
[validationFailures:protected] => Array
(
)
[_new:BaseObject:private] =>
[_deleted:BaseObject:private] =>
[modifiedColumns:protected] => Array
(
)
)
[55] => Category Object
(
[languages:protected] =>
[bok_resources:protected] =>
[bok_topics:protected] =>
[bok_keywords:protected] =>
[id:protected] => 55
[type:protected] => category
[parent:protected] => 2
[label:protected] => Electrical Worker
[alreadyInSave:protected] =>
[alreadyInValidation:protected] =>
[validationFailures:protected] => Array
(
)
[_new:BaseObject:private] =>
[_deleted:BaseObject:private] =>
[modifiedColumns:protected] => Array
(
)
)
[56] => Category Object
(
[languages:protected] =>
[bok_resources:protected] =>
[bok_topics:protected] =>
[bok_keywords:protected] =>
[id:protected] => 56
[type:protected] => category
[parent:protected] => 2
[label:protected] => Elevator Constructor
[alreadyInSave:protected] =>
[alreadyInValidation:protected] =>
[validationFailures:protected] => Array
(
)
[_new:BaseObject:private] =>
[_deleted:BaseObject:private] =>
[modifiedColumns:protected] => Array
(
)
)
[60] => Category Object
(
[languages:protected] =>
[bok_resources:protected] =>
[bok_topics:protected] =>
[bok_keywords:protected] =>
[id:protected] => 60
[type:protected] => category
[parent:protected] => 2
[label:protected] => HVAC
[alreadyInSave:protected] =>
[alreadyInValidation:protected] =>
[validationFailures:protected] => Array
(
)
[_new:BaseObject:private] =>
[_deleted:BaseObject:private] =>
[modifiedColumns:protected] => Array
(
)
)
[64] => Category Object
(
[languages:protected] =>
[bok_resources:protected] =>
[bok_topics:protected] =>
[bok_keywords:protected] =>
[id:protected] => 64
[type:protected] => category
[parent:protected] => 2
[label:protected] => Laborer
[alreadyInSave:protected] =>
[alreadyInValidation:protected] =>
[validationFailures:protected] => Array
(
)
[_new:BaseObject:private] =>
[_deleted:BaseObject:private] =>
[modifiedColumns:protected] => Array
(
)
)
[68] => Category Object
(
[languages:protected] =>
[bok_resources:protected] =>
[bok_topics:protected] =>
[bok_keywords:protected] =>
[id:protected] => 68
[type:protected] => category
[parent:protected] => 2
[label:protected] => Maintenance Worker
[alreadyInSave:protected] =>
[alreadyInValidation:protected] =>
[validationFailures:protected] => Array
(
)
[_new:BaseObject:private] =>
[_deleted:BaseObject:private] =>
[modifiedColumns:protected] => Array
(
)
)
[74] => Category Object
(
[languages:protected] =>
[bok_resources:protected] =>
[bok_topics:protected] =>
[bok_keywords:protected] =>
[id:protected] => 74
[type:protected] => category
[parent:protected] => 2
[label:protected] => Pile Driver
[alreadyInSave:protected] =>
[alreadyInValidation:protected] =>
[validationFailures:protected] => Array
(
)
[_new:BaseObject:private] =>
[_deleted:BaseObject:private] =>
[modifiedColumns:protected] => Array
(
)
)
[63] => Category Object
(
[languages:protected] =>
[bok_resources:protected] =>
[bok_topics:protected] =>
[bok_keywords:protected] =>
[id:protected] => 63
[type:protected] => category
[parent:protected] => 2
[label:protected] => Reinforcing Ironworker
[alreadyInSave:protected] =>
[alreadyInValidation:protected] =>
[validationFailures:protected] => Array
(
)
[_new:BaseObject:private] =>
[_deleted:BaseObject:private] =>
[modifiedColumns:protected] => Array
(
)
)
[78] => Category Object
(
[languages:protected] =>
[bok_resources:protected] =>
[bok_topics:protected] =>
[bok_keywords:protected] =>
[id:protected] => 78
[type:protected] => category
[parent:protected] => 2
[label:protected] => Roofer/Waterproofer
[alreadyInSave:protected] =>
[alreadyInValidation:protected] =>
[validationFailures:protected] => Array
(
)
[_new:BaseObject:private] =>
[_deleted:BaseObject:private] =>
[modifiedColumns:protected] => Array
(
)
)
[79] => Category Object
(
[languages:protected] =>
[bok_resources:protected] =>
[bok_topics:protected] =>
[bok_keywords:protected] =>
[id:protected] => 79
[type:protected] => category
[parent:protected] => 2
[label:protected] => Scaffold Erector
[alreadyInSave:protected] =>
[alreadyInValidation:protected] =>
[validationFailures:protected] => Array
(
)
[_new:BaseObject:private] =>
[_deleted:BaseObject:private] =>
[modifiedColumns:protected] => Array
(
)
)
[80] => Category Object
(
[languages:protected] =>
[bok_resources:protected] =>
[bok_topics:protected] =>
[bok_keywords:protected] =>
[id:protected] => 80
[type:protected] => category
[parent:protected] => 2
[label:protected] => Sheetmetal Worker
[alreadyInSave:protected] =>
[alreadyInValidation:protected] =>
[validationFailures:protected] => Array
(
)
[_new:BaseObject:private] =>
[_deleted:BaseObject:private] =>
[modifiedColumns:protected] => Array
(
)
)
[62] => Category Object
(
[languages:protected] =>
[bok_resources:protected] =>
[bok_topics:protected] =>
[bok_keywords:protected] =>
[id:protected] => 62
[type:protected] => category
[parent:protected] => 2
[label:protected] => Structural Ironworker
[alreadyInSave:protected] =>
[alreadyInValidation:protected] =>
[validationFailures:protected] => Array
(
)
[_new:BaseObject:private] =>
[_deleted:BaseObject:private] =>
[modifiedColumns:protected] => Array
(
)
)
[87] => Category Object
(
[languages:protected] =>
[bok_resources:protected] =>
[bok_topics:protected] =>
[bok_keywords:protected] =>
[id:protected] => 87
[type:protected] => category
[parent:protected] => 3
[label:protected] => Commercial & Institutional
[alreadyInSave:protected] =>
[alreadyInValidation:protected] =>
[validationFailures:protected] => Array
(
)
[_new:BaseObject:private] =>
[_deleted:BaseObject:private] =>
[modifiedColumns:protected] => Array
(
)
)
[90] => Category Object
(
[languages:protected] =>
[bok_resources:protected] =>
[bok_topics:protected] =>
[bok_keywords:protected] =>
[id:protected] => 90
[type:protected] => category
[parent:protected] => 3
[label:protected] => Industrial
[alreadyInSave:protected] =>
[alreadyInValidation:protected] =>
[validationFailures:protected] => Array
(
)
[_new:BaseObject:private] =>
[_deleted:BaseObject:private] =>
[modifiedColumns:protected] => Array
(
)
)
[97] => Category Object
(
[languages:protected] =>
[bok_resources:protected] =>
[bok_topics:protected] =>
[bok_keywords:protected] =>
[id:protected] => 97
[type:protected] => category
[parent:protected] => 5
[label:protected] => Images
[alreadyInSave:protected] =>
[alreadyInValidation:protected] =>
[validationFailures:protected] => Array
(
)
[_new:BaseObject:private] =>
[_deleted:BaseObject:private] =>
[modifiedColumns:protected] => Array
(
)
)
)
[categories_initialized:protected] => 1
[mapped_items:protected] =>
[content:protected] =>
[files:protected] =>
[language:protected] => Language Object
(
[id:protected] => 1
[code:protected] => en
[name:protected] => English
[alreadyInSave:protected] =>
[alreadyInValidation:protected] =>
[validationFailures:protected] => Array
(
)
[_new:BaseObject:private] =>
[_deleted:BaseObject:private] =>
[modifiedColumns:protected] => Array
(
)
)
[old_record:protected] =>
[id:protected] => 3995
[old_id:protected] =>
[elcosh_id:protected] => i002690
[type:protected] => image
[display_type:protected] => Image
[user_id:protected] => 0
[language_id:protected] => 1
[tagging_id:protected] => Bruce Lippy
[priority_id:protected] => 1
[title:protected] => Construction bracing
[total_pages:protected] => 0
[billed_pages:protected] => 0
[publication_number:protected] =>
[part_of:protected] =>
[keywords:protected] => Bracing, support, scaffold
[comments:protected] =>
[summary:protected] => This shows structural support that prevents collapses during construction.
[transition_comments:protected] =>
[external_link:protected] =>
[consol_link:protected] => http://www.cpwrconstructionsolutions.org/masonry/solution/8/adjustable-tower-scaffold.html
[more_like_this:protected] => i002660
[permission_given_by:protected] =>
[published:protected] => T
[billable:protected] => F
[img_name:protected] =>
[img_ext:protected] => jpg
[img_width:protected] =>
[img_height:protected] =>
[img_credit:protected] => Photo by Pam Susi
[img_practice:protected] => good
[vid_source_id:protected] =>
[vid_running_time:protected] =>
[vid_intended_audience:protected] =>
[vid_acquisition_info:protected] =>
[vid_cost:protected] =>
[vid_producer:protected] =>
[vid_filename:protected] =>
[vid_filename_downloadable:protected] =>
[date_summary:protected] => January 2016
[date_permission_requested:protected] =>
[date_permission_received:protected] =>
[date_review_needed:protected] =>
[date_received:protected] => 02/01/16
[date_completed:protected] => 02/01/16
[date_billed:protected] =>
[date_modified:protected] => 02/01/16
[collBokExports:protected] =>
[lastBokExportCriteria:BaseElcoshItem:private] =>
[alreadyInSave:protected] =>
[alreadyInValidation:protected] =>
[validationFailures:protected] => Array
(
)
[_new:BaseObject:private] =>
[_deleted:BaseObject:private] =>
[modifiedColumns:protected] => Array
(
)
)
)
)
[preview_mode] =>
[description] => Toolbox talks have been the main tool for communicating safety information on construction jobs for decades.
Unfortunately, there has been little research on what makes for effective toolbox talks. The IUOE National
Training Fund worked with OSHA and NIOSH to make sure their series of 24 Focus Four toolbox talks were based on the best recommendations for effective design. These toolbox talks accompany an entire package of training materials, but can be used alone. This guide points out the key features of these toolbox talks and how best to deliver them.
[keywords] => toolbox talks, tailgate talks
[related_items] => Array
(
[Toolbox Talks] => Array
(
[0] => DocumentRecord Object
(
[records:protected] => Array
(
)
[recordId:protected] =>
[searchWordClass:protected] =>
[searchWordPeerClass:protected] =>
[bok_record:protected] =>
[authors:protected] =>
[organizations:protected] =>
[collections:protected] =>
[categories:protected] =>
[categories_initialized:protected] =>
[mapped_items:protected] =>
[content:protected] =>
[files:protected] =>
[language:protected] => Language Object
(
[id:protected] => 1
[code:protected] => en
[name:protected] => English
[alreadyInSave:protected] =>
[alreadyInValidation:protected] =>
[validationFailures:protected] => Array
(
)
[_new:BaseObject:private] =>
[_deleted:BaseObject:private] =>
[modifiedColumns:protected] => Array
(
)
)
[old_record:protected] =>
[id:protected] => 1605
[old_id:protected] => 1262
[elcosh_id:protected] => d001137
[type:protected] => document
[display_type:protected] => HTML w/ PDF
[user_id:protected] =>
[language_id:protected] => 1
[tagging_id:protected] => Garber
[priority_id:protected] => 1
[title:protected] => Focus Four Toolbox Talks, Module 1 – Falls, Talk #2 – Falls from debris piles?
[total_pages:protected] => 1
[billed_pages:protected] => 1
[publication_number:protected] =>
[part_of:protected] =>
[keywords:protected] => disaster response, hazard clean-up, uneven surface, disaster site, disaster clean-up
[comments:protected] =>
[summary:protected] => A toolbox talk on preventing falls from debris piles. Includes questions to ask, an incident to discuss with images, and a place to record questions the trainer would like to ask about the incident. Part of a collection. Click on the 'collection' button to access the other items.
[transition_comments:protected] =>
[external_link:protected] =>
[consol_link:protected] => http://www.cpwrconstructionsolutions.org/roofing/hazard/1463/install-asphalt-roofs-fall-from-heights.html
[more_like_this:protected] => a000081,d000478,d000530
[permission_given_by:protected] =>
[published:protected] => T
[billable:protected] => F
[img_name:protected] =>
[img_ext:protected] =>
[img_width:protected] =>
[img_height:protected] =>
[img_credit:protected] =>
[img_practice:protected] =>
[vid_source_id:protected] =>
[vid_running_time:protected] =>
[vid_intended_audience:protected] =>
[vid_acquisition_info:protected] =>
[vid_cost:protected] =>
[vid_producer:protected] =>
[vid_filename:protected] =>
[vid_filename_downloadable:protected] =>
[date_summary:protected] =>
[date_permission_requested:protected] =>
[date_permission_received:protected] =>
[date_review_needed:protected] =>
[date_received:protected] => 02/15/12
[date_completed:protected] => 03/19/12
[date_billed:protected] =>
[date_modified:protected] => 07/10/12
[collBokExports:protected] =>
[lastBokExportCriteria:BaseElcoshItem:private] =>
[alreadyInSave:protected] =>
[alreadyInValidation:protected] =>
[validationFailures:protected] => Array
(
)
[_new:BaseObject:private] =>
[_deleted:BaseObject:private] =>
[modifiedColumns:protected] => Array
(
)
)
[1] => DocumentRecord Object
(
[records:protected] => Array
(
)
[recordId:protected] =>
[searchWordClass:protected] =>
[searchWordPeerClass:protected] =>
[bok_record:protected] =>
[authors:protected] =>
[organizations:protected] =>
[collections:protected] =>
[categories:protected] =>
[categories_initialized:protected] =>
[mapped_items:protected] =>
[content:protected] =>
[files:protected] =>
[language:protected] => Language Object
(
[id:protected] => 1
[code:protected] => en
[name:protected] => English
[alreadyInSave:protected] =>
[alreadyInValidation:protected] =>
[validationFailures:protected] => Array
(
)
[_new:BaseObject:private] =>
[_deleted:BaseObject:private] =>
[modifiedColumns:protected] => Array
(
)
)
[old_record:protected] =>
[id:protected] => 1610
[old_id:protected] => 1271
[elcosh_id:protected] => d001146
[type:protected] => document
[display_type:protected] => HTML w/ PDF
[user_id:protected] => 0
[language_id:protected] => 1
[tagging_id:protected] => Garber
[priority_id:protected] => 1
[title:protected] => Focus Four Toolbox Talks, Module 2 – Struck-by, Talk #5 – Rigging and Securing Loads
[total_pages:protected] => 1
[billed_pages:protected] => 1
[publication_number:protected] =>
[part_of:protected] =>
[keywords:protected] => rigging, lift loads, loading areas, chains
[comments:protected] =>
[summary:protected] => A toolbox talk on preventing struck-by incidents caused by not securing loads properly. Includes questions to ask, an incident to discuss with images, and a place to record questions the trainer would like to ask about the incident. Part of a collection. Click on the 'collection' button to access the other items.
[transition_comments:protected] =>
[external_link:protected] =>
[consol_link:protected] => http://www.cpwrconstructionsolutions.org/heavy_equipment/hazard/1591/move-equipment-to-from-and-between-sites-work-zone-struck-by-injuries-and-fatalities.html
[more_like_this:protected] => d000144,d000360,d000873
[permission_given_by:protected] =>
[published:protected] => T
[billable:protected] => F
[img_name:protected] =>
[img_ext:protected] =>
[img_width:protected] =>
[img_height:protected] =>
[img_credit:protected] =>
[img_practice:protected] =>
[vid_source_id:protected] =>
[vid_running_time:protected] =>
[vid_intended_audience:protected] =>
[vid_acquisition_info:protected] =>
[vid_cost:protected] =>
[vid_producer:protected] =>
[vid_filename:protected] =>
[vid_filename_downloadable:protected] =>
[date_summary:protected] =>
[date_permission_requested:protected] =>
[date_permission_received:protected] =>
[date_review_needed:protected] =>
[date_received:protected] => 02/15/12
[date_completed:protected] => 03/28/12
[date_billed:protected] =>
[date_modified:protected] => 05/12/14
[collBokExports:protected] =>
[lastBokExportCriteria:BaseElcoshItem:private] =>
[alreadyInSave:protected] =>
[alreadyInValidation:protected] =>
[validationFailures:protected] => Array
(
)
[_new:BaseObject:private] =>
[_deleted:BaseObject:private] =>
[modifiedColumns:protected] => Array
(
)
)
[2] => DocumentRecord Object
(
[records:protected] => Array
(
)
[recordId:protected] =>
[searchWordClass:protected] =>
[searchWordPeerClass:protected] =>
[bok_record:protected] =>
[authors:protected] =>
[organizations:protected] =>
[collections:protected] =>
[categories:protected] =>
[categories_initialized:protected] =>
[mapped_items:protected] =>
[content:protected] =>
[files:protected] =>
[language:protected] => Language Object
(
[id:protected] => 1
[code:protected] => en
[name:protected] => English
[alreadyInSave:protected] =>
[alreadyInValidation:protected] =>
[validationFailures:protected] => Array
(
)
[_new:BaseObject:private] =>
[_deleted:BaseObject:private] =>
[modifiedColumns:protected] => Array
(
)
)
[old_record:protected] =>
[id:protected] => 1645
[old_id:protected] => 1274
[elcosh_id:protected] => d001149
[type:protected] => document
[display_type:protected] => HTML w/ PDF
[user_id:protected] => 0
[language_id:protected] => 1
[tagging_id:protected] => Garber
[priority_id:protected] => 1
[title:protected] => Focus Four Toolbox Talks, Module 3 – Caught-in/between, Talk #2 – Trenches & Heavy Equipment
[total_pages:protected] => 1
[billed_pages:protected] => 1
[publication_number:protected] =>
[part_of:protected] =>
[keywords:protected] => back-up alarms, spotter, soil cave-in, spoil pikes, ROPs, trenching, rain
[comments:protected] =>
[summary:protected] => A toolbox talk on preventing incidents involving trenches such as trench collapse. Includes questions to ask, an incident to discuss with images, and a place to record questions the trainer would like to ask about the incident. Part of a collection. Click on the 'collection' button to access the other items.
[transition_comments:protected] =>
[external_link:protected] =>
[consol_link:protected] =>
[more_like_this:protected] => d000019,d000035,d000168
[permission_given_by:protected] =>
[published:protected] => T
[billable:protected] => F
[img_name:protected] =>
[img_ext:protected] =>
[img_width:protected] =>
[img_height:protected] =>
[img_credit:protected] =>
[img_practice:protected] =>
[vid_source_id:protected] =>
[vid_running_time:protected] =>
[vid_intended_audience:protected] =>
[vid_acquisition_info:protected] =>
[vid_cost:protected] =>
[vid_producer:protected] =>
[vid_filename:protected] =>
[vid_filename_downloadable:protected] =>
[date_summary:protected] =>
[date_permission_requested:protected] =>
[date_permission_received:protected] =>
[date_review_needed:protected] =>
[date_received:protected] => 02/15/12
[date_completed:protected] => 04/02/12
[date_billed:protected] =>
[date_modified:protected] => 05/23/23
[collBokExports:protected] =>
[lastBokExportCriteria:BaseElcoshItem:private] =>
[alreadyInSave:protected] =>
[alreadyInValidation:protected] =>
[validationFailures:protected] => Array
(
)
[_new:BaseObject:private] =>
[_deleted:BaseObject:private] =>
[modifiedColumns:protected] => Array
(
)
)
[3] => DocumentRecord Object
(
[records:protected] => Array
(
)
[recordId:protected] =>
[searchWordClass:protected] =>
[searchWordPeerClass:protected] =>
[bok_record:protected] =>
[authors:protected] =>
[organizations:protected] =>
[collections:protected] =>
[categories:protected] =>
[categories_initialized:protected] =>
[mapped_items:protected] =>
[content:protected] =>
[files:protected] =>
[language:protected] => Language Object
(
[id:protected] => 1
[code:protected] => en
[name:protected] => English
[alreadyInSave:protected] =>
[alreadyInValidation:protected] =>
[validationFailures:protected] => Array
(
)
[_new:BaseObject:private] =>
[_deleted:BaseObject:private] =>
[modifiedColumns:protected] => Array
(
)
)
[old_record:protected] =>
[id:protected] => 1654
[old_id:protected] => 1284
[elcosh_id:protected] => d001159
[type:protected] => document
[display_type:protected] => HTML w/ PDF
[user_id:protected] => 0
[language_id:protected] => 1
[tagging_id:protected] => Garber
[priority_id:protected] => 1
[title:protected] => Focus Four Toolbox Talks, Module 4 – Electrocutions, Talk #6 – Hazards on Disaster Sites
[total_pages:protected] => 1
[billed_pages:protected] => 1
[publication_number:protected] =>
[part_of:protected] =>
[keywords:protected] => powerlines, underground, utilities, generators, wet conditions, GFCIs, energized lines, disasters, emergency response
[comments:protected] =>
[summary:protected] => A toolbox talk on how to avoid electrocution on a disaster site. Includes questions to ask, an incident to discuss with images, and a place to record questions the trainer would like to ask about the incident. Part of a collection. Click on the 'collection' button to access the other items.
[transition_comments:protected] =>
[external_link:protected] =>
[consol_link:protected] => http://www.cpwrconstructionsolutions.org/electrical/hazard/1138/install-and-repair-high-voltage-lines-transformers-switches-electrical-shocks-burns-and-or-electrocution.html
[more_like_this:protected] => d000135,d000361,d000437
[permission_given_by:protected] =>
[published:protected] => T
[billable:protected] => F
[img_name:protected] =>
[img_ext:protected] =>
[img_width:protected] =>
[img_height:protected] =>
[img_credit:protected] =>
[img_practice:protected] =>
[vid_source_id:protected] =>
[vid_running_time:protected] =>
[vid_intended_audience:protected] =>
[vid_acquisition_info:protected] =>
[vid_cost:protected] =>
[vid_producer:protected] =>
[vid_filename:protected] =>
[vid_filename_downloadable:protected] =>
[date_summary:protected] =>
[date_permission_requested:protected] =>
[date_permission_received:protected] =>
[date_review_needed:protected] =>
[date_received:protected] => 02/15/12
[date_completed:protected] => 04/02/12
[date_billed:protected] =>
[date_modified:protected] => 05/23/23
[collBokExports:protected] =>
[lastBokExportCriteria:BaseElcoshItem:private] =>
[alreadyInSave:protected] =>
[alreadyInValidation:protected] =>
[validationFailures:protected] => Array
(
)
[_new:BaseObject:private] =>
[_deleted:BaseObject:private] =>
[modifiedColumns:protected] => Array
(
)
)
)
)
[collections] => Array
(
[1294] =>
[1295] =>
[1292] =>
[1293] => CollectionRecord Object
(
[collection_items:protected] =>
[records:protected] => Array
(
)
[recordId:protected] =>
[searchWordClass:protected] =>
[searchWordPeerClass:protected] =>
[bok_record:protected] =>
[authors:protected] =>
[organizations:protected] =>
[collections:protected] =>
[categories:protected] =>
[categories_initialized:protected] =>
[mapped_items:protected] =>
[content:protected] =>
[files:protected] =>
[language:protected] =>
[old_record:protected] =>
[id:protected] => 1293
[old_id:protected] =>
[elcosh_id:protected] => c000026
[type:protected] => collection
[display_type:protected] => Collection
[user_id:protected] =>
[language_id:protected] =>
[tagging_id:protected] =>
[priority_id:protected] =>
[title:protected] => Focus Four-Struck By
[total_pages:protected] =>
[billed_pages:protected] =>
[publication_number:protected] =>
[part_of:protected] =>
[keywords:protected] =>
[comments:protected] =>
[summary:protected] => The following are links to all of the items in this collection:
[transition_comments:protected] =>
[external_link:protected] =>
[consol_link:protected] =>
[more_like_this:protected] =>
[permission_given_by:protected] =>
[published:protected] => T
[billable:protected] => F
[img_name:protected] =>
[img_ext:protected] =>
[img_width:protected] =>
[img_height:protected] =>
[img_credit:protected] =>
[img_practice:protected] =>
[vid_source_id:protected] =>
[vid_running_time:protected] =>
[vid_intended_audience:protected] =>
[vid_acquisition_info:protected] =>
[vid_cost:protected] =>
[vid_producer:protected] =>
[vid_filename:protected] =>
[vid_filename_downloadable:protected] =>
[date_summary:protected] =>
[date_permission_requested:protected] =>
[date_permission_received:protected] =>
[date_review_needed:protected] =>
[date_received:protected] => 05/08/12
[date_completed:protected] => 05/08/12
[date_billed:protected] =>
[date_modified:protected] => 05/08/12
[collBokExports:protected] =>
[lastBokExportCriteria:BaseElcoshItem:private] =>
[alreadyInSave:protected] =>
[alreadyInValidation:protected] =>
[validationFailures:protected] => Array
(
)
[_new:BaseObject:private] =>
[_deleted:BaseObject:private] =>
[modifiedColumns:protected] => Array
(
)
)
)
[record] => DocumentRecord Object
(
[records:protected] => Array
(
)
[recordId:protected] =>
[searchWordClass:protected] =>
[searchWordPeerClass:protected] =>
[bok_record:protected] =>
[authors:protected] => Array
(
)
[organizations:protected] => Array
(
[256] => Organization Object
(
[id:protected] => 256
[elcosh_id:protected] => o000276
[user_id:protected] => 14
[province_id:protected] => 0
[country_id:protected] => 0
[title:protected] => IUOE National Training Fund
[address:protected] =>
[postal_code:protected] =>
[city:protected] =>
[department:protected] =>
[phone:protected] => 304-253-8674
[fax:protected] =>
[email:protected] =>
[website:protected] => http://www.iuoeiettc.org
[filename:protected] =>
[about:protected] =>
[comments:protected] =>
[logo_available:protected] => T
[no_details:protected] => F
[date_received:protected] => 2012-02-13
[date_completed:protected] => 2012-02-13
[date_billed:protected] =>
[alreadyInSave:protected] =>
[alreadyInValidation:protected] =>
[validationFailures:protected] => Array
(
)
[_new:BaseObject:private] =>
[_deleted:BaseObject:private] =>
[modifiedColumns:protected] => Array
(
)
)
)
[collections:protected] => Array
(
[1294] =>
[1295] =>
[1292] =>
[1293] => CollectionRecord Object
(
[collection_items:protected] =>
[records:protected] => Array
(
)
[recordId:protected] =>
[searchWordClass:protected] =>
[searchWordPeerClass:protected] =>
[bok_record:protected] =>
[authors:protected] =>
[organizations:protected] =>
[collections:protected] =>
[categories:protected] =>
[categories_initialized:protected] =>
[mapped_items:protected] =>
[content:protected] =>
[files:protected] =>
[language:protected] =>
[old_record:protected] =>
[id:protected] => 1293
[old_id:protected] =>
[elcosh_id:protected] => c000026
[type:protected] => collection
[display_type:protected] => Collection
[user_id:protected] =>
[language_id:protected] =>
[tagging_id:protected] =>
[priority_id:protected] =>
[title:protected] => Focus Four-Struck By
[total_pages:protected] =>
[billed_pages:protected] =>
[publication_number:protected] =>
[part_of:protected] =>
[keywords:protected] =>
[comments:protected] =>
[summary:protected] => The following are links to all of the items in this collection:
[transition_comments:protected] =>
[external_link:protected] =>
[consol_link:protected] =>
[more_like_this:protected] =>
[permission_given_by:protected] =>
[published:protected] => T
[billable:protected] => F
[img_name:protected] =>
[img_ext:protected] =>
[img_width:protected] =>
[img_height:protected] =>
[img_credit:protected] =>
[img_practice:protected] =>
[vid_source_id:protected] =>
[vid_running_time:protected] =>
[vid_intended_audience:protected] =>
[vid_acquisition_info:protected] =>
[vid_cost:protected] =>
[vid_producer:protected] =>
[vid_filename:protected] =>
[vid_filename_downloadable:protected] =>
[date_summary:protected] =>
[date_permission_requested:protected] =>
[date_permission_received:protected] =>
[date_review_needed:protected] =>
[date_received:protected] => 05/08/12
[date_completed:protected] => 05/08/12
[date_billed:protected] =>
[date_modified:protected] => 05/08/12
[collBokExports:protected] =>
[lastBokExportCriteria:BaseElcoshItem:private] =>
[alreadyInSave:protected] =>
[alreadyInValidation:protected] =>
[validationFailures:protected] => Array
(
)
[_new:BaseObject:private] =>
[_deleted:BaseObject:private] =>
[modifiedColumns:protected] => Array
(
)
)
)
[categories:protected] =>
[categories_initialized:protected] =>
[mapped_items:protected] => Array
(
[1605] => DocumentRecord Object
(
[records:protected] => Array
(
)
[recordId:protected] =>
[searchWordClass:protected] =>
[searchWordPeerClass:protected] =>
[bok_record:protected] =>
[authors:protected] =>
[organizations:protected] =>
[collections:protected] =>
[categories:protected] =>
[categories_initialized:protected] =>
[mapped_items:protected] =>
[content:protected] =>
[files:protected] =>
[language:protected] =>
[old_record:protected] =>
[id:protected] => 1605
[old_id:protected] => 1262
[elcosh_id:protected] => d001137
[type:protected] => document
[display_type:protected] => HTML w/ PDF
[user_id:protected] =>
[language_id:protected] => 1
[tagging_id:protected] => Garber
[priority_id:protected] => 1
[title:protected] => Focus Four Toolbox Talks, Module 1 – Falls, Talk #2 – Falls from debris piles?
[total_pages:protected] => 1
[billed_pages:protected] => 1
[publication_number:protected] =>
[part_of:protected] =>
[keywords:protected] => disaster response, hazard clean-up, uneven surface, disaster site, disaster clean-up
[comments:protected] =>
[summary:protected] => A toolbox talk on preventing falls from debris piles. Includes questions to ask, an incident to discuss with images, and a place to record questions the trainer would like to ask about the incident. Part of a collection. Click on the 'collection' button to access the other items.
[transition_comments:protected] =>
[external_link:protected] =>
[consol_link:protected] => http://www.cpwrconstructionsolutions.org/roofing/hazard/1463/install-asphalt-roofs-fall-from-heights.html
[more_like_this:protected] => a000081,d000478,d000530
[permission_given_by:protected] =>
[published:protected] => T
[billable:protected] => F
[img_name:protected] =>
[img_ext:protected] =>
[img_width:protected] =>
[img_height:protected] =>
[img_credit:protected] =>
[img_practice:protected] =>
[vid_source_id:protected] =>
[vid_running_time:protected] =>
[vid_intended_audience:protected] =>
[vid_acquisition_info:protected] =>
[vid_cost:protected] =>
[vid_producer:protected] =>
[vid_filename:protected] =>
[vid_filename_downloadable:protected] =>
[date_summary:protected] =>
[date_permission_requested:protected] =>
[date_permission_received:protected] =>
[date_review_needed:protected] =>
[date_received:protected] => 02/15/12
[date_completed:protected] => 03/19/12
[date_billed:protected] =>
[date_modified:protected] => 07/10/12
[collBokExports:protected] =>
[lastBokExportCriteria:BaseElcoshItem:private] =>
[alreadyInSave:protected] =>
[alreadyInValidation:protected] =>
[validationFailures:protected] => Array
(
)
[_new:BaseObject:private] =>
[_deleted:BaseObject:private] =>
[modifiedColumns:protected] => Array
(
)
)
[1610] => DocumentRecord Object
(
[records:protected] => Array
(
)
[recordId:protected] =>
[searchWordClass:protected] =>
[searchWordPeerClass:protected] =>
[bok_record:protected] =>
[authors:protected] =>
[organizations:protected] =>
[collections:protected] =>
[categories:protected] =>
[categories_initialized:protected] =>
[mapped_items:protected] =>
[content:protected] =>
[files:protected] =>
[language:protected] =>
[old_record:protected] =>
[id:protected] => 1610
[old_id:protected] => 1271
[elcosh_id:protected] => d001146
[type:protected] => document
[display_type:protected] => HTML w/ PDF
[user_id:protected] => 0
[language_id:protected] => 1
[tagging_id:protected] => Garber
[priority_id:protected] => 1
[title:protected] => Focus Four Toolbox Talks, Module 2 – Struck-by, Talk #5 – Rigging and Securing Loads
[total_pages:protected] => 1
[billed_pages:protected] => 1
[publication_number:protected] =>
[part_of:protected] =>
[keywords:protected] => rigging, lift loads, loading areas, chains
[comments:protected] =>
[summary:protected] => A toolbox talk on preventing struck-by incidents caused by not securing loads properly. Includes questions to ask, an incident to discuss with images, and a place to record questions the trainer would like to ask about the incident. Part of a collection. Click on the 'collection' button to access the other items.
[transition_comments:protected] =>
[external_link:protected] =>
[consol_link:protected] => http://www.cpwrconstructionsolutions.org/heavy_equipment/hazard/1591/move-equipment-to-from-and-between-sites-work-zone-struck-by-injuries-and-fatalities.html
[more_like_this:protected] => d000144,d000360,d000873
[permission_given_by:protected] =>
[published:protected] => T
[billable:protected] => F
[img_name:protected] =>
[img_ext:protected] =>
[img_width:protected] =>
[img_height:protected] =>
[img_credit:protected] =>
[img_practice:protected] =>
[vid_source_id:protected] =>
[vid_running_time:protected] =>
[vid_intended_audience:protected] =>
[vid_acquisition_info:protected] =>
[vid_cost:protected] =>
[vid_producer:protected] =>
[vid_filename:protected] =>
[vid_filename_downloadable:protected] =>
[date_summary:protected] =>
[date_permission_requested:protected] =>
[date_permission_received:protected] =>
[date_review_needed:protected] =>
[date_received:protected] => 02/15/12
[date_completed:protected] => 03/28/12
[date_billed:protected] =>
[date_modified:protected] => 05/12/14
[collBokExports:protected] =>
[lastBokExportCriteria:BaseElcoshItem:private] =>
[alreadyInSave:protected] =>
[alreadyInValidation:protected] =>
[validationFailures:protected] => Array
(
)
[_new:BaseObject:private] =>
[_deleted:BaseObject:private] =>
[modifiedColumns:protected] => Array
(
)
)
[1645] => DocumentRecord Object
(
[records:protected] => Array
(
)
[recordId:protected] =>
[searchWordClass:protected] =>
[searchWordPeerClass:protected] =>
[bok_record:protected] =>
[authors:protected] =>
[organizations:protected] =>
[collections:protected] =>
[categories:protected] =>
[categories_initialized:protected] =>
[mapped_items:protected] =>
[content:protected] =>
[files:protected] =>
[language:protected] =>
[old_record:protected] =>
[id:protected] => 1645
[old_id:protected] => 1274
[elcosh_id:protected] => d001149
[type:protected] => document
[display_type:protected] => HTML w/ PDF
[user_id:protected] => 0
[language_id:protected] => 1
[tagging_id:protected] => Garber
[priority_id:protected] => 1
[title:protected] => Focus Four Toolbox Talks, Module 3 – Caught-in/between, Talk #2 – Trenches & Heavy Equipment
[total_pages:protected] => 1
[billed_pages:protected] => 1
[publication_number:protected] =>
[part_of:protected] =>
[keywords:protected] => back-up alarms, spotter, soil cave-in, spoil pikes, ROPs, trenching, rain
[comments:protected] =>
[summary:protected] => A toolbox talk on preventing incidents involving trenches such as trench collapse. Includes questions to ask, an incident to discuss with images, and a place to record questions the trainer would like to ask about the incident. Part of a collection. Click on the 'collection' button to access the other items.
[transition_comments:protected] =>
[external_link:protected] =>
[consol_link:protected] =>
[more_like_this:protected] => d000019,d000035,d000168
[permission_given_by:protected] =>
[published:protected] => T
[billable:protected] => F
[img_name:protected] =>
[img_ext:protected] =>
[img_width:protected] =>
[img_height:protected] =>
[img_credit:protected] =>
[img_practice:protected] =>
[vid_source_id:protected] =>
[vid_running_time:protected] =>
[vid_intended_audience:protected] =>
[vid_acquisition_info:protected] =>
[vid_cost:protected] =>
[vid_producer:protected] =>
[vid_filename:protected] =>
[vid_filename_downloadable:protected] =>
[date_summary:protected] =>
[date_permission_requested:protected] =>
[date_permission_received:protected] =>
[date_review_needed:protected] =>
[date_received:protected] => 02/15/12
[date_completed:protected] => 04/02/12
[date_billed:protected] =>
[date_modified:protected] => 05/23/23
[collBokExports:protected] =>
[lastBokExportCriteria:BaseElcoshItem:private] =>
[alreadyInSave:protected] =>
[alreadyInValidation:protected] =>
[validationFailures:protected] => Array
(
)
[_new:BaseObject:private] =>
[_deleted:BaseObject:private] =>
[modifiedColumns:protected] => Array
(
)
)
[1654] => DocumentRecord Object
(
[records:protected] => Array
(
)
[recordId:protected] =>
[searchWordClass:protected] =>
[searchWordPeerClass:protected] =>
[bok_record:protected] =>
[authors:protected] =>
[organizations:protected] =>
[collections:protected] =>
[categories:protected] =>
[categories_initialized:protected] =>
[mapped_items:protected] =>
[content:protected] =>
[files:protected] =>
[language:protected] =>
[old_record:protected] =>
[id:protected] => 1654
[old_id:protected] => 1284
[elcosh_id:protected] => d001159
[type:protected] => document
[display_type:protected] => HTML w/ PDF
[user_id:protected] => 0
[language_id:protected] => 1
[tagging_id:protected] => Garber
[priority_id:protected] => 1
[title:protected] => Focus Four Toolbox Talks, Module 4 – Electrocutions, Talk #6 – Hazards on Disaster Sites
[total_pages:protected] => 1
[billed_pages:protected] => 1
[publication_number:protected] =>
[part_of:protected] =>
[keywords:protected] => powerlines, underground, utilities, generators, wet conditions, GFCIs, energized lines, disasters, emergency response
[comments:protected] =>
[summary:protected] => A toolbox talk on how to avoid electrocution on a disaster site. Includes questions to ask, an incident to discuss with images, and a place to record questions the trainer would like to ask about the incident. Part of a collection. Click on the 'collection' button to access the other items.
[transition_comments:protected] =>
[external_link:protected] =>
[consol_link:protected] => http://www.cpwrconstructionsolutions.org/electrical/hazard/1138/install-and-repair-high-voltage-lines-transformers-switches-electrical-shocks-burns-and-or-electrocution.html
[more_like_this:protected] => d000135,d000361,d000437
[permission_given_by:protected] =>
[published:protected] => T
[billable:protected] => F
[img_name:protected] =>
[img_ext:protected] =>
[img_width:protected] =>
[img_height:protected] =>
[img_credit:protected] =>
[img_practice:protected] =>
[vid_source_id:protected] =>
[vid_running_time:protected] =>
[vid_intended_audience:protected] =>
[vid_acquisition_info:protected] =>
[vid_cost:protected] =>
[vid_producer:protected] =>
[vid_filename:protected] =>
[vid_filename_downloadable:protected] =>
[date_summary:protected] =>
[date_permission_requested:protected] =>
[date_permission_received:protected] =>
[date_review_needed:protected] =>
[date_received:protected] => 02/15/12
[date_completed:protected] => 04/02/12
[date_billed:protected] =>
[date_modified:protected] => 05/23/23
[collBokExports:protected] =>
[lastBokExportCriteria:BaseElcoshItem:private] =>
[alreadyInSave:protected] =>
[alreadyInValidation:protected] =>
[validationFailures:protected] => Array
(
)
[_new:BaseObject:private] =>
[_deleted:BaseObject:private] =>
[modifiedColumns:protected] => Array
(
)
)
)
[content:protected] =>
[files:protected] => Array
(
[9400] => File Object
(
[id:protected] => 9400
[filename:protected] => 1.jpg
[downloadable:protected] => F
[timestamp:protected] => 2014-05-08 15:05:37
[alreadyInSave:protected] =>
[alreadyInValidation:protected] =>
[validationFailures:protected] => Array
(
)
[_new:BaseObject:private] =>
[_deleted:BaseObject:private] =>
[modifiedColumns:protected] => Array
(
)
)
[9401] => File Object
(
[id:protected] => 9401
[filename:protected] => d001298.pdf
[downloadable:protected] => T
[timestamp:protected] => 2014-05-08 15:05:37
[alreadyInSave:protected] =>
[alreadyInValidation:protected] =>
[validationFailures:protected] => Array
(
)
[_new:BaseObject:private] =>
[_deleted:BaseObject:private] =>
[modifiedColumns:protected] => Array
(
)
)
)
[language:protected] => Language Object
(
[id:protected] => 1
[code:protected] => en
[name:protected] => English
[alreadyInSave:protected] =>
[alreadyInValidation:protected] =>
[validationFailures:protected] => Array
(
)
[_new:BaseObject:private] =>
[_deleted:BaseObject:private] =>
[modifiedColumns:protected] => Array
(
)
)
[old_record:protected] =>
[id:protected] => 3827
[old_id:protected] =>
[elcosh_id:protected] => d001298
[type:protected] => document
[display_type:protected] => HTML w/ PDF
[user_id:protected] => 23
[language_id:protected] => 1
[tagging_id:protected] => Bruce Lippy
[priority_id:protected] => 1
[title:protected] => Getting the most out of the IUOE Toolbox Talks
[total_pages:protected] => 2
[billed_pages:protected] => 2
[publication_number:protected] =>
[part_of:protected] =>
[keywords:protected] => toolbox talks, tailgate talks
[comments:protected] =>
[summary:protected] => Toolbox talks have been the main tool for communicating safety information on construction jobs for decades.
Unfortunately, there has been little research on what makes for effective toolbox talks. The IUOE National
Training Fund worked with OSHA and NIOSH to make sure their series of 24 Focus Four toolbox talks were based on the best recommendations for effective design. These toolbox talks accompany an entire package of training materials, but can be used alone. This guide points out the key features of these toolbox talks and how best to deliver them.
[transition_comments:protected] =>
[external_link:protected] =>
[consol_link:protected] =>
[more_like_this:protected] => d001137,d001146,d001149,d001159
[permission_given_by:protected] => IUOE National Hazmat Program
[published:protected] => T
[billable:protected] => F
[img_name:protected] =>
[img_ext:protected] => png
[img_width:protected] =>
[img_height:protected] =>
[img_credit:protected] =>
[img_practice:protected] =>
[vid_source_id:protected] =>
[vid_running_time:protected] =>
[vid_intended_audience:protected] =>
[vid_acquisition_info:protected] =>
[vid_cost:protected] =>
[vid_producer:protected] =>
[vid_filename:protected] =>
[vid_filename_downloadable:protected] =>
[date_summary:protected] => 2007
[date_permission_requested:protected] =>
[date_permission_received:protected] =>
[date_review_needed:protected] =>
[date_received:protected] => 05/08/14
[date_completed:protected] => 05/08/14
[date_billed:protected] =>
[date_modified:protected] => 05/08/14
[collBokExports:protected] =>
[lastBokExportCriteria:BaseElcoshItem:private] =>
[alreadyInSave:protected] =>
[alreadyInValidation:protected] =>
[validationFailures:protected] => Array
(
)
[_new:BaseObject:private] =>
[_deleted:BaseObject:private] =>
[modifiedColumns:protected] => Array
(
)
)
[show_text] =>
[document_content] => ElcoshItemDocumentContent Object
(
[id:protected] => 2896
[item_id:protected] => 3827
[type:protected] => main
[title:protected] =>
[content:protected] =>
Why were these talks developed?
Toolbox talks have been the main tool for communicating safety information on construction jobs for decades. Unfortunately, there has been almost no research on what makes for effective toolbox talks. The IUOE National Training Fund has worked with OSHA, the National Institute for Occupational Safety and Health and the Lippy Group, LLC to make sure these Focus Four toolbox talks are based on the latest fi ndings on the most effective design and tailored to the hazards operating engineers face daily. These toolbox talks accompany an entire package of training materials, but can be used alone. The way these are delivered is as important as how well they are designed.
What did NIOSH find out?
- Just handing out factsheets and toolbox talks to workers doesn’t work. Providing copies after toolbox talks doesn’t make much of an impact either.
- Using case studies (real life stories of accidents that ended in fatality or injury) in toolbox talks is effective.
- When toolbox talks containing case studies were accompanied by discussion questions to encourage group participation, they were more effective. Consequently, getting the workers to participate in the discussion about the case study is important. It’s not enough to tell the story, it is better to have the workers engage in problem solving that analyzes why the accident occurred and how it could have been prevented. Active learning is always better than passive.
How should you deliver these toolbox talks?
- Choose a topic that is related to work going on at the site.
- Hold the meeting on the job, preferably where everyone can sit and relax.
- Hold the meeting at the beginning of a shift or after a break. Folks are too tired at the end of a shift to carefully listen and they want to get home.
- Read the toolbox talk sheet on the topic prior to conducting the talk.
- Start at the top of the form and work right through to the end, which should take around 10 to 15 minutes. Guidance is provided in blue print to help you with each section.
- Use the questions provided to generate discussions. Always allow time for the crew to respond to your questions before you provide an answer. Some suggested responses are written in italics.
- Review the case study and emphasize that this was a real incident. Ask the crew for a case study before you review the one provided, however.
- Always end with a discussion of the particular worksite where you are conducting the talk. Tie the talk as closely to hazards on the site as possible and encourage the crew to constantly look for and immediately correct hazards. They should also know how to report any problems that can’t be immediately corrected.
- Provide copies to each person, if you like, but NIOSH has not found that to be particularly effective.
- Encourage workers to do similar talks on their sites and provide them with the IUOE phone number for ordering in bulk.
- Have everyone sign the back of the form to indicate they attended this session and point out it is a pledge to look out for the health and safety of everyone on the site.
What are the key features of these toolbox talks?

[content_transformed:protected] =>
Why were these talks developed?
Toolbox talks have been the main tool for communicating safety information on construction jobs for decades. Unfortunately, there has been almost no research on what makes for effective toolbox talks. The IUOE National Training Fund has worked with OSHA, the National Institute for Occupational Safety and Health and the Lippy Group, LLC to make sure these Focus Four toolbox talks are based on the latest fi ndings on the most effective design and tailored to the hazards operating engineers face daily. These toolbox talks accompany an entire package of training materials, but can be used alone. The way these are delivered is as important as how well they are designed.
What did NIOSH find out?
- Just handing out factsheets and toolbox talks to workers doesn’t work. Providing copies after toolbox talks doesn’t make much of an impact either.
- Using case studies (real life stories of accidents that ended in fatality or injury) in toolbox talks is effective.
- When toolbox talks containing case studies were accompanied by discussion questions to encourage group participation, they were more effective. Consequently, getting the workers to participate in the discussion about the case study is important. It’s not enough to tell the story, it is better to have the workers engage in problem solving that analyzes why the accident occurred and how it could have been prevented. Active learning is always better than passive.
How should you deliver these toolbox talks?
- Choose a topic that is related to work going on at the site.
- Hold the meeting on the job, preferably where everyone can sit and relax.
- Hold the meeting at the beginning of a shift or after a break. Folks are too tired at the end of a shift to carefully listen and they want to get home.
- Read the toolbox talk sheet on the topic prior to conducting the talk.
- Start at the top of the form and work right through to the end, which should take around 10 to 15 minutes. Guidance is provided in blue print to help you with each section.
- Use the questions provided to generate discussions. Always allow time for the crew to respond to your questions before you provide an answer. Some suggested responses are written in italics.
- Review the case study and emphasize that this was a real incident. Ask the crew for a case study before you review the one provided, however.
- Always end with a discussion of the particular worksite where you are conducting the talk. Tie the talk as closely to hazards on the site as possible and encourage the crew to constantly look for and immediately correct hazards. They should also know how to report any problems that can’t be immediately corrected.
- Provide copies to each person, if you like, but NIOSH has not found that to be particularly effective.
- Encourage workers to do similar talks on their sites and provide them with the IUOE phone number for ordering in bulk.
- Have everyone sign the back of the form to indicate they attended this session and point out it is a pledge to look out for the health and safety of everyone on the site.
What are the key features of these toolbox talks?
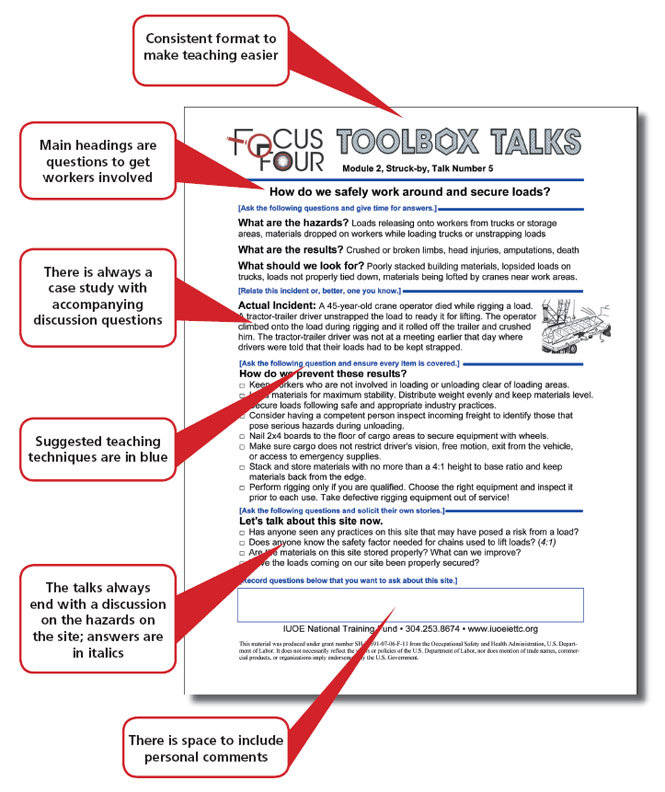
[disclaimer:protected] =>
[disclaimer_transformed:protected] =>
[alreadyInSave:protected] =>
[alreadyInValidation:protected] =>
[validationFailures:protected] => Array
(
)
[_new:BaseObject:private] =>
[_deleted:BaseObject:private] =>
[modifiedColumns:protected] => Array
(
)
)
[template] => record
)
[_globalContext:PHPTAL_Context:private] => stdClass Object
(
)
[_echoDeclarations:PHPTAL_Context:private] =>
[referer] => http://www.elcosh.org/document/3827/d001298/Getting%2Bthe%2Bmost%2Bout%2Bof%2Bthe%2BIUOE%2BToolbox%2BTalks.html
[curr_module] => Record
[styles] => Array
(
)
[javascript] => Array
(
[0] => jquery.min.js
)
[metas] => Array
(
[language] => en
[robots] => index, follow
)
[user] =>
[curr_url] => https://www.elcosh.org/index.php?module=Record&id=3827&type=document
[base_url] => https://www.elcosh.org/index.php?module=Record
[title] => eLCOSH : Getting the most out of the IUOE Toolbox Talks
[language] => en
[search_query] =>
[module] => Record
[new_records] => Array
(
[0] => Search_Result Object
(
[title] => Toolbox Talk: Fixed Ladder
[image] => /record/images/notavailable-p.png
[blurb] => The CPWR Toolbox Talk on Fixed Ladders addresses the potential risks associated with using fixed ladders. The resource includes a brief case example,...
[category] => Array
(
[0] => 15
[1] => 47
[2] => 49
[3] => 51
[4] => 53
[5] => 55
[6] => 60
[7] => 64
[8] => 73
[9] => 76
[10] => 78
[11] => 80
[12] => 86
[13] => 87
[14] => 90
[15] => 92
[16] => 93
[17] => 94
[18] => 100
)
[labels] => Array
(
[0] => Falls
[1] => Work Environment
[2] => Hazards
[3] => Bricklayer
[4] => Trades
[5] => Carpenter
[7] => Cement Mason
[9] => Concrete Polisher
[11] => Electrical Worker
[13] => HVAC
[15] => Laborer
[17] => PCC/Restoration
[19] => Plumber/Pipefitter
[21] => Roofer/Waterproofer
[23] => Sheetmetal Worker
[25] => Welder
[27] => Commercial & Institutional
[28] => Jobsites
[29] => Industrial
[31] => LEED/Green Construction
[33] => Renovations
[35] => Residential
[37] => Toolbox Talks
[38] => Documents
[39] => Media & Documents
)
[type] => Toolbox Talks
[sub_category] =>
[url] => /document/4430/d001660/Toolbox%2BTalk%253A%2BFixed%2BLadder.html
[item:protected] => DocumentRecord Object
(
[records:protected] => Array
(
)
[recordId:protected] =>
[searchWordClass:protected] =>
[searchWordPeerClass:protected] =>
[bok_record:protected] =>
[authors:protected] =>
[organizations:protected] =>
[collections:protected] =>
[categories:protected] => Array
(
[15] => Category Object
(
[languages:protected] =>
[bok_resources:protected] =>
[bok_topics:protected] =>
[bok_keywords:protected] =>
[id:protected] => 15
[type:protected] => category
[parent:protected] => 7
[label:protected] => Falls
[alreadyInSave:protected] =>
[alreadyInValidation:protected] =>
[validationFailures:protected] => Array
(
)
[_new:BaseObject:private] =>
[_deleted:BaseObject:private] =>
[modifiedColumns:protected] => Array
(
)
)
[47] => Category Object
(
[languages:protected] =>
[bok_resources:protected] =>
[bok_topics:protected] =>
[bok_keywords:protected] =>
[id:protected] => 47
[type:protected] => category
[parent:protected] => 2
[label:protected] => Bricklayer
[alreadyInSave:protected] =>
[alreadyInValidation:protected] =>
[validationFailures:protected] => Array
(
)
[_new:BaseObject:private] =>
[_deleted:BaseObject:private] =>
[modifiedColumns:protected] => Array
(
)
)
[49] => Category Object
(
[languages:protected] =>
[bok_resources:protected] =>
[bok_topics:protected] =>
[bok_keywords:protected] =>
[id:protected] => 49
[type:protected] => category
[parent:protected] => 2
[label:protected] => Carpenter
[alreadyInSave:protected] =>
[alreadyInValidation:protected] =>
[validationFailures:protected] => Array
(
)
[_new:BaseObject:private] =>
[_deleted:BaseObject:private] =>
[modifiedColumns:protected] => Array
(
)
)
[51] => Category Object
(
[languages:protected] =>
[bok_resources:protected] =>
[bok_topics:protected] =>
[bok_keywords:protected] =>
[id:protected] => 51
[type:protected] => category
[parent:protected] => 2
[label:protected] => Cement Mason
[alreadyInSave:protected] =>
[alreadyInValidation:protected] =>
[validationFailures:protected] => Array
(
)
[_new:BaseObject:private] =>
[_deleted:BaseObject:private] =>
[modifiedColumns:protected] => Array
(
)
)
[53] => Category Object
(
[languages:protected] =>
[bok_resources:protected] =>
[bok_topics:protected] =>
[bok_keywords:protected] =>
[id:protected] => 53
[type:protected] => category
[parent:protected] => 2
[label:protected] => Concrete Polisher
[alreadyInSave:protected] =>
[alreadyInValidation:protected] =>
[validationFailures:protected] => Array
(
)
[_new:BaseObject:private] =>
[_deleted:BaseObject:private] =>
[modifiedColumns:protected] => Array
(
)
)
[55] => Category Object
(
[languages:protected] =>
[bok_resources:protected] =>
[bok_topics:protected] =>
[bok_keywords:protected] =>
[id:protected] => 55
[type:protected] => category
[parent:protected] => 2
[label:protected] => Electrical Worker
[alreadyInSave:protected] =>
[alreadyInValidation:protected] =>
[validationFailures:protected] => Array
(
)
[_new:BaseObject:private] =>
[_deleted:BaseObject:private] =>
[modifiedColumns:protected] => Array
(
)
)
[60] => Category Object
(
[languages:protected] =>
[bok_resources:protected] =>
[bok_topics:protected] =>
[bok_keywords:protected] =>
[id:protected] => 60
[type:protected] => category
[parent:protected] => 2
[label:protected] => HVAC
[alreadyInSave:protected] =>
[alreadyInValidation:protected] =>
[validationFailures:protected] => Array
(
)
[_new:BaseObject:private] =>
[_deleted:BaseObject:private] =>
[modifiedColumns:protected] => Array
(
)
)
[64] => Category Object
(
[languages:protected] =>
[bok_resources:protected] =>
[bok_topics:protected] =>
[bok_keywords:protected] =>
[id:protected] => 64
[type:protected] => category
[parent:protected] => 2
[label:protected] => Laborer
[alreadyInSave:protected] =>
[alreadyInValidation:protected] =>
[validationFailures:protected] => Array
(
)
[_new:BaseObject:private] =>
[_deleted:BaseObject:private] =>
[modifiedColumns:protected] => Array
(
)
)
[73] => Category Object
(
[languages:protected] =>
[bok_resources:protected] =>
[bok_topics:protected] =>
[bok_keywords:protected] =>
[id:protected] => 73
[type:protected] => category
[parent:protected] => 2
[label:protected] => PCC/Restoration
[alreadyInSave:protected] =>
[alreadyInValidation:protected] =>
[validationFailures:protected] => Array
(
)
[_new:BaseObject:private] =>
[_deleted:BaseObject:private] =>
[modifiedColumns:protected] => Array
(
)
)
[76] => Category Object
(
[languages:protected] =>
[bok_resources:protected] =>
[bok_topics:protected] =>
[bok_keywords:protected] =>
[id:protected] => 76
[type:protected] => category
[parent:protected] => 2
[label:protected] => Plumber/Pipefitter
[alreadyInSave:protected] =>
[alreadyInValidation:protected] =>
[validationFailures:protected] => Array
(
)
[_new:BaseObject:private] =>
[_deleted:BaseObject:private] =>
[modifiedColumns:protected] => Array
(
)
)
[78] => Category Object
(
[languages:protected] =>
[bok_resources:protected] =>
[bok_topics:protected] =>
[bok_keywords:protected] =>
[id:protected] => 78
[type:protected] => category
[parent:protected] => 2
[label:protected] => Roofer/Waterproofer
[alreadyInSave:protected] =>
[alreadyInValidation:protected] =>
[validationFailures:protected] => Array
(
)
[_new:BaseObject:private] =>
[_deleted:BaseObject:private] =>
[modifiedColumns:protected] => Array
(
)
)
[80] => Category Object
(
[languages:protected] =>
[bok_resources:protected] =>
[bok_topics:protected] =>
[bok_keywords:protected] =>
[id:protected] => 80
[type:protected] => category
[parent:protected] => 2
[label:protected] => Sheetmetal Worker
[alreadyInSave:protected] =>
[alreadyInValidation:protected] =>
[validationFailures:protected] => Array
(
)
[_new:BaseObject:private] =>
[_deleted:BaseObject:private] =>
[modifiedColumns:protected] => Array
(
)
)
[86] => Category Object
(
[languages:protected] =>
[bok_resources:protected] =>
[bok_topics:protected] =>
[bok_keywords:protected] =>
[id:protected] => 86
[type:protected] => category
[parent:protected] => 2
[label:protected] => Welder
[alreadyInSave:protected] =>
[alreadyInValidation:protected] =>
[validationFailures:protected] => Array
(
)
[_new:BaseObject:private] =>
[_deleted:BaseObject:private] =>
[modifiedColumns:protected] => Array
(
)
)
[87] => Category Object
(
[languages:protected] =>
[bok_resources:protected] =>
[bok_topics:protected] =>
[bok_keywords:protected] =>
[id:protected] => 87
[type:protected] => category
[parent:protected] => 3
[label:protected] => Commercial & Institutional
[alreadyInSave:protected] =>
[alreadyInValidation:protected] =>
[validationFailures:protected] => Array
(
)
[_new:BaseObject:private] =>
[_deleted:BaseObject:private] =>
[modifiedColumns:protected] => Array
(
)
)
[90] => Category Object
(
[languages:protected] =>
[bok_resources:protected] =>
[bok_topics:protected] =>
[bok_keywords:protected] =>
[id:protected] => 90
[type:protected] => category
[parent:protected] => 3
[label:protected] => Industrial
[alreadyInSave:protected] =>
[alreadyInValidation:protected] =>
[validationFailures:protected] => Array
(
)
[_new:BaseObject:private] =>
[_deleted:BaseObject:private] =>
[modifiedColumns:protected] => Array
(
)
)
[92] => Category Object
(
[languages:protected] =>
[bok_resources:protected] =>
[bok_topics:protected] =>
[bok_keywords:protected] =>
[id:protected] => 92
[type:protected] => category
[parent:protected] => 3
[label:protected] => LEED/Green Construction
[alreadyInSave:protected] =>
[alreadyInValidation:protected] =>
[validationFailures:protected] => Array
(
)
[_new:BaseObject:private] =>
[_deleted:BaseObject:private] =>
[modifiedColumns:protected] => Array
(
)
)
[93] => Category Object
(
[languages:protected] =>
[bok_resources:protected] =>
[bok_topics:protected] =>
[bok_keywords:protected] =>
[id:protected] => 93
[type:protected] => category
[parent:protected] => 3
[label:protected] => Renovations
[alreadyInSave:protected] =>
[alreadyInValidation:protected] =>
[validationFailures:protected] => Array
(
)
[_new:BaseObject:private] =>
[_deleted:BaseObject:private] =>
[modifiedColumns:protected] => Array
(
)
)
[94] => Category Object
(
[languages:protected] =>
[bok_resources:protected] =>
[bok_topics:protected] =>
[bok_keywords:protected] =>
[id:protected] => 94
[type:protected] => category
[parent:protected] => 3
[label:protected] => Residential
[alreadyInSave:protected] =>
[alreadyInValidation:protected] =>
[validationFailures:protected] => Array
(
)
[_new:BaseObject:private] =>
[_deleted:BaseObject:private] =>
[modifiedColumns:protected] => Array
(
)
)
[100] => Category Object
(
[languages:protected] =>
[bok_resources:protected] =>
[bok_topics:protected] =>
[bok_keywords:protected] =>
[id:protected] => 100
[type:protected] => category
[parent:protected] => 6
[label:protected] => Toolbox Talks
[alreadyInSave:protected] =>
[alreadyInValidation:protected] =>
[validationFailures:protected] => Array
(
)
[_new:BaseObject:private] =>
[_deleted:BaseObject:private] =>
[modifiedColumns:protected] => Array
(
)
)
)
[categories_initialized:protected] => 1
[mapped_items:protected] =>
[content:protected] =>
[files:protected] =>
[language:protected] => Language Object
(
[id:protected] => 1
[code:protected] => en
[name:protected] => English
[alreadyInSave:protected] =>
[alreadyInValidation:protected] =>
[validationFailures:protected] => Array
(
)
[_new:BaseObject:private] =>
[_deleted:BaseObject:private] =>
[modifiedColumns:protected] => Array
(
)
)
[old_record:protected] =>
[id:protected] => 4430
[old_id:protected] =>
[elcosh_id:protected] => d001660
[type:protected] => document
[display_type:protected] => HTML only (and links)
[user_id:protected] => 0
[language_id:protected] => 1
[tagging_id:protected] => Mike Aguilar
[priority_id:protected] => 1
[title:protected] => Toolbox Talk: Fixed Ladder
[total_pages:protected] => 0
[billed_pages:protected] => 0
[publication_number:protected] =>
[part_of:protected] =>
[keywords:protected] => Fixed Ladders, Fall Prevention, Falls
[comments:protected] =>
[summary:protected] => The CPWR Toolbox Talk on Fixed Ladders addresses the potential risks associated with using fixed ladders. The resource includes a brief case example, steps to prevent a related injury and questions for discussion. It includes an image that illustrates the hazard, which can be posted in a central location as a reminder of steps to work safely.
Available in
English
and
Spanish.
[transition_comments:protected] =>
[external_link:protected] =>
[consol_link:protected] =>
[more_like_this:protected] => d001257,d001254,d001255,d001256,d001258,d001262,d001279
[permission_given_by:protected] =>
[published:protected] => T
[billable:protected] => F
[img_name:protected] =>
[img_ext:protected] =>
[img_width:protected] =>
[img_height:protected] =>
[img_credit:protected] =>
[img_practice:protected] =>
[vid_source_id:protected] =>
[vid_running_time:protected] =>
[vid_intended_audience:protected] =>
[vid_acquisition_info:protected] =>
[vid_cost:protected] =>
[vid_producer:protected] =>
[vid_filename:protected] =>
[vid_filename_downloadable:protected] =>
[date_summary:protected] =>
[date_permission_requested:protected] =>
[date_permission_received:protected] =>
[date_review_needed:protected] =>
[date_received:protected] => 06/10/22
[date_completed:protected] => 06/10/22
[date_billed:protected] =>
[date_modified:protected] => 05/22/23
[collBokExports:protected] =>
[lastBokExportCriteria:BaseElcoshItem:private] =>
[alreadyInSave:protected] =>
[alreadyInValidation:protected] =>
[validationFailures:protected] => Array
(
)
[_new:BaseObject:private] =>
[_deleted:BaseObject:private] =>
[modifiedColumns:protected] => Array
(
)
)
)
[1] => Search_Result Object
(
[title] => Toolbox Talk: Challenges Preventing Falling Objects
[image] => /record/images/notavailable-p.png
[blurb] => The CPWR Toolbox Talk on Challenges Preventing Falling Objects addresses the hazards of being struck by falling objects on the job site. The resource...
[category] => Array
(
[0] => 12
[1] => 47
[2] => 49
[3] => 51
[4] => 55
[5] => 64
[6] => 68
[7] => 71
[8] => 75
[9] => 78
[10] => 79
[11] => 82
[12] => 62
[13] => 86
[14] => 87
[15] => 88
[16] => 89
[17] => 91
[18] => 90
[19] => 92
[20] => 93
[21] => 94
[22] => 95
[23] => 100
)
[labels] => Array
(
[0] => Crushed/Struck By
[1] => Work Environment
[2] => Hazards
[3] => Bricklayer
[4] => Trades
[5] => Carpenter
[7] => Cement Mason
[9] => Electrical Worker
[11] => Laborer
[13] => Maintenance Worker
[15] => Painter
[17] => Plasterer
[19] => Roofer/Waterproofer
[21] => Scaffold Erector
[23] => Stonemason
[25] => Structural Ironworker
[27] => Welder
[29] => Commercial & Institutional
[30] => Jobsites
[31] => Demolition
[33] => Disasters
[35] => Heavy & Highway
[37] => Industrial
[39] => LEED/Green Construction
[41] => Renovations
[43] => Residential
[45] => Underground
[47] => Toolbox Talks
[48] => Documents
[49] => Media & Documents
)
[type] => Toolbox Talks
[sub_category] =>
[url] => /document/4431/d001661/Toolbox%2BTalk%253A%2BChallenges%2BPreventing%2BFalling%2BObjects.html
[item:protected] => DocumentRecord Object
(
[records:protected] => Array
(
)
[recordId:protected] =>
[searchWordClass:protected] =>
[searchWordPeerClass:protected] =>
[bok_record:protected] =>
[authors:protected] =>
[organizations:protected] =>
[collections:protected] =>
[categories:protected] => Array
(
[12] => Category Object
(
[languages:protected] =>
[bok_resources:protected] =>
[bok_topics:protected] =>
[bok_keywords:protected] =>
[id:protected] => 12
[type:protected] => category
[parent:protected] => 7
[label:protected] => Crushed/Struck By
[alreadyInSave:protected] =>
[alreadyInValidation:protected] =>
[validationFailures:protected] => Array
(
)
[_new:BaseObject:private] =>
[_deleted:BaseObject:private] =>
[modifiedColumns:protected] => Array
(
)
)
[47] => Category Object
(
[languages:protected] =>
[bok_resources:protected] =>
[bok_topics:protected] =>
[bok_keywords:protected] =>
[id:protected] => 47
[type:protected] => category
[parent:protected] => 2
[label:protected] => Bricklayer
[alreadyInSave:protected] =>
[alreadyInValidation:protected] =>
[validationFailures:protected] => Array
(
)
[_new:BaseObject:private] =>
[_deleted:BaseObject:private] =>
[modifiedColumns:protected] => Array
(
)
)
[49] => Category Object
(
[languages:protected] =>
[bok_resources:protected] =>
[bok_topics:protected] =>
[bok_keywords:protected] =>
[id:protected] => 49
[type:protected] => category
[parent:protected] => 2
[label:protected] => Carpenter
[alreadyInSave:protected] =>
[alreadyInValidation:protected] =>
[validationFailures:protected] => Array
(
)
[_new:BaseObject:private] =>
[_deleted:BaseObject:private] =>
[modifiedColumns:protected] => Array
(
)
)
[51] => Category Object
(
[languages:protected] =>
[bok_resources:protected] =>
[bok_topics:protected] =>
[bok_keywords:protected] =>
[id:protected] => 51
[type:protected] => category
[parent:protected] => 2
[label:protected] => Cement Mason
[alreadyInSave:protected] =>
[alreadyInValidation:protected] =>
[validationFailures:protected] => Array
(
)
[_new:BaseObject:private] =>
[_deleted:BaseObject:private] =>
[modifiedColumns:protected] => Array
(
)
)
[55] => Category Object
(
[languages:protected] =>
[bok_resources:protected] =>
[bok_topics:protected] =>
[bok_keywords:protected] =>
[id:protected] => 55
[type:protected] => category
[parent:protected] => 2
[label:protected] => Electrical Worker
[alreadyInSave:protected] =>
[alreadyInValidation:protected] =>
[validationFailures:protected] => Array
(
)
[_new:BaseObject:private] =>
[_deleted:BaseObject:private] =>
[modifiedColumns:protected] => Array
(
)
)
[64] => Category Object
(
[languages:protected] =>
[bok_resources:protected] =>
[bok_topics:protected] =>
[bok_keywords:protected] =>
[id:protected] => 64
[type:protected] => category
[parent:protected] => 2
[label:protected] => Laborer
[alreadyInSave:protected] =>
[alreadyInValidation:protected] =>
[validationFailures:protected] => Array
(
)
[_new:BaseObject:private] =>
[_deleted:BaseObject:private] =>
[modifiedColumns:protected] => Array
(
)
)
[68] => Category Object
(
[languages:protected] =>
[bok_resources:protected] =>
[bok_topics:protected] =>
[bok_keywords:protected] =>
[id:protected] => 68
[type:protected] => category
[parent:protected] => 2
[label:protected] => Maintenance Worker
[alreadyInSave:protected] =>
[alreadyInValidation:protected] =>
[validationFailures:protected] => Array
(
)
[_new:BaseObject:private] =>
[_deleted:BaseObject:private] =>
[modifiedColumns:protected] => Array
(
)
)
[71] => Category Object
(
[languages:protected] =>
[bok_resources:protected] =>
[bok_topics:protected] =>
[bok_keywords:protected] =>
[id:protected] => 71
[type:protected] => category
[parent:protected] => 2
[label:protected] => Painter
[alreadyInSave:protected] =>
[alreadyInValidation:protected] =>
[validationFailures:protected] => Array
(
)
[_new:BaseObject:private] =>
[_deleted:BaseObject:private] =>
[modifiedColumns:protected] => Array
(
)
)
[75] => Category Object
(
[languages:protected] =>
[bok_resources:protected] =>
[bok_topics:protected] =>
[bok_keywords:protected] =>
[id:protected] => 75
[type:protected] => category
[parent:protected] => 2
[label:protected] => Plasterer
[alreadyInSave:protected] =>
[alreadyInValidation:protected] =>
[validationFailures:protected] => Array
(
)
[_new:BaseObject:private] =>
[_deleted:BaseObject:private] =>
[modifiedColumns:protected] => Array
(
)
)
[78] => Category Object
(
[languages:protected] =>
[bok_resources:protected] =>
[bok_topics:protected] =>
[bok_keywords:protected] =>
[id:protected] => 78
[type:protected] => category
[parent:protected] => 2
[label:protected] => Roofer/Waterproofer
[alreadyInSave:protected] =>
[alreadyInValidation:protected] =>
[validationFailures:protected] => Array
(
)
[_new:BaseObject:private] =>
[_deleted:BaseObject:private] =>
[modifiedColumns:protected] => Array
(
)
)
[79] => Category Object
(
[languages:protected] =>
[bok_resources:protected] =>
[bok_topics:protected] =>
[bok_keywords:protected] =>
[id:protected] => 79
[type:protected] => category
[parent:protected] => 2
[label:protected] => Scaffold Erector
[alreadyInSave:protected] =>
[alreadyInValidation:protected] =>
[validationFailures:protected] => Array
(
)
[_new:BaseObject:private] =>
[_deleted:BaseObject:private] =>
[modifiedColumns:protected] => Array
(
)
)
[82] => Category Object
(
[languages:protected] =>
[bok_resources:protected] =>
[bok_topics:protected] =>
[bok_keywords:protected] =>
[id:protected] => 82
[type:protected] => category
[parent:protected] => 2
[label:protected] => Stonemason
[alreadyInSave:protected] =>
[alreadyInValidation:protected] =>
[validationFailures:protected] => Array
(
)
[_new:BaseObject:private] =>
[_deleted:BaseObject:private] =>
[modifiedColumns:protected] => Array
(
)
)
[62] => Category Object
(
[languages:protected] =>
[bok_resources:protected] =>
[bok_topics:protected] =>
[bok_keywords:protected] =>
[id:protected] => 62
[type:protected] => category
[parent:protected] => 2
[label:protected] => Structural Ironworker
[alreadyInSave:protected] =>
[alreadyInValidation:protected] =>
[validationFailures:protected] => Array
(
)
[_new:BaseObject:private] =>
[_deleted:BaseObject:private] =>
[modifiedColumns:protected] => Array
(
)
)
[86] => Category Object
(
[languages:protected] =>
[bok_resources:protected] =>
[bok_topics:protected] =>
[bok_keywords:protected] =>
[id:protected] => 86
[type:protected] => category
[parent:protected] => 2
[label:protected] => Welder
[alreadyInSave:protected] =>
[alreadyInValidation:protected] =>
[validationFailures:protected] => Array
(
)
[_new:BaseObject:private] =>
[_deleted:BaseObject:private] =>
[modifiedColumns:protected] => Array
(
)
)
[87] => Category Object
(
[languages:protected] =>
[bok_resources:protected] =>
[bok_topics:protected] =>
[bok_keywords:protected] =>
[id:protected] => 87
[type:protected] => category
[parent:protected] => 3
[label:protected] => Commercial & Institutional
[alreadyInSave:protected] =>
[alreadyInValidation:protected] =>
[validationFailures:protected] => Array
(
)
[_new:BaseObject:private] =>
[_deleted:BaseObject:private] =>
[modifiedColumns:protected] => Array
(
)
)
[88] => Category Object
(
[languages:protected] =>
[bok_resources:protected] =>
[bok_topics:protected] =>
[bok_keywords:protected] =>
[id:protected] => 88
[type:protected] => category
[parent:protected] => 3
[label:protected] => Demolition
[alreadyInSave:protected] =>
[alreadyInValidation:protected] =>
[validationFailures:protected] => Array
(
)
[_new:BaseObject:private] =>
[_deleted:BaseObject:private] =>
[modifiedColumns:protected] => Array
(
)
)
[89] => Category Object
(
[languages:protected] =>
[bok_resources:protected] =>
[bok_topics:protected] =>
[bok_keywords:protected] =>
[id:protected] => 89
[type:protected] => category
[parent:protected] => 3
[label:protected] => Disasters
[alreadyInSave:protected] =>
[alreadyInValidation:protected] =>
[validationFailures:protected] => Array
(
)
[_new:BaseObject:private] =>
[_deleted:BaseObject:private] =>
[modifiedColumns:protected] => Array
(
)
)
[91] => Category Object
(
[languages:protected] =>
[bok_resources:protected] =>
[bok_topics:protected] =>
[bok_keywords:protected] =>
[id:protected] => 91
[type:protected] => category
[parent:protected] => 3
[label:protected] => Heavy & Highway
[alreadyInSave:protected] =>
[alreadyInValidation:protected] =>
[validationFailures:protected] => Array
(
)
[_new:BaseObject:private] =>
[_deleted:BaseObject:private] =>
[modifiedColumns:protected] => Array
(
)
)
[90] => Category Object
(
[languages:protected] =>
[bok_resources:protected] =>
[bok_topics:protected] =>
[bok_keywords:protected] =>
[id:protected] => 90
[type:protected] => category
[parent:protected] => 3
[label:protected] => Industrial
[alreadyInSave:protected] =>
[alreadyInValidation:protected] =>
[validationFailures:protected] => Array
(
)
[_new:BaseObject:private] =>
[_deleted:BaseObject:private] =>
[modifiedColumns:protected] => Array
(
)
)
[92] => Category Object
(
[languages:protected] =>
[bok_resources:protected] =>
[bok_topics:protected] =>
[bok_keywords:protected] =>
[id:protected] => 92
[type:protected] => category
[parent:protected] => 3
[label:protected] => LEED/Green Construction
[alreadyInSave:protected] =>
[alreadyInValidation:protected] =>
[validationFailures:protected] => Array
(
)
[_new:BaseObject:private] =>
[_deleted:BaseObject:private] =>
[modifiedColumns:protected] => Array
(
)
)
[93] => Category Object
(
[languages:protected] =>
[bok_resources:protected] =>
[bok_topics:protected] =>
[bok_keywords:protected] =>
[id:protected] => 93
[type:protected] => category
[parent:protected] => 3
[label:protected] => Renovations
[alreadyInSave:protected] =>
[alreadyInValidation:protected] =>
[validationFailures:protected] => Array
(
)
[_new:BaseObject:private] =>
[_deleted:BaseObject:private] =>
[modifiedColumns:protected] => Array
(
)
)
[94] => Category Object
(
[languages:protected] =>
[bok_resources:protected] =>
[bok_topics:protected] =>
[bok_keywords:protected] =>
[id:protected] => 94
[type:protected] => category
[parent:protected] => 3
[label:protected] => Residential
[alreadyInSave:protected] =>
[alreadyInValidation:protected] =>
[validationFailures:protected] => Array
(
)
[_new:BaseObject:private] =>
[_deleted:BaseObject:private] =>
[modifiedColumns:protected] => Array
(
)
)
[95] => Category Object
(
[languages:protected] =>
[bok_resources:protected] =>
[bok_topics:protected] =>
[bok_keywords:protected] =>
[id:protected] => 95
[type:protected] => category
[parent:protected] => 3
[label:protected] => Underground
[alreadyInSave:protected] =>
[alreadyInValidation:protected] =>
[validationFailures:protected] => Array
(
)
[_new:BaseObject:private] =>
[_deleted:BaseObject:private] =>
[modifiedColumns:protected] => Array
(
)
)
[100] => Category Object
(
[languages:protected] =>
[bok_resources:protected] =>
[bok_topics:protected] =>
[bok_keywords:protected] =>
[id:protected] => 100
[type:protected] => category
[parent:protected] => 6
[label:protected] => Toolbox Talks
[alreadyInSave:protected] =>
[alreadyInValidation:protected] =>
[validationFailures:protected] => Array
(
)
[_new:BaseObject:private] =>
[_deleted:BaseObject:private] =>
[modifiedColumns:protected] => Array
(
)
)
)
[categories_initialized:protected] => 1
[mapped_items:protected] =>
[content:protected] =>
[files:protected] =>
[language:protected] => Language Object
(
[id:protected] => 1
[code:protected] => en
[name:protected] => English
[alreadyInSave:protected] =>
[alreadyInValidation:protected] =>
[validationFailures:protected] => Array
(
)
[_new:BaseObject:private] =>
[_deleted:BaseObject:private] =>
[modifiedColumns:protected] => Array
(
)
)
[old_record:protected] =>
[id:protected] => 4431
[old_id:protected] =>
[elcosh_id:protected] => d001661
[type:protected] => document
[display_type:protected] => HTML only (and links)
[user_id:protected] => 0
[language_id:protected] => 1
[tagging_id:protected] => Mike Aguilar
[priority_id:protected] => 1
[title:protected] => Toolbox Talk: Challenges Preventing Falling Objects
[total_pages:protected] => 0
[billed_pages:protected] => 0
[publication_number:protected] =>
[part_of:protected] =>
[keywords:protected] => dropped objects, falling objects, struck by incidents, struck by fatalities
[comments:protected] =>
[summary:protected] => The CPWR Toolbox Talk on Challenges Preventing Falling Objects addresses the hazards of being struck by falling objects on the job site. The resource includes a brief example, steps to prevent a related injury, and questions for discussion. It includes a graphic that illustrates a group workers observing a scaffold free of debris during high winds, which can be posted in a central location as a reminder of steps to work safely.
Available in
English and
Spanish.
[transition_comments:protected] =>
[external_link:protected] =>
[consol_link:protected] =>
[more_like_this:protected] => d001234,d001238,d001244,d001251,d001253,d001260,d001268,d001278
[permission_given_by:protected] =>
[published:protected] => T
[billable:protected] => F
[img_name:protected] =>
[img_ext:protected] =>
[img_width:protected] =>
[img_height:protected] =>
[img_credit:protected] =>
[img_practice:protected] =>
[vid_source_id:protected] =>
[vid_running_time:protected] =>
[vid_intended_audience:protected] =>
[vid_acquisition_info:protected] =>
[vid_cost:protected] =>
[vid_producer:protected] =>
[vid_filename:protected] =>
[vid_filename_downloadable:protected] =>
[date_summary:protected] =>
[date_permission_requested:protected] =>
[date_permission_received:protected] =>
[date_review_needed:protected] =>
[date_received:protected] => 06/10/22
[date_completed:protected] => 06/10/22
[date_billed:protected] =>
[date_modified:protected] => 05/22/23
[collBokExports:protected] =>
[lastBokExportCriteria:BaseElcoshItem:private] =>
[alreadyInSave:protected] =>
[alreadyInValidation:protected] =>
[validationFailures:protected] => Array
(
)
[_new:BaseObject:private] =>
[_deleted:BaseObject:private] =>
[modifiedColumns:protected] => Array
(
)
)
)
[2] => Search_Result Object
(
[title] => Toolbox Talk: Tower Crane Safety
[image] => /record/images/notavailable-p.png
[blurb] => The CPWR Toolbox Talk on Tower Crane Safety addresses the potential hazards of Tower Cranes and the importance of following procedure before and durin...
[category] => Array
(
[0] => 11
[1] => 12
[2] => 18
[3] => 70
[4] => 87
[5] => 88
[6] => 91
[7] => 90
[8] => 92
[9] => 100
)
[labels] => Array
(
[0] => Cranes & Hoists
[1] => Work Environment
[2] => Hazards
[3] => Crushed/Struck By
[6] => Motor Vehicles/Heavy Equipment
[9] => Operating Engineer
[10] => Trades
[11] => Commercial & Institutional
[12] => Jobsites
[13] => Demolition
[15] => Heavy & Highway
[17] => Industrial
[19] => LEED/Green Construction
[21] => Toolbox Talks
[22] => Documents
[23] => Media & Documents
)
[type] => Toolbox Talks
[sub_category] =>
[url] => /document/4427/d001657/Toolbox%2BTalk%253A%2BTower%2BCrane%2BSafety.html
[item:protected] => DocumentRecord Object
(
[records:protected] => Array
(
)
[recordId:protected] =>
[searchWordClass:protected] =>
[searchWordPeerClass:protected] =>
[bok_record:protected] =>
[authors:protected] =>
[organizations:protected] =>
[collections:protected] =>
[categories:protected] => Array
(
[11] => Category Object
(
[languages:protected] =>
[bok_resources:protected] =>
[bok_topics:protected] =>
[bok_keywords:protected] =>
[id:protected] => 11
[type:protected] => category
[parent:protected] => 7
[label:protected] => Cranes & Hoists
[alreadyInSave:protected] =>
[alreadyInValidation:protected] =>
[validationFailures:protected] => Array
(
)
[_new:BaseObject:private] =>
[_deleted:BaseObject:private] =>
[modifiedColumns:protected] => Array
(
)
)
[12] => Category Object
(
[languages:protected] =>
[bok_resources:protected] =>
[bok_topics:protected] =>
[bok_keywords:protected] =>
[id:protected] => 12
[type:protected] => category
[parent:protected] => 7
[label:protected] => Crushed/Struck By
[alreadyInSave:protected] =>
[alreadyInValidation:protected] =>
[validationFailures:protected] => Array
(
)
[_new:BaseObject:private] =>
[_deleted:BaseObject:private] =>
[modifiedColumns:protected] => Array
(
)
)
[18] => Category Object
(
[languages:protected] =>
[bok_resources:protected] =>
[bok_topics:protected] =>
[bok_keywords:protected] =>
[id:protected] => 18
[type:protected] => category
[parent:protected] => 7
[label:protected] => Motor Vehicles/Heavy Equipment
[alreadyInSave:protected] =>
[alreadyInValidation:protected] =>
[validationFailures:protected] => Array
(
)
[_new:BaseObject:private] =>
[_deleted:BaseObject:private] =>
[modifiedColumns:protected] => Array
(
)
)
[70] => Category Object
(
[languages:protected] =>
[bok_resources:protected] =>
[bok_topics:protected] =>
[bok_keywords:protected] =>
[id:protected] => 70
[type:protected] => category
[parent:protected] => 2
[label:protected] => Operating Engineer
[alreadyInSave:protected] =>
[alreadyInValidation:protected] =>
[validationFailures:protected] => Array
(
)
[_new:BaseObject:private] =>
[_deleted:BaseObject:private] =>
[modifiedColumns:protected] => Array
(
)
)
[87] => Category Object
(
[languages:protected] =>
[bok_resources:protected] =>
[bok_topics:protected] =>
[bok_keywords:protected] =>
[id:protected] => 87
[type:protected] => category
[parent:protected] => 3
[label:protected] => Commercial & Institutional
[alreadyInSave:protected] =>
[alreadyInValidation:protected] =>
[validationFailures:protected] => Array
(
)
[_new:BaseObject:private] =>
[_deleted:BaseObject:private] =>
[modifiedColumns:protected] => Array
(
)
)
[88] => Category Object
(
[languages:protected] =>
[bok_resources:protected] =>
[bok_topics:protected] =>
[bok_keywords:protected] =>
[id:protected] => 88
[type:protected] => category
[parent:protected] => 3
[label:protected] => Demolition
[alreadyInSave:protected] =>
[alreadyInValidation:protected] =>
[validationFailures:protected] => Array
(
)
[_new:BaseObject:private] =>
[_deleted:BaseObject:private] =>
[modifiedColumns:protected] => Array
(
)
)
[91] => Category Object
(
[languages:protected] =>
[bok_resources:protected] =>
[bok_topics:protected] =>
[bok_keywords:protected] =>
[id:protected] => 91
[type:protected] => category
[parent:protected] => 3
[label:protected] => Heavy & Highway
[alreadyInSave:protected] =>
[alreadyInValidation:protected] =>
[validationFailures:protected] => Array
(
)
[_new:BaseObject:private] =>
[_deleted:BaseObject:private] =>
[modifiedColumns:protected] => Array
(
)
)
[90] => Category Object
(
[languages:protected] =>
[bok_resources:protected] =>
[bok_topics:protected] =>
[bok_keywords:protected] =>
[id:protected] => 90
[type:protected] => category
[parent:protected] => 3
[label:protected] => Industrial
[alreadyInSave:protected] =>
[alreadyInValidation:protected] =>
[validationFailures:protected] => Array
(
)
[_new:BaseObject:private] =>
[_deleted:BaseObject:private] =>
[modifiedColumns:protected] => Array
(
)
)
[92] => Category Object
(
[languages:protected] =>
[bok_resources:protected] =>
[bok_topics:protected] =>
[bok_keywords:protected] =>
[id:protected] => 92
[type:protected] => category
[parent:protected] => 3
[label:protected] => LEED/Green Construction
[alreadyInSave:protected] =>
[alreadyInValidation:protected] =>
[validationFailures:protected] => Array
(
)
[_new:BaseObject:private] =>
[_deleted:BaseObject:private] =>
[modifiedColumns:protected] => Array
(
)
)
[100] => Category Object
(
[languages:protected] =>
[bok_resources:protected] =>
[bok_topics:protected] =>
[bok_keywords:protected] =>
[id:protected] => 100
[type:protected] => category
[parent:protected] => 6
[label:protected] => Toolbox Talks
[alreadyInSave:protected] =>
[alreadyInValidation:protected] =>
[validationFailures:protected] => Array
(
)
[_new:BaseObject:private] =>
[_deleted:BaseObject:private] =>
[modifiedColumns:protected] => Array
(
)
)
)
[categories_initialized:protected] => 1
[mapped_items:protected] =>
[content:protected] =>
[files:protected] =>
[language:protected] => Language Object
(
[id:protected] => 1
[code:protected] => en
[name:protected] => English
[alreadyInSave:protected] =>
[alreadyInValidation:protected] =>
[validationFailures:protected] => Array
(
)
[_new:BaseObject:private] =>
[_deleted:BaseObject:private] =>
[modifiedColumns:protected] => Array
(
)
)
[old_record:protected] =>
[id:protected] => 4427
[old_id:protected] =>
[elcosh_id:protected] => d001657
[type:protected] => document
[display_type:protected] => HTML only (and links)
[user_id:protected] => 0
[language_id:protected] => 1
[tagging_id:protected] => Mike Aguilar
[priority_id:protected] => 1
[title:protected] => Toolbox Talk: Tower Crane Safety
[total_pages:protected] => 0
[billed_pages:protected] => 0
[publication_number:protected] =>
[part_of:protected] =>
[keywords:protected] => Tower Crane, Crane, Stability, Tipping, Lift Zone Safety, Lift, Zone, Safety, Struck by
[comments:protected] =>
[summary:protected] => The CPWR Toolbox Talk on Tower Crane Safety addresses the potential hazards of Tower Cranes and the importance of following procedure before and during Tower Crane operation. The resource includes a brief example, steps to prevent a related injury, and questions for discussion. It includes a graphic that illustrates a worker inspecting a Tower Crane before operation, which can be posted in a central location as a reminder of steps to work safely.
Available in
English and
Spanish.
[transition_comments:protected] =>
[external_link:protected] =>
[consol_link:protected] =>
[more_like_this:protected] => d001234,d001238,d001250,d001251,d001253,d001258,d001262,d001273
[permission_given_by:protected] =>
[published:protected] => T
[billable:protected] => F
[img_name:protected] =>
[img_ext:protected] => jpg
[img_width:protected] =>
[img_height:protected] =>
[img_credit:protected] =>
[img_practice:protected] =>
[vid_source_id:protected] =>
[vid_running_time:protected] =>
[vid_intended_audience:protected] =>
[vid_acquisition_info:protected] =>
[vid_cost:protected] =>
[vid_producer:protected] =>
[vid_filename:protected] =>
[vid_filename_downloadable:protected] =>
[date_summary:protected] =>
[date_permission_requested:protected] =>
[date_permission_received:protected] =>
[date_review_needed:protected] =>
[date_received:protected] => 12/23/21
[date_completed:protected] => 12/23/21
[date_billed:protected] =>
[date_modified:protected] => 05/19/23
[collBokExports:protected] =>
[lastBokExportCriteria:BaseElcoshItem:private] =>
[alreadyInSave:protected] =>
[alreadyInValidation:protected] =>
[validationFailures:protected] => Array
(
)
[_new:BaseObject:private] =>
[_deleted:BaseObject:private] =>
[modifiedColumns:protected] => Array
(
)
)
)
[3] => Search_Result Object
(
[title] => Toolbox Talk: Work Zone Safety: Working Around Vehicles
[image] => /record/images/notavailable-p.png
[blurb] => The CPWR Toolbox Talk on Working Around Vehicles in the Work Zone addresses methods to avoid being struck-by a vehicle on a construction site. The res...
[category] => Array
(
[0] => 12
[1] => 18
[2] => 52
[3] => 57
[4] => 70
[5] => 85
[6] => 87
[7] => 88
[8] => 89
[9] => 91
[10] => 90
[11] => 92
[12] => 93
[13] => 94
[14] => 95
[15] => 100
)
[labels] => Array
(
[0] => Crushed/Struck By
[1] => Work Environment
[2] => Hazards
[3] => Motor Vehicles/Heavy Equipment
[6] => Commercial Diver
[7] => Trades
[8] => Flagger
[10] => Operating Engineer
[12] => Truck Driver
[14] => Commercial & Institutional
[15] => Jobsites
[16] => Demolition
[18] => Disasters
[20] => Heavy & Highway
[22] => Industrial
[24] => LEED/Green Construction
[26] => Renovations
[28] => Residential
[30] => Underground
[32] => Toolbox Talks
[33] => Documents
[34] => Media & Documents
)
[type] => Toolbox Talks
[sub_category] =>
[url] => /document/4428/d001658/Toolbox%2BTalk%253A%2BWork%2BZone%2BSafety%253A%2BWorking%2BAround%2BVehicles.html
[item:protected] => DocumentRecord Object
(
[records:protected] => Array
(
)
[recordId:protected] =>
[searchWordClass:protected] =>
[searchWordPeerClass:protected] =>
[bok_record:protected] =>
[authors:protected] =>
[organizations:protected] =>
[collections:protected] =>
[categories:protected] => Array
(
[12] => Category Object
(
[languages:protected] =>
[bok_resources:protected] =>
[bok_topics:protected] =>
[bok_keywords:protected] =>
[id:protected] => 12
[type:protected] => category
[parent:protected] => 7
[label:protected] => Crushed/Struck By
[alreadyInSave:protected] =>
[alreadyInValidation:protected] =>
[validationFailures:protected] => Array
(
)
[_new:BaseObject:private] =>
[_deleted:BaseObject:private] =>
[modifiedColumns:protected] => Array
(
)
)
[18] => Category Object
(
[languages:protected] =>
[bok_resources:protected] =>
[bok_topics:protected] =>
[bok_keywords:protected] =>
[id:protected] => 18
[type:protected] => category
[parent:protected] => 7
[label:protected] => Motor Vehicles/Heavy Equipment
[alreadyInSave:protected] =>
[alreadyInValidation:protected] =>
[validationFailures:protected] => Array
(
)
[_new:BaseObject:private] =>
[_deleted:BaseObject:private] =>
[modifiedColumns:protected] => Array
(
)
)
[52] => Category Object
(
[languages:protected] =>
[bok_resources:protected] =>
[bok_topics:protected] =>
[bok_keywords:protected] =>
[id:protected] => 52
[type:protected] => category
[parent:protected] => 2
[label:protected] => Commercial Diver
[alreadyInSave:protected] =>
[alreadyInValidation:protected] =>
[validationFailures:protected] => Array
(
)
[_new:BaseObject:private] =>
[_deleted:BaseObject:private] =>
[modifiedColumns:protected] => Array
(
)
)
[57] => Category Object
(
[languages:protected] =>
[bok_resources:protected] =>
[bok_topics:protected] =>
[bok_keywords:protected] =>
[id:protected] => 57
[type:protected] => category
[parent:protected] => 2
[label:protected] => Flagger
[alreadyInSave:protected] =>
[alreadyInValidation:protected] =>
[validationFailures:protected] => Array
(
)
[_new:BaseObject:private] =>
[_deleted:BaseObject:private] =>
[modifiedColumns:protected] => Array
(
)
)
[70] => Category Object
(
[languages:protected] =>
[bok_resources:protected] =>
[bok_topics:protected] =>
[bok_keywords:protected] =>
[id:protected] => 70
[type:protected] => category
[parent:protected] => 2
[label:protected] => Operating Engineer
[alreadyInSave:protected] =>
[alreadyInValidation:protected] =>
[validationFailures:protected] => Array
(
)
[_new:BaseObject:private] =>
[_deleted:BaseObject:private] =>
[modifiedColumns:protected] => Array
(
)
)
[85] => Category Object
(
[languages:protected] =>
[bok_resources:protected] =>
[bok_topics:protected] =>
[bok_keywords:protected] =>
[id:protected] => 85
[type:protected] => category
[parent:protected] => 2
[label:protected] => Truck Driver
[alreadyInSave:protected] =>
[alreadyInValidation:protected] =>
[validationFailures:protected] => Array
(
)
[_new:BaseObject:private] =>
[_deleted:BaseObject:private] =>
[modifiedColumns:protected] => Array
(
)
)
[87] => Category Object
(
[languages:protected] =>
[bok_resources:protected] =>
[bok_topics:protected] =>
[bok_keywords:protected] =>
[id:protected] => 87
[type:protected] => category
[parent:protected] => 3
[label:protected] => Commercial & Institutional
[alreadyInSave:protected] =>
[alreadyInValidation:protected] =>
[validationFailures:protected] => Array
(
)
[_new:BaseObject:private] =>
[_deleted:BaseObject:private] =>
[modifiedColumns:protected] => Array
(
)
)
[88] => Category Object
(
[languages:protected] =>
[bok_resources:protected] =>
[bok_topics:protected] =>
[bok_keywords:protected] =>
[id:protected] => 88
[type:protected] => category
[parent:protected] => 3
[label:protected] => Demolition
[alreadyInSave:protected] =>
[alreadyInValidation:protected] =>
[validationFailures:protected] => Array
(
)
[_new:BaseObject:private] =>
[_deleted:BaseObject:private] =>
[modifiedColumns:protected] => Array
(
)
)
[89] => Category Object
(
[languages:protected] =>
[bok_resources:protected] =>
[bok_topics:protected] =>
[bok_keywords:protected] =>
[id:protected] => 89
[type:protected] => category
[parent:protected] => 3
[label:protected] => Disasters
[alreadyInSave:protected] =>
[alreadyInValidation:protected] =>
[validationFailures:protected] => Array
(
)
[_new:BaseObject:private] =>
[_deleted:BaseObject:private] =>
[modifiedColumns:protected] => Array
(
)
)
[91] => Category Object
(
[languages:protected] =>
[bok_resources:protected] =>
[bok_topics:protected] =>
[bok_keywords:protected] =>
[id:protected] => 91
[type:protected] => category
[parent:protected] => 3
[label:protected] => Heavy & Highway
[alreadyInSave:protected] =>
[alreadyInValidation:protected] =>
[validationFailures:protected] => Array
(
)
[_new:BaseObject:private] =>
[_deleted:BaseObject:private] =>
[modifiedColumns:protected] => Array
(
)
)
[90] => Category Object
(
[languages:protected] =>
[bok_resources:protected] =>
[bok_topics:protected] =>
[bok_keywords:protected] =>
[id:protected] => 90
[type:protected] => category
[parent:protected] => 3
[label:protected] => Industrial
[alreadyInSave:protected] =>
[alreadyInValidation:protected] =>
[validationFailures:protected] => Array
(
)
[_new:BaseObject:private] =>
[_deleted:BaseObject:private] =>
[modifiedColumns:protected] => Array
(
)
)
[92] => Category Object
(
[languages:protected] =>
[bok_resources:protected] =>
[bok_topics:protected] =>
[bok_keywords:protected] =>
[id:protected] => 92
[type:protected] => category
[parent:protected] => 3
[label:protected] => LEED/Green Construction
[alreadyInSave:protected] =>
[alreadyInValidation:protected] =>
[validationFailures:protected] => Array
(
)
[_new:BaseObject:private] =>
[_deleted:BaseObject:private] =>
[modifiedColumns:protected] => Array
(
)
)
[93] => Category Object
(
[languages:protected] =>
[bok_resources:protected] =>
[bok_topics:protected] =>
[bok_keywords:protected] =>
[id:protected] => 93
[type:protected] => category
[parent:protected] => 3
[label:protected] => Renovations
[alreadyInSave:protected] =>
[alreadyInValidation:protected] =>
[validationFailures:protected] => Array
(
)
[_new:BaseObject:private] =>
[_deleted:BaseObject:private] =>
[modifiedColumns:protected] => Array
(
)
)
[94] => Category Object
(
[languages:protected] =>
[bok_resources:protected] =>
[bok_topics:protected] =>
[bok_keywords:protected] =>
[id:protected] => 94
[type:protected] => category
[parent:protected] => 3
[label:protected] => Residential
[alreadyInSave:protected] =>
[alreadyInValidation:protected] =>
[validationFailures:protected] => Array
(
)
[_new:BaseObject:private] =>
[_deleted:BaseObject:private] =>
[modifiedColumns:protected] => Array
(
)
)
[95] => Category Object
(
[languages:protected] =>
[bok_resources:protected] =>
[bok_topics:protected] =>
[bok_keywords:protected] =>
[id:protected] => 95
[type:protected] => category
[parent:protected] => 3
[label:protected] => Underground
[alreadyInSave:protected] =>
[alreadyInValidation:protected] =>
[validationFailures:protected] => Array
(
)
[_new:BaseObject:private] =>
[_deleted:BaseObject:private] =>
[modifiedColumns:protected] => Array
(
)
)
[100] => Category Object
(
[languages:protected] =>
[bok_resources:protected] =>
[bok_topics:protected] =>
[bok_keywords:protected] =>
[id:protected] => 100
[type:protected] => category
[parent:protected] => 6
[label:protected] => Toolbox Talks
[alreadyInSave:protected] =>
[alreadyInValidation:protected] =>
[validationFailures:protected] => Array
(
)
[_new:BaseObject:private] =>
[_deleted:BaseObject:private] =>
[modifiedColumns:protected] => Array
(
)
)
)
[categories_initialized:protected] => 1
[mapped_items:protected] =>
[content:protected] =>
[files:protected] =>
[language:protected] => Language Object
(
[id:protected] => 1
[code:protected] => en
[name:protected] => English
[alreadyInSave:protected] =>
[alreadyInValidation:protected] =>
[validationFailures:protected] => Array
(
)
[_new:BaseObject:private] =>
[_deleted:BaseObject:private] =>
[modifiedColumns:protected] => Array
(
)
)
[old_record:protected] =>
[id:protected] => 4428
[old_id:protected] =>
[elcosh_id:protected] => d001658
[type:protected] => document
[display_type:protected] => HTML only (and links)
[user_id:protected] => 0
[language_id:protected] => 1
[tagging_id:protected] => Daniela Caceres
[priority_id:protected] => 1
[title:protected] => Toolbox Talk: Work Zone Safety: Working Around Vehicles
[total_pages:protected] => 0
[billed_pages:protected] => 0
[publication_number:protected] =>
[part_of:protected] =>
[keywords:protected] => Struck, Struck by, Vehicle, Work Zone Safety, Truck, Operator, Driver, Mobile Equipment
[comments:protected] =>
[summary:protected] => The CPWR Toolbox Talk on Working Around Vehicles in the Work Zone addresses methods to avoid being struck-by a vehicle on a construction site. The resource includes a case example, steps to prevent a related injury, and questions for discussion. It includes a graphic that illustrates the hazard, which can be posted in a central location as a reminder of steps to work safely. Available in
English and
Spanish.
[transition_comments:protected] =>
[external_link:protected] =>
[consol_link:protected] =>
[more_like_this:protected] => d001640
[permission_given_by:protected] =>
[published:protected] => T
[billable:protected] => F
[img_name:protected] =>
[img_ext:protected] =>
[img_width:protected] =>
[img_height:protected] =>
[img_credit:protected] =>
[img_practice:protected] =>
[vid_source_id:protected] =>
[vid_running_time:protected] =>
[vid_intended_audience:protected] =>
[vid_acquisition_info:protected] =>
[vid_cost:protected] =>
[vid_producer:protected] =>
[vid_filename:protected] =>
[vid_filename_downloadable:protected] =>
[date_summary:protected] =>
[date_permission_requested:protected] =>
[date_permission_received:protected] =>
[date_review_needed:protected] =>
[date_received:protected] => 12/23/21
[date_completed:protected] => 12/23/21
[date_billed:protected] =>
[date_modified:protected] => 05/19/23
[collBokExports:protected] =>
[lastBokExportCriteria:BaseElcoshItem:private] =>
[alreadyInSave:protected] =>
[alreadyInValidation:protected] =>
[validationFailures:protected] => Array
(
)
[_new:BaseObject:private] =>
[_deleted:BaseObject:private] =>
[modifiedColumns:protected] => Array
(
)
)
)
[4] => Search_Result Object
(
[title] => Construction Dive -- DeWalt's Jobsite Pro headphones recalled for fire hazards
[image] => /record/images/notavailable-p.png
[blurb] => A recall notice by the United States Consumer Product Safety Commission affects over 300,000 DeWalt Jobsite Pro Headphones. The recall is a result of...
[category] => Array
(
[0] => 16
[1] => 44
[2] => 45
[3] => 46
[4] => 47
[5] => 48
[6] => 49
[7] => 50
[8] => 51
[9] => 52
[10] => 53
[11] => 54
[12] => 55
[13] => 56
[14] => 57
[15] => 58
[16] => 59
[17] => 60
[18] => 61
[19] => 64
[20] => 65
[21] => 66
[22] => 67
[23] => 68
[24] => 69
[25] => 70
[26] => 71
[27] => 72
[28] => 73
[29] => 74
[30] => 75
[31] => 76
[32] => 77
[33] => 63
[34] => 78
[35] => 79
[36] => 80
[37] => 81
[38] => 82
[39] => 62
[40] => 83
[41] => 84
[42] => 85
[43] => 86
[44] => 87
[45] => 88
[46] => 89
[47] => 91
[48] => 90
[49] => 92
[50] => 93
[51] => 94
[52] => 95
)
[labels] => Array
(
[0] => Fire & Explosions
[1] => Work Environment
[2] => Hazards
[3] => Acoustical Ceiling Carpenter
[4] => Trades
[5] => Asbestos/Insulator
[7] => Boilermaker
[9] => Bricklayer
[11] => Cabinetmaker
[13] => Carpenter
[15] => Carpet Layer
[17] => Cement Mason
[19] => Commercial Diver
[21] => Concrete Polisher
[23] => Drywall Applicator Specialist
[25] => Electrical Worker
[27] => Elevator Constructor
[29] => Flagger
[31] => Glazier
[33] => Hazardous Waste Cleanup
[35] => HVAC
[37] => Interior Systems Carpenter
[39] => Laborer
[41] => Landscaper
[43] => Lather
[45] => Lead Abatement Worker
[47] => Maintenance Worker
[49] => Millwright
[51] => Operating Engineer
[53] => Painter
[55] => Paper Hanger
[57] => PCC/Restoration
[59] => Pile Driver
[61] => Plasterer
[63] => Plumber/Pipefitter
[65] => Refractory Worker
[67] => Reinforcing Ironworker
[69] => Roofer/Waterproofer
[71] => Scaffold Erector
[73] => Sheetmetal Worker
[75] => Sprinkler Fitter
[77] => Stonemason
[79] => Structural Ironworker
[81] => Terrazzo Worker
[83] => Tile Setter
[85] => Truck Driver
[87] => Welder
[89] => Commercial & Institutional
[90] => Jobsites
[91] => Demolition
[93] => Disasters
[95] => Heavy & Highway
[97] => Industrial
[99] => LEED/Green Construction
[101] => Renovations
[103] => Residential
[105] => Underground
)
[type] =>
[sub_category] =>
[url] => /document/4426/d001656/Construction%2BDive%2B--%2BDeWalt%2527s%2BJobsite%2BPro%2Bheadphones%2Brecalled%2Bfor%2Bfire%2Bhazards.html
[item:protected] => DocumentRecord Object
(
[records:protected] => Array
(
)
[recordId:protected] =>
[searchWordClass:protected] =>
[searchWordPeerClass:protected] =>
[bok_record:protected] =>
[authors:protected] =>
[organizations:protected] =>
[collections:protected] =>
[categories:protected] => Array
(
[16] => Category Object
(
[languages:protected] =>
[bok_resources:protected] =>
[bok_topics:protected] =>
[bok_keywords:protected] =>
[id:protected] => 16
[type:protected] => category
[parent:protected] => 7
[label:protected] => Fire & Explosions
[alreadyInSave:protected] =>
[alreadyInValidation:protected] =>
[validationFailures:protected] => Array
(
)
[_new:BaseObject:private] =>
[_deleted:BaseObject:private] =>
[modifiedColumns:protected] => Array
(
)
)
[44] => Category Object
(
[languages:protected] =>
[bok_resources:protected] =>
[bok_topics:protected] =>
[bok_keywords:protected] =>
[id:protected] => 44
[type:protected] => category
[parent:protected] => 2
[label:protected] => Acoustical Ceiling Carpenter
[alreadyInSave:protected] =>
[alreadyInValidation:protected] =>
[validationFailures:protected] => Array
(
)
[_new:BaseObject:private] =>
[_deleted:BaseObject:private] =>
[modifiedColumns:protected] => Array
(
)
)
[45] => Category Object
(
[languages:protected] =>
[bok_resources:protected] =>
[bok_topics:protected] =>
[bok_keywords:protected] =>
[id:protected] => 45
[type:protected] => category
[parent:protected] => 2
[label:protected] => Asbestos/Insulator
[alreadyInSave:protected] =>
[alreadyInValidation:protected] =>
[validationFailures:protected] => Array
(
)
[_new:BaseObject:private] =>
[_deleted:BaseObject:private] =>
[modifiedColumns:protected] => Array
(
)
)
[46] => Category Object
(
[languages:protected] =>
[bok_resources:protected] =>
[bok_topics:protected] =>
[bok_keywords:protected] =>
[id:protected] => 46
[type:protected] => category
[parent:protected] => 2
[label:protected] => Boilermaker
[alreadyInSave:protected] =>
[alreadyInValidation:protected] =>
[validationFailures:protected] => Array
(
)
[_new:BaseObject:private] =>
[_deleted:BaseObject:private] =>
[modifiedColumns:protected] => Array
(
)
)
[47] => Category Object
(
[languages:protected] =>
[bok_resources:protected] =>
[bok_topics:protected] =>
[bok_keywords:protected] =>
[id:protected] => 47
[type:protected] => category
[parent:protected] => 2
[label:protected] => Bricklayer
[alreadyInSave:protected] =>
[alreadyInValidation:protected] =>
[validationFailures:protected] => Array
(
)
[_new:BaseObject:private] =>
[_deleted:BaseObject:private] =>
[modifiedColumns:protected] => Array
(
)
)
[48] => Category Object
(
[languages:protected] =>
[bok_resources:protected] =>
[bok_topics:protected] =>
[bok_keywords:protected] =>
[id:protected] => 48
[type:protected] => category
[parent:protected] => 2
[label:protected] => Cabinetmaker
[alreadyInSave:protected] =>
[alreadyInValidation:protected] =>
[validationFailures:protected] => Array
(
)
[_new:BaseObject:private] =>
[_deleted:BaseObject:private] =>
[modifiedColumns:protected] => Array
(
)
)
[49] => Category Object
(
[languages:protected] =>
[bok_resources:protected] =>
[bok_topics:protected] =>
[bok_keywords:protected] =>
[id:protected] => 49
[type:protected] => category
[parent:protected] => 2
[label:protected] => Carpenter
[alreadyInSave:protected] =>
[alreadyInValidation:protected] =>
[validationFailures:protected] => Array
(
)
[_new:BaseObject:private] =>
[_deleted:BaseObject:private] =>
[modifiedColumns:protected] => Array
(
)
)
[50] => Category Object
(
[languages:protected] =>
[bok_resources:protected] =>
[bok_topics:protected] =>
[bok_keywords:protected] =>
[id:protected] => 50
[type:protected] => category
[parent:protected] => 2
[label:protected] => Carpet Layer
[alreadyInSave:protected] =>
[alreadyInValidation:protected] =>
[validationFailures:protected] => Array
(
)
[_new:BaseObject:private] =>
[_deleted:BaseObject:private] =>
[modifiedColumns:protected] => Array
(
)
)
[51] => Category Object
(
[languages:protected] =>
[bok_resources:protected] =>
[bok_topics:protected] =>
[bok_keywords:protected] =>
[id:protected] => 51
[type:protected] => category
[parent:protected] => 2
[label:protected] => Cement Mason
[alreadyInSave:protected] =>
[alreadyInValidation:protected] =>
[validationFailures:protected] => Array
(
)
[_new:BaseObject:private] =>
[_deleted:BaseObject:private] =>
[modifiedColumns:protected] => Array
(
)
)
[52] => Category Object
(
[languages:protected] =>
[bok_resources:protected] =>
[bok_topics:protected] =>
[bok_keywords:protected] =>
[id:protected] => 52
[type:protected] => category
[parent:protected] => 2
[label:protected] => Commercial Diver
[alreadyInSave:protected] =>
[alreadyInValidation:protected] =>
[validationFailures:protected] => Array
(
)
[_new:BaseObject:private] =>
[_deleted:BaseObject:private] =>
[modifiedColumns:protected] => Array
(
)
)
[53] => Category Object
(
[languages:protected] =>
[bok_resources:protected] =>
[bok_topics:protected] =>
[bok_keywords:protected] =>
[id:protected] => 53
[type:protected] => category
[parent:protected] => 2
[label:protected] => Concrete Polisher
[alreadyInSave:protected] =>
[alreadyInValidation:protected] =>
[validationFailures:protected] => Array
(
)
[_new:BaseObject:private] =>
[_deleted:BaseObject:private] =>
[modifiedColumns:protected] => Array
(
)
)
[54] => Category Object
(
[languages:protected] =>
[bok_resources:protected] =>
[bok_topics:protected] =>
[bok_keywords:protected] =>
[id:protected] => 54
[type:protected] => category
[parent:protected] => 2
[label:protected] => Drywall Applicator Specialist
[alreadyInSave:protected] =>
[alreadyInValidation:protected] =>
[validationFailures:protected] => Array
(
)
[_new:BaseObject:private] =>
[_deleted:BaseObject:private] =>
[modifiedColumns:protected] => Array
(
)
)
[55] => Category Object
(
[languages:protected] =>
[bok_resources:protected] =>
[bok_topics:protected] =>
[bok_keywords:protected] =>
[id:protected] => 55
[type:protected] => category
[parent:protected] => 2
[label:protected] => Electrical Worker
[alreadyInSave:protected] =>
[alreadyInValidation:protected] =>
[validationFailures:protected] => Array
(
)
[_new:BaseObject:private] =>
[_deleted:BaseObject:private] =>
[modifiedColumns:protected] => Array
(
)
)
[56] => Category Object
(
[languages:protected] =>
[bok_resources:protected] =>
[bok_topics:protected] =>
[bok_keywords:protected] =>
[id:protected] => 56
[type:protected] => category
[parent:protected] => 2
[label:protected] => Elevator Constructor
[alreadyInSave:protected] =>
[alreadyInValidation:protected] =>
[validationFailures:protected] => Array
(
)
[_new:BaseObject:private] =>
[_deleted:BaseObject:private] =>
[modifiedColumns:protected] => Array
(
)
)
[57] => Category Object
(
[languages:protected] =>
[bok_resources:protected] =>
[bok_topics:protected] =>
[bok_keywords:protected] =>
[id:protected] => 57
[type:protected] => category
[parent:protected] => 2
[label:protected] => Flagger
[alreadyInSave:protected] =>
[alreadyInValidation:protected] =>
[validationFailures:protected] => Array
(
)
[_new:BaseObject:private] =>
[_deleted:BaseObject:private] =>
[modifiedColumns:protected] => Array
(
)
)
[58] => Category Object
(
[languages:protected] =>
[bok_resources:protected] =>
[bok_topics:protected] =>
[bok_keywords:protected] =>
[id:protected] => 58
[type:protected] => category
[parent:protected] => 2
[label:protected] => Glazier
[alreadyInSave:protected] =>
[alreadyInValidation:protected] =>
[validationFailures:protected] => Array
(
)
[_new:BaseObject:private] =>
[_deleted:BaseObject:private] =>
[modifiedColumns:protected] => Array
(
)
)
[59] => Category Object
(
[languages:protected] =>
[bok_resources:protected] =>
[bok_topics:protected] =>
[bok_keywords:protected] =>
[id:protected] => 59
[type:protected] => category
[parent:protected] => 2
[label:protected] => Hazardous Waste Cleanup
[alreadyInSave:protected] =>
[alreadyInValidation:protected] =>
[validationFailures:protected] => Array
(
)
[_new:BaseObject:private] =>
[_deleted:BaseObject:private] =>
[modifiedColumns:protected] => Array
(
)
)
[60] => Category Object
(
[languages:protected] =>
[bok_resources:protected] =>
[bok_topics:protected] =>
[bok_keywords:protected] =>
[id:protected] => 60
[type:protected] => category
[parent:protected] => 2
[label:protected] => HVAC
[alreadyInSave:protected] =>
[alreadyInValidation:protected] =>
[validationFailures:protected] => Array
(
)
[_new:BaseObject:private] =>
[_deleted:BaseObject:private] =>
[modifiedColumns:protected] => Array
(
)
)
[61] => Category Object
(
[languages:protected] =>
[bok_resources:protected] =>
[bok_topics:protected] =>
[bok_keywords:protected] =>
[id:protected] => 61
[type:protected] => category
[parent:protected] => 2
[label:protected] => Interior Systems Carpenter
[alreadyInSave:protected] =>
[alreadyInValidation:protected] =>
[validationFailures:protected] => Array
(
)
[_new:BaseObject:private] =>
[_deleted:BaseObject:private] =>
[modifiedColumns:protected] => Array
(
)
)
[64] => Category Object
(
[languages:protected] =>
[bok_resources:protected] =>
[bok_topics:protected] =>
[bok_keywords:protected] =>
[id:protected] => 64
[type:protected] => category
[parent:protected] => 2
[label:protected] => Laborer
[alreadyInSave:protected] =>
[alreadyInValidation:protected] =>
[validationFailures:protected] => Array
(
)
[_new:BaseObject:private] =>
[_deleted:BaseObject:private] =>
[modifiedColumns:protected] => Array
(
)
)
[65] => Category Object
(
[languages:protected] =>
[bok_resources:protected] =>
[bok_topics:protected] =>
[bok_keywords:protected] =>
[id:protected] => 65
[type:protected] => category
[parent:protected] => 2
[label:protected] => Landscaper
[alreadyInSave:protected] =>
[alreadyInValidation:protected] =>
[validationFailures:protected] => Array
(
)
[_new:BaseObject:private] =>
[_deleted:BaseObject:private] =>
[modifiedColumns:protected] => Array
(
)
)
[66] => Category Object
(
[languages:protected] =>
[bok_resources:protected] =>
[bok_topics:protected] =>
[bok_keywords:protected] =>
[id:protected] => 66
[type:protected] => category
[parent:protected] => 2
[label:protected] => Lather
[alreadyInSave:protected] =>
[alreadyInValidation:protected] =>
[validationFailures:protected] => Array
(
)
[_new:BaseObject:private] =>
[_deleted:BaseObject:private] =>
[modifiedColumns:protected] => Array
(
)
)
[67] => Category Object
(
[languages:protected] =>
[bok_resources:protected] =>
[bok_topics:protected] =>
[bok_keywords:protected] =>
[id:protected] => 67
[type:protected] => category
[parent:protected] => 2
[label:protected] => Lead Abatement Worker
[alreadyInSave:protected] =>
[alreadyInValidation:protected] =>
[validationFailures:protected] => Array
(
)
[_new:BaseObject:private] =>
[_deleted:BaseObject:private] =>
[modifiedColumns:protected] => Array
(
)
)
[68] => Category Object
(
[languages:protected] =>
[bok_resources:protected] =>
[bok_topics:protected] =>
[bok_keywords:protected] =>
[id:protected] => 68
[type:protected] => category
[parent:protected] => 2
[label:protected] => Maintenance Worker
[alreadyInSave:protected] =>
[alreadyInValidation:protected] =>
[validationFailures:protected] => Array
(
)
[_new:BaseObject:private] =>
[_deleted:BaseObject:private] =>
[modifiedColumns:protected] => Array
(
)
)
[69] => Category Object
(
[languages:protected] =>
[bok_resources:protected] =>
[bok_topics:protected] =>
[bok_keywords:protected] =>
[id:protected] => 69
[type:protected] => category
[parent:protected] => 2
[label:protected] => Millwright
[alreadyInSave:protected] =>
[alreadyInValidation:protected] =>
[validationFailures:protected] => Array
(
)
[_new:BaseObject:private] =>
[_deleted:BaseObject:private] =>
[modifiedColumns:protected] => Array
(
)
)
[70] => Category Object
(
[languages:protected] =>
[bok_resources:protected] =>
[bok_topics:protected] =>
[bok_keywords:protected] =>
[id:protected] => 70
[type:protected] => category
[parent:protected] => 2
[label:protected] => Operating Engineer
[alreadyInSave:protected] =>
[alreadyInValidation:protected] =>
[validationFailures:protected] => Array
(
)
[_new:BaseObject:private] =>
[_deleted:BaseObject:private] =>
[modifiedColumns:protected] => Array
(
)
)
[71] => Category Object
(
[languages:protected] =>
[bok_resources:protected] =>
[bok_topics:protected] =>
[bok_keywords:protected] =>
[id:protected] => 71
[type:protected] => category
[parent:protected] => 2
[label:protected] => Painter
[alreadyInSave:protected] =>
[alreadyInValidation:protected] =>
[validationFailures:protected] => Array
(
)
[_new:BaseObject:private] =>
[_deleted:BaseObject:private] =>
[modifiedColumns:protected] => Array
(
)
)
[72] => Category Object
(
[languages:protected] =>
[bok_resources:protected] =>
[bok_topics:protected] =>
[bok_keywords:protected] =>
[id:protected] => 72
[type:protected] => category
[parent:protected] => 2
[label:protected] => Paper Hanger
[alreadyInSave:protected] =>
[alreadyInValidation:protected] =>
[validationFailures:protected] => Array
(
)
[_new:BaseObject:private] =>
[_deleted:BaseObject:private] =>
[modifiedColumns:protected] => Array
(
)
)
[73] => Category Object
(
[languages:protected] =>
[bok_resources:protected] =>
[bok_topics:protected] =>
[bok_keywords:protected] =>
[id:protected] => 73
[type:protected] => category
[parent:protected] => 2
[label:protected] => PCC/Restoration
[alreadyInSave:protected] =>
[alreadyInValidation:protected] =>
[validationFailures:protected] => Array
(
)
[_new:BaseObject:private] =>
[_deleted:BaseObject:private] =>
[modifiedColumns:protected] => Array
(
)
)
[74] => Category Object
(
[languages:protected] =>
[bok_resources:protected] =>
[bok_topics:protected] =>
[bok_keywords:protected] =>
[id:protected] => 74
[type:protected] => category
[parent:protected] => 2
[label:protected] => Pile Driver
[alreadyInSave:protected] =>
[alreadyInValidation:protected] =>
[validationFailures:protected] => Array
(
)
[_new:BaseObject:private] =>
[_deleted:BaseObject:private] =>
[modifiedColumns:protected] => Array
(
)
)
[75] => Category Object
(
[languages:protected] =>
[bok_resources:protected] =>
[bok_topics:protected] =>
[bok_keywords:protected] =>
[id:protected] => 75
[type:protected] => category
[parent:protected] => 2
[label:protected] => Plasterer
[alreadyInSave:protected] =>
[alreadyInValidation:protected] =>
[validationFailures:protected] => Array
(
)
[_new:BaseObject:private] =>
[_deleted:BaseObject:private] =>
[modifiedColumns:protected] => Array
(
)
)
[76] => Category Object
(
[languages:protected] =>
[bok_resources:protected] =>
[bok_topics:protected] =>
[bok_keywords:protected] =>
[id:protected] => 76
[type:protected] => category
[parent:protected] => 2
[label:protected] => Plumber/Pipefitter
[alreadyInSave:protected] =>
[alreadyInValidation:protected] =>
[validationFailures:protected] => Array
(
)
[_new:BaseObject:private] =>
[_deleted:BaseObject:private] =>
[modifiedColumns:protected] => Array
(
)
)
[77] => Category Object
(
[languages:protected] =>
[bok_resources:protected] =>
[bok_topics:protected] =>
[bok_keywords:protected] =>
[id:protected] => 77
[type:protected] => category
[parent:protected] => 2
[label:protected] => Refractory Worker
[alreadyInSave:protected] =>
[alreadyInValidation:protected] =>
[validationFailures:protected] => Array
(
)
[_new:BaseObject:private] =>
[_deleted:BaseObject:private] =>
[modifiedColumns:protected] => Array
(
)
)
[63] => Category Object
(
[languages:protected] =>
[bok_resources:protected] =>
[bok_topics:protected] =>
[bok_keywords:protected] =>
[id:protected] => 63
[type:protected] => category
[parent:protected] => 2
[label:protected] => Reinforcing Ironworker
[alreadyInSave:protected] =>
[alreadyInValidation:protected] =>
[validationFailures:protected] => Array
(
)
[_new:BaseObject:private] =>
[_deleted:BaseObject:private] =>
[modifiedColumns:protected] => Array
(
)
)
[78] => Category Object
(
[languages:protected] =>
[bok_resources:protected] =>
[bok_topics:protected] =>
[bok_keywords:protected] =>
[id:protected] => 78
[type:protected] => category
[parent:protected] => 2
[label:protected] => Roofer/Waterproofer
[alreadyInSave:protected] =>
[alreadyInValidation:protected] =>
[validationFailures:protected] => Array
(
)
[_new:BaseObject:private] =>
[_deleted:BaseObject:private] =>
[modifiedColumns:protected] => Array
(
)
)
[79] => Category Object
(
[languages:protected] =>
[bok_resources:protected] =>
[bok_topics:protected] =>
[bok_keywords:protected] =>
[id:protected] => 79
[type:protected] => category
[parent:protected] => 2
[label:protected] => Scaffold Erector
[alreadyInSave:protected] =>
[alreadyInValidation:protected] =>
[validationFailures:protected] => Array
(
)
[_new:BaseObject:private] =>
[_deleted:BaseObject:private] =>
[modifiedColumns:protected] => Array
(
)
)
[80] => Category Object
(
[languages:protected] =>
[bok_resources:protected] =>
[bok_topics:protected] =>
[bok_keywords:protected] =>
[id:protected] => 80
[type:protected] => category
[parent:protected] => 2
[label:protected] => Sheetmetal Worker
[alreadyInSave:protected] =>
[alreadyInValidation:protected] =>
[validationFailures:protected] => Array
(
)
[_new:BaseObject:private] =>
[_deleted:BaseObject:private] =>
[modifiedColumns:protected] => Array
(
)
)
[81] => Category Object
(
[languages:protected] =>
[bok_resources:protected] =>
[bok_topics:protected] =>
[bok_keywords:protected] =>
[id:protected] => 81
[type:protected] => category
[parent:protected] => 2
[label:protected] => Sprinkler Fitter
[alreadyInSave:protected] =>
[alreadyInValidation:protected] =>
[validationFailures:protected] => Array
(
)
[_new:BaseObject:private] =>
[_deleted:BaseObject:private] =>
[modifiedColumns:protected] => Array
(
)
)
[82] => Category Object
(
[languages:protected] =>
[bok_resources:protected] =>
[bok_topics:protected] =>
[bok_keywords:protected] =>
[id:protected] => 82
[type:protected] => category
[parent:protected] => 2
[label:protected] => Stonemason
[alreadyInSave:protected] =>
[alreadyInValidation:protected] =>
[validationFailures:protected] => Array
(
)
[_new:BaseObject:private] =>
[_deleted:BaseObject:private] =>
[modifiedColumns:protected] => Array
(
)
)
[62] => Category Object
(
[languages:protected] =>
[bok_resources:protected] =>
[bok_topics:protected] =>
[bok_keywords:protected] =>
[id:protected] => 62
[type:protected] => category
[parent:protected] => 2
[label:protected] => Structural Ironworker
[alreadyInSave:protected] =>
[alreadyInValidation:protected] =>
[validationFailures:protected] => Array
(
)
[_new:BaseObject:private] =>
[_deleted:BaseObject:private] =>
[modifiedColumns:protected] => Array
(
)
)
[83] => Category Object
(
[languages:protected] =>
[bok_resources:protected] =>
[bok_topics:protected] =>
[bok_keywords:protected] =>
[id:protected] => 83
[type:protected] => category
[parent:protected] => 2
[label:protected] => Terrazzo Worker
[alreadyInSave:protected] =>
[alreadyInValidation:protected] =>
[validationFailures:protected] => Array
(
)
[_new:BaseObject:private] =>
[_deleted:BaseObject:private] =>
[modifiedColumns:protected] => Array
(
)
)
[84] => Category Object
(
[languages:protected] =>
[bok_resources:protected] =>
[bok_topics:protected] =>
[bok_keywords:protected] =>
[id:protected] => 84
[type:protected] => category
[parent:protected] => 2
[label:protected] => Tile Setter
[alreadyInSave:protected] =>
[alreadyInValidation:protected] =>
[validationFailures:protected] => Array
(
)
[_new:BaseObject:private] =>
[_deleted:BaseObject:private] =>
[modifiedColumns:protected] => Array
(
)
)
[85] => Category Object
(
[languages:protected] =>
[bok_resources:protected] =>
[bok_topics:protected] =>
[bok_keywords:protected] =>
[id:protected] => 85
[type:protected] => category
[parent:protected] => 2
[label:protected] => Truck Driver
[alreadyInSave:protected] =>
[alreadyInValidation:protected] =>
[validationFailures:protected] => Array
(
)
[_new:BaseObject:private] =>
[_deleted:BaseObject:private] =>
[modifiedColumns:protected] => Array
(
)
)
[86] => Category Object
(
[languages:protected] =>
[bok_resources:protected] =>
[bok_topics:protected] =>
[bok_keywords:protected] =>
[id:protected] => 86
[type:protected] => category
[parent:protected] => 2
[label:protected] => Welder
[alreadyInSave:protected] =>
[alreadyInValidation:protected] =>
[validationFailures:protected] => Array
(
)
[_new:BaseObject:private] =>
[_deleted:BaseObject:private] =>
[modifiedColumns:protected] => Array
(
)
)
[87] => Category Object
(
[languages:protected] =>
[bok_resources:protected] =>
[bok_topics:protected] =>
[bok_keywords:protected] =>
[id:protected] => 87
[type:protected] => category
[parent:protected] => 3
[label:protected] => Commercial & Institutional
[alreadyInSave:protected] =>
[alreadyInValidation:protected] =>
[validationFailures:protected] => Array
(
)
[_new:BaseObject:private] =>
[_deleted:BaseObject:private] =>
[modifiedColumns:protected] => Array
(
)
)
[88] => Category Object
(
[languages:protected] =>
[bok_resources:protected] =>
[bok_topics:protected] =>
[bok_keywords:protected] =>
[id:protected] => 88
[type:protected] => category
[parent:protected] => 3
[label:protected] => Demolition
[alreadyInSave:protected] =>
[alreadyInValidation:protected] =>
[validationFailures:protected] => Array
(
)
[_new:BaseObject:private] =>
[_deleted:BaseObject:private] =>
[modifiedColumns:protected] => Array
(
)
)
[89] => Category Object
(
[languages:protected] =>
[bok_resources:protected] =>
[bok_topics:protected] =>
[bok_keywords:protected] =>
[id:protected] => 89
[type:protected] => category
[parent:protected] => 3
[label:protected] => Disasters
[alreadyInSave:protected] =>
[alreadyInValidation:protected] =>
[validationFailures:protected] => Array
(
)
[_new:BaseObject:private] =>
[_deleted:BaseObject:private] =>
[modifiedColumns:protected] => Array
(
)
)
[91] => Category Object
(
[languages:protected] =>
[bok_resources:protected] =>
[bok_topics:protected] =>
[bok_keywords:protected] =>
[id:protected] => 91
[type:protected] => category
[parent:protected] => 3
[label:protected] => Heavy & Highway
[alreadyInSave:protected] =>
[alreadyInValidation:protected] =>
[validationFailures:protected] => Array
(
)
[_new:BaseObject:private] =>
[_deleted:BaseObject:private] =>
[modifiedColumns:protected] => Array
(
)
)
[90] => Category Object
(
[languages:protected] =>
[bok_resources:protected] =>
[bok_topics:protected] =>
[bok_keywords:protected] =>
[id:protected] => 90
[type:protected] => category
[parent:protected] => 3
[label:protected] => Industrial
[alreadyInSave:protected] =>
[alreadyInValidation:protected] =>
[validationFailures:protected] => Array
(
)
[_new:BaseObject:private] =>
[_deleted:BaseObject:private] =>
[modifiedColumns:protected] => Array
(
)
)
[92] => Category Object
(
[languages:protected] =>
[bok_resources:protected] =>
[bok_topics:protected] =>
[bok_keywords:protected] =>
[id:protected] => 92
[type:protected] => category
[parent:protected] => 3
[label:protected] => LEED/Green Construction
[alreadyInSave:protected] =>
[alreadyInValidation:protected] =>
[validationFailures:protected] => Array
(
)
[_new:BaseObject:private] =>
[_deleted:BaseObject:private] =>
[modifiedColumns:protected] => Array
(
)
)
[93] => Category Object
(
[languages:protected] =>
[bok_resources:protected] =>
[bok_topics:protected] =>
[bok_keywords:protected] =>
[id:protected] => 93
[type:protected] => category
[parent:protected] => 3
[label:protected] => Renovations
[alreadyInSave:protected] =>
[alreadyInValidation:protected] =>
[validationFailures:protected] => Array
(
)
[_new:BaseObject:private] =>
[_deleted:BaseObject:private] =>
[modifiedColumns:protected] => Array
(
)
)
[94] => Category Object
(
[languages:protected] =>
[bok_resources:protected] =>
[bok_topics:protected] =>
[bok_keywords:protected] =>
[id:protected] => 94
[type:protected] => category
[parent:protected] => 3
[label:protected] => Residential
[alreadyInSave:protected] =>
[alreadyInValidation:protected] =>
[validationFailures:protected] => Array
(
)
[_new:BaseObject:private] =>
[_deleted:BaseObject:private] =>
[modifiedColumns:protected] => Array
(
)
)
[95] => Category Object
(
[languages:protected] =>
[bok_resources:protected] =>
[bok_topics:protected] =>
[bok_keywords:protected] =>
[id:protected] => 95
[type:protected] => category
[parent:protected] => 3
[label:protected] => Underground
[alreadyInSave:protected] =>
[alreadyInValidation:protected] =>
[validationFailures:protected] => Array
(
)
[_new:BaseObject:private] =>
[_deleted:BaseObject:private] =>
[modifiedColumns:protected] => Array
(
)
)
)
[categories_initialized:protected] => 1
[mapped_items:protected] =>
[content:protected] =>
[files:protected] =>
[language:protected] => Language Object
(
[id:protected] => 1
[code:protected] => en
[name:protected] => English
[alreadyInSave:protected] =>
[alreadyInValidation:protected] =>
[validationFailures:protected] => Array
(
)
[_new:BaseObject:private] =>
[_deleted:BaseObject:private] =>
[modifiedColumns:protected] => Array
(
)
)
[old_record:protected] =>
[id:protected] => 4426
[old_id:protected] =>
[elcosh_id:protected] => d001656
[type:protected] => document
[display_type:protected] => HTML only (and links)
[user_id:protected] => 0
[language_id:protected] => 1
[tagging_id:protected] => Mike Aguilar
[priority_id:protected] => 1
[title:protected] => Construction Dive -- DeWalt's Jobsite Pro headphones recalled for fire hazards
[total_pages:protected] => 1
[billed_pages:protected] => 1
[publication_number:protected] =>
[part_of:protected] =>
[keywords:protected] => DeWalt, Fire Hazards, recall, headphones
[comments:protected] =>
[summary:protected] => A recall notice by the United States Consumer Product Safety Commission affects over 300,000 DeWalt Jobsite Pro Headphones. The recall is a result of a malfunction that can cause earbuds to overheat while charging or during use, leading to fire and burn hazards.
[transition_comments:protected] =>
[external_link:protected] => https://www.constructiondive.com/news/dewalts-jobsite-pro-headphones-recalled-for-fire-hazards/611248/?utm_source=Sailthru&utm_medium=email&utm_campaign=Issue:%202021-12-10%20Construction%20Dive%20Newsletter%20%5Bissue:38532%5D&utm_term=Construction%20Dive
[consol_link:protected] =>
[more_like_this:protected] =>
[permission_given_by:protected] =>
[published:protected] => T
[billable:protected] => F
[img_name:protected] =>
[img_ext:protected] =>
[img_width:protected] =>
[img_height:protected] =>
[img_credit:protected] =>
[img_practice:protected] =>
[vid_source_id:protected] =>
[vid_running_time:protected] =>
[vid_intended_audience:protected] =>
[vid_acquisition_info:protected] =>
[vid_cost:protected] =>
[vid_producer:protected] =>
[vid_filename:protected] =>
[vid_filename_downloadable:protected] =>
[date_summary:protected] =>
[date_permission_requested:protected] =>
[date_permission_received:protected] =>
[date_review_needed:protected] =>
[date_received:protected] => 12/13/21
[date_completed:protected] => 12/13/21
[date_billed:protected] =>
[date_modified:protected] => 12/13/21
[collBokExports:protected] =>
[lastBokExportCriteria:BaseElcoshItem:private] =>
[alreadyInSave:protected] =>
[alreadyInValidation:protected] =>
[validationFailures:protected] => Array
(
)
[_new:BaseObject:private] =>
[_deleted:BaseObject:private] =>
[modifiedColumns:protected] => Array
(
)
)
)
)
[new_images] => Array
(
[0] => Search_Result Object
(
[title] => Morning Toolbox Talk
[image] => /record/images/4003-p.jpg
[blurb] => This photo is from an early morning toolbox talk on a construction job in Mclean, Virginia. It is being delivered in English and Spanish....
[category] => Array
(
[0] => 20
[1] => 51
[2] => 57
[3] => 64
[4] => 70
[5] => 63
[6] => 78
[7] => 82
[8] => 62
[9] => 87
[10] => 88
[11] => 89
[12] => 91
[13] => 90
[14] => 93
[15] => 94
[16] => 97
)
[labels] => Array
(
[0] => Safety Culture
[1] => Work Environment
[2] => Hazards
[3] => Cement Mason
[4] => Trades
[5] => Flagger
[7] => Laborer
[9] => Operating Engineer
[11] => Reinforcing Ironworker
[13] => Roofer/Waterproofer
[15] => Stonemason
[17] => Structural Ironworker
[19] => Commercial & Institutional
[20] => Jobsites
[21] => Demolition
[23] => Disasters
[25] => Heavy & Highway
[27] => Industrial
[29] => Renovations
[31] => Residential
[33] => Images
[34] => Media
[35] => Media & Documents
)
[type] => Images
[sub_category] =>
[url] => /image/4003/i002691/Morning%2BToolbox%2BTalk.html
[item:protected] => ImageRecord Object
(
[records:protected] => Array
(
)
[recordId:protected] =>
[searchWordClass:protected] =>
[searchWordPeerClass:protected] =>
[bok_record:protected] =>
[authors:protected] =>
[organizations:protected] =>
[collections:protected] =>
[categories:protected] => Array
(
[20] => Category Object
(
[languages:protected] =>
[bok_resources:protected] =>
[bok_topics:protected] =>
[bok_keywords:protected] =>
[id:protected] => 20
[type:protected] => category
[parent:protected] => 7
[label:protected] => Safety Culture
[alreadyInSave:protected] =>
[alreadyInValidation:protected] =>
[validationFailures:protected] => Array
(
)
[_new:BaseObject:private] =>
[_deleted:BaseObject:private] =>
[modifiedColumns:protected] => Array
(
)
)
[51] => Category Object
(
[languages:protected] =>
[bok_resources:protected] =>
[bok_topics:protected] =>
[bok_keywords:protected] =>
[id:protected] => 51
[type:protected] => category
[parent:protected] => 2
[label:protected] => Cement Mason
[alreadyInSave:protected] =>
[alreadyInValidation:protected] =>
[validationFailures:protected] => Array
(
)
[_new:BaseObject:private] =>
[_deleted:BaseObject:private] =>
[modifiedColumns:protected] => Array
(
)
)
[57] => Category Object
(
[languages:protected] =>
[bok_resources:protected] =>
[bok_topics:protected] =>
[bok_keywords:protected] =>
[id:protected] => 57
[type:protected] => category
[parent:protected] => 2
[label:protected] => Flagger
[alreadyInSave:protected] =>
[alreadyInValidation:protected] =>
[validationFailures:protected] => Array
(
)
[_new:BaseObject:private] =>
[_deleted:BaseObject:private] =>
[modifiedColumns:protected] => Array
(
)
)
[64] => Category Object
(
[languages:protected] =>
[bok_resources:protected] =>
[bok_topics:protected] =>
[bok_keywords:protected] =>
[id:protected] => 64
[type:protected] => category
[parent:protected] => 2
[label:protected] => Laborer
[alreadyInSave:protected] =>
[alreadyInValidation:protected] =>
[validationFailures:protected] => Array
(
)
[_new:BaseObject:private] =>
[_deleted:BaseObject:private] =>
[modifiedColumns:protected] => Array
(
)
)
[70] => Category Object
(
[languages:protected] =>
[bok_resources:protected] =>
[bok_topics:protected] =>
[bok_keywords:protected] =>
[id:protected] => 70
[type:protected] => category
[parent:protected] => 2
[label:protected] => Operating Engineer
[alreadyInSave:protected] =>
[alreadyInValidation:protected] =>
[validationFailures:protected] => Array
(
)
[_new:BaseObject:private] =>
[_deleted:BaseObject:private] =>
[modifiedColumns:protected] => Array
(
)
)
[63] => Category Object
(
[languages:protected] =>
[bok_resources:protected] =>
[bok_topics:protected] =>
[bok_keywords:protected] =>
[id:protected] => 63
[type:protected] => category
[parent:protected] => 2
[label:protected] => Reinforcing Ironworker
[alreadyInSave:protected] =>
[alreadyInValidation:protected] =>
[validationFailures:protected] => Array
(
)
[_new:BaseObject:private] =>
[_deleted:BaseObject:private] =>
[modifiedColumns:protected] => Array
(
)
)
[78] => Category Object
(
[languages:protected] =>
[bok_resources:protected] =>
[bok_topics:protected] =>
[bok_keywords:protected] =>
[id:protected] => 78
[type:protected] => category
[parent:protected] => 2
[label:protected] => Roofer/Waterproofer
[alreadyInSave:protected] =>
[alreadyInValidation:protected] =>
[validationFailures:protected] => Array
(
)
[_new:BaseObject:private] =>
[_deleted:BaseObject:private] =>
[modifiedColumns:protected] => Array
(
)
)
[82] => Category Object
(
[languages:protected] =>
[bok_resources:protected] =>
[bok_topics:protected] =>
[bok_keywords:protected] =>
[id:protected] => 82
[type:protected] => category
[parent:protected] => 2
[label:protected] => Stonemason
[alreadyInSave:protected] =>
[alreadyInValidation:protected] =>
[validationFailures:protected] => Array
(
)
[_new:BaseObject:private] =>
[_deleted:BaseObject:private] =>
[modifiedColumns:protected] => Array
(
)
)
[62] => Category Object
(
[languages:protected] =>
[bok_resources:protected] =>
[bok_topics:protected] =>
[bok_keywords:protected] =>
[id:protected] => 62
[type:protected] => category
[parent:protected] => 2
[label:protected] => Structural Ironworker
[alreadyInSave:protected] =>
[alreadyInValidation:protected] =>
[validationFailures:protected] => Array
(
)
[_new:BaseObject:private] =>
[_deleted:BaseObject:private] =>
[modifiedColumns:protected] => Array
(
)
)
[87] => Category Object
(
[languages:protected] =>
[bok_resources:protected] =>
[bok_topics:protected] =>
[bok_keywords:protected] =>
[id:protected] => 87
[type:protected] => category
[parent:protected] => 3
[label:protected] => Commercial & Institutional
[alreadyInSave:protected] =>
[alreadyInValidation:protected] =>
[validationFailures:protected] => Array
(
)
[_new:BaseObject:private] =>
[_deleted:BaseObject:private] =>
[modifiedColumns:protected] => Array
(
)
)
[88] => Category Object
(
[languages:protected] =>
[bok_resources:protected] =>
[bok_topics:protected] =>
[bok_keywords:protected] =>
[id:protected] => 88
[type:protected] => category
[parent:protected] => 3
[label:protected] => Demolition
[alreadyInSave:protected] =>
[alreadyInValidation:protected] =>
[validationFailures:protected] => Array
(
)
[_new:BaseObject:private] =>
[_deleted:BaseObject:private] =>
[modifiedColumns:protected] => Array
(
)
)
[89] => Category Object
(
[languages:protected] =>
[bok_resources:protected] =>
[bok_topics:protected] =>
[bok_keywords:protected] =>
[id:protected] => 89
[type:protected] => category
[parent:protected] => 3
[label:protected] => Disasters
[alreadyInSave:protected] =>
[alreadyInValidation:protected] =>
[validationFailures:protected] => Array
(
)
[_new:BaseObject:private] =>
[_deleted:BaseObject:private] =>
[modifiedColumns:protected] => Array
(
)
)
[91] => Category Object
(
[languages:protected] =>
[bok_resources:protected] =>
[bok_topics:protected] =>
[bok_keywords:protected] =>
[id:protected] => 91
[type:protected] => category
[parent:protected] => 3
[label:protected] => Heavy & Highway
[alreadyInSave:protected] =>
[alreadyInValidation:protected] =>
[validationFailures:protected] => Array
(
)
[_new:BaseObject:private] =>
[_deleted:BaseObject:private] =>
[modifiedColumns:protected] => Array
(
)
)
[90] => Category Object
(
[languages:protected] =>
[bok_resources:protected] =>
[bok_topics:protected] =>
[bok_keywords:protected] =>
[id:protected] => 90
[type:protected] => category
[parent:protected] => 3
[label:protected] => Industrial
[alreadyInSave:protected] =>
[alreadyInValidation:protected] =>
[validationFailures:protected] => Array
(
)
[_new:BaseObject:private] =>
[_deleted:BaseObject:private] =>
[modifiedColumns:protected] => Array
(
)
)
[93] => Category Object
(
[languages:protected] =>
[bok_resources:protected] =>
[bok_topics:protected] =>
[bok_keywords:protected] =>
[id:protected] => 93
[type:protected] => category
[parent:protected] => 3
[label:protected] => Renovations
[alreadyInSave:protected] =>
[alreadyInValidation:protected] =>
[validationFailures:protected] => Array
(
)
[_new:BaseObject:private] =>
[_deleted:BaseObject:private] =>
[modifiedColumns:protected] => Array
(
)
)
[94] => Category Object
(
[languages:protected] =>
[bok_resources:protected] =>
[bok_topics:protected] =>
[bok_keywords:protected] =>
[id:protected] => 94
[type:protected] => category
[parent:protected] => 3
[label:protected] => Residential
[alreadyInSave:protected] =>
[alreadyInValidation:protected] =>
[validationFailures:protected] => Array
(
)
[_new:BaseObject:private] =>
[_deleted:BaseObject:private] =>
[modifiedColumns:protected] => Array
(
)
)
[97] => Category Object
(
[languages:protected] =>
[bok_resources:protected] =>
[bok_topics:protected] =>
[bok_keywords:protected] =>
[id:protected] => 97
[type:protected] => category
[parent:protected] => 5
[label:protected] => Images
[alreadyInSave:protected] =>
[alreadyInValidation:protected] =>
[validationFailures:protected] => Array
(
)
[_new:BaseObject:private] =>
[_deleted:BaseObject:private] =>
[modifiedColumns:protected] => Array
(
)
)
)
[categories_initialized:protected] => 1
[mapped_items:protected] =>
[content:protected] =>
[files:protected] =>
[language:protected] => Language Object
(
[id:protected] => 1
[code:protected] => en
[name:protected] => English
[alreadyInSave:protected] =>
[alreadyInValidation:protected] =>
[validationFailures:protected] => Array
(
)
[_new:BaseObject:private] =>
[_deleted:BaseObject:private] =>
[modifiedColumns:protected] => Array
(
)
)
[old_record:protected] =>
[id:protected] => 4003
[old_id:protected] =>
[elcosh_id:protected] => i002691
[type:protected] => image
[display_type:protected] => Image
[user_id:protected] => 0
[language_id:protected] => 1
[tagging_id:protected] => Bruce Lippy
[priority_id:protected] => 1
[title:protected] => Morning Toolbox Talk
[total_pages:protected] => 0
[billed_pages:protected] => 0
[publication_number:protected] =>
[part_of:protected] =>
[keywords:protected] => toolbox talk, tailgate talk, Spanish, bilingual
[comments:protected] =>
[summary:protected] => This photo is from an early morning toolbox talk on a construction job in Mclean, Virginia. It is being delivered in English and Spanish.
[transition_comments:protected] =>
[external_link:protected] =>
[consol_link:protected] => http://www.cpwrconstructionsolutions.org/electrical/solution/662/worker-training.html
[more_like_this:protected] => d001285,d001304,c000079
[permission_given_by:protected] =>
[published:protected] => T
[billable:protected] => F
[img_name:protected] =>
[img_ext:protected] => jpg
[img_width:protected] =>
[img_height:protected] =>
[img_credit:protected] => Morgan Zavertnik and Hoar Construction
[img_practice:protected] => good
[vid_source_id:protected] =>
[vid_running_time:protected] =>
[vid_intended_audience:protected] =>
[vid_acquisition_info:protected] =>
[vid_cost:protected] =>
[vid_producer:protected] =>
[vid_filename:protected] =>
[vid_filename_downloadable:protected] =>
[date_summary:protected] => November 2015
[date_permission_requested:protected] =>
[date_permission_received:protected] =>
[date_review_needed:protected] =>
[date_received:protected] => 03/02/16
[date_completed:protected] => 03/02/16
[date_billed:protected] =>
[date_modified:protected] => 03/02/16
[collBokExports:protected] =>
[lastBokExportCriteria:BaseElcoshItem:private] =>
[alreadyInSave:protected] =>
[alreadyInValidation:protected] =>
[validationFailures:protected] => Array
(
)
[_new:BaseObject:private] =>
[_deleted:BaseObject:private] =>
[modifiedColumns:protected] => Array
(
)
)
)
[1] => Search_Result Object
(
[title] => Toolbox talk - crew view
[image] => /record/images/4005-p.jpg
[blurb] => Photo of crew listening to a toolbox safety talk before starting work....
[category] => Array
(
[0] => 97
[1] => 20
[2] => 47
[3] => 49
[4] => 51
[5] => 55
[6] => 61
[7] => 64
[8] => 71
[9] => 75
[10] => 63
[11] => 79
[12] => 62
[13] => 87
[14] => 88
[15] => 91
[16] => 90
[17] => 93
[18] => 94
[19] => 95
)
[labels] => Array
(
[0] => Images
[1] => Media
[2] => Media & Documents
[3] => Safety Culture
[4] => Work Environment
[5] => Hazards
[6] => Bricklayer
[7] => Trades
[8] => Carpenter
[10] => Cement Mason
[12] => Electrical Worker
[14] => Interior Systems Carpenter
[16] => Laborer
[18] => Painter
[20] => Plasterer
[22] => Reinforcing Ironworker
[24] => Scaffold Erector
[26] => Structural Ironworker
[28] => Commercial & Institutional
[29] => Jobsites
[30] => Demolition
[32] => Heavy & Highway
[34] => Industrial
[36] => Renovations
[38] => Residential
[40] => Underground
)
[type] => Images
[sub_category] =>
[url] => /image/4005/i002692/Toolbox%2Btalk%2B-%2Bcrew%2Bview.html
[item:protected] => ImageRecord Object
(
[records:protected] => Array
(
)
[recordId:protected] =>
[searchWordClass:protected] =>
[searchWordPeerClass:protected] =>
[bok_record:protected] =>
[authors:protected] =>
[organizations:protected] =>
[collections:protected] =>
[categories:protected] => Array
(
[97] => Category Object
(
[languages:protected] =>
[bok_resources:protected] =>
[bok_topics:protected] =>
[bok_keywords:protected] =>
[id:protected] => 97
[type:protected] => category
[parent:protected] => 5
[label:protected] => Images
[alreadyInSave:protected] =>
[alreadyInValidation:protected] =>
[validationFailures:protected] => Array
(
)
[_new:BaseObject:private] =>
[_deleted:BaseObject:private] =>
[modifiedColumns:protected] => Array
(
)
)
[20] => Category Object
(
[languages:protected] =>
[bok_resources:protected] =>
[bok_topics:protected] =>
[bok_keywords:protected] =>
[id:protected] => 20
[type:protected] => category
[parent:protected] => 7
[label:protected] => Safety Culture
[alreadyInSave:protected] =>
[alreadyInValidation:protected] =>
[validationFailures:protected] => Array
(
)
[_new:BaseObject:private] =>
[_deleted:BaseObject:private] =>
[modifiedColumns:protected] => Array
(
)
)
[47] => Category Object
(
[languages:protected] =>
[bok_resources:protected] =>
[bok_topics:protected] =>
[bok_keywords:protected] =>
[id:protected] => 47
[type:protected] => category
[parent:protected] => 2
[label:protected] => Bricklayer
[alreadyInSave:protected] =>
[alreadyInValidation:protected] =>
[validationFailures:protected] => Array
(
)
[_new:BaseObject:private] =>
[_deleted:BaseObject:private] =>
[modifiedColumns:protected] => Array
(
)
)
[49] => Category Object
(
[languages:protected] =>
[bok_resources:protected] =>
[bok_topics:protected] =>
[bok_keywords:protected] =>
[id:protected] => 49
[type:protected] => category
[parent:protected] => 2
[label:protected] => Carpenter
[alreadyInSave:protected] =>
[alreadyInValidation:protected] =>
[validationFailures:protected] => Array
(
)
[_new:BaseObject:private] =>
[_deleted:BaseObject:private] =>
[modifiedColumns:protected] => Array
(
)
)
[51] => Category Object
(
[languages:protected] =>
[bok_resources:protected] =>
[bok_topics:protected] =>
[bok_keywords:protected] =>
[id:protected] => 51
[type:protected] => category
[parent:protected] => 2
[label:protected] => Cement Mason
[alreadyInSave:protected] =>
[alreadyInValidation:protected] =>
[validationFailures:protected] => Array
(
)
[_new:BaseObject:private] =>
[_deleted:BaseObject:private] =>
[modifiedColumns:protected] => Array
(
)
)
[55] => Category Object
(
[languages:protected] =>
[bok_resources:protected] =>
[bok_topics:protected] =>
[bok_keywords:protected] =>
[id:protected] => 55
[type:protected] => category
[parent:protected] => 2
[label:protected] => Electrical Worker
[alreadyInSave:protected] =>
[alreadyInValidation:protected] =>
[validationFailures:protected] => Array
(
)
[_new:BaseObject:private] =>
[_deleted:BaseObject:private] =>
[modifiedColumns:protected] => Array
(
)
)
[61] => Category Object
(
[languages:protected] =>
[bok_resources:protected] =>
[bok_topics:protected] =>
[bok_keywords:protected] =>
[id:protected] => 61
[type:protected] => category
[parent:protected] => 2
[label:protected] => Interior Systems Carpenter
[alreadyInSave:protected] =>
[alreadyInValidation:protected] =>
[validationFailures:protected] => Array
(
)
[_new:BaseObject:private] =>
[_deleted:BaseObject:private] =>
[modifiedColumns:protected] => Array
(
)
)
[64] => Category Object
(
[languages:protected] =>
[bok_resources:protected] =>
[bok_topics:protected] =>
[bok_keywords:protected] =>
[id:protected] => 64
[type:protected] => category
[parent:protected] => 2
[label:protected] => Laborer
[alreadyInSave:protected] =>
[alreadyInValidation:protected] =>
[validationFailures:protected] => Array
(
)
[_new:BaseObject:private] =>
[_deleted:BaseObject:private] =>
[modifiedColumns:protected] => Array
(
)
)
[71] => Category Object
(
[languages:protected] =>
[bok_resources:protected] =>
[bok_topics:protected] =>
[bok_keywords:protected] =>
[id:protected] => 71
[type:protected] => category
[parent:protected] => 2
[label:protected] => Painter
[alreadyInSave:protected] =>
[alreadyInValidation:protected] =>
[validationFailures:protected] => Array
(
)
[_new:BaseObject:private] =>
[_deleted:BaseObject:private] =>
[modifiedColumns:protected] => Array
(
)
)
[75] => Category Object
(
[languages:protected] =>
[bok_resources:protected] =>
[bok_topics:protected] =>
[bok_keywords:protected] =>
[id:protected] => 75
[type:protected] => category
[parent:protected] => 2
[label:protected] => Plasterer
[alreadyInSave:protected] =>
[alreadyInValidation:protected] =>
[validationFailures:protected] => Array
(
)
[_new:BaseObject:private] =>
[_deleted:BaseObject:private] =>
[modifiedColumns:protected] => Array
(
)
)
[63] => Category Object
(
[languages:protected] =>
[bok_resources:protected] =>
[bok_topics:protected] =>
[bok_keywords:protected] =>
[id:protected] => 63
[type:protected] => category
[parent:protected] => 2
[label:protected] => Reinforcing Ironworker
[alreadyInSave:protected] =>
[alreadyInValidation:protected] =>
[validationFailures:protected] => Array
(
)
[_new:BaseObject:private] =>
[_deleted:BaseObject:private] =>
[modifiedColumns:protected] => Array
(
)
)
[79] => Category Object
(
[languages:protected] =>
[bok_resources:protected] =>
[bok_topics:protected] =>
[bok_keywords:protected] =>
[id:protected] => 79
[type:protected] => category
[parent:protected] => 2
[label:protected] => Scaffold Erector
[alreadyInSave:protected] =>
[alreadyInValidation:protected] =>
[validationFailures:protected] => Array
(
)
[_new:BaseObject:private] =>
[_deleted:BaseObject:private] =>
[modifiedColumns:protected] => Array
(
)
)
[62] => Category Object
(
[languages:protected] =>
[bok_resources:protected] =>
[bok_topics:protected] =>
[bok_keywords:protected] =>
[id:protected] => 62
[type:protected] => category
[parent:protected] => 2
[label:protected] => Structural Ironworker
[alreadyInSave:protected] =>
[alreadyInValidation:protected] =>
[validationFailures:protected] => Array
(
)
[_new:BaseObject:private] =>
[_deleted:BaseObject:private] =>
[modifiedColumns:protected] => Array
(
)
)
[87] => Category Object
(
[languages:protected] =>
[bok_resources:protected] =>
[bok_topics:protected] =>
[bok_keywords:protected] =>
[id:protected] => 87
[type:protected] => category
[parent:protected] => 3
[label:protected] => Commercial & Institutional
[alreadyInSave:protected] =>
[alreadyInValidation:protected] =>
[validationFailures:protected] => Array
(
)
[_new:BaseObject:private] =>
[_deleted:BaseObject:private] =>
[modifiedColumns:protected] => Array
(
)
)
[88] => Category Object
(
[languages:protected] =>
[bok_resources:protected] =>
[bok_topics:protected] =>
[bok_keywords:protected] =>
[id:protected] => 88
[type:protected] => category
[parent:protected] => 3
[label:protected] => Demolition
[alreadyInSave:protected] =>
[alreadyInValidation:protected] =>
[validationFailures:protected] => Array
(
)
[_new:BaseObject:private] =>
[_deleted:BaseObject:private] =>
[modifiedColumns:protected] => Array
(
)
)
[91] => Category Object
(
[languages:protected] =>
[bok_resources:protected] =>
[bok_topics:protected] =>
[bok_keywords:protected] =>
[id:protected] => 91
[type:protected] => category
[parent:protected] => 3
[label:protected] => Heavy & Highway
[alreadyInSave:protected] =>
[alreadyInValidation:protected] =>
[validationFailures:protected] => Array
(
)
[_new:BaseObject:private] =>
[_deleted:BaseObject:private] =>
[modifiedColumns:protected] => Array
(
)
)
[90] => Category Object
(
[languages:protected] =>
[bok_resources:protected] =>
[bok_topics:protected] =>
[bok_keywords:protected] =>
[id:protected] => 90
[type:protected] => category
[parent:protected] => 3
[label:protected] => Industrial
[alreadyInSave:protected] =>
[alreadyInValidation:protected] =>
[validationFailures:protected] => Array
(
)
[_new:BaseObject:private] =>
[_deleted:BaseObject:private] =>
[modifiedColumns:protected] => Array
(
)
)
[93] => Category Object
(
[languages:protected] =>
[bok_resources:protected] =>
[bok_topics:protected] =>
[bok_keywords:protected] =>
[id:protected] => 93
[type:protected] => category
[parent:protected] => 3
[label:protected] => Renovations
[alreadyInSave:protected] =>
[alreadyInValidation:protected] =>
[validationFailures:protected] => Array
(
)
[_new:BaseObject:private] =>
[_deleted:BaseObject:private] =>
[modifiedColumns:protected] => Array
(
)
)
[94] => Category Object
(
[languages:protected] =>
[bok_resources:protected] =>
[bok_topics:protected] =>
[bok_keywords:protected] =>
[id:protected] => 94
[type:protected] => category
[parent:protected] => 3
[label:protected] => Residential
[alreadyInSave:protected] =>
[alreadyInValidation:protected] =>
[validationFailures:protected] => Array
(
)
[_new:BaseObject:private] =>
[_deleted:BaseObject:private] =>
[modifiedColumns:protected] => Array
(
)
)
[95] => Category Object
(
[languages:protected] =>
[bok_resources:protected] =>
[bok_topics:protected] =>
[bok_keywords:protected] =>
[id:protected] => 95
[type:protected] => category
[parent:protected] => 3
[label:protected] => Underground
[alreadyInSave:protected] =>
[alreadyInValidation:protected] =>
[validationFailures:protected] => Array
(
)
[_new:BaseObject:private] =>
[_deleted:BaseObject:private] =>
[modifiedColumns:protected] => Array
(
)
)
)
[categories_initialized:protected] => 1
[mapped_items:protected] =>
[content:protected] =>
[files:protected] =>
[language:protected] => Language Object
(
[id:protected] => 1
[code:protected] => en
[name:protected] => English
[alreadyInSave:protected] =>
[alreadyInValidation:protected] =>
[validationFailures:protected] => Array
(
)
[_new:BaseObject:private] =>
[_deleted:BaseObject:private] =>
[modifiedColumns:protected] => Array
(
)
)
[old_record:protected] =>
[id:protected] => 4005
[old_id:protected] =>
[elcosh_id:protected] => i002692
[type:protected] => image
[display_type:protected] => Image
[user_id:protected] => 0
[language_id:protected] => 1
[tagging_id:protected] => Bruce Lippy
[priority_id:protected] => 1
[title:protected] => Toolbox talk - crew view
[total_pages:protected] => 0
[billed_pages:protected] => 0
[publication_number:protected] =>
[part_of:protected] =>
[keywords:protected] => toolbox talk, tailgate talk, safety talk, Spanish
[comments:protected] =>
[summary:protected] => Photo of crew listening to a toolbox safety talk before starting work.
[transition_comments:protected] =>
[external_link:protected] =>
[consol_link:protected] => http://www.cpwrconstructionsolutions.org/electrical/solution/662/worker-training.html
[more_like_this:protected] => i002691,d001269, c000079, d001285
[permission_given_by:protected] =>
[published:protected] => T
[billable:protected] => F
[img_name:protected] =>
[img_ext:protected] => jpg
[img_width:protected] =>
[img_height:protected] =>
[img_credit:protected] => Morgan Zavertnik and Hoar Construction
[img_practice:protected] => good
[vid_source_id:protected] =>
[vid_running_time:protected] =>
[vid_intended_audience:protected] =>
[vid_acquisition_info:protected] =>
[vid_cost:protected] =>
[vid_producer:protected] =>
[vid_filename:protected] =>
[vid_filename_downloadable:protected] =>
[date_summary:protected] => November 2015
[date_permission_requested:protected] =>
[date_permission_received:protected] =>
[date_review_needed:protected] =>
[date_received:protected] => 03/02/16
[date_completed:protected] => 03/02/16
[date_billed:protected] =>
[date_modified:protected] => 03/02/16
[collBokExports:protected] =>
[lastBokExportCriteria:BaseElcoshItem:private] =>
[alreadyInSave:protected] =>
[alreadyInValidation:protected] =>
[validationFailures:protected] => Array
(
)
[_new:BaseObject:private] =>
[_deleted:BaseObject:private] =>
[modifiedColumns:protected] => Array
(
)
)
)
[2] => Search_Result Object
(
[title] => Toolbox talk - long shot
[image] => /record/images/4006-p.jpg
[blurb] => This crew gathered every morning before starting work to discuss a new safety topic....
[category] => Array
(
[0] => 20
[1] => 47
[2] => 49
[3] => 51
[4] => 55
[5] => 64
[6] => 68
[7] => 75
[8] => 76
[9] => 63
[10] => 78
[11] => 79
[12] => 82
[13] => 62
[14] => 87
[15] => 88
[16] => 91
[17] => 90
[18] => 93
[19] => 94
[20] => 95
[21] => 97
)
[labels] => Array
(
[0] => Safety Culture
[1] => Work Environment
[2] => Hazards
[3] => Bricklayer
[4] => Trades
[5] => Carpenter
[7] => Cement Mason
[9] => Electrical Worker
[11] => Laborer
[13] => Maintenance Worker
[15] => Plasterer
[17] => Plumber/Pipefitter
[19] => Reinforcing Ironworker
[21] => Roofer/Waterproofer
[23] => Scaffold Erector
[25] => Stonemason
[27] => Structural Ironworker
[29] => Commercial & Institutional
[30] => Jobsites
[31] => Demolition
[33] => Heavy & Highway
[35] => Industrial
[37] => Renovations
[39] => Residential
[41] => Underground
[43] => Images
[44] => Media
[45] => Media & Documents
)
[type] => Images
[sub_category] =>
[url] => /image/4006/i002693/Toolbox%2Btalk%2B-%2Blong%2Bshot.html
[item:protected] => ImageRecord Object
(
[records:protected] => Array
(
)
[recordId:protected] =>
[searchWordClass:protected] =>
[searchWordPeerClass:protected] =>
[bok_record:protected] =>
[authors:protected] =>
[organizations:protected] =>
[collections:protected] =>
[categories:protected] => Array
(
[20] => Category Object
(
[languages:protected] =>
[bok_resources:protected] =>
[bok_topics:protected] =>
[bok_keywords:protected] =>
[id:protected] => 20
[type:protected] => category
[parent:protected] => 7
[label:protected] => Safety Culture
[alreadyInSave:protected] =>
[alreadyInValidation:protected] =>
[validationFailures:protected] => Array
(
)
[_new:BaseObject:private] =>
[_deleted:BaseObject:private] =>
[modifiedColumns:protected] => Array
(
)
)
[47] => Category Object
(
[languages:protected] =>
[bok_resources:protected] =>
[bok_topics:protected] =>
[bok_keywords:protected] =>
[id:protected] => 47
[type:protected] => category
[parent:protected] => 2
[label:protected] => Bricklayer
[alreadyInSave:protected] =>
[alreadyInValidation:protected] =>
[validationFailures:protected] => Array
(
)
[_new:BaseObject:private] =>
[_deleted:BaseObject:private] =>
[modifiedColumns:protected] => Array
(
)
)
[49] => Category Object
(
[languages:protected] =>
[bok_resources:protected] =>
[bok_topics:protected] =>
[bok_keywords:protected] =>
[id:protected] => 49
[type:protected] => category
[parent:protected] => 2
[label:protected] => Carpenter
[alreadyInSave:protected] =>
[alreadyInValidation:protected] =>
[validationFailures:protected] => Array
(
)
[_new:BaseObject:private] =>
[_deleted:BaseObject:private] =>
[modifiedColumns:protected] => Array
(
)
)
[51] => Category Object
(
[languages:protected] =>
[bok_resources:protected] =>
[bok_topics:protected] =>
[bok_keywords:protected] =>
[id:protected] => 51
[type:protected] => category
[parent:protected] => 2
[label:protected] => Cement Mason
[alreadyInSave:protected] =>
[alreadyInValidation:protected] =>
[validationFailures:protected] => Array
(
)
[_new:BaseObject:private] =>
[_deleted:BaseObject:private] =>
[modifiedColumns:protected] => Array
(
)
)
[55] => Category Object
(
[languages:protected] =>
[bok_resources:protected] =>
[bok_topics:protected] =>
[bok_keywords:protected] =>
[id:protected] => 55
[type:protected] => category
[parent:protected] => 2
[label:protected] => Electrical Worker
[alreadyInSave:protected] =>
[alreadyInValidation:protected] =>
[validationFailures:protected] => Array
(
)
[_new:BaseObject:private] =>
[_deleted:BaseObject:private] =>
[modifiedColumns:protected] => Array
(
)
)
[64] => Category Object
(
[languages:protected] =>
[bok_resources:protected] =>
[bok_topics:protected] =>
[bok_keywords:protected] =>
[id:protected] => 64
[type:protected] => category
[parent:protected] => 2
[label:protected] => Laborer
[alreadyInSave:protected] =>
[alreadyInValidation:protected] =>
[validationFailures:protected] => Array
(
)
[_new:BaseObject:private] =>
[_deleted:BaseObject:private] =>
[modifiedColumns:protected] => Array
(
)
)
[68] => Category Object
(
[languages:protected] =>
[bok_resources:protected] =>
[bok_topics:protected] =>
[bok_keywords:protected] =>
[id:protected] => 68
[type:protected] => category
[parent:protected] => 2
[label:protected] => Maintenance Worker
[alreadyInSave:protected] =>
[alreadyInValidation:protected] =>
[validationFailures:protected] => Array
(
)
[_new:BaseObject:private] =>
[_deleted:BaseObject:private] =>
[modifiedColumns:protected] => Array
(
)
)
[75] => Category Object
(
[languages:protected] =>
[bok_resources:protected] =>
[bok_topics:protected] =>
[bok_keywords:protected] =>
[id:protected] => 75
[type:protected] => category
[parent:protected] => 2
[label:protected] => Plasterer
[alreadyInSave:protected] =>
[alreadyInValidation:protected] =>
[validationFailures:protected] => Array
(
)
[_new:BaseObject:private] =>
[_deleted:BaseObject:private] =>
[modifiedColumns:protected] => Array
(
)
)
[76] => Category Object
(
[languages:protected] =>
[bok_resources:protected] =>
[bok_topics:protected] =>
[bok_keywords:protected] =>
[id:protected] => 76
[type:protected] => category
[parent:protected] => 2
[label:protected] => Plumber/Pipefitter
[alreadyInSave:protected] =>
[alreadyInValidation:protected] =>
[validationFailures:protected] => Array
(
)
[_new:BaseObject:private] =>
[_deleted:BaseObject:private] =>
[modifiedColumns:protected] => Array
(
)
)
[63] => Category Object
(
[languages:protected] =>
[bok_resources:protected] =>
[bok_topics:protected] =>
[bok_keywords:protected] =>
[id:protected] => 63
[type:protected] => category
[parent:protected] => 2
[label:protected] => Reinforcing Ironworker
[alreadyInSave:protected] =>
[alreadyInValidation:protected] =>
[validationFailures:protected] => Array
(
)
[_new:BaseObject:private] =>
[_deleted:BaseObject:private] =>
[modifiedColumns:protected] => Array
(
)
)
[78] => Category Object
(
[languages:protected] =>
[bok_resources:protected] =>
[bok_topics:protected] =>
[bok_keywords:protected] =>
[id:protected] => 78
[type:protected] => category
[parent:protected] => 2
[label:protected] => Roofer/Waterproofer
[alreadyInSave:protected] =>
[alreadyInValidation:protected] =>
[validationFailures:protected] => Array
(
)
[_new:BaseObject:private] =>
[_deleted:BaseObject:private] =>
[modifiedColumns:protected] => Array
(
)
)
[79] => Category Object
(
[languages:protected] =>
[bok_resources:protected] =>
[bok_topics:protected] =>
[bok_keywords:protected] =>
[id:protected] => 79
[type:protected] => category
[parent:protected] => 2
[label:protected] => Scaffold Erector
[alreadyInSave:protected] =>
[alreadyInValidation:protected] =>
[validationFailures:protected] => Array
(
)
[_new:BaseObject:private] =>
[_deleted:BaseObject:private] =>
[modifiedColumns:protected] => Array
(
)
)
[82] => Category Object
(
[languages:protected] =>
[bok_resources:protected] =>
[bok_topics:protected] =>
[bok_keywords:protected] =>
[id:protected] => 82
[type:protected] => category
[parent:protected] => 2
[label:protected] => Stonemason
[alreadyInSave:protected] =>
[alreadyInValidation:protected] =>
[validationFailures:protected] => Array
(
)
[_new:BaseObject:private] =>
[_deleted:BaseObject:private] =>
[modifiedColumns:protected] => Array
(
)
)
[62] => Category Object
(
[languages:protected] =>
[bok_resources:protected] =>
[bok_topics:protected] =>
[bok_keywords:protected] =>
[id:protected] => 62
[type:protected] => category
[parent:protected] => 2
[label:protected] => Structural Ironworker
[alreadyInSave:protected] =>
[alreadyInValidation:protected] =>
[validationFailures:protected] => Array
(
)
[_new:BaseObject:private] =>
[_deleted:BaseObject:private] =>
[modifiedColumns:protected] => Array
(
)
)
[87] => Category Object
(
[languages:protected] =>
[bok_resources:protected] =>
[bok_topics:protected] =>
[bok_keywords:protected] =>
[id:protected] => 87
[type:protected] => category
[parent:protected] => 3
[label:protected] => Commercial & Institutional
[alreadyInSave:protected] =>
[alreadyInValidation:protected] =>
[validationFailures:protected] => Array
(
)
[_new:BaseObject:private] =>
[_deleted:BaseObject:private] =>
[modifiedColumns:protected] => Array
(
)
)
[88] => Category Object
(
[languages:protected] =>
[bok_resources:protected] =>
[bok_topics:protected] =>
[bok_keywords:protected] =>
[id:protected] => 88
[type:protected] => category
[parent:protected] => 3
[label:protected] => Demolition
[alreadyInSave:protected] =>
[alreadyInValidation:protected] =>
[validationFailures:protected] => Array
(
)
[_new:BaseObject:private] =>
[_deleted:BaseObject:private] =>
[modifiedColumns:protected] => Array
(
)
)
[91] => Category Object
(
[languages:protected] =>
[bok_resources:protected] =>
[bok_topics:protected] =>
[bok_keywords:protected] =>
[id:protected] => 91
[type:protected] => category
[parent:protected] => 3
[label:protected] => Heavy & Highway
[alreadyInSave:protected] =>
[alreadyInValidation:protected] =>
[validationFailures:protected] => Array
(
)
[_new:BaseObject:private] =>
[_deleted:BaseObject:private] =>
[modifiedColumns:protected] => Array
(
)
)
[90] => Category Object
(
[languages:protected] =>
[bok_resources:protected] =>
[bok_topics:protected] =>
[bok_keywords:protected] =>
[id:protected] => 90
[type:protected] => category
[parent:protected] => 3
[label:protected] => Industrial
[alreadyInSave:protected] =>
[alreadyInValidation:protected] =>
[validationFailures:protected] => Array
(
)
[_new:BaseObject:private] =>
[_deleted:BaseObject:private] =>
[modifiedColumns:protected] => Array
(
)
)
[93] => Category Object
(
[languages:protected] =>
[bok_resources:protected] =>
[bok_topics:protected] =>
[bok_keywords:protected] =>
[id:protected] => 93
[type:protected] => category
[parent:protected] => 3
[label:protected] => Renovations
[alreadyInSave:protected] =>
[alreadyInValidation:protected] =>
[validationFailures:protected] => Array
(
)
[_new:BaseObject:private] =>
[_deleted:BaseObject:private] =>
[modifiedColumns:protected] => Array
(
)
)
[94] => Category Object
(
[languages:protected] =>
[bok_resources:protected] =>
[bok_topics:protected] =>
[bok_keywords:protected] =>
[id:protected] => 94
[type:protected] => category
[parent:protected] => 3
[label:protected] => Residential
[alreadyInSave:protected] =>
[alreadyInValidation:protected] =>
[validationFailures:protected] => Array
(
)
[_new:BaseObject:private] =>
[_deleted:BaseObject:private] =>
[modifiedColumns:protected] => Array
(
)
)
[95] => Category Object
(
[languages:protected] =>
[bok_resources:protected] =>
[bok_topics:protected] =>
[bok_keywords:protected] =>
[id:protected] => 95
[type:protected] => category
[parent:protected] => 3
[label:protected] => Underground
[alreadyInSave:protected] =>
[alreadyInValidation:protected] =>
[validationFailures:protected] => Array
(
)
[_new:BaseObject:private] =>
[_deleted:BaseObject:private] =>
[modifiedColumns:protected] => Array
(
)
)
[97] => Category Object
(
[languages:protected] =>
[bok_resources:protected] =>
[bok_topics:protected] =>
[bok_keywords:protected] =>
[id:protected] => 97
[type:protected] => category
[parent:protected] => 5
[label:protected] => Images
[alreadyInSave:protected] =>
[alreadyInValidation:protected] =>
[validationFailures:protected] => Array
(
)
[_new:BaseObject:private] =>
[_deleted:BaseObject:private] =>
[modifiedColumns:protected] => Array
(
)
)
)
[categories_initialized:protected] => 1
[mapped_items:protected] =>
[content:protected] =>
[files:protected] =>
[language:protected] => Language Object
(
[id:protected] => 1
[code:protected] => en
[name:protected] => English
[alreadyInSave:protected] =>
[alreadyInValidation:protected] =>
[validationFailures:protected] => Array
(
)
[_new:BaseObject:private] =>
[_deleted:BaseObject:private] =>
[modifiedColumns:protected] => Array
(
)
)
[old_record:protected] =>
[id:protected] => 4006
[old_id:protected] =>
[elcosh_id:protected] => i002693
[type:protected] => image
[display_type:protected] => Image
[user_id:protected] => 0
[language_id:protected] => 1
[tagging_id:protected] => Bruce Lippy
[priority_id:protected] => 1
[title:protected] => Toolbox talk - long shot
[total_pages:protected] => 0
[billed_pages:protected] => 0
[publication_number:protected] =>
[part_of:protected] =>
[keywords:protected] => toolbox talk, tailgate talk, safety minute
[comments:protected] =>
[summary:protected] => This crew gathered every morning before starting work to discuss a new safety topic.
[transition_comments:protected] =>
[external_link:protected] =>
[consol_link:protected] => http://www.cpwrconstructionsolutions.org/electrical/solution/662/worker-training.html
[more_like_this:protected] => i002691,i002692,d001269,d000527
[permission_given_by:protected] =>
[published:protected] => T
[billable:protected] => F
[img_name:protected] =>
[img_ext:protected] => jpg
[img_width:protected] =>
[img_height:protected] =>
[img_credit:protected] => Morgan Zavertnik and Hoar Construction
[img_practice:protected] => good
[vid_source_id:protected] =>
[vid_running_time:protected] =>
[vid_intended_audience:protected] =>
[vid_acquisition_info:protected] =>
[vid_cost:protected] =>
[vid_producer:protected] =>
[vid_filename:protected] =>
[vid_filename_downloadable:protected] =>
[date_summary:protected] => November 2015
[date_permission_requested:protected] =>
[date_permission_received:protected] =>
[date_review_needed:protected] =>
[date_received:protected] => 03/02/16
[date_completed:protected] => 03/02/16
[date_billed:protected] =>
[date_modified:protected] => 03/02/16
[collBokExports:protected] =>
[lastBokExportCriteria:BaseElcoshItem:private] =>
[alreadyInSave:protected] =>
[alreadyInValidation:protected] =>
[validationFailures:protected] => Array
(
)
[_new:BaseObject:private] =>
[_deleted:BaseObject:private] =>
[modifiedColumns:protected] => Array
(
)
)
)
[3] => Search_Result Object
(
[title] => Safety officer discussing ongoing project with marketing coordinator
[image] => /record/images/4014-p.jpg
[blurb] => The safety officer (left) points out the good safety practices on this project that reflect well on the firm and may influence future clients....
[category] => Array
(
[0] => 97
[1] => 20
[2] => 46
[3] => 47
[4] => 49
[5] => 50
[6] => 51
[7] => 54
[8] => 55
[9] => 58
[10] => 60
[11] => 61
[12] => 64
[13] => 71
[14] => 75
[15] => 76
[16] => 63
[17] => 79
[18] => 80
[19] => 82
[20] => 62
[21] => 83
[22] => 87
[23] => 91
[24] => 90
[25] => 93
[26] => 94
)
[labels] => Array
(
[0] => Images
[1] => Media
[2] => Media & Documents
[3] => Safety Culture
[4] => Work Environment
[5] => Hazards
[6] => Boilermaker
[7] => Trades
[8] => Bricklayer
[10] => Carpenter
[12] => Carpet Layer
[14] => Cement Mason
[16] => Drywall Applicator Specialist
[18] => Electrical Worker
[20] => Glazier
[22] => HVAC
[24] => Interior Systems Carpenter
[26] => Laborer
[28] => Painter
[30] => Plasterer
[32] => Plumber/Pipefitter
[34] => Reinforcing Ironworker
[36] => Scaffold Erector
[38] => Sheetmetal Worker
[40] => Stonemason
[42] => Structural Ironworker
[44] => Terrazzo Worker
[46] => Commercial & Institutional
[47] => Jobsites
[48] => Heavy & Highway
[50] => Industrial
[52] => Renovations
[54] => Residential
)
[type] => Images
[sub_category] =>
[url] => /image/4014/i002700/Safety%2Bofficer%2Bdiscussing%2Bongoing%2Bproject%2Bwith%2Bmarketing%2Bcoordinator.html
[item:protected] => ImageRecord Object
(
[records:protected] => Array
(
)
[recordId:protected] =>
[searchWordClass:protected] =>
[searchWordPeerClass:protected] =>
[bok_record:protected] =>
[authors:protected] =>
[organizations:protected] =>
[collections:protected] =>
[categories:protected] => Array
(
[97] => Category Object
(
[languages:protected] =>
[bok_resources:protected] =>
[bok_topics:protected] =>
[bok_keywords:protected] =>
[id:protected] => 97
[type:protected] => category
[parent:protected] => 5
[label:protected] => Images
[alreadyInSave:protected] =>
[alreadyInValidation:protected] =>
[validationFailures:protected] => Array
(
)
[_new:BaseObject:private] =>
[_deleted:BaseObject:private] =>
[modifiedColumns:protected] => Array
(
)
)
[20] => Category Object
(
[languages:protected] =>
[bok_resources:protected] =>
[bok_topics:protected] =>
[bok_keywords:protected] =>
[id:protected] => 20
[type:protected] => category
[parent:protected] => 7
[label:protected] => Safety Culture
[alreadyInSave:protected] =>
[alreadyInValidation:protected] =>
[validationFailures:protected] => Array
(
)
[_new:BaseObject:private] =>
[_deleted:BaseObject:private] =>
[modifiedColumns:protected] => Array
(
)
)
[46] => Category Object
(
[languages:protected] =>
[bok_resources:protected] =>
[bok_topics:protected] =>
[bok_keywords:protected] =>
[id:protected] => 46
[type:protected] => category
[parent:protected] => 2
[label:protected] => Boilermaker
[alreadyInSave:protected] =>
[alreadyInValidation:protected] =>
[validationFailures:protected] => Array
(
)
[_new:BaseObject:private] =>
[_deleted:BaseObject:private] =>
[modifiedColumns:protected] => Array
(
)
)
[47] => Category Object
(
[languages:protected] =>
[bok_resources:protected] =>
[bok_topics:protected] =>
[bok_keywords:protected] =>
[id:protected] => 47
[type:protected] => category
[parent:protected] => 2
[label:protected] => Bricklayer
[alreadyInSave:protected] =>
[alreadyInValidation:protected] =>
[validationFailures:protected] => Array
(
)
[_new:BaseObject:private] =>
[_deleted:BaseObject:private] =>
[modifiedColumns:protected] => Array
(
)
)
[49] => Category Object
(
[languages:protected] =>
[bok_resources:protected] =>
[bok_topics:protected] =>
[bok_keywords:protected] =>
[id:protected] => 49
[type:protected] => category
[parent:protected] => 2
[label:protected] => Carpenter
[alreadyInSave:protected] =>
[alreadyInValidation:protected] =>
[validationFailures:protected] => Array
(
)
[_new:BaseObject:private] =>
[_deleted:BaseObject:private] =>
[modifiedColumns:protected] => Array
(
)
)
[50] => Category Object
(
[languages:protected] =>
[bok_resources:protected] =>
[bok_topics:protected] =>
[bok_keywords:protected] =>
[id:protected] => 50
[type:protected] => category
[parent:protected] => 2
[label:protected] => Carpet Layer
[alreadyInSave:protected] =>
[alreadyInValidation:protected] =>
[validationFailures:protected] => Array
(
)
[_new:BaseObject:private] =>
[_deleted:BaseObject:private] =>
[modifiedColumns:protected] => Array
(
)
)
[51] => Category Object
(
[languages:protected] =>
[bok_resources:protected] =>
[bok_topics:protected] =>
[bok_keywords:protected] =>
[id:protected] => 51
[type:protected] => category
[parent:protected] => 2
[label:protected] => Cement Mason
[alreadyInSave:protected] =>
[alreadyInValidation:protected] =>
[validationFailures:protected] => Array
(
)
[_new:BaseObject:private] =>
[_deleted:BaseObject:private] =>
[modifiedColumns:protected] => Array
(
)
)
[54] => Category Object
(
[languages:protected] =>
[bok_resources:protected] =>
[bok_topics:protected] =>
[bok_keywords:protected] =>
[id:protected] => 54
[type:protected] => category
[parent:protected] => 2
[label:protected] => Drywall Applicator Specialist
[alreadyInSave:protected] =>
[alreadyInValidation:protected] =>
[validationFailures:protected] => Array
(
)
[_new:BaseObject:private] =>
[_deleted:BaseObject:private] =>
[modifiedColumns:protected] => Array
(
)
)
[55] => Category Object
(
[languages:protected] =>
[bok_resources:protected] =>
[bok_topics:protected] =>
[bok_keywords:protected] =>
[id:protected] => 55
[type:protected] => category
[parent:protected] => 2
[label:protected] => Electrical Worker
[alreadyInSave:protected] =>
[alreadyInValidation:protected] =>
[validationFailures:protected] => Array
(
)
[_new:BaseObject:private] =>
[_deleted:BaseObject:private] =>
[modifiedColumns:protected] => Array
(
)
)
[58] => Category Object
(
[languages:protected] =>
[bok_resources:protected] =>
[bok_topics:protected] =>
[bok_keywords:protected] =>
[id:protected] => 58
[type:protected] => category
[parent:protected] => 2
[label:protected] => Glazier
[alreadyInSave:protected] =>
[alreadyInValidation:protected] =>
[validationFailures:protected] => Array
(
)
[_new:BaseObject:private] =>
[_deleted:BaseObject:private] =>
[modifiedColumns:protected] => Array
(
)
)
[60] => Category Object
(
[languages:protected] =>
[bok_resources:protected] =>
[bok_topics:protected] =>
[bok_keywords:protected] =>
[id:protected] => 60
[type:protected] => category
[parent:protected] => 2
[label:protected] => HVAC
[alreadyInSave:protected] =>
[alreadyInValidation:protected] =>
[validationFailures:protected] => Array
(
)
[_new:BaseObject:private] =>
[_deleted:BaseObject:private] =>
[modifiedColumns:protected] => Array
(
)
)
[61] => Category Object
(
[languages:protected] =>
[bok_resources:protected] =>
[bok_topics:protected] =>
[bok_keywords:protected] =>
[id:protected] => 61
[type:protected] => category
[parent:protected] => 2
[label:protected] => Interior Systems Carpenter
[alreadyInSave:protected] =>
[alreadyInValidation:protected] =>
[validationFailures:protected] => Array
(
)
[_new:BaseObject:private] =>
[_deleted:BaseObject:private] =>
[modifiedColumns:protected] => Array
(
)
)
[64] => Category Object
(
[languages:protected] =>
[bok_resources:protected] =>
[bok_topics:protected] =>
[bok_keywords:protected] =>
[id:protected] => 64
[type:protected] => category
[parent:protected] => 2
[label:protected] => Laborer
[alreadyInSave:protected] =>
[alreadyInValidation:protected] =>
[validationFailures:protected] => Array
(
)
[_new:BaseObject:private] =>
[_deleted:BaseObject:private] =>
[modifiedColumns:protected] => Array
(
)
)
[71] => Category Object
(
[languages:protected] =>
[bok_resources:protected] =>
[bok_topics:protected] =>
[bok_keywords:protected] =>
[id:protected] => 71
[type:protected] => category
[parent:protected] => 2
[label:protected] => Painter
[alreadyInSave:protected] =>
[alreadyInValidation:protected] =>
[validationFailures:protected] => Array
(
)
[_new:BaseObject:private] =>
[_deleted:BaseObject:private] =>
[modifiedColumns:protected] => Array
(
)
)
[75] => Category Object
(
[languages:protected] =>
[bok_resources:protected] =>
[bok_topics:protected] =>
[bok_keywords:protected] =>
[id:protected] => 75
[type:protected] => category
[parent:protected] => 2
[label:protected] => Plasterer
[alreadyInSave:protected] =>
[alreadyInValidation:protected] =>
[validationFailures:protected] => Array
(
)
[_new:BaseObject:private] =>
[_deleted:BaseObject:private] =>
[modifiedColumns:protected] => Array
(
)
)
[76] => Category Object
(
[languages:protected] =>
[bok_resources:protected] =>
[bok_topics:protected] =>
[bok_keywords:protected] =>
[id:protected] => 76
[type:protected] => category
[parent:protected] => 2
[label:protected] => Plumber/Pipefitter
[alreadyInSave:protected] =>
[alreadyInValidation:protected] =>
[validationFailures:protected] => Array
(
)
[_new:BaseObject:private] =>
[_deleted:BaseObject:private] =>
[modifiedColumns:protected] => Array
(
)
)
[63] => Category Object
(
[languages:protected] =>
[bok_resources:protected] =>
[bok_topics:protected] =>
[bok_keywords:protected] =>
[id:protected] => 63
[type:protected] => category
[parent:protected] => 2
[label:protected] => Reinforcing Ironworker
[alreadyInSave:protected] =>
[alreadyInValidation:protected] =>
[validationFailures:protected] => Array
(
)
[_new:BaseObject:private] =>
[_deleted:BaseObject:private] =>
[modifiedColumns:protected] => Array
(
)
)
[79] => Category Object
(
[languages:protected] =>
[bok_resources:protected] =>
[bok_topics:protected] =>
[bok_keywords:protected] =>
[id:protected] => 79
[type:protected] => category
[parent:protected] => 2
[label:protected] => Scaffold Erector
[alreadyInSave:protected] =>
[alreadyInValidation:protected] =>
[validationFailures:protected] => Array
(
)
[_new:BaseObject:private] =>
[_deleted:BaseObject:private] =>
[modifiedColumns:protected] => Array
(
)
)
[80] => Category Object
(
[languages:protected] =>
[bok_resources:protected] =>
[bok_topics:protected] =>
[bok_keywords:protected] =>
[id:protected] => 80
[type:protected] => category
[parent:protected] => 2
[label:protected] => Sheetmetal Worker
[alreadyInSave:protected] =>
[alreadyInValidation:protected] =>
[validationFailures:protected] => Array
(
)
[_new:BaseObject:private] =>
[_deleted:BaseObject:private] =>
[modifiedColumns:protected] => Array
(
)
)
[82] => Category Object
(
[languages:protected] =>
[bok_resources:protected] =>
[bok_topics:protected] =>
[bok_keywords:protected] =>
[id:protected] => 82
[type:protected] => category
[parent:protected] => 2
[label:protected] => Stonemason
[alreadyInSave:protected] =>
[alreadyInValidation:protected] =>
[validationFailures:protected] => Array
(
)
[_new:BaseObject:private] =>
[_deleted:BaseObject:private] =>
[modifiedColumns:protected] => Array
(
)
)
[62] => Category Object
(
[languages:protected] =>
[bok_resources:protected] =>
[bok_topics:protected] =>
[bok_keywords:protected] =>
[id:protected] => 62
[type:protected] => category
[parent:protected] => 2
[label:protected] => Structural Ironworker
[alreadyInSave:protected] =>
[alreadyInValidation:protected] =>
[validationFailures:protected] => Array
(
)
[_new:BaseObject:private] =>
[_deleted:BaseObject:private] =>
[modifiedColumns:protected] => Array
(
)
)
[83] => Category Object
(
[languages:protected] =>
[bok_resources:protected] =>
[bok_topics:protected] =>
[bok_keywords:protected] =>
[id:protected] => 83
[type:protected] => category
[parent:protected] => 2
[label:protected] => Terrazzo Worker
[alreadyInSave:protected] =>
[alreadyInValidation:protected] =>
[validationFailures:protected] => Array
(
)
[_new:BaseObject:private] =>
[_deleted:BaseObject:private] =>
[modifiedColumns:protected] => Array
(
)
)
[87] => Category Object
(
[languages:protected] =>
[bok_resources:protected] =>
[bok_topics:protected] =>
[bok_keywords:protected] =>
[id:protected] => 87
[type:protected] => category
[parent:protected] => 3
[label:protected] => Commercial & Institutional
[alreadyInSave:protected] =>
[alreadyInValidation:protected] =>
[validationFailures:protected] => Array
(
)
[_new:BaseObject:private] =>
[_deleted:BaseObject:private] =>
[modifiedColumns:protected] => Array
(
)
)
[91] => Category Object
(
[languages:protected] =>
[bok_resources:protected] =>
[bok_topics:protected] =>
[bok_keywords:protected] =>
[id:protected] => 91
[type:protected] => category
[parent:protected] => 3
[label:protected] => Heavy & Highway
[alreadyInSave:protected] =>
[alreadyInValidation:protected] =>
[validationFailures:protected] => Array
(
)
[_new:BaseObject:private] =>
[_deleted:BaseObject:private] =>
[modifiedColumns:protected] => Array
(
)
)
[90] => Category Object
(
[languages:protected] =>
[bok_resources:protected] =>
[bok_topics:protected] =>
[bok_keywords:protected] =>
[id:protected] => 90
[type:protected] => category
[parent:protected] => 3
[label:protected] => Industrial
[alreadyInSave:protected] =>
[alreadyInValidation:protected] =>
[validationFailures:protected] => Array
(
)
[_new:BaseObject:private] =>
[_deleted:BaseObject:private] =>
[modifiedColumns:protected] => Array
(
)
)
[93] => Category Object
(
[languages:protected] =>
[bok_resources:protected] =>
[bok_topics:protected] =>
[bok_keywords:protected] =>
[id:protected] => 93
[type:protected] => category
[parent:protected] => 3
[label:protected] => Renovations
[alreadyInSave:protected] =>
[alreadyInValidation:protected] =>
[validationFailures:protected] => Array
(
)
[_new:BaseObject:private] =>
[_deleted:BaseObject:private] =>
[modifiedColumns:protected] => Array
(
)
)
[94] => Category Object
(
[languages:protected] =>
[bok_resources:protected] =>
[bok_topics:protected] =>
[bok_keywords:protected] =>
[id:protected] => 94
[type:protected] => category
[parent:protected] => 3
[label:protected] => Residential
[alreadyInSave:protected] =>
[alreadyInValidation:protected] =>
[validationFailures:protected] => Array
(
)
[_new:BaseObject:private] =>
[_deleted:BaseObject:private] =>
[modifiedColumns:protected] => Array
(
)
)
)
[categories_initialized:protected] => 1
[mapped_items:protected] =>
[content:protected] =>
[files:protected] =>
[language:protected] => Language Object
(
[id:protected] => 1
[code:protected] => en
[name:protected] => English
[alreadyInSave:protected] =>
[alreadyInValidation:protected] =>
[validationFailures:protected] => Array
(
)
[_new:BaseObject:private] =>
[_deleted:BaseObject:private] =>
[modifiedColumns:protected] => Array
(
)
)
[old_record:protected] =>
[id:protected] => 4014
[old_id:protected] =>
[elcosh_id:protected] => i002700
[type:protected] => image
[display_type:protected] => Image
[user_id:protected] => 0
[language_id:protected] => 1
[tagging_id:protected] => Bruce Lippy
[priority_id:protected] => 1
[title:protected] => Safety officer discussing ongoing project with marketing coordinator
[total_pages:protected] => 0
[billed_pages:protected] => 0
[publication_number:protected] =>
[part_of:protected] =>
[keywords:protected] => Latino, safety officer, safety culture
[comments:protected] =>
[summary:protected] => The safety officer (left) points out the good safety practices on this project that reflect well on the firm and may influence future clients.
[transition_comments:protected] =>
[external_link:protected] =>
[consol_link:protected] => http://www.cpwrconstructionsolutions.org/index.php
[more_like_this:protected] => d000989,d001351,d001362,d000652, d001101, d000931, d001395
[permission_given_by:protected] =>
[published:protected] => T
[billable:protected] => F
[img_name:protected] =>
[img_ext:protected] => jpg
[img_width:protected] =>
[img_height:protected] =>
[img_credit:protected] => Hoar Construction, Photo by Neil Lippy
[img_practice:protected] => good
[vid_source_id:protected] =>
[vid_running_time:protected] =>
[vid_intended_audience:protected] =>
[vid_acquisition_info:protected] =>
[vid_cost:protected] =>
[vid_producer:protected] =>
[vid_filename:protected] =>
[vid_filename_downloadable:protected] =>
[date_summary:protected] => November 2015
[date_permission_requested:protected] =>
[date_permission_received:protected] =>
[date_review_needed:protected] =>
[date_received:protected] => 03/02/16
[date_completed:protected] => 03/02/16
[date_billed:protected] =>
[date_modified:protected] => 01/30/23
[collBokExports:protected] =>
[lastBokExportCriteria:BaseElcoshItem:private] =>
[alreadyInSave:protected] =>
[alreadyInValidation:protected] =>
[validationFailures:protected] => Array
(
)
[_new:BaseObject:private] =>
[_deleted:BaseObject:private] =>
[modifiedColumns:protected] => Array
(
)
)
)
[4] => Search_Result Object
(
[title] => Scaffolding at top of large column
[image] => /record/images/3994-p.jpg
[blurb] => This shot shows innovative guarding around the top of a large concrete column in the base of a high rise structure going up....
[category] => Array
(
[0] => 15
[1] => 21
[2] => 47
[3] => 51
[4] => 63
[5] => 78
[6] => 79
[7] => 80
[8] => 62
[9] => 87
[10] => 97
[11] => 56
[12] => 64
[13] => 74
)
[labels] => Array
(
[0] => Falls
[1] => Work Environment
[2] => Hazards
[3] => Scaffolds
[6] => Bricklayer
[7] => Trades
[8] => Cement Mason
[10] => Reinforcing Ironworker
[12] => Roofer/Waterproofer
[14] => Scaffold Erector
[16] => Sheetmetal Worker
[18] => Structural Ironworker
[20] => Commercial & Institutional
[21] => Jobsites
[22] => Images
[23] => Media
[24] => Media & Documents
[25] => Elevator Constructor
[27] => Laborer
[29] => Pile Driver
)
[type] => Images
[sub_category] =>
[url] => /image/3994/i002689/Scaffolding%2Bat%2Btop%2Bof%2Blarge%2Bcolumn.html
[item:protected] => ImageRecord Object
(
[records:protected] => Array
(
)
[recordId:protected] =>
[searchWordClass:protected] =>
[searchWordPeerClass:protected] =>
[bok_record:protected] =>
[authors:protected] =>
[organizations:protected] =>
[collections:protected] =>
[categories:protected] => Array
(
[15] => Category Object
(
[languages:protected] =>
[bok_resources:protected] =>
[bok_topics:protected] =>
[bok_keywords:protected] =>
[id:protected] => 15
[type:protected] => category
[parent:protected] => 7
[label:protected] => Falls
[alreadyInSave:protected] =>
[alreadyInValidation:protected] =>
[validationFailures:protected] => Array
(
)
[_new:BaseObject:private] =>
[_deleted:BaseObject:private] =>
[modifiedColumns:protected] => Array
(
)
)
[21] => Category Object
(
[languages:protected] =>
[bok_resources:protected] =>
[bok_topics:protected] =>
[bok_keywords:protected] =>
[id:protected] => 21
[type:protected] => category
[parent:protected] => 7
[label:protected] => Scaffolds
[alreadyInSave:protected] =>
[alreadyInValidation:protected] =>
[validationFailures:protected] => Array
(
)
[_new:BaseObject:private] =>
[_deleted:BaseObject:private] =>
[modifiedColumns:protected] => Array
(
)
)
[47] => Category Object
(
[languages:protected] =>
[bok_resources:protected] =>
[bok_topics:protected] =>
[bok_keywords:protected] =>
[id:protected] => 47
[type:protected] => category
[parent:protected] => 2
[label:protected] => Bricklayer
[alreadyInSave:protected] =>
[alreadyInValidation:protected] =>
[validationFailures:protected] => Array
(
)
[_new:BaseObject:private] =>
[_deleted:BaseObject:private] =>
[modifiedColumns:protected] => Array
(
)
)
[51] => Category Object
(
[languages:protected] =>
[bok_resources:protected] =>
[bok_topics:protected] =>
[bok_keywords:protected] =>
[id:protected] => 51
[type:protected] => category
[parent:protected] => 2
[label:protected] => Cement Mason
[alreadyInSave:protected] =>
[alreadyInValidation:protected] =>
[validationFailures:protected] => Array
(
)
[_new:BaseObject:private] =>
[_deleted:BaseObject:private] =>
[modifiedColumns:protected] => Array
(
)
)
[63] => Category Object
(
[languages:protected] =>
[bok_resources:protected] =>
[bok_topics:protected] =>
[bok_keywords:protected] =>
[id:protected] => 63
[type:protected] => category
[parent:protected] => 2
[label:protected] => Reinforcing Ironworker
[alreadyInSave:protected] =>
[alreadyInValidation:protected] =>
[validationFailures:protected] => Array
(
)
[_new:BaseObject:private] =>
[_deleted:BaseObject:private] =>
[modifiedColumns:protected] => Array
(
)
)
[78] => Category Object
(
[languages:protected] =>
[bok_resources:protected] =>
[bok_topics:protected] =>
[bok_keywords:protected] =>
[id:protected] => 78
[type:protected] => category
[parent:protected] => 2
[label:protected] => Roofer/Waterproofer
[alreadyInSave:protected] =>
[alreadyInValidation:protected] =>
[validationFailures:protected] => Array
(
)
[_new:BaseObject:private] =>
[_deleted:BaseObject:private] =>
[modifiedColumns:protected] => Array
(
)
)
[79] => Category Object
(
[languages:protected] =>
[bok_resources:protected] =>
[bok_topics:protected] =>
[bok_keywords:protected] =>
[id:protected] => 79
[type:protected] => category
[parent:protected] => 2
[label:protected] => Scaffold Erector
[alreadyInSave:protected] =>
[alreadyInValidation:protected] =>
[validationFailures:protected] => Array
(
)
[_new:BaseObject:private] =>
[_deleted:BaseObject:private] =>
[modifiedColumns:protected] => Array
(
)
)
[80] => Category Object
(
[languages:protected] =>
[bok_resources:protected] =>
[bok_topics:protected] =>
[bok_keywords:protected] =>
[id:protected] => 80
[type:protected] => category
[parent:protected] => 2
[label:protected] => Sheetmetal Worker
[alreadyInSave:protected] =>
[alreadyInValidation:protected] =>
[validationFailures:protected] => Array
(
)
[_new:BaseObject:private] =>
[_deleted:BaseObject:private] =>
[modifiedColumns:protected] => Array
(
)
)
[62] => Category Object
(
[languages:protected] =>
[bok_resources:protected] =>
[bok_topics:protected] =>
[bok_keywords:protected] =>
[id:protected] => 62
[type:protected] => category
[parent:protected] => 2
[label:protected] => Structural Ironworker
[alreadyInSave:protected] =>
[alreadyInValidation:protected] =>
[validationFailures:protected] => Array
(
)
[_new:BaseObject:private] =>
[_deleted:BaseObject:private] =>
[modifiedColumns:protected] => Array
(
)
)
[87] => Category Object
(
[languages:protected] =>
[bok_resources:protected] =>
[bok_topics:protected] =>
[bok_keywords:protected] =>
[id:protected] => 87
[type:protected] => category
[parent:protected] => 3
[label:protected] => Commercial & Institutional
[alreadyInSave:protected] =>
[alreadyInValidation:protected] =>
[validationFailures:protected] => Array
(
)
[_new:BaseObject:private] =>
[_deleted:BaseObject:private] =>
[modifiedColumns:protected] => Array
(
)
)
[97] => Category Object
(
[languages:protected] =>
[bok_resources:protected] =>
[bok_topics:protected] =>
[bok_keywords:protected] =>
[id:protected] => 97
[type:protected] => category
[parent:protected] => 5
[label:protected] => Images
[alreadyInSave:protected] =>
[alreadyInValidation:protected] =>
[validationFailures:protected] => Array
(
)
[_new:BaseObject:private] =>
[_deleted:BaseObject:private] =>
[modifiedColumns:protected] => Array
(
)
)
[56] => Category Object
(
[languages:protected] =>
[bok_resources:protected] =>
[bok_topics:protected] =>
[bok_keywords:protected] =>
[id:protected] => 56
[type:protected] => category
[parent:protected] => 2
[label:protected] => Elevator Constructor
[alreadyInSave:protected] =>
[alreadyInValidation:protected] =>
[validationFailures:protected] => Array
(
)
[_new:BaseObject:private] =>
[_deleted:BaseObject:private] =>
[modifiedColumns:protected] => Array
(
)
)
[64] => Category Object
(
[languages:protected] =>
[bok_resources:protected] =>
[bok_topics:protected] =>
[bok_keywords:protected] =>
[id:protected] => 64
[type:protected] => category
[parent:protected] => 2
[label:protected] => Laborer
[alreadyInSave:protected] =>
[alreadyInValidation:protected] =>
[validationFailures:protected] => Array
(
)
[_new:BaseObject:private] =>
[_deleted:BaseObject:private] =>
[modifiedColumns:protected] => Array
(
)
)
[74] => Category Object
(
[languages:protected] =>
[bok_resources:protected] =>
[bok_topics:protected] =>
[bok_keywords:protected] =>
[id:protected] => 74
[type:protected] => category
[parent:protected] => 2
[label:protected] => Pile Driver
[alreadyInSave:protected] =>
[alreadyInValidation:protected] =>
[validationFailures:protected] => Array
(
)
[_new:BaseObject:private] =>
[_deleted:BaseObject:private] =>
[modifiedColumns:protected] => Array
(
)
)
)
[categories_initialized:protected] => 1
[mapped_items:protected] =>
[content:protected] =>
[files:protected] =>
[language:protected] => Language Object
(
[id:protected] => 1
[code:protected] => en
[name:protected] => English
[alreadyInSave:protected] =>
[alreadyInValidation:protected] =>
[validationFailures:protected] => Array
(
)
[_new:BaseObject:private] =>
[_deleted:BaseObject:private] =>
[modifiedColumns:protected] => Array
(
)
)
[old_record:protected] =>
[id:protected] => 3994
[old_id:protected] =>
[elcosh_id:protected] => i002689
[type:protected] => image
[display_type:protected] => Image
[user_id:protected] => 0
[language_id:protected] => 1
[tagging_id:protected] => Bruce Lippy
[priority_id:protected] => 1
[title:protected] => Scaffolding at top of large column
[total_pages:protected] => 0
[billed_pages:protected] => 0
[publication_number:protected] =>
[part_of:protected] =>
[keywords:protected] => Guardrail, railing, fall prevention, falls
[comments:protected] =>
[summary:protected] => This shot shows innovative guarding around the top of a large concrete column in the base of a high rise structure going up.
[transition_comments:protected] =>
[external_link:protected] =>
[consol_link:protected] => http://www.cpwrconstructionsolutions.org/masonry/solution/8/adjustable-tower-scaffold.html
[more_like_this:protected] => c1002680,i002662,d000608,d001255
[permission_given_by:protected] =>
[published:protected] => T
[billable:protected] => F
[img_name:protected] =>
[img_ext:protected] => jpg
[img_width:protected] =>
[img_height:protected] =>
[img_credit:protected] => Photo by Pam Susi
[img_practice:protected] => good
[vid_source_id:protected] =>
[vid_running_time:protected] =>
[vid_intended_audience:protected] =>
[vid_acquisition_info:protected] =>
[vid_cost:protected] =>
[vid_producer:protected] =>
[vid_filename:protected] =>
[vid_filename_downloadable:protected] =>
[date_summary:protected] => January 2016
[date_permission_requested:protected] =>
[date_permission_received:protected] =>
[date_review_needed:protected] =>
[date_received:protected] => 02/01/16
[date_completed:protected] => 02/01/16
[date_billed:protected] =>
[date_modified:protected] => 02/01/16
[collBokExports:protected] =>
[lastBokExportCriteria:BaseElcoshItem:private] =>
[alreadyInSave:protected] =>
[alreadyInValidation:protected] =>
[validationFailures:protected] => Array
(
)
[_new:BaseObject:private] =>
[_deleted:BaseObject:private] =>
[modifiedColumns:protected] => Array
(
)
)
)
[5] => Search_Result Object
(
[title] => Construction bracing
[image] => /record/images/3995-p.jpg
[blurb] => This shows structural support that prevents collapses during construction....
[category] => Array
(
[0] => 12
[1] => 15
[2] => 21
[3] => 49
[4] => 51
[5] => 55
[6] => 56
[7] => 60
[8] => 64
[9] => 68
[10] => 74
[11] => 63
[12] => 78
[13] => 79
[14] => 80
[15] => 62
[16] => 87
[17] => 90
[18] => 97
)
[labels] => Array
(
[0] => Crushed/Struck By
[1] => Work Environment
[2] => Hazards
[3] => Falls
[6] => Scaffolds
[9] => Carpenter
[10] => Trades
[11] => Cement Mason
[13] => Electrical Worker
[15] => Elevator Constructor
[17] => HVAC
[19] => Laborer
[21] => Maintenance Worker
[23] => Pile Driver
[25] => Reinforcing Ironworker
[27] => Roofer/Waterproofer
[29] => Scaffold Erector
[31] => Sheetmetal Worker
[33] => Structural Ironworker
[35] => Commercial & Institutional
[36] => Jobsites
[37] => Industrial
[39] => Images
[40] => Media
[41] => Media & Documents
)
[type] => Images
[sub_category] =>
[url] => /image/3995/i002690/Construction%2Bbracing.html
[item:protected] => ImageRecord Object
(
[records:protected] => Array
(
)
[recordId:protected] =>
[searchWordClass:protected] =>
[searchWordPeerClass:protected] =>
[bok_record:protected] =>
[authors:protected] =>
[organizations:protected] =>
[collections:protected] =>
[categories:protected] => Array
(
[12] => Category Object
(
[languages:protected] =>
[bok_resources:protected] =>
[bok_topics:protected] =>
[bok_keywords:protected] =>
[id:protected] => 12
[type:protected] => category
[parent:protected] => 7
[label:protected] => Crushed/Struck By
[alreadyInSave:protected] =>
[alreadyInValidation:protected] =>
[validationFailures:protected] => Array
(
)
[_new:BaseObject:private] =>
[_deleted:BaseObject:private] =>
[modifiedColumns:protected] => Array
(
)
)
[15] => Category Object
(
[languages:protected] =>
[bok_resources:protected] =>
[bok_topics:protected] =>
[bok_keywords:protected] =>
[id:protected] => 15
[type:protected] => category
[parent:protected] => 7
[label:protected] => Falls
[alreadyInSave:protected] =>
[alreadyInValidation:protected] =>
[validationFailures:protected] => Array
(
)
[_new:BaseObject:private] =>
[_deleted:BaseObject:private] =>
[modifiedColumns:protected] => Array
(
)
)
[21] => Category Object
(
[languages:protected] =>
[bok_resources:protected] =>
[bok_topics:protected] =>
[bok_keywords:protected] =>
[id:protected] => 21
[type:protected] => category
[parent:protected] => 7
[label:protected] => Scaffolds
[alreadyInSave:protected] =>
[alreadyInValidation:protected] =>
[validationFailures:protected] => Array
(
)
[_new:BaseObject:private] =>
[_deleted:BaseObject:private] =>
[modifiedColumns:protected] => Array
(
)
)
[49] => Category Object
(
[languages:protected] =>
[bok_resources:protected] =>
[bok_topics:protected] =>
[bok_keywords:protected] =>
[id:protected] => 49
[type:protected] => category
[parent:protected] => 2
[label:protected] => Carpenter
[alreadyInSave:protected] =>
[alreadyInValidation:protected] =>
[validationFailures:protected] => Array
(
)
[_new:BaseObject:private] =>
[_deleted:BaseObject:private] =>
[modifiedColumns:protected] => Array
(
)
)
[51] => Category Object
(
[languages:protected] =>
[bok_resources:protected] =>
[bok_topics:protected] =>
[bok_keywords:protected] =>
[id:protected] => 51
[type:protected] => category
[parent:protected] => 2
[label:protected] => Cement Mason
[alreadyInSave:protected] =>
[alreadyInValidation:protected] =>
[validationFailures:protected] => Array
(
)
[_new:BaseObject:private] =>
[_deleted:BaseObject:private] =>
[modifiedColumns:protected] => Array
(
)
)
[55] => Category Object
(
[languages:protected] =>
[bok_resources:protected] =>
[bok_topics:protected] =>
[bok_keywords:protected] =>
[id:protected] => 55
[type:protected] => category
[parent:protected] => 2
[label:protected] => Electrical Worker
[alreadyInSave:protected] =>
[alreadyInValidation:protected] =>
[validationFailures:protected] => Array
(
)
[_new:BaseObject:private] =>
[_deleted:BaseObject:private] =>
[modifiedColumns:protected] => Array
(
)
)
[56] => Category Object
(
[languages:protected] =>
[bok_resources:protected] =>
[bok_topics:protected] =>
[bok_keywords:protected] =>
[id:protected] => 56
[type:protected] => category
[parent:protected] => 2
[label:protected] => Elevator Constructor
[alreadyInSave:protected] =>
[alreadyInValidation:protected] =>
[validationFailures:protected] => Array
(
)
[_new:BaseObject:private] =>
[_deleted:BaseObject:private] =>
[modifiedColumns:protected] => Array
(
)
)
[60] => Category Object
(
[languages:protected] =>
[bok_resources:protected] =>
[bok_topics:protected] =>
[bok_keywords:protected] =>
[id:protected] => 60
[type:protected] => category
[parent:protected] => 2
[label:protected] => HVAC
[alreadyInSave:protected] =>
[alreadyInValidation:protected] =>
[validationFailures:protected] => Array
(
)
[_new:BaseObject:private] =>
[_deleted:BaseObject:private] =>
[modifiedColumns:protected] => Array
(
)
)
[64] => Category Object
(
[languages:protected] =>
[bok_resources:protected] =>
[bok_topics:protected] =>
[bok_keywords:protected] =>
[id:protected] => 64
[type:protected] => category
[parent:protected] => 2
[label:protected] => Laborer
[alreadyInSave:protected] =>
[alreadyInValidation:protected] =>
[validationFailures:protected] => Array
(
)
[_new:BaseObject:private] =>
[_deleted:BaseObject:private] =>
[modifiedColumns:protected] => Array
(
)
)
[68] => Category Object
(
[languages:protected] =>
[bok_resources:protected] =>
[bok_topics:protected] =>
[bok_keywords:protected] =>
[id:protected] => 68
[type:protected] => category
[parent:protected] => 2
[label:protected] => Maintenance Worker
[alreadyInSave:protected] =>
[alreadyInValidation:protected] =>
[validationFailures:protected] => Array
(
)
[_new:BaseObject:private] =>
[_deleted:BaseObject:private] =>
[modifiedColumns:protected] => Array
(
)
)
[74] => Category Object
(
[languages:protected] =>
[bok_resources:protected] =>
[bok_topics:protected] =>
[bok_keywords:protected] =>
[id:protected] => 74
[type:protected] => category
[parent:protected] => 2
[label:protected] => Pile Driver
[alreadyInSave:protected] =>
[alreadyInValidation:protected] =>
[validationFailures:protected] => Array
(
)
[_new:BaseObject:private] =>
[_deleted:BaseObject:private] =>
[modifiedColumns:protected] => Array
(
)
)
[63] => Category Object
(
[languages:protected] =>
[bok_resources:protected] =>
[bok_topics:protected] =>
[bok_keywords:protected] =>
[id:protected] => 63
[type:protected] => category
[parent:protected] => 2
[label:protected] => Reinforcing Ironworker
[alreadyInSave:protected] =>
[alreadyInValidation:protected] =>
[validationFailures:protected] => Array
(
)
[_new:BaseObject:private] =>
[_deleted:BaseObject:private] =>
[modifiedColumns:protected] => Array
(
)
)
[78] => Category Object
(
[languages:protected] =>
[bok_resources:protected] =>
[bok_topics:protected] =>
[bok_keywords:protected] =>
[id:protected] => 78
[type:protected] => category
[parent:protected] => 2
[label:protected] => Roofer/Waterproofer
[alreadyInSave:protected] =>
[alreadyInValidation:protected] =>
[validationFailures:protected] => Array
(
)
[_new:BaseObject:private] =>
[_deleted:BaseObject:private] =>
[modifiedColumns:protected] => Array
(
)
)
[79] => Category Object
(
[languages:protected] =>
[bok_resources:protected] =>
[bok_topics:protected] =>
[bok_keywords:protected] =>
[id:protected] => 79
[type:protected] => category
[parent:protected] => 2
[label:protected] => Scaffold Erector
[alreadyInSave:protected] =>
[alreadyInValidation:protected] =>
[validationFailures:protected] => Array
(
)
[_new:BaseObject:private] =>
[_deleted:BaseObject:private] =>
[modifiedColumns:protected] => Array
(
)
)
[80] => Category Object
(
[languages:protected] =>
[bok_resources:protected] =>
[bok_topics:protected] =>
[bok_keywords:protected] =>
[id:protected] => 80
[type:protected] => category
[parent:protected] => 2
[label:protected] => Sheetmetal Worker
[alreadyInSave:protected] =>
[alreadyInValidation:protected] =>
[validationFailures:protected] => Array
(
)
[_new:BaseObject:private] =>
[_deleted:BaseObject:private] =>
[modifiedColumns:protected] => Array
(
)
)
[62] => Category Object
(
[languages:protected] =>
[bok_resources:protected] =>
[bok_topics:protected] =>
[bok_keywords:protected] =>
[id:protected] => 62
[type:protected] => category
[parent:protected] => 2
[label:protected] => Structural Ironworker
[alreadyInSave:protected] =>
[alreadyInValidation:protected] =>
[validationFailures:protected] => Array
(
)
[_new:BaseObject:private] =>
[_deleted:BaseObject:private] =>
[modifiedColumns:protected] => Array
(
)
)
[87] => Category Object
(
[languages:protected] =>
[bok_resources:protected] =>
[bok_topics:protected] =>
[bok_keywords:protected] =>
[id:protected] => 87
[type:protected] => category
[parent:protected] => 3
[label:protected] => Commercial & Institutional
[alreadyInSave:protected] =>
[alreadyInValidation:protected] =>
[validationFailures:protected] => Array
(
)
[_new:BaseObject:private] =>
[_deleted:BaseObject:private] =>
[modifiedColumns:protected] => Array
(
)
)
[90] => Category Object
(
[languages:protected] =>
[bok_resources:protected] =>
[bok_topics:protected] =>
[bok_keywords:protected] =>
[id:protected] => 90
[type:protected] => category
[parent:protected] => 3
[label:protected] => Industrial
[alreadyInSave:protected] =>
[alreadyInValidation:protected] =>
[validationFailures:protected] => Array
(
)
[_new:BaseObject:private] =>
[_deleted:BaseObject:private] =>
[modifiedColumns:protected] => Array
(
)
)
[97] => Category Object
(
[languages:protected] =>
[bok_resources:protected] =>
[bok_topics:protected] =>
[bok_keywords:protected] =>
[id:protected] => 97
[type:protected] => category
[parent:protected] => 5
[label:protected] => Images
[alreadyInSave:protected] =>
[alreadyInValidation:protected] =>
[validationFailures:protected] => Array
(
)
[_new:BaseObject:private] =>
[_deleted:BaseObject:private] =>
[modifiedColumns:protected] => Array
(
)
)
)
[categories_initialized:protected] => 1
[mapped_items:protected] =>
[content:protected] =>
[files:protected] =>
[language:protected] => Language Object
(
[id:protected] => 1
[code:protected] => en
[name:protected] => English
[alreadyInSave:protected] =>
[alreadyInValidation:protected] =>
[validationFailures:protected] => Array
(
)
[_new:BaseObject:private] =>
[_deleted:BaseObject:private] =>
[modifiedColumns:protected] => Array
(
)
)
[old_record:protected] =>
[id:protected] => 3995
[old_id:protected] =>
[elcosh_id:protected] => i002690
[type:protected] => image
[display_type:protected] => Image
[user_id:protected] => 0
[language_id:protected] => 1
[tagging_id:protected] => Bruce Lippy
[priority_id:protected] => 1
[title:protected] => Construction bracing
[total_pages:protected] => 0
[billed_pages:protected] => 0
[publication_number:protected] =>
[part_of:protected] =>
[keywords:protected] => Bracing, support, scaffold
[comments:protected] =>
[summary:protected] => This shows structural support that prevents collapses during construction.
[transition_comments:protected] =>
[external_link:protected] =>
[consol_link:protected] => http://www.cpwrconstructionsolutions.org/masonry/solution/8/adjustable-tower-scaffold.html
[more_like_this:protected] => i002660
[permission_given_by:protected] =>
[published:protected] => T
[billable:protected] => F
[img_name:protected] =>
[img_ext:protected] => jpg
[img_width:protected] =>
[img_height:protected] =>
[img_credit:protected] => Photo by Pam Susi
[img_practice:protected] => good
[vid_source_id:protected] =>
[vid_running_time:protected] =>
[vid_intended_audience:protected] =>
[vid_acquisition_info:protected] =>
[vid_cost:protected] =>
[vid_producer:protected] =>
[vid_filename:protected] =>
[vid_filename_downloadable:protected] =>
[date_summary:protected] => January 2016
[date_permission_requested:protected] =>
[date_permission_received:protected] =>
[date_review_needed:protected] =>
[date_received:protected] => 02/01/16
[date_completed:protected] => 02/01/16
[date_billed:protected] =>
[date_modified:protected] => 02/01/16
[collBokExports:protected] =>
[lastBokExportCriteria:BaseElcoshItem:private] =>
[alreadyInSave:protected] =>
[alreadyInValidation:protected] =>
[validationFailures:protected] => Array
(
)
[_new:BaseObject:private] =>
[_deleted:BaseObject:private] =>
[modifiedColumns:protected] => Array
(
)
)
)
)
[preview_mode] =>
[description] => Toolbox talks have been the main tool for communicating safety information on construction jobs for decades.
Unfortunately, there has been little research on what makes for effective toolbox talks. The IUOE National
Training Fund worked with OSHA and NIOSH to make sure their series of 24 Focus Four toolbox talks were based on the best recommendations for effective design. These toolbox talks accompany an entire package of training materials, but can be used alone. This guide points out the key features of these toolbox talks and how best to deliver them.
[keywords] => toolbox talks, tailgate talks
[related_items] => Array
(
[Toolbox Talks] => Array
(
[0] => DocumentRecord Object
(
[records:protected] => Array
(
)
[recordId:protected] =>
[searchWordClass:protected] =>
[searchWordPeerClass:protected] =>
[bok_record:protected] =>
[authors:protected] =>
[organizations:protected] =>
[collections:protected] =>
[categories:protected] =>
[categories_initialized:protected] =>
[mapped_items:protected] =>
[content:protected] =>
[files:protected] =>
[language:protected] => Language Object
(
[id:protected] => 1
[code:protected] => en
[name:protected] => English
[alreadyInSave:protected] =>
[alreadyInValidation:protected] =>
[validationFailures:protected] => Array
(
)
[_new:BaseObject:private] =>
[_deleted:BaseObject:private] =>
[modifiedColumns:protected] => Array
(
)
)
[old_record:protected] =>
[id:protected] => 1605
[old_id:protected] => 1262
[elcosh_id:protected] => d001137
[type:protected] => document
[display_type:protected] => HTML w/ PDF
[user_id:protected] =>
[language_id:protected] => 1
[tagging_id:protected] => Garber
[priority_id:protected] => 1
[title:protected] => Focus Four Toolbox Talks, Module 1 – Falls, Talk #2 – Falls from debris piles?
[total_pages:protected] => 1
[billed_pages:protected] => 1
[publication_number:protected] =>
[part_of:protected] =>
[keywords:protected] => disaster response, hazard clean-up, uneven surface, disaster site, disaster clean-up
[comments:protected] =>
[summary:protected] => A toolbox talk on preventing falls from debris piles. Includes questions to ask, an incident to discuss with images, and a place to record questions the trainer would like to ask about the incident. Part of a collection. Click on the 'collection' button to access the other items.
[transition_comments:protected] =>
[external_link:protected] =>
[consol_link:protected] => http://www.cpwrconstructionsolutions.org/roofing/hazard/1463/install-asphalt-roofs-fall-from-heights.html
[more_like_this:protected] => a000081,d000478,d000530
[permission_given_by:protected] =>
[published:protected] => T
[billable:protected] => F
[img_name:protected] =>
[img_ext:protected] =>
[img_width:protected] =>
[img_height:protected] =>
[img_credit:protected] =>
[img_practice:protected] =>
[vid_source_id:protected] =>
[vid_running_time:protected] =>
[vid_intended_audience:protected] =>
[vid_acquisition_info:protected] =>
[vid_cost:protected] =>
[vid_producer:protected] =>
[vid_filename:protected] =>
[vid_filename_downloadable:protected] =>
[date_summary:protected] =>
[date_permission_requested:protected] =>
[date_permission_received:protected] =>
[date_review_needed:protected] =>
[date_received:protected] => 02/15/12
[date_completed:protected] => 03/19/12
[date_billed:protected] =>
[date_modified:protected] => 07/10/12
[collBokExports:protected] =>
[lastBokExportCriteria:BaseElcoshItem:private] =>
[alreadyInSave:protected] =>
[alreadyInValidation:protected] =>
[validationFailures:protected] => Array
(
)
[_new:BaseObject:private] =>
[_deleted:BaseObject:private] =>
[modifiedColumns:protected] => Array
(
)
)
[1] => DocumentRecord Object
(
[records:protected] => Array
(
)
[recordId:protected] =>
[searchWordClass:protected] =>
[searchWordPeerClass:protected] =>
[bok_record:protected] =>
[authors:protected] =>
[organizations:protected] =>
[collections:protected] =>
[categories:protected] =>
[categories_initialized:protected] =>
[mapped_items:protected] =>
[content:protected] =>
[files:protected] =>
[language:protected] => Language Object
(
[id:protected] => 1
[code:protected] => en
[name:protected] => English
[alreadyInSave:protected] =>
[alreadyInValidation:protected] =>
[validationFailures:protected] => Array
(
)
[_new:BaseObject:private] =>
[_deleted:BaseObject:private] =>
[modifiedColumns:protected] => Array
(
)
)
[old_record:protected] =>
[id:protected] => 1610
[old_id:protected] => 1271
[elcosh_id:protected] => d001146
[type:protected] => document
[display_type:protected] => HTML w/ PDF
[user_id:protected] => 0
[language_id:protected] => 1
[tagging_id:protected] => Garber
[priority_id:protected] => 1
[title:protected] => Focus Four Toolbox Talks, Module 2 – Struck-by, Talk #5 – Rigging and Securing Loads
[total_pages:protected] => 1
[billed_pages:protected] => 1
[publication_number:protected] =>
[part_of:protected] =>
[keywords:protected] => rigging, lift loads, loading areas, chains
[comments:protected] =>
[summary:protected] => A toolbox talk on preventing struck-by incidents caused by not securing loads properly. Includes questions to ask, an incident to discuss with images, and a place to record questions the trainer would like to ask about the incident. Part of a collection. Click on the 'collection' button to access the other items.
[transition_comments:protected] =>
[external_link:protected] =>
[consol_link:protected] => http://www.cpwrconstructionsolutions.org/heavy_equipment/hazard/1591/move-equipment-to-from-and-between-sites-work-zone-struck-by-injuries-and-fatalities.html
[more_like_this:protected] => d000144,d000360,d000873
[permission_given_by:protected] =>
[published:protected] => T
[billable:protected] => F
[img_name:protected] =>
[img_ext:protected] =>
[img_width:protected] =>
[img_height:protected] =>
[img_credit:protected] =>
[img_practice:protected] =>
[vid_source_id:protected] =>
[vid_running_time:protected] =>
[vid_intended_audience:protected] =>
[vid_acquisition_info:protected] =>
[vid_cost:protected] =>
[vid_producer:protected] =>
[vid_filename:protected] =>
[vid_filename_downloadable:protected] =>
[date_summary:protected] =>
[date_permission_requested:protected] =>
[date_permission_received:protected] =>
[date_review_needed:protected] =>
[date_received:protected] => 02/15/12
[date_completed:protected] => 03/28/12
[date_billed:protected] =>
[date_modified:protected] => 05/12/14
[collBokExports:protected] =>
[lastBokExportCriteria:BaseElcoshItem:private] =>
[alreadyInSave:protected] =>
[alreadyInValidation:protected] =>
[validationFailures:protected] => Array
(
)
[_new:BaseObject:private] =>
[_deleted:BaseObject:private] =>
[modifiedColumns:protected] => Array
(
)
)
[2] => DocumentRecord Object
(
[records:protected] => Array
(
)
[recordId:protected] =>
[searchWordClass:protected] =>
[searchWordPeerClass:protected] =>
[bok_record:protected] =>
[authors:protected] =>
[organizations:protected] =>
[collections:protected] =>
[categories:protected] =>
[categories_initialized:protected] =>
[mapped_items:protected] =>
[content:protected] =>
[files:protected] =>
[language:protected] => Language Object
(
[id:protected] => 1
[code:protected] => en
[name:protected] => English
[alreadyInSave:protected] =>
[alreadyInValidation:protected] =>
[validationFailures:protected] => Array
(
)
[_new:BaseObject:private] =>
[_deleted:BaseObject:private] =>
[modifiedColumns:protected] => Array
(
)
)
[old_record:protected] =>
[id:protected] => 1645
[old_id:protected] => 1274
[elcosh_id:protected] => d001149
[type:protected] => document
[display_type:protected] => HTML w/ PDF
[user_id:protected] => 0
[language_id:protected] => 1
[tagging_id:protected] => Garber
[priority_id:protected] => 1
[title:protected] => Focus Four Toolbox Talks, Module 3 – Caught-in/between, Talk #2 – Trenches & Heavy Equipment
[total_pages:protected] => 1
[billed_pages:protected] => 1
[publication_number:protected] =>
[part_of:protected] =>
[keywords:protected] => back-up alarms, spotter, soil cave-in, spoil pikes, ROPs, trenching, rain
[comments:protected] =>
[summary:protected] => A toolbox talk on preventing incidents involving trenches such as trench collapse. Includes questions to ask, an incident to discuss with images, and a place to record questions the trainer would like to ask about the incident. Part of a collection. Click on the 'collection' button to access the other items.
[transition_comments:protected] =>
[external_link:protected] =>
[consol_link:protected] =>
[more_like_this:protected] => d000019,d000035,d000168
[permission_given_by:protected] =>
[published:protected] => T
[billable:protected] => F
[img_name:protected] =>
[img_ext:protected] =>
[img_width:protected] =>
[img_height:protected] =>
[img_credit:protected] =>
[img_practice:protected] =>
[vid_source_id:protected] =>
[vid_running_time:protected] =>
[vid_intended_audience:protected] =>
[vid_acquisition_info:protected] =>
[vid_cost:protected] =>
[vid_producer:protected] =>
[vid_filename:protected] =>
[vid_filename_downloadable:protected] =>
[date_summary:protected] =>
[date_permission_requested:protected] =>
[date_permission_received:protected] =>
[date_review_needed:protected] =>
[date_received:protected] => 02/15/12
[date_completed:protected] => 04/02/12
[date_billed:protected] =>
[date_modified:protected] => 05/23/23
[collBokExports:protected] =>
[lastBokExportCriteria:BaseElcoshItem:private] =>
[alreadyInSave:protected] =>
[alreadyInValidation:protected] =>
[validationFailures:protected] => Array
(
)
[_new:BaseObject:private] =>
[_deleted:BaseObject:private] =>
[modifiedColumns:protected] => Array
(
)
)
[3] => DocumentRecord Object
(
[records:protected] => Array
(
)
[recordId:protected] =>
[searchWordClass:protected] =>
[searchWordPeerClass:protected] =>
[bok_record:protected] =>
[authors:protected] =>
[organizations:protected] =>
[collections:protected] =>
[categories:protected] =>
[categories_initialized:protected] =>
[mapped_items:protected] =>
[content:protected] =>
[files:protected] =>
[language:protected] => Language Object
(
[id:protected] => 1
[code:protected] => en
[name:protected] => English
[alreadyInSave:protected] =>
[alreadyInValidation:protected] =>
[validationFailures:protected] => Array
(
)
[_new:BaseObject:private] =>
[_deleted:BaseObject:private] =>
[modifiedColumns:protected] => Array
(
)
)
[old_record:protected] =>
[id:protected] => 1654
[old_id:protected] => 1284
[elcosh_id:protected] => d001159
[type:protected] => document
[display_type:protected] => HTML w/ PDF
[user_id:protected] => 0
[language_id:protected] => 1
[tagging_id:protected] => Garber
[priority_id:protected] => 1
[title:protected] => Focus Four Toolbox Talks, Module 4 – Electrocutions, Talk #6 – Hazards on Disaster Sites
[total_pages:protected] => 1
[billed_pages:protected] => 1
[publication_number:protected] =>
[part_of:protected] =>
[keywords:protected] => powerlines, underground, utilities, generators, wet conditions, GFCIs, energized lines, disasters, emergency response
[comments:protected] =>
[summary:protected] => A toolbox talk on how to avoid electrocution on a disaster site. Includes questions to ask, an incident to discuss with images, and a place to record questions the trainer would like to ask about the incident. Part of a collection. Click on the 'collection' button to access the other items.
[transition_comments:protected] =>
[external_link:protected] =>
[consol_link:protected] => http://www.cpwrconstructionsolutions.org/electrical/hazard/1138/install-and-repair-high-voltage-lines-transformers-switches-electrical-shocks-burns-and-or-electrocution.html
[more_like_this:protected] => d000135,d000361,d000437
[permission_given_by:protected] =>
[published:protected] => T
[billable:protected] => F
[img_name:protected] =>
[img_ext:protected] =>
[img_width:protected] =>
[img_height:protected] =>
[img_credit:protected] =>
[img_practice:protected] =>
[vid_source_id:protected] =>
[vid_running_time:protected] =>
[vid_intended_audience:protected] =>
[vid_acquisition_info:protected] =>
[vid_cost:protected] =>
[vid_producer:protected] =>
[vid_filename:protected] =>
[vid_filename_downloadable:protected] =>
[date_summary:protected] =>
[date_permission_requested:protected] =>
[date_permission_received:protected] =>
[date_review_needed:protected] =>
[date_received:protected] => 02/15/12
[date_completed:protected] => 04/02/12
[date_billed:protected] =>
[date_modified:protected] => 05/23/23
[collBokExports:protected] =>
[lastBokExportCriteria:BaseElcoshItem:private] =>
[alreadyInSave:protected] =>
[alreadyInValidation:protected] =>
[validationFailures:protected] => Array
(
)
[_new:BaseObject:private] =>
[_deleted:BaseObject:private] =>
[modifiedColumns:protected] => Array
(
)
)
)
)
[collections] => Array
(
[1294] =>
[1295] =>
[1292] =>
[1293] => CollectionRecord Object
(
[collection_items:protected] =>
[records:protected] => Array
(
)
[recordId:protected] =>
[searchWordClass:protected] =>
[searchWordPeerClass:protected] =>
[bok_record:protected] =>
[authors:protected] =>
[organizations:protected] =>
[collections:protected] =>
[categories:protected] =>
[categories_initialized:protected] =>
[mapped_items:protected] =>
[content:protected] =>
[files:protected] =>
[language:protected] =>
[old_record:protected] =>
[id:protected] => 1293
[old_id:protected] =>
[elcosh_id:protected] => c000026
[type:protected] => collection
[display_type:protected] => Collection
[user_id:protected] =>
[language_id:protected] =>
[tagging_id:protected] =>
[priority_id:protected] =>
[title:protected] => Focus Four-Struck By
[total_pages:protected] =>
[billed_pages:protected] =>
[publication_number:protected] =>
[part_of:protected] =>
[keywords:protected] =>
[comments:protected] =>
[summary:protected] => The following are links to all of the items in this collection:
[transition_comments:protected] =>
[external_link:protected] =>
[consol_link:protected] =>
[more_like_this:protected] =>
[permission_given_by:protected] =>
[published:protected] => T
[billable:protected] => F
[img_name:protected] =>
[img_ext:protected] =>
[img_width:protected] =>
[img_height:protected] =>
[img_credit:protected] =>
[img_practice:protected] =>
[vid_source_id:protected] =>
[vid_running_time:protected] =>
[vid_intended_audience:protected] =>
[vid_acquisition_info:protected] =>
[vid_cost:protected] =>
[vid_producer:protected] =>
[vid_filename:protected] =>
[vid_filename_downloadable:protected] =>
[date_summary:protected] =>
[date_permission_requested:protected] =>
[date_permission_received:protected] =>
[date_review_needed:protected] =>
[date_received:protected] => 05/08/12
[date_completed:protected] => 05/08/12
[date_billed:protected] =>
[date_modified:protected] => 05/08/12
[collBokExports:protected] =>
[lastBokExportCriteria:BaseElcoshItem:private] =>
[alreadyInSave:protected] =>
[alreadyInValidation:protected] =>
[validationFailures:protected] => Array
(
)
[_new:BaseObject:private] =>
[_deleted:BaseObject:private] =>
[modifiedColumns:protected] => Array
(
)
)
)
[record] => DocumentRecord Object
(
[records:protected] => Array
(
)
[recordId:protected] =>
[searchWordClass:protected] =>
[searchWordPeerClass:protected] =>
[bok_record:protected] =>
[authors:protected] => Array
(
)
[organizations:protected] => Array
(
[256] => Organization Object
(
[id:protected] => 256
[elcosh_id:protected] => o000276
[user_id:protected] => 14
[province_id:protected] => 0
[country_id:protected] => 0
[title:protected] => IUOE National Training Fund
[address:protected] =>
[postal_code:protected] =>
[city:protected] =>
[department:protected] =>
[phone:protected] => 304-253-8674
[fax:protected] =>
[email:protected] =>
[website:protected] => http://www.iuoeiettc.org
[filename:protected] =>
[about:protected] =>
[comments:protected] =>
[logo_available:protected] => T
[no_details:protected] => F
[date_received:protected] => 2012-02-13
[date_completed:protected] => 2012-02-13
[date_billed:protected] =>
[alreadyInSave:protected] =>
[alreadyInValidation:protected] =>
[validationFailures:protected] => Array
(
)
[_new:BaseObject:private] =>
[_deleted:BaseObject:private] =>
[modifiedColumns:protected] => Array
(
)
)
)
[collections:protected] => Array
(
[1294] =>
[1295] =>
[1292] =>
[1293] => CollectionRecord Object
(
[collection_items:protected] =>
[records:protected] => Array
(
)
[recordId:protected] =>
[searchWordClass:protected] =>
[searchWordPeerClass:protected] =>
[bok_record:protected] =>
[authors:protected] =>
[organizations:protected] =>
[collections:protected] =>
[categories:protected] =>
[categories_initialized:protected] =>
[mapped_items:protected] =>
[content:protected] =>
[files:protected] =>
[language:protected] =>
[old_record:protected] =>
[id:protected] => 1293
[old_id:protected] =>
[elcosh_id:protected] => c000026
[type:protected] => collection
[display_type:protected] => Collection
[user_id:protected] =>
[language_id:protected] =>
[tagging_id:protected] =>
[priority_id:protected] =>
[title:protected] => Focus Four-Struck By
[total_pages:protected] =>
[billed_pages:protected] =>
[publication_number:protected] =>
[part_of:protected] =>
[keywords:protected] =>
[comments:protected] =>
[summary:protected] => The following are links to all of the items in this collection:
[transition_comments:protected] =>
[external_link:protected] =>
[consol_link:protected] =>
[more_like_this:protected] =>
[permission_given_by:protected] =>
[published:protected] => T
[billable:protected] => F
[img_name:protected] =>
[img_ext:protected] =>
[img_width:protected] =>
[img_height:protected] =>
[img_credit:protected] =>
[img_practice:protected] =>
[vid_source_id:protected] =>
[vid_running_time:protected] =>
[vid_intended_audience:protected] =>
[vid_acquisition_info:protected] =>
[vid_cost:protected] =>
[vid_producer:protected] =>
[vid_filename:protected] =>
[vid_filename_downloadable:protected] =>
[date_summary:protected] =>
[date_permission_requested:protected] =>
[date_permission_received:protected] =>
[date_review_needed:protected] =>
[date_received:protected] => 05/08/12
[date_completed:protected] => 05/08/12
[date_billed:protected] =>
[date_modified:protected] => 05/08/12
[collBokExports:protected] =>
[lastBokExportCriteria:BaseElcoshItem:private] =>
[alreadyInSave:protected] =>
[alreadyInValidation:protected] =>
[validationFailures:protected] => Array
(
)
[_new:BaseObject:private] =>
[_deleted:BaseObject:private] =>
[modifiedColumns:protected] => Array
(
)
)
)
[categories:protected] =>
[categories_initialized:protected] =>
[mapped_items:protected] => Array
(
[1605] => DocumentRecord Object
(
[records:protected] => Array
(
)
[recordId:protected] =>
[searchWordClass:protected] =>
[searchWordPeerClass:protected] =>
[bok_record:protected] =>
[authors:protected] =>
[organizations:protected] =>
[collections:protected] =>
[categories:protected] =>
[categories_initialized:protected] =>
[mapped_items:protected] =>
[content:protected] =>
[files:protected] =>
[language:protected] =>
[old_record:protected] =>
[id:protected] => 1605
[old_id:protected] => 1262
[elcosh_id:protected] => d001137
[type:protected] => document
[display_type:protected] => HTML w/ PDF
[user_id:protected] =>
[language_id:protected] => 1
[tagging_id:protected] => Garber
[priority_id:protected] => 1
[title:protected] => Focus Four Toolbox Talks, Module 1 – Falls, Talk #2 – Falls from debris piles?
[total_pages:protected] => 1
[billed_pages:protected] => 1
[publication_number:protected] =>
[part_of:protected] =>
[keywords:protected] => disaster response, hazard clean-up, uneven surface, disaster site, disaster clean-up
[comments:protected] =>
[summary:protected] => A toolbox talk on preventing falls from debris piles. Includes questions to ask, an incident to discuss with images, and a place to record questions the trainer would like to ask about the incident. Part of a collection. Click on the 'collection' button to access the other items.
[transition_comments:protected] =>
[external_link:protected] =>
[consol_link:protected] => http://www.cpwrconstructionsolutions.org/roofing/hazard/1463/install-asphalt-roofs-fall-from-heights.html
[more_like_this:protected] => a000081,d000478,d000530
[permission_given_by:protected] =>
[published:protected] => T
[billable:protected] => F
[img_name:protected] =>
[img_ext:protected] =>
[img_width:protected] =>
[img_height:protected] =>
[img_credit:protected] =>
[img_practice:protected] =>
[vid_source_id:protected] =>
[vid_running_time:protected] =>
[vid_intended_audience:protected] =>
[vid_acquisition_info:protected] =>
[vid_cost:protected] =>
[vid_producer:protected] =>
[vid_filename:protected] =>
[vid_filename_downloadable:protected] =>
[date_summary:protected] =>
[date_permission_requested:protected] =>
[date_permission_received:protected] =>
[date_review_needed:protected] =>
[date_received:protected] => 02/15/12
[date_completed:protected] => 03/19/12
[date_billed:protected] =>
[date_modified:protected] => 07/10/12
[collBokExports:protected] =>
[lastBokExportCriteria:BaseElcoshItem:private] =>
[alreadyInSave:protected] =>
[alreadyInValidation:protected] =>
[validationFailures:protected] => Array
(
)
[_new:BaseObject:private] =>
[_deleted:BaseObject:private] =>
[modifiedColumns:protected] => Array
(
)
)
[1610] => DocumentRecord Object
(
[records:protected] => Array
(
)
[recordId:protected] =>
[searchWordClass:protected] =>
[searchWordPeerClass:protected] =>
[bok_record:protected] =>
[authors:protected] =>
[organizations:protected] =>
[collections:protected] =>
[categories:protected] =>
[categories_initialized:protected] =>
[mapped_items:protected] =>
[content:protected] =>
[files:protected] =>
[language:protected] =>
[old_record:protected] =>
[id:protected] => 1610
[old_id:protected] => 1271
[elcosh_id:protected] => d001146
[type:protected] => document
[display_type:protected] => HTML w/ PDF
[user_id:protected] => 0
[language_id:protected] => 1
[tagging_id:protected] => Garber
[priority_id:protected] => 1
[title:protected] => Focus Four Toolbox Talks, Module 2 – Struck-by, Talk #5 – Rigging and Securing Loads
[total_pages:protected] => 1
[billed_pages:protected] => 1
[publication_number:protected] =>
[part_of:protected] =>
[keywords:protected] => rigging, lift loads, loading areas, chains
[comments:protected] =>
[summary:protected] => A toolbox talk on preventing struck-by incidents caused by not securing loads properly. Includes questions to ask, an incident to discuss with images, and a place to record questions the trainer would like to ask about the incident. Part of a collection. Click on the 'collection' button to access the other items.
[transition_comments:protected] =>
[external_link:protected] =>
[consol_link:protected] => http://www.cpwrconstructionsolutions.org/heavy_equipment/hazard/1591/move-equipment-to-from-and-between-sites-work-zone-struck-by-injuries-and-fatalities.html
[more_like_this:protected] => d000144,d000360,d000873
[permission_given_by:protected] =>
[published:protected] => T
[billable:protected] => F
[img_name:protected] =>
[img_ext:protected] =>
[img_width:protected] =>
[img_height:protected] =>
[img_credit:protected] =>
[img_practice:protected] =>
[vid_source_id:protected] =>
[vid_running_time:protected] =>
[vid_intended_audience:protected] =>
[vid_acquisition_info:protected] =>
[vid_cost:protected] =>
[vid_producer:protected] =>
[vid_filename:protected] =>
[vid_filename_downloadable:protected] =>
[date_summary:protected] =>
[date_permission_requested:protected] =>
[date_permission_received:protected] =>
[date_review_needed:protected] =>
[date_received:protected] => 02/15/12
[date_completed:protected] => 03/28/12
[date_billed:protected] =>
[date_modified:protected] => 05/12/14
[collBokExports:protected] =>
[lastBokExportCriteria:BaseElcoshItem:private] =>
[alreadyInSave:protected] =>
[alreadyInValidation:protected] =>
[validationFailures:protected] => Array
(
)
[_new:BaseObject:private] =>
[_deleted:BaseObject:private] =>
[modifiedColumns:protected] => Array
(
)
)
[1645] => DocumentRecord Object
(
[records:protected] => Array
(
)
[recordId:protected] =>
[searchWordClass:protected] =>
[searchWordPeerClass:protected] =>
[bok_record:protected] =>
[authors:protected] =>
[organizations:protected] =>
[collections:protected] =>
[categories:protected] =>
[categories_initialized:protected] =>
[mapped_items:protected] =>
[content:protected] =>
[files:protected] =>
[language:protected] =>
[old_record:protected] =>
[id:protected] => 1645
[old_id:protected] => 1274
[elcosh_id:protected] => d001149
[type:protected] => document
[display_type:protected] => HTML w/ PDF
[user_id:protected] => 0
[language_id:protected] => 1
[tagging_id:protected] => Garber
[priority_id:protected] => 1
[title:protected] => Focus Four Toolbox Talks, Module 3 – Caught-in/between, Talk #2 – Trenches & Heavy Equipment
[total_pages:protected] => 1
[billed_pages:protected] => 1
[publication_number:protected] =>
[part_of:protected] =>
[keywords:protected] => back-up alarms, spotter, soil cave-in, spoil pikes, ROPs, trenching, rain
[comments:protected] =>
[summary:protected] => A toolbox talk on preventing incidents involving trenches such as trench collapse. Includes questions to ask, an incident to discuss with images, and a place to record questions the trainer would like to ask about the incident. Part of a collection. Click on the 'collection' button to access the other items.
[transition_comments:protected] =>
[external_link:protected] =>
[consol_link:protected] =>
[more_like_this:protected] => d000019,d000035,d000168
[permission_given_by:protected] =>
[published:protected] => T
[billable:protected] => F
[img_name:protected] =>
[img_ext:protected] =>
[img_width:protected] =>
[img_height:protected] =>
[img_credit:protected] =>
[img_practice:protected] =>
[vid_source_id:protected] =>
[vid_running_time:protected] =>
[vid_intended_audience:protected] =>
[vid_acquisition_info:protected] =>
[vid_cost:protected] =>
[vid_producer:protected] =>
[vid_filename:protected] =>
[vid_filename_downloadable:protected] =>
[date_summary:protected] =>
[date_permission_requested:protected] =>
[date_permission_received:protected] =>
[date_review_needed:protected] =>
[date_received:protected] => 02/15/12
[date_completed:protected] => 04/02/12
[date_billed:protected] =>
[date_modified:protected] => 05/23/23
[collBokExports:protected] =>
[lastBokExportCriteria:BaseElcoshItem:private] =>
[alreadyInSave:protected] =>
[alreadyInValidation:protected] =>
[validationFailures:protected] => Array
(
)
[_new:BaseObject:private] =>
[_deleted:BaseObject:private] =>
[modifiedColumns:protected] => Array
(
)
)
[1654] => DocumentRecord Object
(
[records:protected] => Array
(
)
[recordId:protected] =>
[searchWordClass:protected] =>
[searchWordPeerClass:protected] =>
[bok_record:protected] =>
[authors:protected] =>
[organizations:protected] =>
[collections:protected] =>
[categories:protected] =>
[categories_initialized:protected] =>
[mapped_items:protected] =>
[content:protected] =>
[files:protected] =>
[language:protected] =>
[old_record:protected] =>
[id:protected] => 1654
[old_id:protected] => 1284
[elcosh_id:protected] => d001159
[type:protected] => document
[display_type:protected] => HTML w/ PDF
[user_id:protected] => 0
[language_id:protected] => 1
[tagging_id:protected] => Garber
[priority_id:protected] => 1
[title:protected] => Focus Four Toolbox Talks, Module 4 – Electrocutions, Talk #6 – Hazards on Disaster Sites
[total_pages:protected] => 1
[billed_pages:protected] => 1
[publication_number:protected] =>
[part_of:protected] =>
[keywords:protected] => powerlines, underground, utilities, generators, wet conditions, GFCIs, energized lines, disasters, emergency response
[comments:protected] =>
[summary:protected] => A toolbox talk on how to avoid electrocution on a disaster site. Includes questions to ask, an incident to discuss with images, and a place to record questions the trainer would like to ask about the incident. Part of a collection. Click on the 'collection' button to access the other items.
[transition_comments:protected] =>
[external_link:protected] =>
[consol_link:protected] => http://www.cpwrconstructionsolutions.org/electrical/hazard/1138/install-and-repair-high-voltage-lines-transformers-switches-electrical-shocks-burns-and-or-electrocution.html
[more_like_this:protected] => d000135,d000361,d000437
[permission_given_by:protected] =>
[published:protected] => T
[billable:protected] => F
[img_name:protected] =>
[img_ext:protected] =>
[img_width:protected] =>
[img_height:protected] =>
[img_credit:protected] =>
[img_practice:protected] =>
[vid_source_id:protected] =>
[vid_running_time:protected] =>
[vid_intended_audience:protected] =>
[vid_acquisition_info:protected] =>
[vid_cost:protected] =>
[vid_producer:protected] =>
[vid_filename:protected] =>
[vid_filename_downloadable:protected] =>
[date_summary:protected] =>
[date_permission_requested:protected] =>
[date_permission_received:protected] =>
[date_review_needed:protected] =>
[date_received:protected] => 02/15/12
[date_completed:protected] => 04/02/12
[date_billed:protected] =>
[date_modified:protected] => 05/23/23
[collBokExports:protected] =>
[lastBokExportCriteria:BaseElcoshItem:private] =>
[alreadyInSave:protected] =>
[alreadyInValidation:protected] =>
[validationFailures:protected] => Array
(
)
[_new:BaseObject:private] =>
[_deleted:BaseObject:private] =>
[modifiedColumns:protected] => Array
(
)
)
)
[content:protected] =>
[files:protected] => Array
(
[9400] => File Object
(
[id:protected] => 9400
[filename:protected] => 1.jpg
[downloadable:protected] => F
[timestamp:protected] => 2014-05-08 15:05:37
[alreadyInSave:protected] =>
[alreadyInValidation:protected] =>
[validationFailures:protected] => Array
(
)
[_new:BaseObject:private] =>
[_deleted:BaseObject:private] =>
[modifiedColumns:protected] => Array
(
)
)
[9401] => File Object
(
[id:protected] => 9401
[filename:protected] => d001298.pdf
[downloadable:protected] => T
[timestamp:protected] => 2014-05-08 15:05:37
[alreadyInSave:protected] =>
[alreadyInValidation:protected] =>
[validationFailures:protected] => Array
(
)
[_new:BaseObject:private] =>
[_deleted:BaseObject:private] =>
[modifiedColumns:protected] => Array
(
)
)
)
[language:protected] => Language Object
(
[id:protected] => 1
[code:protected] => en
[name:protected] => English
[alreadyInSave:protected] =>
[alreadyInValidation:protected] =>
[validationFailures:protected] => Array
(
)
[_new:BaseObject:private] =>
[_deleted:BaseObject:private] =>
[modifiedColumns:protected] => Array
(
)
)
[old_record:protected] =>
[id:protected] => 3827
[old_id:protected] =>
[elcosh_id:protected] => d001298
[type:protected] => document
[display_type:protected] => HTML w/ PDF
[user_id:protected] => 23
[language_id:protected] => 1
[tagging_id:protected] => Bruce Lippy
[priority_id:protected] => 1
[title:protected] => Getting the most out of the IUOE Toolbox Talks
[total_pages:protected] => 2
[billed_pages:protected] => 2
[publication_number:protected] =>
[part_of:protected] =>
[keywords:protected] => toolbox talks, tailgate talks
[comments:protected] =>
[summary:protected] => Toolbox talks have been the main tool for communicating safety information on construction jobs for decades.
Unfortunately, there has been little research on what makes for effective toolbox talks. The IUOE National
Training Fund worked with OSHA and NIOSH to make sure their series of 24 Focus Four toolbox talks were based on the best recommendations for effective design. These toolbox talks accompany an entire package of training materials, but can be used alone. This guide points out the key features of these toolbox talks and how best to deliver them.
[transition_comments:protected] =>
[external_link:protected] =>
[consol_link:protected] =>
[more_like_this:protected] => d001137,d001146,d001149,d001159
[permission_given_by:protected] => IUOE National Hazmat Program
[published:protected] => T
[billable:protected] => F
[img_name:protected] =>
[img_ext:protected] => png
[img_width:protected] =>
[img_height:protected] =>
[img_credit:protected] =>
[img_practice:protected] =>
[vid_source_id:protected] =>
[vid_running_time:protected] =>
[vid_intended_audience:protected] =>
[vid_acquisition_info:protected] =>
[vid_cost:protected] =>
[vid_producer:protected] =>
[vid_filename:protected] =>
[vid_filename_downloadable:protected] =>
[date_summary:protected] => 2007
[date_permission_requested:protected] =>
[date_permission_received:protected] =>
[date_review_needed:protected] =>
[date_received:protected] => 05/08/14
[date_completed:protected] => 05/08/14
[date_billed:protected] =>
[date_modified:protected] => 05/08/14
[collBokExports:protected] =>
[lastBokExportCriteria:BaseElcoshItem:private] =>
[alreadyInSave:protected] =>
[alreadyInValidation:protected] =>
[validationFailures:protected] => Array
(
)
[_new:BaseObject:private] =>
[_deleted:BaseObject:private] =>
[modifiedColumns:protected] => Array
(
)
)
[show_text] =>
[document_content] => ElcoshItemDocumentContent Object
(
[id:protected] => 2896
[item_id:protected] => 3827
[type:protected] => main
[title:protected] =>
[content:protected] =>
Why were these talks developed?
Toolbox talks have been the main tool for communicating safety information on construction jobs for decades. Unfortunately, there has been almost no research on what makes for effective toolbox talks. The IUOE National Training Fund has worked with OSHA, the National Institute for Occupational Safety and Health and the Lippy Group, LLC to make sure these Focus Four toolbox talks are based on the latest fi ndings on the most effective design and tailored to the hazards operating engineers face daily. These toolbox talks accompany an entire package of training materials, but can be used alone. The way these are delivered is as important as how well they are designed.
What did NIOSH find out?
- Just handing out factsheets and toolbox talks to workers doesn’t work. Providing copies after toolbox talks doesn’t make much of an impact either.
- Using case studies (real life stories of accidents that ended in fatality or injury) in toolbox talks is effective.
- When toolbox talks containing case studies were accompanied by discussion questions to encourage group participation, they were more effective. Consequently, getting the workers to participate in the discussion about the case study is important. It’s not enough to tell the story, it is better to have the workers engage in problem solving that analyzes why the accident occurred and how it could have been prevented. Active learning is always better than passive.
How should you deliver these toolbox talks?
- Choose a topic that is related to work going on at the site.
- Hold the meeting on the job, preferably where everyone can sit and relax.
- Hold the meeting at the beginning of a shift or after a break. Folks are too tired at the end of a shift to carefully listen and they want to get home.
- Read the toolbox talk sheet on the topic prior to conducting the talk.
- Start at the top of the form and work right through to the end, which should take around 10 to 15 minutes. Guidance is provided in blue print to help you with each section.
- Use the questions provided to generate discussions. Always allow time for the crew to respond to your questions before you provide an answer. Some suggested responses are written in italics.
- Review the case study and emphasize that this was a real incident. Ask the crew for a case study before you review the one provided, however.
- Always end with a discussion of the particular worksite where you are conducting the talk. Tie the talk as closely to hazards on the site as possible and encourage the crew to constantly look for and immediately correct hazards. They should also know how to report any problems that can’t be immediately corrected.
- Provide copies to each person, if you like, but NIOSH has not found that to be particularly effective.
- Encourage workers to do similar talks on their sites and provide them with the IUOE phone number for ordering in bulk.
- Have everyone sign the back of the form to indicate they attended this session and point out it is a pledge to look out for the health and safety of everyone on the site.
What are the key features of these toolbox talks?

[content_transformed:protected] =>
Why were these talks developed?
Toolbox talks have been the main tool for communicating safety information on construction jobs for decades. Unfortunately, there has been almost no research on what makes for effective toolbox talks. The IUOE National Training Fund has worked with OSHA, the National Institute for Occupational Safety and Health and the Lippy Group, LLC to make sure these Focus Four toolbox talks are based on the latest fi ndings on the most effective design and tailored to the hazards operating engineers face daily. These toolbox talks accompany an entire package of training materials, but can be used alone. The way these are delivered is as important as how well they are designed.
What did NIOSH find out?
- Just handing out factsheets and toolbox talks to workers doesn’t work. Providing copies after toolbox talks doesn’t make much of an impact either.
- Using case studies (real life stories of accidents that ended in fatality or injury) in toolbox talks is effective.
- When toolbox talks containing case studies were accompanied by discussion questions to encourage group participation, they were more effective. Consequently, getting the workers to participate in the discussion about the case study is important. It’s not enough to tell the story, it is better to have the workers engage in problem solving that analyzes why the accident occurred and how it could have been prevented. Active learning is always better than passive.
How should you deliver these toolbox talks?
- Choose a topic that is related to work going on at the site.
- Hold the meeting on the job, preferably where everyone can sit and relax.
- Hold the meeting at the beginning of a shift or after a break. Folks are too tired at the end of a shift to carefully listen and they want to get home.
- Read the toolbox talk sheet on the topic prior to conducting the talk.
- Start at the top of the form and work right through to the end, which should take around 10 to 15 minutes. Guidance is provided in blue print to help you with each section.
- Use the questions provided to generate discussions. Always allow time for the crew to respond to your questions before you provide an answer. Some suggested responses are written in italics.
- Review the case study and emphasize that this was a real incident. Ask the crew for a case study before you review the one provided, however.
- Always end with a discussion of the particular worksite where you are conducting the talk. Tie the talk as closely to hazards on the site as possible and encourage the crew to constantly look for and immediately correct hazards. They should also know how to report any problems that can’t be immediately corrected.
- Provide copies to each person, if you like, but NIOSH has not found that to be particularly effective.
- Encourage workers to do similar talks on their sites and provide them with the IUOE phone number for ordering in bulk.
- Have everyone sign the back of the form to indicate they attended this session and point out it is a pledge to look out for the health and safety of everyone on the site.
What are the key features of these toolbox talks?
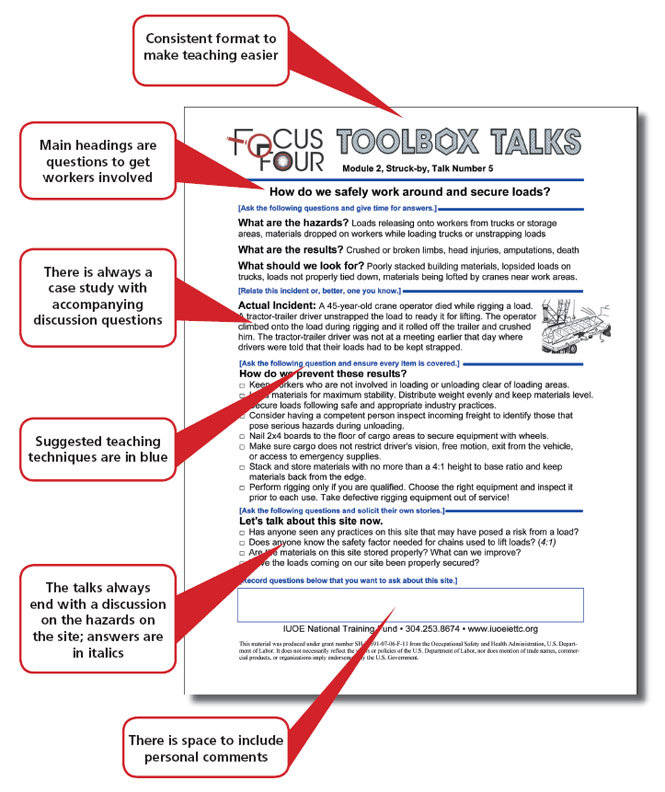
[disclaimer:protected] =>
[disclaimer_transformed:protected] =>
[alreadyInSave:protected] =>
[alreadyInValidation:protected] =>
[validationFailures:protected] => Array
(
)
[_new:BaseObject:private] =>
[_deleted:BaseObject:private] =>
[modifiedColumns:protected] => Array
(
)
)
[template] => record
[collection] =>
)
[_file] => /home/agsafe5/repositories/elcosh/live/templates/elcosh/record.html
[_errors:protected] => Array
(
)
[_encoding:protected] => UTF-8
[_outputMode:protected] => 11
[_forceReparse:protected] =>
[_phpCodeDestination:protected] => /tmp/
[_phpCodeExtension:protected] => php
[_cacheLifetime:protected] => 30
[_cachePurgeFrequency:protected] => 30
[externalMacroTemplatesCache:PHPTAL:private] => Array
(
[macros.html] => PHPTAL Object
(
[_prefilters:protected] => Array
(
)
[_prefilter:PHPTAL:private] => REMOVED: DO NOT USE
[_postfilter:protected] =>
[_repositories:protected] => Array
(
[0] => /home/agsafe5/repositories/elcosh/live/templates/elcosh
)
[_path:protected] => macros.html
[_resolvers:protected] => Array
(
)
[_source:protected] => PHPTAL_FileSource Object
(
[_path:PHPTAL_FileSource:private] => /home/agsafe5/repositories/elcosh/live/templates/elcosh/macros.html
)
[_codeFile:protected] => /tmp/tpl_61515a6c_macros__EnKHR8AWVA3oW7OmomvoZw.php
[_functionName:protected] => tpl_61515a6c_macros__EnKHR8AWVA3oW7OmomvoZw
[_prepared:protected] => 1
[_triggers:protected] => Array
(
)
[_translator:protected] =>
[_globalContext:protected] => stdClass Object
(
)
[_context:protected] => PHPTAL_Context Object
(
[_line] =>
[_file] => /home/agsafe5/repositories/elcosh/live/templates/elcosh/record.html
[repeat] => stdClass Object
(
)
[_xmlDeclaration] =>
[_docType] =>
[_nothrow:PHPTAL_Context:private] =>
[_slots:PHPTAL_Context:private] => Array
(
)
[_slotsStack:PHPTAL_Context:private] => Array
(
[0] => Array
(
)
[1] => Array
(
)
)
[_parentContext:PHPTAL_Context:private] => PHPTAL_Context Object
(
[_line] =>
[_file] => /home/agsafe5/repositories/elcosh/live/templates/elcosh/record.html
[repeat] => stdClass Object
(
)
[_xmlDeclaration] =>
[_docType] =>
[_nothrow:PHPTAL_Context:private] =>
[_slots:PHPTAL_Context:private] => Array
(
)
[_slotsStack:PHPTAL_Context:private] => Array
(
[0] => Array
(
)
[1] => Array
(
)
)
[_parentContext:PHPTAL_Context:private] =>
[_globalContext:PHPTAL_Context:private] => stdClass Object
(
)
[_echoDeclarations:PHPTAL_Context:private] =>
[referer] => http://www.elcosh.org/document/3827/d001298/Getting%2Bthe%2Bmost%2Bout%2Bof%2Bthe%2BIUOE%2BToolbox%2BTalks.html
[curr_module] => Record
[styles] => Array
(
)
[javascript] => Array
(
[0] => jquery.min.js
)
[metas] => Array
(
[language] => en
[robots] => index, follow
)
[user] =>
[curr_url] => https://www.elcosh.org/index.php?module=Record&id=3827&type=document
[base_url] => https://www.elcosh.org/index.php?module=Record
[title] => eLCOSH : Getting the most out of the IUOE Toolbox Talks
[language] => en
[search_query] =>
[module] => Record
[new_records] => Array
(
[0] => Search_Result Object
(
[title] => Toolbox Talk: Fixed Ladder
[image] => /record/images/notavailable-p.png
[blurb] => The CPWR Toolbox Talk on Fixed Ladders addresses the potential risks associated with using fixed ladders. The resource includes a brief case example,...
[category] => Array
(
[0] => 15
[1] => 47
[2] => 49
[3] => 51
[4] => 53
[5] => 55
[6] => 60
[7] => 64
[8] => 73
[9] => 76
[10] => 78
[11] => 80
[12] => 86
[13] => 87
[14] => 90
[15] => 92
[16] => 93
[17] => 94
[18] => 100
)
[labels] => Array
(
[0] => Falls
[1] => Work Environment
[2] => Hazards
[3] => Bricklayer
[4] => Trades
[5] => Carpenter
[7] => Cement Mason
[9] => Concrete Polisher
[11] => Electrical Worker
[13] => HVAC
[15] => Laborer
[17] => PCC/Restoration
[19] => Plumber/Pipefitter
[21] => Roofer/Waterproofer
[23] => Sheetmetal Worker
[25] => Welder
[27] => Commercial & Institutional
[28] => Jobsites
[29] => Industrial
[31] => LEED/Green Construction
[33] => Renovations
[35] => Residential
[37] => Toolbox Talks
[38] => Documents
[39] => Media & Documents
)
[type] => Toolbox Talks
[sub_category] =>
[url] => /document/4430/d001660/Toolbox%2BTalk%253A%2BFixed%2BLadder.html
[item:protected] => DocumentRecord Object
(
[records:protected] => Array
(
)
[recordId:protected] =>
[searchWordClass:protected] =>
[searchWordPeerClass:protected] =>
[bok_record:protected] =>
[authors:protected] =>
[organizations:protected] =>
[collections:protected] =>
[categories:protected] => Array
(
[15] => Category Object
(
[languages:protected] =>
[bok_resources:protected] =>
[bok_topics:protected] =>
[bok_keywords:protected] =>
[id:protected] => 15
[type:protected] => category
[parent:protected] => 7
[label:protected] => Falls
[alreadyInSave:protected] =>
[alreadyInValidation:protected] =>
[validationFailures:protected] => Array
(
)
[_new:BaseObject:private] =>
[_deleted:BaseObject:private] =>
[modifiedColumns:protected] => Array
(
)
)
[47] => Category Object
(
[languages:protected] =>
[bok_resources:protected] =>
[bok_topics:protected] =>
[bok_keywords:protected] =>
[id:protected] => 47
[type:protected] => category
[parent:protected] => 2
[label:protected] => Bricklayer
[alreadyInSave:protected] =>
[alreadyInValidation:protected] =>
[validationFailures:protected] => Array
(
)
[_new:BaseObject:private] =>
[_deleted:BaseObject:private] =>
[modifiedColumns:protected] => Array
(
)
)
[49] => Category Object
(
[languages:protected] =>
[bok_resources:protected] =>
[bok_topics:protected] =>
[bok_keywords:protected] =>
[id:protected] => 49
[type:protected] => category
[parent:protected] => 2
[label:protected] => Carpenter
[alreadyInSave:protected] =>
[alreadyInValidation:protected] =>
[validationFailures:protected] => Array
(
)
[_new:BaseObject:private] =>
[_deleted:BaseObject:private] =>
[modifiedColumns:protected] => Array
(
)
)
[51] => Category Object
(
[languages:protected] =>
[bok_resources:protected] =>
[bok_topics:protected] =>
[bok_keywords:protected] =>
[id:protected] => 51
[type:protected] => category
[parent:protected] => 2
[label:protected] => Cement Mason
[alreadyInSave:protected] =>
[alreadyInValidation:protected] =>
[validationFailures:protected] => Array
(
)
[_new:BaseObject:private] =>
[_deleted:BaseObject:private] =>
[modifiedColumns:protected] => Array
(
)
)
[53] => Category Object
(
[languages:protected] =>
[bok_resources:protected] =>
[bok_topics:protected] =>
[bok_keywords:protected] =>
[id:protected] => 53
[type:protected] => category
[parent:protected] => 2
[label:protected] => Concrete Polisher
[alreadyInSave:protected] =>
[alreadyInValidation:protected] =>
[validationFailures:protected] => Array
(
)
[_new:BaseObject:private] =>
[_deleted:BaseObject:private] =>
[modifiedColumns:protected] => Array
(
)
)
[55] => Category Object
(
[languages:protected] =>
[bok_resources:protected] =>
[bok_topics:protected] =>
[bok_keywords:protected] =>
[id:protected] => 55
[type:protected] => category
[parent:protected] => 2
[label:protected] => Electrical Worker
[alreadyInSave:protected] =>
[alreadyInValidation:protected] =>
[validationFailures:protected] => Array
(
)
[_new:BaseObject:private] =>
[_deleted:BaseObject:private] =>
[modifiedColumns:protected] => Array
(
)
)
[60] => Category Object
(
[languages:protected] =>
[bok_resources:protected] =>
[bok_topics:protected] =>
[bok_keywords:protected] =>
[id:protected] => 60
[type:protected] => category
[parent:protected] => 2
[label:protected] => HVAC
[alreadyInSave:protected] =>
[alreadyInValidation:protected] =>
[validationFailures:protected] => Array
(
)
[_new:BaseObject:private] =>
[_deleted:BaseObject:private] =>
[modifiedColumns:protected] => Array
(
)
)
[64] => Category Object
(
[languages:protected] =>
[bok_resources:protected] =>
[bok_topics:protected] =>
[bok_keywords:protected] =>
[id:protected] => 64
[type:protected] => category
[parent:protected] => 2
[label:protected] => Laborer
[alreadyInSave:protected] =>
[alreadyInValidation:protected] =>
[validationFailures:protected] => Array
(
)
[_new:BaseObject:private] =>
[_deleted:BaseObject:private] =>
[modifiedColumns:protected] => Array
(
)
)
[73] => Category Object
(
[languages:protected] =>
[bok_resources:protected] =>
[bok_topics:protected] =>
[bok_keywords:protected] =>
[id:protected] => 73
[type:protected] => category
[parent:protected] => 2
[label:protected] => PCC/Restoration
[alreadyInSave:protected] =>
[alreadyInValidation:protected] =>
[validationFailures:protected] => Array
(
)
[_new:BaseObject:private] =>
[_deleted:BaseObject:private] =>
[modifiedColumns:protected] => Array
(
)
)
[76] => Category Object
(
[languages:protected] =>
[bok_resources:protected] =>
[bok_topics:protected] =>
[bok_keywords:protected] =>
[id:protected] => 76
[type:protected] => category
[parent:protected] => 2
[label:protected] => Plumber/Pipefitter
[alreadyInSave:protected] =>
[alreadyInValidation:protected] =>
[validationFailures:protected] => Array
(
)
[_new:BaseObject:private] =>
[_deleted:BaseObject:private] =>
[modifiedColumns:protected] => Array
(
)
)
[78] => Category Object
(
[languages:protected] =>
[bok_resources:protected] =>
[bok_topics:protected] =>
[bok_keywords:protected] =>
[id:protected] => 78
[type:protected] => category
[parent:protected] => 2
[label:protected] => Roofer/Waterproofer
[alreadyInSave:protected] =>
[alreadyInValidation:protected] =>
[validationFailures:protected] => Array
(
)
[_new:BaseObject:private] =>
[_deleted:BaseObject:private] =>
[modifiedColumns:protected] => Array
(
)
)
[80] => Category Object
(
[languages:protected] =>
[bok_resources:protected] =>
[bok_topics:protected] =>
[bok_keywords:protected] =>
[id:protected] => 80
[type:protected] => category
[parent:protected] => 2
[label:protected] => Sheetmetal Worker
[alreadyInSave:protected] =>
[alreadyInValidation:protected] =>
[validationFailures:protected] => Array
(
)
[_new:BaseObject:private] =>
[_deleted:BaseObject:private] =>
[modifiedColumns:protected] => Array
(
)
)
[86] => Category Object
(
[languages:protected] =>
[bok_resources:protected] =>
[bok_topics:protected] =>
[bok_keywords:protected] =>
[id:protected] => 86
[type:protected] => category
[parent:protected] => 2
[label:protected] => Welder
[alreadyInSave:protected] =>
[alreadyInValidation:protected] =>
[validationFailures:protected] => Array
(
)
[_new:BaseObject:private] =>
[_deleted:BaseObject:private] =>
[modifiedColumns:protected] => Array
(
)
)
[87] => Category Object
(
[languages:protected] =>
[bok_resources:protected] =>
[bok_topics:protected] =>
[bok_keywords:protected] =>
[id:protected] => 87
[type:protected] => category
[parent:protected] => 3
[label:protected] => Commercial & Institutional
[alreadyInSave:protected] =>
[alreadyInValidation:protected] =>
[validationFailures:protected] => Array
(
)
[_new:BaseObject:private] =>
[_deleted:BaseObject:private] =>
[modifiedColumns:protected] => Array
(
)
)
[90] => Category Object
(
[languages:protected] =>
[bok_resources:protected] =>
[bok_topics:protected] =>
[bok_keywords:protected] =>
[id:protected] => 90
[type:protected] => category
[parent:protected] => 3
[label:protected] => Industrial
[alreadyInSave:protected] =>
[alreadyInValidation:protected] =>
[validationFailures:protected] => Array
(
)
[_new:BaseObject:private] =>
[_deleted:BaseObject:private] =>
[modifiedColumns:protected] => Array
(
)
)
[92] => Category Object
(
[languages:protected] =>
[bok_resources:protected] =>
[bok_topics:protected] =>
[bok_keywords:protected] =>
[id:protected] => 92
[type:protected] => category
[parent:protected] => 3
[label:protected] => LEED/Green Construction
[alreadyInSave:protected] =>
[alreadyInValidation:protected] =>
[validationFailures:protected] => Array
(
)
[_new:BaseObject:private] =>
[_deleted:BaseObject:private] =>
[modifiedColumns:protected] => Array
(
)
)
[93] => Category Object
(
[languages:protected] =>
[bok_resources:protected] =>
[bok_topics:protected] =>
[bok_keywords:protected] =>
[id:protected] => 93
[type:protected] => category
[parent:protected] => 3
[label:protected] => Renovations
[alreadyInSave:protected] =>
[alreadyInValidation:protected] =>
[validationFailures:protected] => Array
(
)
[_new:BaseObject:private] =>
[_deleted:BaseObject:private] =>
[modifiedColumns:protected] => Array
(
)
)
[94] => Category Object
(
[languages:protected] =>
[bok_resources:protected] =>
[bok_topics:protected] =>
[bok_keywords:protected] =>
[id:protected] => 94
[type:protected] => category
[parent:protected] => 3
[label:protected] => Residential
[alreadyInSave:protected] =>
[alreadyInValidation:protected] =>
[validationFailures:protected] => Array
(
)
[_new:BaseObject:private] =>
[_deleted:BaseObject:private] =>
[modifiedColumns:protected] => Array
(
)
)
[100] => Category Object
(
[languages:protected] =>
[bok_resources:protected] =>
[bok_topics:protected] =>
[bok_keywords:protected] =>
[id:protected] => 100
[type:protected] => category
[parent:protected] => 6
[label:protected] => Toolbox Talks
[alreadyInSave:protected] =>
[alreadyInValidation:protected] =>
[validationFailures:protected] => Array
(
)
[_new:BaseObject:private] =>
[_deleted:BaseObject:private] =>
[modifiedColumns:protected] => Array
(
)
)
)
[categories_initialized:protected] => 1
[mapped_items:protected] =>
[content:protected] =>
[files:protected] =>
[language:protected] => Language Object
(
[id:protected] => 1
[code:protected] => en
[name:protected] => English
[alreadyInSave:protected] =>
[alreadyInValidation:protected] =>
[validationFailures:protected] => Array
(
)
[_new:BaseObject:private] =>
[_deleted:BaseObject:private] =>
[modifiedColumns:protected] => Array
(
)
)
[old_record:protected] =>
[id:protected] => 4430
[old_id:protected] =>
[elcosh_id:protected] => d001660
[type:protected] => document
[display_type:protected] => HTML only (and links)
[user_id:protected] => 0
[language_id:protected] => 1
[tagging_id:protected] => Mike Aguilar
[priority_id:protected] => 1
[title:protected] => Toolbox Talk: Fixed Ladder
[total_pages:protected] => 0
[billed_pages:protected] => 0
[publication_number:protected] =>
[part_of:protected] =>
[keywords:protected] => Fixed Ladders, Fall Prevention, Falls
[comments:protected] =>
[summary:protected] => The CPWR Toolbox Talk on Fixed Ladders addresses the potential risks associated with using fixed ladders. The resource includes a brief case example, steps to prevent a related injury and questions for discussion. It includes an image that illustrates the hazard, which can be posted in a central location as a reminder of steps to work safely.
Available in
English
and
Spanish.
[transition_comments:protected] =>
[external_link:protected] =>
[consol_link:protected] =>
[more_like_this:protected] => d001257,d001254,d001255,d001256,d001258,d001262,d001279
[permission_given_by:protected] =>
[published:protected] => T
[billable:protected] => F
[img_name:protected] =>
[img_ext:protected] =>
[img_width:protected] =>
[img_height:protected] =>
[img_credit:protected] =>
[img_practice:protected] =>
[vid_source_id:protected] =>
[vid_running_time:protected] =>
[vid_intended_audience:protected] =>
[vid_acquisition_info:protected] =>
[vid_cost:protected] =>
[vid_producer:protected] =>
[vid_filename:protected] =>
[vid_filename_downloadable:protected] =>
[date_summary:protected] =>
[date_permission_requested:protected] =>
[date_permission_received:protected] =>
[date_review_needed:protected] =>
[date_received:protected] => 06/10/22
[date_completed:protected] => 06/10/22
[date_billed:protected] =>
[date_modified:protected] => 05/22/23
[collBokExports:protected] =>
[lastBokExportCriteria:BaseElcoshItem:private] =>
[alreadyInSave:protected] =>
[alreadyInValidation:protected] =>
[validationFailures:protected] => Array
(
)
[_new:BaseObject:private] =>
[_deleted:BaseObject:private] =>
[modifiedColumns:protected] => Array
(
)
)
)
[1] => Search_Result Object
(
[title] => Toolbox Talk: Challenges Preventing Falling Objects
[image] => /record/images/notavailable-p.png
[blurb] => The CPWR Toolbox Talk on Challenges Preventing Falling Objects addresses the hazards of being struck by falling objects on the job site. The resource...
[category] => Array
(
[0] => 12
[1] => 47
[2] => 49
[3] => 51
[4] => 55
[5] => 64
[6] => 68
[7] => 71
[8] => 75
[9] => 78
[10] => 79
[11] => 82
[12] => 62
[13] => 86
[14] => 87
[15] => 88
[16] => 89
[17] => 91
[18] => 90
[19] => 92
[20] => 93
[21] => 94
[22] => 95
[23] => 100
)
[labels] => Array
(
[0] => Crushed/Struck By
[1] => Work Environment
[2] => Hazards
[3] => Bricklayer
[4] => Trades
[5] => Carpenter
[7] => Cement Mason
[9] => Electrical Worker
[11] => Laborer
[13] => Maintenance Worker
[15] => Painter
[17] => Plasterer
[19] => Roofer/Waterproofer
[21] => Scaffold Erector
[23] => Stonemason
[25] => Structural Ironworker
[27] => Welder
[29] => Commercial & Institutional
[30] => Jobsites
[31] => Demolition
[33] => Disasters
[35] => Heavy & Highway
[37] => Industrial
[39] => LEED/Green Construction
[41] => Renovations
[43] => Residential
[45] => Underground
[47] => Toolbox Talks
[48] => Documents
[49] => Media & Documents
)
[type] => Toolbox Talks
[sub_category] =>
[url] => /document/4431/d001661/Toolbox%2BTalk%253A%2BChallenges%2BPreventing%2BFalling%2BObjects.html
[item:protected] => DocumentRecord Object
(
[records:protected] => Array
(
)
[recordId:protected] =>
[searchWordClass:protected] =>
[searchWordPeerClass:protected] =>
[bok_record:protected] =>
[authors:protected] =>
[organizations:protected] =>
[collections:protected] =>
[categories:protected] => Array
(
[12] => Category Object
(
[languages:protected] =>
[bok_resources:protected] =>
[bok_topics:protected] =>
[bok_keywords:protected] =>
[id:protected] => 12
[type:protected] => category
[parent:protected] => 7
[label:protected] => Crushed/Struck By
[alreadyInSave:protected] =>
[alreadyInValidation:protected] =>
[validationFailures:protected] => Array
(
)
[_new:BaseObject:private] =>
[_deleted:BaseObject:private] =>
[modifiedColumns:protected] => Array
(
)
)
[47] => Category Object
(
[languages:protected] =>
[bok_resources:protected] =>
[bok_topics:protected] =>
[bok_keywords:protected] =>
[id:protected] => 47
[type:protected] => category
[parent:protected] => 2
[label:protected] => Bricklayer
[alreadyInSave:protected] =>
[alreadyInValidation:protected] =>
[validationFailures:protected] => Array
(
)
[_new:BaseObject:private] =>
[_deleted:BaseObject:private] =>
[modifiedColumns:protected] => Array
(
)
)
[49] => Category Object
(
[languages:protected] =>
[bok_resources:protected] =>
[bok_topics:protected] =>
[bok_keywords:protected] =>
[id:protected] => 49
[type:protected] => category
[parent:protected] => 2
[label:protected] => Carpenter
[alreadyInSave:protected] =>
[alreadyInValidation:protected] =>
[validationFailures:protected] => Array
(
)
[_new:BaseObject:private] =>
[_deleted:BaseObject:private] =>
[modifiedColumns:protected] => Array
(
)
)
[51] => Category Object
(
[languages:protected] =>
[bok_resources:protected] =>
[bok_topics:protected] =>
[bok_keywords:protected] =>
[id:protected] => 51
[type:protected] => category
[parent:protected] => 2
[label:protected] => Cement Mason
[alreadyInSave:protected] =>
[alreadyInValidation:protected] =>
[validationFailures:protected] => Array
(
)
[_new:BaseObject:private] =>
[_deleted:BaseObject:private] =>
[modifiedColumns:protected] => Array
(
)
)
[55] => Category Object
(
[languages:protected] =>
[bok_resources:protected] =>
[bok_topics:protected] =>
[bok_keywords:protected] =>
[id:protected] => 55
[type:protected] => category
[parent:protected] => 2
[label:protected] => Electrical Worker
[alreadyInSave:protected] =>
[alreadyInValidation:protected] =>
[validationFailures:protected] => Array
(
)
[_new:BaseObject:private] =>
[_deleted:BaseObject:private] =>
[modifiedColumns:protected] => Array
(
)
)
[64] => Category Object
(
[languages:protected] =>
[bok_resources:protected] =>
[bok_topics:protected] =>
[bok_keywords:protected] =>
[id:protected] => 64
[type:protected] => category
[parent:protected] => 2
[label:protected] => Laborer
[alreadyInSave:protected] =>
[alreadyInValidation:protected] =>
[validationFailures:protected] => Array
(
)
[_new:BaseObject:private] =>
[_deleted:BaseObject:private] =>
[modifiedColumns:protected] => Array
(
)
)
[68] => Category Object
(
[languages:protected] =>
[bok_resources:protected] =>
[bok_topics:protected] =>
[bok_keywords:protected] =>
[id:protected] => 68
[type:protected] => category
[parent:protected] => 2
[label:protected] => Maintenance Worker
[alreadyInSave:protected] =>
[alreadyInValidation:protected] =>
[validationFailures:protected] => Array
(
)
[_new:BaseObject:private] =>
[_deleted:BaseObject:private] =>
[modifiedColumns:protected] => Array
(
)
)
[71] => Category Object
(
[languages:protected] =>
[bok_resources:protected] =>
[bok_topics:protected] =>
[bok_keywords:protected] =>
[id:protected] => 71
[type:protected] => category
[parent:protected] => 2
[label:protected] => Painter
[alreadyInSave:protected] =>
[alreadyInValidation:protected] =>
[validationFailures:protected] => Array
(
)
[_new:BaseObject:private] =>
[_deleted:BaseObject:private] =>
[modifiedColumns:protected] => Array
(
)
)
[75] => Category Object
(
[languages:protected] =>
[bok_resources:protected] =>
[bok_topics:protected] =>
[bok_keywords:protected] =>
[id:protected] => 75
[type:protected] => category
[parent:protected] => 2
[label:protected] => Plasterer
[alreadyInSave:protected] =>
[alreadyInValidation:protected] =>
[validationFailures:protected] => Array
(
)
[_new:BaseObject:private] =>
[_deleted:BaseObject:private] =>
[modifiedColumns:protected] => Array
(
)
)
[78] => Category Object
(
[languages:protected] =>
[bok_resources:protected] =>
[bok_topics:protected] =>
[bok_keywords:protected] =>
[id:protected] => 78
[type:protected] => category
[parent:protected] => 2
[label:protected] => Roofer/Waterproofer
[alreadyInSave:protected] =>
[alreadyInValidation:protected] =>
[validationFailures:protected] => Array
(
)
[_new:BaseObject:private] =>
[_deleted:BaseObject:private] =>
[modifiedColumns:protected] => Array
(
)
)
[79] => Category Object
(
[languages:protected] =>
[bok_resources:protected] =>
[bok_topics:protected] =>
[bok_keywords:protected] =>
[id:protected] => 79
[type:protected] => category
[parent:protected] => 2
[label:protected] => Scaffold Erector
[alreadyInSave:protected] =>
[alreadyInValidation:protected] =>
[validationFailures:protected] => Array
(
)
[_new:BaseObject:private] =>
[_deleted:BaseObject:private] =>
[modifiedColumns:protected] => Array
(
)
)
[82] => Category Object
(
[languages:protected] =>
[bok_resources:protected] =>
[bok_topics:protected] =>
[bok_keywords:protected] =>
[id:protected] => 82
[type:protected] => category
[parent:protected] => 2
[label:protected] => Stonemason
[alreadyInSave:protected] =>
[alreadyInValidation:protected] =>
[validationFailures:protected] => Array
(
)
[_new:BaseObject:private] =>
[_deleted:BaseObject:private] =>
[modifiedColumns:protected] => Array
(
)
)
[62] => Category Object
(
[languages:protected] =>
[bok_resources:protected] =>
[bok_topics:protected] =>
[bok_keywords:protected] =>
[id:protected] => 62
[type:protected] => category
[parent:protected] => 2
[label:protected] => Structural Ironworker
[alreadyInSave:protected] =>
[alreadyInValidation:protected] =>
[validationFailures:protected] => Array
(
)
[_new:BaseObject:private] =>
[_deleted:BaseObject:private] =>
[modifiedColumns:protected] => Array
(
)
)
[86] => Category Object
(
[languages:protected] =>
[bok_resources:protected] =>
[bok_topics:protected] =>
[bok_keywords:protected] =>
[id:protected] => 86
[type:protected] => category
[parent:protected] => 2
[label:protected] => Welder
[alreadyInSave:protected] =>
[alreadyInValidation:protected] =>
[validationFailures:protected] => Array
(
)
[_new:BaseObject:private] =>
[_deleted:BaseObject:private] =>
[modifiedColumns:protected] => Array
(
)
)
[87] => Category Object
(
[languages:protected] =>
[bok_resources:protected] =>
[bok_topics:protected] =>
[bok_keywords:protected] =>
[id:protected] => 87
[type:protected] => category
[parent:protected] => 3
[label:protected] => Commercial & Institutional
[alreadyInSave:protected] =>
[alreadyInValidation:protected] =>
[validationFailures:protected] => Array
(
)
[_new:BaseObject:private] =>
[_deleted:BaseObject:private] =>
[modifiedColumns:protected] => Array
(
)
)
[88] => Category Object
(
[languages:protected] =>
[bok_resources:protected] =>
[bok_topics:protected] =>
[bok_keywords:protected] =>
[id:protected] => 88
[type:protected] => category
[parent:protected] => 3
[label:protected] => Demolition
[alreadyInSave:protected] =>
[alreadyInValidation:protected] =>
[validationFailures:protected] => Array
(
)
[_new:BaseObject:private] =>
[_deleted:BaseObject:private] =>
[modifiedColumns:protected] => Array
(
)
)
[89] => Category Object
(
[languages:protected] =>
[bok_resources:protected] =>
[bok_topics:protected] =>
[bok_keywords:protected] =>
[id:protected] => 89
[type:protected] => category
[parent:protected] => 3
[label:protected] => Disasters
[alreadyInSave:protected] =>
[alreadyInValidation:protected] =>
[validationFailures:protected] => Array
(
)
[_new:BaseObject:private] =>
[_deleted:BaseObject:private] =>
[modifiedColumns:protected] => Array
(
)
)
[91] => Category Object
(
[languages:protected] =>
[bok_resources:protected] =>
[bok_topics:protected] =>
[bok_keywords:protected] =>
[id:protected] => 91
[type:protected] => category
[parent:protected] => 3
[label:protected] => Heavy & Highway
[alreadyInSave:protected] =>
[alreadyInValidation:protected] =>
[validationFailures:protected] => Array
(
)
[_new:BaseObject:private] =>
[_deleted:BaseObject:private] =>
[modifiedColumns:protected] => Array
(
)
)
[90] => Category Object
(
[languages:protected] =>
[bok_resources:protected] =>
[bok_topics:protected] =>
[bok_keywords:protected] =>
[id:protected] => 90
[type:protected] => category
[parent:protected] => 3
[label:protected] => Industrial
[alreadyInSave:protected] =>
[alreadyInValidation:protected] =>
[validationFailures:protected] => Array
(
)
[_new:BaseObject:private] =>
[_deleted:BaseObject:private] =>
[modifiedColumns:protected] => Array
(
)
)
[92] => Category Object
(
[languages:protected] =>
[bok_resources:protected] =>
[bok_topics:protected] =>
[bok_keywords:protected] =>
[id:protected] => 92
[type:protected] => category
[parent:protected] => 3
[label:protected] => LEED/Green Construction
[alreadyInSave:protected] =>
[alreadyInValidation:protected] =>
[validationFailures:protected] => Array
(
)
[_new:BaseObject:private] =>
[_deleted:BaseObject:private] =>
[modifiedColumns:protected] => Array
(
)
)
[93] => Category Object
(
[languages:protected] =>
[bok_resources:protected] =>
[bok_topics:protected] =>
[bok_keywords:protected] =>
[id:protected] => 93
[type:protected] => category
[parent:protected] => 3
[label:protected] => Renovations
[alreadyInSave:protected] =>
[alreadyInValidation:protected] =>
[validationFailures:protected] => Array
(
)
[_new:BaseObject:private] =>
[_deleted:BaseObject:private] =>
[modifiedColumns:protected] => Array
(
)
)
[94] => Category Object
(
[languages:protected] =>
[bok_resources:protected] =>
[bok_topics:protected] =>
[bok_keywords:protected] =>
[id:protected] => 94
[type:protected] => category
[parent:protected] => 3
[label:protected] => Residential
[alreadyInSave:protected] =>
[alreadyInValidation:protected] =>
[validationFailures:protected] => Array
(
)
[_new:BaseObject:private] =>
[_deleted:BaseObject:private] =>
[modifiedColumns:protected] => Array
(
)
)
[95] => Category Object
(
[languages:protected] =>
[bok_resources:protected] =>
[bok_topics:protected] =>
[bok_keywords:protected] =>
[id:protected] => 95
[type:protected] => category
[parent:protected] => 3
[label:protected] => Underground
[alreadyInSave:protected] =>
[alreadyInValidation:protected] =>
[validationFailures:protected] => Array
(
)
[_new:BaseObject:private] =>
[_deleted:BaseObject:private] =>
[modifiedColumns:protected] => Array
(
)
)
[100] => Category Object
(
[languages:protected] =>
[bok_resources:protected] =>
[bok_topics:protected] =>
[bok_keywords:protected] =>
[id:protected] => 100
[type:protected] => category
[parent:protected] => 6
[label:protected] => Toolbox Talks
[alreadyInSave:protected] =>
[alreadyInValidation:protected] =>
[validationFailures:protected] => Array
(
)
[_new:BaseObject:private] =>
[_deleted:BaseObject:private] =>
[modifiedColumns:protected] => Array
(
)
)
)
[categories_initialized:protected] => 1
[mapped_items:protected] =>
[content:protected] =>
[files:protected] =>
[language:protected] => Language Object
(
[id:protected] => 1
[code:protected] => en
[name:protected] => English
[alreadyInSave:protected] =>
[alreadyInValidation:protected] =>
[validationFailures:protected] => Array
(
)
[_new:BaseObject:private] =>
[_deleted:BaseObject:private] =>
[modifiedColumns:protected] => Array
(
)
)
[old_record:protected] =>
[id:protected] => 4431
[old_id:protected] =>
[elcosh_id:protected] => d001661
[type:protected] => document
[display_type:protected] => HTML only (and links)
[user_id:protected] => 0
[language_id:protected] => 1
[tagging_id:protected] => Mike Aguilar
[priority_id:protected] => 1
[title:protected] => Toolbox Talk: Challenges Preventing Falling Objects
[total_pages:protected] => 0
[billed_pages:protected] => 0
[publication_number:protected] =>
[part_of:protected] =>
[keywords:protected] => dropped objects, falling objects, struck by incidents, struck by fatalities
[comments:protected] =>
[summary:protected] => The CPWR Toolbox Talk on Challenges Preventing Falling Objects addresses the hazards of being struck by falling objects on the job site. The resource includes a brief example, steps to prevent a related injury, and questions for discussion. It includes a graphic that illustrates a group workers observing a scaffold free of debris during high winds, which can be posted in a central location as a reminder of steps to work safely.
Available in
English and
Spanish.
[transition_comments:protected] =>
[external_link:protected] =>
[consol_link:protected] =>
[more_like_this:protected] => d001234,d001238,d001244,d001251,d001253,d001260,d001268,d001278
[permission_given_by:protected] =>
[published:protected] => T
[billable:protected] => F
[img_name:protected] =>
[img_ext:protected] =>
[img_width:protected] =>
[img_height:protected] =>
[img_credit:protected] =>
[img_practice:protected] =>
[vid_source_id:protected] =>
[vid_running_time:protected] =>
[vid_intended_audience:protected] =>
[vid_acquisition_info:protected] =>
[vid_cost:protected] =>
[vid_producer:protected] =>
[vid_filename:protected] =>
[vid_filename_downloadable:protected] =>
[date_summary:protected] =>
[date_permission_requested:protected] =>
[date_permission_received:protected] =>
[date_review_needed:protected] =>
[date_received:protected] => 06/10/22
[date_completed:protected] => 06/10/22
[date_billed:protected] =>
[date_modified:protected] => 05/22/23
[collBokExports:protected] =>
[lastBokExportCriteria:BaseElcoshItem:private] =>
[alreadyInSave:protected] =>
[alreadyInValidation:protected] =>
[validationFailures:protected] => Array
(
)
[_new:BaseObject:private] =>
[_deleted:BaseObject:private] =>
[modifiedColumns:protected] => Array
(
)
)
)
[2] => Search_Result Object
(
[title] => Toolbox Talk: Tower Crane Safety
[image] => /record/images/notavailable-p.png
[blurb] => The CPWR Toolbox Talk on Tower Crane Safety addresses the potential hazards of Tower Cranes and the importance of following procedure before and durin...
[category] => Array
(
[0] => 11
[1] => 12
[2] => 18
[3] => 70
[4] => 87
[5] => 88
[6] => 91
[7] => 90
[8] => 92
[9] => 100
)
[labels] => Array
(
[0] => Cranes & Hoists
[1] => Work Environment
[2] => Hazards
[3] => Crushed/Struck By
[6] => Motor Vehicles/Heavy Equipment
[9] => Operating Engineer
[10] => Trades
[11] => Commercial & Institutional
[12] => Jobsites
[13] => Demolition
[15] => Heavy & Highway
[17] => Industrial
[19] => LEED/Green Construction
[21] => Toolbox Talks
[22] => Documents
[23] => Media & Documents
)
[type] => Toolbox Talks
[sub_category] =>
[url] => /document/4427/d001657/Toolbox%2BTalk%253A%2BTower%2BCrane%2BSafety.html
[item:protected] => DocumentRecord Object
(
[records:protected] => Array
(
)
[recordId:protected] =>
[searchWordClass:protected] =>
[searchWordPeerClass:protected] =>
[bok_record:protected] =>
[authors:protected] =>
[organizations:protected] =>
[collections:protected] =>
[categories:protected] => Array
(
[11] => Category Object
(
[languages:protected] =>
[bok_resources:protected] =>
[bok_topics:protected] =>
[bok_keywords:protected] =>
[id:protected] => 11
[type:protected] => category
[parent:protected] => 7
[label:protected] => Cranes & Hoists
[alreadyInSave:protected] =>
[alreadyInValidation:protected] =>
[validationFailures:protected] => Array
(
)
[_new:BaseObject:private] =>
[_deleted:BaseObject:private] =>
[modifiedColumns:protected] => Array
(
)
)
[12] => Category Object
(
[languages:protected] =>
[bok_resources:protected] =>
[bok_topics:protected] =>
[bok_keywords:protected] =>
[id:protected] => 12
[type:protected] => category
[parent:protected] => 7
[label:protected] => Crushed/Struck By
[alreadyInSave:protected] =>
[alreadyInValidation:protected] =>
[validationFailures:protected] => Array
(
)
[_new:BaseObject:private] =>
[_deleted:BaseObject:private] =>
[modifiedColumns:protected] => Array
(
)
)
[18] => Category Object
(
[languages:protected] =>
[bok_resources:protected] =>
[bok_topics:protected] =>
[bok_keywords:protected] =>
[id:protected] => 18
[type:protected] => category
[parent:protected] => 7
[label:protected] => Motor Vehicles/Heavy Equipment
[alreadyInSave:protected] =>
[alreadyInValidation:protected] =>
[validationFailures:protected] => Array
(
)
[_new:BaseObject:private] =>
[_deleted:BaseObject:private] =>
[modifiedColumns:protected] => Array
(
)
)
[70] => Category Object
(
[languages:protected] =>
[bok_resources:protected] =>
[bok_topics:protected] =>
[bok_keywords:protected] =>
[id:protected] => 70
[type:protected] => category
[parent:protected] => 2
[label:protected] => Operating Engineer
[alreadyInSave:protected] =>
[alreadyInValidation:protected] =>
[validationFailures:protected] => Array
(
)
[_new:BaseObject:private] =>
[_deleted:BaseObject:private] =>
[modifiedColumns:protected] => Array
(
)
)
[87] => Category Object
(
[languages:protected] =>
[bok_resources:protected] =>
[bok_topics:protected] =>
[bok_keywords:protected] =>
[id:protected] => 87
[type:protected] => category
[parent:protected] => 3
[label:protected] => Commercial & Institutional
[alreadyInSave:protected] =>
[alreadyInValidation:protected] =>
[validationFailures:protected] => Array
(
)
[_new:BaseObject:private] =>
[_deleted:BaseObject:private] =>
[modifiedColumns:protected] => Array
(
)
)
[88] => Category Object
(
[languages:protected] =>
[bok_resources:protected] =>
[bok_topics:protected] =>
[bok_keywords:protected] =>
[id:protected] => 88
[type:protected] => category
[parent:protected] => 3
[label:protected] => Demolition
[alreadyInSave:protected] =>
[alreadyInValidation:protected] =>
[validationFailures:protected] => Array
(
)
[_new:BaseObject:private] =>
[_deleted:BaseObject:private] =>
[modifiedColumns:protected] => Array
(
)
)
[91] => Category Object
(
[languages:protected] =>
[bok_resources:protected] =>
[bok_topics:protected] =>
[bok_keywords:protected] =>
[id:protected] => 91
[type:protected] => category
[parent:protected] => 3
[label:protected] => Heavy & Highway
[alreadyInSave:protected] =>
[alreadyInValidation:protected] =>
[validationFailures:protected] => Array
(
)
[_new:BaseObject:private] =>
[_deleted:BaseObject:private] =>
[modifiedColumns:protected] => Array
(
)
)
[90] => Category Object
(
[languages:protected] =>
[bok_resources:protected] =>
[bok_topics:protected] =>
[bok_keywords:protected] =>
[id:protected] => 90
[type:protected] => category
[parent:protected] => 3
[label:protected] => Industrial
[alreadyInSave:protected] =>
[alreadyInValidation:protected] =>
[validationFailures:protected] => Array
(
)
[_new:BaseObject:private] =>
[_deleted:BaseObject:private] =>
[modifiedColumns:protected] => Array
(
)
)
[92] => Category Object
(
[languages:protected] =>
[bok_resources:protected] =>
[bok_topics:protected] =>
[bok_keywords:protected] =>
[id:protected] => 92
[type:protected] => category
[parent:protected] => 3
[label:protected] => LEED/Green Construction
[alreadyInSave:protected] =>
[alreadyInValidation:protected] =>
[validationFailures:protected] => Array
(
)
[_new:BaseObject:private] =>
[_deleted:BaseObject:private] =>
[modifiedColumns:protected] => Array
(
)
)
[100] => Category Object
(
[languages:protected] =>
[bok_resources:protected] =>
[bok_topics:protected] =>
[bok_keywords:protected] =>
[id:protected] => 100
[type:protected] => category
[parent:protected] => 6
[label:protected] => Toolbox Talks
[alreadyInSave:protected] =>
[alreadyInValidation:protected] =>
[validationFailures:protected] => Array
(
)
[_new:BaseObject:private] =>
[_deleted:BaseObject:private] =>
[modifiedColumns:protected] => Array
(
)
)
)
[categories_initialized:protected] => 1
[mapped_items:protected] =>
[content:protected] =>
[files:protected] =>
[language:protected] => Language Object
(
[id:protected] => 1
[code:protected] => en
[name:protected] => English
[alreadyInSave:protected] =>
[alreadyInValidation:protected] =>
[validationFailures:protected] => Array
(
)
[_new:BaseObject:private] =>
[_deleted:BaseObject:private] =>
[modifiedColumns:protected] => Array
(
)
)
[old_record:protected] =>
[id:protected] => 4427
[old_id:protected] =>
[elcosh_id:protected] => d001657
[type:protected] => document
[display_type:protected] => HTML only (and links)
[user_id:protected] => 0
[language_id:protected] => 1
[tagging_id:protected] => Mike Aguilar
[priority_id:protected] => 1
[title:protected] => Toolbox Talk: Tower Crane Safety
[total_pages:protected] => 0
[billed_pages:protected] => 0
[publication_number:protected] =>
[part_of:protected] =>
[keywords:protected] => Tower Crane, Crane, Stability, Tipping, Lift Zone Safety, Lift, Zone, Safety, Struck by
[comments:protected] =>
[summary:protected] => The CPWR Toolbox Talk on Tower Crane Safety addresses the potential hazards of Tower Cranes and the importance of following procedure before and during Tower Crane operation. The resource includes a brief example, steps to prevent a related injury, and questions for discussion. It includes a graphic that illustrates a worker inspecting a Tower Crane before operation, which can be posted in a central location as a reminder of steps to work safely.
Available in
English and
Spanish.
[transition_comments:protected] =>
[external_link:protected] =>
[consol_link:protected] =>
[more_like_this:protected] => d001234,d001238,d001250,d001251,d001253,d001258,d001262,d001273
[permission_given_by:protected] =>
[published:protected] => T
[billable:protected] => F
[img_name:protected] =>
[img_ext:protected] => jpg
[img_width:protected] =>
[img_height:protected] =>
[img_credit:protected] =>
[img_practice:protected] =>
[vid_source_id:protected] =>
[vid_running_time:protected] =>
[vid_intended_audience:protected] =>
[vid_acquisition_info:protected] =>
[vid_cost:protected] =>
[vid_producer:protected] =>
[vid_filename:protected] =>
[vid_filename_downloadable:protected] =>
[date_summary:protected] =>
[date_permission_requested:protected] =>
[date_permission_received:protected] =>
[date_review_needed:protected] =>
[date_received:protected] => 12/23/21
[date_completed:protected] => 12/23/21
[date_billed:protected] =>
[date_modified:protected] => 05/19/23
[collBokExports:protected] =>
[lastBokExportCriteria:BaseElcoshItem:private] =>
[alreadyInSave:protected] =>
[alreadyInValidation:protected] =>
[validationFailures:protected] => Array
(
)
[_new:BaseObject:private] =>
[_deleted:BaseObject:private] =>
[modifiedColumns:protected] => Array
(
)
)
)
[3] => Search_Result Object
(
[title] => Toolbox Talk: Work Zone Safety: Working Around Vehicles
[image] => /record/images/notavailable-p.png
[blurb] => The CPWR Toolbox Talk on Working Around Vehicles in the Work Zone addresses methods to avoid being struck-by a vehicle on a construction site. The res...
[category] => Array
(
[0] => 12
[1] => 18
[2] => 52
[3] => 57
[4] => 70
[5] => 85
[6] => 87
[7] => 88
[8] => 89
[9] => 91
[10] => 90
[11] => 92
[12] => 93
[13] => 94
[14] => 95
[15] => 100
)
[labels] => Array
(
[0] => Crushed/Struck By
[1] => Work Environment
[2] => Hazards
[3] => Motor Vehicles/Heavy Equipment
[6] => Commercial Diver
[7] => Trades
[8] => Flagger
[10] => Operating Engineer
[12] => Truck Driver
[14] => Commercial & Institutional
[15] => Jobsites
[16] => Demolition
[18] => Disasters
[20] => Heavy & Highway
[22] => Industrial
[24] => LEED/Green Construction
[26] => Renovations
[28] => Residential
[30] => Underground
[32] => Toolbox Talks
[33] => Documents
[34] => Media & Documents
)
[type] => Toolbox Talks
[sub_category] =>
[url] => /document/4428/d001658/Toolbox%2BTalk%253A%2BWork%2BZone%2BSafety%253A%2BWorking%2BAround%2BVehicles.html
[item:protected] => DocumentRecord Object
(
[records:protected] => Array
(
)
[recordId:protected] =>
[searchWordClass:protected] =>
[searchWordPeerClass:protected] =>
[bok_record:protected] =>
[authors:protected] =>
[organizations:protected] =>
[collections:protected] =>
[categories:protected] => Array
(
[12] => Category Object
(
[languages:protected] =>
[bok_resources:protected] =>
[bok_topics:protected] =>
[bok_keywords:protected] =>
[id:protected] => 12
[type:protected] => category
[parent:protected] => 7
[label:protected] => Crushed/Struck By
[alreadyInSave:protected] =>
[alreadyInValidation:protected] =>
[validationFailures:protected] => Array
(
)
[_new:BaseObject:private] =>
[_deleted:BaseObject:private] =>
[modifiedColumns:protected] => Array
(
)
)
[18] => Category Object
(
[languages:protected] =>
[bok_resources:protected] =>
[bok_topics:protected] =>
[bok_keywords:protected] =>
[id:protected] => 18
[type:protected] => category
[parent:protected] => 7
[label:protected] => Motor Vehicles/Heavy Equipment
[alreadyInSave:protected] =>
[alreadyInValidation:protected] =>
[validationFailures:protected] => Array
(
)
[_new:BaseObject:private] =>
[_deleted:BaseObject:private] =>
[modifiedColumns:protected] => Array
(
)
)
[52] => Category Object
(
[languages:protected] =>
[bok_resources:protected] =>
[bok_topics:protected] =>
[bok_keywords:protected] =>
[id:protected] => 52
[type:protected] => category
[parent:protected] => 2
[label:protected] => Commercial Diver
[alreadyInSave:protected] =>
[alreadyInValidation:protected] =>
[validationFailures:protected] => Array
(
)
[_new:BaseObject:private] =>
[_deleted:BaseObject:private] =>
[modifiedColumns:protected] => Array
(
)
)
[57] => Category Object
(
[languages:protected] =>
[bok_resources:protected] =>
[bok_topics:protected] =>
[bok_keywords:protected] =>
[id:protected] => 57
[type:protected] => category
[parent:protected] => 2
[label:protected] => Flagger
[alreadyInSave:protected] =>
[alreadyInValidation:protected] =>
[validationFailures:protected] => Array
(
)
[_new:BaseObject:private] =>
[_deleted:BaseObject:private] =>
[modifiedColumns:protected] => Array
(
)
)
[70] => Category Object
(
[languages:protected] =>
[bok_resources:protected] =>
[bok_topics:protected] =>
[bok_keywords:protected] =>
[id:protected] => 70
[type:protected] => category
[parent:protected] => 2
[label:protected] => Operating Engineer
[alreadyInSave:protected] =>
[alreadyInValidation:protected] =>
[validationFailures:protected] => Array
(
)
[_new:BaseObject:private] =>
[_deleted:BaseObject:private] =>
[modifiedColumns:protected] => Array
(
)
)
[85] => Category Object
(
[languages:protected] =>
[bok_resources:protected] =>
[bok_topics:protected] =>
[bok_keywords:protected] =>
[id:protected] => 85
[type:protected] => category
[parent:protected] => 2
[label:protected] => Truck Driver
[alreadyInSave:protected] =>
[alreadyInValidation:protected] =>
[validationFailures:protected] => Array
(
)
[_new:BaseObject:private] =>
[_deleted:BaseObject:private] =>
[modifiedColumns:protected] => Array
(
)
)
[87] => Category Object
(
[languages:protected] =>
[bok_resources:protected] =>
[bok_topics:protected] =>
[bok_keywords:protected] =>
[id:protected] => 87
[type:protected] => category
[parent:protected] => 3
[label:protected] => Commercial & Institutional
[alreadyInSave:protected] =>
[alreadyInValidation:protected] =>
[validationFailures:protected] => Array
(
)
[_new:BaseObject:private] =>
[_deleted:BaseObject:private] =>
[modifiedColumns:protected] => Array
(
)
)
[88] => Category Object
(
[languages:protected] =>
[bok_resources:protected] =>
[bok_topics:protected] =>
[bok_keywords:protected] =>
[id:protected] => 88
[type:protected] => category
[parent:protected] => 3
[label:protected] => Demolition
[alreadyInSave:protected] =>
[alreadyInValidation:protected] =>
[validationFailures:protected] => Array
(
)
[_new:BaseObject:private] =>
[_deleted:BaseObject:private] =>
[modifiedColumns:protected] => Array
(
)
)
[89] => Category Object
(
[languages:protected] =>
[bok_resources:protected] =>
[bok_topics:protected] =>
[bok_keywords:protected] =>
[id:protected] => 89
[type:protected] => category
[parent:protected] => 3
[label:protected] => Disasters
[alreadyInSave:protected] =>
[alreadyInValidation:protected] =>
[validationFailures:protected] => Array
(
)
[_new:BaseObject:private] =>
[_deleted:BaseObject:private] =>
[modifiedColumns:protected] => Array
(
)
)
[91] => Category Object
(
[languages:protected] =>
[bok_resources:protected] =>
[bok_topics:protected] =>
[bok_keywords:protected] =>
[id:protected] => 91
[type:protected] => category
[parent:protected] => 3
[label:protected] => Heavy & Highway
[alreadyInSave:protected] =>
[alreadyInValidation:protected] =>
[validationFailures:protected] => Array
(
)
[_new:BaseObject:private] =>
[_deleted:BaseObject:private] =>
[modifiedColumns:protected] => Array
(
)
)
[90] => Category Object
(
[languages:protected] =>
[bok_resources:protected] =>
[bok_topics:protected] =>
[bok_keywords:protected] =>
[id:protected] => 90
[type:protected] => category
[parent:protected] => 3
[label:protected] => Industrial
[alreadyInSave:protected] =>
[alreadyInValidation:protected] =>
[validationFailures:protected] => Array
(
)
[_new:BaseObject:private] =>
[_deleted:BaseObject:private] =>
[modifiedColumns:protected] => Array
(
)
)
[92] => Category Object
(
[languages:protected] =>
[bok_resources:protected] =>
[bok_topics:protected] =>
[bok_keywords:protected] =>
[id:protected] => 92
[type:protected] => category
[parent:protected] => 3
[label:protected] => LEED/Green Construction
[alreadyInSave:protected] =>
[alreadyInValidation:protected] =>
[validationFailures:protected] => Array
(
)
[_new:BaseObject:private] =>
[_deleted:BaseObject:private] =>
[modifiedColumns:protected] => Array
(
)
)
[93] => Category Object
(
[languages:protected] =>
[bok_resources:protected] =>
[bok_topics:protected] =>
[bok_keywords:protected] =>
[id:protected] => 93
[type:protected] => category
[parent:protected] => 3
[label:protected] => Renovations
[alreadyInSave:protected] =>
[alreadyInValidation:protected] =>
[validationFailures:protected] => Array
(
)
[_new:BaseObject:private] =>
[_deleted:BaseObject:private] =>
[modifiedColumns:protected] => Array
(
)
)
[94] => Category Object
(
[languages:protected] =>
[bok_resources:protected] =>
[bok_topics:protected] =>
[bok_keywords:protected] =>
[id:protected] => 94
[type:protected] => category
[parent:protected] => 3
[label:protected] => Residential
[alreadyInSave:protected] =>
[alreadyInValidation:protected] =>
[validationFailures:protected] => Array
(
)
[_new:BaseObject:private] =>
[_deleted:BaseObject:private] =>
[modifiedColumns:protected] => Array
(
)
)
[95] => Category Object
(
[languages:protected] =>
[bok_resources:protected] =>
[bok_topics:protected] =>
[bok_keywords:protected] =>
[id:protected] => 95
[type:protected] => category
[parent:protected] => 3
[label:protected] => Underground
[alreadyInSave:protected] =>
[alreadyInValidation:protected] =>
[validationFailures:protected] => Array
(
)
[_new:BaseObject:private] =>
[_deleted:BaseObject:private] =>
[modifiedColumns:protected] => Array
(
)
)
[100] => Category Object
(
[languages:protected] =>
[bok_resources:protected] =>
[bok_topics:protected] =>
[bok_keywords:protected] =>
[id:protected] => 100
[type:protected] => category
[parent:protected] => 6
[label:protected] => Toolbox Talks
[alreadyInSave:protected] =>
[alreadyInValidation:protected] =>
[validationFailures:protected] => Array
(
)
[_new:BaseObject:private] =>
[_deleted:BaseObject:private] =>
[modifiedColumns:protected] => Array
(
)
)
)
[categories_initialized:protected] => 1
[mapped_items:protected] =>
[content:protected] =>
[files:protected] =>
[language:protected] => Language Object
(
[id:protected] => 1
[code:protected] => en
[name:protected] => English
[alreadyInSave:protected] =>
[alreadyInValidation:protected] =>
[validationFailures:protected] => Array
(
)
[_new:BaseObject:private] =>
[_deleted:BaseObject:private] =>
[modifiedColumns:protected] => Array
(
)
)
[old_record:protected] =>
[id:protected] => 4428
[old_id:protected] =>
[elcosh_id:protected] => d001658
[type:protected] => document
[display_type:protected] => HTML only (and links)
[user_id:protected] => 0
[language_id:protected] => 1
[tagging_id:protected] => Daniela Caceres
[priority_id:protected] => 1
[title:protected] => Toolbox Talk: Work Zone Safety: Working Around Vehicles
[total_pages:protected] => 0
[billed_pages:protected] => 0
[publication_number:protected] =>
[part_of:protected] =>
[keywords:protected] => Struck, Struck by, Vehicle, Work Zone Safety, Truck, Operator, Driver, Mobile Equipment
[comments:protected] =>
[summary:protected] => The CPWR Toolbox Talk on Working Around Vehicles in the Work Zone addresses methods to avoid being struck-by a vehicle on a construction site. The resource includes a case example, steps to prevent a related injury, and questions for discussion. It includes a graphic that illustrates the hazard, which can be posted in a central location as a reminder of steps to work safely. Available in
English and
Spanish.
[transition_comments:protected] =>
[external_link:protected] =>
[consol_link:protected] =>
[more_like_this:protected] => d001640
[permission_given_by:protected] =>
[published:protected] => T
[billable:protected] => F
[img_name:protected] =>
[img_ext:protected] =>
[img_width:protected] =>
[img_height:protected] =>
[img_credit:protected] =>
[img_practice:protected] =>
[vid_source_id:protected] =>
[vid_running_time:protected] =>
[vid_intended_audience:protected] =>
[vid_acquisition_info:protected] =>
[vid_cost:protected] =>
[vid_producer:protected] =>
[vid_filename:protected] =>
[vid_filename_downloadable:protected] =>
[date_summary:protected] =>
[date_permission_requested:protected] =>
[date_permission_received:protected] =>
[date_review_needed:protected] =>
[date_received:protected] => 12/23/21
[date_completed:protected] => 12/23/21
[date_billed:protected] =>
[date_modified:protected] => 05/19/23
[collBokExports:protected] =>
[lastBokExportCriteria:BaseElcoshItem:private] =>
[alreadyInSave:protected] =>
[alreadyInValidation:protected] =>
[validationFailures:protected] => Array
(
)
[_new:BaseObject:private] =>
[_deleted:BaseObject:private] =>
[modifiedColumns:protected] => Array
(
)
)
)
[4] => Search_Result Object
(
[title] => Construction Dive -- DeWalt's Jobsite Pro headphones recalled for fire hazards
[image] => /record/images/notavailable-p.png
[blurb] => A recall notice by the United States Consumer Product Safety Commission affects over 300,000 DeWalt Jobsite Pro Headphones. The recall is a result of...
[category] => Array
(
[0] => 16
[1] => 44
[2] => 45
[3] => 46
[4] => 47
[5] => 48
[6] => 49
[7] => 50
[8] => 51
[9] => 52
[10] => 53
[11] => 54
[12] => 55
[13] => 56
[14] => 57
[15] => 58
[16] => 59
[17] => 60
[18] => 61
[19] => 64
[20] => 65
[21] => 66
[22] => 67
[23] => 68
[24] => 69
[25] => 70
[26] => 71
[27] => 72
[28] => 73
[29] => 74
[30] => 75
[31] => 76
[32] => 77
[33] => 63
[34] => 78
[35] => 79
[36] => 80
[37] => 81
[38] => 82
[39] => 62
[40] => 83
[41] => 84
[42] => 85
[43] => 86
[44] => 87
[45] => 88
[46] => 89
[47] => 91
[48] => 90
[49] => 92
[50] => 93
[51] => 94
[52] => 95
)
[labels] => Array
(
[0] => Fire & Explosions
[1] => Work Environment
[2] => Hazards
[3] => Acoustical Ceiling Carpenter
[4] => Trades
[5] => Asbestos/Insulator
[7] => Boilermaker
[9] => Bricklayer
[11] => Cabinetmaker
[13] => Carpenter
[15] => Carpet Layer
[17] => Cement Mason
[19] => Commercial Diver
[21] => Concrete Polisher
[23] => Drywall Applicator Specialist
[25] => Electrical Worker
[27] => Elevator Constructor
[29] => Flagger
[31] => Glazier
[33] => Hazardous Waste Cleanup
[35] => HVAC
[37] => Interior Systems Carpenter
[39] => Laborer
[41] => Landscaper
[43] => Lather
[45] => Lead Abatement Worker
[47] => Maintenance Worker
[49] => Millwright
[51] => Operating Engineer
[53] => Painter
[55] => Paper Hanger
[57] => PCC/Restoration
[59] => Pile Driver
[61] => Plasterer
[63] => Plumber/Pipefitter
[65] => Refractory Worker
[67] => Reinforcing Ironworker
[69] => Roofer/Waterproofer
[71] => Scaffold Erector
[73] => Sheetmetal Worker
[75] => Sprinkler Fitter
[77] => Stonemason
[79] => Structural Ironworker
[81] => Terrazzo Worker
[83] => Tile Setter
[85] => Truck Driver
[87] => Welder
[89] => Commercial & Institutional
[90] => Jobsites
[91] => Demolition
[93] => Disasters
[95] => Heavy & Highway
[97] => Industrial
[99] => LEED/Green Construction
[101] => Renovations
[103] => Residential
[105] => Underground
)
[type] =>
[sub_category] =>
[url] => /document/4426/d001656/Construction%2BDive%2B--%2BDeWalt%2527s%2BJobsite%2BPro%2Bheadphones%2Brecalled%2Bfor%2Bfire%2Bhazards.html
[item:protected] => DocumentRecord Object
(
[records:protected] => Array
(
)
[recordId:protected] =>
[searchWordClass:protected] =>
[searchWordPeerClass:protected] =>
[bok_record:protected] =>
[authors:protected] =>
[organizations:protected] =>
[collections:protected] =>
[categories:protected] => Array
(
[16] => Category Object
(
[languages:protected] =>
[bok_resources:protected] =>
[bok_topics:protected] =>
[bok_keywords:protected] =>
[id:protected] => 16
[type:protected] => category
[parent:protected] => 7
[label:protected] => Fire & Explosions
[alreadyInSave:protected] =>
[alreadyInValidation:protected] =>
[validationFailures:protected] => Array
(
)
[_new:BaseObject:private] =>
[_deleted:BaseObject:private] =>
[modifiedColumns:protected] => Array
(
)
)
[44] => Category Object
(
[languages:protected] =>
[bok_resources:protected] =>
[bok_topics:protected] =>
[bok_keywords:protected] =>
[id:protected] => 44
[type:protected] => category
[parent:protected] => 2
[label:protected] => Acoustical Ceiling Carpenter
[alreadyInSave:protected] =>
[alreadyInValidation:protected] =>
[validationFailures:protected] => Array
(
)
[_new:BaseObject:private] =>
[_deleted:BaseObject:private] =>
[modifiedColumns:protected] => Array
(
)
)
[45] => Category Object
(
[languages:protected] =>
[bok_resources:protected] =>
[bok_topics:protected] =>
[bok_keywords:protected] =>
[id:protected] => 45
[type:protected] => category
[parent:protected] => 2
[label:protected] => Asbestos/Insulator
[alreadyInSave:protected] =>
[alreadyInValidation:protected] =>
[validationFailures:protected] => Array
(
)
[_new:BaseObject:private] =>
[_deleted:BaseObject:private] =>
[modifiedColumns:protected] => Array
(
)
)
[46] => Category Object
(
[languages:protected] =>
[bok_resources:protected] =>
[bok_topics:protected] =>
[bok_keywords:protected] =>
[id:protected] => 46
[type:protected] => category
[parent:protected] => 2
[label:protected] => Boilermaker
[alreadyInSave:protected] =>
[alreadyInValidation:protected] =>
[validationFailures:protected] => Array
(
)
[_new:BaseObject:private] =>
[_deleted:BaseObject:private] =>
[modifiedColumns:protected] => Array
(
)
)
[47] => Category Object
(
[languages:protected] =>
[bok_resources:protected] =>
[bok_topics:protected] =>
[bok_keywords:protected] =>
[id:protected] => 47
[type:protected] => category
[parent:protected] => 2
[label:protected] => Bricklayer
[alreadyInSave:protected] =>
[alreadyInValidation:protected] =>
[validationFailures:protected] => Array
(
)
[_new:BaseObject:private] =>
[_deleted:BaseObject:private] =>
[modifiedColumns:protected] => Array
(
)
)
[48] => Category Object
(
[languages:protected] =>
[bok_resources:protected] =>
[bok_topics:protected] =>
[bok_keywords:protected] =>
[id:protected] => 48
[type:protected] => category
[parent:protected] => 2
[label:protected] => Cabinetmaker
[alreadyInSave:protected] =>
[alreadyInValidation:protected] =>
[validationFailures:protected] => Array
(
)
[_new:BaseObject:private] =>
[_deleted:BaseObject:private] =>
[modifiedColumns:protected] => Array
(
)
)
[49] => Category Object
(
[languages:protected] =>
[bok_resources:protected] =>
[bok_topics:protected] =>
[bok_keywords:protected] =>
[id:protected] => 49
[type:protected] => category
[parent:protected] => 2
[label:protected] => Carpenter
[alreadyInSave:protected] =>
[alreadyInValidation:protected] =>
[validationFailures:protected] => Array
(
)
[_new:BaseObject:private] =>
[_deleted:BaseObject:private] =>
[modifiedColumns:protected] => Array
(
)
)
[50] => Category Object
(
[languages:protected] =>
[bok_resources:protected] =>
[bok_topics:protected] =>
[bok_keywords:protected] =>
[id:protected] => 50
[type:protected] => category
[parent:protected] => 2
[label:protected] => Carpet Layer
[alreadyInSave:protected] =>
[alreadyInValidation:protected] =>
[validationFailures:protected] => Array
(
)
[_new:BaseObject:private] =>
[_deleted:BaseObject:private] =>
[modifiedColumns:protected] => Array
(
)
)
[51] => Category Object
(
[languages:protected] =>
[bok_resources:protected] =>
[bok_topics:protected] =>
[bok_keywords:protected] =>
[id:protected] => 51
[type:protected] => category
[parent:protected] => 2
[label:protected] => Cement Mason
[alreadyInSave:protected] =>
[alreadyInValidation:protected] =>
[validationFailures:protected] => Array
(
)
[_new:BaseObject:private] =>
[_deleted:BaseObject:private] =>
[modifiedColumns:protected] => Array
(
)
)
[52] => Category Object
(
[languages:protected] =>
[bok_resources:protected] =>
[bok_topics:protected] =>
[bok_keywords:protected] =>
[id:protected] => 52
[type:protected] => category
[parent:protected] => 2
[label:protected] => Commercial Diver
[alreadyInSave:protected] =>
[alreadyInValidation:protected] =>
[validationFailures:protected] => Array
(
)
[_new:BaseObject:private] =>
[_deleted:BaseObject:private] =>
[modifiedColumns:protected] => Array
(
)
)
[53] => Category Object
(
[languages:protected] =>
[bok_resources:protected] =>
[bok_topics:protected] =>
[bok_keywords:protected] =>
[id:protected] => 53
[type:protected] => category
[parent:protected] => 2
[label:protected] => Concrete Polisher
[alreadyInSave:protected] =>
[alreadyInValidation:protected] =>
[validationFailures:protected] => Array
(
)
[_new:BaseObject:private] =>
[_deleted:BaseObject:private] =>
[modifiedColumns:protected] => Array
(
)
)
[54] => Category Object
(
[languages:protected] =>
[bok_resources:protected] =>
[bok_topics:protected] =>
[bok_keywords:protected] =>
[id:protected] => 54
[type:protected] => category
[parent:protected] => 2
[label:protected] => Drywall Applicator Specialist
[alreadyInSave:protected] =>
[alreadyInValidation:protected] =>
[validationFailures:protected] => Array
(
)
[_new:BaseObject:private] =>
[_deleted:BaseObject:private] =>
[modifiedColumns:protected] => Array
(
)
)
[55] => Category Object
(
[languages:protected] =>
[bok_resources:protected] =>
[bok_topics:protected] =>
[bok_keywords:protected] =>
[id:protected] => 55
[type:protected] => category
[parent:protected] => 2
[label:protected] => Electrical Worker
[alreadyInSave:protected] =>
[alreadyInValidation:protected] =>
[validationFailures:protected] => Array
(
)
[_new:BaseObject:private] =>
[_deleted:BaseObject:private] =>
[modifiedColumns:protected] => Array
(
)
)
[56] => Category Object
(
[languages:protected] =>
[bok_resources:protected] =>
[bok_topics:protected] =>
[bok_keywords:protected] =>
[id:protected] => 56
[type:protected] => category
[parent:protected] => 2
[label:protected] => Elevator Constructor
[alreadyInSave:protected] =>
[alreadyInValidation:protected] =>
[validationFailures:protected] => Array
(
)
[_new:BaseObject:private] =>
[_deleted:BaseObject:private] =>
[modifiedColumns:protected] => Array
(
)
)
[57] => Category Object
(
[languages:protected] =>
[bok_resources:protected] =>
[bok_topics:protected] =>
[bok_keywords:protected] =>
[id:protected] => 57
[type:protected] => category
[parent:protected] => 2
[label:protected] => Flagger
[alreadyInSave:protected] =>
[alreadyInValidation:protected] =>
[validationFailures:protected] => Array
(
)
[_new:BaseObject:private] =>
[_deleted:BaseObject:private] =>
[modifiedColumns:protected] => Array
(
)
)
[58] => Category Object
(
[languages:protected] =>
[bok_resources:protected] =>
[bok_topics:protected] =>
[bok_keywords:protected] =>
[id:protected] => 58
[type:protected] => category
[parent:protected] => 2
[label:protected] => Glazier
[alreadyInSave:protected] =>
[alreadyInValidation:protected] =>
[validationFailures:protected] => Array
(
)
[_new:BaseObject:private] =>
[_deleted:BaseObject:private] =>
[modifiedColumns:protected] => Array
(
)
)
[59] => Category Object
(
[languages:protected] =>
[bok_resources:protected] =>
[bok_topics:protected] =>
[bok_keywords:protected] =>
[id:protected] => 59
[type:protected] => category
[parent:protected] => 2
[label:protected] => Hazardous Waste Cleanup
[alreadyInSave:protected] =>
[alreadyInValidation:protected] =>
[validationFailures:protected] => Array
(
)
[_new:BaseObject:private] =>
[_deleted:BaseObject:private] =>
[modifiedColumns:protected] => Array
(
)
)
[60] => Category Object
(
[languages:protected] =>
[bok_resources:protected] =>
[bok_topics:protected] =>
[bok_keywords:protected] =>
[id:protected] => 60
[type:protected] => category
[parent:protected] => 2
[label:protected] => HVAC
[alreadyInSave:protected] =>
[alreadyInValidation:protected] =>
[validationFailures:protected] => Array
(
)
[_new:BaseObject:private] =>
[_deleted:BaseObject:private] =>
[modifiedColumns:protected] => Array
(
)
)
[61] => Category Object
(
[languages:protected] =>
[bok_resources:protected] =>
[bok_topics:protected] =>
[bok_keywords:protected] =>
[id:protected] => 61
[type:protected] => category
[parent:protected] => 2
[label:protected] => Interior Systems Carpenter
[alreadyInSave:protected] =>
[alreadyInValidation:protected] =>
[validationFailures:protected] => Array
(
)
[_new:BaseObject:private] =>
[_deleted:BaseObject:private] =>
[modifiedColumns:protected] => Array
(
)
)
[64] => Category Object
(
[languages:protected] =>
[bok_resources:protected] =>
[bok_topics:protected] =>
[bok_keywords:protected] =>
[id:protected] => 64
[type:protected] => category
[parent:protected] => 2
[label:protected] => Laborer
[alreadyInSave:protected] =>
[alreadyInValidation:protected] =>
[validationFailures:protected] => Array
(
)
[_new:BaseObject:private] =>
[_deleted:BaseObject:private] =>
[modifiedColumns:protected] => Array
(
)
)
[65] => Category Object
(
[languages:protected] =>
[bok_resources:protected] =>
[bok_topics:protected] =>
[bok_keywords:protected] =>
[id:protected] => 65
[type:protected] => category
[parent:protected] => 2
[label:protected] => Landscaper
[alreadyInSave:protected] =>
[alreadyInValidation:protected] =>
[validationFailures:protected] => Array
(
)
[_new:BaseObject:private] =>
[_deleted:BaseObject:private] =>
[modifiedColumns:protected] => Array
(
)
)
[66] => Category Object
(
[languages:protected] =>
[bok_resources:protected] =>
[bok_topics:protected] =>
[bok_keywords:protected] =>
[id:protected] => 66
[type:protected] => category
[parent:protected] => 2
[label:protected] => Lather
[alreadyInSave:protected] =>
[alreadyInValidation:protected] =>
[validationFailures:protected] => Array
(
)
[_new:BaseObject:private] =>
[_deleted:BaseObject:private] =>
[modifiedColumns:protected] => Array
(
)
)
[67] => Category Object
(
[languages:protected] =>
[bok_resources:protected] =>
[bok_topics:protected] =>
[bok_keywords:protected] =>
[id:protected] => 67
[type:protected] => category
[parent:protected] => 2
[label:protected] => Lead Abatement Worker
[alreadyInSave:protected] =>
[alreadyInValidation:protected] =>
[validationFailures:protected] => Array
(
)
[_new:BaseObject:private] =>
[_deleted:BaseObject:private] =>
[modifiedColumns:protected] => Array
(
)
)
[68] => Category Object
(
[languages:protected] =>
[bok_resources:protected] =>
[bok_topics:protected] =>
[bok_keywords:protected] =>
[id:protected] => 68
[type:protected] => category
[parent:protected] => 2
[label:protected] => Maintenance Worker
[alreadyInSave:protected] =>
[alreadyInValidation:protected] =>
[validationFailures:protected] => Array
(
)
[_new:BaseObject:private] =>
[_deleted:BaseObject:private] =>
[modifiedColumns:protected] => Array
(
)
)
[69] => Category Object
(
[languages:protected] =>
[bok_resources:protected] =>
[bok_topics:protected] =>
[bok_keywords:protected] =>
[id:protected] => 69
[type:protected] => category
[parent:protected] => 2
[label:protected] => Millwright
[alreadyInSave:protected] =>
[alreadyInValidation:protected] =>
[validationFailures:protected] => Array
(
)
[_new:BaseObject:private] =>
[_deleted:BaseObject:private] =>
[modifiedColumns:protected] => Array
(
)
)
[70] => Category Object
(
[languages:protected] =>
[bok_resources:protected] =>
[bok_topics:protected] =>
[bok_keywords:protected] =>
[id:protected] => 70
[type:protected] => category
[parent:protected] => 2
[label:protected] => Operating Engineer
[alreadyInSave:protected] =>
[alreadyInValidation:protected] =>
[validationFailures:protected] => Array
(
)
[_new:BaseObject:private] =>
[_deleted:BaseObject:private] =>
[modifiedColumns:protected] => Array
(
)
)
[71] => Category Object
(
[languages:protected] =>
[bok_resources:protected] =>
[bok_topics:protected] =>
[bok_keywords:protected] =>
[id:protected] => 71
[type:protected] => category
[parent:protected] => 2
[label:protected] => Painter
[alreadyInSave:protected] =>
[alreadyInValidation:protected] =>
[validationFailures:protected] => Array
(
)
[_new:BaseObject:private] =>
[_deleted:BaseObject:private] =>
[modifiedColumns:protected] => Array
(
)
)
[72] => Category Object
(
[languages:protected] =>
[bok_resources:protected] =>
[bok_topics:protected] =>
[bok_keywords:protected] =>
[id:protected] => 72
[type:protected] => category
[parent:protected] => 2
[label:protected] => Paper Hanger
[alreadyInSave:protected] =>
[alreadyInValidation:protected] =>
[validationFailures:protected] => Array
(
)
[_new:BaseObject:private] =>
[_deleted:BaseObject:private] =>
[modifiedColumns:protected] => Array
(
)
)
[73] => Category Object
(
[languages:protected] =>
[bok_resources:protected] =>
[bok_topics:protected] =>
[bok_keywords:protected] =>
[id:protected] => 73
[type:protected] => category
[parent:protected] => 2
[label:protected] => PCC/Restoration
[alreadyInSave:protected] =>
[alreadyInValidation:protected] =>
[validationFailures:protected] => Array
(
)
[_new:BaseObject:private] =>
[_deleted:BaseObject:private] =>
[modifiedColumns:protected] => Array
(
)
)
[74] => Category Object
(
[languages:protected] =>
[bok_resources:protected] =>
[bok_topics:protected] =>
[bok_keywords:protected] =>
[id:protected] => 74
[type:protected] => category
[parent:protected] => 2
[label:protected] => Pile Driver
[alreadyInSave:protected] =>
[alreadyInValidation:protected] =>
[validationFailures:protected] => Array
(
)
[_new:BaseObject:private] =>
[_deleted:BaseObject:private] =>
[modifiedColumns:protected] => Array
(
)
)
[75] => Category Object
(
[languages:protected] =>
[bok_resources:protected] =>
[bok_topics:protected] =>
[bok_keywords:protected] =>
[id:protected] => 75
[type:protected] => category
[parent:protected] => 2
[label:protected] => Plasterer
[alreadyInSave:protected] =>
[alreadyInValidation:protected] =>
[validationFailures:protected] => Array
(
)
[_new:BaseObject:private] =>
[_deleted:BaseObject:private] =>
[modifiedColumns:protected] => Array
(
)
)
[76] => Category Object
(
[languages:protected] =>
[bok_resources:protected] =>
[bok_topics:protected] =>
[bok_keywords:protected] =>
[id:protected] => 76
[type:protected] => category
[parent:protected] => 2
[label:protected] => Plumber/Pipefitter
[alreadyInSave:protected] =>
[alreadyInValidation:protected] =>
[validationFailures:protected] => Array
(
)
[_new:BaseObject:private] =>
[_deleted:BaseObject:private] =>
[modifiedColumns:protected] => Array
(
)
)
[77] => Category Object
(
[languages:protected] =>
[bok_resources:protected] =>
[bok_topics:protected] =>
[bok_keywords:protected] =>
[id:protected] => 77
[type:protected] => category
[parent:protected] => 2
[label:protected] => Refractory Worker
[alreadyInSave:protected] =>
[alreadyInValidation:protected] =>
[validationFailures:protected] => Array
(
)
[_new:BaseObject:private] =>
[_deleted:BaseObject:private] =>
[modifiedColumns:protected] => Array
(
)
)
[63] => Category Object
(
[languages:protected] =>
[bok_resources:protected] =>
[bok_topics:protected] =>
[bok_keywords:protected] =>
[id:protected] => 63
[type:protected] => category
[parent:protected] => 2
[label:protected] => Reinforcing Ironworker
[alreadyInSave:protected] =>
[alreadyInValidation:protected] =>
[validationFailures:protected] => Array
(
)
[_new:BaseObject:private] =>
[_deleted:BaseObject:private] =>
[modifiedColumns:protected] => Array
(
)
)
[78] => Category Object
(
[languages:protected] =>
[bok_resources:protected] =>
[bok_topics:protected] =>
[bok_keywords:protected] =>
[id:protected] => 78
[type:protected] => category
[parent:protected] => 2
[label:protected] => Roofer/Waterproofer
[alreadyInSave:protected] =>
[alreadyInValidation:protected] =>
[validationFailures:protected] => Array
(
)
[_new:BaseObject:private] =>
[_deleted:BaseObject:private] =>
[modifiedColumns:protected] => Array
(
)
)
[79] => Category Object
(
[languages:protected] =>
[bok_resources:protected] =>
[bok_topics:protected] =>
[bok_keywords:protected] =>
[id:protected] => 79
[type:protected] => category
[parent:protected] => 2
[label:protected] => Scaffold Erector
[alreadyInSave:protected] =>
[alreadyInValidation:protected] =>
[validationFailures:protected] => Array
(
)
[_new:BaseObject:private] =>
[_deleted:BaseObject:private] =>
[modifiedColumns:protected] => Array
(
)
)
[80] => Category Object
(
[languages:protected] =>
[bok_resources:protected] =>
[bok_topics:protected] =>
[bok_keywords:protected] =>
[id:protected] => 80
[type:protected] => category
[parent:protected] => 2
[label:protected] => Sheetmetal Worker
[alreadyInSave:protected] =>
[alreadyInValidation:protected] =>
[validationFailures:protected] => Array
(
)
[_new:BaseObject:private] =>
[_deleted:BaseObject:private] =>
[modifiedColumns:protected] => Array
(
)
)
[81] => Category Object
(
[languages:protected] =>
[bok_resources:protected] =>
[bok_topics:protected] =>
[bok_keywords:protected] =>
[id:protected] => 81
[type:protected] => category
[parent:protected] => 2
[label:protected] => Sprinkler Fitter
[alreadyInSave:protected] =>
[alreadyInValidation:protected] =>
[validationFailures:protected] => Array
(
)
[_new:BaseObject:private] =>
[_deleted:BaseObject:private] =>
[modifiedColumns:protected] => Array
(
)
)
[82] => Category Object
(
[languages:protected] =>
[bok_resources:protected] =>
[bok_topics:protected] =>
[bok_keywords:protected] =>
[id:protected] => 82
[type:protected] => category
[parent:protected] => 2
[label:protected] => Stonemason
[alreadyInSave:protected] =>
[alreadyInValidation:protected] =>
[validationFailures:protected] => Array
(
)
[_new:BaseObject:private] =>
[_deleted:BaseObject:private] =>
[modifiedColumns:protected] => Array
(
)
)
[62] => Category Object
(
[languages:protected] =>
[bok_resources:protected] =>
[bok_topics:protected] =>
[bok_keywords:protected] =>
[id:protected] => 62
[type:protected] => category
[parent:protected] => 2
[label:protected] => Structural Ironworker
[alreadyInSave:protected] =>
[alreadyInValidation:protected] =>
[validationFailures:protected] => Array
(
)
[_new:BaseObject:private] =>
[_deleted:BaseObject:private] =>
[modifiedColumns:protected] => Array
(
)
)
[83] => Category Object
(
[languages:protected] =>
[bok_resources:protected] =>
[bok_topics:protected] =>
[bok_keywords:protected] =>
[id:protected] => 83
[type:protected] => category
[parent:protected] => 2
[label:protected] => Terrazzo Worker
[alreadyInSave:protected] =>
[alreadyInValidation:protected] =>
[validationFailures:protected] => Array
(
)
[_new:BaseObject:private] =>
[_deleted:BaseObject:private] =>
[modifiedColumns:protected] => Array
(
)
)
[84] => Category Object
(
[languages:protected] =>
[bok_resources:protected] =>
[bok_topics:protected] =>
[bok_keywords:protected] =>
[id:protected] => 84
[type:protected] => category
[parent:protected] => 2
[label:protected] => Tile Setter
[alreadyInSave:protected] =>
[alreadyInValidation:protected] =>
[validationFailures:protected] => Array
(
)
[_new:BaseObject:private] =>
[_deleted:BaseObject:private] =>
[modifiedColumns:protected] => Array
(
)
)
[85] => Category Object
(
[languages:protected] =>
[bok_resources:protected] =>
[bok_topics:protected] =>
[bok_keywords:protected] =>
[id:protected] => 85
[type:protected] => category
[parent:protected] => 2
[label:protected] => Truck Driver
[alreadyInSave:protected] =>
[alreadyInValidation:protected] =>
[validationFailures:protected] => Array
(
)
[_new:BaseObject:private] =>
[_deleted:BaseObject:private] =>
[modifiedColumns:protected] => Array
(
)
)
[86] => Category Object
(
[languages:protected] =>
[bok_resources:protected] =>
[bok_topics:protected] =>
[bok_keywords:protected] =>
[id:protected] => 86
[type:protected] => category
[parent:protected] => 2
[label:protected] => Welder
[alreadyInSave:protected] =>
[alreadyInValidation:protected] =>
[validationFailures:protected] => Array
(
)
[_new:BaseObject:private] =>
[_deleted:BaseObject:private] =>
[modifiedColumns:protected] => Array
(
)
)
[87] => Category Object
(
[languages:protected] =>
[bok_resources:protected] =>
[bok_topics:protected] =>
[bok_keywords:protected] =>
[id:protected] => 87
[type:protected] => category
[parent:protected] => 3
[label:protected] => Commercial & Institutional
[alreadyInSave:protected] =>
[alreadyInValidation:protected] =>
[validationFailures:protected] => Array
(
)
[_new:BaseObject:private] =>
[_deleted:BaseObject:private] =>
[modifiedColumns:protected] => Array
(
)
)
[88] => Category Object
(
[languages:protected] =>
[bok_resources:protected] =>
[bok_topics:protected] =>
[bok_keywords:protected] =>
[id:protected] => 88
[type:protected] => category
[parent:protected] => 3
[label:protected] => Demolition
[alreadyInSave:protected] =>
[alreadyInValidation:protected] =>
[validationFailures:protected] => Array
(
)
[_new:BaseObject:private] =>
[_deleted:BaseObject:private] =>
[modifiedColumns:protected] => Array
(
)
)
[89] => Category Object
(
[languages:protected] =>
[bok_resources:protected] =>
[bok_topics:protected] =>
[bok_keywords:protected] =>
[id:protected] => 89
[type:protected] => category
[parent:protected] => 3
[label:protected] => Disasters
[alreadyInSave:protected] =>
[alreadyInValidation:protected] =>
[validationFailures:protected] => Array
(
)
[_new:BaseObject:private] =>
[_deleted:BaseObject:private] =>
[modifiedColumns:protected] => Array
(
)
)
[91] => Category Object
(
[languages:protected] =>
[bok_resources:protected] =>
[bok_topics:protected] =>
[bok_keywords:protected] =>
[id:protected] => 91
[type:protected] => category
[parent:protected] => 3
[label:protected] => Heavy & Highway
[alreadyInSave:protected] =>
[alreadyInValidation:protected] =>
[validationFailures:protected] => Array
(
)
[_new:BaseObject:private] =>
[_deleted:BaseObject:private] =>
[modifiedColumns:protected] => Array
(
)
)
[90] => Category Object
(
[languages:protected] =>
[bok_resources:protected] =>
[bok_topics:protected] =>
[bok_keywords:protected] =>
[id:protected] => 90
[type:protected] => category
[parent:protected] => 3
[label:protected] => Industrial
[alreadyInSave:protected] =>
[alreadyInValidation:protected] =>
[validationFailures:protected] => Array
(
)
[_new:BaseObject:private] =>
[_deleted:BaseObject:private] =>
[modifiedColumns:protected] => Array
(
)
)
[92] => Category Object
(
[languages:protected] =>
[bok_resources:protected] =>
[bok_topics:protected] =>
[bok_keywords:protected] =>
[id:protected] => 92
[type:protected] => category
[parent:protected] => 3
[label:protected] => LEED/Green Construction
[alreadyInSave:protected] =>
[alreadyInValidation:protected] =>
[validationFailures:protected] => Array
(
)
[_new:BaseObject:private] =>
[_deleted:BaseObject:private] =>
[modifiedColumns:protected] => Array
(
)
)
[93] => Category Object
(
[languages:protected] =>
[bok_resources:protected] =>
[bok_topics:protected] =>
[bok_keywords:protected] =>
[id:protected] => 93
[type:protected] => category
[parent:protected] => 3
[label:protected] => Renovations
[alreadyInSave:protected] =>
[alreadyInValidation:protected] =>
[validationFailures:protected] => Array
(
)
[_new:BaseObject:private] =>
[_deleted:BaseObject:private] =>
[modifiedColumns:protected] => Array
(
)
)
[94] => Category Object
(
[languages:protected] =>
[bok_resources:protected] =>
[bok_topics:protected] =>
[bok_keywords:protected] =>
[id:protected] => 94
[type:protected] => category
[parent:protected] => 3
[label:protected] => Residential
[alreadyInSave:protected] =>
[alreadyInValidation:protected] =>
[validationFailures:protected] => Array
(
)
[_new:BaseObject:private] =>
[_deleted:BaseObject:private] =>
[modifiedColumns:protected] => Array
(
)
)
[95] => Category Object
(
[languages:protected] =>
[bok_resources:protected] =>
[bok_topics:protected] =>
[bok_keywords:protected] =>
[id:protected] => 95
[type:protected] => category
[parent:protected] => 3
[label:protected] => Underground
[alreadyInSave:protected] =>
[alreadyInValidation:protected] =>
[validationFailures:protected] => Array
(
)
[_new:BaseObject:private] =>
[_deleted:BaseObject:private] =>
[modifiedColumns:protected] => Array
(
)
)
)
[categories_initialized:protected] => 1
[mapped_items:protected] =>
[content:protected] =>
[files:protected] =>
[language:protected] => Language Object
(
[id:protected] => 1
[code:protected] => en
[name:protected] => English
[alreadyInSave:protected] =>
[alreadyInValidation:protected] =>
[validationFailures:protected] => Array
(
)
[_new:BaseObject:private] =>
[_deleted:BaseObject:private] =>
[modifiedColumns:protected] => Array
(
)
)
[old_record:protected] =>
[id:protected] => 4426
[old_id:protected] =>
[elcosh_id:protected] => d001656
[type:protected] => document
[display_type:protected] => HTML only (and links)
[user_id:protected] => 0
[language_id:protected] => 1
[tagging_id:protected] => Mike Aguilar
[priority_id:protected] => 1
[title:protected] => Construction Dive -- DeWalt's Jobsite Pro headphones recalled for fire hazards
[total_pages:protected] => 1
[billed_pages:protected] => 1
[publication_number:protected] =>
[part_of:protected] =>
[keywords:protected] => DeWalt, Fire Hazards, recall, headphones
[comments:protected] =>
[summary:protected] => A recall notice by the United States Consumer Product Safety Commission affects over 300,000 DeWalt Jobsite Pro Headphones. The recall is a result of a malfunction that can cause earbuds to overheat while charging or during use, leading to fire and burn hazards.
[transition_comments:protected] =>
[external_link:protected] => https://www.constructiondive.com/news/dewalts-jobsite-pro-headphones-recalled-for-fire-hazards/611248/?utm_source=Sailthru&utm_medium=email&utm_campaign=Issue:%202021-12-10%20Construction%20Dive%20Newsletter%20%5Bissue:38532%5D&utm_term=Construction%20Dive
[consol_link:protected] =>
[more_like_this:protected] =>
[permission_given_by:protected] =>
[published:protected] => T
[billable:protected] => F
[img_name:protected] =>
[img_ext:protected] =>
[img_width:protected] =>
[img_height:protected] =>
[img_credit:protected] =>
[img_practice:protected] =>
[vid_source_id:protected] =>
[vid_running_time:protected] =>
[vid_intended_audience:protected] =>
[vid_acquisition_info:protected] =>
[vid_cost:protected] =>
[vid_producer:protected] =>
[vid_filename:protected] =>
[vid_filename_downloadable:protected] =>
[date_summary:protected] =>
[date_permission_requested:protected] =>
[date_permission_received:protected] =>
[date_review_needed:protected] =>
[date_received:protected] => 12/13/21
[date_completed:protected] => 12/13/21
[date_billed:protected] =>
[date_modified:protected] => 12/13/21
[collBokExports:protected] =>
[lastBokExportCriteria:BaseElcoshItem:private] =>
[alreadyInSave:protected] =>
[alreadyInValidation:protected] =>
[validationFailures:protected] => Array
(
)
[_new:BaseObject:private] =>
[_deleted:BaseObject:private] =>
[modifiedColumns:protected] => Array
(
)
)
)
)
[new_images] => Array
(
[0] => Search_Result Object
(
[title] => Morning Toolbox Talk
[image] => /record/images/4003-p.jpg
[blurb] => This photo is from an early morning toolbox talk on a construction job in Mclean, Virginia. It is being delivered in English and Spanish....
[category] => Array
(
[0] => 20
[1] => 51
[2] => 57
[3] => 64
[4] => 70
[5] => 63
[6] => 78
[7] => 82
[8] => 62
[9] => 87
[10] => 88
[11] => 89
[12] => 91
[13] => 90
[14] => 93
[15] => 94
[16] => 97
)
[labels] => Array
(
[0] => Safety Culture
[1] => Work Environment
[2] => Hazards
[3] => Cement Mason
[4] => Trades
[5] => Flagger
[7] => Laborer
[9] => Operating Engineer
[11] => Reinforcing Ironworker
[13] => Roofer/Waterproofer
[15] => Stonemason
[17] => Structural Ironworker
[19] => Commercial & Institutional
[20] => Jobsites
[21] => Demolition
[23] => Disasters
[25] => Heavy & Highway
[27] => Industrial
[29] => Renovations
[31] => Residential
[33] => Images
[34] => Media
[35] => Media & Documents
)
[type] => Images
[sub_category] =>
[url] => /image/4003/i002691/Morning%2BToolbox%2BTalk.html
[item:protected] => ImageRecord Object
(
[records:protected] => Array
(
)
[recordId:protected] =>
[searchWordClass:protected] =>
[searchWordPeerClass:protected] =>
[bok_record:protected] =>
[authors:protected] =>
[organizations:protected] =>
[collections:protected] =>
[categories:protected] => Array
(
[20] => Category Object
(
[languages:protected] =>
[bok_resources:protected] =>
[bok_topics:protected] =>
[bok_keywords:protected] =>
[id:protected] => 20
[type:protected] => category
[parent:protected] => 7
[label:protected] => Safety Culture
[alreadyInSave:protected] =>
[alreadyInValidation:protected] =>
[validationFailures:protected] => Array
(
)
[_new:BaseObject:private] =>
[_deleted:BaseObject:private] =>
[modifiedColumns:protected] => Array
(
)
)
[51] => Category Object
(
[languages:protected] =>
[bok_resources:protected] =>
[bok_topics:protected] =>
[bok_keywords:protected] =>
[id:protected] => 51
[type:protected] => category
[parent:protected] => 2
[label:protected] => Cement Mason
[alreadyInSave:protected] =>
[alreadyInValidation:protected] =>
[validationFailures:protected] => Array
(
)
[_new:BaseObject:private] =>
[_deleted:BaseObject:private] =>
[modifiedColumns:protected] => Array
(
)
)
[57] => Category Object
(
[languages:protected] =>
[bok_resources:protected] =>
[bok_topics:protected] =>
[bok_keywords:protected] =>
[id:protected] => 57
[type:protected] => category
[parent:protected] => 2
[label:protected] => Flagger
[alreadyInSave:protected] =>
[alreadyInValidation:protected] =>
[validationFailures:protected] => Array
(
)
[_new:BaseObject:private] =>
[_deleted:BaseObject:private] =>
[modifiedColumns:protected] => Array
(
)
)
[64] => Category Object
(
[languages:protected] =>
[bok_resources:protected] =>
[bok_topics:protected] =>
[bok_keywords:protected] =>
[id:protected] => 64
[type:protected] => category
[parent:protected] => 2
[label:protected] => Laborer
[alreadyInSave:protected] =>
[alreadyInValidation:protected] =>
[validationFailures:protected] => Array
(
)
[_new:BaseObject:private] =>
[_deleted:BaseObject:private] =>
[modifiedColumns:protected] => Array
(
)
)
[70] => Category Object
(
[languages:protected] =>
[bok_resources:protected] =>
[bok_topics:protected] =>
[bok_keywords:protected] =>
[id:protected] => 70
[type:protected] => category
[parent:protected] => 2
[label:protected] => Operating Engineer
[alreadyInSave:protected] =>
[alreadyInValidation:protected] =>
[validationFailures:protected] => Array
(
)
[_new:BaseObject:private] =>
[_deleted:BaseObject:private] =>
[modifiedColumns:protected] => Array
(
)
)
[63] => Category Object
(
[languages:protected] =>
[bok_resources:protected] =>
[bok_topics:protected] =>
[bok_keywords:protected] =>
[id:protected] => 63
[type:protected] => category
[parent:protected] => 2
[label:protected] => Reinforcing Ironworker
[alreadyInSave:protected] =>
[alreadyInValidation:protected] =>
[validationFailures:protected] => Array
(
)
[_new:BaseObject:private] =>
[_deleted:BaseObject:private] =>
[modifiedColumns:protected] => Array
(
)
)
[78] => Category Object
(
[languages:protected] =>
[bok_resources:protected] =>
[bok_topics:protected] =>
[bok_keywords:protected] =>
[id:protected] => 78
[type:protected] => category
[parent:protected] => 2
[label:protected] => Roofer/Waterproofer
[alreadyInSave:protected] =>
[alreadyInValidation:protected] =>
[validationFailures:protected] => Array
(
)
[_new:BaseObject:private] =>
[_deleted:BaseObject:private] =>
[modifiedColumns:protected] => Array
(
)
)
[82] => Category Object
(
[languages:protected] =>
[bok_resources:protected] =>
[bok_topics:protected] =>
[bok_keywords:protected] =>
[id:protected] => 82
[type:protected] => category
[parent:protected] => 2
[label:protected] => Stonemason
[alreadyInSave:protected] =>
[alreadyInValidation:protected] =>
[validationFailures:protected] => Array
(
)
[_new:BaseObject:private] =>
[_deleted:BaseObject:private] =>
[modifiedColumns:protected] => Array
(
)
)
[62] => Category Object
(
[languages:protected] =>
[bok_resources:protected] =>
[bok_topics:protected] =>
[bok_keywords:protected] =>
[id:protected] => 62
[type:protected] => category
[parent:protected] => 2
[label:protected] => Structural Ironworker
[alreadyInSave:protected] =>
[alreadyInValidation:protected] =>
[validationFailures:protected] => Array
(
)
[_new:BaseObject:private] =>
[_deleted:BaseObject:private] =>
[modifiedColumns:protected] => Array
(
)
)
[87] => Category Object
(
[languages:protected] =>
[bok_resources:protected] =>
[bok_topics:protected] =>
[bok_keywords:protected] =>
[id:protected] => 87
[type:protected] => category
[parent:protected] => 3
[label:protected] => Commercial & Institutional
[alreadyInSave:protected] =>
[alreadyInValidation:protected] =>
[validationFailures:protected] => Array
(
)
[_new:BaseObject:private] =>
[_deleted:BaseObject:private] =>
[modifiedColumns:protected] => Array
(
)
)
[88] => Category Object
(
[languages:protected] =>
[bok_resources:protected] =>
[bok_topics:protected] =>
[bok_keywords:protected] =>
[id:protected] => 88
[type:protected] => category
[parent:protected] => 3
[label:protected] => Demolition
[alreadyInSave:protected] =>
[alreadyInValidation:protected] =>
[validationFailures:protected] => Array
(
)
[_new:BaseObject:private] =>
[_deleted:BaseObject:private] =>
[modifiedColumns:protected] => Array
(
)
)
[89] => Category Object
(
[languages:protected] =>
[bok_resources:protected] =>
[bok_topics:protected] =>
[bok_keywords:protected] =>
[id:protected] => 89
[type:protected] => category
[parent:protected] => 3
[label:protected] => Disasters
[alreadyInSave:protected] =>
[alreadyInValidation:protected] =>
[validationFailures:protected] => Array
(
)
[_new:BaseObject:private] =>
[_deleted:BaseObject:private] =>
[modifiedColumns:protected] => Array
(
)
)
[91] => Category Object
(
[languages:protected] =>
[bok_resources:protected] =>
[bok_topics:protected] =>
[bok_keywords:protected] =>
[id:protected] => 91
[type:protected] => category
[parent:protected] => 3
[label:protected] => Heavy & Highway
[alreadyInSave:protected] =>
[alreadyInValidation:protected] =>
[validationFailures:protected] => Array
(
)
[_new:BaseObject:private] =>
[_deleted:BaseObject:private] =>
[modifiedColumns:protected] => Array
(
)
)
[90] => Category Object
(
[languages:protected] =>
[bok_resources:protected] =>
[bok_topics:protected] =>
[bok_keywords:protected] =>
[id:protected] => 90
[type:protected] => category
[parent:protected] => 3
[label:protected] => Industrial
[alreadyInSave:protected] =>
[alreadyInValidation:protected] =>
[validationFailures:protected] => Array
(
)
[_new:BaseObject:private] =>
[_deleted:BaseObject:private] =>
[modifiedColumns:protected] => Array
(
)
)
[93] => Category Object
(
[languages:protected] =>
[bok_resources:protected] =>
[bok_topics:protected] =>
[bok_keywords:protected] =>
[id:protected] => 93
[type:protected] => category
[parent:protected] => 3
[label:protected] => Renovations
[alreadyInSave:protected] =>
[alreadyInValidation:protected] =>
[validationFailures:protected] => Array
(
)
[_new:BaseObject:private] =>
[_deleted:BaseObject:private] =>
[modifiedColumns:protected] => Array
(
)
)
[94] => Category Object
(
[languages:protected] =>
[bok_resources:protected] =>
[bok_topics:protected] =>
[bok_keywords:protected] =>
[id:protected] => 94
[type:protected] => category
[parent:protected] => 3
[label:protected] => Residential
[alreadyInSave:protected] =>
[alreadyInValidation:protected] =>
[validationFailures:protected] => Array
(
)
[_new:BaseObject:private] =>
[_deleted:BaseObject:private] =>
[modifiedColumns:protected] => Array
(
)
)
[97] => Category Object
(
[languages:protected] =>
[bok_resources:protected] =>
[bok_topics:protected] =>
[bok_keywords:protected] =>
[id:protected] => 97
[type:protected] => category
[parent:protected] => 5
[label:protected] => Images
[alreadyInSave:protected] =>
[alreadyInValidation:protected] =>
[validationFailures:protected] => Array
(
)
[_new:BaseObject:private] =>
[_deleted:BaseObject:private] =>
[modifiedColumns:protected] => Array
(
)
)
)
[categories_initialized:protected] => 1
[mapped_items:protected] =>
[content:protected] =>
[files:protected] =>
[language:protected] => Language Object
(
[id:protected] => 1
[code:protected] => en
[name:protected] => English
[alreadyInSave:protected] =>
[alreadyInValidation:protected] =>
[validationFailures:protected] => Array
(
)
[_new:BaseObject:private] =>
[_deleted:BaseObject:private] =>
[modifiedColumns:protected] => Array
(
)
)
[old_record:protected] =>
[id:protected] => 4003
[old_id:protected] =>
[elcosh_id:protected] => i002691
[type:protected] => image
[display_type:protected] => Image
[user_id:protected] => 0
[language_id:protected] => 1
[tagging_id:protected] => Bruce Lippy
[priority_id:protected] => 1
[title:protected] => Morning Toolbox Talk
[total_pages:protected] => 0
[billed_pages:protected] => 0
[publication_number:protected] =>
[part_of:protected] =>
[keywords:protected] => toolbox talk, tailgate talk, Spanish, bilingual
[comments:protected] =>
[summary:protected] => This photo is from an early morning toolbox talk on a construction job in Mclean, Virginia. It is being delivered in English and Spanish.
[transition_comments:protected] =>
[external_link:protected] =>
[consol_link:protected] => http://www.cpwrconstructionsolutions.org/electrical/solution/662/worker-training.html
[more_like_this:protected] => d001285,d001304,c000079
[permission_given_by:protected] =>
[published:protected] => T
[billable:protected] => F
[img_name:protected] =>
[img_ext:protected] => jpg
[img_width:protected] =>
[img_height:protected] =>
[img_credit:protected] => Morgan Zavertnik and Hoar Construction
[img_practice:protected] => good
[vid_source_id:protected] =>
[vid_running_time:protected] =>
[vid_intended_audience:protected] =>
[vid_acquisition_info:protected] =>
[vid_cost:protected] =>
[vid_producer:protected] =>
[vid_filename:protected] =>
[vid_filename_downloadable:protected] =>
[date_summary:protected] => November 2015
[date_permission_requested:protected] =>
[date_permission_received:protected] =>
[date_review_needed:protected] =>
[date_received:protected] => 03/02/16
[date_completed:protected] => 03/02/16
[date_billed:protected] =>
[date_modified:protected] => 03/02/16
[collBokExports:protected] =>
[lastBokExportCriteria:BaseElcoshItem:private] =>
[alreadyInSave:protected] =>
[alreadyInValidation:protected] =>
[validationFailures:protected] => Array
(
)
[_new:BaseObject:private] =>
[_deleted:BaseObject:private] =>
[modifiedColumns:protected] => Array
(
)
)
)
[1] => Search_Result Object
(
[title] => Toolbox talk - crew view
[image] => /record/images/4005-p.jpg
[blurb] => Photo of crew listening to a toolbox safety talk before starting work....
[category] => Array
(
[0] => 97
[1] => 20
[2] => 47
[3] => 49
[4] => 51
[5] => 55
[6] => 61
[7] => 64
[8] => 71
[9] => 75
[10] => 63
[11] => 79
[12] => 62
[13] => 87
[14] => 88
[15] => 91
[16] => 90
[17] => 93
[18] => 94
[19] => 95
)
[labels] => Array
(
[0] => Images
[1] => Media
[2] => Media & Documents
[3] => Safety Culture
[4] => Work Environment
[5] => Hazards
[6] => Bricklayer
[7] => Trades
[8] => Carpenter
[10] => Cement Mason
[12] => Electrical Worker
[14] => Interior Systems Carpenter
[16] => Laborer
[18] => Painter
[20] => Plasterer
[22] => Reinforcing Ironworker
[24] => Scaffold Erector
[26] => Structural Ironworker
[28] => Commercial & Institutional
[29] => Jobsites
[30] => Demolition
[32] => Heavy & Highway
[34] => Industrial
[36] => Renovations
[38] => Residential
[40] => Underground
)
[type] => Images
[sub_category] =>
[url] => /image/4005/i002692/Toolbox%2Btalk%2B-%2Bcrew%2Bview.html
[item:protected] => ImageRecord Object
(
[records:protected] => Array
(
)
[recordId:protected] =>
[searchWordClass:protected] =>
[searchWordPeerClass:protected] =>
[bok_record:protected] =>
[authors:protected] =>
[organizations:protected] =>
[collections:protected] =>
[categories:protected] => Array
(
[97] => Category Object
(
[languages:protected] =>
[bok_resources:protected] =>
[bok_topics:protected] =>
[bok_keywords:protected] =>
[id:protected] => 97
[type:protected] => category
[parent:protected] => 5
[label:protected] => Images
[alreadyInSave:protected] =>
[alreadyInValidation:protected] =>
[validationFailures:protected] => Array
(
)
[_new:BaseObject:private] =>
[_deleted:BaseObject:private] =>
[modifiedColumns:protected] => Array
(
)
)
[20] => Category Object
(
[languages:protected] =>
[bok_resources:protected] =>
[bok_topics:protected] =>
[bok_keywords:protected] =>
[id:protected] => 20
[type:protected] => category
[parent:protected] => 7
[label:protected] => Safety Culture
[alreadyInSave:protected] =>
[alreadyInValidation:protected] =>
[validationFailures:protected] => Array
(
)
[_new:BaseObject:private] =>
[_deleted:BaseObject:private] =>
[modifiedColumns:protected] => Array
(
)
)
[47] => Category Object
(
[languages:protected] =>
[bok_resources:protected] =>
[bok_topics:protected] =>
[bok_keywords:protected] =>
[id:protected] => 47
[type:protected] => category
[parent:protected] => 2
[label:protected] => Bricklayer
[alreadyInSave:protected] =>
[alreadyInValidation:protected] =>
[validationFailures:protected] => Array
(
)
[_new:BaseObject:private] =>
[_deleted:BaseObject:private] =>
[modifiedColumns:protected] => Array
(
)
)
[49] => Category Object
(
[languages:protected] =>
[bok_resources:protected] =>
[bok_topics:protected] =>
[bok_keywords:protected] =>
[id:protected] => 49
[type:protected] => category
[parent:protected] => 2
[label:protected] => Carpenter
[alreadyInSave:protected] =>
[alreadyInValidation:protected] =>
[validationFailures:protected] => Array
(
)
[_new:BaseObject:private] =>
[_deleted:BaseObject:private] =>
[modifiedColumns:protected] => Array
(
)
)
[51] => Category Object
(
[languages:protected] =>
[bok_resources:protected] =>
[bok_topics:protected] =>
[bok_keywords:protected] =>
[id:protected] => 51
[type:protected] => category
[parent:protected] => 2
[label:protected] => Cement Mason
[alreadyInSave:protected] =>
[alreadyInValidation:protected] =>
[validationFailures:protected] => Array
(
)
[_new:BaseObject:private] =>
[_deleted:BaseObject:private] =>
[modifiedColumns:protected] => Array
(
)
)
[55] => Category Object
(
[languages:protected] =>
[bok_resources:protected] =>
[bok_topics:protected] =>
[bok_keywords:protected] =>
[id:protected] => 55
[type:protected] => category
[parent:protected] => 2
[label:protected] => Electrical Worker
[alreadyInSave:protected] =>
[alreadyInValidation:protected] =>
[validationFailures:protected] => Array
(
)
[_new:BaseObject:private] =>
[_deleted:BaseObject:private] =>
[modifiedColumns:protected] => Array
(
)
)
[61] => Category Object
(
[languages:protected] =>
[bok_resources:protected] =>
[bok_topics:protected] =>
[bok_keywords:protected] =>
[id:protected] => 61
[type:protected] => category
[parent:protected] => 2
[label:protected] => Interior Systems Carpenter
[alreadyInSave:protected] =>
[alreadyInValidation:protected] =>
[validationFailures:protected] => Array
(
)
[_new:BaseObject:private] =>
[_deleted:BaseObject:private] =>
[modifiedColumns:protected] => Array
(
)
)
[64] => Category Object
(
[languages:protected] =>
[bok_resources:protected] =>
[bok_topics:protected] =>
[bok_keywords:protected] =>
[id:protected] => 64
[type:protected] => category
[parent:protected] => 2
[label:protected] => Laborer
[alreadyInSave:protected] =>
[alreadyInValidation:protected] =>
[validationFailures:protected] => Array
(
)
[_new:BaseObject:private] =>
[_deleted:BaseObject:private] =>
[modifiedColumns:protected] => Array
(
)
)
[71] => Category Object
(
[languages:protected] =>
[bok_resources:protected] =>
[bok_topics:protected] =>
[bok_keywords:protected] =>
[id:protected] => 71
[type:protected] => category
[parent:protected] => 2
[label:protected] => Painter
[alreadyInSave:protected] =>
[alreadyInValidation:protected] =>
[validationFailures:protected] => Array
(
)
[_new:BaseObject:private] =>
[_deleted:BaseObject:private] =>
[modifiedColumns:protected] => Array
(
)
)
[75] => Category Object
(
[languages:protected] =>
[bok_resources:protected] =>
[bok_topics:protected] =>
[bok_keywords:protected] =>
[id:protected] => 75
[type:protected] => category
[parent:protected] => 2
[label:protected] => Plasterer
[alreadyInSave:protected] =>
[alreadyInValidation:protected] =>
[validationFailures:protected] => Array
(
)
[_new:BaseObject:private] =>
[_deleted:BaseObject:private] =>
[modifiedColumns:protected] => Array
(
)
)
[63] => Category Object
(
[languages:protected] =>
[bok_resources:protected] =>
[bok_topics:protected] =>
[bok_keywords:protected] =>
[id:protected] => 63
[type:protected] => category
[parent:protected] => 2
[label:protected] => Reinforcing Ironworker
[alreadyInSave:protected] =>
[alreadyInValidation:protected] =>
[validationFailures:protected] => Array
(
)
[_new:BaseObject:private] =>
[_deleted:BaseObject:private] =>
[modifiedColumns:protected] => Array
(
)
)
[79] => Category Object
(
[languages:protected] =>
[bok_resources:protected] =>
[bok_topics:protected] =>
[bok_keywords:protected] =>
[id:protected] => 79
[type:protected] => category
[parent:protected] => 2
[label:protected] => Scaffold Erector
[alreadyInSave:protected] =>
[alreadyInValidation:protected] =>
[validationFailures:protected] => Array
(
)
[_new:BaseObject:private] =>
[_deleted:BaseObject:private] =>
[modifiedColumns:protected] => Array
(
)
)
[62] => Category Object
(
[languages:protected] =>
[bok_resources:protected] =>
[bok_topics:protected] =>
[bok_keywords:protected] =>
[id:protected] => 62
[type:protected] => category
[parent:protected] => 2
[label:protected] => Structural Ironworker
[alreadyInSave:protected] =>
[alreadyInValidation:protected] =>
[validationFailures:protected] => Array
(
)
[_new:BaseObject:private] =>
[_deleted:BaseObject:private] =>
[modifiedColumns:protected] => Array
(
)
)
[87] => Category Object
(
[languages:protected] =>
[bok_resources:protected] =>
[bok_topics:protected] =>
[bok_keywords:protected] =>
[id:protected] => 87
[type:protected] => category
[parent:protected] => 3
[label:protected] => Commercial & Institutional
[alreadyInSave:protected] =>
[alreadyInValidation:protected] =>
[validationFailures:protected] => Array
(
)
[_new:BaseObject:private] =>
[_deleted:BaseObject:private] =>
[modifiedColumns:protected] => Array
(
)
)
[88] => Category Object
(
[languages:protected] =>
[bok_resources:protected] =>
[bok_topics:protected] =>
[bok_keywords:protected] =>
[id:protected] => 88
[type:protected] => category
[parent:protected] => 3
[label:protected] => Demolition
[alreadyInSave:protected] =>
[alreadyInValidation:protected] =>
[validationFailures:protected] => Array
(
)
[_new:BaseObject:private] =>
[_deleted:BaseObject:private] =>
[modifiedColumns:protected] => Array
(
)
)
[91] => Category Object
(
[languages:protected] =>
[bok_resources:protected] =>
[bok_topics:protected] =>
[bok_keywords:protected] =>
[id:protected] => 91
[type:protected] => category
[parent:protected] => 3
[label:protected] => Heavy & Highway
[alreadyInSave:protected] =>
[alreadyInValidation:protected] =>
[validationFailures:protected] => Array
(
)
[_new:BaseObject:private] =>
[_deleted:BaseObject:private] =>
[modifiedColumns:protected] => Array
(
)
)
[90] => Category Object
(
[languages:protected] =>
[bok_resources:protected] =>
[bok_topics:protected] =>
[bok_keywords:protected] =>
[id:protected] => 90
[type:protected] => category
[parent:protected] => 3
[label:protected] => Industrial
[alreadyInSave:protected] =>
[alreadyInValidation:protected] =>
[validationFailures:protected] => Array
(
)
[_new:BaseObject:private] =>
[_deleted:BaseObject:private] =>
[modifiedColumns:protected] => Array
(
)
)
[93] => Category Object
(
[languages:protected] =>
[bok_resources:protected] =>
[bok_topics:protected] =>
[bok_keywords:protected] =>
[id:protected] => 93
[type:protected] => category
[parent:protected] => 3
[label:protected] => Renovations
[alreadyInSave:protected] =>
[alreadyInValidation:protected] =>
[validationFailures:protected] => Array
(
)
[_new:BaseObject:private] =>
[_deleted:BaseObject:private] =>
[modifiedColumns:protected] => Array
(
)
)
[94] => Category Object
(
[languages:protected] =>
[bok_resources:protected] =>
[bok_topics:protected] =>
[bok_keywords:protected] =>
[id:protected] => 94
[type:protected] => category
[parent:protected] => 3
[label:protected] => Residential
[alreadyInSave:protected] =>
[alreadyInValidation:protected] =>
[validationFailures:protected] => Array
(
)
[_new:BaseObject:private] =>
[_deleted:BaseObject:private] =>
[modifiedColumns:protected] => Array
(
)
)
[95] => Category Object
(
[languages:protected] =>
[bok_resources:protected] =>
[bok_topics:protected] =>
[bok_keywords:protected] =>
[id:protected] => 95
[type:protected] => category
[parent:protected] => 3
[label:protected] => Underground
[alreadyInSave:protected] =>
[alreadyInValidation:protected] =>
[validationFailures:protected] => Array
(
)
[_new:BaseObject:private] =>
[_deleted:BaseObject:private] =>
[modifiedColumns:protected] => Array
(
)
)
)
[categories_initialized:protected] => 1
[mapped_items:protected] =>
[content:protected] =>
[files:protected] =>
[language:protected] => Language Object
(
[id:protected] => 1
[code:protected] => en
[name:protected] => English
[alreadyInSave:protected] =>
[alreadyInValidation:protected] =>
[validationFailures:protected] => Array
(
)
[_new:BaseObject:private] =>
[_deleted:BaseObject:private] =>
[modifiedColumns:protected] => Array
(
)
)
[old_record:protected] =>
[id:protected] => 4005
[old_id:protected] =>
[elcosh_id:protected] => i002692
[type:protected] => image
[display_type:protected] => Image
[user_id:protected] => 0
[language_id:protected] => 1
[tagging_id:protected] => Bruce Lippy
[priority_id:protected] => 1
[title:protected] => Toolbox talk - crew view
[total_pages:protected] => 0
[billed_pages:protected] => 0
[publication_number:protected] =>
[part_of:protected] =>
[keywords:protected] => toolbox talk, tailgate talk, safety talk, Spanish
[comments:protected] =>
[summary:protected] => Photo of crew listening to a toolbox safety talk before starting work.
[transition_comments:protected] =>
[external_link:protected] =>
[consol_link:protected] => http://www.cpwrconstructionsolutions.org/electrical/solution/662/worker-training.html
[more_like_this:protected] => i002691,d001269, c000079, d001285
[permission_given_by:protected] =>
[published:protected] => T
[billable:protected] => F
[img_name:protected] =>
[img_ext:protected] => jpg
[img_width:protected] =>
[img_height:protected] =>
[img_credit:protected] => Morgan Zavertnik and Hoar Construction
[img_practice:protected] => good
[vid_source_id:protected] =>
[vid_running_time:protected] =>
[vid_intended_audience:protected] =>
[vid_acquisition_info:protected] =>
[vid_cost:protected] =>
[vid_producer:protected] =>
[vid_filename:protected] =>
[vid_filename_downloadable:protected] =>
[date_summary:protected] => November 2015
[date_permission_requested:protected] =>
[date_permission_received:protected] =>
[date_review_needed:protected] =>
[date_received:protected] => 03/02/16
[date_completed:protected] => 03/02/16
[date_billed:protected] =>
[date_modified:protected] => 03/02/16
[collBokExports:protected] =>
[lastBokExportCriteria:BaseElcoshItem:private] =>
[alreadyInSave:protected] =>
[alreadyInValidation:protected] =>
[validationFailures:protected] => Array
(
)
[_new:BaseObject:private] =>
[_deleted:BaseObject:private] =>
[modifiedColumns:protected] => Array
(
)
)
)
[2] => Search_Result Object
(
[title] => Toolbox talk - long shot
[image] => /record/images/4006-p.jpg
[blurb] => This crew gathered every morning before starting work to discuss a new safety topic....
[category] => Array
(
[0] => 20
[1] => 47
[2] => 49
[3] => 51
[4] => 55
[5] => 64
[6] => 68
[7] => 75
[8] => 76
[9] => 63
[10] => 78
[11] => 79
[12] => 82
[13] => 62
[14] => 87
[15] => 88
[16] => 91
[17] => 90
[18] => 93
[19] => 94
[20] => 95
[21] => 97
)
[labels] => Array
(
[0] => Safety Culture
[1] => Work Environment
[2] => Hazards
[3] => Bricklayer
[4] => Trades
[5] => Carpenter
[7] => Cement Mason
[9] => Electrical Worker
[11] => Laborer
[13] => Maintenance Worker
[15] => Plasterer
[17] => Plumber/Pipefitter
[19] => Reinforcing Ironworker
[21] => Roofer/Waterproofer
[23] => Scaffold Erector
[25] => Stonemason
[27] => Structural Ironworker
[29] => Commercial & Institutional
[30] => Jobsites
[31] => Demolition
[33] => Heavy & Highway
[35] => Industrial
[37] => Renovations
[39] => Residential
[41] => Underground
[43] => Images
[44] => Media
[45] => Media & Documents
)
[type] => Images
[sub_category] =>
[url] => /image/4006/i002693/Toolbox%2Btalk%2B-%2Blong%2Bshot.html
[item:protected] => ImageRecord Object
(
[records:protected] => Array
(
)
[recordId:protected] =>
[searchWordClass:protected] =>
[searchWordPeerClass:protected] =>
[bok_record:protected] =>
[authors:protected] =>
[organizations:protected] =>
[collections:protected] =>
[categories:protected] => Array
(
[20] => Category Object
(
[languages:protected] =>
[bok_resources:protected] =>
[bok_topics:protected] =>
[bok_keywords:protected] =>
[id:protected] => 20
[type:protected] => category
[parent:protected] => 7
[label:protected] => Safety Culture
[alreadyInSave:protected] =>
[alreadyInValidation:protected] =>
[validationFailures:protected] => Array
(
)
[_new:BaseObject:private] =>
[_deleted:BaseObject:private] =>
[modifiedColumns:protected] => Array
(
)
)
[47] => Category Object
(
[languages:protected] =>
[bok_resources:protected] =>
[bok_topics:protected] =>
[bok_keywords:protected] =>
[id:protected] => 47
[type:protected] => category
[parent:protected] => 2
[label:protected] => Bricklayer
[alreadyInSave:protected] =>
[alreadyInValidation:protected] =>
[validationFailures:protected] => Array
(
)
[_new:BaseObject:private] =>
[_deleted:BaseObject:private] =>
[modifiedColumns:protected] => Array
(
)
)
[49] => Category Object
(
[languages:protected] =>
[bok_resources:protected] =>
[bok_topics:protected] =>
[bok_keywords:protected] =>
[id:protected] => 49
[type:protected] => category
[parent:protected] => 2
[label:protected] => Carpenter
[alreadyInSave:protected] =>
[alreadyInValidation:protected] =>
[validationFailures:protected] => Array
(
)
[_new:BaseObject:private] =>
[_deleted:BaseObject:private] =>
[modifiedColumns:protected] => Array
(
)
)
[51] => Category Object
(
[languages:protected] =>
[bok_resources:protected] =>
[bok_topics:protected] =>
[bok_keywords:protected] =>
[id:protected] => 51
[type:protected] => category
[parent:protected] => 2
[label:protected] => Cement Mason
[alreadyInSave:protected] =>
[alreadyInValidation:protected] =>
[validationFailures:protected] => Array
(
)
[_new:BaseObject:private] =>
[_deleted:BaseObject:private] =>
[modifiedColumns:protected] => Array
(
)
)
[55] => Category Object
(
[languages:protected] =>
[bok_resources:protected] =>
[bok_topics:protected] =>
[bok_keywords:protected] =>
[id:protected] => 55
[type:protected] => category
[parent:protected] => 2
[label:protected] => Electrical Worker
[alreadyInSave:protected] =>
[alreadyInValidation:protected] =>
[validationFailures:protected] => Array
(
)
[_new:BaseObject:private] =>
[_deleted:BaseObject:private] =>
[modifiedColumns:protected] => Array
(
)
)
[64] => Category Object
(
[languages:protected] =>
[bok_resources:protected] =>
[bok_topics:protected] =>
[bok_keywords:protected] =>
[id:protected] => 64
[type:protected] => category
[parent:protected] => 2
[label:protected] => Laborer
[alreadyInSave:protected] =>
[alreadyInValidation:protected] =>
[validationFailures:protected] => Array
(
)
[_new:BaseObject:private] =>
[_deleted:BaseObject:private] =>
[modifiedColumns:protected] => Array
(
)
)
[68] => Category Object
(
[languages:protected] =>
[bok_resources:protected] =>
[bok_topics:protected] =>
[bok_keywords:protected] =>
[id:protected] => 68
[type:protected] => category
[parent:protected] => 2
[label:protected] => Maintenance Worker
[alreadyInSave:protected] =>
[alreadyInValidation:protected] =>
[validationFailures:protected] => Array
(
)
[_new:BaseObject:private] =>
[_deleted:BaseObject:private] =>
[modifiedColumns:protected] => Array
(
)
)
[75] => Category Object
(
[languages:protected] =>
[bok_resources:protected] =>
[bok_topics:protected] =>
[bok_keywords:protected] =>
[id:protected] => 75
[type:protected] => category
[parent:protected] => 2
[label:protected] => Plasterer
[alreadyInSave:protected] =>
[alreadyInValidation:protected] =>
[validationFailures:protected] => Array
(
)
[_new:BaseObject:private] =>
[_deleted:BaseObject:private] =>
[modifiedColumns:protected] => Array
(
)
)
[76] => Category Object
(
[languages:protected] =>
[bok_resources:protected] =>
[bok_topics:protected] =>
[bok_keywords:protected] =>
[id:protected] => 76
[type:protected] => category
[parent:protected] => 2
[label:protected] => Plumber/Pipefitter
[alreadyInSave:protected] =>
[alreadyInValidation:protected] =>
[validationFailures:protected] => Array
(
)
[_new:BaseObject:private] =>
[_deleted:BaseObject:private] =>
[modifiedColumns:protected] => Array
(
)
)
[63] => Category Object
(
[languages:protected] =>
[bok_resources:protected] =>
[bok_topics:protected] =>
[bok_keywords:protected] =>
[id:protected] => 63
[type:protected] => category
[parent:protected] => 2
[label:protected] => Reinforcing Ironworker
[alreadyInSave:protected] =>
[alreadyInValidation:protected] =>
[validationFailures:protected] => Array
(
)
[_new:BaseObject:private] =>
[_deleted:BaseObject:private] =>
[modifiedColumns:protected] => Array
(
)
)
[78] => Category Object
(
[languages:protected] =>
[bok_resources:protected] =>
[bok_topics:protected] =>
[bok_keywords:protected] =>
[id:protected] => 78
[type:protected] => category
[parent:protected] => 2
[label:protected] => Roofer/Waterproofer
[alreadyInSave:protected] =>
[alreadyInValidation:protected] =>
[validationFailures:protected] => Array
(
)
[_new:BaseObject:private] =>
[_deleted:BaseObject:private] =>
[modifiedColumns:protected] => Array
(
)
)
[79] => Category Object
(
[languages:protected] =>
[bok_resources:protected] =>
[bok_topics:protected] =>
[bok_keywords:protected] =>
[id:protected] => 79
[type:protected] => category
[parent:protected] => 2
[label:protected] => Scaffold Erector
[alreadyInSave:protected] =>
[alreadyInValidation:protected] =>
[validationFailures:protected] => Array
(
)
[_new:BaseObject:private] =>
[_deleted:BaseObject:private] =>
[modifiedColumns:protected] => Array
(
)
)
[82] => Category Object
(
[languages:protected] =>
[bok_resources:protected] =>
[bok_topics:protected] =>
[bok_keywords:protected] =>
[id:protected] => 82
[type:protected] => category
[parent:protected] => 2
[label:protected] => Stonemason
[alreadyInSave:protected] =>
[alreadyInValidation:protected] =>
[validationFailures:protected] => Array
(
)
[_new:BaseObject:private] =>
[_deleted:BaseObject:private] =>
[modifiedColumns:protected] => Array
(
)
)
[62] => Category Object
(
[languages:protected] =>
[bok_resources:protected] =>
[bok_topics:protected] =>
[bok_keywords:protected] =>
[id:protected] => 62
[type:protected] => category
[parent:protected] => 2
[label:protected] => Structural Ironworker
[alreadyInSave:protected] =>
[alreadyInValidation:protected] =>
[validationFailures:protected] => Array
(
)
[_new:BaseObject:private] =>
[_deleted:BaseObject:private] =>
[modifiedColumns:protected] => Array
(
)
)
[87] => Category Object
(
[languages:protected] =>
[bok_resources:protected] =>
[bok_topics:protected] =>
[bok_keywords:protected] =>
[id:protected] => 87
[type:protected] => category
[parent:protected] => 3
[label:protected] => Commercial & Institutional
[alreadyInSave:protected] =>
[alreadyInValidation:protected] =>
[validationFailures:protected] => Array
(
)
[_new:BaseObject:private] =>
[_deleted:BaseObject:private] =>
[modifiedColumns:protected] => Array
(
)
)
[88] => Category Object
(
[languages:protected] =>
[bok_resources:protected] =>
[bok_topics:protected] =>
[bok_keywords:protected] =>
[id:protected] => 88
[type:protected] => category
[parent:protected] => 3
[label:protected] => Demolition
[alreadyInSave:protected] =>
[alreadyInValidation:protected] =>
[validationFailures:protected] => Array
(
)
[_new:BaseObject:private] =>
[_deleted:BaseObject:private] =>
[modifiedColumns:protected] => Array
(
)
)
[91] => Category Object
(
[languages:protected] =>
[bok_resources:protected] =>
[bok_topics:protected] =>
[bok_keywords:protected] =>
[id:protected] => 91
[type:protected] => category
[parent:protected] => 3
[label:protected] => Heavy & Highway
[alreadyInSave:protected] =>
[alreadyInValidation:protected] =>
[validationFailures:protected] => Array
(
)
[_new:BaseObject:private] =>
[_deleted:BaseObject:private] =>
[modifiedColumns:protected] => Array
(
)
)
[90] => Category Object
(
[languages:protected] =>
[bok_resources:protected] =>
[bok_topics:protected] =>
[bok_keywords:protected] =>
[id:protected] => 90
[type:protected] => category
[parent:protected] => 3
[label:protected] => Industrial
[alreadyInSave:protected] =>
[alreadyInValidation:protected] =>
[validationFailures:protected] => Array
(
)
[_new:BaseObject:private] =>
[_deleted:BaseObject:private] =>
[modifiedColumns:protected] => Array
(
)
)
[93] => Category Object
(
[languages:protected] =>
[bok_resources:protected] =>
[bok_topics:protected] =>
[bok_keywords:protected] =>
[id:protected] => 93
[type:protected] => category
[parent:protected] => 3
[label:protected] => Renovations
[alreadyInSave:protected] =>
[alreadyInValidation:protected] =>
[validationFailures:protected] => Array
(
)
[_new:BaseObject:private] =>
[_deleted:BaseObject:private] =>
[modifiedColumns:protected] => Array
(
)
)
[94] => Category Object
(
[languages:protected] =>
[bok_resources:protected] =>
[bok_topics:protected] =>
[bok_keywords:protected] =>
[id:protected] => 94
[type:protected] => category
[parent:protected] => 3
[label:protected] => Residential
[alreadyInSave:protected] =>
[alreadyInValidation:protected] =>
[validationFailures:protected] => Array
(
)
[_new:BaseObject:private] =>
[_deleted:BaseObject:private] =>
[modifiedColumns:protected] => Array
(
)
)
[95] => Category Object
(
[languages:protected] =>
[bok_resources:protected] =>
[bok_topics:protected] =>
[bok_keywords:protected] =>
[id:protected] => 95
[type:protected] => category
[parent:protected] => 3
[label:protected] => Underground
[alreadyInSave:protected] =>
[alreadyInValidation:protected] =>
[validationFailures:protected] => Array
(
)
[_new:BaseObject:private] =>
[_deleted:BaseObject:private] =>
[modifiedColumns:protected] => Array
(
)
)
[97] => Category Object
(
[languages:protected] =>
[bok_resources:protected] =>
[bok_topics:protected] =>
[bok_keywords:protected] =>
[id:protected] => 97
[type:protected] => category
[parent:protected] => 5
[label:protected] => Images
[alreadyInSave:protected] =>
[alreadyInValidation:protected] =>
[validationFailures:protected] => Array
(
)
[_new:BaseObject:private] =>
[_deleted:BaseObject:private] =>
[modifiedColumns:protected] => Array
(
)
)
)
[categories_initialized:protected] => 1
[mapped_items:protected] =>
[content:protected] =>
[files:protected] =>
[language:protected] => Language Object
(
[id:protected] => 1
[code:protected] => en
[name:protected] => English
[alreadyInSave:protected] =>
[alreadyInValidation:protected] =>
[validationFailures:protected] => Array
(
)
[_new:BaseObject:private] =>
[_deleted:BaseObject:private] =>
[modifiedColumns:protected] => Array
(
)
)
[old_record:protected] =>
[id:protected] => 4006
[old_id:protected] =>
[elcosh_id:protected] => i002693
[type:protected] => image
[display_type:protected] => Image
[user_id:protected] => 0
[language_id:protected] => 1
[tagging_id:protected] => Bruce Lippy
[priority_id:protected] => 1
[title:protected] => Toolbox talk - long shot
[total_pages:protected] => 0
[billed_pages:protected] => 0
[publication_number:protected] =>
[part_of:protected] =>
[keywords:protected] => toolbox talk, tailgate talk, safety minute
[comments:protected] =>
[summary:protected] => This crew gathered every morning before starting work to discuss a new safety topic.
[transition_comments:protected] =>
[external_link:protected] =>
[consol_link:protected] => http://www.cpwrconstructionsolutions.org/electrical/solution/662/worker-training.html
[more_like_this:protected] => i002691,i002692,d001269,d000527
[permission_given_by:protected] =>
[published:protected] => T
[billable:protected] => F
[img_name:protected] =>
[img_ext:protected] => jpg
[img_width:protected] =>
[img_height:protected] =>
[img_credit:protected] => Morgan Zavertnik and Hoar Construction
[img_practice:protected] => good
[vid_source_id:protected] =>
[vid_running_time:protected] =>
[vid_intended_audience:protected] =>
[vid_acquisition_info:protected] =>
[vid_cost:protected] =>
[vid_producer:protected] =>
[vid_filename:protected] =>
[vid_filename_downloadable:protected] =>
[date_summary:protected] => November 2015
[date_permission_requested:protected] =>
[date_permission_received:protected] =>
[date_review_needed:protected] =>
[date_received:protected] => 03/02/16
[date_completed:protected] => 03/02/16
[date_billed:protected] =>
[date_modified:protected] => 03/02/16
[collBokExports:protected] =>
[lastBokExportCriteria:BaseElcoshItem:private] =>
[alreadyInSave:protected] =>
[alreadyInValidation:protected] =>
[validationFailures:protected] => Array
(
)
[_new:BaseObject:private] =>
[_deleted:BaseObject:private] =>
[modifiedColumns:protected] => Array
(
)
)
)
[3] => Search_Result Object
(
[title] => Safety officer discussing ongoing project with marketing coordinator
[image] => /record/images/4014-p.jpg
[blurb] => The safety officer (left) points out the good safety practices on this project that reflect well on the firm and may influence future clients....
[category] => Array
(
[0] => 97
[1] => 20
[2] => 46
[3] => 47
[4] => 49
[5] => 50
[6] => 51
[7] => 54
[8] => 55
[9] => 58
[10] => 60
[11] => 61
[12] => 64
[13] => 71
[14] => 75
[15] => 76
[16] => 63
[17] => 79
[18] => 80
[19] => 82
[20] => 62
[21] => 83
[22] => 87
[23] => 91
[24] => 90
[25] => 93
[26] => 94
)
[labels] => Array
(
[0] => Images
[1] => Media
[2] => Media & Documents
[3] => Safety Culture
[4] => Work Environment
[5] => Hazards
[6] => Boilermaker
[7] => Trades
[8] => Bricklayer
[10] => Carpenter
[12] => Carpet Layer
[14] => Cement Mason
[16] => Drywall Applicator Specialist
[18] => Electrical Worker
[20] => Glazier
[22] => HVAC
[24] => Interior Systems Carpenter
[26] => Laborer
[28] => Painter
[30] => Plasterer
[32] => Plumber/Pipefitter
[34] => Reinforcing Ironworker
[36] => Scaffold Erector
[38] => Sheetmetal Worker
[40] => Stonemason
[42] => Structural Ironworker
[44] => Terrazzo Worker
[46] => Commercial & Institutional
[47] => Jobsites
[48] => Heavy & Highway
[50] => Industrial
[52] => Renovations
[54] => Residential
)
[type] => Images
[sub_category] =>
[url] => /image/4014/i002700/Safety%2Bofficer%2Bdiscussing%2Bongoing%2Bproject%2Bwith%2Bmarketing%2Bcoordinator.html
[item:protected] => ImageRecord Object
(
[records:protected] => Array
(
)
[recordId:protected] =>
[searchWordClass:protected] =>
[searchWordPeerClass:protected] =>
[bok_record:protected] =>
[authors:protected] =>
[organizations:protected] =>
[collections:protected] =>
[categories:protected] => Array
(
[97] => Category Object
(
[languages:protected] =>
[bok_resources:protected] =>
[bok_topics:protected] =>
[bok_keywords:protected] =>
[id:protected] => 97
[type:protected] => category
[parent:protected] => 5
[label:protected] => Images
[alreadyInSave:protected] =>
[alreadyInValidation:protected] =>
[validationFailures:protected] => Array
(
)
[_new:BaseObject:private] =>
[_deleted:BaseObject:private] =>
[modifiedColumns:protected] => Array
(
)
)
[20] => Category Object
(
[languages:protected] =>
[bok_resources:protected] =>
[bok_topics:protected] =>
[bok_keywords:protected] =>
[id:protected] => 20
[type:protected] => category
[parent:protected] => 7
[label:protected] => Safety Culture
[alreadyInSave:protected] =>
[alreadyInValidation:protected] =>
[validationFailures:protected] => Array
(
)
[_new:BaseObject:private] =>
[_deleted:BaseObject:private] =>
[modifiedColumns:protected] => Array
(
)
)
[46] => Category Object
(
[languages:protected] =>
[bok_resources:protected] =>
[bok_topics:protected] =>
[bok_keywords:protected] =>
[id:protected] => 46
[type:protected] => category
[parent:protected] => 2
[label:protected] => Boilermaker
[alreadyInSave:protected] =>
[alreadyInValidation:protected] =>
[validationFailures:protected] => Array
(
)
[_new:BaseObject:private] =>
[_deleted:BaseObject:private] =>
[modifiedColumns:protected] => Array
(
)
)
[47] => Category Object
(
[languages:protected] =>
[bok_resources:protected] =>
[bok_topics:protected] =>
[bok_keywords:protected] =>
[id:protected] => 47
[type:protected] => category
[parent:protected] => 2
[label:protected] => Bricklayer
[alreadyInSave:protected] =>
[alreadyInValidation:protected] =>
[validationFailures:protected] => Array
(
)
[_new:BaseObject:private] =>
[_deleted:BaseObject:private] =>
[modifiedColumns:protected] => Array
(
)
)
[49] => Category Object
(
[languages:protected] =>
[bok_resources:protected] =>
[bok_topics:protected] =>
[bok_keywords:protected] =>
[id:protected] => 49
[type:protected] => category
[parent:protected] => 2
[label:protected] => Carpenter
[alreadyInSave:protected] =>
[alreadyInValidation:protected] =>
[validationFailures:protected] => Array
(
)
[_new:BaseObject:private] =>
[_deleted:BaseObject:private] =>
[modifiedColumns:protected] => Array
(
)
)
[50] => Category Object
(
[languages:protected] =>
[bok_resources:protected] =>
[bok_topics:protected] =>
[bok_keywords:protected] =>
[id:protected] => 50
[type:protected] => category
[parent:protected] => 2
[label:protected] => Carpet Layer
[alreadyInSave:protected] =>
[alreadyInValidation:protected] =>
[validationFailures:protected] => Array
(
)
[_new:BaseObject:private] =>
[_deleted:BaseObject:private] =>
[modifiedColumns:protected] => Array
(
)
)
[51] => Category Object
(
[languages:protected] =>
[bok_resources:protected] =>
[bok_topics:protected] =>
[bok_keywords:protected] =>
[id:protected] => 51
[type:protected] => category
[parent:protected] => 2
[label:protected] => Cement Mason
[alreadyInSave:protected] =>
[alreadyInValidation:protected] =>
[validationFailures:protected] => Array
(
)
[_new:BaseObject:private] =>
[_deleted:BaseObject:private] =>
[modifiedColumns:protected] => Array
(
)
)
[54] => Category Object
(
[languages:protected] =>
[bok_resources:protected] =>
[bok_topics:protected] =>
[bok_keywords:protected] =>
[id:protected] => 54
[type:protected] => category
[parent:protected] => 2
[label:protected] => Drywall Applicator Specialist
[alreadyInSave:protected] =>
[alreadyInValidation:protected] =>
[validationFailures:protected] => Array
(
)
[_new:BaseObject:private] =>
[_deleted:BaseObject:private] =>
[modifiedColumns:protected] => Array
(
)
)
[55] => Category Object
(
[languages:protected] =>
[bok_resources:protected] =>
[bok_topics:protected] =>
[bok_keywords:protected] =>
[id:protected] => 55
[type:protected] => category
[parent:protected] => 2
[label:protected] => Electrical Worker
[alreadyInSave:protected] =>
[alreadyInValidation:protected] =>
[validationFailures:protected] => Array
(
)
[_new:BaseObject:private] =>
[_deleted:BaseObject:private] =>
[modifiedColumns:protected] => Array
(
)
)
[58] => Category Object
(
[languages:protected] =>
[bok_resources:protected] =>
[bok_topics:protected] =>
[bok_keywords:protected] =>
[id:protected] => 58
[type:protected] => category
[parent:protected] => 2
[label:protected] => Glazier
[alreadyInSave:protected] =>
[alreadyInValidation:protected] =>
[validationFailures:protected] => Array
(
)
[_new:BaseObject:private] =>
[_deleted:BaseObject:private] =>
[modifiedColumns:protected] => Array
(
)
)
[60] => Category Object
(
[languages:protected] =>
[bok_resources:protected] =>
[bok_topics:protected] =>
[bok_keywords:protected] =>
[id:protected] => 60
[type:protected] => category
[parent:protected] => 2
[label:protected] => HVAC
[alreadyInSave:protected] =>
[alreadyInValidation:protected] =>
[validationFailures:protected] => Array
(
)
[_new:BaseObject:private] =>
[_deleted:BaseObject:private] =>
[modifiedColumns:protected] => Array
(
)
)
[61] => Category Object
(
[languages:protected] =>
[bok_resources:protected] =>
[bok_topics:protected] =>
[bok_keywords:protected] =>
[id:protected] => 61
[type:protected] => category
[parent:protected] => 2
[label:protected] => Interior Systems Carpenter
[alreadyInSave:protected] =>
[alreadyInValidation:protected] =>
[validationFailures:protected] => Array
(
)
[_new:BaseObject:private] =>
[_deleted:BaseObject:private] =>
[modifiedColumns:protected] => Array
(
)
)
[64] => Category Object
(
[languages:protected] =>
[bok_resources:protected] =>
[bok_topics:protected] =>
[bok_keywords:protected] =>
[id:protected] => 64
[type:protected] => category
[parent:protected] => 2
[label:protected] => Laborer
[alreadyInSave:protected] =>
[alreadyInValidation:protected] =>
[validationFailures:protected] => Array
(
)
[_new:BaseObject:private] =>
[_deleted:BaseObject:private] =>
[modifiedColumns:protected] => Array
(
)
)
[71] => Category Object
(
[languages:protected] =>
[bok_resources:protected] =>
[bok_topics:protected] =>
[bok_keywords:protected] =>
[id:protected] => 71
[type:protected] => category
[parent:protected] => 2
[label:protected] => Painter
[alreadyInSave:protected] =>
[alreadyInValidation:protected] =>
[validationFailures:protected] => Array
(
)
[_new:BaseObject:private] =>
[_deleted:BaseObject:private] =>
[modifiedColumns:protected] => Array
(
)
)
[75] => Category Object
(
[languages:protected] =>
[bok_resources:protected] =>
[bok_topics:protected] =>
[bok_keywords:protected] =>
[id:protected] => 75
[type:protected] => category
[parent:protected] => 2
[label:protected] => Plasterer
[alreadyInSave:protected] =>
[alreadyInValidation:protected] =>
[validationFailures:protected] => Array
(
)
[_new:BaseObject:private] =>
[_deleted:BaseObject:private] =>
[modifiedColumns:protected] => Array
(
)
)
[76] => Category Object
(
[languages:protected] =>
[bok_resources:protected] =>
[bok_topics:protected] =>
[bok_keywords:protected] =>
[id:protected] => 76
[type:protected] => category
[parent:protected] => 2
[label:protected] => Plumber/Pipefitter
[alreadyInSave:protected] =>
[alreadyInValidation:protected] =>
[validationFailures:protected] => Array
(
)
[_new:BaseObject:private] =>
[_deleted:BaseObject:private] =>
[modifiedColumns:protected] => Array
(
)
)
[63] => Category Object
(
[languages:protected] =>
[bok_resources:protected] =>
[bok_topics:protected] =>
[bok_keywords:protected] =>
[id:protected] => 63
[type:protected] => category
[parent:protected] => 2
[label:protected] => Reinforcing Ironworker
[alreadyInSave:protected] =>
[alreadyInValidation:protected] =>
[validationFailures:protected] => Array
(
)
[_new:BaseObject:private] =>
[_deleted:BaseObject:private] =>
[modifiedColumns:protected] => Array
(
)
)
[79] => Category Object
(
[languages:protected] =>
[bok_resources:protected] =>
[bok_topics:protected] =>
[bok_keywords:protected] =>
[id:protected] => 79
[type:protected] => category
[parent:protected] => 2
[label:protected] => Scaffold Erector
[alreadyInSave:protected] =>
[alreadyInValidation:protected] =>
[validationFailures:protected] => Array
(
)
[_new:BaseObject:private] =>
[_deleted:BaseObject:private] =>
[modifiedColumns:protected] => Array
(
)
)
[80] => Category Object
(
[languages:protected] =>
[bok_resources:protected] =>
[bok_topics:protected] =>
[bok_keywords:protected] =>
[id:protected] => 80
[type:protected] => category
[parent:protected] => 2
[label:protected] => Sheetmetal Worker
[alreadyInSave:protected] =>
[alreadyInValidation:protected] =>
[validationFailures:protected] => Array
(
)
[_new:BaseObject:private] =>
[_deleted:BaseObject:private] =>
[modifiedColumns:protected] => Array
(
)
)
[82] => Category Object
(
[languages:protected] =>
[bok_resources:protected] =>
[bok_topics:protected] =>
[bok_keywords:protected] =>
[id:protected] => 82
[type:protected] => category
[parent:protected] => 2
[label:protected] => Stonemason
[alreadyInSave:protected] =>
[alreadyInValidation:protected] =>
[validationFailures:protected] => Array
(
)
[_new:BaseObject:private] =>
[_deleted:BaseObject:private] =>
[modifiedColumns:protected] => Array
(
)
)
[62] => Category Object
(
[languages:protected] =>
[bok_resources:protected] =>
[bok_topics:protected] =>
[bok_keywords:protected] =>
[id:protected] => 62
[type:protected] => category
[parent:protected] => 2
[label:protected] => Structural Ironworker
[alreadyInSave:protected] =>
[alreadyInValidation:protected] =>
[validationFailures:protected] => Array
(
)
[_new:BaseObject:private] =>
[_deleted:BaseObject:private] =>
[modifiedColumns:protected] => Array
(
)
)
[83] => Category Object
(
[languages:protected] =>
[bok_resources:protected] =>
[bok_topics:protected] =>
[bok_keywords:protected] =>
[id:protected] => 83
[type:protected] => category
[parent:protected] => 2
[label:protected] => Terrazzo Worker
[alreadyInSave:protected] =>
[alreadyInValidation:protected] =>
[validationFailures:protected] => Array
(
)
[_new:BaseObject:private] =>
[_deleted:BaseObject:private] =>
[modifiedColumns:protected] => Array
(
)
)
[87] => Category Object
(
[languages:protected] =>
[bok_resources:protected] =>
[bok_topics:protected] =>
[bok_keywords:protected] =>
[id:protected] => 87
[type:protected] => category
[parent:protected] => 3
[label:protected] => Commercial & Institutional
[alreadyInSave:protected] =>
[alreadyInValidation:protected] =>
[validationFailures:protected] => Array
(
)
[_new:BaseObject:private] =>
[_deleted:BaseObject:private] =>
[modifiedColumns:protected] => Array
(
)
)
[91] => Category Object
(
[languages:protected] =>
[bok_resources:protected] =>
[bok_topics:protected] =>
[bok_keywords:protected] =>
[id:protected] => 91
[type:protected] => category
[parent:protected] => 3
[label:protected] => Heavy & Highway
[alreadyInSave:protected] =>
[alreadyInValidation:protected] =>
[validationFailures:protected] => Array
(
)
[_new:BaseObject:private] =>
[_deleted:BaseObject:private] =>
[modifiedColumns:protected] => Array
(
)
)
[90] => Category Object
(
[languages:protected] =>
[bok_resources:protected] =>
[bok_topics:protected] =>
[bok_keywords:protected] =>
[id:protected] => 90
[type:protected] => category
[parent:protected] => 3
[label:protected] => Industrial
[alreadyInSave:protected] =>
[alreadyInValidation:protected] =>
[validationFailures:protected] => Array
(
)
[_new:BaseObject:private] =>
[_deleted:BaseObject:private] =>
[modifiedColumns:protected] => Array
(
)
)
[93] => Category Object
(
[languages:protected] =>
[bok_resources:protected] =>
[bok_topics:protected] =>
[bok_keywords:protected] =>
[id:protected] => 93
[type:protected] => category
[parent:protected] => 3
[label:protected] => Renovations
[alreadyInSave:protected] =>
[alreadyInValidation:protected] =>
[validationFailures:protected] => Array
(
)
[_new:BaseObject:private] =>
[_deleted:BaseObject:private] =>
[modifiedColumns:protected] => Array
(
)
)
[94] => Category Object
(
[languages:protected] =>
[bok_resources:protected] =>
[bok_topics:protected] =>
[bok_keywords:protected] =>
[id:protected] => 94
[type:protected] => category
[parent:protected] => 3
[label:protected] => Residential
[alreadyInSave:protected] =>
[alreadyInValidation:protected] =>
[validationFailures:protected] => Array
(
)
[_new:BaseObject:private] =>
[_deleted:BaseObject:private] =>
[modifiedColumns:protected] => Array
(
)
)
)
[categories_initialized:protected] => 1
[mapped_items:protected] =>
[content:protected] =>
[files:protected] =>
[language:protected] => Language Object
(
[id:protected] => 1
[code:protected] => en
[name:protected] => English
[alreadyInSave:protected] =>
[alreadyInValidation:protected] =>
[validationFailures:protected] => Array
(
)
[_new:BaseObject:private] =>
[_deleted:BaseObject:private] =>
[modifiedColumns:protected] => Array
(
)
)
[old_record:protected] =>
[id:protected] => 4014
[old_id:protected] =>
[elcosh_id:protected] => i002700
[type:protected] => image
[display_type:protected] => Image
[user_id:protected] => 0
[language_id:protected] => 1
[tagging_id:protected] => Bruce Lippy
[priority_id:protected] => 1
[title:protected] => Safety officer discussing ongoing project with marketing coordinator
[total_pages:protected] => 0
[billed_pages:protected] => 0
[publication_number:protected] =>
[part_of:protected] =>
[keywords:protected] => Latino, safety officer, safety culture
[comments:protected] =>
[summary:protected] => The safety officer (left) points out the good safety practices on this project that reflect well on the firm and may influence future clients.
[transition_comments:protected] =>
[external_link:protected] =>
[consol_link:protected] => http://www.cpwrconstructionsolutions.org/index.php
[more_like_this:protected] => d000989,d001351,d001362,d000652, d001101, d000931, d001395
[permission_given_by:protected] =>
[published:protected] => T
[billable:protected] => F
[img_name:protected] =>
[img_ext:protected] => jpg
[img_width:protected] =>
[img_height:protected] =>
[img_credit:protected] => Hoar Construction, Photo by Neil Lippy
[img_practice:protected] => good
[vid_source_id:protected] =>
[vid_running_time:protected] =>
[vid_intended_audience:protected] =>
[vid_acquisition_info:protected] =>
[vid_cost:protected] =>
[vid_producer:protected] =>
[vid_filename:protected] =>
[vid_filename_downloadable:protected] =>
[date_summary:protected] => November 2015
[date_permission_requested:protected] =>
[date_permission_received:protected] =>
[date_review_needed:protected] =>
[date_received:protected] => 03/02/16
[date_completed:protected] => 03/02/16
[date_billed:protected] =>
[date_modified:protected] => 01/30/23
[collBokExports:protected] =>
[lastBokExportCriteria:BaseElcoshItem:private] =>
[alreadyInSave:protected] =>
[alreadyInValidation:protected] =>
[validationFailures:protected] => Array
(
)
[_new:BaseObject:private] =>
[_deleted:BaseObject:private] =>
[modifiedColumns:protected] => Array
(
)
)
)
[4] => Search_Result Object
(
[title] => Scaffolding at top of large column
[image] => /record/images/3994-p.jpg
[blurb] => This shot shows innovative guarding around the top of a large concrete column in the base of a high rise structure going up....
[category] => Array
(
[0] => 15
[1] => 21
[2] => 47
[3] => 51
[4] => 63
[5] => 78
[6] => 79
[7] => 80
[8] => 62
[9] => 87
[10] => 97
[11] => 56
[12] => 64
[13] => 74
)
[labels] => Array
(
[0] => Falls
[1] => Work Environment
[2] => Hazards
[3] => Scaffolds
[6] => Bricklayer
[7] => Trades
[8] => Cement Mason
[10] => Reinforcing Ironworker
[12] => Roofer/Waterproofer
[14] => Scaffold Erector
[16] => Sheetmetal Worker
[18] => Structural Ironworker
[20] => Commercial & Institutional
[21] => Jobsites
[22] => Images
[23] => Media
[24] => Media & Documents
[25] => Elevator Constructor
[27] => Laborer
[29] => Pile Driver
)
[type] => Images
[sub_category] =>
[url] => /image/3994/i002689/Scaffolding%2Bat%2Btop%2Bof%2Blarge%2Bcolumn.html
[item:protected] => ImageRecord Object
(
[records:protected] => Array
(
)
[recordId:protected] =>
[searchWordClass:protected] =>
[searchWordPeerClass:protected] =>
[bok_record:protected] =>
[authors:protected] =>
[organizations:protected] =>
[collections:protected] =>
[categories:protected] => Array
(
[15] => Category Object
(
[languages:protected] =>
[bok_resources:protected] =>
[bok_topics:protected] =>
[bok_keywords:protected] =>
[id:protected] => 15
[type:protected] => category
[parent:protected] => 7
[label:protected] => Falls
[alreadyInSave:protected] =>
[alreadyInValidation:protected] =>
[validationFailures:protected] => Array
(
)
[_new:BaseObject:private] =>
[_deleted:BaseObject:private] =>
[modifiedColumns:protected] => Array
(
)
)
[21] => Category Object
(
[languages:protected] =>
[bok_resources:protected] =>
[bok_topics:protected] =>
[bok_keywords:protected] =>
[id:protected] => 21
[type:protected] => category
[parent:protected] => 7
[label:protected] => Scaffolds
[alreadyInSave:protected] =>
[alreadyInValidation:protected] =>
[validationFailures:protected] => Array
(
)
[_new:BaseObject:private] =>
[_deleted:BaseObject:private] =>
[modifiedColumns:protected] => Array
(
)
)
[47] => Category Object
(
[languages:protected] =>
[bok_resources:protected] =>
[bok_topics:protected] =>
[bok_keywords:protected] =>
[id:protected] => 47
[type:protected] => category
[parent:protected] => 2
[label:protected] => Bricklayer
[alreadyInSave:protected] =>
[alreadyInValidation:protected] =>
[validationFailures:protected] => Array
(
)
[_new:BaseObject:private] =>
[_deleted:BaseObject:private] =>
[modifiedColumns:protected] => Array
(
)
)
[51] => Category Object
(
[languages:protected] =>
[bok_resources:protected] =>
[bok_topics:protected] =>
[bok_keywords:protected] =>
[id:protected] => 51
[type:protected] => category
[parent:protected] => 2
[label:protected] => Cement Mason
[alreadyInSave:protected] =>
[alreadyInValidation:protected] =>
[validationFailures:protected] => Array
(
)
[_new:BaseObject:private] =>
[_deleted:BaseObject:private] =>
[modifiedColumns:protected] => Array
(
)
)
[63] => Category Object
(
[languages:protected] =>
[bok_resources:protected] =>
[bok_topics:protected] =>
[bok_keywords:protected] =>
[id:protected] => 63
[type:protected] => category
[parent:protected] => 2
[label:protected] => Reinforcing Ironworker
[alreadyInSave:protected] =>
[alreadyInValidation:protected] =>
[validationFailures:protected] => Array
(
)
[_new:BaseObject:private] =>
[_deleted:BaseObject:private] =>
[modifiedColumns:protected] => Array
(
)
)
[78] => Category Object
(
[languages:protected] =>
[bok_resources:protected] =>
[bok_topics:protected] =>
[bok_keywords:protected] =>
[id:protected] => 78
[type:protected] => category
[parent:protected] => 2
[label:protected] => Roofer/Waterproofer
[alreadyInSave:protected] =>
[alreadyInValidation:protected] =>
[validationFailures:protected] => Array
(
)
[_new:BaseObject:private] =>
[_deleted:BaseObject:private] =>
[modifiedColumns:protected] => Array
(
)
)
[79] => Category Object
(
[languages:protected] =>
[bok_resources:protected] =>
[bok_topics:protected] =>
[bok_keywords:protected] =>
[id:protected] => 79
[type:protected] => category
[parent:protected] => 2
[label:protected] => Scaffold Erector
[alreadyInSave:protected] =>
[alreadyInValidation:protected] =>
[validationFailures:protected] => Array
(
)
[_new:BaseObject:private] =>
[_deleted:BaseObject:private] =>
[modifiedColumns:protected] => Array
(
)
)
[80] => Category Object
(
[languages:protected] =>
[bok_resources:protected] =>
[bok_topics:protected] =>
[bok_keywords:protected] =>
[id:protected] => 80
[type:protected] => category
[parent:protected] => 2
[label:protected] => Sheetmetal Worker
[alreadyInSave:protected] =>
[alreadyInValidation:protected] =>
[validationFailures:protected] => Array
(
)
[_new:BaseObject:private] =>
[_deleted:BaseObject:private] =>
[modifiedColumns:protected] => Array
(
)
)
[62] => Category Object
(
[languages:protected] =>
[bok_resources:protected] =>
[bok_topics:protected] =>
[bok_keywords:protected] =>
[id:protected] => 62
[type:protected] => category
[parent:protected] => 2
[label:protected] => Structural Ironworker
[alreadyInSave:protected] =>
[alreadyInValidation:protected] =>
[validationFailures:protected] => Array
(
)
[_new:BaseObject:private] =>
[_deleted:BaseObject:private] =>
[modifiedColumns:protected] => Array
(
)
)
[87] => Category Object
(
[languages:protected] =>
[bok_resources:protected] =>
[bok_topics:protected] =>
[bok_keywords:protected] =>
[id:protected] => 87
[type:protected] => category
[parent:protected] => 3
[label:protected] => Commercial & Institutional
[alreadyInSave:protected] =>
[alreadyInValidation:protected] =>
[validationFailures:protected] => Array
(
)
[_new:BaseObject:private] =>
[_deleted:BaseObject:private] =>
[modifiedColumns:protected] => Array
(
)
)
[97] => Category Object
(
[languages:protected] =>
[bok_resources:protected] =>
[bok_topics:protected] =>
[bok_keywords:protected] =>
[id:protected] => 97
[type:protected] => category
[parent:protected] => 5
[label:protected] => Images
[alreadyInSave:protected] =>
[alreadyInValidation:protected] =>
[validationFailures:protected] => Array
(
)
[_new:BaseObject:private] =>
[_deleted:BaseObject:private] =>
[modifiedColumns:protected] => Array
(
)
)
[56] => Category Object
(
[languages:protected] =>
[bok_resources:protected] =>
[bok_topics:protected] =>
[bok_keywords:protected] =>
[id:protected] => 56
[type:protected] => category
[parent:protected] => 2
[label:protected] => Elevator Constructor
[alreadyInSave:protected] =>
[alreadyInValidation:protected] =>
[validationFailures:protected] => Array
(
)
[_new:BaseObject:private] =>
[_deleted:BaseObject:private] =>
[modifiedColumns:protected] => Array
(
)
)
[64] => Category Object
(
[languages:protected] =>
[bok_resources:protected] =>
[bok_topics:protected] =>
[bok_keywords:protected] =>
[id:protected] => 64
[type:protected] => category
[parent:protected] => 2
[label:protected] => Laborer
[alreadyInSave:protected] =>
[alreadyInValidation:protected] =>
[validationFailures:protected] => Array
(
)
[_new:BaseObject:private] =>
[_deleted:BaseObject:private] =>
[modifiedColumns:protected] => Array
(
)
)
[74] => Category Object
(
[languages:protected] =>
[bok_resources:protected] =>
[bok_topics:protected] =>
[bok_keywords:protected] =>
[id:protected] => 74
[type:protected] => category
[parent:protected] => 2
[label:protected] => Pile Driver
[alreadyInSave:protected] =>
[alreadyInValidation:protected] =>
[validationFailures:protected] => Array
(
)
[_new:BaseObject:private] =>
[_deleted:BaseObject:private] =>
[modifiedColumns:protected] => Array
(
)
)
)
[categories_initialized:protected] => 1
[mapped_items:protected] =>
[content:protected] =>
[files:protected] =>
[language:protected] => Language Object
(
[id:protected] => 1
[code:protected] => en
[name:protected] => English
[alreadyInSave:protected] =>
[alreadyInValidation:protected] =>
[validationFailures:protected] => Array
(
)
[_new:BaseObject:private] =>
[_deleted:BaseObject:private] =>
[modifiedColumns:protected] => Array
(
)
)
[old_record:protected] =>
[id:protected] => 3994
[old_id:protected] =>
[elcosh_id:protected] => i002689
[type:protected] => image
[display_type:protected] => Image
[user_id:protected] => 0
[language_id:protected] => 1
[tagging_id:protected] => Bruce Lippy
[priority_id:protected] => 1
[title:protected] => Scaffolding at top of large column
[total_pages:protected] => 0
[billed_pages:protected] => 0
[publication_number:protected] =>
[part_of:protected] =>
[keywords:protected] => Guardrail, railing, fall prevention, falls
[comments:protected] =>
[summary:protected] => This shot shows innovative guarding around the top of a large concrete column in the base of a high rise structure going up.
[transition_comments:protected] =>
[external_link:protected] =>
[consol_link:protected] => http://www.cpwrconstructionsolutions.org/masonry/solution/8/adjustable-tower-scaffold.html
[more_like_this:protected] => c1002680,i002662,d000608,d001255
[permission_given_by:protected] =>
[published:protected] => T
[billable:protected] => F
[img_name:protected] =>
[img_ext:protected] => jpg
[img_width:protected] =>
[img_height:protected] =>
[img_credit:protected] => Photo by Pam Susi
[img_practice:protected] => good
[vid_source_id:protected] =>
[vid_running_time:protected] =>
[vid_intended_audience:protected] =>
[vid_acquisition_info:protected] =>
[vid_cost:protected] =>
[vid_producer:protected] =>
[vid_filename:protected] =>
[vid_filename_downloadable:protected] =>
[date_summary:protected] => January 2016
[date_permission_requested:protected] =>
[date_permission_received:protected] =>
[date_review_needed:protected] =>
[date_received:protected] => 02/01/16
[date_completed:protected] => 02/01/16
[date_billed:protected] =>
[date_modified:protected] => 02/01/16
[collBokExports:protected] =>
[lastBokExportCriteria:BaseElcoshItem:private] =>
[alreadyInSave:protected] =>
[alreadyInValidation:protected] =>
[validationFailures:protected] => Array
(
)
[_new:BaseObject:private] =>
[_deleted:BaseObject:private] =>
[modifiedColumns:protected] => Array
(
)
)
)
[5] => Search_Result Object
(
[title] => Construction bracing
[image] => /record/images/3995-p.jpg
[blurb] => This shows structural support that prevents collapses during construction....
[category] => Array
(
[0] => 12
[1] => 15
[2] => 21
[3] => 49
[4] => 51
[5] => 55
[6] => 56
[7] => 60
[8] => 64
[9] => 68
[10] => 74
[11] => 63
[12] => 78
[13] => 79
[14] => 80
[15] => 62
[16] => 87
[17] => 90
[18] => 97
)
[labels] => Array
(
[0] => Crushed/Struck By
[1] => Work Environment
[2] => Hazards
[3] => Falls
[6] => Scaffolds
[9] => Carpenter
[10] => Trades
[11] => Cement Mason
[13] => Electrical Worker
[15] => Elevator Constructor
[17] => HVAC
[19] => Laborer
[21] => Maintenance Worker
[23] => Pile Driver
[25] => Reinforcing Ironworker
[27] => Roofer/Waterproofer
[29] => Scaffold Erector
[31] => Sheetmetal Worker
[33] => Structural Ironworker
[35] => Commercial & Institutional
[36] => Jobsites
[37] => Industrial
[39] => Images
[40] => Media
[41] => Media & Documents
)
[type] => Images
[sub_category] =>
[url] => /image/3995/i002690/Construction%2Bbracing.html
[item:protected] => ImageRecord Object
(
[records:protected] => Array
(
)
[recordId:protected] =>
[searchWordClass:protected] =>
[searchWordPeerClass:protected] =>
[bok_record:protected] =>
[authors:protected] =>
[organizations:protected] =>
[collections:protected] =>
[categories:protected] => Array
(
[12] => Category Object
(
[languages:protected] =>
[bok_resources:protected] =>
[bok_topics:protected] =>
[bok_keywords:protected] =>
[id:protected] => 12
[type:protected] => category
[parent:protected] => 7
[label:protected] => Crushed/Struck By
[alreadyInSave:protected] =>
[alreadyInValidation:protected] =>
[validationFailures:protected] => Array
(
)
[_new:BaseObject:private] =>
[_deleted:BaseObject:private] =>
[modifiedColumns:protected] => Array
(
)
)
[15] => Category Object
(
[languages:protected] =>
[bok_resources:protected] =>
[bok_topics:protected] =>
[bok_keywords:protected] =>
[id:protected] => 15
[type:protected] => category
[parent:protected] => 7
[label:protected] => Falls
[alreadyInSave:protected] =>
[alreadyInValidation:protected] =>
[validationFailures:protected] => Array
(
)
[_new:BaseObject:private] =>
[_deleted:BaseObject:private] =>
[modifiedColumns:protected] => Array
(
)
)
[21] => Category Object
(
[languages:protected] =>
[bok_resources:protected] =>
[bok_topics:protected] =>
[bok_keywords:protected] =>
[id:protected] => 21
[type:protected] => category
[parent:protected] => 7
[label:protected] => Scaffolds
[alreadyInSave:protected] =>
[alreadyInValidation:protected] =>
[validationFailures:protected] => Array
(
)
[_new:BaseObject:private] =>
[_deleted:BaseObject:private] =>
[modifiedColumns:protected] => Array
(
)
)
[49] => Category Object
(
[languages:protected] =>
[bok_resources:protected] =>
[bok_topics:protected] =>
[bok_keywords:protected] =>
[id:protected] => 49
[type:protected] => category
[parent:protected] => 2
[label:protected] => Carpenter
[alreadyInSave:protected] =>
[alreadyInValidation:protected] =>
[validationFailures:protected] => Array
(
)
[_new:BaseObject:private] =>
[_deleted:BaseObject:private] =>
[modifiedColumns:protected] => Array
(
)
)
[51] => Category Object
(
[languages:protected] =>
[bok_resources:protected] =>
[bok_topics:protected] =>
[bok_keywords:protected] =>
[id:protected] => 51
[type:protected] => category
[parent:protected] => 2
[label:protected] => Cement Mason
[alreadyInSave:protected] =>
[alreadyInValidation:protected] =>
[validationFailures:protected] => Array
(
)
[_new:BaseObject:private] =>
[_deleted:BaseObject:private] =>
[modifiedColumns:protected] => Array
(
)
)
[55] => Category Object
(
[languages:protected] =>
[bok_resources:protected] =>
[bok_topics:protected] =>
[bok_keywords:protected] =>
[id:protected] => 55
[type:protected] => category
[parent:protected] => 2
[label:protected] => Electrical Worker
[alreadyInSave:protected] =>
[alreadyInValidation:protected] =>
[validationFailures:protected] => Array
(
)
[_new:BaseObject:private] =>
[_deleted:BaseObject:private] =>
[modifiedColumns:protected] => Array
(
)
)
[56] => Category Object
(
[languages:protected] =>
[bok_resources:protected] =>
[bok_topics:protected] =>
[bok_keywords:protected] =>
[id:protected] => 56
[type:protected] => category
[parent:protected] => 2
[label:protected] => Elevator Constructor
[alreadyInSave:protected] =>
[alreadyInValidation:protected] =>
[validationFailures:protected] => Array
(
)
[_new:BaseObject:private] =>
[_deleted:BaseObject:private] =>
[modifiedColumns:protected] => Array
(
)
)
[60] => Category Object
(
[languages:protected] =>
[bok_resources:protected] =>
[bok_topics:protected] =>
[bok_keywords:protected] =>
[id:protected] => 60
[type:protected] => category
[parent:protected] => 2
[label:protected] => HVAC
[alreadyInSave:protected] =>
[alreadyInValidation:protected] =>
[validationFailures:protected] => Array
(
)
[_new:BaseObject:private] =>
[_deleted:BaseObject:private] =>
[modifiedColumns:protected] => Array
(
)
)
[64] => Category Object
(
[languages:protected] =>
[bok_resources:protected] =>
[bok_topics:protected] =>
[bok_keywords:protected] =>
[id:protected] => 64
[type:protected] => category
[parent:protected] => 2
[label:protected] => Laborer
[alreadyInSave:protected] =>
[alreadyInValidation:protected] =>
[validationFailures:protected] => Array
(
)
[_new:BaseObject:private] =>
[_deleted:BaseObject:private] =>
[modifiedColumns:protected] => Array
(
)
)
[68] => Category Object
(
[languages:protected] =>
[bok_resources:protected] =>
[bok_topics:protected] =>
[bok_keywords:protected] =>
[id:protected] => 68
[type:protected] => category
[parent:protected] => 2
[label:protected] => Maintenance Worker
[alreadyInSave:protected] =>
[alreadyInValidation:protected] =>
[validationFailures:protected] => Array
(
)
[_new:BaseObject:private] =>
[_deleted:BaseObject:private] =>
[modifiedColumns:protected] => Array
(
)
)
[74] => Category Object
(
[languages:protected] =>
[bok_resources:protected] =>
[bok_topics:protected] =>
[bok_keywords:protected] =>
[id:protected] => 74
[type:protected] => category
[parent:protected] => 2
[label:protected] => Pile Driver
[alreadyInSave:protected] =>
[alreadyInValidation:protected] =>
[validationFailures:protected] => Array
(
)
[_new:BaseObject:private] =>
[_deleted:BaseObject:private] =>
[modifiedColumns:protected] => Array
(
)
)
[63] => Category Object
(
[languages:protected] =>
[bok_resources:protected] =>
[bok_topics:protected] =>
[bok_keywords:protected] =>
[id:protected] => 63
[type:protected] => category
[parent:protected] => 2
[label:protected] => Reinforcing Ironworker
[alreadyInSave:protected] =>
[alreadyInValidation:protected] =>
[validationFailures:protected] => Array
(
)
[_new:BaseObject:private] =>
[_deleted:BaseObject:private] =>
[modifiedColumns:protected] => Array
(
)
)
[78] => Category Object
(
[languages:protected] =>
[bok_resources:protected] =>
[bok_topics:protected] =>
[bok_keywords:protected] =>
[id:protected] => 78
[type:protected] => category
[parent:protected] => 2
[label:protected] => Roofer/Waterproofer
[alreadyInSave:protected] =>
[alreadyInValidation:protected] =>
[validationFailures:protected] => Array
(
)
[_new:BaseObject:private] =>
[_deleted:BaseObject:private] =>
[modifiedColumns:protected] => Array
(
)
)
[79] => Category Object
(
[languages:protected] =>
[bok_resources:protected] =>
[bok_topics:protected] =>
[bok_keywords:protected] =>
[id:protected] => 79
[type:protected] => category
[parent:protected] => 2
[label:protected] => Scaffold Erector
[alreadyInSave:protected] =>
[alreadyInValidation:protected] =>
[validationFailures:protected] => Array
(
)
[_new:BaseObject:private] =>
[_deleted:BaseObject:private] =>
[modifiedColumns:protected] => Array
(
)
)
[80] => Category Object
(
[languages:protected] =>
[bok_resources:protected] =>
[bok_topics:protected] =>
[bok_keywords:protected] =>
[id:protected] => 80
[type:protected] => category
[parent:protected] => 2
[label:protected] => Sheetmetal Worker
[alreadyInSave:protected] =>
[alreadyInValidation:protected] =>
[validationFailures:protected] => Array
(
)
[_new:BaseObject:private] =>
[_deleted:BaseObject:private] =>
[modifiedColumns:protected] => Array
(
)
)
[62] => Category Object
(
[languages:protected] =>
[bok_resources:protected] =>
[bok_topics:protected] =>
[bok_keywords:protected] =>
[id:protected] => 62
[type:protected] => category
[parent:protected] => 2
[label:protected] => Structural Ironworker
[alreadyInSave:protected] =>
[alreadyInValidation:protected] =>
[validationFailures:protected] => Array
(
)
[_new:BaseObject:private] =>
[_deleted:BaseObject:private] =>
[modifiedColumns:protected] => Array
(
)
)
[87] => Category Object
(
[languages:protected] =>
[bok_resources:protected] =>
[bok_topics:protected] =>
[bok_keywords:protected] =>
[id:protected] => 87
[type:protected] => category
[parent:protected] => 3
[label:protected] => Commercial & Institutional
[alreadyInSave:protected] =>
[alreadyInValidation:protected] =>
[validationFailures:protected] => Array
(
)
[_new:BaseObject:private] =>
[_deleted:BaseObject:private] =>
[modifiedColumns:protected] => Array
(
)
)
[90] => Category Object
(
[languages:protected] =>
[bok_resources:protected] =>
[bok_topics:protected] =>
[bok_keywords:protected] =>
[id:protected] => 90
[type:protected] => category
[parent:protected] => 3
[label:protected] => Industrial
[alreadyInSave:protected] =>
[alreadyInValidation:protected] =>
[validationFailures:protected] => Array
(
)
[_new:BaseObject:private] =>
[_deleted:BaseObject:private] =>
[modifiedColumns:protected] => Array
(
)
)
[97] => Category Object
(
[languages:protected] =>
[bok_resources:protected] =>
[bok_topics:protected] =>
[bok_keywords:protected] =>
[id:protected] => 97
[type:protected] => category
[parent:protected] => 5
[label:protected] => Images
[alreadyInSave:protected] =>
[alreadyInValidation:protected] =>
[validationFailures:protected] => Array
(
)
[_new:BaseObject:private] =>
[_deleted:BaseObject:private] =>
[modifiedColumns:protected] => Array
(
)
)
)
[categories_initialized:protected] => 1
[mapped_items:protected] =>
[content:protected] =>
[files:protected] =>
[language:protected] => Language Object
(
[id:protected] => 1
[code:protected] => en
[name:protected] => English
[alreadyInSave:protected] =>
[alreadyInValidation:protected] =>
[validationFailures:protected] => Array
(
)
[_new:BaseObject:private] =>
[_deleted:BaseObject:private] =>
[modifiedColumns:protected] => Array
(
)
)
[old_record:protected] =>
[id:protected] => 3995
[old_id:protected] =>
[elcosh_id:protected] => i002690
[type:protected] => image
[display_type:protected] => Image
[user_id:protected] => 0
[language_id:protected] => 1
[tagging_id:protected] => Bruce Lippy
[priority_id:protected] => 1
[title:protected] => Construction bracing
[total_pages:protected] => 0
[billed_pages:protected] => 0
[publication_number:protected] =>
[part_of:protected] =>
[keywords:protected] => Bracing, support, scaffold
[comments:protected] =>
[summary:protected] => This shows structural support that prevents collapses during construction.
[transition_comments:protected] =>
[external_link:protected] =>
[consol_link:protected] => http://www.cpwrconstructionsolutions.org/masonry/solution/8/adjustable-tower-scaffold.html
[more_like_this:protected] => i002660
[permission_given_by:protected] =>
[published:protected] => T
[billable:protected] => F
[img_name:protected] =>
[img_ext:protected] => jpg
[img_width:protected] =>
[img_height:protected] =>
[img_credit:protected] => Photo by Pam Susi
[img_practice:protected] => good
[vid_source_id:protected] =>
[vid_running_time:protected] =>
[vid_intended_audience:protected] =>
[vid_acquisition_info:protected] =>
[vid_cost:protected] =>
[vid_producer:protected] =>
[vid_filename:protected] =>
[vid_filename_downloadable:protected] =>
[date_summary:protected] => January 2016
[date_permission_requested:protected] =>
[date_permission_received:protected] =>
[date_review_needed:protected] =>
[date_received:protected] => 02/01/16
[date_completed:protected] => 02/01/16
[date_billed:protected] =>
[date_modified:protected] => 02/01/16
[collBokExports:protected] =>
[lastBokExportCriteria:BaseElcoshItem:private] =>
[alreadyInSave:protected] =>
[alreadyInValidation:protected] =>
[validationFailures:protected] => Array
(
)
[_new:BaseObject:private] =>
[_deleted:BaseObject:private] =>
[modifiedColumns:protected] => Array
(
)
)
)
)
[preview_mode] =>
[description] => Toolbox talks have been the main tool for communicating safety information on construction jobs for decades.
Unfortunately, there has been little research on what makes for effective toolbox talks. The IUOE National
Training Fund worked with OSHA and NIOSH to make sure their series of 24 Focus Four toolbox talks were based on the best recommendations for effective design. These toolbox talks accompany an entire package of training materials, but can be used alone. This guide points out the key features of these toolbox talks and how best to deliver them.
[keywords] => toolbox talks, tailgate talks
[related_items] => Array
(
[Toolbox Talks] => Array
(
[0] => DocumentRecord Object
(
[records:protected] => Array
(
)
[recordId:protected] =>
[searchWordClass:protected] =>
[searchWordPeerClass:protected] =>
[bok_record:protected] =>
[authors:protected] =>
[organizations:protected] =>
[collections:protected] =>
[categories:protected] =>
[categories_initialized:protected] =>
[mapped_items:protected] =>
[content:protected] =>
[files:protected] =>
[language:protected] => Language Object
(
[id:protected] => 1
[code:protected] => en
[name:protected] => English
[alreadyInSave:protected] =>
[alreadyInValidation:protected] =>
[validationFailures:protected] => Array
(
)
[_new:BaseObject:private] =>
[_deleted:BaseObject:private] =>
[modifiedColumns:protected] => Array
(
)
)
[old_record:protected] =>
[id:protected] => 1605
[old_id:protected] => 1262
[elcosh_id:protected] => d001137
[type:protected] => document
[display_type:protected] => HTML w/ PDF
[user_id:protected] =>
[language_id:protected] => 1
[tagging_id:protected] => Garber
[priority_id:protected] => 1
[title:protected] => Focus Four Toolbox Talks, Module 1 – Falls, Talk #2 – Falls from debris piles?
[total_pages:protected] => 1
[billed_pages:protected] => 1
[publication_number:protected] =>
[part_of:protected] =>
[keywords:protected] => disaster response, hazard clean-up, uneven surface, disaster site, disaster clean-up
[comments:protected] =>
[summary:protected] => A toolbox talk on preventing falls from debris piles. Includes questions to ask, an incident to discuss with images, and a place to record questions the trainer would like to ask about the incident. Part of a collection. Click on the 'collection' button to access the other items.
[transition_comments:protected] =>
[external_link:protected] =>
[consol_link:protected] => http://www.cpwrconstructionsolutions.org/roofing/hazard/1463/install-asphalt-roofs-fall-from-heights.html
[more_like_this:protected] => a000081,d000478,d000530
[permission_given_by:protected] =>
[published:protected] => T
[billable:protected] => F
[img_name:protected] =>
[img_ext:protected] =>
[img_width:protected] =>
[img_height:protected] =>
[img_credit:protected] =>
[img_practice:protected] =>
[vid_source_id:protected] =>
[vid_running_time:protected] =>
[vid_intended_audience:protected] =>
[vid_acquisition_info:protected] =>
[vid_cost:protected] =>
[vid_producer:protected] =>
[vid_filename:protected] =>
[vid_filename_downloadable:protected] =>
[date_summary:protected] =>
[date_permission_requested:protected] =>
[date_permission_received:protected] =>
[date_review_needed:protected] =>
[date_received:protected] => 02/15/12
[date_completed:protected] => 03/19/12
[date_billed:protected] =>
[date_modified:protected] => 07/10/12
[collBokExports:protected] =>
[lastBokExportCriteria:BaseElcoshItem:private] =>
[alreadyInSave:protected] =>
[alreadyInValidation:protected] =>
[validationFailures:protected] => Array
(
)
[_new:BaseObject:private] =>
[_deleted:BaseObject:private] =>
[modifiedColumns:protected] => Array
(
)
)
[1] => DocumentRecord Object
(
[records:protected] => Array
(
)
[recordId:protected] =>
[searchWordClass:protected] =>
[searchWordPeerClass:protected] =>
[bok_record:protected] =>
[authors:protected] =>
[organizations:protected] =>
[collections:protected] =>
[categories:protected] =>
[categories_initialized:protected] =>
[mapped_items:protected] =>
[content:protected] =>
[files:protected] =>
[language:protected] => Language Object
(
[id:protected] => 1
[code:protected] => en
[name:protected] => English
[alreadyInSave:protected] =>
[alreadyInValidation:protected] =>
[validationFailures:protected] => Array
(
)
[_new:BaseObject:private] =>
[_deleted:BaseObject:private] =>
[modifiedColumns:protected] => Array
(
)
)
[old_record:protected] =>
[id:protected] => 1610
[old_id:protected] => 1271
[elcosh_id:protected] => d001146
[type:protected] => document
[display_type:protected] => HTML w/ PDF
[user_id:protected] => 0
[language_id:protected] => 1
[tagging_id:protected] => Garber
[priority_id:protected] => 1
[title:protected] => Focus Four Toolbox Talks, Module 2 – Struck-by, Talk #5 – Rigging and Securing Loads
[total_pages:protected] => 1
[billed_pages:protected] => 1
[publication_number:protected] =>
[part_of:protected] =>
[keywords:protected] => rigging, lift loads, loading areas, chains
[comments:protected] =>
[summary:protected] => A toolbox talk on preventing struck-by incidents caused by not securing loads properly. Includes questions to ask, an incident to discuss with images, and a place to record questions the trainer would like to ask about the incident. Part of a collection. Click on the 'collection' button to access the other items.
[transition_comments:protected] =>
[external_link:protected] =>
[consol_link:protected] => http://www.cpwrconstructionsolutions.org/heavy_equipment/hazard/1591/move-equipment-to-from-and-between-sites-work-zone-struck-by-injuries-and-fatalities.html
[more_like_this:protected] => d000144,d000360,d000873
[permission_given_by:protected] =>
[published:protected] => T
[billable:protected] => F
[img_name:protected] =>
[img_ext:protected] =>
[img_width:protected] =>
[img_height:protected] =>
[img_credit:protected] =>
[img_practice:protected] =>
[vid_source_id:protected] =>
[vid_running_time:protected] =>
[vid_intended_audience:protected] =>
[vid_acquisition_info:protected] =>
[vid_cost:protected] =>
[vid_producer:protected] =>
[vid_filename:protected] =>
[vid_filename_downloadable:protected] =>
[date_summary:protected] =>
[date_permission_requested:protected] =>
[date_permission_received:protected] =>
[date_review_needed:protected] =>
[date_received:protected] => 02/15/12
[date_completed:protected] => 03/28/12
[date_billed:protected] =>
[date_modified:protected] => 05/12/14
[collBokExports:protected] =>
[lastBokExportCriteria:BaseElcoshItem:private] =>
[alreadyInSave:protected] =>
[alreadyInValidation:protected] =>
[validationFailures:protected] => Array
(
)
[_new:BaseObject:private] =>
[_deleted:BaseObject:private] =>
[modifiedColumns:protected] => Array
(
)
)
[2] => DocumentRecord Object
(
[records:protected] => Array
(
)
[recordId:protected] =>
[searchWordClass:protected] =>
[searchWordPeerClass:protected] =>
[bok_record:protected] =>
[authors:protected] =>
[organizations:protected] =>
[collections:protected] =>
[categories:protected] =>
[categories_initialized:protected] =>
[mapped_items:protected] =>
[content:protected] =>
[files:protected] =>
[language:protected] => Language Object
(
[id:protected] => 1
[code:protected] => en
[name:protected] => English
[alreadyInSave:protected] =>
[alreadyInValidation:protected] =>
[validationFailures:protected] => Array
(
)
[_new:BaseObject:private] =>
[_deleted:BaseObject:private] =>
[modifiedColumns:protected] => Array
(
)
)
[old_record:protected] =>
[id:protected] => 1645
[old_id:protected] => 1274
[elcosh_id:protected] => d001149
[type:protected] => document
[display_type:protected] => HTML w/ PDF
[user_id:protected] => 0
[language_id:protected] => 1
[tagging_id:protected] => Garber
[priority_id:protected] => 1
[title:protected] => Focus Four Toolbox Talks, Module 3 – Caught-in/between, Talk #2 – Trenches & Heavy Equipment
[total_pages:protected] => 1
[billed_pages:protected] => 1
[publication_number:protected] =>
[part_of:protected] =>
[keywords:protected] => back-up alarms, spotter, soil cave-in, spoil pikes, ROPs, trenching, rain
[comments:protected] =>
[summary:protected] => A toolbox talk on preventing incidents involving trenches such as trench collapse. Includes questions to ask, an incident to discuss with images, and a place to record questions the trainer would like to ask about the incident. Part of a collection. Click on the 'collection' button to access the other items.
[transition_comments:protected] =>
[external_link:protected] =>
[consol_link:protected] =>
[more_like_this:protected] => d000019,d000035,d000168
[permission_given_by:protected] =>
[published:protected] => T
[billable:protected] => F
[img_name:protected] =>
[img_ext:protected] =>
[img_width:protected] =>
[img_height:protected] =>
[img_credit:protected] =>
[img_practice:protected] =>
[vid_source_id:protected] =>
[vid_running_time:protected] =>
[vid_intended_audience:protected] =>
[vid_acquisition_info:protected] =>
[vid_cost:protected] =>
[vid_producer:protected] =>
[vid_filename:protected] =>
[vid_filename_downloadable:protected] =>
[date_summary:protected] =>
[date_permission_requested:protected] =>
[date_permission_received:protected] =>
[date_review_needed:protected] =>
[date_received:protected] => 02/15/12
[date_completed:protected] => 04/02/12
[date_billed:protected] =>
[date_modified:protected] => 05/23/23
[collBokExports:protected] =>
[lastBokExportCriteria:BaseElcoshItem:private] =>
[alreadyInSave:protected] =>
[alreadyInValidation:protected] =>
[validationFailures:protected] => Array
(
)
[_new:BaseObject:private] =>
[_deleted:BaseObject:private] =>
[modifiedColumns:protected] => Array
(
)
)
[3] => DocumentRecord Object
(
[records:protected] => Array
(
)
[recordId:protected] =>
[searchWordClass:protected] =>
[searchWordPeerClass:protected] =>
[bok_record:protected] =>
[authors:protected] =>
[organizations:protected] =>
[collections:protected] =>
[categories:protected] =>
[categories_initialized:protected] =>
[mapped_items:protected] =>
[content:protected] =>
[files:protected] =>
[language:protected] => Language Object
(
[id:protected] => 1
[code:protected] => en
[name:protected] => English
[alreadyInSave:protected] =>
[alreadyInValidation:protected] =>
[validationFailures:protected] => Array
(
)
[_new:BaseObject:private] =>
[_deleted:BaseObject:private] =>
[modifiedColumns:protected] => Array
(
)
)
[old_record:protected] =>
[id:protected] => 1654
[old_id:protected] => 1284
[elcosh_id:protected] => d001159
[type:protected] => document
[display_type:protected] => HTML w/ PDF
[user_id:protected] => 0
[language_id:protected] => 1
[tagging_id:protected] => Garber
[priority_id:protected] => 1
[title:protected] => Focus Four Toolbox Talks, Module 4 – Electrocutions, Talk #6 – Hazards on Disaster Sites
[total_pages:protected] => 1
[billed_pages:protected] => 1
[publication_number:protected] =>
[part_of:protected] =>
[keywords:protected] => powerlines, underground, utilities, generators, wet conditions, GFCIs, energized lines, disasters, emergency response
[comments:protected] =>
[summary:protected] => A toolbox talk on how to avoid electrocution on a disaster site. Includes questions to ask, an incident to discuss with images, and a place to record questions the trainer would like to ask about the incident. Part of a collection. Click on the 'collection' button to access the other items.
[transition_comments:protected] =>
[external_link:protected] =>
[consol_link:protected] => http://www.cpwrconstructionsolutions.org/electrical/hazard/1138/install-and-repair-high-voltage-lines-transformers-switches-electrical-shocks-burns-and-or-electrocution.html
[more_like_this:protected] => d000135,d000361,d000437
[permission_given_by:protected] =>
[published:protected] => T
[billable:protected] => F
[img_name:protected] =>
[img_ext:protected] =>
[img_width:protected] =>
[img_height:protected] =>
[img_credit:protected] =>
[img_practice:protected] =>
[vid_source_id:protected] =>
[vid_running_time:protected] =>
[vid_intended_audience:protected] =>
[vid_acquisition_info:protected] =>
[vid_cost:protected] =>
[vid_producer:protected] =>
[vid_filename:protected] =>
[vid_filename_downloadable:protected] =>
[date_summary:protected] =>
[date_permission_requested:protected] =>
[date_permission_received:protected] =>
[date_review_needed:protected] =>
[date_received:protected] => 02/15/12
[date_completed:protected] => 04/02/12
[date_billed:protected] =>
[date_modified:protected] => 05/23/23
[collBokExports:protected] =>
[lastBokExportCriteria:BaseElcoshItem:private] =>
[alreadyInSave:protected] =>
[alreadyInValidation:protected] =>
[validationFailures:protected] => Array
(
)
[_new:BaseObject:private] =>
[_deleted:BaseObject:private] =>
[modifiedColumns:protected] => Array
(
)
)
)
)
[collections] => Array
(
[1294] =>
[1295] =>
[1292] =>
[1293] => CollectionRecord Object
(
[collection_items:protected] =>
[records:protected] => Array
(
)
[recordId:protected] =>
[searchWordClass:protected] =>
[searchWordPeerClass:protected] =>
[bok_record:protected] =>
[authors:protected] =>
[organizations:protected] =>
[collections:protected] =>
[categories:protected] =>
[categories_initialized:protected] =>
[mapped_items:protected] =>
[content:protected] =>
[files:protected] =>
[language:protected] =>
[old_record:protected] =>
[id:protected] => 1293
[old_id:protected] =>
[elcosh_id:protected] => c000026
[type:protected] => collection
[display_type:protected] => Collection
[user_id:protected] =>
[language_id:protected] =>
[tagging_id:protected] =>
[priority_id:protected] =>
[title:protected] => Focus Four-Struck By
[total_pages:protected] =>
[billed_pages:protected] =>
[publication_number:protected] =>
[part_of:protected] =>
[keywords:protected] =>
[comments:protected] =>
[summary:protected] => The following are links to all of the items in this collection:
[transition_comments:protected] =>
[external_link:protected] =>
[consol_link:protected] =>
[more_like_this:protected] =>
[permission_given_by:protected] =>
[published:protected] => T
[billable:protected] => F
[img_name:protected] =>
[img_ext:protected] =>
[img_width:protected] =>
[img_height:protected] =>
[img_credit:protected] =>
[img_practice:protected] =>
[vid_source_id:protected] =>
[vid_running_time:protected] =>
[vid_intended_audience:protected] =>
[vid_acquisition_info:protected] =>
[vid_cost:protected] =>
[vid_producer:protected] =>
[vid_filename:protected] =>
[vid_filename_downloadable:protected] =>
[date_summary:protected] =>
[date_permission_requested:protected] =>
[date_permission_received:protected] =>
[date_review_needed:protected] =>
[date_received:protected] => 05/08/12
[date_completed:protected] => 05/08/12
[date_billed:protected] =>
[date_modified:protected] => 05/08/12
[collBokExports:protected] =>
[lastBokExportCriteria:BaseElcoshItem:private] =>
[alreadyInSave:protected] =>
[alreadyInValidation:protected] =>
[validationFailures:protected] => Array
(
)
[_new:BaseObject:private] =>
[_deleted:BaseObject:private] =>
[modifiedColumns:protected] => Array
(
)
)
)
[record] => DocumentRecord Object
(
[records:protected] => Array
(
)
[recordId:protected] =>
[searchWordClass:protected] =>
[searchWordPeerClass:protected] =>
[bok_record:protected] =>
[authors:protected] => Array
(
)
[organizations:protected] => Array
(
[256] => Organization Object
(
[id:protected] => 256
[elcosh_id:protected] => o000276
[user_id:protected] => 14
[province_id:protected] => 0
[country_id:protected] => 0
[title:protected] => IUOE National Training Fund
[address:protected] =>
[postal_code:protected] =>
[city:protected] =>
[department:protected] =>
[phone:protected] => 304-253-8674
[fax:protected] =>
[email:protected] =>
[website:protected] => http://www.iuoeiettc.org
[filename:protected] =>
[about:protected] =>
[comments:protected] =>
[logo_available:protected] => T
[no_details:protected] => F
[date_received:protected] => 2012-02-13
[date_completed:protected] => 2012-02-13
[date_billed:protected] =>
[alreadyInSave:protected] =>
[alreadyInValidation:protected] =>
[validationFailures:protected] => Array
(
)
[_new:BaseObject:private] =>
[_deleted:BaseObject:private] =>
[modifiedColumns:protected] => Array
(
)
)
)
[collections:protected] => Array
(
[1294] =>
[1295] =>
[1292] =>
[1293] => CollectionRecord Object
(
[collection_items:protected] =>
[records:protected] => Array
(
)
[recordId:protected] =>
[searchWordClass:protected] =>
[searchWordPeerClass:protected] =>
[bok_record:protected] =>
[authors:protected] =>
[organizations:protected] =>
[collections:protected] =>
[categories:protected] =>
[categories_initialized:protected] =>
[mapped_items:protected] =>
[content:protected] =>
[files:protected] =>
[language:protected] =>
[old_record:protected] =>
[id:protected] => 1293
[old_id:protected] =>
[elcosh_id:protected] => c000026
[type:protected] => collection
[display_type:protected] => Collection
[user_id:protected] =>
[language_id:protected] =>
[tagging_id:protected] =>
[priority_id:protected] =>
[title:protected] => Focus Four-Struck By
[total_pages:protected] =>
[billed_pages:protected] =>
[publication_number:protected] =>
[part_of:protected] =>
[keywords:protected] =>
[comments:protected] =>
[summary:protected] => The following are links to all of the items in this collection:
[transition_comments:protected] =>
[external_link:protected] =>
[consol_link:protected] =>
[more_like_this:protected] =>
[permission_given_by:protected] =>
[published:protected] => T
[billable:protected] => F
[img_name:protected] =>
[img_ext:protected] =>
[img_width:protected] =>
[img_height:protected] =>
[img_credit:protected] =>
[img_practice:protected] =>
[vid_source_id:protected] =>
[vid_running_time:protected] =>
[vid_intended_audience:protected] =>
[vid_acquisition_info:protected] =>
[vid_cost:protected] =>
[vid_producer:protected] =>
[vid_filename:protected] =>
[vid_filename_downloadable:protected] =>
[date_summary:protected] =>
[date_permission_requested:protected] =>
[date_permission_received:protected] =>
[date_review_needed:protected] =>
[date_received:protected] => 05/08/12
[date_completed:protected] => 05/08/12
[date_billed:protected] =>
[date_modified:protected] => 05/08/12
[collBokExports:protected] =>
[lastBokExportCriteria:BaseElcoshItem:private] =>
[alreadyInSave:protected] =>
[alreadyInValidation:protected] =>
[validationFailures:protected] => Array
(
)
[_new:BaseObject:private] =>
[_deleted:BaseObject:private] =>
[modifiedColumns:protected] => Array
(
)
)
)
[categories:protected] =>
[categories_initialized:protected] =>
[mapped_items:protected] => Array
(
[1605] => DocumentRecord Object
(
[records:protected] => Array
(
)
[recordId:protected] =>
[searchWordClass:protected] =>
[searchWordPeerClass:protected] =>
[bok_record:protected] =>
[authors:protected] =>
[organizations:protected] =>
[collections:protected] =>
[categories:protected] =>
[categories_initialized:protected] =>
[mapped_items:protected] =>
[content:protected] =>
[files:protected] =>
[language:protected] =>
[old_record:protected] =>
[id:protected] => 1605
[old_id:protected] => 1262
[elcosh_id:protected] => d001137
[type:protected] => document
[display_type:protected] => HTML w/ PDF
[user_id:protected] =>
[language_id:protected] => 1
[tagging_id:protected] => Garber
[priority_id:protected] => 1
[title:protected] => Focus Four Toolbox Talks, Module 1 – Falls, Talk #2 – Falls from debris piles?
[total_pages:protected] => 1
[billed_pages:protected] => 1
[publication_number:protected] =>
[part_of:protected] =>
[keywords:protected] => disaster response, hazard clean-up, uneven surface, disaster site, disaster clean-up
[comments:protected] =>
[summary:protected] => A toolbox talk on preventing falls from debris piles. Includes questions to ask, an incident to discuss with images, and a place to record questions the trainer would like to ask about the incident. Part of a collection. Click on the 'collection' button to access the other items.
[transition_comments:protected] =>
[external_link:protected] =>
[consol_link:protected] => http://www.cpwrconstructionsolutions.org/roofing/hazard/1463/install-asphalt-roofs-fall-from-heights.html
[more_like_this:protected] => a000081,d000478,d000530
[permission_given_by:protected] =>
[published:protected] => T
[billable:protected] => F
[img_name:protected] =>
[img_ext:protected] =>
[img_width:protected] =>
[img_height:protected] =>
[img_credit:protected] =>
[img_practice:protected] =>
[vid_source_id:protected] =>
[vid_running_time:protected] =>
[vid_intended_audience:protected] =>
[vid_acquisition_info:protected] =>
[vid_cost:protected] =>
[vid_producer:protected] =>
[vid_filename:protected] =>
[vid_filename_downloadable:protected] =>
[date_summary:protected] =>
[date_permission_requested:protected] =>
[date_permission_received:protected] =>
[date_review_needed:protected] =>
[date_received:protected] => 02/15/12
[date_completed:protected] => 03/19/12
[date_billed:protected] =>
[date_modified:protected] => 07/10/12
[collBokExports:protected] =>
[lastBokExportCriteria:BaseElcoshItem:private] =>
[alreadyInSave:protected] =>
[alreadyInValidation:protected] =>
[validationFailures:protected] => Array
(
)
[_new:BaseObject:private] =>
[_deleted:BaseObject:private] =>
[modifiedColumns:protected] => Array
(
)
)
[1610] => DocumentRecord Object
(
[records:protected] => Array
(
)
[recordId:protected] =>
[searchWordClass:protected] =>
[searchWordPeerClass:protected] =>
[bok_record:protected] =>
[authors:protected] =>
[organizations:protected] =>
[collections:protected] =>
[categories:protected] =>
[categories_initialized:protected] =>
[mapped_items:protected] =>
[content:protected] =>
[files:protected] =>
[language:protected] =>
[old_record:protected] =>
[id:protected] => 1610
[old_id:protected] => 1271
[elcosh_id:protected] => d001146
[type:protected] => document
[display_type:protected] => HTML w/ PDF
[user_id:protected] => 0
[language_id:protected] => 1
[tagging_id:protected] => Garber
[priority_id:protected] => 1
[title:protected] => Focus Four Toolbox Talks, Module 2 – Struck-by, Talk #5 – Rigging and Securing Loads
[total_pages:protected] => 1
[billed_pages:protected] => 1
[publication_number:protected] =>
[part_of:protected] =>
[keywords:protected] => rigging, lift loads, loading areas, chains
[comments:protected] =>
[summary:protected] => A toolbox talk on preventing struck-by incidents caused by not securing loads properly. Includes questions to ask, an incident to discuss with images, and a place to record questions the trainer would like to ask about the incident. Part of a collection. Click on the 'collection' button to access the other items.
[transition_comments:protected] =>
[external_link:protected] =>
[consol_link:protected] => http://www.cpwrconstructionsolutions.org/heavy_equipment/hazard/1591/move-equipment-to-from-and-between-sites-work-zone-struck-by-injuries-and-fatalities.html
[more_like_this:protected] => d000144,d000360,d000873
[permission_given_by:protected] =>
[published:protected] => T
[billable:protected] => F
[img_name:protected] =>
[img_ext:protected] =>
[img_width:protected] =>
[img_height:protected] =>
[img_credit:protected] =>
[img_practice:protected] =>
[vid_source_id:protected] =>
[vid_running_time:protected] =>
[vid_intended_audience:protected] =>
[vid_acquisition_info:protected] =>
[vid_cost:protected] =>
[vid_producer:protected] =>
[vid_filename:protected] =>
[vid_filename_downloadable:protected] =>
[date_summary:protected] =>
[date_permission_requested:protected] =>
[date_permission_received:protected] =>
[date_review_needed:protected] =>
[date_received:protected] => 02/15/12
[date_completed:protected] => 03/28/12
[date_billed:protected] =>
[date_modified:protected] => 05/12/14
[collBokExports:protected] =>
[lastBokExportCriteria:BaseElcoshItem:private] =>
[alreadyInSave:protected] =>
[alreadyInValidation:protected] =>
[validationFailures:protected] => Array
(
)
[_new:BaseObject:private] =>
[_deleted:BaseObject:private] =>
[modifiedColumns:protected] => Array
(
)
)
[1645] => DocumentRecord Object
(
[records:protected] => Array
(
)
[recordId:protected] =>
[searchWordClass:protected] =>
[searchWordPeerClass:protected] =>
[bok_record:protected] =>
[authors:protected] =>
[organizations:protected] =>
[collections:protected] =>
[categories:protected] =>
[categories_initialized:protected] =>
[mapped_items:protected] =>
[content:protected] =>
[files:protected] =>
[language:protected] =>
[old_record:protected] =>
[id:protected] => 1645
[old_id:protected] => 1274
[elcosh_id:protected] => d001149
[type:protected] => document
[display_type:protected] => HTML w/ PDF
[user_id:protected] => 0
[language_id:protected] => 1
[tagging_id:protected] => Garber
[priority_id:protected] => 1
[title:protected] => Focus Four Toolbox Talks, Module 3 – Caught-in/between, Talk #2 – Trenches & Heavy Equipment
[total_pages:protected] => 1
[billed_pages:protected] => 1
[publication_number:protected] =>
[part_of:protected] =>
[keywords:protected] => back-up alarms, spotter, soil cave-in, spoil pikes, ROPs, trenching, rain
[comments:protected] =>
[summary:protected] => A toolbox talk on preventing incidents involving trenches such as trench collapse. Includes questions to ask, an incident to discuss with images, and a place to record questions the trainer would like to ask about the incident. Part of a collection. Click on the 'collection' button to access the other items.
[transition_comments:protected] =>
[external_link:protected] =>
[consol_link:protected] =>
[more_like_this:protected] => d000019,d000035,d000168
[permission_given_by:protected] =>
[published:protected] => T
[billable:protected] => F
[img_name:protected] =>
[img_ext:protected] =>
[img_width:protected] =>
[img_height:protected] =>
[img_credit:protected] =>
[img_practice:protected] =>
[vid_source_id:protected] =>
[vid_running_time:protected] =>
[vid_intended_audience:protected] =>
[vid_acquisition_info:protected] =>
[vid_cost:protected] =>
[vid_producer:protected] =>
[vid_filename:protected] =>
[vid_filename_downloadable:protected] =>
[date_summary:protected] =>
[date_permission_requested:protected] =>
[date_permission_received:protected] =>
[date_review_needed:protected] =>
[date_received:protected] => 02/15/12
[date_completed:protected] => 04/02/12
[date_billed:protected] =>
[date_modified:protected] => 05/23/23
[collBokExports:protected] =>
[lastBokExportCriteria:BaseElcoshItem:private] =>
[alreadyInSave:protected] =>
[alreadyInValidation:protected] =>
[validationFailures:protected] => Array
(
)
[_new:BaseObject:private] =>
[_deleted:BaseObject:private] =>
[modifiedColumns:protected] => Array
(
)
)
[1654] => DocumentRecord Object
(
[records:protected] => Array
(
)
[recordId:protected] =>
[searchWordClass:protected] =>
[searchWordPeerClass:protected] =>
[bok_record:protected] =>
[authors:protected] =>
[organizations:protected] =>
[collections:protected] =>
[categories:protected] =>
[categories_initialized:protected] =>
[mapped_items:protected] =>
[content:protected] =>
[files:protected] =>
[language:protected] =>
[old_record:protected] =>
[id:protected] => 1654
[old_id:protected] => 1284
[elcosh_id:protected] => d001159
[type:protected] => document
[display_type:protected] => HTML w/ PDF
[user_id:protected] => 0
[language_id:protected] => 1
[tagging_id:protected] => Garber
[priority_id:protected] => 1
[title:protected] => Focus Four Toolbox Talks, Module 4 – Electrocutions, Talk #6 – Hazards on Disaster Sites
[total_pages:protected] => 1
[billed_pages:protected] => 1
[publication_number:protected] =>
[part_of:protected] =>
[keywords:protected] => powerlines, underground, utilities, generators, wet conditions, GFCIs, energized lines, disasters, emergency response
[comments:protected] =>
[summary:protected] => A toolbox talk on how to avoid electrocution on a disaster site. Includes questions to ask, an incident to discuss with images, and a place to record questions the trainer would like to ask about the incident. Part of a collection. Click on the 'collection' button to access the other items.
[transition_comments:protected] =>
[external_link:protected] =>
[consol_link:protected] => http://www.cpwrconstructionsolutions.org/electrical/hazard/1138/install-and-repair-high-voltage-lines-transformers-switches-electrical-shocks-burns-and-or-electrocution.html
[more_like_this:protected] => d000135,d000361,d000437
[permission_given_by:protected] =>
[published:protected] => T
[billable:protected] => F
[img_name:protected] =>
[img_ext:protected] =>
[img_width:protected] =>
[img_height:protected] =>
[img_credit:protected] =>
[img_practice:protected] =>
[vid_source_id:protected] =>
[vid_running_time:protected] =>
[vid_intended_audience:protected] =>
[vid_acquisition_info:protected] =>
[vid_cost:protected] =>
[vid_producer:protected] =>
[vid_filename:protected] =>
[vid_filename_downloadable:protected] =>
[date_summary:protected] =>
[date_permission_requested:protected] =>
[date_permission_received:protected] =>
[date_review_needed:protected] =>
[date_received:protected] => 02/15/12
[date_completed:protected] => 04/02/12
[date_billed:protected] =>
[date_modified:protected] => 05/23/23
[collBokExports:protected] =>
[lastBokExportCriteria:BaseElcoshItem:private] =>
[alreadyInSave:protected] =>
[alreadyInValidation:protected] =>
[validationFailures:protected] => Array
(
)
[_new:BaseObject:private] =>
[_deleted:BaseObject:private] =>
[modifiedColumns:protected] => Array
(
)
)
)
[content:protected] =>
[files:protected] => Array
(
[9400] => File Object
(
[id:protected] => 9400
[filename:protected] => 1.jpg
[downloadable:protected] => F
[timestamp:protected] => 2014-05-08 15:05:37
[alreadyInSave:protected] =>
[alreadyInValidation:protected] =>
[validationFailures:protected] => Array
(
)
[_new:BaseObject:private] =>
[_deleted:BaseObject:private] =>
[modifiedColumns:protected] => Array
(
)
)
[9401] => File Object
(
[id:protected] => 9401
[filename:protected] => d001298.pdf
[downloadable:protected] => T
[timestamp:protected] => 2014-05-08 15:05:37
[alreadyInSave:protected] =>
[alreadyInValidation:protected] =>
[validationFailures:protected] => Array
(
)
[_new:BaseObject:private] =>
[_deleted:BaseObject:private] =>
[modifiedColumns:protected] => Array
(
)
)
)
[language:protected] => Language Object
(
[id:protected] => 1
[code:protected] => en
[name:protected] => English
[alreadyInSave:protected] =>
[alreadyInValidation:protected] =>
[validationFailures:protected] => Array
(
)
[_new:BaseObject:private] =>
[_deleted:BaseObject:private] =>
[modifiedColumns:protected] => Array
(
)
)
[old_record:protected] =>
[id:protected] => 3827
[old_id:protected] =>
[elcosh_id:protected] => d001298
[type:protected] => document
[display_type:protected] => HTML w/ PDF
[user_id:protected] => 23
[language_id:protected] => 1
[tagging_id:protected] => Bruce Lippy
[priority_id:protected] => 1
[title:protected] => Getting the most out of the IUOE Toolbox Talks
[total_pages:protected] => 2
[billed_pages:protected] => 2
[publication_number:protected] =>
[part_of:protected] =>
[keywords:protected] => toolbox talks, tailgate talks
[comments:protected] =>
[summary:protected] => Toolbox talks have been the main tool for communicating safety information on construction jobs for decades.
Unfortunately, there has been little research on what makes for effective toolbox talks. The IUOE National
Training Fund worked with OSHA and NIOSH to make sure their series of 24 Focus Four toolbox talks were based on the best recommendations for effective design. These toolbox talks accompany an entire package of training materials, but can be used alone. This guide points out the key features of these toolbox talks and how best to deliver them.
[transition_comments:protected] =>
[external_link:protected] =>
[consol_link:protected] =>
[more_like_this:protected] => d001137,d001146,d001149,d001159
[permission_given_by:protected] => IUOE National Hazmat Program
[published:protected] => T
[billable:protected] => F
[img_name:protected] =>
[img_ext:protected] => png
[img_width:protected] =>
[img_height:protected] =>
[img_credit:protected] =>
[img_practice:protected] =>
[vid_source_id:protected] =>
[vid_running_time:protected] =>
[vid_intended_audience:protected] =>
[vid_acquisition_info:protected] =>
[vid_cost:protected] =>
[vid_producer:protected] =>
[vid_filename:protected] =>
[vid_filename_downloadable:protected] =>
[date_summary:protected] => 2007
[date_permission_requested:protected] =>
[date_permission_received:protected] =>
[date_review_needed:protected] =>
[date_received:protected] => 05/08/14
[date_completed:protected] => 05/08/14
[date_billed:protected] =>
[date_modified:protected] => 05/08/14
[collBokExports:protected] =>
[lastBokExportCriteria:BaseElcoshItem:private] =>
[alreadyInSave:protected] =>
[alreadyInValidation:protected] =>
[validationFailures:protected] => Array
(
)
[_new:BaseObject:private] =>
[_deleted:BaseObject:private] =>
[modifiedColumns:protected] => Array
(
)
)
[show_text] =>
[document_content] => ElcoshItemDocumentContent Object
(
[id:protected] => 2896
[item_id:protected] => 3827
[type:protected] => main
[title:protected] =>
[content:protected] =>
Why were these talks developed?
Toolbox talks have been the main tool for communicating safety information on construction jobs for decades. Unfortunately, there has been almost no research on what makes for effective toolbox talks. The IUOE National Training Fund has worked with OSHA, the National Institute for Occupational Safety and Health and the Lippy Group, LLC to make sure these Focus Four toolbox talks are based on the latest fi ndings on the most effective design and tailored to the hazards operating engineers face daily. These toolbox talks accompany an entire package of training materials, but can be used alone. The way these are delivered is as important as how well they are designed.
What did NIOSH find out?
- Just handing out factsheets and toolbox talks to workers doesn’t work. Providing copies after toolbox talks doesn’t make much of an impact either.
- Using case studies (real life stories of accidents that ended in fatality or injury) in toolbox talks is effective.
- When toolbox talks containing case studies were accompanied by discussion questions to encourage group participation, they were more effective. Consequently, getting the workers to participate in the discussion about the case study is important. It’s not enough to tell the story, it is better to have the workers engage in problem solving that analyzes why the accident occurred and how it could have been prevented. Active learning is always better than passive.
How should you deliver these toolbox talks?
- Choose a topic that is related to work going on at the site.
- Hold the meeting on the job, preferably where everyone can sit and relax.
- Hold the meeting at the beginning of a shift or after a break. Folks are too tired at the end of a shift to carefully listen and they want to get home.
- Read the toolbox talk sheet on the topic prior to conducting the talk.
- Start at the top of the form and work right through to the end, which should take around 10 to 15 minutes. Guidance is provided in blue print to help you with each section.
- Use the questions provided to generate discussions. Always allow time for the crew to respond to your questions before you provide an answer. Some suggested responses are written in italics.
- Review the case study and emphasize that this was a real incident. Ask the crew for a case study before you review the one provided, however.
- Always end with a discussion of the particular worksite where you are conducting the talk. Tie the talk as closely to hazards on the site as possible and encourage the crew to constantly look for and immediately correct hazards. They should also know how to report any problems that can’t be immediately corrected.
- Provide copies to each person, if you like, but NIOSH has not found that to be particularly effective.
- Encourage workers to do similar talks on their sites and provide them with the IUOE phone number for ordering in bulk.
- Have everyone sign the back of the form to indicate they attended this session and point out it is a pledge to look out for the health and safety of everyone on the site.
What are the key features of these toolbox talks?

[content_transformed:protected] =>
Why were these talks developed?
Toolbox talks have been the main tool for communicating safety information on construction jobs for decades. Unfortunately, there has been almost no research on what makes for effective toolbox talks. The IUOE National Training Fund has worked with OSHA, the National Institute for Occupational Safety and Health and the Lippy Group, LLC to make sure these Focus Four toolbox talks are based on the latest fi ndings on the most effective design and tailored to the hazards operating engineers face daily. These toolbox talks accompany an entire package of training materials, but can be used alone. The way these are delivered is as important as how well they are designed.
What did NIOSH find out?
- Just handing out factsheets and toolbox talks to workers doesn’t work. Providing copies after toolbox talks doesn’t make much of an impact either.
- Using case studies (real life stories of accidents that ended in fatality or injury) in toolbox talks is effective.
- When toolbox talks containing case studies were accompanied by discussion questions to encourage group participation, they were more effective. Consequently, getting the workers to participate in the discussion about the case study is important. It’s not enough to tell the story, it is better to have the workers engage in problem solving that analyzes why the accident occurred and how it could have been prevented. Active learning is always better than passive.
How should you deliver these toolbox talks?
- Choose a topic that is related to work going on at the site.
- Hold the meeting on the job, preferably where everyone can sit and relax.
- Hold the meeting at the beginning of a shift or after a break. Folks are too tired at the end of a shift to carefully listen and they want to get home.
- Read the toolbox talk sheet on the topic prior to conducting the talk.
- Start at the top of the form and work right through to the end, which should take around 10 to 15 minutes. Guidance is provided in blue print to help you with each section.
- Use the questions provided to generate discussions. Always allow time for the crew to respond to your questions before you provide an answer. Some suggested responses are written in italics.
- Review the case study and emphasize that this was a real incident. Ask the crew for a case study before you review the one provided, however.
- Always end with a discussion of the particular worksite where you are conducting the talk. Tie the talk as closely to hazards on the site as possible and encourage the crew to constantly look for and immediately correct hazards. They should also know how to report any problems that can’t be immediately corrected.
- Provide copies to each person, if you like, but NIOSH has not found that to be particularly effective.
- Encourage workers to do similar talks on their sites and provide them with the IUOE phone number for ordering in bulk.
- Have everyone sign the back of the form to indicate they attended this session and point out it is a pledge to look out for the health and safety of everyone on the site.
What are the key features of these toolbox talks?
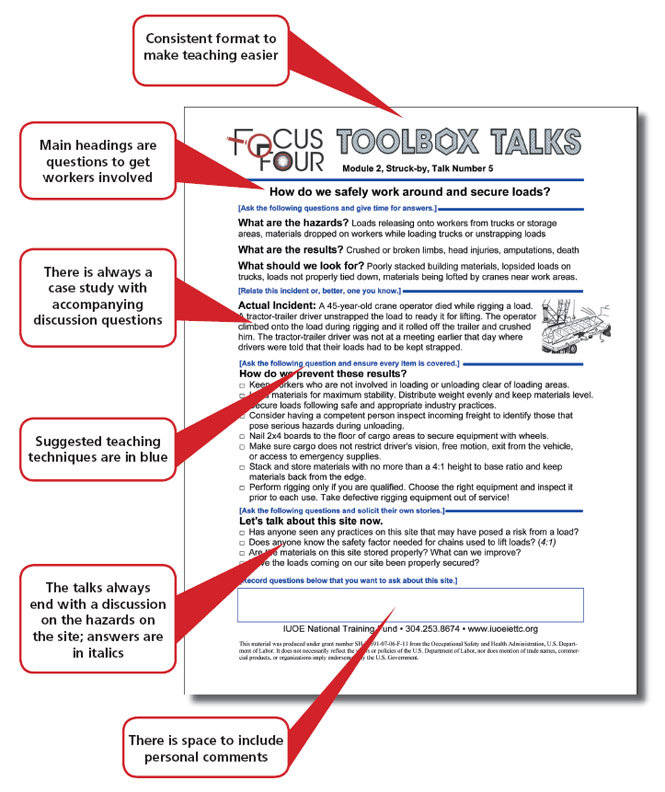
[disclaimer:protected] =>
[disclaimer_transformed:protected] =>
[alreadyInSave:protected] =>
[alreadyInValidation:protected] =>
[validationFailures:protected] => Array
(
)
[_new:BaseObject:private] =>
[_deleted:BaseObject:private] =>
[modifiedColumns:protected] => Array
(
)
)
[template] => record
)
[_globalContext:PHPTAL_Context:private] => stdClass Object
(
)
[_echoDeclarations:PHPTAL_Context:private] =>
[referer] => http://www.elcosh.org/document/3827/d001298/Getting%2Bthe%2Bmost%2Bout%2Bof%2Bthe%2BIUOE%2BToolbox%2BTalks.html
[curr_module] => Record
[styles] => Array
(
)
[javascript] => Array
(
[0] => jquery.min.js
)
[metas] => Array
(
[language] => en
[robots] => index, follow
)
[user] =>
[curr_url] => https://www.elcosh.org/index.php?module=Record&id=3827&type=document
[base_url] => https://www.elcosh.org/index.php?module=Record
[title] => eLCOSH : Getting the most out of the IUOE Toolbox Talks
[language] => en
[search_query] =>
[module] => Record
[new_records] => Array
(
[0] => Search_Result Object
(
[title] => Toolbox Talk: Fixed Ladder
[image] => /record/images/notavailable-p.png
[blurb] => The CPWR Toolbox Talk on Fixed Ladders addresses the potential risks associated with using fixed ladders. The resource includes a brief case example,...
[category] => Array
(
[0] => 15
[1] => 47
[2] => 49
[3] => 51
[4] => 53
[5] => 55
[6] => 60
[7] => 64
[8] => 73
[9] => 76
[10] => 78
[11] => 80
[12] => 86
[13] => 87
[14] => 90
[15] => 92
[16] => 93
[17] => 94
[18] => 100
)
[labels] => Array
(
[0] => Falls
[1] => Work Environment
[2] => Hazards
[3] => Bricklayer
[4] => Trades
[5] => Carpenter
[7] => Cement Mason
[9] => Concrete Polisher
[11] => Electrical Worker
[13] => HVAC
[15] => Laborer
[17] => PCC/Restoration
[19] => Plumber/Pipefitter
[21] => Roofer/Waterproofer
[23] => Sheetmetal Worker
[25] => Welder
[27] => Commercial & Institutional
[28] => Jobsites
[29] => Industrial
[31] => LEED/Green Construction
[33] => Renovations
[35] => Residential
[37] => Toolbox Talks
[38] => Documents
[39] => Media & Documents
)
[type] => Toolbox Talks
[sub_category] =>
[url] => /document/4430/d001660/Toolbox%2BTalk%253A%2BFixed%2BLadder.html
[item:protected] => DocumentRecord Object
(
[records:protected] => Array
(
)
[recordId:protected] =>
[searchWordClass:protected] =>
[searchWordPeerClass:protected] =>
[bok_record:protected] =>
[authors:protected] =>
[organizations:protected] =>
[collections:protected] =>
[categories:protected] => Array
(
[15] => Category Object
(
[languages:protected] =>
[bok_resources:protected] =>
[bok_topics:protected] =>
[bok_keywords:protected] =>
[id:protected] => 15
[type:protected] => category
[parent:protected] => 7
[label:protected] => Falls
[alreadyInSave:protected] =>
[alreadyInValidation:protected] =>
[validationFailures:protected] => Array
(
)
[_new:BaseObject:private] =>
[_deleted:BaseObject:private] =>
[modifiedColumns:protected] => Array
(
)
)
[47] => Category Object
(
[languages:protected] =>
[bok_resources:protected] =>
[bok_topics:protected] =>
[bok_keywords:protected] =>
[id:protected] => 47
[type:protected] => category
[parent:protected] => 2
[label:protected] => Bricklayer
[alreadyInSave:protected] =>
[alreadyInValidation:protected] =>
[validationFailures:protected] => Array
(
)
[_new:BaseObject:private] =>
[_deleted:BaseObject:private] =>
[modifiedColumns:protected] => Array
(
)
)
[49] => Category Object
(
[languages:protected] =>
[bok_resources:protected] =>
[bok_topics:protected] =>
[bok_keywords:protected] =>
[id:protected] => 49
[type:protected] => category
[parent:protected] => 2
[label:protected] => Carpenter
[alreadyInSave:protected] =>
[alreadyInValidation:protected] =>
[validationFailures:protected] => Array
(
)
[_new:BaseObject:private] =>
[_deleted:BaseObject:private] =>
[modifiedColumns:protected] => Array
(
)
)
[51] => Category Object
(
[languages:protected] =>
[bok_resources:protected] =>
[bok_topics:protected] =>
[bok_keywords:protected] =>
[id:protected] => 51
[type:protected] => category
[parent:protected] => 2
[label:protected] => Cement Mason
[alreadyInSave:protected] =>
[alreadyInValidation:protected] =>
[validationFailures:protected] => Array
(
)
[_new:BaseObject:private] =>
[_deleted:BaseObject:private] =>
[modifiedColumns:protected] => Array
(
)
)
[53] => Category Object
(
[languages:protected] =>
[bok_resources:protected] =>
[bok_topics:protected] =>
[bok_keywords:protected] =>
[id:protected] => 53
[type:protected] => category
[parent:protected] => 2
[label:protected] => Concrete Polisher
[alreadyInSave:protected] =>
[alreadyInValidation:protected] =>
[validationFailures:protected] => Array
(
)
[_new:BaseObject:private] =>
[_deleted:BaseObject:private] =>
[modifiedColumns:protected] => Array
(
)
)
[55] => Category Object
(
[languages:protected] =>
[bok_resources:protected] =>
[bok_topics:protected] =>
[bok_keywords:protected] =>
[id:protected] => 55
[type:protected] => category
[parent:protected] => 2
[label:protected] => Electrical Worker
[alreadyInSave:protected] =>
[alreadyInValidation:protected] =>
[validationFailures:protected] => Array
(
)
[_new:BaseObject:private] =>
[_deleted:BaseObject:private] =>
[modifiedColumns:protected] => Array
(
)
)
[60] => Category Object
(
[languages:protected] =>
[bok_resources:protected] =>
[bok_topics:protected] =>
[bok_keywords:protected] =>
[id:protected] => 60
[type:protected] => category
[parent:protected] => 2
[label:protected] => HVAC
[alreadyInSave:protected] =>
[alreadyInValidation:protected] =>
[validationFailures:protected] => Array
(
)
[_new:BaseObject:private] =>
[_deleted:BaseObject:private] =>
[modifiedColumns:protected] => Array
(
)
)
[64] => Category Object
(
[languages:protected] =>
[bok_resources:protected] =>
[bok_topics:protected] =>
[bok_keywords:protected] =>
[id:protected] => 64
[type:protected] => category
[parent:protected] => 2
[label:protected] => Laborer
[alreadyInSave:protected] =>
[alreadyInValidation:protected] =>
[validationFailures:protected] => Array
(
)
[_new:BaseObject:private] =>
[_deleted:BaseObject:private] =>
[modifiedColumns:protected] => Array
(
)
)
[73] => Category Object
(
[languages:protected] =>
[bok_resources:protected] =>
[bok_topics:protected] =>
[bok_keywords:protected] =>
[id:protected] => 73
[type:protected] => category
[parent:protected] => 2
[label:protected] => PCC/Restoration
[alreadyInSave:protected] =>
[alreadyInValidation:protected] =>
[validationFailures:protected] => Array
(
)
[_new:BaseObject:private] =>
[_deleted:BaseObject:private] =>
[modifiedColumns:protected] => Array
(
)
)
[76] => Category Object
(
[languages:protected] =>
[bok_resources:protected] =>
[bok_topics:protected] =>
[bok_keywords:protected] =>
[id:protected] => 76
[type:protected] => category
[parent:protected] => 2
[label:protected] => Plumber/Pipefitter
[alreadyInSave:protected] =>
[alreadyInValidation:protected] =>
[validationFailures:protected] => Array
(
)
[_new:BaseObject:private] =>
[_deleted:BaseObject:private] =>
[modifiedColumns:protected] => Array
(
)
)
[78] => Category Object
(
[languages:protected] =>
[bok_resources:protected] =>
[bok_topics:protected] =>
[bok_keywords:protected] =>
[id:protected] => 78
[type:protected] => category
[parent:protected] => 2
[label:protected] => Roofer/Waterproofer
[alreadyInSave:protected] =>
[alreadyInValidation:protected] =>
[validationFailures:protected] => Array
(
)
[_new:BaseObject:private] =>
[_deleted:BaseObject:private] =>
[modifiedColumns:protected] => Array
(
)
)
[80] => Category Object
(
[languages:protected] =>
[bok_resources:protected] =>
[bok_topics:protected] =>
[bok_keywords:protected] =>
[id:protected] => 80
[type:protected] => category
[parent:protected] => 2
[label:protected] => Sheetmetal Worker
[alreadyInSave:protected] =>
[alreadyInValidation:protected] =>
[validationFailures:protected] => Array
(
)
[_new:BaseObject:private] =>
[_deleted:BaseObject:private] =>
[modifiedColumns:protected] => Array
(
)
)
[86] => Category Object
(
[languages:protected] =>
[bok_resources:protected] =>
[bok_topics:protected] =>
[bok_keywords:protected] =>
[id:protected] => 86
[type:protected] => category
[parent:protected] => 2
[label:protected] => Welder
[alreadyInSave:protected] =>
[alreadyInValidation:protected] =>
[validationFailures:protected] => Array
(
)
[_new:BaseObject:private] =>
[_deleted:BaseObject:private] =>
[modifiedColumns:protected] => Array
(
)
)
[87] => Category Object
(
[languages:protected] =>
[bok_resources:protected] =>
[bok_topics:protected] =>
[bok_keywords:protected] =>
[id:protected] => 87
[type:protected] => category
[parent:protected] => 3
[label:protected] => Commercial & Institutional
[alreadyInSave:protected] =>
[alreadyInValidation:protected] =>
[validationFailures:protected] => Array
(
)
[_new:BaseObject:private] =>
[_deleted:BaseObject:private] =>
[modifiedColumns:protected] => Array
(
)
)
[90] => Category Object
(
[languages:protected] =>
[bok_resources:protected] =>
[bok_topics:protected] =>
[bok_keywords:protected] =>
[id:protected] => 90
[type:protected] => category
[parent:protected] => 3
[label:protected] => Industrial
[alreadyInSave:protected] =>
[alreadyInValidation:protected] =>
[validationFailures:protected] => Array
(
)
[_new:BaseObject:private] =>
[_deleted:BaseObject:private] =>
[modifiedColumns:protected] => Array
(
)
)
[92] => Category Object
(
[languages:protected] =>
[bok_resources:protected] =>
[bok_topics:protected] =>
[bok_keywords:protected] =>
[id:protected] => 92
[type:protected] => category
[parent:protected] => 3
[label:protected] => LEED/Green Construction
[alreadyInSave:protected] =>
[alreadyInValidation:protected] =>
[validationFailures:protected] => Array
(
)
[_new:BaseObject:private] =>
[_deleted:BaseObject:private] =>
[modifiedColumns:protected] => Array
(
)
)
[93] => Category Object
(
[languages:protected] =>
[bok_resources:protected] =>
[bok_topics:protected] =>
[bok_keywords:protected] =>
[id:protected] => 93
[type:protected] => category
[parent:protected] => 3
[label:protected] => Renovations
[alreadyInSave:protected] =>
[alreadyInValidation:protected] =>
[validationFailures:protected] => Array
(
)
[_new:BaseObject:private] =>
[_deleted:BaseObject:private] =>
[modifiedColumns:protected] => Array
(
)
)
[94] => Category Object
(
[languages:protected] =>
[bok_resources:protected] =>
[bok_topics:protected] =>
[bok_keywords:protected] =>
[id:protected] => 94
[type:protected] => category
[parent:protected] => 3
[label:protected] => Residential
[alreadyInSave:protected] =>
[alreadyInValidation:protected] =>
[validationFailures:protected] => Array
(
)
[_new:BaseObject:private] =>
[_deleted:BaseObject:private] =>
[modifiedColumns:protected] => Array
(
)
)
[100] => Category Object
(
[languages:protected] =>
[bok_resources:protected] =>
[bok_topics:protected] =>
[bok_keywords:protected] =>
[id:protected] => 100
[type:protected] => category
[parent:protected] => 6
[label:protected] => Toolbox Talks
[alreadyInSave:protected] =>
[alreadyInValidation:protected] =>
[validationFailures:protected] => Array
(
)
[_new:BaseObject:private] =>
[_deleted:BaseObject:private] =>
[modifiedColumns:protected] => Array
(
)
)
)
[categories_initialized:protected] => 1
[mapped_items:protected] =>
[content:protected] =>
[files:protected] =>
[language:protected] => Language Object
(
[id:protected] => 1
[code:protected] => en
[name:protected] => English
[alreadyInSave:protected] =>
[alreadyInValidation:protected] =>
[validationFailures:protected] => Array
(
)
[_new:BaseObject:private] =>
[_deleted:BaseObject:private] =>
[modifiedColumns:protected] => Array
(
)
)
[old_record:protected] =>
[id:protected] => 4430
[old_id:protected] =>
[elcosh_id:protected] => d001660
[type:protected] => document
[display_type:protected] => HTML only (and links)
[user_id:protected] => 0
[language_id:protected] => 1
[tagging_id:protected] => Mike Aguilar
[priority_id:protected] => 1
[title:protected] => Toolbox Talk: Fixed Ladder
[total_pages:protected] => 0
[billed_pages:protected] => 0
[publication_number:protected] =>
[part_of:protected] =>
[keywords:protected] => Fixed Ladders, Fall Prevention, Falls
[comments:protected] =>
[summary:protected] => The CPWR Toolbox Talk on Fixed Ladders addresses the potential risks associated with using fixed ladders. The resource includes a brief case example, steps to prevent a related injury and questions for discussion. It includes an image that illustrates the hazard, which can be posted in a central location as a reminder of steps to work safely.
Available in
English
and
Spanish.
[transition_comments:protected] =>
[external_link:protected] =>
[consol_link:protected] =>
[more_like_this:protected] => d001257,d001254,d001255,d001256,d001258,d001262,d001279
[permission_given_by:protected] =>
[published:protected] => T
[billable:protected] => F
[img_name:protected] =>
[img_ext:protected] =>
[img_width:protected] =>
[img_height:protected] =>
[img_credit:protected] =>
[img_practice:protected] =>
[vid_source_id:protected] =>
[vid_running_time:protected] =>
[vid_intended_audience:protected] =>
[vid_acquisition_info:protected] =>
[vid_cost:protected] =>
[vid_producer:protected] =>
[vid_filename:protected] =>
[vid_filename_downloadable:protected] =>
[date_summary:protected] =>
[date_permission_requested:protected] =>
[date_permission_received:protected] =>
[date_review_needed:protected] =>
[date_received:protected] => 06/10/22
[date_completed:protected] => 06/10/22
[date_billed:protected] =>
[date_modified:protected] => 05/22/23
[collBokExports:protected] =>
[lastBokExportCriteria:BaseElcoshItem:private] =>
[alreadyInSave:protected] =>
[alreadyInValidation:protected] =>
[validationFailures:protected] => Array
(
)
[_new:BaseObject:private] =>
[_deleted:BaseObject:private] =>
[modifiedColumns:protected] => Array
(
)
)
)
[1] => Search_Result Object
(
[title] => Toolbox Talk: Challenges Preventing Falling Objects
[image] => /record/images/notavailable-p.png
[blurb] => The CPWR Toolbox Talk on Challenges Preventing Falling Objects addresses the hazards of being struck by falling objects on the job site. The resource...
[category] => Array
(
[0] => 12
[1] => 47
[2] => 49
[3] => 51
[4] => 55
[5] => 64
[6] => 68
[7] => 71
[8] => 75
[9] => 78
[10] => 79
[11] => 82
[12] => 62
[13] => 86
[14] => 87
[15] => 88
[16] => 89
[17] => 91
[18] => 90
[19] => 92
[20] => 93
[21] => 94
[22] => 95
[23] => 100
)
[labels] => Array
(
[0] => Crushed/Struck By
[1] => Work Environment
[2] => Hazards
[3] => Bricklayer
[4] => Trades
[5] => Carpenter
[7] => Cement Mason
[9] => Electrical Worker
[11] => Laborer
[13] => Maintenance Worker
[15] => Painter
[17] => Plasterer
[19] => Roofer/Waterproofer
[21] => Scaffold Erector
[23] => Stonemason
[25] => Structural Ironworker
[27] => Welder
[29] => Commercial & Institutional
[30] => Jobsites
[31] => Demolition
[33] => Disasters
[35] => Heavy & Highway
[37] => Industrial
[39] => LEED/Green Construction
[41] => Renovations
[43] => Residential
[45] => Underground
[47] => Toolbox Talks
[48] => Documents
[49] => Media & Documents
)
[type] => Toolbox Talks
[sub_category] =>
[url] => /document/4431/d001661/Toolbox%2BTalk%253A%2BChallenges%2BPreventing%2BFalling%2BObjects.html
[item:protected] => DocumentRecord Object
(
[records:protected] => Array
(
)
[recordId:protected] =>
[searchWordClass:protected] =>
[searchWordPeerClass:protected] =>
[bok_record:protected] =>
[authors:protected] =>
[organizations:protected] =>
[collections:protected] =>
[categories:protected] => Array
(
[12] => Category Object
(
[languages:protected] =>
[bok_resources:protected] =>
[bok_topics:protected] =>
[bok_keywords:protected] =>
[id:protected] => 12
[type:protected] => category
[parent:protected] => 7
[label:protected] => Crushed/Struck By
[alreadyInSave:protected] =>
[alreadyInValidation:protected] =>
[validationFailures:protected] => Array
(
)
[_new:BaseObject:private] =>
[_deleted:BaseObject:private] =>
[modifiedColumns:protected] => Array
(
)
)
[47] => Category Object
(
[languages:protected] =>
[bok_resources:protected] =>
[bok_topics:protected] =>
[bok_keywords:protected] =>
[id:protected] => 47
[type:protected] => category
[parent:protected] => 2
[label:protected] => Bricklayer
[alreadyInSave:protected] =>
[alreadyInValidation:protected] =>
[validationFailures:protected] => Array
(
)
[_new:BaseObject:private] =>
[_deleted:BaseObject:private] =>
[modifiedColumns:protected] => Array
(
)
)
[49] => Category Object
(
[languages:protected] =>
[bok_resources:protected] =>
[bok_topics:protected] =>
[bok_keywords:protected] =>
[id:protected] => 49
[type:protected] => category
[parent:protected] => 2
[label:protected] => Carpenter
[alreadyInSave:protected] =>
[alreadyInValidation:protected] =>
[validationFailures:protected] => Array
(
)
[_new:BaseObject:private] =>
[_deleted:BaseObject:private] =>
[modifiedColumns:protected] => Array
(
)
)
[51] => Category Object
(
[languages:protected] =>
[bok_resources:protected] =>
[bok_topics:protected] =>
[bok_keywords:protected] =>
[id:protected] => 51
[type:protected] => category
[parent:protected] => 2
[label:protected] => Cement Mason
[alreadyInSave:protected] =>
[alreadyInValidation:protected] =>
[validationFailures:protected] => Array
(
)
[_new:BaseObject:private] =>
[_deleted:BaseObject:private] =>
[modifiedColumns:protected] => Array
(
)
)
[55] => Category Object
(
[languages:protected] =>
[bok_resources:protected] =>
[bok_topics:protected] =>
[bok_keywords:protected] =>
[id:protected] => 55
[type:protected] => category
[parent:protected] => 2
[label:protected] => Electrical Worker
[alreadyInSave:protected] =>
[alreadyInValidation:protected] =>
[validationFailures:protected] => Array
(
)
[_new:BaseObject:private] =>
[_deleted:BaseObject:private] =>
[modifiedColumns:protected] => Array
(
)
)
[64] => Category Object
(
[languages:protected] =>
[bok_resources:protected] =>
[bok_topics:protected] =>
[bok_keywords:protected] =>
[id:protected] => 64
[type:protected] => category
[parent:protected] => 2
[label:protected] => Laborer
[alreadyInSave:protected] =>
[alreadyInValidation:protected] =>
[validationFailures:protected] => Array
(
)
[_new:BaseObject:private] =>
[_deleted:BaseObject:private] =>
[modifiedColumns:protected] => Array
(
)
)
[68] => Category Object
(
[languages:protected] =>
[bok_resources:protected] =>
[bok_topics:protected] =>
[bok_keywords:protected] =>
[id:protected] => 68
[type:protected] => category
[parent:protected] => 2
[label:protected] => Maintenance Worker
[alreadyInSave:protected] =>
[alreadyInValidation:protected] =>
[validationFailures:protected] => Array
(
)
[_new:BaseObject:private] =>
[_deleted:BaseObject:private] =>
[modifiedColumns:protected] => Array
(
)
)
[71] => Category Object
(
[languages:protected] =>
[bok_resources:protected] =>
[bok_topics:protected] =>
[bok_keywords:protected] =>
[id:protected] => 71
[type:protected] => category
[parent:protected] => 2
[label:protected] => Painter
[alreadyInSave:protected] =>
[alreadyInValidation:protected] =>
[validationFailures:protected] => Array
(
)
[_new:BaseObject:private] =>
[_deleted:BaseObject:private] =>
[modifiedColumns:protected] => Array
(
)
)
[75] => Category Object
(
[languages:protected] =>
[bok_resources:protected] =>
[bok_topics:protected] =>
[bok_keywords:protected] =>
[id:protected] => 75
[type:protected] => category
[parent:protected] => 2
[label:protected] => Plasterer
[alreadyInSave:protected] =>
[alreadyInValidation:protected] =>
[validationFailures:protected] => Array
(
)
[_new:BaseObject:private] =>
[_deleted:BaseObject:private] =>
[modifiedColumns:protected] => Array
(
)
)
[78] => Category Object
(
[languages:protected] =>
[bok_resources:protected] =>
[bok_topics:protected] =>
[bok_keywords:protected] =>
[id:protected] => 78
[type:protected] => category
[parent:protected] => 2
[label:protected] => Roofer/Waterproofer
[alreadyInSave:protected] =>
[alreadyInValidation:protected] =>
[validationFailures:protected] => Array
(
)
[_new:BaseObject:private] =>
[_deleted:BaseObject:private] =>
[modifiedColumns:protected] => Array
(
)
)
[79] => Category Object
(
[languages:protected] =>
[bok_resources:protected] =>
[bok_topics:protected] =>
[bok_keywords:protected] =>
[id:protected] => 79
[type:protected] => category
[parent:protected] => 2
[label:protected] => Scaffold Erector
[alreadyInSave:protected] =>
[alreadyInValidation:protected] =>
[validationFailures:protected] => Array
(
)
[_new:BaseObject:private] =>
[_deleted:BaseObject:private] =>
[modifiedColumns:protected] => Array
(
)
)
[82] => Category Object
(
[languages:protected] =>
[bok_resources:protected] =>
[bok_topics:protected] =>
[bok_keywords:protected] =>
[id:protected] => 82
[type:protected] => category
[parent:protected] => 2
[label:protected] => Stonemason
[alreadyInSave:protected] =>
[alreadyInValidation:protected] =>
[validationFailures:protected] => Array
(
)
[_new:BaseObject:private] =>
[_deleted:BaseObject:private] =>
[modifiedColumns:protected] => Array
(
)
)
[62] => Category Object
(
[languages:protected] =>
[bok_resources:protected] =>
[bok_topics:protected] =>
[bok_keywords:protected] =>
[id:protected] => 62
[type:protected] => category
[parent:protected] => 2
[label:protected] => Structural Ironworker
[alreadyInSave:protected] =>
[alreadyInValidation:protected] =>
[validationFailures:protected] => Array
(
)
[_new:BaseObject:private] =>
[_deleted:BaseObject:private] =>
[modifiedColumns:protected] => Array
(
)
)
[86] => Category Object
(
[languages:protected] =>
[bok_resources:protected] =>
[bok_topics:protected] =>
[bok_keywords:protected] =>
[id:protected] => 86
[type:protected] => category
[parent:protected] => 2
[label:protected] => Welder
[alreadyInSave:protected] =>
[alreadyInValidation:protected] =>
[validationFailures:protected] => Array
(
)
[_new:BaseObject:private] =>
[_deleted:BaseObject:private] =>
[modifiedColumns:protected] => Array
(
)
)
[87] => Category Object
(
[languages:protected] =>
[bok_resources:protected] =>
[bok_topics:protected] =>
[bok_keywords:protected] =>
[id:protected] => 87
[type:protected] => category
[parent:protected] => 3
[label:protected] => Commercial & Institutional
[alreadyInSave:protected] =>
[alreadyInValidation:protected] =>
[validationFailures:protected] => Array
(
)
[_new:BaseObject:private] =>
[_deleted:BaseObject:private] =>
[modifiedColumns:protected] => Array
(
)
)
[88] => Category Object
(
[languages:protected] =>
[bok_resources:protected] =>
[bok_topics:protected] =>
[bok_keywords:protected] =>
[id:protected] => 88
[type:protected] => category
[parent:protected] => 3
[label:protected] => Demolition
[alreadyInSave:protected] =>
[alreadyInValidation:protected] =>
[validationFailures:protected] => Array
(
)
[_new:BaseObject:private] =>
[_deleted:BaseObject:private] =>
[modifiedColumns:protected] => Array
(
)
)
[89] => Category Object
(
[languages:protected] =>
[bok_resources:protected] =>
[bok_topics:protected] =>
[bok_keywords:protected] =>
[id:protected] => 89
[type:protected] => category
[parent:protected] => 3
[label:protected] => Disasters
[alreadyInSave:protected] =>
[alreadyInValidation:protected] =>
[validationFailures:protected] => Array
(
)
[_new:BaseObject:private] =>
[_deleted:BaseObject:private] =>
[modifiedColumns:protected] => Array
(
)
)
[91] => Category Object
(
[languages:protected] =>
[bok_resources:protected] =>
[bok_topics:protected] =>
[bok_keywords:protected] =>
[id:protected] => 91
[type:protected] => category
[parent:protected] => 3
[label:protected] => Heavy & Highway
[alreadyInSave:protected] =>
[alreadyInValidation:protected] =>
[validationFailures:protected] => Array
(
)
[_new:BaseObject:private] =>
[_deleted:BaseObject:private] =>
[modifiedColumns:protected] => Array
(
)
)
[90] => Category Object
(
[languages:protected] =>
[bok_resources:protected] =>
[bok_topics:protected] =>
[bok_keywords:protected] =>
[id:protected] => 90
[type:protected] => category
[parent:protected] => 3
[label:protected] => Industrial
[alreadyInSave:protected] =>
[alreadyInValidation:protected] =>
[validationFailures:protected] => Array
(
)
[_new:BaseObject:private] =>
[_deleted:BaseObject:private] =>
[modifiedColumns:protected] => Array
(
)
)
[92] => Category Object
(
[languages:protected] =>
[bok_resources:protected] =>
[bok_topics:protected] =>
[bok_keywords:protected] =>
[id:protected] => 92
[type:protected] => category
[parent:protected] => 3
[label:protected] => LEED/Green Construction
[alreadyInSave:protected] =>
[alreadyInValidation:protected] =>
[validationFailures:protected] => Array
(
)
[_new:BaseObject:private] =>
[_deleted:BaseObject:private] =>
[modifiedColumns:protected] => Array
(
)
)
[93] => Category Object
(
[languages:protected] =>
[bok_resources:protected] =>
[bok_topics:protected] =>
[bok_keywords:protected] =>
[id:protected] => 93
[type:protected] => category
[parent:protected] => 3
[label:protected] => Renovations
[alreadyInSave:protected] =>
[alreadyInValidation:protected] =>
[validationFailures:protected] => Array
(
)
[_new:BaseObject:private] =>
[_deleted:BaseObject:private] =>
[modifiedColumns:protected] => Array
(
)
)
[94] => Category Object
(
[languages:protected] =>
[bok_resources:protected] =>
[bok_topics:protected] =>
[bok_keywords:protected] =>
[id:protected] => 94
[type:protected] => category
[parent:protected] => 3
[label:protected] => Residential
[alreadyInSave:protected] =>
[alreadyInValidation:protected] =>
[validationFailures:protected] => Array
(
)
[_new:BaseObject:private] =>
[_deleted:BaseObject:private] =>
[modifiedColumns:protected] => Array
(
)
)
[95] => Category Object
(
[languages:protected] =>
[bok_resources:protected] =>
[bok_topics:protected] =>
[bok_keywords:protected] =>
[id:protected] => 95
[type:protected] => category
[parent:protected] => 3
[label:protected] => Underground
[alreadyInSave:protected] =>
[alreadyInValidation:protected] =>
[validationFailures:protected] => Array
(
)
[_new:BaseObject:private] =>
[_deleted:BaseObject:private] =>
[modifiedColumns:protected] => Array
(
)
)
[100] => Category Object
(
[languages:protected] =>
[bok_resources:protected] =>
[bok_topics:protected] =>
[bok_keywords:protected] =>
[id:protected] => 100
[type:protected] => category
[parent:protected] => 6
[label:protected] => Toolbox Talks
[alreadyInSave:protected] =>
[alreadyInValidation:protected] =>
[validationFailures:protected] => Array
(
)
[_new:BaseObject:private] =>
[_deleted:BaseObject:private] =>
[modifiedColumns:protected] => Array
(
)
)
)
[categories_initialized:protected] => 1
[mapped_items:protected] =>
[content:protected] =>
[files:protected] =>
[language:protected] => Language Object
(
[id:protected] => 1
[code:protected] => en
[name:protected] => English
[alreadyInSave:protected] =>
[alreadyInValidation:protected] =>
[validationFailures:protected] => Array
(
)
[_new:BaseObject:private] =>
[_deleted:BaseObject:private] =>
[modifiedColumns:protected] => Array
(
)
)
[old_record:protected] =>
[id:protected] => 4431
[old_id:protected] =>
[elcosh_id:protected] => d001661
[type:protected] => document
[display_type:protected] => HTML only (and links)
[user_id:protected] => 0
[language_id:protected] => 1
[tagging_id:protected] => Mike Aguilar
[priority_id:protected] => 1
[title:protected] => Toolbox Talk: Challenges Preventing Falling Objects
[total_pages:protected] => 0
[billed_pages:protected] => 0
[publication_number:protected] =>
[part_of:protected] =>
[keywords:protected] => dropped objects, falling objects, struck by incidents, struck by fatalities
[comments:protected] =>
[summary:protected] => The CPWR Toolbox Talk on Challenges Preventing Falling Objects addresses the hazards of being struck by falling objects on the job site. The resource includes a brief example, steps to prevent a related injury, and questions for discussion. It includes a graphic that illustrates a group workers observing a scaffold free of debris during high winds, which can be posted in a central location as a reminder of steps to work safely.
Available in
English and
Spanish.
[transition_comments:protected] =>
[external_link:protected] =>
[consol_link:protected] =>
[more_like_this:protected] => d001234,d001238,d001244,d001251,d001253,d001260,d001268,d001278
[permission_given_by:protected] =>
[published:protected] => T
[billable:protected] => F
[img_name:protected] =>
[img_ext:protected] =>
[img_width:protected] =>
[img_height:protected] =>
[img_credit:protected] =>
[img_practice:protected] =>
[vid_source_id:protected] =>
[vid_running_time:protected] =>
[vid_intended_audience:protected] =>
[vid_acquisition_info:protected] =>
[vid_cost:protected] =>
[vid_producer:protected] =>
[vid_filename:protected] =>
[vid_filename_downloadable:protected] =>
[date_summary:protected] =>
[date_permission_requested:protected] =>
[date_permission_received:protected] =>
[date_review_needed:protected] =>
[date_received:protected] => 06/10/22
[date_completed:protected] => 06/10/22
[date_billed:protected] =>
[date_modified:protected] => 05/22/23
[collBokExports:protected] =>
[lastBokExportCriteria:BaseElcoshItem:private] =>
[alreadyInSave:protected] =>
[alreadyInValidation:protected] =>
[validationFailures:protected] => Array
(
)
[_new:BaseObject:private] =>
[_deleted:BaseObject:private] =>
[modifiedColumns:protected] => Array
(
)
)
)
[2] => Search_Result Object
(
[title] => Toolbox Talk: Tower Crane Safety
[image] => /record/images/notavailable-p.png
[blurb] => The CPWR Toolbox Talk on Tower Crane Safety addresses the potential hazards of Tower Cranes and the importance of following procedure before and durin...
[category] => Array
(
[0] => 11
[1] => 12
[2] => 18
[3] => 70
[4] => 87
[5] => 88
[6] => 91
[7] => 90
[8] => 92
[9] => 100
)
[labels] => Array
(
[0] => Cranes & Hoists
[1] => Work Environment
[2] => Hazards
[3] => Crushed/Struck By
[6] => Motor Vehicles/Heavy Equipment
[9] => Operating Engineer
[10] => Trades
[11] => Commercial & Institutional
[12] => Jobsites
[13] => Demolition
[15] => Heavy & Highway
[17] => Industrial
[19] => LEED/Green Construction
[21] => Toolbox Talks
[22] => Documents
[23] => Media & Documents
)
[type] => Toolbox Talks
[sub_category] =>
[url] => /document/4427/d001657/Toolbox%2BTalk%253A%2BTower%2BCrane%2BSafety.html
[item:protected] => DocumentRecord Object
(
[records:protected] => Array
(
)
[recordId:protected] =>
[searchWordClass:protected] =>
[searchWordPeerClass:protected] =>
[bok_record:protected] =>
[authors:protected] =>
[organizations:protected] =>
[collections:protected] =>
[categories:protected] => Array
(
[11] => Category Object
(
[languages:protected] =>
[bok_resources:protected] =>
[bok_topics:protected] =>
[bok_keywords:protected] =>
[id:protected] => 11
[type:protected] => category
[parent:protected] => 7
[label:protected] => Cranes & Hoists
[alreadyInSave:protected] =>
[alreadyInValidation:protected] =>
[validationFailures:protected] => Array
(
)
[_new:BaseObject:private] =>
[_deleted:BaseObject:private] =>
[modifiedColumns:protected] => Array
(
)
)
[12] => Category Object
(
[languages:protected] =>
[bok_resources:protected] =>
[bok_topics:protected] =>
[bok_keywords:protected] =>
[id:protected] => 12
[type:protected] => category
[parent:protected] => 7
[label:protected] => Crushed/Struck By
[alreadyInSave:protected] =>
[alreadyInValidation:protected] =>
[validationFailures:protected] => Array
(
)
[_new:BaseObject:private] =>
[_deleted:BaseObject:private] =>
[modifiedColumns:protected] => Array
(
)
)
[18] => Category Object
(
[languages:protected] =>
[bok_resources:protected] =>
[bok_topics:protected] =>
[bok_keywords:protected] =>
[id:protected] => 18
[type:protected] => category
[parent:protected] => 7
[label:protected] => Motor Vehicles/Heavy Equipment
[alreadyInSave:protected] =>
[alreadyInValidation:protected] =>
[validationFailures:protected] => Array
(
)
[_new:BaseObject:private] =>
[_deleted:BaseObject:private] =>
[modifiedColumns:protected] => Array
(
)
)
[70] => Category Object
(
[languages:protected] =>
[bok_resources:protected] =>
[bok_topics:protected] =>
[bok_keywords:protected] =>
[id:protected] => 70
[type:protected] => category
[parent:protected] => 2
[label:protected] => Operating Engineer
[alreadyInSave:protected] =>
[alreadyInValidation:protected] =>
[validationFailures:protected] => Array
(
)
[_new:BaseObject:private] =>
[_deleted:BaseObject:private] =>
[modifiedColumns:protected] => Array
(
)
)
[87] => Category Object
(
[languages:protected] =>
[bok_resources:protected] =>
[bok_topics:protected] =>
[bok_keywords:protected] =>
[id:protected] => 87
[type:protected] => category
[parent:protected] => 3
[label:protected] => Commercial & Institutional
[alreadyInSave:protected] =>
[alreadyInValidation:protected] =>
[validationFailures:protected] => Array
(
)
[_new:BaseObject:private] =>
[_deleted:BaseObject:private] =>
[modifiedColumns:protected] => Array
(
)
)
[88] => Category Object
(
[languages:protected] =>
[bok_resources:protected] =>
[bok_topics:protected] =>
[bok_keywords:protected] =>
[id:protected] => 88
[type:protected] => category
[parent:protected] => 3
[label:protected] => Demolition
[alreadyInSave:protected] =>
[alreadyInValidation:protected] =>
[validationFailures:protected] => Array
(
)
[_new:BaseObject:private] =>
[_deleted:BaseObject:private] =>
[modifiedColumns:protected] => Array
(
)
)
[91] => Category Object
(
[languages:protected] =>
[bok_resources:protected] =>
[bok_topics:protected] =>
[bok_keywords:protected] =>
[id:protected] => 91
[type:protected] => category
[parent:protected] => 3
[label:protected] => Heavy & Highway
[alreadyInSave:protected] =>
[alreadyInValidation:protected] =>
[validationFailures:protected] => Array
(
)
[_new:BaseObject:private] =>
[_deleted:BaseObject:private] =>
[modifiedColumns:protected] => Array
(
)
)
[90] => Category Object
(
[languages:protected] =>
[bok_resources:protected] =>
[bok_topics:protected] =>
[bok_keywords:protected] =>
[id:protected] => 90
[type:protected] => category
[parent:protected] => 3
[label:protected] => Industrial
[alreadyInSave:protected] =>
[alreadyInValidation:protected] =>
[validationFailures:protected] => Array
(
)
[_new:BaseObject:private] =>
[_deleted:BaseObject:private] =>
[modifiedColumns:protected] => Array
(
)
)
[92] => Category Object
(
[languages:protected] =>
[bok_resources:protected] =>
[bok_topics:protected] =>
[bok_keywords:protected] =>
[id:protected] => 92
[type:protected] => category
[parent:protected] => 3
[label:protected] => LEED/Green Construction
[alreadyInSave:protected] =>
[alreadyInValidation:protected] =>
[validationFailures:protected] => Array
(
)
[_new:BaseObject:private] =>
[_deleted:BaseObject:private] =>
[modifiedColumns:protected] => Array
(
)
)
[100] => Category Object
(
[languages:protected] =>
[bok_resources:protected] =>
[bok_topics:protected] =>
[bok_keywords:protected] =>
[id:protected] => 100
[type:protected] => category
[parent:protected] => 6
[label:protected] => Toolbox Talks
[alreadyInSave:protected] =>
[alreadyInValidation:protected] =>
[validationFailures:protected] => Array
(
)
[_new:BaseObject:private] =>
[_deleted:BaseObject:private] =>
[modifiedColumns:protected] => Array
(
)
)
)
[categories_initialized:protected] => 1
[mapped_items:protected] =>
[content:protected] =>
[files:protected] =>
[language:protected] => Language Object
(
[id:protected] => 1
[code:protected] => en
[name:protected] => English
[alreadyInSave:protected] =>
[alreadyInValidation:protected] =>
[validationFailures:protected] => Array
(
)
[_new:BaseObject:private] =>
[_deleted:BaseObject:private] =>
[modifiedColumns:protected] => Array
(
)
)
[old_record:protected] =>
[id:protected] => 4427
[old_id:protected] =>
[elcosh_id:protected] => d001657
[type:protected] => document
[display_type:protected] => HTML only (and links)
[user_id:protected] => 0
[language_id:protected] => 1
[tagging_id:protected] => Mike Aguilar
[priority_id:protected] => 1
[title:protected] => Toolbox Talk: Tower Crane Safety
[total_pages:protected] => 0
[billed_pages:protected] => 0
[publication_number:protected] =>
[part_of:protected] =>
[keywords:protected] => Tower Crane, Crane, Stability, Tipping, Lift Zone Safety, Lift, Zone, Safety, Struck by
[comments:protected] =>
[summary:protected] => The CPWR Toolbox Talk on Tower Crane Safety addresses the potential hazards of Tower Cranes and the importance of following procedure before and during Tower Crane operation. The resource includes a brief example, steps to prevent a related injury, and questions for discussion. It includes a graphic that illustrates a worker inspecting a Tower Crane before operation, which can be posted in a central location as a reminder of steps to work safely.
Available in
English and
Spanish.
[transition_comments:protected] =>
[external_link:protected] =>
[consol_link:protected] =>
[more_like_this:protected] => d001234,d001238,d001250,d001251,d001253,d001258,d001262,d001273
[permission_given_by:protected] =>
[published:protected] => T
[billable:protected] => F
[img_name:protected] =>
[img_ext:protected] => jpg
[img_width:protected] =>
[img_height:protected] =>
[img_credit:protected] =>
[img_practice:protected] =>
[vid_source_id:protected] =>
[vid_running_time:protected] =>
[vid_intended_audience:protected] =>
[vid_acquisition_info:protected] =>
[vid_cost:protected] =>
[vid_producer:protected] =>
[vid_filename:protected] =>
[vid_filename_downloadable:protected] =>
[date_summary:protected] =>
[date_permission_requested:protected] =>
[date_permission_received:protected] =>
[date_review_needed:protected] =>
[date_received:protected] => 12/23/21
[date_completed:protected] => 12/23/21
[date_billed:protected] =>
[date_modified:protected] => 05/19/23
[collBokExports:protected] =>
[lastBokExportCriteria:BaseElcoshItem:private] =>
[alreadyInSave:protected] =>
[alreadyInValidation:protected] =>
[validationFailures:protected] => Array
(
)
[_new:BaseObject:private] =>
[_deleted:BaseObject:private] =>
[modifiedColumns:protected] => Array
(
)
)
)
[3] => Search_Result Object
(
[title] => Toolbox Talk: Work Zone Safety: Working Around Vehicles
[image] => /record/images/notavailable-p.png
[blurb] => The CPWR Toolbox Talk on Working Around Vehicles in the Work Zone addresses methods to avoid being struck-by a vehicle on a construction site. The res...
[category] => Array
(
[0] => 12
[1] => 18
[2] => 52
[3] => 57
[4] => 70
[5] => 85
[6] => 87
[7] => 88
[8] => 89
[9] => 91
[10] => 90
[11] => 92
[12] => 93
[13] => 94
[14] => 95
[15] => 100
)
[labels] => Array
(
[0] => Crushed/Struck By
[1] => Work Environment
[2] => Hazards
[3] => Motor Vehicles/Heavy Equipment
[6] => Commercial Diver
[7] => Trades
[8] => Flagger
[10] => Operating Engineer
[12] => Truck Driver
[14] => Commercial & Institutional
[15] => Jobsites
[16] => Demolition
[18] => Disasters
[20] => Heavy & Highway
[22] => Industrial
[24] => LEED/Green Construction
[26] => Renovations
[28] => Residential
[30] => Underground
[32] => Toolbox Talks
[33] => Documents
[34] => Media & Documents
)
[type] => Toolbox Talks
[sub_category] =>
[url] => /document/4428/d001658/Toolbox%2BTalk%253A%2BWork%2BZone%2BSafety%253A%2BWorking%2BAround%2BVehicles.html
[item:protected] => DocumentRecord Object
(
[records:protected] => Array
(
)
[recordId:protected] =>
[searchWordClass:protected] =>
[searchWordPeerClass:protected] =>
[bok_record:protected] =>
[authors:protected] =>
[organizations:protected] =>
[collections:protected] =>
[categories:protected] => Array
(
[12] => Category Object
(
[languages:protected] =>
[bok_resources:protected] =>
[bok_topics:protected] =>
[bok_keywords:protected] =>
[id:protected] => 12
[type:protected] => category
[parent:protected] => 7
[label:protected] => Crushed/Struck By
[alreadyInSave:protected] =>
[alreadyInValidation:protected] =>
[validationFailures:protected] => Array
(
)
[_new:BaseObject:private] =>
[_deleted:BaseObject:private] =>
[modifiedColumns:protected] => Array
(
)
)
[18] => Category Object
(
[languages:protected] =>
[bok_resources:protected] =>
[bok_topics:protected] =>
[bok_keywords:protected] =>
[id:protected] => 18
[type:protected] => category
[parent:protected] => 7
[label:protected] => Motor Vehicles/Heavy Equipment
[alreadyInSave:protected] =>
[alreadyInValidation:protected] =>
[validationFailures:protected] => Array
(
)
[_new:BaseObject:private] =>
[_deleted:BaseObject:private] =>
[modifiedColumns:protected] => Array
(
)
)
[52] => Category Object
(
[languages:protected] =>
[bok_resources:protected] =>
[bok_topics:protected] =>
[bok_keywords:protected] =>
[id:protected] => 52
[type:protected] => category
[parent:protected] => 2
[label:protected] => Commercial Diver
[alreadyInSave:protected] =>
[alreadyInValidation:protected] =>
[validationFailures:protected] => Array
(
)
[_new:BaseObject:private] =>
[_deleted:BaseObject:private] =>
[modifiedColumns:protected] => Array
(
)
)
[57] => Category Object
(
[languages:protected] =>
[bok_resources:protected] =>
[bok_topics:protected] =>
[bok_keywords:protected] =>
[id:protected] => 57
[type:protected] => category
[parent:protected] => 2
[label:protected] => Flagger
[alreadyInSave:protected] =>
[alreadyInValidation:protected] =>
[validationFailures:protected] => Array
(
)
[_new:BaseObject:private] =>
[_deleted:BaseObject:private] =>
[modifiedColumns:protected] => Array
(
)
)
[70] => Category Object
(
[languages:protected] =>
[bok_resources:protected] =>
[bok_topics:protected] =>
[bok_keywords:protected] =>
[id:protected] => 70
[type:protected] => category
[parent:protected] => 2
[label:protected] => Operating Engineer
[alreadyInSave:protected] =>
[alreadyInValidation:protected] =>
[validationFailures:protected] => Array
(
)
[_new:BaseObject:private] =>
[_deleted:BaseObject:private] =>
[modifiedColumns:protected] => Array
(
)
)
[85] => Category Object
(
[languages:protected] =>
[bok_resources:protected] =>
[bok_topics:protected] =>
[bok_keywords:protected] =>
[id:protected] => 85
[type:protected] => category
[parent:protected] => 2
[label:protected] => Truck Driver
[alreadyInSave:protected] =>
[alreadyInValidation:protected] =>
[validationFailures:protected] => Array
(
)
[_new:BaseObject:private] =>
[_deleted:BaseObject:private] =>
[modifiedColumns:protected] => Array
(
)
)
[87] => Category Object
(
[languages:protected] =>
[bok_resources:protected] =>
[bok_topics:protected] =>
[bok_keywords:protected] =>
[id:protected] => 87
[type:protected] => category
[parent:protected] => 3
[label:protected] => Commercial & Institutional
[alreadyInSave:protected] =>
[alreadyInValidation:protected] =>
[validationFailures:protected] => Array
(
)
[_new:BaseObject:private] =>
[_deleted:BaseObject:private] =>
[modifiedColumns:protected] => Array
(
)
)
[88] => Category Object
(
[languages:protected] =>
[bok_resources:protected] =>
[bok_topics:protected] =>
[bok_keywords:protected] =>
[id:protected] => 88
[type:protected] => category
[parent:protected] => 3
[label:protected] => Demolition
[alreadyInSave:protected] =>
[alreadyInValidation:protected] =>
[validationFailures:protected] => Array
(
)
[_new:BaseObject:private] =>
[_deleted:BaseObject:private] =>
[modifiedColumns:protected] => Array
(
)
)
[89] => Category Object
(
[languages:protected] =>
[bok_resources:protected] =>
[bok_topics:protected] =>
[bok_keywords:protected] =>
[id:protected] => 89
[type:protected] => category
[parent:protected] => 3
[label:protected] => Disasters
[alreadyInSave:protected] =>
[alreadyInValidation:protected] =>
[validationFailures:protected] => Array
(
)
[_new:BaseObject:private] =>
[_deleted:BaseObject:private] =>
[modifiedColumns:protected] => Array
(
)
)
[91] => Category Object
(
[languages:protected] =>
[bok_resources:protected] =>
[bok_topics:protected] =>
[bok_keywords:protected] =>
[id:protected] => 91
[type:protected] => category
[parent:protected] => 3
[label:protected] => Heavy & Highway
[alreadyInSave:protected] =>
[alreadyInValidation:protected] =>
[validationFailures:protected] => Array
(
)
[_new:BaseObject:private] =>
[_deleted:BaseObject:private] =>
[modifiedColumns:protected] => Array
(
)
)
[90] => Category Object
(
[languages:protected] =>
[bok_resources:protected] =>
[bok_topics:protected] =>
[bok_keywords:protected] =>
[id:protected] => 90
[type:protected] => category
[parent:protected] => 3
[label:protected] => Industrial
[alreadyInSave:protected] =>
[alreadyInValidation:protected] =>
[validationFailures:protected] => Array
(
)
[_new:BaseObject:private] =>
[_deleted:BaseObject:private] =>
[modifiedColumns:protected] => Array
(
)
)
[92] => Category Object
(
[languages:protected] =>
[bok_resources:protected] =>
[bok_topics:protected] =>
[bok_keywords:protected] =>
[id:protected] => 92
[type:protected] => category
[parent:protected] => 3
[label:protected] => LEED/Green Construction
[alreadyInSave:protected] =>
[alreadyInValidation:protected] =>
[validationFailures:protected] => Array
(
)
[_new:BaseObject:private] =>
[_deleted:BaseObject:private] =>
[modifiedColumns:protected] => Array
(
)
)
[93] => Category Object
(
[languages:protected] =>
[bok_resources:protected] =>
[bok_topics:protected] =>
[bok_keywords:protected] =>
[id:protected] => 93
[type:protected] => category
[parent:protected] => 3
[label:protected] => Renovations
[alreadyInSave:protected] =>
[alreadyInValidation:protected] =>
[validationFailures:protected] => Array
(
)
[_new:BaseObject:private] =>
[_deleted:BaseObject:private] =>
[modifiedColumns:protected] => Array
(
)
)
[94] => Category Object
(
[languages:protected] =>
[bok_resources:protected] =>
[bok_topics:protected] =>
[bok_keywords:protected] =>
[id:protected] => 94
[type:protected] => category
[parent:protected] => 3
[label:protected] => Residential
[alreadyInSave:protected] =>
[alreadyInValidation:protected] =>
[validationFailures:protected] => Array
(
)
[_new:BaseObject:private] =>
[_deleted:BaseObject:private] =>
[modifiedColumns:protected] => Array
(
)
)
[95] => Category Object
(
[languages:protected] =>
[bok_resources:protected] =>
[bok_topics:protected] =>
[bok_keywords:protected] =>
[id:protected] => 95
[type:protected] => category
[parent:protected] => 3
[label:protected] => Underground
[alreadyInSave:protected] =>
[alreadyInValidation:protected] =>
[validationFailures:protected] => Array
(
)
[_new:BaseObject:private] =>
[_deleted:BaseObject:private] =>
[modifiedColumns:protected] => Array
(
)
)
[100] => Category Object
(
[languages:protected] =>
[bok_resources:protected] =>
[bok_topics:protected] =>
[bok_keywords:protected] =>
[id:protected] => 100
[type:protected] => category
[parent:protected] => 6
[label:protected] => Toolbox Talks
[alreadyInSave:protected] =>
[alreadyInValidation:protected] =>
[validationFailures:protected] => Array
(
)
[_new:BaseObject:private] =>
[_deleted:BaseObject:private] =>
[modifiedColumns:protected] => Array
(
)
)
)
[categories_initialized:protected] => 1
[mapped_items:protected] =>
[content:protected] =>
[files:protected] =>
[language:protected] => Language Object
(
[id:protected] => 1
[code:protected] => en
[name:protected] => English
[alreadyInSave:protected] =>
[alreadyInValidation:protected] =>
[validationFailures:protected] => Array
(
)
[_new:BaseObject:private] =>
[_deleted:BaseObject:private] =>
[modifiedColumns:protected] => Array
(
)
)
[old_record:protected] =>
[id:protected] => 4428
[old_id:protected] =>
[elcosh_id:protected] => d001658
[type:protected] => document
[display_type:protected] => HTML only (and links)
[user_id:protected] => 0
[language_id:protected] => 1
[tagging_id:protected] => Daniela Caceres
[priority_id:protected] => 1
[title:protected] => Toolbox Talk: Work Zone Safety: Working Around Vehicles
[total_pages:protected] => 0
[billed_pages:protected] => 0
[publication_number:protected] =>
[part_of:protected] =>
[keywords:protected] => Struck, Struck by, Vehicle, Work Zone Safety, Truck, Operator, Driver, Mobile Equipment
[comments:protected] =>
[summary:protected] => The CPWR Toolbox Talk on Working Around Vehicles in the Work Zone addresses methods to avoid being struck-by a vehicle on a construction site. The resource includes a case example, steps to prevent a related injury, and questions for discussion. It includes a graphic that illustrates the hazard, which can be posted in a central location as a reminder of steps to work safely. Available in
English and
Spanish.
[transition_comments:protected] =>
[external_link:protected] =>
[consol_link:protected] =>
[more_like_this:protected] => d001640
[permission_given_by:protected] =>
[published:protected] => T
[billable:protected] => F
[img_name:protected] =>
[img_ext:protected] =>
[img_width:protected] =>
[img_height:protected] =>
[img_credit:protected] =>
[img_practice:protected] =>
[vid_source_id:protected] =>
[vid_running_time:protected] =>
[vid_intended_audience:protected] =>
[vid_acquisition_info:protected] =>
[vid_cost:protected] =>
[vid_producer:protected] =>
[vid_filename:protected] =>
[vid_filename_downloadable:protected] =>
[date_summary:protected] =>
[date_permission_requested:protected] =>
[date_permission_received:protected] =>
[date_review_needed:protected] =>
[date_received:protected] => 12/23/21
[date_completed:protected] => 12/23/21
[date_billed:protected] =>
[date_modified:protected] => 05/19/23
[collBokExports:protected] =>
[lastBokExportCriteria:BaseElcoshItem:private] =>
[alreadyInSave:protected] =>
[alreadyInValidation:protected] =>
[validationFailures:protected] => Array
(
)
[_new:BaseObject:private] =>
[_deleted:BaseObject:private] =>
[modifiedColumns:protected] => Array
(
)
)
)
[4] => Search_Result Object
(
[title] => Construction Dive -- DeWalt's Jobsite Pro headphones recalled for fire hazards
[image] => /record/images/notavailable-p.png
[blurb] => A recall notice by the United States Consumer Product Safety Commission affects over 300,000 DeWalt Jobsite Pro Headphones. The recall is a result of...
[category] => Array
(
[0] => 16
[1] => 44
[2] => 45
[3] => 46
[4] => 47
[5] => 48
[6] => 49
[7] => 50
[8] => 51
[9] => 52
[10] => 53
[11] => 54
[12] => 55
[13] => 56
[14] => 57
[15] => 58
[16] => 59
[17] => 60
[18] => 61
[19] => 64
[20] => 65
[21] => 66
[22] => 67
[23] => 68
[24] => 69
[25] => 70
[26] => 71
[27] => 72
[28] => 73
[29] => 74
[30] => 75
[31] => 76
[32] => 77
[33] => 63
[34] => 78
[35] => 79
[36] => 80
[37] => 81
[38] => 82
[39] => 62
[40] => 83
[41] => 84
[42] => 85
[43] => 86
[44] => 87
[45] => 88
[46] => 89
[47] => 91
[48] => 90
[49] => 92
[50] => 93
[51] => 94
[52] => 95
)
[labels] => Array
(
[0] => Fire & Explosions
[1] => Work Environment
[2] => Hazards
[3] => Acoustical Ceiling Carpenter
[4] => Trades
[5] => Asbestos/Insulator
[7] => Boilermaker
[9] => Bricklayer
[11] => Cabinetmaker
[13] => Carpenter
[15] => Carpet Layer
[17] => Cement Mason
[19] => Commercial Diver
[21] => Concrete Polisher
[23] => Drywall Applicator Specialist
[25] => Electrical Worker
[27] => Elevator Constructor
[29] => Flagger
[31] => Glazier
[33] => Hazardous Waste Cleanup
[35] => HVAC
[37] => Interior Systems Carpenter
[39] => Laborer
[41] => Landscaper
[43] => Lather
[45] => Lead Abatement Worker
[47] => Maintenance Worker
[49] => Millwright
[51] => Operating Engineer
[53] => Painter
[55] => Paper Hanger
[57] => PCC/Restoration
[59] => Pile Driver
[61] => Plasterer
[63] => Plumber/Pipefitter
[65] => Refractory Worker
[67] => Reinforcing Ironworker
[69] => Roofer/Waterproofer
[71] => Scaffold Erector
[73] => Sheetmetal Worker
[75] => Sprinkler Fitter
[77] => Stonemason
[79] => Structural Ironworker
[81] => Terrazzo Worker
[83] => Tile Setter
[85] => Truck Driver
[87] => Welder
[89] => Commercial & Institutional
[90] => Jobsites
[91] => Demolition
[93] => Disasters
[95] => Heavy & Highway
[97] => Industrial
[99] => LEED/Green Construction
[101] => Renovations
[103] => Residential
[105] => Underground
)
[type] =>
[sub_category] =>
[url] => /document/4426/d001656/Construction%2BDive%2B--%2BDeWalt%2527s%2BJobsite%2BPro%2Bheadphones%2Brecalled%2Bfor%2Bfire%2Bhazards.html
[item:protected] => DocumentRecord Object
(
[records:protected] => Array
(
)
[recordId:protected] =>
[searchWordClass:protected] =>
[searchWordPeerClass:protected] =>
[bok_record:protected] =>
[authors:protected] =>
[organizations:protected] =>
[collections:protected] =>
[categories:protected] => Array
(
[16] => Category Object
(
[languages:protected] =>
[bok_resources:protected] =>
[bok_topics:protected] =>
[bok_keywords:protected] =>
[id:protected] => 16
[type:protected] => category
[parent:protected] => 7
[label:protected] => Fire & Explosions
[alreadyInSave:protected] =>
[alreadyInValidation:protected] =>
[validationFailures:protected] => Array
(
)
[_new:BaseObject:private] =>
[_deleted:BaseObject:private] =>
[modifiedColumns:protected] => Array
(
)
)
[44] => Category Object
(
[languages:protected] =>
[bok_resources:protected] =>
[bok_topics:protected] =>
[bok_keywords:protected] =>
[id:protected] => 44
[type:protected] => category
[parent:protected] => 2
[label:protected] => Acoustical Ceiling Carpenter
[alreadyInSave:protected] =>
[alreadyInValidation:protected] =>
[validationFailures:protected] => Array
(
)
[_new:BaseObject:private] =>
[_deleted:BaseObject:private] =>
[modifiedColumns:protected] => Array
(
)
)
[45] => Category Object
(
[languages:protected] =>
[bok_resources:protected] =>
[bok_topics:protected] =>
[bok_keywords:protected] =>
[id:protected] => 45
[type:protected] => category
[parent:protected] => 2
[label:protected] => Asbestos/Insulator
[alreadyInSave:protected] =>
[alreadyInValidation:protected] =>
[validationFailures:protected] => Array
(
)
[_new:BaseObject:private] =>
[_deleted:BaseObject:private] =>
[modifiedColumns:protected] => Array
(
)
)
[46] => Category Object
(
[languages:protected] =>
[bok_resources:protected] =>
[bok_topics:protected] =>
[bok_keywords:protected] =>
[id:protected] => 46
[type:protected] => category
[parent:protected] => 2
[label:protected] => Boilermaker
[alreadyInSave:protected] =>
[alreadyInValidation:protected] =>
[validationFailures:protected] => Array
(
)
[_new:BaseObject:private] =>
[_deleted:BaseObject:private] =>
[modifiedColumns:protected] => Array
(
)
)
[47] => Category Object
(
[languages:protected] =>
[bok_resources:protected] =>
[bok_topics:protected] =>
[bok_keywords:protected] =>
[id:protected] => 47
[type:protected] => category
[parent:protected] => 2
[label:protected] => Bricklayer
[alreadyInSave:protected] =>
[alreadyInValidation:protected] =>
[validationFailures:protected] => Array
(
)
[_new:BaseObject:private] =>
[_deleted:BaseObject:private] =>
[modifiedColumns:protected] => Array
(
)
)
[48] => Category Object
(
[languages:protected] =>
[bok_resources:protected] =>
[bok_topics:protected] =>
[bok_keywords:protected] =>
[id:protected] => 48
[type:protected] => category
[parent:protected] => 2
[label:protected] => Cabinetmaker
[alreadyInSave:protected] =>
[alreadyInValidation:protected] =>
[validationFailures:protected] => Array
(
)
[_new:BaseObject:private] =>
[_deleted:BaseObject:private] =>
[modifiedColumns:protected] => Array
(
)
)
[49] => Category Object
(
[languages:protected] =>
[bok_resources:protected] =>
[bok_topics:protected] =>
[bok_keywords:protected] =>
[id:protected] => 49
[type:protected] => category
[parent:protected] => 2
[label:protected] => Carpenter
[alreadyInSave:protected] =>
[alreadyInValidation:protected] =>
[validationFailures:protected] => Array
(
)
[_new:BaseObject:private] =>
[_deleted:BaseObject:private] =>
[modifiedColumns:protected] => Array
(
)
)
[50] => Category Object
(
[languages:protected] =>
[bok_resources:protected] =>
[bok_topics:protected] =>
[bok_keywords:protected] =>
[id:protected] => 50
[type:protected] => category
[parent:protected] => 2
[label:protected] => Carpet Layer
[alreadyInSave:protected] =>
[alreadyInValidation:protected] =>
[validationFailures:protected] => Array
(
)
[_new:BaseObject:private] =>
[_deleted:BaseObject:private] =>
[modifiedColumns:protected] => Array
(
)
)
[51] => Category Object
(
[languages:protected] =>
[bok_resources:protected] =>
[bok_topics:protected] =>
[bok_keywords:protected] =>
[id:protected] => 51
[type:protected] => category
[parent:protected] => 2
[label:protected] => Cement Mason
[alreadyInSave:protected] =>
[alreadyInValidation:protected] =>
[validationFailures:protected] => Array
(
)
[_new:BaseObject:private] =>
[_deleted:BaseObject:private] =>
[modifiedColumns:protected] => Array
(
)
)
[52] => Category Object
(
[languages:protected] =>
[bok_resources:protected] =>
[bok_topics:protected] =>
[bok_keywords:protected] =>
[id:protected] => 52
[type:protected] => category
[parent:protected] => 2
[label:protected] => Commercial Diver
[alreadyInSave:protected] =>
[alreadyInValidation:protected] =>
[validationFailures:protected] => Array
(
)
[_new:BaseObject:private] =>
[_deleted:BaseObject:private] =>
[modifiedColumns:protected] => Array
(
)
)
[53] => Category Object
(
[languages:protected] =>
[bok_resources:protected] =>
[bok_topics:protected] =>
[bok_keywords:protected] =>
[id:protected] => 53
[type:protected] => category
[parent:protected] => 2
[label:protected] => Concrete Polisher
[alreadyInSave:protected] =>
[alreadyInValidation:protected] =>
[validationFailures:protected] => Array
(
)
[_new:BaseObject:private] =>
[_deleted:BaseObject:private] =>
[modifiedColumns:protected] => Array
(
)
)
[54] => Category Object
(
[languages:protected] =>
[bok_resources:protected] =>
[bok_topics:protected] =>
[bok_keywords:protected] =>
[id:protected] => 54
[type:protected] => category
[parent:protected] => 2
[label:protected] => Drywall Applicator Specialist
[alreadyInSave:protected] =>
[alreadyInValidation:protected] =>
[validationFailures:protected] => Array
(
)
[_new:BaseObject:private] =>
[_deleted:BaseObject:private] =>
[modifiedColumns:protected] => Array
(
)
)
[55] => Category Object
(
[languages:protected] =>
[bok_resources:protected] =>
[bok_topics:protected] =>
[bok_keywords:protected] =>
[id:protected] => 55
[type:protected] => category
[parent:protected] => 2
[label:protected] => Electrical Worker
[alreadyInSave:protected] =>
[alreadyInValidation:protected] =>
[validationFailures:protected] => Array
(
)
[_new:BaseObject:private] =>
[_deleted:BaseObject:private] =>
[modifiedColumns:protected] => Array
(
)
)
[56] => Category Object
(
[languages:protected] =>
[bok_resources:protected] =>
[bok_topics:protected] =>
[bok_keywords:protected] =>
[id:protected] => 56
[type:protected] => category
[parent:protected] => 2
[label:protected] => Elevator Constructor
[alreadyInSave:protected] =>
[alreadyInValidation:protected] =>
[validationFailures:protected] => Array
(
)
[_new:BaseObject:private] =>
[_deleted:BaseObject:private] =>
[modifiedColumns:protected] => Array
(
)
)
[57] => Category Object
(
[languages:protected] =>
[bok_resources:protected] =>
[bok_topics:protected] =>
[bok_keywords:protected] =>
[id:protected] => 57
[type:protected] => category
[parent:protected] => 2
[label:protected] => Flagger
[alreadyInSave:protected] =>
[alreadyInValidation:protected] =>
[validationFailures:protected] => Array
(
)
[_new:BaseObject:private] =>
[_deleted:BaseObject:private] =>
[modifiedColumns:protected] => Array
(
)
)
[58] => Category Object
(
[languages:protected] =>
[bok_resources:protected] =>
[bok_topics:protected] =>
[bok_keywords:protected] =>
[id:protected] => 58
[type:protected] => category
[parent:protected] => 2
[label:protected] => Glazier
[alreadyInSave:protected] =>
[alreadyInValidation:protected] =>
[validationFailures:protected] => Array
(
)
[_new:BaseObject:private] =>
[_deleted:BaseObject:private] =>
[modifiedColumns:protected] => Array
(
)
)
[59] => Category Object
(
[languages:protected] =>
[bok_resources:protected] =>
[bok_topics:protected] =>
[bok_keywords:protected] =>
[id:protected] => 59
[type:protected] => category
[parent:protected] => 2
[label:protected] => Hazardous Waste Cleanup
[alreadyInSave:protected] =>
[alreadyInValidation:protected] =>
[validationFailures:protected] => Array
(
)
[_new:BaseObject:private] =>
[_deleted:BaseObject:private] =>
[modifiedColumns:protected] => Array
(
)
)
[60] => Category Object
(
[languages:protected] =>
[bok_resources:protected] =>
[bok_topics:protected] =>
[bok_keywords:protected] =>
[id:protected] => 60
[type:protected] => category
[parent:protected] => 2
[label:protected] => HVAC
[alreadyInSave:protected] =>
[alreadyInValidation:protected] =>
[validationFailures:protected] => Array
(
)
[_new:BaseObject:private] =>
[_deleted:BaseObject:private] =>
[modifiedColumns:protected] => Array
(
)
)
[61] => Category Object
(
[languages:protected] =>
[bok_resources:protected] =>
[bok_topics:protected] =>
[bok_keywords:protected] =>
[id:protected] => 61
[type:protected] => category
[parent:protected] => 2
[label:protected] => Interior Systems Carpenter
[alreadyInSave:protected] =>
[alreadyInValidation:protected] =>
[validationFailures:protected] => Array
(
)
[_new:BaseObject:private] =>
[_deleted:BaseObject:private] =>
[modifiedColumns:protected] => Array
(
)
)
[64] => Category Object
(
[languages:protected] =>
[bok_resources:protected] =>
[bok_topics:protected] =>
[bok_keywords:protected] =>
[id:protected] => 64
[type:protected] => category
[parent:protected] => 2
[label:protected] => Laborer
[alreadyInSave:protected] =>
[alreadyInValidation:protected] =>
[validationFailures:protected] => Array
(
)
[_new:BaseObject:private] =>
[_deleted:BaseObject:private] =>
[modifiedColumns:protected] => Array
(
)
)
[65] => Category Object
(
[languages:protected] =>
[bok_resources:protected] =>
[bok_topics:protected] =>
[bok_keywords:protected] =>
[id:protected] => 65
[type:protected] => category
[parent:protected] => 2
[label:protected] => Landscaper
[alreadyInSave:protected] =>
[alreadyInValidation:protected] =>
[validationFailures:protected] => Array
(
)
[_new:BaseObject:private] =>
[_deleted:BaseObject:private] =>
[modifiedColumns:protected] => Array
(
)
)
[66] => Category Object
(
[languages:protected] =>
[bok_resources:protected] =>
[bok_topics:protected] =>
[bok_keywords:protected] =>
[id:protected] => 66
[type:protected] => category
[parent:protected] => 2
[label:protected] => Lather
[alreadyInSave:protected] =>
[alreadyInValidation:protected] =>
[validationFailures:protected] => Array
(
)
[_new:BaseObject:private] =>
[_deleted:BaseObject:private] =>
[modifiedColumns:protected] => Array
(
)
)
[67] => Category Object
(
[languages:protected] =>
[bok_resources:protected] =>
[bok_topics:protected] =>
[bok_keywords:protected] =>
[id:protected] => 67
[type:protected] => category
[parent:protected] => 2
[label:protected] => Lead Abatement Worker
[alreadyInSave:protected] =>
[alreadyInValidation:protected] =>
[validationFailures:protected] => Array
(
)
[_new:BaseObject:private] =>
[_deleted:BaseObject:private] =>
[modifiedColumns:protected] => Array
(
)
)
[68] => Category Object
(
[languages:protected] =>
[bok_resources:protected] =>
[bok_topics:protected] =>
[bok_keywords:protected] =>
[id:protected] => 68
[type:protected] => category
[parent:protected] => 2
[label:protected] => Maintenance Worker
[alreadyInSave:protected] =>
[alreadyInValidation:protected] =>
[validationFailures:protected] => Array
(
)
[_new:BaseObject:private] =>
[_deleted:BaseObject:private] =>
[modifiedColumns:protected] => Array
(
)
)
[69] => Category Object
(
[languages:protected] =>
[bok_resources:protected] =>
[bok_topics:protected] =>
[bok_keywords:protected] =>
[id:protected] => 69
[type:protected] => category
[parent:protected] => 2
[label:protected] => Millwright
[alreadyInSave:protected] =>
[alreadyInValidation:protected] =>
[validationFailures:protected] => Array
(
)
[_new:BaseObject:private] =>
[_deleted:BaseObject:private] =>
[modifiedColumns:protected] => Array
(
)
)
[70] => Category Object
(
[languages:protected] =>
[bok_resources:protected] =>
[bok_topics:protected] =>
[bok_keywords:protected] =>
[id:protected] => 70
[type:protected] => category
[parent:protected] => 2
[label:protected] => Operating Engineer
[alreadyInSave:protected] =>
[alreadyInValidation:protected] =>
[validationFailures:protected] => Array
(
)
[_new:BaseObject:private] =>
[_deleted:BaseObject:private] =>
[modifiedColumns:protected] => Array
(
)
)
[71] => Category Object
(
[languages:protected] =>
[bok_resources:protected] =>
[bok_topics:protected] =>
[bok_keywords:protected] =>
[id:protected] => 71
[type:protected] => category
[parent:protected] => 2
[label:protected] => Painter
[alreadyInSave:protected] =>
[alreadyInValidation:protected] =>
[validationFailures:protected] => Array
(
)
[_new:BaseObject:private] =>
[_deleted:BaseObject:private] =>
[modifiedColumns:protected] => Array
(
)
)
[72] => Category Object
(
[languages:protected] =>
[bok_resources:protected] =>
[bok_topics:protected] =>
[bok_keywords:protected] =>
[id:protected] => 72
[type:protected] => category
[parent:protected] => 2
[label:protected] => Paper Hanger
[alreadyInSave:protected] =>
[alreadyInValidation:protected] =>
[validationFailures:protected] => Array
(
)
[_new:BaseObject:private] =>
[_deleted:BaseObject:private] =>
[modifiedColumns:protected] => Array
(
)
)
[73] => Category Object
(
[languages:protected] =>
[bok_resources:protected] =>
[bok_topics:protected] =>
[bok_keywords:protected] =>
[id:protected] => 73
[type:protected] => category
[parent:protected] => 2
[label:protected] => PCC/Restoration
[alreadyInSave:protected] =>
[alreadyInValidation:protected] =>
[validationFailures:protected] => Array
(
)
[_new:BaseObject:private] =>
[_deleted:BaseObject:private] =>
[modifiedColumns:protected] => Array
(
)
)
[74] => Category Object
(
[languages:protected] =>
[bok_resources:protected] =>
[bok_topics:protected] =>
[bok_keywords:protected] =>
[id:protected] => 74
[type:protected] => category
[parent:protected] => 2
[label:protected] => Pile Driver
[alreadyInSave:protected] =>
[alreadyInValidation:protected] =>
[validationFailures:protected] => Array
(
)
[_new:BaseObject:private] =>
[_deleted:BaseObject:private] =>
[modifiedColumns:protected] => Array
(
)
)
[75] => Category Object
(
[languages:protected] =>
[bok_resources:protected] =>
[bok_topics:protected] =>
[bok_keywords:protected] =>
[id:protected] => 75
[type:protected] => category
[parent:protected] => 2
[label:protected] => Plasterer
[alreadyInSave:protected] =>
[alreadyInValidation:protected] =>
[validationFailures:protected] => Array
(
)
[_new:BaseObject:private] =>
[_deleted:BaseObject:private] =>
[modifiedColumns:protected] => Array
(
)
)
[76] => Category Object
(
[languages:protected] =>
[bok_resources:protected] =>
[bok_topics:protected] =>
[bok_keywords:protected] =>
[id:protected] => 76
[type:protected] => category
[parent:protected] => 2
[label:protected] => Plumber/Pipefitter
[alreadyInSave:protected] =>
[alreadyInValidation:protected] =>
[validationFailures:protected] => Array
(
)
[_new:BaseObject:private] =>
[_deleted:BaseObject:private] =>
[modifiedColumns:protected] => Array
(
)
)
[77] => Category Object
(
[languages:protected] =>
[bok_resources:protected] =>
[bok_topics:protected] =>
[bok_keywords:protected] =>
[id:protected] => 77
[type:protected] => category
[parent:protected] => 2
[label:protected] => Refractory Worker
[alreadyInSave:protected] =>
[alreadyInValidation:protected] =>
[validationFailures:protected] => Array
(
)
[_new:BaseObject:private] =>
[_deleted:BaseObject:private] =>
[modifiedColumns:protected] => Array
(
)
)
[63] => Category Object
(
[languages:protected] =>
[bok_resources:protected] =>
[bok_topics:protected] =>
[bok_keywords:protected] =>
[id:protected] => 63
[type:protected] => category
[parent:protected] => 2
[label:protected] => Reinforcing Ironworker
[alreadyInSave:protected] =>
[alreadyInValidation:protected] =>
[validationFailures:protected] => Array
(
)
[_new:BaseObject:private] =>
[_deleted:BaseObject:private] =>
[modifiedColumns:protected] => Array
(
)
)
[78] => Category Object
(
[languages:protected] =>
[bok_resources:protected] =>
[bok_topics:protected] =>
[bok_keywords:protected] =>
[id:protected] => 78
[type:protected] => category
[parent:protected] => 2
[label:protected] => Roofer/Waterproofer
[alreadyInSave:protected] =>
[alreadyInValidation:protected] =>
[validationFailures:protected] => Array
(
)
[_new:BaseObject:private] =>
[_deleted:BaseObject:private] =>
[modifiedColumns:protected] => Array
(
)
)
[79] => Category Object
(
[languages:protected] =>
[bok_resources:protected] =>
[bok_topics:protected] =>
[bok_keywords:protected] =>
[id:protected] => 79
[type:protected] => category
[parent:protected] => 2
[label:protected] => Scaffold Erector
[alreadyInSave:protected] =>
[alreadyInValidation:protected] =>
[validationFailures:protected] => Array
(
)
[_new:BaseObject:private] =>
[_deleted:BaseObject:private] =>
[modifiedColumns:protected] => Array
(
)
)
[80] => Category Object
(
[languages:protected] =>
[bok_resources:protected] =>
[bok_topics:protected] =>
[bok_keywords:protected] =>
[id:protected] => 80
[type:protected] => category
[parent:protected] => 2
[label:protected] => Sheetmetal Worker
[alreadyInSave:protected] =>
[alreadyInValidation:protected] =>
[validationFailures:protected] => Array
(
)
[_new:BaseObject:private] =>
[_deleted:BaseObject:private] =>
[modifiedColumns:protected] => Array
(
)
)
[81] => Category Object
(
[languages:protected] =>
[bok_resources:protected] =>
[bok_topics:protected] =>
[bok_keywords:protected] =>
[id:protected] => 81
[type:protected] => category
[parent:protected] => 2
[label:protected] => Sprinkler Fitter
[alreadyInSave:protected] =>
[alreadyInValidation:protected] =>
[validationFailures:protected] => Array
(
)
[_new:BaseObject:private] =>
[_deleted:BaseObject:private] =>
[modifiedColumns:protected] => Array
(
)
)
[82] => Category Object
(
[languages:protected] =>
[bok_resources:protected] =>
[bok_topics:protected] =>
[bok_keywords:protected] =>
[id:protected] => 82
[type:protected] => category
[parent:protected] => 2
[label:protected] => Stonemason
[alreadyInSave:protected] =>
[alreadyInValidation:protected] =>
[validationFailures:protected] => Array
(
)
[_new:BaseObject:private] =>
[_deleted:BaseObject:private] =>
[modifiedColumns:protected] => Array
(
)
)
[62] => Category Object
(
[languages:protected] =>
[bok_resources:protected] =>
[bok_topics:protected] =>
[bok_keywords:protected] =>
[id:protected] => 62
[type:protected] => category
[parent:protected] => 2
[label:protected] => Structural Ironworker
[alreadyInSave:protected] =>
[alreadyInValidation:protected] =>
[validationFailures:protected] => Array
(
)
[_new:BaseObject:private] =>
[_deleted:BaseObject:private] =>
[modifiedColumns:protected] => Array
(
)
)
[83] => Category Object
(
[languages:protected] =>
[bok_resources:protected] =>
[bok_topics:protected] =>
[bok_keywords:protected] =>
[id:protected] => 83
[type:protected] => category
[parent:protected] => 2
[label:protected] => Terrazzo Worker
[alreadyInSave:protected] =>
[alreadyInValidation:protected] =>
[validationFailures:protected] => Array
(
)
[_new:BaseObject:private] =>
[_deleted:BaseObject:private] =>
[modifiedColumns:protected] => Array
(
)
)
[84] => Category Object
(
[languages:protected] =>
[bok_resources:protected] =>
[bok_topics:protected] =>
[bok_keywords:protected] =>
[id:protected] => 84
[type:protected] => category
[parent:protected] => 2
[label:protected] => Tile Setter
[alreadyInSave:protected] =>
[alreadyInValidation:protected] =>
[validationFailures:protected] => Array
(
)
[_new:BaseObject:private] =>
[_deleted:BaseObject:private] =>
[modifiedColumns:protected] => Array
(
)
)
[85] => Category Object
(
[languages:protected] =>
[bok_resources:protected] =>
[bok_topics:protected] =>
[bok_keywords:protected] =>
[id:protected] => 85
[type:protected] => category
[parent:protected] => 2
[label:protected] => Truck Driver
[alreadyInSave:protected] =>
[alreadyInValidation:protected] =>
[validationFailures:protected] => Array
(
)
[_new:BaseObject:private] =>
[_deleted:BaseObject:private] =>
[modifiedColumns:protected] => Array
(
)
)
[86] => Category Object
(
[languages:protected] =>
[bok_resources:protected] =>
[bok_topics:protected] =>
[bok_keywords:protected] =>
[id:protected] => 86
[type:protected] => category
[parent:protected] => 2
[label:protected] => Welder
[alreadyInSave:protected] =>
[alreadyInValidation:protected] =>
[validationFailures:protected] => Array
(
)
[_new:BaseObject:private] =>
[_deleted:BaseObject:private] =>
[modifiedColumns:protected] => Array
(
)
)
[87] => Category Object
(
[languages:protected] =>
[bok_resources:protected] =>
[bok_topics:protected] =>
[bok_keywords:protected] =>
[id:protected] => 87
[type:protected] => category
[parent:protected] => 3
[label:protected] => Commercial & Institutional
[alreadyInSave:protected] =>
[alreadyInValidation:protected] =>
[validationFailures:protected] => Array
(
)
[_new:BaseObject:private] =>
[_deleted:BaseObject:private] =>
[modifiedColumns:protected] => Array
(
)
)
[88] => Category Object
(
[languages:protected] =>
[bok_resources:protected] =>
[bok_topics:protected] =>
[bok_keywords:protected] =>
[id:protected] => 88
[type:protected] => category
[parent:protected] => 3
[label:protected] => Demolition
[alreadyInSave:protected] =>
[alreadyInValidation:protected] =>
[validationFailures:protected] => Array
(
)
[_new:BaseObject:private] =>
[_deleted:BaseObject:private] =>
[modifiedColumns:protected] => Array
(
)
)
[89] => Category Object
(
[languages:protected] =>
[bok_resources:protected] =>
[bok_topics:protected] =>
[bok_keywords:protected] =>
[id:protected] => 89
[type:protected] => category
[parent:protected] => 3
[label:protected] => Disasters
[alreadyInSave:protected] =>
[alreadyInValidation:protected] =>
[validationFailures:protected] => Array
(
)
[_new:BaseObject:private] =>
[_deleted:BaseObject:private] =>
[modifiedColumns:protected] => Array
(
)
)
[91] => Category Object
(
[languages:protected] =>
[bok_resources:protected] =>
[bok_topics:protected] =>
[bok_keywords:protected] =>
[id:protected] => 91
[type:protected] => category
[parent:protected] => 3
[label:protected] => Heavy & Highway
[alreadyInSave:protected] =>
[alreadyInValidation:protected] =>
[validationFailures:protected] => Array
(
)
[_new:BaseObject:private] =>
[_deleted:BaseObject:private] =>
[modifiedColumns:protected] => Array
(
)
)
[90] => Category Object
(
[languages:protected] =>
[bok_resources:protected] =>
[bok_topics:protected] =>
[bok_keywords:protected] =>
[id:protected] => 90
[type:protected] => category
[parent:protected] => 3
[label:protected] => Industrial
[alreadyInSave:protected] =>
[alreadyInValidation:protected] =>
[validationFailures:protected] => Array
(
)
[_new:BaseObject:private] =>
[_deleted:BaseObject:private] =>
[modifiedColumns:protected] => Array
(
)
)
[92] => Category Object
(
[languages:protected] =>
[bok_resources:protected] =>
[bok_topics:protected] =>
[bok_keywords:protected] =>
[id:protected] => 92
[type:protected] => category
[parent:protected] => 3
[label:protected] => LEED/Green Construction
[alreadyInSave:protected] =>
[alreadyInValidation:protected] =>
[validationFailures:protected] => Array
(
)
[_new:BaseObject:private] =>
[_deleted:BaseObject:private] =>
[modifiedColumns:protected] => Array
(
)
)
[93] => Category Object
(
[languages:protected] =>
[bok_resources:protected] =>
[bok_topics:protected] =>
[bok_keywords:protected] =>
[id:protected] => 93
[type:protected] => category
[parent:protected] => 3
[label:protected] => Renovations
[alreadyInSave:protected] =>
[alreadyInValidation:protected] =>
[validationFailures:protected] => Array
(
)
[_new:BaseObject:private] =>
[_deleted:BaseObject:private] =>
[modifiedColumns:protected] => Array
(
)
)
[94] => Category Object
(
[languages:protected] =>
[bok_resources:protected] =>
[bok_topics:protected] =>
[bok_keywords:protected] =>
[id:protected] => 94
[type:protected] => category
[parent:protected] => 3
[label:protected] => Residential
[alreadyInSave:protected] =>
[alreadyInValidation:protected] =>
[validationFailures:protected] => Array
(
)
[_new:BaseObject:private] =>
[_deleted:BaseObject:private] =>
[modifiedColumns:protected] => Array
(
)
)
[95] => Category Object
(
[languages:protected] =>
[bok_resources:protected] =>
[bok_topics:protected] =>
[bok_keywords:protected] =>
[id:protected] => 95
[type:protected] => category
[parent:protected] => 3
[label:protected] => Underground
[alreadyInSave:protected] =>
[alreadyInValidation:protected] =>
[validationFailures:protected] => Array
(
)
[_new:BaseObject:private] =>
[_deleted:BaseObject:private] =>
[modifiedColumns:protected] => Array
(
)
)
)
[categories_initialized:protected] => 1
[mapped_items:protected] =>
[content:protected] =>
[files:protected] =>
[language:protected] => Language Object
(
[id:protected] => 1
[code:protected] => en
[name:protected] => English
[alreadyInSave:protected] =>
[alreadyInValidation:protected] =>
[validationFailures:protected] => Array
(
)
[_new:BaseObject:private] =>
[_deleted:BaseObject:private] =>
[modifiedColumns:protected] => Array
(
)
)
[old_record:protected] =>
[id:protected] => 4426
[old_id:protected] =>
[elcosh_id:protected] => d001656
[type:protected] => document
[display_type:protected] => HTML only (and links)
[user_id:protected] => 0
[language_id:protected] => 1
[tagging_id:protected] => Mike Aguilar
[priority_id:protected] => 1
[title:protected] => Construction Dive -- DeWalt's Jobsite Pro headphones recalled for fire hazards
[total_pages:protected] => 1
[billed_pages:protected] => 1
[publication_number:protected] =>
[part_of:protected] =>
[keywords:protected] => DeWalt, Fire Hazards, recall, headphones
[comments:protected] =>
[summary:protected] => A recall notice by the United States Consumer Product Safety Commission affects over 300,000 DeWalt Jobsite Pro Headphones. The recall is a result of a malfunction that can cause earbuds to overheat while charging or during use, leading to fire and burn hazards.
[transition_comments:protected] =>
[external_link:protected] => https://www.constructiondive.com/news/dewalts-jobsite-pro-headphones-recalled-for-fire-hazards/611248/?utm_source=Sailthru&utm_medium=email&utm_campaign=Issue:%202021-12-10%20Construction%20Dive%20Newsletter%20%5Bissue:38532%5D&utm_term=Construction%20Dive
[consol_link:protected] =>
[more_like_this:protected] =>
[permission_given_by:protected] =>
[published:protected] => T
[billable:protected] => F
[img_name:protected] =>
[img_ext:protected] =>
[img_width:protected] =>
[img_height:protected] =>
[img_credit:protected] =>
[img_practice:protected] =>
[vid_source_id:protected] =>
[vid_running_time:protected] =>
[vid_intended_audience:protected] =>
[vid_acquisition_info:protected] =>
[vid_cost:protected] =>
[vid_producer:protected] =>
[vid_filename:protected] =>
[vid_filename_downloadable:protected] =>
[date_summary:protected] =>
[date_permission_requested:protected] =>
[date_permission_received:protected] =>
[date_review_needed:protected] =>
[date_received:protected] => 12/13/21
[date_completed:protected] => 12/13/21
[date_billed:protected] =>
[date_modified:protected] => 12/13/21
[collBokExports:protected] =>
[lastBokExportCriteria:BaseElcoshItem:private] =>
[alreadyInSave:protected] =>
[alreadyInValidation:protected] =>
[validationFailures:protected] => Array
(
)
[_new:BaseObject:private] =>
[_deleted:BaseObject:private] =>
[modifiedColumns:protected] => Array
(
)
)
)
)
[new_images] => Array
(
[0] => Search_Result Object
(
[title] => Morning Toolbox Talk
[image] => /record/images/4003-p.jpg
[blurb] => This photo is from an early morning toolbox talk on a construction job in Mclean, Virginia. It is being delivered in English and Spanish....
[category] => Array
(
[0] => 20
[1] => 51
[2] => 57
[3] => 64
[4] => 70
[5] => 63
[6] => 78
[7] => 82
[8] => 62
[9] => 87
[10] => 88
[11] => 89
[12] => 91
[13] => 90
[14] => 93
[15] => 94
[16] => 97
)
[labels] => Array
(
[0] => Safety Culture
[1] => Work Environment
[2] => Hazards
[3] => Cement Mason
[4] => Trades
[5] => Flagger
[7] => Laborer
[9] => Operating Engineer
[11] => Reinforcing Ironworker
[13] => Roofer/Waterproofer
[15] => Stonemason
[17] => Structural Ironworker
[19] => Commercial & Institutional
[20] => Jobsites
[21] => Demolition
[23] => Disasters
[25] => Heavy & Highway
[27] => Industrial
[29] => Renovations
[31] => Residential
[33] => Images
[34] => Media
[35] => Media & Documents
)
[type] => Images
[sub_category] =>
[url] => /image/4003/i002691/Morning%2BToolbox%2BTalk.html
[item:protected] => ImageRecord Object
(
[records:protected] => Array
(
)
[recordId:protected] =>
[searchWordClass:protected] =>
[searchWordPeerClass:protected] =>
[bok_record:protected] =>
[authors:protected] =>
[organizations:protected] =>
[collections:protected] =>
[categories:protected] => Array
(
[20] => Category Object
(
[languages:protected] =>
[bok_resources:protected] =>
[bok_topics:protected] =>
[bok_keywords:protected] =>
[id:protected] => 20
[type:protected] => category
[parent:protected] => 7
[label:protected] => Safety Culture
[alreadyInSave:protected] =>
[alreadyInValidation:protected] =>
[validationFailures:protected] => Array
(
)
[_new:BaseObject:private] =>
[_deleted:BaseObject:private] =>
[modifiedColumns:protected] => Array
(
)
)
[51] => Category Object
(
[languages:protected] =>
[bok_resources:protected] =>
[bok_topics:protected] =>
[bok_keywords:protected] =>
[id:protected] => 51
[type:protected] => category
[parent:protected] => 2
[label:protected] => Cement Mason
[alreadyInSave:protected] =>
[alreadyInValidation:protected] =>
[validationFailures:protected] => Array
(
)
[_new:BaseObject:private] =>
[_deleted:BaseObject:private] =>
[modifiedColumns:protected] => Array
(
)
)
[57] => Category Object
(
[languages:protected] =>
[bok_resources:protected] =>
[bok_topics:protected] =>
[bok_keywords:protected] =>
[id:protected] => 57
[type:protected] => category
[parent:protected] => 2
[label:protected] => Flagger
[alreadyInSave:protected] =>
[alreadyInValidation:protected] =>
[validationFailures:protected] => Array
(
)
[_new:BaseObject:private] =>
[_deleted:BaseObject:private] =>
[modifiedColumns:protected] => Array
(
)
)
[64] => Category Object
(
[languages:protected] =>
[bok_resources:protected] =>
[bok_topics:protected] =>
[bok_keywords:protected] =>
[id:protected] => 64
[type:protected] => category
[parent:protected] => 2
[label:protected] => Laborer
[alreadyInSave:protected] =>
[alreadyInValidation:protected] =>
[validationFailures:protected] => Array
(
)
[_new:BaseObject:private] =>
[_deleted:BaseObject:private] =>
[modifiedColumns:protected] => Array
(
)
)
[70] => Category Object
(
[languages:protected] =>
[bok_resources:protected] =>
[bok_topics:protected] =>
[bok_keywords:protected] =>
[id:protected] => 70
[type:protected] => category
[parent:protected] => 2
[label:protected] => Operating Engineer
[alreadyInSave:protected] =>
[alreadyInValidation:protected] =>
[validationFailures:protected] => Array
(
)
[_new:BaseObject:private] =>
[_deleted:BaseObject:private] =>
[modifiedColumns:protected] => Array
(
)
)
[63] => Category Object
(
[languages:protected] =>
[bok_resources:protected] =>
[bok_topics:protected] =>
[bok_keywords:protected] =>
[id:protected] => 63
[type:protected] => category
[parent:protected] => 2
[label:protected] => Reinforcing Ironworker
[alreadyInSave:protected] =>
[alreadyInValidation:protected] =>
[validationFailures:protected] => Array
(
)
[_new:BaseObject:private] =>
[_deleted:BaseObject:private] =>
[modifiedColumns:protected] => Array
(
)
)
[78] => Category Object
(
[languages:protected] =>
[bok_resources:protected] =>
[bok_topics:protected] =>
[bok_keywords:protected] =>
[id:protected] => 78
[type:protected] => category
[parent:protected] => 2
[label:protected] => Roofer/Waterproofer
[alreadyInSave:protected] =>
[alreadyInValidation:protected] =>
[validationFailures:protected] => Array
(
)
[_new:BaseObject:private] =>
[_deleted:BaseObject:private] =>
[modifiedColumns:protected] => Array
(
)
)
[82] => Category Object
(
[languages:protected] =>
[bok_resources:protected] =>
[bok_topics:protected] =>
[bok_keywords:protected] =>
[id:protected] => 82
[type:protected] => category
[parent:protected] => 2
[label:protected] => Stonemason
[alreadyInSave:protected] =>
[alreadyInValidation:protected] =>
[validationFailures:protected] => Array
(
)
[_new:BaseObject:private] =>
[_deleted:BaseObject:private] =>
[modifiedColumns:protected] => Array
(
)
)
[62] => Category Object
(
[languages:protected] =>
[bok_resources:protected] =>
[bok_topics:protected] =>
[bok_keywords:protected] =>
[id:protected] => 62
[type:protected] => category
[parent:protected] => 2
[label:protected] => Structural Ironworker
[alreadyInSave:protected] =>
[alreadyInValidation:protected] =>
[validationFailures:protected] => Array
(
)
[_new:BaseObject:private] =>
[_deleted:BaseObject:private] =>
[modifiedColumns:protected] => Array
(
)
)
[87] => Category Object
(
[languages:protected] =>
[bok_resources:protected] =>
[bok_topics:protected] =>
[bok_keywords:protected] =>
[id:protected] => 87
[type:protected] => category
[parent:protected] => 3
[label:protected] => Commercial & Institutional
[alreadyInSave:protected] =>
[alreadyInValidation:protected] =>
[validationFailures:protected] => Array
(
)
[_new:BaseObject:private] =>
[_deleted:BaseObject:private] =>
[modifiedColumns:protected] => Array
(
)
)
[88] => Category Object
(
[languages:protected] =>
[bok_resources:protected] =>
[bok_topics:protected] =>
[bok_keywords:protected] =>
[id:protected] => 88
[type:protected] => category
[parent:protected] => 3
[label:protected] => Demolition
[alreadyInSave:protected] =>
[alreadyInValidation:protected] =>
[validationFailures:protected] => Array
(
)
[_new:BaseObject:private] =>
[_deleted:BaseObject:private] =>
[modifiedColumns:protected] => Array
(
)
)
[89] => Category Object
(
[languages:protected] =>
[bok_resources:protected] =>
[bok_topics:protected] =>
[bok_keywords:protected] =>
[id:protected] => 89
[type:protected] => category
[parent:protected] => 3
[label:protected] => Disasters
[alreadyInSave:protected] =>
[alreadyInValidation:protected] =>
[validationFailures:protected] => Array
(
)
[_new:BaseObject:private] =>
[_deleted:BaseObject:private] =>
[modifiedColumns:protected] => Array
(
)
)
[91] => Category Object
(
[languages:protected] =>
[bok_resources:protected] =>
[bok_topics:protected] =>
[bok_keywords:protected] =>
[id:protected] => 91
[type:protected] => category
[parent:protected] => 3
[label:protected] => Heavy & Highway
[alreadyInSave:protected] =>
[alreadyInValidation:protected] =>
[validationFailures:protected] => Array
(
)
[_new:BaseObject:private] =>
[_deleted:BaseObject:private] =>
[modifiedColumns:protected] => Array
(
)
)
[90] => Category Object
(
[languages:protected] =>
[bok_resources:protected] =>
[bok_topics:protected] =>
[bok_keywords:protected] =>
[id:protected] => 90
[type:protected] => category
[parent:protected] => 3
[label:protected] => Industrial
[alreadyInSave:protected] =>
[alreadyInValidation:protected] =>
[validationFailures:protected] => Array
(
)
[_new:BaseObject:private] =>
[_deleted:BaseObject:private] =>
[modifiedColumns:protected] => Array
(
)
)
[93] => Category Object
(
[languages:protected] =>
[bok_resources:protected] =>
[bok_topics:protected] =>
[bok_keywords:protected] =>
[id:protected] => 93
[type:protected] => category
[parent:protected] => 3
[label:protected] => Renovations
[alreadyInSave:protected] =>
[alreadyInValidation:protected] =>
[validationFailures:protected] => Array
(
)
[_new:BaseObject:private] =>
[_deleted:BaseObject:private] =>
[modifiedColumns:protected] => Array
(
)
)
[94] => Category Object
(
[languages:protected] =>
[bok_resources:protected] =>
[bok_topics:protected] =>
[bok_keywords:protected] =>
[id:protected] => 94
[type:protected] => category
[parent:protected] => 3
[label:protected] => Residential
[alreadyInSave:protected] =>
[alreadyInValidation:protected] =>
[validationFailures:protected] => Array
(
)
[_new:BaseObject:private] =>
[_deleted:BaseObject:private] =>
[modifiedColumns:protected] => Array
(
)
)
[97] => Category Object
(
[languages:protected] =>
[bok_resources:protected] =>
[bok_topics:protected] =>
[bok_keywords:protected] =>
[id:protected] => 97
[type:protected] => category
[parent:protected] => 5
[label:protected] => Images
[alreadyInSave:protected] =>
[alreadyInValidation:protected] =>
[validationFailures:protected] => Array
(
)
[_new:BaseObject:private] =>
[_deleted:BaseObject:private] =>
[modifiedColumns:protected] => Array
(
)
)
)
[categories_initialized:protected] => 1
[mapped_items:protected] =>
[content:protected] =>
[files:protected] =>
[language:protected] => Language Object
(
[id:protected] => 1
[code:protected] => en
[name:protected] => English
[alreadyInSave:protected] =>
[alreadyInValidation:protected] =>
[validationFailures:protected] => Array
(
)
[_new:BaseObject:private] =>
[_deleted:BaseObject:private] =>
[modifiedColumns:protected] => Array
(
)
)
[old_record:protected] =>
[id:protected] => 4003
[old_id:protected] =>
[elcosh_id:protected] => i002691
[type:protected] => image
[display_type:protected] => Image
[user_id:protected] => 0
[language_id:protected] => 1
[tagging_id:protected] => Bruce Lippy
[priority_id:protected] => 1
[title:protected] => Morning Toolbox Talk
[total_pages:protected] => 0
[billed_pages:protected] => 0
[publication_number:protected] =>
[part_of:protected] =>
[keywords:protected] => toolbox talk, tailgate talk, Spanish, bilingual
[comments:protected] =>
[summary:protected] => This photo is from an early morning toolbox talk on a construction job in Mclean, Virginia. It is being delivered in English and Spanish.
[transition_comments:protected] =>
[external_link:protected] =>
[consol_link:protected] => http://www.cpwrconstructionsolutions.org/electrical/solution/662/worker-training.html
[more_like_this:protected] => d001285,d001304,c000079
[permission_given_by:protected] =>
[published:protected] => T
[billable:protected] => F
[img_name:protected] =>
[img_ext:protected] => jpg
[img_width:protected] =>
[img_height:protected] =>
[img_credit:protected] => Morgan Zavertnik and Hoar Construction
[img_practice:protected] => good
[vid_source_id:protected] =>
[vid_running_time:protected] =>
[vid_intended_audience:protected] =>
[vid_acquisition_info:protected] =>
[vid_cost:protected] =>
[vid_producer:protected] =>
[vid_filename:protected] =>
[vid_filename_downloadable:protected] =>
[date_summary:protected] => November 2015
[date_permission_requested:protected] =>
[date_permission_received:protected] =>
[date_review_needed:protected] =>
[date_received:protected] => 03/02/16
[date_completed:protected] => 03/02/16
[date_billed:protected] =>
[date_modified:protected] => 03/02/16
[collBokExports:protected] =>
[lastBokExportCriteria:BaseElcoshItem:private] =>
[alreadyInSave:protected] =>
[alreadyInValidation:protected] =>
[validationFailures:protected] => Array
(
)
[_new:BaseObject:private] =>
[_deleted:BaseObject:private] =>
[modifiedColumns:protected] => Array
(
)
)
)
[1] => Search_Result Object
(
[title] => Toolbox talk - crew view
[image] => /record/images/4005-p.jpg
[blurb] => Photo of crew listening to a toolbox safety talk before starting work....
[category] => Array
(
[0] => 97
[1] => 20
[2] => 47
[3] => 49
[4] => 51
[5] => 55
[6] => 61
[7] => 64
[8] => 71
[9] => 75
[10] => 63
[11] => 79
[12] => 62
[13] => 87
[14] => 88
[15] => 91
[16] => 90
[17] => 93
[18] => 94
[19] => 95
)
[labels] => Array
(
[0] => Images
[1] => Media
[2] => Media & Documents
[3] => Safety Culture
[4] => Work Environment
[5] => Hazards
[6] => Bricklayer
[7] => Trades
[8] => Carpenter
[10] => Cement Mason
[12] => Electrical Worker
[14] => Interior Systems Carpenter
[16] => Laborer
[18] => Painter
[20] => Plasterer
[22] => Reinforcing Ironworker
[24] => Scaffold Erector
[26] => Structural Ironworker
[28] => Commercial & Institutional
[29] => Jobsites
[30] => Demolition
[32] => Heavy & Highway
[34] => Industrial
[36] => Renovations
[38] => Residential
[40] => Underground
)
[type] => Images
[sub_category] =>
[url] => /image/4005/i002692/Toolbox%2Btalk%2B-%2Bcrew%2Bview.html
[item:protected] => ImageRecord Object
(
[records:protected] => Array
(
)
[recordId:protected] =>
[searchWordClass:protected] =>
[searchWordPeerClass:protected] =>
[bok_record:protected] =>
[authors:protected] =>
[organizations:protected] =>
[collections:protected] =>
[categories:protected] => Array
(
[97] => Category Object
(
[languages:protected] =>
[bok_resources:protected] =>
[bok_topics:protected] =>
[bok_keywords:protected] =>
[id:protected] => 97
[type:protected] => category
[parent:protected] => 5
[label:protected] => Images
[alreadyInSave:protected] =>
[alreadyInValidation:protected] =>
[validationFailures:protected] => Array
(
)
[_new:BaseObject:private] =>
[_deleted:BaseObject:private] =>
[modifiedColumns:protected] => Array
(
)
)
[20] => Category Object
(
[languages:protected] =>
[bok_resources:protected] =>
[bok_topics:protected] =>
[bok_keywords:protected] =>
[id:protected] => 20
[type:protected] => category
[parent:protected] => 7
[label:protected] => Safety Culture
[alreadyInSave:protected] =>
[alreadyInValidation:protected] =>
[validationFailures:protected] => Array
(
)
[_new:BaseObject:private] =>
[_deleted:BaseObject:private] =>
[modifiedColumns:protected] => Array
(
)
)
[47] => Category Object
(
[languages:protected] =>
[bok_resources:protected] =>
[bok_topics:protected] =>
[bok_keywords:protected] =>
[id:protected] => 47
[type:protected] => category
[parent:protected] => 2
[label:protected] => Bricklayer
[alreadyInSave:protected] =>
[alreadyInValidation:protected] =>
[validationFailures:protected] => Array
(
)
[_new:BaseObject:private] =>
[_deleted:BaseObject:private] =>
[modifiedColumns:protected] => Array
(
)
)
[49] => Category Object
(
[languages:protected] =>
[bok_resources:protected] =>
[bok_topics:protected] =>
[bok_keywords:protected] =>
[id:protected] => 49
[type:protected] => category
[parent:protected] => 2
[label:protected] => Carpenter
[alreadyInSave:protected] =>
[alreadyInValidation:protected] =>
[validationFailures:protected] => Array
(
)
[_new:BaseObject:private] =>
[_deleted:BaseObject:private] =>
[modifiedColumns:protected] => Array
(
)
)
[51] => Category Object
(
[languages:protected] =>
[bok_resources:protected] =>
[bok_topics:protected] =>
[bok_keywords:protected] =>
[id:protected] => 51
[type:protected] => category
[parent:protected] => 2
[label:protected] => Cement Mason
[alreadyInSave:protected] =>
[alreadyInValidation:protected] =>
[validationFailures:protected] => Array
(
)
[_new:BaseObject:private] =>
[_deleted:BaseObject:private] =>
[modifiedColumns:protected] => Array
(
)
)
[55] => Category Object
(
[languages:protected] =>
[bok_resources:protected] =>
[bok_topics:protected] =>
[bok_keywords:protected] =>
[id:protected] => 55
[type:protected] => category
[parent:protected] => 2
[label:protected] => Electrical Worker
[alreadyInSave:protected] =>
[alreadyInValidation:protected] =>
[validationFailures:protected] => Array
(
)
[_new:BaseObject:private] =>
[_deleted:BaseObject:private] =>
[modifiedColumns:protected] => Array
(
)
)
[61] => Category Object
(
[languages:protected] =>
[bok_resources:protected] =>
[bok_topics:protected] =>
[bok_keywords:protected] =>
[id:protected] => 61
[type:protected] => category
[parent:protected] => 2
[label:protected] => Interior Systems Carpenter
[alreadyInSave:protected] =>
[alreadyInValidation:protected] =>
[validationFailures:protected] => Array
(
)
[_new:BaseObject:private] =>
[_deleted:BaseObject:private] =>
[modifiedColumns:protected] => Array
(
)
)
[64] => Category Object
(
[languages:protected] =>
[bok_resources:protected] =>
[bok_topics:protected] =>
[bok_keywords:protected] =>
[id:protected] => 64
[type:protected] => category
[parent:protected] => 2
[label:protected] => Laborer
[alreadyInSave:protected] =>
[alreadyInValidation:protected] =>
[validationFailures:protected] => Array
(
)
[_new:BaseObject:private] =>
[_deleted:BaseObject:private] =>
[modifiedColumns:protected] => Array
(
)
)
[71] => Category Object
(
[languages:protected] =>
[bok_resources:protected] =>
[bok_topics:protected] =>
[bok_keywords:protected] =>
[id:protected] => 71
[type:protected] => category
[parent:protected] => 2
[label:protected] => Painter
[alreadyInSave:protected] =>
[alreadyInValidation:protected] =>
[validationFailures:protected] => Array
(
)
[_new:BaseObject:private] =>
[_deleted:BaseObject:private] =>
[modifiedColumns:protected] => Array
(
)
)
[75] => Category Object
(
[languages:protected] =>
[bok_resources:protected] =>
[bok_topics:protected] =>
[bok_keywords:protected] =>
[id:protected] => 75
[type:protected] => category
[parent:protected] => 2
[label:protected] => Plasterer
[alreadyInSave:protected] =>
[alreadyInValidation:protected] =>
[validationFailures:protected] => Array
(
)
[_new:BaseObject:private] =>
[_deleted:BaseObject:private] =>
[modifiedColumns:protected] => Array
(
)
)
[63] => Category Object
(
[languages:protected] =>
[bok_resources:protected] =>
[bok_topics:protected] =>
[bok_keywords:protected] =>
[id:protected] => 63
[type:protected] => category
[parent:protected] => 2
[label:protected] => Reinforcing Ironworker
[alreadyInSave:protected] =>
[alreadyInValidation:protected] =>
[validationFailures:protected] => Array
(
)
[_new:BaseObject:private] =>
[_deleted:BaseObject:private] =>
[modifiedColumns:protected] => Array
(
)
)
[79] => Category Object
(
[languages:protected] =>
[bok_resources:protected] =>
[bok_topics:protected] =>
[bok_keywords:protected] =>
[id:protected] => 79
[type:protected] => category
[parent:protected] => 2
[label:protected] => Scaffold Erector
[alreadyInSave:protected] =>
[alreadyInValidation:protected] =>
[validationFailures:protected] => Array
(
)
[_new:BaseObject:private] =>
[_deleted:BaseObject:private] =>
[modifiedColumns:protected] => Array
(
)
)
[62] => Category Object
(
[languages:protected] =>
[bok_resources:protected] =>
[bok_topics:protected] =>
[bok_keywords:protected] =>
[id:protected] => 62
[type:protected] => category
[parent:protected] => 2
[label:protected] => Structural Ironworker
[alreadyInSave:protected] =>
[alreadyInValidation:protected] =>
[validationFailures:protected] => Array
(
)
[_new:BaseObject:private] =>
[_deleted:BaseObject:private] =>
[modifiedColumns:protected] => Array
(
)
)
[87] => Category Object
(
[languages:protected] =>
[bok_resources:protected] =>
[bok_topics:protected] =>
[bok_keywords:protected] =>
[id:protected] => 87
[type:protected] => category
[parent:protected] => 3
[label:protected] => Commercial & Institutional
[alreadyInSave:protected] =>
[alreadyInValidation:protected] =>
[validationFailures:protected] => Array
(
)
[_new:BaseObject:private] =>
[_deleted:BaseObject:private] =>
[modifiedColumns:protected] => Array
(
)
)
[88] => Category Object
(
[languages:protected] =>
[bok_resources:protected] =>
[bok_topics:protected] =>
[bok_keywords:protected] =>
[id:protected] => 88
[type:protected] => category
[parent:protected] => 3
[label:protected] => Demolition
[alreadyInSave:protected] =>
[alreadyInValidation:protected] =>
[validationFailures:protected] => Array
(
)
[_new:BaseObject:private] =>
[_deleted:BaseObject:private] =>
[modifiedColumns:protected] => Array
(
)
)
[91] => Category Object
(
[languages:protected] =>
[bok_resources:protected] =>
[bok_topics:protected] =>
[bok_keywords:protected] =>
[id:protected] => 91
[type:protected] => category
[parent:protected] => 3
[label:protected] => Heavy & Highway
[alreadyInSave:protected] =>
[alreadyInValidation:protected] =>
[validationFailures:protected] => Array
(
)
[_new:BaseObject:private] =>
[_deleted:BaseObject:private] =>
[modifiedColumns:protected] => Array
(
)
)
[90] => Category Object
(
[languages:protected] =>
[bok_resources:protected] =>
[bok_topics:protected] =>
[bok_keywords:protected] =>
[id:protected] => 90
[type:protected] => category
[parent:protected] => 3
[label:protected] => Industrial
[alreadyInSave:protected] =>
[alreadyInValidation:protected] =>
[validationFailures:protected] => Array
(
)
[_new:BaseObject:private] =>
[_deleted:BaseObject:private] =>
[modifiedColumns:protected] => Array
(
)
)
[93] => Category Object
(
[languages:protected] =>
[bok_resources:protected] =>
[bok_topics:protected] =>
[bok_keywords:protected] =>
[id:protected] => 93
[type:protected] => category
[parent:protected] => 3
[label:protected] => Renovations
[alreadyInSave:protected] =>
[alreadyInValidation:protected] =>
[validationFailures:protected] => Array
(
)
[_new:BaseObject:private] =>
[_deleted:BaseObject:private] =>
[modifiedColumns:protected] => Array
(
)
)
[94] => Category Object
(
[languages:protected] =>
[bok_resources:protected] =>
[bok_topics:protected] =>
[bok_keywords:protected] =>
[id:protected] => 94
[type:protected] => category
[parent:protected] => 3
[label:protected] => Residential
[alreadyInSave:protected] =>
[alreadyInValidation:protected] =>
[validationFailures:protected] => Array
(
)
[_new:BaseObject:private] =>
[_deleted:BaseObject:private] =>
[modifiedColumns:protected] => Array
(
)
)
[95] => Category Object
(
[languages:protected] =>
[bok_resources:protected] =>
[bok_topics:protected] =>
[bok_keywords:protected] =>
[id:protected] => 95
[type:protected] => category
[parent:protected] => 3
[label:protected] => Underground
[alreadyInSave:protected] =>
[alreadyInValidation:protected] =>
[validationFailures:protected] => Array
(
)
[_new:BaseObject:private] =>
[_deleted:BaseObject:private] =>
[modifiedColumns:protected] => Array
(
)
)
)
[categories_initialized:protected] => 1
[mapped_items:protected] =>
[content:protected] =>
[files:protected] =>
[language:protected] => Language Object
(
[id:protected] => 1
[code:protected] => en
[name:protected] => English
[alreadyInSave:protected] =>
[alreadyInValidation:protected] =>
[validationFailures:protected] => Array
(
)
[_new:BaseObject:private] =>
[_deleted:BaseObject:private] =>
[modifiedColumns:protected] => Array
(
)
)
[old_record:protected] =>
[id:protected] => 4005
[old_id:protected] =>
[elcosh_id:protected] => i002692
[type:protected] => image
[display_type:protected] => Image
[user_id:protected] => 0
[language_id:protected] => 1
[tagging_id:protected] => Bruce Lippy
[priority_id:protected] => 1
[title:protected] => Toolbox talk - crew view
[total_pages:protected] => 0
[billed_pages:protected] => 0
[publication_number:protected] =>
[part_of:protected] =>
[keywords:protected] => toolbox talk, tailgate talk, safety talk, Spanish
[comments:protected] =>
[summary:protected] => Photo of crew listening to a toolbox safety talk before starting work.
[transition_comments:protected] =>
[external_link:protected] =>
[consol_link:protected] => http://www.cpwrconstructionsolutions.org/electrical/solution/662/worker-training.html
[more_like_this:protected] => i002691,d001269, c000079, d001285
[permission_given_by:protected] =>
[published:protected] => T
[billable:protected] => F
[img_name:protected] =>
[img_ext:protected] => jpg
[img_width:protected] =>
[img_height:protected] =>
[img_credit:protected] => Morgan Zavertnik and Hoar Construction
[img_practice:protected] => good
[vid_source_id:protected] =>
[vid_running_time:protected] =>
[vid_intended_audience:protected] =>
[vid_acquisition_info:protected] =>
[vid_cost:protected] =>
[vid_producer:protected] =>
[vid_filename:protected] =>
[vid_filename_downloadable:protected] =>
[date_summary:protected] => November 2015
[date_permission_requested:protected] =>
[date_permission_received:protected] =>
[date_review_needed:protected] =>
[date_received:protected] => 03/02/16
[date_completed:protected] => 03/02/16
[date_billed:protected] =>
[date_modified:protected] => 03/02/16
[collBokExports:protected] =>
[lastBokExportCriteria:BaseElcoshItem:private] =>
[alreadyInSave:protected] =>
[alreadyInValidation:protected] =>
[validationFailures:protected] => Array
(
)
[_new:BaseObject:private] =>
[_deleted:BaseObject:private] =>
[modifiedColumns:protected] => Array
(
)
)
)
[2] => Search_Result Object
(
[title] => Toolbox talk - long shot
[image] => /record/images/4006-p.jpg
[blurb] => This crew gathered every morning before starting work to discuss a new safety topic....
[category] => Array
(
[0] => 20
[1] => 47
[2] => 49
[3] => 51
[4] => 55
[5] => 64
[6] => 68
[7] => 75
[8] => 76
[9] => 63
[10] => 78
[11] => 79
[12] => 82
[13] => 62
[14] => 87
[15] => 88
[16] => 91
[17] => 90
[18] => 93
[19] => 94
[20] => 95
[21] => 97
)
[labels] => Array
(
[0] => Safety Culture
[1] => Work Environment
[2] => Hazards
[3] => Bricklayer
[4] => Trades
[5] => Carpenter
[7] => Cement Mason
[9] => Electrical Worker
[11] => Laborer
[13] => Maintenance Worker
[15] => Plasterer
[17] => Plumber/Pipefitter
[19] => Reinforcing Ironworker
[21] => Roofer/Waterproofer
[23] => Scaffold Erector
[25] => Stonemason
[27] => Structural Ironworker
[29] => Commercial & Institutional
[30] => Jobsites
[31] => Demolition
[33] => Heavy & Highway
[35] => Industrial
[37] => Renovations
[39] => Residential
[41] => Underground
[43] => Images
[44] => Media
[45] => Media & Documents
)
[type] => Images
[sub_category] =>
[url] => /image/4006/i002693/Toolbox%2Btalk%2B-%2Blong%2Bshot.html
[item:protected] => ImageRecord Object
(
[records:protected] => Array
(
)
[recordId:protected] =>
[searchWordClass:protected] =>
[searchWordPeerClass:protected] =>
[bok_record:protected] =>
[authors:protected] =>
[organizations:protected] =>
[collections:protected] =>
[categories:protected] => Array
(
[20] => Category Object
(
[languages:protected] =>
[bok_resources:protected] =>
[bok_topics:protected] =>
[bok_keywords:protected] =>
[id:protected] => 20
[type:protected] => category
[parent:protected] => 7
[label:protected] => Safety Culture
[alreadyInSave:protected] =>
[alreadyInValidation:protected] =>
[validationFailures:protected] => Array
(
)
[_new:BaseObject:private] =>
[_deleted:BaseObject:private] =>
[modifiedColumns:protected] => Array
(
)
)
[47] => Category Object
(
[languages:protected] =>
[bok_resources:protected] =>
[bok_topics:protected] =>
[bok_keywords:protected] =>
[id:protected] => 47
[type:protected] => category
[parent:protected] => 2
[label:protected] => Bricklayer
[alreadyInSave:protected] =>
[alreadyInValidation:protected] =>
[validationFailures:protected] => Array
(
)
[_new:BaseObject:private] =>
[_deleted:BaseObject:private] =>
[modifiedColumns:protected] => Array
(
)
)
[49] => Category Object
(
[languages:protected] =>
[bok_resources:protected] =>
[bok_topics:protected] =>
[bok_keywords:protected] =>
[id:protected] => 49
[type:protected] => category
[parent:protected] => 2
[label:protected] => Carpenter
[alreadyInSave:protected] =>
[alreadyInValidation:protected] =>
[validationFailures:protected] => Array
(
)
[_new:BaseObject:private] =>
[_deleted:BaseObject:private] =>
[modifiedColumns:protected] => Array
(
)
)
[51] => Category Object
(
[languages:protected] =>
[bok_resources:protected] =>
[bok_topics:protected] =>
[bok_keywords:protected] =>
[id:protected] => 51
[type:protected] => category
[parent:protected] => 2
[label:protected] => Cement Mason
[alreadyInSave:protected] =>
[alreadyInValidation:protected] =>
[validationFailures:protected] => Array
(
)
[_new:BaseObject:private] =>
[_deleted:BaseObject:private] =>
[modifiedColumns:protected] => Array
(
)
)
[55] => Category Object
(
[languages:protected] =>
[bok_resources:protected] =>
[bok_topics:protected] =>
[bok_keywords:protected] =>
[id:protected] => 55
[type:protected] => category
[parent:protected] => 2
[label:protected] => Electrical Worker
[alreadyInSave:protected] =>
[alreadyInValidation:protected] =>
[validationFailures:protected] => Array
(
)
[_new:BaseObject:private] =>
[_deleted:BaseObject:private] =>
[modifiedColumns:protected] => Array
(
)
)
[64] => Category Object
(
[languages:protected] =>
[bok_resources:protected] =>
[bok_topics:protected] =>
[bok_keywords:protected] =>
[id:protected] => 64
[type:protected] => category
[parent:protected] => 2
[label:protected] => Laborer
[alreadyInSave:protected] =>
[alreadyInValidation:protected] =>
[validationFailures:protected] => Array
(
)
[_new:BaseObject:private] =>
[_deleted:BaseObject:private] =>
[modifiedColumns:protected] => Array
(
)
)
[68] => Category Object
(
[languages:protected] =>
[bok_resources:protected] =>
[bok_topics:protected] =>
[bok_keywords:protected] =>
[id:protected] => 68
[type:protected] => category
[parent:protected] => 2
[label:protected] => Maintenance Worker
[alreadyInSave:protected] =>
[alreadyInValidation:protected] =>
[validationFailures:protected] => Array
(
)
[_new:BaseObject:private] =>
[_deleted:BaseObject:private] =>
[modifiedColumns:protected] => Array
(
)
)
[75] => Category Object
(
[languages:protected] =>
[bok_resources:protected] =>
[bok_topics:protected] =>
[bok_keywords:protected] =>
[id:protected] => 75
[type:protected] => category
[parent:protected] => 2
[label:protected] => Plasterer
[alreadyInSave:protected] =>
[alreadyInValidation:protected] =>
[validationFailures:protected] => Array
(
)
[_new:BaseObject:private] =>
[_deleted:BaseObject:private] =>
[modifiedColumns:protected] => Array
(
)
)
[76] => Category Object
(
[languages:protected] =>
[bok_resources:protected] =>
[bok_topics:protected] =>
[bok_keywords:protected] =>
[id:protected] => 76
[type:protected] => category
[parent:protected] => 2
[label:protected] => Plumber/Pipefitter
[alreadyInSave:protected] =>
[alreadyInValidation:protected] =>
[validationFailures:protected] => Array
(
)
[_new:BaseObject:private] =>
[_deleted:BaseObject:private] =>
[modifiedColumns:protected] => Array
(
)
)
[63] => Category Object
(
[languages:protected] =>
[bok_resources:protected] =>
[bok_topics:protected] =>
[bok_keywords:protected] =>
[id:protected] => 63
[type:protected] => category
[parent:protected] => 2
[label:protected] => Reinforcing Ironworker
[alreadyInSave:protected] =>
[alreadyInValidation:protected] =>
[validationFailures:protected] => Array
(
)
[_new:BaseObject:private] =>
[_deleted:BaseObject:private] =>
[modifiedColumns:protected] => Array
(
)
)
[78] => Category Object
(
[languages:protected] =>
[bok_resources:protected] =>
[bok_topics:protected] =>
[bok_keywords:protected] =>
[id:protected] => 78
[type:protected] => category
[parent:protected] => 2
[label:protected] => Roofer/Waterproofer
[alreadyInSave:protected] =>
[alreadyInValidation:protected] =>
[validationFailures:protected] => Array
(
)
[_new:BaseObject:private] =>
[_deleted:BaseObject:private] =>
[modifiedColumns:protected] => Array
(
)
)
[79] => Category Object
(
[languages:protected] =>
[bok_resources:protected] =>
[bok_topics:protected] =>
[bok_keywords:protected] =>
[id:protected] => 79
[type:protected] => category
[parent:protected] => 2
[label:protected] => Scaffold Erector
[alreadyInSave:protected] =>
[alreadyInValidation:protected] =>
[validationFailures:protected] => Array
(
)
[_new:BaseObject:private] =>
[_deleted:BaseObject:private] =>
[modifiedColumns:protected] => Array
(
)
)
[82] => Category Object
(
[languages:protected] =>
[bok_resources:protected] =>
[bok_topics:protected] =>
[bok_keywords:protected] =>
[id:protected] => 82
[type:protected] => category
[parent:protected] => 2
[label:protected] => Stonemason
[alreadyInSave:protected] =>
[alreadyInValidation:protected] =>
[validationFailures:protected] => Array
(
)
[_new:BaseObject:private] =>
[_deleted:BaseObject:private] =>
[modifiedColumns:protected] => Array
(
)
)
[62] => Category Object
(
[languages:protected] =>
[bok_resources:protected] =>
[bok_topics:protected] =>
[bok_keywords:protected] =>
[id:protected] => 62
[type:protected] => category
[parent:protected] => 2
[label:protected] => Structural Ironworker
[alreadyInSave:protected] =>
[alreadyInValidation:protected] =>
[validationFailures:protected] => Array
(
)
[_new:BaseObject:private] =>
[_deleted:BaseObject:private] =>
[modifiedColumns:protected] => Array
(
)
)
[87] => Category Object
(
[languages:protected] =>
[bok_resources:protected] =>
[bok_topics:protected] =>
[bok_keywords:protected] =>
[id:protected] => 87
[type:protected] => category
[parent:protected] => 3
[label:protected] => Commercial & Institutional
[alreadyInSave:protected] =>
[alreadyInValidation:protected] =>
[validationFailures:protected] => Array
(
)
[_new:BaseObject:private] =>
[_deleted:BaseObject:private] =>
[modifiedColumns:protected] => Array
(
)
)
[88] => Category Object
(
[languages:protected] =>
[bok_resources:protected] =>
[bok_topics:protected] =>
[bok_keywords:protected] =>
[id:protected] => 88
[type:protected] => category
[parent:protected] => 3
[label:protected] => Demolition
[alreadyInSave:protected] =>
[alreadyInValidation:protected] =>
[validationFailures:protected] => Array
(
)
[_new:BaseObject:private] =>
[_deleted:BaseObject:private] =>
[modifiedColumns:protected] => Array
(
)
)
[91] => Category Object
(
[languages:protected] =>
[bok_resources:protected] =>
[bok_topics:protected] =>
[bok_keywords:protected] =>
[id:protected] => 91
[type:protected] => category
[parent:protected] => 3
[label:protected] => Heavy & Highway
[alreadyInSave:protected] =>
[alreadyInValidation:protected] =>
[validationFailures:protected] => Array
(
)
[_new:BaseObject:private] =>
[_deleted:BaseObject:private] =>
[modifiedColumns:protected] => Array
(
)
)
[90] => Category Object
(
[languages:protected] =>
[bok_resources:protected] =>
[bok_topics:protected] =>
[bok_keywords:protected] =>
[id:protected] => 90
[type:protected] => category
[parent:protected] => 3
[label:protected] => Industrial
[alreadyInSave:protected] =>
[alreadyInValidation:protected] =>
[validationFailures:protected] => Array
(
)
[_new:BaseObject:private] =>
[_deleted:BaseObject:private] =>
[modifiedColumns:protected] => Array
(
)
)
[93] => Category Object
(
[languages:protected] =>
[bok_resources:protected] =>
[bok_topics:protected] =>
[bok_keywords:protected] =>
[id:protected] => 93
[type:protected] => category
[parent:protected] => 3
[label:protected] => Renovations
[alreadyInSave:protected] =>
[alreadyInValidation:protected] =>
[validationFailures:protected] => Array
(
)
[_new:BaseObject:private] =>
[_deleted:BaseObject:private] =>
[modifiedColumns:protected] => Array
(
)
)
[94] => Category Object
(
[languages:protected] =>
[bok_resources:protected] =>
[bok_topics:protected] =>
[bok_keywords:protected] =>
[id:protected] => 94
[type:protected] => category
[parent:protected] => 3
[label:protected] => Residential
[alreadyInSave:protected] =>
[alreadyInValidation:protected] =>
[validationFailures:protected] => Array
(
)
[_new:BaseObject:private] =>
[_deleted:BaseObject:private] =>
[modifiedColumns:protected] => Array
(
)
)
[95] => Category Object
(
[languages:protected] =>
[bok_resources:protected] =>
[bok_topics:protected] =>
[bok_keywords:protected] =>
[id:protected] => 95
[type:protected] => category
[parent:protected] => 3
[label:protected] => Underground
[alreadyInSave:protected] =>
[alreadyInValidation:protected] =>
[validationFailures:protected] => Array
(
)
[_new:BaseObject:private] =>
[_deleted:BaseObject:private] =>
[modifiedColumns:protected] => Array
(
)
)
[97] => Category Object
(
[languages:protected] =>
[bok_resources:protected] =>
[bok_topics:protected] =>
[bok_keywords:protected] =>
[id:protected] => 97
[type:protected] => category
[parent:protected] => 5
[label:protected] => Images
[alreadyInSave:protected] =>
[alreadyInValidation:protected] =>
[validationFailures:protected] => Array
(
)
[_new:BaseObject:private] =>
[_deleted:BaseObject:private] =>
[modifiedColumns:protected] => Array
(
)
)
)
[categories_initialized:protected] => 1
[mapped_items:protected] =>
[content:protected] =>
[files:protected] =>
[language:protected] => Language Object
(
[id:protected] => 1
[code:protected] => en
[name:protected] => English
[alreadyInSave:protected] =>
[alreadyInValidation:protected] =>
[validationFailures:protected] => Array
(
)
[_new:BaseObject:private] =>
[_deleted:BaseObject:private] =>
[modifiedColumns:protected] => Array
(
)
)
[old_record:protected] =>
[id:protected] => 4006
[old_id:protected] =>
[elcosh_id:protected] => i002693
[type:protected] => image
[display_type:protected] => Image
[user_id:protected] => 0
[language_id:protected] => 1
[tagging_id:protected] => Bruce Lippy
[priority_id:protected] => 1
[title:protected] => Toolbox talk - long shot
[total_pages:protected] => 0
[billed_pages:protected] => 0
[publication_number:protected] =>
[part_of:protected] =>
[keywords:protected] => toolbox talk, tailgate talk, safety minute
[comments:protected] =>
[summary:protected] => This crew gathered every morning before starting work to discuss a new safety topic.
[transition_comments:protected] =>
[external_link:protected] =>
[consol_link:protected] => http://www.cpwrconstructionsolutions.org/electrical/solution/662/worker-training.html
[more_like_this:protected] => i002691,i002692,d001269,d000527
[permission_given_by:protected] =>
[published:protected] => T
[billable:protected] => F
[img_name:protected] =>
[img_ext:protected] => jpg
[img_width:protected] =>
[img_height:protected] =>
[img_credit:protected] => Morgan Zavertnik and Hoar Construction
[img_practice:protected] => good
[vid_source_id:protected] =>
[vid_running_time:protected] =>
[vid_intended_audience:protected] =>
[vid_acquisition_info:protected] =>
[vid_cost:protected] =>
[vid_producer:protected] =>
[vid_filename:protected] =>
[vid_filename_downloadable:protected] =>
[date_summary:protected] => November 2015
[date_permission_requested:protected] =>
[date_permission_received:protected] =>
[date_review_needed:protected] =>
[date_received:protected] => 03/02/16
[date_completed:protected] => 03/02/16
[date_billed:protected] =>
[date_modified:protected] => 03/02/16
[collBokExports:protected] =>
[lastBokExportCriteria:BaseElcoshItem:private] =>
[alreadyInSave:protected] =>
[alreadyInValidation:protected] =>
[validationFailures:protected] => Array
(
)
[_new:BaseObject:private] =>
[_deleted:BaseObject:private] =>
[modifiedColumns:protected] => Array
(
)
)
)
[3] => Search_Result Object
(
[title] => Safety officer discussing ongoing project with marketing coordinator
[image] => /record/images/4014-p.jpg
[blurb] => The safety officer (left) points out the good safety practices on this project that reflect well on the firm and may influence future clients....
[category] => Array
(
[0] => 97
[1] => 20
[2] => 46
[3] => 47
[4] => 49
[5] => 50
[6] => 51
[7] => 54
[8] => 55
[9] => 58
[10] => 60
[11] => 61
[12] => 64
[13] => 71
[14] => 75
[15] => 76
[16] => 63
[17] => 79
[18] => 80
[19] => 82
[20] => 62
[21] => 83
[22] => 87
[23] => 91
[24] => 90
[25] => 93
[26] => 94
)
[labels] => Array
(
[0] => Images
[1] => Media
[2] => Media & Documents
[3] => Safety Culture
[4] => Work Environment
[5] => Hazards
[6] => Boilermaker
[7] => Trades
[8] => Bricklayer
[10] => Carpenter
[12] => Carpet Layer
[14] => Cement Mason
[16] => Drywall Applicator Specialist
[18] => Electrical Worker
[20] => Glazier
[22] => HVAC
[24] => Interior Systems Carpenter
[26] => Laborer
[28] => Painter
[30] => Plasterer
[32] => Plumber/Pipefitter
[34] => Reinforcing Ironworker
[36] => Scaffold Erector
[38] => Sheetmetal Worker
[40] => Stonemason
[42] => Structural Ironworker
[44] => Terrazzo Worker
[46] => Commercial & Institutional
[47] => Jobsites
[48] => Heavy & Highway
[50] => Industrial
[52] => Renovations
[54] => Residential
)
[type] => Images
[sub_category] =>
[url] => /image/4014/i002700/Safety%2Bofficer%2Bdiscussing%2Bongoing%2Bproject%2Bwith%2Bmarketing%2Bcoordinator.html
[item:protected] => ImageRecord Object
(
[records:protected] => Array
(
)
[recordId:protected] =>
[searchWordClass:protected] =>
[searchWordPeerClass:protected] =>
[bok_record:protected] =>
[authors:protected] =>
[organizations:protected] =>
[collections:protected] =>
[categories:protected] => Array
(
[97] => Category Object
(
[languages:protected] =>
[bok_resources:protected] =>
[bok_topics:protected] =>
[bok_keywords:protected] =>
[id:protected] => 97
[type:protected] => category
[parent:protected] => 5
[label:protected] => Images
[alreadyInSave:protected] =>
[alreadyInValidation:protected] =>
[validationFailures:protected] => Array
(
)
[_new:BaseObject:private] =>
[_deleted:BaseObject:private] =>
[modifiedColumns:protected] => Array
(
)
)
[20] => Category Object
(
[languages:protected] =>
[bok_resources:protected] =>
[bok_topics:protected] =>
[bok_keywords:protected] =>
[id:protected] => 20
[type:protected] => category
[parent:protected] => 7
[label:protected] => Safety Culture
[alreadyInSave:protected] =>
[alreadyInValidation:protected] =>
[validationFailures:protected] => Array
(
)
[_new:BaseObject:private] =>
[_deleted:BaseObject:private] =>
[modifiedColumns:protected] => Array
(
)
)
[46] => Category Object
(
[languages:protected] =>
[bok_resources:protected] =>
[bok_topics:protected] =>
[bok_keywords:protected] =>
[id:protected] => 46
[type:protected] => category
[parent:protected] => 2
[label:protected] => Boilermaker
[alreadyInSave:protected] =>
[alreadyInValidation:protected] =>
[validationFailures:protected] => Array
(
)
[_new:BaseObject:private] =>
[_deleted:BaseObject:private] =>
[modifiedColumns:protected] => Array
(
)
)
[47] => Category Object
(
[languages:protected] =>
[bok_resources:protected] =>
[bok_topics:protected] =>
[bok_keywords:protected] =>
[id:protected] => 47
[type:protected] => category
[parent:protected] => 2
[label:protected] => Bricklayer
[alreadyInSave:protected] =>
[alreadyInValidation:protected] =>
[validationFailures:protected] => Array
(
)
[_new:BaseObject:private] =>
[_deleted:BaseObject:private] =>
[modifiedColumns:protected] => Array
(
)
)
[49] => Category Object
(
[languages:protected] =>
[bok_resources:protected] =>
[bok_topics:protected] =>
[bok_keywords:protected] =>
[id:protected] => 49
[type:protected] => category
[parent:protected] => 2
[label:protected] => Carpenter
[alreadyInSave:protected] =>
[alreadyInValidation:protected] =>
[validationFailures:protected] => Array
(
)
[_new:BaseObject:private] =>
[_deleted:BaseObject:private] =>
[modifiedColumns:protected] => Array
(
)
)
[50] => Category Object
(
[languages:protected] =>
[bok_resources:protected] =>
[bok_topics:protected] =>
[bok_keywords:protected] =>
[id:protected] => 50
[type:protected] => category
[parent:protected] => 2
[label:protected] => Carpet Layer
[alreadyInSave:protected] =>
[alreadyInValidation:protected] =>
[validationFailures:protected] => Array
(
)
[_new:BaseObject:private] =>
[_deleted:BaseObject:private] =>
[modifiedColumns:protected] => Array
(
)
)
[51] => Category Object
(
[languages:protected] =>
[bok_resources:protected] =>
[bok_topics:protected] =>
[bok_keywords:protected] =>
[id:protected] => 51
[type:protected] => category
[parent:protected] => 2
[label:protected] => Cement Mason
[alreadyInSave:protected] =>
[alreadyInValidation:protected] =>
[validationFailures:protected] => Array
(
)
[_new:BaseObject:private] =>
[_deleted:BaseObject:private] =>
[modifiedColumns:protected] => Array
(
)
)
[54] => Category Object
(
[languages:protected] =>
[bok_resources:protected] =>
[bok_topics:protected] =>
[bok_keywords:protected] =>
[id:protected] => 54
[type:protected] => category
[parent:protected] => 2
[label:protected] => Drywall Applicator Specialist
[alreadyInSave:protected] =>
[alreadyInValidation:protected] =>
[validationFailures:protected] => Array
(
)
[_new:BaseObject:private] =>
[_deleted:BaseObject:private] =>
[modifiedColumns:protected] => Array
(
)
)
[55] => Category Object
(
[languages:protected] =>
[bok_resources:protected] =>
[bok_topics:protected] =>
[bok_keywords:protected] =>
[id:protected] => 55
[type:protected] => category
[parent:protected] => 2
[label:protected] => Electrical Worker
[alreadyInSave:protected] =>
[alreadyInValidation:protected] =>
[validationFailures:protected] => Array
(
)
[_new:BaseObject:private] =>
[_deleted:BaseObject:private] =>
[modifiedColumns:protected] => Array
(
)
)
[58] => Category Object
(
[languages:protected] =>
[bok_resources:protected] =>
[bok_topics:protected] =>
[bok_keywords:protected] =>
[id:protected] => 58
[type:protected] => category
[parent:protected] => 2
[label:protected] => Glazier
[alreadyInSave:protected] =>
[alreadyInValidation:protected] =>
[validationFailures:protected] => Array
(
)
[_new:BaseObject:private] =>
[_deleted:BaseObject:private] =>
[modifiedColumns:protected] => Array
(
)
)
[60] => Category Object
(
[languages:protected] =>
[bok_resources:protected] =>
[bok_topics:protected] =>
[bok_keywords:protected] =>
[id:protected] => 60
[type:protected] => category
[parent:protected] => 2
[label:protected] => HVAC
[alreadyInSave:protected] =>
[alreadyInValidation:protected] =>
[validationFailures:protected] => Array
(
)
[_new:BaseObject:private] =>
[_deleted:BaseObject:private] =>
[modifiedColumns:protected] => Array
(
)
)
[61] => Category Object
(
[languages:protected] =>
[bok_resources:protected] =>
[bok_topics:protected] =>
[bok_keywords:protected] =>
[id:protected] => 61
[type:protected] => category
[parent:protected] => 2
[label:protected] => Interior Systems Carpenter
[alreadyInSave:protected] =>
[alreadyInValidation:protected] =>
[validationFailures:protected] => Array
(
)
[_new:BaseObject:private] =>
[_deleted:BaseObject:private] =>
[modifiedColumns:protected] => Array
(
)
)
[64] => Category Object
(
[languages:protected] =>
[bok_resources:protected] =>
[bok_topics:protected] =>
[bok_keywords:protected] =>
[id:protected] => 64
[type:protected] => category
[parent:protected] => 2
[label:protected] => Laborer
[alreadyInSave:protected] =>
[alreadyInValidation:protected] =>
[validationFailures:protected] => Array
(
)
[_new:BaseObject:private] =>
[_deleted:BaseObject:private] =>
[modifiedColumns:protected] => Array
(
)
)
[71] => Category Object
(
[languages:protected] =>
[bok_resources:protected] =>
[bok_topics:protected] =>
[bok_keywords:protected] =>
[id:protected] => 71
[type:protected] => category
[parent:protected] => 2
[label:protected] => Painter
[alreadyInSave:protected] =>
[alreadyInValidation:protected] =>
[validationFailures:protected] => Array
(
)
[_new:BaseObject:private] =>
[_deleted:BaseObject:private] =>
[modifiedColumns:protected] => Array
(
)
)
[75] => Category Object
(
[languages:protected] =>
[bok_resources:protected] =>
[bok_topics:protected] =>
[bok_keywords:protected] =>
[id:protected] => 75
[type:protected] => category
[parent:protected] => 2
[label:protected] => Plasterer
[alreadyInSave:protected] =>
[alreadyInValidation:protected] =>
[validationFailures:protected] => Array
(
)
[_new:BaseObject:private] =>
[_deleted:BaseObject:private] =>
[modifiedColumns:protected] => Array
(
)
)
[76] => Category Object
(
[languages:protected] =>
[bok_resources:protected] =>
[bok_topics:protected] =>
[bok_keywords:protected] =>
[id:protected] => 76
[type:protected] => category
[parent:protected] => 2
[label:protected] => Plumber/Pipefitter
[alreadyInSave:protected] =>
[alreadyInValidation:protected] =>
[validationFailures:protected] => Array
(
)
[_new:BaseObject:private] =>
[_deleted:BaseObject:private] =>
[modifiedColumns:protected] => Array
(
)
)
[63] => Category Object
(
[languages:protected] =>
[bok_resources:protected] =>
[bok_topics:protected] =>
[bok_keywords:protected] =>
[id:protected] => 63
[type:protected] => category
[parent:protected] => 2
[label:protected] => Reinforcing Ironworker
[alreadyInSave:protected] =>
[alreadyInValidation:protected] =>
[validationFailures:protected] => Array
(
)
[_new:BaseObject:private] =>
[_deleted:BaseObject:private] =>
[modifiedColumns:protected] => Array
(
)
)
[79] => Category Object
(
[languages:protected] =>
[bok_resources:protected] =>
[bok_topics:protected] =>
[bok_keywords:protected] =>
[id:protected] => 79
[type:protected] => category
[parent:protected] => 2
[label:protected] => Scaffold Erector
[alreadyInSave:protected] =>
[alreadyInValidation:protected] =>
[validationFailures:protected] => Array
(
)
[_new:BaseObject:private] =>
[_deleted:BaseObject:private] =>
[modifiedColumns:protected] => Array
(
)
)
[80] => Category Object
(
[languages:protected] =>
[bok_resources:protected] =>
[bok_topics:protected] =>
[bok_keywords:protected] =>
[id:protected] => 80
[type:protected] => category
[parent:protected] => 2
[label:protected] => Sheetmetal Worker
[alreadyInSave:protected] =>
[alreadyInValidation:protected] =>
[validationFailures:protected] => Array
(
)
[_new:BaseObject:private] =>
[_deleted:BaseObject:private] =>
[modifiedColumns:protected] => Array
(
)
)
[82] => Category Object
(
[languages:protected] =>
[bok_resources:protected] =>
[bok_topics:protected] =>
[bok_keywords:protected] =>
[id:protected] => 82
[type:protected] => category
[parent:protected] => 2
[label:protected] => Stonemason
[alreadyInSave:protected] =>
[alreadyInValidation:protected] =>
[validationFailures:protected] => Array
(
)
[_new:BaseObject:private] =>
[_deleted:BaseObject:private] =>
[modifiedColumns:protected] => Array
(
)
)
[62] => Category Object
(
[languages:protected] =>
[bok_resources:protected] =>
[bok_topics:protected] =>
[bok_keywords:protected] =>
[id:protected] => 62
[type:protected] => category
[parent:protected] => 2
[label:protected] => Structural Ironworker
[alreadyInSave:protected] =>
[alreadyInValidation:protected] =>
[validationFailures:protected] => Array
(
)
[_new:BaseObject:private] =>
[_deleted:BaseObject:private] =>
[modifiedColumns:protected] => Array
(
)
)
[83] => Category Object
(
[languages:protected] =>
[bok_resources:protected] =>
[bok_topics:protected] =>
[bok_keywords:protected] =>
[id:protected] => 83
[type:protected] => category
[parent:protected] => 2
[label:protected] => Terrazzo Worker
[alreadyInSave:protected] =>
[alreadyInValidation:protected] =>
[validationFailures:protected] => Array
(
)
[_new:BaseObject:private] =>
[_deleted:BaseObject:private] =>
[modifiedColumns:protected] => Array
(
)
)
[87] => Category Object
(
[languages:protected] =>
[bok_resources:protected] =>
[bok_topics:protected] =>
[bok_keywords:protected] =>
[id:protected] => 87
[type:protected] => category
[parent:protected] => 3
[label:protected] => Commercial & Institutional
[alreadyInSave:protected] =>
[alreadyInValidation:protected] =>
[validationFailures:protected] => Array
(
)
[_new:BaseObject:private] =>
[_deleted:BaseObject:private] =>
[modifiedColumns:protected] => Array
(
)
)
[91] => Category Object
(
[languages:protected] =>
[bok_resources:protected] =>
[bok_topics:protected] =>
[bok_keywords:protected] =>
[id:protected] => 91
[type:protected] => category
[parent:protected] => 3
[label:protected] => Heavy & Highway
[alreadyInSave:protected] =>
[alreadyInValidation:protected] =>
[validationFailures:protected] => Array
(
)
[_new:BaseObject:private] =>
[_deleted:BaseObject:private] =>
[modifiedColumns:protected] => Array
(
)
)
[90] => Category Object
(
[languages:protected] =>
[bok_resources:protected] =>
[bok_topics:protected] =>
[bok_keywords:protected] =>
[id:protected] => 90
[type:protected] => category
[parent:protected] => 3
[label:protected] => Industrial
[alreadyInSave:protected] =>
[alreadyInValidation:protected] =>
[validationFailures:protected] => Array
(
)
[_new:BaseObject:private] =>
[_deleted:BaseObject:private] =>
[modifiedColumns:protected] => Array
(
)
)
[93] => Category Object
(
[languages:protected] =>
[bok_resources:protected] =>
[bok_topics:protected] =>
[bok_keywords:protected] =>
[id:protected] => 93
[type:protected] => category
[parent:protected] => 3
[label:protected] => Renovations
[alreadyInSave:protected] =>
[alreadyInValidation:protected] =>
[validationFailures:protected] => Array
(
)
[_new:BaseObject:private] =>
[_deleted:BaseObject:private] =>
[modifiedColumns:protected] => Array
(
)
)
[94] => Category Object
(
[languages:protected] =>
[bok_resources:protected] =>
[bok_topics:protected] =>
[bok_keywords:protected] =>
[id:protected] => 94
[type:protected] => category
[parent:protected] => 3
[label:protected] => Residential
[alreadyInSave:protected] =>
[alreadyInValidation:protected] =>
[validationFailures:protected] => Array
(
)
[_new:BaseObject:private] =>
[_deleted:BaseObject:private] =>
[modifiedColumns:protected] => Array
(
)
)
)
[categories_initialized:protected] => 1
[mapped_items:protected] =>
[content:protected] =>
[files:protected] =>
[language:protected] => Language Object
(
[id:protected] => 1
[code:protected] => en
[name:protected] => English
[alreadyInSave:protected] =>
[alreadyInValidation:protected] =>
[validationFailures:protected] => Array
(
)
[_new:BaseObject:private] =>
[_deleted:BaseObject:private] =>
[modifiedColumns:protected] => Array
(
)
)
[old_record:protected] =>
[id:protected] => 4014
[old_id:protected] =>
[elcosh_id:protected] => i002700
[type:protected] => image
[display_type:protected] => Image
[user_id:protected] => 0
[language_id:protected] => 1
[tagging_id:protected] => Bruce Lippy
[priority_id:protected] => 1
[title:protected] => Safety officer discussing ongoing project with marketing coordinator
[total_pages:protected] => 0
[billed_pages:protected] => 0
[publication_number:protected] =>
[part_of:protected] =>
[keywords:protected] => Latino, safety officer, safety culture
[comments:protected] =>
[summary:protected] => The safety officer (left) points out the good safety practices on this project that reflect well on the firm and may influence future clients.
[transition_comments:protected] =>
[external_link:protected] =>
[consol_link:protected] => http://www.cpwrconstructionsolutions.org/index.php
[more_like_this:protected] => d000989,d001351,d001362,d000652, d001101, d000931, d001395
[permission_given_by:protected] =>
[published:protected] => T
[billable:protected] => F
[img_name:protected] =>
[img_ext:protected] => jpg
[img_width:protected] =>
[img_height:protected] =>
[img_credit:protected] => Hoar Construction, Photo by Neil Lippy
[img_practice:protected] => good
[vid_source_id:protected] =>
[vid_running_time:protected] =>
[vid_intended_audience:protected] =>
[vid_acquisition_info:protected] =>
[vid_cost:protected] =>
[vid_producer:protected] =>
[vid_filename:protected] =>
[vid_filename_downloadable:protected] =>
[date_summary:protected] => November 2015
[date_permission_requested:protected] =>
[date_permission_received:protected] =>
[date_review_needed:protected] =>
[date_received:protected] => 03/02/16
[date_completed:protected] => 03/02/16
[date_billed:protected] =>
[date_modified:protected] => 01/30/23
[collBokExports:protected] =>
[lastBokExportCriteria:BaseElcoshItem:private] =>
[alreadyInSave:protected] =>
[alreadyInValidation:protected] =>
[validationFailures:protected] => Array
(
)
[_new:BaseObject:private] =>
[_deleted:BaseObject:private] =>
[modifiedColumns:protected] => Array
(
)
)
)
[4] => Search_Result Object
(
[title] => Scaffolding at top of large column
[image] => /record/images/3994-p.jpg
[blurb] => This shot shows innovative guarding around the top of a large concrete column in the base of a high rise structure going up....
[category] => Array
(
[0] => 15
[1] => 21
[2] => 47
[3] => 51
[4] => 63
[5] => 78
[6] => 79
[7] => 80
[8] => 62
[9] => 87
[10] => 97
[11] => 56
[12] => 64
[13] => 74
)
[labels] => Array
(
[0] => Falls
[1] => Work Environment
[2] => Hazards
[3] => Scaffolds
[6] => Bricklayer
[7] => Trades
[8] => Cement Mason
[10] => Reinforcing Ironworker
[12] => Roofer/Waterproofer
[14] => Scaffold Erector
[16] => Sheetmetal Worker
[18] => Structural Ironworker
[20] => Commercial & Institutional
[21] => Jobsites
[22] => Images
[23] => Media
[24] => Media & Documents
[25] => Elevator Constructor
[27] => Laborer
[29] => Pile Driver
)
[type] => Images
[sub_category] =>
[url] => /image/3994/i002689/Scaffolding%2Bat%2Btop%2Bof%2Blarge%2Bcolumn.html
[item:protected] => ImageRecord Object
(
[records:protected] => Array
(
)
[recordId:protected] =>
[searchWordClass:protected] =>
[searchWordPeerClass:protected] =>
[bok_record:protected] =>
[authors:protected] =>
[organizations:protected] =>
[collections:protected] =>
[categories:protected] => Array
(
[15] => Category Object
(
[languages:protected] =>
[bok_resources:protected] =>
[bok_topics:protected] =>
[bok_keywords:protected] =>
[id:protected] => 15
[type:protected] => category
[parent:protected] => 7
[label:protected] => Falls
[alreadyInSave:protected] =>
[alreadyInValidation:protected] =>
[validationFailures:protected] => Array
(
)
[_new:BaseObject:private] =>
[_deleted:BaseObject:private] =>
[modifiedColumns:protected] => Array
(
)
)
[21] => Category Object
(
[languages:protected] =>
[bok_resources:protected] =>
[bok_topics:protected] =>
[bok_keywords:protected] =>
[id:protected] => 21
[type:protected] => category
[parent:protected] => 7
[label:protected] => Scaffolds
[alreadyInSave:protected] =>
[alreadyInValidation:protected] =>
[validationFailures:protected] => Array
(
)
[_new:BaseObject:private] =>
[_deleted:BaseObject:private] =>
[modifiedColumns:protected] => Array
(
)
)
[47] => Category Object
(
[languages:protected] =>
[bok_resources:protected] =>
[bok_topics:protected] =>
[bok_keywords:protected] =>
[id:protected] => 47
[type:protected] => category
[parent:protected] => 2
[label:protected] => Bricklayer
[alreadyInSave:protected] =>
[alreadyInValidation:protected] =>
[validationFailures:protected] => Array
(
)
[_new:BaseObject:private] =>
[_deleted:BaseObject:private] =>
[modifiedColumns:protected] => Array
(
)
)
[51] => Category Object
(
[languages:protected] =>
[bok_resources:protected] =>
[bok_topics:protected] =>
[bok_keywords:protected] =>
[id:protected] => 51
[type:protected] => category
[parent:protected] => 2
[label:protected] => Cement Mason
[alreadyInSave:protected] =>
[alreadyInValidation:protected] =>
[validationFailures:protected] => Array
(
)
[_new:BaseObject:private] =>
[_deleted:BaseObject:private] =>
[modifiedColumns:protected] => Array
(
)
)
[63] => Category Object
(
[languages:protected] =>
[bok_resources:protected] =>
[bok_topics:protected] =>
[bok_keywords:protected] =>
[id:protected] => 63
[type:protected] => category
[parent:protected] => 2
[label:protected] => Reinforcing Ironworker
[alreadyInSave:protected] =>
[alreadyInValidation:protected] =>
[validationFailures:protected] => Array
(
)
[_new:BaseObject:private] =>
[_deleted:BaseObject:private] =>
[modifiedColumns:protected] => Array
(
)
)
[78] => Category Object
(
[languages:protected] =>
[bok_resources:protected] =>
[bok_topics:protected] =>
[bok_keywords:protected] =>
[id:protected] => 78
[type:protected] => category
[parent:protected] => 2
[label:protected] => Roofer/Waterproofer
[alreadyInSave:protected] =>
[alreadyInValidation:protected] =>
[validationFailures:protected] => Array
(
)
[_new:BaseObject:private] =>
[_deleted:BaseObject:private] =>
[modifiedColumns:protected] => Array
(
)
)
[79] => Category Object
(
[languages:protected] =>
[bok_resources:protected] =>
[bok_topics:protected] =>
[bok_keywords:protected] =>
[id:protected] => 79
[type:protected] => category
[parent:protected] => 2
[label:protected] => Scaffold Erector
[alreadyInSave:protected] =>
[alreadyInValidation:protected] =>
[validationFailures:protected] => Array
(
)
[_new:BaseObject:private] =>
[_deleted:BaseObject:private] =>
[modifiedColumns:protected] => Array
(
)
)
[80] => Category Object
(
[languages:protected] =>
[bok_resources:protected] =>
[bok_topics:protected] =>
[bok_keywords:protected] =>
[id:protected] => 80
[type:protected] => category
[parent:protected] => 2
[label:protected] => Sheetmetal Worker
[alreadyInSave:protected] =>
[alreadyInValidation:protected] =>
[validationFailures:protected] => Array
(
)
[_new:BaseObject:private] =>
[_deleted:BaseObject:private] =>
[modifiedColumns:protected] => Array
(
)
)
[62] => Category Object
(
[languages:protected] =>
[bok_resources:protected] =>
[bok_topics:protected] =>
[bok_keywords:protected] =>
[id:protected] => 62
[type:protected] => category
[parent:protected] => 2
[label:protected] => Structural Ironworker
[alreadyInSave:protected] =>
[alreadyInValidation:protected] =>
[validationFailures:protected] => Array
(
)
[_new:BaseObject:private] =>
[_deleted:BaseObject:private] =>
[modifiedColumns:protected] => Array
(
)
)
[87] => Category Object
(
[languages:protected] =>
[bok_resources:protected] =>
[bok_topics:protected] =>
[bok_keywords:protected] =>
[id:protected] => 87
[type:protected] => category
[parent:protected] => 3
[label:protected] => Commercial & Institutional
[alreadyInSave:protected] =>
[alreadyInValidation:protected] =>
[validationFailures:protected] => Array
(
)
[_new:BaseObject:private] =>
[_deleted:BaseObject:private] =>
[modifiedColumns:protected] => Array
(
)
)
[97] => Category Object
(
[languages:protected] =>
[bok_resources:protected] =>
[bok_topics:protected] =>
[bok_keywords:protected] =>
[id:protected] => 97
[type:protected] => category
[parent:protected] => 5
[label:protected] => Images
[alreadyInSave:protected] =>
[alreadyInValidation:protected] =>
[validationFailures:protected] => Array
(
)
[_new:BaseObject:private] =>
[_deleted:BaseObject:private] =>
[modifiedColumns:protected] => Array
(
)
)
[56] => Category Object
(
[languages:protected] =>
[bok_resources:protected] =>
[bok_topics:protected] =>
[bok_keywords:protected] =>
[id:protected] => 56
[type:protected] => category
[parent:protected] => 2
[label:protected] => Elevator Constructor
[alreadyInSave:protected] =>
[alreadyInValidation:protected] =>
[validationFailures:protected] => Array
(
)
[_new:BaseObject:private] =>
[_deleted:BaseObject:private] =>
[modifiedColumns:protected] => Array
(
)
)
[64] => Category Object
(
[languages:protected] =>
[bok_resources:protected] =>
[bok_topics:protected] =>
[bok_keywords:protected] =>
[id:protected] => 64
[type:protected] => category
[parent:protected] => 2
[label:protected] => Laborer
[alreadyInSave:protected] =>
[alreadyInValidation:protected] =>
[validationFailures:protected] => Array
(
)
[_new:BaseObject:private] =>
[_deleted:BaseObject:private] =>
[modifiedColumns:protected] => Array
(
)
)
[74] => Category Object
(
[languages:protected] =>
[bok_resources:protected] =>
[bok_topics:protected] =>
[bok_keywords:protected] =>
[id:protected] => 74
[type:protected] => category
[parent:protected] => 2
[label:protected] => Pile Driver
[alreadyInSave:protected] =>
[alreadyInValidation:protected] =>
[validationFailures:protected] => Array
(
)
[_new:BaseObject:private] =>
[_deleted:BaseObject:private] =>
[modifiedColumns:protected] => Array
(
)
)
)
[categories_initialized:protected] => 1
[mapped_items:protected] =>
[content:protected] =>
[files:protected] =>
[language:protected] => Language Object
(
[id:protected] => 1
[code:protected] => en
[name:protected] => English
[alreadyInSave:protected] =>
[alreadyInValidation:protected] =>
[validationFailures:protected] => Array
(
)
[_new:BaseObject:private] =>
[_deleted:BaseObject:private] =>
[modifiedColumns:protected] => Array
(
)
)
[old_record:protected] =>
[id:protected] => 3994
[old_id:protected] =>
[elcosh_id:protected] => i002689
[type:protected] => image
[display_type:protected] => Image
[user_id:protected] => 0
[language_id:protected] => 1
[tagging_id:protected] => Bruce Lippy
[priority_id:protected] => 1
[title:protected] => Scaffolding at top of large column
[total_pages:protected] => 0
[billed_pages:protected] => 0
[publication_number:protected] =>
[part_of:protected] =>
[keywords:protected] => Guardrail, railing, fall prevention, falls
[comments:protected] =>
[summary:protected] => This shot shows innovative guarding around the top of a large concrete column in the base of a high rise structure going up.
[transition_comments:protected] =>
[external_link:protected] =>
[consol_link:protected] => http://www.cpwrconstructionsolutions.org/masonry/solution/8/adjustable-tower-scaffold.html
[more_like_this:protected] => c1002680,i002662,d000608,d001255
[permission_given_by:protected] =>
[published:protected] => T
[billable:protected] => F
[img_name:protected] =>
[img_ext:protected] => jpg
[img_width:protected] =>
[img_height:protected] =>
[img_credit:protected] => Photo by Pam Susi
[img_practice:protected] => good
[vid_source_id:protected] =>
[vid_running_time:protected] =>
[vid_intended_audience:protected] =>
[vid_acquisition_info:protected] =>
[vid_cost:protected] =>
[vid_producer:protected] =>
[vid_filename:protected] =>
[vid_filename_downloadable:protected] =>
[date_summary:protected] => January 2016
[date_permission_requested:protected] =>
[date_permission_received:protected] =>
[date_review_needed:protected] =>
[date_received:protected] => 02/01/16
[date_completed:protected] => 02/01/16
[date_billed:protected] =>
[date_modified:protected] => 02/01/16
[collBokExports:protected] =>
[lastBokExportCriteria:BaseElcoshItem:private] =>
[alreadyInSave:protected] =>
[alreadyInValidation:protected] =>
[validationFailures:protected] => Array
(
)
[_new:BaseObject:private] =>
[_deleted:BaseObject:private] =>
[modifiedColumns:protected] => Array
(
)
)
)
[5] => Search_Result Object
(
[title] => Construction bracing
[image] => /record/images/3995-p.jpg
[blurb] => This shows structural support that prevents collapses during construction....
[category] => Array
(
[0] => 12
[1] => 15
[2] => 21
[3] => 49
[4] => 51
[5] => 55
[6] => 56
[7] => 60
[8] => 64
[9] => 68
[10] => 74
[11] => 63
[12] => 78
[13] => 79
[14] => 80
[15] => 62
[16] => 87
[17] => 90
[18] => 97
)
[labels] => Array
(
[0] => Crushed/Struck By
[1] => Work Environment
[2] => Hazards
[3] => Falls
[6] => Scaffolds
[9] => Carpenter
[10] => Trades
[11] => Cement Mason
[13] => Electrical Worker
[15] => Elevator Constructor
[17] => HVAC
[19] => Laborer
[21] => Maintenance Worker
[23] => Pile Driver
[25] => Reinforcing Ironworker
[27] => Roofer/Waterproofer
[29] => Scaffold Erector
[31] => Sheetmetal Worker
[33] => Structural Ironworker
[35] => Commercial & Institutional
[36] => Jobsites
[37] => Industrial
[39] => Images
[40] => Media
[41] => Media & Documents
)
[type] => Images
[sub_category] =>
[url] => /image/3995/i002690/Construction%2Bbracing.html
[item:protected] => ImageRecord Object
(
[records:protected] => Array
(
)
[recordId:protected] =>
[searchWordClass:protected] =>
[searchWordPeerClass:protected] =>
[bok_record:protected] =>
[authors:protected] =>
[organizations:protected] =>
[collections:protected] =>
[categories:protected] => Array
(
[12] => Category Object
(
[languages:protected] =>
[bok_resources:protected] =>
[bok_topics:protected] =>
[bok_keywords:protected] =>
[id:protected] => 12
[type:protected] => category
[parent:protected] => 7
[label:protected] => Crushed/Struck By
[alreadyInSave:protected] =>
[alreadyInValidation:protected] =>
[validationFailures:protected] => Array
(
)
[_new:BaseObject:private] =>
[_deleted:BaseObject:private] =>
[modifiedColumns:protected] => Array
(
)
)
[15] => Category Object
(
[languages:protected] =>
[bok_resources:protected] =>
[bok_topics:protected] =>
[bok_keywords:protected] =>
[id:protected] => 15
[type:protected] => category
[parent:protected] => 7
[label:protected] => Falls
[alreadyInSave:protected] =>
[alreadyInValidation:protected] =>
[validationFailures:protected] => Array
(
)
[_new:BaseObject:private] =>
[_deleted:BaseObject:private] =>
[modifiedColumns:protected] => Array
(
)
)
[21] => Category Object
(
[languages:protected] =>
[bok_resources:protected] =>
[bok_topics:protected] =>
[bok_keywords:protected] =>
[id:protected] => 21
[type:protected] => category
[parent:protected] => 7
[label:protected] => Scaffolds
[alreadyInSave:protected] =>
[alreadyInValidation:protected] =>
[validationFailures:protected] => Array
(
)
[_new:BaseObject:private] =>
[_deleted:BaseObject:private] =>
[modifiedColumns:protected] => Array
(
)
)
[49] => Category Object
(
[languages:protected] =>
[bok_resources:protected] =>
[bok_topics:protected] =>
[bok_keywords:protected] =>
[id:protected] => 49
[type:protected] => category
[parent:protected] => 2
[label:protected] => Carpenter
[alreadyInSave:protected] =>
[alreadyInValidation:protected] =>
[validationFailures:protected] => Array
(
)
[_new:BaseObject:private] =>
[_deleted:BaseObject:private] =>
[modifiedColumns:protected] => Array
(
)
)
[51] => Category Object
(
[languages:protected] =>
[bok_resources:protected] =>
[bok_topics:protected] =>
[bok_keywords:protected] =>
[id:protected] => 51
[type:protected] => category
[parent:protected] => 2
[label:protected] => Cement Mason
[alreadyInSave:protected] =>
[alreadyInValidation:protected] =>
[validationFailures:protected] => Array
(
)
[_new:BaseObject:private] =>
[_deleted:BaseObject:private] =>
[modifiedColumns:protected] => Array
(
)
)
[55] => Category Object
(
[languages:protected] =>
[bok_resources:protected] =>
[bok_topics:protected] =>
[bok_keywords:protected] =>
[id:protected] => 55
[type:protected] => category
[parent:protected] => 2
[label:protected] => Electrical Worker
[alreadyInSave:protected] =>
[alreadyInValidation:protected] =>
[validationFailures:protected] => Array
(
)
[_new:BaseObject:private] =>
[_deleted:BaseObject:private] =>
[modifiedColumns:protected] => Array
(
)
)
[56] => Category Object
(
[languages:protected] =>
[bok_resources:protected] =>
[bok_topics:protected] =>
[bok_keywords:protected] =>
[id:protected] => 56
[type:protected] => category
[parent:protected] => 2
[label:protected] => Elevator Constructor
[alreadyInSave:protected] =>
[alreadyInValidation:protected] =>
[validationFailures:protected] => Array
(
)
[_new:BaseObject:private] =>
[_deleted:BaseObject:private] =>
[modifiedColumns:protected] => Array
(
)
)
[60] => Category Object
(
[languages:protected] =>
[bok_resources:protected] =>
[bok_topics:protected] =>
[bok_keywords:protected] =>
[id:protected] => 60
[type:protected] => category
[parent:protected] => 2
[label:protected] => HVAC
[alreadyInSave:protected] =>
[alreadyInValidation:protected] =>
[validationFailures:protected] => Array
(
)
[_new:BaseObject:private] =>
[_deleted:BaseObject:private] =>
[modifiedColumns:protected] => Array
(
)
)
[64] => Category Object
(
[languages:protected] =>
[bok_resources:protected] =>
[bok_topics:protected] =>
[bok_keywords:protected] =>
[id:protected] => 64
[type:protected] => category
[parent:protected] => 2
[label:protected] => Laborer
[alreadyInSave:protected] =>
[alreadyInValidation:protected] =>
[validationFailures:protected] => Array
(
)
[_new:BaseObject:private] =>
[_deleted:BaseObject:private] =>
[modifiedColumns:protected] => Array
(
)
)
[68] => Category Object
(
[languages:protected] =>
[bok_resources:protected] =>
[bok_topics:protected] =>
[bok_keywords:protected] =>
[id:protected] => 68
[type:protected] => category
[parent:protected] => 2
[label:protected] => Maintenance Worker
[alreadyInSave:protected] =>
[alreadyInValidation:protected] =>
[validationFailures:protected] => Array
(
)
[_new:BaseObject:private] =>
[_deleted:BaseObject:private] =>
[modifiedColumns:protected] => Array
(
)
)
[74] => Category Object
(
[languages:protected] =>
[bok_resources:protected] =>
[bok_topics:protected] =>
[bok_keywords:protected] =>
[id:protected] => 74
[type:protected] => category
[parent:protected] => 2
[label:protected] => Pile Driver
[alreadyInSave:protected] =>
[alreadyInValidation:protected] =>
[validationFailures:protected] => Array
(
)
[_new:BaseObject:private] =>
[_deleted:BaseObject:private] =>
[modifiedColumns:protected] => Array
(
)
)
[63] => Category Object
(
[languages:protected] =>
[bok_resources:protected] =>
[bok_topics:protected] =>
[bok_keywords:protected] =>
[id:protected] => 63
[type:protected] => category
[parent:protected] => 2
[label:protected] => Reinforcing Ironworker
[alreadyInSave:protected] =>
[alreadyInValidation:protected] =>
[validationFailures:protected] => Array
(
)
[_new:BaseObject:private] =>
[_deleted:BaseObject:private] =>
[modifiedColumns:protected] => Array
(
)
)
[78] => Category Object
(
[languages:protected] =>
[bok_resources:protected] =>
[bok_topics:protected] =>
[bok_keywords:protected] =>
[id:protected] => 78
[type:protected] => category
[parent:protected] => 2
[label:protected] => Roofer/Waterproofer
[alreadyInSave:protected] =>
[alreadyInValidation:protected] =>
[validationFailures:protected] => Array
(
)
[_new:BaseObject:private] =>
[_deleted:BaseObject:private] =>
[modifiedColumns:protected] => Array
(
)
)
[79] => Category Object
(
[languages:protected] =>
[bok_resources:protected] =>
[bok_topics:protected] =>
[bok_keywords:protected] =>
[id:protected] => 79
[type:protected] => category
[parent:protected] => 2
[label:protected] => Scaffold Erector
[alreadyInSave:protected] =>
[alreadyInValidation:protected] =>
[validationFailures:protected] => Array
(
)
[_new:BaseObject:private] =>
[_deleted:BaseObject:private] =>
[modifiedColumns:protected] => Array
(
)
)
[80] => Category Object
(
[languages:protected] =>
[bok_resources:protected] =>
[bok_topics:protected] =>
[bok_keywords:protected] =>
[id:protected] => 80
[type:protected] => category
[parent:protected] => 2
[label:protected] => Sheetmetal Worker
[alreadyInSave:protected] =>
[alreadyInValidation:protected] =>
[validationFailures:protected] => Array
(
)
[_new:BaseObject:private] =>
[_deleted:BaseObject:private] =>
[modifiedColumns:protected] => Array
(
)
)
[62] => Category Object
(
[languages:protected] =>
[bok_resources:protected] =>
[bok_topics:protected] =>
[bok_keywords:protected] =>
[id:protected] => 62
[type:protected] => category
[parent:protected] => 2
[label:protected] => Structural Ironworker
[alreadyInSave:protected] =>
[alreadyInValidation:protected] =>
[validationFailures:protected] => Array
(
)
[_new:BaseObject:private] =>
[_deleted:BaseObject:private] =>
[modifiedColumns:protected] => Array
(
)
)
[87] => Category Object
(
[languages:protected] =>
[bok_resources:protected] =>
[bok_topics:protected] =>
[bok_keywords:protected] =>
[id:protected] => 87
[type:protected] => category
[parent:protected] => 3
[label:protected] => Commercial & Institutional
[alreadyInSave:protected] =>
[alreadyInValidation:protected] =>
[validationFailures:protected] => Array
(
)
[_new:BaseObject:private] =>
[_deleted:BaseObject:private] =>
[modifiedColumns:protected] => Array
(
)
)
[90] => Category Object
(
[languages:protected] =>
[bok_resources:protected] =>
[bok_topics:protected] =>
[bok_keywords:protected] =>
[id:protected] => 90
[type:protected] => category
[parent:protected] => 3
[label:protected] => Industrial
[alreadyInSave:protected] =>
[alreadyInValidation:protected] =>
[validationFailures:protected] => Array
(
)
[_new:BaseObject:private] =>
[_deleted:BaseObject:private] =>
[modifiedColumns:protected] => Array
(
)
)
[97] => Category Object
(
[languages:protected] =>
[bok_resources:protected] =>
[bok_topics:protected] =>
[bok_keywords:protected] =>
[id:protected] => 97
[type:protected] => category
[parent:protected] => 5
[label:protected] => Images
[alreadyInSave:protected] =>
[alreadyInValidation:protected] =>
[validationFailures:protected] => Array
(
)
[_new:BaseObject:private] =>
[_deleted:BaseObject:private] =>
[modifiedColumns:protected] => Array
(
)
)
)
[categories_initialized:protected] => 1
[mapped_items:protected] =>
[content:protected] =>
[files:protected] =>
[language:protected] => Language Object
(
[id:protected] => 1
[code:protected] => en
[name:protected] => English
[alreadyInSave:protected] =>
[alreadyInValidation:protected] =>
[validationFailures:protected] => Array
(
)
[_new:BaseObject:private] =>
[_deleted:BaseObject:private] =>
[modifiedColumns:protected] => Array
(
)
)
[old_record:protected] =>
[id:protected] => 3995
[old_id:protected] =>
[elcosh_id:protected] => i002690
[type:protected] => image
[display_type:protected] => Image
[user_id:protected] => 0
[language_id:protected] => 1
[tagging_id:protected] => Bruce Lippy
[priority_id:protected] => 1
[title:protected] => Construction bracing
[total_pages:protected] => 0
[billed_pages:protected] => 0
[publication_number:protected] =>
[part_of:protected] =>
[keywords:protected] => Bracing, support, scaffold
[comments:protected] =>
[summary:protected] => This shows structural support that prevents collapses during construction.
[transition_comments:protected] =>
[external_link:protected] =>
[consol_link:protected] => http://www.cpwrconstructionsolutions.org/masonry/solution/8/adjustable-tower-scaffold.html
[more_like_this:protected] => i002660
[permission_given_by:protected] =>
[published:protected] => T
[billable:protected] => F
[img_name:protected] =>
[img_ext:protected] => jpg
[img_width:protected] =>
[img_height:protected] =>
[img_credit:protected] => Photo by Pam Susi
[img_practice:protected] => good
[vid_source_id:protected] =>
[vid_running_time:protected] =>
[vid_intended_audience:protected] =>
[vid_acquisition_info:protected] =>
[vid_cost:protected] =>
[vid_producer:protected] =>
[vid_filename:protected] =>
[vid_filename_downloadable:protected] =>
[date_summary:protected] => January 2016
[date_permission_requested:protected] =>
[date_permission_received:protected] =>
[date_review_needed:protected] =>
[date_received:protected] => 02/01/16
[date_completed:protected] => 02/01/16
[date_billed:protected] =>
[date_modified:protected] => 02/01/16
[collBokExports:protected] =>
[lastBokExportCriteria:BaseElcoshItem:private] =>
[alreadyInSave:protected] =>
[alreadyInValidation:protected] =>
[validationFailures:protected] => Array
(
)
[_new:BaseObject:private] =>
[_deleted:BaseObject:private] =>
[modifiedColumns:protected] => Array
(
)
)
)
)
[preview_mode] =>
[description] => Toolbox talks have been the main tool for communicating safety information on construction jobs for decades.
Unfortunately, there has been little research on what makes for effective toolbox talks. The IUOE National
Training Fund worked with OSHA and NIOSH to make sure their series of 24 Focus Four toolbox talks were based on the best recommendations for effective design. These toolbox talks accompany an entire package of training materials, but can be used alone. This guide points out the key features of these toolbox talks and how best to deliver them.
[keywords] => toolbox talks, tailgate talks
[related_items] => Array
(
[Toolbox Talks] => Array
(
[0] => DocumentRecord Object
(
[records:protected] => Array
(
)
[recordId:protected] =>
[searchWordClass:protected] =>
[searchWordPeerClass:protected] =>
[bok_record:protected] =>
[authors:protected] =>
[organizations:protected] =>
[collections:protected] =>
[categories:protected] =>
[categories_initialized:protected] =>
[mapped_items:protected] =>
[content:protected] =>
[files:protected] =>
[language:protected] => Language Object
(
[id:protected] => 1
[code:protected] => en
[name:protected] => English
[alreadyInSave:protected] =>
[alreadyInValidation:protected] =>
[validationFailures:protected] => Array
(
)
[_new:BaseObject:private] =>
[_deleted:BaseObject:private] =>
[modifiedColumns:protected] => Array
(
)
)
[old_record:protected] =>
[id:protected] => 1605
[old_id:protected] => 1262
[elcosh_id:protected] => d001137
[type:protected] => document
[display_type:protected] => HTML w/ PDF
[user_id:protected] =>
[language_id:protected] => 1
[tagging_id:protected] => Garber
[priority_id:protected] => 1
[title:protected] => Focus Four Toolbox Talks, Module 1 – Falls, Talk #2 – Falls from debris piles?
[total_pages:protected] => 1
[billed_pages:protected] => 1
[publication_number:protected] =>
[part_of:protected] =>
[keywords:protected] => disaster response, hazard clean-up, uneven surface, disaster site, disaster clean-up
[comments:protected] =>
[summary:protected] => A toolbox talk on preventing falls from debris piles. Includes questions to ask, an incident to discuss with images, and a place to record questions the trainer would like to ask about the incident. Part of a collection. Click on the 'collection' button to access the other items.
[transition_comments:protected] =>
[external_link:protected] =>
[consol_link:protected] => http://www.cpwrconstructionsolutions.org/roofing/hazard/1463/install-asphalt-roofs-fall-from-heights.html
[more_like_this:protected] => a000081,d000478,d000530
[permission_given_by:protected] =>
[published:protected] => T
[billable:protected] => F
[img_name:protected] =>
[img_ext:protected] =>
[img_width:protected] =>
[img_height:protected] =>
[img_credit:protected] =>
[img_practice:protected] =>
[vid_source_id:protected] =>
[vid_running_time:protected] =>
[vid_intended_audience:protected] =>
[vid_acquisition_info:protected] =>
[vid_cost:protected] =>
[vid_producer:protected] =>
[vid_filename:protected] =>
[vid_filename_downloadable:protected] =>
[date_summary:protected] =>
[date_permission_requested:protected] =>
[date_permission_received:protected] =>
[date_review_needed:protected] =>
[date_received:protected] => 02/15/12
[date_completed:protected] => 03/19/12
[date_billed:protected] =>
[date_modified:protected] => 07/10/12
[collBokExports:protected] =>
[lastBokExportCriteria:BaseElcoshItem:private] =>
[alreadyInSave:protected] =>
[alreadyInValidation:protected] =>
[validationFailures:protected] => Array
(
)
[_new:BaseObject:private] =>
[_deleted:BaseObject:private] =>
[modifiedColumns:protected] => Array
(
)
)
[1] => DocumentRecord Object
(
[records:protected] => Array
(
)
[recordId:protected] =>
[searchWordClass:protected] =>
[searchWordPeerClass:protected] =>
[bok_record:protected] =>
[authors:protected] =>
[organizations:protected] =>
[collections:protected] =>
[categories:protected] =>
[categories_initialized:protected] =>
[mapped_items:protected] =>
[content:protected] =>
[files:protected] =>
[language:protected] => Language Object
(
[id:protected] => 1
[code:protected] => en
[name:protected] => English
[alreadyInSave:protected] =>
[alreadyInValidation:protected] =>
[validationFailures:protected] => Array
(
)
[_new:BaseObject:private] =>
[_deleted:BaseObject:private] =>
[modifiedColumns:protected] => Array
(
)
)
[old_record:protected] =>
[id:protected] => 1610
[old_id:protected] => 1271
[elcosh_id:protected] => d001146
[type:protected] => document
[display_type:protected] => HTML w/ PDF
[user_id:protected] => 0
[language_id:protected] => 1
[tagging_id:protected] => Garber
[priority_id:protected] => 1
[title:protected] => Focus Four Toolbox Talks, Module 2 – Struck-by, Talk #5 – Rigging and Securing Loads
[total_pages:protected] => 1
[billed_pages:protected] => 1
[publication_number:protected] =>
[part_of:protected] =>
[keywords:protected] => rigging, lift loads, loading areas, chains
[comments:protected] =>
[summary:protected] => A toolbox talk on preventing struck-by incidents caused by not securing loads properly. Includes questions to ask, an incident to discuss with images, and a place to record questions the trainer would like to ask about the incident. Part of a collection. Click on the 'collection' button to access the other items.
[transition_comments:protected] =>
[external_link:protected] =>
[consol_link:protected] => http://www.cpwrconstructionsolutions.org/heavy_equipment/hazard/1591/move-equipment-to-from-and-between-sites-work-zone-struck-by-injuries-and-fatalities.html
[more_like_this:protected] => d000144,d000360,d000873
[permission_given_by:protected] =>
[published:protected] => T
[billable:protected] => F
[img_name:protected] =>
[img_ext:protected] =>
[img_width:protected] =>
[img_height:protected] =>
[img_credit:protected] =>
[img_practice:protected] =>
[vid_source_id:protected] =>
[vid_running_time:protected] =>
[vid_intended_audience:protected] =>
[vid_acquisition_info:protected] =>
[vid_cost:protected] =>
[vid_producer:protected] =>
[vid_filename:protected] =>
[vid_filename_downloadable:protected] =>
[date_summary:protected] =>
[date_permission_requested:protected] =>
[date_permission_received:protected] =>
[date_review_needed:protected] =>
[date_received:protected] => 02/15/12
[date_completed:protected] => 03/28/12
[date_billed:protected] =>
[date_modified:protected] => 05/12/14
[collBokExports:protected] =>
[lastBokExportCriteria:BaseElcoshItem:private] =>
[alreadyInSave:protected] =>
[alreadyInValidation:protected] =>
[validationFailures:protected] => Array
(
)
[_new:BaseObject:private] =>
[_deleted:BaseObject:private] =>
[modifiedColumns:protected] => Array
(
)
)
[2] => DocumentRecord Object
(
[records:protected] => Array
(
)
[recordId:protected] =>
[searchWordClass:protected] =>
[searchWordPeerClass:protected] =>
[bok_record:protected] =>
[authors:protected] =>
[organizations:protected] =>
[collections:protected] =>
[categories:protected] =>
[categories_initialized:protected] =>
[mapped_items:protected] =>
[content:protected] =>
[files:protected] =>
[language:protected] => Language Object
(
[id:protected] => 1
[code:protected] => en
[name:protected] => English
[alreadyInSave:protected] =>
[alreadyInValidation:protected] =>
[validationFailures:protected] => Array
(
)
[_new:BaseObject:private] =>
[_deleted:BaseObject:private] =>
[modifiedColumns:protected] => Array
(
)
)
[old_record:protected] =>
[id:protected] => 1645
[old_id:protected] => 1274
[elcosh_id:protected] => d001149
[type:protected] => document
[display_type:protected] => HTML w/ PDF
[user_id:protected] => 0
[language_id:protected] => 1
[tagging_id:protected] => Garber
[priority_id:protected] => 1
[title:protected] => Focus Four Toolbox Talks, Module 3 – Caught-in/between, Talk #2 – Trenches & Heavy Equipment
[total_pages:protected] => 1
[billed_pages:protected] => 1
[publication_number:protected] =>
[part_of:protected] =>
[keywords:protected] => back-up alarms, spotter, soil cave-in, spoil pikes, ROPs, trenching, rain
[comments:protected] =>
[summary:protected] => A toolbox talk on preventing incidents involving trenches such as trench collapse. Includes questions to ask, an incident to discuss with images, and a place to record questions the trainer would like to ask about the incident. Part of a collection. Click on the 'collection' button to access the other items.
[transition_comments:protected] =>
[external_link:protected] =>
[consol_link:protected] =>
[more_like_this:protected] => d000019,d000035,d000168
[permission_given_by:protected] =>
[published:protected] => T
[billable:protected] => F
[img_name:protected] =>
[img_ext:protected] =>
[img_width:protected] =>
[img_height:protected] =>
[img_credit:protected] =>
[img_practice:protected] =>
[vid_source_id:protected] =>
[vid_running_time:protected] =>
[vid_intended_audience:protected] =>
[vid_acquisition_info:protected] =>
[vid_cost:protected] =>
[vid_producer:protected] =>
[vid_filename:protected] =>
[vid_filename_downloadable:protected] =>
[date_summary:protected] =>
[date_permission_requested:protected] =>
[date_permission_received:protected] =>
[date_review_needed:protected] =>
[date_received:protected] => 02/15/12
[date_completed:protected] => 04/02/12
[date_billed:protected] =>
[date_modified:protected] => 05/23/23
[collBokExports:protected] =>
[lastBokExportCriteria:BaseElcoshItem:private] =>
[alreadyInSave:protected] =>
[alreadyInValidation:protected] =>
[validationFailures:protected] => Array
(
)
[_new:BaseObject:private] =>
[_deleted:BaseObject:private] =>
[modifiedColumns:protected] => Array
(
)
)
[3] => DocumentRecord Object
(
[records:protected] => Array
(
)
[recordId:protected] =>
[searchWordClass:protected] =>
[searchWordPeerClass:protected] =>
[bok_record:protected] =>
[authors:protected] =>
[organizations:protected] =>
[collections:protected] =>
[categories:protected] =>
[categories_initialized:protected] =>
[mapped_items:protected] =>
[content:protected] =>
[files:protected] =>
[language:protected] => Language Object
(
[id:protected] => 1
[code:protected] => en
[name:protected] => English
[alreadyInSave:protected] =>
[alreadyInValidation:protected] =>
[validationFailures:protected] => Array
(
)
[_new:BaseObject:private] =>
[_deleted:BaseObject:private] =>
[modifiedColumns:protected] => Array
(
)
)
[old_record:protected] =>
[id:protected] => 1654
[old_id:protected] => 1284
[elcosh_id:protected] => d001159
[type:protected] => document
[display_type:protected] => HTML w/ PDF
[user_id:protected] => 0
[language_id:protected] => 1
[tagging_id:protected] => Garber
[priority_id:protected] => 1
[title:protected] => Focus Four Toolbox Talks, Module 4 – Electrocutions, Talk #6 – Hazards on Disaster Sites
[total_pages:protected] => 1
[billed_pages:protected] => 1
[publication_number:protected] =>
[part_of:protected] =>
[keywords:protected] => powerlines, underground, utilities, generators, wet conditions, GFCIs, energized lines, disasters, emergency response
[comments:protected] =>
[summary:protected] => A toolbox talk on how to avoid electrocution on a disaster site. Includes questions to ask, an incident to discuss with images, and a place to record questions the trainer would like to ask about the incident. Part of a collection. Click on the 'collection' button to access the other items.
[transition_comments:protected] =>
[external_link:protected] =>
[consol_link:protected] => http://www.cpwrconstructionsolutions.org/electrical/hazard/1138/install-and-repair-high-voltage-lines-transformers-switches-electrical-shocks-burns-and-or-electrocution.html
[more_like_this:protected] => d000135,d000361,d000437
[permission_given_by:protected] =>
[published:protected] => T
[billable:protected] => F
[img_name:protected] =>
[img_ext:protected] =>
[img_width:protected] =>
[img_height:protected] =>
[img_credit:protected] =>
[img_practice:protected] =>
[vid_source_id:protected] =>
[vid_running_time:protected] =>
[vid_intended_audience:protected] =>
[vid_acquisition_info:protected] =>
[vid_cost:protected] =>
[vid_producer:protected] =>
[vid_filename:protected] =>
[vid_filename_downloadable:protected] =>
[date_summary:protected] =>
[date_permission_requested:protected] =>
[date_permission_received:protected] =>
[date_review_needed:protected] =>
[date_received:protected] => 02/15/12
[date_completed:protected] => 04/02/12
[date_billed:protected] =>
[date_modified:protected] => 05/23/23
[collBokExports:protected] =>
[lastBokExportCriteria:BaseElcoshItem:private] =>
[alreadyInSave:protected] =>
[alreadyInValidation:protected] =>
[validationFailures:protected] => Array
(
)
[_new:BaseObject:private] =>
[_deleted:BaseObject:private] =>
[modifiedColumns:protected] => Array
(
)
)
)
)
[collections] => Array
(
[1294] =>
[1295] =>
[1292] =>
[1293] => CollectionRecord Object
(
[collection_items:protected] =>
[records:protected] => Array
(
)
[recordId:protected] =>
[searchWordClass:protected] =>
[searchWordPeerClass:protected] =>
[bok_record:protected] =>
[authors:protected] =>
[organizations:protected] =>
[collections:protected] =>
[categories:protected] =>
[categories_initialized:protected] =>
[mapped_items:protected] =>
[content:protected] =>
[files:protected] =>
[language:protected] =>
[old_record:protected] =>
[id:protected] => 1293
[old_id:protected] =>
[elcosh_id:protected] => c000026
[type:protected] => collection
[display_type:protected] => Collection
[user_id:protected] =>
[language_id:protected] =>
[tagging_id:protected] =>
[priority_id:protected] =>
[title:protected] => Focus Four-Struck By
[total_pages:protected] =>
[billed_pages:protected] =>
[publication_number:protected] =>
[part_of:protected] =>
[keywords:protected] =>
[comments:protected] =>
[summary:protected] => The following are links to all of the items in this collection:
[transition_comments:protected] =>
[external_link:protected] =>
[consol_link:protected] =>
[more_like_this:protected] =>
[permission_given_by:protected] =>
[published:protected] => T
[billable:protected] => F
[img_name:protected] =>
[img_ext:protected] =>
[img_width:protected] =>
[img_height:protected] =>
[img_credit:protected] =>
[img_practice:protected] =>
[vid_source_id:protected] =>
[vid_running_time:protected] =>
[vid_intended_audience:protected] =>
[vid_acquisition_info:protected] =>
[vid_cost:protected] =>
[vid_producer:protected] =>
[vid_filename:protected] =>
[vid_filename_downloadable:protected] =>
[date_summary:protected] =>
[date_permission_requested:protected] =>
[date_permission_received:protected] =>
[date_review_needed:protected] =>
[date_received:protected] => 05/08/12
[date_completed:protected] => 05/08/12
[date_billed:protected] =>
[date_modified:protected] => 05/08/12
[collBokExports:protected] =>
[lastBokExportCriteria:BaseElcoshItem:private] =>
[alreadyInSave:protected] =>
[alreadyInValidation:protected] =>
[validationFailures:protected] => Array
(
)
[_new:BaseObject:private] =>
[_deleted:BaseObject:private] =>
[modifiedColumns:protected] => Array
(
)
)
)
[record] => DocumentRecord Object
(
[records:protected] => Array
(
)
[recordId:protected] =>
[searchWordClass:protected] =>
[searchWordPeerClass:protected] =>
[bok_record:protected] =>
[authors:protected] => Array
(
)
[organizations:protected] => Array
(
[256] => Organization Object
(
[id:protected] => 256
[elcosh_id:protected] => o000276
[user_id:protected] => 14
[province_id:protected] => 0
[country_id:protected] => 0
[title:protected] => IUOE National Training Fund
[address:protected] =>
[postal_code:protected] =>
[city:protected] =>
[department:protected] =>
[phone:protected] => 304-253-8674
[fax:protected] =>
[email:protected] =>
[website:protected] => http://www.iuoeiettc.org
[filename:protected] =>
[about:protected] =>
[comments:protected] =>
[logo_available:protected] => T
[no_details:protected] => F
[date_received:protected] => 2012-02-13
[date_completed:protected] => 2012-02-13
[date_billed:protected] =>
[alreadyInSave:protected] =>
[alreadyInValidation:protected] =>
[validationFailures:protected] => Array
(
)
[_new:BaseObject:private] =>
[_deleted:BaseObject:private] =>
[modifiedColumns:protected] => Array
(
)
)
)
[collections:protected] => Array
(
[1294] =>
[1295] =>
[1292] =>
[1293] => CollectionRecord Object
(
[collection_items:protected] =>
[records:protected] => Array
(
)
[recordId:protected] =>
[searchWordClass:protected] =>
[searchWordPeerClass:protected] =>
[bok_record:protected] =>
[authors:protected] =>
[organizations:protected] =>
[collections:protected] =>
[categories:protected] =>
[categories_initialized:protected] =>
[mapped_items:protected] =>
[content:protected] =>
[files:protected] =>
[language:protected] =>
[old_record:protected] =>
[id:protected] => 1293
[old_id:protected] =>
[elcosh_id:protected] => c000026
[type:protected] => collection
[display_type:protected] => Collection
[user_id:protected] =>
[language_id:protected] =>
[tagging_id:protected] =>
[priority_id:protected] =>
[title:protected] => Focus Four-Struck By
[total_pages:protected] =>
[billed_pages:protected] =>
[publication_number:protected] =>
[part_of:protected] =>
[keywords:protected] =>
[comments:protected] =>
[summary:protected] => The following are links to all of the items in this collection:
[transition_comments:protected] =>
[external_link:protected] =>
[consol_link:protected] =>
[more_like_this:protected] =>
[permission_given_by:protected] =>
[published:protected] => T
[billable:protected] => F
[img_name:protected] =>
[img_ext:protected] =>
[img_width:protected] =>
[img_height:protected] =>
[img_credit:protected] =>
[img_practice:protected] =>
[vid_source_id:protected] =>
[vid_running_time:protected] =>
[vid_intended_audience:protected] =>
[vid_acquisition_info:protected] =>
[vid_cost:protected] =>
[vid_producer:protected] =>
[vid_filename:protected] =>
[vid_filename_downloadable:protected] =>
[date_summary:protected] =>
[date_permission_requested:protected] =>
[date_permission_received:protected] =>
[date_review_needed:protected] =>
[date_received:protected] => 05/08/12
[date_completed:protected] => 05/08/12
[date_billed:protected] =>
[date_modified:protected] => 05/08/12
[collBokExports:protected] =>
[lastBokExportCriteria:BaseElcoshItem:private] =>
[alreadyInSave:protected] =>
[alreadyInValidation:protected] =>
[validationFailures:protected] => Array
(
)
[_new:BaseObject:private] =>
[_deleted:BaseObject:private] =>
[modifiedColumns:protected] => Array
(
)
)
)
[categories:protected] =>
[categories_initialized:protected] =>
[mapped_items:protected] => Array
(
[1605] => DocumentRecord Object
(
[records:protected] => Array
(
)
[recordId:protected] =>
[searchWordClass:protected] =>
[searchWordPeerClass:protected] =>
[bok_record:protected] =>
[authors:protected] =>
[organizations:protected] =>
[collections:protected] =>
[categories:protected] =>
[categories_initialized:protected] =>
[mapped_items:protected] =>
[content:protected] =>
[files:protected] =>
[language:protected] =>
[old_record:protected] =>
[id:protected] => 1605
[old_id:protected] => 1262
[elcosh_id:protected] => d001137
[type:protected] => document
[display_type:protected] => HTML w/ PDF
[user_id:protected] =>
[language_id:protected] => 1
[tagging_id:protected] => Garber
[priority_id:protected] => 1
[title:protected] => Focus Four Toolbox Talks, Module 1 – Falls, Talk #2 – Falls from debris piles?
[total_pages:protected] => 1
[billed_pages:protected] => 1
[publication_number:protected] =>
[part_of:protected] =>
[keywords:protected] => disaster response, hazard clean-up, uneven surface, disaster site, disaster clean-up
[comments:protected] =>
[summary:protected] => A toolbox talk on preventing falls from debris piles. Includes questions to ask, an incident to discuss with images, and a place to record questions the trainer would like to ask about the incident. Part of a collection. Click on the 'collection' button to access the other items.
[transition_comments:protected] =>
[external_link:protected] =>
[consol_link:protected] => http://www.cpwrconstructionsolutions.org/roofing/hazard/1463/install-asphalt-roofs-fall-from-heights.html
[more_like_this:protected] => a000081,d000478,d000530
[permission_given_by:protected] =>
[published:protected] => T
[billable:protected] => F
[img_name:protected] =>
[img_ext:protected] =>
[img_width:protected] =>
[img_height:protected] =>
[img_credit:protected] =>
[img_practice:protected] =>
[vid_source_id:protected] =>
[vid_running_time:protected] =>
[vid_intended_audience:protected] =>
[vid_acquisition_info:protected] =>
[vid_cost:protected] =>
[vid_producer:protected] =>
[vid_filename:protected] =>
[vid_filename_downloadable:protected] =>
[date_summary:protected] =>
[date_permission_requested:protected] =>
[date_permission_received:protected] =>
[date_review_needed:protected] =>
[date_received:protected] => 02/15/12
[date_completed:protected] => 03/19/12
[date_billed:protected] =>
[date_modified:protected] => 07/10/12
[collBokExports:protected] =>
[lastBokExportCriteria:BaseElcoshItem:private] =>
[alreadyInSave:protected] =>
[alreadyInValidation:protected] =>
[validationFailures:protected] => Array
(
)
[_new:BaseObject:private] =>
[_deleted:BaseObject:private] =>
[modifiedColumns:protected] => Array
(
)
)
[1610] => DocumentRecord Object
(
[records:protected] => Array
(
)
[recordId:protected] =>
[searchWordClass:protected] =>
[searchWordPeerClass:protected] =>
[bok_record:protected] =>
[authors:protected] =>
[organizations:protected] =>
[collections:protected] =>
[categories:protected] =>
[categories_initialized:protected] =>
[mapped_items:protected] =>
[content:protected] =>
[files:protected] =>
[language:protected] =>
[old_record:protected] =>
[id:protected] => 1610
[old_id:protected] => 1271
[elcosh_id:protected] => d001146
[type:protected] => document
[display_type:protected] => HTML w/ PDF
[user_id:protected] => 0
[language_id:protected] => 1
[tagging_id:protected] => Garber
[priority_id:protected] => 1
[title:protected] => Focus Four Toolbox Talks, Module 2 – Struck-by, Talk #5 – Rigging and Securing Loads
[total_pages:protected] => 1
[billed_pages:protected] => 1
[publication_number:protected] =>
[part_of:protected] =>
[keywords:protected] => rigging, lift loads, loading areas, chains
[comments:protected] =>
[summary:protected] => A toolbox talk on preventing struck-by incidents caused by not securing loads properly. Includes questions to ask, an incident to discuss with images, and a place to record questions the trainer would like to ask about the incident. Part of a collection. Click on the 'collection' button to access the other items.
[transition_comments:protected] =>
[external_link:protected] =>
[consol_link:protected] => http://www.cpwrconstructionsolutions.org/heavy_equipment/hazard/1591/move-equipment-to-from-and-between-sites-work-zone-struck-by-injuries-and-fatalities.html
[more_like_this:protected] => d000144,d000360,d000873
[permission_given_by:protected] =>
[published:protected] => T
[billable:protected] => F
[img_name:protected] =>
[img_ext:protected] =>
[img_width:protected] =>
[img_height:protected] =>
[img_credit:protected] =>
[img_practice:protected] =>
[vid_source_id:protected] =>
[vid_running_time:protected] =>
[vid_intended_audience:protected] =>
[vid_acquisition_info:protected] =>
[vid_cost:protected] =>
[vid_producer:protected] =>
[vid_filename:protected] =>
[vid_filename_downloadable:protected] =>
[date_summary:protected] =>
[date_permission_requested:protected] =>
[date_permission_received:protected] =>
[date_review_needed:protected] =>
[date_received:protected] => 02/15/12
[date_completed:protected] => 03/28/12
[date_billed:protected] =>
[date_modified:protected] => 05/12/14
[collBokExports:protected] =>
[lastBokExportCriteria:BaseElcoshItem:private] =>
[alreadyInSave:protected] =>
[alreadyInValidation:protected] =>
[validationFailures:protected] => Array
(
)
[_new:BaseObject:private] =>
[_deleted:BaseObject:private] =>
[modifiedColumns:protected] => Array
(
)
)
[1645] => DocumentRecord Object
(
[records:protected] => Array
(
)
[recordId:protected] =>
[searchWordClass:protected] =>
[searchWordPeerClass:protected] =>
[bok_record:protected] =>
[authors:protected] =>
[organizations:protected] =>
[collections:protected] =>
[categories:protected] =>
[categories_initialized:protected] =>
[mapped_items:protected] =>
[content:protected] =>
[files:protected] =>
[language:protected] =>
[old_record:protected] =>
[id:protected] => 1645
[old_id:protected] => 1274
[elcosh_id:protected] => d001149
[type:protected] => document
[display_type:protected] => HTML w/ PDF
[user_id:protected] => 0
[language_id:protected] => 1
[tagging_id:protected] => Garber
[priority_id:protected] => 1
[title:protected] => Focus Four Toolbox Talks, Module 3 – Caught-in/between, Talk #2 – Trenches & Heavy Equipment
[total_pages:protected] => 1
[billed_pages:protected] => 1
[publication_number:protected] =>
[part_of:protected] =>
[keywords:protected] => back-up alarms, spotter, soil cave-in, spoil pikes, ROPs, trenching, rain
[comments:protected] =>
[summary:protected] => A toolbox talk on preventing incidents involving trenches such as trench collapse. Includes questions to ask, an incident to discuss with images, and a place to record questions the trainer would like to ask about the incident. Part of a collection. Click on the 'collection' button to access the other items.
[transition_comments:protected] =>
[external_link:protected] =>
[consol_link:protected] =>
[more_like_this:protected] => d000019,d000035,d000168
[permission_given_by:protected] =>
[published:protected] => T
[billable:protected] => F
[img_name:protected] =>
[img_ext:protected] =>
[img_width:protected] =>
[img_height:protected] =>
[img_credit:protected] =>
[img_practice:protected] =>
[vid_source_id:protected] =>
[vid_running_time:protected] =>
[vid_intended_audience:protected] =>
[vid_acquisition_info:protected] =>
[vid_cost:protected] =>
[vid_producer:protected] =>
[vid_filename:protected] =>
[vid_filename_downloadable:protected] =>
[date_summary:protected] =>
[date_permission_requested:protected] =>
[date_permission_received:protected] =>
[date_review_needed:protected] =>
[date_received:protected] => 02/15/12
[date_completed:protected] => 04/02/12
[date_billed:protected] =>
[date_modified:protected] => 05/23/23
[collBokExports:protected] =>
[lastBokExportCriteria:BaseElcoshItem:private] =>
[alreadyInSave:protected] =>
[alreadyInValidation:protected] =>
[validationFailures:protected] => Array
(
)
[_new:BaseObject:private] =>
[_deleted:BaseObject:private] =>
[modifiedColumns:protected] => Array
(
)
)
[1654] => DocumentRecord Object
(
[records:protected] => Array
(
)
[recordId:protected] =>
[searchWordClass:protected] =>
[searchWordPeerClass:protected] =>
[bok_record:protected] =>
[authors:protected] =>
[organizations:protected] =>
[collections:protected] =>
[categories:protected] =>
[categories_initialized:protected] =>
[mapped_items:protected] =>
[content:protected] =>
[files:protected] =>
[language:protected] =>
[old_record:protected] =>
[id:protected] => 1654
[old_id:protected] => 1284
[elcosh_id:protected] => d001159
[type:protected] => document
[display_type:protected] => HTML w/ PDF
[user_id:protected] => 0
[language_id:protected] => 1
[tagging_id:protected] => Garber
[priority_id:protected] => 1
[title:protected] => Focus Four Toolbox Talks, Module 4 – Electrocutions, Talk #6 – Hazards on Disaster Sites
[total_pages:protected] => 1
[billed_pages:protected] => 1
[publication_number:protected] =>
[part_of:protected] =>
[keywords:protected] => powerlines, underground, utilities, generators, wet conditions, GFCIs, energized lines, disasters, emergency response
[comments:protected] =>
[summary:protected] => A toolbox talk on how to avoid electrocution on a disaster site. Includes questions to ask, an incident to discuss with images, and a place to record questions the trainer would like to ask about the incident. Part of a collection. Click on the 'collection' button to access the other items.
[transition_comments:protected] =>
[external_link:protected] =>
[consol_link:protected] => http://www.cpwrconstructionsolutions.org/electrical/hazard/1138/install-and-repair-high-voltage-lines-transformers-switches-electrical-shocks-burns-and-or-electrocution.html
[more_like_this:protected] => d000135,d000361,d000437
[permission_given_by:protected] =>
[published:protected] => T
[billable:protected] => F
[img_name:protected] =>
[img_ext:protected] =>
[img_width:protected] =>
[img_height:protected] =>
[img_credit:protected] =>
[img_practice:protected] =>
[vid_source_id:protected] =>
[vid_running_time:protected] =>
[vid_intended_audience:protected] =>
[vid_acquisition_info:protected] =>
[vid_cost:protected] =>
[vid_producer:protected] =>
[vid_filename:protected] =>
[vid_filename_downloadable:protected] =>
[date_summary:protected] =>
[date_permission_requested:protected] =>
[date_permission_received:protected] =>
[date_review_needed:protected] =>
[date_received:protected] => 02/15/12
[date_completed:protected] => 04/02/12
[date_billed:protected] =>
[date_modified:protected] => 05/23/23
[collBokExports:protected] =>
[lastBokExportCriteria:BaseElcoshItem:private] =>
[alreadyInSave:protected] =>
[alreadyInValidation:protected] =>
[validationFailures:protected] => Array
(
)
[_new:BaseObject:private] =>
[_deleted:BaseObject:private] =>
[modifiedColumns:protected] => Array
(
)
)
)
[content:protected] =>
[files:protected] => Array
(
[9400] => File Object
(
[id:protected] => 9400
[filename:protected] => 1.jpg
[downloadable:protected] => F
[timestamp:protected] => 2014-05-08 15:05:37
[alreadyInSave:protected] =>
[alreadyInValidation:protected] =>
[validationFailures:protected] => Array
(
)
[_new:BaseObject:private] =>
[_deleted:BaseObject:private] =>
[modifiedColumns:protected] => Array
(
)
)
[9401] => File Object
(
[id:protected] => 9401
[filename:protected] => d001298.pdf
[downloadable:protected] => T
[timestamp:protected] => 2014-05-08 15:05:37
[alreadyInSave:protected] =>
[alreadyInValidation:protected] =>
[validationFailures:protected] => Array
(
)
[_new:BaseObject:private] =>
[_deleted:BaseObject:private] =>
[modifiedColumns:protected] => Array
(
)
)
)
[language:protected] => Language Object
(
[id:protected] => 1
[code:protected] => en
[name:protected] => English
[alreadyInSave:protected] =>
[alreadyInValidation:protected] =>
[validationFailures:protected] => Array
(
)
[_new:BaseObject:private] =>
[_deleted:BaseObject:private] =>
[modifiedColumns:protected] => Array
(
)
)
[old_record:protected] =>
[id:protected] => 3827
[old_id:protected] =>
[elcosh_id:protected] => d001298
[type:protected] => document
[display_type:protected] => HTML w/ PDF
[user_id:protected] => 23
[language_id:protected] => 1
[tagging_id:protected] => Bruce Lippy
[priority_id:protected] => 1
[title:protected] => Getting the most out of the IUOE Toolbox Talks
[total_pages:protected] => 2
[billed_pages:protected] => 2
[publication_number:protected] =>
[part_of:protected] =>
[keywords:protected] => toolbox talks, tailgate talks
[comments:protected] =>
[summary:protected] => Toolbox talks have been the main tool for communicating safety information on construction jobs for decades.
Unfortunately, there has been little research on what makes for effective toolbox talks. The IUOE National
Training Fund worked with OSHA and NIOSH to make sure their series of 24 Focus Four toolbox talks were based on the best recommendations for effective design. These toolbox talks accompany an entire package of training materials, but can be used alone. This guide points out the key features of these toolbox talks and how best to deliver them.
[transition_comments:protected] =>
[external_link:protected] =>
[consol_link:protected] =>
[more_like_this:protected] => d001137,d001146,d001149,d001159
[permission_given_by:protected] => IUOE National Hazmat Program
[published:protected] => T
[billable:protected] => F
[img_name:protected] =>
[img_ext:protected] => png
[img_width:protected] =>
[img_height:protected] =>
[img_credit:protected] =>
[img_practice:protected] =>
[vid_source_id:protected] =>
[vid_running_time:protected] =>
[vid_intended_audience:protected] =>
[vid_acquisition_info:protected] =>
[vid_cost:protected] =>
[vid_producer:protected] =>
[vid_filename:protected] =>
[vid_filename_downloadable:protected] =>
[date_summary:protected] => 2007
[date_permission_requested:protected] =>
[date_permission_received:protected] =>
[date_review_needed:protected] =>
[date_received:protected] => 05/08/14
[date_completed:protected] => 05/08/14
[date_billed:protected] =>
[date_modified:protected] => 05/08/14
[collBokExports:protected] =>
[lastBokExportCriteria:BaseElcoshItem:private] =>
[alreadyInSave:protected] =>
[alreadyInValidation:protected] =>
[validationFailures:protected] => Array
(
)
[_new:BaseObject:private] =>
[_deleted:BaseObject:private] =>
[modifiedColumns:protected] => Array
(
)
)
[show_text] =>
[document_content] => ElcoshItemDocumentContent Object
(
[id:protected] => 2896
[item_id:protected] => 3827
[type:protected] => main
[title:protected] =>
[content:protected] =>
Why were these talks developed?
Toolbox talks have been the main tool for communicating safety information on construction jobs for decades. Unfortunately, there has been almost no research on what makes for effective toolbox talks. The IUOE National Training Fund has worked with OSHA, the National Institute for Occupational Safety and Health and the Lippy Group, LLC to make sure these Focus Four toolbox talks are based on the latest fi ndings on the most effective design and tailored to the hazards operating engineers face daily. These toolbox talks accompany an entire package of training materials, but can be used alone. The way these are delivered is as important as how well they are designed.
What did NIOSH find out?
- Just handing out factsheets and toolbox talks to workers doesn’t work. Providing copies after toolbox talks doesn’t make much of an impact either.
- Using case studies (real life stories of accidents that ended in fatality or injury) in toolbox talks is effective.
- When toolbox talks containing case studies were accompanied by discussion questions to encourage group participation, they were more effective. Consequently, getting the workers to participate in the discussion about the case study is important. It’s not enough to tell the story, it is better to have the workers engage in problem solving that analyzes why the accident occurred and how it could have been prevented. Active learning is always better than passive.
How should you deliver these toolbox talks?
- Choose a topic that is related to work going on at the site.
- Hold the meeting on the job, preferably where everyone can sit and relax.
- Hold the meeting at the beginning of a shift or after a break. Folks are too tired at the end of a shift to carefully listen and they want to get home.
- Read the toolbox talk sheet on the topic prior to conducting the talk.
- Start at the top of the form and work right through to the end, which should take around 10 to 15 minutes. Guidance is provided in blue print to help you with each section.
- Use the questions provided to generate discussions. Always allow time for the crew to respond to your questions before you provide an answer. Some suggested responses are written in italics.
- Review the case study and emphasize that this was a real incident. Ask the crew for a case study before you review the one provided, however.
- Always end with a discussion of the particular worksite where you are conducting the talk. Tie the talk as closely to hazards on the site as possible and encourage the crew to constantly look for and immediately correct hazards. They should also know how to report any problems that can’t be immediately corrected.
- Provide copies to each person, if you like, but NIOSH has not found that to be particularly effective.
- Encourage workers to do similar talks on their sites and provide them with the IUOE phone number for ordering in bulk.
- Have everyone sign the back of the form to indicate they attended this session and point out it is a pledge to look out for the health and safety of everyone on the site.
What are the key features of these toolbox talks?

[content_transformed:protected] =>
Why were these talks developed?
Toolbox talks have been the main tool for communicating safety information on construction jobs for decades. Unfortunately, there has been almost no research on what makes for effective toolbox talks. The IUOE National Training Fund has worked with OSHA, the National Institute for Occupational Safety and Health and the Lippy Group, LLC to make sure these Focus Four toolbox talks are based on the latest fi ndings on the most effective design and tailored to the hazards operating engineers face daily. These toolbox talks accompany an entire package of training materials, but can be used alone. The way these are delivered is as important as how well they are designed.
What did NIOSH find out?
- Just handing out factsheets and toolbox talks to workers doesn’t work. Providing copies after toolbox talks doesn’t make much of an impact either.
- Using case studies (real life stories of accidents that ended in fatality or injury) in toolbox talks is effective.
- When toolbox talks containing case studies were accompanied by discussion questions to encourage group participation, they were more effective. Consequently, getting the workers to participate in the discussion about the case study is important. It’s not enough to tell the story, it is better to have the workers engage in problem solving that analyzes why the accident occurred and how it could have been prevented. Active learning is always better than passive.
How should you deliver these toolbox talks?
- Choose a topic that is related to work going on at the site.
- Hold the meeting on the job, preferably where everyone can sit and relax.
- Hold the meeting at the beginning of a shift or after a break. Folks are too tired at the end of a shift to carefully listen and they want to get home.
- Read the toolbox talk sheet on the topic prior to conducting the talk.
- Start at the top of the form and work right through to the end, which should take around 10 to 15 minutes. Guidance is provided in blue print to help you with each section.
- Use the questions provided to generate discussions. Always allow time for the crew to respond to your questions before you provide an answer. Some suggested responses are written in italics.
- Review the case study and emphasize that this was a real incident. Ask the crew for a case study before you review the one provided, however.
- Always end with a discussion of the particular worksite where you are conducting the talk. Tie the talk as closely to hazards on the site as possible and encourage the crew to constantly look for and immediately correct hazards. They should also know how to report any problems that can’t be immediately corrected.
- Provide copies to each person, if you like, but NIOSH has not found that to be particularly effective.
- Encourage workers to do similar talks on their sites and provide them with the IUOE phone number for ordering in bulk.
- Have everyone sign the back of the form to indicate they attended this session and point out it is a pledge to look out for the health and safety of everyone on the site.
What are the key features of these toolbox talks?
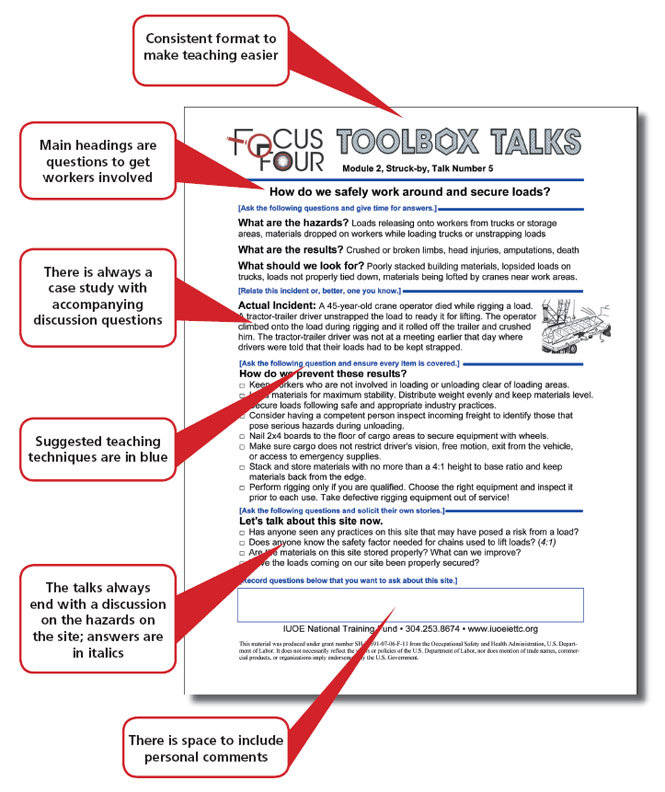
[disclaimer:protected] =>
[disclaimer_transformed:protected] =>
[alreadyInSave:protected] =>
[alreadyInValidation:protected] =>
[validationFailures:protected] => Array
(
)
[_new:BaseObject:private] =>
[_deleted:BaseObject:private] =>
[modifiedColumns:protected] => Array
(
)
)
[template] => record
)
[_file] => /home/agsafe5/repositories/elcosh/live/templates/elcosh/macros.html
[_errors:protected] => Array
(
)
[_encoding:protected] => UTF-8
[_outputMode:protected] => 11
[_forceReparse:protected] =>
[_phpCodeDestination:protected] => /tmp/
[_phpCodeExtension:protected] => php
[_cacheLifetime:protected] => 30
[_cachePurgeFrequency:protected] => 30
[externalMacroTemplatesCache:PHPTAL:private] => Array
(
)
)
[record_macros.html] => PHPTAL Object
(
[_prefilters:protected] => Array
(
)
[_prefilter:PHPTAL:private] => REMOVED: DO NOT USE
[_postfilter:protected] =>
[_repositories:protected] => Array
(
[0] => /home/agsafe5/repositories/elcosh/live/templates/elcosh
)
[_path:protected] => record_macros.html
[_resolvers:protected] => Array
(
)
[_source:protected] => PHPTAL_FileSource Object
(
[_path:PHPTAL_FileSource:private] => /home/agsafe5/repositories/elcosh/live/templates/elcosh/record_macros.html
)
[_codeFile:protected] => /tmp/tpl_61515a6c_record_macros__gMFg5NvPLybiFfYjAv9Aag.php
[_functionName:protected] => tpl_61515a6c_record_macros__gMFg5NvPLybiFfYjAv9Aag
[_prepared:protected] => 1
[_triggers:protected] => Array
(
)
[_translator:protected] =>
[_globalContext:protected] => stdClass Object
(
)
[_context:protected] => PHPTAL_Context Object
(
[_line] =>
[_file] => /home/agsafe5/repositories/elcosh/live/templates/elcosh/record.html
[repeat] => stdClass Object
(
)
[_xmlDeclaration] =>
[_docType] =>
[_nothrow:PHPTAL_Context:private] =>
[_slots:PHPTAL_Context:private] => Array
(
)
[_slotsStack:PHPTAL_Context:private] => Array
(
[0] => Array
(
)
[1] => Array
(
)
)
[_parentContext:PHPTAL_Context:private] => PHPTAL_Context Object
(
[_line] =>
[_file] => /home/agsafe5/repositories/elcosh/live/templates/elcosh/record.html
[repeat] => stdClass Object
(
)
[_xmlDeclaration] =>
[_docType] =>
[_nothrow:PHPTAL_Context:private] =>
[_slots:PHPTAL_Context:private] => Array
(
)
[_slotsStack:PHPTAL_Context:private] => Array
(
[0] => Array
(
)
[1] => Array
(
)
)
[_parentContext:PHPTAL_Context:private] =>
[_globalContext:PHPTAL_Context:private] => stdClass Object
(
)
[_echoDeclarations:PHPTAL_Context:private] =>
[referer] => http://www.elcosh.org/document/3827/d001298/Getting%2Bthe%2Bmost%2Bout%2Bof%2Bthe%2BIUOE%2BToolbox%2BTalks.html
[curr_module] => Record
[styles] => Array
(
)
[javascript] => Array
(
[0] => jquery.min.js
)
[metas] => Array
(
[language] => en
[robots] => index, follow
)
[user] =>
[curr_url] => https://www.elcosh.org/index.php?module=Record&id=3827&type=document
[base_url] => https://www.elcosh.org/index.php?module=Record
[title] => eLCOSH : Getting the most out of the IUOE Toolbox Talks
[language] => en
[search_query] =>
[module] => Record
[new_records] => Array
(
[0] => Search_Result Object
(
[title] => Toolbox Talk: Fixed Ladder
[image] => /record/images/notavailable-p.png
[blurb] => The CPWR Toolbox Talk on Fixed Ladders addresses the potential risks associated with using fixed ladders. The resource includes a brief case example,...
[category] => Array
(
[0] => 15
[1] => 47
[2] => 49
[3] => 51
[4] => 53
[5] => 55
[6] => 60
[7] => 64
[8] => 73
[9] => 76
[10] => 78
[11] => 80
[12] => 86
[13] => 87
[14] => 90
[15] => 92
[16] => 93
[17] => 94
[18] => 100
)
[labels] => Array
(
[0] => Falls
[1] => Work Environment
[2] => Hazards
[3] => Bricklayer
[4] => Trades
[5] => Carpenter
[7] => Cement Mason
[9] => Concrete Polisher
[11] => Electrical Worker
[13] => HVAC
[15] => Laborer
[17] => PCC/Restoration
[19] => Plumber/Pipefitter
[21] => Roofer/Waterproofer
[23] => Sheetmetal Worker
[25] => Welder
[27] => Commercial & Institutional
[28] => Jobsites
[29] => Industrial
[31] => LEED/Green Construction
[33] => Renovations
[35] => Residential
[37] => Toolbox Talks
[38] => Documents
[39] => Media & Documents
)
[type] => Toolbox Talks
[sub_category] =>
[url] => /document/4430/d001660/Toolbox%2BTalk%253A%2BFixed%2BLadder.html
[item:protected] => DocumentRecord Object
(
[records:protected] => Array
(
)
[recordId:protected] =>
[searchWordClass:protected] =>
[searchWordPeerClass:protected] =>
[bok_record:protected] =>
[authors:protected] =>
[organizations:protected] =>
[collections:protected] =>
[categories:protected] => Array
(
[15] => Category Object
(
[languages:protected] =>
[bok_resources:protected] =>
[bok_topics:protected] =>
[bok_keywords:protected] =>
[id:protected] => 15
[type:protected] => category
[parent:protected] => 7
[label:protected] => Falls
[alreadyInSave:protected] =>
[alreadyInValidation:protected] =>
[validationFailures:protected] => Array
(
)
[_new:BaseObject:private] =>
[_deleted:BaseObject:private] =>
[modifiedColumns:protected] => Array
(
)
)
[47] => Category Object
(
[languages:protected] =>
[bok_resources:protected] =>
[bok_topics:protected] =>
[bok_keywords:protected] =>
[id:protected] => 47
[type:protected] => category
[parent:protected] => 2
[label:protected] => Bricklayer
[alreadyInSave:protected] =>
[alreadyInValidation:protected] =>
[validationFailures:protected] => Array
(
)
[_new:BaseObject:private] =>
[_deleted:BaseObject:private] =>
[modifiedColumns:protected] => Array
(
)
)
[49] => Category Object
(
[languages:protected] =>
[bok_resources:protected] =>
[bok_topics:protected] =>
[bok_keywords:protected] =>
[id:protected] => 49
[type:protected] => category
[parent:protected] => 2
[label:protected] => Carpenter
[alreadyInSave:protected] =>
[alreadyInValidation:protected] =>
[validationFailures:protected] => Array
(
)
[_new:BaseObject:private] =>
[_deleted:BaseObject:private] =>
[modifiedColumns:protected] => Array
(
)
)
[51] => Category Object
(
[languages:protected] =>
[bok_resources:protected] =>
[bok_topics:protected] =>
[bok_keywords:protected] =>
[id:protected] => 51
[type:protected] => category
[parent:protected] => 2
[label:protected] => Cement Mason
[alreadyInSave:protected] =>
[alreadyInValidation:protected] =>
[validationFailures:protected] => Array
(
)
[_new:BaseObject:private] =>
[_deleted:BaseObject:private] =>
[modifiedColumns:protected] => Array
(
)
)
[53] => Category Object
(
[languages:protected] =>
[bok_resources:protected] =>
[bok_topics:protected] =>
[bok_keywords:protected] =>
[id:protected] => 53
[type:protected] => category
[parent:protected] => 2
[label:protected] => Concrete Polisher
[alreadyInSave:protected] =>
[alreadyInValidation:protected] =>
[validationFailures:protected] => Array
(
)
[_new:BaseObject:private] =>
[_deleted:BaseObject:private] =>
[modifiedColumns:protected] => Array
(
)
)
[55] => Category Object
(
[languages:protected] =>
[bok_resources:protected] =>
[bok_topics:protected] =>
[bok_keywords:protected] =>
[id:protected] => 55
[type:protected] => category
[parent:protected] => 2
[label:protected] => Electrical Worker
[alreadyInSave:protected] =>
[alreadyInValidation:protected] =>
[validationFailures:protected] => Array
(
)
[_new:BaseObject:private] =>
[_deleted:BaseObject:private] =>
[modifiedColumns:protected] => Array
(
)
)
[60] => Category Object
(
[languages:protected] =>
[bok_resources:protected] =>
[bok_topics:protected] =>
[bok_keywords:protected] =>
[id:protected] => 60
[type:protected] => category
[parent:protected] => 2
[label:protected] => HVAC
[alreadyInSave:protected] =>
[alreadyInValidation:protected] =>
[validationFailures:protected] => Array
(
)
[_new:BaseObject:private] =>
[_deleted:BaseObject:private] =>
[modifiedColumns:protected] => Array
(
)
)
[64] => Category Object
(
[languages:protected] =>
[bok_resources:protected] =>
[bok_topics:protected] =>
[bok_keywords:protected] =>
[id:protected] => 64
[type:protected] => category
[parent:protected] => 2
[label:protected] => Laborer
[alreadyInSave:protected] =>
[alreadyInValidation:protected] =>
[validationFailures:protected] => Array
(
)
[_new:BaseObject:private] =>
[_deleted:BaseObject:private] =>
[modifiedColumns:protected] => Array
(
)
)
[73] => Category Object
(
[languages:protected] =>
[bok_resources:protected] =>
[bok_topics:protected] =>
[bok_keywords:protected] =>
[id:protected] => 73
[type:protected] => category
[parent:protected] => 2
[label:protected] => PCC/Restoration
[alreadyInSave:protected] =>
[alreadyInValidation:protected] =>
[validationFailures:protected] => Array
(
)
[_new:BaseObject:private] =>
[_deleted:BaseObject:private] =>
[modifiedColumns:protected] => Array
(
)
)
[76] => Category Object
(
[languages:protected] =>
[bok_resources:protected] =>
[bok_topics:protected] =>
[bok_keywords:protected] =>
[id:protected] => 76
[type:protected] => category
[parent:protected] => 2
[label:protected] => Plumber/Pipefitter
[alreadyInSave:protected] =>
[alreadyInValidation:protected] =>
[validationFailures:protected] => Array
(
)
[_new:BaseObject:private] =>
[_deleted:BaseObject:private] =>
[modifiedColumns:protected] => Array
(
)
)
[78] => Category Object
(
[languages:protected] =>
[bok_resources:protected] =>
[bok_topics:protected] =>
[bok_keywords:protected] =>
[id:protected] => 78
[type:protected] => category
[parent:protected] => 2
[label:protected] => Roofer/Waterproofer
[alreadyInSave:protected] =>
[alreadyInValidation:protected] =>
[validationFailures:protected] => Array
(
)
[_new:BaseObject:private] =>
[_deleted:BaseObject:private] =>
[modifiedColumns:protected] => Array
(
)
)
[80] => Category Object
(
[languages:protected] =>
[bok_resources:protected] =>
[bok_topics:protected] =>
[bok_keywords:protected] =>
[id:protected] => 80
[type:protected] => category
[parent:protected] => 2
[label:protected] => Sheetmetal Worker
[alreadyInSave:protected] =>
[alreadyInValidation:protected] =>
[validationFailures:protected] => Array
(
)
[_new:BaseObject:private] =>
[_deleted:BaseObject:private] =>
[modifiedColumns:protected] => Array
(
)
)
[86] => Category Object
(
[languages:protected] =>
[bok_resources:protected] =>
[bok_topics:protected] =>
[bok_keywords:protected] =>
[id:protected] => 86
[type:protected] => category
[parent:protected] => 2
[label:protected] => Welder
[alreadyInSave:protected] =>
[alreadyInValidation:protected] =>
[validationFailures:protected] => Array
(
)
[_new:BaseObject:private] =>
[_deleted:BaseObject:private] =>
[modifiedColumns:protected] => Array
(
)
)
[87] => Category Object
(
[languages:protected] =>
[bok_resources:protected] =>
[bok_topics:protected] =>
[bok_keywords:protected] =>
[id:protected] => 87
[type:protected] => category
[parent:protected] => 3
[label:protected] => Commercial & Institutional
[alreadyInSave:protected] =>
[alreadyInValidation:protected] =>
[validationFailures:protected] => Array
(
)
[_new:BaseObject:private] =>
[_deleted:BaseObject:private] =>
[modifiedColumns:protected] => Array
(
)
)
[90] => Category Object
(
[languages:protected] =>
[bok_resources:protected] =>
[bok_topics:protected] =>
[bok_keywords:protected] =>
[id:protected] => 90
[type:protected] => category
[parent:protected] => 3
[label:protected] => Industrial
[alreadyInSave:protected] =>
[alreadyInValidation:protected] =>
[validationFailures:protected] => Array
(
)
[_new:BaseObject:private] =>
[_deleted:BaseObject:private] =>
[modifiedColumns:protected] => Array
(
)
)
[92] => Category Object
(
[languages:protected] =>
[bok_resources:protected] =>
[bok_topics:protected] =>
[bok_keywords:protected] =>
[id:protected] => 92
[type:protected] => category
[parent:protected] => 3
[label:protected] => LEED/Green Construction
[alreadyInSave:protected] =>
[alreadyInValidation:protected] =>
[validationFailures:protected] => Array
(
)
[_new:BaseObject:private] =>
[_deleted:BaseObject:private] =>
[modifiedColumns:protected] => Array
(
)
)
[93] => Category Object
(
[languages:protected] =>
[bok_resources:protected] =>
[bok_topics:protected] =>
[bok_keywords:protected] =>
[id:protected] => 93
[type:protected] => category
[parent:protected] => 3
[label:protected] => Renovations
[alreadyInSave:protected] =>
[alreadyInValidation:protected] =>
[validationFailures:protected] => Array
(
)
[_new:BaseObject:private] =>
[_deleted:BaseObject:private] =>
[modifiedColumns:protected] => Array
(
)
)
[94] => Category Object
(
[languages:protected] =>
[bok_resources:protected] =>
[bok_topics:protected] =>
[bok_keywords:protected] =>
[id:protected] => 94
[type:protected] => category
[parent:protected] => 3
[label:protected] => Residential
[alreadyInSave:protected] =>
[alreadyInValidation:protected] =>
[validationFailures:protected] => Array
(
)
[_new:BaseObject:private] =>
[_deleted:BaseObject:private] =>
[modifiedColumns:protected] => Array
(
)
)
[100] => Category Object
(
[languages:protected] =>
[bok_resources:protected] =>
[bok_topics:protected] =>
[bok_keywords:protected] =>
[id:protected] => 100
[type:protected] => category
[parent:protected] => 6
[label:protected] => Toolbox Talks
[alreadyInSave:protected] =>
[alreadyInValidation:protected] =>
[validationFailures:protected] => Array
(
)
[_new:BaseObject:private] =>
[_deleted:BaseObject:private] =>
[modifiedColumns:protected] => Array
(
)
)
)
[categories_initialized:protected] => 1
[mapped_items:protected] =>
[content:protected] =>
[files:protected] =>
[language:protected] => Language Object
(
[id:protected] => 1
[code:protected] => en
[name:protected] => English
[alreadyInSave:protected] =>
[alreadyInValidation:protected] =>
[validationFailures:protected] => Array
(
)
[_new:BaseObject:private] =>
[_deleted:BaseObject:private] =>
[modifiedColumns:protected] => Array
(
)
)
[old_record:protected] =>
[id:protected] => 4430
[old_id:protected] =>
[elcosh_id:protected] => d001660
[type:protected] => document
[display_type:protected] => HTML only (and links)
[user_id:protected] => 0
[language_id:protected] => 1
[tagging_id:protected] => Mike Aguilar
[priority_id:protected] => 1
[title:protected] => Toolbox Talk: Fixed Ladder
[total_pages:protected] => 0
[billed_pages:protected] => 0
[publication_number:protected] =>
[part_of:protected] =>
[keywords:protected] => Fixed Ladders, Fall Prevention, Falls
[comments:protected] =>
[summary:protected] => The CPWR Toolbox Talk on Fixed Ladders addresses the potential risks associated with using fixed ladders. The resource includes a brief case example, steps to prevent a related injury and questions for discussion. It includes an image that illustrates the hazard, which can be posted in a central location as a reminder of steps to work safely.
Available in
English
and
Spanish.
[transition_comments:protected] =>
[external_link:protected] =>
[consol_link:protected] =>
[more_like_this:protected] => d001257,d001254,d001255,d001256,d001258,d001262,d001279
[permission_given_by:protected] =>
[published:protected] => T
[billable:protected] => F
[img_name:protected] =>
[img_ext:protected] =>
[img_width:protected] =>
[img_height:protected] =>
[img_credit:protected] =>
[img_practice:protected] =>
[vid_source_id:protected] =>
[vid_running_time:protected] =>
[vid_intended_audience:protected] =>
[vid_acquisition_info:protected] =>
[vid_cost:protected] =>
[vid_producer:protected] =>
[vid_filename:protected] =>
[vid_filename_downloadable:protected] =>
[date_summary:protected] =>
[date_permission_requested:protected] =>
[date_permission_received:protected] =>
[date_review_needed:protected] =>
[date_received:protected] => 06/10/22
[date_completed:protected] => 06/10/22
[date_billed:protected] =>
[date_modified:protected] => 05/22/23
[collBokExports:protected] =>
[lastBokExportCriteria:BaseElcoshItem:private] =>
[alreadyInSave:protected] =>
[alreadyInValidation:protected] =>
[validationFailures:protected] => Array
(
)
[_new:BaseObject:private] =>
[_deleted:BaseObject:private] =>
[modifiedColumns:protected] => Array
(
)
)
)
[1] => Search_Result Object
(
[title] => Toolbox Talk: Challenges Preventing Falling Objects
[image] => /record/images/notavailable-p.png
[blurb] => The CPWR Toolbox Talk on Challenges Preventing Falling Objects addresses the hazards of being struck by falling objects on the job site. The resource...
[category] => Array
(
[0] => 12
[1] => 47
[2] => 49
[3] => 51
[4] => 55
[5] => 64
[6] => 68
[7] => 71
[8] => 75
[9] => 78
[10] => 79
[11] => 82
[12] => 62
[13] => 86
[14] => 87
[15] => 88
[16] => 89
[17] => 91
[18] => 90
[19] => 92
[20] => 93
[21] => 94
[22] => 95
[23] => 100
)
[labels] => Array
(
[0] => Crushed/Struck By
[1] => Work Environment
[2] => Hazards
[3] => Bricklayer
[4] => Trades
[5] => Carpenter
[7] => Cement Mason
[9] => Electrical Worker
[11] => Laborer
[13] => Maintenance Worker
[15] => Painter
[17] => Plasterer
[19] => Roofer/Waterproofer
[21] => Scaffold Erector
[23] => Stonemason
[25] => Structural Ironworker
[27] => Welder
[29] => Commercial & Institutional
[30] => Jobsites
[31] => Demolition
[33] => Disasters
[35] => Heavy & Highway
[37] => Industrial
[39] => LEED/Green Construction
[41] => Renovations
[43] => Residential
[45] => Underground
[47] => Toolbox Talks
[48] => Documents
[49] => Media & Documents
)
[type] => Toolbox Talks
[sub_category] =>
[url] => /document/4431/d001661/Toolbox%2BTalk%253A%2BChallenges%2BPreventing%2BFalling%2BObjects.html
[item:protected] => DocumentRecord Object
(
[records:protected] => Array
(
)
[recordId:protected] =>
[searchWordClass:protected] =>
[searchWordPeerClass:protected] =>
[bok_record:protected] =>
[authors:protected] =>
[organizations:protected] =>
[collections:protected] =>
[categories:protected] => Array
(
[12] => Category Object
(
[languages:protected] =>
[bok_resources:protected] =>
[bok_topics:protected] =>
[bok_keywords:protected] =>
[id:protected] => 12
[type:protected] => category
[parent:protected] => 7
[label:protected] => Crushed/Struck By
[alreadyInSave:protected] =>
[alreadyInValidation:protected] =>
[validationFailures:protected] => Array
(
)
[_new:BaseObject:private] =>
[_deleted:BaseObject:private] =>
[modifiedColumns:protected] => Array
(
)
)
[47] => Category Object
(
[languages:protected] =>
[bok_resources:protected] =>
[bok_topics:protected] =>
[bok_keywords:protected] =>
[id:protected] => 47
[type:protected] => category
[parent:protected] => 2
[label:protected] => Bricklayer
[alreadyInSave:protected] =>
[alreadyInValidation:protected] =>
[validationFailures:protected] => Array
(
)
[_new:BaseObject:private] =>
[_deleted:BaseObject:private] =>
[modifiedColumns:protected] => Array
(
)
)
[49] => Category Object
(
[languages:protected] =>
[bok_resources:protected] =>
[bok_topics:protected] =>
[bok_keywords:protected] =>
[id:protected] => 49
[type:protected] => category
[parent:protected] => 2
[label:protected] => Carpenter
[alreadyInSave:protected] =>
[alreadyInValidation:protected] =>
[validationFailures:protected] => Array
(
)
[_new:BaseObject:private] =>
[_deleted:BaseObject:private] =>
[modifiedColumns:protected] => Array
(
)
)
[51] => Category Object
(
[languages:protected] =>
[bok_resources:protected] =>
[bok_topics:protected] =>
[bok_keywords:protected] =>
[id:protected] => 51
[type:protected] => category
[parent:protected] => 2
[label:protected] => Cement Mason
[alreadyInSave:protected] =>
[alreadyInValidation:protected] =>
[validationFailures:protected] => Array
(
)
[_new:BaseObject:private] =>
[_deleted:BaseObject:private] =>
[modifiedColumns:protected] => Array
(
)
)
[55] => Category Object
(
[languages:protected] =>
[bok_resources:protected] =>
[bok_topics:protected] =>
[bok_keywords:protected] =>
[id:protected] => 55
[type:protected] => category
[parent:protected] => 2
[label:protected] => Electrical Worker
[alreadyInSave:protected] =>
[alreadyInValidation:protected] =>
[validationFailures:protected] => Array
(
)
[_new:BaseObject:private] =>
[_deleted:BaseObject:private] =>
[modifiedColumns:protected] => Array
(
)
)
[64] => Category Object
(
[languages:protected] =>
[bok_resources:protected] =>
[bok_topics:protected] =>
[bok_keywords:protected] =>
[id:protected] => 64
[type:protected] => category
[parent:protected] => 2
[label:protected] => Laborer
[alreadyInSave:protected] =>
[alreadyInValidation:protected] =>
[validationFailures:protected] => Array
(
)
[_new:BaseObject:private] =>
[_deleted:BaseObject:private] =>
[modifiedColumns:protected] => Array
(
)
)
[68] => Category Object
(
[languages:protected] =>
[bok_resources:protected] =>
[bok_topics:protected] =>
[bok_keywords:protected] =>
[id:protected] => 68
[type:protected] => category
[parent:protected] => 2
[label:protected] => Maintenance Worker
[alreadyInSave:protected] =>
[alreadyInValidation:protected] =>
[validationFailures:protected] => Array
(
)
[_new:BaseObject:private] =>
[_deleted:BaseObject:private] =>
[modifiedColumns:protected] => Array
(
)
)
[71] => Category Object
(
[languages:protected] =>
[bok_resources:protected] =>
[bok_topics:protected] =>
[bok_keywords:protected] =>
[id:protected] => 71
[type:protected] => category
[parent:protected] => 2
[label:protected] => Painter
[alreadyInSave:protected] =>
[alreadyInValidation:protected] =>
[validationFailures:protected] => Array
(
)
[_new:BaseObject:private] =>
[_deleted:BaseObject:private] =>
[modifiedColumns:protected] => Array
(
)
)
[75] => Category Object
(
[languages:protected] =>
[bok_resources:protected] =>
[bok_topics:protected] =>
[bok_keywords:protected] =>
[id:protected] => 75
[type:protected] => category
[parent:protected] => 2
[label:protected] => Plasterer
[alreadyInSave:protected] =>
[alreadyInValidation:protected] =>
[validationFailures:protected] => Array
(
)
[_new:BaseObject:private] =>
[_deleted:BaseObject:private] =>
[modifiedColumns:protected] => Array
(
)
)
[78] => Category Object
(
[languages:protected] =>
[bok_resources:protected] =>
[bok_topics:protected] =>
[bok_keywords:protected] =>
[id:protected] => 78
[type:protected] => category
[parent:protected] => 2
[label:protected] => Roofer/Waterproofer
[alreadyInSave:protected] =>
[alreadyInValidation:protected] =>
[validationFailures:protected] => Array
(
)
[_new:BaseObject:private] =>
[_deleted:BaseObject:private] =>
[modifiedColumns:protected] => Array
(
)
)
[79] => Category Object
(
[languages:protected] =>
[bok_resources:protected] =>
[bok_topics:protected] =>
[bok_keywords:protected] =>
[id:protected] => 79
[type:protected] => category
[parent:protected] => 2
[label:protected] => Scaffold Erector
[alreadyInSave:protected] =>
[alreadyInValidation:protected] =>
[validationFailures:protected] => Array
(
)
[_new:BaseObject:private] =>
[_deleted:BaseObject:private] =>
[modifiedColumns:protected] => Array
(
)
)
[82] => Category Object
(
[languages:protected] =>
[bok_resources:protected] =>
[bok_topics:protected] =>
[bok_keywords:protected] =>
[id:protected] => 82
[type:protected] => category
[parent:protected] => 2
[label:protected] => Stonemason
[alreadyInSave:protected] =>
[alreadyInValidation:protected] =>
[validationFailures:protected] => Array
(
)
[_new:BaseObject:private] =>
[_deleted:BaseObject:private] =>
[modifiedColumns:protected] => Array
(
)
)
[62] => Category Object
(
[languages:protected] =>
[bok_resources:protected] =>
[bok_topics:protected] =>
[bok_keywords:protected] =>
[id:protected] => 62
[type:protected] => category
[parent:protected] => 2
[label:protected] => Structural Ironworker
[alreadyInSave:protected] =>
[alreadyInValidation:protected] =>
[validationFailures:protected] => Array
(
)
[_new:BaseObject:private] =>
[_deleted:BaseObject:private] =>
[modifiedColumns:protected] => Array
(
)
)
[86] => Category Object
(
[languages:protected] =>
[bok_resources:protected] =>
[bok_topics:protected] =>
[bok_keywords:protected] =>
[id:protected] => 86
[type:protected] => category
[parent:protected] => 2
[label:protected] => Welder
[alreadyInSave:protected] =>
[alreadyInValidation:protected] =>
[validationFailures:protected] => Array
(
)
[_new:BaseObject:private] =>
[_deleted:BaseObject:private] =>
[modifiedColumns:protected] => Array
(
)
)
[87] => Category Object
(
[languages:protected] =>
[bok_resources:protected] =>
[bok_topics:protected] =>
[bok_keywords:protected] =>
[id:protected] => 87
[type:protected] => category
[parent:protected] => 3
[label:protected] => Commercial & Institutional
[alreadyInSave:protected] =>
[alreadyInValidation:protected] =>
[validationFailures:protected] => Array
(
)
[_new:BaseObject:private] =>
[_deleted:BaseObject:private] =>
[modifiedColumns:protected] => Array
(
)
)
[88] => Category Object
(
[languages:protected] =>
[bok_resources:protected] =>
[bok_topics:protected] =>
[bok_keywords:protected] =>
[id:protected] => 88
[type:protected] => category
[parent:protected] => 3
[label:protected] => Demolition
[alreadyInSave:protected] =>
[alreadyInValidation:protected] =>
[validationFailures:protected] => Array
(
)
[_new:BaseObject:private] =>
[_deleted:BaseObject:private] =>
[modifiedColumns:protected] => Array
(
)
)
[89] => Category Object
(
[languages:protected] =>
[bok_resources:protected] =>
[bok_topics:protected] =>
[bok_keywords:protected] =>
[id:protected] => 89
[type:protected] => category
[parent:protected] => 3
[label:protected] => Disasters
[alreadyInSave:protected] =>
[alreadyInValidation:protected] =>
[validationFailures:protected] => Array
(
)
[_new:BaseObject:private] =>
[_deleted:BaseObject:private] =>
[modifiedColumns:protected] => Array
(
)
)
[91] => Category Object
(
[languages:protected] =>
[bok_resources:protected] =>
[bok_topics:protected] =>
[bok_keywords:protected] =>
[id:protected] => 91
[type:protected] => category
[parent:protected] => 3
[label:protected] => Heavy & Highway
[alreadyInSave:protected] =>
[alreadyInValidation:protected] =>
[validationFailures:protected] => Array
(
)
[_new:BaseObject:private] =>
[_deleted:BaseObject:private] =>
[modifiedColumns:protected] => Array
(
)
)
[90] => Category Object
(
[languages:protected] =>
[bok_resources:protected] =>
[bok_topics:protected] =>
[bok_keywords:protected] =>
[id:protected] => 90
[type:protected] => category
[parent:protected] => 3
[label:protected] => Industrial
[alreadyInSave:protected] =>
[alreadyInValidation:protected] =>
[validationFailures:protected] => Array
(
)
[_new:BaseObject:private] =>
[_deleted:BaseObject:private] =>
[modifiedColumns:protected] => Array
(
)
)
[92] => Category Object
(
[languages:protected] =>
[bok_resources:protected] =>
[bok_topics:protected] =>
[bok_keywords:protected] =>
[id:protected] => 92
[type:protected] => category
[parent:protected] => 3
[label:protected] => LEED/Green Construction
[alreadyInSave:protected] =>
[alreadyInValidation:protected] =>
[validationFailures:protected] => Array
(
)
[_new:BaseObject:private] =>
[_deleted:BaseObject:private] =>
[modifiedColumns:protected] => Array
(
)
)
[93] => Category Object
(
[languages:protected] =>
[bok_resources:protected] =>
[bok_topics:protected] =>
[bok_keywords:protected] =>
[id:protected] => 93
[type:protected] => category
[parent:protected] => 3
[label:protected] => Renovations
[alreadyInSave:protected] =>
[alreadyInValidation:protected] =>
[validationFailures:protected] => Array
(
)
[_new:BaseObject:private] =>
[_deleted:BaseObject:private] =>
[modifiedColumns:protected] => Array
(
)
)
[94] => Category Object
(
[languages:protected] =>
[bok_resources:protected] =>
[bok_topics:protected] =>
[bok_keywords:protected] =>
[id:protected] => 94
[type:protected] => category
[parent:protected] => 3
[label:protected] => Residential
[alreadyInSave:protected] =>
[alreadyInValidation:protected] =>
[validationFailures:protected] => Array
(
)
[_new:BaseObject:private] =>
[_deleted:BaseObject:private] =>
[modifiedColumns:protected] => Array
(
)
)
[95] => Category Object
(
[languages:protected] =>
[bok_resources:protected] =>
[bok_topics:protected] =>
[bok_keywords:protected] =>
[id:protected] => 95
[type:protected] => category
[parent:protected] => 3
[label:protected] => Underground
[alreadyInSave:protected] =>
[alreadyInValidation:protected] =>
[validationFailures:protected] => Array
(
)
[_new:BaseObject:private] =>
[_deleted:BaseObject:private] =>
[modifiedColumns:protected] => Array
(
)
)
[100] => Category Object
(
[languages:protected] =>
[bok_resources:protected] =>
[bok_topics:protected] =>
[bok_keywords:protected] =>
[id:protected] => 100
[type:protected] => category
[parent:protected] => 6
[label:protected] => Toolbox Talks
[alreadyInSave:protected] =>
[alreadyInValidation:protected] =>
[validationFailures:protected] => Array
(
)
[_new:BaseObject:private] =>
[_deleted:BaseObject:private] =>
[modifiedColumns:protected] => Array
(
)
)
)
[categories_initialized:protected] => 1
[mapped_items:protected] =>
[content:protected] =>
[files:protected] =>
[language:protected] => Language Object
(
[id:protected] => 1
[code:protected] => en
[name:protected] => English
[alreadyInSave:protected] =>
[alreadyInValidation:protected] =>
[validationFailures:protected] => Array
(
)
[_new:BaseObject:private] =>
[_deleted:BaseObject:private] =>
[modifiedColumns:protected] => Array
(
)
)
[old_record:protected] =>
[id:protected] => 4431
[old_id:protected] =>
[elcosh_id:protected] => d001661
[type:protected] => document
[display_type:protected] => HTML only (and links)
[user_id:protected] => 0
[language_id:protected] => 1
[tagging_id:protected] => Mike Aguilar
[priority_id:protected] => 1
[title:protected] => Toolbox Talk: Challenges Preventing Falling Objects
[total_pages:protected] => 0
[billed_pages:protected] => 0
[publication_number:protected] =>
[part_of:protected] =>
[keywords:protected] => dropped objects, falling objects, struck by incidents, struck by fatalities
[comments:protected] =>
[summary:protected] => The CPWR Toolbox Talk on Challenges Preventing Falling Objects addresses the hazards of being struck by falling objects on the job site. The resource includes a brief example, steps to prevent a related injury, and questions for discussion. It includes a graphic that illustrates a group workers observing a scaffold free of debris during high winds, which can be posted in a central location as a reminder of steps to work safely.
Available in
English and
Spanish.
[transition_comments:protected] =>
[external_link:protected] =>
[consol_link:protected] =>
[more_like_this:protected] => d001234,d001238,d001244,d001251,d001253,d001260,d001268,d001278
[permission_given_by:protected] =>
[published:protected] => T
[billable:protected] => F
[img_name:protected] =>
[img_ext:protected] =>
[img_width:protected] =>
[img_height:protected] =>
[img_credit:protected] =>
[img_practice:protected] =>
[vid_source_id:protected] =>
[vid_running_time:protected] =>
[vid_intended_audience:protected] =>
[vid_acquisition_info:protected] =>
[vid_cost:protected] =>
[vid_producer:protected] =>
[vid_filename:protected] =>
[vid_filename_downloadable:protected] =>
[date_summary:protected] =>
[date_permission_requested:protected] =>
[date_permission_received:protected] =>
[date_review_needed:protected] =>
[date_received:protected] => 06/10/22
[date_completed:protected] => 06/10/22
[date_billed:protected] =>
[date_modified:protected] => 05/22/23
[collBokExports:protected] =>
[lastBokExportCriteria:BaseElcoshItem:private] =>
[alreadyInSave:protected] =>
[alreadyInValidation:protected] =>
[validationFailures:protected] => Array
(
)
[_new:BaseObject:private] =>
[_deleted:BaseObject:private] =>
[modifiedColumns:protected] => Array
(
)
)
)
[2] => Search_Result Object
(
[title] => Toolbox Talk: Tower Crane Safety
[image] => /record/images/notavailable-p.png
[blurb] => The CPWR Toolbox Talk on Tower Crane Safety addresses the potential hazards of Tower Cranes and the importance of following procedure before and durin...
[category] => Array
(
[0] => 11
[1] => 12
[2] => 18
[3] => 70
[4] => 87
[5] => 88
[6] => 91
[7] => 90
[8] => 92
[9] => 100
)
[labels] => Array
(
[0] => Cranes & Hoists
[1] => Work Environment
[2] => Hazards
[3] => Crushed/Struck By
[6] => Motor Vehicles/Heavy Equipment
[9] => Operating Engineer
[10] => Trades
[11] => Commercial & Institutional
[12] => Jobsites
[13] => Demolition
[15] => Heavy & Highway
[17] => Industrial
[19] => LEED/Green Construction
[21] => Toolbox Talks
[22] => Documents
[23] => Media & Documents
)
[type] => Toolbox Talks
[sub_category] =>
[url] => /document/4427/d001657/Toolbox%2BTalk%253A%2BTower%2BCrane%2BSafety.html
[item:protected] => DocumentRecord Object
(
[records:protected] => Array
(
)
[recordId:protected] =>
[searchWordClass:protected] =>
[searchWordPeerClass:protected] =>
[bok_record:protected] =>
[authors:protected] =>
[organizations:protected] =>
[collections:protected] =>
[categories:protected] => Array
(
[11] => Category Object
(
[languages:protected] =>
[bok_resources:protected] =>
[bok_topics:protected] =>
[bok_keywords:protected] =>
[id:protected] => 11
[type:protected] => category
[parent:protected] => 7
[label:protected] => Cranes & Hoists
[alreadyInSave:protected] =>
[alreadyInValidation:protected] =>
[validationFailures:protected] => Array
(
)
[_new:BaseObject:private] =>
[_deleted:BaseObject:private] =>
[modifiedColumns:protected] => Array
(
)
)
[12] => Category Object
(
[languages:protected] =>
[bok_resources:protected] =>
[bok_topics:protected] =>
[bok_keywords:protected] =>
[id:protected] => 12
[type:protected] => category
[parent:protected] => 7
[label:protected] => Crushed/Struck By
[alreadyInSave:protected] =>
[alreadyInValidation:protected] =>
[validationFailures:protected] => Array
(
)
[_new:BaseObject:private] =>
[_deleted:BaseObject:private] =>
[modifiedColumns:protected] => Array
(
)
)
[18] => Category Object
(
[languages:protected] =>
[bok_resources:protected] =>
[bok_topics:protected] =>
[bok_keywords:protected] =>
[id:protected] => 18
[type:protected] => category
[parent:protected] => 7
[label:protected] => Motor Vehicles/Heavy Equipment
[alreadyInSave:protected] =>
[alreadyInValidation:protected] =>
[validationFailures:protected] => Array
(
)
[_new:BaseObject:private] =>
[_deleted:BaseObject:private] =>
[modifiedColumns:protected] => Array
(
)
)
[70] => Category Object
(
[languages:protected] =>
[bok_resources:protected] =>
[bok_topics:protected] =>
[bok_keywords:protected] =>
[id:protected] => 70
[type:protected] => category
[parent:protected] => 2
[label:protected] => Operating Engineer
[alreadyInSave:protected] =>
[alreadyInValidation:protected] =>
[validationFailures:protected] => Array
(
)
[_new:BaseObject:private] =>
[_deleted:BaseObject:private] =>
[modifiedColumns:protected] => Array
(
)
)
[87] => Category Object
(
[languages:protected] =>
[bok_resources:protected] =>
[bok_topics:protected] =>
[bok_keywords:protected] =>
[id:protected] => 87
[type:protected] => category
[parent:protected] => 3
[label:protected] => Commercial & Institutional
[alreadyInSave:protected] =>
[alreadyInValidation:protected] =>
[validationFailures:protected] => Array
(
)
[_new:BaseObject:private] =>
[_deleted:BaseObject:private] =>
[modifiedColumns:protected] => Array
(
)
)
[88] => Category Object
(
[languages:protected] =>
[bok_resources:protected] =>
[bok_topics:protected] =>
[bok_keywords:protected] =>
[id:protected] => 88
[type:protected] => category
[parent:protected] => 3
[label:protected] => Demolition
[alreadyInSave:protected] =>
[alreadyInValidation:protected] =>
[validationFailures:protected] => Array
(
)
[_new:BaseObject:private] =>
[_deleted:BaseObject:private] =>
[modifiedColumns:protected] => Array
(
)
)
[91] => Category Object
(
[languages:protected] =>
[bok_resources:protected] =>
[bok_topics:protected] =>
[bok_keywords:protected] =>
[id:protected] => 91
[type:protected] => category
[parent:protected] => 3
[label:protected] => Heavy & Highway
[alreadyInSave:protected] =>
[alreadyInValidation:protected] =>
[validationFailures:protected] => Array
(
)
[_new:BaseObject:private] =>
[_deleted:BaseObject:private] =>
[modifiedColumns:protected] => Array
(
)
)
[90] => Category Object
(
[languages:protected] =>
[bok_resources:protected] =>
[bok_topics:protected] =>
[bok_keywords:protected] =>
[id:protected] => 90
[type:protected] => category
[parent:protected] => 3
[label:protected] => Industrial
[alreadyInSave:protected] =>
[alreadyInValidation:protected] =>
[validationFailures:protected] => Array
(
)
[_new:BaseObject:private] =>
[_deleted:BaseObject:private] =>
[modifiedColumns:protected] => Array
(
)
)
[92] => Category Object
(
[languages:protected] =>
[bok_resources:protected] =>
[bok_topics:protected] =>
[bok_keywords:protected] =>
[id:protected] => 92
[type:protected] => category
[parent:protected] => 3
[label:protected] => LEED/Green Construction
[alreadyInSave:protected] =>
[alreadyInValidation:protected] =>
[validationFailures:protected] => Array
(
)
[_new:BaseObject:private] =>
[_deleted:BaseObject:private] =>
[modifiedColumns:protected] => Array
(
)
)
[100] => Category Object
(
[languages:protected] =>
[bok_resources:protected] =>
[bok_topics:protected] =>
[bok_keywords:protected] =>
[id:protected] => 100
[type:protected] => category
[parent:protected] => 6
[label:protected] => Toolbox Talks
[alreadyInSave:protected] =>
[alreadyInValidation:protected] =>
[validationFailures:protected] => Array
(
)
[_new:BaseObject:private] =>
[_deleted:BaseObject:private] =>
[modifiedColumns:protected] => Array
(
)
)
)
[categories_initialized:protected] => 1
[mapped_items:protected] =>
[content:protected] =>
[files:protected] =>
[language:protected] => Language Object
(
[id:protected] => 1
[code:protected] => en
[name:protected] => English
[alreadyInSave:protected] =>
[alreadyInValidation:protected] =>
[validationFailures:protected] => Array
(
)
[_new:BaseObject:private] =>
[_deleted:BaseObject:private] =>
[modifiedColumns:protected] => Array
(
)
)
[old_record:protected] =>
[id:protected] => 4427
[old_id:protected] =>
[elcosh_id:protected] => d001657
[type:protected] => document
[display_type:protected] => HTML only (and links)
[user_id:protected] => 0
[language_id:protected] => 1
[tagging_id:protected] => Mike Aguilar
[priority_id:protected] => 1
[title:protected] => Toolbox Talk: Tower Crane Safety
[total_pages:protected] => 0
[billed_pages:protected] => 0
[publication_number:protected] =>
[part_of:protected] =>
[keywords:protected] => Tower Crane, Crane, Stability, Tipping, Lift Zone Safety, Lift, Zone, Safety, Struck by
[comments:protected] =>
[summary:protected] => The CPWR Toolbox Talk on Tower Crane Safety addresses the potential hazards of Tower Cranes and the importance of following procedure before and during Tower Crane operation. The resource includes a brief example, steps to prevent a related injury, and questions for discussion. It includes a graphic that illustrates a worker inspecting a Tower Crane before operation, which can be posted in a central location as a reminder of steps to work safely.
Available in
English and
Spanish.
[transition_comments:protected] =>
[external_link:protected] =>
[consol_link:protected] =>
[more_like_this:protected] => d001234,d001238,d001250,d001251,d001253,d001258,d001262,d001273
[permission_given_by:protected] =>
[published:protected] => T
[billable:protected] => F
[img_name:protected] =>
[img_ext:protected] => jpg
[img_width:protected] =>
[img_height:protected] =>
[img_credit:protected] =>
[img_practice:protected] =>
[vid_source_id:protected] =>
[vid_running_time:protected] =>
[vid_intended_audience:protected] =>
[vid_acquisition_info:protected] =>
[vid_cost:protected] =>
[vid_producer:protected] =>
[vid_filename:protected] =>
[vid_filename_downloadable:protected] =>
[date_summary:protected] =>
[date_permission_requested:protected] =>
[date_permission_received:protected] =>
[date_review_needed:protected] =>
[date_received:protected] => 12/23/21
[date_completed:protected] => 12/23/21
[date_billed:protected] =>
[date_modified:protected] => 05/19/23
[collBokExports:protected] =>
[lastBokExportCriteria:BaseElcoshItem:private] =>
[alreadyInSave:protected] =>
[alreadyInValidation:protected] =>
[validationFailures:protected] => Array
(
)
[_new:BaseObject:private] =>
[_deleted:BaseObject:private] =>
[modifiedColumns:protected] => Array
(
)
)
)
[3] => Search_Result Object
(
[title] => Toolbox Talk: Work Zone Safety: Working Around Vehicles
[image] => /record/images/notavailable-p.png
[blurb] => The CPWR Toolbox Talk on Working Around Vehicles in the Work Zone addresses methods to avoid being struck-by a vehicle on a construction site. The res...
[category] => Array
(
[0] => 12
[1] => 18
[2] => 52
[3] => 57
[4] => 70
[5] => 85
[6] => 87
[7] => 88
[8] => 89
[9] => 91
[10] => 90
[11] => 92
[12] => 93
[13] => 94
[14] => 95
[15] => 100
)
[labels] => Array
(
[0] => Crushed/Struck By
[1] => Work Environment
[2] => Hazards
[3] => Motor Vehicles/Heavy Equipment
[6] => Commercial Diver
[7] => Trades
[8] => Flagger
[10] => Operating Engineer
[12] => Truck Driver
[14] => Commercial & Institutional
[15] => Jobsites
[16] => Demolition
[18] => Disasters
[20] => Heavy & Highway
[22] => Industrial
[24] => LEED/Green Construction
[26] => Renovations
[28] => Residential
[30] => Underground
[32] => Toolbox Talks
[33] => Documents
[34] => Media & Documents
)
[type] => Toolbox Talks
[sub_category] =>
[url] => /document/4428/d001658/Toolbox%2BTalk%253A%2BWork%2BZone%2BSafety%253A%2BWorking%2BAround%2BVehicles.html
[item:protected] => DocumentRecord Object
(
[records:protected] => Array
(
)
[recordId:protected] =>
[searchWordClass:protected] =>
[searchWordPeerClass:protected] =>
[bok_record:protected] =>
[authors:protected] =>
[organizations:protected] =>
[collections:protected] =>
[categories:protected] => Array
(
[12] => Category Object
(
[languages:protected] =>
[bok_resources:protected] =>
[bok_topics:protected] =>
[bok_keywords:protected] =>
[id:protected] => 12
[type:protected] => category
[parent:protected] => 7
[label:protected] => Crushed/Struck By
[alreadyInSave:protected] =>
[alreadyInValidation:protected] =>
[validationFailures:protected] => Array
(
)
[_new:BaseObject:private] =>
[_deleted:BaseObject:private] =>
[modifiedColumns:protected] => Array
(
)
)
[18] => Category Object
(
[languages:protected] =>
[bok_resources:protected] =>
[bok_topics:protected] =>
[bok_keywords:protected] =>
[id:protected] => 18
[type:protected] => category
[parent:protected] => 7
[label:protected] => Motor Vehicles/Heavy Equipment
[alreadyInSave:protected] =>
[alreadyInValidation:protected] =>
[validationFailures:protected] => Array
(
)
[_new:BaseObject:private] =>
[_deleted:BaseObject:private] =>
[modifiedColumns:protected] => Array
(
)
)
[52] => Category Object
(
[languages:protected] =>
[bok_resources:protected] =>
[bok_topics:protected] =>
[bok_keywords:protected] =>
[id:protected] => 52
[type:protected] => category
[parent:protected] => 2
[label:protected] => Commercial Diver
[alreadyInSave:protected] =>
[alreadyInValidation:protected] =>
[validationFailures:protected] => Array
(
)
[_new:BaseObject:private] =>
[_deleted:BaseObject:private] =>
[modifiedColumns:protected] => Array
(
)
)
[57] => Category Object
(
[languages:protected] =>
[bok_resources:protected] =>
[bok_topics:protected] =>
[bok_keywords:protected] =>
[id:protected] => 57
[type:protected] => category
[parent:protected] => 2
[label:protected] => Flagger
[alreadyInSave:protected] =>
[alreadyInValidation:protected] =>
[validationFailures:protected] => Array
(
)
[_new:BaseObject:private] =>
[_deleted:BaseObject:private] =>
[modifiedColumns:protected] => Array
(
)
)
[70] => Category Object
(
[languages:protected] =>
[bok_resources:protected] =>
[bok_topics:protected] =>
[bok_keywords:protected] =>
[id:protected] => 70
[type:protected] => category
[parent:protected] => 2
[label:protected] => Operating Engineer
[alreadyInSave:protected] =>
[alreadyInValidation:protected] =>
[validationFailures:protected] => Array
(
)
[_new:BaseObject:private] =>
[_deleted:BaseObject:private] =>
[modifiedColumns:protected] => Array
(
)
)
[85] => Category Object
(
[languages:protected] =>
[bok_resources:protected] =>
[bok_topics:protected] =>
[bok_keywords:protected] =>
[id:protected] => 85
[type:protected] => category
[parent:protected] => 2
[label:protected] => Truck Driver
[alreadyInSave:protected] =>
[alreadyInValidation:protected] =>
[validationFailures:protected] => Array
(
)
[_new:BaseObject:private] =>
[_deleted:BaseObject:private] =>
[modifiedColumns:protected] => Array
(
)
)
[87] => Category Object
(
[languages:protected] =>
[bok_resources:protected] =>
[bok_topics:protected] =>
[bok_keywords:protected] =>
[id:protected] => 87
[type:protected] => category
[parent:protected] => 3
[label:protected] => Commercial & Institutional
[alreadyInSave:protected] =>
[alreadyInValidation:protected] =>
[validationFailures:protected] => Array
(
)
[_new:BaseObject:private] =>
[_deleted:BaseObject:private] =>
[modifiedColumns:protected] => Array
(
)
)
[88] => Category Object
(
[languages:protected] =>
[bok_resources:protected] =>
[bok_topics:protected] =>
[bok_keywords:protected] =>
[id:protected] => 88
[type:protected] => category
[parent:protected] => 3
[label:protected] => Demolition
[alreadyInSave:protected] =>
[alreadyInValidation:protected] =>
[validationFailures:protected] => Array
(
)
[_new:BaseObject:private] =>
[_deleted:BaseObject:private] =>
[modifiedColumns:protected] => Array
(
)
)
[89] => Category Object
(
[languages:protected] =>
[bok_resources:protected] =>
[bok_topics:protected] =>
[bok_keywords:protected] =>
[id:protected] => 89
[type:protected] => category
[parent:protected] => 3
[label:protected] => Disasters
[alreadyInSave:protected] =>
[alreadyInValidation:protected] =>
[validationFailures:protected] => Array
(
)
[_new:BaseObject:private] =>
[_deleted:BaseObject:private] =>
[modifiedColumns:protected] => Array
(
)
)
[91] => Category Object
(
[languages:protected] =>
[bok_resources:protected] =>
[bok_topics:protected] =>
[bok_keywords:protected] =>
[id:protected] => 91
[type:protected] => category
[parent:protected] => 3
[label:protected] => Heavy & Highway
[alreadyInSave:protected] =>
[alreadyInValidation:protected] =>
[validationFailures:protected] => Array
(
)
[_new:BaseObject:private] =>
[_deleted:BaseObject:private] =>
[modifiedColumns:protected] => Array
(
)
)
[90] => Category Object
(
[languages:protected] =>
[bok_resources:protected] =>
[bok_topics:protected] =>
[bok_keywords:protected] =>
[id:protected] => 90
[type:protected] => category
[parent:protected] => 3
[label:protected] => Industrial
[alreadyInSave:protected] =>
[alreadyInValidation:protected] =>
[validationFailures:protected] => Array
(
)
[_new:BaseObject:private] =>
[_deleted:BaseObject:private] =>
[modifiedColumns:protected] => Array
(
)
)
[92] => Category Object
(
[languages:protected] =>
[bok_resources:protected] =>
[bok_topics:protected] =>
[bok_keywords:protected] =>
[id:protected] => 92
[type:protected] => category
[parent:protected] => 3
[label:protected] => LEED/Green Construction
[alreadyInSave:protected] =>
[alreadyInValidation:protected] =>
[validationFailures:protected] => Array
(
)
[_new:BaseObject:private] =>
[_deleted:BaseObject:private] =>
[modifiedColumns:protected] => Array
(
)
)
[93] => Category Object
(
[languages:protected] =>
[bok_resources:protected] =>
[bok_topics:protected] =>
[bok_keywords:protected] =>
[id:protected] => 93
[type:protected] => category
[parent:protected] => 3
[label:protected] => Renovations
[alreadyInSave:protected] =>
[alreadyInValidation:protected] =>
[validationFailures:protected] => Array
(
)
[_new:BaseObject:private] =>
[_deleted:BaseObject:private] =>
[modifiedColumns:protected] => Array
(
)
)
[94] => Category Object
(
[languages:protected] =>
[bok_resources:protected] =>
[bok_topics:protected] =>
[bok_keywords:protected] =>
[id:protected] => 94
[type:protected] => category
[parent:protected] => 3
[label:protected] => Residential
[alreadyInSave:protected] =>
[alreadyInValidation:protected] =>
[validationFailures:protected] => Array
(
)
[_new:BaseObject:private] =>
[_deleted:BaseObject:private] =>
[modifiedColumns:protected] => Array
(
)
)
[95] => Category Object
(
[languages:protected] =>
[bok_resources:protected] =>
[bok_topics:protected] =>
[bok_keywords:protected] =>
[id:protected] => 95
[type:protected] => category
[parent:protected] => 3
[label:protected] => Underground
[alreadyInSave:protected] =>
[alreadyInValidation:protected] =>
[validationFailures:protected] => Array
(
)
[_new:BaseObject:private] =>
[_deleted:BaseObject:private] =>
[modifiedColumns:protected] => Array
(
)
)
[100] => Category Object
(
[languages:protected] =>
[bok_resources:protected] =>
[bok_topics:protected] =>
[bok_keywords:protected] =>
[id:protected] => 100
[type:protected] => category
[parent:protected] => 6
[label:protected] => Toolbox Talks
[alreadyInSave:protected] =>
[alreadyInValidation:protected] =>
[validationFailures:protected] => Array
(
)
[_new:BaseObject:private] =>
[_deleted:BaseObject:private] =>
[modifiedColumns:protected] => Array
(
)
)
)
[categories_initialized:protected] => 1
[mapped_items:protected] =>
[content:protected] =>
[files:protected] =>
[language:protected] => Language Object
(
[id:protected] => 1
[code:protected] => en
[name:protected] => English
[alreadyInSave:protected] =>
[alreadyInValidation:protected] =>
[validationFailures:protected] => Array
(
)
[_new:BaseObject:private] =>
[_deleted:BaseObject:private] =>
[modifiedColumns:protected] => Array
(
)
)
[old_record:protected] =>
[id:protected] => 4428
[old_id:protected] =>
[elcosh_id:protected] => d001658
[type:protected] => document
[display_type:protected] => HTML only (and links)
[user_id:protected] => 0
[language_id:protected] => 1
[tagging_id:protected] => Daniela Caceres
[priority_id:protected] => 1
[title:protected] => Toolbox Talk: Work Zone Safety: Working Around Vehicles
[total_pages:protected] => 0
[billed_pages:protected] => 0
[publication_number:protected] =>
[part_of:protected] =>
[keywords:protected] => Struck, Struck by, Vehicle, Work Zone Safety, Truck, Operator, Driver, Mobile Equipment
[comments:protected] =>
[summary:protected] => The CPWR Toolbox Talk on Working Around Vehicles in the Work Zone addresses methods to avoid being struck-by a vehicle on a construction site. The resource includes a case example, steps to prevent a related injury, and questions for discussion. It includes a graphic that illustrates the hazard, which can be posted in a central location as a reminder of steps to work safely. Available in
English and
Spanish.
[transition_comments:protected] =>
[external_link:protected] =>
[consol_link:protected] =>
[more_like_this:protected] => d001640
[permission_given_by:protected] =>
[published:protected] => T
[billable:protected] => F
[img_name:protected] =>
[img_ext:protected] =>
[img_width:protected] =>
[img_height:protected] =>
[img_credit:protected] =>
[img_practice:protected] =>
[vid_source_id:protected] =>
[vid_running_time:protected] =>
[vid_intended_audience:protected] =>
[vid_acquisition_info:protected] =>
[vid_cost:protected] =>
[vid_producer:protected] =>
[vid_filename:protected] =>
[vid_filename_downloadable:protected] =>
[date_summary:protected] =>
[date_permission_requested:protected] =>
[date_permission_received:protected] =>
[date_review_needed:protected] =>
[date_received:protected] => 12/23/21
[date_completed:protected] => 12/23/21
[date_billed:protected] =>
[date_modified:protected] => 05/19/23
[collBokExports:protected] =>
[lastBokExportCriteria:BaseElcoshItem:private] =>
[alreadyInSave:protected] =>
[alreadyInValidation:protected] =>
[validationFailures:protected] => Array
(
)
[_new:BaseObject:private] =>
[_deleted:BaseObject:private] =>
[modifiedColumns:protected] => Array
(
)
)
)
[4] => Search_Result Object
(
[title] => Construction Dive -- DeWalt's Jobsite Pro headphones recalled for fire hazards
[image] => /record/images/notavailable-p.png
[blurb] => A recall notice by the United States Consumer Product Safety Commission affects over 300,000 DeWalt Jobsite Pro Headphones. The recall is a result of...
[category] => Array
(
[0] => 16
[1] => 44
[2] => 45
[3] => 46
[4] => 47
[5] => 48
[6] => 49
[7] => 50
[8] => 51
[9] => 52
[10] => 53
[11] => 54
[12] => 55
[13] => 56
[14] => 57
[15] => 58
[16] => 59
[17] => 60
[18] => 61
[19] => 64
[20] => 65
[21] => 66
[22] => 67
[23] => 68
[24] => 69
[25] => 70
[26] => 71
[27] => 72
[28] => 73
[29] => 74
[30] => 75
[31] => 76
[32] => 77
[33] => 63
[34] => 78
[35] => 79
[36] => 80
[37] => 81
[38] => 82
[39] => 62
[40] => 83
[41] => 84
[42] => 85
[43] => 86
[44] => 87
[45] => 88
[46] => 89
[47] => 91
[48] => 90
[49] => 92
[50] => 93
[51] => 94
[52] => 95
)
[labels] => Array
(
[0] => Fire & Explosions
[1] => Work Environment
[2] => Hazards
[3] => Acoustical Ceiling Carpenter
[4] => Trades
[5] => Asbestos/Insulator
[7] => Boilermaker
[9] => Bricklayer
[11] => Cabinetmaker
[13] => Carpenter
[15] => Carpet Layer
[17] => Cement Mason
[19] => Commercial Diver
[21] => Concrete Polisher
[23] => Drywall Applicator Specialist
[25] => Electrical Worker
[27] => Elevator Constructor
[29] => Flagger
[31] => Glazier
[33] => Hazardous Waste Cleanup
[35] => HVAC
[37] => Interior Systems Carpenter
[39] => Laborer
[41] => Landscaper
[43] => Lather
[45] => Lead Abatement Worker
[47] => Maintenance Worker
[49] => Millwright
[51] => Operating Engineer
[53] => Painter
[55] => Paper Hanger
[57] => PCC/Restoration
[59] => Pile Driver
[61] => Plasterer
[63] => Plumber/Pipefitter
[65] => Refractory Worker
[67] => Reinforcing Ironworker
[69] => Roofer/Waterproofer
[71] => Scaffold Erector
[73] => Sheetmetal Worker
[75] => Sprinkler Fitter
[77] => Stonemason
[79] => Structural Ironworker
[81] => Terrazzo Worker
[83] => Tile Setter
[85] => Truck Driver
[87] => Welder
[89] => Commercial & Institutional
[90] => Jobsites
[91] => Demolition
[93] => Disasters
[95] => Heavy & Highway
[97] => Industrial
[99] => LEED/Green Construction
[101] => Renovations
[103] => Residential
[105] => Underground
)
[type] =>
[sub_category] =>
[url] => /document/4426/d001656/Construction%2BDive%2B--%2BDeWalt%2527s%2BJobsite%2BPro%2Bheadphones%2Brecalled%2Bfor%2Bfire%2Bhazards.html
[item:protected] => DocumentRecord Object
(
[records:protected] => Array
(
)
[recordId:protected] =>
[searchWordClass:protected] =>
[searchWordPeerClass:protected] =>
[bok_record:protected] =>
[authors:protected] =>
[organizations:protected] =>
[collections:protected] =>
[categories:protected] => Array
(
[16] => Category Object
(
[languages:protected] =>
[bok_resources:protected] =>
[bok_topics:protected] =>
[bok_keywords:protected] =>
[id:protected] => 16
[type:protected] => category
[parent:protected] => 7
[label:protected] => Fire & Explosions
[alreadyInSave:protected] =>
[alreadyInValidation:protected] =>
[validationFailures:protected] => Array
(
)
[_new:BaseObject:private] =>
[_deleted:BaseObject:private] =>
[modifiedColumns:protected] => Array
(
)
)
[44] => Category Object
(
[languages:protected] =>
[bok_resources:protected] =>
[bok_topics:protected] =>
[bok_keywords:protected] =>
[id:protected] => 44
[type:protected] => category
[parent:protected] => 2
[label:protected] => Acoustical Ceiling Carpenter
[alreadyInSave:protected] =>
[alreadyInValidation:protected] =>
[validationFailures:protected] => Array
(
)
[_new:BaseObject:private] =>
[_deleted:BaseObject:private] =>
[modifiedColumns:protected] => Array
(
)
)
[45] => Category Object
(
[languages:protected] =>
[bok_resources:protected] =>
[bok_topics:protected] =>
[bok_keywords:protected] =>
[id:protected] => 45
[type:protected] => category
[parent:protected] => 2
[label:protected] => Asbestos/Insulator
[alreadyInSave:protected] =>
[alreadyInValidation:protected] =>
[validationFailures:protected] => Array
(
)
[_new:BaseObject:private] =>
[_deleted:BaseObject:private] =>
[modifiedColumns:protected] => Array
(
)
)
[46] => Category Object
(
[languages:protected] =>
[bok_resources:protected] =>
[bok_topics:protected] =>
[bok_keywords:protected] =>
[id:protected] => 46
[type:protected] => category
[parent:protected] => 2
[label:protected] => Boilermaker
[alreadyInSave:protected] =>
[alreadyInValidation:protected] =>
[validationFailures:protected] => Array
(
)
[_new:BaseObject:private] =>
[_deleted:BaseObject:private] =>
[modifiedColumns:protected] => Array
(
)
)
[47] => Category Object
(
[languages:protected] =>
[bok_resources:protected] =>
[bok_topics:protected] =>
[bok_keywords:protected] =>
[id:protected] => 47
[type:protected] => category
[parent:protected] => 2
[label:protected] => Bricklayer
[alreadyInSave:protected] =>
[alreadyInValidation:protected] =>
[validationFailures:protected] => Array
(
)
[_new:BaseObject:private] =>
[_deleted:BaseObject:private] =>
[modifiedColumns:protected] => Array
(
)
)
[48] => Category Object
(
[languages:protected] =>
[bok_resources:protected] =>
[bok_topics:protected] =>
[bok_keywords:protected] =>
[id:protected] => 48
[type:protected] => category
[parent:protected] => 2
[label:protected] => Cabinetmaker
[alreadyInSave:protected] =>
[alreadyInValidation:protected] =>
[validationFailures:protected] => Array
(
)
[_new:BaseObject:private] =>
[_deleted:BaseObject:private] =>
[modifiedColumns:protected] => Array
(
)
)
[49] => Category Object
(
[languages:protected] =>
[bok_resources:protected] =>
[bok_topics:protected] =>
[bok_keywords:protected] =>
[id:protected] => 49
[type:protected] => category
[parent:protected] => 2
[label:protected] => Carpenter
[alreadyInSave:protected] =>
[alreadyInValidation:protected] =>
[validationFailures:protected] => Array
(
)
[_new:BaseObject:private] =>
[_deleted:BaseObject:private] =>
[modifiedColumns:protected] => Array
(
)
)
[50] => Category Object
(
[languages:protected] =>
[bok_resources:protected] =>
[bok_topics:protected] =>
[bok_keywords:protected] =>
[id:protected] => 50
[type:protected] => category
[parent:protected] => 2
[label:protected] => Carpet Layer
[alreadyInSave:protected] =>
[alreadyInValidation:protected] =>
[validationFailures:protected] => Array
(
)
[_new:BaseObject:private] =>
[_deleted:BaseObject:private] =>
[modifiedColumns:protected] => Array
(
)
)
[51] => Category Object
(
[languages:protected] =>
[bok_resources:protected] =>
[bok_topics:protected] =>
[bok_keywords:protected] =>
[id:protected] => 51
[type:protected] => category
[parent:protected] => 2
[label:protected] => Cement Mason
[alreadyInSave:protected] =>
[alreadyInValidation:protected] =>
[validationFailures:protected] => Array
(
)
[_new:BaseObject:private] =>
[_deleted:BaseObject:private] =>
[modifiedColumns:protected] => Array
(
)
)
[52] => Category Object
(
[languages:protected] =>
[bok_resources:protected] =>
[bok_topics:protected] =>
[bok_keywords:protected] =>
[id:protected] => 52
[type:protected] => category
[parent:protected] => 2
[label:protected] => Commercial Diver
[alreadyInSave:protected] =>
[alreadyInValidation:protected] =>
[validationFailures:protected] => Array
(
)
[_new:BaseObject:private] =>
[_deleted:BaseObject:private] =>
[modifiedColumns:protected] => Array
(
)
)
[53] => Category Object
(
[languages:protected] =>
[bok_resources:protected] =>
[bok_topics:protected] =>
[bok_keywords:protected] =>
[id:protected] => 53
[type:protected] => category
[parent:protected] => 2
[label:protected] => Concrete Polisher
[alreadyInSave:protected] =>
[alreadyInValidation:protected] =>
[validationFailures:protected] => Array
(
)
[_new:BaseObject:private] =>
[_deleted:BaseObject:private] =>
[modifiedColumns:protected] => Array
(
)
)
[54] => Category Object
(
[languages:protected] =>
[bok_resources:protected] =>
[bok_topics:protected] =>
[bok_keywords:protected] =>
[id:protected] => 54
[type:protected] => category
[parent:protected] => 2
[label:protected] => Drywall Applicator Specialist
[alreadyInSave:protected] =>
[alreadyInValidation:protected] =>
[validationFailures:protected] => Array
(
)
[_new:BaseObject:private] =>
[_deleted:BaseObject:private] =>
[modifiedColumns:protected] => Array
(
)
)
[55] => Category Object
(
[languages:protected] =>
[bok_resources:protected] =>
[bok_topics:protected] =>
[bok_keywords:protected] =>
[id:protected] => 55
[type:protected] => category
[parent:protected] => 2
[label:protected] => Electrical Worker
[alreadyInSave:protected] =>
[alreadyInValidation:protected] =>
[validationFailures:protected] => Array
(
)
[_new:BaseObject:private] =>
[_deleted:BaseObject:private] =>
[modifiedColumns:protected] => Array
(
)
)
[56] => Category Object
(
[languages:protected] =>
[bok_resources:protected] =>
[bok_topics:protected] =>
[bok_keywords:protected] =>
[id:protected] => 56
[type:protected] => category
[parent:protected] => 2
[label:protected] => Elevator Constructor
[alreadyInSave:protected] =>
[alreadyInValidation:protected] =>
[validationFailures:protected] => Array
(
)
[_new:BaseObject:private] =>
[_deleted:BaseObject:private] =>
[modifiedColumns:protected] => Array
(
)
)
[57] => Category Object
(
[languages:protected] =>
[bok_resources:protected] =>
[bok_topics:protected] =>
[bok_keywords:protected] =>
[id:protected] => 57
[type:protected] => category
[parent:protected] => 2
[label:protected] => Flagger
[alreadyInSave:protected] =>
[alreadyInValidation:protected] =>
[validationFailures:protected] => Array
(
)
[_new:BaseObject:private] =>
[_deleted:BaseObject:private] =>
[modifiedColumns:protected] => Array
(
)
)
[58] => Category Object
(
[languages:protected] =>
[bok_resources:protected] =>
[bok_topics:protected] =>
[bok_keywords:protected] =>
[id:protected] => 58
[type:protected] => category
[parent:protected] => 2
[label:protected] => Glazier
[alreadyInSave:protected] =>
[alreadyInValidation:protected] =>
[validationFailures:protected] => Array
(
)
[_new:BaseObject:private] =>
[_deleted:BaseObject:private] =>
[modifiedColumns:protected] => Array
(
)
)
[59] => Category Object
(
[languages:protected] =>
[bok_resources:protected] =>
[bok_topics:protected] =>
[bok_keywords:protected] =>
[id:protected] => 59
[type:protected] => category
[parent:protected] => 2
[label:protected] => Hazardous Waste Cleanup
[alreadyInSave:protected] =>
[alreadyInValidation:protected] =>
[validationFailures:protected] => Array
(
)
[_new:BaseObject:private] =>
[_deleted:BaseObject:private] =>
[modifiedColumns:protected] => Array
(
)
)
[60] => Category Object
(
[languages:protected] =>
[bok_resources:protected] =>
[bok_topics:protected] =>
[bok_keywords:protected] =>
[id:protected] => 60
[type:protected] => category
[parent:protected] => 2
[label:protected] => HVAC
[alreadyInSave:protected] =>
[alreadyInValidation:protected] =>
[validationFailures:protected] => Array
(
)
[_new:BaseObject:private] =>
[_deleted:BaseObject:private] =>
[modifiedColumns:protected] => Array
(
)
)
[61] => Category Object
(
[languages:protected] =>
[bok_resources:protected] =>
[bok_topics:protected] =>
[bok_keywords:protected] =>
[id:protected] => 61
[type:protected] => category
[parent:protected] => 2
[label:protected] => Interior Systems Carpenter
[alreadyInSave:protected] =>
[alreadyInValidation:protected] =>
[validationFailures:protected] => Array
(
)
[_new:BaseObject:private] =>
[_deleted:BaseObject:private] =>
[modifiedColumns:protected] => Array
(
)
)
[64] => Category Object
(
[languages:protected] =>
[bok_resources:protected] =>
[bok_topics:protected] =>
[bok_keywords:protected] =>
[id:protected] => 64
[type:protected] => category
[parent:protected] => 2
[label:protected] => Laborer
[alreadyInSave:protected] =>
[alreadyInValidation:protected] =>
[validationFailures:protected] => Array
(
)
[_new:BaseObject:private] =>
[_deleted:BaseObject:private] =>
[modifiedColumns:protected] => Array
(
)
)
[65] => Category Object
(
[languages:protected] =>
[bok_resources:protected] =>
[bok_topics:protected] =>
[bok_keywords:protected] =>
[id:protected] => 65
[type:protected] => category
[parent:protected] => 2
[label:protected] => Landscaper
[alreadyInSave:protected] =>
[alreadyInValidation:protected] =>
[validationFailures:protected] => Array
(
)
[_new:BaseObject:private] =>
[_deleted:BaseObject:private] =>
[modifiedColumns:protected] => Array
(
)
)
[66] => Category Object
(
[languages:protected] =>
[bok_resources:protected] =>
[bok_topics:protected] =>
[bok_keywords:protected] =>
[id:protected] => 66
[type:protected] => category
[parent:protected] => 2
[label:protected] => Lather
[alreadyInSave:protected] =>
[alreadyInValidation:protected] =>
[validationFailures:protected] => Array
(
)
[_new:BaseObject:private] =>
[_deleted:BaseObject:private] =>
[modifiedColumns:protected] => Array
(
)
)
[67] => Category Object
(
[languages:protected] =>
[bok_resources:protected] =>
[bok_topics:protected] =>
[bok_keywords:protected] =>
[id:protected] => 67
[type:protected] => category
[parent:protected] => 2
[label:protected] => Lead Abatement Worker
[alreadyInSave:protected] =>
[alreadyInValidation:protected] =>
[validationFailures:protected] => Array
(
)
[_new:BaseObject:private] =>
[_deleted:BaseObject:private] =>
[modifiedColumns:protected] => Array
(
)
)
[68] => Category Object
(
[languages:protected] =>
[bok_resources:protected] =>
[bok_topics:protected] =>
[bok_keywords:protected] =>
[id:protected] => 68
[type:protected] => category
[parent:protected] => 2
[label:protected] => Maintenance Worker
[alreadyInSave:protected] =>
[alreadyInValidation:protected] =>
[validationFailures:protected] => Array
(
)
[_new:BaseObject:private] =>
[_deleted:BaseObject:private] =>
[modifiedColumns:protected] => Array
(
)
)
[69] => Category Object
(
[languages:protected] =>
[bok_resources:protected] =>
[bok_topics:protected] =>
[bok_keywords:protected] =>
[id:protected] => 69
[type:protected] => category
[parent:protected] => 2
[label:protected] => Millwright
[alreadyInSave:protected] =>
[alreadyInValidation:protected] =>
[validationFailures:protected] => Array
(
)
[_new:BaseObject:private] =>
[_deleted:BaseObject:private] =>
[modifiedColumns:protected] => Array
(
)
)
[70] => Category Object
(
[languages:protected] =>
[bok_resources:protected] =>
[bok_topics:protected] =>
[bok_keywords:protected] =>
[id:protected] => 70
[type:protected] => category
[parent:protected] => 2
[label:protected] => Operating Engineer
[alreadyInSave:protected] =>
[alreadyInValidation:protected] =>
[validationFailures:protected] => Array
(
)
[_new:BaseObject:private] =>
[_deleted:BaseObject:private] =>
[modifiedColumns:protected] => Array
(
)
)
[71] => Category Object
(
[languages:protected] =>
[bok_resources:protected] =>
[bok_topics:protected] =>
[bok_keywords:protected] =>
[id:protected] => 71
[type:protected] => category
[parent:protected] => 2
[label:protected] => Painter
[alreadyInSave:protected] =>
[alreadyInValidation:protected] =>
[validationFailures:protected] => Array
(
)
[_new:BaseObject:private] =>
[_deleted:BaseObject:private] =>
[modifiedColumns:protected] => Array
(
)
)
[72] => Category Object
(
[languages:protected] =>
[bok_resources:protected] =>
[bok_topics:protected] =>
[bok_keywords:protected] =>
[id:protected] => 72
[type:protected] => category
[parent:protected] => 2
[label:protected] => Paper Hanger
[alreadyInSave:protected] =>
[alreadyInValidation:protected] =>
[validationFailures:protected] => Array
(
)
[_new:BaseObject:private] =>
[_deleted:BaseObject:private] =>
[modifiedColumns:protected] => Array
(
)
)
[73] => Category Object
(
[languages:protected] =>
[bok_resources:protected] =>
[bok_topics:protected] =>
[bok_keywords:protected] =>
[id:protected] => 73
[type:protected] => category
[parent:protected] => 2
[label:protected] => PCC/Restoration
[alreadyInSave:protected] =>
[alreadyInValidation:protected] =>
[validationFailures:protected] => Array
(
)
[_new:BaseObject:private] =>
[_deleted:BaseObject:private] =>
[modifiedColumns:protected] => Array
(
)
)
[74] => Category Object
(
[languages:protected] =>
[bok_resources:protected] =>
[bok_topics:protected] =>
[bok_keywords:protected] =>
[id:protected] => 74
[type:protected] => category
[parent:protected] => 2
[label:protected] => Pile Driver
[alreadyInSave:protected] =>
[alreadyInValidation:protected] =>
[validationFailures:protected] => Array
(
)
[_new:BaseObject:private] =>
[_deleted:BaseObject:private] =>
[modifiedColumns:protected] => Array
(
)
)
[75] => Category Object
(
[languages:protected] =>
[bok_resources:protected] =>
[bok_topics:protected] =>
[bok_keywords:protected] =>
[id:protected] => 75
[type:protected] => category
[parent:protected] => 2
[label:protected] => Plasterer
[alreadyInSave:protected] =>
[alreadyInValidation:protected] =>
[validationFailures:protected] => Array
(
)
[_new:BaseObject:private] =>
[_deleted:BaseObject:private] =>
[modifiedColumns:protected] => Array
(
)
)
[76] => Category Object
(
[languages:protected] =>
[bok_resources:protected] =>
[bok_topics:protected] =>
[bok_keywords:protected] =>
[id:protected] => 76
[type:protected] => category
[parent:protected] => 2
[label:protected] => Plumber/Pipefitter
[alreadyInSave:protected] =>
[alreadyInValidation:protected] =>
[validationFailures:protected] => Array
(
)
[_new:BaseObject:private] =>
[_deleted:BaseObject:private] =>
[modifiedColumns:protected] => Array
(
)
)
[77] => Category Object
(
[languages:protected] =>
[bok_resources:protected] =>
[bok_topics:protected] =>
[bok_keywords:protected] =>
[id:protected] => 77
[type:protected] => category
[parent:protected] => 2
[label:protected] => Refractory Worker
[alreadyInSave:protected] =>
[alreadyInValidation:protected] =>
[validationFailures:protected] => Array
(
)
[_new:BaseObject:private] =>
[_deleted:BaseObject:private] =>
[modifiedColumns:protected] => Array
(
)
)
[63] => Category Object
(
[languages:protected] =>
[bok_resources:protected] =>
[bok_topics:protected] =>
[bok_keywords:protected] =>
[id:protected] => 63
[type:protected] => category
[parent:protected] => 2
[label:protected] => Reinforcing Ironworker
[alreadyInSave:protected] =>
[alreadyInValidation:protected] =>
[validationFailures:protected] => Array
(
)
[_new:BaseObject:private] =>
[_deleted:BaseObject:private] =>
[modifiedColumns:protected] => Array
(
)
)
[78] => Category Object
(
[languages:protected] =>
[bok_resources:protected] =>
[bok_topics:protected] =>
[bok_keywords:protected] =>
[id:protected] => 78
[type:protected] => category
[parent:protected] => 2
[label:protected] => Roofer/Waterproofer
[alreadyInSave:protected] =>
[alreadyInValidation:protected] =>
[validationFailures:protected] => Array
(
)
[_new:BaseObject:private] =>
[_deleted:BaseObject:private] =>
[modifiedColumns:protected] => Array
(
)
)
[79] => Category Object
(
[languages:protected] =>
[bok_resources:protected] =>
[bok_topics:protected] =>
[bok_keywords:protected] =>
[id:protected] => 79
[type:protected] => category
[parent:protected] => 2
[label:protected] => Scaffold Erector
[alreadyInSave:protected] =>
[alreadyInValidation:protected] =>
[validationFailures:protected] => Array
(
)
[_new:BaseObject:private] =>
[_deleted:BaseObject:private] =>
[modifiedColumns:protected] => Array
(
)
)
[80] => Category Object
(
[languages:protected] =>
[bok_resources:protected] =>
[bok_topics:protected] =>
[bok_keywords:protected] =>
[id:protected] => 80
[type:protected] => category
[parent:protected] => 2
[label:protected] => Sheetmetal Worker
[alreadyInSave:protected] =>
[alreadyInValidation:protected] =>
[validationFailures:protected] => Array
(
)
[_new:BaseObject:private] =>
[_deleted:BaseObject:private] =>
[modifiedColumns:protected] => Array
(
)
)
[81] => Category Object
(
[languages:protected] =>
[bok_resources:protected] =>
[bok_topics:protected] =>
[bok_keywords:protected] =>
[id:protected] => 81
[type:protected] => category
[parent:protected] => 2
[label:protected] => Sprinkler Fitter
[alreadyInSave:protected] =>
[alreadyInValidation:protected] =>
[validationFailures:protected] => Array
(
)
[_new:BaseObject:private] =>
[_deleted:BaseObject:private] =>
[modifiedColumns:protected] => Array
(
)
)
[82] => Category Object
(
[languages:protected] =>
[bok_resources:protected] =>
[bok_topics:protected] =>
[bok_keywords:protected] =>
[id:protected] => 82
[type:protected] => category
[parent:protected] => 2
[label:protected] => Stonemason
[alreadyInSave:protected] =>
[alreadyInValidation:protected] =>
[validationFailures:protected] => Array
(
)
[_new:BaseObject:private] =>
[_deleted:BaseObject:private] =>
[modifiedColumns:protected] => Array
(
)
)
[62] => Category Object
(
[languages:protected] =>
[bok_resources:protected] =>
[bok_topics:protected] =>
[bok_keywords:protected] =>
[id:protected] => 62
[type:protected] => category
[parent:protected] => 2
[label:protected] => Structural Ironworker
[alreadyInSave:protected] =>
[alreadyInValidation:protected] =>
[validationFailures:protected] => Array
(
)
[_new:BaseObject:private] =>
[_deleted:BaseObject:private] =>
[modifiedColumns:protected] => Array
(
)
)
[83] => Category Object
(
[languages:protected] =>
[bok_resources:protected] =>
[bok_topics:protected] =>
[bok_keywords:protected] =>
[id:protected] => 83
[type:protected] => category
[parent:protected] => 2
[label:protected] => Terrazzo Worker
[alreadyInSave:protected] =>
[alreadyInValidation:protected] =>
[validationFailures:protected] => Array
(
)
[_new:BaseObject:private] =>
[_deleted:BaseObject:private] =>
[modifiedColumns:protected] => Array
(
)
)
[84] => Category Object
(
[languages:protected] =>
[bok_resources:protected] =>
[bok_topics:protected] =>
[bok_keywords:protected] =>
[id:protected] => 84
[type:protected] => category
[parent:protected] => 2
[label:protected] => Tile Setter
[alreadyInSave:protected] =>
[alreadyInValidation:protected] =>
[validationFailures:protected] => Array
(
)
[_new:BaseObject:private] =>
[_deleted:BaseObject:private] =>
[modifiedColumns:protected] => Array
(
)
)
[85] => Category Object
(
[languages:protected] =>
[bok_resources:protected] =>
[bok_topics:protected] =>
[bok_keywords:protected] =>
[id:protected] => 85
[type:protected] => category
[parent:protected] => 2
[label:protected] => Truck Driver
[alreadyInSave:protected] =>
[alreadyInValidation:protected] =>
[validationFailures:protected] => Array
(
)
[_new:BaseObject:private] =>
[_deleted:BaseObject:private] =>
[modifiedColumns:protected] => Array
(
)
)
[86] => Category Object
(
[languages:protected] =>
[bok_resources:protected] =>
[bok_topics:protected] =>
[bok_keywords:protected] =>
[id:protected] => 86
[type:protected] => category
[parent:protected] => 2
[label:protected] => Welder
[alreadyInSave:protected] =>
[alreadyInValidation:protected] =>
[validationFailures:protected] => Array
(
)
[_new:BaseObject:private] =>
[_deleted:BaseObject:private] =>
[modifiedColumns:protected] => Array
(
)
)
[87] => Category Object
(
[languages:protected] =>
[bok_resources:protected] =>
[bok_topics:protected] =>
[bok_keywords:protected] =>
[id:protected] => 87
[type:protected] => category
[parent:protected] => 3
[label:protected] => Commercial & Institutional
[alreadyInSave:protected] =>
[alreadyInValidation:protected] =>
[validationFailures:protected] => Array
(
)
[_new:BaseObject:private] =>
[_deleted:BaseObject:private] =>
[modifiedColumns:protected] => Array
(
)
)
[88] => Category Object
(
[languages:protected] =>
[bok_resources:protected] =>
[bok_topics:protected] =>
[bok_keywords:protected] =>
[id:protected] => 88
[type:protected] => category
[parent:protected] => 3
[label:protected] => Demolition
[alreadyInSave:protected] =>
[alreadyInValidation:protected] =>
[validationFailures:protected] => Array
(
)
[_new:BaseObject:private] =>
[_deleted:BaseObject:private] =>
[modifiedColumns:protected] => Array
(
)
)
[89] => Category Object
(
[languages:protected] =>
[bok_resources:protected] =>
[bok_topics:protected] =>
[bok_keywords:protected] =>
[id:protected] => 89
[type:protected] => category
[parent:protected] => 3
[label:protected] => Disasters
[alreadyInSave:protected] =>
[alreadyInValidation:protected] =>
[validationFailures:protected] => Array
(
)
[_new:BaseObject:private] =>
[_deleted:BaseObject:private] =>
[modifiedColumns:protected] => Array
(
)
)
[91] => Category Object
(
[languages:protected] =>
[bok_resources:protected] =>
[bok_topics:protected] =>
[bok_keywords:protected] =>
[id:protected] => 91
[type:protected] => category
[parent:protected] => 3
[label:protected] => Heavy & Highway
[alreadyInSave:protected] =>
[alreadyInValidation:protected] =>
[validationFailures:protected] => Array
(
)
[_new:BaseObject:private] =>
[_deleted:BaseObject:private] =>
[modifiedColumns:protected] => Array
(
)
)
[90] => Category Object
(
[languages:protected] =>
[bok_resources:protected] =>
[bok_topics:protected] =>
[bok_keywords:protected] =>
[id:protected] => 90
[type:protected] => category
[parent:protected] => 3
[label:protected] => Industrial
[alreadyInSave:protected] =>
[alreadyInValidation:protected] =>
[validationFailures:protected] => Array
(
)
[_new:BaseObject:private] =>
[_deleted:BaseObject:private] =>
[modifiedColumns:protected] => Array
(
)
)
[92] => Category Object
(
[languages:protected] =>
[bok_resources:protected] =>
[bok_topics:protected] =>
[bok_keywords:protected] =>
[id:protected] => 92
[type:protected] => category
[parent:protected] => 3
[label:protected] => LEED/Green Construction
[alreadyInSave:protected] =>
[alreadyInValidation:protected] =>
[validationFailures:protected] => Array
(
)
[_new:BaseObject:private] =>
[_deleted:BaseObject:private] =>
[modifiedColumns:protected] => Array
(
)
)
[93] => Category Object
(
[languages:protected] =>
[bok_resources:protected] =>
[bok_topics:protected] =>
[bok_keywords:protected] =>
[id:protected] => 93
[type:protected] => category
[parent:protected] => 3
[label:protected] => Renovations
[alreadyInSave:protected] =>
[alreadyInValidation:protected] =>
[validationFailures:protected] => Array
(
)
[_new:BaseObject:private] =>
[_deleted:BaseObject:private] =>
[modifiedColumns:protected] => Array
(
)
)
[94] => Category Object
(
[languages:protected] =>
[bok_resources:protected] =>
[bok_topics:protected] =>
[bok_keywords:protected] =>
[id:protected] => 94
[type:protected] => category
[parent:protected] => 3
[label:protected] => Residential
[alreadyInSave:protected] =>
[alreadyInValidation:protected] =>
[validationFailures:protected] => Array
(
)
[_new:BaseObject:private] =>
[_deleted:BaseObject:private] =>
[modifiedColumns:protected] => Array
(
)
)
[95] => Category Object
(
[languages:protected] =>
[bok_resources:protected] =>
[bok_topics:protected] =>
[bok_keywords:protected] =>
[id:protected] => 95
[type:protected] => category
[parent:protected] => 3
[label:protected] => Underground
[alreadyInSave:protected] =>
[alreadyInValidation:protected] =>
[validationFailures:protected] => Array
(
)
[_new:BaseObject:private] =>
[_deleted:BaseObject:private] =>
[modifiedColumns:protected] => Array
(
)
)
)
[categories_initialized:protected] => 1
[mapped_items:protected] =>
[content:protected] =>
[files:protected] =>
[language:protected] => Language Object
(
[id:protected] => 1
[code:protected] => en
[name:protected] => English
[alreadyInSave:protected] =>
[alreadyInValidation:protected] =>
[validationFailures:protected] => Array
(
)
[_new:BaseObject:private] =>
[_deleted:BaseObject:private] =>
[modifiedColumns:protected] => Array
(
)
)
[old_record:protected] =>
[id:protected] => 4426
[old_id:protected] =>
[elcosh_id:protected] => d001656
[type:protected] => document
[display_type:protected] => HTML only (and links)
[user_id:protected] => 0
[language_id:protected] => 1
[tagging_id:protected] => Mike Aguilar
[priority_id:protected] => 1
[title:protected] => Construction Dive -- DeWalt's Jobsite Pro headphones recalled for fire hazards
[total_pages:protected] => 1
[billed_pages:protected] => 1
[publication_number:protected] =>
[part_of:protected] =>
[keywords:protected] => DeWalt, Fire Hazards, recall, headphones
[comments:protected] =>
[summary:protected] => A recall notice by the United States Consumer Product Safety Commission affects over 300,000 DeWalt Jobsite Pro Headphones. The recall is a result of a malfunction that can cause earbuds to overheat while charging or during use, leading to fire and burn hazards.
[transition_comments:protected] =>
[external_link:protected] => https://www.constructiondive.com/news/dewalts-jobsite-pro-headphones-recalled-for-fire-hazards/611248/?utm_source=Sailthru&utm_medium=email&utm_campaign=Issue:%202021-12-10%20Construction%20Dive%20Newsletter%20%5Bissue:38532%5D&utm_term=Construction%20Dive
[consol_link:protected] =>
[more_like_this:protected] =>
[permission_given_by:protected] =>
[published:protected] => T
[billable:protected] => F
[img_name:protected] =>
[img_ext:protected] =>
[img_width:protected] =>
[img_height:protected] =>
[img_credit:protected] =>
[img_practice:protected] =>
[vid_source_id:protected] =>
[vid_running_time:protected] =>
[vid_intended_audience:protected] =>
[vid_acquisition_info:protected] =>
[vid_cost:protected] =>
[vid_producer:protected] =>
[vid_filename:protected] =>
[vid_filename_downloadable:protected] =>
[date_summary:protected] =>
[date_permission_requested:protected] =>
[date_permission_received:protected] =>
[date_review_needed:protected] =>
[date_received:protected] => 12/13/21
[date_completed:protected] => 12/13/21
[date_billed:protected] =>
[date_modified:protected] => 12/13/21
[collBokExports:protected] =>
[lastBokExportCriteria:BaseElcoshItem:private] =>
[alreadyInSave:protected] =>
[alreadyInValidation:protected] =>
[validationFailures:protected] => Array
(
)
[_new:BaseObject:private] =>
[_deleted:BaseObject:private] =>
[modifiedColumns:protected] => Array
(
)
)
)
)
[new_images] => Array
(
[0] => Search_Result Object
(
[title] => Morning Toolbox Talk
[image] => /record/images/4003-p.jpg
[blurb] => This photo is from an early morning toolbox talk on a construction job in Mclean, Virginia. It is being delivered in English and Spanish....
[category] => Array
(
[0] => 20
[1] => 51
[2] => 57
[3] => 64
[4] => 70
[5] => 63
[6] => 78
[7] => 82
[8] => 62
[9] => 87
[10] => 88
[11] => 89
[12] => 91
[13] => 90
[14] => 93
[15] => 94
[16] => 97
)
[labels] => Array
(
[0] => Safety Culture
[1] => Work Environment
[2] => Hazards
[3] => Cement Mason
[4] => Trades
[5] => Flagger
[7] => Laborer
[9] => Operating Engineer
[11] => Reinforcing Ironworker
[13] => Roofer/Waterproofer
[15] => Stonemason
[17] => Structural Ironworker
[19] => Commercial & Institutional
[20] => Jobsites
[21] => Demolition
[23] => Disasters
[25] => Heavy & Highway
[27] => Industrial
[29] => Renovations
[31] => Residential
[33] => Images
[34] => Media
[35] => Media & Documents
)
[type] => Images
[sub_category] =>
[url] => /image/4003/i002691/Morning%2BToolbox%2BTalk.html
[item:protected] => ImageRecord Object
(
[records:protected] => Array
(
)
[recordId:protected] =>
[searchWordClass:protected] =>
[searchWordPeerClass:protected] =>
[bok_record:protected] =>
[authors:protected] =>
[organizations:protected] =>
[collections:protected] =>
[categories:protected] => Array
(
[20] => Category Object
(
[languages:protected] =>
[bok_resources:protected] =>
[bok_topics:protected] =>
[bok_keywords:protected] =>
[id:protected] => 20
[type:protected] => category
[parent:protected] => 7
[label:protected] => Safety Culture
[alreadyInSave:protected] =>
[alreadyInValidation:protected] =>
[validationFailures:protected] => Array
(
)
[_new:BaseObject:private] =>
[_deleted:BaseObject:private] =>
[modifiedColumns:protected] => Array
(
)
)
[51] => Category Object
(
[languages:protected] =>
[bok_resources:protected] =>
[bok_topics:protected] =>
[bok_keywords:protected] =>
[id:protected] => 51
[type:protected] => category
[parent:protected] => 2
[label:protected] => Cement Mason
[alreadyInSave:protected] =>
[alreadyInValidation:protected] =>
[validationFailures:protected] => Array
(
)
[_new:BaseObject:private] =>
[_deleted:BaseObject:private] =>
[modifiedColumns:protected] => Array
(
)
)
[57] => Category Object
(
[languages:protected] =>
[bok_resources:protected] =>
[bok_topics:protected] =>
[bok_keywords:protected] =>
[id:protected] => 57
[type:protected] => category
[parent:protected] => 2
[label:protected] => Flagger
[alreadyInSave:protected] =>
[alreadyInValidation:protected] =>
[validationFailures:protected] => Array
(
)
[_new:BaseObject:private] =>
[_deleted:BaseObject:private] =>
[modifiedColumns:protected] => Array
(
)
)
[64] => Category Object
(
[languages:protected] =>
[bok_resources:protected] =>
[bok_topics:protected] =>
[bok_keywords:protected] =>
[id:protected] => 64
[type:protected] => category
[parent:protected] => 2
[label:protected] => Laborer
[alreadyInSave:protected] =>
[alreadyInValidation:protected] =>
[validationFailures:protected] => Array
(
)
[_new:BaseObject:private] =>
[_deleted:BaseObject:private] =>
[modifiedColumns:protected] => Array
(
)
)
[70] => Category Object
(
[languages:protected] =>
[bok_resources:protected] =>
[bok_topics:protected] =>
[bok_keywords:protected] =>
[id:protected] => 70
[type:protected] => category
[parent:protected] => 2
[label:protected] => Operating Engineer
[alreadyInSave:protected] =>
[alreadyInValidation:protected] =>
[validationFailures:protected] => Array
(
)
[_new:BaseObject:private] =>
[_deleted:BaseObject:private] =>
[modifiedColumns:protected] => Array
(
)
)
[63] => Category Object
(
[languages:protected] =>
[bok_resources:protected] =>
[bok_topics:protected] =>
[bok_keywords:protected] =>
[id:protected] => 63
[type:protected] => category
[parent:protected] => 2
[label:protected] => Reinforcing Ironworker
[alreadyInSave:protected] =>
[alreadyInValidation:protected] =>
[validationFailures:protected] => Array
(
)
[_new:BaseObject:private] =>
[_deleted:BaseObject:private] =>
[modifiedColumns:protected] => Array
(
)
)
[78] => Category Object
(
[languages:protected] =>
[bok_resources:protected] =>
[bok_topics:protected] =>
[bok_keywords:protected] =>
[id:protected] => 78
[type:protected] => category
[parent:protected] => 2
[label:protected] => Roofer/Waterproofer
[alreadyInSave:protected] =>
[alreadyInValidation:protected] =>
[validationFailures:protected] => Array
(
)
[_new:BaseObject:private] =>
[_deleted:BaseObject:private] =>
[modifiedColumns:protected] => Array
(
)
)
[82] => Category Object
(
[languages:protected] =>
[bok_resources:protected] =>
[bok_topics:protected] =>
[bok_keywords:protected] =>
[id:protected] => 82
[type:protected] => category
[parent:protected] => 2
[label:protected] => Stonemason
[alreadyInSave:protected] =>
[alreadyInValidation:protected] =>
[validationFailures:protected] => Array
(
)
[_new:BaseObject:private] =>
[_deleted:BaseObject:private] =>
[modifiedColumns:protected] => Array
(
)
)
[62] => Category Object
(
[languages:protected] =>
[bok_resources:protected] =>
[bok_topics:protected] =>
[bok_keywords:protected] =>
[id:protected] => 62
[type:protected] => category
[parent:protected] => 2
[label:protected] => Structural Ironworker
[alreadyInSave:protected] =>
[alreadyInValidation:protected] =>
[validationFailures:protected] => Array
(
)
[_new:BaseObject:private] =>
[_deleted:BaseObject:private] =>
[modifiedColumns:protected] => Array
(
)
)
[87] => Category Object
(
[languages:protected] =>
[bok_resources:protected] =>
[bok_topics:protected] =>
[bok_keywords:protected] =>
[id:protected] => 87
[type:protected] => category
[parent:protected] => 3
[label:protected] => Commercial & Institutional
[alreadyInSave:protected] =>
[alreadyInValidation:protected] =>
[validationFailures:protected] => Array
(
)
[_new:BaseObject:private] =>
[_deleted:BaseObject:private] =>
[modifiedColumns:protected] => Array
(
)
)
[88] => Category Object
(
[languages:protected] =>
[bok_resources:protected] =>
[bok_topics:protected] =>
[bok_keywords:protected] =>
[id:protected] => 88
[type:protected] => category
[parent:protected] => 3
[label:protected] => Demolition
[alreadyInSave:protected] =>
[alreadyInValidation:protected] =>
[validationFailures:protected] => Array
(
)
[_new:BaseObject:private] =>
[_deleted:BaseObject:private] =>
[modifiedColumns:protected] => Array
(
)
)
[89] => Category Object
(
[languages:protected] =>
[bok_resources:protected] =>
[bok_topics:protected] =>
[bok_keywords:protected] =>
[id:protected] => 89
[type:protected] => category
[parent:protected] => 3
[label:protected] => Disasters
[alreadyInSave:protected] =>
[alreadyInValidation:protected] =>
[validationFailures:protected] => Array
(
)
[_new:BaseObject:private] =>
[_deleted:BaseObject:private] =>
[modifiedColumns:protected] => Array
(
)
)
[91] => Category Object
(
[languages:protected] =>
[bok_resources:protected] =>
[bok_topics:protected] =>
[bok_keywords:protected] =>
[id:protected] => 91
[type:protected] => category
[parent:protected] => 3
[label:protected] => Heavy & Highway
[alreadyInSave:protected] =>
[alreadyInValidation:protected] =>
[validationFailures:protected] => Array
(
)
[_new:BaseObject:private] =>
[_deleted:BaseObject:private] =>
[modifiedColumns:protected] => Array
(
)
)
[90] => Category Object
(
[languages:protected] =>
[bok_resources:protected] =>
[bok_topics:protected] =>
[bok_keywords:protected] =>
[id:protected] => 90
[type:protected] => category
[parent:protected] => 3
[label:protected] => Industrial
[alreadyInSave:protected] =>
[alreadyInValidation:protected] =>
[validationFailures:protected] => Array
(
)
[_new:BaseObject:private] =>
[_deleted:BaseObject:private] =>
[modifiedColumns:protected] => Array
(
)
)
[93] => Category Object
(
[languages:protected] =>
[bok_resources:protected] =>
[bok_topics:protected] =>
[bok_keywords:protected] =>
[id:protected] => 93
[type:protected] => category
[parent:protected] => 3
[label:protected] => Renovations
[alreadyInSave:protected] =>
[alreadyInValidation:protected] =>
[validationFailures:protected] => Array
(
)
[_new:BaseObject:private] =>
[_deleted:BaseObject:private] =>
[modifiedColumns:protected] => Array
(
)
)
[94] => Category Object
(
[languages:protected] =>
[bok_resources:protected] =>
[bok_topics:protected] =>
[bok_keywords:protected] =>
[id:protected] => 94
[type:protected] => category
[parent:protected] => 3
[label:protected] => Residential
[alreadyInSave:protected] =>
[alreadyInValidation:protected] =>
[validationFailures:protected] => Array
(
)
[_new:BaseObject:private] =>
[_deleted:BaseObject:private] =>
[modifiedColumns:protected] => Array
(
)
)
[97] => Category Object
(
[languages:protected] =>
[bok_resources:protected] =>
[bok_topics:protected] =>
[bok_keywords:protected] =>
[id:protected] => 97
[type:protected] => category
[parent:protected] => 5
[label:protected] => Images
[alreadyInSave:protected] =>
[alreadyInValidation:protected] =>
[validationFailures:protected] => Array
(
)
[_new:BaseObject:private] =>
[_deleted:BaseObject:private] =>
[modifiedColumns:protected] => Array
(
)
)
)
[categories_initialized:protected] => 1
[mapped_items:protected] =>
[content:protected] =>
[files:protected] =>
[language:protected] => Language Object
(
[id:protected] => 1
[code:protected] => en
[name:protected] => English
[alreadyInSave:protected] =>
[alreadyInValidation:protected] =>
[validationFailures:protected] => Array
(
)
[_new:BaseObject:private] =>
[_deleted:BaseObject:private] =>
[modifiedColumns:protected] => Array
(
)
)
[old_record:protected] =>
[id:protected] => 4003
[old_id:protected] =>
[elcosh_id:protected] => i002691
[type:protected] => image
[display_type:protected] => Image
[user_id:protected] => 0
[language_id:protected] => 1
[tagging_id:protected] => Bruce Lippy
[priority_id:protected] => 1
[title:protected] => Morning Toolbox Talk
[total_pages:protected] => 0
[billed_pages:protected] => 0
[publication_number:protected] =>
[part_of:protected] =>
[keywords:protected] => toolbox talk, tailgate talk, Spanish, bilingual
[comments:protected] =>
[summary:protected] => This photo is from an early morning toolbox talk on a construction job in Mclean, Virginia. It is being delivered in English and Spanish.
[transition_comments:protected] =>
[external_link:protected] =>
[consol_link:protected] => http://www.cpwrconstructionsolutions.org/electrical/solution/662/worker-training.html
[more_like_this:protected] => d001285,d001304,c000079
[permission_given_by:protected] =>
[published:protected] => T
[billable:protected] => F
[img_name:protected] =>
[img_ext:protected] => jpg
[img_width:protected] =>
[img_height:protected] =>
[img_credit:protected] => Morgan Zavertnik and Hoar Construction
[img_practice:protected] => good
[vid_source_id:protected] =>
[vid_running_time:protected] =>
[vid_intended_audience:protected] =>
[vid_acquisition_info:protected] =>
[vid_cost:protected] =>
[vid_producer:protected] =>
[vid_filename:protected] =>
[vid_filename_downloadable:protected] =>
[date_summary:protected] => November 2015
[date_permission_requested:protected] =>
[date_permission_received:protected] =>
[date_review_needed:protected] =>
[date_received:protected] => 03/02/16
[date_completed:protected] => 03/02/16
[date_billed:protected] =>
[date_modified:protected] => 03/02/16
[collBokExports:protected] =>
[lastBokExportCriteria:BaseElcoshItem:private] =>
[alreadyInSave:protected] =>
[alreadyInValidation:protected] =>
[validationFailures:protected] => Array
(
)
[_new:BaseObject:private] =>
[_deleted:BaseObject:private] =>
[modifiedColumns:protected] => Array
(
)
)
)
[1] => Search_Result Object
(
[title] => Toolbox talk - crew view
[image] => /record/images/4005-p.jpg
[blurb] => Photo of crew listening to a toolbox safety talk before starting work....
[category] => Array
(
[0] => 97
[1] => 20
[2] => 47
[3] => 49
[4] => 51
[5] => 55
[6] => 61
[7] => 64
[8] => 71
[9] => 75
[10] => 63
[11] => 79
[12] => 62
[13] => 87
[14] => 88
[15] => 91
[16] => 90
[17] => 93
[18] => 94
[19] => 95
)
[labels] => Array
(
[0] => Images
[1] => Media
[2] => Media & Documents
[3] => Safety Culture
[4] => Work Environment
[5] => Hazards
[6] => Bricklayer
[7] => Trades
[8] => Carpenter
[10] => Cement Mason
[12] => Electrical Worker
[14] => Interior Systems Carpenter
[16] => Laborer
[18] => Painter
[20] => Plasterer
[22] => Reinforcing Ironworker
[24] => Scaffold Erector
[26] => Structural Ironworker
[28] => Commercial & Institutional
[29] => Jobsites
[30] => Demolition
[32] => Heavy & Highway
[34] => Industrial
[36] => Renovations
[38] => Residential
[40] => Underground
)
[type] => Images
[sub_category] =>
[url] => /image/4005/i002692/Toolbox%2Btalk%2B-%2Bcrew%2Bview.html
[item:protected] => ImageRecord Object
(
[records:protected] => Array
(
)
[recordId:protected] =>
[searchWordClass:protected] =>
[searchWordPeerClass:protected] =>
[bok_record:protected] =>
[authors:protected] =>
[organizations:protected] =>
[collections:protected] =>
[categories:protected] => Array
(
[97] => Category Object
(
[languages:protected] =>
[bok_resources:protected] =>
[bok_topics:protected] =>
[bok_keywords:protected] =>
[id:protected] => 97
[type:protected] => category
[parent:protected] => 5
[label:protected] => Images
[alreadyInSave:protected] =>
[alreadyInValidation:protected] =>
[validationFailures:protected] => Array
(
)
[_new:BaseObject:private] =>
[_deleted:BaseObject:private] =>
[modifiedColumns:protected] => Array
(
)
)
[20] => Category Object
(
[languages:protected] =>
[bok_resources:protected] =>
[bok_topics:protected] =>
[bok_keywords:protected] =>
[id:protected] => 20
[type:protected] => category
[parent:protected] => 7
[label:protected] => Safety Culture
[alreadyInSave:protected] =>
[alreadyInValidation:protected] =>
[validationFailures:protected] => Array
(
)
[_new:BaseObject:private] =>
[_deleted:BaseObject:private] =>
[modifiedColumns:protected] => Array
(
)
)
[47] => Category Object
(
[languages:protected] =>
[bok_resources:protected] =>
[bok_topics:protected] =>
[bok_keywords:protected] =>
[id:protected] => 47
[type:protected] => category
[parent:protected] => 2
[label:protected] => Bricklayer
[alreadyInSave:protected] =>
[alreadyInValidation:protected] =>
[validationFailures:protected] => Array
(
)
[_new:BaseObject:private] =>
[_deleted:BaseObject:private] =>
[modifiedColumns:protected] => Array
(
)
)
[49] => Category Object
(
[languages:protected] =>
[bok_resources:protected] =>
[bok_topics:protected] =>
[bok_keywords:protected] =>
[id:protected] => 49
[type:protected] => category
[parent:protected] => 2
[label:protected] => Carpenter
[alreadyInSave:protected] =>
[alreadyInValidation:protected] =>
[validationFailures:protected] => Array
(
)
[_new:BaseObject:private] =>
[_deleted:BaseObject:private] =>
[modifiedColumns:protected] => Array
(
)
)
[51] => Category Object
(
[languages:protected] =>
[bok_resources:protected] =>
[bok_topics:protected] =>
[bok_keywords:protected] =>
[id:protected] => 51
[type:protected] => category
[parent:protected] => 2
[label:protected] => Cement Mason
[alreadyInSave:protected] =>
[alreadyInValidation:protected] =>
[validationFailures:protected] => Array
(
)
[_new:BaseObject:private] =>
[_deleted:BaseObject:private] =>
[modifiedColumns:protected] => Array
(
)
)
[55] => Category Object
(
[languages:protected] =>
[bok_resources:protected] =>
[bok_topics:protected] =>
[bok_keywords:protected] =>
[id:protected] => 55
[type:protected] => category
[parent:protected] => 2
[label:protected] => Electrical Worker
[alreadyInSave:protected] =>
[alreadyInValidation:protected] =>
[validationFailures:protected] => Array
(
)
[_new:BaseObject:private] =>
[_deleted:BaseObject:private] =>
[modifiedColumns:protected] => Array
(
)
)
[61] => Category Object
(
[languages:protected] =>
[bok_resources:protected] =>
[bok_topics:protected] =>
[bok_keywords:protected] =>
[id:protected] => 61
[type:protected] => category
[parent:protected] => 2
[label:protected] => Interior Systems Carpenter
[alreadyInSave:protected] =>
[alreadyInValidation:protected] =>
[validationFailures:protected] => Array
(
)
[_new:BaseObject:private] =>
[_deleted:BaseObject:private] =>
[modifiedColumns:protected] => Array
(
)
)
[64] => Category Object
(
[languages:protected] =>
[bok_resources:protected] =>
[bok_topics:protected] =>
[bok_keywords:protected] =>
[id:protected] => 64
[type:protected] => category
[parent:protected] => 2
[label:protected] => Laborer
[alreadyInSave:protected] =>
[alreadyInValidation:protected] =>
[validationFailures:protected] => Array
(
)
[_new:BaseObject:private] =>
[_deleted:BaseObject:private] =>
[modifiedColumns:protected] => Array
(
)
)
[71] => Category Object
(
[languages:protected] =>
[bok_resources:protected] =>
[bok_topics:protected] =>
[bok_keywords:protected] =>
[id:protected] => 71
[type:protected] => category
[parent:protected] => 2
[label:protected] => Painter
[alreadyInSave:protected] =>
[alreadyInValidation:protected] =>
[validationFailures:protected] => Array
(
)
[_new:BaseObject:private] =>
[_deleted:BaseObject:private] =>
[modifiedColumns:protected] => Array
(
)
)
[75] => Category Object
(
[languages:protected] =>
[bok_resources:protected] =>
[bok_topics:protected] =>
[bok_keywords:protected] =>
[id:protected] => 75
[type:protected] => category
[parent:protected] => 2
[label:protected] => Plasterer
[alreadyInSave:protected] =>
[alreadyInValidation:protected] =>
[validationFailures:protected] => Array
(
)
[_new:BaseObject:private] =>
[_deleted:BaseObject:private] =>
[modifiedColumns:protected] => Array
(
)
)
[63] => Category Object
(
[languages:protected] =>
[bok_resources:protected] =>
[bok_topics:protected] =>
[bok_keywords:protected] =>
[id:protected] => 63
[type:protected] => category
[parent:protected] => 2
[label:protected] => Reinforcing Ironworker
[alreadyInSave:protected] =>
[alreadyInValidation:protected] =>
[validationFailures:protected] => Array
(
)
[_new:BaseObject:private] =>
[_deleted:BaseObject:private] =>
[modifiedColumns:protected] => Array
(
)
)
[79] => Category Object
(
[languages:protected] =>
[bok_resources:protected] =>
[bok_topics:protected] =>
[bok_keywords:protected] =>
[id:protected] => 79
[type:protected] => category
[parent:protected] => 2
[label:protected] => Scaffold Erector
[alreadyInSave:protected] =>
[alreadyInValidation:protected] =>
[validationFailures:protected] => Array
(
)
[_new:BaseObject:private] =>
[_deleted:BaseObject:private] =>
[modifiedColumns:protected] => Array
(
)
)
[62] => Category Object
(
[languages:protected] =>
[bok_resources:protected] =>
[bok_topics:protected] =>
[bok_keywords:protected] =>
[id:protected] => 62
[type:protected] => category
[parent:protected] => 2
[label:protected] => Structural Ironworker
[alreadyInSave:protected] =>
[alreadyInValidation:protected] =>
[validationFailures:protected] => Array
(
)
[_new:BaseObject:private] =>
[_deleted:BaseObject:private] =>
[modifiedColumns:protected] => Array
(
)
)
[87] => Category Object
(
[languages:protected] =>
[bok_resources:protected] =>
[bok_topics:protected] =>
[bok_keywords:protected] =>
[id:protected] => 87
[type:protected] => category
[parent:protected] => 3
[label:protected] => Commercial & Institutional
[alreadyInSave:protected] =>
[alreadyInValidation:protected] =>
[validationFailures:protected] => Array
(
)
[_new:BaseObject:private] =>
[_deleted:BaseObject:private] =>
[modifiedColumns:protected] => Array
(
)
)
[88] => Category Object
(
[languages:protected] =>
[bok_resources:protected] =>
[bok_topics:protected] =>
[bok_keywords:protected] =>
[id:protected] => 88
[type:protected] => category
[parent:protected] => 3
[label:protected] => Demolition
[alreadyInSave:protected] =>
[alreadyInValidation:protected] =>
[validationFailures:protected] => Array
(
)
[_new:BaseObject:private] =>
[_deleted:BaseObject:private] =>
[modifiedColumns:protected] => Array
(
)
)
[91] => Category Object
(
[languages:protected] =>
[bok_resources:protected] =>
[bok_topics:protected] =>
[bok_keywords:protected] =>
[id:protected] => 91
[type:protected] => category
[parent:protected] => 3
[label:protected] => Heavy & Highway
[alreadyInSave:protected] =>
[alreadyInValidation:protected] =>
[validationFailures:protected] => Array
(
)
[_new:BaseObject:private] =>
[_deleted:BaseObject:private] =>
[modifiedColumns:protected] => Array
(
)
)
[90] => Category Object
(
[languages:protected] =>
[bok_resources:protected] =>
[bok_topics:protected] =>
[bok_keywords:protected] =>
[id:protected] => 90
[type:protected] => category
[parent:protected] => 3
[label:protected] => Industrial
[alreadyInSave:protected] =>
[alreadyInValidation:protected] =>
[validationFailures:protected] => Array
(
)
[_new:BaseObject:private] =>
[_deleted:BaseObject:private] =>
[modifiedColumns:protected] => Array
(
)
)
[93] => Category Object
(
[languages:protected] =>
[bok_resources:protected] =>
[bok_topics:protected] =>
[bok_keywords:protected] =>
[id:protected] => 93
[type:protected] => category
[parent:protected] => 3
[label:protected] => Renovations
[alreadyInSave:protected] =>
[alreadyInValidation:protected] =>
[validationFailures:protected] => Array
(
)
[_new:BaseObject:private] =>
[_deleted:BaseObject:private] =>
[modifiedColumns:protected] => Array
(
)
)
[94] => Category Object
(
[languages:protected] =>
[bok_resources:protected] =>
[bok_topics:protected] =>
[bok_keywords:protected] =>
[id:protected] => 94
[type:protected] => category
[parent:protected] => 3
[label:protected] => Residential
[alreadyInSave:protected] =>
[alreadyInValidation:protected] =>
[validationFailures:protected] => Array
(
)
[_new:BaseObject:private] =>
[_deleted:BaseObject:private] =>
[modifiedColumns:protected] => Array
(
)
)
[95] => Category Object
(
[languages:protected] =>
[bok_resources:protected] =>
[bok_topics:protected] =>
[bok_keywords:protected] =>
[id:protected] => 95
[type:protected] => category
[parent:protected] => 3
[label:protected] => Underground
[alreadyInSave:protected] =>
[alreadyInValidation:protected] =>
[validationFailures:protected] => Array
(
)
[_new:BaseObject:private] =>
[_deleted:BaseObject:private] =>
[modifiedColumns:protected] => Array
(
)
)
)
[categories_initialized:protected] => 1
[mapped_items:protected] =>
[content:protected] =>
[files:protected] =>
[language:protected] => Language Object
(
[id:protected] => 1
[code:protected] => en
[name:protected] => English
[alreadyInSave:protected] =>
[alreadyInValidation:protected] =>
[validationFailures:protected] => Array
(
)
[_new:BaseObject:private] =>
[_deleted:BaseObject:private] =>
[modifiedColumns:protected] => Array
(
)
)
[old_record:protected] =>
[id:protected] => 4005
[old_id:protected] =>
[elcosh_id:protected] => i002692
[type:protected] => image
[display_type:protected] => Image
[user_id:protected] => 0
[language_id:protected] => 1
[tagging_id:protected] => Bruce Lippy
[priority_id:protected] => 1
[title:protected] => Toolbox talk - crew view
[total_pages:protected] => 0
[billed_pages:protected] => 0
[publication_number:protected] =>
[part_of:protected] =>
[keywords:protected] => toolbox talk, tailgate talk, safety talk, Spanish
[comments:protected] =>
[summary:protected] => Photo of crew listening to a toolbox safety talk before starting work.
[transition_comments:protected] =>
[external_link:protected] =>
[consol_link:protected] => http://www.cpwrconstructionsolutions.org/electrical/solution/662/worker-training.html
[more_like_this:protected] => i002691,d001269, c000079, d001285
[permission_given_by:protected] =>
[published:protected] => T
[billable:protected] => F
[img_name:protected] =>
[img_ext:protected] => jpg
[img_width:protected] =>
[img_height:protected] =>
[img_credit:protected] => Morgan Zavertnik and Hoar Construction
[img_practice:protected] => good
[vid_source_id:protected] =>
[vid_running_time:protected] =>
[vid_intended_audience:protected] =>
[vid_acquisition_info:protected] =>
[vid_cost:protected] =>
[vid_producer:protected] =>
[vid_filename:protected] =>
[vid_filename_downloadable:protected] =>
[date_summary:protected] => November 2015
[date_permission_requested:protected] =>
[date_permission_received:protected] =>
[date_review_needed:protected] =>
[date_received:protected] => 03/02/16
[date_completed:protected] => 03/02/16
[date_billed:protected] =>
[date_modified:protected] => 03/02/16
[collBokExports:protected] =>
[lastBokExportCriteria:BaseElcoshItem:private] =>
[alreadyInSave:protected] =>
[alreadyInValidation:protected] =>
[validationFailures:protected] => Array
(
)
[_new:BaseObject:private] =>
[_deleted:BaseObject:private] =>
[modifiedColumns:protected] => Array
(
)
)
)
[2] => Search_Result Object
(
[title] => Toolbox talk - long shot
[image] => /record/images/4006-p.jpg
[blurb] => This crew gathered every morning before starting work to discuss a new safety topic....
[category] => Array
(
[0] => 20
[1] => 47
[2] => 49
[3] => 51
[4] => 55
[5] => 64
[6] => 68
[7] => 75
[8] => 76
[9] => 63
[10] => 78
[11] => 79
[12] => 82
[13] => 62
[14] => 87
[15] => 88
[16] => 91
[17] => 90
[18] => 93
[19] => 94
[20] => 95
[21] => 97
)
[labels] => Array
(
[0] => Safety Culture
[1] => Work Environment
[2] => Hazards
[3] => Bricklayer
[4] => Trades
[5] => Carpenter
[7] => Cement Mason
[9] => Electrical Worker
[11] => Laborer
[13] => Maintenance Worker
[15] => Plasterer
[17] => Plumber/Pipefitter
[19] => Reinforcing Ironworker
[21] => Roofer/Waterproofer
[23] => Scaffold Erector
[25] => Stonemason
[27] => Structural Ironworker
[29] => Commercial & Institutional
[30] => Jobsites
[31] => Demolition
[33] => Heavy & Highway
[35] => Industrial
[37] => Renovations
[39] => Residential
[41] => Underground
[43] => Images
[44] => Media
[45] => Media & Documents
)
[type] => Images
[sub_category] =>
[url] => /image/4006/i002693/Toolbox%2Btalk%2B-%2Blong%2Bshot.html
[item:protected] => ImageRecord Object
(
[records:protected] => Array
(
)
[recordId:protected] =>
[searchWordClass:protected] =>
[searchWordPeerClass:protected] =>
[bok_record:protected] =>
[authors:protected] =>
[organizations:protected] =>
[collections:protected] =>
[categories:protected] => Array
(
[20] => Category Object
(
[languages:protected] =>
[bok_resources:protected] =>
[bok_topics:protected] =>
[bok_keywords:protected] =>
[id:protected] => 20
[type:protected] => category
[parent:protected] => 7
[label:protected] => Safety Culture
[alreadyInSave:protected] =>
[alreadyInValidation:protected] =>
[validationFailures:protected] => Array
(
)
[_new:BaseObject:private] =>
[_deleted:BaseObject:private] =>
[modifiedColumns:protected] => Array
(
)
)
[47] => Category Object
(
[languages:protected] =>
[bok_resources:protected] =>
[bok_topics:protected] =>
[bok_keywords:protected] =>
[id:protected] => 47
[type:protected] => category
[parent:protected] => 2
[label:protected] => Bricklayer
[alreadyInSave:protected] =>
[alreadyInValidation:protected] =>
[validationFailures:protected] => Array
(
)
[_new:BaseObject:private] =>
[_deleted:BaseObject:private] =>
[modifiedColumns:protected] => Array
(
)
)
[49] => Category Object
(
[languages:protected] =>
[bok_resources:protected] =>
[bok_topics:protected] =>
[bok_keywords:protected] =>
[id:protected] => 49
[type:protected] => category
[parent:protected] => 2
[label:protected] => Carpenter
[alreadyInSave:protected] =>
[alreadyInValidation:protected] =>
[validationFailures:protected] => Array
(
)
[_new:BaseObject:private] =>
[_deleted:BaseObject:private] =>
[modifiedColumns:protected] => Array
(
)
)
[51] => Category Object
(
[languages:protected] =>
[bok_resources:protected] =>
[bok_topics:protected] =>
[bok_keywords:protected] =>
[id:protected] => 51
[type:protected] => category
[parent:protected] => 2
[label:protected] => Cement Mason
[alreadyInSave:protected] =>
[alreadyInValidation:protected] =>
[validationFailures:protected] => Array
(
)
[_new:BaseObject:private] =>
[_deleted:BaseObject:private] =>
[modifiedColumns:protected] => Array
(
)
)
[55] => Category Object
(
[languages:protected] =>
[bok_resources:protected] =>
[bok_topics:protected] =>
[bok_keywords:protected] =>
[id:protected] => 55
[type:protected] => category
[parent:protected] => 2
[label:protected] => Electrical Worker
[alreadyInSave:protected] =>
[alreadyInValidation:protected] =>
[validationFailures:protected] => Array
(
)
[_new:BaseObject:private] =>
[_deleted:BaseObject:private] =>
[modifiedColumns:protected] => Array
(
)
)
[64] => Category Object
(
[languages:protected] =>
[bok_resources:protected] =>
[bok_topics:protected] =>
[bok_keywords:protected] =>
[id:protected] => 64
[type:protected] => category
[parent:protected] => 2
[label:protected] => Laborer
[alreadyInSave:protected] =>
[alreadyInValidation:protected] =>
[validationFailures:protected] => Array
(
)
[_new:BaseObject:private] =>
[_deleted:BaseObject:private] =>
[modifiedColumns:protected] => Array
(
)
)
[68] => Category Object
(
[languages:protected] =>
[bok_resources:protected] =>
[bok_topics:protected] =>
[bok_keywords:protected] =>
[id:protected] => 68
[type:protected] => category
[parent:protected] => 2
[label:protected] => Maintenance Worker
[alreadyInSave:protected] =>
[alreadyInValidation:protected] =>
[validationFailures:protected] => Array
(
)
[_new:BaseObject:private] =>
[_deleted:BaseObject:private] =>
[modifiedColumns:protected] => Array
(
)
)
[75] => Category Object
(
[languages:protected] =>
[bok_resources:protected] =>
[bok_topics:protected] =>
[bok_keywords:protected] =>
[id:protected] => 75
[type:protected] => category
[parent:protected] => 2
[label:protected] => Plasterer
[alreadyInSave:protected] =>
[alreadyInValidation:protected] =>
[validationFailures:protected] => Array
(
)
[_new:BaseObject:private] =>
[_deleted:BaseObject:private] =>
[modifiedColumns:protected] => Array
(
)
)
[76] => Category Object
(
[languages:protected] =>
[bok_resources:protected] =>
[bok_topics:protected] =>
[bok_keywords:protected] =>
[id:protected] => 76
[type:protected] => category
[parent:protected] => 2
[label:protected] => Plumber/Pipefitter
[alreadyInSave:protected] =>
[alreadyInValidation:protected] =>
[validationFailures:protected] => Array
(
)
[_new:BaseObject:private] =>
[_deleted:BaseObject:private] =>
[modifiedColumns:protected] => Array
(
)
)
[63] => Category Object
(
[languages:protected] =>
[bok_resources:protected] =>
[bok_topics:protected] =>
[bok_keywords:protected] =>
[id:protected] => 63
[type:protected] => category
[parent:protected] => 2
[label:protected] => Reinforcing Ironworker
[alreadyInSave:protected] =>
[alreadyInValidation:protected] =>
[validationFailures:protected] => Array
(
)
[_new:BaseObject:private] =>
[_deleted:BaseObject:private] =>
[modifiedColumns:protected] => Array
(
)
)
[78] => Category Object
(
[languages:protected] =>
[bok_resources:protected] =>
[bok_topics:protected] =>
[bok_keywords:protected] =>
[id:protected] => 78
[type:protected] => category
[parent:protected] => 2
[label:protected] => Roofer/Waterproofer
[alreadyInSave:protected] =>
[alreadyInValidation:protected] =>
[validationFailures:protected] => Array
(
)
[_new:BaseObject:private] =>
[_deleted:BaseObject:private] =>
[modifiedColumns:protected] => Array
(
)
)
[79] => Category Object
(
[languages:protected] =>
[bok_resources:protected] =>
[bok_topics:protected] =>
[bok_keywords:protected] =>
[id:protected] => 79
[type:protected] => category
[parent:protected] => 2
[label:protected] => Scaffold Erector
[alreadyInSave:protected] =>
[alreadyInValidation:protected] =>
[validationFailures:protected] => Array
(
)
[_new:BaseObject:private] =>
[_deleted:BaseObject:private] =>
[modifiedColumns:protected] => Array
(
)
)
[82] => Category Object
(
[languages:protected] =>
[bok_resources:protected] =>
[bok_topics:protected] =>
[bok_keywords:protected] =>
[id:protected] => 82
[type:protected] => category
[parent:protected] => 2
[label:protected] => Stonemason
[alreadyInSave:protected] =>
[alreadyInValidation:protected] =>
[validationFailures:protected] => Array
(
)
[_new:BaseObject:private] =>
[_deleted:BaseObject:private] =>
[modifiedColumns:protected] => Array
(
)
)
[62] => Category Object
(
[languages:protected] =>
[bok_resources:protected] =>
[bok_topics:protected] =>
[bok_keywords:protected] =>
[id:protected] => 62
[type:protected] => category
[parent:protected] => 2
[label:protected] => Structural Ironworker
[alreadyInSave:protected] =>
[alreadyInValidation:protected] =>
[validationFailures:protected] => Array
(
)
[_new:BaseObject:private] =>
[_deleted:BaseObject:private] =>
[modifiedColumns:protected] => Array
(
)
)
[87] => Category Object
(
[languages:protected] =>
[bok_resources:protected] =>
[bok_topics:protected] =>
[bok_keywords:protected] =>
[id:protected] => 87
[type:protected] => category
[parent:protected] => 3
[label:protected] => Commercial & Institutional
[alreadyInSave:protected] =>
[alreadyInValidation:protected] =>
[validationFailures:protected] => Array
(
)
[_new:BaseObject:private] =>
[_deleted:BaseObject:private] =>
[modifiedColumns:protected] => Array
(
)
)
[88] => Category Object
(
[languages:protected] =>
[bok_resources:protected] =>
[bok_topics:protected] =>
[bok_keywords:protected] =>
[id:protected] => 88
[type:protected] => category
[parent:protected] => 3
[label:protected] => Demolition
[alreadyInSave:protected] =>
[alreadyInValidation:protected] =>
[validationFailures:protected] => Array
(
)
[_new:BaseObject:private] =>
[_deleted:BaseObject:private] =>
[modifiedColumns:protected] => Array
(
)
)
[91] => Category Object
(
[languages:protected] =>
[bok_resources:protected] =>
[bok_topics:protected] =>
[bok_keywords:protected] =>
[id:protected] => 91
[type:protected] => category
[parent:protected] => 3
[label:protected] => Heavy & Highway
[alreadyInSave:protected] =>
[alreadyInValidation:protected] =>
[validationFailures:protected] => Array
(
)
[_new:BaseObject:private] =>
[_deleted:BaseObject:private] =>
[modifiedColumns:protected] => Array
(
)
)
[90] => Category Object
(
[languages:protected] =>
[bok_resources:protected] =>
[bok_topics:protected] =>
[bok_keywords:protected] =>
[id:protected] => 90
[type:protected] => category
[parent:protected] => 3
[label:protected] => Industrial
[alreadyInSave:protected] =>
[alreadyInValidation:protected] =>
[validationFailures:protected] => Array
(
)
[_new:BaseObject:private] =>
[_deleted:BaseObject:private] =>
[modifiedColumns:protected] => Array
(
)
)
[93] => Category Object
(
[languages:protected] =>
[bok_resources:protected] =>
[bok_topics:protected] =>
[bok_keywords:protected] =>
[id:protected] => 93
[type:protected] => category
[parent:protected] => 3
[label:protected] => Renovations
[alreadyInSave:protected] =>
[alreadyInValidation:protected] =>
[validationFailures:protected] => Array
(
)
[_new:BaseObject:private] =>
[_deleted:BaseObject:private] =>
[modifiedColumns:protected] => Array
(
)
)
[94] => Category Object
(
[languages:protected] =>
[bok_resources:protected] =>
[bok_topics:protected] =>
[bok_keywords:protected] =>
[id:protected] => 94
[type:protected] => category
[parent:protected] => 3
[label:protected] => Residential
[alreadyInSave:protected] =>
[alreadyInValidation:protected] =>
[validationFailures:protected] => Array
(
)
[_new:BaseObject:private] =>
[_deleted:BaseObject:private] =>
[modifiedColumns:protected] => Array
(
)
)
[95] => Category Object
(
[languages:protected] =>
[bok_resources:protected] =>
[bok_topics:protected] =>
[bok_keywords:protected] =>
[id:protected] => 95
[type:protected] => category
[parent:protected] => 3
[label:protected] => Underground
[alreadyInSave:protected] =>
[alreadyInValidation:protected] =>
[validationFailures:protected] => Array
(
)
[_new:BaseObject:private] =>
[_deleted:BaseObject:private] =>
[modifiedColumns:protected] => Array
(
)
)
[97] => Category Object
(
[languages:protected] =>
[bok_resources:protected] =>
[bok_topics:protected] =>
[bok_keywords:protected] =>
[id:protected] => 97
[type:protected] => category
[parent:protected] => 5
[label:protected] => Images
[alreadyInSave:protected] =>
[alreadyInValidation:protected] =>
[validationFailures:protected] => Array
(
)
[_new:BaseObject:private] =>
[_deleted:BaseObject:private] =>
[modifiedColumns:protected] => Array
(
)
)
)
[categories_initialized:protected] => 1
[mapped_items:protected] =>
[content:protected] =>
[files:protected] =>
[language:protected] => Language Object
(
[id:protected] => 1
[code:protected] => en
[name:protected] => English
[alreadyInSave:protected] =>
[alreadyInValidation:protected] =>
[validationFailures:protected] => Array
(
)
[_new:BaseObject:private] =>
[_deleted:BaseObject:private] =>
[modifiedColumns:protected] => Array
(
)
)
[old_record:protected] =>
[id:protected] => 4006
[old_id:protected] =>
[elcosh_id:protected] => i002693
[type:protected] => image
[display_type:protected] => Image
[user_id:protected] => 0
[language_id:protected] => 1
[tagging_id:protected] => Bruce Lippy
[priority_id:protected] => 1
[title:protected] => Toolbox talk - long shot
[total_pages:protected] => 0
[billed_pages:protected] => 0
[publication_number:protected] =>
[part_of:protected] =>
[keywords:protected] => toolbox talk, tailgate talk, safety minute
[comments:protected] =>
[summary:protected] => This crew gathered every morning before starting work to discuss a new safety topic.
[transition_comments:protected] =>
[external_link:protected] =>
[consol_link:protected] => http://www.cpwrconstructionsolutions.org/electrical/solution/662/worker-training.html
[more_like_this:protected] => i002691,i002692,d001269,d000527
[permission_given_by:protected] =>
[published:protected] => T
[billable:protected] => F
[img_name:protected] =>
[img_ext:protected] => jpg
[img_width:protected] =>
[img_height:protected] =>
[img_credit:protected] => Morgan Zavertnik and Hoar Construction
[img_practice:protected] => good
[vid_source_id:protected] =>
[vid_running_time:protected] =>
[vid_intended_audience:protected] =>
[vid_acquisition_info:protected] =>
[vid_cost:protected] =>
[vid_producer:protected] =>
[vid_filename:protected] =>
[vid_filename_downloadable:protected] =>
[date_summary:protected] => November 2015
[date_permission_requested:protected] =>
[date_permission_received:protected] =>
[date_review_needed:protected] =>
[date_received:protected] => 03/02/16
[date_completed:protected] => 03/02/16
[date_billed:protected] =>
[date_modified:protected] => 03/02/16
[collBokExports:protected] =>
[lastBokExportCriteria:BaseElcoshItem:private] =>
[alreadyInSave:protected] =>
[alreadyInValidation:protected] =>
[validationFailures:protected] => Array
(
)
[_new:BaseObject:private] =>
[_deleted:BaseObject:private] =>
[modifiedColumns:protected] => Array
(
)
)
)
[3] => Search_Result Object
(
[title] => Safety officer discussing ongoing project with marketing coordinator
[image] => /record/images/4014-p.jpg
[blurb] => The safety officer (left) points out the good safety practices on this project that reflect well on the firm and may influence future clients....
[category] => Array
(
[0] => 97
[1] => 20
[2] => 46
[3] => 47
[4] => 49
[5] => 50
[6] => 51
[7] => 54
[8] => 55
[9] => 58
[10] => 60
[11] => 61
[12] => 64
[13] => 71
[14] => 75
[15] => 76
[16] => 63
[17] => 79
[18] => 80
[19] => 82
[20] => 62
[21] => 83
[22] => 87
[23] => 91
[24] => 90
[25] => 93
[26] => 94
)
[labels] => Array
(
[0] => Images
[1] => Media
[2] => Media & Documents
[3] => Safety Culture
[4] => Work Environment
[5] => Hazards
[6] => Boilermaker
[7] => Trades
[8] => Bricklayer
[10] => Carpenter
[12] => Carpet Layer
[14] => Cement Mason
[16] => Drywall Applicator Specialist
[18] => Electrical Worker
[20] => Glazier
[22] => HVAC
[24] => Interior Systems Carpenter
[26] => Laborer
[28] => Painter
[30] => Plasterer
[32] => Plumber/Pipefitter
[34] => Reinforcing Ironworker
[36] => Scaffold Erector
[38] => Sheetmetal Worker
[40] => Stonemason
[42] => Structural Ironworker
[44] => Terrazzo Worker
[46] => Commercial & Institutional
[47] => Jobsites
[48] => Heavy & Highway
[50] => Industrial
[52] => Renovations
[54] => Residential
)
[type] => Images
[sub_category] =>
[url] => /image/4014/i002700/Safety%2Bofficer%2Bdiscussing%2Bongoing%2Bproject%2Bwith%2Bmarketing%2Bcoordinator.html
[item:protected] => ImageRecord Object
(
[records:protected] => Array
(
)
[recordId:protected] =>
[searchWordClass:protected] =>
[searchWordPeerClass:protected] =>
[bok_record:protected] =>
[authors:protected] =>
[organizations:protected] =>
[collections:protected] =>
[categories:protected] => Array
(
[97] => Category Object
(
[languages:protected] =>
[bok_resources:protected] =>
[bok_topics:protected] =>
[bok_keywords:protected] =>
[id:protected] => 97
[type:protected] => category
[parent:protected] => 5
[label:protected] => Images
[alreadyInSave:protected] =>
[alreadyInValidation:protected] =>
[validationFailures:protected] => Array
(
)
[_new:BaseObject:private] =>
[_deleted:BaseObject:private] =>
[modifiedColumns:protected] => Array
(
)
)
[20] => Category Object
(
[languages:protected] =>
[bok_resources:protected] =>
[bok_topics:protected] =>
[bok_keywords:protected] =>
[id:protected] => 20
[type:protected] => category
[parent:protected] => 7
[label:protected] => Safety Culture
[alreadyInSave:protected] =>
[alreadyInValidation:protected] =>
[validationFailures:protected] => Array
(
)
[_new:BaseObject:private] =>
[_deleted:BaseObject:private] =>
[modifiedColumns:protected] => Array
(
)
)
[46] => Category Object
(
[languages:protected] =>
[bok_resources:protected] =>
[bok_topics:protected] =>
[bok_keywords:protected] =>
[id:protected] => 46
[type:protected] => category
[parent:protected] => 2
[label:protected] => Boilermaker
[alreadyInSave:protected] =>
[alreadyInValidation:protected] =>
[validationFailures:protected] => Array
(
)
[_new:BaseObject:private] =>
[_deleted:BaseObject:private] =>
[modifiedColumns:protected] => Array
(
)
)
[47] => Category Object
(
[languages:protected] =>
[bok_resources:protected] =>
[bok_topics:protected] =>
[bok_keywords:protected] =>
[id:protected] => 47
[type:protected] => category
[parent:protected] => 2
[label:protected] => Bricklayer
[alreadyInSave:protected] =>
[alreadyInValidation:protected] =>
[validationFailures:protected] => Array
(
)
[_new:BaseObject:private] =>
[_deleted:BaseObject:private] =>
[modifiedColumns:protected] => Array
(
)
)
[49] => Category Object
(
[languages:protected] =>
[bok_resources:protected] =>
[bok_topics:protected] =>
[bok_keywords:protected] =>
[id:protected] => 49
[type:protected] => category
[parent:protected] => 2
[label:protected] => Carpenter
[alreadyInSave:protected] =>
[alreadyInValidation:protected] =>
[validationFailures:protected] => Array
(
)
[_new:BaseObject:private] =>
[_deleted:BaseObject:private] =>
[modifiedColumns:protected] => Array
(
)
)
[50] => Category Object
(
[languages:protected] =>
[bok_resources:protected] =>
[bok_topics:protected] =>
[bok_keywords:protected] =>
[id:protected] => 50
[type:protected] => category
[parent:protected] => 2
[label:protected] => Carpet Layer
[alreadyInSave:protected] =>
[alreadyInValidation:protected] =>
[validationFailures:protected] => Array
(
)
[_new:BaseObject:private] =>
[_deleted:BaseObject:private] =>
[modifiedColumns:protected] => Array
(
)
)
[51] => Category Object
(
[languages:protected] =>
[bok_resources:protected] =>
[bok_topics:protected] =>
[bok_keywords:protected] =>
[id:protected] => 51
[type:protected] => category
[parent:protected] => 2
[label:protected] => Cement Mason
[alreadyInSave:protected] =>
[alreadyInValidation:protected] =>
[validationFailures:protected] => Array
(
)
[_new:BaseObject:private] =>
[_deleted:BaseObject:private] =>
[modifiedColumns:protected] => Array
(
)
)
[54] => Category Object
(
[languages:protected] =>
[bok_resources:protected] =>
[bok_topics:protected] =>
[bok_keywords:protected] =>
[id:protected] => 54
[type:protected] => category
[parent:protected] => 2
[label:protected] => Drywall Applicator Specialist
[alreadyInSave:protected] =>
[alreadyInValidation:protected] =>
[validationFailures:protected] => Array
(
)
[_new:BaseObject:private] =>
[_deleted:BaseObject:private] =>
[modifiedColumns:protected] => Array
(
)
)
[55] => Category Object
(
[languages:protected] =>
[bok_resources:protected] =>
[bok_topics:protected] =>
[bok_keywords:protected] =>
[id:protected] => 55
[type:protected] => category
[parent:protected] => 2
[label:protected] => Electrical Worker
[alreadyInSave:protected] =>
[alreadyInValidation:protected] =>
[validationFailures:protected] => Array
(
)
[_new:BaseObject:private] =>
[_deleted:BaseObject:private] =>
[modifiedColumns:protected] => Array
(
)
)
[58] => Category Object
(
[languages:protected] =>
[bok_resources:protected] =>
[bok_topics:protected] =>
[bok_keywords:protected] =>
[id:protected] => 58
[type:protected] => category
[parent:protected] => 2
[label:protected] => Glazier
[alreadyInSave:protected] =>
[alreadyInValidation:protected] =>
[validationFailures:protected] => Array
(
)
[_new:BaseObject:private] =>
[_deleted:BaseObject:private] =>
[modifiedColumns:protected] => Array
(
)
)
[60] => Category Object
(
[languages:protected] =>
[bok_resources:protected] =>
[bok_topics:protected] =>
[bok_keywords:protected] =>
[id:protected] => 60
[type:protected] => category
[parent:protected] => 2
[label:protected] => HVAC
[alreadyInSave:protected] =>
[alreadyInValidation:protected] =>
[validationFailures:protected] => Array
(
)
[_new:BaseObject:private] =>
[_deleted:BaseObject:private] =>
[modifiedColumns:protected] => Array
(
)
)
[61] => Category Object
(
[languages:protected] =>
[bok_resources:protected] =>
[bok_topics:protected] =>
[bok_keywords:protected] =>
[id:protected] => 61
[type:protected] => category
[parent:protected] => 2
[label:protected] => Interior Systems Carpenter
[alreadyInSave:protected] =>
[alreadyInValidation:protected] =>
[validationFailures:protected] => Array
(
)
[_new:BaseObject:private] =>
[_deleted:BaseObject:private] =>
[modifiedColumns:protected] => Array
(
)
)
[64] => Category Object
(
[languages:protected] =>
[bok_resources:protected] =>
[bok_topics:protected] =>
[bok_keywords:protected] =>
[id:protected] => 64
[type:protected] => category
[parent:protected] => 2
[label:protected] => Laborer
[alreadyInSave:protected] =>
[alreadyInValidation:protected] =>
[validationFailures:protected] => Array
(
)
[_new:BaseObject:private] =>
[_deleted:BaseObject:private] =>
[modifiedColumns:protected] => Array
(
)
)
[71] => Category Object
(
[languages:protected] =>
[bok_resources:protected] =>
[bok_topics:protected] =>
[bok_keywords:protected] =>
[id:protected] => 71
[type:protected] => category
[parent:protected] => 2
[label:protected] => Painter
[alreadyInSave:protected] =>
[alreadyInValidation:protected] =>
[validationFailures:protected] => Array
(
)
[_new:BaseObject:private] =>
[_deleted:BaseObject:private] =>
[modifiedColumns:protected] => Array
(
)
)
[75] => Category Object
(
[languages:protected] =>
[bok_resources:protected] =>
[bok_topics:protected] =>
[bok_keywords:protected] =>
[id:protected] => 75
[type:protected] => category
[parent:protected] => 2
[label:protected] => Plasterer
[alreadyInSave:protected] =>
[alreadyInValidation:protected] =>
[validationFailures:protected] => Array
(
)
[_new:BaseObject:private] =>
[_deleted:BaseObject:private] =>
[modifiedColumns:protected] => Array
(
)
)
[76] => Category Object
(
[languages:protected] =>
[bok_resources:protected] =>
[bok_topics:protected] =>
[bok_keywords:protected] =>
[id:protected] => 76
[type:protected] => category
[parent:protected] => 2
[label:protected] => Plumber/Pipefitter
[alreadyInSave:protected] =>
[alreadyInValidation:protected] =>
[validationFailures:protected] => Array
(
)
[_new:BaseObject:private] =>
[_deleted:BaseObject:private] =>
[modifiedColumns:protected] => Array
(
)
)
[63] => Category Object
(
[languages:protected] =>
[bok_resources:protected] =>
[bok_topics:protected] =>
[bok_keywords:protected] =>
[id:protected] => 63
[type:protected] => category
[parent:protected] => 2
[label:protected] => Reinforcing Ironworker
[alreadyInSave:protected] =>
[alreadyInValidation:protected] =>
[validationFailures:protected] => Array
(
)
[_new:BaseObject:private] =>
[_deleted:BaseObject:private] =>
[modifiedColumns:protected] => Array
(
)
)
[79] => Category Object
(
[languages:protected] =>
[bok_resources:protected] =>
[bok_topics:protected] =>
[bok_keywords:protected] =>
[id:protected] => 79
[type:protected] => category
[parent:protected] => 2
[label:protected] => Scaffold Erector
[alreadyInSave:protected] =>
[alreadyInValidation:protected] =>
[validationFailures:protected] => Array
(
)
[_new:BaseObject:private] =>
[_deleted:BaseObject:private] =>
[modifiedColumns:protected] => Array
(
)
)
[80] => Category Object
(
[languages:protected] =>
[bok_resources:protected] =>
[bok_topics:protected] =>
[bok_keywords:protected] =>
[id:protected] => 80
[type:protected] => category
[parent:protected] => 2
[label:protected] => Sheetmetal Worker
[alreadyInSave:protected] =>
[alreadyInValidation:protected] =>
[validationFailures:protected] => Array
(
)
[_new:BaseObject:private] =>
[_deleted:BaseObject:private] =>
[modifiedColumns:protected] => Array
(
)
)
[82] => Category Object
(
[languages:protected] =>
[bok_resources:protected] =>
[bok_topics:protected] =>
[bok_keywords:protected] =>
[id:protected] => 82
[type:protected] => category
[parent:protected] => 2
[label:protected] => Stonemason
[alreadyInSave:protected] =>
[alreadyInValidation:protected] =>
[validationFailures:protected] => Array
(
)
[_new:BaseObject:private] =>
[_deleted:BaseObject:private] =>
[modifiedColumns:protected] => Array
(
)
)
[62] => Category Object
(
[languages:protected] =>
[bok_resources:protected] =>
[bok_topics:protected] =>
[bok_keywords:protected] =>
[id:protected] => 62
[type:protected] => category
[parent:protected] => 2
[label:protected] => Structural Ironworker
[alreadyInSave:protected] =>
[alreadyInValidation:protected] =>
[validationFailures:protected] => Array
(
)
[_new:BaseObject:private] =>
[_deleted:BaseObject:private] =>
[modifiedColumns:protected] => Array
(
)
)
[83] => Category Object
(
[languages:protected] =>
[bok_resources:protected] =>
[bok_topics:protected] =>
[bok_keywords:protected] =>
[id:protected] => 83
[type:protected] => category
[parent:protected] => 2
[label:protected] => Terrazzo Worker
[alreadyInSave:protected] =>
[alreadyInValidation:protected] =>
[validationFailures:protected] => Array
(
)
[_new:BaseObject:private] =>
[_deleted:BaseObject:private] =>
[modifiedColumns:protected] => Array
(
)
)
[87] => Category Object
(
[languages:protected] =>
[bok_resources:protected] =>
[bok_topics:protected] =>
[bok_keywords:protected] =>
[id:protected] => 87
[type:protected] => category
[parent:protected] => 3
[label:protected] => Commercial & Institutional
[alreadyInSave:protected] =>
[alreadyInValidation:protected] =>
[validationFailures:protected] => Array
(
)
[_new:BaseObject:private] =>
[_deleted:BaseObject:private] =>
[modifiedColumns:protected] => Array
(
)
)
[91] => Category Object
(
[languages:protected] =>
[bok_resources:protected] =>
[bok_topics:protected] =>
[bok_keywords:protected] =>
[id:protected] => 91
[type:protected] => category
[parent:protected] => 3
[label:protected] => Heavy & Highway
[alreadyInSave:protected] =>
[alreadyInValidation:protected] =>
[validationFailures:protected] => Array
(
)
[_new:BaseObject:private] =>
[_deleted:BaseObject:private] =>
[modifiedColumns:protected] => Array
(
)
)
[90] => Category Object
(
[languages:protected] =>
[bok_resources:protected] =>
[bok_topics:protected] =>
[bok_keywords:protected] =>
[id:protected] => 90
[type:protected] => category
[parent:protected] => 3
[label:protected] => Industrial
[alreadyInSave:protected] =>
[alreadyInValidation:protected] =>
[validationFailures:protected] => Array
(
)
[_new:BaseObject:private] =>
[_deleted:BaseObject:private] =>
[modifiedColumns:protected] => Array
(
)
)
[93] => Category Object
(
[languages:protected] =>
[bok_resources:protected] =>
[bok_topics:protected] =>
[bok_keywords:protected] =>
[id:protected] => 93
[type:protected] => category
[parent:protected] => 3
[label:protected] => Renovations
[alreadyInSave:protected] =>
[alreadyInValidation:protected] =>
[validationFailures:protected] => Array
(
)
[_new:BaseObject:private] =>
[_deleted:BaseObject:private] =>
[modifiedColumns:protected] => Array
(
)
)
[94] => Category Object
(
[languages:protected] =>
[bok_resources:protected] =>
[bok_topics:protected] =>
[bok_keywords:protected] =>
[id:protected] => 94
[type:protected] => category
[parent:protected] => 3
[label:protected] => Residential
[alreadyInSave:protected] =>
[alreadyInValidation:protected] =>
[validationFailures:protected] => Array
(
)
[_new:BaseObject:private] =>
[_deleted:BaseObject:private] =>
[modifiedColumns:protected] => Array
(
)
)
)
[categories_initialized:protected] => 1
[mapped_items:protected] =>
[content:protected] =>
[files:protected] =>
[language:protected] => Language Object
(
[id:protected] => 1
[code:protected] => en
[name:protected] => English
[alreadyInSave:protected] =>
[alreadyInValidation:protected] =>
[validationFailures:protected] => Array
(
)
[_new:BaseObject:private] =>
[_deleted:BaseObject:private] =>
[modifiedColumns:protected] => Array
(
)
)
[old_record:protected] =>
[id:protected] => 4014
[old_id:protected] =>
[elcosh_id:protected] => i002700
[type:protected] => image
[display_type:protected] => Image
[user_id:protected] => 0
[language_id:protected] => 1
[tagging_id:protected] => Bruce Lippy
[priority_id:protected] => 1
[title:protected] => Safety officer discussing ongoing project with marketing coordinator
[total_pages:protected] => 0
[billed_pages:protected] => 0
[publication_number:protected] =>
[part_of:protected] =>
[keywords:protected] => Latino, safety officer, safety culture
[comments:protected] =>
[summary:protected] => The safety officer (left) points out the good safety practices on this project that reflect well on the firm and may influence future clients.
[transition_comments:protected] =>
[external_link:protected] =>
[consol_link:protected] => http://www.cpwrconstructionsolutions.org/index.php
[more_like_this:protected] => d000989,d001351,d001362,d000652, d001101, d000931, d001395
[permission_given_by:protected] =>
[published:protected] => T
[billable:protected] => F
[img_name:protected] =>
[img_ext:protected] => jpg
[img_width:protected] =>
[img_height:protected] =>
[img_credit:protected] => Hoar Construction, Photo by Neil Lippy
[img_practice:protected] => good
[vid_source_id:protected] =>
[vid_running_time:protected] =>
[vid_intended_audience:protected] =>
[vid_acquisition_info:protected] =>
[vid_cost:protected] =>
[vid_producer:protected] =>
[vid_filename:protected] =>
[vid_filename_downloadable:protected] =>
[date_summary:protected] => November 2015
[date_permission_requested:protected] =>
[date_permission_received:protected] =>
[date_review_needed:protected] =>
[date_received:protected] => 03/02/16
[date_completed:protected] => 03/02/16
[date_billed:protected] =>
[date_modified:protected] => 01/30/23
[collBokExports:protected] =>
[lastBokExportCriteria:BaseElcoshItem:private] =>
[alreadyInSave:protected] =>
[alreadyInValidation:protected] =>
[validationFailures:protected] => Array
(
)
[_new:BaseObject:private] =>
[_deleted:BaseObject:private] =>
[modifiedColumns:protected] => Array
(
)
)
)
[4] => Search_Result Object
(
[title] => Scaffolding at top of large column
[image] => /record/images/3994-p.jpg
[blurb] => This shot shows innovative guarding around the top of a large concrete column in the base of a high rise structure going up....
[category] => Array
(
[0] => 15
[1] => 21
[2] => 47
[3] => 51
[4] => 63
[5] => 78
[6] => 79
[7] => 80
[8] => 62
[9] => 87
[10] => 97
[11] => 56
[12] => 64
[13] => 74
)
[labels] => Array
(
[0] => Falls
[1] => Work Environment
[2] => Hazards
[3] => Scaffolds
[6] => Bricklayer
[7] => Trades
[8] => Cement Mason
[10] => Reinforcing Ironworker
[12] => Roofer/Waterproofer
[14] => Scaffold Erector
[16] => Sheetmetal Worker
[18] => Structural Ironworker
[20] => Commercial & Institutional
[21] => Jobsites
[22] => Images
[23] => Media
[24] => Media & Documents
[25] => Elevator Constructor
[27] => Laborer
[29] => Pile Driver
)
[type] => Images
[sub_category] =>
[url] => /image/3994/i002689/Scaffolding%2Bat%2Btop%2Bof%2Blarge%2Bcolumn.html
[item:protected] => ImageRecord Object
(
[records:protected] => Array
(
)
[recordId:protected] =>
[searchWordClass:protected] =>
[searchWordPeerClass:protected] =>
[bok_record:protected] =>
[authors:protected] =>
[organizations:protected] =>
[collections:protected] =>
[categories:protected] => Array
(
[15] => Category Object
(
[languages:protected] =>
[bok_resources:protected] =>
[bok_topics:protected] =>
[bok_keywords:protected] =>
[id:protected] => 15
[type:protected] => category
[parent:protected] => 7
[label:protected] => Falls
[alreadyInSave:protected] =>
[alreadyInValidation:protected] =>
[validationFailures:protected] => Array
(
)
[_new:BaseObject:private] =>
[_deleted:BaseObject:private] =>
[modifiedColumns:protected] => Array
(
)
)
[21] => Category Object
(
[languages:protected] =>
[bok_resources:protected] =>
[bok_topics:protected] =>
[bok_keywords:protected] =>
[id:protected] => 21
[type:protected] => category
[parent:protected] => 7
[label:protected] => Scaffolds
[alreadyInSave:protected] =>
[alreadyInValidation:protected] =>
[validationFailures:protected] => Array
(
)
[_new:BaseObject:private] =>
[_deleted:BaseObject:private] =>
[modifiedColumns:protected] => Array
(
)
)
[47] => Category Object
(
[languages:protected] =>
[bok_resources:protected] =>
[bok_topics:protected] =>
[bok_keywords:protected] =>
[id:protected] => 47
[type:protected] => category
[parent:protected] => 2
[label:protected] => Bricklayer
[alreadyInSave:protected] =>
[alreadyInValidation:protected] =>
[validationFailures:protected] => Array
(
)
[_new:BaseObject:private] =>
[_deleted:BaseObject:private] =>
[modifiedColumns:protected] => Array
(
)
)
[51] => Category Object
(
[languages:protected] =>
[bok_resources:protected] =>
[bok_topics:protected] =>
[bok_keywords:protected] =>
[id:protected] => 51
[type:protected] => category
[parent:protected] => 2
[label:protected] => Cement Mason
[alreadyInSave:protected] =>
[alreadyInValidation:protected] =>
[validationFailures:protected] => Array
(
)
[_new:BaseObject:private] =>
[_deleted:BaseObject:private] =>
[modifiedColumns:protected] => Array
(
)
)
[63] => Category Object
(
[languages:protected] =>
[bok_resources:protected] =>
[bok_topics:protected] =>
[bok_keywords:protected] =>
[id:protected] => 63
[type:protected] => category
[parent:protected] => 2
[label:protected] => Reinforcing Ironworker
[alreadyInSave:protected] =>
[alreadyInValidation:protected] =>
[validationFailures:protected] => Array
(
)
[_new:BaseObject:private] =>
[_deleted:BaseObject:private] =>
[modifiedColumns:protected] => Array
(
)
)
[78] => Category Object
(
[languages:protected] =>
[bok_resources:protected] =>
[bok_topics:protected] =>
[bok_keywords:protected] =>
[id:protected] => 78
[type:protected] => category
[parent:protected] => 2
[label:protected] => Roofer/Waterproofer
[alreadyInSave:protected] =>
[alreadyInValidation:protected] =>
[validationFailures:protected] => Array
(
)
[_new:BaseObject:private] =>
[_deleted:BaseObject:private] =>
[modifiedColumns:protected] => Array
(
)
)
[79] => Category Object
(
[languages:protected] =>
[bok_resources:protected] =>
[bok_topics:protected] =>
[bok_keywords:protected] =>
[id:protected] => 79
[type:protected] => category
[parent:protected] => 2
[label:protected] => Scaffold Erector
[alreadyInSave:protected] =>
[alreadyInValidation:protected] =>
[validationFailures:protected] => Array
(
)
[_new:BaseObject:private] =>
[_deleted:BaseObject:private] =>
[modifiedColumns:protected] => Array
(
)
)
[80] => Category Object
(
[languages:protected] =>
[bok_resources:protected] =>
[bok_topics:protected] =>
[bok_keywords:protected] =>
[id:protected] => 80
[type:protected] => category
[parent:protected] => 2
[label:protected] => Sheetmetal Worker
[alreadyInSave:protected] =>
[alreadyInValidation:protected] =>
[validationFailures:protected] => Array
(
)
[_new:BaseObject:private] =>
[_deleted:BaseObject:private] =>
[modifiedColumns:protected] => Array
(
)
)
[62] => Category Object
(
[languages:protected] =>
[bok_resources:protected] =>
[bok_topics:protected] =>
[bok_keywords:protected] =>
[id:protected] => 62
[type:protected] => category
[parent:protected] => 2
[label:protected] => Structural Ironworker
[alreadyInSave:protected] =>
[alreadyInValidation:protected] =>
[validationFailures:protected] => Array
(
)
[_new:BaseObject:private] =>
[_deleted:BaseObject:private] =>
[modifiedColumns:protected] => Array
(
)
)
[87] => Category Object
(
[languages:protected] =>
[bok_resources:protected] =>
[bok_topics:protected] =>
[bok_keywords:protected] =>
[id:protected] => 87
[type:protected] => category
[parent:protected] => 3
[label:protected] => Commercial & Institutional
[alreadyInSave:protected] =>
[alreadyInValidation:protected] =>
[validationFailures:protected] => Array
(
)
[_new:BaseObject:private] =>
[_deleted:BaseObject:private] =>
[modifiedColumns:protected] => Array
(
)
)
[97] => Category Object
(
[languages:protected] =>
[bok_resources:protected] =>
[bok_topics:protected] =>
[bok_keywords:protected] =>
[id:protected] => 97
[type:protected] => category
[parent:protected] => 5
[label:protected] => Images
[alreadyInSave:protected] =>
[alreadyInValidation:protected] =>
[validationFailures:protected] => Array
(
)
[_new:BaseObject:private] =>
[_deleted:BaseObject:private] =>
[modifiedColumns:protected] => Array
(
)
)
[56] => Category Object
(
[languages:protected] =>
[bok_resources:protected] =>
[bok_topics:protected] =>
[bok_keywords:protected] =>
[id:protected] => 56
[type:protected] => category
[parent:protected] => 2
[label:protected] => Elevator Constructor
[alreadyInSave:protected] =>
[alreadyInValidation:protected] =>
[validationFailures:protected] => Array
(
)
[_new:BaseObject:private] =>
[_deleted:BaseObject:private] =>
[modifiedColumns:protected] => Array
(
)
)
[64] => Category Object
(
[languages:protected] =>
[bok_resources:protected] =>
[bok_topics:protected] =>
[bok_keywords:protected] =>
[id:protected] => 64
[type:protected] => category
[parent:protected] => 2
[label:protected] => Laborer
[alreadyInSave:protected] =>
[alreadyInValidation:protected] =>
[validationFailures:protected] => Array
(
)
[_new:BaseObject:private] =>
[_deleted:BaseObject:private] =>
[modifiedColumns:protected] => Array
(
)
)
[74] => Category Object
(
[languages:protected] =>
[bok_resources:protected] =>
[bok_topics:protected] =>
[bok_keywords:protected] =>
[id:protected] => 74
[type:protected] => category
[parent:protected] => 2
[label:protected] => Pile Driver
[alreadyInSave:protected] =>
[alreadyInValidation:protected] =>
[validationFailures:protected] => Array
(
)
[_new:BaseObject:private] =>
[_deleted:BaseObject:private] =>
[modifiedColumns:protected] => Array
(
)
)
)
[categories_initialized:protected] => 1
[mapped_items:protected] =>
[content:protected] =>
[files:protected] =>
[language:protected] => Language Object
(
[id:protected] => 1
[code:protected] => en
[name:protected] => English
[alreadyInSave:protected] =>
[alreadyInValidation:protected] =>
[validationFailures:protected] => Array
(
)
[_new:BaseObject:private] =>
[_deleted:BaseObject:private] =>
[modifiedColumns:protected] => Array
(
)
)
[old_record:protected] =>
[id:protected] => 3994
[old_id:protected] =>
[elcosh_id:protected] => i002689
[type:protected] => image
[display_type:protected] => Image
[user_id:protected] => 0
[language_id:protected] => 1
[tagging_id:protected] => Bruce Lippy
[priority_id:protected] => 1
[title:protected] => Scaffolding at top of large column
[total_pages:protected] => 0
[billed_pages:protected] => 0
[publication_number:protected] =>
[part_of:protected] =>
[keywords:protected] => Guardrail, railing, fall prevention, falls
[comments:protected] =>
[summary:protected] => This shot shows innovative guarding around the top of a large concrete column in the base of a high rise structure going up.
[transition_comments:protected] =>
[external_link:protected] =>
[consol_link:protected] => http://www.cpwrconstructionsolutions.org/masonry/solution/8/adjustable-tower-scaffold.html
[more_like_this:protected] => c1002680,i002662,d000608,d001255
[permission_given_by:protected] =>
[published:protected] => T
[billable:protected] => F
[img_name:protected] =>
[img_ext:protected] => jpg
[img_width:protected] =>
[img_height:protected] =>
[img_credit:protected] => Photo by Pam Susi
[img_practice:protected] => good
[vid_source_id:protected] =>
[vid_running_time:protected] =>
[vid_intended_audience:protected] =>
[vid_acquisition_info:protected] =>
[vid_cost:protected] =>
[vid_producer:protected] =>
[vid_filename:protected] =>
[vid_filename_downloadable:protected] =>
[date_summary:protected] => January 2016
[date_permission_requested:protected] =>
[date_permission_received:protected] =>
[date_review_needed:protected] =>
[date_received:protected] => 02/01/16
[date_completed:protected] => 02/01/16
[date_billed:protected] =>
[date_modified:protected] => 02/01/16
[collBokExports:protected] =>
[lastBokExportCriteria:BaseElcoshItem:private] =>
[alreadyInSave:protected] =>
[alreadyInValidation:protected] =>
[validationFailures:protected] => Array
(
)
[_new:BaseObject:private] =>
[_deleted:BaseObject:private] =>
[modifiedColumns:protected] => Array
(
)
)
)
[5] => Search_Result Object
(
[title] => Construction bracing
[image] => /record/images/3995-p.jpg
[blurb] => This shows structural support that prevents collapses during construction....
[category] => Array
(
[0] => 12
[1] => 15
[2] => 21
[3] => 49
[4] => 51
[5] => 55
[6] => 56
[7] => 60
[8] => 64
[9] => 68
[10] => 74
[11] => 63
[12] => 78
[13] => 79
[14] => 80
[15] => 62
[16] => 87
[17] => 90
[18] => 97
)
[labels] => Array
(
[0] => Crushed/Struck By
[1] => Work Environment
[2] => Hazards
[3] => Falls
[6] => Scaffolds
[9] => Carpenter
[10] => Trades
[11] => Cement Mason
[13] => Electrical Worker
[15] => Elevator Constructor
[17] => HVAC
[19] => Laborer
[21] => Maintenance Worker
[23] => Pile Driver
[25] => Reinforcing Ironworker
[27] => Roofer/Waterproofer
[29] => Scaffold Erector
[31] => Sheetmetal Worker
[33] => Structural Ironworker
[35] => Commercial & Institutional
[36] => Jobsites
[37] => Industrial
[39] => Images
[40] => Media
[41] => Media & Documents
)
[type] => Images
[sub_category] =>
[url] => /image/3995/i002690/Construction%2Bbracing.html
[item:protected] => ImageRecord Object
(
[records:protected] => Array
(
)
[recordId:protected] =>
[searchWordClass:protected] =>
[searchWordPeerClass:protected] =>
[bok_record:protected] =>
[authors:protected] =>
[organizations:protected] =>
[collections:protected] =>
[categories:protected] => Array
(
[12] => Category Object
(
[languages:protected] =>
[bok_resources:protected] =>
[bok_topics:protected] =>
[bok_keywords:protected] =>
[id:protected] => 12
[type:protected] => category
[parent:protected] => 7
[label:protected] => Crushed/Struck By
[alreadyInSave:protected] =>
[alreadyInValidation:protected] =>
[validationFailures:protected] => Array
(
)
[_new:BaseObject:private] =>
[_deleted:BaseObject:private] =>
[modifiedColumns:protected] => Array
(
)
)
[15] => Category Object
(
[languages:protected] =>
[bok_resources:protected] =>
[bok_topics:protected] =>
[bok_keywords:protected] =>
[id:protected] => 15
[type:protected] => category
[parent:protected] => 7
[label:protected] => Falls
[alreadyInSave:protected] =>
[alreadyInValidation:protected] =>
[validationFailures:protected] => Array
(
)
[_new:BaseObject:private] =>
[_deleted:BaseObject:private] =>
[modifiedColumns:protected] => Array
(
)
)
[21] => Category Object
(
[languages:protected] =>
[bok_resources:protected] =>
[bok_topics:protected] =>
[bok_keywords:protected] =>
[id:protected] => 21
[type:protected] => category
[parent:protected] => 7
[label:protected] => Scaffolds
[alreadyInSave:protected] =>
[alreadyInValidation:protected] =>
[validationFailures:protected] => Array
(
)
[_new:BaseObject:private] =>
[_deleted:BaseObject:private] =>
[modifiedColumns:protected] => Array
(
)
)
[49] => Category Object
(
[languages:protected] =>
[bok_resources:protected] =>
[bok_topics:protected] =>
[bok_keywords:protected] =>
[id:protected] => 49
[type:protected] => category
[parent:protected] => 2
[label:protected] => Carpenter
[alreadyInSave:protected] =>
[alreadyInValidation:protected] =>
[validationFailures:protected] => Array
(
)
[_new:BaseObject:private] =>
[_deleted:BaseObject:private] =>
[modifiedColumns:protected] => Array
(
)
)
[51] => Category Object
(
[languages:protected] =>
[bok_resources:protected] =>
[bok_topics:protected] =>
[bok_keywords:protected] =>
[id:protected] => 51
[type:protected] => category
[parent:protected] => 2
[label:protected] => Cement Mason
[alreadyInSave:protected] =>
[alreadyInValidation:protected] =>
[validationFailures:protected] => Array
(
)
[_new:BaseObject:private] =>
[_deleted:BaseObject:private] =>
[modifiedColumns:protected] => Array
(
)
)
[55] => Category Object
(
[languages:protected] =>
[bok_resources:protected] =>
[bok_topics:protected] =>
[bok_keywords:protected] =>
[id:protected] => 55
[type:protected] => category
[parent:protected] => 2
[label:protected] => Electrical Worker
[alreadyInSave:protected] =>
[alreadyInValidation:protected] =>
[validationFailures:protected] => Array
(
)
[_new:BaseObject:private] =>
[_deleted:BaseObject:private] =>
[modifiedColumns:protected] => Array
(
)
)
[56] => Category Object
(
[languages:protected] =>
[bok_resources:protected] =>
[bok_topics:protected] =>
[bok_keywords:protected] =>
[id:protected] => 56
[type:protected] => category
[parent:protected] => 2
[label:protected] => Elevator Constructor
[alreadyInSave:protected] =>
[alreadyInValidation:protected] =>
[validationFailures:protected] => Array
(
)
[_new:BaseObject:private] =>
[_deleted:BaseObject:private] =>
[modifiedColumns:protected] => Array
(
)
)
[60] => Category Object
(
[languages:protected] =>
[bok_resources:protected] =>
[bok_topics:protected] =>
[bok_keywords:protected] =>
[id:protected] => 60
[type:protected] => category
[parent:protected] => 2
[label:protected] => HVAC
[alreadyInSave:protected] =>
[alreadyInValidation:protected] =>
[validationFailures:protected] => Array
(
)
[_new:BaseObject:private] =>
[_deleted:BaseObject:private] =>
[modifiedColumns:protected] => Array
(
)
)
[64] => Category Object
(
[languages:protected] =>
[bok_resources:protected] =>
[bok_topics:protected] =>
[bok_keywords:protected] =>
[id:protected] => 64
[type:protected] => category
[parent:protected] => 2
[label:protected] => Laborer
[alreadyInSave:protected] =>
[alreadyInValidation:protected] =>
[validationFailures:protected] => Array
(
)
[_new:BaseObject:private] =>
[_deleted:BaseObject:private] =>
[modifiedColumns:protected] => Array
(
)
)
[68] => Category Object
(
[languages:protected] =>
[bok_resources:protected] =>
[bok_topics:protected] =>
[bok_keywords:protected] =>
[id:protected] => 68
[type:protected] => category
[parent:protected] => 2
[label:protected] => Maintenance Worker
[alreadyInSave:protected] =>
[alreadyInValidation:protected] =>
[validationFailures:protected] => Array
(
)
[_new:BaseObject:private] =>
[_deleted:BaseObject:private] =>
[modifiedColumns:protected] => Array
(
)
)
[74] => Category Object
(
[languages:protected] =>
[bok_resources:protected] =>
[bok_topics:protected] =>
[bok_keywords:protected] =>
[id:protected] => 74
[type:protected] => category
[parent:protected] => 2
[label:protected] => Pile Driver
[alreadyInSave:protected] =>
[alreadyInValidation:protected] =>
[validationFailures:protected] => Array
(
)
[_new:BaseObject:private] =>
[_deleted:BaseObject:private] =>
[modifiedColumns:protected] => Array
(
)
)
[63] => Category Object
(
[languages:protected] =>
[bok_resources:protected] =>
[bok_topics:protected] =>
[bok_keywords:protected] =>
[id:protected] => 63
[type:protected] => category
[parent:protected] => 2
[label:protected] => Reinforcing Ironworker
[alreadyInSave:protected] =>
[alreadyInValidation:protected] =>
[validationFailures:protected] => Array
(
)
[_new:BaseObject:private] =>
[_deleted:BaseObject:private] =>
[modifiedColumns:protected] => Array
(
)
)
[78] => Category Object
(
[languages:protected] =>
[bok_resources:protected] =>
[bok_topics:protected] =>
[bok_keywords:protected] =>
[id:protected] => 78
[type:protected] => category
[parent:protected] => 2
[label:protected] => Roofer/Waterproofer
[alreadyInSave:protected] =>
[alreadyInValidation:protected] =>
[validationFailures:protected] => Array
(
)
[_new:BaseObject:private] =>
[_deleted:BaseObject:private] =>
[modifiedColumns:protected] => Array
(
)
)
[79] => Category Object
(
[languages:protected] =>
[bok_resources:protected] =>
[bok_topics:protected] =>
[bok_keywords:protected] =>
[id:protected] => 79
[type:protected] => category
[parent:protected] => 2
[label:protected] => Scaffold Erector
[alreadyInSave:protected] =>
[alreadyInValidation:protected] =>
[validationFailures:protected] => Array
(
)
[_new:BaseObject:private] =>
[_deleted:BaseObject:private] =>
[modifiedColumns:protected] => Array
(
)
)
[80] => Category Object
(
[languages:protected] =>
[bok_resources:protected] =>
[bok_topics:protected] =>
[bok_keywords:protected] =>
[id:protected] => 80
[type:protected] => category
[parent:protected] => 2
[label:protected] => Sheetmetal Worker
[alreadyInSave:protected] =>
[alreadyInValidation:protected] =>
[validationFailures:protected] => Array
(
)
[_new:BaseObject:private] =>
[_deleted:BaseObject:private] =>
[modifiedColumns:protected] => Array
(
)
)
[62] => Category Object
(
[languages:protected] =>
[bok_resources:protected] =>
[bok_topics:protected] =>
[bok_keywords:protected] =>
[id:protected] => 62
[type:protected] => category
[parent:protected] => 2
[label:protected] => Structural Ironworker
[alreadyInSave:protected] =>
[alreadyInValidation:protected] =>
[validationFailures:protected] => Array
(
)
[_new:BaseObject:private] =>
[_deleted:BaseObject:private] =>
[modifiedColumns:protected] => Array
(
)
)
[87] => Category Object
(
[languages:protected] =>
[bok_resources:protected] =>
[bok_topics:protected] =>
[bok_keywords:protected] =>
[id:protected] => 87
[type:protected] => category
[parent:protected] => 3
[label:protected] => Commercial & Institutional
[alreadyInSave:protected] =>
[alreadyInValidation:protected] =>
[validationFailures:protected] => Array
(
)
[_new:BaseObject:private] =>
[_deleted:BaseObject:private] =>
[modifiedColumns:protected] => Array
(
)
)
[90] => Category Object
(
[languages:protected] =>
[bok_resources:protected] =>
[bok_topics:protected] =>
[bok_keywords:protected] =>
[id:protected] => 90
[type:protected] => category
[parent:protected] => 3
[label:protected] => Industrial
[alreadyInSave:protected] =>
[alreadyInValidation:protected] =>
[validationFailures:protected] => Array
(
)
[_new:BaseObject:private] =>
[_deleted:BaseObject:private] =>
[modifiedColumns:protected] => Array
(
)
)
[97] => Category Object
(
[languages:protected] =>
[bok_resources:protected] =>
[bok_topics:protected] =>
[bok_keywords:protected] =>
[id:protected] => 97
[type:protected] => category
[parent:protected] => 5
[label:protected] => Images
[alreadyInSave:protected] =>
[alreadyInValidation:protected] =>
[validationFailures:protected] => Array
(
)
[_new:BaseObject:private] =>
[_deleted:BaseObject:private] =>
[modifiedColumns:protected] => Array
(
)
)
)
[categories_initialized:protected] => 1
[mapped_items:protected] =>
[content:protected] =>
[files:protected] =>
[language:protected] => Language Object
(
[id:protected] => 1
[code:protected] => en
[name:protected] => English
[alreadyInSave:protected] =>
[alreadyInValidation:protected] =>
[validationFailures:protected] => Array
(
)
[_new:BaseObject:private] =>
[_deleted:BaseObject:private] =>
[modifiedColumns:protected] => Array
(
)
)
[old_record:protected] =>
[id:protected] => 3995
[old_id:protected] =>
[elcosh_id:protected] => i002690
[type:protected] => image
[display_type:protected] => Image
[user_id:protected] => 0
[language_id:protected] => 1
[tagging_id:protected] => Bruce Lippy
[priority_id:protected] => 1
[title:protected] => Construction bracing
[total_pages:protected] => 0
[billed_pages:protected] => 0
[publication_number:protected] =>
[part_of:protected] =>
[keywords:protected] => Bracing, support, scaffold
[comments:protected] =>
[summary:protected] => This shows structural support that prevents collapses during construction.
[transition_comments:protected] =>
[external_link:protected] =>
[consol_link:protected] => http://www.cpwrconstructionsolutions.org/masonry/solution/8/adjustable-tower-scaffold.html
[more_like_this:protected] => i002660
[permission_given_by:protected] =>
[published:protected] => T
[billable:protected] => F
[img_name:protected] =>
[img_ext:protected] => jpg
[img_width:protected] =>
[img_height:protected] =>
[img_credit:protected] => Photo by Pam Susi
[img_practice:protected] => good
[vid_source_id:protected] =>
[vid_running_time:protected] =>
[vid_intended_audience:protected] =>
[vid_acquisition_info:protected] =>
[vid_cost:protected] =>
[vid_producer:protected] =>
[vid_filename:protected] =>
[vid_filename_downloadable:protected] =>
[date_summary:protected] => January 2016
[date_permission_requested:protected] =>
[date_permission_received:protected] =>
[date_review_needed:protected] =>
[date_received:protected] => 02/01/16
[date_completed:protected] => 02/01/16
[date_billed:protected] =>
[date_modified:protected] => 02/01/16
[collBokExports:protected] =>
[lastBokExportCriteria:BaseElcoshItem:private] =>
[alreadyInSave:protected] =>
[alreadyInValidation:protected] =>
[validationFailures:protected] => Array
(
)
[_new:BaseObject:private] =>
[_deleted:BaseObject:private] =>
[modifiedColumns:protected] => Array
(
)
)
)
)
[preview_mode] =>
[description] => Toolbox talks have been the main tool for communicating safety information on construction jobs for decades.
Unfortunately, there has been little research on what makes for effective toolbox talks. The IUOE National
Training Fund worked with OSHA and NIOSH to make sure their series of 24 Focus Four toolbox talks were based on the best recommendations for effective design. These toolbox talks accompany an entire package of training materials, but can be used alone. This guide points out the key features of these toolbox talks and how best to deliver them.
[keywords] => toolbox talks, tailgate talks
[related_items] => Array
(
[Toolbox Talks] => Array
(
[0] => DocumentRecord Object
(
[records:protected] => Array
(
)
[recordId:protected] =>
[searchWordClass:protected] =>
[searchWordPeerClass:protected] =>
[bok_record:protected] =>
[authors:protected] =>
[organizations:protected] =>
[collections:protected] =>
[categories:protected] =>
[categories_initialized:protected] =>
[mapped_items:protected] =>
[content:protected] =>
[files:protected] =>
[language:protected] => Language Object
(
[id:protected] => 1
[code:protected] => en
[name:protected] => English
[alreadyInSave:protected] =>
[alreadyInValidation:protected] =>
[validationFailures:protected] => Array
(
)
[_new:BaseObject:private] =>
[_deleted:BaseObject:private] =>
[modifiedColumns:protected] => Array
(
)
)
[old_record:protected] =>
[id:protected] => 1605
[old_id:protected] => 1262
[elcosh_id:protected] => d001137
[type:protected] => document
[display_type:protected] => HTML w/ PDF
[user_id:protected] =>
[language_id:protected] => 1
[tagging_id:protected] => Garber
[priority_id:protected] => 1
[title:protected] => Focus Four Toolbox Talks, Module 1 – Falls, Talk #2 – Falls from debris piles?
[total_pages:protected] => 1
[billed_pages:protected] => 1
[publication_number:protected] =>
[part_of:protected] =>
[keywords:protected] => disaster response, hazard clean-up, uneven surface, disaster site, disaster clean-up
[comments:protected] =>
[summary:protected] => A toolbox talk on preventing falls from debris piles. Includes questions to ask, an incident to discuss with images, and a place to record questions the trainer would like to ask about the incident. Part of a collection. Click on the 'collection' button to access the other items.
[transition_comments:protected] =>
[external_link:protected] =>
[consol_link:protected] => http://www.cpwrconstructionsolutions.org/roofing/hazard/1463/install-asphalt-roofs-fall-from-heights.html
[more_like_this:protected] => a000081,d000478,d000530
[permission_given_by:protected] =>
[published:protected] => T
[billable:protected] => F
[img_name:protected] =>
[img_ext:protected] =>
[img_width:protected] =>
[img_height:protected] =>
[img_credit:protected] =>
[img_practice:protected] =>
[vid_source_id:protected] =>
[vid_running_time:protected] =>
[vid_intended_audience:protected] =>
[vid_acquisition_info:protected] =>
[vid_cost:protected] =>
[vid_producer:protected] =>
[vid_filename:protected] =>
[vid_filename_downloadable:protected] =>
[date_summary:protected] =>
[date_permission_requested:protected] =>
[date_permission_received:protected] =>
[date_review_needed:protected] =>
[date_received:protected] => 02/15/12
[date_completed:protected] => 03/19/12
[date_billed:protected] =>
[date_modified:protected] => 07/10/12
[collBokExports:protected] =>
[lastBokExportCriteria:BaseElcoshItem:private] =>
[alreadyInSave:protected] =>
[alreadyInValidation:protected] =>
[validationFailures:protected] => Array
(
)
[_new:BaseObject:private] =>
[_deleted:BaseObject:private] =>
[modifiedColumns:protected] => Array
(
)
)
[1] => DocumentRecord Object
(
[records:protected] => Array
(
)
[recordId:protected] =>
[searchWordClass:protected] =>
[searchWordPeerClass:protected] =>
[bok_record:protected] =>
[authors:protected] =>
[organizations:protected] =>
[collections:protected] =>
[categories:protected] =>
[categories_initialized:protected] =>
[mapped_items:protected] =>
[content:protected] =>
[files:protected] =>
[language:protected] => Language Object
(
[id:protected] => 1
[code:protected] => en
[name:protected] => English
[alreadyInSave:protected] =>
[alreadyInValidation:protected] =>
[validationFailures:protected] => Array
(
)
[_new:BaseObject:private] =>
[_deleted:BaseObject:private] =>
[modifiedColumns:protected] => Array
(
)
)
[old_record:protected] =>
[id:protected] => 1610
[old_id:protected] => 1271
[elcosh_id:protected] => d001146
[type:protected] => document
[display_type:protected] => HTML w/ PDF
[user_id:protected] => 0
[language_id:protected] => 1
[tagging_id:protected] => Garber
[priority_id:protected] => 1
[title:protected] => Focus Four Toolbox Talks, Module 2 – Struck-by, Talk #5 – Rigging and Securing Loads
[total_pages:protected] => 1
[billed_pages:protected] => 1
[publication_number:protected] =>
[part_of:protected] =>
[keywords:protected] => rigging, lift loads, loading areas, chains
[comments:protected] =>
[summary:protected] => A toolbox talk on preventing struck-by incidents caused by not securing loads properly. Includes questions to ask, an incident to discuss with images, and a place to record questions the trainer would like to ask about the incident. Part of a collection. Click on the 'collection' button to access the other items.
[transition_comments:protected] =>
[external_link:protected] =>
[consol_link:protected] => http://www.cpwrconstructionsolutions.org/heavy_equipment/hazard/1591/move-equipment-to-from-and-between-sites-work-zone-struck-by-injuries-and-fatalities.html
[more_like_this:protected] => d000144,d000360,d000873
[permission_given_by:protected] =>
[published:protected] => T
[billable:protected] => F
[img_name:protected] =>
[img_ext:protected] =>
[img_width:protected] =>
[img_height:protected] =>
[img_credit:protected] =>
[img_practice:protected] =>
[vid_source_id:protected] =>
[vid_running_time:protected] =>
[vid_intended_audience:protected] =>
[vid_acquisition_info:protected] =>
[vid_cost:protected] =>
[vid_producer:protected] =>
[vid_filename:protected] =>
[vid_filename_downloadable:protected] =>
[date_summary:protected] =>
[date_permission_requested:protected] =>
[date_permission_received:protected] =>
[date_review_needed:protected] =>
[date_received:protected] => 02/15/12
[date_completed:protected] => 03/28/12
[date_billed:protected] =>
[date_modified:protected] => 05/12/14
[collBokExports:protected] =>
[lastBokExportCriteria:BaseElcoshItem:private] =>
[alreadyInSave:protected] =>
[alreadyInValidation:protected] =>
[validationFailures:protected] => Array
(
)
[_new:BaseObject:private] =>
[_deleted:BaseObject:private] =>
[modifiedColumns:protected] => Array
(
)
)
[2] => DocumentRecord Object
(
[records:protected] => Array
(
)
[recordId:protected] =>
[searchWordClass:protected] =>
[searchWordPeerClass:protected] =>
[bok_record:protected] =>
[authors:protected] =>
[organizations:protected] =>
[collections:protected] =>
[categories:protected] =>
[categories_initialized:protected] =>
[mapped_items:protected] =>
[content:protected] =>
[files:protected] =>
[language:protected] => Language Object
(
[id:protected] => 1
[code:protected] => en
[name:protected] => English
[alreadyInSave:protected] =>
[alreadyInValidation:protected] =>
[validationFailures:protected] => Array
(
)
[_new:BaseObject:private] =>
[_deleted:BaseObject:private] =>
[modifiedColumns:protected] => Array
(
)
)
[old_record:protected] =>
[id:protected] => 1645
[old_id:protected] => 1274
[elcosh_id:protected] => d001149
[type:protected] => document
[display_type:protected] => HTML w/ PDF
[user_id:protected] => 0
[language_id:protected] => 1
[tagging_id:protected] => Garber
[priority_id:protected] => 1
[title:protected] => Focus Four Toolbox Talks, Module 3 – Caught-in/between, Talk #2 – Trenches & Heavy Equipment
[total_pages:protected] => 1
[billed_pages:protected] => 1
[publication_number:protected] =>
[part_of:protected] =>
[keywords:protected] => back-up alarms, spotter, soil cave-in, spoil pikes, ROPs, trenching, rain
[comments:protected] =>
[summary:protected] => A toolbox talk on preventing incidents involving trenches such as trench collapse. Includes questions to ask, an incident to discuss with images, and a place to record questions the trainer would like to ask about the incident. Part of a collection. Click on the 'collection' button to access the other items.
[transition_comments:protected] =>
[external_link:protected] =>
[consol_link:protected] =>
[more_like_this:protected] => d000019,d000035,d000168
[permission_given_by:protected] =>
[published:protected] => T
[billable:protected] => F
[img_name:protected] =>
[img_ext:protected] =>
[img_width:protected] =>
[img_height:protected] =>
[img_credit:protected] =>
[img_practice:protected] =>
[vid_source_id:protected] =>
[vid_running_time:protected] =>
[vid_intended_audience:protected] =>
[vid_acquisition_info:protected] =>
[vid_cost:protected] =>
[vid_producer:protected] =>
[vid_filename:protected] =>
[vid_filename_downloadable:protected] =>
[date_summary:protected] =>
[date_permission_requested:protected] =>
[date_permission_received:protected] =>
[date_review_needed:protected] =>
[date_received:protected] => 02/15/12
[date_completed:protected] => 04/02/12
[date_billed:protected] =>
[date_modified:protected] => 05/23/23
[collBokExports:protected] =>
[lastBokExportCriteria:BaseElcoshItem:private] =>
[alreadyInSave:protected] =>
[alreadyInValidation:protected] =>
[validationFailures:protected] => Array
(
)
[_new:BaseObject:private] =>
[_deleted:BaseObject:private] =>
[modifiedColumns:protected] => Array
(
)
)
[3] => DocumentRecord Object
(
[records:protected] => Array
(
)
[recordId:protected] =>
[searchWordClass:protected] =>
[searchWordPeerClass:protected] =>
[bok_record:protected] =>
[authors:protected] =>
[organizations:protected] =>
[collections:protected] =>
[categories:protected] =>
[categories_initialized:protected] =>
[mapped_items:protected] =>
[content:protected] =>
[files:protected] =>
[language:protected] => Language Object
(
[id:protected] => 1
[code:protected] => en
[name:protected] => English
[alreadyInSave:protected] =>
[alreadyInValidation:protected] =>
[validationFailures:protected] => Array
(
)
[_new:BaseObject:private] =>
[_deleted:BaseObject:private] =>
[modifiedColumns:protected] => Array
(
)
)
[old_record:protected] =>
[id:protected] => 1654
[old_id:protected] => 1284
[elcosh_id:protected] => d001159
[type:protected] => document
[display_type:protected] => HTML w/ PDF
[user_id:protected] => 0
[language_id:protected] => 1
[tagging_id:protected] => Garber
[priority_id:protected] => 1
[title:protected] => Focus Four Toolbox Talks, Module 4 – Electrocutions, Talk #6 – Hazards on Disaster Sites
[total_pages:protected] => 1
[billed_pages:protected] => 1
[publication_number:protected] =>
[part_of:protected] =>
[keywords:protected] => powerlines, underground, utilities, generators, wet conditions, GFCIs, energized lines, disasters, emergency response
[comments:protected] =>
[summary:protected] => A toolbox talk on how to avoid electrocution on a disaster site. Includes questions to ask, an incident to discuss with images, and a place to record questions the trainer would like to ask about the incident. Part of a collection. Click on the 'collection' button to access the other items.
[transition_comments:protected] =>
[external_link:protected] =>
[consol_link:protected] => http://www.cpwrconstructionsolutions.org/electrical/hazard/1138/install-and-repair-high-voltage-lines-transformers-switches-electrical-shocks-burns-and-or-electrocution.html
[more_like_this:protected] => d000135,d000361,d000437
[permission_given_by:protected] =>
[published:protected] => T
[billable:protected] => F
[img_name:protected] =>
[img_ext:protected] =>
[img_width:protected] =>
[img_height:protected] =>
[img_credit:protected] =>
[img_practice:protected] =>
[vid_source_id:protected] =>
[vid_running_time:protected] =>
[vid_intended_audience:protected] =>
[vid_acquisition_info:protected] =>
[vid_cost:protected] =>
[vid_producer:protected] =>
[vid_filename:protected] =>
[vid_filename_downloadable:protected] =>
[date_summary:protected] =>
[date_permission_requested:protected] =>
[date_permission_received:protected] =>
[date_review_needed:protected] =>
[date_received:protected] => 02/15/12
[date_completed:protected] => 04/02/12
[date_billed:protected] =>
[date_modified:protected] => 05/23/23
[collBokExports:protected] =>
[lastBokExportCriteria:BaseElcoshItem:private] =>
[alreadyInSave:protected] =>
[alreadyInValidation:protected] =>
[validationFailures:protected] => Array
(
)
[_new:BaseObject:private] =>
[_deleted:BaseObject:private] =>
[modifiedColumns:protected] => Array
(
)
)
)
)
[collections] => Array
(
[1294] =>
[1295] =>
[1292] =>
[1293] => CollectionRecord Object
(
[collection_items:protected] =>
[records:protected] => Array
(
)
[recordId:protected] =>
[searchWordClass:protected] =>
[searchWordPeerClass:protected] =>
[bok_record:protected] =>
[authors:protected] =>
[organizations:protected] =>
[collections:protected] =>
[categories:protected] =>
[categories_initialized:protected] =>
[mapped_items:protected] =>
[content:protected] =>
[files:protected] =>
[language:protected] =>
[old_record:protected] =>
[id:protected] => 1293
[old_id:protected] =>
[elcosh_id:protected] => c000026
[type:protected] => collection
[display_type:protected] => Collection
[user_id:protected] =>
[language_id:protected] =>
[tagging_id:protected] =>
[priority_id:protected] =>
[title:protected] => Focus Four-Struck By
[total_pages:protected] =>
[billed_pages:protected] =>
[publication_number:protected] =>
[part_of:protected] =>
[keywords:protected] =>
[comments:protected] =>
[summary:protected] => The following are links to all of the items in this collection:
[transition_comments:protected] =>
[external_link:protected] =>
[consol_link:protected] =>
[more_like_this:protected] =>
[permission_given_by:protected] =>
[published:protected] => T
[billable:protected] => F
[img_name:protected] =>
[img_ext:protected] =>
[img_width:protected] =>
[img_height:protected] =>
[img_credit:protected] =>
[img_practice:protected] =>
[vid_source_id:protected] =>
[vid_running_time:protected] =>
[vid_intended_audience:protected] =>
[vid_acquisition_info:protected] =>
[vid_cost:protected] =>
[vid_producer:protected] =>
[vid_filename:protected] =>
[vid_filename_downloadable:protected] =>
[date_summary:protected] =>
[date_permission_requested:protected] =>
[date_permission_received:protected] =>
[date_review_needed:protected] =>
[date_received:protected] => 05/08/12
[date_completed:protected] => 05/08/12
[date_billed:protected] =>
[date_modified:protected] => 05/08/12
[collBokExports:protected] =>
[lastBokExportCriteria:BaseElcoshItem:private] =>
[alreadyInSave:protected] =>
[alreadyInValidation:protected] =>
[validationFailures:protected] => Array
(
)
[_new:BaseObject:private] =>
[_deleted:BaseObject:private] =>
[modifiedColumns:protected] => Array
(
)
)
)
[record] => DocumentRecord Object
(
[records:protected] => Array
(
)
[recordId:protected] =>
[searchWordClass:protected] =>
[searchWordPeerClass:protected] =>
[bok_record:protected] =>
[authors:protected] => Array
(
)
[organizations:protected] => Array
(
[256] => Organization Object
(
[id:protected] => 256
[elcosh_id:protected] => o000276
[user_id:protected] => 14
[province_id:protected] => 0
[country_id:protected] => 0
[title:protected] => IUOE National Training Fund
[address:protected] =>
[postal_code:protected] =>
[city:protected] =>
[department:protected] =>
[phone:protected] => 304-253-8674
[fax:protected] =>
[email:protected] =>
[website:protected] => http://www.iuoeiettc.org
[filename:protected] =>
[about:protected] =>
[comments:protected] =>
[logo_available:protected] => T
[no_details:protected] => F
[date_received:protected] => 2012-02-13
[date_completed:protected] => 2012-02-13
[date_billed:protected] =>
[alreadyInSave:protected] =>
[alreadyInValidation:protected] =>
[validationFailures:protected] => Array
(
)
[_new:BaseObject:private] =>
[_deleted:BaseObject:private] =>
[modifiedColumns:protected] => Array
(
)
)
)
[collections:protected] => Array
(
[1294] =>
[1295] =>
[1292] =>
[1293] => CollectionRecord Object
(
[collection_items:protected] =>
[records:protected] => Array
(
)
[recordId:protected] =>
[searchWordClass:protected] =>
[searchWordPeerClass:protected] =>
[bok_record:protected] =>
[authors:protected] =>
[organizations:protected] =>
[collections:protected] =>
[categories:protected] =>
[categories_initialized:protected] =>
[mapped_items:protected] =>
[content:protected] =>
[files:protected] =>
[language:protected] =>
[old_record:protected] =>
[id:protected] => 1293
[old_id:protected] =>
[elcosh_id:protected] => c000026
[type:protected] => collection
[display_type:protected] => Collection
[user_id:protected] =>
[language_id:protected] =>
[tagging_id:protected] =>
[priority_id:protected] =>
[title:protected] => Focus Four-Struck By
[total_pages:protected] =>
[billed_pages:protected] =>
[publication_number:protected] =>
[part_of:protected] =>
[keywords:protected] =>
[comments:protected] =>
[summary:protected] => The following are links to all of the items in this collection:
[transition_comments:protected] =>
[external_link:protected] =>
[consol_link:protected] =>
[more_like_this:protected] =>
[permission_given_by:protected] =>
[published:protected] => T
[billable:protected] => F
[img_name:protected] =>
[img_ext:protected] =>
[img_width:protected] =>
[img_height:protected] =>
[img_credit:protected] =>
[img_practice:protected] =>
[vid_source_id:protected] =>
[vid_running_time:protected] =>
[vid_intended_audience:protected] =>
[vid_acquisition_info:protected] =>
[vid_cost:protected] =>
[vid_producer:protected] =>
[vid_filename:protected] =>
[vid_filename_downloadable:protected] =>
[date_summary:protected] =>
[date_permission_requested:protected] =>
[date_permission_received:protected] =>
[date_review_needed:protected] =>
[date_received:protected] => 05/08/12
[date_completed:protected] => 05/08/12
[date_billed:protected] =>
[date_modified:protected] => 05/08/12
[collBokExports:protected] =>
[lastBokExportCriteria:BaseElcoshItem:private] =>
[alreadyInSave:protected] =>
[alreadyInValidation:protected] =>
[validationFailures:protected] => Array
(
)
[_new:BaseObject:private] =>
[_deleted:BaseObject:private] =>
[modifiedColumns:protected] => Array
(
)
)
)
[categories:protected] =>
[categories_initialized:protected] =>
[mapped_items:protected] => Array
(
[1605] => DocumentRecord Object
(
[records:protected] => Array
(
)
[recordId:protected] =>
[searchWordClass:protected] =>
[searchWordPeerClass:protected] =>
[bok_record:protected] =>
[authors:protected] =>
[organizations:protected] =>
[collections:protected] =>
[categories:protected] =>
[categories_initialized:protected] =>
[mapped_items:protected] =>
[content:protected] =>
[files:protected] =>
[language:protected] =>
[old_record:protected] =>
[id:protected] => 1605
[old_id:protected] => 1262
[elcosh_id:protected] => d001137
[type:protected] => document
[display_type:protected] => HTML w/ PDF
[user_id:protected] =>
[language_id:protected] => 1
[tagging_id:protected] => Garber
[priority_id:protected] => 1
[title:protected] => Focus Four Toolbox Talks, Module 1 – Falls, Talk #2 – Falls from debris piles?
[total_pages:protected] => 1
[billed_pages:protected] => 1
[publication_number:protected] =>
[part_of:protected] =>
[keywords:protected] => disaster response, hazard clean-up, uneven surface, disaster site, disaster clean-up
[comments:protected] =>
[summary:protected] => A toolbox talk on preventing falls from debris piles. Includes questions to ask, an incident to discuss with images, and a place to record questions the trainer would like to ask about the incident. Part of a collection. Click on the 'collection' button to access the other items.
[transition_comments:protected] =>
[external_link:protected] =>
[consol_link:protected] => http://www.cpwrconstructionsolutions.org/roofing/hazard/1463/install-asphalt-roofs-fall-from-heights.html
[more_like_this:protected] => a000081,d000478,d000530
[permission_given_by:protected] =>
[published:protected] => T
[billable:protected] => F
[img_name:protected] =>
[img_ext:protected] =>
[img_width:protected] =>
[img_height:protected] =>
[img_credit:protected] =>
[img_practice:protected] =>
[vid_source_id:protected] =>
[vid_running_time:protected] =>
[vid_intended_audience:protected] =>
[vid_acquisition_info:protected] =>
[vid_cost:protected] =>
[vid_producer:protected] =>
[vid_filename:protected] =>
[vid_filename_downloadable:protected] =>
[date_summary:protected] =>
[date_permission_requested:protected] =>
[date_permission_received:protected] =>
[date_review_needed:protected] =>
[date_received:protected] => 02/15/12
[date_completed:protected] => 03/19/12
[date_billed:protected] =>
[date_modified:protected] => 07/10/12
[collBokExports:protected] =>
[lastBokExportCriteria:BaseElcoshItem:private] =>
[alreadyInSave:protected] =>
[alreadyInValidation:protected] =>
[validationFailures:protected] => Array
(
)
[_new:BaseObject:private] =>
[_deleted:BaseObject:private] =>
[modifiedColumns:protected] => Array
(
)
)
[1610] => DocumentRecord Object
(
[records:protected] => Array
(
)
[recordId:protected] =>
[searchWordClass:protected] =>
[searchWordPeerClass:protected] =>
[bok_record:protected] =>
[authors:protected] =>
[organizations:protected] =>
[collections:protected] =>
[categories:protected] =>
[categories_initialized:protected] =>
[mapped_items:protected] =>
[content:protected] =>
[files:protected] =>
[language:protected] =>
[old_record:protected] =>
[id:protected] => 1610
[old_id:protected] => 1271
[elcosh_id:protected] => d001146
[type:protected] => document
[display_type:protected] => HTML w/ PDF
[user_id:protected] => 0
[language_id:protected] => 1
[tagging_id:protected] => Garber
[priority_id:protected] => 1
[title:protected] => Focus Four Toolbox Talks, Module 2 – Struck-by, Talk #5 – Rigging and Securing Loads
[total_pages:protected] => 1
[billed_pages:protected] => 1
[publication_number:protected] =>
[part_of:protected] =>
[keywords:protected] => rigging, lift loads, loading areas, chains
[comments:protected] =>
[summary:protected] => A toolbox talk on preventing struck-by incidents caused by not securing loads properly. Includes questions to ask, an incident to discuss with images, and a place to record questions the trainer would like to ask about the incident. Part of a collection. Click on the 'collection' button to access the other items.
[transition_comments:protected] =>
[external_link:protected] =>
[consol_link:protected] => http://www.cpwrconstructionsolutions.org/heavy_equipment/hazard/1591/move-equipment-to-from-and-between-sites-work-zone-struck-by-injuries-and-fatalities.html
[more_like_this:protected] => d000144,d000360,d000873
[permission_given_by:protected] =>
[published:protected] => T
[billable:protected] => F
[img_name:protected] =>
[img_ext:protected] =>
[img_width:protected] =>
[img_height:protected] =>
[img_credit:protected] =>
[img_practice:protected] =>
[vid_source_id:protected] =>
[vid_running_time:protected] =>
[vid_intended_audience:protected] =>
[vid_acquisition_info:protected] =>
[vid_cost:protected] =>
[vid_producer:protected] =>
[vid_filename:protected] =>
[vid_filename_downloadable:protected] =>
[date_summary:protected] =>
[date_permission_requested:protected] =>
[date_permission_received:protected] =>
[date_review_needed:protected] =>
[date_received:protected] => 02/15/12
[date_completed:protected] => 03/28/12
[date_billed:protected] =>
[date_modified:protected] => 05/12/14
[collBokExports:protected] =>
[lastBokExportCriteria:BaseElcoshItem:private] =>
[alreadyInSave:protected] =>
[alreadyInValidation:protected] =>
[validationFailures:protected] => Array
(
)
[_new:BaseObject:private] =>
[_deleted:BaseObject:private] =>
[modifiedColumns:protected] => Array
(
)
)
[1645] => DocumentRecord Object
(
[records:protected] => Array
(
)
[recordId:protected] =>
[searchWordClass:protected] =>
[searchWordPeerClass:protected] =>
[bok_record:protected] =>
[authors:protected] =>
[organizations:protected] =>
[collections:protected] =>
[categories:protected] =>
[categories_initialized:protected] =>
[mapped_items:protected] =>
[content:protected] =>
[files:protected] =>
[language:protected] =>
[old_record:protected] =>
[id:protected] => 1645
[old_id:protected] => 1274
[elcosh_id:protected] => d001149
[type:protected] => document
[display_type:protected] => HTML w/ PDF
[user_id:protected] => 0
[language_id:protected] => 1
[tagging_id:protected] => Garber
[priority_id:protected] => 1
[title:protected] => Focus Four Toolbox Talks, Module 3 – Caught-in/between, Talk #2 – Trenches & Heavy Equipment
[total_pages:protected] => 1
[billed_pages:protected] => 1
[publication_number:protected] =>
[part_of:protected] =>
[keywords:protected] => back-up alarms, spotter, soil cave-in, spoil pikes, ROPs, trenching, rain
[comments:protected] =>
[summary:protected] => A toolbox talk on preventing incidents involving trenches such as trench collapse. Includes questions to ask, an incident to discuss with images, and a place to record questions the trainer would like to ask about the incident. Part of a collection. Click on the 'collection' button to access the other items.
[transition_comments:protected] =>
[external_link:protected] =>
[consol_link:protected] =>
[more_like_this:protected] => d000019,d000035,d000168
[permission_given_by:protected] =>
[published:protected] => T
[billable:protected] => F
[img_name:protected] =>
[img_ext:protected] =>
[img_width:protected] =>
[img_height:protected] =>
[img_credit:protected] =>
[img_practice:protected] =>
[vid_source_id:protected] =>
[vid_running_time:protected] =>
[vid_intended_audience:protected] =>
[vid_acquisition_info:protected] =>
[vid_cost:protected] =>
[vid_producer:protected] =>
[vid_filename:protected] =>
[vid_filename_downloadable:protected] =>
[date_summary:protected] =>
[date_permission_requested:protected] =>
[date_permission_received:protected] =>
[date_review_needed:protected] =>
[date_received:protected] => 02/15/12
[date_completed:protected] => 04/02/12
[date_billed:protected] =>
[date_modified:protected] => 05/23/23
[collBokExports:protected] =>
[lastBokExportCriteria:BaseElcoshItem:private] =>
[alreadyInSave:protected] =>
[alreadyInValidation:protected] =>
[validationFailures:protected] => Array
(
)
[_new:BaseObject:private] =>
[_deleted:BaseObject:private] =>
[modifiedColumns:protected] => Array
(
)
)
[1654] => DocumentRecord Object
(
[records:protected] => Array
(
)
[recordId:protected] =>
[searchWordClass:protected] =>
[searchWordPeerClass:protected] =>
[bok_record:protected] =>
[authors:protected] =>
[organizations:protected] =>
[collections:protected] =>
[categories:protected] =>
[categories_initialized:protected] =>
[mapped_items:protected] =>
[content:protected] =>
[files:protected] =>
[language:protected] =>
[old_record:protected] =>
[id:protected] => 1654
[old_id:protected] => 1284
[elcosh_id:protected] => d001159
[type:protected] => document
[display_type:protected] => HTML w/ PDF
[user_id:protected] => 0
[language_id:protected] => 1
[tagging_id:protected] => Garber
[priority_id:protected] => 1
[title:protected] => Focus Four Toolbox Talks, Module 4 – Electrocutions, Talk #6 – Hazards on Disaster Sites
[total_pages:protected] => 1
[billed_pages:protected] => 1
[publication_number:protected] =>
[part_of:protected] =>
[keywords:protected] => powerlines, underground, utilities, generators, wet conditions, GFCIs, energized lines, disasters, emergency response
[comments:protected] =>
[summary:protected] => A toolbox talk on how to avoid electrocution on a disaster site. Includes questions to ask, an incident to discuss with images, and a place to record questions the trainer would like to ask about the incident. Part of a collection. Click on the 'collection' button to access the other items.
[transition_comments:protected] =>
[external_link:protected] =>
[consol_link:protected] => http://www.cpwrconstructionsolutions.org/electrical/hazard/1138/install-and-repair-high-voltage-lines-transformers-switches-electrical-shocks-burns-and-or-electrocution.html
[more_like_this:protected] => d000135,d000361,d000437
[permission_given_by:protected] =>
[published:protected] => T
[billable:protected] => F
[img_name:protected] =>
[img_ext:protected] =>
[img_width:protected] =>
[img_height:protected] =>
[img_credit:protected] =>
[img_practice:protected] =>
[vid_source_id:protected] =>
[vid_running_time:protected] =>
[vid_intended_audience:protected] =>
[vid_acquisition_info:protected] =>
[vid_cost:protected] =>
[vid_producer:protected] =>
[vid_filename:protected] =>
[vid_filename_downloadable:protected] =>
[date_summary:protected] =>
[date_permission_requested:protected] =>
[date_permission_received:protected] =>
[date_review_needed:protected] =>
[date_received:protected] => 02/15/12
[date_completed:protected] => 04/02/12
[date_billed:protected] =>
[date_modified:protected] => 05/23/23
[collBokExports:protected] =>
[lastBokExportCriteria:BaseElcoshItem:private] =>
[alreadyInSave:protected] =>
[alreadyInValidation:protected] =>
[validationFailures:protected] => Array
(
)
[_new:BaseObject:private] =>
[_deleted:BaseObject:private] =>
[modifiedColumns:protected] => Array
(
)
)
)
[content:protected] =>
[files:protected] => Array
(
[9400] => File Object
(
[id:protected] => 9400
[filename:protected] => 1.jpg
[downloadable:protected] => F
[timestamp:protected] => 2014-05-08 15:05:37
[alreadyInSave:protected] =>
[alreadyInValidation:protected] =>
[validationFailures:protected] => Array
(
)
[_new:BaseObject:private] =>
[_deleted:BaseObject:private] =>
[modifiedColumns:protected] => Array
(
)
)
[9401] => File Object
(
[id:protected] => 9401
[filename:protected] => d001298.pdf
[downloadable:protected] => T
[timestamp:protected] => 2014-05-08 15:05:37
[alreadyInSave:protected] =>
[alreadyInValidation:protected] =>
[validationFailures:protected] => Array
(
)
[_new:BaseObject:private] =>
[_deleted:BaseObject:private] =>
[modifiedColumns:protected] => Array
(
)
)
)
[language:protected] => Language Object
(
[id:protected] => 1
[code:protected] => en
[name:protected] => English
[alreadyInSave:protected] =>
[alreadyInValidation:protected] =>
[validationFailures:protected] => Array
(
)
[_new:BaseObject:private] =>
[_deleted:BaseObject:private] =>
[modifiedColumns:protected] => Array
(
)
)
[old_record:protected] =>
[id:protected] => 3827
[old_id:protected] =>
[elcosh_id:protected] => d001298
[type:protected] => document
[display_type:protected] => HTML w/ PDF
[user_id:protected] => 23
[language_id:protected] => 1
[tagging_id:protected] => Bruce Lippy
[priority_id:protected] => 1
[title:protected] => Getting the most out of the IUOE Toolbox Talks
[total_pages:protected] => 2
[billed_pages:protected] => 2
[publication_number:protected] =>
[part_of:protected] =>
[keywords:protected] => toolbox talks, tailgate talks
[comments:protected] =>
[summary:protected] => Toolbox talks have been the main tool for communicating safety information on construction jobs for decades.
Unfortunately, there has been little research on what makes for effective toolbox talks. The IUOE National
Training Fund worked with OSHA and NIOSH to make sure their series of 24 Focus Four toolbox talks were based on the best recommendations for effective design. These toolbox talks accompany an entire package of training materials, but can be used alone. This guide points out the key features of these toolbox talks and how best to deliver them.
[transition_comments:protected] =>
[external_link:protected] =>
[consol_link:protected] =>
[more_like_this:protected] => d001137,d001146,d001149,d001159
[permission_given_by:protected] => IUOE National Hazmat Program
[published:protected] => T
[billable:protected] => F
[img_name:protected] =>
[img_ext:protected] => png
[img_width:protected] =>
[img_height:protected] =>
[img_credit:protected] =>
[img_practice:protected] =>
[vid_source_id:protected] =>
[vid_running_time:protected] =>
[vid_intended_audience:protected] =>
[vid_acquisition_info:protected] =>
[vid_cost:protected] =>
[vid_producer:protected] =>
[vid_filename:protected] =>
[vid_filename_downloadable:protected] =>
[date_summary:protected] => 2007
[date_permission_requested:protected] =>
[date_permission_received:protected] =>
[date_review_needed:protected] =>
[date_received:protected] => 05/08/14
[date_completed:protected] => 05/08/14
[date_billed:protected] =>
[date_modified:protected] => 05/08/14
[collBokExports:protected] =>
[lastBokExportCriteria:BaseElcoshItem:private] =>
[alreadyInSave:protected] =>
[alreadyInValidation:protected] =>
[validationFailures:protected] => Array
(
)
[_new:BaseObject:private] =>
[_deleted:BaseObject:private] =>
[modifiedColumns:protected] => Array
(
)
)
[show_text] =>
[document_content] => ElcoshItemDocumentContent Object
(
[id:protected] => 2896
[item_id:protected] => 3827
[type:protected] => main
[title:protected] =>
[content:protected] =>
Why were these talks developed?
Toolbox talks have been the main tool for communicating safety information on construction jobs for decades. Unfortunately, there has been almost no research on what makes for effective toolbox talks. The IUOE National Training Fund has worked with OSHA, the National Institute for Occupational Safety and Health and the Lippy Group, LLC to make sure these Focus Four toolbox talks are based on the latest fi ndings on the most effective design and tailored to the hazards operating engineers face daily. These toolbox talks accompany an entire package of training materials, but can be used alone. The way these are delivered is as important as how well they are designed.
What did NIOSH find out?
- Just handing out factsheets and toolbox talks to workers doesn’t work. Providing copies after toolbox talks doesn’t make much of an impact either.
- Using case studies (real life stories of accidents that ended in fatality or injury) in toolbox talks is effective.
- When toolbox talks containing case studies were accompanied by discussion questions to encourage group participation, they were more effective. Consequently, getting the workers to participate in the discussion about the case study is important. It’s not enough to tell the story, it is better to have the workers engage in problem solving that analyzes why the accident occurred and how it could have been prevented. Active learning is always better than passive.
How should you deliver these toolbox talks?
- Choose a topic that is related to work going on at the site.
- Hold the meeting on the job, preferably where everyone can sit and relax.
- Hold the meeting at the beginning of a shift or after a break. Folks are too tired at the end of a shift to carefully listen and they want to get home.
- Read the toolbox talk sheet on the topic prior to conducting the talk.
- Start at the top of the form and work right through to the end, which should take around 10 to 15 minutes. Guidance is provided in blue print to help you with each section.
- Use the questions provided to generate discussions. Always allow time for the crew to respond to your questions before you provide an answer. Some suggested responses are written in italics.
- Review the case study and emphasize that this was a real incident. Ask the crew for a case study before you review the one provided, however.
- Always end with a discussion of the particular worksite where you are conducting the talk. Tie the talk as closely to hazards on the site as possible and encourage the crew to constantly look for and immediately correct hazards. They should also know how to report any problems that can’t be immediately corrected.
- Provide copies to each person, if you like, but NIOSH has not found that to be particularly effective.
- Encourage workers to do similar talks on their sites and provide them with the IUOE phone number for ordering in bulk.
- Have everyone sign the back of the form to indicate they attended this session and point out it is a pledge to look out for the health and safety of everyone on the site.
What are the key features of these toolbox talks?

[content_transformed:protected] =>
Why were these talks developed?
Toolbox talks have been the main tool for communicating safety information on construction jobs for decades. Unfortunately, there has been almost no research on what makes for effective toolbox talks. The IUOE National Training Fund has worked with OSHA, the National Institute for Occupational Safety and Health and the Lippy Group, LLC to make sure these Focus Four toolbox talks are based on the latest fi ndings on the most effective design and tailored to the hazards operating engineers face daily. These toolbox talks accompany an entire package of training materials, but can be used alone. The way these are delivered is as important as how well they are designed.
What did NIOSH find out?
- Just handing out factsheets and toolbox talks to workers doesn’t work. Providing copies after toolbox talks doesn’t make much of an impact either.
- Using case studies (real life stories of accidents that ended in fatality or injury) in toolbox talks is effective.
- When toolbox talks containing case studies were accompanied by discussion questions to encourage group participation, they were more effective. Consequently, getting the workers to participate in the discussion about the case study is important. It’s not enough to tell the story, it is better to have the workers engage in problem solving that analyzes why the accident occurred and how it could have been prevented. Active learning is always better than passive.
How should you deliver these toolbox talks?
- Choose a topic that is related to work going on at the site.
- Hold the meeting on the job, preferably where everyone can sit and relax.
- Hold the meeting at the beginning of a shift or after a break. Folks are too tired at the end of a shift to carefully listen and they want to get home.
- Read the toolbox talk sheet on the topic prior to conducting the talk.
- Start at the top of the form and work right through to the end, which should take around 10 to 15 minutes. Guidance is provided in blue print to help you with each section.
- Use the questions provided to generate discussions. Always allow time for the crew to respond to your questions before you provide an answer. Some suggested responses are written in italics.
- Review the case study and emphasize that this was a real incident. Ask the crew for a case study before you review the one provided, however.
- Always end with a discussion of the particular worksite where you are conducting the talk. Tie the talk as closely to hazards on the site as possible and encourage the crew to constantly look for and immediately correct hazards. They should also know how to report any problems that can’t be immediately corrected.
- Provide copies to each person, if you like, but NIOSH has not found that to be particularly effective.
- Encourage workers to do similar talks on their sites and provide them with the IUOE phone number for ordering in bulk.
- Have everyone sign the back of the form to indicate they attended this session and point out it is a pledge to look out for the health and safety of everyone on the site.
What are the key features of these toolbox talks?
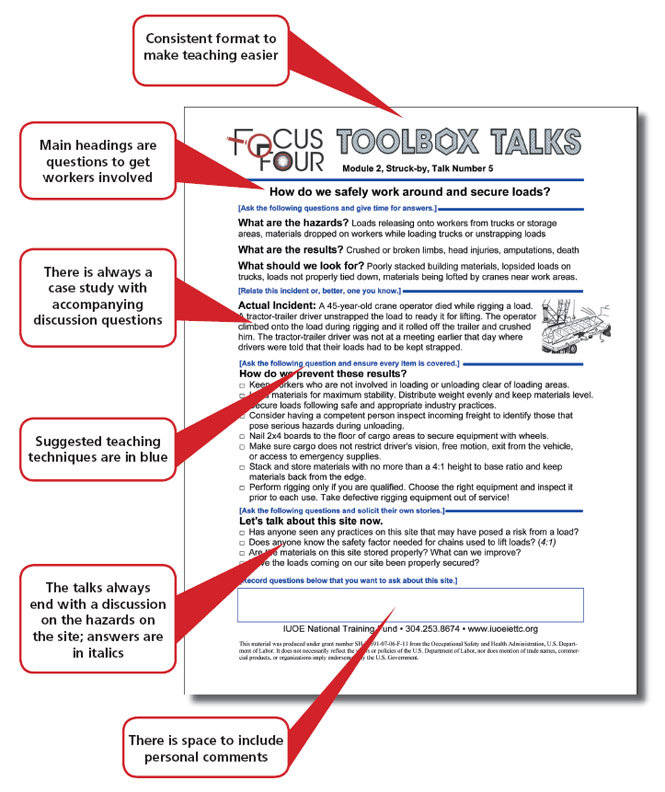
[disclaimer:protected] =>
[disclaimer_transformed:protected] =>
[alreadyInSave:protected] =>
[alreadyInValidation:protected] =>
[validationFailures:protected] => Array
(
)
[_new:BaseObject:private] =>
[_deleted:BaseObject:private] =>
[modifiedColumns:protected] => Array
(
)
)
[template] => record
)
[_globalContext:PHPTAL_Context:private] => stdClass Object
(
)
[_echoDeclarations:PHPTAL_Context:private] =>
[referer] => http://www.elcosh.org/document/3827/d001298/Getting%2Bthe%2Bmost%2Bout%2Bof%2Bthe%2BIUOE%2BToolbox%2BTalks.html
[curr_module] => Record
[styles] => Array
(
)
[javascript] => Array
(
[0] => jquery.min.js
)
[metas] => Array
(
[language] => en
[robots] => index, follow
)
[user] =>
[curr_url] => https://www.elcosh.org/index.php?module=Record&id=3827&type=document
[base_url] => https://www.elcosh.org/index.php?module=Record
[title] => eLCOSH : Getting the most out of the IUOE Toolbox Talks
[language] => en
[search_query] =>
[module] => Record
[new_records] => Array
(
[0] => Search_Result Object
(
[title] => Toolbox Talk: Fixed Ladder
[image] => /record/images/notavailable-p.png
[blurb] => The CPWR Toolbox Talk on Fixed Ladders addresses the potential risks associated with using fixed ladders. The resource includes a brief case example,...
[category] => Array
(
[0] => 15
[1] => 47
[2] => 49
[3] => 51
[4] => 53
[5] => 55
[6] => 60
[7] => 64
[8] => 73
[9] => 76
[10] => 78
[11] => 80
[12] => 86
[13] => 87
[14] => 90
[15] => 92
[16] => 93
[17] => 94
[18] => 100
)
[labels] => Array
(
[0] => Falls
[1] => Work Environment
[2] => Hazards
[3] => Bricklayer
[4] => Trades
[5] => Carpenter
[7] => Cement Mason
[9] => Concrete Polisher
[11] => Electrical Worker
[13] => HVAC
[15] => Laborer
[17] => PCC/Restoration
[19] => Plumber/Pipefitter
[21] => Roofer/Waterproofer
[23] => Sheetmetal Worker
[25] => Welder
[27] => Commercial & Institutional
[28] => Jobsites
[29] => Industrial
[31] => LEED/Green Construction
[33] => Renovations
[35] => Residential
[37] => Toolbox Talks
[38] => Documents
[39] => Media & Documents
)
[type] => Toolbox Talks
[sub_category] =>
[url] => /document/4430/d001660/Toolbox%2BTalk%253A%2BFixed%2BLadder.html
[item:protected] => DocumentRecord Object
(
[records:protected] => Array
(
)
[recordId:protected] =>
[searchWordClass:protected] =>
[searchWordPeerClass:protected] =>
[bok_record:protected] =>
[authors:protected] =>
[organizations:protected] =>
[collections:protected] =>
[categories:protected] => Array
(
[15] => Category Object
(
[languages:protected] =>
[bok_resources:protected] =>
[bok_topics:protected] =>
[bok_keywords:protected] =>
[id:protected] => 15
[type:protected] => category
[parent:protected] => 7
[label:protected] => Falls
[alreadyInSave:protected] =>
[alreadyInValidation:protected] =>
[validationFailures:protected] => Array
(
)
[_new:BaseObject:private] =>
[_deleted:BaseObject:private] =>
[modifiedColumns:protected] => Array
(
)
)
[47] => Category Object
(
[languages:protected] =>
[bok_resources:protected] =>
[bok_topics:protected] =>
[bok_keywords:protected] =>
[id:protected] => 47
[type:protected] => category
[parent:protected] => 2
[label:protected] => Bricklayer
[alreadyInSave:protected] =>
[alreadyInValidation:protected] =>
[validationFailures:protected] => Array
(
)
[_new:BaseObject:private] =>
[_deleted:BaseObject:private] =>
[modifiedColumns:protected] => Array
(
)
)
[49] => Category Object
(
[languages:protected] =>
[bok_resources:protected] =>
[bok_topics:protected] =>
[bok_keywords:protected] =>
[id:protected] => 49
[type:protected] => category
[parent:protected] => 2
[label:protected] => Carpenter
[alreadyInSave:protected] =>
[alreadyInValidation:protected] =>
[validationFailures:protected] => Array
(
)
[_new:BaseObject:private] =>
[_deleted:BaseObject:private] =>
[modifiedColumns:protected] => Array
(
)
)
[51] => Category Object
(
[languages:protected] =>
[bok_resources:protected] =>
[bok_topics:protected] =>
[bok_keywords:protected] =>
[id:protected] => 51
[type:protected] => category
[parent:protected] => 2
[label:protected] => Cement Mason
[alreadyInSave:protected] =>
[alreadyInValidation:protected] =>
[validationFailures:protected] => Array
(
)
[_new:BaseObject:private] =>
[_deleted:BaseObject:private] =>
[modifiedColumns:protected] => Array
(
)
)
[53] => Category Object
(
[languages:protected] =>
[bok_resources:protected] =>
[bok_topics:protected] =>
[bok_keywords:protected] =>
[id:protected] => 53
[type:protected] => category
[parent:protected] => 2
[label:protected] => Concrete Polisher
[alreadyInSave:protected] =>
[alreadyInValidation:protected] =>
[validationFailures:protected] => Array
(
)
[_new:BaseObject:private] =>
[_deleted:BaseObject:private] =>
[modifiedColumns:protected] => Array
(
)
)
[55] => Category Object
(
[languages:protected] =>
[bok_resources:protected] =>
[bok_topics:protected] =>
[bok_keywords:protected] =>
[id:protected] => 55
[type:protected] => category
[parent:protected] => 2
[label:protected] => Electrical Worker
[alreadyInSave:protected] =>
[alreadyInValidation:protected] =>
[validationFailures:protected] => Array
(
)
[_new:BaseObject:private] =>
[_deleted:BaseObject:private] =>
[modifiedColumns:protected] => Array
(
)
)
[60] => Category Object
(
[languages:protected] =>
[bok_resources:protected] =>
[bok_topics:protected] =>
[bok_keywords:protected] =>
[id:protected] => 60
[type:protected] => category
[parent:protected] => 2
[label:protected] => HVAC
[alreadyInSave:protected] =>
[alreadyInValidation:protected] =>
[validationFailures:protected] => Array
(
)
[_new:BaseObject:private] =>
[_deleted:BaseObject:private] =>
[modifiedColumns:protected] => Array
(
)
)
[64] => Category Object
(
[languages:protected] =>
[bok_resources:protected] =>
[bok_topics:protected] =>
[bok_keywords:protected] =>
[id:protected] => 64
[type:protected] => category
[parent:protected] => 2
[label:protected] => Laborer
[alreadyInSave:protected] =>
[alreadyInValidation:protected] =>
[validationFailures:protected] => Array
(
)
[_new:BaseObject:private] =>
[_deleted:BaseObject:private] =>
[modifiedColumns:protected] => Array
(
)
)
[73] => Category Object
(
[languages:protected] =>
[bok_resources:protected] =>
[bok_topics:protected] =>
[bok_keywords:protected] =>
[id:protected] => 73
[type:protected] => category
[parent:protected] => 2
[label:protected] => PCC/Restoration
[alreadyInSave:protected] =>
[alreadyInValidation:protected] =>
[validationFailures:protected] => Array
(
)
[_new:BaseObject:private] =>
[_deleted:BaseObject:private] =>
[modifiedColumns:protected] => Array
(
)
)
[76] => Category Object
(
[languages:protected] =>
[bok_resources:protected] =>
[bok_topics:protected] =>
[bok_keywords:protected] =>
[id:protected] => 76
[type:protected] => category
[parent:protected] => 2
[label:protected] => Plumber/Pipefitter
[alreadyInSave:protected] =>
[alreadyInValidation:protected] =>
[validationFailures:protected] => Array
(
)
[_new:BaseObject:private] =>
[_deleted:BaseObject:private] =>
[modifiedColumns:protected] => Array
(
)
)
[78] => Category Object
(
[languages:protected] =>
[bok_resources:protected] =>
[bok_topics:protected] =>
[bok_keywords:protected] =>
[id:protected] => 78
[type:protected] => category
[parent:protected] => 2
[label:protected] => Roofer/Waterproofer
[alreadyInSave:protected] =>
[alreadyInValidation:protected] =>
[validationFailures:protected] => Array
(
)
[_new:BaseObject:private] =>
[_deleted:BaseObject:private] =>
[modifiedColumns:protected] => Array
(
)
)
[80] => Category Object
(
[languages:protected] =>
[bok_resources:protected] =>
[bok_topics:protected] =>
[bok_keywords:protected] =>
[id:protected] => 80
[type:protected] => category
[parent:protected] => 2
[label:protected] => Sheetmetal Worker
[alreadyInSave:protected] =>
[alreadyInValidation:protected] =>
[validationFailures:protected] => Array
(
)
[_new:BaseObject:private] =>
[_deleted:BaseObject:private] =>
[modifiedColumns:protected] => Array
(
)
)
[86] => Category Object
(
[languages:protected] =>
[bok_resources:protected] =>
[bok_topics:protected] =>
[bok_keywords:protected] =>
[id:protected] => 86
[type:protected] => category
[parent:protected] => 2
[label:protected] => Welder
[alreadyInSave:protected] =>
[alreadyInValidation:protected] =>
[validationFailures:protected] => Array
(
)
[_new:BaseObject:private] =>
[_deleted:BaseObject:private] =>
[modifiedColumns:protected] => Array
(
)
)
[87] => Category Object
(
[languages:protected] =>
[bok_resources:protected] =>
[bok_topics:protected] =>
[bok_keywords:protected] =>
[id:protected] => 87
[type:protected] => category
[parent:protected] => 3
[label:protected] => Commercial & Institutional
[alreadyInSave:protected] =>
[alreadyInValidation:protected] =>
[validationFailures:protected] => Array
(
)
[_new:BaseObject:private] =>
[_deleted:BaseObject:private] =>
[modifiedColumns:protected] => Array
(
)
)
[90] => Category Object
(
[languages:protected] =>
[bok_resources:protected] =>
[bok_topics:protected] =>
[bok_keywords:protected] =>
[id:protected] => 90
[type:protected] => category
[parent:protected] => 3
[label:protected] => Industrial
[alreadyInSave:protected] =>
[alreadyInValidation:protected] =>
[validationFailures:protected] => Array
(
)
[_new:BaseObject:private] =>
[_deleted:BaseObject:private] =>
[modifiedColumns:protected] => Array
(
)
)
[92] => Category Object
(
[languages:protected] =>
[bok_resources:protected] =>
[bok_topics:protected] =>
[bok_keywords:protected] =>
[id:protected] => 92
[type:protected] => category
[parent:protected] => 3
[label:protected] => LEED/Green Construction
[alreadyInSave:protected] =>
[alreadyInValidation:protected] =>
[validationFailures:protected] => Array
(
)
[_new:BaseObject:private] =>
[_deleted:BaseObject:private] =>
[modifiedColumns:protected] => Array
(
)
)
[93] => Category Object
(
[languages:protected] =>
[bok_resources:protected] =>
[bok_topics:protected] =>
[bok_keywords:protected] =>
[id:protected] => 93
[type:protected] => category
[parent:protected] => 3
[label:protected] => Renovations
[alreadyInSave:protected] =>
[alreadyInValidation:protected] =>
[validationFailures:protected] => Array
(
)
[_new:BaseObject:private] =>
[_deleted:BaseObject:private] =>
[modifiedColumns:protected] => Array
(
)
)
[94] => Category Object
(
[languages:protected] =>
[bok_resources:protected] =>
[bok_topics:protected] =>
[bok_keywords:protected] =>
[id:protected] => 94
[type:protected] => category
[parent:protected] => 3
[label:protected] => Residential
[alreadyInSave:protected] =>
[alreadyInValidation:protected] =>
[validationFailures:protected] => Array
(
)
[_new:BaseObject:private] =>
[_deleted:BaseObject:private] =>
[modifiedColumns:protected] => Array
(
)
)
[100] => Category Object
(
[languages:protected] =>
[bok_resources:protected] =>
[bok_topics:protected] =>
[bok_keywords:protected] =>
[id:protected] => 100
[type:protected] => category
[parent:protected] => 6
[label:protected] => Toolbox Talks
[alreadyInSave:protected] =>
[alreadyInValidation:protected] =>
[validationFailures:protected] => Array
(
)
[_new:BaseObject:private] =>
[_deleted:BaseObject:private] =>
[modifiedColumns:protected] => Array
(
)
)
)
[categories_initialized:protected] => 1
[mapped_items:protected] =>
[content:protected] =>
[files:protected] =>
[language:protected] => Language Object
(
[id:protected] => 1
[code:protected] => en
[name:protected] => English
[alreadyInSave:protected] =>
[alreadyInValidation:protected] =>
[validationFailures:protected] => Array
(
)
[_new:BaseObject:private] =>
[_deleted:BaseObject:private] =>
[modifiedColumns:protected] => Array
(
)
)
[old_record:protected] =>
[id:protected] => 4430
[old_id:protected] =>
[elcosh_id:protected] => d001660
[type:protected] => document
[display_type:protected] => HTML only (and links)
[user_id:protected] => 0
[language_id:protected] => 1
[tagging_id:protected] => Mike Aguilar
[priority_id:protected] => 1
[title:protected] => Toolbox Talk: Fixed Ladder
[total_pages:protected] => 0
[billed_pages:protected] => 0
[publication_number:protected] =>
[part_of:protected] =>
[keywords:protected] => Fixed Ladders, Fall Prevention, Falls
[comments:protected] =>
[summary:protected] => The CPWR Toolbox Talk on Fixed Ladders addresses the potential risks associated with using fixed ladders. The resource includes a brief case example, steps to prevent a related injury and questions for discussion. It includes an image that illustrates the hazard, which can be posted in a central location as a reminder of steps to work safely.
Available in
English
and
Spanish.
[transition_comments:protected] =>
[external_link:protected] =>
[consol_link:protected] =>
[more_like_this:protected] => d001257,d001254,d001255,d001256,d001258,d001262,d001279
[permission_given_by:protected] =>
[published:protected] => T
[billable:protected] => F
[img_name:protected] =>
[img_ext:protected] =>
[img_width:protected] =>
[img_height:protected] =>
[img_credit:protected] =>
[img_practice:protected] =>
[vid_source_id:protected] =>
[vid_running_time:protected] =>
[vid_intended_audience:protected] =>
[vid_acquisition_info:protected] =>
[vid_cost:protected] =>
[vid_producer:protected] =>
[vid_filename:protected] =>
[vid_filename_downloadable:protected] =>
[date_summary:protected] =>
[date_permission_requested:protected] =>
[date_permission_received:protected] =>
[date_review_needed:protected] =>
[date_received:protected] => 06/10/22
[date_completed:protected] => 06/10/22
[date_billed:protected] =>
[date_modified:protected] => 05/22/23
[collBokExports:protected] =>
[lastBokExportCriteria:BaseElcoshItem:private] =>
[alreadyInSave:protected] =>
[alreadyInValidation:protected] =>
[validationFailures:protected] => Array
(
)
[_new:BaseObject:private] =>
[_deleted:BaseObject:private] =>
[modifiedColumns:protected] => Array
(
)
)
)
[1] => Search_Result Object
(
[title] => Toolbox Talk: Challenges Preventing Falling Objects
[image] => /record/images/notavailable-p.png
[blurb] => The CPWR Toolbox Talk on Challenges Preventing Falling Objects addresses the hazards of being struck by falling objects on the job site. The resource...
[category] => Array
(
[0] => 12
[1] => 47
[2] => 49
[3] => 51
[4] => 55
[5] => 64
[6] => 68
[7] => 71
[8] => 75
[9] => 78
[10] => 79
[11] => 82
[12] => 62
[13] => 86
[14] => 87
[15] => 88
[16] => 89
[17] => 91
[18] => 90
[19] => 92
[20] => 93
[21] => 94
[22] => 95
[23] => 100
)
[labels] => Array
(
[0] => Crushed/Struck By
[1] => Work Environment
[2] => Hazards
[3] => Bricklayer
[4] => Trades
[5] => Carpenter
[7] => Cement Mason
[9] => Electrical Worker
[11] => Laborer
[13] => Maintenance Worker
[15] => Painter
[17] => Plasterer
[19] => Roofer/Waterproofer
[21] => Scaffold Erector
[23] => Stonemason
[25] => Structural Ironworker
[27] => Welder
[29] => Commercial & Institutional
[30] => Jobsites
[31] => Demolition
[33] => Disasters
[35] => Heavy & Highway
[37] => Industrial
[39] => LEED/Green Construction
[41] => Renovations
[43] => Residential
[45] => Underground
[47] => Toolbox Talks
[48] => Documents
[49] => Media & Documents
)
[type] => Toolbox Talks
[sub_category] =>
[url] => /document/4431/d001661/Toolbox%2BTalk%253A%2BChallenges%2BPreventing%2BFalling%2BObjects.html
[item:protected] => DocumentRecord Object
(
[records:protected] => Array
(
)
[recordId:protected] =>
[searchWordClass:protected] =>
[searchWordPeerClass:protected] =>
[bok_record:protected] =>
[authors:protected] =>
[organizations:protected] =>
[collections:protected] =>
[categories:protected] => Array
(
[12] => Category Object
(
[languages:protected] =>
[bok_resources:protected] =>
[bok_topics:protected] =>
[bok_keywords:protected] =>
[id:protected] => 12
[type:protected] => category
[parent:protected] => 7
[label:protected] => Crushed/Struck By
[alreadyInSave:protected] =>
[alreadyInValidation:protected] =>
[validationFailures:protected] => Array
(
)
[_new:BaseObject:private] =>
[_deleted:BaseObject:private] =>
[modifiedColumns:protected] => Array
(
)
)
[47] => Category Object
(
[languages:protected] =>
[bok_resources:protected] =>
[bok_topics:protected] =>
[bok_keywords:protected] =>
[id:protected] => 47
[type:protected] => category
[parent:protected] => 2
[label:protected] => Bricklayer
[alreadyInSave:protected] =>
[alreadyInValidation:protected] =>
[validationFailures:protected] => Array
(
)
[_new:BaseObject:private] =>
[_deleted:BaseObject:private] =>
[modifiedColumns:protected] => Array
(
)
)
[49] => Category Object
(
[languages:protected] =>
[bok_resources:protected] =>
[bok_topics:protected] =>
[bok_keywords:protected] =>
[id:protected] => 49
[type:protected] => category
[parent:protected] => 2
[label:protected] => Carpenter
[alreadyInSave:protected] =>
[alreadyInValidation:protected] =>
[validationFailures:protected] => Array
(
)
[_new:BaseObject:private] =>
[_deleted:BaseObject:private] =>
[modifiedColumns:protected] => Array
(
)
)
[51] => Category Object
(
[languages:protected] =>
[bok_resources:protected] =>
[bok_topics:protected] =>
[bok_keywords:protected] =>
[id:protected] => 51
[type:protected] => category
[parent:protected] => 2
[label:protected] => Cement Mason
[alreadyInSave:protected] =>
[alreadyInValidation:protected] =>
[validationFailures:protected] => Array
(
)
[_new:BaseObject:private] =>
[_deleted:BaseObject:private] =>
[modifiedColumns:protected] => Array
(
)
)
[55] => Category Object
(
[languages:protected] =>
[bok_resources:protected] =>
[bok_topics:protected] =>
[bok_keywords:protected] =>
[id:protected] => 55
[type:protected] => category
[parent:protected] => 2
[label:protected] => Electrical Worker
[alreadyInSave:protected] =>
[alreadyInValidation:protected] =>
[validationFailures:protected] => Array
(
)
[_new:BaseObject:private] =>
[_deleted:BaseObject:private] =>
[modifiedColumns:protected] => Array
(
)
)
[64] => Category Object
(
[languages:protected] =>
[bok_resources:protected] =>
[bok_topics:protected] =>
[bok_keywords:protected] =>
[id:protected] => 64
[type:protected] => category
[parent:protected] => 2
[label:protected] => Laborer
[alreadyInSave:protected] =>
[alreadyInValidation:protected] =>
[validationFailures:protected] => Array
(
)
[_new:BaseObject:private] =>
[_deleted:BaseObject:private] =>
[modifiedColumns:protected] => Array
(
)
)
[68] => Category Object
(
[languages:protected] =>
[bok_resources:protected] =>
[bok_topics:protected] =>
[bok_keywords:protected] =>
[id:protected] => 68
[type:protected] => category
[parent:protected] => 2
[label:protected] => Maintenance Worker
[alreadyInSave:protected] =>
[alreadyInValidation:protected] =>
[validationFailures:protected] => Array
(
)
[_new:BaseObject:private] =>
[_deleted:BaseObject:private] =>
[modifiedColumns:protected] => Array
(
)
)
[71] => Category Object
(
[languages:protected] =>
[bok_resources:protected] =>
[bok_topics:protected] =>
[bok_keywords:protected] =>
[id:protected] => 71
[type:protected] => category
[parent:protected] => 2
[label:protected] => Painter
[alreadyInSave:protected] =>
[alreadyInValidation:protected] =>
[validationFailures:protected] => Array
(
)
[_new:BaseObject:private] =>
[_deleted:BaseObject:private] =>
[modifiedColumns:protected] => Array
(
)
)
[75] => Category Object
(
[languages:protected] =>
[bok_resources:protected] =>
[bok_topics:protected] =>
[bok_keywords:protected] =>
[id:protected] => 75
[type:protected] => category
[parent:protected] => 2
[label:protected] => Plasterer
[alreadyInSave:protected] =>
[alreadyInValidation:protected] =>
[validationFailures:protected] => Array
(
)
[_new:BaseObject:private] =>
[_deleted:BaseObject:private] =>
[modifiedColumns:protected] => Array
(
)
)
[78] => Category Object
(
[languages:protected] =>
[bok_resources:protected] =>
[bok_topics:protected] =>
[bok_keywords:protected] =>
[id:protected] => 78
[type:protected] => category
[parent:protected] => 2
[label:protected] => Roofer/Waterproofer
[alreadyInSave:protected] =>
[alreadyInValidation:protected] =>
[validationFailures:protected] => Array
(
)
[_new:BaseObject:private] =>
[_deleted:BaseObject:private] =>
[modifiedColumns:protected] => Array
(
)
)
[79] => Category Object
(
[languages:protected] =>
[bok_resources:protected] =>
[bok_topics:protected] =>
[bok_keywords:protected] =>
[id:protected] => 79
[type:protected] => category
[parent:protected] => 2
[label:protected] => Scaffold Erector
[alreadyInSave:protected] =>
[alreadyInValidation:protected] =>
[validationFailures:protected] => Array
(
)
[_new:BaseObject:private] =>
[_deleted:BaseObject:private] =>
[modifiedColumns:protected] => Array
(
)
)
[82] => Category Object
(
[languages:protected] =>
[bok_resources:protected] =>
[bok_topics:protected] =>
[bok_keywords:protected] =>
[id:protected] => 82
[type:protected] => category
[parent:protected] => 2
[label:protected] => Stonemason
[alreadyInSave:protected] =>
[alreadyInValidation:protected] =>
[validationFailures:protected] => Array
(
)
[_new:BaseObject:private] =>
[_deleted:BaseObject:private] =>
[modifiedColumns:protected] => Array
(
)
)
[62] => Category Object
(
[languages:protected] =>
[bok_resources:protected] =>
[bok_topics:protected] =>
[bok_keywords:protected] =>
[id:protected] => 62
[type:protected] => category
[parent:protected] => 2
[label:protected] => Structural Ironworker
[alreadyInSave:protected] =>
[alreadyInValidation:protected] =>
[validationFailures:protected] => Array
(
)
[_new:BaseObject:private] =>
[_deleted:BaseObject:private] =>
[modifiedColumns:protected] => Array
(
)
)
[86] => Category Object
(
[languages:protected] =>
[bok_resources:protected] =>
[bok_topics:protected] =>
[bok_keywords:protected] =>
[id:protected] => 86
[type:protected] => category
[parent:protected] => 2
[label:protected] => Welder
[alreadyInSave:protected] =>
[alreadyInValidation:protected] =>
[validationFailures:protected] => Array
(
)
[_new:BaseObject:private] =>
[_deleted:BaseObject:private] =>
[modifiedColumns:protected] => Array
(
)
)
[87] => Category Object
(
[languages:protected] =>
[bok_resources:protected] =>
[bok_topics:protected] =>
[bok_keywords:protected] =>
[id:protected] => 87
[type:protected] => category
[parent:protected] => 3
[label:protected] => Commercial & Institutional
[alreadyInSave:protected] =>
[alreadyInValidation:protected] =>
[validationFailures:protected] => Array
(
)
[_new:BaseObject:private] =>
[_deleted:BaseObject:private] =>
[modifiedColumns:protected] => Array
(
)
)
[88] => Category Object
(
[languages:protected] =>
[bok_resources:protected] =>
[bok_topics:protected] =>
[bok_keywords:protected] =>
[id:protected] => 88
[type:protected] => category
[parent:protected] => 3
[label:protected] => Demolition
[alreadyInSave:protected] =>
[alreadyInValidation:protected] =>
[validationFailures:protected] => Array
(
)
[_new:BaseObject:private] =>
[_deleted:BaseObject:private] =>
[modifiedColumns:protected] => Array
(
)
)
[89] => Category Object
(
[languages:protected] =>
[bok_resources:protected] =>
[bok_topics:protected] =>
[bok_keywords:protected] =>
[id:protected] => 89
[type:protected] => category
[parent:protected] => 3
[label:protected] => Disasters
[alreadyInSave:protected] =>
[alreadyInValidation:protected] =>
[validationFailures:protected] => Array
(
)
[_new:BaseObject:private] =>
[_deleted:BaseObject:private] =>
[modifiedColumns:protected] => Array
(
)
)
[91] => Category Object
(
[languages:protected] =>
[bok_resources:protected] =>
[bok_topics:protected] =>
[bok_keywords:protected] =>
[id:protected] => 91
[type:protected] => category
[parent:protected] => 3
[label:protected] => Heavy & Highway
[alreadyInSave:protected] =>
[alreadyInValidation:protected] =>
[validationFailures:protected] => Array
(
)
[_new:BaseObject:private] =>
[_deleted:BaseObject:private] =>
[modifiedColumns:protected] => Array
(
)
)
[90] => Category Object
(
[languages:protected] =>
[bok_resources:protected] =>
[bok_topics:protected] =>
[bok_keywords:protected] =>
[id:protected] => 90
[type:protected] => category
[parent:protected] => 3
[label:protected] => Industrial
[alreadyInSave:protected] =>
[alreadyInValidation:protected] =>
[validationFailures:protected] => Array
(
)
[_new:BaseObject:private] =>
[_deleted:BaseObject:private] =>
[modifiedColumns:protected] => Array
(
)
)
[92] => Category Object
(
[languages:protected] =>
[bok_resources:protected] =>
[bok_topics:protected] =>
[bok_keywords:protected] =>
[id:protected] => 92
[type:protected] => category
[parent:protected] => 3
[label:protected] => LEED/Green Construction
[alreadyInSave:protected] =>
[alreadyInValidation:protected] =>
[validationFailures:protected] => Array
(
)
[_new:BaseObject:private] =>
[_deleted:BaseObject:private] =>
[modifiedColumns:protected] => Array
(
)
)
[93] => Category Object
(
[languages:protected] =>
[bok_resources:protected] =>
[bok_topics:protected] =>
[bok_keywords:protected] =>
[id:protected] => 93
[type:protected] => category
[parent:protected] => 3
[label:protected] => Renovations
[alreadyInSave:protected] =>
[alreadyInValidation:protected] =>
[validationFailures:protected] => Array
(
)
[_new:BaseObject:private] =>
[_deleted:BaseObject:private] =>
[modifiedColumns:protected] => Array
(
)
)
[94] => Category Object
(
[languages:protected] =>
[bok_resources:protected] =>
[bok_topics:protected] =>
[bok_keywords:protected] =>
[id:protected] => 94
[type:protected] => category
[parent:protected] => 3
[label:protected] => Residential
[alreadyInSave:protected] =>
[alreadyInValidation:protected] =>
[validationFailures:protected] => Array
(
)
[_new:BaseObject:private] =>
[_deleted:BaseObject:private] =>
[modifiedColumns:protected] => Array
(
)
)
[95] => Category Object
(
[languages:protected] =>
[bok_resources:protected] =>
[bok_topics:protected] =>
[bok_keywords:protected] =>
[id:protected] => 95
[type:protected] => category
[parent:protected] => 3
[label:protected] => Underground
[alreadyInSave:protected] =>
[alreadyInValidation:protected] =>
[validationFailures:protected] => Array
(
)
[_new:BaseObject:private] =>
[_deleted:BaseObject:private] =>
[modifiedColumns:protected] => Array
(
)
)
[100] => Category Object
(
[languages:protected] =>
[bok_resources:protected] =>
[bok_topics:protected] =>
[bok_keywords:protected] =>
[id:protected] => 100
[type:protected] => category
[parent:protected] => 6
[label:protected] => Toolbox Talks
[alreadyInSave:protected] =>
[alreadyInValidation:protected] =>
[validationFailures:protected] => Array
(
)
[_new:BaseObject:private] =>
[_deleted:BaseObject:private] =>
[modifiedColumns:protected] => Array
(
)
)
)
[categories_initialized:protected] => 1
[mapped_items:protected] =>
[content:protected] =>
[files:protected] =>
[language:protected] => Language Object
(
[id:protected] => 1
[code:protected] => en
[name:protected] => English
[alreadyInSave:protected] =>
[alreadyInValidation:protected] =>
[validationFailures:protected] => Array
(
)
[_new:BaseObject:private] =>
[_deleted:BaseObject:private] =>
[modifiedColumns:protected] => Array
(
)
)
[old_record:protected] =>
[id:protected] => 4431
[old_id:protected] =>
[elcosh_id:protected] => d001661
[type:protected] => document
[display_type:protected] => HTML only (and links)
[user_id:protected] => 0
[language_id:protected] => 1
[tagging_id:protected] => Mike Aguilar
[priority_id:protected] => 1
[title:protected] => Toolbox Talk: Challenges Preventing Falling Objects
[total_pages:protected] => 0
[billed_pages:protected] => 0
[publication_number:protected] =>
[part_of:protected] =>
[keywords:protected] => dropped objects, falling objects, struck by incidents, struck by fatalities
[comments:protected] =>
[summary:protected] => The CPWR Toolbox Talk on Challenges Preventing Falling Objects addresses the hazards of being struck by falling objects on the job site. The resource includes a brief example, steps to prevent a related injury, and questions for discussion. It includes a graphic that illustrates a group workers observing a scaffold free of debris during high winds, which can be posted in a central location as a reminder of steps to work safely.
Available in
English and
Spanish.
[transition_comments:protected] =>
[external_link:protected] =>
[consol_link:protected] =>
[more_like_this:protected] => d001234,d001238,d001244,d001251,d001253,d001260,d001268,d001278
[permission_given_by:protected] =>
[published:protected] => T
[billable:protected] => F
[img_name:protected] =>
[img_ext:protected] =>
[img_width:protected] =>
[img_height:protected] =>
[img_credit:protected] =>
[img_practice:protected] =>
[vid_source_id:protected] =>
[vid_running_time:protected] =>
[vid_intended_audience:protected] =>
[vid_acquisition_info:protected] =>
[vid_cost:protected] =>
[vid_producer:protected] =>
[vid_filename:protected] =>
[vid_filename_downloadable:protected] =>
[date_summary:protected] =>
[date_permission_requested:protected] =>
[date_permission_received:protected] =>
[date_review_needed:protected] =>
[date_received:protected] => 06/10/22
[date_completed:protected] => 06/10/22
[date_billed:protected] =>
[date_modified:protected] => 05/22/23
[collBokExports:protected] =>
[lastBokExportCriteria:BaseElcoshItem:private] =>
[alreadyInSave:protected] =>
[alreadyInValidation:protected] =>
[validationFailures:protected] => Array
(
)
[_new:BaseObject:private] =>
[_deleted:BaseObject:private] =>
[modifiedColumns:protected] => Array
(
)
)
)
[2] => Search_Result Object
(
[title] => Toolbox Talk: Tower Crane Safety
[image] => /record/images/notavailable-p.png
[blurb] => The CPWR Toolbox Talk on Tower Crane Safety addresses the potential hazards of Tower Cranes and the importance of following procedure before and durin...
[category] => Array
(
[0] => 11
[1] => 12
[2] => 18
[3] => 70
[4] => 87
[5] => 88
[6] => 91
[7] => 90
[8] => 92
[9] => 100
)
[labels] => Array
(
[0] => Cranes & Hoists
[1] => Work Environment
[2] => Hazards
[3] => Crushed/Struck By
[6] => Motor Vehicles/Heavy Equipment
[9] => Operating Engineer
[10] => Trades
[11] => Commercial & Institutional
[12] => Jobsites
[13] => Demolition
[15] => Heavy & Highway
[17] => Industrial
[19] => LEED/Green Construction
[21] => Toolbox Talks
[22] => Documents
[23] => Media & Documents
)
[type] => Toolbox Talks
[sub_category] =>
[url] => /document/4427/d001657/Toolbox%2BTalk%253A%2BTower%2BCrane%2BSafety.html
[item:protected] => DocumentRecord Object
(
[records:protected] => Array
(
)
[recordId:protected] =>
[searchWordClass:protected] =>
[searchWordPeerClass:protected] =>
[bok_record:protected] =>
[authors:protected] =>
[organizations:protected] =>
[collections:protected] =>
[categories:protected] => Array
(
[11] => Category Object
(
[languages:protected] =>
[bok_resources:protected] =>
[bok_topics:protected] =>
[bok_keywords:protected] =>
[id:protected] => 11
[type:protected] => category
[parent:protected] => 7
[label:protected] => Cranes & Hoists
[alreadyInSave:protected] =>
[alreadyInValidation:protected] =>
[validationFailures:protected] => Array
(
)
[_new:BaseObject:private] =>
[_deleted:BaseObject:private] =>
[modifiedColumns:protected] => Array
(
)
)
[12] => Category Object
(
[languages:protected] =>
[bok_resources:protected] =>
[bok_topics:protected] =>
[bok_keywords:protected] =>
[id:protected] => 12
[type:protected] => category
[parent:protected] => 7
[label:protected] => Crushed/Struck By
[alreadyInSave:protected] =>
[alreadyInValidation:protected] =>
[validationFailures:protected] => Array
(
)
[_new:BaseObject:private] =>
[_deleted:BaseObject:private] =>
[modifiedColumns:protected] => Array
(
)
)
[18] => Category Object
(
[languages:protected] =>
[bok_resources:protected] =>
[bok_topics:protected] =>
[bok_keywords:protected] =>
[id:protected] => 18
[type:protected] => category
[parent:protected] => 7
[label:protected] => Motor Vehicles/Heavy Equipment
[alreadyInSave:protected] =>
[alreadyInValidation:protected] =>
[validationFailures:protected] => Array
(
)
[_new:BaseObject:private] =>
[_deleted:BaseObject:private] =>
[modifiedColumns:protected] => Array
(
)
)
[70] => Category Object
(
[languages:protected] =>
[bok_resources:protected] =>
[bok_topics:protected] =>
[bok_keywords:protected] =>
[id:protected] => 70
[type:protected] => category
[parent:protected] => 2
[label:protected] => Operating Engineer
[alreadyInSave:protected] =>
[alreadyInValidation:protected] =>
[validationFailures:protected] => Array
(
)
[_new:BaseObject:private] =>
[_deleted:BaseObject:private] =>
[modifiedColumns:protected] => Array
(
)
)
[87] => Category Object
(
[languages:protected] =>
[bok_resources:protected] =>
[bok_topics:protected] =>
[bok_keywords:protected] =>
[id:protected] => 87
[type:protected] => category
[parent:protected] => 3
[label:protected] => Commercial & Institutional
[alreadyInSave:protected] =>
[alreadyInValidation:protected] =>
[validationFailures:protected] => Array
(
)
[_new:BaseObject:private] =>
[_deleted:BaseObject:private] =>
[modifiedColumns:protected] => Array
(
)
)
[88] => Category Object
(
[languages:protected] =>
[bok_resources:protected] =>
[bok_topics:protected] =>
[bok_keywords:protected] =>
[id:protected] => 88
[type:protected] => category
[parent:protected] => 3
[label:protected] => Demolition
[alreadyInSave:protected] =>
[alreadyInValidation:protected] =>
[validationFailures:protected] => Array
(
)
[_new:BaseObject:private] =>
[_deleted:BaseObject:private] =>
[modifiedColumns:protected] => Array
(
)
)
[91] => Category Object
(
[languages:protected] =>
[bok_resources:protected] =>
[bok_topics:protected] =>
[bok_keywords:protected] =>
[id:protected] => 91
[type:protected] => category
[parent:protected] => 3
[label:protected] => Heavy & Highway
[alreadyInSave:protected] =>
[alreadyInValidation:protected] =>
[validationFailures:protected] => Array
(
)
[_new:BaseObject:private] =>
[_deleted:BaseObject:private] =>
[modifiedColumns:protected] => Array
(
)
)
[90] => Category Object
(
[languages:protected] =>
[bok_resources:protected] =>
[bok_topics:protected] =>
[bok_keywords:protected] =>
[id:protected] => 90
[type:protected] => category
[parent:protected] => 3
[label:protected] => Industrial
[alreadyInSave:protected] =>
[alreadyInValidation:protected] =>
[validationFailures:protected] => Array
(
)
[_new:BaseObject:private] =>
[_deleted:BaseObject:private] =>
[modifiedColumns:protected] => Array
(
)
)
[92] => Category Object
(
[languages:protected] =>
[bok_resources:protected] =>
[bok_topics:protected] =>
[bok_keywords:protected] =>
[id:protected] => 92
[type:protected] => category
[parent:protected] => 3
[label:protected] => LEED/Green Construction
[alreadyInSave:protected] =>
[alreadyInValidation:protected] =>
[validationFailures:protected] => Array
(
)
[_new:BaseObject:private] =>
[_deleted:BaseObject:private] =>
[modifiedColumns:protected] => Array
(
)
)
[100] => Category Object
(
[languages:protected] =>
[bok_resources:protected] =>
[bok_topics:protected] =>
[bok_keywords:protected] =>
[id:protected] => 100
[type:protected] => category
[parent:protected] => 6
[label:protected] => Toolbox Talks
[alreadyInSave:protected] =>
[alreadyInValidation:protected] =>
[validationFailures:protected] => Array
(
)
[_new:BaseObject:private] =>
[_deleted:BaseObject:private] =>
[modifiedColumns:protected] => Array
(
)
)
)
[categories_initialized:protected] => 1
[mapped_items:protected] =>
[content:protected] =>
[files:protected] =>
[language:protected] => Language Object
(
[id:protected] => 1
[code:protected] => en
[name:protected] => English
[alreadyInSave:protected] =>
[alreadyInValidation:protected] =>
[validationFailures:protected] => Array
(
)
[_new:BaseObject:private] =>
[_deleted:BaseObject:private] =>
[modifiedColumns:protected] => Array
(
)
)
[old_record:protected] =>
[id:protected] => 4427
[old_id:protected] =>
[elcosh_id:protected] => d001657
[type:protected] => document
[display_type:protected] => HTML only (and links)
[user_id:protected] => 0
[language_id:protected] => 1
[tagging_id:protected] => Mike Aguilar
[priority_id:protected] => 1
[title:protected] => Toolbox Talk: Tower Crane Safety
[total_pages:protected] => 0
[billed_pages:protected] => 0
[publication_number:protected] =>
[part_of:protected] =>
[keywords:protected] => Tower Crane, Crane, Stability, Tipping, Lift Zone Safety, Lift, Zone, Safety, Struck by
[comments:protected] =>
[summary:protected] => The CPWR Toolbox Talk on Tower Crane Safety addresses the potential hazards of Tower Cranes and the importance of following procedure before and during Tower Crane operation. The resource includes a brief example, steps to prevent a related injury, and questions for discussion. It includes a graphic that illustrates a worker inspecting a Tower Crane before operation, which can be posted in a central location as a reminder of steps to work safely.
Available in
English and
Spanish.
[transition_comments:protected] =>
[external_link:protected] =>
[consol_link:protected] =>
[more_like_this:protected] => d001234,d001238,d001250,d001251,d001253,d001258,d001262,d001273
[permission_given_by:protected] =>
[published:protected] => T
[billable:protected] => F
[img_name:protected] =>
[img_ext:protected] => jpg
[img_width:protected] =>
[img_height:protected] =>
[img_credit:protected] =>
[img_practice:protected] =>
[vid_source_id:protected] =>
[vid_running_time:protected] =>
[vid_intended_audience:protected] =>
[vid_acquisition_info:protected] =>
[vid_cost:protected] =>
[vid_producer:protected] =>
[vid_filename:protected] =>
[vid_filename_downloadable:protected] =>
[date_summary:protected] =>
[date_permission_requested:protected] =>
[date_permission_received:protected] =>
[date_review_needed:protected] =>
[date_received:protected] => 12/23/21
[date_completed:protected] => 12/23/21
[date_billed:protected] =>
[date_modified:protected] => 05/19/23
[collBokExports:protected] =>
[lastBokExportCriteria:BaseElcoshItem:private] =>
[alreadyInSave:protected] =>
[alreadyInValidation:protected] =>
[validationFailures:protected] => Array
(
)
[_new:BaseObject:private] =>
[_deleted:BaseObject:private] =>
[modifiedColumns:protected] => Array
(
)
)
)
[3] => Search_Result Object
(
[title] => Toolbox Talk: Work Zone Safety: Working Around Vehicles
[image] => /record/images/notavailable-p.png
[blurb] => The CPWR Toolbox Talk on Working Around Vehicles in the Work Zone addresses methods to avoid being struck-by a vehicle on a construction site. The res...
[category] => Array
(
[0] => 12
[1] => 18
[2] => 52
[3] => 57
[4] => 70
[5] => 85
[6] => 87
[7] => 88
[8] => 89
[9] => 91
[10] => 90
[11] => 92
[12] => 93
[13] => 94
[14] => 95
[15] => 100
)
[labels] => Array
(
[0] => Crushed/Struck By
[1] => Work Environment
[2] => Hazards
[3] => Motor Vehicles/Heavy Equipment
[6] => Commercial Diver
[7] => Trades
[8] => Flagger
[10] => Operating Engineer
[12] => Truck Driver
[14] => Commercial & Institutional
[15] => Jobsites
[16] => Demolition
[18] => Disasters
[20] => Heavy & Highway
[22] => Industrial
[24] => LEED/Green Construction
[26] => Renovations
[28] => Residential
[30] => Underground
[32] => Toolbox Talks
[33] => Documents
[34] => Media & Documents
)
[type] => Toolbox Talks
[sub_category] =>
[url] => /document/4428/d001658/Toolbox%2BTalk%253A%2BWork%2BZone%2BSafety%253A%2BWorking%2BAround%2BVehicles.html
[item:protected] => DocumentRecord Object
(
[records:protected] => Array
(
)
[recordId:protected] =>
[searchWordClass:protected] =>
[searchWordPeerClass:protected] =>
[bok_record:protected] =>
[authors:protected] =>
[organizations:protected] =>
[collections:protected] =>
[categories:protected] => Array
(
[12] => Category Object
(
[languages:protected] =>
[bok_resources:protected] =>
[bok_topics:protected] =>
[bok_keywords:protected] =>
[id:protected] => 12
[type:protected] => category
[parent:protected] => 7
[label:protected] => Crushed/Struck By
[alreadyInSave:protected] =>
[alreadyInValidation:protected] =>
[validationFailures:protected] => Array
(
)
[_new:BaseObject:private] =>
[_deleted:BaseObject:private] =>
[modifiedColumns:protected] => Array
(
)
)
[18] => Category Object
(
[languages:protected] =>
[bok_resources:protected] =>
[bok_topics:protected] =>
[bok_keywords:protected] =>
[id:protected] => 18
[type:protected] => category
[parent:protected] => 7
[label:protected] => Motor Vehicles/Heavy Equipment
[alreadyInSave:protected] =>
[alreadyInValidation:protected] =>
[validationFailures:protected] => Array
(
)
[_new:BaseObject:private] =>
[_deleted:BaseObject:private] =>
[modifiedColumns:protected] => Array
(
)
)
[52] => Category Object
(
[languages:protected] =>
[bok_resources:protected] =>
[bok_topics:protected] =>
[bok_keywords:protected] =>
[id:protected] => 52
[type:protected] => category
[parent:protected] => 2
[label:protected] => Commercial Diver
[alreadyInSave:protected] =>
[alreadyInValidation:protected] =>
[validationFailures:protected] => Array
(
)
[_new:BaseObject:private] =>
[_deleted:BaseObject:private] =>
[modifiedColumns:protected] => Array
(
)
)
[57] => Category Object
(
[languages:protected] =>
[bok_resources:protected] =>
[bok_topics:protected] =>
[bok_keywords:protected] =>
[id:protected] => 57
[type:protected] => category
[parent:protected] => 2
[label:protected] => Flagger
[alreadyInSave:protected] =>
[alreadyInValidation:protected] =>
[validationFailures:protected] => Array
(
)
[_new:BaseObject:private] =>
[_deleted:BaseObject:private] =>
[modifiedColumns:protected] => Array
(
)
)
[70] => Category Object
(
[languages:protected] =>
[bok_resources:protected] =>
[bok_topics:protected] =>
[bok_keywords:protected] =>
[id:protected] => 70
[type:protected] => category
[parent:protected] => 2
[label:protected] => Operating Engineer
[alreadyInSave:protected] =>
[alreadyInValidation:protected] =>
[validationFailures:protected] => Array
(
)
[_new:BaseObject:private] =>
[_deleted:BaseObject:private] =>
[modifiedColumns:protected] => Array
(
)
)
[85] => Category Object
(
[languages:protected] =>
[bok_resources:protected] =>
[bok_topics:protected] =>
[bok_keywords:protected] =>
[id:protected] => 85
[type:protected] => category
[parent:protected] => 2
[label:protected] => Truck Driver
[alreadyInSave:protected] =>
[alreadyInValidation:protected] =>
[validationFailures:protected] => Array
(
)
[_new:BaseObject:private] =>
[_deleted:BaseObject:private] =>
[modifiedColumns:protected] => Array
(
)
)
[87] => Category Object
(
[languages:protected] =>
[bok_resources:protected] =>
[bok_topics:protected] =>
[bok_keywords:protected] =>
[id:protected] => 87
[type:protected] => category
[parent:protected] => 3
[label:protected] => Commercial & Institutional
[alreadyInSave:protected] =>
[alreadyInValidation:protected] =>
[validationFailures:protected] => Array
(
)
[_new:BaseObject:private] =>
[_deleted:BaseObject:private] =>
[modifiedColumns:protected] => Array
(
)
)
[88] => Category Object
(
[languages:protected] =>
[bok_resources:protected] =>
[bok_topics:protected] =>
[bok_keywords:protected] =>
[id:protected] => 88
[type:protected] => category
[parent:protected] => 3
[label:protected] => Demolition
[alreadyInSave:protected] =>
[alreadyInValidation:protected] =>
[validationFailures:protected] => Array
(
)
[_new:BaseObject:private] =>
[_deleted:BaseObject:private] =>
[modifiedColumns:protected] => Array
(
)
)
[89] => Category Object
(
[languages:protected] =>
[bok_resources:protected] =>
[bok_topics:protected] =>
[bok_keywords:protected] =>
[id:protected] => 89
[type:protected] => category
[parent:protected] => 3
[label:protected] => Disasters
[alreadyInSave:protected] =>
[alreadyInValidation:protected] =>
[validationFailures:protected] => Array
(
)
[_new:BaseObject:private] =>
[_deleted:BaseObject:private] =>
[modifiedColumns:protected] => Array
(
)
)
[91] => Category Object
(
[languages:protected] =>
[bok_resources:protected] =>
[bok_topics:protected] =>
[bok_keywords:protected] =>
[id:protected] => 91
[type:protected] => category
[parent:protected] => 3
[label:protected] => Heavy & Highway
[alreadyInSave:protected] =>
[alreadyInValidation:protected] =>
[validationFailures:protected] => Array
(
)
[_new:BaseObject:private] =>
[_deleted:BaseObject:private] =>
[modifiedColumns:protected] => Array
(
)
)
[90] => Category Object
(
[languages:protected] =>
[bok_resources:protected] =>
[bok_topics:protected] =>
[bok_keywords:protected] =>
[id:protected] => 90
[type:protected] => category
[parent:protected] => 3
[label:protected] => Industrial
[alreadyInSave:protected] =>
[alreadyInValidation:protected] =>
[validationFailures:protected] => Array
(
)
[_new:BaseObject:private] =>
[_deleted:BaseObject:private] =>
[modifiedColumns:protected] => Array
(
)
)
[92] => Category Object
(
[languages:protected] =>
[bok_resources:protected] =>
[bok_topics:protected] =>
[bok_keywords:protected] =>
[id:protected] => 92
[type:protected] => category
[parent:protected] => 3
[label:protected] => LEED/Green Construction
[alreadyInSave:protected] =>
[alreadyInValidation:protected] =>
[validationFailures:protected] => Array
(
)
[_new:BaseObject:private] =>
[_deleted:BaseObject:private] =>
[modifiedColumns:protected] => Array
(
)
)
[93] => Category Object
(
[languages:protected] =>
[bok_resources:protected] =>
[bok_topics:protected] =>
[bok_keywords:protected] =>
[id:protected] => 93
[type:protected] => category
[parent:protected] => 3
[label:protected] => Renovations
[alreadyInSave:protected] =>
[alreadyInValidation:protected] =>
[validationFailures:protected] => Array
(
)
[_new:BaseObject:private] =>
[_deleted:BaseObject:private] =>
[modifiedColumns:protected] => Array
(
)
)
[94] => Category Object
(
[languages:protected] =>
[bok_resources:protected] =>
[bok_topics:protected] =>
[bok_keywords:protected] =>
[id:protected] => 94
[type:protected] => category
[parent:protected] => 3
[label:protected] => Residential
[alreadyInSave:protected] =>
[alreadyInValidation:protected] =>
[validationFailures:protected] => Array
(
)
[_new:BaseObject:private] =>
[_deleted:BaseObject:private] =>
[modifiedColumns:protected] => Array
(
)
)
[95] => Category Object
(
[languages:protected] =>
[bok_resources:protected] =>
[bok_topics:protected] =>
[bok_keywords:protected] =>
[id:protected] => 95
[type:protected] => category
[parent:protected] => 3
[label:protected] => Underground
[alreadyInSave:protected] =>
[alreadyInValidation:protected] =>
[validationFailures:protected] => Array
(
)
[_new:BaseObject:private] =>
[_deleted:BaseObject:private] =>
[modifiedColumns:protected] => Array
(
)
)
[100] => Category Object
(
[languages:protected] =>
[bok_resources:protected] =>
[bok_topics:protected] =>
[bok_keywords:protected] =>
[id:protected] => 100
[type:protected] => category
[parent:protected] => 6
[label:protected] => Toolbox Talks
[alreadyInSave:protected] =>
[alreadyInValidation:protected] =>
[validationFailures:protected] => Array
(
)
[_new:BaseObject:private] =>
[_deleted:BaseObject:private] =>
[modifiedColumns:protected] => Array
(
)
)
)
[categories_initialized:protected] => 1
[mapped_items:protected] =>
[content:protected] =>
[files:protected] =>
[language:protected] => Language Object
(
[id:protected] => 1
[code:protected] => en
[name:protected] => English
[alreadyInSave:protected] =>
[alreadyInValidation:protected] =>
[validationFailures:protected] => Array
(
)
[_new:BaseObject:private] =>
[_deleted:BaseObject:private] =>
[modifiedColumns:protected] => Array
(
)
)
[old_record:protected] =>
[id:protected] => 4428
[old_id:protected] =>
[elcosh_id:protected] => d001658
[type:protected] => document
[display_type:protected] => HTML only (and links)
[user_id:protected] => 0
[language_id:protected] => 1
[tagging_id:protected] => Daniela Caceres
[priority_id:protected] => 1
[title:protected] => Toolbox Talk: Work Zone Safety: Working Around Vehicles
[total_pages:protected] => 0
[billed_pages:protected] => 0
[publication_number:protected] =>
[part_of:protected] =>
[keywords:protected] => Struck, Struck by, Vehicle, Work Zone Safety, Truck, Operator, Driver, Mobile Equipment
[comments:protected] =>
[summary:protected] => The CPWR Toolbox Talk on Working Around Vehicles in the Work Zone addresses methods to avoid being struck-by a vehicle on a construction site. The resource includes a case example, steps to prevent a related injury, and questions for discussion. It includes a graphic that illustrates the hazard, which can be posted in a central location as a reminder of steps to work safely. Available in
English and
Spanish.
[transition_comments:protected] =>
[external_link:protected] =>
[consol_link:protected] =>
[more_like_this:protected] => d001640
[permission_given_by:protected] =>
[published:protected] => T
[billable:protected] => F
[img_name:protected] =>
[img_ext:protected] =>
[img_width:protected] =>
[img_height:protected] =>
[img_credit:protected] =>
[img_practice:protected] =>
[vid_source_id:protected] =>
[vid_running_time:protected] =>
[vid_intended_audience:protected] =>
[vid_acquisition_info:protected] =>
[vid_cost:protected] =>
[vid_producer:protected] =>
[vid_filename:protected] =>
[vid_filename_downloadable:protected] =>
[date_summary:protected] =>
[date_permission_requested:protected] =>
[date_permission_received:protected] =>
[date_review_needed:protected] =>
[date_received:protected] => 12/23/21
[date_completed:protected] => 12/23/21
[date_billed:protected] =>
[date_modified:protected] => 05/19/23
[collBokExports:protected] =>
[lastBokExportCriteria:BaseElcoshItem:private] =>
[alreadyInSave:protected] =>
[alreadyInValidation:protected] =>
[validationFailures:protected] => Array
(
)
[_new:BaseObject:private] =>
[_deleted:BaseObject:private] =>
[modifiedColumns:protected] => Array
(
)
)
)
[4] => Search_Result Object
(
[title] => Construction Dive -- DeWalt's Jobsite Pro headphones recalled for fire hazards
[image] => /record/images/notavailable-p.png
[blurb] => A recall notice by the United States Consumer Product Safety Commission affects over 300,000 DeWalt Jobsite Pro Headphones. The recall is a result of...
[category] => Array
(
[0] => 16
[1] => 44
[2] => 45
[3] => 46
[4] => 47
[5] => 48
[6] => 49
[7] => 50
[8] => 51
[9] => 52
[10] => 53
[11] => 54
[12] => 55
[13] => 56
[14] => 57
[15] => 58
[16] => 59
[17] => 60
[18] => 61
[19] => 64
[20] => 65
[21] => 66
[22] => 67
[23] => 68
[24] => 69
[25] => 70
[26] => 71
[27] => 72
[28] => 73
[29] => 74
[30] => 75
[31] => 76
[32] => 77
[33] => 63
[34] => 78
[35] => 79
[36] => 80
[37] => 81
[38] => 82
[39] => 62
[40] => 83
[41] => 84
[42] => 85
[43] => 86
[44] => 87
[45] => 88
[46] => 89
[47] => 91
[48] => 90
[49] => 92
[50] => 93
[51] => 94
[52] => 95
)
[labels] => Array
(
[0] => Fire & Explosions
[1] => Work Environment
[2] => Hazards
[3] => Acoustical Ceiling Carpenter
[4] => Trades
[5] => Asbestos/Insulator
[7] => Boilermaker
[9] => Bricklayer
[11] => Cabinetmaker
[13] => Carpenter
[15] => Carpet Layer
[17] => Cement Mason
[19] => Commercial Diver
[21] => Concrete Polisher
[23] => Drywall Applicator Specialist
[25] => Electrical Worker
[27] => Elevator Constructor
[29] => Flagger
[31] => Glazier
[33] => Hazardous Waste Cleanup
[35] => HVAC
[37] => Interior Systems Carpenter
[39] => Laborer
[41] => Landscaper
[43] => Lather
[45] => Lead Abatement Worker
[47] => Maintenance Worker
[49] => Millwright
[51] => Operating Engineer
[53] => Painter
[55] => Paper Hanger
[57] => PCC/Restoration
[59] => Pile Driver
[61] => Plasterer
[63] => Plumber/Pipefitter
[65] => Refractory Worker
[67] => Reinforcing Ironworker
[69] => Roofer/Waterproofer
[71] => Scaffold Erector
[73] => Sheetmetal Worker
[75] => Sprinkler Fitter
[77] => Stonemason
[79] => Structural Ironworker
[81] => Terrazzo Worker
[83] => Tile Setter
[85] => Truck Driver
[87] => Welder
[89] => Commercial & Institutional
[90] => Jobsites
[91] => Demolition
[93] => Disasters
[95] => Heavy & Highway
[97] => Industrial
[99] => LEED/Green Construction
[101] => Renovations
[103] => Residential
[105] => Underground
)
[type] =>
[sub_category] =>
[url] => /document/4426/d001656/Construction%2BDive%2B--%2BDeWalt%2527s%2BJobsite%2BPro%2Bheadphones%2Brecalled%2Bfor%2Bfire%2Bhazards.html
[item:protected] => DocumentRecord Object
(
[records:protected] => Array
(
)
[recordId:protected] =>
[searchWordClass:protected] =>
[searchWordPeerClass:protected] =>
[bok_record:protected] =>
[authors:protected] =>
[organizations:protected] =>
[collections:protected] =>
[categories:protected] => Array
(
[16] => Category Object
(
[languages:protected] =>
[bok_resources:protected] =>
[bok_topics:protected] =>
[bok_keywords:protected] =>
[id:protected] => 16
[type:protected] => category
[parent:protected] => 7
[label:protected] => Fire & Explosions
[alreadyInSave:protected] =>
[alreadyInValidation:protected] =>
[validationFailures:protected] => Array
(
)
[_new:BaseObject:private] =>
[_deleted:BaseObject:private] =>
[modifiedColumns:protected] => Array
(
)
)
[44] => Category Object
(
[languages:protected] =>
[bok_resources:protected] =>
[bok_topics:protected] =>
[bok_keywords:protected] =>
[id:protected] => 44
[type:protected] => category
[parent:protected] => 2
[label:protected] => Acoustical Ceiling Carpenter
[alreadyInSave:protected] =>
[alreadyInValidation:protected] =>
[validationFailures:protected] => Array
(
)
[_new:BaseObject:private] =>
[_deleted:BaseObject:private] =>
[modifiedColumns:protected] => Array
(
)
)
[45] => Category Object
(
[languages:protected] =>
[bok_resources:protected] =>
[bok_topics:protected] =>
[bok_keywords:protected] =>
[id:protected] => 45
[type:protected] => category
[parent:protected] => 2
[label:protected] => Asbestos/Insulator
[alreadyInSave:protected] =>
[alreadyInValidation:protected] =>
[validationFailures:protected] => Array
(
)
[_new:BaseObject:private] =>
[_deleted:BaseObject:private] =>
[modifiedColumns:protected] => Array
(
)
)
[46] => Category Object
(
[languages:protected] =>
[bok_resources:protected] =>
[bok_topics:protected] =>
[bok_keywords:protected] =>
[id:protected] => 46
[type:protected] => category
[parent:protected] => 2
[label:protected] => Boilermaker
[alreadyInSave:protected] =>
[alreadyInValidation:protected] =>
[validationFailures:protected] => Array
(
)
[_new:BaseObject:private] =>
[_deleted:BaseObject:private] =>
[modifiedColumns:protected] => Array
(
)
)
[47] => Category Object
(
[languages:protected] =>
[bok_resources:protected] =>
[bok_topics:protected] =>
[bok_keywords:protected] =>
[id:protected] => 47
[type:protected] => category
[parent:protected] => 2
[label:protected] => Bricklayer
[alreadyInSave:protected] =>
[alreadyInValidation:protected] =>
[validationFailures:protected] => Array
(
)
[_new:BaseObject:private] =>
[_deleted:BaseObject:private] =>
[modifiedColumns:protected] => Array
(
)
)
[48] => Category Object
(
[languages:protected] =>
[bok_resources:protected] =>
[bok_topics:protected] =>
[bok_keywords:protected] =>
[id:protected] => 48
[type:protected] => category
[parent:protected] => 2
[label:protected] => Cabinetmaker
[alreadyInSave:protected] =>
[alreadyInValidation:protected] =>
[validationFailures:protected] => Array
(
)
[_new:BaseObject:private] =>
[_deleted:BaseObject:private] =>
[modifiedColumns:protected] => Array
(
)
)
[49] => Category Object
(
[languages:protected] =>
[bok_resources:protected] =>
[bok_topics:protected] =>
[bok_keywords:protected] =>
[id:protected] => 49
[type:protected] => category
[parent:protected] => 2
[label:protected] => Carpenter
[alreadyInSave:protected] =>
[alreadyInValidation:protected] =>
[validationFailures:protected] => Array
(
)
[_new:BaseObject:private] =>
[_deleted:BaseObject:private] =>
[modifiedColumns:protected] => Array
(
)
)
[50] => Category Object
(
[languages:protected] =>
[bok_resources:protected] =>
[bok_topics:protected] =>
[bok_keywords:protected] =>
[id:protected] => 50
[type:protected] => category
[parent:protected] => 2
[label:protected] => Carpet Layer
[alreadyInSave:protected] =>
[alreadyInValidation:protected] =>
[validationFailures:protected] => Array
(
)
[_new:BaseObject:private] =>
[_deleted:BaseObject:private] =>
[modifiedColumns:protected] => Array
(
)
)
[51] => Category Object
(
[languages:protected] =>
[bok_resources:protected] =>
[bok_topics:protected] =>
[bok_keywords:protected] =>
[id:protected] => 51
[type:protected] => category
[parent:protected] => 2
[label:protected] => Cement Mason
[alreadyInSave:protected] =>
[alreadyInValidation:protected] =>
[validationFailures:protected] => Array
(
)
[_new:BaseObject:private] =>
[_deleted:BaseObject:private] =>
[modifiedColumns:protected] => Array
(
)
)
[52] => Category Object
(
[languages:protected] =>
[bok_resources:protected] =>
[bok_topics:protected] =>
[bok_keywords:protected] =>
[id:protected] => 52
[type:protected] => category
[parent:protected] => 2
[label:protected] => Commercial Diver
[alreadyInSave:protected] =>
[alreadyInValidation:protected] =>
[validationFailures:protected] => Array
(
)
[_new:BaseObject:private] =>
[_deleted:BaseObject:private] =>
[modifiedColumns:protected] => Array
(
)
)
[53] => Category Object
(
[languages:protected] =>
[bok_resources:protected] =>
[bok_topics:protected] =>
[bok_keywords:protected] =>
[id:protected] => 53
[type:protected] => category
[parent:protected] => 2
[label:protected] => Concrete Polisher
[alreadyInSave:protected] =>
[alreadyInValidation:protected] =>
[validationFailures:protected] => Array
(
)
[_new:BaseObject:private] =>
[_deleted:BaseObject:private] =>
[modifiedColumns:protected] => Array
(
)
)
[54] => Category Object
(
[languages:protected] =>
[bok_resources:protected] =>
[bok_topics:protected] =>
[bok_keywords:protected] =>
[id:protected] => 54
[type:protected] => category
[parent:protected] => 2
[label:protected] => Drywall Applicator Specialist
[alreadyInSave:protected] =>
[alreadyInValidation:protected] =>
[validationFailures:protected] => Array
(
)
[_new:BaseObject:private] =>
[_deleted:BaseObject:private] =>
[modifiedColumns:protected] => Array
(
)
)
[55] => Category Object
(
[languages:protected] =>
[bok_resources:protected] =>
[bok_topics:protected] =>
[bok_keywords:protected] =>
[id:protected] => 55
[type:protected] => category
[parent:protected] => 2
[label:protected] => Electrical Worker
[alreadyInSave:protected] =>
[alreadyInValidation:protected] =>
[validationFailures:protected] => Array
(
)
[_new:BaseObject:private] =>
[_deleted:BaseObject:private] =>
[modifiedColumns:protected] => Array
(
)
)
[56] => Category Object
(
[languages:protected] =>
[bok_resources:protected] =>
[bok_topics:protected] =>
[bok_keywords:protected] =>
[id:protected] => 56
[type:protected] => category
[parent:protected] => 2
[label:protected] => Elevator Constructor
[alreadyInSave:protected] =>
[alreadyInValidation:protected] =>
[validationFailures:protected] => Array
(
)
[_new:BaseObject:private] =>
[_deleted:BaseObject:private] =>
[modifiedColumns:protected] => Array
(
)
)
[57] => Category Object
(
[languages:protected] =>
[bok_resources:protected] =>
[bok_topics:protected] =>
[bok_keywords:protected] =>
[id:protected] => 57
[type:protected] => category
[parent:protected] => 2
[label:protected] => Flagger
[alreadyInSave:protected] =>
[alreadyInValidation:protected] =>
[validationFailures:protected] => Array
(
)
[_new:BaseObject:private] =>
[_deleted:BaseObject:private] =>
[modifiedColumns:protected] => Array
(
)
)
[58] => Category Object
(
[languages:protected] =>
[bok_resources:protected] =>
[bok_topics:protected] =>
[bok_keywords:protected] =>
[id:protected] => 58
[type:protected] => category
[parent:protected] => 2
[label:protected] => Glazier
[alreadyInSave:protected] =>
[alreadyInValidation:protected] =>
[validationFailures:protected] => Array
(
)
[_new:BaseObject:private] =>
[_deleted:BaseObject:private] =>
[modifiedColumns:protected] => Array
(
)
)
[59] => Category Object
(
[languages:protected] =>
[bok_resources:protected] =>
[bok_topics:protected] =>
[bok_keywords:protected] =>
[id:protected] => 59
[type:protected] => category
[parent:protected] => 2
[label:protected] => Hazardous Waste Cleanup
[alreadyInSave:protected] =>
[alreadyInValidation:protected] =>
[validationFailures:protected] => Array
(
)
[_new:BaseObject:private] =>
[_deleted:BaseObject:private] =>
[modifiedColumns:protected] => Array
(
)
)
[60] => Category Object
(
[languages:protected] =>
[bok_resources:protected] =>
[bok_topics:protected] =>
[bok_keywords:protected] =>
[id:protected] => 60
[type:protected] => category
[parent:protected] => 2
[label:protected] => HVAC
[alreadyInSave:protected] =>
[alreadyInValidation:protected] =>
[validationFailures:protected] => Array
(
)
[_new:BaseObject:private] =>
[_deleted:BaseObject:private] =>
[modifiedColumns:protected] => Array
(
)
)
[61] => Category Object
(
[languages:protected] =>
[bok_resources:protected] =>
[bok_topics:protected] =>
[bok_keywords:protected] =>
[id:protected] => 61
[type:protected] => category
[parent:protected] => 2
[label:protected] => Interior Systems Carpenter
[alreadyInSave:protected] =>
[alreadyInValidation:protected] =>
[validationFailures:protected] => Array
(
)
[_new:BaseObject:private] =>
[_deleted:BaseObject:private] =>
[modifiedColumns:protected] => Array
(
)
)
[64] => Category Object
(
[languages:protected] =>
[bok_resources:protected] =>
[bok_topics:protected] =>
[bok_keywords:protected] =>
[id:protected] => 64
[type:protected] => category
[parent:protected] => 2
[label:protected] => Laborer
[alreadyInSave:protected] =>
[alreadyInValidation:protected] =>
[validationFailures:protected] => Array
(
)
[_new:BaseObject:private] =>
[_deleted:BaseObject:private] =>
[modifiedColumns:protected] => Array
(
)
)
[65] => Category Object
(
[languages:protected] =>
[bok_resources:protected] =>
[bok_topics:protected] =>
[bok_keywords:protected] =>
[id:protected] => 65
[type:protected] => category
[parent:protected] => 2
[label:protected] => Landscaper
[alreadyInSave:protected] =>
[alreadyInValidation:protected] =>
[validationFailures:protected] => Array
(
)
[_new:BaseObject:private] =>
[_deleted:BaseObject:private] =>
[modifiedColumns:protected] => Array
(
)
)
[66] => Category Object
(
[languages:protected] =>
[bok_resources:protected] =>
[bok_topics:protected] =>
[bok_keywords:protected] =>
[id:protected] => 66
[type:protected] => category
[parent:protected] => 2
[label:protected] => Lather
[alreadyInSave:protected] =>
[alreadyInValidation:protected] =>
[validationFailures:protected] => Array
(
)
[_new:BaseObject:private] =>
[_deleted:BaseObject:private] =>
[modifiedColumns:protected] => Array
(
)
)
[67] => Category Object
(
[languages:protected] =>
[bok_resources:protected] =>
[bok_topics:protected] =>
[bok_keywords:protected] =>
[id:protected] => 67
[type:protected] => category
[parent:protected] => 2
[label:protected] => Lead Abatement Worker
[alreadyInSave:protected] =>
[alreadyInValidation:protected] =>
[validationFailures:protected] => Array
(
)
[_new:BaseObject:private] =>
[_deleted:BaseObject:private] =>
[modifiedColumns:protected] => Array
(
)
)
[68] => Category Object
(
[languages:protected] =>
[bok_resources:protected] =>
[bok_topics:protected] =>
[bok_keywords:protected] =>
[id:protected] => 68
[type:protected] => category
[parent:protected] => 2
[label:protected] => Maintenance Worker
[alreadyInSave:protected] =>
[alreadyInValidation:protected] =>
[validationFailures:protected] => Array
(
)
[_new:BaseObject:private] =>
[_deleted:BaseObject:private] =>
[modifiedColumns:protected] => Array
(
)
)
[69] => Category Object
(
[languages:protected] =>
[bok_resources:protected] =>
[bok_topics:protected] =>
[bok_keywords:protected] =>
[id:protected] => 69
[type:protected] => category
[parent:protected] => 2
[label:protected] => Millwright
[alreadyInSave:protected] =>
[alreadyInValidation:protected] =>
[validationFailures:protected] => Array
(
)
[_new:BaseObject:private] =>
[_deleted:BaseObject:private] =>
[modifiedColumns:protected] => Array
(
)
)
[70] => Category Object
(
[languages:protected] =>
[bok_resources:protected] =>
[bok_topics:protected] =>
[bok_keywords:protected] =>
[id:protected] => 70
[type:protected] => category
[parent:protected] => 2
[label:protected] => Operating Engineer
[alreadyInSave:protected] =>
[alreadyInValidation:protected] =>
[validationFailures:protected] => Array
(
)
[_new:BaseObject:private] =>
[_deleted:BaseObject:private] =>
[modifiedColumns:protected] => Array
(
)
)
[71] => Category Object
(
[languages:protected] =>
[bok_resources:protected] =>
[bok_topics:protected] =>
[bok_keywords:protected] =>
[id:protected] => 71
[type:protected] => category
[parent:protected] => 2
[label:protected] => Painter
[alreadyInSave:protected] =>
[alreadyInValidation:protected] =>
[validationFailures:protected] => Array
(
)
[_new:BaseObject:private] =>
[_deleted:BaseObject:private] =>
[modifiedColumns:protected] => Array
(
)
)
[72] => Category Object
(
[languages:protected] =>
[bok_resources:protected] =>
[bok_topics:protected] =>
[bok_keywords:protected] =>
[id:protected] => 72
[type:protected] => category
[parent:protected] => 2
[label:protected] => Paper Hanger
[alreadyInSave:protected] =>
[alreadyInValidation:protected] =>
[validationFailures:protected] => Array
(
)
[_new:BaseObject:private] =>
[_deleted:BaseObject:private] =>
[modifiedColumns:protected] => Array
(
)
)
[73] => Category Object
(
[languages:protected] =>
[bok_resources:protected] =>
[bok_topics:protected] =>
[bok_keywords:protected] =>
[id:protected] => 73
[type:protected] => category
[parent:protected] => 2
[label:protected] => PCC/Restoration
[alreadyInSave:protected] =>
[alreadyInValidation:protected] =>
[validationFailures:protected] => Array
(
)
[_new:BaseObject:private] =>
[_deleted:BaseObject:private] =>
[modifiedColumns:protected] => Array
(
)
)
[74] => Category Object
(
[languages:protected] =>
[bok_resources:protected] =>
[bok_topics:protected] =>
[bok_keywords:protected] =>
[id:protected] => 74
[type:protected] => category
[parent:protected] => 2
[label:protected] => Pile Driver
[alreadyInSave:protected] =>
[alreadyInValidation:protected] =>
[validationFailures:protected] => Array
(
)
[_new:BaseObject:private] =>
[_deleted:BaseObject:private] =>
[modifiedColumns:protected] => Array
(
)
)
[75] => Category Object
(
[languages:protected] =>
[bok_resources:protected] =>
[bok_topics:protected] =>
[bok_keywords:protected] =>
[id:protected] => 75
[type:protected] => category
[parent:protected] => 2
[label:protected] => Plasterer
[alreadyInSave:protected] =>
[alreadyInValidation:protected] =>
[validationFailures:protected] => Array
(
)
[_new:BaseObject:private] =>
[_deleted:BaseObject:private] =>
[modifiedColumns:protected] => Array
(
)
)
[76] => Category Object
(
[languages:protected] =>
[bok_resources:protected] =>
[bok_topics:protected] =>
[bok_keywords:protected] =>
[id:protected] => 76
[type:protected] => category
[parent:protected] => 2
[label:protected] => Plumber/Pipefitter
[alreadyInSave:protected] =>
[alreadyInValidation:protected] =>
[validationFailures:protected] => Array
(
)
[_new:BaseObject:private] =>
[_deleted:BaseObject:private] =>
[modifiedColumns:protected] => Array
(
)
)
[77] => Category Object
(
[languages:protected] =>
[bok_resources:protected] =>
[bok_topics:protected] =>
[bok_keywords:protected] =>
[id:protected] => 77
[type:protected] => category
[parent:protected] => 2
[label:protected] => Refractory Worker
[alreadyInSave:protected] =>
[alreadyInValidation:protected] =>
[validationFailures:protected] => Array
(
)
[_new:BaseObject:private] =>
[_deleted:BaseObject:private] =>
[modifiedColumns:protected] => Array
(
)
)
[63] => Category Object
(
[languages:protected] =>
[bok_resources:protected] =>
[bok_topics:protected] =>
[bok_keywords:protected] =>
[id:protected] => 63
[type:protected] => category
[parent:protected] => 2
[label:protected] => Reinforcing Ironworker
[alreadyInSave:protected] =>
[alreadyInValidation:protected] =>
[validationFailures:protected] => Array
(
)
[_new:BaseObject:private] =>
[_deleted:BaseObject:private] =>
[modifiedColumns:protected] => Array
(
)
)
[78] => Category Object
(
[languages:protected] =>
[bok_resources:protected] =>
[bok_topics:protected] =>
[bok_keywords:protected] =>
[id:protected] => 78
[type:protected] => category
[parent:protected] => 2
[label:protected] => Roofer/Waterproofer
[alreadyInSave:protected] =>
[alreadyInValidation:protected] =>
[validationFailures:protected] => Array
(
)
[_new:BaseObject:private] =>
[_deleted:BaseObject:private] =>
[modifiedColumns:protected] => Array
(
)
)
[79] => Category Object
(
[languages:protected] =>
[bok_resources:protected] =>
[bok_topics:protected] =>
[bok_keywords:protected] =>
[id:protected] => 79
[type:protected] => category
[parent:protected] => 2
[label:protected] => Scaffold Erector
[alreadyInSave:protected] =>
[alreadyInValidation:protected] =>
[validationFailures:protected] => Array
(
)
[_new:BaseObject:private] =>
[_deleted:BaseObject:private] =>
[modifiedColumns:protected] => Array
(
)
)
[80] => Category Object
(
[languages:protected] =>
[bok_resources:protected] =>
[bok_topics:protected] =>
[bok_keywords:protected] =>
[id:protected] => 80
[type:protected] => category
[parent:protected] => 2
[label:protected] => Sheetmetal Worker
[alreadyInSave:protected] =>
[alreadyInValidation:protected] =>
[validationFailures:protected] => Array
(
)
[_new:BaseObject:private] =>
[_deleted:BaseObject:private] =>
[modifiedColumns:protected] => Array
(
)
)
[81] => Category Object
(
[languages:protected] =>
[bok_resources:protected] =>
[bok_topics:protected] =>
[bok_keywords:protected] =>
[id:protected] => 81
[type:protected] => category
[parent:protected] => 2
[label:protected] => Sprinkler Fitter
[alreadyInSave:protected] =>
[alreadyInValidation:protected] =>
[validationFailures:protected] => Array
(
)
[_new:BaseObject:private] =>
[_deleted:BaseObject:private] =>
[modifiedColumns:protected] => Array
(
)
)
[82] => Category Object
(
[languages:protected] =>
[bok_resources:protected] =>
[bok_topics:protected] =>
[bok_keywords:protected] =>
[id:protected] => 82
[type:protected] => category
[parent:protected] => 2
[label:protected] => Stonemason
[alreadyInSave:protected] =>
[alreadyInValidation:protected] =>
[validationFailures:protected] => Array
(
)
[_new:BaseObject:private] =>
[_deleted:BaseObject:private] =>
[modifiedColumns:protected] => Array
(
)
)
[62] => Category Object
(
[languages:protected] =>
[bok_resources:protected] =>
[bok_topics:protected] =>
[bok_keywords:protected] =>
[id:protected] => 62
[type:protected] => category
[parent:protected] => 2
[label:protected] => Structural Ironworker
[alreadyInSave:protected] =>
[alreadyInValidation:protected] =>
[validationFailures:protected] => Array
(
)
[_new:BaseObject:private] =>
[_deleted:BaseObject:private] =>
[modifiedColumns:protected] => Array
(
)
)
[83] => Category Object
(
[languages:protected] =>
[bok_resources:protected] =>
[bok_topics:protected] =>
[bok_keywords:protected] =>
[id:protected] => 83
[type:protected] => category
[parent:protected] => 2
[label:protected] => Terrazzo Worker
[alreadyInSave:protected] =>
[alreadyInValidation:protected] =>
[validationFailures:protected] => Array
(
)
[_new:BaseObject:private] =>
[_deleted:BaseObject:private] =>
[modifiedColumns:protected] => Array
(
)
)
[84] => Category Object
(
[languages:protected] =>
[bok_resources:protected] =>
[bok_topics:protected] =>
[bok_keywords:protected] =>
[id:protected] => 84
[type:protected] => category
[parent:protected] => 2
[label:protected] => Tile Setter
[alreadyInSave:protected] =>
[alreadyInValidation:protected] =>
[validationFailures:protected] => Array
(
)
[_new:BaseObject:private] =>
[_deleted:BaseObject:private] =>
[modifiedColumns:protected] => Array
(
)
)
[85] => Category Object
(
[languages:protected] =>
[bok_resources:protected] =>
[bok_topics:protected] =>
[bok_keywords:protected] =>
[id:protected] => 85
[type:protected] => category
[parent:protected] => 2
[label:protected] => Truck Driver
[alreadyInSave:protected] =>
[alreadyInValidation:protected] =>
[validationFailures:protected] => Array
(
)
[_new:BaseObject:private] =>
[_deleted:BaseObject:private] =>
[modifiedColumns:protected] => Array
(
)
)
[86] => Category Object
(
[languages:protected] =>
[bok_resources:protected] =>
[bok_topics:protected] =>
[bok_keywords:protected] =>
[id:protected] => 86
[type:protected] => category
[parent:protected] => 2
[label:protected] => Welder
[alreadyInSave:protected] =>
[alreadyInValidation:protected] =>
[validationFailures:protected] => Array
(
)
[_new:BaseObject:private] =>
[_deleted:BaseObject:private] =>
[modifiedColumns:protected] => Array
(
)
)
[87] => Category Object
(
[languages:protected] =>
[bok_resources:protected] =>
[bok_topics:protected] =>
[bok_keywords:protected] =>
[id:protected] => 87
[type:protected] => category
[parent:protected] => 3
[label:protected] => Commercial & Institutional
[alreadyInSave:protected] =>
[alreadyInValidation:protected] =>
[validationFailures:protected] => Array
(
)
[_new:BaseObject:private] =>
[_deleted:BaseObject:private] =>
[modifiedColumns:protected] => Array
(
)
)
[88] => Category Object
(
[languages:protected] =>
[bok_resources:protected] =>
[bok_topics:protected] =>
[bok_keywords:protected] =>
[id:protected] => 88
[type:protected] => category
[parent:protected] => 3
[label:protected] => Demolition
[alreadyInSave:protected] =>
[alreadyInValidation:protected] =>
[validationFailures:protected] => Array
(
)
[_new:BaseObject:private] =>
[_deleted:BaseObject:private] =>
[modifiedColumns:protected] => Array
(
)
)
[89] => Category Object
(
[languages:protected] =>
[bok_resources:protected] =>
[bok_topics:protected] =>
[bok_keywords:protected] =>
[id:protected] => 89
[type:protected] => category
[parent:protected] => 3
[label:protected] => Disasters
[alreadyInSave:protected] =>
[alreadyInValidation:protected] =>
[validationFailures:protected] => Array
(
)
[_new:BaseObject:private] =>
[_deleted:BaseObject:private] =>
[modifiedColumns:protected] => Array
(
)
)
[91] => Category Object
(
[languages:protected] =>
[bok_resources:protected] =>
[bok_topics:protected] =>
[bok_keywords:protected] =>
[id:protected] => 91
[type:protected] => category
[parent:protected] => 3
[label:protected] => Heavy & Highway
[alreadyInSave:protected] =>
[alreadyInValidation:protected] =>
[validationFailures:protected] => Array
(
)
[_new:BaseObject:private] =>
[_deleted:BaseObject:private] =>
[modifiedColumns:protected] => Array
(
)
)
[90] => Category Object
(
[languages:protected] =>
[bok_resources:protected] =>
[bok_topics:protected] =>
[bok_keywords:protected] =>
[id:protected] => 90
[type:protected] => category
[parent:protected] => 3
[label:protected] => Industrial
[alreadyInSave:protected] =>
[alreadyInValidation:protected] =>
[validationFailures:protected] => Array
(
)
[_new:BaseObject:private] =>
[_deleted:BaseObject:private] =>
[modifiedColumns:protected] => Array
(
)
)
[92] => Category Object
(
[languages:protected] =>
[bok_resources:protected] =>
[bok_topics:protected] =>
[bok_keywords:protected] =>
[id:protected] => 92
[type:protected] => category
[parent:protected] => 3
[label:protected] => LEED/Green Construction
[alreadyInSave:protected] =>
[alreadyInValidation:protected] =>
[validationFailures:protected] => Array
(
)
[_new:BaseObject:private] =>
[_deleted:BaseObject:private] =>
[modifiedColumns:protected] => Array
(
)
)
[93] => Category Object
(
[languages:protected] =>
[bok_resources:protected] =>
[bok_topics:protected] =>
[bok_keywords:protected] =>
[id:protected] => 93
[type:protected] => category
[parent:protected] => 3
[label:protected] => Renovations
[alreadyInSave:protected] =>
[alreadyInValidation:protected] =>
[validationFailures:protected] => Array
(
)
[_new:BaseObject:private] =>
[_deleted:BaseObject:private] =>
[modifiedColumns:protected] => Array
(
)
)
[94] => Category Object
(
[languages:protected] =>
[bok_resources:protected] =>
[bok_topics:protected] =>
[bok_keywords:protected] =>
[id:protected] => 94
[type:protected] => category
[parent:protected] => 3
[label:protected] => Residential
[alreadyInSave:protected] =>
[alreadyInValidation:protected] =>
[validationFailures:protected] => Array
(
)
[_new:BaseObject:private] =>
[_deleted:BaseObject:private] =>
[modifiedColumns:protected] => Array
(
)
)
[95] => Category Object
(
[languages:protected] =>
[bok_resources:protected] =>
[bok_topics:protected] =>
[bok_keywords:protected] =>
[id:protected] => 95
[type:protected] => category
[parent:protected] => 3
[label:protected] => Underground
[alreadyInSave:protected] =>
[alreadyInValidation:protected] =>
[validationFailures:protected] => Array
(
)
[_new:BaseObject:private] =>
[_deleted:BaseObject:private] =>
[modifiedColumns:protected] => Array
(
)
)
)
[categories_initialized:protected] => 1
[mapped_items:protected] =>
[content:protected] =>
[files:protected] =>
[language:protected] => Language Object
(
[id:protected] => 1
[code:protected] => en
[name:protected] => English
[alreadyInSave:protected] =>
[alreadyInValidation:protected] =>
[validationFailures:protected] => Array
(
)
[_new:BaseObject:private] =>
[_deleted:BaseObject:private] =>
[modifiedColumns:protected] => Array
(
)
)
[old_record:protected] =>
[id:protected] => 4426
[old_id:protected] =>
[elcosh_id:protected] => d001656
[type:protected] => document
[display_type:protected] => HTML only (and links)
[user_id:protected] => 0
[language_id:protected] => 1
[tagging_id:protected] => Mike Aguilar
[priority_id:protected] => 1
[title:protected] => Construction Dive -- DeWalt's Jobsite Pro headphones recalled for fire hazards
[total_pages:protected] => 1
[billed_pages:protected] => 1
[publication_number:protected] =>
[part_of:protected] =>
[keywords:protected] => DeWalt, Fire Hazards, recall, headphones
[comments:protected] =>
[summary:protected] => A recall notice by the United States Consumer Product Safety Commission affects over 300,000 DeWalt Jobsite Pro Headphones. The recall is a result of a malfunction that can cause earbuds to overheat while charging or during use, leading to fire and burn hazards.
[transition_comments:protected] =>
[external_link:protected] => https://www.constructiondive.com/news/dewalts-jobsite-pro-headphones-recalled-for-fire-hazards/611248/?utm_source=Sailthru&utm_medium=email&utm_campaign=Issue:%202021-12-10%20Construction%20Dive%20Newsletter%20%5Bissue:38532%5D&utm_term=Construction%20Dive
[consol_link:protected] =>
[more_like_this:protected] =>
[permission_given_by:protected] =>
[published:protected] => T
[billable:protected] => F
[img_name:protected] =>
[img_ext:protected] =>
[img_width:protected] =>
[img_height:protected] =>
[img_credit:protected] =>
[img_practice:protected] =>
[vid_source_id:protected] =>
[vid_running_time:protected] =>
[vid_intended_audience:protected] =>
[vid_acquisition_info:protected] =>
[vid_cost:protected] =>
[vid_producer:protected] =>
[vid_filename:protected] =>
[vid_filename_downloadable:protected] =>
[date_summary:protected] =>
[date_permission_requested:protected] =>
[date_permission_received:protected] =>
[date_review_needed:protected] =>
[date_received:protected] => 12/13/21
[date_completed:protected] => 12/13/21
[date_billed:protected] =>
[date_modified:protected] => 12/13/21
[collBokExports:protected] =>
[lastBokExportCriteria:BaseElcoshItem:private] =>
[alreadyInSave:protected] =>
[alreadyInValidation:protected] =>
[validationFailures:protected] => Array
(
)
[_new:BaseObject:private] =>
[_deleted:BaseObject:private] =>
[modifiedColumns:protected] => Array
(
)
)
)
)
[new_images] => Array
(
[0] => Search_Result Object
(
[title] => Morning Toolbox Talk
[image] => /record/images/4003-p.jpg
[blurb] => This photo is from an early morning toolbox talk on a construction job in Mclean, Virginia. It is being delivered in English and Spanish....
[category] => Array
(
[0] => 20
[1] => 51
[2] => 57
[3] => 64
[4] => 70
[5] => 63
[6] => 78
[7] => 82
[8] => 62
[9] => 87
[10] => 88
[11] => 89
[12] => 91
[13] => 90
[14] => 93
[15] => 94
[16] => 97
)
[labels] => Array
(
[0] => Safety Culture
[1] => Work Environment
[2] => Hazards
[3] => Cement Mason
[4] => Trades
[5] => Flagger
[7] => Laborer
[9] => Operating Engineer
[11] => Reinforcing Ironworker
[13] => Roofer/Waterproofer
[15] => Stonemason
[17] => Structural Ironworker
[19] => Commercial & Institutional
[20] => Jobsites
[21] => Demolition
[23] => Disasters
[25] => Heavy & Highway
[27] => Industrial
[29] => Renovations
[31] => Residential
[33] => Images
[34] => Media
[35] => Media & Documents
)
[type] => Images
[sub_category] =>
[url] => /image/4003/i002691/Morning%2BToolbox%2BTalk.html
[item:protected] => ImageRecord Object
(
[records:protected] => Array
(
)
[recordId:protected] =>
[searchWordClass:protected] =>
[searchWordPeerClass:protected] =>
[bok_record:protected] =>
[authors:protected] =>
[organizations:protected] =>
[collections:protected] =>
[categories:protected] => Array
(
[20] => Category Object
(
[languages:protected] =>
[bok_resources:protected] =>
[bok_topics:protected] =>
[bok_keywords:protected] =>
[id:protected] => 20
[type:protected] => category
[parent:protected] => 7
[label:protected] => Safety Culture
[alreadyInSave:protected] =>
[alreadyInValidation:protected] =>
[validationFailures:protected] => Array
(
)
[_new:BaseObject:private] =>
[_deleted:BaseObject:private] =>
[modifiedColumns:protected] => Array
(
)
)
[51] => Category Object
(
[languages:protected] =>
[bok_resources:protected] =>
[bok_topics:protected] =>
[bok_keywords:protected] =>
[id:protected] => 51
[type:protected] => category
[parent:protected] => 2
[label:protected] => Cement Mason
[alreadyInSave:protected] =>
[alreadyInValidation:protected] =>
[validationFailures:protected] => Array
(
)
[_new:BaseObject:private] =>
[_deleted:BaseObject:private] =>
[modifiedColumns:protected] => Array
(
)
)
[57] => Category Object
(
[languages:protected] =>
[bok_resources:protected] =>
[bok_topics:protected] =>
[bok_keywords:protected] =>
[id:protected] => 57
[type:protected] => category
[parent:protected] => 2
[label:protected] => Flagger
[alreadyInSave:protected] =>
[alreadyInValidation:protected] =>
[validationFailures:protected] => Array
(
)
[_new:BaseObject:private] =>
[_deleted:BaseObject:private] =>
[modifiedColumns:protected] => Array
(
)
)
[64] => Category Object
(
[languages:protected] =>
[bok_resources:protected] =>
[bok_topics:protected] =>
[bok_keywords:protected] =>
[id:protected] => 64
[type:protected] => category
[parent:protected] => 2
[label:protected] => Laborer
[alreadyInSave:protected] =>
[alreadyInValidation:protected] =>
[validationFailures:protected] => Array
(
)
[_new:BaseObject:private] =>
[_deleted:BaseObject:private] =>
[modifiedColumns:protected] => Array
(
)
)
[70] => Category Object
(
[languages:protected] =>
[bok_resources:protected] =>
[bok_topics:protected] =>
[bok_keywords:protected] =>
[id:protected] => 70
[type:protected] => category
[parent:protected] => 2
[label:protected] => Operating Engineer
[alreadyInSave:protected] =>
[alreadyInValidation:protected] =>
[validationFailures:protected] => Array
(
)
[_new:BaseObject:private] =>
[_deleted:BaseObject:private] =>
[modifiedColumns:protected] => Array
(
)
)
[63] => Category Object
(
[languages:protected] =>
[bok_resources:protected] =>
[bok_topics:protected] =>
[bok_keywords:protected] =>
[id:protected] => 63
[type:protected] => category
[parent:protected] => 2
[label:protected] => Reinforcing Ironworker
[alreadyInSave:protected] =>
[alreadyInValidation:protected] =>
[validationFailures:protected] => Array
(
)
[_new:BaseObject:private] =>
[_deleted:BaseObject:private] =>
[modifiedColumns:protected] => Array
(
)
)
[78] => Category Object
(
[languages:protected] =>
[bok_resources:protected] =>
[bok_topics:protected] =>
[bok_keywords:protected] =>
[id:protected] => 78
[type:protected] => category
[parent:protected] => 2
[label:protected] => Roofer/Waterproofer
[alreadyInSave:protected] =>
[alreadyInValidation:protected] =>
[validationFailures:protected] => Array
(
)
[_new:BaseObject:private] =>
[_deleted:BaseObject:private] =>
[modifiedColumns:protected] => Array
(
)
)
[82] => Category Object
(
[languages:protected] =>
[bok_resources:protected] =>
[bok_topics:protected] =>
[bok_keywords:protected] =>
[id:protected] => 82
[type:protected] => category
[parent:protected] => 2
[label:protected] => Stonemason
[alreadyInSave:protected] =>
[alreadyInValidation:protected] =>
[validationFailures:protected] => Array
(
)
[_new:BaseObject:private] =>
[_deleted:BaseObject:private] =>
[modifiedColumns:protected] => Array
(
)
)
[62] => Category Object
(
[languages:protected] =>
[bok_resources:protected] =>
[bok_topics:protected] =>
[bok_keywords:protected] =>
[id:protected] => 62
[type:protected] => category
[parent:protected] => 2
[label:protected] => Structural Ironworker
[alreadyInSave:protected] =>
[alreadyInValidation:protected] =>
[validationFailures:protected] => Array
(
)
[_new:BaseObject:private] =>
[_deleted:BaseObject:private] =>
[modifiedColumns:protected] => Array
(
)
)
[87] => Category Object
(
[languages:protected] =>
[bok_resources:protected] =>
[bok_topics:protected] =>
[bok_keywords:protected] =>
[id:protected] => 87
[type:protected] => category
[parent:protected] => 3
[label:protected] => Commercial & Institutional
[alreadyInSave:protected] =>
[alreadyInValidation:protected] =>
[validationFailures:protected] => Array
(
)
[_new:BaseObject:private] =>
[_deleted:BaseObject:private] =>
[modifiedColumns:protected] => Array
(
)
)
[88] => Category Object
(
[languages:protected] =>
[bok_resources:protected] =>
[bok_topics:protected] =>
[bok_keywords:protected] =>
[id:protected] => 88
[type:protected] => category
[parent:protected] => 3
[label:protected] => Demolition
[alreadyInSave:protected] =>
[alreadyInValidation:protected] =>
[validationFailures:protected] => Array
(
)
[_new:BaseObject:private] =>
[_deleted:BaseObject:private] =>
[modifiedColumns:protected] => Array
(
)
)
[89] => Category Object
(
[languages:protected] =>
[bok_resources:protected] =>
[bok_topics:protected] =>
[bok_keywords:protected] =>
[id:protected] => 89
[type:protected] => category
[parent:protected] => 3
[label:protected] => Disasters
[alreadyInSave:protected] =>
[alreadyInValidation:protected] =>
[validationFailures:protected] => Array
(
)
[_new:BaseObject:private] =>
[_deleted:BaseObject:private] =>
[modifiedColumns:protected] => Array
(
)
)
[91] => Category Object
(
[languages:protected] =>
[bok_resources:protected] =>
[bok_topics:protected] =>
[bok_keywords:protected] =>
[id:protected] => 91
[type:protected] => category
[parent:protected] => 3
[label:protected] => Heavy & Highway
[alreadyInSave:protected] =>
[alreadyInValidation:protected] =>
[validationFailures:protected] => Array
(
)
[_new:BaseObject:private] =>
[_deleted:BaseObject:private] =>
[modifiedColumns:protected] => Array
(
)
)
[90] => Category Object
(
[languages:protected] =>
[bok_resources:protected] =>
[bok_topics:protected] =>
[bok_keywords:protected] =>
[id:protected] => 90
[type:protected] => category
[parent:protected] => 3
[label:protected] => Industrial
[alreadyInSave:protected] =>
[alreadyInValidation:protected] =>
[validationFailures:protected] => Array
(
)
[_new:BaseObject:private] =>
[_deleted:BaseObject:private] =>
[modifiedColumns:protected] => Array
(
)
)
[93] => Category Object
(
[languages:protected] =>
[bok_resources:protected] =>
[bok_topics:protected] =>
[bok_keywords:protected] =>
[id:protected] => 93
[type:protected] => category
[parent:protected] => 3
[label:protected] => Renovations
[alreadyInSave:protected] =>
[alreadyInValidation:protected] =>
[validationFailures:protected] => Array
(
)
[_new:BaseObject:private] =>
[_deleted:BaseObject:private] =>
[modifiedColumns:protected] => Array
(
)
)
[94] => Category Object
(
[languages:protected] =>
[bok_resources:protected] =>
[bok_topics:protected] =>
[bok_keywords:protected] =>
[id:protected] => 94
[type:protected] => category
[parent:protected] => 3
[label:protected] => Residential
[alreadyInSave:protected] =>
[alreadyInValidation:protected] =>
[validationFailures:protected] => Array
(
)
[_new:BaseObject:private] =>
[_deleted:BaseObject:private] =>
[modifiedColumns:protected] => Array
(
)
)
[97] => Category Object
(
[languages:protected] =>
[bok_resources:protected] =>
[bok_topics:protected] =>
[bok_keywords:protected] =>
[id:protected] => 97
[type:protected] => category
[parent:protected] => 5
[label:protected] => Images
[alreadyInSave:protected] =>
[alreadyInValidation:protected] =>
[validationFailures:protected] => Array
(
)
[_new:BaseObject:private] =>
[_deleted:BaseObject:private] =>
[modifiedColumns:protected] => Array
(
)
)
)
[categories_initialized:protected] => 1
[mapped_items:protected] =>
[content:protected] =>
[files:protected] =>
[language:protected] => Language Object
(
[id:protected] => 1
[code:protected] => en
[name:protected] => English
[alreadyInSave:protected] =>
[alreadyInValidation:protected] =>
[validationFailures:protected] => Array
(
)
[_new:BaseObject:private] =>
[_deleted:BaseObject:private] =>
[modifiedColumns:protected] => Array
(
)
)
[old_record:protected] =>
[id:protected] => 4003
[old_id:protected] =>
[elcosh_id:protected] => i002691
[type:protected] => image
[display_type:protected] => Image
[user_id:protected] => 0
[language_id:protected] => 1
[tagging_id:protected] => Bruce Lippy
[priority_id:protected] => 1
[title:protected] => Morning Toolbox Talk
[total_pages:protected] => 0
[billed_pages:protected] => 0
[publication_number:protected] =>
[part_of:protected] =>
[keywords:protected] => toolbox talk, tailgate talk, Spanish, bilingual
[comments:protected] =>
[summary:protected] => This photo is from an early morning toolbox talk on a construction job in Mclean, Virginia. It is being delivered in English and Spanish.
[transition_comments:protected] =>
[external_link:protected] =>
[consol_link:protected] => http://www.cpwrconstructionsolutions.org/electrical/solution/662/worker-training.html
[more_like_this:protected] => d001285,d001304,c000079
[permission_given_by:protected] =>
[published:protected] => T
[billable:protected] => F
[img_name:protected] =>
[img_ext:protected] => jpg
[img_width:protected] =>
[img_height:protected] =>
[img_credit:protected] => Morgan Zavertnik and Hoar Construction
[img_practice:protected] => good
[vid_source_id:protected] =>
[vid_running_time:protected] =>
[vid_intended_audience:protected] =>
[vid_acquisition_info:protected] =>
[vid_cost:protected] =>
[vid_producer:protected] =>
[vid_filename:protected] =>
[vid_filename_downloadable:protected] =>
[date_summary:protected] => November 2015
[date_permission_requested:protected] =>
[date_permission_received:protected] =>
[date_review_needed:protected] =>
[date_received:protected] => 03/02/16
[date_completed:protected] => 03/02/16
[date_billed:protected] =>
[date_modified:protected] => 03/02/16
[collBokExports:protected] =>
[lastBokExportCriteria:BaseElcoshItem:private] =>
[alreadyInSave:protected] =>
[alreadyInValidation:protected] =>
[validationFailures:protected] => Array
(
)
[_new:BaseObject:private] =>
[_deleted:BaseObject:private] =>
[modifiedColumns:protected] => Array
(
)
)
)
[1] => Search_Result Object
(
[title] => Toolbox talk - crew view
[image] => /record/images/4005-p.jpg
[blurb] => Photo of crew listening to a toolbox safety talk before starting work....
[category] => Array
(
[0] => 97
[1] => 20
[2] => 47
[3] => 49
[4] => 51
[5] => 55
[6] => 61
[7] => 64
[8] => 71
[9] => 75
[10] => 63
[11] => 79
[12] => 62
[13] => 87
[14] => 88
[15] => 91
[16] => 90
[17] => 93
[18] => 94
[19] => 95
)
[labels] => Array
(
[0] => Images
[1] => Media
[2] => Media & Documents
[3] => Safety Culture
[4] => Work Environment
[5] => Hazards
[6] => Bricklayer
[7] => Trades
[8] => Carpenter
[10] => Cement Mason
[12] => Electrical Worker
[14] => Interior Systems Carpenter
[16] => Laborer
[18] => Painter
[20] => Plasterer
[22] => Reinforcing Ironworker
[24] => Scaffold Erector
[26] => Structural Ironworker
[28] => Commercial & Institutional
[29] => Jobsites
[30] => Demolition
[32] => Heavy & Highway
[34] => Industrial
[36] => Renovations
[38] => Residential
[40] => Underground
)
[type] => Images
[sub_category] =>
[url] => /image/4005/i002692/Toolbox%2Btalk%2B-%2Bcrew%2Bview.html
[item:protected] => ImageRecord Object
(
[records:protected] => Array
(
)
[recordId:protected] =>
[searchWordClass:protected] =>
[searchWordPeerClass:protected] =>
[bok_record:protected] =>
[authors:protected] =>
[organizations:protected] =>
[collections:protected] =>
[categories:protected] => Array
(
[97] => Category Object
(
[languages:protected] =>
[bok_resources:protected] =>
[bok_topics:protected] =>
[bok_keywords:protected] =>
[id:protected] => 97
[type:protected] => category
[parent:protected] => 5
[label:protected] => Images
[alreadyInSave:protected] =>
[alreadyInValidation:protected] =>
[validationFailures:protected] => Array
(
)
[_new:BaseObject:private] =>
[_deleted:BaseObject:private] =>
[modifiedColumns:protected] => Array
(
)
)
[20] => Category Object
(
[languages:protected] =>
[bok_resources:protected] =>
[bok_topics:protected] =>
[bok_keywords:protected] =>
[id:protected] => 20
[type:protected] => category
[parent:protected] => 7
[label:protected] => Safety Culture
[alreadyInSave:protected] =>
[alreadyInValidation:protected] =>
[validationFailures:protected] => Array
(
)
[_new:BaseObject:private] =>
[_deleted:BaseObject:private] =>
[modifiedColumns:protected] => Array
(
)
)
[47] => Category Object
(
[languages:protected] =>
[bok_resources:protected] =>
[bok_topics:protected] =>
[bok_keywords:protected] =>
[id:protected] => 47
[type:protected] => category
[parent:protected] => 2
[label:protected] => Bricklayer
[alreadyInSave:protected] =>
[alreadyInValidation:protected] =>
[validationFailures:protected] => Array
(
)
[_new:BaseObject:private] =>
[_deleted:BaseObject:private] =>
[modifiedColumns:protected] => Array
(
)
)
[49] => Category Object
(
[languages:protected] =>
[bok_resources:protected] =>
[bok_topics:protected] =>
[bok_keywords:protected] =>
[id:protected] => 49
[type:protected] => category
[parent:protected] => 2
[label:protected] => Carpenter
[alreadyInSave:protected] =>
[alreadyInValidation:protected] =>
[validationFailures:protected] => Array
(
)
[_new:BaseObject:private] =>
[_deleted:BaseObject:private] =>
[modifiedColumns:protected] => Array
(
)
)
[51] => Category Object
(
[languages:protected] =>
[bok_resources:protected] =>
[bok_topics:protected] =>
[bok_keywords:protected] =>
[id:protected] => 51
[type:protected] => category
[parent:protected] => 2
[label:protected] => Cement Mason
[alreadyInSave:protected] =>
[alreadyInValidation:protected] =>
[validationFailures:protected] => Array
(
)
[_new:BaseObject:private] =>
[_deleted:BaseObject:private] =>
[modifiedColumns:protected] => Array
(
)
)
[55] => Category Object
(
[languages:protected] =>
[bok_resources:protected] =>
[bok_topics:protected] =>
[bok_keywords:protected] =>
[id:protected] => 55
[type:protected] => category
[parent:protected] => 2
[label:protected] => Electrical Worker
[alreadyInSave:protected] =>
[alreadyInValidation:protected] =>
[validationFailures:protected] => Array
(
)
[_new:BaseObject:private] =>
[_deleted:BaseObject:private] =>
[modifiedColumns:protected] => Array
(
)
)
[61] => Category Object
(
[languages:protected] =>
[bok_resources:protected] =>
[bok_topics:protected] =>
[bok_keywords:protected] =>
[id:protected] => 61
[type:protected] => category
[parent:protected] => 2
[label:protected] => Interior Systems Carpenter
[alreadyInSave:protected] =>
[alreadyInValidation:protected] =>
[validationFailures:protected] => Array
(
)
[_new:BaseObject:private] =>
[_deleted:BaseObject:private] =>
[modifiedColumns:protected] => Array
(
)
)
[64] => Category Object
(
[languages:protected] =>
[bok_resources:protected] =>
[bok_topics:protected] =>
[bok_keywords:protected] =>
[id:protected] => 64
[type:protected] => category
[parent:protected] => 2
[label:protected] => Laborer
[alreadyInSave:protected] =>
[alreadyInValidation:protected] =>
[validationFailures:protected] => Array
(
)
[_new:BaseObject:private] =>
[_deleted:BaseObject:private] =>
[modifiedColumns:protected] => Array
(
)
)
[71] => Category Object
(
[languages:protected] =>
[bok_resources:protected] =>
[bok_topics:protected] =>
[bok_keywords:protected] =>
[id:protected] => 71
[type:protected] => category
[parent:protected] => 2
[label:protected] => Painter
[alreadyInSave:protected] =>
[alreadyInValidation:protected] =>
[validationFailures:protected] => Array
(
)
[_new:BaseObject:private] =>
[_deleted:BaseObject:private] =>
[modifiedColumns:protected] => Array
(
)
)
[75] => Category Object
(
[languages:protected] =>
[bok_resources:protected] =>
[bok_topics:protected] =>
[bok_keywords:protected] =>
[id:protected] => 75
[type:protected] => category
[parent:protected] => 2
[label:protected] => Plasterer
[alreadyInSave:protected] =>
[alreadyInValidation:protected] =>
[validationFailures:protected] => Array
(
)
[_new:BaseObject:private] =>
[_deleted:BaseObject:private] =>
[modifiedColumns:protected] => Array
(
)
)
[63] => Category Object
(
[languages:protected] =>
[bok_resources:protected] =>
[bok_topics:protected] =>
[bok_keywords:protected] =>
[id:protected] => 63
[type:protected] => category
[parent:protected] => 2
[label:protected] => Reinforcing Ironworker
[alreadyInSave:protected] =>
[alreadyInValidation:protected] =>
[validationFailures:protected] => Array
(
)
[_new:BaseObject:private] =>
[_deleted:BaseObject:private] =>
[modifiedColumns:protected] => Array
(
)
)
[79] => Category Object
(
[languages:protected] =>
[bok_resources:protected] =>
[bok_topics:protected] =>
[bok_keywords:protected] =>
[id:protected] => 79
[type:protected] => category
[parent:protected] => 2
[label:protected] => Scaffold Erector
[alreadyInSave:protected] =>
[alreadyInValidation:protected] =>
[validationFailures:protected] => Array
(
)
[_new:BaseObject:private] =>
[_deleted:BaseObject:private] =>
[modifiedColumns:protected] => Array
(
)
)
[62] => Category Object
(
[languages:protected] =>
[bok_resources:protected] =>
[bok_topics:protected] =>
[bok_keywords:protected] =>
[id:protected] => 62
[type:protected] => category
[parent:protected] => 2
[label:protected] => Structural Ironworker
[alreadyInSave:protected] =>
[alreadyInValidation:protected] =>
[validationFailures:protected] => Array
(
)
[_new:BaseObject:private] =>
[_deleted:BaseObject:private] =>
[modifiedColumns:protected] => Array
(
)
)
[87] => Category Object
(
[languages:protected] =>
[bok_resources:protected] =>
[bok_topics:protected] =>
[bok_keywords:protected] =>
[id:protected] => 87
[type:protected] => category
[parent:protected] => 3
[label:protected] => Commercial & Institutional
[alreadyInSave:protected] =>
[alreadyInValidation:protected] =>
[validationFailures:protected] => Array
(
)
[_new:BaseObject:private] =>
[_deleted:BaseObject:private] =>
[modifiedColumns:protected] => Array
(
)
)
[88] => Category Object
(
[languages:protected] =>
[bok_resources:protected] =>
[bok_topics:protected] =>
[bok_keywords:protected] =>
[id:protected] => 88
[type:protected] => category
[parent:protected] => 3
[label:protected] => Demolition
[alreadyInSave:protected] =>
[alreadyInValidation:protected] =>
[validationFailures:protected] => Array
(
)
[_new:BaseObject:private] =>
[_deleted:BaseObject:private] =>
[modifiedColumns:protected] => Array
(
)
)
[91] => Category Object
(
[languages:protected] =>
[bok_resources:protected] =>
[bok_topics:protected] =>
[bok_keywords:protected] =>
[id:protected] => 91
[type:protected] => category
[parent:protected] => 3
[label:protected] => Heavy & Highway
[alreadyInSave:protected] =>
[alreadyInValidation:protected] =>
[validationFailures:protected] => Array
(
)
[_new:BaseObject:private] =>
[_deleted:BaseObject:private] =>
[modifiedColumns:protected] => Array
(
)
)
[90] => Category Object
(
[languages:protected] =>
[bok_resources:protected] =>
[bok_topics:protected] =>
[bok_keywords:protected] =>
[id:protected] => 90
[type:protected] => category
[parent:protected] => 3
[label:protected] => Industrial
[alreadyInSave:protected] =>
[alreadyInValidation:protected] =>
[validationFailures:protected] => Array
(
)
[_new:BaseObject:private] =>
[_deleted:BaseObject:private] =>
[modifiedColumns:protected] => Array
(
)
)
[93] => Category Object
(
[languages:protected] =>
[bok_resources:protected] =>
[bok_topics:protected] =>
[bok_keywords:protected] =>
[id:protected] => 93
[type:protected] => category
[parent:protected] => 3
[label:protected] => Renovations
[alreadyInSave:protected] =>
[alreadyInValidation:protected] =>
[validationFailures:protected] => Array
(
)
[_new:BaseObject:private] =>
[_deleted:BaseObject:private] =>
[modifiedColumns:protected] => Array
(
)
)
[94] => Category Object
(
[languages:protected] =>
[bok_resources:protected] =>
[bok_topics:protected] =>
[bok_keywords:protected] =>
[id:protected] => 94
[type:protected] => category
[parent:protected] => 3
[label:protected] => Residential
[alreadyInSave:protected] =>
[alreadyInValidation:protected] =>
[validationFailures:protected] => Array
(
)
[_new:BaseObject:private] =>
[_deleted:BaseObject:private] =>
[modifiedColumns:protected] => Array
(
)
)
[95] => Category Object
(
[languages:protected] =>
[bok_resources:protected] =>
[bok_topics:protected] =>
[bok_keywords:protected] =>
[id:protected] => 95
[type:protected] => category
[parent:protected] => 3
[label:protected] => Underground
[alreadyInSave:protected] =>
[alreadyInValidation:protected] =>
[validationFailures:protected] => Array
(
)
[_new:BaseObject:private] =>
[_deleted:BaseObject:private] =>
[modifiedColumns:protected] => Array
(
)
)
)
[categories_initialized:protected] => 1
[mapped_items:protected] =>
[content:protected] =>
[files:protected] =>
[language:protected] => Language Object
(
[id:protected] => 1
[code:protected] => en
[name:protected] => English
[alreadyInSave:protected] =>
[alreadyInValidation:protected] =>
[validationFailures:protected] => Array
(
)
[_new:BaseObject:private] =>
[_deleted:BaseObject:private] =>
[modifiedColumns:protected] => Array
(
)
)
[old_record:protected] =>
[id:protected] => 4005
[old_id:protected] =>
[elcosh_id:protected] => i002692
[type:protected] => image
[display_type:protected] => Image
[user_id:protected] => 0
[language_id:protected] => 1
[tagging_id:protected] => Bruce Lippy
[priority_id:protected] => 1
[title:protected] => Toolbox talk - crew view
[total_pages:protected] => 0
[billed_pages:protected] => 0
[publication_number:protected] =>
[part_of:protected] =>
[keywords:protected] => toolbox talk, tailgate talk, safety talk, Spanish
[comments:protected] =>
[summary:protected] => Photo of crew listening to a toolbox safety talk before starting work.
[transition_comments:protected] =>
[external_link:protected] =>
[consol_link:protected] => http://www.cpwrconstructionsolutions.org/electrical/solution/662/worker-training.html
[more_like_this:protected] => i002691,d001269, c000079, d001285
[permission_given_by:protected] =>
[published:protected] => T
[billable:protected] => F
[img_name:protected] =>
[img_ext:protected] => jpg
[img_width:protected] =>
[img_height:protected] =>
[img_credit:protected] => Morgan Zavertnik and Hoar Construction
[img_practice:protected] => good
[vid_source_id:protected] =>
[vid_running_time:protected] =>
[vid_intended_audience:protected] =>
[vid_acquisition_info:protected] =>
[vid_cost:protected] =>
[vid_producer:protected] =>
[vid_filename:protected] =>
[vid_filename_downloadable:protected] =>
[date_summary:protected] => November 2015
[date_permission_requested:protected] =>
[date_permission_received:protected] =>
[date_review_needed:protected] =>
[date_received:protected] => 03/02/16
[date_completed:protected] => 03/02/16
[date_billed:protected] =>
[date_modified:protected] => 03/02/16
[collBokExports:protected] =>
[lastBokExportCriteria:BaseElcoshItem:private] =>
[alreadyInSave:protected] =>
[alreadyInValidation:protected] =>
[validationFailures:protected] => Array
(
)
[_new:BaseObject:private] =>
[_deleted:BaseObject:private] =>
[modifiedColumns:protected] => Array
(
)
)
)
[2] => Search_Result Object
(
[title] => Toolbox talk - long shot
[image] => /record/images/4006-p.jpg
[blurb] => This crew gathered every morning before starting work to discuss a new safety topic....
[category] => Array
(
[0] => 20
[1] => 47
[2] => 49
[3] => 51
[4] => 55
[5] => 64
[6] => 68
[7] => 75
[8] => 76
[9] => 63
[10] => 78
[11] => 79
[12] => 82
[13] => 62
[14] => 87
[15] => 88
[16] => 91
[17] => 90
[18] => 93
[19] => 94
[20] => 95
[21] => 97
)
[labels] => Array
(
[0] => Safety Culture
[1] => Work Environment
[2] => Hazards
[3] => Bricklayer
[4] => Trades
[5] => Carpenter
[7] => Cement Mason
[9] => Electrical Worker
[11] => Laborer
[13] => Maintenance Worker
[15] => Plasterer
[17] => Plumber/Pipefitter
[19] => Reinforcing Ironworker
[21] => Roofer/Waterproofer
[23] => Scaffold Erector
[25] => Stonemason
[27] => Structural Ironworker
[29] => Commercial & Institutional
[30] => Jobsites
[31] => Demolition
[33] => Heavy & Highway
[35] => Industrial
[37] => Renovations
[39] => Residential
[41] => Underground
[43] => Images
[44] => Media
[45] => Media & Documents
)
[type] => Images
[sub_category] =>
[url] => /image/4006/i002693/Toolbox%2Btalk%2B-%2Blong%2Bshot.html
[item:protected] => ImageRecord Object
(
[records:protected] => Array
(
)
[recordId:protected] =>
[searchWordClass:protected] =>
[searchWordPeerClass:protected] =>
[bok_record:protected] =>
[authors:protected] =>
[organizations:protected] =>
[collections:protected] =>
[categories:protected] => Array
(
[20] => Category Object
(
[languages:protected] =>
[bok_resources:protected] =>
[bok_topics:protected] =>
[bok_keywords:protected] =>
[id:protected] => 20
[type:protected] => category
[parent:protected] => 7
[label:protected] => Safety Culture
[alreadyInSave:protected] =>
[alreadyInValidation:protected] =>
[validationFailures:protected] => Array
(
)
[_new:BaseObject:private] =>
[_deleted:BaseObject:private] =>
[modifiedColumns:protected] => Array
(
)
)
[47] => Category Object
(
[languages:protected] =>
[bok_resources:protected] =>
[bok_topics:protected] =>
[bok_keywords:protected] =>
[id:protected] => 47
[type:protected] => category
[parent:protected] => 2
[label:protected] => Bricklayer
[alreadyInSave:protected] =>
[alreadyInValidation:protected] =>
[validationFailures:protected] => Array
(
)
[_new:BaseObject:private] =>
[_deleted:BaseObject:private] =>
[modifiedColumns:protected] => Array
(
)
)
[49] => Category Object
(
[languages:protected] =>
[bok_resources:protected] =>
[bok_topics:protected] =>
[bok_keywords:protected] =>
[id:protected] => 49
[type:protected] => category
[parent:protected] => 2
[label:protected] => Carpenter
[alreadyInSave:protected] =>
[alreadyInValidation:protected] =>
[validationFailures:protected] => Array
(
)
[_new:BaseObject:private] =>
[_deleted:BaseObject:private] =>
[modifiedColumns:protected] => Array
(
)
)
[51] => Category Object
(
[languages:protected] =>
[bok_resources:protected] =>
[bok_topics:protected] =>
[bok_keywords:protected] =>
[id:protected] => 51
[type:protected] => category
[parent:protected] => 2
[label:protected] => Cement Mason
[alreadyInSave:protected] =>
[alreadyInValidation:protected] =>
[validationFailures:protected] => Array
(
)
[_new:BaseObject:private] =>
[_deleted:BaseObject:private] =>
[modifiedColumns:protected] => Array
(
)
)
[55] => Category Object
(
[languages:protected] =>
[bok_resources:protected] =>
[bok_topics:protected] =>
[bok_keywords:protected] =>
[id:protected] => 55
[type:protected] => category
[parent:protected] => 2
[label:protected] => Electrical Worker
[alreadyInSave:protected] =>
[alreadyInValidation:protected] =>
[validationFailures:protected] => Array
(
)
[_new:BaseObject:private] =>
[_deleted:BaseObject:private] =>
[modifiedColumns:protected] => Array
(
)
)
[64] => Category Object
(
[languages:protected] =>
[bok_resources:protected] =>
[bok_topics:protected] =>
[bok_keywords:protected] =>
[id:protected] => 64
[type:protected] => category
[parent:protected] => 2
[label:protected] => Laborer
[alreadyInSave:protected] =>
[alreadyInValidation:protected] =>
[validationFailures:protected] => Array
(
)
[_new:BaseObject:private] =>
[_deleted:BaseObject:private] =>
[modifiedColumns:protected] => Array
(
)
)
[68] => Category Object
(
[languages:protected] =>
[bok_resources:protected] =>
[bok_topics:protected] =>
[bok_keywords:protected] =>
[id:protected] => 68
[type:protected] => category
[parent:protected] => 2
[label:protected] => Maintenance Worker
[alreadyInSave:protected] =>
[alreadyInValidation:protected] =>
[validationFailures:protected] => Array
(
)
[_new:BaseObject:private] =>
[_deleted:BaseObject:private] =>
[modifiedColumns:protected] => Array
(
)
)
[75] => Category Object
(
[languages:protected] =>
[bok_resources:protected] =>
[bok_topics:protected] =>
[bok_keywords:protected] =>
[id:protected] => 75
[type:protected] => category
[parent:protected] => 2
[label:protected] => Plasterer
[alreadyInSave:protected] =>
[alreadyInValidation:protected] =>
[validationFailures:protected] => Array
(
)
[_new:BaseObject:private] =>
[_deleted:BaseObject:private] =>
[modifiedColumns:protected] => Array
(
)
)
[76] => Category Object
(
[languages:protected] =>
[bok_resources:protected] =>
[bok_topics:protected] =>
[bok_keywords:protected] =>
[id:protected] => 76
[type:protected] => category
[parent:protected] => 2
[label:protected] => Plumber/Pipefitter
[alreadyInSave:protected] =>
[alreadyInValidation:protected] =>
[validationFailures:protected] => Array
(
)
[_new:BaseObject:private] =>
[_deleted:BaseObject:private] =>
[modifiedColumns:protected] => Array
(
)
)
[63] => Category Object
(
[languages:protected] =>
[bok_resources:protected] =>
[bok_topics:protected] =>
[bok_keywords:protected] =>
[id:protected] => 63
[type:protected] => category
[parent:protected] => 2
[label:protected] => Reinforcing Ironworker
[alreadyInSave:protected] =>
[alreadyInValidation:protected] =>
[validationFailures:protected] => Array
(
)
[_new:BaseObject:private] =>
[_deleted:BaseObject:private] =>
[modifiedColumns:protected] => Array
(
)
)
[78] => Category Object
(
[languages:protected] =>
[bok_resources:protected] =>
[bok_topics:protected] =>
[bok_keywords:protected] =>
[id:protected] => 78
[type:protected] => category
[parent:protected] => 2
[label:protected] => Roofer/Waterproofer
[alreadyInSave:protected] =>
[alreadyInValidation:protected] =>
[validationFailures:protected] => Array
(
)
[_new:BaseObject:private] =>
[_deleted:BaseObject:private] =>
[modifiedColumns:protected] => Array
(
)
)
[79] => Category Object
(
[languages:protected] =>
[bok_resources:protected] =>
[bok_topics:protected] =>
[bok_keywords:protected] =>
[id:protected] => 79
[type:protected] => category
[parent:protected] => 2
[label:protected] => Scaffold Erector
[alreadyInSave:protected] =>
[alreadyInValidation:protected] =>
[validationFailures:protected] => Array
(
)
[_new:BaseObject:private] =>
[_deleted:BaseObject:private] =>
[modifiedColumns:protected] => Array
(
)
)
[82] => Category Object
(
[languages:protected] =>
[bok_resources:protected] =>
[bok_topics:protected] =>
[bok_keywords:protected] =>
[id:protected] => 82
[type:protected] => category
[parent:protected] => 2
[label:protected] => Stonemason
[alreadyInSave:protected] =>
[alreadyInValidation:protected] =>
[validationFailures:protected] => Array
(
)
[_new:BaseObject:private] =>
[_deleted:BaseObject:private] =>
[modifiedColumns:protected] => Array
(
)
)
[62] => Category Object
(
[languages:protected] =>
[bok_resources:protected] =>
[bok_topics:protected] =>
[bok_keywords:protected] =>
[id:protected] => 62
[type:protected] => category
[parent:protected] => 2
[label:protected] => Structural Ironworker
[alreadyInSave:protected] =>
[alreadyInValidation:protected] =>
[validationFailures:protected] => Array
(
)
[_new:BaseObject:private] =>
[_deleted:BaseObject:private] =>
[modifiedColumns:protected] => Array
(
)
)
[87] => Category Object
(
[languages:protected] =>
[bok_resources:protected] =>
[bok_topics:protected] =>
[bok_keywords:protected] =>
[id:protected] => 87
[type:protected] => category
[parent:protected] => 3
[label:protected] => Commercial & Institutional
[alreadyInSave:protected] =>
[alreadyInValidation:protected] =>
[validationFailures:protected] => Array
(
)
[_new:BaseObject:private] =>
[_deleted:BaseObject:private] =>
[modifiedColumns:protected] => Array
(
)
)
[88] => Category Object
(
[languages:protected] =>
[bok_resources:protected] =>
[bok_topics:protected] =>
[bok_keywords:protected] =>
[id:protected] => 88
[type:protected] => category
[parent:protected] => 3
[label:protected] => Demolition
[alreadyInSave:protected] =>
[alreadyInValidation:protected] =>
[validationFailures:protected] => Array
(
)
[_new:BaseObject:private] =>
[_deleted:BaseObject:private] =>
[modifiedColumns:protected] => Array
(
)
)
[91] => Category Object
(
[languages:protected] =>
[bok_resources:protected] =>
[bok_topics:protected] =>
[bok_keywords:protected] =>
[id:protected] => 91
[type:protected] => category
[parent:protected] => 3
[label:protected] => Heavy & Highway
[alreadyInSave:protected] =>
[alreadyInValidation:protected] =>
[validationFailures:protected] => Array
(
)
[_new:BaseObject:private] =>
[_deleted:BaseObject:private] =>
[modifiedColumns:protected] => Array
(
)
)
[90] => Category Object
(
[languages:protected] =>
[bok_resources:protected] =>
[bok_topics:protected] =>
[bok_keywords:protected] =>
[id:protected] => 90
[type:protected] => category
[parent:protected] => 3
[label:protected] => Industrial
[alreadyInSave:protected] =>
[alreadyInValidation:protected] =>
[validationFailures:protected] => Array
(
)
[_new:BaseObject:private] =>
[_deleted:BaseObject:private] =>
[modifiedColumns:protected] => Array
(
)
)
[93] => Category Object
(
[languages:protected] =>
[bok_resources:protected] =>
[bok_topics:protected] =>
[bok_keywords:protected] =>
[id:protected] => 93
[type:protected] => category
[parent:protected] => 3
[label:protected] => Renovations
[alreadyInSave:protected] =>
[alreadyInValidation:protected] =>
[validationFailures:protected] => Array
(
)
[_new:BaseObject:private] =>
[_deleted:BaseObject:private] =>
[modifiedColumns:protected] => Array
(
)
)
[94] => Category Object
(
[languages:protected] =>
[bok_resources:protected] =>
[bok_topics:protected] =>
[bok_keywords:protected] =>
[id:protected] => 94
[type:protected] => category
[parent:protected] => 3
[label:protected] => Residential
[alreadyInSave:protected] =>
[alreadyInValidation:protected] =>
[validationFailures:protected] => Array
(
)
[_new:BaseObject:private] =>
[_deleted:BaseObject:private] =>
[modifiedColumns:protected] => Array
(
)
)
[95] => Category Object
(
[languages:protected] =>
[bok_resources:protected] =>
[bok_topics:protected] =>
[bok_keywords:protected] =>
[id:protected] => 95
[type:protected] => category
[parent:protected] => 3
[label:protected] => Underground
[alreadyInSave:protected] =>
[alreadyInValidation:protected] =>
[validationFailures:protected] => Array
(
)
[_new:BaseObject:private] =>
[_deleted:BaseObject:private] =>
[modifiedColumns:protected] => Array
(
)
)
[97] => Category Object
(
[languages:protected] =>
[bok_resources:protected] =>
[bok_topics:protected] =>
[bok_keywords:protected] =>
[id:protected] => 97
[type:protected] => category
[parent:protected] => 5
[label:protected] => Images
[alreadyInSave:protected] =>
[alreadyInValidation:protected] =>
[validationFailures:protected] => Array
(
)
[_new:BaseObject:private] =>
[_deleted:BaseObject:private] =>
[modifiedColumns:protected] => Array
(
)
)
)
[categories_initialized:protected] => 1
[mapped_items:protected] =>
[content:protected] =>
[files:protected] =>
[language:protected] => Language Object
(
[id:protected] => 1
[code:protected] => en
[name:protected] => English
[alreadyInSave:protected] =>
[alreadyInValidation:protected] =>
[validationFailures:protected] => Array
(
)
[_new:BaseObject:private] =>
[_deleted:BaseObject:private] =>
[modifiedColumns:protected] => Array
(
)
)
[old_record:protected] =>
[id:protected] => 4006
[old_id:protected] =>
[elcosh_id:protected] => i002693
[type:protected] => image
[display_type:protected] => Image
[user_id:protected] => 0
[language_id:protected] => 1
[tagging_id:protected] => Bruce Lippy
[priority_id:protected] => 1
[title:protected] => Toolbox talk - long shot
[total_pages:protected] => 0
[billed_pages:protected] => 0
[publication_number:protected] =>
[part_of:protected] =>
[keywords:protected] => toolbox talk, tailgate talk, safety minute
[comments:protected] =>
[summary:protected] => This crew gathered every morning before starting work to discuss a new safety topic.
[transition_comments:protected] =>
[external_link:protected] =>
[consol_link:protected] => http://www.cpwrconstructionsolutions.org/electrical/solution/662/worker-training.html
[more_like_this:protected] => i002691,i002692,d001269,d000527
[permission_given_by:protected] =>
[published:protected] => T
[billable:protected] => F
[img_name:protected] =>
[img_ext:protected] => jpg
[img_width:protected] =>
[img_height:protected] =>
[img_credit:protected] => Morgan Zavertnik and Hoar Construction
[img_practice:protected] => good
[vid_source_id:protected] =>
[vid_running_time:protected] =>
[vid_intended_audience:protected] =>
[vid_acquisition_info:protected] =>
[vid_cost:protected] =>
[vid_producer:protected] =>
[vid_filename:protected] =>
[vid_filename_downloadable:protected] =>
[date_summary:protected] => November 2015
[date_permission_requested:protected] =>
[date_permission_received:protected] =>
[date_review_needed:protected] =>
[date_received:protected] => 03/02/16
[date_completed:protected] => 03/02/16
[date_billed:protected] =>
[date_modified:protected] => 03/02/16
[collBokExports:protected] =>
[lastBokExportCriteria:BaseElcoshItem:private] =>
[alreadyInSave:protected] =>
[alreadyInValidation:protected] =>
[validationFailures:protected] => Array
(
)
[_new:BaseObject:private] =>
[_deleted:BaseObject:private] =>
[modifiedColumns:protected] => Array
(
)
)
)
[3] => Search_Result Object
(
[title] => Safety officer discussing ongoing project with marketing coordinator
[image] => /record/images/4014-p.jpg
[blurb] => The safety officer (left) points out the good safety practices on this project that reflect well on the firm and may influence future clients....
[category] => Array
(
[0] => 97
[1] => 20
[2] => 46
[3] => 47
[4] => 49
[5] => 50
[6] => 51
[7] => 54
[8] => 55
[9] => 58
[10] => 60
[11] => 61
[12] => 64
[13] => 71
[14] => 75
[15] => 76
[16] => 63
[17] => 79
[18] => 80
[19] => 82
[20] => 62
[21] => 83
[22] => 87
[23] => 91
[24] => 90
[25] => 93
[26] => 94
)
[labels] => Array
(
[0] => Images
[1] => Media
[2] => Media & Documents
[3] => Safety Culture
[4] => Work Environment
[5] => Hazards
[6] => Boilermaker
[7] => Trades
[8] => Bricklayer
[10] => Carpenter
[12] => Carpet Layer
[14] => Cement Mason
[16] => Drywall Applicator Specialist
[18] => Electrical Worker
[20] => Glazier
[22] => HVAC
[24] => Interior Systems Carpenter
[26] => Laborer
[28] => Painter
[30] => Plasterer
[32] => Plumber/Pipefitter
[34] => Reinforcing Ironworker
[36] => Scaffold Erector
[38] => Sheetmetal Worker
[40] => Stonemason
[42] => Structural Ironworker
[44] => Terrazzo Worker
[46] => Commercial & Institutional
[47] => Jobsites
[48] => Heavy & Highway
[50] => Industrial
[52] => Renovations
[54] => Residential
)
[type] => Images
[sub_category] =>
[url] => /image/4014/i002700/Safety%2Bofficer%2Bdiscussing%2Bongoing%2Bproject%2Bwith%2Bmarketing%2Bcoordinator.html
[item:protected] => ImageRecord Object
(
[records:protected] => Array
(
)
[recordId:protected] =>
[searchWordClass:protected] =>
[searchWordPeerClass:protected] =>
[bok_record:protected] =>
[authors:protected] =>
[organizations:protected] =>
[collections:protected] =>
[categories:protected] => Array
(
[97] => Category Object
(
[languages:protected] =>
[bok_resources:protected] =>
[bok_topics:protected] =>
[bok_keywords:protected] =>
[id:protected] => 97
[type:protected] => category
[parent:protected] => 5
[label:protected] => Images
[alreadyInSave:protected] =>
[alreadyInValidation:protected] =>
[validationFailures:protected] => Array
(
)
[_new:BaseObject:private] =>
[_deleted:BaseObject:private] =>
[modifiedColumns:protected] => Array
(
)
)
[20] => Category Object
(
[languages:protected] =>
[bok_resources:protected] =>
[bok_topics:protected] =>
[bok_keywords:protected] =>
[id:protected] => 20
[type:protected] => category
[parent:protected] => 7
[label:protected] => Safety Culture
[alreadyInSave:protected] =>
[alreadyInValidation:protected] =>
[validationFailures:protected] => Array
(
)
[_new:BaseObject:private] =>
[_deleted:BaseObject:private] =>
[modifiedColumns:protected] => Array
(
)
)
[46] => Category Object
(
[languages:protected] =>
[bok_resources:protected] =>
[bok_topics:protected] =>
[bok_keywords:protected] =>
[id:protected] => 46
[type:protected] => category
[parent:protected] => 2
[label:protected] => Boilermaker
[alreadyInSave:protected] =>
[alreadyInValidation:protected] =>
[validationFailures:protected] => Array
(
)
[_new:BaseObject:private] =>
[_deleted:BaseObject:private] =>
[modifiedColumns:protected] => Array
(
)
)
[47] => Category Object
(
[languages:protected] =>
[bok_resources:protected] =>
[bok_topics:protected] =>
[bok_keywords:protected] =>
[id:protected] => 47
[type:protected] => category
[parent:protected] => 2
[label:protected] => Bricklayer
[alreadyInSave:protected] =>
[alreadyInValidation:protected] =>
[validationFailures:protected] => Array
(
)
[_new:BaseObject:private] =>
[_deleted:BaseObject:private] =>
[modifiedColumns:protected] => Array
(
)
)
[49] => Category Object
(
[languages:protected] =>
[bok_resources:protected] =>
[bok_topics:protected] =>
[bok_keywords:protected] =>
[id:protected] => 49
[type:protected] => category
[parent:protected] => 2
[label:protected] => Carpenter
[alreadyInSave:protected] =>
[alreadyInValidation:protected] =>
[validationFailures:protected] => Array
(
)
[_new:BaseObject:private] =>
[_deleted:BaseObject:private] =>
[modifiedColumns:protected] => Array
(
)
)
[50] => Category Object
(
[languages:protected] =>
[bok_resources:protected] =>
[bok_topics:protected] =>
[bok_keywords:protected] =>
[id:protected] => 50
[type:protected] => category
[parent:protected] => 2
[label:protected] => Carpet Layer
[alreadyInSave:protected] =>
[alreadyInValidation:protected] =>
[validationFailures:protected] => Array
(
)
[_new:BaseObject:private] =>
[_deleted:BaseObject:private] =>
[modifiedColumns:protected] => Array
(
)
)
[51] => Category Object
(
[languages:protected] =>
[bok_resources:protected] =>
[bok_topics:protected] =>
[bok_keywords:protected] =>
[id:protected] => 51
[type:protected] => category
[parent:protected] => 2
[label:protected] => Cement Mason
[alreadyInSave:protected] =>
[alreadyInValidation:protected] =>
[validationFailures:protected] => Array
(
)
[_new:BaseObject:private] =>
[_deleted:BaseObject:private] =>
[modifiedColumns:protected] => Array
(
)
)
[54] => Category Object
(
[languages:protected] =>
[bok_resources:protected] =>
[bok_topics:protected] =>
[bok_keywords:protected] =>
[id:protected] => 54
[type:protected] => category
[parent:protected] => 2
[label:protected] => Drywall Applicator Specialist
[alreadyInSave:protected] =>
[alreadyInValidation:protected] =>
[validationFailures:protected] => Array
(
)
[_new:BaseObject:private] =>
[_deleted:BaseObject:private] =>
[modifiedColumns:protected] => Array
(
)
)
[55] => Category Object
(
[languages:protected] =>
[bok_resources:protected] =>
[bok_topics:protected] =>
[bok_keywords:protected] =>
[id:protected] => 55
[type:protected] => category
[parent:protected] => 2
[label:protected] => Electrical Worker
[alreadyInSave:protected] =>
[alreadyInValidation:protected] =>
[validationFailures:protected] => Array
(
)
[_new:BaseObject:private] =>
[_deleted:BaseObject:private] =>
[modifiedColumns:protected] => Array
(
)
)
[58] => Category Object
(
[languages:protected] =>
[bok_resources:protected] =>
[bok_topics:protected] =>
[bok_keywords:protected] =>
[id:protected] => 58
[type:protected] => category
[parent:protected] => 2
[label:protected] => Glazier
[alreadyInSave:protected] =>
[alreadyInValidation:protected] =>
[validationFailures:protected] => Array
(
)
[_new:BaseObject:private] =>
[_deleted:BaseObject:private] =>
[modifiedColumns:protected] => Array
(
)
)
[60] => Category Object
(
[languages:protected] =>
[bok_resources:protected] =>
[bok_topics:protected] =>
[bok_keywords:protected] =>
[id:protected] => 60
[type:protected] => category
[parent:protected] => 2
[label:protected] => HVAC
[alreadyInSave:protected] =>
[alreadyInValidation:protected] =>
[validationFailures:protected] => Array
(
)
[_new:BaseObject:private] =>
[_deleted:BaseObject:private] =>
[modifiedColumns:protected] => Array
(
)
)
[61] => Category Object
(
[languages:protected] =>
[bok_resources:protected] =>
[bok_topics:protected] =>
[bok_keywords:protected] =>
[id:protected] => 61
[type:protected] => category
[parent:protected] => 2
[label:protected] => Interior Systems Carpenter
[alreadyInSave:protected] =>
[alreadyInValidation:protected] =>
[validationFailures:protected] => Array
(
)
[_new:BaseObject:private] =>
[_deleted:BaseObject:private] =>
[modifiedColumns:protected] => Array
(
)
)
[64] => Category Object
(
[languages:protected] =>
[bok_resources:protected] =>
[bok_topics:protected] =>
[bok_keywords:protected] =>
[id:protected] => 64
[type:protected] => category
[parent:protected] => 2
[label:protected] => Laborer
[alreadyInSave:protected] =>
[alreadyInValidation:protected] =>
[validationFailures:protected] => Array
(
)
[_new:BaseObject:private] =>
[_deleted:BaseObject:private] =>
[modifiedColumns:protected] => Array
(
)
)
[71] => Category Object
(
[languages:protected] =>
[bok_resources:protected] =>
[bok_topics:protected] =>
[bok_keywords:protected] =>
[id:protected] => 71
[type:protected] => category
[parent:protected] => 2
[label:protected] => Painter
[alreadyInSave:protected] =>
[alreadyInValidation:protected] =>
[validationFailures:protected] => Array
(
)
[_new:BaseObject:private] =>
[_deleted:BaseObject:private] =>
[modifiedColumns:protected] => Array
(
)
)
[75] => Category Object
(
[languages:protected] =>
[bok_resources:protected] =>
[bok_topics:protected] =>
[bok_keywords:protected] =>
[id:protected] => 75
[type:protected] => category
[parent:protected] => 2
[label:protected] => Plasterer
[alreadyInSave:protected] =>
[alreadyInValidation:protected] =>
[validationFailures:protected] => Array
(
)
[_new:BaseObject:private] =>
[_deleted:BaseObject:private] =>
[modifiedColumns:protected] => Array
(
)
)
[76] => Category Object
(
[languages:protected] =>
[bok_resources:protected] =>
[bok_topics:protected] =>
[bok_keywords:protected] =>
[id:protected] => 76
[type:protected] => category
[parent:protected] => 2
[label:protected] => Plumber/Pipefitter
[alreadyInSave:protected] =>
[alreadyInValidation:protected] =>
[validationFailures:protected] => Array
(
)
[_new:BaseObject:private] =>
[_deleted:BaseObject:private] =>
[modifiedColumns:protected] => Array
(
)
)
[63] => Category Object
(
[languages:protected] =>
[bok_resources:protected] =>
[bok_topics:protected] =>
[bok_keywords:protected] =>
[id:protected] => 63
[type:protected] => category
[parent:protected] => 2
[label:protected] => Reinforcing Ironworker
[alreadyInSave:protected] =>
[alreadyInValidation:protected] =>
[validationFailures:protected] => Array
(
)
[_new:BaseObject:private] =>
[_deleted:BaseObject:private] =>
[modifiedColumns:protected] => Array
(
)
)
[79] => Category Object
(
[languages:protected] =>
[bok_resources:protected] =>
[bok_topics:protected] =>
[bok_keywords:protected] =>
[id:protected] => 79
[type:protected] => category
[parent:protected] => 2
[label:protected] => Scaffold Erector
[alreadyInSave:protected] =>
[alreadyInValidation:protected] =>
[validationFailures:protected] => Array
(
)
[_new:BaseObject:private] =>
[_deleted:BaseObject:private] =>
[modifiedColumns:protected] => Array
(
)
)
[80] => Category Object
(
[languages:protected] =>
[bok_resources:protected] =>
[bok_topics:protected] =>
[bok_keywords:protected] =>
[id:protected] => 80
[type:protected] => category
[parent:protected] => 2
[label:protected] => Sheetmetal Worker
[alreadyInSave:protected] =>
[alreadyInValidation:protected] =>
[validationFailures:protected] => Array
(
)
[_new:BaseObject:private] =>
[_deleted:BaseObject:private] =>
[modifiedColumns:protected] => Array
(
)
)
[82] => Category Object
(
[languages:protected] =>
[bok_resources:protected] =>
[bok_topics:protected] =>
[bok_keywords:protected] =>
[id:protected] => 82
[type:protected] => category
[parent:protected] => 2
[label:protected] => Stonemason
[alreadyInSave:protected] =>
[alreadyInValidation:protected] =>
[validationFailures:protected] => Array
(
)
[_new:BaseObject:private] =>
[_deleted:BaseObject:private] =>
[modifiedColumns:protected] => Array
(
)
)
[62] => Category Object
(
[languages:protected] =>
[bok_resources:protected] =>
[bok_topics:protected] =>
[bok_keywords:protected] =>
[id:protected] => 62
[type:protected] => category
[parent:protected] => 2
[label:protected] => Structural Ironworker
[alreadyInSave:protected] =>
[alreadyInValidation:protected] =>
[validationFailures:protected] => Array
(
)
[_new:BaseObject:private] =>
[_deleted:BaseObject:private] =>
[modifiedColumns:protected] => Array
(
)
)
[83] => Category Object
(
[languages:protected] =>
[bok_resources:protected] =>
[bok_topics:protected] =>
[bok_keywords:protected] =>
[id:protected] => 83
[type:protected] => category
[parent:protected] => 2
[label:protected] => Terrazzo Worker
[alreadyInSave:protected] =>
[alreadyInValidation:protected] =>
[validationFailures:protected] => Array
(
)
[_new:BaseObject:private] =>
[_deleted:BaseObject:private] =>
[modifiedColumns:protected] => Array
(
)
)
[87] => Category Object
(
[languages:protected] =>
[bok_resources:protected] =>
[bok_topics:protected] =>
[bok_keywords:protected] =>
[id:protected] => 87
[type:protected] => category
[parent:protected] => 3
[label:protected] => Commercial & Institutional
[alreadyInSave:protected] =>
[alreadyInValidation:protected] =>
[validationFailures:protected] => Array
(
)
[_new:BaseObject:private] =>
[_deleted:BaseObject:private] =>
[modifiedColumns:protected] => Array
(
)
)
[91] => Category Object
(
[languages:protected] =>
[bok_resources:protected] =>
[bok_topics:protected] =>
[bok_keywords:protected] =>
[id:protected] => 91
[type:protected] => category
[parent:protected] => 3
[label:protected] => Heavy & Highway
[alreadyInSave:protected] =>
[alreadyInValidation:protected] =>
[validationFailures:protected] => Array
(
)
[_new:BaseObject:private] =>
[_deleted:BaseObject:private] =>
[modifiedColumns:protected] => Array
(
)
)
[90] => Category Object
(
[languages:protected] =>
[bok_resources:protected] =>
[bok_topics:protected] =>
[bok_keywords:protected] =>
[id:protected] => 90
[type:protected] => category
[parent:protected] => 3
[label:protected] => Industrial
[alreadyInSave:protected] =>
[alreadyInValidation:protected] =>
[validationFailures:protected] => Array
(
)
[_new:BaseObject:private] =>
[_deleted:BaseObject:private] =>
[modifiedColumns:protected] => Array
(
)
)
[93] => Category Object
(
[languages:protected] =>
[bok_resources:protected] =>
[bok_topics:protected] =>
[bok_keywords:protected] =>
[id:protected] => 93
[type:protected] => category
[parent:protected] => 3
[label:protected] => Renovations
[alreadyInSave:protected] =>
[alreadyInValidation:protected] =>
[validationFailures:protected] => Array
(
)
[_new:BaseObject:private] =>
[_deleted:BaseObject:private] =>
[modifiedColumns:protected] => Array
(
)
)
[94] => Category Object
(
[languages:protected] =>
[bok_resources:protected] =>
[bok_topics:protected] =>
[bok_keywords:protected] =>
[id:protected] => 94
[type:protected] => category
[parent:protected] => 3
[label:protected] => Residential
[alreadyInSave:protected] =>
[alreadyInValidation:protected] =>
[validationFailures:protected] => Array
(
)
[_new:BaseObject:private] =>
[_deleted:BaseObject:private] =>
[modifiedColumns:protected] => Array
(
)
)
)
[categories_initialized:protected] => 1
[mapped_items:protected] =>
[content:protected] =>
[files:protected] =>
[language:protected] => Language Object
(
[id:protected] => 1
[code:protected] => en
[name:protected] => English
[alreadyInSave:protected] =>
[alreadyInValidation:protected] =>
[validationFailures:protected] => Array
(
)
[_new:BaseObject:private] =>
[_deleted:BaseObject:private] =>
[modifiedColumns:protected] => Array
(
)
)
[old_record:protected] =>
[id:protected] => 4014
[old_id:protected] =>
[elcosh_id:protected] => i002700
[type:protected] => image
[display_type:protected] => Image
[user_id:protected] => 0
[language_id:protected] => 1
[tagging_id:protected] => Bruce Lippy
[priority_id:protected] => 1
[title:protected] => Safety officer discussing ongoing project with marketing coordinator
[total_pages:protected] => 0
[billed_pages:protected] => 0
[publication_number:protected] =>
[part_of:protected] =>
[keywords:protected] => Latino, safety officer, safety culture
[comments:protected] =>
[summary:protected] => The safety officer (left) points out the good safety practices on this project that reflect well on the firm and may influence future clients.
[transition_comments:protected] =>
[external_link:protected] =>
[consol_link:protected] => http://www.cpwrconstructionsolutions.org/index.php
[more_like_this:protected] => d000989,d001351,d001362,d000652, d001101, d000931, d001395
[permission_given_by:protected] =>
[published:protected] => T
[billable:protected] => F
[img_name:protected] =>
[img_ext:protected] => jpg
[img_width:protected] =>
[img_height:protected] =>
[img_credit:protected] => Hoar Construction, Photo by Neil Lippy
[img_practice:protected] => good
[vid_source_id:protected] =>
[vid_running_time:protected] =>
[vid_intended_audience:protected] =>
[vid_acquisition_info:protected] =>
[vid_cost:protected] =>
[vid_producer:protected] =>
[vid_filename:protected] =>
[vid_filename_downloadable:protected] =>
[date_summary:protected] => November 2015
[date_permission_requested:protected] =>
[date_permission_received:protected] =>
[date_review_needed:protected] =>
[date_received:protected] => 03/02/16
[date_completed:protected] => 03/02/16
[date_billed:protected] =>
[date_modified:protected] => 01/30/23
[collBokExports:protected] =>
[lastBokExportCriteria:BaseElcoshItem:private] =>
[alreadyInSave:protected] =>
[alreadyInValidation:protected] =>
[validationFailures:protected] => Array
(
)
[_new:BaseObject:private] =>
[_deleted:BaseObject:private] =>
[modifiedColumns:protected] => Array
(
)
)
)
[4] => Search_Result Object
(
[title] => Scaffolding at top of large column
[image] => /record/images/3994-p.jpg
[blurb] => This shot shows innovative guarding around the top of a large concrete column in the base of a high rise structure going up....
[category] => Array
(
[0] => 15
[1] => 21
[2] => 47
[3] => 51
[4] => 63
[5] => 78
[6] => 79
[7] => 80
[8] => 62
[9] => 87
[10] => 97
[11] => 56
[12] => 64
[13] => 74
)
[labels] => Array
(
[0] => Falls
[1] => Work Environment
[2] => Hazards
[3] => Scaffolds
[6] => Bricklayer
[7] => Trades
[8] => Cement Mason
[10] => Reinforcing Ironworker
[12] => Roofer/Waterproofer
[14] => Scaffold Erector
[16] => Sheetmetal Worker
[18] => Structural Ironworker
[20] => Commercial & Institutional
[21] => Jobsites
[22] => Images
[23] => Media
[24] => Media & Documents
[25] => Elevator Constructor
[27] => Laborer
[29] => Pile Driver
)
[type] => Images
[sub_category] =>
[url] => /image/3994/i002689/Scaffolding%2Bat%2Btop%2Bof%2Blarge%2Bcolumn.html
[item:protected] => ImageRecord Object
(
[records:protected] => Array
(
)
[recordId:protected] =>
[searchWordClass:protected] =>
[searchWordPeerClass:protected] =>
[bok_record:protected] =>
[authors:protected] =>
[organizations:protected] =>
[collections:protected] =>
[categories:protected] => Array
(
[15] => Category Object
(
[languages:protected] =>
[bok_resources:protected] =>
[bok_topics:protected] =>
[bok_keywords:protected] =>
[id:protected] => 15
[type:protected] => category
[parent:protected] => 7
[label:protected] => Falls
[alreadyInSave:protected] =>
[alreadyInValidation:protected] =>
[validationFailures:protected] => Array
(
)
[_new:BaseObject:private] =>
[_deleted:BaseObject:private] =>
[modifiedColumns:protected] => Array
(
)
)
[21] => Category Object
(
[languages:protected] =>
[bok_resources:protected] =>
[bok_topics:protected] =>
[bok_keywords:protected] =>
[id:protected] => 21
[type:protected] => category
[parent:protected] => 7
[label:protected] => Scaffolds
[alreadyInSave:protected] =>
[alreadyInValidation:protected] =>
[validationFailures:protected] => Array
(
)
[_new:BaseObject:private] =>
[_deleted:BaseObject:private] =>
[modifiedColumns:protected] => Array
(
)
)
[47] => Category Object
(
[languages:protected] =>
[bok_resources:protected] =>
[bok_topics:protected] =>
[bok_keywords:protected] =>
[id:protected] => 47
[type:protected] => category
[parent:protected] => 2
[label:protected] => Bricklayer
[alreadyInSave:protected] =>
[alreadyInValidation:protected] =>
[validationFailures:protected] => Array
(
)
[_new:BaseObject:private] =>
[_deleted:BaseObject:private] =>
[modifiedColumns:protected] => Array
(
)
)
[51] => Category Object
(
[languages:protected] =>
[bok_resources:protected] =>
[bok_topics:protected] =>
[bok_keywords:protected] =>
[id:protected] => 51
[type:protected] => category
[parent:protected] => 2
[label:protected] => Cement Mason
[alreadyInSave:protected] =>
[alreadyInValidation:protected] =>
[validationFailures:protected] => Array
(
)
[_new:BaseObject:private] =>
[_deleted:BaseObject:private] =>
[modifiedColumns:protected] => Array
(
)
)
[63] => Category Object
(
[languages:protected] =>
[bok_resources:protected] =>
[bok_topics:protected] =>
[bok_keywords:protected] =>
[id:protected] => 63
[type:protected] => category
[parent:protected] => 2
[label:protected] => Reinforcing Ironworker
[alreadyInSave:protected] =>
[alreadyInValidation:protected] =>
[validationFailures:protected] => Array
(
)
[_new:BaseObject:private] =>
[_deleted:BaseObject:private] =>
[modifiedColumns:protected] => Array
(
)
)
[78] => Category Object
(
[languages:protected] =>
[bok_resources:protected] =>
[bok_topics:protected] =>
[bok_keywords:protected] =>
[id:protected] => 78
[type:protected] => category
[parent:protected] => 2
[label:protected] => Roofer/Waterproofer
[alreadyInSave:protected] =>
[alreadyInValidation:protected] =>
[validationFailures:protected] => Array
(
)
[_new:BaseObject:private] =>
[_deleted:BaseObject:private] =>
[modifiedColumns:protected] => Array
(
)
)
[79] => Category Object
(
[languages:protected] =>
[bok_resources:protected] =>
[bok_topics:protected] =>
[bok_keywords:protected] =>
[id:protected] => 79
[type:protected] => category
[parent:protected] => 2
[label:protected] => Scaffold Erector
[alreadyInSave:protected] =>
[alreadyInValidation:protected] =>
[validationFailures:protected] => Array
(
)
[_new:BaseObject:private] =>
[_deleted:BaseObject:private] =>
[modifiedColumns:protected] => Array
(
)
)
[80] => Category Object
(
[languages:protected] =>
[bok_resources:protected] =>
[bok_topics:protected] =>
[bok_keywords:protected] =>
[id:protected] => 80
[type:protected] => category
[parent:protected] => 2
[label:protected] => Sheetmetal Worker
[alreadyInSave:protected] =>
[alreadyInValidation:protected] =>
[validationFailures:protected] => Array
(
)
[_new:BaseObject:private] =>
[_deleted:BaseObject:private] =>
[modifiedColumns:protected] => Array
(
)
)
[62] => Category Object
(
[languages:protected] =>
[bok_resources:protected] =>
[bok_topics:protected] =>
[bok_keywords:protected] =>
[id:protected] => 62
[type:protected] => category
[parent:protected] => 2
[label:protected] => Structural Ironworker
[alreadyInSave:protected] =>
[alreadyInValidation:protected] =>
[validationFailures:protected] => Array
(
)
[_new:BaseObject:private] =>
[_deleted:BaseObject:private] =>
[modifiedColumns:protected] => Array
(
)
)
[87] => Category Object
(
[languages:protected] =>
[bok_resources:protected] =>
[bok_topics:protected] =>
[bok_keywords:protected] =>
[id:protected] => 87
[type:protected] => category
[parent:protected] => 3
[label:protected] => Commercial & Institutional
[alreadyInSave:protected] =>
[alreadyInValidation:protected] =>
[validationFailures:protected] => Array
(
)
[_new:BaseObject:private] =>
[_deleted:BaseObject:private] =>
[modifiedColumns:protected] => Array
(
)
)
[97] => Category Object
(
[languages:protected] =>
[bok_resources:protected] =>
[bok_topics:protected] =>
[bok_keywords:protected] =>
[id:protected] => 97
[type:protected] => category
[parent:protected] => 5
[label:protected] => Images
[alreadyInSave:protected] =>
[alreadyInValidation:protected] =>
[validationFailures:protected] => Array
(
)
[_new:BaseObject:private] =>
[_deleted:BaseObject:private] =>
[modifiedColumns:protected] => Array
(
)
)
[56] => Category Object
(
[languages:protected] =>
[bok_resources:protected] =>
[bok_topics:protected] =>
[bok_keywords:protected] =>
[id:protected] => 56
[type:protected] => category
[parent:protected] => 2
[label:protected] => Elevator Constructor
[alreadyInSave:protected] =>
[alreadyInValidation:protected] =>
[validationFailures:protected] => Array
(
)
[_new:BaseObject:private] =>
[_deleted:BaseObject:private] =>
[modifiedColumns:protected] => Array
(
)
)
[64] => Category Object
(
[languages:protected] =>
[bok_resources:protected] =>
[bok_topics:protected] =>
[bok_keywords:protected] =>
[id:protected] => 64
[type:protected] => category
[parent:protected] => 2
[label:protected] => Laborer
[alreadyInSave:protected] =>
[alreadyInValidation:protected] =>
[validationFailures:protected] => Array
(
)
[_new:BaseObject:private] =>
[_deleted:BaseObject:private] =>
[modifiedColumns:protected] => Array
(
)
)
[74] => Category Object
(
[languages:protected] =>
[bok_resources:protected] =>
[bok_topics:protected] =>
[bok_keywords:protected] =>
[id:protected] => 74
[type:protected] => category
[parent:protected] => 2
[label:protected] => Pile Driver
[alreadyInSave:protected] =>
[alreadyInValidation:protected] =>
[validationFailures:protected] => Array
(
)
[_new:BaseObject:private] =>
[_deleted:BaseObject:private] =>
[modifiedColumns:protected] => Array
(
)
)
)
[categories_initialized:protected] => 1
[mapped_items:protected] =>
[content:protected] =>
[files:protected] =>
[language:protected] => Language Object
(
[id:protected] => 1
[code:protected] => en
[name:protected] => English
[alreadyInSave:protected] =>
[alreadyInValidation:protected] =>
[validationFailures:protected] => Array
(
)
[_new:BaseObject:private] =>
[_deleted:BaseObject:private] =>
[modifiedColumns:protected] => Array
(
)
)
[old_record:protected] =>
[id:protected] => 3994
[old_id:protected] =>
[elcosh_id:protected] => i002689
[type:protected] => image
[display_type:protected] => Image
[user_id:protected] => 0
[language_id:protected] => 1
[tagging_id:protected] => Bruce Lippy
[priority_id:protected] => 1
[title:protected] => Scaffolding at top of large column
[total_pages:protected] => 0
[billed_pages:protected] => 0
[publication_number:protected] =>
[part_of:protected] =>
[keywords:protected] => Guardrail, railing, fall prevention, falls
[comments:protected] =>
[summary:protected] => This shot shows innovative guarding around the top of a large concrete column in the base of a high rise structure going up.
[transition_comments:protected] =>
[external_link:protected] =>
[consol_link:protected] => http://www.cpwrconstructionsolutions.org/masonry/solution/8/adjustable-tower-scaffold.html
[more_like_this:protected] => c1002680,i002662,d000608,d001255
[permission_given_by:protected] =>
[published:protected] => T
[billable:protected] => F
[img_name:protected] =>
[img_ext:protected] => jpg
[img_width:protected] =>
[img_height:protected] =>
[img_credit:protected] => Photo by Pam Susi
[img_practice:protected] => good
[vid_source_id:protected] =>
[vid_running_time:protected] =>
[vid_intended_audience:protected] =>
[vid_acquisition_info:protected] =>
[vid_cost:protected] =>
[vid_producer:protected] =>
[vid_filename:protected] =>
[vid_filename_downloadable:protected] =>
[date_summary:protected] => January 2016
[date_permission_requested:protected] =>
[date_permission_received:protected] =>
[date_review_needed:protected] =>
[date_received:protected] => 02/01/16
[date_completed:protected] => 02/01/16
[date_billed:protected] =>
[date_modified:protected] => 02/01/16
[collBokExports:protected] =>
[lastBokExportCriteria:BaseElcoshItem:private] =>
[alreadyInSave:protected] =>
[alreadyInValidation:protected] =>
[validationFailures:protected] => Array
(
)
[_new:BaseObject:private] =>
[_deleted:BaseObject:private] =>
[modifiedColumns:protected] => Array
(
)
)
)
[5] => Search_Result Object
(
[title] => Construction bracing
[image] => /record/images/3995-p.jpg
[blurb] => This shows structural support that prevents collapses during construction....
[category] => Array
(
[0] => 12
[1] => 15
[2] => 21
[3] => 49
[4] => 51
[5] => 55
[6] => 56
[7] => 60
[8] => 64
[9] => 68
[10] => 74
[11] => 63
[12] => 78
[13] => 79
[14] => 80
[15] => 62
[16] => 87
[17] => 90
[18] => 97
)
[labels] => Array
(
[0] => Crushed/Struck By
[1] => Work Environment
[2] => Hazards
[3] => Falls
[6] => Scaffolds
[9] => Carpenter
[10] => Trades
[11] => Cement Mason
[13] => Electrical Worker
[15] => Elevator Constructor
[17] => HVAC
[19] => Laborer
[21] => Maintenance Worker
[23] => Pile Driver
[25] => Reinforcing Ironworker
[27] => Roofer/Waterproofer
[29] => Scaffold Erector
[31] => Sheetmetal Worker
[33] => Structural Ironworker
[35] => Commercial & Institutional
[36] => Jobsites
[37] => Industrial
[39] => Images
[40] => Media
[41] => Media & Documents
)
[type] => Images
[sub_category] =>
[url] => /image/3995/i002690/Construction%2Bbracing.html
[item:protected] => ImageRecord Object
(
[records:protected] => Array
(
)
[recordId:protected] =>
[searchWordClass:protected] =>
[searchWordPeerClass:protected] =>
[bok_record:protected] =>
[authors:protected] =>
[organizations:protected] =>
[collections:protected] =>
[categories:protected] => Array
(
[12] => Category Object
(
[languages:protected] =>
[bok_resources:protected] =>
[bok_topics:protected] =>
[bok_keywords:protected] =>
[id:protected] => 12
[type:protected] => category
[parent:protected] => 7
[label:protected] => Crushed/Struck By
[alreadyInSave:protected] =>
[alreadyInValidation:protected] =>
[validationFailures:protected] => Array
(
)
[_new:BaseObject:private] =>
[_deleted:BaseObject:private] =>
[modifiedColumns:protected] => Array
(
)
)
[15] => Category Object
(
[languages:protected] =>
[bok_resources:protected] =>
[bok_topics:protected] =>
[bok_keywords:protected] =>
[id:protected] => 15
[type:protected] => category
[parent:protected] => 7
[label:protected] => Falls
[alreadyInSave:protected] =>
[alreadyInValidation:protected] =>
[validationFailures:protected] => Array
(
)
[_new:BaseObject:private] =>
[_deleted:BaseObject:private] =>
[modifiedColumns:protected] => Array
(
)
)
[21] => Category Object
(
[languages:protected] =>
[bok_resources:protected] =>
[bok_topics:protected] =>
[bok_keywords:protected] =>
[id:protected] => 21
[type:protected] => category
[parent:protected] => 7
[label:protected] => Scaffolds
[alreadyInSave:protected] =>
[alreadyInValidation:protected] =>
[validationFailures:protected] => Array
(
)
[_new:BaseObject:private] =>
[_deleted:BaseObject:private] =>
[modifiedColumns:protected] => Array
(
)
)
[49] => Category Object
(
[languages:protected] =>
[bok_resources:protected] =>
[bok_topics:protected] =>
[bok_keywords:protected] =>
[id:protected] => 49
[type:protected] => category
[parent:protected] => 2
[label:protected] => Carpenter
[alreadyInSave:protected] =>
[alreadyInValidation:protected] =>
[validationFailures:protected] => Array
(
)
[_new:BaseObject:private] =>
[_deleted:BaseObject:private] =>
[modifiedColumns:protected] => Array
(
)
)
[51] => Category Object
(
[languages:protected] =>
[bok_resources:protected] =>
[bok_topics:protected] =>
[bok_keywords:protected] =>
[id:protected] => 51
[type:protected] => category
[parent:protected] => 2
[label:protected] => Cement Mason
[alreadyInSave:protected] =>
[alreadyInValidation:protected] =>
[validationFailures:protected] => Array
(
)
[_new:BaseObject:private] =>
[_deleted:BaseObject:private] =>
[modifiedColumns:protected] => Array
(
)
)
[55] => Category Object
(
[languages:protected] =>
[bok_resources:protected] =>
[bok_topics:protected] =>
[bok_keywords:protected] =>
[id:protected] => 55
[type:protected] => category
[parent:protected] => 2
[label:protected] => Electrical Worker
[alreadyInSave:protected] =>
[alreadyInValidation:protected] =>
[validationFailures:protected] => Array
(
)
[_new:BaseObject:private] =>
[_deleted:BaseObject:private] =>
[modifiedColumns:protected] => Array
(
)
)
[56] => Category Object
(
[languages:protected] =>
[bok_resources:protected] =>
[bok_topics:protected] =>
[bok_keywords:protected] =>
[id:protected] => 56
[type:protected] => category
[parent:protected] => 2
[label:protected] => Elevator Constructor
[alreadyInSave:protected] =>
[alreadyInValidation:protected] =>
[validationFailures:protected] => Array
(
)
[_new:BaseObject:private] =>
[_deleted:BaseObject:private] =>
[modifiedColumns:protected] => Array
(
)
)
[60] => Category Object
(
[languages:protected] =>
[bok_resources:protected] =>
[bok_topics:protected] =>
[bok_keywords:protected] =>
[id:protected] => 60
[type:protected] => category
[parent:protected] => 2
[label:protected] => HVAC
[alreadyInSave:protected] =>
[alreadyInValidation:protected] =>
[validationFailures:protected] => Array
(
)
[_new:BaseObject:private] =>
[_deleted:BaseObject:private] =>
[modifiedColumns:protected] => Array
(
)
)
[64] => Category Object
(
[languages:protected] =>
[bok_resources:protected] =>
[bok_topics:protected] =>
[bok_keywords:protected] =>
[id:protected] => 64
[type:protected] => category
[parent:protected] => 2
[label:protected] => Laborer
[alreadyInSave:protected] =>
[alreadyInValidation:protected] =>
[validationFailures:protected] => Array
(
)
[_new:BaseObject:private] =>
[_deleted:BaseObject:private] =>
[modifiedColumns:protected] => Array
(
)
)
[68] => Category Object
(
[languages:protected] =>
[bok_resources:protected] =>
[bok_topics:protected] =>
[bok_keywords:protected] =>
[id:protected] => 68
[type:protected] => category
[parent:protected] => 2
[label:protected] => Maintenance Worker
[alreadyInSave:protected] =>
[alreadyInValidation:protected] =>
[validationFailures:protected] => Array
(
)
[_new:BaseObject:private] =>
[_deleted:BaseObject:private] =>
[modifiedColumns:protected] => Array
(
)
)
[74] => Category Object
(
[languages:protected] =>
[bok_resources:protected] =>
[bok_topics:protected] =>
[bok_keywords:protected] =>
[id:protected] => 74
[type:protected] => category
[parent:protected] => 2
[label:protected] => Pile Driver
[alreadyInSave:protected] =>
[alreadyInValidation:protected] =>
[validationFailures:protected] => Array
(
)
[_new:BaseObject:private] =>
[_deleted:BaseObject:private] =>
[modifiedColumns:protected] => Array
(
)
)
[63] => Category Object
(
[languages:protected] =>
[bok_resources:protected] =>
[bok_topics:protected] =>
[bok_keywords:protected] =>
[id:protected] => 63
[type:protected] => category
[parent:protected] => 2
[label:protected] => Reinforcing Ironworker
[alreadyInSave:protected] =>
[alreadyInValidation:protected] =>
[validationFailures:protected] => Array
(
)
[_new:BaseObject:private] =>
[_deleted:BaseObject:private] =>
[modifiedColumns:protected] => Array
(
)
)
[78] => Category Object
(
[languages:protected] =>
[bok_resources:protected] =>
[bok_topics:protected] =>
[bok_keywords:protected] =>
[id:protected] => 78
[type:protected] => category
[parent:protected] => 2
[label:protected] => Roofer/Waterproofer
[alreadyInSave:protected] =>
[alreadyInValidation:protected] =>
[validationFailures:protected] => Array
(
)
[_new:BaseObject:private] =>
[_deleted:BaseObject:private] =>
[modifiedColumns:protected] => Array
(
)
)
[79] => Category Object
(
[languages:protected] =>
[bok_resources:protected] =>
[bok_topics:protected] =>
[bok_keywords:protected] =>
[id:protected] => 79
[type:protected] => category
[parent:protected] => 2
[label:protected] => Scaffold Erector
[alreadyInSave:protected] =>
[alreadyInValidation:protected] =>
[validationFailures:protected] => Array
(
)
[_new:BaseObject:private] =>
[_deleted:BaseObject:private] =>
[modifiedColumns:protected] => Array
(
)
)
[80] => Category Object
(
[languages:protected] =>
[bok_resources:protected] =>
[bok_topics:protected] =>
[bok_keywords:protected] =>
[id:protected] => 80
[type:protected] => category
[parent:protected] => 2
[label:protected] => Sheetmetal Worker
[alreadyInSave:protected] =>
[alreadyInValidation:protected] =>
[validationFailures:protected] => Array
(
)
[_new:BaseObject:private] =>
[_deleted:BaseObject:private] =>
[modifiedColumns:protected] => Array
(
)
)
[62] => Category Object
(
[languages:protected] =>
[bok_resources:protected] =>
[bok_topics:protected] =>
[bok_keywords:protected] =>
[id:protected] => 62
[type:protected] => category
[parent:protected] => 2
[label:protected] => Structural Ironworker
[alreadyInSave:protected] =>
[alreadyInValidation:protected] =>
[validationFailures:protected] => Array
(
)
[_new:BaseObject:private] =>
[_deleted:BaseObject:private] =>
[modifiedColumns:protected] => Array
(
)
)
[87] => Category Object
(
[languages:protected] =>
[bok_resources:protected] =>
[bok_topics:protected] =>
[bok_keywords:protected] =>
[id:protected] => 87
[type:protected] => category
[parent:protected] => 3
[label:protected] => Commercial & Institutional
[alreadyInSave:protected] =>
[alreadyInValidation:protected] =>
[validationFailures:protected] => Array
(
)
[_new:BaseObject:private] =>
[_deleted:BaseObject:private] =>
[modifiedColumns:protected] => Array
(
)
)
[90] => Category Object
(
[languages:protected] =>
[bok_resources:protected] =>
[bok_topics:protected] =>
[bok_keywords:protected] =>
[id:protected] => 90
[type:protected] => category
[parent:protected] => 3
[label:protected] => Industrial
[alreadyInSave:protected] =>
[alreadyInValidation:protected] =>
[validationFailures:protected] => Array
(
)
[_new:BaseObject:private] =>
[_deleted:BaseObject:private] =>
[modifiedColumns:protected] => Array
(
)
)
[97] => Category Object
(
[languages:protected] =>
[bok_resources:protected] =>
[bok_topics:protected] =>
[bok_keywords:protected] =>
[id:protected] => 97
[type:protected] => category
[parent:protected] => 5
[label:protected] => Images
[alreadyInSave:protected] =>
[alreadyInValidation:protected] =>
[validationFailures:protected] => Array
(
)
[_new:BaseObject:private] =>
[_deleted:BaseObject:private] =>
[modifiedColumns:protected] => Array
(
)
)
)
[categories_initialized:protected] => 1
[mapped_items:protected] =>
[content:protected] =>
[files:protected] =>
[language:protected] => Language Object
(
[id:protected] => 1
[code:protected] => en
[name:protected] => English
[alreadyInSave:protected] =>
[alreadyInValidation:protected] =>
[validationFailures:protected] => Array
(
)
[_new:BaseObject:private] =>
[_deleted:BaseObject:private] =>
[modifiedColumns:protected] => Array
(
)
)
[old_record:protected] =>
[id:protected] => 3995
[old_id:protected] =>
[elcosh_id:protected] => i002690
[type:protected] => image
[display_type:protected] => Image
[user_id:protected] => 0
[language_id:protected] => 1
[tagging_id:protected] => Bruce Lippy
[priority_id:protected] => 1
[title:protected] => Construction bracing
[total_pages:protected] => 0
[billed_pages:protected] => 0
[publication_number:protected] =>
[part_of:protected] =>
[keywords:protected] => Bracing, support, scaffold
[comments:protected] =>
[summary:protected] => This shows structural support that prevents collapses during construction.
[transition_comments:protected] =>
[external_link:protected] =>
[consol_link:protected] => http://www.cpwrconstructionsolutions.org/masonry/solution/8/adjustable-tower-scaffold.html
[more_like_this:protected] => i002660
[permission_given_by:protected] =>
[published:protected] => T
[billable:protected] => F
[img_name:protected] =>
[img_ext:protected] => jpg
[img_width:protected] =>
[img_height:protected] =>
[img_credit:protected] => Photo by Pam Susi
[img_practice:protected] => good
[vid_source_id:protected] =>
[vid_running_time:protected] =>
[vid_intended_audience:protected] =>
[vid_acquisition_info:protected] =>
[vid_cost:protected] =>
[vid_producer:protected] =>
[vid_filename:protected] =>
[vid_filename_downloadable:protected] =>
[date_summary:protected] => January 2016
[date_permission_requested:protected] =>
[date_permission_received:protected] =>
[date_review_needed:protected] =>
[date_received:protected] => 02/01/16
[date_completed:protected] => 02/01/16
[date_billed:protected] =>
[date_modified:protected] => 02/01/16
[collBokExports:protected] =>
[lastBokExportCriteria:BaseElcoshItem:private] =>
[alreadyInSave:protected] =>
[alreadyInValidation:protected] =>
[validationFailures:protected] => Array
(
)
[_new:BaseObject:private] =>
[_deleted:BaseObject:private] =>
[modifiedColumns:protected] => Array
(
)
)
)
)
[preview_mode] =>
[description] => Toolbox talks have been the main tool for communicating safety information on construction jobs for decades.
Unfortunately, there has been little research on what makes for effective toolbox talks. The IUOE National
Training Fund worked with OSHA and NIOSH to make sure their series of 24 Focus Four toolbox talks were based on the best recommendations for effective design. These toolbox talks accompany an entire package of training materials, but can be used alone. This guide points out the key features of these toolbox talks and how best to deliver them.
[keywords] => toolbox talks, tailgate talks
[related_items] => Array
(
[Toolbox Talks] => Array
(
[0] => DocumentRecord Object
(
[records:protected] => Array
(
)
[recordId:protected] =>
[searchWordClass:protected] =>
[searchWordPeerClass:protected] =>
[bok_record:protected] =>
[authors:protected] =>
[organizations:protected] =>
[collections:protected] =>
[categories:protected] =>
[categories_initialized:protected] =>
[mapped_items:protected] =>
[content:protected] =>
[files:protected] =>
[language:protected] => Language Object
(
[id:protected] => 1
[code:protected] => en
[name:protected] => English
[alreadyInSave:protected] =>
[alreadyInValidation:protected] =>
[validationFailures:protected] => Array
(
)
[_new:BaseObject:private] =>
[_deleted:BaseObject:private] =>
[modifiedColumns:protected] => Array
(
)
)
[old_record:protected] =>
[id:protected] => 1605
[old_id:protected] => 1262
[elcosh_id:protected] => d001137
[type:protected] => document
[display_type:protected] => HTML w/ PDF
[user_id:protected] =>
[language_id:protected] => 1
[tagging_id:protected] => Garber
[priority_id:protected] => 1
[title:protected] => Focus Four Toolbox Talks, Module 1 – Falls, Talk #2 – Falls from debris piles?
[total_pages:protected] => 1
[billed_pages:protected] => 1
[publication_number:protected] =>
[part_of:protected] =>
[keywords:protected] => disaster response, hazard clean-up, uneven surface, disaster site, disaster clean-up
[comments:protected] =>
[summary:protected] => A toolbox talk on preventing falls from debris piles. Includes questions to ask, an incident to discuss with images, and a place to record questions the trainer would like to ask about the incident. Part of a collection. Click on the 'collection' button to access the other items.
[transition_comments:protected] =>
[external_link:protected] =>
[consol_link:protected] => http://www.cpwrconstructionsolutions.org/roofing/hazard/1463/install-asphalt-roofs-fall-from-heights.html
[more_like_this:protected] => a000081,d000478,d000530
[permission_given_by:protected] =>
[published:protected] => T
[billable:protected] => F
[img_name:protected] =>
[img_ext:protected] =>
[img_width:protected] =>
[img_height:protected] =>
[img_credit:protected] =>
[img_practice:protected] =>
[vid_source_id:protected] =>
[vid_running_time:protected] =>
[vid_intended_audience:protected] =>
[vid_acquisition_info:protected] =>
[vid_cost:protected] =>
[vid_producer:protected] =>
[vid_filename:protected] =>
[vid_filename_downloadable:protected] =>
[date_summary:protected] =>
[date_permission_requested:protected] =>
[date_permission_received:protected] =>
[date_review_needed:protected] =>
[date_received:protected] => 02/15/12
[date_completed:protected] => 03/19/12
[date_billed:protected] =>
[date_modified:protected] => 07/10/12
[collBokExports:protected] =>
[lastBokExportCriteria:BaseElcoshItem:private] =>
[alreadyInSave:protected] =>
[alreadyInValidation:protected] =>
[validationFailures:protected] => Array
(
)
[_new:BaseObject:private] =>
[_deleted:BaseObject:private] =>
[modifiedColumns:protected] => Array
(
)
)
[1] => DocumentRecord Object
(
[records:protected] => Array
(
)
[recordId:protected] =>
[searchWordClass:protected] =>
[searchWordPeerClass:protected] =>
[bok_record:protected] =>
[authors:protected] =>
[organizations:protected] =>
[collections:protected] =>
[categories:protected] =>
[categories_initialized:protected] =>
[mapped_items:protected] =>
[content:protected] =>
[files:protected] =>
[language:protected] => Language Object
(
[id:protected] => 1
[code:protected] => en
[name:protected] => English
[alreadyInSave:protected] =>
[alreadyInValidation:protected] =>
[validationFailures:protected] => Array
(
)
[_new:BaseObject:private] =>
[_deleted:BaseObject:private] =>
[modifiedColumns:protected] => Array
(
)
)
[old_record:protected] =>
[id:protected] => 1610
[old_id:protected] => 1271
[elcosh_id:protected] => d001146
[type:protected] => document
[display_type:protected] => HTML w/ PDF
[user_id:protected] => 0
[language_id:protected] => 1
[tagging_id:protected] => Garber
[priority_id:protected] => 1
[title:protected] => Focus Four Toolbox Talks, Module 2 – Struck-by, Talk #5 – Rigging and Securing Loads
[total_pages:protected] => 1
[billed_pages:protected] => 1
[publication_number:protected] =>
[part_of:protected] =>
[keywords:protected] => rigging, lift loads, loading areas, chains
[comments:protected] =>
[summary:protected] => A toolbox talk on preventing struck-by incidents caused by not securing loads properly. Includes questions to ask, an incident to discuss with images, and a place to record questions the trainer would like to ask about the incident. Part of a collection. Click on the 'collection' button to access the other items.
[transition_comments:protected] =>
[external_link:protected] =>
[consol_link:protected] => http://www.cpwrconstructionsolutions.org/heavy_equipment/hazard/1591/move-equipment-to-from-and-between-sites-work-zone-struck-by-injuries-and-fatalities.html
[more_like_this:protected] => d000144,d000360,d000873
[permission_given_by:protected] =>
[published:protected] => T
[billable:protected] => F
[img_name:protected] =>
[img_ext:protected] =>
[img_width:protected] =>
[img_height:protected] =>
[img_credit:protected] =>
[img_practice:protected] =>
[vid_source_id:protected] =>
[vid_running_time:protected] =>
[vid_intended_audience:protected] =>
[vid_acquisition_info:protected] =>
[vid_cost:protected] =>
[vid_producer:protected] =>
[vid_filename:protected] =>
[vid_filename_downloadable:protected] =>
[date_summary:protected] =>
[date_permission_requested:protected] =>
[date_permission_received:protected] =>
[date_review_needed:protected] =>
[date_received:protected] => 02/15/12
[date_completed:protected] => 03/28/12
[date_billed:protected] =>
[date_modified:protected] => 05/12/14
[collBokExports:protected] =>
[lastBokExportCriteria:BaseElcoshItem:private] =>
[alreadyInSave:protected] =>
[alreadyInValidation:protected] =>
[validationFailures:protected] => Array
(
)
[_new:BaseObject:private] =>
[_deleted:BaseObject:private] =>
[modifiedColumns:protected] => Array
(
)
)
[2] => DocumentRecord Object
(
[records:protected] => Array
(
)
[recordId:protected] =>
[searchWordClass:protected] =>
[searchWordPeerClass:protected] =>
[bok_record:protected] =>
[authors:protected] =>
[organizations:protected] =>
[collections:protected] =>
[categories:protected] =>
[categories_initialized:protected] =>
[mapped_items:protected] =>
[content:protected] =>
[files:protected] =>
[language:protected] => Language Object
(
[id:protected] => 1
[code:protected] => en
[name:protected] => English
[alreadyInSave:protected] =>
[alreadyInValidation:protected] =>
[validationFailures:protected] => Array
(
)
[_new:BaseObject:private] =>
[_deleted:BaseObject:private] =>
[modifiedColumns:protected] => Array
(
)
)
[old_record:protected] =>
[id:protected] => 1645
[old_id:protected] => 1274
[elcosh_id:protected] => d001149
[type:protected] => document
[display_type:protected] => HTML w/ PDF
[user_id:protected] => 0
[language_id:protected] => 1
[tagging_id:protected] => Garber
[priority_id:protected] => 1
[title:protected] => Focus Four Toolbox Talks, Module 3 – Caught-in/between, Talk #2 – Trenches & Heavy Equipment
[total_pages:protected] => 1
[billed_pages:protected] => 1
[publication_number:protected] =>
[part_of:protected] =>
[keywords:protected] => back-up alarms, spotter, soil cave-in, spoil pikes, ROPs, trenching, rain
[comments:protected] =>
[summary:protected] => A toolbox talk on preventing incidents involving trenches such as trench collapse. Includes questions to ask, an incident to discuss with images, and a place to record questions the trainer would like to ask about the incident. Part of a collection. Click on the 'collection' button to access the other items.
[transition_comments:protected] =>
[external_link:protected] =>
[consol_link:protected] =>
[more_like_this:protected] => d000019,d000035,d000168
[permission_given_by:protected] =>
[published:protected] => T
[billable:protected] => F
[img_name:protected] =>
[img_ext:protected] =>
[img_width:protected] =>
[img_height:protected] =>
[img_credit:protected] =>
[img_practice:protected] =>
[vid_source_id:protected] =>
[vid_running_time:protected] =>
[vid_intended_audience:protected] =>
[vid_acquisition_info:protected] =>
[vid_cost:protected] =>
[vid_producer:protected] =>
[vid_filename:protected] =>
[vid_filename_downloadable:protected] =>
[date_summary:protected] =>
[date_permission_requested:protected] =>
[date_permission_received:protected] =>
[date_review_needed:protected] =>
[date_received:protected] => 02/15/12
[date_completed:protected] => 04/02/12
[date_billed:protected] =>
[date_modified:protected] => 05/23/23
[collBokExports:protected] =>
[lastBokExportCriteria:BaseElcoshItem:private] =>
[alreadyInSave:protected] =>
[alreadyInValidation:protected] =>
[validationFailures:protected] => Array
(
)
[_new:BaseObject:private] =>
[_deleted:BaseObject:private] =>
[modifiedColumns:protected] => Array
(
)
)
[3] => DocumentRecord Object
(
[records:protected] => Array
(
)
[recordId:protected] =>
[searchWordClass:protected] =>
[searchWordPeerClass:protected] =>
[bok_record:protected] =>
[authors:protected] =>
[organizations:protected] =>
[collections:protected] =>
[categories:protected] =>
[categories_initialized:protected] =>
[mapped_items:protected] =>
[content:protected] =>
[files:protected] =>
[language:protected] => Language Object
(
[id:protected] => 1
[code:protected] => en
[name:protected] => English
[alreadyInSave:protected] =>
[alreadyInValidation:protected] =>
[validationFailures:protected] => Array
(
)
[_new:BaseObject:private] =>
[_deleted:BaseObject:private] =>
[modifiedColumns:protected] => Array
(
)
)
[old_record:protected] =>
[id:protected] => 1654
[old_id:protected] => 1284
[elcosh_id:protected] => d001159
[type:protected] => document
[display_type:protected] => HTML w/ PDF
[user_id:protected] => 0
[language_id:protected] => 1
[tagging_id:protected] => Garber
[priority_id:protected] => 1
[title:protected] => Focus Four Toolbox Talks, Module 4 – Electrocutions, Talk #6 – Hazards on Disaster Sites
[total_pages:protected] => 1
[billed_pages:protected] => 1
[publication_number:protected] =>
[part_of:protected] =>
[keywords:protected] => powerlines, underground, utilities, generators, wet conditions, GFCIs, energized lines, disasters, emergency response
[comments:protected] =>
[summary:protected] => A toolbox talk on how to avoid electrocution on a disaster site. Includes questions to ask, an incident to discuss with images, and a place to record questions the trainer would like to ask about the incident. Part of a collection. Click on the 'collection' button to access the other items.
[transition_comments:protected] =>
[external_link:protected] =>
[consol_link:protected] => http://www.cpwrconstructionsolutions.org/electrical/hazard/1138/install-and-repair-high-voltage-lines-transformers-switches-electrical-shocks-burns-and-or-electrocution.html
[more_like_this:protected] => d000135,d000361,d000437
[permission_given_by:protected] =>
[published:protected] => T
[billable:protected] => F
[img_name:protected] =>
[img_ext:protected] =>
[img_width:protected] =>
[img_height:protected] =>
[img_credit:protected] =>
[img_practice:protected] =>
[vid_source_id:protected] =>
[vid_running_time:protected] =>
[vid_intended_audience:protected] =>
[vid_acquisition_info:protected] =>
[vid_cost:protected] =>
[vid_producer:protected] =>
[vid_filename:protected] =>
[vid_filename_downloadable:protected] =>
[date_summary:protected] =>
[date_permission_requested:protected] =>
[date_permission_received:protected] =>
[date_review_needed:protected] =>
[date_received:protected] => 02/15/12
[date_completed:protected] => 04/02/12
[date_billed:protected] =>
[date_modified:protected] => 05/23/23
[collBokExports:protected] =>
[lastBokExportCriteria:BaseElcoshItem:private] =>
[alreadyInSave:protected] =>
[alreadyInValidation:protected] =>
[validationFailures:protected] => Array
(
)
[_new:BaseObject:private] =>
[_deleted:BaseObject:private] =>
[modifiedColumns:protected] => Array
(
)
)
)
)
[collections] => Array
(
[1294] =>
[1295] =>
[1292] =>
[1293] => CollectionRecord Object
(
[collection_items:protected] =>
[records:protected] => Array
(
)
[recordId:protected] =>
[searchWordClass:protected] =>
[searchWordPeerClass:protected] =>
[bok_record:protected] =>
[authors:protected] =>
[organizations:protected] =>
[collections:protected] =>
[categories:protected] =>
[categories_initialized:protected] =>
[mapped_items:protected] =>
[content:protected] =>
[files:protected] =>
[language:protected] =>
[old_record:protected] =>
[id:protected] => 1293
[old_id:protected] =>
[elcosh_id:protected] => c000026
[type:protected] => collection
[display_type:protected] => Collection
[user_id:protected] =>
[language_id:protected] =>
[tagging_id:protected] =>
[priority_id:protected] =>
[title:protected] => Focus Four-Struck By
[total_pages:protected] =>
[billed_pages:protected] =>
[publication_number:protected] =>
[part_of:protected] =>
[keywords:protected] =>
[comments:protected] =>
[summary:protected] => The following are links to all of the items in this collection:
[transition_comments:protected] =>
[external_link:protected] =>
[consol_link:protected] =>
[more_like_this:protected] =>
[permission_given_by:protected] =>
[published:protected] => T
[billable:protected] => F
[img_name:protected] =>
[img_ext:protected] =>
[img_width:protected] =>
[img_height:protected] =>
[img_credit:protected] =>
[img_practice:protected] =>
[vid_source_id:protected] =>
[vid_running_time:protected] =>
[vid_intended_audience:protected] =>
[vid_acquisition_info:protected] =>
[vid_cost:protected] =>
[vid_producer:protected] =>
[vid_filename:protected] =>
[vid_filename_downloadable:protected] =>
[date_summary:protected] =>
[date_permission_requested:protected] =>
[date_permission_received:protected] =>
[date_review_needed:protected] =>
[date_received:protected] => 05/08/12
[date_completed:protected] => 05/08/12
[date_billed:protected] =>
[date_modified:protected] => 05/08/12
[collBokExports:protected] =>
[lastBokExportCriteria:BaseElcoshItem:private] =>
[alreadyInSave:protected] =>
[alreadyInValidation:protected] =>
[validationFailures:protected] => Array
(
)
[_new:BaseObject:private] =>
[_deleted:BaseObject:private] =>
[modifiedColumns:protected] => Array
(
)
)
)
[record] => DocumentRecord Object
(
[records:protected] => Array
(
)
[recordId:protected] =>
[searchWordClass:protected] =>
[searchWordPeerClass:protected] =>
[bok_record:protected] =>
[authors:protected] => Array
(
)
[organizations:protected] => Array
(
[256] => Organization Object
(
[id:protected] => 256
[elcosh_id:protected] => o000276
[user_id:protected] => 14
[province_id:protected] => 0
[country_id:protected] => 0
[title:protected] => IUOE National Training Fund
[address:protected] =>
[postal_code:protected] =>
[city:protected] =>
[department:protected] =>
[phone:protected] => 304-253-8674
[fax:protected] =>
[email:protected] =>
[website:protected] => http://www.iuoeiettc.org
[filename:protected] =>
[about:protected] =>
[comments:protected] =>
[logo_available:protected] => T
[no_details:protected] => F
[date_received:protected] => 2012-02-13
[date_completed:protected] => 2012-02-13
[date_billed:protected] =>
[alreadyInSave:protected] =>
[alreadyInValidation:protected] =>
[validationFailures:protected] => Array
(
)
[_new:BaseObject:private] =>
[_deleted:BaseObject:private] =>
[modifiedColumns:protected] => Array
(
)
)
)
[collections:protected] => Array
(
[1294] =>
[1295] =>
[1292] =>
[1293] => CollectionRecord Object
(
[collection_items:protected] =>
[records:protected] => Array
(
)
[recordId:protected] =>
[searchWordClass:protected] =>
[searchWordPeerClass:protected] =>
[bok_record:protected] =>
[authors:protected] =>
[organizations:protected] =>
[collections:protected] =>
[categories:protected] =>
[categories_initialized:protected] =>
[mapped_items:protected] =>
[content:protected] =>
[files:protected] =>
[language:protected] =>
[old_record:protected] =>
[id:protected] => 1293
[old_id:protected] =>
[elcosh_id:protected] => c000026
[type:protected] => collection
[display_type:protected] => Collection
[user_id:protected] =>
[language_id:protected] =>
[tagging_id:protected] =>
[priority_id:protected] =>
[title:protected] => Focus Four-Struck By
[total_pages:protected] =>
[billed_pages:protected] =>
[publication_number:protected] =>
[part_of:protected] =>
[keywords:protected] =>
[comments:protected] =>
[summary:protected] => The following are links to all of the items in this collection:
[transition_comments:protected] =>
[external_link:protected] =>
[consol_link:protected] =>
[more_like_this:protected] =>
[permission_given_by:protected] =>
[published:protected] => T
[billable:protected] => F
[img_name:protected] =>
[img_ext:protected] =>
[img_width:protected] =>
[img_height:protected] =>
[img_credit:protected] =>
[img_practice:protected] =>
[vid_source_id:protected] =>
[vid_running_time:protected] =>
[vid_intended_audience:protected] =>
[vid_acquisition_info:protected] =>
[vid_cost:protected] =>
[vid_producer:protected] =>
[vid_filename:protected] =>
[vid_filename_downloadable:protected] =>
[date_summary:protected] =>
[date_permission_requested:protected] =>
[date_permission_received:protected] =>
[date_review_needed:protected] =>
[date_received:protected] => 05/08/12
[date_completed:protected] => 05/08/12
[date_billed:protected] =>
[date_modified:protected] => 05/08/12
[collBokExports:protected] =>
[lastBokExportCriteria:BaseElcoshItem:private] =>
[alreadyInSave:protected] =>
[alreadyInValidation:protected] =>
[validationFailures:protected] => Array
(
)
[_new:BaseObject:private] =>
[_deleted:BaseObject:private] =>
[modifiedColumns:protected] => Array
(
)
)
)
[categories:protected] =>
[categories_initialized:protected] =>
[mapped_items:protected] => Array
(
[1605] => DocumentRecord Object
(
[records:protected] => Array
(
)
[recordId:protected] =>
[searchWordClass:protected] =>
[searchWordPeerClass:protected] =>
[bok_record:protected] =>
[authors:protected] =>
[organizations:protected] =>
[collections:protected] =>
[categories:protected] =>
[categories_initialized:protected] =>
[mapped_items:protected] =>
[content:protected] =>
[files:protected] =>
[language:protected] =>
[old_record:protected] =>
[id:protected] => 1605
[old_id:protected] => 1262
[elcosh_id:protected] => d001137
[type:protected] => document
[display_type:protected] => HTML w/ PDF
[user_id:protected] =>
[language_id:protected] => 1
[tagging_id:protected] => Garber
[priority_id:protected] => 1
[title:protected] => Focus Four Toolbox Talks, Module 1 – Falls, Talk #2 – Falls from debris piles?
[total_pages:protected] => 1
[billed_pages:protected] => 1
[publication_number:protected] =>
[part_of:protected] =>
[keywords:protected] => disaster response, hazard clean-up, uneven surface, disaster site, disaster clean-up
[comments:protected] =>
[summary:protected] => A toolbox talk on preventing falls from debris piles. Includes questions to ask, an incident to discuss with images, and a place to record questions the trainer would like to ask about the incident. Part of a collection. Click on the 'collection' button to access the other items.
[transition_comments:protected] =>
[external_link:protected] =>
[consol_link:protected] => http://www.cpwrconstructionsolutions.org/roofing/hazard/1463/install-asphalt-roofs-fall-from-heights.html
[more_like_this:protected] => a000081,d000478,d000530
[permission_given_by:protected] =>
[published:protected] => T
[billable:protected] => F
[img_name:protected] =>
[img_ext:protected] =>
[img_width:protected] =>
[img_height:protected] =>
[img_credit:protected] =>
[img_practice:protected] =>
[vid_source_id:protected] =>
[vid_running_time:protected] =>
[vid_intended_audience:protected] =>
[vid_acquisition_info:protected] =>
[vid_cost:protected] =>
[vid_producer:protected] =>
[vid_filename:protected] =>
[vid_filename_downloadable:protected] =>
[date_summary:protected] =>
[date_permission_requested:protected] =>
[date_permission_received:protected] =>
[date_review_needed:protected] =>
[date_received:protected] => 02/15/12
[date_completed:protected] => 03/19/12
[date_billed:protected] =>
[date_modified:protected] => 07/10/12
[collBokExports:protected] =>
[lastBokExportCriteria:BaseElcoshItem:private] =>
[alreadyInSave:protected] =>
[alreadyInValidation:protected] =>
[validationFailures:protected] => Array
(
)
[_new:BaseObject:private] =>
[_deleted:BaseObject:private] =>
[modifiedColumns:protected] => Array
(
)
)
[1610] => DocumentRecord Object
(
[records:protected] => Array
(
)
[recordId:protected] =>
[searchWordClass:protected] =>
[searchWordPeerClass:protected] =>
[bok_record:protected] =>
[authors:protected] =>
[organizations:protected] =>
[collections:protected] =>
[categories:protected] =>
[categories_initialized:protected] =>
[mapped_items:protected] =>
[content:protected] =>
[files:protected] =>
[language:protected] =>
[old_record:protected] =>
[id:protected] => 1610
[old_id:protected] => 1271
[elcosh_id:protected] => d001146
[type:protected] => document
[display_type:protected] => HTML w/ PDF
[user_id:protected] => 0
[language_id:protected] => 1
[tagging_id:protected] => Garber
[priority_id:protected] => 1
[title:protected] => Focus Four Toolbox Talks, Module 2 – Struck-by, Talk #5 – Rigging and Securing Loads
[total_pages:protected] => 1
[billed_pages:protected] => 1
[publication_number:protected] =>
[part_of:protected] =>
[keywords:protected] => rigging, lift loads, loading areas, chains
[comments:protected] =>
[summary:protected] => A toolbox talk on preventing struck-by incidents caused by not securing loads properly. Includes questions to ask, an incident to discuss with images, and a place to record questions the trainer would like to ask about the incident. Part of a collection. Click on the 'collection' button to access the other items.
[transition_comments:protected] =>
[external_link:protected] =>
[consol_link:protected] => http://www.cpwrconstructionsolutions.org/heavy_equipment/hazard/1591/move-equipment-to-from-and-between-sites-work-zone-struck-by-injuries-and-fatalities.html
[more_like_this:protected] => d000144,d000360,d000873
[permission_given_by:protected] =>
[published:protected] => T
[billable:protected] => F
[img_name:protected] =>
[img_ext:protected] =>
[img_width:protected] =>
[img_height:protected] =>
[img_credit:protected] =>
[img_practice:protected] =>
[vid_source_id:protected] =>
[vid_running_time:protected] =>
[vid_intended_audience:protected] =>
[vid_acquisition_info:protected] =>
[vid_cost:protected] =>
[vid_producer:protected] =>
[vid_filename:protected] =>
[vid_filename_downloadable:protected] =>
[date_summary:protected] =>
[date_permission_requested:protected] =>
[date_permission_received:protected] =>
[date_review_needed:protected] =>
[date_received:protected] => 02/15/12
[date_completed:protected] => 03/28/12
[date_billed:protected] =>
[date_modified:protected] => 05/12/14
[collBokExports:protected] =>
[lastBokExportCriteria:BaseElcoshItem:private] =>
[alreadyInSave:protected] =>
[alreadyInValidation:protected] =>
[validationFailures:protected] => Array
(
)
[_new:BaseObject:private] =>
[_deleted:BaseObject:private] =>
[modifiedColumns:protected] => Array
(
)
)
[1645] => DocumentRecord Object
(
[records:protected] => Array
(
)
[recordId:protected] =>
[searchWordClass:protected] =>
[searchWordPeerClass:protected] =>
[bok_record:protected] =>
[authors:protected] =>
[organizations:protected] =>
[collections:protected] =>
[categories:protected] =>
[categories_initialized:protected] =>
[mapped_items:protected] =>
[content:protected] =>
[files:protected] =>
[language:protected] =>
[old_record:protected] =>
[id:protected] => 1645
[old_id:protected] => 1274
[elcosh_id:protected] => d001149
[type:protected] => document
[display_type:protected] => HTML w/ PDF
[user_id:protected] => 0
[language_id:protected] => 1
[tagging_id:protected] => Garber
[priority_id:protected] => 1
[title:protected] => Focus Four Toolbox Talks, Module 3 – Caught-in/between, Talk #2 – Trenches & Heavy Equipment
[total_pages:protected] => 1
[billed_pages:protected] => 1
[publication_number:protected] =>
[part_of:protected] =>
[keywords:protected] => back-up alarms, spotter, soil cave-in, spoil pikes, ROPs, trenching, rain
[comments:protected] =>
[summary:protected] => A toolbox talk on preventing incidents involving trenches such as trench collapse. Includes questions to ask, an incident to discuss with images, and a place to record questions the trainer would like to ask about the incident. Part of a collection. Click on the 'collection' button to access the other items.
[transition_comments:protected] =>
[external_link:protected] =>
[consol_link:protected] =>
[more_like_this:protected] => d000019,d000035,d000168
[permission_given_by:protected] =>
[published:protected] => T
[billable:protected] => F
[img_name:protected] =>
[img_ext:protected] =>
[img_width:protected] =>
[img_height:protected] =>
[img_credit:protected] =>
[img_practice:protected] =>
[vid_source_id:protected] =>
[vid_running_time:protected] =>
[vid_intended_audience:protected] =>
[vid_acquisition_info:protected] =>
[vid_cost:protected] =>
[vid_producer:protected] =>
[vid_filename:protected] =>
[vid_filename_downloadable:protected] =>
[date_summary:protected] =>
[date_permission_requested:protected] =>
[date_permission_received:protected] =>
[date_review_needed:protected] =>
[date_received:protected] => 02/15/12
[date_completed:protected] => 04/02/12
[date_billed:protected] =>
[date_modified:protected] => 05/23/23
[collBokExports:protected] =>
[lastBokExportCriteria:BaseElcoshItem:private] =>
[alreadyInSave:protected] =>
[alreadyInValidation:protected] =>
[validationFailures:protected] => Array
(
)
[_new:BaseObject:private] =>
[_deleted:BaseObject:private] =>
[modifiedColumns:protected] => Array
(
)
)
[1654] => DocumentRecord Object
(
[records:protected] => Array
(
)
[recordId:protected] =>
[searchWordClass:protected] =>
[searchWordPeerClass:protected] =>
[bok_record:protected] =>
[authors:protected] =>
[organizations:protected] =>
[collections:protected] =>
[categories:protected] =>
[categories_initialized:protected] =>
[mapped_items:protected] =>
[content:protected] =>
[files:protected] =>
[language:protected] =>
[old_record:protected] =>
[id:protected] => 1654
[old_id:protected] => 1284
[elcosh_id:protected] => d001159
[type:protected] => document
[display_type:protected] => HTML w/ PDF
[user_id:protected] => 0
[language_id:protected] => 1
[tagging_id:protected] => Garber
[priority_id:protected] => 1
[title:protected] => Focus Four Toolbox Talks, Module 4 – Electrocutions, Talk #6 – Hazards on Disaster Sites
[total_pages:protected] => 1
[billed_pages:protected] => 1
[publication_number:protected] =>
[part_of:protected] =>
[keywords:protected] => powerlines, underground, utilities, generators, wet conditions, GFCIs, energized lines, disasters, emergency response
[comments:protected] =>
[summary:protected] => A toolbox talk on how to avoid electrocution on a disaster site. Includes questions to ask, an incident to discuss with images, and a place to record questions the trainer would like to ask about the incident. Part of a collection. Click on the 'collection' button to access the other items.
[transition_comments:protected] =>
[external_link:protected] =>
[consol_link:protected] => http://www.cpwrconstructionsolutions.org/electrical/hazard/1138/install-and-repair-high-voltage-lines-transformers-switches-electrical-shocks-burns-and-or-electrocution.html
[more_like_this:protected] => d000135,d000361,d000437
[permission_given_by:protected] =>
[published:protected] => T
[billable:protected] => F
[img_name:protected] =>
[img_ext:protected] =>
[img_width:protected] =>
[img_height:protected] =>
[img_credit:protected] =>
[img_practice:protected] =>
[vid_source_id:protected] =>
[vid_running_time:protected] =>
[vid_intended_audience:protected] =>
[vid_acquisition_info:protected] =>
[vid_cost:protected] =>
[vid_producer:protected] =>
[vid_filename:protected] =>
[vid_filename_downloadable:protected] =>
[date_summary:protected] =>
[date_permission_requested:protected] =>
[date_permission_received:protected] =>
[date_review_needed:protected] =>
[date_received:protected] => 02/15/12
[date_completed:protected] => 04/02/12
[date_billed:protected] =>
[date_modified:protected] => 05/23/23
[collBokExports:protected] =>
[lastBokExportCriteria:BaseElcoshItem:private] =>
[alreadyInSave:protected] =>
[alreadyInValidation:protected] =>
[validationFailures:protected] => Array
(
)
[_new:BaseObject:private] =>
[_deleted:BaseObject:private] =>
[modifiedColumns:protected] => Array
(
)
)
)
[content:protected] =>
[files:protected] => Array
(
[9400] => File Object
(
[id:protected] => 9400
[filename:protected] => 1.jpg
[downloadable:protected] => F
[timestamp:protected] => 2014-05-08 15:05:37
[alreadyInSave:protected] =>
[alreadyInValidation:protected] =>
[validationFailures:protected] => Array
(
)
[_new:BaseObject:private] =>
[_deleted:BaseObject:private] =>
[modifiedColumns:protected] => Array
(
)
)
[9401] => File Object
(
[id:protected] => 9401
[filename:protected] => d001298.pdf
[downloadable:protected] => T
[timestamp:protected] => 2014-05-08 15:05:37
[alreadyInSave:protected] =>
[alreadyInValidation:protected] =>
[validationFailures:protected] => Array
(
)
[_new:BaseObject:private] =>
[_deleted:BaseObject:private] =>
[modifiedColumns:protected] => Array
(
)
)
)
[language:protected] => Language Object
(
[id:protected] => 1
[code:protected] => en
[name:protected] => English
[alreadyInSave:protected] =>
[alreadyInValidation:protected] =>
[validationFailures:protected] => Array
(
)
[_new:BaseObject:private] =>
[_deleted:BaseObject:private] =>
[modifiedColumns:protected] => Array
(
)
)
[old_record:protected] =>
[id:protected] => 3827
[old_id:protected] =>
[elcosh_id:protected] => d001298
[type:protected] => document
[display_type:protected] => HTML w/ PDF
[user_id:protected] => 23
[language_id:protected] => 1
[tagging_id:protected] => Bruce Lippy
[priority_id:protected] => 1
[title:protected] => Getting the most out of the IUOE Toolbox Talks
[total_pages:protected] => 2
[billed_pages:protected] => 2
[publication_number:protected] =>
[part_of:protected] =>
[keywords:protected] => toolbox talks, tailgate talks
[comments:protected] =>
[summary:protected] => Toolbox talks have been the main tool for communicating safety information on construction jobs for decades.
Unfortunately, there has been little research on what makes for effective toolbox talks. The IUOE National
Training Fund worked with OSHA and NIOSH to make sure their series of 24 Focus Four toolbox talks were based on the best recommendations for effective design. These toolbox talks accompany an entire package of training materials, but can be used alone. This guide points out the key features of these toolbox talks and how best to deliver them.
[transition_comments:protected] =>
[external_link:protected] =>
[consol_link:protected] =>
[more_like_this:protected] => d001137,d001146,d001149,d001159
[permission_given_by:protected] => IUOE National Hazmat Program
[published:protected] => T
[billable:protected] => F
[img_name:protected] =>
[img_ext:protected] => png
[img_width:protected] =>
[img_height:protected] =>
[img_credit:protected] =>
[img_practice:protected] =>
[vid_source_id:protected] =>
[vid_running_time:protected] =>
[vid_intended_audience:protected] =>
[vid_acquisition_info:protected] =>
[vid_cost:protected] =>
[vid_producer:protected] =>
[vid_filename:protected] =>
[vid_filename_downloadable:protected] =>
[date_summary:protected] => 2007
[date_permission_requested:protected] =>
[date_permission_received:protected] =>
[date_review_needed:protected] =>
[date_received:protected] => 05/08/14
[date_completed:protected] => 05/08/14
[date_billed:protected] =>
[date_modified:protected] => 05/08/14
[collBokExports:protected] =>
[lastBokExportCriteria:BaseElcoshItem:private] =>
[alreadyInSave:protected] =>
[alreadyInValidation:protected] =>
[validationFailures:protected] => Array
(
)
[_new:BaseObject:private] =>
[_deleted:BaseObject:private] =>
[modifiedColumns:protected] => Array
(
)
)
[show_text] =>
[document_content] => ElcoshItemDocumentContent Object
(
[id:protected] => 2896
[item_id:protected] => 3827
[type:protected] => main
[title:protected] =>
[content:protected] =>
Why were these talks developed?
Toolbox talks have been the main tool for communicating safety information on construction jobs for decades. Unfortunately, there has been almost no research on what makes for effective toolbox talks. The IUOE National Training Fund has worked with OSHA, the National Institute for Occupational Safety and Health and the Lippy Group, LLC to make sure these Focus Four toolbox talks are based on the latest fi ndings on the most effective design and tailored to the hazards operating engineers face daily. These toolbox talks accompany an entire package of training materials, but can be used alone. The way these are delivered is as important as how well they are designed.
What did NIOSH find out?
- Just handing out factsheets and toolbox talks to workers doesn’t work. Providing copies after toolbox talks doesn’t make much of an impact either.
- Using case studies (real life stories of accidents that ended in fatality or injury) in toolbox talks is effective.
- When toolbox talks containing case studies were accompanied by discussion questions to encourage group participation, they were more effective. Consequently, getting the workers to participate in the discussion about the case study is important. It’s not enough to tell the story, it is better to have the workers engage in problem solving that analyzes why the accident occurred and how it could have been prevented. Active learning is always better than passive.
How should you deliver these toolbox talks?
- Choose a topic that is related to work going on at the site.
- Hold the meeting on the job, preferably where everyone can sit and relax.
- Hold the meeting at the beginning of a shift or after a break. Folks are too tired at the end of a shift to carefully listen and they want to get home.
- Read the toolbox talk sheet on the topic prior to conducting the talk.
- Start at the top of the form and work right through to the end, which should take around 10 to 15 minutes. Guidance is provided in blue print to help you with each section.
- Use the questions provided to generate discussions. Always allow time for the crew to respond to your questions before you provide an answer. Some suggested responses are written in italics.
- Review the case study and emphasize that this was a real incident. Ask the crew for a case study before you review the one provided, however.
- Always end with a discussion of the particular worksite where you are conducting the talk. Tie the talk as closely to hazards on the site as possible and encourage the crew to constantly look for and immediately correct hazards. They should also know how to report any problems that can’t be immediately corrected.
- Provide copies to each person, if you like, but NIOSH has not found that to be particularly effective.
- Encourage workers to do similar talks on their sites and provide them with the IUOE phone number for ordering in bulk.
- Have everyone sign the back of the form to indicate they attended this session and point out it is a pledge to look out for the health and safety of everyone on the site.
What are the key features of these toolbox talks?

[content_transformed:protected] =>
Why were these talks developed?
Toolbox talks have been the main tool for communicating safety information on construction jobs for decades. Unfortunately, there has been almost no research on what makes for effective toolbox talks. The IUOE National Training Fund has worked with OSHA, the National Institute for Occupational Safety and Health and the Lippy Group, LLC to make sure these Focus Four toolbox talks are based on the latest fi ndings on the most effective design and tailored to the hazards operating engineers face daily. These toolbox talks accompany an entire package of training materials, but can be used alone. The way these are delivered is as important as how well they are designed.
What did NIOSH find out?
- Just handing out factsheets and toolbox talks to workers doesn’t work. Providing copies after toolbox talks doesn’t make much of an impact either.
- Using case studies (real life stories of accidents that ended in fatality or injury) in toolbox talks is effective.
- When toolbox talks containing case studies were accompanied by discussion questions to encourage group participation, they were more effective. Consequently, getting the workers to participate in the discussion about the case study is important. It’s not enough to tell the story, it is better to have the workers engage in problem solving that analyzes why the accident occurred and how it could have been prevented. Active learning is always better than passive.
How should you deliver these toolbox talks?
- Choose a topic that is related to work going on at the site.
- Hold the meeting on the job, preferably where everyone can sit and relax.
- Hold the meeting at the beginning of a shift or after a break. Folks are too tired at the end of a shift to carefully listen and they want to get home.
- Read the toolbox talk sheet on the topic prior to conducting the talk.
- Start at the top of the form and work right through to the end, which should take around 10 to 15 minutes. Guidance is provided in blue print to help you with each section.
- Use the questions provided to generate discussions. Always allow time for the crew to respond to your questions before you provide an answer. Some suggested responses are written in italics.
- Review the case study and emphasize that this was a real incident. Ask the crew for a case study before you review the one provided, however.
- Always end with a discussion of the particular worksite where you are conducting the talk. Tie the talk as closely to hazards on the site as possible and encourage the crew to constantly look for and immediately correct hazards. They should also know how to report any problems that can’t be immediately corrected.
- Provide copies to each person, if you like, but NIOSH has not found that to be particularly effective.
- Encourage workers to do similar talks on their sites and provide them with the IUOE phone number for ordering in bulk.
- Have everyone sign the back of the form to indicate they attended this session and point out it is a pledge to look out for the health and safety of everyone on the site.
What are the key features of these toolbox talks?
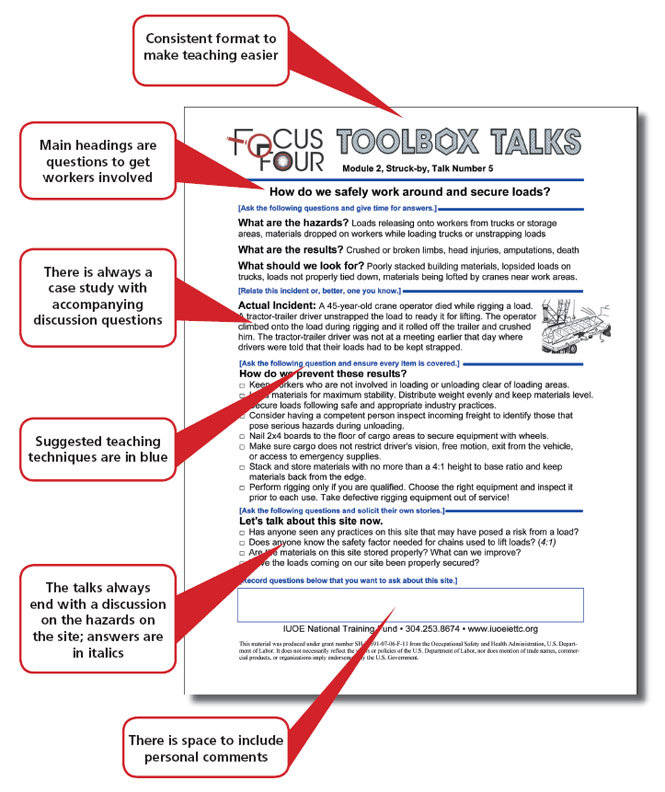
[disclaimer:protected] =>
[disclaimer_transformed:protected] =>
[alreadyInSave:protected] =>
[alreadyInValidation:protected] =>
[validationFailures:protected] => Array
(
)
[_new:BaseObject:private] =>
[_deleted:BaseObject:private] =>
[modifiedColumns:protected] => Array
(
)
)
[template] => record
)
[_file] => /home/agsafe5/repositories/elcosh/live/templates/elcosh/record_macros.html
[_errors:protected] => Array
(
)
[_encoding:protected] => UTF-8
[_outputMode:protected] => 11
[_forceReparse:protected] =>
[_phpCodeDestination:protected] => /tmp/
[_phpCodeExtension:protected] => php
[_cacheLifetime:protected] => 30
[_cachePurgeFrequency:protected] => 30
[externalMacroTemplatesCache:PHPTAL:private] => Array
(
)
)
)
)
)
)
[3] => Array
(
[file] => /tmp/tpl_61515a6c_record__uvBJJSo8xT_sgOY5gjP7ug.php
[line] => 44
[function] => _executeMacroOfTemplate
[class] => PHPTAL
[type] => ->
[args] => Array
(
[0] => record_macros.html/collections
[1] => PHPTAL Object
(
[_prefilters:protected] => Array
(
)
[_prefilter:PHPTAL:private] => REMOVED: DO NOT USE
[_postfilter:protected] =>
[_repositories:protected] => Array
(
)
[_path:protected] => /home/agsafe5/repositories/elcosh/live/templates/elcosh/record.html
[_resolvers:protected] => Array
(
)
[_source:protected] => PHPTAL_FileSource Object
(
[_path:PHPTAL_FileSource:private] => /home/agsafe5/repositories/elcosh/live/templates/elcosh/record.html
)
[_codeFile:protected] => /tmp/tpl_61515a6c_record__uvBJJSo8xT_sgOY5gjP7ug.php
[_functionName:protected] => tpl_61515a6c_record__uvBJJSo8xT_sgOY5gjP7ug
[_prepared:protected] => 1
[_triggers:protected] => Array
(
)
[_translator:protected] =>
[_globalContext:protected] => stdClass Object
(
)
[_context:protected] => PHPTAL_Context Object
(
[_line] =>
[_file] => /home/agsafe5/repositories/elcosh/live/templates/elcosh/record.html
[repeat] => stdClass Object
(
)
[_xmlDeclaration] =>
[_docType] =>
[_nothrow:PHPTAL_Context:private] =>
[_slots:PHPTAL_Context:private] => Array
(
)
[_slotsStack:PHPTAL_Context:private] => Array
(
[0] => Array
(
)
[1] => Array
(
)
)
[_parentContext:PHPTAL_Context:private] =>
[_globalContext:PHPTAL_Context:private] => stdClass Object
(
)
[_echoDeclarations:PHPTAL_Context:private] =>
[referer] => http://www.elcosh.org/document/3827/d001298/Getting%2Bthe%2Bmost%2Bout%2Bof%2Bthe%2BIUOE%2BToolbox%2BTalks.html
[curr_module] => Record
[styles] => Array
(
)
[javascript] => Array
(
[0] => jquery.min.js
)
[metas] => Array
(
[language] => en
[robots] => index, follow
)
[user] =>
[curr_url] => https://www.elcosh.org/index.php?module=Record&id=3827&type=document
[base_url] => https://www.elcosh.org/index.php?module=Record
[title] => eLCOSH : Getting the most out of the IUOE Toolbox Talks
[language] => en
[search_query] =>
[module] => Record
[new_records] => Array
(
[0] => Search_Result Object
(
[title] => Toolbox Talk: Fixed Ladder
[image] => /record/images/notavailable-p.png
[blurb] => The CPWR Toolbox Talk on Fixed Ladders addresses the potential risks associated with using fixed ladders. The resource includes a brief case example,...
[category] => Array
(
[0] => 15
[1] => 47
[2] => 49
[3] => 51
[4] => 53
[5] => 55
[6] => 60
[7] => 64
[8] => 73
[9] => 76
[10] => 78
[11] => 80
[12] => 86
[13] => 87
[14] => 90
[15] => 92
[16] => 93
[17] => 94
[18] => 100
)
[labels] => Array
(
[0] => Falls
[1] => Work Environment
[2] => Hazards
[3] => Bricklayer
[4] => Trades
[5] => Carpenter
[7] => Cement Mason
[9] => Concrete Polisher
[11] => Electrical Worker
[13] => HVAC
[15] => Laborer
[17] => PCC/Restoration
[19] => Plumber/Pipefitter
[21] => Roofer/Waterproofer
[23] => Sheetmetal Worker
[25] => Welder
[27] => Commercial & Institutional
[28] => Jobsites
[29] => Industrial
[31] => LEED/Green Construction
[33] => Renovations
[35] => Residential
[37] => Toolbox Talks
[38] => Documents
[39] => Media & Documents
)
[type] => Toolbox Talks
[sub_category] =>
[url] => /document/4430/d001660/Toolbox%2BTalk%253A%2BFixed%2BLadder.html
[item:protected] => DocumentRecord Object
(
[records:protected] => Array
(
)
[recordId:protected] =>
[searchWordClass:protected] =>
[searchWordPeerClass:protected] =>
[bok_record:protected] =>
[authors:protected] =>
[organizations:protected] =>
[collections:protected] =>
[categories:protected] => Array
(
[15] => Category Object
(
[languages:protected] =>
[bok_resources:protected] =>
[bok_topics:protected] =>
[bok_keywords:protected] =>
[id:protected] => 15
[type:protected] => category
[parent:protected] => 7
[label:protected] => Falls
[alreadyInSave:protected] =>
[alreadyInValidation:protected] =>
[validationFailures:protected] => Array
(
)
[_new:BaseObject:private] =>
[_deleted:BaseObject:private] =>
[modifiedColumns:protected] => Array
(
)
)
[47] => Category Object
(
[languages:protected] =>
[bok_resources:protected] =>
[bok_topics:protected] =>
[bok_keywords:protected] =>
[id:protected] => 47
[type:protected] => category
[parent:protected] => 2
[label:protected] => Bricklayer
[alreadyInSave:protected] =>
[alreadyInValidation:protected] =>
[validationFailures:protected] => Array
(
)
[_new:BaseObject:private] =>
[_deleted:BaseObject:private] =>
[modifiedColumns:protected] => Array
(
)
)
[49] => Category Object
(
[languages:protected] =>
[bok_resources:protected] =>
[bok_topics:protected] =>
[bok_keywords:protected] =>
[id:protected] => 49
[type:protected] => category
[parent:protected] => 2
[label:protected] => Carpenter
[alreadyInSave:protected] =>
[alreadyInValidation:protected] =>
[validationFailures:protected] => Array
(
)
[_new:BaseObject:private] =>
[_deleted:BaseObject:private] =>
[modifiedColumns:protected] => Array
(
)
)
[51] => Category Object
(
[languages:protected] =>
[bok_resources:protected] =>
[bok_topics:protected] =>
[bok_keywords:protected] =>
[id:protected] => 51
[type:protected] => category
[parent:protected] => 2
[label:protected] => Cement Mason
[alreadyInSave:protected] =>
[alreadyInValidation:protected] =>
[validationFailures:protected] => Array
(
)
[_new:BaseObject:private] =>
[_deleted:BaseObject:private] =>
[modifiedColumns:protected] => Array
(
)
)
[53] => Category Object
(
[languages:protected] =>
[bok_resources:protected] =>
[bok_topics:protected] =>
[bok_keywords:protected] =>
[id:protected] => 53
[type:protected] => category
[parent:protected] => 2
[label:protected] => Concrete Polisher
[alreadyInSave:protected] =>
[alreadyInValidation:protected] =>
[validationFailures:protected] => Array
(
)
[_new:BaseObject:private] =>
[_deleted:BaseObject:private] =>
[modifiedColumns:protected] => Array
(
)
)
[55] => Category Object
(
[languages:protected] =>
[bok_resources:protected] =>
[bok_topics:protected] =>
[bok_keywords:protected] =>
[id:protected] => 55
[type:protected] => category
[parent:protected] => 2
[label:protected] => Electrical Worker
[alreadyInSave:protected] =>
[alreadyInValidation:protected] =>
[validationFailures:protected] => Array
(
)
[_new:BaseObject:private] =>
[_deleted:BaseObject:private] =>
[modifiedColumns:protected] => Array
(
)
)
[60] => Category Object
(
[languages:protected] =>
[bok_resources:protected] =>
[bok_topics:protected] =>
[bok_keywords:protected] =>
[id:protected] => 60
[type:protected] => category
[parent:protected] => 2
[label:protected] => HVAC
[alreadyInSave:protected] =>
[alreadyInValidation:protected] =>
[validationFailures:protected] => Array
(
)
[_new:BaseObject:private] =>
[_deleted:BaseObject:private] =>
[modifiedColumns:protected] => Array
(
)
)
[64] => Category Object
(
[languages:protected] =>
[bok_resources:protected] =>
[bok_topics:protected] =>
[bok_keywords:protected] =>
[id:protected] => 64
[type:protected] => category
[parent:protected] => 2
[label:protected] => Laborer
[alreadyInSave:protected] =>
[alreadyInValidation:protected] =>
[validationFailures:protected] => Array
(
)
[_new:BaseObject:private] =>
[_deleted:BaseObject:private] =>
[modifiedColumns:protected] => Array
(
)
)
[73] => Category Object
(
[languages:protected] =>
[bok_resources:protected] =>
[bok_topics:protected] =>
[bok_keywords:protected] =>
[id:protected] => 73
[type:protected] => category
[parent:protected] => 2
[label:protected] => PCC/Restoration
[alreadyInSave:protected] =>
[alreadyInValidation:protected] =>
[validationFailures:protected] => Array
(
)
[_new:BaseObject:private] =>
[_deleted:BaseObject:private] =>
[modifiedColumns:protected] => Array
(
)
)
[76] => Category Object
(
[languages:protected] =>
[bok_resources:protected] =>
[bok_topics:protected] =>
[bok_keywords:protected] =>
[id:protected] => 76
[type:protected] => category
[parent:protected] => 2
[label:protected] => Plumber/Pipefitter
[alreadyInSave:protected] =>
[alreadyInValidation:protected] =>
[validationFailures:protected] => Array
(
)
[_new:BaseObject:private] =>
[_deleted:BaseObject:private] =>
[modifiedColumns:protected] => Array
(
)
)
[78] => Category Object
(
[languages:protected] =>
[bok_resources:protected] =>
[bok_topics:protected] =>
[bok_keywords:protected] =>
[id:protected] => 78
[type:protected] => category
[parent:protected] => 2
[label:protected] => Roofer/Waterproofer
[alreadyInSave:protected] =>
[alreadyInValidation:protected] =>
[validationFailures:protected] => Array
(
)
[_new:BaseObject:private] =>
[_deleted:BaseObject:private] =>
[modifiedColumns:protected] => Array
(
)
)
[80] => Category Object
(
[languages:protected] =>
[bok_resources:protected] =>
[bok_topics:protected] =>
[bok_keywords:protected] =>
[id:protected] => 80
[type:protected] => category
[parent:protected] => 2
[label:protected] => Sheetmetal Worker
[alreadyInSave:protected] =>
[alreadyInValidation:protected] =>
[validationFailures:protected] => Array
(
)
[_new:BaseObject:private] =>
[_deleted:BaseObject:private] =>
[modifiedColumns:protected] => Array
(
)
)
[86] => Category Object
(
[languages:protected] =>
[bok_resources:protected] =>
[bok_topics:protected] =>
[bok_keywords:protected] =>
[id:protected] => 86
[type:protected] => category
[parent:protected] => 2
[label:protected] => Welder
[alreadyInSave:protected] =>
[alreadyInValidation:protected] =>
[validationFailures:protected] => Array
(
)
[_new:BaseObject:private] =>
[_deleted:BaseObject:private] =>
[modifiedColumns:protected] => Array
(
)
)
[87] => Category Object
(
[languages:protected] =>
[bok_resources:protected] =>
[bok_topics:protected] =>
[bok_keywords:protected] =>
[id:protected] => 87
[type:protected] => category
[parent:protected] => 3
[label:protected] => Commercial & Institutional
[alreadyInSave:protected] =>
[alreadyInValidation:protected] =>
[validationFailures:protected] => Array
(
)
[_new:BaseObject:private] =>
[_deleted:BaseObject:private] =>
[modifiedColumns:protected] => Array
(
)
)
[90] => Category Object
(
[languages:protected] =>
[bok_resources:protected] =>
[bok_topics:protected] =>
[bok_keywords:protected] =>
[id:protected] => 90
[type:protected] => category
[parent:protected] => 3
[label:protected] => Industrial
[alreadyInSave:protected] =>
[alreadyInValidation:protected] =>
[validationFailures:protected] => Array
(
)
[_new:BaseObject:private] =>
[_deleted:BaseObject:private] =>
[modifiedColumns:protected] => Array
(
)
)
[92] => Category Object
(
[languages:protected] =>
[bok_resources:protected] =>
[bok_topics:protected] =>
[bok_keywords:protected] =>
[id:protected] => 92
[type:protected] => category
[parent:protected] => 3
[label:protected] => LEED/Green Construction
[alreadyInSave:protected] =>
[alreadyInValidation:protected] =>
[validationFailures:protected] => Array
(
)
[_new:BaseObject:private] =>
[_deleted:BaseObject:private] =>
[modifiedColumns:protected] => Array
(
)
)
[93] => Category Object
(
[languages:protected] =>
[bok_resources:protected] =>
[bok_topics:protected] =>
[bok_keywords:protected] =>
[id:protected] => 93
[type:protected] => category
[parent:protected] => 3
[label:protected] => Renovations
[alreadyInSave:protected] =>
[alreadyInValidation:protected] =>
[validationFailures:protected] => Array
(
)
[_new:BaseObject:private] =>
[_deleted:BaseObject:private] =>
[modifiedColumns:protected] => Array
(
)
)
[94] => Category Object
(
[languages:protected] =>
[bok_resources:protected] =>
[bok_topics:protected] =>
[bok_keywords:protected] =>
[id:protected] => 94
[type:protected] => category
[parent:protected] => 3
[label:protected] => Residential
[alreadyInSave:protected] =>
[alreadyInValidation:protected] =>
[validationFailures:protected] => Array
(
)
[_new:BaseObject:private] =>
[_deleted:BaseObject:private] =>
[modifiedColumns:protected] => Array
(
)
)
[100] => Category Object
(
[languages:protected] =>
[bok_resources:protected] =>
[bok_topics:protected] =>
[bok_keywords:protected] =>
[id:protected] => 100
[type:protected] => category
[parent:protected] => 6
[label:protected] => Toolbox Talks
[alreadyInSave:protected] =>
[alreadyInValidation:protected] =>
[validationFailures:protected] => Array
(
)
[_new:BaseObject:private] =>
[_deleted:BaseObject:private] =>
[modifiedColumns:protected] => Array
(
)
)
)
[categories_initialized:protected] => 1
[mapped_items:protected] =>
[content:protected] =>
[files:protected] =>
[language:protected] => Language Object
(
[id:protected] => 1
[code:protected] => en
[name:protected] => English
[alreadyInSave:protected] =>
[alreadyInValidation:protected] =>
[validationFailures:protected] => Array
(
)
[_new:BaseObject:private] =>
[_deleted:BaseObject:private] =>
[modifiedColumns:protected] => Array
(
)
)
[old_record:protected] =>
[id:protected] => 4430
[old_id:protected] =>
[elcosh_id:protected] => d001660
[type:protected] => document
[display_type:protected] => HTML only (and links)
[user_id:protected] => 0
[language_id:protected] => 1
[tagging_id:protected] => Mike Aguilar
[priority_id:protected] => 1
[title:protected] => Toolbox Talk: Fixed Ladder
[total_pages:protected] => 0
[billed_pages:protected] => 0
[publication_number:protected] =>
[part_of:protected] =>
[keywords:protected] => Fixed Ladders, Fall Prevention, Falls
[comments:protected] =>
[summary:protected] => The CPWR Toolbox Talk on Fixed Ladders addresses the potential risks associated with using fixed ladders. The resource includes a brief case example, steps to prevent a related injury and questions for discussion. It includes an image that illustrates the hazard, which can be posted in a central location as a reminder of steps to work safely.
Available in
English
and
Spanish.
[transition_comments:protected] =>
[external_link:protected] =>
[consol_link:protected] =>
[more_like_this:protected] => d001257,d001254,d001255,d001256,d001258,d001262,d001279
[permission_given_by:protected] =>
[published:protected] => T
[billable:protected] => F
[img_name:protected] =>
[img_ext:protected] =>
[img_width:protected] =>
[img_height:protected] =>
[img_credit:protected] =>
[img_practice:protected] =>
[vid_source_id:protected] =>
[vid_running_time:protected] =>
[vid_intended_audience:protected] =>
[vid_acquisition_info:protected] =>
[vid_cost:protected] =>
[vid_producer:protected] =>
[vid_filename:protected] =>
[vid_filename_downloadable:protected] =>
[date_summary:protected] =>
[date_permission_requested:protected] =>
[date_permission_received:protected] =>
[date_review_needed:protected] =>
[date_received:protected] => 06/10/22
[date_completed:protected] => 06/10/22
[date_billed:protected] =>
[date_modified:protected] => 05/22/23
[collBokExports:protected] =>
[lastBokExportCriteria:BaseElcoshItem:private] =>
[alreadyInSave:protected] =>
[alreadyInValidation:protected] =>
[validationFailures:protected] => Array
(
)
[_new:BaseObject:private] =>
[_deleted:BaseObject:private] =>
[modifiedColumns:protected] => Array
(
)
)
)
[1] => Search_Result Object
(
[title] => Toolbox Talk: Challenges Preventing Falling Objects
[image] => /record/images/notavailable-p.png
[blurb] => The CPWR Toolbox Talk on Challenges Preventing Falling Objects addresses the hazards of being struck by falling objects on the job site. The resource...
[category] => Array
(
[0] => 12
[1] => 47
[2] => 49
[3] => 51
[4] => 55
[5] => 64
[6] => 68
[7] => 71
[8] => 75
[9] => 78
[10] => 79
[11] => 82
[12] => 62
[13] => 86
[14] => 87
[15] => 88
[16] => 89
[17] => 91
[18] => 90
[19] => 92
[20] => 93
[21] => 94
[22] => 95
[23] => 100
)
[labels] => Array
(
[0] => Crushed/Struck By
[1] => Work Environment
[2] => Hazards
[3] => Bricklayer
[4] => Trades
[5] => Carpenter
[7] => Cement Mason
[9] => Electrical Worker
[11] => Laborer
[13] => Maintenance Worker
[15] => Painter
[17] => Plasterer
[19] => Roofer/Waterproofer
[21] => Scaffold Erector
[23] => Stonemason
[25] => Structural Ironworker
[27] => Welder
[29] => Commercial & Institutional
[30] => Jobsites
[31] => Demolition
[33] => Disasters
[35] => Heavy & Highway
[37] => Industrial
[39] => LEED/Green Construction
[41] => Renovations
[43] => Residential
[45] => Underground
[47] => Toolbox Talks
[48] => Documents
[49] => Media & Documents
)
[type] => Toolbox Talks
[sub_category] =>
[url] => /document/4431/d001661/Toolbox%2BTalk%253A%2BChallenges%2BPreventing%2BFalling%2BObjects.html
[item:protected] => DocumentRecord Object
(
[records:protected] => Array
(
)
[recordId:protected] =>
[searchWordClass:protected] =>
[searchWordPeerClass:protected] =>
[bok_record:protected] =>
[authors:protected] =>
[organizations:protected] =>
[collections:protected] =>
[categories:protected] => Array
(
[12] => Category Object
(
[languages:protected] =>
[bok_resources:protected] =>
[bok_topics:protected] =>
[bok_keywords:protected] =>
[id:protected] => 12
[type:protected] => category
[parent:protected] => 7
[label:protected] => Crushed/Struck By
[alreadyInSave:protected] =>
[alreadyInValidation:protected] =>
[validationFailures:protected] => Array
(
)
[_new:BaseObject:private] =>
[_deleted:BaseObject:private] =>
[modifiedColumns:protected] => Array
(
)
)
[47] => Category Object
(
[languages:protected] =>
[bok_resources:protected] =>
[bok_topics:protected] =>
[bok_keywords:protected] =>
[id:protected] => 47
[type:protected] => category
[parent:protected] => 2
[label:protected] => Bricklayer
[alreadyInSave:protected] =>
[alreadyInValidation:protected] =>
[validationFailures:protected] => Array
(
)
[_new:BaseObject:private] =>
[_deleted:BaseObject:private] =>
[modifiedColumns:protected] => Array
(
)
)
[49] => Category Object
(
[languages:protected] =>
[bok_resources:protected] =>
[bok_topics:protected] =>
[bok_keywords:protected] =>
[id:protected] => 49
[type:protected] => category
[parent:protected] => 2
[label:protected] => Carpenter
[alreadyInSave:protected] =>
[alreadyInValidation:protected] =>
[validationFailures:protected] => Array
(
)
[_new:BaseObject:private] =>
[_deleted:BaseObject:private] =>
[modifiedColumns:protected] => Array
(
)
)
[51] => Category Object
(
[languages:protected] =>
[bok_resources:protected] =>
[bok_topics:protected] =>
[bok_keywords:protected] =>
[id:protected] => 51
[type:protected] => category
[parent:protected] => 2
[label:protected] => Cement Mason
[alreadyInSave:protected] =>
[alreadyInValidation:protected] =>
[validationFailures:protected] => Array
(
)
[_new:BaseObject:private] =>
[_deleted:BaseObject:private] =>
[modifiedColumns:protected] => Array
(
)
)
[55] => Category Object
(
[languages:protected] =>
[bok_resources:protected] =>
[bok_topics:protected] =>
[bok_keywords:protected] =>
[id:protected] => 55
[type:protected] => category
[parent:protected] => 2
[label:protected] => Electrical Worker
[alreadyInSave:protected] =>
[alreadyInValidation:protected] =>
[validationFailures:protected] => Array
(
)
[_new:BaseObject:private] =>
[_deleted:BaseObject:private] =>
[modifiedColumns:protected] => Array
(
)
)
[64] => Category Object
(
[languages:protected] =>
[bok_resources:protected] =>
[bok_topics:protected] =>
[bok_keywords:protected] =>
[id:protected] => 64
[type:protected] => category
[parent:protected] => 2
[label:protected] => Laborer
[alreadyInSave:protected] =>
[alreadyInValidation:protected] =>
[validationFailures:protected] => Array
(
)
[_new:BaseObject:private] =>
[_deleted:BaseObject:private] =>
[modifiedColumns:protected] => Array
(
)
)
[68] => Category Object
(
[languages:protected] =>
[bok_resources:protected] =>
[bok_topics:protected] =>
[bok_keywords:protected] =>
[id:protected] => 68
[type:protected] => category
[parent:protected] => 2
[label:protected] => Maintenance Worker
[alreadyInSave:protected] =>
[alreadyInValidation:protected] =>
[validationFailures:protected] => Array
(
)
[_new:BaseObject:private] =>
[_deleted:BaseObject:private] =>
[modifiedColumns:protected] => Array
(
)
)
[71] => Category Object
(
[languages:protected] =>
[bok_resources:protected] =>
[bok_topics:protected] =>
[bok_keywords:protected] =>
[id:protected] => 71
[type:protected] => category
[parent:protected] => 2
[label:protected] => Painter
[alreadyInSave:protected] =>
[alreadyInValidation:protected] =>
[validationFailures:protected] => Array
(
)
[_new:BaseObject:private] =>
[_deleted:BaseObject:private] =>
[modifiedColumns:protected] => Array
(
)
)
[75] => Category Object
(
[languages:protected] =>
[bok_resources:protected] =>
[bok_topics:protected] =>
[bok_keywords:protected] =>
[id:protected] => 75
[type:protected] => category
[parent:protected] => 2
[label:protected] => Plasterer
[alreadyInSave:protected] =>
[alreadyInValidation:protected] =>
[validationFailures:protected] => Array
(
)
[_new:BaseObject:private] =>
[_deleted:BaseObject:private] =>
[modifiedColumns:protected] => Array
(
)
)
[78] => Category Object
(
[languages:protected] =>
[bok_resources:protected] =>
[bok_topics:protected] =>
[bok_keywords:protected] =>
[id:protected] => 78
[type:protected] => category
[parent:protected] => 2
[label:protected] => Roofer/Waterproofer
[alreadyInSave:protected] =>
[alreadyInValidation:protected] =>
[validationFailures:protected] => Array
(
)
[_new:BaseObject:private] =>
[_deleted:BaseObject:private] =>
[modifiedColumns:protected] => Array
(
)
)
[79] => Category Object
(
[languages:protected] =>
[bok_resources:protected] =>
[bok_topics:protected] =>
[bok_keywords:protected] =>
[id:protected] => 79
[type:protected] => category
[parent:protected] => 2
[label:protected] => Scaffold Erector
[alreadyInSave:protected] =>
[alreadyInValidation:protected] =>
[validationFailures:protected] => Array
(
)
[_new:BaseObject:private] =>
[_deleted:BaseObject:private] =>
[modifiedColumns:protected] => Array
(
)
)
[82] => Category Object
(
[languages:protected] =>
[bok_resources:protected] =>
[bok_topics:protected] =>
[bok_keywords:protected] =>
[id:protected] => 82
[type:protected] => category
[parent:protected] => 2
[label:protected] => Stonemason
[alreadyInSave:protected] =>
[alreadyInValidation:protected] =>
[validationFailures:protected] => Array
(
)
[_new:BaseObject:private] =>
[_deleted:BaseObject:private] =>
[modifiedColumns:protected] => Array
(
)
)
[62] => Category Object
(
[languages:protected] =>
[bok_resources:protected] =>
[bok_topics:protected] =>
[bok_keywords:protected] =>
[id:protected] => 62
[type:protected] => category
[parent:protected] => 2
[label:protected] => Structural Ironworker
[alreadyInSave:protected] =>
[alreadyInValidation:protected] =>
[validationFailures:protected] => Array
(
)
[_new:BaseObject:private] =>
[_deleted:BaseObject:private] =>
[modifiedColumns:protected] => Array
(
)
)
[86] => Category Object
(
[languages:protected] =>
[bok_resources:protected] =>
[bok_topics:protected] =>
[bok_keywords:protected] =>
[id:protected] => 86
[type:protected] => category
[parent:protected] => 2
[label:protected] => Welder
[alreadyInSave:protected] =>
[alreadyInValidation:protected] =>
[validationFailures:protected] => Array
(
)
[_new:BaseObject:private] =>
[_deleted:BaseObject:private] =>
[modifiedColumns:protected] => Array
(
)
)
[87] => Category Object
(
[languages:protected] =>
[bok_resources:protected] =>
[bok_topics:protected] =>
[bok_keywords:protected] =>
[id:protected] => 87
[type:protected] => category
[parent:protected] => 3
[label:protected] => Commercial & Institutional
[alreadyInSave:protected] =>
[alreadyInValidation:protected] =>
[validationFailures:protected] => Array
(
)
[_new:BaseObject:private] =>
[_deleted:BaseObject:private] =>
[modifiedColumns:protected] => Array
(
)
)
[88] => Category Object
(
[languages:protected] =>
[bok_resources:protected] =>
[bok_topics:protected] =>
[bok_keywords:protected] =>
[id:protected] => 88
[type:protected] => category
[parent:protected] => 3
[label:protected] => Demolition
[alreadyInSave:protected] =>
[alreadyInValidation:protected] =>
[validationFailures:protected] => Array
(
)
[_new:BaseObject:private] =>
[_deleted:BaseObject:private] =>
[modifiedColumns:protected] => Array
(
)
)
[89] => Category Object
(
[languages:protected] =>
[bok_resources:protected] =>
[bok_topics:protected] =>
[bok_keywords:protected] =>
[id:protected] => 89
[type:protected] => category
[parent:protected] => 3
[label:protected] => Disasters
[alreadyInSave:protected] =>
[alreadyInValidation:protected] =>
[validationFailures:protected] => Array
(
)
[_new:BaseObject:private] =>
[_deleted:BaseObject:private] =>
[modifiedColumns:protected] => Array
(
)
)
[91] => Category Object
(
[languages:protected] =>
[bok_resources:protected] =>
[bok_topics:protected] =>
[bok_keywords:protected] =>
[id:protected] => 91
[type:protected] => category
[parent:protected] => 3
[label:protected] => Heavy & Highway
[alreadyInSave:protected] =>
[alreadyInValidation:protected] =>
[validationFailures:protected] => Array
(
)
[_new:BaseObject:private] =>
[_deleted:BaseObject:private] =>
[modifiedColumns:protected] => Array
(
)
)
[90] => Category Object
(
[languages:protected] =>
[bok_resources:protected] =>
[bok_topics:protected] =>
[bok_keywords:protected] =>
[id:protected] => 90
[type:protected] => category
[parent:protected] => 3
[label:protected] => Industrial
[alreadyInSave:protected] =>
[alreadyInValidation:protected] =>
[validationFailures:protected] => Array
(
)
[_new:BaseObject:private] =>
[_deleted:BaseObject:private] =>
[modifiedColumns:protected] => Array
(
)
)
[92] => Category Object
(
[languages:protected] =>
[bok_resources:protected] =>
[bok_topics:protected] =>
[bok_keywords:protected] =>
[id:protected] => 92
[type:protected] => category
[parent:protected] => 3
[label:protected] => LEED/Green Construction
[alreadyInSave:protected] =>
[alreadyInValidation:protected] =>
[validationFailures:protected] => Array
(
)
[_new:BaseObject:private] =>
[_deleted:BaseObject:private] =>
[modifiedColumns:protected] => Array
(
)
)
[93] => Category Object
(
[languages:protected] =>
[bok_resources:protected] =>
[bok_topics:protected] =>
[bok_keywords:protected] =>
[id:protected] => 93
[type:protected] => category
[parent:protected] => 3
[label:protected] => Renovations
[alreadyInSave:protected] =>
[alreadyInValidation:protected] =>
[validationFailures:protected] => Array
(
)
[_new:BaseObject:private] =>
[_deleted:BaseObject:private] =>
[modifiedColumns:protected] => Array
(
)
)
[94] => Category Object
(
[languages:protected] =>
[bok_resources:protected] =>
[bok_topics:protected] =>
[bok_keywords:protected] =>
[id:protected] => 94
[type:protected] => category
[parent:protected] => 3
[label:protected] => Residential
[alreadyInSave:protected] =>
[alreadyInValidation:protected] =>
[validationFailures:protected] => Array
(
)
[_new:BaseObject:private] =>
[_deleted:BaseObject:private] =>
[modifiedColumns:protected] => Array
(
)
)
[95] => Category Object
(
[languages:protected] =>
[bok_resources:protected] =>
[bok_topics:protected] =>
[bok_keywords:protected] =>
[id:protected] => 95
[type:protected] => category
[parent:protected] => 3
[label:protected] => Underground
[alreadyInSave:protected] =>
[alreadyInValidation:protected] =>
[validationFailures:protected] => Array
(
)
[_new:BaseObject:private] =>
[_deleted:BaseObject:private] =>
[modifiedColumns:protected] => Array
(
)
)
[100] => Category Object
(
[languages:protected] =>
[bok_resources:protected] =>
[bok_topics:protected] =>
[bok_keywords:protected] =>
[id:protected] => 100
[type:protected] => category
[parent:protected] => 6
[label:protected] => Toolbox Talks
[alreadyInSave:protected] =>
[alreadyInValidation:protected] =>
[validationFailures:protected] => Array
(
)
[_new:BaseObject:private] =>
[_deleted:BaseObject:private] =>
[modifiedColumns:protected] => Array
(
)
)
)
[categories_initialized:protected] => 1
[mapped_items:protected] =>
[content:protected] =>
[files:protected] =>
[language:protected] => Language Object
(
[id:protected] => 1
[code:protected] => en
[name:protected] => English
[alreadyInSave:protected] =>
[alreadyInValidation:protected] =>
[validationFailures:protected] => Array
(
)
[_new:BaseObject:private] =>
[_deleted:BaseObject:private] =>
[modifiedColumns:protected] => Array
(
)
)
[old_record:protected] =>
[id:protected] => 4431
[old_id:protected] =>
[elcosh_id:protected] => d001661
[type:protected] => document
[display_type:protected] => HTML only (and links)
[user_id:protected] => 0
[language_id:protected] => 1
[tagging_id:protected] => Mike Aguilar
[priority_id:protected] => 1
[title:protected] => Toolbox Talk: Challenges Preventing Falling Objects
[total_pages:protected] => 0
[billed_pages:protected] => 0
[publication_number:protected] =>
[part_of:protected] =>
[keywords:protected] => dropped objects, falling objects, struck by incidents, struck by fatalities
[comments:protected] =>
[summary:protected] => The CPWR Toolbox Talk on Challenges Preventing Falling Objects addresses the hazards of being struck by falling objects on the job site. The resource includes a brief example, steps to prevent a related injury, and questions for discussion. It includes a graphic that illustrates a group workers observing a scaffold free of debris during high winds, which can be posted in a central location as a reminder of steps to work safely.
Available in
English and
Spanish.
[transition_comments:protected] =>
[external_link:protected] =>
[consol_link:protected] =>
[more_like_this:protected] => d001234,d001238,d001244,d001251,d001253,d001260,d001268,d001278
[permission_given_by:protected] =>
[published:protected] => T
[billable:protected] => F
[img_name:protected] =>
[img_ext:protected] =>
[img_width:protected] =>
[img_height:protected] =>
[img_credit:protected] =>
[img_practice:protected] =>
[vid_source_id:protected] =>
[vid_running_time:protected] =>
[vid_intended_audience:protected] =>
[vid_acquisition_info:protected] =>
[vid_cost:protected] =>
[vid_producer:protected] =>
[vid_filename:protected] =>
[vid_filename_downloadable:protected] =>
[date_summary:protected] =>
[date_permission_requested:protected] =>
[date_permission_received:protected] =>
[date_review_needed:protected] =>
[date_received:protected] => 06/10/22
[date_completed:protected] => 06/10/22
[date_billed:protected] =>
[date_modified:protected] => 05/22/23
[collBokExports:protected] =>
[lastBokExportCriteria:BaseElcoshItem:private] =>
[alreadyInSave:protected] =>
[alreadyInValidation:protected] =>
[validationFailures:protected] => Array
(
)
[_new:BaseObject:private] =>
[_deleted:BaseObject:private] =>
[modifiedColumns:protected] => Array
(
)
)
)
[2] => Search_Result Object
(
[title] => Toolbox Talk: Tower Crane Safety
[image] => /record/images/notavailable-p.png
[blurb] => The CPWR Toolbox Talk on Tower Crane Safety addresses the potential hazards of Tower Cranes and the importance of following procedure before and durin...
[category] => Array
(
[0] => 11
[1] => 12
[2] => 18
[3] => 70
[4] => 87
[5] => 88
[6] => 91
[7] => 90
[8] => 92
[9] => 100
)
[labels] => Array
(
[0] => Cranes & Hoists
[1] => Work Environment
[2] => Hazards
[3] => Crushed/Struck By
[6] => Motor Vehicles/Heavy Equipment
[9] => Operating Engineer
[10] => Trades
[11] => Commercial & Institutional
[12] => Jobsites
[13] => Demolition
[15] => Heavy & Highway
[17] => Industrial
[19] => LEED/Green Construction
[21] => Toolbox Talks
[22] => Documents
[23] => Media & Documents
)
[type] => Toolbox Talks
[sub_category] =>
[url] => /document/4427/d001657/Toolbox%2BTalk%253A%2BTower%2BCrane%2BSafety.html
[item:protected] => DocumentRecord Object
(
[records:protected] => Array
(
)
[recordId:protected] =>
[searchWordClass:protected] =>
[searchWordPeerClass:protected] =>
[bok_record:protected] =>
[authors:protected] =>
[organizations:protected] =>
[collections:protected] =>
[categories:protected] => Array
(
[11] => Category Object
(
[languages:protected] =>
[bok_resources:protected] =>
[bok_topics:protected] =>
[bok_keywords:protected] =>
[id:protected] => 11
[type:protected] => category
[parent:protected] => 7
[label:protected] => Cranes & Hoists
[alreadyInSave:protected] =>
[alreadyInValidation:protected] =>
[validationFailures:protected] => Array
(
)
[_new:BaseObject:private] =>
[_deleted:BaseObject:private] =>
[modifiedColumns:protected] => Array
(
)
)
[12] => Category Object
(
[languages:protected] =>
[bok_resources:protected] =>
[bok_topics:protected] =>
[bok_keywords:protected] =>
[id:protected] => 12
[type:protected] => category
[parent:protected] => 7
[label:protected] => Crushed/Struck By
[alreadyInSave:protected] =>
[alreadyInValidation:protected] =>
[validationFailures:protected] => Array
(
)
[_new:BaseObject:private] =>
[_deleted:BaseObject:private] =>
[modifiedColumns:protected] => Array
(
)
)
[18] => Category Object
(
[languages:protected] =>
[bok_resources:protected] =>
[bok_topics:protected] =>
[bok_keywords:protected] =>
[id:protected] => 18
[type:protected] => category
[parent:protected] => 7
[label:protected] => Motor Vehicles/Heavy Equipment
[alreadyInSave:protected] =>
[alreadyInValidation:protected] =>
[validationFailures:protected] => Array
(
)
[_new:BaseObject:private] =>
[_deleted:BaseObject:private] =>
[modifiedColumns:protected] => Array
(
)
)
[70] => Category Object
(
[languages:protected] =>
[bok_resources:protected] =>
[bok_topics:protected] =>
[bok_keywords:protected] =>
[id:protected] => 70
[type:protected] => category
[parent:protected] => 2
[label:protected] => Operating Engineer
[alreadyInSave:protected] =>
[alreadyInValidation:protected] =>
[validationFailures:protected] => Array
(
)
[_new:BaseObject:private] =>
[_deleted:BaseObject:private] =>
[modifiedColumns:protected] => Array
(
)
)
[87] => Category Object
(
[languages:protected] =>
[bok_resources:protected] =>
[bok_topics:protected] =>
[bok_keywords:protected] =>
[id:protected] => 87
[type:protected] => category
[parent:protected] => 3
[label:protected] => Commercial & Institutional
[alreadyInSave:protected] =>
[alreadyInValidation:protected] =>
[validationFailures:protected] => Array
(
)
[_new:BaseObject:private] =>
[_deleted:BaseObject:private] =>
[modifiedColumns:protected] => Array
(
)
)
[88] => Category Object
(
[languages:protected] =>
[bok_resources:protected] =>
[bok_topics:protected] =>
[bok_keywords:protected] =>
[id:protected] => 88
[type:protected] => category
[parent:protected] => 3
[label:protected] => Demolition
[alreadyInSave:protected] =>
[alreadyInValidation:protected] =>
[validationFailures:protected] => Array
(
)
[_new:BaseObject:private] =>
[_deleted:BaseObject:private] =>
[modifiedColumns:protected] => Array
(
)
)
[91] => Category Object
(
[languages:protected] =>
[bok_resources:protected] =>
[bok_topics:protected] =>
[bok_keywords:protected] =>
[id:protected] => 91
[type:protected] => category
[parent:protected] => 3
[label:protected] => Heavy & Highway
[alreadyInSave:protected] =>
[alreadyInValidation:protected] =>
[validationFailures:protected] => Array
(
)
[_new:BaseObject:private] =>
[_deleted:BaseObject:private] =>
[modifiedColumns:protected] => Array
(
)
)
[90] => Category Object
(
[languages:protected] =>
[bok_resources:protected] =>
[bok_topics:protected] =>
[bok_keywords:protected] =>
[id:protected] => 90
[type:protected] => category
[parent:protected] => 3
[label:protected] => Industrial
[alreadyInSave:protected] =>
[alreadyInValidation:protected] =>
[validationFailures:protected] => Array
(
)
[_new:BaseObject:private] =>
[_deleted:BaseObject:private] =>
[modifiedColumns:protected] => Array
(
)
)
[92] => Category Object
(
[languages:protected] =>
[bok_resources:protected] =>
[bok_topics:protected] =>
[bok_keywords:protected] =>
[id:protected] => 92
[type:protected] => category
[parent:protected] => 3
[label:protected] => LEED/Green Construction
[alreadyInSave:protected] =>
[alreadyInValidation:protected] =>
[validationFailures:protected] => Array
(
)
[_new:BaseObject:private] =>
[_deleted:BaseObject:private] =>
[modifiedColumns:protected] => Array
(
)
)
[100] => Category Object
(
[languages:protected] =>
[bok_resources:protected] =>
[bok_topics:protected] =>
[bok_keywords:protected] =>
[id:protected] => 100
[type:protected] => category
[parent:protected] => 6
[label:protected] => Toolbox Talks
[alreadyInSave:protected] =>
[alreadyInValidation:protected] =>
[validationFailures:protected] => Array
(
)
[_new:BaseObject:private] =>
[_deleted:BaseObject:private] =>
[modifiedColumns:protected] => Array
(
)
)
)
[categories_initialized:protected] => 1
[mapped_items:protected] =>
[content:protected] =>
[files:protected] =>
[language:protected] => Language Object
(
[id:protected] => 1
[code:protected] => en
[name:protected] => English
[alreadyInSave:protected] =>
[alreadyInValidation:protected] =>
[validationFailures:protected] => Array
(
)
[_new:BaseObject:private] =>
[_deleted:BaseObject:private] =>
[modifiedColumns:protected] => Array
(
)
)
[old_record:protected] =>
[id:protected] => 4427
[old_id:protected] =>
[elcosh_id:protected] => d001657
[type:protected] => document
[display_type:protected] => HTML only (and links)
[user_id:protected] => 0
[language_id:protected] => 1
[tagging_id:protected] => Mike Aguilar
[priority_id:protected] => 1
[title:protected] => Toolbox Talk: Tower Crane Safety
[total_pages:protected] => 0
[billed_pages:protected] => 0
[publication_number:protected] =>
[part_of:protected] =>
[keywords:protected] => Tower Crane, Crane, Stability, Tipping, Lift Zone Safety, Lift, Zone, Safety, Struck by
[comments:protected] =>
[summary:protected] => The CPWR Toolbox Talk on Tower Crane Safety addresses the potential hazards of Tower Cranes and the importance of following procedure before and during Tower Crane operation. The resource includes a brief example, steps to prevent a related injury, and questions for discussion. It includes a graphic that illustrates a worker inspecting a Tower Crane before operation, which can be posted in a central location as a reminder of steps to work safely.
Available in
English and
Spanish.
[transition_comments:protected] =>
[external_link:protected] =>
[consol_link:protected] =>
[more_like_this:protected] => d001234,d001238,d001250,d001251,d001253,d001258,d001262,d001273
[permission_given_by:protected] =>
[published:protected] => T
[billable:protected] => F
[img_name:protected] =>
[img_ext:protected] => jpg
[img_width:protected] =>
[img_height:protected] =>
[img_credit:protected] =>
[img_practice:protected] =>
[vid_source_id:protected] =>
[vid_running_time:protected] =>
[vid_intended_audience:protected] =>
[vid_acquisition_info:protected] =>
[vid_cost:protected] =>
[vid_producer:protected] =>
[vid_filename:protected] =>
[vid_filename_downloadable:protected] =>
[date_summary:protected] =>
[date_permission_requested:protected] =>
[date_permission_received:protected] =>
[date_review_needed:protected] =>
[date_received:protected] => 12/23/21
[date_completed:protected] => 12/23/21
[date_billed:protected] =>
[date_modified:protected] => 05/19/23
[collBokExports:protected] =>
[lastBokExportCriteria:BaseElcoshItem:private] =>
[alreadyInSave:protected] =>
[alreadyInValidation:protected] =>
[validationFailures:protected] => Array
(
)
[_new:BaseObject:private] =>
[_deleted:BaseObject:private] =>
[modifiedColumns:protected] => Array
(
)
)
)
[3] => Search_Result Object
(
[title] => Toolbox Talk: Work Zone Safety: Working Around Vehicles
[image] => /record/images/notavailable-p.png
[blurb] => The CPWR Toolbox Talk on Working Around Vehicles in the Work Zone addresses methods to avoid being struck-by a vehicle on a construction site. The res...
[category] => Array
(
[0] => 12
[1] => 18
[2] => 52
[3] => 57
[4] => 70
[5] => 85
[6] => 87
[7] => 88
[8] => 89
[9] => 91
[10] => 90
[11] => 92
[12] => 93
[13] => 94
[14] => 95
[15] => 100
)
[labels] => Array
(
[0] => Crushed/Struck By
[1] => Work Environment
[2] => Hazards
[3] => Motor Vehicles/Heavy Equipment
[6] => Commercial Diver
[7] => Trades
[8] => Flagger
[10] => Operating Engineer
[12] => Truck Driver
[14] => Commercial & Institutional
[15] => Jobsites
[16] => Demolition
[18] => Disasters
[20] => Heavy & Highway
[22] => Industrial
[24] => LEED/Green Construction
[26] => Renovations
[28] => Residential
[30] => Underground
[32] => Toolbox Talks
[33] => Documents
[34] => Media & Documents
)
[type] => Toolbox Talks
[sub_category] =>
[url] => /document/4428/d001658/Toolbox%2BTalk%253A%2BWork%2BZone%2BSafety%253A%2BWorking%2BAround%2BVehicles.html
[item:protected] => DocumentRecord Object
(
[records:protected] => Array
(
)
[recordId:protected] =>
[searchWordClass:protected] =>
[searchWordPeerClass:protected] =>
[bok_record:protected] =>
[authors:protected] =>
[organizations:protected] =>
[collections:protected] =>
[categories:protected] => Array
(
[12] => Category Object
(
[languages:protected] =>
[bok_resources:protected] =>
[bok_topics:protected] =>
[bok_keywords:protected] =>
[id:protected] => 12
[type:protected] => category
[parent:protected] => 7
[label:protected] => Crushed/Struck By
[alreadyInSave:protected] =>
[alreadyInValidation:protected] =>
[validationFailures:protected] => Array
(
)
[_new:BaseObject:private] =>
[_deleted:BaseObject:private] =>
[modifiedColumns:protected] => Array
(
)
)
[18] => Category Object
(
[languages:protected] =>
[bok_resources:protected] =>
[bok_topics:protected] =>
[bok_keywords:protected] =>
[id:protected] => 18
[type:protected] => category
[parent:protected] => 7
[label:protected] => Motor Vehicles/Heavy Equipment
[alreadyInSave:protected] =>
[alreadyInValidation:protected] =>
[validationFailures:protected] => Array
(
)
[_new:BaseObject:private] =>
[_deleted:BaseObject:private] =>
[modifiedColumns:protected] => Array
(
)
)
[52] => Category Object
(
[languages:protected] =>
[bok_resources:protected] =>
[bok_topics:protected] =>
[bok_keywords:protected] =>
[id:protected] => 52
[type:protected] => category
[parent:protected] => 2
[label:protected] => Commercial Diver
[alreadyInSave:protected] =>
[alreadyInValidation:protected] =>
[validationFailures:protected] => Array
(
)
[_new:BaseObject:private] =>
[_deleted:BaseObject:private] =>
[modifiedColumns:protected] => Array
(
)
)
[57] => Category Object
(
[languages:protected] =>
[bok_resources:protected] =>
[bok_topics:protected] =>
[bok_keywords:protected] =>
[id:protected] => 57
[type:protected] => category
[parent:protected] => 2
[label:protected] => Flagger
[alreadyInSave:protected] =>
[alreadyInValidation:protected] =>
[validationFailures:protected] => Array
(
)
[_new:BaseObject:private] =>
[_deleted:BaseObject:private] =>
[modifiedColumns:protected] => Array
(
)
)
[70] => Category Object
(
[languages:protected] =>
[bok_resources:protected] =>
[bok_topics:protected] =>
[bok_keywords:protected] =>
[id:protected] => 70
[type:protected] => category
[parent:protected] => 2
[label:protected] => Operating Engineer
[alreadyInSave:protected] =>
[alreadyInValidation:protected] =>
[validationFailures:protected] => Array
(
)
[_new:BaseObject:private] =>
[_deleted:BaseObject:private] =>
[modifiedColumns:protected] => Array
(
)
)
[85] => Category Object
(
[languages:protected] =>
[bok_resources:protected] =>
[bok_topics:protected] =>
[bok_keywords:protected] =>
[id:protected] => 85
[type:protected] => category
[parent:protected] => 2
[label:protected] => Truck Driver
[alreadyInSave:protected] =>
[alreadyInValidation:protected] =>
[validationFailures:protected] => Array
(
)
[_new:BaseObject:private] =>
[_deleted:BaseObject:private] =>
[modifiedColumns:protected] => Array
(
)
)
[87] => Category Object
(
[languages:protected] =>
[bok_resources:protected] =>
[bok_topics:protected] =>
[bok_keywords:protected] =>
[id:protected] => 87
[type:protected] => category
[parent:protected] => 3
[label:protected] => Commercial & Institutional
[alreadyInSave:protected] =>
[alreadyInValidation:protected] =>
[validationFailures:protected] => Array
(
)
[_new:BaseObject:private] =>
[_deleted:BaseObject:private] =>
[modifiedColumns:protected] => Array
(
)
)
[88] => Category Object
(
[languages:protected] =>
[bok_resources:protected] =>
[bok_topics:protected] =>
[bok_keywords:protected] =>
[id:protected] => 88
[type:protected] => category
[parent:protected] => 3
[label:protected] => Demolition
[alreadyInSave:protected] =>
[alreadyInValidation:protected] =>
[validationFailures:protected] => Array
(
)
[_new:BaseObject:private] =>
[_deleted:BaseObject:private] =>
[modifiedColumns:protected] => Array
(
)
)
[89] => Category Object
(
[languages:protected] =>
[bok_resources:protected] =>
[bok_topics:protected] =>
[bok_keywords:protected] =>
[id:protected] => 89
[type:protected] => category
[parent:protected] => 3
[label:protected] => Disasters
[alreadyInSave:protected] =>
[alreadyInValidation:protected] =>
[validationFailures:protected] => Array
(
)
[_new:BaseObject:private] =>
[_deleted:BaseObject:private] =>
[modifiedColumns:protected] => Array
(
)
)
[91] => Category Object
(
[languages:protected] =>
[bok_resources:protected] =>
[bok_topics:protected] =>
[bok_keywords:protected] =>
[id:protected] => 91
[type:protected] => category
[parent:protected] => 3
[label:protected] => Heavy & Highway
[alreadyInSave:protected] =>
[alreadyInValidation:protected] =>
[validationFailures:protected] => Array
(
)
[_new:BaseObject:private] =>
[_deleted:BaseObject:private] =>
[modifiedColumns:protected] => Array
(
)
)
[90] => Category Object
(
[languages:protected] =>
[bok_resources:protected] =>
[bok_topics:protected] =>
[bok_keywords:protected] =>
[id:protected] => 90
[type:protected] => category
[parent:protected] => 3
[label:protected] => Industrial
[alreadyInSave:protected] =>
[alreadyInValidation:protected] =>
[validationFailures:protected] => Array
(
)
[_new:BaseObject:private] =>
[_deleted:BaseObject:private] =>
[modifiedColumns:protected] => Array
(
)
)
[92] => Category Object
(
[languages:protected] =>
[bok_resources:protected] =>
[bok_topics:protected] =>
[bok_keywords:protected] =>
[id:protected] => 92
[type:protected] => category
[parent:protected] => 3
[label:protected] => LEED/Green Construction
[alreadyInSave:protected] =>
[alreadyInValidation:protected] =>
[validationFailures:protected] => Array
(
)
[_new:BaseObject:private] =>
[_deleted:BaseObject:private] =>
[modifiedColumns:protected] => Array
(
)
)
[93] => Category Object
(
[languages:protected] =>
[bok_resources:protected] =>
[bok_topics:protected] =>
[bok_keywords:protected] =>
[id:protected] => 93
[type:protected] => category
[parent:protected] => 3
[label:protected] => Renovations
[alreadyInSave:protected] =>
[alreadyInValidation:protected] =>
[validationFailures:protected] => Array
(
)
[_new:BaseObject:private] =>
[_deleted:BaseObject:private] =>
[modifiedColumns:protected] => Array
(
)
)
[94] => Category Object
(
[languages:protected] =>
[bok_resources:protected] =>
[bok_topics:protected] =>
[bok_keywords:protected] =>
[id:protected] => 94
[type:protected] => category
[parent:protected] => 3
[label:protected] => Residential
[alreadyInSave:protected] =>
[alreadyInValidation:protected] =>
[validationFailures:protected] => Array
(
)
[_new:BaseObject:private] =>
[_deleted:BaseObject:private] =>
[modifiedColumns:protected] => Array
(
)
)
[95] => Category Object
(
[languages:protected] =>
[bok_resources:protected] =>
[bok_topics:protected] =>
[bok_keywords:protected] =>
[id:protected] => 95
[type:protected] => category
[parent:protected] => 3
[label:protected] => Underground
[alreadyInSave:protected] =>
[alreadyInValidation:protected] =>
[validationFailures:protected] => Array
(
)
[_new:BaseObject:private] =>
[_deleted:BaseObject:private] =>
[modifiedColumns:protected] => Array
(
)
)
[100] => Category Object
(
[languages:protected] =>
[bok_resources:protected] =>
[bok_topics:protected] =>
[bok_keywords:protected] =>
[id:protected] => 100
[type:protected] => category
[parent:protected] => 6
[label:protected] => Toolbox Talks
[alreadyInSave:protected] =>
[alreadyInValidation:protected] =>
[validationFailures:protected] => Array
(
)
[_new:BaseObject:private] =>
[_deleted:BaseObject:private] =>
[modifiedColumns:protected] => Array
(
)
)
)
[categories_initialized:protected] => 1
[mapped_items:protected] =>
[content:protected] =>
[files:protected] =>
[language:protected] => Language Object
(
[id:protected] => 1
[code:protected] => en
[name:protected] => English
[alreadyInSave:protected] =>
[alreadyInValidation:protected] =>
[validationFailures:protected] => Array
(
)
[_new:BaseObject:private] =>
[_deleted:BaseObject:private] =>
[modifiedColumns:protected] => Array
(
)
)
[old_record:protected] =>
[id:protected] => 4428
[old_id:protected] =>
[elcosh_id:protected] => d001658
[type:protected] => document
[display_type:protected] => HTML only (and links)
[user_id:protected] => 0
[language_id:protected] => 1
[tagging_id:protected] => Daniela Caceres
[priority_id:protected] => 1
[title:protected] => Toolbox Talk: Work Zone Safety: Working Around Vehicles
[total_pages:protected] => 0
[billed_pages:protected] => 0
[publication_number:protected] =>
[part_of:protected] =>
[keywords:protected] => Struck, Struck by, Vehicle, Work Zone Safety, Truck, Operator, Driver, Mobile Equipment
[comments:protected] =>
[summary:protected] => The CPWR Toolbox Talk on Working Around Vehicles in the Work Zone addresses methods to avoid being struck-by a vehicle on a construction site. The resource includes a case example, steps to prevent a related injury, and questions for discussion. It includes a graphic that illustrates the hazard, which can be posted in a central location as a reminder of steps to work safely. Available in
English and
Spanish.
[transition_comments:protected] =>
[external_link:protected] =>
[consol_link:protected] =>
[more_like_this:protected] => d001640
[permission_given_by:protected] =>
[published:protected] => T
[billable:protected] => F
[img_name:protected] =>
[img_ext:protected] =>
[img_width:protected] =>
[img_height:protected] =>
[img_credit:protected] =>
[img_practice:protected] =>
[vid_source_id:protected] =>
[vid_running_time:protected] =>
[vid_intended_audience:protected] =>
[vid_acquisition_info:protected] =>
[vid_cost:protected] =>
[vid_producer:protected] =>
[vid_filename:protected] =>
[vid_filename_downloadable:protected] =>
[date_summary:protected] =>
[date_permission_requested:protected] =>
[date_permission_received:protected] =>
[date_review_needed:protected] =>
[date_received:protected] => 12/23/21
[date_completed:protected] => 12/23/21
[date_billed:protected] =>
[date_modified:protected] => 05/19/23
[collBokExports:protected] =>
[lastBokExportCriteria:BaseElcoshItem:private] =>
[alreadyInSave:protected] =>
[alreadyInValidation:protected] =>
[validationFailures:protected] => Array
(
)
[_new:BaseObject:private] =>
[_deleted:BaseObject:private] =>
[modifiedColumns:protected] => Array
(
)
)
)
[4] => Search_Result Object
(
[title] => Construction Dive -- DeWalt's Jobsite Pro headphones recalled for fire hazards
[image] => /record/images/notavailable-p.png
[blurb] => A recall notice by the United States Consumer Product Safety Commission affects over 300,000 DeWalt Jobsite Pro Headphones. The recall is a result of...
[category] => Array
(
[0] => 16
[1] => 44
[2] => 45
[3] => 46
[4] => 47
[5] => 48
[6] => 49
[7] => 50
[8] => 51
[9] => 52
[10] => 53
[11] => 54
[12] => 55
[13] => 56
[14] => 57
[15] => 58
[16] => 59
[17] => 60
[18] => 61
[19] => 64
[20] => 65
[21] => 66
[22] => 67
[23] => 68
[24] => 69
[25] => 70
[26] => 71
[27] => 72
[28] => 73
[29] => 74
[30] => 75
[31] => 76
[32] => 77
[33] => 63
[34] => 78
[35] => 79
[36] => 80
[37] => 81
[38] => 82
[39] => 62
[40] => 83
[41] => 84
[42] => 85
[43] => 86
[44] => 87
[45] => 88
[46] => 89
[47] => 91
[48] => 90
[49] => 92
[50] => 93
[51] => 94
[52] => 95
)
[labels] => Array
(
[0] => Fire & Explosions
[1] => Work Environment
[2] => Hazards
[3] => Acoustical Ceiling Carpenter
[4] => Trades
[5] => Asbestos/Insulator
[7] => Boilermaker
[9] => Bricklayer
[11] => Cabinetmaker
[13] => Carpenter
[15] => Carpet Layer
[17] => Cement Mason
[19] => Commercial Diver
[21] => Concrete Polisher
[23] => Drywall Applicator Specialist
[25] => Electrical Worker
[27] => Elevator Constructor
[29] => Flagger
[31] => Glazier
[33] => Hazardous Waste Cleanup
[35] => HVAC
[37] => Interior Systems Carpenter
[39] => Laborer
[41] => Landscaper
[43] => Lather
[45] => Lead Abatement Worker
[47] => Maintenance Worker
[49] => Millwright
[51] => Operating Engineer
[53] => Painter
[55] => Paper Hanger
[57] => PCC/Restoration
[59] => Pile Driver
[61] => Plasterer
[63] => Plumber/Pipefitter
[65] => Refractory Worker
[67] => Reinforcing Ironworker
[69] => Roofer/Waterproofer
[71] => Scaffold Erector
[73] => Sheetmetal Worker
[75] => Sprinkler Fitter
[77] => Stonemason
[79] => Structural Ironworker
[81] => Terrazzo Worker
[83] => Tile Setter
[85] => Truck Driver
[87] => Welder
[89] => Commercial & Institutional
[90] => Jobsites
[91] => Demolition
[93] => Disasters
[95] => Heavy & Highway
[97] => Industrial
[99] => LEED/Green Construction
[101] => Renovations
[103] => Residential
[105] => Underground
)
[type] =>
[sub_category] =>
[url] => /document/4426/d001656/Construction%2BDive%2B--%2BDeWalt%2527s%2BJobsite%2BPro%2Bheadphones%2Brecalled%2Bfor%2Bfire%2Bhazards.html
[item:protected] => DocumentRecord Object
(
[records:protected] => Array
(
)
[recordId:protected] =>
[searchWordClass:protected] =>
[searchWordPeerClass:protected] =>
[bok_record:protected] =>
[authors:protected] =>
[organizations:protected] =>
[collections:protected] =>
[categories:protected] => Array
(
[16] => Category Object
(
[languages:protected] =>
[bok_resources:protected] =>
[bok_topics:protected] =>
[bok_keywords:protected] =>
[id:protected] => 16
[type:protected] => category
[parent:protected] => 7
[label:protected] => Fire & Explosions
[alreadyInSave:protected] =>
[alreadyInValidation:protected] =>
[validationFailures:protected] => Array
(
)
[_new:BaseObject:private] =>
[_deleted:BaseObject:private] =>
[modifiedColumns:protected] => Array
(
)
)
[44] => Category Object
(
[languages:protected] =>
[bok_resources:protected] =>
[bok_topics:protected] =>
[bok_keywords:protected] =>
[id:protected] => 44
[type:protected] => category
[parent:protected] => 2
[label:protected] => Acoustical Ceiling Carpenter
[alreadyInSave:protected] =>
[alreadyInValidation:protected] =>
[validationFailures:protected] => Array
(
)
[_new:BaseObject:private] =>
[_deleted:BaseObject:private] =>
[modifiedColumns:protected] => Array
(
)
)
[45] => Category Object
(
[languages:protected] =>
[bok_resources:protected] =>
[bok_topics:protected] =>
[bok_keywords:protected] =>
[id:protected] => 45
[type:protected] => category
[parent:protected] => 2
[label:protected] => Asbestos/Insulator
[alreadyInSave:protected] =>
[alreadyInValidation:protected] =>
[validationFailures:protected] => Array
(
)
[_new:BaseObject:private] =>
[_deleted:BaseObject:private] =>
[modifiedColumns:protected] => Array
(
)
)
[46] => Category Object
(
[languages:protected] =>
[bok_resources:protected] =>
[bok_topics:protected] =>
[bok_keywords:protected] =>
[id:protected] => 46
[type:protected] => category
[parent:protected] => 2
[label:protected] => Boilermaker
[alreadyInSave:protected] =>
[alreadyInValidation:protected] =>
[validationFailures:protected] => Array
(
)
[_new:BaseObject:private] =>
[_deleted:BaseObject:private] =>
[modifiedColumns:protected] => Array
(
)
)
[47] => Category Object
(
[languages:protected] =>
[bok_resources:protected] =>
[bok_topics:protected] =>
[bok_keywords:protected] =>
[id:protected] => 47
[type:protected] => category
[parent:protected] => 2
[label:protected] => Bricklayer
[alreadyInSave:protected] =>
[alreadyInValidation:protected] =>
[validationFailures:protected] => Array
(
)
[_new:BaseObject:private] =>
[_deleted:BaseObject:private] =>
[modifiedColumns:protected] => Array
(
)
)
[48] => Category Object
(
[languages:protected] =>
[bok_resources:protected] =>
[bok_topics:protected] =>
[bok_keywords:protected] =>
[id:protected] => 48
[type:protected] => category
[parent:protected] => 2
[label:protected] => Cabinetmaker
[alreadyInSave:protected] =>
[alreadyInValidation:protected] =>
[validationFailures:protected] => Array
(
)
[_new:BaseObject:private] =>
[_deleted:BaseObject:private] =>
[modifiedColumns:protected] => Array
(
)
)
[49] => Category Object
(
[languages:protected] =>
[bok_resources:protected] =>
[bok_topics:protected] =>
[bok_keywords:protected] =>
[id:protected] => 49
[type:protected] => category
[parent:protected] => 2
[label:protected] => Carpenter
[alreadyInSave:protected] =>
[alreadyInValidation:protected] =>
[validationFailures:protected] => Array
(
)
[_new:BaseObject:private] =>
[_deleted:BaseObject:private] =>
[modifiedColumns:protected] => Array
(
)
)
[50] => Category Object
(
[languages:protected] =>
[bok_resources:protected] =>
[bok_topics:protected] =>
[bok_keywords:protected] =>
[id:protected] => 50
[type:protected] => category
[parent:protected] => 2
[label:protected] => Carpet Layer
[alreadyInSave:protected] =>
[alreadyInValidation:protected] =>
[validationFailures:protected] => Array
(
)
[_new:BaseObject:private] =>
[_deleted:BaseObject:private] =>
[modifiedColumns:protected] => Array
(
)
)
[51] => Category Object
(
[languages:protected] =>
[bok_resources:protected] =>
[bok_topics:protected] =>
[bok_keywords:protected] =>
[id:protected] => 51
[type:protected] => category
[parent:protected] => 2
[label:protected] => Cement Mason
[alreadyInSave:protected] =>
[alreadyInValidation:protected] =>
[validationFailures:protected] => Array
(
)
[_new:BaseObject:private] =>
[_deleted:BaseObject:private] =>
[modifiedColumns:protected] => Array
(
)
)
[52] => Category Object
(
[languages:protected] =>
[bok_resources:protected] =>
[bok_topics:protected] =>
[bok_keywords:protected] =>
[id:protected] => 52
[type:protected] => category
[parent:protected] => 2
[label:protected] => Commercial Diver
[alreadyInSave:protected] =>
[alreadyInValidation:protected] =>
[validationFailures:protected] => Array
(
)
[_new:BaseObject:private] =>
[_deleted:BaseObject:private] =>
[modifiedColumns:protected] => Array
(
)
)
[53] => Category Object
(
[languages:protected] =>
[bok_resources:protected] =>
[bok_topics:protected] =>
[bok_keywords:protected] =>
[id:protected] => 53
[type:protected] => category
[parent:protected] => 2
[label:protected] => Concrete Polisher
[alreadyInSave:protected] =>
[alreadyInValidation:protected] =>
[validationFailures:protected] => Array
(
)
[_new:BaseObject:private] =>
[_deleted:BaseObject:private] =>
[modifiedColumns:protected] => Array
(
)
)
[54] => Category Object
(
[languages:protected] =>
[bok_resources:protected] =>
[bok_topics:protected] =>
[bok_keywords:protected] =>
[id:protected] => 54
[type:protected] => category
[parent:protected] => 2
[label:protected] => Drywall Applicator Specialist
[alreadyInSave:protected] =>
[alreadyInValidation:protected] =>
[validationFailures:protected] => Array
(
)
[_new:BaseObject:private] =>
[_deleted:BaseObject:private] =>
[modifiedColumns:protected] => Array
(
)
)
[55] => Category Object
(
[languages:protected] =>
[bok_resources:protected] =>
[bok_topics:protected] =>
[bok_keywords:protected] =>
[id:protected] => 55
[type:protected] => category
[parent:protected] => 2
[label:protected] => Electrical Worker
[alreadyInSave:protected] =>
[alreadyInValidation:protected] =>
[validationFailures:protected] => Array
(
)
[_new:BaseObject:private] =>
[_deleted:BaseObject:private] =>
[modifiedColumns:protected] => Array
(
)
)
[56] => Category Object
(
[languages:protected] =>
[bok_resources:protected] =>
[bok_topics:protected] =>
[bok_keywords:protected] =>
[id:protected] => 56
[type:protected] => category
[parent:protected] => 2
[label:protected] => Elevator Constructor
[alreadyInSave:protected] =>
[alreadyInValidation:protected] =>
[validationFailures:protected] => Array
(
)
[_new:BaseObject:private] =>
[_deleted:BaseObject:private] =>
[modifiedColumns:protected] => Array
(
)
)
[57] => Category Object
(
[languages:protected] =>
[bok_resources:protected] =>
[bok_topics:protected] =>
[bok_keywords:protected] =>
[id:protected] => 57
[type:protected] => category
[parent:protected] => 2
[label:protected] => Flagger
[alreadyInSave:protected] =>
[alreadyInValidation:protected] =>
[validationFailures:protected] => Array
(
)
[_new:BaseObject:private] =>
[_deleted:BaseObject:private] =>
[modifiedColumns:protected] => Array
(
)
)
[58] => Category Object
(
[languages:protected] =>
[bok_resources:protected] =>
[bok_topics:protected] =>
[bok_keywords:protected] =>
[id:protected] => 58
[type:protected] => category
[parent:protected] => 2
[label:protected] => Glazier
[alreadyInSave:protected] =>
[alreadyInValidation:protected] =>
[validationFailures:protected] => Array
(
)
[_new:BaseObject:private] =>
[_deleted:BaseObject:private] =>
[modifiedColumns:protected] => Array
(
)
)
[59] => Category Object
(
[languages:protected] =>
[bok_resources:protected] =>
[bok_topics:protected] =>
[bok_keywords:protected] =>
[id:protected] => 59
[type:protected] => category
[parent:protected] => 2
[label:protected] => Hazardous Waste Cleanup
[alreadyInSave:protected] =>
[alreadyInValidation:protected] =>
[validationFailures:protected] => Array
(
)
[_new:BaseObject:private] =>
[_deleted:BaseObject:private] =>
[modifiedColumns:protected] => Array
(
)
)
[60] => Category Object
(
[languages:protected] =>
[bok_resources:protected] =>
[bok_topics:protected] =>
[bok_keywords:protected] =>
[id:protected] => 60
[type:protected] => category
[parent:protected] => 2
[label:protected] => HVAC
[alreadyInSave:protected] =>
[alreadyInValidation:protected] =>
[validationFailures:protected] => Array
(
)
[_new:BaseObject:private] =>
[_deleted:BaseObject:private] =>
[modifiedColumns:protected] => Array
(
)
)
[61] => Category Object
(
[languages:protected] =>
[bok_resources:protected] =>
[bok_topics:protected] =>
[bok_keywords:protected] =>
[id:protected] => 61
[type:protected] => category
[parent:protected] => 2
[label:protected] => Interior Systems Carpenter
[alreadyInSave:protected] =>
[alreadyInValidation:protected] =>
[validationFailures:protected] => Array
(
)
[_new:BaseObject:private] =>
[_deleted:BaseObject:private] =>
[modifiedColumns:protected] => Array
(
)
)
[64] => Category Object
(
[languages:protected] =>
[bok_resources:protected] =>
[bok_topics:protected] =>
[bok_keywords:protected] =>
[id:protected] => 64
[type:protected] => category
[parent:protected] => 2
[label:protected] => Laborer
[alreadyInSave:protected] =>
[alreadyInValidation:protected] =>
[validationFailures:protected] => Array
(
)
[_new:BaseObject:private] =>
[_deleted:BaseObject:private] =>
[modifiedColumns:protected] => Array
(
)
)
[65] => Category Object
(
[languages:protected] =>
[bok_resources:protected] =>
[bok_topics:protected] =>
[bok_keywords:protected] =>
[id:protected] => 65
[type:protected] => category
[parent:protected] => 2
[label:protected] => Landscaper
[alreadyInSave:protected] =>
[alreadyInValidation:protected] =>
[validationFailures:protected] => Array
(
)
[_new:BaseObject:private] =>
[_deleted:BaseObject:private] =>
[modifiedColumns:protected] => Array
(
)
)
[66] => Category Object
(
[languages:protected] =>
[bok_resources:protected] =>
[bok_topics:protected] =>
[bok_keywords:protected] =>
[id:protected] => 66
[type:protected] => category
[parent:protected] => 2
[label:protected] => Lather
[alreadyInSave:protected] =>
[alreadyInValidation:protected] =>
[validationFailures:protected] => Array
(
)
[_new:BaseObject:private] =>
[_deleted:BaseObject:private] =>
[modifiedColumns:protected] => Array
(
)
)
[67] => Category Object
(
[languages:protected] =>
[bok_resources:protected] =>
[bok_topics:protected] =>
[bok_keywords:protected] =>
[id:protected] => 67
[type:protected] => category
[parent:protected] => 2
[label:protected] => Lead Abatement Worker
[alreadyInSave:protected] =>
[alreadyInValidation:protected] =>
[validationFailures:protected] => Array
(
)
[_new:BaseObject:private] =>
[_deleted:BaseObject:private] =>
[modifiedColumns:protected] => Array
(
)
)
[68] => Category Object
(
[languages:protected] =>
[bok_resources:protected] =>
[bok_topics:protected] =>
[bok_keywords:protected] =>
[id:protected] => 68
[type:protected] => category
[parent:protected] => 2
[label:protected] => Maintenance Worker
[alreadyInSave:protected] =>
[alreadyInValidation:protected] =>
[validationFailures:protected] => Array
(
)
[_new:BaseObject:private] =>
[_deleted:BaseObject:private] =>
[modifiedColumns:protected] => Array
(
)
)
[69] => Category Object
(
[languages:protected] =>
[bok_resources:protected] =>
[bok_topics:protected] =>
[bok_keywords:protected] =>
[id:protected] => 69
[type:protected] => category
[parent:protected] => 2
[label:protected] => Millwright
[alreadyInSave:protected] =>
[alreadyInValidation:protected] =>
[validationFailures:protected] => Array
(
)
[_new:BaseObject:private] =>
[_deleted:BaseObject:private] =>
[modifiedColumns:protected] => Array
(
)
)
[70] => Category Object
(
[languages:protected] =>
[bok_resources:protected] =>
[bok_topics:protected] =>
[bok_keywords:protected] =>
[id:protected] => 70
[type:protected] => category
[parent:protected] => 2
[label:protected] => Operating Engineer
[alreadyInSave:protected] =>
[alreadyInValidation:protected] =>
[validationFailures:protected] => Array
(
)
[_new:BaseObject:private] =>
[_deleted:BaseObject:private] =>
[modifiedColumns:protected] => Array
(
)
)
[71] => Category Object
(
[languages:protected] =>
[bok_resources:protected] =>
[bok_topics:protected] =>
[bok_keywords:protected] =>
[id:protected] => 71
[type:protected] => category
[parent:protected] => 2
[label:protected] => Painter
[alreadyInSave:protected] =>
[alreadyInValidation:protected] =>
[validationFailures:protected] => Array
(
)
[_new:BaseObject:private] =>
[_deleted:BaseObject:private] =>
[modifiedColumns:protected] => Array
(
)
)
[72] => Category Object
(
[languages:protected] =>
[bok_resources:protected] =>
[bok_topics:protected] =>
[bok_keywords:protected] =>
[id:protected] => 72
[type:protected] => category
[parent:protected] => 2
[label:protected] => Paper Hanger
[alreadyInSave:protected] =>
[alreadyInValidation:protected] =>
[validationFailures:protected] => Array
(
)
[_new:BaseObject:private] =>
[_deleted:BaseObject:private] =>
[modifiedColumns:protected] => Array
(
)
)
[73] => Category Object
(
[languages:protected] =>
[bok_resources:protected] =>
[bok_topics:protected] =>
[bok_keywords:protected] =>
[id:protected] => 73
[type:protected] => category
[parent:protected] => 2
[label:protected] => PCC/Restoration
[alreadyInSave:protected] =>
[alreadyInValidation:protected] =>
[validationFailures:protected] => Array
(
)
[_new:BaseObject:private] =>
[_deleted:BaseObject:private] =>
[modifiedColumns:protected] => Array
(
)
)
[74] => Category Object
(
[languages:protected] =>
[bok_resources:protected] =>
[bok_topics:protected] =>
[bok_keywords:protected] =>
[id:protected] => 74
[type:protected] => category
[parent:protected] => 2
[label:protected] => Pile Driver
[alreadyInSave:protected] =>
[alreadyInValidation:protected] =>
[validationFailures:protected] => Array
(
)
[_new:BaseObject:private] =>
[_deleted:BaseObject:private] =>
[modifiedColumns:protected] => Array
(
)
)
[75] => Category Object
(
[languages:protected] =>
[bok_resources:protected] =>
[bok_topics:protected] =>
[bok_keywords:protected] =>
[id:protected] => 75
[type:protected] => category
[parent:protected] => 2
[label:protected] => Plasterer
[alreadyInSave:protected] =>
[alreadyInValidation:protected] =>
[validationFailures:protected] => Array
(
)
[_new:BaseObject:private] =>
[_deleted:BaseObject:private] =>
[modifiedColumns:protected] => Array
(
)
)
[76] => Category Object
(
[languages:protected] =>
[bok_resources:protected] =>
[bok_topics:protected] =>
[bok_keywords:protected] =>
[id:protected] => 76
[type:protected] => category
[parent:protected] => 2
[label:protected] => Plumber/Pipefitter
[alreadyInSave:protected] =>
[alreadyInValidation:protected] =>
[validationFailures:protected] => Array
(
)
[_new:BaseObject:private] =>
[_deleted:BaseObject:private] =>
[modifiedColumns:protected] => Array
(
)
)
[77] => Category Object
(
[languages:protected] =>
[bok_resources:protected] =>
[bok_topics:protected] =>
[bok_keywords:protected] =>
[id:protected] => 77
[type:protected] => category
[parent:protected] => 2
[label:protected] => Refractory Worker
[alreadyInSave:protected] =>
[alreadyInValidation:protected] =>
[validationFailures:protected] => Array
(
)
[_new:BaseObject:private] =>
[_deleted:BaseObject:private] =>
[modifiedColumns:protected] => Array
(
)
)
[63] => Category Object
(
[languages:protected] =>
[bok_resources:protected] =>
[bok_topics:protected] =>
[bok_keywords:protected] =>
[id:protected] => 63
[type:protected] => category
[parent:protected] => 2
[label:protected] => Reinforcing Ironworker
[alreadyInSave:protected] =>
[alreadyInValidation:protected] =>
[validationFailures:protected] => Array
(
)
[_new:BaseObject:private] =>
[_deleted:BaseObject:private] =>
[modifiedColumns:protected] => Array
(
)
)
[78] => Category Object
(
[languages:protected] =>
[bok_resources:protected] =>
[bok_topics:protected] =>
[bok_keywords:protected] =>
[id:protected] => 78
[type:protected] => category
[parent:protected] => 2
[label:protected] => Roofer/Waterproofer
[alreadyInSave:protected] =>
[alreadyInValidation:protected] =>
[validationFailures:protected] => Array
(
)
[_new:BaseObject:private] =>
[_deleted:BaseObject:private] =>
[modifiedColumns:protected] => Array
(
)
)
[79] => Category Object
(
[languages:protected] =>
[bok_resources:protected] =>
[bok_topics:protected] =>
[bok_keywords:protected] =>
[id:protected] => 79
[type:protected] => category
[parent:protected] => 2
[label:protected] => Scaffold Erector
[alreadyInSave:protected] =>
[alreadyInValidation:protected] =>
[validationFailures:protected] => Array
(
)
[_new:BaseObject:private] =>
[_deleted:BaseObject:private] =>
[modifiedColumns:protected] => Array
(
)
)
[80] => Category Object
(
[languages:protected] =>
[bok_resources:protected] =>
[bok_topics:protected] =>
[bok_keywords:protected] =>
[id:protected] => 80
[type:protected] => category
[parent:protected] => 2
[label:protected] => Sheetmetal Worker
[alreadyInSave:protected] =>
[alreadyInValidation:protected] =>
[validationFailures:protected] => Array
(
)
[_new:BaseObject:private] =>
[_deleted:BaseObject:private] =>
[modifiedColumns:protected] => Array
(
)
)
[81] => Category Object
(
[languages:protected] =>
[bok_resources:protected] =>
[bok_topics:protected] =>
[bok_keywords:protected] =>
[id:protected] => 81
[type:protected] => category
[parent:protected] => 2
[label:protected] => Sprinkler Fitter
[alreadyInSave:protected] =>
[alreadyInValidation:protected] =>
[validationFailures:protected] => Array
(
)
[_new:BaseObject:private] =>
[_deleted:BaseObject:private] =>
[modifiedColumns:protected] => Array
(
)
)
[82] => Category Object
(
[languages:protected] =>
[bok_resources:protected] =>
[bok_topics:protected] =>
[bok_keywords:protected] =>
[id:protected] => 82
[type:protected] => category
[parent:protected] => 2
[label:protected] => Stonemason
[alreadyInSave:protected] =>
[alreadyInValidation:protected] =>
[validationFailures:protected] => Array
(
)
[_new:BaseObject:private] =>
[_deleted:BaseObject:private] =>
[modifiedColumns:protected] => Array
(
)
)
[62] => Category Object
(
[languages:protected] =>
[bok_resources:protected] =>
[bok_topics:protected] =>
[bok_keywords:protected] =>
[id:protected] => 62
[type:protected] => category
[parent:protected] => 2
[label:protected] => Structural Ironworker
[alreadyInSave:protected] =>
[alreadyInValidation:protected] =>
[validationFailures:protected] => Array
(
)
[_new:BaseObject:private] =>
[_deleted:BaseObject:private] =>
[modifiedColumns:protected] => Array
(
)
)
[83] => Category Object
(
[languages:protected] =>
[bok_resources:protected] =>
[bok_topics:protected] =>
[bok_keywords:protected] =>
[id:protected] => 83
[type:protected] => category
[parent:protected] => 2
[label:protected] => Terrazzo Worker
[alreadyInSave:protected] =>
[alreadyInValidation:protected] =>
[validationFailures:protected] => Array
(
)
[_new:BaseObject:private] =>
[_deleted:BaseObject:private] =>
[modifiedColumns:protected] => Array
(
)
)
[84] => Category Object
(
[languages:protected] =>
[bok_resources:protected] =>
[bok_topics:protected] =>
[bok_keywords:protected] =>
[id:protected] => 84
[type:protected] => category
[parent:protected] => 2
[label:protected] => Tile Setter
[alreadyInSave:protected] =>
[alreadyInValidation:protected] =>
[validationFailures:protected] => Array
(
)
[_new:BaseObject:private] =>
[_deleted:BaseObject:private] =>
[modifiedColumns:protected] => Array
(
)
)
[85] => Category Object
(
[languages:protected] =>
[bok_resources:protected] =>
[bok_topics:protected] =>
[bok_keywords:protected] =>
[id:protected] => 85
[type:protected] => category
[parent:protected] => 2
[label:protected] => Truck Driver
[alreadyInSave:protected] =>
[alreadyInValidation:protected] =>
[validationFailures:protected] => Array
(
)
[_new:BaseObject:private] =>
[_deleted:BaseObject:private] =>
[modifiedColumns:protected] => Array
(
)
)
[86] => Category Object
(
[languages:protected] =>
[bok_resources:protected] =>
[bok_topics:protected] =>
[bok_keywords:protected] =>
[id:protected] => 86
[type:protected] => category
[parent:protected] => 2
[label:protected] => Welder
[alreadyInSave:protected] =>
[alreadyInValidation:protected] =>
[validationFailures:protected] => Array
(
)
[_new:BaseObject:private] =>
[_deleted:BaseObject:private] =>
[modifiedColumns:protected] => Array
(
)
)
[87] => Category Object
(
[languages:protected] =>
[bok_resources:protected] =>
[bok_topics:protected] =>
[bok_keywords:protected] =>
[id:protected] => 87
[type:protected] => category
[parent:protected] => 3
[label:protected] => Commercial & Institutional
[alreadyInSave:protected] =>
[alreadyInValidation:protected] =>
[validationFailures:protected] => Array
(
)
[_new:BaseObject:private] =>
[_deleted:BaseObject:private] =>
[modifiedColumns:protected] => Array
(
)
)
[88] => Category Object
(
[languages:protected] =>
[bok_resources:protected] =>
[bok_topics:protected] =>
[bok_keywords:protected] =>
[id:protected] => 88
[type:protected] => category
[parent:protected] => 3
[label:protected] => Demolition
[alreadyInSave:protected] =>
[alreadyInValidation:protected] =>
[validationFailures:protected] => Array
(
)
[_new:BaseObject:private] =>
[_deleted:BaseObject:private] =>
[modifiedColumns:protected] => Array
(
)
)
[89] => Category Object
(
[languages:protected] =>
[bok_resources:protected] =>
[bok_topics:protected] =>
[bok_keywords:protected] =>
[id:protected] => 89
[type:protected] => category
[parent:protected] => 3
[label:protected] => Disasters
[alreadyInSave:protected] =>
[alreadyInValidation:protected] =>
[validationFailures:protected] => Array
(
)
[_new:BaseObject:private] =>
[_deleted:BaseObject:private] =>
[modifiedColumns:protected] => Array
(
)
)
[91] => Category Object
(
[languages:protected] =>
[bok_resources:protected] =>
[bok_topics:protected] =>
[bok_keywords:protected] =>
[id:protected] => 91
[type:protected] => category
[parent:protected] => 3
[label:protected] => Heavy & Highway
[alreadyInSave:protected] =>
[alreadyInValidation:protected] =>
[validationFailures:protected] => Array
(
)
[_new:BaseObject:private] =>
[_deleted:BaseObject:private] =>
[modifiedColumns:protected] => Array
(
)
)
[90] => Category Object
(
[languages:protected] =>
[bok_resources:protected] =>
[bok_topics:protected] =>
[bok_keywords:protected] =>
[id:protected] => 90
[type:protected] => category
[parent:protected] => 3
[label:protected] => Industrial
[alreadyInSave:protected] =>
[alreadyInValidation:protected] =>
[validationFailures:protected] => Array
(
)
[_new:BaseObject:private] =>
[_deleted:BaseObject:private] =>
[modifiedColumns:protected] => Array
(
)
)
[92] => Category Object
(
[languages:protected] =>
[bok_resources:protected] =>
[bok_topics:protected] =>
[bok_keywords:protected] =>
[id:protected] => 92
[type:protected] => category
[parent:protected] => 3
[label:protected] => LEED/Green Construction
[alreadyInSave:protected] =>
[alreadyInValidation:protected] =>
[validationFailures:protected] => Array
(
)
[_new:BaseObject:private] =>
[_deleted:BaseObject:private] =>
[modifiedColumns:protected] => Array
(
)
)
[93] => Category Object
(
[languages:protected] =>
[bok_resources:protected] =>
[bok_topics:protected] =>
[bok_keywords:protected] =>
[id:protected] => 93
[type:protected] => category
[parent:protected] => 3
[label:protected] => Renovations
[alreadyInSave:protected] =>
[alreadyInValidation:protected] =>
[validationFailures:protected] => Array
(
)
[_new:BaseObject:private] =>
[_deleted:BaseObject:private] =>
[modifiedColumns:protected] => Array
(
)
)
[94] => Category Object
(
[languages:protected] =>
[bok_resources:protected] =>
[bok_topics:protected] =>
[bok_keywords:protected] =>
[id:protected] => 94
[type:protected] => category
[parent:protected] => 3
[label:protected] => Residential
[alreadyInSave:protected] =>
[alreadyInValidation:protected] =>
[validationFailures:protected] => Array
(
)
[_new:BaseObject:private] =>
[_deleted:BaseObject:private] =>
[modifiedColumns:protected] => Array
(
)
)
[95] => Category Object
(
[languages:protected] =>
[bok_resources:protected] =>
[bok_topics:protected] =>
[bok_keywords:protected] =>
[id:protected] => 95
[type:protected] => category
[parent:protected] => 3
[label:protected] => Underground
[alreadyInSave:protected] =>
[alreadyInValidation:protected] =>
[validationFailures:protected] => Array
(
)
[_new:BaseObject:private] =>
[_deleted:BaseObject:private] =>
[modifiedColumns:protected] => Array
(
)
)
)
[categories_initialized:protected] => 1
[mapped_items:protected] =>
[content:protected] =>
[files:protected] =>
[language:protected] => Language Object
(
[id:protected] => 1
[code:protected] => en
[name:protected] => English
[alreadyInSave:protected] =>
[alreadyInValidation:protected] =>
[validationFailures:protected] => Array
(
)
[_new:BaseObject:private] =>
[_deleted:BaseObject:private] =>
[modifiedColumns:protected] => Array
(
)
)
[old_record:protected] =>
[id:protected] => 4426
[old_id:protected] =>
[elcosh_id:protected] => d001656
[type:protected] => document
[display_type:protected] => HTML only (and links)
[user_id:protected] => 0
[language_id:protected] => 1
[tagging_id:protected] => Mike Aguilar
[priority_id:protected] => 1
[title:protected] => Construction Dive -- DeWalt's Jobsite Pro headphones recalled for fire hazards
[total_pages:protected] => 1
[billed_pages:protected] => 1
[publication_number:protected] =>
[part_of:protected] =>
[keywords:protected] => DeWalt, Fire Hazards, recall, headphones
[comments:protected] =>
[summary:protected] => A recall notice by the United States Consumer Product Safety Commission affects over 300,000 DeWalt Jobsite Pro Headphones. The recall is a result of a malfunction that can cause earbuds to overheat while charging or during use, leading to fire and burn hazards.
[transition_comments:protected] =>
[external_link:protected] => https://www.constructiondive.com/news/dewalts-jobsite-pro-headphones-recalled-for-fire-hazards/611248/?utm_source=Sailthru&utm_medium=email&utm_campaign=Issue:%202021-12-10%20Construction%20Dive%20Newsletter%20%5Bissue:38532%5D&utm_term=Construction%20Dive
[consol_link:protected] =>
[more_like_this:protected] =>
[permission_given_by:protected] =>
[published:protected] => T
[billable:protected] => F
[img_name:protected] =>
[img_ext:protected] =>
[img_width:protected] =>
[img_height:protected] =>
[img_credit:protected] =>
[img_practice:protected] =>
[vid_source_id:protected] =>
[vid_running_time:protected] =>
[vid_intended_audience:protected] =>
[vid_acquisition_info:protected] =>
[vid_cost:protected] =>
[vid_producer:protected] =>
[vid_filename:protected] =>
[vid_filename_downloadable:protected] =>
[date_summary:protected] =>
[date_permission_requested:protected] =>
[date_permission_received:protected] =>
[date_review_needed:protected] =>
[date_received:protected] => 12/13/21
[date_completed:protected] => 12/13/21
[date_billed:protected] =>
[date_modified:protected] => 12/13/21
[collBokExports:protected] =>
[lastBokExportCriteria:BaseElcoshItem:private] =>
[alreadyInSave:protected] =>
[alreadyInValidation:protected] =>
[validationFailures:protected] => Array
(
)
[_new:BaseObject:private] =>
[_deleted:BaseObject:private] =>
[modifiedColumns:protected] => Array
(
)
)
)
)
[new_images] => Array
(
[0] => Search_Result Object
(
[title] => Morning Toolbox Talk
[image] => /record/images/4003-p.jpg
[blurb] => This photo is from an early morning toolbox talk on a construction job in Mclean, Virginia. It is being delivered in English and Spanish....
[category] => Array
(
[0] => 20
[1] => 51
[2] => 57
[3] => 64
[4] => 70
[5] => 63
[6] => 78
[7] => 82
[8] => 62
[9] => 87
[10] => 88
[11] => 89
[12] => 91
[13] => 90
[14] => 93
[15] => 94
[16] => 97
)
[labels] => Array
(
[0] => Safety Culture
[1] => Work Environment
[2] => Hazards
[3] => Cement Mason
[4] => Trades
[5] => Flagger
[7] => Laborer
[9] => Operating Engineer
[11] => Reinforcing Ironworker
[13] => Roofer/Waterproofer
[15] => Stonemason
[17] => Structural Ironworker
[19] => Commercial & Institutional
[20] => Jobsites
[21] => Demolition
[23] => Disasters
[25] => Heavy & Highway
[27] => Industrial
[29] => Renovations
[31] => Residential
[33] => Images
[34] => Media
[35] => Media & Documents
)
[type] => Images
[sub_category] =>
[url] => /image/4003/i002691/Morning%2BToolbox%2BTalk.html
[item:protected] => ImageRecord Object
(
[records:protected] => Array
(
)
[recordId:protected] =>
[searchWordClass:protected] =>
[searchWordPeerClass:protected] =>
[bok_record:protected] =>
[authors:protected] =>
[organizations:protected] =>
[collections:protected] =>
[categories:protected] => Array
(
[20] => Category Object
(
[languages:protected] =>
[bok_resources:protected] =>
[bok_topics:protected] =>
[bok_keywords:protected] =>
[id:protected] => 20
[type:protected] => category
[parent:protected] => 7
[label:protected] => Safety Culture
[alreadyInSave:protected] =>
[alreadyInValidation:protected] =>
[validationFailures:protected] => Array
(
)
[_new:BaseObject:private] =>
[_deleted:BaseObject:private] =>
[modifiedColumns:protected] => Array
(
)
)
[51] => Category Object
(
[languages:protected] =>
[bok_resources:protected] =>
[bok_topics:protected] =>
[bok_keywords:protected] =>
[id:protected] => 51
[type:protected] => category
[parent:protected] => 2
[label:protected] => Cement Mason
[alreadyInSave:protected] =>
[alreadyInValidation:protected] =>
[validationFailures:protected] => Array
(
)
[_new:BaseObject:private] =>
[_deleted:BaseObject:private] =>
[modifiedColumns:protected] => Array
(
)
)
[57] => Category Object
(
[languages:protected] =>
[bok_resources:protected] =>
[bok_topics:protected] =>
[bok_keywords:protected] =>
[id:protected] => 57
[type:protected] => category
[parent:protected] => 2
[label:protected] => Flagger
[alreadyInSave:protected] =>
[alreadyInValidation:protected] =>
[validationFailures:protected] => Array
(
)
[_new:BaseObject:private] =>
[_deleted:BaseObject:private] =>
[modifiedColumns:protected] => Array
(
)
)
[64] => Category Object
(
[languages:protected] =>
[bok_resources:protected] =>
[bok_topics:protected] =>
[bok_keywords:protected] =>
[id:protected] => 64
[type:protected] => category
[parent:protected] => 2
[label:protected] => Laborer
[alreadyInSave:protected] =>
[alreadyInValidation:protected] =>
[validationFailures:protected] => Array
(
)
[_new:BaseObject:private] =>
[_deleted:BaseObject:private] =>
[modifiedColumns:protected] => Array
(
)
)
[70] => Category Object
(
[languages:protected] =>
[bok_resources:protected] =>
[bok_topics:protected] =>
[bok_keywords:protected] =>
[id:protected] => 70
[type:protected] => category
[parent:protected] => 2
[label:protected] => Operating Engineer
[alreadyInSave:protected] =>
[alreadyInValidation:protected] =>
[validationFailures:protected] => Array
(
)
[_new:BaseObject:private] =>
[_deleted:BaseObject:private] =>
[modifiedColumns:protected] => Array
(
)
)
[63] => Category Object
(
[languages:protected] =>
[bok_resources:protected] =>
[bok_topics:protected] =>
[bok_keywords:protected] =>
[id:protected] => 63
[type:protected] => category
[parent:protected] => 2
[label:protected] => Reinforcing Ironworker
[alreadyInSave:protected] =>
[alreadyInValidation:protected] =>
[validationFailures:protected] => Array
(
)
[_new:BaseObject:private] =>
[_deleted:BaseObject:private] =>
[modifiedColumns:protected] => Array
(
)
)
[78] => Category Object
(
[languages:protected] =>
[bok_resources:protected] =>
[bok_topics:protected] =>
[bok_keywords:protected] =>
[id:protected] => 78
[type:protected] => category
[parent:protected] => 2
[label:protected] => Roofer/Waterproofer
[alreadyInSave:protected] =>
[alreadyInValidation:protected] =>
[validationFailures:protected] => Array
(
)
[_new:BaseObject:private] =>
[_deleted:BaseObject:private] =>
[modifiedColumns:protected] => Array
(
)
)
[82] => Category Object
(
[languages:protected] =>
[bok_resources:protected] =>
[bok_topics:protected] =>
[bok_keywords:protected] =>
[id:protected] => 82
[type:protected] => category
[parent:protected] => 2
[label:protected] => Stonemason
[alreadyInSave:protected] =>
[alreadyInValidation:protected] =>
[validationFailures:protected] => Array
(
)
[_new:BaseObject:private] =>
[_deleted:BaseObject:private] =>
[modifiedColumns:protected] => Array
(
)
)
[62] => Category Object
(
[languages:protected] =>
[bok_resources:protected] =>
[bok_topics:protected] =>
[bok_keywords:protected] =>
[id:protected] => 62
[type:protected] => category
[parent:protected] => 2
[label:protected] => Structural Ironworker
[alreadyInSave:protected] =>
[alreadyInValidation:protected] =>
[validationFailures:protected] => Array
(
)
[_new:BaseObject:private] =>
[_deleted:BaseObject:private] =>
[modifiedColumns:protected] => Array
(
)
)
[87] => Category Object
(
[languages:protected] =>
[bok_resources:protected] =>
[bok_topics:protected] =>
[bok_keywords:protected] =>
[id:protected] => 87
[type:protected] => category
[parent:protected] => 3
[label:protected] => Commercial & Institutional
[alreadyInSave:protected] =>
[alreadyInValidation:protected] =>
[validationFailures:protected] => Array
(
)
[_new:BaseObject:private] =>
[_deleted:BaseObject:private] =>
[modifiedColumns:protected] => Array
(
)
)
[88] => Category Object
(
[languages:protected] =>
[bok_resources:protected] =>
[bok_topics:protected] =>
[bok_keywords:protected] =>
[id:protected] => 88
[type:protected] => category
[parent:protected] => 3
[label:protected] => Demolition
[alreadyInSave:protected] =>
[alreadyInValidation:protected] =>
[validationFailures:protected] => Array
(
)
[_new:BaseObject:private] =>
[_deleted:BaseObject:private] =>
[modifiedColumns:protected] => Array
(
)
)
[89] => Category Object
(
[languages:protected] =>
[bok_resources:protected] =>
[bok_topics:protected] =>
[bok_keywords:protected] =>
[id:protected] => 89
[type:protected] => category
[parent:protected] => 3
[label:protected] => Disasters
[alreadyInSave:protected] =>
[alreadyInValidation:protected] =>
[validationFailures:protected] => Array
(
)
[_new:BaseObject:private] =>
[_deleted:BaseObject:private] =>
[modifiedColumns:protected] => Array
(
)
)
[91] => Category Object
(
[languages:protected] =>
[bok_resources:protected] =>
[bok_topics:protected] =>
[bok_keywords:protected] =>
[id:protected] => 91
[type:protected] => category
[parent:protected] => 3
[label:protected] => Heavy & Highway
[alreadyInSave:protected] =>
[alreadyInValidation:protected] =>
[validationFailures:protected] => Array
(
)
[_new:BaseObject:private] =>
[_deleted:BaseObject:private] =>
[modifiedColumns:protected] => Array
(
)
)
[90] => Category Object
(
[languages:protected] =>
[bok_resources:protected] =>
[bok_topics:protected] =>
[bok_keywords:protected] =>
[id:protected] => 90
[type:protected] => category
[parent:protected] => 3
[label:protected] => Industrial
[alreadyInSave:protected] =>
[alreadyInValidation:protected] =>
[validationFailures:protected] => Array
(
)
[_new:BaseObject:private] =>
[_deleted:BaseObject:private] =>
[modifiedColumns:protected] => Array
(
)
)
[93] => Category Object
(
[languages:protected] =>
[bok_resources:protected] =>
[bok_topics:protected] =>
[bok_keywords:protected] =>
[id:protected] => 93
[type:protected] => category
[parent:protected] => 3
[label:protected] => Renovations
[alreadyInSave:protected] =>
[alreadyInValidation:protected] =>
[validationFailures:protected] => Array
(
)
[_new:BaseObject:private] =>
[_deleted:BaseObject:private] =>
[modifiedColumns:protected] => Array
(
)
)
[94] => Category Object
(
[languages:protected] =>
[bok_resources:protected] =>
[bok_topics:protected] =>
[bok_keywords:protected] =>
[id:protected] => 94
[type:protected] => category
[parent:protected] => 3
[label:protected] => Residential
[alreadyInSave:protected] =>
[alreadyInValidation:protected] =>
[validationFailures:protected] => Array
(
)
[_new:BaseObject:private] =>
[_deleted:BaseObject:private] =>
[modifiedColumns:protected] => Array
(
)
)
[97] => Category Object
(
[languages:protected] =>
[bok_resources:protected] =>
[bok_topics:protected] =>
[bok_keywords:protected] =>
[id:protected] => 97
[type:protected] => category
[parent:protected] => 5
[label:protected] => Images
[alreadyInSave:protected] =>
[alreadyInValidation:protected] =>
[validationFailures:protected] => Array
(
)
[_new:BaseObject:private] =>
[_deleted:BaseObject:private] =>
[modifiedColumns:protected] => Array
(
)
)
)
[categories_initialized:protected] => 1
[mapped_items:protected] =>
[content:protected] =>
[files:protected] =>
[language:protected] => Language Object
(
[id:protected] => 1
[code:protected] => en
[name:protected] => English
[alreadyInSave:protected] =>
[alreadyInValidation:protected] =>
[validationFailures:protected] => Array
(
)
[_new:BaseObject:private] =>
[_deleted:BaseObject:private] =>
[modifiedColumns:protected] => Array
(
)
)
[old_record:protected] =>
[id:protected] => 4003
[old_id:protected] =>
[elcosh_id:protected] => i002691
[type:protected] => image
[display_type:protected] => Image
[user_id:protected] => 0
[language_id:protected] => 1
[tagging_id:protected] => Bruce Lippy
[priority_id:protected] => 1
[title:protected] => Morning Toolbox Talk
[total_pages:protected] => 0
[billed_pages:protected] => 0
[publication_number:protected] =>
[part_of:protected] =>
[keywords:protected] => toolbox talk, tailgate talk, Spanish, bilingual
[comments:protected] =>
[summary:protected] => This photo is from an early morning toolbox talk on a construction job in Mclean, Virginia. It is being delivered in English and Spanish.
[transition_comments:protected] =>
[external_link:protected] =>
[consol_link:protected] => http://www.cpwrconstructionsolutions.org/electrical/solution/662/worker-training.html
[more_like_this:protected] => d001285,d001304,c000079
[permission_given_by:protected] =>
[published:protected] => T
[billable:protected] => F
[img_name:protected] =>
[img_ext:protected] => jpg
[img_width:protected] =>
[img_height:protected] =>
[img_credit:protected] => Morgan Zavertnik and Hoar Construction
[img_practice:protected] => good
[vid_source_id:protected] =>
[vid_running_time:protected] =>
[vid_intended_audience:protected] =>
[vid_acquisition_info:protected] =>
[vid_cost:protected] =>
[vid_producer:protected] =>
[vid_filename:protected] =>
[vid_filename_downloadable:protected] =>
[date_summary:protected] => November 2015
[date_permission_requested:protected] =>
[date_permission_received:protected] =>
[date_review_needed:protected] =>
[date_received:protected] => 03/02/16
[date_completed:protected] => 03/02/16
[date_billed:protected] =>
[date_modified:protected] => 03/02/16
[collBokExports:protected] =>
[lastBokExportCriteria:BaseElcoshItem:private] =>
[alreadyInSave:protected] =>
[alreadyInValidation:protected] =>
[validationFailures:protected] => Array
(
)
[_new:BaseObject:private] =>
[_deleted:BaseObject:private] =>
[modifiedColumns:protected] => Array
(
)
)
)
[1] => Search_Result Object
(
[title] => Toolbox talk - crew view
[image] => /record/images/4005-p.jpg
[blurb] => Photo of crew listening to a toolbox safety talk before starting work....
[category] => Array
(
[0] => 97
[1] => 20
[2] => 47
[3] => 49
[4] => 51
[5] => 55
[6] => 61
[7] => 64
[8] => 71
[9] => 75
[10] => 63
[11] => 79
[12] => 62
[13] => 87
[14] => 88
[15] => 91
[16] => 90
[17] => 93
[18] => 94
[19] => 95
)
[labels] => Array
(
[0] => Images
[1] => Media
[2] => Media & Documents
[3] => Safety Culture
[4] => Work Environment
[5] => Hazards
[6] => Bricklayer
[7] => Trades
[8] => Carpenter
[10] => Cement Mason
[12] => Electrical Worker
[14] => Interior Systems Carpenter
[16] => Laborer
[18] => Painter
[20] => Plasterer
[22] => Reinforcing Ironworker
[24] => Scaffold Erector
[26] => Structural Ironworker
[28] => Commercial & Institutional
[29] => Jobsites
[30] => Demolition
[32] => Heavy & Highway
[34] => Industrial
[36] => Renovations
[38] => Residential
[40] => Underground
)
[type] => Images
[sub_category] =>
[url] => /image/4005/i002692/Toolbox%2Btalk%2B-%2Bcrew%2Bview.html
[item:protected] => ImageRecord Object
(
[records:protected] => Array
(
)
[recordId:protected] =>
[searchWordClass:protected] =>
[searchWordPeerClass:protected] =>
[bok_record:protected] =>
[authors:protected] =>
[organizations:protected] =>
[collections:protected] =>
[categories:protected] => Array
(
[97] => Category Object
(
[languages:protected] =>
[bok_resources:protected] =>
[bok_topics:protected] =>
[bok_keywords:protected] =>
[id:protected] => 97
[type:protected] => category
[parent:protected] => 5
[label:protected] => Images
[alreadyInSave:protected] =>
[alreadyInValidation:protected] =>
[validationFailures:protected] => Array
(
)
[_new:BaseObject:private] =>
[_deleted:BaseObject:private] =>
[modifiedColumns:protected] => Array
(
)
)
[20] => Category Object
(
[languages:protected] =>
[bok_resources:protected] =>
[bok_topics:protected] =>
[bok_keywords:protected] =>
[id:protected] => 20
[type:protected] => category
[parent:protected] => 7
[label:protected] => Safety Culture
[alreadyInSave:protected] =>
[alreadyInValidation:protected] =>
[validationFailures:protected] => Array
(
)
[_new:BaseObject:private] =>
[_deleted:BaseObject:private] =>
[modifiedColumns:protected] => Array
(
)
)
[47] => Category Object
(
[languages:protected] =>
[bok_resources:protected] =>
[bok_topics:protected] =>
[bok_keywords:protected] =>
[id:protected] => 47
[type:protected] => category
[parent:protected] => 2
[label:protected] => Bricklayer
[alreadyInSave:protected] =>
[alreadyInValidation:protected] =>
[validationFailures:protected] => Array
(
)
[_new:BaseObject:private] =>
[_deleted:BaseObject:private] =>
[modifiedColumns:protected] => Array
(
)
)
[49] => Category Object
(
[languages:protected] =>
[bok_resources:protected] =>
[bok_topics:protected] =>
[bok_keywords:protected] =>
[id:protected] => 49
[type:protected] => category
[parent:protected] => 2
[label:protected] => Carpenter
[alreadyInSave:protected] =>
[alreadyInValidation:protected] =>
[validationFailures:protected] => Array
(
)
[_new:BaseObject:private] =>
[_deleted:BaseObject:private] =>
[modifiedColumns:protected] => Array
(
)
)
[51] => Category Object
(
[languages:protected] =>
[bok_resources:protected] =>
[bok_topics:protected] =>
[bok_keywords:protected] =>
[id:protected] => 51
[type:protected] => category
[parent:protected] => 2
[label:protected] => Cement Mason
[alreadyInSave:protected] =>
[alreadyInValidation:protected] =>
[validationFailures:protected] => Array
(
)
[_new:BaseObject:private] =>
[_deleted:BaseObject:private] =>
[modifiedColumns:protected] => Array
(
)
)
[55] => Category Object
(
[languages:protected] =>
[bok_resources:protected] =>
[bok_topics:protected] =>
[bok_keywords:protected] =>
[id:protected] => 55
[type:protected] => category
[parent:protected] => 2
[label:protected] => Electrical Worker
[alreadyInSave:protected] =>
[alreadyInValidation:protected] =>
[validationFailures:protected] => Array
(
)
[_new:BaseObject:private] =>
[_deleted:BaseObject:private] =>
[modifiedColumns:protected] => Array
(
)
)
[61] => Category Object
(
[languages:protected] =>
[bok_resources:protected] =>
[bok_topics:protected] =>
[bok_keywords:protected] =>
[id:protected] => 61
[type:protected] => category
[parent:protected] => 2
[label:protected] => Interior Systems Carpenter
[alreadyInSave:protected] =>
[alreadyInValidation:protected] =>
[validationFailures:protected] => Array
(
)
[_new:BaseObject:private] =>
[_deleted:BaseObject:private] =>
[modifiedColumns:protected] => Array
(
)
)
[64] => Category Object
(
[languages:protected] =>
[bok_resources:protected] =>
[bok_topics:protected] =>
[bok_keywords:protected] =>
[id:protected] => 64
[type:protected] => category
[parent:protected] => 2
[label:protected] => Laborer
[alreadyInSave:protected] =>
[alreadyInValidation:protected] =>
[validationFailures:protected] => Array
(
)
[_new:BaseObject:private] =>
[_deleted:BaseObject:private] =>
[modifiedColumns:protected] => Array
(
)
)
[71] => Category Object
(
[languages:protected] =>
[bok_resources:protected] =>
[bok_topics:protected] =>
[bok_keywords:protected] =>
[id:protected] => 71
[type:protected] => category
[parent:protected] => 2
[label:protected] => Painter
[alreadyInSave:protected] =>
[alreadyInValidation:protected] =>
[validationFailures:protected] => Array
(
)
[_new:BaseObject:private] =>
[_deleted:BaseObject:private] =>
[modifiedColumns:protected] => Array
(
)
)
[75] => Category Object
(
[languages:protected] =>
[bok_resources:protected] =>
[bok_topics:protected] =>
[bok_keywords:protected] =>
[id:protected] => 75
[type:protected] => category
[parent:protected] => 2
[label:protected] => Plasterer
[alreadyInSave:protected] =>
[alreadyInValidation:protected] =>
[validationFailures:protected] => Array
(
)
[_new:BaseObject:private] =>
[_deleted:BaseObject:private] =>
[modifiedColumns:protected] => Array
(
)
)
[63] => Category Object
(
[languages:protected] =>
[bok_resources:protected] =>
[bok_topics:protected] =>
[bok_keywords:protected] =>
[id:protected] => 63
[type:protected] => category
[parent:protected] => 2
[label:protected] => Reinforcing Ironworker
[alreadyInSave:protected] =>
[alreadyInValidation:protected] =>
[validationFailures:protected] => Array
(
)
[_new:BaseObject:private] =>
[_deleted:BaseObject:private] =>
[modifiedColumns:protected] => Array
(
)
)
[79] => Category Object
(
[languages:protected] =>
[bok_resources:protected] =>
[bok_topics:protected] =>
[bok_keywords:protected] =>
[id:protected] => 79
[type:protected] => category
[parent:protected] => 2
[label:protected] => Scaffold Erector
[alreadyInSave:protected] =>
[alreadyInValidation:protected] =>
[validationFailures:protected] => Array
(
)
[_new:BaseObject:private] =>
[_deleted:BaseObject:private] =>
[modifiedColumns:protected] => Array
(
)
)
[62] => Category Object
(
[languages:protected] =>
[bok_resources:protected] =>
[bok_topics:protected] =>
[bok_keywords:protected] =>
[id:protected] => 62
[type:protected] => category
[parent:protected] => 2
[label:protected] => Structural Ironworker
[alreadyInSave:protected] =>
[alreadyInValidation:protected] =>
[validationFailures:protected] => Array
(
)
[_new:BaseObject:private] =>
[_deleted:BaseObject:private] =>
[modifiedColumns:protected] => Array
(
)
)
[87] => Category Object
(
[languages:protected] =>
[bok_resources:protected] =>
[bok_topics:protected] =>
[bok_keywords:protected] =>
[id:protected] => 87
[type:protected] => category
[parent:protected] => 3
[label:protected] => Commercial & Institutional
[alreadyInSave:protected] =>
[alreadyInValidation:protected] =>
[validationFailures:protected] => Array
(
)
[_new:BaseObject:private] =>
[_deleted:BaseObject:private] =>
[modifiedColumns:protected] => Array
(
)
)
[88] => Category Object
(
[languages:protected] =>
[bok_resources:protected] =>
[bok_topics:protected] =>
[bok_keywords:protected] =>
[id:protected] => 88
[type:protected] => category
[parent:protected] => 3
[label:protected] => Demolition
[alreadyInSave:protected] =>
[alreadyInValidation:protected] =>
[validationFailures:protected] => Array
(
)
[_new:BaseObject:private] =>
[_deleted:BaseObject:private] =>
[modifiedColumns:protected] => Array
(
)
)
[91] => Category Object
(
[languages:protected] =>
[bok_resources:protected] =>
[bok_topics:protected] =>
[bok_keywords:protected] =>
[id:protected] => 91
[type:protected] => category
[parent:protected] => 3
[label:protected] => Heavy & Highway
[alreadyInSave:protected] =>
[alreadyInValidation:protected] =>
[validationFailures:protected] => Array
(
)
[_new:BaseObject:private] =>
[_deleted:BaseObject:private] =>
[modifiedColumns:protected] => Array
(
)
)
[90] => Category Object
(
[languages:protected] =>
[bok_resources:protected] =>
[bok_topics:protected] =>
[bok_keywords:protected] =>
[id:protected] => 90
[type:protected] => category
[parent:protected] => 3
[label:protected] => Industrial
[alreadyInSave:protected] =>
[alreadyInValidation:protected] =>
[validationFailures:protected] => Array
(
)
[_new:BaseObject:private] =>
[_deleted:BaseObject:private] =>
[modifiedColumns:protected] => Array
(
)
)
[93] => Category Object
(
[languages:protected] =>
[bok_resources:protected] =>
[bok_topics:protected] =>
[bok_keywords:protected] =>
[id:protected] => 93
[type:protected] => category
[parent:protected] => 3
[label:protected] => Renovations
[alreadyInSave:protected] =>
[alreadyInValidation:protected] =>
[validationFailures:protected] => Array
(
)
[_new:BaseObject:private] =>
[_deleted:BaseObject:private] =>
[modifiedColumns:protected] => Array
(
)
)
[94] => Category Object
(
[languages:protected] =>
[bok_resources:protected] =>
[bok_topics:protected] =>
[bok_keywords:protected] =>
[id:protected] => 94
[type:protected] => category
[parent:protected] => 3
[label:protected] => Residential
[alreadyInSave:protected] =>
[alreadyInValidation:protected] =>
[validationFailures:protected] => Array
(
)
[_new:BaseObject:private] =>
[_deleted:BaseObject:private] =>
[modifiedColumns:protected] => Array
(
)
)
[95] => Category Object
(
[languages:protected] =>
[bok_resources:protected] =>
[bok_topics:protected] =>
[bok_keywords:protected] =>
[id:protected] => 95
[type:protected] => category
[parent:protected] => 3
[label:protected] => Underground
[alreadyInSave:protected] =>
[alreadyInValidation:protected] =>
[validationFailures:protected] => Array
(
)
[_new:BaseObject:private] =>
[_deleted:BaseObject:private] =>
[modifiedColumns:protected] => Array
(
)
)
)
[categories_initialized:protected] => 1
[mapped_items:protected] =>
[content:protected] =>
[files:protected] =>
[language:protected] => Language Object
(
[id:protected] => 1
[code:protected] => en
[name:protected] => English
[alreadyInSave:protected] =>
[alreadyInValidation:protected] =>
[validationFailures:protected] => Array
(
)
[_new:BaseObject:private] =>
[_deleted:BaseObject:private] =>
[modifiedColumns:protected] => Array
(
)
)
[old_record:protected] =>
[id:protected] => 4005
[old_id:protected] =>
[elcosh_id:protected] => i002692
[type:protected] => image
[display_type:protected] => Image
[user_id:protected] => 0
[language_id:protected] => 1
[tagging_id:protected] => Bruce Lippy
[priority_id:protected] => 1
[title:protected] => Toolbox talk - crew view
[total_pages:protected] => 0
[billed_pages:protected] => 0
[publication_number:protected] =>
[part_of:protected] =>
[keywords:protected] => toolbox talk, tailgate talk, safety talk, Spanish
[comments:protected] =>
[summary:protected] => Photo of crew listening to a toolbox safety talk before starting work.
[transition_comments:protected] =>
[external_link:protected] =>
[consol_link:protected] => http://www.cpwrconstructionsolutions.org/electrical/solution/662/worker-training.html
[more_like_this:protected] => i002691,d001269, c000079, d001285
[permission_given_by:protected] =>
[published:protected] => T
[billable:protected] => F
[img_name:protected] =>
[img_ext:protected] => jpg
[img_width:protected] =>
[img_height:protected] =>
[img_credit:protected] => Morgan Zavertnik and Hoar Construction
[img_practice:protected] => good
[vid_source_id:protected] =>
[vid_running_time:protected] =>
[vid_intended_audience:protected] =>
[vid_acquisition_info:protected] =>
[vid_cost:protected] =>
[vid_producer:protected] =>
[vid_filename:protected] =>
[vid_filename_downloadable:protected] =>
[date_summary:protected] => November 2015
[date_permission_requested:protected] =>
[date_permission_received:protected] =>
[date_review_needed:protected] =>
[date_received:protected] => 03/02/16
[date_completed:protected] => 03/02/16
[date_billed:protected] =>
[date_modified:protected] => 03/02/16
[collBokExports:protected] =>
[lastBokExportCriteria:BaseElcoshItem:private] =>
[alreadyInSave:protected] =>
[alreadyInValidation:protected] =>
[validationFailures:protected] => Array
(
)
[_new:BaseObject:private] =>
[_deleted:BaseObject:private] =>
[modifiedColumns:protected] => Array
(
)
)
)
[2] => Search_Result Object
(
[title] => Toolbox talk - long shot
[image] => /record/images/4006-p.jpg
[blurb] => This crew gathered every morning before starting work to discuss a new safety topic....
[category] => Array
(
[0] => 20
[1] => 47
[2] => 49
[3] => 51
[4] => 55
[5] => 64
[6] => 68
[7] => 75
[8] => 76
[9] => 63
[10] => 78
[11] => 79
[12] => 82
[13] => 62
[14] => 87
[15] => 88
[16] => 91
[17] => 90
[18] => 93
[19] => 94
[20] => 95
[21] => 97
)
[labels] => Array
(
[0] => Safety Culture
[1] => Work Environment
[2] => Hazards
[3] => Bricklayer
[4] => Trades
[5] => Carpenter
[7] => Cement Mason
[9] => Electrical Worker
[11] => Laborer
[13] => Maintenance Worker
[15] => Plasterer
[17] => Plumber/Pipefitter
[19] => Reinforcing Ironworker
[21] => Roofer/Waterproofer
[23] => Scaffold Erector
[25] => Stonemason
[27] => Structural Ironworker
[29] => Commercial & Institutional
[30] => Jobsites
[31] => Demolition
[33] => Heavy & Highway
[35] => Industrial
[37] => Renovations
[39] => Residential
[41] => Underground
[43] => Images
[44] => Media
[45] => Media & Documents
)
[type] => Images
[sub_category] =>
[url] => /image/4006/i002693/Toolbox%2Btalk%2B-%2Blong%2Bshot.html
[item:protected] => ImageRecord Object
(
[records:protected] => Array
(
)
[recordId:protected] =>
[searchWordClass:protected] =>
[searchWordPeerClass:protected] =>
[bok_record:protected] =>
[authors:protected] =>
[organizations:protected] =>
[collections:protected] =>
[categories:protected] => Array
(
[20] => Category Object
(
[languages:protected] =>
[bok_resources:protected] =>
[bok_topics:protected] =>
[bok_keywords:protected] =>
[id:protected] => 20
[type:protected] => category
[parent:protected] => 7
[label:protected] => Safety Culture
[alreadyInSave:protected] =>
[alreadyInValidation:protected] =>
[validationFailures:protected] => Array
(
)
[_new:BaseObject:private] =>
[_deleted:BaseObject:private] =>
[modifiedColumns:protected] => Array
(
)
)
[47] => Category Object
(
[languages:protected] =>
[bok_resources:protected] =>
[bok_topics:protected] =>
[bok_keywords:protected] =>
[id:protected] => 47
[type:protected] => category
[parent:protected] => 2
[label:protected] => Bricklayer
[alreadyInSave:protected] =>
[alreadyInValidation:protected] =>
[validationFailures:protected] => Array
(
)
[_new:BaseObject:private] =>
[_deleted:BaseObject:private] =>
[modifiedColumns:protected] => Array
(
)
)
[49] => Category Object
(
[languages:protected] =>
[bok_resources:protected] =>
[bok_topics:protected] =>
[bok_keywords:protected] =>
[id:protected] => 49
[type:protected] => category
[parent:protected] => 2
[label:protected] => Carpenter
[alreadyInSave:protected] =>
[alreadyInValidation:protected] =>
[validationFailures:protected] => Array
(
)
[_new:BaseObject:private] =>
[_deleted:BaseObject:private] =>
[modifiedColumns:protected] => Array
(
)
)
[51] => Category Object
(
[languages:protected] =>
[bok_resources:protected] =>
[bok_topics:protected] =>
[bok_keywords:protected] =>
[id:protected] => 51
[type:protected] => category
[parent:protected] => 2
[label:protected] => Cement Mason
[alreadyInSave:protected] =>
[alreadyInValidation:protected] =>
[validationFailures:protected] => Array
(
)
[_new:BaseObject:private] =>
[_deleted:BaseObject:private] =>
[modifiedColumns:protected] => Array
(
)
)
[55] => Category Object
(
[languages:protected] =>
[bok_resources:protected] =>
[bok_topics:protected] =>
[bok_keywords:protected] =>
[id:protected] => 55
[type:protected] => category
[parent:protected] => 2
[label:protected] => Electrical Worker
[alreadyInSave:protected] =>
[alreadyInValidation:protected] =>
[validationFailures:protected] => Array
(
)
[_new:BaseObject:private] =>
[_deleted:BaseObject:private] =>
[modifiedColumns:protected] => Array
(
)
)
[64] => Category Object
(
[languages:protected] =>
[bok_resources:protected] =>
[bok_topics:protected] =>
[bok_keywords:protected] =>
[id:protected] => 64
[type:protected] => category
[parent:protected] => 2
[label:protected] => Laborer
[alreadyInSave:protected] =>
[alreadyInValidation:protected] =>
[validationFailures:protected] => Array
(
)
[_new:BaseObject:private] =>
[_deleted:BaseObject:private] =>
[modifiedColumns:protected] => Array
(
)
)
[68] => Category Object
(
[languages:protected] =>
[bok_resources:protected] =>
[bok_topics:protected] =>
[bok_keywords:protected] =>
[id:protected] => 68
[type:protected] => category
[parent:protected] => 2
[label:protected] => Maintenance Worker
[alreadyInSave:protected] =>
[alreadyInValidation:protected] =>
[validationFailures:protected] => Array
(
)
[_new:BaseObject:private] =>
[_deleted:BaseObject:private] =>
[modifiedColumns:protected] => Array
(
)
)
[75] => Category Object
(
[languages:protected] =>
[bok_resources:protected] =>
[bok_topics:protected] =>
[bok_keywords:protected] =>
[id:protected] => 75
[type:protected] => category
[parent:protected] => 2
[label:protected] => Plasterer
[alreadyInSave:protected] =>
[alreadyInValidation:protected] =>
[validationFailures:protected] => Array
(
)
[_new:BaseObject:private] =>
[_deleted:BaseObject:private] =>
[modifiedColumns:protected] => Array
(
)
)
[76] => Category Object
(
[languages:protected] =>
[bok_resources:protected] =>
[bok_topics:protected] =>
[bok_keywords:protected] =>
[id:protected] => 76
[type:protected] => category
[parent:protected] => 2
[label:protected] => Plumber/Pipefitter
[alreadyInSave:protected] =>
[alreadyInValidation:protected] =>
[validationFailures:protected] => Array
(
)
[_new:BaseObject:private] =>
[_deleted:BaseObject:private] =>
[modifiedColumns:protected] => Array
(
)
)
[63] => Category Object
(
[languages:protected] =>
[bok_resources:protected] =>
[bok_topics:protected] =>
[bok_keywords:protected] =>
[id:protected] => 63
[type:protected] => category
[parent:protected] => 2
[label:protected] => Reinforcing Ironworker
[alreadyInSave:protected] =>
[alreadyInValidation:protected] =>
[validationFailures:protected] => Array
(
)
[_new:BaseObject:private] =>
[_deleted:BaseObject:private] =>
[modifiedColumns:protected] => Array
(
)
)
[78] => Category Object
(
[languages:protected] =>
[bok_resources:protected] =>
[bok_topics:protected] =>
[bok_keywords:protected] =>
[id:protected] => 78
[type:protected] => category
[parent:protected] => 2
[label:protected] => Roofer/Waterproofer
[alreadyInSave:protected] =>
[alreadyInValidation:protected] =>
[validationFailures:protected] => Array
(
)
[_new:BaseObject:private] =>
[_deleted:BaseObject:private] =>
[modifiedColumns:protected] => Array
(
)
)
[79] => Category Object
(
[languages:protected] =>
[bok_resources:protected] =>
[bok_topics:protected] =>
[bok_keywords:protected] =>
[id:protected] => 79
[type:protected] => category
[parent:protected] => 2
[label:protected] => Scaffold Erector
[alreadyInSave:protected] =>
[alreadyInValidation:protected] =>
[validationFailures:protected] => Array
(
)
[_new:BaseObject:private] =>
[_deleted:BaseObject:private] =>
[modifiedColumns:protected] => Array
(
)
)
[82] => Category Object
(
[languages:protected] =>
[bok_resources:protected] =>
[bok_topics:protected] =>
[bok_keywords:protected] =>
[id:protected] => 82
[type:protected] => category
[parent:protected] => 2
[label:protected] => Stonemason
[alreadyInSave:protected] =>
[alreadyInValidation:protected] =>
[validationFailures:protected] => Array
(
)
[_new:BaseObject:private] =>
[_deleted:BaseObject:private] =>
[modifiedColumns:protected] => Array
(
)
)
[62] => Category Object
(
[languages:protected] =>
[bok_resources:protected] =>
[bok_topics:protected] =>
[bok_keywords:protected] =>
[id:protected] => 62
[type:protected] => category
[parent:protected] => 2
[label:protected] => Structural Ironworker
[alreadyInSave:protected] =>
[alreadyInValidation:protected] =>
[validationFailures:protected] => Array
(
)
[_new:BaseObject:private] =>
[_deleted:BaseObject:private] =>
[modifiedColumns:protected] => Array
(
)
)
[87] => Category Object
(
[languages:protected] =>
[bok_resources:protected] =>
[bok_topics:protected] =>
[bok_keywords:protected] =>
[id:protected] => 87
[type:protected] => category
[parent:protected] => 3
[label:protected] => Commercial & Institutional
[alreadyInSave:protected] =>
[alreadyInValidation:protected] =>
[validationFailures:protected] => Array
(
)
[_new:BaseObject:private] =>
[_deleted:BaseObject:private] =>
[modifiedColumns:protected] => Array
(
)
)
[88] => Category Object
(
[languages:protected] =>
[bok_resources:protected] =>
[bok_topics:protected] =>
[bok_keywords:protected] =>
[id:protected] => 88
[type:protected] => category
[parent:protected] => 3
[label:protected] => Demolition
[alreadyInSave:protected] =>
[alreadyInValidation:protected] =>
[validationFailures:protected] => Array
(
)
[_new:BaseObject:private] =>
[_deleted:BaseObject:private] =>
[modifiedColumns:protected] => Array
(
)
)
[91] => Category Object
(
[languages:protected] =>
[bok_resources:protected] =>
[bok_topics:protected] =>
[bok_keywords:protected] =>
[id:protected] => 91
[type:protected] => category
[parent:protected] => 3
[label:protected] => Heavy & Highway
[alreadyInSave:protected] =>
[alreadyInValidation:protected] =>
[validationFailures:protected] => Array
(
)
[_new:BaseObject:private] =>
[_deleted:BaseObject:private] =>
[modifiedColumns:protected] => Array
(
)
)
[90] => Category Object
(
[languages:protected] =>
[bok_resources:protected] =>
[bok_topics:protected] =>
[bok_keywords:protected] =>
[id:protected] => 90
[type:protected] => category
[parent:protected] => 3
[label:protected] => Industrial
[alreadyInSave:protected] =>
[alreadyInValidation:protected] =>
[validationFailures:protected] => Array
(
)
[_new:BaseObject:private] =>
[_deleted:BaseObject:private] =>
[modifiedColumns:protected] => Array
(
)
)
[93] => Category Object
(
[languages:protected] =>
[bok_resources:protected] =>
[bok_topics:protected] =>
[bok_keywords:protected] =>
[id:protected] => 93
[type:protected] => category
[parent:protected] => 3
[label:protected] => Renovations
[alreadyInSave:protected] =>
[alreadyInValidation:protected] =>
[validationFailures:protected] => Array
(
)
[_new:BaseObject:private] =>
[_deleted:BaseObject:private] =>
[modifiedColumns:protected] => Array
(
)
)
[94] => Category Object
(
[languages:protected] =>
[bok_resources:protected] =>
[bok_topics:protected] =>
[bok_keywords:protected] =>
[id:protected] => 94
[type:protected] => category
[parent:protected] => 3
[label:protected] => Residential
[alreadyInSave:protected] =>
[alreadyInValidation:protected] =>
[validationFailures:protected] => Array
(
)
[_new:BaseObject:private] =>
[_deleted:BaseObject:private] =>
[modifiedColumns:protected] => Array
(
)
)
[95] => Category Object
(
[languages:protected] =>
[bok_resources:protected] =>
[bok_topics:protected] =>
[bok_keywords:protected] =>
[id:protected] => 95
[type:protected] => category
[parent:protected] => 3
[label:protected] => Underground
[alreadyInSave:protected] =>
[alreadyInValidation:protected] =>
[validationFailures:protected] => Array
(
)
[_new:BaseObject:private] =>
[_deleted:BaseObject:private] =>
[modifiedColumns:protected] => Array
(
)
)
[97] => Category Object
(
[languages:protected] =>
[bok_resources:protected] =>
[bok_topics:protected] =>
[bok_keywords:protected] =>
[id:protected] => 97
[type:protected] => category
[parent:protected] => 5
[label:protected] => Images
[alreadyInSave:protected] =>
[alreadyInValidation:protected] =>
[validationFailures:protected] => Array
(
)
[_new:BaseObject:private] =>
[_deleted:BaseObject:private] =>
[modifiedColumns:protected] => Array
(
)
)
)
[categories_initialized:protected] => 1
[mapped_items:protected] =>
[content:protected] =>
[files:protected] =>
[language:protected] => Language Object
(
[id:protected] => 1
[code:protected] => en
[name:protected] => English
[alreadyInSave:protected] =>
[alreadyInValidation:protected] =>
[validationFailures:protected] => Array
(
)
[_new:BaseObject:private] =>
[_deleted:BaseObject:private] =>
[modifiedColumns:protected] => Array
(
)
)
[old_record:protected] =>
[id:protected] => 4006
[old_id:protected] =>
[elcosh_id:protected] => i002693
[type:protected] => image
[display_type:protected] => Image
[user_id:protected] => 0
[language_id:protected] => 1
[tagging_id:protected] => Bruce Lippy
[priority_id:protected] => 1
[title:protected] => Toolbox talk - long shot
[total_pages:protected] => 0
[billed_pages:protected] => 0
[publication_number:protected] =>
[part_of:protected] =>
[keywords:protected] => toolbox talk, tailgate talk, safety minute
[comments:protected] =>
[summary:protected] => This crew gathered every morning before starting work to discuss a new safety topic.
[transition_comments:protected] =>
[external_link:protected] =>
[consol_link:protected] => http://www.cpwrconstructionsolutions.org/electrical/solution/662/worker-training.html
[more_like_this:protected] => i002691,i002692,d001269,d000527
[permission_given_by:protected] =>
[published:protected] => T
[billable:protected] => F
[img_name:protected] =>
[img_ext:protected] => jpg
[img_width:protected] =>
[img_height:protected] =>
[img_credit:protected] => Morgan Zavertnik and Hoar Construction
[img_practice:protected] => good
[vid_source_id:protected] =>
[vid_running_time:protected] =>
[vid_intended_audience:protected] =>
[vid_acquisition_info:protected] =>
[vid_cost:protected] =>
[vid_producer:protected] =>
[vid_filename:protected] =>
[vid_filename_downloadable:protected] =>
[date_summary:protected] => November 2015
[date_permission_requested:protected] =>
[date_permission_received:protected] =>
[date_review_needed:protected] =>
[date_received:protected] => 03/02/16
[date_completed:protected] => 03/02/16
[date_billed:protected] =>
[date_modified:protected] => 03/02/16
[collBokExports:protected] =>
[lastBokExportCriteria:BaseElcoshItem:private] =>
[alreadyInSave:protected] =>
[alreadyInValidation:protected] =>
[validationFailures:protected] => Array
(
)
[_new:BaseObject:private] =>
[_deleted:BaseObject:private] =>
[modifiedColumns:protected] => Array
(
)
)
)
[3] => Search_Result Object
(
[title] => Safety officer discussing ongoing project with marketing coordinator
[image] => /record/images/4014-p.jpg
[blurb] => The safety officer (left) points out the good safety practices on this project that reflect well on the firm and may influence future clients....
[category] => Array
(
[0] => 97
[1] => 20
[2] => 46
[3] => 47
[4] => 49
[5] => 50
[6] => 51
[7] => 54
[8] => 55
[9] => 58
[10] => 60
[11] => 61
[12] => 64
[13] => 71
[14] => 75
[15] => 76
[16] => 63
[17] => 79
[18] => 80
[19] => 82
[20] => 62
[21] => 83
[22] => 87
[23] => 91
[24] => 90
[25] => 93
[26] => 94
)
[labels] => Array
(
[0] => Images
[1] => Media
[2] => Media & Documents
[3] => Safety Culture
[4] => Work Environment
[5] => Hazards
[6] => Boilermaker
[7] => Trades
[8] => Bricklayer
[10] => Carpenter
[12] => Carpet Layer
[14] => Cement Mason
[16] => Drywall Applicator Specialist
[18] => Electrical Worker
[20] => Glazier
[22] => HVAC
[24] => Interior Systems Carpenter
[26] => Laborer
[28] => Painter
[30] => Plasterer
[32] => Plumber/Pipefitter
[34] => Reinforcing Ironworker
[36] => Scaffold Erector
[38] => Sheetmetal Worker
[40] => Stonemason
[42] => Structural Ironworker
[44] => Terrazzo Worker
[46] => Commercial & Institutional
[47] => Jobsites
[48] => Heavy & Highway
[50] => Industrial
[52] => Renovations
[54] => Residential
)
[type] => Images
[sub_category] =>
[url] => /image/4014/i002700/Safety%2Bofficer%2Bdiscussing%2Bongoing%2Bproject%2Bwith%2Bmarketing%2Bcoordinator.html
[item:protected] => ImageRecord Object
(
[records:protected] => Array
(
)
[recordId:protected] =>
[searchWordClass:protected] =>
[searchWordPeerClass:protected] =>
[bok_record:protected] =>
[authors:protected] =>
[organizations:protected] =>
[collections:protected] =>
[categories:protected] => Array
(
[97] => Category Object
(
[languages:protected] =>
[bok_resources:protected] =>
[bok_topics:protected] =>
[bok_keywords:protected] =>
[id:protected] => 97
[type:protected] => category
[parent:protected] => 5
[label:protected] => Images
[alreadyInSave:protected] =>
[alreadyInValidation:protected] =>
[validationFailures:protected] => Array
(
)
[_new:BaseObject:private] =>
[_deleted:BaseObject:private] =>
[modifiedColumns:protected] => Array
(
)
)
[20] => Category Object
(
[languages:protected] =>
[bok_resources:protected] =>
[bok_topics:protected] =>
[bok_keywords:protected] =>
[id:protected] => 20
[type:protected] => category
[parent:protected] => 7
[label:protected] => Safety Culture
[alreadyInSave:protected] =>
[alreadyInValidation:protected] =>
[validationFailures:protected] => Array
(
)
[_new:BaseObject:private] =>
[_deleted:BaseObject:private] =>
[modifiedColumns:protected] => Array
(
)
)
[46] => Category Object
(
[languages:protected] =>
[bok_resources:protected] =>
[bok_topics:protected] =>
[bok_keywords:protected] =>
[id:protected] => 46
[type:protected] => category
[parent:protected] => 2
[label:protected] => Boilermaker
[alreadyInSave:protected] =>
[alreadyInValidation:protected] =>
[validationFailures:protected] => Array
(
)
[_new:BaseObject:private] =>
[_deleted:BaseObject:private] =>
[modifiedColumns:protected] => Array
(
)
)
[47] => Category Object
(
[languages:protected] =>
[bok_resources:protected] =>
[bok_topics:protected] =>
[bok_keywords:protected] =>
[id:protected] => 47
[type:protected] => category
[parent:protected] => 2
[label:protected] => Bricklayer
[alreadyInSave:protected] =>
[alreadyInValidation:protected] =>
[validationFailures:protected] => Array
(
)
[_new:BaseObject:private] =>
[_deleted:BaseObject:private] =>
[modifiedColumns:protected] => Array
(
)
)
[49] => Category Object
(
[languages:protected] =>
[bok_resources:protected] =>
[bok_topics:protected] =>
[bok_keywords:protected] =>
[id:protected] => 49
[type:protected] => category
[parent:protected] => 2
[label:protected] => Carpenter
[alreadyInSave:protected] =>
[alreadyInValidation:protected] =>
[validationFailures:protected] => Array
(
)
[_new:BaseObject:private] =>
[_deleted:BaseObject:private] =>
[modifiedColumns:protected] => Array
(
)
)
[50] => Category Object
(
[languages:protected] =>
[bok_resources:protected] =>
[bok_topics:protected] =>
[bok_keywords:protected] =>
[id:protected] => 50
[type:protected] => category
[parent:protected] => 2
[label:protected] => Carpet Layer
[alreadyInSave:protected] =>
[alreadyInValidation:protected] =>
[validationFailures:protected] => Array
(
)
[_new:BaseObject:private] =>
[_deleted:BaseObject:private] =>
[modifiedColumns:protected] => Array
(
)
)
[51] => Category Object
(
[languages:protected] =>
[bok_resources:protected] =>
[bok_topics:protected] =>
[bok_keywords:protected] =>
[id:protected] => 51
[type:protected] => category
[parent:protected] => 2
[label:protected] => Cement Mason
[alreadyInSave:protected] =>
[alreadyInValidation:protected] =>
[validationFailures:protected] => Array
(
)
[_new:BaseObject:private] =>
[_deleted:BaseObject:private] =>
[modifiedColumns:protected] => Array
(
)
)
[54] => Category Object
(
[languages:protected] =>
[bok_resources:protected] =>
[bok_topics:protected] =>
[bok_keywords:protected] =>
[id:protected] => 54
[type:protected] => category
[parent:protected] => 2
[label:protected] => Drywall Applicator Specialist
[alreadyInSave:protected] =>
[alreadyInValidation:protected] =>
[validationFailures:protected] => Array
(
)
[_new:BaseObject:private] =>
[_deleted:BaseObject:private] =>
[modifiedColumns:protected] => Array
(
)
)
[55] => Category Object
(
[languages:protected] =>
[bok_resources:protected] =>
[bok_topics:protected] =>
[bok_keywords:protected] =>
[id:protected] => 55
[type:protected] => category
[parent:protected] => 2
[label:protected] => Electrical Worker
[alreadyInSave:protected] =>
[alreadyInValidation:protected] =>
[validationFailures:protected] => Array
(
)
[_new:BaseObject:private] =>
[_deleted:BaseObject:private] =>
[modifiedColumns:protected] => Array
(
)
)
[58] => Category Object
(
[languages:protected] =>
[bok_resources:protected] =>
[bok_topics:protected] =>
[bok_keywords:protected] =>
[id:protected] => 58
[type:protected] => category
[parent:protected] => 2
[label:protected] => Glazier
[alreadyInSave:protected] =>
[alreadyInValidation:protected] =>
[validationFailures:protected] => Array
(
)
[_new:BaseObject:private] =>
[_deleted:BaseObject:private] =>
[modifiedColumns:protected] => Array
(
)
)
[60] => Category Object
(
[languages:protected] =>
[bok_resources:protected] =>
[bok_topics:protected] =>
[bok_keywords:protected] =>
[id:protected] => 60
[type:protected] => category
[parent:protected] => 2
[label:protected] => HVAC
[alreadyInSave:protected] =>
[alreadyInValidation:protected] =>
[validationFailures:protected] => Array
(
)
[_new:BaseObject:private] =>
[_deleted:BaseObject:private] =>
[modifiedColumns:protected] => Array
(
)
)
[61] => Category Object
(
[languages:protected] =>
[bok_resources:protected] =>
[bok_topics:protected] =>
[bok_keywords:protected] =>
[id:protected] => 61
[type:protected] => category
[parent:protected] => 2
[label:protected] => Interior Systems Carpenter
[alreadyInSave:protected] =>
[alreadyInValidation:protected] =>
[validationFailures:protected] => Array
(
)
[_new:BaseObject:private] =>
[_deleted:BaseObject:private] =>
[modifiedColumns:protected] => Array
(
)
)
[64] => Category Object
(
[languages:protected] =>
[bok_resources:protected] =>
[bok_topics:protected] =>
[bok_keywords:protected] =>
[id:protected] => 64
[type:protected] => category
[parent:protected] => 2
[label:protected] => Laborer
[alreadyInSave:protected] =>
[alreadyInValidation:protected] =>
[validationFailures:protected] => Array
(
)
[_new:BaseObject:private] =>
[_deleted:BaseObject:private] =>
[modifiedColumns:protected] => Array
(
)
)
[71] => Category Object
(
[languages:protected] =>
[bok_resources:protected] =>
[bok_topics:protected] =>
[bok_keywords:protected] =>
[id:protected] => 71
[type:protected] => category
[parent:protected] => 2
[label:protected] => Painter
[alreadyInSave:protected] =>
[alreadyInValidation:protected] =>
[validationFailures:protected] => Array
(
)
[_new:BaseObject:private] =>
[_deleted:BaseObject:private] =>
[modifiedColumns:protected] => Array
(
)
)
[75] => Category Object
(
[languages:protected] =>
[bok_resources:protected] =>
[bok_topics:protected] =>
[bok_keywords:protected] =>
[id:protected] => 75
[type:protected] => category
[parent:protected] => 2
[label:protected] => Plasterer
[alreadyInSave:protected] =>
[alreadyInValidation:protected] =>
[validationFailures:protected] => Array
(
)
[_new:BaseObject:private] =>
[_deleted:BaseObject:private] =>
[modifiedColumns:protected] => Array
(
)
)
[76] => Category Object
(
[languages:protected] =>
[bok_resources:protected] =>
[bok_topics:protected] =>
[bok_keywords:protected] =>
[id:protected] => 76
[type:protected] => category
[parent:protected] => 2
[label:protected] => Plumber/Pipefitter
[alreadyInSave:protected] =>
[alreadyInValidation:protected] =>
[validationFailures:protected] => Array
(
)
[_new:BaseObject:private] =>
[_deleted:BaseObject:private] =>
[modifiedColumns:protected] => Array
(
)
)
[63] => Category Object
(
[languages:protected] =>
[bok_resources:protected] =>
[bok_topics:protected] =>
[bok_keywords:protected] =>
[id:protected] => 63
[type:protected] => category
[parent:protected] => 2
[label:protected] => Reinforcing Ironworker
[alreadyInSave:protected] =>
[alreadyInValidation:protected] =>
[validationFailures:protected] => Array
(
)
[_new:BaseObject:private] =>
[_deleted:BaseObject:private] =>
[modifiedColumns:protected] => Array
(
)
)
[79] => Category Object
(
[languages:protected] =>
[bok_resources:protected] =>
[bok_topics:protected] =>
[bok_keywords:protected] =>
[id:protected] => 79
[type:protected] => category
[parent:protected] => 2
[label:protected] => Scaffold Erector
[alreadyInSave:protected] =>
[alreadyInValidation:protected] =>
[validationFailures:protected] => Array
(
)
[_new:BaseObject:private] =>
[_deleted:BaseObject:private] =>
[modifiedColumns:protected] => Array
(
)
)
[80] => Category Object
(
[languages:protected] =>
[bok_resources:protected] =>
[bok_topics:protected] =>
[bok_keywords:protected] =>
[id:protected] => 80
[type:protected] => category
[parent:protected] => 2
[label:protected] => Sheetmetal Worker
[alreadyInSave:protected] =>
[alreadyInValidation:protected] =>
[validationFailures:protected] => Array
(
)
[_new:BaseObject:private] =>
[_deleted:BaseObject:private] =>
[modifiedColumns:protected] => Array
(
)
)
[82] => Category Object
(
[languages:protected] =>
[bok_resources:protected] =>
[bok_topics:protected] =>
[bok_keywords:protected] =>
[id:protected] => 82
[type:protected] => category
[parent:protected] => 2
[label:protected] => Stonemason
[alreadyInSave:protected] =>
[alreadyInValidation:protected] =>
[validationFailures:protected] => Array
(
)
[_new:BaseObject:private] =>
[_deleted:BaseObject:private] =>
[modifiedColumns:protected] => Array
(
)
)
[62] => Category Object
(
[languages:protected] =>
[bok_resources:protected] =>
[bok_topics:protected] =>
[bok_keywords:protected] =>
[id:protected] => 62
[type:protected] => category
[parent:protected] => 2
[label:protected] => Structural Ironworker
[alreadyInSave:protected] =>
[alreadyInValidation:protected] =>
[validationFailures:protected] => Array
(
)
[_new:BaseObject:private] =>
[_deleted:BaseObject:private] =>
[modifiedColumns:protected] => Array
(
)
)
[83] => Category Object
(
[languages:protected] =>
[bok_resources:protected] =>
[bok_topics:protected] =>
[bok_keywords:protected] =>
[id:protected] => 83
[type:protected] => category
[parent:protected] => 2
[label:protected] => Terrazzo Worker
[alreadyInSave:protected] =>
[alreadyInValidation:protected] =>
[validationFailures:protected] => Array
(
)
[_new:BaseObject:private] =>
[_deleted:BaseObject:private] =>
[modifiedColumns:protected] => Array
(
)
)
[87] => Category Object
(
[languages:protected] =>
[bok_resources:protected] =>
[bok_topics:protected] =>
[bok_keywords:protected] =>
[id:protected] => 87
[type:protected] => category
[parent:protected] => 3
[label:protected] => Commercial & Institutional
[alreadyInSave:protected] =>
[alreadyInValidation:protected] =>
[validationFailures:protected] => Array
(
)
[_new:BaseObject:private] =>
[_deleted:BaseObject:private] =>
[modifiedColumns:protected] => Array
(
)
)
[91] => Category Object
(
[languages:protected] =>
[bok_resources:protected] =>
[bok_topics:protected] =>
[bok_keywords:protected] =>
[id:protected] => 91
[type:protected] => category
[parent:protected] => 3
[label:protected] => Heavy & Highway
[alreadyInSave:protected] =>
[alreadyInValidation:protected] =>
[validationFailures:protected] => Array
(
)
[_new:BaseObject:private] =>
[_deleted:BaseObject:private] =>
[modifiedColumns:protected] => Array
(
)
)
[90] => Category Object
(
[languages:protected] =>
[bok_resources:protected] =>
[bok_topics:protected] =>
[bok_keywords:protected] =>
[id:protected] => 90
[type:protected] => category
[parent:protected] => 3
[label:protected] => Industrial
[alreadyInSave:protected] =>
[alreadyInValidation:protected] =>
[validationFailures:protected] => Array
(
)
[_new:BaseObject:private] =>
[_deleted:BaseObject:private] =>
[modifiedColumns:protected] => Array
(
)
)
[93] => Category Object
(
[languages:protected] =>
[bok_resources:protected] =>
[bok_topics:protected] =>
[bok_keywords:protected] =>
[id:protected] => 93
[type:protected] => category
[parent:protected] => 3
[label:protected] => Renovations
[alreadyInSave:protected] =>
[alreadyInValidation:protected] =>
[validationFailures:protected] => Array
(
)
[_new:BaseObject:private] =>
[_deleted:BaseObject:private] =>
[modifiedColumns:protected] => Array
(
)
)
[94] => Category Object
(
[languages:protected] =>
[bok_resources:protected] =>
[bok_topics:protected] =>
[bok_keywords:protected] =>
[id:protected] => 94
[type:protected] => category
[parent:protected] => 3
[label:protected] => Residential
[alreadyInSave:protected] =>
[alreadyInValidation:protected] =>
[validationFailures:protected] => Array
(
)
[_new:BaseObject:private] =>
[_deleted:BaseObject:private] =>
[modifiedColumns:protected] => Array
(
)
)
)
[categories_initialized:protected] => 1
[mapped_items:protected] =>
[content:protected] =>
[files:protected] =>
[language:protected] => Language Object
(
[id:protected] => 1
[code:protected] => en
[name:protected] => English
[alreadyInSave:protected] =>
[alreadyInValidation:protected] =>
[validationFailures:protected] => Array
(
)
[_new:BaseObject:private] =>
[_deleted:BaseObject:private] =>
[modifiedColumns:protected] => Array
(
)
)
[old_record:protected] =>
[id:protected] => 4014
[old_id:protected] =>
[elcosh_id:protected] => i002700
[type:protected] => image
[display_type:protected] => Image
[user_id:protected] => 0
[language_id:protected] => 1
[tagging_id:protected] => Bruce Lippy
[priority_id:protected] => 1
[title:protected] => Safety officer discussing ongoing project with marketing coordinator
[total_pages:protected] => 0
[billed_pages:protected] => 0
[publication_number:protected] =>
[part_of:protected] =>
[keywords:protected] => Latino, safety officer, safety culture
[comments:protected] =>
[summary:protected] => The safety officer (left) points out the good safety practices on this project that reflect well on the firm and may influence future clients.
[transition_comments:protected] =>
[external_link:protected] =>
[consol_link:protected] => http://www.cpwrconstructionsolutions.org/index.php
[more_like_this:protected] => d000989,d001351,d001362,d000652, d001101, d000931, d001395
[permission_given_by:protected] =>
[published:protected] => T
[billable:protected] => F
[img_name:protected] =>
[img_ext:protected] => jpg
[img_width:protected] =>
[img_height:protected] =>
[img_credit:protected] => Hoar Construction, Photo by Neil Lippy
[img_practice:protected] => good
[vid_source_id:protected] =>
[vid_running_time:protected] =>
[vid_intended_audience:protected] =>
[vid_acquisition_info:protected] =>
[vid_cost:protected] =>
[vid_producer:protected] =>
[vid_filename:protected] =>
[vid_filename_downloadable:protected] =>
[date_summary:protected] => November 2015
[date_permission_requested:protected] =>
[date_permission_received:protected] =>
[date_review_needed:protected] =>
[date_received:protected] => 03/02/16
[date_completed:protected] => 03/02/16
[date_billed:protected] =>
[date_modified:protected] => 01/30/23
[collBokExports:protected] =>
[lastBokExportCriteria:BaseElcoshItem:private] =>
[alreadyInSave:protected] =>
[alreadyInValidation:protected] =>
[validationFailures:protected] => Array
(
)
[_new:BaseObject:private] =>
[_deleted:BaseObject:private] =>
[modifiedColumns:protected] => Array
(
)
)
)
[4] => Search_Result Object
(
[title] => Scaffolding at top of large column
[image] => /record/images/3994-p.jpg
[blurb] => This shot shows innovative guarding around the top of a large concrete column in the base of a high rise structure going up....
[category] => Array
(
[0] => 15
[1] => 21
[2] => 47
[3] => 51
[4] => 63
[5] => 78
[6] => 79
[7] => 80
[8] => 62
[9] => 87
[10] => 97
[11] => 56
[12] => 64
[13] => 74
)
[labels] => Array
(
[0] => Falls
[1] => Work Environment
[2] => Hazards
[3] => Scaffolds
[6] => Bricklayer
[7] => Trades
[8] => Cement Mason
[10] => Reinforcing Ironworker
[12] => Roofer/Waterproofer
[14] => Scaffold Erector
[16] => Sheetmetal Worker
[18] => Structural Ironworker
[20] => Commercial & Institutional
[21] => Jobsites
[22] => Images
[23] => Media
[24] => Media & Documents
[25] => Elevator Constructor
[27] => Laborer
[29] => Pile Driver
)
[type] => Images
[sub_category] =>
[url] => /image/3994/i002689/Scaffolding%2Bat%2Btop%2Bof%2Blarge%2Bcolumn.html
[item:protected] => ImageRecord Object
(
[records:protected] => Array
(
)
[recordId:protected] =>
[searchWordClass:protected] =>
[searchWordPeerClass:protected] =>
[bok_record:protected] =>
[authors:protected] =>
[organizations:protected] =>
[collections:protected] =>
[categories:protected] => Array
(
[15] => Category Object
(
[languages:protected] =>
[bok_resources:protected] =>
[bok_topics:protected] =>
[bok_keywords:protected] =>
[id:protected] => 15
[type:protected] => category
[parent:protected] => 7
[label:protected] => Falls
[alreadyInSave:protected] =>
[alreadyInValidation:protected] =>
[validationFailures:protected] => Array
(
)
[_new:BaseObject:private] =>
[_deleted:BaseObject:private] =>
[modifiedColumns:protected] => Array
(
)
)
[21] => Category Object
(
[languages:protected] =>
[bok_resources:protected] =>
[bok_topics:protected] =>
[bok_keywords:protected] =>
[id:protected] => 21
[type:protected] => category
[parent:protected] => 7
[label:protected] => Scaffolds
[alreadyInSave:protected] =>
[alreadyInValidation:protected] =>
[validationFailures:protected] => Array
(
)
[_new:BaseObject:private] =>
[_deleted:BaseObject:private] =>
[modifiedColumns:protected] => Array
(
)
)
[47] => Category Object
(
[languages:protected] =>
[bok_resources:protected] =>
[bok_topics:protected] =>
[bok_keywords:protected] =>
[id:protected] => 47
[type:protected] => category
[parent:protected] => 2
[label:protected] => Bricklayer
[alreadyInSave:protected] =>
[alreadyInValidation:protected] =>
[validationFailures:protected] => Array
(
)
[_new:BaseObject:private] =>
[_deleted:BaseObject:private] =>
[modifiedColumns:protected] => Array
(
)
)
[51] => Category Object
(
[languages:protected] =>
[bok_resources:protected] =>
[bok_topics:protected] =>
[bok_keywords:protected] =>
[id:protected] => 51
[type:protected] => category
[parent:protected] => 2
[label:protected] => Cement Mason
[alreadyInSave:protected] =>
[alreadyInValidation:protected] =>
[validationFailures:protected] => Array
(
)
[_new:BaseObject:private] =>
[_deleted:BaseObject:private] =>
[modifiedColumns:protected] => Array
(
)
)
[63] => Category Object
(
[languages:protected] =>
[bok_resources:protected] =>
[bok_topics:protected] =>
[bok_keywords:protected] =>
[id:protected] => 63
[type:protected] => category
[parent:protected] => 2
[label:protected] => Reinforcing Ironworker
[alreadyInSave:protected] =>
[alreadyInValidation:protected] =>
[validationFailures:protected] => Array
(
)
[_new:BaseObject:private] =>
[_deleted:BaseObject:private] =>
[modifiedColumns:protected] => Array
(
)
)
[78] => Category Object
(
[languages:protected] =>
[bok_resources:protected] =>
[bok_topics:protected] =>
[bok_keywords:protected] =>
[id:protected] => 78
[type:protected] => category
[parent:protected] => 2
[label:protected] => Roofer/Waterproofer
[alreadyInSave:protected] =>
[alreadyInValidation:protected] =>
[validationFailures:protected] => Array
(
)
[_new:BaseObject:private] =>
[_deleted:BaseObject:private] =>
[modifiedColumns:protected] => Array
(
)
)
[79] => Category Object
(
[languages:protected] =>
[bok_resources:protected] =>
[bok_topics:protected] =>
[bok_keywords:protected] =>
[id:protected] => 79
[type:protected] => category
[parent:protected] => 2
[label:protected] => Scaffold Erector
[alreadyInSave:protected] =>
[alreadyInValidation:protected] =>
[validationFailures:protected] => Array
(
)
[_new:BaseObject:private] =>
[_deleted:BaseObject:private] =>
[modifiedColumns:protected] => Array
(
)
)
[80] => Category Object
(
[languages:protected] =>
[bok_resources:protected] =>
[bok_topics:protected] =>
[bok_keywords:protected] =>
[id:protected] => 80
[type:protected] => category
[parent:protected] => 2
[label:protected] => Sheetmetal Worker
[alreadyInSave:protected] =>
[alreadyInValidation:protected] =>
[validationFailures:protected] => Array
(
)
[_new:BaseObject:private] =>
[_deleted:BaseObject:private] =>
[modifiedColumns:protected] => Array
(
)
)
[62] => Category Object
(
[languages:protected] =>
[bok_resources:protected] =>
[bok_topics:protected] =>
[bok_keywords:protected] =>
[id:protected] => 62
[type:protected] => category
[parent:protected] => 2
[label:protected] => Structural Ironworker
[alreadyInSave:protected] =>
[alreadyInValidation:protected] =>
[validationFailures:protected] => Array
(
)
[_new:BaseObject:private] =>
[_deleted:BaseObject:private] =>
[modifiedColumns:protected] => Array
(
)
)
[87] => Category Object
(
[languages:protected] =>
[bok_resources:protected] =>
[bok_topics:protected] =>
[bok_keywords:protected] =>
[id:protected] => 87
[type:protected] => category
[parent:protected] => 3
[label:protected] => Commercial & Institutional
[alreadyInSave:protected] =>
[alreadyInValidation:protected] =>
[validationFailures:protected] => Array
(
)
[_new:BaseObject:private] =>
[_deleted:BaseObject:private] =>
[modifiedColumns:protected] => Array
(
)
)
[97] => Category Object
(
[languages:protected] =>
[bok_resources:protected] =>
[bok_topics:protected] =>
[bok_keywords:protected] =>
[id:protected] => 97
[type:protected] => category
[parent:protected] => 5
[label:protected] => Images
[alreadyInSave:protected] =>
[alreadyInValidation:protected] =>
[validationFailures:protected] => Array
(
)
[_new:BaseObject:private] =>
[_deleted:BaseObject:private] =>
[modifiedColumns:protected] => Array
(
)
)
[56] => Category Object
(
[languages:protected] =>
[bok_resources:protected] =>
[bok_topics:protected] =>
[bok_keywords:protected] =>
[id:protected] => 56
[type:protected] => category
[parent:protected] => 2
[label:protected] => Elevator Constructor
[alreadyInSave:protected] =>
[alreadyInValidation:protected] =>
[validationFailures:protected] => Array
(
)
[_new:BaseObject:private] =>
[_deleted:BaseObject:private] =>
[modifiedColumns:protected] => Array
(
)
)
[64] => Category Object
(
[languages:protected] =>
[bok_resources:protected] =>
[bok_topics:protected] =>
[bok_keywords:protected] =>
[id:protected] => 64
[type:protected] => category
[parent:protected] => 2
[label:protected] => Laborer
[alreadyInSave:protected] =>
[alreadyInValidation:protected] =>
[validationFailures:protected] => Array
(
)
[_new:BaseObject:private] =>
[_deleted:BaseObject:private] =>
[modifiedColumns:protected] => Array
(
)
)
[74] => Category Object
(
[languages:protected] =>
[bok_resources:protected] =>
[bok_topics:protected] =>
[bok_keywords:protected] =>
[id:protected] => 74
[type:protected] => category
[parent:protected] => 2
[label:protected] => Pile Driver
[alreadyInSave:protected] =>
[alreadyInValidation:protected] =>
[validationFailures:protected] => Array
(
)
[_new:BaseObject:private] =>
[_deleted:BaseObject:private] =>
[modifiedColumns:protected] => Array
(
)
)
)
[categories_initialized:protected] => 1
[mapped_items:protected] =>
[content:protected] =>
[files:protected] =>
[language:protected] => Language Object
(
[id:protected] => 1
[code:protected] => en
[name:protected] => English
[alreadyInSave:protected] =>
[alreadyInValidation:protected] =>
[validationFailures:protected] => Array
(
)
[_new:BaseObject:private] =>
[_deleted:BaseObject:private] =>
[modifiedColumns:protected] => Array
(
)
)
[old_record:protected] =>
[id:protected] => 3994
[old_id:protected] =>
[elcosh_id:protected] => i002689
[type:protected] => image
[display_type:protected] => Image
[user_id:protected] => 0
[language_id:protected] => 1
[tagging_id:protected] => Bruce Lippy
[priority_id:protected] => 1
[title:protected] => Scaffolding at top of large column
[total_pages:protected] => 0
[billed_pages:protected] => 0
[publication_number:protected] =>
[part_of:protected] =>
[keywords:protected] => Guardrail, railing, fall prevention, falls
[comments:protected] =>
[summary:protected] => This shot shows innovative guarding around the top of a large concrete column in the base of a high rise structure going up.
[transition_comments:protected] =>
[external_link:protected] =>
[consol_link:protected] => http://www.cpwrconstructionsolutions.org/masonry/solution/8/adjustable-tower-scaffold.html
[more_like_this:protected] => c1002680,i002662,d000608,d001255
[permission_given_by:protected] =>
[published:protected] => T
[billable:protected] => F
[img_name:protected] =>
[img_ext:protected] => jpg
[img_width:protected] =>
[img_height:protected] =>
[img_credit:protected] => Photo by Pam Susi
[img_practice:protected] => good
[vid_source_id:protected] =>
[vid_running_time:protected] =>
[vid_intended_audience:protected] =>
[vid_acquisition_info:protected] =>
[vid_cost:protected] =>
[vid_producer:protected] =>
[vid_filename:protected] =>
[vid_filename_downloadable:protected] =>
[date_summary:protected] => January 2016
[date_permission_requested:protected] =>
[date_permission_received:protected] =>
[date_review_needed:protected] =>
[date_received:protected] => 02/01/16
[date_completed:protected] => 02/01/16
[date_billed:protected] =>
[date_modified:protected] => 02/01/16
[collBokExports:protected] =>
[lastBokExportCriteria:BaseElcoshItem:private] =>
[alreadyInSave:protected] =>
[alreadyInValidation:protected] =>
[validationFailures:protected] => Array
(
)
[_new:BaseObject:private] =>
[_deleted:BaseObject:private] =>
[modifiedColumns:protected] => Array
(
)
)
)
[5] => Search_Result Object
(
[title] => Construction bracing
[image] => /record/images/3995-p.jpg
[blurb] => This shows structural support that prevents collapses during construction....
[category] => Array
(
[0] => 12
[1] => 15
[2] => 21
[3] => 49
[4] => 51
[5] => 55
[6] => 56
[7] => 60
[8] => 64
[9] => 68
[10] => 74
[11] => 63
[12] => 78
[13] => 79
[14] => 80
[15] => 62
[16] => 87
[17] => 90
[18] => 97
)
[labels] => Array
(
[0] => Crushed/Struck By
[1] => Work Environment
[2] => Hazards
[3] => Falls
[6] => Scaffolds
[9] => Carpenter
[10] => Trades
[11] => Cement Mason
[13] => Electrical Worker
[15] => Elevator Constructor
[17] => HVAC
[19] => Laborer
[21] => Maintenance Worker
[23] => Pile Driver
[25] => Reinforcing Ironworker
[27] => Roofer/Waterproofer
[29] => Scaffold Erector
[31] => Sheetmetal Worker
[33] => Structural Ironworker
[35] => Commercial & Institutional
[36] => Jobsites
[37] => Industrial
[39] => Images
[40] => Media
[41] => Media & Documents
)
[type] => Images
[sub_category] =>
[url] => /image/3995/i002690/Construction%2Bbracing.html
[item:protected] => ImageRecord Object
(
[records:protected] => Array
(
)
[recordId:protected] =>
[searchWordClass:protected] =>
[searchWordPeerClass:protected] =>
[bok_record:protected] =>
[authors:protected] =>
[organizations:protected] =>
[collections:protected] =>
[categories:protected] => Array
(
[12] => Category Object
(
[languages:protected] =>
[bok_resources:protected] =>
[bok_topics:protected] =>
[bok_keywords:protected] =>
[id:protected] => 12
[type:protected] => category
[parent:protected] => 7
[label:protected] => Crushed/Struck By
[alreadyInSave:protected] =>
[alreadyInValidation:protected] =>
[validationFailures:protected] => Array
(
)
[_new:BaseObject:private] =>
[_deleted:BaseObject:private] =>
[modifiedColumns:protected] => Array
(
)
)
[15] => Category Object
(
[languages:protected] =>
[bok_resources:protected] =>
[bok_topics:protected] =>
[bok_keywords:protected] =>
[id:protected] => 15
[type:protected] => category
[parent:protected] => 7
[label:protected] => Falls
[alreadyInSave:protected] =>
[alreadyInValidation:protected] =>
[validationFailures:protected] => Array
(
)
[_new:BaseObject:private] =>
[_deleted:BaseObject:private] =>
[modifiedColumns:protected] => Array
(
)
)
[21] => Category Object
(
[languages:protected] =>
[bok_resources:protected] =>
[bok_topics:protected] =>
[bok_keywords:protected] =>
[id:protected] => 21
[type:protected] => category
[parent:protected] => 7
[label:protected] => Scaffolds
[alreadyInSave:protected] =>
[alreadyInValidation:protected] =>
[validationFailures:protected] => Array
(
)
[_new:BaseObject:private] =>
[_deleted:BaseObject:private] =>
[modifiedColumns:protected] => Array
(
)
)
[49] => Category Object
(
[languages:protected] =>
[bok_resources:protected] =>
[bok_topics:protected] =>
[bok_keywords:protected] =>
[id:protected] => 49
[type:protected] => category
[parent:protected] => 2
[label:protected] => Carpenter
[alreadyInSave:protected] =>
[alreadyInValidation:protected] =>
[validationFailures:protected] => Array
(
)
[_new:BaseObject:private] =>
[_deleted:BaseObject:private] =>
[modifiedColumns:protected] => Array
(
)
)
[51] => Category Object
(
[languages:protected] =>
[bok_resources:protected] =>
[bok_topics:protected] =>
[bok_keywords:protected] =>
[id:protected] => 51
[type:protected] => category
[parent:protected] => 2
[label:protected] => Cement Mason
[alreadyInSave:protected] =>
[alreadyInValidation:protected] =>
[validationFailures:protected] => Array
(
)
[_new:BaseObject:private] =>
[_deleted:BaseObject:private] =>
[modifiedColumns:protected] => Array
(
)
)
[55] => Category Object
(
[languages:protected] =>
[bok_resources:protected] =>
[bok_topics:protected] =>
[bok_keywords:protected] =>
[id:protected] => 55
[type:protected] => category
[parent:protected] => 2
[label:protected] => Electrical Worker
[alreadyInSave:protected] =>
[alreadyInValidation:protected] =>
[validationFailures:protected] => Array
(
)
[_new:BaseObject:private] =>
[_deleted:BaseObject:private] =>
[modifiedColumns:protected] => Array
(
)
)
[56] => Category Object
(
[languages:protected] =>
[bok_resources:protected] =>
[bok_topics:protected] =>
[bok_keywords:protected] =>
[id:protected] => 56
[type:protected] => category
[parent:protected] => 2
[label:protected] => Elevator Constructor
[alreadyInSave:protected] =>
[alreadyInValidation:protected] =>
[validationFailures:protected] => Array
(
)
[_new:BaseObject:private] =>
[_deleted:BaseObject:private] =>
[modifiedColumns:protected] => Array
(
)
)
[60] => Category Object
(
[languages:protected] =>
[bok_resources:protected] =>
[bok_topics:protected] =>
[bok_keywords:protected] =>
[id:protected] => 60
[type:protected] => category
[parent:protected] => 2
[label:protected] => HVAC
[alreadyInSave:protected] =>
[alreadyInValidation:protected] =>
[validationFailures:protected] => Array
(
)
[_new:BaseObject:private] =>
[_deleted:BaseObject:private] =>
[modifiedColumns:protected] => Array
(
)
)
[64] => Category Object
(
[languages:protected] =>
[bok_resources:protected] =>
[bok_topics:protected] =>
[bok_keywords:protected] =>
[id:protected] => 64
[type:protected] => category
[parent:protected] => 2
[label:protected] => Laborer
[alreadyInSave:protected] =>
[alreadyInValidation:protected] =>
[validationFailures:protected] => Array
(
)
[_new:BaseObject:private] =>
[_deleted:BaseObject:private] =>
[modifiedColumns:protected] => Array
(
)
)
[68] => Category Object
(
[languages:protected] =>
[bok_resources:protected] =>
[bok_topics:protected] =>
[bok_keywords:protected] =>
[id:protected] => 68
[type:protected] => category
[parent:protected] => 2
[label:protected] => Maintenance Worker
[alreadyInSave:protected] =>
[alreadyInValidation:protected] =>
[validationFailures:protected] => Array
(
)
[_new:BaseObject:private] =>
[_deleted:BaseObject:private] =>
[modifiedColumns:protected] => Array
(
)
)
[74] => Category Object
(
[languages:protected] =>
[bok_resources:protected] =>
[bok_topics:protected] =>
[bok_keywords:protected] =>
[id:protected] => 74
[type:protected] => category
[parent:protected] => 2
[label:protected] => Pile Driver
[alreadyInSave:protected] =>
[alreadyInValidation:protected] =>
[validationFailures:protected] => Array
(
)
[_new:BaseObject:private] =>
[_deleted:BaseObject:private] =>
[modifiedColumns:protected] => Array
(
)
)
[63] => Category Object
(
[languages:protected] =>
[bok_resources:protected] =>
[bok_topics:protected] =>
[bok_keywords:protected] =>
[id:protected] => 63
[type:protected] => category
[parent:protected] => 2
[label:protected] => Reinforcing Ironworker
[alreadyInSave:protected] =>
[alreadyInValidation:protected] =>
[validationFailures:protected] => Array
(
)
[_new:BaseObject:private] =>
[_deleted:BaseObject:private] =>
[modifiedColumns:protected] => Array
(
)
)
[78] => Category Object
(
[languages:protected] =>
[bok_resources:protected] =>
[bok_topics:protected] =>
[bok_keywords:protected] =>
[id:protected] => 78
[type:protected] => category
[parent:protected] => 2
[label:protected] => Roofer/Waterproofer
[alreadyInSave:protected] =>
[alreadyInValidation:protected] =>
[validationFailures:protected] => Array
(
)
[_new:BaseObject:private] =>
[_deleted:BaseObject:private] =>
[modifiedColumns:protected] => Array
(
)
)
[79] => Category Object
(
[languages:protected] =>
[bok_resources:protected] =>
[bok_topics:protected] =>
[bok_keywords:protected] =>
[id:protected] => 79
[type:protected] => category
[parent:protected] => 2
[label:protected] => Scaffold Erector
[alreadyInSave:protected] =>
[alreadyInValidation:protected] =>
[validationFailures:protected] => Array
(
)
[_new:BaseObject:private] =>
[_deleted:BaseObject:private] =>
[modifiedColumns:protected] => Array
(
)
)
[80] => Category Object
(
[languages:protected] =>
[bok_resources:protected] =>
[bok_topics:protected] =>
[bok_keywords:protected] =>
[id:protected] => 80
[type:protected] => category
[parent:protected] => 2
[label:protected] => Sheetmetal Worker
[alreadyInSave:protected] =>
[alreadyInValidation:protected] =>
[validationFailures:protected] => Array
(
)
[_new:BaseObject:private] =>
[_deleted:BaseObject:private] =>
[modifiedColumns:protected] => Array
(
)
)
[62] => Category Object
(
[languages:protected] =>
[bok_resources:protected] =>
[bok_topics:protected] =>
[bok_keywords:protected] =>
[id:protected] => 62
[type:protected] => category
[parent:protected] => 2
[label:protected] => Structural Ironworker
[alreadyInSave:protected] =>
[alreadyInValidation:protected] =>
[validationFailures:protected] => Array
(
)
[_new:BaseObject:private] =>
[_deleted:BaseObject:private] =>
[modifiedColumns:protected] => Array
(
)
)
[87] => Category Object
(
[languages:protected] =>
[bok_resources:protected] =>
[bok_topics:protected] =>
[bok_keywords:protected] =>
[id:protected] => 87
[type:protected] => category
[parent:protected] => 3
[label:protected] => Commercial & Institutional
[alreadyInSave:protected] =>
[alreadyInValidation:protected] =>
[validationFailures:protected] => Array
(
)
[_new:BaseObject:private] =>
[_deleted:BaseObject:private] =>
[modifiedColumns:protected] => Array
(
)
)
[90] => Category Object
(
[languages:protected] =>
[bok_resources:protected] =>
[bok_topics:protected] =>
[bok_keywords:protected] =>
[id:protected] => 90
[type:protected] => category
[parent:protected] => 3
[label:protected] => Industrial
[alreadyInSave:protected] =>
[alreadyInValidation:protected] =>
[validationFailures:protected] => Array
(
)
[_new:BaseObject:private] =>
[_deleted:BaseObject:private] =>
[modifiedColumns:protected] => Array
(
)
)
[97] => Category Object
(
[languages:protected] =>
[bok_resources:protected] =>
[bok_topics:protected] =>
[bok_keywords:protected] =>
[id:protected] => 97
[type:protected] => category
[parent:protected] => 5
[label:protected] => Images
[alreadyInSave:protected] =>
[alreadyInValidation:protected] =>
[validationFailures:protected] => Array
(
)
[_new:BaseObject:private] =>
[_deleted:BaseObject:private] =>
[modifiedColumns:protected] => Array
(
)
)
)
[categories_initialized:protected] => 1
[mapped_items:protected] =>
[content:protected] =>
[files:protected] =>
[language:protected] => Language Object
(
[id:protected] => 1
[code:protected] => en
[name:protected] => English
[alreadyInSave:protected] =>
[alreadyInValidation:protected] =>
[validationFailures:protected] => Array
(
)
[_new:BaseObject:private] =>
[_deleted:BaseObject:private] =>
[modifiedColumns:protected] => Array
(
)
)
[old_record:protected] =>
[id:protected] => 3995
[old_id:protected] =>
[elcosh_id:protected] => i002690
[type:protected] => image
[display_type:protected] => Image
[user_id:protected] => 0
[language_id:protected] => 1
[tagging_id:protected] => Bruce Lippy
[priority_id:protected] => 1
[title:protected] => Construction bracing
[total_pages:protected] => 0
[billed_pages:protected] => 0
[publication_number:protected] =>
[part_of:protected] =>
[keywords:protected] => Bracing, support, scaffold
[comments:protected] =>
[summary:protected] => This shows structural support that prevents collapses during construction.
[transition_comments:protected] =>
[external_link:protected] =>
[consol_link:protected] => http://www.cpwrconstructionsolutions.org/masonry/solution/8/adjustable-tower-scaffold.html
[more_like_this:protected] => i002660
[permission_given_by:protected] =>
[published:protected] => T
[billable:protected] => F
[img_name:protected] =>
[img_ext:protected] => jpg
[img_width:protected] =>
[img_height:protected] =>
[img_credit:protected] => Photo by Pam Susi
[img_practice:protected] => good
[vid_source_id:protected] =>
[vid_running_time:protected] =>
[vid_intended_audience:protected] =>
[vid_acquisition_info:protected] =>
[vid_cost:protected] =>
[vid_producer:protected] =>
[vid_filename:protected] =>
[vid_filename_downloadable:protected] =>
[date_summary:protected] => January 2016
[date_permission_requested:protected] =>
[date_permission_received:protected] =>
[date_review_needed:protected] =>
[date_received:protected] => 02/01/16
[date_completed:protected] => 02/01/16
[date_billed:protected] =>
[date_modified:protected] => 02/01/16
[collBokExports:protected] =>
[lastBokExportCriteria:BaseElcoshItem:private] =>
[alreadyInSave:protected] =>
[alreadyInValidation:protected] =>
[validationFailures:protected] => Array
(
)
[_new:BaseObject:private] =>
[_deleted:BaseObject:private] =>
[modifiedColumns:protected] => Array
(
)
)
)
)
[preview_mode] =>
[description] => Toolbox talks have been the main tool for communicating safety information on construction jobs for decades.
Unfortunately, there has been little research on what makes for effective toolbox talks. The IUOE National
Training Fund worked with OSHA and NIOSH to make sure their series of 24 Focus Four toolbox talks were based on the best recommendations for effective design. These toolbox talks accompany an entire package of training materials, but can be used alone. This guide points out the key features of these toolbox talks and how best to deliver them.
[keywords] => toolbox talks, tailgate talks
[related_items] => Array
(
[Toolbox Talks] => Array
(
[0] => DocumentRecord Object
(
[records:protected] => Array
(
)
[recordId:protected] =>
[searchWordClass:protected] =>
[searchWordPeerClass:protected] =>
[bok_record:protected] =>
[authors:protected] =>
[organizations:protected] =>
[collections:protected] =>
[categories:protected] =>
[categories_initialized:protected] =>
[mapped_items:protected] =>
[content:protected] =>
[files:protected] =>
[language:protected] => Language Object
(
[id:protected] => 1
[code:protected] => en
[name:protected] => English
[alreadyInSave:protected] =>
[alreadyInValidation:protected] =>
[validationFailures:protected] => Array
(
)
[_new:BaseObject:private] =>
[_deleted:BaseObject:private] =>
[modifiedColumns:protected] => Array
(
)
)
[old_record:protected] =>
[id:protected] => 1605
[old_id:protected] => 1262
[elcosh_id:protected] => d001137
[type:protected] => document
[display_type:protected] => HTML w/ PDF
[user_id:protected] =>
[language_id:protected] => 1
[tagging_id:protected] => Garber
[priority_id:protected] => 1
[title:protected] => Focus Four Toolbox Talks, Module 1 – Falls, Talk #2 – Falls from debris piles?
[total_pages:protected] => 1
[billed_pages:protected] => 1
[publication_number:protected] =>
[part_of:protected] =>
[keywords:protected] => disaster response, hazard clean-up, uneven surface, disaster site, disaster clean-up
[comments:protected] =>
[summary:protected] => A toolbox talk on preventing falls from debris piles. Includes questions to ask, an incident to discuss with images, and a place to record questions the trainer would like to ask about the incident. Part of a collection. Click on the 'collection' button to access the other items.
[transition_comments:protected] =>
[external_link:protected] =>
[consol_link:protected] => http://www.cpwrconstructionsolutions.org/roofing/hazard/1463/install-asphalt-roofs-fall-from-heights.html
[more_like_this:protected] => a000081,d000478,d000530
[permission_given_by:protected] =>
[published:protected] => T
[billable:protected] => F
[img_name:protected] =>
[img_ext:protected] =>
[img_width:protected] =>
[img_height:protected] =>
[img_credit:protected] =>
[img_practice:protected] =>
[vid_source_id:protected] =>
[vid_running_time:protected] =>
[vid_intended_audience:protected] =>
[vid_acquisition_info:protected] =>
[vid_cost:protected] =>
[vid_producer:protected] =>
[vid_filename:protected] =>
[vid_filename_downloadable:protected] =>
[date_summary:protected] =>
[date_permission_requested:protected] =>
[date_permission_received:protected] =>
[date_review_needed:protected] =>
[date_received:protected] => 02/15/12
[date_completed:protected] => 03/19/12
[date_billed:protected] =>
[date_modified:protected] => 07/10/12
[collBokExports:protected] =>
[lastBokExportCriteria:BaseElcoshItem:private] =>
[alreadyInSave:protected] =>
[alreadyInValidation:protected] =>
[validationFailures:protected] => Array
(
)
[_new:BaseObject:private] =>
[_deleted:BaseObject:private] =>
[modifiedColumns:protected] => Array
(
)
)
[1] => DocumentRecord Object
(
[records:protected] => Array
(
)
[recordId:protected] =>
[searchWordClass:protected] =>
[searchWordPeerClass:protected] =>
[bok_record:protected] =>
[authors:protected] =>
[organizations:protected] =>
[collections:protected] =>
[categories:protected] =>
[categories_initialized:protected] =>
[mapped_items:protected] =>
[content:protected] =>
[files:protected] =>
[language:protected] => Language Object
(
[id:protected] => 1
[code:protected] => en
[name:protected] => English
[alreadyInSave:protected] =>
[alreadyInValidation:protected] =>
[validationFailures:protected] => Array
(
)
[_new:BaseObject:private] =>
[_deleted:BaseObject:private] =>
[modifiedColumns:protected] => Array
(
)
)
[old_record:protected] =>
[id:protected] => 1610
[old_id:protected] => 1271
[elcosh_id:protected] => d001146
[type:protected] => document
[display_type:protected] => HTML w/ PDF
[user_id:protected] => 0
[language_id:protected] => 1
[tagging_id:protected] => Garber
[priority_id:protected] => 1
[title:protected] => Focus Four Toolbox Talks, Module 2 – Struck-by, Talk #5 – Rigging and Securing Loads
[total_pages:protected] => 1
[billed_pages:protected] => 1
[publication_number:protected] =>
[part_of:protected] =>
[keywords:protected] => rigging, lift loads, loading areas, chains
[comments:protected] =>
[summary:protected] => A toolbox talk on preventing struck-by incidents caused by not securing loads properly. Includes questions to ask, an incident to discuss with images, and a place to record questions the trainer would like to ask about the incident. Part of a collection. Click on the 'collection' button to access the other items.
[transition_comments:protected] =>
[external_link:protected] =>
[consol_link:protected] => http://www.cpwrconstructionsolutions.org/heavy_equipment/hazard/1591/move-equipment-to-from-and-between-sites-work-zone-struck-by-injuries-and-fatalities.html
[more_like_this:protected] => d000144,d000360,d000873
[permission_given_by:protected] =>
[published:protected] => T
[billable:protected] => F
[img_name:protected] =>
[img_ext:protected] =>
[img_width:protected] =>
[img_height:protected] =>
[img_credit:protected] =>
[img_practice:protected] =>
[vid_source_id:protected] =>
[vid_running_time:protected] =>
[vid_intended_audience:protected] =>
[vid_acquisition_info:protected] =>
[vid_cost:protected] =>
[vid_producer:protected] =>
[vid_filename:protected] =>
[vid_filename_downloadable:protected] =>
[date_summary:protected] =>
[date_permission_requested:protected] =>
[date_permission_received:protected] =>
[date_review_needed:protected] =>
[date_received:protected] => 02/15/12
[date_completed:protected] => 03/28/12
[date_billed:protected] =>
[date_modified:protected] => 05/12/14
[collBokExports:protected] =>
[lastBokExportCriteria:BaseElcoshItem:private] =>
[alreadyInSave:protected] =>
[alreadyInValidation:protected] =>
[validationFailures:protected] => Array
(
)
[_new:BaseObject:private] =>
[_deleted:BaseObject:private] =>
[modifiedColumns:protected] => Array
(
)
)
[2] => DocumentRecord Object
(
[records:protected] => Array
(
)
[recordId:protected] =>
[searchWordClass:protected] =>
[searchWordPeerClass:protected] =>
[bok_record:protected] =>
[authors:protected] =>
[organizations:protected] =>
[collections:protected] =>
[categories:protected] =>
[categories_initialized:protected] =>
[mapped_items:protected] =>
[content:protected] =>
[files:protected] =>
[language:protected] => Language Object
(
[id:protected] => 1
[code:protected] => en
[name:protected] => English
[alreadyInSave:protected] =>
[alreadyInValidation:protected] =>
[validationFailures:protected] => Array
(
)
[_new:BaseObject:private] =>
[_deleted:BaseObject:private] =>
[modifiedColumns:protected] => Array
(
)
)
[old_record:protected] =>
[id:protected] => 1645
[old_id:protected] => 1274
[elcosh_id:protected] => d001149
[type:protected] => document
[display_type:protected] => HTML w/ PDF
[user_id:protected] => 0
[language_id:protected] => 1
[tagging_id:protected] => Garber
[priority_id:protected] => 1
[title:protected] => Focus Four Toolbox Talks, Module 3 – Caught-in/between, Talk #2 – Trenches & Heavy Equipment
[total_pages:protected] => 1
[billed_pages:protected] => 1
[publication_number:protected] =>
[part_of:protected] =>
[keywords:protected] => back-up alarms, spotter, soil cave-in, spoil pikes, ROPs, trenching, rain
[comments:protected] =>
[summary:protected] => A toolbox talk on preventing incidents involving trenches such as trench collapse. Includes questions to ask, an incident to discuss with images, and a place to record questions the trainer would like to ask about the incident. Part of a collection. Click on the 'collection' button to access the other items.
[transition_comments:protected] =>
[external_link:protected] =>
[consol_link:protected] =>
[more_like_this:protected] => d000019,d000035,d000168
[permission_given_by:protected] =>
[published:protected] => T
[billable:protected] => F
[img_name:protected] =>
[img_ext:protected] =>
[img_width:protected] =>
[img_height:protected] =>
[img_credit:protected] =>
[img_practice:protected] =>
[vid_source_id:protected] =>
[vid_running_time:protected] =>
[vid_intended_audience:protected] =>
[vid_acquisition_info:protected] =>
[vid_cost:protected] =>
[vid_producer:protected] =>
[vid_filename:protected] =>
[vid_filename_downloadable:protected] =>
[date_summary:protected] =>
[date_permission_requested:protected] =>
[date_permission_received:protected] =>
[date_review_needed:protected] =>
[date_received:protected] => 02/15/12
[date_completed:protected] => 04/02/12
[date_billed:protected] =>
[date_modified:protected] => 05/23/23
[collBokExports:protected] =>
[lastBokExportCriteria:BaseElcoshItem:private] =>
[alreadyInSave:protected] =>
[alreadyInValidation:protected] =>
[validationFailures:protected] => Array
(
)
[_new:BaseObject:private] =>
[_deleted:BaseObject:private] =>
[modifiedColumns:protected] => Array
(
)
)
[3] => DocumentRecord Object
(
[records:protected] => Array
(
)
[recordId:protected] =>
[searchWordClass:protected] =>
[searchWordPeerClass:protected] =>
[bok_record:protected] =>
[authors:protected] =>
[organizations:protected] =>
[collections:protected] =>
[categories:protected] =>
[categories_initialized:protected] =>
[mapped_items:protected] =>
[content:protected] =>
[files:protected] =>
[language:protected] => Language Object
(
[id:protected] => 1
[code:protected] => en
[name:protected] => English
[alreadyInSave:protected] =>
[alreadyInValidation:protected] =>
[validationFailures:protected] => Array
(
)
[_new:BaseObject:private] =>
[_deleted:BaseObject:private] =>
[modifiedColumns:protected] => Array
(
)
)
[old_record:protected] =>
[id:protected] => 1654
[old_id:protected] => 1284
[elcosh_id:protected] => d001159
[type:protected] => document
[display_type:protected] => HTML w/ PDF
[user_id:protected] => 0
[language_id:protected] => 1
[tagging_id:protected] => Garber
[priority_id:protected] => 1
[title:protected] => Focus Four Toolbox Talks, Module 4 – Electrocutions, Talk #6 – Hazards on Disaster Sites
[total_pages:protected] => 1
[billed_pages:protected] => 1
[publication_number:protected] =>
[part_of:protected] =>
[keywords:protected] => powerlines, underground, utilities, generators, wet conditions, GFCIs, energized lines, disasters, emergency response
[comments:protected] =>
[summary:protected] => A toolbox talk on how to avoid electrocution on a disaster site. Includes questions to ask, an incident to discuss with images, and a place to record questions the trainer would like to ask about the incident. Part of a collection. Click on the 'collection' button to access the other items.
[transition_comments:protected] =>
[external_link:protected] =>
[consol_link:protected] => http://www.cpwrconstructionsolutions.org/electrical/hazard/1138/install-and-repair-high-voltage-lines-transformers-switches-electrical-shocks-burns-and-or-electrocution.html
[more_like_this:protected] => d000135,d000361,d000437
[permission_given_by:protected] =>
[published:protected] => T
[billable:protected] => F
[img_name:protected] =>
[img_ext:protected] =>
[img_width:protected] =>
[img_height:protected] =>
[img_credit:protected] =>
[img_practice:protected] =>
[vid_source_id:protected] =>
[vid_running_time:protected] =>
[vid_intended_audience:protected] =>
[vid_acquisition_info:protected] =>
[vid_cost:protected] =>
[vid_producer:protected] =>
[vid_filename:protected] =>
[vid_filename_downloadable:protected] =>
[date_summary:protected] =>
[date_permission_requested:protected] =>
[date_permission_received:protected] =>
[date_review_needed:protected] =>
[date_received:protected] => 02/15/12
[date_completed:protected] => 04/02/12
[date_billed:protected] =>
[date_modified:protected] => 05/23/23
[collBokExports:protected] =>
[lastBokExportCriteria:BaseElcoshItem:private] =>
[alreadyInSave:protected] =>
[alreadyInValidation:protected] =>
[validationFailures:protected] => Array
(
)
[_new:BaseObject:private] =>
[_deleted:BaseObject:private] =>
[modifiedColumns:protected] => Array
(
)
)
)
)
[collections] => Array
(
[1294] =>
[1295] =>
[1292] =>
[1293] => CollectionRecord Object
(
[collection_items:protected] =>
[records:protected] => Array
(
)
[recordId:protected] =>
[searchWordClass:protected] =>
[searchWordPeerClass:protected] =>
[bok_record:protected] =>
[authors:protected] =>
[organizations:protected] =>
[collections:protected] =>
[categories:protected] =>
[categories_initialized:protected] =>
[mapped_items:protected] =>
[content:protected] =>
[files:protected] =>
[language:protected] =>
[old_record:protected] =>
[id:protected] => 1293
[old_id:protected] =>
[elcosh_id:protected] => c000026
[type:protected] => collection
[display_type:protected] => Collection
[user_id:protected] =>
[language_id:protected] =>
[tagging_id:protected] =>
[priority_id:protected] =>
[title:protected] => Focus Four-Struck By
[total_pages:protected] =>
[billed_pages:protected] =>
[publication_number:protected] =>
[part_of:protected] =>
[keywords:protected] =>
[comments:protected] =>
[summary:protected] => The following are links to all of the items in this collection:
[transition_comments:protected] =>
[external_link:protected] =>
[consol_link:protected] =>
[more_like_this:protected] =>
[permission_given_by:protected] =>
[published:protected] => T
[billable:protected] => F
[img_name:protected] =>
[img_ext:protected] =>
[img_width:protected] =>
[img_height:protected] =>
[img_credit:protected] =>
[img_practice:protected] =>
[vid_source_id:protected] =>
[vid_running_time:protected] =>
[vid_intended_audience:protected] =>
[vid_acquisition_info:protected] =>
[vid_cost:protected] =>
[vid_producer:protected] =>
[vid_filename:protected] =>
[vid_filename_downloadable:protected] =>
[date_summary:protected] =>
[date_permission_requested:protected] =>
[date_permission_received:protected] =>
[date_review_needed:protected] =>
[date_received:protected] => 05/08/12
[date_completed:protected] => 05/08/12
[date_billed:protected] =>
[date_modified:protected] => 05/08/12
[collBokExports:protected] =>
[lastBokExportCriteria:BaseElcoshItem:private] =>
[alreadyInSave:protected] =>
[alreadyInValidation:protected] =>
[validationFailures:protected] => Array
(
)
[_new:BaseObject:private] =>
[_deleted:BaseObject:private] =>
[modifiedColumns:protected] => Array
(
)
)
)
[record] => DocumentRecord Object
(
[records:protected] => Array
(
)
[recordId:protected] =>
[searchWordClass:protected] =>
[searchWordPeerClass:protected] =>
[bok_record:protected] =>
[authors:protected] => Array
(
)
[organizations:protected] => Array
(
[256] => Organization Object
(
[id:protected] => 256
[elcosh_id:protected] => o000276
[user_id:protected] => 14
[province_id:protected] => 0
[country_id:protected] => 0
[title:protected] => IUOE National Training Fund
[address:protected] =>
[postal_code:protected] =>
[city:protected] =>
[department:protected] =>
[phone:protected] => 304-253-8674
[fax:protected] =>
[email:protected] =>
[website:protected] => http://www.iuoeiettc.org
[filename:protected] =>
[about:protected] =>
[comments:protected] =>
[logo_available:protected] => T
[no_details:protected] => F
[date_received:protected] => 2012-02-13
[date_completed:protected] => 2012-02-13
[date_billed:protected] =>
[alreadyInSave:protected] =>
[alreadyInValidation:protected] =>
[validationFailures:protected] => Array
(
)
[_new:BaseObject:private] =>
[_deleted:BaseObject:private] =>
[modifiedColumns:protected] => Array
(
)
)
)
[collections:protected] => Array
(
[1294] =>
[1295] =>
[1292] =>
[1293] => CollectionRecord Object
(
[collection_items:protected] =>
[records:protected] => Array
(
)
[recordId:protected] =>
[searchWordClass:protected] =>
[searchWordPeerClass:protected] =>
[bok_record:protected] =>
[authors:protected] =>
[organizations:protected] =>
[collections:protected] =>
[categories:protected] =>
[categories_initialized:protected] =>
[mapped_items:protected] =>
[content:protected] =>
[files:protected] =>
[language:protected] =>
[old_record:protected] =>
[id:protected] => 1293
[old_id:protected] =>
[elcosh_id:protected] => c000026
[type:protected] => collection
[display_type:protected] => Collection
[user_id:protected] =>
[language_id:protected] =>
[tagging_id:protected] =>
[priority_id:protected] =>
[title:protected] => Focus Four-Struck By
[total_pages:protected] =>
[billed_pages:protected] =>
[publication_number:protected] =>
[part_of:protected] =>
[keywords:protected] =>
[comments:protected] =>
[summary:protected] => The following are links to all of the items in this collection:
[transition_comments:protected] =>
[external_link:protected] =>
[consol_link:protected] =>
[more_like_this:protected] =>
[permission_given_by:protected] =>
[published:protected] => T
[billable:protected] => F
[img_name:protected] =>
[img_ext:protected] =>
[img_width:protected] =>
[img_height:protected] =>
[img_credit:protected] =>
[img_practice:protected] =>
[vid_source_id:protected] =>
[vid_running_time:protected] =>
[vid_intended_audience:protected] =>
[vid_acquisition_info:protected] =>
[vid_cost:protected] =>
[vid_producer:protected] =>
[vid_filename:protected] =>
[vid_filename_downloadable:protected] =>
[date_summary:protected] =>
[date_permission_requested:protected] =>
[date_permission_received:protected] =>
[date_review_needed:protected] =>
[date_received:protected] => 05/08/12
[date_completed:protected] => 05/08/12
[date_billed:protected] =>
[date_modified:protected] => 05/08/12
[collBokExports:protected] =>
[lastBokExportCriteria:BaseElcoshItem:private] =>
[alreadyInSave:protected] =>
[alreadyInValidation:protected] =>
[validationFailures:protected] => Array
(
)
[_new:BaseObject:private] =>
[_deleted:BaseObject:private] =>
[modifiedColumns:protected] => Array
(
)
)
)
[categories:protected] =>
[categories_initialized:protected] =>
[mapped_items:protected] => Array
(
[1605] => DocumentRecord Object
(
[records:protected] => Array
(
)
[recordId:protected] =>
[searchWordClass:protected] =>
[searchWordPeerClass:protected] =>
[bok_record:protected] =>
[authors:protected] =>
[organizations:protected] =>
[collections:protected] =>
[categories:protected] =>
[categories_initialized:protected] =>
[mapped_items:protected] =>
[content:protected] =>
[files:protected] =>
[language:protected] =>
[old_record:protected] =>
[id:protected] => 1605
[old_id:protected] => 1262
[elcosh_id:protected] => d001137
[type:protected] => document
[display_type:protected] => HTML w/ PDF
[user_id:protected] =>
[language_id:protected] => 1
[tagging_id:protected] => Garber
[priority_id:protected] => 1
[title:protected] => Focus Four Toolbox Talks, Module 1 – Falls, Talk #2 – Falls from debris piles?
[total_pages:protected] => 1
[billed_pages:protected] => 1
[publication_number:protected] =>
[part_of:protected] =>
[keywords:protected] => disaster response, hazard clean-up, uneven surface, disaster site, disaster clean-up
[comments:protected] =>
[summary:protected] => A toolbox talk on preventing falls from debris piles. Includes questions to ask, an incident to discuss with images, and a place to record questions the trainer would like to ask about the incident. Part of a collection. Click on the 'collection' button to access the other items.
[transition_comments:protected] =>
[external_link:protected] =>
[consol_link:protected] => http://www.cpwrconstructionsolutions.org/roofing/hazard/1463/install-asphalt-roofs-fall-from-heights.html
[more_like_this:protected] => a000081,d000478,d000530
[permission_given_by:protected] =>
[published:protected] => T
[billable:protected] => F
[img_name:protected] =>
[img_ext:protected] =>
[img_width:protected] =>
[img_height:protected] =>
[img_credit:protected] =>
[img_practice:protected] =>
[vid_source_id:protected] =>
[vid_running_time:protected] =>
[vid_intended_audience:protected] =>
[vid_acquisition_info:protected] =>
[vid_cost:protected] =>
[vid_producer:protected] =>
[vid_filename:protected] =>
[vid_filename_downloadable:protected] =>
[date_summary:protected] =>
[date_permission_requested:protected] =>
[date_permission_received:protected] =>
[date_review_needed:protected] =>
[date_received:protected] => 02/15/12
[date_completed:protected] => 03/19/12
[date_billed:protected] =>
[date_modified:protected] => 07/10/12
[collBokExports:protected] =>
[lastBokExportCriteria:BaseElcoshItem:private] =>
[alreadyInSave:protected] =>
[alreadyInValidation:protected] =>
[validationFailures:protected] => Array
(
)
[_new:BaseObject:private] =>
[_deleted:BaseObject:private] =>
[modifiedColumns:protected] => Array
(
)
)
[1610] => DocumentRecord Object
(
[records:protected] => Array
(
)
[recordId:protected] =>
[searchWordClass:protected] =>
[searchWordPeerClass:protected] =>
[bok_record:protected] =>
[authors:protected] =>
[organizations:protected] =>
[collections:protected] =>
[categories:protected] =>
[categories_initialized:protected] =>
[mapped_items:protected] =>
[content:protected] =>
[files:protected] =>
[language:protected] =>
[old_record:protected] =>
[id:protected] => 1610
[old_id:protected] => 1271
[elcosh_id:protected] => d001146
[type:protected] => document
[display_type:protected] => HTML w/ PDF
[user_id:protected] => 0
[language_id:protected] => 1
[tagging_id:protected] => Garber
[priority_id:protected] => 1
[title:protected] => Focus Four Toolbox Talks, Module 2 – Struck-by, Talk #5 – Rigging and Securing Loads
[total_pages:protected] => 1
[billed_pages:protected] => 1
[publication_number:protected] =>
[part_of:protected] =>
[keywords:protected] => rigging, lift loads, loading areas, chains
[comments:protected] =>
[summary:protected] => A toolbox talk on preventing struck-by incidents caused by not securing loads properly. Includes questions to ask, an incident to discuss with images, and a place to record questions the trainer would like to ask about the incident. Part of a collection. Click on the 'collection' button to access the other items.
[transition_comments:protected] =>
[external_link:protected] =>
[consol_link:protected] => http://www.cpwrconstructionsolutions.org/heavy_equipment/hazard/1591/move-equipment-to-from-and-between-sites-work-zone-struck-by-injuries-and-fatalities.html
[more_like_this:protected] => d000144,d000360,d000873
[permission_given_by:protected] =>
[published:protected] => T
[billable:protected] => F
[img_name:protected] =>
[img_ext:protected] =>
[img_width:protected] =>
[img_height:protected] =>
[img_credit:protected] =>
[img_practice:protected] =>
[vid_source_id:protected] =>
[vid_running_time:protected] =>
[vid_intended_audience:protected] =>
[vid_acquisition_info:protected] =>
[vid_cost:protected] =>
[vid_producer:protected] =>
[vid_filename:protected] =>
[vid_filename_downloadable:protected] =>
[date_summary:protected] =>
[date_permission_requested:protected] =>
[date_permission_received:protected] =>
[date_review_needed:protected] =>
[date_received:protected] => 02/15/12
[date_completed:protected] => 03/28/12
[date_billed:protected] =>
[date_modified:protected] => 05/12/14
[collBokExports:protected] =>
[lastBokExportCriteria:BaseElcoshItem:private] =>
[alreadyInSave:protected] =>
[alreadyInValidation:protected] =>
[validationFailures:protected] => Array
(
)
[_new:BaseObject:private] =>
[_deleted:BaseObject:private] =>
[modifiedColumns:protected] => Array
(
)
)
[1645] => DocumentRecord Object
(
[records:protected] => Array
(
)
[recordId:protected] =>
[searchWordClass:protected] =>
[searchWordPeerClass:protected] =>
[bok_record:protected] =>
[authors:protected] =>
[organizations:protected] =>
[collections:protected] =>
[categories:protected] =>
[categories_initialized:protected] =>
[mapped_items:protected] =>
[content:protected] =>
[files:protected] =>
[language:protected] =>
[old_record:protected] =>
[id:protected] => 1645
[old_id:protected] => 1274
[elcosh_id:protected] => d001149
[type:protected] => document
[display_type:protected] => HTML w/ PDF
[user_id:protected] => 0
[language_id:protected] => 1
[tagging_id:protected] => Garber
[priority_id:protected] => 1
[title:protected] => Focus Four Toolbox Talks, Module 3 – Caught-in/between, Talk #2 – Trenches & Heavy Equipment
[total_pages:protected] => 1
[billed_pages:protected] => 1
[publication_number:protected] =>
[part_of:protected] =>
[keywords:protected] => back-up alarms, spotter, soil cave-in, spoil pikes, ROPs, trenching, rain
[comments:protected] =>
[summary:protected] => A toolbox talk on preventing incidents involving trenches such as trench collapse. Includes questions to ask, an incident to discuss with images, and a place to record questions the trainer would like to ask about the incident. Part of a collection. Click on the 'collection' button to access the other items.
[transition_comments:protected] =>
[external_link:protected] =>
[consol_link:protected] =>
[more_like_this:protected] => d000019,d000035,d000168
[permission_given_by:protected] =>
[published:protected] => T
[billable:protected] => F
[img_name:protected] =>
[img_ext:protected] =>
[img_width:protected] =>
[img_height:protected] =>
[img_credit:protected] =>
[img_practice:protected] =>
[vid_source_id:protected] =>
[vid_running_time:protected] =>
[vid_intended_audience:protected] =>
[vid_acquisition_info:protected] =>
[vid_cost:protected] =>
[vid_producer:protected] =>
[vid_filename:protected] =>
[vid_filename_downloadable:protected] =>
[date_summary:protected] =>
[date_permission_requested:protected] =>
[date_permission_received:protected] =>
[date_review_needed:protected] =>
[date_received:protected] => 02/15/12
[date_completed:protected] => 04/02/12
[date_billed:protected] =>
[date_modified:protected] => 05/23/23
[collBokExports:protected] =>
[lastBokExportCriteria:BaseElcoshItem:private] =>
[alreadyInSave:protected] =>
[alreadyInValidation:protected] =>
[validationFailures:protected] => Array
(
)
[_new:BaseObject:private] =>
[_deleted:BaseObject:private] =>
[modifiedColumns:protected] => Array
(
)
)
[1654] => DocumentRecord Object
(
[records:protected] => Array
(
)
[recordId:protected] =>
[searchWordClass:protected] =>
[searchWordPeerClass:protected] =>
[bok_record:protected] =>
[authors:protected] =>
[organizations:protected] =>
[collections:protected] =>
[categories:protected] =>
[categories_initialized:protected] =>
[mapped_items:protected] =>
[content:protected] =>
[files:protected] =>
[language:protected] =>
[old_record:protected] =>
[id:protected] => 1654
[old_id:protected] => 1284
[elcosh_id:protected] => d001159
[type:protected] => document
[display_type:protected] => HTML w/ PDF
[user_id:protected] => 0
[language_id:protected] => 1
[tagging_id:protected] => Garber
[priority_id:protected] => 1
[title:protected] => Focus Four Toolbox Talks, Module 4 – Electrocutions, Talk #6 – Hazards on Disaster Sites
[total_pages:protected] => 1
[billed_pages:protected] => 1
[publication_number:protected] =>
[part_of:protected] =>
[keywords:protected] => powerlines, underground, utilities, generators, wet conditions, GFCIs, energized lines, disasters, emergency response
[comments:protected] =>
[summary:protected] => A toolbox talk on how to avoid electrocution on a disaster site. Includes questions to ask, an incident to discuss with images, and a place to record questions the trainer would like to ask about the incident. Part of a collection. Click on the 'collection' button to access the other items.
[transition_comments:protected] =>
[external_link:protected] =>
[consol_link:protected] => http://www.cpwrconstructionsolutions.org/electrical/hazard/1138/install-and-repair-high-voltage-lines-transformers-switches-electrical-shocks-burns-and-or-electrocution.html
[more_like_this:protected] => d000135,d000361,d000437
[permission_given_by:protected] =>
[published:protected] => T
[billable:protected] => F
[img_name:protected] =>
[img_ext:protected] =>
[img_width:protected] =>
[img_height:protected] =>
[img_credit:protected] =>
[img_practice:protected] =>
[vid_source_id:protected] =>
[vid_running_time:protected] =>
[vid_intended_audience:protected] =>
[vid_acquisition_info:protected] =>
[vid_cost:protected] =>
[vid_producer:protected] =>
[vid_filename:protected] =>
[vid_filename_downloadable:protected] =>
[date_summary:protected] =>
[date_permission_requested:protected] =>
[date_permission_received:protected] =>
[date_review_needed:protected] =>
[date_received:protected] => 02/15/12
[date_completed:protected] => 04/02/12
[date_billed:protected] =>
[date_modified:protected] => 05/23/23
[collBokExports:protected] =>
[lastBokExportCriteria:BaseElcoshItem:private] =>
[alreadyInSave:protected] =>
[alreadyInValidation:protected] =>
[validationFailures:protected] => Array
(
)
[_new:BaseObject:private] =>
[_deleted:BaseObject:private] =>
[modifiedColumns:protected] => Array
(
)
)
)
[content:protected] =>
[files:protected] => Array
(
[9400] => File Object
(
[id:protected] => 9400
[filename:protected] => 1.jpg
[downloadable:protected] => F
[timestamp:protected] => 2014-05-08 15:05:37
[alreadyInSave:protected] =>
[alreadyInValidation:protected] =>
[validationFailures:protected] => Array
(
)
[_new:BaseObject:private] =>
[_deleted:BaseObject:private] =>
[modifiedColumns:protected] => Array
(
)
)
[9401] => File Object
(
[id:protected] => 9401
[filename:protected] => d001298.pdf
[downloadable:protected] => T
[timestamp:protected] => 2014-05-08 15:05:37
[alreadyInSave:protected] =>
[alreadyInValidation:protected] =>
[validationFailures:protected] => Array
(
)
[_new:BaseObject:private] =>
[_deleted:BaseObject:private] =>
[modifiedColumns:protected] => Array
(
)
)
)
[language:protected] => Language Object
(
[id:protected] => 1
[code:protected] => en
[name:protected] => English
[alreadyInSave:protected] =>
[alreadyInValidation:protected] =>
[validationFailures:protected] => Array
(
)
[_new:BaseObject:private] =>
[_deleted:BaseObject:private] =>
[modifiedColumns:protected] => Array
(
)
)
[old_record:protected] =>
[id:protected] => 3827
[old_id:protected] =>
[elcosh_id:protected] => d001298
[type:protected] => document
[display_type:protected] => HTML w/ PDF
[user_id:protected] => 23
[language_id:protected] => 1
[tagging_id:protected] => Bruce Lippy
[priority_id:protected] => 1
[title:protected] => Getting the most out of the IUOE Toolbox Talks
[total_pages:protected] => 2
[billed_pages:protected] => 2
[publication_number:protected] =>
[part_of:protected] =>
[keywords:protected] => toolbox talks, tailgate talks
[comments:protected] =>
[summary:protected] => Toolbox talks have been the main tool for communicating safety information on construction jobs for decades.
Unfortunately, there has been little research on what makes for effective toolbox talks. The IUOE National
Training Fund worked with OSHA and NIOSH to make sure their series of 24 Focus Four toolbox talks were based on the best recommendations for effective design. These toolbox talks accompany an entire package of training materials, but can be used alone. This guide points out the key features of these toolbox talks and how best to deliver them.
[transition_comments:protected] =>
[external_link:protected] =>
[consol_link:protected] =>
[more_like_this:protected] => d001137,d001146,d001149,d001159
[permission_given_by:protected] => IUOE National Hazmat Program
[published:protected] => T
[billable:protected] => F
[img_name:protected] =>
[img_ext:protected] => png
[img_width:protected] =>
[img_height:protected] =>
[img_credit:protected] =>
[img_practice:protected] =>
[vid_source_id:protected] =>
[vid_running_time:protected] =>
[vid_intended_audience:protected] =>
[vid_acquisition_info:protected] =>
[vid_cost:protected] =>
[vid_producer:protected] =>
[vid_filename:protected] =>
[vid_filename_downloadable:protected] =>
[date_summary:protected] => 2007
[date_permission_requested:protected] =>
[date_permission_received:protected] =>
[date_review_needed:protected] =>
[date_received:protected] => 05/08/14
[date_completed:protected] => 05/08/14
[date_billed:protected] =>
[date_modified:protected] => 05/08/14
[collBokExports:protected] =>
[lastBokExportCriteria:BaseElcoshItem:private] =>
[alreadyInSave:protected] =>
[alreadyInValidation:protected] =>
[validationFailures:protected] => Array
(
)
[_new:BaseObject:private] =>
[_deleted:BaseObject:private] =>
[modifiedColumns:protected] => Array
(
)
)
[show_text] =>
[document_content] => ElcoshItemDocumentContent Object
(
[id:protected] => 2896
[item_id:protected] => 3827
[type:protected] => main
[title:protected] =>
[content:protected] =>
Why were these talks developed?
Toolbox talks have been the main tool for communicating safety information on construction jobs for decades. Unfortunately, there has been almost no research on what makes for effective toolbox talks. The IUOE National Training Fund has worked with OSHA, the National Institute for Occupational Safety and Health and the Lippy Group, LLC to make sure these Focus Four toolbox talks are based on the latest fi ndings on the most effective design and tailored to the hazards operating engineers face daily. These toolbox talks accompany an entire package of training materials, but can be used alone. The way these are delivered is as important as how well they are designed.
What did NIOSH find out?
- Just handing out factsheets and toolbox talks to workers doesn’t work. Providing copies after toolbox talks doesn’t make much of an impact either.
- Using case studies (real life stories of accidents that ended in fatality or injury) in toolbox talks is effective.
- When toolbox talks containing case studies were accompanied by discussion questions to encourage group participation, they were more effective. Consequently, getting the workers to participate in the discussion about the case study is important. It’s not enough to tell the story, it is better to have the workers engage in problem solving that analyzes why the accident occurred and how it could have been prevented. Active learning is always better than passive.
How should you deliver these toolbox talks?
- Choose a topic that is related to work going on at the site.
- Hold the meeting on the job, preferably where everyone can sit and relax.
- Hold the meeting at the beginning of a shift or after a break. Folks are too tired at the end of a shift to carefully listen and they want to get home.
- Read the toolbox talk sheet on the topic prior to conducting the talk.
- Start at the top of the form and work right through to the end, which should take around 10 to 15 minutes. Guidance is provided in blue print to help you with each section.
- Use the questions provided to generate discussions. Always allow time for the crew to respond to your questions before you provide an answer. Some suggested responses are written in italics.
- Review the case study and emphasize that this was a real incident. Ask the crew for a case study before you review the one provided, however.
- Always end with a discussion of the particular worksite where you are conducting the talk. Tie the talk as closely to hazards on the site as possible and encourage the crew to constantly look for and immediately correct hazards. They should also know how to report any problems that can’t be immediately corrected.
- Provide copies to each person, if you like, but NIOSH has not found that to be particularly effective.
- Encourage workers to do similar talks on their sites and provide them with the IUOE phone number for ordering in bulk.
- Have everyone sign the back of the form to indicate they attended this session and point out it is a pledge to look out for the health and safety of everyone on the site.
What are the key features of these toolbox talks?

[content_transformed:protected] =>
Why were these talks developed?
Toolbox talks have been the main tool for communicating safety information on construction jobs for decades. Unfortunately, there has been almost no research on what makes for effective toolbox talks. The IUOE National Training Fund has worked with OSHA, the National Institute for Occupational Safety and Health and the Lippy Group, LLC to make sure these Focus Four toolbox talks are based on the latest fi ndings on the most effective design and tailored to the hazards operating engineers face daily. These toolbox talks accompany an entire package of training materials, but can be used alone. The way these are delivered is as important as how well they are designed.
What did NIOSH find out?
- Just handing out factsheets and toolbox talks to workers doesn’t work. Providing copies after toolbox talks doesn’t make much of an impact either.
- Using case studies (real life stories of accidents that ended in fatality or injury) in toolbox talks is effective.
- When toolbox talks containing case studies were accompanied by discussion questions to encourage group participation, they were more effective. Consequently, getting the workers to participate in the discussion about the case study is important. It’s not enough to tell the story, it is better to have the workers engage in problem solving that analyzes why the accident occurred and how it could have been prevented. Active learning is always better than passive.
How should you deliver these toolbox talks?
- Choose a topic that is related to work going on at the site.
- Hold the meeting on the job, preferably where everyone can sit and relax.
- Hold the meeting at the beginning of a shift or after a break. Folks are too tired at the end of a shift to carefully listen and they want to get home.
- Read the toolbox talk sheet on the topic prior to conducting the talk.
- Start at the top of the form and work right through to the end, which should take around 10 to 15 minutes. Guidance is provided in blue print to help you with each section.
- Use the questions provided to generate discussions. Always allow time for the crew to respond to your questions before you provide an answer. Some suggested responses are written in italics.
- Review the case study and emphasize that this was a real incident. Ask the crew for a case study before you review the one provided, however.
- Always end with a discussion of the particular worksite where you are conducting the talk. Tie the talk as closely to hazards on the site as possible and encourage the crew to constantly look for and immediately correct hazards. They should also know how to report any problems that can’t be immediately corrected.
- Provide copies to each person, if you like, but NIOSH has not found that to be particularly effective.
- Encourage workers to do similar talks on their sites and provide them with the IUOE phone number for ordering in bulk.
- Have everyone sign the back of the form to indicate they attended this session and point out it is a pledge to look out for the health and safety of everyone on the site.
What are the key features of these toolbox talks?
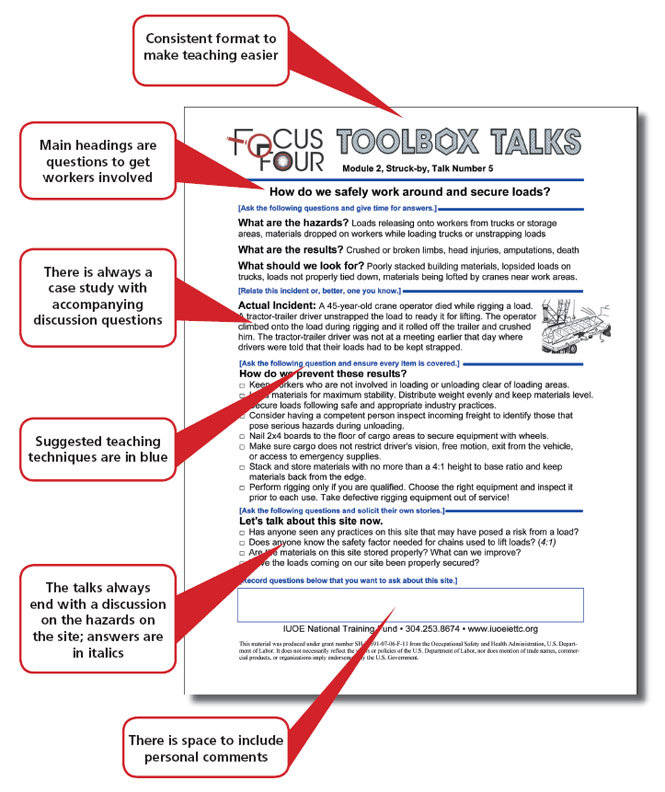
[disclaimer:protected] =>
[disclaimer_transformed:protected] =>
[alreadyInSave:protected] =>
[alreadyInValidation:protected] =>
[validationFailures:protected] => Array
(
)
[_new:BaseObject:private] =>
[_deleted:BaseObject:private] =>
[modifiedColumns:protected] => Array
(
)
)
[template] => record
)
[_file] => /home/agsafe5/repositories/elcosh/live/templates/elcosh/record.html
[_errors:protected] => Array
(
)
[_encoding:protected] => UTF-8
[_outputMode:protected] => 11
[_forceReparse:protected] =>
[_phpCodeDestination:protected] => /tmp/
[_phpCodeExtension:protected] => php
[_cacheLifetime:protected] => 30
[_cachePurgeFrequency:protected] => 30
[externalMacroTemplatesCache:PHPTAL:private] => Array
(
[macros.html] => PHPTAL Object
(
[_prefilters:protected] => Array
(
)
[_prefilter:PHPTAL:private] => REMOVED: DO NOT USE
[_postfilter:protected] =>
[_repositories:protected] => Array
(
[0] => /home/agsafe5/repositories/elcosh/live/templates/elcosh
)
[_path:protected] => macros.html
[_resolvers:protected] => Array
(
)
[_source:protected] => PHPTAL_FileSource Object
(
[_path:PHPTAL_FileSource:private] => /home/agsafe5/repositories/elcosh/live/templates/elcosh/macros.html
)
[_codeFile:protected] => /tmp/tpl_61515a6c_macros__EnKHR8AWVA3oW7OmomvoZw.php
[_functionName:protected] => tpl_61515a6c_macros__EnKHR8AWVA3oW7OmomvoZw
[_prepared:protected] => 1
[_triggers:protected] => Array
(
)
[_translator:protected] =>
[_globalContext:protected] => stdClass Object
(
)
[_context:protected] => PHPTAL_Context Object
(
[_line] =>
[_file] => /home/agsafe5/repositories/elcosh/live/templates/elcosh/record.html
[repeat] => stdClass Object
(
)
[_xmlDeclaration] =>
[_docType] =>
[_nothrow:PHPTAL_Context:private] =>
[_slots:PHPTAL_Context:private] => Array
(
)
[_slotsStack:PHPTAL_Context:private] => Array
(
[0] => Array
(
)
[1] => Array
(
)
)
[_parentContext:PHPTAL_Context:private] => PHPTAL_Context Object
(
[_line] =>
[_file] => /home/agsafe5/repositories/elcosh/live/templates/elcosh/record.html
[repeat] => stdClass Object
(
)
[_xmlDeclaration] =>
[_docType] =>
[_nothrow:PHPTAL_Context:private] =>
[_slots:PHPTAL_Context:private] => Array
(
)
[_slotsStack:PHPTAL_Context:private] => Array
(
[0] => Array
(
)
[1] => Array
(
)
)
[_parentContext:PHPTAL_Context:private] =>
[_globalContext:PHPTAL_Context:private] => stdClass Object
(
)
[_echoDeclarations:PHPTAL_Context:private] =>
[referer] => http://www.elcosh.org/document/3827/d001298/Getting%2Bthe%2Bmost%2Bout%2Bof%2Bthe%2BIUOE%2BToolbox%2BTalks.html
[curr_module] => Record
[styles] => Array
(
)
[javascript] => Array
(
[0] => jquery.min.js
)
[metas] => Array
(
[language] => en
[robots] => index, follow
)
[user] =>
[curr_url] => https://www.elcosh.org/index.php?module=Record&id=3827&type=document
[base_url] => https://www.elcosh.org/index.php?module=Record
[title] => eLCOSH : Getting the most out of the IUOE Toolbox Talks
[language] => en
[search_query] =>
[module] => Record
[new_records] => Array
(
[0] => Search_Result Object
(
[title] => Toolbox Talk: Fixed Ladder
[image] => /record/images/notavailable-p.png
[blurb] => The CPWR Toolbox Talk on Fixed Ladders addresses the potential risks associated with using fixed ladders. The resource includes a brief case example,...
[category] => Array
(
[0] => 15
[1] => 47
[2] => 49
[3] => 51
[4] => 53
[5] => 55
[6] => 60
[7] => 64
[8] => 73
[9] => 76
[10] => 78
[11] => 80
[12] => 86
[13] => 87
[14] => 90
[15] => 92
[16] => 93
[17] => 94
[18] => 100
)
[labels] => Array
(
[0] => Falls
[1] => Work Environment
[2] => Hazards
[3] => Bricklayer
[4] => Trades
[5] => Carpenter
[7] => Cement Mason
[9] => Concrete Polisher
[11] => Electrical Worker
[13] => HVAC
[15] => Laborer
[17] => PCC/Restoration
[19] => Plumber/Pipefitter
[21] => Roofer/Waterproofer
[23] => Sheetmetal Worker
[25] => Welder
[27] => Commercial & Institutional
[28] => Jobsites
[29] => Industrial
[31] => LEED/Green Construction
[33] => Renovations
[35] => Residential
[37] => Toolbox Talks
[38] => Documents
[39] => Media & Documents
)
[type] => Toolbox Talks
[sub_category] =>
[url] => /document/4430/d001660/Toolbox%2BTalk%253A%2BFixed%2BLadder.html
[item:protected] => DocumentRecord Object
(
[records:protected] => Array
(
)
[recordId:protected] =>
[searchWordClass:protected] =>
[searchWordPeerClass:protected] =>
[bok_record:protected] =>
[authors:protected] =>
[organizations:protected] =>
[collections:protected] =>
[categories:protected] => Array
(
[15] => Category Object
(
[languages:protected] =>
[bok_resources:protected] =>
[bok_topics:protected] =>
[bok_keywords:protected] =>
[id:protected] => 15
[type:protected] => category
[parent:protected] => 7
[label:protected] => Falls
[alreadyInSave:protected] =>
[alreadyInValidation:protected] =>
[validationFailures:protected] => Array
(
)
[_new:BaseObject:private] =>
[_deleted:BaseObject:private] =>
[modifiedColumns:protected] => Array
(
)
)
[47] => Category Object
(
[languages:protected] =>
[bok_resources:protected] =>
[bok_topics:protected] =>
[bok_keywords:protected] =>
[id:protected] => 47
[type:protected] => category
[parent:protected] => 2
[label:protected] => Bricklayer
[alreadyInSave:protected] =>
[alreadyInValidation:protected] =>
[validationFailures:protected] => Array
(
)
[_new:BaseObject:private] =>
[_deleted:BaseObject:private] =>
[modifiedColumns:protected] => Array
(
)
)
[49] => Category Object
(
[languages:protected] =>
[bok_resources:protected] =>
[bok_topics:protected] =>
[bok_keywords:protected] =>
[id:protected] => 49
[type:protected] => category
[parent:protected] => 2
[label:protected] => Carpenter
[alreadyInSave:protected] =>
[alreadyInValidation:protected] =>
[validationFailures:protected] => Array
(
)
[_new:BaseObject:private] =>
[_deleted:BaseObject:private] =>
[modifiedColumns:protected] => Array
(
)
)
[51] => Category Object
(
[languages:protected] =>
[bok_resources:protected] =>
[bok_topics:protected] =>
[bok_keywords:protected] =>
[id:protected] => 51
[type:protected] => category
[parent:protected] => 2
[label:protected] => Cement Mason
[alreadyInSave:protected] =>
[alreadyInValidation:protected] =>
[validationFailures:protected] => Array
(
)
[_new:BaseObject:private] =>
[_deleted:BaseObject:private] =>
[modifiedColumns:protected] => Array
(
)
)
[53] => Category Object
(
[languages:protected] =>
[bok_resources:protected] =>
[bok_topics:protected] =>
[bok_keywords:protected] =>
[id:protected] => 53
[type:protected] => category
[parent:protected] => 2
[label:protected] => Concrete Polisher
[alreadyInSave:protected] =>
[alreadyInValidation:protected] =>
[validationFailures:protected] => Array
(
)
[_new:BaseObject:private] =>
[_deleted:BaseObject:private] =>
[modifiedColumns:protected] => Array
(
)
)
[55] => Category Object
(
[languages:protected] =>
[bok_resources:protected] =>
[bok_topics:protected] =>
[bok_keywords:protected] =>
[id:protected] => 55
[type:protected] => category
[parent:protected] => 2
[label:protected] => Electrical Worker
[alreadyInSave:protected] =>
[alreadyInValidation:protected] =>
[validationFailures:protected] => Array
(
)
[_new:BaseObject:private] =>
[_deleted:BaseObject:private] =>
[modifiedColumns:protected] => Array
(
)
)
[60] => Category Object
(
[languages:protected] =>
[bok_resources:protected] =>
[bok_topics:protected] =>
[bok_keywords:protected] =>
[id:protected] => 60
[type:protected] => category
[parent:protected] => 2
[label:protected] => HVAC
[alreadyInSave:protected] =>
[alreadyInValidation:protected] =>
[validationFailures:protected] => Array
(
)
[_new:BaseObject:private] =>
[_deleted:BaseObject:private] =>
[modifiedColumns:protected] => Array
(
)
)
[64] => Category Object
(
[languages:protected] =>
[bok_resources:protected] =>
[bok_topics:protected] =>
[bok_keywords:protected] =>
[id:protected] => 64
[type:protected] => category
[parent:protected] => 2
[label:protected] => Laborer
[alreadyInSave:protected] =>
[alreadyInValidation:protected] =>
[validationFailures:protected] => Array
(
)
[_new:BaseObject:private] =>
[_deleted:BaseObject:private] =>
[modifiedColumns:protected] => Array
(
)
)
[73] => Category Object
(
[languages:protected] =>
[bok_resources:protected] =>
[bok_topics:protected] =>
[bok_keywords:protected] =>
[id:protected] => 73
[type:protected] => category
[parent:protected] => 2
[label:protected] => PCC/Restoration
[alreadyInSave:protected] =>
[alreadyInValidation:protected] =>
[validationFailures:protected] => Array
(
)
[_new:BaseObject:private] =>
[_deleted:BaseObject:private] =>
[modifiedColumns:protected] => Array
(
)
)
[76] => Category Object
(
[languages:protected] =>
[bok_resources:protected] =>
[bok_topics:protected] =>
[bok_keywords:protected] =>
[id:protected] => 76
[type:protected] => category
[parent:protected] => 2
[label:protected] => Plumber/Pipefitter
[alreadyInSave:protected] =>
[alreadyInValidation:protected] =>
[validationFailures:protected] => Array
(
)
[_new:BaseObject:private] =>
[_deleted:BaseObject:private] =>
[modifiedColumns:protected] => Array
(
)
)
[78] => Category Object
(
[languages:protected] =>
[bok_resources:protected] =>
[bok_topics:protected] =>
[bok_keywords:protected] =>
[id:protected] => 78
[type:protected] => category
[parent:protected] => 2
[label:protected] => Roofer/Waterproofer
[alreadyInSave:protected] =>
[alreadyInValidation:protected] =>
[validationFailures:protected] => Array
(
)
[_new:BaseObject:private] =>
[_deleted:BaseObject:private] =>
[modifiedColumns:protected] => Array
(
)
)
[80] => Category Object
(
[languages:protected] =>
[bok_resources:protected] =>
[bok_topics:protected] =>
[bok_keywords:protected] =>
[id:protected] => 80
[type:protected] => category
[parent:protected] => 2
[label:protected] => Sheetmetal Worker
[alreadyInSave:protected] =>
[alreadyInValidation:protected] =>
[validationFailures:protected] => Array
(
)
[_new:BaseObject:private] =>
[_deleted:BaseObject:private] =>
[modifiedColumns:protected] => Array
(
)
)
[86] => Category Object
(
[languages:protected] =>
[bok_resources:protected] =>
[bok_topics:protected] =>
[bok_keywords:protected] =>
[id:protected] => 86
[type:protected] => category
[parent:protected] => 2
[label:protected] => Welder
[alreadyInSave:protected] =>
[alreadyInValidation:protected] =>
[validationFailures:protected] => Array
(
)
[_new:BaseObject:private] =>
[_deleted:BaseObject:private] =>
[modifiedColumns:protected] => Array
(
)
)
[87] => Category Object
(
[languages:protected] =>
[bok_resources:protected] =>
[bok_topics:protected] =>
[bok_keywords:protected] =>
[id:protected] => 87
[type:protected] => category
[parent:protected] => 3
[label:protected] => Commercial & Institutional
[alreadyInSave:protected] =>
[alreadyInValidation:protected] =>
[validationFailures:protected] => Array
(
)
[_new:BaseObject:private] =>
[_deleted:BaseObject:private] =>
[modifiedColumns:protected] => Array
(
)
)
[90] => Category Object
(
[languages:protected] =>
[bok_resources:protected] =>
[bok_topics:protected] =>
[bok_keywords:protected] =>
[id:protected] => 90
[type:protected] => category
[parent:protected] => 3
[label:protected] => Industrial
[alreadyInSave:protected] =>
[alreadyInValidation:protected] =>
[validationFailures:protected] => Array
(
)
[_new:BaseObject:private] =>
[_deleted:BaseObject:private] =>
[modifiedColumns:protected] => Array
(
)
)
[92] => Category Object
(
[languages:protected] =>
[bok_resources:protected] =>
[bok_topics:protected] =>
[bok_keywords:protected] =>
[id:protected] => 92
[type:protected] => category
[parent:protected] => 3
[label:protected] => LEED/Green Construction
[alreadyInSave:protected] =>
[alreadyInValidation:protected] =>
[validationFailures:protected] => Array
(
)
[_new:BaseObject:private] =>
[_deleted:BaseObject:private] =>
[modifiedColumns:protected] => Array
(
)
)
[93] => Category Object
(
[languages:protected] =>
[bok_resources:protected] =>
[bok_topics:protected] =>
[bok_keywords:protected] =>
[id:protected] => 93
[type:protected] => category
[parent:protected] => 3
[label:protected] => Renovations
[alreadyInSave:protected] =>
[alreadyInValidation:protected] =>
[validationFailures:protected] => Array
(
)
[_new:BaseObject:private] =>
[_deleted:BaseObject:private] =>
[modifiedColumns:protected] => Array
(
)
)
[94] => Category Object
(
[languages:protected] =>
[bok_resources:protected] =>
[bok_topics:protected] =>
[bok_keywords:protected] =>
[id:protected] => 94
[type:protected] => category
[parent:protected] => 3
[label:protected] => Residential
[alreadyInSave:protected] =>
[alreadyInValidation:protected] =>
[validationFailures:protected] => Array
(
)
[_new:BaseObject:private] =>
[_deleted:BaseObject:private] =>
[modifiedColumns:protected] => Array
(
)
)
[100] => Category Object
(
[languages:protected] =>
[bok_resources:protected] =>
[bok_topics:protected] =>
[bok_keywords:protected] =>
[id:protected] => 100
[type:protected] => category
[parent:protected] => 6
[label:protected] => Toolbox Talks
[alreadyInSave:protected] =>
[alreadyInValidation:protected] =>
[validationFailures:protected] => Array
(
)
[_new:BaseObject:private] =>
[_deleted:BaseObject:private] =>
[modifiedColumns:protected] => Array
(
)
)
)
[categories_initialized:protected] => 1
[mapped_items:protected] =>
[content:protected] =>
[files:protected] =>
[language:protected] => Language Object
(
[id:protected] => 1
[code:protected] => en
[name:protected] => English
[alreadyInSave:protected] =>
[alreadyInValidation:protected] =>
[validationFailures:protected] => Array
(
)
[_new:BaseObject:private] =>
[_deleted:BaseObject:private] =>
[modifiedColumns:protected] => Array
(
)
)
[old_record:protected] =>
[id:protected] => 4430
[old_id:protected] =>
[elcosh_id:protected] => d001660
[type:protected] => document
[display_type:protected] => HTML only (and links)
[user_id:protected] => 0
[language_id:protected] => 1
[tagging_id:protected] => Mike Aguilar
[priority_id:protected] => 1
[title:protected] => Toolbox Talk: Fixed Ladder
[total_pages:protected] => 0
[billed_pages:protected] => 0
[publication_number:protected] =>
[part_of:protected] =>
[keywords:protected] => Fixed Ladders, Fall Prevention, Falls
[comments:protected] =>
[summary:protected] => The CPWR Toolbox Talk on Fixed Ladders addresses the potential risks associated with using fixed ladders. The resource includes a brief case example, steps to prevent a related injury and questions for discussion. It includes an image that illustrates the hazard, which can be posted in a central location as a reminder of steps to work safely.
Available in
English
and
Spanish.
[transition_comments:protected] =>
[external_link:protected] =>
[consol_link:protected] =>
[more_like_this:protected] => d001257,d001254,d001255,d001256,d001258,d001262,d001279
[permission_given_by:protected] =>
[published:protected] => T
[billable:protected] => F
[img_name:protected] =>
[img_ext:protected] =>
[img_width:protected] =>
[img_height:protected] =>
[img_credit:protected] =>
[img_practice:protected] =>
[vid_source_id:protected] =>
[vid_running_time:protected] =>
[vid_intended_audience:protected] =>
[vid_acquisition_info:protected] =>
[vid_cost:protected] =>
[vid_producer:protected] =>
[vid_filename:protected] =>
[vid_filename_downloadable:protected] =>
[date_summary:protected] =>
[date_permission_requested:protected] =>
[date_permission_received:protected] =>
[date_review_needed:protected] =>
[date_received:protected] => 06/10/22
[date_completed:protected] => 06/10/22
[date_billed:protected] =>
[date_modified:protected] => 05/22/23
[collBokExports:protected] =>
[lastBokExportCriteria:BaseElcoshItem:private] =>
[alreadyInSave:protected] =>
[alreadyInValidation:protected] =>
[validationFailures:protected] => Array
(
)
[_new:BaseObject:private] =>
[_deleted:BaseObject:private] =>
[modifiedColumns:protected] => Array
(
)
)
)
[1] => Search_Result Object
(
[title] => Toolbox Talk: Challenges Preventing Falling Objects
[image] => /record/images/notavailable-p.png
[blurb] => The CPWR Toolbox Talk on Challenges Preventing Falling Objects addresses the hazards of being struck by falling objects on the job site. The resource...
[category] => Array
(
[0] => 12
[1] => 47
[2] => 49
[3] => 51
[4] => 55
[5] => 64
[6] => 68
[7] => 71
[8] => 75
[9] => 78
[10] => 79
[11] => 82
[12] => 62
[13] => 86
[14] => 87
[15] => 88
[16] => 89
[17] => 91
[18] => 90
[19] => 92
[20] => 93
[21] => 94
[22] => 95
[23] => 100
)
[labels] => Array
(
[0] => Crushed/Struck By
[1] => Work Environment
[2] => Hazards
[3] => Bricklayer
[4] => Trades
[5] => Carpenter
[7] => Cement Mason
[9] => Electrical Worker
[11] => Laborer
[13] => Maintenance Worker
[15] => Painter
[17] => Plasterer
[19] => Roofer/Waterproofer
[21] => Scaffold Erector
[23] => Stonemason
[25] => Structural Ironworker
[27] => Welder
[29] => Commercial & Institutional
[30] => Jobsites
[31] => Demolition
[33] => Disasters
[35] => Heavy & Highway
[37] => Industrial
[39] => LEED/Green Construction
[41] => Renovations
[43] => Residential
[45] => Underground
[47] => Toolbox Talks
[48] => Documents
[49] => Media & Documents
)
[type] => Toolbox Talks
[sub_category] =>
[url] => /document/4431/d001661/Toolbox%2BTalk%253A%2BChallenges%2BPreventing%2BFalling%2BObjects.html
[item:protected] => DocumentRecord Object
(
[records:protected] => Array
(
)
[recordId:protected] =>
[searchWordClass:protected] =>
[searchWordPeerClass:protected] =>
[bok_record:protected] =>
[authors:protected] =>
[organizations:protected] =>
[collections:protected] =>
[categories:protected] => Array
(
[12] => Category Object
(
[languages:protected] =>
[bok_resources:protected] =>
[bok_topics:protected] =>
[bok_keywords:protected] =>
[id:protected] => 12
[type:protected] => category
[parent:protected] => 7
[label:protected] => Crushed/Struck By
[alreadyInSave:protected] =>
[alreadyInValidation:protected] =>
[validationFailures:protected] => Array
(
)
[_new:BaseObject:private] =>
[_deleted:BaseObject:private] =>
[modifiedColumns:protected] => Array
(
)
)
[47] => Category Object
(
[languages:protected] =>
[bok_resources:protected] =>
[bok_topics:protected] =>
[bok_keywords:protected] =>
[id:protected] => 47
[type:protected] => category
[parent:protected] => 2
[label:protected] => Bricklayer
[alreadyInSave:protected] =>
[alreadyInValidation:protected] =>
[validationFailures:protected] => Array
(
)
[_new:BaseObject:private] =>
[_deleted:BaseObject:private] =>
[modifiedColumns:protected] => Array
(
)
)
[49] => Category Object
(
[languages:protected] =>
[bok_resources:protected] =>
[bok_topics:protected] =>
[bok_keywords:protected] =>
[id:protected] => 49
[type:protected] => category
[parent:protected] => 2
[label:protected] => Carpenter
[alreadyInSave:protected] =>
[alreadyInValidation:protected] =>
[validationFailures:protected] => Array
(
)
[_new:BaseObject:private] =>
[_deleted:BaseObject:private] =>
[modifiedColumns:protected] => Array
(
)
)
[51] => Category Object
(
[languages:protected] =>
[bok_resources:protected] =>
[bok_topics:protected] =>
[bok_keywords:protected] =>
[id:protected] => 51
[type:protected] => category
[parent:protected] => 2
[label:protected] => Cement Mason
[alreadyInSave:protected] =>
[alreadyInValidation:protected] =>
[validationFailures:protected] => Array
(
)
[_new:BaseObject:private] =>
[_deleted:BaseObject:private] =>
[modifiedColumns:protected] => Array
(
)
)
[55] => Category Object
(
[languages:protected] =>
[bok_resources:protected] =>
[bok_topics:protected] =>
[bok_keywords:protected] =>
[id:protected] => 55
[type:protected] => category
[parent:protected] => 2
[label:protected] => Electrical Worker
[alreadyInSave:protected] =>
[alreadyInValidation:protected] =>
[validationFailures:protected] => Array
(
)
[_new:BaseObject:private] =>
[_deleted:BaseObject:private] =>
[modifiedColumns:protected] => Array
(
)
)
[64] => Category Object
(
[languages:protected] =>
[bok_resources:protected] =>
[bok_topics:protected] =>
[bok_keywords:protected] =>
[id:protected] => 64
[type:protected] => category
[parent:protected] => 2
[label:protected] => Laborer
[alreadyInSave:protected] =>
[alreadyInValidation:protected] =>
[validationFailures:protected] => Array
(
)
[_new:BaseObject:private] =>
[_deleted:BaseObject:private] =>
[modifiedColumns:protected] => Array
(
)
)
[68] => Category Object
(
[languages:protected] =>
[bok_resources:protected] =>
[bok_topics:protected] =>
[bok_keywords:protected] =>
[id:protected] => 68
[type:protected] => category
[parent:protected] => 2
[label:protected] => Maintenance Worker
[alreadyInSave:protected] =>
[alreadyInValidation:protected] =>
[validationFailures:protected] => Array
(
)
[_new:BaseObject:private] =>
[_deleted:BaseObject:private] =>
[modifiedColumns:protected] => Array
(
)
)
[71] => Category Object
(
[languages:protected] =>
[bok_resources:protected] =>
[bok_topics:protected] =>
[bok_keywords:protected] =>
[id:protected] => 71
[type:protected] => category
[parent:protected] => 2
[label:protected] => Painter
[alreadyInSave:protected] =>
[alreadyInValidation:protected] =>
[validationFailures:protected] => Array
(
)
[_new:BaseObject:private] =>
[_deleted:BaseObject:private] =>
[modifiedColumns:protected] => Array
(
)
)
[75] => Category Object
(
[languages:protected] =>
[bok_resources:protected] =>
[bok_topics:protected] =>
[bok_keywords:protected] =>
[id:protected] => 75
[type:protected] => category
[parent:protected] => 2
[label:protected] => Plasterer
[alreadyInSave:protected] =>
[alreadyInValidation:protected] =>
[validationFailures:protected] => Array
(
)
[_new:BaseObject:private] =>
[_deleted:BaseObject:private] =>
[modifiedColumns:protected] => Array
(
)
)
[78] => Category Object
(
[languages:protected] =>
[bok_resources:protected] =>
[bok_topics:protected] =>
[bok_keywords:protected] =>
[id:protected] => 78
[type:protected] => category
[parent:protected] => 2
[label:protected] => Roofer/Waterproofer
[alreadyInSave:protected] =>
[alreadyInValidation:protected] =>
[validationFailures:protected] => Array
(
)
[_new:BaseObject:private] =>
[_deleted:BaseObject:private] =>
[modifiedColumns:protected] => Array
(
)
)
[79] => Category Object
(
[languages:protected] =>
[bok_resources:protected] =>
[bok_topics:protected] =>
[bok_keywords:protected] =>
[id:protected] => 79
[type:protected] => category
[parent:protected] => 2
[label:protected] => Scaffold Erector
[alreadyInSave:protected] =>
[alreadyInValidation:protected] =>
[validationFailures:protected] => Array
(
)
[_new:BaseObject:private] =>
[_deleted:BaseObject:private] =>
[modifiedColumns:protected] => Array
(
)
)
[82] => Category Object
(
[languages:protected] =>
[bok_resources:protected] =>
[bok_topics:protected] =>
[bok_keywords:protected] =>
[id:protected] => 82
[type:protected] => category
[parent:protected] => 2
[label:protected] => Stonemason
[alreadyInSave:protected] =>
[alreadyInValidation:protected] =>
[validationFailures:protected] => Array
(
)
[_new:BaseObject:private] =>
[_deleted:BaseObject:private] =>
[modifiedColumns:protected] => Array
(
)
)
[62] => Category Object
(
[languages:protected] =>
[bok_resources:protected] =>
[bok_topics:protected] =>
[bok_keywords:protected] =>
[id:protected] => 62
[type:protected] => category
[parent:protected] => 2
[label:protected] => Structural Ironworker
[alreadyInSave:protected] =>
[alreadyInValidation:protected] =>
[validationFailures:protected] => Array
(
)
[_new:BaseObject:private] =>
[_deleted:BaseObject:private] =>
[modifiedColumns:protected] => Array
(
)
)
[86] => Category Object
(
[languages:protected] =>
[bok_resources:protected] =>
[bok_topics:protected] =>
[bok_keywords:protected] =>
[id:protected] => 86
[type:protected] => category
[parent:protected] => 2
[label:protected] => Welder
[alreadyInSave:protected] =>
[alreadyInValidation:protected] =>
[validationFailures:protected] => Array
(
)
[_new:BaseObject:private] =>
[_deleted:BaseObject:private] =>
[modifiedColumns:protected] => Array
(
)
)
[87] => Category Object
(
[languages:protected] =>
[bok_resources:protected] =>
[bok_topics:protected] =>
[bok_keywords:protected] =>
[id:protected] => 87
[type:protected] => category
[parent:protected] => 3
[label:protected] => Commercial & Institutional
[alreadyInSave:protected] =>
[alreadyInValidation:protected] =>
[validationFailures:protected] => Array
(
)
[_new:BaseObject:private] =>
[_deleted:BaseObject:private] =>
[modifiedColumns:protected] => Array
(
)
)
[88] => Category Object
(
[languages:protected] =>
[bok_resources:protected] =>
[bok_topics:protected] =>
[bok_keywords:protected] =>
[id:protected] => 88
[type:protected] => category
[parent:protected] => 3
[label:protected] => Demolition
[alreadyInSave:protected] =>
[alreadyInValidation:protected] =>
[validationFailures:protected] => Array
(
)
[_new:BaseObject:private] =>
[_deleted:BaseObject:private] =>
[modifiedColumns:protected] => Array
(
)
)
[89] => Category Object
(
[languages:protected] =>
[bok_resources:protected] =>
[bok_topics:protected] =>
[bok_keywords:protected] =>
[id:protected] => 89
[type:protected] => category
[parent:protected] => 3
[label:protected] => Disasters
[alreadyInSave:protected] =>
[alreadyInValidation:protected] =>
[validationFailures:protected] => Array
(
)
[_new:BaseObject:private] =>
[_deleted:BaseObject:private] =>
[modifiedColumns:protected] => Array
(
)
)
[91] => Category Object
(
[languages:protected] =>
[bok_resources:protected] =>
[bok_topics:protected] =>
[bok_keywords:protected] =>
[id:protected] => 91
[type:protected] => category
[parent:protected] => 3
[label:protected] => Heavy & Highway
[alreadyInSave:protected] =>
[alreadyInValidation:protected] =>
[validationFailures:protected] => Array
(
)
[_new:BaseObject:private] =>
[_deleted:BaseObject:private] =>
[modifiedColumns:protected] => Array
(
)
)
[90] => Category Object
(
[languages:protected] =>
[bok_resources:protected] =>
[bok_topics:protected] =>
[bok_keywords:protected] =>
[id:protected] => 90
[type:protected] => category
[parent:protected] => 3
[label:protected] => Industrial
[alreadyInSave:protected] =>
[alreadyInValidation:protected] =>
[validationFailures:protected] => Array
(
)
[_new:BaseObject:private] =>
[_deleted:BaseObject:private] =>
[modifiedColumns:protected] => Array
(
)
)
[92] => Category Object
(
[languages:protected] =>
[bok_resources:protected] =>
[bok_topics:protected] =>
[bok_keywords:protected] =>
[id:protected] => 92
[type:protected] => category
[parent:protected] => 3
[label:protected] => LEED/Green Construction
[alreadyInSave:protected] =>
[alreadyInValidation:protected] =>
[validationFailures:protected] => Array
(
)
[_new:BaseObject:private] =>
[_deleted:BaseObject:private] =>
[modifiedColumns:protected] => Array
(
)
)
[93] => Category Object
(
[languages:protected] =>
[bok_resources:protected] =>
[bok_topics:protected] =>
[bok_keywords:protected] =>
[id:protected] => 93
[type:protected] => category
[parent:protected] => 3
[label:protected] => Renovations
[alreadyInSave:protected] =>
[alreadyInValidation:protected] =>
[validationFailures:protected] => Array
(
)
[_new:BaseObject:private] =>
[_deleted:BaseObject:private] =>
[modifiedColumns:protected] => Array
(
)
)
[94] => Category Object
(
[languages:protected] =>
[bok_resources:protected] =>
[bok_topics:protected] =>
[bok_keywords:protected] =>
[id:protected] => 94
[type:protected] => category
[parent:protected] => 3
[label:protected] => Residential
[alreadyInSave:protected] =>
[alreadyInValidation:protected] =>
[validationFailures:protected] => Array
(
)
[_new:BaseObject:private] =>
[_deleted:BaseObject:private] =>
[modifiedColumns:protected] => Array
(
)
)
[95] => Category Object
(
[languages:protected] =>
[bok_resources:protected] =>
[bok_topics:protected] =>
[bok_keywords:protected] =>
[id:protected] => 95
[type:protected] => category
[parent:protected] => 3
[label:protected] => Underground
[alreadyInSave:protected] =>
[alreadyInValidation:protected] =>
[validationFailures:protected] => Array
(
)
[_new:BaseObject:private] =>
[_deleted:BaseObject:private] =>
[modifiedColumns:protected] => Array
(
)
)
[100] => Category Object
(
[languages:protected] =>
[bok_resources:protected] =>
[bok_topics:protected] =>
[bok_keywords:protected] =>
[id:protected] => 100
[type:protected] => category
[parent:protected] => 6
[label:protected] => Toolbox Talks
[alreadyInSave:protected] =>
[alreadyInValidation:protected] =>
[validationFailures:protected] => Array
(
)
[_new:BaseObject:private] =>
[_deleted:BaseObject:private] =>
[modifiedColumns:protected] => Array
(
)
)
)
[categories_initialized:protected] => 1
[mapped_items:protected] =>
[content:protected] =>
[files:protected] =>
[language:protected] => Language Object
(
[id:protected] => 1
[code:protected] => en
[name:protected] => English
[alreadyInSave:protected] =>
[alreadyInValidation:protected] =>
[validationFailures:protected] => Array
(
)
[_new:BaseObject:private] =>
[_deleted:BaseObject:private] =>
[modifiedColumns:protected] => Array
(
)
)
[old_record:protected] =>
[id:protected] => 4431
[old_id:protected] =>
[elcosh_id:protected] => d001661
[type:protected] => document
[display_type:protected] => HTML only (and links)
[user_id:protected] => 0
[language_id:protected] => 1
[tagging_id:protected] => Mike Aguilar
[priority_id:protected] => 1
[title:protected] => Toolbox Talk: Challenges Preventing Falling Objects
[total_pages:protected] => 0
[billed_pages:protected] => 0
[publication_number:protected] =>
[part_of:protected] =>
[keywords:protected] => dropped objects, falling objects, struck by incidents, struck by fatalities
[comments:protected] =>
[summary:protected] => The CPWR Toolbox Talk on Challenges Preventing Falling Objects addresses the hazards of being struck by falling objects on the job site. The resource includes a brief example, steps to prevent a related injury, and questions for discussion. It includes a graphic that illustrates a group workers observing a scaffold free of debris during high winds, which can be posted in a central location as a reminder of steps to work safely.
Available in
English and
Spanish.
[transition_comments:protected] =>
[external_link:protected] =>
[consol_link:protected] =>
[more_like_this:protected] => d001234,d001238,d001244,d001251,d001253,d001260,d001268,d001278
[permission_given_by:protected] =>
[published:protected] => T
[billable:protected] => F
[img_name:protected] =>
[img_ext:protected] =>
[img_width:protected] =>
[img_height:protected] =>
[img_credit:protected] =>
[img_practice:protected] =>
[vid_source_id:protected] =>
[vid_running_time:protected] =>
[vid_intended_audience:protected] =>
[vid_acquisition_info:protected] =>
[vid_cost:protected] =>
[vid_producer:protected] =>
[vid_filename:protected] =>
[vid_filename_downloadable:protected] =>
[date_summary:protected] =>
[date_permission_requested:protected] =>
[date_permission_received:protected] =>
[date_review_needed:protected] =>
[date_received:protected] => 06/10/22
[date_completed:protected] => 06/10/22
[date_billed:protected] =>
[date_modified:protected] => 05/22/23
[collBokExports:protected] =>
[lastBokExportCriteria:BaseElcoshItem:private] =>
[alreadyInSave:protected] =>
[alreadyInValidation:protected] =>
[validationFailures:protected] => Array
(
)
[_new:BaseObject:private] =>
[_deleted:BaseObject:private] =>
[modifiedColumns:protected] => Array
(
)
)
)
[2] => Search_Result Object
(
[title] => Toolbox Talk: Tower Crane Safety
[image] => /record/images/notavailable-p.png
[blurb] => The CPWR Toolbox Talk on Tower Crane Safety addresses the potential hazards of Tower Cranes and the importance of following procedure before and durin...
[category] => Array
(
[0] => 11
[1] => 12
[2] => 18
[3] => 70
[4] => 87
[5] => 88
[6] => 91
[7] => 90
[8] => 92
[9] => 100
)
[labels] => Array
(
[0] => Cranes & Hoists
[1] => Work Environment
[2] => Hazards
[3] => Crushed/Struck By
[6] => Motor Vehicles/Heavy Equipment
[9] => Operating Engineer
[10] => Trades
[11] => Commercial & Institutional
[12] => Jobsites
[13] => Demolition
[15] => Heavy & Highway
[17] => Industrial
[19] => LEED/Green Construction
[21] => Toolbox Talks
[22] => Documents
[23] => Media & Documents
)
[type] => Toolbox Talks
[sub_category] =>
[url] => /document/4427/d001657/Toolbox%2BTalk%253A%2BTower%2BCrane%2BSafety.html
[item:protected] => DocumentRecord Object
(
[records:protected] => Array
(
)
[recordId:protected] =>
[searchWordClass:protected] =>
[searchWordPeerClass:protected] =>
[bok_record:protected] =>
[authors:protected] =>
[organizations:protected] =>
[collections:protected] =>
[categories:protected] => Array
(
[11] => Category Object
(
[languages:protected] =>
[bok_resources:protected] =>
[bok_topics:protected] =>
[bok_keywords:protected] =>
[id:protected] => 11
[type:protected] => category
[parent:protected] => 7
[label:protected] => Cranes & Hoists
[alreadyInSave:protected] =>
[alreadyInValidation:protected] =>
[validationFailures:protected] => Array
(
)
[_new:BaseObject:private] =>
[_deleted:BaseObject:private] =>
[modifiedColumns:protected] => Array
(
)
)
[12] => Category Object
(
[languages:protected] =>
[bok_resources:protected] =>
[bok_topics:protected] =>
[bok_keywords:protected] =>
[id:protected] => 12
[type:protected] => category
[parent:protected] => 7
[label:protected] => Crushed/Struck By
[alreadyInSave:protected] =>
[alreadyInValidation:protected] =>
[validationFailures:protected] => Array
(
)
[_new:BaseObject:private] =>
[_deleted:BaseObject:private] =>
[modifiedColumns:protected] => Array
(
)
)
[18] => Category Object
(
[languages:protected] =>
[bok_resources:protected] =>
[bok_topics:protected] =>
[bok_keywords:protected] =>
[id:protected] => 18
[type:protected] => category
[parent:protected] => 7
[label:protected] => Motor Vehicles/Heavy Equipment
[alreadyInSave:protected] =>
[alreadyInValidation:protected] =>
[validationFailures:protected] => Array
(
)
[_new:BaseObject:private] =>
[_deleted:BaseObject:private] =>
[modifiedColumns:protected] => Array
(
)
)
[70] => Category Object
(
[languages:protected] =>
[bok_resources:protected] =>
[bok_topics:protected] =>
[bok_keywords:protected] =>
[id:protected] => 70
[type:protected] => category
[parent:protected] => 2
[label:protected] => Operating Engineer
[alreadyInSave:protected] =>
[alreadyInValidation:protected] =>
[validationFailures:protected] => Array
(
)
[_new:BaseObject:private] =>
[_deleted:BaseObject:private] =>
[modifiedColumns:protected] => Array
(
)
)
[87] => Category Object
(
[languages:protected] =>
[bok_resources:protected] =>
[bok_topics:protected] =>
[bok_keywords:protected] =>
[id:protected] => 87
[type:protected] => category
[parent:protected] => 3
[label:protected] => Commercial & Institutional
[alreadyInSave:protected] =>
[alreadyInValidation:protected] =>
[validationFailures:protected] => Array
(
)
[_new:BaseObject:private] =>
[_deleted:BaseObject:private] =>
[modifiedColumns:protected] => Array
(
)
)
[88] => Category Object
(
[languages:protected] =>
[bok_resources:protected] =>
[bok_topics:protected] =>
[bok_keywords:protected] =>
[id:protected] => 88
[type:protected] => category
[parent:protected] => 3
[label:protected] => Demolition
[alreadyInSave:protected] =>
[alreadyInValidation:protected] =>
[validationFailures:protected] => Array
(
)
[_new:BaseObject:private] =>
[_deleted:BaseObject:private] =>
[modifiedColumns:protected] => Array
(
)
)
[91] => Category Object
(
[languages:protected] =>
[bok_resources:protected] =>
[bok_topics:protected] =>
[bok_keywords:protected] =>
[id:protected] => 91
[type:protected] => category
[parent:protected] => 3
[label:protected] => Heavy & Highway
[alreadyInSave:protected] =>
[alreadyInValidation:protected] =>
[validationFailures:protected] => Array
(
)
[_new:BaseObject:private] =>
[_deleted:BaseObject:private] =>
[modifiedColumns:protected] => Array
(
)
)
[90] => Category Object
(
[languages:protected] =>
[bok_resources:protected] =>
[bok_topics:protected] =>
[bok_keywords:protected] =>
[id:protected] => 90
[type:protected] => category
[parent:protected] => 3
[label:protected] => Industrial
[alreadyInSave:protected] =>
[alreadyInValidation:protected] =>
[validationFailures:protected] => Array
(
)
[_new:BaseObject:private] =>
[_deleted:BaseObject:private] =>
[modifiedColumns:protected] => Array
(
)
)
[92] => Category Object
(
[languages:protected] =>
[bok_resources:protected] =>
[bok_topics:protected] =>
[bok_keywords:protected] =>
[id:protected] => 92
[type:protected] => category
[parent:protected] => 3
[label:protected] => LEED/Green Construction
[alreadyInSave:protected] =>
[alreadyInValidation:protected] =>
[validationFailures:protected] => Array
(
)
[_new:BaseObject:private] =>
[_deleted:BaseObject:private] =>
[modifiedColumns:protected] => Array
(
)
)
[100] => Category Object
(
[languages:protected] =>
[bok_resources:protected] =>
[bok_topics:protected] =>
[bok_keywords:protected] =>
[id:protected] => 100
[type:protected] => category
[parent:protected] => 6
[label:protected] => Toolbox Talks
[alreadyInSave:protected] =>
[alreadyInValidation:protected] =>
[validationFailures:protected] => Array
(
)
[_new:BaseObject:private] =>
[_deleted:BaseObject:private] =>
[modifiedColumns:protected] => Array
(
)
)
)
[categories_initialized:protected] => 1
[mapped_items:protected] =>
[content:protected] =>
[files:protected] =>
[language:protected] => Language Object
(
[id:protected] => 1
[code:protected] => en
[name:protected] => English
[alreadyInSave:protected] =>
[alreadyInValidation:protected] =>
[validationFailures:protected] => Array
(
)
[_new:BaseObject:private] =>
[_deleted:BaseObject:private] =>
[modifiedColumns:protected] => Array
(
)
)
[old_record:protected] =>
[id:protected] => 4427
[old_id:protected] =>
[elcosh_id:protected] => d001657
[type:protected] => document
[display_type:protected] => HTML only (and links)
[user_id:protected] => 0
[language_id:protected] => 1
[tagging_id:protected] => Mike Aguilar
[priority_id:protected] => 1
[title:protected] => Toolbox Talk: Tower Crane Safety
[total_pages:protected] => 0
[billed_pages:protected] => 0
[publication_number:protected] =>
[part_of:protected] =>
[keywords:protected] => Tower Crane, Crane, Stability, Tipping, Lift Zone Safety, Lift, Zone, Safety, Struck by
[comments:protected] =>
[summary:protected] => The CPWR Toolbox Talk on Tower Crane Safety addresses the potential hazards of Tower Cranes and the importance of following procedure before and during Tower Crane operation. The resource includes a brief example, steps to prevent a related injury, and questions for discussion. It includes a graphic that illustrates a worker inspecting a Tower Crane before operation, which can be posted in a central location as a reminder of steps to work safely.
Available in
English and
Spanish.
[transition_comments:protected] =>
[external_link:protected] =>
[consol_link:protected] =>
[more_like_this:protected] => d001234,d001238,d001250,d001251,d001253,d001258,d001262,d001273
[permission_given_by:protected] =>
[published:protected] => T
[billable:protected] => F
[img_name:protected] =>
[img_ext:protected] => jpg
[img_width:protected] =>
[img_height:protected] =>
[img_credit:protected] =>
[img_practice:protected] =>
[vid_source_id:protected] =>
[vid_running_time:protected] =>
[vid_intended_audience:protected] =>
[vid_acquisition_info:protected] =>
[vid_cost:protected] =>
[vid_producer:protected] =>
[vid_filename:protected] =>
[vid_filename_downloadable:protected] =>
[date_summary:protected] =>
[date_permission_requested:protected] =>
[date_permission_received:protected] =>
[date_review_needed:protected] =>
[date_received:protected] => 12/23/21
[date_completed:protected] => 12/23/21
[date_billed:protected] =>
[date_modified:protected] => 05/19/23
[collBokExports:protected] =>
[lastBokExportCriteria:BaseElcoshItem:private] =>
[alreadyInSave:protected] =>
[alreadyInValidation:protected] =>
[validationFailures:protected] => Array
(
)
[_new:BaseObject:private] =>
[_deleted:BaseObject:private] =>
[modifiedColumns:protected] => Array
(
)
)
)
[3] => Search_Result Object
(
[title] => Toolbox Talk: Work Zone Safety: Working Around Vehicles
[image] => /record/images/notavailable-p.png
[blurb] => The CPWR Toolbox Talk on Working Around Vehicles in the Work Zone addresses methods to avoid being struck-by a vehicle on a construction site. The res...
[category] => Array
(
[0] => 12
[1] => 18
[2] => 52
[3] => 57
[4] => 70
[5] => 85
[6] => 87
[7] => 88
[8] => 89
[9] => 91
[10] => 90
[11] => 92
[12] => 93
[13] => 94
[14] => 95
[15] => 100
)
[labels] => Array
(
[0] => Crushed/Struck By
[1] => Work Environment
[2] => Hazards
[3] => Motor Vehicles/Heavy Equipment
[6] => Commercial Diver
[7] => Trades
[8] => Flagger
[10] => Operating Engineer
[12] => Truck Driver
[14] => Commercial & Institutional
[15] => Jobsites
[16] => Demolition
[18] => Disasters
[20] => Heavy & Highway
[22] => Industrial
[24] => LEED/Green Construction
[26] => Renovations
[28] => Residential
[30] => Underground
[32] => Toolbox Talks
[33] => Documents
[34] => Media & Documents
)
[type] => Toolbox Talks
[sub_category] =>
[url] => /document/4428/d001658/Toolbox%2BTalk%253A%2BWork%2BZone%2BSafety%253A%2BWorking%2BAround%2BVehicles.html
[item:protected] => DocumentRecord Object
(
[records:protected] => Array
(
)
[recordId:protected] =>
[searchWordClass:protected] =>
[searchWordPeerClass:protected] =>
[bok_record:protected] =>
[authors:protected] =>
[organizations:protected] =>
[collections:protected] =>
[categories:protected] => Array
(
[12] => Category Object
(
[languages:protected] =>
[bok_resources:protected] =>
[bok_topics:protected] =>
[bok_keywords:protected] =>
[id:protected] => 12
[type:protected] => category
[parent:protected] => 7
[label:protected] => Crushed/Struck By
[alreadyInSave:protected] =>
[alreadyInValidation:protected] =>
[validationFailures:protected] => Array
(
)
[_new:BaseObject:private] =>
[_deleted:BaseObject:private] =>
[modifiedColumns:protected] => Array
(
)
)
[18] => Category Object
(
[languages:protected] =>
[bok_resources:protected] =>
[bok_topics:protected] =>
[bok_keywords:protected] =>
[id:protected] => 18
[type:protected] => category
[parent:protected] => 7
[label:protected] => Motor Vehicles/Heavy Equipment
[alreadyInSave:protected] =>
[alreadyInValidation:protected] =>
[validationFailures:protected] => Array
(
)
[_new:BaseObject:private] =>
[_deleted:BaseObject:private] =>
[modifiedColumns:protected] => Array
(
)
)
[52] => Category Object
(
[languages:protected] =>
[bok_resources:protected] =>
[bok_topics:protected] =>
[bok_keywords:protected] =>
[id:protected] => 52
[type:protected] => category
[parent:protected] => 2
[label:protected] => Commercial Diver
[alreadyInSave:protected] =>
[alreadyInValidation:protected] =>
[validationFailures:protected] => Array
(
)
[_new:BaseObject:private] =>
[_deleted:BaseObject:private] =>
[modifiedColumns:protected] => Array
(
)
)
[57] => Category Object
(
[languages:protected] =>
[bok_resources:protected] =>
[bok_topics:protected] =>
[bok_keywords:protected] =>
[id:protected] => 57
[type:protected] => category
[parent:protected] => 2
[label:protected] => Flagger
[alreadyInSave:protected] =>
[alreadyInValidation:protected] =>
[validationFailures:protected] => Array
(
)
[_new:BaseObject:private] =>
[_deleted:BaseObject:private] =>
[modifiedColumns:protected] => Array
(
)
)
[70] => Category Object
(
[languages:protected] =>
[bok_resources:protected] =>
[bok_topics:protected] =>
[bok_keywords:protected] =>
[id:protected] => 70
[type:protected] => category
[parent:protected] => 2
[label:protected] => Operating Engineer
[alreadyInSave:protected] =>
[alreadyInValidation:protected] =>
[validationFailures:protected] => Array
(
)
[_new:BaseObject:private] =>
[_deleted:BaseObject:private] =>
[modifiedColumns:protected] => Array
(
)
)
[85] => Category Object
(
[languages:protected] =>
[bok_resources:protected] =>
[bok_topics:protected] =>
[bok_keywords:protected] =>
[id:protected] => 85
[type:protected] => category
[parent:protected] => 2
[label:protected] => Truck Driver
[alreadyInSave:protected] =>
[alreadyInValidation:protected] =>
[validationFailures:protected] => Array
(
)
[_new:BaseObject:private] =>
[_deleted:BaseObject:private] =>
[modifiedColumns:protected] => Array
(
)
)
[87] => Category Object
(
[languages:protected] =>
[bok_resources:protected] =>
[bok_topics:protected] =>
[bok_keywords:protected] =>
[id:protected] => 87
[type:protected] => category
[parent:protected] => 3
[label:protected] => Commercial & Institutional
[alreadyInSave:protected] =>
[alreadyInValidation:protected] =>
[validationFailures:protected] => Array
(
)
[_new:BaseObject:private] =>
[_deleted:BaseObject:private] =>
[modifiedColumns:protected] => Array
(
)
)
[88] => Category Object
(
[languages:protected] =>
[bok_resources:protected] =>
[bok_topics:protected] =>
[bok_keywords:protected] =>
[id:protected] => 88
[type:protected] => category
[parent:protected] => 3
[label:protected] => Demolition
[alreadyInSave:protected] =>
[alreadyInValidation:protected] =>
[validationFailures:protected] => Array
(
)
[_new:BaseObject:private] =>
[_deleted:BaseObject:private] =>
[modifiedColumns:protected] => Array
(
)
)
[89] => Category Object
(
[languages:protected] =>
[bok_resources:protected] =>
[bok_topics:protected] =>
[bok_keywords:protected] =>
[id:protected] => 89
[type:protected] => category
[parent:protected] => 3
[label:protected] => Disasters
[alreadyInSave:protected] =>
[alreadyInValidation:protected] =>
[validationFailures:protected] => Array
(
)
[_new:BaseObject:private] =>
[_deleted:BaseObject:private] =>
[modifiedColumns:protected] => Array
(
)
)
[91] => Category Object
(
[languages:protected] =>
[bok_resources:protected] =>
[bok_topics:protected] =>
[bok_keywords:protected] =>
[id:protected] => 91
[type:protected] => category
[parent:protected] => 3
[label:protected] => Heavy & Highway
[alreadyInSave:protected] =>
[alreadyInValidation:protected] =>
[validationFailures:protected] => Array
(
)
[_new:BaseObject:private] =>
[_deleted:BaseObject:private] =>
[modifiedColumns:protected] => Array
(
)
)
[90] => Category Object
(
[languages:protected] =>
[bok_resources:protected] =>
[bok_topics:protected] =>
[bok_keywords:protected] =>
[id:protected] => 90
[type:protected] => category
[parent:protected] => 3
[label:protected] => Industrial
[alreadyInSave:protected] =>
[alreadyInValidation:protected] =>
[validationFailures:protected] => Array
(
)
[_new:BaseObject:private] =>
[_deleted:BaseObject:private] =>
[modifiedColumns:protected] => Array
(
)
)
[92] => Category Object
(
[languages:protected] =>
[bok_resources:protected] =>
[bok_topics:protected] =>
[bok_keywords:protected] =>
[id:protected] => 92
[type:protected] => category
[parent:protected] => 3
[label:protected] => LEED/Green Construction
[alreadyInSave:protected] =>
[alreadyInValidation:protected] =>
[validationFailures:protected] => Array
(
)
[_new:BaseObject:private] =>
[_deleted:BaseObject:private] =>
[modifiedColumns:protected] => Array
(
)
)
[93] => Category Object
(
[languages:protected] =>
[bok_resources:protected] =>
[bok_topics:protected] =>
[bok_keywords:protected] =>
[id:protected] => 93
[type:protected] => category
[parent:protected] => 3
[label:protected] => Renovations
[alreadyInSave:protected] =>
[alreadyInValidation:protected] =>
[validationFailures:protected] => Array
(
)
[_new:BaseObject:private] =>
[_deleted:BaseObject:private] =>
[modifiedColumns:protected] => Array
(
)
)
[94] => Category Object
(
[languages:protected] =>
[bok_resources:protected] =>
[bok_topics:protected] =>
[bok_keywords:protected] =>
[id:protected] => 94
[type:protected] => category
[parent:protected] => 3
[label:protected] => Residential
[alreadyInSave:protected] =>
[alreadyInValidation:protected] =>
[validationFailures:protected] => Array
(
)
[_new:BaseObject:private] =>
[_deleted:BaseObject:private] =>
[modifiedColumns:protected] => Array
(
)
)
[95] => Category Object
(
[languages:protected] =>
[bok_resources:protected] =>
[bok_topics:protected] =>
[bok_keywords:protected] =>
[id:protected] => 95
[type:protected] => category
[parent:protected] => 3
[label:protected] => Underground
[alreadyInSave:protected] =>
[alreadyInValidation:protected] =>
[validationFailures:protected] => Array
(
)
[_new:BaseObject:private] =>
[_deleted:BaseObject:private] =>
[modifiedColumns:protected] => Array
(
)
)
[100] => Category Object
(
[languages:protected] =>
[bok_resources:protected] =>
[bok_topics:protected] =>
[bok_keywords:protected] =>
[id:protected] => 100
[type:protected] => category
[parent:protected] => 6
[label:protected] => Toolbox Talks
[alreadyInSave:protected] =>
[alreadyInValidation:protected] =>
[validationFailures:protected] => Array
(
)
[_new:BaseObject:private] =>
[_deleted:BaseObject:private] =>
[modifiedColumns:protected] => Array
(
)
)
)
[categories_initialized:protected] => 1
[mapped_items:protected] =>
[content:protected] =>
[files:protected] =>
[language:protected] => Language Object
(
[id:protected] => 1
[code:protected] => en
[name:protected] => English
[alreadyInSave:protected] =>
[alreadyInValidation:protected] =>
[validationFailures:protected] => Array
(
)
[_new:BaseObject:private] =>
[_deleted:BaseObject:private] =>
[modifiedColumns:protected] => Array
(
)
)
[old_record:protected] =>
[id:protected] => 4428
[old_id:protected] =>
[elcosh_id:protected] => d001658
[type:protected] => document
[display_type:protected] => HTML only (and links)
[user_id:protected] => 0
[language_id:protected] => 1
[tagging_id:protected] => Daniela Caceres
[priority_id:protected] => 1
[title:protected] => Toolbox Talk: Work Zone Safety: Working Around Vehicles
[total_pages:protected] => 0
[billed_pages:protected] => 0
[publication_number:protected] =>
[part_of:protected] =>
[keywords:protected] => Struck, Struck by, Vehicle, Work Zone Safety, Truck, Operator, Driver, Mobile Equipment
[comments:protected] =>
[summary:protected] => The CPWR Toolbox Talk on Working Around Vehicles in the Work Zone addresses methods to avoid being struck-by a vehicle on a construction site. The resource includes a case example, steps to prevent a related injury, and questions for discussion. It includes a graphic that illustrates the hazard, which can be posted in a central location as a reminder of steps to work safely. Available in
English and
Spanish.
[transition_comments:protected] =>
[external_link:protected] =>
[consol_link:protected] =>
[more_like_this:protected] => d001640
[permission_given_by:protected] =>
[published:protected] => T
[billable:protected] => F
[img_name:protected] =>
[img_ext:protected] =>
[img_width:protected] =>
[img_height:protected] =>
[img_credit:protected] =>
[img_practice:protected] =>
[vid_source_id:protected] =>
[vid_running_time:protected] =>
[vid_intended_audience:protected] =>
[vid_acquisition_info:protected] =>
[vid_cost:protected] =>
[vid_producer:protected] =>
[vid_filename:protected] =>
[vid_filename_downloadable:protected] =>
[date_summary:protected] =>
[date_permission_requested:protected] =>
[date_permission_received:protected] =>
[date_review_needed:protected] =>
[date_received:protected] => 12/23/21
[date_completed:protected] => 12/23/21
[date_billed:protected] =>
[date_modified:protected] => 05/19/23
[collBokExports:protected] =>
[lastBokExportCriteria:BaseElcoshItem:private] =>
[alreadyInSave:protected] =>
[alreadyInValidation:protected] =>
[validationFailures:protected] => Array
(
)
[_new:BaseObject:private] =>
[_deleted:BaseObject:private] =>
[modifiedColumns:protected] => Array
(
)
)
)
[4] => Search_Result Object
(
[title] => Construction Dive -- DeWalt's Jobsite Pro headphones recalled for fire hazards
[image] => /record/images/notavailable-p.png
[blurb] => A recall notice by the United States Consumer Product Safety Commission affects over 300,000 DeWalt Jobsite Pro Headphones. The recall is a result of...
[category] => Array
(
[0] => 16
[1] => 44
[2] => 45
[3] => 46
[4] => 47
[5] => 48
[6] => 49
[7] => 50
[8] => 51
[9] => 52
[10] => 53
[11] => 54
[12] => 55
[13] => 56
[14] => 57
[15] => 58
[16] => 59
[17] => 60
[18] => 61
[19] => 64
[20] => 65
[21] => 66
[22] => 67
[23] => 68
[24] => 69
[25] => 70
[26] => 71
[27] => 72
[28] => 73
[29] => 74
[30] => 75
[31] => 76
[32] => 77
[33] => 63
[34] => 78
[35] => 79
[36] => 80
[37] => 81
[38] => 82
[39] => 62
[40] => 83
[41] => 84
[42] => 85
[43] => 86
[44] => 87
[45] => 88
[46] => 89
[47] => 91
[48] => 90
[49] => 92
[50] => 93
[51] => 94
[52] => 95
)
[labels] => Array
(
[0] => Fire & Explosions
[1] => Work Environment
[2] => Hazards
[3] => Acoustical Ceiling Carpenter
[4] => Trades
[5] => Asbestos/Insulator
[7] => Boilermaker
[9] => Bricklayer
[11] => Cabinetmaker
[13] => Carpenter
[15] => Carpet Layer
[17] => Cement Mason
[19] => Commercial Diver
[21] => Concrete Polisher
[23] => Drywall Applicator Specialist
[25] => Electrical Worker
[27] => Elevator Constructor
[29] => Flagger
[31] => Glazier
[33] => Hazardous Waste Cleanup
[35] => HVAC
[37] => Interior Systems Carpenter
[39] => Laborer
[41] => Landscaper
[43] => Lather
[45] => Lead Abatement Worker
[47] => Maintenance Worker
[49] => Millwright
[51] => Operating Engineer
[53] => Painter
[55] => Paper Hanger
[57] => PCC/Restoration
[59] => Pile Driver
[61] => Plasterer
[63] => Plumber/Pipefitter
[65] => Refractory Worker
[67] => Reinforcing Ironworker
[69] => Roofer/Waterproofer
[71] => Scaffold Erector
[73] => Sheetmetal Worker
[75] => Sprinkler Fitter
[77] => Stonemason
[79] => Structural Ironworker
[81] => Terrazzo Worker
[83] => Tile Setter
[85] => Truck Driver
[87] => Welder
[89] => Commercial & Institutional
[90] => Jobsites
[91] => Demolition
[93] => Disasters
[95] => Heavy & Highway
[97] => Industrial
[99] => LEED/Green Construction
[101] => Renovations
[103] => Residential
[105] => Underground
)
[type] =>
[sub_category] =>
[url] => /document/4426/d001656/Construction%2BDive%2B--%2BDeWalt%2527s%2BJobsite%2BPro%2Bheadphones%2Brecalled%2Bfor%2Bfire%2Bhazards.html
[item:protected] => DocumentRecord Object
(
[records:protected] => Array
(
)
[recordId:protected] =>
[searchWordClass:protected] =>
[searchWordPeerClass:protected] =>
[bok_record:protected] =>
[authors:protected] =>
[organizations:protected] =>
[collections:protected] =>
[categories:protected] => Array
(
[16] => Category Object
(
[languages:protected] =>
[bok_resources:protected] =>
[bok_topics:protected] =>
[bok_keywords:protected] =>
[id:protected] => 16
[type:protected] => category
[parent:protected] => 7
[label:protected] => Fire & Explosions
[alreadyInSave:protected] =>
[alreadyInValidation:protected] =>
[validationFailures:protected] => Array
(
)
[_new:BaseObject:private] =>
[_deleted:BaseObject:private] =>
[modifiedColumns:protected] => Array
(
)
)
[44] => Category Object
(
[languages:protected] =>
[bok_resources:protected] =>
[bok_topics:protected] =>
[bok_keywords:protected] =>
[id:protected] => 44
[type:protected] => category
[parent:protected] => 2
[label:protected] => Acoustical Ceiling Carpenter
[alreadyInSave:protected] =>
[alreadyInValidation:protected] =>
[validationFailures:protected] => Array
(
)
[_new:BaseObject:private] =>
[_deleted:BaseObject:private] =>
[modifiedColumns:protected] => Array
(
)
)
[45] => Category Object
(
[languages:protected] =>
[bok_resources:protected] =>
[bok_topics:protected] =>
[bok_keywords:protected] =>
[id:protected] => 45
[type:protected] => category
[parent:protected] => 2
[label:protected] => Asbestos/Insulator
[alreadyInSave:protected] =>
[alreadyInValidation:protected] =>
[validationFailures:protected] => Array
(
)
[_new:BaseObject:private] =>
[_deleted:BaseObject:private] =>
[modifiedColumns:protected] => Array
(
)
)
[46] => Category Object
(
[languages:protected] =>
[bok_resources:protected] =>
[bok_topics:protected] =>
[bok_keywords:protected] =>
[id:protected] => 46
[type:protected] => category
[parent:protected] => 2
[label:protected] => Boilermaker
[alreadyInSave:protected] =>
[alreadyInValidation:protected] =>
[validationFailures:protected] => Array
(
)
[_new:BaseObject:private] =>
[_deleted:BaseObject:private] =>
[modifiedColumns:protected] => Array
(
)
)
[47] => Category Object
(
[languages:protected] =>
[bok_resources:protected] =>
[bok_topics:protected] =>
[bok_keywords:protected] =>
[id:protected] => 47
[type:protected] => category
[parent:protected] => 2
[label:protected] => Bricklayer
[alreadyInSave:protected] =>
[alreadyInValidation:protected] =>
[validationFailures:protected] => Array
(
)
[_new:BaseObject:private] =>
[_deleted:BaseObject:private] =>
[modifiedColumns:protected] => Array
(
)
)
[48] => Category Object
(
[languages:protected] =>
[bok_resources:protected] =>
[bok_topics:protected] =>
[bok_keywords:protected] =>
[id:protected] => 48
[type:protected] => category
[parent:protected] => 2
[label:protected] => Cabinetmaker
[alreadyInSave:protected] =>
[alreadyInValidation:protected] =>
[validationFailures:protected] => Array
(
)
[_new:BaseObject:private] =>
[_deleted:BaseObject:private] =>
[modifiedColumns:protected] => Array
(
)
)
[49] => Category Object
(
[languages:protected] =>
[bok_resources:protected] =>
[bok_topics:protected] =>
[bok_keywords:protected] =>
[id:protected] => 49
[type:protected] => category
[parent:protected] => 2
[label:protected] => Carpenter
[alreadyInSave:protected] =>
[alreadyInValidation:protected] =>
[validationFailures:protected] => Array
(
)
[_new:BaseObject:private] =>
[_deleted:BaseObject:private] =>
[modifiedColumns:protected] => Array
(
)
)
[50] => Category Object
(
[languages:protected] =>
[bok_resources:protected] =>
[bok_topics:protected] =>
[bok_keywords:protected] =>
[id:protected] => 50
[type:protected] => category
[parent:protected] => 2
[label:protected] => Carpet Layer
[alreadyInSave:protected] =>
[alreadyInValidation:protected] =>
[validationFailures:protected] => Array
(
)
[_new:BaseObject:private] =>
[_deleted:BaseObject:private] =>
[modifiedColumns:protected] => Array
(
)
)
[51] => Category Object
(
[languages:protected] =>
[bok_resources:protected] =>
[bok_topics:protected] =>
[bok_keywords:protected] =>
[id:protected] => 51
[type:protected] => category
[parent:protected] => 2
[label:protected] => Cement Mason
[alreadyInSave:protected] =>
[alreadyInValidation:protected] =>
[validationFailures:protected] => Array
(
)
[_new:BaseObject:private] =>
[_deleted:BaseObject:private] =>
[modifiedColumns:protected] => Array
(
)
)
[52] => Category Object
(
[languages:protected] =>
[bok_resources:protected] =>
[bok_topics:protected] =>
[bok_keywords:protected] =>
[id:protected] => 52
[type:protected] => category
[parent:protected] => 2
[label:protected] => Commercial Diver
[alreadyInSave:protected] =>
[alreadyInValidation:protected] =>
[validationFailures:protected] => Array
(
)
[_new:BaseObject:private] =>
[_deleted:BaseObject:private] =>
[modifiedColumns:protected] => Array
(
)
)
[53] => Category Object
(
[languages:protected] =>
[bok_resources:protected] =>
[bok_topics:protected] =>
[bok_keywords:protected] =>
[id:protected] => 53
[type:protected] => category
[parent:protected] => 2
[label:protected] => Concrete Polisher
[alreadyInSave:protected] =>
[alreadyInValidation:protected] =>
[validationFailures:protected] => Array
(
)
[_new:BaseObject:private] =>
[_deleted:BaseObject:private] =>
[modifiedColumns:protected] => Array
(
)
)
[54] => Category Object
(
[languages:protected] =>
[bok_resources:protected] =>
[bok_topics:protected] =>
[bok_keywords:protected] =>
[id:protected] => 54
[type:protected] => category
[parent:protected] => 2
[label:protected] => Drywall Applicator Specialist
[alreadyInSave:protected] =>
[alreadyInValidation:protected] =>
[validationFailures:protected] => Array
(
)
[_new:BaseObject:private] =>
[_deleted:BaseObject:private] =>
[modifiedColumns:protected] => Array
(
)
)
[55] => Category Object
(
[languages:protected] =>
[bok_resources:protected] =>
[bok_topics:protected] =>
[bok_keywords:protected] =>
[id:protected] => 55
[type:protected] => category
[parent:protected] => 2
[label:protected] => Electrical Worker
[alreadyInSave:protected] =>
[alreadyInValidation:protected] =>
[validationFailures:protected] => Array
(
)
[_new:BaseObject:private] =>
[_deleted:BaseObject:private] =>
[modifiedColumns:protected] => Array
(
)
)
[56] => Category Object
(
[languages:protected] =>
[bok_resources:protected] =>
[bok_topics:protected] =>
[bok_keywords:protected] =>
[id:protected] => 56
[type:protected] => category
[parent:protected] => 2
[label:protected] => Elevator Constructor
[alreadyInSave:protected] =>
[alreadyInValidation:protected] =>
[validationFailures:protected] => Array
(
)
[_new:BaseObject:private] =>
[_deleted:BaseObject:private] =>
[modifiedColumns:protected] => Array
(
)
)
[57] => Category Object
(
[languages:protected] =>
[bok_resources:protected] =>
[bok_topics:protected] =>
[bok_keywords:protected] =>
[id:protected] => 57
[type:protected] => category
[parent:protected] => 2
[label:protected] => Flagger
[alreadyInSave:protected] =>
[alreadyInValidation:protected] =>
[validationFailures:protected] => Array
(
)
[_new:BaseObject:private] =>
[_deleted:BaseObject:private] =>
[modifiedColumns:protected] => Array
(
)
)
[58] => Category Object
(
[languages:protected] =>
[bok_resources:protected] =>
[bok_topics:protected] =>
[bok_keywords:protected] =>
[id:protected] => 58
[type:protected] => category
[parent:protected] => 2
[label:protected] => Glazier
[alreadyInSave:protected] =>
[alreadyInValidation:protected] =>
[validationFailures:protected] => Array
(
)
[_new:BaseObject:private] =>
[_deleted:BaseObject:private] =>
[modifiedColumns:protected] => Array
(
)
)
[59] => Category Object
(
[languages:protected] =>
[bok_resources:protected] =>
[bok_topics:protected] =>
[bok_keywords:protected] =>
[id:protected] => 59
[type:protected] => category
[parent:protected] => 2
[label:protected] => Hazardous Waste Cleanup
[alreadyInSave:protected] =>
[alreadyInValidation:protected] =>
[validationFailures:protected] => Array
(
)
[_new:BaseObject:private] =>
[_deleted:BaseObject:private] =>
[modifiedColumns:protected] => Array
(
)
)
[60] => Category Object
(
[languages:protected] =>
[bok_resources:protected] =>
[bok_topics:protected] =>
[bok_keywords:protected] =>
[id:protected] => 60
[type:protected] => category
[parent:protected] => 2
[label:protected] => HVAC
[alreadyInSave:protected] =>
[alreadyInValidation:protected] =>
[validationFailures:protected] => Array
(
)
[_new:BaseObject:private] =>
[_deleted:BaseObject:private] =>
[modifiedColumns:protected] => Array
(
)
)
[61] => Category Object
(
[languages:protected] =>
[bok_resources:protected] =>
[bok_topics:protected] =>
[bok_keywords:protected] =>
[id:protected] => 61
[type:protected] => category
[parent:protected] => 2
[label:protected] => Interior Systems Carpenter
[alreadyInSave:protected] =>
[alreadyInValidation:protected] =>
[validationFailures:protected] => Array
(
)
[_new:BaseObject:private] =>
[_deleted:BaseObject:private] =>
[modifiedColumns:protected] => Array
(
)
)
[64] => Category Object
(
[languages:protected] =>
[bok_resources:protected] =>
[bok_topics:protected] =>
[bok_keywords:protected] =>
[id:protected] => 64
[type:protected] => category
[parent:protected] => 2
[label:protected] => Laborer
[alreadyInSave:protected] =>
[alreadyInValidation:protected] =>
[validationFailures:protected] => Array
(
)
[_new:BaseObject:private] =>
[_deleted:BaseObject:private] =>
[modifiedColumns:protected] => Array
(
)
)
[65] => Category Object
(
[languages:protected] =>
[bok_resources:protected] =>
[bok_topics:protected] =>
[bok_keywords:protected] =>
[id:protected] => 65
[type:protected] => category
[parent:protected] => 2
[label:protected] => Landscaper
[alreadyInSave:protected] =>
[alreadyInValidation:protected] =>
[validationFailures:protected] => Array
(
)
[_new:BaseObject:private] =>
[_deleted:BaseObject:private] =>
[modifiedColumns:protected] => Array
(
)
)
[66] => Category Object
(
[languages:protected] =>
[bok_resources:protected] =>
[bok_topics:protected] =>
[bok_keywords:protected] =>
[id:protected] => 66
[type:protected] => category
[parent:protected] => 2
[label:protected] => Lather
[alreadyInSave:protected] =>
[alreadyInValidation:protected] =>
[validationFailures:protected] => Array
(
)
[_new:BaseObject:private] =>
[_deleted:BaseObject:private] =>
[modifiedColumns:protected] => Array
(
)
)
[67] => Category Object
(
[languages:protected] =>
[bok_resources:protected] =>
[bok_topics:protected] =>
[bok_keywords:protected] =>
[id:protected] => 67
[type:protected] => category
[parent:protected] => 2
[label:protected] => Lead Abatement Worker
[alreadyInSave:protected] =>
[alreadyInValidation:protected] =>
[validationFailures:protected] => Array
(
)
[_new:BaseObject:private] =>
[_deleted:BaseObject:private] =>
[modifiedColumns:protected] => Array
(
)
)
[68] => Category Object
(
[languages:protected] =>
[bok_resources:protected] =>
[bok_topics:protected] =>
[bok_keywords:protected] =>
[id:protected] => 68
[type:protected] => category
[parent:protected] => 2
[label:protected] => Maintenance Worker
[alreadyInSave:protected] =>
[alreadyInValidation:protected] =>
[validationFailures:protected] => Array
(
)
[_new:BaseObject:private] =>
[_deleted:BaseObject:private] =>
[modifiedColumns:protected] => Array
(
)
)
[69] => Category Object
(
[languages:protected] =>
[bok_resources:protected] =>
[bok_topics:protected] =>
[bok_keywords:protected] =>
[id:protected] => 69
[type:protected] => category
[parent:protected] => 2
[label:protected] => Millwright
[alreadyInSave:protected] =>
[alreadyInValidation:protected] =>
[validationFailures:protected] => Array
(
)
[_new:BaseObject:private] =>
[_deleted:BaseObject:private] =>
[modifiedColumns:protected] => Array
(
)
)
[70] => Category Object
(
[languages:protected] =>
[bok_resources:protected] =>
[bok_topics:protected] =>
[bok_keywords:protected] =>
[id:protected] => 70
[type:protected] => category
[parent:protected] => 2
[label:protected] => Operating Engineer
[alreadyInSave:protected] =>
[alreadyInValidation:protected] =>
[validationFailures:protected] => Array
(
)
[_new:BaseObject:private] =>
[_deleted:BaseObject:private] =>
[modifiedColumns:protected] => Array
(
)
)
[71] => Category Object
(
[languages:protected] =>
[bok_resources:protected] =>
[bok_topics:protected] =>
[bok_keywords:protected] =>
[id:protected] => 71
[type:protected] => category
[parent:protected] => 2
[label:protected] => Painter
[alreadyInSave:protected] =>
[alreadyInValidation:protected] =>
[validationFailures:protected] => Array
(
)
[_new:BaseObject:private] =>
[_deleted:BaseObject:private] =>
[modifiedColumns:protected] => Array
(
)
)
[72] => Category Object
(
[languages:protected] =>
[bok_resources:protected] =>
[bok_topics:protected] =>
[bok_keywords:protected] =>
[id:protected] => 72
[type:protected] => category
[parent:protected] => 2
[label:protected] => Paper Hanger
[alreadyInSave:protected] =>
[alreadyInValidation:protected] =>
[validationFailures:protected] => Array
(
)
[_new:BaseObject:private] =>
[_deleted:BaseObject:private] =>
[modifiedColumns:protected] => Array
(
)
)
[73] => Category Object
(
[languages:protected] =>
[bok_resources:protected] =>
[bok_topics:protected] =>
[bok_keywords:protected] =>
[id:protected] => 73
[type:protected] => category
[parent:protected] => 2
[label:protected] => PCC/Restoration
[alreadyInSave:protected] =>
[alreadyInValidation:protected] =>
[validationFailures:protected] => Array
(
)
[_new:BaseObject:private] =>
[_deleted:BaseObject:private] =>
[modifiedColumns:protected] => Array
(
)
)
[74] => Category Object
(
[languages:protected] =>
[bok_resources:protected] =>
[bok_topics:protected] =>
[bok_keywords:protected] =>
[id:protected] => 74
[type:protected] => category
[parent:protected] => 2
[label:protected] => Pile Driver
[alreadyInSave:protected] =>
[alreadyInValidation:protected] =>
[validationFailures:protected] => Array
(
)
[_new:BaseObject:private] =>
[_deleted:BaseObject:private] =>
[modifiedColumns:protected] => Array
(
)
)
[75] => Category Object
(
[languages:protected] =>
[bok_resources:protected] =>
[bok_topics:protected] =>
[bok_keywords:protected] =>
[id:protected] => 75
[type:protected] => category
[parent:protected] => 2
[label:protected] => Plasterer
[alreadyInSave:protected] =>
[alreadyInValidation:protected] =>
[validationFailures:protected] => Array
(
)
[_new:BaseObject:private] =>
[_deleted:BaseObject:private] =>
[modifiedColumns:protected] => Array
(
)
)
[76] => Category Object
(
[languages:protected] =>
[bok_resources:protected] =>
[bok_topics:protected] =>
[bok_keywords:protected] =>
[id:protected] => 76
[type:protected] => category
[parent:protected] => 2
[label:protected] => Plumber/Pipefitter
[alreadyInSave:protected] =>
[alreadyInValidation:protected] =>
[validationFailures:protected] => Array
(
)
[_new:BaseObject:private] =>
[_deleted:BaseObject:private] =>
[modifiedColumns:protected] => Array
(
)
)
[77] => Category Object
(
[languages:protected] =>
[bok_resources:protected] =>
[bok_topics:protected] =>
[bok_keywords:protected] =>
[id:protected] => 77
[type:protected] => category
[parent:protected] => 2
[label:protected] => Refractory Worker
[alreadyInSave:protected] =>
[alreadyInValidation:protected] =>
[validationFailures:protected] => Array
(
)
[_new:BaseObject:private] =>
[_deleted:BaseObject:private] =>
[modifiedColumns:protected] => Array
(
)
)
[63] => Category Object
(
[languages:protected] =>
[bok_resources:protected] =>
[bok_topics:protected] =>
[bok_keywords:protected] =>
[id:protected] => 63
[type:protected] => category
[parent:protected] => 2
[label:protected] => Reinforcing Ironworker
[alreadyInSave:protected] =>
[alreadyInValidation:protected] =>
[validationFailures:protected] => Array
(
)
[_new:BaseObject:private] =>
[_deleted:BaseObject:private] =>
[modifiedColumns:protected] => Array
(
)
)
[78] => Category Object
(
[languages:protected] =>
[bok_resources:protected] =>
[bok_topics:protected] =>
[bok_keywords:protected] =>
[id:protected] => 78
[type:protected] => category
[parent:protected] => 2
[label:protected] => Roofer/Waterproofer
[alreadyInSave:protected] =>
[alreadyInValidation:protected] =>
[validationFailures:protected] => Array
(
)
[_new:BaseObject:private] =>
[_deleted:BaseObject:private] =>
[modifiedColumns:protected] => Array
(
)
)
[79] => Category Object
(
[languages:protected] =>
[bok_resources:protected] =>
[bok_topics:protected] =>
[bok_keywords:protected] =>
[id:protected] => 79
[type:protected] => category
[parent:protected] => 2
[label:protected] => Scaffold Erector
[alreadyInSave:protected] =>
[alreadyInValidation:protected] =>
[validationFailures:protected] => Array
(
)
[_new:BaseObject:private] =>
[_deleted:BaseObject:private] =>
[modifiedColumns:protected] => Array
(
)
)
[80] => Category Object
(
[languages:protected] =>
[bok_resources:protected] =>
[bok_topics:protected] =>
[bok_keywords:protected] =>
[id:protected] => 80
[type:protected] => category
[parent:protected] => 2
[label:protected] => Sheetmetal Worker
[alreadyInSave:protected] =>
[alreadyInValidation:protected] =>
[validationFailures:protected] => Array
(
)
[_new:BaseObject:private] =>
[_deleted:BaseObject:private] =>
[modifiedColumns:protected] => Array
(
)
)
[81] => Category Object
(
[languages:protected] =>
[bok_resources:protected] =>
[bok_topics:protected] =>
[bok_keywords:protected] =>
[id:protected] => 81
[type:protected] => category
[parent:protected] => 2
[label:protected] => Sprinkler Fitter
[alreadyInSave:protected] =>
[alreadyInValidation:protected] =>
[validationFailures:protected] => Array
(
)
[_new:BaseObject:private] =>
[_deleted:BaseObject:private] =>
[modifiedColumns:protected] => Array
(
)
)
[82] => Category Object
(
[languages:protected] =>
[bok_resources:protected] =>
[bok_topics:protected] =>
[bok_keywords:protected] =>
[id:protected] => 82
[type:protected] => category
[parent:protected] => 2
[label:protected] => Stonemason
[alreadyInSave:protected] =>
[alreadyInValidation:protected] =>
[validationFailures:protected] => Array
(
)
[_new:BaseObject:private] =>
[_deleted:BaseObject:private] =>
[modifiedColumns:protected] => Array
(
)
)
[62] => Category Object
(
[languages:protected] =>
[bok_resources:protected] =>
[bok_topics:protected] =>
[bok_keywords:protected] =>
[id:protected] => 62
[type:protected] => category
[parent:protected] => 2
[label:protected] => Structural Ironworker
[alreadyInSave:protected] =>
[alreadyInValidation:protected] =>
[validationFailures:protected] => Array
(
)
[_new:BaseObject:private] =>
[_deleted:BaseObject:private] =>
[modifiedColumns:protected] => Array
(
)
)
[83] => Category Object
(
[languages:protected] =>
[bok_resources:protected] =>
[bok_topics:protected] =>
[bok_keywords:protected] =>
[id:protected] => 83
[type:protected] => category
[parent:protected] => 2
[label:protected] => Terrazzo Worker
[alreadyInSave:protected] =>
[alreadyInValidation:protected] =>
[validationFailures:protected] => Array
(
)
[_new:BaseObject:private] =>
[_deleted:BaseObject:private] =>
[modifiedColumns:protected] => Array
(
)
)
[84] => Category Object
(
[languages:protected] =>
[bok_resources:protected] =>
[bok_topics:protected] =>
[bok_keywords:protected] =>
[id:protected] => 84
[type:protected] => category
[parent:protected] => 2
[label:protected] => Tile Setter
[alreadyInSave:protected] =>
[alreadyInValidation:protected] =>
[validationFailures:protected] => Array
(
)
[_new:BaseObject:private] =>
[_deleted:BaseObject:private] =>
[modifiedColumns:protected] => Array
(
)
)
[85] => Category Object
(
[languages:protected] =>
[bok_resources:protected] =>
[bok_topics:protected] =>
[bok_keywords:protected] =>
[id:protected] => 85
[type:protected] => category
[parent:protected] => 2
[label:protected] => Truck Driver
[alreadyInSave:protected] =>
[alreadyInValidation:protected] =>
[validationFailures:protected] => Array
(
)
[_new:BaseObject:private] =>
[_deleted:BaseObject:private] =>
[modifiedColumns:protected] => Array
(
)
)
[86] => Category Object
(
[languages:protected] =>
[bok_resources:protected] =>
[bok_topics:protected] =>
[bok_keywords:protected] =>
[id:protected] => 86
[type:protected] => category
[parent:protected] => 2
[label:protected] => Welder
[alreadyInSave:protected] =>
[alreadyInValidation:protected] =>
[validationFailures:protected] => Array
(
)
[_new:BaseObject:private] =>
[_deleted:BaseObject:private] =>
[modifiedColumns:protected] => Array
(
)
)
[87] => Category Object
(
[languages:protected] =>
[bok_resources:protected] =>
[bok_topics:protected] =>
[bok_keywords:protected] =>
[id:protected] => 87
[type:protected] => category
[parent:protected] => 3
[label:protected] => Commercial & Institutional
[alreadyInSave:protected] =>
[alreadyInValidation:protected] =>
[validationFailures:protected] => Array
(
)
[_new:BaseObject:private] =>
[_deleted:BaseObject:private] =>
[modifiedColumns:protected] => Array
(
)
)
[88] => Category Object
(
[languages:protected] =>
[bok_resources:protected] =>
[bok_topics:protected] =>
[bok_keywords:protected] =>
[id:protected] => 88
[type:protected] => category
[parent:protected] => 3
[label:protected] => Demolition
[alreadyInSave:protected] =>
[alreadyInValidation:protected] =>
[validationFailures:protected] => Array
(
)
[_new:BaseObject:private] =>
[_deleted:BaseObject:private] =>
[modifiedColumns:protected] => Array
(
)
)
[89] => Category Object
(
[languages:protected] =>
[bok_resources:protected] =>
[bok_topics:protected] =>
[bok_keywords:protected] =>
[id:protected] => 89
[type:protected] => category
[parent:protected] => 3
[label:protected] => Disasters
[alreadyInSave:protected] =>
[alreadyInValidation:protected] =>
[validationFailures:protected] => Array
(
)
[_new:BaseObject:private] =>
[_deleted:BaseObject:private] =>
[modifiedColumns:protected] => Array
(
)
)
[91] => Category Object
(
[languages:protected] =>
[bok_resources:protected] =>
[bok_topics:protected] =>
[bok_keywords:protected] =>
[id:protected] => 91
[type:protected] => category
[parent:protected] => 3
[label:protected] => Heavy & Highway
[alreadyInSave:protected] =>
[alreadyInValidation:protected] =>
[validationFailures:protected] => Array
(
)
[_new:BaseObject:private] =>
[_deleted:BaseObject:private] =>
[modifiedColumns:protected] => Array
(
)
)
[90] => Category Object
(
[languages:protected] =>
[bok_resources:protected] =>
[bok_topics:protected] =>
[bok_keywords:protected] =>
[id:protected] => 90
[type:protected] => category
[parent:protected] => 3
[label:protected] => Industrial
[alreadyInSave:protected] =>
[alreadyInValidation:protected] =>
[validationFailures:protected] => Array
(
)
[_new:BaseObject:private] =>
[_deleted:BaseObject:private] =>
[modifiedColumns:protected] => Array
(
)
)
[92] => Category Object
(
[languages:protected] =>
[bok_resources:protected] =>
[bok_topics:protected] =>
[bok_keywords:protected] =>
[id:protected] => 92
[type:protected] => category
[parent:protected] => 3
[label:protected] => LEED/Green Construction
[alreadyInSave:protected] =>
[alreadyInValidation:protected] =>
[validationFailures:protected] => Array
(
)
[_new:BaseObject:private] =>
[_deleted:BaseObject:private] =>
[modifiedColumns:protected] => Array
(
)
)
[93] => Category Object
(
[languages:protected] =>
[bok_resources:protected] =>
[bok_topics:protected] =>
[bok_keywords:protected] =>
[id:protected] => 93
[type:protected] => category
[parent:protected] => 3
[label:protected] => Renovations
[alreadyInSave:protected] =>
[alreadyInValidation:protected] =>
[validationFailures:protected] => Array
(
)
[_new:BaseObject:private] =>
[_deleted:BaseObject:private] =>
[modifiedColumns:protected] => Array
(
)
)
[94] => Category Object
(
[languages:protected] =>
[bok_resources:protected] =>
[bok_topics:protected] =>
[bok_keywords:protected] =>
[id:protected] => 94
[type:protected] => category
[parent:protected] => 3
[label:protected] => Residential
[alreadyInSave:protected] =>
[alreadyInValidation:protected] =>
[validationFailures:protected] => Array
(
)
[_new:BaseObject:private] =>
[_deleted:BaseObject:private] =>
[modifiedColumns:protected] => Array
(
)
)
[95] => Category Object
(
[languages:protected] =>
[bok_resources:protected] =>
[bok_topics:protected] =>
[bok_keywords:protected] =>
[id:protected] => 95
[type:protected] => category
[parent:protected] => 3
[label:protected] => Underground
[alreadyInSave:protected] =>
[alreadyInValidation:protected] =>
[validationFailures:protected] => Array
(
)
[_new:BaseObject:private] =>
[_deleted:BaseObject:private] =>
[modifiedColumns:protected] => Array
(
)
)
)
[categories_initialized:protected] => 1
[mapped_items:protected] =>
[content:protected] =>
[files:protected] =>
[language:protected] => Language Object
(
[id:protected] => 1
[code:protected] => en
[name:protected] => English
[alreadyInSave:protected] =>
[alreadyInValidation:protected] =>
[validationFailures:protected] => Array
(
)
[_new:BaseObject:private] =>
[_deleted:BaseObject:private] =>
[modifiedColumns:protected] => Array
(
)
)
[old_record:protected] =>
[id:protected] => 4426
[old_id:protected] =>
[elcosh_id:protected] => d001656
[type:protected] => document
[display_type:protected] => HTML only (and links)
[user_id:protected] => 0
[language_id:protected] => 1
[tagging_id:protected] => Mike Aguilar
[priority_id:protected] => 1
[title:protected] => Construction Dive -- DeWalt's Jobsite Pro headphones recalled for fire hazards
[total_pages:protected] => 1
[billed_pages:protected] => 1
[publication_number:protected] =>
[part_of:protected] =>
[keywords:protected] => DeWalt, Fire Hazards, recall, headphones
[comments:protected] =>
[summary:protected] => A recall notice by the United States Consumer Product Safety Commission affects over 300,000 DeWalt Jobsite Pro Headphones. The recall is a result of a malfunction that can cause earbuds to overheat while charging or during use, leading to fire and burn hazards.
[transition_comments:protected] =>
[external_link:protected] => https://www.constructiondive.com/news/dewalts-jobsite-pro-headphones-recalled-for-fire-hazards/611248/?utm_source=Sailthru&utm_medium=email&utm_campaign=Issue:%202021-12-10%20Construction%20Dive%20Newsletter%20%5Bissue:38532%5D&utm_term=Construction%20Dive
[consol_link:protected] =>
[more_like_this:protected] =>
[permission_given_by:protected] =>
[published:protected] => T
[billable:protected] => F
[img_name:protected] =>
[img_ext:protected] =>
[img_width:protected] =>
[img_height:protected] =>
[img_credit:protected] =>
[img_practice:protected] =>
[vid_source_id:protected] =>
[vid_running_time:protected] =>
[vid_intended_audience:protected] =>
[vid_acquisition_info:protected] =>
[vid_cost:protected] =>
[vid_producer:protected] =>
[vid_filename:protected] =>
[vid_filename_downloadable:protected] =>
[date_summary:protected] =>
[date_permission_requested:protected] =>
[date_permission_received:protected] =>
[date_review_needed:protected] =>
[date_received:protected] => 12/13/21
[date_completed:protected] => 12/13/21
[date_billed:protected] =>
[date_modified:protected] => 12/13/21
[collBokExports:protected] =>
[lastBokExportCriteria:BaseElcoshItem:private] =>
[alreadyInSave:protected] =>
[alreadyInValidation:protected] =>
[validationFailures:protected] => Array
(
)
[_new:BaseObject:private] =>
[_deleted:BaseObject:private] =>
[modifiedColumns:protected] => Array
(
)
)
)
)
[new_images] => Array
(
[0] => Search_Result Object
(
[title] => Morning Toolbox Talk
[image] => /record/images/4003-p.jpg
[blurb] => This photo is from an early morning toolbox talk on a construction job in Mclean, Virginia. It is being delivered in English and Spanish....
[category] => Array
(
[0] => 20
[1] => 51
[2] => 57
[3] => 64
[4] => 70
[5] => 63
[6] => 78
[7] => 82
[8] => 62
[9] => 87
[10] => 88
[11] => 89
[12] => 91
[13] => 90
[14] => 93
[15] => 94
[16] => 97
)
[labels] => Array
(
[0] => Safety Culture
[1] => Work Environment
[2] => Hazards
[3] => Cement Mason
[4] => Trades
[5] => Flagger
[7] => Laborer
[9] => Operating Engineer
[11] => Reinforcing Ironworker
[13] => Roofer/Waterproofer
[15] => Stonemason
[17] => Structural Ironworker
[19] => Commercial & Institutional
[20] => Jobsites
[21] => Demolition
[23] => Disasters
[25] => Heavy & Highway
[27] => Industrial
[29] => Renovations
[31] => Residential
[33] => Images
[34] => Media
[35] => Media & Documents
)
[type] => Images
[sub_category] =>
[url] => /image/4003/i002691/Morning%2BToolbox%2BTalk.html
[item:protected] => ImageRecord Object
(
[records:protected] => Array
(
)
[recordId:protected] =>
[searchWordClass:protected] =>
[searchWordPeerClass:protected] =>
[bok_record:protected] =>
[authors:protected] =>
[organizations:protected] =>
[collections:protected] =>
[categories:protected] => Array
(
[20] => Category Object
(
[languages:protected] =>
[bok_resources:protected] =>
[bok_topics:protected] =>
[bok_keywords:protected] =>
[id:protected] => 20
[type:protected] => category
[parent:protected] => 7
[label:protected] => Safety Culture
[alreadyInSave:protected] =>
[alreadyInValidation:protected] =>
[validationFailures:protected] => Array
(
)
[_new:BaseObject:private] =>
[_deleted:BaseObject:private] =>
[modifiedColumns:protected] => Array
(
)
)
[51] => Category Object
(
[languages:protected] =>
[bok_resources:protected] =>
[bok_topics:protected] =>
[bok_keywords:protected] =>
[id:protected] => 51
[type:protected] => category
[parent:protected] => 2
[label:protected] => Cement Mason
[alreadyInSave:protected] =>
[alreadyInValidation:protected] =>
[validationFailures:protected] => Array
(
)
[_new:BaseObject:private] =>
[_deleted:BaseObject:private] =>
[modifiedColumns:protected] => Array
(
)
)
[57] => Category Object
(
[languages:protected] =>
[bok_resources:protected] =>
[bok_topics:protected] =>
[bok_keywords:protected] =>
[id:protected] => 57
[type:protected] => category
[parent:protected] => 2
[label:protected] => Flagger
[alreadyInSave:protected] =>
[alreadyInValidation:protected] =>
[validationFailures:protected] => Array
(
)
[_new:BaseObject:private] =>
[_deleted:BaseObject:private] =>
[modifiedColumns:protected] => Array
(
)
)
[64] => Category Object
(
[languages:protected] =>
[bok_resources:protected] =>
[bok_topics:protected] =>
[bok_keywords:protected] =>
[id:protected] => 64
[type:protected] => category
[parent:protected] => 2
[label:protected] => Laborer
[alreadyInSave:protected] =>
[alreadyInValidation:protected] =>
[validationFailures:protected] => Array
(
)
[_new:BaseObject:private] =>
[_deleted:BaseObject:private] =>
[modifiedColumns:protected] => Array
(
)
)
[70] => Category Object
(
[languages:protected] =>
[bok_resources:protected] =>
[bok_topics:protected] =>
[bok_keywords:protected] =>
[id:protected] => 70
[type:protected] => category
[parent:protected] => 2
[label:protected] => Operating Engineer
[alreadyInSave:protected] =>
[alreadyInValidation:protected] =>
[validationFailures:protected] => Array
(
)
[_new:BaseObject:private] =>
[_deleted:BaseObject:private] =>
[modifiedColumns:protected] => Array
(
)
)
[63] => Category Object
(
[languages:protected] =>
[bok_resources:protected] =>
[bok_topics:protected] =>
[bok_keywords:protected] =>
[id:protected] => 63
[type:protected] => category
[parent:protected] => 2
[label:protected] => Reinforcing Ironworker
[alreadyInSave:protected] =>
[alreadyInValidation:protected] =>
[validationFailures:protected] => Array
(
)
[_new:BaseObject:private] =>
[_deleted:BaseObject:private] =>
[modifiedColumns:protected] => Array
(
)
)
[78] => Category Object
(
[languages:protected] =>
[bok_resources:protected] =>
[bok_topics:protected] =>
[bok_keywords:protected] =>
[id:protected] => 78
[type:protected] => category
[parent:protected] => 2
[label:protected] => Roofer/Waterproofer
[alreadyInSave:protected] =>
[alreadyInValidation:protected] =>
[validationFailures:protected] => Array
(
)
[_new:BaseObject:private] =>
[_deleted:BaseObject:private] =>
[modifiedColumns:protected] => Array
(
)
)
[82] => Category Object
(
[languages:protected] =>
[bok_resources:protected] =>
[bok_topics:protected] =>
[bok_keywords:protected] =>
[id:protected] => 82
[type:protected] => category
[parent:protected] => 2
[label:protected] => Stonemason
[alreadyInSave:protected] =>
[alreadyInValidation:protected] =>
[validationFailures:protected] => Array
(
)
[_new:BaseObject:private] =>
[_deleted:BaseObject:private] =>
[modifiedColumns:protected] => Array
(
)
)
[62] => Category Object
(
[languages:protected] =>
[bok_resources:protected] =>
[bok_topics:protected] =>
[bok_keywords:protected] =>
[id:protected] => 62
[type:protected] => category
[parent:protected] => 2
[label:protected] => Structural Ironworker
[alreadyInSave:protected] =>
[alreadyInValidation:protected] =>
[validationFailures:protected] => Array
(
)
[_new:BaseObject:private] =>
[_deleted:BaseObject:private] =>
[modifiedColumns:protected] => Array
(
)
)
[87] => Category Object
(
[languages:protected] =>
[bok_resources:protected] =>
[bok_topics:protected] =>
[bok_keywords:protected] =>
[id:protected] => 87
[type:protected] => category
[parent:protected] => 3
[label:protected] => Commercial & Institutional
[alreadyInSave:protected] =>
[alreadyInValidation:protected] =>
[validationFailures:protected] => Array
(
)
[_new:BaseObject:private] =>
[_deleted:BaseObject:private] =>
[modifiedColumns:protected] => Array
(
)
)
[88] => Category Object
(
[languages:protected] =>
[bok_resources:protected] =>
[bok_topics:protected] =>
[bok_keywords:protected] =>
[id:protected] => 88
[type:protected] => category
[parent:protected] => 3
[label:protected] => Demolition
[alreadyInSave:protected] =>
[alreadyInValidation:protected] =>
[validationFailures:protected] => Array
(
)
[_new:BaseObject:private] =>
[_deleted:BaseObject:private] =>
[modifiedColumns:protected] => Array
(
)
)
[89] => Category Object
(
[languages:protected] =>
[bok_resources:protected] =>
[bok_topics:protected] =>
[bok_keywords:protected] =>
[id:protected] => 89
[type:protected] => category
[parent:protected] => 3
[label:protected] => Disasters
[alreadyInSave:protected] =>
[alreadyInValidation:protected] =>
[validationFailures:protected] => Array
(
)
[_new:BaseObject:private] =>
[_deleted:BaseObject:private] =>
[modifiedColumns:protected] => Array
(
)
)
[91] => Category Object
(
[languages:protected] =>
[bok_resources:protected] =>
[bok_topics:protected] =>
[bok_keywords:protected] =>
[id:protected] => 91
[type:protected] => category
[parent:protected] => 3
[label:protected] => Heavy & Highway
[alreadyInSave:protected] =>
[alreadyInValidation:protected] =>
[validationFailures:protected] => Array
(
)
[_new:BaseObject:private] =>
[_deleted:BaseObject:private] =>
[modifiedColumns:protected] => Array
(
)
)
[90] => Category Object
(
[languages:protected] =>
[bok_resources:protected] =>
[bok_topics:protected] =>
[bok_keywords:protected] =>
[id:protected] => 90
[type:protected] => category
[parent:protected] => 3
[label:protected] => Industrial
[alreadyInSave:protected] =>
[alreadyInValidation:protected] =>
[validationFailures:protected] => Array
(
)
[_new:BaseObject:private] =>
[_deleted:BaseObject:private] =>
[modifiedColumns:protected] => Array
(
)
)
[93] => Category Object
(
[languages:protected] =>
[bok_resources:protected] =>
[bok_topics:protected] =>
[bok_keywords:protected] =>
[id:protected] => 93
[type:protected] => category
[parent:protected] => 3
[label:protected] => Renovations
[alreadyInSave:protected] =>
[alreadyInValidation:protected] =>
[validationFailures:protected] => Array
(
)
[_new:BaseObject:private] =>
[_deleted:BaseObject:private] =>
[modifiedColumns:protected] => Array
(
)
)
[94] => Category Object
(
[languages:protected] =>
[bok_resources:protected] =>
[bok_topics:protected] =>
[bok_keywords:protected] =>
[id:protected] => 94
[type:protected] => category
[parent:protected] => 3
[label:protected] => Residential
[alreadyInSave:protected] =>
[alreadyInValidation:protected] =>
[validationFailures:protected] => Array
(
)
[_new:BaseObject:private] =>
[_deleted:BaseObject:private] =>
[modifiedColumns:protected] => Array
(
)
)
[97] => Category Object
(
[languages:protected] =>
[bok_resources:protected] =>
[bok_topics:protected] =>
[bok_keywords:protected] =>
[id:protected] => 97
[type:protected] => category
[parent:protected] => 5
[label:protected] => Images
[alreadyInSave:protected] =>
[alreadyInValidation:protected] =>
[validationFailures:protected] => Array
(
)
[_new:BaseObject:private] =>
[_deleted:BaseObject:private] =>
[modifiedColumns:protected] => Array
(
)
)
)
[categories_initialized:protected] => 1
[mapped_items:protected] =>
[content:protected] =>
[files:protected] =>
[language:protected] => Language Object
(
[id:protected] => 1
[code:protected] => en
[name:protected] => English
[alreadyInSave:protected] =>
[alreadyInValidation:protected] =>
[validationFailures:protected] => Array
(
)
[_new:BaseObject:private] =>
[_deleted:BaseObject:private] =>
[modifiedColumns:protected] => Array
(
)
)
[old_record:protected] =>
[id:protected] => 4003
[old_id:protected] =>
[elcosh_id:protected] => i002691
[type:protected] => image
[display_type:protected] => Image
[user_id:protected] => 0
[language_id:protected] => 1
[tagging_id:protected] => Bruce Lippy
[priority_id:protected] => 1
[title:protected] => Morning Toolbox Talk
[total_pages:protected] => 0
[billed_pages:protected] => 0
[publication_number:protected] =>
[part_of:protected] =>
[keywords:protected] => toolbox talk, tailgate talk, Spanish, bilingual
[comments:protected] =>
[summary:protected] => This photo is from an early morning toolbox talk on a construction job in Mclean, Virginia. It is being delivered in English and Spanish.
[transition_comments:protected] =>
[external_link:protected] =>
[consol_link:protected] => http://www.cpwrconstructionsolutions.org/electrical/solution/662/worker-training.html
[more_like_this:protected] => d001285,d001304,c000079
[permission_given_by:protected] =>
[published:protected] => T
[billable:protected] => F
[img_name:protected] =>
[img_ext:protected] => jpg
[img_width:protected] =>
[img_height:protected] =>
[img_credit:protected] => Morgan Zavertnik and Hoar Construction
[img_practice:protected] => good
[vid_source_id:protected] =>
[vid_running_time:protected] =>
[vid_intended_audience:protected] =>
[vid_acquisition_info:protected] =>
[vid_cost:protected] =>
[vid_producer:protected] =>
[vid_filename:protected] =>
[vid_filename_downloadable:protected] =>
[date_summary:protected] => November 2015
[date_permission_requested:protected] =>
[date_permission_received:protected] =>
[date_review_needed:protected] =>
[date_received:protected] => 03/02/16
[date_completed:protected] => 03/02/16
[date_billed:protected] =>
[date_modified:protected] => 03/02/16
[collBokExports:protected] =>
[lastBokExportCriteria:BaseElcoshItem:private] =>
[alreadyInSave:protected] =>
[alreadyInValidation:protected] =>
[validationFailures:protected] => Array
(
)
[_new:BaseObject:private] =>
[_deleted:BaseObject:private] =>
[modifiedColumns:protected] => Array
(
)
)
)
[1] => Search_Result Object
(
[title] => Toolbox talk - crew view
[image] => /record/images/4005-p.jpg
[blurb] => Photo of crew listening to a toolbox safety talk before starting work....
[category] => Array
(
[0] => 97
[1] => 20
[2] => 47
[3] => 49
[4] => 51
[5] => 55
[6] => 61
[7] => 64
[8] => 71
[9] => 75
[10] => 63
[11] => 79
[12] => 62
[13] => 87
[14] => 88
[15] => 91
[16] => 90
[17] => 93
[18] => 94
[19] => 95
)
[labels] => Array
(
[0] => Images
[1] => Media
[2] => Media & Documents
[3] => Safety Culture
[4] => Work Environment
[5] => Hazards
[6] => Bricklayer
[7] => Trades
[8] => Carpenter
[10] => Cement Mason
[12] => Electrical Worker
[14] => Interior Systems Carpenter
[16] => Laborer
[18] => Painter
[20] => Plasterer
[22] => Reinforcing Ironworker
[24] => Scaffold Erector
[26] => Structural Ironworker
[28] => Commercial & Institutional
[29] => Jobsites
[30] => Demolition
[32] => Heavy & Highway
[34] => Industrial
[36] => Renovations
[38] => Residential
[40] => Underground
)
[type] => Images
[sub_category] =>
[url] => /image/4005/i002692/Toolbox%2Btalk%2B-%2Bcrew%2Bview.html
[item:protected] => ImageRecord Object
(
[records:protected] => Array
(
)
[recordId:protected] =>
[searchWordClass:protected] =>
[searchWordPeerClass:protected] =>
[bok_record:protected] =>
[authors:protected] =>
[organizations:protected] =>
[collections:protected] =>
[categories:protected] => Array
(
[97] => Category Object
(
[languages:protected] =>
[bok_resources:protected] =>
[bok_topics:protected] =>
[bok_keywords:protected] =>
[id:protected] => 97
[type:protected] => category
[parent:protected] => 5
[label:protected] => Images
[alreadyInSave:protected] =>
[alreadyInValidation:protected] =>
[validationFailures:protected] => Array
(
)
[_new:BaseObject:private] =>
[_deleted:BaseObject:private] =>
[modifiedColumns:protected] => Array
(
)
)
[20] => Category Object
(
[languages:protected] =>
[bok_resources:protected] =>
[bok_topics:protected] =>
[bok_keywords:protected] =>
[id:protected] => 20
[type:protected] => category
[parent:protected] => 7
[label:protected] => Safety Culture
[alreadyInSave:protected] =>
[alreadyInValidation:protected] =>
[validationFailures:protected] => Array
(
)
[_new:BaseObject:private] =>
[_deleted:BaseObject:private] =>
[modifiedColumns:protected] => Array
(
)
)
[47] => Category Object
(
[languages:protected] =>
[bok_resources:protected] =>
[bok_topics:protected] =>
[bok_keywords:protected] =>
[id:protected] => 47
[type:protected] => category
[parent:protected] => 2
[label:protected] => Bricklayer
[alreadyInSave:protected] =>
[alreadyInValidation:protected] =>
[validationFailures:protected] => Array
(
)
[_new:BaseObject:private] =>
[_deleted:BaseObject:private] =>
[modifiedColumns:protected] => Array
(
)
)
[49] => Category Object
(
[languages:protected] =>
[bok_resources:protected] =>
[bok_topics:protected] =>
[bok_keywords:protected] =>
[id:protected] => 49
[type:protected] => category
[parent:protected] => 2
[label:protected] => Carpenter
[alreadyInSave:protected] =>
[alreadyInValidation:protected] =>
[validationFailures:protected] => Array
(
)
[_new:BaseObject:private] =>
[_deleted:BaseObject:private] =>
[modifiedColumns:protected] => Array
(
)
)
[51] => Category Object
(
[languages:protected] =>
[bok_resources:protected] =>
[bok_topics:protected] =>
[bok_keywords:protected] =>
[id:protected] => 51
[type:protected] => category
[parent:protected] => 2
[label:protected] => Cement Mason
[alreadyInSave:protected] =>
[alreadyInValidation:protected] =>
[validationFailures:protected] => Array
(
)
[_new:BaseObject:private] =>
[_deleted:BaseObject:private] =>
[modifiedColumns:protected] => Array
(
)
)
[55] => Category Object
(
[languages:protected] =>
[bok_resources:protected] =>
[bok_topics:protected] =>
[bok_keywords:protected] =>
[id:protected] => 55
[type:protected] => category
[parent:protected] => 2
[label:protected] => Electrical Worker
[alreadyInSave:protected] =>
[alreadyInValidation:protected] =>
[validationFailures:protected] => Array
(
)
[_new:BaseObject:private] =>
[_deleted:BaseObject:private] =>
[modifiedColumns:protected] => Array
(
)
)
[61] => Category Object
(
[languages:protected] =>
[bok_resources:protected] =>
[bok_topics:protected] =>
[bok_keywords:protected] =>
[id:protected] => 61
[type:protected] => category
[parent:protected] => 2
[label:protected] => Interior Systems Carpenter
[alreadyInSave:protected] =>
[alreadyInValidation:protected] =>
[validationFailures:protected] => Array
(
)
[_new:BaseObject:private] =>
[_deleted:BaseObject:private] =>
[modifiedColumns:protected] => Array
(
)
)
[64] => Category Object
(
[languages:protected] =>
[bok_resources:protected] =>
[bok_topics:protected] =>
[bok_keywords:protected] =>
[id:protected] => 64
[type:protected] => category
[parent:protected] => 2
[label:protected] => Laborer
[alreadyInSave:protected] =>
[alreadyInValidation:protected] =>
[validationFailures:protected] => Array
(
)
[_new:BaseObject:private] =>
[_deleted:BaseObject:private] =>
[modifiedColumns:protected] => Array
(
)
)
[71] => Category Object
(
[languages:protected] =>
[bok_resources:protected] =>
[bok_topics:protected] =>
[bok_keywords:protected] =>
[id:protected] => 71
[type:protected] => category
[parent:protected] => 2
[label:protected] => Painter
[alreadyInSave:protected] =>
[alreadyInValidation:protected] =>
[validationFailures:protected] => Array
(
)
[_new:BaseObject:private] =>
[_deleted:BaseObject:private] =>
[modifiedColumns:protected] => Array
(
)
)
[75] => Category Object
(
[languages:protected] =>
[bok_resources:protected] =>
[bok_topics:protected] =>
[bok_keywords:protected] =>
[id:protected] => 75
[type:protected] => category
[parent:protected] => 2
[label:protected] => Plasterer
[alreadyInSave:protected] =>
[alreadyInValidation:protected] =>
[validationFailures:protected] => Array
(
)
[_new:BaseObject:private] =>
[_deleted:BaseObject:private] =>
[modifiedColumns:protected] => Array
(
)
)
[63] => Category Object
(
[languages:protected] =>
[bok_resources:protected] =>
[bok_topics:protected] =>
[bok_keywords:protected] =>
[id:protected] => 63
[type:protected] => category
[parent:protected] => 2
[label:protected] => Reinforcing Ironworker
[alreadyInSave:protected] =>
[alreadyInValidation:protected] =>
[validationFailures:protected] => Array
(
)
[_new:BaseObject:private] =>
[_deleted:BaseObject:private] =>
[modifiedColumns:protected] => Array
(
)
)
[79] => Category Object
(
[languages:protected] =>
[bok_resources:protected] =>
[bok_topics:protected] =>
[bok_keywords:protected] =>
[id:protected] => 79
[type:protected] => category
[parent:protected] => 2
[label:protected] => Scaffold Erector
[alreadyInSave:protected] =>
[alreadyInValidation:protected] =>
[validationFailures:protected] => Array
(
)
[_new:BaseObject:private] =>
[_deleted:BaseObject:private] =>
[modifiedColumns:protected] => Array
(
)
)
[62] => Category Object
(
[languages:protected] =>
[bok_resources:protected] =>
[bok_topics:protected] =>
[bok_keywords:protected] =>
[id:protected] => 62
[type:protected] => category
[parent:protected] => 2
[label:protected] => Structural Ironworker
[alreadyInSave:protected] =>
[alreadyInValidation:protected] =>
[validationFailures:protected] => Array
(
)
[_new:BaseObject:private] =>
[_deleted:BaseObject:private] =>
[modifiedColumns:protected] => Array
(
)
)
[87] => Category Object
(
[languages:protected] =>
[bok_resources:protected] =>
[bok_topics:protected] =>
[bok_keywords:protected] =>
[id:protected] => 87
[type:protected] => category
[parent:protected] => 3
[label:protected] => Commercial & Institutional
[alreadyInSave:protected] =>
[alreadyInValidation:protected] =>
[validationFailures:protected] => Array
(
)
[_new:BaseObject:private] =>
[_deleted:BaseObject:private] =>
[modifiedColumns:protected] => Array
(
)
)
[88] => Category Object
(
[languages:protected] =>
[bok_resources:protected] =>
[bok_topics:protected] =>
[bok_keywords:protected] =>
[id:protected] => 88
[type:protected] => category
[parent:protected] => 3
[label:protected] => Demolition
[alreadyInSave:protected] =>
[alreadyInValidation:protected] =>
[validationFailures:protected] => Array
(
)
[_new:BaseObject:private] =>
[_deleted:BaseObject:private] =>
[modifiedColumns:protected] => Array
(
)
)
[91] => Category Object
(
[languages:protected] =>
[bok_resources:protected] =>
[bok_topics:protected] =>
[bok_keywords:protected] =>
[id:protected] => 91
[type:protected] => category
[parent:protected] => 3
[label:protected] => Heavy & Highway
[alreadyInSave:protected] =>
[alreadyInValidation:protected] =>
[validationFailures:protected] => Array
(
)
[_new:BaseObject:private] =>
[_deleted:BaseObject:private] =>
[modifiedColumns:protected] => Array
(
)
)
[90] => Category Object
(
[languages:protected] =>
[bok_resources:protected] =>
[bok_topics:protected] =>
[bok_keywords:protected] =>
[id:protected] => 90
[type:protected] => category
[parent:protected] => 3
[label:protected] => Industrial
[alreadyInSave:protected] =>
[alreadyInValidation:protected] =>
[validationFailures:protected] => Array
(
)
[_new:BaseObject:private] =>
[_deleted:BaseObject:private] =>
[modifiedColumns:protected] => Array
(
)
)
[93] => Category Object
(
[languages:protected] =>
[bok_resources:protected] =>
[bok_topics:protected] =>
[bok_keywords:protected] =>
[id:protected] => 93
[type:protected] => category
[parent:protected] => 3
[label:protected] => Renovations
[alreadyInSave:protected] =>
[alreadyInValidation:protected] =>
[validationFailures:protected] => Array
(
)
[_new:BaseObject:private] =>
[_deleted:BaseObject:private] =>
[modifiedColumns:protected] => Array
(
)
)
[94] => Category Object
(
[languages:protected] =>
[bok_resources:protected] =>
[bok_topics:protected] =>
[bok_keywords:protected] =>
[id:protected] => 94
[type:protected] => category
[parent:protected] => 3
[label:protected] => Residential
[alreadyInSave:protected] =>
[alreadyInValidation:protected] =>
[validationFailures:protected] => Array
(
)
[_new:BaseObject:private] =>
[_deleted:BaseObject:private] =>
[modifiedColumns:protected] => Array
(
)
)
[95] => Category Object
(
[languages:protected] =>
[bok_resources:protected] =>
[bok_topics:protected] =>
[bok_keywords:protected] =>
[id:protected] => 95
[type:protected] => category
[parent:protected] => 3
[label:protected] => Underground
[alreadyInSave:protected] =>
[alreadyInValidation:protected] =>
[validationFailures:protected] => Array
(
)
[_new:BaseObject:private] =>
[_deleted:BaseObject:private] =>
[modifiedColumns:protected] => Array
(
)
)
)
[categories_initialized:protected] => 1
[mapped_items:protected] =>
[content:protected] =>
[files:protected] =>
[language:protected] => Language Object
(
[id:protected] => 1
[code:protected] => en
[name:protected] => English
[alreadyInSave:protected] =>
[alreadyInValidation:protected] =>
[validationFailures:protected] => Array
(
)
[_new:BaseObject:private] =>
[_deleted:BaseObject:private] =>
[modifiedColumns:protected] => Array
(
)
)
[old_record:protected] =>
[id:protected] => 4005
[old_id:protected] =>
[elcosh_id:protected] => i002692
[type:protected] => image
[display_type:protected] => Image
[user_id:protected] => 0
[language_id:protected] => 1
[tagging_id:protected] => Bruce Lippy
[priority_id:protected] => 1
[title:protected] => Toolbox talk - crew view
[total_pages:protected] => 0
[billed_pages:protected] => 0
[publication_number:protected] =>
[part_of:protected] =>
[keywords:protected] => toolbox talk, tailgate talk, safety talk, Spanish
[comments:protected] =>
[summary:protected] => Photo of crew listening to a toolbox safety talk before starting work.
[transition_comments:protected] =>
[external_link:protected] =>
[consol_link:protected] => http://www.cpwrconstructionsolutions.org/electrical/solution/662/worker-training.html
[more_like_this:protected] => i002691,d001269, c000079, d001285
[permission_given_by:protected] =>
[published:protected] => T
[billable:protected] => F
[img_name:protected] =>
[img_ext:protected] => jpg
[img_width:protected] =>
[img_height:protected] =>
[img_credit:protected] => Morgan Zavertnik and Hoar Construction
[img_practice:protected] => good
[vid_source_id:protected] =>
[vid_running_time:protected] =>
[vid_intended_audience:protected] =>
[vid_acquisition_info:protected] =>
[vid_cost:protected] =>
[vid_producer:protected] =>
[vid_filename:protected] =>
[vid_filename_downloadable:protected] =>
[date_summary:protected] => November 2015
[date_permission_requested:protected] =>
[date_permission_received:protected] =>
[date_review_needed:protected] =>
[date_received:protected] => 03/02/16
[date_completed:protected] => 03/02/16
[date_billed:protected] =>
[date_modified:protected] => 03/02/16
[collBokExports:protected] =>
[lastBokExportCriteria:BaseElcoshItem:private] =>
[alreadyInSave:protected] =>
[alreadyInValidation:protected] =>
[validationFailures:protected] => Array
(
)
[_new:BaseObject:private] =>
[_deleted:BaseObject:private] =>
[modifiedColumns:protected] => Array
(
)
)
)
[2] => Search_Result Object
(
[title] => Toolbox talk - long shot
[image] => /record/images/4006-p.jpg
[blurb] => This crew gathered every morning before starting work to discuss a new safety topic....
[category] => Array
(
[0] => 20
[1] => 47
[2] => 49
[3] => 51
[4] => 55
[5] => 64
[6] => 68
[7] => 75
[8] => 76
[9] => 63
[10] => 78
[11] => 79
[12] => 82
[13] => 62
[14] => 87
[15] => 88
[16] => 91
[17] => 90
[18] => 93
[19] => 94
[20] => 95
[21] => 97
)
[labels] => Array
(
[0] => Safety Culture
[1] => Work Environment
[2] => Hazards
[3] => Bricklayer
[4] => Trades
[5] => Carpenter
[7] => Cement Mason
[9] => Electrical Worker
[11] => Laborer
[13] => Maintenance Worker
[15] => Plasterer
[17] => Plumber/Pipefitter
[19] => Reinforcing Ironworker
[21] => Roofer/Waterproofer
[23] => Scaffold Erector
[25] => Stonemason
[27] => Structural Ironworker
[29] => Commercial & Institutional
[30] => Jobsites
[31] => Demolition
[33] => Heavy & Highway
[35] => Industrial
[37] => Renovations
[39] => Residential
[41] => Underground
[43] => Images
[44] => Media
[45] => Media & Documents
)
[type] => Images
[sub_category] =>
[url] => /image/4006/i002693/Toolbox%2Btalk%2B-%2Blong%2Bshot.html
[item:protected] => ImageRecord Object
(
[records:protected] => Array
(
)
[recordId:protected] =>
[searchWordClass:protected] =>
[searchWordPeerClass:protected] =>
[bok_record:protected] =>
[authors:protected] =>
[organizations:protected] =>
[collections:protected] =>
[categories:protected] => Array
(
[20] => Category Object
(
[languages:protected] =>
[bok_resources:protected] =>
[bok_topics:protected] =>
[bok_keywords:protected] =>
[id:protected] => 20
[type:protected] => category
[parent:protected] => 7
[label:protected] => Safety Culture
[alreadyInSave:protected] =>
[alreadyInValidation:protected] =>
[validationFailures:protected] => Array
(
)
[_new:BaseObject:private] =>
[_deleted:BaseObject:private] =>
[modifiedColumns:protected] => Array
(
)
)
[47] => Category Object
(
[languages:protected] =>
[bok_resources:protected] =>
[bok_topics:protected] =>
[bok_keywords:protected] =>
[id:protected] => 47
[type:protected] => category
[parent:protected] => 2
[label:protected] => Bricklayer
[alreadyInSave:protected] =>
[alreadyInValidation:protected] =>
[validationFailures:protected] => Array
(
)
[_new:BaseObject:private] =>
[_deleted:BaseObject:private] =>
[modifiedColumns:protected] => Array
(
)
)
[49] => Category Object
(
[languages:protected] =>
[bok_resources:protected] =>
[bok_topics:protected] =>
[bok_keywords:protected] =>
[id:protected] => 49
[type:protected] => category
[parent:protected] => 2
[label:protected] => Carpenter
[alreadyInSave:protected] =>
[alreadyInValidation:protected] =>
[validationFailures:protected] => Array
(
)
[_new:BaseObject:private] =>
[_deleted:BaseObject:private] =>
[modifiedColumns:protected] => Array
(
)
)
[51] => Category Object
(
[languages:protected] =>
[bok_resources:protected] =>
[bok_topics:protected] =>
[bok_keywords:protected] =>
[id:protected] => 51
[type:protected] => category
[parent:protected] => 2
[label:protected] => Cement Mason
[alreadyInSave:protected] =>
[alreadyInValidation:protected] =>
[validationFailures:protected] => Array
(
)
[_new:BaseObject:private] =>
[_deleted:BaseObject:private] =>
[modifiedColumns:protected] => Array
(
)
)
[55] => Category Object
(
[languages:protected] =>
[bok_resources:protected] =>
[bok_topics:protected] =>
[bok_keywords:protected] =>
[id:protected] => 55
[type:protected] => category
[parent:protected] => 2
[label:protected] => Electrical Worker
[alreadyInSave:protected] =>
[alreadyInValidation:protected] =>
[validationFailures:protected] => Array
(
)
[_new:BaseObject:private] =>
[_deleted:BaseObject:private] =>
[modifiedColumns:protected] => Array
(
)
)
[64] => Category Object
(
[languages:protected] =>
[bok_resources:protected] =>
[bok_topics:protected] =>
[bok_keywords:protected] =>
[id:protected] => 64
[type:protected] => category
[parent:protected] => 2
[label:protected] => Laborer
[alreadyInSave:protected] =>
[alreadyInValidation:protected] =>
[validationFailures:protected] => Array
(
)
[_new:BaseObject:private] =>
[_deleted:BaseObject:private] =>
[modifiedColumns:protected] => Array
(
)
)
[68] => Category Object
(
[languages:protected] =>
[bok_resources:protected] =>
[bok_topics:protected] =>
[bok_keywords:protected] =>
[id:protected] => 68
[type:protected] => category
[parent:protected] => 2
[label:protected] => Maintenance Worker
[alreadyInSave:protected] =>
[alreadyInValidation:protected] =>
[validationFailures:protected] => Array
(
)
[_new:BaseObject:private] =>
[_deleted:BaseObject:private] =>
[modifiedColumns:protected] => Array
(
)
)
[75] => Category Object
(
[languages:protected] =>
[bok_resources:protected] =>
[bok_topics:protected] =>
[bok_keywords:protected] =>
[id:protected] => 75
[type:protected] => category
[parent:protected] => 2
[label:protected] => Plasterer
[alreadyInSave:protected] =>
[alreadyInValidation:protected] =>
[validationFailures:protected] => Array
(
)
[_new:BaseObject:private] =>
[_deleted:BaseObject:private] =>
[modifiedColumns:protected] => Array
(
)
)
[76] => Category Object
(
[languages:protected] =>
[bok_resources:protected] =>
[bok_topics:protected] =>
[bok_keywords:protected] =>
[id:protected] => 76
[type:protected] => category
[parent:protected] => 2
[label:protected] => Plumber/Pipefitter
[alreadyInSave:protected] =>
[alreadyInValidation:protected] =>
[validationFailures:protected] => Array
(
)
[_new:BaseObject:private] =>
[_deleted:BaseObject:private] =>
[modifiedColumns:protected] => Array
(
)
)
[63] => Category Object
(
[languages:protected] =>
[bok_resources:protected] =>
[bok_topics:protected] =>
[bok_keywords:protected] =>
[id:protected] => 63
[type:protected] => category
[parent:protected] => 2
[label:protected] => Reinforcing Ironworker
[alreadyInSave:protected] =>
[alreadyInValidation:protected] =>
[validationFailures:protected] => Array
(
)
[_new:BaseObject:private] =>
[_deleted:BaseObject:private] =>
[modifiedColumns:protected] => Array
(
)
)
[78] => Category Object
(
[languages:protected] =>
[bok_resources:protected] =>
[bok_topics:protected] =>
[bok_keywords:protected] =>
[id:protected] => 78
[type:protected] => category
[parent:protected] => 2
[label:protected] => Roofer/Waterproofer
[alreadyInSave:protected] =>
[alreadyInValidation:protected] =>
[validationFailures:protected] => Array
(
)
[_new:BaseObject:private] =>
[_deleted:BaseObject:private] =>
[modifiedColumns:protected] => Array
(
)
)
[79] => Category Object
(
[languages:protected] =>
[bok_resources:protected] =>
[bok_topics:protected] =>
[bok_keywords:protected] =>
[id:protected] => 79
[type:protected] => category
[parent:protected] => 2
[label:protected] => Scaffold Erector
[alreadyInSave:protected] =>
[alreadyInValidation:protected] =>
[validationFailures:protected] => Array
(
)
[_new:BaseObject:private] =>
[_deleted:BaseObject:private] =>
[modifiedColumns:protected] => Array
(
)
)
[82] => Category Object
(
[languages:protected] =>
[bok_resources:protected] =>
[bok_topics:protected] =>
[bok_keywords:protected] =>
[id:protected] => 82
[type:protected] => category
[parent:protected] => 2
[label:protected] => Stonemason
[alreadyInSave:protected] =>
[alreadyInValidation:protected] =>
[validationFailures:protected] => Array
(
)
[_new:BaseObject:private] =>
[_deleted:BaseObject:private] =>
[modifiedColumns:protected] => Array
(
)
)
[62] => Category Object
(
[languages:protected] =>
[bok_resources:protected] =>
[bok_topics:protected] =>
[bok_keywords:protected] =>
[id:protected] => 62
[type:protected] => category
[parent:protected] => 2
[label:protected] => Structural Ironworker
[alreadyInSave:protected] =>
[alreadyInValidation:protected] =>
[validationFailures:protected] => Array
(
)
[_new:BaseObject:private] =>
[_deleted:BaseObject:private] =>
[modifiedColumns:protected] => Array
(
)
)
[87] => Category Object
(
[languages:protected] =>
[bok_resources:protected] =>
[bok_topics:protected] =>
[bok_keywords:protected] =>
[id:protected] => 87
[type:protected] => category
[parent:protected] => 3
[label:protected] => Commercial & Institutional
[alreadyInSave:protected] =>
[alreadyInValidation:protected] =>
[validationFailures:protected] => Array
(
)
[_new:BaseObject:private] =>
[_deleted:BaseObject:private] =>
[modifiedColumns:protected] => Array
(
)
)
[88] => Category Object
(
[languages:protected] =>
[bok_resources:protected] =>
[bok_topics:protected] =>
[bok_keywords:protected] =>
[id:protected] => 88
[type:protected] => category
[parent:protected] => 3
[label:protected] => Demolition
[alreadyInSave:protected] =>
[alreadyInValidation:protected] =>
[validationFailures:protected] => Array
(
)
[_new:BaseObject:private] =>
[_deleted:BaseObject:private] =>
[modifiedColumns:protected] => Array
(
)
)
[91] => Category Object
(
[languages:protected] =>
[bok_resources:protected] =>
[bok_topics:protected] =>
[bok_keywords:protected] =>
[id:protected] => 91
[type:protected] => category
[parent:protected] => 3
[label:protected] => Heavy & Highway
[alreadyInSave:protected] =>
[alreadyInValidation:protected] =>
[validationFailures:protected] => Array
(
)
[_new:BaseObject:private] =>
[_deleted:BaseObject:private] =>
[modifiedColumns:protected] => Array
(
)
)
[90] => Category Object
(
[languages:protected] =>
[bok_resources:protected] =>
[bok_topics:protected] =>
[bok_keywords:protected] =>
[id:protected] => 90
[type:protected] => category
[parent:protected] => 3
[label:protected] => Industrial
[alreadyInSave:protected] =>
[alreadyInValidation:protected] =>
[validationFailures:protected] => Array
(
)
[_new:BaseObject:private] =>
[_deleted:BaseObject:private] =>
[modifiedColumns:protected] => Array
(
)
)
[93] => Category Object
(
[languages:protected] =>
[bok_resources:protected] =>
[bok_topics:protected] =>
[bok_keywords:protected] =>
[id:protected] => 93
[type:protected] => category
[parent:protected] => 3
[label:protected] => Renovations
[alreadyInSave:protected] =>
[alreadyInValidation:protected] =>
[validationFailures:protected] => Array
(
)
[_new:BaseObject:private] =>
[_deleted:BaseObject:private] =>
[modifiedColumns:protected] => Array
(
)
)
[94] => Category Object
(
[languages:protected] =>
[bok_resources:protected] =>
[bok_topics:protected] =>
[bok_keywords:protected] =>
[id:protected] => 94
[type:protected] => category
[parent:protected] => 3
[label:protected] => Residential
[alreadyInSave:protected] =>
[alreadyInValidation:protected] =>
[validationFailures:protected] => Array
(
)
[_new:BaseObject:private] =>
[_deleted:BaseObject:private] =>
[modifiedColumns:protected] => Array
(
)
)
[95] => Category Object
(
[languages:protected] =>
[bok_resources:protected] =>
[bok_topics:protected] =>
[bok_keywords:protected] =>
[id:protected] => 95
[type:protected] => category
[parent:protected] => 3
[label:protected] => Underground
[alreadyInSave:protected] =>
[alreadyInValidation:protected] =>
[validationFailures:protected] => Array
(
)
[_new:BaseObject:private] =>
[_deleted:BaseObject:private] =>
[modifiedColumns:protected] => Array
(
)
)
[97] => Category Object
(
[languages:protected] =>
[bok_resources:protected] =>
[bok_topics:protected] =>
[bok_keywords:protected] =>
[id:protected] => 97
[type:protected] => category
[parent:protected] => 5
[label:protected] => Images
[alreadyInSave:protected] =>
[alreadyInValidation:protected] =>
[validationFailures:protected] => Array
(
)
[_new:BaseObject:private] =>
[_deleted:BaseObject:private] =>
[modifiedColumns:protected] => Array
(
)
)
)
[categories_initialized:protected] => 1
[mapped_items:protected] =>
[content:protected] =>
[files:protected] =>
[language:protected] => Language Object
(
[id:protected] => 1
[code:protected] => en
[name:protected] => English
[alreadyInSave:protected] =>
[alreadyInValidation:protected] =>
[validationFailures:protected] => Array
(
)
[_new:BaseObject:private] =>
[_deleted:BaseObject:private] =>
[modifiedColumns:protected] => Array
(
)
)
[old_record:protected] =>
[id:protected] => 4006
[old_id:protected] =>
[elcosh_id:protected] => i002693
[type:protected] => image
[display_type:protected] => Image
[user_id:protected] => 0
[language_id:protected] => 1
[tagging_id:protected] => Bruce Lippy
[priority_id:protected] => 1
[title:protected] => Toolbox talk - long shot
[total_pages:protected] => 0
[billed_pages:protected] => 0
[publication_number:protected] =>
[part_of:protected] =>
[keywords:protected] => toolbox talk, tailgate talk, safety minute
[comments:protected] =>
[summary:protected] => This crew gathered every morning before starting work to discuss a new safety topic.
[transition_comments:protected] =>
[external_link:protected] =>
[consol_link:protected] => http://www.cpwrconstructionsolutions.org/electrical/solution/662/worker-training.html
[more_like_this:protected] => i002691,i002692,d001269,d000527
[permission_given_by:protected] =>
[published:protected] => T
[billable:protected] => F
[img_name:protected] =>
[img_ext:protected] => jpg
[img_width:protected] =>
[img_height:protected] =>
[img_credit:protected] => Morgan Zavertnik and Hoar Construction
[img_practice:protected] => good
[vid_source_id:protected] =>
[vid_running_time:protected] =>
[vid_intended_audience:protected] =>
[vid_acquisition_info:protected] =>
[vid_cost:protected] =>
[vid_producer:protected] =>
[vid_filename:protected] =>
[vid_filename_downloadable:protected] =>
[date_summary:protected] => November 2015
[date_permission_requested:protected] =>
[date_permission_received:protected] =>
[date_review_needed:protected] =>
[date_received:protected] => 03/02/16
[date_completed:protected] => 03/02/16
[date_billed:protected] =>
[date_modified:protected] => 03/02/16
[collBokExports:protected] =>
[lastBokExportCriteria:BaseElcoshItem:private] =>
[alreadyInSave:protected] =>
[alreadyInValidation:protected] =>
[validationFailures:protected] => Array
(
)
[_new:BaseObject:private] =>
[_deleted:BaseObject:private] =>
[modifiedColumns:protected] => Array
(
)
)
)
[3] => Search_Result Object
(
[title] => Safety officer discussing ongoing project with marketing coordinator
[image] => /record/images/4014-p.jpg
[blurb] => The safety officer (left) points out the good safety practices on this project that reflect well on the firm and may influence future clients....
[category] => Array
(
[0] => 97
[1] => 20
[2] => 46
[3] => 47
[4] => 49
[5] => 50
[6] => 51
[7] => 54
[8] => 55
[9] => 58
[10] => 60
[11] => 61
[12] => 64
[13] => 71
[14] => 75
[15] => 76
[16] => 63
[17] => 79
[18] => 80
[19] => 82
[20] => 62
[21] => 83
[22] => 87
[23] => 91
[24] => 90
[25] => 93
[26] => 94
)
[labels] => Array
(
[0] => Images
[1] => Media
[2] => Media & Documents
[3] => Safety Culture
[4] => Work Environment
[5] => Hazards
[6] => Boilermaker
[7] => Trades
[8] => Bricklayer
[10] => Carpenter
[12] => Carpet Layer
[14] => Cement Mason
[16] => Drywall Applicator Specialist
[18] => Electrical Worker
[20] => Glazier
[22] => HVAC
[24] => Interior Systems Carpenter
[26] => Laborer
[28] => Painter
[30] => Plasterer
[32] => Plumber/Pipefitter
[34] => Reinforcing Ironworker
[36] => Scaffold Erector
[38] => Sheetmetal Worker
[40] => Stonemason
[42] => Structural Ironworker
[44] => Terrazzo Worker
[46] => Commercial & Institutional
[47] => Jobsites
[48] => Heavy & Highway
[50] => Industrial
[52] => Renovations
[54] => Residential
)
[type] => Images
[sub_category] =>
[url] => /image/4014/i002700/Safety%2Bofficer%2Bdiscussing%2Bongoing%2Bproject%2Bwith%2Bmarketing%2Bcoordinator.html
[item:protected] => ImageRecord Object
(
[records:protected] => Array
(
)
[recordId:protected] =>
[searchWordClass:protected] =>
[searchWordPeerClass:protected] =>
[bok_record:protected] =>
[authors:protected] =>
[organizations:protected] =>
[collections:protected] =>
[categories:protected] => Array
(
[97] => Category Object
(
[languages:protected] =>
[bok_resources:protected] =>
[bok_topics:protected] =>
[bok_keywords:protected] =>
[id:protected] => 97
[type:protected] => category
[parent:protected] => 5
[label:protected] => Images
[alreadyInSave:protected] =>
[alreadyInValidation:protected] =>
[validationFailures:protected] => Array
(
)
[_new:BaseObject:private] =>
[_deleted:BaseObject:private] =>
[modifiedColumns:protected] => Array
(
)
)
[20] => Category Object
(
[languages:protected] =>
[bok_resources:protected] =>
[bok_topics:protected] =>
[bok_keywords:protected] =>
[id:protected] => 20
[type:protected] => category
[parent:protected] => 7
[label:protected] => Safety Culture
[alreadyInSave:protected] =>
[alreadyInValidation:protected] =>
[validationFailures:protected] => Array
(
)
[_new:BaseObject:private] =>
[_deleted:BaseObject:private] =>
[modifiedColumns:protected] => Array
(
)
)
[46] => Category Object
(
[languages:protected] =>
[bok_resources:protected] =>
[bok_topics:protected] =>
[bok_keywords:protected] =>
[id:protected] => 46
[type:protected] => category
[parent:protected] => 2
[label:protected] => Boilermaker
[alreadyInSave:protected] =>
[alreadyInValidation:protected] =>
[validationFailures:protected] => Array
(
)
[_new:BaseObject:private] =>
[_deleted:BaseObject:private] =>
[modifiedColumns:protected] => Array
(
)
)
[47] => Category Object
(
[languages:protected] =>
[bok_resources:protected] =>
[bok_topics:protected] =>
[bok_keywords:protected] =>
[id:protected] => 47
[type:protected] => category
[parent:protected] => 2
[label:protected] => Bricklayer
[alreadyInSave:protected] =>
[alreadyInValidation:protected] =>
[validationFailures:protected] => Array
(
)
[_new:BaseObject:private] =>
[_deleted:BaseObject:private] =>
[modifiedColumns:protected] => Array
(
)
)
[49] => Category Object
(
[languages:protected] =>
[bok_resources:protected] =>
[bok_topics:protected] =>
[bok_keywords:protected] =>
[id:protected] => 49
[type:protected] => category
[parent:protected] => 2
[label:protected] => Carpenter
[alreadyInSave:protected] =>
[alreadyInValidation:protected] =>
[validationFailures:protected] => Array
(
)
[_new:BaseObject:private] =>
[_deleted:BaseObject:private] =>
[modifiedColumns:protected] => Array
(
)
)
[50] => Category Object
(
[languages:protected] =>
[bok_resources:protected] =>
[bok_topics:protected] =>
[bok_keywords:protected] =>
[id:protected] => 50
[type:protected] => category
[parent:protected] => 2
[label:protected] => Carpet Layer
[alreadyInSave:protected] =>
[alreadyInValidation:protected] =>
[validationFailures:protected] => Array
(
)
[_new:BaseObject:private] =>
[_deleted:BaseObject:private] =>
[modifiedColumns:protected] => Array
(
)
)
[51] => Category Object
(
[languages:protected] =>
[bok_resources:protected] =>
[bok_topics:protected] =>
[bok_keywords:protected] =>
[id:protected] => 51
[type:protected] => category
[parent:protected] => 2
[label:protected] => Cement Mason
[alreadyInSave:protected] =>
[alreadyInValidation:protected] =>
[validationFailures:protected] => Array
(
)
[_new:BaseObject:private] =>
[_deleted:BaseObject:private] =>
[modifiedColumns:protected] => Array
(
)
)
[54] => Category Object
(
[languages:protected] =>
[bok_resources:protected] =>
[bok_topics:protected] =>
[bok_keywords:protected] =>
[id:protected] => 54
[type:protected] => category
[parent:protected] => 2
[label:protected] => Drywall Applicator Specialist
[alreadyInSave:protected] =>
[alreadyInValidation:protected] =>
[validationFailures:protected] => Array
(
)
[_new:BaseObject:private] =>
[_deleted:BaseObject:private] =>
[modifiedColumns:protected] => Array
(
)
)
[55] => Category Object
(
[languages:protected] =>
[bok_resources:protected] =>
[bok_topics:protected] =>
[bok_keywords:protected] =>
[id:protected] => 55
[type:protected] => category
[parent:protected] => 2
[label:protected] => Electrical Worker
[alreadyInSave:protected] =>
[alreadyInValidation:protected] =>
[validationFailures:protected] => Array
(
)
[_new:BaseObject:private] =>
[_deleted:BaseObject:private] =>
[modifiedColumns:protected] => Array
(
)
)
[58] => Category Object
(
[languages:protected] =>
[bok_resources:protected] =>
[bok_topics:protected] =>
[bok_keywords:protected] =>
[id:protected] => 58
[type:protected] => category
[parent:protected] => 2
[label:protected] => Glazier
[alreadyInSave:protected] =>
[alreadyInValidation:protected] =>
[validationFailures:protected] => Array
(
)
[_new:BaseObject:private] =>
[_deleted:BaseObject:private] =>
[modifiedColumns:protected] => Array
(
)
)
[60] => Category Object
(
[languages:protected] =>
[bok_resources:protected] =>
[bok_topics:protected] =>
[bok_keywords:protected] =>
[id:protected] => 60
[type:protected] => category
[parent:protected] => 2
[label:protected] => HVAC
[alreadyInSave:protected] =>
[alreadyInValidation:protected] =>
[validationFailures:protected] => Array
(
)
[_new:BaseObject:private] =>
[_deleted:BaseObject:private] =>
[modifiedColumns:protected] => Array
(
)
)
[61] => Category Object
(
[languages:protected] =>
[bok_resources:protected] =>
[bok_topics:protected] =>
[bok_keywords:protected] =>
[id:protected] => 61
[type:protected] => category
[parent:protected] => 2
[label:protected] => Interior Systems Carpenter
[alreadyInSave:protected] =>
[alreadyInValidation:protected] =>
[validationFailures:protected] => Array
(
)
[_new:BaseObject:private] =>
[_deleted:BaseObject:private] =>
[modifiedColumns:protected] => Array
(
)
)
[64] => Category Object
(
[languages:protected] =>
[bok_resources:protected] =>
[bok_topics:protected] =>
[bok_keywords:protected] =>
[id:protected] => 64
[type:protected] => category
[parent:protected] => 2
[label:protected] => Laborer
[alreadyInSave:protected] =>
[alreadyInValidation:protected] =>
[validationFailures:protected] => Array
(
)
[_new:BaseObject:private] =>
[_deleted:BaseObject:private] =>
[modifiedColumns:protected] => Array
(
)
)
[71] => Category Object
(
[languages:protected] =>
[bok_resources:protected] =>
[bok_topics:protected] =>
[bok_keywords:protected] =>
[id:protected] => 71
[type:protected] => category
[parent:protected] => 2
[label:protected] => Painter
[alreadyInSave:protected] =>
[alreadyInValidation:protected] =>
[validationFailures:protected] => Array
(
)
[_new:BaseObject:private] =>
[_deleted:BaseObject:private] =>
[modifiedColumns:protected] => Array
(
)
)
[75] => Category Object
(
[languages:protected] =>
[bok_resources:protected] =>
[bok_topics:protected] =>
[bok_keywords:protected] =>
[id:protected] => 75
[type:protected] => category
[parent:protected] => 2
[label:protected] => Plasterer
[alreadyInSave:protected] =>
[alreadyInValidation:protected] =>
[validationFailures:protected] => Array
(
)
[_new:BaseObject:private] =>
[_deleted:BaseObject:private] =>
[modifiedColumns:protected] => Array
(
)
)
[76] => Category Object
(
[languages:protected] =>
[bok_resources:protected] =>
[bok_topics:protected] =>
[bok_keywords:protected] =>
[id:protected] => 76
[type:protected] => category
[parent:protected] => 2
[label:protected] => Plumber/Pipefitter
[alreadyInSave:protected] =>
[alreadyInValidation:protected] =>
[validationFailures:protected] => Array
(
)
[_new:BaseObject:private] =>
[_deleted:BaseObject:private] =>
[modifiedColumns:protected] => Array
(
)
)
[63] => Category Object
(
[languages:protected] =>
[bok_resources:protected] =>
[bok_topics:protected] =>
[bok_keywords:protected] =>
[id:protected] => 63
[type:protected] => category
[parent:protected] => 2
[label:protected] => Reinforcing Ironworker
[alreadyInSave:protected] =>
[alreadyInValidation:protected] =>
[validationFailures:protected] => Array
(
)
[_new:BaseObject:private] =>
[_deleted:BaseObject:private] =>
[modifiedColumns:protected] => Array
(
)
)
[79] => Category Object
(
[languages:protected] =>
[bok_resources:protected] =>
[bok_topics:protected] =>
[bok_keywords:protected] =>
[id:protected] => 79
[type:protected] => category
[parent:protected] => 2
[label:protected] => Scaffold Erector
[alreadyInSave:protected] =>
[alreadyInValidation:protected] =>
[validationFailures:protected] => Array
(
)
[_new:BaseObject:private] =>
[_deleted:BaseObject:private] =>
[modifiedColumns:protected] => Array
(
)
)
[80] => Category Object
(
[languages:protected] =>
[bok_resources:protected] =>
[bok_topics:protected] =>
[bok_keywords:protected] =>
[id:protected] => 80
[type:protected] => category
[parent:protected] => 2
[label:protected] => Sheetmetal Worker
[alreadyInSave:protected] =>
[alreadyInValidation:protected] =>
[validationFailures:protected] => Array
(
)
[_new:BaseObject:private] =>
[_deleted:BaseObject:private] =>
[modifiedColumns:protected] => Array
(
)
)
[82] => Category Object
(
[languages:protected] =>
[bok_resources:protected] =>
[bok_topics:protected] =>
[bok_keywords:protected] =>
[id:protected] => 82
[type:protected] => category
[parent:protected] => 2
[label:protected] => Stonemason
[alreadyInSave:protected] =>
[alreadyInValidation:protected] =>
[validationFailures:protected] => Array
(
)
[_new:BaseObject:private] =>
[_deleted:BaseObject:private] =>
[modifiedColumns:protected] => Array
(
)
)
[62] => Category Object
(
[languages:protected] =>
[bok_resources:protected] =>
[bok_topics:protected] =>
[bok_keywords:protected] =>
[id:protected] => 62
[type:protected] => category
[parent:protected] => 2
[label:protected] => Structural Ironworker
[alreadyInSave:protected] =>
[alreadyInValidation:protected] =>
[validationFailures:protected] => Array
(
)
[_new:BaseObject:private] =>
[_deleted:BaseObject:private] =>
[modifiedColumns:protected] => Array
(
)
)
[83] => Category Object
(
[languages:protected] =>
[bok_resources:protected] =>
[bok_topics:protected] =>
[bok_keywords:protected] =>
[id:protected] => 83
[type:protected] => category
[parent:protected] => 2
[label:protected] => Terrazzo Worker
[alreadyInSave:protected] =>
[alreadyInValidation:protected] =>
[validationFailures:protected] => Array
(
)
[_new:BaseObject:private] =>
[_deleted:BaseObject:private] =>
[modifiedColumns:protected] => Array
(
)
)
[87] => Category Object
(
[languages:protected] =>
[bok_resources:protected] =>
[bok_topics:protected] =>
[bok_keywords:protected] =>
[id:protected] => 87
[type:protected] => category
[parent:protected] => 3
[label:protected] => Commercial & Institutional
[alreadyInSave:protected] =>
[alreadyInValidation:protected] =>
[validationFailures:protected] => Array
(
)
[_new:BaseObject:private] =>
[_deleted:BaseObject:private] =>
[modifiedColumns:protected] => Array
(
)
)
[91] => Category Object
(
[languages:protected] =>
[bok_resources:protected] =>
[bok_topics:protected] =>
[bok_keywords:protected] =>
[id:protected] => 91
[type:protected] => category
[parent:protected] => 3
[label:protected] => Heavy & Highway
[alreadyInSave:protected] =>
[alreadyInValidation:protected] =>
[validationFailures:protected] => Array
(
)
[_new:BaseObject:private] =>
[_deleted:BaseObject:private] =>
[modifiedColumns:protected] => Array
(
)
)
[90] => Category Object
(
[languages:protected] =>
[bok_resources:protected] =>
[bok_topics:protected] =>
[bok_keywords:protected] =>
[id:protected] => 90
[type:protected] => category
[parent:protected] => 3
[label:protected] => Industrial
[alreadyInSave:protected] =>
[alreadyInValidation:protected] =>
[validationFailures:protected] => Array
(
)
[_new:BaseObject:private] =>
[_deleted:BaseObject:private] =>
[modifiedColumns:protected] => Array
(
)
)
[93] => Category Object
(
[languages:protected] =>
[bok_resources:protected] =>
[bok_topics:protected] =>
[bok_keywords:protected] =>
[id:protected] => 93
[type:protected] => category
[parent:protected] => 3
[label:protected] => Renovations
[alreadyInSave:protected] =>
[alreadyInValidation:protected] =>
[validationFailures:protected] => Array
(
)
[_new:BaseObject:private] =>
[_deleted:BaseObject:private] =>
[modifiedColumns:protected] => Array
(
)
)
[94] => Category Object
(
[languages:protected] =>
[bok_resources:protected] =>
[bok_topics:protected] =>
[bok_keywords:protected] =>
[id:protected] => 94
[type:protected] => category
[parent:protected] => 3
[label:protected] => Residential
[alreadyInSave:protected] =>
[alreadyInValidation:protected] =>
[validationFailures:protected] => Array
(
)
[_new:BaseObject:private] =>
[_deleted:BaseObject:private] =>
[modifiedColumns:protected] => Array
(
)
)
)
[categories_initialized:protected] => 1
[mapped_items:protected] =>
[content:protected] =>
[files:protected] =>
[language:protected] => Language Object
(
[id:protected] => 1
[code:protected] => en
[name:protected] => English
[alreadyInSave:protected] =>
[alreadyInValidation:protected] =>
[validationFailures:protected] => Array
(
)
[_new:BaseObject:private] =>
[_deleted:BaseObject:private] =>
[modifiedColumns:protected] => Array
(
)
)
[old_record:protected] =>
[id:protected] => 4014
[old_id:protected] =>
[elcosh_id:protected] => i002700
[type:protected] => image
[display_type:protected] => Image
[user_id:protected] => 0
[language_id:protected] => 1
[tagging_id:protected] => Bruce Lippy
[priority_id:protected] => 1
[title:protected] => Safety officer discussing ongoing project with marketing coordinator
[total_pages:protected] => 0
[billed_pages:protected] => 0
[publication_number:protected] =>
[part_of:protected] =>
[keywords:protected] => Latino, safety officer, safety culture
[comments:protected] =>
[summary:protected] => The safety officer (left) points out the good safety practices on this project that reflect well on the firm and may influence future clients.
[transition_comments:protected] =>
[external_link:protected] =>
[consol_link:protected] => http://www.cpwrconstructionsolutions.org/index.php
[more_like_this:protected] => d000989,d001351,d001362,d000652, d001101, d000931, d001395
[permission_given_by:protected] =>
[published:protected] => T
[billable:protected] => F
[img_name:protected] =>
[img_ext:protected] => jpg
[img_width:protected] =>
[img_height:protected] =>
[img_credit:protected] => Hoar Construction, Photo by Neil Lippy
[img_practice:protected] => good
[vid_source_id:protected] =>
[vid_running_time:protected] =>
[vid_intended_audience:protected] =>
[vid_acquisition_info:protected] =>
[vid_cost:protected] =>
[vid_producer:protected] =>
[vid_filename:protected] =>
[vid_filename_downloadable:protected] =>
[date_summary:protected] => November 2015
[date_permission_requested:protected] =>
[date_permission_received:protected] =>
[date_review_needed:protected] =>
[date_received:protected] => 03/02/16
[date_completed:protected] => 03/02/16
[date_billed:protected] =>
[date_modified:protected] => 01/30/23
[collBokExports:protected] =>
[lastBokExportCriteria:BaseElcoshItem:private] =>
[alreadyInSave:protected] =>
[alreadyInValidation:protected] =>
[validationFailures:protected] => Array
(
)
[_new:BaseObject:private] =>
[_deleted:BaseObject:private] =>
[modifiedColumns:protected] => Array
(
)
)
)
[4] => Search_Result Object
(
[title] => Scaffolding at top of large column
[image] => /record/images/3994-p.jpg
[blurb] => This shot shows innovative guarding around the top of a large concrete column in the base of a high rise structure going up....
[category] => Array
(
[0] => 15
[1] => 21
[2] => 47
[3] => 51
[4] => 63
[5] => 78
[6] => 79
[7] => 80
[8] => 62
[9] => 87
[10] => 97
[11] => 56
[12] => 64
[13] => 74
)
[labels] => Array
(
[0] => Falls
[1] => Work Environment
[2] => Hazards
[3] => Scaffolds
[6] => Bricklayer
[7] => Trades
[8] => Cement Mason
[10] => Reinforcing Ironworker
[12] => Roofer/Waterproofer
[14] => Scaffold Erector
[16] => Sheetmetal Worker
[18] => Structural Ironworker
[20] => Commercial & Institutional
[21] => Jobsites
[22] => Images
[23] => Media
[24] => Media & Documents
[25] => Elevator Constructor
[27] => Laborer
[29] => Pile Driver
)
[type] => Images
[sub_category] =>
[url] => /image/3994/i002689/Scaffolding%2Bat%2Btop%2Bof%2Blarge%2Bcolumn.html
[item:protected] => ImageRecord Object
(
[records:protected] => Array
(
)
[recordId:protected] =>
[searchWordClass:protected] =>
[searchWordPeerClass:protected] =>
[bok_record:protected] =>
[authors:protected] =>
[organizations:protected] =>
[collections:protected] =>
[categories:protected] => Array
(
[15] => Category Object
(
[languages:protected] =>
[bok_resources:protected] =>
[bok_topics:protected] =>
[bok_keywords:protected] =>
[id:protected] => 15
[type:protected] => category
[parent:protected] => 7
[label:protected] => Falls
[alreadyInSave:protected] =>
[alreadyInValidation:protected] =>
[validationFailures:protected] => Array
(
)
[_new:BaseObject:private] =>
[_deleted:BaseObject:private] =>
[modifiedColumns:protected] => Array
(
)
)
[21] => Category Object
(
[languages:protected] =>
[bok_resources:protected] =>
[bok_topics:protected] =>
[bok_keywords:protected] =>
[id:protected] => 21
[type:protected] => category
[parent:protected] => 7
[label:protected] => Scaffolds
[alreadyInSave:protected] =>
[alreadyInValidation:protected] =>
[validationFailures:protected] => Array
(
)
[_new:BaseObject:private] =>
[_deleted:BaseObject:private] =>
[modifiedColumns:protected] => Array
(
)
)
[47] => Category Object
(
[languages:protected] =>
[bok_resources:protected] =>
[bok_topics:protected] =>
[bok_keywords:protected] =>
[id:protected] => 47
[type:protected] => category
[parent:protected] => 2
[label:protected] => Bricklayer
[alreadyInSave:protected] =>
[alreadyInValidation:protected] =>
[validationFailures:protected] => Array
(
)
[_new:BaseObject:private] =>
[_deleted:BaseObject:private] =>
[modifiedColumns:protected] => Array
(
)
)
[51] => Category Object
(
[languages:protected] =>
[bok_resources:protected] =>
[bok_topics:protected] =>
[bok_keywords:protected] =>
[id:protected] => 51
[type:protected] => category
[parent:protected] => 2
[label:protected] => Cement Mason
[alreadyInSave:protected] =>
[alreadyInValidation:protected] =>
[validationFailures:protected] => Array
(
)
[_new:BaseObject:private] =>
[_deleted:BaseObject:private] =>
[modifiedColumns:protected] => Array
(
)
)
[63] => Category Object
(
[languages:protected] =>
[bok_resources:protected] =>
[bok_topics:protected] =>
[bok_keywords:protected] =>
[id:protected] => 63
[type:protected] => category
[parent:protected] => 2
[label:protected] => Reinforcing Ironworker
[alreadyInSave:protected] =>
[alreadyInValidation:protected] =>
[validationFailures:protected] => Array
(
)
[_new:BaseObject:private] =>
[_deleted:BaseObject:private] =>
[modifiedColumns:protected] => Array
(
)
)
[78] => Category Object
(
[languages:protected] =>
[bok_resources:protected] =>
[bok_topics:protected] =>
[bok_keywords:protected] =>
[id:protected] => 78
[type:protected] => category
[parent:protected] => 2
[label:protected] => Roofer/Waterproofer
[alreadyInSave:protected] =>
[alreadyInValidation:protected] =>
[validationFailures:protected] => Array
(
)
[_new:BaseObject:private] =>
[_deleted:BaseObject:private] =>
[modifiedColumns:protected] => Array
(
)
)
[79] => Category Object
(
[languages:protected] =>
[bok_resources:protected] =>
[bok_topics:protected] =>
[bok_keywords:protected] =>
[id:protected] => 79
[type:protected] => category
[parent:protected] => 2
[label:protected] => Scaffold Erector
[alreadyInSave:protected] =>
[alreadyInValidation:protected] =>
[validationFailures:protected] => Array
(
)
[_new:BaseObject:private] =>
[_deleted:BaseObject:private] =>
[modifiedColumns:protected] => Array
(
)
)
[80] => Category Object
(
[languages:protected] =>
[bok_resources:protected] =>
[bok_topics:protected] =>
[bok_keywords:protected] =>
[id:protected] => 80
[type:protected] => category
[parent:protected] => 2
[label:protected] => Sheetmetal Worker
[alreadyInSave:protected] =>
[alreadyInValidation:protected] =>
[validationFailures:protected] => Array
(
)
[_new:BaseObject:private] =>
[_deleted:BaseObject:private] =>
[modifiedColumns:protected] => Array
(
)
)
[62] => Category Object
(
[languages:protected] =>
[bok_resources:protected] =>
[bok_topics:protected] =>
[bok_keywords:protected] =>
[id:protected] => 62
[type:protected] => category
[parent:protected] => 2
[label:protected] => Structural Ironworker
[alreadyInSave:protected] =>
[alreadyInValidation:protected] =>
[validationFailures:protected] => Array
(
)
[_new:BaseObject:private] =>
[_deleted:BaseObject:private] =>
[modifiedColumns:protected] => Array
(
)
)
[87] => Category Object
(
[languages:protected] =>
[bok_resources:protected] =>
[bok_topics:protected] =>
[bok_keywords:protected] =>
[id:protected] => 87
[type:protected] => category
[parent:protected] => 3
[label:protected] => Commercial & Institutional
[alreadyInSave:protected] =>
[alreadyInValidation:protected] =>
[validationFailures:protected] => Array
(
)
[_new:BaseObject:private] =>
[_deleted:BaseObject:private] =>
[modifiedColumns:protected] => Array
(
)
)
[97] => Category Object
(
[languages:protected] =>
[bok_resources:protected] =>
[bok_topics:protected] =>
[bok_keywords:protected] =>
[id:protected] => 97
[type:protected] => category
[parent:protected] => 5
[label:protected] => Images
[alreadyInSave:protected] =>
[alreadyInValidation:protected] =>
[validationFailures:protected] => Array
(
)
[_new:BaseObject:private] =>
[_deleted:BaseObject:private] =>
[modifiedColumns:protected] => Array
(
)
)
[56] => Category Object
(
[languages:protected] =>
[bok_resources:protected] =>
[bok_topics:protected] =>
[bok_keywords:protected] =>
[id:protected] => 56
[type:protected] => category
[parent:protected] => 2
[label:protected] => Elevator Constructor
[alreadyInSave:protected] =>
[alreadyInValidation:protected] =>
[validationFailures:protected] => Array
(
)
[_new:BaseObject:private] =>
[_deleted:BaseObject:private] =>
[modifiedColumns:protected] => Array
(
)
)
[64] => Category Object
(
[languages:protected] =>
[bok_resources:protected] =>
[bok_topics:protected] =>
[bok_keywords:protected] =>
[id:protected] => 64
[type:protected] => category
[parent:protected] => 2
[label:protected] => Laborer
[alreadyInSave:protected] =>
[alreadyInValidation:protected] =>
[validationFailures:protected] => Array
(
)
[_new:BaseObject:private] =>
[_deleted:BaseObject:private] =>
[modifiedColumns:protected] => Array
(
)
)
[74] => Category Object
(
[languages:protected] =>
[bok_resources:protected] =>
[bok_topics:protected] =>
[bok_keywords:protected] =>
[id:protected] => 74
[type:protected] => category
[parent:protected] => 2
[label:protected] => Pile Driver
[alreadyInSave:protected] =>
[alreadyInValidation:protected] =>
[validationFailures:protected] => Array
(
)
[_new:BaseObject:private] =>
[_deleted:BaseObject:private] =>
[modifiedColumns:protected] => Array
(
)
)
)
[categories_initialized:protected] => 1
[mapped_items:protected] =>
[content:protected] =>
[files:protected] =>
[language:protected] => Language Object
(
[id:protected] => 1
[code:protected] => en
[name:protected] => English
[alreadyInSave:protected] =>
[alreadyInValidation:protected] =>
[validationFailures:protected] => Array
(
)
[_new:BaseObject:private] =>
[_deleted:BaseObject:private] =>
[modifiedColumns:protected] => Array
(
)
)
[old_record:protected] =>
[id:protected] => 3994
[old_id:protected] =>
[elcosh_id:protected] => i002689
[type:protected] => image
[display_type:protected] => Image
[user_id:protected] => 0
[language_id:protected] => 1
[tagging_id:protected] => Bruce Lippy
[priority_id:protected] => 1
[title:protected] => Scaffolding at top of large column
[total_pages:protected] => 0
[billed_pages:protected] => 0
[publication_number:protected] =>
[part_of:protected] =>
[keywords:protected] => Guardrail, railing, fall prevention, falls
[comments:protected] =>
[summary:protected] => This shot shows innovative guarding around the top of a large concrete column in the base of a high rise structure going up.
[transition_comments:protected] =>
[external_link:protected] =>
[consol_link:protected] => http://www.cpwrconstructionsolutions.org/masonry/solution/8/adjustable-tower-scaffold.html
[more_like_this:protected] => c1002680,i002662,d000608,d001255
[permission_given_by:protected] =>
[published:protected] => T
[billable:protected] => F
[img_name:protected] =>
[img_ext:protected] => jpg
[img_width:protected] =>
[img_height:protected] =>
[img_credit:protected] => Photo by Pam Susi
[img_practice:protected] => good
[vid_source_id:protected] =>
[vid_running_time:protected] =>
[vid_intended_audience:protected] =>
[vid_acquisition_info:protected] =>
[vid_cost:protected] =>
[vid_producer:protected] =>
[vid_filename:protected] =>
[vid_filename_downloadable:protected] =>
[date_summary:protected] => January 2016
[date_permission_requested:protected] =>
[date_permission_received:protected] =>
[date_review_needed:protected] =>
[date_received:protected] => 02/01/16
[date_completed:protected] => 02/01/16
[date_billed:protected] =>
[date_modified:protected] => 02/01/16
[collBokExports:protected] =>
[lastBokExportCriteria:BaseElcoshItem:private] =>
[alreadyInSave:protected] =>
[alreadyInValidation:protected] =>
[validationFailures:protected] => Array
(
)
[_new:BaseObject:private] =>
[_deleted:BaseObject:private] =>
[modifiedColumns:protected] => Array
(
)
)
)
[5] => Search_Result Object
(
[title] => Construction bracing
[image] => /record/images/3995-p.jpg
[blurb] => This shows structural support that prevents collapses during construction....
[category] => Array
(
[0] => 12
[1] => 15
[2] => 21
[3] => 49
[4] => 51
[5] => 55
[6] => 56
[7] => 60
[8] => 64
[9] => 68
[10] => 74
[11] => 63
[12] => 78
[13] => 79
[14] => 80
[15] => 62
[16] => 87
[17] => 90
[18] => 97
)
[labels] => Array
(
[0] => Crushed/Struck By
[1] => Work Environment
[2] => Hazards
[3] => Falls
[6] => Scaffolds
[9] => Carpenter
[10] => Trades
[11] => Cement Mason
[13] => Electrical Worker
[15] => Elevator Constructor
[17] => HVAC
[19] => Laborer
[21] => Maintenance Worker
[23] => Pile Driver
[25] => Reinforcing Ironworker
[27] => Roofer/Waterproofer
[29] => Scaffold Erector
[31] => Sheetmetal Worker
[33] => Structural Ironworker
[35] => Commercial & Institutional
[36] => Jobsites
[37] => Industrial
[39] => Images
[40] => Media
[41] => Media & Documents
)
[type] => Images
[sub_category] =>
[url] => /image/3995/i002690/Construction%2Bbracing.html
[item:protected] => ImageRecord Object
(
[records:protected] => Array
(
)
[recordId:protected] =>
[searchWordClass:protected] =>
[searchWordPeerClass:protected] =>
[bok_record:protected] =>
[authors:protected] =>
[organizations:protected] =>
[collections:protected] =>
[categories:protected] => Array
(
[12] => Category Object
(
[languages:protected] =>
[bok_resources:protected] =>
[bok_topics:protected] =>
[bok_keywords:protected] =>
[id:protected] => 12
[type:protected] => category
[parent:protected] => 7
[label:protected] => Crushed/Struck By
[alreadyInSave:protected] =>
[alreadyInValidation:protected] =>
[validationFailures:protected] => Array
(
)
[_new:BaseObject:private] =>
[_deleted:BaseObject:private] =>
[modifiedColumns:protected] => Array
(
)
)
[15] => Category Object
(
[languages:protected] =>
[bok_resources:protected] =>
[bok_topics:protected] =>
[bok_keywords:protected] =>
[id:protected] => 15
[type:protected] => category
[parent:protected] => 7
[label:protected] => Falls
[alreadyInSave:protected] =>
[alreadyInValidation:protected] =>
[validationFailures:protected] => Array
(
)
[_new:BaseObject:private] =>
[_deleted:BaseObject:private] =>
[modifiedColumns:protected] => Array
(
)
)
[21] => Category Object
(
[languages:protected] =>
[bok_resources:protected] =>
[bok_topics:protected] =>
[bok_keywords:protected] =>
[id:protected] => 21
[type:protected] => category
[parent:protected] => 7
[label:protected] => Scaffolds
[alreadyInSave:protected] =>
[alreadyInValidation:protected] =>
[validationFailures:protected] => Array
(
)
[_new:BaseObject:private] =>
[_deleted:BaseObject:private] =>
[modifiedColumns:protected] => Array
(
)
)
[49] => Category Object
(
[languages:protected] =>
[bok_resources:protected] =>
[bok_topics:protected] =>
[bok_keywords:protected] =>
[id:protected] => 49
[type:protected] => category
[parent:protected] => 2
[label:protected] => Carpenter
[alreadyInSave:protected] =>
[alreadyInValidation:protected] =>
[validationFailures:protected] => Array
(
)
[_new:BaseObject:private] =>
[_deleted:BaseObject:private] =>
[modifiedColumns:protected] => Array
(
)
)
[51] => Category Object
(
[languages:protected] =>
[bok_resources:protected] =>
[bok_topics:protected] =>
[bok_keywords:protected] =>
[id:protected] => 51
[type:protected] => category
[parent:protected] => 2
[label:protected] => Cement Mason
[alreadyInSave:protected] =>
[alreadyInValidation:protected] =>
[validationFailures:protected] => Array
(
)
[_new:BaseObject:private] =>
[_deleted:BaseObject:private] =>
[modifiedColumns:protected] => Array
(
)
)
[55] => Category Object
(
[languages:protected] =>
[bok_resources:protected] =>
[bok_topics:protected] =>
[bok_keywords:protected] =>
[id:protected] => 55
[type:protected] => category
[parent:protected] => 2
[label:protected] => Electrical Worker
[alreadyInSave:protected] =>
[alreadyInValidation:protected] =>
[validationFailures:protected] => Array
(
)
[_new:BaseObject:private] =>
[_deleted:BaseObject:private] =>
[modifiedColumns:protected] => Array
(
)
)
[56] => Category Object
(
[languages:protected] =>
[bok_resources:protected] =>
[bok_topics:protected] =>
[bok_keywords:protected] =>
[id:protected] => 56
[type:protected] => category
[parent:protected] => 2
[label:protected] => Elevator Constructor
[alreadyInSave:protected] =>
[alreadyInValidation:protected] =>
[validationFailures:protected] => Array
(
)
[_new:BaseObject:private] =>
[_deleted:BaseObject:private] =>
[modifiedColumns:protected] => Array
(
)
)
[60] => Category Object
(
[languages:protected] =>
[bok_resources:protected] =>
[bok_topics:protected] =>
[bok_keywords:protected] =>
[id:protected] => 60
[type:protected] => category
[parent:protected] => 2
[label:protected] => HVAC
[alreadyInSave:protected] =>
[alreadyInValidation:protected] =>
[validationFailures:protected] => Array
(
)
[_new:BaseObject:private] =>
[_deleted:BaseObject:private] =>
[modifiedColumns:protected] => Array
(
)
)
[64] => Category Object
(
[languages:protected] =>
[bok_resources:protected] =>
[bok_topics:protected] =>
[bok_keywords:protected] =>
[id:protected] => 64
[type:protected] => category
[parent:protected] => 2
[label:protected] => Laborer
[alreadyInSave:protected] =>
[alreadyInValidation:protected] =>
[validationFailures:protected] => Array
(
)
[_new:BaseObject:private] =>
[_deleted:BaseObject:private] =>
[modifiedColumns:protected] => Array
(
)
)
[68] => Category Object
(
[languages:protected] =>
[bok_resources:protected] =>
[bok_topics:protected] =>
[bok_keywords:protected] =>
[id:protected] => 68
[type:protected] => category
[parent:protected] => 2
[label:protected] => Maintenance Worker
[alreadyInSave:protected] =>
[alreadyInValidation:protected] =>
[validationFailures:protected] => Array
(
)
[_new:BaseObject:private] =>
[_deleted:BaseObject:private] =>
[modifiedColumns:protected] => Array
(
)
)
[74] => Category Object
(
[languages:protected] =>
[bok_resources:protected] =>
[bok_topics:protected] =>
[bok_keywords:protected] =>
[id:protected] => 74
[type:protected] => category
[parent:protected] => 2
[label:protected] => Pile Driver
[alreadyInSave:protected] =>
[alreadyInValidation:protected] =>
[validationFailures:protected] => Array
(
)
[_new:BaseObject:private] =>
[_deleted:BaseObject:private] =>
[modifiedColumns:protected] => Array
(
)
)
[63] => Category Object
(
[languages:protected] =>
[bok_resources:protected] =>
[bok_topics:protected] =>
[bok_keywords:protected] =>
[id:protected] => 63
[type:protected] => category
[parent:protected] => 2
[label:protected] => Reinforcing Ironworker
[alreadyInSave:protected] =>
[alreadyInValidation:protected] =>
[validationFailures:protected] => Array
(
)
[_new:BaseObject:private] =>
[_deleted:BaseObject:private] =>
[modifiedColumns:protected] => Array
(
)
)
[78] => Category Object
(
[languages:protected] =>
[bok_resources:protected] =>
[bok_topics:protected] =>
[bok_keywords:protected] =>
[id:protected] => 78
[type:protected] => category
[parent:protected] => 2
[label:protected] => Roofer/Waterproofer
[alreadyInSave:protected] =>
[alreadyInValidation:protected] =>
[validationFailures:protected] => Array
(
)
[_new:BaseObject:private] =>
[_deleted:BaseObject:private] =>
[modifiedColumns:protected] => Array
(
)
)
[79] => Category Object
(
[languages:protected] =>
[bok_resources:protected] =>
[bok_topics:protected] =>
[bok_keywords:protected] =>
[id:protected] => 79
[type:protected] => category
[parent:protected] => 2
[label:protected] => Scaffold Erector
[alreadyInSave:protected] =>
[alreadyInValidation:protected] =>
[validationFailures:protected] => Array
(
)
[_new:BaseObject:private] =>
[_deleted:BaseObject:private] =>
[modifiedColumns:protected] => Array
(
)
)
[80] => Category Object
(
[languages:protected] =>
[bok_resources:protected] =>
[bok_topics:protected] =>
[bok_keywords:protected] =>
[id:protected] => 80
[type:protected] => category
[parent:protected] => 2
[label:protected] => Sheetmetal Worker
[alreadyInSave:protected] =>
[alreadyInValidation:protected] =>
[validationFailures:protected] => Array
(
)
[_new:BaseObject:private] =>
[_deleted:BaseObject:private] =>
[modifiedColumns:protected] => Array
(
)
)
[62] => Category Object
(
[languages:protected] =>
[bok_resources:protected] =>
[bok_topics:protected] =>
[bok_keywords:protected] =>
[id:protected] => 62
[type:protected] => category
[parent:protected] => 2
[label:protected] => Structural Ironworker
[alreadyInSave:protected] =>
[alreadyInValidation:protected] =>
[validationFailures:protected] => Array
(
)
[_new:BaseObject:private] =>
[_deleted:BaseObject:private] =>
[modifiedColumns:protected] => Array
(
)
)
[87] => Category Object
(
[languages:protected] =>
[bok_resources:protected] =>
[bok_topics:protected] =>
[bok_keywords:protected] =>
[id:protected] => 87
[type:protected] => category
[parent:protected] => 3
[label:protected] => Commercial & Institutional
[alreadyInSave:protected] =>
[alreadyInValidation:protected] =>
[validationFailures:protected] => Array
(
)
[_new:BaseObject:private] =>
[_deleted:BaseObject:private] =>
[modifiedColumns:protected] => Array
(
)
)
[90] => Category Object
(
[languages:protected] =>
[bok_resources:protected] =>
[bok_topics:protected] =>
[bok_keywords:protected] =>
[id:protected] => 90
[type:protected] => category
[parent:protected] => 3
[label:protected] => Industrial
[alreadyInSave:protected] =>
[alreadyInValidation:protected] =>
[validationFailures:protected] => Array
(
)
[_new:BaseObject:private] =>
[_deleted:BaseObject:private] =>
[modifiedColumns:protected] => Array
(
)
)
[97] => Category Object
(
[languages:protected] =>
[bok_resources:protected] =>
[bok_topics:protected] =>
[bok_keywords:protected] =>
[id:protected] => 97
[type:protected] => category
[parent:protected] => 5
[label:protected] => Images
[alreadyInSave:protected] =>
[alreadyInValidation:protected] =>
[validationFailures:protected] => Array
(
)
[_new:BaseObject:private] =>
[_deleted:BaseObject:private] =>
[modifiedColumns:protected] => Array
(
)
)
)
[categories_initialized:protected] => 1
[mapped_items:protected] =>
[content:protected] =>
[files:protected] =>
[language:protected] => Language Object
(
[id:protected] => 1
[code:protected] => en
[name:protected] => English
[alreadyInSave:protected] =>
[alreadyInValidation:protected] =>
[validationFailures:protected] => Array
(
)
[_new:BaseObject:private] =>
[_deleted:BaseObject:private] =>
[modifiedColumns:protected] => Array
(
)
)
[old_record:protected] =>
[id:protected] => 3995
[old_id:protected] =>
[elcosh_id:protected] => i002690
[type:protected] => image
[display_type:protected] => Image
[user_id:protected] => 0
[language_id:protected] => 1
[tagging_id:protected] => Bruce Lippy
[priority_id:protected] => 1
[title:protected] => Construction bracing
[total_pages:protected] => 0
[billed_pages:protected] => 0
[publication_number:protected] =>
[part_of:protected] =>
[keywords:protected] => Bracing, support, scaffold
[comments:protected] =>
[summary:protected] => This shows structural support that prevents collapses during construction.
[transition_comments:protected] =>
[external_link:protected] =>
[consol_link:protected] => http://www.cpwrconstructionsolutions.org/masonry/solution/8/adjustable-tower-scaffold.html
[more_like_this:protected] => i002660
[permission_given_by:protected] =>
[published:protected] => T
[billable:protected] => F
[img_name:protected] =>
[img_ext:protected] => jpg
[img_width:protected] =>
[img_height:protected] =>
[img_credit:protected] => Photo by Pam Susi
[img_practice:protected] => good
[vid_source_id:protected] =>
[vid_running_time:protected] =>
[vid_intended_audience:protected] =>
[vid_acquisition_info:protected] =>
[vid_cost:protected] =>
[vid_producer:protected] =>
[vid_filename:protected] =>
[vid_filename_downloadable:protected] =>
[date_summary:protected] => January 2016
[date_permission_requested:protected] =>
[date_permission_received:protected] =>
[date_review_needed:protected] =>
[date_received:protected] => 02/01/16
[date_completed:protected] => 02/01/16
[date_billed:protected] =>
[date_modified:protected] => 02/01/16
[collBokExports:protected] =>
[lastBokExportCriteria:BaseElcoshItem:private] =>
[alreadyInSave:protected] =>
[alreadyInValidation:protected] =>
[validationFailures:protected] => Array
(
)
[_new:BaseObject:private] =>
[_deleted:BaseObject:private] =>
[modifiedColumns:protected] => Array
(
)
)
)
)
[preview_mode] =>
[description] => Toolbox talks have been the main tool for communicating safety information on construction jobs for decades.
Unfortunately, there has been little research on what makes for effective toolbox talks. The IUOE National
Training Fund worked with OSHA and NIOSH to make sure their series of 24 Focus Four toolbox talks were based on the best recommendations for effective design. These toolbox talks accompany an entire package of training materials, but can be used alone. This guide points out the key features of these toolbox talks and how best to deliver them.
[keywords] => toolbox talks, tailgate talks
[related_items] => Array
(
[Toolbox Talks] => Array
(
[0] => DocumentRecord Object
(
[records:protected] => Array
(
)
[recordId:protected] =>
[searchWordClass:protected] =>
[searchWordPeerClass:protected] =>
[bok_record:protected] =>
[authors:protected] =>
[organizations:protected] =>
[collections:protected] =>
[categories:protected] =>
[categories_initialized:protected] =>
[mapped_items:protected] =>
[content:protected] =>
[files:protected] =>
[language:protected] => Language Object
(
[id:protected] => 1
[code:protected] => en
[name:protected] => English
[alreadyInSave:protected] =>
[alreadyInValidation:protected] =>
[validationFailures:protected] => Array
(
)
[_new:BaseObject:private] =>
[_deleted:BaseObject:private] =>
[modifiedColumns:protected] => Array
(
)
)
[old_record:protected] =>
[id:protected] => 1605
[old_id:protected] => 1262
[elcosh_id:protected] => d001137
[type:protected] => document
[display_type:protected] => HTML w/ PDF
[user_id:protected] =>
[language_id:protected] => 1
[tagging_id:protected] => Garber
[priority_id:protected] => 1
[title:protected] => Focus Four Toolbox Talks, Module 1 – Falls, Talk #2 – Falls from debris piles?
[total_pages:protected] => 1
[billed_pages:protected] => 1
[publication_number:protected] =>
[part_of:protected] =>
[keywords:protected] => disaster response, hazard clean-up, uneven surface, disaster site, disaster clean-up
[comments:protected] =>
[summary:protected] => A toolbox talk on preventing falls from debris piles. Includes questions to ask, an incident to discuss with images, and a place to record questions the trainer would like to ask about the incident. Part of a collection. Click on the 'collection' button to access the other items.
[transition_comments:protected] =>
[external_link:protected] =>
[consol_link:protected] => http://www.cpwrconstructionsolutions.org/roofing/hazard/1463/install-asphalt-roofs-fall-from-heights.html
[more_like_this:protected] => a000081,d000478,d000530
[permission_given_by:protected] =>
[published:protected] => T
[billable:protected] => F
[img_name:protected] =>
[img_ext:protected] =>
[img_width:protected] =>
[img_height:protected] =>
[img_credit:protected] =>
[img_practice:protected] =>
[vid_source_id:protected] =>
[vid_running_time:protected] =>
[vid_intended_audience:protected] =>
[vid_acquisition_info:protected] =>
[vid_cost:protected] =>
[vid_producer:protected] =>
[vid_filename:protected] =>
[vid_filename_downloadable:protected] =>
[date_summary:protected] =>
[date_permission_requested:protected] =>
[date_permission_received:protected] =>
[date_review_needed:protected] =>
[date_received:protected] => 02/15/12
[date_completed:protected] => 03/19/12
[date_billed:protected] =>
[date_modified:protected] => 07/10/12
[collBokExports:protected] =>
[lastBokExportCriteria:BaseElcoshItem:private] =>
[alreadyInSave:protected] =>
[alreadyInValidation:protected] =>
[validationFailures:protected] => Array
(
)
[_new:BaseObject:private] =>
[_deleted:BaseObject:private] =>
[modifiedColumns:protected] => Array
(
)
)
[1] => DocumentRecord Object
(
[records:protected] => Array
(
)
[recordId:protected] =>
[searchWordClass:protected] =>
[searchWordPeerClass:protected] =>
[bok_record:protected] =>
[authors:protected] =>
[organizations:protected] =>
[collections:protected] =>
[categories:protected] =>
[categories_initialized:protected] =>
[mapped_items:protected] =>
[content:protected] =>
[files:protected] =>
[language:protected] => Language Object
(
[id:protected] => 1
[code:protected] => en
[name:protected] => English
[alreadyInSave:protected] =>
[alreadyInValidation:protected] =>
[validationFailures:protected] => Array
(
)
[_new:BaseObject:private] =>
[_deleted:BaseObject:private] =>
[modifiedColumns:protected] => Array
(
)
)
[old_record:protected] =>
[id:protected] => 1610
[old_id:protected] => 1271
[elcosh_id:protected] => d001146
[type:protected] => document
[display_type:protected] => HTML w/ PDF
[user_id:protected] => 0
[language_id:protected] => 1
[tagging_id:protected] => Garber
[priority_id:protected] => 1
[title:protected] => Focus Four Toolbox Talks, Module 2 – Struck-by, Talk #5 – Rigging and Securing Loads
[total_pages:protected] => 1
[billed_pages:protected] => 1
[publication_number:protected] =>
[part_of:protected] =>
[keywords:protected] => rigging, lift loads, loading areas, chains
[comments:protected] =>
[summary:protected] => A toolbox talk on preventing struck-by incidents caused by not securing loads properly. Includes questions to ask, an incident to discuss with images, and a place to record questions the trainer would like to ask about the incident. Part of a collection. Click on the 'collection' button to access the other items.
[transition_comments:protected] =>
[external_link:protected] =>
[consol_link:protected] => http://www.cpwrconstructionsolutions.org/heavy_equipment/hazard/1591/move-equipment-to-from-and-between-sites-work-zone-struck-by-injuries-and-fatalities.html
[more_like_this:protected] => d000144,d000360,d000873
[permission_given_by:protected] =>
[published:protected] => T
[billable:protected] => F
[img_name:protected] =>
[img_ext:protected] =>
[img_width:protected] =>
[img_height:protected] =>
[img_credit:protected] =>
[img_practice:protected] =>
[vid_source_id:protected] =>
[vid_running_time:protected] =>
[vid_intended_audience:protected] =>
[vid_acquisition_info:protected] =>
[vid_cost:protected] =>
[vid_producer:protected] =>
[vid_filename:protected] =>
[vid_filename_downloadable:protected] =>
[date_summary:protected] =>
[date_permission_requested:protected] =>
[date_permission_received:protected] =>
[date_review_needed:protected] =>
[date_received:protected] => 02/15/12
[date_completed:protected] => 03/28/12
[date_billed:protected] =>
[date_modified:protected] => 05/12/14
[collBokExports:protected] =>
[lastBokExportCriteria:BaseElcoshItem:private] =>
[alreadyInSave:protected] =>
[alreadyInValidation:protected] =>
[validationFailures:protected] => Array
(
)
[_new:BaseObject:private] =>
[_deleted:BaseObject:private] =>
[modifiedColumns:protected] => Array
(
)
)
[2] => DocumentRecord Object
(
[records:protected] => Array
(
)
[recordId:protected] =>
[searchWordClass:protected] =>
[searchWordPeerClass:protected] =>
[bok_record:protected] =>
[authors:protected] =>
[organizations:protected] =>
[collections:protected] =>
[categories:protected] =>
[categories_initialized:protected] =>
[mapped_items:protected] =>
[content:protected] =>
[files:protected] =>
[language:protected] => Language Object
(
[id:protected] => 1
[code:protected] => en
[name:protected] => English
[alreadyInSave:protected] =>
[alreadyInValidation:protected] =>
[validationFailures:protected] => Array
(
)
[_new:BaseObject:private] =>
[_deleted:BaseObject:private] =>
[modifiedColumns:protected] => Array
(
)
)
[old_record:protected] =>
[id:protected] => 1645
[old_id:protected] => 1274
[elcosh_id:protected] => d001149
[type:protected] => document
[display_type:protected] => HTML w/ PDF
[user_id:protected] => 0
[language_id:protected] => 1
[tagging_id:protected] => Garber
[priority_id:protected] => 1
[title:protected] => Focus Four Toolbox Talks, Module 3 – Caught-in/between, Talk #2 – Trenches & Heavy Equipment
[total_pages:protected] => 1
[billed_pages:protected] => 1
[publication_number:protected] =>
[part_of:protected] =>
[keywords:protected] => back-up alarms, spotter, soil cave-in, spoil pikes, ROPs, trenching, rain
[comments:protected] =>
[summary:protected] => A toolbox talk on preventing incidents involving trenches such as trench collapse. Includes questions to ask, an incident to discuss with images, and a place to record questions the trainer would like to ask about the incident. Part of a collection. Click on the 'collection' button to access the other items.
[transition_comments:protected] =>
[external_link:protected] =>
[consol_link:protected] =>
[more_like_this:protected] => d000019,d000035,d000168
[permission_given_by:protected] =>
[published:protected] => T
[billable:protected] => F
[img_name:protected] =>
[img_ext:protected] =>
[img_width:protected] =>
[img_height:protected] =>
[img_credit:protected] =>
[img_practice:protected] =>
[vid_source_id:protected] =>
[vid_running_time:protected] =>
[vid_intended_audience:protected] =>
[vid_acquisition_info:protected] =>
[vid_cost:protected] =>
[vid_producer:protected] =>
[vid_filename:protected] =>
[vid_filename_downloadable:protected] =>
[date_summary:protected] =>
[date_permission_requested:protected] =>
[date_permission_received:protected] =>
[date_review_needed:protected] =>
[date_received:protected] => 02/15/12
[date_completed:protected] => 04/02/12
[date_billed:protected] =>
[date_modified:protected] => 05/23/23
[collBokExports:protected] =>
[lastBokExportCriteria:BaseElcoshItem:private] =>
[alreadyInSave:protected] =>
[alreadyInValidation:protected] =>
[validationFailures:protected] => Array
(
)
[_new:BaseObject:private] =>
[_deleted:BaseObject:private] =>
[modifiedColumns:protected] => Array
(
)
)
[3] => DocumentRecord Object
(
[records:protected] => Array
(
)
[recordId:protected] =>
[searchWordClass:protected] =>
[searchWordPeerClass:protected] =>
[bok_record:protected] =>
[authors:protected] =>
[organizations:protected] =>
[collections:protected] =>
[categories:protected] =>
[categories_initialized:protected] =>
[mapped_items:protected] =>
[content:protected] =>
[files:protected] =>
[language:protected] => Language Object
(
[id:protected] => 1
[code:protected] => en
[name:protected] => English
[alreadyInSave:protected] =>
[alreadyInValidation:protected] =>
[validationFailures:protected] => Array
(
)
[_new:BaseObject:private] =>
[_deleted:BaseObject:private] =>
[modifiedColumns:protected] => Array
(
)
)
[old_record:protected] =>
[id:protected] => 1654
[old_id:protected] => 1284
[elcosh_id:protected] => d001159
[type:protected] => document
[display_type:protected] => HTML w/ PDF
[user_id:protected] => 0
[language_id:protected] => 1
[tagging_id:protected] => Garber
[priority_id:protected] => 1
[title:protected] => Focus Four Toolbox Talks, Module 4 – Electrocutions, Talk #6 – Hazards on Disaster Sites
[total_pages:protected] => 1
[billed_pages:protected] => 1
[publication_number:protected] =>
[part_of:protected] =>
[keywords:protected] => powerlines, underground, utilities, generators, wet conditions, GFCIs, energized lines, disasters, emergency response
[comments:protected] =>
[summary:protected] => A toolbox talk on how to avoid electrocution on a disaster site. Includes questions to ask, an incident to discuss with images, and a place to record questions the trainer would like to ask about the incident. Part of a collection. Click on the 'collection' button to access the other items.
[transition_comments:protected] =>
[external_link:protected] =>
[consol_link:protected] => http://www.cpwrconstructionsolutions.org/electrical/hazard/1138/install-and-repair-high-voltage-lines-transformers-switches-electrical-shocks-burns-and-or-electrocution.html
[more_like_this:protected] => d000135,d000361,d000437
[permission_given_by:protected] =>
[published:protected] => T
[billable:protected] => F
[img_name:protected] =>
[img_ext:protected] =>
[img_width:protected] =>
[img_height:protected] =>
[img_credit:protected] =>
[img_practice:protected] =>
[vid_source_id:protected] =>
[vid_running_time:protected] =>
[vid_intended_audience:protected] =>
[vid_acquisition_info:protected] =>
[vid_cost:protected] =>
[vid_producer:protected] =>
[vid_filename:protected] =>
[vid_filename_downloadable:protected] =>
[date_summary:protected] =>
[date_permission_requested:protected] =>
[date_permission_received:protected] =>
[date_review_needed:protected] =>
[date_received:protected] => 02/15/12
[date_completed:protected] => 04/02/12
[date_billed:protected] =>
[date_modified:protected] => 05/23/23
[collBokExports:protected] =>
[lastBokExportCriteria:BaseElcoshItem:private] =>
[alreadyInSave:protected] =>
[alreadyInValidation:protected] =>
[validationFailures:protected] => Array
(
)
[_new:BaseObject:private] =>
[_deleted:BaseObject:private] =>
[modifiedColumns:protected] => Array
(
)
)
)
)
[collections] => Array
(
[1294] =>
[1295] =>
[1292] =>
[1293] => CollectionRecord Object
(
[collection_items:protected] =>
[records:protected] => Array
(
)
[recordId:protected] =>
[searchWordClass:protected] =>
[searchWordPeerClass:protected] =>
[bok_record:protected] =>
[authors:protected] =>
[organizations:protected] =>
[collections:protected] =>
[categories:protected] =>
[categories_initialized:protected] =>
[mapped_items:protected] =>
[content:protected] =>
[files:protected] =>
[language:protected] =>
[old_record:protected] =>
[id:protected] => 1293
[old_id:protected] =>
[elcosh_id:protected] => c000026
[type:protected] => collection
[display_type:protected] => Collection
[user_id:protected] =>
[language_id:protected] =>
[tagging_id:protected] =>
[priority_id:protected] =>
[title:protected] => Focus Four-Struck By
[total_pages:protected] =>
[billed_pages:protected] =>
[publication_number:protected] =>
[part_of:protected] =>
[keywords:protected] =>
[comments:protected] =>
[summary:protected] => The following are links to all of the items in this collection:
[transition_comments:protected] =>
[external_link:protected] =>
[consol_link:protected] =>
[more_like_this:protected] =>
[permission_given_by:protected] =>
[published:protected] => T
[billable:protected] => F
[img_name:protected] =>
[img_ext:protected] =>
[img_width:protected] =>
[img_height:protected] =>
[img_credit:protected] =>
[img_practice:protected] =>
[vid_source_id:protected] =>
[vid_running_time:protected] =>
[vid_intended_audience:protected] =>
[vid_acquisition_info:protected] =>
[vid_cost:protected] =>
[vid_producer:protected] =>
[vid_filename:protected] =>
[vid_filename_downloadable:protected] =>
[date_summary:protected] =>
[date_permission_requested:protected] =>
[date_permission_received:protected] =>
[date_review_needed:protected] =>
[date_received:protected] => 05/08/12
[date_completed:protected] => 05/08/12
[date_billed:protected] =>
[date_modified:protected] => 05/08/12
[collBokExports:protected] =>
[lastBokExportCriteria:BaseElcoshItem:private] =>
[alreadyInSave:protected] =>
[alreadyInValidation:protected] =>
[validationFailures:protected] => Array
(
)
[_new:BaseObject:private] =>
[_deleted:BaseObject:private] =>
[modifiedColumns:protected] => Array
(
)
)
)
[record] => DocumentRecord Object
(
[records:protected] => Array
(
)
[recordId:protected] =>
[searchWordClass:protected] =>
[searchWordPeerClass:protected] =>
[bok_record:protected] =>
[authors:protected] => Array
(
)
[organizations:protected] => Array
(
[256] => Organization Object
(
[id:protected] => 256
[elcosh_id:protected] => o000276
[user_id:protected] => 14
[province_id:protected] => 0
[country_id:protected] => 0
[title:protected] => IUOE National Training Fund
[address:protected] =>
[postal_code:protected] =>
[city:protected] =>
[department:protected] =>
[phone:protected] => 304-253-8674
[fax:protected] =>
[email:protected] =>
[website:protected] => http://www.iuoeiettc.org
[filename:protected] =>
[about:protected] =>
[comments:protected] =>
[logo_available:protected] => T
[no_details:protected] => F
[date_received:protected] => 2012-02-13
[date_completed:protected] => 2012-02-13
[date_billed:protected] =>
[alreadyInSave:protected] =>
[alreadyInValidation:protected] =>
[validationFailures:protected] => Array
(
)
[_new:BaseObject:private] =>
[_deleted:BaseObject:private] =>
[modifiedColumns:protected] => Array
(
)
)
)
[collections:protected] => Array
(
[1294] =>
[1295] =>
[1292] =>
[1293] => CollectionRecord Object
(
[collection_items:protected] =>
[records:protected] => Array
(
)
[recordId:protected] =>
[searchWordClass:protected] =>
[searchWordPeerClass:protected] =>
[bok_record:protected] =>
[authors:protected] =>
[organizations:protected] =>
[collections:protected] =>
[categories:protected] =>
[categories_initialized:protected] =>
[mapped_items:protected] =>
[content:protected] =>
[files:protected] =>
[language:protected] =>
[old_record:protected] =>
[id:protected] => 1293
[old_id:protected] =>
[elcosh_id:protected] => c000026
[type:protected] => collection
[display_type:protected] => Collection
[user_id:protected] =>
[language_id:protected] =>
[tagging_id:protected] =>
[priority_id:protected] =>
[title:protected] => Focus Four-Struck By
[total_pages:protected] =>
[billed_pages:protected] =>
[publication_number:protected] =>
[part_of:protected] =>
[keywords:protected] =>
[comments:protected] =>
[summary:protected] => The following are links to all of the items in this collection:
[transition_comments:protected] =>
[external_link:protected] =>
[consol_link:protected] =>
[more_like_this:protected] =>
[permission_given_by:protected] =>
[published:protected] => T
[billable:protected] => F
[img_name:protected] =>
[img_ext:protected] =>
[img_width:protected] =>
[img_height:protected] =>
[img_credit:protected] =>
[img_practice:protected] =>
[vid_source_id:protected] =>
[vid_running_time:protected] =>
[vid_intended_audience:protected] =>
[vid_acquisition_info:protected] =>
[vid_cost:protected] =>
[vid_producer:protected] =>
[vid_filename:protected] =>
[vid_filename_downloadable:protected] =>
[date_summary:protected] =>
[date_permission_requested:protected] =>
[date_permission_received:protected] =>
[date_review_needed:protected] =>
[date_received:protected] => 05/08/12
[date_completed:protected] => 05/08/12
[date_billed:protected] =>
[date_modified:protected] => 05/08/12
[collBokExports:protected] =>
[lastBokExportCriteria:BaseElcoshItem:private] =>
[alreadyInSave:protected] =>
[alreadyInValidation:protected] =>
[validationFailures:protected] => Array
(
)
[_new:BaseObject:private] =>
[_deleted:BaseObject:private] =>
[modifiedColumns:protected] => Array
(
)
)
)
[categories:protected] =>
[categories_initialized:protected] =>
[mapped_items:protected] => Array
(
[1605] => DocumentRecord Object
(
[records:protected] => Array
(
)
[recordId:protected] =>
[searchWordClass:protected] =>
[searchWordPeerClass:protected] =>
[bok_record:protected] =>
[authors:protected] =>
[organizations:protected] =>
[collections:protected] =>
[categories:protected] =>
[categories_initialized:protected] =>
[mapped_items:protected] =>
[content:protected] =>
[files:protected] =>
[language:protected] =>
[old_record:protected] =>
[id:protected] => 1605
[old_id:protected] => 1262
[elcosh_id:protected] => d001137
[type:protected] => document
[display_type:protected] => HTML w/ PDF
[user_id:protected] =>
[language_id:protected] => 1
[tagging_id:protected] => Garber
[priority_id:protected] => 1
[title:protected] => Focus Four Toolbox Talks, Module 1 – Falls, Talk #2 – Falls from debris piles?
[total_pages:protected] => 1
[billed_pages:protected] => 1
[publication_number:protected] =>
[part_of:protected] =>
[keywords:protected] => disaster response, hazard clean-up, uneven surface, disaster site, disaster clean-up
[comments:protected] =>
[summary:protected] => A toolbox talk on preventing falls from debris piles. Includes questions to ask, an incident to discuss with images, and a place to record questions the trainer would like to ask about the incident. Part of a collection. Click on the 'collection' button to access the other items.
[transition_comments:protected] =>
[external_link:protected] =>
[consol_link:protected] => http://www.cpwrconstructionsolutions.org/roofing/hazard/1463/install-asphalt-roofs-fall-from-heights.html
[more_like_this:protected] => a000081,d000478,d000530
[permission_given_by:protected] =>
[published:protected] => T
[billable:protected] => F
[img_name:protected] =>
[img_ext:protected] =>
[img_width:protected] =>
[img_height:protected] =>
[img_credit:protected] =>
[img_practice:protected] =>
[vid_source_id:protected] =>
[vid_running_time:protected] =>
[vid_intended_audience:protected] =>
[vid_acquisition_info:protected] =>
[vid_cost:protected] =>
[vid_producer:protected] =>
[vid_filename:protected] =>
[vid_filename_downloadable:protected] =>
[date_summary:protected] =>
[date_permission_requested:protected] =>
[date_permission_received:protected] =>
[date_review_needed:protected] =>
[date_received:protected] => 02/15/12
[date_completed:protected] => 03/19/12
[date_billed:protected] =>
[date_modified:protected] => 07/10/12
[collBokExports:protected] =>
[lastBokExportCriteria:BaseElcoshItem:private] =>
[alreadyInSave:protected] =>
[alreadyInValidation:protected] =>
[validationFailures:protected] => Array
(
)
[_new:BaseObject:private] =>
[_deleted:BaseObject:private] =>
[modifiedColumns:protected] => Array
(
)
)
[1610] => DocumentRecord Object
(
[records:protected] => Array
(
)
[recordId:protected] =>
[searchWordClass:protected] =>
[searchWordPeerClass:protected] =>
[bok_record:protected] =>
[authors:protected] =>
[organizations:protected] =>
[collections:protected] =>
[categories:protected] =>
[categories_initialized:protected] =>
[mapped_items:protected] =>
[content:protected] =>
[files:protected] =>
[language:protected] =>
[old_record:protected] =>
[id:protected] => 1610
[old_id:protected] => 1271
[elcosh_id:protected] => d001146
[type:protected] => document
[display_type:protected] => HTML w/ PDF
[user_id:protected] => 0
[language_id:protected] => 1
[tagging_id:protected] => Garber
[priority_id:protected] => 1
[title:protected] => Focus Four Toolbox Talks, Module 2 – Struck-by, Talk #5 – Rigging and Securing Loads
[total_pages:protected] => 1
[billed_pages:protected] => 1
[publication_number:protected] =>
[part_of:protected] =>
[keywords:protected] => rigging, lift loads, loading areas, chains
[comments:protected] =>
[summary:protected] => A toolbox talk on preventing struck-by incidents caused by not securing loads properly. Includes questions to ask, an incident to discuss with images, and a place to record questions the trainer would like to ask about the incident. Part of a collection. Click on the 'collection' button to access the other items.
[transition_comments:protected] =>
[external_link:protected] =>
[consol_link:protected] => http://www.cpwrconstructionsolutions.org/heavy_equipment/hazard/1591/move-equipment-to-from-and-between-sites-work-zone-struck-by-injuries-and-fatalities.html
[more_like_this:protected] => d000144,d000360,d000873
[permission_given_by:protected] =>
[published:protected] => T
[billable:protected] => F
[img_name:protected] =>
[img_ext:protected] =>
[img_width:protected] =>
[img_height:protected] =>
[img_credit:protected] =>
[img_practice:protected] =>
[vid_source_id:protected] =>
[vid_running_time:protected] =>
[vid_intended_audience:protected] =>
[vid_acquisition_info:protected] =>
[vid_cost:protected] =>
[vid_producer:protected] =>
[vid_filename:protected] =>
[vid_filename_downloadable:protected] =>
[date_summary:protected] =>
[date_permission_requested:protected] =>
[date_permission_received:protected] =>
[date_review_needed:protected] =>
[date_received:protected] => 02/15/12
[date_completed:protected] => 03/28/12
[date_billed:protected] =>
[date_modified:protected] => 05/12/14
[collBokExports:protected] =>
[lastBokExportCriteria:BaseElcoshItem:private] =>
[alreadyInSave:protected] =>
[alreadyInValidation:protected] =>
[validationFailures:protected] => Array
(
)
[_new:BaseObject:private] =>
[_deleted:BaseObject:private] =>
[modifiedColumns:protected] => Array
(
)
)
[1645] => DocumentRecord Object
(
[records:protected] => Array
(
)
[recordId:protected] =>
[searchWordClass:protected] =>
[searchWordPeerClass:protected] =>
[bok_record:protected] =>
[authors:protected] =>
[organizations:protected] =>
[collections:protected] =>
[categories:protected] =>
[categories_initialized:protected] =>
[mapped_items:protected] =>
[content:protected] =>
[files:protected] =>
[language:protected] =>
[old_record:protected] =>
[id:protected] => 1645
[old_id:protected] => 1274
[elcosh_id:protected] => d001149
[type:protected] => document
[display_type:protected] => HTML w/ PDF
[user_id:protected] => 0
[language_id:protected] => 1
[tagging_id:protected] => Garber
[priority_id:protected] => 1
[title:protected] => Focus Four Toolbox Talks, Module 3 – Caught-in/between, Talk #2 – Trenches & Heavy Equipment
[total_pages:protected] => 1
[billed_pages:protected] => 1
[publication_number:protected] =>
[part_of:protected] =>
[keywords:protected] => back-up alarms, spotter, soil cave-in, spoil pikes, ROPs, trenching, rain
[comments:protected] =>
[summary:protected] => A toolbox talk on preventing incidents involving trenches such as trench collapse. Includes questions to ask, an incident to discuss with images, and a place to record questions the trainer would like to ask about the incident. Part of a collection. Click on the 'collection' button to access the other items.
[transition_comments:protected] =>
[external_link:protected] =>
[consol_link:protected] =>
[more_like_this:protected] => d000019,d000035,d000168
[permission_given_by:protected] =>
[published:protected] => T
[billable:protected] => F
[img_name:protected] =>
[img_ext:protected] =>
[img_width:protected] =>
[img_height:protected] =>
[img_credit:protected] =>
[img_practice:protected] =>
[vid_source_id:protected] =>
[vid_running_time:protected] =>
[vid_intended_audience:protected] =>
[vid_acquisition_info:protected] =>
[vid_cost:protected] =>
[vid_producer:protected] =>
[vid_filename:protected] =>
[vid_filename_downloadable:protected] =>
[date_summary:protected] =>
[date_permission_requested:protected] =>
[date_permission_received:protected] =>
[date_review_needed:protected] =>
[date_received:protected] => 02/15/12
[date_completed:protected] => 04/02/12
[date_billed:protected] =>
[date_modified:protected] => 05/23/23
[collBokExports:protected] =>
[lastBokExportCriteria:BaseElcoshItem:private] =>
[alreadyInSave:protected] =>
[alreadyInValidation:protected] =>
[validationFailures:protected] => Array
(
)
[_new:BaseObject:private] =>
[_deleted:BaseObject:private] =>
[modifiedColumns:protected] => Array
(
)
)
[1654] => DocumentRecord Object
(
[records:protected] => Array
(
)
[recordId:protected] =>
[searchWordClass:protected] =>
[searchWordPeerClass:protected] =>
[bok_record:protected] =>
[authors:protected] =>
[organizations:protected] =>
[collections:protected] =>
[categories:protected] =>
[categories_initialized:protected] =>
[mapped_items:protected] =>
[content:protected] =>
[files:protected] =>
[language:protected] =>
[old_record:protected] =>
[id:protected] => 1654
[old_id:protected] => 1284
[elcosh_id:protected] => d001159
[type:protected] => document
[display_type:protected] => HTML w/ PDF
[user_id:protected] => 0
[language_id:protected] => 1
[tagging_id:protected] => Garber
[priority_id:protected] => 1
[title:protected] => Focus Four Toolbox Talks, Module 4 – Electrocutions, Talk #6 – Hazards on Disaster Sites
[total_pages:protected] => 1
[billed_pages:protected] => 1
[publication_number:protected] =>
[part_of:protected] =>
[keywords:protected] => powerlines, underground, utilities, generators, wet conditions, GFCIs, energized lines, disasters, emergency response
[comments:protected] =>
[summary:protected] => A toolbox talk on how to avoid electrocution on a disaster site. Includes questions to ask, an incident to discuss with images, and a place to record questions the trainer would like to ask about the incident. Part of a collection. Click on the 'collection' button to access the other items.
[transition_comments:protected] =>
[external_link:protected] =>
[consol_link:protected] => http://www.cpwrconstructionsolutions.org/electrical/hazard/1138/install-and-repair-high-voltage-lines-transformers-switches-electrical-shocks-burns-and-or-electrocution.html
[more_like_this:protected] => d000135,d000361,d000437
[permission_given_by:protected] =>
[published:protected] => T
[billable:protected] => F
[img_name:protected] =>
[img_ext:protected] =>
[img_width:protected] =>
[img_height:protected] =>
[img_credit:protected] =>
[img_practice:protected] =>
[vid_source_id:protected] =>
[vid_running_time:protected] =>
[vid_intended_audience:protected] =>
[vid_acquisition_info:protected] =>
[vid_cost:protected] =>
[vid_producer:protected] =>
[vid_filename:protected] =>
[vid_filename_downloadable:protected] =>
[date_summary:protected] =>
[date_permission_requested:protected] =>
[date_permission_received:protected] =>
[date_review_needed:protected] =>
[date_received:protected] => 02/15/12
[date_completed:protected] => 04/02/12
[date_billed:protected] =>
[date_modified:protected] => 05/23/23
[collBokExports:protected] =>
[lastBokExportCriteria:BaseElcoshItem:private] =>
[alreadyInSave:protected] =>
[alreadyInValidation:protected] =>
[validationFailures:protected] => Array
(
)
[_new:BaseObject:private] =>
[_deleted:BaseObject:private] =>
[modifiedColumns:protected] => Array
(
)
)
)
[content:protected] =>
[files:protected] => Array
(
[9400] => File Object
(
[id:protected] => 9400
[filename:protected] => 1.jpg
[downloadable:protected] => F
[timestamp:protected] => 2014-05-08 15:05:37
[alreadyInSave:protected] =>
[alreadyInValidation:protected] =>
[validationFailures:protected] => Array
(
)
[_new:BaseObject:private] =>
[_deleted:BaseObject:private] =>
[modifiedColumns:protected] => Array
(
)
)
[9401] => File Object
(
[id:protected] => 9401
[filename:protected] => d001298.pdf
[downloadable:protected] => T
[timestamp:protected] => 2014-05-08 15:05:37
[alreadyInSave:protected] =>
[alreadyInValidation:protected] =>
[validationFailures:protected] => Array
(
)
[_new:BaseObject:private] =>
[_deleted:BaseObject:private] =>
[modifiedColumns:protected] => Array
(
)
)
)
[language:protected] => Language Object
(
[id:protected] => 1
[code:protected] => en
[name:protected] => English
[alreadyInSave:protected] =>
[alreadyInValidation:protected] =>
[validationFailures:protected] => Array
(
)
[_new:BaseObject:private] =>
[_deleted:BaseObject:private] =>
[modifiedColumns:protected] => Array
(
)
)
[old_record:protected] =>
[id:protected] => 3827
[old_id:protected] =>
[elcosh_id:protected] => d001298
[type:protected] => document
[display_type:protected] => HTML w/ PDF
[user_id:protected] => 23
[language_id:protected] => 1
[tagging_id:protected] => Bruce Lippy
[priority_id:protected] => 1
[title:protected] => Getting the most out of the IUOE Toolbox Talks
[total_pages:protected] => 2
[billed_pages:protected] => 2
[publication_number:protected] =>
[part_of:protected] =>
[keywords:protected] => toolbox talks, tailgate talks
[comments:protected] =>
[summary:protected] => Toolbox talks have been the main tool for communicating safety information on construction jobs for decades.
Unfortunately, there has been little research on what makes for effective toolbox talks. The IUOE National
Training Fund worked with OSHA and NIOSH to make sure their series of 24 Focus Four toolbox talks were based on the best recommendations for effective design. These toolbox talks accompany an entire package of training materials, but can be used alone. This guide points out the key features of these toolbox talks and how best to deliver them.
[transition_comments:protected] =>
[external_link:protected] =>
[consol_link:protected] =>
[more_like_this:protected] => d001137,d001146,d001149,d001159
[permission_given_by:protected] => IUOE National Hazmat Program
[published:protected] => T
[billable:protected] => F
[img_name:protected] =>
[img_ext:protected] => png
[img_width:protected] =>
[img_height:protected] =>
[img_credit:protected] =>
[img_practice:protected] =>
[vid_source_id:protected] =>
[vid_running_time:protected] =>
[vid_intended_audience:protected] =>
[vid_acquisition_info:protected] =>
[vid_cost:protected] =>
[vid_producer:protected] =>
[vid_filename:protected] =>
[vid_filename_downloadable:protected] =>
[date_summary:protected] => 2007
[date_permission_requested:protected] =>
[date_permission_received:protected] =>
[date_review_needed:protected] =>
[date_received:protected] => 05/08/14
[date_completed:protected] => 05/08/14
[date_billed:protected] =>
[date_modified:protected] => 05/08/14
[collBokExports:protected] =>
[lastBokExportCriteria:BaseElcoshItem:private] =>
[alreadyInSave:protected] =>
[alreadyInValidation:protected] =>
[validationFailures:protected] => Array
(
)
[_new:BaseObject:private] =>
[_deleted:BaseObject:private] =>
[modifiedColumns:protected] => Array
(
)
)
[show_text] =>
[document_content] => ElcoshItemDocumentContent Object
(
[id:protected] => 2896
[item_id:protected] => 3827
[type:protected] => main
[title:protected] =>
[content:protected] =>
Why were these talks developed?
Toolbox talks have been the main tool for communicating safety information on construction jobs for decades. Unfortunately, there has been almost no research on what makes for effective toolbox talks. The IUOE National Training Fund has worked with OSHA, the National Institute for Occupational Safety and Health and the Lippy Group, LLC to make sure these Focus Four toolbox talks are based on the latest fi ndings on the most effective design and tailored to the hazards operating engineers face daily. These toolbox talks accompany an entire package of training materials, but can be used alone. The way these are delivered is as important as how well they are designed.
What did NIOSH find out?
- Just handing out factsheets and toolbox talks to workers doesn’t work. Providing copies after toolbox talks doesn’t make much of an impact either.
- Using case studies (real life stories of accidents that ended in fatality or injury) in toolbox talks is effective.
- When toolbox talks containing case studies were accompanied by discussion questions to encourage group participation, they were more effective. Consequently, getting the workers to participate in the discussion about the case study is important. It’s not enough to tell the story, it is better to have the workers engage in problem solving that analyzes why the accident occurred and how it could have been prevented. Active learning is always better than passive.
How should you deliver these toolbox talks?
- Choose a topic that is related to work going on at the site.
- Hold the meeting on the job, preferably where everyone can sit and relax.
- Hold the meeting at the beginning of a shift or after a break. Folks are too tired at the end of a shift to carefully listen and they want to get home.
- Read the toolbox talk sheet on the topic prior to conducting the talk.
- Start at the top of the form and work right through to the end, which should take around 10 to 15 minutes. Guidance is provided in blue print to help you with each section.
- Use the questions provided to generate discussions. Always allow time for the crew to respond to your questions before you provide an answer. Some suggested responses are written in italics.
- Review the case study and emphasize that this was a real incident. Ask the crew for a case study before you review the one provided, however.
- Always end with a discussion of the particular worksite where you are conducting the talk. Tie the talk as closely to hazards on the site as possible and encourage the crew to constantly look for and immediately correct hazards. They should also know how to report any problems that can’t be immediately corrected.
- Provide copies to each person, if you like, but NIOSH has not found that to be particularly effective.
- Encourage workers to do similar talks on their sites and provide them with the IUOE phone number for ordering in bulk.
- Have everyone sign the back of the form to indicate they attended this session and point out it is a pledge to look out for the health and safety of everyone on the site.
What are the key features of these toolbox talks?

[content_transformed:protected] =>
Why were these talks developed?
Toolbox talks have been the main tool for communicating safety information on construction jobs for decades. Unfortunately, there has been almost no research on what makes for effective toolbox talks. The IUOE National Training Fund has worked with OSHA, the National Institute for Occupational Safety and Health and the Lippy Group, LLC to make sure these Focus Four toolbox talks are based on the latest fi ndings on the most effective design and tailored to the hazards operating engineers face daily. These toolbox talks accompany an entire package of training materials, but can be used alone. The way these are delivered is as important as how well they are designed.
What did NIOSH find out?
- Just handing out factsheets and toolbox talks to workers doesn’t work. Providing copies after toolbox talks doesn’t make much of an impact either.
- Using case studies (real life stories of accidents that ended in fatality or injury) in toolbox talks is effective.
- When toolbox talks containing case studies were accompanied by discussion questions to encourage group participation, they were more effective. Consequently, getting the workers to participate in the discussion about the case study is important. It’s not enough to tell the story, it is better to have the workers engage in problem solving that analyzes why the accident occurred and how it could have been prevented. Active learning is always better than passive.
How should you deliver these toolbox talks?
- Choose a topic that is related to work going on at the site.
- Hold the meeting on the job, preferably where everyone can sit and relax.
- Hold the meeting at the beginning of a shift or after a break. Folks are too tired at the end of a shift to carefully listen and they want to get home.
- Read the toolbox talk sheet on the topic prior to conducting the talk.
- Start at the top of the form and work right through to the end, which should take around 10 to 15 minutes. Guidance is provided in blue print to help you with each section.
- Use the questions provided to generate discussions. Always allow time for the crew to respond to your questions before you provide an answer. Some suggested responses are written in italics.
- Review the case study and emphasize that this was a real incident. Ask the crew for a case study before you review the one provided, however.
- Always end with a discussion of the particular worksite where you are conducting the talk. Tie the talk as closely to hazards on the site as possible and encourage the crew to constantly look for and immediately correct hazards. They should also know how to report any problems that can’t be immediately corrected.
- Provide copies to each person, if you like, but NIOSH has not found that to be particularly effective.
- Encourage workers to do similar talks on their sites and provide them with the IUOE phone number for ordering in bulk.
- Have everyone sign the back of the form to indicate they attended this session and point out it is a pledge to look out for the health and safety of everyone on the site.
What are the key features of these toolbox talks?
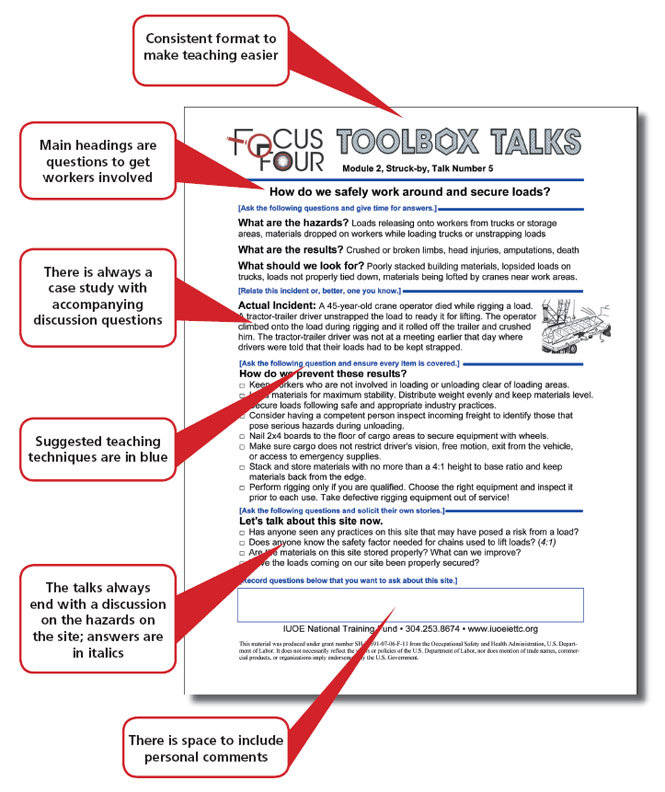
[disclaimer:protected] =>
[disclaimer_transformed:protected] =>
[alreadyInSave:protected] =>
[alreadyInValidation:protected] =>
[validationFailures:protected] => Array
(
)
[_new:BaseObject:private] =>
[_deleted:BaseObject:private] =>
[modifiedColumns:protected] => Array
(
)
)
[template] => record
)
[_globalContext:PHPTAL_Context:private] => stdClass Object
(
)
[_echoDeclarations:PHPTAL_Context:private] =>
[referer] => http://www.elcosh.org/document/3827/d001298/Getting%2Bthe%2Bmost%2Bout%2Bof%2Bthe%2BIUOE%2BToolbox%2BTalks.html
[curr_module] => Record
[styles] => Array
(
)
[javascript] => Array
(
[0] => jquery.min.js
)
[metas] => Array
(
[language] => en
[robots] => index, follow
)
[user] =>
[curr_url] => https://www.elcosh.org/index.php?module=Record&id=3827&type=document
[base_url] => https://www.elcosh.org/index.php?module=Record
[title] => eLCOSH : Getting the most out of the IUOE Toolbox Talks
[language] => en
[search_query] =>
[module] => Record
[new_records] => Array
(
[0] => Search_Result Object
(
[title] => Toolbox Talk: Fixed Ladder
[image] => /record/images/notavailable-p.png
[blurb] => The CPWR Toolbox Talk on Fixed Ladders addresses the potential risks associated with using fixed ladders. The resource includes a brief case example,...
[category] => Array
(
[0] => 15
[1] => 47
[2] => 49
[3] => 51
[4] => 53
[5] => 55
[6] => 60
[7] => 64
[8] => 73
[9] => 76
[10] => 78
[11] => 80
[12] => 86
[13] => 87
[14] => 90
[15] => 92
[16] => 93
[17] => 94
[18] => 100
)
[labels] => Array
(
[0] => Falls
[1] => Work Environment
[2] => Hazards
[3] => Bricklayer
[4] => Trades
[5] => Carpenter
[7] => Cement Mason
[9] => Concrete Polisher
[11] => Electrical Worker
[13] => HVAC
[15] => Laborer
[17] => PCC/Restoration
[19] => Plumber/Pipefitter
[21] => Roofer/Waterproofer
[23] => Sheetmetal Worker
[25] => Welder
[27] => Commercial & Institutional
[28] => Jobsites
[29] => Industrial
[31] => LEED/Green Construction
[33] => Renovations
[35] => Residential
[37] => Toolbox Talks
[38] => Documents
[39] => Media & Documents
)
[type] => Toolbox Talks
[sub_category] =>
[url] => /document/4430/d001660/Toolbox%2BTalk%253A%2BFixed%2BLadder.html
[item:protected] => DocumentRecord Object
(
[records:protected] => Array
(
)
[recordId:protected] =>
[searchWordClass:protected] =>
[searchWordPeerClass:protected] =>
[bok_record:protected] =>
[authors:protected] =>
[organizations:protected] =>
[collections:protected] =>
[categories:protected] => Array
(
[15] => Category Object
(
[languages:protected] =>
[bok_resources:protected] =>
[bok_topics:protected] =>
[bok_keywords:protected] =>
[id:protected] => 15
[type:protected] => category
[parent:protected] => 7
[label:protected] => Falls
[alreadyInSave:protected] =>
[alreadyInValidation:protected] =>
[validationFailures:protected] => Array
(
)
[_new:BaseObject:private] =>
[_deleted:BaseObject:private] =>
[modifiedColumns:protected] => Array
(
)
)
[47] => Category Object
(
[languages:protected] =>
[bok_resources:protected] =>
[bok_topics:protected] =>
[bok_keywords:protected] =>
[id:protected] => 47
[type:protected] => category
[parent:protected] => 2
[label:protected] => Bricklayer
[alreadyInSave:protected] =>
[alreadyInValidation:protected] =>
[validationFailures:protected] => Array
(
)
[_new:BaseObject:private] =>
[_deleted:BaseObject:private] =>
[modifiedColumns:protected] => Array
(
)
)
[49] => Category Object
(
[languages:protected] =>
[bok_resources:protected] =>
[bok_topics:protected] =>
[bok_keywords:protected] =>
[id:protected] => 49
[type:protected] => category
[parent:protected] => 2
[label:protected] => Carpenter
[alreadyInSave:protected] =>
[alreadyInValidation:protected] =>
[validationFailures:protected] => Array
(
)
[_new:BaseObject:private] =>
[_deleted:BaseObject:private] =>
[modifiedColumns:protected] => Array
(
)
)
[51] => Category Object
(
[languages:protected] =>
[bok_resources:protected] =>
[bok_topics:protected] =>
[bok_keywords:protected] =>
[id:protected] => 51
[type:protected] => category
[parent:protected] => 2
[label:protected] => Cement Mason
[alreadyInSave:protected] =>
[alreadyInValidation:protected] =>
[validationFailures:protected] => Array
(
)
[_new:BaseObject:private] =>
[_deleted:BaseObject:private] =>
[modifiedColumns:protected] => Array
(
)
)
[53] => Category Object
(
[languages:protected] =>
[bok_resources:protected] =>
[bok_topics:protected] =>
[bok_keywords:protected] =>
[id:protected] => 53
[type:protected] => category
[parent:protected] => 2
[label:protected] => Concrete Polisher
[alreadyInSave:protected] =>
[alreadyInValidation:protected] =>
[validationFailures:protected] => Array
(
)
[_new:BaseObject:private] =>
[_deleted:BaseObject:private] =>
[modifiedColumns:protected] => Array
(
)
)
[55] => Category Object
(
[languages:protected] =>
[bok_resources:protected] =>
[bok_topics:protected] =>
[bok_keywords:protected] =>
[id:protected] => 55
[type:protected] => category
[parent:protected] => 2
[label:protected] => Electrical Worker
[alreadyInSave:protected] =>
[alreadyInValidation:protected] =>
[validationFailures:protected] => Array
(
)
[_new:BaseObject:private] =>
[_deleted:BaseObject:private] =>
[modifiedColumns:protected] => Array
(
)
)
[60] => Category Object
(
[languages:protected] =>
[bok_resources:protected] =>
[bok_topics:protected] =>
[bok_keywords:protected] =>
[id:protected] => 60
[type:protected] => category
[parent:protected] => 2
[label:protected] => HVAC
[alreadyInSave:protected] =>
[alreadyInValidation:protected] =>
[validationFailures:protected] => Array
(
)
[_new:BaseObject:private] =>
[_deleted:BaseObject:private] =>
[modifiedColumns:protected] => Array
(
)
)
[64] => Category Object
(
[languages:protected] =>
[bok_resources:protected] =>
[bok_topics:protected] =>
[bok_keywords:protected] =>
[id:protected] => 64
[type:protected] => category
[parent:protected] => 2
[label:protected] => Laborer
[alreadyInSave:protected] =>
[alreadyInValidation:protected] =>
[validationFailures:protected] => Array
(
)
[_new:BaseObject:private] =>
[_deleted:BaseObject:private] =>
[modifiedColumns:protected] => Array
(
)
)
[73] => Category Object
(
[languages:protected] =>
[bok_resources:protected] =>
[bok_topics:protected] =>
[bok_keywords:protected] =>
[id:protected] => 73
[type:protected] => category
[parent:protected] => 2
[label:protected] => PCC/Restoration
[alreadyInSave:protected] =>
[alreadyInValidation:protected] =>
[validationFailures:protected] => Array
(
)
[_new:BaseObject:private] =>
[_deleted:BaseObject:private] =>
[modifiedColumns:protected] => Array
(
)
)
[76] => Category Object
(
[languages:protected] =>
[bok_resources:protected] =>
[bok_topics:protected] =>
[bok_keywords:protected] =>
[id:protected] => 76
[type:protected] => category
[parent:protected] => 2
[label:protected] => Plumber/Pipefitter
[alreadyInSave:protected] =>
[alreadyInValidation:protected] =>
[validationFailures:protected] => Array
(
)
[_new:BaseObject:private] =>
[_deleted:BaseObject:private] =>
[modifiedColumns:protected] => Array
(
)
)
[78] => Category Object
(
[languages:protected] =>
[bok_resources:protected] =>
[bok_topics:protected] =>
[bok_keywords:protected] =>
[id:protected] => 78
[type:protected] => category
[parent:protected] => 2
[label:protected] => Roofer/Waterproofer
[alreadyInSave:protected] =>
[alreadyInValidation:protected] =>
[validationFailures:protected] => Array
(
)
[_new:BaseObject:private] =>
[_deleted:BaseObject:private] =>
[modifiedColumns:protected] => Array
(
)
)
[80] => Category Object
(
[languages:protected] =>
[bok_resources:protected] =>
[bok_topics:protected] =>
[bok_keywords:protected] =>
[id:protected] => 80
[type:protected] => category
[parent:protected] => 2
[label:protected] => Sheetmetal Worker
[alreadyInSave:protected] =>
[alreadyInValidation:protected] =>
[validationFailures:protected] => Array
(
)
[_new:BaseObject:private] =>
[_deleted:BaseObject:private] =>
[modifiedColumns:protected] => Array
(
)
)
[86] => Category Object
(
[languages:protected] =>
[bok_resources:protected] =>
[bok_topics:protected] =>
[bok_keywords:protected] =>
[id:protected] => 86
[type:protected] => category
[parent:protected] => 2
[label:protected] => Welder
[alreadyInSave:protected] =>
[alreadyInValidation:protected] =>
[validationFailures:protected] => Array
(
)
[_new:BaseObject:private] =>
[_deleted:BaseObject:private] =>
[modifiedColumns:protected] => Array
(
)
)
[87] => Category Object
(
[languages:protected] =>
[bok_resources:protected] =>
[bok_topics:protected] =>
[bok_keywords:protected] =>
[id:protected] => 87
[type:protected] => category
[parent:protected] => 3
[label:protected] => Commercial & Institutional
[alreadyInSave:protected] =>
[alreadyInValidation:protected] =>
[validationFailures:protected] => Array
(
)
[_new:BaseObject:private] =>
[_deleted:BaseObject:private] =>
[modifiedColumns:protected] => Array
(
)
)
[90] => Category Object
(
[languages:protected] =>
[bok_resources:protected] =>
[bok_topics:protected] =>
[bok_keywords:protected] =>
[id:protected] => 90
[type:protected] => category
[parent:protected] => 3
[label:protected] => Industrial
[alreadyInSave:protected] =>
[alreadyInValidation:protected] =>
[validationFailures:protected] => Array
(
)
[_new:BaseObject:private] =>
[_deleted:BaseObject:private] =>
[modifiedColumns:protected] => Array
(
)
)
[92] => Category Object
(
[languages:protected] =>
[bok_resources:protected] =>
[bok_topics:protected] =>
[bok_keywords:protected] =>
[id:protected] => 92
[type:protected] => category
[parent:protected] => 3
[label:protected] => LEED/Green Construction
[alreadyInSave:protected] =>
[alreadyInValidation:protected] =>
[validationFailures:protected] => Array
(
)
[_new:BaseObject:private] =>
[_deleted:BaseObject:private] =>
[modifiedColumns:protected] => Array
(
)
)
[93] => Category Object
(
[languages:protected] =>
[bok_resources:protected] =>
[bok_topics:protected] =>
[bok_keywords:protected] =>
[id:protected] => 93
[type:protected] => category
[parent:protected] => 3
[label:protected] => Renovations
[alreadyInSave:protected] =>
[alreadyInValidation:protected] =>
[validationFailures:protected] => Array
(
)
[_new:BaseObject:private] =>
[_deleted:BaseObject:private] =>
[modifiedColumns:protected] => Array
(
)
)
[94] => Category Object
(
[languages:protected] =>
[bok_resources:protected] =>
[bok_topics:protected] =>
[bok_keywords:protected] =>
[id:protected] => 94
[type:protected] => category
[parent:protected] => 3
[label:protected] => Residential
[alreadyInSave:protected] =>
[alreadyInValidation:protected] =>
[validationFailures:protected] => Array
(
)
[_new:BaseObject:private] =>
[_deleted:BaseObject:private] =>
[modifiedColumns:protected] => Array
(
)
)
[100] => Category Object
(
[languages:protected] =>
[bok_resources:protected] =>
[bok_topics:protected] =>
[bok_keywords:protected] =>
[id:protected] => 100
[type:protected] => category
[parent:protected] => 6
[label:protected] => Toolbox Talks
[alreadyInSave:protected] =>
[alreadyInValidation:protected] =>
[validationFailures:protected] => Array
(
)
[_new:BaseObject:private] =>
[_deleted:BaseObject:private] =>
[modifiedColumns:protected] => Array
(
)
)
)
[categories_initialized:protected] => 1
[mapped_items:protected] =>
[content:protected] =>
[files:protected] =>
[language:protected] => Language Object
(
[id:protected] => 1
[code:protected] => en
[name:protected] => English
[alreadyInSave:protected] =>
[alreadyInValidation:protected] =>
[validationFailures:protected] => Array
(
)
[_new:BaseObject:private] =>
[_deleted:BaseObject:private] =>
[modifiedColumns:protected] => Array
(
)
)
[old_record:protected] =>
[id:protected] => 4430
[old_id:protected] =>
[elcosh_id:protected] => d001660
[type:protected] => document
[display_type:protected] => HTML only (and links)
[user_id:protected] => 0
[language_id:protected] => 1
[tagging_id:protected] => Mike Aguilar
[priority_id:protected] => 1
[title:protected] => Toolbox Talk: Fixed Ladder
[total_pages:protected] => 0
[billed_pages:protected] => 0
[publication_number:protected] =>
[part_of:protected] =>
[keywords:protected] => Fixed Ladders, Fall Prevention, Falls
[comments:protected] =>
[summary:protected] => The CPWR Toolbox Talk on Fixed Ladders addresses the potential risks associated with using fixed ladders. The resource includes a brief case example, steps to prevent a related injury and questions for discussion. It includes an image that illustrates the hazard, which can be posted in a central location as a reminder of steps to work safely.
Available in
English
and
Spanish.
[transition_comments:protected] =>
[external_link:protected] =>
[consol_link:protected] =>
[more_like_this:protected] => d001257,d001254,d001255,d001256,d001258,d001262,d001279
[permission_given_by:protected] =>
[published:protected] => T
[billable:protected] => F
[img_name:protected] =>
[img_ext:protected] =>
[img_width:protected] =>
[img_height:protected] =>
[img_credit:protected] =>
[img_practice:protected] =>
[vid_source_id:protected] =>
[vid_running_time:protected] =>
[vid_intended_audience:protected] =>
[vid_acquisition_info:protected] =>
[vid_cost:protected] =>
[vid_producer:protected] =>
[vid_filename:protected] =>
[vid_filename_downloadable:protected] =>
[date_summary:protected] =>
[date_permission_requested:protected] =>
[date_permission_received:protected] =>
[date_review_needed:protected] =>
[date_received:protected] => 06/10/22
[date_completed:protected] => 06/10/22
[date_billed:protected] =>
[date_modified:protected] => 05/22/23
[collBokExports:protected] =>
[lastBokExportCriteria:BaseElcoshItem:private] =>
[alreadyInSave:protected] =>
[alreadyInValidation:protected] =>
[validationFailures:protected] => Array
(
)
[_new:BaseObject:private] =>
[_deleted:BaseObject:private] =>
[modifiedColumns:protected] => Array
(
)
)
)
[1] => Search_Result Object
(
[title] => Toolbox Talk: Challenges Preventing Falling Objects
[image] => /record/images/notavailable-p.png
[blurb] => The CPWR Toolbox Talk on Challenges Preventing Falling Objects addresses the hazards of being struck by falling objects on the job site. The resource...
[category] => Array
(
[0] => 12
[1] => 47
[2] => 49
[3] => 51
[4] => 55
[5] => 64
[6] => 68
[7] => 71
[8] => 75
[9] => 78
[10] => 79
[11] => 82
[12] => 62
[13] => 86
[14] => 87
[15] => 88
[16] => 89
[17] => 91
[18] => 90
[19] => 92
[20] => 93
[21] => 94
[22] => 95
[23] => 100
)
[labels] => Array
(
[0] => Crushed/Struck By
[1] => Work Environment
[2] => Hazards
[3] => Bricklayer
[4] => Trades
[5] => Carpenter
[7] => Cement Mason
[9] => Electrical Worker
[11] => Laborer
[13] => Maintenance Worker
[15] => Painter
[17] => Plasterer
[19] => Roofer/Waterproofer
[21] => Scaffold Erector
[23] => Stonemason
[25] => Structural Ironworker
[27] => Welder
[29] => Commercial & Institutional
[30] => Jobsites
[31] => Demolition
[33] => Disasters
[35] => Heavy & Highway
[37] => Industrial
[39] => LEED/Green Construction
[41] => Renovations
[43] => Residential
[45] => Underground
[47] => Toolbox Talks
[48] => Documents
[49] => Media & Documents
)
[type] => Toolbox Talks
[sub_category] =>
[url] => /document/4431/d001661/Toolbox%2BTalk%253A%2BChallenges%2BPreventing%2BFalling%2BObjects.html
[item:protected] => DocumentRecord Object
(
[records:protected] => Array
(
)
[recordId:protected] =>
[searchWordClass:protected] =>
[searchWordPeerClass:protected] =>
[bok_record:protected] =>
[authors:protected] =>
[organizations:protected] =>
[collections:protected] =>
[categories:protected] => Array
(
[12] => Category Object
(
[languages:protected] =>
[bok_resources:protected] =>
[bok_topics:protected] =>
[bok_keywords:protected] =>
[id:protected] => 12
[type:protected] => category
[parent:protected] => 7
[label:protected] => Crushed/Struck By
[alreadyInSave:protected] =>
[alreadyInValidation:protected] =>
[validationFailures:protected] => Array
(
)
[_new:BaseObject:private] =>
[_deleted:BaseObject:private] =>
[modifiedColumns:protected] => Array
(
)
)
[47] => Category Object
(
[languages:protected] =>
[bok_resources:protected] =>
[bok_topics:protected] =>
[bok_keywords:protected] =>
[id:protected] => 47
[type:protected] => category
[parent:protected] => 2
[label:protected] => Bricklayer
[alreadyInSave:protected] =>
[alreadyInValidation:protected] =>
[validationFailures:protected] => Array
(
)
[_new:BaseObject:private] =>
[_deleted:BaseObject:private] =>
[modifiedColumns:protected] => Array
(
)
)
[49] => Category Object
(
[languages:protected] =>
[bok_resources:protected] =>
[bok_topics:protected] =>
[bok_keywords:protected] =>
[id:protected] => 49
[type:protected] => category
[parent:protected] => 2
[label:protected] => Carpenter
[alreadyInSave:protected] =>
[alreadyInValidation:protected] =>
[validationFailures:protected] => Array
(
)
[_new:BaseObject:private] =>
[_deleted:BaseObject:private] =>
[modifiedColumns:protected] => Array
(
)
)
[51] => Category Object
(
[languages:protected] =>
[bok_resources:protected] =>
[bok_topics:protected] =>
[bok_keywords:protected] =>
[id:protected] => 51
[type:protected] => category
[parent:protected] => 2
[label:protected] => Cement Mason
[alreadyInSave:protected] =>
[alreadyInValidation:protected] =>
[validationFailures:protected] => Array
(
)
[_new:BaseObject:private] =>
[_deleted:BaseObject:private] =>
[modifiedColumns:protected] => Array
(
)
)
[55] => Category Object
(
[languages:protected] =>
[bok_resources:protected] =>
[bok_topics:protected] =>
[bok_keywords:protected] =>
[id:protected] => 55
[type:protected] => category
[parent:protected] => 2
[label:protected] => Electrical Worker
[alreadyInSave:protected] =>
[alreadyInValidation:protected] =>
[validationFailures:protected] => Array
(
)
[_new:BaseObject:private] =>
[_deleted:BaseObject:private] =>
[modifiedColumns:protected] => Array
(
)
)
[64] => Category Object
(
[languages:protected] =>
[bok_resources:protected] =>
[bok_topics:protected] =>
[bok_keywords:protected] =>
[id:protected] => 64
[type:protected] => category
[parent:protected] => 2
[label:protected] => Laborer
[alreadyInSave:protected] =>
[alreadyInValidation:protected] =>
[validationFailures:protected] => Array
(
)
[_new:BaseObject:private] =>
[_deleted:BaseObject:private] =>
[modifiedColumns:protected] => Array
(
)
)
[68] => Category Object
(
[languages:protected] =>
[bok_resources:protected] =>
[bok_topics:protected] =>
[bok_keywords:protected] =>
[id:protected] => 68
[type:protected] => category
[parent:protected] => 2
[label:protected] => Maintenance Worker
[alreadyInSave:protected] =>
[alreadyInValidation:protected] =>
[validationFailures:protected] => Array
(
)
[_new:BaseObject:private] =>
[_deleted:BaseObject:private] =>
[modifiedColumns:protected] => Array
(
)
)
[71] => Category Object
(
[languages:protected] =>
[bok_resources:protected] =>
[bok_topics:protected] =>
[bok_keywords:protected] =>
[id:protected] => 71
[type:protected] => category
[parent:protected] => 2
[label:protected] => Painter
[alreadyInSave:protected] =>
[alreadyInValidation:protected] =>
[validationFailures:protected] => Array
(
)
[_new:BaseObject:private] =>
[_deleted:BaseObject:private] =>
[modifiedColumns:protected] => Array
(
)
)
[75] => Category Object
(
[languages:protected] =>
[bok_resources:protected] =>
[bok_topics:protected] =>
[bok_keywords:protected] =>
[id:protected] => 75
[type:protected] => category
[parent:protected] => 2
[label:protected] => Plasterer
[alreadyInSave:protected] =>
[alreadyInValidation:protected] =>
[validationFailures:protected] => Array
(
)
[_new:BaseObject:private] =>
[_deleted:BaseObject:private] =>
[modifiedColumns:protected] => Array
(
)
)
[78] => Category Object
(
[languages:protected] =>
[bok_resources:protected] =>
[bok_topics:protected] =>
[bok_keywords:protected] =>
[id:protected] => 78
[type:protected] => category
[parent:protected] => 2
[label:protected] => Roofer/Waterproofer
[alreadyInSave:protected] =>
[alreadyInValidation:protected] =>
[validationFailures:protected] => Array
(
)
[_new:BaseObject:private] =>
[_deleted:BaseObject:private] =>
[modifiedColumns:protected] => Array
(
)
)
[79] => Category Object
(
[languages:protected] =>
[bok_resources:protected] =>
[bok_topics:protected] =>
[bok_keywords:protected] =>
[id:protected] => 79
[type:protected] => category
[parent:protected] => 2
[label:protected] => Scaffold Erector
[alreadyInSave:protected] =>
[alreadyInValidation:protected] =>
[validationFailures:protected] => Array
(
)
[_new:BaseObject:private] =>
[_deleted:BaseObject:private] =>
[modifiedColumns:protected] => Array
(
)
)
[82] => Category Object
(
[languages:protected] =>
[bok_resources:protected] =>
[bok_topics:protected] =>
[bok_keywords:protected] =>
[id:protected] => 82
[type:protected] => category
[parent:protected] => 2
[label:protected] => Stonemason
[alreadyInSave:protected] =>
[alreadyInValidation:protected] =>
[validationFailures:protected] => Array
(
)
[_new:BaseObject:private] =>
[_deleted:BaseObject:private] =>
[modifiedColumns:protected] => Array
(
)
)
[62] => Category Object
(
[languages:protected] =>
[bok_resources:protected] =>
[bok_topics:protected] =>
[bok_keywords:protected] =>
[id:protected] => 62
[type:protected] => category
[parent:protected] => 2
[label:protected] => Structural Ironworker
[alreadyInSave:protected] =>
[alreadyInValidation:protected] =>
[validationFailures:protected] => Array
(
)
[_new:BaseObject:private] =>
[_deleted:BaseObject:private] =>
[modifiedColumns:protected] => Array
(
)
)
[86] => Category Object
(
[languages:protected] =>
[bok_resources:protected] =>
[bok_topics:protected] =>
[bok_keywords:protected] =>
[id:protected] => 86
[type:protected] => category
[parent:protected] => 2
[label:protected] => Welder
[alreadyInSave:protected] =>
[alreadyInValidation:protected] =>
[validationFailures:protected] => Array
(
)
[_new:BaseObject:private] =>
[_deleted:BaseObject:private] =>
[modifiedColumns:protected] => Array
(
)
)
[87] => Category Object
(
[languages:protected] =>
[bok_resources:protected] =>
[bok_topics:protected] =>
[bok_keywords:protected] =>
[id:protected] => 87
[type:protected] => category
[parent:protected] => 3
[label:protected] => Commercial & Institutional
[alreadyInSave:protected] =>
[alreadyInValidation:protected] =>
[validationFailures:protected] => Array
(
)
[_new:BaseObject:private] =>
[_deleted:BaseObject:private] =>
[modifiedColumns:protected] => Array
(
)
)
[88] => Category Object
(
[languages:protected] =>
[bok_resources:protected] =>
[bok_topics:protected] =>
[bok_keywords:protected] =>
[id:protected] => 88
[type:protected] => category
[parent:protected] => 3
[label:protected] => Demolition
[alreadyInSave:protected] =>
[alreadyInValidation:protected] =>
[validationFailures:protected] => Array
(
)
[_new:BaseObject:private] =>
[_deleted:BaseObject:private] =>
[modifiedColumns:protected] => Array
(
)
)
[89] => Category Object
(
[languages:protected] =>
[bok_resources:protected] =>
[bok_topics:protected] =>
[bok_keywords:protected] =>
[id:protected] => 89
[type:protected] => category
[parent:protected] => 3
[label:protected] => Disasters
[alreadyInSave:protected] =>
[alreadyInValidation:protected] =>
[validationFailures:protected] => Array
(
)
[_new:BaseObject:private] =>
[_deleted:BaseObject:private] =>
[modifiedColumns:protected] => Array
(
)
)
[91] => Category Object
(
[languages:protected] =>
[bok_resources:protected] =>
[bok_topics:protected] =>
[bok_keywords:protected] =>
[id:protected] => 91
[type:protected] => category
[parent:protected] => 3
[label:protected] => Heavy & Highway
[alreadyInSave:protected] =>
[alreadyInValidation:protected] =>
[validationFailures:protected] => Array
(
)
[_new:BaseObject:private] =>
[_deleted:BaseObject:private] =>
[modifiedColumns:protected] => Array
(
)
)
[90] => Category Object
(
[languages:protected] =>
[bok_resources:protected] =>
[bok_topics:protected] =>
[bok_keywords:protected] =>
[id:protected] => 90
[type:protected] => category
[parent:protected] => 3
[label:protected] => Industrial
[alreadyInSave:protected] =>
[alreadyInValidation:protected] =>
[validationFailures:protected] => Array
(
)
[_new:BaseObject:private] =>
[_deleted:BaseObject:private] =>
[modifiedColumns:protected] => Array
(
)
)
[92] => Category Object
(
[languages:protected] =>
[bok_resources:protected] =>
[bok_topics:protected] =>
[bok_keywords:protected] =>
[id:protected] => 92
[type:protected] => category
[parent:protected] => 3
[label:protected] => LEED/Green Construction
[alreadyInSave:protected] =>
[alreadyInValidation:protected] =>
[validationFailures:protected] => Array
(
)
[_new:BaseObject:private] =>
[_deleted:BaseObject:private] =>
[modifiedColumns:protected] => Array
(
)
)
[93] => Category Object
(
[languages:protected] =>
[bok_resources:protected] =>
[bok_topics:protected] =>
[bok_keywords:protected] =>
[id:protected] => 93
[type:protected] => category
[parent:protected] => 3
[label:protected] => Renovations
[alreadyInSave:protected] =>
[alreadyInValidation:protected] =>
[validationFailures:protected] => Array
(
)
[_new:BaseObject:private] =>
[_deleted:BaseObject:private] =>
[modifiedColumns:protected] => Array
(
)
)
[94] => Category Object
(
[languages:protected] =>
[bok_resources:protected] =>
[bok_topics:protected] =>
[bok_keywords:protected] =>
[id:protected] => 94
[type:protected] => category
[parent:protected] => 3
[label:protected] => Residential
[alreadyInSave:protected] =>
[alreadyInValidation:protected] =>
[validationFailures:protected] => Array
(
)
[_new:BaseObject:private] =>
[_deleted:BaseObject:private] =>
[modifiedColumns:protected] => Array
(
)
)
[95] => Category Object
(
[languages:protected] =>
[bok_resources:protected] =>
[bok_topics:protected] =>
[bok_keywords:protected] =>
[id:protected] => 95
[type:protected] => category
[parent:protected] => 3
[label:protected] => Underground
[alreadyInSave:protected] =>
[alreadyInValidation:protected] =>
[validationFailures:protected] => Array
(
)
[_new:BaseObject:private] =>
[_deleted:BaseObject:private] =>
[modifiedColumns:protected] => Array
(
)
)
[100] => Category Object
(
[languages:protected] =>
[bok_resources:protected] =>
[bok_topics:protected] =>
[bok_keywords:protected] =>
[id:protected] => 100
[type:protected] => category
[parent:protected] => 6
[label:protected] => Toolbox Talks
[alreadyInSave:protected] =>
[alreadyInValidation:protected] =>
[validationFailures:protected] => Array
(
)
[_new:BaseObject:private] =>
[_deleted:BaseObject:private] =>
[modifiedColumns:protected] => Array
(
)
)
)
[categories_initialized:protected] => 1
[mapped_items:protected] =>
[content:protected] =>
[files:protected] =>
[language:protected] => Language Object
(
[id:protected] => 1
[code:protected] => en
[name:protected] => English
[alreadyInSave:protected] =>
[alreadyInValidation:protected] =>
[validationFailures:protected] => Array
(
)
[_new:BaseObject:private] =>
[_deleted:BaseObject:private] =>
[modifiedColumns:protected] => Array
(
)
)
[old_record:protected] =>
[id:protected] => 4431
[old_id:protected] =>
[elcosh_id:protected] => d001661
[type:protected] => document
[display_type:protected] => HTML only (and links)
[user_id:protected] => 0
[language_id:protected] => 1
[tagging_id:protected] => Mike Aguilar
[priority_id:protected] => 1
[title:protected] => Toolbox Talk: Challenges Preventing Falling Objects
[total_pages:protected] => 0
[billed_pages:protected] => 0
[publication_number:protected] =>
[part_of:protected] =>
[keywords:protected] => dropped objects, falling objects, struck by incidents, struck by fatalities
[comments:protected] =>
[summary:protected] => The CPWR Toolbox Talk on Challenges Preventing Falling Objects addresses the hazards of being struck by falling objects on the job site. The resource includes a brief example, steps to prevent a related injury, and questions for discussion. It includes a graphic that illustrates a group workers observing a scaffold free of debris during high winds, which can be posted in a central location as a reminder of steps to work safely.
Available in
English and
Spanish.
[transition_comments:protected] =>
[external_link:protected] =>
[consol_link:protected] =>
[more_like_this:protected] => d001234,d001238,d001244,d001251,d001253,d001260,d001268,d001278
[permission_given_by:protected] =>
[published:protected] => T
[billable:protected] => F
[img_name:protected] =>
[img_ext:protected] =>
[img_width:protected] =>
[img_height:protected] =>
[img_credit:protected] =>
[img_practice:protected] =>
[vid_source_id:protected] =>
[vid_running_time:protected] =>
[vid_intended_audience:protected] =>
[vid_acquisition_info:protected] =>
[vid_cost:protected] =>
[vid_producer:protected] =>
[vid_filename:protected] =>
[vid_filename_downloadable:protected] =>
[date_summary:protected] =>
[date_permission_requested:protected] =>
[date_permission_received:protected] =>
[date_review_needed:protected] =>
[date_received:protected] => 06/10/22
[date_completed:protected] => 06/10/22
[date_billed:protected] =>
[date_modified:protected] => 05/22/23
[collBokExports:protected] =>
[lastBokExportCriteria:BaseElcoshItem:private] =>
[alreadyInSave:protected] =>
[alreadyInValidation:protected] =>
[validationFailures:protected] => Array
(
)
[_new:BaseObject:private] =>
[_deleted:BaseObject:private] =>
[modifiedColumns:protected] => Array
(
)
)
)
[2] => Search_Result Object
(
[title] => Toolbox Talk: Tower Crane Safety
[image] => /record/images/notavailable-p.png
[blurb] => The CPWR Toolbox Talk on Tower Crane Safety addresses the potential hazards of Tower Cranes and the importance of following procedure before and durin...
[category] => Array
(
[0] => 11
[1] => 12
[2] => 18
[3] => 70
[4] => 87
[5] => 88
[6] => 91
[7] => 90
[8] => 92
[9] => 100
)
[labels] => Array
(
[0] => Cranes & Hoists
[1] => Work Environment
[2] => Hazards
[3] => Crushed/Struck By
[6] => Motor Vehicles/Heavy Equipment
[9] => Operating Engineer
[10] => Trades
[11] => Commercial & Institutional
[12] => Jobsites
[13] => Demolition
[15] => Heavy & Highway
[17] => Industrial
[19] => LEED/Green Construction
[21] => Toolbox Talks
[22] => Documents
[23] => Media & Documents
)
[type] => Toolbox Talks
[sub_category] =>
[url] => /document/4427/d001657/Toolbox%2BTalk%253A%2BTower%2BCrane%2BSafety.html
[item:protected] => DocumentRecord Object
(
[records:protected] => Array
(
)
[recordId:protected] =>
[searchWordClass:protected] =>
[searchWordPeerClass:protected] =>
[bok_record:protected] =>
[authors:protected] =>
[organizations:protected] =>
[collections:protected] =>
[categories:protected] => Array
(
[11] => Category Object
(
[languages:protected] =>
[bok_resources:protected] =>
[bok_topics:protected] =>
[bok_keywords:protected] =>
[id:protected] => 11
[type:protected] => category
[parent:protected] => 7
[label:protected] => Cranes & Hoists
[alreadyInSave:protected] =>
[alreadyInValidation:protected] =>
[validationFailures:protected] => Array
(
)
[_new:BaseObject:private] =>
[_deleted:BaseObject:private] =>
[modifiedColumns:protected] => Array
(
)
)
[12] => Category Object
(
[languages:protected] =>
[bok_resources:protected] =>
[bok_topics:protected] =>
[bok_keywords:protected] =>
[id:protected] => 12
[type:protected] => category
[parent:protected] => 7
[label:protected] => Crushed/Struck By
[alreadyInSave:protected] =>
[alreadyInValidation:protected] =>
[validationFailures:protected] => Array
(
)
[_new:BaseObject:private] =>
[_deleted:BaseObject:private] =>
[modifiedColumns:protected] => Array
(
)
)
[18] => Category Object
(
[languages:protected] =>
[bok_resources:protected] =>
[bok_topics:protected] =>
[bok_keywords:protected] =>
[id:protected] => 18
[type:protected] => category
[parent:protected] => 7
[label:protected] => Motor Vehicles/Heavy Equipment
[alreadyInSave:protected] =>
[alreadyInValidation:protected] =>
[validationFailures:protected] => Array
(
)
[_new:BaseObject:private] =>
[_deleted:BaseObject:private] =>
[modifiedColumns:protected] => Array
(
)
)
[70] => Category Object
(
[languages:protected] =>
[bok_resources:protected] =>
[bok_topics:protected] =>
[bok_keywords:protected] =>
[id:protected] => 70
[type:protected] => category
[parent:protected] => 2
[label:protected] => Operating Engineer
[alreadyInSave:protected] =>
[alreadyInValidation:protected] =>
[validationFailures:protected] => Array
(
)
[_new:BaseObject:private] =>
[_deleted:BaseObject:private] =>
[modifiedColumns:protected] => Array
(
)
)
[87] => Category Object
(
[languages:protected] =>
[bok_resources:protected] =>
[bok_topics:protected] =>
[bok_keywords:protected] =>
[id:protected] => 87
[type:protected] => category
[parent:protected] => 3
[label:protected] => Commercial & Institutional
[alreadyInSave:protected] =>
[alreadyInValidation:protected] =>
[validationFailures:protected] => Array
(
)
[_new:BaseObject:private] =>
[_deleted:BaseObject:private] =>
[modifiedColumns:protected] => Array
(
)
)
[88] => Category Object
(
[languages:protected] =>
[bok_resources:protected] =>
[bok_topics:protected] =>
[bok_keywords:protected] =>
[id:protected] => 88
[type:protected] => category
[parent:protected] => 3
[label:protected] => Demolition
[alreadyInSave:protected] =>
[alreadyInValidation:protected] =>
[validationFailures:protected] => Array
(
)
[_new:BaseObject:private] =>
[_deleted:BaseObject:private] =>
[modifiedColumns:protected] => Array
(
)
)
[91] => Category Object
(
[languages:protected] =>
[bok_resources:protected] =>
[bok_topics:protected] =>
[bok_keywords:protected] =>
[id:protected] => 91
[type:protected] => category
[parent:protected] => 3
[label:protected] => Heavy & Highway
[alreadyInSave:protected] =>
[alreadyInValidation:protected] =>
[validationFailures:protected] => Array
(
)
[_new:BaseObject:private] =>
[_deleted:BaseObject:private] =>
[modifiedColumns:protected] => Array
(
)
)
[90] => Category Object
(
[languages:protected] =>
[bok_resources:protected] =>
[bok_topics:protected] =>
[bok_keywords:protected] =>
[id:protected] => 90
[type:protected] => category
[parent:protected] => 3
[label:protected] => Industrial
[alreadyInSave:protected] =>
[alreadyInValidation:protected] =>
[validationFailures:protected] => Array
(
)
[_new:BaseObject:private] =>
[_deleted:BaseObject:private] =>
[modifiedColumns:protected] => Array
(
)
)
[92] => Category Object
(
[languages:protected] =>
[bok_resources:protected] =>
[bok_topics:protected] =>
[bok_keywords:protected] =>
[id:protected] => 92
[type:protected] => category
[parent:protected] => 3
[label:protected] => LEED/Green Construction
[alreadyInSave:protected] =>
[alreadyInValidation:protected] =>
[validationFailures:protected] => Array
(
)
[_new:BaseObject:private] =>
[_deleted:BaseObject:private] =>
[modifiedColumns:protected] => Array
(
)
)
[100] => Category Object
(
[languages:protected] =>
[bok_resources:protected] =>
[bok_topics:protected] =>
[bok_keywords:protected] =>
[id:protected] => 100
[type:protected] => category
[parent:protected] => 6
[label:protected] => Toolbox Talks
[alreadyInSave:protected] =>
[alreadyInValidation:protected] =>
[validationFailures:protected] => Array
(
)
[_new:BaseObject:private] =>
[_deleted:BaseObject:private] =>
[modifiedColumns:protected] => Array
(
)
)
)
[categories_initialized:protected] => 1
[mapped_items:protected] =>
[content:protected] =>
[files:protected] =>
[language:protected] => Language Object
(
[id:protected] => 1
[code:protected] => en
[name:protected] => English
[alreadyInSave:protected] =>
[alreadyInValidation:protected] =>
[validationFailures:protected] => Array
(
)
[_new:BaseObject:private] =>
[_deleted:BaseObject:private] =>
[modifiedColumns:protected] => Array
(
)
)
[old_record:protected] =>
[id:protected] => 4427
[old_id:protected] =>
[elcosh_id:protected] => d001657
[type:protected] => document
[display_type:protected] => HTML only (and links)
[user_id:protected] => 0
[language_id:protected] => 1
[tagging_id:protected] => Mike Aguilar
[priority_id:protected] => 1
[title:protected] => Toolbox Talk: Tower Crane Safety
[total_pages:protected] => 0
[billed_pages:protected] => 0
[publication_number:protected] =>
[part_of:protected] =>
[keywords:protected] => Tower Crane, Crane, Stability, Tipping, Lift Zone Safety, Lift, Zone, Safety, Struck by
[comments:protected] =>
[summary:protected] => The CPWR Toolbox Talk on Tower Crane Safety addresses the potential hazards of Tower Cranes and the importance of following procedure before and during Tower Crane operation. The resource includes a brief example, steps to prevent a related injury, and questions for discussion. It includes a graphic that illustrates a worker inspecting a Tower Crane before operation, which can be posted in a central location as a reminder of steps to work safely.
Available in
English and
Spanish.
[transition_comments:protected] =>
[external_link:protected] =>
[consol_link:protected] =>
[more_like_this:protected] => d001234,d001238,d001250,d001251,d001253,d001258,d001262,d001273
[permission_given_by:protected] =>
[published:protected] => T
[billable:protected] => F
[img_name:protected] =>
[img_ext:protected] => jpg
[img_width:protected] =>
[img_height:protected] =>
[img_credit:protected] =>
[img_practice:protected] =>
[vid_source_id:protected] =>
[vid_running_time:protected] =>
[vid_intended_audience:protected] =>
[vid_acquisition_info:protected] =>
[vid_cost:protected] =>
[vid_producer:protected] =>
[vid_filename:protected] =>
[vid_filename_downloadable:protected] =>
[date_summary:protected] =>
[date_permission_requested:protected] =>
[date_permission_received:protected] =>
[date_review_needed:protected] =>
[date_received:protected] => 12/23/21
[date_completed:protected] => 12/23/21
[date_billed:protected] =>
[date_modified:protected] => 05/19/23
[collBokExports:protected] =>
[lastBokExportCriteria:BaseElcoshItem:private] =>
[alreadyInSave:protected] =>
[alreadyInValidation:protected] =>
[validationFailures:protected] => Array
(
)
[_new:BaseObject:private] =>
[_deleted:BaseObject:private] =>
[modifiedColumns:protected] => Array
(
)
)
)
[3] => Search_Result Object
(
[title] => Toolbox Talk: Work Zone Safety: Working Around Vehicles
[image] => /record/images/notavailable-p.png
[blurb] => The CPWR Toolbox Talk on Working Around Vehicles in the Work Zone addresses methods to avoid being struck-by a vehicle on a construction site. The res...
[category] => Array
(
[0] => 12
[1] => 18
[2] => 52
[3] => 57
[4] => 70
[5] => 85
[6] => 87
[7] => 88
[8] => 89
[9] => 91
[10] => 90
[11] => 92
[12] => 93
[13] => 94
[14] => 95
[15] => 100
)
[labels] => Array
(
[0] => Crushed/Struck By
[1] => Work Environment
[2] => Hazards
[3] => Motor Vehicles/Heavy Equipment
[6] => Commercial Diver
[7] => Trades
[8] => Flagger
[10] => Operating Engineer
[12] => Truck Driver
[14] => Commercial & Institutional
[15] => Jobsites
[16] => Demolition
[18] => Disasters
[20] => Heavy & Highway
[22] => Industrial
[24] => LEED/Green Construction
[26] => Renovations
[28] => Residential
[30] => Underground
[32] => Toolbox Talks
[33] => Documents
[34] => Media & Documents
)
[type] => Toolbox Talks
[sub_category] =>
[url] => /document/4428/d001658/Toolbox%2BTalk%253A%2BWork%2BZone%2BSafety%253A%2BWorking%2BAround%2BVehicles.html
[item:protected] => DocumentRecord Object
(
[records:protected] => Array
(
)
[recordId:protected] =>
[searchWordClass:protected] =>
[searchWordPeerClass:protected] =>
[bok_record:protected] =>
[authors:protected] =>
[organizations:protected] =>
[collections:protected] =>
[categories:protected] => Array
(
[12] => Category Object
(
[languages:protected] =>
[bok_resources:protected] =>
[bok_topics:protected] =>
[bok_keywords:protected] =>
[id:protected] => 12
[type:protected] => category
[parent:protected] => 7
[label:protected] => Crushed/Struck By
[alreadyInSave:protected] =>
[alreadyInValidation:protected] =>
[validationFailures:protected] => Array
(
)
[_new:BaseObject:private] =>
[_deleted:BaseObject:private] =>
[modifiedColumns:protected] => Array
(
)
)
[18] => Category Object
(
[languages:protected] =>
[bok_resources:protected] =>
[bok_topics:protected] =>
[bok_keywords:protected] =>
[id:protected] => 18
[type:protected] => category
[parent:protected] => 7
[label:protected] => Motor Vehicles/Heavy Equipment
[alreadyInSave:protected] =>
[alreadyInValidation:protected] =>
[validationFailures:protected] => Array
(
)
[_new:BaseObject:private] =>
[_deleted:BaseObject:private] =>
[modifiedColumns:protected] => Array
(
)
)
[52] => Category Object
(
[languages:protected] =>
[bok_resources:protected] =>
[bok_topics:protected] =>
[bok_keywords:protected] =>
[id:protected] => 52
[type:protected] => category
[parent:protected] => 2
[label:protected] => Commercial Diver
[alreadyInSave:protected] =>
[alreadyInValidation:protected] =>
[validationFailures:protected] => Array
(
)
[_new:BaseObject:private] =>
[_deleted:BaseObject:private] =>
[modifiedColumns:protected] => Array
(
)
)
[57] => Category Object
(
[languages:protected] =>
[bok_resources:protected] =>
[bok_topics:protected] =>
[bok_keywords:protected] =>
[id:protected] => 57
[type:protected] => category
[parent:protected] => 2
[label:protected] => Flagger
[alreadyInSave:protected] =>
[alreadyInValidation:protected] =>
[validationFailures:protected] => Array
(
)
[_new:BaseObject:private] =>
[_deleted:BaseObject:private] =>
[modifiedColumns:protected] => Array
(
)
)
[70] => Category Object
(
[languages:protected] =>
[bok_resources:protected] =>
[bok_topics:protected] =>
[bok_keywords:protected] =>
[id:protected] => 70
[type:protected] => category
[parent:protected] => 2
[label:protected] => Operating Engineer
[alreadyInSave:protected] =>
[alreadyInValidation:protected] =>
[validationFailures:protected] => Array
(
)
[_new:BaseObject:private] =>
[_deleted:BaseObject:private] =>
[modifiedColumns:protected] => Array
(
)
)
[85] => Category Object
(
[languages:protected] =>
[bok_resources:protected] =>
[bok_topics:protected] =>
[bok_keywords:protected] =>
[id:protected] => 85
[type:protected] => category
[parent:protected] => 2
[label:protected] => Truck Driver
[alreadyInSave:protected] =>
[alreadyInValidation:protected] =>
[validationFailures:protected] => Array
(
)
[_new:BaseObject:private] =>
[_deleted:BaseObject:private] =>
[modifiedColumns:protected] => Array
(
)
)
[87] => Category Object
(
[languages:protected] =>
[bok_resources:protected] =>
[bok_topics:protected] =>
[bok_keywords:protected] =>
[id:protected] => 87
[type:protected] => category
[parent:protected] => 3
[label:protected] => Commercial & Institutional
[alreadyInSave:protected] =>
[alreadyInValidation:protected] =>
[validationFailures:protected] => Array
(
)
[_new:BaseObject:private] =>
[_deleted:BaseObject:private] =>
[modifiedColumns:protected] => Array
(
)
)
[88] => Category Object
(
[languages:protected] =>
[bok_resources:protected] =>
[bok_topics:protected] =>
[bok_keywords:protected] =>
[id:protected] => 88
[type:protected] => category
[parent:protected] => 3
[label:protected] => Demolition
[alreadyInSave:protected] =>
[alreadyInValidation:protected] =>
[validationFailures:protected] => Array
(
)
[_new:BaseObject:private] =>
[_deleted:BaseObject:private] =>
[modifiedColumns:protected] => Array
(
)
)
[89] => Category Object
(
[languages:protected] =>
[bok_resources:protected] =>
[bok_topics:protected] =>
[bok_keywords:protected] =>
[id:protected] => 89
[type:protected] => category
[parent:protected] => 3
[label:protected] => Disasters
[alreadyInSave:protected] =>
[alreadyInValidation:protected] =>
[validationFailures:protected] => Array
(
)
[_new:BaseObject:private] =>
[_deleted:BaseObject:private] =>
[modifiedColumns:protected] => Array
(
)
)
[91] => Category Object
(
[languages:protected] =>
[bok_resources:protected] =>
[bok_topics:protected] =>
[bok_keywords:protected] =>
[id:protected] => 91
[type:protected] => category
[parent:protected] => 3
[label:protected] => Heavy & Highway
[alreadyInSave:protected] =>
[alreadyInValidation:protected] =>
[validationFailures:protected] => Array
(
)
[_new:BaseObject:private] =>
[_deleted:BaseObject:private] =>
[modifiedColumns:protected] => Array
(
)
)
[90] => Category Object
(
[languages:protected] =>
[bok_resources:protected] =>
[bok_topics:protected] =>
[bok_keywords:protected] =>
[id:protected] => 90
[type:protected] => category
[parent:protected] => 3
[label:protected] => Industrial
[alreadyInSave:protected] =>
[alreadyInValidation:protected] =>
[validationFailures:protected] => Array
(
)
[_new:BaseObject:private] =>
[_deleted:BaseObject:private] =>
[modifiedColumns:protected] => Array
(
)
)
[92] => Category Object
(
[languages:protected] =>
[bok_resources:protected] =>
[bok_topics:protected] =>
[bok_keywords:protected] =>
[id:protected] => 92
[type:protected] => category
[parent:protected] => 3
[label:protected] => LEED/Green Construction
[alreadyInSave:protected] =>
[alreadyInValidation:protected] =>
[validationFailures:protected] => Array
(
)
[_new:BaseObject:private] =>
[_deleted:BaseObject:private] =>
[modifiedColumns:protected] => Array
(
)
)
[93] => Category Object
(
[languages:protected] =>
[bok_resources:protected] =>
[bok_topics:protected] =>
[bok_keywords:protected] =>
[id:protected] => 93
[type:protected] => category
[parent:protected] => 3
[label:protected] => Renovations
[alreadyInSave:protected] =>
[alreadyInValidation:protected] =>
[validationFailures:protected] => Array
(
)
[_new:BaseObject:private] =>
[_deleted:BaseObject:private] =>
[modifiedColumns:protected] => Array
(
)
)
[94] => Category Object
(
[languages:protected] =>
[bok_resources:protected] =>
[bok_topics:protected] =>
[bok_keywords:protected] =>
[id:protected] => 94
[type:protected] => category
[parent:protected] => 3
[label:protected] => Residential
[alreadyInSave:protected] =>
[alreadyInValidation:protected] =>
[validationFailures:protected] => Array
(
)
[_new:BaseObject:private] =>
[_deleted:BaseObject:private] =>
[modifiedColumns:protected] => Array
(
)
)
[95] => Category Object
(
[languages:protected] =>
[bok_resources:protected] =>
[bok_topics:protected] =>
[bok_keywords:protected] =>
[id:protected] => 95
[type:protected] => category
[parent:protected] => 3
[label:protected] => Underground
[alreadyInSave:protected] =>
[alreadyInValidation:protected] =>
[validationFailures:protected] => Array
(
)
[_new:BaseObject:private] =>
[_deleted:BaseObject:private] =>
[modifiedColumns:protected] => Array
(
)
)
[100] => Category Object
(
[languages:protected] =>
[bok_resources:protected] =>
[bok_topics:protected] =>
[bok_keywords:protected] =>
[id:protected] => 100
[type:protected] => category
[parent:protected] => 6
[label:protected] => Toolbox Talks
[alreadyInSave:protected] =>
[alreadyInValidation:protected] =>
[validationFailures:protected] => Array
(
)
[_new:BaseObject:private] =>
[_deleted:BaseObject:private] =>
[modifiedColumns:protected] => Array
(
)
)
)
[categories_initialized:protected] => 1
[mapped_items:protected] =>
[content:protected] =>
[files:protected] =>
[language:protected] => Language Object
(
[id:protected] => 1
[code:protected] => en
[name:protected] => English
[alreadyInSave:protected] =>
[alreadyInValidation:protected] =>
[validationFailures:protected] => Array
(
)
[_new:BaseObject:private] =>
[_deleted:BaseObject:private] =>
[modifiedColumns:protected] => Array
(
)
)
[old_record:protected] =>
[id:protected] => 4428
[old_id:protected] =>
[elcosh_id:protected] => d001658
[type:protected] => document
[display_type:protected] => HTML only (and links)
[user_id:protected] => 0
[language_id:protected] => 1
[tagging_id:protected] => Daniela Caceres
[priority_id:protected] => 1
[title:protected] => Toolbox Talk: Work Zone Safety: Working Around Vehicles
[total_pages:protected] => 0
[billed_pages:protected] => 0
[publication_number:protected] =>
[part_of:protected] =>
[keywords:protected] => Struck, Struck by, Vehicle, Work Zone Safety, Truck, Operator, Driver, Mobile Equipment
[comments:protected] =>
[summary:protected] => The CPWR Toolbox Talk on Working Around Vehicles in the Work Zone addresses methods to avoid being struck-by a vehicle on a construction site. The resource includes a case example, steps to prevent a related injury, and questions for discussion. It includes a graphic that illustrates the hazard, which can be posted in a central location as a reminder of steps to work safely. Available in
English and
Spanish.
[transition_comments:protected] =>
[external_link:protected] =>
[consol_link:protected] =>
[more_like_this:protected] => d001640
[permission_given_by:protected] =>
[published:protected] => T
[billable:protected] => F
[img_name:protected] =>
[img_ext:protected] =>
[img_width:protected] =>
[img_height:protected] =>
[img_credit:protected] =>
[img_practice:protected] =>
[vid_source_id:protected] =>
[vid_running_time:protected] =>
[vid_intended_audience:protected] =>
[vid_acquisition_info:protected] =>
[vid_cost:protected] =>
[vid_producer:protected] =>
[vid_filename:protected] =>
[vid_filename_downloadable:protected] =>
[date_summary:protected] =>
[date_permission_requested:protected] =>
[date_permission_received:protected] =>
[date_review_needed:protected] =>
[date_received:protected] => 12/23/21
[date_completed:protected] => 12/23/21
[date_billed:protected] =>
[date_modified:protected] => 05/19/23
[collBokExports:protected] =>
[lastBokExportCriteria:BaseElcoshItem:private] =>
[alreadyInSave:protected] =>
[alreadyInValidation:protected] =>
[validationFailures:protected] => Array
(
)
[_new:BaseObject:private] =>
[_deleted:BaseObject:private] =>
[modifiedColumns:protected] => Array
(
)
)
)
[4] => Search_Result Object
(
[title] => Construction Dive -- DeWalt's Jobsite Pro headphones recalled for fire hazards
[image] => /record/images/notavailable-p.png
[blurb] => A recall notice by the United States Consumer Product Safety Commission affects over 300,000 DeWalt Jobsite Pro Headphones. The recall is a result of...
[category] => Array
(
[0] => 16
[1] => 44
[2] => 45
[3] => 46
[4] => 47
[5] => 48
[6] => 49
[7] => 50
[8] => 51
[9] => 52
[10] => 53
[11] => 54
[12] => 55
[13] => 56
[14] => 57
[15] => 58
[16] => 59
[17] => 60
[18] => 61
[19] => 64
[20] => 65
[21] => 66
[22] => 67
[23] => 68
[24] => 69
[25] => 70
[26] => 71
[27] => 72
[28] => 73
[29] => 74
[30] => 75
[31] => 76
[32] => 77
[33] => 63
[34] => 78
[35] => 79
[36] => 80
[37] => 81
[38] => 82
[39] => 62
[40] => 83
[41] => 84
[42] => 85
[43] => 86
[44] => 87
[45] => 88
[46] => 89
[47] => 91
[48] => 90
[49] => 92
[50] => 93
[51] => 94
[52] => 95
)
[labels] => Array
(
[0] => Fire & Explosions
[1] => Work Environment
[2] => Hazards
[3] => Acoustical Ceiling Carpenter
[4] => Trades
[5] => Asbestos/Insulator
[7] => Boilermaker
[9] => Bricklayer
[11] => Cabinetmaker
[13] => Carpenter
[15] => Carpet Layer
[17] => Cement Mason
[19] => Commercial Diver
[21] => Concrete Polisher
[23] => Drywall Applicator Specialist
[25] => Electrical Worker
[27] => Elevator Constructor
[29] => Flagger
[31] => Glazier
[33] => Hazardous Waste Cleanup
[35] => HVAC
[37] => Interior Systems Carpenter
[39] => Laborer
[41] => Landscaper
[43] => Lather
[45] => Lead Abatement Worker
[47] => Maintenance Worker
[49] => Millwright
[51] => Operating Engineer
[53] => Painter
[55] => Paper Hanger
[57] => PCC/Restoration
[59] => Pile Driver
[61] => Plasterer
[63] => Plumber/Pipefitter
[65] => Refractory Worker
[67] => Reinforcing Ironworker
[69] => Roofer/Waterproofer
[71] => Scaffold Erector
[73] => Sheetmetal Worker
[75] => Sprinkler Fitter
[77] => Stonemason
[79] => Structural Ironworker
[81] => Terrazzo Worker
[83] => Tile Setter
[85] => Truck Driver
[87] => Welder
[89] => Commercial & Institutional
[90] => Jobsites
[91] => Demolition
[93] => Disasters
[95] => Heavy & Highway
[97] => Industrial
[99] => LEED/Green Construction
[101] => Renovations
[103] => Residential
[105] => Underground
)
[type] =>
[sub_category] =>
[url] => /document/4426/d001656/Construction%2BDive%2B--%2BDeWalt%2527s%2BJobsite%2BPro%2Bheadphones%2Brecalled%2Bfor%2Bfire%2Bhazards.html
[item:protected] => DocumentRecord Object
(
[records:protected] => Array
(
)
[recordId:protected] =>
[searchWordClass:protected] =>
[searchWordPeerClass:protected] =>
[bok_record:protected] =>
[authors:protected] =>
[organizations:protected] =>
[collections:protected] =>
[categories:protected] => Array
(
[16] => Category Object
(
[languages:protected] =>
[bok_resources:protected] =>
[bok_topics:protected] =>
[bok_keywords:protected] =>
[id:protected] => 16
[type:protected] => category
[parent:protected] => 7
[label:protected] => Fire & Explosions
[alreadyInSave:protected] =>
[alreadyInValidation:protected] =>
[validationFailures:protected] => Array
(
)
[_new:BaseObject:private] =>
[_deleted:BaseObject:private] =>
[modifiedColumns:protected] => Array
(
)
)
[44] => Category Object
(
[languages:protected] =>
[bok_resources:protected] =>
[bok_topics:protected] =>
[bok_keywords:protected] =>
[id:protected] => 44
[type:protected] => category
[parent:protected] => 2
[label:protected] => Acoustical Ceiling Carpenter
[alreadyInSave:protected] =>
[alreadyInValidation:protected] =>
[validationFailures:protected] => Array
(
)
[_new:BaseObject:private] =>
[_deleted:BaseObject:private] =>
[modifiedColumns:protected] => Array
(
)
)
[45] => Category Object
(
[languages:protected] =>
[bok_resources:protected] =>
[bok_topics:protected] =>
[bok_keywords:protected] =>
[id:protected] => 45
[type:protected] => category
[parent:protected] => 2
[label:protected] => Asbestos/Insulator
[alreadyInSave:protected] =>
[alreadyInValidation:protected] =>
[validationFailures:protected] => Array
(
)
[_new:BaseObject:private] =>
[_deleted:BaseObject:private] =>
[modifiedColumns:protected] => Array
(
)
)
[46] => Category Object
(
[languages:protected] =>
[bok_resources:protected] =>
[bok_topics:protected] =>
[bok_keywords:protected] =>
[id:protected] => 46
[type:protected] => category
[parent:protected] => 2
[label:protected] => Boilermaker
[alreadyInSave:protected] =>
[alreadyInValidation:protected] =>
[validationFailures:protected] => Array
(
)
[_new:BaseObject:private] =>
[_deleted:BaseObject:private] =>
[modifiedColumns:protected] => Array
(
)
)
[47] => Category Object
(
[languages:protected] =>
[bok_resources:protected] =>
[bok_topics:protected] =>
[bok_keywords:protected] =>
[id:protected] => 47
[type:protected] => category
[parent:protected] => 2
[label:protected] => Bricklayer
[alreadyInSave:protected] =>
[alreadyInValidation:protected] =>
[validationFailures:protected] => Array
(
)
[_new:BaseObject:private] =>
[_deleted:BaseObject:private] =>
[modifiedColumns:protected] => Array
(
)
)
[48] => Category Object
(
[languages:protected] =>
[bok_resources:protected] =>
[bok_topics:protected] =>
[bok_keywords:protected] =>
[id:protected] => 48
[type:protected] => category
[parent:protected] => 2
[label:protected] => Cabinetmaker
[alreadyInSave:protected] =>
[alreadyInValidation:protected] =>
[validationFailures:protected] => Array
(
)
[_new:BaseObject:private] =>
[_deleted:BaseObject:private] =>
[modifiedColumns:protected] => Array
(
)
)
[49] => Category Object
(
[languages:protected] =>
[bok_resources:protected] =>
[bok_topics:protected] =>
[bok_keywords:protected] =>
[id:protected] => 49
[type:protected] => category
[parent:protected] => 2
[label:protected] => Carpenter
[alreadyInSave:protected] =>
[alreadyInValidation:protected] =>
[validationFailures:protected] => Array
(
)
[_new:BaseObject:private] =>
[_deleted:BaseObject:private] =>
[modifiedColumns:protected] => Array
(
)
)
[50] => Category Object
(
[languages:protected] =>
[bok_resources:protected] =>
[bok_topics:protected] =>
[bok_keywords:protected] =>
[id:protected] => 50
[type:protected] => category
[parent:protected] => 2
[label:protected] => Carpet Layer
[alreadyInSave:protected] =>
[alreadyInValidation:protected] =>
[validationFailures:protected] => Array
(
)
[_new:BaseObject:private] =>
[_deleted:BaseObject:private] =>
[modifiedColumns:protected] => Array
(
)
)
[51] => Category Object
(
[languages:protected] =>
[bok_resources:protected] =>
[bok_topics:protected] =>
[bok_keywords:protected] =>
[id:protected] => 51
[type:protected] => category
[parent:protected] => 2
[label:protected] => Cement Mason
[alreadyInSave:protected] =>
[alreadyInValidation:protected] =>
[validationFailures:protected] => Array
(
)
[_new:BaseObject:private] =>
[_deleted:BaseObject:private] =>
[modifiedColumns:protected] => Array
(
)
)
[52] => Category Object
(
[languages:protected] =>
[bok_resources:protected] =>
[bok_topics:protected] =>
[bok_keywords:protected] =>
[id:protected] => 52
[type:protected] => category
[parent:protected] => 2
[label:protected] => Commercial Diver
[alreadyInSave:protected] =>
[alreadyInValidation:protected] =>
[validationFailures:protected] => Array
(
)
[_new:BaseObject:private] =>
[_deleted:BaseObject:private] =>
[modifiedColumns:protected] => Array
(
)
)
[53] => Category Object
(
[languages:protected] =>
[bok_resources:protected] =>
[bok_topics:protected] =>
[bok_keywords:protected] =>
[id:protected] => 53
[type:protected] => category
[parent:protected] => 2
[label:protected] => Concrete Polisher
[alreadyInSave:protected] =>
[alreadyInValidation:protected] =>
[validationFailures:protected] => Array
(
)
[_new:BaseObject:private] =>
[_deleted:BaseObject:private] =>
[modifiedColumns:protected] => Array
(
)
)
[54] => Category Object
(
[languages:protected] =>
[bok_resources:protected] =>
[bok_topics:protected] =>
[bok_keywords:protected] =>
[id:protected] => 54
[type:protected] => category
[parent:protected] => 2
[label:protected] => Drywall Applicator Specialist
[alreadyInSave:protected] =>
[alreadyInValidation:protected] =>
[validationFailures:protected] => Array
(
)
[_new:BaseObject:private] =>
[_deleted:BaseObject:private] =>
[modifiedColumns:protected] => Array
(
)
)
[55] => Category Object
(
[languages:protected] =>
[bok_resources:protected] =>
[bok_topics:protected] =>
[bok_keywords:protected] =>
[id:protected] => 55
[type:protected] => category
[parent:protected] => 2
[label:protected] => Electrical Worker
[alreadyInSave:protected] =>
[alreadyInValidation:protected] =>
[validationFailures:protected] => Array
(
)
[_new:BaseObject:private] =>
[_deleted:BaseObject:private] =>
[modifiedColumns:protected] => Array
(
)
)
[56] => Category Object
(
[languages:protected] =>
[bok_resources:protected] =>
[bok_topics:protected] =>
[bok_keywords:protected] =>
[id:protected] => 56
[type:protected] => category
[parent:protected] => 2
[label:protected] => Elevator Constructor
[alreadyInSave:protected] =>
[alreadyInValidation:protected] =>
[validationFailures:protected] => Array
(
)
[_new:BaseObject:private] =>
[_deleted:BaseObject:private] =>
[modifiedColumns:protected] => Array
(
)
)
[57] => Category Object
(
[languages:protected] =>
[bok_resources:protected] =>
[bok_topics:protected] =>
[bok_keywords:protected] =>
[id:protected] => 57
[type:protected] => category
[parent:protected] => 2
[label:protected] => Flagger
[alreadyInSave:protected] =>
[alreadyInValidation:protected] =>
[validationFailures:protected] => Array
(
)
[_new:BaseObject:private] =>
[_deleted:BaseObject:private] =>
[modifiedColumns:protected] => Array
(
)
)
[58] => Category Object
(
[languages:protected] =>
[bok_resources:protected] =>
[bok_topics:protected] =>
[bok_keywords:protected] =>
[id:protected] => 58
[type:protected] => category
[parent:protected] => 2
[label:protected] => Glazier
[alreadyInSave:protected] =>
[alreadyInValidation:protected] =>
[validationFailures:protected] => Array
(
)
[_new:BaseObject:private] =>
[_deleted:BaseObject:private] =>
[modifiedColumns:protected] => Array
(
)
)
[59] => Category Object
(
[languages:protected] =>
[bok_resources:protected] =>
[bok_topics:protected] =>
[bok_keywords:protected] =>
[id:protected] => 59
[type:protected] => category
[parent:protected] => 2
[label:protected] => Hazardous Waste Cleanup
[alreadyInSave:protected] =>
[alreadyInValidation:protected] =>
[validationFailures:protected] => Array
(
)
[_new:BaseObject:private] =>
[_deleted:BaseObject:private] =>
[modifiedColumns:protected] => Array
(
)
)
[60] => Category Object
(
[languages:protected] =>
[bok_resources:protected] =>
[bok_topics:protected] =>
[bok_keywords:protected] =>
[id:protected] => 60
[type:protected] => category
[parent:protected] => 2
[label:protected] => HVAC
[alreadyInSave:protected] =>
[alreadyInValidation:protected] =>
[validationFailures:protected] => Array
(
)
[_new:BaseObject:private] =>
[_deleted:BaseObject:private] =>
[modifiedColumns:protected] => Array
(
)
)
[61] => Category Object
(
[languages:protected] =>
[bok_resources:protected] =>
[bok_topics:protected] =>
[bok_keywords:protected] =>
[id:protected] => 61
[type:protected] => category
[parent:protected] => 2
[label:protected] => Interior Systems Carpenter
[alreadyInSave:protected] =>
[alreadyInValidation:protected] =>
[validationFailures:protected] => Array
(
)
[_new:BaseObject:private] =>
[_deleted:BaseObject:private] =>
[modifiedColumns:protected] => Array
(
)
)
[64] => Category Object
(
[languages:protected] =>
[bok_resources:protected] =>
[bok_topics:protected] =>
[bok_keywords:protected] =>
[id:protected] => 64
[type:protected] => category
[parent:protected] => 2
[label:protected] => Laborer
[alreadyInSave:protected] =>
[alreadyInValidation:protected] =>
[validationFailures:protected] => Array
(
)
[_new:BaseObject:private] =>
[_deleted:BaseObject:private] =>
[modifiedColumns:protected] => Array
(
)
)
[65] => Category Object
(
[languages:protected] =>
[bok_resources:protected] =>
[bok_topics:protected] =>
[bok_keywords:protected] =>
[id:protected] => 65
[type:protected] => category
[parent:protected] => 2
[label:protected] => Landscaper
[alreadyInSave:protected] =>
[alreadyInValidation:protected] =>
[validationFailures:protected] => Array
(
)
[_new:BaseObject:private] =>
[_deleted:BaseObject:private] =>
[modifiedColumns:protected] => Array
(
)
)
[66] => Category Object
(
[languages:protected] =>
[bok_resources:protected] =>
[bok_topics:protected] =>
[bok_keywords:protected] =>
[id:protected] => 66
[type:protected] => category
[parent:protected] => 2
[label:protected] => Lather
[alreadyInSave:protected] =>
[alreadyInValidation:protected] =>
[validationFailures:protected] => Array
(
)
[_new:BaseObject:private] =>
[_deleted:BaseObject:private] =>
[modifiedColumns:protected] => Array
(
)
)
[67] => Category Object
(
[languages:protected] =>
[bok_resources:protected] =>
[bok_topics:protected] =>
[bok_keywords:protected] =>
[id:protected] => 67
[type:protected] => category
[parent:protected] => 2
[label:protected] => Lead Abatement Worker
[alreadyInSave:protected] =>
[alreadyInValidation:protected] =>
[validationFailures:protected] => Array
(
)
[_new:BaseObject:private] =>
[_deleted:BaseObject:private] =>
[modifiedColumns:protected] => Array
(
)
)
[68] => Category Object
(
[languages:protected] =>
[bok_resources:protected] =>
[bok_topics:protected] =>
[bok_keywords:protected] =>
[id:protected] => 68
[type:protected] => category
[parent:protected] => 2
[label:protected] => Maintenance Worker
[alreadyInSave:protected] =>
[alreadyInValidation:protected] =>
[validationFailures:protected] => Array
(
)
[_new:BaseObject:private] =>
[_deleted:BaseObject:private] =>
[modifiedColumns:protected] => Array
(
)
)
[69] => Category Object
(
[languages:protected] =>
[bok_resources:protected] =>
[bok_topics:protected] =>
[bok_keywords:protected] =>
[id:protected] => 69
[type:protected] => category
[parent:protected] => 2
[label:protected] => Millwright
[alreadyInSave:protected] =>
[alreadyInValidation:protected] =>
[validationFailures:protected] => Array
(
)
[_new:BaseObject:private] =>
[_deleted:BaseObject:private] =>
[modifiedColumns:protected] => Array
(
)
)
[70] => Category Object
(
[languages:protected] =>
[bok_resources:protected] =>
[bok_topics:protected] =>
[bok_keywords:protected] =>
[id:protected] => 70
[type:protected] => category
[parent:protected] => 2
[label:protected] => Operating Engineer
[alreadyInSave:protected] =>
[alreadyInValidation:protected] =>
[validationFailures:protected] => Array
(
)
[_new:BaseObject:private] =>
[_deleted:BaseObject:private] =>
[modifiedColumns:protected] => Array
(
)
)
[71] => Category Object
(
[languages:protected] =>
[bok_resources:protected] =>
[bok_topics:protected] =>
[bok_keywords:protected] =>
[id:protected] => 71
[type:protected] => category
[parent:protected] => 2
[label:protected] => Painter
[alreadyInSave:protected] =>
[alreadyInValidation:protected] =>
[validationFailures:protected] => Array
(
)
[_new:BaseObject:private] =>
[_deleted:BaseObject:private] =>
[modifiedColumns:protected] => Array
(
)
)
[72] => Category Object
(
[languages:protected] =>
[bok_resources:protected] =>
[bok_topics:protected] =>
[bok_keywords:protected] =>
[id:protected] => 72
[type:protected] => category
[parent:protected] => 2
[label:protected] => Paper Hanger
[alreadyInSave:protected] =>
[alreadyInValidation:protected] =>
[validationFailures:protected] => Array
(
)
[_new:BaseObject:private] =>
[_deleted:BaseObject:private] =>
[modifiedColumns:protected] => Array
(
)
)
[73] => Category Object
(
[languages:protected] =>
[bok_resources:protected] =>
[bok_topics:protected] =>
[bok_keywords:protected] =>
[id:protected] => 73
[type:protected] => category
[parent:protected] => 2
[label:protected] => PCC/Restoration
[alreadyInSave:protected] =>
[alreadyInValidation:protected] =>
[validationFailures:protected] => Array
(
)
[_new:BaseObject:private] =>
[_deleted:BaseObject:private] =>
[modifiedColumns:protected] => Array
(
)
)
[74] => Category Object
(
[languages:protected] =>
[bok_resources:protected] =>
[bok_topics:protected] =>
[bok_keywords:protected] =>
[id:protected] => 74
[type:protected] => category
[parent:protected] => 2
[label:protected] => Pile Driver
[alreadyInSave:protected] =>
[alreadyInValidation:protected] =>
[validationFailures:protected] => Array
(
)
[_new:BaseObject:private] =>
[_deleted:BaseObject:private] =>
[modifiedColumns:protected] => Array
(
)
)
[75] => Category Object
(
[languages:protected] =>
[bok_resources:protected] =>
[bok_topics:protected] =>
[bok_keywords:protected] =>
[id:protected] => 75
[type:protected] => category
[parent:protected] => 2
[label:protected] => Plasterer
[alreadyInSave:protected] =>
[alreadyInValidation:protected] =>
[validationFailures:protected] => Array
(
)
[_new:BaseObject:private] =>
[_deleted:BaseObject:private] =>
[modifiedColumns:protected] => Array
(
)
)
[76] => Category Object
(
[languages:protected] =>
[bok_resources:protected] =>
[bok_topics:protected] =>
[bok_keywords:protected] =>
[id:protected] => 76
[type:protected] => category
[parent:protected] => 2
[label:protected] => Plumber/Pipefitter
[alreadyInSave:protected] =>
[alreadyInValidation:protected] =>
[validationFailures:protected] => Array
(
)
[_new:BaseObject:private] =>
[_deleted:BaseObject:private] =>
[modifiedColumns:protected] => Array
(
)
)
[77] => Category Object
(
[languages:protected] =>
[bok_resources:protected] =>
[bok_topics:protected] =>
[bok_keywords:protected] =>
[id:protected] => 77
[type:protected] => category
[parent:protected] => 2
[label:protected] => Refractory Worker
[alreadyInSave:protected] =>
[alreadyInValidation:protected] =>
[validationFailures:protected] => Array
(
)
[_new:BaseObject:private] =>
[_deleted:BaseObject:private] =>
[modifiedColumns:protected] => Array
(
)
)
[63] => Category Object
(
[languages:protected] =>
[bok_resources:protected] =>
[bok_topics:protected] =>
[bok_keywords:protected] =>
[id:protected] => 63
[type:protected] => category
[parent:protected] => 2
[label:protected] => Reinforcing Ironworker
[alreadyInSave:protected] =>
[alreadyInValidation:protected] =>
[validationFailures:protected] => Array
(
)
[_new:BaseObject:private] =>
[_deleted:BaseObject:private] =>
[modifiedColumns:protected] => Array
(
)
)
[78] => Category Object
(
[languages:protected] =>
[bok_resources:protected] =>
[bok_topics:protected] =>
[bok_keywords:protected] =>
[id:protected] => 78
[type:protected] => category
[parent:protected] => 2
[label:protected] => Roofer/Waterproofer
[alreadyInSave:protected] =>
[alreadyInValidation:protected] =>
[validationFailures:protected] => Array
(
)
[_new:BaseObject:private] =>
[_deleted:BaseObject:private] =>
[modifiedColumns:protected] => Array
(
)
)
[79] => Category Object
(
[languages:protected] =>
[bok_resources:protected] =>
[bok_topics:protected] =>
[bok_keywords:protected] =>
[id:protected] => 79
[type:protected] => category
[parent:protected] => 2
[label:protected] => Scaffold Erector
[alreadyInSave:protected] =>
[alreadyInValidation:protected] =>
[validationFailures:protected] => Array
(
)
[_new:BaseObject:private] =>
[_deleted:BaseObject:private] =>
[modifiedColumns:protected] => Array
(
)
)
[80] => Category Object
(
[languages:protected] =>
[bok_resources:protected] =>
[bok_topics:protected] =>
[bok_keywords:protected] =>
[id:protected] => 80
[type:protected] => category
[parent:protected] => 2
[label:protected] => Sheetmetal Worker
[alreadyInSave:protected] =>
[alreadyInValidation:protected] =>
[validationFailures:protected] => Array
(
)
[_new:BaseObject:private] =>
[_deleted:BaseObject:private] =>
[modifiedColumns:protected] => Array
(
)
)
[81] => Category Object
(
[languages:protected] =>
[bok_resources:protected] =>
[bok_topics:protected] =>
[bok_keywords:protected] =>
[id:protected] => 81
[type:protected] => category
[parent:protected] => 2
[label:protected] => Sprinkler Fitter
[alreadyInSave:protected] =>
[alreadyInValidation:protected] =>
[validationFailures:protected] => Array
(
)
[_new:BaseObject:private] =>
[_deleted:BaseObject:private] =>
[modifiedColumns:protected] => Array
(
)
)
[82] => Category Object
(
[languages:protected] =>
[bok_resources:protected] =>
[bok_topics:protected] =>
[bok_keywords:protected] =>
[id:protected] => 82
[type:protected] => category
[parent:protected] => 2
[label:protected] => Stonemason
[alreadyInSave:protected] =>
[alreadyInValidation:protected] =>
[validationFailures:protected] => Array
(
)
[_new:BaseObject:private] =>
[_deleted:BaseObject:private] =>
[modifiedColumns:protected] => Array
(
)
)
[62] => Category Object
(
[languages:protected] =>
[bok_resources:protected] =>
[bok_topics:protected] =>
[bok_keywords:protected] =>
[id:protected] => 62
[type:protected] => category
[parent:protected] => 2
[label:protected] => Structural Ironworker
[alreadyInSave:protected] =>
[alreadyInValidation:protected] =>
[validationFailures:protected] => Array
(
)
[_new:BaseObject:private] =>
[_deleted:BaseObject:private] =>
[modifiedColumns:protected] => Array
(
)
)
[83] => Category Object
(
[languages:protected] =>
[bok_resources:protected] =>
[bok_topics:protected] =>
[bok_keywords:protected] =>
[id:protected] => 83
[type:protected] => category
[parent:protected] => 2
[label:protected] => Terrazzo Worker
[alreadyInSave:protected] =>
[alreadyInValidation:protected] =>
[validationFailures:protected] => Array
(
)
[_new:BaseObject:private] =>
[_deleted:BaseObject:private] =>
[modifiedColumns:protected] => Array
(
)
)
[84] => Category Object
(
[languages:protected] =>
[bok_resources:protected] =>
[bok_topics:protected] =>
[bok_keywords:protected] =>
[id:protected] => 84
[type:protected] => category
[parent:protected] => 2
[label:protected] => Tile Setter
[alreadyInSave:protected] =>
[alreadyInValidation:protected] =>
[validationFailures:protected] => Array
(
)
[_new:BaseObject:private] =>
[_deleted:BaseObject:private] =>
[modifiedColumns:protected] => Array
(
)
)
[85] => Category Object
(
[languages:protected] =>
[bok_resources:protected] =>
[bok_topics:protected] =>
[bok_keywords:protected] =>
[id:protected] => 85
[type:protected] => category
[parent:protected] => 2
[label:protected] => Truck Driver
[alreadyInSave:protected] =>
[alreadyInValidation:protected] =>
[validationFailures:protected] => Array
(
)
[_new:BaseObject:private] =>
[_deleted:BaseObject:private] =>
[modifiedColumns:protected] => Array
(
)
)
[86] => Category Object
(
[languages:protected] =>
[bok_resources:protected] =>
[bok_topics:protected] =>
[bok_keywords:protected] =>
[id:protected] => 86
[type:protected] => category
[parent:protected] => 2
[label:protected] => Welder
[alreadyInSave:protected] =>
[alreadyInValidation:protected] =>
[validationFailures:protected] => Array
(
)
[_new:BaseObject:private] =>
[_deleted:BaseObject:private] =>
[modifiedColumns:protected] => Array
(
)
)
[87] => Category Object
(
[languages:protected] =>
[bok_resources:protected] =>
[bok_topics:protected] =>
[bok_keywords:protected] =>
[id:protected] => 87
[type:protected] => category
[parent:protected] => 3
[label:protected] => Commercial & Institutional
[alreadyInSave:protected] =>
[alreadyInValidation:protected] =>
[validationFailures:protected] => Array
(
)
[_new:BaseObject:private] =>
[_deleted:BaseObject:private] =>
[modifiedColumns:protected] => Array
(
)
)
[88] => Category Object
(
[languages:protected] =>
[bok_resources:protected] =>
[bok_topics:protected] =>
[bok_keywords:protected] =>
[id:protected] => 88
[type:protected] => category
[parent:protected] => 3
[label:protected] => Demolition
[alreadyInSave:protected] =>
[alreadyInValidation:protected] =>
[validationFailures:protected] => Array
(
)
[_new:BaseObject:private] =>
[_deleted:BaseObject:private] =>
[modifiedColumns:protected] => Array
(
)
)
[89] => Category Object
(
[languages:protected] =>
[bok_resources:protected] =>
[bok_topics:protected] =>
[bok_keywords:protected] =>
[id:protected] => 89
[type:protected] => category
[parent:protected] => 3
[label:protected] => Disasters
[alreadyInSave:protected] =>
[alreadyInValidation:protected] =>
[validationFailures:protected] => Array
(
)
[_new:BaseObject:private] =>
[_deleted:BaseObject:private] =>
[modifiedColumns:protected] => Array
(
)
)
[91] => Category Object
(
[languages:protected] =>
[bok_resources:protected] =>
[bok_topics:protected] =>
[bok_keywords:protected] =>
[id:protected] => 91
[type:protected] => category
[parent:protected] => 3
[label:protected] => Heavy & Highway
[alreadyInSave:protected] =>
[alreadyInValidation:protected] =>
[validationFailures:protected] => Array
(
)
[_new:BaseObject:private] =>
[_deleted:BaseObject:private] =>
[modifiedColumns:protected] => Array
(
)
)
[90] => Category Object
(
[languages:protected] =>
[bok_resources:protected] =>
[bok_topics:protected] =>
[bok_keywords:protected] =>
[id:protected] => 90
[type:protected] => category
[parent:protected] => 3
[label:protected] => Industrial
[alreadyInSave:protected] =>
[alreadyInValidation:protected] =>
[validationFailures:protected] => Array
(
)
[_new:BaseObject:private] =>
[_deleted:BaseObject:private] =>
[modifiedColumns:protected] => Array
(
)
)
[92] => Category Object
(
[languages:protected] =>
[bok_resources:protected] =>
[bok_topics:protected] =>
[bok_keywords:protected] =>
[id:protected] => 92
[type:protected] => category
[parent:protected] => 3
[label:protected] => LEED/Green Construction
[alreadyInSave:protected] =>
[alreadyInValidation:protected] =>
[validationFailures:protected] => Array
(
)
[_new:BaseObject:private] =>
[_deleted:BaseObject:private] =>
[modifiedColumns:protected] => Array
(
)
)
[93] => Category Object
(
[languages:protected] =>
[bok_resources:protected] =>
[bok_topics:protected] =>
[bok_keywords:protected] =>
[id:protected] => 93
[type:protected] => category
[parent:protected] => 3
[label:protected] => Renovations
[alreadyInSave:protected] =>
[alreadyInValidation:protected] =>
[validationFailures:protected] => Array
(
)
[_new:BaseObject:private] =>
[_deleted:BaseObject:private] =>
[modifiedColumns:protected] => Array
(
)
)
[94] => Category Object
(
[languages:protected] =>
[bok_resources:protected] =>
[bok_topics:protected] =>
[bok_keywords:protected] =>
[id:protected] => 94
[type:protected] => category
[parent:protected] => 3
[label:protected] => Residential
[alreadyInSave:protected] =>
[alreadyInValidation:protected] =>
[validationFailures:protected] => Array
(
)
[_new:BaseObject:private] =>
[_deleted:BaseObject:private] =>
[modifiedColumns:protected] => Array
(
)
)
[95] => Category Object
(
[languages:protected] =>
[bok_resources:protected] =>
[bok_topics:protected] =>
[bok_keywords:protected] =>
[id:protected] => 95
[type:protected] => category
[parent:protected] => 3
[label:protected] => Underground
[alreadyInSave:protected] =>
[alreadyInValidation:protected] =>
[validationFailures:protected] => Array
(
)
[_new:BaseObject:private] =>
[_deleted:BaseObject:private] =>
[modifiedColumns:protected] => Array
(
)
)
)
[categories_initialized:protected] => 1
[mapped_items:protected] =>
[content:protected] =>
[files:protected] =>
[language:protected] => Language Object
(
[id:protected] => 1
[code:protected] => en
[name:protected] => English
[alreadyInSave:protected] =>
[alreadyInValidation:protected] =>
[validationFailures:protected] => Array
(
)
[_new:BaseObject:private] =>
[_deleted:BaseObject:private] =>
[modifiedColumns:protected] => Array
(
)
)
[old_record:protected] =>
[id:protected] => 4426
[old_id:protected] =>
[elcosh_id:protected] => d001656
[type:protected] => document
[display_type:protected] => HTML only (and links)
[user_id:protected] => 0
[language_id:protected] => 1
[tagging_id:protected] => Mike Aguilar
[priority_id:protected] => 1
[title:protected] => Construction Dive -- DeWalt's Jobsite Pro headphones recalled for fire hazards
[total_pages:protected] => 1
[billed_pages:protected] => 1
[publication_number:protected] =>
[part_of:protected] =>
[keywords:protected] => DeWalt, Fire Hazards, recall, headphones
[comments:protected] =>
[summary:protected] => A recall notice by the United States Consumer Product Safety Commission affects over 300,000 DeWalt Jobsite Pro Headphones. The recall is a result of a malfunction that can cause earbuds to overheat while charging or during use, leading to fire and burn hazards.
[transition_comments:protected] =>
[external_link:protected] => https://www.constructiondive.com/news/dewalts-jobsite-pro-headphones-recalled-for-fire-hazards/611248/?utm_source=Sailthru&utm_medium=email&utm_campaign=Issue:%202021-12-10%20Construction%20Dive%20Newsletter%20%5Bissue:38532%5D&utm_term=Construction%20Dive
[consol_link:protected] =>
[more_like_this:protected] =>
[permission_given_by:protected] =>
[published:protected] => T
[billable:protected] => F
[img_name:protected] =>
[img_ext:protected] =>
[img_width:protected] =>
[img_height:protected] =>
[img_credit:protected] =>
[img_practice:protected] =>
[vid_source_id:protected] =>
[vid_running_time:protected] =>
[vid_intended_audience:protected] =>
[vid_acquisition_info:protected] =>
[vid_cost:protected] =>
[vid_producer:protected] =>
[vid_filename:protected] =>
[vid_filename_downloadable:protected] =>
[date_summary:protected] =>
[date_permission_requested:protected] =>
[date_permission_received:protected] =>
[date_review_needed:protected] =>
[date_received:protected] => 12/13/21
[date_completed:protected] => 12/13/21
[date_billed:protected] =>
[date_modified:protected] => 12/13/21
[collBokExports:protected] =>
[lastBokExportCriteria:BaseElcoshItem:private] =>
[alreadyInSave:protected] =>
[alreadyInValidation:protected] =>
[validationFailures:protected] => Array
(
)
[_new:BaseObject:private] =>
[_deleted:BaseObject:private] =>
[modifiedColumns:protected] => Array
(
)
)
)
)
[new_images] => Array
(
[0] => Search_Result Object
(
[title] => Morning Toolbox Talk
[image] => /record/images/4003-p.jpg
[blurb] => This photo is from an early morning toolbox talk on a construction job in Mclean, Virginia. It is being delivered in English and Spanish....
[category] => Array
(
[0] => 20
[1] => 51
[2] => 57
[3] => 64
[4] => 70
[5] => 63
[6] => 78
[7] => 82
[8] => 62
[9] => 87
[10] => 88
[11] => 89
[12] => 91
[13] => 90
[14] => 93
[15] => 94
[16] => 97
)
[labels] => Array
(
[0] => Safety Culture
[1] => Work Environment
[2] => Hazards
[3] => Cement Mason
[4] => Trades
[5] => Flagger
[7] => Laborer
[9] => Operating Engineer
[11] => Reinforcing Ironworker
[13] => Roofer/Waterproofer
[15] => Stonemason
[17] => Structural Ironworker
[19] => Commercial & Institutional
[20] => Jobsites
[21] => Demolition
[23] => Disasters
[25] => Heavy & Highway
[27] => Industrial
[29] => Renovations
[31] => Residential
[33] => Images
[34] => Media
[35] => Media & Documents
)
[type] => Images
[sub_category] =>
[url] => /image/4003/i002691/Morning%2BToolbox%2BTalk.html
[item:protected] => ImageRecord Object
(
[records:protected] => Array
(
)
[recordId:protected] =>
[searchWordClass:protected] =>
[searchWordPeerClass:protected] =>
[bok_record:protected] =>
[authors:protected] =>
[organizations:protected] =>
[collections:protected] =>
[categories:protected] => Array
(
[20] => Category Object
(
[languages:protected] =>
[bok_resources:protected] =>
[bok_topics:protected] =>
[bok_keywords:protected] =>
[id:protected] => 20
[type:protected] => category
[parent:protected] => 7
[label:protected] => Safety Culture
[alreadyInSave:protected] =>
[alreadyInValidation:protected] =>
[validationFailures:protected] => Array
(
)
[_new:BaseObject:private] =>
[_deleted:BaseObject:private] =>
[modifiedColumns:protected] => Array
(
)
)
[51] => Category Object
(
[languages:protected] =>
[bok_resources:protected] =>
[bok_topics:protected] =>
[bok_keywords:protected] =>
[id:protected] => 51
[type:protected] => category
[parent:protected] => 2
[label:protected] => Cement Mason
[alreadyInSave:protected] =>
[alreadyInValidation:protected] =>
[validationFailures:protected] => Array
(
)
[_new:BaseObject:private] =>
[_deleted:BaseObject:private] =>
[modifiedColumns:protected] => Array
(
)
)
[57] => Category Object
(
[languages:protected] =>
[bok_resources:protected] =>
[bok_topics:protected] =>
[bok_keywords:protected] =>
[id:protected] => 57
[type:protected] => category
[parent:protected] => 2
[label:protected] => Flagger
[alreadyInSave:protected] =>
[alreadyInValidation:protected] =>
[validationFailures:protected] => Array
(
)
[_new:BaseObject:private] =>
[_deleted:BaseObject:private] =>
[modifiedColumns:protected] => Array
(
)
)
[64] => Category Object
(
[languages:protected] =>
[bok_resources:protected] =>
[bok_topics:protected] =>
[bok_keywords:protected] =>
[id:protected] => 64
[type:protected] => category
[parent:protected] => 2
[label:protected] => Laborer
[alreadyInSave:protected] =>
[alreadyInValidation:protected] =>
[validationFailures:protected] => Array
(
)
[_new:BaseObject:private] =>
[_deleted:BaseObject:private] =>
[modifiedColumns:protected] => Array
(
)
)
[70] => Category Object
(
[languages:protected] =>
[bok_resources:protected] =>
[bok_topics:protected] =>
[bok_keywords:protected] =>
[id:protected] => 70
[type:protected] => category
[parent:protected] => 2
[label:protected] => Operating Engineer
[alreadyInSave:protected] =>
[alreadyInValidation:protected] =>
[validationFailures:protected] => Array
(
)
[_new:BaseObject:private] =>
[_deleted:BaseObject:private] =>
[modifiedColumns:protected] => Array
(
)
)
[63] => Category Object
(
[languages:protected] =>
[bok_resources:protected] =>
[bok_topics:protected] =>
[bok_keywords:protected] =>
[id:protected] => 63
[type:protected] => category
[parent:protected] => 2
[label:protected] => Reinforcing Ironworker
[alreadyInSave:protected] =>
[alreadyInValidation:protected] =>
[validationFailures:protected] => Array
(
)
[_new:BaseObject:private] =>
[_deleted:BaseObject:private] =>
[modifiedColumns:protected] => Array
(
)
)
[78] => Category Object
(
[languages:protected] =>
[bok_resources:protected] =>
[bok_topics:protected] =>
[bok_keywords:protected] =>
[id:protected] => 78
[type:protected] => category
[parent:protected] => 2
[label:protected] => Roofer/Waterproofer
[alreadyInSave:protected] =>
[alreadyInValidation:protected] =>
[validationFailures:protected] => Array
(
)
[_new:BaseObject:private] =>
[_deleted:BaseObject:private] =>
[modifiedColumns:protected] => Array
(
)
)
[82] => Category Object
(
[languages:protected] =>
[bok_resources:protected] =>
[bok_topics:protected] =>
[bok_keywords:protected] =>
[id:protected] => 82
[type:protected] => category
[parent:protected] => 2
[label:protected] => Stonemason
[alreadyInSave:protected] =>
[alreadyInValidation:protected] =>
[validationFailures:protected] => Array
(
)
[_new:BaseObject:private] =>
[_deleted:BaseObject:private] =>
[modifiedColumns:protected] => Array
(
)
)
[62] => Category Object
(
[languages:protected] =>
[bok_resources:protected] =>
[bok_topics:protected] =>
[bok_keywords:protected] =>
[id:protected] => 62
[type:protected] => category
[parent:protected] => 2
[label:protected] => Structural Ironworker
[alreadyInSave:protected] =>
[alreadyInValidation:protected] =>
[validationFailures:protected] => Array
(
)
[_new:BaseObject:private] =>
[_deleted:BaseObject:private] =>
[modifiedColumns:protected] => Array
(
)
)
[87] => Category Object
(
[languages:protected] =>
[bok_resources:protected] =>
[bok_topics:protected] =>
[bok_keywords:protected] =>
[id:protected] => 87
[type:protected] => category
[parent:protected] => 3
[label:protected] => Commercial & Institutional
[alreadyInSave:protected] =>
[alreadyInValidation:protected] =>
[validationFailures:protected] => Array
(
)
[_new:BaseObject:private] =>
[_deleted:BaseObject:private] =>
[modifiedColumns:protected] => Array
(
)
)
[88] => Category Object
(
[languages:protected] =>
[bok_resources:protected] =>
[bok_topics:protected] =>
[bok_keywords:protected] =>
[id:protected] => 88
[type:protected] => category
[parent:protected] => 3
[label:protected] => Demolition
[alreadyInSave:protected] =>
[alreadyInValidation:protected] =>
[validationFailures:protected] => Array
(
)
[_new:BaseObject:private] =>
[_deleted:BaseObject:private] =>
[modifiedColumns:protected] => Array
(
)
)
[89] => Category Object
(
[languages:protected] =>
[bok_resources:protected] =>
[bok_topics:protected] =>
[bok_keywords:protected] =>
[id:protected] => 89
[type:protected] => category
[parent:protected] => 3
[label:protected] => Disasters
[alreadyInSave:protected] =>
[alreadyInValidation:protected] =>
[validationFailures:protected] => Array
(
)
[_new:BaseObject:private] =>
[_deleted:BaseObject:private] =>
[modifiedColumns:protected] => Array
(
)
)
[91] => Category Object
(
[languages:protected] =>
[bok_resources:protected] =>
[bok_topics:protected] =>
[bok_keywords:protected] =>
[id:protected] => 91
[type:protected] => category
[parent:protected] => 3
[label:protected] => Heavy & Highway
[alreadyInSave:protected] =>
[alreadyInValidation:protected] =>
[validationFailures:protected] => Array
(
)
[_new:BaseObject:private] =>
[_deleted:BaseObject:private] =>
[modifiedColumns:protected] => Array
(
)
)
[90] => Category Object
(
[languages:protected] =>
[bok_resources:protected] =>
[bok_topics:protected] =>
[bok_keywords:protected] =>
[id:protected] => 90
[type:protected] => category
[parent:protected] => 3
[label:protected] => Industrial
[alreadyInSave:protected] =>
[alreadyInValidation:protected] =>
[validationFailures:protected] => Array
(
)
[_new:BaseObject:private] =>
[_deleted:BaseObject:private] =>
[modifiedColumns:protected] => Array
(
)
)
[93] => Category Object
(
[languages:protected] =>
[bok_resources:protected] =>
[bok_topics:protected] =>
[bok_keywords:protected] =>
[id:protected] => 93
[type:protected] => category
[parent:protected] => 3
[label:protected] => Renovations
[alreadyInSave:protected] =>
[alreadyInValidation:protected] =>
[validationFailures:protected] => Array
(
)
[_new:BaseObject:private] =>
[_deleted:BaseObject:private] =>
[modifiedColumns:protected] => Array
(
)
)
[94] => Category Object
(
[languages:protected] =>
[bok_resources:protected] =>
[bok_topics:protected] =>
[bok_keywords:protected] =>
[id:protected] => 94
[type:protected] => category
[parent:protected] => 3
[label:protected] => Residential
[alreadyInSave:protected] =>
[alreadyInValidation:protected] =>
[validationFailures:protected] => Array
(
)
[_new:BaseObject:private] =>
[_deleted:BaseObject:private] =>
[modifiedColumns:protected] => Array
(
)
)
[97] => Category Object
(
[languages:protected] =>
[bok_resources:protected] =>
[bok_topics:protected] =>
[bok_keywords:protected] =>
[id:protected] => 97
[type:protected] => category
[parent:protected] => 5
[label:protected] => Images
[alreadyInSave:protected] =>
[alreadyInValidation:protected] =>
[validationFailures:protected] => Array
(
)
[_new:BaseObject:private] =>
[_deleted:BaseObject:private] =>
[modifiedColumns:protected] => Array
(
)
)
)
[categories_initialized:protected] => 1
[mapped_items:protected] =>
[content:protected] =>
[files:protected] =>
[language:protected] => Language Object
(
[id:protected] => 1
[code:protected] => en
[name:protected] => English
[alreadyInSave:protected] =>
[alreadyInValidation:protected] =>
[validationFailures:protected] => Array
(
)
[_new:BaseObject:private] =>
[_deleted:BaseObject:private] =>
[modifiedColumns:protected] => Array
(
)
)
[old_record:protected] =>
[id:protected] => 4003
[old_id:protected] =>
[elcosh_id:protected] => i002691
[type:protected] => image
[display_type:protected] => Image
[user_id:protected] => 0
[language_id:protected] => 1
[tagging_id:protected] => Bruce Lippy
[priority_id:protected] => 1
[title:protected] => Morning Toolbox Talk
[total_pages:protected] => 0
[billed_pages:protected] => 0
[publication_number:protected] =>
[part_of:protected] =>
[keywords:protected] => toolbox talk, tailgate talk, Spanish, bilingual
[comments:protected] =>
[summary:protected] => This photo is from an early morning toolbox talk on a construction job in Mclean, Virginia. It is being delivered in English and Spanish.
[transition_comments:protected] =>
[external_link:protected] =>
[consol_link:protected] => http://www.cpwrconstructionsolutions.org/electrical/solution/662/worker-training.html
[more_like_this:protected] => d001285,d001304,c000079
[permission_given_by:protected] =>
[published:protected] => T
[billable:protected] => F
[img_name:protected] =>
[img_ext:protected] => jpg
[img_width:protected] =>
[img_height:protected] =>
[img_credit:protected] => Morgan Zavertnik and Hoar Construction
[img_practice:protected] => good
[vid_source_id:protected] =>
[vid_running_time:protected] =>
[vid_intended_audience:protected] =>
[vid_acquisition_info:protected] =>
[vid_cost:protected] =>
[vid_producer:protected] =>
[vid_filename:protected] =>
[vid_filename_downloadable:protected] =>
[date_summary:protected] => November 2015
[date_permission_requested:protected] =>
[date_permission_received:protected] =>
[date_review_needed:protected] =>
[date_received:protected] => 03/02/16
[date_completed:protected] => 03/02/16
[date_billed:protected] =>
[date_modified:protected] => 03/02/16
[collBokExports:protected] =>
[lastBokExportCriteria:BaseElcoshItem:private] =>
[alreadyInSave:protected] =>
[alreadyInValidation:protected] =>
[validationFailures:protected] => Array
(
)
[_new:BaseObject:private] =>
[_deleted:BaseObject:private] =>
[modifiedColumns:protected] => Array
(
)
)
)
[1] => Search_Result Object
(
[title] => Toolbox talk - crew view
[image] => /record/images/4005-p.jpg
[blurb] => Photo of crew listening to a toolbox safety talk before starting work....
[category] => Array
(
[0] => 97
[1] => 20
[2] => 47
[3] => 49
[4] => 51
[5] => 55
[6] => 61
[7] => 64
[8] => 71
[9] => 75
[10] => 63
[11] => 79
[12] => 62
[13] => 87
[14] => 88
[15] => 91
[16] => 90
[17] => 93
[18] => 94
[19] => 95
)
[labels] => Array
(
[0] => Images
[1] => Media
[2] => Media & Documents
[3] => Safety Culture
[4] => Work Environment
[5] => Hazards
[6] => Bricklayer
[7] => Trades
[8] => Carpenter
[10] => Cement Mason
[12] => Electrical Worker
[14] => Interior Systems Carpenter
[16] => Laborer
[18] => Painter
[20] => Plasterer
[22] => Reinforcing Ironworker
[24] => Scaffold Erector
[26] => Structural Ironworker
[28] => Commercial & Institutional
[29] => Jobsites
[30] => Demolition
[32] => Heavy & Highway
[34] => Industrial
[36] => Renovations
[38] => Residential
[40] => Underground
)
[type] => Images
[sub_category] =>
[url] => /image/4005/i002692/Toolbox%2Btalk%2B-%2Bcrew%2Bview.html
[item:protected] => ImageRecord Object
(
[records:protected] => Array
(
)
[recordId:protected] =>
[searchWordClass:protected] =>
[searchWordPeerClass:protected] =>
[bok_record:protected] =>
[authors:protected] =>
[organizations:protected] =>
[collections:protected] =>
[categories:protected] => Array
(
[97] => Category Object
(
[languages:protected] =>
[bok_resources:protected] =>
[bok_topics:protected] =>
[bok_keywords:protected] =>
[id:protected] => 97
[type:protected] => category
[parent:protected] => 5
[label:protected] => Images
[alreadyInSave:protected] =>
[alreadyInValidation:protected] =>
[validationFailures:protected] => Array
(
)
[_new:BaseObject:private] =>
[_deleted:BaseObject:private] =>
[modifiedColumns:protected] => Array
(
)
)
[20] => Category Object
(
[languages:protected] =>
[bok_resources:protected] =>
[bok_topics:protected] =>
[bok_keywords:protected] =>
[id:protected] => 20
[type:protected] => category
[parent:protected] => 7
[label:protected] => Safety Culture
[alreadyInSave:protected] =>
[alreadyInValidation:protected] =>
[validationFailures:protected] => Array
(
)
[_new:BaseObject:private] =>
[_deleted:BaseObject:private] =>
[modifiedColumns:protected] => Array
(
)
)
[47] => Category Object
(
[languages:protected] =>
[bok_resources:protected] =>
[bok_topics:protected] =>
[bok_keywords:protected] =>
[id:protected] => 47
[type:protected] => category
[parent:protected] => 2
[label:protected] => Bricklayer
[alreadyInSave:protected] =>
[alreadyInValidation:protected] =>
[validationFailures:protected] => Array
(
)
[_new:BaseObject:private] =>
[_deleted:BaseObject:private] =>
[modifiedColumns:protected] => Array
(
)
)
[49] => Category Object
(
[languages:protected] =>
[bok_resources:protected] =>
[bok_topics:protected] =>
[bok_keywords:protected] =>
[id:protected] => 49
[type:protected] => category
[parent:protected] => 2
[label:protected] => Carpenter
[alreadyInSave:protected] =>
[alreadyInValidation:protected] =>
[validationFailures:protected] => Array
(
)
[_new:BaseObject:private] =>
[_deleted:BaseObject:private] =>
[modifiedColumns:protected] => Array
(
)
)
[51] => Category Object
(
[languages:protected] =>
[bok_resources:protected] =>
[bok_topics:protected] =>
[bok_keywords:protected] =>
[id:protected] => 51
[type:protected] => category
[parent:protected] => 2
[label:protected] => Cement Mason
[alreadyInSave:protected] =>
[alreadyInValidation:protected] =>
[validationFailures:protected] => Array
(
)
[_new:BaseObject:private] =>
[_deleted:BaseObject:private] =>
[modifiedColumns:protected] => Array
(
)
)
[55] => Category Object
(
[languages:protected] =>
[bok_resources:protected] =>
[bok_topics:protected] =>
[bok_keywords:protected] =>
[id:protected] => 55
[type:protected] => category
[parent:protected] => 2
[label:protected] => Electrical Worker
[alreadyInSave:protected] =>
[alreadyInValidation:protected] =>
[validationFailures:protected] => Array
(
)
[_new:BaseObject:private] =>
[_deleted:BaseObject:private] =>
[modifiedColumns:protected] => Array
(
)
)
[61] => Category Object
(
[languages:protected] =>
[bok_resources:protected] =>
[bok_topics:protected] =>
[bok_keywords:protected] =>
[id:protected] => 61
[type:protected] => category
[parent:protected] => 2
[label:protected] => Interior Systems Carpenter
[alreadyInSave:protected] =>
[alreadyInValidation:protected] =>
[validationFailures:protected] => Array
(
)
[_new:BaseObject:private] =>
[_deleted:BaseObject:private] =>
[modifiedColumns:protected] => Array
(
)
)
[64] => Category Object
(
[languages:protected] =>
[bok_resources:protected] =>
[bok_topics:protected] =>
[bok_keywords:protected] =>
[id:protected] => 64
[type:protected] => category
[parent:protected] => 2
[label:protected] => Laborer
[alreadyInSave:protected] =>
[alreadyInValidation:protected] =>
[validationFailures:protected] => Array
(
)
[_new:BaseObject:private] =>
[_deleted:BaseObject:private] =>
[modifiedColumns:protected] => Array
(
)
)
[71] => Category Object
(
[languages:protected] =>
[bok_resources:protected] =>
[bok_topics:protected] =>
[bok_keywords:protected] =>
[id:protected] => 71
[type:protected] => category
[parent:protected] => 2
[label:protected] => Painter
[alreadyInSave:protected] =>
[alreadyInValidation:protected] =>
[validationFailures:protected] => Array
(
)
[_new:BaseObject:private] =>
[_deleted:BaseObject:private] =>
[modifiedColumns:protected] => Array
(
)
)
[75] => Category Object
(
[languages:protected] =>
[bok_resources:protected] =>
[bok_topics:protected] =>
[bok_keywords:protected] =>
[id:protected] => 75
[type:protected] => category
[parent:protected] => 2
[label:protected] => Plasterer
[alreadyInSave:protected] =>
[alreadyInValidation:protected] =>
[validationFailures:protected] => Array
(
)
[_new:BaseObject:private] =>
[_deleted:BaseObject:private] =>
[modifiedColumns:protected] => Array
(
)
)
[63] => Category Object
(
[languages:protected] =>
[bok_resources:protected] =>
[bok_topics:protected] =>
[bok_keywords:protected] =>
[id:protected] => 63
[type:protected] => category
[parent:protected] => 2
[label:protected] => Reinforcing Ironworker
[alreadyInSave:protected] =>
[alreadyInValidation:protected] =>
[validationFailures:protected] => Array
(
)
[_new:BaseObject:private] =>
[_deleted:BaseObject:private] =>
[modifiedColumns:protected] => Array
(
)
)
[79] => Category Object
(
[languages:protected] =>
[bok_resources:protected] =>
[bok_topics:protected] =>
[bok_keywords:protected] =>
[id:protected] => 79
[type:protected] => category
[parent:protected] => 2
[label:protected] => Scaffold Erector
[alreadyInSave:protected] =>
[alreadyInValidation:protected] =>
[validationFailures:protected] => Array
(
)
[_new:BaseObject:private] =>
[_deleted:BaseObject:private] =>
[modifiedColumns:protected] => Array
(
)
)
[62] => Category Object
(
[languages:protected] =>
[bok_resources:protected] =>
[bok_topics:protected] =>
[bok_keywords:protected] =>
[id:protected] => 62
[type:protected] => category
[parent:protected] => 2
[label:protected] => Structural Ironworker
[alreadyInSave:protected] =>
[alreadyInValidation:protected] =>
[validationFailures:protected] => Array
(
)
[_new:BaseObject:private] =>
[_deleted:BaseObject:private] =>
[modifiedColumns:protected] => Array
(
)
)
[87] => Category Object
(
[languages:protected] =>
[bok_resources:protected] =>
[bok_topics:protected] =>
[bok_keywords:protected] =>
[id:protected] => 87
[type:protected] => category
[parent:protected] => 3
[label:protected] => Commercial & Institutional
[alreadyInSave:protected] =>
[alreadyInValidation:protected] =>
[validationFailures:protected] => Array
(
)
[_new:BaseObject:private] =>
[_deleted:BaseObject:private] =>
[modifiedColumns:protected] => Array
(
)
)
[88] => Category Object
(
[languages:protected] =>
[bok_resources:protected] =>
[bok_topics:protected] =>
[bok_keywords:protected] =>
[id:protected] => 88
[type:protected] => category
[parent:protected] => 3
[label:protected] => Demolition
[alreadyInSave:protected] =>
[alreadyInValidation:protected] =>
[validationFailures:protected] => Array
(
)
[_new:BaseObject:private] =>
[_deleted:BaseObject:private] =>
[modifiedColumns:protected] => Array
(
)
)
[91] => Category Object
(
[languages:protected] =>
[bok_resources:protected] =>
[bok_topics:protected] =>
[bok_keywords:protected] =>
[id:protected] => 91
[type:protected] => category
[parent:protected] => 3
[label:protected] => Heavy & Highway
[alreadyInSave:protected] =>
[alreadyInValidation:protected] =>
[validationFailures:protected] => Array
(
)
[_new:BaseObject:private] =>
[_deleted:BaseObject:private] =>
[modifiedColumns:protected] => Array
(
)
)
[90] => Category Object
(
[languages:protected] =>
[bok_resources:protected] =>
[bok_topics:protected] =>
[bok_keywords:protected] =>
[id:protected] => 90
[type:protected] => category
[parent:protected] => 3
[label:protected] => Industrial
[alreadyInSave:protected] =>
[alreadyInValidation:protected] =>
[validationFailures:protected] => Array
(
)
[_new:BaseObject:private] =>
[_deleted:BaseObject:private] =>
[modifiedColumns:protected] => Array
(
)
)
[93] => Category Object
(
[languages:protected] =>
[bok_resources:protected] =>
[bok_topics:protected] =>
[bok_keywords:protected] =>
[id:protected] => 93
[type:protected] => category
[parent:protected] => 3
[label:protected] => Renovations
[alreadyInSave:protected] =>
[alreadyInValidation:protected] =>
[validationFailures:protected] => Array
(
)
[_new:BaseObject:private] =>
[_deleted:BaseObject:private] =>
[modifiedColumns:protected] => Array
(
)
)
[94] => Category Object
(
[languages:protected] =>
[bok_resources:protected] =>
[bok_topics:protected] =>
[bok_keywords:protected] =>
[id:protected] => 94
[type:protected] => category
[parent:protected] => 3
[label:protected] => Residential
[alreadyInSave:protected] =>
[alreadyInValidation:protected] =>
[validationFailures:protected] => Array
(
)
[_new:BaseObject:private] =>
[_deleted:BaseObject:private] =>
[modifiedColumns:protected] => Array
(
)
)
[95] => Category Object
(
[languages:protected] =>
[bok_resources:protected] =>
[bok_topics:protected] =>
[bok_keywords:protected] =>
[id:protected] => 95
[type:protected] => category
[parent:protected] => 3
[label:protected] => Underground
[alreadyInSave:protected] =>
[alreadyInValidation:protected] =>
[validationFailures:protected] => Array
(
)
[_new:BaseObject:private] =>
[_deleted:BaseObject:private] =>
[modifiedColumns:protected] => Array
(
)
)
)
[categories_initialized:protected] => 1
[mapped_items:protected] =>
[content:protected] =>
[files:protected] =>
[language:protected] => Language Object
(
[id:protected] => 1
[code:protected] => en
[name:protected] => English
[alreadyInSave:protected] =>
[alreadyInValidation:protected] =>
[validationFailures:protected] => Array
(
)
[_new:BaseObject:private] =>
[_deleted:BaseObject:private] =>
[modifiedColumns:protected] => Array
(
)
)
[old_record:protected] =>
[id:protected] => 4005
[old_id:protected] =>
[elcosh_id:protected] => i002692
[type:protected] => image
[display_type:protected] => Image
[user_id:protected] => 0
[language_id:protected] => 1
[tagging_id:protected] => Bruce Lippy
[priority_id:protected] => 1
[title:protected] => Toolbox talk - crew view
[total_pages:protected] => 0
[billed_pages:protected] => 0
[publication_number:protected] =>
[part_of:protected] =>
[keywords:protected] => toolbox talk, tailgate talk, safety talk, Spanish
[comments:protected] =>
[summary:protected] => Photo of crew listening to a toolbox safety talk before starting work.
[transition_comments:protected] =>
[external_link:protected] =>
[consol_link:protected] => http://www.cpwrconstructionsolutions.org/electrical/solution/662/worker-training.html
[more_like_this:protected] => i002691,d001269, c000079, d001285
[permission_given_by:protected] =>
[published:protected] => T
[billable:protected] => F
[img_name:protected] =>
[img_ext:protected] => jpg
[img_width:protected] =>
[img_height:protected] =>
[img_credit:protected] => Morgan Zavertnik and Hoar Construction
[img_practice:protected] => good
[vid_source_id:protected] =>
[vid_running_time:protected] =>
[vid_intended_audience:protected] =>
[vid_acquisition_info:protected] =>
[vid_cost:protected] =>
[vid_producer:protected] =>
[vid_filename:protected] =>
[vid_filename_downloadable:protected] =>
[date_summary:protected] => November 2015
[date_permission_requested:protected] =>
[date_permission_received:protected] =>
[date_review_needed:protected] =>
[date_received:protected] => 03/02/16
[date_completed:protected] => 03/02/16
[date_billed:protected] =>
[date_modified:protected] => 03/02/16
[collBokExports:protected] =>
[lastBokExportCriteria:BaseElcoshItem:private] =>
[alreadyInSave:protected] =>
[alreadyInValidation:protected] =>
[validationFailures:protected] => Array
(
)
[_new:BaseObject:private] =>
[_deleted:BaseObject:private] =>
[modifiedColumns:protected] => Array
(
)
)
)
[2] => Search_Result Object
(
[title] => Toolbox talk - long shot
[image] => /record/images/4006-p.jpg
[blurb] => This crew gathered every morning before starting work to discuss a new safety topic....
[category] => Array
(
[0] => 20
[1] => 47
[2] => 49
[3] => 51
[4] => 55
[5] => 64
[6] => 68
[7] => 75
[8] => 76
[9] => 63
[10] => 78
[11] => 79
[12] => 82
[13] => 62
[14] => 87
[15] => 88
[16] => 91
[17] => 90
[18] => 93
[19] => 94
[20] => 95
[21] => 97
)
[labels] => Array
(
[0] => Safety Culture
[1] => Work Environment
[2] => Hazards
[3] => Bricklayer
[4] => Trades
[5] => Carpenter
[7] => Cement Mason
[9] => Electrical Worker
[11] => Laborer
[13] => Maintenance Worker
[15] => Plasterer
[17] => Plumber/Pipefitter
[19] => Reinforcing Ironworker
[21] => Roofer/Waterproofer
[23] => Scaffold Erector
[25] => Stonemason
[27] => Structural Ironworker
[29] => Commercial & Institutional
[30] => Jobsites
[31] => Demolition
[33] => Heavy & Highway
[35] => Industrial
[37] => Renovations
[39] => Residential
[41] => Underground
[43] => Images
[44] => Media
[45] => Media & Documents
)
[type] => Images
[sub_category] =>
[url] => /image/4006/i002693/Toolbox%2Btalk%2B-%2Blong%2Bshot.html
[item:protected] => ImageRecord Object
(
[records:protected] => Array
(
)
[recordId:protected] =>
[searchWordClass:protected] =>
[searchWordPeerClass:protected] =>
[bok_record:protected] =>
[authors:protected] =>
[organizations:protected] =>
[collections:protected] =>
[categories:protected] => Array
(
[20] => Category Object
(
[languages:protected] =>
[bok_resources:protected] =>
[bok_topics:protected] =>
[bok_keywords:protected] =>
[id:protected] => 20
[type:protected] => category
[parent:protected] => 7
[label:protected] => Safety Culture
[alreadyInSave:protected] =>
[alreadyInValidation:protected] =>
[validationFailures:protected] => Array
(
)
[_new:BaseObject:private] =>
[_deleted:BaseObject:private] =>
[modifiedColumns:protected] => Array
(
)
)
[47] => Category Object
(
[languages:protected] =>
[bok_resources:protected] =>
[bok_topics:protected] =>
[bok_keywords:protected] =>
[id:protected] => 47
[type:protected] => category
[parent:protected] => 2
[label:protected] => Bricklayer
[alreadyInSave:protected] =>
[alreadyInValidation:protected] =>
[validationFailures:protected] => Array
(
)
[_new:BaseObject:private] =>
[_deleted:BaseObject:private] =>
[modifiedColumns:protected] => Array
(
)
)
[49] => Category Object
(
[languages:protected] =>
[bok_resources:protected] =>
[bok_topics:protected] =>
[bok_keywords:protected] =>
[id:protected] => 49
[type:protected] => category
[parent:protected] => 2
[label:protected] => Carpenter
[alreadyInSave:protected] =>
[alreadyInValidation:protected] =>
[validationFailures:protected] => Array
(
)
[_new:BaseObject:private] =>
[_deleted:BaseObject:private] =>
[modifiedColumns:protected] => Array
(
)
)
[51] => Category Object
(
[languages:protected] =>
[bok_resources:protected] =>
[bok_topics:protected] =>
[bok_keywords:protected] =>
[id:protected] => 51
[type:protected] => category
[parent:protected] => 2
[label:protected] => Cement Mason
[alreadyInSave:protected] =>
[alreadyInValidation:protected] =>
[validationFailures:protected] => Array
(
)
[_new:BaseObject:private] =>
[_deleted:BaseObject:private] =>
[modifiedColumns:protected] => Array
(
)
)
[55] => Category Object
(
[languages:protected] =>
[bok_resources:protected] =>
[bok_topics:protected] =>
[bok_keywords:protected] =>
[id:protected] => 55
[type:protected] => category
[parent:protected] => 2
[label:protected] => Electrical Worker
[alreadyInSave:protected] =>
[alreadyInValidation:protected] =>
[validationFailures:protected] => Array
(
)
[_new:BaseObject:private] =>
[_deleted:BaseObject:private] =>
[modifiedColumns:protected] => Array
(
)
)
[64] => Category Object
(
[languages:protected] =>
[bok_resources:protected] =>
[bok_topics:protected] =>
[bok_keywords:protected] =>
[id:protected] => 64
[type:protected] => category
[parent:protected] => 2
[label:protected] => Laborer
[alreadyInSave:protected] =>
[alreadyInValidation:protected] =>
[validationFailures:protected] => Array
(
)
[_new:BaseObject:private] =>
[_deleted:BaseObject:private] =>
[modifiedColumns:protected] => Array
(
)
)
[68] => Category Object
(
[languages:protected] =>
[bok_resources:protected] =>
[bok_topics:protected] =>
[bok_keywords:protected] =>
[id:protected] => 68
[type:protected] => category
[parent:protected] => 2
[label:protected] => Maintenance Worker
[alreadyInSave:protected] =>
[alreadyInValidation:protected] =>
[validationFailures:protected] => Array
(
)
[_new:BaseObject:private] =>
[_deleted:BaseObject:private] =>
[modifiedColumns:protected] => Array
(
)
)
[75] => Category Object
(
[languages:protected] =>
[bok_resources:protected] =>
[bok_topics:protected] =>
[bok_keywords:protected] =>
[id:protected] => 75
[type:protected] => category
[parent:protected] => 2
[label:protected] => Plasterer
[alreadyInSave:protected] =>
[alreadyInValidation:protected] =>
[validationFailures:protected] => Array
(
)
[_new:BaseObject:private] =>
[_deleted:BaseObject:private] =>
[modifiedColumns:protected] => Array
(
)
)
[76] => Category Object
(
[languages:protected] =>
[bok_resources:protected] =>
[bok_topics:protected] =>
[bok_keywords:protected] =>
[id:protected] => 76
[type:protected] => category
[parent:protected] => 2
[label:protected] => Plumber/Pipefitter
[alreadyInSave:protected] =>
[alreadyInValidation:protected] =>
[validationFailures:protected] => Array
(
)
[_new:BaseObject:private] =>
[_deleted:BaseObject:private] =>
[modifiedColumns:protected] => Array
(
)
)
[63] => Category Object
(
[languages:protected] =>
[bok_resources:protected] =>
[bok_topics:protected] =>
[bok_keywords:protected] =>
[id:protected] => 63
[type:protected] => category
[parent:protected] => 2
[label:protected] => Reinforcing Ironworker
[alreadyInSave:protected] =>
[alreadyInValidation:protected] =>
[validationFailures:protected] => Array
(
)
[_new:BaseObject:private] =>
[_deleted:BaseObject:private] =>
[modifiedColumns:protected] => Array
(
)
)
[78] => Category Object
(
[languages:protected] =>
[bok_resources:protected] =>
[bok_topics:protected] =>
[bok_keywords:protected] =>
[id:protected] => 78
[type:protected] => category
[parent:protected] => 2
[label:protected] => Roofer/Waterproofer
[alreadyInSave:protected] =>
[alreadyInValidation:protected] =>
[validationFailures:protected] => Array
(
)
[_new:BaseObject:private] =>
[_deleted:BaseObject:private] =>
[modifiedColumns:protected] => Array
(
)
)
[79] => Category Object
(
[languages:protected] =>
[bok_resources:protected] =>
[bok_topics:protected] =>
[bok_keywords:protected] =>
[id:protected] => 79
[type:protected] => category
[parent:protected] => 2
[label:protected] => Scaffold Erector
[alreadyInSave:protected] =>
[alreadyInValidation:protected] =>
[validationFailures:protected] => Array
(
)
[_new:BaseObject:private] =>
[_deleted:BaseObject:private] =>
[modifiedColumns:protected] => Array
(
)
)
[82] => Category Object
(
[languages:protected] =>
[bok_resources:protected] =>
[bok_topics:protected] =>
[bok_keywords:protected] =>
[id:protected] => 82
[type:protected] => category
[parent:protected] => 2
[label:protected] => Stonemason
[alreadyInSave:protected] =>
[alreadyInValidation:protected] =>
[validationFailures:protected] => Array
(
)
[_new:BaseObject:private] =>
[_deleted:BaseObject:private] =>
[modifiedColumns:protected] => Array
(
)
)
[62] => Category Object
(
[languages:protected] =>
[bok_resources:protected] =>
[bok_topics:protected] =>
[bok_keywords:protected] =>
[id:protected] => 62
[type:protected] => category
[parent:protected] => 2
[label:protected] => Structural Ironworker
[alreadyInSave:protected] =>
[alreadyInValidation:protected] =>
[validationFailures:protected] => Array
(
)
[_new:BaseObject:private] =>
[_deleted:BaseObject:private] =>
[modifiedColumns:protected] => Array
(
)
)
[87] => Category Object
(
[languages:protected] =>
[bok_resources:protected] =>
[bok_topics:protected] =>
[bok_keywords:protected] =>
[id:protected] => 87
[type:protected] => category
[parent:protected] => 3
[label:protected] => Commercial & Institutional
[alreadyInSave:protected] =>
[alreadyInValidation:protected] =>
[validationFailures:protected] => Array
(
)
[_new:BaseObject:private] =>
[_deleted:BaseObject:private] =>
[modifiedColumns:protected] => Array
(
)
)
[88] => Category Object
(
[languages:protected] =>
[bok_resources:protected] =>
[bok_topics:protected] =>
[bok_keywords:protected] =>
[id:protected] => 88
[type:protected] => category
[parent:protected] => 3
[label:protected] => Demolition
[alreadyInSave:protected] =>
[alreadyInValidation:protected] =>
[validationFailures:protected] => Array
(
)
[_new:BaseObject:private] =>
[_deleted:BaseObject:private] =>
[modifiedColumns:protected] => Array
(
)
)
[91] => Category Object
(
[languages:protected] =>
[bok_resources:protected] =>
[bok_topics:protected] =>
[bok_keywords:protected] =>
[id:protected] => 91
[type:protected] => category
[parent:protected] => 3
[label:protected] => Heavy & Highway
[alreadyInSave:protected] =>
[alreadyInValidation:protected] =>
[validationFailures:protected] => Array
(
)
[_new:BaseObject:private] =>
[_deleted:BaseObject:private] =>
[modifiedColumns:protected] => Array
(
)
)
[90] => Category Object
(
[languages:protected] =>
[bok_resources:protected] =>
[bok_topics:protected] =>
[bok_keywords:protected] =>
[id:protected] => 90
[type:protected] => category
[parent:protected] => 3
[label:protected] => Industrial
[alreadyInSave:protected] =>
[alreadyInValidation:protected] =>
[validationFailures:protected] => Array
(
)
[_new:BaseObject:private] =>
[_deleted:BaseObject:private] =>
[modifiedColumns:protected] => Array
(
)
)
[93] => Category Object
(
[languages:protected] =>
[bok_resources:protected] =>
[bok_topics:protected] =>
[bok_keywords:protected] =>
[id:protected] => 93
[type:protected] => category
[parent:protected] => 3
[label:protected] => Renovations
[alreadyInSave:protected] =>
[alreadyInValidation:protected] =>
[validationFailures:protected] => Array
(
)
[_new:BaseObject:private] =>
[_deleted:BaseObject:private] =>
[modifiedColumns:protected] => Array
(
)
)
[94] => Category Object
(
[languages:protected] =>
[bok_resources:protected] =>
[bok_topics:protected] =>
[bok_keywords:protected] =>
[id:protected] => 94
[type:protected] => category
[parent:protected] => 3
[label:protected] => Residential
[alreadyInSave:protected] =>
[alreadyInValidation:protected] =>
[validationFailures:protected] => Array
(
)
[_new:BaseObject:private] =>
[_deleted:BaseObject:private] =>
[modifiedColumns:protected] => Array
(
)
)
[95] => Category Object
(
[languages:protected] =>
[bok_resources:protected] =>
[bok_topics:protected] =>
[bok_keywords:protected] =>
[id:protected] => 95
[type:protected] => category
[parent:protected] => 3
[label:protected] => Underground
[alreadyInSave:protected] =>
[alreadyInValidation:protected] =>
[validationFailures:protected] => Array
(
)
[_new:BaseObject:private] =>
[_deleted:BaseObject:private] =>
[modifiedColumns:protected] => Array
(
)
)
[97] => Category Object
(
[languages:protected] =>
[bok_resources:protected] =>
[bok_topics:protected] =>
[bok_keywords:protected] =>
[id:protected] => 97
[type:protected] => category
[parent:protected] => 5
[label:protected] => Images
[alreadyInSave:protected] =>
[alreadyInValidation:protected] =>
[validationFailures:protected] => Array
(
)
[_new:BaseObject:private] =>
[_deleted:BaseObject:private] =>
[modifiedColumns:protected] => Array
(
)
)
)
[categories_initialized:protected] => 1
[mapped_items:protected] =>
[content:protected] =>
[files:protected] =>
[language:protected] => Language Object
(
[id:protected] => 1
[code:protected] => en
[name:protected] => English
[alreadyInSave:protected] =>
[alreadyInValidation:protected] =>
[validationFailures:protected] => Array
(
)
[_new:BaseObject:private] =>
[_deleted:BaseObject:private] =>
[modifiedColumns:protected] => Array
(
)
)
[old_record:protected] =>
[id:protected] => 4006
[old_id:protected] =>
[elcosh_id:protected] => i002693
[type:protected] => image
[display_type:protected] => Image
[user_id:protected] => 0
[language_id:protected] => 1
[tagging_id:protected] => Bruce Lippy
[priority_id:protected] => 1
[title:protected] => Toolbox talk - long shot
[total_pages:protected] => 0
[billed_pages:protected] => 0
[publication_number:protected] =>
[part_of:protected] =>
[keywords:protected] => toolbox talk, tailgate talk, safety minute
[comments:protected] =>
[summary:protected] => This crew gathered every morning before starting work to discuss a new safety topic.
[transition_comments:protected] =>
[external_link:protected] =>
[consol_link:protected] => http://www.cpwrconstructionsolutions.org/electrical/solution/662/worker-training.html
[more_like_this:protected] => i002691,i002692,d001269,d000527
[permission_given_by:protected] =>
[published:protected] => T
[billable:protected] => F
[img_name:protected] =>
[img_ext:protected] => jpg
[img_width:protected] =>
[img_height:protected] =>
[img_credit:protected] => Morgan Zavertnik and Hoar Construction
[img_practice:protected] => good
[vid_source_id:protected] =>
[vid_running_time:protected] =>
[vid_intended_audience:protected] =>
[vid_acquisition_info:protected] =>
[vid_cost:protected] =>
[vid_producer:protected] =>
[vid_filename:protected] =>
[vid_filename_downloadable:protected] =>
[date_summary:protected] => November 2015
[date_permission_requested:protected] =>
[date_permission_received:protected] =>
[date_review_needed:protected] =>
[date_received:protected] => 03/02/16
[date_completed:protected] => 03/02/16
[date_billed:protected] =>
[date_modified:protected] => 03/02/16
[collBokExports:protected] =>
[lastBokExportCriteria:BaseElcoshItem:private] =>
[alreadyInSave:protected] =>
[alreadyInValidation:protected] =>
[validationFailures:protected] => Array
(
)
[_new:BaseObject:private] =>
[_deleted:BaseObject:private] =>
[modifiedColumns:protected] => Array
(
)
)
)
[3] => Search_Result Object
(
[title] => Safety officer discussing ongoing project with marketing coordinator
[image] => /record/images/4014-p.jpg
[blurb] => The safety officer (left) points out the good safety practices on this project that reflect well on the firm and may influence future clients....
[category] => Array
(
[0] => 97
[1] => 20
[2] => 46
[3] => 47
[4] => 49
[5] => 50
[6] => 51
[7] => 54
[8] => 55
[9] => 58
[10] => 60
[11] => 61
[12] => 64
[13] => 71
[14] => 75
[15] => 76
[16] => 63
[17] => 79
[18] => 80
[19] => 82
[20] => 62
[21] => 83
[22] => 87
[23] => 91
[24] => 90
[25] => 93
[26] => 94
)
[labels] => Array
(
[0] => Images
[1] => Media
[2] => Media & Documents
[3] => Safety Culture
[4] => Work Environment
[5] => Hazards
[6] => Boilermaker
[7] => Trades
[8] => Bricklayer
[10] => Carpenter
[12] => Carpet Layer
[14] => Cement Mason
[16] => Drywall Applicator Specialist
[18] => Electrical Worker
[20] => Glazier
[22] => HVAC
[24] => Interior Systems Carpenter
[26] => Laborer
[28] => Painter
[30] => Plasterer
[32] => Plumber/Pipefitter
[34] => Reinforcing Ironworker
[36] => Scaffold Erector
[38] => Sheetmetal Worker
[40] => Stonemason
[42] => Structural Ironworker
[44] => Terrazzo Worker
[46] => Commercial & Institutional
[47] => Jobsites
[48] => Heavy & Highway
[50] => Industrial
[52] => Renovations
[54] => Residential
)
[type] => Images
[sub_category] =>
[url] => /image/4014/i002700/Safety%2Bofficer%2Bdiscussing%2Bongoing%2Bproject%2Bwith%2Bmarketing%2Bcoordinator.html
[item:protected] => ImageRecord Object
(
[records:protected] => Array
(
)
[recordId:protected] =>
[searchWordClass:protected] =>
[searchWordPeerClass:protected] =>
[bok_record:protected] =>
[authors:protected] =>
[organizations:protected] =>
[collections:protected] =>
[categories:protected] => Array
(
[97] => Category Object
(
[languages:protected] =>
[bok_resources:protected] =>
[bok_topics:protected] =>
[bok_keywords:protected] =>
[id:protected] => 97
[type:protected] => category
[parent:protected] => 5
[label:protected] => Images
[alreadyInSave:protected] =>
[alreadyInValidation:protected] =>
[validationFailures:protected] => Array
(
)
[_new:BaseObject:private] =>
[_deleted:BaseObject:private] =>
[modifiedColumns:protected] => Array
(
)
)
[20] => Category Object
(
[languages:protected] =>
[bok_resources:protected] =>
[bok_topics:protected] =>
[bok_keywords:protected] =>
[id:protected] => 20
[type:protected] => category
[parent:protected] => 7
[label:protected] => Safety Culture
[alreadyInSave:protected] =>
[alreadyInValidation:protected] =>
[validationFailures:protected] => Array
(
)
[_new:BaseObject:private] =>
[_deleted:BaseObject:private] =>
[modifiedColumns:protected] => Array
(
)
)
[46] => Category Object
(
[languages:protected] =>
[bok_resources:protected] =>
[bok_topics:protected] =>
[bok_keywords:protected] =>
[id:protected] => 46
[type:protected] => category
[parent:protected] => 2
[label:protected] => Boilermaker
[alreadyInSave:protected] =>
[alreadyInValidation:protected] =>
[validationFailures:protected] => Array
(
)
[_new:BaseObject:private] =>
[_deleted:BaseObject:private] =>
[modifiedColumns:protected] => Array
(
)
)
[47] => Category Object
(
[languages:protected] =>
[bok_resources:protected] =>
[bok_topics:protected] =>
[bok_keywords:protected] =>
[id:protected] => 47
[type:protected] => category
[parent:protected] => 2
[label:protected] => Bricklayer
[alreadyInSave:protected] =>
[alreadyInValidation:protected] =>
[validationFailures:protected] => Array
(
)
[_new:BaseObject:private] =>
[_deleted:BaseObject:private] =>
[modifiedColumns:protected] => Array
(
)
)
[49] => Category Object
(
[languages:protected] =>
[bok_resources:protected] =>
[bok_topics:protected] =>
[bok_keywords:protected] =>
[id:protected] => 49
[type:protected] => category
[parent:protected] => 2
[label:protected] => Carpenter
[alreadyInSave:protected] =>
[alreadyInValidation:protected] =>
[validationFailures:protected] => Array
(
)
[_new:BaseObject:private] =>
[_deleted:BaseObject:private] =>
[modifiedColumns:protected] => Array
(
)
)
[50] => Category Object
(
[languages:protected] =>
[bok_resources:protected] =>
[bok_topics:protected] =>
[bok_keywords:protected] =>
[id:protected] => 50
[type:protected] => category
[parent:protected] => 2
[label:protected] => Carpet Layer
[alreadyInSave:protected] =>
[alreadyInValidation:protected] =>
[validationFailures:protected] => Array
(
)
[_new:BaseObject:private] =>
[_deleted:BaseObject:private] =>
[modifiedColumns:protected] => Array
(
)
)
[51] => Category Object
(
[languages:protected] =>
[bok_resources:protected] =>
[bok_topics:protected] =>
[bok_keywords:protected] =>
[id:protected] => 51
[type:protected] => category
[parent:protected] => 2
[label:protected] => Cement Mason
[alreadyInSave:protected] =>
[alreadyInValidation:protected] =>
[validationFailures:protected] => Array
(
)
[_new:BaseObject:private] =>
[_deleted:BaseObject:private] =>
[modifiedColumns:protected] => Array
(
)
)
[54] => Category Object
(
[languages:protected] =>
[bok_resources:protected] =>
[bok_topics:protected] =>
[bok_keywords:protected] =>
[id:protected] => 54
[type:protected] => category
[parent:protected] => 2
[label:protected] => Drywall Applicator Specialist
[alreadyInSave:protected] =>
[alreadyInValidation:protected] =>
[validationFailures:protected] => Array
(
)
[_new:BaseObject:private] =>
[_deleted:BaseObject:private] =>
[modifiedColumns:protected] => Array
(
)
)
[55] => Category Object
(
[languages:protected] =>
[bok_resources:protected] =>
[bok_topics:protected] =>
[bok_keywords:protected] =>
[id:protected] => 55
[type:protected] => category
[parent:protected] => 2
[label:protected] => Electrical Worker
[alreadyInSave:protected] =>
[alreadyInValidation:protected] =>
[validationFailures:protected] => Array
(
)
[_new:BaseObject:private] =>
[_deleted:BaseObject:private] =>
[modifiedColumns:protected] => Array
(
)
)
[58] => Category Object
(
[languages:protected] =>
[bok_resources:protected] =>
[bok_topics:protected] =>
[bok_keywords:protected] =>
[id:protected] => 58
[type:protected] => category
[parent:protected] => 2
[label:protected] => Glazier
[alreadyInSave:protected] =>
[alreadyInValidation:protected] =>
[validationFailures:protected] => Array
(
)
[_new:BaseObject:private] =>
[_deleted:BaseObject:private] =>
[modifiedColumns:protected] => Array
(
)
)
[60] => Category Object
(
[languages:protected] =>
[bok_resources:protected] =>
[bok_topics:protected] =>
[bok_keywords:protected] =>
[id:protected] => 60
[type:protected] => category
[parent:protected] => 2
[label:protected] => HVAC
[alreadyInSave:protected] =>
[alreadyInValidation:protected] =>
[validationFailures:protected] => Array
(
)
[_new:BaseObject:private] =>
[_deleted:BaseObject:private] =>
[modifiedColumns:protected] => Array
(
)
)
[61] => Category Object
(
[languages:protected] =>
[bok_resources:protected] =>
[bok_topics:protected] =>
[bok_keywords:protected] =>
[id:protected] => 61
[type:protected] => category
[parent:protected] => 2
[label:protected] => Interior Systems Carpenter
[alreadyInSave:protected] =>
[alreadyInValidation:protected] =>
[validationFailures:protected] => Array
(
)
[_new:BaseObject:private] =>
[_deleted:BaseObject:private] =>
[modifiedColumns:protected] => Array
(
)
)
[64] => Category Object
(
[languages:protected] =>
[bok_resources:protected] =>
[bok_topics:protected] =>
[bok_keywords:protected] =>
[id:protected] => 64
[type:protected] => category
[parent:protected] => 2
[label:protected] => Laborer
[alreadyInSave:protected] =>
[alreadyInValidation:protected] =>
[validationFailures:protected] => Array
(
)
[_new:BaseObject:private] =>
[_deleted:BaseObject:private] =>
[modifiedColumns:protected] => Array
(
)
)
[71] => Category Object
(
[languages:protected] =>
[bok_resources:protected] =>
[bok_topics:protected] =>
[bok_keywords:protected] =>
[id:protected] => 71
[type:protected] => category
[parent:protected] => 2
[label:protected] => Painter
[alreadyInSave:protected] =>
[alreadyInValidation:protected] =>
[validationFailures:protected] => Array
(
)
[_new:BaseObject:private] =>
[_deleted:BaseObject:private] =>
[modifiedColumns:protected] => Array
(
)
)
[75] => Category Object
(
[languages:protected] =>
[bok_resources:protected] =>
[bok_topics:protected] =>
[bok_keywords:protected] =>
[id:protected] => 75
[type:protected] => category
[parent:protected] => 2
[label:protected] => Plasterer
[alreadyInSave:protected] =>
[alreadyInValidation:protected] =>
[validationFailures:protected] => Array
(
)
[_new:BaseObject:private] =>
[_deleted:BaseObject:private] =>
[modifiedColumns:protected] => Array
(
)
)
[76] => Category Object
(
[languages:protected] =>
[bok_resources:protected] =>
[bok_topics:protected] =>
[bok_keywords:protected] =>
[id:protected] => 76
[type:protected] => category
[parent:protected] => 2
[label:protected] => Plumber/Pipefitter
[alreadyInSave:protected] =>
[alreadyInValidation:protected] =>
[validationFailures:protected] => Array
(
)
[_new:BaseObject:private] =>
[_deleted:BaseObject:private] =>
[modifiedColumns:protected] => Array
(
)
)
[63] => Category Object
(
[languages:protected] =>
[bok_resources:protected] =>
[bok_topics:protected] =>
[bok_keywords:protected] =>
[id:protected] => 63
[type:protected] => category
[parent:protected] => 2
[label:protected] => Reinforcing Ironworker
[alreadyInSave:protected] =>
[alreadyInValidation:protected] =>
[validationFailures:protected] => Array
(
)
[_new:BaseObject:private] =>
[_deleted:BaseObject:private] =>
[modifiedColumns:protected] => Array
(
)
)
[79] => Category Object
(
[languages:protected] =>
[bok_resources:protected] =>
[bok_topics:protected] =>
[bok_keywords:protected] =>
[id:protected] => 79
[type:protected] => category
[parent:protected] => 2
[label:protected] => Scaffold Erector
[alreadyInSave:protected] =>
[alreadyInValidation:protected] =>
[validationFailures:protected] => Array
(
)
[_new:BaseObject:private] =>
[_deleted:BaseObject:private] =>
[modifiedColumns:protected] => Array
(
)
)
[80] => Category Object
(
[languages:protected] =>
[bok_resources:protected] =>
[bok_topics:protected] =>
[bok_keywords:protected] =>
[id:protected] => 80
[type:protected] => category
[parent:protected] => 2
[label:protected] => Sheetmetal Worker
[alreadyInSave:protected] =>
[alreadyInValidation:protected] =>
[validationFailures:protected] => Array
(
)
[_new:BaseObject:private] =>
[_deleted:BaseObject:private] =>
[modifiedColumns:protected] => Array
(
)
)
[82] => Category Object
(
[languages:protected] =>
[bok_resources:protected] =>
[bok_topics:protected] =>
[bok_keywords:protected] =>
[id:protected] => 82
[type:protected] => category
[parent:protected] => 2
[label:protected] => Stonemason
[alreadyInSave:protected] =>
[alreadyInValidation:protected] =>
[validationFailures:protected] => Array
(
)
[_new:BaseObject:private] =>
[_deleted:BaseObject:private] =>
[modifiedColumns:protected] => Array
(
)
)
[62] => Category Object
(
[languages:protected] =>
[bok_resources:protected] =>
[bok_topics:protected] =>
[bok_keywords:protected] =>
[id:protected] => 62
[type:protected] => category
[parent:protected] => 2
[label:protected] => Structural Ironworker
[alreadyInSave:protected] =>
[alreadyInValidation:protected] =>
[validationFailures:protected] => Array
(
)
[_new:BaseObject:private] =>
[_deleted:BaseObject:private] =>
[modifiedColumns:protected] => Array
(
)
)
[83] => Category Object
(
[languages:protected] =>
[bok_resources:protected] =>
[bok_topics:protected] =>
[bok_keywords:protected] =>
[id:protected] => 83
[type:protected] => category
[parent:protected] => 2
[label:protected] => Terrazzo Worker
[alreadyInSave:protected] =>
[alreadyInValidation:protected] =>
[validationFailures:protected] => Array
(
)
[_new:BaseObject:private] =>
[_deleted:BaseObject:private] =>
[modifiedColumns:protected] => Array
(
)
)
[87] => Category Object
(
[languages:protected] =>
[bok_resources:protected] =>
[bok_topics:protected] =>
[bok_keywords:protected] =>
[id:protected] => 87
[type:protected] => category
[parent:protected] => 3
[label:protected] => Commercial & Institutional
[alreadyInSave:protected] =>
[alreadyInValidation:protected] =>
[validationFailures:protected] => Array
(
)
[_new:BaseObject:private] =>
[_deleted:BaseObject:private] =>
[modifiedColumns:protected] => Array
(
)
)
[91] => Category Object
(
[languages:protected] =>
[bok_resources:protected] =>
[bok_topics:protected] =>
[bok_keywords:protected] =>
[id:protected] => 91
[type:protected] => category
[parent:protected] => 3
[label:protected] => Heavy & Highway
[alreadyInSave:protected] =>
[alreadyInValidation:protected] =>
[validationFailures:protected] => Array
(
)
[_new:BaseObject:private] =>
[_deleted:BaseObject:private] =>
[modifiedColumns:protected] => Array
(
)
)
[90] => Category Object
(
[languages:protected] =>
[bok_resources:protected] =>
[bok_topics:protected] =>
[bok_keywords:protected] =>
[id:protected] => 90
[type:protected] => category
[parent:protected] => 3
[label:protected] => Industrial
[alreadyInSave:protected] =>
[alreadyInValidation:protected] =>
[validationFailures:protected] => Array
(
)
[_new:BaseObject:private] =>
[_deleted:BaseObject:private] =>
[modifiedColumns:protected] => Array
(
)
)
[93] => Category Object
(
[languages:protected] =>
[bok_resources:protected] =>
[bok_topics:protected] =>
[bok_keywords:protected] =>
[id:protected] => 93
[type:protected] => category
[parent:protected] => 3
[label:protected] => Renovations
[alreadyInSave:protected] =>
[alreadyInValidation:protected] =>
[validationFailures:protected] => Array
(
)
[_new:BaseObject:private] =>
[_deleted:BaseObject:private] =>
[modifiedColumns:protected] => Array
(
)
)
[94] => Category Object
(
[languages:protected] =>
[bok_resources:protected] =>
[bok_topics:protected] =>
[bok_keywords:protected] =>
[id:protected] => 94
[type:protected] => category
[parent:protected] => 3
[label:protected] => Residential
[alreadyInSave:protected] =>
[alreadyInValidation:protected] =>
[validationFailures:protected] => Array
(
)
[_new:BaseObject:private] =>
[_deleted:BaseObject:private] =>
[modifiedColumns:protected] => Array
(
)
)
)
[categories_initialized:protected] => 1
[mapped_items:protected] =>
[content:protected] =>
[files:protected] =>
[language:protected] => Language Object
(
[id:protected] => 1
[code:protected] => en
[name:protected] => English
[alreadyInSave:protected] =>
[alreadyInValidation:protected] =>
[validationFailures:protected] => Array
(
)
[_new:BaseObject:private] =>
[_deleted:BaseObject:private] =>
[modifiedColumns:protected] => Array
(
)
)
[old_record:protected] =>
[id:protected] => 4014
[old_id:protected] =>
[elcosh_id:protected] => i002700
[type:protected] => image
[display_type:protected] => Image
[user_id:protected] => 0
[language_id:protected] => 1
[tagging_id:protected] => Bruce Lippy
[priority_id:protected] => 1
[title:protected] => Safety officer discussing ongoing project with marketing coordinator
[total_pages:protected] => 0
[billed_pages:protected] => 0
[publication_number:protected] =>
[part_of:protected] =>
[keywords:protected] => Latino, safety officer, safety culture
[comments:protected] =>
[summary:protected] => The safety officer (left) points out the good safety practices on this project that reflect well on the firm and may influence future clients.
[transition_comments:protected] =>
[external_link:protected] =>
[consol_link:protected] => http://www.cpwrconstructionsolutions.org/index.php
[more_like_this:protected] => d000989,d001351,d001362,d000652, d001101, d000931, d001395
[permission_given_by:protected] =>
[published:protected] => T
[billable:protected] => F
[img_name:protected] =>
[img_ext:protected] => jpg
[img_width:protected] =>
[img_height:protected] =>
[img_credit:protected] => Hoar Construction, Photo by Neil Lippy
[img_practice:protected] => good
[vid_source_id:protected] =>
[vid_running_time:protected] =>
[vid_intended_audience:protected] =>
[vid_acquisition_info:protected] =>
[vid_cost:protected] =>
[vid_producer:protected] =>
[vid_filename:protected] =>
[vid_filename_downloadable:protected] =>
[date_summary:protected] => November 2015
[date_permission_requested:protected] =>
[date_permission_received:protected] =>
[date_review_needed:protected] =>
[date_received:protected] => 03/02/16
[date_completed:protected] => 03/02/16
[date_billed:protected] =>
[date_modified:protected] => 01/30/23
[collBokExports:protected] =>
[lastBokExportCriteria:BaseElcoshItem:private] =>
[alreadyInSave:protected] =>
[alreadyInValidation:protected] =>
[validationFailures:protected] => Array
(
)
[_new:BaseObject:private] =>
[_deleted:BaseObject:private] =>
[modifiedColumns:protected] => Array
(
)
)
)
[4] => Search_Result Object
(
[title] => Scaffolding at top of large column
[image] => /record/images/3994-p.jpg
[blurb] => This shot shows innovative guarding around the top of a large concrete column in the base of a high rise structure going up....
[category] => Array
(
[0] => 15
[1] => 21
[2] => 47
[3] => 51
[4] => 63
[5] => 78
[6] => 79
[7] => 80
[8] => 62
[9] => 87
[10] => 97
[11] => 56
[12] => 64
[13] => 74
)
[labels] => Array
(
[0] => Falls
[1] => Work Environment
[2] => Hazards
[3] => Scaffolds
[6] => Bricklayer
[7] => Trades
[8] => Cement Mason
[10] => Reinforcing Ironworker
[12] => Roofer/Waterproofer
[14] => Scaffold Erector
[16] => Sheetmetal Worker
[18] => Structural Ironworker
[20] => Commercial & Institutional
[21] => Jobsites
[22] => Images
[23] => Media
[24] => Media & Documents
[25] => Elevator Constructor
[27] => Laborer
[29] => Pile Driver
)
[type] => Images
[sub_category] =>
[url] => /image/3994/i002689/Scaffolding%2Bat%2Btop%2Bof%2Blarge%2Bcolumn.html
[item:protected] => ImageRecord Object
(
[records:protected] => Array
(
)
[recordId:protected] =>
[searchWordClass:protected] =>
[searchWordPeerClass:protected] =>
[bok_record:protected] =>
[authors:protected] =>
[organizations:protected] =>
[collections:protected] =>
[categories:protected] => Array
(
[15] => Category Object
(
[languages:protected] =>
[bok_resources:protected] =>
[bok_topics:protected] =>
[bok_keywords:protected] =>
[id:protected] => 15
[type:protected] => category
[parent:protected] => 7
[label:protected] => Falls
[alreadyInSave:protected] =>
[alreadyInValidation:protected] =>
[validationFailures:protected] => Array
(
)
[_new:BaseObject:private] =>
[_deleted:BaseObject:private] =>
[modifiedColumns:protected] => Array
(
)
)
[21] => Category Object
(
[languages:protected] =>
[bok_resources:protected] =>
[bok_topics:protected] =>
[bok_keywords:protected] =>
[id:protected] => 21
[type:protected] => category
[parent:protected] => 7
[label:protected] => Scaffolds
[alreadyInSave:protected] =>
[alreadyInValidation:protected] =>
[validationFailures:protected] => Array
(
)
[_new:BaseObject:private] =>
[_deleted:BaseObject:private] =>
[modifiedColumns:protected] => Array
(
)
)
[47] => Category Object
(
[languages:protected] =>
[bok_resources:protected] =>
[bok_topics:protected] =>
[bok_keywords:protected] =>
[id:protected] => 47
[type:protected] => category
[parent:protected] => 2
[label:protected] => Bricklayer
[alreadyInSave:protected] =>
[alreadyInValidation:protected] =>
[validationFailures:protected] => Array
(
)
[_new:BaseObject:private] =>
[_deleted:BaseObject:private] =>
[modifiedColumns:protected] => Array
(
)
)
[51] => Category Object
(
[languages:protected] =>
[bok_resources:protected] =>
[bok_topics:protected] =>
[bok_keywords:protected] =>
[id:protected] => 51
[type:protected] => category
[parent:protected] => 2
[label:protected] => Cement Mason
[alreadyInSave:protected] =>
[alreadyInValidation:protected] =>
[validationFailures:protected] => Array
(
)
[_new:BaseObject:private] =>
[_deleted:BaseObject:private] =>
[modifiedColumns:protected] => Array
(
)
)
[63] => Category Object
(
[languages:protected] =>
[bok_resources:protected] =>
[bok_topics:protected] =>
[bok_keywords:protected] =>
[id:protected] => 63
[type:protected] => category
[parent:protected] => 2
[label:protected] => Reinforcing Ironworker
[alreadyInSave:protected] =>
[alreadyInValidation:protected] =>
[validationFailures:protected] => Array
(
)
[_new:BaseObject:private] =>
[_deleted:BaseObject:private] =>
[modifiedColumns:protected] => Array
(
)
)
[78] => Category Object
(
[languages:protected] =>
[bok_resources:protected] =>
[bok_topics:protected] =>
[bok_keywords:protected] =>
[id:protected] => 78
[type:protected] => category
[parent:protected] => 2
[label:protected] => Roofer/Waterproofer
[alreadyInSave:protected] =>
[alreadyInValidation:protected] =>
[validationFailures:protected] => Array
(
)
[_new:BaseObject:private] =>
[_deleted:BaseObject:private] =>
[modifiedColumns:protected] => Array
(
)
)
[79] => Category Object
(
[languages:protected] =>
[bok_resources:protected] =>
[bok_topics:protected] =>
[bok_keywords:protected] =>
[id:protected] => 79
[type:protected] => category
[parent:protected] => 2
[label:protected] => Scaffold Erector
[alreadyInSave:protected] =>
[alreadyInValidation:protected] =>
[validationFailures:protected] => Array
(
)
[_new:BaseObject:private] =>
[_deleted:BaseObject:private] =>
[modifiedColumns:protected] => Array
(
)
)
[80] => Category Object
(
[languages:protected] =>
[bok_resources:protected] =>
[bok_topics:protected] =>
[bok_keywords:protected] =>
[id:protected] => 80
[type:protected] => category
[parent:protected] => 2
[label:protected] => Sheetmetal Worker
[alreadyInSave:protected] =>
[alreadyInValidation:protected] =>
[validationFailures:protected] => Array
(
)
[_new:BaseObject:private] =>
[_deleted:BaseObject:private] =>
[modifiedColumns:protected] => Array
(
)
)
[62] => Category Object
(
[languages:protected] =>
[bok_resources:protected] =>
[bok_topics:protected] =>
[bok_keywords:protected] =>
[id:protected] => 62
[type:protected] => category
[parent:protected] => 2
[label:protected] => Structural Ironworker
[alreadyInSave:protected] =>
[alreadyInValidation:protected] =>
[validationFailures:protected] => Array
(
)
[_new:BaseObject:private] =>
[_deleted:BaseObject:private] =>
[modifiedColumns:protected] => Array
(
)
)
[87] => Category Object
(
[languages:protected] =>
[bok_resources:protected] =>
[bok_topics:protected] =>
[bok_keywords:protected] =>
[id:protected] => 87
[type:protected] => category
[parent:protected] => 3
[label:protected] => Commercial & Institutional
[alreadyInSave:protected] =>
[alreadyInValidation:protected] =>
[validationFailures:protected] => Array
(
)
[_new:BaseObject:private] =>
[_deleted:BaseObject:private] =>
[modifiedColumns:protected] => Array
(
)
)
[97] => Category Object
(
[languages:protected] =>
[bok_resources:protected] =>
[bok_topics:protected] =>
[bok_keywords:protected] =>
[id:protected] => 97
[type:protected] => category
[parent:protected] => 5
[label:protected] => Images
[alreadyInSave:protected] =>
[alreadyInValidation:protected] =>
[validationFailures:protected] => Array
(
)
[_new:BaseObject:private] =>
[_deleted:BaseObject:private] =>
[modifiedColumns:protected] => Array
(
)
)
[56] => Category Object
(
[languages:protected] =>
[bok_resources:protected] =>
[bok_topics:protected] =>
[bok_keywords:protected] =>
[id:protected] => 56
[type:protected] => category
[parent:protected] => 2
[label:protected] => Elevator Constructor
[alreadyInSave:protected] =>
[alreadyInValidation:protected] =>
[validationFailures:protected] => Array
(
)
[_new:BaseObject:private] =>
[_deleted:BaseObject:private] =>
[modifiedColumns:protected] => Array
(
)
)
[64] => Category Object
(
[languages:protected] =>
[bok_resources:protected] =>
[bok_topics:protected] =>
[bok_keywords:protected] =>
[id:protected] => 64
[type:protected] => category
[parent:protected] => 2
[label:protected] => Laborer
[alreadyInSave:protected] =>
[alreadyInValidation:protected] =>
[validationFailures:protected] => Array
(
)
[_new:BaseObject:private] =>
[_deleted:BaseObject:private] =>
[modifiedColumns:protected] => Array
(
)
)
[74] => Category Object
(
[languages:protected] =>
[bok_resources:protected] =>
[bok_topics:protected] =>
[bok_keywords:protected] =>
[id:protected] => 74
[type:protected] => category
[parent:protected] => 2
[label:protected] => Pile Driver
[alreadyInSave:protected] =>
[alreadyInValidation:protected] =>
[validationFailures:protected] => Array
(
)
[_new:BaseObject:private] =>
[_deleted:BaseObject:private] =>
[modifiedColumns:protected] => Array
(
)
)
)
[categories_initialized:protected] => 1
[mapped_items:protected] =>
[content:protected] =>
[files:protected] =>
[language:protected] => Language Object
(
[id:protected] => 1
[code:protected] => en
[name:protected] => English
[alreadyInSave:protected] =>
[alreadyInValidation:protected] =>
[validationFailures:protected] => Array
(
)
[_new:BaseObject:private] =>
[_deleted:BaseObject:private] =>
[modifiedColumns:protected] => Array
(
)
)
[old_record:protected] =>
[id:protected] => 3994
[old_id:protected] =>
[elcosh_id:protected] => i002689
[type:protected] => image
[display_type:protected] => Image
[user_id:protected] => 0
[language_id:protected] => 1
[tagging_id:protected] => Bruce Lippy
[priority_id:protected] => 1
[title:protected] => Scaffolding at top of large column
[total_pages:protected] => 0
[billed_pages:protected] => 0
[publication_number:protected] =>
[part_of:protected] =>
[keywords:protected] => Guardrail, railing, fall prevention, falls
[comments:protected] =>
[summary:protected] => This shot shows innovative guarding around the top of a large concrete column in the base of a high rise structure going up.
[transition_comments:protected] =>
[external_link:protected] =>
[consol_link:protected] => http://www.cpwrconstructionsolutions.org/masonry/solution/8/adjustable-tower-scaffold.html
[more_like_this:protected] => c1002680,i002662,d000608,d001255
[permission_given_by:protected] =>
[published:protected] => T
[billable:protected] => F
[img_name:protected] =>
[img_ext:protected] => jpg
[img_width:protected] =>
[img_height:protected] =>
[img_credit:protected] => Photo by Pam Susi
[img_practice:protected] => good
[vid_source_id:protected] =>
[vid_running_time:protected] =>
[vid_intended_audience:protected] =>
[vid_acquisition_info:protected] =>
[vid_cost:protected] =>
[vid_producer:protected] =>
[vid_filename:protected] =>
[vid_filename_downloadable:protected] =>
[date_summary:protected] => January 2016
[date_permission_requested:protected] =>
[date_permission_received:protected] =>
[date_review_needed:protected] =>
[date_received:protected] => 02/01/16
[date_completed:protected] => 02/01/16
[date_billed:protected] =>
[date_modified:protected] => 02/01/16
[collBokExports:protected] =>
[lastBokExportCriteria:BaseElcoshItem:private] =>
[alreadyInSave:protected] =>
[alreadyInValidation:protected] =>
[validationFailures:protected] => Array
(
)
[_new:BaseObject:private] =>
[_deleted:BaseObject:private] =>
[modifiedColumns:protected] => Array
(
)
)
)
[5] => Search_Result Object
(
[title] => Construction bracing
[image] => /record/images/3995-p.jpg
[blurb] => This shows structural support that prevents collapses during construction....
[category] => Array
(
[0] => 12
[1] => 15
[2] => 21
[3] => 49
[4] => 51
[5] => 55
[6] => 56
[7] => 60
[8] => 64
[9] => 68
[10] => 74
[11] => 63
[12] => 78
[13] => 79
[14] => 80
[15] => 62
[16] => 87
[17] => 90
[18] => 97
)
[labels] => Array
(
[0] => Crushed/Struck By
[1] => Work Environment
[2] => Hazards
[3] => Falls
[6] => Scaffolds
[9] => Carpenter
[10] => Trades
[11] => Cement Mason
[13] => Electrical Worker
[15] => Elevator Constructor
[17] => HVAC
[19] => Laborer
[21] => Maintenance Worker
[23] => Pile Driver
[25] => Reinforcing Ironworker
[27] => Roofer/Waterproofer
[29] => Scaffold Erector
[31] => Sheetmetal Worker
[33] => Structural Ironworker
[35] => Commercial & Institutional
[36] => Jobsites
[37] => Industrial
[39] => Images
[40] => Media
[41] => Media & Documents
)
[type] => Images
[sub_category] =>
[url] => /image/3995/i002690/Construction%2Bbracing.html
[item:protected] => ImageRecord Object
(
[records:protected] => Array
(
)
[recordId:protected] =>
[searchWordClass:protected] =>
[searchWordPeerClass:protected] =>
[bok_record:protected] =>
[authors:protected] =>
[organizations:protected] =>
[collections:protected] =>
[categories:protected] => Array
(
[12] => Category Object
(
[languages:protected] =>
[bok_resources:protected] =>
[bok_topics:protected] =>
[bok_keywords:protected] =>
[id:protected] => 12
[type:protected] => category
[parent:protected] => 7
[label:protected] => Crushed/Struck By
[alreadyInSave:protected] =>
[alreadyInValidation:protected] =>
[validationFailures:protected] => Array
(
)
[_new:BaseObject:private] =>
[_deleted:BaseObject:private] =>
[modifiedColumns:protected] => Array
(
)
)
[15] => Category Object
(
[languages:protected] =>
[bok_resources:protected] =>
[bok_topics:protected] =>
[bok_keywords:protected] =>
[id:protected] => 15
[type:protected] => category
[parent:protected] => 7
[label:protected] => Falls
[alreadyInSave:protected] =>
[alreadyInValidation:protected] =>
[validationFailures:protected] => Array
(
)
[_new:BaseObject:private] =>
[_deleted:BaseObject:private] =>
[modifiedColumns:protected] => Array
(
)
)
[21] => Category Object
(
[languages:protected] =>
[bok_resources:protected] =>
[bok_topics:protected] =>
[bok_keywords:protected] =>
[id:protected] => 21
[type:protected] => category
[parent:protected] => 7
[label:protected] => Scaffolds
[alreadyInSave:protected] =>
[alreadyInValidation:protected] =>
[validationFailures:protected] => Array
(
)
[_new:BaseObject:private] =>
[_deleted:BaseObject:private] =>
[modifiedColumns:protected] => Array
(
)
)
[49] => Category Object
(
[languages:protected] =>
[bok_resources:protected] =>
[bok_topics:protected] =>
[bok_keywords:protected] =>
[id:protected] => 49
[type:protected] => category
[parent:protected] => 2
[label:protected] => Carpenter
[alreadyInSave:protected] =>
[alreadyInValidation:protected] =>
[validationFailures:protected] => Array
(
)
[_new:BaseObject:private] =>
[_deleted:BaseObject:private] =>
[modifiedColumns:protected] => Array
(
)
)
[51] => Category Object
(
[languages:protected] =>
[bok_resources:protected] =>
[bok_topics:protected] =>
[bok_keywords:protected] =>
[id:protected] => 51
[type:protected] => category
[parent:protected] => 2
[label:protected] => Cement Mason
[alreadyInSave:protected] =>
[alreadyInValidation:protected] =>
[validationFailures:protected] => Array
(
)
[_new:BaseObject:private] =>
[_deleted:BaseObject:private] =>
[modifiedColumns:protected] => Array
(
)
)
[55] => Category Object
(
[languages:protected] =>
[bok_resources:protected] =>
[bok_topics:protected] =>
[bok_keywords:protected] =>
[id:protected] => 55
[type:protected] => category
[parent:protected] => 2
[label:protected] => Electrical Worker
[alreadyInSave:protected] =>
[alreadyInValidation:protected] =>
[validationFailures:protected] => Array
(
)
[_new:BaseObject:private] =>
[_deleted:BaseObject:private] =>
[modifiedColumns:protected] => Array
(
)
)
[56] => Category Object
(
[languages:protected] =>
[bok_resources:protected] =>
[bok_topics:protected] =>
[bok_keywords:protected] =>
[id:protected] => 56
[type:protected] => category
[parent:protected] => 2
[label:protected] => Elevator Constructor
[alreadyInSave:protected] =>
[alreadyInValidation:protected] =>
[validationFailures:protected] => Array
(
)
[_new:BaseObject:private] =>
[_deleted:BaseObject:private] =>
[modifiedColumns:protected] => Array
(
)
)
[60] => Category Object
(
[languages:protected] =>
[bok_resources:protected] =>
[bok_topics:protected] =>
[bok_keywords:protected] =>
[id:protected] => 60
[type:protected] => category
[parent:protected] => 2
[label:protected] => HVAC
[alreadyInSave:protected] =>
[alreadyInValidation:protected] =>
[validationFailures:protected] => Array
(
)
[_new:BaseObject:private] =>
[_deleted:BaseObject:private] =>
[modifiedColumns:protected] => Array
(
)
)
[64] => Category Object
(
[languages:protected] =>
[bok_resources:protected] =>
[bok_topics:protected] =>
[bok_keywords:protected] =>
[id:protected] => 64
[type:protected] => category
[parent:protected] => 2
[label:protected] => Laborer
[alreadyInSave:protected] =>
[alreadyInValidation:protected] =>
[validationFailures:protected] => Array
(
)
[_new:BaseObject:private] =>
[_deleted:BaseObject:private] =>
[modifiedColumns:protected] => Array
(
)
)
[68] => Category Object
(
[languages:protected] =>
[bok_resources:protected] =>
[bok_topics:protected] =>
[bok_keywords:protected] =>
[id:protected] => 68
[type:protected] => category
[parent:protected] => 2
[label:protected] => Maintenance Worker
[alreadyInSave:protected] =>
[alreadyInValidation:protected] =>
[validationFailures:protected] => Array
(
)
[_new:BaseObject:private] =>
[_deleted:BaseObject:private] =>
[modifiedColumns:protected] => Array
(
)
)
[74] => Category Object
(
[languages:protected] =>
[bok_resources:protected] =>
[bok_topics:protected] =>
[bok_keywords:protected] =>
[id:protected] => 74
[type:protected] => category
[parent:protected] => 2
[label:protected] => Pile Driver
[alreadyInSave:protected] =>
[alreadyInValidation:protected] =>
[validationFailures:protected] => Array
(
)
[_new:BaseObject:private] =>
[_deleted:BaseObject:private] =>
[modifiedColumns:protected] => Array
(
)
)
[63] => Category Object
(
[languages:protected] =>
[bok_resources:protected] =>
[bok_topics:protected] =>
[bok_keywords:protected] =>
[id:protected] => 63
[type:protected] => category
[parent:protected] => 2
[label:protected] => Reinforcing Ironworker
[alreadyInSave:protected] =>
[alreadyInValidation:protected] =>
[validationFailures:protected] => Array
(
)
[_new:BaseObject:private] =>
[_deleted:BaseObject:private] =>
[modifiedColumns:protected] => Array
(
)
)
[78] => Category Object
(
[languages:protected] =>
[bok_resources:protected] =>
[bok_topics:protected] =>
[bok_keywords:protected] =>
[id:protected] => 78
[type:protected] => category
[parent:protected] => 2
[label:protected] => Roofer/Waterproofer
[alreadyInSave:protected] =>
[alreadyInValidation:protected] =>
[validationFailures:protected] => Array
(
)
[_new:BaseObject:private] =>
[_deleted:BaseObject:private] =>
[modifiedColumns:protected] => Array
(
)
)
[79] => Category Object
(
[languages:protected] =>
[bok_resources:protected] =>
[bok_topics:protected] =>
[bok_keywords:protected] =>
[id:protected] => 79
[type:protected] => category
[parent:protected] => 2
[label:protected] => Scaffold Erector
[alreadyInSave:protected] =>
[alreadyInValidation:protected] =>
[validationFailures:protected] => Array
(
)
[_new:BaseObject:private] =>
[_deleted:BaseObject:private] =>
[modifiedColumns:protected] => Array
(
)
)
[80] => Category Object
(
[languages:protected] =>
[bok_resources:protected] =>
[bok_topics:protected] =>
[bok_keywords:protected] =>
[id:protected] => 80
[type:protected] => category
[parent:protected] => 2
[label:protected] => Sheetmetal Worker
[alreadyInSave:protected] =>
[alreadyInValidation:protected] =>
[validationFailures:protected] => Array
(
)
[_new:BaseObject:private] =>
[_deleted:BaseObject:private] =>
[modifiedColumns:protected] => Array
(
)
)
[62] => Category Object
(
[languages:protected] =>
[bok_resources:protected] =>
[bok_topics:protected] =>
[bok_keywords:protected] =>
[id:protected] => 62
[type:protected] => category
[parent:protected] => 2
[label:protected] => Structural Ironworker
[alreadyInSave:protected] =>
[alreadyInValidation:protected] =>
[validationFailures:protected] => Array
(
)
[_new:BaseObject:private] =>
[_deleted:BaseObject:private] =>
[modifiedColumns:protected] => Array
(
)
)
[87] => Category Object
(
[languages:protected] =>
[bok_resources:protected] =>
[bok_topics:protected] =>
[bok_keywords:protected] =>
[id:protected] => 87
[type:protected] => category
[parent:protected] => 3
[label:protected] => Commercial & Institutional
[alreadyInSave:protected] =>
[alreadyInValidation:protected] =>
[validationFailures:protected] => Array
(
)
[_new:BaseObject:private] =>
[_deleted:BaseObject:private] =>
[modifiedColumns:protected] => Array
(
)
)
[90] => Category Object
(
[languages:protected] =>
[bok_resources:protected] =>
[bok_topics:protected] =>
[bok_keywords:protected] =>
[id:protected] => 90
[type:protected] => category
[parent:protected] => 3
[label:protected] => Industrial
[alreadyInSave:protected] =>
[alreadyInValidation:protected] =>
[validationFailures:protected] => Array
(
)
[_new:BaseObject:private] =>
[_deleted:BaseObject:private] =>
[modifiedColumns:protected] => Array
(
)
)
[97] => Category Object
(
[languages:protected] =>
[bok_resources:protected] =>
[bok_topics:protected] =>
[bok_keywords:protected] =>
[id:protected] => 97
[type:protected] => category
[parent:protected] => 5
[label:protected] => Images
[alreadyInSave:protected] =>
[alreadyInValidation:protected] =>
[validationFailures:protected] => Array
(
)
[_new:BaseObject:private] =>
[_deleted:BaseObject:private] =>
[modifiedColumns:protected] => Array
(
)
)
)
[categories_initialized:protected] => 1
[mapped_items:protected] =>
[content:protected] =>
[files:protected] =>
[language:protected] => Language Object
(
[id:protected] => 1
[code:protected] => en
[name:protected] => English
[alreadyInSave:protected] =>
[alreadyInValidation:protected] =>
[validationFailures:protected] => Array
(
)
[_new:BaseObject:private] =>
[_deleted:BaseObject:private] =>
[modifiedColumns:protected] => Array
(
)
)
[old_record:protected] =>
[id:protected] => 3995
[old_id:protected] =>
[elcosh_id:protected] => i002690
[type:protected] => image
[display_type:protected] => Image
[user_id:protected] => 0
[language_id:protected] => 1
[tagging_id:protected] => Bruce Lippy
[priority_id:protected] => 1
[title:protected] => Construction bracing
[total_pages:protected] => 0
[billed_pages:protected] => 0
[publication_number:protected] =>
[part_of:protected] =>
[keywords:protected] => Bracing, support, scaffold
[comments:protected] =>
[summary:protected] => This shows structural support that prevents collapses during construction.
[transition_comments:protected] =>
[external_link:protected] =>
[consol_link:protected] => http://www.cpwrconstructionsolutions.org/masonry/solution/8/adjustable-tower-scaffold.html
[more_like_this:protected] => i002660
[permission_given_by:protected] =>
[published:protected] => T
[billable:protected] => F
[img_name:protected] =>
[img_ext:protected] => jpg
[img_width:protected] =>
[img_height:protected] =>
[img_credit:protected] => Photo by Pam Susi
[img_practice:protected] => good
[vid_source_id:protected] =>
[vid_running_time:protected] =>
[vid_intended_audience:protected] =>
[vid_acquisition_info:protected] =>
[vid_cost:protected] =>
[vid_producer:protected] =>
[vid_filename:protected] =>
[vid_filename_downloadable:protected] =>
[date_summary:protected] => January 2016
[date_permission_requested:protected] =>
[date_permission_received:protected] =>
[date_review_needed:protected] =>
[date_received:protected] => 02/01/16
[date_completed:protected] => 02/01/16
[date_billed:protected] =>
[date_modified:protected] => 02/01/16
[collBokExports:protected] =>
[lastBokExportCriteria:BaseElcoshItem:private] =>
[alreadyInSave:protected] =>
[alreadyInValidation:protected] =>
[validationFailures:protected] => Array
(
)
[_new:BaseObject:private] =>
[_deleted:BaseObject:private] =>
[modifiedColumns:protected] => Array
(
)
)
)
)
[preview_mode] =>
[description] => Toolbox talks have been the main tool for communicating safety information on construction jobs for decades.
Unfortunately, there has been little research on what makes for effective toolbox talks. The IUOE National
Training Fund worked with OSHA and NIOSH to make sure their series of 24 Focus Four toolbox talks were based on the best recommendations for effective design. These toolbox talks accompany an entire package of training materials, but can be used alone. This guide points out the key features of these toolbox talks and how best to deliver them.
[keywords] => toolbox talks, tailgate talks
[related_items] => Array
(
[Toolbox Talks] => Array
(
[0] => DocumentRecord Object
(
[records:protected] => Array
(
)
[recordId:protected] =>
[searchWordClass:protected] =>
[searchWordPeerClass:protected] =>
[bok_record:protected] =>
[authors:protected] =>
[organizations:protected] =>
[collections:protected] =>
[categories:protected] =>
[categories_initialized:protected] =>
[mapped_items:protected] =>
[content:protected] =>
[files:protected] =>
[language:protected] => Language Object
(
[id:protected] => 1
[code:protected] => en
[name:protected] => English
[alreadyInSave:protected] =>
[alreadyInValidation:protected] =>
[validationFailures:protected] => Array
(
)
[_new:BaseObject:private] =>
[_deleted:BaseObject:private] =>
[modifiedColumns:protected] => Array
(
)
)
[old_record:protected] =>
[id:protected] => 1605
[old_id:protected] => 1262
[elcosh_id:protected] => d001137
[type:protected] => document
[display_type:protected] => HTML w/ PDF
[user_id:protected] =>
[language_id:protected] => 1
[tagging_id:protected] => Garber
[priority_id:protected] => 1
[title:protected] => Focus Four Toolbox Talks, Module 1 – Falls, Talk #2 – Falls from debris piles?
[total_pages:protected] => 1
[billed_pages:protected] => 1
[publication_number:protected] =>
[part_of:protected] =>
[keywords:protected] => disaster response, hazard clean-up, uneven surface, disaster site, disaster clean-up
[comments:protected] =>
[summary:protected] => A toolbox talk on preventing falls from debris piles. Includes questions to ask, an incident to discuss with images, and a place to record questions the trainer would like to ask about the incident. Part of a collection. Click on the 'collection' button to access the other items.
[transition_comments:protected] =>
[external_link:protected] =>
[consol_link:protected] => http://www.cpwrconstructionsolutions.org/roofing/hazard/1463/install-asphalt-roofs-fall-from-heights.html
[more_like_this:protected] => a000081,d000478,d000530
[permission_given_by:protected] =>
[published:protected] => T
[billable:protected] => F
[img_name:protected] =>
[img_ext:protected] =>
[img_width:protected] =>
[img_height:protected] =>
[img_credit:protected] =>
[img_practice:protected] =>
[vid_source_id:protected] =>
[vid_running_time:protected] =>
[vid_intended_audience:protected] =>
[vid_acquisition_info:protected] =>
[vid_cost:protected] =>
[vid_producer:protected] =>
[vid_filename:protected] =>
[vid_filename_downloadable:protected] =>
[date_summary:protected] =>
[date_permission_requested:protected] =>
[date_permission_received:protected] =>
[date_review_needed:protected] =>
[date_received:protected] => 02/15/12
[date_completed:protected] => 03/19/12
[date_billed:protected] =>
[date_modified:protected] => 07/10/12
[collBokExports:protected] =>
[lastBokExportCriteria:BaseElcoshItem:private] =>
[alreadyInSave:protected] =>
[alreadyInValidation:protected] =>
[validationFailures:protected] => Array
(
)
[_new:BaseObject:private] =>
[_deleted:BaseObject:private] =>
[modifiedColumns:protected] => Array
(
)
)
[1] => DocumentRecord Object
(
[records:protected] => Array
(
)
[recordId:protected] =>
[searchWordClass:protected] =>
[searchWordPeerClass:protected] =>
[bok_record:protected] =>
[authors:protected] =>
[organizations:protected] =>
[collections:protected] =>
[categories:protected] =>
[categories_initialized:protected] =>
[mapped_items:protected] =>
[content:protected] =>
[files:protected] =>
[language:protected] => Language Object
(
[id:protected] => 1
[code:protected] => en
[name:protected] => English
[alreadyInSave:protected] =>
[alreadyInValidation:protected] =>
[validationFailures:protected] => Array
(
)
[_new:BaseObject:private] =>
[_deleted:BaseObject:private] =>
[modifiedColumns:protected] => Array
(
)
)
[old_record:protected] =>
[id:protected] => 1610
[old_id:protected] => 1271
[elcosh_id:protected] => d001146
[type:protected] => document
[display_type:protected] => HTML w/ PDF
[user_id:protected] => 0
[language_id:protected] => 1
[tagging_id:protected] => Garber
[priority_id:protected] => 1
[title:protected] => Focus Four Toolbox Talks, Module 2 – Struck-by, Talk #5 – Rigging and Securing Loads
[total_pages:protected] => 1
[billed_pages:protected] => 1
[publication_number:protected] =>
[part_of:protected] =>
[keywords:protected] => rigging, lift loads, loading areas, chains
[comments:protected] =>
[summary:protected] => A toolbox talk on preventing struck-by incidents caused by not securing loads properly. Includes questions to ask, an incident to discuss with images, and a place to record questions the trainer would like to ask about the incident. Part of a collection. Click on the 'collection' button to access the other items.
[transition_comments:protected] =>
[external_link:protected] =>
[consol_link:protected] => http://www.cpwrconstructionsolutions.org/heavy_equipment/hazard/1591/move-equipment-to-from-and-between-sites-work-zone-struck-by-injuries-and-fatalities.html
[more_like_this:protected] => d000144,d000360,d000873
[permission_given_by:protected] =>
[published:protected] => T
[billable:protected] => F
[img_name:protected] =>
[img_ext:protected] =>
[img_width:protected] =>
[img_height:protected] =>
[img_credit:protected] =>
[img_practice:protected] =>
[vid_source_id:protected] =>
[vid_running_time:protected] =>
[vid_intended_audience:protected] =>
[vid_acquisition_info:protected] =>
[vid_cost:protected] =>
[vid_producer:protected] =>
[vid_filename:protected] =>
[vid_filename_downloadable:protected] =>
[date_summary:protected] =>
[date_permission_requested:protected] =>
[date_permission_received:protected] =>
[date_review_needed:protected] =>
[date_received:protected] => 02/15/12
[date_completed:protected] => 03/28/12
[date_billed:protected] =>
[date_modified:protected] => 05/12/14
[collBokExports:protected] =>
[lastBokExportCriteria:BaseElcoshItem:private] =>
[alreadyInSave:protected] =>
[alreadyInValidation:protected] =>
[validationFailures:protected] => Array
(
)
[_new:BaseObject:private] =>
[_deleted:BaseObject:private] =>
[modifiedColumns:protected] => Array
(
)
)
[2] => DocumentRecord Object
(
[records:protected] => Array
(
)
[recordId:protected] =>
[searchWordClass:protected] =>
[searchWordPeerClass:protected] =>
[bok_record:protected] =>
[authors:protected] =>
[organizations:protected] =>
[collections:protected] =>
[categories:protected] =>
[categories_initialized:protected] =>
[mapped_items:protected] =>
[content:protected] =>
[files:protected] =>
[language:protected] => Language Object
(
[id:protected] => 1
[code:protected] => en
[name:protected] => English
[alreadyInSave:protected] =>
[alreadyInValidation:protected] =>
[validationFailures:protected] => Array
(
)
[_new:BaseObject:private] =>
[_deleted:BaseObject:private] =>
[modifiedColumns:protected] => Array
(
)
)
[old_record:protected] =>
[id:protected] => 1645
[old_id:protected] => 1274
[elcosh_id:protected] => d001149
[type:protected] => document
[display_type:protected] => HTML w/ PDF
[user_id:protected] => 0
[language_id:protected] => 1
[tagging_id:protected] => Garber
[priority_id:protected] => 1
[title:protected] => Focus Four Toolbox Talks, Module 3 – Caught-in/between, Talk #2 – Trenches & Heavy Equipment
[total_pages:protected] => 1
[billed_pages:protected] => 1
[publication_number:protected] =>
[part_of:protected] =>
[keywords:protected] => back-up alarms, spotter, soil cave-in, spoil pikes, ROPs, trenching, rain
[comments:protected] =>
[summary:protected] => A toolbox talk on preventing incidents involving trenches such as trench collapse. Includes questions to ask, an incident to discuss with images, and a place to record questions the trainer would like to ask about the incident. Part of a collection. Click on the 'collection' button to access the other items.
[transition_comments:protected] =>
[external_link:protected] =>
[consol_link:protected] =>
[more_like_this:protected] => d000019,d000035,d000168
[permission_given_by:protected] =>
[published:protected] => T
[billable:protected] => F
[img_name:protected] =>
[img_ext:protected] =>
[img_width:protected] =>
[img_height:protected] =>
[img_credit:protected] =>
[img_practice:protected] =>
[vid_source_id:protected] =>
[vid_running_time:protected] =>
[vid_intended_audience:protected] =>
[vid_acquisition_info:protected] =>
[vid_cost:protected] =>
[vid_producer:protected] =>
[vid_filename:protected] =>
[vid_filename_downloadable:protected] =>
[date_summary:protected] =>
[date_permission_requested:protected] =>
[date_permission_received:protected] =>
[date_review_needed:protected] =>
[date_received:protected] => 02/15/12
[date_completed:protected] => 04/02/12
[date_billed:protected] =>
[date_modified:protected] => 05/23/23
[collBokExports:protected] =>
[lastBokExportCriteria:BaseElcoshItem:private] =>
[alreadyInSave:protected] =>
[alreadyInValidation:protected] =>
[validationFailures:protected] => Array
(
)
[_new:BaseObject:private] =>
[_deleted:BaseObject:private] =>
[modifiedColumns:protected] => Array
(
)
)
[3] => DocumentRecord Object
(
[records:protected] => Array
(
)
[recordId:protected] =>
[searchWordClass:protected] =>
[searchWordPeerClass:protected] =>
[bok_record:protected] =>
[authors:protected] =>
[organizations:protected] =>
[collections:protected] =>
[categories:protected] =>
[categories_initialized:protected] =>
[mapped_items:protected] =>
[content:protected] =>
[files:protected] =>
[language:protected] => Language Object
(
[id:protected] => 1
[code:protected] => en
[name:protected] => English
[alreadyInSave:protected] =>
[alreadyInValidation:protected] =>
[validationFailures:protected] => Array
(
)
[_new:BaseObject:private] =>
[_deleted:BaseObject:private] =>
[modifiedColumns:protected] => Array
(
)
)
[old_record:protected] =>
[id:protected] => 1654
[old_id:protected] => 1284
[elcosh_id:protected] => d001159
[type:protected] => document
[display_type:protected] => HTML w/ PDF
[user_id:protected] => 0
[language_id:protected] => 1
[tagging_id:protected] => Garber
[priority_id:protected] => 1
[title:protected] => Focus Four Toolbox Talks, Module 4 – Electrocutions, Talk #6 – Hazards on Disaster Sites
[total_pages:protected] => 1
[billed_pages:protected] => 1
[publication_number:protected] =>
[part_of:protected] =>
[keywords:protected] => powerlines, underground, utilities, generators, wet conditions, GFCIs, energized lines, disasters, emergency response
[comments:protected] =>
[summary:protected] => A toolbox talk on how to avoid electrocution on a disaster site. Includes questions to ask, an incident to discuss with images, and a place to record questions the trainer would like to ask about the incident. Part of a collection. Click on the 'collection' button to access the other items.
[transition_comments:protected] =>
[external_link:protected] =>
[consol_link:protected] => http://www.cpwrconstructionsolutions.org/electrical/hazard/1138/install-and-repair-high-voltage-lines-transformers-switches-electrical-shocks-burns-and-or-electrocution.html
[more_like_this:protected] => d000135,d000361,d000437
[permission_given_by:protected] =>
[published:protected] => T
[billable:protected] => F
[img_name:protected] =>
[img_ext:protected] =>
[img_width:protected] =>
[img_height:protected] =>
[img_credit:protected] =>
[img_practice:protected] =>
[vid_source_id:protected] =>
[vid_running_time:protected] =>
[vid_intended_audience:protected] =>
[vid_acquisition_info:protected] =>
[vid_cost:protected] =>
[vid_producer:protected] =>
[vid_filename:protected] =>
[vid_filename_downloadable:protected] =>
[date_summary:protected] =>
[date_permission_requested:protected] =>
[date_permission_received:protected] =>
[date_review_needed:protected] =>
[date_received:protected] => 02/15/12
[date_completed:protected] => 04/02/12
[date_billed:protected] =>
[date_modified:protected] => 05/23/23
[collBokExports:protected] =>
[lastBokExportCriteria:BaseElcoshItem:private] =>
[alreadyInSave:protected] =>
[alreadyInValidation:protected] =>
[validationFailures:protected] => Array
(
)
[_new:BaseObject:private] =>
[_deleted:BaseObject:private] =>
[modifiedColumns:protected] => Array
(
)
)
)
)
[collections] => Array
(
[1294] =>
[1295] =>
[1292] =>
[1293] => CollectionRecord Object
(
[collection_items:protected] =>
[records:protected] => Array
(
)
[recordId:protected] =>
[searchWordClass:protected] =>
[searchWordPeerClass:protected] =>
[bok_record:protected] =>
[authors:protected] =>
[organizations:protected] =>
[collections:protected] =>
[categories:protected] =>
[categories_initialized:protected] =>
[mapped_items:protected] =>
[content:protected] =>
[files:protected] =>
[language:protected] =>
[old_record:protected] =>
[id:protected] => 1293
[old_id:protected] =>
[elcosh_id:protected] => c000026
[type:protected] => collection
[display_type:protected] => Collection
[user_id:protected] =>
[language_id:protected] =>
[tagging_id:protected] =>
[priority_id:protected] =>
[title:protected] => Focus Four-Struck By
[total_pages:protected] =>
[billed_pages:protected] =>
[publication_number:protected] =>
[part_of:protected] =>
[keywords:protected] =>
[comments:protected] =>
[summary:protected] => The following are links to all of the items in this collection:
[transition_comments:protected] =>
[external_link:protected] =>
[consol_link:protected] =>
[more_like_this:protected] =>
[permission_given_by:protected] =>
[published:protected] => T
[billable:protected] => F
[img_name:protected] =>
[img_ext:protected] =>
[img_width:protected] =>
[img_height:protected] =>
[img_credit:protected] =>
[img_practice:protected] =>
[vid_source_id:protected] =>
[vid_running_time:protected] =>
[vid_intended_audience:protected] =>
[vid_acquisition_info:protected] =>
[vid_cost:protected] =>
[vid_producer:protected] =>
[vid_filename:protected] =>
[vid_filename_downloadable:protected] =>
[date_summary:protected] =>
[date_permission_requested:protected] =>
[date_permission_received:protected] =>
[date_review_needed:protected] =>
[date_received:protected] => 05/08/12
[date_completed:protected] => 05/08/12
[date_billed:protected] =>
[date_modified:protected] => 05/08/12
[collBokExports:protected] =>
[lastBokExportCriteria:BaseElcoshItem:private] =>
[alreadyInSave:protected] =>
[alreadyInValidation:protected] =>
[validationFailures:protected] => Array
(
)
[_new:BaseObject:private] =>
[_deleted:BaseObject:private] =>
[modifiedColumns:protected] => Array
(
)
)
)
[record] => DocumentRecord Object
(
[records:protected] => Array
(
)
[recordId:protected] =>
[searchWordClass:protected] =>
[searchWordPeerClass:protected] =>
[bok_record:protected] =>
[authors:protected] => Array
(
)
[organizations:protected] => Array
(
[256] => Organization Object
(
[id:protected] => 256
[elcosh_id:protected] => o000276
[user_id:protected] => 14
[province_id:protected] => 0
[country_id:protected] => 0
[title:protected] => IUOE National Training Fund
[address:protected] =>
[postal_code:protected] =>
[city:protected] =>
[department:protected] =>
[phone:protected] => 304-253-8674
[fax:protected] =>
[email:protected] =>
[website:protected] => http://www.iuoeiettc.org
[filename:protected] =>
[about:protected] =>
[comments:protected] =>
[logo_available:protected] => T
[no_details:protected] => F
[date_received:protected] => 2012-02-13
[date_completed:protected] => 2012-02-13
[date_billed:protected] =>
[alreadyInSave:protected] =>
[alreadyInValidation:protected] =>
[validationFailures:protected] => Array
(
)
[_new:BaseObject:private] =>
[_deleted:BaseObject:private] =>
[modifiedColumns:protected] => Array
(
)
)
)
[collections:protected] => Array
(
[1294] =>
[1295] =>
[1292] =>
[1293] => CollectionRecord Object
(
[collection_items:protected] =>
[records:protected] => Array
(
)
[recordId:protected] =>
[searchWordClass:protected] =>
[searchWordPeerClass:protected] =>
[bok_record:protected] =>
[authors:protected] =>
[organizations:protected] =>
[collections:protected] =>
[categories:protected] =>
[categories_initialized:protected] =>
[mapped_items:protected] =>
[content:protected] =>
[files:protected] =>
[language:protected] =>
[old_record:protected] =>
[id:protected] => 1293
[old_id:protected] =>
[elcosh_id:protected] => c000026
[type:protected] => collection
[display_type:protected] => Collection
[user_id:protected] =>
[language_id:protected] =>
[tagging_id:protected] =>
[priority_id:protected] =>
[title:protected] => Focus Four-Struck By
[total_pages:protected] =>
[billed_pages:protected] =>
[publication_number:protected] =>
[part_of:protected] =>
[keywords:protected] =>
[comments:protected] =>
[summary:protected] => The following are links to all of the items in this collection:
[transition_comments:protected] =>
[external_link:protected] =>
[consol_link:protected] =>
[more_like_this:protected] =>
[permission_given_by:protected] =>
[published:protected] => T
[billable:protected] => F
[img_name:protected] =>
[img_ext:protected] =>
[img_width:protected] =>
[img_height:protected] =>
[img_credit:protected] =>
[img_practice:protected] =>
[vid_source_id:protected] =>
[vid_running_time:protected] =>
[vid_intended_audience:protected] =>
[vid_acquisition_info:protected] =>
[vid_cost:protected] =>
[vid_producer:protected] =>
[vid_filename:protected] =>
[vid_filename_downloadable:protected] =>
[date_summary:protected] =>
[date_permission_requested:protected] =>
[date_permission_received:protected] =>
[date_review_needed:protected] =>
[date_received:protected] => 05/08/12
[date_completed:protected] => 05/08/12
[date_billed:protected] =>
[date_modified:protected] => 05/08/12
[collBokExports:protected] =>
[lastBokExportCriteria:BaseElcoshItem:private] =>
[alreadyInSave:protected] =>
[alreadyInValidation:protected] =>
[validationFailures:protected] => Array
(
)
[_new:BaseObject:private] =>
[_deleted:BaseObject:private] =>
[modifiedColumns:protected] => Array
(
)
)
)
[categories:protected] =>
[categories_initialized:protected] =>
[mapped_items:protected] => Array
(
[1605] => DocumentRecord Object
(
[records:protected] => Array
(
)
[recordId:protected] =>
[searchWordClass:protected] =>
[searchWordPeerClass:protected] =>
[bok_record:protected] =>
[authors:protected] =>
[organizations:protected] =>
[collections:protected] =>
[categories:protected] =>
[categories_initialized:protected] =>
[mapped_items:protected] =>
[content:protected] =>
[files:protected] =>
[language:protected] =>
[old_record:protected] =>
[id:protected] => 1605
[old_id:protected] => 1262
[elcosh_id:protected] => d001137
[type:protected] => document
[display_type:protected] => HTML w/ PDF
[user_id:protected] =>
[language_id:protected] => 1
[tagging_id:protected] => Garber
[priority_id:protected] => 1
[title:protected] => Focus Four Toolbox Talks, Module 1 – Falls, Talk #2 – Falls from debris piles?
[total_pages:protected] => 1
[billed_pages:protected] => 1
[publication_number:protected] =>
[part_of:protected] =>
[keywords:protected] => disaster response, hazard clean-up, uneven surface, disaster site, disaster clean-up
[comments:protected] =>
[summary:protected] => A toolbox talk on preventing falls from debris piles. Includes questions to ask, an incident to discuss with images, and a place to record questions the trainer would like to ask about the incident. Part of a collection. Click on the 'collection' button to access the other items.
[transition_comments:protected] =>
[external_link:protected] =>
[consol_link:protected] => http://www.cpwrconstructionsolutions.org/roofing/hazard/1463/install-asphalt-roofs-fall-from-heights.html
[more_like_this:protected] => a000081,d000478,d000530
[permission_given_by:protected] =>
[published:protected] => T
[billable:protected] => F
[img_name:protected] =>
[img_ext:protected] =>
[img_width:protected] =>
[img_height:protected] =>
[img_credit:protected] =>
[img_practice:protected] =>
[vid_source_id:protected] =>
[vid_running_time:protected] =>
[vid_intended_audience:protected] =>
[vid_acquisition_info:protected] =>
[vid_cost:protected] =>
[vid_producer:protected] =>
[vid_filename:protected] =>
[vid_filename_downloadable:protected] =>
[date_summary:protected] =>
[date_permission_requested:protected] =>
[date_permission_received:protected] =>
[date_review_needed:protected] =>
[date_received:protected] => 02/15/12
[date_completed:protected] => 03/19/12
[date_billed:protected] =>
[date_modified:protected] => 07/10/12
[collBokExports:protected] =>
[lastBokExportCriteria:BaseElcoshItem:private] =>
[alreadyInSave:protected] =>
[alreadyInValidation:protected] =>
[validationFailures:protected] => Array
(
)
[_new:BaseObject:private] =>
[_deleted:BaseObject:private] =>
[modifiedColumns:protected] => Array
(
)
)
[1610] => DocumentRecord Object
(
[records:protected] => Array
(
)
[recordId:protected] =>
[searchWordClass:protected] =>
[searchWordPeerClass:protected] =>
[bok_record:protected] =>
[authors:protected] =>
[organizations:protected] =>
[collections:protected] =>
[categories:protected] =>
[categories_initialized:protected] =>
[mapped_items:protected] =>
[content:protected] =>
[files:protected] =>
[language:protected] =>
[old_record:protected] =>
[id:protected] => 1610
[old_id:protected] => 1271
[elcosh_id:protected] => d001146
[type:protected] => document
[display_type:protected] => HTML w/ PDF
[user_id:protected] => 0
[language_id:protected] => 1
[tagging_id:protected] => Garber
[priority_id:protected] => 1
[title:protected] => Focus Four Toolbox Talks, Module 2 – Struck-by, Talk #5 – Rigging and Securing Loads
[total_pages:protected] => 1
[billed_pages:protected] => 1
[publication_number:protected] =>
[part_of:protected] =>
[keywords:protected] => rigging, lift loads, loading areas, chains
[comments:protected] =>
[summary:protected] => A toolbox talk on preventing struck-by incidents caused by not securing loads properly. Includes questions to ask, an incident to discuss with images, and a place to record questions the trainer would like to ask about the incident. Part of a collection. Click on the 'collection' button to access the other items.
[transition_comments:protected] =>
[external_link:protected] =>
[consol_link:protected] => http://www.cpwrconstructionsolutions.org/heavy_equipment/hazard/1591/move-equipment-to-from-and-between-sites-work-zone-struck-by-injuries-and-fatalities.html
[more_like_this:protected] => d000144,d000360,d000873
[permission_given_by:protected] =>
[published:protected] => T
[billable:protected] => F
[img_name:protected] =>
[img_ext:protected] =>
[img_width:protected] =>
[img_height:protected] =>
[img_credit:protected] =>
[img_practice:protected] =>
[vid_source_id:protected] =>
[vid_running_time:protected] =>
[vid_intended_audience:protected] =>
[vid_acquisition_info:protected] =>
[vid_cost:protected] =>
[vid_producer:protected] =>
[vid_filename:protected] =>
[vid_filename_downloadable:protected] =>
[date_summary:protected] =>
[date_permission_requested:protected] =>
[date_permission_received:protected] =>
[date_review_needed:protected] =>
[date_received:protected] => 02/15/12
[date_completed:protected] => 03/28/12
[date_billed:protected] =>
[date_modified:protected] => 05/12/14
[collBokExports:protected] =>
[lastBokExportCriteria:BaseElcoshItem:private] =>
[alreadyInSave:protected] =>
[alreadyInValidation:protected] =>
[validationFailures:protected] => Array
(
)
[_new:BaseObject:private] =>
[_deleted:BaseObject:private] =>
[modifiedColumns:protected] => Array
(
)
)
[1645] => DocumentRecord Object
(
[records:protected] => Array
(
)
[recordId:protected] =>
[searchWordClass:protected] =>
[searchWordPeerClass:protected] =>
[bok_record:protected] =>
[authors:protected] =>
[organizations:protected] =>
[collections:protected] =>
[categories:protected] =>
[categories_initialized:protected] =>
[mapped_items:protected] =>
[content:protected] =>
[files:protected] =>
[language:protected] =>
[old_record:protected] =>
[id:protected] => 1645
[old_id:protected] => 1274
[elcosh_id:protected] => d001149
[type:protected] => document
[display_type:protected] => HTML w/ PDF
[user_id:protected] => 0
[language_id:protected] => 1
[tagging_id:protected] => Garber
[priority_id:protected] => 1
[title:protected] => Focus Four Toolbox Talks, Module 3 – Caught-in/between, Talk #2 – Trenches & Heavy Equipment
[total_pages:protected] => 1
[billed_pages:protected] => 1
[publication_number:protected] =>
[part_of:protected] =>
[keywords:protected] => back-up alarms, spotter, soil cave-in, spoil pikes, ROPs, trenching, rain
[comments:protected] =>
[summary:protected] => A toolbox talk on preventing incidents involving trenches such as trench collapse. Includes questions to ask, an incident to discuss with images, and a place to record questions the trainer would like to ask about the incident. Part of a collection. Click on the 'collection' button to access the other items.
[transition_comments:protected] =>
[external_link:protected] =>
[consol_link:protected] =>
[more_like_this:protected] => d000019,d000035,d000168
[permission_given_by:protected] =>
[published:protected] => T
[billable:protected] => F
[img_name:protected] =>
[img_ext:protected] =>
[img_width:protected] =>
[img_height:protected] =>
[img_credit:protected] =>
[img_practice:protected] =>
[vid_source_id:protected] =>
[vid_running_time:protected] =>
[vid_intended_audience:protected] =>
[vid_acquisition_info:protected] =>
[vid_cost:protected] =>
[vid_producer:protected] =>
[vid_filename:protected] =>
[vid_filename_downloadable:protected] =>
[date_summary:protected] =>
[date_permission_requested:protected] =>
[date_permission_received:protected] =>
[date_review_needed:protected] =>
[date_received:protected] => 02/15/12
[date_completed:protected] => 04/02/12
[date_billed:protected] =>
[date_modified:protected] => 05/23/23
[collBokExports:protected] =>
[lastBokExportCriteria:BaseElcoshItem:private] =>
[alreadyInSave:protected] =>
[alreadyInValidation:protected] =>
[validationFailures:protected] => Array
(
)
[_new:BaseObject:private] =>
[_deleted:BaseObject:private] =>
[modifiedColumns:protected] => Array
(
)
)
[1654] => DocumentRecord Object
(
[records:protected] => Array
(
)
[recordId:protected] =>
[searchWordClass:protected] =>
[searchWordPeerClass:protected] =>
[bok_record:protected] =>
[authors:protected] =>
[organizations:protected] =>
[collections:protected] =>
[categories:protected] =>
[categories_initialized:protected] =>
[mapped_items:protected] =>
[content:protected] =>
[files:protected] =>
[language:protected] =>
[old_record:protected] =>
[id:protected] => 1654
[old_id:protected] => 1284
[elcosh_id:protected] => d001159
[type:protected] => document
[display_type:protected] => HTML w/ PDF
[user_id:protected] => 0
[language_id:protected] => 1
[tagging_id:protected] => Garber
[priority_id:protected] => 1
[title:protected] => Focus Four Toolbox Talks, Module 4 – Electrocutions, Talk #6 – Hazards on Disaster Sites
[total_pages:protected] => 1
[billed_pages:protected] => 1
[publication_number:protected] =>
[part_of:protected] =>
[keywords:protected] => powerlines, underground, utilities, generators, wet conditions, GFCIs, energized lines, disasters, emergency response
[comments:protected] =>
[summary:protected] => A toolbox talk on how to avoid electrocution on a disaster site. Includes questions to ask, an incident to discuss with images, and a place to record questions the trainer would like to ask about the incident. Part of a collection. Click on the 'collection' button to access the other items.
[transition_comments:protected] =>
[external_link:protected] =>
[consol_link:protected] => http://www.cpwrconstructionsolutions.org/electrical/hazard/1138/install-and-repair-high-voltage-lines-transformers-switches-electrical-shocks-burns-and-or-electrocution.html
[more_like_this:protected] => d000135,d000361,d000437
[permission_given_by:protected] =>
[published:protected] => T
[billable:protected] => F
[img_name:protected] =>
[img_ext:protected] =>
[img_width:protected] =>
[img_height:protected] =>
[img_credit:protected] =>
[img_practice:protected] =>
[vid_source_id:protected] =>
[vid_running_time:protected] =>
[vid_intended_audience:protected] =>
[vid_acquisition_info:protected] =>
[vid_cost:protected] =>
[vid_producer:protected] =>
[vid_filename:protected] =>
[vid_filename_downloadable:protected] =>
[date_summary:protected] =>
[date_permission_requested:protected] =>
[date_permission_received:protected] =>
[date_review_needed:protected] =>
[date_received:protected] => 02/15/12
[date_completed:protected] => 04/02/12
[date_billed:protected] =>
[date_modified:protected] => 05/23/23
[collBokExports:protected] =>
[lastBokExportCriteria:BaseElcoshItem:private] =>
[alreadyInSave:protected] =>
[alreadyInValidation:protected] =>
[validationFailures:protected] => Array
(
)
[_new:BaseObject:private] =>
[_deleted:BaseObject:private] =>
[modifiedColumns:protected] => Array
(
)
)
)
[content:protected] =>
[files:protected] => Array
(
[9400] => File Object
(
[id:protected] => 9400
[filename:protected] => 1.jpg
[downloadable:protected] => F
[timestamp:protected] => 2014-05-08 15:05:37
[alreadyInSave:protected] =>
[alreadyInValidation:protected] =>
[validationFailures:protected] => Array
(
)
[_new:BaseObject:private] =>
[_deleted:BaseObject:private] =>
[modifiedColumns:protected] => Array
(
)
)
[9401] => File Object
(
[id:protected] => 9401
[filename:protected] => d001298.pdf
[downloadable:protected] => T
[timestamp:protected] => 2014-05-08 15:05:37
[alreadyInSave:protected] =>
[alreadyInValidation:protected] =>
[validationFailures:protected] => Array
(
)
[_new:BaseObject:private] =>
[_deleted:BaseObject:private] =>
[modifiedColumns:protected] => Array
(
)
)
)
[language:protected] => Language Object
(
[id:protected] => 1
[code:protected] => en
[name:protected] => English
[alreadyInSave:protected] =>
[alreadyInValidation:protected] =>
[validationFailures:protected] => Array
(
)
[_new:BaseObject:private] =>
[_deleted:BaseObject:private] =>
[modifiedColumns:protected] => Array
(
)
)
[old_record:protected] =>
[id:protected] => 3827
[old_id:protected] =>
[elcosh_id:protected] => d001298
[type:protected] => document
[display_type:protected] => HTML w/ PDF
[user_id:protected] => 23
[language_id:protected] => 1
[tagging_id:protected] => Bruce Lippy
[priority_id:protected] => 1
[title:protected] => Getting the most out of the IUOE Toolbox Talks
[total_pages:protected] => 2
[billed_pages:protected] => 2
[publication_number:protected] =>
[part_of:protected] =>
[keywords:protected] => toolbox talks, tailgate talks
[comments:protected] =>
[summary:protected] => Toolbox talks have been the main tool for communicating safety information on construction jobs for decades.
Unfortunately, there has been little research on what makes for effective toolbox talks. The IUOE National
Training Fund worked with OSHA and NIOSH to make sure their series of 24 Focus Four toolbox talks were based on the best recommendations for effective design. These toolbox talks accompany an entire package of training materials, but can be used alone. This guide points out the key features of these toolbox talks and how best to deliver them.
[transition_comments:protected] =>
[external_link:protected] =>
[consol_link:protected] =>
[more_like_this:protected] => d001137,d001146,d001149,d001159
[permission_given_by:protected] => IUOE National Hazmat Program
[published:protected] => T
[billable:protected] => F
[img_name:protected] =>
[img_ext:protected] => png
[img_width:protected] =>
[img_height:protected] =>
[img_credit:protected] =>
[img_practice:protected] =>
[vid_source_id:protected] =>
[vid_running_time:protected] =>
[vid_intended_audience:protected] =>
[vid_acquisition_info:protected] =>
[vid_cost:protected] =>
[vid_producer:protected] =>
[vid_filename:protected] =>
[vid_filename_downloadable:protected] =>
[date_summary:protected] => 2007
[date_permission_requested:protected] =>
[date_permission_received:protected] =>
[date_review_needed:protected] =>
[date_received:protected] => 05/08/14
[date_completed:protected] => 05/08/14
[date_billed:protected] =>
[date_modified:protected] => 05/08/14
[collBokExports:protected] =>
[lastBokExportCriteria:BaseElcoshItem:private] =>
[alreadyInSave:protected] =>
[alreadyInValidation:protected] =>
[validationFailures:protected] => Array
(
)
[_new:BaseObject:private] =>
[_deleted:BaseObject:private] =>
[modifiedColumns:protected] => Array
(
)
)
[show_text] =>
[document_content] => ElcoshItemDocumentContent Object
(
[id:protected] => 2896
[item_id:protected] => 3827
[type:protected] => main
[title:protected] =>
[content:protected] =>
Why were these talks developed?
Toolbox talks have been the main tool for communicating safety information on construction jobs for decades. Unfortunately, there has been almost no research on what makes for effective toolbox talks. The IUOE National Training Fund has worked with OSHA, the National Institute for Occupational Safety and Health and the Lippy Group, LLC to make sure these Focus Four toolbox talks are based on the latest fi ndings on the most effective design and tailored to the hazards operating engineers face daily. These toolbox talks accompany an entire package of training materials, but can be used alone. The way these are delivered is as important as how well they are designed.
What did NIOSH find out?
- Just handing out factsheets and toolbox talks to workers doesn’t work. Providing copies after toolbox talks doesn’t make much of an impact either.
- Using case studies (real life stories of accidents that ended in fatality or injury) in toolbox talks is effective.
- When toolbox talks containing case studies were accompanied by discussion questions to encourage group participation, they were more effective. Consequently, getting the workers to participate in the discussion about the case study is important. It’s not enough to tell the story, it is better to have the workers engage in problem solving that analyzes why the accident occurred and how it could have been prevented. Active learning is always better than passive.
How should you deliver these toolbox talks?
- Choose a topic that is related to work going on at the site.
- Hold the meeting on the job, preferably where everyone can sit and relax.
- Hold the meeting at the beginning of a shift or after a break. Folks are too tired at the end of a shift to carefully listen and they want to get home.
- Read the toolbox talk sheet on the topic prior to conducting the talk.
- Start at the top of the form and work right through to the end, which should take around 10 to 15 minutes. Guidance is provided in blue print to help you with each section.
- Use the questions provided to generate discussions. Always allow time for the crew to respond to your questions before you provide an answer. Some suggested responses are written in italics.
- Review the case study and emphasize that this was a real incident. Ask the crew for a case study before you review the one provided, however.
- Always end with a discussion of the particular worksite where you are conducting the talk. Tie the talk as closely to hazards on the site as possible and encourage the crew to constantly look for and immediately correct hazards. They should also know how to report any problems that can’t be immediately corrected.
- Provide copies to each person, if you like, but NIOSH has not found that to be particularly effective.
- Encourage workers to do similar talks on their sites and provide them with the IUOE phone number for ordering in bulk.
- Have everyone sign the back of the form to indicate they attended this session and point out it is a pledge to look out for the health and safety of everyone on the site.
What are the key features of these toolbox talks?

[content_transformed:protected] =>
Why were these talks developed?
Toolbox talks have been the main tool for communicating safety information on construction jobs for decades. Unfortunately, there has been almost no research on what makes for effective toolbox talks. The IUOE National Training Fund has worked with OSHA, the National Institute for Occupational Safety and Health and the Lippy Group, LLC to make sure these Focus Four toolbox talks are based on the latest fi ndings on the most effective design and tailored to the hazards operating engineers face daily. These toolbox talks accompany an entire package of training materials, but can be used alone. The way these are delivered is as important as how well they are designed.
What did NIOSH find out?
- Just handing out factsheets and toolbox talks to workers doesn’t work. Providing copies after toolbox talks doesn’t make much of an impact either.
- Using case studies (real life stories of accidents that ended in fatality or injury) in toolbox talks is effective.
- When toolbox talks containing case studies were accompanied by discussion questions to encourage group participation, they were more effective. Consequently, getting the workers to participate in the discussion about the case study is important. It’s not enough to tell the story, it is better to have the workers engage in problem solving that analyzes why the accident occurred and how it could have been prevented. Active learning is always better than passive.
How should you deliver these toolbox talks?
- Choose a topic that is related to work going on at the site.
- Hold the meeting on the job, preferably where everyone can sit and relax.
- Hold the meeting at the beginning of a shift or after a break. Folks are too tired at the end of a shift to carefully listen and they want to get home.
- Read the toolbox talk sheet on the topic prior to conducting the talk.
- Start at the top of the form and work right through to the end, which should take around 10 to 15 minutes. Guidance is provided in blue print to help you with each section.
- Use the questions provided to generate discussions. Always allow time for the crew to respond to your questions before you provide an answer. Some suggested responses are written in italics.
- Review the case study and emphasize that this was a real incident. Ask the crew for a case study before you review the one provided, however.
- Always end with a discussion of the particular worksite where you are conducting the talk. Tie the talk as closely to hazards on the site as possible and encourage the crew to constantly look for and immediately correct hazards. They should also know how to report any problems that can’t be immediately corrected.
- Provide copies to each person, if you like, but NIOSH has not found that to be particularly effective.
- Encourage workers to do similar talks on their sites and provide them with the IUOE phone number for ordering in bulk.
- Have everyone sign the back of the form to indicate they attended this session and point out it is a pledge to look out for the health and safety of everyone on the site.
What are the key features of these toolbox talks?
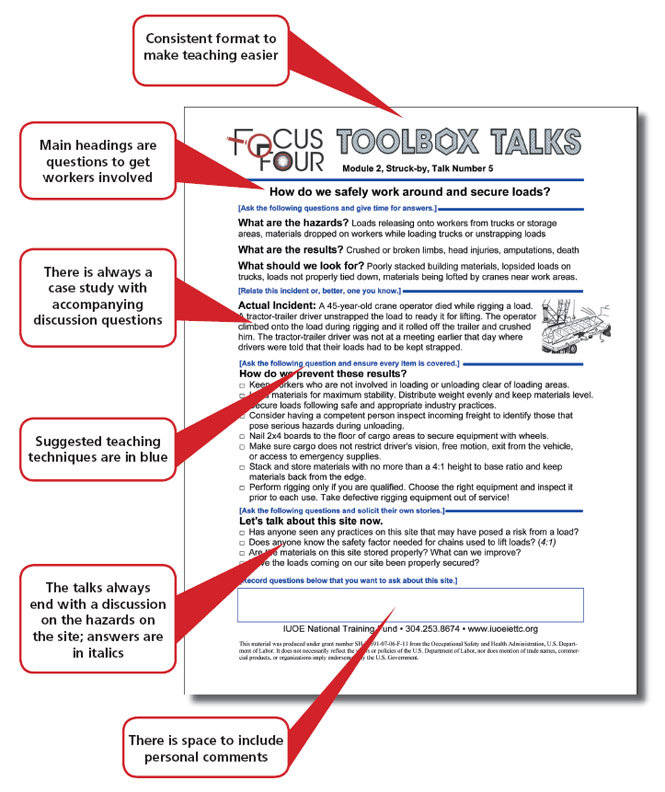
[disclaimer:protected] =>
[disclaimer_transformed:protected] =>
[alreadyInSave:protected] =>
[alreadyInValidation:protected] =>
[validationFailures:protected] => Array
(
)
[_new:BaseObject:private] =>
[_deleted:BaseObject:private] =>
[modifiedColumns:protected] => Array
(
)
)
[template] => record
)
[_file] => /home/agsafe5/repositories/elcosh/live/templates/elcosh/macros.html
[_errors:protected] => Array
(
)
[_encoding:protected] => UTF-8
[_outputMode:protected] => 11
[_forceReparse:protected] =>
[_phpCodeDestination:protected] => /tmp/
[_phpCodeExtension:protected] => php
[_cacheLifetime:protected] => 30
[_cachePurgeFrequency:protected] => 30
[externalMacroTemplatesCache:PHPTAL:private] => Array
(
)
)
[record_macros.html] => PHPTAL Object
(
[_prefilters:protected] => Array
(
)
[_prefilter:PHPTAL:private] => REMOVED: DO NOT USE
[_postfilter:protected] =>
[_repositories:protected] => Array
(
[0] => /home/agsafe5/repositories/elcosh/live/templates/elcosh
)
[_path:protected] => record_macros.html
[_resolvers:protected] => Array
(
)
[_source:protected] => PHPTAL_FileSource Object
(
[_path:PHPTAL_FileSource:private] => /home/agsafe5/repositories/elcosh/live/templates/elcosh/record_macros.html
)
[_codeFile:protected] => /tmp/tpl_61515a6c_record_macros__gMFg5NvPLybiFfYjAv9Aag.php
[_functionName:protected] => tpl_61515a6c_record_macros__gMFg5NvPLybiFfYjAv9Aag
[_prepared:protected] => 1
[_triggers:protected] => Array
(
)
[_translator:protected] =>
[_globalContext:protected] => stdClass Object
(
)
[_context:protected] => PHPTAL_Context Object
(
[_line] =>
[_file] => /home/agsafe5/repositories/elcosh/live/templates/elcosh/record.html
[repeat] => stdClass Object
(
)
[_xmlDeclaration] =>
[_docType] =>
[_nothrow:PHPTAL_Context:private] =>
[_slots:PHPTAL_Context:private] => Array
(
)
[_slotsStack:PHPTAL_Context:private] => Array
(
[0] => Array
(
)
[1] => Array
(
)
)
[_parentContext:PHPTAL_Context:private] => PHPTAL_Context Object
(
[_line] =>
[_file] => /home/agsafe5/repositories/elcosh/live/templates/elcosh/record.html
[repeat] => stdClass Object
(
)
[_xmlDeclaration] =>
[_docType] =>
[_nothrow:PHPTAL_Context:private] =>
[_slots:PHPTAL_Context:private] => Array
(
)
[_slotsStack:PHPTAL_Context:private] => Array
(
[0] => Array
(
)
[1] => Array
(
)
)
[_parentContext:PHPTAL_Context:private] =>
[_globalContext:PHPTAL_Context:private] => stdClass Object
(
)
[_echoDeclarations:PHPTAL_Context:private] =>
[referer] => http://www.elcosh.org/document/3827/d001298/Getting%2Bthe%2Bmost%2Bout%2Bof%2Bthe%2BIUOE%2BToolbox%2BTalks.html
[curr_module] => Record
[styles] => Array
(
)
[javascript] => Array
(
[0] => jquery.min.js
)
[metas] => Array
(
[language] => en
[robots] => index, follow
)
[user] =>
[curr_url] => https://www.elcosh.org/index.php?module=Record&id=3827&type=document
[base_url] => https://www.elcosh.org/index.php?module=Record
[title] => eLCOSH : Getting the most out of the IUOE Toolbox Talks
[language] => en
[search_query] =>
[module] => Record
[new_records] => Array
(
[0] => Search_Result Object
(
[title] => Toolbox Talk: Fixed Ladder
[image] => /record/images/notavailable-p.png
[blurb] => The CPWR Toolbox Talk on Fixed Ladders addresses the potential risks associated with using fixed ladders. The resource includes a brief case example,...
[category] => Array
(
[0] => 15
[1] => 47
[2] => 49
[3] => 51
[4] => 53
[5] => 55
[6] => 60
[7] => 64
[8] => 73
[9] => 76
[10] => 78
[11] => 80
[12] => 86
[13] => 87
[14] => 90
[15] => 92
[16] => 93
[17] => 94
[18] => 100
)
[labels] => Array
(
[0] => Falls
[1] => Work Environment
[2] => Hazards
[3] => Bricklayer
[4] => Trades
[5] => Carpenter
[7] => Cement Mason
[9] => Concrete Polisher
[11] => Electrical Worker
[13] => HVAC
[15] => Laborer
[17] => PCC/Restoration
[19] => Plumber/Pipefitter
[21] => Roofer/Waterproofer
[23] => Sheetmetal Worker
[25] => Welder
[27] => Commercial & Institutional
[28] => Jobsites
[29] => Industrial
[31] => LEED/Green Construction
[33] => Renovations
[35] => Residential
[37] => Toolbox Talks
[38] => Documents
[39] => Media & Documents
)
[type] => Toolbox Talks
[sub_category] =>
[url] => /document/4430/d001660/Toolbox%2BTalk%253A%2BFixed%2BLadder.html
[item:protected] => DocumentRecord Object
(
[records:protected] => Array
(
)
[recordId:protected] =>
[searchWordClass:protected] =>
[searchWordPeerClass:protected] =>
[bok_record:protected] =>
[authors:protected] =>
[organizations:protected] =>
[collections:protected] =>
[categories:protected] => Array
(
[15] => Category Object
(
[languages:protected] =>
[bok_resources:protected] =>
[bok_topics:protected] =>
[bok_keywords:protected] =>
[id:protected] => 15
[type:protected] => category
[parent:protected] => 7
[label:protected] => Falls
[alreadyInSave:protected] =>
[alreadyInValidation:protected] =>
[validationFailures:protected] => Array
(
)
[_new:BaseObject:private] =>
[_deleted:BaseObject:private] =>
[modifiedColumns:protected] => Array
(
)
)
[47] => Category Object
(
[languages:protected] =>
[bok_resources:protected] =>
[bok_topics:protected] =>
[bok_keywords:protected] =>
[id:protected] => 47
[type:protected] => category
[parent:protected] => 2
[label:protected] => Bricklayer
[alreadyInSave:protected] =>
[alreadyInValidation:protected] =>
[validationFailures:protected] => Array
(
)
[_new:BaseObject:private] =>
[_deleted:BaseObject:private] =>
[modifiedColumns:protected] => Array
(
)
)
[49] => Category Object
(
[languages:protected] =>
[bok_resources:protected] =>
[bok_topics:protected] =>
[bok_keywords:protected] =>
[id:protected] => 49
[type:protected] => category
[parent:protected] => 2
[label:protected] => Carpenter
[alreadyInSave:protected] =>
[alreadyInValidation:protected] =>
[validationFailures:protected] => Array
(
)
[_new:BaseObject:private] =>
[_deleted:BaseObject:private] =>
[modifiedColumns:protected] => Array
(
)
)
[51] => Category Object
(
[languages:protected] =>
[bok_resources:protected] =>
[bok_topics:protected] =>
[bok_keywords:protected] =>
[id:protected] => 51
[type:protected] => category
[parent:protected] => 2
[label:protected] => Cement Mason
[alreadyInSave:protected] =>
[alreadyInValidation:protected] =>
[validationFailures:protected] => Array
(
)
[_new:BaseObject:private] =>
[_deleted:BaseObject:private] =>
[modifiedColumns:protected] => Array
(
)
)
[53] => Category Object
(
[languages:protected] =>
[bok_resources:protected] =>
[bok_topics:protected] =>
[bok_keywords:protected] =>
[id:protected] => 53
[type:protected] => category
[parent:protected] => 2
[label:protected] => Concrete Polisher
[alreadyInSave:protected] =>
[alreadyInValidation:protected] =>
[validationFailures:protected] => Array
(
)
[_new:BaseObject:private] =>
[_deleted:BaseObject:private] =>
[modifiedColumns:protected] => Array
(
)
)
[55] => Category Object
(
[languages:protected] =>
[bok_resources:protected] =>
[bok_topics:protected] =>
[bok_keywords:protected] =>
[id:protected] => 55
[type:protected] => category
[parent:protected] => 2
[label:protected] => Electrical Worker
[alreadyInSave:protected] =>
[alreadyInValidation:protected] =>
[validationFailures:protected] => Array
(
)
[_new:BaseObject:private] =>
[_deleted:BaseObject:private] =>
[modifiedColumns:protected] => Array
(
)
)
[60] => Category Object
(
[languages:protected] =>
[bok_resources:protected] =>
[bok_topics:protected] =>
[bok_keywords:protected] =>
[id:protected] => 60
[type:protected] => category
[parent:protected] => 2
[label:protected] => HVAC
[alreadyInSave:protected] =>
[alreadyInValidation:protected] =>
[validationFailures:protected] => Array
(
)
[_new:BaseObject:private] =>
[_deleted:BaseObject:private] =>
[modifiedColumns:protected] => Array
(
)
)
[64] => Category Object
(
[languages:protected] =>
[bok_resources:protected] =>
[bok_topics:protected] =>
[bok_keywords:protected] =>
[id:protected] => 64
[type:protected] => category
[parent:protected] => 2
[label:protected] => Laborer
[alreadyInSave:protected] =>
[alreadyInValidation:protected] =>
[validationFailures:protected] => Array
(
)
[_new:BaseObject:private] =>
[_deleted:BaseObject:private] =>
[modifiedColumns:protected] => Array
(
)
)
[73] => Category Object
(
[languages:protected] =>
[bok_resources:protected] =>
[bok_topics:protected] =>
[bok_keywords:protected] =>
[id:protected] => 73
[type:protected] => category
[parent:protected] => 2
[label:protected] => PCC/Restoration
[alreadyInSave:protected] =>
[alreadyInValidation:protected] =>
[validationFailures:protected] => Array
(
)
[_new:BaseObject:private] =>
[_deleted:BaseObject:private] =>
[modifiedColumns:protected] => Array
(
)
)
[76] => Category Object
(
[languages:protected] =>
[bok_resources:protected] =>
[bok_topics:protected] =>
[bok_keywords:protected] =>
[id:protected] => 76
[type:protected] => category
[parent:protected] => 2
[label:protected] => Plumber/Pipefitter
[alreadyInSave:protected] =>
[alreadyInValidation:protected] =>
[validationFailures:protected] => Array
(
)
[_new:BaseObject:private] =>
[_deleted:BaseObject:private] =>
[modifiedColumns:protected] => Array
(
)
)
[78] => Category Object
(
[languages:protected] =>
[bok_resources:protected] =>
[bok_topics:protected] =>
[bok_keywords:protected] =>
[id:protected] => 78
[type:protected] => category
[parent:protected] => 2
[label:protected] => Roofer/Waterproofer
[alreadyInSave:protected] =>
[alreadyInValidation:protected] =>
[validationFailures:protected] => Array
(
)
[_new:BaseObject:private] =>
[_deleted:BaseObject:private] =>
[modifiedColumns:protected] => Array
(
)
)
[80] => Category Object
(
[languages:protected] =>
[bok_resources:protected] =>
[bok_topics:protected] =>
[bok_keywords:protected] =>
[id:protected] => 80
[type:protected] => category
[parent:protected] => 2
[label:protected] => Sheetmetal Worker
[alreadyInSave:protected] =>
[alreadyInValidation:protected] =>
[validationFailures:protected] => Array
(
)
[_new:BaseObject:private] =>
[_deleted:BaseObject:private] =>
[modifiedColumns:protected] => Array
(
)
)
[86] => Category Object
(
[languages:protected] =>
[bok_resources:protected] =>
[bok_topics:protected] =>
[bok_keywords:protected] =>
[id:protected] => 86
[type:protected] => category
[parent:protected] => 2
[label:protected] => Welder
[alreadyInSave:protected] =>
[alreadyInValidation:protected] =>
[validationFailures:protected] => Array
(
)
[_new:BaseObject:private] =>
[_deleted:BaseObject:private] =>
[modifiedColumns:protected] => Array
(
)
)
[87] => Category Object
(
[languages:protected] =>
[bok_resources:protected] =>
[bok_topics:protected] =>
[bok_keywords:protected] =>
[id:protected] => 87
[type:protected] => category
[parent:protected] => 3
[label:protected] => Commercial & Institutional
[alreadyInSave:protected] =>
[alreadyInValidation:protected] =>
[validationFailures:protected] => Array
(
)
[_new:BaseObject:private] =>
[_deleted:BaseObject:private] =>
[modifiedColumns:protected] => Array
(
)
)
[90] => Category Object
(
[languages:protected] =>
[bok_resources:protected] =>
[bok_topics:protected] =>
[bok_keywords:protected] =>
[id:protected] => 90
[type:protected] => category
[parent:protected] => 3
[label:protected] => Industrial
[alreadyInSave:protected] =>
[alreadyInValidation:protected] =>
[validationFailures:protected] => Array
(
)
[_new:BaseObject:private] =>
[_deleted:BaseObject:private] =>
[modifiedColumns:protected] => Array
(
)
)
[92] => Category Object
(
[languages:protected] =>
[bok_resources:protected] =>
[bok_topics:protected] =>
[bok_keywords:protected] =>
[id:protected] => 92
[type:protected] => category
[parent:protected] => 3
[label:protected] => LEED/Green Construction
[alreadyInSave:protected] =>
[alreadyInValidation:protected] =>
[validationFailures:protected] => Array
(
)
[_new:BaseObject:private] =>
[_deleted:BaseObject:private] =>
[modifiedColumns:protected] => Array
(
)
)
[93] => Category Object
(
[languages:protected] =>
[bok_resources:protected] =>
[bok_topics:protected] =>
[bok_keywords:protected] =>
[id:protected] => 93
[type:protected] => category
[parent:protected] => 3
[label:protected] => Renovations
[alreadyInSave:protected] =>
[alreadyInValidation:protected] =>
[validationFailures:protected] => Array
(
)
[_new:BaseObject:private] =>
[_deleted:BaseObject:private] =>
[modifiedColumns:protected] => Array
(
)
)
[94] => Category Object
(
[languages:protected] =>
[bok_resources:protected] =>
[bok_topics:protected] =>
[bok_keywords:protected] =>
[id:protected] => 94
[type:protected] => category
[parent:protected] => 3
[label:protected] => Residential
[alreadyInSave:protected] =>
[alreadyInValidation:protected] =>
[validationFailures:protected] => Array
(
)
[_new:BaseObject:private] =>
[_deleted:BaseObject:private] =>
[modifiedColumns:protected] => Array
(
)
)
[100] => Category Object
(
[languages:protected] =>
[bok_resources:protected] =>
[bok_topics:protected] =>
[bok_keywords:protected] =>
[id:protected] => 100
[type:protected] => category
[parent:protected] => 6
[label:protected] => Toolbox Talks
[alreadyInSave:protected] =>
[alreadyInValidation:protected] =>
[validationFailures:protected] => Array
(
)
[_new:BaseObject:private] =>
[_deleted:BaseObject:private] =>
[modifiedColumns:protected] => Array
(
)
)
)
[categories_initialized:protected] => 1
[mapped_items:protected] =>
[content:protected] =>
[files:protected] =>
[language:protected] => Language Object
(
[id:protected] => 1
[code:protected] => en
[name:protected] => English
[alreadyInSave:protected] =>
[alreadyInValidation:protected] =>
[validationFailures:protected] => Array
(
)
[_new:BaseObject:private] =>
[_deleted:BaseObject:private] =>
[modifiedColumns:protected] => Array
(
)
)
[old_record:protected] =>
[id:protected] => 4430
[old_id:protected] =>
[elcosh_id:protected] => d001660
[type:protected] => document
[display_type:protected] => HTML only (and links)
[user_id:protected] => 0
[language_id:protected] => 1
[tagging_id:protected] => Mike Aguilar
[priority_id:protected] => 1
[title:protected] => Toolbox Talk: Fixed Ladder
[total_pages:protected] => 0
[billed_pages:protected] => 0
[publication_number:protected] =>
[part_of:protected] =>
[keywords:protected] => Fixed Ladders, Fall Prevention, Falls
[comments:protected] =>
[summary:protected] => The CPWR Toolbox Talk on Fixed Ladders addresses the potential risks associated with using fixed ladders. The resource includes a brief case example, steps to prevent a related injury and questions for discussion. It includes an image that illustrates the hazard, which can be posted in a central location as a reminder of steps to work safely.
Available in
English
and
Spanish.
[transition_comments:protected] =>
[external_link:protected] =>
[consol_link:protected] =>
[more_like_this:protected] => d001257,d001254,d001255,d001256,d001258,d001262,d001279
[permission_given_by:protected] =>
[published:protected] => T
[billable:protected] => F
[img_name:protected] =>
[img_ext:protected] =>
[img_width:protected] =>
[img_height:protected] =>
[img_credit:protected] =>
[img_practice:protected] =>
[vid_source_id:protected] =>
[vid_running_time:protected] =>
[vid_intended_audience:protected] =>
[vid_acquisition_info:protected] =>
[vid_cost:protected] =>
[vid_producer:protected] =>
[vid_filename:protected] =>
[vid_filename_downloadable:protected] =>
[date_summary:protected] =>
[date_permission_requested:protected] =>
[date_permission_received:protected] =>
[date_review_needed:protected] =>
[date_received:protected] => 06/10/22
[date_completed:protected] => 06/10/22
[date_billed:protected] =>
[date_modified:protected] => 05/22/23
[collBokExports:protected] =>
[lastBokExportCriteria:BaseElcoshItem:private] =>
[alreadyInSave:protected] =>
[alreadyInValidation:protected] =>
[validationFailures:protected] => Array
(
)
[_new:BaseObject:private] =>
[_deleted:BaseObject:private] =>
[modifiedColumns:protected] => Array
(
)
)
)
[1] => Search_Result Object
(
[title] => Toolbox Talk: Challenges Preventing Falling Objects
[image] => /record/images/notavailable-p.png
[blurb] => The CPWR Toolbox Talk on Challenges Preventing Falling Objects addresses the hazards of being struck by falling objects on the job site. The resource...
[category] => Array
(
[0] => 12
[1] => 47
[2] => 49
[3] => 51
[4] => 55
[5] => 64
[6] => 68
[7] => 71
[8] => 75
[9] => 78
[10] => 79
[11] => 82
[12] => 62
[13] => 86
[14] => 87
[15] => 88
[16] => 89
[17] => 91
[18] => 90
[19] => 92
[20] => 93
[21] => 94
[22] => 95
[23] => 100
)
[labels] => Array
(
[0] => Crushed/Struck By
[1] => Work Environment
[2] => Hazards
[3] => Bricklayer
[4] => Trades
[5] => Carpenter
[7] => Cement Mason
[9] => Electrical Worker
[11] => Laborer
[13] => Maintenance Worker
[15] => Painter
[17] => Plasterer
[19] => Roofer/Waterproofer
[21] => Scaffold Erector
[23] => Stonemason
[25] => Structural Ironworker
[27] => Welder
[29] => Commercial & Institutional
[30] => Jobsites
[31] => Demolition
[33] => Disasters
[35] => Heavy & Highway
[37] => Industrial
[39] => LEED/Green Construction
[41] => Renovations
[43] => Residential
[45] => Underground
[47] => Toolbox Talks
[48] => Documents
[49] => Media & Documents
)
[type] => Toolbox Talks
[sub_category] =>
[url] => /document/4431/d001661/Toolbox%2BTalk%253A%2BChallenges%2BPreventing%2BFalling%2BObjects.html
[item:protected] => DocumentRecord Object
(
[records:protected] => Array
(
)
[recordId:protected] =>
[searchWordClass:protected] =>
[searchWordPeerClass:protected] =>
[bok_record:protected] =>
[authors:protected] =>
[organizations:protected] =>
[collections:protected] =>
[categories:protected] => Array
(
[12] => Category Object
(
[languages:protected] =>
[bok_resources:protected] =>
[bok_topics:protected] =>
[bok_keywords:protected] =>
[id:protected] => 12
[type:protected] => category
[parent:protected] => 7
[label:protected] => Crushed/Struck By
[alreadyInSave:protected] =>
[alreadyInValidation:protected] =>
[validationFailures:protected] => Array
(
)
[_new:BaseObject:private] =>
[_deleted:BaseObject:private] =>
[modifiedColumns:protected] => Array
(
)
)
[47] => Category Object
(
[languages:protected] =>
[bok_resources:protected] =>
[bok_topics:protected] =>
[bok_keywords:protected] =>
[id:protected] => 47
[type:protected] => category
[parent:protected] => 2
[label:protected] => Bricklayer
[alreadyInSave:protected] =>
[alreadyInValidation:protected] =>
[validationFailures:protected] => Array
(
)
[_new:BaseObject:private] =>
[_deleted:BaseObject:private] =>
[modifiedColumns:protected] => Array
(
)
)
[49] => Category Object
(
[languages:protected] =>
[bok_resources:protected] =>
[bok_topics:protected] =>
[bok_keywords:protected] =>
[id:protected] => 49
[type:protected] => category
[parent:protected] => 2
[label:protected] => Carpenter
[alreadyInSave:protected] =>
[alreadyInValidation:protected] =>
[validationFailures:protected] => Array
(
)
[_new:BaseObject:private] =>
[_deleted:BaseObject:private] =>
[modifiedColumns:protected] => Array
(
)
)
[51] => Category Object
(
[languages:protected] =>
[bok_resources:protected] =>
[bok_topics:protected] =>
[bok_keywords:protected] =>
[id:protected] => 51
[type:protected] => category
[parent:protected] => 2
[label:protected] => Cement Mason
[alreadyInSave:protected] =>
[alreadyInValidation:protected] =>
[validationFailures:protected] => Array
(
)
[_new:BaseObject:private] =>
[_deleted:BaseObject:private] =>
[modifiedColumns:protected] => Array
(
)
)
[55] => Category Object
(
[languages:protected] =>
[bok_resources:protected] =>
[bok_topics:protected] =>
[bok_keywords:protected] =>
[id:protected] => 55
[type:protected] => category
[parent:protected] => 2
[label:protected] => Electrical Worker
[alreadyInSave:protected] =>
[alreadyInValidation:protected] =>
[validationFailures:protected] => Array
(
)
[_new:BaseObject:private] =>
[_deleted:BaseObject:private] =>
[modifiedColumns:protected] => Array
(
)
)
[64] => Category Object
(
[languages:protected] =>
[bok_resources:protected] =>
[bok_topics:protected] =>
[bok_keywords:protected] =>
[id:protected] => 64
[type:protected] => category
[parent:protected] => 2
[label:protected] => Laborer
[alreadyInSave:protected] =>
[alreadyInValidation:protected] =>
[validationFailures:protected] => Array
(
)
[_new:BaseObject:private] =>
[_deleted:BaseObject:private] =>
[modifiedColumns:protected] => Array
(
)
)
[68] => Category Object
(
[languages:protected] =>
[bok_resources:protected] =>
[bok_topics:protected] =>
[bok_keywords:protected] =>
[id:protected] => 68
[type:protected] => category
[parent:protected] => 2
[label:protected] => Maintenance Worker
[alreadyInSave:protected] =>
[alreadyInValidation:protected] =>
[validationFailures:protected] => Array
(
)
[_new:BaseObject:private] =>
[_deleted:BaseObject:private] =>
[modifiedColumns:protected] => Array
(
)
)
[71] => Category Object
(
[languages:protected] =>
[bok_resources:protected] =>
[bok_topics:protected] =>
[bok_keywords:protected] =>
[id:protected] => 71
[type:protected] => category
[parent:protected] => 2
[label:protected] => Painter
[alreadyInSave:protected] =>
[alreadyInValidation:protected] =>
[validationFailures:protected] => Array
(
)
[_new:BaseObject:private] =>
[_deleted:BaseObject:private] =>
[modifiedColumns:protected] => Array
(
)
)
[75] => Category Object
(
[languages:protected] =>
[bok_resources:protected] =>
[bok_topics:protected] =>
[bok_keywords:protected] =>
[id:protected] => 75
[type:protected] => category
[parent:protected] => 2
[label:protected] => Plasterer
[alreadyInSave:protected] =>
[alreadyInValidation:protected] =>
[validationFailures:protected] => Array
(
)
[_new:BaseObject:private] =>
[_deleted:BaseObject:private] =>
[modifiedColumns:protected] => Array
(
)
)
[78] => Category Object
(
[languages:protected] =>
[bok_resources:protected] =>
[bok_topics:protected] =>
[bok_keywords:protected] =>
[id:protected] => 78
[type:protected] => category
[parent:protected] => 2
[label:protected] => Roofer/Waterproofer
[alreadyInSave:protected] =>
[alreadyInValidation:protected] =>
[validationFailures:protected] => Array
(
)
[_new:BaseObject:private] =>
[_deleted:BaseObject:private] =>
[modifiedColumns:protected] => Array
(
)
)
[79] => Category Object
(
[languages:protected] =>
[bok_resources:protected] =>
[bok_topics:protected] =>
[bok_keywords:protected] =>
[id:protected] => 79
[type:protected] => category
[parent:protected] => 2
[label:protected] => Scaffold Erector
[alreadyInSave:protected] =>
[alreadyInValidation:protected] =>
[validationFailures:protected] => Array
(
)
[_new:BaseObject:private] =>
[_deleted:BaseObject:private] =>
[modifiedColumns:protected] => Array
(
)
)
[82] => Category Object
(
[languages:protected] =>
[bok_resources:protected] =>
[bok_topics:protected] =>
[bok_keywords:protected] =>
[id:protected] => 82
[type:protected] => category
[parent:protected] => 2
[label:protected] => Stonemason
[alreadyInSave:protected] =>
[alreadyInValidation:protected] =>
[validationFailures:protected] => Array
(
)
[_new:BaseObject:private] =>
[_deleted:BaseObject:private] =>
[modifiedColumns:protected] => Array
(
)
)
[62] => Category Object
(
[languages:protected] =>
[bok_resources:protected] =>
[bok_topics:protected] =>
[bok_keywords:protected] =>
[id:protected] => 62
[type:protected] => category
[parent:protected] => 2
[label:protected] => Structural Ironworker
[alreadyInSave:protected] =>
[alreadyInValidation:protected] =>
[validationFailures:protected] => Array
(
)
[_new:BaseObject:private] =>
[_deleted:BaseObject:private] =>
[modifiedColumns:protected] => Array
(
)
)
[86] => Category Object
(
[languages:protected] =>
[bok_resources:protected] =>
[bok_topics:protected] =>
[bok_keywords:protected] =>
[id:protected] => 86
[type:protected] => category
[parent:protected] => 2
[label:protected] => Welder
[alreadyInSave:protected] =>
[alreadyInValidation:protected] =>
[validationFailures:protected] => Array
(
)
[_new:BaseObject:private] =>
[_deleted:BaseObject:private] =>
[modifiedColumns:protected] => Array
(
)
)
[87] => Category Object
(
[languages:protected] =>
[bok_resources:protected] =>
[bok_topics:protected] =>
[bok_keywords:protected] =>
[id:protected] => 87
[type:protected] => category
[parent:protected] => 3
[label:protected] => Commercial & Institutional
[alreadyInSave:protected] =>
[alreadyInValidation:protected] =>
[validationFailures:protected] => Array
(
)
[_new:BaseObject:private] =>
[_deleted:BaseObject:private] =>
[modifiedColumns:protected] => Array
(
)
)
[88] => Category Object
(
[languages:protected] =>
[bok_resources:protected] =>
[bok_topics:protected] =>
[bok_keywords:protected] =>
[id:protected] => 88
[type:protected] => category
[parent:protected] => 3
[label:protected] => Demolition
[alreadyInSave:protected] =>
[alreadyInValidation:protected] =>
[validationFailures:protected] => Array
(
)
[_new:BaseObject:private] =>
[_deleted:BaseObject:private] =>
[modifiedColumns:protected] => Array
(
)
)
[89] => Category Object
(
[languages:protected] =>
[bok_resources:protected] =>
[bok_topics:protected] =>
[bok_keywords:protected] =>
[id:protected] => 89
[type:protected] => category
[parent:protected] => 3
[label:protected] => Disasters
[alreadyInSave:protected] =>
[alreadyInValidation:protected] =>
[validationFailures:protected] => Array
(
)
[_new:BaseObject:private] =>
[_deleted:BaseObject:private] =>
[modifiedColumns:protected] => Array
(
)
)
[91] => Category Object
(
[languages:protected] =>
[bok_resources:protected] =>
[bok_topics:protected] =>
[bok_keywords:protected] =>
[id:protected] => 91
[type:protected] => category
[parent:protected] => 3
[label:protected] => Heavy & Highway
[alreadyInSave:protected] =>
[alreadyInValidation:protected] =>
[validationFailures:protected] => Array
(
)
[_new:BaseObject:private] =>
[_deleted:BaseObject:private] =>
[modifiedColumns:protected] => Array
(
)
)
[90] => Category Object
(
[languages:protected] =>
[bok_resources:protected] =>
[bok_topics:protected] =>
[bok_keywords:protected] =>
[id:protected] => 90
[type:protected] => category
[parent:protected] => 3
[label:protected] => Industrial
[alreadyInSave:protected] =>
[alreadyInValidation:protected] =>
[validationFailures:protected] => Array
(
)
[_new:BaseObject:private] =>
[_deleted:BaseObject:private] =>
[modifiedColumns:protected] => Array
(
)
)
[92] => Category Object
(
[languages:protected] =>
[bok_resources:protected] =>
[bok_topics:protected] =>
[bok_keywords:protected] =>
[id:protected] => 92
[type:protected] => category
[parent:protected] => 3
[label:protected] => LEED/Green Construction
[alreadyInSave:protected] =>
[alreadyInValidation:protected] =>
[validationFailures:protected] => Array
(
)
[_new:BaseObject:private] =>
[_deleted:BaseObject:private] =>
[modifiedColumns:protected] => Array
(
)
)
[93] => Category Object
(
[languages:protected] =>
[bok_resources:protected] =>
[bok_topics:protected] =>
[bok_keywords:protected] =>
[id:protected] => 93
[type:protected] => category
[parent:protected] => 3
[label:protected] => Renovations
[alreadyInSave:protected] =>
[alreadyInValidation:protected] =>
[validationFailures:protected] => Array
(
)
[_new:BaseObject:private] =>
[_deleted:BaseObject:private] =>
[modifiedColumns:protected] => Array
(
)
)
[94] => Category Object
(
[languages:protected] =>
[bok_resources:protected] =>
[bok_topics:protected] =>
[bok_keywords:protected] =>
[id:protected] => 94
[type:protected] => category
[parent:protected] => 3
[label:protected] => Residential
[alreadyInSave:protected] =>
[alreadyInValidation:protected] =>
[validationFailures:protected] => Array
(
)
[_new:BaseObject:private] =>
[_deleted:BaseObject:private] =>
[modifiedColumns:protected] => Array
(
)
)
[95] => Category Object
(
[languages:protected] =>
[bok_resources:protected] =>
[bok_topics:protected] =>
[bok_keywords:protected] =>
[id:protected] => 95
[type:protected] => category
[parent:protected] => 3
[label:protected] => Underground
[alreadyInSave:protected] =>
[alreadyInValidation:protected] =>
[validationFailures:protected] => Array
(
)
[_new:BaseObject:private] =>
[_deleted:BaseObject:private] =>
[modifiedColumns:protected] => Array
(
)
)
[100] => Category Object
(
[languages:protected] =>
[bok_resources:protected] =>
[bok_topics:protected] =>
[bok_keywords:protected] =>
[id:protected] => 100
[type:protected] => category
[parent:protected] => 6
[label:protected] => Toolbox Talks
[alreadyInSave:protected] =>
[alreadyInValidation:protected] =>
[validationFailures:protected] => Array
(
)
[_new:BaseObject:private] =>
[_deleted:BaseObject:private] =>
[modifiedColumns:protected] => Array
(
)
)
)
[categories_initialized:protected] => 1
[mapped_items:protected] =>
[content:protected] =>
[files:protected] =>
[language:protected] => Language Object
(
[id:protected] => 1
[code:protected] => en
[name:protected] => English
[alreadyInSave:protected] =>
[alreadyInValidation:protected] =>
[validationFailures:protected] => Array
(
)
[_new:BaseObject:private] =>
[_deleted:BaseObject:private] =>
[modifiedColumns:protected] => Array
(
)
)
[old_record:protected] =>
[id:protected] => 4431
[old_id:protected] =>
[elcosh_id:protected] => d001661
[type:protected] => document
[display_type:protected] => HTML only (and links)
[user_id:protected] => 0
[language_id:protected] => 1
[tagging_id:protected] => Mike Aguilar
[priority_id:protected] => 1
[title:protected] => Toolbox Talk: Challenges Preventing Falling Objects
[total_pages:protected] => 0
[billed_pages:protected] => 0
[publication_number:protected] =>
[part_of:protected] =>
[keywords:protected] => dropped objects, falling objects, struck by incidents, struck by fatalities
[comments:protected] =>
[summary:protected] => The CPWR Toolbox Talk on Challenges Preventing Falling Objects addresses the hazards of being struck by falling objects on the job site. The resource includes a brief example, steps to prevent a related injury, and questions for discussion. It includes a graphic that illustrates a group workers observing a scaffold free of debris during high winds, which can be posted in a central location as a reminder of steps to work safely.
Available in
English and
Spanish.
[transition_comments:protected] =>
[external_link:protected] =>
[consol_link:protected] =>
[more_like_this:protected] => d001234,d001238,d001244,d001251,d001253,d001260,d001268,d001278
[permission_given_by:protected] =>
[published:protected] => T
[billable:protected] => F
[img_name:protected] =>
[img_ext:protected] =>
[img_width:protected] =>
[img_height:protected] =>
[img_credit:protected] =>
[img_practice:protected] =>
[vid_source_id:protected] =>
[vid_running_time:protected] =>
[vid_intended_audience:protected] =>
[vid_acquisition_info:protected] =>
[vid_cost:protected] =>
[vid_producer:protected] =>
[vid_filename:protected] =>
[vid_filename_downloadable:protected] =>
[date_summary:protected] =>
[date_permission_requested:protected] =>
[date_permission_received:protected] =>
[date_review_needed:protected] =>
[date_received:protected] => 06/10/22
[date_completed:protected] => 06/10/22
[date_billed:protected] =>
[date_modified:protected] => 05/22/23
[collBokExports:protected] =>
[lastBokExportCriteria:BaseElcoshItem:private] =>
[alreadyInSave:protected] =>
[alreadyInValidation:protected] =>
[validationFailures:protected] => Array
(
)
[_new:BaseObject:private] =>
[_deleted:BaseObject:private] =>
[modifiedColumns:protected] => Array
(
)
)
)
[2] => Search_Result Object
(
[title] => Toolbox Talk: Tower Crane Safety
[image] => /record/images/notavailable-p.png
[blurb] => The CPWR Toolbox Talk on Tower Crane Safety addresses the potential hazards of Tower Cranes and the importance of following procedure before and durin...
[category] => Array
(
[0] => 11
[1] => 12
[2] => 18
[3] => 70
[4] => 87
[5] => 88
[6] => 91
[7] => 90
[8] => 92
[9] => 100
)
[labels] => Array
(
[0] => Cranes & Hoists
[1] => Work Environment
[2] => Hazards
[3] => Crushed/Struck By
[6] => Motor Vehicles/Heavy Equipment
[9] => Operating Engineer
[10] => Trades
[11] => Commercial & Institutional
[12] => Jobsites
[13] => Demolition
[15] => Heavy & Highway
[17] => Industrial
[19] => LEED/Green Construction
[21] => Toolbox Talks
[22] => Documents
[23] => Media & Documents
)
[type] => Toolbox Talks
[sub_category] =>
[url] => /document/4427/d001657/Toolbox%2BTalk%253A%2BTower%2BCrane%2BSafety.html
[item:protected] => DocumentRecord Object
(
[records:protected] => Array
(
)
[recordId:protected] =>
[searchWordClass:protected] =>
[searchWordPeerClass:protected] =>
[bok_record:protected] =>
[authors:protected] =>
[organizations:protected] =>
[collections:protected] =>
[categories:protected] => Array
(
[11] => Category Object
(
[languages:protected] =>
[bok_resources:protected] =>
[bok_topics:protected] =>
[bok_keywords:protected] =>
[id:protected] => 11
[type:protected] => category
[parent:protected] => 7
[label:protected] => Cranes & Hoists
[alreadyInSave:protected] =>
[alreadyInValidation:protected] =>
[validationFailures:protected] => Array
(
)
[_new:BaseObject:private] =>
[_deleted:BaseObject:private] =>
[modifiedColumns:protected] => Array
(
)
)
[12] => Category Object
(
[languages:protected] =>
[bok_resources:protected] =>
[bok_topics:protected] =>
[bok_keywords:protected] =>
[id:protected] => 12
[type:protected] => category
[parent:protected] => 7
[label:protected] => Crushed/Struck By
[alreadyInSave:protected] =>
[alreadyInValidation:protected] =>
[validationFailures:protected] => Array
(
)
[_new:BaseObject:private] =>
[_deleted:BaseObject:private] =>
[modifiedColumns:protected] => Array
(
)
)
[18] => Category Object
(
[languages:protected] =>
[bok_resources:protected] =>
[bok_topics:protected] =>
[bok_keywords:protected] =>
[id:protected] => 18
[type:protected] => category
[parent:protected] => 7
[label:protected] => Motor Vehicles/Heavy Equipment
[alreadyInSave:protected] =>
[alreadyInValidation:protected] =>
[validationFailures:protected] => Array
(
)
[_new:BaseObject:private] =>
[_deleted:BaseObject:private] =>
[modifiedColumns:protected] => Array
(
)
)
[70] => Category Object
(
[languages:protected] =>
[bok_resources:protected] =>
[bok_topics:protected] =>
[bok_keywords:protected] =>
[id:protected] => 70
[type:protected] => category
[parent:protected] => 2
[label:protected] => Operating Engineer
[alreadyInSave:protected] =>
[alreadyInValidation:protected] =>
[validationFailures:protected] => Array
(
)
[_new:BaseObject:private] =>
[_deleted:BaseObject:private] =>
[modifiedColumns:protected] => Array
(
)
)
[87] => Category Object
(
[languages:protected] =>
[bok_resources:protected] =>
[bok_topics:protected] =>
[bok_keywords:protected] =>
[id:protected] => 87
[type:protected] => category
[parent:protected] => 3
[label:protected] => Commercial & Institutional
[alreadyInSave:protected] =>
[alreadyInValidation:protected] =>
[validationFailures:protected] => Array
(
)
[_new:BaseObject:private] =>
[_deleted:BaseObject:private] =>
[modifiedColumns:protected] => Array
(
)
)
[88] => Category Object
(
[languages:protected] =>
[bok_resources:protected] =>
[bok_topics:protected] =>
[bok_keywords:protected] =>
[id:protected] => 88
[type:protected] => category
[parent:protected] => 3
[label:protected] => Demolition
[alreadyInSave:protected] =>
[alreadyInValidation:protected] =>
[validationFailures:protected] => Array
(
)
[_new:BaseObject:private] =>
[_deleted:BaseObject:private] =>
[modifiedColumns:protected] => Array
(
)
)
[91] => Category Object
(
[languages:protected] =>
[bok_resources:protected] =>
[bok_topics:protected] =>
[bok_keywords:protected] =>
[id:protected] => 91
[type:protected] => category
[parent:protected] => 3
[label:protected] => Heavy & Highway
[alreadyInSave:protected] =>
[alreadyInValidation:protected] =>
[validationFailures:protected] => Array
(
)
[_new:BaseObject:private] =>
[_deleted:BaseObject:private] =>
[modifiedColumns:protected] => Array
(
)
)
[90] => Category Object
(
[languages:protected] =>
[bok_resources:protected] =>
[bok_topics:protected] =>
[bok_keywords:protected] =>
[id:protected] => 90
[type:protected] => category
[parent:protected] => 3
[label:protected] => Industrial
[alreadyInSave:protected] =>
[alreadyInValidation:protected] =>
[validationFailures:protected] => Array
(
)
[_new:BaseObject:private] =>
[_deleted:BaseObject:private] =>
[modifiedColumns:protected] => Array
(
)
)
[92] => Category Object
(
[languages:protected] =>
[bok_resources:protected] =>
[bok_topics:protected] =>
[bok_keywords:protected] =>
[id:protected] => 92
[type:protected] => category
[parent:protected] => 3
[label:protected] => LEED/Green Construction
[alreadyInSave:protected] =>
[alreadyInValidation:protected] =>
[validationFailures:protected] => Array
(
)
[_new:BaseObject:private] =>
[_deleted:BaseObject:private] =>
[modifiedColumns:protected] => Array
(
)
)
[100] => Category Object
(
[languages:protected] =>
[bok_resources:protected] =>
[bok_topics:protected] =>
[bok_keywords:protected] =>
[id:protected] => 100
[type:protected] => category
[parent:protected] => 6
[label:protected] => Toolbox Talks
[alreadyInSave:protected] =>
[alreadyInValidation:protected] =>
[validationFailures:protected] => Array
(
)
[_new:BaseObject:private] =>
[_deleted:BaseObject:private] =>
[modifiedColumns:protected] => Array
(
)
)
)
[categories_initialized:protected] => 1
[mapped_items:protected] =>
[content:protected] =>
[files:protected] =>
[language:protected] => Language Object
(
[id:protected] => 1
[code:protected] => en
[name:protected] => English
[alreadyInSave:protected] =>
[alreadyInValidation:protected] =>
[validationFailures:protected] => Array
(
)
[_new:BaseObject:private] =>
[_deleted:BaseObject:private] =>
[modifiedColumns:protected] => Array
(
)
)
[old_record:protected] =>
[id:protected] => 4427
[old_id:protected] =>
[elcosh_id:protected] => d001657
[type:protected] => document
[display_type:protected] => HTML only (and links)
[user_id:protected] => 0
[language_id:protected] => 1
[tagging_id:protected] => Mike Aguilar
[priority_id:protected] => 1
[title:protected] => Toolbox Talk: Tower Crane Safety
[total_pages:protected] => 0
[billed_pages:protected] => 0
[publication_number:protected] =>
[part_of:protected] =>
[keywords:protected] => Tower Crane, Crane, Stability, Tipping, Lift Zone Safety, Lift, Zone, Safety, Struck by
[comments:protected] =>
[summary:protected] => The CPWR Toolbox Talk on Tower Crane Safety addresses the potential hazards of Tower Cranes and the importance of following procedure before and during Tower Crane operation. The resource includes a brief example, steps to prevent a related injury, and questions for discussion. It includes a graphic that illustrates a worker inspecting a Tower Crane before operation, which can be posted in a central location as a reminder of steps to work safely.
Available in
English and
Spanish.
[transition_comments:protected] =>
[external_link:protected] =>
[consol_link:protected] =>
[more_like_this:protected] => d001234,d001238,d001250,d001251,d001253,d001258,d001262,d001273
[permission_given_by:protected] =>
[published:protected] => T
[billable:protected] => F
[img_name:protected] =>
[img_ext:protected] => jpg
[img_width:protected] =>
[img_height:protected] =>
[img_credit:protected] =>
[img_practice:protected] =>
[vid_source_id:protected] =>
[vid_running_time:protected] =>
[vid_intended_audience:protected] =>
[vid_acquisition_info:protected] =>
[vid_cost:protected] =>
[vid_producer:protected] =>
[vid_filename:protected] =>
[vid_filename_downloadable:protected] =>
[date_summary:protected] =>
[date_permission_requested:protected] =>
[date_permission_received:protected] =>
[date_review_needed:protected] =>
[date_received:protected] => 12/23/21
[date_completed:protected] => 12/23/21
[date_billed:protected] =>
[date_modified:protected] => 05/19/23
[collBokExports:protected] =>
[lastBokExportCriteria:BaseElcoshItem:private] =>
[alreadyInSave:protected] =>
[alreadyInValidation:protected] =>
[validationFailures:protected] => Array
(
)
[_new:BaseObject:private] =>
[_deleted:BaseObject:private] =>
[modifiedColumns:protected] => Array
(
)
)
)
[3] => Search_Result Object
(
[title] => Toolbox Talk: Work Zone Safety: Working Around Vehicles
[image] => /record/images/notavailable-p.png
[blurb] => The CPWR Toolbox Talk on Working Around Vehicles in the Work Zone addresses methods to avoid being struck-by a vehicle on a construction site. The res...
[category] => Array
(
[0] => 12
[1] => 18
[2] => 52
[3] => 57
[4] => 70
[5] => 85
[6] => 87
[7] => 88
[8] => 89
[9] => 91
[10] => 90
[11] => 92
[12] => 93
[13] => 94
[14] => 95
[15] => 100
)
[labels] => Array
(
[0] => Crushed/Struck By
[1] => Work Environment
[2] => Hazards
[3] => Motor Vehicles/Heavy Equipment
[6] => Commercial Diver
[7] => Trades
[8] => Flagger
[10] => Operating Engineer
[12] => Truck Driver
[14] => Commercial & Institutional
[15] => Jobsites
[16] => Demolition
[18] => Disasters
[20] => Heavy & Highway
[22] => Industrial
[24] => LEED/Green Construction
[26] => Renovations
[28] => Residential
[30] => Underground
[32] => Toolbox Talks
[33] => Documents
[34] => Media & Documents
)
[type] => Toolbox Talks
[sub_category] =>
[url] => /document/4428/d001658/Toolbox%2BTalk%253A%2BWork%2BZone%2BSafety%253A%2BWorking%2BAround%2BVehicles.html
[item:protected] => DocumentRecord Object
(
[records:protected] => Array
(
)
[recordId:protected] =>
[searchWordClass:protected] =>
[searchWordPeerClass:protected] =>
[bok_record:protected] =>
[authors:protected] =>
[organizations:protected] =>
[collections:protected] =>
[categories:protected] => Array
(
[12] => Category Object
(
[languages:protected] =>
[bok_resources:protected] =>
[bok_topics:protected] =>
[bok_keywords:protected] =>
[id:protected] => 12
[type:protected] => category
[parent:protected] => 7
[label:protected] => Crushed/Struck By
[alreadyInSave:protected] =>
[alreadyInValidation:protected] =>
[validationFailures:protected] => Array
(
)
[_new:BaseObject:private] =>
[_deleted:BaseObject:private] =>
[modifiedColumns:protected] => Array
(
)
)
[18] => Category Object
(
[languages:protected] =>
[bok_resources:protected] =>
[bok_topics:protected] =>
[bok_keywords:protected] =>
[id:protected] => 18
[type:protected] => category
[parent:protected] => 7
[label:protected] => Motor Vehicles/Heavy Equipment
[alreadyInSave:protected] =>
[alreadyInValidation:protected] =>
[validationFailures:protected] => Array
(
)
[_new:BaseObject:private] =>
[_deleted:BaseObject:private] =>
[modifiedColumns:protected] => Array
(
)
)
[52] => Category Object
(
[languages:protected] =>
[bok_resources:protected] =>
[bok_topics:protected] =>
[bok_keywords:protected] =>
[id:protected] => 52
[type:protected] => category
[parent:protected] => 2
[label:protected] => Commercial Diver
[alreadyInSave:protected] =>
[alreadyInValidation:protected] =>
[validationFailures:protected] => Array
(
)
[_new:BaseObject:private] =>
[_deleted:BaseObject:private] =>
[modifiedColumns:protected] => Array
(
)
)
[57] => Category Object
(
[languages:protected] =>
[bok_resources:protected] =>
[bok_topics:protected] =>
[bok_keywords:protected] =>
[id:protected] => 57
[type:protected] => category
[parent:protected] => 2
[label:protected] => Flagger
[alreadyInSave:protected] =>
[alreadyInValidation:protected] =>
[validationFailures:protected] => Array
(
)
[_new:BaseObject:private] =>
[_deleted:BaseObject:private] =>
[modifiedColumns:protected] => Array
(
)
)
[70] => Category Object
(
[languages:protected] =>
[bok_resources:protected] =>
[bok_topics:protected] =>
[bok_keywords:protected] =>
[id:protected] => 70
[type:protected] => category
[parent:protected] => 2
[label:protected] => Operating Engineer
[alreadyInSave:protected] =>
[alreadyInValidation:protected] =>
[validationFailures:protected] => Array
(
)
[_new:BaseObject:private] =>
[_deleted:BaseObject:private] =>
[modifiedColumns:protected] => Array
(
)
)
[85] => Category Object
(
[languages:protected] =>
[bok_resources:protected] =>
[bok_topics:protected] =>
[bok_keywords:protected] =>
[id:protected] => 85
[type:protected] => category
[parent:protected] => 2
[label:protected] => Truck Driver
[alreadyInSave:protected] =>
[alreadyInValidation:protected] =>
[validationFailures:protected] => Array
(
)
[_new:BaseObject:private] =>
[_deleted:BaseObject:private] =>
[modifiedColumns:protected] => Array
(
)
)
[87] => Category Object
(
[languages:protected] =>
[bok_resources:protected] =>
[bok_topics:protected] =>
[bok_keywords:protected] =>
[id:protected] => 87
[type:protected] => category
[parent:protected] => 3
[label:protected] => Commercial & Institutional
[alreadyInSave:protected] =>
[alreadyInValidation:protected] =>
[validationFailures:protected] => Array
(
)
[_new:BaseObject:private] =>
[_deleted:BaseObject:private] =>
[modifiedColumns:protected] => Array
(
)
)
[88] => Category Object
(
[languages:protected] =>
[bok_resources:protected] =>
[bok_topics:protected] =>
[bok_keywords:protected] =>
[id:protected] => 88
[type:protected] => category
[parent:protected] => 3
[label:protected] => Demolition
[alreadyInSave:protected] =>
[alreadyInValidation:protected] =>
[validationFailures:protected] => Array
(
)
[_new:BaseObject:private] =>
[_deleted:BaseObject:private] =>
[modifiedColumns:protected] => Array
(
)
)
[89] => Category Object
(
[languages:protected] =>
[bok_resources:protected] =>
[bok_topics:protected] =>
[bok_keywords:protected] =>
[id:protected] => 89
[type:protected] => category
[parent:protected] => 3
[label:protected] => Disasters
[alreadyInSave:protected] =>
[alreadyInValidation:protected] =>
[validationFailures:protected] => Array
(
)
[_new:BaseObject:private] =>
[_deleted:BaseObject:private] =>
[modifiedColumns:protected] => Array
(
)
)
[91] => Category Object
(
[languages:protected] =>
[bok_resources:protected] =>
[bok_topics:protected] =>
[bok_keywords:protected] =>
[id:protected] => 91
[type:protected] => category
[parent:protected] => 3
[label:protected] => Heavy & Highway
[alreadyInSave:protected] =>
[alreadyInValidation:protected] =>
[validationFailures:protected] => Array
(
)
[_new:BaseObject:private] =>
[_deleted:BaseObject:private] =>
[modifiedColumns:protected] => Array
(
)
)
[90] => Category Object
(
[languages:protected] =>
[bok_resources:protected] =>
[bok_topics:protected] =>
[bok_keywords:protected] =>
[id:protected] => 90
[type:protected] => category
[parent:protected] => 3
[label:protected] => Industrial
[alreadyInSave:protected] =>
[alreadyInValidation:protected] =>
[validationFailures:protected] => Array
(
)
[_new:BaseObject:private] =>
[_deleted:BaseObject:private] =>
[modifiedColumns:protected] => Array
(
)
)
[92] => Category Object
(
[languages:protected] =>
[bok_resources:protected] =>
[bok_topics:protected] =>
[bok_keywords:protected] =>
[id:protected] => 92
[type:protected] => category
[parent:protected] => 3
[label:protected] => LEED/Green Construction
[alreadyInSave:protected] =>
[alreadyInValidation:protected] =>
[validationFailures:protected] => Array
(
)
[_new:BaseObject:private] =>
[_deleted:BaseObject:private] =>
[modifiedColumns:protected] => Array
(
)
)
[93] => Category Object
(
[languages:protected] =>
[bok_resources:protected] =>
[bok_topics:protected] =>
[bok_keywords:protected] =>
[id:protected] => 93
[type:protected] => category
[parent:protected] => 3
[label:protected] => Renovations
[alreadyInSave:protected] =>
[alreadyInValidation:protected] =>
[validationFailures:protected] => Array
(
)
[_new:BaseObject:private] =>
[_deleted:BaseObject:private] =>
[modifiedColumns:protected] => Array
(
)
)
[94] => Category Object
(
[languages:protected] =>
[bok_resources:protected] =>
[bok_topics:protected] =>
[bok_keywords:protected] =>
[id:protected] => 94
[type:protected] => category
[parent:protected] => 3
[label:protected] => Residential
[alreadyInSave:protected] =>
[alreadyInValidation:protected] =>
[validationFailures:protected] => Array
(
)
[_new:BaseObject:private] =>
[_deleted:BaseObject:private] =>
[modifiedColumns:protected] => Array
(
)
)
[95] => Category Object
(
[languages:protected] =>
[bok_resources:protected] =>
[bok_topics:protected] =>
[bok_keywords:protected] =>
[id:protected] => 95
[type:protected] => category
[parent:protected] => 3
[label:protected] => Underground
[alreadyInSave:protected] =>
[alreadyInValidation:protected] =>
[validationFailures:protected] => Array
(
)
[_new:BaseObject:private] =>
[_deleted:BaseObject:private] =>
[modifiedColumns:protected] => Array
(
)
)
[100] => Category Object
(
[languages:protected] =>
[bok_resources:protected] =>
[bok_topics:protected] =>
[bok_keywords:protected] =>
[id:protected] => 100
[type:protected] => category
[parent:protected] => 6
[label:protected] => Toolbox Talks
[alreadyInSave:protected] =>
[alreadyInValidation:protected] =>
[validationFailures:protected] => Array
(
)
[_new:BaseObject:private] =>
[_deleted:BaseObject:private] =>
[modifiedColumns:protected] => Array
(
)
)
)
[categories_initialized:protected] => 1
[mapped_items:protected] =>
[content:protected] =>
[files:protected] =>
[language:protected] => Language Object
(
[id:protected] => 1
[code:protected] => en
[name:protected] => English
[alreadyInSave:protected] =>
[alreadyInValidation:protected] =>
[validationFailures:protected] => Array
(
)
[_new:BaseObject:private] =>
[_deleted:BaseObject:private] =>
[modifiedColumns:protected] => Array
(
)
)
[old_record:protected] =>
[id:protected] => 4428
[old_id:protected] =>
[elcosh_id:protected] => d001658
[type:protected] => document
[display_type:protected] => HTML only (and links)
[user_id:protected] => 0
[language_id:protected] => 1
[tagging_id:protected] => Daniela Caceres
[priority_id:protected] => 1
[title:protected] => Toolbox Talk: Work Zone Safety: Working Around Vehicles
[total_pages:protected] => 0
[billed_pages:protected] => 0
[publication_number:protected] =>
[part_of:protected] =>
[keywords:protected] => Struck, Struck by, Vehicle, Work Zone Safety, Truck, Operator, Driver, Mobile Equipment
[comments:protected] =>
[summary:protected] => The CPWR Toolbox Talk on Working Around Vehicles in the Work Zone addresses methods to avoid being struck-by a vehicle on a construction site. The resource includes a case example, steps to prevent a related injury, and questions for discussion. It includes a graphic that illustrates the hazard, which can be posted in a central location as a reminder of steps to work safely. Available in
English and
Spanish.
[transition_comments:protected] =>
[external_link:protected] =>
[consol_link:protected] =>
[more_like_this:protected] => d001640
[permission_given_by:protected] =>
[published:protected] => T
[billable:protected] => F
[img_name:protected] =>
[img_ext:protected] =>
[img_width:protected] =>
[img_height:protected] =>
[img_credit:protected] =>
[img_practice:protected] =>
[vid_source_id:protected] =>
[vid_running_time:protected] =>
[vid_intended_audience:protected] =>
[vid_acquisition_info:protected] =>
[vid_cost:protected] =>
[vid_producer:protected] =>
[vid_filename:protected] =>
[vid_filename_downloadable:protected] =>
[date_summary:protected] =>
[date_permission_requested:protected] =>
[date_permission_received:protected] =>
[date_review_needed:protected] =>
[date_received:protected] => 12/23/21
[date_completed:protected] => 12/23/21
[date_billed:protected] =>
[date_modified:protected] => 05/19/23
[collBokExports:protected] =>
[lastBokExportCriteria:BaseElcoshItem:private] =>
[alreadyInSave:protected] =>
[alreadyInValidation:protected] =>
[validationFailures:protected] => Array
(
)
[_new:BaseObject:private] =>
[_deleted:BaseObject:private] =>
[modifiedColumns:protected] => Array
(
)
)
)
[4] => Search_Result Object
(
[title] => Construction Dive -- DeWalt's Jobsite Pro headphones recalled for fire hazards
[image] => /record/images/notavailable-p.png
[blurb] => A recall notice by the United States Consumer Product Safety Commission affects over 300,000 DeWalt Jobsite Pro Headphones. The recall is a result of...
[category] => Array
(
[0] => 16
[1] => 44
[2] => 45
[3] => 46
[4] => 47
[5] => 48
[6] => 49
[7] => 50
[8] => 51
[9] => 52
[10] => 53
[11] => 54
[12] => 55
[13] => 56
[14] => 57
[15] => 58
[16] => 59
[17] => 60
[18] => 61
[19] => 64
[20] => 65
[21] => 66
[22] => 67
[23] => 68
[24] => 69
[25] => 70
[26] => 71
[27] => 72
[28] => 73
[29] => 74
[30] => 75
[31] => 76
[32] => 77
[33] => 63
[34] => 78
[35] => 79
[36] => 80
[37] => 81
[38] => 82
[39] => 62
[40] => 83
[41] => 84
[42] => 85
[43] => 86
[44] => 87
[45] => 88
[46] => 89
[47] => 91
[48] => 90
[49] => 92
[50] => 93
[51] => 94
[52] => 95
)
[labels] => Array
(
[0] => Fire & Explosions
[1] => Work Environment
[2] => Hazards
[3] => Acoustical Ceiling Carpenter
[4] => Trades
[5] => Asbestos/Insulator
[7] => Boilermaker
[9] => Bricklayer
[11] => Cabinetmaker
[13] => Carpenter
[15] => Carpet Layer
[17] => Cement Mason
[19] => Commercial Diver
[21] => Concrete Polisher
[23] => Drywall Applicator Specialist
[25] => Electrical Worker
[27] => Elevator Constructor
[29] => Flagger
[31] => Glazier
[33] => Hazardous Waste Cleanup
[35] => HVAC
[37] => Interior Systems Carpenter
[39] => Laborer
[41] => Landscaper
[43] => Lather
[45] => Lead Abatement Worker
[47] => Maintenance Worker
[49] => Millwright
[51] => Operating Engineer
[53] => Painter
[55] => Paper Hanger
[57] => PCC/Restoration
[59] => Pile Driver
[61] => Plasterer
[63] => Plumber/Pipefitter
[65] => Refractory Worker
[67] => Reinforcing Ironworker
[69] => Roofer/Waterproofer
[71] => Scaffold Erector
[73] => Sheetmetal Worker
[75] => Sprinkler Fitter
[77] => Stonemason
[79] => Structural Ironworker
[81] => Terrazzo Worker
[83] => Tile Setter
[85] => Truck Driver
[87] => Welder
[89] => Commercial & Institutional
[90] => Jobsites
[91] => Demolition
[93] => Disasters
[95] => Heavy & Highway
[97] => Industrial
[99] => LEED/Green Construction
[101] => Renovations
[103] => Residential
[105] => Underground
)
[type] =>
[sub_category] =>
[url] => /document/4426/d001656/Construction%2BDive%2B--%2BDeWalt%2527s%2BJobsite%2BPro%2Bheadphones%2Brecalled%2Bfor%2Bfire%2Bhazards.html
[item:protected] => DocumentRecord Object
(
[records:protected] => Array
(
)
[recordId:protected] =>
[searchWordClass:protected] =>
[searchWordPeerClass:protected] =>
[bok_record:protected] =>
[authors:protected] =>
[organizations:protected] =>
[collections:protected] =>
[categories:protected] => Array
(
[16] => Category Object
(
[languages:protected] =>
[bok_resources:protected] =>
[bok_topics:protected] =>
[bok_keywords:protected] =>
[id:protected] => 16
[type:protected] => category
[parent:protected] => 7
[label:protected] => Fire & Explosions
[alreadyInSave:protected] =>
[alreadyInValidation:protected] =>
[validationFailures:protected] => Array
(
)
[_new:BaseObject:private] =>
[_deleted:BaseObject:private] =>
[modifiedColumns:protected] => Array
(
)
)
[44] => Category Object
(
[languages:protected] =>
[bok_resources:protected] =>
[bok_topics:protected] =>
[bok_keywords:protected] =>
[id:protected] => 44
[type:protected] => category
[parent:protected] => 2
[label:protected] => Acoustical Ceiling Carpenter
[alreadyInSave:protected] =>
[alreadyInValidation:protected] =>
[validationFailures:protected] => Array
(
)
[_new:BaseObject:private] =>
[_deleted:BaseObject:private] =>
[modifiedColumns:protected] => Array
(
)
)
[45] => Category Object
(
[languages:protected] =>
[bok_resources:protected] =>
[bok_topics:protected] =>
[bok_keywords:protected] =>
[id:protected] => 45
[type:protected] => category
[parent:protected] => 2
[label:protected] => Asbestos/Insulator
[alreadyInSave:protected] =>
[alreadyInValidation:protected] =>
[validationFailures:protected] => Array
(
)
[_new:BaseObject:private] =>
[_deleted:BaseObject:private] =>
[modifiedColumns:protected] => Array
(
)
)
[46] => Category Object
(
[languages:protected] =>
[bok_resources:protected] =>
[bok_topics:protected] =>
[bok_keywords:protected] =>
[id:protected] => 46
[type:protected] => category
[parent:protected] => 2
[label:protected] => Boilermaker
[alreadyInSave:protected] =>
[alreadyInValidation:protected] =>
[validationFailures:protected] => Array
(
)
[_new:BaseObject:private] =>
[_deleted:BaseObject:private] =>
[modifiedColumns:protected] => Array
(
)
)
[47] => Category Object
(
[languages:protected] =>
[bok_resources:protected] =>
[bok_topics:protected] =>
[bok_keywords:protected] =>
[id:protected] => 47
[type:protected] => category
[parent:protected] => 2
[label:protected] => Bricklayer
[alreadyInSave:protected] =>
[alreadyInValidation:protected] =>
[validationFailures:protected] => Array
(
)
[_new:BaseObject:private] =>
[_deleted:BaseObject:private] =>
[modifiedColumns:protected] => Array
(
)
)
[48] => Category Object
(
[languages:protected] =>
[bok_resources:protected] =>
[bok_topics:protected] =>
[bok_keywords:protected] =>
[id:protected] => 48
[type:protected] => category
[parent:protected] => 2
[label:protected] => Cabinetmaker
[alreadyInSave:protected] =>
[alreadyInValidation:protected] =>
[validationFailures:protected] => Array
(
)
[_new:BaseObject:private] =>
[_deleted:BaseObject:private] =>
[modifiedColumns:protected] => Array
(
)
)
[49] => Category Object
(
[languages:protected] =>
[bok_resources:protected] =>
[bok_topics:protected] =>
[bok_keywords:protected] =>
[id:protected] => 49
[type:protected] => category
[parent:protected] => 2
[label:protected] => Carpenter
[alreadyInSave:protected] =>
[alreadyInValidation:protected] =>
[validationFailures:protected] => Array
(
)
[_new:BaseObject:private] =>
[_deleted:BaseObject:private] =>
[modifiedColumns:protected] => Array
(
)
)
[50] => Category Object
(
[languages:protected] =>
[bok_resources:protected] =>
[bok_topics:protected] =>
[bok_keywords:protected] =>
[id:protected] => 50
[type:protected] => category
[parent:protected] => 2
[label:protected] => Carpet Layer
[alreadyInSave:protected] =>
[alreadyInValidation:protected] =>
[validationFailures:protected] => Array
(
)
[_new:BaseObject:private] =>
[_deleted:BaseObject:private] =>
[modifiedColumns:protected] => Array
(
)
)
[51] => Category Object
(
[languages:protected] =>
[bok_resources:protected] =>
[bok_topics:protected] =>
[bok_keywords:protected] =>
[id:protected] => 51
[type:protected] => category
[parent:protected] => 2
[label:protected] => Cement Mason
[alreadyInSave:protected] =>
[alreadyInValidation:protected] =>
[validationFailures:protected] => Array
(
)
[_new:BaseObject:private] =>
[_deleted:BaseObject:private] =>
[modifiedColumns:protected] => Array
(
)
)
[52] => Category Object
(
[languages:protected] =>
[bok_resources:protected] =>
[bok_topics:protected] =>
[bok_keywords:protected] =>
[id:protected] => 52
[type:protected] => category
[parent:protected] => 2
[label:protected] => Commercial Diver
[alreadyInSave:protected] =>
[alreadyInValidation:protected] =>
[validationFailures:protected] => Array
(
)
[_new:BaseObject:private] =>
[_deleted:BaseObject:private] =>
[modifiedColumns:protected] => Array
(
)
)
[53] => Category Object
(
[languages:protected] =>
[bok_resources:protected] =>
[bok_topics:protected] =>
[bok_keywords:protected] =>
[id:protected] => 53
[type:protected] => category
[parent:protected] => 2
[label:protected] => Concrete Polisher
[alreadyInSave:protected] =>
[alreadyInValidation:protected] =>
[validationFailures:protected] => Array
(
)
[_new:BaseObject:private] =>
[_deleted:BaseObject:private] =>
[modifiedColumns:protected] => Array
(
)
)
[54] => Category Object
(
[languages:protected] =>
[bok_resources:protected] =>
[bok_topics:protected] =>
[bok_keywords:protected] =>
[id:protected] => 54
[type:protected] => category
[parent:protected] => 2
[label:protected] => Drywall Applicator Specialist
[alreadyInSave:protected] =>
[alreadyInValidation:protected] =>
[validationFailures:protected] => Array
(
)
[_new:BaseObject:private] =>
[_deleted:BaseObject:private] =>
[modifiedColumns:protected] => Array
(
)
)
[55] => Category Object
(
[languages:protected] =>
[bok_resources:protected] =>
[bok_topics:protected] =>
[bok_keywords:protected] =>
[id:protected] => 55
[type:protected] => category
[parent:protected] => 2
[label:protected] => Electrical Worker
[alreadyInSave:protected] =>
[alreadyInValidation:protected] =>
[validationFailures:protected] => Array
(
)
[_new:BaseObject:private] =>
[_deleted:BaseObject:private] =>
[modifiedColumns:protected] => Array
(
)
)
[56] => Category Object
(
[languages:protected] =>
[bok_resources:protected] =>
[bok_topics:protected] =>
[bok_keywords:protected] =>
[id:protected] => 56
[type:protected] => category
[parent:protected] => 2
[label:protected] => Elevator Constructor
[alreadyInSave:protected] =>
[alreadyInValidation:protected] =>
[validationFailures:protected] => Array
(
)
[_new:BaseObject:private] =>
[_deleted:BaseObject:private] =>
[modifiedColumns:protected] => Array
(
)
)
[57] => Category Object
(
[languages:protected] =>
[bok_resources:protected] =>
[bok_topics:protected] =>
[bok_keywords:protected] =>
[id:protected] => 57
[type:protected] => category
[parent:protected] => 2
[label:protected] => Flagger
[alreadyInSave:protected] =>
[alreadyInValidation:protected] =>
[validationFailures:protected] => Array
(
)
[_new:BaseObject:private] =>
[_deleted:BaseObject:private] =>
[modifiedColumns:protected] => Array
(
)
)
[58] => Category Object
(
[languages:protected] =>
[bok_resources:protected] =>
[bok_topics:protected] =>
[bok_keywords:protected] =>
[id:protected] => 58
[type:protected] => category
[parent:protected] => 2
[label:protected] => Glazier
[alreadyInSave:protected] =>
[alreadyInValidation:protected] =>
[validationFailures:protected] => Array
(
)
[_new:BaseObject:private] =>
[_deleted:BaseObject:private] =>
[modifiedColumns:protected] => Array
(
)
)
[59] => Category Object
(
[languages:protected] =>
[bok_resources:protected] =>
[bok_topics:protected] =>
[bok_keywords:protected] =>
[id:protected] => 59
[type:protected] => category
[parent:protected] => 2
[label:protected] => Hazardous Waste Cleanup
[alreadyInSave:protected] =>
[alreadyInValidation:protected] =>
[validationFailures:protected] => Array
(
)
[_new:BaseObject:private] =>
[_deleted:BaseObject:private] =>
[modifiedColumns:protected] => Array
(
)
)
[60] => Category Object
(
[languages:protected] =>
[bok_resources:protected] =>
[bok_topics:protected] =>
[bok_keywords:protected] =>
[id:protected] => 60
[type:protected] => category
[parent:protected] => 2
[label:protected] => HVAC
[alreadyInSave:protected] =>
[alreadyInValidation:protected] =>
[validationFailures:protected] => Array
(
)
[_new:BaseObject:private] =>
[_deleted:BaseObject:private] =>
[modifiedColumns:protected] => Array
(
)
)
[61] => Category Object
(
[languages:protected] =>
[bok_resources:protected] =>
[bok_topics:protected] =>
[bok_keywords:protected] =>
[id:protected] => 61
[type:protected] => category
[parent:protected] => 2
[label:protected] => Interior Systems Carpenter
[alreadyInSave:protected] =>
[alreadyInValidation:protected] =>
[validationFailures:protected] => Array
(
)
[_new:BaseObject:private] =>
[_deleted:BaseObject:private] =>
[modifiedColumns:protected] => Array
(
)
)
[64] => Category Object
(
[languages:protected] =>
[bok_resources:protected] =>
[bok_topics:protected] =>
[bok_keywords:protected] =>
[id:protected] => 64
[type:protected] => category
[parent:protected] => 2
[label:protected] => Laborer
[alreadyInSave:protected] =>
[alreadyInValidation:protected] =>
[validationFailures:protected] => Array
(
)
[_new:BaseObject:private] =>
[_deleted:BaseObject:private] =>
[modifiedColumns:protected] => Array
(
)
)
[65] => Category Object
(
[languages:protected] =>
[bok_resources:protected] =>
[bok_topics:protected] =>
[bok_keywords:protected] =>
[id:protected] => 65
[type:protected] => category
[parent:protected] => 2
[label:protected] => Landscaper
[alreadyInSave:protected] =>
[alreadyInValidation:protected] =>
[validationFailures:protected] => Array
(
)
[_new:BaseObject:private] =>
[_deleted:BaseObject:private] =>
[modifiedColumns:protected] => Array
(
)
)
[66] => Category Object
(
[languages:protected] =>
[bok_resources:protected] =>
[bok_topics:protected] =>
[bok_keywords:protected] =>
[id:protected] => 66
[type:protected] => category
[parent:protected] => 2
[label:protected] => Lather
[alreadyInSave:protected] =>
[alreadyInValidation:protected] =>
[validationFailures:protected] => Array
(
)
[_new:BaseObject:private] =>
[_deleted:BaseObject:private] =>
[modifiedColumns:protected] => Array
(
)
)
[67] => Category Object
(
[languages:protected] =>
[bok_resources:protected] =>
[bok_topics:protected] =>
[bok_keywords:protected] =>
[id:protected] => 67
[type:protected] => category
[parent:protected] => 2
[label:protected] => Lead Abatement Worker
[alreadyInSave:protected] =>
[alreadyInValidation:protected] =>
[validationFailures:protected] => Array
(
)
[_new:BaseObject:private] =>
[_deleted:BaseObject:private] =>
[modifiedColumns:protected] => Array
(
)
)
[68] => Category Object
(
[languages:protected] =>
[bok_resources:protected] =>
[bok_topics:protected] =>
[bok_keywords:protected] =>
[id:protected] => 68
[type:protected] => category
[parent:protected] => 2
[label:protected] => Maintenance Worker
[alreadyInSave:protected] =>
[alreadyInValidation:protected] =>
[validationFailures:protected] => Array
(
)
[_new:BaseObject:private] =>
[_deleted:BaseObject:private] =>
[modifiedColumns:protected] => Array
(
)
)
[69] => Category Object
(
[languages:protected] =>
[bok_resources:protected] =>
[bok_topics:protected] =>
[bok_keywords:protected] =>
[id:protected] => 69
[type:protected] => category
[parent:protected] => 2
[label:protected] => Millwright
[alreadyInSave:protected] =>
[alreadyInValidation:protected] =>
[validationFailures:protected] => Array
(
)
[_new:BaseObject:private] =>
[_deleted:BaseObject:private] =>
[modifiedColumns:protected] => Array
(
)
)
[70] => Category Object
(
[languages:protected] =>
[bok_resources:protected] =>
[bok_topics:protected] =>
[bok_keywords:protected] =>
[id:protected] => 70
[type:protected] => category
[parent:protected] => 2
[label:protected] => Operating Engineer
[alreadyInSave:protected] =>
[alreadyInValidation:protected] =>
[validationFailures:protected] => Array
(
)
[_new:BaseObject:private] =>
[_deleted:BaseObject:private] =>
[modifiedColumns:protected] => Array
(
)
)
[71] => Category Object
(
[languages:protected] =>
[bok_resources:protected] =>
[bok_topics:protected] =>
[bok_keywords:protected] =>
[id:protected] => 71
[type:protected] => category
[parent:protected] => 2
[label:protected] => Painter
[alreadyInSave:protected] =>
[alreadyInValidation:protected] =>
[validationFailures:protected] => Array
(
)
[_new:BaseObject:private] =>
[_deleted:BaseObject:private] =>
[modifiedColumns:protected] => Array
(
)
)
[72] => Category Object
(
[languages:protected] =>
[bok_resources:protected] =>
[bok_topics:protected] =>
[bok_keywords:protected] =>
[id:protected] => 72
[type:protected] => category
[parent:protected] => 2
[label:protected] => Paper Hanger
[alreadyInSave:protected] =>
[alreadyInValidation:protected] =>
[validationFailures:protected] => Array
(
)
[_new:BaseObject:private] =>
[_deleted:BaseObject:private] =>
[modifiedColumns:protected] => Array
(
)
)
[73] => Category Object
(
[languages:protected] =>
[bok_resources:protected] =>
[bok_topics:protected] =>
[bok_keywords:protected] =>
[id:protected] => 73
[type:protected] => category
[parent:protected] => 2
[label:protected] => PCC/Restoration
[alreadyInSave:protected] =>
[alreadyInValidation:protected] =>
[validationFailures:protected] => Array
(
)
[_new:BaseObject:private] =>
[_deleted:BaseObject:private] =>
[modifiedColumns:protected] => Array
(
)
)
[74] => Category Object
(
[languages:protected] =>
[bok_resources:protected] =>
[bok_topics:protected] =>
[bok_keywords:protected] =>
[id:protected] => 74
[type:protected] => category
[parent:protected] => 2
[label:protected] => Pile Driver
[alreadyInSave:protected] =>
[alreadyInValidation:protected] =>
[validationFailures:protected] => Array
(
)
[_new:BaseObject:private] =>
[_deleted:BaseObject:private] =>
[modifiedColumns:protected] => Array
(
)
)
[75] => Category Object
(
[languages:protected] =>
[bok_resources:protected] =>
[bok_topics:protected] =>
[bok_keywords:protected] =>
[id:protected] => 75
[type:protected] => category
[parent:protected] => 2
[label:protected] => Plasterer
[alreadyInSave:protected] =>
[alreadyInValidation:protected] =>
[validationFailures:protected] => Array
(
)
[_new:BaseObject:private] =>
[_deleted:BaseObject:private] =>
[modifiedColumns:protected] => Array
(
)
)
[76] => Category Object
(
[languages:protected] =>
[bok_resources:protected] =>
[bok_topics:protected] =>
[bok_keywords:protected] =>
[id:protected] => 76
[type:protected] => category
[parent:protected] => 2
[label:protected] => Plumber/Pipefitter
[alreadyInSave:protected] =>
[alreadyInValidation:protected] =>
[validationFailures:protected] => Array
(
)
[_new:BaseObject:private] =>
[_deleted:BaseObject:private] =>
[modifiedColumns:protected] => Array
(
)
)
[77] => Category Object
(
[languages:protected] =>
[bok_resources:protected] =>
[bok_topics:protected] =>
[bok_keywords:protected] =>
[id:protected] => 77
[type:protected] => category
[parent:protected] => 2
[label:protected] => Refractory Worker
[alreadyInSave:protected] =>
[alreadyInValidation:protected] =>
[validationFailures:protected] => Array
(
)
[_new:BaseObject:private] =>
[_deleted:BaseObject:private] =>
[modifiedColumns:protected] => Array
(
)
)
[63] => Category Object
(
[languages:protected] =>
[bok_resources:protected] =>
[bok_topics:protected] =>
[bok_keywords:protected] =>
[id:protected] => 63
[type:protected] => category
[parent:protected] => 2
[label:protected] => Reinforcing Ironworker
[alreadyInSave:protected] =>
[alreadyInValidation:protected] =>
[validationFailures:protected] => Array
(
)
[_new:BaseObject:private] =>
[_deleted:BaseObject:private] =>
[modifiedColumns:protected] => Array
(
)
)
[78] => Category Object
(
[languages:protected] =>
[bok_resources:protected] =>
[bok_topics:protected] =>
[bok_keywords:protected] =>
[id:protected] => 78
[type:protected] => category
[parent:protected] => 2
[label:protected] => Roofer/Waterproofer
[alreadyInSave:protected] =>
[alreadyInValidation:protected] =>
[validationFailures:protected] => Array
(
)
[_new:BaseObject:private] =>
[_deleted:BaseObject:private] =>
[modifiedColumns:protected] => Array
(
)
)
[79] => Category Object
(
[languages:protected] =>
[bok_resources:protected] =>
[bok_topics:protected] =>
[bok_keywords:protected] =>
[id:protected] => 79
[type:protected] => category
[parent:protected] => 2
[label:protected] => Scaffold Erector
[alreadyInSave:protected] =>
[alreadyInValidation:protected] =>
[validationFailures:protected] => Array
(
)
[_new:BaseObject:private] =>
[_deleted:BaseObject:private] =>
[modifiedColumns:protected] => Array
(
)
)
[80] => Category Object
(
[languages:protected] =>
[bok_resources:protected] =>
[bok_topics:protected] =>
[bok_keywords:protected] =>
[id:protected] => 80
[type:protected] => category
[parent:protected] => 2
[label:protected] => Sheetmetal Worker
[alreadyInSave:protected] =>
[alreadyInValidation:protected] =>
[validationFailures:protected] => Array
(
)
[_new:BaseObject:private] =>
[_deleted:BaseObject:private] =>
[modifiedColumns:protected] => Array
(
)
)
[81] => Category Object
(
[languages:protected] =>
[bok_resources:protected] =>
[bok_topics:protected] =>
[bok_keywords:protected] =>
[id:protected] => 81
[type:protected] => category
[parent:protected] => 2
[label:protected] => Sprinkler Fitter
[alreadyInSave:protected] =>
[alreadyInValidation:protected] =>
[validationFailures:protected] => Array
(
)
[_new:BaseObject:private] =>
[_deleted:BaseObject:private] =>
[modifiedColumns:protected] => Array
(
)
)
[82] => Category Object
(
[languages:protected] =>
[bok_resources:protected] =>
[bok_topics:protected] =>
[bok_keywords:protected] =>
[id:protected] => 82
[type:protected] => category
[parent:protected] => 2
[label:protected] => Stonemason
[alreadyInSave:protected] =>
[alreadyInValidation:protected] =>
[validationFailures:protected] => Array
(
)
[_new:BaseObject:private] =>
[_deleted:BaseObject:private] =>
[modifiedColumns:protected] => Array
(
)
)
[62] => Category Object
(
[languages:protected] =>
[bok_resources:protected] =>
[bok_topics:protected] =>
[bok_keywords:protected] =>
[id:protected] => 62
[type:protected] => category
[parent:protected] => 2
[label:protected] => Structural Ironworker
[alreadyInSave:protected] =>
[alreadyInValidation:protected] =>
[validationFailures:protected] => Array
(
)
[_new:BaseObject:private] =>
[_deleted:BaseObject:private] =>
[modifiedColumns:protected] => Array
(
)
)
[83] => Category Object
(
[languages:protected] =>
[bok_resources:protected] =>
[bok_topics:protected] =>
[bok_keywords:protected] =>
[id:protected] => 83
[type:protected] => category
[parent:protected] => 2
[label:protected] => Terrazzo Worker
[alreadyInSave:protected] =>
[alreadyInValidation:protected] =>
[validationFailures:protected] => Array
(
)
[_new:BaseObject:private] =>
[_deleted:BaseObject:private] =>
[modifiedColumns:protected] => Array
(
)
)
[84] => Category Object
(
[languages:protected] =>
[bok_resources:protected] =>
[bok_topics:protected] =>
[bok_keywords:protected] =>
[id:protected] => 84
[type:protected] => category
[parent:protected] => 2
[label:protected] => Tile Setter
[alreadyInSave:protected] =>
[alreadyInValidation:protected] =>
[validationFailures:protected] => Array
(
)
[_new:BaseObject:private] =>
[_deleted:BaseObject:private] =>
[modifiedColumns:protected] => Array
(
)
)
[85] => Category Object
(
[languages:protected] =>
[bok_resources:protected] =>
[bok_topics:protected] =>
[bok_keywords:protected] =>
[id:protected] => 85
[type:protected] => category
[parent:protected] => 2
[label:protected] => Truck Driver
[alreadyInSave:protected] =>
[alreadyInValidation:protected] =>
[validationFailures:protected] => Array
(
)
[_new:BaseObject:private] =>
[_deleted:BaseObject:private] =>
[modifiedColumns:protected] => Array
(
)
)
[86] => Category Object
(
[languages:protected] =>
[bok_resources:protected] =>
[bok_topics:protected] =>
[bok_keywords:protected] =>
[id:protected] => 86
[type:protected] => category
[parent:protected] => 2
[label:protected] => Welder
[alreadyInSave:protected] =>
[alreadyInValidation:protected] =>
[validationFailures:protected] => Array
(
)
[_new:BaseObject:private] =>
[_deleted:BaseObject:private] =>
[modifiedColumns:protected] => Array
(
)
)
[87] => Category Object
(
[languages:protected] =>
[bok_resources:protected] =>
[bok_topics:protected] =>
[bok_keywords:protected] =>
[id:protected] => 87
[type:protected] => category
[parent:protected] => 3
[label:protected] => Commercial & Institutional
[alreadyInSave:protected] =>
[alreadyInValidation:protected] =>
[validationFailures:protected] => Array
(
)
[_new:BaseObject:private] =>
[_deleted:BaseObject:private] =>
[modifiedColumns:protected] => Array
(
)
)
[88] => Category Object
(
[languages:protected] =>
[bok_resources:protected] =>
[bok_topics:protected] =>
[bok_keywords:protected] =>
[id:protected] => 88
[type:protected] => category
[parent:protected] => 3
[label:protected] => Demolition
[alreadyInSave:protected] =>
[alreadyInValidation:protected] =>
[validationFailures:protected] => Array
(
)
[_new:BaseObject:private] =>
[_deleted:BaseObject:private] =>
[modifiedColumns:protected] => Array
(
)
)
[89] => Category Object
(
[languages:protected] =>
[bok_resources:protected] =>
[bok_topics:protected] =>
[bok_keywords:protected] =>
[id:protected] => 89
[type:protected] => category
[parent:protected] => 3
[label:protected] => Disasters
[alreadyInSave:protected] =>
[alreadyInValidation:protected] =>
[validationFailures:protected] => Array
(
)
[_new:BaseObject:private] =>
[_deleted:BaseObject:private] =>
[modifiedColumns:protected] => Array
(
)
)
[91] => Category Object
(
[languages:protected] =>
[bok_resources:protected] =>
[bok_topics:protected] =>
[bok_keywords:protected] =>
[id:protected] => 91
[type:protected] => category
[parent:protected] => 3
[label:protected] => Heavy & Highway
[alreadyInSave:protected] =>
[alreadyInValidation:protected] =>
[validationFailures:protected] => Array
(
)
[_new:BaseObject:private] =>
[_deleted:BaseObject:private] =>
[modifiedColumns:protected] => Array
(
)
)
[90] => Category Object
(
[languages:protected] =>
[bok_resources:protected] =>
[bok_topics:protected] =>
[bok_keywords:protected] =>
[id:protected] => 90
[type:protected] => category
[parent:protected] => 3
[label:protected] => Industrial
[alreadyInSave:protected] =>
[alreadyInValidation:protected] =>
[validationFailures:protected] => Array
(
)
[_new:BaseObject:private] =>
[_deleted:BaseObject:private] =>
[modifiedColumns:protected] => Array
(
)
)
[92] => Category Object
(
[languages:protected] =>
[bok_resources:protected] =>
[bok_topics:protected] =>
[bok_keywords:protected] =>
[id:protected] => 92
[type:protected] => category
[parent:protected] => 3
[label:protected] => LEED/Green Construction
[alreadyInSave:protected] =>
[alreadyInValidation:protected] =>
[validationFailures:protected] => Array
(
)
[_new:BaseObject:private] =>
[_deleted:BaseObject:private] =>
[modifiedColumns:protected] => Array
(
)
)
[93] => Category Object
(
[languages:protected] =>
[bok_resources:protected] =>
[bok_topics:protected] =>
[bok_keywords:protected] =>
[id:protected] => 93
[type:protected] => category
[parent:protected] => 3
[label:protected] => Renovations
[alreadyInSave:protected] =>
[alreadyInValidation:protected] =>
[validationFailures:protected] => Array
(
)
[_new:BaseObject:private] =>
[_deleted:BaseObject:private] =>
[modifiedColumns:protected] => Array
(
)
)
[94] => Category Object
(
[languages:protected] =>
[bok_resources:protected] =>
[bok_topics:protected] =>
[bok_keywords:protected] =>
[id:protected] => 94
[type:protected] => category
[parent:protected] => 3
[label:protected] => Residential
[alreadyInSave:protected] =>
[alreadyInValidation:protected] =>
[validationFailures:protected] => Array
(
)
[_new:BaseObject:private] =>
[_deleted:BaseObject:private] =>
[modifiedColumns:protected] => Array
(
)
)
[95] => Category Object
(
[languages:protected] =>
[bok_resources:protected] =>
[bok_topics:protected] =>
[bok_keywords:protected] =>
[id:protected] => 95
[type:protected] => category
[parent:protected] => 3
[label:protected] => Underground
[alreadyInSave:protected] =>
[alreadyInValidation:protected] =>
[validationFailures:protected] => Array
(
)
[_new:BaseObject:private] =>
[_deleted:BaseObject:private] =>
[modifiedColumns:protected] => Array
(
)
)
)
[categories_initialized:protected] => 1
[mapped_items:protected] =>
[content:protected] =>
[files:protected] =>
[language:protected] => Language Object
(
[id:protected] => 1
[code:protected] => en
[name:protected] => English
[alreadyInSave:protected] =>
[alreadyInValidation:protected] =>
[validationFailures:protected] => Array
(
)
[_new:BaseObject:private] =>
[_deleted:BaseObject:private] =>
[modifiedColumns:protected] => Array
(
)
)
[old_record:protected] =>
[id:protected] => 4426
[old_id:protected] =>
[elcosh_id:protected] => d001656
[type:protected] => document
[display_type:protected] => HTML only (and links)
[user_id:protected] => 0
[language_id:protected] => 1
[tagging_id:protected] => Mike Aguilar
[priority_id:protected] => 1
[title:protected] => Construction Dive -- DeWalt's Jobsite Pro headphones recalled for fire hazards
[total_pages:protected] => 1
[billed_pages:protected] => 1
[publication_number:protected] =>
[part_of:protected] =>
[keywords:protected] => DeWalt, Fire Hazards, recall, headphones
[comments:protected] =>
[summary:protected] => A recall notice by the United States Consumer Product Safety Commission affects over 300,000 DeWalt Jobsite Pro Headphones. The recall is a result of a malfunction that can cause earbuds to overheat while charging or during use, leading to fire and burn hazards.
[transition_comments:protected] =>
[external_link:protected] => https://www.constructiondive.com/news/dewalts-jobsite-pro-headphones-recalled-for-fire-hazards/611248/?utm_source=Sailthru&utm_medium=email&utm_campaign=Issue:%202021-12-10%20Construction%20Dive%20Newsletter%20%5Bissue:38532%5D&utm_term=Construction%20Dive
[consol_link:protected] =>
[more_like_this:protected] =>
[permission_given_by:protected] =>
[published:protected] => T
[billable:protected] => F
[img_name:protected] =>
[img_ext:protected] =>
[img_width:protected] =>
[img_height:protected] =>
[img_credit:protected] =>
[img_practice:protected] =>
[vid_source_id:protected] =>
[vid_running_time:protected] =>
[vid_intended_audience:protected] =>
[vid_acquisition_info:protected] =>
[vid_cost:protected] =>
[vid_producer:protected] =>
[vid_filename:protected] =>
[vid_filename_downloadable:protected] =>
[date_summary:protected] =>
[date_permission_requested:protected] =>
[date_permission_received:protected] =>
[date_review_needed:protected] =>
[date_received:protected] => 12/13/21
[date_completed:protected] => 12/13/21
[date_billed:protected] =>
[date_modified:protected] => 12/13/21
[collBokExports:protected] =>
[lastBokExportCriteria:BaseElcoshItem:private] =>
[alreadyInSave:protected] =>
[alreadyInValidation:protected] =>
[validationFailures:protected] => Array
(
)
[_new:BaseObject:private] =>
[_deleted:BaseObject:private] =>
[modifiedColumns:protected] => Array
(
)
)
)
)
[new_images] => Array
(
[0] => Search_Result Object
(
[title] => Morning Toolbox Talk
[image] => /record/images/4003-p.jpg
[blurb] => This photo is from an early morning toolbox talk on a construction job in Mclean, Virginia. It is being delivered in English and Spanish....
[category] => Array
(
[0] => 20
[1] => 51
[2] => 57
[3] => 64
[4] => 70
[5] => 63
[6] => 78
[7] => 82
[8] => 62
[9] => 87
[10] => 88
[11] => 89
[12] => 91
[13] => 90
[14] => 93
[15] => 94
[16] => 97
)
[labels] => Array
(
[0] => Safety Culture
[1] => Work Environment
[2] => Hazards
[3] => Cement Mason
[4] => Trades
[5] => Flagger
[7] => Laborer
[9] => Operating Engineer
[11] => Reinforcing Ironworker
[13] => Roofer/Waterproofer
[15] => Stonemason
[17] => Structural Ironworker
[19] => Commercial & Institutional
[20] => Jobsites
[21] => Demolition
[23] => Disasters
[25] => Heavy & Highway
[27] => Industrial
[29] => Renovations
[31] => Residential
[33] => Images
[34] => Media
[35] => Media & Documents
)
[type] => Images
[sub_category] =>
[url] => /image/4003/i002691/Morning%2BToolbox%2BTalk.html
[item:protected] => ImageRecord Object
(
[records:protected] => Array
(
)
[recordId:protected] =>
[searchWordClass:protected] =>
[searchWordPeerClass:protected] =>
[bok_record:protected] =>
[authors:protected] =>
[organizations:protected] =>
[collections:protected] =>
[categories:protected] => Array
(
[20] => Category Object
(
[languages:protected] =>
[bok_resources:protected] =>
[bok_topics:protected] =>
[bok_keywords:protected] =>
[id:protected] => 20
[type:protected] => category
[parent:protected] => 7
[label:protected] => Safety Culture
[alreadyInSave:protected] =>
[alreadyInValidation:protected] =>
[validationFailures:protected] => Array
(
)
[_new:BaseObject:private] =>
[_deleted:BaseObject:private] =>
[modifiedColumns:protected] => Array
(
)
)
[51] => Category Object
(
[languages:protected] =>
[bok_resources:protected] =>
[bok_topics:protected] =>
[bok_keywords:protected] =>
[id:protected] => 51
[type:protected] => category
[parent:protected] => 2
[label:protected] => Cement Mason
[alreadyInSave:protected] =>
[alreadyInValidation:protected] =>
[validationFailures:protected] => Array
(
)
[_new:BaseObject:private] =>
[_deleted:BaseObject:private] =>
[modifiedColumns:protected] => Array
(
)
)
[57] => Category Object
(
[languages:protected] =>
[bok_resources:protected] =>
[bok_topics:protected] =>
[bok_keywords:protected] =>
[id:protected] => 57
[type:protected] => category
[parent:protected] => 2
[label:protected] => Flagger
[alreadyInSave:protected] =>
[alreadyInValidation:protected] =>
[validationFailures:protected] => Array
(
)
[_new:BaseObject:private] =>
[_deleted:BaseObject:private] =>
[modifiedColumns:protected] => Array
(
)
)
[64] => Category Object
(
[languages:protected] =>
[bok_resources:protected] =>
[bok_topics:protected] =>
[bok_keywords:protected] =>
[id:protected] => 64
[type:protected] => category
[parent:protected] => 2
[label:protected] => Laborer
[alreadyInSave:protected] =>
[alreadyInValidation:protected] =>
[validationFailures:protected] => Array
(
)
[_new:BaseObject:private] =>
[_deleted:BaseObject:private] =>
[modifiedColumns:protected] => Array
(
)
)
[70] => Category Object
(
[languages:protected] =>
[bok_resources:protected] =>
[bok_topics:protected] =>
[bok_keywords:protected] =>
[id:protected] => 70
[type:protected] => category
[parent:protected] => 2
[label:protected] => Operating Engineer
[alreadyInSave:protected] =>
[alreadyInValidation:protected] =>
[validationFailures:protected] => Array
(
)
[_new:BaseObject:private] =>
[_deleted:BaseObject:private] =>
[modifiedColumns:protected] => Array
(
)
)
[63] => Category Object
(
[languages:protected] =>
[bok_resources:protected] =>
[bok_topics:protected] =>
[bok_keywords:protected] =>
[id:protected] => 63
[type:protected] => category
[parent:protected] => 2
[label:protected] => Reinforcing Ironworker
[alreadyInSave:protected] =>
[alreadyInValidation:protected] =>
[validationFailures:protected] => Array
(
)
[_new:BaseObject:private] =>
[_deleted:BaseObject:private] =>
[modifiedColumns:protected] => Array
(
)
)
[78] => Category Object
(
[languages:protected] =>
[bok_resources:protected] =>
[bok_topics:protected] =>
[bok_keywords:protected] =>
[id:protected] => 78
[type:protected] => category
[parent:protected] => 2
[label:protected] => Roofer/Waterproofer
[alreadyInSave:protected] =>
[alreadyInValidation:protected] =>
[validationFailures:protected] => Array
(
)
[_new:BaseObject:private] =>
[_deleted:BaseObject:private] =>
[modifiedColumns:protected] => Array
(
)
)
[82] => Category Object
(
[languages:protected] =>
[bok_resources:protected] =>
[bok_topics:protected] =>
[bok_keywords:protected] =>
[id:protected] => 82
[type:protected] => category
[parent:protected] => 2
[label:protected] => Stonemason
[alreadyInSave:protected] =>
[alreadyInValidation:protected] =>
[validationFailures:protected] => Array
(
)
[_new:BaseObject:private] =>
[_deleted:BaseObject:private] =>
[modifiedColumns:protected] => Array
(
)
)
[62] => Category Object
(
[languages:protected] =>
[bok_resources:protected] =>
[bok_topics:protected] =>
[bok_keywords:protected] =>
[id:protected] => 62
[type:protected] => category
[parent:protected] => 2
[label:protected] => Structural Ironworker
[alreadyInSave:protected] =>
[alreadyInValidation:protected] =>
[validationFailures:protected] => Array
(
)
[_new:BaseObject:private] =>
[_deleted:BaseObject:private] =>
[modifiedColumns:protected] => Array
(
)
)
[87] => Category Object
(
[languages:protected] =>
[bok_resources:protected] =>
[bok_topics:protected] =>
[bok_keywords:protected] =>
[id:protected] => 87
[type:protected] => category
[parent:protected] => 3
[label:protected] => Commercial & Institutional
[alreadyInSave:protected] =>
[alreadyInValidation:protected] =>
[validationFailures:protected] => Array
(
)
[_new:BaseObject:private] =>
[_deleted:BaseObject:private] =>
[modifiedColumns:protected] => Array
(
)
)
[88] => Category Object
(
[languages:protected] =>
[bok_resources:protected] =>
[bok_topics:protected] =>
[bok_keywords:protected] =>
[id:protected] => 88
[type:protected] => category
[parent:protected] => 3
[label:protected] => Demolition
[alreadyInSave:protected] =>
[alreadyInValidation:protected] =>
[validationFailures:protected] => Array
(
)
[_new:BaseObject:private] =>
[_deleted:BaseObject:private] =>
[modifiedColumns:protected] => Array
(
)
)
[89] => Category Object
(
[languages:protected] =>
[bok_resources:protected] =>
[bok_topics:protected] =>
[bok_keywords:protected] =>
[id:protected] => 89
[type:protected] => category
[parent:protected] => 3
[label:protected] => Disasters
[alreadyInSave:protected] =>
[alreadyInValidation:protected] =>
[validationFailures:protected] => Array
(
)
[_new:BaseObject:private] =>
[_deleted:BaseObject:private] =>
[modifiedColumns:protected] => Array
(
)
)
[91] => Category Object
(
[languages:protected] =>
[bok_resources:protected] =>
[bok_topics:protected] =>
[bok_keywords:protected] =>
[id:protected] => 91
[type:protected] => category
[parent:protected] => 3
[label:protected] => Heavy & Highway
[alreadyInSave:protected] =>
[alreadyInValidation:protected] =>
[validationFailures:protected] => Array
(
)
[_new:BaseObject:private] =>
[_deleted:BaseObject:private] =>
[modifiedColumns:protected] => Array
(
)
)
[90] => Category Object
(
[languages:protected] =>
[bok_resources:protected] =>
[bok_topics:protected] =>
[bok_keywords:protected] =>
[id:protected] => 90
[type:protected] => category
[parent:protected] => 3
[label:protected] => Industrial
[alreadyInSave:protected] =>
[alreadyInValidation:protected] =>
[validationFailures:protected] => Array
(
)
[_new:BaseObject:private] =>
[_deleted:BaseObject:private] =>
[modifiedColumns:protected] => Array
(
)
)
[93] => Category Object
(
[languages:protected] =>
[bok_resources:protected] =>
[bok_topics:protected] =>
[bok_keywords:protected] =>
[id:protected] => 93
[type:protected] => category
[parent:protected] => 3
[label:protected] => Renovations
[alreadyInSave:protected] =>
[alreadyInValidation:protected] =>
[validationFailures:protected] => Array
(
)
[_new:BaseObject:private] =>
[_deleted:BaseObject:private] =>
[modifiedColumns:protected] => Array
(
)
)
[94] => Category Object
(
[languages:protected] =>
[bok_resources:protected] =>
[bok_topics:protected] =>
[bok_keywords:protected] =>
[id:protected] => 94
[type:protected] => category
[parent:protected] => 3
[label:protected] => Residential
[alreadyInSave:protected] =>
[alreadyInValidation:protected] =>
[validationFailures:protected] => Array
(
)
[_new:BaseObject:private] =>
[_deleted:BaseObject:private] =>
[modifiedColumns:protected] => Array
(
)
)
[97] => Category Object
(
[languages:protected] =>
[bok_resources:protected] =>
[bok_topics:protected] =>
[bok_keywords:protected] =>
[id:protected] => 97
[type:protected] => category
[parent:protected] => 5
[label:protected] => Images
[alreadyInSave:protected] =>
[alreadyInValidation:protected] =>
[validationFailures:protected] => Array
(
)
[_new:BaseObject:private] =>
[_deleted:BaseObject:private] =>
[modifiedColumns:protected] => Array
(
)
)
)
[categories_initialized:protected] => 1
[mapped_items:protected] =>
[content:protected] =>
[files:protected] =>
[language:protected] => Language Object
(
[id:protected] => 1
[code:protected] => en
[name:protected] => English
[alreadyInSave:protected] =>
[alreadyInValidation:protected] =>
[validationFailures:protected] => Array
(
)
[_new:BaseObject:private] =>
[_deleted:BaseObject:private] =>
[modifiedColumns:protected] => Array
(
)
)
[old_record:protected] =>
[id:protected] => 4003
[old_id:protected] =>
[elcosh_id:protected] => i002691
[type:protected] => image
[display_type:protected] => Image
[user_id:protected] => 0
[language_id:protected] => 1
[tagging_id:protected] => Bruce Lippy
[priority_id:protected] => 1
[title:protected] => Morning Toolbox Talk
[total_pages:protected] => 0
[billed_pages:protected] => 0
[publication_number:protected] =>
[part_of:protected] =>
[keywords:protected] => toolbox talk, tailgate talk, Spanish, bilingual
[comments:protected] =>
[summary:protected] => This photo is from an early morning toolbox talk on a construction job in Mclean, Virginia. It is being delivered in English and Spanish.
[transition_comments:protected] =>
[external_link:protected] =>
[consol_link:protected] => http://www.cpwrconstructionsolutions.org/electrical/solution/662/worker-training.html
[more_like_this:protected] => d001285,d001304,c000079
[permission_given_by:protected] =>
[published:protected] => T
[billable:protected] => F
[img_name:protected] =>
[img_ext:protected] => jpg
[img_width:protected] =>
[img_height:protected] =>
[img_credit:protected] => Morgan Zavertnik and Hoar Construction
[img_practice:protected] => good
[vid_source_id:protected] =>
[vid_running_time:protected] =>
[vid_intended_audience:protected] =>
[vid_acquisition_info:protected] =>
[vid_cost:protected] =>
[vid_producer:protected] =>
[vid_filename:protected] =>
[vid_filename_downloadable:protected] =>
[date_summary:protected] => November 2015
[date_permission_requested:protected] =>
[date_permission_received:protected] =>
[date_review_needed:protected] =>
[date_received:protected] => 03/02/16
[date_completed:protected] => 03/02/16
[date_billed:protected] =>
[date_modified:protected] => 03/02/16
[collBokExports:protected] =>
[lastBokExportCriteria:BaseElcoshItem:private] =>
[alreadyInSave:protected] =>
[alreadyInValidation:protected] =>
[validationFailures:protected] => Array
(
)
[_new:BaseObject:private] =>
[_deleted:BaseObject:private] =>
[modifiedColumns:protected] => Array
(
)
)
)
[1] => Search_Result Object
(
[title] => Toolbox talk - crew view
[image] => /record/images/4005-p.jpg
[blurb] => Photo of crew listening to a toolbox safety talk before starting work....
[category] => Array
(
[0] => 97
[1] => 20
[2] => 47
[3] => 49
[4] => 51
[5] => 55
[6] => 61
[7] => 64
[8] => 71
[9] => 75
[10] => 63
[11] => 79
[12] => 62
[13] => 87
[14] => 88
[15] => 91
[16] => 90
[17] => 93
[18] => 94
[19] => 95
)
[labels] => Array
(
[0] => Images
[1] => Media
[2] => Media & Documents
[3] => Safety Culture
[4] => Work Environment
[5] => Hazards
[6] => Bricklayer
[7] => Trades
[8] => Carpenter
[10] => Cement Mason
[12] => Electrical Worker
[14] => Interior Systems Carpenter
[16] => Laborer
[18] => Painter
[20] => Plasterer
[22] => Reinforcing Ironworker
[24] => Scaffold Erector
[26] => Structural Ironworker
[28] => Commercial & Institutional
[29] => Jobsites
[30] => Demolition
[32] => Heavy & Highway
[34] => Industrial
[36] => Renovations
[38] => Residential
[40] => Underground
)
[type] => Images
[sub_category] =>
[url] => /image/4005/i002692/Toolbox%2Btalk%2B-%2Bcrew%2Bview.html
[item:protected] => ImageRecord Object
(
[records:protected] => Array
(
)
[recordId:protected] =>
[searchWordClass:protected] =>
[searchWordPeerClass:protected] =>
[bok_record:protected] =>
[authors:protected] =>
[organizations:protected] =>
[collections:protected] =>
[categories:protected] => Array
(
[97] => Category Object
(
[languages:protected] =>
[bok_resources:protected] =>
[bok_topics:protected] =>
[bok_keywords:protected] =>
[id:protected] => 97
[type:protected] => category
[parent:protected] => 5
[label:protected] => Images
[alreadyInSave:protected] =>
[alreadyInValidation:protected] =>
[validationFailures:protected] => Array
(
)
[_new:BaseObject:private] =>
[_deleted:BaseObject:private] =>
[modifiedColumns:protected] => Array
(
)
)
[20] => Category Object
(
[languages:protected] =>
[bok_resources:protected] =>
[bok_topics:protected] =>
[bok_keywords:protected] =>
[id:protected] => 20
[type:protected] => category
[parent:protected] => 7
[label:protected] => Safety Culture
[alreadyInSave:protected] =>
[alreadyInValidation:protected] =>
[validationFailures:protected] => Array
(
)
[_new:BaseObject:private] =>
[_deleted:BaseObject:private] =>
[modifiedColumns:protected] => Array
(
)
)
[47] => Category Object
(
[languages:protected] =>
[bok_resources:protected] =>
[bok_topics:protected] =>
[bok_keywords:protected] =>
[id:protected] => 47
[type:protected] => category
[parent:protected] => 2
[label:protected] => Bricklayer
[alreadyInSave:protected] =>
[alreadyInValidation:protected] =>
[validationFailures:protected] => Array
(
)
[_new:BaseObject:private] =>
[_deleted:BaseObject:private] =>
[modifiedColumns:protected] => Array
(
)
)
[49] => Category Object
(
[languages:protected] =>
[bok_resources:protected] =>
[bok_topics:protected] =>
[bok_keywords:protected] =>
[id:protected] => 49
[type:protected] => category
[parent:protected] => 2
[label:protected] => Carpenter
[alreadyInSave:protected] =>
[alreadyInValidation:protected] =>
[validationFailures:protected] => Array
(
)
[_new:BaseObject:private] =>
[_deleted:BaseObject:private] =>
[modifiedColumns:protected] => Array
(
)
)
[51] => Category Object
(
[languages:protected] =>
[bok_resources:protected] =>
[bok_topics:protected] =>
[bok_keywords:protected] =>
[id:protected] => 51
[type:protected] => category
[parent:protected] => 2
[label:protected] => Cement Mason
[alreadyInSave:protected] =>
[alreadyInValidation:protected] =>
[validationFailures:protected] => Array
(
)
[_new:BaseObject:private] =>
[_deleted:BaseObject:private] =>
[modifiedColumns:protected] => Array
(
)
)
[55] => Category Object
(
[languages:protected] =>
[bok_resources:protected] =>
[bok_topics:protected] =>
[bok_keywords:protected] =>
[id:protected] => 55
[type:protected] => category
[parent:protected] => 2
[label:protected] => Electrical Worker
[alreadyInSave:protected] =>
[alreadyInValidation:protected] =>
[validationFailures:protected] => Array
(
)
[_new:BaseObject:private] =>
[_deleted:BaseObject:private] =>
[modifiedColumns:protected] => Array
(
)
)
[61] => Category Object
(
[languages:protected] =>
[bok_resources:protected] =>
[bok_topics:protected] =>
[bok_keywords:protected] =>
[id:protected] => 61
[type:protected] => category
[parent:protected] => 2
[label:protected] => Interior Systems Carpenter
[alreadyInSave:protected] =>
[alreadyInValidation:protected] =>
[validationFailures:protected] => Array
(
)
[_new:BaseObject:private] =>
[_deleted:BaseObject:private] =>
[modifiedColumns:protected] => Array
(
)
)
[64] => Category Object
(
[languages:protected] =>
[bok_resources:protected] =>
[bok_topics:protected] =>
[bok_keywords:protected] =>
[id:protected] => 64
[type:protected] => category
[parent:protected] => 2
[label:protected] => Laborer
[alreadyInSave:protected] =>
[alreadyInValidation:protected] =>
[validationFailures:protected] => Array
(
)
[_new:BaseObject:private] =>
[_deleted:BaseObject:private] =>
[modifiedColumns:protected] => Array
(
)
)
[71] => Category Object
(
[languages:protected] =>
[bok_resources:protected] =>
[bok_topics:protected] =>
[bok_keywords:protected] =>
[id:protected] => 71
[type:protected] => category
[parent:protected] => 2
[label:protected] => Painter
[alreadyInSave:protected] =>
[alreadyInValidation:protected] =>
[validationFailures:protected] => Array
(
)
[_new:BaseObject:private] =>
[_deleted:BaseObject:private] =>
[modifiedColumns:protected] => Array
(
)
)
[75] => Category Object
(
[languages:protected] =>
[bok_resources:protected] =>
[bok_topics:protected] =>
[bok_keywords:protected] =>
[id:protected] => 75
[type:protected] => category
[parent:protected] => 2
[label:protected] => Plasterer
[alreadyInSave:protected] =>
[alreadyInValidation:protected] =>
[validationFailures:protected] => Array
(
)
[_new:BaseObject:private] =>
[_deleted:BaseObject:private] =>
[modifiedColumns:protected] => Array
(
)
)
[63] => Category Object
(
[languages:protected] =>
[bok_resources:protected] =>
[bok_topics:protected] =>
[bok_keywords:protected] =>
[id:protected] => 63
[type:protected] => category
[parent:protected] => 2
[label:protected] => Reinforcing Ironworker
[alreadyInSave:protected] =>
[alreadyInValidation:protected] =>
[validationFailures:protected] => Array
(
)
[_new:BaseObject:private] =>
[_deleted:BaseObject:private] =>
[modifiedColumns:protected] => Array
(
)
)
[79] => Category Object
(
[languages:protected] =>
[bok_resources:protected] =>
[bok_topics:protected] =>
[bok_keywords:protected] =>
[id:protected] => 79
[type:protected] => category
[parent:protected] => 2
[label:protected] => Scaffold Erector
[alreadyInSave:protected] =>
[alreadyInValidation:protected] =>
[validationFailures:protected] => Array
(
)
[_new:BaseObject:private] =>
[_deleted:BaseObject:private] =>
[modifiedColumns:protected] => Array
(
)
)
[62] => Category Object
(
[languages:protected] =>
[bok_resources:protected] =>
[bok_topics:protected] =>
[bok_keywords:protected] =>
[id:protected] => 62
[type:protected] => category
[parent:protected] => 2
[label:protected] => Structural Ironworker
[alreadyInSave:protected] =>
[alreadyInValidation:protected] =>
[validationFailures:protected] => Array
(
)
[_new:BaseObject:private] =>
[_deleted:BaseObject:private] =>
[modifiedColumns:protected] => Array
(
)
)
[87] => Category Object
(
[languages:protected] =>
[bok_resources:protected] =>
[bok_topics:protected] =>
[bok_keywords:protected] =>
[id:protected] => 87
[type:protected] => category
[parent:protected] => 3
[label:protected] => Commercial & Institutional
[alreadyInSave:protected] =>
[alreadyInValidation:protected] =>
[validationFailures:protected] => Array
(
)
[_new:BaseObject:private] =>
[_deleted:BaseObject:private] =>
[modifiedColumns:protected] => Array
(
)
)
[88] => Category Object
(
[languages:protected] =>
[bok_resources:protected] =>
[bok_topics:protected] =>
[bok_keywords:protected] =>
[id:protected] => 88
[type:protected] => category
[parent:protected] => 3
[label:protected] => Demolition
[alreadyInSave:protected] =>
[alreadyInValidation:protected] =>
[validationFailures:protected] => Array
(
)
[_new:BaseObject:private] =>
[_deleted:BaseObject:private] =>
[modifiedColumns:protected] => Array
(
)
)
[91] => Category Object
(
[languages:protected] =>
[bok_resources:protected] =>
[bok_topics:protected] =>
[bok_keywords:protected] =>
[id:protected] => 91
[type:protected] => category
[parent:protected] => 3
[label:protected] => Heavy & Highway
[alreadyInSave:protected] =>
[alreadyInValidation:protected] =>
[validationFailures:protected] => Array
(
)
[_new:BaseObject:private] =>
[_deleted:BaseObject:private] =>
[modifiedColumns:protected] => Array
(
)
)
[90] => Category Object
(
[languages:protected] =>
[bok_resources:protected] =>
[bok_topics:protected] =>
[bok_keywords:protected] =>
[id:protected] => 90
[type:protected] => category
[parent:protected] => 3
[label:protected] => Industrial
[alreadyInSave:protected] =>
[alreadyInValidation:protected] =>
[validationFailures:protected] => Array
(
)
[_new:BaseObject:private] =>
[_deleted:BaseObject:private] =>
[modifiedColumns:protected] => Array
(
)
)
[93] => Category Object
(
[languages:protected] =>
[bok_resources:protected] =>
[bok_topics:protected] =>
[bok_keywords:protected] =>
[id:protected] => 93
[type:protected] => category
[parent:protected] => 3
[label:protected] => Renovations
[alreadyInSave:protected] =>
[alreadyInValidation:protected] =>
[validationFailures:protected] => Array
(
)
[_new:BaseObject:private] =>
[_deleted:BaseObject:private] =>
[modifiedColumns:protected] => Array
(
)
)
[94] => Category Object
(
[languages:protected] =>
[bok_resources:protected] =>
[bok_topics:protected] =>
[bok_keywords:protected] =>
[id:protected] => 94
[type:protected] => category
[parent:protected] => 3
[label:protected] => Residential
[alreadyInSave:protected] =>
[alreadyInValidation:protected] =>
[validationFailures:protected] => Array
(
)
[_new:BaseObject:private] =>
[_deleted:BaseObject:private] =>
[modifiedColumns:protected] => Array
(
)
)
[95] => Category Object
(
[languages:protected] =>
[bok_resources:protected] =>
[bok_topics:protected] =>
[bok_keywords:protected] =>
[id:protected] => 95
[type:protected] => category
[parent:protected] => 3
[label:protected] => Underground
[alreadyInSave:protected] =>
[alreadyInValidation:protected] =>
[validationFailures:protected] => Array
(
)
[_new:BaseObject:private] =>
[_deleted:BaseObject:private] =>
[modifiedColumns:protected] => Array
(
)
)
)
[categories_initialized:protected] => 1
[mapped_items:protected] =>
[content:protected] =>
[files:protected] =>
[language:protected] => Language Object
(
[id:protected] => 1
[code:protected] => en
[name:protected] => English
[alreadyInSave:protected] =>
[alreadyInValidation:protected] =>
[validationFailures:protected] => Array
(
)
[_new:BaseObject:private] =>
[_deleted:BaseObject:private] =>
[modifiedColumns:protected] => Array
(
)
)
[old_record:protected] =>
[id:protected] => 4005
[old_id:protected] =>
[elcosh_id:protected] => i002692
[type:protected] => image
[display_type:protected] => Image
[user_id:protected] => 0
[language_id:protected] => 1
[tagging_id:protected] => Bruce Lippy
[priority_id:protected] => 1
[title:protected] => Toolbox talk - crew view
[total_pages:protected] => 0
[billed_pages:protected] => 0
[publication_number:protected] =>
[part_of:protected] =>
[keywords:protected] => toolbox talk, tailgate talk, safety talk, Spanish
[comments:protected] =>
[summary:protected] => Photo of crew listening to a toolbox safety talk before starting work.
[transition_comments:protected] =>
[external_link:protected] =>
[consol_link:protected] => http://www.cpwrconstructionsolutions.org/electrical/solution/662/worker-training.html
[more_like_this:protected] => i002691,d001269, c000079, d001285
[permission_given_by:protected] =>
[published:protected] => T
[billable:protected] => F
[img_name:protected] =>
[img_ext:protected] => jpg
[img_width:protected] =>
[img_height:protected] =>
[img_credit:protected] => Morgan Zavertnik and Hoar Construction
[img_practice:protected] => good
[vid_source_id:protected] =>
[vid_running_time:protected] =>
[vid_intended_audience:protected] =>
[vid_acquisition_info:protected] =>
[vid_cost:protected] =>
[vid_producer:protected] =>
[vid_filename:protected] =>
[vid_filename_downloadable:protected] =>
[date_summary:protected] => November 2015
[date_permission_requested:protected] =>
[date_permission_received:protected] =>
[date_review_needed:protected] =>
[date_received:protected] => 03/02/16
[date_completed:protected] => 03/02/16
[date_billed:protected] =>
[date_modified:protected] => 03/02/16
[collBokExports:protected] =>
[lastBokExportCriteria:BaseElcoshItem:private] =>
[alreadyInSave:protected] =>
[alreadyInValidation:protected] =>
[validationFailures:protected] => Array
(
)
[_new:BaseObject:private] =>
[_deleted:BaseObject:private] =>
[modifiedColumns:protected] => Array
(
)
)
)
[2] => Search_Result Object
(
[title] => Toolbox talk - long shot
[image] => /record/images/4006-p.jpg
[blurb] => This crew gathered every morning before starting work to discuss a new safety topic....
[category] => Array
(
[0] => 20
[1] => 47
[2] => 49
[3] => 51
[4] => 55
[5] => 64
[6] => 68
[7] => 75
[8] => 76
[9] => 63
[10] => 78
[11] => 79
[12] => 82
[13] => 62
[14] => 87
[15] => 88
[16] => 91
[17] => 90
[18] => 93
[19] => 94
[20] => 95
[21] => 97
)
[labels] => Array
(
[0] => Safety Culture
[1] => Work Environment
[2] => Hazards
[3] => Bricklayer
[4] => Trades
[5] => Carpenter
[7] => Cement Mason
[9] => Electrical Worker
[11] => Laborer
[13] => Maintenance Worker
[15] => Plasterer
[17] => Plumber/Pipefitter
[19] => Reinforcing Ironworker
[21] => Roofer/Waterproofer
[23] => Scaffold Erector
[25] => Stonemason
[27] => Structural Ironworker
[29] => Commercial & Institutional
[30] => Jobsites
[31] => Demolition
[33] => Heavy & Highway
[35] => Industrial
[37] => Renovations
[39] => Residential
[41] => Underground
[43] => Images
[44] => Media
[45] => Media & Documents
)
[type] => Images
[sub_category] =>
[url] => /image/4006/i002693/Toolbox%2Btalk%2B-%2Blong%2Bshot.html
[item:protected] => ImageRecord Object
(
[records:protected] => Array
(
)
[recordId:protected] =>
[searchWordClass:protected] =>
[searchWordPeerClass:protected] =>
[bok_record:protected] =>
[authors:protected] =>
[organizations:protected] =>
[collections:protected] =>
[categories:protected] => Array
(
[20] => Category Object
(
[languages:protected] =>
[bok_resources:protected] =>
[bok_topics:protected] =>
[bok_keywords:protected] =>
[id:protected] => 20
[type:protected] => category
[parent:protected] => 7
[label:protected] => Safety Culture
[alreadyInSave:protected] =>
[alreadyInValidation:protected] =>
[validationFailures:protected] => Array
(
)
[_new:BaseObject:private] =>
[_deleted:BaseObject:private] =>
[modifiedColumns:protected] => Array
(
)
)
[47] => Category Object
(
[languages:protected] =>
[bok_resources:protected] =>
[bok_topics:protected] =>
[bok_keywords:protected] =>
[id:protected] => 47
[type:protected] => category
[parent:protected] => 2
[label:protected] => Bricklayer
[alreadyInSave:protected] =>
[alreadyInValidation:protected] =>
[validationFailures:protected] => Array
(
)
[_new:BaseObject:private] =>
[_deleted:BaseObject:private] =>
[modifiedColumns:protected] => Array
(
)
)
[49] => Category Object
(
[languages:protected] =>
[bok_resources:protected] =>
[bok_topics:protected] =>
[bok_keywords:protected] =>
[id:protected] => 49
[type:protected] => category
[parent:protected] => 2
[label:protected] => Carpenter
[alreadyInSave:protected] =>
[alreadyInValidation:protected] =>
[validationFailures:protected] => Array
(
)
[_new:BaseObject:private] =>
[_deleted:BaseObject:private] =>
[modifiedColumns:protected] => Array
(
)
)
[51] => Category Object
(
[languages:protected] =>
[bok_resources:protected] =>
[bok_topics:protected] =>
[bok_keywords:protected] =>
[id:protected] => 51
[type:protected] => category
[parent:protected] => 2
[label:protected] => Cement Mason
[alreadyInSave:protected] =>
[alreadyInValidation:protected] =>
[validationFailures:protected] => Array
(
)
[_new:BaseObject:private] =>
[_deleted:BaseObject:private] =>
[modifiedColumns:protected] => Array
(
)
)
[55] => Category Object
(
[languages:protected] =>
[bok_resources:protected] =>
[bok_topics:protected] =>
[bok_keywords:protected] =>
[id:protected] => 55
[type:protected] => category
[parent:protected] => 2
[label:protected] => Electrical Worker
[alreadyInSave:protected] =>
[alreadyInValidation:protected] =>
[validationFailures:protected] => Array
(
)
[_new:BaseObject:private] =>
[_deleted:BaseObject:private] =>
[modifiedColumns:protected] => Array
(
)
)
[64] => Category Object
(
[languages:protected] =>
[bok_resources:protected] =>
[bok_topics:protected] =>
[bok_keywords:protected] =>
[id:protected] => 64
[type:protected] => category
[parent:protected] => 2
[label:protected] => Laborer
[alreadyInSave:protected] =>
[alreadyInValidation:protected] =>
[validationFailures:protected] => Array
(
)
[_new:BaseObject:private] =>
[_deleted:BaseObject:private] =>
[modifiedColumns:protected] => Array
(
)
)
[68] => Category Object
(
[languages:protected] =>
[bok_resources:protected] =>
[bok_topics:protected] =>
[bok_keywords:protected] =>
[id:protected] => 68
[type:protected] => category
[parent:protected] => 2
[label:protected] => Maintenance Worker
[alreadyInSave:protected] =>
[alreadyInValidation:protected] =>
[validationFailures:protected] => Array
(
)
[_new:BaseObject:private] =>
[_deleted:BaseObject:private] =>
[modifiedColumns:protected] => Array
(
)
)
[75] => Category Object
(
[languages:protected] =>
[bok_resources:protected] =>
[bok_topics:protected] =>
[bok_keywords:protected] =>
[id:protected] => 75
[type:protected] => category
[parent:protected] => 2
[label:protected] => Plasterer
[alreadyInSave:protected] =>
[alreadyInValidation:protected] =>
[validationFailures:protected] => Array
(
)
[_new:BaseObject:private] =>
[_deleted:BaseObject:private] =>
[modifiedColumns:protected] => Array
(
)
)
[76] => Category Object
(
[languages:protected] =>
[bok_resources:protected] =>
[bok_topics:protected] =>
[bok_keywords:protected] =>
[id:protected] => 76
[type:protected] => category
[parent:protected] => 2
[label:protected] => Plumber/Pipefitter
[alreadyInSave:protected] =>
[alreadyInValidation:protected] =>
[validationFailures:protected] => Array
(
)
[_new:BaseObject:private] =>
[_deleted:BaseObject:private] =>
[modifiedColumns:protected] => Array
(
)
)
[63] => Category Object
(
[languages:protected] =>
[bok_resources:protected] =>
[bok_topics:protected] =>
[bok_keywords:protected] =>
[id:protected] => 63
[type:protected] => category
[parent:protected] => 2
[label:protected] => Reinforcing Ironworker
[alreadyInSave:protected] =>
[alreadyInValidation:protected] =>
[validationFailures:protected] => Array
(
)
[_new:BaseObject:private] =>
[_deleted:BaseObject:private] =>
[modifiedColumns:protected] => Array
(
)
)
[78] => Category Object
(
[languages:protected] =>
[bok_resources:protected] =>
[bok_topics:protected] =>
[bok_keywords:protected] =>
[id:protected] => 78
[type:protected] => category
[parent:protected] => 2
[label:protected] => Roofer/Waterproofer
[alreadyInSave:protected] =>
[alreadyInValidation:protected] =>
[validationFailures:protected] => Array
(
)
[_new:BaseObject:private] =>
[_deleted:BaseObject:private] =>
[modifiedColumns:protected] => Array
(
)
)
[79] => Category Object
(
[languages:protected] =>
[bok_resources:protected] =>
[bok_topics:protected] =>
[bok_keywords:protected] =>
[id:protected] => 79
[type:protected] => category
[parent:protected] => 2
[label:protected] => Scaffold Erector
[alreadyInSave:protected] =>
[alreadyInValidation:protected] =>
[validationFailures:protected] => Array
(
)
[_new:BaseObject:private] =>
[_deleted:BaseObject:private] =>
[modifiedColumns:protected] => Array
(
)
)
[82] => Category Object
(
[languages:protected] =>
[bok_resources:protected] =>
[bok_topics:protected] =>
[bok_keywords:protected] =>
[id:protected] => 82
[type:protected] => category
[parent:protected] => 2
[label:protected] => Stonemason
[alreadyInSave:protected] =>
[alreadyInValidation:protected] =>
[validationFailures:protected] => Array
(
)
[_new:BaseObject:private] =>
[_deleted:BaseObject:private] =>
[modifiedColumns:protected] => Array
(
)
)
[62] => Category Object
(
[languages:protected] =>
[bok_resources:protected] =>
[bok_topics:protected] =>
[bok_keywords:protected] =>
[id:protected] => 62
[type:protected] => category
[parent:protected] => 2
[label:protected] => Structural Ironworker
[alreadyInSave:protected] =>
[alreadyInValidation:protected] =>
[validationFailures:protected] => Array
(
)
[_new:BaseObject:private] =>
[_deleted:BaseObject:private] =>
[modifiedColumns:protected] => Array
(
)
)
[87] => Category Object
(
[languages:protected] =>
[bok_resources:protected] =>
[bok_topics:protected] =>
[bok_keywords:protected] =>
[id:protected] => 87
[type:protected] => category
[parent:protected] => 3
[label:protected] => Commercial & Institutional
[alreadyInSave:protected] =>
[alreadyInValidation:protected] =>
[validationFailures:protected] => Array
(
)
[_new:BaseObject:private] =>
[_deleted:BaseObject:private] =>
[modifiedColumns:protected] => Array
(
)
)
[88] => Category Object
(
[languages:protected] =>
[bok_resources:protected] =>
[bok_topics:protected] =>
[bok_keywords:protected] =>
[id:protected] => 88
[type:protected] => category
[parent:protected] => 3
[label:protected] => Demolition
[alreadyInSave:protected] =>
[alreadyInValidation:protected] =>
[validationFailures:protected] => Array
(
)
[_new:BaseObject:private] =>
[_deleted:BaseObject:private] =>
[modifiedColumns:protected] => Array
(
)
)
[91] => Category Object
(
[languages:protected] =>
[bok_resources:protected] =>
[bok_topics:protected] =>
[bok_keywords:protected] =>
[id:protected] => 91
[type:protected] => category
[parent:protected] => 3
[label:protected] => Heavy & Highway
[alreadyInSave:protected] =>
[alreadyInValidation:protected] =>
[validationFailures:protected] => Array
(
)
[_new:BaseObject:private] =>
[_deleted:BaseObject:private] =>
[modifiedColumns:protected] => Array
(
)
)
[90] => Category Object
(
[languages:protected] =>
[bok_resources:protected] =>
[bok_topics:protected] =>
[bok_keywords:protected] =>
[id:protected] => 90
[type:protected] => category
[parent:protected] => 3
[label:protected] => Industrial
[alreadyInSave:protected] =>
[alreadyInValidation:protected] =>
[validationFailures:protected] => Array
(
)
[_new:BaseObject:private] =>
[_deleted:BaseObject:private] =>
[modifiedColumns:protected] => Array
(
)
)
[93] => Category Object
(
[languages:protected] =>
[bok_resources:protected] =>
[bok_topics:protected] =>
[bok_keywords:protected] =>
[id:protected] => 93
[type:protected] => category
[parent:protected] => 3
[label:protected] => Renovations
[alreadyInSave:protected] =>
[alreadyInValidation:protected] =>
[validationFailures:protected] => Array
(
)
[_new:BaseObject:private] =>
[_deleted:BaseObject:private] =>
[modifiedColumns:protected] => Array
(
)
)
[94] => Category Object
(
[languages:protected] =>
[bok_resources:protected] =>
[bok_topics:protected] =>
[bok_keywords:protected] =>
[id:protected] => 94
[type:protected] => category
[parent:protected] => 3
[label:protected] => Residential
[alreadyInSave:protected] =>
[alreadyInValidation:protected] =>
[validationFailures:protected] => Array
(
)
[_new:BaseObject:private] =>
[_deleted:BaseObject:private] =>
[modifiedColumns:protected] => Array
(
)
)
[95] => Category Object
(
[languages:protected] =>
[bok_resources:protected] =>
[bok_topics:protected] =>
[bok_keywords:protected] =>
[id:protected] => 95
[type:protected] => category
[parent:protected] => 3
[label:protected] => Underground
[alreadyInSave:protected] =>
[alreadyInValidation:protected] =>
[validationFailures:protected] => Array
(
)
[_new:BaseObject:private] =>
[_deleted:BaseObject:private] =>
[modifiedColumns:protected] => Array
(
)
)
[97] => Category Object
(
[languages:protected] =>
[bok_resources:protected] =>
[bok_topics:protected] =>
[bok_keywords:protected] =>
[id:protected] => 97
[type:protected] => category
[parent:protected] => 5
[label:protected] => Images
[alreadyInSave:protected] =>
[alreadyInValidation:protected] =>
[validationFailures:protected] => Array
(
)
[_new:BaseObject:private] =>
[_deleted:BaseObject:private] =>
[modifiedColumns:protected] => Array
(
)
)
)
[categories_initialized:protected] => 1
[mapped_items:protected] =>
[content:protected] =>
[files:protected] =>
[language:protected] => Language Object
(
[id:protected] => 1
[code:protected] => en
[name:protected] => English
[alreadyInSave:protected] =>
[alreadyInValidation:protected] =>
[validationFailures:protected] => Array
(
)
[_new:BaseObject:private] =>
[_deleted:BaseObject:private] =>
[modifiedColumns:protected] => Array
(
)
)
[old_record:protected] =>
[id:protected] => 4006
[old_id:protected] =>
[elcosh_id:protected] => i002693
[type:protected] => image
[display_type:protected] => Image
[user_id:protected] => 0
[language_id:protected] => 1
[tagging_id:protected] => Bruce Lippy
[priority_id:protected] => 1
[title:protected] => Toolbox talk - long shot
[total_pages:protected] => 0
[billed_pages:protected] => 0
[publication_number:protected] =>
[part_of:protected] =>
[keywords:protected] => toolbox talk, tailgate talk, safety minute
[comments:protected] =>
[summary:protected] => This crew gathered every morning before starting work to discuss a new safety topic.
[transition_comments:protected] =>
[external_link:protected] =>
[consol_link:protected] => http://www.cpwrconstructionsolutions.org/electrical/solution/662/worker-training.html
[more_like_this:protected] => i002691,i002692,d001269,d000527
[permission_given_by:protected] =>
[published:protected] => T
[billable:protected] => F
[img_name:protected] =>
[img_ext:protected] => jpg
[img_width:protected] =>
[img_height:protected] =>
[img_credit:protected] => Morgan Zavertnik and Hoar Construction
[img_practice:protected] => good
[vid_source_id:protected] =>
[vid_running_time:protected] =>
[vid_intended_audience:protected] =>
[vid_acquisition_info:protected] =>
[vid_cost:protected] =>
[vid_producer:protected] =>
[vid_filename:protected] =>
[vid_filename_downloadable:protected] =>
[date_summary:protected] => November 2015
[date_permission_requested:protected] =>
[date_permission_received:protected] =>
[date_review_needed:protected] =>
[date_received:protected] => 03/02/16
[date_completed:protected] => 03/02/16
[date_billed:protected] =>
[date_modified:protected] => 03/02/16
[collBokExports:protected] =>
[lastBokExportCriteria:BaseElcoshItem:private] =>
[alreadyInSave:protected] =>
[alreadyInValidation:protected] =>
[validationFailures:protected] => Array
(
)
[_new:BaseObject:private] =>
[_deleted:BaseObject:private] =>
[modifiedColumns:protected] => Array
(
)
)
)
[3] => Search_Result Object
(
[title] => Safety officer discussing ongoing project with marketing coordinator
[image] => /record/images/4014-p.jpg
[blurb] => The safety officer (left) points out the good safety practices on this project that reflect well on the firm and may influence future clients....
[category] => Array
(
[0] => 97
[1] => 20
[2] => 46
[3] => 47
[4] => 49
[5] => 50
[6] => 51
[7] => 54
[8] => 55
[9] => 58
[10] => 60
[11] => 61
[12] => 64
[13] => 71
[14] => 75
[15] => 76
[16] => 63
[17] => 79
[18] => 80
[19] => 82
[20] => 62
[21] => 83
[22] => 87
[23] => 91
[24] => 90
[25] => 93
[26] => 94
)
[labels] => Array
(
[0] => Images
[1] => Media
[2] => Media & Documents
[3] => Safety Culture
[4] => Work Environment
[5] => Hazards
[6] => Boilermaker
[7] => Trades
[8] => Bricklayer
[10] => Carpenter
[12] => Carpet Layer
[14] => Cement Mason
[16] => Drywall Applicator Specialist
[18] => Electrical Worker
[20] => Glazier
[22] => HVAC
[24] => Interior Systems Carpenter
[26] => Laborer
[28] => Painter
[30] => Plasterer
[32] => Plumber/Pipefitter
[34] => Reinforcing Ironworker
[36] => Scaffold Erector
[38] => Sheetmetal Worker
[40] => Stonemason
[42] => Structural Ironworker
[44] => Terrazzo Worker
[46] => Commercial & Institutional
[47] => Jobsites
[48] => Heavy & Highway
[50] => Industrial
[52] => Renovations
[54] => Residential
)
[type] => Images
[sub_category] =>
[url] => /image/4014/i002700/Safety%2Bofficer%2Bdiscussing%2Bongoing%2Bproject%2Bwith%2Bmarketing%2Bcoordinator.html
[item:protected] => ImageRecord Object
(
[records:protected] => Array
(
)
[recordId:protected] =>
[searchWordClass:protected] =>
[searchWordPeerClass:protected] =>
[bok_record:protected] =>
[authors:protected] =>
[organizations:protected] =>
[collections:protected] =>
[categories:protected] => Array
(
[97] => Category Object
(
[languages:protected] =>
[bok_resources:protected] =>
[bok_topics:protected] =>
[bok_keywords:protected] =>
[id:protected] => 97
[type:protected] => category
[parent:protected] => 5
[label:protected] => Images
[alreadyInSave:protected] =>
[alreadyInValidation:protected] =>
[validationFailures:protected] => Array
(
)
[_new:BaseObject:private] =>
[_deleted:BaseObject:private] =>
[modifiedColumns:protected] => Array
(
)
)
[20] => Category Object
(
[languages:protected] =>
[bok_resources:protected] =>
[bok_topics:protected] =>
[bok_keywords:protected] =>
[id:protected] => 20
[type:protected] => category
[parent:protected] => 7
[label:protected] => Safety Culture
[alreadyInSave:protected] =>
[alreadyInValidation:protected] =>
[validationFailures:protected] => Array
(
)
[_new:BaseObject:private] =>
[_deleted:BaseObject:private] =>
[modifiedColumns:protected] => Array
(
)
)
[46] => Category Object
(
[languages:protected] =>
[bok_resources:protected] =>
[bok_topics:protected] =>
[bok_keywords:protected] =>
[id:protected] => 46
[type:protected] => category
[parent:protected] => 2
[label:protected] => Boilermaker
[alreadyInSave:protected] =>
[alreadyInValidation:protected] =>
[validationFailures:protected] => Array
(
)
[_new:BaseObject:private] =>
[_deleted:BaseObject:private] =>
[modifiedColumns:protected] => Array
(
)
)
[47] => Category Object
(
[languages:protected] =>
[bok_resources:protected] =>
[bok_topics:protected] =>
[bok_keywords:protected] =>
[id:protected] => 47
[type:protected] => category
[parent:protected] => 2
[label:protected] => Bricklayer
[alreadyInSave:protected] =>
[alreadyInValidation:protected] =>
[validationFailures:protected] => Array
(
)
[_new:BaseObject:private] =>
[_deleted:BaseObject:private] =>
[modifiedColumns:protected] => Array
(
)
)
[49] => Category Object
(
[languages:protected] =>
[bok_resources:protected] =>
[bok_topics:protected] =>
[bok_keywords:protected] =>
[id:protected] => 49
[type:protected] => category
[parent:protected] => 2
[label:protected] => Carpenter
[alreadyInSave:protected] =>
[alreadyInValidation:protected] =>
[validationFailures:protected] => Array
(
)
[_new:BaseObject:private] =>
[_deleted:BaseObject:private] =>
[modifiedColumns:protected] => Array
(
)
)
[50] => Category Object
(
[languages:protected] =>
[bok_resources:protected] =>
[bok_topics:protected] =>
[bok_keywords:protected] =>
[id:protected] => 50
[type:protected] => category
[parent:protected] => 2
[label:protected] => Carpet Layer
[alreadyInSave:protected] =>
[alreadyInValidation:protected] =>
[validationFailures:protected] => Array
(
)
[_new:BaseObject:private] =>
[_deleted:BaseObject:private] =>
[modifiedColumns:protected] => Array
(
)
)
[51] => Category Object
(
[languages:protected] =>
[bok_resources:protected] =>
[bok_topics:protected] =>
[bok_keywords:protected] =>
[id:protected] => 51
[type:protected] => category
[parent:protected] => 2
[label:protected] => Cement Mason
[alreadyInSave:protected] =>
[alreadyInValidation:protected] =>
[validationFailures:protected] => Array
(
)
[_new:BaseObject:private] =>
[_deleted:BaseObject:private] =>
[modifiedColumns:protected] => Array
(
)
)
[54] => Category Object
(
[languages:protected] =>
[bok_resources:protected] =>
[bok_topics:protected] =>
[bok_keywords:protected] =>
[id:protected] => 54
[type:protected] => category
[parent:protected] => 2
[label:protected] => Drywall Applicator Specialist
[alreadyInSave:protected] =>
[alreadyInValidation:protected] =>
[validationFailures:protected] => Array
(
)
[_new:BaseObject:private] =>
[_deleted:BaseObject:private] =>
[modifiedColumns:protected] => Array
(
)
)
[55] => Category Object
(
[languages:protected] =>
[bok_resources:protected] =>
[bok_topics:protected] =>
[bok_keywords:protected] =>
[id:protected] => 55
[type:protected] => category
[parent:protected] => 2
[label:protected] => Electrical Worker
[alreadyInSave:protected] =>
[alreadyInValidation:protected] =>
[validationFailures:protected] => Array
(
)
[_new:BaseObject:private] =>
[_deleted:BaseObject:private] =>
[modifiedColumns:protected] => Array
(
)
)
[58] => Category Object
(
[languages:protected] =>
[bok_resources:protected] =>
[bok_topics:protected] =>
[bok_keywords:protected] =>
[id:protected] => 58
[type:protected] => category
[parent:protected] => 2
[label:protected] => Glazier
[alreadyInSave:protected] =>
[alreadyInValidation:protected] =>
[validationFailures:protected] => Array
(
)
[_new:BaseObject:private] =>
[_deleted:BaseObject:private] =>
[modifiedColumns:protected] => Array
(
)
)
[60] => Category Object
(
[languages:protected] =>
[bok_resources:protected] =>
[bok_topics:protected] =>
[bok_keywords:protected] =>
[id:protected] => 60
[type:protected] => category
[parent:protected] => 2
[label:protected] => HVAC
[alreadyInSave:protected] =>
[alreadyInValidation:protected] =>
[validationFailures:protected] => Array
(
)
[_new:BaseObject:private] =>
[_deleted:BaseObject:private] =>
[modifiedColumns:protected] => Array
(
)
)
[61] => Category Object
(
[languages:protected] =>
[bok_resources:protected] =>
[bok_topics:protected] =>
[bok_keywords:protected] =>
[id:protected] => 61
[type:protected] => category
[parent:protected] => 2
[label:protected] => Interior Systems Carpenter
[alreadyInSave:protected] =>
[alreadyInValidation:protected] =>
[validationFailures:protected] => Array
(
)
[_new:BaseObject:private] =>
[_deleted:BaseObject:private] =>
[modifiedColumns:protected] => Array
(
)
)
[64] => Category Object
(
[languages:protected] =>
[bok_resources:protected] =>
[bok_topics:protected] =>
[bok_keywords:protected] =>
[id:protected] => 64
[type:protected] => category
[parent:protected] => 2
[label:protected] => Laborer
[alreadyInSave:protected] =>
[alreadyInValidation:protected] =>
[validationFailures:protected] => Array
(
)
[_new:BaseObject:private] =>
[_deleted:BaseObject:private] =>
[modifiedColumns:protected] => Array
(
)
)
[71] => Category Object
(
[languages:protected] =>
[bok_resources:protected] =>
[bok_topics:protected] =>
[bok_keywords:protected] =>
[id:protected] => 71
[type:protected] => category
[parent:protected] => 2
[label:protected] => Painter
[alreadyInSave:protected] =>
[alreadyInValidation:protected] =>
[validationFailures:protected] => Array
(
)
[_new:BaseObject:private] =>
[_deleted:BaseObject:private] =>
[modifiedColumns:protected] => Array
(
)
)
[75] => Category Object
(
[languages:protected] =>
[bok_resources:protected] =>
[bok_topics:protected] =>
[bok_keywords:protected] =>
[id:protected] => 75
[type:protected] => category
[parent:protected] => 2
[label:protected] => Plasterer
[alreadyInSave:protected] =>
[alreadyInValidation:protected] =>
[validationFailures:protected] => Array
(
)
[_new:BaseObject:private] =>
[_deleted:BaseObject:private] =>
[modifiedColumns:protected] => Array
(
)
)
[76] => Category Object
(
[languages:protected] =>
[bok_resources:protected] =>
[bok_topics:protected] =>
[bok_keywords:protected] =>
[id:protected] => 76
[type:protected] => category
[parent:protected] => 2
[label:protected] => Plumber/Pipefitter
[alreadyInSave:protected] =>
[alreadyInValidation:protected] =>
[validationFailures:protected] => Array
(
)
[_new:BaseObject:private] =>
[_deleted:BaseObject:private] =>
[modifiedColumns:protected] => Array
(
)
)
[63] => Category Object
(
[languages:protected] =>
[bok_resources:protected] =>
[bok_topics:protected] =>
[bok_keywords:protected] =>
[id:protected] => 63
[type:protected] => category
[parent:protected] => 2
[label:protected] => Reinforcing Ironworker
[alreadyInSave:protected] =>
[alreadyInValidation:protected] =>
[validationFailures:protected] => Array
(
)
[_new:BaseObject:private] =>
[_deleted:BaseObject:private] =>
[modifiedColumns:protected] => Array
(
)
)
[79] => Category Object
(
[languages:protected] =>
[bok_resources:protected] =>
[bok_topics:protected] =>
[bok_keywords:protected] =>
[id:protected] => 79
[type:protected] => category
[parent:protected] => 2
[label:protected] => Scaffold Erector
[alreadyInSave:protected] =>
[alreadyInValidation:protected] =>
[validationFailures:protected] => Array
(
)
[_new:BaseObject:private] =>
[_deleted:BaseObject:private] =>
[modifiedColumns:protected] => Array
(
)
)
[80] => Category Object
(
[languages:protected] =>
[bok_resources:protected] =>
[bok_topics:protected] =>
[bok_keywords:protected] =>
[id:protected] => 80
[type:protected] => category
[parent:protected] => 2
[label:protected] => Sheetmetal Worker
[alreadyInSave:protected] =>
[alreadyInValidation:protected] =>
[validationFailures:protected] => Array
(
)
[_new:BaseObject:private] =>
[_deleted:BaseObject:private] =>
[modifiedColumns:protected] => Array
(
)
)
[82] => Category Object
(
[languages:protected] =>
[bok_resources:protected] =>
[bok_topics:protected] =>
[bok_keywords:protected] =>
[id:protected] => 82
[type:protected] => category
[parent:protected] => 2
[label:protected] => Stonemason
[alreadyInSave:protected] =>
[alreadyInValidation:protected] =>
[validationFailures:protected] => Array
(
)
[_new:BaseObject:private] =>
[_deleted:BaseObject:private] =>
[modifiedColumns:protected] => Array
(
)
)
[62] => Category Object
(
[languages:protected] =>
[bok_resources:protected] =>
[bok_topics:protected] =>
[bok_keywords:protected] =>
[id:protected] => 62
[type:protected] => category
[parent:protected] => 2
[label:protected] => Structural Ironworker
[alreadyInSave:protected] =>
[alreadyInValidation:protected] =>
[validationFailures:protected] => Array
(
)
[_new:BaseObject:private] =>
[_deleted:BaseObject:private] =>
[modifiedColumns:protected] => Array
(
)
)
[83] => Category Object
(
[languages:protected] =>
[bok_resources:protected] =>
[bok_topics:protected] =>
[bok_keywords:protected] =>
[id:protected] => 83
[type:protected] => category
[parent:protected] => 2
[label:protected] => Terrazzo Worker
[alreadyInSave:protected] =>
[alreadyInValidation:protected] =>
[validationFailures:protected] => Array
(
)
[_new:BaseObject:private] =>
[_deleted:BaseObject:private] =>
[modifiedColumns:protected] => Array
(
)
)
[87] => Category Object
(
[languages:protected] =>
[bok_resources:protected] =>
[bok_topics:protected] =>
[bok_keywords:protected] =>
[id:protected] => 87
[type:protected] => category
[parent:protected] => 3
[label:protected] => Commercial & Institutional
[alreadyInSave:protected] =>
[alreadyInValidation:protected] =>
[validationFailures:protected] => Array
(
)
[_new:BaseObject:private] =>
[_deleted:BaseObject:private] =>
[modifiedColumns:protected] => Array
(
)
)
[91] => Category Object
(
[languages:protected] =>
[bok_resources:protected] =>
[bok_topics:protected] =>
[bok_keywords:protected] =>
[id:protected] => 91
[type:protected] => category
[parent:protected] => 3
[label:protected] => Heavy & Highway
[alreadyInSave:protected] =>
[alreadyInValidation:protected] =>
[validationFailures:protected] => Array
(
)
[_new:BaseObject:private] =>
[_deleted:BaseObject:private] =>
[modifiedColumns:protected] => Array
(
)
)
[90] => Category Object
(
[languages:protected] =>
[bok_resources:protected] =>
[bok_topics:protected] =>
[bok_keywords:protected] =>
[id:protected] => 90
[type:protected] => category
[parent:protected] => 3
[label:protected] => Industrial
[alreadyInSave:protected] =>
[alreadyInValidation:protected] =>
[validationFailures:protected] => Array
(
)
[_new:BaseObject:private] =>
[_deleted:BaseObject:private] =>
[modifiedColumns:protected] => Array
(
)
)
[93] => Category Object
(
[languages:protected] =>
[bok_resources:protected] =>
[bok_topics:protected] =>
[bok_keywords:protected] =>
[id:protected] => 93
[type:protected] => category
[parent:protected] => 3
[label:protected] => Renovations
[alreadyInSave:protected] =>
[alreadyInValidation:protected] =>
[validationFailures:protected] => Array
(
)
[_new:BaseObject:private] =>
[_deleted:BaseObject:private] =>
[modifiedColumns:protected] => Array
(
)
)
[94] => Category Object
(
[languages:protected] =>
[bok_resources:protected] =>
[bok_topics:protected] =>
[bok_keywords:protected] =>
[id:protected] => 94
[type:protected] => category
[parent:protected] => 3
[label:protected] => Residential
[alreadyInSave:protected] =>
[alreadyInValidation:protected] =>
[validationFailures:protected] => Array
(
)
[_new:BaseObject:private] =>
[_deleted:BaseObject:private] =>
[modifiedColumns:protected] => Array
(
)
)
)
[categories_initialized:protected] => 1
[mapped_items:protected] =>
[content:protected] =>
[files:protected] =>
[language:protected] => Language Object
(
[id:protected] => 1
[code:protected] => en
[name:protected] => English
[alreadyInSave:protected] =>
[alreadyInValidation:protected] =>
[validationFailures:protected] => Array
(
)
[_new:BaseObject:private] =>
[_deleted:BaseObject:private] =>
[modifiedColumns:protected] => Array
(
)
)
[old_record:protected] =>
[id:protected] => 4014
[old_id:protected] =>
[elcosh_id:protected] => i002700
[type:protected] => image
[display_type:protected] => Image
[user_id:protected] => 0
[language_id:protected] => 1
[tagging_id:protected] => Bruce Lippy
[priority_id:protected] => 1
[title:protected] => Safety officer discussing ongoing project with marketing coordinator
[total_pages:protected] => 0
[billed_pages:protected] => 0
[publication_number:protected] =>
[part_of:protected] =>
[keywords:protected] => Latino, safety officer, safety culture
[comments:protected] =>
[summary:protected] => The safety officer (left) points out the good safety practices on this project that reflect well on the firm and may influence future clients.
[transition_comments:protected] =>
[external_link:protected] =>
[consol_link:protected] => http://www.cpwrconstructionsolutions.org/index.php
[more_like_this:protected] => d000989,d001351,d001362,d000652, d001101, d000931, d001395
[permission_given_by:protected] =>
[published:protected] => T
[billable:protected] => F
[img_name:protected] =>
[img_ext:protected] => jpg
[img_width:protected] =>
[img_height:protected] =>
[img_credit:protected] => Hoar Construction, Photo by Neil Lippy
[img_practice:protected] => good
[vid_source_id:protected] =>
[vid_running_time:protected] =>
[vid_intended_audience:protected] =>
[vid_acquisition_info:protected] =>
[vid_cost:protected] =>
[vid_producer:protected] =>
[vid_filename:protected] =>
[vid_filename_downloadable:protected] =>
[date_summary:protected] => November 2015
[date_permission_requested:protected] =>
[date_permission_received:protected] =>
[date_review_needed:protected] =>
[date_received:protected] => 03/02/16
[date_completed:protected] => 03/02/16
[date_billed:protected] =>
[date_modified:protected] => 01/30/23
[collBokExports:protected] =>
[lastBokExportCriteria:BaseElcoshItem:private] =>
[alreadyInSave:protected] =>
[alreadyInValidation:protected] =>
[validationFailures:protected] => Array
(
)
[_new:BaseObject:private] =>
[_deleted:BaseObject:private] =>
[modifiedColumns:protected] => Array
(
)
)
)
[4] => Search_Result Object
(
[title] => Scaffolding at top of large column
[image] => /record/images/3994-p.jpg
[blurb] => This shot shows innovative guarding around the top of a large concrete column in the base of a high rise structure going up....
[category] => Array
(
[0] => 15
[1] => 21
[2] => 47
[3] => 51
[4] => 63
[5] => 78
[6] => 79
[7] => 80
[8] => 62
[9] => 87
[10] => 97
[11] => 56
[12] => 64
[13] => 74
)
[labels] => Array
(
[0] => Falls
[1] => Work Environment
[2] => Hazards
[3] => Scaffolds
[6] => Bricklayer
[7] => Trades
[8] => Cement Mason
[10] => Reinforcing Ironworker
[12] => Roofer/Waterproofer
[14] => Scaffold Erector
[16] => Sheetmetal Worker
[18] => Structural Ironworker
[20] => Commercial & Institutional
[21] => Jobsites
[22] => Images
[23] => Media
[24] => Media & Documents
[25] => Elevator Constructor
[27] => Laborer
[29] => Pile Driver
)
[type] => Images
[sub_category] =>
[url] => /image/3994/i002689/Scaffolding%2Bat%2Btop%2Bof%2Blarge%2Bcolumn.html
[item:protected] => ImageRecord Object
(
[records:protected] => Array
(
)
[recordId:protected] =>
[searchWordClass:protected] =>
[searchWordPeerClass:protected] =>
[bok_record:protected] =>
[authors:protected] =>
[organizations:protected] =>
[collections:protected] =>
[categories:protected] => Array
(
[15] => Category Object
(
[languages:protected] =>
[bok_resources:protected] =>
[bok_topics:protected] =>
[bok_keywords:protected] =>
[id:protected] => 15
[type:protected] => category
[parent:protected] => 7
[label:protected] => Falls
[alreadyInSave:protected] =>
[alreadyInValidation:protected] =>
[validationFailures:protected] => Array
(
)
[_new:BaseObject:private] =>
[_deleted:BaseObject:private] =>
[modifiedColumns:protected] => Array
(
)
)
[21] => Category Object
(
[languages:protected] =>
[bok_resources:protected] =>
[bok_topics:protected] =>
[bok_keywords:protected] =>
[id:protected] => 21
[type:protected] => category
[parent:protected] => 7
[label:protected] => Scaffolds
[alreadyInSave:protected] =>
[alreadyInValidation:protected] =>
[validationFailures:protected] => Array
(
)
[_new:BaseObject:private] =>
[_deleted:BaseObject:private] =>
[modifiedColumns:protected] => Array
(
)
)
[47] => Category Object
(
[languages:protected] =>
[bok_resources:protected] =>
[bok_topics:protected] =>
[bok_keywords:protected] =>
[id:protected] => 47
[type:protected] => category
[parent:protected] => 2
[label:protected] => Bricklayer
[alreadyInSave:protected] =>
[alreadyInValidation:protected] =>
[validationFailures:protected] => Array
(
)
[_new:BaseObject:private] =>
[_deleted:BaseObject:private] =>
[modifiedColumns:protected] => Array
(
)
)
[51] => Category Object
(
[languages:protected] =>
[bok_resources:protected] =>
[bok_topics:protected] =>
[bok_keywords:protected] =>
[id:protected] => 51
[type:protected] => category
[parent:protected] => 2
[label:protected] => Cement Mason
[alreadyInSave:protected] =>
[alreadyInValidation:protected] =>
[validationFailures:protected] => Array
(
)
[_new:BaseObject:private] =>
[_deleted:BaseObject:private] =>
[modifiedColumns:protected] => Array
(
)
)
[63] => Category Object
(
[languages:protected] =>
[bok_resources:protected] =>
[bok_topics:protected] =>
[bok_keywords:protected] =>
[id:protected] => 63
[type:protected] => category
[parent:protected] => 2
[label:protected] => Reinforcing Ironworker
[alreadyInSave:protected] =>
[alreadyInValidation:protected] =>
[validationFailures:protected] => Array
(
)
[_new:BaseObject:private] =>
[_deleted:BaseObject:private] =>
[modifiedColumns:protected] => Array
(
)
)
[78] => Category Object
(
[languages:protected] =>
[bok_resources:protected] =>
[bok_topics:protected] =>
[bok_keywords:protected] =>
[id:protected] => 78
[type:protected] => category
[parent:protected] => 2
[label:protected] => Roofer/Waterproofer
[alreadyInSave:protected] =>
[alreadyInValidation:protected] =>
[validationFailures:protected] => Array
(
)
[_new:BaseObject:private] =>
[_deleted:BaseObject:private] =>
[modifiedColumns:protected] => Array
(
)
)
[79] => Category Object
(
[languages:protected] =>
[bok_resources:protected] =>
[bok_topics:protected] =>
[bok_keywords:protected] =>
[id:protected] => 79
[type:protected] => category
[parent:protected] => 2
[label:protected] => Scaffold Erector
[alreadyInSave:protected] =>
[alreadyInValidation:protected] =>
[validationFailures:protected] => Array
(
)
[_new:BaseObject:private] =>
[_deleted:BaseObject:private] =>
[modifiedColumns:protected] => Array
(
)
)
[80] => Category Object
(
[languages:protected] =>
[bok_resources:protected] =>
[bok_topics:protected] =>
[bok_keywords:protected] =>
[id:protected] => 80
[type:protected] => category
[parent:protected] => 2
[label:protected] => Sheetmetal Worker
[alreadyInSave:protected] =>
[alreadyInValidation:protected] =>
[validationFailures:protected] => Array
(
)
[_new:BaseObject:private] =>
[_deleted:BaseObject:private] =>
[modifiedColumns:protected] => Array
(
)
)
[62] => Category Object
(
[languages:protected] =>
[bok_resources:protected] =>
[bok_topics:protected] =>
[bok_keywords:protected] =>
[id:protected] => 62
[type:protected] => category
[parent:protected] => 2
[label:protected] => Structural Ironworker
[alreadyInSave:protected] =>
[alreadyInValidation:protected] =>
[validationFailures:protected] => Array
(
)
[_new:BaseObject:private] =>
[_deleted:BaseObject:private] =>
[modifiedColumns:protected] => Array
(
)
)
[87] => Category Object
(
[languages:protected] =>
[bok_resources:protected] =>
[bok_topics:protected] =>
[bok_keywords:protected] =>
[id:protected] => 87
[type:protected] => category
[parent:protected] => 3
[label:protected] => Commercial & Institutional
[alreadyInSave:protected] =>
[alreadyInValidation:protected] =>
[validationFailures:protected] => Array
(
)
[_new:BaseObject:private] =>
[_deleted:BaseObject:private] =>
[modifiedColumns:protected] => Array
(
)
)
[97] => Category Object
(
[languages:protected] =>
[bok_resources:protected] =>
[bok_topics:protected] =>
[bok_keywords:protected] =>
[id:protected] => 97
[type:protected] => category
[parent:protected] => 5
[label:protected] => Images
[alreadyInSave:protected] =>
[alreadyInValidation:protected] =>
[validationFailures:protected] => Array
(
)
[_new:BaseObject:private] =>
[_deleted:BaseObject:private] =>
[modifiedColumns:protected] => Array
(
)
)
[56] => Category Object
(
[languages:protected] =>
[bok_resources:protected] =>
[bok_topics:protected] =>
[bok_keywords:protected] =>
[id:protected] => 56
[type:protected] => category
[parent:protected] => 2
[label:protected] => Elevator Constructor
[alreadyInSave:protected] =>
[alreadyInValidation:protected] =>
[validationFailures:protected] => Array
(
)
[_new:BaseObject:private] =>
[_deleted:BaseObject:private] =>
[modifiedColumns:protected] => Array
(
)
)
[64] => Category Object
(
[languages:protected] =>
[bok_resources:protected] =>
[bok_topics:protected] =>
[bok_keywords:protected] =>
[id:protected] => 64
[type:protected] => category
[parent:protected] => 2
[label:protected] => Laborer
[alreadyInSave:protected] =>
[alreadyInValidation:protected] =>
[validationFailures:protected] => Array
(
)
[_new:BaseObject:private] =>
[_deleted:BaseObject:private] =>
[modifiedColumns:protected] => Array
(
)
)
[74] => Category Object
(
[languages:protected] =>
[bok_resources:protected] =>
[bok_topics:protected] =>
[bok_keywords:protected] =>
[id:protected] => 74
[type:protected] => category
[parent:protected] => 2
[label:protected] => Pile Driver
[alreadyInSave:protected] =>
[alreadyInValidation:protected] =>
[validationFailures:protected] => Array
(
)
[_new:BaseObject:private] =>
[_deleted:BaseObject:private] =>
[modifiedColumns:protected] => Array
(
)
)
)
[categories_initialized:protected] => 1
[mapped_items:protected] =>
[content:protected] =>
[files:protected] =>
[language:protected] => Language Object
(
[id:protected] => 1
[code:protected] => en
[name:protected] => English
[alreadyInSave:protected] =>
[alreadyInValidation:protected] =>
[validationFailures:protected] => Array
(
)
[_new:BaseObject:private] =>
[_deleted:BaseObject:private] =>
[modifiedColumns:protected] => Array
(
)
)
[old_record:protected] =>
[id:protected] => 3994
[old_id:protected] =>
[elcosh_id:protected] => i002689
[type:protected] => image
[display_type:protected] => Image
[user_id:protected] => 0
[language_id:protected] => 1
[tagging_id:protected] => Bruce Lippy
[priority_id:protected] => 1
[title:protected] => Scaffolding at top of large column
[total_pages:protected] => 0
[billed_pages:protected] => 0
[publication_number:protected] =>
[part_of:protected] =>
[keywords:protected] => Guardrail, railing, fall prevention, falls
[comments:protected] =>
[summary:protected] => This shot shows innovative guarding around the top of a large concrete column in the base of a high rise structure going up.
[transition_comments:protected] =>
[external_link:protected] =>
[consol_link:protected] => http://www.cpwrconstructionsolutions.org/masonry/solution/8/adjustable-tower-scaffold.html
[more_like_this:protected] => c1002680,i002662,d000608,d001255
[permission_given_by:protected] =>
[published:protected] => T
[billable:protected] => F
[img_name:protected] =>
[img_ext:protected] => jpg
[img_width:protected] =>
[img_height:protected] =>
[img_credit:protected] => Photo by Pam Susi
[img_practice:protected] => good
[vid_source_id:protected] =>
[vid_running_time:protected] =>
[vid_intended_audience:protected] =>
[vid_acquisition_info:protected] =>
[vid_cost:protected] =>
[vid_producer:protected] =>
[vid_filename:protected] =>
[vid_filename_downloadable:protected] =>
[date_summary:protected] => January 2016
[date_permission_requested:protected] =>
[date_permission_received:protected] =>
[date_review_needed:protected] =>
[date_received:protected] => 02/01/16
[date_completed:protected] => 02/01/16
[date_billed:protected] =>
[date_modified:protected] => 02/01/16
[collBokExports:protected] =>
[lastBokExportCriteria:BaseElcoshItem:private] =>
[alreadyInSave:protected] =>
[alreadyInValidation:protected] =>
[validationFailures:protected] => Array
(
)
[_new:BaseObject:private] =>
[_deleted:BaseObject:private] =>
[modifiedColumns:protected] => Array
(
)
)
)
[5] => Search_Result Object
(
[title] => Construction bracing
[image] => /record/images/3995-p.jpg
[blurb] => This shows structural support that prevents collapses during construction....
[category] => Array
(
[0] => 12
[1] => 15
[2] => 21
[3] => 49
[4] => 51
[5] => 55
[6] => 56
[7] => 60
[8] => 64
[9] => 68
[10] => 74
[11] => 63
[12] => 78
[13] => 79
[14] => 80
[15] => 62
[16] => 87
[17] => 90
[18] => 97
)
[labels] => Array
(
[0] => Crushed/Struck By
[1] => Work Environment
[2] => Hazards
[3] => Falls
[6] => Scaffolds
[9] => Carpenter
[10] => Trades
[11] => Cement Mason
[13] => Electrical Worker
[15] => Elevator Constructor
[17] => HVAC
[19] => Laborer
[21] => Maintenance Worker
[23] => Pile Driver
[25] => Reinforcing Ironworker
[27] => Roofer/Waterproofer
[29] => Scaffold Erector
[31] => Sheetmetal Worker
[33] => Structural Ironworker
[35] => Commercial & Institutional
[36] => Jobsites
[37] => Industrial
[39] => Images
[40] => Media
[41] => Media & Documents
)
[type] => Images
[sub_category] =>
[url] => /image/3995/i002690/Construction%2Bbracing.html
[item:protected] => ImageRecord Object
(
[records:protected] => Array
(
)
[recordId:protected] =>
[searchWordClass:protected] =>
[searchWordPeerClass:protected] =>
[bok_record:protected] =>
[authors:protected] =>
[organizations:protected] =>
[collections:protected] =>
[categories:protected] => Array
(
[12] => Category Object
(
[languages:protected] =>
[bok_resources:protected] =>
[bok_topics:protected] =>
[bok_keywords:protected] =>
[id:protected] => 12
[type:protected] => category
[parent:protected] => 7
[label:protected] => Crushed/Struck By
[alreadyInSave:protected] =>
[alreadyInValidation:protected] =>
[validationFailures:protected] => Array
(
)
[_new:BaseObject:private] =>
[_deleted:BaseObject:private] =>
[modifiedColumns:protected] => Array
(
)
)
[15] => Category Object
(
[languages:protected] =>
[bok_resources:protected] =>
[bok_topics:protected] =>
[bok_keywords:protected] =>
[id:protected] => 15
[type:protected] => category
[parent:protected] => 7
[label:protected] => Falls
[alreadyInSave:protected] =>
[alreadyInValidation:protected] =>
[validationFailures:protected] => Array
(
)
[_new:BaseObject:private] =>
[_deleted:BaseObject:private] =>
[modifiedColumns:protected] => Array
(
)
)
[21] => Category Object
(
[languages:protected] =>
[bok_resources:protected] =>
[bok_topics:protected] =>
[bok_keywords:protected] =>
[id:protected] => 21
[type:protected] => category
[parent:protected] => 7
[label:protected] => Scaffolds
[alreadyInSave:protected] =>
[alreadyInValidation:protected] =>
[validationFailures:protected] => Array
(
)
[_new:BaseObject:private] =>
[_deleted:BaseObject:private] =>
[modifiedColumns:protected] => Array
(
)
)
[49] => Category Object
(
[languages:protected] =>
[bok_resources:protected] =>
[bok_topics:protected] =>
[bok_keywords:protected] =>
[id:protected] => 49
[type:protected] => category
[parent:protected] => 2
[label:protected] => Carpenter
[alreadyInSave:protected] =>
[alreadyInValidation:protected] =>
[validationFailures:protected] => Array
(
)
[_new:BaseObject:private] =>
[_deleted:BaseObject:private] =>
[modifiedColumns:protected] => Array
(
)
)
[51] => Category Object
(
[languages:protected] =>
[bok_resources:protected] =>
[bok_topics:protected] =>
[bok_keywords:protected] =>
[id:protected] => 51
[type:protected] => category
[parent:protected] => 2
[label:protected] => Cement Mason
[alreadyInSave:protected] =>
[alreadyInValidation:protected] =>
[validationFailures:protected] => Array
(
)
[_new:BaseObject:private] =>
[_deleted:BaseObject:private] =>
[modifiedColumns:protected] => Array
(
)
)
[55] => Category Object
(
[languages:protected] =>
[bok_resources:protected] =>
[bok_topics:protected] =>
[bok_keywords:protected] =>
[id:protected] => 55
[type:protected] => category
[parent:protected] => 2
[label:protected] => Electrical Worker
[alreadyInSave:protected] =>
[alreadyInValidation:protected] =>
[validationFailures:protected] => Array
(
)
[_new:BaseObject:private] =>
[_deleted:BaseObject:private] =>
[modifiedColumns:protected] => Array
(
)
)
[56] => Category Object
(
[languages:protected] =>
[bok_resources:protected] =>
[bok_topics:protected] =>
[bok_keywords:protected] =>
[id:protected] => 56
[type:protected] => category
[parent:protected] => 2
[label:protected] => Elevator Constructor
[alreadyInSave:protected] =>
[alreadyInValidation:protected] =>
[validationFailures:protected] => Array
(
)
[_new:BaseObject:private] =>
[_deleted:BaseObject:private] =>
[modifiedColumns:protected] => Array
(
)
)
[60] => Category Object
(
[languages:protected] =>
[bok_resources:protected] =>
[bok_topics:protected] =>
[bok_keywords:protected] =>
[id:protected] => 60
[type:protected] => category
[parent:protected] => 2
[label:protected] => HVAC
[alreadyInSave:protected] =>
[alreadyInValidation:protected] =>
[validationFailures:protected] => Array
(
)
[_new:BaseObject:private] =>
[_deleted:BaseObject:private] =>
[modifiedColumns:protected] => Array
(
)
)
[64] => Category Object
(
[languages:protected] =>
[bok_resources:protected] =>
[bok_topics:protected] =>
[bok_keywords:protected] =>
[id:protected] => 64
[type:protected] => category
[parent:protected] => 2
[label:protected] => Laborer
[alreadyInSave:protected] =>
[alreadyInValidation:protected] =>
[validationFailures:protected] => Array
(
)
[_new:BaseObject:private] =>
[_deleted:BaseObject:private] =>
[modifiedColumns:protected] => Array
(
)
)
[68] => Category Object
(
[languages:protected] =>
[bok_resources:protected] =>
[bok_topics:protected] =>
[bok_keywords:protected] =>
[id:protected] => 68
[type:protected] => category
[parent:protected] => 2
[label:protected] => Maintenance Worker
[alreadyInSave:protected] =>
[alreadyInValidation:protected] =>
[validationFailures:protected] => Array
(
)
[_new:BaseObject:private] =>
[_deleted:BaseObject:private] =>
[modifiedColumns:protected] => Array
(
)
)
[74] => Category Object
(
[languages:protected] =>
[bok_resources:protected] =>
[bok_topics:protected] =>
[bok_keywords:protected] =>
[id:protected] => 74
[type:protected] => category
[parent:protected] => 2
[label:protected] => Pile Driver
[alreadyInSave:protected] =>
[alreadyInValidation:protected] =>
[validationFailures:protected] => Array
(
)
[_new:BaseObject:private] =>
[_deleted:BaseObject:private] =>
[modifiedColumns:protected] => Array
(
)
)
[63] => Category Object
(
[languages:protected] =>
[bok_resources:protected] =>
[bok_topics:protected] =>
[bok_keywords:protected] =>
[id:protected] => 63
[type:protected] => category
[parent:protected] => 2
[label:protected] => Reinforcing Ironworker
[alreadyInSave:protected] =>
[alreadyInValidation:protected] =>
[validationFailures:protected] => Array
(
)
[_new:BaseObject:private] =>
[_deleted:BaseObject:private] =>
[modifiedColumns:protected] => Array
(
)
)
[78] => Category Object
(
[languages:protected] =>
[bok_resources:protected] =>
[bok_topics:protected] =>
[bok_keywords:protected] =>
[id:protected] => 78
[type:protected] => category
[parent:protected] => 2
[label:protected] => Roofer/Waterproofer
[alreadyInSave:protected] =>
[alreadyInValidation:protected] =>
[validationFailures:protected] => Array
(
)
[_new:BaseObject:private] =>
[_deleted:BaseObject:private] =>
[modifiedColumns:protected] => Array
(
)
)
[79] => Category Object
(
[languages:protected] =>
[bok_resources:protected] =>
[bok_topics:protected] =>
[bok_keywords:protected] =>
[id:protected] => 79
[type:protected] => category
[parent:protected] => 2
[label:protected] => Scaffold Erector
[alreadyInSave:protected] =>
[alreadyInValidation:protected] =>
[validationFailures:protected] => Array
(
)
[_new:BaseObject:private] =>
[_deleted:BaseObject:private] =>
[modifiedColumns:protected] => Array
(
)
)
[80] => Category Object
(
[languages:protected] =>
[bok_resources:protected] =>
[bok_topics:protected] =>
[bok_keywords:protected] =>
[id:protected] => 80
[type:protected] => category
[parent:protected] => 2
[label:protected] => Sheetmetal Worker
[alreadyInSave:protected] =>
[alreadyInValidation:protected] =>
[validationFailures:protected] => Array
(
)
[_new:BaseObject:private] =>
[_deleted:BaseObject:private] =>
[modifiedColumns:protected] => Array
(
)
)
[62] => Category Object
(
[languages:protected] =>
[bok_resources:protected] =>
[bok_topics:protected] =>
[bok_keywords:protected] =>
[id:protected] => 62
[type:protected] => category
[parent:protected] => 2
[label:protected] => Structural Ironworker
[alreadyInSave:protected] =>
[alreadyInValidation:protected] =>
[validationFailures:protected] => Array
(
)
[_new:BaseObject:private] =>
[_deleted:BaseObject:private] =>
[modifiedColumns:protected] => Array
(
)
)
[87] => Category Object
(
[languages:protected] =>
[bok_resources:protected] =>
[bok_topics:protected] =>
[bok_keywords:protected] =>
[id:protected] => 87
[type:protected] => category
[parent:protected] => 3
[label:protected] => Commercial & Institutional
[alreadyInSave:protected] =>
[alreadyInValidation:protected] =>
[validationFailures:protected] => Array
(
)
[_new:BaseObject:private] =>
[_deleted:BaseObject:private] =>
[modifiedColumns:protected] => Array
(
)
)
[90] => Category Object
(
[languages:protected] =>
[bok_resources:protected] =>
[bok_topics:protected] =>
[bok_keywords:protected] =>
[id:protected] => 90
[type:protected] => category
[parent:protected] => 3
[label:protected] => Industrial
[alreadyInSave:protected] =>
[alreadyInValidation:protected] =>
[validationFailures:protected] => Array
(
)
[_new:BaseObject:private] =>
[_deleted:BaseObject:private] =>
[modifiedColumns:protected] => Array
(
)
)
[97] => Category Object
(
[languages:protected] =>
[bok_resources:protected] =>
[bok_topics:protected] =>
[bok_keywords:protected] =>
[id:protected] => 97
[type:protected] => category
[parent:protected] => 5
[label:protected] => Images
[alreadyInSave:protected] =>
[alreadyInValidation:protected] =>
[validationFailures:protected] => Array
(
)
[_new:BaseObject:private] =>
[_deleted:BaseObject:private] =>
[modifiedColumns:protected] => Array
(
)
)
)
[categories_initialized:protected] => 1
[mapped_items:protected] =>
[content:protected] =>
[files:protected] =>
[language:protected] => Language Object
(
[id:protected] => 1
[code:protected] => en
[name:protected] => English
[alreadyInSave:protected] =>
[alreadyInValidation:protected] =>
[validationFailures:protected] => Array
(
)
[_new:BaseObject:private] =>
[_deleted:BaseObject:private] =>
[modifiedColumns:protected] => Array
(
)
)
[old_record:protected] =>
[id:protected] => 3995
[old_id:protected] =>
[elcosh_id:protected] => i002690
[type:protected] => image
[display_type:protected] => Image
[user_id:protected] => 0
[language_id:protected] => 1
[tagging_id:protected] => Bruce Lippy
[priority_id:protected] => 1
[title:protected] => Construction bracing
[total_pages:protected] => 0
[billed_pages:protected] => 0
[publication_number:protected] =>
[part_of:protected] =>
[keywords:protected] => Bracing, support, scaffold
[comments:protected] =>
[summary:protected] => This shows structural support that prevents collapses during construction.
[transition_comments:protected] =>
[external_link:protected] =>
[consol_link:protected] => http://www.cpwrconstructionsolutions.org/masonry/solution/8/adjustable-tower-scaffold.html
[more_like_this:protected] => i002660
[permission_given_by:protected] =>
[published:protected] => T
[billable:protected] => F
[img_name:protected] =>
[img_ext:protected] => jpg
[img_width:protected] =>
[img_height:protected] =>
[img_credit:protected] => Photo by Pam Susi
[img_practice:protected] => good
[vid_source_id:protected] =>
[vid_running_time:protected] =>
[vid_intended_audience:protected] =>
[vid_acquisition_info:protected] =>
[vid_cost:protected] =>
[vid_producer:protected] =>
[vid_filename:protected] =>
[vid_filename_downloadable:protected] =>
[date_summary:protected] => January 2016
[date_permission_requested:protected] =>
[date_permission_received:protected] =>
[date_review_needed:protected] =>
[date_received:protected] => 02/01/16
[date_completed:protected] => 02/01/16
[date_billed:protected] =>
[date_modified:protected] => 02/01/16
[collBokExports:protected] =>
[lastBokExportCriteria:BaseElcoshItem:private] =>
[alreadyInSave:protected] =>
[alreadyInValidation:protected] =>
[validationFailures:protected] => Array
(
)
[_new:BaseObject:private] =>
[_deleted:BaseObject:private] =>
[modifiedColumns:protected] => Array
(
)
)
)
)
[preview_mode] =>
[description] => Toolbox talks have been the main tool for communicating safety information on construction jobs for decades.
Unfortunately, there has been little research on what makes for effective toolbox talks. The IUOE National
Training Fund worked with OSHA and NIOSH to make sure their series of 24 Focus Four toolbox talks were based on the best recommendations for effective design. These toolbox talks accompany an entire package of training materials, but can be used alone. This guide points out the key features of these toolbox talks and how best to deliver them.
[keywords] => toolbox talks, tailgate talks
[related_items] => Array
(
[Toolbox Talks] => Array
(
[0] => DocumentRecord Object
(
[records:protected] => Array
(
)
[recordId:protected] =>
[searchWordClass:protected] =>
[searchWordPeerClass:protected] =>
[bok_record:protected] =>
[authors:protected] =>
[organizations:protected] =>
[collections:protected] =>
[categories:protected] =>
[categories_initialized:protected] =>
[mapped_items:protected] =>
[content:protected] =>
[files:protected] =>
[language:protected] => Language Object
(
[id:protected] => 1
[code:protected] => en
[name:protected] => English
[alreadyInSave:protected] =>
[alreadyInValidation:protected] =>
[validationFailures:protected] => Array
(
)
[_new:BaseObject:private] =>
[_deleted:BaseObject:private] =>
[modifiedColumns:protected] => Array
(
)
)
[old_record:protected] =>
[id:protected] => 1605
[old_id:protected] => 1262
[elcosh_id:protected] => d001137
[type:protected] => document
[display_type:protected] => HTML w/ PDF
[user_id:protected] =>
[language_id:protected] => 1
[tagging_id:protected] => Garber
[priority_id:protected] => 1
[title:protected] => Focus Four Toolbox Talks, Module 1 – Falls, Talk #2 – Falls from debris piles?
[total_pages:protected] => 1
[billed_pages:protected] => 1
[publication_number:protected] =>
[part_of:protected] =>
[keywords:protected] => disaster response, hazard clean-up, uneven surface, disaster site, disaster clean-up
[comments:protected] =>
[summary:protected] => A toolbox talk on preventing falls from debris piles. Includes questions to ask, an incident to discuss with images, and a place to record questions the trainer would like to ask about the incident. Part of a collection. Click on the 'collection' button to access the other items.
[transition_comments:protected] =>
[external_link:protected] =>
[consol_link:protected] => http://www.cpwrconstructionsolutions.org/roofing/hazard/1463/install-asphalt-roofs-fall-from-heights.html
[more_like_this:protected] => a000081,d000478,d000530
[permission_given_by:protected] =>
[published:protected] => T
[billable:protected] => F
[img_name:protected] =>
[img_ext:protected] =>
[img_width:protected] =>
[img_height:protected] =>
[img_credit:protected] =>
[img_practice:protected] =>
[vid_source_id:protected] =>
[vid_running_time:protected] =>
[vid_intended_audience:protected] =>
[vid_acquisition_info:protected] =>
[vid_cost:protected] =>
[vid_producer:protected] =>
[vid_filename:protected] =>
[vid_filename_downloadable:protected] =>
[date_summary:protected] =>
[date_permission_requested:protected] =>
[date_permission_received:protected] =>
[date_review_needed:protected] =>
[date_received:protected] => 02/15/12
[date_completed:protected] => 03/19/12
[date_billed:protected] =>
[date_modified:protected] => 07/10/12
[collBokExports:protected] =>
[lastBokExportCriteria:BaseElcoshItem:private] =>
[alreadyInSave:protected] =>
[alreadyInValidation:protected] =>
[validationFailures:protected] => Array
(
)
[_new:BaseObject:private] =>
[_deleted:BaseObject:private] =>
[modifiedColumns:protected] => Array
(
)
)
[1] => DocumentRecord Object
(
[records:protected] => Array
(
)
[recordId:protected] =>
[searchWordClass:protected] =>
[searchWordPeerClass:protected] =>
[bok_record:protected] =>
[authors:protected] =>
[organizations:protected] =>
[collections:protected] =>
[categories:protected] =>
[categories_initialized:protected] =>
[mapped_items:protected] =>
[content:protected] =>
[files:protected] =>
[language:protected] => Language Object
(
[id:protected] => 1
[code:protected] => en
[name:protected] => English
[alreadyInSave:protected] =>
[alreadyInValidation:protected] =>
[validationFailures:protected] => Array
(
)
[_new:BaseObject:private] =>
[_deleted:BaseObject:private] =>
[modifiedColumns:protected] => Array
(
)
)
[old_record:protected] =>
[id:protected] => 1610
[old_id:protected] => 1271
[elcosh_id:protected] => d001146
[type:protected] => document
[display_type:protected] => HTML w/ PDF
[user_id:protected] => 0
[language_id:protected] => 1
[tagging_id:protected] => Garber
[priority_id:protected] => 1
[title:protected] => Focus Four Toolbox Talks, Module 2 – Struck-by, Talk #5 – Rigging and Securing Loads
[total_pages:protected] => 1
[billed_pages:protected] => 1
[publication_number:protected] =>
[part_of:protected] =>
[keywords:protected] => rigging, lift loads, loading areas, chains
[comments:protected] =>
[summary:protected] => A toolbox talk on preventing struck-by incidents caused by not securing loads properly. Includes questions to ask, an incident to discuss with images, and a place to record questions the trainer would like to ask about the incident. Part of a collection. Click on the 'collection' button to access the other items.
[transition_comments:protected] =>
[external_link:protected] =>
[consol_link:protected] => http://www.cpwrconstructionsolutions.org/heavy_equipment/hazard/1591/move-equipment-to-from-and-between-sites-work-zone-struck-by-injuries-and-fatalities.html
[more_like_this:protected] => d000144,d000360,d000873
[permission_given_by:protected] =>
[published:protected] => T
[billable:protected] => F
[img_name:protected] =>
[img_ext:protected] =>
[img_width:protected] =>
[img_height:protected] =>
[img_credit:protected] =>
[img_practice:protected] =>
[vid_source_id:protected] =>
[vid_running_time:protected] =>
[vid_intended_audience:protected] =>
[vid_acquisition_info:protected] =>
[vid_cost:protected] =>
[vid_producer:protected] =>
[vid_filename:protected] =>
[vid_filename_downloadable:protected] =>
[date_summary:protected] =>
[date_permission_requested:protected] =>
[date_permission_received:protected] =>
[date_review_needed:protected] =>
[date_received:protected] => 02/15/12
[date_completed:protected] => 03/28/12
[date_billed:protected] =>
[date_modified:protected] => 05/12/14
[collBokExports:protected] =>
[lastBokExportCriteria:BaseElcoshItem:private] =>
[alreadyInSave:protected] =>
[alreadyInValidation:protected] =>
[validationFailures:protected] => Array
(
)
[_new:BaseObject:private] =>
[_deleted:BaseObject:private] =>
[modifiedColumns:protected] => Array
(
)
)
[2] => DocumentRecord Object
(
[records:protected] => Array
(
)
[recordId:protected] =>
[searchWordClass:protected] =>
[searchWordPeerClass:protected] =>
[bok_record:protected] =>
[authors:protected] =>
[organizations:protected] =>
[collections:protected] =>
[categories:protected] =>
[categories_initialized:protected] =>
[mapped_items:protected] =>
[content:protected] =>
[files:protected] =>
[language:protected] => Language Object
(
[id:protected] => 1
[code:protected] => en
[name:protected] => English
[alreadyInSave:protected] =>
[alreadyInValidation:protected] =>
[validationFailures:protected] => Array
(
)
[_new:BaseObject:private] =>
[_deleted:BaseObject:private] =>
[modifiedColumns:protected] => Array
(
)
)
[old_record:protected] =>
[id:protected] => 1645
[old_id:protected] => 1274
[elcosh_id:protected] => d001149
[type:protected] => document
[display_type:protected] => HTML w/ PDF
[user_id:protected] => 0
[language_id:protected] => 1
[tagging_id:protected] => Garber
[priority_id:protected] => 1
[title:protected] => Focus Four Toolbox Talks, Module 3 – Caught-in/between, Talk #2 – Trenches & Heavy Equipment
[total_pages:protected] => 1
[billed_pages:protected] => 1
[publication_number:protected] =>
[part_of:protected] =>
[keywords:protected] => back-up alarms, spotter, soil cave-in, spoil pikes, ROPs, trenching, rain
[comments:protected] =>
[summary:protected] => A toolbox talk on preventing incidents involving trenches such as trench collapse. Includes questions to ask, an incident to discuss with images, and a place to record questions the trainer would like to ask about the incident. Part of a collection. Click on the 'collection' button to access the other items.
[transition_comments:protected] =>
[external_link:protected] =>
[consol_link:protected] =>
[more_like_this:protected] => d000019,d000035,d000168
[permission_given_by:protected] =>
[published:protected] => T
[billable:protected] => F
[img_name:protected] =>
[img_ext:protected] =>
[img_width:protected] =>
[img_height:protected] =>
[img_credit:protected] =>
[img_practice:protected] =>
[vid_source_id:protected] =>
[vid_running_time:protected] =>
[vid_intended_audience:protected] =>
[vid_acquisition_info:protected] =>
[vid_cost:protected] =>
[vid_producer:protected] =>
[vid_filename:protected] =>
[vid_filename_downloadable:protected] =>
[date_summary:protected] =>
[date_permission_requested:protected] =>
[date_permission_received:protected] =>
[date_review_needed:protected] =>
[date_received:protected] => 02/15/12
[date_completed:protected] => 04/02/12
[date_billed:protected] =>
[date_modified:protected] => 05/23/23
[collBokExports:protected] =>
[lastBokExportCriteria:BaseElcoshItem:private] =>
[alreadyInSave:protected] =>
[alreadyInValidation:protected] =>
[validationFailures:protected] => Array
(
)
[_new:BaseObject:private] =>
[_deleted:BaseObject:private] =>
[modifiedColumns:protected] => Array
(
)
)
[3] => DocumentRecord Object
(
[records:protected] => Array
(
)
[recordId:protected] =>
[searchWordClass:protected] =>
[searchWordPeerClass:protected] =>
[bok_record:protected] =>
[authors:protected] =>
[organizations:protected] =>
[collections:protected] =>
[categories:protected] =>
[categories_initialized:protected] =>
[mapped_items:protected] =>
[content:protected] =>
[files:protected] =>
[language:protected] => Language Object
(
[id:protected] => 1
[code:protected] => en
[name:protected] => English
[alreadyInSave:protected] =>
[alreadyInValidation:protected] =>
[validationFailures:protected] => Array
(
)
[_new:BaseObject:private] =>
[_deleted:BaseObject:private] =>
[modifiedColumns:protected] => Array
(
)
)
[old_record:protected] =>
[id:protected] => 1654
[old_id:protected] => 1284
[elcosh_id:protected] => d001159
[type:protected] => document
[display_type:protected] => HTML w/ PDF
[user_id:protected] => 0
[language_id:protected] => 1
[tagging_id:protected] => Garber
[priority_id:protected] => 1
[title:protected] => Focus Four Toolbox Talks, Module 4 – Electrocutions, Talk #6 – Hazards on Disaster Sites
[total_pages:protected] => 1
[billed_pages:protected] => 1
[publication_number:protected] =>
[part_of:protected] =>
[keywords:protected] => powerlines, underground, utilities, generators, wet conditions, GFCIs, energized lines, disasters, emergency response
[comments:protected] =>
[summary:protected] => A toolbox talk on how to avoid electrocution on a disaster site. Includes questions to ask, an incident to discuss with images, and a place to record questions the trainer would like to ask about the incident. Part of a collection. Click on the 'collection' button to access the other items.
[transition_comments:protected] =>
[external_link:protected] =>
[consol_link:protected] => http://www.cpwrconstructionsolutions.org/electrical/hazard/1138/install-and-repair-high-voltage-lines-transformers-switches-electrical-shocks-burns-and-or-electrocution.html
[more_like_this:protected] => d000135,d000361,d000437
[permission_given_by:protected] =>
[published:protected] => T
[billable:protected] => F
[img_name:protected] =>
[img_ext:protected] =>
[img_width:protected] =>
[img_height:protected] =>
[img_credit:protected] =>
[img_practice:protected] =>
[vid_source_id:protected] =>
[vid_running_time:protected] =>
[vid_intended_audience:protected] =>
[vid_acquisition_info:protected] =>
[vid_cost:protected] =>
[vid_producer:protected] =>
[vid_filename:protected] =>
[vid_filename_downloadable:protected] =>
[date_summary:protected] =>
[date_permission_requested:protected] =>
[date_permission_received:protected] =>
[date_review_needed:protected] =>
[date_received:protected] => 02/15/12
[date_completed:protected] => 04/02/12
[date_billed:protected] =>
[date_modified:protected] => 05/23/23
[collBokExports:protected] =>
[lastBokExportCriteria:BaseElcoshItem:private] =>
[alreadyInSave:protected] =>
[alreadyInValidation:protected] =>
[validationFailures:protected] => Array
(
)
[_new:BaseObject:private] =>
[_deleted:BaseObject:private] =>
[modifiedColumns:protected] => Array
(
)
)
)
)
[collections] => Array
(
[1294] =>
[1295] =>
[1292] =>
[1293] => CollectionRecord Object
(
[collection_items:protected] =>
[records:protected] => Array
(
)
[recordId:protected] =>
[searchWordClass:protected] =>
[searchWordPeerClass:protected] =>
[bok_record:protected] =>
[authors:protected] =>
[organizations:protected] =>
[collections:protected] =>
[categories:protected] =>
[categories_initialized:protected] =>
[mapped_items:protected] =>
[content:protected] =>
[files:protected] =>
[language:protected] =>
[old_record:protected] =>
[id:protected] => 1293
[old_id:protected] =>
[elcosh_id:protected] => c000026
[type:protected] => collection
[display_type:protected] => Collection
[user_id:protected] =>
[language_id:protected] =>
[tagging_id:protected] =>
[priority_id:protected] =>
[title:protected] => Focus Four-Struck By
[total_pages:protected] =>
[billed_pages:protected] =>
[publication_number:protected] =>
[part_of:protected] =>
[keywords:protected] =>
[comments:protected] =>
[summary:protected] => The following are links to all of the items in this collection:
[transition_comments:protected] =>
[external_link:protected] =>
[consol_link:protected] =>
[more_like_this:protected] =>
[permission_given_by:protected] =>
[published:protected] => T
[billable:protected] => F
[img_name:protected] =>
[img_ext:protected] =>
[img_width:protected] =>
[img_height:protected] =>
[img_credit:protected] =>
[img_practice:protected] =>
[vid_source_id:protected] =>
[vid_running_time:protected] =>
[vid_intended_audience:protected] =>
[vid_acquisition_info:protected] =>
[vid_cost:protected] =>
[vid_producer:protected] =>
[vid_filename:protected] =>
[vid_filename_downloadable:protected] =>
[date_summary:protected] =>
[date_permission_requested:protected] =>
[date_permission_received:protected] =>
[date_review_needed:protected] =>
[date_received:protected] => 05/08/12
[date_completed:protected] => 05/08/12
[date_billed:protected] =>
[date_modified:protected] => 05/08/12
[collBokExports:protected] =>
[lastBokExportCriteria:BaseElcoshItem:private] =>
[alreadyInSave:protected] =>
[alreadyInValidation:protected] =>
[validationFailures:protected] => Array
(
)
[_new:BaseObject:private] =>
[_deleted:BaseObject:private] =>
[modifiedColumns:protected] => Array
(
)
)
)
[record] => DocumentRecord Object
(
[records:protected] => Array
(
)
[recordId:protected] =>
[searchWordClass:protected] =>
[searchWordPeerClass:protected] =>
[bok_record:protected] =>
[authors:protected] => Array
(
)
[organizations:protected] => Array
(
[256] => Organization Object
(
[id:protected] => 256
[elcosh_id:protected] => o000276
[user_id:protected] => 14
[province_id:protected] => 0
[country_id:protected] => 0
[title:protected] => IUOE National Training Fund
[address:protected] =>
[postal_code:protected] =>
[city:protected] =>
[department:protected] =>
[phone:protected] => 304-253-8674
[fax:protected] =>
[email:protected] =>
[website:protected] => http://www.iuoeiettc.org
[filename:protected] =>
[about:protected] =>
[comments:protected] =>
[logo_available:protected] => T
[no_details:protected] => F
[date_received:protected] => 2012-02-13
[date_completed:protected] => 2012-02-13
[date_billed:protected] =>
[alreadyInSave:protected] =>
[alreadyInValidation:protected] =>
[validationFailures:protected] => Array
(
)
[_new:BaseObject:private] =>
[_deleted:BaseObject:private] =>
[modifiedColumns:protected] => Array
(
)
)
)
[collections:protected] => Array
(
[1294] =>
[1295] =>
[1292] =>
[1293] => CollectionRecord Object
(
[collection_items:protected] =>
[records:protected] => Array
(
)
[recordId:protected] =>
[searchWordClass:protected] =>
[searchWordPeerClass:protected] =>
[bok_record:protected] =>
[authors:protected] =>
[organizations:protected] =>
[collections:protected] =>
[categories:protected] =>
[categories_initialized:protected] =>
[mapped_items:protected] =>
[content:protected] =>
[files:protected] =>
[language:protected] =>
[old_record:protected] =>
[id:protected] => 1293
[old_id:protected] =>
[elcosh_id:protected] => c000026
[type:protected] => collection
[display_type:protected] => Collection
[user_id:protected] =>
[language_id:protected] =>
[tagging_id:protected] =>
[priority_id:protected] =>
[title:protected] => Focus Four-Struck By
[total_pages:protected] =>
[billed_pages:protected] =>
[publication_number:protected] =>
[part_of:protected] =>
[keywords:protected] =>
[comments:protected] =>
[summary:protected] => The following are links to all of the items in this collection:
[transition_comments:protected] =>
[external_link:protected] =>
[consol_link:protected] =>
[more_like_this:protected] =>
[permission_given_by:protected] =>
[published:protected] => T
[billable:protected] => F
[img_name:protected] =>
[img_ext:protected] =>
[img_width:protected] =>
[img_height:protected] =>
[img_credit:protected] =>
[img_practice:protected] =>
[vid_source_id:protected] =>
[vid_running_time:protected] =>
[vid_intended_audience:protected] =>
[vid_acquisition_info:protected] =>
[vid_cost:protected] =>
[vid_producer:protected] =>
[vid_filename:protected] =>
[vid_filename_downloadable:protected] =>
[date_summary:protected] =>
[date_permission_requested:protected] =>
[date_permission_received:protected] =>
[date_review_needed:protected] =>
[date_received:protected] => 05/08/12
[date_completed:protected] => 05/08/12
[date_billed:protected] =>
[date_modified:protected] => 05/08/12
[collBokExports:protected] =>
[lastBokExportCriteria:BaseElcoshItem:private] =>
[alreadyInSave:protected] =>
[alreadyInValidation:protected] =>
[validationFailures:protected] => Array
(
)
[_new:BaseObject:private] =>
[_deleted:BaseObject:private] =>
[modifiedColumns:protected] => Array
(
)
)
)
[categories:protected] =>
[categories_initialized:protected] =>
[mapped_items:protected] => Array
(
[1605] => DocumentRecord Object
(
[records:protected] => Array
(
)
[recordId:protected] =>
[searchWordClass:protected] =>
[searchWordPeerClass:protected] =>
[bok_record:protected] =>
[authors:protected] =>
[organizations:protected] =>
[collections:protected] =>
[categories:protected] =>
[categories_initialized:protected] =>
[mapped_items:protected] =>
[content:protected] =>
[files:protected] =>
[language:protected] =>
[old_record:protected] =>
[id:protected] => 1605
[old_id:protected] => 1262
[elcosh_id:protected] => d001137
[type:protected] => document
[display_type:protected] => HTML w/ PDF
[user_id:protected] =>
[language_id:protected] => 1
[tagging_id:protected] => Garber
[priority_id:protected] => 1
[title:protected] => Focus Four Toolbox Talks, Module 1 – Falls, Talk #2 – Falls from debris piles?
[total_pages:protected] => 1
[billed_pages:protected] => 1
[publication_number:protected] =>
[part_of:protected] =>
[keywords:protected] => disaster response, hazard clean-up, uneven surface, disaster site, disaster clean-up
[comments:protected] =>
[summary:protected] => A toolbox talk on preventing falls from debris piles. Includes questions to ask, an incident to discuss with images, and a place to record questions the trainer would like to ask about the incident. Part of a collection. Click on the 'collection' button to access the other items.
[transition_comments:protected] =>
[external_link:protected] =>
[consol_link:protected] => http://www.cpwrconstructionsolutions.org/roofing/hazard/1463/install-asphalt-roofs-fall-from-heights.html
[more_like_this:protected] => a000081,d000478,d000530
[permission_given_by:protected] =>
[published:protected] => T
[billable:protected] => F
[img_name:protected] =>
[img_ext:protected] =>
[img_width:protected] =>
[img_height:protected] =>
[img_credit:protected] =>
[img_practice:protected] =>
[vid_source_id:protected] =>
[vid_running_time:protected] =>
[vid_intended_audience:protected] =>
[vid_acquisition_info:protected] =>
[vid_cost:protected] =>
[vid_producer:protected] =>
[vid_filename:protected] =>
[vid_filename_downloadable:protected] =>
[date_summary:protected] =>
[date_permission_requested:protected] =>
[date_permission_received:protected] =>
[date_review_needed:protected] =>
[date_received:protected] => 02/15/12
[date_completed:protected] => 03/19/12
[date_billed:protected] =>
[date_modified:protected] => 07/10/12
[collBokExports:protected] =>
[lastBokExportCriteria:BaseElcoshItem:private] =>
[alreadyInSave:protected] =>
[alreadyInValidation:protected] =>
[validationFailures:protected] => Array
(
)
[_new:BaseObject:private] =>
[_deleted:BaseObject:private] =>
[modifiedColumns:protected] => Array
(
)
)
[1610] => DocumentRecord Object
(
[records:protected] => Array
(
)
[recordId:protected] =>
[searchWordClass:protected] =>
[searchWordPeerClass:protected] =>
[bok_record:protected] =>
[authors:protected] =>
[organizations:protected] =>
[collections:protected] =>
[categories:protected] =>
[categories_initialized:protected] =>
[mapped_items:protected] =>
[content:protected] =>
[files:protected] =>
[language:protected] =>
[old_record:protected] =>
[id:protected] => 1610
[old_id:protected] => 1271
[elcosh_id:protected] => d001146
[type:protected] => document
[display_type:protected] => HTML w/ PDF
[user_id:protected] => 0
[language_id:protected] => 1
[tagging_id:protected] => Garber
[priority_id:protected] => 1
[title:protected] => Focus Four Toolbox Talks, Module 2 – Struck-by, Talk #5 – Rigging and Securing Loads
[total_pages:protected] => 1
[billed_pages:protected] => 1
[publication_number:protected] =>
[part_of:protected] =>
[keywords:protected] => rigging, lift loads, loading areas, chains
[comments:protected] =>
[summary:protected] => A toolbox talk on preventing struck-by incidents caused by not securing loads properly. Includes questions to ask, an incident to discuss with images, and a place to record questions the trainer would like to ask about the incident. Part of a collection. Click on the 'collection' button to access the other items.
[transition_comments:protected] =>
[external_link:protected] =>
[consol_link:protected] => http://www.cpwrconstructionsolutions.org/heavy_equipment/hazard/1591/move-equipment-to-from-and-between-sites-work-zone-struck-by-injuries-and-fatalities.html
[more_like_this:protected] => d000144,d000360,d000873
[permission_given_by:protected] =>
[published:protected] => T
[billable:protected] => F
[img_name:protected] =>
[img_ext:protected] =>
[img_width:protected] =>
[img_height:protected] =>
[img_credit:protected] =>
[img_practice:protected] =>
[vid_source_id:protected] =>
[vid_running_time:protected] =>
[vid_intended_audience:protected] =>
[vid_acquisition_info:protected] =>
[vid_cost:protected] =>
[vid_producer:protected] =>
[vid_filename:protected] =>
[vid_filename_downloadable:protected] =>
[date_summary:protected] =>
[date_permission_requested:protected] =>
[date_permission_received:protected] =>
[date_review_needed:protected] =>
[date_received:protected] => 02/15/12
[date_completed:protected] => 03/28/12
[date_billed:protected] =>
[date_modified:protected] => 05/12/14
[collBokExports:protected] =>
[lastBokExportCriteria:BaseElcoshItem:private] =>
[alreadyInSave:protected] =>
[alreadyInValidation:protected] =>
[validationFailures:protected] => Array
(
)
[_new:BaseObject:private] =>
[_deleted:BaseObject:private] =>
[modifiedColumns:protected] => Array
(
)
)
[1645] => DocumentRecord Object
(
[records:protected] => Array
(
)
[recordId:protected] =>
[searchWordClass:protected] =>
[searchWordPeerClass:protected] =>
[bok_record:protected] =>
[authors:protected] =>
[organizations:protected] =>
[collections:protected] =>
[categories:protected] =>
[categories_initialized:protected] =>
[mapped_items:protected] =>
[content:protected] =>
[files:protected] =>
[language:protected] =>
[old_record:protected] =>
[id:protected] => 1645
[old_id:protected] => 1274
[elcosh_id:protected] => d001149
[type:protected] => document
[display_type:protected] => HTML w/ PDF
[user_id:protected] => 0
[language_id:protected] => 1
[tagging_id:protected] => Garber
[priority_id:protected] => 1
[title:protected] => Focus Four Toolbox Talks, Module 3 – Caught-in/between, Talk #2 – Trenches & Heavy Equipment
[total_pages:protected] => 1
[billed_pages:protected] => 1
[publication_number:protected] =>
[part_of:protected] =>
[keywords:protected] => back-up alarms, spotter, soil cave-in, spoil pikes, ROPs, trenching, rain
[comments:protected] =>
[summary:protected] => A toolbox talk on preventing incidents involving trenches such as trench collapse. Includes questions to ask, an incident to discuss with images, and a place to record questions the trainer would like to ask about the incident. Part of a collection. Click on the 'collection' button to access the other items.
[transition_comments:protected] =>
[external_link:protected] =>
[consol_link:protected] =>
[more_like_this:protected] => d000019,d000035,d000168
[permission_given_by:protected] =>
[published:protected] => T
[billable:protected] => F
[img_name:protected] =>
[img_ext:protected] =>
[img_width:protected] =>
[img_height:protected] =>
[img_credit:protected] =>
[img_practice:protected] =>
[vid_source_id:protected] =>
[vid_running_time:protected] =>
[vid_intended_audience:protected] =>
[vid_acquisition_info:protected] =>
[vid_cost:protected] =>
[vid_producer:protected] =>
[vid_filename:protected] =>
[vid_filename_downloadable:protected] =>
[date_summary:protected] =>
[date_permission_requested:protected] =>
[date_permission_received:protected] =>
[date_review_needed:protected] =>
[date_received:protected] => 02/15/12
[date_completed:protected] => 04/02/12
[date_billed:protected] =>
[date_modified:protected] => 05/23/23
[collBokExports:protected] =>
[lastBokExportCriteria:BaseElcoshItem:private] =>
[alreadyInSave:protected] =>
[alreadyInValidation:protected] =>
[validationFailures:protected] => Array
(
)
[_new:BaseObject:private] =>
[_deleted:BaseObject:private] =>
[modifiedColumns:protected] => Array
(
)
)
[1654] => DocumentRecord Object
(
[records:protected] => Array
(
)
[recordId:protected] =>
[searchWordClass:protected] =>
[searchWordPeerClass:protected] =>
[bok_record:protected] =>
[authors:protected] =>
[organizations:protected] =>
[collections:protected] =>
[categories:protected] =>
[categories_initialized:protected] =>
[mapped_items:protected] =>
[content:protected] =>
[files:protected] =>
[language:protected] =>
[old_record:protected] =>
[id:protected] => 1654
[old_id:protected] => 1284
[elcosh_id:protected] => d001159
[type:protected] => document
[display_type:protected] => HTML w/ PDF
[user_id:protected] => 0
[language_id:protected] => 1
[tagging_id:protected] => Garber
[priority_id:protected] => 1
[title:protected] => Focus Four Toolbox Talks, Module 4 – Electrocutions, Talk #6 – Hazards on Disaster Sites
[total_pages:protected] => 1
[billed_pages:protected] => 1
[publication_number:protected] =>
[part_of:protected] =>
[keywords:protected] => powerlines, underground, utilities, generators, wet conditions, GFCIs, energized lines, disasters, emergency response
[comments:protected] =>
[summary:protected] => A toolbox talk on how to avoid electrocution on a disaster site. Includes questions to ask, an incident to discuss with images, and a place to record questions the trainer would like to ask about the incident. Part of a collection. Click on the 'collection' button to access the other items.
[transition_comments:protected] =>
[external_link:protected] =>
[consol_link:protected] => http://www.cpwrconstructionsolutions.org/electrical/hazard/1138/install-and-repair-high-voltage-lines-transformers-switches-electrical-shocks-burns-and-or-electrocution.html
[more_like_this:protected] => d000135,d000361,d000437
[permission_given_by:protected] =>
[published:protected] => T
[billable:protected] => F
[img_name:protected] =>
[img_ext:protected] =>
[img_width:protected] =>
[img_height:protected] =>
[img_credit:protected] =>
[img_practice:protected] =>
[vid_source_id:protected] =>
[vid_running_time:protected] =>
[vid_intended_audience:protected] =>
[vid_acquisition_info:protected] =>
[vid_cost:protected] =>
[vid_producer:protected] =>
[vid_filename:protected] =>
[vid_filename_downloadable:protected] =>
[date_summary:protected] =>
[date_permission_requested:protected] =>
[date_permission_received:protected] =>
[date_review_needed:protected] =>
[date_received:protected] => 02/15/12
[date_completed:protected] => 04/02/12
[date_billed:protected] =>
[date_modified:protected] => 05/23/23
[collBokExports:protected] =>
[lastBokExportCriteria:BaseElcoshItem:private] =>
[alreadyInSave:protected] =>
[alreadyInValidation:protected] =>
[validationFailures:protected] => Array
(
)
[_new:BaseObject:private] =>
[_deleted:BaseObject:private] =>
[modifiedColumns:protected] => Array
(
)
)
)
[content:protected] =>
[files:protected] => Array
(
[9400] => File Object
(
[id:protected] => 9400
[filename:protected] => 1.jpg
[downloadable:protected] => F
[timestamp:protected] => 2014-05-08 15:05:37
[alreadyInSave:protected] =>
[alreadyInValidation:protected] =>
[validationFailures:protected] => Array
(
)
[_new:BaseObject:private] =>
[_deleted:BaseObject:private] =>
[modifiedColumns:protected] => Array
(
)
)
[9401] => File Object
(
[id:protected] => 9401
[filename:protected] => d001298.pdf
[downloadable:protected] => T
[timestamp:protected] => 2014-05-08 15:05:37
[alreadyInSave:protected] =>
[alreadyInValidation:protected] =>
[validationFailures:protected] => Array
(
)
[_new:BaseObject:private] =>
[_deleted:BaseObject:private] =>
[modifiedColumns:protected] => Array
(
)
)
)
[language:protected] => Language Object
(
[id:protected] => 1
[code:protected] => en
[name:protected] => English
[alreadyInSave:protected] =>
[alreadyInValidation:protected] =>
[validationFailures:protected] => Array
(
)
[_new:BaseObject:private] =>
[_deleted:BaseObject:private] =>
[modifiedColumns:protected] => Array
(
)
)
[old_record:protected] =>
[id:protected] => 3827
[old_id:protected] =>
[elcosh_id:protected] => d001298
[type:protected] => document
[display_type:protected] => HTML w/ PDF
[user_id:protected] => 23
[language_id:protected] => 1
[tagging_id:protected] => Bruce Lippy
[priority_id:protected] => 1
[title:protected] => Getting the most out of the IUOE Toolbox Talks
[total_pages:protected] => 2
[billed_pages:protected] => 2
[publication_number:protected] =>
[part_of:protected] =>
[keywords:protected] => toolbox talks, tailgate talks
[comments:protected] =>
[summary:protected] => Toolbox talks have been the main tool for communicating safety information on construction jobs for decades.
Unfortunately, there has been little research on what makes for effective toolbox talks. The IUOE National
Training Fund worked with OSHA and NIOSH to make sure their series of 24 Focus Four toolbox talks were based on the best recommendations for effective design. These toolbox talks accompany an entire package of training materials, but can be used alone. This guide points out the key features of these toolbox talks and how best to deliver them.
[transition_comments:protected] =>
[external_link:protected] =>
[consol_link:protected] =>
[more_like_this:protected] => d001137,d001146,d001149,d001159
[permission_given_by:protected] => IUOE National Hazmat Program
[published:protected] => T
[billable:protected] => F
[img_name:protected] =>
[img_ext:protected] => png
[img_width:protected] =>
[img_height:protected] =>
[img_credit:protected] =>
[img_practice:protected] =>
[vid_source_id:protected] =>
[vid_running_time:protected] =>
[vid_intended_audience:protected] =>
[vid_acquisition_info:protected] =>
[vid_cost:protected] =>
[vid_producer:protected] =>
[vid_filename:protected] =>
[vid_filename_downloadable:protected] =>
[date_summary:protected] => 2007
[date_permission_requested:protected] =>
[date_permission_received:protected] =>
[date_review_needed:protected] =>
[date_received:protected] => 05/08/14
[date_completed:protected] => 05/08/14
[date_billed:protected] =>
[date_modified:protected] => 05/08/14
[collBokExports:protected] =>
[lastBokExportCriteria:BaseElcoshItem:private] =>
[alreadyInSave:protected] =>
[alreadyInValidation:protected] =>
[validationFailures:protected] => Array
(
)
[_new:BaseObject:private] =>
[_deleted:BaseObject:private] =>
[modifiedColumns:protected] => Array
(
)
)
[show_text] =>
[document_content] => ElcoshItemDocumentContent Object
(
[id:protected] => 2896
[item_id:protected] => 3827
[type:protected] => main
[title:protected] =>
[content:protected] =>
Why were these talks developed?
Toolbox talks have been the main tool for communicating safety information on construction jobs for decades. Unfortunately, there has been almost no research on what makes for effective toolbox talks. The IUOE National Training Fund has worked with OSHA, the National Institute for Occupational Safety and Health and the Lippy Group, LLC to make sure these Focus Four toolbox talks are based on the latest fi ndings on the most effective design and tailored to the hazards operating engineers face daily. These toolbox talks accompany an entire package of training materials, but can be used alone. The way these are delivered is as important as how well they are designed.
What did NIOSH find out?
- Just handing out factsheets and toolbox talks to workers doesn’t work. Providing copies after toolbox talks doesn’t make much of an impact either.
- Using case studies (real life stories of accidents that ended in fatality or injury) in toolbox talks is effective.
- When toolbox talks containing case studies were accompanied by discussion questions to encourage group participation, they were more effective. Consequently, getting the workers to participate in the discussion about the case study is important. It’s not enough to tell the story, it is better to have the workers engage in problem solving that analyzes why the accident occurred and how it could have been prevented. Active learning is always better than passive.
How should you deliver these toolbox talks?
- Choose a topic that is related to work going on at the site.
- Hold the meeting on the job, preferably where everyone can sit and relax.
- Hold the meeting at the beginning of a shift or after a break. Folks are too tired at the end of a shift to carefully listen and they want to get home.
- Read the toolbox talk sheet on the topic prior to conducting the talk.
- Start at the top of the form and work right through to the end, which should take around 10 to 15 minutes. Guidance is provided in blue print to help you with each section.
- Use the questions provided to generate discussions. Always allow time for the crew to respond to your questions before you provide an answer. Some suggested responses are written in italics.
- Review the case study and emphasize that this was a real incident. Ask the crew for a case study before you review the one provided, however.
- Always end with a discussion of the particular worksite where you are conducting the talk. Tie the talk as closely to hazards on the site as possible and encourage the crew to constantly look for and immediately correct hazards. They should also know how to report any problems that can’t be immediately corrected.
- Provide copies to each person, if you like, but NIOSH has not found that to be particularly effective.
- Encourage workers to do similar talks on their sites and provide them with the IUOE phone number for ordering in bulk.
- Have everyone sign the back of the form to indicate they attended this session and point out it is a pledge to look out for the health and safety of everyone on the site.
What are the key features of these toolbox talks?

[content_transformed:protected] =>
Why were these talks developed?
Toolbox talks have been the main tool for communicating safety information on construction jobs for decades. Unfortunately, there has been almost no research on what makes for effective toolbox talks. The IUOE National Training Fund has worked with OSHA, the National Institute for Occupational Safety and Health and the Lippy Group, LLC to make sure these Focus Four toolbox talks are based on the latest fi ndings on the most effective design and tailored to the hazards operating engineers face daily. These toolbox talks accompany an entire package of training materials, but can be used alone. The way these are delivered is as important as how well they are designed.
What did NIOSH find out?
- Just handing out factsheets and toolbox talks to workers doesn’t work. Providing copies after toolbox talks doesn’t make much of an impact either.
- Using case studies (real life stories of accidents that ended in fatality or injury) in toolbox talks is effective.
- When toolbox talks containing case studies were accompanied by discussion questions to encourage group participation, they were more effective. Consequently, getting the workers to participate in the discussion about the case study is important. It’s not enough to tell the story, it is better to have the workers engage in problem solving that analyzes why the accident occurred and how it could have been prevented. Active learning is always better than passive.
How should you deliver these toolbox talks?
- Choose a topic that is related to work going on at the site.
- Hold the meeting on the job, preferably where everyone can sit and relax.
- Hold the meeting at the beginning of a shift or after a break. Folks are too tired at the end of a shift to carefully listen and they want to get home.
- Read the toolbox talk sheet on the topic prior to conducting the talk.
- Start at the top of the form and work right through to the end, which should take around 10 to 15 minutes. Guidance is provided in blue print to help you with each section.
- Use the questions provided to generate discussions. Always allow time for the crew to respond to your questions before you provide an answer. Some suggested responses are written in italics.
- Review the case study and emphasize that this was a real incident. Ask the crew for a case study before you review the one provided, however.
- Always end with a discussion of the particular worksite where you are conducting the talk. Tie the talk as closely to hazards on the site as possible and encourage the crew to constantly look for and immediately correct hazards. They should also know how to report any problems that can’t be immediately corrected.
- Provide copies to each person, if you like, but NIOSH has not found that to be particularly effective.
- Encourage workers to do similar talks on their sites and provide them with the IUOE phone number for ordering in bulk.
- Have everyone sign the back of the form to indicate they attended this session and point out it is a pledge to look out for the health and safety of everyone on the site.
What are the key features of these toolbox talks?
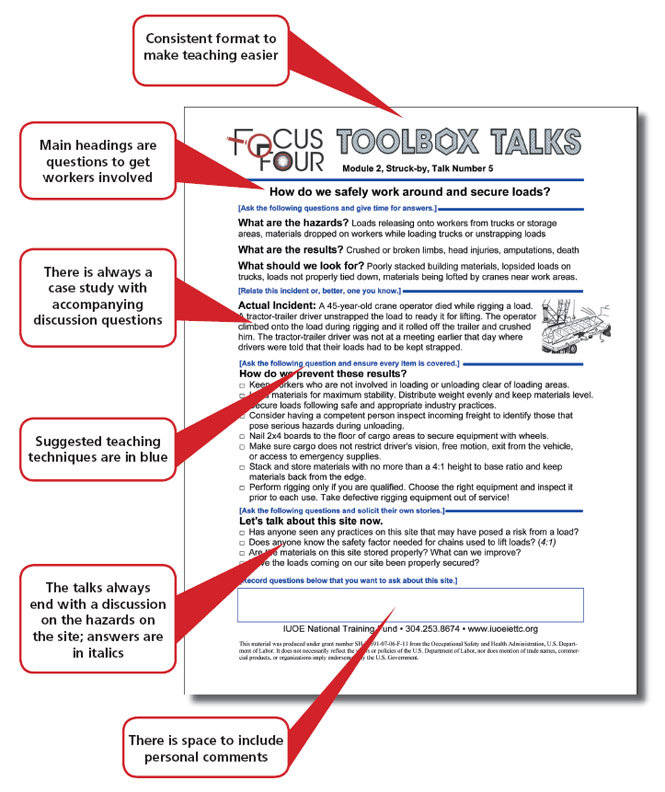
[disclaimer:protected] =>
[disclaimer_transformed:protected] =>
[alreadyInSave:protected] =>
[alreadyInValidation:protected] =>
[validationFailures:protected] => Array
(
)
[_new:BaseObject:private] =>
[_deleted:BaseObject:private] =>
[modifiedColumns:protected] => Array
(
)
)
[template] => record
)
[_globalContext:PHPTAL_Context:private] => stdClass Object
(
)
[_echoDeclarations:PHPTAL_Context:private] =>
[referer] => http://www.elcosh.org/document/3827/d001298/Getting%2Bthe%2Bmost%2Bout%2Bof%2Bthe%2BIUOE%2BToolbox%2BTalks.html
[curr_module] => Record
[styles] => Array
(
)
[javascript] => Array
(
[0] => jquery.min.js
)
[metas] => Array
(
[language] => en
[robots] => index, follow
)
[user] =>
[curr_url] => https://www.elcosh.org/index.php?module=Record&id=3827&type=document
[base_url] => https://www.elcosh.org/index.php?module=Record
[title] => eLCOSH : Getting the most out of the IUOE Toolbox Talks
[language] => en
[search_query] =>
[module] => Record
[new_records] => Array
(
[0] => Search_Result Object
(
[title] => Toolbox Talk: Fixed Ladder
[image] => /record/images/notavailable-p.png
[blurb] => The CPWR Toolbox Talk on Fixed Ladders addresses the potential risks associated with using fixed ladders. The resource includes a brief case example,...
[category] => Array
(
[0] => 15
[1] => 47
[2] => 49
[3] => 51
[4] => 53
[5] => 55
[6] => 60
[7] => 64
[8] => 73
[9] => 76
[10] => 78
[11] => 80
[12] => 86
[13] => 87
[14] => 90
[15] => 92
[16] => 93
[17] => 94
[18] => 100
)
[labels] => Array
(
[0] => Falls
[1] => Work Environment
[2] => Hazards
[3] => Bricklayer
[4] => Trades
[5] => Carpenter
[7] => Cement Mason
[9] => Concrete Polisher
[11] => Electrical Worker
[13] => HVAC
[15] => Laborer
[17] => PCC/Restoration
[19] => Plumber/Pipefitter
[21] => Roofer/Waterproofer
[23] => Sheetmetal Worker
[25] => Welder
[27] => Commercial & Institutional
[28] => Jobsites
[29] => Industrial
[31] => LEED/Green Construction
[33] => Renovations
[35] => Residential
[37] => Toolbox Talks
[38] => Documents
[39] => Media & Documents
)
[type] => Toolbox Talks
[sub_category] =>
[url] => /document/4430/d001660/Toolbox%2BTalk%253A%2BFixed%2BLadder.html
[item:protected] => DocumentRecord Object
(
[records:protected] => Array
(
)
[recordId:protected] =>
[searchWordClass:protected] =>
[searchWordPeerClass:protected] =>
[bok_record:protected] =>
[authors:protected] =>
[organizations:protected] =>
[collections:protected] =>
[categories:protected] => Array
(
[15] => Category Object
(
[languages:protected] =>
[bok_resources:protected] =>
[bok_topics:protected] =>
[bok_keywords:protected] =>
[id:protected] => 15
[type:protected] => category
[parent:protected] => 7
[label:protected] => Falls
[alreadyInSave:protected] =>
[alreadyInValidation:protected] =>
[validationFailures:protected] => Array
(
)
[_new:BaseObject:private] =>
[_deleted:BaseObject:private] =>
[modifiedColumns:protected] => Array
(
)
)
[47] => Category Object
(
[languages:protected] =>
[bok_resources:protected] =>
[bok_topics:protected] =>
[bok_keywords:protected] =>
[id:protected] => 47
[type:protected] => category
[parent:protected] => 2
[label:protected] => Bricklayer
[alreadyInSave:protected] =>
[alreadyInValidation:protected] =>
[validationFailures:protected] => Array
(
)
[_new:BaseObject:private] =>
[_deleted:BaseObject:private] =>
[modifiedColumns:protected] => Array
(
)
)
[49] => Category Object
(
[languages:protected] =>
[bok_resources:protected] =>
[bok_topics:protected] =>
[bok_keywords:protected] =>
[id:protected] => 49
[type:protected] => category
[parent:protected] => 2
[label:protected] => Carpenter
[alreadyInSave:protected] =>
[alreadyInValidation:protected] =>
[validationFailures:protected] => Array
(
)
[_new:BaseObject:private] =>
[_deleted:BaseObject:private] =>
[modifiedColumns:protected] => Array
(
)
)
[51] => Category Object
(
[languages:protected] =>
[bok_resources:protected] =>
[bok_topics:protected] =>
[bok_keywords:protected] =>
[id:protected] => 51
[type:protected] => category
[parent:protected] => 2
[label:protected] => Cement Mason
[alreadyInSave:protected] =>
[alreadyInValidation:protected] =>
[validationFailures:protected] => Array
(
)
[_new:BaseObject:private] =>
[_deleted:BaseObject:private] =>
[modifiedColumns:protected] => Array
(
)
)
[53] => Category Object
(
[languages:protected] =>
[bok_resources:protected] =>
[bok_topics:protected] =>
[bok_keywords:protected] =>
[id:protected] => 53
[type:protected] => category
[parent:protected] => 2
[label:protected] => Concrete Polisher
[alreadyInSave:protected] =>
[alreadyInValidation:protected] =>
[validationFailures:protected] => Array
(
)
[_new:BaseObject:private] =>
[_deleted:BaseObject:private] =>
[modifiedColumns:protected] => Array
(
)
)
[55] => Category Object
(
[languages:protected] =>
[bok_resources:protected] =>
[bok_topics:protected] =>
[bok_keywords:protected] =>
[id:protected] => 55
[type:protected] => category
[parent:protected] => 2
[label:protected] => Electrical Worker
[alreadyInSave:protected] =>
[alreadyInValidation:protected] =>
[validationFailures:protected] => Array
(
)
[_new:BaseObject:private] =>
[_deleted:BaseObject:private] =>
[modifiedColumns:protected] => Array
(
)
)
[60] => Category Object
(
[languages:protected] =>
[bok_resources:protected] =>
[bok_topics:protected] =>
[bok_keywords:protected] =>
[id:protected] => 60
[type:protected] => category
[parent:protected] => 2
[label:protected] => HVAC
[alreadyInSave:protected] =>
[alreadyInValidation:protected] =>
[validationFailures:protected] => Array
(
)
[_new:BaseObject:private] =>
[_deleted:BaseObject:private] =>
[modifiedColumns:protected] => Array
(
)
)
[64] => Category Object
(
[languages:protected] =>
[bok_resources:protected] =>
[bok_topics:protected] =>
[bok_keywords:protected] =>
[id:protected] => 64
[type:protected] => category
[parent:protected] => 2
[label:protected] => Laborer
[alreadyInSave:protected] =>
[alreadyInValidation:protected] =>
[validationFailures:protected] => Array
(
)
[_new:BaseObject:private] =>
[_deleted:BaseObject:private] =>
[modifiedColumns:protected] => Array
(
)
)
[73] => Category Object
(
[languages:protected] =>
[bok_resources:protected] =>
[bok_topics:protected] =>
[bok_keywords:protected] =>
[id:protected] => 73
[type:protected] => category
[parent:protected] => 2
[label:protected] => PCC/Restoration
[alreadyInSave:protected] =>
[alreadyInValidation:protected] =>
[validationFailures:protected] => Array
(
)
[_new:BaseObject:private] =>
[_deleted:BaseObject:private] =>
[modifiedColumns:protected] => Array
(
)
)
[76] => Category Object
(
[languages:protected] =>
[bok_resources:protected] =>
[bok_topics:protected] =>
[bok_keywords:protected] =>
[id:protected] => 76
[type:protected] => category
[parent:protected] => 2
[label:protected] => Plumber/Pipefitter
[alreadyInSave:protected] =>
[alreadyInValidation:protected] =>
[validationFailures:protected] => Array
(
)
[_new:BaseObject:private] =>
[_deleted:BaseObject:private] =>
[modifiedColumns:protected] => Array
(
)
)
[78] => Category Object
(
[languages:protected] =>
[bok_resources:protected] =>
[bok_topics:protected] =>
[bok_keywords:protected] =>
[id:protected] => 78
[type:protected] => category
[parent:protected] => 2
[label:protected] => Roofer/Waterproofer
[alreadyInSave:protected] =>
[alreadyInValidation:protected] =>
[validationFailures:protected] => Array
(
)
[_new:BaseObject:private] =>
[_deleted:BaseObject:private] =>
[modifiedColumns:protected] => Array
(
)
)
[80] => Category Object
(
[languages:protected] =>
[bok_resources:protected] =>
[bok_topics:protected] =>
[bok_keywords:protected] =>
[id:protected] => 80
[type:protected] => category
[parent:protected] => 2
[label:protected] => Sheetmetal Worker
[alreadyInSave:protected] =>
[alreadyInValidation:protected] =>
[validationFailures:protected] => Array
(
)
[_new:BaseObject:private] =>
[_deleted:BaseObject:private] =>
[modifiedColumns:protected] => Array
(
)
)
[86] => Category Object
(
[languages:protected] =>
[bok_resources:protected] =>
[bok_topics:protected] =>
[bok_keywords:protected] =>
[id:protected] => 86
[type:protected] => category
[parent:protected] => 2
[label:protected] => Welder
[alreadyInSave:protected] =>
[alreadyInValidation:protected] =>
[validationFailures:protected] => Array
(
)
[_new:BaseObject:private] =>
[_deleted:BaseObject:private] =>
[modifiedColumns:protected] => Array
(
)
)
[87] => Category Object
(
[languages:protected] =>
[bok_resources:protected] =>
[bok_topics:protected] =>
[bok_keywords:protected] =>
[id:protected] => 87
[type:protected] => category
[parent:protected] => 3
[label:protected] => Commercial & Institutional
[alreadyInSave:protected] =>
[alreadyInValidation:protected] =>
[validationFailures:protected] => Array
(
)
[_new:BaseObject:private] =>
[_deleted:BaseObject:private] =>
[modifiedColumns:protected] => Array
(
)
)
[90] => Category Object
(
[languages:protected] =>
[bok_resources:protected] =>
[bok_topics:protected] =>
[bok_keywords:protected] =>
[id:protected] => 90
[type:protected] => category
[parent:protected] => 3
[label:protected] => Industrial
[alreadyInSave:protected] =>
[alreadyInValidation:protected] =>
[validationFailures:protected] => Array
(
)
[_new:BaseObject:private] =>
[_deleted:BaseObject:private] =>
[modifiedColumns:protected] => Array
(
)
)
[92] => Category Object
(
[languages:protected] =>
[bok_resources:protected] =>
[bok_topics:protected] =>
[bok_keywords:protected] =>
[id:protected] => 92
[type:protected] => category
[parent:protected] => 3
[label:protected] => LEED/Green Construction
[alreadyInSave:protected] =>
[alreadyInValidation:protected] =>
[validationFailures:protected] => Array
(
)
[_new:BaseObject:private] =>
[_deleted:BaseObject:private] =>
[modifiedColumns:protected] => Array
(
)
)
[93] => Category Object
(
[languages:protected] =>
[bok_resources:protected] =>
[bok_topics:protected] =>
[bok_keywords:protected] =>
[id:protected] => 93
[type:protected] => category
[parent:protected] => 3
[label:protected] => Renovations
[alreadyInSave:protected] =>
[alreadyInValidation:protected] =>
[validationFailures:protected] => Array
(
)
[_new:BaseObject:private] =>
[_deleted:BaseObject:private] =>
[modifiedColumns:protected] => Array
(
)
)
[94] => Category Object
(
[languages:protected] =>
[bok_resources:protected] =>
[bok_topics:protected] =>
[bok_keywords:protected] =>
[id:protected] => 94
[type:protected] => category
[parent:protected] => 3
[label:protected] => Residential
[alreadyInSave:protected] =>
[alreadyInValidation:protected] =>
[validationFailures:protected] => Array
(
)
[_new:BaseObject:private] =>
[_deleted:BaseObject:private] =>
[modifiedColumns:protected] => Array
(
)
)
[100] => Category Object
(
[languages:protected] =>
[bok_resources:protected] =>
[bok_topics:protected] =>
[bok_keywords:protected] =>
[id:protected] => 100
[type:protected] => category
[parent:protected] => 6
[label:protected] => Toolbox Talks
[alreadyInSave:protected] =>
[alreadyInValidation:protected] =>
[validationFailures:protected] => Array
(
)
[_new:BaseObject:private] =>
[_deleted:BaseObject:private] =>
[modifiedColumns:protected] => Array
(
)
)
)
[categories_initialized:protected] => 1
[mapped_items:protected] =>
[content:protected] =>
[files:protected] =>
[language:protected] => Language Object
(
[id:protected] => 1
[code:protected] => en
[name:protected] => English
[alreadyInSave:protected] =>
[alreadyInValidation:protected] =>
[validationFailures:protected] => Array
(
)
[_new:BaseObject:private] =>
[_deleted:BaseObject:private] =>
[modifiedColumns:protected] => Array
(
)
)
[old_record:protected] =>
[id:protected] => 4430
[old_id:protected] =>
[elcosh_id:protected] => d001660
[type:protected] => document
[display_type:protected] => HTML only (and links)
[user_id:protected] => 0
[language_id:protected] => 1
[tagging_id:protected] => Mike Aguilar
[priority_id:protected] => 1
[title:protected] => Toolbox Talk: Fixed Ladder
[total_pages:protected] => 0
[billed_pages:protected] => 0
[publication_number:protected] =>
[part_of:protected] =>
[keywords:protected] => Fixed Ladders, Fall Prevention, Falls
[comments:protected] =>
[summary:protected] => The CPWR Toolbox Talk on Fixed Ladders addresses the potential risks associated with using fixed ladders. The resource includes a brief case example, steps to prevent a related injury and questions for discussion. It includes an image that illustrates the hazard, which can be posted in a central location as a reminder of steps to work safely.
Available in
English
and
Spanish.
[transition_comments:protected] =>
[external_link:protected] =>
[consol_link:protected] =>
[more_like_this:protected] => d001257,d001254,d001255,d001256,d001258,d001262,d001279
[permission_given_by:protected] =>
[published:protected] => T
[billable:protected] => F
[img_name:protected] =>
[img_ext:protected] =>
[img_width:protected] =>
[img_height:protected] =>
[img_credit:protected] =>
[img_practice:protected] =>
[vid_source_id:protected] =>
[vid_running_time:protected] =>
[vid_intended_audience:protected] =>
[vid_acquisition_info:protected] =>
[vid_cost:protected] =>
[vid_producer:protected] =>
[vid_filename:protected] =>
[vid_filename_downloadable:protected] =>
[date_summary:protected] =>
[date_permission_requested:protected] =>
[date_permission_received:protected] =>
[date_review_needed:protected] =>
[date_received:protected] => 06/10/22
[date_completed:protected] => 06/10/22
[date_billed:protected] =>
[date_modified:protected] => 05/22/23
[collBokExports:protected] =>
[lastBokExportCriteria:BaseElcoshItem:private] =>
[alreadyInSave:protected] =>
[alreadyInValidation:protected] =>
[validationFailures:protected] => Array
(
)
[_new:BaseObject:private] =>
[_deleted:BaseObject:private] =>
[modifiedColumns:protected] => Array
(
)
)
)
[1] => Search_Result Object
(
[title] => Toolbox Talk: Challenges Preventing Falling Objects
[image] => /record/images/notavailable-p.png
[blurb] => The CPWR Toolbox Talk on Challenges Preventing Falling Objects addresses the hazards of being struck by falling objects on the job site. The resource...
[category] => Array
(
[0] => 12
[1] => 47
[2] => 49
[3] => 51
[4] => 55
[5] => 64
[6] => 68
[7] => 71
[8] => 75
[9] => 78
[10] => 79
[11] => 82
[12] => 62
[13] => 86
[14] => 87
[15] => 88
[16] => 89
[17] => 91
[18] => 90
[19] => 92
[20] => 93
[21] => 94
[22] => 95
[23] => 100
)
[labels] => Array
(
[0] => Crushed/Struck By
[1] => Work Environment
[2] => Hazards
[3] => Bricklayer
[4] => Trades
[5] => Carpenter
[7] => Cement Mason
[9] => Electrical Worker
[11] => Laborer
[13] => Maintenance Worker
[15] => Painter
[17] => Plasterer
[19] => Roofer/Waterproofer
[21] => Scaffold Erector
[23] => Stonemason
[25] => Structural Ironworker
[27] => Welder
[29] => Commercial & Institutional
[30] => Jobsites
[31] => Demolition
[33] => Disasters
[35] => Heavy & Highway
[37] => Industrial
[39] => LEED/Green Construction
[41] => Renovations
[43] => Residential
[45] => Underground
[47] => Toolbox Talks
[48] => Documents
[49] => Media & Documents
)
[type] => Toolbox Talks
[sub_category] =>
[url] => /document/4431/d001661/Toolbox%2BTalk%253A%2BChallenges%2BPreventing%2BFalling%2BObjects.html
[item:protected] => DocumentRecord Object
(
[records:protected] => Array
(
)
[recordId:protected] =>
[searchWordClass:protected] =>
[searchWordPeerClass:protected] =>
[bok_record:protected] =>
[authors:protected] =>
[organizations:protected] =>
[collections:protected] =>
[categories:protected] => Array
(
[12] => Category Object
(
[languages:protected] =>
[bok_resources:protected] =>
[bok_topics:protected] =>
[bok_keywords:protected] =>
[id:protected] => 12
[type:protected] => category
[parent:protected] => 7
[label:protected] => Crushed/Struck By
[alreadyInSave:protected] =>
[alreadyInValidation:protected] =>
[validationFailures:protected] => Array
(
)
[_new:BaseObject:private] =>
[_deleted:BaseObject:private] =>
[modifiedColumns:protected] => Array
(
)
)
[47] => Category Object
(
[languages:protected] =>
[bok_resources:protected] =>
[bok_topics:protected] =>
[bok_keywords:protected] =>
[id:protected] => 47
[type:protected] => category
[parent:protected] => 2
[label:protected] => Bricklayer
[alreadyInSave:protected] =>
[alreadyInValidation:protected] =>
[validationFailures:protected] => Array
(
)
[_new:BaseObject:private] =>
[_deleted:BaseObject:private] =>
[modifiedColumns:protected] => Array
(
)
)
[49] => Category Object
(
[languages:protected] =>
[bok_resources:protected] =>
[bok_topics:protected] =>
[bok_keywords:protected] =>
[id:protected] => 49
[type:protected] => category
[parent:protected] => 2
[label:protected] => Carpenter
[alreadyInSave:protected] =>
[alreadyInValidation:protected] =>
[validationFailures:protected] => Array
(
)
[_new:BaseObject:private] =>
[_deleted:BaseObject:private] =>
[modifiedColumns:protected] => Array
(
)
)
[51] => Category Object
(
[languages:protected] =>
[bok_resources:protected] =>
[bok_topics:protected] =>
[bok_keywords:protected] =>
[id:protected] => 51
[type:protected] => category
[parent:protected] => 2
[label:protected] => Cement Mason
[alreadyInSave:protected] =>
[alreadyInValidation:protected] =>
[validationFailures:protected] => Array
(
)
[_new:BaseObject:private] =>
[_deleted:BaseObject:private] =>
[modifiedColumns:protected] => Array
(
)
)
[55] => Category Object
(
[languages:protected] =>
[bok_resources:protected] =>
[bok_topics:protected] =>
[bok_keywords:protected] =>
[id:protected] => 55
[type:protected] => category
[parent:protected] => 2
[label:protected] => Electrical Worker
[alreadyInSave:protected] =>
[alreadyInValidation:protected] =>
[validationFailures:protected] => Array
(
)
[_new:BaseObject:private] =>
[_deleted:BaseObject:private] =>
[modifiedColumns:protected] => Array
(
)
)
[64] => Category Object
(
[languages:protected] =>
[bok_resources:protected] =>
[bok_topics:protected] =>
[bok_keywords:protected] =>
[id:protected] => 64
[type:protected] => category
[parent:protected] => 2
[label:protected] => Laborer
[alreadyInSave:protected] =>
[alreadyInValidation:protected] =>
[validationFailures:protected] => Array
(
)
[_new:BaseObject:private] =>
[_deleted:BaseObject:private] =>
[modifiedColumns:protected] => Array
(
)
)
[68] => Category Object
(
[languages:protected] =>
[bok_resources:protected] =>
[bok_topics:protected] =>
[bok_keywords:protected] =>
[id:protected] => 68
[type:protected] => category
[parent:protected] => 2
[label:protected] => Maintenance Worker
[alreadyInSave:protected] =>
[alreadyInValidation:protected] =>
[validationFailures:protected] => Array
(
)
[_new:BaseObject:private] =>
[_deleted:BaseObject:private] =>
[modifiedColumns:protected] => Array
(
)
)
[71] => Category Object
(
[languages:protected] =>
[bok_resources:protected] =>
[bok_topics:protected] =>
[bok_keywords:protected] =>
[id:protected] => 71
[type:protected] => category
[parent:protected] => 2
[label:protected] => Painter
[alreadyInSave:protected] =>
[alreadyInValidation:protected] =>
[validationFailures:protected] => Array
(
)
[_new:BaseObject:private] =>
[_deleted:BaseObject:private] =>
[modifiedColumns:protected] => Array
(
)
)
[75] => Category Object
(
[languages:protected] =>
[bok_resources:protected] =>
[bok_topics:protected] =>
[bok_keywords:protected] =>
[id:protected] => 75
[type:protected] => category
[parent:protected] => 2
[label:protected] => Plasterer
[alreadyInSave:protected] =>
[alreadyInValidation:protected] =>
[validationFailures:protected] => Array
(
)
[_new:BaseObject:private] =>
[_deleted:BaseObject:private] =>
[modifiedColumns:protected] => Array
(
)
)
[78] => Category Object
(
[languages:protected] =>
[bok_resources:protected] =>
[bok_topics:protected] =>
[bok_keywords:protected] =>
[id:protected] => 78
[type:protected] => category
[parent:protected] => 2
[label:protected] => Roofer/Waterproofer
[alreadyInSave:protected] =>
[alreadyInValidation:protected] =>
[validationFailures:protected] => Array
(
)
[_new:BaseObject:private] =>
[_deleted:BaseObject:private] =>
[modifiedColumns:protected] => Array
(
)
)
[79] => Category Object
(
[languages:protected] =>
[bok_resources:protected] =>
[bok_topics:protected] =>
[bok_keywords:protected] =>
[id:protected] => 79
[type:protected] => category
[parent:protected] => 2
[label:protected] => Scaffold Erector
[alreadyInSave:protected] =>
[alreadyInValidation:protected] =>
[validationFailures:protected] => Array
(
)
[_new:BaseObject:private] =>
[_deleted:BaseObject:private] =>
[modifiedColumns:protected] => Array
(
)
)
[82] => Category Object
(
[languages:protected] =>
[bok_resources:protected] =>
[bok_topics:protected] =>
[bok_keywords:protected] =>
[id:protected] => 82
[type:protected] => category
[parent:protected] => 2
[label:protected] => Stonemason
[alreadyInSave:protected] =>
[alreadyInValidation:protected] =>
[validationFailures:protected] => Array
(
)
[_new:BaseObject:private] =>
[_deleted:BaseObject:private] =>
[modifiedColumns:protected] => Array
(
)
)
[62] => Category Object
(
[languages:protected] =>
[bok_resources:protected] =>
[bok_topics:protected] =>
[bok_keywords:protected] =>
[id:protected] => 62
[type:protected] => category
[parent:protected] => 2
[label:protected] => Structural Ironworker
[alreadyInSave:protected] =>
[alreadyInValidation:protected] =>
[validationFailures:protected] => Array
(
)
[_new:BaseObject:private] =>
[_deleted:BaseObject:private] =>
[modifiedColumns:protected] => Array
(
)
)
[86] => Category Object
(
[languages:protected] =>
[bok_resources:protected] =>
[bok_topics:protected] =>
[bok_keywords:protected] =>
[id:protected] => 86
[type:protected] => category
[parent:protected] => 2
[label:protected] => Welder
[alreadyInSave:protected] =>
[alreadyInValidation:protected] =>
[validationFailures:protected] => Array
(
)
[_new:BaseObject:private] =>
[_deleted:BaseObject:private] =>
[modifiedColumns:protected] => Array
(
)
)
[87] => Category Object
(
[languages:protected] =>
[bok_resources:protected] =>
[bok_topics:protected] =>
[bok_keywords:protected] =>
[id:protected] => 87
[type:protected] => category
[parent:protected] => 3
[label:protected] => Commercial & Institutional
[alreadyInSave:protected] =>
[alreadyInValidation:protected] =>
[validationFailures:protected] => Array
(
)
[_new:BaseObject:private] =>
[_deleted:BaseObject:private] =>
[modifiedColumns:protected] => Array
(
)
)
[88] => Category Object
(
[languages:protected] =>
[bok_resources:protected] =>
[bok_topics:protected] =>
[bok_keywords:protected] =>
[id:protected] => 88
[type:protected] => category
[parent:protected] => 3
[label:protected] => Demolition
[alreadyInSave:protected] =>
[alreadyInValidation:protected] =>
[validationFailures:protected] => Array
(
)
[_new:BaseObject:private] =>
[_deleted:BaseObject:private] =>
[modifiedColumns:protected] => Array
(
)
)
[89] => Category Object
(
[languages:protected] =>
[bok_resources:protected] =>
[bok_topics:protected] =>
[bok_keywords:protected] =>
[id:protected] => 89
[type:protected] => category
[parent:protected] => 3
[label:protected] => Disasters
[alreadyInSave:protected] =>
[alreadyInValidation:protected] =>
[validationFailures:protected] => Array
(
)
[_new:BaseObject:private] =>
[_deleted:BaseObject:private] =>
[modifiedColumns:protected] => Array
(
)
)
[91] => Category Object
(
[languages:protected] =>
[bok_resources:protected] =>
[bok_topics:protected] =>
[bok_keywords:protected] =>
[id:protected] => 91
[type:protected] => category
[parent:protected] => 3
[label:protected] => Heavy & Highway
[alreadyInSave:protected] =>
[alreadyInValidation:protected] =>
[validationFailures:protected] => Array
(
)
[_new:BaseObject:private] =>
[_deleted:BaseObject:private] =>
[modifiedColumns:protected] => Array
(
)
)
[90] => Category Object
(
[languages:protected] =>
[bok_resources:protected] =>
[bok_topics:protected] =>
[bok_keywords:protected] =>
[id:protected] => 90
[type:protected] => category
[parent:protected] => 3
[label:protected] => Industrial
[alreadyInSave:protected] =>
[alreadyInValidation:protected] =>
[validationFailures:protected] => Array
(
)
[_new:BaseObject:private] =>
[_deleted:BaseObject:private] =>
[modifiedColumns:protected] => Array
(
)
)
[92] => Category Object
(
[languages:protected] =>
[bok_resources:protected] =>
[bok_topics:protected] =>
[bok_keywords:protected] =>
[id:protected] => 92
[type:protected] => category
[parent:protected] => 3
[label:protected] => LEED/Green Construction
[alreadyInSave:protected] =>
[alreadyInValidation:protected] =>
[validationFailures:protected] => Array
(
)
[_new:BaseObject:private] =>
[_deleted:BaseObject:private] =>
[modifiedColumns:protected] => Array
(
)
)
[93] => Category Object
(
[languages:protected] =>
[bok_resources:protected] =>
[bok_topics:protected] =>
[bok_keywords:protected] =>
[id:protected] => 93
[type:protected] => category
[parent:protected] => 3
[label:protected] => Renovations
[alreadyInSave:protected] =>
[alreadyInValidation:protected] =>
[validationFailures:protected] => Array
(
)
[_new:BaseObject:private] =>
[_deleted:BaseObject:private] =>
[modifiedColumns:protected] => Array
(
)
)
[94] => Category Object
(
[languages:protected] =>
[bok_resources:protected] =>
[bok_topics:protected] =>
[bok_keywords:protected] =>
[id:protected] => 94
[type:protected] => category
[parent:protected] => 3
[label:protected] => Residential
[alreadyInSave:protected] =>
[alreadyInValidation:protected] =>
[validationFailures:protected] => Array
(
)
[_new:BaseObject:private] =>
[_deleted:BaseObject:private] =>
[modifiedColumns:protected] => Array
(
)
)
[95] => Category Object
(
[languages:protected] =>
[bok_resources:protected] =>
[bok_topics:protected] =>
[bok_keywords:protected] =>
[id:protected] => 95
[type:protected] => category
[parent:protected] => 3
[label:protected] => Underground
[alreadyInSave:protected] =>
[alreadyInValidation:protected] =>
[validationFailures:protected] => Array
(
)
[_new:BaseObject:private] =>
[_deleted:BaseObject:private] =>
[modifiedColumns:protected] => Array
(
)
)
[100] => Category Object
(
[languages:protected] =>
[bok_resources:protected] =>
[bok_topics:protected] =>
[bok_keywords:protected] =>
[id:protected] => 100
[type:protected] => category
[parent:protected] => 6
[label:protected] => Toolbox Talks
[alreadyInSave:protected] =>
[alreadyInValidation:protected] =>
[validationFailures:protected] => Array
(
)
[_new:BaseObject:private] =>
[_deleted:BaseObject:private] =>
[modifiedColumns:protected] => Array
(
)
)
)
[categories_initialized:protected] => 1
[mapped_items:protected] =>
[content:protected] =>
[files:protected] =>
[language:protected] => Language Object
(
[id:protected] => 1
[code:protected] => en
[name:protected] => English
[alreadyInSave:protected] =>
[alreadyInValidation:protected] =>
[validationFailures:protected] => Array
(
)
[_new:BaseObject:private] =>
[_deleted:BaseObject:private] =>
[modifiedColumns:protected] => Array
(
)
)
[old_record:protected] =>
[id:protected] => 4431
[old_id:protected] =>
[elcosh_id:protected] => d001661
[type:protected] => document
[display_type:protected] => HTML only (and links)
[user_id:protected] => 0
[language_id:protected] => 1
[tagging_id:protected] => Mike Aguilar
[priority_id:protected] => 1
[title:protected] => Toolbox Talk: Challenges Preventing Falling Objects
[total_pages:protected] => 0
[billed_pages:protected] => 0
[publication_number:protected] =>
[part_of:protected] =>
[keywords:protected] => dropped objects, falling objects, struck by incidents, struck by fatalities
[comments:protected] =>
[summary:protected] => The CPWR Toolbox Talk on Challenges Preventing Falling Objects addresses the hazards of being struck by falling objects on the job site. The resource includes a brief example, steps to prevent a related injury, and questions for discussion. It includes a graphic that illustrates a group workers observing a scaffold free of debris during high winds, which can be posted in a central location as a reminder of steps to work safely.
Available in
English and
Spanish.
[transition_comments:protected] =>
[external_link:protected] =>
[consol_link:protected] =>
[more_like_this:protected] => d001234,d001238,d001244,d001251,d001253,d001260,d001268,d001278
[permission_given_by:protected] =>
[published:protected] => T
[billable:protected] => F
[img_name:protected] =>
[img_ext:protected] =>
[img_width:protected] =>
[img_height:protected] =>
[img_credit:protected] =>
[img_practice:protected] =>
[vid_source_id:protected] =>
[vid_running_time:protected] =>
[vid_intended_audience:protected] =>
[vid_acquisition_info:protected] =>
[vid_cost:protected] =>
[vid_producer:protected] =>
[vid_filename:protected] =>
[vid_filename_downloadable:protected] =>
[date_summary:protected] =>
[date_permission_requested:protected] =>
[date_permission_received:protected] =>
[date_review_needed:protected] =>
[date_received:protected] => 06/10/22
[date_completed:protected] => 06/10/22
[date_billed:protected] =>
[date_modified:protected] => 05/22/23
[collBokExports:protected] =>
[lastBokExportCriteria:BaseElcoshItem:private] =>
[alreadyInSave:protected] =>
[alreadyInValidation:protected] =>
[validationFailures:protected] => Array
(
)
[_new:BaseObject:private] =>
[_deleted:BaseObject:private] =>
[modifiedColumns:protected] => Array
(
)
)
)
[2] => Search_Result Object
(
[title] => Toolbox Talk: Tower Crane Safety
[image] => /record/images/notavailable-p.png
[blurb] => The CPWR Toolbox Talk on Tower Crane Safety addresses the potential hazards of Tower Cranes and the importance of following procedure before and durin...
[category] => Array
(
[0] => 11
[1] => 12
[2] => 18
[3] => 70
[4] => 87
[5] => 88
[6] => 91
[7] => 90
[8] => 92
[9] => 100
)
[labels] => Array
(
[0] => Cranes & Hoists
[1] => Work Environment
[2] => Hazards
[3] => Crushed/Struck By
[6] => Motor Vehicles/Heavy Equipment
[9] => Operating Engineer
[10] => Trades
[11] => Commercial & Institutional
[12] => Jobsites
[13] => Demolition
[15] => Heavy & Highway
[17] => Industrial
[19] => LEED/Green Construction
[21] => Toolbox Talks
[22] => Documents
[23] => Media & Documents
)
[type] => Toolbox Talks
[sub_category] =>
[url] => /document/4427/d001657/Toolbox%2BTalk%253A%2BTower%2BCrane%2BSafety.html
[item:protected] => DocumentRecord Object
(
[records:protected] => Array
(
)
[recordId:protected] =>
[searchWordClass:protected] =>
[searchWordPeerClass:protected] =>
[bok_record:protected] =>
[authors:protected] =>
[organizations:protected] =>
[collections:protected] =>
[categories:protected] => Array
(
[11] => Category Object
(
[languages:protected] =>
[bok_resources:protected] =>
[bok_topics:protected] =>
[bok_keywords:protected] =>
[id:protected] => 11
[type:protected] => category
[parent:protected] => 7
[label:protected] => Cranes & Hoists
[alreadyInSave:protected] =>
[alreadyInValidation:protected] =>
[validationFailures:protected] => Array
(
)
[_new:BaseObject:private] =>
[_deleted:BaseObject:private] =>
[modifiedColumns:protected] => Array
(
)
)
[12] => Category Object
(
[languages:protected] =>
[bok_resources:protected] =>
[bok_topics:protected] =>
[bok_keywords:protected] =>
[id:protected] => 12
[type:protected] => category
[parent:protected] => 7
[label:protected] => Crushed/Struck By
[alreadyInSave:protected] =>
[alreadyInValidation:protected] =>
[validationFailures:protected] => Array
(
)
[_new:BaseObject:private] =>
[_deleted:BaseObject:private] =>
[modifiedColumns:protected] => Array
(
)
)
[18] => Category Object
(
[languages:protected] =>
[bok_resources:protected] =>
[bok_topics:protected] =>
[bok_keywords:protected] =>
[id:protected] => 18
[type:protected] => category
[parent:protected] => 7
[label:protected] => Motor Vehicles/Heavy Equipment
[alreadyInSave:protected] =>
[alreadyInValidation:protected] =>
[validationFailures:protected] => Array
(
)
[_new:BaseObject:private] =>
[_deleted:BaseObject:private] =>
[modifiedColumns:protected] => Array
(
)
)
[70] => Category Object
(
[languages:protected] =>
[bok_resources:protected] =>
[bok_topics:protected] =>
[bok_keywords:protected] =>
[id:protected] => 70
[type:protected] => category
[parent:protected] => 2
[label:protected] => Operating Engineer
[alreadyInSave:protected] =>
[alreadyInValidation:protected] =>
[validationFailures:protected] => Array
(
)
[_new:BaseObject:private] =>
[_deleted:BaseObject:private] =>
[modifiedColumns:protected] => Array
(
)
)
[87] => Category Object
(
[languages:protected] =>
[bok_resources:protected] =>
[bok_topics:protected] =>
[bok_keywords:protected] =>
[id:protected] => 87
[type:protected] => category
[parent:protected] => 3
[label:protected] => Commercial & Institutional
[alreadyInSave:protected] =>
[alreadyInValidation:protected] =>
[validationFailures:protected] => Array
(
)
[_new:BaseObject:private] =>
[_deleted:BaseObject:private] =>
[modifiedColumns:protected] => Array
(
)
)
[88] => Category Object
(
[languages:protected] =>
[bok_resources:protected] =>
[bok_topics:protected] =>
[bok_keywords:protected] =>
[id:protected] => 88
[type:protected] => category
[parent:protected] => 3
[label:protected] => Demolition
[alreadyInSave:protected] =>
[alreadyInValidation:protected] =>
[validationFailures:protected] => Array
(
)
[_new:BaseObject:private] =>
[_deleted:BaseObject:private] =>
[modifiedColumns:protected] => Array
(
)
)
[91] => Category Object
(
[languages:protected] =>
[bok_resources:protected] =>
[bok_topics:protected] =>
[bok_keywords:protected] =>
[id:protected] => 91
[type:protected] => category
[parent:protected] => 3
[label:protected] => Heavy & Highway
[alreadyInSave:protected] =>
[alreadyInValidation:protected] =>
[validationFailures:protected] => Array
(
)
[_new:BaseObject:private] =>
[_deleted:BaseObject:private] =>
[modifiedColumns:protected] => Array
(
)
)
[90] => Category Object
(
[languages:protected] =>
[bok_resources:protected] =>
[bok_topics:protected] =>
[bok_keywords:protected] =>
[id:protected] => 90
[type:protected] => category
[parent:protected] => 3
[label:protected] => Industrial
[alreadyInSave:protected] =>
[alreadyInValidation:protected] =>
[validationFailures:protected] => Array
(
)
[_new:BaseObject:private] =>
[_deleted:BaseObject:private] =>
[modifiedColumns:protected] => Array
(
)
)
[92] => Category Object
(
[languages:protected] =>
[bok_resources:protected] =>
[bok_topics:protected] =>
[bok_keywords:protected] =>
[id:protected] => 92
[type:protected] => category
[parent:protected] => 3
[label:protected] => LEED/Green Construction
[alreadyInSave:protected] =>
[alreadyInValidation:protected] =>
[validationFailures:protected] => Array
(
)
[_new:BaseObject:private] =>
[_deleted:BaseObject:private] =>
[modifiedColumns:protected] => Array
(
)
)
[100] => Category Object
(
[languages:protected] =>
[bok_resources:protected] =>
[bok_topics:protected] =>
[bok_keywords:protected] =>
[id:protected] => 100
[type:protected] => category
[parent:protected] => 6
[label:protected] => Toolbox Talks
[alreadyInSave:protected] =>
[alreadyInValidation:protected] =>
[validationFailures:protected] => Array
(
)
[_new:BaseObject:private] =>
[_deleted:BaseObject:private] =>
[modifiedColumns:protected] => Array
(
)
)
)
[categories_initialized:protected] => 1
[mapped_items:protected] =>
[content:protected] =>
[files:protected] =>
[language:protected] => Language Object
(
[id:protected] => 1
[code:protected] => en
[name:protected] => English
[alreadyInSave:protected] =>
[alreadyInValidation:protected] =>
[validationFailures:protected] => Array
(
)
[_new:BaseObject:private] =>
[_deleted:BaseObject:private] =>
[modifiedColumns:protected] => Array
(
)
)
[old_record:protected] =>
[id:protected] => 4427
[old_id:protected] =>
[elcosh_id:protected] => d001657
[type:protected] => document
[display_type:protected] => HTML only (and links)
[user_id:protected] => 0
[language_id:protected] => 1
[tagging_id:protected] => Mike Aguilar
[priority_id:protected] => 1
[title:protected] => Toolbox Talk: Tower Crane Safety
[total_pages:protected] => 0
[billed_pages:protected] => 0
[publication_number:protected] =>
[part_of:protected] =>
[keywords:protected] => Tower Crane, Crane, Stability, Tipping, Lift Zone Safety, Lift, Zone, Safety, Struck by
[comments:protected] =>
[summary:protected] => The CPWR Toolbox Talk on Tower Crane Safety addresses the potential hazards of Tower Cranes and the importance of following procedure before and during Tower Crane operation. The resource includes a brief example, steps to prevent a related injury, and questions for discussion. It includes a graphic that illustrates a worker inspecting a Tower Crane before operation, which can be posted in a central location as a reminder of steps to work safely.
Available in
English and
Spanish.
[transition_comments:protected] =>
[external_link:protected] =>
[consol_link:protected] =>
[more_like_this:protected] => d001234,d001238,d001250,d001251,d001253,d001258,d001262,d001273
[permission_given_by:protected] =>
[published:protected] => T
[billable:protected] => F
[img_name:protected] =>
[img_ext:protected] => jpg
[img_width:protected] =>
[img_height:protected] =>
[img_credit:protected] =>
[img_practice:protected] =>
[vid_source_id:protected] =>
[vid_running_time:protected] =>
[vid_intended_audience:protected] =>
[vid_acquisition_info:protected] =>
[vid_cost:protected] =>
[vid_producer:protected] =>
[vid_filename:protected] =>
[vid_filename_downloadable:protected] =>
[date_summary:protected] =>
[date_permission_requested:protected] =>
[date_permission_received:protected] =>
[date_review_needed:protected] =>
[date_received:protected] => 12/23/21
[date_completed:protected] => 12/23/21
[date_billed:protected] =>
[date_modified:protected] => 05/19/23
[collBokExports:protected] =>
[lastBokExportCriteria:BaseElcoshItem:private] =>
[alreadyInSave:protected] =>
[alreadyInValidation:protected] =>
[validationFailures:protected] => Array
(
)
[_new:BaseObject:private] =>
[_deleted:BaseObject:private] =>
[modifiedColumns:protected] => Array
(
)
)
)
[3] => Search_Result Object
(
[title] => Toolbox Talk: Work Zone Safety: Working Around Vehicles
[image] => /record/images/notavailable-p.png
[blurb] => The CPWR Toolbox Talk on Working Around Vehicles in the Work Zone addresses methods to avoid being struck-by a vehicle on a construction site. The res...
[category] => Array
(
[0] => 12
[1] => 18
[2] => 52
[3] => 57
[4] => 70
[5] => 85
[6] => 87
[7] => 88
[8] => 89
[9] => 91
[10] => 90
[11] => 92
[12] => 93
[13] => 94
[14] => 95
[15] => 100
)
[labels] => Array
(
[0] => Crushed/Struck By
[1] => Work Environment
[2] => Hazards
[3] => Motor Vehicles/Heavy Equipment
[6] => Commercial Diver
[7] => Trades
[8] => Flagger
[10] => Operating Engineer
[12] => Truck Driver
[14] => Commercial & Institutional
[15] => Jobsites
[16] => Demolition
[18] => Disasters
[20] => Heavy & Highway
[22] => Industrial
[24] => LEED/Green Construction
[26] => Renovations
[28] => Residential
[30] => Underground
[32] => Toolbox Talks
[33] => Documents
[34] => Media & Documents
)
[type] => Toolbox Talks
[sub_category] =>
[url] => /document/4428/d001658/Toolbox%2BTalk%253A%2BWork%2BZone%2BSafety%253A%2BWorking%2BAround%2BVehicles.html
[item:protected] => DocumentRecord Object
(
[records:protected] => Array
(
)
[recordId:protected] =>
[searchWordClass:protected] =>
[searchWordPeerClass:protected] =>
[bok_record:protected] =>
[authors:protected] =>
[organizations:protected] =>
[collections:protected] =>
[categories:protected] => Array
(
[12] => Category Object
(
[languages:protected] =>
[bok_resources:protected] =>
[bok_topics:protected] =>
[bok_keywords:protected] =>
[id:protected] => 12
[type:protected] => category
[parent:protected] => 7
[label:protected] => Crushed/Struck By
[alreadyInSave:protected] =>
[alreadyInValidation:protected] =>
[validationFailures:protected] => Array
(
)
[_new:BaseObject:private] =>
[_deleted:BaseObject:private] =>
[modifiedColumns:protected] => Array
(
)
)
[18] => Category Object
(
[languages:protected] =>
[bok_resources:protected] =>
[bok_topics:protected] =>
[bok_keywords:protected] =>
[id:protected] => 18
[type:protected] => category
[parent:protected] => 7
[label:protected] => Motor Vehicles/Heavy Equipment
[alreadyInSave:protected] =>
[alreadyInValidation:protected] =>
[validationFailures:protected] => Array
(
)
[_new:BaseObject:private] =>
[_deleted:BaseObject:private] =>
[modifiedColumns:protected] => Array
(
)
)
[52] => Category Object
(
[languages:protected] =>
[bok_resources:protected] =>
[bok_topics:protected] =>
[bok_keywords:protected] =>
[id:protected] => 52
[type:protected] => category
[parent:protected] => 2
[label:protected] => Commercial Diver
[alreadyInSave:protected] =>
[alreadyInValidation:protected] =>
[validationFailures:protected] => Array
(
)
[_new:BaseObject:private] =>
[_deleted:BaseObject:private] =>
[modifiedColumns:protected] => Array
(
)
)
[57] => Category Object
(
[languages:protected] =>
[bok_resources:protected] =>
[bok_topics:protected] =>
[bok_keywords:protected] =>
[id:protected] => 57
[type:protected] => category
[parent:protected] => 2
[label:protected] => Flagger
[alreadyInSave:protected] =>
[alreadyInValidation:protected] =>
[validationFailures:protected] => Array
(
)
[_new:BaseObject:private] =>
[_deleted:BaseObject:private] =>
[modifiedColumns:protected] => Array
(
)
)
[70] => Category Object
(
[languages:protected] =>
[bok_resources:protected] =>
[bok_topics:protected] =>
[bok_keywords:protected] =>
[id:protected] => 70
[type:protected] => category
[parent:protected] => 2
[label:protected] => Operating Engineer
[alreadyInSave:protected] =>
[alreadyInValidation:protected] =>
[validationFailures:protected] => Array
(
)
[_new:BaseObject:private] =>
[_deleted:BaseObject:private] =>
[modifiedColumns:protected] => Array
(
)
)
[85] => Category Object
(
[languages:protected] =>
[bok_resources:protected] =>
[bok_topics:protected] =>
[bok_keywords:protected] =>
[id:protected] => 85
[type:protected] => category
[parent:protected] => 2
[label:protected] => Truck Driver
[alreadyInSave:protected] =>
[alreadyInValidation:protected] =>
[validationFailures:protected] => Array
(
)
[_new:BaseObject:private] =>
[_deleted:BaseObject:private] =>
[modifiedColumns:protected] => Array
(
)
)
[87] => Category Object
(
[languages:protected] =>
[bok_resources:protected] =>
[bok_topics:protected] =>
[bok_keywords:protected] =>
[id:protected] => 87
[type:protected] => category
[parent:protected] => 3
[label:protected] => Commercial & Institutional
[alreadyInSave:protected] =>
[alreadyInValidation:protected] =>
[validationFailures:protected] => Array
(
)
[_new:BaseObject:private] =>
[_deleted:BaseObject:private] =>
[modifiedColumns:protected] => Array
(
)
)
[88] => Category Object
(
[languages:protected] =>
[bok_resources:protected] =>
[bok_topics:protected] =>
[bok_keywords:protected] =>
[id:protected] => 88
[type:protected] => category
[parent:protected] => 3
[label:protected] => Demolition
[alreadyInSave:protected] =>
[alreadyInValidation:protected] =>
[validationFailures:protected] => Array
(
)
[_new:BaseObject:private] =>
[_deleted:BaseObject:private] =>
[modifiedColumns:protected] => Array
(
)
)
[89] => Category Object
(
[languages:protected] =>
[bok_resources:protected] =>
[bok_topics:protected] =>
[bok_keywords:protected] =>
[id:protected] => 89
[type:protected] => category
[parent:protected] => 3
[label:protected] => Disasters
[alreadyInSave:protected] =>
[alreadyInValidation:protected] =>
[validationFailures:protected] => Array
(
)
[_new:BaseObject:private] =>
[_deleted:BaseObject:private] =>
[modifiedColumns:protected] => Array
(
)
)
[91] => Category Object
(
[languages:protected] =>
[bok_resources:protected] =>
[bok_topics:protected] =>
[bok_keywords:protected] =>
[id:protected] => 91
[type:protected] => category
[parent:protected] => 3
[label:protected] => Heavy & Highway
[alreadyInSave:protected] =>
[alreadyInValidation:protected] =>
[validationFailures:protected] => Array
(
)
[_new:BaseObject:private] =>
[_deleted:BaseObject:private] =>
[modifiedColumns:protected] => Array
(
)
)
[90] => Category Object
(
[languages:protected] =>
[bok_resources:protected] =>
[bok_topics:protected] =>
[bok_keywords:protected] =>
[id:protected] => 90
[type:protected] => category
[parent:protected] => 3
[label:protected] => Industrial
[alreadyInSave:protected] =>
[alreadyInValidation:protected] =>
[validationFailures:protected] => Array
(
)
[_new:BaseObject:private] =>
[_deleted:BaseObject:private] =>
[modifiedColumns:protected] => Array
(
)
)
[92] => Category Object
(
[languages:protected] =>
[bok_resources:protected] =>
[bok_topics:protected] =>
[bok_keywords:protected] =>
[id:protected] => 92
[type:protected] => category
[parent:protected] => 3
[label:protected] => LEED/Green Construction
[alreadyInSave:protected] =>
[alreadyInValidation:protected] =>
[validationFailures:protected] => Array
(
)
[_new:BaseObject:private] =>
[_deleted:BaseObject:private] =>
[modifiedColumns:protected] => Array
(
)
)
[93] => Category Object
(
[languages:protected] =>
[bok_resources:protected] =>
[bok_topics:protected] =>
[bok_keywords:protected] =>
[id:protected] => 93
[type:protected] => category
[parent:protected] => 3
[label:protected] => Renovations
[alreadyInSave:protected] =>
[alreadyInValidation:protected] =>
[validationFailures:protected] => Array
(
)
[_new:BaseObject:private] =>
[_deleted:BaseObject:private] =>
[modifiedColumns:protected] => Array
(
)
)
[94] => Category Object
(
[languages:protected] =>
[bok_resources:protected] =>
[bok_topics:protected] =>
[bok_keywords:protected] =>
[id:protected] => 94
[type:protected] => category
[parent:protected] => 3
[label:protected] => Residential
[alreadyInSave:protected] =>
[alreadyInValidation:protected] =>
[validationFailures:protected] => Array
(
)
[_new:BaseObject:private] =>
[_deleted:BaseObject:private] =>
[modifiedColumns:protected] => Array
(
)
)
[95] => Category Object
(
[languages:protected] =>
[bok_resources:protected] =>
[bok_topics:protected] =>
[bok_keywords:protected] =>
[id:protected] => 95
[type:protected] => category
[parent:protected] => 3
[label:protected] => Underground
[alreadyInSave:protected] =>
[alreadyInValidation:protected] =>
[validationFailures:protected] => Array
(
)
[_new:BaseObject:private] =>
[_deleted:BaseObject:private] =>
[modifiedColumns:protected] => Array
(
)
)
[100] => Category Object
(
[languages:protected] =>
[bok_resources:protected] =>
[bok_topics:protected] =>
[bok_keywords:protected] =>
[id:protected] => 100
[type:protected] => category
[parent:protected] => 6
[label:protected] => Toolbox Talks
[alreadyInSave:protected] =>
[alreadyInValidation:protected] =>
[validationFailures:protected] => Array
(
)
[_new:BaseObject:private] =>
[_deleted:BaseObject:private] =>
[modifiedColumns:protected] => Array
(
)
)
)
[categories_initialized:protected] => 1
[mapped_items:protected] =>
[content:protected] =>
[files:protected] =>
[language:protected] => Language Object
(
[id:protected] => 1
[code:protected] => en
[name:protected] => English
[alreadyInSave:protected] =>
[alreadyInValidation:protected] =>
[validationFailures:protected] => Array
(
)
[_new:BaseObject:private] =>
[_deleted:BaseObject:private] =>
[modifiedColumns:protected] => Array
(
)
)
[old_record:protected] =>
[id:protected] => 4428
[old_id:protected] =>
[elcosh_id:protected] => d001658
[type:protected] => document
[display_type:protected] => HTML only (and links)
[user_id:protected] => 0
[language_id:protected] => 1
[tagging_id:protected] => Daniela Caceres
[priority_id:protected] => 1
[title:protected] => Toolbox Talk: Work Zone Safety: Working Around Vehicles
[total_pages:protected] => 0
[billed_pages:protected] => 0
[publication_number:protected] =>
[part_of:protected] =>
[keywords:protected] => Struck, Struck by, Vehicle, Work Zone Safety, Truck, Operator, Driver, Mobile Equipment
[comments:protected] =>
[summary:protected] => The CPWR Toolbox Talk on Working Around Vehicles in the Work Zone addresses methods to avoid being struck-by a vehicle on a construction site. The resource includes a case example, steps to prevent a related injury, and questions for discussion. It includes a graphic that illustrates the hazard, which can be posted in a central location as a reminder of steps to work safely. Available in
English and
Spanish.
[transition_comments:protected] =>
[external_link:protected] =>
[consol_link:protected] =>
[more_like_this:protected] => d001640
[permission_given_by:protected] =>
[published:protected] => T
[billable:protected] => F
[img_name:protected] =>
[img_ext:protected] =>
[img_width:protected] =>
[img_height:protected] =>
[img_credit:protected] =>
[img_practice:protected] =>
[vid_source_id:protected] =>
[vid_running_time:protected] =>
[vid_intended_audience:protected] =>
[vid_acquisition_info:protected] =>
[vid_cost:protected] =>
[vid_producer:protected] =>
[vid_filename:protected] =>
[vid_filename_downloadable:protected] =>
[date_summary:protected] =>
[date_permission_requested:protected] =>
[date_permission_received:protected] =>
[date_review_needed:protected] =>
[date_received:protected] => 12/23/21
[date_completed:protected] => 12/23/21
[date_billed:protected] =>
[date_modified:protected] => 05/19/23
[collBokExports:protected] =>
[lastBokExportCriteria:BaseElcoshItem:private] =>
[alreadyInSave:protected] =>
[alreadyInValidation:protected] =>
[validationFailures:protected] => Array
(
)
[_new:BaseObject:private] =>
[_deleted:BaseObject:private] =>
[modifiedColumns:protected] => Array
(
)
)
)
[4] => Search_Result Object
(
[title] => Construction Dive -- DeWalt's Jobsite Pro headphones recalled for fire hazards
[image] => /record/images/notavailable-p.png
[blurb] => A recall notice by the United States Consumer Product Safety Commission affects over 300,000 DeWalt Jobsite Pro Headphones. The recall is a result of...
[category] => Array
(
[0] => 16
[1] => 44
[2] => 45
[3] => 46
[4] => 47
[5] => 48
[6] => 49
[7] => 50
[8] => 51
[9] => 52
[10] => 53
[11] => 54
[12] => 55
[13] => 56
[14] => 57
[15] => 58
[16] => 59
[17] => 60
[18] => 61
[19] => 64
[20] => 65
[21] => 66
[22] => 67
[23] => 68
[24] => 69
[25] => 70
[26] => 71
[27] => 72
[28] => 73
[29] => 74
[30] => 75
[31] => 76
[32] => 77
[33] => 63
[34] => 78
[35] => 79
[36] => 80
[37] => 81
[38] => 82
[39] => 62
[40] => 83
[41] => 84
[42] => 85
[43] => 86
[44] => 87
[45] => 88
[46] => 89
[47] => 91
[48] => 90
[49] => 92
[50] => 93
[51] => 94
[52] => 95
)
[labels] => Array
(
[0] => Fire & Explosions
[1] => Work Environment
[2] => Hazards
[3] => Acoustical Ceiling Carpenter
[4] => Trades
[5] => Asbestos/Insulator
[7] => Boilermaker
[9] => Bricklayer
[11] => Cabinetmaker
[13] => Carpenter
[15] => Carpet Layer
[17] => Cement Mason
[19] => Commercial Diver
[21] => Concrete Polisher
[23] => Drywall Applicator Specialist
[25] => Electrical Worker
[27] => Elevator Constructor
[29] => Flagger
[31] => Glazier
[33] => Hazardous Waste Cleanup
[35] => HVAC
[37] => Interior Systems Carpenter
[39] => Laborer
[41] => Landscaper
[43] => Lather
[45] => Lead Abatement Worker
[47] => Maintenance Worker
[49] => Millwright
[51] => Operating Engineer
[53] => Painter
[55] => Paper Hanger
[57] => PCC/Restoration
[59] => Pile Driver
[61] => Plasterer
[63] => Plumber/Pipefitter
[65] => Refractory Worker
[67] => Reinforcing Ironworker
[69] => Roofer/Waterproofer
[71] => Scaffold Erector
[73] => Sheetmetal Worker
[75] => Sprinkler Fitter
[77] => Stonemason
[79] => Structural Ironworker
[81] => Terrazzo Worker
[83] => Tile Setter
[85] => Truck Driver
[87] => Welder
[89] => Commercial & Institutional
[90] => Jobsites
[91] => Demolition
[93] => Disasters
[95] => Heavy & Highway
[97] => Industrial
[99] => LEED/Green Construction
[101] => Renovations
[103] => Residential
[105] => Underground
)
[type] =>
[sub_category] =>
[url] => /document/4426/d001656/Construction%2BDive%2B--%2BDeWalt%2527s%2BJobsite%2BPro%2Bheadphones%2Brecalled%2Bfor%2Bfire%2Bhazards.html
[item:protected] => DocumentRecord Object
(
[records:protected] => Array
(
)
[recordId:protected] =>
[searchWordClass:protected] =>
[searchWordPeerClass:protected] =>
[bok_record:protected] =>
[authors:protected] =>
[organizations:protected] =>
[collections:protected] =>
[categories:protected] => Array
(
[16] => Category Object
(
[languages:protected] =>
[bok_resources:protected] =>
[bok_topics:protected] =>
[bok_keywords:protected] =>
[id:protected] => 16
[type:protected] => category
[parent:protected] => 7
[label:protected] => Fire & Explosions
[alreadyInSave:protected] =>
[alreadyInValidation:protected] =>
[validationFailures:protected] => Array
(
)
[_new:BaseObject:private] =>
[_deleted:BaseObject:private] =>
[modifiedColumns:protected] => Array
(
)
)
[44] => Category Object
(
[languages:protected] =>
[bok_resources:protected] =>
[bok_topics:protected] =>
[bok_keywords:protected] =>
[id:protected] => 44
[type:protected] => category
[parent:protected] => 2
[label:protected] => Acoustical Ceiling Carpenter
[alreadyInSave:protected] =>
[alreadyInValidation:protected] =>
[validationFailures:protected] => Array
(
)
[_new:BaseObject:private] =>
[_deleted:BaseObject:private] =>
[modifiedColumns:protected] => Array
(
)
)
[45] => Category Object
(
[languages:protected] =>
[bok_resources:protected] =>
[bok_topics:protected] =>
[bok_keywords:protected] =>
[id:protected] => 45
[type:protected] => category
[parent:protected] => 2
[label:protected] => Asbestos/Insulator
[alreadyInSave:protected] =>
[alreadyInValidation:protected] =>
[validationFailures:protected] => Array
(
)
[_new:BaseObject:private] =>
[_deleted:BaseObject:private] =>
[modifiedColumns:protected] => Array
(
)
)
[46] => Category Object
(
[languages:protected] =>
[bok_resources:protected] =>
[bok_topics:protected] =>
[bok_keywords:protected] =>
[id:protected] => 46
[type:protected] => category
[parent:protected] => 2
[label:protected] => Boilermaker
[alreadyInSave:protected] =>
[alreadyInValidation:protected] =>
[validationFailures:protected] => Array
(
)
[_new:BaseObject:private] =>
[_deleted:BaseObject:private] =>
[modifiedColumns:protected] => Array
(
)
)
[47] => Category Object
(
[languages:protected] =>
[bok_resources:protected] =>
[bok_topics:protected] =>
[bok_keywords:protected] =>
[id:protected] => 47
[type:protected] => category
[parent:protected] => 2
[label:protected] => Bricklayer
[alreadyInSave:protected] =>
[alreadyInValidation:protected] =>
[validationFailures:protected] => Array
(
)
[_new:BaseObject:private] =>
[_deleted:BaseObject:private] =>
[modifiedColumns:protected] => Array
(
)
)
[48] => Category Object
(
[languages:protected] =>
[bok_resources:protected] =>
[bok_topics:protected] =>
[bok_keywords:protected] =>
[id:protected] => 48
[type:protected] => category
[parent:protected] => 2
[label:protected] => Cabinetmaker
[alreadyInSave:protected] =>
[alreadyInValidation:protected] =>
[validationFailures:protected] => Array
(
)
[_new:BaseObject:private] =>
[_deleted:BaseObject:private] =>
[modifiedColumns:protected] => Array
(
)
)
[49] => Category Object
(
[languages:protected] =>
[bok_resources:protected] =>
[bok_topics:protected] =>
[bok_keywords:protected] =>
[id:protected] => 49
[type:protected] => category
[parent:protected] => 2
[label:protected] => Carpenter
[alreadyInSave:protected] =>
[alreadyInValidation:protected] =>
[validationFailures:protected] => Array
(
)
[_new:BaseObject:private] =>
[_deleted:BaseObject:private] =>
[modifiedColumns:protected] => Array
(
)
)
[50] => Category Object
(
[languages:protected] =>
[bok_resources:protected] =>
[bok_topics:protected] =>
[bok_keywords:protected] =>
[id:protected] => 50
[type:protected] => category
[parent:protected] => 2
[label:protected] => Carpet Layer
[alreadyInSave:protected] =>
[alreadyInValidation:protected] =>
[validationFailures:protected] => Array
(
)
[_new:BaseObject:private] =>
[_deleted:BaseObject:private] =>
[modifiedColumns:protected] => Array
(
)
)
[51] => Category Object
(
[languages:protected] =>
[bok_resources:protected] =>
[bok_topics:protected] =>
[bok_keywords:protected] =>
[id:protected] => 51
[type:protected] => category
[parent:protected] => 2
[label:protected] => Cement Mason
[alreadyInSave:protected] =>
[alreadyInValidation:protected] =>
[validationFailures:protected] => Array
(
)
[_new:BaseObject:private] =>
[_deleted:BaseObject:private] =>
[modifiedColumns:protected] => Array
(
)
)
[52] => Category Object
(
[languages:protected] =>
[bok_resources:protected] =>
[bok_topics:protected] =>
[bok_keywords:protected] =>
[id:protected] => 52
[type:protected] => category
[parent:protected] => 2
[label:protected] => Commercial Diver
[alreadyInSave:protected] =>
[alreadyInValidation:protected] =>
[validationFailures:protected] => Array
(
)
[_new:BaseObject:private] =>
[_deleted:BaseObject:private] =>
[modifiedColumns:protected] => Array
(
)
)
[53] => Category Object
(
[languages:protected] =>
[bok_resources:protected] =>
[bok_topics:protected] =>
[bok_keywords:protected] =>
[id:protected] => 53
[type:protected] => category
[parent:protected] => 2
[label:protected] => Concrete Polisher
[alreadyInSave:protected] =>
[alreadyInValidation:protected] =>
[validationFailures:protected] => Array
(
)
[_new:BaseObject:private] =>
[_deleted:BaseObject:private] =>
[modifiedColumns:protected] => Array
(
)
)
[54] => Category Object
(
[languages:protected] =>
[bok_resources:protected] =>
[bok_topics:protected] =>
[bok_keywords:protected] =>
[id:protected] => 54
[type:protected] => category
[parent:protected] => 2
[label:protected] => Drywall Applicator Specialist
[alreadyInSave:protected] =>
[alreadyInValidation:protected] =>
[validationFailures:protected] => Array
(
)
[_new:BaseObject:private] =>
[_deleted:BaseObject:private] =>
[modifiedColumns:protected] => Array
(
)
)
[55] => Category Object
(
[languages:protected] =>
[bok_resources:protected] =>
[bok_topics:protected] =>
[bok_keywords:protected] =>
[id:protected] => 55
[type:protected] => category
[parent:protected] => 2
[label:protected] => Electrical Worker
[alreadyInSave:protected] =>
[alreadyInValidation:protected] =>
[validationFailures:protected] => Array
(
)
[_new:BaseObject:private] =>
[_deleted:BaseObject:private] =>
[modifiedColumns:protected] => Array
(
)
)
[56] => Category Object
(
[languages:protected] =>
[bok_resources:protected] =>
[bok_topics:protected] =>
[bok_keywords:protected] =>
[id:protected] => 56
[type:protected] => category
[parent:protected] => 2
[label:protected] => Elevator Constructor
[alreadyInSave:protected] =>
[alreadyInValidation:protected] =>
[validationFailures:protected] => Array
(
)
[_new:BaseObject:private] =>
[_deleted:BaseObject:private] =>
[modifiedColumns:protected] => Array
(
)
)
[57] => Category Object
(
[languages:protected] =>
[bok_resources:protected] =>
[bok_topics:protected] =>
[bok_keywords:protected] =>
[id:protected] => 57
[type:protected] => category
[parent:protected] => 2
[label:protected] => Flagger
[alreadyInSave:protected] =>
[alreadyInValidation:protected] =>
[validationFailures:protected] => Array
(
)
[_new:BaseObject:private] =>
[_deleted:BaseObject:private] =>
[modifiedColumns:protected] => Array
(
)
)
[58] => Category Object
(
[languages:protected] =>
[bok_resources:protected] =>
[bok_topics:protected] =>
[bok_keywords:protected] =>
[id:protected] => 58
[type:protected] => category
[parent:protected] => 2
[label:protected] => Glazier
[alreadyInSave:protected] =>
[alreadyInValidation:protected] =>
[validationFailures:protected] => Array
(
)
[_new:BaseObject:private] =>
[_deleted:BaseObject:private] =>
[modifiedColumns:protected] => Array
(
)
)
[59] => Category Object
(
[languages:protected] =>
[bok_resources:protected] =>
[bok_topics:protected] =>
[bok_keywords:protected] =>
[id:protected] => 59
[type:protected] => category
[parent:protected] => 2
[label:protected] => Hazardous Waste Cleanup
[alreadyInSave:protected] =>
[alreadyInValidation:protected] =>
[validationFailures:protected] => Array
(
)
[_new:BaseObject:private] =>
[_deleted:BaseObject:private] =>
[modifiedColumns:protected] => Array
(
)
)
[60] => Category Object
(
[languages:protected] =>
[bok_resources:protected] =>
[bok_topics:protected] =>
[bok_keywords:protected] =>
[id:protected] => 60
[type:protected] => category
[parent:protected] => 2
[label:protected] => HVAC
[alreadyInSave:protected] =>
[alreadyInValidation:protected] =>
[validationFailures:protected] => Array
(
)
[_new:BaseObject:private] =>
[_deleted:BaseObject:private] =>
[modifiedColumns:protected] => Array
(
)
)
[61] => Category Object
(
[languages:protected] =>
[bok_resources:protected] =>
[bok_topics:protected] =>
[bok_keywords:protected] =>
[id:protected] => 61
[type:protected] => category
[parent:protected] => 2
[label:protected] => Interior Systems Carpenter
[alreadyInSave:protected] =>
[alreadyInValidation:protected] =>
[validationFailures:protected] => Array
(
)
[_new:BaseObject:private] =>
[_deleted:BaseObject:private] =>
[modifiedColumns:protected] => Array
(
)
)
[64] => Category Object
(
[languages:protected] =>
[bok_resources:protected] =>
[bok_topics:protected] =>
[bok_keywords:protected] =>
[id:protected] => 64
[type:protected] => category
[parent:protected] => 2
[label:protected] => Laborer
[alreadyInSave:protected] =>
[alreadyInValidation:protected] =>
[validationFailures:protected] => Array
(
)
[_new:BaseObject:private] =>
[_deleted:BaseObject:private] =>
[modifiedColumns:protected] => Array
(
)
)
[65] => Category Object
(
[languages:protected] =>
[bok_resources:protected] =>
[bok_topics:protected] =>
[bok_keywords:protected] =>
[id:protected] => 65
[type:protected] => category
[parent:protected] => 2
[label:protected] => Landscaper
[alreadyInSave:protected] =>
[alreadyInValidation:protected] =>
[validationFailures:protected] => Array
(
)
[_new:BaseObject:private] =>
[_deleted:BaseObject:private] =>
[modifiedColumns:protected] => Array
(
)
)
[66] => Category Object
(
[languages:protected] =>
[bok_resources:protected] =>
[bok_topics:protected] =>
[bok_keywords:protected] =>
[id:protected] => 66
[type:protected] => category
[parent:protected] => 2
[label:protected] => Lather
[alreadyInSave:protected] =>
[alreadyInValidation:protected] =>
[validationFailures:protected] => Array
(
)
[_new:BaseObject:private] =>
[_deleted:BaseObject:private] =>
[modifiedColumns:protected] => Array
(
)
)
[67] => Category Object
(
[languages:protected] =>
[bok_resources:protected] =>
[bok_topics:protected] =>
[bok_keywords:protected] =>
[id:protected] => 67
[type:protected] => category
[parent:protected] => 2
[label:protected] => Lead Abatement Worker
[alreadyInSave:protected] =>
[alreadyInValidation:protected] =>
[validationFailures:protected] => Array
(
)
[_new:BaseObject:private] =>
[_deleted:BaseObject:private] =>
[modifiedColumns:protected] => Array
(
)
)
[68] => Category Object
(
[languages:protected] =>
[bok_resources:protected] =>
[bok_topics:protected] =>
[bok_keywords:protected] =>
[id:protected] => 68
[type:protected] => category
[parent:protected] => 2
[label:protected] => Maintenance Worker
[alreadyInSave:protected] =>
[alreadyInValidation:protected] =>
[validationFailures:protected] => Array
(
)
[_new:BaseObject:private] =>
[_deleted:BaseObject:private] =>
[modifiedColumns:protected] => Array
(
)
)
[69] => Category Object
(
[languages:protected] =>
[bok_resources:protected] =>
[bok_topics:protected] =>
[bok_keywords:protected] =>
[id:protected] => 69
[type:protected] => category
[parent:protected] => 2
[label:protected] => Millwright
[alreadyInSave:protected] =>
[alreadyInValidation:protected] =>
[validationFailures:protected] => Array
(
)
[_new:BaseObject:private] =>
[_deleted:BaseObject:private] =>
[modifiedColumns:protected] => Array
(
)
)
[70] => Category Object
(
[languages:protected] =>
[bok_resources:protected] =>
[bok_topics:protected] =>
[bok_keywords:protected] =>
[id:protected] => 70
[type:protected] => category
[parent:protected] => 2
[label:protected] => Operating Engineer
[alreadyInSave:protected] =>
[alreadyInValidation:protected] =>
[validationFailures:protected] => Array
(
)
[_new:BaseObject:private] =>
[_deleted:BaseObject:private] =>
[modifiedColumns:protected] => Array
(
)
)
[71] => Category Object
(
[languages:protected] =>
[bok_resources:protected] =>
[bok_topics:protected] =>
[bok_keywords:protected] =>
[id:protected] => 71
[type:protected] => category
[parent:protected] => 2
[label:protected] => Painter
[alreadyInSave:protected] =>
[alreadyInValidation:protected] =>
[validationFailures:protected] => Array
(
)
[_new:BaseObject:private] =>
[_deleted:BaseObject:private] =>
[modifiedColumns:protected] => Array
(
)
)
[72] => Category Object
(
[languages:protected] =>
[bok_resources:protected] =>
[bok_topics:protected] =>
[bok_keywords:protected] =>
[id:protected] => 72
[type:protected] => category
[parent:protected] => 2
[label:protected] => Paper Hanger
[alreadyInSave:protected] =>
[alreadyInValidation:protected] =>
[validationFailures:protected] => Array
(
)
[_new:BaseObject:private] =>
[_deleted:BaseObject:private] =>
[modifiedColumns:protected] => Array
(
)
)
[73] => Category Object
(
[languages:protected] =>
[bok_resources:protected] =>
[bok_topics:protected] =>
[bok_keywords:protected] =>
[id:protected] => 73
[type:protected] => category
[parent:protected] => 2
[label:protected] => PCC/Restoration
[alreadyInSave:protected] =>
[alreadyInValidation:protected] =>
[validationFailures:protected] => Array
(
)
[_new:BaseObject:private] =>
[_deleted:BaseObject:private] =>
[modifiedColumns:protected] => Array
(
)
)
[74] => Category Object
(
[languages:protected] =>
[bok_resources:protected] =>
[bok_topics:protected] =>
[bok_keywords:protected] =>
[id:protected] => 74
[type:protected] => category
[parent:protected] => 2
[label:protected] => Pile Driver
[alreadyInSave:protected] =>
[alreadyInValidation:protected] =>
[validationFailures:protected] => Array
(
)
[_new:BaseObject:private] =>
[_deleted:BaseObject:private] =>
[modifiedColumns:protected] => Array
(
)
)
[75] => Category Object
(
[languages:protected] =>
[bok_resources:protected] =>
[bok_topics:protected] =>
[bok_keywords:protected] =>
[id:protected] => 75
[type:protected] => category
[parent:protected] => 2
[label:protected] => Plasterer
[alreadyInSave:protected] =>
[alreadyInValidation:protected] =>
[validationFailures:protected] => Array
(
)
[_new:BaseObject:private] =>
[_deleted:BaseObject:private] =>
[modifiedColumns:protected] => Array
(
)
)
[76] => Category Object
(
[languages:protected] =>
[bok_resources:protected] =>
[bok_topics:protected] =>
[bok_keywords:protected] =>
[id:protected] => 76
[type:protected] => category
[parent:protected] => 2
[label:protected] => Plumber/Pipefitter
[alreadyInSave:protected] =>
[alreadyInValidation:protected] =>
[validationFailures:protected] => Array
(
)
[_new:BaseObject:private] =>
[_deleted:BaseObject:private] =>
[modifiedColumns:protected] => Array
(
)
)
[77] => Category Object
(
[languages:protected] =>
[bok_resources:protected] =>
[bok_topics:protected] =>
[bok_keywords:protected] =>
[id:protected] => 77
[type:protected] => category
[parent:protected] => 2
[label:protected] => Refractory Worker
[alreadyInSave:protected] =>
[alreadyInValidation:protected] =>
[validationFailures:protected] => Array
(
)
[_new:BaseObject:private] =>
[_deleted:BaseObject:private] =>
[modifiedColumns:protected] => Array
(
)
)
[63] => Category Object
(
[languages:protected] =>
[bok_resources:protected] =>
[bok_topics:protected] =>
[bok_keywords:protected] =>
[id:protected] => 63
[type:protected] => category
[parent:protected] => 2
[label:protected] => Reinforcing Ironworker
[alreadyInSave:protected] =>
[alreadyInValidation:protected] =>
[validationFailures:protected] => Array
(
)
[_new:BaseObject:private] =>
[_deleted:BaseObject:private] =>
[modifiedColumns:protected] => Array
(
)
)
[78] => Category Object
(
[languages:protected] =>
[bok_resources:protected] =>
[bok_topics:protected] =>
[bok_keywords:protected] =>
[id:protected] => 78
[type:protected] => category
[parent:protected] => 2
[label:protected] => Roofer/Waterproofer
[alreadyInSave:protected] =>
[alreadyInValidation:protected] =>
[validationFailures:protected] => Array
(
)
[_new:BaseObject:private] =>
[_deleted:BaseObject:private] =>
[modifiedColumns:protected] => Array
(
)
)
[79] => Category Object
(
[languages:protected] =>
[bok_resources:protected] =>
[bok_topics:protected] =>
[bok_keywords:protected] =>
[id:protected] => 79
[type:protected] => category
[parent:protected] => 2
[label:protected] => Scaffold Erector
[alreadyInSave:protected] =>
[alreadyInValidation:protected] =>
[validationFailures:protected] => Array
(
)
[_new:BaseObject:private] =>
[_deleted:BaseObject:private] =>
[modifiedColumns:protected] => Array
(
)
)
[80] => Category Object
(
[languages:protected] =>
[bok_resources:protected] =>
[bok_topics:protected] =>
[bok_keywords:protected] =>
[id:protected] => 80
[type:protected] => category
[parent:protected] => 2
[label:protected] => Sheetmetal Worker
[alreadyInSave:protected] =>
[alreadyInValidation:protected] =>
[validationFailures:protected] => Array
(
)
[_new:BaseObject:private] =>
[_deleted:BaseObject:private] =>
[modifiedColumns:protected] => Array
(
)
)
[81] => Category Object
(
[languages:protected] =>
[bok_resources:protected] =>
[bok_topics:protected] =>
[bok_keywords:protected] =>
[id:protected] => 81
[type:protected] => category
[parent:protected] => 2
[label:protected] => Sprinkler Fitter
[alreadyInSave:protected] =>
[alreadyInValidation:protected] =>
[validationFailures:protected] => Array
(
)
[_new:BaseObject:private] =>
[_deleted:BaseObject:private] =>
[modifiedColumns:protected] => Array
(
)
)
[82] => Category Object
(
[languages:protected] =>
[bok_resources:protected] =>
[bok_topics:protected] =>
[bok_keywords:protected] =>
[id:protected] => 82
[type:protected] => category
[parent:protected] => 2
[label:protected] => Stonemason
[alreadyInSave:protected] =>
[alreadyInValidation:protected] =>
[validationFailures:protected] => Array
(
)
[_new:BaseObject:private] =>
[_deleted:BaseObject:private] =>
[modifiedColumns:protected] => Array
(
)
)
[62] => Category Object
(
[languages:protected] =>
[bok_resources:protected] =>
[bok_topics:protected] =>
[bok_keywords:protected] =>
[id:protected] => 62
[type:protected] => category
[parent:protected] => 2
[label:protected] => Structural Ironworker
[alreadyInSave:protected] =>
[alreadyInValidation:protected] =>
[validationFailures:protected] => Array
(
)
[_new:BaseObject:private] =>
[_deleted:BaseObject:private] =>
[modifiedColumns:protected] => Array
(
)
)
[83] => Category Object
(
[languages:protected] =>
[bok_resources:protected] =>
[bok_topics:protected] =>
[bok_keywords:protected] =>
[id:protected] => 83
[type:protected] => category
[parent:protected] => 2
[label:protected] => Terrazzo Worker
[alreadyInSave:protected] =>
[alreadyInValidation:protected] =>
[validationFailures:protected] => Array
(
)
[_new:BaseObject:private] =>
[_deleted:BaseObject:private] =>
[modifiedColumns:protected] => Array
(
)
)
[84] => Category Object
(
[languages:protected] =>
[bok_resources:protected] =>
[bok_topics:protected] =>
[bok_keywords:protected] =>
[id:protected] => 84
[type:protected] => category
[parent:protected] => 2
[label:protected] => Tile Setter
[alreadyInSave:protected] =>
[alreadyInValidation:protected] =>
[validationFailures:protected] => Array
(
)
[_new:BaseObject:private] =>
[_deleted:BaseObject:private] =>
[modifiedColumns:protected] => Array
(
)
)
[85] => Category Object
(
[languages:protected] =>
[bok_resources:protected] =>
[bok_topics:protected] =>
[bok_keywords:protected] =>
[id:protected] => 85
[type:protected] => category
[parent:protected] => 2
[label:protected] => Truck Driver
[alreadyInSave:protected] =>
[alreadyInValidation:protected] =>
[validationFailures:protected] => Array
(
)
[_new:BaseObject:private] =>
[_deleted:BaseObject:private] =>
[modifiedColumns:protected] => Array
(
)
)
[86] => Category Object
(
[languages:protected] =>
[bok_resources:protected] =>
[bok_topics:protected] =>
[bok_keywords:protected] =>
[id:protected] => 86
[type:protected] => category
[parent:protected] => 2
[label:protected] => Welder
[alreadyInSave:protected] =>
[alreadyInValidation:protected] =>
[validationFailures:protected] => Array
(
)
[_new:BaseObject:private] =>
[_deleted:BaseObject:private] =>
[modifiedColumns:protected] => Array
(
)
)
[87] => Category Object
(
[languages:protected] =>
[bok_resources:protected] =>
[bok_topics:protected] =>
[bok_keywords:protected] =>
[id:protected] => 87
[type:protected] => category
[parent:protected] => 3
[label:protected] => Commercial & Institutional
[alreadyInSave:protected] =>
[alreadyInValidation:protected] =>
[validationFailures:protected] => Array
(
)
[_new:BaseObject:private] =>
[_deleted:BaseObject:private] =>
[modifiedColumns:protected] => Array
(
)
)
[88] => Category Object
(
[languages:protected] =>
[bok_resources:protected] =>
[bok_topics:protected] =>
[bok_keywords:protected] =>
[id:protected] => 88
[type:protected] => category
[parent:protected] => 3
[label:protected] => Demolition
[alreadyInSave:protected] =>
[alreadyInValidation:protected] =>
[validationFailures:protected] => Array
(
)
[_new:BaseObject:private] =>
[_deleted:BaseObject:private] =>
[modifiedColumns:protected] => Array
(
)
)
[89] => Category Object
(
[languages:protected] =>
[bok_resources:protected] =>
[bok_topics:protected] =>
[bok_keywords:protected] =>
[id:protected] => 89
[type:protected] => category
[parent:protected] => 3
[label:protected] => Disasters
[alreadyInSave:protected] =>
[alreadyInValidation:protected] =>
[validationFailures:protected] => Array
(
)
[_new:BaseObject:private] =>
[_deleted:BaseObject:private] =>
[modifiedColumns:protected] => Array
(
)
)
[91] => Category Object
(
[languages:protected] =>
[bok_resources:protected] =>
[bok_topics:protected] =>
[bok_keywords:protected] =>
[id:protected] => 91
[type:protected] => category
[parent:protected] => 3
[label:protected] => Heavy & Highway
[alreadyInSave:protected] =>
[alreadyInValidation:protected] =>
[validationFailures:protected] => Array
(
)
[_new:BaseObject:private] =>
[_deleted:BaseObject:private] =>
[modifiedColumns:protected] => Array
(
)
)
[90] => Category Object
(
[languages:protected] =>
[bok_resources:protected] =>
[bok_topics:protected] =>
[bok_keywords:protected] =>
[id:protected] => 90
[type:protected] => category
[parent:protected] => 3
[label:protected] => Industrial
[alreadyInSave:protected] =>
[alreadyInValidation:protected] =>
[validationFailures:protected] => Array
(
)
[_new:BaseObject:private] =>
[_deleted:BaseObject:private] =>
[modifiedColumns:protected] => Array
(
)
)
[92] => Category Object
(
[languages:protected] =>
[bok_resources:protected] =>
[bok_topics:protected] =>
[bok_keywords:protected] =>
[id:protected] => 92
[type:protected] => category
[parent:protected] => 3
[label:protected] => LEED/Green Construction
[alreadyInSave:protected] =>
[alreadyInValidation:protected] =>
[validationFailures:protected] => Array
(
)
[_new:BaseObject:private] =>
[_deleted:BaseObject:private] =>
[modifiedColumns:protected] => Array
(
)
)
[93] => Category Object
(
[languages:protected] =>
[bok_resources:protected] =>
[bok_topics:protected] =>
[bok_keywords:protected] =>
[id:protected] => 93
[type:protected] => category
[parent:protected] => 3
[label:protected] => Renovations
[alreadyInSave:protected] =>
[alreadyInValidation:protected] =>
[validationFailures:protected] => Array
(
)
[_new:BaseObject:private] =>
[_deleted:BaseObject:private] =>
[modifiedColumns:protected] => Array
(
)
)
[94] => Category Object
(
[languages:protected] =>
[bok_resources:protected] =>
[bok_topics:protected] =>
[bok_keywords:protected] =>
[id:protected] => 94
[type:protected] => category
[parent:protected] => 3
[label:protected] => Residential
[alreadyInSave:protected] =>
[alreadyInValidation:protected] =>
[validationFailures:protected] => Array
(
)
[_new:BaseObject:private] =>
[_deleted:BaseObject:private] =>
[modifiedColumns:protected] => Array
(
)
)
[95] => Category Object
(
[languages:protected] =>
[bok_resources:protected] =>
[bok_topics:protected] =>
[bok_keywords:protected] =>
[id:protected] => 95
[type:protected] => category
[parent:protected] => 3
[label:protected] => Underground
[alreadyInSave:protected] =>
[alreadyInValidation:protected] =>
[validationFailures:protected] => Array
(
)
[_new:BaseObject:private] =>
[_deleted:BaseObject:private] =>
[modifiedColumns:protected] => Array
(
)
)
)
[categories_initialized:protected] => 1
[mapped_items:protected] =>
[content:protected] =>
[files:protected] =>
[language:protected] => Language Object
(
[id:protected] => 1
[code:protected] => en
[name:protected] => English
[alreadyInSave:protected] =>
[alreadyInValidation:protected] =>
[validationFailures:protected] => Array
(
)
[_new:BaseObject:private] =>
[_deleted:BaseObject:private] =>
[modifiedColumns:protected] => Array
(
)
)
[old_record:protected] =>
[id:protected] => 4426
[old_id:protected] =>
[elcosh_id:protected] => d001656
[type:protected] => document
[display_type:protected] => HTML only (and links)
[user_id:protected] => 0
[language_id:protected] => 1
[tagging_id:protected] => Mike Aguilar
[priority_id:protected] => 1
[title:protected] => Construction Dive -- DeWalt's Jobsite Pro headphones recalled for fire hazards
[total_pages:protected] => 1
[billed_pages:protected] => 1
[publication_number:protected] =>
[part_of:protected] =>
[keywords:protected] => DeWalt, Fire Hazards, recall, headphones
[comments:protected] =>
[summary:protected] => A recall notice by the United States Consumer Product Safety Commission affects over 300,000 DeWalt Jobsite Pro Headphones. The recall is a result of a malfunction that can cause earbuds to overheat while charging or during use, leading to fire and burn hazards.
[transition_comments:protected] =>
[external_link:protected] => https://www.constructiondive.com/news/dewalts-jobsite-pro-headphones-recalled-for-fire-hazards/611248/?utm_source=Sailthru&utm_medium=email&utm_campaign=Issue:%202021-12-10%20Construction%20Dive%20Newsletter%20%5Bissue:38532%5D&utm_term=Construction%20Dive
[consol_link:protected] =>
[more_like_this:protected] =>
[permission_given_by:protected] =>
[published:protected] => T
[billable:protected] => F
[img_name:protected] =>
[img_ext:protected] =>
[img_width:protected] =>
[img_height:protected] =>
[img_credit:protected] =>
[img_practice:protected] =>
[vid_source_id:protected] =>
[vid_running_time:protected] =>
[vid_intended_audience:protected] =>
[vid_acquisition_info:protected] =>
[vid_cost:protected] =>
[vid_producer:protected] =>
[vid_filename:protected] =>
[vid_filename_downloadable:protected] =>
[date_summary:protected] =>
[date_permission_requested:protected] =>
[date_permission_received:protected] =>
[date_review_needed:protected] =>
[date_received:protected] => 12/13/21
[date_completed:protected] => 12/13/21
[date_billed:protected] =>
[date_modified:protected] => 12/13/21
[collBokExports:protected] =>
[lastBokExportCriteria:BaseElcoshItem:private] =>
[alreadyInSave:protected] =>
[alreadyInValidation:protected] =>
[validationFailures:protected] => Array
(
)
[_new:BaseObject:private] =>
[_deleted:BaseObject:private] =>
[modifiedColumns:protected] => Array
(
)
)
)
)
[new_images] => Array
(
[0] => Search_Result Object
(
[title] => Morning Toolbox Talk
[image] => /record/images/4003-p.jpg
[blurb] => This photo is from an early morning toolbox talk on a construction job in Mclean, Virginia. It is being delivered in English and Spanish....
[category] => Array
(
[0] => 20
[1] => 51
[2] => 57
[3] => 64
[4] => 70
[5] => 63
[6] => 78
[7] => 82
[8] => 62
[9] => 87
[10] => 88
[11] => 89
[12] => 91
[13] => 90
[14] => 93
[15] => 94
[16] => 97
)
[labels] => Array
(
[0] => Safety Culture
[1] => Work Environment
[2] => Hazards
[3] => Cement Mason
[4] => Trades
[5] => Flagger
[7] => Laborer
[9] => Operating Engineer
[11] => Reinforcing Ironworker
[13] => Roofer/Waterproofer
[15] => Stonemason
[17] => Structural Ironworker
[19] => Commercial & Institutional
[20] => Jobsites
[21] => Demolition
[23] => Disasters
[25] => Heavy & Highway
[27] => Industrial
[29] => Renovations
[31] => Residential
[33] => Images
[34] => Media
[35] => Media & Documents
)
[type] => Images
[sub_category] =>
[url] => /image/4003/i002691/Morning%2BToolbox%2BTalk.html
[item:protected] => ImageRecord Object
(
[records:protected] => Array
(
)
[recordId:protected] =>
[searchWordClass:protected] =>
[searchWordPeerClass:protected] =>
[bok_record:protected] =>
[authors:protected] =>
[organizations:protected] =>
[collections:protected] =>
[categories:protected] => Array
(
[20] => Category Object
(
[languages:protected] =>
[bok_resources:protected] =>
[bok_topics:protected] =>
[bok_keywords:protected] =>
[id:protected] => 20
[type:protected] => category
[parent:protected] => 7
[label:protected] => Safety Culture
[alreadyInSave:protected] =>
[alreadyInValidation:protected] =>
[validationFailures:protected] => Array
(
)
[_new:BaseObject:private] =>
[_deleted:BaseObject:private] =>
[modifiedColumns:protected] => Array
(
)
)
[51] => Category Object
(
[languages:protected] =>
[bok_resources:protected] =>
[bok_topics:protected] =>
[bok_keywords:protected] =>
[id:protected] => 51
[type:protected] => category
[parent:protected] => 2
[label:protected] => Cement Mason
[alreadyInSave:protected] =>
[alreadyInValidation:protected] =>
[validationFailures:protected] => Array
(
)
[_new:BaseObject:private] =>
[_deleted:BaseObject:private] =>
[modifiedColumns:protected] => Array
(
)
)
[57] => Category Object
(
[languages:protected] =>
[bok_resources:protected] =>
[bok_topics:protected] =>
[bok_keywords:protected] =>
[id:protected] => 57
[type:protected] => category
[parent:protected] => 2
[label:protected] => Flagger
[alreadyInSave:protected] =>
[alreadyInValidation:protected] =>
[validationFailures:protected] => Array
(
)
[_new:BaseObject:private] =>
[_deleted:BaseObject:private] =>
[modifiedColumns:protected] => Array
(
)
)
[64] => Category Object
(
[languages:protected] =>
[bok_resources:protected] =>
[bok_topics:protected] =>
[bok_keywords:protected] =>
[id:protected] => 64
[type:protected] => category
[parent:protected] => 2
[label:protected] => Laborer
[alreadyInSave:protected] =>
[alreadyInValidation:protected] =>
[validationFailures:protected] => Array
(
)
[_new:BaseObject:private] =>
[_deleted:BaseObject:private] =>
[modifiedColumns:protected] => Array
(
)
)
[70] => Category Object
(
[languages:protected] =>
[bok_resources:protected] =>
[bok_topics:protected] =>
[bok_keywords:protected] =>
[id:protected] => 70
[type:protected] => category
[parent:protected] => 2
[label:protected] => Operating Engineer
[alreadyInSave:protected] =>
[alreadyInValidation:protected] =>
[validationFailures:protected] => Array
(
)
[_new:BaseObject:private] =>
[_deleted:BaseObject:private] =>
[modifiedColumns:protected] => Array
(
)
)
[63] => Category Object
(
[languages:protected] =>
[bok_resources:protected] =>
[bok_topics:protected] =>
[bok_keywords:protected] =>
[id:protected] => 63
[type:protected] => category
[parent:protected] => 2
[label:protected] => Reinforcing Ironworker
[alreadyInSave:protected] =>
[alreadyInValidation:protected] =>
[validationFailures:protected] => Array
(
)
[_new:BaseObject:private] =>
[_deleted:BaseObject:private] =>
[modifiedColumns:protected] => Array
(
)
)
[78] => Category Object
(
[languages:protected] =>
[bok_resources:protected] =>
[bok_topics:protected] =>
[bok_keywords:protected] =>
[id:protected] => 78
[type:protected] => category
[parent:protected] => 2
[label:protected] => Roofer/Waterproofer
[alreadyInSave:protected] =>
[alreadyInValidation:protected] =>
[validationFailures:protected] => Array
(
)
[_new:BaseObject:private] =>
[_deleted:BaseObject:private] =>
[modifiedColumns:protected] => Array
(
)
)
[82] => Category Object
(
[languages:protected] =>
[bok_resources:protected] =>
[bok_topics:protected] =>
[bok_keywords:protected] =>
[id:protected] => 82
[type:protected] => category
[parent:protected] => 2
[label:protected] => Stonemason
[alreadyInSave:protected] =>
[alreadyInValidation:protected] =>
[validationFailures:protected] => Array
(
)
[_new:BaseObject:private] =>
[_deleted:BaseObject:private] =>
[modifiedColumns:protected] => Array
(
)
)
[62] => Category Object
(
[languages:protected] =>
[bok_resources:protected] =>
[bok_topics:protected] =>
[bok_keywords:protected] =>
[id:protected] => 62
[type:protected] => category
[parent:protected] => 2
[label:protected] => Structural Ironworker
[alreadyInSave:protected] =>
[alreadyInValidation:protected] =>
[validationFailures:protected] => Array
(
)
[_new:BaseObject:private] =>
[_deleted:BaseObject:private] =>
[modifiedColumns:protected] => Array
(
)
)
[87] => Category Object
(
[languages:protected] =>
[bok_resources:protected] =>
[bok_topics:protected] =>
[bok_keywords:protected] =>
[id:protected] => 87
[type:protected] => category
[parent:protected] => 3
[label:protected] => Commercial & Institutional
[alreadyInSave:protected] =>
[alreadyInValidation:protected] =>
[validationFailures:protected] => Array
(
)
[_new:BaseObject:private] =>
[_deleted:BaseObject:private] =>
[modifiedColumns:protected] => Array
(
)
)
[88] => Category Object
(
[languages:protected] =>
[bok_resources:protected] =>
[bok_topics:protected] =>
[bok_keywords:protected] =>
[id:protected] => 88
[type:protected] => category
[parent:protected] => 3
[label:protected] => Demolition
[alreadyInSave:protected] =>
[alreadyInValidation:protected] =>
[validationFailures:protected] => Array
(
)
[_new:BaseObject:private] =>
[_deleted:BaseObject:private] =>
[modifiedColumns:protected] => Array
(
)
)
[89] => Category Object
(
[languages:protected] =>
[bok_resources:protected] =>
[bok_topics:protected] =>
[bok_keywords:protected] =>
[id:protected] => 89
[type:protected] => category
[parent:protected] => 3
[label:protected] => Disasters
[alreadyInSave:protected] =>
[alreadyInValidation:protected] =>
[validationFailures:protected] => Array
(
)
[_new:BaseObject:private] =>
[_deleted:BaseObject:private] =>
[modifiedColumns:protected] => Array
(
)
)
[91] => Category Object
(
[languages:protected] =>
[bok_resources:protected] =>
[bok_topics:protected] =>
[bok_keywords:protected] =>
[id:protected] => 91
[type:protected] => category
[parent:protected] => 3
[label:protected] => Heavy & Highway
[alreadyInSave:protected] =>
[alreadyInValidation:protected] =>
[validationFailures:protected] => Array
(
)
[_new:BaseObject:private] =>
[_deleted:BaseObject:private] =>
[modifiedColumns:protected] => Array
(
)
)
[90] => Category Object
(
[languages:protected] =>
[bok_resources:protected] =>
[bok_topics:protected] =>
[bok_keywords:protected] =>
[id:protected] => 90
[type:protected] => category
[parent:protected] => 3
[label:protected] => Industrial
[alreadyInSave:protected] =>
[alreadyInValidation:protected] =>
[validationFailures:protected] => Array
(
)
[_new:BaseObject:private] =>
[_deleted:BaseObject:private] =>
[modifiedColumns:protected] => Array
(
)
)
[93] => Category Object
(
[languages:protected] =>
[bok_resources:protected] =>
[bok_topics:protected] =>
[bok_keywords:protected] =>
[id:protected] => 93
[type:protected] => category
[parent:protected] => 3
[label:protected] => Renovations
[alreadyInSave:protected] =>
[alreadyInValidation:protected] =>
[validationFailures:protected] => Array
(
)
[_new:BaseObject:private] =>
[_deleted:BaseObject:private] =>
[modifiedColumns:protected] => Array
(
)
)
[94] => Category Object
(
[languages:protected] =>
[bok_resources:protected] =>
[bok_topics:protected] =>
[bok_keywords:protected] =>
[id:protected] => 94
[type:protected] => category
[parent:protected] => 3
[label:protected] => Residential
[alreadyInSave:protected] =>
[alreadyInValidation:protected] =>
[validationFailures:protected] => Array
(
)
[_new:BaseObject:private] =>
[_deleted:BaseObject:private] =>
[modifiedColumns:protected] => Array
(
)
)
[97] => Category Object
(
[languages:protected] =>
[bok_resources:protected] =>
[bok_topics:protected] =>
[bok_keywords:protected] =>
[id:protected] => 97
[type:protected] => category
[parent:protected] => 5
[label:protected] => Images
[alreadyInSave:protected] =>
[alreadyInValidation:protected] =>
[validationFailures:protected] => Array
(
)
[_new:BaseObject:private] =>
[_deleted:BaseObject:private] =>
[modifiedColumns:protected] => Array
(
)
)
)
[categories_initialized:protected] => 1
[mapped_items:protected] =>
[content:protected] =>
[files:protected] =>
[language:protected] => Language Object
(
[id:protected] => 1
[code:protected] => en
[name:protected] => English
[alreadyInSave:protected] =>
[alreadyInValidation:protected] =>
[validationFailures:protected] => Array
(
)
[_new:BaseObject:private] =>
[_deleted:BaseObject:private] =>
[modifiedColumns:protected] => Array
(
)
)
[old_record:protected] =>
[id:protected] => 4003
[old_id:protected] =>
[elcosh_id:protected] => i002691
[type:protected] => image
[display_type:protected] => Image
[user_id:protected] => 0
[language_id:protected] => 1
[tagging_id:protected] => Bruce Lippy
[priority_id:protected] => 1
[title:protected] => Morning Toolbox Talk
[total_pages:protected] => 0
[billed_pages:protected] => 0
[publication_number:protected] =>
[part_of:protected] =>
[keywords:protected] => toolbox talk, tailgate talk, Spanish, bilingual
[comments:protected] =>
[summary:protected] => This photo is from an early morning toolbox talk on a construction job in Mclean, Virginia. It is being delivered in English and Spanish.
[transition_comments:protected] =>
[external_link:protected] =>
[consol_link:protected] => http://www.cpwrconstructionsolutions.org/electrical/solution/662/worker-training.html
[more_like_this:protected] => d001285,d001304,c000079
[permission_given_by:protected] =>
[published:protected] => T
[billable:protected] => F
[img_name:protected] =>
[img_ext:protected] => jpg
[img_width:protected] =>
[img_height:protected] =>
[img_credit:protected] => Morgan Zavertnik and Hoar Construction
[img_practice:protected] => good
[vid_source_id:protected] =>
[vid_running_time:protected] =>
[vid_intended_audience:protected] =>
[vid_acquisition_info:protected] =>
[vid_cost:protected] =>
[vid_producer:protected] =>
[vid_filename:protected] =>
[vid_filename_downloadable:protected] =>
[date_summary:protected] => November 2015
[date_permission_requested:protected] =>
[date_permission_received:protected] =>
[date_review_needed:protected] =>
[date_received:protected] => 03/02/16
[date_completed:protected] => 03/02/16
[date_billed:protected] =>
[date_modified:protected] => 03/02/16
[collBokExports:protected] =>
[lastBokExportCriteria:BaseElcoshItem:private] =>
[alreadyInSave:protected] =>
[alreadyInValidation:protected] =>
[validationFailures:protected] => Array
(
)
[_new:BaseObject:private] =>
[_deleted:BaseObject:private] =>
[modifiedColumns:protected] => Array
(
)
)
)
[1] => Search_Result Object
(
[title] => Toolbox talk - crew view
[image] => /record/images/4005-p.jpg
[blurb] => Photo of crew listening to a toolbox safety talk before starting work....
[category] => Array
(
[0] => 97
[1] => 20
[2] => 47
[3] => 49
[4] => 51
[5] => 55
[6] => 61
[7] => 64
[8] => 71
[9] => 75
[10] => 63
[11] => 79
[12] => 62
[13] => 87
[14] => 88
[15] => 91
[16] => 90
[17] => 93
[18] => 94
[19] => 95
)
[labels] => Array
(
[0] => Images
[1] => Media
[2] => Media & Documents
[3] => Safety Culture
[4] => Work Environment
[5] => Hazards
[6] => Bricklayer
[7] => Trades
[8] => Carpenter
[10] => Cement Mason
[12] => Electrical Worker
[14] => Interior Systems Carpenter
[16] => Laborer
[18] => Painter
[20] => Plasterer
[22] => Reinforcing Ironworker
[24] => Scaffold Erector
[26] => Structural Ironworker
[28] => Commercial & Institutional
[29] => Jobsites
[30] => Demolition
[32] => Heavy & Highway
[34] => Industrial
[36] => Renovations
[38] => Residential
[40] => Underground
)
[type] => Images
[sub_category] =>
[url] => /image/4005/i002692/Toolbox%2Btalk%2B-%2Bcrew%2Bview.html
[item:protected] => ImageRecord Object
(
[records:protected] => Array
(
)
[recordId:protected] =>
[searchWordClass:protected] =>
[searchWordPeerClass:protected] =>
[bok_record:protected] =>
[authors:protected] =>
[organizations:protected] =>
[collections:protected] =>
[categories:protected] => Array
(
[97] => Category Object
(
[languages:protected] =>
[bok_resources:protected] =>
[bok_topics:protected] =>
[bok_keywords:protected] =>
[id:protected] => 97
[type:protected] => category
[parent:protected] => 5
[label:protected] => Images
[alreadyInSave:protected] =>
[alreadyInValidation:protected] =>
[validationFailures:protected] => Array
(
)
[_new:BaseObject:private] =>
[_deleted:BaseObject:private] =>
[modifiedColumns:protected] => Array
(
)
)
[20] => Category Object
(
[languages:protected] =>
[bok_resources:protected] =>
[bok_topics:protected] =>
[bok_keywords:protected] =>
[id:protected] => 20
[type:protected] => category
[parent:protected] => 7
[label:protected] => Safety Culture
[alreadyInSave:protected] =>
[alreadyInValidation:protected] =>
[validationFailures:protected] => Array
(
)
[_new:BaseObject:private] =>
[_deleted:BaseObject:private] =>
[modifiedColumns:protected] => Array
(
)
)
[47] => Category Object
(
[languages:protected] =>
[bok_resources:protected] =>
[bok_topics:protected] =>
[bok_keywords:protected] =>
[id:protected] => 47
[type:protected] => category
[parent:protected] => 2
[label:protected] => Bricklayer
[alreadyInSave:protected] =>
[alreadyInValidation:protected] =>
[validationFailures:protected] => Array
(
)
[_new:BaseObject:private] =>
[_deleted:BaseObject:private] =>
[modifiedColumns:protected] => Array
(
)
)
[49] => Category Object
(
[languages:protected] =>
[bok_resources:protected] =>
[bok_topics:protected] =>
[bok_keywords:protected] =>
[id:protected] => 49
[type:protected] => category
[parent:protected] => 2
[label:protected] => Carpenter
[alreadyInSave:protected] =>
[alreadyInValidation:protected] =>
[validationFailures:protected] => Array
(
)
[_new:BaseObject:private] =>
[_deleted:BaseObject:private] =>
[modifiedColumns:protected] => Array
(
)
)
[51] => Category Object
(
[languages:protected] =>
[bok_resources:protected] =>
[bok_topics:protected] =>
[bok_keywords:protected] =>
[id:protected] => 51
[type:protected] => category
[parent:protected] => 2
[label:protected] => Cement Mason
[alreadyInSave:protected] =>
[alreadyInValidation:protected] =>
[validationFailures:protected] => Array
(
)
[_new:BaseObject:private] =>
[_deleted:BaseObject:private] =>
[modifiedColumns:protected] => Array
(
)
)
[55] => Category Object
(
[languages:protected] =>
[bok_resources:protected] =>
[bok_topics:protected] =>
[bok_keywords:protected] =>
[id:protected] => 55
[type:protected] => category
[parent:protected] => 2
[label:protected] => Electrical Worker
[alreadyInSave:protected] =>
[alreadyInValidation:protected] =>
[validationFailures:protected] => Array
(
)
[_new:BaseObject:private] =>
[_deleted:BaseObject:private] =>
[modifiedColumns:protected] => Array
(
)
)
[61] => Category Object
(
[languages:protected] =>
[bok_resources:protected] =>
[bok_topics:protected] =>
[bok_keywords:protected] =>
[id:protected] => 61
[type:protected] => category
[parent:protected] => 2
[label:protected] => Interior Systems Carpenter
[alreadyInSave:protected] =>
[alreadyInValidation:protected] =>
[validationFailures:protected] => Array
(
)
[_new:BaseObject:private] =>
[_deleted:BaseObject:private] =>
[modifiedColumns:protected] => Array
(
)
)
[64] => Category Object
(
[languages:protected] =>
[bok_resources:protected] =>
[bok_topics:protected] =>
[bok_keywords:protected] =>
[id:protected] => 64
[type:protected] => category
[parent:protected] => 2
[label:protected] => Laborer
[alreadyInSave:protected] =>
[alreadyInValidation:protected] =>
[validationFailures:protected] => Array
(
)
[_new:BaseObject:private] =>
[_deleted:BaseObject:private] =>
[modifiedColumns:protected] => Array
(
)
)
[71] => Category Object
(
[languages:protected] =>
[bok_resources:protected] =>
[bok_topics:protected] =>
[bok_keywords:protected] =>
[id:protected] => 71
[type:protected] => category
[parent:protected] => 2
[label:protected] => Painter
[alreadyInSave:protected] =>
[alreadyInValidation:protected] =>
[validationFailures:protected] => Array
(
)
[_new:BaseObject:private] =>
[_deleted:BaseObject:private] =>
[modifiedColumns:protected] => Array
(
)
)
[75] => Category Object
(
[languages:protected] =>
[bok_resources:protected] =>
[bok_topics:protected] =>
[bok_keywords:protected] =>
[id:protected] => 75
[type:protected] => category
[parent:protected] => 2
[label:protected] => Plasterer
[alreadyInSave:protected] =>
[alreadyInValidation:protected] =>
[validationFailures:protected] => Array
(
)
[_new:BaseObject:private] =>
[_deleted:BaseObject:private] =>
[modifiedColumns:protected] => Array
(
)
)
[63] => Category Object
(
[languages:protected] =>
[bok_resources:protected] =>
[bok_topics:protected] =>
[bok_keywords:protected] =>
[id:protected] => 63
[type:protected] => category
[parent:protected] => 2
[label:protected] => Reinforcing Ironworker
[alreadyInSave:protected] =>
[alreadyInValidation:protected] =>
[validationFailures:protected] => Array
(
)
[_new:BaseObject:private] =>
[_deleted:BaseObject:private] =>
[modifiedColumns:protected] => Array
(
)
)
[79] => Category Object
(
[languages:protected] =>
[bok_resources:protected] =>
[bok_topics:protected] =>
[bok_keywords:protected] =>
[id:protected] => 79
[type:protected] => category
[parent:protected] => 2
[label:protected] => Scaffold Erector
[alreadyInSave:protected] =>
[alreadyInValidation:protected] =>
[validationFailures:protected] => Array
(
)
[_new:BaseObject:private] =>
[_deleted:BaseObject:private] =>
[modifiedColumns:protected] => Array
(
)
)
[62] => Category Object
(
[languages:protected] =>
[bok_resources:protected] =>
[bok_topics:protected] =>
[bok_keywords:protected] =>
[id:protected] => 62
[type:protected] => category
[parent:protected] => 2
[label:protected] => Structural Ironworker
[alreadyInSave:protected] =>
[alreadyInValidation:protected] =>
[validationFailures:protected] => Array
(
)
[_new:BaseObject:private] =>
[_deleted:BaseObject:private] =>
[modifiedColumns:protected] => Array
(
)
)
[87] => Category Object
(
[languages:protected] =>
[bok_resources:protected] =>
[bok_topics:protected] =>
[bok_keywords:protected] =>
[id:protected] => 87
[type:protected] => category
[parent:protected] => 3
[label:protected] => Commercial & Institutional
[alreadyInSave:protected] =>
[alreadyInValidation:protected] =>
[validationFailures:protected] => Array
(
)
[_new:BaseObject:private] =>
[_deleted:BaseObject:private] =>
[modifiedColumns:protected] => Array
(
)
)
[88] => Category Object
(
[languages:protected] =>
[bok_resources:protected] =>
[bok_topics:protected] =>
[bok_keywords:protected] =>
[id:protected] => 88
[type:protected] => category
[parent:protected] => 3
[label:protected] => Demolition
[alreadyInSave:protected] =>
[alreadyInValidation:protected] =>
[validationFailures:protected] => Array
(
)
[_new:BaseObject:private] =>
[_deleted:BaseObject:private] =>
[modifiedColumns:protected] => Array
(
)
)
[91] => Category Object
(
[languages:protected] =>
[bok_resources:protected] =>
[bok_topics:protected] =>
[bok_keywords:protected] =>
[id:protected] => 91
[type:protected] => category
[parent:protected] => 3
[label:protected] => Heavy & Highway
[alreadyInSave:protected] =>
[alreadyInValidation:protected] =>
[validationFailures:protected] => Array
(
)
[_new:BaseObject:private] =>
[_deleted:BaseObject:private] =>
[modifiedColumns:protected] => Array
(
)
)
[90] => Category Object
(
[languages:protected] =>
[bok_resources:protected] =>
[bok_topics:protected] =>
[bok_keywords:protected] =>
[id:protected] => 90
[type:protected] => category
[parent:protected] => 3
[label:protected] => Industrial
[alreadyInSave:protected] =>
[alreadyInValidation:protected] =>
[validationFailures:protected] => Array
(
)
[_new:BaseObject:private] =>
[_deleted:BaseObject:private] =>
[modifiedColumns:protected] => Array
(
)
)
[93] => Category Object
(
[languages:protected] =>
[bok_resources:protected] =>
[bok_topics:protected] =>
[bok_keywords:protected] =>
[id:protected] => 93
[type:protected] => category
[parent:protected] => 3
[label:protected] => Renovations
[alreadyInSave:protected] =>
[alreadyInValidation:protected] =>
[validationFailures:protected] => Array
(
)
[_new:BaseObject:private] =>
[_deleted:BaseObject:private] =>
[modifiedColumns:protected] => Array
(
)
)
[94] => Category Object
(
[languages:protected] =>
[bok_resources:protected] =>
[bok_topics:protected] =>
[bok_keywords:protected] =>
[id:protected] => 94
[type:protected] => category
[parent:protected] => 3
[label:protected] => Residential
[alreadyInSave:protected] =>
[alreadyInValidation:protected] =>
[validationFailures:protected] => Array
(
)
[_new:BaseObject:private] =>
[_deleted:BaseObject:private] =>
[modifiedColumns:protected] => Array
(
)
)
[95] => Category Object
(
[languages:protected] =>
[bok_resources:protected] =>
[bok_topics:protected] =>
[bok_keywords:protected] =>
[id:protected] => 95
[type:protected] => category
[parent:protected] => 3
[label:protected] => Underground
[alreadyInSave:protected] =>
[alreadyInValidation:protected] =>
[validationFailures:protected] => Array
(
)
[_new:BaseObject:private] =>
[_deleted:BaseObject:private] =>
[modifiedColumns:protected] => Array
(
)
)
)
[categories_initialized:protected] => 1
[mapped_items:protected] =>
[content:protected] =>
[files:protected] =>
[language:protected] => Language Object
(
[id:protected] => 1
[code:protected] => en
[name:protected] => English
[alreadyInSave:protected] =>
[alreadyInValidation:protected] =>
[validationFailures:protected] => Array
(
)
[_new:BaseObject:private] =>
[_deleted:BaseObject:private] =>
[modifiedColumns:protected] => Array
(
)
)
[old_record:protected] =>
[id:protected] => 4005
[old_id:protected] =>
[elcosh_id:protected] => i002692
[type:protected] => image
[display_type:protected] => Image
[user_id:protected] => 0
[language_id:protected] => 1
[tagging_id:protected] => Bruce Lippy
[priority_id:protected] => 1
[title:protected] => Toolbox talk - crew view
[total_pages:protected] => 0
[billed_pages:protected] => 0
[publication_number:protected] =>
[part_of:protected] =>
[keywords:protected] => toolbox talk, tailgate talk, safety talk, Spanish
[comments:protected] =>
[summary:protected] => Photo of crew listening to a toolbox safety talk before starting work.
[transition_comments:protected] =>
[external_link:protected] =>
[consol_link:protected] => http://www.cpwrconstructionsolutions.org/electrical/solution/662/worker-training.html
[more_like_this:protected] => i002691,d001269, c000079, d001285
[permission_given_by:protected] =>
[published:protected] => T
[billable:protected] => F
[img_name:protected] =>
[img_ext:protected] => jpg
[img_width:protected] =>
[img_height:protected] =>
[img_credit:protected] => Morgan Zavertnik and Hoar Construction
[img_practice:protected] => good
[vid_source_id:protected] =>
[vid_running_time:protected] =>
[vid_intended_audience:protected] =>
[vid_acquisition_info:protected] =>
[vid_cost:protected] =>
[vid_producer:protected] =>
[vid_filename:protected] =>
[vid_filename_downloadable:protected] =>
[date_summary:protected] => November 2015
[date_permission_requested:protected] =>
[date_permission_received:protected] =>
[date_review_needed:protected] =>
[date_received:protected] => 03/02/16
[date_completed:protected] => 03/02/16
[date_billed:protected] =>
[date_modified:protected] => 03/02/16
[collBokExports:protected] =>
[lastBokExportCriteria:BaseElcoshItem:private] =>
[alreadyInSave:protected] =>
[alreadyInValidation:protected] =>
[validationFailures:protected] => Array
(
)
[_new:BaseObject:private] =>
[_deleted:BaseObject:private] =>
[modifiedColumns:protected] => Array
(
)
)
)
[2] => Search_Result Object
(
[title] => Toolbox talk - long shot
[image] => /record/images/4006-p.jpg
[blurb] => This crew gathered every morning before starting work to discuss a new safety topic....
[category] => Array
(
[0] => 20
[1] => 47
[2] => 49
[3] => 51
[4] => 55
[5] => 64
[6] => 68
[7] => 75
[8] => 76
[9] => 63
[10] => 78
[11] => 79
[12] => 82
[13] => 62
[14] => 87
[15] => 88
[16] => 91
[17] => 90
[18] => 93
[19] => 94
[20] => 95
[21] => 97
)
[labels] => Array
(
[0] => Safety Culture
[1] => Work Environment
[2] => Hazards
[3] => Bricklayer
[4] => Trades
[5] => Carpenter
[7] => Cement Mason
[9] => Electrical Worker
[11] => Laborer
[13] => Maintenance Worker
[15] => Plasterer
[17] => Plumber/Pipefitter
[19] => Reinforcing Ironworker
[21] => Roofer/Waterproofer
[23] => Scaffold Erector
[25] => Stonemason
[27] => Structural Ironworker
[29] => Commercial & Institutional
[30] => Jobsites
[31] => Demolition
[33] => Heavy & Highway
[35] => Industrial
[37] => Renovations
[39] => Residential
[41] => Underground
[43] => Images
[44] => Media
[45] => Media & Documents
)
[type] => Images
[sub_category] =>
[url] => /image/4006/i002693/Toolbox%2Btalk%2B-%2Blong%2Bshot.html
[item:protected] => ImageRecord Object
(
[records:protected] => Array
(
)
[recordId:protected] =>
[searchWordClass:protected] =>
[searchWordPeerClass:protected] =>
[bok_record:protected] =>
[authors:protected] =>
[organizations:protected] =>
[collections:protected] =>
[categories:protected] => Array
(
[20] => Category Object
(
[languages:protected] =>
[bok_resources:protected] =>
[bok_topics:protected] =>
[bok_keywords:protected] =>
[id:protected] => 20
[type:protected] => category
[parent:protected] => 7
[label:protected] => Safety Culture
[alreadyInSave:protected] =>
[alreadyInValidation:protected] =>
[validationFailures:protected] => Array
(
)
[_new:BaseObject:private] =>
[_deleted:BaseObject:private] =>
[modifiedColumns:protected] => Array
(
)
)
[47] => Category Object
(
[languages:protected] =>
[bok_resources:protected] =>
[bok_topics:protected] =>
[bok_keywords:protected] =>
[id:protected] => 47
[type:protected] => category
[parent:protected] => 2
[label:protected] => Bricklayer
[alreadyInSave:protected] =>
[alreadyInValidation:protected] =>
[validationFailures:protected] => Array
(
)
[_new:BaseObject:private] =>
[_deleted:BaseObject:private] =>
[modifiedColumns:protected] => Array
(
)
)
[49] => Category Object
(
[languages:protected] =>
[bok_resources:protected] =>
[bok_topics:protected] =>
[bok_keywords:protected] =>
[id:protected] => 49
[type:protected] => category
[parent:protected] => 2
[label:protected] => Carpenter
[alreadyInSave:protected] =>
[alreadyInValidation:protected] =>
[validationFailures:protected] => Array
(
)
[_new:BaseObject:private] =>
[_deleted:BaseObject:private] =>
[modifiedColumns:protected] => Array
(
)
)
[51] => Category Object
(
[languages:protected] =>
[bok_resources:protected] =>
[bok_topics:protected] =>
[bok_keywords:protected] =>
[id:protected] => 51
[type:protected] => category
[parent:protected] => 2
[label:protected] => Cement Mason
[alreadyInSave:protected] =>
[alreadyInValidation:protected] =>
[validationFailures:protected] => Array
(
)
[_new:BaseObject:private] =>
[_deleted:BaseObject:private] =>
[modifiedColumns:protected] => Array
(
)
)
[55] => Category Object
(
[languages:protected] =>
[bok_resources:protected] =>
[bok_topics:protected] =>
[bok_keywords:protected] =>
[id:protected] => 55
[type:protected] => category
[parent:protected] => 2
[label:protected] => Electrical Worker
[alreadyInSave:protected] =>
[alreadyInValidation:protected] =>
[validationFailures:protected] => Array
(
)
[_new:BaseObject:private] =>
[_deleted:BaseObject:private] =>
[modifiedColumns:protected] => Array
(
)
)
[64] => Category Object
(
[languages:protected] =>
[bok_resources:protected] =>
[bok_topics:protected] =>
[bok_keywords:protected] =>
[id:protected] => 64
[type:protected] => category
[parent:protected] => 2
[label:protected] => Laborer
[alreadyInSave:protected] =>
[alreadyInValidation:protected] =>
[validationFailures:protected] => Array
(
)
[_new:BaseObject:private] =>
[_deleted:BaseObject:private] =>
[modifiedColumns:protected] => Array
(
)
)
[68] => Category Object
(
[languages:protected] =>
[bok_resources:protected] =>
[bok_topics:protected] =>
[bok_keywords:protected] =>
[id:protected] => 68
[type:protected] => category
[parent:protected] => 2
[label:protected] => Maintenance Worker
[alreadyInSave:protected] =>
[alreadyInValidation:protected] =>
[validationFailures:protected] => Array
(
)
[_new:BaseObject:private] =>
[_deleted:BaseObject:private] =>
[modifiedColumns:protected] => Array
(
)
)
[75] => Category Object
(
[languages:protected] =>
[bok_resources:protected] =>
[bok_topics:protected] =>
[bok_keywords:protected] =>
[id:protected] => 75
[type:protected] => category
[parent:protected] => 2
[label:protected] => Plasterer
[alreadyInSave:protected] =>
[alreadyInValidation:protected] =>
[validationFailures:protected] => Array
(
)
[_new:BaseObject:private] =>
[_deleted:BaseObject:private] =>
[modifiedColumns:protected] => Array
(
)
)
[76] => Category Object
(
[languages:protected] =>
[bok_resources:protected] =>
[bok_topics:protected] =>
[bok_keywords:protected] =>
[id:protected] => 76
[type:protected] => category
[parent:protected] => 2
[label:protected] => Plumber/Pipefitter
[alreadyInSave:protected] =>
[alreadyInValidation:protected] =>
[validationFailures:protected] => Array
(
)
[_new:BaseObject:private] =>
[_deleted:BaseObject:private] =>
[modifiedColumns:protected] => Array
(
)
)
[63] => Category Object
(
[languages:protected] =>
[bok_resources:protected] =>
[bok_topics:protected] =>
[bok_keywords:protected] =>
[id:protected] => 63
[type:protected] => category
[parent:protected] => 2
[label:protected] => Reinforcing Ironworker
[alreadyInSave:protected] =>
[alreadyInValidation:protected] =>
[validationFailures:protected] => Array
(
)
[_new:BaseObject:private] =>
[_deleted:BaseObject:private] =>
[modifiedColumns:protected] => Array
(
)
)
[78] => Category Object
(
[languages:protected] =>
[bok_resources:protected] =>
[bok_topics:protected] =>
[bok_keywords:protected] =>
[id:protected] => 78
[type:protected] => category
[parent:protected] => 2
[label:protected] => Roofer/Waterproofer
[alreadyInSave:protected] =>
[alreadyInValidation:protected] =>
[validationFailures:protected] => Array
(
)
[_new:BaseObject:private] =>
[_deleted:BaseObject:private] =>
[modifiedColumns:protected] => Array
(
)
)
[79] => Category Object
(
[languages:protected] =>
[bok_resources:protected] =>
[bok_topics:protected] =>
[bok_keywords:protected] =>
[id:protected] => 79
[type:protected] => category
[parent:protected] => 2
[label:protected] => Scaffold Erector
[alreadyInSave:protected] =>
[alreadyInValidation:protected] =>
[validationFailures:protected] => Array
(
)
[_new:BaseObject:private] =>
[_deleted:BaseObject:private] =>
[modifiedColumns:protected] => Array
(
)
)
[82] => Category Object
(
[languages:protected] =>
[bok_resources:protected] =>
[bok_topics:protected] =>
[bok_keywords:protected] =>
[id:protected] => 82
[type:protected] => category
[parent:protected] => 2
[label:protected] => Stonemason
[alreadyInSave:protected] =>
[alreadyInValidation:protected] =>
[validationFailures:protected] => Array
(
)
[_new:BaseObject:private] =>
[_deleted:BaseObject:private] =>
[modifiedColumns:protected] => Array
(
)
)
[62] => Category Object
(
[languages:protected] =>
[bok_resources:protected] =>
[bok_topics:protected] =>
[bok_keywords:protected] =>
[id:protected] => 62
[type:protected] => category
[parent:protected] => 2
[label:protected] => Structural Ironworker
[alreadyInSave:protected] =>
[alreadyInValidation:protected] =>
[validationFailures:protected] => Array
(
)
[_new:BaseObject:private] =>
[_deleted:BaseObject:private] =>
[modifiedColumns:protected] => Array
(
)
)
[87] => Category Object
(
[languages:protected] =>
[bok_resources:protected] =>
[bok_topics:protected] =>
[bok_keywords:protected] =>
[id:protected] => 87
[type:protected] => category
[parent:protected] => 3
[label:protected] => Commercial & Institutional
[alreadyInSave:protected] =>
[alreadyInValidation:protected] =>
[validationFailures:protected] => Array
(
)
[_new:BaseObject:private] =>
[_deleted:BaseObject:private] =>
[modifiedColumns:protected] => Array
(
)
)
[88] => Category Object
(
[languages:protected] =>
[bok_resources:protected] =>
[bok_topics:protected] =>
[bok_keywords:protected] =>
[id:protected] => 88
[type:protected] => category
[parent:protected] => 3
[label:protected] => Demolition
[alreadyInSave:protected] =>
[alreadyInValidation:protected] =>
[validationFailures:protected] => Array
(
)
[_new:BaseObject:private] =>
[_deleted:BaseObject:private] =>
[modifiedColumns:protected] => Array
(
)
)
[91] => Category Object
(
[languages:protected] =>
[bok_resources:protected] =>
[bok_topics:protected] =>
[bok_keywords:protected] =>
[id:protected] => 91
[type:protected] => category
[parent:protected] => 3
[label:protected] => Heavy & Highway
[alreadyInSave:protected] =>
[alreadyInValidation:protected] =>
[validationFailures:protected] => Array
(
)
[_new:BaseObject:private] =>
[_deleted:BaseObject:private] =>
[modifiedColumns:protected] => Array
(
)
)
[90] => Category Object
(
[languages:protected] =>
[bok_resources:protected] =>
[bok_topics:protected] =>
[bok_keywords:protected] =>
[id:protected] => 90
[type:protected] => category
[parent:protected] => 3
[label:protected] => Industrial
[alreadyInSave:protected] =>
[alreadyInValidation:protected] =>
[validationFailures:protected] => Array
(
)
[_new:BaseObject:private] =>
[_deleted:BaseObject:private] =>
[modifiedColumns:protected] => Array
(
)
)
[93] => Category Object
(
[languages:protected] =>
[bok_resources:protected] =>
[bok_topics:protected] =>
[bok_keywords:protected] =>
[id:protected] => 93
[type:protected] => category
[parent:protected] => 3
[label:protected] => Renovations
[alreadyInSave:protected] =>
[alreadyInValidation:protected] =>
[validationFailures:protected] => Array
(
)
[_new:BaseObject:private] =>
[_deleted:BaseObject:private] =>
[modifiedColumns:protected] => Array
(
)
)
[94] => Category Object
(
[languages:protected] =>
[bok_resources:protected] =>
[bok_topics:protected] =>
[bok_keywords:protected] =>
[id:protected] => 94
[type:protected] => category
[parent:protected] => 3
[label:protected] => Residential
[alreadyInSave:protected] =>
[alreadyInValidation:protected] =>
[validationFailures:protected] => Array
(
)
[_new:BaseObject:private] =>
[_deleted:BaseObject:private] =>
[modifiedColumns:protected] => Array
(
)
)
[95] => Category Object
(
[languages:protected] =>
[bok_resources:protected] =>
[bok_topics:protected] =>
[bok_keywords:protected] =>
[id:protected] => 95
[type:protected] => category
[parent:protected] => 3
[label:protected] => Underground
[alreadyInSave:protected] =>
[alreadyInValidation:protected] =>
[validationFailures:protected] => Array
(
)
[_new:BaseObject:private] =>
[_deleted:BaseObject:private] =>
[modifiedColumns:protected] => Array
(
)
)
[97] => Category Object
(
[languages:protected] =>
[bok_resources:protected] =>
[bok_topics:protected] =>
[bok_keywords:protected] =>
[id:protected] => 97
[type:protected] => category
[parent:protected] => 5
[label:protected] => Images
[alreadyInSave:protected] =>
[alreadyInValidation:protected] =>
[validationFailures:protected] => Array
(
)
[_new:BaseObject:private] =>
[_deleted:BaseObject:private] =>
[modifiedColumns:protected] => Array
(
)
)
)
[categories_initialized:protected] => 1
[mapped_items:protected] =>
[content:protected] =>
[files:protected] =>
[language:protected] => Language Object
(
[id:protected] => 1
[code:protected] => en
[name:protected] => English
[alreadyInSave:protected] =>
[alreadyInValidation:protected] =>
[validationFailures:protected] => Array
(
)
[_new:BaseObject:private] =>
[_deleted:BaseObject:private] =>
[modifiedColumns:protected] => Array
(
)
)
[old_record:protected] =>
[id:protected] => 4006
[old_id:protected] =>
[elcosh_id:protected] => i002693
[type:protected] => image
[display_type:protected] => Image
[user_id:protected] => 0
[language_id:protected] => 1
[tagging_id:protected] => Bruce Lippy
[priority_id:protected] => 1
[title:protected] => Toolbox talk - long shot
[total_pages:protected] => 0
[billed_pages:protected] => 0
[publication_number:protected] =>
[part_of:protected] =>
[keywords:protected] => toolbox talk, tailgate talk, safety minute
[comments:protected] =>
[summary:protected] => This crew gathered every morning before starting work to discuss a new safety topic.
[transition_comments:protected] =>
[external_link:protected] =>
[consol_link:protected] => http://www.cpwrconstructionsolutions.org/electrical/solution/662/worker-training.html
[more_like_this:protected] => i002691,i002692,d001269,d000527
[permission_given_by:protected] =>
[published:protected] => T
[billable:protected] => F
[img_name:protected] =>
[img_ext:protected] => jpg
[img_width:protected] =>
[img_height:protected] =>
[img_credit:protected] => Morgan Zavertnik and Hoar Construction
[img_practice:protected] => good
[vid_source_id:protected] =>
[vid_running_time:protected] =>
[vid_intended_audience:protected] =>
[vid_acquisition_info:protected] =>
[vid_cost:protected] =>
[vid_producer:protected] =>
[vid_filename:protected] =>
[vid_filename_downloadable:protected] =>
[date_summary:protected] => November 2015
[date_permission_requested:protected] =>
[date_permission_received:protected] =>
[date_review_needed:protected] =>
[date_received:protected] => 03/02/16
[date_completed:protected] => 03/02/16
[date_billed:protected] =>
[date_modified:protected] => 03/02/16
[collBokExports:protected] =>
[lastBokExportCriteria:BaseElcoshItem:private] =>
[alreadyInSave:protected] =>
[alreadyInValidation:protected] =>
[validationFailures:protected] => Array
(
)
[_new:BaseObject:private] =>
[_deleted:BaseObject:private] =>
[modifiedColumns:protected] => Array
(
)
)
)
[3] => Search_Result Object
(
[title] => Safety officer discussing ongoing project with marketing coordinator
[image] => /record/images/4014-p.jpg
[blurb] => The safety officer (left) points out the good safety practices on this project that reflect well on the firm and may influence future clients....
[category] => Array
(
[0] => 97
[1] => 20
[2] => 46
[3] => 47
[4] => 49
[5] => 50
[6] => 51
[7] => 54
[8] => 55
[9] => 58
[10] => 60
[11] => 61
[12] => 64
[13] => 71
[14] => 75
[15] => 76
[16] => 63
[17] => 79
[18] => 80
[19] => 82
[20] => 62
[21] => 83
[22] => 87
[23] => 91
[24] => 90
[25] => 93
[26] => 94
)
[labels] => Array
(
[0] => Images
[1] => Media
[2] => Media & Documents
[3] => Safety Culture
[4] => Work Environment
[5] => Hazards
[6] => Boilermaker
[7] => Trades
[8] => Bricklayer
[10] => Carpenter
[12] => Carpet Layer
[14] => Cement Mason
[16] => Drywall Applicator Specialist
[18] => Electrical Worker
[20] => Glazier
[22] => HVAC
[24] => Interior Systems Carpenter
[26] => Laborer
[28] => Painter
[30] => Plasterer
[32] => Plumber/Pipefitter
[34] => Reinforcing Ironworker
[36] => Scaffold Erector
[38] => Sheetmetal Worker
[40] => Stonemason
[42] => Structural Ironworker
[44] => Terrazzo Worker
[46] => Commercial & Institutional
[47] => Jobsites
[48] => Heavy & Highway
[50] => Industrial
[52] => Renovations
[54] => Residential
)
[type] => Images
[sub_category] =>
[url] => /image/4014/i002700/Safety%2Bofficer%2Bdiscussing%2Bongoing%2Bproject%2Bwith%2Bmarketing%2Bcoordinator.html
[item:protected] => ImageRecord Object
(
[records:protected] => Array
(
)
[recordId:protected] =>
[searchWordClass:protected] =>
[searchWordPeerClass:protected] =>
[bok_record:protected] =>
[authors:protected] =>
[organizations:protected] =>
[collections:protected] =>
[categories:protected] => Array
(
[97] => Category Object
(
[languages:protected] =>
[bok_resources:protected] =>
[bok_topics:protected] =>
[bok_keywords:protected] =>
[id:protected] => 97
[type:protected] => category
[parent:protected] => 5
[label:protected] => Images
[alreadyInSave:protected] =>
[alreadyInValidation:protected] =>
[validationFailures:protected] => Array
(
)
[_new:BaseObject:private] =>
[_deleted:BaseObject:private] =>
[modifiedColumns:protected] => Array
(
)
)
[20] => Category Object
(
[languages:protected] =>
[bok_resources:protected] =>
[bok_topics:protected] =>
[bok_keywords:protected] =>
[id:protected] => 20
[type:protected] => category
[parent:protected] => 7
[label:protected] => Safety Culture
[alreadyInSave:protected] =>
[alreadyInValidation:protected] =>
[validationFailures:protected] => Array
(
)
[_new:BaseObject:private] =>
[_deleted:BaseObject:private] =>
[modifiedColumns:protected] => Array
(
)
)
[46] => Category Object
(
[languages:protected] =>
[bok_resources:protected] =>
[bok_topics:protected] =>
[bok_keywords:protected] =>
[id:protected] => 46
[type:protected] => category
[parent:protected] => 2
[label:protected] => Boilermaker
[alreadyInSave:protected] =>
[alreadyInValidation:protected] =>
[validationFailures:protected] => Array
(
)
[_new:BaseObject:private] =>
[_deleted:BaseObject:private] =>
[modifiedColumns:protected] => Array
(
)
)
[47] => Category Object
(
[languages:protected] =>
[bok_resources:protected] =>
[bok_topics:protected] =>
[bok_keywords:protected] =>
[id:protected] => 47
[type:protected] => category
[parent:protected] => 2
[label:protected] => Bricklayer
[alreadyInSave:protected] =>
[alreadyInValidation:protected] =>
[validationFailures:protected] => Array
(
)
[_new:BaseObject:private] =>
[_deleted:BaseObject:private] =>
[modifiedColumns:protected] => Array
(
)
)
[49] => Category Object
(
[languages:protected] =>
[bok_resources:protected] =>
[bok_topics:protected] =>
[bok_keywords:protected] =>
[id:protected] => 49
[type:protected] => category
[parent:protected] => 2
[label:protected] => Carpenter
[alreadyInSave:protected] =>
[alreadyInValidation:protected] =>
[validationFailures:protected] => Array
(
)
[_new:BaseObject:private] =>
[_deleted:BaseObject:private] =>
[modifiedColumns:protected] => Array
(
)
)
[50] => Category Object
(
[languages:protected] =>
[bok_resources:protected] =>
[bok_topics:protected] =>
[bok_keywords:protected] =>
[id:protected] => 50
[type:protected] => category
[parent:protected] => 2
[label:protected] => Carpet Layer
[alreadyInSave:protected] =>
[alreadyInValidation:protected] =>
[validationFailures:protected] => Array
(
)
[_new:BaseObject:private] =>
[_deleted:BaseObject:private] =>
[modifiedColumns:protected] => Array
(
)
)
[51] => Category Object
(
[languages:protected] =>
[bok_resources:protected] =>
[bok_topics:protected] =>
[bok_keywords:protected] =>
[id:protected] => 51
[type:protected] => category
[parent:protected] => 2
[label:protected] => Cement Mason
[alreadyInSave:protected] =>
[alreadyInValidation:protected] =>
[validationFailures:protected] => Array
(
)
[_new:BaseObject:private] =>
[_deleted:BaseObject:private] =>
[modifiedColumns:protected] => Array
(
)
)
[54] => Category Object
(
[languages:protected] =>
[bok_resources:protected] =>
[bok_topics:protected] =>
[bok_keywords:protected] =>
[id:protected] => 54
[type:protected] => category
[parent:protected] => 2
[label:protected] => Drywall Applicator Specialist
[alreadyInSave:protected] =>
[alreadyInValidation:protected] =>
[validationFailures:protected] => Array
(
)
[_new:BaseObject:private] =>
[_deleted:BaseObject:private] =>
[modifiedColumns:protected] => Array
(
)
)
[55] => Category Object
(
[languages:protected] =>
[bok_resources:protected] =>
[bok_topics:protected] =>
[bok_keywords:protected] =>
[id:protected] => 55
[type:protected] => category
[parent:protected] => 2
[label:protected] => Electrical Worker
[alreadyInSave:protected] =>
[alreadyInValidation:protected] =>
[validationFailures:protected] => Array
(
)
[_new:BaseObject:private] =>
[_deleted:BaseObject:private] =>
[modifiedColumns:protected] => Array
(
)
)
[58] => Category Object
(
[languages:protected] =>
[bok_resources:protected] =>
[bok_topics:protected] =>
[bok_keywords:protected] =>
[id:protected] => 58
[type:protected] => category
[parent:protected] => 2
[label:protected] => Glazier
[alreadyInSave:protected] =>
[alreadyInValidation:protected] =>
[validationFailures:protected] => Array
(
)
[_new:BaseObject:private] =>
[_deleted:BaseObject:private] =>
[modifiedColumns:protected] => Array
(
)
)
[60] => Category Object
(
[languages:protected] =>
[bok_resources:protected] =>
[bok_topics:protected] =>
[bok_keywords:protected] =>
[id:protected] => 60
[type:protected] => category
[parent:protected] => 2
[label:protected] => HVAC
[alreadyInSave:protected] =>
[alreadyInValidation:protected] =>
[validationFailures:protected] => Array
(
)
[_new:BaseObject:private] =>
[_deleted:BaseObject:private] =>
[modifiedColumns:protected] => Array
(
)
)
[61] => Category Object
(
[languages:protected] =>
[bok_resources:protected] =>
[bok_topics:protected] =>
[bok_keywords:protected] =>
[id:protected] => 61
[type:protected] => category
[parent:protected] => 2
[label:protected] => Interior Systems Carpenter
[alreadyInSave:protected] =>
[alreadyInValidation:protected] =>
[validationFailures:protected] => Array
(
)
[_new:BaseObject:private] =>
[_deleted:BaseObject:private] =>
[modifiedColumns:protected] => Array
(
)
)
[64] => Category Object
(
[languages:protected] =>
[bok_resources:protected] =>
[bok_topics:protected] =>
[bok_keywords:protected] =>
[id:protected] => 64
[type:protected] => category
[parent:protected] => 2
[label:protected] => Laborer
[alreadyInSave:protected] =>
[alreadyInValidation:protected] =>
[validationFailures:protected] => Array
(
)
[_new:BaseObject:private] =>
[_deleted:BaseObject:private] =>
[modifiedColumns:protected] => Array
(
)
)
[71] => Category Object
(
[languages:protected] =>
[bok_resources:protected] =>
[bok_topics:protected] =>
[bok_keywords:protected] =>
[id:protected] => 71
[type:protected] => category
[parent:protected] => 2
[label:protected] => Painter
[alreadyInSave:protected] =>
[alreadyInValidation:protected] =>
[validationFailures:protected] => Array
(
)
[_new:BaseObject:private] =>
[_deleted:BaseObject:private] =>
[modifiedColumns:protected] => Array
(
)
)
[75] => Category Object
(
[languages:protected] =>
[bok_resources:protected] =>
[bok_topics:protected] =>
[bok_keywords:protected] =>
[id:protected] => 75
[type:protected] => category
[parent:protected] => 2
[label:protected] => Plasterer
[alreadyInSave:protected] =>
[alreadyInValidation:protected] =>
[validationFailures:protected] => Array
(
)
[_new:BaseObject:private] =>
[_deleted:BaseObject:private] =>
[modifiedColumns:protected] => Array
(
)
)
[76] => Category Object
(
[languages:protected] =>
[bok_resources:protected] =>
[bok_topics:protected] =>
[bok_keywords:protected] =>
[id:protected] => 76
[type:protected] => category
[parent:protected] => 2
[label:protected] => Plumber/Pipefitter
[alreadyInSave:protected] =>
[alreadyInValidation:protected] =>
[validationFailures:protected] => Array
(
)
[_new:BaseObject:private] =>
[_deleted:BaseObject:private] =>
[modifiedColumns:protected] => Array
(
)
)
[63] => Category Object
(
[languages:protected] =>
[bok_resources:protected] =>
[bok_topics:protected] =>
[bok_keywords:protected] =>
[id:protected] => 63
[type:protected] => category
[parent:protected] => 2
[label:protected] => Reinforcing Ironworker
[alreadyInSave:protected] =>
[alreadyInValidation:protected] =>
[validationFailures:protected] => Array
(
)
[_new:BaseObject:private] =>
[_deleted:BaseObject:private] =>
[modifiedColumns:protected] => Array
(
)
)
[79] => Category Object
(
[languages:protected] =>
[bok_resources:protected] =>
[bok_topics:protected] =>
[bok_keywords:protected] =>
[id:protected] => 79
[type:protected] => category
[parent:protected] => 2
[label:protected] => Scaffold Erector
[alreadyInSave:protected] =>
[alreadyInValidation:protected] =>
[validationFailures:protected] => Array
(
)
[_new:BaseObject:private] =>
[_deleted:BaseObject:private] =>
[modifiedColumns:protected] => Array
(
)
)
[80] => Category Object
(
[languages:protected] =>
[bok_resources:protected] =>
[bok_topics:protected] =>
[bok_keywords:protected] =>
[id:protected] => 80
[type:protected] => category
[parent:protected] => 2
[label:protected] => Sheetmetal Worker
[alreadyInSave:protected] =>
[alreadyInValidation:protected] =>
[validationFailures:protected] => Array
(
)
[_new:BaseObject:private] =>
[_deleted:BaseObject:private] =>
[modifiedColumns:protected] => Array
(
)
)
[82] => Category Object
(
[languages:protected] =>
[bok_resources:protected] =>
[bok_topics:protected] =>
[bok_keywords:protected] =>
[id:protected] => 82
[type:protected] => category
[parent:protected] => 2
[label:protected] => Stonemason
[alreadyInSave:protected] =>
[alreadyInValidation:protected] =>
[validationFailures:protected] => Array
(
)
[_new:BaseObject:private] =>
[_deleted:BaseObject:private] =>
[modifiedColumns:protected] => Array
(
)
)
[62] => Category Object
(
[languages:protected] =>
[bok_resources:protected] =>
[bok_topics:protected] =>
[bok_keywords:protected] =>
[id:protected] => 62
[type:protected] => category
[parent:protected] => 2
[label:protected] => Structural Ironworker
[alreadyInSave:protected] =>
[alreadyInValidation:protected] =>
[validationFailures:protected] => Array
(
)
[_new:BaseObject:private] =>
[_deleted:BaseObject:private] =>
[modifiedColumns:protected] => Array
(
)
)
[83] => Category Object
(
[languages:protected] =>
[bok_resources:protected] =>
[bok_topics:protected] =>
[bok_keywords:protected] =>
[id:protected] => 83
[type:protected] => category
[parent:protected] => 2
[label:protected] => Terrazzo Worker
[alreadyInSave:protected] =>
[alreadyInValidation:protected] =>
[validationFailures:protected] => Array
(
)
[_new:BaseObject:private] =>
[_deleted:BaseObject:private] =>
[modifiedColumns:protected] => Array
(
)
)
[87] => Category Object
(
[languages:protected] =>
[bok_resources:protected] =>
[bok_topics:protected] =>
[bok_keywords:protected] =>
[id:protected] => 87
[type:protected] => category
[parent:protected] => 3
[label:protected] => Commercial & Institutional
[alreadyInSave:protected] =>
[alreadyInValidation:protected] =>
[validationFailures:protected] => Array
(
)
[_new:BaseObject:private] =>
[_deleted:BaseObject:private] =>
[modifiedColumns:protected] => Array
(
)
)
[91] => Category Object
(
[languages:protected] =>
[bok_resources:protected] =>
[bok_topics:protected] =>
[bok_keywords:protected] =>
[id:protected] => 91
[type:protected] => category
[parent:protected] => 3
[label:protected] => Heavy & Highway
[alreadyInSave:protected] =>
[alreadyInValidation:protected] =>
[validationFailures:protected] => Array
(
)
[_new:BaseObject:private] =>
[_deleted:BaseObject:private] =>
[modifiedColumns:protected] => Array
(
)
)
[90] => Category Object
(
[languages:protected] =>
[bok_resources:protected] =>
[bok_topics:protected] =>
[bok_keywords:protected] =>
[id:protected] => 90
[type:protected] => category
[parent:protected] => 3
[label:protected] => Industrial
[alreadyInSave:protected] =>
[alreadyInValidation:protected] =>
[validationFailures:protected] => Array
(
)
[_new:BaseObject:private] =>
[_deleted:BaseObject:private] =>
[modifiedColumns:protected] => Array
(
)
)
[93] => Category Object
(
[languages:protected] =>
[bok_resources:protected] =>
[bok_topics:protected] =>
[bok_keywords:protected] =>
[id:protected] => 93
[type:protected] => category
[parent:protected] => 3
[label:protected] => Renovations
[alreadyInSave:protected] =>
[alreadyInValidation:protected] =>
[validationFailures:protected] => Array
(
)
[_new:BaseObject:private] =>
[_deleted:BaseObject:private] =>
[modifiedColumns:protected] => Array
(
)
)
[94] => Category Object
(
[languages:protected] =>
[bok_resources:protected] =>
[bok_topics:protected] =>
[bok_keywords:protected] =>
[id:protected] => 94
[type:protected] => category
[parent:protected] => 3
[label:protected] => Residential
[alreadyInSave:protected] =>
[alreadyInValidation:protected] =>
[validationFailures:protected] => Array
(
)
[_new:BaseObject:private] =>
[_deleted:BaseObject:private] =>
[modifiedColumns:protected] => Array
(
)
)
)
[categories_initialized:protected] => 1
[mapped_items:protected] =>
[content:protected] =>
[files:protected] =>
[language:protected] => Language Object
(
[id:protected] => 1
[code:protected] => en
[name:protected] => English
[alreadyInSave:protected] =>
[alreadyInValidation:protected] =>
[validationFailures:protected] => Array
(
)
[_new:BaseObject:private] =>
[_deleted:BaseObject:private] =>
[modifiedColumns:protected] => Array
(
)
)
[old_record:protected] =>
[id:protected] => 4014
[old_id:protected] =>
[elcosh_id:protected] => i002700
[type:protected] => image
[display_type:protected] => Image
[user_id:protected] => 0
[language_id:protected] => 1
[tagging_id:protected] => Bruce Lippy
[priority_id:protected] => 1
[title:protected] => Safety officer discussing ongoing project with marketing coordinator
[total_pages:protected] => 0
[billed_pages:protected] => 0
[publication_number:protected] =>
[part_of:protected] =>
[keywords:protected] => Latino, safety officer, safety culture
[comments:protected] =>
[summary:protected] => The safety officer (left) points out the good safety practices on this project that reflect well on the firm and may influence future clients.
[transition_comments:protected] =>
[external_link:protected] =>
[consol_link:protected] => http://www.cpwrconstructionsolutions.org/index.php
[more_like_this:protected] => d000989,d001351,d001362,d000652, d001101, d000931, d001395
[permission_given_by:protected] =>
[published:protected] => T
[billable:protected] => F
[img_name:protected] =>
[img_ext:protected] => jpg
[img_width:protected] =>
[img_height:protected] =>
[img_credit:protected] => Hoar Construction, Photo by Neil Lippy
[img_practice:protected] => good
[vid_source_id:protected] =>
[vid_running_time:protected] =>
[vid_intended_audience:protected] =>
[vid_acquisition_info:protected] =>
[vid_cost:protected] =>
[vid_producer:protected] =>
[vid_filename:protected] =>
[vid_filename_downloadable:protected] =>
[date_summary:protected] => November 2015
[date_permission_requested:protected] =>
[date_permission_received:protected] =>
[date_review_needed:protected] =>
[date_received:protected] => 03/02/16
[date_completed:protected] => 03/02/16
[date_billed:protected] =>
[date_modified:protected] => 01/30/23
[collBokExports:protected] =>
[lastBokExportCriteria:BaseElcoshItem:private] =>
[alreadyInSave:protected] =>
[alreadyInValidation:protected] =>
[validationFailures:protected] => Array
(
)
[_new:BaseObject:private] =>
[_deleted:BaseObject:private] =>
[modifiedColumns:protected] => Array
(
)
)
)
[4] => Search_Result Object
(
[title] => Scaffolding at top of large column
[image] => /record/images/3994-p.jpg
[blurb] => This shot shows innovative guarding around the top of a large concrete column in the base of a high rise structure going up....
[category] => Array
(
[0] => 15
[1] => 21
[2] => 47
[3] => 51
[4] => 63
[5] => 78
[6] => 79
[7] => 80
[8] => 62
[9] => 87
[10] => 97
[11] => 56
[12] => 64
[13] => 74
)
[labels] => Array
(
[0] => Falls
[1] => Work Environment
[2] => Hazards
[3] => Scaffolds
[6] => Bricklayer
[7] => Trades
[8] => Cement Mason
[10] => Reinforcing Ironworker
[12] => Roofer/Waterproofer
[14] => Scaffold Erector
[16] => Sheetmetal Worker
[18] => Structural Ironworker
[20] => Commercial & Institutional
[21] => Jobsites
[22] => Images
[23] => Media
[24] => Media & Documents
[25] => Elevator Constructor
[27] => Laborer
[29] => Pile Driver
)
[type] => Images
[sub_category] =>
[url] => /image/3994/i002689/Scaffolding%2Bat%2Btop%2Bof%2Blarge%2Bcolumn.html
[item:protected] => ImageRecord Object
(
[records:protected] => Array
(
)
[recordId:protected] =>
[searchWordClass:protected] =>
[searchWordPeerClass:protected] =>
[bok_record:protected] =>
[authors:protected] =>
[organizations:protected] =>
[collections:protected] =>
[categories:protected] => Array
(
[15] => Category Object
(
[languages:protected] =>
[bok_resources:protected] =>
[bok_topics:protected] =>
[bok_keywords:protected] =>
[id:protected] => 15
[type:protected] => category
[parent:protected] => 7
[label:protected] => Falls
[alreadyInSave:protected] =>
[alreadyInValidation:protected] =>
[validationFailures:protected] => Array
(
)
[_new:BaseObject:private] =>
[_deleted:BaseObject:private] =>
[modifiedColumns:protected] => Array
(
)
)
[21] => Category Object
(
[languages:protected] =>
[bok_resources:protected] =>
[bok_topics:protected] =>
[bok_keywords:protected] =>
[id:protected] => 21
[type:protected] => category
[parent:protected] => 7
[label:protected] => Scaffolds
[alreadyInSave:protected] =>
[alreadyInValidation:protected] =>
[validationFailures:protected] => Array
(
)
[_new:BaseObject:private] =>
[_deleted:BaseObject:private] =>
[modifiedColumns:protected] => Array
(
)
)
[47] => Category Object
(
[languages:protected] =>
[bok_resources:protected] =>
[bok_topics:protected] =>
[bok_keywords:protected] =>
[id:protected] => 47
[type:protected] => category
[parent:protected] => 2
[label:protected] => Bricklayer
[alreadyInSave:protected] =>
[alreadyInValidation:protected] =>
[validationFailures:protected] => Array
(
)
[_new:BaseObject:private] =>
[_deleted:BaseObject:private] =>
[modifiedColumns:protected] => Array
(
)
)
[51] => Category Object
(
[languages:protected] =>
[bok_resources:protected] =>
[bok_topics:protected] =>
[bok_keywords:protected] =>
[id:protected] => 51
[type:protected] => category
[parent:protected] => 2
[label:protected] => Cement Mason
[alreadyInSave:protected] =>
[alreadyInValidation:protected] =>
[validationFailures:protected] => Array
(
)
[_new:BaseObject:private] =>
[_deleted:BaseObject:private] =>
[modifiedColumns:protected] => Array
(
)
)
[63] => Category Object
(
[languages:protected] =>
[bok_resources:protected] =>
[bok_topics:protected] =>
[bok_keywords:protected] =>
[id:protected] => 63
[type:protected] => category
[parent:protected] => 2
[label:protected] => Reinforcing Ironworker
[alreadyInSave:protected] =>
[alreadyInValidation:protected] =>
[validationFailures:protected] => Array
(
)
[_new:BaseObject:private] =>
[_deleted:BaseObject:private] =>
[modifiedColumns:protected] => Array
(
)
)
[78] => Category Object
(
[languages:protected] =>
[bok_resources:protected] =>
[bok_topics:protected] =>
[bok_keywords:protected] =>
[id:protected] => 78
[type:protected] => category
[parent:protected] => 2
[label:protected] => Roofer/Waterproofer
[alreadyInSave:protected] =>
[alreadyInValidation:protected] =>
[validationFailures:protected] => Array
(
)
[_new:BaseObject:private] =>
[_deleted:BaseObject:private] =>
[modifiedColumns:protected] => Array
(
)
)
[79] => Category Object
(
[languages:protected] =>
[bok_resources:protected] =>
[bok_topics:protected] =>
[bok_keywords:protected] =>
[id:protected] => 79
[type:protected] => category
[parent:protected] => 2
[label:protected] => Scaffold Erector
[alreadyInSave:protected] =>
[alreadyInValidation:protected] =>
[validationFailures:protected] => Array
(
)
[_new:BaseObject:private] =>
[_deleted:BaseObject:private] =>
[modifiedColumns:protected] => Array
(
)
)
[80] => Category Object
(
[languages:protected] =>
[bok_resources:protected] =>
[bok_topics:protected] =>
[bok_keywords:protected] =>
[id:protected] => 80
[type:protected] => category
[parent:protected] => 2
[label:protected] => Sheetmetal Worker
[alreadyInSave:protected] =>
[alreadyInValidation:protected] =>
[validationFailures:protected] => Array
(
)
[_new:BaseObject:private] =>
[_deleted:BaseObject:private] =>
[modifiedColumns:protected] => Array
(
)
)
[62] => Category Object
(
[languages:protected] =>
[bok_resources:protected] =>
[bok_topics:protected] =>
[bok_keywords:protected] =>
[id:protected] => 62
[type:protected] => category
[parent:protected] => 2
[label:protected] => Structural Ironworker
[alreadyInSave:protected] =>
[alreadyInValidation:protected] =>
[validationFailures:protected] => Array
(
)
[_new:BaseObject:private] =>
[_deleted:BaseObject:private] =>
[modifiedColumns:protected] => Array
(
)
)
[87] => Category Object
(
[languages:protected] =>
[bok_resources:protected] =>
[bok_topics:protected] =>
[bok_keywords:protected] =>
[id:protected] => 87
[type:protected] => category
[parent:protected] => 3
[label:protected] => Commercial & Institutional
[alreadyInSave:protected] =>
[alreadyInValidation:protected] =>
[validationFailures:protected] => Array
(
)
[_new:BaseObject:private] =>
[_deleted:BaseObject:private] =>
[modifiedColumns:protected] => Array
(
)
)
[97] => Category Object
(
[languages:protected] =>
[bok_resources:protected] =>
[bok_topics:protected] =>
[bok_keywords:protected] =>
[id:protected] => 97
[type:protected] => category
[parent:protected] => 5
[label:protected] => Images
[alreadyInSave:protected] =>
[alreadyInValidation:protected] =>
[validationFailures:protected] => Array
(
)
[_new:BaseObject:private] =>
[_deleted:BaseObject:private] =>
[modifiedColumns:protected] => Array
(
)
)
[56] => Category Object
(
[languages:protected] =>
[bok_resources:protected] =>
[bok_topics:protected] =>
[bok_keywords:protected] =>
[id:protected] => 56
[type:protected] => category
[parent:protected] => 2
[label:protected] => Elevator Constructor
[alreadyInSave:protected] =>
[alreadyInValidation:protected] =>
[validationFailures:protected] => Array
(
)
[_new:BaseObject:private] =>
[_deleted:BaseObject:private] =>
[modifiedColumns:protected] => Array
(
)
)
[64] => Category Object
(
[languages:protected] =>
[bok_resources:protected] =>
[bok_topics:protected] =>
[bok_keywords:protected] =>
[id:protected] => 64
[type:protected] => category
[parent:protected] => 2
[label:protected] => Laborer
[alreadyInSave:protected] =>
[alreadyInValidation:protected] =>
[validationFailures:protected] => Array
(
)
[_new:BaseObject:private] =>
[_deleted:BaseObject:private] =>
[modifiedColumns:protected] => Array
(
)
)
[74] => Category Object
(
[languages:protected] =>
[bok_resources:protected] =>
[bok_topics:protected] =>
[bok_keywords:protected] =>
[id:protected] => 74
[type:protected] => category
[parent:protected] => 2
[label:protected] => Pile Driver
[alreadyInSave:protected] =>
[alreadyInValidation:protected] =>
[validationFailures:protected] => Array
(
)
[_new:BaseObject:private] =>
[_deleted:BaseObject:private] =>
[modifiedColumns:protected] => Array
(
)
)
)
[categories_initialized:protected] => 1
[mapped_items:protected] =>
[content:protected] =>
[files:protected] =>
[language:protected] => Language Object
(
[id:protected] => 1
[code:protected] => en
[name:protected] => English
[alreadyInSave:protected] =>
[alreadyInValidation:protected] =>
[validationFailures:protected] => Array
(
)
[_new:BaseObject:private] =>
[_deleted:BaseObject:private] =>
[modifiedColumns:protected] => Array
(
)
)
[old_record:protected] =>
[id:protected] => 3994
[old_id:protected] =>
[elcosh_id:protected] => i002689
[type:protected] => image
[display_type:protected] => Image
[user_id:protected] => 0
[language_id:protected] => 1
[tagging_id:protected] => Bruce Lippy
[priority_id:protected] => 1
[title:protected] => Scaffolding at top of large column
[total_pages:protected] => 0
[billed_pages:protected] => 0
[publication_number:protected] =>
[part_of:protected] =>
[keywords:protected] => Guardrail, railing, fall prevention, falls
[comments:protected] =>
[summary:protected] => This shot shows innovative guarding around the top of a large concrete column in the base of a high rise structure going up.
[transition_comments:protected] =>
[external_link:protected] =>
[consol_link:protected] => http://www.cpwrconstructionsolutions.org/masonry/solution/8/adjustable-tower-scaffold.html
[more_like_this:protected] => c1002680,i002662,d000608,d001255
[permission_given_by:protected] =>
[published:protected] => T
[billable:protected] => F
[img_name:protected] =>
[img_ext:protected] => jpg
[img_width:protected] =>
[img_height:protected] =>
[img_credit:protected] => Photo by Pam Susi
[img_practice:protected] => good
[vid_source_id:protected] =>
[vid_running_time:protected] =>
[vid_intended_audience:protected] =>
[vid_acquisition_info:protected] =>
[vid_cost:protected] =>
[vid_producer:protected] =>
[vid_filename:protected] =>
[vid_filename_downloadable:protected] =>
[date_summary:protected] => January 2016
[date_permission_requested:protected] =>
[date_permission_received:protected] =>
[date_review_needed:protected] =>
[date_received:protected] => 02/01/16
[date_completed:protected] => 02/01/16
[date_billed:protected] =>
[date_modified:protected] => 02/01/16
[collBokExports:protected] =>
[lastBokExportCriteria:BaseElcoshItem:private] =>
[alreadyInSave:protected] =>
[alreadyInValidation:protected] =>
[validationFailures:protected] => Array
(
)
[_new:BaseObject:private] =>
[_deleted:BaseObject:private] =>
[modifiedColumns:protected] => Array
(
)
)
)
[5] => Search_Result Object
(
[title] => Construction bracing
[image] => /record/images/3995-p.jpg
[blurb] => This shows structural support that prevents collapses during construction....
[category] => Array
(
[0] => 12
[1] => 15
[2] => 21
[3] => 49
[4] => 51
[5] => 55
[6] => 56
[7] => 60
[8] => 64
[9] => 68
[10] => 74
[11] => 63
[12] => 78
[13] => 79
[14] => 80
[15] => 62
[16] => 87
[17] => 90
[18] => 97
)
[labels] => Array
(
[0] => Crushed/Struck By
[1] => Work Environment
[2] => Hazards
[3] => Falls
[6] => Scaffolds
[9] => Carpenter
[10] => Trades
[11] => Cement Mason
[13] => Electrical Worker
[15] => Elevator Constructor
[17] => HVAC
[19] => Laborer
[21] => Maintenance Worker
[23] => Pile Driver
[25] => Reinforcing Ironworker
[27] => Roofer/Waterproofer
[29] => Scaffold Erector
[31] => Sheetmetal Worker
[33] => Structural Ironworker
[35] => Commercial & Institutional
[36] => Jobsites
[37] => Industrial
[39] => Images
[40] => Media
[41] => Media & Documents
)
[type] => Images
[sub_category] =>
[url] => /image/3995/i002690/Construction%2Bbracing.html
[item:protected] => ImageRecord Object
(
[records:protected] => Array
(
)
[recordId:protected] =>
[searchWordClass:protected] =>
[searchWordPeerClass:protected] =>
[bok_record:protected] =>
[authors:protected] =>
[organizations:protected] =>
[collections:protected] =>
[categories:protected] => Array
(
[12] => Category Object
(
[languages:protected] =>
[bok_resources:protected] =>
[bok_topics:protected] =>
[bok_keywords:protected] =>
[id:protected] => 12
[type:protected] => category
[parent:protected] => 7
[label:protected] => Crushed/Struck By
[alreadyInSave:protected] =>
[alreadyInValidation:protected] =>
[validationFailures:protected] => Array
(
)
[_new:BaseObject:private] =>
[_deleted:BaseObject:private] =>
[modifiedColumns:protected] => Array
(
)
)
[15] => Category Object
(
[languages:protected] =>
[bok_resources:protected] =>
[bok_topics:protected] =>
[bok_keywords:protected] =>
[id:protected] => 15
[type:protected] => category
[parent:protected] => 7
[label:protected] => Falls
[alreadyInSave:protected] =>
[alreadyInValidation:protected] =>
[validationFailures:protected] => Array
(
)
[_new:BaseObject:private] =>
[_deleted:BaseObject:private] =>
[modifiedColumns:protected] => Array
(
)
)
[21] => Category Object
(
[languages:protected] =>
[bok_resources:protected] =>
[bok_topics:protected] =>
[bok_keywords:protected] =>
[id:protected] => 21
[type:protected] => category
[parent:protected] => 7
[label:protected] => Scaffolds
[alreadyInSave:protected] =>
[alreadyInValidation:protected] =>
[validationFailures:protected] => Array
(
)
[_new:BaseObject:private] =>
[_deleted:BaseObject:private] =>
[modifiedColumns:protected] => Array
(
)
)
[49] => Category Object
(
[languages:protected] =>
[bok_resources:protected] =>
[bok_topics:protected] =>
[bok_keywords:protected] =>
[id:protected] => 49
[type:protected] => category
[parent:protected] => 2
[label:protected] => Carpenter
[alreadyInSave:protected] =>
[alreadyInValidation:protected] =>
[validationFailures:protected] => Array
(
)
[_new:BaseObject:private] =>
[_deleted:BaseObject:private] =>
[modifiedColumns:protected] => Array
(
)
)
[51] => Category Object
(
[languages:protected] =>
[bok_resources:protected] =>
[bok_topics:protected] =>
[bok_keywords:protected] =>
[id:protected] => 51
[type:protected] => category
[parent:protected] => 2
[label:protected] => Cement Mason
[alreadyInSave:protected] =>
[alreadyInValidation:protected] =>
[validationFailures:protected] => Array
(
)
[_new:BaseObject:private] =>
[_deleted:BaseObject:private] =>
[modifiedColumns:protected] => Array
(
)
)
[55] => Category Object
(
[languages:protected] =>
[bok_resources:protected] =>
[bok_topics:protected] =>
[bok_keywords:protected] =>
[id:protected] => 55
[type:protected] => category
[parent:protected] => 2
[label:protected] => Electrical Worker
[alreadyInSave:protected] =>
[alreadyInValidation:protected] =>
[validationFailures:protected] => Array
(
)
[_new:BaseObject:private] =>
[_deleted:BaseObject:private] =>
[modifiedColumns:protected] => Array
(
)
)
[56] => Category Object
(
[languages:protected] =>
[bok_resources:protected] =>
[bok_topics:protected] =>
[bok_keywords:protected] =>
[id:protected] => 56
[type:protected] => category
[parent:protected] => 2
[label:protected] => Elevator Constructor
[alreadyInSave:protected] =>
[alreadyInValidation:protected] =>
[validationFailures:protected] => Array
(
)
[_new:BaseObject:private] =>
[_deleted:BaseObject:private] =>
[modifiedColumns:protected] => Array
(
)
)
[60] => Category Object
(
[languages:protected] =>
[bok_resources:protected] =>
[bok_topics:protected] =>
[bok_keywords:protected] =>
[id:protected] => 60
[type:protected] => category
[parent:protected] => 2
[label:protected] => HVAC
[alreadyInSave:protected] =>
[alreadyInValidation:protected] =>
[validationFailures:protected] => Array
(
)
[_new:BaseObject:private] =>
[_deleted:BaseObject:private] =>
[modifiedColumns:protected] => Array
(
)
)
[64] => Category Object
(
[languages:protected] =>
[bok_resources:protected] =>
[bok_topics:protected] =>
[bok_keywords:protected] =>
[id:protected] => 64
[type:protected] => category
[parent:protected] => 2
[label:protected] => Laborer
[alreadyInSave:protected] =>
[alreadyInValidation:protected] =>
[validationFailures:protected] => Array
(
)
[_new:BaseObject:private] =>
[_deleted:BaseObject:private] =>
[modifiedColumns:protected] => Array
(
)
)
[68] => Category Object
(
[languages:protected] =>
[bok_resources:protected] =>
[bok_topics:protected] =>
[bok_keywords:protected] =>
[id:protected] => 68
[type:protected] => category
[parent:protected] => 2
[label:protected] => Maintenance Worker
[alreadyInSave:protected] =>
[alreadyInValidation:protected] =>
[validationFailures:protected] => Array
(
)
[_new:BaseObject:private] =>
[_deleted:BaseObject:private] =>
[modifiedColumns:protected] => Array
(
)
)
[74] => Category Object
(
[languages:protected] =>
[bok_resources:protected] =>
[bok_topics:protected] =>
[bok_keywords:protected] =>
[id:protected] => 74
[type:protected] => category
[parent:protected] => 2
[label:protected] => Pile Driver
[alreadyInSave:protected] =>
[alreadyInValidation:protected] =>
[validationFailures:protected] => Array
(
)
[_new:BaseObject:private] =>
[_deleted:BaseObject:private] =>
[modifiedColumns:protected] => Array
(
)
)
[63] => Category Object
(
[languages:protected] =>
[bok_resources:protected] =>
[bok_topics:protected] =>
[bok_keywords:protected] =>
[id:protected] => 63
[type:protected] => category
[parent:protected] => 2
[label:protected] => Reinforcing Ironworker
[alreadyInSave:protected] =>
[alreadyInValidation:protected] =>
[validationFailures:protected] => Array
(
)
[_new:BaseObject:private] =>
[_deleted:BaseObject:private] =>
[modifiedColumns:protected] => Array
(
)
)
[78] => Category Object
(
[languages:protected] =>
[bok_resources:protected] =>
[bok_topics:protected] =>
[bok_keywords:protected] =>
[id:protected] => 78
[type:protected] => category
[parent:protected] => 2
[label:protected] => Roofer/Waterproofer
[alreadyInSave:protected] =>
[alreadyInValidation:protected] =>
[validationFailures:protected] => Array
(
)
[_new:BaseObject:private] =>
[_deleted:BaseObject:private] =>
[modifiedColumns:protected] => Array
(
)
)
[79] => Category Object
(
[languages:protected] =>
[bok_resources:protected] =>
[bok_topics:protected] =>
[bok_keywords:protected] =>
[id:protected] => 79
[type:protected] => category
[parent:protected] => 2
[label:protected] => Scaffold Erector
[alreadyInSave:protected] =>
[alreadyInValidation:protected] =>
[validationFailures:protected] => Array
(
)
[_new:BaseObject:private] =>
[_deleted:BaseObject:private] =>
[modifiedColumns:protected] => Array
(
)
)
[80] => Category Object
(
[languages:protected] =>
[bok_resources:protected] =>
[bok_topics:protected] =>
[bok_keywords:protected] =>
[id:protected] => 80
[type:protected] => category
[parent:protected] => 2
[label:protected] => Sheetmetal Worker
[alreadyInSave:protected] =>
[alreadyInValidation:protected] =>
[validationFailures:protected] => Array
(
)
[_new:BaseObject:private] =>
[_deleted:BaseObject:private] =>
[modifiedColumns:protected] => Array
(
)
)
[62] => Category Object
(
[languages:protected] =>
[bok_resources:protected] =>
[bok_topics:protected] =>
[bok_keywords:protected] =>
[id:protected] => 62
[type:protected] => category
[parent:protected] => 2
[label:protected] => Structural Ironworker
[alreadyInSave:protected] =>
[alreadyInValidation:protected] =>
[validationFailures:protected] => Array
(
)
[_new:BaseObject:private] =>
[_deleted:BaseObject:private] =>
[modifiedColumns:protected] => Array
(
)
)
[87] => Category Object
(
[languages:protected] =>
[bok_resources:protected] =>
[bok_topics:protected] =>
[bok_keywords:protected] =>
[id:protected] => 87
[type:protected] => category
[parent:protected] => 3
[label:protected] => Commercial & Institutional
[alreadyInSave:protected] =>
[alreadyInValidation:protected] =>
[validationFailures:protected] => Array
(
)
[_new:BaseObject:private] =>
[_deleted:BaseObject:private] =>
[modifiedColumns:protected] => Array
(
)
)
[90] => Category Object
(
[languages:protected] =>
[bok_resources:protected] =>
[bok_topics:protected] =>
[bok_keywords:protected] =>
[id:protected] => 90
[type:protected] => category
[parent:protected] => 3
[label:protected] => Industrial
[alreadyInSave:protected] =>
[alreadyInValidation:protected] =>
[validationFailures:protected] => Array
(
)
[_new:BaseObject:private] =>
[_deleted:BaseObject:private] =>
[modifiedColumns:protected] => Array
(
)
)
[97] => Category Object
(
[languages:protected] =>
[bok_resources:protected] =>
[bok_topics:protected] =>
[bok_keywords:protected] =>
[id:protected] => 97
[type:protected] => category
[parent:protected] => 5
[label:protected] => Images
[alreadyInSave:protected] =>
[alreadyInValidation:protected] =>
[validationFailures:protected] => Array
(
)
[_new:BaseObject:private] =>
[_deleted:BaseObject:private] =>
[modifiedColumns:protected] => Array
(
)
)
)
[categories_initialized:protected] => 1
[mapped_items:protected] =>
[content:protected] =>
[files:protected] =>
[language:protected] => Language Object
(
[id:protected] => 1
[code:protected] => en
[name:protected] => English
[alreadyInSave:protected] =>
[alreadyInValidation:protected] =>
[validationFailures:protected] => Array
(
)
[_new:BaseObject:private] =>
[_deleted:BaseObject:private] =>
[modifiedColumns:protected] => Array
(
)
)
[old_record:protected] =>
[id:protected] => 3995
[old_id:protected] =>
[elcosh_id:protected] => i002690
[type:protected] => image
[display_type:protected] => Image
[user_id:protected] => 0
[language_id:protected] => 1
[tagging_id:protected] => Bruce Lippy
[priority_id:protected] => 1
[title:protected] => Construction bracing
[total_pages:protected] => 0
[billed_pages:protected] => 0
[publication_number:protected] =>
[part_of:protected] =>
[keywords:protected] => Bracing, support, scaffold
[comments:protected] =>
[summary:protected] => This shows structural support that prevents collapses during construction.
[transition_comments:protected] =>
[external_link:protected] =>
[consol_link:protected] => http://www.cpwrconstructionsolutions.org/masonry/solution/8/adjustable-tower-scaffold.html
[more_like_this:protected] => i002660
[permission_given_by:protected] =>
[published:protected] => T
[billable:protected] => F
[img_name:protected] =>
[img_ext:protected] => jpg
[img_width:protected] =>
[img_height:protected] =>
[img_credit:protected] => Photo by Pam Susi
[img_practice:protected] => good
[vid_source_id:protected] =>
[vid_running_time:protected] =>
[vid_intended_audience:protected] =>
[vid_acquisition_info:protected] =>
[vid_cost:protected] =>
[vid_producer:protected] =>
[vid_filename:protected] =>
[vid_filename_downloadable:protected] =>
[date_summary:protected] => January 2016
[date_permission_requested:protected] =>
[date_permission_received:protected] =>
[date_review_needed:protected] =>
[date_received:protected] => 02/01/16
[date_completed:protected] => 02/01/16
[date_billed:protected] =>
[date_modified:protected] => 02/01/16
[collBokExports:protected] =>
[lastBokExportCriteria:BaseElcoshItem:private] =>
[alreadyInSave:protected] =>
[alreadyInValidation:protected] =>
[validationFailures:protected] => Array
(
)
[_new:BaseObject:private] =>
[_deleted:BaseObject:private] =>
[modifiedColumns:protected] => Array
(
)
)
)
)
[preview_mode] =>
[description] => Toolbox talks have been the main tool for communicating safety information on construction jobs for decades.
Unfortunately, there has been little research on what makes for effective toolbox talks. The IUOE National
Training Fund worked with OSHA and NIOSH to make sure their series of 24 Focus Four toolbox talks were based on the best recommendations for effective design. These toolbox talks accompany an entire package of training materials, but can be used alone. This guide points out the key features of these toolbox talks and how best to deliver them.
[keywords] => toolbox talks, tailgate talks
[related_items] => Array
(
[Toolbox Talks] => Array
(
[0] => DocumentRecord Object
(
[records:protected] => Array
(
)
[recordId:protected] =>
[searchWordClass:protected] =>
[searchWordPeerClass:protected] =>
[bok_record:protected] =>
[authors:protected] =>
[organizations:protected] =>
[collections:protected] =>
[categories:protected] =>
[categories_initialized:protected] =>
[mapped_items:protected] =>
[content:protected] =>
[files:protected] =>
[language:protected] => Language Object
(
[id:protected] => 1
[code:protected] => en
[name:protected] => English
[alreadyInSave:protected] =>
[alreadyInValidation:protected] =>
[validationFailures:protected] => Array
(
)
[_new:BaseObject:private] =>
[_deleted:BaseObject:private] =>
[modifiedColumns:protected] => Array
(
)
)
[old_record:protected] =>
[id:protected] => 1605
[old_id:protected] => 1262
[elcosh_id:protected] => d001137
[type:protected] => document
[display_type:protected] => HTML w/ PDF
[user_id:protected] =>
[language_id:protected] => 1
[tagging_id:protected] => Garber
[priority_id:protected] => 1
[title:protected] => Focus Four Toolbox Talks, Module 1 – Falls, Talk #2 – Falls from debris piles?
[total_pages:protected] => 1
[billed_pages:protected] => 1
[publication_number:protected] =>
[part_of:protected] =>
[keywords:protected] => disaster response, hazard clean-up, uneven surface, disaster site, disaster clean-up
[comments:protected] =>
[summary:protected] => A toolbox talk on preventing falls from debris piles. Includes questions to ask, an incident to discuss with images, and a place to record questions the trainer would like to ask about the incident. Part of a collection. Click on the 'collection' button to access the other items.
[transition_comments:protected] =>
[external_link:protected] =>
[consol_link:protected] => http://www.cpwrconstructionsolutions.org/roofing/hazard/1463/install-asphalt-roofs-fall-from-heights.html
[more_like_this:protected] => a000081,d000478,d000530
[permission_given_by:protected] =>
[published:protected] => T
[billable:protected] => F
[img_name:protected] =>
[img_ext:protected] =>
[img_width:protected] =>
[img_height:protected] =>
[img_credit:protected] =>
[img_practice:protected] =>
[vid_source_id:protected] =>
[vid_running_time:protected] =>
[vid_intended_audience:protected] =>
[vid_acquisition_info:protected] =>
[vid_cost:protected] =>
[vid_producer:protected] =>
[vid_filename:protected] =>
[vid_filename_downloadable:protected] =>
[date_summary:protected] =>
[date_permission_requested:protected] =>
[date_permission_received:protected] =>
[date_review_needed:protected] =>
[date_received:protected] => 02/15/12
[date_completed:protected] => 03/19/12
[date_billed:protected] =>
[date_modified:protected] => 07/10/12
[collBokExports:protected] =>
[lastBokExportCriteria:BaseElcoshItem:private] =>
[alreadyInSave:protected] =>
[alreadyInValidation:protected] =>
[validationFailures:protected] => Array
(
)
[_new:BaseObject:private] =>
[_deleted:BaseObject:private] =>
[modifiedColumns:protected] => Array
(
)
)
[1] => DocumentRecord Object
(
[records:protected] => Array
(
)
[recordId:protected] =>
[searchWordClass:protected] =>
[searchWordPeerClass:protected] =>
[bok_record:protected] =>
[authors:protected] =>
[organizations:protected] =>
[collections:protected] =>
[categories:protected] =>
[categories_initialized:protected] =>
[mapped_items:protected] =>
[content:protected] =>
[files:protected] =>
[language:protected] => Language Object
(
[id:protected] => 1
[code:protected] => en
[name:protected] => English
[alreadyInSave:protected] =>
[alreadyInValidation:protected] =>
[validationFailures:protected] => Array
(
)
[_new:BaseObject:private] =>
[_deleted:BaseObject:private] =>
[modifiedColumns:protected] => Array
(
)
)
[old_record:protected] =>
[id:protected] => 1610
[old_id:protected] => 1271
[elcosh_id:protected] => d001146
[type:protected] => document
[display_type:protected] => HTML w/ PDF
[user_id:protected] => 0
[language_id:protected] => 1
[tagging_id:protected] => Garber
[priority_id:protected] => 1
[title:protected] => Focus Four Toolbox Talks, Module 2 – Struck-by, Talk #5 – Rigging and Securing Loads
[total_pages:protected] => 1
[billed_pages:protected] => 1
[publication_number:protected] =>
[part_of:protected] =>
[keywords:protected] => rigging, lift loads, loading areas, chains
[comments:protected] =>
[summary:protected] => A toolbox talk on preventing struck-by incidents caused by not securing loads properly. Includes questions to ask, an incident to discuss with images, and a place to record questions the trainer would like to ask about the incident. Part of a collection. Click on the 'collection' button to access the other items.
[transition_comments:protected] =>
[external_link:protected] =>
[consol_link:protected] => http://www.cpwrconstructionsolutions.org/heavy_equipment/hazard/1591/move-equipment-to-from-and-between-sites-work-zone-struck-by-injuries-and-fatalities.html
[more_like_this:protected] => d000144,d000360,d000873
[permission_given_by:protected] =>
[published:protected] => T
[billable:protected] => F
[img_name:protected] =>
[img_ext:protected] =>
[img_width:protected] =>
[img_height:protected] =>
[img_credit:protected] =>
[img_practice:protected] =>
[vid_source_id:protected] =>
[vid_running_time:protected] =>
[vid_intended_audience:protected] =>
[vid_acquisition_info:protected] =>
[vid_cost:protected] =>
[vid_producer:protected] =>
[vid_filename:protected] =>
[vid_filename_downloadable:protected] =>
[date_summary:protected] =>
[date_permission_requested:protected] =>
[date_permission_received:protected] =>
[date_review_needed:protected] =>
[date_received:protected] => 02/15/12
[date_completed:protected] => 03/28/12
[date_billed:protected] =>
[date_modified:protected] => 05/12/14
[collBokExports:protected] =>
[lastBokExportCriteria:BaseElcoshItem:private] =>
[alreadyInSave:protected] =>
[alreadyInValidation:protected] =>
[validationFailures:protected] => Array
(
)
[_new:BaseObject:private] =>
[_deleted:BaseObject:private] =>
[modifiedColumns:protected] => Array
(
)
)
[2] => DocumentRecord Object
(
[records:protected] => Array
(
)
[recordId:protected] =>
[searchWordClass:protected] =>
[searchWordPeerClass:protected] =>
[bok_record:protected] =>
[authors:protected] =>
[organizations:protected] =>
[collections:protected] =>
[categories:protected] =>
[categories_initialized:protected] =>
[mapped_items:protected] =>
[content:protected] =>
[files:protected] =>
[language:protected] => Language Object
(
[id:protected] => 1
[code:protected] => en
[name:protected] => English
[alreadyInSave:protected] =>
[alreadyInValidation:protected] =>
[validationFailures:protected] => Array
(
)
[_new:BaseObject:private] =>
[_deleted:BaseObject:private] =>
[modifiedColumns:protected] => Array
(
)
)
[old_record:protected] =>
[id:protected] => 1645
[old_id:protected] => 1274
[elcosh_id:protected] => d001149
[type:protected] => document
[display_type:protected] => HTML w/ PDF
[user_id:protected] => 0
[language_id:protected] => 1
[tagging_id:protected] => Garber
[priority_id:protected] => 1
[title:protected] => Focus Four Toolbox Talks, Module 3 – Caught-in/between, Talk #2 – Trenches & Heavy Equipment
[total_pages:protected] => 1
[billed_pages:protected] => 1
[publication_number:protected] =>
[part_of:protected] =>
[keywords:protected] => back-up alarms, spotter, soil cave-in, spoil pikes, ROPs, trenching, rain
[comments:protected] =>
[summary:protected] => A toolbox talk on preventing incidents involving trenches such as trench collapse. Includes questions to ask, an incident to discuss with images, and a place to record questions the trainer would like to ask about the incident. Part of a collection. Click on the 'collection' button to access the other items.
[transition_comments:protected] =>
[external_link:protected] =>
[consol_link:protected] =>
[more_like_this:protected] => d000019,d000035,d000168
[permission_given_by:protected] =>
[published:protected] => T
[billable:protected] => F
[img_name:protected] =>
[img_ext:protected] =>
[img_width:protected] =>
[img_height:protected] =>
[img_credit:protected] =>
[img_practice:protected] =>
[vid_source_id:protected] =>
[vid_running_time:protected] =>
[vid_intended_audience:protected] =>
[vid_acquisition_info:protected] =>
[vid_cost:protected] =>
[vid_producer:protected] =>
[vid_filename:protected] =>
[vid_filename_downloadable:protected] =>
[date_summary:protected] =>
[date_permission_requested:protected] =>
[date_permission_received:protected] =>
[date_review_needed:protected] =>
[date_received:protected] => 02/15/12
[date_completed:protected] => 04/02/12
[date_billed:protected] =>
[date_modified:protected] => 05/23/23
[collBokExports:protected] =>
[lastBokExportCriteria:BaseElcoshItem:private] =>
[alreadyInSave:protected] =>
[alreadyInValidation:protected] =>
[validationFailures:protected] => Array
(
)
[_new:BaseObject:private] =>
[_deleted:BaseObject:private] =>
[modifiedColumns:protected] => Array
(
)
)
[3] => DocumentRecord Object
(
[records:protected] => Array
(
)
[recordId:protected] =>
[searchWordClass:protected] =>
[searchWordPeerClass:protected] =>
[bok_record:protected] =>
[authors:protected] =>
[organizations:protected] =>
[collections:protected] =>
[categories:protected] =>
[categories_initialized:protected] =>
[mapped_items:protected] =>
[content:protected] =>
[files:protected] =>
[language:protected] => Language Object
(
[id:protected] => 1
[code:protected] => en
[name:protected] => English
[alreadyInSave:protected] =>
[alreadyInValidation:protected] =>
[validationFailures:protected] => Array
(
)
[_new:BaseObject:private] =>
[_deleted:BaseObject:private] =>
[modifiedColumns:protected] => Array
(
)
)
[old_record:protected] =>
[id:protected] => 1654
[old_id:protected] => 1284
[elcosh_id:protected] => d001159
[type:protected] => document
[display_type:protected] => HTML w/ PDF
[user_id:protected] => 0
[language_id:protected] => 1
[tagging_id:protected] => Garber
[priority_id:protected] => 1
[title:protected] => Focus Four Toolbox Talks, Module 4 – Electrocutions, Talk #6 – Hazards on Disaster Sites
[total_pages:protected] => 1
[billed_pages:protected] => 1
[publication_number:protected] =>
[part_of:protected] =>
[keywords:protected] => powerlines, underground, utilities, generators, wet conditions, GFCIs, energized lines, disasters, emergency response
[comments:protected] =>
[summary:protected] => A toolbox talk on how to avoid electrocution on a disaster site. Includes questions to ask, an incident to discuss with images, and a place to record questions the trainer would like to ask about the incident. Part of a collection. Click on the 'collection' button to access the other items.
[transition_comments:protected] =>
[external_link:protected] =>
[consol_link:protected] => http://www.cpwrconstructionsolutions.org/electrical/hazard/1138/install-and-repair-high-voltage-lines-transformers-switches-electrical-shocks-burns-and-or-electrocution.html
[more_like_this:protected] => d000135,d000361,d000437
[permission_given_by:protected] =>
[published:protected] => T
[billable:protected] => F
[img_name:protected] =>
[img_ext:protected] =>
[img_width:protected] =>
[img_height:protected] =>
[img_credit:protected] =>
[img_practice:protected] =>
[vid_source_id:protected] =>
[vid_running_time:protected] =>
[vid_intended_audience:protected] =>
[vid_acquisition_info:protected] =>
[vid_cost:protected] =>
[vid_producer:protected] =>
[vid_filename:protected] =>
[vid_filename_downloadable:protected] =>
[date_summary:protected] =>
[date_permission_requested:protected] =>
[date_permission_received:protected] =>
[date_review_needed:protected] =>
[date_received:protected] => 02/15/12
[date_completed:protected] => 04/02/12
[date_billed:protected] =>
[date_modified:protected] => 05/23/23
[collBokExports:protected] =>
[lastBokExportCriteria:BaseElcoshItem:private] =>
[alreadyInSave:protected] =>
[alreadyInValidation:protected] =>
[validationFailures:protected] => Array
(
)
[_new:BaseObject:private] =>
[_deleted:BaseObject:private] =>
[modifiedColumns:protected] => Array
(
)
)
)
)
[collections] => Array
(
[1294] =>
[1295] =>
[1292] =>
[1293] => CollectionRecord Object
(
[collection_items:protected] =>
[records:protected] => Array
(
)
[recordId:protected] =>
[searchWordClass:protected] =>
[searchWordPeerClass:protected] =>
[bok_record:protected] =>
[authors:protected] =>
[organizations:protected] =>
[collections:protected] =>
[categories:protected] =>
[categories_initialized:protected] =>
[mapped_items:protected] =>
[content:protected] =>
[files:protected] =>
[language:protected] =>
[old_record:protected] =>
[id:protected] => 1293
[old_id:protected] =>
[elcosh_id:protected] => c000026
[type:protected] => collection
[display_type:protected] => Collection
[user_id:protected] =>
[language_id:protected] =>
[tagging_id:protected] =>
[priority_id:protected] =>
[title:protected] => Focus Four-Struck By
[total_pages:protected] =>
[billed_pages:protected] =>
[publication_number:protected] =>
[part_of:protected] =>
[keywords:protected] =>
[comments:protected] =>
[summary:protected] => The following are links to all of the items in this collection:
[transition_comments:protected] =>
[external_link:protected] =>
[consol_link:protected] =>
[more_like_this:protected] =>
[permission_given_by:protected] =>
[published:protected] => T
[billable:protected] => F
[img_name:protected] =>
[img_ext:protected] =>
[img_width:protected] =>
[img_height:protected] =>
[img_credit:protected] =>
[img_practice:protected] =>
[vid_source_id:protected] =>
[vid_running_time:protected] =>
[vid_intended_audience:protected] =>
[vid_acquisition_info:protected] =>
[vid_cost:protected] =>
[vid_producer:protected] =>
[vid_filename:protected] =>
[vid_filename_downloadable:protected] =>
[date_summary:protected] =>
[date_permission_requested:protected] =>
[date_permission_received:protected] =>
[date_review_needed:protected] =>
[date_received:protected] => 05/08/12
[date_completed:protected] => 05/08/12
[date_billed:protected] =>
[date_modified:protected] => 05/08/12
[collBokExports:protected] =>
[lastBokExportCriteria:BaseElcoshItem:private] =>
[alreadyInSave:protected] =>
[alreadyInValidation:protected] =>
[validationFailures:protected] => Array
(
)
[_new:BaseObject:private] =>
[_deleted:BaseObject:private] =>
[modifiedColumns:protected] => Array
(
)
)
)
[record] => DocumentRecord Object
(
[records:protected] => Array
(
)
[recordId:protected] =>
[searchWordClass:protected] =>
[searchWordPeerClass:protected] =>
[bok_record:protected] =>
[authors:protected] => Array
(
)
[organizations:protected] => Array
(
[256] => Organization Object
(
[id:protected] => 256
[elcosh_id:protected] => o000276
[user_id:protected] => 14
[province_id:protected] => 0
[country_id:protected] => 0
[title:protected] => IUOE National Training Fund
[address:protected] =>
[postal_code:protected] =>
[city:protected] =>
[department:protected] =>
[phone:protected] => 304-253-8674
[fax:protected] =>
[email:protected] =>
[website:protected] => http://www.iuoeiettc.org
[filename:protected] =>
[about:protected] =>
[comments:protected] =>
[logo_available:protected] => T
[no_details:protected] => F
[date_received:protected] => 2012-02-13
[date_completed:protected] => 2012-02-13
[date_billed:protected] =>
[alreadyInSave:protected] =>
[alreadyInValidation:protected] =>
[validationFailures:protected] => Array
(
)
[_new:BaseObject:private] =>
[_deleted:BaseObject:private] =>
[modifiedColumns:protected] => Array
(
)
)
)
[collections:protected] => Array
(
[1294] =>
[1295] =>
[1292] =>
[1293] => CollectionRecord Object
(
[collection_items:protected] =>
[records:protected] => Array
(
)
[recordId:protected] =>
[searchWordClass:protected] =>
[searchWordPeerClass:protected] =>
[bok_record:protected] =>
[authors:protected] =>
[organizations:protected] =>
[collections:protected] =>
[categories:protected] =>
[categories_initialized:protected] =>
[mapped_items:protected] =>
[content:protected] =>
[files:protected] =>
[language:protected] =>
[old_record:protected] =>
[id:protected] => 1293
[old_id:protected] =>
[elcosh_id:protected] => c000026
[type:protected] => collection
[display_type:protected] => Collection
[user_id:protected] =>
[language_id:protected] =>
[tagging_id:protected] =>
[priority_id:protected] =>
[title:protected] => Focus Four-Struck By
[total_pages:protected] =>
[billed_pages:protected] =>
[publication_number:protected] =>
[part_of:protected] =>
[keywords:protected] =>
[comments:protected] =>
[summary:protected] => The following are links to all of the items in this collection:
[transition_comments:protected] =>
[external_link:protected] =>
[consol_link:protected] =>
[more_like_this:protected] =>
[permission_given_by:protected] =>
[published:protected] => T
[billable:protected] => F
[img_name:protected] =>
[img_ext:protected] =>
[img_width:protected] =>
[img_height:protected] =>
[img_credit:protected] =>
[img_practice:protected] =>
[vid_source_id:protected] =>
[vid_running_time:protected] =>
[vid_intended_audience:protected] =>
[vid_acquisition_info:protected] =>
[vid_cost:protected] =>
[vid_producer:protected] =>
[vid_filename:protected] =>
[vid_filename_downloadable:protected] =>
[date_summary:protected] =>
[date_permission_requested:protected] =>
[date_permission_received:protected] =>
[date_review_needed:protected] =>
[date_received:protected] => 05/08/12
[date_completed:protected] => 05/08/12
[date_billed:protected] =>
[date_modified:protected] => 05/08/12
[collBokExports:protected] =>
[lastBokExportCriteria:BaseElcoshItem:private] =>
[alreadyInSave:protected] =>
[alreadyInValidation:protected] =>
[validationFailures:protected] => Array
(
)
[_new:BaseObject:private] =>
[_deleted:BaseObject:private] =>
[modifiedColumns:protected] => Array
(
)
)
)
[categories:protected] =>
[categories_initialized:protected] =>
[mapped_items:protected] => Array
(
[1605] => DocumentRecord Object
(
[records:protected] => Array
(
)
[recordId:protected] =>
[searchWordClass:protected] =>
[searchWordPeerClass:protected] =>
[bok_record:protected] =>
[authors:protected] =>
[organizations:protected] =>
[collections:protected] =>
[categories:protected] =>
[categories_initialized:protected] =>
[mapped_items:protected] =>
[content:protected] =>
[files:protected] =>
[language:protected] =>
[old_record:protected] =>
[id:protected] => 1605
[old_id:protected] => 1262
[elcosh_id:protected] => d001137
[type:protected] => document
[display_type:protected] => HTML w/ PDF
[user_id:protected] =>
[language_id:protected] => 1
[tagging_id:protected] => Garber
[priority_id:protected] => 1
[title:protected] => Focus Four Toolbox Talks, Module 1 – Falls, Talk #2 – Falls from debris piles?
[total_pages:protected] => 1
[billed_pages:protected] => 1
[publication_number:protected] =>
[part_of:protected] =>
[keywords:protected] => disaster response, hazard clean-up, uneven surface, disaster site, disaster clean-up
[comments:protected] =>
[summary:protected] => A toolbox talk on preventing falls from debris piles. Includes questions to ask, an incident to discuss with images, and a place to record questions the trainer would like to ask about the incident. Part of a collection. Click on the 'collection' button to access the other items.
[transition_comments:protected] =>
[external_link:protected] =>
[consol_link:protected] => http://www.cpwrconstructionsolutions.org/roofing/hazard/1463/install-asphalt-roofs-fall-from-heights.html
[more_like_this:protected] => a000081,d000478,d000530
[permission_given_by:protected] =>
[published:protected] => T
[billable:protected] => F
[img_name:protected] =>
[img_ext:protected] =>
[img_width:protected] =>
[img_height:protected] =>
[img_credit:protected] =>
[img_practice:protected] =>
[vid_source_id:protected] =>
[vid_running_time:protected] =>
[vid_intended_audience:protected] =>
[vid_acquisition_info:protected] =>
[vid_cost:protected] =>
[vid_producer:protected] =>
[vid_filename:protected] =>
[vid_filename_downloadable:protected] =>
[date_summary:protected] =>
[date_permission_requested:protected] =>
[date_permission_received:protected] =>
[date_review_needed:protected] =>
[date_received:protected] => 02/15/12
[date_completed:protected] => 03/19/12
[date_billed:protected] =>
[date_modified:protected] => 07/10/12
[collBokExports:protected] =>
[lastBokExportCriteria:BaseElcoshItem:private] =>
[alreadyInSave:protected] =>
[alreadyInValidation:protected] =>
[validationFailures:protected] => Array
(
)
[_new:BaseObject:private] =>
[_deleted:BaseObject:private] =>
[modifiedColumns:protected] => Array
(
)
)
[1610] => DocumentRecord Object
(
[records:protected] => Array
(
)
[recordId:protected] =>
[searchWordClass:protected] =>
[searchWordPeerClass:protected] =>
[bok_record:protected] =>
[authors:protected] =>
[organizations:protected] =>
[collections:protected] =>
[categories:protected] =>
[categories_initialized:protected] =>
[mapped_items:protected] =>
[content:protected] =>
[files:protected] =>
[language:protected] =>
[old_record:protected] =>
[id:protected] => 1610
[old_id:protected] => 1271
[elcosh_id:protected] => d001146
[type:protected] => document
[display_type:protected] => HTML w/ PDF
[user_id:protected] => 0
[language_id:protected] => 1
[tagging_id:protected] => Garber
[priority_id:protected] => 1
[title:protected] => Focus Four Toolbox Talks, Module 2 – Struck-by, Talk #5 – Rigging and Securing Loads
[total_pages:protected] => 1
[billed_pages:protected] => 1
[publication_number:protected] =>
[part_of:protected] =>
[keywords:protected] => rigging, lift loads, loading areas, chains
[comments:protected] =>
[summary:protected] => A toolbox talk on preventing struck-by incidents caused by not securing loads properly. Includes questions to ask, an incident to discuss with images, and a place to record questions the trainer would like to ask about the incident. Part of a collection. Click on the 'collection' button to access the other items.
[transition_comments:protected] =>
[external_link:protected] =>
[consol_link:protected] => http://www.cpwrconstructionsolutions.org/heavy_equipment/hazard/1591/move-equipment-to-from-and-between-sites-work-zone-struck-by-injuries-and-fatalities.html
[more_like_this:protected] => d000144,d000360,d000873
[permission_given_by:protected] =>
[published:protected] => T
[billable:protected] => F
[img_name:protected] =>
[img_ext:protected] =>
[img_width:protected] =>
[img_height:protected] =>
[img_credit:protected] =>
[img_practice:protected] =>
[vid_source_id:protected] =>
[vid_running_time:protected] =>
[vid_intended_audience:protected] =>
[vid_acquisition_info:protected] =>
[vid_cost:protected] =>
[vid_producer:protected] =>
[vid_filename:protected] =>
[vid_filename_downloadable:protected] =>
[date_summary:protected] =>
[date_permission_requested:protected] =>
[date_permission_received:protected] =>
[date_review_needed:protected] =>
[date_received:protected] => 02/15/12
[date_completed:protected] => 03/28/12
[date_billed:protected] =>
[date_modified:protected] => 05/12/14
[collBokExports:protected] =>
[lastBokExportCriteria:BaseElcoshItem:private] =>
[alreadyInSave:protected] =>
[alreadyInValidation:protected] =>
[validationFailures:protected] => Array
(
)
[_new:BaseObject:private] =>
[_deleted:BaseObject:private] =>
[modifiedColumns:protected] => Array
(
)
)
[1645] => DocumentRecord Object
(
[records:protected] => Array
(
)
[recordId:protected] =>
[searchWordClass:protected] =>
[searchWordPeerClass:protected] =>
[bok_record:protected] =>
[authors:protected] =>
[organizations:protected] =>
[collections:protected] =>
[categories:protected] =>
[categories_initialized:protected] =>
[mapped_items:protected] =>
[content:protected] =>
[files:protected] =>
[language:protected] =>
[old_record:protected] =>
[id:protected] => 1645
[old_id:protected] => 1274
[elcosh_id:protected] => d001149
[type:protected] => document
[display_type:protected] => HTML w/ PDF
[user_id:protected] => 0
[language_id:protected] => 1
[tagging_id:protected] => Garber
[priority_id:protected] => 1
[title:protected] => Focus Four Toolbox Talks, Module 3 – Caught-in/between, Talk #2 – Trenches & Heavy Equipment
[total_pages:protected] => 1
[billed_pages:protected] => 1
[publication_number:protected] =>
[part_of:protected] =>
[keywords:protected] => back-up alarms, spotter, soil cave-in, spoil pikes, ROPs, trenching, rain
[comments:protected] =>
[summary:protected] => A toolbox talk on preventing incidents involving trenches such as trench collapse. Includes questions to ask, an incident to discuss with images, and a place to record questions the trainer would like to ask about the incident. Part of a collection. Click on the 'collection' button to access the other items.
[transition_comments:protected] =>
[external_link:protected] =>
[consol_link:protected] =>
[more_like_this:protected] => d000019,d000035,d000168
[permission_given_by:protected] =>
[published:protected] => T
[billable:protected] => F
[img_name:protected] =>
[img_ext:protected] =>
[img_width:protected] =>
[img_height:protected] =>
[img_credit:protected] =>
[img_practice:protected] =>
[vid_source_id:protected] =>
[vid_running_time:protected] =>
[vid_intended_audience:protected] =>
[vid_acquisition_info:protected] =>
[vid_cost:protected] =>
[vid_producer:protected] =>
[vid_filename:protected] =>
[vid_filename_downloadable:protected] =>
[date_summary:protected] =>
[date_permission_requested:protected] =>
[date_permission_received:protected] =>
[date_review_needed:protected] =>
[date_received:protected] => 02/15/12
[date_completed:protected] => 04/02/12
[date_billed:protected] =>
[date_modified:protected] => 05/23/23
[collBokExports:protected] =>
[lastBokExportCriteria:BaseElcoshItem:private] =>
[alreadyInSave:protected] =>
[alreadyInValidation:protected] =>
[validationFailures:protected] => Array
(
)
[_new:BaseObject:private] =>
[_deleted:BaseObject:private] =>
[modifiedColumns:protected] => Array
(
)
)
[1654] => DocumentRecord Object
(
[records:protected] => Array
(
)
[recordId:protected] =>
[searchWordClass:protected] =>
[searchWordPeerClass:protected] =>
[bok_record:protected] =>
[authors:protected] =>
[organizations:protected] =>
[collections:protected] =>
[categories:protected] =>
[categories_initialized:protected] =>
[mapped_items:protected] =>
[content:protected] =>
[files:protected] =>
[language:protected] =>
[old_record:protected] =>
[id:protected] => 1654
[old_id:protected] => 1284
[elcosh_id:protected] => d001159
[type:protected] => document
[display_type:protected] => HTML w/ PDF
[user_id:protected] => 0
[language_id:protected] => 1
[tagging_id:protected] => Garber
[priority_id:protected] => 1
[title:protected] => Focus Four Toolbox Talks, Module 4 – Electrocutions, Talk #6 – Hazards on Disaster Sites
[total_pages:protected] => 1
[billed_pages:protected] => 1
[publication_number:protected] =>
[part_of:protected] =>
[keywords:protected] => powerlines, underground, utilities, generators, wet conditions, GFCIs, energized lines, disasters, emergency response
[comments:protected] =>
[summary:protected] => A toolbox talk on how to avoid electrocution on a disaster site. Includes questions to ask, an incident to discuss with images, and a place to record questions the trainer would like to ask about the incident. Part of a collection. Click on the 'collection' button to access the other items.
[transition_comments:protected] =>
[external_link:protected] =>
[consol_link:protected] => http://www.cpwrconstructionsolutions.org/electrical/hazard/1138/install-and-repair-high-voltage-lines-transformers-switches-electrical-shocks-burns-and-or-electrocution.html
[more_like_this:protected] => d000135,d000361,d000437
[permission_given_by:protected] =>
[published:protected] => T
[billable:protected] => F
[img_name:protected] =>
[img_ext:protected] =>
[img_width:protected] =>
[img_height:protected] =>
[img_credit:protected] =>
[img_practice:protected] =>
[vid_source_id:protected] =>
[vid_running_time:protected] =>
[vid_intended_audience:protected] =>
[vid_acquisition_info:protected] =>
[vid_cost:protected] =>
[vid_producer:protected] =>
[vid_filename:protected] =>
[vid_filename_downloadable:protected] =>
[date_summary:protected] =>
[date_permission_requested:protected] =>
[date_permission_received:protected] =>
[date_review_needed:protected] =>
[date_received:protected] => 02/15/12
[date_completed:protected] => 04/02/12
[date_billed:protected] =>
[date_modified:protected] => 05/23/23
[collBokExports:protected] =>
[lastBokExportCriteria:BaseElcoshItem:private] =>
[alreadyInSave:protected] =>
[alreadyInValidation:protected] =>
[validationFailures:protected] => Array
(
)
[_new:BaseObject:private] =>
[_deleted:BaseObject:private] =>
[modifiedColumns:protected] => Array
(
)
)
)
[content:protected] =>
[files:protected] => Array
(
[9400] => File Object
(
[id:protected] => 9400
[filename:protected] => 1.jpg
[downloadable:protected] => F
[timestamp:protected] => 2014-05-08 15:05:37
[alreadyInSave:protected] =>
[alreadyInValidation:protected] =>
[validationFailures:protected] => Array
(
)
[_new:BaseObject:private] =>
[_deleted:BaseObject:private] =>
[modifiedColumns:protected] => Array
(
)
)
[9401] => File Object
(
[id:protected] => 9401
[filename:protected] => d001298.pdf
[downloadable:protected] => T
[timestamp:protected] => 2014-05-08 15:05:37
[alreadyInSave:protected] =>
[alreadyInValidation:protected] =>
[validationFailures:protected] => Array
(
)
[_new:BaseObject:private] =>
[_deleted:BaseObject:private] =>
[modifiedColumns:protected] => Array
(
)
)
)
[language:protected] => Language Object
(
[id:protected] => 1
[code:protected] => en
[name:protected] => English
[alreadyInSave:protected] =>
[alreadyInValidation:protected] =>
[validationFailures:protected] => Array
(
)
[_new:BaseObject:private] =>
[_deleted:BaseObject:private] =>
[modifiedColumns:protected] => Array
(
)
)
[old_record:protected] =>
[id:protected] => 3827
[old_id:protected] =>
[elcosh_id:protected] => d001298
[type:protected] => document
[display_type:protected] => HTML w/ PDF
[user_id:protected] => 23
[language_id:protected] => 1
[tagging_id:protected] => Bruce Lippy
[priority_id:protected] => 1
[title:protected] => Getting the most out of the IUOE Toolbox Talks
[total_pages:protected] => 2
[billed_pages:protected] => 2
[publication_number:protected] =>
[part_of:protected] =>
[keywords:protected] => toolbox talks, tailgate talks
[comments:protected] =>
[summary:protected] => Toolbox talks have been the main tool for communicating safety information on construction jobs for decades.
Unfortunately, there has been little research on what makes for effective toolbox talks. The IUOE National
Training Fund worked with OSHA and NIOSH to make sure their series of 24 Focus Four toolbox talks were based on the best recommendations for effective design. These toolbox talks accompany an entire package of training materials, but can be used alone. This guide points out the key features of these toolbox talks and how best to deliver them.
[transition_comments:protected] =>
[external_link:protected] =>
[consol_link:protected] =>
[more_like_this:protected] => d001137,d001146,d001149,d001159
[permission_given_by:protected] => IUOE National Hazmat Program
[published:protected] => T
[billable:protected] => F
[img_name:protected] =>
[img_ext:protected] => png
[img_width:protected] =>
[img_height:protected] =>
[img_credit:protected] =>
[img_practice:protected] =>
[vid_source_id:protected] =>
[vid_running_time:protected] =>
[vid_intended_audience:protected] =>
[vid_acquisition_info:protected] =>
[vid_cost:protected] =>
[vid_producer:protected] =>
[vid_filename:protected] =>
[vid_filename_downloadable:protected] =>
[date_summary:protected] => 2007
[date_permission_requested:protected] =>
[date_permission_received:protected] =>
[date_review_needed:protected] =>
[date_received:protected] => 05/08/14
[date_completed:protected] => 05/08/14
[date_billed:protected] =>
[date_modified:protected] => 05/08/14
[collBokExports:protected] =>
[lastBokExportCriteria:BaseElcoshItem:private] =>
[alreadyInSave:protected] =>
[alreadyInValidation:protected] =>
[validationFailures:protected] => Array
(
)
[_new:BaseObject:private] =>
[_deleted:BaseObject:private] =>
[modifiedColumns:protected] => Array
(
)
)
[show_text] =>
[document_content] => ElcoshItemDocumentContent Object
(
[id:protected] => 2896
[item_id:protected] => 3827
[type:protected] => main
[title:protected] =>
[content:protected] =>
Why were these talks developed?
Toolbox talks have been the main tool for communicating safety information on construction jobs for decades. Unfortunately, there has been almost no research on what makes for effective toolbox talks. The IUOE National Training Fund has worked with OSHA, the National Institute for Occupational Safety and Health and the Lippy Group, LLC to make sure these Focus Four toolbox talks are based on the latest fi ndings on the most effective design and tailored to the hazards operating engineers face daily. These toolbox talks accompany an entire package of training materials, but can be used alone. The way these are delivered is as important as how well they are designed.
What did NIOSH find out?
- Just handing out factsheets and toolbox talks to workers doesn’t work. Providing copies after toolbox talks doesn’t make much of an impact either.
- Using case studies (real life stories of accidents that ended in fatality or injury) in toolbox talks is effective.
- When toolbox talks containing case studies were accompanied by discussion questions to encourage group participation, they were more effective. Consequently, getting the workers to participate in the discussion about the case study is important. It’s not enough to tell the story, it is better to have the workers engage in problem solving that analyzes why the accident occurred and how it could have been prevented. Active learning is always better than passive.
How should you deliver these toolbox talks?
- Choose a topic that is related to work going on at the site.
- Hold the meeting on the job, preferably where everyone can sit and relax.
- Hold the meeting at the beginning of a shift or after a break. Folks are too tired at the end of a shift to carefully listen and they want to get home.
- Read the toolbox talk sheet on the topic prior to conducting the talk.
- Start at the top of the form and work right through to the end, which should take around 10 to 15 minutes. Guidance is provided in blue print to help you with each section.
- Use the questions provided to generate discussions. Always allow time for the crew to respond to your questions before you provide an answer. Some suggested responses are written in italics.
- Review the case study and emphasize that this was a real incident. Ask the crew for a case study before you review the one provided, however.
- Always end with a discussion of the particular worksite where you are conducting the talk. Tie the talk as closely to hazards on the site as possible and encourage the crew to constantly look for and immediately correct hazards. They should also know how to report any problems that can’t be immediately corrected.
- Provide copies to each person, if you like, but NIOSH has not found that to be particularly effective.
- Encourage workers to do similar talks on their sites and provide them with the IUOE phone number for ordering in bulk.
- Have everyone sign the back of the form to indicate they attended this session and point out it is a pledge to look out for the health and safety of everyone on the site.
What are the key features of these toolbox talks?

[content_transformed:protected] =>
Why were these talks developed?
Toolbox talks have been the main tool for communicating safety information on construction jobs for decades. Unfortunately, there has been almost no research on what makes for effective toolbox talks. The IUOE National Training Fund has worked with OSHA, the National Institute for Occupational Safety and Health and the Lippy Group, LLC to make sure these Focus Four toolbox talks are based on the latest fi ndings on the most effective design and tailored to the hazards operating engineers face daily. These toolbox talks accompany an entire package of training materials, but can be used alone. The way these are delivered is as important as how well they are designed.
What did NIOSH find out?
- Just handing out factsheets and toolbox talks to workers doesn’t work. Providing copies after toolbox talks doesn’t make much of an impact either.
- Using case studies (real life stories of accidents that ended in fatality or injury) in toolbox talks is effective.
- When toolbox talks containing case studies were accompanied by discussion questions to encourage group participation, they were more effective. Consequently, getting the workers to participate in the discussion about the case study is important. It’s not enough to tell the story, it is better to have the workers engage in problem solving that analyzes why the accident occurred and how it could have been prevented. Active learning is always better than passive.
How should you deliver these toolbox talks?
- Choose a topic that is related to work going on at the site.
- Hold the meeting on the job, preferably where everyone can sit and relax.
- Hold the meeting at the beginning of a shift or after a break. Folks are too tired at the end of a shift to carefully listen and they want to get home.
- Read the toolbox talk sheet on the topic prior to conducting the talk.
- Start at the top of the form and work right through to the end, which should take around 10 to 15 minutes. Guidance is provided in blue print to help you with each section.
- Use the questions provided to generate discussions. Always allow time for the crew to respond to your questions before you provide an answer. Some suggested responses are written in italics.
- Review the case study and emphasize that this was a real incident. Ask the crew for a case study before you review the one provided, however.
- Always end with a discussion of the particular worksite where you are conducting the talk. Tie the talk as closely to hazards on the site as possible and encourage the crew to constantly look for and immediately correct hazards. They should also know how to report any problems that can’t be immediately corrected.
- Provide copies to each person, if you like, but NIOSH has not found that to be particularly effective.
- Encourage workers to do similar talks on their sites and provide them with the IUOE phone number for ordering in bulk.
- Have everyone sign the back of the form to indicate they attended this session and point out it is a pledge to look out for the health and safety of everyone on the site.
What are the key features of these toolbox talks?
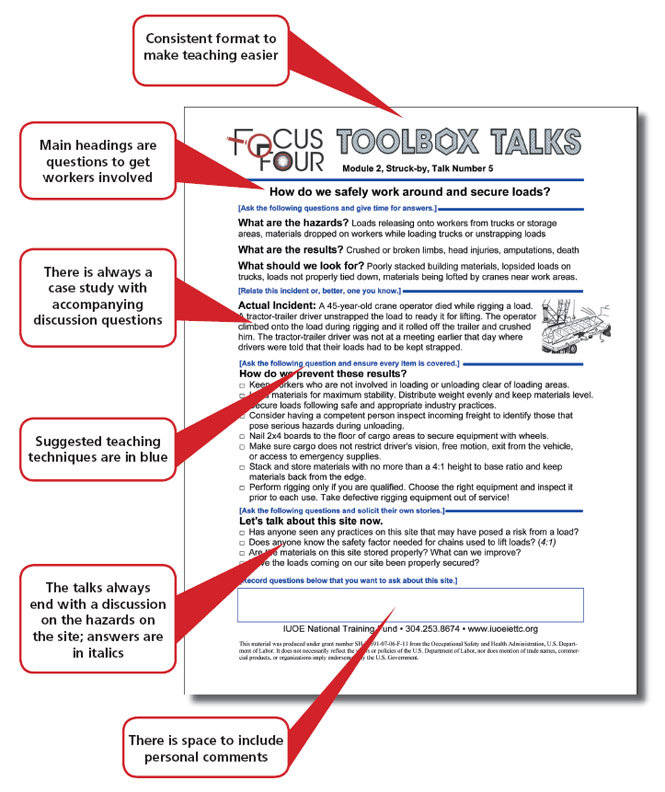
[disclaimer:protected] =>
[disclaimer_transformed:protected] =>
[alreadyInSave:protected] =>
[alreadyInValidation:protected] =>
[validationFailures:protected] => Array
(
)
[_new:BaseObject:private] =>
[_deleted:BaseObject:private] =>
[modifiedColumns:protected] => Array
(
)
)
[template] => record
)
[_file] => /home/agsafe5/repositories/elcosh/live/templates/elcosh/record_macros.html
[_errors:protected] => Array
(
)
[_encoding:protected] => UTF-8
[_outputMode:protected] => 11
[_forceReparse:protected] =>
[_phpCodeDestination:protected] => /tmp/
[_phpCodeExtension:protected] => php
[_cacheLifetime:protected] => 30
[_cachePurgeFrequency:protected] => 30
[externalMacroTemplatesCache:PHPTAL:private] => Array
(
)
)
)
)
)
)
[4] => Array
(
[file] => /home/agsafe5/repositories/elcosh/live/sblib/core/SB_PHPTAL/PHPTAL/PHPTAL.php
[line] => 659
[function] => tpl_61515a6c_record__uvBJJSo8xT_sgOY5gjP7ug
[args] => Array
(
[0] => PHPTAL Object
(
[_prefilters:protected] => Array
(
)
[_prefilter:PHPTAL:private] => REMOVED: DO NOT USE
[_postfilter:protected] =>
[_repositories:protected] => Array
(
)
[_path:protected] => /home/agsafe5/repositories/elcosh/live/templates/elcosh/record.html
[_resolvers:protected] => Array
(
)
[_source:protected] => PHPTAL_FileSource Object
(
[_path:PHPTAL_FileSource:private] => /home/agsafe5/repositories/elcosh/live/templates/elcosh/record.html
)
[_codeFile:protected] => /tmp/tpl_61515a6c_record__uvBJJSo8xT_sgOY5gjP7ug.php
[_functionName:protected] => tpl_61515a6c_record__uvBJJSo8xT_sgOY5gjP7ug
[_prepared:protected] => 1
[_triggers:protected] => Array
(
)
[_translator:protected] =>
[_globalContext:protected] => stdClass Object
(
)
[_context:protected] => PHPTAL_Context Object
(
[_line] =>
[_file] => /home/agsafe5/repositories/elcosh/live/templates/elcosh/record.html
[repeat] => stdClass Object
(
)
[_xmlDeclaration] =>
[_docType] =>
[_nothrow:PHPTAL_Context:private] =>
[_slots:PHPTAL_Context:private] => Array
(
)
[_slotsStack:PHPTAL_Context:private] => Array
(
[0] => Array
(
)
[1] => Array
(
)
)
[_parentContext:PHPTAL_Context:private] =>
[_globalContext:PHPTAL_Context:private] => stdClass Object
(
)
[_echoDeclarations:PHPTAL_Context:private] =>
[referer] => http://www.elcosh.org/document/3827/d001298/Getting%2Bthe%2Bmost%2Bout%2Bof%2Bthe%2BIUOE%2BToolbox%2BTalks.html
[curr_module] => Record
[styles] => Array
(
)
[javascript] => Array
(
[0] => jquery.min.js
)
[metas] => Array
(
[language] => en
[robots] => index, follow
)
[user] =>
[curr_url] => https://www.elcosh.org/index.php?module=Record&id=3827&type=document
[base_url] => https://www.elcosh.org/index.php?module=Record
[title] => eLCOSH : Getting the most out of the IUOE Toolbox Talks
[language] => en
[search_query] =>
[module] => Record
[new_records] => Array
(
[0] => Search_Result Object
(
[title] => Toolbox Talk: Fixed Ladder
[image] => /record/images/notavailable-p.png
[blurb] => The CPWR Toolbox Talk on Fixed Ladders addresses the potential risks associated with using fixed ladders. The resource includes a brief case example,...
[category] => Array
(
[0] => 15
[1] => 47
[2] => 49
[3] => 51
[4] => 53
[5] => 55
[6] => 60
[7] => 64
[8] => 73
[9] => 76
[10] => 78
[11] => 80
[12] => 86
[13] => 87
[14] => 90
[15] => 92
[16] => 93
[17] => 94
[18] => 100
)
[labels] => Array
(
[0] => Falls
[1] => Work Environment
[2] => Hazards
[3] => Bricklayer
[4] => Trades
[5] => Carpenter
[7] => Cement Mason
[9] => Concrete Polisher
[11] => Electrical Worker
[13] => HVAC
[15] => Laborer
[17] => PCC/Restoration
[19] => Plumber/Pipefitter
[21] => Roofer/Waterproofer
[23] => Sheetmetal Worker
[25] => Welder
[27] => Commercial & Institutional
[28] => Jobsites
[29] => Industrial
[31] => LEED/Green Construction
[33] => Renovations
[35] => Residential
[37] => Toolbox Talks
[38] => Documents
[39] => Media & Documents
)
[type] => Toolbox Talks
[sub_category] =>
[url] => /document/4430/d001660/Toolbox%2BTalk%253A%2BFixed%2BLadder.html
[item:protected] => DocumentRecord Object
(
[records:protected] => Array
(
)
[recordId:protected] =>
[searchWordClass:protected] =>
[searchWordPeerClass:protected] =>
[bok_record:protected] =>
[authors:protected] =>
[organizations:protected] =>
[collections:protected] =>
[categories:protected] => Array
(
[15] => Category Object
(
[languages:protected] =>
[bok_resources:protected] =>
[bok_topics:protected] =>
[bok_keywords:protected] =>
[id:protected] => 15
[type:protected] => category
[parent:protected] => 7
[label:protected] => Falls
[alreadyInSave:protected] =>
[alreadyInValidation:protected] =>
[validationFailures:protected] => Array
(
)
[_new:BaseObject:private] =>
[_deleted:BaseObject:private] =>
[modifiedColumns:protected] => Array
(
)
)
[47] => Category Object
(
[languages:protected] =>
[bok_resources:protected] =>
[bok_topics:protected] =>
[bok_keywords:protected] =>
[id:protected] => 47
[type:protected] => category
[parent:protected] => 2
[label:protected] => Bricklayer
[alreadyInSave:protected] =>
[alreadyInValidation:protected] =>
[validationFailures:protected] => Array
(
)
[_new:BaseObject:private] =>
[_deleted:BaseObject:private] =>
[modifiedColumns:protected] => Array
(
)
)
[49] => Category Object
(
[languages:protected] =>
[bok_resources:protected] =>
[bok_topics:protected] =>
[bok_keywords:protected] =>
[id:protected] => 49
[type:protected] => category
[parent:protected] => 2
[label:protected] => Carpenter
[alreadyInSave:protected] =>
[alreadyInValidation:protected] =>
[validationFailures:protected] => Array
(
)
[_new:BaseObject:private] =>
[_deleted:BaseObject:private] =>
[modifiedColumns:protected] => Array
(
)
)
[51] => Category Object
(
[languages:protected] =>
[bok_resources:protected] =>
[bok_topics:protected] =>
[bok_keywords:protected] =>
[id:protected] => 51
[type:protected] => category
[parent:protected] => 2
[label:protected] => Cement Mason
[alreadyInSave:protected] =>
[alreadyInValidation:protected] =>
[validationFailures:protected] => Array
(
)
[_new:BaseObject:private] =>
[_deleted:BaseObject:private] =>
[modifiedColumns:protected] => Array
(
)
)
[53] => Category Object
(
[languages:protected] =>
[bok_resources:protected] =>
[bok_topics:protected] =>
[bok_keywords:protected] =>
[id:protected] => 53
[type:protected] => category
[parent:protected] => 2
[label:protected] => Concrete Polisher
[alreadyInSave:protected] =>
[alreadyInValidation:protected] =>
[validationFailures:protected] => Array
(
)
[_new:BaseObject:private] =>
[_deleted:BaseObject:private] =>
[modifiedColumns:protected] => Array
(
)
)
[55] => Category Object
(
[languages:protected] =>
[bok_resources:protected] =>
[bok_topics:protected] =>
[bok_keywords:protected] =>
[id:protected] => 55
[type:protected] => category
[parent:protected] => 2
[label:protected] => Electrical Worker
[alreadyInSave:protected] =>
[alreadyInValidation:protected] =>
[validationFailures:protected] => Array
(
)
[_new:BaseObject:private] =>
[_deleted:BaseObject:private] =>
[modifiedColumns:protected] => Array
(
)
)
[60] => Category Object
(
[languages:protected] =>
[bok_resources:protected] =>
[bok_topics:protected] =>
[bok_keywords:protected] =>
[id:protected] => 60
[type:protected] => category
[parent:protected] => 2
[label:protected] => HVAC
[alreadyInSave:protected] =>
[alreadyInValidation:protected] =>
[validationFailures:protected] => Array
(
)
[_new:BaseObject:private] =>
[_deleted:BaseObject:private] =>
[modifiedColumns:protected] => Array
(
)
)
[64] => Category Object
(
[languages:protected] =>
[bok_resources:protected] =>
[bok_topics:protected] =>
[bok_keywords:protected] =>
[id:protected] => 64
[type:protected] => category
[parent:protected] => 2
[label:protected] => Laborer
[alreadyInSave:protected] =>
[alreadyInValidation:protected] =>
[validationFailures:protected] => Array
(
)
[_new:BaseObject:private] =>
[_deleted:BaseObject:private] =>
[modifiedColumns:protected] => Array
(
)
)
[73] => Category Object
(
[languages:protected] =>
[bok_resources:protected] =>
[bok_topics:protected] =>
[bok_keywords:protected] =>
[id:protected] => 73
[type:protected] => category
[parent:protected] => 2
[label:protected] => PCC/Restoration
[alreadyInSave:protected] =>
[alreadyInValidation:protected] =>
[validationFailures:protected] => Array
(
)
[_new:BaseObject:private] =>
[_deleted:BaseObject:private] =>
[modifiedColumns:protected] => Array
(
)
)
[76] => Category Object
(
[languages:protected] =>
[bok_resources:protected] =>
[bok_topics:protected] =>
[bok_keywords:protected] =>
[id:protected] => 76
[type:protected] => category
[parent:protected] => 2
[label:protected] => Plumber/Pipefitter
[alreadyInSave:protected] =>
[alreadyInValidation:protected] =>
[validationFailures:protected] => Array
(
)
[_new:BaseObject:private] =>
[_deleted:BaseObject:private] =>
[modifiedColumns:protected] => Array
(
)
)
[78] => Category Object
(
[languages:protected] =>
[bok_resources:protected] =>
[bok_topics:protected] =>
[bok_keywords:protected] =>
[id:protected] => 78
[type:protected] => category
[parent:protected] => 2
[label:protected] => Roofer/Waterproofer
[alreadyInSave:protected] =>
[alreadyInValidation:protected] =>
[validationFailures:protected] => Array
(
)
[_new:BaseObject:private] =>
[_deleted:BaseObject:private] =>
[modifiedColumns:protected] => Array
(
)
)
[80] => Category Object
(
[languages:protected] =>
[bok_resources:protected] =>
[bok_topics:protected] =>
[bok_keywords:protected] =>
[id:protected] => 80
[type:protected] => category
[parent:protected] => 2
[label:protected] => Sheetmetal Worker
[alreadyInSave:protected] =>
[alreadyInValidation:protected] =>
[validationFailures:protected] => Array
(
)
[_new:BaseObject:private] =>
[_deleted:BaseObject:private] =>
[modifiedColumns:protected] => Array
(
)
)
[86] => Category Object
(
[languages:protected] =>
[bok_resources:protected] =>
[bok_topics:protected] =>
[bok_keywords:protected] =>
[id:protected] => 86
[type:protected] => category
[parent:protected] => 2
[label:protected] => Welder
[alreadyInSave:protected] =>
[alreadyInValidation:protected] =>
[validationFailures:protected] => Array
(
)
[_new:BaseObject:private] =>
[_deleted:BaseObject:private] =>
[modifiedColumns:protected] => Array
(
)
)
[87] => Category Object
(
[languages:protected] =>
[bok_resources:protected] =>
[bok_topics:protected] =>
[bok_keywords:protected] =>
[id:protected] => 87
[type:protected] => category
[parent:protected] => 3
[label:protected] => Commercial & Institutional
[alreadyInSave:protected] =>
[alreadyInValidation:protected] =>
[validationFailures:protected] => Array
(
)
[_new:BaseObject:private] =>
[_deleted:BaseObject:private] =>
[modifiedColumns:protected] => Array
(
)
)
[90] => Category Object
(
[languages:protected] =>
[bok_resources:protected] =>
[bok_topics:protected] =>
[bok_keywords:protected] =>
[id:protected] => 90
[type:protected] => category
[parent:protected] => 3
[label:protected] => Industrial
[alreadyInSave:protected] =>
[alreadyInValidation:protected] =>
[validationFailures:protected] => Array
(
)
[_new:BaseObject:private] =>
[_deleted:BaseObject:private] =>
[modifiedColumns:protected] => Array
(
)
)
[92] => Category Object
(
[languages:protected] =>
[bok_resources:protected] =>
[bok_topics:protected] =>
[bok_keywords:protected] =>
[id:protected] => 92
[type:protected] => category
[parent:protected] => 3
[label:protected] => LEED/Green Construction
[alreadyInSave:protected] =>
[alreadyInValidation:protected] =>
[validationFailures:protected] => Array
(
)
[_new:BaseObject:private] =>
[_deleted:BaseObject:private] =>
[modifiedColumns:protected] => Array
(
)
)
[93] => Category Object
(
[languages:protected] =>
[bok_resources:protected] =>
[bok_topics:protected] =>
[bok_keywords:protected] =>
[id:protected] => 93
[type:protected] => category
[parent:protected] => 3
[label:protected] => Renovations
[alreadyInSave:protected] =>
[alreadyInValidation:protected] =>
[validationFailures:protected] => Array
(
)
[_new:BaseObject:private] =>
[_deleted:BaseObject:private] =>
[modifiedColumns:protected] => Array
(
)
)
[94] => Category Object
(
[languages:protected] =>
[bok_resources:protected] =>
[bok_topics:protected] =>
[bok_keywords:protected] =>
[id:protected] => 94
[type:protected] => category
[parent:protected] => 3
[label:protected] => Residential
[alreadyInSave:protected] =>
[alreadyInValidation:protected] =>
[validationFailures:protected] => Array
(
)
[_new:BaseObject:private] =>
[_deleted:BaseObject:private] =>
[modifiedColumns:protected] => Array
(
)
)
[100] => Category Object
(
[languages:protected] =>
[bok_resources:protected] =>
[bok_topics:protected] =>
[bok_keywords:protected] =>
[id:protected] => 100
[type:protected] => category
[parent:protected] => 6
[label:protected] => Toolbox Talks
[alreadyInSave:protected] =>
[alreadyInValidation:protected] =>
[validationFailures:protected] => Array
(
)
[_new:BaseObject:private] =>
[_deleted:BaseObject:private] =>
[modifiedColumns:protected] => Array
(
)
)
)
[categories_initialized:protected] => 1
[mapped_items:protected] =>
[content:protected] =>
[files:protected] =>
[language:protected] => Language Object
(
[id:protected] => 1
[code:protected] => en
[name:protected] => English
[alreadyInSave:protected] =>
[alreadyInValidation:protected] =>
[validationFailures:protected] => Array
(
)
[_new:BaseObject:private] =>
[_deleted:BaseObject:private] =>
[modifiedColumns:protected] => Array
(
)
)
[old_record:protected] =>
[id:protected] => 4430
[old_id:protected] =>
[elcosh_id:protected] => d001660
[type:protected] => document
[display_type:protected] => HTML only (and links)
[user_id:protected] => 0
[language_id:protected] => 1
[tagging_id:protected] => Mike Aguilar
[priority_id:protected] => 1
[title:protected] => Toolbox Talk: Fixed Ladder
[total_pages:protected] => 0
[billed_pages:protected] => 0
[publication_number:protected] =>
[part_of:protected] =>
[keywords:protected] => Fixed Ladders, Fall Prevention, Falls
[comments:protected] =>
[summary:protected] => The CPWR Toolbox Talk on Fixed Ladders addresses the potential risks associated with using fixed ladders. The resource includes a brief case example, steps to prevent a related injury and questions for discussion. It includes an image that illustrates the hazard, which can be posted in a central location as a reminder of steps to work safely.
Available in
English
and
Spanish.
[transition_comments:protected] =>
[external_link:protected] =>
[consol_link:protected] =>
[more_like_this:protected] => d001257,d001254,d001255,d001256,d001258,d001262,d001279
[permission_given_by:protected] =>
[published:protected] => T
[billable:protected] => F
[img_name:protected] =>
[img_ext:protected] =>
[img_width:protected] =>
[img_height:protected] =>
[img_credit:protected] =>
[img_practice:protected] =>
[vid_source_id:protected] =>
[vid_running_time:protected] =>
[vid_intended_audience:protected] =>
[vid_acquisition_info:protected] =>
[vid_cost:protected] =>
[vid_producer:protected] =>
[vid_filename:protected] =>
[vid_filename_downloadable:protected] =>
[date_summary:protected] =>
[date_permission_requested:protected] =>
[date_permission_received:protected] =>
[date_review_needed:protected] =>
[date_received:protected] => 06/10/22
[date_completed:protected] => 06/10/22
[date_billed:protected] =>
[date_modified:protected] => 05/22/23
[collBokExports:protected] =>
[lastBokExportCriteria:BaseElcoshItem:private] =>
[alreadyInSave:protected] =>
[alreadyInValidation:protected] =>
[validationFailures:protected] => Array
(
)
[_new:BaseObject:private] =>
[_deleted:BaseObject:private] =>
[modifiedColumns:protected] => Array
(
)
)
)
[1] => Search_Result Object
(
[title] => Toolbox Talk: Challenges Preventing Falling Objects
[image] => /record/images/notavailable-p.png
[blurb] => The CPWR Toolbox Talk on Challenges Preventing Falling Objects addresses the hazards of being struck by falling objects on the job site. The resource...
[category] => Array
(
[0] => 12
[1] => 47
[2] => 49
[3] => 51
[4] => 55
[5] => 64
[6] => 68
[7] => 71
[8] => 75
[9] => 78
[10] => 79
[11] => 82
[12] => 62
[13] => 86
[14] => 87
[15] => 88
[16] => 89
[17] => 91
[18] => 90
[19] => 92
[20] => 93
[21] => 94
[22] => 95
[23] => 100
)
[labels] => Array
(
[0] => Crushed/Struck By
[1] => Work Environment
[2] => Hazards
[3] => Bricklayer
[4] => Trades
[5] => Carpenter
[7] => Cement Mason
[9] => Electrical Worker
[11] => Laborer
[13] => Maintenance Worker
[15] => Painter
[17] => Plasterer
[19] => Roofer/Waterproofer
[21] => Scaffold Erector
[23] => Stonemason
[25] => Structural Ironworker
[27] => Welder
[29] => Commercial & Institutional
[30] => Jobsites
[31] => Demolition
[33] => Disasters
[35] => Heavy & Highway
[37] => Industrial
[39] => LEED/Green Construction
[41] => Renovations
[43] => Residential
[45] => Underground
[47] => Toolbox Talks
[48] => Documents
[49] => Media & Documents
)
[type] => Toolbox Talks
[sub_category] =>
[url] => /document/4431/d001661/Toolbox%2BTalk%253A%2BChallenges%2BPreventing%2BFalling%2BObjects.html
[item:protected] => DocumentRecord Object
(
[records:protected] => Array
(
)
[recordId:protected] =>
[searchWordClass:protected] =>
[searchWordPeerClass:protected] =>
[bok_record:protected] =>
[authors:protected] =>
[organizations:protected] =>
[collections:protected] =>
[categories:protected] => Array
(
[12] => Category Object
(
[languages:protected] =>
[bok_resources:protected] =>
[bok_topics:protected] =>
[bok_keywords:protected] =>
[id:protected] => 12
[type:protected] => category
[parent:protected] => 7
[label:protected] => Crushed/Struck By
[alreadyInSave:protected] =>
[alreadyInValidation:protected] =>
[validationFailures:protected] => Array
(
)
[_new:BaseObject:private] =>
[_deleted:BaseObject:private] =>
[modifiedColumns:protected] => Array
(
)
)
[47] => Category Object
(
[languages:protected] =>
[bok_resources:protected] =>
[bok_topics:protected] =>
[bok_keywords:protected] =>
[id:protected] => 47
[type:protected] => category
[parent:protected] => 2
[label:protected] => Bricklayer
[alreadyInSave:protected] =>
[alreadyInValidation:protected] =>
[validationFailures:protected] => Array
(
)
[_new:BaseObject:private] =>
[_deleted:BaseObject:private] =>
[modifiedColumns:protected] => Array
(
)
)
[49] => Category Object
(
[languages:protected] =>
[bok_resources:protected] =>
[bok_topics:protected] =>
[bok_keywords:protected] =>
[id:protected] => 49
[type:protected] => category
[parent:protected] => 2
[label:protected] => Carpenter
[alreadyInSave:protected] =>
[alreadyInValidation:protected] =>
[validationFailures:protected] => Array
(
)
[_new:BaseObject:private] =>
[_deleted:BaseObject:private] =>
[modifiedColumns:protected] => Array
(
)
)
[51] => Category Object
(
[languages:protected] =>
[bok_resources:protected] =>
[bok_topics:protected] =>
[bok_keywords:protected] =>
[id:protected] => 51
[type:protected] => category
[parent:protected] => 2
[label:protected] => Cement Mason
[alreadyInSave:protected] =>
[alreadyInValidation:protected] =>
[validationFailures:protected] => Array
(
)
[_new:BaseObject:private] =>
[_deleted:BaseObject:private] =>
[modifiedColumns:protected] => Array
(
)
)
[55] => Category Object
(
[languages:protected] =>
[bok_resources:protected] =>
[bok_topics:protected] =>
[bok_keywords:protected] =>
[id:protected] => 55
[type:protected] => category
[parent:protected] => 2
[label:protected] => Electrical Worker
[alreadyInSave:protected] =>
[alreadyInValidation:protected] =>
[validationFailures:protected] => Array
(
)
[_new:BaseObject:private] =>
[_deleted:BaseObject:private] =>
[modifiedColumns:protected] => Array
(
)
)
[64] => Category Object
(
[languages:protected] =>
[bok_resources:protected] =>
[bok_topics:protected] =>
[bok_keywords:protected] =>
[id:protected] => 64
[type:protected] => category
[parent:protected] => 2
[label:protected] => Laborer
[alreadyInSave:protected] =>
[alreadyInValidation:protected] =>
[validationFailures:protected] => Array
(
)
[_new:BaseObject:private] =>
[_deleted:BaseObject:private] =>
[modifiedColumns:protected] => Array
(
)
)
[68] => Category Object
(
[languages:protected] =>
[bok_resources:protected] =>
[bok_topics:protected] =>
[bok_keywords:protected] =>
[id:protected] => 68
[type:protected] => category
[parent:protected] => 2
[label:protected] => Maintenance Worker
[alreadyInSave:protected] =>
[alreadyInValidation:protected] =>
[validationFailures:protected] => Array
(
)
[_new:BaseObject:private] =>
[_deleted:BaseObject:private] =>
[modifiedColumns:protected] => Array
(
)
)
[71] => Category Object
(
[languages:protected] =>
[bok_resources:protected] =>
[bok_topics:protected] =>
[bok_keywords:protected] =>
[id:protected] => 71
[type:protected] => category
[parent:protected] => 2
[label:protected] => Painter
[alreadyInSave:protected] =>
[alreadyInValidation:protected] =>
[validationFailures:protected] => Array
(
)
[_new:BaseObject:private] =>
[_deleted:BaseObject:private] =>
[modifiedColumns:protected] => Array
(
)
)
[75] => Category Object
(
[languages:protected] =>
[bok_resources:protected] =>
[bok_topics:protected] =>
[bok_keywords:protected] =>
[id:protected] => 75
[type:protected] => category
[parent:protected] => 2
[label:protected] => Plasterer
[alreadyInSave:protected] =>
[alreadyInValidation:protected] =>
[validationFailures:protected] => Array
(
)
[_new:BaseObject:private] =>
[_deleted:BaseObject:private] =>
[modifiedColumns:protected] => Array
(
)
)
[78] => Category Object
(
[languages:protected] =>
[bok_resources:protected] =>
[bok_topics:protected] =>
[bok_keywords:protected] =>
[id:protected] => 78
[type:protected] => category
[parent:protected] => 2
[label:protected] => Roofer/Waterproofer
[alreadyInSave:protected] =>
[alreadyInValidation:protected] =>
[validationFailures:protected] => Array
(
)
[_new:BaseObject:private] =>
[_deleted:BaseObject:private] =>
[modifiedColumns:protected] => Array
(
)
)
[79] => Category Object
(
[languages:protected] =>
[bok_resources:protected] =>
[bok_topics:protected] =>
[bok_keywords:protected] =>
[id:protected] => 79
[type:protected] => category
[parent:protected] => 2
[label:protected] => Scaffold Erector
[alreadyInSave:protected] =>
[alreadyInValidation:protected] =>
[validationFailures:protected] => Array
(
)
[_new:BaseObject:private] =>
[_deleted:BaseObject:private] =>
[modifiedColumns:protected] => Array
(
)
)
[82] => Category Object
(
[languages:protected] =>
[bok_resources:protected] =>
[bok_topics:protected] =>
[bok_keywords:protected] =>
[id:protected] => 82
[type:protected] => category
[parent:protected] => 2
[label:protected] => Stonemason
[alreadyInSave:protected] =>
[alreadyInValidation:protected] =>
[validationFailures:protected] => Array
(
)
[_new:BaseObject:private] =>
[_deleted:BaseObject:private] =>
[modifiedColumns:protected] => Array
(
)
)
[62] => Category Object
(
[languages:protected] =>
[bok_resources:protected] =>
[bok_topics:protected] =>
[bok_keywords:protected] =>
[id:protected] => 62
[type:protected] => category
[parent:protected] => 2
[label:protected] => Structural Ironworker
[alreadyInSave:protected] =>
[alreadyInValidation:protected] =>
[validationFailures:protected] => Array
(
)
[_new:BaseObject:private] =>
[_deleted:BaseObject:private] =>
[modifiedColumns:protected] => Array
(
)
)
[86] => Category Object
(
[languages:protected] =>
[bok_resources:protected] =>
[bok_topics:protected] =>
[bok_keywords:protected] =>
[id:protected] => 86
[type:protected] => category
[parent:protected] => 2
[label:protected] => Welder
[alreadyInSave:protected] =>
[alreadyInValidation:protected] =>
[validationFailures:protected] => Array
(
)
[_new:BaseObject:private] =>
[_deleted:BaseObject:private] =>
[modifiedColumns:protected] => Array
(
)
)
[87] => Category Object
(
[languages:protected] =>
[bok_resources:protected] =>
[bok_topics:protected] =>
[bok_keywords:protected] =>
[id:protected] => 87
[type:protected] => category
[parent:protected] => 3
[label:protected] => Commercial & Institutional
[alreadyInSave:protected] =>
[alreadyInValidation:protected] =>
[validationFailures:protected] => Array
(
)
[_new:BaseObject:private] =>
[_deleted:BaseObject:private] =>
[modifiedColumns:protected] => Array
(
)
)
[88] => Category Object
(
[languages:protected] =>
[bok_resources:protected] =>
[bok_topics:protected] =>
[bok_keywords:protected] =>
[id:protected] => 88
[type:protected] => category
[parent:protected] => 3
[label:protected] => Demolition
[alreadyInSave:protected] =>
[alreadyInValidation:protected] =>
[validationFailures:protected] => Array
(
)
[_new:BaseObject:private] =>
[_deleted:BaseObject:private] =>
[modifiedColumns:protected] => Array
(
)
)
[89] => Category Object
(
[languages:protected] =>
[bok_resources:protected] =>
[bok_topics:protected] =>
[bok_keywords:protected] =>
[id:protected] => 89
[type:protected] => category
[parent:protected] => 3
[label:protected] => Disasters
[alreadyInSave:protected] =>
[alreadyInValidation:protected] =>
[validationFailures:protected] => Array
(
)
[_new:BaseObject:private] =>
[_deleted:BaseObject:private] =>
[modifiedColumns:protected] => Array
(
)
)
[91] => Category Object
(
[languages:protected] =>
[bok_resources:protected] =>
[bok_topics:protected] =>
[bok_keywords:protected] =>
[id:protected] => 91
[type:protected] => category
[parent:protected] => 3
[label:protected] => Heavy & Highway
[alreadyInSave:protected] =>
[alreadyInValidation:protected] =>
[validationFailures:protected] => Array
(
)
[_new:BaseObject:private] =>
[_deleted:BaseObject:private] =>
[modifiedColumns:protected] => Array
(
)
)
[90] => Category Object
(
[languages:protected] =>
[bok_resources:protected] =>
[bok_topics:protected] =>
[bok_keywords:protected] =>
[id:protected] => 90
[type:protected] => category
[parent:protected] => 3
[label:protected] => Industrial
[alreadyInSave:protected] =>
[alreadyInValidation:protected] =>
[validationFailures:protected] => Array
(
)
[_new:BaseObject:private] =>
[_deleted:BaseObject:private] =>
[modifiedColumns:protected] => Array
(
)
)
[92] => Category Object
(
[languages:protected] =>
[bok_resources:protected] =>
[bok_topics:protected] =>
[bok_keywords:protected] =>
[id:protected] => 92
[type:protected] => category
[parent:protected] => 3
[label:protected] => LEED/Green Construction
[alreadyInSave:protected] =>
[alreadyInValidation:protected] =>
[validationFailures:protected] => Array
(
)
[_new:BaseObject:private] =>
[_deleted:BaseObject:private] =>
[modifiedColumns:protected] => Array
(
)
)
[93] => Category Object
(
[languages:protected] =>
[bok_resources:protected] =>
[bok_topics:protected] =>
[bok_keywords:protected] =>
[id:protected] => 93
[type:protected] => category
[parent:protected] => 3
[label:protected] => Renovations
[alreadyInSave:protected] =>
[alreadyInValidation:protected] =>
[validationFailures:protected] => Array
(
)
[_new:BaseObject:private] =>
[_deleted:BaseObject:private] =>
[modifiedColumns:protected] => Array
(
)
)
[94] => Category Object
(
[languages:protected] =>
[bok_resources:protected] =>
[bok_topics:protected] =>
[bok_keywords:protected] =>
[id:protected] => 94
[type:protected] => category
[parent:protected] => 3
[label:protected] => Residential
[alreadyInSave:protected] =>
[alreadyInValidation:protected] =>
[validationFailures:protected] => Array
(
)
[_new:BaseObject:private] =>
[_deleted:BaseObject:private] =>
[modifiedColumns:protected] => Array
(
)
)
[95] => Category Object
(
[languages:protected] =>
[bok_resources:protected] =>
[bok_topics:protected] =>
[bok_keywords:protected] =>
[id:protected] => 95
[type:protected] => category
[parent:protected] => 3
[label:protected] => Underground
[alreadyInSave:protected] =>
[alreadyInValidation:protected] =>
[validationFailures:protected] => Array
(
)
[_new:BaseObject:private] =>
[_deleted:BaseObject:private] =>
[modifiedColumns:protected] => Array
(
)
)
[100] => Category Object
(
[languages:protected] =>
[bok_resources:protected] =>
[bok_topics:protected] =>
[bok_keywords:protected] =>
[id:protected] => 100
[type:protected] => category
[parent:protected] => 6
[label:protected] => Toolbox Talks
[alreadyInSave:protected] =>
[alreadyInValidation:protected] =>
[validationFailures:protected] => Array
(
)
[_new:BaseObject:private] =>
[_deleted:BaseObject:private] =>
[modifiedColumns:protected] => Array
(
)
)
)
[categories_initialized:protected] => 1
[mapped_items:protected] =>
[content:protected] =>
[files:protected] =>
[language:protected] => Language Object
(
[id:protected] => 1
[code:protected] => en
[name:protected] => English
[alreadyInSave:protected] =>
[alreadyInValidation:protected] =>
[validationFailures:protected] => Array
(
)
[_new:BaseObject:private] =>
[_deleted:BaseObject:private] =>
[modifiedColumns:protected] => Array
(
)
)
[old_record:protected] =>
[id:protected] => 4431
[old_id:protected] =>
[elcosh_id:protected] => d001661
[type:protected] => document
[display_type:protected] => HTML only (and links)
[user_id:protected] => 0
[language_id:protected] => 1
[tagging_id:protected] => Mike Aguilar
[priority_id:protected] => 1
[title:protected] => Toolbox Talk: Challenges Preventing Falling Objects
[total_pages:protected] => 0
[billed_pages:protected] => 0
[publication_number:protected] =>
[part_of:protected] =>
[keywords:protected] => dropped objects, falling objects, struck by incidents, struck by fatalities
[comments:protected] =>
[summary:protected] => The CPWR Toolbox Talk on Challenges Preventing Falling Objects addresses the hazards of being struck by falling objects on the job site. The resource includes a brief example, steps to prevent a related injury, and questions for discussion. It includes a graphic that illustrates a group workers observing a scaffold free of debris during high winds, which can be posted in a central location as a reminder of steps to work safely.
Available in
English and
Spanish.
[transition_comments:protected] =>
[external_link:protected] =>
[consol_link:protected] =>
[more_like_this:protected] => d001234,d001238,d001244,d001251,d001253,d001260,d001268,d001278
[permission_given_by:protected] =>
[published:protected] => T
[billable:protected] => F
[img_name:protected] =>
[img_ext:protected] =>
[img_width:protected] =>
[img_height:protected] =>
[img_credit:protected] =>
[img_practice:protected] =>
[vid_source_id:protected] =>
[vid_running_time:protected] =>
[vid_intended_audience:protected] =>
[vid_acquisition_info:protected] =>
[vid_cost:protected] =>
[vid_producer:protected] =>
[vid_filename:protected] =>
[vid_filename_downloadable:protected] =>
[date_summary:protected] =>
[date_permission_requested:protected] =>
[date_permission_received:protected] =>
[date_review_needed:protected] =>
[date_received:protected] => 06/10/22
[date_completed:protected] => 06/10/22
[date_billed:protected] =>
[date_modified:protected] => 05/22/23
[collBokExports:protected] =>
[lastBokExportCriteria:BaseElcoshItem:private] =>
[alreadyInSave:protected] =>
[alreadyInValidation:protected] =>
[validationFailures:protected] => Array
(
)
[_new:BaseObject:private] =>
[_deleted:BaseObject:private] =>
[modifiedColumns:protected] => Array
(
)
)
)
[2] => Search_Result Object
(
[title] => Toolbox Talk: Tower Crane Safety
[image] => /record/images/notavailable-p.png
[blurb] => The CPWR Toolbox Talk on Tower Crane Safety addresses the potential hazards of Tower Cranes and the importance of following procedure before and durin...
[category] => Array
(
[0] => 11
[1] => 12
[2] => 18
[3] => 70
[4] => 87
[5] => 88
[6] => 91
[7] => 90
[8] => 92
[9] => 100
)
[labels] => Array
(
[0] => Cranes & Hoists
[1] => Work Environment
[2] => Hazards
[3] => Crushed/Struck By
[6] => Motor Vehicles/Heavy Equipment
[9] => Operating Engineer
[10] => Trades
[11] => Commercial & Institutional
[12] => Jobsites
[13] => Demolition
[15] => Heavy & Highway
[17] => Industrial
[19] => LEED/Green Construction
[21] => Toolbox Talks
[22] => Documents
[23] => Media & Documents
)
[type] => Toolbox Talks
[sub_category] =>
[url] => /document/4427/d001657/Toolbox%2BTalk%253A%2BTower%2BCrane%2BSafety.html
[item:protected] => DocumentRecord Object
(
[records:protected] => Array
(
)
[recordId:protected] =>
[searchWordClass:protected] =>
[searchWordPeerClass:protected] =>
[bok_record:protected] =>
[authors:protected] =>
[organizations:protected] =>
[collections:protected] =>
[categories:protected] => Array
(
[11] => Category Object
(
[languages:protected] =>
[bok_resources:protected] =>
[bok_topics:protected] =>
[bok_keywords:protected] =>
[id:protected] => 11
[type:protected] => category
[parent:protected] => 7
[label:protected] => Cranes & Hoists
[alreadyInSave:protected] =>
[alreadyInValidation:protected] =>
[validationFailures:protected] => Array
(
)
[_new:BaseObject:private] =>
[_deleted:BaseObject:private] =>
[modifiedColumns:protected] => Array
(
)
)
[12] => Category Object
(
[languages:protected] =>
[bok_resources:protected] =>
[bok_topics:protected] =>
[bok_keywords:protected] =>
[id:protected] => 12
[type:protected] => category
[parent:protected] => 7
[label:protected] => Crushed/Struck By
[alreadyInSave:protected] =>
[alreadyInValidation:protected] =>
[validationFailures:protected] => Array
(
)
[_new:BaseObject:private] =>
[_deleted:BaseObject:private] =>
[modifiedColumns:protected] => Array
(
)
)
[18] => Category Object
(
[languages:protected] =>
[bok_resources:protected] =>
[bok_topics:protected] =>
[bok_keywords:protected] =>
[id:protected] => 18
[type:protected] => category
[parent:protected] => 7
[label:protected] => Motor Vehicles/Heavy Equipment
[alreadyInSave:protected] =>
[alreadyInValidation:protected] =>
[validationFailures:protected] => Array
(
)
[_new:BaseObject:private] =>
[_deleted:BaseObject:private] =>
[modifiedColumns:protected] => Array
(
)
)
[70] => Category Object
(
[languages:protected] =>
[bok_resources:protected] =>
[bok_topics:protected] =>
[bok_keywords:protected] =>
[id:protected] => 70
[type:protected] => category
[parent:protected] => 2
[label:protected] => Operating Engineer
[alreadyInSave:protected] =>
[alreadyInValidation:protected] =>
[validationFailures:protected] => Array
(
)
[_new:BaseObject:private] =>
[_deleted:BaseObject:private] =>
[modifiedColumns:protected] => Array
(
)
)
[87] => Category Object
(
[languages:protected] =>
[bok_resources:protected] =>
[bok_topics:protected] =>
[bok_keywords:protected] =>
[id:protected] => 87
[type:protected] => category
[parent:protected] => 3
[label:protected] => Commercial & Institutional
[alreadyInSave:protected] =>
[alreadyInValidation:protected] =>
[validationFailures:protected] => Array
(
)
[_new:BaseObject:private] =>
[_deleted:BaseObject:private] =>
[modifiedColumns:protected] => Array
(
)
)
[88] => Category Object
(
[languages:protected] =>
[bok_resources:protected] =>
[bok_topics:protected] =>
[bok_keywords:protected] =>
[id:protected] => 88
[type:protected] => category
[parent:protected] => 3
[label:protected] => Demolition
[alreadyInSave:protected] =>
[alreadyInValidation:protected] =>
[validationFailures:protected] => Array
(
)
[_new:BaseObject:private] =>
[_deleted:BaseObject:private] =>
[modifiedColumns:protected] => Array
(
)
)
[91] => Category Object
(
[languages:protected] =>
[bok_resources:protected] =>
[bok_topics:protected] =>
[bok_keywords:protected] =>
[id:protected] => 91
[type:protected] => category
[parent:protected] => 3
[label:protected] => Heavy & Highway
[alreadyInSave:protected] =>
[alreadyInValidation:protected] =>
[validationFailures:protected] => Array
(
)
[_new:BaseObject:private] =>
[_deleted:BaseObject:private] =>
[modifiedColumns:protected] => Array
(
)
)
[90] => Category Object
(
[languages:protected] =>
[bok_resources:protected] =>
[bok_topics:protected] =>
[bok_keywords:protected] =>
[id:protected] => 90
[type:protected] => category
[parent:protected] => 3
[label:protected] => Industrial
[alreadyInSave:protected] =>
[alreadyInValidation:protected] =>
[validationFailures:protected] => Array
(
)
[_new:BaseObject:private] =>
[_deleted:BaseObject:private] =>
[modifiedColumns:protected] => Array
(
)
)
[92] => Category Object
(
[languages:protected] =>
[bok_resources:protected] =>
[bok_topics:protected] =>
[bok_keywords:protected] =>
[id:protected] => 92
[type:protected] => category
[parent:protected] => 3
[label:protected] => LEED/Green Construction
[alreadyInSave:protected] =>
[alreadyInValidation:protected] =>
[validationFailures:protected] => Array
(
)
[_new:BaseObject:private] =>
[_deleted:BaseObject:private] =>
[modifiedColumns:protected] => Array
(
)
)
[100] => Category Object
(
[languages:protected] =>
[bok_resources:protected] =>
[bok_topics:protected] =>
[bok_keywords:protected] =>
[id:protected] => 100
[type:protected] => category
[parent:protected] => 6
[label:protected] => Toolbox Talks
[alreadyInSave:protected] =>
[alreadyInValidation:protected] =>
[validationFailures:protected] => Array
(
)
[_new:BaseObject:private] =>
[_deleted:BaseObject:private] =>
[modifiedColumns:protected] => Array
(
)
)
)
[categories_initialized:protected] => 1
[mapped_items:protected] =>
[content:protected] =>
[files:protected] =>
[language:protected] => Language Object
(
[id:protected] => 1
[code:protected] => en
[name:protected] => English
[alreadyInSave:protected] =>
[alreadyInValidation:protected] =>
[validationFailures:protected] => Array
(
)
[_new:BaseObject:private] =>
[_deleted:BaseObject:private] =>
[modifiedColumns:protected] => Array
(
)
)
[old_record:protected] =>
[id:protected] => 4427
[old_id:protected] =>
[elcosh_id:protected] => d001657
[type:protected] => document
[display_type:protected] => HTML only (and links)
[user_id:protected] => 0
[language_id:protected] => 1
[tagging_id:protected] => Mike Aguilar
[priority_id:protected] => 1
[title:protected] => Toolbox Talk: Tower Crane Safety
[total_pages:protected] => 0
[billed_pages:protected] => 0
[publication_number:protected] =>
[part_of:protected] =>
[keywords:protected] => Tower Crane, Crane, Stability, Tipping, Lift Zone Safety, Lift, Zone, Safety, Struck by
[comments:protected] =>
[summary:protected] => The CPWR Toolbox Talk on Tower Crane Safety addresses the potential hazards of Tower Cranes and the importance of following procedure before and during Tower Crane operation. The resource includes a brief example, steps to prevent a related injury, and questions for discussion. It includes a graphic that illustrates a worker inspecting a Tower Crane before operation, which can be posted in a central location as a reminder of steps to work safely.
Available in
English and
Spanish.
[transition_comments:protected] =>
[external_link:protected] =>
[consol_link:protected] =>
[more_like_this:protected] => d001234,d001238,d001250,d001251,d001253,d001258,d001262,d001273
[permission_given_by:protected] =>
[published:protected] => T
[billable:protected] => F
[img_name:protected] =>
[img_ext:protected] => jpg
[img_width:protected] =>
[img_height:protected] =>
[img_credit:protected] =>
[img_practice:protected] =>
[vid_source_id:protected] =>
[vid_running_time:protected] =>
[vid_intended_audience:protected] =>
[vid_acquisition_info:protected] =>
[vid_cost:protected] =>
[vid_producer:protected] =>
[vid_filename:protected] =>
[vid_filename_downloadable:protected] =>
[date_summary:protected] =>
[date_permission_requested:protected] =>
[date_permission_received:protected] =>
[date_review_needed:protected] =>
[date_received:protected] => 12/23/21
[date_completed:protected] => 12/23/21
[date_billed:protected] =>
[date_modified:protected] => 05/19/23
[collBokExports:protected] =>
[lastBokExportCriteria:BaseElcoshItem:private] =>
[alreadyInSave:protected] =>
[alreadyInValidation:protected] =>
[validationFailures:protected] => Array
(
)
[_new:BaseObject:private] =>
[_deleted:BaseObject:private] =>
[modifiedColumns:protected] => Array
(
)
)
)
[3] => Search_Result Object
(
[title] => Toolbox Talk: Work Zone Safety: Working Around Vehicles
[image] => /record/images/notavailable-p.png
[blurb] => The CPWR Toolbox Talk on Working Around Vehicles in the Work Zone addresses methods to avoid being struck-by a vehicle on a construction site. The res...
[category] => Array
(
[0] => 12
[1] => 18
[2] => 52
[3] => 57
[4] => 70
[5] => 85
[6] => 87
[7] => 88
[8] => 89
[9] => 91
[10] => 90
[11] => 92
[12] => 93
[13] => 94
[14] => 95
[15] => 100
)
[labels] => Array
(
[0] => Crushed/Struck By
[1] => Work Environment
[2] => Hazards
[3] => Motor Vehicles/Heavy Equipment
[6] => Commercial Diver
[7] => Trades
[8] => Flagger
[10] => Operating Engineer
[12] => Truck Driver
[14] => Commercial & Institutional
[15] => Jobsites
[16] => Demolition
[18] => Disasters
[20] => Heavy & Highway
[22] => Industrial
[24] => LEED/Green Construction
[26] => Renovations
[28] => Residential
[30] => Underground
[32] => Toolbox Talks
[33] => Documents
[34] => Media & Documents
)
[type] => Toolbox Talks
[sub_category] =>
[url] => /document/4428/d001658/Toolbox%2BTalk%253A%2BWork%2BZone%2BSafety%253A%2BWorking%2BAround%2BVehicles.html
[item:protected] => DocumentRecord Object
(
[records:protected] => Array
(
)
[recordId:protected] =>
[searchWordClass:protected] =>
[searchWordPeerClass:protected] =>
[bok_record:protected] =>
[authors:protected] =>
[organizations:protected] =>
[collections:protected] =>
[categories:protected] => Array
(
[12] => Category Object
(
[languages:protected] =>
[bok_resources:protected] =>
[bok_topics:protected] =>
[bok_keywords:protected] =>
[id:protected] => 12
[type:protected] => category
[parent:protected] => 7
[label:protected] => Crushed/Struck By
[alreadyInSave:protected] =>
[alreadyInValidation:protected] =>
[validationFailures:protected] => Array
(
)
[_new:BaseObject:private] =>
[_deleted:BaseObject:private] =>
[modifiedColumns:protected] => Array
(
)
)
[18] => Category Object
(
[languages:protected] =>
[bok_resources:protected] =>
[bok_topics:protected] =>
[bok_keywords:protected] =>
[id:protected] => 18
[type:protected] => category
[parent:protected] => 7
[label:protected] => Motor Vehicles/Heavy Equipment
[alreadyInSave:protected] =>
[alreadyInValidation:protected] =>
[validationFailures:protected] => Array
(
)
[_new:BaseObject:private] =>
[_deleted:BaseObject:private] =>
[modifiedColumns:protected] => Array
(
)
)
[52] => Category Object
(
[languages:protected] =>
[bok_resources:protected] =>
[bok_topics:protected] =>
[bok_keywords:protected] =>
[id:protected] => 52
[type:protected] => category
[parent:protected] => 2
[label:protected] => Commercial Diver
[alreadyInSave:protected] =>
[alreadyInValidation:protected] =>
[validationFailures:protected] => Array
(
)
[_new:BaseObject:private] =>
[_deleted:BaseObject:private] =>
[modifiedColumns:protected] => Array
(
)
)
[57] => Category Object
(
[languages:protected] =>
[bok_resources:protected] =>
[bok_topics:protected] =>
[bok_keywords:protected] =>
[id:protected] => 57
[type:protected] => category
[parent:protected] => 2
[label:protected] => Flagger
[alreadyInSave:protected] =>
[alreadyInValidation:protected] =>
[validationFailures:protected] => Array
(
)
[_new:BaseObject:private] =>
[_deleted:BaseObject:private] =>
[modifiedColumns:protected] => Array
(
)
)
[70] => Category Object
(
[languages:protected] =>
[bok_resources:protected] =>
[bok_topics:protected] =>
[bok_keywords:protected] =>
[id:protected] => 70
[type:protected] => category
[parent:protected] => 2
[label:protected] => Operating Engineer
[alreadyInSave:protected] =>
[alreadyInValidation:protected] =>
[validationFailures:protected] => Array
(
)
[_new:BaseObject:private] =>
[_deleted:BaseObject:private] =>
[modifiedColumns:protected] => Array
(
)
)
[85] => Category Object
(
[languages:protected] =>
[bok_resources:protected] =>
[bok_topics:protected] =>
[bok_keywords:protected] =>
[id:protected] => 85
[type:protected] => category
[parent:protected] => 2
[label:protected] => Truck Driver
[alreadyInSave:protected] =>
[alreadyInValidation:protected] =>
[validationFailures:protected] => Array
(
)
[_new:BaseObject:private] =>
[_deleted:BaseObject:private] =>
[modifiedColumns:protected] => Array
(
)
)
[87] => Category Object
(
[languages:protected] =>
[bok_resources:protected] =>
[bok_topics:protected] =>
[bok_keywords:protected] =>
[id:protected] => 87
[type:protected] => category
[parent:protected] => 3
[label:protected] => Commercial & Institutional
[alreadyInSave:protected] =>
[alreadyInValidation:protected] =>
[validationFailures:protected] => Array
(
)
[_new:BaseObject:private] =>
[_deleted:BaseObject:private] =>
[modifiedColumns:protected] => Array
(
)
)
[88] => Category Object
(
[languages:protected] =>
[bok_resources:protected] =>
[bok_topics:protected] =>
[bok_keywords:protected] =>
[id:protected] => 88
[type:protected] => category
[parent:protected] => 3
[label:protected] => Demolition
[alreadyInSave:protected] =>
[alreadyInValidation:protected] =>
[validationFailures:protected] => Array
(
)
[_new:BaseObject:private] =>
[_deleted:BaseObject:private] =>
[modifiedColumns:protected] => Array
(
)
)
[89] => Category Object
(
[languages:protected] =>
[bok_resources:protected] =>
[bok_topics:protected] =>
[bok_keywords:protected] =>
[id:protected] => 89
[type:protected] => category
[parent:protected] => 3
[label:protected] => Disasters
[alreadyInSave:protected] =>
[alreadyInValidation:protected] =>
[validationFailures:protected] => Array
(
)
[_new:BaseObject:private] =>
[_deleted:BaseObject:private] =>
[modifiedColumns:protected] => Array
(
)
)
[91] => Category Object
(
[languages:protected] =>
[bok_resources:protected] =>
[bok_topics:protected] =>
[bok_keywords:protected] =>
[id:protected] => 91
[type:protected] => category
[parent:protected] => 3
[label:protected] => Heavy & Highway
[alreadyInSave:protected] =>
[alreadyInValidation:protected] =>
[validationFailures:protected] => Array
(
)
[_new:BaseObject:private] =>
[_deleted:BaseObject:private] =>
[modifiedColumns:protected] => Array
(
)
)
[90] => Category Object
(
[languages:protected] =>
[bok_resources:protected] =>
[bok_topics:protected] =>
[bok_keywords:protected] =>
[id:protected] => 90
[type:protected] => category
[parent:protected] => 3
[label:protected] => Industrial
[alreadyInSave:protected] =>
[alreadyInValidation:protected] =>
[validationFailures:protected] => Array
(
)
[_new:BaseObject:private] =>
[_deleted:BaseObject:private] =>
[modifiedColumns:protected] => Array
(
)
)
[92] => Category Object
(
[languages:protected] =>
[bok_resources:protected] =>
[bok_topics:protected] =>
[bok_keywords:protected] =>
[id:protected] => 92
[type:protected] => category
[parent:protected] => 3
[label:protected] => LEED/Green Construction
[alreadyInSave:protected] =>
[alreadyInValidation:protected] =>
[validationFailures:protected] => Array
(
)
[_new:BaseObject:private] =>
[_deleted:BaseObject:private] =>
[modifiedColumns:protected] => Array
(
)
)
[93] => Category Object
(
[languages:protected] =>
[bok_resources:protected] =>
[bok_topics:protected] =>
[bok_keywords:protected] =>
[id:protected] => 93
[type:protected] => category
[parent:protected] => 3
[label:protected] => Renovations
[alreadyInSave:protected] =>
[alreadyInValidation:protected] =>
[validationFailures:protected] => Array
(
)
[_new:BaseObject:private] =>
[_deleted:BaseObject:private] =>
[modifiedColumns:protected] => Array
(
)
)
[94] => Category Object
(
[languages:protected] =>
[bok_resources:protected] =>
[bok_topics:protected] =>
[bok_keywords:protected] =>
[id:protected] => 94
[type:protected] => category
[parent:protected] => 3
[label:protected] => Residential
[alreadyInSave:protected] =>
[alreadyInValidation:protected] =>
[validationFailures:protected] => Array
(
)
[_new:BaseObject:private] =>
[_deleted:BaseObject:private] =>
[modifiedColumns:protected] => Array
(
)
)
[95] => Category Object
(
[languages:protected] =>
[bok_resources:protected] =>
[bok_topics:protected] =>
[bok_keywords:protected] =>
[id:protected] => 95
[type:protected] => category
[parent:protected] => 3
[label:protected] => Underground
[alreadyInSave:protected] =>
[alreadyInValidation:protected] =>
[validationFailures:protected] => Array
(
)
[_new:BaseObject:private] =>
[_deleted:BaseObject:private] =>
[modifiedColumns:protected] => Array
(
)
)
[100] => Category Object
(
[languages:protected] =>
[bok_resources:protected] =>
[bok_topics:protected] =>
[bok_keywords:protected] =>
[id:protected] => 100
[type:protected] => category
[parent:protected] => 6
[label:protected] => Toolbox Talks
[alreadyInSave:protected] =>
[alreadyInValidation:protected] =>
[validationFailures:protected] => Array
(
)
[_new:BaseObject:private] =>
[_deleted:BaseObject:private] =>
[modifiedColumns:protected] => Array
(
)
)
)
[categories_initialized:protected] => 1
[mapped_items:protected] =>
[content:protected] =>
[files:protected] =>
[language:protected] => Language Object
(
[id:protected] => 1
[code:protected] => en
[name:protected] => English
[alreadyInSave:protected] =>
[alreadyInValidation:protected] =>
[validationFailures:protected] => Array
(
)
[_new:BaseObject:private] =>
[_deleted:BaseObject:private] =>
[modifiedColumns:protected] => Array
(
)
)
[old_record:protected] =>
[id:protected] => 4428
[old_id:protected] =>
[elcosh_id:protected] => d001658
[type:protected] => document
[display_type:protected] => HTML only (and links)
[user_id:protected] => 0
[language_id:protected] => 1
[tagging_id:protected] => Daniela Caceres
[priority_id:protected] => 1
[title:protected] => Toolbox Talk: Work Zone Safety: Working Around Vehicles
[total_pages:protected] => 0
[billed_pages:protected] => 0
[publication_number:protected] =>
[part_of:protected] =>
[keywords:protected] => Struck, Struck by, Vehicle, Work Zone Safety, Truck, Operator, Driver, Mobile Equipment
[comments:protected] =>
[summary:protected] => The CPWR Toolbox Talk on Working Around Vehicles in the Work Zone addresses methods to avoid being struck-by a vehicle on a construction site. The resource includes a case example, steps to prevent a related injury, and questions for discussion. It includes a graphic that illustrates the hazard, which can be posted in a central location as a reminder of steps to work safely. Available in
English and
Spanish.
[transition_comments:protected] =>
[external_link:protected] =>
[consol_link:protected] =>
[more_like_this:protected] => d001640
[permission_given_by:protected] =>
[published:protected] => T
[billable:protected] => F
[img_name:protected] =>
[img_ext:protected] =>
[img_width:protected] =>
[img_height:protected] =>
[img_credit:protected] =>
[img_practice:protected] =>
[vid_source_id:protected] =>
[vid_running_time:protected] =>
[vid_intended_audience:protected] =>
[vid_acquisition_info:protected] =>
[vid_cost:protected] =>
[vid_producer:protected] =>
[vid_filename:protected] =>
[vid_filename_downloadable:protected] =>
[date_summary:protected] =>
[date_permission_requested:protected] =>
[date_permission_received:protected] =>
[date_review_needed:protected] =>
[date_received:protected] => 12/23/21
[date_completed:protected] => 12/23/21
[date_billed:protected] =>
[date_modified:protected] => 05/19/23
[collBokExports:protected] =>
[lastBokExportCriteria:BaseElcoshItem:private] =>
[alreadyInSave:protected] =>
[alreadyInValidation:protected] =>
[validationFailures:protected] => Array
(
)
[_new:BaseObject:private] =>
[_deleted:BaseObject:private] =>
[modifiedColumns:protected] => Array
(
)
)
)
[4] => Search_Result Object
(
[title] => Construction Dive -- DeWalt's Jobsite Pro headphones recalled for fire hazards
[image] => /record/images/notavailable-p.png
[blurb] => A recall notice by the United States Consumer Product Safety Commission affects over 300,000 DeWalt Jobsite Pro Headphones. The recall is a result of...
[category] => Array
(
[0] => 16
[1] => 44
[2] => 45
[3] => 46
[4] => 47
[5] => 48
[6] => 49
[7] => 50
[8] => 51
[9] => 52
[10] => 53
[11] => 54
[12] => 55
[13] => 56
[14] => 57
[15] => 58
[16] => 59
[17] => 60
[18] => 61
[19] => 64
[20] => 65
[21] => 66
[22] => 67
[23] => 68
[24] => 69
[25] => 70
[26] => 71
[27] => 72
[28] => 73
[29] => 74
[30] => 75
[31] => 76
[32] => 77
[33] => 63
[34] => 78
[35] => 79
[36] => 80
[37] => 81
[38] => 82
[39] => 62
[40] => 83
[41] => 84
[42] => 85
[43] => 86
[44] => 87
[45] => 88
[46] => 89
[47] => 91
[48] => 90
[49] => 92
[50] => 93
[51] => 94
[52] => 95
)
[labels] => Array
(
[0] => Fire & Explosions
[1] => Work Environment
[2] => Hazards
[3] => Acoustical Ceiling Carpenter
[4] => Trades
[5] => Asbestos/Insulator
[7] => Boilermaker
[9] => Bricklayer
[11] => Cabinetmaker
[13] => Carpenter
[15] => Carpet Layer
[17] => Cement Mason
[19] => Commercial Diver
[21] => Concrete Polisher
[23] => Drywall Applicator Specialist
[25] => Electrical Worker
[27] => Elevator Constructor
[29] => Flagger
[31] => Glazier
[33] => Hazardous Waste Cleanup
[35] => HVAC
[37] => Interior Systems Carpenter
[39] => Laborer
[41] => Landscaper
[43] => Lather
[45] => Lead Abatement Worker
[47] => Maintenance Worker
[49] => Millwright
[51] => Operating Engineer
[53] => Painter
[55] => Paper Hanger
[57] => PCC/Restoration
[59] => Pile Driver
[61] => Plasterer
[63] => Plumber/Pipefitter
[65] => Refractory Worker
[67] => Reinforcing Ironworker
[69] => Roofer/Waterproofer
[71] => Scaffold Erector
[73] => Sheetmetal Worker
[75] => Sprinkler Fitter
[77] => Stonemason
[79] => Structural Ironworker
[81] => Terrazzo Worker
[83] => Tile Setter
[85] => Truck Driver
[87] => Welder
[89] => Commercial & Institutional
[90] => Jobsites
[91] => Demolition
[93] => Disasters
[95] => Heavy & Highway
[97] => Industrial
[99] => LEED/Green Construction
[101] => Renovations
[103] => Residential
[105] => Underground
)
[type] =>
[sub_category] =>
[url] => /document/4426/d001656/Construction%2BDive%2B--%2BDeWalt%2527s%2BJobsite%2BPro%2Bheadphones%2Brecalled%2Bfor%2Bfire%2Bhazards.html
[item:protected] => DocumentRecord Object
(
[records:protected] => Array
(
)
[recordId:protected] =>
[searchWordClass:protected] =>
[searchWordPeerClass:protected] =>
[bok_record:protected] =>
[authors:protected] =>
[organizations:protected] =>
[collections:protected] =>
[categories:protected] => Array
(
[16] => Category Object
(
[languages:protected] =>
[bok_resources:protected] =>
[bok_topics:protected] =>
[bok_keywords:protected] =>
[id:protected] => 16
[type:protected] => category
[parent:protected] => 7
[label:protected] => Fire & Explosions
[alreadyInSave:protected] =>
[alreadyInValidation:protected] =>
[validationFailures:protected] => Array
(
)
[_new:BaseObject:private] =>
[_deleted:BaseObject:private] =>
[modifiedColumns:protected] => Array
(
)
)
[44] => Category Object
(
[languages:protected] =>
[bok_resources:protected] =>
[bok_topics:protected] =>
[bok_keywords:protected] =>
[id:protected] => 44
[type:protected] => category
[parent:protected] => 2
[label:protected] => Acoustical Ceiling Carpenter
[alreadyInSave:protected] =>
[alreadyInValidation:protected] =>
[validationFailures:protected] => Array
(
)
[_new:BaseObject:private] =>
[_deleted:BaseObject:private] =>
[modifiedColumns:protected] => Array
(
)
)
[45] => Category Object
(
[languages:protected] =>
[bok_resources:protected] =>
[bok_topics:protected] =>
[bok_keywords:protected] =>
[id:protected] => 45
[type:protected] => category
[parent:protected] => 2
[label:protected] => Asbestos/Insulator
[alreadyInSave:protected] =>
[alreadyInValidation:protected] =>
[validationFailures:protected] => Array
(
)
[_new:BaseObject:private] =>
[_deleted:BaseObject:private] =>
[modifiedColumns:protected] => Array
(
)
)
[46] => Category Object
(
[languages:protected] =>
[bok_resources:protected] =>
[bok_topics:protected] =>
[bok_keywords:protected] =>
[id:protected] => 46
[type:protected] => category
[parent:protected] => 2
[label:protected] => Boilermaker
[alreadyInSave:protected] =>
[alreadyInValidation:protected] =>
[validationFailures:protected] => Array
(
)
[_new:BaseObject:private] =>
[_deleted:BaseObject:private] =>
[modifiedColumns:protected] => Array
(
)
)
[47] => Category Object
(
[languages:protected] =>
[bok_resources:protected] =>
[bok_topics:protected] =>
[bok_keywords:protected] =>
[id:protected] => 47
[type:protected] => category
[parent:protected] => 2
[label:protected] => Bricklayer
[alreadyInSave:protected] =>
[alreadyInValidation:protected] =>
[validationFailures:protected] => Array
(
)
[_new:BaseObject:private] =>
[_deleted:BaseObject:private] =>
[modifiedColumns:protected] => Array
(
)
)
[48] => Category Object
(
[languages:protected] =>
[bok_resources:protected] =>
[bok_topics:protected] =>
[bok_keywords:protected] =>
[id:protected] => 48
[type:protected] => category
[parent:protected] => 2
[label:protected] => Cabinetmaker
[alreadyInSave:protected] =>
[alreadyInValidation:protected] =>
[validationFailures:protected] => Array
(
)
[_new:BaseObject:private] =>
[_deleted:BaseObject:private] =>
[modifiedColumns:protected] => Array
(
)
)
[49] => Category Object
(
[languages:protected] =>
[bok_resources:protected] =>
[bok_topics:protected] =>
[bok_keywords:protected] =>
[id:protected] => 49
[type:protected] => category
[parent:protected] => 2
[label:protected] => Carpenter
[alreadyInSave:protected] =>
[alreadyInValidation:protected] =>
[validationFailures:protected] => Array
(
)
[_new:BaseObject:private] =>
[_deleted:BaseObject:private] =>
[modifiedColumns:protected] => Array
(
)
)
[50] => Category Object
(
[languages:protected] =>
[bok_resources:protected] =>
[bok_topics:protected] =>
[bok_keywords:protected] =>
[id:protected] => 50
[type:protected] => category
[parent:protected] => 2
[label:protected] => Carpet Layer
[alreadyInSave:protected] =>
[alreadyInValidation:protected] =>
[validationFailures:protected] => Array
(
)
[_new:BaseObject:private] =>
[_deleted:BaseObject:private] =>
[modifiedColumns:protected] => Array
(
)
)
[51] => Category Object
(
[languages:protected] =>
[bok_resources:protected] =>
[bok_topics:protected] =>
[bok_keywords:protected] =>
[id:protected] => 51
[type:protected] => category
[parent:protected] => 2
[label:protected] => Cement Mason
[alreadyInSave:protected] =>
[alreadyInValidation:protected] =>
[validationFailures:protected] => Array
(
)
[_new:BaseObject:private] =>
[_deleted:BaseObject:private] =>
[modifiedColumns:protected] => Array
(
)
)
[52] => Category Object
(
[languages:protected] =>
[bok_resources:protected] =>
[bok_topics:protected] =>
[bok_keywords:protected] =>
[id:protected] => 52
[type:protected] => category
[parent:protected] => 2
[label:protected] => Commercial Diver
[alreadyInSave:protected] =>
[alreadyInValidation:protected] =>
[validationFailures:protected] => Array
(
)
[_new:BaseObject:private] =>
[_deleted:BaseObject:private] =>
[modifiedColumns:protected] => Array
(
)
)
[53] => Category Object
(
[languages:protected] =>
[bok_resources:protected] =>
[bok_topics:protected] =>
[bok_keywords:protected] =>
[id:protected] => 53
[type:protected] => category
[parent:protected] => 2
[label:protected] => Concrete Polisher
[alreadyInSave:protected] =>
[alreadyInValidation:protected] =>
[validationFailures:protected] => Array
(
)
[_new:BaseObject:private] =>
[_deleted:BaseObject:private] =>
[modifiedColumns:protected] => Array
(
)
)
[54] => Category Object
(
[languages:protected] =>
[bok_resources:protected] =>
[bok_topics:protected] =>
[bok_keywords:protected] =>
[id:protected] => 54
[type:protected] => category
[parent:protected] => 2
[label:protected] => Drywall Applicator Specialist
[alreadyInSave:protected] =>
[alreadyInValidation:protected] =>
[validationFailures:protected] => Array
(
)
[_new:BaseObject:private] =>
[_deleted:BaseObject:private] =>
[modifiedColumns:protected] => Array
(
)
)
[55] => Category Object
(
[languages:protected] =>
[bok_resources:protected] =>
[bok_topics:protected] =>
[bok_keywords:protected] =>
[id:protected] => 55
[type:protected] => category
[parent:protected] => 2
[label:protected] => Electrical Worker
[alreadyInSave:protected] =>
[alreadyInValidation:protected] =>
[validationFailures:protected] => Array
(
)
[_new:BaseObject:private] =>
[_deleted:BaseObject:private] =>
[modifiedColumns:protected] => Array
(
)
)
[56] => Category Object
(
[languages:protected] =>
[bok_resources:protected] =>
[bok_topics:protected] =>
[bok_keywords:protected] =>
[id:protected] => 56
[type:protected] => category
[parent:protected] => 2
[label:protected] => Elevator Constructor
[alreadyInSave:protected] =>
[alreadyInValidation:protected] =>
[validationFailures:protected] => Array
(
)
[_new:BaseObject:private] =>
[_deleted:BaseObject:private] =>
[modifiedColumns:protected] => Array
(
)
)
[57] => Category Object
(
[languages:protected] =>
[bok_resources:protected] =>
[bok_topics:protected] =>
[bok_keywords:protected] =>
[id:protected] => 57
[type:protected] => category
[parent:protected] => 2
[label:protected] => Flagger
[alreadyInSave:protected] =>
[alreadyInValidation:protected] =>
[validationFailures:protected] => Array
(
)
[_new:BaseObject:private] =>
[_deleted:BaseObject:private] =>
[modifiedColumns:protected] => Array
(
)
)
[58] => Category Object
(
[languages:protected] =>
[bok_resources:protected] =>
[bok_topics:protected] =>
[bok_keywords:protected] =>
[id:protected] => 58
[type:protected] => category
[parent:protected] => 2
[label:protected] => Glazier
[alreadyInSave:protected] =>
[alreadyInValidation:protected] =>
[validationFailures:protected] => Array
(
)
[_new:BaseObject:private] =>
[_deleted:BaseObject:private] =>
[modifiedColumns:protected] => Array
(
)
)
[59] => Category Object
(
[languages:protected] =>
[bok_resources:protected] =>
[bok_topics:protected] =>
[bok_keywords:protected] =>
[id:protected] => 59
[type:protected] => category
[parent:protected] => 2
[label:protected] => Hazardous Waste Cleanup
[alreadyInSave:protected] =>
[alreadyInValidation:protected] =>
[validationFailures:protected] => Array
(
)
[_new:BaseObject:private] =>
[_deleted:BaseObject:private] =>
[modifiedColumns:protected] => Array
(
)
)
[60] => Category Object
(
[languages:protected] =>
[bok_resources:protected] =>
[bok_topics:protected] =>
[bok_keywords:protected] =>
[id:protected] => 60
[type:protected] => category
[parent:protected] => 2
[label:protected] => HVAC
[alreadyInSave:protected] =>
[alreadyInValidation:protected] =>
[validationFailures:protected] => Array
(
)
[_new:BaseObject:private] =>
[_deleted:BaseObject:private] =>
[modifiedColumns:protected] => Array
(
)
)
[61] => Category Object
(
[languages:protected] =>
[bok_resources:protected] =>
[bok_topics:protected] =>
[bok_keywords:protected] =>
[id:protected] => 61
[type:protected] => category
[parent:protected] => 2
[label:protected] => Interior Systems Carpenter
[alreadyInSave:protected] =>
[alreadyInValidation:protected] =>
[validationFailures:protected] => Array
(
)
[_new:BaseObject:private] =>
[_deleted:BaseObject:private] =>
[modifiedColumns:protected] => Array
(
)
)
[64] => Category Object
(
[languages:protected] =>
[bok_resources:protected] =>
[bok_topics:protected] =>
[bok_keywords:protected] =>
[id:protected] => 64
[type:protected] => category
[parent:protected] => 2
[label:protected] => Laborer
[alreadyInSave:protected] =>
[alreadyInValidation:protected] =>
[validationFailures:protected] => Array
(
)
[_new:BaseObject:private] =>
[_deleted:BaseObject:private] =>
[modifiedColumns:protected] => Array
(
)
)
[65] => Category Object
(
[languages:protected] =>
[bok_resources:protected] =>
[bok_topics:protected] =>
[bok_keywords:protected] =>
[id:protected] => 65
[type:protected] => category
[parent:protected] => 2
[label:protected] => Landscaper
[alreadyInSave:protected] =>
[alreadyInValidation:protected] =>
[validationFailures:protected] => Array
(
)
[_new:BaseObject:private] =>
[_deleted:BaseObject:private] =>
[modifiedColumns:protected] => Array
(
)
)
[66] => Category Object
(
[languages:protected] =>
[bok_resources:protected] =>
[bok_topics:protected] =>
[bok_keywords:protected] =>
[id:protected] => 66
[type:protected] => category
[parent:protected] => 2
[label:protected] => Lather
[alreadyInSave:protected] =>
[alreadyInValidation:protected] =>
[validationFailures:protected] => Array
(
)
[_new:BaseObject:private] =>
[_deleted:BaseObject:private] =>
[modifiedColumns:protected] => Array
(
)
)
[67] => Category Object
(
[languages:protected] =>
[bok_resources:protected] =>
[bok_topics:protected] =>
[bok_keywords:protected] =>
[id:protected] => 67
[type:protected] => category
[parent:protected] => 2
[label:protected] => Lead Abatement Worker
[alreadyInSave:protected] =>
[alreadyInValidation:protected] =>
[validationFailures:protected] => Array
(
)
[_new:BaseObject:private] =>
[_deleted:BaseObject:private] =>
[modifiedColumns:protected] => Array
(
)
)
[68] => Category Object
(
[languages:protected] =>
[bok_resources:protected] =>
[bok_topics:protected] =>
[bok_keywords:protected] =>
[id:protected] => 68
[type:protected] => category
[parent:protected] => 2
[label:protected] => Maintenance Worker
[alreadyInSave:protected] =>
[alreadyInValidation:protected] =>
[validationFailures:protected] => Array
(
)
[_new:BaseObject:private] =>
[_deleted:BaseObject:private] =>
[modifiedColumns:protected] => Array
(
)
)
[69] => Category Object
(
[languages:protected] =>
[bok_resources:protected] =>
[bok_topics:protected] =>
[bok_keywords:protected] =>
[id:protected] => 69
[type:protected] => category
[parent:protected] => 2
[label:protected] => Millwright
[alreadyInSave:protected] =>
[alreadyInValidation:protected] =>
[validationFailures:protected] => Array
(
)
[_new:BaseObject:private] =>
[_deleted:BaseObject:private] =>
[modifiedColumns:protected] => Array
(
)
)
[70] => Category Object
(
[languages:protected] =>
[bok_resources:protected] =>
[bok_topics:protected] =>
[bok_keywords:protected] =>
[id:protected] => 70
[type:protected] => category
[parent:protected] => 2
[label:protected] => Operating Engineer
[alreadyInSave:protected] =>
[alreadyInValidation:protected] =>
[validationFailures:protected] => Array
(
)
[_new:BaseObject:private] =>
[_deleted:BaseObject:private] =>
[modifiedColumns:protected] => Array
(
)
)
[71] => Category Object
(
[languages:protected] =>
[bok_resources:protected] =>
[bok_topics:protected] =>
[bok_keywords:protected] =>
[id:protected] => 71
[type:protected] => category
[parent:protected] => 2
[label:protected] => Painter
[alreadyInSave:protected] =>
[alreadyInValidation:protected] =>
[validationFailures:protected] => Array
(
)
[_new:BaseObject:private] =>
[_deleted:BaseObject:private] =>
[modifiedColumns:protected] => Array
(
)
)
[72] => Category Object
(
[languages:protected] =>
[bok_resources:protected] =>
[bok_topics:protected] =>
[bok_keywords:protected] =>
[id:protected] => 72
[type:protected] => category
[parent:protected] => 2
[label:protected] => Paper Hanger
[alreadyInSave:protected] =>
[alreadyInValidation:protected] =>
[validationFailures:protected] => Array
(
)
[_new:BaseObject:private] =>
[_deleted:BaseObject:private] =>
[modifiedColumns:protected] => Array
(
)
)
[73] => Category Object
(
[languages:protected] =>
[bok_resources:protected] =>
[bok_topics:protected] =>
[bok_keywords:protected] =>
[id:protected] => 73
[type:protected] => category
[parent:protected] => 2
[label:protected] => PCC/Restoration
[alreadyInSave:protected] =>
[alreadyInValidation:protected] =>
[validationFailures:protected] => Array
(
)
[_new:BaseObject:private] =>
[_deleted:BaseObject:private] =>
[modifiedColumns:protected] => Array
(
)
)
[74] => Category Object
(
[languages:protected] =>
[bok_resources:protected] =>
[bok_topics:protected] =>
[bok_keywords:protected] =>
[id:protected] => 74
[type:protected] => category
[parent:protected] => 2
[label:protected] => Pile Driver
[alreadyInSave:protected] =>
[alreadyInValidation:protected] =>
[validationFailures:protected] => Array
(
)
[_new:BaseObject:private] =>
[_deleted:BaseObject:private] =>
[modifiedColumns:protected] => Array
(
)
)
[75] => Category Object
(
[languages:protected] =>
[bok_resources:protected] =>
[bok_topics:protected] =>
[bok_keywords:protected] =>
[id:protected] => 75
[type:protected] => category
[parent:protected] => 2
[label:protected] => Plasterer
[alreadyInSave:protected] =>
[alreadyInValidation:protected] =>
[validationFailures:protected] => Array
(
)
[_new:BaseObject:private] =>
[_deleted:BaseObject:private] =>
[modifiedColumns:protected] => Array
(
)
)
[76] => Category Object
(
[languages:protected] =>
[bok_resources:protected] =>
[bok_topics:protected] =>
[bok_keywords:protected] =>
[id:protected] => 76
[type:protected] => category
[parent:protected] => 2
[label:protected] => Plumber/Pipefitter
[alreadyInSave:protected] =>
[alreadyInValidation:protected] =>
[validationFailures:protected] => Array
(
)
[_new:BaseObject:private] =>
[_deleted:BaseObject:private] =>
[modifiedColumns:protected] => Array
(
)
)
[77] => Category Object
(
[languages:protected] =>
[bok_resources:protected] =>
[bok_topics:protected] =>
[bok_keywords:protected] =>
[id:protected] => 77
[type:protected] => category
[parent:protected] => 2
[label:protected] => Refractory Worker
[alreadyInSave:protected] =>
[alreadyInValidation:protected] =>
[validationFailures:protected] => Array
(
)
[_new:BaseObject:private] =>
[_deleted:BaseObject:private] =>
[modifiedColumns:protected] => Array
(
)
)
[63] => Category Object
(
[languages:protected] =>
[bok_resources:protected] =>
[bok_topics:protected] =>
[bok_keywords:protected] =>
[id:protected] => 63
[type:protected] => category
[parent:protected] => 2
[label:protected] => Reinforcing Ironworker
[alreadyInSave:protected] =>
[alreadyInValidation:protected] =>
[validationFailures:protected] => Array
(
)
[_new:BaseObject:private] =>
[_deleted:BaseObject:private] =>
[modifiedColumns:protected] => Array
(
)
)
[78] => Category Object
(
[languages:protected] =>
[bok_resources:protected] =>
[bok_topics:protected] =>
[bok_keywords:protected] =>
[id:protected] => 78
[type:protected] => category
[parent:protected] => 2
[label:protected] => Roofer/Waterproofer
[alreadyInSave:protected] =>
[alreadyInValidation:protected] =>
[validationFailures:protected] => Array
(
)
[_new:BaseObject:private] =>
[_deleted:BaseObject:private] =>
[modifiedColumns:protected] => Array
(
)
)
[79] => Category Object
(
[languages:protected] =>
[bok_resources:protected] =>
[bok_topics:protected] =>
[bok_keywords:protected] =>
[id:protected] => 79
[type:protected] => category
[parent:protected] => 2
[label:protected] => Scaffold Erector
[alreadyInSave:protected] =>
[alreadyInValidation:protected] =>
[validationFailures:protected] => Array
(
)
[_new:BaseObject:private] =>
[_deleted:BaseObject:private] =>
[modifiedColumns:protected] => Array
(
)
)
[80] => Category Object
(
[languages:protected] =>
[bok_resources:protected] =>
[bok_topics:protected] =>
[bok_keywords:protected] =>
[id:protected] => 80
[type:protected] => category
[parent:protected] => 2
[label:protected] => Sheetmetal Worker
[alreadyInSave:protected] =>
[alreadyInValidation:protected] =>
[validationFailures:protected] => Array
(
)
[_new:BaseObject:private] =>
[_deleted:BaseObject:private] =>
[modifiedColumns:protected] => Array
(
)
)
[81] => Category Object
(
[languages:protected] =>
[bok_resources:protected] =>
[bok_topics:protected] =>
[bok_keywords:protected] =>
[id:protected] => 81
[type:protected] => category
[parent:protected] => 2
[label:protected] => Sprinkler Fitter
[alreadyInSave:protected] =>
[alreadyInValidation:protected] =>
[validationFailures:protected] => Array
(
)
[_new:BaseObject:private] =>
[_deleted:BaseObject:private] =>
[modifiedColumns:protected] => Array
(
)
)
[82] => Category Object
(
[languages:protected] =>
[bok_resources:protected] =>
[bok_topics:protected] =>
[bok_keywords:protected] =>
[id:protected] => 82
[type:protected] => category
[parent:protected] => 2
[label:protected] => Stonemason
[alreadyInSave:protected] =>
[alreadyInValidation:protected] =>
[validationFailures:protected] => Array
(
)
[_new:BaseObject:private] =>
[_deleted:BaseObject:private] =>
[modifiedColumns:protected] => Array
(
)
)
[62] => Category Object
(
[languages:protected] =>
[bok_resources:protected] =>
[bok_topics:protected] =>
[bok_keywords:protected] =>
[id:protected] => 62
[type:protected] => category
[parent:protected] => 2
[label:protected] => Structural Ironworker
[alreadyInSave:protected] =>
[alreadyInValidation:protected] =>
[validationFailures:protected] => Array
(
)
[_new:BaseObject:private] =>
[_deleted:BaseObject:private] =>
[modifiedColumns:protected] => Array
(
)
)
[83] => Category Object
(
[languages:protected] =>
[bok_resources:protected] =>
[bok_topics:protected] =>
[bok_keywords:protected] =>
[id:protected] => 83
[type:protected] => category
[parent:protected] => 2
[label:protected] => Terrazzo Worker
[alreadyInSave:protected] =>
[alreadyInValidation:protected] =>
[validationFailures:protected] => Array
(
)
[_new:BaseObject:private] =>
[_deleted:BaseObject:private] =>
[modifiedColumns:protected] => Array
(
)
)
[84] => Category Object
(
[languages:protected] =>
[bok_resources:protected] =>
[bok_topics:protected] =>
[bok_keywords:protected] =>
[id:protected] => 84
[type:protected] => category
[parent:protected] => 2
[label:protected] => Tile Setter
[alreadyInSave:protected] =>
[alreadyInValidation:protected] =>
[validationFailures:protected] => Array
(
)
[_new:BaseObject:private] =>
[_deleted:BaseObject:private] =>
[modifiedColumns:protected] => Array
(
)
)
[85] => Category Object
(
[languages:protected] =>
[bok_resources:protected] =>
[bok_topics:protected] =>
[bok_keywords:protected] =>
[id:protected] => 85
[type:protected] => category
[parent:protected] => 2
[label:protected] => Truck Driver
[alreadyInSave:protected] =>
[alreadyInValidation:protected] =>
[validationFailures:protected] => Array
(
)
[_new:BaseObject:private] =>
[_deleted:BaseObject:private] =>
[modifiedColumns:protected] => Array
(
)
)
[86] => Category Object
(
[languages:protected] =>
[bok_resources:protected] =>
[bok_topics:protected] =>
[bok_keywords:protected] =>
[id:protected] => 86
[type:protected] => category
[parent:protected] => 2
[label:protected] => Welder
[alreadyInSave:protected] =>
[alreadyInValidation:protected] =>
[validationFailures:protected] => Array
(
)
[_new:BaseObject:private] =>
[_deleted:BaseObject:private] =>
[modifiedColumns:protected] => Array
(
)
)
[87] => Category Object
(
[languages:protected] =>
[bok_resources:protected] =>
[bok_topics:protected] =>
[bok_keywords:protected] =>
[id:protected] => 87
[type:protected] => category
[parent:protected] => 3
[label:protected] => Commercial & Institutional
[alreadyInSave:protected] =>
[alreadyInValidation:protected] =>
[validationFailures:protected] => Array
(
)
[_new:BaseObject:private] =>
[_deleted:BaseObject:private] =>
[modifiedColumns:protected] => Array
(
)
)
[88] => Category Object
(
[languages:protected] =>
[bok_resources:protected] =>
[bok_topics:protected] =>
[bok_keywords:protected] =>
[id:protected] => 88
[type:protected] => category
[parent:protected] => 3
[label:protected] => Demolition
[alreadyInSave:protected] =>
[alreadyInValidation:protected] =>
[validationFailures:protected] => Array
(
)
[_new:BaseObject:private] =>
[_deleted:BaseObject:private] =>
[modifiedColumns:protected] => Array
(
)
)
[89] => Category Object
(
[languages:protected] =>
[bok_resources:protected] =>
[bok_topics:protected] =>
[bok_keywords:protected] =>
[id:protected] => 89
[type:protected] => category
[parent:protected] => 3
[label:protected] => Disasters
[alreadyInSave:protected] =>
[alreadyInValidation:protected] =>
[validationFailures:protected] => Array
(
)
[_new:BaseObject:private] =>
[_deleted:BaseObject:private] =>
[modifiedColumns:protected] => Array
(
)
)
[91] => Category Object
(
[languages:protected] =>
[bok_resources:protected] =>
[bok_topics:protected] =>
[bok_keywords:protected] =>
[id:protected] => 91
[type:protected] => category
[parent:protected] => 3
[label:protected] => Heavy & Highway
[alreadyInSave:protected] =>
[alreadyInValidation:protected] =>
[validationFailures:protected] => Array
(
)
[_new:BaseObject:private] =>
[_deleted:BaseObject:private] =>
[modifiedColumns:protected] => Array
(
)
)
[90] => Category Object
(
[languages:protected] =>
[bok_resources:protected] =>
[bok_topics:protected] =>
[bok_keywords:protected] =>
[id:protected] => 90
[type:protected] => category
[parent:protected] => 3
[label:protected] => Industrial
[alreadyInSave:protected] =>
[alreadyInValidation:protected] =>
[validationFailures:protected] => Array
(
)
[_new:BaseObject:private] =>
[_deleted:BaseObject:private] =>
[modifiedColumns:protected] => Array
(
)
)
[92] => Category Object
(
[languages:protected] =>
[bok_resources:protected] =>
[bok_topics:protected] =>
[bok_keywords:protected] =>
[id:protected] => 92
[type:protected] => category
[parent:protected] => 3
[label:protected] => LEED/Green Construction
[alreadyInSave:protected] =>
[alreadyInValidation:protected] =>
[validationFailures:protected] => Array
(
)
[_new:BaseObject:private] =>
[_deleted:BaseObject:private] =>
[modifiedColumns:protected] => Array
(
)
)
[93] => Category Object
(
[languages:protected] =>
[bok_resources:protected] =>
[bok_topics:protected] =>
[bok_keywords:protected] =>
[id:protected] => 93
[type:protected] => category
[parent:protected] => 3
[label:protected] => Renovations
[alreadyInSave:protected] =>
[alreadyInValidation:protected] =>
[validationFailures:protected] => Array
(
)
[_new:BaseObject:private] =>
[_deleted:BaseObject:private] =>
[modifiedColumns:protected] => Array
(
)
)
[94] => Category Object
(
[languages:protected] =>
[bok_resources:protected] =>
[bok_topics:protected] =>
[bok_keywords:protected] =>
[id:protected] => 94
[type:protected] => category
[parent:protected] => 3
[label:protected] => Residential
[alreadyInSave:protected] =>
[alreadyInValidation:protected] =>
[validationFailures:protected] => Array
(
)
[_new:BaseObject:private] =>
[_deleted:BaseObject:private] =>
[modifiedColumns:protected] => Array
(
)
)
[95] => Category Object
(
[languages:protected] =>
[bok_resources:protected] =>
[bok_topics:protected] =>
[bok_keywords:protected] =>
[id:protected] => 95
[type:protected] => category
[parent:protected] => 3
[label:protected] => Underground
[alreadyInSave:protected] =>
[alreadyInValidation:protected] =>
[validationFailures:protected] => Array
(
)
[_new:BaseObject:private] =>
[_deleted:BaseObject:private] =>
[modifiedColumns:protected] => Array
(
)
)
)
[categories_initialized:protected] => 1
[mapped_items:protected] =>
[content:protected] =>
[files:protected] =>
[language:protected] => Language Object
(
[id:protected] => 1
[code:protected] => en
[name:protected] => English
[alreadyInSave:protected] =>
[alreadyInValidation:protected] =>
[validationFailures:protected] => Array
(
)
[_new:BaseObject:private] =>
[_deleted:BaseObject:private] =>
[modifiedColumns:protected] => Array
(
)
)
[old_record:protected] =>
[id:protected] => 4426
[old_id:protected] =>
[elcosh_id:protected] => d001656
[type:protected] => document
[display_type:protected] => HTML only (and links)
[user_id:protected] => 0
[language_id:protected] => 1
[tagging_id:protected] => Mike Aguilar
[priority_id:protected] => 1
[title:protected] => Construction Dive -- DeWalt's Jobsite Pro headphones recalled for fire hazards
[total_pages:protected] => 1
[billed_pages:protected] => 1
[publication_number:protected] =>
[part_of:protected] =>
[keywords:protected] => DeWalt, Fire Hazards, recall, headphones
[comments:protected] =>
[summary:protected] => A recall notice by the United States Consumer Product Safety Commission affects over 300,000 DeWalt Jobsite Pro Headphones. The recall is a result of a malfunction that can cause earbuds to overheat while charging or during use, leading to fire and burn hazards.
[transition_comments:protected] =>
[external_link:protected] => https://www.constructiondive.com/news/dewalts-jobsite-pro-headphones-recalled-for-fire-hazards/611248/?utm_source=Sailthru&utm_medium=email&utm_campaign=Issue:%202021-12-10%20Construction%20Dive%20Newsletter%20%5Bissue:38532%5D&utm_term=Construction%20Dive
[consol_link:protected] =>
[more_like_this:protected] =>
[permission_given_by:protected] =>
[published:protected] => T
[billable:protected] => F
[img_name:protected] =>
[img_ext:protected] =>
[img_width:protected] =>
[img_height:protected] =>
[img_credit:protected] =>
[img_practice:protected] =>
[vid_source_id:protected] =>
[vid_running_time:protected] =>
[vid_intended_audience:protected] =>
[vid_acquisition_info:protected] =>
[vid_cost:protected] =>
[vid_producer:protected] =>
[vid_filename:protected] =>
[vid_filename_downloadable:protected] =>
[date_summary:protected] =>
[date_permission_requested:protected] =>
[date_permission_received:protected] =>
[date_review_needed:protected] =>
[date_received:protected] => 12/13/21
[date_completed:protected] => 12/13/21
[date_billed:protected] =>
[date_modified:protected] => 12/13/21
[collBokExports:protected] =>
[lastBokExportCriteria:BaseElcoshItem:private] =>
[alreadyInSave:protected] =>
[alreadyInValidation:protected] =>
[validationFailures:protected] => Array
(
)
[_new:BaseObject:private] =>
[_deleted:BaseObject:private] =>
[modifiedColumns:protected] => Array
(
)
)
)
)
[new_images] => Array
(
[0] => Search_Result Object
(
[title] => Morning Toolbox Talk
[image] => /record/images/4003-p.jpg
[blurb] => This photo is from an early morning toolbox talk on a construction job in Mclean, Virginia. It is being delivered in English and Spanish....
[category] => Array
(
[0] => 20
[1] => 51
[2] => 57
[3] => 64
[4] => 70
[5] => 63
[6] => 78
[7] => 82
[8] => 62
[9] => 87
[10] => 88
[11] => 89
[12] => 91
[13] => 90
[14] => 93
[15] => 94
[16] => 97
)
[labels] => Array
(
[0] => Safety Culture
[1] => Work Environment
[2] => Hazards
[3] => Cement Mason
[4] => Trades
[5] => Flagger
[7] => Laborer
[9] => Operating Engineer
[11] => Reinforcing Ironworker
[13] => Roofer/Waterproofer
[15] => Stonemason
[17] => Structural Ironworker
[19] => Commercial & Institutional
[20] => Jobsites
[21] => Demolition
[23] => Disasters
[25] => Heavy & Highway
[27] => Industrial
[29] => Renovations
[31] => Residential
[33] => Images
[34] => Media
[35] => Media & Documents
)
[type] => Images
[sub_category] =>
[url] => /image/4003/i002691/Morning%2BToolbox%2BTalk.html
[item:protected] => ImageRecord Object
(
[records:protected] => Array
(
)
[recordId:protected] =>
[searchWordClass:protected] =>
[searchWordPeerClass:protected] =>
[bok_record:protected] =>
[authors:protected] =>
[organizations:protected] =>
[collections:protected] =>
[categories:protected] => Array
(
[20] => Category Object
(
[languages:protected] =>
[bok_resources:protected] =>
[bok_topics:protected] =>
[bok_keywords:protected] =>
[id:protected] => 20
[type:protected] => category
[parent:protected] => 7
[label:protected] => Safety Culture
[alreadyInSave:protected] =>
[alreadyInValidation:protected] =>
[validationFailures:protected] => Array
(
)
[_new:BaseObject:private] =>
[_deleted:BaseObject:private] =>
[modifiedColumns:protected] => Array
(
)
)
[51] => Category Object
(
[languages:protected] =>
[bok_resources:protected] =>
[bok_topics:protected] =>
[bok_keywords:protected] =>
[id:protected] => 51
[type:protected] => category
[parent:protected] => 2
[label:protected] => Cement Mason
[alreadyInSave:protected] =>
[alreadyInValidation:protected] =>
[validationFailures:protected] => Array
(
)
[_new:BaseObject:private] =>
[_deleted:BaseObject:private] =>
[modifiedColumns:protected] => Array
(
)
)
[57] => Category Object
(
[languages:protected] =>
[bok_resources:protected] =>
[bok_topics:protected] =>
[bok_keywords:protected] =>
[id:protected] => 57
[type:protected] => category
[parent:protected] => 2
[label:protected] => Flagger
[alreadyInSave:protected] =>
[alreadyInValidation:protected] =>
[validationFailures:protected] => Array
(
)
[_new:BaseObject:private] =>
[_deleted:BaseObject:private] =>
[modifiedColumns:protected] => Array
(
)
)
[64] => Category Object
(
[languages:protected] =>
[bok_resources:protected] =>
[bok_topics:protected] =>
[bok_keywords:protected] =>
[id:protected] => 64
[type:protected] => category
[parent:protected] => 2
[label:protected] => Laborer
[alreadyInSave:protected] =>
[alreadyInValidation:protected] =>
[validationFailures:protected] => Array
(
)
[_new:BaseObject:private] =>
[_deleted:BaseObject:private] =>
[modifiedColumns:protected] => Array
(
)
)
[70] => Category Object
(
[languages:protected] =>
[bok_resources:protected] =>
[bok_topics:protected] =>
[bok_keywords:protected] =>
[id:protected] => 70
[type:protected] => category
[parent:protected] => 2
[label:protected] => Operating Engineer
[alreadyInSave:protected] =>
[alreadyInValidation:protected] =>
[validationFailures:protected] => Array
(
)
[_new:BaseObject:private] =>
[_deleted:BaseObject:private] =>
[modifiedColumns:protected] => Array
(
)
)
[63] => Category Object
(
[languages:protected] =>
[bok_resources:protected] =>
[bok_topics:protected] =>
[bok_keywords:protected] =>
[id:protected] => 63
[type:protected] => category
[parent:protected] => 2
[label:protected] => Reinforcing Ironworker
[alreadyInSave:protected] =>
[alreadyInValidation:protected] =>
[validationFailures:protected] => Array
(
)
[_new:BaseObject:private] =>
[_deleted:BaseObject:private] =>
[modifiedColumns:protected] => Array
(
)
)
[78] => Category Object
(
[languages:protected] =>
[bok_resources:protected] =>
[bok_topics:protected] =>
[bok_keywords:protected] =>
[id:protected] => 78
[type:protected] => category
[parent:protected] => 2
[label:protected] => Roofer/Waterproofer
[alreadyInSave:protected] =>
[alreadyInValidation:protected] =>
[validationFailures:protected] => Array
(
)
[_new:BaseObject:private] =>
[_deleted:BaseObject:private] =>
[modifiedColumns:protected] => Array
(
)
)
[82] => Category Object
(
[languages:protected] =>
[bok_resources:protected] =>
[bok_topics:protected] =>
[bok_keywords:protected] =>
[id:protected] => 82
[type:protected] => category
[parent:protected] => 2
[label:protected] => Stonemason
[alreadyInSave:protected] =>
[alreadyInValidation:protected] =>
[validationFailures:protected] => Array
(
)
[_new:BaseObject:private] =>
[_deleted:BaseObject:private] =>
[modifiedColumns:protected] => Array
(
)
)
[62] => Category Object
(
[languages:protected] =>
[bok_resources:protected] =>
[bok_topics:protected] =>
[bok_keywords:protected] =>
[id:protected] => 62
[type:protected] => category
[parent:protected] => 2
[label:protected] => Structural Ironworker
[alreadyInSave:protected] =>
[alreadyInValidation:protected] =>
[validationFailures:protected] => Array
(
)
[_new:BaseObject:private] =>
[_deleted:BaseObject:private] =>
[modifiedColumns:protected] => Array
(
)
)
[87] => Category Object
(
[languages:protected] =>
[bok_resources:protected] =>
[bok_topics:protected] =>
[bok_keywords:protected] =>
[id:protected] => 87
[type:protected] => category
[parent:protected] => 3
[label:protected] => Commercial & Institutional
[alreadyInSave:protected] =>
[alreadyInValidation:protected] =>
[validationFailures:protected] => Array
(
)
[_new:BaseObject:private] =>
[_deleted:BaseObject:private] =>
[modifiedColumns:protected] => Array
(
)
)
[88] => Category Object
(
[languages:protected] =>
[bok_resources:protected] =>
[bok_topics:protected] =>
[bok_keywords:protected] =>
[id:protected] => 88
[type:protected] => category
[parent:protected] => 3
[label:protected] => Demolition
[alreadyInSave:protected] =>
[alreadyInValidation:protected] =>
[validationFailures:protected] => Array
(
)
[_new:BaseObject:private] =>
[_deleted:BaseObject:private] =>
[modifiedColumns:protected] => Array
(
)
)
[89] => Category Object
(
[languages:protected] =>
[bok_resources:protected] =>
[bok_topics:protected] =>
[bok_keywords:protected] =>
[id:protected] => 89
[type:protected] => category
[parent:protected] => 3
[label:protected] => Disasters
[alreadyInSave:protected] =>
[alreadyInValidation:protected] =>
[validationFailures:protected] => Array
(
)
[_new:BaseObject:private] =>
[_deleted:BaseObject:private] =>
[modifiedColumns:protected] => Array
(
)
)
[91] => Category Object
(
[languages:protected] =>
[bok_resources:protected] =>
[bok_topics:protected] =>
[bok_keywords:protected] =>
[id:protected] => 91
[type:protected] => category
[parent:protected] => 3
[label:protected] => Heavy & Highway
[alreadyInSave:protected] =>
[alreadyInValidation:protected] =>
[validationFailures:protected] => Array
(
)
[_new:BaseObject:private] =>
[_deleted:BaseObject:private] =>
[modifiedColumns:protected] => Array
(
)
)
[90] => Category Object
(
[languages:protected] =>
[bok_resources:protected] =>
[bok_topics:protected] =>
[bok_keywords:protected] =>
[id:protected] => 90
[type:protected] => category
[parent:protected] => 3
[label:protected] => Industrial
[alreadyInSave:protected] =>
[alreadyInValidation:protected] =>
[validationFailures:protected] => Array
(
)
[_new:BaseObject:private] =>
[_deleted:BaseObject:private] =>
[modifiedColumns:protected] => Array
(
)
)
[93] => Category Object
(
[languages:protected] =>
[bok_resources:protected] =>
[bok_topics:protected] =>
[bok_keywords:protected] =>
[id:protected] => 93
[type:protected] => category
[parent:protected] => 3
[label:protected] => Renovations
[alreadyInSave:protected] =>
[alreadyInValidation:protected] =>
[validationFailures:protected] => Array
(
)
[_new:BaseObject:private] =>
[_deleted:BaseObject:private] =>
[modifiedColumns:protected] => Array
(
)
)
[94] => Category Object
(
[languages:protected] =>
[bok_resources:protected] =>
[bok_topics:protected] =>
[bok_keywords:protected] =>
[id:protected] => 94
[type:protected] => category
[parent:protected] => 3
[label:protected] => Residential
[alreadyInSave:protected] =>
[alreadyInValidation:protected] =>
[validationFailures:protected] => Array
(
)
[_new:BaseObject:private] =>
[_deleted:BaseObject:private] =>
[modifiedColumns:protected] => Array
(
)
)
[97] => Category Object
(
[languages:protected] =>
[bok_resources:protected] =>
[bok_topics:protected] =>
[bok_keywords:protected] =>
[id:protected] => 97
[type:protected] => category
[parent:protected] => 5
[label:protected] => Images
[alreadyInSave:protected] =>
[alreadyInValidation:protected] =>
[validationFailures:protected] => Array
(
)
[_new:BaseObject:private] =>
[_deleted:BaseObject:private] =>
[modifiedColumns:protected] => Array
(
)
)
)
[categories_initialized:protected] => 1
[mapped_items:protected] =>
[content:protected] =>
[files:protected] =>
[language:protected] => Language Object
(
[id:protected] => 1
[code:protected] => en
[name:protected] => English
[alreadyInSave:protected] =>
[alreadyInValidation:protected] =>
[validationFailures:protected] => Array
(
)
[_new:BaseObject:private] =>
[_deleted:BaseObject:private] =>
[modifiedColumns:protected] => Array
(
)
)
[old_record:protected] =>
[id:protected] => 4003
[old_id:protected] =>
[elcosh_id:protected] => i002691
[type:protected] => image
[display_type:protected] => Image
[user_id:protected] => 0
[language_id:protected] => 1
[tagging_id:protected] => Bruce Lippy
[priority_id:protected] => 1
[title:protected] => Morning Toolbox Talk
[total_pages:protected] => 0
[billed_pages:protected] => 0
[publication_number:protected] =>
[part_of:protected] =>
[keywords:protected] => toolbox talk, tailgate talk, Spanish, bilingual
[comments:protected] =>
[summary:protected] => This photo is from an early morning toolbox talk on a construction job in Mclean, Virginia. It is being delivered in English and Spanish.
[transition_comments:protected] =>
[external_link:protected] =>
[consol_link:protected] => http://www.cpwrconstructionsolutions.org/electrical/solution/662/worker-training.html
[more_like_this:protected] => d001285,d001304,c000079
[permission_given_by:protected] =>
[published:protected] => T
[billable:protected] => F
[img_name:protected] =>
[img_ext:protected] => jpg
[img_width:protected] =>
[img_height:protected] =>
[img_credit:protected] => Morgan Zavertnik and Hoar Construction
[img_practice:protected] => good
[vid_source_id:protected] =>
[vid_running_time:protected] =>
[vid_intended_audience:protected] =>
[vid_acquisition_info:protected] =>
[vid_cost:protected] =>
[vid_producer:protected] =>
[vid_filename:protected] =>
[vid_filename_downloadable:protected] =>
[date_summary:protected] => November 2015
[date_permission_requested:protected] =>
[date_permission_received:protected] =>
[date_review_needed:protected] =>
[date_received:protected] => 03/02/16
[date_completed:protected] => 03/02/16
[date_billed:protected] =>
[date_modified:protected] => 03/02/16
[collBokExports:protected] =>
[lastBokExportCriteria:BaseElcoshItem:private] =>
[alreadyInSave:protected] =>
[alreadyInValidation:protected] =>
[validationFailures:protected] => Array
(
)
[_new:BaseObject:private] =>
[_deleted:BaseObject:private] =>
[modifiedColumns:protected] => Array
(
)
)
)
[1] => Search_Result Object
(
[title] => Toolbox talk - crew view
[image] => /record/images/4005-p.jpg
[blurb] => Photo of crew listening to a toolbox safety talk before starting work....
[category] => Array
(
[0] => 97
[1] => 20
[2] => 47
[3] => 49
[4] => 51
[5] => 55
[6] => 61
[7] => 64
[8] => 71
[9] => 75
[10] => 63
[11] => 79
[12] => 62
[13] => 87
[14] => 88
[15] => 91
[16] => 90
[17] => 93
[18] => 94
[19] => 95
)
[labels] => Array
(
[0] => Images
[1] => Media
[2] => Media & Documents
[3] => Safety Culture
[4] => Work Environment
[5] => Hazards
[6] => Bricklayer
[7] => Trades
[8] => Carpenter
[10] => Cement Mason
[12] => Electrical Worker
[14] => Interior Systems Carpenter
[16] => Laborer
[18] => Painter
[20] => Plasterer
[22] => Reinforcing Ironworker
[24] => Scaffold Erector
[26] => Structural Ironworker
[28] => Commercial & Institutional
[29] => Jobsites
[30] => Demolition
[32] => Heavy & Highway
[34] => Industrial
[36] => Renovations
[38] => Residential
[40] => Underground
)
[type] => Images
[sub_category] =>
[url] => /image/4005/i002692/Toolbox%2Btalk%2B-%2Bcrew%2Bview.html
[item:protected] => ImageRecord Object
(
[records:protected] => Array
(
)
[recordId:protected] =>
[searchWordClass:protected] =>
[searchWordPeerClass:protected] =>
[bok_record:protected] =>
[authors:protected] =>
[organizations:protected] =>
[collections:protected] =>
[categories:protected] => Array
(
[97] => Category Object
(
[languages:protected] =>
[bok_resources:protected] =>
[bok_topics:protected] =>
[bok_keywords:protected] =>
[id:protected] => 97
[type:protected] => category
[parent:protected] => 5
[label:protected] => Images
[alreadyInSave:protected] =>
[alreadyInValidation:protected] =>
[validationFailures:protected] => Array
(
)
[_new:BaseObject:private] =>
[_deleted:BaseObject:private] =>
[modifiedColumns:protected] => Array
(
)
)
[20] => Category Object
(
[languages:protected] =>
[bok_resources:protected] =>
[bok_topics:protected] =>
[bok_keywords:protected] =>
[id:protected] => 20
[type:protected] => category
[parent:protected] => 7
[label:protected] => Safety Culture
[alreadyInSave:protected] =>
[alreadyInValidation:protected] =>
[validationFailures:protected] => Array
(
)
[_new:BaseObject:private] =>
[_deleted:BaseObject:private] =>
[modifiedColumns:protected] => Array
(
)
)
[47] => Category Object
(
[languages:protected] =>
[bok_resources:protected] =>
[bok_topics:protected] =>
[bok_keywords:protected] =>
[id:protected] => 47
[type:protected] => category
[parent:protected] => 2
[label:protected] => Bricklayer
[alreadyInSave:protected] =>
[alreadyInValidation:protected] =>
[validationFailures:protected] => Array
(
)
[_new:BaseObject:private] =>
[_deleted:BaseObject:private] =>
[modifiedColumns:protected] => Array
(
)
)
[49] => Category Object
(
[languages:protected] =>
[bok_resources:protected] =>
[bok_topics:protected] =>
[bok_keywords:protected] =>
[id:protected] => 49
[type:protected] => category
[parent:protected] => 2
[label:protected] => Carpenter
[alreadyInSave:protected] =>
[alreadyInValidation:protected] =>
[validationFailures:protected] => Array
(
)
[_new:BaseObject:private] =>
[_deleted:BaseObject:private] =>
[modifiedColumns:protected] => Array
(
)
)
[51] => Category Object
(
[languages:protected] =>
[bok_resources:protected] =>
[bok_topics:protected] =>
[bok_keywords:protected] =>
[id:protected] => 51
[type:protected] => category
[parent:protected] => 2
[label:protected] => Cement Mason
[alreadyInSave:protected] =>
[alreadyInValidation:protected] =>
[validationFailures:protected] => Array
(
)
[_new:BaseObject:private] =>
[_deleted:BaseObject:private] =>
[modifiedColumns:protected] => Array
(
)
)
[55] => Category Object
(
[languages:protected] =>
[bok_resources:protected] =>
[bok_topics:protected] =>
[bok_keywords:protected] =>
[id:protected] => 55
[type:protected] => category
[parent:protected] => 2
[label:protected] => Electrical Worker
[alreadyInSave:protected] =>
[alreadyInValidation:protected] =>
[validationFailures:protected] => Array
(
)
[_new:BaseObject:private] =>
[_deleted:BaseObject:private] =>
[modifiedColumns:protected] => Array
(
)
)
[61] => Category Object
(
[languages:protected] =>
[bok_resources:protected] =>
[bok_topics:protected] =>
[bok_keywords:protected] =>
[id:protected] => 61
[type:protected] => category
[parent:protected] => 2
[label:protected] => Interior Systems Carpenter
[alreadyInSave:protected] =>
[alreadyInValidation:protected] =>
[validationFailures:protected] => Array
(
)
[_new:BaseObject:private] =>
[_deleted:BaseObject:private] =>
[modifiedColumns:protected] => Array
(
)
)
[64] => Category Object
(
[languages:protected] =>
[bok_resources:protected] =>
[bok_topics:protected] =>
[bok_keywords:protected] =>
[id:protected] => 64
[type:protected] => category
[parent:protected] => 2
[label:protected] => Laborer
[alreadyInSave:protected] =>
[alreadyInValidation:protected] =>
[validationFailures:protected] => Array
(
)
[_new:BaseObject:private] =>
[_deleted:BaseObject:private] =>
[modifiedColumns:protected] => Array
(
)
)
[71] => Category Object
(
[languages:protected] =>
[bok_resources:protected] =>
[bok_topics:protected] =>
[bok_keywords:protected] =>
[id:protected] => 71
[type:protected] => category
[parent:protected] => 2
[label:protected] => Painter
[alreadyInSave:protected] =>
[alreadyInValidation:protected] =>
[validationFailures:protected] => Array
(
)
[_new:BaseObject:private] =>
[_deleted:BaseObject:private] =>
[modifiedColumns:protected] => Array
(
)
)
[75] => Category Object
(
[languages:protected] =>
[bok_resources:protected] =>
[bok_topics:protected] =>
[bok_keywords:protected] =>
[id:protected] => 75
[type:protected] => category
[parent:protected] => 2
[label:protected] => Plasterer
[alreadyInSave:protected] =>
[alreadyInValidation:protected] =>
[validationFailures:protected] => Array
(
)
[_new:BaseObject:private] =>
[_deleted:BaseObject:private] =>
[modifiedColumns:protected] => Array
(
)
)
[63] => Category Object
(
[languages:protected] =>
[bok_resources:protected] =>
[bok_topics:protected] =>
[bok_keywords:protected] =>
[id:protected] => 63
[type:protected] => category
[parent:protected] => 2
[label:protected] => Reinforcing Ironworker
[alreadyInSave:protected] =>
[alreadyInValidation:protected] =>
[validationFailures:protected] => Array
(
)
[_new:BaseObject:private] =>
[_deleted:BaseObject:private] =>
[modifiedColumns:protected] => Array
(
)
)
[79] => Category Object
(
[languages:protected] =>
[bok_resources:protected] =>
[bok_topics:protected] =>
[bok_keywords:protected] =>
[id:protected] => 79
[type:protected] => category
[parent:protected] => 2
[label:protected] => Scaffold Erector
[alreadyInSave:protected] =>
[alreadyInValidation:protected] =>
[validationFailures:protected] => Array
(
)
[_new:BaseObject:private] =>
[_deleted:BaseObject:private] =>
[modifiedColumns:protected] => Array
(
)
)
[62] => Category Object
(
[languages:protected] =>
[bok_resources:protected] =>
[bok_topics:protected] =>
[bok_keywords:protected] =>
[id:protected] => 62
[type:protected] => category
[parent:protected] => 2
[label:protected] => Structural Ironworker
[alreadyInSave:protected] =>
[alreadyInValidation:protected] =>
[validationFailures:protected] => Array
(
)
[_new:BaseObject:private] =>
[_deleted:BaseObject:private] =>
[modifiedColumns:protected] => Array
(
)
)
[87] => Category Object
(
[languages:protected] =>
[bok_resources:protected] =>
[bok_topics:protected] =>
[bok_keywords:protected] =>
[id:protected] => 87
[type:protected] => category
[parent:protected] => 3
[label:protected] => Commercial & Institutional
[alreadyInSave:protected] =>
[alreadyInValidation:protected] =>
[validationFailures:protected] => Array
(
)
[_new:BaseObject:private] =>
[_deleted:BaseObject:private] =>
[modifiedColumns:protected] => Array
(
)
)
[88] => Category Object
(
[languages:protected] =>
[bok_resources:protected] =>
[bok_topics:protected] =>
[bok_keywords:protected] =>
[id:protected] => 88
[type:protected] => category
[parent:protected] => 3
[label:protected] => Demolition
[alreadyInSave:protected] =>
[alreadyInValidation:protected] =>
[validationFailures:protected] => Array
(
)
[_new:BaseObject:private] =>
[_deleted:BaseObject:private] =>
[modifiedColumns:protected] => Array
(
)
)
[91] => Category Object
(
[languages:protected] =>
[bok_resources:protected] =>
[bok_topics:protected] =>
[bok_keywords:protected] =>
[id:protected] => 91
[type:protected] => category
[parent:protected] => 3
[label:protected] => Heavy & Highway
[alreadyInSave:protected] =>
[alreadyInValidation:protected] =>
[validationFailures:protected] => Array
(
)
[_new:BaseObject:private] =>
[_deleted:BaseObject:private] =>
[modifiedColumns:protected] => Array
(
)
)
[90] => Category Object
(
[languages:protected] =>
[bok_resources:protected] =>
[bok_topics:protected] =>
[bok_keywords:protected] =>
[id:protected] => 90
[type:protected] => category
[parent:protected] => 3
[label:protected] => Industrial
[alreadyInSave:protected] =>
[alreadyInValidation:protected] =>
[validationFailures:protected] => Array
(
)
[_new:BaseObject:private] =>
[_deleted:BaseObject:private] =>
[modifiedColumns:protected] => Array
(
)
)
[93] => Category Object
(
[languages:protected] =>
[bok_resources:protected] =>
[bok_topics:protected] =>
[bok_keywords:protected] =>
[id:protected] => 93
[type:protected] => category
[parent:protected] => 3
[label:protected] => Renovations
[alreadyInSave:protected] =>
[alreadyInValidation:protected] =>
[validationFailures:protected] => Array
(
)
[_new:BaseObject:private] =>
[_deleted:BaseObject:private] =>
[modifiedColumns:protected] => Array
(
)
)
[94] => Category Object
(
[languages:protected] =>
[bok_resources:protected] =>
[bok_topics:protected] =>
[bok_keywords:protected] =>
[id:protected] => 94
[type:protected] => category
[parent:protected] => 3
[label:protected] => Residential
[alreadyInSave:protected] =>
[alreadyInValidation:protected] =>
[validationFailures:protected] => Array
(
)
[_new:BaseObject:private] =>
[_deleted:BaseObject:private] =>
[modifiedColumns:protected] => Array
(
)
)
[95] => Category Object
(
[languages:protected] =>
[bok_resources:protected] =>
[bok_topics:protected] =>
[bok_keywords:protected] =>
[id:protected] => 95
[type:protected] => category
[parent:protected] => 3
[label:protected] => Underground
[alreadyInSave:protected] =>
[alreadyInValidation:protected] =>
[validationFailures:protected] => Array
(
)
[_new:BaseObject:private] =>
[_deleted:BaseObject:private] =>
[modifiedColumns:protected] => Array
(
)
)
)
[categories_initialized:protected] => 1
[mapped_items:protected] =>
[content:protected] =>
[files:protected] =>
[language:protected] => Language Object
(
[id:protected] => 1
[code:protected] => en
[name:protected] => English
[alreadyInSave:protected] =>
[alreadyInValidation:protected] =>
[validationFailures:protected] => Array
(
)
[_new:BaseObject:private] =>
[_deleted:BaseObject:private] =>
[modifiedColumns:protected] => Array
(
)
)
[old_record:protected] =>
[id:protected] => 4005
[old_id:protected] =>
[elcosh_id:protected] => i002692
[type:protected] => image
[display_type:protected] => Image
[user_id:protected] => 0
[language_id:protected] => 1
[tagging_id:protected] => Bruce Lippy
[priority_id:protected] => 1
[title:protected] => Toolbox talk - crew view
[total_pages:protected] => 0
[billed_pages:protected] => 0
[publication_number:protected] =>
[part_of:protected] =>
[keywords:protected] => toolbox talk, tailgate talk, safety talk, Spanish
[comments:protected] =>
[summary:protected] => Photo of crew listening to a toolbox safety talk before starting work.
[transition_comments:protected] =>
[external_link:protected] =>
[consol_link:protected] => http://www.cpwrconstructionsolutions.org/electrical/solution/662/worker-training.html
[more_like_this:protected] => i002691,d001269, c000079, d001285
[permission_given_by:protected] =>
[published:protected] => T
[billable:protected] => F
[img_name:protected] =>
[img_ext:protected] => jpg
[img_width:protected] =>
[img_height:protected] =>
[img_credit:protected] => Morgan Zavertnik and Hoar Construction
[img_practice:protected] => good
[vid_source_id:protected] =>
[vid_running_time:protected] =>
[vid_intended_audience:protected] =>
[vid_acquisition_info:protected] =>
[vid_cost:protected] =>
[vid_producer:protected] =>
[vid_filename:protected] =>
[vid_filename_downloadable:protected] =>
[date_summary:protected] => November 2015
[date_permission_requested:protected] =>
[date_permission_received:protected] =>
[date_review_needed:protected] =>
[date_received:protected] => 03/02/16
[date_completed:protected] => 03/02/16
[date_billed:protected] =>
[date_modified:protected] => 03/02/16
[collBokExports:protected] =>
[lastBokExportCriteria:BaseElcoshItem:private] =>
[alreadyInSave:protected] =>
[alreadyInValidation:protected] =>
[validationFailures:protected] => Array
(
)
[_new:BaseObject:private] =>
[_deleted:BaseObject:private] =>
[modifiedColumns:protected] => Array
(
)
)
)
[2] => Search_Result Object
(
[title] => Toolbox talk - long shot
[image] => /record/images/4006-p.jpg
[blurb] => This crew gathered every morning before starting work to discuss a new safety topic....
[category] => Array
(
[0] => 20
[1] => 47
[2] => 49
[3] => 51
[4] => 55
[5] => 64
[6] => 68
[7] => 75
[8] => 76
[9] => 63
[10] => 78
[11] => 79
[12] => 82
[13] => 62
[14] => 87
[15] => 88
[16] => 91
[17] => 90
[18] => 93
[19] => 94
[20] => 95
[21] => 97
)
[labels] => Array
(
[0] => Safety Culture
[1] => Work Environment
[2] => Hazards
[3] => Bricklayer
[4] => Trades
[5] => Carpenter
[7] => Cement Mason
[9] => Electrical Worker
[11] => Laborer
[13] => Maintenance Worker
[15] => Plasterer
[17] => Plumber/Pipefitter
[19] => Reinforcing Ironworker
[21] => Roofer/Waterproofer
[23] => Scaffold Erector
[25] => Stonemason
[27] => Structural Ironworker
[29] => Commercial & Institutional
[30] => Jobsites
[31] => Demolition
[33] => Heavy & Highway
[35] => Industrial
[37] => Renovations
[39] => Residential
[41] => Underground
[43] => Images
[44] => Media
[45] => Media & Documents
)
[type] => Images
[sub_category] =>
[url] => /image/4006/i002693/Toolbox%2Btalk%2B-%2Blong%2Bshot.html
[item:protected] => ImageRecord Object
(
[records:protected] => Array
(
)
[recordId:protected] =>
[searchWordClass:protected] =>
[searchWordPeerClass:protected] =>
[bok_record:protected] =>
[authors:protected] =>
[organizations:protected] =>
[collections:protected] =>
[categories:protected] => Array
(
[20] => Category Object
(
[languages:protected] =>
[bok_resources:protected] =>
[bok_topics:protected] =>
[bok_keywords:protected] =>
[id:protected] => 20
[type:protected] => category
[parent:protected] => 7
[label:protected] => Safety Culture
[alreadyInSave:protected] =>
[alreadyInValidation:protected] =>
[validationFailures:protected] => Array
(
)
[_new:BaseObject:private] =>
[_deleted:BaseObject:private] =>
[modifiedColumns:protected] => Array
(
)
)
[47] => Category Object
(
[languages:protected] =>
[bok_resources:protected] =>
[bok_topics:protected] =>
[bok_keywords:protected] =>
[id:protected] => 47
[type:protected] => category
[parent:protected] => 2
[label:protected] => Bricklayer
[alreadyInSave:protected] =>
[alreadyInValidation:protected] =>
[validationFailures:protected] => Array
(
)
[_new:BaseObject:private] =>
[_deleted:BaseObject:private] =>
[modifiedColumns:protected] => Array
(
)
)
[49] => Category Object
(
[languages:protected] =>
[bok_resources:protected] =>
[bok_topics:protected] =>
[bok_keywords:protected] =>
[id:protected] => 49
[type:protected] => category
[parent:protected] => 2
[label:protected] => Carpenter
[alreadyInSave:protected] =>
[alreadyInValidation:protected] =>
[validationFailures:protected] => Array
(
)
[_new:BaseObject:private] =>
[_deleted:BaseObject:private] =>
[modifiedColumns:protected] => Array
(
)
)
[51] => Category Object
(
[languages:protected] =>
[bok_resources:protected] =>
[bok_topics:protected] =>
[bok_keywords:protected] =>
[id:protected] => 51
[type:protected] => category
[parent:protected] => 2
[label:protected] => Cement Mason
[alreadyInSave:protected] =>
[alreadyInValidation:protected] =>
[validationFailures:protected] => Array
(
)
[_new:BaseObject:private] =>
[_deleted:BaseObject:private] =>
[modifiedColumns:protected] => Array
(
)
)
[55] => Category Object
(
[languages:protected] =>
[bok_resources:protected] =>
[bok_topics:protected] =>
[bok_keywords:protected] =>
[id:protected] => 55
[type:protected] => category
[parent:protected] => 2
[label:protected] => Electrical Worker
[alreadyInSave:protected] =>
[alreadyInValidation:protected] =>
[validationFailures:protected] => Array
(
)
[_new:BaseObject:private] =>
[_deleted:BaseObject:private] =>
[modifiedColumns:protected] => Array
(
)
)
[64] => Category Object
(
[languages:protected] =>
[bok_resources:protected] =>
[bok_topics:protected] =>
[bok_keywords:protected] =>
[id:protected] => 64
[type:protected] => category
[parent:protected] => 2
[label:protected] => Laborer
[alreadyInSave:protected] =>
[alreadyInValidation:protected] =>
[validationFailures:protected] => Array
(
)
[_new:BaseObject:private] =>
[_deleted:BaseObject:private] =>
[modifiedColumns:protected] => Array
(
)
)
[68] => Category Object
(
[languages:protected] =>
[bok_resources:protected] =>
[bok_topics:protected] =>
[bok_keywords:protected] =>
[id:protected] => 68
[type:protected] => category
[parent:protected] => 2
[label:protected] => Maintenance Worker
[alreadyInSave:protected] =>
[alreadyInValidation:protected] =>
[validationFailures:protected] => Array
(
)
[_new:BaseObject:private] =>
[_deleted:BaseObject:private] =>
[modifiedColumns:protected] => Array
(
)
)
[75] => Category Object
(
[languages:protected] =>
[bok_resources:protected] =>
[bok_topics:protected] =>
[bok_keywords:protected] =>
[id:protected] => 75
[type:protected] => category
[parent:protected] => 2
[label:protected] => Plasterer
[alreadyInSave:protected] =>
[alreadyInValidation:protected] =>
[validationFailures:protected] => Array
(
)
[_new:BaseObject:private] =>
[_deleted:BaseObject:private] =>
[modifiedColumns:protected] => Array
(
)
)
[76] => Category Object
(
[languages:protected] =>
[bok_resources:protected] =>
[bok_topics:protected] =>
[bok_keywords:protected] =>
[id:protected] => 76
[type:protected] => category
[parent:protected] => 2
[label:protected] => Plumber/Pipefitter
[alreadyInSave:protected] =>
[alreadyInValidation:protected] =>
[validationFailures:protected] => Array
(
)
[_new:BaseObject:private] =>
[_deleted:BaseObject:private] =>
[modifiedColumns:protected] => Array
(
)
)
[63] => Category Object
(
[languages:protected] =>
[bok_resources:protected] =>
[bok_topics:protected] =>
[bok_keywords:protected] =>
[id:protected] => 63
[type:protected] => category
[parent:protected] => 2
[label:protected] => Reinforcing Ironworker
[alreadyInSave:protected] =>
[alreadyInValidation:protected] =>
[validationFailures:protected] => Array
(
)
[_new:BaseObject:private] =>
[_deleted:BaseObject:private] =>
[modifiedColumns:protected] => Array
(
)
)
[78] => Category Object
(
[languages:protected] =>
[bok_resources:protected] =>
[bok_topics:protected] =>
[bok_keywords:protected] =>
[id:protected] => 78
[type:protected] => category
[parent:protected] => 2
[label:protected] => Roofer/Waterproofer
[alreadyInSave:protected] =>
[alreadyInValidation:protected] =>
[validationFailures:protected] => Array
(
)
[_new:BaseObject:private] =>
[_deleted:BaseObject:private] =>
[modifiedColumns:protected] => Array
(
)
)
[79] => Category Object
(
[languages:protected] =>
[bok_resources:protected] =>
[bok_topics:protected] =>
[bok_keywords:protected] =>
[id:protected] => 79
[type:protected] => category
[parent:protected] => 2
[label:protected] => Scaffold Erector
[alreadyInSave:protected] =>
[alreadyInValidation:protected] =>
[validationFailures:protected] => Array
(
)
[_new:BaseObject:private] =>
[_deleted:BaseObject:private] =>
[modifiedColumns:protected] => Array
(
)
)
[82] => Category Object
(
[languages:protected] =>
[bok_resources:protected] =>
[bok_topics:protected] =>
[bok_keywords:protected] =>
[id:protected] => 82
[type:protected] => category
[parent:protected] => 2
[label:protected] => Stonemason
[alreadyInSave:protected] =>
[alreadyInValidation:protected] =>
[validationFailures:protected] => Array
(
)
[_new:BaseObject:private] =>
[_deleted:BaseObject:private] =>
[modifiedColumns:protected] => Array
(
)
)
[62] => Category Object
(
[languages:protected] =>
[bok_resources:protected] =>
[bok_topics:protected] =>
[bok_keywords:protected] =>
[id:protected] => 62
[type:protected] => category
[parent:protected] => 2
[label:protected] => Structural Ironworker
[alreadyInSave:protected] =>
[alreadyInValidation:protected] =>
[validationFailures:protected] => Array
(
)
[_new:BaseObject:private] =>
[_deleted:BaseObject:private] =>
[modifiedColumns:protected] => Array
(
)
)
[87] => Category Object
(
[languages:protected] =>
[bok_resources:protected] =>
[bok_topics:protected] =>
[bok_keywords:protected] =>
[id:protected] => 87
[type:protected] => category
[parent:protected] => 3
[label:protected] => Commercial & Institutional
[alreadyInSave:protected] =>
[alreadyInValidation:protected] =>
[validationFailures:protected] => Array
(
)
[_new:BaseObject:private] =>
[_deleted:BaseObject:private] =>
[modifiedColumns:protected] => Array
(
)
)
[88] => Category Object
(
[languages:protected] =>
[bok_resources:protected] =>
[bok_topics:protected] =>
[bok_keywords:protected] =>
[id:protected] => 88
[type:protected] => category
[parent:protected] => 3
[label:protected] => Demolition
[alreadyInSave:protected] =>
[alreadyInValidation:protected] =>
[validationFailures:protected] => Array
(
)
[_new:BaseObject:private] =>
[_deleted:BaseObject:private] =>
[modifiedColumns:protected] => Array
(
)
)
[91] => Category Object
(
[languages:protected] =>
[bok_resources:protected] =>
[bok_topics:protected] =>
[bok_keywords:protected] =>
[id:protected] => 91
[type:protected] => category
[parent:protected] => 3
[label:protected] => Heavy & Highway
[alreadyInSave:protected] =>
[alreadyInValidation:protected] =>
[validationFailures:protected] => Array
(
)
[_new:BaseObject:private] =>
[_deleted:BaseObject:private] =>
[modifiedColumns:protected] => Array
(
)
)
[90] => Category Object
(
[languages:protected] =>
[bok_resources:protected] =>
[bok_topics:protected] =>
[bok_keywords:protected] =>
[id:protected] => 90
[type:protected] => category
[parent:protected] => 3
[label:protected] => Industrial
[alreadyInSave:protected] =>
[alreadyInValidation:protected] =>
[validationFailures:protected] => Array
(
)
[_new:BaseObject:private] =>
[_deleted:BaseObject:private] =>
[modifiedColumns:protected] => Array
(
)
)
[93] => Category Object
(
[languages:protected] =>
[bok_resources:protected] =>
[bok_topics:protected] =>
[bok_keywords:protected] =>
[id:protected] => 93
[type:protected] => category
[parent:protected] => 3
[label:protected] => Renovations
[alreadyInSave:protected] =>
[alreadyInValidation:protected] =>
[validationFailures:protected] => Array
(
)
[_new:BaseObject:private] =>
[_deleted:BaseObject:private] =>
[modifiedColumns:protected] => Array
(
)
)
[94] => Category Object
(
[languages:protected] =>
[bok_resources:protected] =>
[bok_topics:protected] =>
[bok_keywords:protected] =>
[id:protected] => 94
[type:protected] => category
[parent:protected] => 3
[label:protected] => Residential
[alreadyInSave:protected] =>
[alreadyInValidation:protected] =>
[validationFailures:protected] => Array
(
)
[_new:BaseObject:private] =>
[_deleted:BaseObject:private] =>
[modifiedColumns:protected] => Array
(
)
)
[95] => Category Object
(
[languages:protected] =>
[bok_resources:protected] =>
[bok_topics:protected] =>
[bok_keywords:protected] =>
[id:protected] => 95
[type:protected] => category
[parent:protected] => 3
[label:protected] => Underground
[alreadyInSave:protected] =>
[alreadyInValidation:protected] =>
[validationFailures:protected] => Array
(
)
[_new:BaseObject:private] =>
[_deleted:BaseObject:private] =>
[modifiedColumns:protected] => Array
(
)
)
[97] => Category Object
(
[languages:protected] =>
[bok_resources:protected] =>
[bok_topics:protected] =>
[bok_keywords:protected] =>
[id:protected] => 97
[type:protected] => category
[parent:protected] => 5
[label:protected] => Images
[alreadyInSave:protected] =>
[alreadyInValidation:protected] =>
[validationFailures:protected] => Array
(
)
[_new:BaseObject:private] =>
[_deleted:BaseObject:private] =>
[modifiedColumns:protected] => Array
(
)
)
)
[categories_initialized:protected] => 1
[mapped_items:protected] =>
[content:protected] =>
[files:protected] =>
[language:protected] => Language Object
(
[id:protected] => 1
[code:protected] => en
[name:protected] => English
[alreadyInSave:protected] =>
[alreadyInValidation:protected] =>
[validationFailures:protected] => Array
(
)
[_new:BaseObject:private] =>
[_deleted:BaseObject:private] =>
[modifiedColumns:protected] => Array
(
)
)
[old_record:protected] =>
[id:protected] => 4006
[old_id:protected] =>
[elcosh_id:protected] => i002693
[type:protected] => image
[display_type:protected] => Image
[user_id:protected] => 0
[language_id:protected] => 1
[tagging_id:protected] => Bruce Lippy
[priority_id:protected] => 1
[title:protected] => Toolbox talk - long shot
[total_pages:protected] => 0
[billed_pages:protected] => 0
[publication_number:protected] =>
[part_of:protected] =>
[keywords:protected] => toolbox talk, tailgate talk, safety minute
[comments:protected] =>
[summary:protected] => This crew gathered every morning before starting work to discuss a new safety topic.
[transition_comments:protected] =>
[external_link:protected] =>
[consol_link:protected] => http://www.cpwrconstructionsolutions.org/electrical/solution/662/worker-training.html
[more_like_this:protected] => i002691,i002692,d001269,d000527
[permission_given_by:protected] =>
[published:protected] => T
[billable:protected] => F
[img_name:protected] =>
[img_ext:protected] => jpg
[img_width:protected] =>
[img_height:protected] =>
[img_credit:protected] => Morgan Zavertnik and Hoar Construction
[img_practice:protected] => good
[vid_source_id:protected] =>
[vid_running_time:protected] =>
[vid_intended_audience:protected] =>
[vid_acquisition_info:protected] =>
[vid_cost:protected] =>
[vid_producer:protected] =>
[vid_filename:protected] =>
[vid_filename_downloadable:protected] =>
[date_summary:protected] => November 2015
[date_permission_requested:protected] =>
[date_permission_received:protected] =>
[date_review_needed:protected] =>
[date_received:protected] => 03/02/16
[date_completed:protected] => 03/02/16
[date_billed:protected] =>
[date_modified:protected] => 03/02/16
[collBokExports:protected] =>
[lastBokExportCriteria:BaseElcoshItem:private] =>
[alreadyInSave:protected] =>
[alreadyInValidation:protected] =>
[validationFailures:protected] => Array
(
)
[_new:BaseObject:private] =>
[_deleted:BaseObject:private] =>
[modifiedColumns:protected] => Array
(
)
)
)
[3] => Search_Result Object
(
[title] => Safety officer discussing ongoing project with marketing coordinator
[image] => /record/images/4014-p.jpg
[blurb] => The safety officer (left) points out the good safety practices on this project that reflect well on the firm and may influence future clients....
[category] => Array
(
[0] => 97
[1] => 20
[2] => 46
[3] => 47
[4] => 49
[5] => 50
[6] => 51
[7] => 54
[8] => 55
[9] => 58
[10] => 60
[11] => 61
[12] => 64
[13] => 71
[14] => 75
[15] => 76
[16] => 63
[17] => 79
[18] => 80
[19] => 82
[20] => 62
[21] => 83
[22] => 87
[23] => 91
[24] => 90
[25] => 93
[26] => 94
)
[labels] => Array
(
[0] => Images
[1] => Media
[2] => Media & Documents
[3] => Safety Culture
[4] => Work Environment
[5] => Hazards
[6] => Boilermaker
[7] => Trades
[8] => Bricklayer
[10] => Carpenter
[12] => Carpet Layer
[14] => Cement Mason
[16] => Drywall Applicator Specialist
[18] => Electrical Worker
[20] => Glazier
[22] => HVAC
[24] => Interior Systems Carpenter
[26] => Laborer
[28] => Painter
[30] => Plasterer
[32] => Plumber/Pipefitter
[34] => Reinforcing Ironworker
[36] => Scaffold Erector
[38] => Sheetmetal Worker
[40] => Stonemason
[42] => Structural Ironworker
[44] => Terrazzo Worker
[46] => Commercial & Institutional
[47] => Jobsites
[48] => Heavy & Highway
[50] => Industrial
[52] => Renovations
[54] => Residential
)
[type] => Images
[sub_category] =>
[url] => /image/4014/i002700/Safety%2Bofficer%2Bdiscussing%2Bongoing%2Bproject%2Bwith%2Bmarketing%2Bcoordinator.html
[item:protected] => ImageRecord Object
(
[records:protected] => Array
(
)
[recordId:protected] =>
[searchWordClass:protected] =>
[searchWordPeerClass:protected] =>
[bok_record:protected] =>
[authors:protected] =>
[organizations:protected] =>
[collections:protected] =>
[categories:protected] => Array
(
[97] => Category Object
(
[languages:protected] =>
[bok_resources:protected] =>
[bok_topics:protected] =>
[bok_keywords:protected] =>
[id:protected] => 97
[type:protected] => category
[parent:protected] => 5
[label:protected] => Images
[alreadyInSave:protected] =>
[alreadyInValidation:protected] =>
[validationFailures:protected] => Array
(
)
[_new:BaseObject:private] =>
[_deleted:BaseObject:private] =>
[modifiedColumns:protected] => Array
(
)
)
[20] => Category Object
(
[languages:protected] =>
[bok_resources:protected] =>
[bok_topics:protected] =>
[bok_keywords:protected] =>
[id:protected] => 20
[type:protected] => category
[parent:protected] => 7
[label:protected] => Safety Culture
[alreadyInSave:protected] =>
[alreadyInValidation:protected] =>
[validationFailures:protected] => Array
(
)
[_new:BaseObject:private] =>
[_deleted:BaseObject:private] =>
[modifiedColumns:protected] => Array
(
)
)
[46] => Category Object
(
[languages:protected] =>
[bok_resources:protected] =>
[bok_topics:protected] =>
[bok_keywords:protected] =>
[id:protected] => 46
[type:protected] => category
[parent:protected] => 2
[label:protected] => Boilermaker
[alreadyInSave:protected] =>
[alreadyInValidation:protected] =>
[validationFailures:protected] => Array
(
)
[_new:BaseObject:private] =>
[_deleted:BaseObject:private] =>
[modifiedColumns:protected] => Array
(
)
)
[47] => Category Object
(
[languages:protected] =>
[bok_resources:protected] =>
[bok_topics:protected] =>
[bok_keywords:protected] =>
[id:protected] => 47
[type:protected] => category
[parent:protected] => 2
[label:protected] => Bricklayer
[alreadyInSave:protected] =>
[alreadyInValidation:protected] =>
[validationFailures:protected] => Array
(
)
[_new:BaseObject:private] =>
[_deleted:BaseObject:private] =>
[modifiedColumns:protected] => Array
(
)
)
[49] => Category Object
(
[languages:protected] =>
[bok_resources:protected] =>
[bok_topics:protected] =>
[bok_keywords:protected] =>
[id:protected] => 49
[type:protected] => category
[parent:protected] => 2
[label:protected] => Carpenter
[alreadyInSave:protected] =>
[alreadyInValidation:protected] =>
[validationFailures:protected] => Array
(
)
[_new:BaseObject:private] =>
[_deleted:BaseObject:private] =>
[modifiedColumns:protected] => Array
(
)
)
[50] => Category Object
(
[languages:protected] =>
[bok_resources:protected] =>
[bok_topics:protected] =>
[bok_keywords:protected] =>
[id:protected] => 50
[type:protected] => category
[parent:protected] => 2
[label:protected] => Carpet Layer
[alreadyInSave:protected] =>
[alreadyInValidation:protected] =>
[validationFailures:protected] => Array
(
)
[_new:BaseObject:private] =>
[_deleted:BaseObject:private] =>
[modifiedColumns:protected] => Array
(
)
)
[51] => Category Object
(
[languages:protected] =>
[bok_resources:protected] =>
[bok_topics:protected] =>
[bok_keywords:protected] =>
[id:protected] => 51
[type:protected] => category
[parent:protected] => 2
[label:protected] => Cement Mason
[alreadyInSave:protected] =>
[alreadyInValidation:protected] =>
[validationFailures:protected] => Array
(
)
[_new:BaseObject:private] =>
[_deleted:BaseObject:private] =>
[modifiedColumns:protected] => Array
(
)
)
[54] => Category Object
(
[languages:protected] =>
[bok_resources:protected] =>
[bok_topics:protected] =>
[bok_keywords:protected] =>
[id:protected] => 54
[type:protected] => category
[parent:protected] => 2
[label:protected] => Drywall Applicator Specialist
[alreadyInSave:protected] =>
[alreadyInValidation:protected] =>
[validationFailures:protected] => Array
(
)
[_new:BaseObject:private] =>
[_deleted:BaseObject:private] =>
[modifiedColumns:protected] => Array
(
)
)
[55] => Category Object
(
[languages:protected] =>
[bok_resources:protected] =>
[bok_topics:protected] =>
[bok_keywords:protected] =>
[id:protected] => 55
[type:protected] => category
[parent:protected] => 2
[label:protected] => Electrical Worker
[alreadyInSave:protected] =>
[alreadyInValidation:protected] =>
[validationFailures:protected] => Array
(
)
[_new:BaseObject:private] =>
[_deleted:BaseObject:private] =>
[modifiedColumns:protected] => Array
(
)
)
[58] => Category Object
(
[languages:protected] =>
[bok_resources:protected] =>
[bok_topics:protected] =>
[bok_keywords:protected] =>
[id:protected] => 58
[type:protected] => category
[parent:protected] => 2
[label:protected] => Glazier
[alreadyInSave:protected] =>
[alreadyInValidation:protected] =>
[validationFailures:protected] => Array
(
)
[_new:BaseObject:private] =>
[_deleted:BaseObject:private] =>
[modifiedColumns:protected] => Array
(
)
)
[60] => Category Object
(
[languages:protected] =>
[bok_resources:protected] =>
[bok_topics:protected] =>
[bok_keywords:protected] =>
[id:protected] => 60
[type:protected] => category
[parent:protected] => 2
[label:protected] => HVAC
[alreadyInSave:protected] =>
[alreadyInValidation:protected] =>
[validationFailures:protected] => Array
(
)
[_new:BaseObject:private] =>
[_deleted:BaseObject:private] =>
[modifiedColumns:protected] => Array
(
)
)
[61] => Category Object
(
[languages:protected] =>
[bok_resources:protected] =>
[bok_topics:protected] =>
[bok_keywords:protected] =>
[id:protected] => 61
[type:protected] => category
[parent:protected] => 2
[label:protected] => Interior Systems Carpenter
[alreadyInSave:protected] =>
[alreadyInValidation:protected] =>
[validationFailures:protected] => Array
(
)
[_new:BaseObject:private] =>
[_deleted:BaseObject:private] =>
[modifiedColumns:protected] => Array
(
)
)
[64] => Category Object
(
[languages:protected] =>
[bok_resources:protected] =>
[bok_topics:protected] =>
[bok_keywords:protected] =>
[id:protected] => 64
[type:protected] => category
[parent:protected] => 2
[label:protected] => Laborer
[alreadyInSave:protected] =>
[alreadyInValidation:protected] =>
[validationFailures:protected] => Array
(
)
[_new:BaseObject:private] =>
[_deleted:BaseObject:private] =>
[modifiedColumns:protected] => Array
(
)
)
[71] => Category Object
(
[languages:protected] =>
[bok_resources:protected] =>
[bok_topics:protected] =>
[bok_keywords:protected] =>
[id:protected] => 71
[type:protected] => category
[parent:protected] => 2
[label:protected] => Painter
[alreadyInSave:protected] =>
[alreadyInValidation:protected] =>
[validationFailures:protected] => Array
(
)
[_new:BaseObject:private] =>
[_deleted:BaseObject:private] =>
[modifiedColumns:protected] => Array
(
)
)
[75] => Category Object
(
[languages:protected] =>
[bok_resources:protected] =>
[bok_topics:protected] =>
[bok_keywords:protected] =>
[id:protected] => 75
[type:protected] => category
[parent:protected] => 2
[label:protected] => Plasterer
[alreadyInSave:protected] =>
[alreadyInValidation:protected] =>
[validationFailures:protected] => Array
(
)
[_new:BaseObject:private] =>
[_deleted:BaseObject:private] =>
[modifiedColumns:protected] => Array
(
)
)
[76] => Category Object
(
[languages:protected] =>
[bok_resources:protected] =>
[bok_topics:protected] =>
[bok_keywords:protected] =>
[id:protected] => 76
[type:protected] => category
[parent:protected] => 2
[label:protected] => Plumber/Pipefitter
[alreadyInSave:protected] =>
[alreadyInValidation:protected] =>
[validationFailures:protected] => Array
(
)
[_new:BaseObject:private] =>
[_deleted:BaseObject:private] =>
[modifiedColumns:protected] => Array
(
)
)
[63] => Category Object
(
[languages:protected] =>
[bok_resources:protected] =>
[bok_topics:protected] =>
[bok_keywords:protected] =>
[id:protected] => 63
[type:protected] => category
[parent:protected] => 2
[label:protected] => Reinforcing Ironworker
[alreadyInSave:protected] =>
[alreadyInValidation:protected] =>
[validationFailures:protected] => Array
(
)
[_new:BaseObject:private] =>
[_deleted:BaseObject:private] =>
[modifiedColumns:protected] => Array
(
)
)
[79] => Category Object
(
[languages:protected] =>
[bok_resources:protected] =>
[bok_topics:protected] =>
[bok_keywords:protected] =>
[id:protected] => 79
[type:protected] => category
[parent:protected] => 2
[label:protected] => Scaffold Erector
[alreadyInSave:protected] =>
[alreadyInValidation:protected] =>
[validationFailures:protected] => Array
(
)
[_new:BaseObject:private] =>
[_deleted:BaseObject:private] =>
[modifiedColumns:protected] => Array
(
)
)
[80] => Category Object
(
[languages:protected] =>
[bok_resources:protected] =>
[bok_topics:protected] =>
[bok_keywords:protected] =>
[id:protected] => 80
[type:protected] => category
[parent:protected] => 2
[label:protected] => Sheetmetal Worker
[alreadyInSave:protected] =>
[alreadyInValidation:protected] =>
[validationFailures:protected] => Array
(
)
[_new:BaseObject:private] =>
[_deleted:BaseObject:private] =>
[modifiedColumns:protected] => Array
(
)
)
[82] => Category Object
(
[languages:protected] =>
[bok_resources:protected] =>
[bok_topics:protected] =>
[bok_keywords:protected] =>
[id:protected] => 82
[type:protected] => category
[parent:protected] => 2
[label:protected] => Stonemason
[alreadyInSave:protected] =>
[alreadyInValidation:protected] =>
[validationFailures:protected] => Array
(
)
[_new:BaseObject:private] =>
[_deleted:BaseObject:private] =>
[modifiedColumns:protected] => Array
(
)
)
[62] => Category Object
(
[languages:protected] =>
[bok_resources:protected] =>
[bok_topics:protected] =>
[bok_keywords:protected] =>
[id:protected] => 62
[type:protected] => category
[parent:protected] => 2
[label:protected] => Structural Ironworker
[alreadyInSave:protected] =>
[alreadyInValidation:protected] =>
[validationFailures:protected] => Array
(
)
[_new:BaseObject:private] =>
[_deleted:BaseObject:private] =>
[modifiedColumns:protected] => Array
(
)
)
[83] => Category Object
(
[languages:protected] =>
[bok_resources:protected] =>
[bok_topics:protected] =>
[bok_keywords:protected] =>
[id:protected] => 83
[type:protected] => category
[parent:protected] => 2
[label:protected] => Terrazzo Worker
[alreadyInSave:protected] =>
[alreadyInValidation:protected] =>
[validationFailures:protected] => Array
(
)
[_new:BaseObject:private] =>
[_deleted:BaseObject:private] =>
[modifiedColumns:protected] => Array
(
)
)
[87] => Category Object
(
[languages:protected] =>
[bok_resources:protected] =>
[bok_topics:protected] =>
[bok_keywords:protected] =>
[id:protected] => 87
[type:protected] => category
[parent:protected] => 3
[label:protected] => Commercial & Institutional
[alreadyInSave:protected] =>
[alreadyInValidation:protected] =>
[validationFailures:protected] => Array
(
)
[_new:BaseObject:private] =>
[_deleted:BaseObject:private] =>
[modifiedColumns:protected] => Array
(
)
)
[91] => Category Object
(
[languages:protected] =>
[bok_resources:protected] =>
[bok_topics:protected] =>
[bok_keywords:protected] =>
[id:protected] => 91
[type:protected] => category
[parent:protected] => 3
[label:protected] => Heavy & Highway
[alreadyInSave:protected] =>
[alreadyInValidation:protected] =>
[validationFailures:protected] => Array
(
)
[_new:BaseObject:private] =>
[_deleted:BaseObject:private] =>
[modifiedColumns:protected] => Array
(
)
)
[90] => Category Object
(
[languages:protected] =>
[bok_resources:protected] =>
[bok_topics:protected] =>
[bok_keywords:protected] =>
[id:protected] => 90
[type:protected] => category
[parent:protected] => 3
[label:protected] => Industrial
[alreadyInSave:protected] =>
[alreadyInValidation:protected] =>
[validationFailures:protected] => Array
(
)
[_new:BaseObject:private] =>
[_deleted:BaseObject:private] =>
[modifiedColumns:protected] => Array
(
)
)
[93] => Category Object
(
[languages:protected] =>
[bok_resources:protected] =>
[bok_topics:protected] =>
[bok_keywords:protected] =>
[id:protected] => 93
[type:protected] => category
[parent:protected] => 3
[label:protected] => Renovations
[alreadyInSave:protected] =>
[alreadyInValidation:protected] =>
[validationFailures:protected] => Array
(
)
[_new:BaseObject:private] =>
[_deleted:BaseObject:private] =>
[modifiedColumns:protected] => Array
(
)
)
[94] => Category Object
(
[languages:protected] =>
[bok_resources:protected] =>
[bok_topics:protected] =>
[bok_keywords:protected] =>
[id:protected] => 94
[type:protected] => category
[parent:protected] => 3
[label:protected] => Residential
[alreadyInSave:protected] =>
[alreadyInValidation:protected] =>
[validationFailures:protected] => Array
(
)
[_new:BaseObject:private] =>
[_deleted:BaseObject:private] =>
[modifiedColumns:protected] => Array
(
)
)
)
[categories_initialized:protected] => 1
[mapped_items:protected] =>
[content:protected] =>
[files:protected] =>
[language:protected] => Language Object
(
[id:protected] => 1
[code:protected] => en
[name:protected] => English
[alreadyInSave:protected] =>
[alreadyInValidation:protected] =>
[validationFailures:protected] => Array
(
)
[_new:BaseObject:private] =>
[_deleted:BaseObject:private] =>
[modifiedColumns:protected] => Array
(
)
)
[old_record:protected] =>
[id:protected] => 4014
[old_id:protected] =>
[elcosh_id:protected] => i002700
[type:protected] => image
[display_type:protected] => Image
[user_id:protected] => 0
[language_id:protected] => 1
[tagging_id:protected] => Bruce Lippy
[priority_id:protected] => 1
[title:protected] => Safety officer discussing ongoing project with marketing coordinator
[total_pages:protected] => 0
[billed_pages:protected] => 0
[publication_number:protected] =>
[part_of:protected] =>
[keywords:protected] => Latino, safety officer, safety culture
[comments:protected] =>
[summary:protected] => The safety officer (left) points out the good safety practices on this project that reflect well on the firm and may influence future clients.
[transition_comments:protected] =>
[external_link:protected] =>
[consol_link:protected] => http://www.cpwrconstructionsolutions.org/index.php
[more_like_this:protected] => d000989,d001351,d001362,d000652, d001101, d000931, d001395
[permission_given_by:protected] =>
[published:protected] => T
[billable:protected] => F
[img_name:protected] =>
[img_ext:protected] => jpg
[img_width:protected] =>
[img_height:protected] =>
[img_credit:protected] => Hoar Construction, Photo by Neil Lippy
[img_practice:protected] => good
[vid_source_id:protected] =>
[vid_running_time:protected] =>
[vid_intended_audience:protected] =>
[vid_acquisition_info:protected] =>
[vid_cost:protected] =>
[vid_producer:protected] =>
[vid_filename:protected] =>
[vid_filename_downloadable:protected] =>
[date_summary:protected] => November 2015
[date_permission_requested:protected] =>
[date_permission_received:protected] =>
[date_review_needed:protected] =>
[date_received:protected] => 03/02/16
[date_completed:protected] => 03/02/16
[date_billed:protected] =>
[date_modified:protected] => 01/30/23
[collBokExports:protected] =>
[lastBokExportCriteria:BaseElcoshItem:private] =>
[alreadyInSave:protected] =>
[alreadyInValidation:protected] =>
[validationFailures:protected] => Array
(
)
[_new:BaseObject:private] =>
[_deleted:BaseObject:private] =>
[modifiedColumns:protected] => Array
(
)
)
)
[4] => Search_Result Object
(
[title] => Scaffolding at top of large column
[image] => /record/images/3994-p.jpg
[blurb] => This shot shows innovative guarding around the top of a large concrete column in the base of a high rise structure going up....
[category] => Array
(
[0] => 15
[1] => 21
[2] => 47
[3] => 51
[4] => 63
[5] => 78
[6] => 79
[7] => 80
[8] => 62
[9] => 87
[10] => 97
[11] => 56
[12] => 64
[13] => 74
)
[labels] => Array
(
[0] => Falls
[1] => Work Environment
[2] => Hazards
[3] => Scaffolds
[6] => Bricklayer
[7] => Trades
[8] => Cement Mason
[10] => Reinforcing Ironworker
[12] => Roofer/Waterproofer
[14] => Scaffold Erector
[16] => Sheetmetal Worker
[18] => Structural Ironworker
[20] => Commercial & Institutional
[21] => Jobsites
[22] => Images
[23] => Media
[24] => Media & Documents
[25] => Elevator Constructor
[27] => Laborer
[29] => Pile Driver
)
[type] => Images
[sub_category] =>
[url] => /image/3994/i002689/Scaffolding%2Bat%2Btop%2Bof%2Blarge%2Bcolumn.html
[item:protected] => ImageRecord Object
(
[records:protected] => Array
(
)
[recordId:protected] =>
[searchWordClass:protected] =>
[searchWordPeerClass:protected] =>
[bok_record:protected] =>
[authors:protected] =>
[organizations:protected] =>
[collections:protected] =>
[categories:protected] => Array
(
[15] => Category Object
(
[languages:protected] =>
[bok_resources:protected] =>
[bok_topics:protected] =>
[bok_keywords:protected] =>
[id:protected] => 15
[type:protected] => category
[parent:protected] => 7
[label:protected] => Falls
[alreadyInSave:protected] =>
[alreadyInValidation:protected] =>
[validationFailures:protected] => Array
(
)
[_new:BaseObject:private] =>
[_deleted:BaseObject:private] =>
[modifiedColumns:protected] => Array
(
)
)
[21] => Category Object
(
[languages:protected] =>
[bok_resources:protected] =>
[bok_topics:protected] =>
[bok_keywords:protected] =>
[id:protected] => 21
[type:protected] => category
[parent:protected] => 7
[label:protected] => Scaffolds
[alreadyInSave:protected] =>
[alreadyInValidation:protected] =>
[validationFailures:protected] => Array
(
)
[_new:BaseObject:private] =>
[_deleted:BaseObject:private] =>
[modifiedColumns:protected] => Array
(
)
)
[47] => Category Object
(
[languages:protected] =>
[bok_resources:protected] =>
[bok_topics:protected] =>
[bok_keywords:protected] =>
[id:protected] => 47
[type:protected] => category
[parent:protected] => 2
[label:protected] => Bricklayer
[alreadyInSave:protected] =>
[alreadyInValidation:protected] =>
[validationFailures:protected] => Array
(
)
[_new:BaseObject:private] =>
[_deleted:BaseObject:private] =>
[modifiedColumns:protected] => Array
(
)
)
[51] => Category Object
(
[languages:protected] =>
[bok_resources:protected] =>
[bok_topics:protected] =>
[bok_keywords:protected] =>
[id:protected] => 51
[type:protected] => category
[parent:protected] => 2
[label:protected] => Cement Mason
[alreadyInSave:protected] =>
[alreadyInValidation:protected] =>
[validationFailures:protected] => Array
(
)
[_new:BaseObject:private] =>
[_deleted:BaseObject:private] =>
[modifiedColumns:protected] => Array
(
)
)
[63] => Category Object
(
[languages:protected] =>
[bok_resources:protected] =>
[bok_topics:protected] =>
[bok_keywords:protected] =>
[id:protected] => 63
[type:protected] => category
[parent:protected] => 2
[label:protected] => Reinforcing Ironworker
[alreadyInSave:protected] =>
[alreadyInValidation:protected] =>
[validationFailures:protected] => Array
(
)
[_new:BaseObject:private] =>
[_deleted:BaseObject:private] =>
[modifiedColumns:protected] => Array
(
)
)
[78] => Category Object
(
[languages:protected] =>
[bok_resources:protected] =>
[bok_topics:protected] =>
[bok_keywords:protected] =>
[id:protected] => 78
[type:protected] => category
[parent:protected] => 2
[label:protected] => Roofer/Waterproofer
[alreadyInSave:protected] =>
[alreadyInValidation:protected] =>
[validationFailures:protected] => Array
(
)
[_new:BaseObject:private] =>
[_deleted:BaseObject:private] =>
[modifiedColumns:protected] => Array
(
)
)
[79] => Category Object
(
[languages:protected] =>
[bok_resources:protected] =>
[bok_topics:protected] =>
[bok_keywords:protected] =>
[id:protected] => 79
[type:protected] => category
[parent:protected] => 2
[label:protected] => Scaffold Erector
[alreadyInSave:protected] =>
[alreadyInValidation:protected] =>
[validationFailures:protected] => Array
(
)
[_new:BaseObject:private] =>
[_deleted:BaseObject:private] =>
[modifiedColumns:protected] => Array
(
)
)
[80] => Category Object
(
[languages:protected] =>
[bok_resources:protected] =>
[bok_topics:protected] =>
[bok_keywords:protected] =>
[id:protected] => 80
[type:protected] => category
[parent:protected] => 2
[label:protected] => Sheetmetal Worker
[alreadyInSave:protected] =>
[alreadyInValidation:protected] =>
[validationFailures:protected] => Array
(
)
[_new:BaseObject:private] =>
[_deleted:BaseObject:private] =>
[modifiedColumns:protected] => Array
(
)
)
[62] => Category Object
(
[languages:protected] =>
[bok_resources:protected] =>
[bok_topics:protected] =>
[bok_keywords:protected] =>
[id:protected] => 62
[type:protected] => category
[parent:protected] => 2
[label:protected] => Structural Ironworker
[alreadyInSave:protected] =>
[alreadyInValidation:protected] =>
[validationFailures:protected] => Array
(
)
[_new:BaseObject:private] =>
[_deleted:BaseObject:private] =>
[modifiedColumns:protected] => Array
(
)
)
[87] => Category Object
(
[languages:protected] =>
[bok_resources:protected] =>
[bok_topics:protected] =>
[bok_keywords:protected] =>
[id:protected] => 87
[type:protected] => category
[parent:protected] => 3
[label:protected] => Commercial & Institutional
[alreadyInSave:protected] =>
[alreadyInValidation:protected] =>
[validationFailures:protected] => Array
(
)
[_new:BaseObject:private] =>
[_deleted:BaseObject:private] =>
[modifiedColumns:protected] => Array
(
)
)
[97] => Category Object
(
[languages:protected] =>
[bok_resources:protected] =>
[bok_topics:protected] =>
[bok_keywords:protected] =>
[id:protected] => 97
[type:protected] => category
[parent:protected] => 5
[label:protected] => Images
[alreadyInSave:protected] =>
[alreadyInValidation:protected] =>
[validationFailures:protected] => Array
(
)
[_new:BaseObject:private] =>
[_deleted:BaseObject:private] =>
[modifiedColumns:protected] => Array
(
)
)
[56] => Category Object
(
[languages:protected] =>
[bok_resources:protected] =>
[bok_topics:protected] =>
[bok_keywords:protected] =>
[id:protected] => 56
[type:protected] => category
[parent:protected] => 2
[label:protected] => Elevator Constructor
[alreadyInSave:protected] =>
[alreadyInValidation:protected] =>
[validationFailures:protected] => Array
(
)
[_new:BaseObject:private] =>
[_deleted:BaseObject:private] =>
[modifiedColumns:protected] => Array
(
)
)
[64] => Category Object
(
[languages:protected] =>
[bok_resources:protected] =>
[bok_topics:protected] =>
[bok_keywords:protected] =>
[id:protected] => 64
[type:protected] => category
[parent:protected] => 2
[label:protected] => Laborer
[alreadyInSave:protected] =>
[alreadyInValidation:protected] =>
[validationFailures:protected] => Array
(
)
[_new:BaseObject:private] =>
[_deleted:BaseObject:private] =>
[modifiedColumns:protected] => Array
(
)
)
[74] => Category Object
(
[languages:protected] =>
[bok_resources:protected] =>
[bok_topics:protected] =>
[bok_keywords:protected] =>
[id:protected] => 74
[type:protected] => category
[parent:protected] => 2
[label:protected] => Pile Driver
[alreadyInSave:protected] =>
[alreadyInValidation:protected] =>
[validationFailures:protected] => Array
(
)
[_new:BaseObject:private] =>
[_deleted:BaseObject:private] =>
[modifiedColumns:protected] => Array
(
)
)
)
[categories_initialized:protected] => 1
[mapped_items:protected] =>
[content:protected] =>
[files:protected] =>
[language:protected] => Language Object
(
[id:protected] => 1
[code:protected] => en
[name:protected] => English
[alreadyInSave:protected] =>
[alreadyInValidation:protected] =>
[validationFailures:protected] => Array
(
)
[_new:BaseObject:private] =>
[_deleted:BaseObject:private] =>
[modifiedColumns:protected] => Array
(
)
)
[old_record:protected] =>
[id:protected] => 3994
[old_id:protected] =>
[elcosh_id:protected] => i002689
[type:protected] => image
[display_type:protected] => Image
[user_id:protected] => 0
[language_id:protected] => 1
[tagging_id:protected] => Bruce Lippy
[priority_id:protected] => 1
[title:protected] => Scaffolding at top of large column
[total_pages:protected] => 0
[billed_pages:protected] => 0
[publication_number:protected] =>
[part_of:protected] =>
[keywords:protected] => Guardrail, railing, fall prevention, falls
[comments:protected] =>
[summary:protected] => This shot shows innovative guarding around the top of a large concrete column in the base of a high rise structure going up.
[transition_comments:protected] =>
[external_link:protected] =>
[consol_link:protected] => http://www.cpwrconstructionsolutions.org/masonry/solution/8/adjustable-tower-scaffold.html
[more_like_this:protected] => c1002680,i002662,d000608,d001255
[permission_given_by:protected] =>
[published:protected] => T
[billable:protected] => F
[img_name:protected] =>
[img_ext:protected] => jpg
[img_width:protected] =>
[img_height:protected] =>
[img_credit:protected] => Photo by Pam Susi
[img_practice:protected] => good
[vid_source_id:protected] =>
[vid_running_time:protected] =>
[vid_intended_audience:protected] =>
[vid_acquisition_info:protected] =>
[vid_cost:protected] =>
[vid_producer:protected] =>
[vid_filename:protected] =>
[vid_filename_downloadable:protected] =>
[date_summary:protected] => January 2016
[date_permission_requested:protected] =>
[date_permission_received:protected] =>
[date_review_needed:protected] =>
[date_received:protected] => 02/01/16
[date_completed:protected] => 02/01/16
[date_billed:protected] =>
[date_modified:protected] => 02/01/16
[collBokExports:protected] =>
[lastBokExportCriteria:BaseElcoshItem:private] =>
[alreadyInSave:protected] =>
[alreadyInValidation:protected] =>
[validationFailures:protected] => Array
(
)
[_new:BaseObject:private] =>
[_deleted:BaseObject:private] =>
[modifiedColumns:protected] => Array
(
)
)
)
[5] => Search_Result Object
(
[title] => Construction bracing
[image] => /record/images/3995-p.jpg
[blurb] => This shows structural support that prevents collapses during construction....
[category] => Array
(
[0] => 12
[1] => 15
[2] => 21
[3] => 49
[4] => 51
[5] => 55
[6] => 56
[7] => 60
[8] => 64
[9] => 68
[10] => 74
[11] => 63
[12] => 78
[13] => 79
[14] => 80
[15] => 62
[16] => 87
[17] => 90
[18] => 97
)
[labels] => Array
(
[0] => Crushed/Struck By
[1] => Work Environment
[2] => Hazards
[3] => Falls
[6] => Scaffolds
[9] => Carpenter
[10] => Trades
[11] => Cement Mason
[13] => Electrical Worker
[15] => Elevator Constructor
[17] => HVAC
[19] => Laborer
[21] => Maintenance Worker
[23] => Pile Driver
[25] => Reinforcing Ironworker
[27] => Roofer/Waterproofer
[29] => Scaffold Erector
[31] => Sheetmetal Worker
[33] => Structural Ironworker
[35] => Commercial & Institutional
[36] => Jobsites
[37] => Industrial
[39] => Images
[40] => Media
[41] => Media & Documents
)
[type] => Images
[sub_category] =>
[url] => /image/3995/i002690/Construction%2Bbracing.html
[item:protected] => ImageRecord Object
(
[records:protected] => Array
(
)
[recordId:protected] =>
[searchWordClass:protected] =>
[searchWordPeerClass:protected] =>
[bok_record:protected] =>
[authors:protected] =>
[organizations:protected] =>
[collections:protected] =>
[categories:protected] => Array
(
[12] => Category Object
(
[languages:protected] =>
[bok_resources:protected] =>
[bok_topics:protected] =>
[bok_keywords:protected] =>
[id:protected] => 12
[type:protected] => category
[parent:protected] => 7
[label:protected] => Crushed/Struck By
[alreadyInSave:protected] =>
[alreadyInValidation:protected] =>
[validationFailures:protected] => Array
(
)
[_new:BaseObject:private] =>
[_deleted:BaseObject:private] =>
[modifiedColumns:protected] => Array
(
)
)
[15] => Category Object
(
[languages:protected] =>
[bok_resources:protected] =>
[bok_topics:protected] =>
[bok_keywords:protected] =>
[id:protected] => 15
[type:protected] => category
[parent:protected] => 7
[label:protected] => Falls
[alreadyInSave:protected] =>
[alreadyInValidation:protected] =>
[validationFailures:protected] => Array
(
)
[_new:BaseObject:private] =>
[_deleted:BaseObject:private] =>
[modifiedColumns:protected] => Array
(
)
)
[21] => Category Object
(
[languages:protected] =>
[bok_resources:protected] =>
[bok_topics:protected] =>
[bok_keywords:protected] =>
[id:protected] => 21
[type:protected] => category
[parent:protected] => 7
[label:protected] => Scaffolds
[alreadyInSave:protected] =>
[alreadyInValidation:protected] =>
[validationFailures:protected] => Array
(
)
[_new:BaseObject:private] =>
[_deleted:BaseObject:private] =>
[modifiedColumns:protected] => Array
(
)
)
[49] => Category Object
(
[languages:protected] =>
[bok_resources:protected] =>
[bok_topics:protected] =>
[bok_keywords:protected] =>
[id:protected] => 49
[type:protected] => category
[parent:protected] => 2
[label:protected] => Carpenter
[alreadyInSave:protected] =>
[alreadyInValidation:protected] =>
[validationFailures:protected] => Array
(
)
[_new:BaseObject:private] =>
[_deleted:BaseObject:private] =>
[modifiedColumns:protected] => Array
(
)
)
[51] => Category Object
(
[languages:protected] =>
[bok_resources:protected] =>
[bok_topics:protected] =>
[bok_keywords:protected] =>
[id:protected] => 51
[type:protected] => category
[parent:protected] => 2
[label:protected] => Cement Mason
[alreadyInSave:protected] =>
[alreadyInValidation:protected] =>
[validationFailures:protected] => Array
(
)
[_new:BaseObject:private] =>
[_deleted:BaseObject:private] =>
[modifiedColumns:protected] => Array
(
)
)
[55] => Category Object
(
[languages:protected] =>
[bok_resources:protected] =>
[bok_topics:protected] =>
[bok_keywords:protected] =>
[id:protected] => 55
[type:protected] => category
[parent:protected] => 2
[label:protected] => Electrical Worker
[alreadyInSave:protected] =>
[alreadyInValidation:protected] =>
[validationFailures:protected] => Array
(
)
[_new:BaseObject:private] =>
[_deleted:BaseObject:private] =>
[modifiedColumns:protected] => Array
(
)
)
[56] => Category Object
(
[languages:protected] =>
[bok_resources:protected] =>
[bok_topics:protected] =>
[bok_keywords:protected] =>
[id:protected] => 56
[type:protected] => category
[parent:protected] => 2
[label:protected] => Elevator Constructor
[alreadyInSave:protected] =>
[alreadyInValidation:protected] =>
[validationFailures:protected] => Array
(
)
[_new:BaseObject:private] =>
[_deleted:BaseObject:private] =>
[modifiedColumns:protected] => Array
(
)
)
[60] => Category Object
(
[languages:protected] =>
[bok_resources:protected] =>
[bok_topics:protected] =>
[bok_keywords:protected] =>
[id:protected] => 60
[type:protected] => category
[parent:protected] => 2
[label:protected] => HVAC
[alreadyInSave:protected] =>
[alreadyInValidation:protected] =>
[validationFailures:protected] => Array
(
)
[_new:BaseObject:private] =>
[_deleted:BaseObject:private] =>
[modifiedColumns:protected] => Array
(
)
)
[64] => Category Object
(
[languages:protected] =>
[bok_resources:protected] =>
[bok_topics:protected] =>
[bok_keywords:protected] =>
[id:protected] => 64
[type:protected] => category
[parent:protected] => 2
[label:protected] => Laborer
[alreadyInSave:protected] =>
[alreadyInValidation:protected] =>
[validationFailures:protected] => Array
(
)
[_new:BaseObject:private] =>
[_deleted:BaseObject:private] =>
[modifiedColumns:protected] => Array
(
)
)
[68] => Category Object
(
[languages:protected] =>
[bok_resources:protected] =>
[bok_topics:protected] =>
[bok_keywords:protected] =>
[id:protected] => 68
[type:protected] => category
[parent:protected] => 2
[label:protected] => Maintenance Worker
[alreadyInSave:protected] =>
[alreadyInValidation:protected] =>
[validationFailures:protected] => Array
(
)
[_new:BaseObject:private] =>
[_deleted:BaseObject:private] =>
[modifiedColumns:protected] => Array
(
)
)
[74] => Category Object
(
[languages:protected] =>
[bok_resources:protected] =>
[bok_topics:protected] =>
[bok_keywords:protected] =>
[id:protected] => 74
[type:protected] => category
[parent:protected] => 2
[label:protected] => Pile Driver
[alreadyInSave:protected] =>
[alreadyInValidation:protected] =>
[validationFailures:protected] => Array
(
)
[_new:BaseObject:private] =>
[_deleted:BaseObject:private] =>
[modifiedColumns:protected] => Array
(
)
)
[63] => Category Object
(
[languages:protected] =>
[bok_resources:protected] =>
[bok_topics:protected] =>
[bok_keywords:protected] =>
[id:protected] => 63
[type:protected] => category
[parent:protected] => 2
[label:protected] => Reinforcing Ironworker
[alreadyInSave:protected] =>
[alreadyInValidation:protected] =>
[validationFailures:protected] => Array
(
)
[_new:BaseObject:private] =>
[_deleted:BaseObject:private] =>
[modifiedColumns:protected] => Array
(
)
)
[78] => Category Object
(
[languages:protected] =>
[bok_resources:protected] =>
[bok_topics:protected] =>
[bok_keywords:protected] =>
[id:protected] => 78
[type:protected] => category
[parent:protected] => 2
[label:protected] => Roofer/Waterproofer
[alreadyInSave:protected] =>
[alreadyInValidation:protected] =>
[validationFailures:protected] => Array
(
)
[_new:BaseObject:private] =>
[_deleted:BaseObject:private] =>
[modifiedColumns:protected] => Array
(
)
)
[79] => Category Object
(
[languages:protected] =>
[bok_resources:protected] =>
[bok_topics:protected] =>
[bok_keywords:protected] =>
[id:protected] => 79
[type:protected] => category
[parent:protected] => 2
[label:protected] => Scaffold Erector
[alreadyInSave:protected] =>
[alreadyInValidation:protected] =>
[validationFailures:protected] => Array
(
)
[_new:BaseObject:private] =>
[_deleted:BaseObject:private] =>
[modifiedColumns:protected] => Array
(
)
)
[80] => Category Object
(
[languages:protected] =>
[bok_resources:protected] =>
[bok_topics:protected] =>
[bok_keywords:protected] =>
[id:protected] => 80
[type:protected] => category
[parent:protected] => 2
[label:protected] => Sheetmetal Worker
[alreadyInSave:protected] =>
[alreadyInValidation:protected] =>
[validationFailures:protected] => Array
(
)
[_new:BaseObject:private] =>
[_deleted:BaseObject:private] =>
[modifiedColumns:protected] => Array
(
)
)
[62] => Category Object
(
[languages:protected] =>
[bok_resources:protected] =>
[bok_topics:protected] =>
[bok_keywords:protected] =>
[id:protected] => 62
[type:protected] => category
[parent:protected] => 2
[label:protected] => Structural Ironworker
[alreadyInSave:protected] =>
[alreadyInValidation:protected] =>
[validationFailures:protected] => Array
(
)
[_new:BaseObject:private] =>
[_deleted:BaseObject:private] =>
[modifiedColumns:protected] => Array
(
)
)
[87] => Category Object
(
[languages:protected] =>
[bok_resources:protected] =>
[bok_topics:protected] =>
[bok_keywords:protected] =>
[id:protected] => 87
[type:protected] => category
[parent:protected] => 3
[label:protected] => Commercial & Institutional
[alreadyInSave:protected] =>
[alreadyInValidation:protected] =>
[validationFailures:protected] => Array
(
)
[_new:BaseObject:private] =>
[_deleted:BaseObject:private] =>
[modifiedColumns:protected] => Array
(
)
)
[90] => Category Object
(
[languages:protected] =>
[bok_resources:protected] =>
[bok_topics:protected] =>
[bok_keywords:protected] =>
[id:protected] => 90
[type:protected] => category
[parent:protected] => 3
[label:protected] => Industrial
[alreadyInSave:protected] =>
[alreadyInValidation:protected] =>
[validationFailures:protected] => Array
(
)
[_new:BaseObject:private] =>
[_deleted:BaseObject:private] =>
[modifiedColumns:protected] => Array
(
)
)
[97] => Category Object
(
[languages:protected] =>
[bok_resources:protected] =>
[bok_topics:protected] =>
[bok_keywords:protected] =>
[id:protected] => 97
[type:protected] => category
[parent:protected] => 5
[label:protected] => Images
[alreadyInSave:protected] =>
[alreadyInValidation:protected] =>
[validationFailures:protected] => Array
(
)
[_new:BaseObject:private] =>
[_deleted:BaseObject:private] =>
[modifiedColumns:protected] => Array
(
)
)
)
[categories_initialized:protected] => 1
[mapped_items:protected] =>
[content:protected] =>
[files:protected] =>
[language:protected] => Language Object
(
[id:protected] => 1
[code:protected] => en
[name:protected] => English
[alreadyInSave:protected] =>
[alreadyInValidation:protected] =>
[validationFailures:protected] => Array
(
)
[_new:BaseObject:private] =>
[_deleted:BaseObject:private] =>
[modifiedColumns:protected] => Array
(
)
)
[old_record:protected] =>
[id:protected] => 3995
[old_id:protected] =>
[elcosh_id:protected] => i002690
[type:protected] => image
[display_type:protected] => Image
[user_id:protected] => 0
[language_id:protected] => 1
[tagging_id:protected] => Bruce Lippy
[priority_id:protected] => 1
[title:protected] => Construction bracing
[total_pages:protected] => 0
[billed_pages:protected] => 0
[publication_number:protected] =>
[part_of:protected] =>
[keywords:protected] => Bracing, support, scaffold
[comments:protected] =>
[summary:protected] => This shows structural support that prevents collapses during construction.
[transition_comments:protected] =>
[external_link:protected] =>
[consol_link:protected] => http://www.cpwrconstructionsolutions.org/masonry/solution/8/adjustable-tower-scaffold.html
[more_like_this:protected] => i002660
[permission_given_by:protected] =>
[published:protected] => T
[billable:protected] => F
[img_name:protected] =>
[img_ext:protected] => jpg
[img_width:protected] =>
[img_height:protected] =>
[img_credit:protected] => Photo by Pam Susi
[img_practice:protected] => good
[vid_source_id:protected] =>
[vid_running_time:protected] =>
[vid_intended_audience:protected] =>
[vid_acquisition_info:protected] =>
[vid_cost:protected] =>
[vid_producer:protected] =>
[vid_filename:protected] =>
[vid_filename_downloadable:protected] =>
[date_summary:protected] => January 2016
[date_permission_requested:protected] =>
[date_permission_received:protected] =>
[date_review_needed:protected] =>
[date_received:protected] => 02/01/16
[date_completed:protected] => 02/01/16
[date_billed:protected] =>
[date_modified:protected] => 02/01/16
[collBokExports:protected] =>
[lastBokExportCriteria:BaseElcoshItem:private] =>
[alreadyInSave:protected] =>
[alreadyInValidation:protected] =>
[validationFailures:protected] => Array
(
)
[_new:BaseObject:private] =>
[_deleted:BaseObject:private] =>
[modifiedColumns:protected] => Array
(
)
)
)
)
[preview_mode] =>
[description] => Toolbox talks have been the main tool for communicating safety information on construction jobs for decades.
Unfortunately, there has been little research on what makes for effective toolbox talks. The IUOE National
Training Fund worked with OSHA and NIOSH to make sure their series of 24 Focus Four toolbox talks were based on the best recommendations for effective design. These toolbox talks accompany an entire package of training materials, but can be used alone. This guide points out the key features of these toolbox talks and how best to deliver them.
[keywords] => toolbox talks, tailgate talks
[related_items] => Array
(
[Toolbox Talks] => Array
(
[0] => DocumentRecord Object
(
[records:protected] => Array
(
)
[recordId:protected] =>
[searchWordClass:protected] =>
[searchWordPeerClass:protected] =>
[bok_record:protected] =>
[authors:protected] =>
[organizations:protected] =>
[collections:protected] =>
[categories:protected] =>
[categories_initialized:protected] =>
[mapped_items:protected] =>
[content:protected] =>
[files:protected] =>
[language:protected] => Language Object
(
[id:protected] => 1
[code:protected] => en
[name:protected] => English
[alreadyInSave:protected] =>
[alreadyInValidation:protected] =>
[validationFailures:protected] => Array
(
)
[_new:BaseObject:private] =>
[_deleted:BaseObject:private] =>
[modifiedColumns:protected] => Array
(
)
)
[old_record:protected] =>
[id:protected] => 1605
[old_id:protected] => 1262
[elcosh_id:protected] => d001137
[type:protected] => document
[display_type:protected] => HTML w/ PDF
[user_id:protected] =>
[language_id:protected] => 1
[tagging_id:protected] => Garber
[priority_id:protected] => 1
[title:protected] => Focus Four Toolbox Talks, Module 1 – Falls, Talk #2 – Falls from debris piles?
[total_pages:protected] => 1
[billed_pages:protected] => 1
[publication_number:protected] =>
[part_of:protected] =>
[keywords:protected] => disaster response, hazard clean-up, uneven surface, disaster site, disaster clean-up
[comments:protected] =>
[summary:protected] => A toolbox talk on preventing falls from debris piles. Includes questions to ask, an incident to discuss with images, and a place to record questions the trainer would like to ask about the incident. Part of a collection. Click on the 'collection' button to access the other items.
[transition_comments:protected] =>
[external_link:protected] =>
[consol_link:protected] => http://www.cpwrconstructionsolutions.org/roofing/hazard/1463/install-asphalt-roofs-fall-from-heights.html
[more_like_this:protected] => a000081,d000478,d000530
[permission_given_by:protected] =>
[published:protected] => T
[billable:protected] => F
[img_name:protected] =>
[img_ext:protected] =>
[img_width:protected] =>
[img_height:protected] =>
[img_credit:protected] =>
[img_practice:protected] =>
[vid_source_id:protected] =>
[vid_running_time:protected] =>
[vid_intended_audience:protected] =>
[vid_acquisition_info:protected] =>
[vid_cost:protected] =>
[vid_producer:protected] =>
[vid_filename:protected] =>
[vid_filename_downloadable:protected] =>
[date_summary:protected] =>
[date_permission_requested:protected] =>
[date_permission_received:protected] =>
[date_review_needed:protected] =>
[date_received:protected] => 02/15/12
[date_completed:protected] => 03/19/12
[date_billed:protected] =>
[date_modified:protected] => 07/10/12
[collBokExports:protected] =>
[lastBokExportCriteria:BaseElcoshItem:private] =>
[alreadyInSave:protected] =>
[alreadyInValidation:protected] =>
[validationFailures:protected] => Array
(
)
[_new:BaseObject:private] =>
[_deleted:BaseObject:private] =>
[modifiedColumns:protected] => Array
(
)
)
[1] => DocumentRecord Object
(
[records:protected] => Array
(
)
[recordId:protected] =>
[searchWordClass:protected] =>
[searchWordPeerClass:protected] =>
[bok_record:protected] =>
[authors:protected] =>
[organizations:protected] =>
[collections:protected] =>
[categories:protected] =>
[categories_initialized:protected] =>
[mapped_items:protected] =>
[content:protected] =>
[files:protected] =>
[language:protected] => Language Object
(
[id:protected] => 1
[code:protected] => en
[name:protected] => English
[alreadyInSave:protected] =>
[alreadyInValidation:protected] =>
[validationFailures:protected] => Array
(
)
[_new:BaseObject:private] =>
[_deleted:BaseObject:private] =>
[modifiedColumns:protected] => Array
(
)
)
[old_record:protected] =>
[id:protected] => 1610
[old_id:protected] => 1271
[elcosh_id:protected] => d001146
[type:protected] => document
[display_type:protected] => HTML w/ PDF
[user_id:protected] => 0
[language_id:protected] => 1
[tagging_id:protected] => Garber
[priority_id:protected] => 1
[title:protected] => Focus Four Toolbox Talks, Module 2 – Struck-by, Talk #5 – Rigging and Securing Loads
[total_pages:protected] => 1
[billed_pages:protected] => 1
[publication_number:protected] =>
[part_of:protected] =>
[keywords:protected] => rigging, lift loads, loading areas, chains
[comments:protected] =>
[summary:protected] => A toolbox talk on preventing struck-by incidents caused by not securing loads properly. Includes questions to ask, an incident to discuss with images, and a place to record questions the trainer would like to ask about the incident. Part of a collection. Click on the 'collection' button to access the other items.
[transition_comments:protected] =>
[external_link:protected] =>
[consol_link:protected] => http://www.cpwrconstructionsolutions.org/heavy_equipment/hazard/1591/move-equipment-to-from-and-between-sites-work-zone-struck-by-injuries-and-fatalities.html
[more_like_this:protected] => d000144,d000360,d000873
[permission_given_by:protected] =>
[published:protected] => T
[billable:protected] => F
[img_name:protected] =>
[img_ext:protected] =>
[img_width:protected] =>
[img_height:protected] =>
[img_credit:protected] =>
[img_practice:protected] =>
[vid_source_id:protected] =>
[vid_running_time:protected] =>
[vid_intended_audience:protected] =>
[vid_acquisition_info:protected] =>
[vid_cost:protected] =>
[vid_producer:protected] =>
[vid_filename:protected] =>
[vid_filename_downloadable:protected] =>
[date_summary:protected] =>
[date_permission_requested:protected] =>
[date_permission_received:protected] =>
[date_review_needed:protected] =>
[date_received:protected] => 02/15/12
[date_completed:protected] => 03/28/12
[date_billed:protected] =>
[date_modified:protected] => 05/12/14
[collBokExports:protected] =>
[lastBokExportCriteria:BaseElcoshItem:private] =>
[alreadyInSave:protected] =>
[alreadyInValidation:protected] =>
[validationFailures:protected] => Array
(
)
[_new:BaseObject:private] =>
[_deleted:BaseObject:private] =>
[modifiedColumns:protected] => Array
(
)
)
[2] => DocumentRecord Object
(
[records:protected] => Array
(
)
[recordId:protected] =>
[searchWordClass:protected] =>
[searchWordPeerClass:protected] =>
[bok_record:protected] =>
[authors:protected] =>
[organizations:protected] =>
[collections:protected] =>
[categories:protected] =>
[categories_initialized:protected] =>
[mapped_items:protected] =>
[content:protected] =>
[files:protected] =>
[language:protected] => Language Object
(
[id:protected] => 1
[code:protected] => en
[name:protected] => English
[alreadyInSave:protected] =>
[alreadyInValidation:protected] =>
[validationFailures:protected] => Array
(
)
[_new:BaseObject:private] =>
[_deleted:BaseObject:private] =>
[modifiedColumns:protected] => Array
(
)
)
[old_record:protected] =>
[id:protected] => 1645
[old_id:protected] => 1274
[elcosh_id:protected] => d001149
[type:protected] => document
[display_type:protected] => HTML w/ PDF
[user_id:protected] => 0
[language_id:protected] => 1
[tagging_id:protected] => Garber
[priority_id:protected] => 1
[title:protected] => Focus Four Toolbox Talks, Module 3 – Caught-in/between, Talk #2 – Trenches & Heavy Equipment
[total_pages:protected] => 1
[billed_pages:protected] => 1
[publication_number:protected] =>
[part_of:protected] =>
[keywords:protected] => back-up alarms, spotter, soil cave-in, spoil pikes, ROPs, trenching, rain
[comments:protected] =>
[summary:protected] => A toolbox talk on preventing incidents involving trenches such as trench collapse. Includes questions to ask, an incident to discuss with images, and a place to record questions the trainer would like to ask about the incident. Part of a collection. Click on the 'collection' button to access the other items.
[transition_comments:protected] =>
[external_link:protected] =>
[consol_link:protected] =>
[more_like_this:protected] => d000019,d000035,d000168
[permission_given_by:protected] =>
[published:protected] => T
[billable:protected] => F
[img_name:protected] =>
[img_ext:protected] =>
[img_width:protected] =>
[img_height:protected] =>
[img_credit:protected] =>
[img_practice:protected] =>
[vid_source_id:protected] =>
[vid_running_time:protected] =>
[vid_intended_audience:protected] =>
[vid_acquisition_info:protected] =>
[vid_cost:protected] =>
[vid_producer:protected] =>
[vid_filename:protected] =>
[vid_filename_downloadable:protected] =>
[date_summary:protected] =>
[date_permission_requested:protected] =>
[date_permission_received:protected] =>
[date_review_needed:protected] =>
[date_received:protected] => 02/15/12
[date_completed:protected] => 04/02/12
[date_billed:protected] =>
[date_modified:protected] => 05/23/23
[collBokExports:protected] =>
[lastBokExportCriteria:BaseElcoshItem:private] =>
[alreadyInSave:protected] =>
[alreadyInValidation:protected] =>
[validationFailures:protected] => Array
(
)
[_new:BaseObject:private] =>
[_deleted:BaseObject:private] =>
[modifiedColumns:protected] => Array
(
)
)
[3] => DocumentRecord Object
(
[records:protected] => Array
(
)
[recordId:protected] =>
[searchWordClass:protected] =>
[searchWordPeerClass:protected] =>
[bok_record:protected] =>
[authors:protected] =>
[organizations:protected] =>
[collections:protected] =>
[categories:protected] =>
[categories_initialized:protected] =>
[mapped_items:protected] =>
[content:protected] =>
[files:protected] =>
[language:protected] => Language Object
(
[id:protected] => 1
[code:protected] => en
[name:protected] => English
[alreadyInSave:protected] =>
[alreadyInValidation:protected] =>
[validationFailures:protected] => Array
(
)
[_new:BaseObject:private] =>
[_deleted:BaseObject:private] =>
[modifiedColumns:protected] => Array
(
)
)
[old_record:protected] =>
[id:protected] => 1654
[old_id:protected] => 1284
[elcosh_id:protected] => d001159
[type:protected] => document
[display_type:protected] => HTML w/ PDF
[user_id:protected] => 0
[language_id:protected] => 1
[tagging_id:protected] => Garber
[priority_id:protected] => 1
[title:protected] => Focus Four Toolbox Talks, Module 4 – Electrocutions, Talk #6 – Hazards on Disaster Sites
[total_pages:protected] => 1
[billed_pages:protected] => 1
[publication_number:protected] =>
[part_of:protected] =>
[keywords:protected] => powerlines, underground, utilities, generators, wet conditions, GFCIs, energized lines, disasters, emergency response
[comments:protected] =>
[summary:protected] => A toolbox talk on how to avoid electrocution on a disaster site. Includes questions to ask, an incident to discuss with images, and a place to record questions the trainer would like to ask about the incident. Part of a collection. Click on the 'collection' button to access the other items.
[transition_comments:protected] =>
[external_link:protected] =>
[consol_link:protected] => http://www.cpwrconstructionsolutions.org/electrical/hazard/1138/install-and-repair-high-voltage-lines-transformers-switches-electrical-shocks-burns-and-or-electrocution.html
[more_like_this:protected] => d000135,d000361,d000437
[permission_given_by:protected] =>
[published:protected] => T
[billable:protected] => F
[img_name:protected] =>
[img_ext:protected] =>
[img_width:protected] =>
[img_height:protected] =>
[img_credit:protected] =>
[img_practice:protected] =>
[vid_source_id:protected] =>
[vid_running_time:protected] =>
[vid_intended_audience:protected] =>
[vid_acquisition_info:protected] =>
[vid_cost:protected] =>
[vid_producer:protected] =>
[vid_filename:protected] =>
[vid_filename_downloadable:protected] =>
[date_summary:protected] =>
[date_permission_requested:protected] =>
[date_permission_received:protected] =>
[date_review_needed:protected] =>
[date_received:protected] => 02/15/12
[date_completed:protected] => 04/02/12
[date_billed:protected] =>
[date_modified:protected] => 05/23/23
[collBokExports:protected] =>
[lastBokExportCriteria:BaseElcoshItem:private] =>
[alreadyInSave:protected] =>
[alreadyInValidation:protected] =>
[validationFailures:protected] => Array
(
)
[_new:BaseObject:private] =>
[_deleted:BaseObject:private] =>
[modifiedColumns:protected] => Array
(
)
)
)
)
[collections] => Array
(
[1294] =>
[1295] =>
[1292] =>
[1293] => CollectionRecord Object
(
[collection_items:protected] =>
[records:protected] => Array
(
)
[recordId:protected] =>
[searchWordClass:protected] =>
[searchWordPeerClass:protected] =>
[bok_record:protected] =>
[authors:protected] =>
[organizations:protected] =>
[collections:protected] =>
[categories:protected] =>
[categories_initialized:protected] =>
[mapped_items:protected] =>
[content:protected] =>
[files:protected] =>
[language:protected] =>
[old_record:protected] =>
[id:protected] => 1293
[old_id:protected] =>
[elcosh_id:protected] => c000026
[type:protected] => collection
[display_type:protected] => Collection
[user_id:protected] =>
[language_id:protected] =>
[tagging_id:protected] =>
[priority_id:protected] =>
[title:protected] => Focus Four-Struck By
[total_pages:protected] =>
[billed_pages:protected] =>
[publication_number:protected] =>
[part_of:protected] =>
[keywords:protected] =>
[comments:protected] =>
[summary:protected] => The following are links to all of the items in this collection:
[transition_comments:protected] =>
[external_link:protected] =>
[consol_link:protected] =>
[more_like_this:protected] =>
[permission_given_by:protected] =>
[published:protected] => T
[billable:protected] => F
[img_name:protected] =>
[img_ext:protected] =>
[img_width:protected] =>
[img_height:protected] =>
[img_credit:protected] =>
[img_practice:protected] =>
[vid_source_id:protected] =>
[vid_running_time:protected] =>
[vid_intended_audience:protected] =>
[vid_acquisition_info:protected] =>
[vid_cost:protected] =>
[vid_producer:protected] =>
[vid_filename:protected] =>
[vid_filename_downloadable:protected] =>
[date_summary:protected] =>
[date_permission_requested:protected] =>
[date_permission_received:protected] =>
[date_review_needed:protected] =>
[date_received:protected] => 05/08/12
[date_completed:protected] => 05/08/12
[date_billed:protected] =>
[date_modified:protected] => 05/08/12
[collBokExports:protected] =>
[lastBokExportCriteria:BaseElcoshItem:private] =>
[alreadyInSave:protected] =>
[alreadyInValidation:protected] =>
[validationFailures:protected] => Array
(
)
[_new:BaseObject:private] =>
[_deleted:BaseObject:private] =>
[modifiedColumns:protected] => Array
(
)
)
)
[record] => DocumentRecord Object
(
[records:protected] => Array
(
)
[recordId:protected] =>
[searchWordClass:protected] =>
[searchWordPeerClass:protected] =>
[bok_record:protected] =>
[authors:protected] => Array
(
)
[organizations:protected] => Array
(
[256] => Organization Object
(
[id:protected] => 256
[elcosh_id:protected] => o000276
[user_id:protected] => 14
[province_id:protected] => 0
[country_id:protected] => 0
[title:protected] => IUOE National Training Fund
[address:protected] =>
[postal_code:protected] =>
[city:protected] =>
[department:protected] =>
[phone:protected] => 304-253-8674
[fax:protected] =>
[email:protected] =>
[website:protected] => http://www.iuoeiettc.org
[filename:protected] =>
[about:protected] =>
[comments:protected] =>
[logo_available:protected] => T
[no_details:protected] => F
[date_received:protected] => 2012-02-13
[date_completed:protected] => 2012-02-13
[date_billed:protected] =>
[alreadyInSave:protected] =>
[alreadyInValidation:protected] =>
[validationFailures:protected] => Array
(
)
[_new:BaseObject:private] =>
[_deleted:BaseObject:private] =>
[modifiedColumns:protected] => Array
(
)
)
)
[collections:protected] => Array
(
[1294] =>
[1295] =>
[1292] =>
[1293] => CollectionRecord Object
(
[collection_items:protected] =>
[records:protected] => Array
(
)
[recordId:protected] =>
[searchWordClass:protected] =>
[searchWordPeerClass:protected] =>
[bok_record:protected] =>
[authors:protected] =>
[organizations:protected] =>
[collections:protected] =>
[categories:protected] =>
[categories_initialized:protected] =>
[mapped_items:protected] =>
[content:protected] =>
[files:protected] =>
[language:protected] =>
[old_record:protected] =>
[id:protected] => 1293
[old_id:protected] =>
[elcosh_id:protected] => c000026
[type:protected] => collection
[display_type:protected] => Collection
[user_id:protected] =>
[language_id:protected] =>
[tagging_id:protected] =>
[priority_id:protected] =>
[title:protected] => Focus Four-Struck By
[total_pages:protected] =>
[billed_pages:protected] =>
[publication_number:protected] =>
[part_of:protected] =>
[keywords:protected] =>
[comments:protected] =>
[summary:protected] => The following are links to all of the items in this collection:
[transition_comments:protected] =>
[external_link:protected] =>
[consol_link:protected] =>
[more_like_this:protected] =>
[permission_given_by:protected] =>
[published:protected] => T
[billable:protected] => F
[img_name:protected] =>
[img_ext:protected] =>
[img_width:protected] =>
[img_height:protected] =>
[img_credit:protected] =>
[img_practice:protected] =>
[vid_source_id:protected] =>
[vid_running_time:protected] =>
[vid_intended_audience:protected] =>
[vid_acquisition_info:protected] =>
[vid_cost:protected] =>
[vid_producer:protected] =>
[vid_filename:protected] =>
[vid_filename_downloadable:protected] =>
[date_summary:protected] =>
[date_permission_requested:protected] =>
[date_permission_received:protected] =>
[date_review_needed:protected] =>
[date_received:protected] => 05/08/12
[date_completed:protected] => 05/08/12
[date_billed:protected] =>
[date_modified:protected] => 05/08/12
[collBokExports:protected] =>
[lastBokExportCriteria:BaseElcoshItem:private] =>
[alreadyInSave:protected] =>
[alreadyInValidation:protected] =>
[validationFailures:protected] => Array
(
)
[_new:BaseObject:private] =>
[_deleted:BaseObject:private] =>
[modifiedColumns:protected] => Array
(
)
)
)
[categories:protected] =>
[categories_initialized:protected] =>
[mapped_items:protected] => Array
(
[1605] => DocumentRecord Object
(
[records:protected] => Array
(
)
[recordId:protected] =>
[searchWordClass:protected] =>
[searchWordPeerClass:protected] =>
[bok_record:protected] =>
[authors:protected] =>
[organizations:protected] =>
[collections:protected] =>
[categories:protected] =>
[categories_initialized:protected] =>
[mapped_items:protected] =>
[content:protected] =>
[files:protected] =>
[language:protected] =>
[old_record:protected] =>
[id:protected] => 1605
[old_id:protected] => 1262
[elcosh_id:protected] => d001137
[type:protected] => document
[display_type:protected] => HTML w/ PDF
[user_id:protected] =>
[language_id:protected] => 1
[tagging_id:protected] => Garber
[priority_id:protected] => 1
[title:protected] => Focus Four Toolbox Talks, Module 1 – Falls, Talk #2 – Falls from debris piles?
[total_pages:protected] => 1
[billed_pages:protected] => 1
[publication_number:protected] =>
[part_of:protected] =>
[keywords:protected] => disaster response, hazard clean-up, uneven surface, disaster site, disaster clean-up
[comments:protected] =>
[summary:protected] => A toolbox talk on preventing falls from debris piles. Includes questions to ask, an incident to discuss with images, and a place to record questions the trainer would like to ask about the incident. Part of a collection. Click on the 'collection' button to access the other items.
[transition_comments:protected] =>
[external_link:protected] =>
[consol_link:protected] => http://www.cpwrconstructionsolutions.org/roofing/hazard/1463/install-asphalt-roofs-fall-from-heights.html
[more_like_this:protected] => a000081,d000478,d000530
[permission_given_by:protected] =>
[published:protected] => T
[billable:protected] => F
[img_name:protected] =>
[img_ext:protected] =>
[img_width:protected] =>
[img_height:protected] =>
[img_credit:protected] =>
[img_practice:protected] =>
[vid_source_id:protected] =>
[vid_running_time:protected] =>
[vid_intended_audience:protected] =>
[vid_acquisition_info:protected] =>
[vid_cost:protected] =>
[vid_producer:protected] =>
[vid_filename:protected] =>
[vid_filename_downloadable:protected] =>
[date_summary:protected] =>
[date_permission_requested:protected] =>
[date_permission_received:protected] =>
[date_review_needed:protected] =>
[date_received:protected] => 02/15/12
[date_completed:protected] => 03/19/12
[date_billed:protected] =>
[date_modified:protected] => 07/10/12
[collBokExports:protected] =>
[lastBokExportCriteria:BaseElcoshItem:private] =>
[alreadyInSave:protected] =>
[alreadyInValidation:protected] =>
[validationFailures:protected] => Array
(
)
[_new:BaseObject:private] =>
[_deleted:BaseObject:private] =>
[modifiedColumns:protected] => Array
(
)
)
[1610] => DocumentRecord Object
(
[records:protected] => Array
(
)
[recordId:protected] =>
[searchWordClass:protected] =>
[searchWordPeerClass:protected] =>
[bok_record:protected] =>
[authors:protected] =>
[organizations:protected] =>
[collections:protected] =>
[categories:protected] =>
[categories_initialized:protected] =>
[mapped_items:protected] =>
[content:protected] =>
[files:protected] =>
[language:protected] =>
[old_record:protected] =>
[id:protected] => 1610
[old_id:protected] => 1271
[elcosh_id:protected] => d001146
[type:protected] => document
[display_type:protected] => HTML w/ PDF
[user_id:protected] => 0
[language_id:protected] => 1
[tagging_id:protected] => Garber
[priority_id:protected] => 1
[title:protected] => Focus Four Toolbox Talks, Module 2 – Struck-by, Talk #5 – Rigging and Securing Loads
[total_pages:protected] => 1
[billed_pages:protected] => 1
[publication_number:protected] =>
[part_of:protected] =>
[keywords:protected] => rigging, lift loads, loading areas, chains
[comments:protected] =>
[summary:protected] => A toolbox talk on preventing struck-by incidents caused by not securing loads properly. Includes questions to ask, an incident to discuss with images, and a place to record questions the trainer would like to ask about the incident. Part of a collection. Click on the 'collection' button to access the other items.
[transition_comments:protected] =>
[external_link:protected] =>
[consol_link:protected] => http://www.cpwrconstructionsolutions.org/heavy_equipment/hazard/1591/move-equipment-to-from-and-between-sites-work-zone-struck-by-injuries-and-fatalities.html
[more_like_this:protected] => d000144,d000360,d000873
[permission_given_by:protected] =>
[published:protected] => T
[billable:protected] => F
[img_name:protected] =>
[img_ext:protected] =>
[img_width:protected] =>
[img_height:protected] =>
[img_credit:protected] =>
[img_practice:protected] =>
[vid_source_id:protected] =>
[vid_running_time:protected] =>
[vid_intended_audience:protected] =>
[vid_acquisition_info:protected] =>
[vid_cost:protected] =>
[vid_producer:protected] =>
[vid_filename:protected] =>
[vid_filename_downloadable:protected] =>
[date_summary:protected] =>
[date_permission_requested:protected] =>
[date_permission_received:protected] =>
[date_review_needed:protected] =>
[date_received:protected] => 02/15/12
[date_completed:protected] => 03/28/12
[date_billed:protected] =>
[date_modified:protected] => 05/12/14
[collBokExports:protected] =>
[lastBokExportCriteria:BaseElcoshItem:private] =>
[alreadyInSave:protected] =>
[alreadyInValidation:protected] =>
[validationFailures:protected] => Array
(
)
[_new:BaseObject:private] =>
[_deleted:BaseObject:private] =>
[modifiedColumns:protected] => Array
(
)
)
[1645] => DocumentRecord Object
(
[records:protected] => Array
(
)
[recordId:protected] =>
[searchWordClass:protected] =>
[searchWordPeerClass:protected] =>
[bok_record:protected] =>
[authors:protected] =>
[organizations:protected] =>
[collections:protected] =>
[categories:protected] =>
[categories_initialized:protected] =>
[mapped_items:protected] =>
[content:protected] =>
[files:protected] =>
[language:protected] =>
[old_record:protected] =>
[id:protected] => 1645
[old_id:protected] => 1274
[elcosh_id:protected] => d001149
[type:protected] => document
[display_type:protected] => HTML w/ PDF
[user_id:protected] => 0
[language_id:protected] => 1
[tagging_id:protected] => Garber
[priority_id:protected] => 1
[title:protected] => Focus Four Toolbox Talks, Module 3 – Caught-in/between, Talk #2 – Trenches & Heavy Equipment
[total_pages:protected] => 1
[billed_pages:protected] => 1
[publication_number:protected] =>
[part_of:protected] =>
[keywords:protected] => back-up alarms, spotter, soil cave-in, spoil pikes, ROPs, trenching, rain
[comments:protected] =>
[summary:protected] => A toolbox talk on preventing incidents involving trenches such as trench collapse. Includes questions to ask, an incident to discuss with images, and a place to record questions the trainer would like to ask about the incident. Part of a collection. Click on the 'collection' button to access the other items.
[transition_comments:protected] =>
[external_link:protected] =>
[consol_link:protected] =>
[more_like_this:protected] => d000019,d000035,d000168
[permission_given_by:protected] =>
[published:protected] => T
[billable:protected] => F
[img_name:protected] =>
[img_ext:protected] =>
[img_width:protected] =>
[img_height:protected] =>
[img_credit:protected] =>
[img_practice:protected] =>
[vid_source_id:protected] =>
[vid_running_time:protected] =>
[vid_intended_audience:protected] =>
[vid_acquisition_info:protected] =>
[vid_cost:protected] =>
[vid_producer:protected] =>
[vid_filename:protected] =>
[vid_filename_downloadable:protected] =>
[date_summary:protected] =>
[date_permission_requested:protected] =>
[date_permission_received:protected] =>
[date_review_needed:protected] =>
[date_received:protected] => 02/15/12
[date_completed:protected] => 04/02/12
[date_billed:protected] =>
[date_modified:protected] => 05/23/23
[collBokExports:protected] =>
[lastBokExportCriteria:BaseElcoshItem:private] =>
[alreadyInSave:protected] =>
[alreadyInValidation:protected] =>
[validationFailures:protected] => Array
(
)
[_new:BaseObject:private] =>
[_deleted:BaseObject:private] =>
[modifiedColumns:protected] => Array
(
)
)
[1654] => DocumentRecord Object
(
[records:protected] => Array
(
)
[recordId:protected] =>
[searchWordClass:protected] =>
[searchWordPeerClass:protected] =>
[bok_record:protected] =>
[authors:protected] =>
[organizations:protected] =>
[collections:protected] =>
[categories:protected] =>
[categories_initialized:protected] =>
[mapped_items:protected] =>
[content:protected] =>
[files:protected] =>
[language:protected] =>
[old_record:protected] =>
[id:protected] => 1654
[old_id:protected] => 1284
[elcosh_id:protected] => d001159
[type:protected] => document
[display_type:protected] => HTML w/ PDF
[user_id:protected] => 0
[language_id:protected] => 1
[tagging_id:protected] => Garber
[priority_id:protected] => 1
[title:protected] => Focus Four Toolbox Talks, Module 4 – Electrocutions, Talk #6 – Hazards on Disaster Sites
[total_pages:protected] => 1
[billed_pages:protected] => 1
[publication_number:protected] =>
[part_of:protected] =>
[keywords:protected] => powerlines, underground, utilities, generators, wet conditions, GFCIs, energized lines, disasters, emergency response
[comments:protected] =>
[summary:protected] => A toolbox talk on how to avoid electrocution on a disaster site. Includes questions to ask, an incident to discuss with images, and a place to record questions the trainer would like to ask about the incident. Part of a collection. Click on the 'collection' button to access the other items.
[transition_comments:protected] =>
[external_link:protected] =>
[consol_link:protected] => http://www.cpwrconstructionsolutions.org/electrical/hazard/1138/install-and-repair-high-voltage-lines-transformers-switches-electrical-shocks-burns-and-or-electrocution.html
[more_like_this:protected] => d000135,d000361,d000437
[permission_given_by:protected] =>
[published:protected] => T
[billable:protected] => F
[img_name:protected] =>
[img_ext:protected] =>
[img_width:protected] =>
[img_height:protected] =>
[img_credit:protected] =>
[img_practice:protected] =>
[vid_source_id:protected] =>
[vid_running_time:protected] =>
[vid_intended_audience:protected] =>
[vid_acquisition_info:protected] =>
[vid_cost:protected] =>
[vid_producer:protected] =>
[vid_filename:protected] =>
[vid_filename_downloadable:protected] =>
[date_summary:protected] =>
[date_permission_requested:protected] =>
[date_permission_received:protected] =>
[date_review_needed:protected] =>
[date_received:protected] => 02/15/12
[date_completed:protected] => 04/02/12
[date_billed:protected] =>
[date_modified:protected] => 05/23/23
[collBokExports:protected] =>
[lastBokExportCriteria:BaseElcoshItem:private] =>
[alreadyInSave:protected] =>
[alreadyInValidation:protected] =>
[validationFailures:protected] => Array
(
)
[_new:BaseObject:private] =>
[_deleted:BaseObject:private] =>
[modifiedColumns:protected] => Array
(
)
)
)
[content:protected] =>
[files:protected] => Array
(
[9400] => File Object
(
[id:protected] => 9400
[filename:protected] => 1.jpg
[downloadable:protected] => F
[timestamp:protected] => 2014-05-08 15:05:37
[alreadyInSave:protected] =>
[alreadyInValidation:protected] =>
[validationFailures:protected] => Array
(
)
[_new:BaseObject:private] =>
[_deleted:BaseObject:private] =>
[modifiedColumns:protected] => Array
(
)
)
[9401] => File Object
(
[id:protected] => 9401
[filename:protected] => d001298.pdf
[downloadable:protected] => T
[timestamp:protected] => 2014-05-08 15:05:37
[alreadyInSave:protected] =>
[alreadyInValidation:protected] =>
[validationFailures:protected] => Array
(
)
[_new:BaseObject:private] =>
[_deleted:BaseObject:private] =>
[modifiedColumns:protected] => Array
(
)
)
)
[language:protected] => Language Object
(
[id:protected] => 1
[code:protected] => en
[name:protected] => English
[alreadyInSave:protected] =>
[alreadyInValidation:protected] =>
[validationFailures:protected] => Array
(
)
[_new:BaseObject:private] =>
[_deleted:BaseObject:private] =>
[modifiedColumns:protected] => Array
(
)
)
[old_record:protected] =>
[id:protected] => 3827
[old_id:protected] =>
[elcosh_id:protected] => d001298
[type:protected] => document
[display_type:protected] => HTML w/ PDF
[user_id:protected] => 23
[language_id:protected] => 1
[tagging_id:protected] => Bruce Lippy
[priority_id:protected] => 1
[title:protected] => Getting the most out of the IUOE Toolbox Talks
[total_pages:protected] => 2
[billed_pages:protected] => 2
[publication_number:protected] =>
[part_of:protected] =>
[keywords:protected] => toolbox talks, tailgate talks
[comments:protected] =>
[summary:protected] => Toolbox talks have been the main tool for communicating safety information on construction jobs for decades.
Unfortunately, there has been little research on what makes for effective toolbox talks. The IUOE National
Training Fund worked with OSHA and NIOSH to make sure their series of 24 Focus Four toolbox talks were based on the best recommendations for effective design. These toolbox talks accompany an entire package of training materials, but can be used alone. This guide points out the key features of these toolbox talks and how best to deliver them.
[transition_comments:protected] =>
[external_link:protected] =>
[consol_link:protected] =>
[more_like_this:protected] => d001137,d001146,d001149,d001159
[permission_given_by:protected] => IUOE National Hazmat Program
[published:protected] => T
[billable:protected] => F
[img_name:protected] =>
[img_ext:protected] => png
[img_width:protected] =>
[img_height:protected] =>
[img_credit:protected] =>
[img_practice:protected] =>
[vid_source_id:protected] =>
[vid_running_time:protected] =>
[vid_intended_audience:protected] =>
[vid_acquisition_info:protected] =>
[vid_cost:protected] =>
[vid_producer:protected] =>
[vid_filename:protected] =>
[vid_filename_downloadable:protected] =>
[date_summary:protected] => 2007
[date_permission_requested:protected] =>
[date_permission_received:protected] =>
[date_review_needed:protected] =>
[date_received:protected] => 05/08/14
[date_completed:protected] => 05/08/14
[date_billed:protected] =>
[date_modified:protected] => 05/08/14
[collBokExports:protected] =>
[lastBokExportCriteria:BaseElcoshItem:private] =>
[alreadyInSave:protected] =>
[alreadyInValidation:protected] =>
[validationFailures:protected] => Array
(
)
[_new:BaseObject:private] =>
[_deleted:BaseObject:private] =>
[modifiedColumns:protected] => Array
(
)
)
[show_text] =>
[document_content] => ElcoshItemDocumentContent Object
(
[id:protected] => 2896
[item_id:protected] => 3827
[type:protected] => main
[title:protected] =>
[content:protected] =>
Why were these talks developed?
Toolbox talks have been the main tool for communicating safety information on construction jobs for decades. Unfortunately, there has been almost no research on what makes for effective toolbox talks. The IUOE National Training Fund has worked with OSHA, the National Institute for Occupational Safety and Health and the Lippy Group, LLC to make sure these Focus Four toolbox talks are based on the latest fi ndings on the most effective design and tailored to the hazards operating engineers face daily. These toolbox talks accompany an entire package of training materials, but can be used alone. The way these are delivered is as important as how well they are designed.
What did NIOSH find out?
- Just handing out factsheets and toolbox talks to workers doesn’t work. Providing copies after toolbox talks doesn’t make much of an impact either.
- Using case studies (real life stories of accidents that ended in fatality or injury) in toolbox talks is effective.
- When toolbox talks containing case studies were accompanied by discussion questions to encourage group participation, they were more effective. Consequently, getting the workers to participate in the discussion about the case study is important. It’s not enough to tell the story, it is better to have the workers engage in problem solving that analyzes why the accident occurred and how it could have been prevented. Active learning is always better than passive.
How should you deliver these toolbox talks?
- Choose a topic that is related to work going on at the site.
- Hold the meeting on the job, preferably where everyone can sit and relax.
- Hold the meeting at the beginning of a shift or after a break. Folks are too tired at the end of a shift to carefully listen and they want to get home.
- Read the toolbox talk sheet on the topic prior to conducting the talk.
- Start at the top of the form and work right through to the end, which should take around 10 to 15 minutes. Guidance is provided in blue print to help you with each section.
- Use the questions provided to generate discussions. Always allow time for the crew to respond to your questions before you provide an answer. Some suggested responses are written in italics.
- Review the case study and emphasize that this was a real incident. Ask the crew for a case study before you review the one provided, however.
- Always end with a discussion of the particular worksite where you are conducting the talk. Tie the talk as closely to hazards on the site as possible and encourage the crew to constantly look for and immediately correct hazards. They should also know how to report any problems that can’t be immediately corrected.
- Provide copies to each person, if you like, but NIOSH has not found that to be particularly effective.
- Encourage workers to do similar talks on their sites and provide them with the IUOE phone number for ordering in bulk.
- Have everyone sign the back of the form to indicate they attended this session and point out it is a pledge to look out for the health and safety of everyone on the site.
What are the key features of these toolbox talks?

[content_transformed:protected] =>
Why were these talks developed?
Toolbox talks have been the main tool for communicating safety information on construction jobs for decades. Unfortunately, there has been almost no research on what makes for effective toolbox talks. The IUOE National Training Fund has worked with OSHA, the National Institute for Occupational Safety and Health and the Lippy Group, LLC to make sure these Focus Four toolbox talks are based on the latest fi ndings on the most effective design and tailored to the hazards operating engineers face daily. These toolbox talks accompany an entire package of training materials, but can be used alone. The way these are delivered is as important as how well they are designed.
What did NIOSH find out?
- Just handing out factsheets and toolbox talks to workers doesn’t work. Providing copies after toolbox talks doesn’t make much of an impact either.
- Using case studies (real life stories of accidents that ended in fatality or injury) in toolbox talks is effective.
- When toolbox talks containing case studies were accompanied by discussion questions to encourage group participation, they were more effective. Consequently, getting the workers to participate in the discussion about the case study is important. It’s not enough to tell the story, it is better to have the workers engage in problem solving that analyzes why the accident occurred and how it could have been prevented. Active learning is always better than passive.
How should you deliver these toolbox talks?
- Choose a topic that is related to work going on at the site.
- Hold the meeting on the job, preferably where everyone can sit and relax.
- Hold the meeting at the beginning of a shift or after a break. Folks are too tired at the end of a shift to carefully listen and they want to get home.
- Read the toolbox talk sheet on the topic prior to conducting the talk.
- Start at the top of the form and work right through to the end, which should take around 10 to 15 minutes. Guidance is provided in blue print to help you with each section.
- Use the questions provided to generate discussions. Always allow time for the crew to respond to your questions before you provide an answer. Some suggested responses are written in italics.
- Review the case study and emphasize that this was a real incident. Ask the crew for a case study before you review the one provided, however.
- Always end with a discussion of the particular worksite where you are conducting the talk. Tie the talk as closely to hazards on the site as possible and encourage the crew to constantly look for and immediately correct hazards. They should also know how to report any problems that can’t be immediately corrected.
- Provide copies to each person, if you like, but NIOSH has not found that to be particularly effective.
- Encourage workers to do similar talks on their sites and provide them with the IUOE phone number for ordering in bulk.
- Have everyone sign the back of the form to indicate they attended this session and point out it is a pledge to look out for the health and safety of everyone on the site.
What are the key features of these toolbox talks?
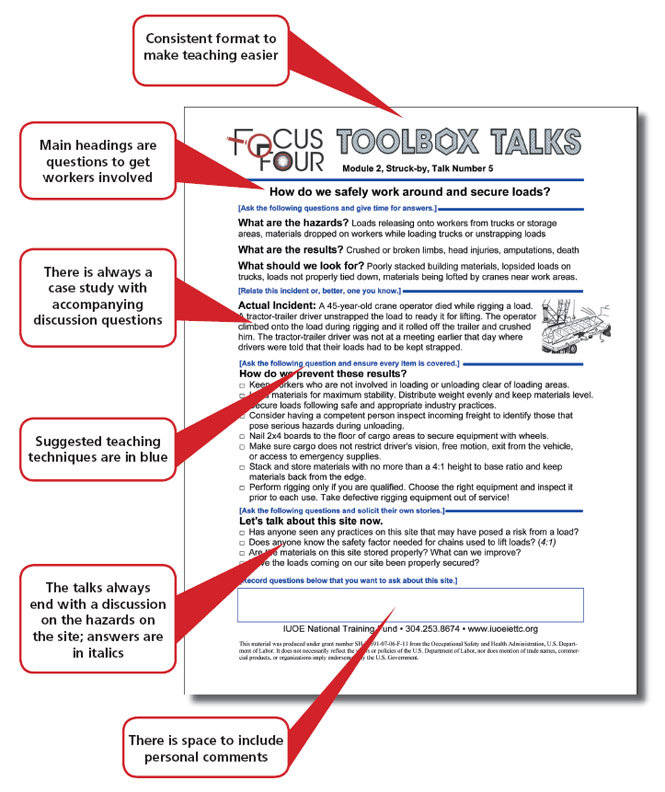
[disclaimer:protected] =>
[disclaimer_transformed:protected] =>
[alreadyInSave:protected] =>
[alreadyInValidation:protected] =>
[validationFailures:protected] => Array
(
)
[_new:BaseObject:private] =>
[_deleted:BaseObject:private] =>
[modifiedColumns:protected] => Array
(
)
)
[template] => record
)
[_file] => /home/agsafe5/repositories/elcosh/live/templates/elcosh/record.html
[_errors:protected] => Array
(
)
[_encoding:protected] => UTF-8
[_outputMode:protected] => 11
[_forceReparse:protected] =>
[_phpCodeDestination:protected] => /tmp/
[_phpCodeExtension:protected] => php
[_cacheLifetime:protected] => 30
[_cachePurgeFrequency:protected] => 30
[externalMacroTemplatesCache:PHPTAL:private] => Array
(
[macros.html] => PHPTAL Object
(
[_prefilters:protected] => Array
(
)
[_prefilter:PHPTAL:private] => REMOVED: DO NOT USE
[_postfilter:protected] =>
[_repositories:protected] => Array
(
[0] => /home/agsafe5/repositories/elcosh/live/templates/elcosh
)
[_path:protected] => macros.html
[_resolvers:protected] => Array
(
)
[_source:protected] => PHPTAL_FileSource Object
(
[_path:PHPTAL_FileSource:private] => /home/agsafe5/repositories/elcosh/live/templates/elcosh/macros.html
)
[_codeFile:protected] => /tmp/tpl_61515a6c_macros__EnKHR8AWVA3oW7OmomvoZw.php
[_functionName:protected] => tpl_61515a6c_macros__EnKHR8AWVA3oW7OmomvoZw
[_prepared:protected] => 1
[_triggers:protected] => Array
(
)
[_translator:protected] =>
[_globalContext:protected] => stdClass Object
(
)
[_context:protected] => PHPTAL_Context Object
(
[_line] =>
[_file] => /home/agsafe5/repositories/elcosh/live/templates/elcosh/record.html
[repeat] => stdClass Object
(
)
[_xmlDeclaration] =>
[_docType] =>
[_nothrow:PHPTAL_Context:private] =>
[_slots:PHPTAL_Context:private] => Array
(
)
[_slotsStack:PHPTAL_Context:private] => Array
(
[0] => Array
(
)
[1] => Array
(
)
)
[_parentContext:PHPTAL_Context:private] => PHPTAL_Context Object
(
[_line] =>
[_file] => /home/agsafe5/repositories/elcosh/live/templates/elcosh/record.html
[repeat] => stdClass Object
(
)
[_xmlDeclaration] =>
[_docType] =>
[_nothrow:PHPTAL_Context:private] =>
[_slots:PHPTAL_Context:private] => Array
(
)
[_slotsStack:PHPTAL_Context:private] => Array
(
[0] => Array
(
)
[1] => Array
(
)
)
[_parentContext:PHPTAL_Context:private] =>
[_globalContext:PHPTAL_Context:private] => stdClass Object
(
)
[_echoDeclarations:PHPTAL_Context:private] =>
[referer] => http://www.elcosh.org/document/3827/d001298/Getting%2Bthe%2Bmost%2Bout%2Bof%2Bthe%2BIUOE%2BToolbox%2BTalks.html
[curr_module] => Record
[styles] => Array
(
)
[javascript] => Array
(
[0] => jquery.min.js
)
[metas] => Array
(
[language] => en
[robots] => index, follow
)
[user] =>
[curr_url] => https://www.elcosh.org/index.php?module=Record&id=3827&type=document
[base_url] => https://www.elcosh.org/index.php?module=Record
[title] => eLCOSH : Getting the most out of the IUOE Toolbox Talks
[language] => en
[search_query] =>
[module] => Record
[new_records] => Array
(
[0] => Search_Result Object
(
[title] => Toolbox Talk: Fixed Ladder
[image] => /record/images/notavailable-p.png
[blurb] => The CPWR Toolbox Talk on Fixed Ladders addresses the potential risks associated with using fixed ladders. The resource includes a brief case example,...
[category] => Array
(
[0] => 15
[1] => 47
[2] => 49
[3] => 51
[4] => 53
[5] => 55
[6] => 60
[7] => 64
[8] => 73
[9] => 76
[10] => 78
[11] => 80
[12] => 86
[13] => 87
[14] => 90
[15] => 92
[16] => 93
[17] => 94
[18] => 100
)
[labels] => Array
(
[0] => Falls
[1] => Work Environment
[2] => Hazards
[3] => Bricklayer
[4] => Trades
[5] => Carpenter
[7] => Cement Mason
[9] => Concrete Polisher
[11] => Electrical Worker
[13] => HVAC
[15] => Laborer
[17] => PCC/Restoration
[19] => Plumber/Pipefitter
[21] => Roofer/Waterproofer
[23] => Sheetmetal Worker
[25] => Welder
[27] => Commercial & Institutional
[28] => Jobsites
[29] => Industrial
[31] => LEED/Green Construction
[33] => Renovations
[35] => Residential
[37] => Toolbox Talks
[38] => Documents
[39] => Media & Documents
)
[type] => Toolbox Talks
[sub_category] =>
[url] => /document/4430/d001660/Toolbox%2BTalk%253A%2BFixed%2BLadder.html
[item:protected] => DocumentRecord Object
(
[records:protected] => Array
(
)
[recordId:protected] =>
[searchWordClass:protected] =>
[searchWordPeerClass:protected] =>
[bok_record:protected] =>
[authors:protected] =>
[organizations:protected] =>
[collections:protected] =>
[categories:protected] => Array
(
[15] => Category Object
(
[languages:protected] =>
[bok_resources:protected] =>
[bok_topics:protected] =>
[bok_keywords:protected] =>
[id:protected] => 15
[type:protected] => category
[parent:protected] => 7
[label:protected] => Falls
[alreadyInSave:protected] =>
[alreadyInValidation:protected] =>
[validationFailures:protected] => Array
(
)
[_new:BaseObject:private] =>
[_deleted:BaseObject:private] =>
[modifiedColumns:protected] => Array
(
)
)
[47] => Category Object
(
[languages:protected] =>
[bok_resources:protected] =>
[bok_topics:protected] =>
[bok_keywords:protected] =>
[id:protected] => 47
[type:protected] => category
[parent:protected] => 2
[label:protected] => Bricklayer
[alreadyInSave:protected] =>
[alreadyInValidation:protected] =>
[validationFailures:protected] => Array
(
)
[_new:BaseObject:private] =>
[_deleted:BaseObject:private] =>
[modifiedColumns:protected] => Array
(
)
)
[49] => Category Object
(
[languages:protected] =>
[bok_resources:protected] =>
[bok_topics:protected] =>
[bok_keywords:protected] =>
[id:protected] => 49
[type:protected] => category
[parent:protected] => 2
[label:protected] => Carpenter
[alreadyInSave:protected] =>
[alreadyInValidation:protected] =>
[validationFailures:protected] => Array
(
)
[_new:BaseObject:private] =>
[_deleted:BaseObject:private] =>
[modifiedColumns:protected] => Array
(
)
)
[51] => Category Object
(
[languages:protected] =>
[bok_resources:protected] =>
[bok_topics:protected] =>
[bok_keywords:protected] =>
[id:protected] => 51
[type:protected] => category
[parent:protected] => 2
[label:protected] => Cement Mason
[alreadyInSave:protected] =>
[alreadyInValidation:protected] =>
[validationFailures:protected] => Array
(
)
[_new:BaseObject:private] =>
[_deleted:BaseObject:private] =>
[modifiedColumns:protected] => Array
(
)
)
[53] => Category Object
(
[languages:protected] =>
[bok_resources:protected] =>
[bok_topics:protected] =>
[bok_keywords:protected] =>
[id:protected] => 53
[type:protected] => category
[parent:protected] => 2
[label:protected] => Concrete Polisher
[alreadyInSave:protected] =>
[alreadyInValidation:protected] =>
[validationFailures:protected] => Array
(
)
[_new:BaseObject:private] =>
[_deleted:BaseObject:private] =>
[modifiedColumns:protected] => Array
(
)
)
[55] => Category Object
(
[languages:protected] =>
[bok_resources:protected] =>
[bok_topics:protected] =>
[bok_keywords:protected] =>
[id:protected] => 55
[type:protected] => category
[parent:protected] => 2
[label:protected] => Electrical Worker
[alreadyInSave:protected] =>
[alreadyInValidation:protected] =>
[validationFailures:protected] => Array
(
)
[_new:BaseObject:private] =>
[_deleted:BaseObject:private] =>
[modifiedColumns:protected] => Array
(
)
)
[60] => Category Object
(
[languages:protected] =>
[bok_resources:protected] =>
[bok_topics:protected] =>
[bok_keywords:protected] =>
[id:protected] => 60
[type:protected] => category
[parent:protected] => 2
[label:protected] => HVAC
[alreadyInSave:protected] =>
[alreadyInValidation:protected] =>
[validationFailures:protected] => Array
(
)
[_new:BaseObject:private] =>
[_deleted:BaseObject:private] =>
[modifiedColumns:protected] => Array
(
)
)
[64] => Category Object
(
[languages:protected] =>
[bok_resources:protected] =>
[bok_topics:protected] =>
[bok_keywords:protected] =>
[id:protected] => 64
[type:protected] => category
[parent:protected] => 2
[label:protected] => Laborer
[alreadyInSave:protected] =>
[alreadyInValidation:protected] =>
[validationFailures:protected] => Array
(
)
[_new:BaseObject:private] =>
[_deleted:BaseObject:private] =>
[modifiedColumns:protected] => Array
(
)
)
[73] => Category Object
(
[languages:protected] =>
[bok_resources:protected] =>
[bok_topics:protected] =>
[bok_keywords:protected] =>
[id:protected] => 73
[type:protected] => category
[parent:protected] => 2
[label:protected] => PCC/Restoration
[alreadyInSave:protected] =>
[alreadyInValidation:protected] =>
[validationFailures:protected] => Array
(
)
[_new:BaseObject:private] =>
[_deleted:BaseObject:private] =>
[modifiedColumns:protected] => Array
(
)
)
[76] => Category Object
(
[languages:protected] =>
[bok_resources:protected] =>
[bok_topics:protected] =>
[bok_keywords:protected] =>
[id:protected] => 76
[type:protected] => category
[parent:protected] => 2
[label:protected] => Plumber/Pipefitter
[alreadyInSave:protected] =>
[alreadyInValidation:protected] =>
[validationFailures:protected] => Array
(
)
[_new:BaseObject:private] =>
[_deleted:BaseObject:private] =>
[modifiedColumns:protected] => Array
(
)
)
[78] => Category Object
(
[languages:protected] =>
[bok_resources:protected] =>
[bok_topics:protected] =>
[bok_keywords:protected] =>
[id:protected] => 78
[type:protected] => category
[parent:protected] => 2
[label:protected] => Roofer/Waterproofer
[alreadyInSave:protected] =>
[alreadyInValidation:protected] =>
[validationFailures:protected] => Array
(
)
[_new:BaseObject:private] =>
[_deleted:BaseObject:private] =>
[modifiedColumns:protected] => Array
(
)
)
[80] => Category Object
(
[languages:protected] =>
[bok_resources:protected] =>
[bok_topics:protected] =>
[bok_keywords:protected] =>
[id:protected] => 80
[type:protected] => category
[parent:protected] => 2
[label:protected] => Sheetmetal Worker
[alreadyInSave:protected] =>
[alreadyInValidation:protected] =>
[validationFailures:protected] => Array
(
)
[_new:BaseObject:private] =>
[_deleted:BaseObject:private] =>
[modifiedColumns:protected] => Array
(
)
)
[86] => Category Object
(
[languages:protected] =>
[bok_resources:protected] =>
[bok_topics:protected] =>
[bok_keywords:protected] =>
[id:protected] => 86
[type:protected] => category
[parent:protected] => 2
[label:protected] => Welder
[alreadyInSave:protected] =>
[alreadyInValidation:protected] =>
[validationFailures:protected] => Array
(
)
[_new:BaseObject:private] =>
[_deleted:BaseObject:private] =>
[modifiedColumns:protected] => Array
(
)
)
[87] => Category Object
(
[languages:protected] =>
[bok_resources:protected] =>
[bok_topics:protected] =>
[bok_keywords:protected] =>
[id:protected] => 87
[type:protected] => category
[parent:protected] => 3
[label:protected] => Commercial & Institutional
[alreadyInSave:protected] =>
[alreadyInValidation:protected] =>
[validationFailures:protected] => Array
(
)
[_new:BaseObject:private] =>
[_deleted:BaseObject:private] =>
[modifiedColumns:protected] => Array
(
)
)
[90] => Category Object
(
[languages:protected] =>
[bok_resources:protected] =>
[bok_topics:protected] =>
[bok_keywords:protected] =>
[id:protected] => 90
[type:protected] => category
[parent:protected] => 3
[label:protected] => Industrial
[alreadyInSave:protected] =>
[alreadyInValidation:protected] =>
[validationFailures:protected] => Array
(
)
[_new:BaseObject:private] =>
[_deleted:BaseObject:private] =>
[modifiedColumns:protected] => Array
(
)
)
[92] => Category Object
(
[languages:protected] =>
[bok_resources:protected] =>
[bok_topics:protected] =>
[bok_keywords:protected] =>
[id:protected] => 92
[type:protected] => category
[parent:protected] => 3
[label:protected] => LEED/Green Construction
[alreadyInSave:protected] =>
[alreadyInValidation:protected] =>
[validationFailures:protected] => Array
(
)
[_new:BaseObject:private] =>
[_deleted:BaseObject:private] =>
[modifiedColumns:protected] => Array
(
)
)
[93] => Category Object
(
[languages:protected] =>
[bok_resources:protected] =>
[bok_topics:protected] =>
[bok_keywords:protected] =>
[id:protected] => 93
[type:protected] => category
[parent:protected] => 3
[label:protected] => Renovations
[alreadyInSave:protected] =>
[alreadyInValidation:protected] =>
[validationFailures:protected] => Array
(
)
[_new:BaseObject:private] =>
[_deleted:BaseObject:private] =>
[modifiedColumns:protected] => Array
(
)
)
[94] => Category Object
(
[languages:protected] =>
[bok_resources:protected] =>
[bok_topics:protected] =>
[bok_keywords:protected] =>
[id:protected] => 94
[type:protected] => category
[parent:protected] => 3
[label:protected] => Residential
[alreadyInSave:protected] =>
[alreadyInValidation:protected] =>
[validationFailures:protected] => Array
(
)
[_new:BaseObject:private] =>
[_deleted:BaseObject:private] =>
[modifiedColumns:protected] => Array
(
)
)
[100] => Category Object
(
[languages:protected] =>
[bok_resources:protected] =>
[bok_topics:protected] =>
[bok_keywords:protected] =>
[id:protected] => 100
[type:protected] => category
[parent:protected] => 6
[label:protected] => Toolbox Talks
[alreadyInSave:protected] =>
[alreadyInValidation:protected] =>
[validationFailures:protected] => Array
(
)
[_new:BaseObject:private] =>
[_deleted:BaseObject:private] =>
[modifiedColumns:protected] => Array
(
)
)
)
[categories_initialized:protected] => 1
[mapped_items:protected] =>
[content:protected] =>
[files:protected] =>
[language:protected] => Language Object
(
[id:protected] => 1
[code:protected] => en
[name:protected] => English
[alreadyInSave:protected] =>
[alreadyInValidation:protected] =>
[validationFailures:protected] => Array
(
)
[_new:BaseObject:private] =>
[_deleted:BaseObject:private] =>
[modifiedColumns:protected] => Array
(
)
)
[old_record:protected] =>
[id:protected] => 4430
[old_id:protected] =>
[elcosh_id:protected] => d001660
[type:protected] => document
[display_type:protected] => HTML only (and links)
[user_id:protected] => 0
[language_id:protected] => 1
[tagging_id:protected] => Mike Aguilar
[priority_id:protected] => 1
[title:protected] => Toolbox Talk: Fixed Ladder
[total_pages:protected] => 0
[billed_pages:protected] => 0
[publication_number:protected] =>
[part_of:protected] =>
[keywords:protected] => Fixed Ladders, Fall Prevention, Falls
[comments:protected] =>
[summary:protected] => The CPWR Toolbox Talk on Fixed Ladders addresses the potential risks associated with using fixed ladders. The resource includes a brief case example, steps to prevent a related injury and questions for discussion. It includes an image that illustrates the hazard, which can be posted in a central location as a reminder of steps to work safely.
Available in
English
and
Spanish.
[transition_comments:protected] =>
[external_link:protected] =>
[consol_link:protected] =>
[more_like_this:protected] => d001257,d001254,d001255,d001256,d001258,d001262,d001279
[permission_given_by:protected] =>
[published:protected] => T
[billable:protected] => F
[img_name:protected] =>
[img_ext:protected] =>
[img_width:protected] =>
[img_height:protected] =>
[img_credit:protected] =>
[img_practice:protected] =>
[vid_source_id:protected] =>
[vid_running_time:protected] =>
[vid_intended_audience:protected] =>
[vid_acquisition_info:protected] =>
[vid_cost:protected] =>
[vid_producer:protected] =>
[vid_filename:protected] =>
[vid_filename_downloadable:protected] =>
[date_summary:protected] =>
[date_permission_requested:protected] =>
[date_permission_received:protected] =>
[date_review_needed:protected] =>
[date_received:protected] => 06/10/22
[date_completed:protected] => 06/10/22
[date_billed:protected] =>
[date_modified:protected] => 05/22/23
[collBokExports:protected] =>
[lastBokExportCriteria:BaseElcoshItem:private] =>
[alreadyInSave:protected] =>
[alreadyInValidation:protected] =>
[validationFailures:protected] => Array
(
)
[_new:BaseObject:private] =>
[_deleted:BaseObject:private] =>
[modifiedColumns:protected] => Array
(
)
)
)
[1] => Search_Result Object
(
[title] => Toolbox Talk: Challenges Preventing Falling Objects
[image] => /record/images/notavailable-p.png
[blurb] => The CPWR Toolbox Talk on Challenges Preventing Falling Objects addresses the hazards of being struck by falling objects on the job site. The resource...
[category] => Array
(
[0] => 12
[1] => 47
[2] => 49
[3] => 51
[4] => 55
[5] => 64
[6] => 68
[7] => 71
[8] => 75
[9] => 78
[10] => 79
[11] => 82
[12] => 62
[13] => 86
[14] => 87
[15] => 88
[16] => 89
[17] => 91
[18] => 90
[19] => 92
[20] => 93
[21] => 94
[22] => 95
[23] => 100
)
[labels] => Array
(
[0] => Crushed/Struck By
[1] => Work Environment
[2] => Hazards
[3] => Bricklayer
[4] => Trades
[5] => Carpenter
[7] => Cement Mason
[9] => Electrical Worker
[11] => Laborer
[13] => Maintenance Worker
[15] => Painter
[17] => Plasterer
[19] => Roofer/Waterproofer
[21] => Scaffold Erector
[23] => Stonemason
[25] => Structural Ironworker
[27] => Welder
[29] => Commercial & Institutional
[30] => Jobsites
[31] => Demolition
[33] => Disasters
[35] => Heavy & Highway
[37] => Industrial
[39] => LEED/Green Construction
[41] => Renovations
[43] => Residential
[45] => Underground
[47] => Toolbox Talks
[48] => Documents
[49] => Media & Documents
)
[type] => Toolbox Talks
[sub_category] =>
[url] => /document/4431/d001661/Toolbox%2BTalk%253A%2BChallenges%2BPreventing%2BFalling%2BObjects.html
[item:protected] => DocumentRecord Object
(
[records:protected] => Array
(
)
[recordId:protected] =>
[searchWordClass:protected] =>
[searchWordPeerClass:protected] =>
[bok_record:protected] =>
[authors:protected] =>
[organizations:protected] =>
[collections:protected] =>
[categories:protected] => Array
(
[12] => Category Object
(
[languages:protected] =>
[bok_resources:protected] =>
[bok_topics:protected] =>
[bok_keywords:protected] =>
[id:protected] => 12
[type:protected] => category
[parent:protected] => 7
[label:protected] => Crushed/Struck By
[alreadyInSave:protected] =>
[alreadyInValidation:protected] =>
[validationFailures:protected] => Array
(
)
[_new:BaseObject:private] =>
[_deleted:BaseObject:private] =>
[modifiedColumns:protected] => Array
(
)
)
[47] => Category Object
(
[languages:protected] =>
[bok_resources:protected] =>
[bok_topics:protected] =>
[bok_keywords:protected] =>
[id:protected] => 47
[type:protected] => category
[parent:protected] => 2
[label:protected] => Bricklayer
[alreadyInSave:protected] =>
[alreadyInValidation:protected] =>
[validationFailures:protected] => Array
(
)
[_new:BaseObject:private] =>
[_deleted:BaseObject:private] =>
[modifiedColumns:protected] => Array
(
)
)
[49] => Category Object
(
[languages:protected] =>
[bok_resources:protected] =>
[bok_topics:protected] =>
[bok_keywords:protected] =>
[id:protected] => 49
[type:protected] => category
[parent:protected] => 2
[label:protected] => Carpenter
[alreadyInSave:protected] =>
[alreadyInValidation:protected] =>
[validationFailures:protected] => Array
(
)
[_new:BaseObject:private] =>
[_deleted:BaseObject:private] =>
[modifiedColumns:protected] => Array
(
)
)
[51] => Category Object
(
[languages:protected] =>
[bok_resources:protected] =>
[bok_topics:protected] =>
[bok_keywords:protected] =>
[id:protected] => 51
[type:protected] => category
[parent:protected] => 2
[label:protected] => Cement Mason
[alreadyInSave:protected] =>
[alreadyInValidation:protected] =>
[validationFailures:protected] => Array
(
)
[_new:BaseObject:private] =>
[_deleted:BaseObject:private] =>
[modifiedColumns:protected] => Array
(
)
)
[55] => Category Object
(
[languages:protected] =>
[bok_resources:protected] =>
[bok_topics:protected] =>
[bok_keywords:protected] =>
[id:protected] => 55
[type:protected] => category
[parent:protected] => 2
[label:protected] => Electrical Worker
[alreadyInSave:protected] =>
[alreadyInValidation:protected] =>
[validationFailures:protected] => Array
(
)
[_new:BaseObject:private] =>
[_deleted:BaseObject:private] =>
[modifiedColumns:protected] => Array
(
)
)
[64] => Category Object
(
[languages:protected] =>
[bok_resources:protected] =>
[bok_topics:protected] =>
[bok_keywords:protected] =>
[id:protected] => 64
[type:protected] => category
[parent:protected] => 2
[label:protected] => Laborer
[alreadyInSave:protected] =>
[alreadyInValidation:protected] =>
[validationFailures:protected] => Array
(
)
[_new:BaseObject:private] =>
[_deleted:BaseObject:private] =>
[modifiedColumns:protected] => Array
(
)
)
[68] => Category Object
(
[languages:protected] =>
[bok_resources:protected] =>
[bok_topics:protected] =>
[bok_keywords:protected] =>
[id:protected] => 68
[type:protected] => category
[parent:protected] => 2
[label:protected] => Maintenance Worker
[alreadyInSave:protected] =>
[alreadyInValidation:protected] =>
[validationFailures:protected] => Array
(
)
[_new:BaseObject:private] =>
[_deleted:BaseObject:private] =>
[modifiedColumns:protected] => Array
(
)
)
[71] => Category Object
(
[languages:protected] =>
[bok_resources:protected] =>
[bok_topics:protected] =>
[bok_keywords:protected] =>
[id:protected] => 71
[type:protected] => category
[parent:protected] => 2
[label:protected] => Painter
[alreadyInSave:protected] =>
[alreadyInValidation:protected] =>
[validationFailures:protected] => Array
(
)
[_new:BaseObject:private] =>
[_deleted:BaseObject:private] =>
[modifiedColumns:protected] => Array
(
)
)
[75] => Category Object
(
[languages:protected] =>
[bok_resources:protected] =>
[bok_topics:protected] =>
[bok_keywords:protected] =>
[id:protected] => 75
[type:protected] => category
[parent:protected] => 2
[label:protected] => Plasterer
[alreadyInSave:protected] =>
[alreadyInValidation:protected] =>
[validationFailures:protected] => Array
(
)
[_new:BaseObject:private] =>
[_deleted:BaseObject:private] =>
[modifiedColumns:protected] => Array
(
)
)
[78] => Category Object
(
[languages:protected] =>
[bok_resources:protected] =>
[bok_topics:protected] =>
[bok_keywords:protected] =>
[id:protected] => 78
[type:protected] => category
[parent:protected] => 2
[label:protected] => Roofer/Waterproofer
[alreadyInSave:protected] =>
[alreadyInValidation:protected] =>
[validationFailures:protected] => Array
(
)
[_new:BaseObject:private] =>
[_deleted:BaseObject:private] =>
[modifiedColumns:protected] => Array
(
)
)
[79] => Category Object
(
[languages:protected] =>
[bok_resources:protected] =>
[bok_topics:protected] =>
[bok_keywords:protected] =>
[id:protected] => 79
[type:protected] => category
[parent:protected] => 2
[label:protected] => Scaffold Erector
[alreadyInSave:protected] =>
[alreadyInValidation:protected] =>
[validationFailures:protected] => Array
(
)
[_new:BaseObject:private] =>
[_deleted:BaseObject:private] =>
[modifiedColumns:protected] => Array
(
)
)
[82] => Category Object
(
[languages:protected] =>
[bok_resources:protected] =>
[bok_topics:protected] =>
[bok_keywords:protected] =>
[id:protected] => 82
[type:protected] => category
[parent:protected] => 2
[label:protected] => Stonemason
[alreadyInSave:protected] =>
[alreadyInValidation:protected] =>
[validationFailures:protected] => Array
(
)
[_new:BaseObject:private] =>
[_deleted:BaseObject:private] =>
[modifiedColumns:protected] => Array
(
)
)
[62] => Category Object
(
[languages:protected] =>
[bok_resources:protected] =>
[bok_topics:protected] =>
[bok_keywords:protected] =>
[id:protected] => 62
[type:protected] => category
[parent:protected] => 2
[label:protected] => Structural Ironworker
[alreadyInSave:protected] =>
[alreadyInValidation:protected] =>
[validationFailures:protected] => Array
(
)
[_new:BaseObject:private] =>
[_deleted:BaseObject:private] =>
[modifiedColumns:protected] => Array
(
)
)
[86] => Category Object
(
[languages:protected] =>
[bok_resources:protected] =>
[bok_topics:protected] =>
[bok_keywords:protected] =>
[id:protected] => 86
[type:protected] => category
[parent:protected] => 2
[label:protected] => Welder
[alreadyInSave:protected] =>
[alreadyInValidation:protected] =>
[validationFailures:protected] => Array
(
)
[_new:BaseObject:private] =>
[_deleted:BaseObject:private] =>
[modifiedColumns:protected] => Array
(
)
)
[87] => Category Object
(
[languages:protected] =>
[bok_resources:protected] =>
[bok_topics:protected] =>
[bok_keywords:protected] =>
[id:protected] => 87
[type:protected] => category
[parent:protected] => 3
[label:protected] => Commercial & Institutional
[alreadyInSave:protected] =>
[alreadyInValidation:protected] =>
[validationFailures:protected] => Array
(
)
[_new:BaseObject:private] =>
[_deleted:BaseObject:private] =>
[modifiedColumns:protected] => Array
(
)
)
[88] => Category Object
(
[languages:protected] =>
[bok_resources:protected] =>
[bok_topics:protected] =>
[bok_keywords:protected] =>
[id:protected] => 88
[type:protected] => category
[parent:protected] => 3
[label:protected] => Demolition
[alreadyInSave:protected] =>
[alreadyInValidation:protected] =>
[validationFailures:protected] => Array
(
)
[_new:BaseObject:private] =>
[_deleted:BaseObject:private] =>
[modifiedColumns:protected] => Array
(
)
)
[89] => Category Object
(
[languages:protected] =>
[bok_resources:protected] =>
[bok_topics:protected] =>
[bok_keywords:protected] =>
[id:protected] => 89
[type:protected] => category
[parent:protected] => 3
[label:protected] => Disasters
[alreadyInSave:protected] =>
[alreadyInValidation:protected] =>
[validationFailures:protected] => Array
(
)
[_new:BaseObject:private] =>
[_deleted:BaseObject:private] =>
[modifiedColumns:protected] => Array
(
)
)
[91] => Category Object
(
[languages:protected] =>
[bok_resources:protected] =>
[bok_topics:protected] =>
[bok_keywords:protected] =>
[id:protected] => 91
[type:protected] => category
[parent:protected] => 3
[label:protected] => Heavy & Highway
[alreadyInSave:protected] =>
[alreadyInValidation:protected] =>
[validationFailures:protected] => Array
(
)
[_new:BaseObject:private] =>
[_deleted:BaseObject:private] =>
[modifiedColumns:protected] => Array
(
)
)
[90] => Category Object
(
[languages:protected] =>
[bok_resources:protected] =>
[bok_topics:protected] =>
[bok_keywords:protected] =>
[id:protected] => 90
[type:protected] => category
[parent:protected] => 3
[label:protected] => Industrial
[alreadyInSave:protected] =>
[alreadyInValidation:protected] =>
[validationFailures:protected] => Array
(
)
[_new:BaseObject:private] =>
[_deleted:BaseObject:private] =>
[modifiedColumns:protected] => Array
(
)
)
[92] => Category Object
(
[languages:protected] =>
[bok_resources:protected] =>
[bok_topics:protected] =>
[bok_keywords:protected] =>
[id:protected] => 92
[type:protected] => category
[parent:protected] => 3
[label:protected] => LEED/Green Construction
[alreadyInSave:protected] =>
[alreadyInValidation:protected] =>
[validationFailures:protected] => Array
(
)
[_new:BaseObject:private] =>
[_deleted:BaseObject:private] =>
[modifiedColumns:protected] => Array
(
)
)
[93] => Category Object
(
[languages:protected] =>
[bok_resources:protected] =>
[bok_topics:protected] =>
[bok_keywords:protected] =>
[id:protected] => 93
[type:protected] => category
[parent:protected] => 3
[label:protected] => Renovations
[alreadyInSave:protected] =>
[alreadyInValidation:protected] =>
[validationFailures:protected] => Array
(
)
[_new:BaseObject:private] =>
[_deleted:BaseObject:private] =>
[modifiedColumns:protected] => Array
(
)
)
[94] => Category Object
(
[languages:protected] =>
[bok_resources:protected] =>
[bok_topics:protected] =>
[bok_keywords:protected] =>
[id:protected] => 94
[type:protected] => category
[parent:protected] => 3
[label:protected] => Residential
[alreadyInSave:protected] =>
[alreadyInValidation:protected] =>
[validationFailures:protected] => Array
(
)
[_new:BaseObject:private] =>
[_deleted:BaseObject:private] =>
[modifiedColumns:protected] => Array
(
)
)
[95] => Category Object
(
[languages:protected] =>
[bok_resources:protected] =>
[bok_topics:protected] =>
[bok_keywords:protected] =>
[id:protected] => 95
[type:protected] => category
[parent:protected] => 3
[label:protected] => Underground
[alreadyInSave:protected] =>
[alreadyInValidation:protected] =>
[validationFailures:protected] => Array
(
)
[_new:BaseObject:private] =>
[_deleted:BaseObject:private] =>
[modifiedColumns:protected] => Array
(
)
)
[100] => Category Object
(
[languages:protected] =>
[bok_resources:protected] =>
[bok_topics:protected] =>
[bok_keywords:protected] =>
[id:protected] => 100
[type:protected] => category
[parent:protected] => 6
[label:protected] => Toolbox Talks
[alreadyInSave:protected] =>
[alreadyInValidation:protected] =>
[validationFailures:protected] => Array
(
)
[_new:BaseObject:private] =>
[_deleted:BaseObject:private] =>
[modifiedColumns:protected] => Array
(
)
)
)
[categories_initialized:protected] => 1
[mapped_items:protected] =>
[content:protected] =>
[files:protected] =>
[language:protected] => Language Object
(
[id:protected] => 1
[code:protected] => en
[name:protected] => English
[alreadyInSave:protected] =>
[alreadyInValidation:protected] =>
[validationFailures:protected] => Array
(
)
[_new:BaseObject:private] =>
[_deleted:BaseObject:private] =>
[modifiedColumns:protected] => Array
(
)
)
[old_record:protected] =>
[id:protected] => 4431
[old_id:protected] =>
[elcosh_id:protected] => d001661
[type:protected] => document
[display_type:protected] => HTML only (and links)
[user_id:protected] => 0
[language_id:protected] => 1
[tagging_id:protected] => Mike Aguilar
[priority_id:protected] => 1
[title:protected] => Toolbox Talk: Challenges Preventing Falling Objects
[total_pages:protected] => 0
[billed_pages:protected] => 0
[publication_number:protected] =>
[part_of:protected] =>
[keywords:protected] => dropped objects, falling objects, struck by incidents, struck by fatalities
[comments:protected] =>
[summary:protected] => The CPWR Toolbox Talk on Challenges Preventing Falling Objects addresses the hazards of being struck by falling objects on the job site. The resource includes a brief example, steps to prevent a related injury, and questions for discussion. It includes a graphic that illustrates a group workers observing a scaffold free of debris during high winds, which can be posted in a central location as a reminder of steps to work safely.
Available in
English and
Spanish.
[transition_comments:protected] =>
[external_link:protected] =>
[consol_link:protected] =>
[more_like_this:protected] => d001234,d001238,d001244,d001251,d001253,d001260,d001268,d001278
[permission_given_by:protected] =>
[published:protected] => T
[billable:protected] => F
[img_name:protected] =>
[img_ext:protected] =>
[img_width:protected] =>
[img_height:protected] =>
[img_credit:protected] =>
[img_practice:protected] =>
[vid_source_id:protected] =>
[vid_running_time:protected] =>
[vid_intended_audience:protected] =>
[vid_acquisition_info:protected] =>
[vid_cost:protected] =>
[vid_producer:protected] =>
[vid_filename:protected] =>
[vid_filename_downloadable:protected] =>
[date_summary:protected] =>
[date_permission_requested:protected] =>
[date_permission_received:protected] =>
[date_review_needed:protected] =>
[date_received:protected] => 06/10/22
[date_completed:protected] => 06/10/22
[date_billed:protected] =>
[date_modified:protected] => 05/22/23
[collBokExports:protected] =>
[lastBokExportCriteria:BaseElcoshItem:private] =>
[alreadyInSave:protected] =>
[alreadyInValidation:protected] =>
[validationFailures:protected] => Array
(
)
[_new:BaseObject:private] =>
[_deleted:BaseObject:private] =>
[modifiedColumns:protected] => Array
(
)
)
)
[2] => Search_Result Object
(
[title] => Toolbox Talk: Tower Crane Safety
[image] => /record/images/notavailable-p.png
[blurb] => The CPWR Toolbox Talk on Tower Crane Safety addresses the potential hazards of Tower Cranes and the importance of following procedure before and durin...
[category] => Array
(
[0] => 11
[1] => 12
[2] => 18
[3] => 70
[4] => 87
[5] => 88
[6] => 91
[7] => 90
[8] => 92
[9] => 100
)
[labels] => Array
(
[0] => Cranes & Hoists
[1] => Work Environment
[2] => Hazards
[3] => Crushed/Struck By
[6] => Motor Vehicles/Heavy Equipment
[9] => Operating Engineer
[10] => Trades
[11] => Commercial & Institutional
[12] => Jobsites
[13] => Demolition
[15] => Heavy & Highway
[17] => Industrial
[19] => LEED/Green Construction
[21] => Toolbox Talks
[22] => Documents
[23] => Media & Documents
)
[type] => Toolbox Talks
[sub_category] =>
[url] => /document/4427/d001657/Toolbox%2BTalk%253A%2BTower%2BCrane%2BSafety.html
[item:protected] => DocumentRecord Object
(
[records:protected] => Array
(
)
[recordId:protected] =>
[searchWordClass:protected] =>
[searchWordPeerClass:protected] =>
[bok_record:protected] =>
[authors:protected] =>
[organizations:protected] =>
[collections:protected] =>
[categories:protected] => Array
(
[11] => Category Object
(
[languages:protected] =>
[bok_resources:protected] =>
[bok_topics:protected] =>
[bok_keywords:protected] =>
[id:protected] => 11
[type:protected] => category
[parent:protected] => 7
[label:protected] => Cranes & Hoists
[alreadyInSave:protected] =>
[alreadyInValidation:protected] =>
[validationFailures:protected] => Array
(
)
[_new:BaseObject:private] =>
[_deleted:BaseObject:private] =>
[modifiedColumns:protected] => Array
(
)
)
[12] => Category Object
(
[languages:protected] =>
[bok_resources:protected] =>
[bok_topics:protected] =>
[bok_keywords:protected] =>
[id:protected] => 12
[type:protected] => category
[parent:protected] => 7
[label:protected] => Crushed/Struck By
[alreadyInSave:protected] =>
[alreadyInValidation:protected] =>
[validationFailures:protected] => Array
(
)
[_new:BaseObject:private] =>
[_deleted:BaseObject:private] =>
[modifiedColumns:protected] => Array
(
)
)
[18] => Category Object
(
[languages:protected] =>
[bok_resources:protected] =>
[bok_topics:protected] =>
[bok_keywords:protected] =>
[id:protected] => 18
[type:protected] => category
[parent:protected] => 7
[label:protected] => Motor Vehicles/Heavy Equipment
[alreadyInSave:protected] =>
[alreadyInValidation:protected] =>
[validationFailures:protected] => Array
(
)
[_new:BaseObject:private] =>
[_deleted:BaseObject:private] =>
[modifiedColumns:protected] => Array
(
)
)
[70] => Category Object
(
[languages:protected] =>
[bok_resources:protected] =>
[bok_topics:protected] =>
[bok_keywords:protected] =>
[id:protected] => 70
[type:protected] => category
[parent:protected] => 2
[label:protected] => Operating Engineer
[alreadyInSave:protected] =>
[alreadyInValidation:protected] =>
[validationFailures:protected] => Array
(
)
[_new:BaseObject:private] =>
[_deleted:BaseObject:private] =>
[modifiedColumns:protected] => Array
(
)
)
[87] => Category Object
(
[languages:protected] =>
[bok_resources:protected] =>
[bok_topics:protected] =>
[bok_keywords:protected] =>
[id:protected] => 87
[type:protected] => category
[parent:protected] => 3
[label:protected] => Commercial & Institutional
[alreadyInSave:protected] =>
[alreadyInValidation:protected] =>
[validationFailures:protected] => Array
(
)
[_new:BaseObject:private] =>
[_deleted:BaseObject:private] =>
[modifiedColumns:protected] => Array
(
)
)
[88] => Category Object
(
[languages:protected] =>
[bok_resources:protected] =>
[bok_topics:protected] =>
[bok_keywords:protected] =>
[id:protected] => 88
[type:protected] => category
[parent:protected] => 3
[label:protected] => Demolition
[alreadyInSave:protected] =>
[alreadyInValidation:protected] =>
[validationFailures:protected] => Array
(
)
[_new:BaseObject:private] =>
[_deleted:BaseObject:private] =>
[modifiedColumns:protected] => Array
(
)
)
[91] => Category Object
(
[languages:protected] =>
[bok_resources:protected] =>
[bok_topics:protected] =>
[bok_keywords:protected] =>
[id:protected] => 91
[type:protected] => category
[parent:protected] => 3
[label:protected] => Heavy & Highway
[alreadyInSave:protected] =>
[alreadyInValidation:protected] =>
[validationFailures:protected] => Array
(
)
[_new:BaseObject:private] =>
[_deleted:BaseObject:private] =>
[modifiedColumns:protected] => Array
(
)
)
[90] => Category Object
(
[languages:protected] =>
[bok_resources:protected] =>
[bok_topics:protected] =>
[bok_keywords:protected] =>
[id:protected] => 90
[type:protected] => category
[parent:protected] => 3
[label:protected] => Industrial
[alreadyInSave:protected] =>
[alreadyInValidation:protected] =>
[validationFailures:protected] => Array
(
)
[_new:BaseObject:private] =>
[_deleted:BaseObject:private] =>
[modifiedColumns:protected] => Array
(
)
)
[92] => Category Object
(
[languages:protected] =>
[bok_resources:protected] =>
[bok_topics:protected] =>
[bok_keywords:protected] =>
[id:protected] => 92
[type:protected] => category
[parent:protected] => 3
[label:protected] => LEED/Green Construction
[alreadyInSave:protected] =>
[alreadyInValidation:protected] =>
[validationFailures:protected] => Array
(
)
[_new:BaseObject:private] =>
[_deleted:BaseObject:private] =>
[modifiedColumns:protected] => Array
(
)
)
[100] => Category Object
(
[languages:protected] =>
[bok_resources:protected] =>
[bok_topics:protected] =>
[bok_keywords:protected] =>
[id:protected] => 100
[type:protected] => category
[parent:protected] => 6
[label:protected] => Toolbox Talks
[alreadyInSave:protected] =>
[alreadyInValidation:protected] =>
[validationFailures:protected] => Array
(
)
[_new:BaseObject:private] =>
[_deleted:BaseObject:private] =>
[modifiedColumns:protected] => Array
(
)
)
)
[categories_initialized:protected] => 1
[mapped_items:protected] =>
[content:protected] =>
[files:protected] =>
[language:protected] => Language Object
(
[id:protected] => 1
[code:protected] => en
[name:protected] => English
[alreadyInSave:protected] =>
[alreadyInValidation:protected] =>
[validationFailures:protected] => Array
(
)
[_new:BaseObject:private] =>
[_deleted:BaseObject:private] =>
[modifiedColumns:protected] => Array
(
)
)
[old_record:protected] =>
[id:protected] => 4427
[old_id:protected] =>
[elcosh_id:protected] => d001657
[type:protected] => document
[display_type:protected] => HTML only (and links)
[user_id:protected] => 0
[language_id:protected] => 1
[tagging_id:protected] => Mike Aguilar
[priority_id:protected] => 1
[title:protected] => Toolbox Talk: Tower Crane Safety
[total_pages:protected] => 0
[billed_pages:protected] => 0
[publication_number:protected] =>
[part_of:protected] =>
[keywords:protected] => Tower Crane, Crane, Stability, Tipping, Lift Zone Safety, Lift, Zone, Safety, Struck by
[comments:protected] =>
[summary:protected] => The CPWR Toolbox Talk on Tower Crane Safety addresses the potential hazards of Tower Cranes and the importance of following procedure before and during Tower Crane operation. The resource includes a brief example, steps to prevent a related injury, and questions for discussion. It includes a graphic that illustrates a worker inspecting a Tower Crane before operation, which can be posted in a central location as a reminder of steps to work safely.
Available in
English and
Spanish.
[transition_comments:protected] =>
[external_link:protected] =>
[consol_link:protected] =>
[more_like_this:protected] => d001234,d001238,d001250,d001251,d001253,d001258,d001262,d001273
[permission_given_by:protected] =>
[published:protected] => T
[billable:protected] => F
[img_name:protected] =>
[img_ext:protected] => jpg
[img_width:protected] =>
[img_height:protected] =>
[img_credit:protected] =>
[img_practice:protected] =>
[vid_source_id:protected] =>
[vid_running_time:protected] =>
[vid_intended_audience:protected] =>
[vid_acquisition_info:protected] =>
[vid_cost:protected] =>
[vid_producer:protected] =>
[vid_filename:protected] =>
[vid_filename_downloadable:protected] =>
[date_summary:protected] =>
[date_permission_requested:protected] =>
[date_permission_received:protected] =>
[date_review_needed:protected] =>
[date_received:protected] => 12/23/21
[date_completed:protected] => 12/23/21
[date_billed:protected] =>
[date_modified:protected] => 05/19/23
[collBokExports:protected] =>
[lastBokExportCriteria:BaseElcoshItem:private] =>
[alreadyInSave:protected] =>
[alreadyInValidation:protected] =>
[validationFailures:protected] => Array
(
)
[_new:BaseObject:private] =>
[_deleted:BaseObject:private] =>
[modifiedColumns:protected] => Array
(
)
)
)
[3] => Search_Result Object
(
[title] => Toolbox Talk: Work Zone Safety: Working Around Vehicles
[image] => /record/images/notavailable-p.png
[blurb] => The CPWR Toolbox Talk on Working Around Vehicles in the Work Zone addresses methods to avoid being struck-by a vehicle on a construction site. The res...
[category] => Array
(
[0] => 12
[1] => 18
[2] => 52
[3] => 57
[4] => 70
[5] => 85
[6] => 87
[7] => 88
[8] => 89
[9] => 91
[10] => 90
[11] => 92
[12] => 93
[13] => 94
[14] => 95
[15] => 100
)
[labels] => Array
(
[0] => Crushed/Struck By
[1] => Work Environment
[2] => Hazards
[3] => Motor Vehicles/Heavy Equipment
[6] => Commercial Diver
[7] => Trades
[8] => Flagger
[10] => Operating Engineer
[12] => Truck Driver
[14] => Commercial & Institutional
[15] => Jobsites
[16] => Demolition
[18] => Disasters
[20] => Heavy & Highway
[22] => Industrial
[24] => LEED/Green Construction
[26] => Renovations
[28] => Residential
[30] => Underground
[32] => Toolbox Talks
[33] => Documents
[34] => Media & Documents
)
[type] => Toolbox Talks
[sub_category] =>
[url] => /document/4428/d001658/Toolbox%2BTalk%253A%2BWork%2BZone%2BSafety%253A%2BWorking%2BAround%2BVehicles.html
[item:protected] => DocumentRecord Object
(
[records:protected] => Array
(
)
[recordId:protected] =>
[searchWordClass:protected] =>
[searchWordPeerClass:protected] =>
[bok_record:protected] =>
[authors:protected] =>
[organizations:protected] =>
[collections:protected] =>
[categories:protected] => Array
(
[12] => Category Object
(
[languages:protected] =>
[bok_resources:protected] =>
[bok_topics:protected] =>
[bok_keywords:protected] =>
[id:protected] => 12
[type:protected] => category
[parent:protected] => 7
[label:protected] => Crushed/Struck By
[alreadyInSave:protected] =>
[alreadyInValidation:protected] =>
[validationFailures:protected] => Array
(
)
[_new:BaseObject:private] =>
[_deleted:BaseObject:private] =>
[modifiedColumns:protected] => Array
(
)
)
[18] => Category Object
(
[languages:protected] =>
[bok_resources:protected] =>
[bok_topics:protected] =>
[bok_keywords:protected] =>
[id:protected] => 18
[type:protected] => category
[parent:protected] => 7
[label:protected] => Motor Vehicles/Heavy Equipment
[alreadyInSave:protected] =>
[alreadyInValidation:protected] =>
[validationFailures:protected] => Array
(
)
[_new:BaseObject:private] =>
[_deleted:BaseObject:private] =>
[modifiedColumns:protected] => Array
(
)
)
[52] => Category Object
(
[languages:protected] =>
[bok_resources:protected] =>
[bok_topics:protected] =>
[bok_keywords:protected] =>
[id:protected] => 52
[type:protected] => category
[parent:protected] => 2
[label:protected] => Commercial Diver
[alreadyInSave:protected] =>
[alreadyInValidation:protected] =>
[validationFailures:protected] => Array
(
)
[_new:BaseObject:private] =>
[_deleted:BaseObject:private] =>
[modifiedColumns:protected] => Array
(
)
)
[57] => Category Object
(
[languages:protected] =>
[bok_resources:protected] =>
[bok_topics:protected] =>
[bok_keywords:protected] =>
[id:protected] => 57
[type:protected] => category
[parent:protected] => 2
[label:protected] => Flagger
[alreadyInSave:protected] =>
[alreadyInValidation:protected] =>
[validationFailures:protected] => Array
(
)
[_new:BaseObject:private] =>
[_deleted:BaseObject:private] =>
[modifiedColumns:protected] => Array
(
)
)
[70] => Category Object
(
[languages:protected] =>
[bok_resources:protected] =>
[bok_topics:protected] =>
[bok_keywords:protected] =>
[id:protected] => 70
[type:protected] => category
[parent:protected] => 2
[label:protected] => Operating Engineer
[alreadyInSave:protected] =>
[alreadyInValidation:protected] =>
[validationFailures:protected] => Array
(
)
[_new:BaseObject:private] =>
[_deleted:BaseObject:private] =>
[modifiedColumns:protected] => Array
(
)
)
[85] => Category Object
(
[languages:protected] =>
[bok_resources:protected] =>
[bok_topics:protected] =>
[bok_keywords:protected] =>
[id:protected] => 85
[type:protected] => category
[parent:protected] => 2
[label:protected] => Truck Driver
[alreadyInSave:protected] =>
[alreadyInValidation:protected] =>
[validationFailures:protected] => Array
(
)
[_new:BaseObject:private] =>
[_deleted:BaseObject:private] =>
[modifiedColumns:protected] => Array
(
)
)
[87] => Category Object
(
[languages:protected] =>
[bok_resources:protected] =>
[bok_topics:protected] =>
[bok_keywords:protected] =>
[id:protected] => 87
[type:protected] => category
[parent:protected] => 3
[label:protected] => Commercial & Institutional
[alreadyInSave:protected] =>
[alreadyInValidation:protected] =>
[validationFailures:protected] => Array
(
)
[_new:BaseObject:private] =>
[_deleted:BaseObject:private] =>
[modifiedColumns:protected] => Array
(
)
)
[88] => Category Object
(
[languages:protected] =>
[bok_resources:protected] =>
[bok_topics:protected] =>
[bok_keywords:protected] =>
[id:protected] => 88
[type:protected] => category
[parent:protected] => 3
[label:protected] => Demolition
[alreadyInSave:protected] =>
[alreadyInValidation:protected] =>
[validationFailures:protected] => Array
(
)
[_new:BaseObject:private] =>
[_deleted:BaseObject:private] =>
[modifiedColumns:protected] => Array
(
)
)
[89] => Category Object
(
[languages:protected] =>
[bok_resources:protected] =>
[bok_topics:protected] =>
[bok_keywords:protected] =>
[id:protected] => 89
[type:protected] => category
[parent:protected] => 3
[label:protected] => Disasters
[alreadyInSave:protected] =>
[alreadyInValidation:protected] =>
[validationFailures:protected] => Array
(
)
[_new:BaseObject:private] =>
[_deleted:BaseObject:private] =>
[modifiedColumns:protected] => Array
(
)
)
[91] => Category Object
(
[languages:protected] =>
[bok_resources:protected] =>
[bok_topics:protected] =>
[bok_keywords:protected] =>
[id:protected] => 91
[type:protected] => category
[parent:protected] => 3
[label:protected] => Heavy & Highway
[alreadyInSave:protected] =>
[alreadyInValidation:protected] =>
[validationFailures:protected] => Array
(
)
[_new:BaseObject:private] =>
[_deleted:BaseObject:private] =>
[modifiedColumns:protected] => Array
(
)
)
[90] => Category Object
(
[languages:protected] =>
[bok_resources:protected] =>
[bok_topics:protected] =>
[bok_keywords:protected] =>
[id:protected] => 90
[type:protected] => category
[parent:protected] => 3
[label:protected] => Industrial
[alreadyInSave:protected] =>
[alreadyInValidation:protected] =>
[validationFailures:protected] => Array
(
)
[_new:BaseObject:private] =>
[_deleted:BaseObject:private] =>
[modifiedColumns:protected] => Array
(
)
)
[92] => Category Object
(
[languages:protected] =>
[bok_resources:protected] =>
[bok_topics:protected] =>
[bok_keywords:protected] =>
[id:protected] => 92
[type:protected] => category
[parent:protected] => 3
[label:protected] => LEED/Green Construction
[alreadyInSave:protected] =>
[alreadyInValidation:protected] =>
[validationFailures:protected] => Array
(
)
[_new:BaseObject:private] =>
[_deleted:BaseObject:private] =>
[modifiedColumns:protected] => Array
(
)
)
[93] => Category Object
(
[languages:protected] =>
[bok_resources:protected] =>
[bok_topics:protected] =>
[bok_keywords:protected] =>
[id:protected] => 93
[type:protected] => category
[parent:protected] => 3
[label:protected] => Renovations
[alreadyInSave:protected] =>
[alreadyInValidation:protected] =>
[validationFailures:protected] => Array
(
)
[_new:BaseObject:private] =>
[_deleted:BaseObject:private] =>
[modifiedColumns:protected] => Array
(
)
)
[94] => Category Object
(
[languages:protected] =>
[bok_resources:protected] =>
[bok_topics:protected] =>
[bok_keywords:protected] =>
[id:protected] => 94
[type:protected] => category
[parent:protected] => 3
[label:protected] => Residential
[alreadyInSave:protected] =>
[alreadyInValidation:protected] =>
[validationFailures:protected] => Array
(
)
[_new:BaseObject:private] =>
[_deleted:BaseObject:private] =>
[modifiedColumns:protected] => Array
(
)
)
[95] => Category Object
(
[languages:protected] =>
[bok_resources:protected] =>
[bok_topics:protected] =>
[bok_keywords:protected] =>
[id:protected] => 95
[type:protected] => category
[parent:protected] => 3
[label:protected] => Underground
[alreadyInSave:protected] =>
[alreadyInValidation:protected] =>
[validationFailures:protected] => Array
(
)
[_new:BaseObject:private] =>
[_deleted:BaseObject:private] =>
[modifiedColumns:protected] => Array
(
)
)
[100] => Category Object
(
[languages:protected] =>
[bok_resources:protected] =>
[bok_topics:protected] =>
[bok_keywords:protected] =>
[id:protected] => 100
[type:protected] => category
[parent:protected] => 6
[label:protected] => Toolbox Talks
[alreadyInSave:protected] =>
[alreadyInValidation:protected] =>
[validationFailures:protected] => Array
(
)
[_new:BaseObject:private] =>
[_deleted:BaseObject:private] =>
[modifiedColumns:protected] => Array
(
)
)
)
[categories_initialized:protected] => 1
[mapped_items:protected] =>
[content:protected] =>
[files:protected] =>
[language:protected] => Language Object
(
[id:protected] => 1
[code:protected] => en
[name:protected] => English
[alreadyInSave:protected] =>
[alreadyInValidation:protected] =>
[validationFailures:protected] => Array
(
)
[_new:BaseObject:private] =>
[_deleted:BaseObject:private] =>
[modifiedColumns:protected] => Array
(
)
)
[old_record:protected] =>
[id:protected] => 4428
[old_id:protected] =>
[elcosh_id:protected] => d001658
[type:protected] => document
[display_type:protected] => HTML only (and links)
[user_id:protected] => 0
[language_id:protected] => 1
[tagging_id:protected] => Daniela Caceres
[priority_id:protected] => 1
[title:protected] => Toolbox Talk: Work Zone Safety: Working Around Vehicles
[total_pages:protected] => 0
[billed_pages:protected] => 0
[publication_number:protected] =>
[part_of:protected] =>
[keywords:protected] => Struck, Struck by, Vehicle, Work Zone Safety, Truck, Operator, Driver, Mobile Equipment
[comments:protected] =>
[summary:protected] => The CPWR Toolbox Talk on Working Around Vehicles in the Work Zone addresses methods to avoid being struck-by a vehicle on a construction site. The resource includes a case example, steps to prevent a related injury, and questions for discussion. It includes a graphic that illustrates the hazard, which can be posted in a central location as a reminder of steps to work safely. Available in
English and
Spanish.
[transition_comments:protected] =>
[external_link:protected] =>
[consol_link:protected] =>
[more_like_this:protected] => d001640
[permission_given_by:protected] =>
[published:protected] => T
[billable:protected] => F
[img_name:protected] =>
[img_ext:protected] =>
[img_width:protected] =>
[img_height:protected] =>
[img_credit:protected] =>
[img_practice:protected] =>
[vid_source_id:protected] =>
[vid_running_time:protected] =>
[vid_intended_audience:protected] =>
[vid_acquisition_info:protected] =>
[vid_cost:protected] =>
[vid_producer:protected] =>
[vid_filename:protected] =>
[vid_filename_downloadable:protected] =>
[date_summary:protected] =>
[date_permission_requested:protected] =>
[date_permission_received:protected] =>
[date_review_needed:protected] =>
[date_received:protected] => 12/23/21
[date_completed:protected] => 12/23/21
[date_billed:protected] =>
[date_modified:protected] => 05/19/23
[collBokExports:protected] =>
[lastBokExportCriteria:BaseElcoshItem:private] =>
[alreadyInSave:protected] =>
[alreadyInValidation:protected] =>
[validationFailures:protected] => Array
(
)
[_new:BaseObject:private] =>
[_deleted:BaseObject:private] =>
[modifiedColumns:protected] => Array
(
)
)
)
[4] => Search_Result Object
(
[title] => Construction Dive -- DeWalt's Jobsite Pro headphones recalled for fire hazards
[image] => /record/images/notavailable-p.png
[blurb] => A recall notice by the United States Consumer Product Safety Commission affects over 300,000 DeWalt Jobsite Pro Headphones. The recall is a result of...
[category] => Array
(
[0] => 16
[1] => 44
[2] => 45
[3] => 46
[4] => 47
[5] => 48
[6] => 49
[7] => 50
[8] => 51
[9] => 52
[10] => 53
[11] => 54
[12] => 55
[13] => 56
[14] => 57
[15] => 58
[16] => 59
[17] => 60
[18] => 61
[19] => 64
[20] => 65
[21] => 66
[22] => 67
[23] => 68
[24] => 69
[25] => 70
[26] => 71
[27] => 72
[28] => 73
[29] => 74
[30] => 75
[31] => 76
[32] => 77
[33] => 63
[34] => 78
[35] => 79
[36] => 80
[37] => 81
[38] => 82
[39] => 62
[40] => 83
[41] => 84
[42] => 85
[43] => 86
[44] => 87
[45] => 88
[46] => 89
[47] => 91
[48] => 90
[49] => 92
[50] => 93
[51] => 94
[52] => 95
)
[labels] => Array
(
[0] => Fire & Explosions
[1] => Work Environment
[2] => Hazards
[3] => Acoustical Ceiling Carpenter
[4] => Trades
[5] => Asbestos/Insulator
[7] => Boilermaker
[9] => Bricklayer
[11] => Cabinetmaker
[13] => Carpenter
[15] => Carpet Layer
[17] => Cement Mason
[19] => Commercial Diver
[21] => Concrete Polisher
[23] => Drywall Applicator Specialist
[25] => Electrical Worker
[27] => Elevator Constructor
[29] => Flagger
[31] => Glazier
[33] => Hazardous Waste Cleanup
[35] => HVAC
[37] => Interior Systems Carpenter
[39] => Laborer
[41] => Landscaper
[43] => Lather
[45] => Lead Abatement Worker
[47] => Maintenance Worker
[49] => Millwright
[51] => Operating Engineer
[53] => Painter
[55] => Paper Hanger
[57] => PCC/Restoration
[59] => Pile Driver
[61] => Plasterer
[63] => Plumber/Pipefitter
[65] => Refractory Worker
[67] => Reinforcing Ironworker
[69] => Roofer/Waterproofer
[71] => Scaffold Erector
[73] => Sheetmetal Worker
[75] => Sprinkler Fitter
[77] => Stonemason
[79] => Structural Ironworker
[81] => Terrazzo Worker
[83] => Tile Setter
[85] => Truck Driver
[87] => Welder
[89] => Commercial & Institutional
[90] => Jobsites
[91] => Demolition
[93] => Disasters
[95] => Heavy & Highway
[97] => Industrial
[99] => LEED/Green Construction
[101] => Renovations
[103] => Residential
[105] => Underground
)
[type] =>
[sub_category] =>
[url] => /document/4426/d001656/Construction%2BDive%2B--%2BDeWalt%2527s%2BJobsite%2BPro%2Bheadphones%2Brecalled%2Bfor%2Bfire%2Bhazards.html
[item:protected] => DocumentRecord Object
(
[records:protected] => Array
(
)
[recordId:protected] =>
[searchWordClass:protected] =>
[searchWordPeerClass:protected] =>
[bok_record:protected] =>
[authors:protected] =>
[organizations:protected] =>
[collections:protected] =>
[categories:protected] => Array
(
[16] => Category Object
(
[languages:protected] =>
[bok_resources:protected] =>
[bok_topics:protected] =>
[bok_keywords:protected] =>
[id:protected] => 16
[type:protected] => category
[parent:protected] => 7
[label:protected] => Fire & Explosions
[alreadyInSave:protected] =>
[alreadyInValidation:protected] =>
[validationFailures:protected] => Array
(
)
[_new:BaseObject:private] =>
[_deleted:BaseObject:private] =>
[modifiedColumns:protected] => Array
(
)
)
[44] => Category Object
(
[languages:protected] =>
[bok_resources:protected] =>
[bok_topics:protected] =>
[bok_keywords:protected] =>
[id:protected] => 44
[type:protected] => category
[parent:protected] => 2
[label:protected] => Acoustical Ceiling Carpenter
[alreadyInSave:protected] =>
[alreadyInValidation:protected] =>
[validationFailures:protected] => Array
(
)
[_new:BaseObject:private] =>
[_deleted:BaseObject:private] =>
[modifiedColumns:protected] => Array
(
)
)
[45] => Category Object
(
[languages:protected] =>
[bok_resources:protected] =>
[bok_topics:protected] =>
[bok_keywords:protected] =>
[id:protected] => 45
[type:protected] => category
[parent:protected] => 2
[label:protected] => Asbestos/Insulator
[alreadyInSave:protected] =>
[alreadyInValidation:protected] =>
[validationFailures:protected] => Array
(
)
[_new:BaseObject:private] =>
[_deleted:BaseObject:private] =>
[modifiedColumns:protected] => Array
(
)
)
[46] => Category Object
(
[languages:protected] =>
[bok_resources:protected] =>
[bok_topics:protected] =>
[bok_keywords:protected] =>
[id:protected] => 46
[type:protected] => category
[parent:protected] => 2
[label:protected] => Boilermaker
[alreadyInSave:protected] =>
[alreadyInValidation:protected] =>
[validationFailures:protected] => Array
(
)
[_new:BaseObject:private] =>
[_deleted:BaseObject:private] =>
[modifiedColumns:protected] => Array
(
)
)
[47] => Category Object
(
[languages:protected] =>
[bok_resources:protected] =>
[bok_topics:protected] =>
[bok_keywords:protected] =>
[id:protected] => 47
[type:protected] => category
[parent:protected] => 2
[label:protected] => Bricklayer
[alreadyInSave:protected] =>
[alreadyInValidation:protected] =>
[validationFailures:protected] => Array
(
)
[_new:BaseObject:private] =>
[_deleted:BaseObject:private] =>
[modifiedColumns:protected] => Array
(
)
)
[48] => Category Object
(
[languages:protected] =>
[bok_resources:protected] =>
[bok_topics:protected] =>
[bok_keywords:protected] =>
[id:protected] => 48
[type:protected] => category
[parent:protected] => 2
[label:protected] => Cabinetmaker
[alreadyInSave:protected] =>
[alreadyInValidation:protected] =>
[validationFailures:protected] => Array
(
)
[_new:BaseObject:private] =>
[_deleted:BaseObject:private] =>
[modifiedColumns:protected] => Array
(
)
)
[49] => Category Object
(
[languages:protected] =>
[bok_resources:protected] =>
[bok_topics:protected] =>
[bok_keywords:protected] =>
[id:protected] => 49
[type:protected] => category
[parent:protected] => 2
[label:protected] => Carpenter
[alreadyInSave:protected] =>
[alreadyInValidation:protected] =>
[validationFailures:protected] => Array
(
)
[_new:BaseObject:private] =>
[_deleted:BaseObject:private] =>
[modifiedColumns:protected] => Array
(
)
)
[50] => Category Object
(
[languages:protected] =>
[bok_resources:protected] =>
[bok_topics:protected] =>
[bok_keywords:protected] =>
[id:protected] => 50
[type:protected] => category
[parent:protected] => 2
[label:protected] => Carpet Layer
[alreadyInSave:protected] =>
[alreadyInValidation:protected] =>
[validationFailures:protected] => Array
(
)
[_new:BaseObject:private] =>
[_deleted:BaseObject:private] =>
[modifiedColumns:protected] => Array
(
)
)
[51] => Category Object
(
[languages:protected] =>
[bok_resources:protected] =>
[bok_topics:protected] =>
[bok_keywords:protected] =>
[id:protected] => 51
[type:protected] => category
[parent:protected] => 2
[label:protected] => Cement Mason
[alreadyInSave:protected] =>
[alreadyInValidation:protected] =>
[validationFailures:protected] => Array
(
)
[_new:BaseObject:private] =>
[_deleted:BaseObject:private] =>
[modifiedColumns:protected] => Array
(
)
)
[52] => Category Object
(
[languages:protected] =>
[bok_resources:protected] =>
[bok_topics:protected] =>
[bok_keywords:protected] =>
[id:protected] => 52
[type:protected] => category
[parent:protected] => 2
[label:protected] => Commercial Diver
[alreadyInSave:protected] =>
[alreadyInValidation:protected] =>
[validationFailures:protected] => Array
(
)
[_new:BaseObject:private] =>
[_deleted:BaseObject:private] =>
[modifiedColumns:protected] => Array
(
)
)
[53] => Category Object
(
[languages:protected] =>
[bok_resources:protected] =>
[bok_topics:protected] =>
[bok_keywords:protected] =>
[id:protected] => 53
[type:protected] => category
[parent:protected] => 2
[label:protected] => Concrete Polisher
[alreadyInSave:protected] =>
[alreadyInValidation:protected] =>
[validationFailures:protected] => Array
(
)
[_new:BaseObject:private] =>
[_deleted:BaseObject:private] =>
[modifiedColumns:protected] => Array
(
)
)
[54] => Category Object
(
[languages:protected] =>
[bok_resources:protected] =>
[bok_topics:protected] =>
[bok_keywords:protected] =>
[id:protected] => 54
[type:protected] => category
[parent:protected] => 2
[label:protected] => Drywall Applicator Specialist
[alreadyInSave:protected] =>
[alreadyInValidation:protected] =>
[validationFailures:protected] => Array
(
)
[_new:BaseObject:private] =>
[_deleted:BaseObject:private] =>
[modifiedColumns:protected] => Array
(
)
)
[55] => Category Object
(
[languages:protected] =>
[bok_resources:protected] =>
[bok_topics:protected] =>
[bok_keywords:protected] =>
[id:protected] => 55
[type:protected] => category
[parent:protected] => 2
[label:protected] => Electrical Worker
[alreadyInSave:protected] =>
[alreadyInValidation:protected] =>
[validationFailures:protected] => Array
(
)
[_new:BaseObject:private] =>
[_deleted:BaseObject:private] =>
[modifiedColumns:protected] => Array
(
)
)
[56] => Category Object
(
[languages:protected] =>
[bok_resources:protected] =>
[bok_topics:protected] =>
[bok_keywords:protected] =>
[id:protected] => 56
[type:protected] => category
[parent:protected] => 2
[label:protected] => Elevator Constructor
[alreadyInSave:protected] =>
[alreadyInValidation:protected] =>
[validationFailures:protected] => Array
(
)
[_new:BaseObject:private] =>
[_deleted:BaseObject:private] =>
[modifiedColumns:protected] => Array
(
)
)
[57] => Category Object
(
[languages:protected] =>
[bok_resources:protected] =>
[bok_topics:protected] =>
[bok_keywords:protected] =>
[id:protected] => 57
[type:protected] => category
[parent:protected] => 2
[label:protected] => Flagger
[alreadyInSave:protected] =>
[alreadyInValidation:protected] =>
[validationFailures:protected] => Array
(
)
[_new:BaseObject:private] =>
[_deleted:BaseObject:private] =>
[modifiedColumns:protected] => Array
(
)
)
[58] => Category Object
(
[languages:protected] =>
[bok_resources:protected] =>
[bok_topics:protected] =>
[bok_keywords:protected] =>
[id:protected] => 58
[type:protected] => category
[parent:protected] => 2
[label:protected] => Glazier
[alreadyInSave:protected] =>
[alreadyInValidation:protected] =>
[validationFailures:protected] => Array
(
)
[_new:BaseObject:private] =>
[_deleted:BaseObject:private] =>
[modifiedColumns:protected] => Array
(
)
)
[59] => Category Object
(
[languages:protected] =>
[bok_resources:protected] =>
[bok_topics:protected] =>
[bok_keywords:protected] =>
[id:protected] => 59
[type:protected] => category
[parent:protected] => 2
[label:protected] => Hazardous Waste Cleanup
[alreadyInSave:protected] =>
[alreadyInValidation:protected] =>
[validationFailures:protected] => Array
(
)
[_new:BaseObject:private] =>
[_deleted:BaseObject:private] =>
[modifiedColumns:protected] => Array
(
)
)
[60] => Category Object
(
[languages:protected] =>
[bok_resources:protected] =>
[bok_topics:protected] =>
[bok_keywords:protected] =>
[id:protected] => 60
[type:protected] => category
[parent:protected] => 2
[label:protected] => HVAC
[alreadyInSave:protected] =>
[alreadyInValidation:protected] =>
[validationFailures:protected] => Array
(
)
[_new:BaseObject:private] =>
[_deleted:BaseObject:private] =>
[modifiedColumns:protected] => Array
(
)
)
[61] => Category Object
(
[languages:protected] =>
[bok_resources:protected] =>
[bok_topics:protected] =>
[bok_keywords:protected] =>
[id:protected] => 61
[type:protected] => category
[parent:protected] => 2
[label:protected] => Interior Systems Carpenter
[alreadyInSave:protected] =>
[alreadyInValidation:protected] =>
[validationFailures:protected] => Array
(
)
[_new:BaseObject:private] =>
[_deleted:BaseObject:private] =>
[modifiedColumns:protected] => Array
(
)
)
[64] => Category Object
(
[languages:protected] =>
[bok_resources:protected] =>
[bok_topics:protected] =>
[bok_keywords:protected] =>
[id:protected] => 64
[type:protected] => category
[parent:protected] => 2
[label:protected] => Laborer
[alreadyInSave:protected] =>
[alreadyInValidation:protected] =>
[validationFailures:protected] => Array
(
)
[_new:BaseObject:private] =>
[_deleted:BaseObject:private] =>
[modifiedColumns:protected] => Array
(
)
)
[65] => Category Object
(
[languages:protected] =>
[bok_resources:protected] =>
[bok_topics:protected] =>
[bok_keywords:protected] =>
[id:protected] => 65
[type:protected] => category
[parent:protected] => 2
[label:protected] => Landscaper
[alreadyInSave:protected] =>
[alreadyInValidation:protected] =>
[validationFailures:protected] => Array
(
)
[_new:BaseObject:private] =>
[_deleted:BaseObject:private] =>
[modifiedColumns:protected] => Array
(
)
)
[66] => Category Object
(
[languages:protected] =>
[bok_resources:protected] =>
[bok_topics:protected] =>
[bok_keywords:protected] =>
[id:protected] => 66
[type:protected] => category
[parent:protected] => 2
[label:protected] => Lather
[alreadyInSave:protected] =>
[alreadyInValidation:protected] =>
[validationFailures:protected] => Array
(
)
[_new:BaseObject:private] =>
[_deleted:BaseObject:private] =>
[modifiedColumns:protected] => Array
(
)
)
[67] => Category Object
(
[languages:protected] =>
[bok_resources:protected] =>
[bok_topics:protected] =>
[bok_keywords:protected] =>
[id:protected] => 67
[type:protected] => category
[parent:protected] => 2
[label:protected] => Lead Abatement Worker
[alreadyInSave:protected] =>
[alreadyInValidation:protected] =>
[validationFailures:protected] => Array
(
)
[_new:BaseObject:private] =>
[_deleted:BaseObject:private] =>
[modifiedColumns:protected] => Array
(
)
)
[68] => Category Object
(
[languages:protected] =>
[bok_resources:protected] =>
[bok_topics:protected] =>
[bok_keywords:protected] =>
[id:protected] => 68
[type:protected] => category
[parent:protected] => 2
[label:protected] => Maintenance Worker
[alreadyInSave:protected] =>
[alreadyInValidation:protected] =>
[validationFailures:protected] => Array
(
)
[_new:BaseObject:private] =>
[_deleted:BaseObject:private] =>
[modifiedColumns:protected] => Array
(
)
)
[69] => Category Object
(
[languages:protected] =>
[bok_resources:protected] =>
[bok_topics:protected] =>
[bok_keywords:protected] =>
[id:protected] => 69
[type:protected] => category
[parent:protected] => 2
[label:protected] => Millwright
[alreadyInSave:protected] =>
[alreadyInValidation:protected] =>
[validationFailures:protected] => Array
(
)
[_new:BaseObject:private] =>
[_deleted:BaseObject:private] =>
[modifiedColumns:protected] => Array
(
)
)
[70] => Category Object
(
[languages:protected] =>
[bok_resources:protected] =>
[bok_topics:protected] =>
[bok_keywords:protected] =>
[id:protected] => 70
[type:protected] => category
[parent:protected] => 2
[label:protected] => Operating Engineer
[alreadyInSave:protected] =>
[alreadyInValidation:protected] =>
[validationFailures:protected] => Array
(
)
[_new:BaseObject:private] =>
[_deleted:BaseObject:private] =>
[modifiedColumns:protected] => Array
(
)
)
[71] => Category Object
(
[languages:protected] =>
[bok_resources:protected] =>
[bok_topics:protected] =>
[bok_keywords:protected] =>
[id:protected] => 71
[type:protected] => category
[parent:protected] => 2
[label:protected] => Painter
[alreadyInSave:protected] =>
[alreadyInValidation:protected] =>
[validationFailures:protected] => Array
(
)
[_new:BaseObject:private] =>
[_deleted:BaseObject:private] =>
[modifiedColumns:protected] => Array
(
)
)
[72] => Category Object
(
[languages:protected] =>
[bok_resources:protected] =>
[bok_topics:protected] =>
[bok_keywords:protected] =>
[id:protected] => 72
[type:protected] => category
[parent:protected] => 2
[label:protected] => Paper Hanger
[alreadyInSave:protected] =>
[alreadyInValidation:protected] =>
[validationFailures:protected] => Array
(
)
[_new:BaseObject:private] =>
[_deleted:BaseObject:private] =>
[modifiedColumns:protected] => Array
(
)
)
[73] => Category Object
(
[languages:protected] =>
[bok_resources:protected] =>
[bok_topics:protected] =>
[bok_keywords:protected] =>
[id:protected] => 73
[type:protected] => category
[parent:protected] => 2
[label:protected] => PCC/Restoration
[alreadyInSave:protected] =>
[alreadyInValidation:protected] =>
[validationFailures:protected] => Array
(
)
[_new:BaseObject:private] =>
[_deleted:BaseObject:private] =>
[modifiedColumns:protected] => Array
(
)
)
[74] => Category Object
(
[languages:protected] =>
[bok_resources:protected] =>
[bok_topics:protected] =>
[bok_keywords:protected] =>
[id:protected] => 74
[type:protected] => category
[parent:protected] => 2
[label:protected] => Pile Driver
[alreadyInSave:protected] =>
[alreadyInValidation:protected] =>
[validationFailures:protected] => Array
(
)
[_new:BaseObject:private] =>
[_deleted:BaseObject:private] =>
[modifiedColumns:protected] => Array
(
)
)
[75] => Category Object
(
[languages:protected] =>
[bok_resources:protected] =>
[bok_topics:protected] =>
[bok_keywords:protected] =>
[id:protected] => 75
[type:protected] => category
[parent:protected] => 2
[label:protected] => Plasterer
[alreadyInSave:protected] =>
[alreadyInValidation:protected] =>
[validationFailures:protected] => Array
(
)
[_new:BaseObject:private] =>
[_deleted:BaseObject:private] =>
[modifiedColumns:protected] => Array
(
)
)
[76] => Category Object
(
[languages:protected] =>
[bok_resources:protected] =>
[bok_topics:protected] =>
[bok_keywords:protected] =>
[id:protected] => 76
[type:protected] => category
[parent:protected] => 2
[label:protected] => Plumber/Pipefitter
[alreadyInSave:protected] =>
[alreadyInValidation:protected] =>
[validationFailures:protected] => Array
(
)
[_new:BaseObject:private] =>
[_deleted:BaseObject:private] =>
[modifiedColumns:protected] => Array
(
)
)
[77] => Category Object
(
[languages:protected] =>
[bok_resources:protected] =>
[bok_topics:protected] =>
[bok_keywords:protected] =>
[id:protected] => 77
[type:protected] => category
[parent:protected] => 2
[label:protected] => Refractory Worker
[alreadyInSave:protected] =>
[alreadyInValidation:protected] =>
[validationFailures:protected] => Array
(
)
[_new:BaseObject:private] =>
[_deleted:BaseObject:private] =>
[modifiedColumns:protected] => Array
(
)
)
[63] => Category Object
(
[languages:protected] =>
[bok_resources:protected] =>
[bok_topics:protected] =>
[bok_keywords:protected] =>
[id:protected] => 63
[type:protected] => category
[parent:protected] => 2
[label:protected] => Reinforcing Ironworker
[alreadyInSave:protected] =>
[alreadyInValidation:protected] =>
[validationFailures:protected] => Array
(
)
[_new:BaseObject:private] =>
[_deleted:BaseObject:private] =>
[modifiedColumns:protected] => Array
(
)
)
[78] => Category Object
(
[languages:protected] =>
[bok_resources:protected] =>
[bok_topics:protected] =>
[bok_keywords:protected] =>
[id:protected] => 78
[type:protected] => category
[parent:protected] => 2
[label:protected] => Roofer/Waterproofer
[alreadyInSave:protected] =>
[alreadyInValidation:protected] =>
[validationFailures:protected] => Array
(
)
[_new:BaseObject:private] =>
[_deleted:BaseObject:private] =>
[modifiedColumns:protected] => Array
(
)
)
[79] => Category Object
(
[languages:protected] =>
[bok_resources:protected] =>
[bok_topics:protected] =>
[bok_keywords:protected] =>
[id:protected] => 79
[type:protected] => category
[parent:protected] => 2
[label:protected] => Scaffold Erector
[alreadyInSave:protected] =>
[alreadyInValidation:protected] =>
[validationFailures:protected] => Array
(
)
[_new:BaseObject:private] =>
[_deleted:BaseObject:private] =>
[modifiedColumns:protected] => Array
(
)
)
[80] => Category Object
(
[languages:protected] =>
[bok_resources:protected] =>
[bok_topics:protected] =>
[bok_keywords:protected] =>
[id:protected] => 80
[type:protected] => category
[parent:protected] => 2
[label:protected] => Sheetmetal Worker
[alreadyInSave:protected] =>
[alreadyInValidation:protected] =>
[validationFailures:protected] => Array
(
)
[_new:BaseObject:private] =>
[_deleted:BaseObject:private] =>
[modifiedColumns:protected] => Array
(
)
)
[81] => Category Object
(
[languages:protected] =>
[bok_resources:protected] =>
[bok_topics:protected] =>
[bok_keywords:protected] =>
[id:protected] => 81
[type:protected] => category
[parent:protected] => 2
[label:protected] => Sprinkler Fitter
[alreadyInSave:protected] =>
[alreadyInValidation:protected] =>
[validationFailures:protected] => Array
(
)
[_new:BaseObject:private] =>
[_deleted:BaseObject:private] =>
[modifiedColumns:protected] => Array
(
)
)
[82] => Category Object
(
[languages:protected] =>
[bok_resources:protected] =>
[bok_topics:protected] =>
[bok_keywords:protected] =>
[id:protected] => 82
[type:protected] => category
[parent:protected] => 2
[label:protected] => Stonemason
[alreadyInSave:protected] =>
[alreadyInValidation:protected] =>
[validationFailures:protected] => Array
(
)
[_new:BaseObject:private] =>
[_deleted:BaseObject:private] =>
[modifiedColumns:protected] => Array
(
)
)
[62] => Category Object
(
[languages:protected] =>
[bok_resources:protected] =>
[bok_topics:protected] =>
[bok_keywords:protected] =>
[id:protected] => 62
[type:protected] => category
[parent:protected] => 2
[label:protected] => Structural Ironworker
[alreadyInSave:protected] =>
[alreadyInValidation:protected] =>
[validationFailures:protected] => Array
(
)
[_new:BaseObject:private] =>
[_deleted:BaseObject:private] =>
[modifiedColumns:protected] => Array
(
)
)
[83] => Category Object
(
[languages:protected] =>
[bok_resources:protected] =>
[bok_topics:protected] =>
[bok_keywords:protected] =>
[id:protected] => 83
[type:protected] => category
[parent:protected] => 2
[label:protected] => Terrazzo Worker
[alreadyInSave:protected] =>
[alreadyInValidation:protected] =>
[validationFailures:protected] => Array
(
)
[_new:BaseObject:private] =>
[_deleted:BaseObject:private] =>
[modifiedColumns:protected] => Array
(
)
)
[84] => Category Object
(
[languages:protected] =>
[bok_resources:protected] =>
[bok_topics:protected] =>
[bok_keywords:protected] =>
[id:protected] => 84
[type:protected] => category
[parent:protected] => 2
[label:protected] => Tile Setter
[alreadyInSave:protected] =>
[alreadyInValidation:protected] =>
[validationFailures:protected] => Array
(
)
[_new:BaseObject:private] =>
[_deleted:BaseObject:private] =>
[modifiedColumns:protected] => Array
(
)
)
[85] => Category Object
(
[languages:protected] =>
[bok_resources:protected] =>
[bok_topics:protected] =>
[bok_keywords:protected] =>
[id:protected] => 85
[type:protected] => category
[parent:protected] => 2
[label:protected] => Truck Driver
[alreadyInSave:protected] =>
[alreadyInValidation:protected] =>
[validationFailures:protected] => Array
(
)
[_new:BaseObject:private] =>
[_deleted:BaseObject:private] =>
[modifiedColumns:protected] => Array
(
)
)
[86] => Category Object
(
[languages:protected] =>
[bok_resources:protected] =>
[bok_topics:protected] =>
[bok_keywords:protected] =>
[id:protected] => 86
[type:protected] => category
[parent:protected] => 2
[label:protected] => Welder
[alreadyInSave:protected] =>
[alreadyInValidation:protected] =>
[validationFailures:protected] => Array
(
)
[_new:BaseObject:private] =>
[_deleted:BaseObject:private] =>
[modifiedColumns:protected] => Array
(
)
)
[87] => Category Object
(
[languages:protected] =>
[bok_resources:protected] =>
[bok_topics:protected] =>
[bok_keywords:protected] =>
[id:protected] => 87
[type:protected] => category
[parent:protected] => 3
[label:protected] => Commercial & Institutional
[alreadyInSave:protected] =>
[alreadyInValidation:protected] =>
[validationFailures:protected] => Array
(
)
[_new:BaseObject:private] =>
[_deleted:BaseObject:private] =>
[modifiedColumns:protected] => Array
(
)
)
[88] => Category Object
(
[languages:protected] =>
[bok_resources:protected] =>
[bok_topics:protected] =>
[bok_keywords:protected] =>
[id:protected] => 88
[type:protected] => category
[parent:protected] => 3
[label:protected] => Demolition
[alreadyInSave:protected] =>
[alreadyInValidation:protected] =>
[validationFailures:protected] => Array
(
)
[_new:BaseObject:private] =>
[_deleted:BaseObject:private] =>
[modifiedColumns:protected] => Array
(
)
)
[89] => Category Object
(
[languages:protected] =>
[bok_resources:protected] =>
[bok_topics:protected] =>
[bok_keywords:protected] =>
[id:protected] => 89
[type:protected] => category
[parent:protected] => 3
[label:protected] => Disasters
[alreadyInSave:protected] =>
[alreadyInValidation:protected] =>
[validationFailures:protected] => Array
(
)
[_new:BaseObject:private] =>
[_deleted:BaseObject:private] =>
[modifiedColumns:protected] => Array
(
)
)
[91] => Category Object
(
[languages:protected] =>
[bok_resources:protected] =>
[bok_topics:protected] =>
[bok_keywords:protected] =>
[id:protected] => 91
[type:protected] => category
[parent:protected] => 3
[label:protected] => Heavy & Highway
[alreadyInSave:protected] =>
[alreadyInValidation:protected] =>
[validationFailures:protected] => Array
(
)
[_new:BaseObject:private] =>
[_deleted:BaseObject:private] =>
[modifiedColumns:protected] => Array
(
)
)
[90] => Category Object
(
[languages:protected] =>
[bok_resources:protected] =>
[bok_topics:protected] =>
[bok_keywords:protected] =>
[id:protected] => 90
[type:protected] => category
[parent:protected] => 3
[label:protected] => Industrial
[alreadyInSave:protected] =>
[alreadyInValidation:protected] =>
[validationFailures:protected] => Array
(
)
[_new:BaseObject:private] =>
[_deleted:BaseObject:private] =>
[modifiedColumns:protected] => Array
(
)
)
[92] => Category Object
(
[languages:protected] =>
[bok_resources:protected] =>
[bok_topics:protected] =>
[bok_keywords:protected] =>
[id:protected] => 92
[type:protected] => category
[parent:protected] => 3
[label:protected] => LEED/Green Construction
[alreadyInSave:protected] =>
[alreadyInValidation:protected] =>
[validationFailures:protected] => Array
(
)
[_new:BaseObject:private] =>
[_deleted:BaseObject:private] =>
[modifiedColumns:protected] => Array
(
)
)
[93] => Category Object
(
[languages:protected] =>
[bok_resources:protected] =>
[bok_topics:protected] =>
[bok_keywords:protected] =>
[id:protected] => 93
[type:protected] => category
[parent:protected] => 3
[label:protected] => Renovations
[alreadyInSave:protected] =>
[alreadyInValidation:protected] =>
[validationFailures:protected] => Array
(
)
[_new:BaseObject:private] =>
[_deleted:BaseObject:private] =>
[modifiedColumns:protected] => Array
(
)
)
[94] => Category Object
(
[languages:protected] =>
[bok_resources:protected] =>
[bok_topics:protected] =>
[bok_keywords:protected] =>
[id:protected] => 94
[type:protected] => category
[parent:protected] => 3
[label:protected] => Residential
[alreadyInSave:protected] =>
[alreadyInValidation:protected] =>
[validationFailures:protected] => Array
(
)
[_new:BaseObject:private] =>
[_deleted:BaseObject:private] =>
[modifiedColumns:protected] => Array
(
)
)
[95] => Category Object
(
[languages:protected] =>
[bok_resources:protected] =>
[bok_topics:protected] =>
[bok_keywords:protected] =>
[id:protected] => 95
[type:protected] => category
[parent:protected] => 3
[label:protected] => Underground
[alreadyInSave:protected] =>
[alreadyInValidation:protected] =>
[validationFailures:protected] => Array
(
)
[_new:BaseObject:private] =>
[_deleted:BaseObject:private] =>
[modifiedColumns:protected] => Array
(
)
)
)
[categories_initialized:protected] => 1
[mapped_items:protected] =>
[content:protected] =>
[files:protected] =>
[language:protected] => Language Object
(
[id:protected] => 1
[code:protected] => en
[name:protected] => English
[alreadyInSave:protected] =>
[alreadyInValidation:protected] =>
[validationFailures:protected] => Array
(
)
[_new:BaseObject:private] =>
[_deleted:BaseObject:private] =>
[modifiedColumns:protected] => Array
(
)
)
[old_record:protected] =>
[id:protected] => 4426
[old_id:protected] =>
[elcosh_id:protected] => d001656
[type:protected] => document
[display_type:protected] => HTML only (and links)
[user_id:protected] => 0
[language_id:protected] => 1
[tagging_id:protected] => Mike Aguilar
[priority_id:protected] => 1
[title:protected] => Construction Dive -- DeWalt's Jobsite Pro headphones recalled for fire hazards
[total_pages:protected] => 1
[billed_pages:protected] => 1
[publication_number:protected] =>
[part_of:protected] =>
[keywords:protected] => DeWalt, Fire Hazards, recall, headphones
[comments:protected] =>
[summary:protected] => A recall notice by the United States Consumer Product Safety Commission affects over 300,000 DeWalt Jobsite Pro Headphones. The recall is a result of a malfunction that can cause earbuds to overheat while charging or during use, leading to fire and burn hazards.
[transition_comments:protected] =>
[external_link:protected] => https://www.constructiondive.com/news/dewalts-jobsite-pro-headphones-recalled-for-fire-hazards/611248/?utm_source=Sailthru&utm_medium=email&utm_campaign=Issue:%202021-12-10%20Construction%20Dive%20Newsletter%20%5Bissue:38532%5D&utm_term=Construction%20Dive
[consol_link:protected] =>
[more_like_this:protected] =>
[permission_given_by:protected] =>
[published:protected] => T
[billable:protected] => F
[img_name:protected] =>
[img_ext:protected] =>
[img_width:protected] =>
[img_height:protected] =>
[img_credit:protected] =>
[img_practice:protected] =>
[vid_source_id:protected] =>
[vid_running_time:protected] =>
[vid_intended_audience:protected] =>
[vid_acquisition_info:protected] =>
[vid_cost:protected] =>
[vid_producer:protected] =>
[vid_filename:protected] =>
[vid_filename_downloadable:protected] =>
[date_summary:protected] =>
[date_permission_requested:protected] =>
[date_permission_received:protected] =>
[date_review_needed:protected] =>
[date_received:protected] => 12/13/21
[date_completed:protected] => 12/13/21
[date_billed:protected] =>
[date_modified:protected] => 12/13/21
[collBokExports:protected] =>
[lastBokExportCriteria:BaseElcoshItem:private] =>
[alreadyInSave:protected] =>
[alreadyInValidation:protected] =>
[validationFailures:protected] => Array
(
)
[_new:BaseObject:private] =>
[_deleted:BaseObject:private] =>
[modifiedColumns:protected] => Array
(
)
)
)
)
[new_images] => Array
(
[0] => Search_Result Object
(
[title] => Morning Toolbox Talk
[image] => /record/images/4003-p.jpg
[blurb] => This photo is from an early morning toolbox talk on a construction job in Mclean, Virginia. It is being delivered in English and Spanish....
[category] => Array
(
[0] => 20
[1] => 51
[2] => 57
[3] => 64
[4] => 70
[5] => 63
[6] => 78
[7] => 82
[8] => 62
[9] => 87
[10] => 88
[11] => 89
[12] => 91
[13] => 90
[14] => 93
[15] => 94
[16] => 97
)
[labels] => Array
(
[0] => Safety Culture
[1] => Work Environment
[2] => Hazards
[3] => Cement Mason
[4] => Trades
[5] => Flagger
[7] => Laborer
[9] => Operating Engineer
[11] => Reinforcing Ironworker
[13] => Roofer/Waterproofer
[15] => Stonemason
[17] => Structural Ironworker
[19] => Commercial & Institutional
[20] => Jobsites
[21] => Demolition
[23] => Disasters
[25] => Heavy & Highway
[27] => Industrial
[29] => Renovations
[31] => Residential
[33] => Images
[34] => Media
[35] => Media & Documents
)
[type] => Images
[sub_category] =>
[url] => /image/4003/i002691/Morning%2BToolbox%2BTalk.html
[item:protected] => ImageRecord Object
(
[records:protected] => Array
(
)
[recordId:protected] =>
[searchWordClass:protected] =>
[searchWordPeerClass:protected] =>
[bok_record:protected] =>
[authors:protected] =>
[organizations:protected] =>
[collections:protected] =>
[categories:protected] => Array
(
[20] => Category Object
(
[languages:protected] =>
[bok_resources:protected] =>
[bok_topics:protected] =>
[bok_keywords:protected] =>
[id:protected] => 20
[type:protected] => category
[parent:protected] => 7
[label:protected] => Safety Culture
[alreadyInSave:protected] =>
[alreadyInValidation:protected] =>
[validationFailures:protected] => Array
(
)
[_new:BaseObject:private] =>
[_deleted:BaseObject:private] =>
[modifiedColumns:protected] => Array
(
)
)
[51] => Category Object
(
[languages:protected] =>
[bok_resources:protected] =>
[bok_topics:protected] =>
[bok_keywords:protected] =>
[id:protected] => 51
[type:protected] => category
[parent:protected] => 2
[label:protected] => Cement Mason
[alreadyInSave:protected] =>
[alreadyInValidation:protected] =>
[validationFailures:protected] => Array
(
)
[_new:BaseObject:private] =>
[_deleted:BaseObject:private] =>
[modifiedColumns:protected] => Array
(
)
)
[57] => Category Object
(
[languages:protected] =>
[bok_resources:protected] =>
[bok_topics:protected] =>
[bok_keywords:protected] =>
[id:protected] => 57
[type:protected] => category
[parent:protected] => 2
[label:protected] => Flagger
[alreadyInSave:protected] =>
[alreadyInValidation:protected] =>
[validationFailures:protected] => Array
(
)
[_new:BaseObject:private] =>
[_deleted:BaseObject:private] =>
[modifiedColumns:protected] => Array
(
)
)
[64] => Category Object
(
[languages:protected] =>
[bok_resources:protected] =>
[bok_topics:protected] =>
[bok_keywords:protected] =>
[id:protected] => 64
[type:protected] => category
[parent:protected] => 2
[label:protected] => Laborer
[alreadyInSave:protected] =>
[alreadyInValidation:protected] =>
[validationFailures:protected] => Array
(
)
[_new:BaseObject:private] =>
[_deleted:BaseObject:private] =>
[modifiedColumns:protected] => Array
(
)
)
[70] => Category Object
(
[languages:protected] =>
[bok_resources:protected] =>
[bok_topics:protected] =>
[bok_keywords:protected] =>
[id:protected] => 70
[type:protected] => category
[parent:protected] => 2
[label:protected] => Operating Engineer
[alreadyInSave:protected] =>
[alreadyInValidation:protected] =>
[validationFailures:protected] => Array
(
)
[_new:BaseObject:private] =>
[_deleted:BaseObject:private] =>
[modifiedColumns:protected] => Array
(
)
)
[63] => Category Object
(
[languages:protected] =>
[bok_resources:protected] =>
[bok_topics:protected] =>
[bok_keywords:protected] =>
[id:protected] => 63
[type:protected] => category
[parent:protected] => 2
[label:protected] => Reinforcing Ironworker
[alreadyInSave:protected] =>
[alreadyInValidation:protected] =>
[validationFailures:protected] => Array
(
)
[_new:BaseObject:private] =>
[_deleted:BaseObject:private] =>
[modifiedColumns:protected] => Array
(
)
)
[78] => Category Object
(
[languages:protected] =>
[bok_resources:protected] =>
[bok_topics:protected] =>
[bok_keywords:protected] =>
[id:protected] => 78
[type:protected] => category
[parent:protected] => 2
[label:protected] => Roofer/Waterproofer
[alreadyInSave:protected] =>
[alreadyInValidation:protected] =>
[validationFailures:protected] => Array
(
)
[_new:BaseObject:private] =>
[_deleted:BaseObject:private] =>
[modifiedColumns:protected] => Array
(
)
)
[82] => Category Object
(
[languages:protected] =>
[bok_resources:protected] =>
[bok_topics:protected] =>
[bok_keywords:protected] =>
[id:protected] => 82
[type:protected] => category
[parent:protected] => 2
[label:protected] => Stonemason
[alreadyInSave:protected] =>
[alreadyInValidation:protected] =>
[validationFailures:protected] => Array
(
)
[_new:BaseObject:private] =>
[_deleted:BaseObject:private] =>
[modifiedColumns:protected] => Array
(
)
)
[62] => Category Object
(
[languages:protected] =>
[bok_resources:protected] =>
[bok_topics:protected] =>
[bok_keywords:protected] =>
[id:protected] => 62
[type:protected] => category
[parent:protected] => 2
[label:protected] => Structural Ironworker
[alreadyInSave:protected] =>
[alreadyInValidation:protected] =>
[validationFailures:protected] => Array
(
)
[_new:BaseObject:private] =>
[_deleted:BaseObject:private] =>
[modifiedColumns:protected] => Array
(
)
)
[87] => Category Object
(
[languages:protected] =>
[bok_resources:protected] =>
[bok_topics:protected] =>
[bok_keywords:protected] =>
[id:protected] => 87
[type:protected] => category
[parent:protected] => 3
[label:protected] => Commercial & Institutional
[alreadyInSave:protected] =>
[alreadyInValidation:protected] =>
[validationFailures:protected] => Array
(
)
[_new:BaseObject:private] =>
[_deleted:BaseObject:private] =>
[modifiedColumns:protected] => Array
(
)
)
[88] => Category Object
(
[languages:protected] =>
[bok_resources:protected] =>
[bok_topics:protected] =>
[bok_keywords:protected] =>
[id:protected] => 88
[type:protected] => category
[parent:protected] => 3
[label:protected] => Demolition
[alreadyInSave:protected] =>
[alreadyInValidation:protected] =>
[validationFailures:protected] => Array
(
)
[_new:BaseObject:private] =>
[_deleted:BaseObject:private] =>
[modifiedColumns:protected] => Array
(
)
)
[89] => Category Object
(
[languages:protected] =>
[bok_resources:protected] =>
[bok_topics:protected] =>
[bok_keywords:protected] =>
[id:protected] => 89
[type:protected] => category
[parent:protected] => 3
[label:protected] => Disasters
[alreadyInSave:protected] =>
[alreadyInValidation:protected] =>
[validationFailures:protected] => Array
(
)
[_new:BaseObject:private] =>
[_deleted:BaseObject:private] =>
[modifiedColumns:protected] => Array
(
)
)
[91] => Category Object
(
[languages:protected] =>
[bok_resources:protected] =>
[bok_topics:protected] =>
[bok_keywords:protected] =>
[id:protected] => 91
[type:protected] => category
[parent:protected] => 3
[label:protected] => Heavy & Highway
[alreadyInSave:protected] =>
[alreadyInValidation:protected] =>
[validationFailures:protected] => Array
(
)
[_new:BaseObject:private] =>
[_deleted:BaseObject:private] =>
[modifiedColumns:protected] => Array
(
)
)
[90] => Category Object
(
[languages:protected] =>
[bok_resources:protected] =>
[bok_topics:protected] =>
[bok_keywords:protected] =>
[id:protected] => 90
[type:protected] => category
[parent:protected] => 3
[label:protected] => Industrial
[alreadyInSave:protected] =>
[alreadyInValidation:protected] =>
[validationFailures:protected] => Array
(
)
[_new:BaseObject:private] =>
[_deleted:BaseObject:private] =>
[modifiedColumns:protected] => Array
(
)
)
[93] => Category Object
(
[languages:protected] =>
[bok_resources:protected] =>
[bok_topics:protected] =>
[bok_keywords:protected] =>
[id:protected] => 93
[type:protected] => category
[parent:protected] => 3
[label:protected] => Renovations
[alreadyInSave:protected] =>
[alreadyInValidation:protected] =>
[validationFailures:protected] => Array
(
)
[_new:BaseObject:private] =>
[_deleted:BaseObject:private] =>
[modifiedColumns:protected] => Array
(
)
)
[94] => Category Object
(
[languages:protected] =>
[bok_resources:protected] =>
[bok_topics:protected] =>
[bok_keywords:protected] =>
[id:protected] => 94
[type:protected] => category
[parent:protected] => 3
[label:protected] => Residential
[alreadyInSave:protected] =>
[alreadyInValidation:protected] =>
[validationFailures:protected] => Array
(
)
[_new:BaseObject:private] =>
[_deleted:BaseObject:private] =>
[modifiedColumns:protected] => Array
(
)
)
[97] => Category Object
(
[languages:protected] =>
[bok_resources:protected] =>
[bok_topics:protected] =>
[bok_keywords:protected] =>
[id:protected] => 97
[type:protected] => category
[parent:protected] => 5
[label:protected] => Images
[alreadyInSave:protected] =>
[alreadyInValidation:protected] =>
[validationFailures:protected] => Array
(
)
[_new:BaseObject:private] =>
[_deleted:BaseObject:private] =>
[modifiedColumns:protected] => Array
(
)
)
)
[categories_initialized:protected] => 1
[mapped_items:protected] =>
[content:protected] =>
[files:protected] =>
[language:protected] => Language Object
(
[id:protected] => 1
[code:protected] => en
[name:protected] => English
[alreadyInSave:protected] =>
[alreadyInValidation:protected] =>
[validationFailures:protected] => Array
(
)
[_new:BaseObject:private] =>
[_deleted:BaseObject:private] =>
[modifiedColumns:protected] => Array
(
)
)
[old_record:protected] =>
[id:protected] => 4003
[old_id:protected] =>
[elcosh_id:protected] => i002691
[type:protected] => image
[display_type:protected] => Image
[user_id:protected] => 0
[language_id:protected] => 1
[tagging_id:protected] => Bruce Lippy
[priority_id:protected] => 1
[title:protected] => Morning Toolbox Talk
[total_pages:protected] => 0
[billed_pages:protected] => 0
[publication_number:protected] =>
[part_of:protected] =>
[keywords:protected] => toolbox talk, tailgate talk, Spanish, bilingual
[comments:protected] =>
[summary:protected] => This photo is from an early morning toolbox talk on a construction job in Mclean, Virginia. It is being delivered in English and Spanish.
[transition_comments:protected] =>
[external_link:protected] =>
[consol_link:protected] => http://www.cpwrconstructionsolutions.org/electrical/solution/662/worker-training.html
[more_like_this:protected] => d001285,d001304,c000079
[permission_given_by:protected] =>
[published:protected] => T
[billable:protected] => F
[img_name:protected] =>
[img_ext:protected] => jpg
[img_width:protected] =>
[img_height:protected] =>
[img_credit:protected] => Morgan Zavertnik and Hoar Construction
[img_practice:protected] => good
[vid_source_id:protected] =>
[vid_running_time:protected] =>
[vid_intended_audience:protected] =>
[vid_acquisition_info:protected] =>
[vid_cost:protected] =>
[vid_producer:protected] =>
[vid_filename:protected] =>
[vid_filename_downloadable:protected] =>
[date_summary:protected] => November 2015
[date_permission_requested:protected] =>
[date_permission_received:protected] =>
[date_review_needed:protected] =>
[date_received:protected] => 03/02/16
[date_completed:protected] => 03/02/16
[date_billed:protected] =>
[date_modified:protected] => 03/02/16
[collBokExports:protected] =>
[lastBokExportCriteria:BaseElcoshItem:private] =>
[alreadyInSave:protected] =>
[alreadyInValidation:protected] =>
[validationFailures:protected] => Array
(
)
[_new:BaseObject:private] =>
[_deleted:BaseObject:private] =>
[modifiedColumns:protected] => Array
(
)
)
)
[1] => Search_Result Object
(
[title] => Toolbox talk - crew view
[image] => /record/images/4005-p.jpg
[blurb] => Photo of crew listening to a toolbox safety talk before starting work....
[category] => Array
(
[0] => 97
[1] => 20
[2] => 47
[3] => 49
[4] => 51
[5] => 55
[6] => 61
[7] => 64
[8] => 71
[9] => 75
[10] => 63
[11] => 79
[12] => 62
[13] => 87
[14] => 88
[15] => 91
[16] => 90
[17] => 93
[18] => 94
[19] => 95
)
[labels] => Array
(
[0] => Images
[1] => Media
[2] => Media & Documents
[3] => Safety Culture
[4] => Work Environment
[5] => Hazards
[6] => Bricklayer
[7] => Trades
[8] => Carpenter
[10] => Cement Mason
[12] => Electrical Worker
[14] => Interior Systems Carpenter
[16] => Laborer
[18] => Painter
[20] => Plasterer
[22] => Reinforcing Ironworker
[24] => Scaffold Erector
[26] => Structural Ironworker
[28] => Commercial & Institutional
[29] => Jobsites
[30] => Demolition
[32] => Heavy & Highway
[34] => Industrial
[36] => Renovations
[38] => Residential
[40] => Underground
)
[type] => Images
[sub_category] =>
[url] => /image/4005/i002692/Toolbox%2Btalk%2B-%2Bcrew%2Bview.html
[item:protected] => ImageRecord Object
(
[records:protected] => Array
(
)
[recordId:protected] =>
[searchWordClass:protected] =>
[searchWordPeerClass:protected] =>
[bok_record:protected] =>
[authors:protected] =>
[organizations:protected] =>
[collections:protected] =>
[categories:protected] => Array
(
[97] => Category Object
(
[languages:protected] =>
[bok_resources:protected] =>
[bok_topics:protected] =>
[bok_keywords:protected] =>
[id:protected] => 97
[type:protected] => category
[parent:protected] => 5
[label:protected] => Images
[alreadyInSave:protected] =>
[alreadyInValidation:protected] =>
[validationFailures:protected] => Array
(
)
[_new:BaseObject:private] =>
[_deleted:BaseObject:private] =>
[modifiedColumns:protected] => Array
(
)
)
[20] => Category Object
(
[languages:protected] =>
[bok_resources:protected] =>
[bok_topics:protected] =>
[bok_keywords:protected] =>
[id:protected] => 20
[type:protected] => category
[parent:protected] => 7
[label:protected] => Safety Culture
[alreadyInSave:protected] =>
[alreadyInValidation:protected] =>
[validationFailures:protected] => Array
(
)
[_new:BaseObject:private] =>
[_deleted:BaseObject:private] =>
[modifiedColumns:protected] => Array
(
)
)
[47] => Category Object
(
[languages:protected] =>
[bok_resources:protected] =>
[bok_topics:protected] =>
[bok_keywords:protected] =>
[id:protected] => 47
[type:protected] => category
[parent:protected] => 2
[label:protected] => Bricklayer
[alreadyInSave:protected] =>
[alreadyInValidation:protected] =>
[validationFailures:protected] => Array
(
)
[_new:BaseObject:private] =>
[_deleted:BaseObject:private] =>
[modifiedColumns:protected] => Array
(
)
)
[49] => Category Object
(
[languages:protected] =>
[bok_resources:protected] =>
[bok_topics:protected] =>
[bok_keywords:protected] =>
[id:protected] => 49
[type:protected] => category
[parent:protected] => 2
[label:protected] => Carpenter
[alreadyInSave:protected] =>
[alreadyInValidation:protected] =>
[validationFailures:protected] => Array
(
)
[_new:BaseObject:private] =>
[_deleted:BaseObject:private] =>
[modifiedColumns:protected] => Array
(
)
)
[51] => Category Object
(
[languages:protected] =>
[bok_resources:protected] =>
[bok_topics:protected] =>
[bok_keywords:protected] =>
[id:protected] => 51
[type:protected] => category
[parent:protected] => 2
[label:protected] => Cement Mason
[alreadyInSave:protected] =>
[alreadyInValidation:protected] =>
[validationFailures:protected] => Array
(
)
[_new:BaseObject:private] =>
[_deleted:BaseObject:private] =>
[modifiedColumns:protected] => Array
(
)
)
[55] => Category Object
(
[languages:protected] =>
[bok_resources:protected] =>
[bok_topics:protected] =>
[bok_keywords:protected] =>
[id:protected] => 55
[type:protected] => category
[parent:protected] => 2
[label:protected] => Electrical Worker
[alreadyInSave:protected] =>
[alreadyInValidation:protected] =>
[validationFailures:protected] => Array
(
)
[_new:BaseObject:private] =>
[_deleted:BaseObject:private] =>
[modifiedColumns:protected] => Array
(
)
)
[61] => Category Object
(
[languages:protected] =>
[bok_resources:protected] =>
[bok_topics:protected] =>
[bok_keywords:protected] =>
[id:protected] => 61
[type:protected] => category
[parent:protected] => 2
[label:protected] => Interior Systems Carpenter
[alreadyInSave:protected] =>
[alreadyInValidation:protected] =>
[validationFailures:protected] => Array
(
)
[_new:BaseObject:private] =>
[_deleted:BaseObject:private] =>
[modifiedColumns:protected] => Array
(
)
)
[64] => Category Object
(
[languages:protected] =>
[bok_resources:protected] =>
[bok_topics:protected] =>
[bok_keywords:protected] =>
[id:protected] => 64
[type:protected] => category
[parent:protected] => 2
[label:protected] => Laborer
[alreadyInSave:protected] =>
[alreadyInValidation:protected] =>
[validationFailures:protected] => Array
(
)
[_new:BaseObject:private] =>
[_deleted:BaseObject:private] =>
[modifiedColumns:protected] => Array
(
)
)
[71] => Category Object
(
[languages:protected] =>
[bok_resources:protected] =>
[bok_topics:protected] =>
[bok_keywords:protected] =>
[id:protected] => 71
[type:protected] => category
[parent:protected] => 2
[label:protected] => Painter
[alreadyInSave:protected] =>
[alreadyInValidation:protected] =>
[validationFailures:protected] => Array
(
)
[_new:BaseObject:private] =>
[_deleted:BaseObject:private] =>
[modifiedColumns:protected] => Array
(
)
)
[75] => Category Object
(
[languages:protected] =>
[bok_resources:protected] =>
[bok_topics:protected] =>
[bok_keywords:protected] =>
[id:protected] => 75
[type:protected] => category
[parent:protected] => 2
[label:protected] => Plasterer
[alreadyInSave:protected] =>
[alreadyInValidation:protected] =>
[validationFailures:protected] => Array
(
)
[_new:BaseObject:private] =>
[_deleted:BaseObject:private] =>
[modifiedColumns:protected] => Array
(
)
)
[63] => Category Object
(
[languages:protected] =>
[bok_resources:protected] =>
[bok_topics:protected] =>
[bok_keywords:protected] =>
[id:protected] => 63
[type:protected] => category
[parent:protected] => 2
[label:protected] => Reinforcing Ironworker
[alreadyInSave:protected] =>
[alreadyInValidation:protected] =>
[validationFailures:protected] => Array
(
)
[_new:BaseObject:private] =>
[_deleted:BaseObject:private] =>
[modifiedColumns:protected] => Array
(
)
)
[79] => Category Object
(
[languages:protected] =>
[bok_resources:protected] =>
[bok_topics:protected] =>
[bok_keywords:protected] =>
[id:protected] => 79
[type:protected] => category
[parent:protected] => 2
[label:protected] => Scaffold Erector
[alreadyInSave:protected] =>
[alreadyInValidation:protected] =>
[validationFailures:protected] => Array
(
)
[_new:BaseObject:private] =>
[_deleted:BaseObject:private] =>
[modifiedColumns:protected] => Array
(
)
)
[62] => Category Object
(
[languages:protected] =>
[bok_resources:protected] =>
[bok_topics:protected] =>
[bok_keywords:protected] =>
[id:protected] => 62
[type:protected] => category
[parent:protected] => 2
[label:protected] => Structural Ironworker
[alreadyInSave:protected] =>
[alreadyInValidation:protected] =>
[validationFailures:protected] => Array
(
)
[_new:BaseObject:private] =>
[_deleted:BaseObject:private] =>
[modifiedColumns:protected] => Array
(
)
)
[87] => Category Object
(
[languages:protected] =>
[bok_resources:protected] =>
[bok_topics:protected] =>
[bok_keywords:protected] =>
[id:protected] => 87
[type:protected] => category
[parent:protected] => 3
[label:protected] => Commercial & Institutional
[alreadyInSave:protected] =>
[alreadyInValidation:protected] =>
[validationFailures:protected] => Array
(
)
[_new:BaseObject:private] =>
[_deleted:BaseObject:private] =>
[modifiedColumns:protected] => Array
(
)
)
[88] => Category Object
(
[languages:protected] =>
[bok_resources:protected] =>
[bok_topics:protected] =>
[bok_keywords:protected] =>
[id:protected] => 88
[type:protected] => category
[parent:protected] => 3
[label:protected] => Demolition
[alreadyInSave:protected] =>
[alreadyInValidation:protected] =>
[validationFailures:protected] => Array
(
)
[_new:BaseObject:private] =>
[_deleted:BaseObject:private] =>
[modifiedColumns:protected] => Array
(
)
)
[91] => Category Object
(
[languages:protected] =>
[bok_resources:protected] =>
[bok_topics:protected] =>
[bok_keywords:protected] =>
[id:protected] => 91
[type:protected] => category
[parent:protected] => 3
[label:protected] => Heavy & Highway
[alreadyInSave:protected] =>
[alreadyInValidation:protected] =>
[validationFailures:protected] => Array
(
)
[_new:BaseObject:private] =>
[_deleted:BaseObject:private] =>
[modifiedColumns:protected] => Array
(
)
)
[90] => Category Object
(
[languages:protected] =>
[bok_resources:protected] =>
[bok_topics:protected] =>
[bok_keywords:protected] =>
[id:protected] => 90
[type:protected] => category
[parent:protected] => 3
[label:protected] => Industrial
[alreadyInSave:protected] =>
[alreadyInValidation:protected] =>
[validationFailures:protected] => Array
(
)
[_new:BaseObject:private] =>
[_deleted:BaseObject:private] =>
[modifiedColumns:protected] => Array
(
)
)
[93] => Category Object
(
[languages:protected] =>
[bok_resources:protected] =>
[bok_topics:protected] =>
[bok_keywords:protected] =>
[id:protected] => 93
[type:protected] => category
[parent:protected] => 3
[label:protected] => Renovations
[alreadyInSave:protected] =>
[alreadyInValidation:protected] =>
[validationFailures:protected] => Array
(
)
[_new:BaseObject:private] =>
[_deleted:BaseObject:private] =>
[modifiedColumns:protected] => Array
(
)
)
[94] => Category Object
(
[languages:protected] =>
[bok_resources:protected] =>
[bok_topics:protected] =>
[bok_keywords:protected] =>
[id:protected] => 94
[type:protected] => category
[parent:protected] => 3
[label:protected] => Residential
[alreadyInSave:protected] =>
[alreadyInValidation:protected] =>
[validationFailures:protected] => Array
(
)
[_new:BaseObject:private] =>
[_deleted:BaseObject:private] =>
[modifiedColumns:protected] => Array
(
)
)
[95] => Category Object
(
[languages:protected] =>
[bok_resources:protected] =>
[bok_topics:protected] =>
[bok_keywords:protected] =>
[id:protected] => 95
[type:protected] => category
[parent:protected] => 3
[label:protected] => Underground
[alreadyInSave:protected] =>
[alreadyInValidation:protected] =>
[validationFailures:protected] => Array
(
)
[_new:BaseObject:private] =>
[_deleted:BaseObject:private] =>
[modifiedColumns:protected] => Array
(
)
)
)
[categories_initialized:protected] => 1
[mapped_items:protected] =>
[content:protected] =>
[files:protected] =>
[language:protected] => Language Object
(
[id:protected] => 1
[code:protected] => en
[name:protected] => English
[alreadyInSave:protected] =>
[alreadyInValidation:protected] =>
[validationFailures:protected] => Array
(
)
[_new:BaseObject:private] =>
[_deleted:BaseObject:private] =>
[modifiedColumns:protected] => Array
(
)
)
[old_record:protected] =>
[id:protected] => 4005
[old_id:protected] =>
[elcosh_id:protected] => i002692
[type:protected] => image
[display_type:protected] => Image
[user_id:protected] => 0
[language_id:protected] => 1
[tagging_id:protected] => Bruce Lippy
[priority_id:protected] => 1
[title:protected] => Toolbox talk - crew view
[total_pages:protected] => 0
[billed_pages:protected] => 0
[publication_number:protected] =>
[part_of:protected] =>
[keywords:protected] => toolbox talk, tailgate talk, safety talk, Spanish
[comments:protected] =>
[summary:protected] => Photo of crew listening to a toolbox safety talk before starting work.
[transition_comments:protected] =>
[external_link:protected] =>
[consol_link:protected] => http://www.cpwrconstructionsolutions.org/electrical/solution/662/worker-training.html
[more_like_this:protected] => i002691,d001269, c000079, d001285
[permission_given_by:protected] =>
[published:protected] => T
[billable:protected] => F
[img_name:protected] =>
[img_ext:protected] => jpg
[img_width:protected] =>
[img_height:protected] =>
[img_credit:protected] => Morgan Zavertnik and Hoar Construction
[img_practice:protected] => good
[vid_source_id:protected] =>
[vid_running_time:protected] =>
[vid_intended_audience:protected] =>
[vid_acquisition_info:protected] =>
[vid_cost:protected] =>
[vid_producer:protected] =>
[vid_filename:protected] =>
[vid_filename_downloadable:protected] =>
[date_summary:protected] => November 2015
[date_permission_requested:protected] =>
[date_permission_received:protected] =>
[date_review_needed:protected] =>
[date_received:protected] => 03/02/16
[date_completed:protected] => 03/02/16
[date_billed:protected] =>
[date_modified:protected] => 03/02/16
[collBokExports:protected] =>
[lastBokExportCriteria:BaseElcoshItem:private] =>
[alreadyInSave:protected] =>
[alreadyInValidation:protected] =>
[validationFailures:protected] => Array
(
)
[_new:BaseObject:private] =>
[_deleted:BaseObject:private] =>
[modifiedColumns:protected] => Array
(
)
)
)
[2] => Search_Result Object
(
[title] => Toolbox talk - long shot
[image] => /record/images/4006-p.jpg
[blurb] => This crew gathered every morning before starting work to discuss a new safety topic....
[category] => Array
(
[0] => 20
[1] => 47
[2] => 49
[3] => 51
[4] => 55
[5] => 64
[6] => 68
[7] => 75
[8] => 76
[9] => 63
[10] => 78
[11] => 79
[12] => 82
[13] => 62
[14] => 87
[15] => 88
[16] => 91
[17] => 90
[18] => 93
[19] => 94
[20] => 95
[21] => 97
)
[labels] => Array
(
[0] => Safety Culture
[1] => Work Environment
[2] => Hazards
[3] => Bricklayer
[4] => Trades
[5] => Carpenter
[7] => Cement Mason
[9] => Electrical Worker
[11] => Laborer
[13] => Maintenance Worker
[15] => Plasterer
[17] => Plumber/Pipefitter
[19] => Reinforcing Ironworker
[21] => Roofer/Waterproofer
[23] => Scaffold Erector
[25] => Stonemason
[27] => Structural Ironworker
[29] => Commercial & Institutional
[30] => Jobsites
[31] => Demolition
[33] => Heavy & Highway
[35] => Industrial
[37] => Renovations
[39] => Residential
[41] => Underground
[43] => Images
[44] => Media
[45] => Media & Documents
)
[type] => Images
[sub_category] =>
[url] => /image/4006/i002693/Toolbox%2Btalk%2B-%2Blong%2Bshot.html
[item:protected] => ImageRecord Object
(
[records:protected] => Array
(
)
[recordId:protected] =>
[searchWordClass:protected] =>
[searchWordPeerClass:protected] =>
[bok_record:protected] =>
[authors:protected] =>
[organizations:protected] =>
[collections:protected] =>
[categories:protected] => Array
(
[20] => Category Object
(
[languages:protected] =>
[bok_resources:protected] =>
[bok_topics:protected] =>
[bok_keywords:protected] =>
[id:protected] => 20
[type:protected] => category
[parent:protected] => 7
[label:protected] => Safety Culture
[alreadyInSave:protected] =>
[alreadyInValidation:protected] =>
[validationFailures:protected] => Array
(
)
[_new:BaseObject:private] =>
[_deleted:BaseObject:private] =>
[modifiedColumns:protected] => Array
(
)
)
[47] => Category Object
(
[languages:protected] =>
[bok_resources:protected] =>
[bok_topics:protected] =>
[bok_keywords:protected] =>
[id:protected] => 47
[type:protected] => category
[parent:protected] => 2
[label:protected] => Bricklayer
[alreadyInSave:protected] =>
[alreadyInValidation:protected] =>
[validationFailures:protected] => Array
(
)
[_new:BaseObject:private] =>
[_deleted:BaseObject:private] =>
[modifiedColumns:protected] => Array
(
)
)
[49] => Category Object
(
[languages:protected] =>
[bok_resources:protected] =>
[bok_topics:protected] =>
[bok_keywords:protected] =>
[id:protected] => 49
[type:protected] => category
[parent:protected] => 2
[label:protected] => Carpenter
[alreadyInSave:protected] =>
[alreadyInValidation:protected] =>
[validationFailures:protected] => Array
(
)
[_new:BaseObject:private] =>
[_deleted:BaseObject:private] =>
[modifiedColumns:protected] => Array
(
)
)
[51] => Category Object
(
[languages:protected] =>
[bok_resources:protected] =>
[bok_topics:protected] =>
[bok_keywords:protected] =>
[id:protected] => 51
[type:protected] => category
[parent:protected] => 2
[label:protected] => Cement Mason
[alreadyInSave:protected] =>
[alreadyInValidation:protected] =>
[validationFailures:protected] => Array
(
)
[_new:BaseObject:private] =>
[_deleted:BaseObject:private] =>
[modifiedColumns:protected] => Array
(
)
)
[55] => Category Object
(
[languages:protected] =>
[bok_resources:protected] =>
[bok_topics:protected] =>
[bok_keywords:protected] =>
[id:protected] => 55
[type:protected] => category
[parent:protected] => 2
[label:protected] => Electrical Worker
[alreadyInSave:protected] =>
[alreadyInValidation:protected] =>
[validationFailures:protected] => Array
(
)
[_new:BaseObject:private] =>
[_deleted:BaseObject:private] =>
[modifiedColumns:protected] => Array
(
)
)
[64] => Category Object
(
[languages:protected] =>
[bok_resources:protected] =>
[bok_topics:protected] =>
[bok_keywords:protected] =>
[id:protected] => 64
[type:protected] => category
[parent:protected] => 2
[label:protected] => Laborer
[alreadyInSave:protected] =>
[alreadyInValidation:protected] =>
[validationFailures:protected] => Array
(
)
[_new:BaseObject:private] =>
[_deleted:BaseObject:private] =>
[modifiedColumns:protected] => Array
(
)
)
[68] => Category Object
(
[languages:protected] =>
[bok_resources:protected] =>
[bok_topics:protected] =>
[bok_keywords:protected] =>
[id:protected] => 68
[type:protected] => category
[parent:protected] => 2
[label:protected] => Maintenance Worker
[alreadyInSave:protected] =>
[alreadyInValidation:protected] =>
[validationFailures:protected] => Array
(
)
[_new:BaseObject:private] =>
[_deleted:BaseObject:private] =>
[modifiedColumns:protected] => Array
(
)
)
[75] => Category Object
(
[languages:protected] =>
[bok_resources:protected] =>
[bok_topics:protected] =>
[bok_keywords:protected] =>
[id:protected] => 75
[type:protected] => category
[parent:protected] => 2
[label:protected] => Plasterer
[alreadyInSave:protected] =>
[alreadyInValidation:protected] =>
[validationFailures:protected] => Array
(
)
[_new:BaseObject:private] =>
[_deleted:BaseObject:private] =>
[modifiedColumns:protected] => Array
(
)
)
[76] => Category Object
(
[languages:protected] =>
[bok_resources:protected] =>
[bok_topics:protected] =>
[bok_keywords:protected] =>
[id:protected] => 76
[type:protected] => category
[parent:protected] => 2
[label:protected] => Plumber/Pipefitter
[alreadyInSave:protected] =>
[alreadyInValidation:protected] =>
[validationFailures:protected] => Array
(
)
[_new:BaseObject:private] =>
[_deleted:BaseObject:private] =>
[modifiedColumns:protected] => Array
(
)
)
[63] => Category Object
(
[languages:protected] =>
[bok_resources:protected] =>
[bok_topics:protected] =>
[bok_keywords:protected] =>
[id:protected] => 63
[type:protected] => category
[parent:protected] => 2
[label:protected] => Reinforcing Ironworker
[alreadyInSave:protected] =>
[alreadyInValidation:protected] =>
[validationFailures:protected] => Array
(
)
[_new:BaseObject:private] =>
[_deleted:BaseObject:private] =>
[modifiedColumns:protected] => Array
(
)
)
[78] => Category Object
(
[languages:protected] =>
[bok_resources:protected] =>
[bok_topics:protected] =>
[bok_keywords:protected] =>
[id:protected] => 78
[type:protected] => category
[parent:protected] => 2
[label:protected] => Roofer/Waterproofer
[alreadyInSave:protected] =>
[alreadyInValidation:protected] =>
[validationFailures:protected] => Array
(
)
[_new:BaseObject:private] =>
[_deleted:BaseObject:private] =>
[modifiedColumns:protected] => Array
(
)
)
[79] => Category Object
(
[languages:protected] =>
[bok_resources:protected] =>
[bok_topics:protected] =>
[bok_keywords:protected] =>
[id:protected] => 79
[type:protected] => category
[parent:protected] => 2
[label:protected] => Scaffold Erector
[alreadyInSave:protected] =>
[alreadyInValidation:protected] =>
[validationFailures:protected] => Array
(
)
[_new:BaseObject:private] =>
[_deleted:BaseObject:private] =>
[modifiedColumns:protected] => Array
(
)
)
[82] => Category Object
(
[languages:protected] =>
[bok_resources:protected] =>
[bok_topics:protected] =>
[bok_keywords:protected] =>
[id:protected] => 82
[type:protected] => category
[parent:protected] => 2
[label:protected] => Stonemason
[alreadyInSave:protected] =>
[alreadyInValidation:protected] =>
[validationFailures:protected] => Array
(
)
[_new:BaseObject:private] =>
[_deleted:BaseObject:private] =>
[modifiedColumns:protected] => Array
(
)
)
[62] => Category Object
(
[languages:protected] =>
[bok_resources:protected] =>
[bok_topics:protected] =>
[bok_keywords:protected] =>
[id:protected] => 62
[type:protected] => category
[parent:protected] => 2
[label:protected] => Structural Ironworker
[alreadyInSave:protected] =>
[alreadyInValidation:protected] =>
[validationFailures:protected] => Array
(
)
[_new:BaseObject:private] =>
[_deleted:BaseObject:private] =>
[modifiedColumns:protected] => Array
(
)
)
[87] => Category Object
(
[languages:protected] =>
[bok_resources:protected] =>
[bok_topics:protected] =>
[bok_keywords:protected] =>
[id:protected] => 87
[type:protected] => category
[parent:protected] => 3
[label:protected] => Commercial & Institutional
[alreadyInSave:protected] =>
[alreadyInValidation:protected] =>
[validationFailures:protected] => Array
(
)
[_new:BaseObject:private] =>
[_deleted:BaseObject:private] =>
[modifiedColumns:protected] => Array
(
)
)
[88] => Category Object
(
[languages:protected] =>
[bok_resources:protected] =>
[bok_topics:protected] =>
[bok_keywords:protected] =>
[id:protected] => 88
[type:protected] => category
[parent:protected] => 3
[label:protected] => Demolition
[alreadyInSave:protected] =>
[alreadyInValidation:protected] =>
[validationFailures:protected] => Array
(
)
[_new:BaseObject:private] =>
[_deleted:BaseObject:private] =>
[modifiedColumns:protected] => Array
(
)
)
[91] => Category Object
(
[languages:protected] =>
[bok_resources:protected] =>
[bok_topics:protected] =>
[bok_keywords:protected] =>
[id:protected] => 91
[type:protected] => category
[parent:protected] => 3
[label:protected] => Heavy & Highway
[alreadyInSave:protected] =>
[alreadyInValidation:protected] =>
[validationFailures:protected] => Array
(
)
[_new:BaseObject:private] =>
[_deleted:BaseObject:private] =>
[modifiedColumns:protected] => Array
(
)
)
[90] => Category Object
(
[languages:protected] =>
[bok_resources:protected] =>
[bok_topics:protected] =>
[bok_keywords:protected] =>
[id:protected] => 90
[type:protected] => category
[parent:protected] => 3
[label:protected] => Industrial
[alreadyInSave:protected] =>
[alreadyInValidation:protected] =>
[validationFailures:protected] => Array
(
)
[_new:BaseObject:private] =>
[_deleted:BaseObject:private] =>
[modifiedColumns:protected] => Array
(
)
)
[93] => Category Object
(
[languages:protected] =>
[bok_resources:protected] =>
[bok_topics:protected] =>
[bok_keywords:protected] =>
[id:protected] => 93
[type:protected] => category
[parent:protected] => 3
[label:protected] => Renovations
[alreadyInSave:protected] =>
[alreadyInValidation:protected] =>
[validationFailures:protected] => Array
(
)
[_new:BaseObject:private] =>
[_deleted:BaseObject:private] =>
[modifiedColumns:protected] => Array
(
)
)
[94] => Category Object
(
[languages:protected] =>
[bok_resources:protected] =>
[bok_topics:protected] =>
[bok_keywords:protected] =>
[id:protected] => 94
[type:protected] => category
[parent:protected] => 3
[label:protected] => Residential
[alreadyInSave:protected] =>
[alreadyInValidation:protected] =>
[validationFailures:protected] => Array
(
)
[_new:BaseObject:private] =>
[_deleted:BaseObject:private] =>
[modifiedColumns:protected] => Array
(
)
)
[95] => Category Object
(
[languages:protected] =>
[bok_resources:protected] =>
[bok_topics:protected] =>
[bok_keywords:protected] =>
[id:protected] => 95
[type:protected] => category
[parent:protected] => 3
[label:protected] => Underground
[alreadyInSave:protected] =>
[alreadyInValidation:protected] =>
[validationFailures:protected] => Array
(
)
[_new:BaseObject:private] =>
[_deleted:BaseObject:private] =>
[modifiedColumns:protected] => Array
(
)
)
[97] => Category Object
(
[languages:protected] =>
[bok_resources:protected] =>
[bok_topics:protected] =>
[bok_keywords:protected] =>
[id:protected] => 97
[type:protected] => category
[parent:protected] => 5
[label:protected] => Images
[alreadyInSave:protected] =>
[alreadyInValidation:protected] =>
[validationFailures:protected] => Array
(
)
[_new:BaseObject:private] =>
[_deleted:BaseObject:private] =>
[modifiedColumns:protected] => Array
(
)
)
)
[categories_initialized:protected] => 1
[mapped_items:protected] =>
[content:protected] =>
[files:protected] =>
[language:protected] => Language Object
(
[id:protected] => 1
[code:protected] => en
[name:protected] => English
[alreadyInSave:protected] =>
[alreadyInValidation:protected] =>
[validationFailures:protected] => Array
(
)
[_new:BaseObject:private] =>
[_deleted:BaseObject:private] =>
[modifiedColumns:protected] => Array
(
)
)
[old_record:protected] =>
[id:protected] => 4006
[old_id:protected] =>
[elcosh_id:protected] => i002693
[type:protected] => image
[display_type:protected] => Image
[user_id:protected] => 0
[language_id:protected] => 1
[tagging_id:protected] => Bruce Lippy
[priority_id:protected] => 1
[title:protected] => Toolbox talk - long shot
[total_pages:protected] => 0
[billed_pages:protected] => 0
[publication_number:protected] =>
[part_of:protected] =>
[keywords:protected] => toolbox talk, tailgate talk, safety minute
[comments:protected] =>
[summary:protected] => This crew gathered every morning before starting work to discuss a new safety topic.
[transition_comments:protected] =>
[external_link:protected] =>
[consol_link:protected] => http://www.cpwrconstructionsolutions.org/electrical/solution/662/worker-training.html
[more_like_this:protected] => i002691,i002692,d001269,d000527
[permission_given_by:protected] =>
[published:protected] => T
[billable:protected] => F
[img_name:protected] =>
[img_ext:protected] => jpg
[img_width:protected] =>
[img_height:protected] =>
[img_credit:protected] => Morgan Zavertnik and Hoar Construction
[img_practice:protected] => good
[vid_source_id:protected] =>
[vid_running_time:protected] =>
[vid_intended_audience:protected] =>
[vid_acquisition_info:protected] =>
[vid_cost:protected] =>
[vid_producer:protected] =>
[vid_filename:protected] =>
[vid_filename_downloadable:protected] =>
[date_summary:protected] => November 2015
[date_permission_requested:protected] =>
[date_permission_received:protected] =>
[date_review_needed:protected] =>
[date_received:protected] => 03/02/16
[date_completed:protected] => 03/02/16
[date_billed:protected] =>
[date_modified:protected] => 03/02/16
[collBokExports:protected] =>
[lastBokExportCriteria:BaseElcoshItem:private] =>
[alreadyInSave:protected] =>
[alreadyInValidation:protected] =>
[validationFailures:protected] => Array
(
)
[_new:BaseObject:private] =>
[_deleted:BaseObject:private] =>
[modifiedColumns:protected] => Array
(
)
)
)
[3] => Search_Result Object
(
[title] => Safety officer discussing ongoing project with marketing coordinator
[image] => /record/images/4014-p.jpg
[blurb] => The safety officer (left) points out the good safety practices on this project that reflect well on the firm and may influence future clients....
[category] => Array
(
[0] => 97
[1] => 20
[2] => 46
[3] => 47
[4] => 49
[5] => 50
[6] => 51
[7] => 54
[8] => 55
[9] => 58
[10] => 60
[11] => 61
[12] => 64
[13] => 71
[14] => 75
[15] => 76
[16] => 63
[17] => 79
[18] => 80
[19] => 82
[20] => 62
[21] => 83
[22] => 87
[23] => 91
[24] => 90
[25] => 93
[26] => 94
)
[labels] => Array
(
[0] => Images
[1] => Media
[2] => Media & Documents
[3] => Safety Culture
[4] => Work Environment
[5] => Hazards
[6] => Boilermaker
[7] => Trades
[8] => Bricklayer
[10] => Carpenter
[12] => Carpet Layer
[14] => Cement Mason
[16] => Drywall Applicator Specialist
[18] => Electrical Worker
[20] => Glazier
[22] => HVAC
[24] => Interior Systems Carpenter
[26] => Laborer
[28] => Painter
[30] => Plasterer
[32] => Plumber/Pipefitter
[34] => Reinforcing Ironworker
[36] => Scaffold Erector
[38] => Sheetmetal Worker
[40] => Stonemason
[42] => Structural Ironworker
[44] => Terrazzo Worker
[46] => Commercial & Institutional
[47] => Jobsites
[48] => Heavy & Highway
[50] => Industrial
[52] => Renovations
[54] => Residential
)
[type] => Images
[sub_category] =>
[url] => /image/4014/i002700/Safety%2Bofficer%2Bdiscussing%2Bongoing%2Bproject%2Bwith%2Bmarketing%2Bcoordinator.html
[item:protected] => ImageRecord Object
(
[records:protected] => Array
(
)
[recordId:protected] =>
[searchWordClass:protected] =>
[searchWordPeerClass:protected] =>
[bok_record:protected] =>
[authors:protected] =>
[organizations:protected] =>
[collections:protected] =>
[categories:protected] => Array
(
[97] => Category Object
(
[languages:protected] =>
[bok_resources:protected] =>
[bok_topics:protected] =>
[bok_keywords:protected] =>
[id:protected] => 97
[type:protected] => category
[parent:protected] => 5
[label:protected] => Images
[alreadyInSave:protected] =>
[alreadyInValidation:protected] =>
[validationFailures:protected] => Array
(
)
[_new:BaseObject:private] =>
[_deleted:BaseObject:private] =>
[modifiedColumns:protected] => Array
(
)
)
[20] => Category Object
(
[languages:protected] =>
[bok_resources:protected] =>
[bok_topics:protected] =>
[bok_keywords:protected] =>
[id:protected] => 20
[type:protected] => category
[parent:protected] => 7
[label:protected] => Safety Culture
[alreadyInSave:protected] =>
[alreadyInValidation:protected] =>
[validationFailures:protected] => Array
(
)
[_new:BaseObject:private] =>
[_deleted:BaseObject:private] =>
[modifiedColumns:protected] => Array
(
)
)
[46] => Category Object
(
[languages:protected] =>
[bok_resources:protected] =>
[bok_topics:protected] =>
[bok_keywords:protected] =>
[id:protected] => 46
[type:protected] => category
[parent:protected] => 2
[label:protected] => Boilermaker
[alreadyInSave:protected] =>
[alreadyInValidation:protected] =>
[validationFailures:protected] => Array
(
)
[_new:BaseObject:private] =>
[_deleted:BaseObject:private] =>
[modifiedColumns:protected] => Array
(
)
)
[47] => Category Object
(
[languages:protected] =>
[bok_resources:protected] =>
[bok_topics:protected] =>
[bok_keywords:protected] =>
[id:protected] => 47
[type:protected] => category
[parent:protected] => 2
[label:protected] => Bricklayer
[alreadyInSave:protected] =>
[alreadyInValidation:protected] =>
[validationFailures:protected] => Array
(
)
[_new:BaseObject:private] =>
[_deleted:BaseObject:private] =>
[modifiedColumns:protected] => Array
(
)
)
[49] => Category Object
(
[languages:protected] =>
[bok_resources:protected] =>
[bok_topics:protected] =>
[bok_keywords:protected] =>
[id:protected] => 49
[type:protected] => category
[parent:protected] => 2
[label:protected] => Carpenter
[alreadyInSave:protected] =>
[alreadyInValidation:protected] =>
[validationFailures:protected] => Array
(
)
[_new:BaseObject:private] =>
[_deleted:BaseObject:private] =>
[modifiedColumns:protected] => Array
(
)
)
[50] => Category Object
(
[languages:protected] =>
[bok_resources:protected] =>
[bok_topics:protected] =>
[bok_keywords:protected] =>
[id:protected] => 50
[type:protected] => category
[parent:protected] => 2
[label:protected] => Carpet Layer
[alreadyInSave:protected] =>
[alreadyInValidation:protected] =>
[validationFailures:protected] => Array
(
)
[_new:BaseObject:private] =>
[_deleted:BaseObject:private] =>
[modifiedColumns:protected] => Array
(
)
)
[51] => Category Object
(
[languages:protected] =>
[bok_resources:protected] =>
[bok_topics:protected] =>
[bok_keywords:protected] =>
[id:protected] => 51
[type:protected] => category
[parent:protected] => 2
[label:protected] => Cement Mason
[alreadyInSave:protected] =>
[alreadyInValidation:protected] =>
[validationFailures:protected] => Array
(
)
[_new:BaseObject:private] =>
[_deleted:BaseObject:private] =>
[modifiedColumns:protected] => Array
(
)
)
[54] => Category Object
(
[languages:protected] =>
[bok_resources:protected] =>
[bok_topics:protected] =>
[bok_keywords:protected] =>
[id:protected] => 54
[type:protected] => category
[parent:protected] => 2
[label:protected] => Drywall Applicator Specialist
[alreadyInSave:protected] =>
[alreadyInValidation:protected] =>
[validationFailures:protected] => Array
(
)
[_new:BaseObject:private] =>
[_deleted:BaseObject:private] =>
[modifiedColumns:protected] => Array
(
)
)
[55] => Category Object
(
[languages:protected] =>
[bok_resources:protected] =>
[bok_topics:protected] =>
[bok_keywords:protected] =>
[id:protected] => 55
[type:protected] => category
[parent:protected] => 2
[label:protected] => Electrical Worker
[alreadyInSave:protected] =>
[alreadyInValidation:protected] =>
[validationFailures:protected] => Array
(
)
[_new:BaseObject:private] =>
[_deleted:BaseObject:private] =>
[modifiedColumns:protected] => Array
(
)
)
[58] => Category Object
(
[languages:protected] =>
[bok_resources:protected] =>
[bok_topics:protected] =>
[bok_keywords:protected] =>
[id:protected] => 58
[type:protected] => category
[parent:protected] => 2
[label:protected] => Glazier
[alreadyInSave:protected] =>
[alreadyInValidation:protected] =>
[validationFailures:protected] => Array
(
)
[_new:BaseObject:private] =>
[_deleted:BaseObject:private] =>
[modifiedColumns:protected] => Array
(
)
)
[60] => Category Object
(
[languages:protected] =>
[bok_resources:protected] =>
[bok_topics:protected] =>
[bok_keywords:protected] =>
[id:protected] => 60
[type:protected] => category
[parent:protected] => 2
[label:protected] => HVAC
[alreadyInSave:protected] =>
[alreadyInValidation:protected] =>
[validationFailures:protected] => Array
(
)
[_new:BaseObject:private] =>
[_deleted:BaseObject:private] =>
[modifiedColumns:protected] => Array
(
)
)
[61] => Category Object
(
[languages:protected] =>
[bok_resources:protected] =>
[bok_topics:protected] =>
[bok_keywords:protected] =>
[id:protected] => 61
[type:protected] => category
[parent:protected] => 2
[label:protected] => Interior Systems Carpenter
[alreadyInSave:protected] =>
[alreadyInValidation:protected] =>
[validationFailures:protected] => Array
(
)
[_new:BaseObject:private] =>
[_deleted:BaseObject:private] =>
[modifiedColumns:protected] => Array
(
)
)
[64] => Category Object
(
[languages:protected] =>
[bok_resources:protected] =>
[bok_topics:protected] =>
[bok_keywords:protected] =>
[id:protected] => 64
[type:protected] => category
[parent:protected] => 2
[label:protected] => Laborer
[alreadyInSave:protected] =>
[alreadyInValidation:protected] =>
[validationFailures:protected] => Array
(
)
[_new:BaseObject:private] =>
[_deleted:BaseObject:private] =>
[modifiedColumns:protected] => Array
(
)
)
[71] => Category Object
(
[languages:protected] =>
[bok_resources:protected] =>
[bok_topics:protected] =>
[bok_keywords:protected] =>
[id:protected] => 71
[type:protected] => category
[parent:protected] => 2
[label:protected] => Painter
[alreadyInSave:protected] =>
[alreadyInValidation:protected] =>
[validationFailures:protected] => Array
(
)
[_new:BaseObject:private] =>
[_deleted:BaseObject:private] =>
[modifiedColumns:protected] => Array
(
)
)
[75] => Category Object
(
[languages:protected] =>
[bok_resources:protected] =>
[bok_topics:protected] =>
[bok_keywords:protected] =>
[id:protected] => 75
[type:protected] => category
[parent:protected] => 2
[label:protected] => Plasterer
[alreadyInSave:protected] =>
[alreadyInValidation:protected] =>
[validationFailures:protected] => Array
(
)
[_new:BaseObject:private] =>
[_deleted:BaseObject:private] =>
[modifiedColumns:protected] => Array
(
)
)
[76] => Category Object
(
[languages:protected] =>
[bok_resources:protected] =>
[bok_topics:protected] =>
[bok_keywords:protected] =>
[id:protected] => 76
[type:protected] => category
[parent:protected] => 2
[label:protected] => Plumber/Pipefitter
[alreadyInSave:protected] =>
[alreadyInValidation:protected] =>
[validationFailures:protected] => Array
(
)
[_new:BaseObject:private] =>
[_deleted:BaseObject:private] =>
[modifiedColumns:protected] => Array
(
)
)
[63] => Category Object
(
[languages:protected] =>
[bok_resources:protected] =>
[bok_topics:protected] =>
[bok_keywords:protected] =>
[id:protected] => 63
[type:protected] => category
[parent:protected] => 2
[label:protected] => Reinforcing Ironworker
[alreadyInSave:protected] =>
[alreadyInValidation:protected] =>
[validationFailures:protected] => Array
(
)
[_new:BaseObject:private] =>
[_deleted:BaseObject:private] =>
[modifiedColumns:protected] => Array
(
)
)
[79] => Category Object
(
[languages:protected] =>
[bok_resources:protected] =>
[bok_topics:protected] =>
[bok_keywords:protected] =>
[id:protected] => 79
[type:protected] => category
[parent:protected] => 2
[label:protected] => Scaffold Erector
[alreadyInSave:protected] =>
[alreadyInValidation:protected] =>
[validationFailures:protected] => Array
(
)
[_new:BaseObject:private] =>
[_deleted:BaseObject:private] =>
[modifiedColumns:protected] => Array
(
)
)
[80] => Category Object
(
[languages:protected] =>
[bok_resources:protected] =>
[bok_topics:protected] =>
[bok_keywords:protected] =>
[id:protected] => 80
[type:protected] => category
[parent:protected] => 2
[label:protected] => Sheetmetal Worker
[alreadyInSave:protected] =>
[alreadyInValidation:protected] =>
[validationFailures:protected] => Array
(
)
[_new:BaseObject:private] =>
[_deleted:BaseObject:private] =>
[modifiedColumns:protected] => Array
(
)
)
[82] => Category Object
(
[languages:protected] =>
[bok_resources:protected] =>
[bok_topics:protected] =>
[bok_keywords:protected] =>
[id:protected] => 82
[type:protected] => category
[parent:protected] => 2
[label:protected] => Stonemason
[alreadyInSave:protected] =>
[alreadyInValidation:protected] =>
[validationFailures:protected] => Array
(
)
[_new:BaseObject:private] =>
[_deleted:BaseObject:private] =>
[modifiedColumns:protected] => Array
(
)
)
[62] => Category Object
(
[languages:protected] =>
[bok_resources:protected] =>
[bok_topics:protected] =>
[bok_keywords:protected] =>
[id:protected] => 62
[type:protected] => category
[parent:protected] => 2
[label:protected] => Structural Ironworker
[alreadyInSave:protected] =>
[alreadyInValidation:protected] =>
[validationFailures:protected] => Array
(
)
[_new:BaseObject:private] =>
[_deleted:BaseObject:private] =>
[modifiedColumns:protected] => Array
(
)
)
[83] => Category Object
(
[languages:protected] =>
[bok_resources:protected] =>
[bok_topics:protected] =>
[bok_keywords:protected] =>
[id:protected] => 83
[type:protected] => category
[parent:protected] => 2
[label:protected] => Terrazzo Worker
[alreadyInSave:protected] =>
[alreadyInValidation:protected] =>
[validationFailures:protected] => Array
(
)
[_new:BaseObject:private] =>
[_deleted:BaseObject:private] =>
[modifiedColumns:protected] => Array
(
)
)
[87] => Category Object
(
[languages:protected] =>
[bok_resources:protected] =>
[bok_topics:protected] =>
[bok_keywords:protected] =>
[id:protected] => 87
[type:protected] => category
[parent:protected] => 3
[label:protected] => Commercial & Institutional
[alreadyInSave:protected] =>
[alreadyInValidation:protected] =>
[validationFailures:protected] => Array
(
)
[_new:BaseObject:private] =>
[_deleted:BaseObject:private] =>
[modifiedColumns:protected] => Array
(
)
)
[91] => Category Object
(
[languages:protected] =>
[bok_resources:protected] =>
[bok_topics:protected] =>
[bok_keywords:protected] =>
[id:protected] => 91
[type:protected] => category
[parent:protected] => 3
[label:protected] => Heavy & Highway
[alreadyInSave:protected] =>
[alreadyInValidation:protected] =>
[validationFailures:protected] => Array
(
)
[_new:BaseObject:private] =>
[_deleted:BaseObject:private] =>
[modifiedColumns:protected] => Array
(
)
)
[90] => Category Object
(
[languages:protected] =>
[bok_resources:protected] =>
[bok_topics:protected] =>
[bok_keywords:protected] =>
[id:protected] => 90
[type:protected] => category
[parent:protected] => 3
[label:protected] => Industrial
[alreadyInSave:protected] =>
[alreadyInValidation:protected] =>
[validationFailures:protected] => Array
(
)
[_new:BaseObject:private] =>
[_deleted:BaseObject:private] =>
[modifiedColumns:protected] => Array
(
)
)
[93] => Category Object
(
[languages:protected] =>
[bok_resources:protected] =>
[bok_topics:protected] =>
[bok_keywords:protected] =>
[id:protected] => 93
[type:protected] => category
[parent:protected] => 3
[label:protected] => Renovations
[alreadyInSave:protected] =>
[alreadyInValidation:protected] =>
[validationFailures:protected] => Array
(
)
[_new:BaseObject:private] =>
[_deleted:BaseObject:private] =>
[modifiedColumns:protected] => Array
(
)
)
[94] => Category Object
(
[languages:protected] =>
[bok_resources:protected] =>
[bok_topics:protected] =>
[bok_keywords:protected] =>
[id:protected] => 94
[type:protected] => category
[parent:protected] => 3
[label:protected] => Residential
[alreadyInSave:protected] =>
[alreadyInValidation:protected] =>
[validationFailures:protected] => Array
(
)
[_new:BaseObject:private] =>
[_deleted:BaseObject:private] =>
[modifiedColumns:protected] => Array
(
)
)
)
[categories_initialized:protected] => 1
[mapped_items:protected] =>
[content:protected] =>
[files:protected] =>
[language:protected] => Language Object
(
[id:protected] => 1
[code:protected] => en
[name:protected] => English
[alreadyInSave:protected] =>
[alreadyInValidation:protected] =>
[validationFailures:protected] => Array
(
)
[_new:BaseObject:private] =>
[_deleted:BaseObject:private] =>
[modifiedColumns:protected] => Array
(
)
)
[old_record:protected] =>
[id:protected] => 4014
[old_id:protected] =>
[elcosh_id:protected] => i002700
[type:protected] => image
[display_type:protected] => Image
[user_id:protected] => 0
[language_id:protected] => 1
[tagging_id:protected] => Bruce Lippy
[priority_id:protected] => 1
[title:protected] => Safety officer discussing ongoing project with marketing coordinator
[total_pages:protected] => 0
[billed_pages:protected] => 0
[publication_number:protected] =>
[part_of:protected] =>
[keywords:protected] => Latino, safety officer, safety culture
[comments:protected] =>
[summary:protected] => The safety officer (left) points out the good safety practices on this project that reflect well on the firm and may influence future clients.
[transition_comments:protected] =>
[external_link:protected] =>
[consol_link:protected] => http://www.cpwrconstructionsolutions.org/index.php
[more_like_this:protected] => d000989,d001351,d001362,d000652, d001101, d000931, d001395
[permission_given_by:protected] =>
[published:protected] => T
[billable:protected] => F
[img_name:protected] =>
[img_ext:protected] => jpg
[img_width:protected] =>
[img_height:protected] =>
[img_credit:protected] => Hoar Construction, Photo by Neil Lippy
[img_practice:protected] => good
[vid_source_id:protected] =>
[vid_running_time:protected] =>
[vid_intended_audience:protected] =>
[vid_acquisition_info:protected] =>
[vid_cost:protected] =>
[vid_producer:protected] =>
[vid_filename:protected] =>
[vid_filename_downloadable:protected] =>
[date_summary:protected] => November 2015
[date_permission_requested:protected] =>
[date_permission_received:protected] =>
[date_review_needed:protected] =>
[date_received:protected] => 03/02/16
[date_completed:protected] => 03/02/16
[date_billed:protected] =>
[date_modified:protected] => 01/30/23
[collBokExports:protected] =>
[lastBokExportCriteria:BaseElcoshItem:private] =>
[alreadyInSave:protected] =>
[alreadyInValidation:protected] =>
[validationFailures:protected] => Array
(
)
[_new:BaseObject:private] =>
[_deleted:BaseObject:private] =>
[modifiedColumns:protected] => Array
(
)
)
)
[4] => Search_Result Object
(
[title] => Scaffolding at top of large column
[image] => /record/images/3994-p.jpg
[blurb] => This shot shows innovative guarding around the top of a large concrete column in the base of a high rise structure going up....
[category] => Array
(
[0] => 15
[1] => 21
[2] => 47
[3] => 51
[4] => 63
[5] => 78
[6] => 79
[7] => 80
[8] => 62
[9] => 87
[10] => 97
[11] => 56
[12] => 64
[13] => 74
)
[labels] => Array
(
[0] => Falls
[1] => Work Environment
[2] => Hazards
[3] => Scaffolds
[6] => Bricklayer
[7] => Trades
[8] => Cement Mason
[10] => Reinforcing Ironworker
[12] => Roofer/Waterproofer
[14] => Scaffold Erector
[16] => Sheetmetal Worker
[18] => Structural Ironworker
[20] => Commercial & Institutional
[21] => Jobsites
[22] => Images
[23] => Media
[24] => Media & Documents
[25] => Elevator Constructor
[27] => Laborer
[29] => Pile Driver
)
[type] => Images
[sub_category] =>
[url] => /image/3994/i002689/Scaffolding%2Bat%2Btop%2Bof%2Blarge%2Bcolumn.html
[item:protected] => ImageRecord Object
(
[records:protected] => Array
(
)
[recordId:protected] =>
[searchWordClass:protected] =>
[searchWordPeerClass:protected] =>
[bok_record:protected] =>
[authors:protected] =>
[organizations:protected] =>
[collections:protected] =>
[categories:protected] => Array
(
[15] => Category Object
(
[languages:protected] =>
[bok_resources:protected] =>
[bok_topics:protected] =>
[bok_keywords:protected] =>
[id:protected] => 15
[type:protected] => category
[parent:protected] => 7
[label:protected] => Falls
[alreadyInSave:protected] =>
[alreadyInValidation:protected] =>
[validationFailures:protected] => Array
(
)
[_new:BaseObject:private] =>
[_deleted:BaseObject:private] =>
[modifiedColumns:protected] => Array
(
)
)
[21] => Category Object
(
[languages:protected] =>
[bok_resources:protected] =>
[bok_topics:protected] =>
[bok_keywords:protected] =>
[id:protected] => 21
[type:protected] => category
[parent:protected] => 7
[label:protected] => Scaffolds
[alreadyInSave:protected] =>
[alreadyInValidation:protected] =>
[validationFailures:protected] => Array
(
)
[_new:BaseObject:private] =>
[_deleted:BaseObject:private] =>
[modifiedColumns:protected] => Array
(
)
)
[47] => Category Object
(
[languages:protected] =>
[bok_resources:protected] =>
[bok_topics:protected] =>
[bok_keywords:protected] =>
[id:protected] => 47
[type:protected] => category
[parent:protected] => 2
[label:protected] => Bricklayer
[alreadyInSave:protected] =>
[alreadyInValidation:protected] =>
[validationFailures:protected] => Array
(
)
[_new:BaseObject:private] =>
[_deleted:BaseObject:private] =>
[modifiedColumns:protected] => Array
(
)
)
[51] => Category Object
(
[languages:protected] =>
[bok_resources:protected] =>
[bok_topics:protected] =>
[bok_keywords:protected] =>
[id:protected] => 51
[type:protected] => category
[parent:protected] => 2
[label:protected] => Cement Mason
[alreadyInSave:protected] =>
[alreadyInValidation:protected] =>
[validationFailures:protected] => Array
(
)
[_new:BaseObject:private] =>
[_deleted:BaseObject:private] =>
[modifiedColumns:protected] => Array
(
)
)
[63] => Category Object
(
[languages:protected] =>
[bok_resources:protected] =>
[bok_topics:protected] =>
[bok_keywords:protected] =>
[id:protected] => 63
[type:protected] => category
[parent:protected] => 2
[label:protected] => Reinforcing Ironworker
[alreadyInSave:protected] =>
[alreadyInValidation:protected] =>
[validationFailures:protected] => Array
(
)
[_new:BaseObject:private] =>
[_deleted:BaseObject:private] =>
[modifiedColumns:protected] => Array
(
)
)
[78] => Category Object
(
[languages:protected] =>
[bok_resources:protected] =>
[bok_topics:protected] =>
[bok_keywords:protected] =>
[id:protected] => 78
[type:protected] => category
[parent:protected] => 2
[label:protected] => Roofer/Waterproofer
[alreadyInSave:protected] =>
[alreadyInValidation:protected] =>
[validationFailures:protected] => Array
(
)
[_new:BaseObject:private] =>
[_deleted:BaseObject:private] =>
[modifiedColumns:protected] => Array
(
)
)
[79] => Category Object
(
[languages:protected] =>
[bok_resources:protected] =>
[bok_topics:protected] =>
[bok_keywords:protected] =>
[id:protected] => 79
[type:protected] => category
[parent:protected] => 2
[label:protected] => Scaffold Erector
[alreadyInSave:protected] =>
[alreadyInValidation:protected] =>
[validationFailures:protected] => Array
(
)
[_new:BaseObject:private] =>
[_deleted:BaseObject:private] =>
[modifiedColumns:protected] => Array
(
)
)
[80] => Category Object
(
[languages:protected] =>
[bok_resources:protected] =>
[bok_topics:protected] =>
[bok_keywords:protected] =>
[id:protected] => 80
[type:protected] => category
[parent:protected] => 2
[label:protected] => Sheetmetal Worker
[alreadyInSave:protected] =>
[alreadyInValidation:protected] =>
[validationFailures:protected] => Array
(
)
[_new:BaseObject:private] =>
[_deleted:BaseObject:private] =>
[modifiedColumns:protected] => Array
(
)
)
[62] => Category Object
(
[languages:protected] =>
[bok_resources:protected] =>
[bok_topics:protected] =>
[bok_keywords:protected] =>
[id:protected] => 62
[type:protected] => category
[parent:protected] => 2
[label:protected] => Structural Ironworker
[alreadyInSave:protected] =>
[alreadyInValidation:protected] =>
[validationFailures:protected] => Array
(
)
[_new:BaseObject:private] =>
[_deleted:BaseObject:private] =>
[modifiedColumns:protected] => Array
(
)
)
[87] => Category Object
(
[languages:protected] =>
[bok_resources:protected] =>
[bok_topics:protected] =>
[bok_keywords:protected] =>
[id:protected] => 87
[type:protected] => category
[parent:protected] => 3
[label:protected] => Commercial & Institutional
[alreadyInSave:protected] =>
[alreadyInValidation:protected] =>
[validationFailures:protected] => Array
(
)
[_new:BaseObject:private] =>
[_deleted:BaseObject:private] =>
[modifiedColumns:protected] => Array
(
)
)
[97] => Category Object
(
[languages:protected] =>
[bok_resources:protected] =>
[bok_topics:protected] =>
[bok_keywords:protected] =>
[id:protected] => 97
[type:protected] => category
[parent:protected] => 5
[label:protected] => Images
[alreadyInSave:protected] =>
[alreadyInValidation:protected] =>
[validationFailures:protected] => Array
(
)
[_new:BaseObject:private] =>
[_deleted:BaseObject:private] =>
[modifiedColumns:protected] => Array
(
)
)
[56] => Category Object
(
[languages:protected] =>
[bok_resources:protected] =>
[bok_topics:protected] =>
[bok_keywords:protected] =>
[id:protected] => 56
[type:protected] => category
[parent:protected] => 2
[label:protected] => Elevator Constructor
[alreadyInSave:protected] =>
[alreadyInValidation:protected] =>
[validationFailures:protected] => Array
(
)
[_new:BaseObject:private] =>
[_deleted:BaseObject:private] =>
[modifiedColumns:protected] => Array
(
)
)
[64] => Category Object
(
[languages:protected] =>
[bok_resources:protected] =>
[bok_topics:protected] =>
[bok_keywords:protected] =>
[id:protected] => 64
[type:protected] => category
[parent:protected] => 2
[label:protected] => Laborer
[alreadyInSave:protected] =>
[alreadyInValidation:protected] =>
[validationFailures:protected] => Array
(
)
[_new:BaseObject:private] =>
[_deleted:BaseObject:private] =>
[modifiedColumns:protected] => Array
(
)
)
[74] => Category Object
(
[languages:protected] =>
[bok_resources:protected] =>
[bok_topics:protected] =>
[bok_keywords:protected] =>
[id:protected] => 74
[type:protected] => category
[parent:protected] => 2
[label:protected] => Pile Driver
[alreadyInSave:protected] =>
[alreadyInValidation:protected] =>
[validationFailures:protected] => Array
(
)
[_new:BaseObject:private] =>
[_deleted:BaseObject:private] =>
[modifiedColumns:protected] => Array
(
)
)
)
[categories_initialized:protected] => 1
[mapped_items:protected] =>
[content:protected] =>
[files:protected] =>
[language:protected] => Language Object
(
[id:protected] => 1
[code:protected] => en
[name:protected] => English
[alreadyInSave:protected] =>
[alreadyInValidation:protected] =>
[validationFailures:protected] => Array
(
)
[_new:BaseObject:private] =>
[_deleted:BaseObject:private] =>
[modifiedColumns:protected] => Array
(
)
)
[old_record:protected] =>
[id:protected] => 3994
[old_id:protected] =>
[elcosh_id:protected] => i002689
[type:protected] => image
[display_type:protected] => Image
[user_id:protected] => 0
[language_id:protected] => 1
[tagging_id:protected] => Bruce Lippy
[priority_id:protected] => 1
[title:protected] => Scaffolding at top of large column
[total_pages:protected] => 0
[billed_pages:protected] => 0
[publication_number:protected] =>
[part_of:protected] =>
[keywords:protected] => Guardrail, railing, fall prevention, falls
[comments:protected] =>
[summary:protected] => This shot shows innovative guarding around the top of a large concrete column in the base of a high rise structure going up.
[transition_comments:protected] =>
[external_link:protected] =>
[consol_link:protected] => http://www.cpwrconstructionsolutions.org/masonry/solution/8/adjustable-tower-scaffold.html
[more_like_this:protected] => c1002680,i002662,d000608,d001255
[permission_given_by:protected] =>
[published:protected] => T
[billable:protected] => F
[img_name:protected] =>
[img_ext:protected] => jpg
[img_width:protected] =>
[img_height:protected] =>
[img_credit:protected] => Photo by Pam Susi
[img_practice:protected] => good
[vid_source_id:protected] =>
[vid_running_time:protected] =>
[vid_intended_audience:protected] =>
[vid_acquisition_info:protected] =>
[vid_cost:protected] =>
[vid_producer:protected] =>
[vid_filename:protected] =>
[vid_filename_downloadable:protected] =>
[date_summary:protected] => January 2016
[date_permission_requested:protected] =>
[date_permission_received:protected] =>
[date_review_needed:protected] =>
[date_received:protected] => 02/01/16
[date_completed:protected] => 02/01/16
[date_billed:protected] =>
[date_modified:protected] => 02/01/16
[collBokExports:protected] =>
[lastBokExportCriteria:BaseElcoshItem:private] =>
[alreadyInSave:protected] =>
[alreadyInValidation:protected] =>
[validationFailures:protected] => Array
(
)
[_new:BaseObject:private] =>
[_deleted:BaseObject:private] =>
[modifiedColumns:protected] => Array
(
)
)
)
[5] => Search_Result Object
(
[title] => Construction bracing
[image] => /record/images/3995-p.jpg
[blurb] => This shows structural support that prevents collapses during construction....
[category] => Array
(
[0] => 12
[1] => 15
[2] => 21
[3] => 49
[4] => 51
[5] => 55
[6] => 56
[7] => 60
[8] => 64
[9] => 68
[10] => 74
[11] => 63
[12] => 78
[13] => 79
[14] => 80
[15] => 62
[16] => 87
[17] => 90
[18] => 97
)
[labels] => Array
(
[0] => Crushed/Struck By
[1] => Work Environment
[2] => Hazards
[3] => Falls
[6] => Scaffolds
[9] => Carpenter
[10] => Trades
[11] => Cement Mason
[13] => Electrical Worker
[15] => Elevator Constructor
[17] => HVAC
[19] => Laborer
[21] => Maintenance Worker
[23] => Pile Driver
[25] => Reinforcing Ironworker
[27] => Roofer/Waterproofer
[29] => Scaffold Erector
[31] => Sheetmetal Worker
[33] => Structural Ironworker
[35] => Commercial & Institutional
[36] => Jobsites
[37] => Industrial
[39] => Images
[40] => Media
[41] => Media & Documents
)
[type] => Images
[sub_category] =>
[url] => /image/3995/i002690/Construction%2Bbracing.html
[item:protected] => ImageRecord Object
(
[records:protected] => Array
(
)
[recordId:protected] =>
[searchWordClass:protected] =>
[searchWordPeerClass:protected] =>
[bok_record:protected] =>
[authors:protected] =>
[organizations:protected] =>
[collections:protected] =>
[categories:protected] => Array
(
[12] => Category Object
(
[languages:protected] =>
[bok_resources:protected] =>
[bok_topics:protected] =>
[bok_keywords:protected] =>
[id:protected] => 12
[type:protected] => category
[parent:protected] => 7
[label:protected] => Crushed/Struck By
[alreadyInSave:protected] =>
[alreadyInValidation:protected] =>
[validationFailures:protected] => Array
(
)
[_new:BaseObject:private] =>
[_deleted:BaseObject:private] =>
[modifiedColumns:protected] => Array
(
)
)
[15] => Category Object
(
[languages:protected] =>
[bok_resources:protected] =>
[bok_topics:protected] =>
[bok_keywords:protected] =>
[id:protected] => 15
[type:protected] => category
[parent:protected] => 7
[label:protected] => Falls
[alreadyInSave:protected] =>
[alreadyInValidation:protected] =>
[validationFailures:protected] => Array
(
)
[_new:BaseObject:private] =>
[_deleted:BaseObject:private] =>
[modifiedColumns:protected] => Array
(
)
)
[21] => Category Object
(
[languages:protected] =>
[bok_resources:protected] =>
[bok_topics:protected] =>
[bok_keywords:protected] =>
[id:protected] => 21
[type:protected] => category
[parent:protected] => 7
[label:protected] => Scaffolds
[alreadyInSave:protected] =>
[alreadyInValidation:protected] =>
[validationFailures:protected] => Array
(
)
[_new:BaseObject:private] =>
[_deleted:BaseObject:private] =>
[modifiedColumns:protected] => Array
(
)
)
[49] => Category Object
(
[languages:protected] =>
[bok_resources:protected] =>
[bok_topics:protected] =>
[bok_keywords:protected] =>
[id:protected] => 49
[type:protected] => category
[parent:protected] => 2
[label:protected] => Carpenter
[alreadyInSave:protected] =>
[alreadyInValidation:protected] =>
[validationFailures:protected] => Array
(
)
[_new:BaseObject:private] =>
[_deleted:BaseObject:private] =>
[modifiedColumns:protected] => Array
(
)
)
[51] => Category Object
(
[languages:protected] =>
[bok_resources:protected] =>
[bok_topics:protected] =>
[bok_keywords:protected] =>
[id:protected] => 51
[type:protected] => category
[parent:protected] => 2
[label:protected] => Cement Mason
[alreadyInSave:protected] =>
[alreadyInValidation:protected] =>
[validationFailures:protected] => Array
(
)
[_new:BaseObject:private] =>
[_deleted:BaseObject:private] =>
[modifiedColumns:protected] => Array
(
)
)
[55] => Category Object
(
[languages:protected] =>
[bok_resources:protected] =>
[bok_topics:protected] =>
[bok_keywords:protected] =>
[id:protected] => 55
[type:protected] => category
[parent:protected] => 2
[label:protected] => Electrical Worker
[alreadyInSave:protected] =>
[alreadyInValidation:protected] =>
[validationFailures:protected] => Array
(
)
[_new:BaseObject:private] =>
[_deleted:BaseObject:private] =>
[modifiedColumns:protected] => Array
(
)
)
[56] => Category Object
(
[languages:protected] =>
[bok_resources:protected] =>
[bok_topics:protected] =>
[bok_keywords:protected] =>
[id:protected] => 56
[type:protected] => category
[parent:protected] => 2
[label:protected] => Elevator Constructor
[alreadyInSave:protected] =>
[alreadyInValidation:protected] =>
[validationFailures:protected] => Array
(
)
[_new:BaseObject:private] =>
[_deleted:BaseObject:private] =>
[modifiedColumns:protected] => Array
(
)
)
[60] => Category Object
(
[languages:protected] =>
[bok_resources:protected] =>
[bok_topics:protected] =>
[bok_keywords:protected] =>
[id:protected] => 60
[type:protected] => category
[parent:protected] => 2
[label:protected] => HVAC
[alreadyInSave:protected] =>
[alreadyInValidation:protected] =>
[validationFailures:protected] => Array
(
)
[_new:BaseObject:private] =>
[_deleted:BaseObject:private] =>
[modifiedColumns:protected] => Array
(
)
)
[64] => Category Object
(
[languages:protected] =>
[bok_resources:protected] =>
[bok_topics:protected] =>
[bok_keywords:protected] =>
[id:protected] => 64
[type:protected] => category
[parent:protected] => 2
[label:protected] => Laborer
[alreadyInSave:protected] =>
[alreadyInValidation:protected] =>
[validationFailures:protected] => Array
(
)
[_new:BaseObject:private] =>
[_deleted:BaseObject:private] =>
[modifiedColumns:protected] => Array
(
)
)
[68] => Category Object
(
[languages:protected] =>
[bok_resources:protected] =>
[bok_topics:protected] =>
[bok_keywords:protected] =>
[id:protected] => 68
[type:protected] => category
[parent:protected] => 2
[label:protected] => Maintenance Worker
[alreadyInSave:protected] =>
[alreadyInValidation:protected] =>
[validationFailures:protected] => Array
(
)
[_new:BaseObject:private] =>
[_deleted:BaseObject:private] =>
[modifiedColumns:protected] => Array
(
)
)
[74] => Category Object
(
[languages:protected] =>
[bok_resources:protected] =>
[bok_topics:protected] =>
[bok_keywords:protected] =>
[id:protected] => 74
[type:protected] => category
[parent:protected] => 2
[label:protected] => Pile Driver
[alreadyInSave:protected] =>
[alreadyInValidation:protected] =>
[validationFailures:protected] => Array
(
)
[_new:BaseObject:private] =>
[_deleted:BaseObject:private] =>
[modifiedColumns:protected] => Array
(
)
)
[63] => Category Object
(
[languages:protected] =>
[bok_resources:protected] =>
[bok_topics:protected] =>
[bok_keywords:protected] =>
[id:protected] => 63
[type:protected] => category
[parent:protected] => 2
[label:protected] => Reinforcing Ironworker
[alreadyInSave:protected] =>
[alreadyInValidation:protected] =>
[validationFailures:protected] => Array
(
)
[_new:BaseObject:private] =>
[_deleted:BaseObject:private] =>
[modifiedColumns:protected] => Array
(
)
)
[78] => Category Object
(
[languages:protected] =>
[bok_resources:protected] =>
[bok_topics:protected] =>
[bok_keywords:protected] =>
[id:protected] => 78
[type:protected] => category
[parent:protected] => 2
[label:protected] => Roofer/Waterproofer
[alreadyInSave:protected] =>
[alreadyInValidation:protected] =>
[validationFailures:protected] => Array
(
)
[_new:BaseObject:private] =>
[_deleted:BaseObject:private] =>
[modifiedColumns:protected] => Array
(
)
)
[79] => Category Object
(
[languages:protected] =>
[bok_resources:protected] =>
[bok_topics:protected] =>
[bok_keywords:protected] =>
[id:protected] => 79
[type:protected] => category
[parent:protected] => 2
[label:protected] => Scaffold Erector
[alreadyInSave:protected] =>
[alreadyInValidation:protected] =>
[validationFailures:protected] => Array
(
)
[_new:BaseObject:private] =>
[_deleted:BaseObject:private] =>
[modifiedColumns:protected] => Array
(
)
)
[80] => Category Object
(
[languages:protected] =>
[bok_resources:protected] =>
[bok_topics:protected] =>
[bok_keywords:protected] =>
[id:protected] => 80
[type:protected] => category
[parent:protected] => 2
[label:protected] => Sheetmetal Worker
[alreadyInSave:protected] =>
[alreadyInValidation:protected] =>
[validationFailures:protected] => Array
(
)
[_new:BaseObject:private] =>
[_deleted:BaseObject:private] =>
[modifiedColumns:protected] => Array
(
)
)
[62] => Category Object
(
[languages:protected] =>
[bok_resources:protected] =>
[bok_topics:protected] =>
[bok_keywords:protected] =>
[id:protected] => 62
[type:protected] => category
[parent:protected] => 2
[label:protected] => Structural Ironworker
[alreadyInSave:protected] =>
[alreadyInValidation:protected] =>
[validationFailures:protected] => Array
(
)
[_new:BaseObject:private] =>
[_deleted:BaseObject:private] =>
[modifiedColumns:protected] => Array
(
)
)
[87] => Category Object
(
[languages:protected] =>
[bok_resources:protected] =>
[bok_topics:protected] =>
[bok_keywords:protected] =>
[id:protected] => 87
[type:protected] => category
[parent:protected] => 3
[label:protected] => Commercial & Institutional
[alreadyInSave:protected] =>
[alreadyInValidation:protected] =>
[validationFailures:protected] => Array
(
)
[_new:BaseObject:private] =>
[_deleted:BaseObject:private] =>
[modifiedColumns:protected] => Array
(
)
)
[90] => Category Object
(
[languages:protected] =>
[bok_resources:protected] =>
[bok_topics:protected] =>
[bok_keywords:protected] =>
[id:protected] => 90
[type:protected] => category
[parent:protected] => 3
[label:protected] => Industrial
[alreadyInSave:protected] =>
[alreadyInValidation:protected] =>
[validationFailures:protected] => Array
(
)
[_new:BaseObject:private] =>
[_deleted:BaseObject:private] =>
[modifiedColumns:protected] => Array
(
)
)
[97] => Category Object
(
[languages:protected] =>
[bok_resources:protected] =>
[bok_topics:protected] =>
[bok_keywords:protected] =>
[id:protected] => 97
[type:protected] => category
[parent:protected] => 5
[label:protected] => Images
[alreadyInSave:protected] =>
[alreadyInValidation:protected] =>
[validationFailures:protected] => Array
(
)
[_new:BaseObject:private] =>
[_deleted:BaseObject:private] =>
[modifiedColumns:protected] => Array
(
)
)
)
[categories_initialized:protected] => 1
[mapped_items:protected] =>
[content:protected] =>
[files:protected] =>
[language:protected] => Language Object
(
[id:protected] => 1
[code:protected] => en
[name:protected] => English
[alreadyInSave:protected] =>
[alreadyInValidation:protected] =>
[validationFailures:protected] => Array
(
)
[_new:BaseObject:private] =>
[_deleted:BaseObject:private] =>
[modifiedColumns:protected] => Array
(
)
)
[old_record:protected] =>
[id:protected] => 3995
[old_id:protected] =>
[elcosh_id:protected] => i002690
[type:protected] => image
[display_type:protected] => Image
[user_id:protected] => 0
[language_id:protected] => 1
[tagging_id:protected] => Bruce Lippy
[priority_id:protected] => 1
[title:protected] => Construction bracing
[total_pages:protected] => 0
[billed_pages:protected] => 0
[publication_number:protected] =>
[part_of:protected] =>
[keywords:protected] => Bracing, support, scaffold
[comments:protected] =>
[summary:protected] => This shows structural support that prevents collapses during construction.
[transition_comments:protected] =>
[external_link:protected] =>
[consol_link:protected] => http://www.cpwrconstructionsolutions.org/masonry/solution/8/adjustable-tower-scaffold.html
[more_like_this:protected] => i002660
[permission_given_by:protected] =>
[published:protected] => T
[billable:protected] => F
[img_name:protected] =>
[img_ext:protected] => jpg
[img_width:protected] =>
[img_height:protected] =>
[img_credit:protected] => Photo by Pam Susi
[img_practice:protected] => good
[vid_source_id:protected] =>
[vid_running_time:protected] =>
[vid_intended_audience:protected] =>
[vid_acquisition_info:protected] =>
[vid_cost:protected] =>
[vid_producer:protected] =>
[vid_filename:protected] =>
[vid_filename_downloadable:protected] =>
[date_summary:protected] => January 2016
[date_permission_requested:protected] =>
[date_permission_received:protected] =>
[date_review_needed:protected] =>
[date_received:protected] => 02/01/16
[date_completed:protected] => 02/01/16
[date_billed:protected] =>
[date_modified:protected] => 02/01/16
[collBokExports:protected] =>
[lastBokExportCriteria:BaseElcoshItem:private] =>
[alreadyInSave:protected] =>
[alreadyInValidation:protected] =>
[validationFailures:protected] => Array
(
)
[_new:BaseObject:private] =>
[_deleted:BaseObject:private] =>
[modifiedColumns:protected] => Array
(
)
)
)
)
[preview_mode] =>
[description] => Toolbox talks have been the main tool for communicating safety information on construction jobs for decades.
Unfortunately, there has been little research on what makes for effective toolbox talks. The IUOE National
Training Fund worked with OSHA and NIOSH to make sure their series of 24 Focus Four toolbox talks were based on the best recommendations for effective design. These toolbox talks accompany an entire package of training materials, but can be used alone. This guide points out the key features of these toolbox talks and how best to deliver them.
[keywords] => toolbox talks, tailgate talks
[related_items] => Array
(
[Toolbox Talks] => Array
(
[0] => DocumentRecord Object
(
[records:protected] => Array
(
)
[recordId:protected] =>
[searchWordClass:protected] =>
[searchWordPeerClass:protected] =>
[bok_record:protected] =>
[authors:protected] =>
[organizations:protected] =>
[collections:protected] =>
[categories:protected] =>
[categories_initialized:protected] =>
[mapped_items:protected] =>
[content:protected] =>
[files:protected] =>
[language:protected] => Language Object
(
[id:protected] => 1
[code:protected] => en
[name:protected] => English
[alreadyInSave:protected] =>
[alreadyInValidation:protected] =>
[validationFailures:protected] => Array
(
)
[_new:BaseObject:private] =>
[_deleted:BaseObject:private] =>
[modifiedColumns:protected] => Array
(
)
)
[old_record:protected] =>
[id:protected] => 1605
[old_id:protected] => 1262
[elcosh_id:protected] => d001137
[type:protected] => document
[display_type:protected] => HTML w/ PDF
[user_id:protected] =>
[language_id:protected] => 1
[tagging_id:protected] => Garber
[priority_id:protected] => 1
[title:protected] => Focus Four Toolbox Talks, Module 1 – Falls, Talk #2 – Falls from debris piles?
[total_pages:protected] => 1
[billed_pages:protected] => 1
[publication_number:protected] =>
[part_of:protected] =>
[keywords:protected] => disaster response, hazard clean-up, uneven surface, disaster site, disaster clean-up
[comments:protected] =>
[summary:protected] => A toolbox talk on preventing falls from debris piles. Includes questions to ask, an incident to discuss with images, and a place to record questions the trainer would like to ask about the incident. Part of a collection. Click on the 'collection' button to access the other items.
[transition_comments:protected] =>
[external_link:protected] =>
[consol_link:protected] => http://www.cpwrconstructionsolutions.org/roofing/hazard/1463/install-asphalt-roofs-fall-from-heights.html
[more_like_this:protected] => a000081,d000478,d000530
[permission_given_by:protected] =>
[published:protected] => T
[billable:protected] => F
[img_name:protected] =>
[img_ext:protected] =>
[img_width:protected] =>
[img_height:protected] =>
[img_credit:protected] =>
[img_practice:protected] =>
[vid_source_id:protected] =>
[vid_running_time:protected] =>
[vid_intended_audience:protected] =>
[vid_acquisition_info:protected] =>
[vid_cost:protected] =>
[vid_producer:protected] =>
[vid_filename:protected] =>
[vid_filename_downloadable:protected] =>
[date_summary:protected] =>
[date_permission_requested:protected] =>
[date_permission_received:protected] =>
[date_review_needed:protected] =>
[date_received:protected] => 02/15/12
[date_completed:protected] => 03/19/12
[date_billed:protected] =>
[date_modified:protected] => 07/10/12
[collBokExports:protected] =>
[lastBokExportCriteria:BaseElcoshItem:private] =>
[alreadyInSave:protected] =>
[alreadyInValidation:protected] =>
[validationFailures:protected] => Array
(
)
[_new:BaseObject:private] =>
[_deleted:BaseObject:private] =>
[modifiedColumns:protected] => Array
(
)
)
[1] => DocumentRecord Object
(
[records:protected] => Array
(
)
[recordId:protected] =>
[searchWordClass:protected] =>
[searchWordPeerClass:protected] =>
[bok_record:protected] =>
[authors:protected] =>
[organizations:protected] =>
[collections:protected] =>
[categories:protected] =>
[categories_initialized:protected] =>
[mapped_items:protected] =>
[content:protected] =>
[files:protected] =>
[language:protected] => Language Object
(
[id:protected] => 1
[code:protected] => en
[name:protected] => English
[alreadyInSave:protected] =>
[alreadyInValidation:protected] =>
[validationFailures:protected] => Array
(
)
[_new:BaseObject:private] =>
[_deleted:BaseObject:private] =>
[modifiedColumns:protected] => Array
(
)
)
[old_record:protected] =>
[id:protected] => 1610
[old_id:protected] => 1271
[elcosh_id:protected] => d001146
[type:protected] => document
[display_type:protected] => HTML w/ PDF
[user_id:protected] => 0
[language_id:protected] => 1
[tagging_id:protected] => Garber
[priority_id:protected] => 1
[title:protected] => Focus Four Toolbox Talks, Module 2 – Struck-by, Talk #5 – Rigging and Securing Loads
[total_pages:protected] => 1
[billed_pages:protected] => 1
[publication_number:protected] =>
[part_of:protected] =>
[keywords:protected] => rigging, lift loads, loading areas, chains
[comments:protected] =>
[summary:protected] => A toolbox talk on preventing struck-by incidents caused by not securing loads properly. Includes questions to ask, an incident to discuss with images, and a place to record questions the trainer would like to ask about the incident. Part of a collection. Click on the 'collection' button to access the other items.
[transition_comments:protected] =>
[external_link:protected] =>
[consol_link:protected] => http://www.cpwrconstructionsolutions.org/heavy_equipment/hazard/1591/move-equipment-to-from-and-between-sites-work-zone-struck-by-injuries-and-fatalities.html
[more_like_this:protected] => d000144,d000360,d000873
[permission_given_by:protected] =>
[published:protected] => T
[billable:protected] => F
[img_name:protected] =>
[img_ext:protected] =>
[img_width:protected] =>
[img_height:protected] =>
[img_credit:protected] =>
[img_practice:protected] =>
[vid_source_id:protected] =>
[vid_running_time:protected] =>
[vid_intended_audience:protected] =>
[vid_acquisition_info:protected] =>
[vid_cost:protected] =>
[vid_producer:protected] =>
[vid_filename:protected] =>
[vid_filename_downloadable:protected] =>
[date_summary:protected] =>
[date_permission_requested:protected] =>
[date_permission_received:protected] =>
[date_review_needed:protected] =>
[date_received:protected] => 02/15/12
[date_completed:protected] => 03/28/12
[date_billed:protected] =>
[date_modified:protected] => 05/12/14
[collBokExports:protected] =>
[lastBokExportCriteria:BaseElcoshItem:private] =>
[alreadyInSave:protected] =>
[alreadyInValidation:protected] =>
[validationFailures:protected] => Array
(
)
[_new:BaseObject:private] =>
[_deleted:BaseObject:private] =>
[modifiedColumns:protected] => Array
(
)
)
[2] => DocumentRecord Object
(
[records:protected] => Array
(
)
[recordId:protected] =>
[searchWordClass:protected] =>
[searchWordPeerClass:protected] =>
[bok_record:protected] =>
[authors:protected] =>
[organizations:protected] =>
[collections:protected] =>
[categories:protected] =>
[categories_initialized:protected] =>
[mapped_items:protected] =>
[content:protected] =>
[files:protected] =>
[language:protected] => Language Object
(
[id:protected] => 1
[code:protected] => en
[name:protected] => English
[alreadyInSave:protected] =>
[alreadyInValidation:protected] =>
[validationFailures:protected] => Array
(
)
[_new:BaseObject:private] =>
[_deleted:BaseObject:private] =>
[modifiedColumns:protected] => Array
(
)
)
[old_record:protected] =>
[id:protected] => 1645
[old_id:protected] => 1274
[elcosh_id:protected] => d001149
[type:protected] => document
[display_type:protected] => HTML w/ PDF
[user_id:protected] => 0
[language_id:protected] => 1
[tagging_id:protected] => Garber
[priority_id:protected] => 1
[title:protected] => Focus Four Toolbox Talks, Module 3 – Caught-in/between, Talk #2 – Trenches & Heavy Equipment
[total_pages:protected] => 1
[billed_pages:protected] => 1
[publication_number:protected] =>
[part_of:protected] =>
[keywords:protected] => back-up alarms, spotter, soil cave-in, spoil pikes, ROPs, trenching, rain
[comments:protected] =>
[summary:protected] => A toolbox talk on preventing incidents involving trenches such as trench collapse. Includes questions to ask, an incident to discuss with images, and a place to record questions the trainer would like to ask about the incident. Part of a collection. Click on the 'collection' button to access the other items.
[transition_comments:protected] =>
[external_link:protected] =>
[consol_link:protected] =>
[more_like_this:protected] => d000019,d000035,d000168
[permission_given_by:protected] =>
[published:protected] => T
[billable:protected] => F
[img_name:protected] =>
[img_ext:protected] =>
[img_width:protected] =>
[img_height:protected] =>
[img_credit:protected] =>
[img_practice:protected] =>
[vid_source_id:protected] =>
[vid_running_time:protected] =>
[vid_intended_audience:protected] =>
[vid_acquisition_info:protected] =>
[vid_cost:protected] =>
[vid_producer:protected] =>
[vid_filename:protected] =>
[vid_filename_downloadable:protected] =>
[date_summary:protected] =>
[date_permission_requested:protected] =>
[date_permission_received:protected] =>
[date_review_needed:protected] =>
[date_received:protected] => 02/15/12
[date_completed:protected] => 04/02/12
[date_billed:protected] =>
[date_modified:protected] => 05/23/23
[collBokExports:protected] =>
[lastBokExportCriteria:BaseElcoshItem:private] =>
[alreadyInSave:protected] =>
[alreadyInValidation:protected] =>
[validationFailures:protected] => Array
(
)
[_new:BaseObject:private] =>
[_deleted:BaseObject:private] =>
[modifiedColumns:protected] => Array
(
)
)
[3] => DocumentRecord Object
(
[records:protected] => Array
(
)
[recordId:protected] =>
[searchWordClass:protected] =>
[searchWordPeerClass:protected] =>
[bok_record:protected] =>
[authors:protected] =>
[organizations:protected] =>
[collections:protected] =>
[categories:protected] =>
[categories_initialized:protected] =>
[mapped_items:protected] =>
[content:protected] =>
[files:protected] =>
[language:protected] => Language Object
(
[id:protected] => 1
[code:protected] => en
[name:protected] => English
[alreadyInSave:protected] =>
[alreadyInValidation:protected] =>
[validationFailures:protected] => Array
(
)
[_new:BaseObject:private] =>
[_deleted:BaseObject:private] =>
[modifiedColumns:protected] => Array
(
)
)
[old_record:protected] =>
[id:protected] => 1654
[old_id:protected] => 1284
[elcosh_id:protected] => d001159
[type:protected] => document
[display_type:protected] => HTML w/ PDF
[user_id:protected] => 0
[language_id:protected] => 1
[tagging_id:protected] => Garber
[priority_id:protected] => 1
[title:protected] => Focus Four Toolbox Talks, Module 4 – Electrocutions, Talk #6 – Hazards on Disaster Sites
[total_pages:protected] => 1
[billed_pages:protected] => 1
[publication_number:protected] =>
[part_of:protected] =>
[keywords:protected] => powerlines, underground, utilities, generators, wet conditions, GFCIs, energized lines, disasters, emergency response
[comments:protected] =>
[summary:protected] => A toolbox talk on how to avoid electrocution on a disaster site. Includes questions to ask, an incident to discuss with images, and a place to record questions the trainer would like to ask about the incident. Part of a collection. Click on the 'collection' button to access the other items.
[transition_comments:protected] =>
[external_link:protected] =>
[consol_link:protected] => http://www.cpwrconstructionsolutions.org/electrical/hazard/1138/install-and-repair-high-voltage-lines-transformers-switches-electrical-shocks-burns-and-or-electrocution.html
[more_like_this:protected] => d000135,d000361,d000437
[permission_given_by:protected] =>
[published:protected] => T
[billable:protected] => F
[img_name:protected] =>
[img_ext:protected] =>
[img_width:protected] =>
[img_height:protected] =>
[img_credit:protected] =>
[img_practice:protected] =>
[vid_source_id:protected] =>
[vid_running_time:protected] =>
[vid_intended_audience:protected] =>
[vid_acquisition_info:protected] =>
[vid_cost:protected] =>
[vid_producer:protected] =>
[vid_filename:protected] =>
[vid_filename_downloadable:protected] =>
[date_summary:protected] =>
[date_permission_requested:protected] =>
[date_permission_received:protected] =>
[date_review_needed:protected] =>
[date_received:protected] => 02/15/12
[date_completed:protected] => 04/02/12
[date_billed:protected] =>
[date_modified:protected] => 05/23/23
[collBokExports:protected] =>
[lastBokExportCriteria:BaseElcoshItem:private] =>
[alreadyInSave:protected] =>
[alreadyInValidation:protected] =>
[validationFailures:protected] => Array
(
)
[_new:BaseObject:private] =>
[_deleted:BaseObject:private] =>
[modifiedColumns:protected] => Array
(
)
)
)
)
[collections] => Array
(
[1294] =>
[1295] =>
[1292] =>
[1293] => CollectionRecord Object
(
[collection_items:protected] =>
[records:protected] => Array
(
)
[recordId:protected] =>
[searchWordClass:protected] =>
[searchWordPeerClass:protected] =>
[bok_record:protected] =>
[authors:protected] =>
[organizations:protected] =>
[collections:protected] =>
[categories:protected] =>
[categories_initialized:protected] =>
[mapped_items:protected] =>
[content:protected] =>
[files:protected] =>
[language:protected] =>
[old_record:protected] =>
[id:protected] => 1293
[old_id:protected] =>
[elcosh_id:protected] => c000026
[type:protected] => collection
[display_type:protected] => Collection
[user_id:protected] =>
[language_id:protected] =>
[tagging_id:protected] =>
[priority_id:protected] =>
[title:protected] => Focus Four-Struck By
[total_pages:protected] =>
[billed_pages:protected] =>
[publication_number:protected] =>
[part_of:protected] =>
[keywords:protected] =>
[comments:protected] =>
[summary:protected] => The following are links to all of the items in this collection:
[transition_comments:protected] =>
[external_link:protected] =>
[consol_link:protected] =>
[more_like_this:protected] =>
[permission_given_by:protected] =>
[published:protected] => T
[billable:protected] => F
[img_name:protected] =>
[img_ext:protected] =>
[img_width:protected] =>
[img_height:protected] =>
[img_credit:protected] =>
[img_practice:protected] =>
[vid_source_id:protected] =>
[vid_running_time:protected] =>
[vid_intended_audience:protected] =>
[vid_acquisition_info:protected] =>
[vid_cost:protected] =>
[vid_producer:protected] =>
[vid_filename:protected] =>
[vid_filename_downloadable:protected] =>
[date_summary:protected] =>
[date_permission_requested:protected] =>
[date_permission_received:protected] =>
[date_review_needed:protected] =>
[date_received:protected] => 05/08/12
[date_completed:protected] => 05/08/12
[date_billed:protected] =>
[date_modified:protected] => 05/08/12
[collBokExports:protected] =>
[lastBokExportCriteria:BaseElcoshItem:private] =>
[alreadyInSave:protected] =>
[alreadyInValidation:protected] =>
[validationFailures:protected] => Array
(
)
[_new:BaseObject:private] =>
[_deleted:BaseObject:private] =>
[modifiedColumns:protected] => Array
(
)
)
)
[record] => DocumentRecord Object
(
[records:protected] => Array
(
)
[recordId:protected] =>
[searchWordClass:protected] =>
[searchWordPeerClass:protected] =>
[bok_record:protected] =>
[authors:protected] => Array
(
)
[organizations:protected] => Array
(
[256] => Organization Object
(
[id:protected] => 256
[elcosh_id:protected] => o000276
[user_id:protected] => 14
[province_id:protected] => 0
[country_id:protected] => 0
[title:protected] => IUOE National Training Fund
[address:protected] =>
[postal_code:protected] =>
[city:protected] =>
[department:protected] =>
[phone:protected] => 304-253-8674
[fax:protected] =>
[email:protected] =>
[website:protected] => http://www.iuoeiettc.org
[filename:protected] =>
[about:protected] =>
[comments:protected] =>
[logo_available:protected] => T
[no_details:protected] => F
[date_received:protected] => 2012-02-13
[date_completed:protected] => 2012-02-13
[date_billed:protected] =>
[alreadyInSave:protected] =>
[alreadyInValidation:protected] =>
[validationFailures:protected] => Array
(
)
[_new:BaseObject:private] =>
[_deleted:BaseObject:private] =>
[modifiedColumns:protected] => Array
(
)
)
)
[collections:protected] => Array
(
[1294] =>
[1295] =>
[1292] =>
[1293] => CollectionRecord Object
(
[collection_items:protected] =>
[records:protected] => Array
(
)
[recordId:protected] =>
[searchWordClass:protected] =>
[searchWordPeerClass:protected] =>
[bok_record:protected] =>
[authors:protected] =>
[organizations:protected] =>
[collections:protected] =>
[categories:protected] =>
[categories_initialized:protected] =>
[mapped_items:protected] =>
[content:protected] =>
[files:protected] =>
[language:protected] =>
[old_record:protected] =>
[id:protected] => 1293
[old_id:protected] =>
[elcosh_id:protected] => c000026
[type:protected] => collection
[display_type:protected] => Collection
[user_id:protected] =>
[language_id:protected] =>
[tagging_id:protected] =>
[priority_id:protected] =>
[title:protected] => Focus Four-Struck By
[total_pages:protected] =>
[billed_pages:protected] =>
[publication_number:protected] =>
[part_of:protected] =>
[keywords:protected] =>
[comments:protected] =>
[summary:protected] => The following are links to all of the items in this collection:
[transition_comments:protected] =>
[external_link:protected] =>
[consol_link:protected] =>
[more_like_this:protected] =>
[permission_given_by:protected] =>
[published:protected] => T
[billable:protected] => F
[img_name:protected] =>
[img_ext:protected] =>
[img_width:protected] =>
[img_height:protected] =>
[img_credit:protected] =>
[img_practice:protected] =>
[vid_source_id:protected] =>
[vid_running_time:protected] =>
[vid_intended_audience:protected] =>
[vid_acquisition_info:protected] =>
[vid_cost:protected] =>
[vid_producer:protected] =>
[vid_filename:protected] =>
[vid_filename_downloadable:protected] =>
[date_summary:protected] =>
[date_permission_requested:protected] =>
[date_permission_received:protected] =>
[date_review_needed:protected] =>
[date_received:protected] => 05/08/12
[date_completed:protected] => 05/08/12
[date_billed:protected] =>
[date_modified:protected] => 05/08/12
[collBokExports:protected] =>
[lastBokExportCriteria:BaseElcoshItem:private] =>
[alreadyInSave:protected] =>
[alreadyInValidation:protected] =>
[validationFailures:protected] => Array
(
)
[_new:BaseObject:private] =>
[_deleted:BaseObject:private] =>
[modifiedColumns:protected] => Array
(
)
)
)
[categories:protected] =>
[categories_initialized:protected] =>
[mapped_items:protected] => Array
(
[1605] => DocumentRecord Object
(
[records:protected] => Array
(
)
[recordId:protected] =>
[searchWordClass:protected] =>
[searchWordPeerClass:protected] =>
[bok_record:protected] =>
[authors:protected] =>
[organizations:protected] =>
[collections:protected] =>
[categories:protected] =>
[categories_initialized:protected] =>
[mapped_items:protected] =>
[content:protected] =>
[files:protected] =>
[language:protected] =>
[old_record:protected] =>
[id:protected] => 1605
[old_id:protected] => 1262
[elcosh_id:protected] => d001137
[type:protected] => document
[display_type:protected] => HTML w/ PDF
[user_id:protected] =>
[language_id:protected] => 1
[tagging_id:protected] => Garber
[priority_id:protected] => 1
[title:protected] => Focus Four Toolbox Talks, Module 1 – Falls, Talk #2 – Falls from debris piles?
[total_pages:protected] => 1
[billed_pages:protected] => 1
[publication_number:protected] =>
[part_of:protected] =>
[keywords:protected] => disaster response, hazard clean-up, uneven surface, disaster site, disaster clean-up
[comments:protected] =>
[summary:protected] => A toolbox talk on preventing falls from debris piles. Includes questions to ask, an incident to discuss with images, and a place to record questions the trainer would like to ask about the incident. Part of a collection. Click on the 'collection' button to access the other items.
[transition_comments:protected] =>
[external_link:protected] =>
[consol_link:protected] => http://www.cpwrconstructionsolutions.org/roofing/hazard/1463/install-asphalt-roofs-fall-from-heights.html
[more_like_this:protected] => a000081,d000478,d000530
[permission_given_by:protected] =>
[published:protected] => T
[billable:protected] => F
[img_name:protected] =>
[img_ext:protected] =>
[img_width:protected] =>
[img_height:protected] =>
[img_credit:protected] =>
[img_practice:protected] =>
[vid_source_id:protected] =>
[vid_running_time:protected] =>
[vid_intended_audience:protected] =>
[vid_acquisition_info:protected] =>
[vid_cost:protected] =>
[vid_producer:protected] =>
[vid_filename:protected] =>
[vid_filename_downloadable:protected] =>
[date_summary:protected] =>
[date_permission_requested:protected] =>
[date_permission_received:protected] =>
[date_review_needed:protected] =>
[date_received:protected] => 02/15/12
[date_completed:protected] => 03/19/12
[date_billed:protected] =>
[date_modified:protected] => 07/10/12
[collBokExports:protected] =>
[lastBokExportCriteria:BaseElcoshItem:private] =>
[alreadyInSave:protected] =>
[alreadyInValidation:protected] =>
[validationFailures:protected] => Array
(
)
[_new:BaseObject:private] =>
[_deleted:BaseObject:private] =>
[modifiedColumns:protected] => Array
(
)
)
[1610] => DocumentRecord Object
(
[records:protected] => Array
(
)
[recordId:protected] =>
[searchWordClass:protected] =>
[searchWordPeerClass:protected] =>
[bok_record:protected] =>
[authors:protected] =>
[organizations:protected] =>
[collections:protected] =>
[categories:protected] =>
[categories_initialized:protected] =>
[mapped_items:protected] =>
[content:protected] =>
[files:protected] =>
[language:protected] =>
[old_record:protected] =>
[id:protected] => 1610
[old_id:protected] => 1271
[elcosh_id:protected] => d001146
[type:protected] => document
[display_type:protected] => HTML w/ PDF
[user_id:protected] => 0
[language_id:protected] => 1
[tagging_id:protected] => Garber
[priority_id:protected] => 1
[title:protected] => Focus Four Toolbox Talks, Module 2 – Struck-by, Talk #5 – Rigging and Securing Loads
[total_pages:protected] => 1
[billed_pages:protected] => 1
[publication_number:protected] =>
[part_of:protected] =>
[keywords:protected] => rigging, lift loads, loading areas, chains
[comments:protected] =>
[summary:protected] => A toolbox talk on preventing struck-by incidents caused by not securing loads properly. Includes questions to ask, an incident to discuss with images, and a place to record questions the trainer would like to ask about the incident. Part of a collection. Click on the 'collection' button to access the other items.
[transition_comments:protected] =>
[external_link:protected] =>
[consol_link:protected] => http://www.cpwrconstructionsolutions.org/heavy_equipment/hazard/1591/move-equipment-to-from-and-between-sites-work-zone-struck-by-injuries-and-fatalities.html
[more_like_this:protected] => d000144,d000360,d000873
[permission_given_by:protected] =>
[published:protected] => T
[billable:protected] => F
[img_name:protected] =>
[img_ext:protected] =>
[img_width:protected] =>
[img_height:protected] =>
[img_credit:protected] =>
[img_practice:protected] =>
[vid_source_id:protected] =>
[vid_running_time:protected] =>
[vid_intended_audience:protected] =>
[vid_acquisition_info:protected] =>
[vid_cost:protected] =>
[vid_producer:protected] =>
[vid_filename:protected] =>
[vid_filename_downloadable:protected] =>
[date_summary:protected] =>
[date_permission_requested:protected] =>
[date_permission_received:protected] =>
[date_review_needed:protected] =>
[date_received:protected] => 02/15/12
[date_completed:protected] => 03/28/12
[date_billed:protected] =>
[date_modified:protected] => 05/12/14
[collBokExports:protected] =>
[lastBokExportCriteria:BaseElcoshItem:private] =>
[alreadyInSave:protected] =>
[alreadyInValidation:protected] =>
[validationFailures:protected] => Array
(
)
[_new:BaseObject:private] =>
[_deleted:BaseObject:private] =>
[modifiedColumns:protected] => Array
(
)
)
[1645] => DocumentRecord Object
(
[records:protected] => Array
(
)
[recordId:protected] =>
[searchWordClass:protected] =>
[searchWordPeerClass:protected] =>
[bok_record:protected] =>
[authors:protected] =>
[organizations:protected] =>
[collections:protected] =>
[categories:protected] =>
[categories_initialized:protected] =>
[mapped_items:protected] =>
[content:protected] =>
[files:protected] =>
[language:protected] =>
[old_record:protected] =>
[id:protected] => 1645
[old_id:protected] => 1274
[elcosh_id:protected] => d001149
[type:protected] => document
[display_type:protected] => HTML w/ PDF
[user_id:protected] => 0
[language_id:protected] => 1
[tagging_id:protected] => Garber
[priority_id:protected] => 1
[title:protected] => Focus Four Toolbox Talks, Module 3 – Caught-in/between, Talk #2 – Trenches & Heavy Equipment
[total_pages:protected] => 1
[billed_pages:protected] => 1
[publication_number:protected] =>
[part_of:protected] =>
[keywords:protected] => back-up alarms, spotter, soil cave-in, spoil pikes, ROPs, trenching, rain
[comments:protected] =>
[summary:protected] => A toolbox talk on preventing incidents involving trenches such as trench collapse. Includes questions to ask, an incident to discuss with images, and a place to record questions the trainer would like to ask about the incident. Part of a collection. Click on the 'collection' button to access the other items.
[transition_comments:protected] =>
[external_link:protected] =>
[consol_link:protected] =>
[more_like_this:protected] => d000019,d000035,d000168
[permission_given_by:protected] =>
[published:protected] => T
[billable:protected] => F
[img_name:protected] =>
[img_ext:protected] =>
[img_width:protected] =>
[img_height:protected] =>
[img_credit:protected] =>
[img_practice:protected] =>
[vid_source_id:protected] =>
[vid_running_time:protected] =>
[vid_intended_audience:protected] =>
[vid_acquisition_info:protected] =>
[vid_cost:protected] =>
[vid_producer:protected] =>
[vid_filename:protected] =>
[vid_filename_downloadable:protected] =>
[date_summary:protected] =>
[date_permission_requested:protected] =>
[date_permission_received:protected] =>
[date_review_needed:protected] =>
[date_received:protected] => 02/15/12
[date_completed:protected] => 04/02/12
[date_billed:protected] =>
[date_modified:protected] => 05/23/23
[collBokExports:protected] =>
[lastBokExportCriteria:BaseElcoshItem:private] =>
[alreadyInSave:protected] =>
[alreadyInValidation:protected] =>
[validationFailures:protected] => Array
(
)
[_new:BaseObject:private] =>
[_deleted:BaseObject:private] =>
[modifiedColumns:protected] => Array
(
)
)
[1654] => DocumentRecord Object
(
[records:protected] => Array
(
)
[recordId:protected] =>
[searchWordClass:protected] =>
[searchWordPeerClass:protected] =>
[bok_record:protected] =>
[authors:protected] =>
[organizations:protected] =>
[collections:protected] =>
[categories:protected] =>
[categories_initialized:protected] =>
[mapped_items:protected] =>
[content:protected] =>
[files:protected] =>
[language:protected] =>
[old_record:protected] =>
[id:protected] => 1654
[old_id:protected] => 1284
[elcosh_id:protected] => d001159
[type:protected] => document
[display_type:protected] => HTML w/ PDF
[user_id:protected] => 0
[language_id:protected] => 1
[tagging_id:protected] => Garber
[priority_id:protected] => 1
[title:protected] => Focus Four Toolbox Talks, Module 4 – Electrocutions, Talk #6 – Hazards on Disaster Sites
[total_pages:protected] => 1
[billed_pages:protected] => 1
[publication_number:protected] =>
[part_of:protected] =>
[keywords:protected] => powerlines, underground, utilities, generators, wet conditions, GFCIs, energized lines, disasters, emergency response
[comments:protected] =>
[summary:protected] => A toolbox talk on how to avoid electrocution on a disaster site. Includes questions to ask, an incident to discuss with images, and a place to record questions the trainer would like to ask about the incident. Part of a collection. Click on the 'collection' button to access the other items.
[transition_comments:protected] =>
[external_link:protected] =>
[consol_link:protected] => http://www.cpwrconstructionsolutions.org/electrical/hazard/1138/install-and-repair-high-voltage-lines-transformers-switches-electrical-shocks-burns-and-or-electrocution.html
[more_like_this:protected] => d000135,d000361,d000437
[permission_given_by:protected] =>
[published:protected] => T
[billable:protected] => F
[img_name:protected] =>
[img_ext:protected] =>
[img_width:protected] =>
[img_height:protected] =>
[img_credit:protected] =>
[img_practice:protected] =>
[vid_source_id:protected] =>
[vid_running_time:protected] =>
[vid_intended_audience:protected] =>
[vid_acquisition_info:protected] =>
[vid_cost:protected] =>
[vid_producer:protected] =>
[vid_filename:protected] =>
[vid_filename_downloadable:protected] =>
[date_summary:protected] =>
[date_permission_requested:protected] =>
[date_permission_received:protected] =>
[date_review_needed:protected] =>
[date_received:protected] => 02/15/12
[date_completed:protected] => 04/02/12
[date_billed:protected] =>
[date_modified:protected] => 05/23/23
[collBokExports:protected] =>
[lastBokExportCriteria:BaseElcoshItem:private] =>
[alreadyInSave:protected] =>
[alreadyInValidation:protected] =>
[validationFailures:protected] => Array
(
)
[_new:BaseObject:private] =>
[_deleted:BaseObject:private] =>
[modifiedColumns:protected] => Array
(
)
)
)
[content:protected] =>
[files:protected] => Array
(
[9400] => File Object
(
[id:protected] => 9400
[filename:protected] => 1.jpg
[downloadable:protected] => F
[timestamp:protected] => 2014-05-08 15:05:37
[alreadyInSave:protected] =>
[alreadyInValidation:protected] =>
[validationFailures:protected] => Array
(
)
[_new:BaseObject:private] =>
[_deleted:BaseObject:private] =>
[modifiedColumns:protected] => Array
(
)
)
[9401] => File Object
(
[id:protected] => 9401
[filename:protected] => d001298.pdf
[downloadable:protected] => T
[timestamp:protected] => 2014-05-08 15:05:37
[alreadyInSave:protected] =>
[alreadyInValidation:protected] =>
[validationFailures:protected] => Array
(
)
[_new:BaseObject:private] =>
[_deleted:BaseObject:private] =>
[modifiedColumns:protected] => Array
(
)
)
)
[language:protected] => Language Object
(
[id:protected] => 1
[code:protected] => en
[name:protected] => English
[alreadyInSave:protected] =>
[alreadyInValidation:protected] =>
[validationFailures:protected] => Array
(
)
[_new:BaseObject:private] =>
[_deleted:BaseObject:private] =>
[modifiedColumns:protected] => Array
(
)
)
[old_record:protected] =>
[id:protected] => 3827
[old_id:protected] =>
[elcosh_id:protected] => d001298
[type:protected] => document
[display_type:protected] => HTML w/ PDF
[user_id:protected] => 23
[language_id:protected] => 1
[tagging_id:protected] => Bruce Lippy
[priority_id:protected] => 1
[title:protected] => Getting the most out of the IUOE Toolbox Talks
[total_pages:protected] => 2
[billed_pages:protected] => 2
[publication_number:protected] =>
[part_of:protected] =>
[keywords:protected] => toolbox talks, tailgate talks
[comments:protected] =>
[summary:protected] => Toolbox talks have been the main tool for communicating safety information on construction jobs for decades.
Unfortunately, there has been little research on what makes for effective toolbox talks. The IUOE National
Training Fund worked with OSHA and NIOSH to make sure their series of 24 Focus Four toolbox talks were based on the best recommendations for effective design. These toolbox talks accompany an entire package of training materials, but can be used alone. This guide points out the key features of these toolbox talks and how best to deliver them.
[transition_comments:protected] =>
[external_link:protected] =>
[consol_link:protected] =>
[more_like_this:protected] => d001137,d001146,d001149,d001159
[permission_given_by:protected] => IUOE National Hazmat Program
[published:protected] => T
[billable:protected] => F
[img_name:protected] =>
[img_ext:protected] => png
[img_width:protected] =>
[img_height:protected] =>
[img_credit:protected] =>
[img_practice:protected] =>
[vid_source_id:protected] =>
[vid_running_time:protected] =>
[vid_intended_audience:protected] =>
[vid_acquisition_info:protected] =>
[vid_cost:protected] =>
[vid_producer:protected] =>
[vid_filename:protected] =>
[vid_filename_downloadable:protected] =>
[date_summary:protected] => 2007
[date_permission_requested:protected] =>
[date_permission_received:protected] =>
[date_review_needed:protected] =>
[date_received:protected] => 05/08/14
[date_completed:protected] => 05/08/14
[date_billed:protected] =>
[date_modified:protected] => 05/08/14
[collBokExports:protected] =>
[lastBokExportCriteria:BaseElcoshItem:private] =>
[alreadyInSave:protected] =>
[alreadyInValidation:protected] =>
[validationFailures:protected] => Array
(
)
[_new:BaseObject:private] =>
[_deleted:BaseObject:private] =>
[modifiedColumns:protected] => Array
(
)
)
[show_text] =>
[document_content] => ElcoshItemDocumentContent Object
(
[id:protected] => 2896
[item_id:protected] => 3827
[type:protected] => main
[title:protected] =>
[content:protected] =>
Why were these talks developed?
Toolbox talks have been the main tool for communicating safety information on construction jobs for decades. Unfortunately, there has been almost no research on what makes for effective toolbox talks. The IUOE National Training Fund has worked with OSHA, the National Institute for Occupational Safety and Health and the Lippy Group, LLC to make sure these Focus Four toolbox talks are based on the latest fi ndings on the most effective design and tailored to the hazards operating engineers face daily. These toolbox talks accompany an entire package of training materials, but can be used alone. The way these are delivered is as important as how well they are designed.
What did NIOSH find out?
- Just handing out factsheets and toolbox talks to workers doesn’t work. Providing copies after toolbox talks doesn’t make much of an impact either.
- Using case studies (real life stories of accidents that ended in fatality or injury) in toolbox talks is effective.
- When toolbox talks containing case studies were accompanied by discussion questions to encourage group participation, they were more effective. Consequently, getting the workers to participate in the discussion about the case study is important. It’s not enough to tell the story, it is better to have the workers engage in problem solving that analyzes why the accident occurred and how it could have been prevented. Active learning is always better than passive.
How should you deliver these toolbox talks?
- Choose a topic that is related to work going on at the site.
- Hold the meeting on the job, preferably where everyone can sit and relax.
- Hold the meeting at the beginning of a shift or after a break. Folks are too tired at the end of a shift to carefully listen and they want to get home.
- Read the toolbox talk sheet on the topic prior to conducting the talk.
- Start at the top of the form and work right through to the end, which should take around 10 to 15 minutes. Guidance is provided in blue print to help you with each section.
- Use the questions provided to generate discussions. Always allow time for the crew to respond to your questions before you provide an answer. Some suggested responses are written in italics.
- Review the case study and emphasize that this was a real incident. Ask the crew for a case study before you review the one provided, however.
- Always end with a discussion of the particular worksite where you are conducting the talk. Tie the talk as closely to hazards on the site as possible and encourage the crew to constantly look for and immediately correct hazards. They should also know how to report any problems that can’t be immediately corrected.
- Provide copies to each person, if you like, but NIOSH has not found that to be particularly effective.
- Encourage workers to do similar talks on their sites and provide them with the IUOE phone number for ordering in bulk.
- Have everyone sign the back of the form to indicate they attended this session and point out it is a pledge to look out for the health and safety of everyone on the site.
What are the key features of these toolbox talks?

[content_transformed:protected] =>
Why were these talks developed?
Toolbox talks have been the main tool for communicating safety information on construction jobs for decades. Unfortunately, there has been almost no research on what makes for effective toolbox talks. The IUOE National Training Fund has worked with OSHA, the National Institute for Occupational Safety and Health and the Lippy Group, LLC to make sure these Focus Four toolbox talks are based on the latest fi ndings on the most effective design and tailored to the hazards operating engineers face daily. These toolbox talks accompany an entire package of training materials, but can be used alone. The way these are delivered is as important as how well they are designed.
What did NIOSH find out?
- Just handing out factsheets and toolbox talks to workers doesn’t work. Providing copies after toolbox talks doesn’t make much of an impact either.
- Using case studies (real life stories of accidents that ended in fatality or injury) in toolbox talks is effective.
- When toolbox talks containing case studies were accompanied by discussion questions to encourage group participation, they were more effective. Consequently, getting the workers to participate in the discussion about the case study is important. It’s not enough to tell the story, it is better to have the workers engage in problem solving that analyzes why the accident occurred and how it could have been prevented. Active learning is always better than passive.
How should you deliver these toolbox talks?
- Choose a topic that is related to work going on at the site.
- Hold the meeting on the job, preferably where everyone can sit and relax.
- Hold the meeting at the beginning of a shift or after a break. Folks are too tired at the end of a shift to carefully listen and they want to get home.
- Read the toolbox talk sheet on the topic prior to conducting the talk.
- Start at the top of the form and work right through to the end, which should take around 10 to 15 minutes. Guidance is provided in blue print to help you with each section.
- Use the questions provided to generate discussions. Always allow time for the crew to respond to your questions before you provide an answer. Some suggested responses are written in italics.
- Review the case study and emphasize that this was a real incident. Ask the crew for a case study before you review the one provided, however.
- Always end with a discussion of the particular worksite where you are conducting the talk. Tie the talk as closely to hazards on the site as possible and encourage the crew to constantly look for and immediately correct hazards. They should also know how to report any problems that can’t be immediately corrected.
- Provide copies to each person, if you like, but NIOSH has not found that to be particularly effective.
- Encourage workers to do similar talks on their sites and provide them with the IUOE phone number for ordering in bulk.
- Have everyone sign the back of the form to indicate they attended this session and point out it is a pledge to look out for the health and safety of everyone on the site.
What are the key features of these toolbox talks?
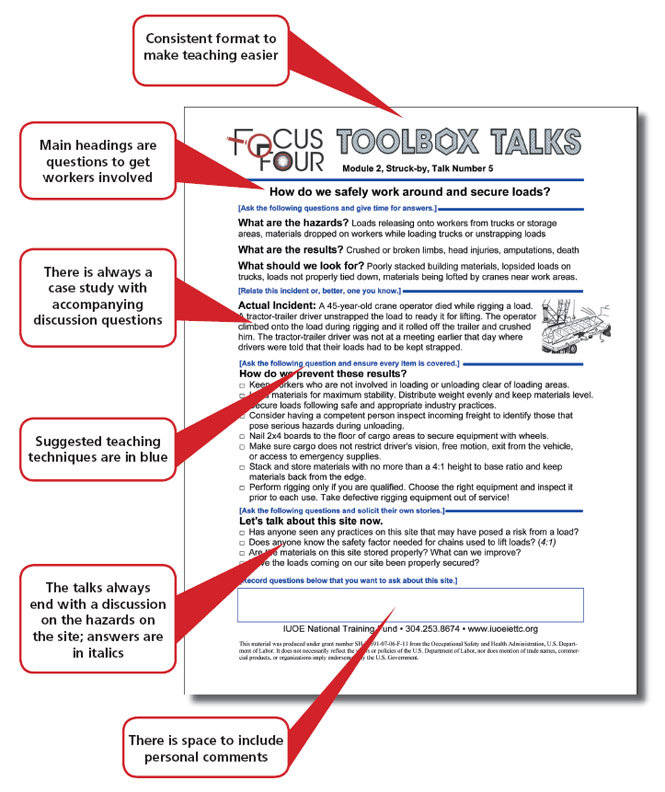
[disclaimer:protected] =>
[disclaimer_transformed:protected] =>
[alreadyInSave:protected] =>
[alreadyInValidation:protected] =>
[validationFailures:protected] => Array
(
)
[_new:BaseObject:private] =>
[_deleted:BaseObject:private] =>
[modifiedColumns:protected] => Array
(
)
)
[template] => record
)
[_globalContext:PHPTAL_Context:private] => stdClass Object
(
)
[_echoDeclarations:PHPTAL_Context:private] =>
[referer] => http://www.elcosh.org/document/3827/d001298/Getting%2Bthe%2Bmost%2Bout%2Bof%2Bthe%2BIUOE%2BToolbox%2BTalks.html
[curr_module] => Record
[styles] => Array
(
)
[javascript] => Array
(
[0] => jquery.min.js
)
[metas] => Array
(
[language] => en
[robots] => index, follow
)
[user] =>
[curr_url] => https://www.elcosh.org/index.php?module=Record&id=3827&type=document
[base_url] => https://www.elcosh.org/index.php?module=Record
[title] => eLCOSH : Getting the most out of the IUOE Toolbox Talks
[language] => en
[search_query] =>
[module] => Record
[new_records] => Array
(
[0] => Search_Result Object
(
[title] => Toolbox Talk: Fixed Ladder
[image] => /record/images/notavailable-p.png
[blurb] => The CPWR Toolbox Talk on Fixed Ladders addresses the potential risks associated with using fixed ladders. The resource includes a brief case example,...
[category] => Array
(
[0] => 15
[1] => 47
[2] => 49
[3] => 51
[4] => 53
[5] => 55
[6] => 60
[7] => 64
[8] => 73
[9] => 76
[10] => 78
[11] => 80
[12] => 86
[13] => 87
[14] => 90
[15] => 92
[16] => 93
[17] => 94
[18] => 100
)
[labels] => Array
(
[0] => Falls
[1] => Work Environment
[2] => Hazards
[3] => Bricklayer
[4] => Trades
[5] => Carpenter
[7] => Cement Mason
[9] => Concrete Polisher
[11] => Electrical Worker
[13] => HVAC
[15] => Laborer
[17] => PCC/Restoration
[19] => Plumber/Pipefitter
[21] => Roofer/Waterproofer
[23] => Sheetmetal Worker
[25] => Welder
[27] => Commercial & Institutional
[28] => Jobsites
[29] => Industrial
[31] => LEED/Green Construction
[33] => Renovations
[35] => Residential
[37] => Toolbox Talks
[38] => Documents
[39] => Media & Documents
)
[type] => Toolbox Talks
[sub_category] =>
[url] => /document/4430/d001660/Toolbox%2BTalk%253A%2BFixed%2BLadder.html
[item:protected] => DocumentRecord Object
(
[records:protected] => Array
(
)
[recordId:protected] =>
[searchWordClass:protected] =>
[searchWordPeerClass:protected] =>
[bok_record:protected] =>
[authors:protected] =>
[organizations:protected] =>
[collections:protected] =>
[categories:protected] => Array
(
[15] => Category Object
(
[languages:protected] =>
[bok_resources:protected] =>
[bok_topics:protected] =>
[bok_keywords:protected] =>
[id:protected] => 15
[type:protected] => category
[parent:protected] => 7
[label:protected] => Falls
[alreadyInSave:protected] =>
[alreadyInValidation:protected] =>
[validationFailures:protected] => Array
(
)
[_new:BaseObject:private] =>
[_deleted:BaseObject:private] =>
[modifiedColumns:protected] => Array
(
)
)
[47] => Category Object
(
[languages:protected] =>
[bok_resources:protected] =>
[bok_topics:protected] =>
[bok_keywords:protected] =>
[id:protected] => 47
[type:protected] => category
[parent:protected] => 2
[label:protected] => Bricklayer
[alreadyInSave:protected] =>
[alreadyInValidation:protected] =>
[validationFailures:protected] => Array
(
)
[_new:BaseObject:private] =>
[_deleted:BaseObject:private] =>
[modifiedColumns:protected] => Array
(
)
)
[49] => Category Object
(
[languages:protected] =>
[bok_resources:protected] =>
[bok_topics:protected] =>
[bok_keywords:protected] =>
[id:protected] => 49
[type:protected] => category
[parent:protected] => 2
[label:protected] => Carpenter
[alreadyInSave:protected] =>
[alreadyInValidation:protected] =>
[validationFailures:protected] => Array
(
)
[_new:BaseObject:private] =>
[_deleted:BaseObject:private] =>
[modifiedColumns:protected] => Array
(
)
)
[51] => Category Object
(
[languages:protected] =>
[bok_resources:protected] =>
[bok_topics:protected] =>
[bok_keywords:protected] =>
[id:protected] => 51
[type:protected] => category
[parent:protected] => 2
[label:protected] => Cement Mason
[alreadyInSave:protected] =>
[alreadyInValidation:protected] =>
[validationFailures:protected] => Array
(
)
[_new:BaseObject:private] =>
[_deleted:BaseObject:private] =>
[modifiedColumns:protected] => Array
(
)
)
[53] => Category Object
(
[languages:protected] =>
[bok_resources:protected] =>
[bok_topics:protected] =>
[bok_keywords:protected] =>
[id:protected] => 53
[type:protected] => category
[parent:protected] => 2
[label:protected] => Concrete Polisher
[alreadyInSave:protected] =>
[alreadyInValidation:protected] =>
[validationFailures:protected] => Array
(
)
[_new:BaseObject:private] =>
[_deleted:BaseObject:private] =>
[modifiedColumns:protected] => Array
(
)
)
[55] => Category Object
(
[languages:protected] =>
[bok_resources:protected] =>
[bok_topics:protected] =>
[bok_keywords:protected] =>
[id:protected] => 55
[type:protected] => category
[parent:protected] => 2
[label:protected] => Electrical Worker
[alreadyInSave:protected] =>
[alreadyInValidation:protected] =>
[validationFailures:protected] => Array
(
)
[_new:BaseObject:private] =>
[_deleted:BaseObject:private] =>
[modifiedColumns:protected] => Array
(
)
)
[60] => Category Object
(
[languages:protected] =>
[bok_resources:protected] =>
[bok_topics:protected] =>
[bok_keywords:protected] =>
[id:protected] => 60
[type:protected] => category
[parent:protected] => 2
[label:protected] => HVAC
[alreadyInSave:protected] =>
[alreadyInValidation:protected] =>
[validationFailures:protected] => Array
(
)
[_new:BaseObject:private] =>
[_deleted:BaseObject:private] =>
[modifiedColumns:protected] => Array
(
)
)
[64] => Category Object
(
[languages:protected] =>
[bok_resources:protected] =>
[bok_topics:protected] =>
[bok_keywords:protected] =>
[id:protected] => 64
[type:protected] => category
[parent:protected] => 2
[label:protected] => Laborer
[alreadyInSave:protected] =>
[alreadyInValidation:protected] =>
[validationFailures:protected] => Array
(
)
[_new:BaseObject:private] =>
[_deleted:BaseObject:private] =>
[modifiedColumns:protected] => Array
(
)
)
[73] => Category Object
(
[languages:protected] =>
[bok_resources:protected] =>
[bok_topics:protected] =>
[bok_keywords:protected] =>
[id:protected] => 73
[type:protected] => category
[parent:protected] => 2
[label:protected] => PCC/Restoration
[alreadyInSave:protected] =>
[alreadyInValidation:protected] =>
[validationFailures:protected] => Array
(
)
[_new:BaseObject:private] =>
[_deleted:BaseObject:private] =>
[modifiedColumns:protected] => Array
(
)
)
[76] => Category Object
(
[languages:protected] =>
[bok_resources:protected] =>
[bok_topics:protected] =>
[bok_keywords:protected] =>
[id:protected] => 76
[type:protected] => category
[parent:protected] => 2
[label:protected] => Plumber/Pipefitter
[alreadyInSave:protected] =>
[alreadyInValidation:protected] =>
[validationFailures:protected] => Array
(
)
[_new:BaseObject:private] =>
[_deleted:BaseObject:private] =>
[modifiedColumns:protected] => Array
(
)
)
[78] => Category Object
(
[languages:protected] =>
[bok_resources:protected] =>
[bok_topics:protected] =>
[bok_keywords:protected] =>
[id:protected] => 78
[type:protected] => category
[parent:protected] => 2
[label:protected] => Roofer/Waterproofer
[alreadyInSave:protected] =>
[alreadyInValidation:protected] =>
[validationFailures:protected] => Array
(
)
[_new:BaseObject:private] =>
[_deleted:BaseObject:private] =>
[modifiedColumns:protected] => Array
(
)
)
[80] => Category Object
(
[languages:protected] =>
[bok_resources:protected] =>
[bok_topics:protected] =>
[bok_keywords:protected] =>
[id:protected] => 80
[type:protected] => category
[parent:protected] => 2
[label:protected] => Sheetmetal Worker
[alreadyInSave:protected] =>
[alreadyInValidation:protected] =>
[validationFailures:protected] => Array
(
)
[_new:BaseObject:private] =>
[_deleted:BaseObject:private] =>
[modifiedColumns:protected] => Array
(
)
)
[86] => Category Object
(
[languages:protected] =>
[bok_resources:protected] =>
[bok_topics:protected] =>
[bok_keywords:protected] =>
[id:protected] => 86
[type:protected] => category
[parent:protected] => 2
[label:protected] => Welder
[alreadyInSave:protected] =>
[alreadyInValidation:protected] =>
[validationFailures:protected] => Array
(
)
[_new:BaseObject:private] =>
[_deleted:BaseObject:private] =>
[modifiedColumns:protected] => Array
(
)
)
[87] => Category Object
(
[languages:protected] =>
[bok_resources:protected] =>
[bok_topics:protected] =>
[bok_keywords:protected] =>
[id:protected] => 87
[type:protected] => category
[parent:protected] => 3
[label:protected] => Commercial & Institutional
[alreadyInSave:protected] =>
[alreadyInValidation:protected] =>
[validationFailures:protected] => Array
(
)
[_new:BaseObject:private] =>
[_deleted:BaseObject:private] =>
[modifiedColumns:protected] => Array
(
)
)
[90] => Category Object
(
[languages:protected] =>
[bok_resources:protected] =>
[bok_topics:protected] =>
[bok_keywords:protected] =>
[id:protected] => 90
[type:protected] => category
[parent:protected] => 3
[label:protected] => Industrial
[alreadyInSave:protected] =>
[alreadyInValidation:protected] =>
[validationFailures:protected] => Array
(
)
[_new:BaseObject:private] =>
[_deleted:BaseObject:private] =>
[modifiedColumns:protected] => Array
(
)
)
[92] => Category Object
(
[languages:protected] =>
[bok_resources:protected] =>
[bok_topics:protected] =>
[bok_keywords:protected] =>
[id:protected] => 92
[type:protected] => category
[parent:protected] => 3
[label:protected] => LEED/Green Construction
[alreadyInSave:protected] =>
[alreadyInValidation:protected] =>
[validationFailures:protected] => Array
(
)
[_new:BaseObject:private] =>
[_deleted:BaseObject:private] =>
[modifiedColumns:protected] => Array
(
)
)
[93] => Category Object
(
[languages:protected] =>
[bok_resources:protected] =>
[bok_topics:protected] =>
[bok_keywords:protected] =>
[id:protected] => 93
[type:protected] => category
[parent:protected] => 3
[label:protected] => Renovations
[alreadyInSave:protected] =>
[alreadyInValidation:protected] =>
[validationFailures:protected] => Array
(
)
[_new:BaseObject:private] =>
[_deleted:BaseObject:private] =>
[modifiedColumns:protected] => Array
(
)
)
[94] => Category Object
(
[languages:protected] =>
[bok_resources:protected] =>
[bok_topics:protected] =>
[bok_keywords:protected] =>
[id:protected] => 94
[type:protected] => category
[parent:protected] => 3
[label:protected] => Residential
[alreadyInSave:protected] =>
[alreadyInValidation:protected] =>
[validationFailures:protected] => Array
(
)
[_new:BaseObject:private] =>
[_deleted:BaseObject:private] =>
[modifiedColumns:protected] => Array
(
)
)
[100] => Category Object
(
[languages:protected] =>
[bok_resources:protected] =>
[bok_topics:protected] =>
[bok_keywords:protected] =>
[id:protected] => 100
[type:protected] => category
[parent:protected] => 6
[label:protected] => Toolbox Talks
[alreadyInSave:protected] =>
[alreadyInValidation:protected] =>
[validationFailures:protected] => Array
(
)
[_new:BaseObject:private] =>
[_deleted:BaseObject:private] =>
[modifiedColumns:protected] => Array
(
)
)
)
[categories_initialized:protected] => 1
[mapped_items:protected] =>
[content:protected] =>
[files:protected] =>
[language:protected] => Language Object
(
[id:protected] => 1
[code:protected] => en
[name:protected] => English
[alreadyInSave:protected] =>
[alreadyInValidation:protected] =>
[validationFailures:protected] => Array
(
)
[_new:BaseObject:private] =>
[_deleted:BaseObject:private] =>
[modifiedColumns:protected] => Array
(
)
)
[old_record:protected] =>
[id:protected] => 4430
[old_id:protected] =>
[elcosh_id:protected] => d001660
[type:protected] => document
[display_type:protected] => HTML only (and links)
[user_id:protected] => 0
[language_id:protected] => 1
[tagging_id:protected] => Mike Aguilar
[priority_id:protected] => 1
[title:protected] => Toolbox Talk: Fixed Ladder
[total_pages:protected] => 0
[billed_pages:protected] => 0
[publication_number:protected] =>
[part_of:protected] =>
[keywords:protected] => Fixed Ladders, Fall Prevention, Falls
[comments:protected] =>
[summary:protected] => The CPWR Toolbox Talk on Fixed Ladders addresses the potential risks associated with using fixed ladders. The resource includes a brief case example, steps to prevent a related injury and questions for discussion. It includes an image that illustrates the hazard, which can be posted in a central location as a reminder of steps to work safely.
Available in
English
and
Spanish.
[transition_comments:protected] =>
[external_link:protected] =>
[consol_link:protected] =>
[more_like_this:protected] => d001257,d001254,d001255,d001256,d001258,d001262,d001279
[permission_given_by:protected] =>
[published:protected] => T
[billable:protected] => F
[img_name:protected] =>
[img_ext:protected] =>
[img_width:protected] =>
[img_height:protected] =>
[img_credit:protected] =>
[img_practice:protected] =>
[vid_source_id:protected] =>
[vid_running_time:protected] =>
[vid_intended_audience:protected] =>
[vid_acquisition_info:protected] =>
[vid_cost:protected] =>
[vid_producer:protected] =>
[vid_filename:protected] =>
[vid_filename_downloadable:protected] =>
[date_summary:protected] =>
[date_permission_requested:protected] =>
[date_permission_received:protected] =>
[date_review_needed:protected] =>
[date_received:protected] => 06/10/22
[date_completed:protected] => 06/10/22
[date_billed:protected] =>
[date_modified:protected] => 05/22/23
[collBokExports:protected] =>
[lastBokExportCriteria:BaseElcoshItem:private] =>
[alreadyInSave:protected] =>
[alreadyInValidation:protected] =>
[validationFailures:protected] => Array
(
)
[_new:BaseObject:private] =>
[_deleted:BaseObject:private] =>
[modifiedColumns:protected] => Array
(
)
)
)
[1] => Search_Result Object
(
[title] => Toolbox Talk: Challenges Preventing Falling Objects
[image] => /record/images/notavailable-p.png
[blurb] => The CPWR Toolbox Talk on Challenges Preventing Falling Objects addresses the hazards of being struck by falling objects on the job site. The resource...
[category] => Array
(
[0] => 12
[1] => 47
[2] => 49
[3] => 51
[4] => 55
[5] => 64
[6] => 68
[7] => 71
[8] => 75
[9] => 78
[10] => 79
[11] => 82
[12] => 62
[13] => 86
[14] => 87
[15] => 88
[16] => 89
[17] => 91
[18] => 90
[19] => 92
[20] => 93
[21] => 94
[22] => 95
[23] => 100
)
[labels] => Array
(
[0] => Crushed/Struck By
[1] => Work Environment
[2] => Hazards
[3] => Bricklayer
[4] => Trades
[5] => Carpenter
[7] => Cement Mason
[9] => Electrical Worker
[11] => Laborer
[13] => Maintenance Worker
[15] => Painter
[17] => Plasterer
[19] => Roofer/Waterproofer
[21] => Scaffold Erector
[23] => Stonemason
[25] => Structural Ironworker
[27] => Welder
[29] => Commercial & Institutional
[30] => Jobsites
[31] => Demolition
[33] => Disasters
[35] => Heavy & Highway
[37] => Industrial
[39] => LEED/Green Construction
[41] => Renovations
[43] => Residential
[45] => Underground
[47] => Toolbox Talks
[48] => Documents
[49] => Media & Documents
)
[type] => Toolbox Talks
[sub_category] =>
[url] => /document/4431/d001661/Toolbox%2BTalk%253A%2BChallenges%2BPreventing%2BFalling%2BObjects.html
[item:protected] => DocumentRecord Object
(
[records:protected] => Array
(
)
[recordId:protected] =>
[searchWordClass:protected] =>
[searchWordPeerClass:protected] =>
[bok_record:protected] =>
[authors:protected] =>
[organizations:protected] =>
[collections:protected] =>
[categories:protected] => Array
(
[12] => Category Object
(
[languages:protected] =>
[bok_resources:protected] =>
[bok_topics:protected] =>
[bok_keywords:protected] =>
[id:protected] => 12
[type:protected] => category
[parent:protected] => 7
[label:protected] => Crushed/Struck By
[alreadyInSave:protected] =>
[alreadyInValidation:protected] =>
[validationFailures:protected] => Array
(
)
[_new:BaseObject:private] =>
[_deleted:BaseObject:private] =>
[modifiedColumns:protected] => Array
(
)
)
[47] => Category Object
(
[languages:protected] =>
[bok_resources:protected] =>
[bok_topics:protected] =>
[bok_keywords:protected] =>
[id:protected] => 47
[type:protected] => category
[parent:protected] => 2
[label:protected] => Bricklayer
[alreadyInSave:protected] =>
[alreadyInValidation:protected] =>
[validationFailures:protected] => Array
(
)
[_new:BaseObject:private] =>
[_deleted:BaseObject:private] =>
[modifiedColumns:protected] => Array
(
)
)
[49] => Category Object
(
[languages:protected] =>
[bok_resources:protected] =>
[bok_topics:protected] =>
[bok_keywords:protected] =>
[id:protected] => 49
[type:protected] => category
[parent:protected] => 2
[label:protected] => Carpenter
[alreadyInSave:protected] =>
[alreadyInValidation:protected] =>
[validationFailures:protected] => Array
(
)
[_new:BaseObject:private] =>
[_deleted:BaseObject:private] =>
[modifiedColumns:protected] => Array
(
)
)
[51] => Category Object
(
[languages:protected] =>
[bok_resources:protected] =>
[bok_topics:protected] =>
[bok_keywords:protected] =>
[id:protected] => 51
[type:protected] => category
[parent:protected] => 2
[label:protected] => Cement Mason
[alreadyInSave:protected] =>
[alreadyInValidation:protected] =>
[validationFailures:protected] => Array
(
)
[_new:BaseObject:private] =>
[_deleted:BaseObject:private] =>
[modifiedColumns:protected] => Array
(
)
)
[55] => Category Object
(
[languages:protected] =>
[bok_resources:protected] =>
[bok_topics:protected] =>
[bok_keywords:protected] =>
[id:protected] => 55
[type:protected] => category
[parent:protected] => 2
[label:protected] => Electrical Worker
[alreadyInSave:protected] =>
[alreadyInValidation:protected] =>
[validationFailures:protected] => Array
(
)
[_new:BaseObject:private] =>
[_deleted:BaseObject:private] =>
[modifiedColumns:protected] => Array
(
)
)
[64] => Category Object
(
[languages:protected] =>
[bok_resources:protected] =>
[bok_topics:protected] =>
[bok_keywords:protected] =>
[id:protected] => 64
[type:protected] => category
[parent:protected] => 2
[label:protected] => Laborer
[alreadyInSave:protected] =>
[alreadyInValidation:protected] =>
[validationFailures:protected] => Array
(
)
[_new:BaseObject:private] =>
[_deleted:BaseObject:private] =>
[modifiedColumns:protected] => Array
(
)
)
[68] => Category Object
(
[languages:protected] =>
[bok_resources:protected] =>
[bok_topics:protected] =>
[bok_keywords:protected] =>
[id:protected] => 68
[type:protected] => category
[parent:protected] => 2
[label:protected] => Maintenance Worker
[alreadyInSave:protected] =>
[alreadyInValidation:protected] =>
[validationFailures:protected] => Array
(
)
[_new:BaseObject:private] =>
[_deleted:BaseObject:private] =>
[modifiedColumns:protected] => Array
(
)
)
[71] => Category Object
(
[languages:protected] =>
[bok_resources:protected] =>
[bok_topics:protected] =>
[bok_keywords:protected] =>
[id:protected] => 71
[type:protected] => category
[parent:protected] => 2
[label:protected] => Painter
[alreadyInSave:protected] =>
[alreadyInValidation:protected] =>
[validationFailures:protected] => Array
(
)
[_new:BaseObject:private] =>
[_deleted:BaseObject:private] =>
[modifiedColumns:protected] => Array
(
)
)
[75] => Category Object
(
[languages:protected] =>
[bok_resources:protected] =>
[bok_topics:protected] =>
[bok_keywords:protected] =>
[id:protected] => 75
[type:protected] => category
[parent:protected] => 2
[label:protected] => Plasterer
[alreadyInSave:protected] =>
[alreadyInValidation:protected] =>
[validationFailures:protected] => Array
(
)
[_new:BaseObject:private] =>
[_deleted:BaseObject:private] =>
[modifiedColumns:protected] => Array
(
)
)
[78] => Category Object
(
[languages:protected] =>
[bok_resources:protected] =>
[bok_topics:protected] =>
[bok_keywords:protected] =>
[id:protected] => 78
[type:protected] => category
[parent:protected] => 2
[label:protected] => Roofer/Waterproofer
[alreadyInSave:protected] =>
[alreadyInValidation:protected] =>
[validationFailures:protected] => Array
(
)
[_new:BaseObject:private] =>
[_deleted:BaseObject:private] =>
[modifiedColumns:protected] => Array
(
)
)
[79] => Category Object
(
[languages:protected] =>
[bok_resources:protected] =>
[bok_topics:protected] =>
[bok_keywords:protected] =>
[id:protected] => 79
[type:protected] => category
[parent:protected] => 2
[label:protected] => Scaffold Erector
[alreadyInSave:protected] =>
[alreadyInValidation:protected] =>
[validationFailures:protected] => Array
(
)
[_new:BaseObject:private] =>
[_deleted:BaseObject:private] =>
[modifiedColumns:protected] => Array
(
)
)
[82] => Category Object
(
[languages:protected] =>
[bok_resources:protected] =>
[bok_topics:protected] =>
[bok_keywords:protected] =>
[id:protected] => 82
[type:protected] => category
[parent:protected] => 2
[label:protected] => Stonemason
[alreadyInSave:protected] =>
[alreadyInValidation:protected] =>
[validationFailures:protected] => Array
(
)
[_new:BaseObject:private] =>
[_deleted:BaseObject:private] =>
[modifiedColumns:protected] => Array
(
)
)
[62] => Category Object
(
[languages:protected] =>
[bok_resources:protected] =>
[bok_topics:protected] =>
[bok_keywords:protected] =>
[id:protected] => 62
[type:protected] => category
[parent:protected] => 2
[label:protected] => Structural Ironworker
[alreadyInSave:protected] =>
[alreadyInValidation:protected] =>
[validationFailures:protected] => Array
(
)
[_new:BaseObject:private] =>
[_deleted:BaseObject:private] =>
[modifiedColumns:protected] => Array
(
)
)
[86] => Category Object
(
[languages:protected] =>
[bok_resources:protected] =>
[bok_topics:protected] =>
[bok_keywords:protected] =>
[id:protected] => 86
[type:protected] => category
[parent:protected] => 2
[label:protected] => Welder
[alreadyInSave:protected] =>
[alreadyInValidation:protected] =>
[validationFailures:protected] => Array
(
)
[_new:BaseObject:private] =>
[_deleted:BaseObject:private] =>
[modifiedColumns:protected] => Array
(
)
)
[87] => Category Object
(
[languages:protected] =>
[bok_resources:protected] =>
[bok_topics:protected] =>
[bok_keywords:protected] =>
[id:protected] => 87
[type:protected] => category
[parent:protected] => 3
[label:protected] => Commercial & Institutional
[alreadyInSave:protected] =>
[alreadyInValidation:protected] =>
[validationFailures:protected] => Array
(
)
[_new:BaseObject:private] =>
[_deleted:BaseObject:private] =>
[modifiedColumns:protected] => Array
(
)
)
[88] => Category Object
(
[languages:protected] =>
[bok_resources:protected] =>
[bok_topics:protected] =>
[bok_keywords:protected] =>
[id:protected] => 88
[type:protected] => category
[parent:protected] => 3
[label:protected] => Demolition
[alreadyInSave:protected] =>
[alreadyInValidation:protected] =>
[validationFailures:protected] => Array
(
)
[_new:BaseObject:private] =>
[_deleted:BaseObject:private] =>
[modifiedColumns:protected] => Array
(
)
)
[89] => Category Object
(
[languages:protected] =>
[bok_resources:protected] =>
[bok_topics:protected] =>
[bok_keywords:protected] =>
[id:protected] => 89
[type:protected] => category
[parent:protected] => 3
[label:protected] => Disasters
[alreadyInSave:protected] =>
[alreadyInValidation:protected] =>
[validationFailures:protected] => Array
(
)
[_new:BaseObject:private] =>
[_deleted:BaseObject:private] =>
[modifiedColumns:protected] => Array
(
)
)
[91] => Category Object
(
[languages:protected] =>
[bok_resources:protected] =>
[bok_topics:protected] =>
[bok_keywords:protected] =>
[id:protected] => 91
[type:protected] => category
[parent:protected] => 3
[label:protected] => Heavy & Highway
[alreadyInSave:protected] =>
[alreadyInValidation:protected] =>
[validationFailures:protected] => Array
(
)
[_new:BaseObject:private] =>
[_deleted:BaseObject:private] =>
[modifiedColumns:protected] => Array
(
)
)
[90] => Category Object
(
[languages:protected] =>
[bok_resources:protected] =>
[bok_topics:protected] =>
[bok_keywords:protected] =>
[id:protected] => 90
[type:protected] => category
[parent:protected] => 3
[label:protected] => Industrial
[alreadyInSave:protected] =>
[alreadyInValidation:protected] =>
[validationFailures:protected] => Array
(
)
[_new:BaseObject:private] =>
[_deleted:BaseObject:private] =>
[modifiedColumns:protected] => Array
(
)
)
[92] => Category Object
(
[languages:protected] =>
[bok_resources:protected] =>
[bok_topics:protected] =>
[bok_keywords:protected] =>
[id:protected] => 92
[type:protected] => category
[parent:protected] => 3
[label:protected] => LEED/Green Construction
[alreadyInSave:protected] =>
[alreadyInValidation:protected] =>
[validationFailures:protected] => Array
(
)
[_new:BaseObject:private] =>
[_deleted:BaseObject:private] =>
[modifiedColumns:protected] => Array
(
)
)
[93] => Category Object
(
[languages:protected] =>
[bok_resources:protected] =>
[bok_topics:protected] =>
[bok_keywords:protected] =>
[id:protected] => 93
[type:protected] => category
[parent:protected] => 3
[label:protected] => Renovations
[alreadyInSave:protected] =>
[alreadyInValidation:protected] =>
[validationFailures:protected] => Array
(
)
[_new:BaseObject:private] =>
[_deleted:BaseObject:private] =>
[modifiedColumns:protected] => Array
(
)
)
[94] => Category Object
(
[languages:protected] =>
[bok_resources:protected] =>
[bok_topics:protected] =>
[bok_keywords:protected] =>
[id:protected] => 94
[type:protected] => category
[parent:protected] => 3
[label:protected] => Residential
[alreadyInSave:protected] =>
[alreadyInValidation:protected] =>
[validationFailures:protected] => Array
(
)
[_new:BaseObject:private] =>
[_deleted:BaseObject:private] =>
[modifiedColumns:protected] => Array
(
)
)
[95] => Category Object
(
[languages:protected] =>
[bok_resources:protected] =>
[bok_topics:protected] =>
[bok_keywords:protected] =>
[id:protected] => 95
[type:protected] => category
[parent:protected] => 3
[label:protected] => Underground
[alreadyInSave:protected] =>
[alreadyInValidation:protected] =>
[validationFailures:protected] => Array
(
)
[_new:BaseObject:private] =>
[_deleted:BaseObject:private] =>
[modifiedColumns:protected] => Array
(
)
)
[100] => Category Object
(
[languages:protected] =>
[bok_resources:protected] =>
[bok_topics:protected] =>
[bok_keywords:protected] =>
[id:protected] => 100
[type:protected] => category
[parent:protected] => 6
[label:protected] => Toolbox Talks
[alreadyInSave:protected] =>
[alreadyInValidation:protected] =>
[validationFailures:protected] => Array
(
)
[_new:BaseObject:private] =>
[_deleted:BaseObject:private] =>
[modifiedColumns:protected] => Array
(
)
)
)
[categories_initialized:protected] => 1
[mapped_items:protected] =>
[content:protected] =>
[files:protected] =>
[language:protected] => Language Object
(
[id:protected] => 1
[code:protected] => en
[name:protected] => English
[alreadyInSave:protected] =>
[alreadyInValidation:protected] =>
[validationFailures:protected] => Array
(
)
[_new:BaseObject:private] =>
[_deleted:BaseObject:private] =>
[modifiedColumns:protected] => Array
(
)
)
[old_record:protected] =>
[id:protected] => 4431
[old_id:protected] =>
[elcosh_id:protected] => d001661
[type:protected] => document
[display_type:protected] => HTML only (and links)
[user_id:protected] => 0
[language_id:protected] => 1
[tagging_id:protected] => Mike Aguilar
[priority_id:protected] => 1
[title:protected] => Toolbox Talk: Challenges Preventing Falling Objects
[total_pages:protected] => 0
[billed_pages:protected] => 0
[publication_number:protected] =>
[part_of:protected] =>
[keywords:protected] => dropped objects, falling objects, struck by incidents, struck by fatalities
[comments:protected] =>
[summary:protected] => The CPWR Toolbox Talk on Challenges Preventing Falling Objects addresses the hazards of being struck by falling objects on the job site. The resource includes a brief example, steps to prevent a related injury, and questions for discussion. It includes a graphic that illustrates a group workers observing a scaffold free of debris during high winds, which can be posted in a central location as a reminder of steps to work safely.
Available in
English and
Spanish.
[transition_comments:protected] =>
[external_link:protected] =>
[consol_link:protected] =>
[more_like_this:protected] => d001234,d001238,d001244,d001251,d001253,d001260,d001268,d001278
[permission_given_by:protected] =>
[published:protected] => T
[billable:protected] => F
[img_name:protected] =>
[img_ext:protected] =>
[img_width:protected] =>
[img_height:protected] =>
[img_credit:protected] =>
[img_practice:protected] =>
[vid_source_id:protected] =>
[vid_running_time:protected] =>
[vid_intended_audience:protected] =>
[vid_acquisition_info:protected] =>
[vid_cost:protected] =>
[vid_producer:protected] =>
[vid_filename:protected] =>
[vid_filename_downloadable:protected] =>
[date_summary:protected] =>
[date_permission_requested:protected] =>
[date_permission_received:protected] =>
[date_review_needed:protected] =>
[date_received:protected] => 06/10/22
[date_completed:protected] => 06/10/22
[date_billed:protected] =>
[date_modified:protected] => 05/22/23
[collBokExports:protected] =>
[lastBokExportCriteria:BaseElcoshItem:private] =>
[alreadyInSave:protected] =>
[alreadyInValidation:protected] =>
[validationFailures:protected] => Array
(
)
[_new:BaseObject:private] =>
[_deleted:BaseObject:private] =>
[modifiedColumns:protected] => Array
(
)
)
)
[2] => Search_Result Object
(
[title] => Toolbox Talk: Tower Crane Safety
[image] => /record/images/notavailable-p.png
[blurb] => The CPWR Toolbox Talk on Tower Crane Safety addresses the potential hazards of Tower Cranes and the importance of following procedure before and durin...
[category] => Array
(
[0] => 11
[1] => 12
[2] => 18
[3] => 70
[4] => 87
[5] => 88
[6] => 91
[7] => 90
[8] => 92
[9] => 100
)
[labels] => Array
(
[0] => Cranes & Hoists
[1] => Work Environment
[2] => Hazards
[3] => Crushed/Struck By
[6] => Motor Vehicles/Heavy Equipment
[9] => Operating Engineer
[10] => Trades
[11] => Commercial & Institutional
[12] => Jobsites
[13] => Demolition
[15] => Heavy & Highway
[17] => Industrial
[19] => LEED/Green Construction
[21] => Toolbox Talks
[22] => Documents
[23] => Media & Documents
)
[type] => Toolbox Talks
[sub_category] =>
[url] => /document/4427/d001657/Toolbox%2BTalk%253A%2BTower%2BCrane%2BSafety.html
[item:protected] => DocumentRecord Object
(
[records:protected] => Array
(
)
[recordId:protected] =>
[searchWordClass:protected] =>
[searchWordPeerClass:protected] =>
[bok_record:protected] =>
[authors:protected] =>
[organizations:protected] =>
[collections:protected] =>
[categories:protected] => Array
(
[11] => Category Object
(
[languages:protected] =>
[bok_resources:protected] =>
[bok_topics:protected] =>
[bok_keywords:protected] =>
[id:protected] => 11
[type:protected] => category
[parent:protected] => 7
[label:protected] => Cranes & Hoists
[alreadyInSave:protected] =>
[alreadyInValidation:protected] =>
[validationFailures:protected] => Array
(
)
[_new:BaseObject:private] =>
[_deleted:BaseObject:private] =>
[modifiedColumns:protected] => Array
(
)
)
[12] => Category Object
(
[languages:protected] =>
[bok_resources:protected] =>
[bok_topics:protected] =>
[bok_keywords:protected] =>
[id:protected] => 12
[type:protected] => category
[parent:protected] => 7
[label:protected] => Crushed/Struck By
[alreadyInSave:protected] =>
[alreadyInValidation:protected] =>
[validationFailures:protected] => Array
(
)
[_new:BaseObject:private] =>
[_deleted:BaseObject:private] =>
[modifiedColumns:protected] => Array
(
)
)
[18] => Category Object
(
[languages:protected] =>
[bok_resources:protected] =>
[bok_topics:protected] =>
[bok_keywords:protected] =>
[id:protected] => 18
[type:protected] => category
[parent:protected] => 7
[label:protected] => Motor Vehicles/Heavy Equipment
[alreadyInSave:protected] =>
[alreadyInValidation:protected] =>
[validationFailures:protected] => Array
(
)
[_new:BaseObject:private] =>
[_deleted:BaseObject:private] =>
[modifiedColumns:protected] => Array
(
)
)
[70] => Category Object
(
[languages:protected] =>
[bok_resources:protected] =>
[bok_topics:protected] =>
[bok_keywords:protected] =>
[id:protected] => 70
[type:protected] => category
[parent:protected] => 2
[label:protected] => Operating Engineer
[alreadyInSave:protected] =>
[alreadyInValidation:protected] =>
[validationFailures:protected] => Array
(
)
[_new:BaseObject:private] =>
[_deleted:BaseObject:private] =>
[modifiedColumns:protected] => Array
(
)
)
[87] => Category Object
(
[languages:protected] =>
[bok_resources:protected] =>
[bok_topics:protected] =>
[bok_keywords:protected] =>
[id:protected] => 87
[type:protected] => category
[parent:protected] => 3
[label:protected] => Commercial & Institutional
[alreadyInSave:protected] =>
[alreadyInValidation:protected] =>
[validationFailures:protected] => Array
(
)
[_new:BaseObject:private] =>
[_deleted:BaseObject:private] =>
[modifiedColumns:protected] => Array
(
)
)
[88] => Category Object
(
[languages:protected] =>
[bok_resources:protected] =>
[bok_topics:protected] =>
[bok_keywords:protected] =>
[id:protected] => 88
[type:protected] => category
[parent:protected] => 3
[label:protected] => Demolition
[alreadyInSave:protected] =>
[alreadyInValidation:protected] =>
[validationFailures:protected] => Array
(
)
[_new:BaseObject:private] =>
[_deleted:BaseObject:private] =>
[modifiedColumns:protected] => Array
(
)
)
[91] => Category Object
(
[languages:protected] =>
[bok_resources:protected] =>
[bok_topics:protected] =>
[bok_keywords:protected] =>
[id:protected] => 91
[type:protected] => category
[parent:protected] => 3
[label:protected] => Heavy & Highway
[alreadyInSave:protected] =>
[alreadyInValidation:protected] =>
[validationFailures:protected] => Array
(
)
[_new:BaseObject:private] =>
[_deleted:BaseObject:private] =>
[modifiedColumns:protected] => Array
(
)
)
[90] => Category Object
(
[languages:protected] =>
[bok_resources:protected] =>
[bok_topics:protected] =>
[bok_keywords:protected] =>
[id:protected] => 90
[type:protected] => category
[parent:protected] => 3
[label:protected] => Industrial
[alreadyInSave:protected] =>
[alreadyInValidation:protected] =>
[validationFailures:protected] => Array
(
)
[_new:BaseObject:private] =>
[_deleted:BaseObject:private] =>
[modifiedColumns:protected] => Array
(
)
)
[92] => Category Object
(
[languages:protected] =>
[bok_resources:protected] =>
[bok_topics:protected] =>
[bok_keywords:protected] =>
[id:protected] => 92
[type:protected] => category
[parent:protected] => 3
[label:protected] => LEED/Green Construction
[alreadyInSave:protected] =>
[alreadyInValidation:protected] =>
[validationFailures:protected] => Array
(
)
[_new:BaseObject:private] =>
[_deleted:BaseObject:private] =>
[modifiedColumns:protected] => Array
(
)
)
[100] => Category Object
(
[languages:protected] =>
[bok_resources:protected] =>
[bok_topics:protected] =>
[bok_keywords:protected] =>
[id:protected] => 100
[type:protected] => category
[parent:protected] => 6
[label:protected] => Toolbox Talks
[alreadyInSave:protected] =>
[alreadyInValidation:protected] =>
[validationFailures:protected] => Array
(
)
[_new:BaseObject:private] =>
[_deleted:BaseObject:private] =>
[modifiedColumns:protected] => Array
(
)
)
)
[categories_initialized:protected] => 1
[mapped_items:protected] =>
[content:protected] =>
[files:protected] =>
[language:protected] => Language Object
(
[id:protected] => 1
[code:protected] => en
[name:protected] => English
[alreadyInSave:protected] =>
[alreadyInValidation:protected] =>
[validationFailures:protected] => Array
(
)
[_new:BaseObject:private] =>
[_deleted:BaseObject:private] =>
[modifiedColumns:protected] => Array
(
)
)
[old_record:protected] =>
[id:protected] => 4427
[old_id:protected] =>
[elcosh_id:protected] => d001657
[type:protected] => document
[display_type:protected] => HTML only (and links)
[user_id:protected] => 0
[language_id:protected] => 1
[tagging_id:protected] => Mike Aguilar
[priority_id:protected] => 1
[title:protected] => Toolbox Talk: Tower Crane Safety
[total_pages:protected] => 0
[billed_pages:protected] => 0
[publication_number:protected] =>
[part_of:protected] =>
[keywords:protected] => Tower Crane, Crane, Stability, Tipping, Lift Zone Safety, Lift, Zone, Safety, Struck by
[comments:protected] =>
[summary:protected] => The CPWR Toolbox Talk on Tower Crane Safety addresses the potential hazards of Tower Cranes and the importance of following procedure before and during Tower Crane operation. The resource includes a brief example, steps to prevent a related injury, and questions for discussion. It includes a graphic that illustrates a worker inspecting a Tower Crane before operation, which can be posted in a central location as a reminder of steps to work safely.
Available in
English and
Spanish.
[transition_comments:protected] =>
[external_link:protected] =>
[consol_link:protected] =>
[more_like_this:protected] => d001234,d001238,d001250,d001251,d001253,d001258,d001262,d001273
[permission_given_by:protected] =>
[published:protected] => T
[billable:protected] => F
[img_name:protected] =>
[img_ext:protected] => jpg
[img_width:protected] =>
[img_height:protected] =>
[img_credit:protected] =>
[img_practice:protected] =>
[vid_source_id:protected] =>
[vid_running_time:protected] =>
[vid_intended_audience:protected] =>
[vid_acquisition_info:protected] =>
[vid_cost:protected] =>
[vid_producer:protected] =>
[vid_filename:protected] =>
[vid_filename_downloadable:protected] =>
[date_summary:protected] =>
[date_permission_requested:protected] =>
[date_permission_received:protected] =>
[date_review_needed:protected] =>
[date_received:protected] => 12/23/21
[date_completed:protected] => 12/23/21
[date_billed:protected] =>
[date_modified:protected] => 05/19/23
[collBokExports:protected] =>
[lastBokExportCriteria:BaseElcoshItem:private] =>
[alreadyInSave:protected] =>
[alreadyInValidation:protected] =>
[validationFailures:protected] => Array
(
)
[_new:BaseObject:private] =>
[_deleted:BaseObject:private] =>
[modifiedColumns:protected] => Array
(
)
)
)
[3] => Search_Result Object
(
[title] => Toolbox Talk: Work Zone Safety: Working Around Vehicles
[image] => /record/images/notavailable-p.png
[blurb] => The CPWR Toolbox Talk on Working Around Vehicles in the Work Zone addresses methods to avoid being struck-by a vehicle on a construction site. The res...
[category] => Array
(
[0] => 12
[1] => 18
[2] => 52
[3] => 57
[4] => 70
[5] => 85
[6] => 87
[7] => 88
[8] => 89
[9] => 91
[10] => 90
[11] => 92
[12] => 93
[13] => 94
[14] => 95
[15] => 100
)
[labels] => Array
(
[0] => Crushed/Struck By
[1] => Work Environment
[2] => Hazards
[3] => Motor Vehicles/Heavy Equipment
[6] => Commercial Diver
[7] => Trades
[8] => Flagger
[10] => Operating Engineer
[12] => Truck Driver
[14] => Commercial & Institutional
[15] => Jobsites
[16] => Demolition
[18] => Disasters
[20] => Heavy & Highway
[22] => Industrial
[24] => LEED/Green Construction
[26] => Renovations
[28] => Residential
[30] => Underground
[32] => Toolbox Talks
[33] => Documents
[34] => Media & Documents
)
[type] => Toolbox Talks
[sub_category] =>
[url] => /document/4428/d001658/Toolbox%2BTalk%253A%2BWork%2BZone%2BSafety%253A%2BWorking%2BAround%2BVehicles.html
[item:protected] => DocumentRecord Object
(
[records:protected] => Array
(
)
[recordId:protected] =>
[searchWordClass:protected] =>
[searchWordPeerClass:protected] =>
[bok_record:protected] =>
[authors:protected] =>
[organizations:protected] =>
[collections:protected] =>
[categories:protected] => Array
(
[12] => Category Object
(
[languages:protected] =>
[bok_resources:protected] =>
[bok_topics:protected] =>
[bok_keywords:protected] =>
[id:protected] => 12
[type:protected] => category
[parent:protected] => 7
[label:protected] => Crushed/Struck By
[alreadyInSave:protected] =>
[alreadyInValidation:protected] =>
[validationFailures:protected] => Array
(
)
[_new:BaseObject:private] =>
[_deleted:BaseObject:private] =>
[modifiedColumns:protected] => Array
(
)
)
[18] => Category Object
(
[languages:protected] =>
[bok_resources:protected] =>
[bok_topics:protected] =>
[bok_keywords:protected] =>
[id:protected] => 18
[type:protected] => category
[parent:protected] => 7
[label:protected] => Motor Vehicles/Heavy Equipment
[alreadyInSave:protected] =>
[alreadyInValidation:protected] =>
[validationFailures:protected] => Array
(
)
[_new:BaseObject:private] =>
[_deleted:BaseObject:private] =>
[modifiedColumns:protected] => Array
(
)
)
[52] => Category Object
(
[languages:protected] =>
[bok_resources:protected] =>
[bok_topics:protected] =>
[bok_keywords:protected] =>
[id:protected] => 52
[type:protected] => category
[parent:protected] => 2
[label:protected] => Commercial Diver
[alreadyInSave:protected] =>
[alreadyInValidation:protected] =>
[validationFailures:protected] => Array
(
)
[_new:BaseObject:private] =>
[_deleted:BaseObject:private] =>
[modifiedColumns:protected] => Array
(
)
)
[57] => Category Object
(
[languages:protected] =>
[bok_resources:protected] =>
[bok_topics:protected] =>
[bok_keywords:protected] =>
[id:protected] => 57
[type:protected] => category
[parent:protected] => 2
[label:protected] => Flagger
[alreadyInSave:protected] =>
[alreadyInValidation:protected] =>
[validationFailures:protected] => Array
(
)
[_new:BaseObject:private] =>
[_deleted:BaseObject:private] =>
[modifiedColumns:protected] => Array
(
)
)
[70] => Category Object
(
[languages:protected] =>
[bok_resources:protected] =>
[bok_topics:protected] =>
[bok_keywords:protected] =>
[id:protected] => 70
[type:protected] => category
[parent:protected] => 2
[label:protected] => Operating Engineer
[alreadyInSave:protected] =>
[alreadyInValidation:protected] =>
[validationFailures:protected] => Array
(
)
[_new:BaseObject:private] =>
[_deleted:BaseObject:private] =>
[modifiedColumns:protected] => Array
(
)
)
[85] => Category Object
(
[languages:protected] =>
[bok_resources:protected] =>
[bok_topics:protected] =>
[bok_keywords:protected] =>
[id:protected] => 85
[type:protected] => category
[parent:protected] => 2
[label:protected] => Truck Driver
[alreadyInSave:protected] =>
[alreadyInValidation:protected] =>
[validationFailures:protected] => Array
(
)
[_new:BaseObject:private] =>
[_deleted:BaseObject:private] =>
[modifiedColumns:protected] => Array
(
)
)
[87] => Category Object
(
[languages:protected] =>
[bok_resources:protected] =>
[bok_topics:protected] =>
[bok_keywords:protected] =>
[id:protected] => 87
[type:protected] => category
[parent:protected] => 3
[label:protected] => Commercial & Institutional
[alreadyInSave:protected] =>
[alreadyInValidation:protected] =>
[validationFailures:protected] => Array
(
)
[_new:BaseObject:private] =>
[_deleted:BaseObject:private] =>
[modifiedColumns:protected] => Array
(
)
)
[88] => Category Object
(
[languages:protected] =>
[bok_resources:protected] =>
[bok_topics:protected] =>
[bok_keywords:protected] =>
[id:protected] => 88
[type:protected] => category
[parent:protected] => 3
[label:protected] => Demolition
[alreadyInSave:protected] =>
[alreadyInValidation:protected] =>
[validationFailures:protected] => Array
(
)
[_new:BaseObject:private] =>
[_deleted:BaseObject:private] =>
[modifiedColumns:protected] => Array
(
)
)
[89] => Category Object
(
[languages:protected] =>
[bok_resources:protected] =>
[bok_topics:protected] =>
[bok_keywords:protected] =>
[id:protected] => 89
[type:protected] => category
[parent:protected] => 3
[label:protected] => Disasters
[alreadyInSave:protected] =>
[alreadyInValidation:protected] =>
[validationFailures:protected] => Array
(
)
[_new:BaseObject:private] =>
[_deleted:BaseObject:private] =>
[modifiedColumns:protected] => Array
(
)
)
[91] => Category Object
(
[languages:protected] =>
[bok_resources:protected] =>
[bok_topics:protected] =>
[bok_keywords:protected] =>
[id:protected] => 91
[type:protected] => category
[parent:protected] => 3
[label:protected] => Heavy & Highway
[alreadyInSave:protected] =>
[alreadyInValidation:protected] =>
[validationFailures:protected] => Array
(
)
[_new:BaseObject:private] =>
[_deleted:BaseObject:private] =>
[modifiedColumns:protected] => Array
(
)
)
[90] => Category Object
(
[languages:protected] =>
[bok_resources:protected] =>
[bok_topics:protected] =>
[bok_keywords:protected] =>
[id:protected] => 90
[type:protected] => category
[parent:protected] => 3
[label:protected] => Industrial
[alreadyInSave:protected] =>
[alreadyInValidation:protected] =>
[validationFailures:protected] => Array
(
)
[_new:BaseObject:private] =>
[_deleted:BaseObject:private] =>
[modifiedColumns:protected] => Array
(
)
)
[92] => Category Object
(
[languages:protected] =>
[bok_resources:protected] =>
[bok_topics:protected] =>
[bok_keywords:protected] =>
[id:protected] => 92
[type:protected] => category
[parent:protected] => 3
[label:protected] => LEED/Green Construction
[alreadyInSave:protected] =>
[alreadyInValidation:protected] =>
[validationFailures:protected] => Array
(
)
[_new:BaseObject:private] =>
[_deleted:BaseObject:private] =>
[modifiedColumns:protected] => Array
(
)
)
[93] => Category Object
(
[languages:protected] =>
[bok_resources:protected] =>
[bok_topics:protected] =>
[bok_keywords:protected] =>
[id:protected] => 93
[type:protected] => category
[parent:protected] => 3
[label:protected] => Renovations
[alreadyInSave:protected] =>
[alreadyInValidation:protected] =>
[validationFailures:protected] => Array
(
)
[_new:BaseObject:private] =>
[_deleted:BaseObject:private] =>
[modifiedColumns:protected] => Array
(
)
)
[94] => Category Object
(
[languages:protected] =>
[bok_resources:protected] =>
[bok_topics:protected] =>
[bok_keywords:protected] =>
[id:protected] => 94
[type:protected] => category
[parent:protected] => 3
[label:protected] => Residential
[alreadyInSave:protected] =>
[alreadyInValidation:protected] =>
[validationFailures:protected] => Array
(
)
[_new:BaseObject:private] =>
[_deleted:BaseObject:private] =>
[modifiedColumns:protected] => Array
(
)
)
[95] => Category Object
(
[languages:protected] =>
[bok_resources:protected] =>
[bok_topics:protected] =>
[bok_keywords:protected] =>
[id:protected] => 95
[type:protected] => category
[parent:protected] => 3
[label:protected] => Underground
[alreadyInSave:protected] =>
[alreadyInValidation:protected] =>
[validationFailures:protected] => Array
(
)
[_new:BaseObject:private] =>
[_deleted:BaseObject:private] =>
[modifiedColumns:protected] => Array
(
)
)
[100] => Category Object
(
[languages:protected] =>
[bok_resources:protected] =>
[bok_topics:protected] =>
[bok_keywords:protected] =>
[id:protected] => 100
[type:protected] => category
[parent:protected] => 6
[label:protected] => Toolbox Talks
[alreadyInSave:protected] =>
[alreadyInValidation:protected] =>
[validationFailures:protected] => Array
(
)
[_new:BaseObject:private] =>
[_deleted:BaseObject:private] =>
[modifiedColumns:protected] => Array
(
)
)
)
[categories_initialized:protected] => 1
[mapped_items:protected] =>
[content:protected] =>
[files:protected] =>
[language:protected] => Language Object
(
[id:protected] => 1
[code:protected] => en
[name:protected] => English
[alreadyInSave:protected] =>
[alreadyInValidation:protected] =>
[validationFailures:protected] => Array
(
)
[_new:BaseObject:private] =>
[_deleted:BaseObject:private] =>
[modifiedColumns:protected] => Array
(
)
)
[old_record:protected] =>
[id:protected] => 4428
[old_id:protected] =>
[elcosh_id:protected] => d001658
[type:protected] => document
[display_type:protected] => HTML only (and links)
[user_id:protected] => 0
[language_id:protected] => 1
[tagging_id:protected] => Daniela Caceres
[priority_id:protected] => 1
[title:protected] => Toolbox Talk: Work Zone Safety: Working Around Vehicles
[total_pages:protected] => 0
[billed_pages:protected] => 0
[publication_number:protected] =>
[part_of:protected] =>
[keywords:protected] => Struck, Struck by, Vehicle, Work Zone Safety, Truck, Operator, Driver, Mobile Equipment
[comments:protected] =>
[summary:protected] => The CPWR Toolbox Talk on Working Around Vehicles in the Work Zone addresses methods to avoid being struck-by a vehicle on a construction site. The resource includes a case example, steps to prevent a related injury, and questions for discussion. It includes a graphic that illustrates the hazard, which can be posted in a central location as a reminder of steps to work safely. Available in
English and
Spanish.
[transition_comments:protected] =>
[external_link:protected] =>
[consol_link:protected] =>
[more_like_this:protected] => d001640
[permission_given_by:protected] =>
[published:protected] => T
[billable:protected] => F
[img_name:protected] =>
[img_ext:protected] =>
[img_width:protected] =>
[img_height:protected] =>
[img_credit:protected] =>
[img_practice:protected] =>
[vid_source_id:protected] =>
[vid_running_time:protected] =>
[vid_intended_audience:protected] =>
[vid_acquisition_info:protected] =>
[vid_cost:protected] =>
[vid_producer:protected] =>
[vid_filename:protected] =>
[vid_filename_downloadable:protected] =>
[date_summary:protected] =>
[date_permission_requested:protected] =>
[date_permission_received:protected] =>
[date_review_needed:protected] =>
[date_received:protected] => 12/23/21
[date_completed:protected] => 12/23/21
[date_billed:protected] =>
[date_modified:protected] => 05/19/23
[collBokExports:protected] =>
[lastBokExportCriteria:BaseElcoshItem:private] =>
[alreadyInSave:protected] =>
[alreadyInValidation:protected] =>
[validationFailures:protected] => Array
(
)
[_new:BaseObject:private] =>
[_deleted:BaseObject:private] =>
[modifiedColumns:protected] => Array
(
)
)
)
[4] => Search_Result Object
(
[title] => Construction Dive -- DeWalt's Jobsite Pro headphones recalled for fire hazards
[image] => /record/images/notavailable-p.png
[blurb] => A recall notice by the United States Consumer Product Safety Commission affects over 300,000 DeWalt Jobsite Pro Headphones. The recall is a result of...
[category] => Array
(
[0] => 16
[1] => 44
[2] => 45
[3] => 46
[4] => 47
[5] => 48
[6] => 49
[7] => 50
[8] => 51
[9] => 52
[10] => 53
[11] => 54
[12] => 55
[13] => 56
[14] => 57
[15] => 58
[16] => 59
[17] => 60
[18] => 61
[19] => 64
[20] => 65
[21] => 66
[22] => 67
[23] => 68
[24] => 69
[25] => 70
[26] => 71
[27] => 72
[28] => 73
[29] => 74
[30] => 75
[31] => 76
[32] => 77
[33] => 63
[34] => 78
[35] => 79
[36] => 80
[37] => 81
[38] => 82
[39] => 62
[40] => 83
[41] => 84
[42] => 85
[43] => 86
[44] => 87
[45] => 88
[46] => 89
[47] => 91
[48] => 90
[49] => 92
[50] => 93
[51] => 94
[52] => 95
)
[labels] => Array
(
[0] => Fire & Explosions
[1] => Work Environment
[2] => Hazards
[3] => Acoustical Ceiling Carpenter
[4] => Trades
[5] => Asbestos/Insulator
[7] => Boilermaker
[9] => Bricklayer
[11] => Cabinetmaker
[13] => Carpenter
[15] => Carpet Layer
[17] => Cement Mason
[19] => Commercial Diver
[21] => Concrete Polisher
[23] => Drywall Applicator Specialist
[25] => Electrical Worker
[27] => Elevator Constructor
[29] => Flagger
[31] => Glazier
[33] => Hazardous Waste Cleanup
[35] => HVAC
[37] => Interior Systems Carpenter
[39] => Laborer
[41] => Landscaper
[43] => Lather
[45] => Lead Abatement Worker
[47] => Maintenance Worker
[49] => Millwright
[51] => Operating Engineer
[53] => Painter
[55] => Paper Hanger
[57] => PCC/Restoration
[59] => Pile Driver
[61] => Plasterer
[63] => Plumber/Pipefitter
[65] => Refractory Worker
[67] => Reinforcing Ironworker
[69] => Roofer/Waterproofer
[71] => Scaffold Erector
[73] => Sheetmetal Worker
[75] => Sprinkler Fitter
[77] => Stonemason
[79] => Structural Ironworker
[81] => Terrazzo Worker
[83] => Tile Setter
[85] => Truck Driver
[87] => Welder
[89] => Commercial & Institutional
[90] => Jobsites
[91] => Demolition
[93] => Disasters
[95] => Heavy & Highway
[97] => Industrial
[99] => LEED/Green Construction
[101] => Renovations
[103] => Residential
[105] => Underground
)
[type] =>
[sub_category] =>
[url] => /document/4426/d001656/Construction%2BDive%2B--%2BDeWalt%2527s%2BJobsite%2BPro%2Bheadphones%2Brecalled%2Bfor%2Bfire%2Bhazards.html
[item:protected] => DocumentRecord Object
(
[records:protected] => Array
(
)
[recordId:protected] =>
[searchWordClass:protected] =>
[searchWordPeerClass:protected] =>
[bok_record:protected] =>
[authors:protected] =>
[organizations:protected] =>
[collections:protected] =>
[categories:protected] => Array
(
[16] => Category Object
(
[languages:protected] =>
[bok_resources:protected] =>
[bok_topics:protected] =>
[bok_keywords:protected] =>
[id:protected] => 16
[type:protected] => category
[parent:protected] => 7
[label:protected] => Fire & Explosions
[alreadyInSave:protected] =>
[alreadyInValidation:protected] =>
[validationFailures:protected] => Array
(
)
[_new:BaseObject:private] =>
[_deleted:BaseObject:private] =>
[modifiedColumns:protected] => Array
(
)
)
[44] => Category Object
(
[languages:protected] =>
[bok_resources:protected] =>
[bok_topics:protected] =>
[bok_keywords:protected] =>
[id:protected] => 44
[type:protected] => category
[parent:protected] => 2
[label:protected] => Acoustical Ceiling Carpenter
[alreadyInSave:protected] =>
[alreadyInValidation:protected] =>
[validationFailures:protected] => Array
(
)
[_new:BaseObject:private] =>
[_deleted:BaseObject:private] =>
[modifiedColumns:protected] => Array
(
)
)
[45] => Category Object
(
[languages:protected] =>
[bok_resources:protected] =>
[bok_topics:protected] =>
[bok_keywords:protected] =>
[id:protected] => 45
[type:protected] => category
[parent:protected] => 2
[label:protected] => Asbestos/Insulator
[alreadyInSave:protected] =>
[alreadyInValidation:protected] =>
[validationFailures:protected] => Array
(
)
[_new:BaseObject:private] =>
[_deleted:BaseObject:private] =>
[modifiedColumns:protected] => Array
(
)
)
[46] => Category Object
(
[languages:protected] =>
[bok_resources:protected] =>
[bok_topics:protected] =>
[bok_keywords:protected] =>
[id:protected] => 46
[type:protected] => category
[parent:protected] => 2
[label:protected] => Boilermaker
[alreadyInSave:protected] =>
[alreadyInValidation:protected] =>
[validationFailures:protected] => Array
(
)
[_new:BaseObject:private] =>
[_deleted:BaseObject:private] =>
[modifiedColumns:protected] => Array
(
)
)
[47] => Category Object
(
[languages:protected] =>
[bok_resources:protected] =>
[bok_topics:protected] =>
[bok_keywords:protected] =>
[id:protected] => 47
[type:protected] => category
[parent:protected] => 2
[label:protected] => Bricklayer
[alreadyInSave:protected] =>
[alreadyInValidation:protected] =>
[validationFailures:protected] => Array
(
)
[_new:BaseObject:private] =>
[_deleted:BaseObject:private] =>
[modifiedColumns:protected] => Array
(
)
)
[48] => Category Object
(
[languages:protected] =>
[bok_resources:protected] =>
[bok_topics:protected] =>
[bok_keywords:protected] =>
[id:protected] => 48
[type:protected] => category
[parent:protected] => 2
[label:protected] => Cabinetmaker
[alreadyInSave:protected] =>
[alreadyInValidation:protected] =>
[validationFailures:protected] => Array
(
)
[_new:BaseObject:private] =>
[_deleted:BaseObject:private] =>
[modifiedColumns:protected] => Array
(
)
)
[49] => Category Object
(
[languages:protected] =>
[bok_resources:protected] =>
[bok_topics:protected] =>
[bok_keywords:protected] =>
[id:protected] => 49
[type:protected] => category
[parent:protected] => 2
[label:protected] => Carpenter
[alreadyInSave:protected] =>
[alreadyInValidation:protected] =>
[validationFailures:protected] => Array
(
)
[_new:BaseObject:private] =>
[_deleted:BaseObject:private] =>
[modifiedColumns:protected] => Array
(
)
)
[50] => Category Object
(
[languages:protected] =>
[bok_resources:protected] =>
[bok_topics:protected] =>
[bok_keywords:protected] =>
[id:protected] => 50
[type:protected] => category
[parent:protected] => 2
[label:protected] => Carpet Layer
[alreadyInSave:protected] =>
[alreadyInValidation:protected] =>
[validationFailures:protected] => Array
(
)
[_new:BaseObject:private] =>
[_deleted:BaseObject:private] =>
[modifiedColumns:protected] => Array
(
)
)
[51] => Category Object
(
[languages:protected] =>
[bok_resources:protected] =>
[bok_topics:protected] =>
[bok_keywords:protected] =>
[id:protected] => 51
[type:protected] => category
[parent:protected] => 2
[label:protected] => Cement Mason
[alreadyInSave:protected] =>
[alreadyInValidation:protected] =>
[validationFailures:protected] => Array
(
)
[_new:BaseObject:private] =>
[_deleted:BaseObject:private] =>
[modifiedColumns:protected] => Array
(
)
)
[52] => Category Object
(
[languages:protected] =>
[bok_resources:protected] =>
[bok_topics:protected] =>
[bok_keywords:protected] =>
[id:protected] => 52
[type:protected] => category
[parent:protected] => 2
[label:protected] => Commercial Diver
[alreadyInSave:protected] =>
[alreadyInValidation:protected] =>
[validationFailures:protected] => Array
(
)
[_new:BaseObject:private] =>
[_deleted:BaseObject:private] =>
[modifiedColumns:protected] => Array
(
)
)
[53] => Category Object
(
[languages:protected] =>
[bok_resources:protected] =>
[bok_topics:protected] =>
[bok_keywords:protected] =>
[id:protected] => 53
[type:protected] => category
[parent:protected] => 2
[label:protected] => Concrete Polisher
[alreadyInSave:protected] =>
[alreadyInValidation:protected] =>
[validationFailures:protected] => Array
(
)
[_new:BaseObject:private] =>
[_deleted:BaseObject:private] =>
[modifiedColumns:protected] => Array
(
)
)
[54] => Category Object
(
[languages:protected] =>
[bok_resources:protected] =>
[bok_topics:protected] =>
[bok_keywords:protected] =>
[id:protected] => 54
[type:protected] => category
[parent:protected] => 2
[label:protected] => Drywall Applicator Specialist
[alreadyInSave:protected] =>
[alreadyInValidation:protected] =>
[validationFailures:protected] => Array
(
)
[_new:BaseObject:private] =>
[_deleted:BaseObject:private] =>
[modifiedColumns:protected] => Array
(
)
)
[55] => Category Object
(
[languages:protected] =>
[bok_resources:protected] =>
[bok_topics:protected] =>
[bok_keywords:protected] =>
[id:protected] => 55
[type:protected] => category
[parent:protected] => 2
[label:protected] => Electrical Worker
[alreadyInSave:protected] =>
[alreadyInValidation:protected] =>
[validationFailures:protected] => Array
(
)
[_new:BaseObject:private] =>
[_deleted:BaseObject:private] =>
[modifiedColumns:protected] => Array
(
)
)
[56] => Category Object
(
[languages:protected] =>
[bok_resources:protected] =>
[bok_topics:protected] =>
[bok_keywords:protected] =>
[id:protected] => 56
[type:protected] => category
[parent:protected] => 2
[label:protected] => Elevator Constructor
[alreadyInSave:protected] =>
[alreadyInValidation:protected] =>
[validationFailures:protected] => Array
(
)
[_new:BaseObject:private] =>
[_deleted:BaseObject:private] =>
[modifiedColumns:protected] => Array
(
)
)
[57] => Category Object
(
[languages:protected] =>
[bok_resources:protected] =>
[bok_topics:protected] =>
[bok_keywords:protected] =>
[id:protected] => 57
[type:protected] => category
[parent:protected] => 2
[label:protected] => Flagger
[alreadyInSave:protected] =>
[alreadyInValidation:protected] =>
[validationFailures:protected] => Array
(
)
[_new:BaseObject:private] =>
[_deleted:BaseObject:private] =>
[modifiedColumns:protected] => Array
(
)
)
[58] => Category Object
(
[languages:protected] =>
[bok_resources:protected] =>
[bok_topics:protected] =>
[bok_keywords:protected] =>
[id:protected] => 58
[type:protected] => category
[parent:protected] => 2
[label:protected] => Glazier
[alreadyInSave:protected] =>
[alreadyInValidation:protected] =>
[validationFailures:protected] => Array
(
)
[_new:BaseObject:private] =>
[_deleted:BaseObject:private] =>
[modifiedColumns:protected] => Array
(
)
)
[59] => Category Object
(
[languages:protected] =>
[bok_resources:protected] =>
[bok_topics:protected] =>
[bok_keywords:protected] =>
[id:protected] => 59
[type:protected] => category
[parent:protected] => 2
[label:protected] => Hazardous Waste Cleanup
[alreadyInSave:protected] =>
[alreadyInValidation:protected] =>
[validationFailures:protected] => Array
(
)
[_new:BaseObject:private] =>
[_deleted:BaseObject:private] =>
[modifiedColumns:protected] => Array
(
)
)
[60] => Category Object
(
[languages:protected] =>
[bok_resources:protected] =>
[bok_topics:protected] =>
[bok_keywords:protected] =>
[id:protected] => 60
[type:protected] => category
[parent:protected] => 2
[label:protected] => HVAC
[alreadyInSave:protected] =>
[alreadyInValidation:protected] =>
[validationFailures:protected] => Array
(
)
[_new:BaseObject:private] =>
[_deleted:BaseObject:private] =>
[modifiedColumns:protected] => Array
(
)
)
[61] => Category Object
(
[languages:protected] =>
[bok_resources:protected] =>
[bok_topics:protected] =>
[bok_keywords:protected] =>
[id:protected] => 61
[type:protected] => category
[parent:protected] => 2
[label:protected] => Interior Systems Carpenter
[alreadyInSave:protected] =>
[alreadyInValidation:protected] =>
[validationFailures:protected] => Array
(
)
[_new:BaseObject:private] =>
[_deleted:BaseObject:private] =>
[modifiedColumns:protected] => Array
(
)
)
[64] => Category Object
(
[languages:protected] =>
[bok_resources:protected] =>
[bok_topics:protected] =>
[bok_keywords:protected] =>
[id:protected] => 64
[type:protected] => category
[parent:protected] => 2
[label:protected] => Laborer
[alreadyInSave:protected] =>
[alreadyInValidation:protected] =>
[validationFailures:protected] => Array
(
)
[_new:BaseObject:private] =>
[_deleted:BaseObject:private] =>
[modifiedColumns:protected] => Array
(
)
)
[65] => Category Object
(
[languages:protected] =>
[bok_resources:protected] =>
[bok_topics:protected] =>
[bok_keywords:protected] =>
[id:protected] => 65
[type:protected] => category
[parent:protected] => 2
[label:protected] => Landscaper
[alreadyInSave:protected] =>
[alreadyInValidation:protected] =>
[validationFailures:protected] => Array
(
)
[_new:BaseObject:private] =>
[_deleted:BaseObject:private] =>
[modifiedColumns:protected] => Array
(
)
)
[66] => Category Object
(
[languages:protected] =>
[bok_resources:protected] =>
[bok_topics:protected] =>
[bok_keywords:protected] =>
[id:protected] => 66
[type:protected] => category
[parent:protected] => 2
[label:protected] => Lather
[alreadyInSave:protected] =>
[alreadyInValidation:protected] =>
[validationFailures:protected] => Array
(
)
[_new:BaseObject:private] =>
[_deleted:BaseObject:private] =>
[modifiedColumns:protected] => Array
(
)
)
[67] => Category Object
(
[languages:protected] =>
[bok_resources:protected] =>
[bok_topics:protected] =>
[bok_keywords:protected] =>
[id:protected] => 67
[type:protected] => category
[parent:protected] => 2
[label:protected] => Lead Abatement Worker
[alreadyInSave:protected] =>
[alreadyInValidation:protected] =>
[validationFailures:protected] => Array
(
)
[_new:BaseObject:private] =>
[_deleted:BaseObject:private] =>
[modifiedColumns:protected] => Array
(
)
)
[68] => Category Object
(
[languages:protected] =>
[bok_resources:protected] =>
[bok_topics:protected] =>
[bok_keywords:protected] =>
[id:protected] => 68
[type:protected] => category
[parent:protected] => 2
[label:protected] => Maintenance Worker
[alreadyInSave:protected] =>
[alreadyInValidation:protected] =>
[validationFailures:protected] => Array
(
)
[_new:BaseObject:private] =>
[_deleted:BaseObject:private] =>
[modifiedColumns:protected] => Array
(
)
)
[69] => Category Object
(
[languages:protected] =>
[bok_resources:protected] =>
[bok_topics:protected] =>
[bok_keywords:protected] =>
[id:protected] => 69
[type:protected] => category
[parent:protected] => 2
[label:protected] => Millwright
[alreadyInSave:protected] =>
[alreadyInValidation:protected] =>
[validationFailures:protected] => Array
(
)
[_new:BaseObject:private] =>
[_deleted:BaseObject:private] =>
[modifiedColumns:protected] => Array
(
)
)
[70] => Category Object
(
[languages:protected] =>
[bok_resources:protected] =>
[bok_topics:protected] =>
[bok_keywords:protected] =>
[id:protected] => 70
[type:protected] => category
[parent:protected] => 2
[label:protected] => Operating Engineer
[alreadyInSave:protected] =>
[alreadyInValidation:protected] =>
[validationFailures:protected] => Array
(
)
[_new:BaseObject:private] =>
[_deleted:BaseObject:private] =>
[modifiedColumns:protected] => Array
(
)
)
[71] => Category Object
(
[languages:protected] =>
[bok_resources:protected] =>
[bok_topics:protected] =>
[bok_keywords:protected] =>
[id:protected] => 71
[type:protected] => category
[parent:protected] => 2
[label:protected] => Painter
[alreadyInSave:protected] =>
[alreadyInValidation:protected] =>
[validationFailures:protected] => Array
(
)
[_new:BaseObject:private] =>
[_deleted:BaseObject:private] =>
[modifiedColumns:protected] => Array
(
)
)
[72] => Category Object
(
[languages:protected] =>
[bok_resources:protected] =>
[bok_topics:protected] =>
[bok_keywords:protected] =>
[id:protected] => 72
[type:protected] => category
[parent:protected] => 2
[label:protected] => Paper Hanger
[alreadyInSave:protected] =>
[alreadyInValidation:protected] =>
[validationFailures:protected] => Array
(
)
[_new:BaseObject:private] =>
[_deleted:BaseObject:private] =>
[modifiedColumns:protected] => Array
(
)
)
[73] => Category Object
(
[languages:protected] =>
[bok_resources:protected] =>
[bok_topics:protected] =>
[bok_keywords:protected] =>
[id:protected] => 73
[type:protected] => category
[parent:protected] => 2
[label:protected] => PCC/Restoration
[alreadyInSave:protected] =>
[alreadyInValidation:protected] =>
[validationFailures:protected] => Array
(
)
[_new:BaseObject:private] =>
[_deleted:BaseObject:private] =>
[modifiedColumns:protected] => Array
(
)
)
[74] => Category Object
(
[languages:protected] =>
[bok_resources:protected] =>
[bok_topics:protected] =>
[bok_keywords:protected] =>
[id:protected] => 74
[type:protected] => category
[parent:protected] => 2
[label:protected] => Pile Driver
[alreadyInSave:protected] =>
[alreadyInValidation:protected] =>
[validationFailures:protected] => Array
(
)
[_new:BaseObject:private] =>
[_deleted:BaseObject:private] =>
[modifiedColumns:protected] => Array
(
)
)
[75] => Category Object
(
[languages:protected] =>
[bok_resources:protected] =>
[bok_topics:protected] =>
[bok_keywords:protected] =>
[id:protected] => 75
[type:protected] => category
[parent:protected] => 2
[label:protected] => Plasterer
[alreadyInSave:protected] =>
[alreadyInValidation:protected] =>
[validationFailures:protected] => Array
(
)
[_new:BaseObject:private] =>
[_deleted:BaseObject:private] =>
[modifiedColumns:protected] => Array
(
)
)
[76] => Category Object
(
[languages:protected] =>
[bok_resources:protected] =>
[bok_topics:protected] =>
[bok_keywords:protected] =>
[id:protected] => 76
[type:protected] => category
[parent:protected] => 2
[label:protected] => Plumber/Pipefitter
[alreadyInSave:protected] =>
[alreadyInValidation:protected] =>
[validationFailures:protected] => Array
(
)
[_new:BaseObject:private] =>
[_deleted:BaseObject:private] =>
[modifiedColumns:protected] => Array
(
)
)
[77] => Category Object
(
[languages:protected] =>
[bok_resources:protected] =>
[bok_topics:protected] =>
[bok_keywords:protected] =>
[id:protected] => 77
[type:protected] => category
[parent:protected] => 2
[label:protected] => Refractory Worker
[alreadyInSave:protected] =>
[alreadyInValidation:protected] =>
[validationFailures:protected] => Array
(
)
[_new:BaseObject:private] =>
[_deleted:BaseObject:private] =>
[modifiedColumns:protected] => Array
(
)
)
[63] => Category Object
(
[languages:protected] =>
[bok_resources:protected] =>
[bok_topics:protected] =>
[bok_keywords:protected] =>
[id:protected] => 63
[type:protected] => category
[parent:protected] => 2
[label:protected] => Reinforcing Ironworker
[alreadyInSave:protected] =>
[alreadyInValidation:protected] =>
[validationFailures:protected] => Array
(
)
[_new:BaseObject:private] =>
[_deleted:BaseObject:private] =>
[modifiedColumns:protected] => Array
(
)
)
[78] => Category Object
(
[languages:protected] =>
[bok_resources:protected] =>
[bok_topics:protected] =>
[bok_keywords:protected] =>
[id:protected] => 78
[type:protected] => category
[parent:protected] => 2
[label:protected] => Roofer/Waterproofer
[alreadyInSave:protected] =>
[alreadyInValidation:protected] =>
[validationFailures:protected] => Array
(
)
[_new:BaseObject:private] =>
[_deleted:BaseObject:private] =>
[modifiedColumns:protected] => Array
(
)
)
[79] => Category Object
(
[languages:protected] =>
[bok_resources:protected] =>
[bok_topics:protected] =>
[bok_keywords:protected] =>
[id:protected] => 79
[type:protected] => category
[parent:protected] => 2
[label:protected] => Scaffold Erector
[alreadyInSave:protected] =>
[alreadyInValidation:protected] =>
[validationFailures:protected] => Array
(
)
[_new:BaseObject:private] =>
[_deleted:BaseObject:private] =>
[modifiedColumns:protected] => Array
(
)
)
[80] => Category Object
(
[languages:protected] =>
[bok_resources:protected] =>
[bok_topics:protected] =>
[bok_keywords:protected] =>
[id:protected] => 80
[type:protected] => category
[parent:protected] => 2
[label:protected] => Sheetmetal Worker
[alreadyInSave:protected] =>
[alreadyInValidation:protected] =>
[validationFailures:protected] => Array
(
)
[_new:BaseObject:private] =>
[_deleted:BaseObject:private] =>
[modifiedColumns:protected] => Array
(
)
)
[81] => Category Object
(
[languages:protected] =>
[bok_resources:protected] =>
[bok_topics:protected] =>
[bok_keywords:protected] =>
[id:protected] => 81
[type:protected] => category
[parent:protected] => 2
[label:protected] => Sprinkler Fitter
[alreadyInSave:protected] =>
[alreadyInValidation:protected] =>
[validationFailures:protected] => Array
(
)
[_new:BaseObject:private] =>
[_deleted:BaseObject:private] =>
[modifiedColumns:protected] => Array
(
)
)
[82] => Category Object
(
[languages:protected] =>
[bok_resources:protected] =>
[bok_topics:protected] =>
[bok_keywords:protected] =>
[id:protected] => 82
[type:protected] => category
[parent:protected] => 2
[label:protected] => Stonemason
[alreadyInSave:protected] =>
[alreadyInValidation:protected] =>
[validationFailures:protected] => Array
(
)
[_new:BaseObject:private] =>
[_deleted:BaseObject:private] =>
[modifiedColumns:protected] => Array
(
)
)
[62] => Category Object
(
[languages:protected] =>
[bok_resources:protected] =>
[bok_topics:protected] =>
[bok_keywords:protected] =>
[id:protected] => 62
[type:protected] => category
[parent:protected] => 2
[label:protected] => Structural Ironworker
[alreadyInSave:protected] =>
[alreadyInValidation:protected] =>
[validationFailures:protected] => Array
(
)
[_new:BaseObject:private] =>
[_deleted:BaseObject:private] =>
[modifiedColumns:protected] => Array
(
)
)
[83] => Category Object
(
[languages:protected] =>
[bok_resources:protected] =>
[bok_topics:protected] =>
[bok_keywords:protected] =>
[id:protected] => 83
[type:protected] => category
[parent:protected] => 2
[label:protected] => Terrazzo Worker
[alreadyInSave:protected] =>
[alreadyInValidation:protected] =>
[validationFailures:protected] => Array
(
)
[_new:BaseObject:private] =>
[_deleted:BaseObject:private] =>
[modifiedColumns:protected] => Array
(
)
)
[84] => Category Object
(
[languages:protected] =>
[bok_resources:protected] =>
[bok_topics:protected] =>
[bok_keywords:protected] =>
[id:protected] => 84
[type:protected] => category
[parent:protected] => 2
[label:protected] => Tile Setter
[alreadyInSave:protected] =>
[alreadyInValidation:protected] =>
[validationFailures:protected] => Array
(
)
[_new:BaseObject:private] =>
[_deleted:BaseObject:private] =>
[modifiedColumns:protected] => Array
(
)
)
[85] => Category Object
(
[languages:protected] =>
[bok_resources:protected] =>
[bok_topics:protected] =>
[bok_keywords:protected] =>
[id:protected] => 85
[type:protected] => category
[parent:protected] => 2
[label:protected] => Truck Driver
[alreadyInSave:protected] =>
[alreadyInValidation:protected] =>
[validationFailures:protected] => Array
(
)
[_new:BaseObject:private] =>
[_deleted:BaseObject:private] =>
[modifiedColumns:protected] => Array
(
)
)
[86] => Category Object
(
[languages:protected] =>
[bok_resources:protected] =>
[bok_topics:protected] =>
[bok_keywords:protected] =>
[id:protected] => 86
[type:protected] => category
[parent:protected] => 2
[label:protected] => Welder
[alreadyInSave:protected] =>
[alreadyInValidation:protected] =>
[validationFailures:protected] => Array
(
)
[_new:BaseObject:private] =>
[_deleted:BaseObject:private] =>
[modifiedColumns:protected] => Array
(
)
)
[87] => Category Object
(
[languages:protected] =>
[bok_resources:protected] =>
[bok_topics:protected] =>
[bok_keywords:protected] =>
[id:protected] => 87
[type:protected] => category
[parent:protected] => 3
[label:protected] => Commercial & Institutional
[alreadyInSave:protected] =>
[alreadyInValidation:protected] =>
[validationFailures:protected] => Array
(
)
[_new:BaseObject:private] =>
[_deleted:BaseObject:private] =>
[modifiedColumns:protected] => Array
(
)
)
[88] => Category Object
(
[languages:protected] =>
[bok_resources:protected] =>
[bok_topics:protected] =>
[bok_keywords:protected] =>
[id:protected] => 88
[type:protected] => category
[parent:protected] => 3
[label:protected] => Demolition
[alreadyInSave:protected] =>
[alreadyInValidation:protected] =>
[validationFailures:protected] => Array
(
)
[_new:BaseObject:private] =>
[_deleted:BaseObject:private] =>
[modifiedColumns:protected] => Array
(
)
)
[89] => Category Object
(
[languages:protected] =>
[bok_resources:protected] =>
[bok_topics:protected] =>
[bok_keywords:protected] =>
[id:protected] => 89
[type:protected] => category
[parent:protected] => 3
[label:protected] => Disasters
[alreadyInSave:protected] =>
[alreadyInValidation:protected] =>
[validationFailures:protected] => Array
(
)
[_new:BaseObject:private] =>
[_deleted:BaseObject:private] =>
[modifiedColumns:protected] => Array
(
)
)
[91] => Category Object
(
[languages:protected] =>
[bok_resources:protected] =>
[bok_topics:protected] =>
[bok_keywords:protected] =>
[id:protected] => 91
[type:protected] => category
[parent:protected] => 3
[label:protected] => Heavy & Highway
[alreadyInSave:protected] =>
[alreadyInValidation:protected] =>
[validationFailures:protected] => Array
(
)
[_new:BaseObject:private] =>
[_deleted:BaseObject:private] =>
[modifiedColumns:protected] => Array
(
)
)
[90] => Category Object
(
[languages:protected] =>
[bok_resources:protected] =>
[bok_topics:protected] =>
[bok_keywords:protected] =>
[id:protected] => 90
[type:protected] => category
[parent:protected] => 3
[label:protected] => Industrial
[alreadyInSave:protected] =>
[alreadyInValidation:protected] =>
[validationFailures:protected] => Array
(
)
[_new:BaseObject:private] =>
[_deleted:BaseObject:private] =>
[modifiedColumns:protected] => Array
(
)
)
[92] => Category Object
(
[languages:protected] =>
[bok_resources:protected] =>
[bok_topics:protected] =>
[bok_keywords:protected] =>
[id:protected] => 92
[type:protected] => category
[parent:protected] => 3
[label:protected] => LEED/Green Construction
[alreadyInSave:protected] =>
[alreadyInValidation:protected] =>
[validationFailures:protected] => Array
(
)
[_new:BaseObject:private] =>
[_deleted:BaseObject:private] =>
[modifiedColumns:protected] => Array
(
)
)
[93] => Category Object
(
[languages:protected] =>
[bok_resources:protected] =>
[bok_topics:protected] =>
[bok_keywords:protected] =>
[id:protected] => 93
[type:protected] => category
[parent:protected] => 3
[label:protected] => Renovations
[alreadyInSave:protected] =>
[alreadyInValidation:protected] =>
[validationFailures:protected] => Array
(
)
[_new:BaseObject:private] =>
[_deleted:BaseObject:private] =>
[modifiedColumns:protected] => Array
(
)
)
[94] => Category Object
(
[languages:protected] =>
[bok_resources:protected] =>
[bok_topics:protected] =>
[bok_keywords:protected] =>
[id:protected] => 94
[type:protected] => category
[parent:protected] => 3
[label:protected] => Residential
[alreadyInSave:protected] =>
[alreadyInValidation:protected] =>
[validationFailures:protected] => Array
(
)
[_new:BaseObject:private] =>
[_deleted:BaseObject:private] =>
[modifiedColumns:protected] => Array
(
)
)
[95] => Category Object
(
[languages:protected] =>
[bok_resources:protected] =>
[bok_topics:protected] =>
[bok_keywords:protected] =>
[id:protected] => 95
[type:protected] => category
[parent:protected] => 3
[label:protected] => Underground
[alreadyInSave:protected] =>
[alreadyInValidation:protected] =>
[validationFailures:protected] => Array
(
)
[_new:BaseObject:private] =>
[_deleted:BaseObject:private] =>
[modifiedColumns:protected] => Array
(
)
)
)
[categories_initialized:protected] => 1
[mapped_items:protected] =>
[content:protected] =>
[files:protected] =>
[language:protected] => Language Object
(
[id:protected] => 1
[code:protected] => en
[name:protected] => English
[alreadyInSave:protected] =>
[alreadyInValidation:protected] =>
[validationFailures:protected] => Array
(
)
[_new:BaseObject:private] =>
[_deleted:BaseObject:private] =>
[modifiedColumns:protected] => Array
(
)
)
[old_record:protected] =>
[id:protected] => 4426
[old_id:protected] =>
[elcosh_id:protected] => d001656
[type:protected] => document
[display_type:protected] => HTML only (and links)
[user_id:protected] => 0
[language_id:protected] => 1
[tagging_id:protected] => Mike Aguilar
[priority_id:protected] => 1
[title:protected] => Construction Dive -- DeWalt's Jobsite Pro headphones recalled for fire hazards
[total_pages:protected] => 1
[billed_pages:protected] => 1
[publication_number:protected] =>
[part_of:protected] =>
[keywords:protected] => DeWalt, Fire Hazards, recall, headphones
[comments:protected] =>
[summary:protected] => A recall notice by the United States Consumer Product Safety Commission affects over 300,000 DeWalt Jobsite Pro Headphones. The recall is a result of a malfunction that can cause earbuds to overheat while charging or during use, leading to fire and burn hazards.
[transition_comments:protected] =>
[external_link:protected] => https://www.constructiondive.com/news/dewalts-jobsite-pro-headphones-recalled-for-fire-hazards/611248/?utm_source=Sailthru&utm_medium=email&utm_campaign=Issue:%202021-12-10%20Construction%20Dive%20Newsletter%20%5Bissue:38532%5D&utm_term=Construction%20Dive
[consol_link:protected] =>
[more_like_this:protected] =>
[permission_given_by:protected] =>
[published:protected] => T
[billable:protected] => F
[img_name:protected] =>
[img_ext:protected] =>
[img_width:protected] =>
[img_height:protected] =>
[img_credit:protected] =>
[img_practice:protected] =>
[vid_source_id:protected] =>
[vid_running_time:protected] =>
[vid_intended_audience:protected] =>
[vid_acquisition_info:protected] =>
[vid_cost:protected] =>
[vid_producer:protected] =>
[vid_filename:protected] =>
[vid_filename_downloadable:protected] =>
[date_summary:protected] =>
[date_permission_requested:protected] =>
[date_permission_received:protected] =>
[date_review_needed:protected] =>
[date_received:protected] => 12/13/21
[date_completed:protected] => 12/13/21
[date_billed:protected] =>
[date_modified:protected] => 12/13/21
[collBokExports:protected] =>
[lastBokExportCriteria:BaseElcoshItem:private] =>
[alreadyInSave:protected] =>
[alreadyInValidation:protected] =>
[validationFailures:protected] => Array
(
)
[_new:BaseObject:private] =>
[_deleted:BaseObject:private] =>
[modifiedColumns:protected] => Array
(
)
)
)
)
[new_images] => Array
(
[0] => Search_Result Object
(
[title] => Morning Toolbox Talk
[image] => /record/images/4003-p.jpg
[blurb] => This photo is from an early morning toolbox talk on a construction job in Mclean, Virginia. It is being delivered in English and Spanish....
[category] => Array
(
[0] => 20
[1] => 51
[2] => 57
[3] => 64
[4] => 70
[5] => 63
[6] => 78
[7] => 82
[8] => 62
[9] => 87
[10] => 88
[11] => 89
[12] => 91
[13] => 90
[14] => 93
[15] => 94
[16] => 97
)
[labels] => Array
(
[0] => Safety Culture
[1] => Work Environment
[2] => Hazards
[3] => Cement Mason
[4] => Trades
[5] => Flagger
[7] => Laborer
[9] => Operating Engineer
[11] => Reinforcing Ironworker
[13] => Roofer/Waterproofer
[15] => Stonemason
[17] => Structural Ironworker
[19] => Commercial & Institutional
[20] => Jobsites
[21] => Demolition
[23] => Disasters
[25] => Heavy & Highway
[27] => Industrial
[29] => Renovations
[31] => Residential
[33] => Images
[34] => Media
[35] => Media & Documents
)
[type] => Images
[sub_category] =>
[url] => /image/4003/i002691/Morning%2BToolbox%2BTalk.html
[item:protected] => ImageRecord Object
(
[records:protected] => Array
(
)
[recordId:protected] =>
[searchWordClass:protected] =>
[searchWordPeerClass:protected] =>
[bok_record:protected] =>
[authors:protected] =>
[organizations:protected] =>
[collections:protected] =>
[categories:protected] => Array
(
[20] => Category Object
(
[languages:protected] =>
[bok_resources:protected] =>
[bok_topics:protected] =>
[bok_keywords:protected] =>
[id:protected] => 20
[type:protected] => category
[parent:protected] => 7
[label:protected] => Safety Culture
[alreadyInSave:protected] =>
[alreadyInValidation:protected] =>
[validationFailures:protected] => Array
(
)
[_new:BaseObject:private] =>
[_deleted:BaseObject:private] =>
[modifiedColumns:protected] => Array
(
)
)
[51] => Category Object
(
[languages:protected] =>
[bok_resources:protected] =>
[bok_topics:protected] =>
[bok_keywords:protected] =>
[id:protected] => 51
[type:protected] => category
[parent:protected] => 2
[label:protected] => Cement Mason
[alreadyInSave:protected] =>
[alreadyInValidation:protected] =>
[validationFailures:protected] => Array
(
)
[_new:BaseObject:private] =>
[_deleted:BaseObject:private] =>
[modifiedColumns:protected] => Array
(
)
)
[57] => Category Object
(
[languages:protected] =>
[bok_resources:protected] =>
[bok_topics:protected] =>
[bok_keywords:protected] =>
[id:protected] => 57
[type:protected] => category
[parent:protected] => 2
[label:protected] => Flagger
[alreadyInSave:protected] =>
[alreadyInValidation:protected] =>
[validationFailures:protected] => Array
(
)
[_new:BaseObject:private] =>
[_deleted:BaseObject:private] =>
[modifiedColumns:protected] => Array
(
)
)
[64] => Category Object
(
[languages:protected] =>
[bok_resources:protected] =>
[bok_topics:protected] =>
[bok_keywords:protected] =>
[id:protected] => 64
[type:protected] => category
[parent:protected] => 2
[label:protected] => Laborer
[alreadyInSave:protected] =>
[alreadyInValidation:protected] =>
[validationFailures:protected] => Array
(
)
[_new:BaseObject:private] =>
[_deleted:BaseObject:private] =>
[modifiedColumns:protected] => Array
(
)
)
[70] => Category Object
(
[languages:protected] =>
[bok_resources:protected] =>
[bok_topics:protected] =>
[bok_keywords:protected] =>
[id:protected] => 70
[type:protected] => category
[parent:protected] => 2
[label:protected] => Operating Engineer
[alreadyInSave:protected] =>
[alreadyInValidation:protected] =>
[validationFailures:protected] => Array
(
)
[_new:BaseObject:private] =>
[_deleted:BaseObject:private] =>
[modifiedColumns:protected] => Array
(
)
)
[63] => Category Object
(
[languages:protected] =>
[bok_resources:protected] =>
[bok_topics:protected] =>
[bok_keywords:protected] =>
[id:protected] => 63
[type:protected] => category
[parent:protected] => 2
[label:protected] => Reinforcing Ironworker
[alreadyInSave:protected] =>
[alreadyInValidation:protected] =>
[validationFailures:protected] => Array
(
)
[_new:BaseObject:private] =>
[_deleted:BaseObject:private] =>
[modifiedColumns:protected] => Array
(
)
)
[78] => Category Object
(
[languages:protected] =>
[bok_resources:protected] =>
[bok_topics:protected] =>
[bok_keywords:protected] =>
[id:protected] => 78
[type:protected] => category
[parent:protected] => 2
[label:protected] => Roofer/Waterproofer
[alreadyInSave:protected] =>
[alreadyInValidation:protected] =>
[validationFailures:protected] => Array
(
)
[_new:BaseObject:private] =>
[_deleted:BaseObject:private] =>
[modifiedColumns:protected] => Array
(
)
)
[82] => Category Object
(
[languages:protected] =>
[bok_resources:protected] =>
[bok_topics:protected] =>
[bok_keywords:protected] =>
[id:protected] => 82
[type:protected] => category
[parent:protected] => 2
[label:protected] => Stonemason
[alreadyInSave:protected] =>
[alreadyInValidation:protected] =>
[validationFailures:protected] => Array
(
)
[_new:BaseObject:private] =>
[_deleted:BaseObject:private] =>
[modifiedColumns:protected] => Array
(
)
)
[62] => Category Object
(
[languages:protected] =>
[bok_resources:protected] =>
[bok_topics:protected] =>
[bok_keywords:protected] =>
[id:protected] => 62
[type:protected] => category
[parent:protected] => 2
[label:protected] => Structural Ironworker
[alreadyInSave:protected] =>
[alreadyInValidation:protected] =>
[validationFailures:protected] => Array
(
)
[_new:BaseObject:private] =>
[_deleted:BaseObject:private] =>
[modifiedColumns:protected] => Array
(
)
)
[87] => Category Object
(
[languages:protected] =>
[bok_resources:protected] =>
[bok_topics:protected] =>
[bok_keywords:protected] =>
[id:protected] => 87
[type:protected] => category
[parent:protected] => 3
[label:protected] => Commercial & Institutional
[alreadyInSave:protected] =>
[alreadyInValidation:protected] =>
[validationFailures:protected] => Array
(
)
[_new:BaseObject:private] =>
[_deleted:BaseObject:private] =>
[modifiedColumns:protected] => Array
(
)
)
[88] => Category Object
(
[languages:protected] =>
[bok_resources:protected] =>
[bok_topics:protected] =>
[bok_keywords:protected] =>
[id:protected] => 88
[type:protected] => category
[parent:protected] => 3
[label:protected] => Demolition
[alreadyInSave:protected] =>
[alreadyInValidation:protected] =>
[validationFailures:protected] => Array
(
)
[_new:BaseObject:private] =>
[_deleted:BaseObject:private] =>
[modifiedColumns:protected] => Array
(
)
)
[89] => Category Object
(
[languages:protected] =>
[bok_resources:protected] =>
[bok_topics:protected] =>
[bok_keywords:protected] =>
[id:protected] => 89
[type:protected] => category
[parent:protected] => 3
[label:protected] => Disasters
[alreadyInSave:protected] =>
[alreadyInValidation:protected] =>
[validationFailures:protected] => Array
(
)
[_new:BaseObject:private] =>
[_deleted:BaseObject:private] =>
[modifiedColumns:protected] => Array
(
)
)
[91] => Category Object
(
[languages:protected] =>
[bok_resources:protected] =>
[bok_topics:protected] =>
[bok_keywords:protected] =>
[id:protected] => 91
[type:protected] => category
[parent:protected] => 3
[label:protected] => Heavy & Highway
[alreadyInSave:protected] =>
[alreadyInValidation:protected] =>
[validationFailures:protected] => Array
(
)
[_new:BaseObject:private] =>
[_deleted:BaseObject:private] =>
[modifiedColumns:protected] => Array
(
)
)
[90] => Category Object
(
[languages:protected] =>
[bok_resources:protected] =>
[bok_topics:protected] =>
[bok_keywords:protected] =>
[id:protected] => 90
[type:protected] => category
[parent:protected] => 3
[label:protected] => Industrial
[alreadyInSave:protected] =>
[alreadyInValidation:protected] =>
[validationFailures:protected] => Array
(
)
[_new:BaseObject:private] =>
[_deleted:BaseObject:private] =>
[modifiedColumns:protected] => Array
(
)
)
[93] => Category Object
(
[languages:protected] =>
[bok_resources:protected] =>
[bok_topics:protected] =>
[bok_keywords:protected] =>
[id:protected] => 93
[type:protected] => category
[parent:protected] => 3
[label:protected] => Renovations
[alreadyInSave:protected] =>
[alreadyInValidation:protected] =>
[validationFailures:protected] => Array
(
)
[_new:BaseObject:private] =>
[_deleted:BaseObject:private] =>
[modifiedColumns:protected] => Array
(
)
)
[94] => Category Object
(
[languages:protected] =>
[bok_resources:protected] =>
[bok_topics:protected] =>
[bok_keywords:protected] =>
[id:protected] => 94
[type:protected] => category
[parent:protected] => 3
[label:protected] => Residential
[alreadyInSave:protected] =>
[alreadyInValidation:protected] =>
[validationFailures:protected] => Array
(
)
[_new:BaseObject:private] =>
[_deleted:BaseObject:private] =>
[modifiedColumns:protected] => Array
(
)
)
[97] => Category Object
(
[languages:protected] =>
[bok_resources:protected] =>
[bok_topics:protected] =>
[bok_keywords:protected] =>
[id:protected] => 97
[type:protected] => category
[parent:protected] => 5
[label:protected] => Images
[alreadyInSave:protected] =>
[alreadyInValidation:protected] =>
[validationFailures:protected] => Array
(
)
[_new:BaseObject:private] =>
[_deleted:BaseObject:private] =>
[modifiedColumns:protected] => Array
(
)
)
)
[categories_initialized:protected] => 1
[mapped_items:protected] =>
[content:protected] =>
[files:protected] =>
[language:protected] => Language Object
(
[id:protected] => 1
[code:protected] => en
[name:protected] => English
[alreadyInSave:protected] =>
[alreadyInValidation:protected] =>
[validationFailures:protected] => Array
(
)
[_new:BaseObject:private] =>
[_deleted:BaseObject:private] =>
[modifiedColumns:protected] => Array
(
)
)
[old_record:protected] =>
[id:protected] => 4003
[old_id:protected] =>
[elcosh_id:protected] => i002691
[type:protected] => image
[display_type:protected] => Image
[user_id:protected] => 0
[language_id:protected] => 1
[tagging_id:protected] => Bruce Lippy
[priority_id:protected] => 1
[title:protected] => Morning Toolbox Talk
[total_pages:protected] => 0
[billed_pages:protected] => 0
[publication_number:protected] =>
[part_of:protected] =>
[keywords:protected] => toolbox talk, tailgate talk, Spanish, bilingual
[comments:protected] =>
[summary:protected] => This photo is from an early morning toolbox talk on a construction job in Mclean, Virginia. It is being delivered in English and Spanish.
[transition_comments:protected] =>
[external_link:protected] =>
[consol_link:protected] => http://www.cpwrconstructionsolutions.org/electrical/solution/662/worker-training.html
[more_like_this:protected] => d001285,d001304,c000079
[permission_given_by:protected] =>
[published:protected] => T
[billable:protected] => F
[img_name:protected] =>
[img_ext:protected] => jpg
[img_width:protected] =>
[img_height:protected] =>
[img_credit:protected] => Morgan Zavertnik and Hoar Construction
[img_practice:protected] => good
[vid_source_id:protected] =>
[vid_running_time:protected] =>
[vid_intended_audience:protected] =>
[vid_acquisition_info:protected] =>
[vid_cost:protected] =>
[vid_producer:protected] =>
[vid_filename:protected] =>
[vid_filename_downloadable:protected] =>
[date_summary:protected] => November 2015
[date_permission_requested:protected] =>
[date_permission_received:protected] =>
[date_review_needed:protected] =>
[date_received:protected] => 03/02/16
[date_completed:protected] => 03/02/16
[date_billed:protected] =>
[date_modified:protected] => 03/02/16
[collBokExports:protected] =>
[lastBokExportCriteria:BaseElcoshItem:private] =>
[alreadyInSave:protected] =>
[alreadyInValidation:protected] =>
[validationFailures:protected] => Array
(
)
[_new:BaseObject:private] =>
[_deleted:BaseObject:private] =>
[modifiedColumns:protected] => Array
(
)
)
)
[1] => Search_Result Object
(
[title] => Toolbox talk - crew view
[image] => /record/images/4005-p.jpg
[blurb] => Photo of crew listening to a toolbox safety talk before starting work....
[category] => Array
(
[0] => 97
[1] => 20
[2] => 47
[3] => 49
[4] => 51
[5] => 55
[6] => 61
[7] => 64
[8] => 71
[9] => 75
[10] => 63
[11] => 79
[12] => 62
[13] => 87
[14] => 88
[15] => 91
[16] => 90
[17] => 93
[18] => 94
[19] => 95
)
[labels] => Array
(
[0] => Images
[1] => Media
[2] => Media & Documents
[3] => Safety Culture
[4] => Work Environment
[5] => Hazards
[6] => Bricklayer
[7] => Trades
[8] => Carpenter
[10] => Cement Mason
[12] => Electrical Worker
[14] => Interior Systems Carpenter
[16] => Laborer
[18] => Painter
[20] => Plasterer
[22] => Reinforcing Ironworker
[24] => Scaffold Erector
[26] => Structural Ironworker
[28] => Commercial & Institutional
[29] => Jobsites
[30] => Demolition
[32] => Heavy & Highway
[34] => Industrial
[36] => Renovations
[38] => Residential
[40] => Underground
)
[type] => Images
[sub_category] =>
[url] => /image/4005/i002692/Toolbox%2Btalk%2B-%2Bcrew%2Bview.html
[item:protected] => ImageRecord Object
(
[records:protected] => Array
(
)
[recordId:protected] =>
[searchWordClass:protected] =>
[searchWordPeerClass:protected] =>
[bok_record:protected] =>
[authors:protected] =>
[organizations:protected] =>
[collections:protected] =>
[categories:protected] => Array
(
[97] => Category Object
(
[languages:protected] =>
[bok_resources:protected] =>
[bok_topics:protected] =>
[bok_keywords:protected] =>
[id:protected] => 97
[type:protected] => category
[parent:protected] => 5
[label:protected] => Images
[alreadyInSave:protected] =>
[alreadyInValidation:protected] =>
[validationFailures:protected] => Array
(
)
[_new:BaseObject:private] =>
[_deleted:BaseObject:private] =>
[modifiedColumns:protected] => Array
(
)
)
[20] => Category Object
(
[languages:protected] =>
[bok_resources:protected] =>
[bok_topics:protected] =>
[bok_keywords:protected] =>
[id:protected] => 20
[type:protected] => category
[parent:protected] => 7
[label:protected] => Safety Culture
[alreadyInSave:protected] =>
[alreadyInValidation:protected] =>
[validationFailures:protected] => Array
(
)
[_new:BaseObject:private] =>
[_deleted:BaseObject:private] =>
[modifiedColumns:protected] => Array
(
)
)
[47] => Category Object
(
[languages:protected] =>
[bok_resources:protected] =>
[bok_topics:protected] =>
[bok_keywords:protected] =>
[id:protected] => 47
[type:protected] => category
[parent:protected] => 2
[label:protected] => Bricklayer
[alreadyInSave:protected] =>
[alreadyInValidation:protected] =>
[validationFailures:protected] => Array
(
)
[_new:BaseObject:private] =>
[_deleted:BaseObject:private] =>
[modifiedColumns:protected] => Array
(
)
)
[49] => Category Object
(
[languages:protected] =>
[bok_resources:protected] =>
[bok_topics:protected] =>
[bok_keywords:protected] =>
[id:protected] => 49
[type:protected] => category
[parent:protected] => 2
[label:protected] => Carpenter
[alreadyInSave:protected] =>
[alreadyInValidation:protected] =>
[validationFailures:protected] => Array
(
)
[_new:BaseObject:private] =>
[_deleted:BaseObject:private] =>
[modifiedColumns:protected] => Array
(
)
)
[51] => Category Object
(
[languages:protected] =>
[bok_resources:protected] =>
[bok_topics:protected] =>
[bok_keywords:protected] =>
[id:protected] => 51
[type:protected] => category
[parent:protected] => 2
[label:protected] => Cement Mason
[alreadyInSave:protected] =>
[alreadyInValidation:protected] =>
[validationFailures:protected] => Array
(
)
[_new:BaseObject:private] =>
[_deleted:BaseObject:private] =>
[modifiedColumns:protected] => Array
(
)
)
[55] => Category Object
(
[languages:protected] =>
[bok_resources:protected] =>
[bok_topics:protected] =>
[bok_keywords:protected] =>
[id:protected] => 55
[type:protected] => category
[parent:protected] => 2
[label:protected] => Electrical Worker
[alreadyInSave:protected] =>
[alreadyInValidation:protected] =>
[validationFailures:protected] => Array
(
)
[_new:BaseObject:private] =>
[_deleted:BaseObject:private] =>
[modifiedColumns:protected] => Array
(
)
)
[61] => Category Object
(
[languages:protected] =>
[bok_resources:protected] =>
[bok_topics:protected] =>
[bok_keywords:protected] =>
[id:protected] => 61
[type:protected] => category
[parent:protected] => 2
[label:protected] => Interior Systems Carpenter
[alreadyInSave:protected] =>
[alreadyInValidation:protected] =>
[validationFailures:protected] => Array
(
)
[_new:BaseObject:private] =>
[_deleted:BaseObject:private] =>
[modifiedColumns:protected] => Array
(
)
)
[64] => Category Object
(
[languages:protected] =>
[bok_resources:protected] =>
[bok_topics:protected] =>
[bok_keywords:protected] =>
[id:protected] => 64
[type:protected] => category
[parent:protected] => 2
[label:protected] => Laborer
[alreadyInSave:protected] =>
[alreadyInValidation:protected] =>
[validationFailures:protected] => Array
(
)
[_new:BaseObject:private] =>
[_deleted:BaseObject:private] =>
[modifiedColumns:protected] => Array
(
)
)
[71] => Category Object
(
[languages:protected] =>
[bok_resources:protected] =>
[bok_topics:protected] =>
[bok_keywords:protected] =>
[id:protected] => 71
[type:protected] => category
[parent:protected] => 2
[label:protected] => Painter
[alreadyInSave:protected] =>
[alreadyInValidation:protected] =>
[validationFailures:protected] => Array
(
)
[_new:BaseObject:private] =>
[_deleted:BaseObject:private] =>
[modifiedColumns:protected] => Array
(
)
)
[75] => Category Object
(
[languages:protected] =>
[bok_resources:protected] =>
[bok_topics:protected] =>
[bok_keywords:protected] =>
[id:protected] => 75
[type:protected] => category
[parent:protected] => 2
[label:protected] => Plasterer
[alreadyInSave:protected] =>
[alreadyInValidation:protected] =>
[validationFailures:protected] => Array
(
)
[_new:BaseObject:private] =>
[_deleted:BaseObject:private] =>
[modifiedColumns:protected] => Array
(
)
)
[63] => Category Object
(
[languages:protected] =>
[bok_resources:protected] =>
[bok_topics:protected] =>
[bok_keywords:protected] =>
[id:protected] => 63
[type:protected] => category
[parent:protected] => 2
[label:protected] => Reinforcing Ironworker
[alreadyInSave:protected] =>
[alreadyInValidation:protected] =>
[validationFailures:protected] => Array
(
)
[_new:BaseObject:private] =>
[_deleted:BaseObject:private] =>
[modifiedColumns:protected] => Array
(
)
)
[79] => Category Object
(
[languages:protected] =>
[bok_resources:protected] =>
[bok_topics:protected] =>
[bok_keywords:protected] =>
[id:protected] => 79
[type:protected] => category
[parent:protected] => 2
[label:protected] => Scaffold Erector
[alreadyInSave:protected] =>
[alreadyInValidation:protected] =>
[validationFailures:protected] => Array
(
)
[_new:BaseObject:private] =>
[_deleted:BaseObject:private] =>
[modifiedColumns:protected] => Array
(
)
)
[62] => Category Object
(
[languages:protected] =>
[bok_resources:protected] =>
[bok_topics:protected] =>
[bok_keywords:protected] =>
[id:protected] => 62
[type:protected] => category
[parent:protected] => 2
[label:protected] => Structural Ironworker
[alreadyInSave:protected] =>
[alreadyInValidation:protected] =>
[validationFailures:protected] => Array
(
)
[_new:BaseObject:private] =>
[_deleted:BaseObject:private] =>
[modifiedColumns:protected] => Array
(
)
)
[87] => Category Object
(
[languages:protected] =>
[bok_resources:protected] =>
[bok_topics:protected] =>
[bok_keywords:protected] =>
[id:protected] => 87
[type:protected] => category
[parent:protected] => 3
[label:protected] => Commercial & Institutional
[alreadyInSave:protected] =>
[alreadyInValidation:protected] =>
[validationFailures:protected] => Array
(
)
[_new:BaseObject:private] =>
[_deleted:BaseObject:private] =>
[modifiedColumns:protected] => Array
(
)
)
[88] => Category Object
(
[languages:protected] =>
[bok_resources:protected] =>
[bok_topics:protected] =>
[bok_keywords:protected] =>
[id:protected] => 88
[type:protected] => category
[parent:protected] => 3
[label:protected] => Demolition
[alreadyInSave:protected] =>
[alreadyInValidation:protected] =>
[validationFailures:protected] => Array
(
)
[_new:BaseObject:private] =>
[_deleted:BaseObject:private] =>
[modifiedColumns:protected] => Array
(
)
)
[91] => Category Object
(
[languages:protected] =>
[bok_resources:protected] =>
[bok_topics:protected] =>
[bok_keywords:protected] =>
[id:protected] => 91
[type:protected] => category
[parent:protected] => 3
[label:protected] => Heavy & Highway
[alreadyInSave:protected] =>
[alreadyInValidation:protected] =>
[validationFailures:protected] => Array
(
)
[_new:BaseObject:private] =>
[_deleted:BaseObject:private] =>
[modifiedColumns:protected] => Array
(
)
)
[90] => Category Object
(
[languages:protected] =>
[bok_resources:protected] =>
[bok_topics:protected] =>
[bok_keywords:protected] =>
[id:protected] => 90
[type:protected] => category
[parent:protected] => 3
[label:protected] => Industrial
[alreadyInSave:protected] =>
[alreadyInValidation:protected] =>
[validationFailures:protected] => Array
(
)
[_new:BaseObject:private] =>
[_deleted:BaseObject:private] =>
[modifiedColumns:protected] => Array
(
)
)
[93] => Category Object
(
[languages:protected] =>
[bok_resources:protected] =>
[bok_topics:protected] =>
[bok_keywords:protected] =>
[id:protected] => 93
[type:protected] => category
[parent:protected] => 3
[label:protected] => Renovations
[alreadyInSave:protected] =>
[alreadyInValidation:protected] =>
[validationFailures:protected] => Array
(
)
[_new:BaseObject:private] =>
[_deleted:BaseObject:private] =>
[modifiedColumns:protected] => Array
(
)
)
[94] => Category Object
(
[languages:protected] =>
[bok_resources:protected] =>
[bok_topics:protected] =>
[bok_keywords:protected] =>
[id:protected] => 94
[type:protected] => category
[parent:protected] => 3
[label:protected] => Residential
[alreadyInSave:protected] =>
[alreadyInValidation:protected] =>
[validationFailures:protected] => Array
(
)
[_new:BaseObject:private] =>
[_deleted:BaseObject:private] =>
[modifiedColumns:protected] => Array
(
)
)
[95] => Category Object
(
[languages:protected] =>
[bok_resources:protected] =>
[bok_topics:protected] =>
[bok_keywords:protected] =>
[id:protected] => 95
[type:protected] => category
[parent:protected] => 3
[label:protected] => Underground
[alreadyInSave:protected] =>
[alreadyInValidation:protected] =>
[validationFailures:protected] => Array
(
)
[_new:BaseObject:private] =>
[_deleted:BaseObject:private] =>
[modifiedColumns:protected] => Array
(
)
)
)
[categories_initialized:protected] => 1
[mapped_items:protected] =>
[content:protected] =>
[files:protected] =>
[language:protected] => Language Object
(
[id:protected] => 1
[code:protected] => en
[name:protected] => English
[alreadyInSave:protected] =>
[alreadyInValidation:protected] =>
[validationFailures:protected] => Array
(
)
[_new:BaseObject:private] =>
[_deleted:BaseObject:private] =>
[modifiedColumns:protected] => Array
(
)
)
[old_record:protected] =>
[id:protected] => 4005
[old_id:protected] =>
[elcosh_id:protected] => i002692
[type:protected] => image
[display_type:protected] => Image
[user_id:protected] => 0
[language_id:protected] => 1
[tagging_id:protected] => Bruce Lippy
[priority_id:protected] => 1
[title:protected] => Toolbox talk - crew view
[total_pages:protected] => 0
[billed_pages:protected] => 0
[publication_number:protected] =>
[part_of:protected] =>
[keywords:protected] => toolbox talk, tailgate talk, safety talk, Spanish
[comments:protected] =>
[summary:protected] => Photo of crew listening to a toolbox safety talk before starting work.
[transition_comments:protected] =>
[external_link:protected] =>
[consol_link:protected] => http://www.cpwrconstructionsolutions.org/electrical/solution/662/worker-training.html
[more_like_this:protected] => i002691,d001269, c000079, d001285
[permission_given_by:protected] =>
[published:protected] => T
[billable:protected] => F
[img_name:protected] =>
[img_ext:protected] => jpg
[img_width:protected] =>
[img_height:protected] =>
[img_credit:protected] => Morgan Zavertnik and Hoar Construction
[img_practice:protected] => good
[vid_source_id:protected] =>
[vid_running_time:protected] =>
[vid_intended_audience:protected] =>
[vid_acquisition_info:protected] =>
[vid_cost:protected] =>
[vid_producer:protected] =>
[vid_filename:protected] =>
[vid_filename_downloadable:protected] =>
[date_summary:protected] => November 2015
[date_permission_requested:protected] =>
[date_permission_received:protected] =>
[date_review_needed:protected] =>
[date_received:protected] => 03/02/16
[date_completed:protected] => 03/02/16
[date_billed:protected] =>
[date_modified:protected] => 03/02/16
[collBokExports:protected] =>
[lastBokExportCriteria:BaseElcoshItem:private] =>
[alreadyInSave:protected] =>
[alreadyInValidation:protected] =>
[validationFailures:protected] => Array
(
)
[_new:BaseObject:private] =>
[_deleted:BaseObject:private] =>
[modifiedColumns:protected] => Array
(
)
)
)
[2] => Search_Result Object
(
[title] => Toolbox talk - long shot
[image] => /record/images/4006-p.jpg
[blurb] => This crew gathered every morning before starting work to discuss a new safety topic....
[category] => Array
(
[0] => 20
[1] => 47
[2] => 49
[3] => 51
[4] => 55
[5] => 64
[6] => 68
[7] => 75
[8] => 76
[9] => 63
[10] => 78
[11] => 79
[12] => 82
[13] => 62
[14] => 87
[15] => 88
[16] => 91
[17] => 90
[18] => 93
[19] => 94
[20] => 95
[21] => 97
)
[labels] => Array
(
[0] => Safety Culture
[1] => Work Environment
[2] => Hazards
[3] => Bricklayer
[4] => Trades
[5] => Carpenter
[7] => Cement Mason
[9] => Electrical Worker
[11] => Laborer
[13] => Maintenance Worker
[15] => Plasterer
[17] => Plumber/Pipefitter
[19] => Reinforcing Ironworker
[21] => Roofer/Waterproofer
[23] => Scaffold Erector
[25] => Stonemason
[27] => Structural Ironworker
[29] => Commercial & Institutional
[30] => Jobsites
[31] => Demolition
[33] => Heavy & Highway
[35] => Industrial
[37] => Renovations
[39] => Residential
[41] => Underground
[43] => Images
[44] => Media
[45] => Media & Documents
)
[type] => Images
[sub_category] =>
[url] => /image/4006/i002693/Toolbox%2Btalk%2B-%2Blong%2Bshot.html
[item:protected] => ImageRecord Object
(
[records:protected] => Array
(
)
[recordId:protected] =>
[searchWordClass:protected] =>
[searchWordPeerClass:protected] =>
[bok_record:protected] =>
[authors:protected] =>
[organizations:protected] =>
[collections:protected] =>
[categories:protected] => Array
(
[20] => Category Object
(
[languages:protected] =>
[bok_resources:protected] =>
[bok_topics:protected] =>
[bok_keywords:protected] =>
[id:protected] => 20
[type:protected] => category
[parent:protected] => 7
[label:protected] => Safety Culture
[alreadyInSave:protected] =>
[alreadyInValidation:protected] =>
[validationFailures:protected] => Array
(
)
[_new:BaseObject:private] =>
[_deleted:BaseObject:private] =>
[modifiedColumns:protected] => Array
(
)
)
[47] => Category Object
(
[languages:protected] =>
[bok_resources:protected] =>
[bok_topics:protected] =>
[bok_keywords:protected] =>
[id:protected] => 47
[type:protected] => category
[parent:protected] => 2
[label:protected] => Bricklayer
[alreadyInSave:protected] =>
[alreadyInValidation:protected] =>
[validationFailures:protected] => Array
(
)
[_new:BaseObject:private] =>
[_deleted:BaseObject:private] =>
[modifiedColumns:protected] => Array
(
)
)
[49] => Category Object
(
[languages:protected] =>
[bok_resources:protected] =>
[bok_topics:protected] =>
[bok_keywords:protected] =>
[id:protected] => 49
[type:protected] => category
[parent:protected] => 2
[label:protected] => Carpenter
[alreadyInSave:protected] =>
[alreadyInValidation:protected] =>
[validationFailures:protected] => Array
(
)
[_new:BaseObject:private] =>
[_deleted:BaseObject:private] =>
[modifiedColumns:protected] => Array
(
)
)
[51] => Category Object
(
[languages:protected] =>
[bok_resources:protected] =>
[bok_topics:protected] =>
[bok_keywords:protected] =>
[id:protected] => 51
[type:protected] => category
[parent:protected] => 2
[label:protected] => Cement Mason
[alreadyInSave:protected] =>
[alreadyInValidation:protected] =>
[validationFailures:protected] => Array
(
)
[_new:BaseObject:private] =>
[_deleted:BaseObject:private] =>
[modifiedColumns:protected] => Array
(
)
)
[55] => Category Object
(
[languages:protected] =>
[bok_resources:protected] =>
[bok_topics:protected] =>
[bok_keywords:protected] =>
[id:protected] => 55
[type:protected] => category
[parent:protected] => 2
[label:protected] => Electrical Worker
[alreadyInSave:protected] =>
[alreadyInValidation:protected] =>
[validationFailures:protected] => Array
(
)
[_new:BaseObject:private] =>
[_deleted:BaseObject:private] =>
[modifiedColumns:protected] => Array
(
)
)
[64] => Category Object
(
[languages:protected] =>
[bok_resources:protected] =>
[bok_topics:protected] =>
[bok_keywords:protected] =>
[id:protected] => 64
[type:protected] => category
[parent:protected] => 2
[label:protected] => Laborer
[alreadyInSave:protected] =>
[alreadyInValidation:protected] =>
[validationFailures:protected] => Array
(
)
[_new:BaseObject:private] =>
[_deleted:BaseObject:private] =>
[modifiedColumns:protected] => Array
(
)
)
[68] => Category Object
(
[languages:protected] =>
[bok_resources:protected] =>
[bok_topics:protected] =>
[bok_keywords:protected] =>
[id:protected] => 68
[type:protected] => category
[parent:protected] => 2
[label:protected] => Maintenance Worker
[alreadyInSave:protected] =>
[alreadyInValidation:protected] =>
[validationFailures:protected] => Array
(
)
[_new:BaseObject:private] =>
[_deleted:BaseObject:private] =>
[modifiedColumns:protected] => Array
(
)
)
[75] => Category Object
(
[languages:protected] =>
[bok_resources:protected] =>
[bok_topics:protected] =>
[bok_keywords:protected] =>
[id:protected] => 75
[type:protected] => category
[parent:protected] => 2
[label:protected] => Plasterer
[alreadyInSave:protected] =>
[alreadyInValidation:protected] =>
[validationFailures:protected] => Array
(
)
[_new:BaseObject:private] =>
[_deleted:BaseObject:private] =>
[modifiedColumns:protected] => Array
(
)
)
[76] => Category Object
(
[languages:protected] =>
[bok_resources:protected] =>
[bok_topics:protected] =>
[bok_keywords:protected] =>
[id:protected] => 76
[type:protected] => category
[parent:protected] => 2
[label:protected] => Plumber/Pipefitter
[alreadyInSave:protected] =>
[alreadyInValidation:protected] =>
[validationFailures:protected] => Array
(
)
[_new:BaseObject:private] =>
[_deleted:BaseObject:private] =>
[modifiedColumns:protected] => Array
(
)
)
[63] => Category Object
(
[languages:protected] =>
[bok_resources:protected] =>
[bok_topics:protected] =>
[bok_keywords:protected] =>
[id:protected] => 63
[type:protected] => category
[parent:protected] => 2
[label:protected] => Reinforcing Ironworker
[alreadyInSave:protected] =>
[alreadyInValidation:protected] =>
[validationFailures:protected] => Array
(
)
[_new:BaseObject:private] =>
[_deleted:BaseObject:private] =>
[modifiedColumns:protected] => Array
(
)
)
[78] => Category Object
(
[languages:protected] =>
[bok_resources:protected] =>
[bok_topics:protected] =>
[bok_keywords:protected] =>
[id:protected] => 78
[type:protected] => category
[parent:protected] => 2
[label:protected] => Roofer/Waterproofer
[alreadyInSave:protected] =>
[alreadyInValidation:protected] =>
[validationFailures:protected] => Array
(
)
[_new:BaseObject:private] =>
[_deleted:BaseObject:private] =>
[modifiedColumns:protected] => Array
(
)
)
[79] => Category Object
(
[languages:protected] =>
[bok_resources:protected] =>
[bok_topics:protected] =>
[bok_keywords:protected] =>
[id:protected] => 79
[type:protected] => category
[parent:protected] => 2
[label:protected] => Scaffold Erector
[alreadyInSave:protected] =>
[alreadyInValidation:protected] =>
[validationFailures:protected] => Array
(
)
[_new:BaseObject:private] =>
[_deleted:BaseObject:private] =>
[modifiedColumns:protected] => Array
(
)
)
[82] => Category Object
(
[languages:protected] =>
[bok_resources:protected] =>
[bok_topics:protected] =>
[bok_keywords:protected] =>
[id:protected] => 82
[type:protected] => category
[parent:protected] => 2
[label:protected] => Stonemason
[alreadyInSave:protected] =>
[alreadyInValidation:protected] =>
[validationFailures:protected] => Array
(
)
[_new:BaseObject:private] =>
[_deleted:BaseObject:private] =>
[modifiedColumns:protected] => Array
(
)
)
[62] => Category Object
(
[languages:protected] =>
[bok_resources:protected] =>
[bok_topics:protected] =>
[bok_keywords:protected] =>
[id:protected] => 62
[type:protected] => category
[parent:protected] => 2
[label:protected] => Structural Ironworker
[alreadyInSave:protected] =>
[alreadyInValidation:protected] =>
[validationFailures:protected] => Array
(
)
[_new:BaseObject:private] =>
[_deleted:BaseObject:private] =>
[modifiedColumns:protected] => Array
(
)
)
[87] => Category Object
(
[languages:protected] =>
[bok_resources:protected] =>
[bok_topics:protected] =>
[bok_keywords:protected] =>
[id:protected] => 87
[type:protected] => category
[parent:protected] => 3
[label:protected] => Commercial & Institutional
[alreadyInSave:protected] =>
[alreadyInValidation:protected] =>
[validationFailures:protected] => Array
(
)
[_new:BaseObject:private] =>
[_deleted:BaseObject:private] =>
[modifiedColumns:protected] => Array
(
)
)
[88] => Category Object
(
[languages:protected] =>
[bok_resources:protected] =>
[bok_topics:protected] =>
[bok_keywords:protected] =>
[id:protected] => 88
[type:protected] => category
[parent:protected] => 3
[label:protected] => Demolition
[alreadyInSave:protected] =>
[alreadyInValidation:protected] =>
[validationFailures:protected] => Array
(
)
[_new:BaseObject:private] =>
[_deleted:BaseObject:private] =>
[modifiedColumns:protected] => Array
(
)
)
[91] => Category Object
(
[languages:protected] =>
[bok_resources:protected] =>
[bok_topics:protected] =>
[bok_keywords:protected] =>
[id:protected] => 91
[type:protected] => category
[parent:protected] => 3
[label:protected] => Heavy & Highway
[alreadyInSave:protected] =>
[alreadyInValidation:protected] =>
[validationFailures:protected] => Array
(
)
[_new:BaseObject:private] =>
[_deleted:BaseObject:private] =>
[modifiedColumns:protected] => Array
(
)
)
[90] => Category Object
(
[languages:protected] =>
[bok_resources:protected] =>
[bok_topics:protected] =>
[bok_keywords:protected] =>
[id:protected] => 90
[type:protected] => category
[parent:protected] => 3
[label:protected] => Industrial
[alreadyInSave:protected] =>
[alreadyInValidation:protected] =>
[validationFailures:protected] => Array
(
)
[_new:BaseObject:private] =>
[_deleted:BaseObject:private] =>
[modifiedColumns:protected] => Array
(
)
)
[93] => Category Object
(
[languages:protected] =>
[bok_resources:protected] =>
[bok_topics:protected] =>
[bok_keywords:protected] =>
[id:protected] => 93
[type:protected] => category
[parent:protected] => 3
[label:protected] => Renovations
[alreadyInSave:protected] =>
[alreadyInValidation:protected] =>
[validationFailures:protected] => Array
(
)
[_new:BaseObject:private] =>
[_deleted:BaseObject:private] =>
[modifiedColumns:protected] => Array
(
)
)
[94] => Category Object
(
[languages:protected] =>
[bok_resources:protected] =>
[bok_topics:protected] =>
[bok_keywords:protected] =>
[id:protected] => 94
[type:protected] => category
[parent:protected] => 3
[label:protected] => Residential
[alreadyInSave:protected] =>
[alreadyInValidation:protected] =>
[validationFailures:protected] => Array
(
)
[_new:BaseObject:private] =>
[_deleted:BaseObject:private] =>
[modifiedColumns:protected] => Array
(
)
)
[95] => Category Object
(
[languages:protected] =>
[bok_resources:protected] =>
[bok_topics:protected] =>
[bok_keywords:protected] =>
[id:protected] => 95
[type:protected] => category
[parent:protected] => 3
[label:protected] => Underground
[alreadyInSave:protected] =>
[alreadyInValidation:protected] =>
[validationFailures:protected] => Array
(
)
[_new:BaseObject:private] =>
[_deleted:BaseObject:private] =>
[modifiedColumns:protected] => Array
(
)
)
[97] => Category Object
(
[languages:protected] =>
[bok_resources:protected] =>
[bok_topics:protected] =>
[bok_keywords:protected] =>
[id:protected] => 97
[type:protected] => category
[parent:protected] => 5
[label:protected] => Images
[alreadyInSave:protected] =>
[alreadyInValidation:protected] =>
[validationFailures:protected] => Array
(
)
[_new:BaseObject:private] =>
[_deleted:BaseObject:private] =>
[modifiedColumns:protected] => Array
(
)
)
)
[categories_initialized:protected] => 1
[mapped_items:protected] =>
[content:protected] =>
[files:protected] =>
[language:protected] => Language Object
(
[id:protected] => 1
[code:protected] => en
[name:protected] => English
[alreadyInSave:protected] =>
[alreadyInValidation:protected] =>
[validationFailures:protected] => Array
(
)
[_new:BaseObject:private] =>
[_deleted:BaseObject:private] =>
[modifiedColumns:protected] => Array
(
)
)
[old_record:protected] =>
[id:protected] => 4006
[old_id:protected] =>
[elcosh_id:protected] => i002693
[type:protected] => image
[display_type:protected] => Image
[user_id:protected] => 0
[language_id:protected] => 1
[tagging_id:protected] => Bruce Lippy
[priority_id:protected] => 1
[title:protected] => Toolbox talk - long shot
[total_pages:protected] => 0
[billed_pages:protected] => 0
[publication_number:protected] =>
[part_of:protected] =>
[keywords:protected] => toolbox talk, tailgate talk, safety minute
[comments:protected] =>
[summary:protected] => This crew gathered every morning before starting work to discuss a new safety topic.
[transition_comments:protected] =>
[external_link:protected] =>
[consol_link:protected] => http://www.cpwrconstructionsolutions.org/electrical/solution/662/worker-training.html
[more_like_this:protected] => i002691,i002692,d001269,d000527
[permission_given_by:protected] =>
[published:protected] => T
[billable:protected] => F
[img_name:protected] =>
[img_ext:protected] => jpg
[img_width:protected] =>
[img_height:protected] =>
[img_credit:protected] => Morgan Zavertnik and Hoar Construction
[img_practice:protected] => good
[vid_source_id:protected] =>
[vid_running_time:protected] =>
[vid_intended_audience:protected] =>
[vid_acquisition_info:protected] =>
[vid_cost:protected] =>
[vid_producer:protected] =>
[vid_filename:protected] =>
[vid_filename_downloadable:protected] =>
[date_summary:protected] => November 2015
[date_permission_requested:protected] =>
[date_permission_received:protected] =>
[date_review_needed:protected] =>
[date_received:protected] => 03/02/16
[date_completed:protected] => 03/02/16
[date_billed:protected] =>
[date_modified:protected] => 03/02/16
[collBokExports:protected] =>
[lastBokExportCriteria:BaseElcoshItem:private] =>
[alreadyInSave:protected] =>
[alreadyInValidation:protected] =>
[validationFailures:protected] => Array
(
)
[_new:BaseObject:private] =>
[_deleted:BaseObject:private] =>
[modifiedColumns:protected] => Array
(
)
)
)
[3] => Search_Result Object
(
[title] => Safety officer discussing ongoing project with marketing coordinator
[image] => /record/images/4014-p.jpg
[blurb] => The safety officer (left) points out the good safety practices on this project that reflect well on the firm and may influence future clients....
[category] => Array
(
[0] => 97
[1] => 20
[2] => 46
[3] => 47
[4] => 49
[5] => 50
[6] => 51
[7] => 54
[8] => 55
[9] => 58
[10] => 60
[11] => 61
[12] => 64
[13] => 71
[14] => 75
[15] => 76
[16] => 63
[17] => 79
[18] => 80
[19] => 82
[20] => 62
[21] => 83
[22] => 87
[23] => 91
[24] => 90
[25] => 93
[26] => 94
)
[labels] => Array
(
[0] => Images
[1] => Media
[2] => Media & Documents
[3] => Safety Culture
[4] => Work Environment
[5] => Hazards
[6] => Boilermaker
[7] => Trades
[8] => Bricklayer
[10] => Carpenter
[12] => Carpet Layer
[14] => Cement Mason
[16] => Drywall Applicator Specialist
[18] => Electrical Worker
[20] => Glazier
[22] => HVAC
[24] => Interior Systems Carpenter
[26] => Laborer
[28] => Painter
[30] => Plasterer
[32] => Plumber/Pipefitter
[34] => Reinforcing Ironworker
[36] => Scaffold Erector
[38] => Sheetmetal Worker
[40] => Stonemason
[42] => Structural Ironworker
[44] => Terrazzo Worker
[46] => Commercial & Institutional
[47] => Jobsites
[48] => Heavy & Highway
[50] => Industrial
[52] => Renovations
[54] => Residential
)
[type] => Images
[sub_category] =>
[url] => /image/4014/i002700/Safety%2Bofficer%2Bdiscussing%2Bongoing%2Bproject%2Bwith%2Bmarketing%2Bcoordinator.html
[item:protected] => ImageRecord Object
(
[records:protected] => Array
(
)
[recordId:protected] =>
[searchWordClass:protected] =>
[searchWordPeerClass:protected] =>
[bok_record:protected] =>
[authors:protected] =>
[organizations:protected] =>
[collections:protected] =>
[categories:protected] => Array
(
[97] => Category Object
(
[languages:protected] =>
[bok_resources:protected] =>
[bok_topics:protected] =>
[bok_keywords:protected] =>
[id:protected] => 97
[type:protected] => category
[parent:protected] => 5
[label:protected] => Images
[alreadyInSave:protected] =>
[alreadyInValidation:protected] =>
[validationFailures:protected] => Array
(
)
[_new:BaseObject:private] =>
[_deleted:BaseObject:private] =>
[modifiedColumns:protected] => Array
(
)
)
[20] => Category Object
(
[languages:protected] =>
[bok_resources:protected] =>
[bok_topics:protected] =>
[bok_keywords:protected] =>
[id:protected] => 20
[type:protected] => category
[parent:protected] => 7
[label:protected] => Safety Culture
[alreadyInSave:protected] =>
[alreadyInValidation:protected] =>
[validationFailures:protected] => Array
(
)
[_new:BaseObject:private] =>
[_deleted:BaseObject:private] =>
[modifiedColumns:protected] => Array
(
)
)
[46] => Category Object
(
[languages:protected] =>
[bok_resources:protected] =>
[bok_topics:protected] =>
[bok_keywords:protected] =>
[id:protected] => 46
[type:protected] => category
[parent:protected] => 2
[label:protected] => Boilermaker
[alreadyInSave:protected] =>
[alreadyInValidation:protected] =>
[validationFailures:protected] => Array
(
)
[_new:BaseObject:private] =>
[_deleted:BaseObject:private] =>
[modifiedColumns:protected] => Array
(
)
)
[47] => Category Object
(
[languages:protected] =>
[bok_resources:protected] =>
[bok_topics:protected] =>
[bok_keywords:protected] =>
[id:protected] => 47
[type:protected] => category
[parent:protected] => 2
[label:protected] => Bricklayer
[alreadyInSave:protected] =>
[alreadyInValidation:protected] =>
[validationFailures:protected] => Array
(
)
[_new:BaseObject:private] =>
[_deleted:BaseObject:private] =>
[modifiedColumns:protected] => Array
(
)
)
[49] => Category Object
(
[languages:protected] =>
[bok_resources:protected] =>
[bok_topics:protected] =>
[bok_keywords:protected] =>
[id:protected] => 49
[type:protected] => category
[parent:protected] => 2
[label:protected] => Carpenter
[alreadyInSave:protected] =>
[alreadyInValidation:protected] =>
[validationFailures:protected] => Array
(
)
[_new:BaseObject:private] =>
[_deleted:BaseObject:private] =>
[modifiedColumns:protected] => Array
(
)
)
[50] => Category Object
(
[languages:protected] =>
[bok_resources:protected] =>
[bok_topics:protected] =>
[bok_keywords:protected] =>
[id:protected] => 50
[type:protected] => category
[parent:protected] => 2
[label:protected] => Carpet Layer
[alreadyInSave:protected] =>
[alreadyInValidation:protected] =>
[validationFailures:protected] => Array
(
)
[_new:BaseObject:private] =>
[_deleted:BaseObject:private] =>
[modifiedColumns:protected] => Array
(
)
)
[51] => Category Object
(
[languages:protected] =>
[bok_resources:protected] =>
[bok_topics:protected] =>
[bok_keywords:protected] =>
[id:protected] => 51
[type:protected] => category
[parent:protected] => 2
[label:protected] => Cement Mason
[alreadyInSave:protected] =>
[alreadyInValidation:protected] =>
[validationFailures:protected] => Array
(
)
[_new:BaseObject:private] =>
[_deleted:BaseObject:private] =>
[modifiedColumns:protected] => Array
(
)
)
[54] => Category Object
(
[languages:protected] =>
[bok_resources:protected] =>
[bok_topics:protected] =>
[bok_keywords:protected] =>
[id:protected] => 54
[type:protected] => category
[parent:protected] => 2
[label:protected] => Drywall Applicator Specialist
[alreadyInSave:protected] =>
[alreadyInValidation:protected] =>
[validationFailures:protected] => Array
(
)
[_new:BaseObject:private] =>
[_deleted:BaseObject:private] =>
[modifiedColumns:protected] => Array
(
)
)
[55] => Category Object
(
[languages:protected] =>
[bok_resources:protected] =>
[bok_topics:protected] =>
[bok_keywords:protected] =>
[id:protected] => 55
[type:protected] => category
[parent:protected] => 2
[label:protected] => Electrical Worker
[alreadyInSave:protected] =>
[alreadyInValidation:protected] =>
[validationFailures:protected] => Array
(
)
[_new:BaseObject:private] =>
[_deleted:BaseObject:private] =>
[modifiedColumns:protected] => Array
(
)
)
[58] => Category Object
(
[languages:protected] =>
[bok_resources:protected] =>
[bok_topics:protected] =>
[bok_keywords:protected] =>
[id:protected] => 58
[type:protected] => category
[parent:protected] => 2
[label:protected] => Glazier
[alreadyInSave:protected] =>
[alreadyInValidation:protected] =>
[validationFailures:protected] => Array
(
)
[_new:BaseObject:private] =>
[_deleted:BaseObject:private] =>
[modifiedColumns:protected] => Array
(
)
)
[60] => Category Object
(
[languages:protected] =>
[bok_resources:protected] =>
[bok_topics:protected] =>
[bok_keywords:protected] =>
[id:protected] => 60
[type:protected] => category
[parent:protected] => 2
[label:protected] => HVAC
[alreadyInSave:protected] =>
[alreadyInValidation:protected] =>
[validationFailures:protected] => Array
(
)
[_new:BaseObject:private] =>
[_deleted:BaseObject:private] =>
[modifiedColumns:protected] => Array
(
)
)
[61] => Category Object
(
[languages:protected] =>
[bok_resources:protected] =>
[bok_topics:protected] =>
[bok_keywords:protected] =>
[id:protected] => 61
[type:protected] => category
[parent:protected] => 2
[label:protected] => Interior Systems Carpenter
[alreadyInSave:protected] =>
[alreadyInValidation:protected] =>
[validationFailures:protected] => Array
(
)
[_new:BaseObject:private] =>
[_deleted:BaseObject:private] =>
[modifiedColumns:protected] => Array
(
)
)
[64] => Category Object
(
[languages:protected] =>
[bok_resources:protected] =>
[bok_topics:protected] =>
[bok_keywords:protected] =>
[id:protected] => 64
[type:protected] => category
[parent:protected] => 2
[label:protected] => Laborer
[alreadyInSave:protected] =>
[alreadyInValidation:protected] =>
[validationFailures:protected] => Array
(
)
[_new:BaseObject:private] =>
[_deleted:BaseObject:private] =>
[modifiedColumns:protected] => Array
(
)
)
[71] => Category Object
(
[languages:protected] =>
[bok_resources:protected] =>
[bok_topics:protected] =>
[bok_keywords:protected] =>
[id:protected] => 71
[type:protected] => category
[parent:protected] => 2
[label:protected] => Painter
[alreadyInSave:protected] =>
[alreadyInValidation:protected] =>
[validationFailures:protected] => Array
(
)
[_new:BaseObject:private] =>
[_deleted:BaseObject:private] =>
[modifiedColumns:protected] => Array
(
)
)
[75] => Category Object
(
[languages:protected] =>
[bok_resources:protected] =>
[bok_topics:protected] =>
[bok_keywords:protected] =>
[id:protected] => 75
[type:protected] => category
[parent:protected] => 2
[label:protected] => Plasterer
[alreadyInSave:protected] =>
[alreadyInValidation:protected] =>
[validationFailures:protected] => Array
(
)
[_new:BaseObject:private] =>
[_deleted:BaseObject:private] =>
[modifiedColumns:protected] => Array
(
)
)
[76] => Category Object
(
[languages:protected] =>
[bok_resources:protected] =>
[bok_topics:protected] =>
[bok_keywords:protected] =>
[id:protected] => 76
[type:protected] => category
[parent:protected] => 2
[label:protected] => Plumber/Pipefitter
[alreadyInSave:protected] =>
[alreadyInValidation:protected] =>
[validationFailures:protected] => Array
(
)
[_new:BaseObject:private] =>
[_deleted:BaseObject:private] =>
[modifiedColumns:protected] => Array
(
)
)
[63] => Category Object
(
[languages:protected] =>
[bok_resources:protected] =>
[bok_topics:protected] =>
[bok_keywords:protected] =>
[id:protected] => 63
[type:protected] => category
[parent:protected] => 2
[label:protected] => Reinforcing Ironworker
[alreadyInSave:protected] =>
[alreadyInValidation:protected] =>
[validationFailures:protected] => Array
(
)
[_new:BaseObject:private] =>
[_deleted:BaseObject:private] =>
[modifiedColumns:protected] => Array
(
)
)
[79] => Category Object
(
[languages:protected] =>
[bok_resources:protected] =>
[bok_topics:protected] =>
[bok_keywords:protected] =>
[id:protected] => 79
[type:protected] => category
[parent:protected] => 2
[label:protected] => Scaffold Erector
[alreadyInSave:protected] =>
[alreadyInValidation:protected] =>
[validationFailures:protected] => Array
(
)
[_new:BaseObject:private] =>
[_deleted:BaseObject:private] =>
[modifiedColumns:protected] => Array
(
)
)
[80] => Category Object
(
[languages:protected] =>
[bok_resources:protected] =>
[bok_topics:protected] =>
[bok_keywords:protected] =>
[id:protected] => 80
[type:protected] => category
[parent:protected] => 2
[label:protected] => Sheetmetal Worker
[alreadyInSave:protected] =>
[alreadyInValidation:protected] =>
[validationFailures:protected] => Array
(
)
[_new:BaseObject:private] =>
[_deleted:BaseObject:private] =>
[modifiedColumns:protected] => Array
(
)
)
[82] => Category Object
(
[languages:protected] =>
[bok_resources:protected] =>
[bok_topics:protected] =>
[bok_keywords:protected] =>
[id:protected] => 82
[type:protected] => category
[parent:protected] => 2
[label:protected] => Stonemason
[alreadyInSave:protected] =>
[alreadyInValidation:protected] =>
[validationFailures:protected] => Array
(
)
[_new:BaseObject:private] =>
[_deleted:BaseObject:private] =>
[modifiedColumns:protected] => Array
(
)
)
[62] => Category Object
(
[languages:protected] =>
[bok_resources:protected] =>
[bok_topics:protected] =>
[bok_keywords:protected] =>
[id:protected] => 62
[type:protected] => category
[parent:protected] => 2
[label:protected] => Structural Ironworker
[alreadyInSave:protected] =>
[alreadyInValidation:protected] =>
[validationFailures:protected] => Array
(
)
[_new:BaseObject:private] =>
[_deleted:BaseObject:private] =>
[modifiedColumns:protected] => Array
(
)
)
[83] => Category Object
(
[languages:protected] =>
[bok_resources:protected] =>
[bok_topics:protected] =>
[bok_keywords:protected] =>
[id:protected] => 83
[type:protected] => category
[parent:protected] => 2
[label:protected] => Terrazzo Worker
[alreadyInSave:protected] =>
[alreadyInValidation:protected] =>
[validationFailures:protected] => Array
(
)
[_new:BaseObject:private] =>
[_deleted:BaseObject:private] =>
[modifiedColumns:protected] => Array
(
)
)
[87] => Category Object
(
[languages:protected] =>
[bok_resources:protected] =>
[bok_topics:protected] =>
[bok_keywords:protected] =>
[id:protected] => 87
[type:protected] => category
[parent:protected] => 3
[label:protected] => Commercial & Institutional
[alreadyInSave:protected] =>
[alreadyInValidation:protected] =>
[validationFailures:protected] => Array
(
)
[_new:BaseObject:private] =>
[_deleted:BaseObject:private] =>
[modifiedColumns:protected] => Array
(
)
)
[91] => Category Object
(
[languages:protected] =>
[bok_resources:protected] =>
[bok_topics:protected] =>
[bok_keywords:protected] =>
[id:protected] => 91
[type:protected] => category
[parent:protected] => 3
[label:protected] => Heavy & Highway
[alreadyInSave:protected] =>
[alreadyInValidation:protected] =>
[validationFailures:protected] => Array
(
)
[_new:BaseObject:private] =>
[_deleted:BaseObject:private] =>
[modifiedColumns:protected] => Array
(
)
)
[90] => Category Object
(
[languages:protected] =>
[bok_resources:protected] =>
[bok_topics:protected] =>
[bok_keywords:protected] =>
[id:protected] => 90
[type:protected] => category
[parent:protected] => 3
[label:protected] => Industrial
[alreadyInSave:protected] =>
[alreadyInValidation:protected] =>
[validationFailures:protected] => Array
(
)
[_new:BaseObject:private] =>
[_deleted:BaseObject:private] =>
[modifiedColumns:protected] => Array
(
)
)
[93] => Category Object
(
[languages:protected] =>
[bok_resources:protected] =>
[bok_topics:protected] =>
[bok_keywords:protected] =>
[id:protected] => 93
[type:protected] => category
[parent:protected] => 3
[label:protected] => Renovations
[alreadyInSave:protected] =>
[alreadyInValidation:protected] =>
[validationFailures:protected] => Array
(
)
[_new:BaseObject:private] =>
[_deleted:BaseObject:private] =>
[modifiedColumns:protected] => Array
(
)
)
[94] => Category Object
(
[languages:protected] =>
[bok_resources:protected] =>
[bok_topics:protected] =>
[bok_keywords:protected] =>
[id:protected] => 94
[type:protected] => category
[parent:protected] => 3
[label:protected] => Residential
[alreadyInSave:protected] =>
[alreadyInValidation:protected] =>
[validationFailures:protected] => Array
(
)
[_new:BaseObject:private] =>
[_deleted:BaseObject:private] =>
[modifiedColumns:protected] => Array
(
)
)
)
[categories_initialized:protected] => 1
[mapped_items:protected] =>
[content:protected] =>
[files:protected] =>
[language:protected] => Language Object
(
[id:protected] => 1
[code:protected] => en
[name:protected] => English
[alreadyInSave:protected] =>
[alreadyInValidation:protected] =>
[validationFailures:protected] => Array
(
)
[_new:BaseObject:private] =>
[_deleted:BaseObject:private] =>
[modifiedColumns:protected] => Array
(
)
)
[old_record:protected] =>
[id:protected] => 4014
[old_id:protected] =>
[elcosh_id:protected] => i002700
[type:protected] => image
[display_type:protected] => Image
[user_id:protected] => 0
[language_id:protected] => 1
[tagging_id:protected] => Bruce Lippy
[priority_id:protected] => 1
[title:protected] => Safety officer discussing ongoing project with marketing coordinator
[total_pages:protected] => 0
[billed_pages:protected] => 0
[publication_number:protected] =>
[part_of:protected] =>
[keywords:protected] => Latino, safety officer, safety culture
[comments:protected] =>
[summary:protected] => The safety officer (left) points out the good safety practices on this project that reflect well on the firm and may influence future clients.
[transition_comments:protected] =>
[external_link:protected] =>
[consol_link:protected] => http://www.cpwrconstructionsolutions.org/index.php
[more_like_this:protected] => d000989,d001351,d001362,d000652, d001101, d000931, d001395
[permission_given_by:protected] =>
[published:protected] => T
[billable:protected] => F
[img_name:protected] =>
[img_ext:protected] => jpg
[img_width:protected] =>
[img_height:protected] =>
[img_credit:protected] => Hoar Construction, Photo by Neil Lippy
[img_practice:protected] => good
[vid_source_id:protected] =>
[vid_running_time:protected] =>
[vid_intended_audience:protected] =>
[vid_acquisition_info:protected] =>
[vid_cost:protected] =>
[vid_producer:protected] =>
[vid_filename:protected] =>
[vid_filename_downloadable:protected] =>
[date_summary:protected] => November 2015
[date_permission_requested:protected] =>
[date_permission_received:protected] =>
[date_review_needed:protected] =>
[date_received:protected] => 03/02/16
[date_completed:protected] => 03/02/16
[date_billed:protected] =>
[date_modified:protected] => 01/30/23
[collBokExports:protected] =>
[lastBokExportCriteria:BaseElcoshItem:private] =>
[alreadyInSave:protected] =>
[alreadyInValidation:protected] =>
[validationFailures:protected] => Array
(
)
[_new:BaseObject:private] =>
[_deleted:BaseObject:private] =>
[modifiedColumns:protected] => Array
(
)
)
)
[4] => Search_Result Object
(
[title] => Scaffolding at top of large column
[image] => /record/images/3994-p.jpg
[blurb] => This shot shows innovative guarding around the top of a large concrete column in the base of a high rise structure going up....
[category] => Array
(
[0] => 15
[1] => 21
[2] => 47
[3] => 51
[4] => 63
[5] => 78
[6] => 79
[7] => 80
[8] => 62
[9] => 87
[10] => 97
[11] => 56
[12] => 64
[13] => 74
)
[labels] => Array
(
[0] => Falls
[1] => Work Environment
[2] => Hazards
[3] => Scaffolds
[6] => Bricklayer
[7] => Trades
[8] => Cement Mason
[10] => Reinforcing Ironworker
[12] => Roofer/Waterproofer
[14] => Scaffold Erector
[16] => Sheetmetal Worker
[18] => Structural Ironworker
[20] => Commercial & Institutional
[21] => Jobsites
[22] => Images
[23] => Media
[24] => Media & Documents
[25] => Elevator Constructor
[27] => Laborer
[29] => Pile Driver
)
[type] => Images
[sub_category] =>
[url] => /image/3994/i002689/Scaffolding%2Bat%2Btop%2Bof%2Blarge%2Bcolumn.html
[item:protected] => ImageRecord Object
(
[records:protected] => Array
(
)
[recordId:protected] =>
[searchWordClass:protected] =>
[searchWordPeerClass:protected] =>
[bok_record:protected] =>
[authors:protected] =>
[organizations:protected] =>
[collections:protected] =>
[categories:protected] => Array
(
[15] => Category Object
(
[languages:protected] =>
[bok_resources:protected] =>
[bok_topics:protected] =>
[bok_keywords:protected] =>
[id:protected] => 15
[type:protected] => category
[parent:protected] => 7
[label:protected] => Falls
[alreadyInSave:protected] =>
[alreadyInValidation:protected] =>
[validationFailures:protected] => Array
(
)
[_new:BaseObject:private] =>
[_deleted:BaseObject:private] =>
[modifiedColumns:protected] => Array
(
)
)
[21] => Category Object
(
[languages:protected] =>
[bok_resources:protected] =>
[bok_topics:protected] =>
[bok_keywords:protected] =>
[id:protected] => 21
[type:protected] => category
[parent:protected] => 7
[label:protected] => Scaffolds
[alreadyInSave:protected] =>
[alreadyInValidation:protected] =>
[validationFailures:protected] => Array
(
)
[_new:BaseObject:private] =>
[_deleted:BaseObject:private] =>
[modifiedColumns:protected] => Array
(
)
)
[47] => Category Object
(
[languages:protected] =>
[bok_resources:protected] =>
[bok_topics:protected] =>
[bok_keywords:protected] =>
[id:protected] => 47
[type:protected] => category
[parent:protected] => 2
[label:protected] => Bricklayer
[alreadyInSave:protected] =>
[alreadyInValidation:protected] =>
[validationFailures:protected] => Array
(
)
[_new:BaseObject:private] =>
[_deleted:BaseObject:private] =>
[modifiedColumns:protected] => Array
(
)
)
[51] => Category Object
(
[languages:protected] =>
[bok_resources:protected] =>
[bok_topics:protected] =>
[bok_keywords:protected] =>
[id:protected] => 51
[type:protected] => category
[parent:protected] => 2
[label:protected] => Cement Mason
[alreadyInSave:protected] =>
[alreadyInValidation:protected] =>
[validationFailures:protected] => Array
(
)
[_new:BaseObject:private] =>
[_deleted:BaseObject:private] =>
[modifiedColumns:protected] => Array
(
)
)
[63] => Category Object
(
[languages:protected] =>
[bok_resources:protected] =>
[bok_topics:protected] =>
[bok_keywords:protected] =>
[id:protected] => 63
[type:protected] => category
[parent:protected] => 2
[label:protected] => Reinforcing Ironworker
[alreadyInSave:protected] =>
[alreadyInValidation:protected] =>
[validationFailures:protected] => Array
(
)
[_new:BaseObject:private] =>
[_deleted:BaseObject:private] =>
[modifiedColumns:protected] => Array
(
)
)
[78] => Category Object
(
[languages:protected] =>
[bok_resources:protected] =>
[bok_topics:protected] =>
[bok_keywords:protected] =>
[id:protected] => 78
[type:protected] => category
[parent:protected] => 2
[label:protected] => Roofer/Waterproofer
[alreadyInSave:protected] =>
[alreadyInValidation:protected] =>
[validationFailures:protected] => Array
(
)
[_new:BaseObject:private] =>
[_deleted:BaseObject:private] =>
[modifiedColumns:protected] => Array
(
)
)
[79] => Category Object
(
[languages:protected] =>
[bok_resources:protected] =>
[bok_topics:protected] =>
[bok_keywords:protected] =>
[id:protected] => 79
[type:protected] => category
[parent:protected] => 2
[label:protected] => Scaffold Erector
[alreadyInSave:protected] =>
[alreadyInValidation:protected] =>
[validationFailures:protected] => Array
(
)
[_new:BaseObject:private] =>
[_deleted:BaseObject:private] =>
[modifiedColumns:protected] => Array
(
)
)
[80] => Category Object
(
[languages:protected] =>
[bok_resources:protected] =>
[bok_topics:protected] =>
[bok_keywords:protected] =>
[id:protected] => 80
[type:protected] => category
[parent:protected] => 2
[label:protected] => Sheetmetal Worker
[alreadyInSave:protected] =>
[alreadyInValidation:protected] =>
[validationFailures:protected] => Array
(
)
[_new:BaseObject:private] =>
[_deleted:BaseObject:private] =>
[modifiedColumns:protected] => Array
(
)
)
[62] => Category Object
(
[languages:protected] =>
[bok_resources:protected] =>
[bok_topics:protected] =>
[bok_keywords:protected] =>
[id:protected] => 62
[type:protected] => category
[parent:protected] => 2
[label:protected] => Structural Ironworker
[alreadyInSave:protected] =>
[alreadyInValidation:protected] =>
[validationFailures:protected] => Array
(
)
[_new:BaseObject:private] =>
[_deleted:BaseObject:private] =>
[modifiedColumns:protected] => Array
(
)
)
[87] => Category Object
(
[languages:protected] =>
[bok_resources:protected] =>
[bok_topics:protected] =>
[bok_keywords:protected] =>
[id:protected] => 87
[type:protected] => category
[parent:protected] => 3
[label:protected] => Commercial & Institutional
[alreadyInSave:protected] =>
[alreadyInValidation:protected] =>
[validationFailures:protected] => Array
(
)
[_new:BaseObject:private] =>
[_deleted:BaseObject:private] =>
[modifiedColumns:protected] => Array
(
)
)
[97] => Category Object
(
[languages:protected] =>
[bok_resources:protected] =>
[bok_topics:protected] =>
[bok_keywords:protected] =>
[id:protected] => 97
[type:protected] => category
[parent:protected] => 5
[label:protected] => Images
[alreadyInSave:protected] =>
[alreadyInValidation:protected] =>
[validationFailures:protected] => Array
(
)
[_new:BaseObject:private] =>
[_deleted:BaseObject:private] =>
[modifiedColumns:protected] => Array
(
)
)
[56] => Category Object
(
[languages:protected] =>
[bok_resources:protected] =>
[bok_topics:protected] =>
[bok_keywords:protected] =>
[id:protected] => 56
[type:protected] => category
[parent:protected] => 2
[label:protected] => Elevator Constructor
[alreadyInSave:protected] =>
[alreadyInValidation:protected] =>
[validationFailures:protected] => Array
(
)
[_new:BaseObject:private] =>
[_deleted:BaseObject:private] =>
[modifiedColumns:protected] => Array
(
)
)
[64] => Category Object
(
[languages:protected] =>
[bok_resources:protected] =>
[bok_topics:protected] =>
[bok_keywords:protected] =>
[id:protected] => 64
[type:protected] => category
[parent:protected] => 2
[label:protected] => Laborer
[alreadyInSave:protected] =>
[alreadyInValidation:protected] =>
[validationFailures:protected] => Array
(
)
[_new:BaseObject:private] =>
[_deleted:BaseObject:private] =>
[modifiedColumns:protected] => Array
(
)
)
[74] => Category Object
(
[languages:protected] =>
[bok_resources:protected] =>
[bok_topics:protected] =>
[bok_keywords:protected] =>
[id:protected] => 74
[type:protected] => category
[parent:protected] => 2
[label:protected] => Pile Driver
[alreadyInSave:protected] =>
[alreadyInValidation:protected] =>
[validationFailures:protected] => Array
(
)
[_new:BaseObject:private] =>
[_deleted:BaseObject:private] =>
[modifiedColumns:protected] => Array
(
)
)
)
[categories_initialized:protected] => 1
[mapped_items:protected] =>
[content:protected] =>
[files:protected] =>
[language:protected] => Language Object
(
[id:protected] => 1
[code:protected] => en
[name:protected] => English
[alreadyInSave:protected] =>
[alreadyInValidation:protected] =>
[validationFailures:protected] => Array
(
)
[_new:BaseObject:private] =>
[_deleted:BaseObject:private] =>
[modifiedColumns:protected] => Array
(
)
)
[old_record:protected] =>
[id:protected] => 3994
[old_id:protected] =>
[elcosh_id:protected] => i002689
[type:protected] => image
[display_type:protected] => Image
[user_id:protected] => 0
[language_id:protected] => 1
[tagging_id:protected] => Bruce Lippy
[priority_id:protected] => 1
[title:protected] => Scaffolding at top of large column
[total_pages:protected] => 0
[billed_pages:protected] => 0
[publication_number:protected] =>
[part_of:protected] =>
[keywords:protected] => Guardrail, railing, fall prevention, falls
[comments:protected] =>
[summary:protected] => This shot shows innovative guarding around the top of a large concrete column in the base of a high rise structure going up.
[transition_comments:protected] =>
[external_link:protected] =>
[consol_link:protected] => http://www.cpwrconstructionsolutions.org/masonry/solution/8/adjustable-tower-scaffold.html
[more_like_this:protected] => c1002680,i002662,d000608,d001255
[permission_given_by:protected] =>
[published:protected] => T
[billable:protected] => F
[img_name:protected] =>
[img_ext:protected] => jpg
[img_width:protected] =>
[img_height:protected] =>
[img_credit:protected] => Photo by Pam Susi
[img_practice:protected] => good
[vid_source_id:protected] =>
[vid_running_time:protected] =>
[vid_intended_audience:protected] =>
[vid_acquisition_info:protected] =>
[vid_cost:protected] =>
[vid_producer:protected] =>
[vid_filename:protected] =>
[vid_filename_downloadable:protected] =>
[date_summary:protected] => January 2016
[date_permission_requested:protected] =>
[date_permission_received:protected] =>
[date_review_needed:protected] =>
[date_received:protected] => 02/01/16
[date_completed:protected] => 02/01/16
[date_billed:protected] =>
[date_modified:protected] => 02/01/16
[collBokExports:protected] =>
[lastBokExportCriteria:BaseElcoshItem:private] =>
[alreadyInSave:protected] =>
[alreadyInValidation:protected] =>
[validationFailures:protected] => Array
(
)
[_new:BaseObject:private] =>
[_deleted:BaseObject:private] =>
[modifiedColumns:protected] => Array
(
)
)
)
[5] => Search_Result Object
(
[title] => Construction bracing
[image] => /record/images/3995-p.jpg
[blurb] => This shows structural support that prevents collapses during construction....
[category] => Array
(
[0] => 12
[1] => 15
[2] => 21
[3] => 49
[4] => 51
[5] => 55
[6] => 56
[7] => 60
[8] => 64
[9] => 68
[10] => 74
[11] => 63
[12] => 78
[13] => 79
[14] => 80
[15] => 62
[16] => 87
[17] => 90
[18] => 97
)
[labels] => Array
(
[0] => Crushed/Struck By
[1] => Work Environment
[2] => Hazards
[3] => Falls
[6] => Scaffolds
[9] => Carpenter
[10] => Trades
[11] => Cement Mason
[13] => Electrical Worker
[15] => Elevator Constructor
[17] => HVAC
[19] => Laborer
[21] => Maintenance Worker
[23] => Pile Driver
[25] => Reinforcing Ironworker
[27] => Roofer/Waterproofer
[29] => Scaffold Erector
[31] => Sheetmetal Worker
[33] => Structural Ironworker
[35] => Commercial & Institutional
[36] => Jobsites
[37] => Industrial
[39] => Images
[40] => Media
[41] => Media & Documents
)
[type] => Images
[sub_category] =>
[url] => /image/3995/i002690/Construction%2Bbracing.html
[item:protected] => ImageRecord Object
(
[records:protected] => Array
(
)
[recordId:protected] =>
[searchWordClass:protected] =>
[searchWordPeerClass:protected] =>
[bok_record:protected] =>
[authors:protected] =>
[organizations:protected] =>
[collections:protected] =>
[categories:protected] => Array
(
[12] => Category Object
(
[languages:protected] =>
[bok_resources:protected] =>
[bok_topics:protected] =>
[bok_keywords:protected] =>
[id:protected] => 12
[type:protected] => category
[parent:protected] => 7
[label:protected] => Crushed/Struck By
[alreadyInSave:protected] =>
[alreadyInValidation:protected] =>
[validationFailures:protected] => Array
(
)
[_new:BaseObject:private] =>
[_deleted:BaseObject:private] =>
[modifiedColumns:protected] => Array
(
)
)
[15] => Category Object
(
[languages:protected] =>
[bok_resources:protected] =>
[bok_topics:protected] =>
[bok_keywords:protected] =>
[id:protected] => 15
[type:protected] => category
[parent:protected] => 7
[label:protected] => Falls
[alreadyInSave:protected] =>
[alreadyInValidation:protected] =>
[validationFailures:protected] => Array
(
)
[_new:BaseObject:private] =>
[_deleted:BaseObject:private] =>
[modifiedColumns:protected] => Array
(
)
)
[21] => Category Object
(
[languages:protected] =>
[bok_resources:protected] =>
[bok_topics:protected] =>
[bok_keywords:protected] =>
[id:protected] => 21
[type:protected] => category
[parent:protected] => 7
[label:protected] => Scaffolds
[alreadyInSave:protected] =>
[alreadyInValidation:protected] =>
[validationFailures:protected] => Array
(
)
[_new:BaseObject:private] =>
[_deleted:BaseObject:private] =>
[modifiedColumns:protected] => Array
(
)
)
[49] => Category Object
(
[languages:protected] =>
[bok_resources:protected] =>
[bok_topics:protected] =>
[bok_keywords:protected] =>
[id:protected] => 49
[type:protected] => category
[parent:protected] => 2
[label:protected] => Carpenter
[alreadyInSave:protected] =>
[alreadyInValidation:protected] =>
[validationFailures:protected] => Array
(
)
[_new:BaseObject:private] =>
[_deleted:BaseObject:private] =>
[modifiedColumns:protected] => Array
(
)
)
[51] => Category Object
(
[languages:protected] =>
[bok_resources:protected] =>
[bok_topics:protected] =>
[bok_keywords:protected] =>
[id:protected] => 51
[type:protected] => category
[parent:protected] => 2
[label:protected] => Cement Mason
[alreadyInSave:protected] =>
[alreadyInValidation:protected] =>
[validationFailures:protected] => Array
(
)
[_new:BaseObject:private] =>
[_deleted:BaseObject:private] =>
[modifiedColumns:protected] => Array
(
)
)
[55] => Category Object
(
[languages:protected] =>
[bok_resources:protected] =>
[bok_topics:protected] =>
[bok_keywords:protected] =>
[id:protected] => 55
[type:protected] => category
[parent:protected] => 2
[label:protected] => Electrical Worker
[alreadyInSave:protected] =>
[alreadyInValidation:protected] =>
[validationFailures:protected] => Array
(
)
[_new:BaseObject:private] =>
[_deleted:BaseObject:private] =>
[modifiedColumns:protected] => Array
(
)
)
[56] => Category Object
(
[languages:protected] =>
[bok_resources:protected] =>
[bok_topics:protected] =>
[bok_keywords:protected] =>
[id:protected] => 56
[type:protected] => category
[parent:protected] => 2
[label:protected] => Elevator Constructor
[alreadyInSave:protected] =>
[alreadyInValidation:protected] =>
[validationFailures:protected] => Array
(
)
[_new:BaseObject:private] =>
[_deleted:BaseObject:private] =>
[modifiedColumns:protected] => Array
(
)
)
[60] => Category Object
(
[languages:protected] =>
[bok_resources:protected] =>
[bok_topics:protected] =>
[bok_keywords:protected] =>
[id:protected] => 60
[type:protected] => category
[parent:protected] => 2
[label:protected] => HVAC
[alreadyInSave:protected] =>
[alreadyInValidation:protected] =>
[validationFailures:protected] => Array
(
)
[_new:BaseObject:private] =>
[_deleted:BaseObject:private] =>
[modifiedColumns:protected] => Array
(
)
)
[64] => Category Object
(
[languages:protected] =>
[bok_resources:protected] =>
[bok_topics:protected] =>
[bok_keywords:protected] =>
[id:protected] => 64
[type:protected] => category
[parent:protected] => 2
[label:protected] => Laborer
[alreadyInSave:protected] =>
[alreadyInValidation:protected] =>
[validationFailures:protected] => Array
(
)
[_new:BaseObject:private] =>
[_deleted:BaseObject:private] =>
[modifiedColumns:protected] => Array
(
)
)
[68] => Category Object
(
[languages:protected] =>
[bok_resources:protected] =>
[bok_topics:protected] =>
[bok_keywords:protected] =>
[id:protected] => 68
[type:protected] => category
[parent:protected] => 2
[label:protected] => Maintenance Worker
[alreadyInSave:protected] =>
[alreadyInValidation:protected] =>
[validationFailures:protected] => Array
(
)
[_new:BaseObject:private] =>
[_deleted:BaseObject:private] =>
[modifiedColumns:protected] => Array
(
)
)
[74] => Category Object
(
[languages:protected] =>
[bok_resources:protected] =>
[bok_topics:protected] =>
[bok_keywords:protected] =>
[id:protected] => 74
[type:protected] => category
[parent:protected] => 2
[label:protected] => Pile Driver
[alreadyInSave:protected] =>
[alreadyInValidation:protected] =>
[validationFailures:protected] => Array
(
)
[_new:BaseObject:private] =>
[_deleted:BaseObject:private] =>
[modifiedColumns:protected] => Array
(
)
)
[63] => Category Object
(
[languages:protected] =>
[bok_resources:protected] =>
[bok_topics:protected] =>
[bok_keywords:protected] =>
[id:protected] => 63
[type:protected] => category
[parent:protected] => 2
[label:protected] => Reinforcing Ironworker
[alreadyInSave:protected] =>
[alreadyInValidation:protected] =>
[validationFailures:protected] => Array
(
)
[_new:BaseObject:private] =>
[_deleted:BaseObject:private] =>
[modifiedColumns:protected] => Array
(
)
)
[78] => Category Object
(
[languages:protected] =>
[bok_resources:protected] =>
[bok_topics:protected] =>
[bok_keywords:protected] =>
[id:protected] => 78
[type:protected] => category
[parent:protected] => 2
[label:protected] => Roofer/Waterproofer
[alreadyInSave:protected] =>
[alreadyInValidation:protected] =>
[validationFailures:protected] => Array
(
)
[_new:BaseObject:private] =>
[_deleted:BaseObject:private] =>
[modifiedColumns:protected] => Array
(
)
)
[79] => Category Object
(
[languages:protected] =>
[bok_resources:protected] =>
[bok_topics:protected] =>
[bok_keywords:protected] =>
[id:protected] => 79
[type:protected] => category
[parent:protected] => 2
[label:protected] => Scaffold Erector
[alreadyInSave:protected] =>
[alreadyInValidation:protected] =>
[validationFailures:protected] => Array
(
)
[_new:BaseObject:private] =>
[_deleted:BaseObject:private] =>
[modifiedColumns:protected] => Array
(
)
)
[80] => Category Object
(
[languages:protected] =>
[bok_resources:protected] =>
[bok_topics:protected] =>
[bok_keywords:protected] =>
[id:protected] => 80
[type:protected] => category
[parent:protected] => 2
[label:protected] => Sheetmetal Worker
[alreadyInSave:protected] =>
[alreadyInValidation:protected] =>
[validationFailures:protected] => Array
(
)
[_new:BaseObject:private] =>
[_deleted:BaseObject:private] =>
[modifiedColumns:protected] => Array
(
)
)
[62] => Category Object
(
[languages:protected] =>
[bok_resources:protected] =>
[bok_topics:protected] =>
[bok_keywords:protected] =>
[id:protected] => 62
[type:protected] => category
[parent:protected] => 2
[label:protected] => Structural Ironworker
[alreadyInSave:protected] =>
[alreadyInValidation:protected] =>
[validationFailures:protected] => Array
(
)
[_new:BaseObject:private] =>
[_deleted:BaseObject:private] =>
[modifiedColumns:protected] => Array
(
)
)
[87] => Category Object
(
[languages:protected] =>
[bok_resources:protected] =>
[bok_topics:protected] =>
[bok_keywords:protected] =>
[id:protected] => 87
[type:protected] => category
[parent:protected] => 3
[label:protected] => Commercial & Institutional
[alreadyInSave:protected] =>
[alreadyInValidation:protected] =>
[validationFailures:protected] => Array
(
)
[_new:BaseObject:private] =>
[_deleted:BaseObject:private] =>
[modifiedColumns:protected] => Array
(
)
)
[90] => Category Object
(
[languages:protected] =>
[bok_resources:protected] =>
[bok_topics:protected] =>
[bok_keywords:protected] =>
[id:protected] => 90
[type:protected] => category
[parent:protected] => 3
[label:protected] => Industrial
[alreadyInSave:protected] =>
[alreadyInValidation:protected] =>
[validationFailures:protected] => Array
(
)
[_new:BaseObject:private] =>
[_deleted:BaseObject:private] =>
[modifiedColumns:protected] => Array
(
)
)
[97] => Category Object
(
[languages:protected] =>
[bok_resources:protected] =>
[bok_topics:protected] =>
[bok_keywords:protected] =>
[id:protected] => 97
[type:protected] => category
[parent:protected] => 5
[label:protected] => Images
[alreadyInSave:protected] =>
[alreadyInValidation:protected] =>
[validationFailures:protected] => Array
(
)
[_new:BaseObject:private] =>
[_deleted:BaseObject:private] =>
[modifiedColumns:protected] => Array
(
)
)
)
[categories_initialized:protected] => 1
[mapped_items:protected] =>
[content:protected] =>
[files:protected] =>
[language:protected] => Language Object
(
[id:protected] => 1
[code:protected] => en
[name:protected] => English
[alreadyInSave:protected] =>
[alreadyInValidation:protected] =>
[validationFailures:protected] => Array
(
)
[_new:BaseObject:private] =>
[_deleted:BaseObject:private] =>
[modifiedColumns:protected] => Array
(
)
)
[old_record:protected] =>
[id:protected] => 3995
[old_id:protected] =>
[elcosh_id:protected] => i002690
[type:protected] => image
[display_type:protected] => Image
[user_id:protected] => 0
[language_id:protected] => 1
[tagging_id:protected] => Bruce Lippy
[priority_id:protected] => 1
[title:protected] => Construction bracing
[total_pages:protected] => 0
[billed_pages:protected] => 0
[publication_number:protected] =>
[part_of:protected] =>
[keywords:protected] => Bracing, support, scaffold
[comments:protected] =>
[summary:protected] => This shows structural support that prevents collapses during construction.
[transition_comments:protected] =>
[external_link:protected] =>
[consol_link:protected] => http://www.cpwrconstructionsolutions.org/masonry/solution/8/adjustable-tower-scaffold.html
[more_like_this:protected] => i002660
[permission_given_by:protected] =>
[published:protected] => T
[billable:protected] => F
[img_name:protected] =>
[img_ext:protected] => jpg
[img_width:protected] =>
[img_height:protected] =>
[img_credit:protected] => Photo by Pam Susi
[img_practice:protected] => good
[vid_source_id:protected] =>
[vid_running_time:protected] =>
[vid_intended_audience:protected] =>
[vid_acquisition_info:protected] =>
[vid_cost:protected] =>
[vid_producer:protected] =>
[vid_filename:protected] =>
[vid_filename_downloadable:protected] =>
[date_summary:protected] => January 2016
[date_permission_requested:protected] =>
[date_permission_received:protected] =>
[date_review_needed:protected] =>
[date_received:protected] => 02/01/16
[date_completed:protected] => 02/01/16
[date_billed:protected] =>
[date_modified:protected] => 02/01/16
[collBokExports:protected] =>
[lastBokExportCriteria:BaseElcoshItem:private] =>
[alreadyInSave:protected] =>
[alreadyInValidation:protected] =>
[validationFailures:protected] => Array
(
)
[_new:BaseObject:private] =>
[_deleted:BaseObject:private] =>
[modifiedColumns:protected] => Array
(
)
)
)
)
[preview_mode] =>
[description] => Toolbox talks have been the main tool for communicating safety information on construction jobs for decades.
Unfortunately, there has been little research on what makes for effective toolbox talks. The IUOE National
Training Fund worked with OSHA and NIOSH to make sure their series of 24 Focus Four toolbox talks were based on the best recommendations for effective design. These toolbox talks accompany an entire package of training materials, but can be used alone. This guide points out the key features of these toolbox talks and how best to deliver them.
[keywords] => toolbox talks, tailgate talks
[related_items] => Array
(
[Toolbox Talks] => Array
(
[0] => DocumentRecord Object
(
[records:protected] => Array
(
)
[recordId:protected] =>
[searchWordClass:protected] =>
[searchWordPeerClass:protected] =>
[bok_record:protected] =>
[authors:protected] =>
[organizations:protected] =>
[collections:protected] =>
[categories:protected] =>
[categories_initialized:protected] =>
[mapped_items:protected] =>
[content:protected] =>
[files:protected] =>
[language:protected] => Language Object
(
[id:protected] => 1
[code:protected] => en
[name:protected] => English
[alreadyInSave:protected] =>
[alreadyInValidation:protected] =>
[validationFailures:protected] => Array
(
)
[_new:BaseObject:private] =>
[_deleted:BaseObject:private] =>
[modifiedColumns:protected] => Array
(
)
)
[old_record:protected] =>
[id:protected] => 1605
[old_id:protected] => 1262
[elcosh_id:protected] => d001137
[type:protected] => document
[display_type:protected] => HTML w/ PDF
[user_id:protected] =>
[language_id:protected] => 1
[tagging_id:protected] => Garber
[priority_id:protected] => 1
[title:protected] => Focus Four Toolbox Talks, Module 1 – Falls, Talk #2 – Falls from debris piles?
[total_pages:protected] => 1
[billed_pages:protected] => 1
[publication_number:protected] =>
[part_of:protected] =>
[keywords:protected] => disaster response, hazard clean-up, uneven surface, disaster site, disaster clean-up
[comments:protected] =>
[summary:protected] => A toolbox talk on preventing falls from debris piles. Includes questions to ask, an incident to discuss with images, and a place to record questions the trainer would like to ask about the incident. Part of a collection. Click on the 'collection' button to access the other items.
[transition_comments:protected] =>
[external_link:protected] =>
[consol_link:protected] => http://www.cpwrconstructionsolutions.org/roofing/hazard/1463/install-asphalt-roofs-fall-from-heights.html
[more_like_this:protected] => a000081,d000478,d000530
[permission_given_by:protected] =>
[published:protected] => T
[billable:protected] => F
[img_name:protected] =>
[img_ext:protected] =>
[img_width:protected] =>
[img_height:protected] =>
[img_credit:protected] =>
[img_practice:protected] =>
[vid_source_id:protected] =>
[vid_running_time:protected] =>
[vid_intended_audience:protected] =>
[vid_acquisition_info:protected] =>
[vid_cost:protected] =>
[vid_producer:protected] =>
[vid_filename:protected] =>
[vid_filename_downloadable:protected] =>
[date_summary:protected] =>
[date_permission_requested:protected] =>
[date_permission_received:protected] =>
[date_review_needed:protected] =>
[date_received:protected] => 02/15/12
[date_completed:protected] => 03/19/12
[date_billed:protected] =>
[date_modified:protected] => 07/10/12
[collBokExports:protected] =>
[lastBokExportCriteria:BaseElcoshItem:private] =>
[alreadyInSave:protected] =>
[alreadyInValidation:protected] =>
[validationFailures:protected] => Array
(
)
[_new:BaseObject:private] =>
[_deleted:BaseObject:private] =>
[modifiedColumns:protected] => Array
(
)
)
[1] => DocumentRecord Object
(
[records:protected] => Array
(
)
[recordId:protected] =>
[searchWordClass:protected] =>
[searchWordPeerClass:protected] =>
[bok_record:protected] =>
[authors:protected] =>
[organizations:protected] =>
[collections:protected] =>
[categories:protected] =>
[categories_initialized:protected] =>
[mapped_items:protected] =>
[content:protected] =>
[files:protected] =>
[language:protected] => Language Object
(
[id:protected] => 1
[code:protected] => en
[name:protected] => English
[alreadyInSave:protected] =>
[alreadyInValidation:protected] =>
[validationFailures:protected] => Array
(
)
[_new:BaseObject:private] =>
[_deleted:BaseObject:private] =>
[modifiedColumns:protected] => Array
(
)
)
[old_record:protected] =>
[id:protected] => 1610
[old_id:protected] => 1271
[elcosh_id:protected] => d001146
[type:protected] => document
[display_type:protected] => HTML w/ PDF
[user_id:protected] => 0
[language_id:protected] => 1
[tagging_id:protected] => Garber
[priority_id:protected] => 1
[title:protected] => Focus Four Toolbox Talks, Module 2 – Struck-by, Talk #5 – Rigging and Securing Loads
[total_pages:protected] => 1
[billed_pages:protected] => 1
[publication_number:protected] =>
[part_of:protected] =>
[keywords:protected] => rigging, lift loads, loading areas, chains
[comments:protected] =>
[summary:protected] => A toolbox talk on preventing struck-by incidents caused by not securing loads properly. Includes questions to ask, an incident to discuss with images, and a place to record questions the trainer would like to ask about the incident. Part of a collection. Click on the 'collection' button to access the other items.
[transition_comments:protected] =>
[external_link:protected] =>
[consol_link:protected] => http://www.cpwrconstructionsolutions.org/heavy_equipment/hazard/1591/move-equipment-to-from-and-between-sites-work-zone-struck-by-injuries-and-fatalities.html
[more_like_this:protected] => d000144,d000360,d000873
[permission_given_by:protected] =>
[published:protected] => T
[billable:protected] => F
[img_name:protected] =>
[img_ext:protected] =>
[img_width:protected] =>
[img_height:protected] =>
[img_credit:protected] =>
[img_practice:protected] =>
[vid_source_id:protected] =>
[vid_running_time:protected] =>
[vid_intended_audience:protected] =>
[vid_acquisition_info:protected] =>
[vid_cost:protected] =>
[vid_producer:protected] =>
[vid_filename:protected] =>
[vid_filename_downloadable:protected] =>
[date_summary:protected] =>
[date_permission_requested:protected] =>
[date_permission_received:protected] =>
[date_review_needed:protected] =>
[date_received:protected] => 02/15/12
[date_completed:protected] => 03/28/12
[date_billed:protected] =>
[date_modified:protected] => 05/12/14
[collBokExports:protected] =>
[lastBokExportCriteria:BaseElcoshItem:private] =>
[alreadyInSave:protected] =>
[alreadyInValidation:protected] =>
[validationFailures:protected] => Array
(
)
[_new:BaseObject:private] =>
[_deleted:BaseObject:private] =>
[modifiedColumns:protected] => Array
(
)
)
[2] => DocumentRecord Object
(
[records:protected] => Array
(
)
[recordId:protected] =>
[searchWordClass:protected] =>
[searchWordPeerClass:protected] =>
[bok_record:protected] =>
[authors:protected] =>
[organizations:protected] =>
[collections:protected] =>
[categories:protected] =>
[categories_initialized:protected] =>
[mapped_items:protected] =>
[content:protected] =>
[files:protected] =>
[language:protected] => Language Object
(
[id:protected] => 1
[code:protected] => en
[name:protected] => English
[alreadyInSave:protected] =>
[alreadyInValidation:protected] =>
[validationFailures:protected] => Array
(
)
[_new:BaseObject:private] =>
[_deleted:BaseObject:private] =>
[modifiedColumns:protected] => Array
(
)
)
[old_record:protected] =>
[id:protected] => 1645
[old_id:protected] => 1274
[elcosh_id:protected] => d001149
[type:protected] => document
[display_type:protected] => HTML w/ PDF
[user_id:protected] => 0
[language_id:protected] => 1
[tagging_id:protected] => Garber
[priority_id:protected] => 1
[title:protected] => Focus Four Toolbox Talks, Module 3 – Caught-in/between, Talk #2 – Trenches & Heavy Equipment
[total_pages:protected] => 1
[billed_pages:protected] => 1
[publication_number:protected] =>
[part_of:protected] =>
[keywords:protected] => back-up alarms, spotter, soil cave-in, spoil pikes, ROPs, trenching, rain
[comments:protected] =>
[summary:protected] => A toolbox talk on preventing incidents involving trenches such as trench collapse. Includes questions to ask, an incident to discuss with images, and a place to record questions the trainer would like to ask about the incident. Part of a collection. Click on the 'collection' button to access the other items.
[transition_comments:protected] =>
[external_link:protected] =>
[consol_link:protected] =>
[more_like_this:protected] => d000019,d000035,d000168
[permission_given_by:protected] =>
[published:protected] => T
[billable:protected] => F
[img_name:protected] =>
[img_ext:protected] =>
[img_width:protected] =>
[img_height:protected] =>
[img_credit:protected] =>
[img_practice:protected] =>
[vid_source_id:protected] =>
[vid_running_time:protected] =>
[vid_intended_audience:protected] =>
[vid_acquisition_info:protected] =>
[vid_cost:protected] =>
[vid_producer:protected] =>
[vid_filename:protected] =>
[vid_filename_downloadable:protected] =>
[date_summary:protected] =>
[date_permission_requested:protected] =>
[date_permission_received:protected] =>
[date_review_needed:protected] =>
[date_received:protected] => 02/15/12
[date_completed:protected] => 04/02/12
[date_billed:protected] =>
[date_modified:protected] => 05/23/23
[collBokExports:protected] =>
[lastBokExportCriteria:BaseElcoshItem:private] =>
[alreadyInSave:protected] =>
[alreadyInValidation:protected] =>
[validationFailures:protected] => Array
(
)
[_new:BaseObject:private] =>
[_deleted:BaseObject:private] =>
[modifiedColumns:protected] => Array
(
)
)
[3] => DocumentRecord Object
(
[records:protected] => Array
(
)
[recordId:protected] =>
[searchWordClass:protected] =>
[searchWordPeerClass:protected] =>
[bok_record:protected] =>
[authors:protected] =>
[organizations:protected] =>
[collections:protected] =>
[categories:protected] =>
[categories_initialized:protected] =>
[mapped_items:protected] =>
[content:protected] =>
[files:protected] =>
[language:protected] => Language Object
(
[id:protected] => 1
[code:protected] => en
[name:protected] => English
[alreadyInSave:protected] =>
[alreadyInValidation:protected] =>
[validationFailures:protected] => Array
(
)
[_new:BaseObject:private] =>
[_deleted:BaseObject:private] =>
[modifiedColumns:protected] => Array
(
)
)
[old_record:protected] =>
[id:protected] => 1654
[old_id:protected] => 1284
[elcosh_id:protected] => d001159
[type:protected] => document
[display_type:protected] => HTML w/ PDF
[user_id:protected] => 0
[language_id:protected] => 1
[tagging_id:protected] => Garber
[priority_id:protected] => 1
[title:protected] => Focus Four Toolbox Talks, Module 4 – Electrocutions, Talk #6 – Hazards on Disaster Sites
[total_pages:protected] => 1
[billed_pages:protected] => 1
[publication_number:protected] =>
[part_of:protected] =>
[keywords:protected] => powerlines, underground, utilities, generators, wet conditions, GFCIs, energized lines, disasters, emergency response
[comments:protected] =>
[summary:protected] => A toolbox talk on how to avoid electrocution on a disaster site. Includes questions to ask, an incident to discuss with images, and a place to record questions the trainer would like to ask about the incident. Part of a collection. Click on the 'collection' button to access the other items.
[transition_comments:protected] =>
[external_link:protected] =>
[consol_link:protected] => http://www.cpwrconstructionsolutions.org/electrical/hazard/1138/install-and-repair-high-voltage-lines-transformers-switches-electrical-shocks-burns-and-or-electrocution.html
[more_like_this:protected] => d000135,d000361,d000437
[permission_given_by:protected] =>
[published:protected] => T
[billable:protected] => F
[img_name:protected] =>
[img_ext:protected] =>
[img_width:protected] =>
[img_height:protected] =>
[img_credit:protected] =>
[img_practice:protected] =>
[vid_source_id:protected] =>
[vid_running_time:protected] =>
[vid_intended_audience:protected] =>
[vid_acquisition_info:protected] =>
[vid_cost:protected] =>
[vid_producer:protected] =>
[vid_filename:protected] =>
[vid_filename_downloadable:protected] =>
[date_summary:protected] =>
[date_permission_requested:protected] =>
[date_permission_received:protected] =>
[date_review_needed:protected] =>
[date_received:protected] => 02/15/12
[date_completed:protected] => 04/02/12
[date_billed:protected] =>
[date_modified:protected] => 05/23/23
[collBokExports:protected] =>
[lastBokExportCriteria:BaseElcoshItem:private] =>
[alreadyInSave:protected] =>
[alreadyInValidation:protected] =>
[validationFailures:protected] => Array
(
)
[_new:BaseObject:private] =>
[_deleted:BaseObject:private] =>
[modifiedColumns:protected] => Array
(
)
)
)
)
[collections] => Array
(
[1294] =>
[1295] =>
[1292] =>
[1293] => CollectionRecord Object
(
[collection_items:protected] =>
[records:protected] => Array
(
)
[recordId:protected] =>
[searchWordClass:protected] =>
[searchWordPeerClass:protected] =>
[bok_record:protected] =>
[authors:protected] =>
[organizations:protected] =>
[collections:protected] =>
[categories:protected] =>
[categories_initialized:protected] =>
[mapped_items:protected] =>
[content:protected] =>
[files:protected] =>
[language:protected] =>
[old_record:protected] =>
[id:protected] => 1293
[old_id:protected] =>
[elcosh_id:protected] => c000026
[type:protected] => collection
[display_type:protected] => Collection
[user_id:protected] =>
[language_id:protected] =>
[tagging_id:protected] =>
[priority_id:protected] =>
[title:protected] => Focus Four-Struck By
[total_pages:protected] =>
[billed_pages:protected] =>
[publication_number:protected] =>
[part_of:protected] =>
[keywords:protected] =>
[comments:protected] =>
[summary:protected] => The following are links to all of the items in this collection:
[transition_comments:protected] =>
[external_link:protected] =>
[consol_link:protected] =>
[more_like_this:protected] =>
[permission_given_by:protected] =>
[published:protected] => T
[billable:protected] => F
[img_name:protected] =>
[img_ext:protected] =>
[img_width:protected] =>
[img_height:protected] =>
[img_credit:protected] =>
[img_practice:protected] =>
[vid_source_id:protected] =>
[vid_running_time:protected] =>
[vid_intended_audience:protected] =>
[vid_acquisition_info:protected] =>
[vid_cost:protected] =>
[vid_producer:protected] =>
[vid_filename:protected] =>
[vid_filename_downloadable:protected] =>
[date_summary:protected] =>
[date_permission_requested:protected] =>
[date_permission_received:protected] =>
[date_review_needed:protected] =>
[date_received:protected] => 05/08/12
[date_completed:protected] => 05/08/12
[date_billed:protected] =>
[date_modified:protected] => 05/08/12
[collBokExports:protected] =>
[lastBokExportCriteria:BaseElcoshItem:private] =>
[alreadyInSave:protected] =>
[alreadyInValidation:protected] =>
[validationFailures:protected] => Array
(
)
[_new:BaseObject:private] =>
[_deleted:BaseObject:private] =>
[modifiedColumns:protected] => Array
(
)
)
)
[record] => DocumentRecord Object
(
[records:protected] => Array
(
)
[recordId:protected] =>
[searchWordClass:protected] =>
[searchWordPeerClass:protected] =>
[bok_record:protected] =>
[authors:protected] => Array
(
)
[organizations:protected] => Array
(
[256] => Organization Object
(
[id:protected] => 256
[elcosh_id:protected] => o000276
[user_id:protected] => 14
[province_id:protected] => 0
[country_id:protected] => 0
[title:protected] => IUOE National Training Fund
[address:protected] =>
[postal_code:protected] =>
[city:protected] =>
[department:protected] =>
[phone:protected] => 304-253-8674
[fax:protected] =>
[email:protected] =>
[website:protected] => http://www.iuoeiettc.org
[filename:protected] =>
[about:protected] =>
[comments:protected] =>
[logo_available:protected] => T
[no_details:protected] => F
[date_received:protected] => 2012-02-13
[date_completed:protected] => 2012-02-13
[date_billed:protected] =>
[alreadyInSave:protected] =>
[alreadyInValidation:protected] =>
[validationFailures:protected] => Array
(
)
[_new:BaseObject:private] =>
[_deleted:BaseObject:private] =>
[modifiedColumns:protected] => Array
(
)
)
)
[collections:protected] => Array
(
[1294] =>
[1295] =>
[1292] =>
[1293] => CollectionRecord Object
(
[collection_items:protected] =>
[records:protected] => Array
(
)
[recordId:protected] =>
[searchWordClass:protected] =>
[searchWordPeerClass:protected] =>
[bok_record:protected] =>
[authors:protected] =>
[organizations:protected] =>
[collections:protected] =>
[categories:protected] =>
[categories_initialized:protected] =>
[mapped_items:protected] =>
[content:protected] =>
[files:protected] =>
[language:protected] =>
[old_record:protected] =>
[id:protected] => 1293
[old_id:protected] =>
[elcosh_id:protected] => c000026
[type:protected] => collection
[display_type:protected] => Collection
[user_id:protected] =>
[language_id:protected] =>
[tagging_id:protected] =>
[priority_id:protected] =>
[title:protected] => Focus Four-Struck By
[total_pages:protected] =>
[billed_pages:protected] =>
[publication_number:protected] =>
[part_of:protected] =>
[keywords:protected] =>
[comments:protected] =>
[summary:protected] => The following are links to all of the items in this collection:
[transition_comments:protected] =>
[external_link:protected] =>
[consol_link:protected] =>
[more_like_this:protected] =>
[permission_given_by:protected] =>
[published:protected] => T
[billable:protected] => F
[img_name:protected] =>
[img_ext:protected] =>
[img_width:protected] =>
[img_height:protected] =>
[img_credit:protected] =>
[img_practice:protected] =>
[vid_source_id:protected] =>
[vid_running_time:protected] =>
[vid_intended_audience:protected] =>
[vid_acquisition_info:protected] =>
[vid_cost:protected] =>
[vid_producer:protected] =>
[vid_filename:protected] =>
[vid_filename_downloadable:protected] =>
[date_summary:protected] =>
[date_permission_requested:protected] =>
[date_permission_received:protected] =>
[date_review_needed:protected] =>
[date_received:protected] => 05/08/12
[date_completed:protected] => 05/08/12
[date_billed:protected] =>
[date_modified:protected] => 05/08/12
[collBokExports:protected] =>
[lastBokExportCriteria:BaseElcoshItem:private] =>
[alreadyInSave:protected] =>
[alreadyInValidation:protected] =>
[validationFailures:protected] => Array
(
)
[_new:BaseObject:private] =>
[_deleted:BaseObject:private] =>
[modifiedColumns:protected] => Array
(
)
)
)
[categories:protected] =>
[categories_initialized:protected] =>
[mapped_items:protected] => Array
(
[1605] => DocumentRecord Object
(
[records:protected] => Array
(
)
[recordId:protected] =>
[searchWordClass:protected] =>
[searchWordPeerClass:protected] =>
[bok_record:protected] =>
[authors:protected] =>
[organizations:protected] =>
[collections:protected] =>
[categories:protected] =>
[categories_initialized:protected] =>
[mapped_items:protected] =>
[content:protected] =>
[files:protected] =>
[language:protected] =>
[old_record:protected] =>
[id:protected] => 1605
[old_id:protected] => 1262
[elcosh_id:protected] => d001137
[type:protected] => document
[display_type:protected] => HTML w/ PDF
[user_id:protected] =>
[language_id:protected] => 1
[tagging_id:protected] => Garber
[priority_id:protected] => 1
[title:protected] => Focus Four Toolbox Talks, Module 1 – Falls, Talk #2 – Falls from debris piles?
[total_pages:protected] => 1
[billed_pages:protected] => 1
[publication_number:protected] =>
[part_of:protected] =>
[keywords:protected] => disaster response, hazard clean-up, uneven surface, disaster site, disaster clean-up
[comments:protected] =>
[summary:protected] => A toolbox talk on preventing falls from debris piles. Includes questions to ask, an incident to discuss with images, and a place to record questions the trainer would like to ask about the incident. Part of a collection. Click on the 'collection' button to access the other items.
[transition_comments:protected] =>
[external_link:protected] =>
[consol_link:protected] => http://www.cpwrconstructionsolutions.org/roofing/hazard/1463/install-asphalt-roofs-fall-from-heights.html
[more_like_this:protected] => a000081,d000478,d000530
[permission_given_by:protected] =>
[published:protected] => T
[billable:protected] => F
[img_name:protected] =>
[img_ext:protected] =>
[img_width:protected] =>
[img_height:protected] =>
[img_credit:protected] =>
[img_practice:protected] =>
[vid_source_id:protected] =>
[vid_running_time:protected] =>
[vid_intended_audience:protected] =>
[vid_acquisition_info:protected] =>
[vid_cost:protected] =>
[vid_producer:protected] =>
[vid_filename:protected] =>
[vid_filename_downloadable:protected] =>
[date_summary:protected] =>
[date_permission_requested:protected] =>
[date_permission_received:protected] =>
[date_review_needed:protected] =>
[date_received:protected] => 02/15/12
[date_completed:protected] => 03/19/12
[date_billed:protected] =>
[date_modified:protected] => 07/10/12
[collBokExports:protected] =>
[lastBokExportCriteria:BaseElcoshItem:private] =>
[alreadyInSave:protected] =>
[alreadyInValidation:protected] =>
[validationFailures:protected] => Array
(
)
[_new:BaseObject:private] =>
[_deleted:BaseObject:private] =>
[modifiedColumns:protected] => Array
(
)
)
[1610] => DocumentRecord Object
(
[records:protected] => Array
(
)
[recordId:protected] =>
[searchWordClass:protected] =>
[searchWordPeerClass:protected] =>
[bok_record:protected] =>
[authors:protected] =>
[organizations:protected] =>
[collections:protected] =>
[categories:protected] =>
[categories_initialized:protected] =>
[mapped_items:protected] =>
[content:protected] =>
[files:protected] =>
[language:protected] =>
[old_record:protected] =>
[id:protected] => 1610
[old_id:protected] => 1271
[elcosh_id:protected] => d001146
[type:protected] => document
[display_type:protected] => HTML w/ PDF
[user_id:protected] => 0
[language_id:protected] => 1
[tagging_id:protected] => Garber
[priority_id:protected] => 1
[title:protected] => Focus Four Toolbox Talks, Module 2 – Struck-by, Talk #5 – Rigging and Securing Loads
[total_pages:protected] => 1
[billed_pages:protected] => 1
[publication_number:protected] =>
[part_of:protected] =>
[keywords:protected] => rigging, lift loads, loading areas, chains
[comments:protected] =>
[summary:protected] => A toolbox talk on preventing struck-by incidents caused by not securing loads properly. Includes questions to ask, an incident to discuss with images, and a place to record questions the trainer would like to ask about the incident. Part of a collection. Click on the 'collection' button to access the other items.
[transition_comments:protected] =>
[external_link:protected] =>
[consol_link:protected] => http://www.cpwrconstructionsolutions.org/heavy_equipment/hazard/1591/move-equipment-to-from-and-between-sites-work-zone-struck-by-injuries-and-fatalities.html
[more_like_this:protected] => d000144,d000360,d000873
[permission_given_by:protected] =>
[published:protected] => T
[billable:protected] => F
[img_name:protected] =>
[img_ext:protected] =>
[img_width:protected] =>
[img_height:protected] =>
[img_credit:protected] =>
[img_practice:protected] =>
[vid_source_id:protected] =>
[vid_running_time:protected] =>
[vid_intended_audience:protected] =>
[vid_acquisition_info:protected] =>
[vid_cost:protected] =>
[vid_producer:protected] =>
[vid_filename:protected] =>
[vid_filename_downloadable:protected] =>
[date_summary:protected] =>
[date_permission_requested:protected] =>
[date_permission_received:protected] =>
[date_review_needed:protected] =>
[date_received:protected] => 02/15/12
[date_completed:protected] => 03/28/12
[date_billed:protected] =>
[date_modified:protected] => 05/12/14
[collBokExports:protected] =>
[lastBokExportCriteria:BaseElcoshItem:private] =>
[alreadyInSave:protected] =>
[alreadyInValidation:protected] =>
[validationFailures:protected] => Array
(
)
[_new:BaseObject:private] =>
[_deleted:BaseObject:private] =>
[modifiedColumns:protected] => Array
(
)
)
[1645] => DocumentRecord Object
(
[records:protected] => Array
(
)
[recordId:protected] =>
[searchWordClass:protected] =>
[searchWordPeerClass:protected] =>
[bok_record:protected] =>
[authors:protected] =>
[organizations:protected] =>
[collections:protected] =>
[categories:protected] =>
[categories_initialized:protected] =>
[mapped_items:protected] =>
[content:protected] =>
[files:protected] =>
[language:protected] =>
[old_record:protected] =>
[id:protected] => 1645
[old_id:protected] => 1274
[elcosh_id:protected] => d001149
[type:protected] => document
[display_type:protected] => HTML w/ PDF
[user_id:protected] => 0
[language_id:protected] => 1
[tagging_id:protected] => Garber
[priority_id:protected] => 1
[title:protected] => Focus Four Toolbox Talks, Module 3 – Caught-in/between, Talk #2 – Trenches & Heavy Equipment
[total_pages:protected] => 1
[billed_pages:protected] => 1
[publication_number:protected] =>
[part_of:protected] =>
[keywords:protected] => back-up alarms, spotter, soil cave-in, spoil pikes, ROPs, trenching, rain
[comments:protected] =>
[summary:protected] => A toolbox talk on preventing incidents involving trenches such as trench collapse. Includes questions to ask, an incident to discuss with images, and a place to record questions the trainer would like to ask about the incident. Part of a collection. Click on the 'collection' button to access the other items.
[transition_comments:protected] =>
[external_link:protected] =>
[consol_link:protected] =>
[more_like_this:protected] => d000019,d000035,d000168
[permission_given_by:protected] =>
[published:protected] => T
[billable:protected] => F
[img_name:protected] =>
[img_ext:protected] =>
[img_width:protected] =>
[img_height:protected] =>
[img_credit:protected] =>
[img_practice:protected] =>
[vid_source_id:protected] =>
[vid_running_time:protected] =>
[vid_intended_audience:protected] =>
[vid_acquisition_info:protected] =>
[vid_cost:protected] =>
[vid_producer:protected] =>
[vid_filename:protected] =>
[vid_filename_downloadable:protected] =>
[date_summary:protected] =>
[date_permission_requested:protected] =>
[date_permission_received:protected] =>
[date_review_needed:protected] =>
[date_received:protected] => 02/15/12
[date_completed:protected] => 04/02/12
[date_billed:protected] =>
[date_modified:protected] => 05/23/23
[collBokExports:protected] =>
[lastBokExportCriteria:BaseElcoshItem:private] =>
[alreadyInSave:protected] =>
[alreadyInValidation:protected] =>
[validationFailures:protected] => Array
(
)
[_new:BaseObject:private] =>
[_deleted:BaseObject:private] =>
[modifiedColumns:protected] => Array
(
)
)
[1654] => DocumentRecord Object
(
[records:protected] => Array
(
)
[recordId:protected] =>
[searchWordClass:protected] =>
[searchWordPeerClass:protected] =>
[bok_record:protected] =>
[authors:protected] =>
[organizations:protected] =>
[collections:protected] =>
[categories:protected] =>
[categories_initialized:protected] =>
[mapped_items:protected] =>
[content:protected] =>
[files:protected] =>
[language:protected] =>
[old_record:protected] =>
[id:protected] => 1654
[old_id:protected] => 1284
[elcosh_id:protected] => d001159
[type:protected] => document
[display_type:protected] => HTML w/ PDF
[user_id:protected] => 0
[language_id:protected] => 1
[tagging_id:protected] => Garber
[priority_id:protected] => 1
[title:protected] => Focus Four Toolbox Talks, Module 4 – Electrocutions, Talk #6 – Hazards on Disaster Sites
[total_pages:protected] => 1
[billed_pages:protected] => 1
[publication_number:protected] =>
[part_of:protected] =>
[keywords:protected] => powerlines, underground, utilities, generators, wet conditions, GFCIs, energized lines, disasters, emergency response
[comments:protected] =>
[summary:protected] => A toolbox talk on how to avoid electrocution on a disaster site. Includes questions to ask, an incident to discuss with images, and a place to record questions the trainer would like to ask about the incident. Part of a collection. Click on the 'collection' button to access the other items.
[transition_comments:protected] =>
[external_link:protected] =>
[consol_link:protected] => http://www.cpwrconstructionsolutions.org/electrical/hazard/1138/install-and-repair-high-voltage-lines-transformers-switches-electrical-shocks-burns-and-or-electrocution.html
[more_like_this:protected] => d000135,d000361,d000437
[permission_given_by:protected] =>
[published:protected] => T
[billable:protected] => F
[img_name:protected] =>
[img_ext:protected] =>
[img_width:protected] =>
[img_height:protected] =>
[img_credit:protected] =>
[img_practice:protected] =>
[vid_source_id:protected] =>
[vid_running_time:protected] =>
[vid_intended_audience:protected] =>
[vid_acquisition_info:protected] =>
[vid_cost:protected] =>
[vid_producer:protected] =>
[vid_filename:protected] =>
[vid_filename_downloadable:protected] =>
[date_summary:protected] =>
[date_permission_requested:protected] =>
[date_permission_received:protected] =>
[date_review_needed:protected] =>
[date_received:protected] => 02/15/12
[date_completed:protected] => 04/02/12
[date_billed:protected] =>
[date_modified:protected] => 05/23/23
[collBokExports:protected] =>
[lastBokExportCriteria:BaseElcoshItem:private] =>
[alreadyInSave:protected] =>
[alreadyInValidation:protected] =>
[validationFailures:protected] => Array
(
)
[_new:BaseObject:private] =>
[_deleted:BaseObject:private] =>
[modifiedColumns:protected] => Array
(
)
)
)
[content:protected] =>
[files:protected] => Array
(
[9400] => File Object
(
[id:protected] => 9400
[filename:protected] => 1.jpg
[downloadable:protected] => F
[timestamp:protected] => 2014-05-08 15:05:37
[alreadyInSave:protected] =>
[alreadyInValidation:protected] =>
[validationFailures:protected] => Array
(
)
[_new:BaseObject:private] =>
[_deleted:BaseObject:private] =>
[modifiedColumns:protected] => Array
(
)
)
[9401] => File Object
(
[id:protected] => 9401
[filename:protected] => d001298.pdf
[downloadable:protected] => T
[timestamp:protected] => 2014-05-08 15:05:37
[alreadyInSave:protected] =>
[alreadyInValidation:protected] =>
[validationFailures:protected] => Array
(
)
[_new:BaseObject:private] =>
[_deleted:BaseObject:private] =>
[modifiedColumns:protected] => Array
(
)
)
)
[language:protected] => Language Object
(
[id:protected] => 1
[code:protected] => en
[name:protected] => English
[alreadyInSave:protected] =>
[alreadyInValidation:protected] =>
[validationFailures:protected] => Array
(
)
[_new:BaseObject:private] =>
[_deleted:BaseObject:private] =>
[modifiedColumns:protected] => Array
(
)
)
[old_record:protected] =>
[id:protected] => 3827
[old_id:protected] =>
[elcosh_id:protected] => d001298
[type:protected] => document
[display_type:protected] => HTML w/ PDF
[user_id:protected] => 23
[language_id:protected] => 1
[tagging_id:protected] => Bruce Lippy
[priority_id:protected] => 1
[title:protected] => Getting the most out of the IUOE Toolbox Talks
[total_pages:protected] => 2
[billed_pages:protected] => 2
[publication_number:protected] =>
[part_of:protected] =>
[keywords:protected] => toolbox talks, tailgate talks
[comments:protected] =>
[summary:protected] => Toolbox talks have been the main tool for communicating safety information on construction jobs for decades.
Unfortunately, there has been little research on what makes for effective toolbox talks. The IUOE National
Training Fund worked with OSHA and NIOSH to make sure their series of 24 Focus Four toolbox talks were based on the best recommendations for effective design. These toolbox talks accompany an entire package of training materials, but can be used alone. This guide points out the key features of these toolbox talks and how best to deliver them.
[transition_comments:protected] =>
[external_link:protected] =>
[consol_link:protected] =>
[more_like_this:protected] => d001137,d001146,d001149,d001159
[permission_given_by:protected] => IUOE National Hazmat Program
[published:protected] => T
[billable:protected] => F
[img_name:protected] =>
[img_ext:protected] => png
[img_width:protected] =>
[img_height:protected] =>
[img_credit:protected] =>
[img_practice:protected] =>
[vid_source_id:protected] =>
[vid_running_time:protected] =>
[vid_intended_audience:protected] =>
[vid_acquisition_info:protected] =>
[vid_cost:protected] =>
[vid_producer:protected] =>
[vid_filename:protected] =>
[vid_filename_downloadable:protected] =>
[date_summary:protected] => 2007
[date_permission_requested:protected] =>
[date_permission_received:protected] =>
[date_review_needed:protected] =>
[date_received:protected] => 05/08/14
[date_completed:protected] => 05/08/14
[date_billed:protected] =>
[date_modified:protected] => 05/08/14
[collBokExports:protected] =>
[lastBokExportCriteria:BaseElcoshItem:private] =>
[alreadyInSave:protected] =>
[alreadyInValidation:protected] =>
[validationFailures:protected] => Array
(
)
[_new:BaseObject:private] =>
[_deleted:BaseObject:private] =>
[modifiedColumns:protected] => Array
(
)
)
[show_text] =>
[document_content] => ElcoshItemDocumentContent Object
(
[id:protected] => 2896
[item_id:protected] => 3827
[type:protected] => main
[title:protected] =>
[content:protected] =>
Why were these talks developed?
Toolbox talks have been the main tool for communicating safety information on construction jobs for decades. Unfortunately, there has been almost no research on what makes for effective toolbox talks. The IUOE National Training Fund has worked with OSHA, the National Institute for Occupational Safety and Health and the Lippy Group, LLC to make sure these Focus Four toolbox talks are based on the latest fi ndings on the most effective design and tailored to the hazards operating engineers face daily. These toolbox talks accompany an entire package of training materials, but can be used alone. The way these are delivered is as important as how well they are designed.
What did NIOSH find out?
- Just handing out factsheets and toolbox talks to workers doesn’t work. Providing copies after toolbox talks doesn’t make much of an impact either.
- Using case studies (real life stories of accidents that ended in fatality or injury) in toolbox talks is effective.
- When toolbox talks containing case studies were accompanied by discussion questions to encourage group participation, they were more effective. Consequently, getting the workers to participate in the discussion about the case study is important. It’s not enough to tell the story, it is better to have the workers engage in problem solving that analyzes why the accident occurred and how it could have been prevented. Active learning is always better than passive.
How should you deliver these toolbox talks?
- Choose a topic that is related to work going on at the site.
- Hold the meeting on the job, preferably where everyone can sit and relax.
- Hold the meeting at the beginning of a shift or after a break. Folks are too tired at the end of a shift to carefully listen and they want to get home.
- Read the toolbox talk sheet on the topic prior to conducting the talk.
- Start at the top of the form and work right through to the end, which should take around 10 to 15 minutes. Guidance is provided in blue print to help you with each section.
- Use the questions provided to generate discussions. Always allow time for the crew to respond to your questions before you provide an answer. Some suggested responses are written in italics.
- Review the case study and emphasize that this was a real incident. Ask the crew for a case study before you review the one provided, however.
- Always end with a discussion of the particular worksite where you are conducting the talk. Tie the talk as closely to hazards on the site as possible and encourage the crew to constantly look for and immediately correct hazards. They should also know how to report any problems that can’t be immediately corrected.
- Provide copies to each person, if you like, but NIOSH has not found that to be particularly effective.
- Encourage workers to do similar talks on their sites and provide them with the IUOE phone number for ordering in bulk.
- Have everyone sign the back of the form to indicate they attended this session and point out it is a pledge to look out for the health and safety of everyone on the site.
What are the key features of these toolbox talks?

[content_transformed:protected] =>
Why were these talks developed?
Toolbox talks have been the main tool for communicating safety information on construction jobs for decades. Unfortunately, there has been almost no research on what makes for effective toolbox talks. The IUOE National Training Fund has worked with OSHA, the National Institute for Occupational Safety and Health and the Lippy Group, LLC to make sure these Focus Four toolbox talks are based on the latest fi ndings on the most effective design and tailored to the hazards operating engineers face daily. These toolbox talks accompany an entire package of training materials, but can be used alone. The way these are delivered is as important as how well they are designed.
What did NIOSH find out?
- Just handing out factsheets and toolbox talks to workers doesn’t work. Providing copies after toolbox talks doesn’t make much of an impact either.
- Using case studies (real life stories of accidents that ended in fatality or injury) in toolbox talks is effective.
- When toolbox talks containing case studies were accompanied by discussion questions to encourage group participation, they were more effective. Consequently, getting the workers to participate in the discussion about the case study is important. It’s not enough to tell the story, it is better to have the workers engage in problem solving that analyzes why the accident occurred and how it could have been prevented. Active learning is always better than passive.
How should you deliver these toolbox talks?
- Choose a topic that is related to work going on at the site.
- Hold the meeting on the job, preferably where everyone can sit and relax.
- Hold the meeting at the beginning of a shift or after a break. Folks are too tired at the end of a shift to carefully listen and they want to get home.
- Read the toolbox talk sheet on the topic prior to conducting the talk.
- Start at the top of the form and work right through to the end, which should take around 10 to 15 minutes. Guidance is provided in blue print to help you with each section.
- Use the questions provided to generate discussions. Always allow time for the crew to respond to your questions before you provide an answer. Some suggested responses are written in italics.
- Review the case study and emphasize that this was a real incident. Ask the crew for a case study before you review the one provided, however.
- Always end with a discussion of the particular worksite where you are conducting the talk. Tie the talk as closely to hazards on the site as possible and encourage the crew to constantly look for and immediately correct hazards. They should also know how to report any problems that can’t be immediately corrected.
- Provide copies to each person, if you like, but NIOSH has not found that to be particularly effective.
- Encourage workers to do similar talks on their sites and provide them with the IUOE phone number for ordering in bulk.
- Have everyone sign the back of the form to indicate they attended this session and point out it is a pledge to look out for the health and safety of everyone on the site.
What are the key features of these toolbox talks?
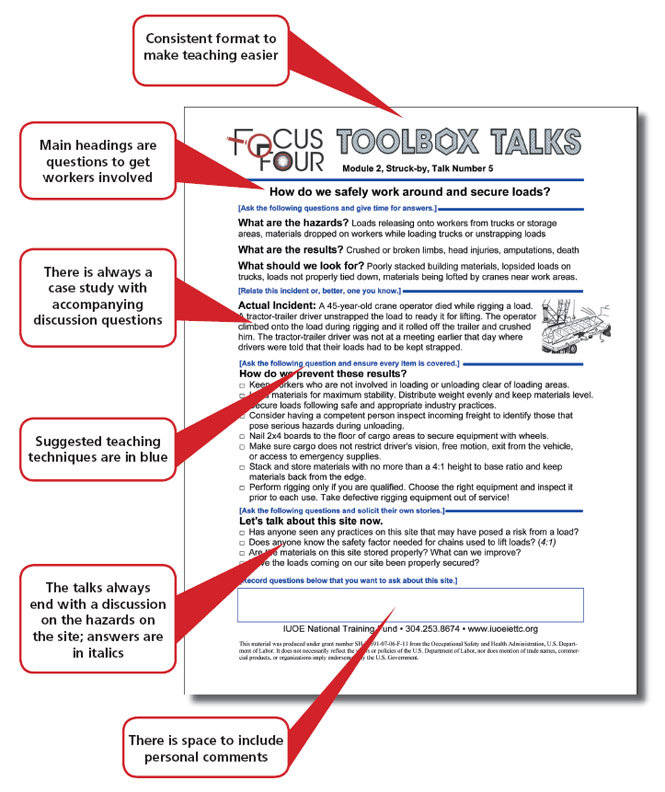
[disclaimer:protected] =>
[disclaimer_transformed:protected] =>
[alreadyInSave:protected] =>
[alreadyInValidation:protected] =>
[validationFailures:protected] => Array
(
)
[_new:BaseObject:private] =>
[_deleted:BaseObject:private] =>
[modifiedColumns:protected] => Array
(
)
)
[template] => record
)
[_file] => /home/agsafe5/repositories/elcosh/live/templates/elcosh/macros.html
[_errors:protected] => Array
(
)
[_encoding:protected] => UTF-8
[_outputMode:protected] => 11
[_forceReparse:protected] =>
[_phpCodeDestination:protected] => /tmp/
[_phpCodeExtension:protected] => php
[_cacheLifetime:protected] => 30
[_cachePurgeFrequency:protected] => 30
[externalMacroTemplatesCache:PHPTAL:private] => Array
(
)
)
[record_macros.html] => PHPTAL Object
(
[_prefilters:protected] => Array
(
)
[_prefilter:PHPTAL:private] => REMOVED: DO NOT USE
[_postfilter:protected] =>
[_repositories:protected] => Array
(
[0] => /home/agsafe5/repositories/elcosh/live/templates/elcosh
)
[_path:protected] => record_macros.html
[_resolvers:protected] => Array
(
)
[_source:protected] => PHPTAL_FileSource Object
(
[_path:PHPTAL_FileSource:private] => /home/agsafe5/repositories/elcosh/live/templates/elcosh/record_macros.html
)
[_codeFile:protected] => /tmp/tpl_61515a6c_record_macros__gMFg5NvPLybiFfYjAv9Aag.php
[_functionName:protected] => tpl_61515a6c_record_macros__gMFg5NvPLybiFfYjAv9Aag
[_prepared:protected] => 1
[_triggers:protected] => Array
(
)
[_translator:protected] =>
[_globalContext:protected] => stdClass Object
(
)
[_context:protected] => PHPTAL_Context Object
(
[_line] =>
[_file] => /home/agsafe5/repositories/elcosh/live/templates/elcosh/record.html
[repeat] => stdClass Object
(
)
[_xmlDeclaration] =>
[_docType] =>
[_nothrow:PHPTAL_Context:private] =>
[_slots:PHPTAL_Context:private] => Array
(
)
[_slotsStack:PHPTAL_Context:private] => Array
(
[0] => Array
(
)
[1] => Array
(
)
)
[_parentContext:PHPTAL_Context:private] => PHPTAL_Context Object
(
[_line] =>
[_file] => /home/agsafe5/repositories/elcosh/live/templates/elcosh/record.html
[repeat] => stdClass Object
(
)
[_xmlDeclaration] =>
[_docType] =>
[_nothrow:PHPTAL_Context:private] =>
[_slots:PHPTAL_Context:private] => Array
(
)
[_slotsStack:PHPTAL_Context:private] => Array
(
[0] => Array
(
)
[1] => Array
(
)
)
[_parentContext:PHPTAL_Context:private] =>
[_globalContext:PHPTAL_Context:private] => stdClass Object
(
)
[_echoDeclarations:PHPTAL_Context:private] =>
[referer] => http://www.elcosh.org/document/3827/d001298/Getting%2Bthe%2Bmost%2Bout%2Bof%2Bthe%2BIUOE%2BToolbox%2BTalks.html
[curr_module] => Record
[styles] => Array
(
)
[javascript] => Array
(
[0] => jquery.min.js
)
[metas] => Array
(
[language] => en
[robots] => index, follow
)
[user] =>
[curr_url] => https://www.elcosh.org/index.php?module=Record&id=3827&type=document
[base_url] => https://www.elcosh.org/index.php?module=Record
[title] => eLCOSH : Getting the most out of the IUOE Toolbox Talks
[language] => en
[search_query] =>
[module] => Record
[new_records] => Array
(
[0] => Search_Result Object
(
[title] => Toolbox Talk: Fixed Ladder
[image] => /record/images/notavailable-p.png
[blurb] => The CPWR Toolbox Talk on Fixed Ladders addresses the potential risks associated with using fixed ladders. The resource includes a brief case example,...
[category] => Array
(
[0] => 15
[1] => 47
[2] => 49
[3] => 51
[4] => 53
[5] => 55
[6] => 60
[7] => 64
[8] => 73
[9] => 76
[10] => 78
[11] => 80
[12] => 86
[13] => 87
[14] => 90
[15] => 92
[16] => 93
[17] => 94
[18] => 100
)
[labels] => Array
(
[0] => Falls
[1] => Work Environment
[2] => Hazards
[3] => Bricklayer
[4] => Trades
[5] => Carpenter
[7] => Cement Mason
[9] => Concrete Polisher
[11] => Electrical Worker
[13] => HVAC
[15] => Laborer
[17] => PCC/Restoration
[19] => Plumber/Pipefitter
[21] => Roofer/Waterproofer
[23] => Sheetmetal Worker
[25] => Welder
[27] => Commercial & Institutional
[28] => Jobsites
[29] => Industrial
[31] => LEED/Green Construction
[33] => Renovations
[35] => Residential
[37] => Toolbox Talks
[38] => Documents
[39] => Media & Documents
)
[type] => Toolbox Talks
[sub_category] =>
[url] => /document/4430/d001660/Toolbox%2BTalk%253A%2BFixed%2BLadder.html
[item:protected] => DocumentRecord Object
(
[records:protected] => Array
(
)
[recordId:protected] =>
[searchWordClass:protected] =>
[searchWordPeerClass:protected] =>
[bok_record:protected] =>
[authors:protected] =>
[organizations:protected] =>
[collections:protected] =>
[categories:protected] => Array
(
[15] => Category Object
(
[languages:protected] =>
[bok_resources:protected] =>
[bok_topics:protected] =>
[bok_keywords:protected] =>
[id:protected] => 15
[type:protected] => category
[parent:protected] => 7
[label:protected] => Falls
[alreadyInSave:protected] =>
[alreadyInValidation:protected] =>
[validationFailures:protected] => Array
(
)
[_new:BaseObject:private] =>
[_deleted:BaseObject:private] =>
[modifiedColumns:protected] => Array
(
)
)
[47] => Category Object
(
[languages:protected] =>
[bok_resources:protected] =>
[bok_topics:protected] =>
[bok_keywords:protected] =>
[id:protected] => 47
[type:protected] => category
[parent:protected] => 2
[label:protected] => Bricklayer
[alreadyInSave:protected] =>
[alreadyInValidation:protected] =>
[validationFailures:protected] => Array
(
)
[_new:BaseObject:private] =>
[_deleted:BaseObject:private] =>
[modifiedColumns:protected] => Array
(
)
)
[49] => Category Object
(
[languages:protected] =>
[bok_resources:protected] =>
[bok_topics:protected] =>
[bok_keywords:protected] =>
[id:protected] => 49
[type:protected] => category
[parent:protected] => 2
[label:protected] => Carpenter
[alreadyInSave:protected] =>
[alreadyInValidation:protected] =>
[validationFailures:protected] => Array
(
)
[_new:BaseObject:private] =>
[_deleted:BaseObject:private] =>
[modifiedColumns:protected] => Array
(
)
)
[51] => Category Object
(
[languages:protected] =>
[bok_resources:protected] =>
[bok_topics:protected] =>
[bok_keywords:protected] =>
[id:protected] => 51
[type:protected] => category
[parent:protected] => 2
[label:protected] => Cement Mason
[alreadyInSave:protected] =>
[alreadyInValidation:protected] =>
[validationFailures:protected] => Array
(
)
[_new:BaseObject:private] =>
[_deleted:BaseObject:private] =>
[modifiedColumns:protected] => Array
(
)
)
[53] => Category Object
(
[languages:protected] =>
[bok_resources:protected] =>
[bok_topics:protected] =>
[bok_keywords:protected] =>
[id:protected] => 53
[type:protected] => category
[parent:protected] => 2
[label:protected] => Concrete Polisher
[alreadyInSave:protected] =>
[alreadyInValidation:protected] =>
[validationFailures:protected] => Array
(
)
[_new:BaseObject:private] =>
[_deleted:BaseObject:private] =>
[modifiedColumns:protected] => Array
(
)
)
[55] => Category Object
(
[languages:protected] =>
[bok_resources:protected] =>
[bok_topics:protected] =>
[bok_keywords:protected] =>
[id:protected] => 55
[type:protected] => category
[parent:protected] => 2
[label:protected] => Electrical Worker
[alreadyInSave:protected] =>
[alreadyInValidation:protected] =>
[validationFailures:protected] => Array
(
)
[_new:BaseObject:private] =>
[_deleted:BaseObject:private] =>
[modifiedColumns:protected] => Array
(
)
)
[60] => Category Object
(
[languages:protected] =>
[bok_resources:protected] =>
[bok_topics:protected] =>
[bok_keywords:protected] =>
[id:protected] => 60
[type:protected] => category
[parent:protected] => 2
[label:protected] => HVAC
[alreadyInSave:protected] =>
[alreadyInValidation:protected] =>
[validationFailures:protected] => Array
(
)
[_new:BaseObject:private] =>
[_deleted:BaseObject:private] =>
[modifiedColumns:protected] => Array
(
)
)
[64] => Category Object
(
[languages:protected] =>
[bok_resources:protected] =>
[bok_topics:protected] =>
[bok_keywords:protected] =>
[id:protected] => 64
[type:protected] => category
[parent:protected] => 2
[label:protected] => Laborer
[alreadyInSave:protected] =>
[alreadyInValidation:protected] =>
[validationFailures:protected] => Array
(
)
[_new:BaseObject:private] =>
[_deleted:BaseObject:private] =>
[modifiedColumns:protected] => Array
(
)
)
[73] => Category Object
(
[languages:protected] =>
[bok_resources:protected] =>
[bok_topics:protected] =>
[bok_keywords:protected] =>
[id:protected] => 73
[type:protected] => category
[parent:protected] => 2
[label:protected] => PCC/Restoration
[alreadyInSave:protected] =>
[alreadyInValidation:protected] =>
[validationFailures:protected] => Array
(
)
[_new:BaseObject:private] =>
[_deleted:BaseObject:private] =>
[modifiedColumns:protected] => Array
(
)
)
[76] => Category Object
(
[languages:protected] =>
[bok_resources:protected] =>
[bok_topics:protected] =>
[bok_keywords:protected] =>
[id:protected] => 76
[type:protected] => category
[parent:protected] => 2
[label:protected] => Plumber/Pipefitter
[alreadyInSave:protected] =>
[alreadyInValidation:protected] =>
[validationFailures:protected] => Array
(
)
[_new:BaseObject:private] =>
[_deleted:BaseObject:private] =>
[modifiedColumns:protected] => Array
(
)
)
[78] => Category Object
(
[languages:protected] =>
[bok_resources:protected] =>
[bok_topics:protected] =>
[bok_keywords:protected] =>
[id:protected] => 78
[type:protected] => category
[parent:protected] => 2
[label:protected] => Roofer/Waterproofer
[alreadyInSave:protected] =>
[alreadyInValidation:protected] =>
[validationFailures:protected] => Array
(
)
[_new:BaseObject:private] =>
[_deleted:BaseObject:private] =>
[modifiedColumns:protected] => Array
(
)
)
[80] => Category Object
(
[languages:protected] =>
[bok_resources:protected] =>
[bok_topics:protected] =>
[bok_keywords:protected] =>
[id:protected] => 80
[type:protected] => category
[parent:protected] => 2
[label:protected] => Sheetmetal Worker
[alreadyInSave:protected] =>
[alreadyInValidation:protected] =>
[validationFailures:protected] => Array
(
)
[_new:BaseObject:private] =>
[_deleted:BaseObject:private] =>
[modifiedColumns:protected] => Array
(
)
)
[86] => Category Object
(
[languages:protected] =>
[bok_resources:protected] =>
[bok_topics:protected] =>
[bok_keywords:protected] =>
[id:protected] => 86
[type:protected] => category
[parent:protected] => 2
[label:protected] => Welder
[alreadyInSave:protected] =>
[alreadyInValidation:protected] =>
[validationFailures:protected] => Array
(
)
[_new:BaseObject:private] =>
[_deleted:BaseObject:private] =>
[modifiedColumns:protected] => Array
(
)
)
[87] => Category Object
(
[languages:protected] =>
[bok_resources:protected] =>
[bok_topics:protected] =>
[bok_keywords:protected] =>
[id:protected] => 87
[type:protected] => category
[parent:protected] => 3
[label:protected] => Commercial & Institutional
[alreadyInSave:protected] =>
[alreadyInValidation:protected] =>
[validationFailures:protected] => Array
(
)
[_new:BaseObject:private] =>
[_deleted:BaseObject:private] =>
[modifiedColumns:protected] => Array
(
)
)
[90] => Category Object
(
[languages:protected] =>
[bok_resources:protected] =>
[bok_topics:protected] =>
[bok_keywords:protected] =>
[id:protected] => 90
[type:protected] => category
[parent:protected] => 3
[label:protected] => Industrial
[alreadyInSave:protected] =>
[alreadyInValidation:protected] =>
[validationFailures:protected] => Array
(
)
[_new:BaseObject:private] =>
[_deleted:BaseObject:private] =>
[modifiedColumns:protected] => Array
(
)
)
[92] => Category Object
(
[languages:protected] =>
[bok_resources:protected] =>
[bok_topics:protected] =>
[bok_keywords:protected] =>
[id:protected] => 92
[type:protected] => category
[parent:protected] => 3
[label:protected] => LEED/Green Construction
[alreadyInSave:protected] =>
[alreadyInValidation:protected] =>
[validationFailures:protected] => Array
(
)
[_new:BaseObject:private] =>
[_deleted:BaseObject:private] =>
[modifiedColumns:protected] => Array
(
)
)
[93] => Category Object
(
[languages:protected] =>
[bok_resources:protected] =>
[bok_topics:protected] =>
[bok_keywords:protected] =>
[id:protected] => 93
[type:protected] => category
[parent:protected] => 3
[label:protected] => Renovations
[alreadyInSave:protected] =>
[alreadyInValidation:protected] =>
[validationFailures:protected] => Array
(
)
[_new:BaseObject:private] =>
[_deleted:BaseObject:private] =>
[modifiedColumns:protected] => Array
(
)
)
[94] => Category Object
(
[languages:protected] =>
[bok_resources:protected] =>
[bok_topics:protected] =>
[bok_keywords:protected] =>
[id:protected] => 94
[type:protected] => category
[parent:protected] => 3
[label:protected] => Residential
[alreadyInSave:protected] =>
[alreadyInValidation:protected] =>
[validationFailures:protected] => Array
(
)
[_new:BaseObject:private] =>
[_deleted:BaseObject:private] =>
[modifiedColumns:protected] => Array
(
)
)
[100] => Category Object
(
[languages:protected] =>
[bok_resources:protected] =>
[bok_topics:protected] =>
[bok_keywords:protected] =>
[id:protected] => 100
[type:protected] => category
[parent:protected] => 6
[label:protected] => Toolbox Talks
[alreadyInSave:protected] =>
[alreadyInValidation:protected] =>
[validationFailures:protected] => Array
(
)
[_new:BaseObject:private] =>
[_deleted:BaseObject:private] =>
[modifiedColumns:protected] => Array
(
)
)
)
[categories_initialized:protected] => 1
[mapped_items:protected] =>
[content:protected] =>
[files:protected] =>
[language:protected] => Language Object
(
[id:protected] => 1
[code:protected] => en
[name:protected] => English
[alreadyInSave:protected] =>
[alreadyInValidation:protected] =>
[validationFailures:protected] => Array
(
)
[_new:BaseObject:private] =>
[_deleted:BaseObject:private] =>
[modifiedColumns:protected] => Array
(
)
)
[old_record:protected] =>
[id:protected] => 4430
[old_id:protected] =>
[elcosh_id:protected] => d001660
[type:protected] => document
[display_type:protected] => HTML only (and links)
[user_id:protected] => 0
[language_id:protected] => 1
[tagging_id:protected] => Mike Aguilar
[priority_id:protected] => 1
[title:protected] => Toolbox Talk: Fixed Ladder
[total_pages:protected] => 0
[billed_pages:protected] => 0
[publication_number:protected] =>
[part_of:protected] =>
[keywords:protected] => Fixed Ladders, Fall Prevention, Falls
[comments:protected] =>
[summary:protected] => The CPWR Toolbox Talk on Fixed Ladders addresses the potential risks associated with using fixed ladders. The resource includes a brief case example, steps to prevent a related injury and questions for discussion. It includes an image that illustrates the hazard, which can be posted in a central location as a reminder of steps to work safely.
Available in
English
and
Spanish.
[transition_comments:protected] =>
[external_link:protected] =>
[consol_link:protected] =>
[more_like_this:protected] => d001257,d001254,d001255,d001256,d001258,d001262,d001279
[permission_given_by:protected] =>
[published:protected] => T
[billable:protected] => F
[img_name:protected] =>
[img_ext:protected] =>
[img_width:protected] =>
[img_height:protected] =>
[img_credit:protected] =>
[img_practice:protected] =>
[vid_source_id:protected] =>
[vid_running_time:protected] =>
[vid_intended_audience:protected] =>
[vid_acquisition_info:protected] =>
[vid_cost:protected] =>
[vid_producer:protected] =>
[vid_filename:protected] =>
[vid_filename_downloadable:protected] =>
[date_summary:protected] =>
[date_permission_requested:protected] =>
[date_permission_received:protected] =>
[date_review_needed:protected] =>
[date_received:protected] => 06/10/22
[date_completed:protected] => 06/10/22
[date_billed:protected] =>
[date_modified:protected] => 05/22/23
[collBokExports:protected] =>
[lastBokExportCriteria:BaseElcoshItem:private] =>
[alreadyInSave:protected] =>
[alreadyInValidation:protected] =>
[validationFailures:protected] => Array
(
)
[_new:BaseObject:private] =>
[_deleted:BaseObject:private] =>
[modifiedColumns:protected] => Array
(
)
)
)
[1] => Search_Result Object
(
[title] => Toolbox Talk: Challenges Preventing Falling Objects
[image] => /record/images/notavailable-p.png
[blurb] => The CPWR Toolbox Talk on Challenges Preventing Falling Objects addresses the hazards of being struck by falling objects on the job site. The resource...
[category] => Array
(
[0] => 12
[1] => 47
[2] => 49
[3] => 51
[4] => 55
[5] => 64
[6] => 68
[7] => 71
[8] => 75
[9] => 78
[10] => 79
[11] => 82
[12] => 62
[13] => 86
[14] => 87
[15] => 88
[16] => 89
[17] => 91
[18] => 90
[19] => 92
[20] => 93
[21] => 94
[22] => 95
[23] => 100
)
[labels] => Array
(
[0] => Crushed/Struck By
[1] => Work Environment
[2] => Hazards
[3] => Bricklayer
[4] => Trades
[5] => Carpenter
[7] => Cement Mason
[9] => Electrical Worker
[11] => Laborer
[13] => Maintenance Worker
[15] => Painter
[17] => Plasterer
[19] => Roofer/Waterproofer
[21] => Scaffold Erector
[23] => Stonemason
[25] => Structural Ironworker
[27] => Welder
[29] => Commercial & Institutional
[30] => Jobsites
[31] => Demolition
[33] => Disasters
[35] => Heavy & Highway
[37] => Industrial
[39] => LEED/Green Construction
[41] => Renovations
[43] => Residential
[45] => Underground
[47] => Toolbox Talks
[48] => Documents
[49] => Media & Documents
)
[type] => Toolbox Talks
[sub_category] =>
[url] => /document/4431/d001661/Toolbox%2BTalk%253A%2BChallenges%2BPreventing%2BFalling%2BObjects.html
[item:protected] => DocumentRecord Object
(
[records:protected] => Array
(
)
[recordId:protected] =>
[searchWordClass:protected] =>
[searchWordPeerClass:protected] =>
[bok_record:protected] =>
[authors:protected] =>
[organizations:protected] =>
[collections:protected] =>
[categories:protected] => Array
(
[12] => Category Object
(
[languages:protected] =>
[bok_resources:protected] =>
[bok_topics:protected] =>
[bok_keywords:protected] =>
[id:protected] => 12
[type:protected] => category
[parent:protected] => 7
[label:protected] => Crushed/Struck By
[alreadyInSave:protected] =>
[alreadyInValidation:protected] =>
[validationFailures:protected] => Array
(
)
[_new:BaseObject:private] =>
[_deleted:BaseObject:private] =>
[modifiedColumns:protected] => Array
(
)
)
[47] => Category Object
(
[languages:protected] =>
[bok_resources:protected] =>
[bok_topics:protected] =>
[bok_keywords:protected] =>
[id:protected] => 47
[type:protected] => category
[parent:protected] => 2
[label:protected] => Bricklayer
[alreadyInSave:protected] =>
[alreadyInValidation:protected] =>
[validationFailures:protected] => Array
(
)
[_new:BaseObject:private] =>
[_deleted:BaseObject:private] =>
[modifiedColumns:protected] => Array
(
)
)
[49] => Category Object
(
[languages:protected] =>
[bok_resources:protected] =>
[bok_topics:protected] =>
[bok_keywords:protected] =>
[id:protected] => 49
[type:protected] => category
[parent:protected] => 2
[label:protected] => Carpenter
[alreadyInSave:protected] =>
[alreadyInValidation:protected] =>
[validationFailures:protected] => Array
(
)
[_new:BaseObject:private] =>
[_deleted:BaseObject:private] =>
[modifiedColumns:protected] => Array
(
)
)
[51] => Category Object
(
[languages:protected] =>
[bok_resources:protected] =>
[bok_topics:protected] =>
[bok_keywords:protected] =>
[id:protected] => 51
[type:protected] => category
[parent:protected] => 2
[label:protected] => Cement Mason
[alreadyInSave:protected] =>
[alreadyInValidation:protected] =>
[validationFailures:protected] => Array
(
)
[_new:BaseObject:private] =>
[_deleted:BaseObject:private] =>
[modifiedColumns:protected] => Array
(
)
)
[55] => Category Object
(
[languages:protected] =>
[bok_resources:protected] =>
[bok_topics:protected] =>
[bok_keywords:protected] =>
[id:protected] => 55
[type:protected] => category
[parent:protected] => 2
[label:protected] => Electrical Worker
[alreadyInSave:protected] =>
[alreadyInValidation:protected] =>
[validationFailures:protected] => Array
(
)
[_new:BaseObject:private] =>
[_deleted:BaseObject:private] =>
[modifiedColumns:protected] => Array
(
)
)
[64] => Category Object
(
[languages:protected] =>
[bok_resources:protected] =>
[bok_topics:protected] =>
[bok_keywords:protected] =>
[id:protected] => 64
[type:protected] => category
[parent:protected] => 2
[label:protected] => Laborer
[alreadyInSave:protected] =>
[alreadyInValidation:protected] =>
[validationFailures:protected] => Array
(
)
[_new:BaseObject:private] =>
[_deleted:BaseObject:private] =>
[modifiedColumns:protected] => Array
(
)
)
[68] => Category Object
(
[languages:protected] =>
[bok_resources:protected] =>
[bok_topics:protected] =>
[bok_keywords:protected] =>
[id:protected] => 68
[type:protected] => category
[parent:protected] => 2
[label:protected] => Maintenance Worker
[alreadyInSave:protected] =>
[alreadyInValidation:protected] =>
[validationFailures:protected] => Array
(
)
[_new:BaseObject:private] =>
[_deleted:BaseObject:private] =>
[modifiedColumns:protected] => Array
(
)
)
[71] => Category Object
(
[languages:protected] =>
[bok_resources:protected] =>
[bok_topics:protected] =>
[bok_keywords:protected] =>
[id:protected] => 71
[type:protected] => category
[parent:protected] => 2
[label:protected] => Painter
[alreadyInSave:protected] =>
[alreadyInValidation:protected] =>
[validationFailures:protected] => Array
(
)
[_new:BaseObject:private] =>
[_deleted:BaseObject:private] =>
[modifiedColumns:protected] => Array
(
)
)
[75] => Category Object
(
[languages:protected] =>
[bok_resources:protected] =>
[bok_topics:protected] =>
[bok_keywords:protected] =>
[id:protected] => 75
[type:protected] => category
[parent:protected] => 2
[label:protected] => Plasterer
[alreadyInSave:protected] =>
[alreadyInValidation:protected] =>
[validationFailures:protected] => Array
(
)
[_new:BaseObject:private] =>
[_deleted:BaseObject:private] =>
[modifiedColumns:protected] => Array
(
)
)
[78] => Category Object
(
[languages:protected] =>
[bok_resources:protected] =>
[bok_topics:protected] =>
[bok_keywords:protected] =>
[id:protected] => 78
[type:protected] => category
[parent:protected] => 2
[label:protected] => Roofer/Waterproofer
[alreadyInSave:protected] =>
[alreadyInValidation:protected] =>
[validationFailures:protected] => Array
(
)
[_new:BaseObject:private] =>
[_deleted:BaseObject:private] =>
[modifiedColumns:protected] => Array
(
)
)
[79] => Category Object
(
[languages:protected] =>
[bok_resources:protected] =>
[bok_topics:protected] =>
[bok_keywords:protected] =>
[id:protected] => 79
[type:protected] => category
[parent:protected] => 2
[label:protected] => Scaffold Erector
[alreadyInSave:protected] =>
[alreadyInValidation:protected] =>
[validationFailures:protected] => Array
(
)
[_new:BaseObject:private] =>
[_deleted:BaseObject:private] =>
[modifiedColumns:protected] => Array
(
)
)
[82] => Category Object
(
[languages:protected] =>
[bok_resources:protected] =>
[bok_topics:protected] =>
[bok_keywords:protected] =>
[id:protected] => 82
[type:protected] => category
[parent:protected] => 2
[label:protected] => Stonemason
[alreadyInSave:protected] =>
[alreadyInValidation:protected] =>
[validationFailures:protected] => Array
(
)
[_new:BaseObject:private] =>
[_deleted:BaseObject:private] =>
[modifiedColumns:protected] => Array
(
)
)
[62] => Category Object
(
[languages:protected] =>
[bok_resources:protected] =>
[bok_topics:protected] =>
[bok_keywords:protected] =>
[id:protected] => 62
[type:protected] => category
[parent:protected] => 2
[label:protected] => Structural Ironworker
[alreadyInSave:protected] =>
[alreadyInValidation:protected] =>
[validationFailures:protected] => Array
(
)
[_new:BaseObject:private] =>
[_deleted:BaseObject:private] =>
[modifiedColumns:protected] => Array
(
)
)
[86] => Category Object
(
[languages:protected] =>
[bok_resources:protected] =>
[bok_topics:protected] =>
[bok_keywords:protected] =>
[id:protected] => 86
[type:protected] => category
[parent:protected] => 2
[label:protected] => Welder
[alreadyInSave:protected] =>
[alreadyInValidation:protected] =>
[validationFailures:protected] => Array
(
)
[_new:BaseObject:private] =>
[_deleted:BaseObject:private] =>
[modifiedColumns:protected] => Array
(
)
)
[87] => Category Object
(
[languages:protected] =>
[bok_resources:protected] =>
[bok_topics:protected] =>
[bok_keywords:protected] =>
[id:protected] => 87
[type:protected] => category
[parent:protected] => 3
[label:protected] => Commercial & Institutional
[alreadyInSave:protected] =>
[alreadyInValidation:protected] =>
[validationFailures:protected] => Array
(
)
[_new:BaseObject:private] =>
[_deleted:BaseObject:private] =>
[modifiedColumns:protected] => Array
(
)
)
[88] => Category Object
(
[languages:protected] =>
[bok_resources:protected] =>
[bok_topics:protected] =>
[bok_keywords:protected] =>
[id:protected] => 88
[type:protected] => category
[parent:protected] => 3
[label:protected] => Demolition
[alreadyInSave:protected] =>
[alreadyInValidation:protected] =>
[validationFailures:protected] => Array
(
)
[_new:BaseObject:private] =>
[_deleted:BaseObject:private] =>
[modifiedColumns:protected] => Array
(
)
)
[89] => Category Object
(
[languages:protected] =>
[bok_resources:protected] =>
[bok_topics:protected] =>
[bok_keywords:protected] =>
[id:protected] => 89
[type:protected] => category
[parent:protected] => 3
[label:protected] => Disasters
[alreadyInSave:protected] =>
[alreadyInValidation:protected] =>
[validationFailures:protected] => Array
(
)
[_new:BaseObject:private] =>
[_deleted:BaseObject:private] =>
[modifiedColumns:protected] => Array
(
)
)
[91] => Category Object
(
[languages:protected] =>
[bok_resources:protected] =>
[bok_topics:protected] =>
[bok_keywords:protected] =>
[id:protected] => 91
[type:protected] => category
[parent:protected] => 3
[label:protected] => Heavy & Highway
[alreadyInSave:protected] =>
[alreadyInValidation:protected] =>
[validationFailures:protected] => Array
(
)
[_new:BaseObject:private] =>
[_deleted:BaseObject:private] =>
[modifiedColumns:protected] => Array
(
)
)
[90] => Category Object
(
[languages:protected] =>
[bok_resources:protected] =>
[bok_topics:protected] =>
[bok_keywords:protected] =>
[id:protected] => 90
[type:protected] => category
[parent:protected] => 3
[label:protected] => Industrial
[alreadyInSave:protected] =>
[alreadyInValidation:protected] =>
[validationFailures:protected] => Array
(
)
[_new:BaseObject:private] =>
[_deleted:BaseObject:private] =>
[modifiedColumns:protected] => Array
(
)
)
[92] => Category Object
(
[languages:protected] =>
[bok_resources:protected] =>
[bok_topics:protected] =>
[bok_keywords:protected] =>
[id:protected] => 92
[type:protected] => category
[parent:protected] => 3
[label:protected] => LEED/Green Construction
[alreadyInSave:protected] =>
[alreadyInValidation:protected] =>
[validationFailures:protected] => Array
(
)
[_new:BaseObject:private] =>
[_deleted:BaseObject:private] =>
[modifiedColumns:protected] => Array
(
)
)
[93] => Category Object
(
[languages:protected] =>
[bok_resources:protected] =>
[bok_topics:protected] =>
[bok_keywords:protected] =>
[id:protected] => 93
[type:protected] => category
[parent:protected] => 3
[label:protected] => Renovations
[alreadyInSave:protected] =>
[alreadyInValidation:protected] =>
[validationFailures:protected] => Array
(
)
[_new:BaseObject:private] =>
[_deleted:BaseObject:private] =>
[modifiedColumns:protected] => Array
(
)
)
[94] => Category Object
(
[languages:protected] =>
[bok_resources:protected] =>
[bok_topics:protected] =>
[bok_keywords:protected] =>
[id:protected] => 94
[type:protected] => category
[parent:protected] => 3
[label:protected] => Residential
[alreadyInSave:protected] =>
[alreadyInValidation:protected] =>
[validationFailures:protected] => Array
(
)
[_new:BaseObject:private] =>
[_deleted:BaseObject:private] =>
[modifiedColumns:protected] => Array
(
)
)
[95] => Category Object
(
[languages:protected] =>
[bok_resources:protected] =>
[bok_topics:protected] =>
[bok_keywords:protected] =>
[id:protected] => 95
[type:protected] => category
[parent:protected] => 3
[label:protected] => Underground
[alreadyInSave:protected] =>
[alreadyInValidation:protected] =>
[validationFailures:protected] => Array
(
)
[_new:BaseObject:private] =>
[_deleted:BaseObject:private] =>
[modifiedColumns:protected] => Array
(
)
)
[100] => Category Object
(
[languages:protected] =>
[bok_resources:protected] =>
[bok_topics:protected] =>
[bok_keywords:protected] =>
[id:protected] => 100
[type:protected] => category
[parent:protected] => 6
[label:protected] => Toolbox Talks
[alreadyInSave:protected] =>
[alreadyInValidation:protected] =>
[validationFailures:protected] => Array
(
)
[_new:BaseObject:private] =>
[_deleted:BaseObject:private] =>
[modifiedColumns:protected] => Array
(
)
)
)
[categories_initialized:protected] => 1
[mapped_items:protected] =>
[content:protected] =>
[files:protected] =>
[language:protected] => Language Object
(
[id:protected] => 1
[code:protected] => en
[name:protected] => English
[alreadyInSave:protected] =>
[alreadyInValidation:protected] =>
[validationFailures:protected] => Array
(
)
[_new:BaseObject:private] =>
[_deleted:BaseObject:private] =>
[modifiedColumns:protected] => Array
(
)
)
[old_record:protected] =>
[id:protected] => 4431
[old_id:protected] =>
[elcosh_id:protected] => d001661
[type:protected] => document
[display_type:protected] => HTML only (and links)
[user_id:protected] => 0
[language_id:protected] => 1
[tagging_id:protected] => Mike Aguilar
[priority_id:protected] => 1
[title:protected] => Toolbox Talk: Challenges Preventing Falling Objects
[total_pages:protected] => 0
[billed_pages:protected] => 0
[publication_number:protected] =>
[part_of:protected] =>
[keywords:protected] => dropped objects, falling objects, struck by incidents, struck by fatalities
[comments:protected] =>
[summary:protected] => The CPWR Toolbox Talk on Challenges Preventing Falling Objects addresses the hazards of being struck by falling objects on the job site. The resource includes a brief example, steps to prevent a related injury, and questions for discussion. It includes a graphic that illustrates a group workers observing a scaffold free of debris during high winds, which can be posted in a central location as a reminder of steps to work safely.
Available in
English and
Spanish.
[transition_comments:protected] =>
[external_link:protected] =>
[consol_link:protected] =>
[more_like_this:protected] => d001234,d001238,d001244,d001251,d001253,d001260,d001268,d001278
[permission_given_by:protected] =>
[published:protected] => T
[billable:protected] => F
[img_name:protected] =>
[img_ext:protected] =>
[img_width:protected] =>
[img_height:protected] =>
[img_credit:protected] =>
[img_practice:protected] =>
[vid_source_id:protected] =>
[vid_running_time:protected] =>
[vid_intended_audience:protected] =>
[vid_acquisition_info:protected] =>
[vid_cost:protected] =>
[vid_producer:protected] =>
[vid_filename:protected] =>
[vid_filename_downloadable:protected] =>
[date_summary:protected] =>
[date_permission_requested:protected] =>
[date_permission_received:protected] =>
[date_review_needed:protected] =>
[date_received:protected] => 06/10/22
[date_completed:protected] => 06/10/22
[date_billed:protected] =>
[date_modified:protected] => 05/22/23
[collBokExports:protected] =>
[lastBokExportCriteria:BaseElcoshItem:private] =>
[alreadyInSave:protected] =>
[alreadyInValidation:protected] =>
[validationFailures:protected] => Array
(
)
[_new:BaseObject:private] =>
[_deleted:BaseObject:private] =>
[modifiedColumns:protected] => Array
(
)
)
)
[2] => Search_Result Object
(
[title] => Toolbox Talk: Tower Crane Safety
[image] => /record/images/notavailable-p.png
[blurb] => The CPWR Toolbox Talk on Tower Crane Safety addresses the potential hazards of Tower Cranes and the importance of following procedure before and durin...
[category] => Array
(
[0] => 11
[1] => 12
[2] => 18
[3] => 70
[4] => 87
[5] => 88
[6] => 91
[7] => 90
[8] => 92
[9] => 100
)
[labels] => Array
(
[0] => Cranes & Hoists
[1] => Work Environment
[2] => Hazards
[3] => Crushed/Struck By
[6] => Motor Vehicles/Heavy Equipment
[9] => Operating Engineer
[10] => Trades
[11] => Commercial & Institutional
[12] => Jobsites
[13] => Demolition
[15] => Heavy & Highway
[17] => Industrial
[19] => LEED/Green Construction
[21] => Toolbox Talks
[22] => Documents
[23] => Media & Documents
)
[type] => Toolbox Talks
[sub_category] =>
[url] => /document/4427/d001657/Toolbox%2BTalk%253A%2BTower%2BCrane%2BSafety.html
[item:protected] => DocumentRecord Object
(
[records:protected] => Array
(
)
[recordId:protected] =>
[searchWordClass:protected] =>
[searchWordPeerClass:protected] =>
[bok_record:protected] =>
[authors:protected] =>
[organizations:protected] =>
[collections:protected] =>
[categories:protected] => Array
(
[11] => Category Object
(
[languages:protected] =>
[bok_resources:protected] =>
[bok_topics:protected] =>
[bok_keywords:protected] =>
[id:protected] => 11
[type:protected] => category
[parent:protected] => 7
[label:protected] => Cranes & Hoists
[alreadyInSave:protected] =>
[alreadyInValidation:protected] =>
[validationFailures:protected] => Array
(
)
[_new:BaseObject:private] =>
[_deleted:BaseObject:private] =>
[modifiedColumns:protected] => Array
(
)
)
[12] => Category Object
(
[languages:protected] =>
[bok_resources:protected] =>
[bok_topics:protected] =>
[bok_keywords:protected] =>
[id:protected] => 12
[type:protected] => category
[parent:protected] => 7
[label:protected] => Crushed/Struck By
[alreadyInSave:protected] =>
[alreadyInValidation:protected] =>
[validationFailures:protected] => Array
(
)
[_new:BaseObject:private] =>
[_deleted:BaseObject:private] =>
[modifiedColumns:protected] => Array
(
)
)
[18] => Category Object
(
[languages:protected] =>
[bok_resources:protected] =>
[bok_topics:protected] =>
[bok_keywords:protected] =>
[id:protected] => 18
[type:protected] => category
[parent:protected] => 7
[label:protected] => Motor Vehicles/Heavy Equipment
[alreadyInSave:protected] =>
[alreadyInValidation:protected] =>
[validationFailures:protected] => Array
(
)
[_new:BaseObject:private] =>
[_deleted:BaseObject:private] =>
[modifiedColumns:protected] => Array
(
)
)
[70] => Category Object
(
[languages:protected] =>
[bok_resources:protected] =>
[bok_topics:protected] =>
[bok_keywords:protected] =>
[id:protected] => 70
[type:protected] => category
[parent:protected] => 2
[label:protected] => Operating Engineer
[alreadyInSave:protected] =>
[alreadyInValidation:protected] =>
[validationFailures:protected] => Array
(
)
[_new:BaseObject:private] =>
[_deleted:BaseObject:private] =>
[modifiedColumns:protected] => Array
(
)
)
[87] => Category Object
(
[languages:protected] =>
[bok_resources:protected] =>
[bok_topics:protected] =>
[bok_keywords:protected] =>
[id:protected] => 87
[type:protected] => category
[parent:protected] => 3
[label:protected] => Commercial & Institutional
[alreadyInSave:protected] =>
[alreadyInValidation:protected] =>
[validationFailures:protected] => Array
(
)
[_new:BaseObject:private] =>
[_deleted:BaseObject:private] =>
[modifiedColumns:protected] => Array
(
)
)
[88] => Category Object
(
[languages:protected] =>
[bok_resources:protected] =>
[bok_topics:protected] =>
[bok_keywords:protected] =>
[id:protected] => 88
[type:protected] => category
[parent:protected] => 3
[label:protected] => Demolition
[alreadyInSave:protected] =>
[alreadyInValidation:protected] =>
[validationFailures:protected] => Array
(
)
[_new:BaseObject:private] =>
[_deleted:BaseObject:private] =>
[modifiedColumns:protected] => Array
(
)
)
[91] => Category Object
(
[languages:protected] =>
[bok_resources:protected] =>
[bok_topics:protected] =>
[bok_keywords:protected] =>
[id:protected] => 91
[type:protected] => category
[parent:protected] => 3
[label:protected] => Heavy & Highway
[alreadyInSave:protected] =>
[alreadyInValidation:protected] =>
[validationFailures:protected] => Array
(
)
[_new:BaseObject:private] =>
[_deleted:BaseObject:private] =>
[modifiedColumns:protected] => Array
(
)
)
[90] => Category Object
(
[languages:protected] =>
[bok_resources:protected] =>
[bok_topics:protected] =>
[bok_keywords:protected] =>
[id:protected] => 90
[type:protected] => category
[parent:protected] => 3
[label:protected] => Industrial
[alreadyInSave:protected] =>
[alreadyInValidation:protected] =>
[validationFailures:protected] => Array
(
)
[_new:BaseObject:private] =>
[_deleted:BaseObject:private] =>
[modifiedColumns:protected] => Array
(
)
)
[92] => Category Object
(
[languages:protected] =>
[bok_resources:protected] =>
[bok_topics:protected] =>
[bok_keywords:protected] =>
[id:protected] => 92
[type:protected] => category
[parent:protected] => 3
[label:protected] => LEED/Green Construction
[alreadyInSave:protected] =>
[alreadyInValidation:protected] =>
[validationFailures:protected] => Array
(
)
[_new:BaseObject:private] =>
[_deleted:BaseObject:private] =>
[modifiedColumns:protected] => Array
(
)
)
[100] => Category Object
(
[languages:protected] =>
[bok_resources:protected] =>
[bok_topics:protected] =>
[bok_keywords:protected] =>
[id:protected] => 100
[type:protected] => category
[parent:protected] => 6
[label:protected] => Toolbox Talks
[alreadyInSave:protected] =>
[alreadyInValidation:protected] =>
[validationFailures:protected] => Array
(
)
[_new:BaseObject:private] =>
[_deleted:BaseObject:private] =>
[modifiedColumns:protected] => Array
(
)
)
)
[categories_initialized:protected] => 1
[mapped_items:protected] =>
[content:protected] =>
[files:protected] =>
[language:protected] => Language Object
(
[id:protected] => 1
[code:protected] => en
[name:protected] => English
[alreadyInSave:protected] =>
[alreadyInValidation:protected] =>
[validationFailures:protected] => Array
(
)
[_new:BaseObject:private] =>
[_deleted:BaseObject:private] =>
[modifiedColumns:protected] => Array
(
)
)
[old_record:protected] =>
[id:protected] => 4427
[old_id:protected] =>
[elcosh_id:protected] => d001657
[type:protected] => document
[display_type:protected] => HTML only (and links)
[user_id:protected] => 0
[language_id:protected] => 1
[tagging_id:protected] => Mike Aguilar
[priority_id:protected] => 1
[title:protected] => Toolbox Talk: Tower Crane Safety
[total_pages:protected] => 0
[billed_pages:protected] => 0
[publication_number:protected] =>
[part_of:protected] =>
[keywords:protected] => Tower Crane, Crane, Stability, Tipping, Lift Zone Safety, Lift, Zone, Safety, Struck by
[comments:protected] =>
[summary:protected] => The CPWR Toolbox Talk on Tower Crane Safety addresses the potential hazards of Tower Cranes and the importance of following procedure before and during Tower Crane operation. The resource includes a brief example, steps to prevent a related injury, and questions for discussion. It includes a graphic that illustrates a worker inspecting a Tower Crane before operation, which can be posted in a central location as a reminder of steps to work safely.
Available in
English and
Spanish.
[transition_comments:protected] =>
[external_link:protected] =>
[consol_link:protected] =>
[more_like_this:protected] => d001234,d001238,d001250,d001251,d001253,d001258,d001262,d001273
[permission_given_by:protected] =>
[published:protected] => T
[billable:protected] => F
[img_name:protected] =>
[img_ext:protected] => jpg
[img_width:protected] =>
[img_height:protected] =>
[img_credit:protected] =>
[img_practice:protected] =>
[vid_source_id:protected] =>
[vid_running_time:protected] =>
[vid_intended_audience:protected] =>
[vid_acquisition_info:protected] =>
[vid_cost:protected] =>
[vid_producer:protected] =>
[vid_filename:protected] =>
[vid_filename_downloadable:protected] =>
[date_summary:protected] =>
[date_permission_requested:protected] =>
[date_permission_received:protected] =>
[date_review_needed:protected] =>
[date_received:protected] => 12/23/21
[date_completed:protected] => 12/23/21
[date_billed:protected] =>
[date_modified:protected] => 05/19/23
[collBokExports:protected] =>
[lastBokExportCriteria:BaseElcoshItem:private] =>
[alreadyInSave:protected] =>
[alreadyInValidation:protected] =>
[validationFailures:protected] => Array
(
)
[_new:BaseObject:private] =>
[_deleted:BaseObject:private] =>
[modifiedColumns:protected] => Array
(
)
)
)
[3] => Search_Result Object
(
[title] => Toolbox Talk: Work Zone Safety: Working Around Vehicles
[image] => /record/images/notavailable-p.png
[blurb] => The CPWR Toolbox Talk on Working Around Vehicles in the Work Zone addresses methods to avoid being struck-by a vehicle on a construction site. The res...
[category] => Array
(
[0] => 12
[1] => 18
[2] => 52
[3] => 57
[4] => 70
[5] => 85
[6] => 87
[7] => 88
[8] => 89
[9] => 91
[10] => 90
[11] => 92
[12] => 93
[13] => 94
[14] => 95
[15] => 100
)
[labels] => Array
(
[0] => Crushed/Struck By
[1] => Work Environment
[2] => Hazards
[3] => Motor Vehicles/Heavy Equipment
[6] => Commercial Diver
[7] => Trades
[8] => Flagger
[10] => Operating Engineer
[12] => Truck Driver
[14] => Commercial & Institutional
[15] => Jobsites
[16] => Demolition
[18] => Disasters
[20] => Heavy & Highway
[22] => Industrial
[24] => LEED/Green Construction
[26] => Renovations
[28] => Residential
[30] => Underground
[32] => Toolbox Talks
[33] => Documents
[34] => Media & Documents
)
[type] => Toolbox Talks
[sub_category] =>
[url] => /document/4428/d001658/Toolbox%2BTalk%253A%2BWork%2BZone%2BSafety%253A%2BWorking%2BAround%2BVehicles.html
[item:protected] => DocumentRecord Object
(
[records:protected] => Array
(
)
[recordId:protected] =>
[searchWordClass:protected] =>
[searchWordPeerClass:protected] =>
[bok_record:protected] =>
[authors:protected] =>
[organizations:protected] =>
[collections:protected] =>
[categories:protected] => Array
(
[12] => Category Object
(
[languages:protected] =>
[bok_resources:protected] =>
[bok_topics:protected] =>
[bok_keywords:protected] =>
[id:protected] => 12
[type:protected] => category
[parent:protected] => 7
[label:protected] => Crushed/Struck By
[alreadyInSave:protected] =>
[alreadyInValidation:protected] =>
[validationFailures:protected] => Array
(
)
[_new:BaseObject:private] =>
[_deleted:BaseObject:private] =>
[modifiedColumns:protected] => Array
(
)
)
[18] => Category Object
(
[languages:protected] =>
[bok_resources:protected] =>
[bok_topics:protected] =>
[bok_keywords:protected] =>
[id:protected] => 18
[type:protected] => category
[parent:protected] => 7
[label:protected] => Motor Vehicles/Heavy Equipment
[alreadyInSave:protected] =>
[alreadyInValidation:protected] =>
[validationFailures:protected] => Array
(
)
[_new:BaseObject:private] =>
[_deleted:BaseObject:private] =>
[modifiedColumns:protected] => Array
(
)
)
[52] => Category Object
(
[languages:protected] =>
[bok_resources:protected] =>
[bok_topics:protected] =>
[bok_keywords:protected] =>
[id:protected] => 52
[type:protected] => category
[parent:protected] => 2
[label:protected] => Commercial Diver
[alreadyInSave:protected] =>
[alreadyInValidation:protected] =>
[validationFailures:protected] => Array
(
)
[_new:BaseObject:private] =>
[_deleted:BaseObject:private] =>
[modifiedColumns:protected] => Array
(
)
)
[57] => Category Object
(
[languages:protected] =>
[bok_resources:protected] =>
[bok_topics:protected] =>
[bok_keywords:protected] =>
[id:protected] => 57
[type:protected] => category
[parent:protected] => 2
[label:protected] => Flagger
[alreadyInSave:protected] =>
[alreadyInValidation:protected] =>
[validationFailures:protected] => Array
(
)
[_new:BaseObject:private] =>
[_deleted:BaseObject:private] =>
[modifiedColumns:protected] => Array
(
)
)
[70] => Category Object
(
[languages:protected] =>
[bok_resources:protected] =>
[bok_topics:protected] =>
[bok_keywords:protected] =>
[id:protected] => 70
[type:protected] => category
[parent:protected] => 2
[label:protected] => Operating Engineer
[alreadyInSave:protected] =>
[alreadyInValidation:protected] =>
[validationFailures:protected] => Array
(
)
[_new:BaseObject:private] =>
[_deleted:BaseObject:private] =>
[modifiedColumns:protected] => Array
(
)
)
[85] => Category Object
(
[languages:protected] =>
[bok_resources:protected] =>
[bok_topics:protected] =>
[bok_keywords:protected] =>
[id:protected] => 85
[type:protected] => category
[parent:protected] => 2
[label:protected] => Truck Driver
[alreadyInSave:protected] =>
[alreadyInValidation:protected] =>
[validationFailures:protected] => Array
(
)
[_new:BaseObject:private] =>
[_deleted:BaseObject:private] =>
[modifiedColumns:protected] => Array
(
)
)
[87] => Category Object
(
[languages:protected] =>
[bok_resources:protected] =>
[bok_topics:protected] =>
[bok_keywords:protected] =>
[id:protected] => 87
[type:protected] => category
[parent:protected] => 3
[label:protected] => Commercial & Institutional
[alreadyInSave:protected] =>
[alreadyInValidation:protected] =>
[validationFailures:protected] => Array
(
)
[_new:BaseObject:private] =>
[_deleted:BaseObject:private] =>
[modifiedColumns:protected] => Array
(
)
)
[88] => Category Object
(
[languages:protected] =>
[bok_resources:protected] =>
[bok_topics:protected] =>
[bok_keywords:protected] =>
[id:protected] => 88
[type:protected] => category
[parent:protected] => 3
[label:protected] => Demolition
[alreadyInSave:protected] =>
[alreadyInValidation:protected] =>
[validationFailures:protected] => Array
(
)
[_new:BaseObject:private] =>
[_deleted:BaseObject:private] =>
[modifiedColumns:protected] => Array
(
)
)
[89] => Category Object
(
[languages:protected] =>
[bok_resources:protected] =>
[bok_topics:protected] =>
[bok_keywords:protected] =>
[id:protected] => 89
[type:protected] => category
[parent:protected] => 3
[label:protected] => Disasters
[alreadyInSave:protected] =>
[alreadyInValidation:protected] =>
[validationFailures:protected] => Array
(
)
[_new:BaseObject:private] =>
[_deleted:BaseObject:private] =>
[modifiedColumns:protected] => Array
(
)
)
[91] => Category Object
(
[languages:protected] =>
[bok_resources:protected] =>
[bok_topics:protected] =>
[bok_keywords:protected] =>
[id:protected] => 91
[type:protected] => category
[parent:protected] => 3
[label:protected] => Heavy & Highway
[alreadyInSave:protected] =>
[alreadyInValidation:protected] =>
[validationFailures:protected] => Array
(
)
[_new:BaseObject:private] =>
[_deleted:BaseObject:private] =>
[modifiedColumns:protected] => Array
(
)
)
[90] => Category Object
(
[languages:protected] =>
[bok_resources:protected] =>
[bok_topics:protected] =>
[bok_keywords:protected] =>
[id:protected] => 90
[type:protected] => category
[parent:protected] => 3
[label:protected] => Industrial
[alreadyInSave:protected] =>
[alreadyInValidation:protected] =>
[validationFailures:protected] => Array
(
)
[_new:BaseObject:private] =>
[_deleted:BaseObject:private] =>
[modifiedColumns:protected] => Array
(
)
)
[92] => Category Object
(
[languages:protected] =>
[bok_resources:protected] =>
[bok_topics:protected] =>
[bok_keywords:protected] =>
[id:protected] => 92
[type:protected] => category
[parent:protected] => 3
[label:protected] => LEED/Green Construction
[alreadyInSave:protected] =>
[alreadyInValidation:protected] =>
[validationFailures:protected] => Array
(
)
[_new:BaseObject:private] =>
[_deleted:BaseObject:private] =>
[modifiedColumns:protected] => Array
(
)
)
[93] => Category Object
(
[languages:protected] =>
[bok_resources:protected] =>
[bok_topics:protected] =>
[bok_keywords:protected] =>
[id:protected] => 93
[type:protected] => category
[parent:protected] => 3
[label:protected] => Renovations
[alreadyInSave:protected] =>
[alreadyInValidation:protected] =>
[validationFailures:protected] => Array
(
)
[_new:BaseObject:private] =>
[_deleted:BaseObject:private] =>
[modifiedColumns:protected] => Array
(
)
)
[94] => Category Object
(
[languages:protected] =>
[bok_resources:protected] =>
[bok_topics:protected] =>
[bok_keywords:protected] =>
[id:protected] => 94
[type:protected] => category
[parent:protected] => 3
[label:protected] => Residential
[alreadyInSave:protected] =>
[alreadyInValidation:protected] =>
[validationFailures:protected] => Array
(
)
[_new:BaseObject:private] =>
[_deleted:BaseObject:private] =>
[modifiedColumns:protected] => Array
(
)
)
[95] => Category Object
(
[languages:protected] =>
[bok_resources:protected] =>
[bok_topics:protected] =>
[bok_keywords:protected] =>
[id:protected] => 95
[type:protected] => category
[parent:protected] => 3
[label:protected] => Underground
[alreadyInSave:protected] =>
[alreadyInValidation:protected] =>
[validationFailures:protected] => Array
(
)
[_new:BaseObject:private] =>
[_deleted:BaseObject:private] =>
[modifiedColumns:protected] => Array
(
)
)
[100] => Category Object
(
[languages:protected] =>
[bok_resources:protected] =>
[bok_topics:protected] =>
[bok_keywords:protected] =>
[id:protected] => 100
[type:protected] => category
[parent:protected] => 6
[label:protected] => Toolbox Talks
[alreadyInSave:protected] =>
[alreadyInValidation:protected] =>
[validationFailures:protected] => Array
(
)
[_new:BaseObject:private] =>
[_deleted:BaseObject:private] =>
[modifiedColumns:protected] => Array
(
)
)
)
[categories_initialized:protected] => 1
[mapped_items:protected] =>
[content:protected] =>
[files:protected] =>
[language:protected] => Language Object
(
[id:protected] => 1
[code:protected] => en
[name:protected] => English
[alreadyInSave:protected] =>
[alreadyInValidation:protected] =>
[validationFailures:protected] => Array
(
)
[_new:BaseObject:private] =>
[_deleted:BaseObject:private] =>
[modifiedColumns:protected] => Array
(
)
)
[old_record:protected] =>
[id:protected] => 4428
[old_id:protected] =>
[elcosh_id:protected] => d001658
[type:protected] => document
[display_type:protected] => HTML only (and links)
[user_id:protected] => 0
[language_id:protected] => 1
[tagging_id:protected] => Daniela Caceres
[priority_id:protected] => 1
[title:protected] => Toolbox Talk: Work Zone Safety: Working Around Vehicles
[total_pages:protected] => 0
[billed_pages:protected] => 0
[publication_number:protected] =>
[part_of:protected] =>
[keywords:protected] => Struck, Struck by, Vehicle, Work Zone Safety, Truck, Operator, Driver, Mobile Equipment
[comments:protected] =>
[summary:protected] => The CPWR Toolbox Talk on Working Around Vehicles in the Work Zone addresses methods to avoid being struck-by a vehicle on a construction site. The resource includes a case example, steps to prevent a related injury, and questions for discussion. It includes a graphic that illustrates the hazard, which can be posted in a central location as a reminder of steps to work safely. Available in
English and
Spanish.
[transition_comments:protected] =>
[external_link:protected] =>
[consol_link:protected] =>
[more_like_this:protected] => d001640
[permission_given_by:protected] =>
[published:protected] => T
[billable:protected] => F
[img_name:protected] =>
[img_ext:protected] =>
[img_width:protected] =>
[img_height:protected] =>
[img_credit:protected] =>
[img_practice:protected] =>
[vid_source_id:protected] =>
[vid_running_time:protected] =>
[vid_intended_audience:protected] =>
[vid_acquisition_info:protected] =>
[vid_cost:protected] =>
[vid_producer:protected] =>
[vid_filename:protected] =>
[vid_filename_downloadable:protected] =>
[date_summary:protected] =>
[date_permission_requested:protected] =>
[date_permission_received:protected] =>
[date_review_needed:protected] =>
[date_received:protected] => 12/23/21
[date_completed:protected] => 12/23/21
[date_billed:protected] =>
[date_modified:protected] => 05/19/23
[collBokExports:protected] =>
[lastBokExportCriteria:BaseElcoshItem:private] =>
[alreadyInSave:protected] =>
[alreadyInValidation:protected] =>
[validationFailures:protected] => Array
(
)
[_new:BaseObject:private] =>
[_deleted:BaseObject:private] =>
[modifiedColumns:protected] => Array
(
)
)
)
[4] => Search_Result Object
(
[title] => Construction Dive -- DeWalt's Jobsite Pro headphones recalled for fire hazards
[image] => /record/images/notavailable-p.png
[blurb] => A recall notice by the United States Consumer Product Safety Commission affects over 300,000 DeWalt Jobsite Pro Headphones. The recall is a result of...
[category] => Array
(
[0] => 16
[1] => 44
[2] => 45
[3] => 46
[4] => 47
[5] => 48
[6] => 49
[7] => 50
[8] => 51
[9] => 52
[10] => 53
[11] => 54
[12] => 55
[13] => 56
[14] => 57
[15] => 58
[16] => 59
[17] => 60
[18] => 61
[19] => 64
[20] => 65
[21] => 66
[22] => 67
[23] => 68
[24] => 69
[25] => 70
[26] => 71
[27] => 72
[28] => 73
[29] => 74
[30] => 75
[31] => 76
[32] => 77
[33] => 63
[34] => 78
[35] => 79
[36] => 80
[37] => 81
[38] => 82
[39] => 62
[40] => 83
[41] => 84
[42] => 85
[43] => 86
[44] => 87
[45] => 88
[46] => 89
[47] => 91
[48] => 90
[49] => 92
[50] => 93
[51] => 94
[52] => 95
)
[labels] => Array
(
[0] => Fire & Explosions
[1] => Work Environment
[2] => Hazards
[3] => Acoustical Ceiling Carpenter
[4] => Trades
[5] => Asbestos/Insulator
[7] => Boilermaker
[9] => Bricklayer
[11] => Cabinetmaker
[13] => Carpenter
[15] => Carpet Layer
[17] => Cement Mason
[19] => Commercial Diver
[21] => Concrete Polisher
[23] => Drywall Applicator Specialist
[25] => Electrical Worker
[27] => Elevator Constructor
[29] => Flagger
[31] => Glazier
[33] => Hazardous Waste Cleanup
[35] => HVAC
[37] => Interior Systems Carpenter
[39] => Laborer
[41] => Landscaper
[43] => Lather
[45] => Lead Abatement Worker
[47] => Maintenance Worker
[49] => Millwright
[51] => Operating Engineer
[53] => Painter
[55] => Paper Hanger
[57] => PCC/Restoration
[59] => Pile Driver
[61] => Plasterer
[63] => Plumber/Pipefitter
[65] => Refractory Worker
[67] => Reinforcing Ironworker
[69] => Roofer/Waterproofer
[71] => Scaffold Erector
[73] => Sheetmetal Worker
[75] => Sprinkler Fitter
[77] => Stonemason
[79] => Structural Ironworker
[81] => Terrazzo Worker
[83] => Tile Setter
[85] => Truck Driver
[87] => Welder
[89] => Commercial & Institutional
[90] => Jobsites
[91] => Demolition
[93] => Disasters
[95] => Heavy & Highway
[97] => Industrial
[99] => LEED/Green Construction
[101] => Renovations
[103] => Residential
[105] => Underground
)
[type] =>
[sub_category] =>
[url] => /document/4426/d001656/Construction%2BDive%2B--%2BDeWalt%2527s%2BJobsite%2BPro%2Bheadphones%2Brecalled%2Bfor%2Bfire%2Bhazards.html
[item:protected] => DocumentRecord Object
(
[records:protected] => Array
(
)
[recordId:protected] =>
[searchWordClass:protected] =>
[searchWordPeerClass:protected] =>
[bok_record:protected] =>
[authors:protected] =>
[organizations:protected] =>
[collections:protected] =>
[categories:protected] => Array
(
[16] => Category Object
(
[languages:protected] =>
[bok_resources:protected] =>
[bok_topics:protected] =>
[bok_keywords:protected] =>
[id:protected] => 16
[type:protected] => category
[parent:protected] => 7
[label:protected] => Fire & Explosions
[alreadyInSave:protected] =>
[alreadyInValidation:protected] =>
[validationFailures:protected] => Array
(
)
[_new:BaseObject:private] =>
[_deleted:BaseObject:private] =>
[modifiedColumns:protected] => Array
(
)
)
[44] => Category Object
(
[languages:protected] =>
[bok_resources:protected] =>
[bok_topics:protected] =>
[bok_keywords:protected] =>
[id:protected] => 44
[type:protected] => category
[parent:protected] => 2
[label:protected] => Acoustical Ceiling Carpenter
[alreadyInSave:protected] =>
[alreadyInValidation:protected] =>
[validationFailures:protected] => Array
(
)
[_new:BaseObject:private] =>
[_deleted:BaseObject:private] =>
[modifiedColumns:protected] => Array
(
)
)
[45] => Category Object
(
[languages:protected] =>
[bok_resources:protected] =>
[bok_topics:protected] =>
[bok_keywords:protected] =>
[id:protected] => 45
[type:protected] => category
[parent:protected] => 2
[label:protected] => Asbestos/Insulator
[alreadyInSave:protected] =>
[alreadyInValidation:protected] =>
[validationFailures:protected] => Array
(
)
[_new:BaseObject:private] =>
[_deleted:BaseObject:private] =>
[modifiedColumns:protected] => Array
(
)
)
[46] => Category Object
(
[languages:protected] =>
[bok_resources:protected] =>
[bok_topics:protected] =>
[bok_keywords:protected] =>
[id:protected] => 46
[type:protected] => category
[parent:protected] => 2
[label:protected] => Boilermaker
[alreadyInSave:protected] =>
[alreadyInValidation:protected] =>
[validationFailures:protected] => Array
(
)
[_new:BaseObject:private] =>
[_deleted:BaseObject:private] =>
[modifiedColumns:protected] => Array
(
)
)
[47] => Category Object
(
[languages:protected] =>
[bok_resources:protected] =>
[bok_topics:protected] =>
[bok_keywords:protected] =>
[id:protected] => 47
[type:protected] => category
[parent:protected] => 2
[label:protected] => Bricklayer
[alreadyInSave:protected] =>
[alreadyInValidation:protected] =>
[validationFailures:protected] => Array
(
)
[_new:BaseObject:private] =>
[_deleted:BaseObject:private] =>
[modifiedColumns:protected] => Array
(
)
)
[48] => Category Object
(
[languages:protected] =>
[bok_resources:protected] =>
[bok_topics:protected] =>
[bok_keywords:protected] =>
[id:protected] => 48
[type:protected] => category
[parent:protected] => 2
[label:protected] => Cabinetmaker
[alreadyInSave:protected] =>
[alreadyInValidation:protected] =>
[validationFailures:protected] => Array
(
)
[_new:BaseObject:private] =>
[_deleted:BaseObject:private] =>
[modifiedColumns:protected] => Array
(
)
)
[49] => Category Object
(
[languages:protected] =>
[bok_resources:protected] =>
[bok_topics:protected] =>
[bok_keywords:protected] =>
[id:protected] => 49
[type:protected] => category
[parent:protected] => 2
[label:protected] => Carpenter
[alreadyInSave:protected] =>
[alreadyInValidation:protected] =>
[validationFailures:protected] => Array
(
)
[_new:BaseObject:private] =>
[_deleted:BaseObject:private] =>
[modifiedColumns:protected] => Array
(
)
)
[50] => Category Object
(
[languages:protected] =>
[bok_resources:protected] =>
[bok_topics:protected] =>
[bok_keywords:protected] =>
[id:protected] => 50
[type:protected] => category
[parent:protected] => 2
[label:protected] => Carpet Layer
[alreadyInSave:protected] =>
[alreadyInValidation:protected] =>
[validationFailures:protected] => Array
(
)
[_new:BaseObject:private] =>
[_deleted:BaseObject:private] =>
[modifiedColumns:protected] => Array
(
)
)
[51] => Category Object
(
[languages:protected] =>
[bok_resources:protected] =>
[bok_topics:protected] =>
[bok_keywords:protected] =>
[id:protected] => 51
[type:protected] => category
[parent:protected] => 2
[label:protected] => Cement Mason
[alreadyInSave:protected] =>
[alreadyInValidation:protected] =>
[validationFailures:protected] => Array
(
)
[_new:BaseObject:private] =>
[_deleted:BaseObject:private] =>
[modifiedColumns:protected] => Array
(
)
)
[52] => Category Object
(
[languages:protected] =>
[bok_resources:protected] =>
[bok_topics:protected] =>
[bok_keywords:protected] =>
[id:protected] => 52
[type:protected] => category
[parent:protected] => 2
[label:protected] => Commercial Diver
[alreadyInSave:protected] =>
[alreadyInValidation:protected] =>
[validationFailures:protected] => Array
(
)
[_new:BaseObject:private] =>
[_deleted:BaseObject:private] =>
[modifiedColumns:protected] => Array
(
)
)
[53] => Category Object
(
[languages:protected] =>
[bok_resources:protected] =>
[bok_topics:protected] =>
[bok_keywords:protected] =>
[id:protected] => 53
[type:protected] => category
[parent:protected] => 2
[label:protected] => Concrete Polisher
[alreadyInSave:protected] =>
[alreadyInValidation:protected] =>
[validationFailures:protected] => Array
(
)
[_new:BaseObject:private] =>
[_deleted:BaseObject:private] =>
[modifiedColumns:protected] => Array
(
)
)
[54] => Category Object
(
[languages:protected] =>
[bok_resources:protected] =>
[bok_topics:protected] =>
[bok_keywords:protected] =>
[id:protected] => 54
[type:protected] => category
[parent:protected] => 2
[label:protected] => Drywall Applicator Specialist
[alreadyInSave:protected] =>
[alreadyInValidation:protected] =>
[validationFailures:protected] => Array
(
)
[_new:BaseObject:private] =>
[_deleted:BaseObject:private] =>
[modifiedColumns:protected] => Array
(
)
)
[55] => Category Object
(
[languages:protected] =>
[bok_resources:protected] =>
[bok_topics:protected] =>
[bok_keywords:protected] =>
[id:protected] => 55
[type:protected] => category
[parent:protected] => 2
[label:protected] => Electrical Worker
[alreadyInSave:protected] =>
[alreadyInValidation:protected] =>
[validationFailures:protected] => Array
(
)
[_new:BaseObject:private] =>
[_deleted:BaseObject:private] =>
[modifiedColumns:protected] => Array
(
)
)
[56] => Category Object
(
[languages:protected] =>
[bok_resources:protected] =>
[bok_topics:protected] =>
[bok_keywords:protected] =>
[id:protected] => 56
[type:protected] => category
[parent:protected] => 2
[label:protected] => Elevator Constructor
[alreadyInSave:protected] =>
[alreadyInValidation:protected] =>
[validationFailures:protected] => Array
(
)
[_new:BaseObject:private] =>
[_deleted:BaseObject:private] =>
[modifiedColumns:protected] => Array
(
)
)
[57] => Category Object
(
[languages:protected] =>
[bok_resources:protected] =>
[bok_topics:protected] =>
[bok_keywords:protected] =>
[id:protected] => 57
[type:protected] => category
[parent:protected] => 2
[label:protected] => Flagger
[alreadyInSave:protected] =>
[alreadyInValidation:protected] =>
[validationFailures:protected] => Array
(
)
[_new:BaseObject:private] =>
[_deleted:BaseObject:private] =>
[modifiedColumns:protected] => Array
(
)
)
[58] => Category Object
(
[languages:protected] =>
[bok_resources:protected] =>
[bok_topics:protected] =>
[bok_keywords:protected] =>
[id:protected] => 58
[type:protected] => category
[parent:protected] => 2
[label:protected] => Glazier
[alreadyInSave:protected] =>
[alreadyInValidation:protected] =>
[validationFailures:protected] => Array
(
)
[_new:BaseObject:private] =>
[_deleted:BaseObject:private] =>
[modifiedColumns:protected] => Array
(
)
)
[59] => Category Object
(
[languages:protected] =>
[bok_resources:protected] =>
[bok_topics:protected] =>
[bok_keywords:protected] =>
[id:protected] => 59
[type:protected] => category
[parent:protected] => 2
[label:protected] => Hazardous Waste Cleanup
[alreadyInSave:protected] =>
[alreadyInValidation:protected] =>
[validationFailures:protected] => Array
(
)
[_new:BaseObject:private] =>
[_deleted:BaseObject:private] =>
[modifiedColumns:protected] => Array
(
)
)
[60] => Category Object
(
[languages:protected] =>
[bok_resources:protected] =>
[bok_topics:protected] =>
[bok_keywords:protected] =>
[id:protected] => 60
[type:protected] => category
[parent:protected] => 2
[label:protected] => HVAC
[alreadyInSave:protected] =>
[alreadyInValidation:protected] =>
[validationFailures:protected] => Array
(
)
[_new:BaseObject:private] =>
[_deleted:BaseObject:private] =>
[modifiedColumns:protected] => Array
(
)
)
[61] => Category Object
(
[languages:protected] =>
[bok_resources:protected] =>
[bok_topics:protected] =>
[bok_keywords:protected] =>
[id:protected] => 61
[type:protected] => category
[parent:protected] => 2
[label:protected] => Interior Systems Carpenter
[alreadyInSave:protected] =>
[alreadyInValidation:protected] =>
[validationFailures:protected] => Array
(
)
[_new:BaseObject:private] =>
[_deleted:BaseObject:private] =>
[modifiedColumns:protected] => Array
(
)
)
[64] => Category Object
(
[languages:protected] =>
[bok_resources:protected] =>
[bok_topics:protected] =>
[bok_keywords:protected] =>
[id:protected] => 64
[type:protected] => category
[parent:protected] => 2
[label:protected] => Laborer
[alreadyInSave:protected] =>
[alreadyInValidation:protected] =>
[validationFailures:protected] => Array
(
)
[_new:BaseObject:private] =>
[_deleted:BaseObject:private] =>
[modifiedColumns:protected] => Array
(
)
)
[65] => Category Object
(
[languages:protected] =>
[bok_resources:protected] =>
[bok_topics:protected] =>
[bok_keywords:protected] =>
[id:protected] => 65
[type:protected] => category
[parent:protected] => 2
[label:protected] => Landscaper
[alreadyInSave:protected] =>
[alreadyInValidation:protected] =>
[validationFailures:protected] => Array
(
)
[_new:BaseObject:private] =>
[_deleted:BaseObject:private] =>
[modifiedColumns:protected] => Array
(
)
)
[66] => Category Object
(
[languages:protected] =>
[bok_resources:protected] =>
[bok_topics:protected] =>
[bok_keywords:protected] =>
[id:protected] => 66
[type:protected] => category
[parent:protected] => 2
[label:protected] => Lather
[alreadyInSave:protected] =>
[alreadyInValidation:protected] =>
[validationFailures:protected] => Array
(
)
[_new:BaseObject:private] =>
[_deleted:BaseObject:private] =>
[modifiedColumns:protected] => Array
(
)
)
[67] => Category Object
(
[languages:protected] =>
[bok_resources:protected] =>
[bok_topics:protected] =>
[bok_keywords:protected] =>
[id:protected] => 67
[type:protected] => category
[parent:protected] => 2
[label:protected] => Lead Abatement Worker
[alreadyInSave:protected] =>
[alreadyInValidation:protected] =>
[validationFailures:protected] => Array
(
)
[_new:BaseObject:private] =>
[_deleted:BaseObject:private] =>
[modifiedColumns:protected] => Array
(
)
)
[68] => Category Object
(
[languages:protected] =>
[bok_resources:protected] =>
[bok_topics:protected] =>
[bok_keywords:protected] =>
[id:protected] => 68
[type:protected] => category
[parent:protected] => 2
[label:protected] => Maintenance Worker
[alreadyInSave:protected] =>
[alreadyInValidation:protected] =>
[validationFailures:protected] => Array
(
)
[_new:BaseObject:private] =>
[_deleted:BaseObject:private] =>
[modifiedColumns:protected] => Array
(
)
)
[69] => Category Object
(
[languages:protected] =>
[bok_resources:protected] =>
[bok_topics:protected] =>
[bok_keywords:protected] =>
[id:protected] => 69
[type:protected] => category
[parent:protected] => 2
[label:protected] => Millwright
[alreadyInSave:protected] =>
[alreadyInValidation:protected] =>
[validationFailures:protected] => Array
(
)
[_new:BaseObject:private] =>
[_deleted:BaseObject:private] =>
[modifiedColumns:protected] => Array
(
)
)
[70] => Category Object
(
[languages:protected] =>
[bok_resources:protected] =>
[bok_topics:protected] =>
[bok_keywords:protected] =>
[id:protected] => 70
[type:protected] => category
[parent:protected] => 2
[label:protected] => Operating Engineer
[alreadyInSave:protected] =>
[alreadyInValidation:protected] =>
[validationFailures:protected] => Array
(
)
[_new:BaseObject:private] =>
[_deleted:BaseObject:private] =>
[modifiedColumns:protected] => Array
(
)
)
[71] => Category Object
(
[languages:protected] =>
[bok_resources:protected] =>
[bok_topics:protected] =>
[bok_keywords:protected] =>
[id:protected] => 71
[type:protected] => category
[parent:protected] => 2
[label:protected] => Painter
[alreadyInSave:protected] =>
[alreadyInValidation:protected] =>
[validationFailures:protected] => Array
(
)
[_new:BaseObject:private] =>
[_deleted:BaseObject:private] =>
[modifiedColumns:protected] => Array
(
)
)
[72] => Category Object
(
[languages:protected] =>
[bok_resources:protected] =>
[bok_topics:protected] =>
[bok_keywords:protected] =>
[id:protected] => 72
[type:protected] => category
[parent:protected] => 2
[label:protected] => Paper Hanger
[alreadyInSave:protected] =>
[alreadyInValidation:protected] =>
[validationFailures:protected] => Array
(
)
[_new:BaseObject:private] =>
[_deleted:BaseObject:private] =>
[modifiedColumns:protected] => Array
(
)
)
[73] => Category Object
(
[languages:protected] =>
[bok_resources:protected] =>
[bok_topics:protected] =>
[bok_keywords:protected] =>
[id:protected] => 73
[type:protected] => category
[parent:protected] => 2
[label:protected] => PCC/Restoration
[alreadyInSave:protected] =>
[alreadyInValidation:protected] =>
[validationFailures:protected] => Array
(
)
[_new:BaseObject:private] =>
[_deleted:BaseObject:private] =>
[modifiedColumns:protected] => Array
(
)
)
[74] => Category Object
(
[languages:protected] =>
[bok_resources:protected] =>
[bok_topics:protected] =>
[bok_keywords:protected] =>
[id:protected] => 74
[type:protected] => category
[parent:protected] => 2
[label:protected] => Pile Driver
[alreadyInSave:protected] =>
[alreadyInValidation:protected] =>
[validationFailures:protected] => Array
(
)
[_new:BaseObject:private] =>
[_deleted:BaseObject:private] =>
[modifiedColumns:protected] => Array
(
)
)
[75] => Category Object
(
[languages:protected] =>
[bok_resources:protected] =>
[bok_topics:protected] =>
[bok_keywords:protected] =>
[id:protected] => 75
[type:protected] => category
[parent:protected] => 2
[label:protected] => Plasterer
[alreadyInSave:protected] =>
[alreadyInValidation:protected] =>
[validationFailures:protected] => Array
(
)
[_new:BaseObject:private] =>
[_deleted:BaseObject:private] =>
[modifiedColumns:protected] => Array
(
)
)
[76] => Category Object
(
[languages:protected] =>
[bok_resources:protected] =>
[bok_topics:protected] =>
[bok_keywords:protected] =>
[id:protected] => 76
[type:protected] => category
[parent:protected] => 2
[label:protected] => Plumber/Pipefitter
[alreadyInSave:protected] =>
[alreadyInValidation:protected] =>
[validationFailures:protected] => Array
(
)
[_new:BaseObject:private] =>
[_deleted:BaseObject:private] =>
[modifiedColumns:protected] => Array
(
)
)
[77] => Category Object
(
[languages:protected] =>
[bok_resources:protected] =>
[bok_topics:protected] =>
[bok_keywords:protected] =>
[id:protected] => 77
[type:protected] => category
[parent:protected] => 2
[label:protected] => Refractory Worker
[alreadyInSave:protected] =>
[alreadyInValidation:protected] =>
[validationFailures:protected] => Array
(
)
[_new:BaseObject:private] =>
[_deleted:BaseObject:private] =>
[modifiedColumns:protected] => Array
(
)
)
[63] => Category Object
(
[languages:protected] =>
[bok_resources:protected] =>
[bok_topics:protected] =>
[bok_keywords:protected] =>
[id:protected] => 63
[type:protected] => category
[parent:protected] => 2
[label:protected] => Reinforcing Ironworker
[alreadyInSave:protected] =>
[alreadyInValidation:protected] =>
[validationFailures:protected] => Array
(
)
[_new:BaseObject:private] =>
[_deleted:BaseObject:private] =>
[modifiedColumns:protected] => Array
(
)
)
[78] => Category Object
(
[languages:protected] =>
[bok_resources:protected] =>
[bok_topics:protected] =>
[bok_keywords:protected] =>
[id:protected] => 78
[type:protected] => category
[parent:protected] => 2
[label:protected] => Roofer/Waterproofer
[alreadyInSave:protected] =>
[alreadyInValidation:protected] =>
[validationFailures:protected] => Array
(
)
[_new:BaseObject:private] =>
[_deleted:BaseObject:private] =>
[modifiedColumns:protected] => Array
(
)
)
[79] => Category Object
(
[languages:protected] =>
[bok_resources:protected] =>
[bok_topics:protected] =>
[bok_keywords:protected] =>
[id:protected] => 79
[type:protected] => category
[parent:protected] => 2
[label:protected] => Scaffold Erector
[alreadyInSave:protected] =>
[alreadyInValidation:protected] =>
[validationFailures:protected] => Array
(
)
[_new:BaseObject:private] =>
[_deleted:BaseObject:private] =>
[modifiedColumns:protected] => Array
(
)
)
[80] => Category Object
(
[languages:protected] =>
[bok_resources:protected] =>
[bok_topics:protected] =>
[bok_keywords:protected] =>
[id:protected] => 80
[type:protected] => category
[parent:protected] => 2
[label:protected] => Sheetmetal Worker
[alreadyInSave:protected] =>
[alreadyInValidation:protected] =>
[validationFailures:protected] => Array
(
)
[_new:BaseObject:private] =>
[_deleted:BaseObject:private] =>
[modifiedColumns:protected] => Array
(
)
)
[81] => Category Object
(
[languages:protected] =>
[bok_resources:protected] =>
[bok_topics:protected] =>
[bok_keywords:protected] =>
[id:protected] => 81
[type:protected] => category
[parent:protected] => 2
[label:protected] => Sprinkler Fitter
[alreadyInSave:protected] =>
[alreadyInValidation:protected] =>
[validationFailures:protected] => Array
(
)
[_new:BaseObject:private] =>
[_deleted:BaseObject:private] =>
[modifiedColumns:protected] => Array
(
)
)
[82] => Category Object
(
[languages:protected] =>
[bok_resources:protected] =>
[bok_topics:protected] =>
[bok_keywords:protected] =>
[id:protected] => 82
[type:protected] => category
[parent:protected] => 2
[label:protected] => Stonemason
[alreadyInSave:protected] =>
[alreadyInValidation:protected] =>
[validationFailures:protected] => Array
(
)
[_new:BaseObject:private] =>
[_deleted:BaseObject:private] =>
[modifiedColumns:protected] => Array
(
)
)
[62] => Category Object
(
[languages:protected] =>
[bok_resources:protected] =>
[bok_topics:protected] =>
[bok_keywords:protected] =>
[id:protected] => 62
[type:protected] => category
[parent:protected] => 2
[label:protected] => Structural Ironworker
[alreadyInSave:protected] =>
[alreadyInValidation:protected] =>
[validationFailures:protected] => Array
(
)
[_new:BaseObject:private] =>
[_deleted:BaseObject:private] =>
[modifiedColumns:protected] => Array
(
)
)
[83] => Category Object
(
[languages:protected] =>
[bok_resources:protected] =>
[bok_topics:protected] =>
[bok_keywords:protected] =>
[id:protected] => 83
[type:protected] => category
[parent:protected] => 2
[label:protected] => Terrazzo Worker
[alreadyInSave:protected] =>
[alreadyInValidation:protected] =>
[validationFailures:protected] => Array
(
)
[_new:BaseObject:private] =>
[_deleted:BaseObject:private] =>
[modifiedColumns:protected] => Array
(
)
)
[84] => Category Object
(
[languages:protected] =>
[bok_resources:protected] =>
[bok_topics:protected] =>
[bok_keywords:protected] =>
[id:protected] => 84
[type:protected] => category
[parent:protected] => 2
[label:protected] => Tile Setter
[alreadyInSave:protected] =>
[alreadyInValidation:protected] =>
[validationFailures:protected] => Array
(
)
[_new:BaseObject:private] =>
[_deleted:BaseObject:private] =>
[modifiedColumns:protected] => Array
(
)
)
[85] => Category Object
(
[languages:protected] =>
[bok_resources:protected] =>
[bok_topics:protected] =>
[bok_keywords:protected] =>
[id:protected] => 85
[type:protected] => category
[parent:protected] => 2
[label:protected] => Truck Driver
[alreadyInSave:protected] =>
[alreadyInValidation:protected] =>
[validationFailures:protected] => Array
(
)
[_new:BaseObject:private] =>
[_deleted:BaseObject:private] =>
[modifiedColumns:protected] => Array
(
)
)
[86] => Category Object
(
[languages:protected] =>
[bok_resources:protected] =>
[bok_topics:protected] =>
[bok_keywords:protected] =>
[id:protected] => 86
[type:protected] => category
[parent:protected] => 2
[label:protected] => Welder
[alreadyInSave:protected] =>
[alreadyInValidation:protected] =>
[validationFailures:protected] => Array
(
)
[_new:BaseObject:private] =>
[_deleted:BaseObject:private] =>
[modifiedColumns:protected] => Array
(
)
)
[87] => Category Object
(
[languages:protected] =>
[bok_resources:protected] =>
[bok_topics:protected] =>
[bok_keywords:protected] =>
[id:protected] => 87
[type:protected] => category
[parent:protected] => 3
[label:protected] => Commercial & Institutional
[alreadyInSave:protected] =>
[alreadyInValidation:protected] =>
[validationFailures:protected] => Array
(
)
[_new:BaseObject:private] =>
[_deleted:BaseObject:private] =>
[modifiedColumns:protected] => Array
(
)
)
[88] => Category Object
(
[languages:protected] =>
[bok_resources:protected] =>
[bok_topics:protected] =>
[bok_keywords:protected] =>
[id:protected] => 88
[type:protected] => category
[parent:protected] => 3
[label:protected] => Demolition
[alreadyInSave:protected] =>
[alreadyInValidation:protected] =>
[validationFailures:protected] => Array
(
)
[_new:BaseObject:private] =>
[_deleted:BaseObject:private] =>
[modifiedColumns:protected] => Array
(
)
)
[89] => Category Object
(
[languages:protected] =>
[bok_resources:protected] =>
[bok_topics:protected] =>
[bok_keywords:protected] =>
[id:protected] => 89
[type:protected] => category
[parent:protected] => 3
[label:protected] => Disasters
[alreadyInSave:protected] =>
[alreadyInValidation:protected] =>
[validationFailures:protected] => Array
(
)
[_new:BaseObject:private] =>
[_deleted:BaseObject:private] =>
[modifiedColumns:protected] => Array
(
)
)
[91] => Category Object
(
[languages:protected] =>
[bok_resources:protected] =>
[bok_topics:protected] =>
[bok_keywords:protected] =>
[id:protected] => 91
[type:protected] => category
[parent:protected] => 3
[label:protected] => Heavy & Highway
[alreadyInSave:protected] =>
[alreadyInValidation:protected] =>
[validationFailures:protected] => Array
(
)
[_new:BaseObject:private] =>
[_deleted:BaseObject:private] =>
[modifiedColumns:protected] => Array
(
)
)
[90] => Category Object
(
[languages:protected] =>
[bok_resources:protected] =>
[bok_topics:protected] =>
[bok_keywords:protected] =>
[id:protected] => 90
[type:protected] => category
[parent:protected] => 3
[label:protected] => Industrial
[alreadyInSave:protected] =>
[alreadyInValidation:protected] =>
[validationFailures:protected] => Array
(
)
[_new:BaseObject:private] =>
[_deleted:BaseObject:private] =>
[modifiedColumns:protected] => Array
(
)
)
[92] => Category Object
(
[languages:protected] =>
[bok_resources:protected] =>
[bok_topics:protected] =>
[bok_keywords:protected] =>
[id:protected] => 92
[type:protected] => category
[parent:protected] => 3
[label:protected] => LEED/Green Construction
[alreadyInSave:protected] =>
[alreadyInValidation:protected] =>
[validationFailures:protected] => Array
(
)
[_new:BaseObject:private] =>
[_deleted:BaseObject:private] =>
[modifiedColumns:protected] => Array
(
)
)
[93] => Category Object
(
[languages:protected] =>
[bok_resources:protected] =>
[bok_topics:protected] =>
[bok_keywords:protected] =>
[id:protected] => 93
[type:protected] => category
[parent:protected] => 3
[label:protected] => Renovations
[alreadyInSave:protected] =>
[alreadyInValidation:protected] =>
[validationFailures:protected] => Array
(
)
[_new:BaseObject:private] =>
[_deleted:BaseObject:private] =>
[modifiedColumns:protected] => Array
(
)
)
[94] => Category Object
(
[languages:protected] =>
[bok_resources:protected] =>
[bok_topics:protected] =>
[bok_keywords:protected] =>
[id:protected] => 94
[type:protected] => category
[parent:protected] => 3
[label:protected] => Residential
[alreadyInSave:protected] =>
[alreadyInValidation:protected] =>
[validationFailures:protected] => Array
(
)
[_new:BaseObject:private] =>
[_deleted:BaseObject:private] =>
[modifiedColumns:protected] => Array
(
)
)
[95] => Category Object
(
[languages:protected] =>
[bok_resources:protected] =>
[bok_topics:protected] =>
[bok_keywords:protected] =>
[id:protected] => 95
[type:protected] => category
[parent:protected] => 3
[label:protected] => Underground
[alreadyInSave:protected] =>
[alreadyInValidation:protected] =>
[validationFailures:protected] => Array
(
)
[_new:BaseObject:private] =>
[_deleted:BaseObject:private] =>
[modifiedColumns:protected] => Array
(
)
)
)
[categories_initialized:protected] => 1
[mapped_items:protected] =>
[content:protected] =>
[files:protected] =>
[language:protected] => Language Object
(
[id:protected] => 1
[code:protected] => en
[name:protected] => English
[alreadyInSave:protected] =>
[alreadyInValidation:protected] =>
[validationFailures:protected] => Array
(
)
[_new:BaseObject:private] =>
[_deleted:BaseObject:private] =>
[modifiedColumns:protected] => Array
(
)
)
[old_record:protected] =>
[id:protected] => 4426
[old_id:protected] =>
[elcosh_id:protected] => d001656
[type:protected] => document
[display_type:protected] => HTML only (and links)
[user_id:protected] => 0
[language_id:protected] => 1
[tagging_id:protected] => Mike Aguilar
[priority_id:protected] => 1
[title:protected] => Construction Dive -- DeWalt's Jobsite Pro headphones recalled for fire hazards
[total_pages:protected] => 1
[billed_pages:protected] => 1
[publication_number:protected] =>
[part_of:protected] =>
[keywords:protected] => DeWalt, Fire Hazards, recall, headphones
[comments:protected] =>
[summary:protected] => A recall notice by the United States Consumer Product Safety Commission affects over 300,000 DeWalt Jobsite Pro Headphones. The recall is a result of a malfunction that can cause earbuds to overheat while charging or during use, leading to fire and burn hazards.
[transition_comments:protected] =>
[external_link:protected] => https://www.constructiondive.com/news/dewalts-jobsite-pro-headphones-recalled-for-fire-hazards/611248/?utm_source=Sailthru&utm_medium=email&utm_campaign=Issue:%202021-12-10%20Construction%20Dive%20Newsletter%20%5Bissue:38532%5D&utm_term=Construction%20Dive
[consol_link:protected] =>
[more_like_this:protected] =>
[permission_given_by:protected] =>
[published:protected] => T
[billable:protected] => F
[img_name:protected] =>
[img_ext:protected] =>
[img_width:protected] =>
[img_height:protected] =>
[img_credit:protected] =>
[img_practice:protected] =>
[vid_source_id:protected] =>
[vid_running_time:protected] =>
[vid_intended_audience:protected] =>
[vid_acquisition_info:protected] =>
[vid_cost:protected] =>
[vid_producer:protected] =>
[vid_filename:protected] =>
[vid_filename_downloadable:protected] =>
[date_summary:protected] =>
[date_permission_requested:protected] =>
[date_permission_received:protected] =>
[date_review_needed:protected] =>
[date_received:protected] => 12/13/21
[date_completed:protected] => 12/13/21
[date_billed:protected] =>
[date_modified:protected] => 12/13/21
[collBokExports:protected] =>
[lastBokExportCriteria:BaseElcoshItem:private] =>
[alreadyInSave:protected] =>
[alreadyInValidation:protected] =>
[validationFailures:protected] => Array
(
)
[_new:BaseObject:private] =>
[_deleted:BaseObject:private] =>
[modifiedColumns:protected] => Array
(
)
)
)
)
[new_images] => Array
(
[0] => Search_Result Object
(
[title] => Morning Toolbox Talk
[image] => /record/images/4003-p.jpg
[blurb] => This photo is from an early morning toolbox talk on a construction job in Mclean, Virginia. It is being delivered in English and Spanish....
[category] => Array
(
[0] => 20
[1] => 51
[2] => 57
[3] => 64
[4] => 70
[5] => 63
[6] => 78
[7] => 82
[8] => 62
[9] => 87
[10] => 88
[11] => 89
[12] => 91
[13] => 90
[14] => 93
[15] => 94
[16] => 97
)
[labels] => Array
(
[0] => Safety Culture
[1] => Work Environment
[2] => Hazards
[3] => Cement Mason
[4] => Trades
[5] => Flagger
[7] => Laborer
[9] => Operating Engineer
[11] => Reinforcing Ironworker
[13] => Roofer/Waterproofer
[15] => Stonemason
[17] => Structural Ironworker
[19] => Commercial & Institutional
[20] => Jobsites
[21] => Demolition
[23] => Disasters
[25] => Heavy & Highway
[27] => Industrial
[29] => Renovations
[31] => Residential
[33] => Images
[34] => Media
[35] => Media & Documents
)
[type] => Images
[sub_category] =>
[url] => /image/4003/i002691/Morning%2BToolbox%2BTalk.html
[item:protected] => ImageRecord Object
(
[records:protected] => Array
(
)
[recordId:protected] =>
[searchWordClass:protected] =>
[searchWordPeerClass:protected] =>
[bok_record:protected] =>
[authors:protected] =>
[organizations:protected] =>
[collections:protected] =>
[categories:protected] => Array
(
[20] => Category Object
(
[languages:protected] =>
[bok_resources:protected] =>
[bok_topics:protected] =>
[bok_keywords:protected] =>
[id:protected] => 20
[type:protected] => category
[parent:protected] => 7
[label:protected] => Safety Culture
[alreadyInSave:protected] =>
[alreadyInValidation:protected] =>
[validationFailures:protected] => Array
(
)
[_new:BaseObject:private] =>
[_deleted:BaseObject:private] =>
[modifiedColumns:protected] => Array
(
)
)
[51] => Category Object
(
[languages:protected] =>
[bok_resources:protected] =>
[bok_topics:protected] =>
[bok_keywords:protected] =>
[id:protected] => 51
[type:protected] => category
[parent:protected] => 2
[label:protected] => Cement Mason
[alreadyInSave:protected] =>
[alreadyInValidation:protected] =>
[validationFailures:protected] => Array
(
)
[_new:BaseObject:private] =>
[_deleted:BaseObject:private] =>
[modifiedColumns:protected] => Array
(
)
)
[57] => Category Object
(
[languages:protected] =>
[bok_resources:protected] =>
[bok_topics:protected] =>
[bok_keywords:protected] =>
[id:protected] => 57
[type:protected] => category
[parent:protected] => 2
[label:protected] => Flagger
[alreadyInSave:protected] =>
[alreadyInValidation:protected] =>
[validationFailures:protected] => Array
(
)
[_new:BaseObject:private] =>
[_deleted:BaseObject:private] =>
[modifiedColumns:protected] => Array
(
)
)
[64] => Category Object
(
[languages:protected] =>
[bok_resources:protected] =>
[bok_topics:protected] =>
[bok_keywords:protected] =>
[id:protected] => 64
[type:protected] => category
[parent:protected] => 2
[label:protected] => Laborer
[alreadyInSave:protected] =>
[alreadyInValidation:protected] =>
[validationFailures:protected] => Array
(
)
[_new:BaseObject:private] =>
[_deleted:BaseObject:private] =>
[modifiedColumns:protected] => Array
(
)
)
[70] => Category Object
(
[languages:protected] =>
[bok_resources:protected] =>
[bok_topics:protected] =>
[bok_keywords:protected] =>
[id:protected] => 70
[type:protected] => category
[parent:protected] => 2
[label:protected] => Operating Engineer
[alreadyInSave:protected] =>
[alreadyInValidation:protected] =>
[validationFailures:protected] => Array
(
)
[_new:BaseObject:private] =>
[_deleted:BaseObject:private] =>
[modifiedColumns:protected] => Array
(
)
)
[63] => Category Object
(
[languages:protected] =>
[bok_resources:protected] =>
[bok_topics:protected] =>
[bok_keywords:protected] =>
[id:protected] => 63
[type:protected] => category
[parent:protected] => 2
[label:protected] => Reinforcing Ironworker
[alreadyInSave:protected] =>
[alreadyInValidation:protected] =>
[validationFailures:protected] => Array
(
)
[_new:BaseObject:private] =>
[_deleted:BaseObject:private] =>
[modifiedColumns:protected] => Array
(
)
)
[78] => Category Object
(
[languages:protected] =>
[bok_resources:protected] =>
[bok_topics:protected] =>
[bok_keywords:protected] =>
[id:protected] => 78
[type:protected] => category
[parent:protected] => 2
[label:protected] => Roofer/Waterproofer
[alreadyInSave:protected] =>
[alreadyInValidation:protected] =>
[validationFailures:protected] => Array
(
)
[_new:BaseObject:private] =>
[_deleted:BaseObject:private] =>
[modifiedColumns:protected] => Array
(
)
)
[82] => Category Object
(
[languages:protected] =>
[bok_resources:protected] =>
[bok_topics:protected] =>
[bok_keywords:protected] =>
[id:protected] => 82
[type:protected] => category
[parent:protected] => 2
[label:protected] => Stonemason
[alreadyInSave:protected] =>
[alreadyInValidation:protected] =>
[validationFailures:protected] => Array
(
)
[_new:BaseObject:private] =>
[_deleted:BaseObject:private] =>
[modifiedColumns:protected] => Array
(
)
)
[62] => Category Object
(
[languages:protected] =>
[bok_resources:protected] =>
[bok_topics:protected] =>
[bok_keywords:protected] =>
[id:protected] => 62
[type:protected] => category
[parent:protected] => 2
[label:protected] => Structural Ironworker
[alreadyInSave:protected] =>
[alreadyInValidation:protected] =>
[validationFailures:protected] => Array
(
)
[_new:BaseObject:private] =>
[_deleted:BaseObject:private] =>
[modifiedColumns:protected] => Array
(
)
)
[87] => Category Object
(
[languages:protected] =>
[bok_resources:protected] =>
[bok_topics:protected] =>
[bok_keywords:protected] =>
[id:protected] => 87
[type:protected] => category
[parent:protected] => 3
[label:protected] => Commercial & Institutional
[alreadyInSave:protected] =>
[alreadyInValidation:protected] =>
[validationFailures:protected] => Array
(
)
[_new:BaseObject:private] =>
[_deleted:BaseObject:private] =>
[modifiedColumns:protected] => Array
(
)
)
[88] => Category Object
(
[languages:protected] =>
[bok_resources:protected] =>
[bok_topics:protected] =>
[bok_keywords:protected] =>
[id:protected] => 88
[type:protected] => category
[parent:protected] => 3
[label:protected] => Demolition
[alreadyInSave:protected] =>
[alreadyInValidation:protected] =>
[validationFailures:protected] => Array
(
)
[_new:BaseObject:private] =>
[_deleted:BaseObject:private] =>
[modifiedColumns:protected] => Array
(
)
)
[89] => Category Object
(
[languages:protected] =>
[bok_resources:protected] =>
[bok_topics:protected] =>
[bok_keywords:protected] =>
[id:protected] => 89
[type:protected] => category
[parent:protected] => 3
[label:protected] => Disasters
[alreadyInSave:protected] =>
[alreadyInValidation:protected] =>
[validationFailures:protected] => Array
(
)
[_new:BaseObject:private] =>
[_deleted:BaseObject:private] =>
[modifiedColumns:protected] => Array
(
)
)
[91] => Category Object
(
[languages:protected] =>
[bok_resources:protected] =>
[bok_topics:protected] =>
[bok_keywords:protected] =>
[id:protected] => 91
[type:protected] => category
[parent:protected] => 3
[label:protected] => Heavy & Highway
[alreadyInSave:protected] =>
[alreadyInValidation:protected] =>
[validationFailures:protected] => Array
(
)
[_new:BaseObject:private] =>
[_deleted:BaseObject:private] =>
[modifiedColumns:protected] => Array
(
)
)
[90] => Category Object
(
[languages:protected] =>
[bok_resources:protected] =>
[bok_topics:protected] =>
[bok_keywords:protected] =>
[id:protected] => 90
[type:protected] => category
[parent:protected] => 3
[label:protected] => Industrial
[alreadyInSave:protected] =>
[alreadyInValidation:protected] =>
[validationFailures:protected] => Array
(
)
[_new:BaseObject:private] =>
[_deleted:BaseObject:private] =>
[modifiedColumns:protected] => Array
(
)
)
[93] => Category Object
(
[languages:protected] =>
[bok_resources:protected] =>
[bok_topics:protected] =>
[bok_keywords:protected] =>
[id:protected] => 93
[type:protected] => category
[parent:protected] => 3
[label:protected] => Renovations
[alreadyInSave:protected] =>
[alreadyInValidation:protected] =>
[validationFailures:protected] => Array
(
)
[_new:BaseObject:private] =>
[_deleted:BaseObject:private] =>
[modifiedColumns:protected] => Array
(
)
)
[94] => Category Object
(
[languages:protected] =>
[bok_resources:protected] =>
[bok_topics:protected] =>
[bok_keywords:protected] =>
[id:protected] => 94
[type:protected] => category
[parent:protected] => 3
[label:protected] => Residential
[alreadyInSave:protected] =>
[alreadyInValidation:protected] =>
[validationFailures:protected] => Array
(
)
[_new:BaseObject:private] =>
[_deleted:BaseObject:private] =>
[modifiedColumns:protected] => Array
(
)
)
[97] => Category Object
(
[languages:protected] =>
[bok_resources:protected] =>
[bok_topics:protected] =>
[bok_keywords:protected] =>
[id:protected] => 97
[type:protected] => category
[parent:protected] => 5
[label:protected] => Images
[alreadyInSave:protected] =>
[alreadyInValidation:protected] =>
[validationFailures:protected] => Array
(
)
[_new:BaseObject:private] =>
[_deleted:BaseObject:private] =>
[modifiedColumns:protected] => Array
(
)
)
)
[categories_initialized:protected] => 1
[mapped_items:protected] =>
[content:protected] =>
[files:protected] =>
[language:protected] => Language Object
(
[id:protected] => 1
[code:protected] => en
[name:protected] => English
[alreadyInSave:protected] =>
[alreadyInValidation:protected] =>
[validationFailures:protected] => Array
(
)
[_new:BaseObject:private] =>
[_deleted:BaseObject:private] =>
[modifiedColumns:protected] => Array
(
)
)
[old_record:protected] =>
[id:protected] => 4003
[old_id:protected] =>
[elcosh_id:protected] => i002691
[type:protected] => image
[display_type:protected] => Image
[user_id:protected] => 0
[language_id:protected] => 1
[tagging_id:protected] => Bruce Lippy
[priority_id:protected] => 1
[title:protected] => Morning Toolbox Talk
[total_pages:protected] => 0
[billed_pages:protected] => 0
[publication_number:protected] =>
[part_of:protected] =>
[keywords:protected] => toolbox talk, tailgate talk, Spanish, bilingual
[comments:protected] =>
[summary:protected] => This photo is from an early morning toolbox talk on a construction job in Mclean, Virginia. It is being delivered in English and Spanish.
[transition_comments:protected] =>
[external_link:protected] =>
[consol_link:protected] => http://www.cpwrconstructionsolutions.org/electrical/solution/662/worker-training.html
[more_like_this:protected] => d001285,d001304,c000079
[permission_given_by:protected] =>
[published:protected] => T
[billable:protected] => F
[img_name:protected] =>
[img_ext:protected] => jpg
[img_width:protected] =>
[img_height:protected] =>
[img_credit:protected] => Morgan Zavertnik and Hoar Construction
[img_practice:protected] => good
[vid_source_id:protected] =>
[vid_running_time:protected] =>
[vid_intended_audience:protected] =>
[vid_acquisition_info:protected] =>
[vid_cost:protected] =>
[vid_producer:protected] =>
[vid_filename:protected] =>
[vid_filename_downloadable:protected] =>
[date_summary:protected] => November 2015
[date_permission_requested:protected] =>
[date_permission_received:protected] =>
[date_review_needed:protected] =>
[date_received:protected] => 03/02/16
[date_completed:protected] => 03/02/16
[date_billed:protected] =>
[date_modified:protected] => 03/02/16
[collBokExports:protected] =>
[lastBokExportCriteria:BaseElcoshItem:private] =>
[alreadyInSave:protected] =>
[alreadyInValidation:protected] =>
[validationFailures:protected] => Array
(
)
[_new:BaseObject:private] =>
[_deleted:BaseObject:private] =>
[modifiedColumns:protected] => Array
(
)
)
)
[1] => Search_Result Object
(
[title] => Toolbox talk - crew view
[image] => /record/images/4005-p.jpg
[blurb] => Photo of crew listening to a toolbox safety talk before starting work....
[category] => Array
(
[0] => 97
[1] => 20
[2] => 47
[3] => 49
[4] => 51
[5] => 55
[6] => 61
[7] => 64
[8] => 71
[9] => 75
[10] => 63
[11] => 79
[12] => 62
[13] => 87
[14] => 88
[15] => 91
[16] => 90
[17] => 93
[18] => 94
[19] => 95
)
[labels] => Array
(
[0] => Images
[1] => Media
[2] => Media & Documents
[3] => Safety Culture
[4] => Work Environment
[5] => Hazards
[6] => Bricklayer
[7] => Trades
[8] => Carpenter
[10] => Cement Mason
[12] => Electrical Worker
[14] => Interior Systems Carpenter
[16] => Laborer
[18] => Painter
[20] => Plasterer
[22] => Reinforcing Ironworker
[24] => Scaffold Erector
[26] => Structural Ironworker
[28] => Commercial & Institutional
[29] => Jobsites
[30] => Demolition
[32] => Heavy & Highway
[34] => Industrial
[36] => Renovations
[38] => Residential
[40] => Underground
)
[type] => Images
[sub_category] =>
[url] => /image/4005/i002692/Toolbox%2Btalk%2B-%2Bcrew%2Bview.html
[item:protected] => ImageRecord Object
(
[records:protected] => Array
(
)
[recordId:protected] =>
[searchWordClass:protected] =>
[searchWordPeerClass:protected] =>
[bok_record:protected] =>
[authors:protected] =>
[organizations:protected] =>
[collections:protected] =>
[categories:protected] => Array
(
[97] => Category Object
(
[languages:protected] =>
[bok_resources:protected] =>
[bok_topics:protected] =>
[bok_keywords:protected] =>
[id:protected] => 97
[type:protected] => category
[parent:protected] => 5
[label:protected] => Images
[alreadyInSave:protected] =>
[alreadyInValidation:protected] =>
[validationFailures:protected] => Array
(
)
[_new:BaseObject:private] =>
[_deleted:BaseObject:private] =>
[modifiedColumns:protected] => Array
(
)
)
[20] => Category Object
(
[languages:protected] =>
[bok_resources:protected] =>
[bok_topics:protected] =>
[bok_keywords:protected] =>
[id:protected] => 20
[type:protected] => category
[parent:protected] => 7
[label:protected] => Safety Culture
[alreadyInSave:protected] =>
[alreadyInValidation:protected] =>
[validationFailures:protected] => Array
(
)
[_new:BaseObject:private] =>
[_deleted:BaseObject:private] =>
[modifiedColumns:protected] => Array
(
)
)
[47] => Category Object
(
[languages:protected] =>
[bok_resources:protected] =>
[bok_topics:protected] =>
[bok_keywords:protected] =>
[id:protected] => 47
[type:protected] => category
[parent:protected] => 2
[label:protected] => Bricklayer
[alreadyInSave:protected] =>
[alreadyInValidation:protected] =>
[validationFailures:protected] => Array
(
)
[_new:BaseObject:private] =>
[_deleted:BaseObject:private] =>
[modifiedColumns:protected] => Array
(
)
)
[49] => Category Object
(
[languages:protected] =>
[bok_resources:protected] =>
[bok_topics:protected] =>
[bok_keywords:protected] =>
[id:protected] => 49
[type:protected] => category
[parent:protected] => 2
[label:protected] => Carpenter
[alreadyInSave:protected] =>
[alreadyInValidation:protected] =>
[validationFailures:protected] => Array
(
)
[_new:BaseObject:private] =>
[_deleted:BaseObject:private] =>
[modifiedColumns:protected] => Array
(
)
)
[51] => Category Object
(
[languages:protected] =>
[bok_resources:protected] =>
[bok_topics:protected] =>
[bok_keywords:protected] =>
[id:protected] => 51
[type:protected] => category
[parent:protected] => 2
[label:protected] => Cement Mason
[alreadyInSave:protected] =>
[alreadyInValidation:protected] =>
[validationFailures:protected] => Array
(
)
[_new:BaseObject:private] =>
[_deleted:BaseObject:private] =>
[modifiedColumns:protected] => Array
(
)
)
[55] => Category Object
(
[languages:protected] =>
[bok_resources:protected] =>
[bok_topics:protected] =>
[bok_keywords:protected] =>
[id:protected] => 55
[type:protected] => category
[parent:protected] => 2
[label:protected] => Electrical Worker
[alreadyInSave:protected] =>
[alreadyInValidation:protected] =>
[validationFailures:protected] => Array
(
)
[_new:BaseObject:private] =>
[_deleted:BaseObject:private] =>
[modifiedColumns:protected] => Array
(
)
)
[61] => Category Object
(
[languages:protected] =>
[bok_resources:protected] =>
[bok_topics:protected] =>
[bok_keywords:protected] =>
[id:protected] => 61
[type:protected] => category
[parent:protected] => 2
[label:protected] => Interior Systems Carpenter
[alreadyInSave:protected] =>
[alreadyInValidation:protected] =>
[validationFailures:protected] => Array
(
)
[_new:BaseObject:private] =>
[_deleted:BaseObject:private] =>
[modifiedColumns:protected] => Array
(
)
)
[64] => Category Object
(
[languages:protected] =>
[bok_resources:protected] =>
[bok_topics:protected] =>
[bok_keywords:protected] =>
[id:protected] => 64
[type:protected] => category
[parent:protected] => 2
[label:protected] => Laborer
[alreadyInSave:protected] =>
[alreadyInValidation:protected] =>
[validationFailures:protected] => Array
(
)
[_new:BaseObject:private] =>
[_deleted:BaseObject:private] =>
[modifiedColumns:protected] => Array
(
)
)
[71] => Category Object
(
[languages:protected] =>
[bok_resources:protected] =>
[bok_topics:protected] =>
[bok_keywords:protected] =>
[id:protected] => 71
[type:protected] => category
[parent:protected] => 2
[label:protected] => Painter
[alreadyInSave:protected] =>
[alreadyInValidation:protected] =>
[validationFailures:protected] => Array
(
)
[_new:BaseObject:private] =>
[_deleted:BaseObject:private] =>
[modifiedColumns:protected] => Array
(
)
)
[75] => Category Object
(
[languages:protected] =>
[bok_resources:protected] =>
[bok_topics:protected] =>
[bok_keywords:protected] =>
[id:protected] => 75
[type:protected] => category
[parent:protected] => 2
[label:protected] => Plasterer
[alreadyInSave:protected] =>
[alreadyInValidation:protected] =>
[validationFailures:protected] => Array
(
)
[_new:BaseObject:private] =>
[_deleted:BaseObject:private] =>
[modifiedColumns:protected] => Array
(
)
)
[63] => Category Object
(
[languages:protected] =>
[bok_resources:protected] =>
[bok_topics:protected] =>
[bok_keywords:protected] =>
[id:protected] => 63
[type:protected] => category
[parent:protected] => 2
[label:protected] => Reinforcing Ironworker
[alreadyInSave:protected] =>
[alreadyInValidation:protected] =>
[validationFailures:protected] => Array
(
)
[_new:BaseObject:private] =>
[_deleted:BaseObject:private] =>
[modifiedColumns:protected] => Array
(
)
)
[79] => Category Object
(
[languages:protected] =>
[bok_resources:protected] =>
[bok_topics:protected] =>
[bok_keywords:protected] =>
[id:protected] => 79
[type:protected] => category
[parent:protected] => 2
[label:protected] => Scaffold Erector
[alreadyInSave:protected] =>
[alreadyInValidation:protected] =>
[validationFailures:protected] => Array
(
)
[_new:BaseObject:private] =>
[_deleted:BaseObject:private] =>
[modifiedColumns:protected] => Array
(
)
)
[62] => Category Object
(
[languages:protected] =>
[bok_resources:protected] =>
[bok_topics:protected] =>
[bok_keywords:protected] =>
[id:protected] => 62
[type:protected] => category
[parent:protected] => 2
[label:protected] => Structural Ironworker
[alreadyInSave:protected] =>
[alreadyInValidation:protected] =>
[validationFailures:protected] => Array
(
)
[_new:BaseObject:private] =>
[_deleted:BaseObject:private] =>
[modifiedColumns:protected] => Array
(
)
)
[87] => Category Object
(
[languages:protected] =>
[bok_resources:protected] =>
[bok_topics:protected] =>
[bok_keywords:protected] =>
[id:protected] => 87
[type:protected] => category
[parent:protected] => 3
[label:protected] => Commercial & Institutional
[alreadyInSave:protected] =>
[alreadyInValidation:protected] =>
[validationFailures:protected] => Array
(
)
[_new:BaseObject:private] =>
[_deleted:BaseObject:private] =>
[modifiedColumns:protected] => Array
(
)
)
[88] => Category Object
(
[languages:protected] =>
[bok_resources:protected] =>
[bok_topics:protected] =>
[bok_keywords:protected] =>
[id:protected] => 88
[type:protected] => category
[parent:protected] => 3
[label:protected] => Demolition
[alreadyInSave:protected] =>
[alreadyInValidation:protected] =>
[validationFailures:protected] => Array
(
)
[_new:BaseObject:private] =>
[_deleted:BaseObject:private] =>
[modifiedColumns:protected] => Array
(
)
)
[91] => Category Object
(
[languages:protected] =>
[bok_resources:protected] =>
[bok_topics:protected] =>
[bok_keywords:protected] =>
[id:protected] => 91
[type:protected] => category
[parent:protected] => 3
[label:protected] => Heavy & Highway
[alreadyInSave:protected] =>
[alreadyInValidation:protected] =>
[validationFailures:protected] => Array
(
)
[_new:BaseObject:private] =>
[_deleted:BaseObject:private] =>
[modifiedColumns:protected] => Array
(
)
)
[90] => Category Object
(
[languages:protected] =>
[bok_resources:protected] =>
[bok_topics:protected] =>
[bok_keywords:protected] =>
[id:protected] => 90
[type:protected] => category
[parent:protected] => 3
[label:protected] => Industrial
[alreadyInSave:protected] =>
[alreadyInValidation:protected] =>
[validationFailures:protected] => Array
(
)
[_new:BaseObject:private] =>
[_deleted:BaseObject:private] =>
[modifiedColumns:protected] => Array
(
)
)
[93] => Category Object
(
[languages:protected] =>
[bok_resources:protected] =>
[bok_topics:protected] =>
[bok_keywords:protected] =>
[id:protected] => 93
[type:protected] => category
[parent:protected] => 3
[label:protected] => Renovations
[alreadyInSave:protected] =>
[alreadyInValidation:protected] =>
[validationFailures:protected] => Array
(
)
[_new:BaseObject:private] =>
[_deleted:BaseObject:private] =>
[modifiedColumns:protected] => Array
(
)
)
[94] => Category Object
(
[languages:protected] =>
[bok_resources:protected] =>
[bok_topics:protected] =>
[bok_keywords:protected] =>
[id:protected] => 94
[type:protected] => category
[parent:protected] => 3
[label:protected] => Residential
[alreadyInSave:protected] =>
[alreadyInValidation:protected] =>
[validationFailures:protected] => Array
(
)
[_new:BaseObject:private] =>
[_deleted:BaseObject:private] =>
[modifiedColumns:protected] => Array
(
)
)
[95] => Category Object
(
[languages:protected] =>
[bok_resources:protected] =>
[bok_topics:protected] =>
[bok_keywords:protected] =>
[id:protected] => 95
[type:protected] => category
[parent:protected] => 3
[label:protected] => Underground
[alreadyInSave:protected] =>
[alreadyInValidation:protected] =>
[validationFailures:protected] => Array
(
)
[_new:BaseObject:private] =>
[_deleted:BaseObject:private] =>
[modifiedColumns:protected] => Array
(
)
)
)
[categories_initialized:protected] => 1
[mapped_items:protected] =>
[content:protected] =>
[files:protected] =>
[language:protected] => Language Object
(
[id:protected] => 1
[code:protected] => en
[name:protected] => English
[alreadyInSave:protected] =>
[alreadyInValidation:protected] =>
[validationFailures:protected] => Array
(
)
[_new:BaseObject:private] =>
[_deleted:BaseObject:private] =>
[modifiedColumns:protected] => Array
(
)
)
[old_record:protected] =>
[id:protected] => 4005
[old_id:protected] =>
[elcosh_id:protected] => i002692
[type:protected] => image
[display_type:protected] => Image
[user_id:protected] => 0
[language_id:protected] => 1
[tagging_id:protected] => Bruce Lippy
[priority_id:protected] => 1
[title:protected] => Toolbox talk - crew view
[total_pages:protected] => 0
[billed_pages:protected] => 0
[publication_number:protected] =>
[part_of:protected] =>
[keywords:protected] => toolbox talk, tailgate talk, safety talk, Spanish
[comments:protected] =>
[summary:protected] => Photo of crew listening to a toolbox safety talk before starting work.
[transition_comments:protected] =>
[external_link:protected] =>
[consol_link:protected] => http://www.cpwrconstructionsolutions.org/electrical/solution/662/worker-training.html
[more_like_this:protected] => i002691,d001269, c000079, d001285
[permission_given_by:protected] =>
[published:protected] => T
[billable:protected] => F
[img_name:protected] =>
[img_ext:protected] => jpg
[img_width:protected] =>
[img_height:protected] =>
[img_credit:protected] => Morgan Zavertnik and Hoar Construction
[img_practice:protected] => good
[vid_source_id:protected] =>
[vid_running_time:protected] =>
[vid_intended_audience:protected] =>
[vid_acquisition_info:protected] =>
[vid_cost:protected] =>
[vid_producer:protected] =>
[vid_filename:protected] =>
[vid_filename_downloadable:protected] =>
[date_summary:protected] => November 2015
[date_permission_requested:protected] =>
[date_permission_received:protected] =>
[date_review_needed:protected] =>
[date_received:protected] => 03/02/16
[date_completed:protected] => 03/02/16
[date_billed:protected] =>
[date_modified:protected] => 03/02/16
[collBokExports:protected] =>
[lastBokExportCriteria:BaseElcoshItem:private] =>
[alreadyInSave:protected] =>
[alreadyInValidation:protected] =>
[validationFailures:protected] => Array
(
)
[_new:BaseObject:private] =>
[_deleted:BaseObject:private] =>
[modifiedColumns:protected] => Array
(
)
)
)
[2] => Search_Result Object
(
[title] => Toolbox talk - long shot
[image] => /record/images/4006-p.jpg
[blurb] => This crew gathered every morning before starting work to discuss a new safety topic....
[category] => Array
(
[0] => 20
[1] => 47
[2] => 49
[3] => 51
[4] => 55
[5] => 64
[6] => 68
[7] => 75
[8] => 76
[9] => 63
[10] => 78
[11] => 79
[12] => 82
[13] => 62
[14] => 87
[15] => 88
[16] => 91
[17] => 90
[18] => 93
[19] => 94
[20] => 95
[21] => 97
)
[labels] => Array
(
[0] => Safety Culture
[1] => Work Environment
[2] => Hazards
[3] => Bricklayer
[4] => Trades
[5] => Carpenter
[7] => Cement Mason
[9] => Electrical Worker
[11] => Laborer
[13] => Maintenance Worker
[15] => Plasterer
[17] => Plumber/Pipefitter
[19] => Reinforcing Ironworker
[21] => Roofer/Waterproofer
[23] => Scaffold Erector
[25] => Stonemason
[27] => Structural Ironworker
[29] => Commercial & Institutional
[30] => Jobsites
[31] => Demolition
[33] => Heavy & Highway
[35] => Industrial
[37] => Renovations
[39] => Residential
[41] => Underground
[43] => Images
[44] => Media
[45] => Media & Documents
)
[type] => Images
[sub_category] =>
[url] => /image/4006/i002693/Toolbox%2Btalk%2B-%2Blong%2Bshot.html
[item:protected] => ImageRecord Object
(
[records:protected] => Array
(
)
[recordId:protected] =>
[searchWordClass:protected] =>
[searchWordPeerClass:protected] =>
[bok_record:protected] =>
[authors:protected] =>
[organizations:protected] =>
[collections:protected] =>
[categories:protected] => Array
(
[20] => Category Object
(
[languages:protected] =>
[bok_resources:protected] =>
[bok_topics:protected] =>
[bok_keywords:protected] =>
[id:protected] => 20
[type:protected] => category
[parent:protected] => 7
[label:protected] => Safety Culture
[alreadyInSave:protected] =>
[alreadyInValidation:protected] =>
[validationFailures:protected] => Array
(
)
[_new:BaseObject:private] =>
[_deleted:BaseObject:private] =>
[modifiedColumns:protected] => Array
(
)
)
[47] => Category Object
(
[languages:protected] =>
[bok_resources:protected] =>
[bok_topics:protected] =>
[bok_keywords:protected] =>
[id:protected] => 47
[type:protected] => category
[parent:protected] => 2
[label:protected] => Bricklayer
[alreadyInSave:protected] =>
[alreadyInValidation:protected] =>
[validationFailures:protected] => Array
(
)
[_new:BaseObject:private] =>
[_deleted:BaseObject:private] =>
[modifiedColumns:protected] => Array
(
)
)
[49] => Category Object
(
[languages:protected] =>
[bok_resources:protected] =>
[bok_topics:protected] =>
[bok_keywords:protected] =>
[id:protected] => 49
[type:protected] => category
[parent:protected] => 2
[label:protected] => Carpenter
[alreadyInSave:protected] =>
[alreadyInValidation:protected] =>
[validationFailures:protected] => Array
(
)
[_new:BaseObject:private] =>
[_deleted:BaseObject:private] =>
[modifiedColumns:protected] => Array
(
)
)
[51] => Category Object
(
[languages:protected] =>
[bok_resources:protected] =>
[bok_topics:protected] =>
[bok_keywords:protected] =>
[id:protected] => 51
[type:protected] => category
[parent:protected] => 2
[label:protected] => Cement Mason
[alreadyInSave:protected] =>
[alreadyInValidation:protected] =>
[validationFailures:protected] => Array
(
)
[_new:BaseObject:private] =>
[_deleted:BaseObject:private] =>
[modifiedColumns:protected] => Array
(
)
)
[55] => Category Object
(
[languages:protected] =>
[bok_resources:protected] =>
[bok_topics:protected] =>
[bok_keywords:protected] =>
[id:protected] => 55
[type:protected] => category
[parent:protected] => 2
[label:protected] => Electrical Worker
[alreadyInSave:protected] =>
[alreadyInValidation:protected] =>
[validationFailures:protected] => Array
(
)
[_new:BaseObject:private] =>
[_deleted:BaseObject:private] =>
[modifiedColumns:protected] => Array
(
)
)
[64] => Category Object
(
[languages:protected] =>
[bok_resources:protected] =>
[bok_topics:protected] =>
[bok_keywords:protected] =>
[id:protected] => 64
[type:protected] => category
[parent:protected] => 2
[label:protected] => Laborer
[alreadyInSave:protected] =>
[alreadyInValidation:protected] =>
[validationFailures:protected] => Array
(
)
[_new:BaseObject:private] =>
[_deleted:BaseObject:private] =>
[modifiedColumns:protected] => Array
(
)
)
[68] => Category Object
(
[languages:protected] =>
[bok_resources:protected] =>
[bok_topics:protected] =>
[bok_keywords:protected] =>
[id:protected] => 68
[type:protected] => category
[parent:protected] => 2
[label:protected] => Maintenance Worker
[alreadyInSave:protected] =>
[alreadyInValidation:protected] =>
[validationFailures:protected] => Array
(
)
[_new:BaseObject:private] =>
[_deleted:BaseObject:private] =>
[modifiedColumns:protected] => Array
(
)
)
[75] => Category Object
(
[languages:protected] =>
[bok_resources:protected] =>
[bok_topics:protected] =>
[bok_keywords:protected] =>
[id:protected] => 75
[type:protected] => category
[parent:protected] => 2
[label:protected] => Plasterer
[alreadyInSave:protected] =>
[alreadyInValidation:protected] =>
[validationFailures:protected] => Array
(
)
[_new:BaseObject:private] =>
[_deleted:BaseObject:private] =>
[modifiedColumns:protected] => Array
(
)
)
[76] => Category Object
(
[languages:protected] =>
[bok_resources:protected] =>
[bok_topics:protected] =>
[bok_keywords:protected] =>
[id:protected] => 76
[type:protected] => category
[parent:protected] => 2
[label:protected] => Plumber/Pipefitter
[alreadyInSave:protected] =>
[alreadyInValidation:protected] =>
[validationFailures:protected] => Array
(
)
[_new:BaseObject:private] =>
[_deleted:BaseObject:private] =>
[modifiedColumns:protected] => Array
(
)
)
[63] => Category Object
(
[languages:protected] =>
[bok_resources:protected] =>
[bok_topics:protected] =>
[bok_keywords:protected] =>
[id:protected] => 63
[type:protected] => category
[parent:protected] => 2
[label:protected] => Reinforcing Ironworker
[alreadyInSave:protected] =>
[alreadyInValidation:protected] =>
[validationFailures:protected] => Array
(
)
[_new:BaseObject:private] =>
[_deleted:BaseObject:private] =>
[modifiedColumns:protected] => Array
(
)
)
[78] => Category Object
(
[languages:protected] =>
[bok_resources:protected] =>
[bok_topics:protected] =>
[bok_keywords:protected] =>
[id:protected] => 78
[type:protected] => category
[parent:protected] => 2
[label:protected] => Roofer/Waterproofer
[alreadyInSave:protected] =>
[alreadyInValidation:protected] =>
[validationFailures:protected] => Array
(
)
[_new:BaseObject:private] =>
[_deleted:BaseObject:private] =>
[modifiedColumns:protected] => Array
(
)
)
[79] => Category Object
(
[languages:protected] =>
[bok_resources:protected] =>
[bok_topics:protected] =>
[bok_keywords:protected] =>
[id:protected] => 79
[type:protected] => category
[parent:protected] => 2
[label:protected] => Scaffold Erector
[alreadyInSave:protected] =>
[alreadyInValidation:protected] =>
[validationFailures:protected] => Array
(
)
[_new:BaseObject:private] =>
[_deleted:BaseObject:private] =>
[modifiedColumns:protected] => Array
(
)
)
[82] => Category Object
(
[languages:protected] =>
[bok_resources:protected] =>
[bok_topics:protected] =>
[bok_keywords:protected] =>
[id:protected] => 82
[type:protected] => category
[parent:protected] => 2
[label:protected] => Stonemason
[alreadyInSave:protected] =>
[alreadyInValidation:protected] =>
[validationFailures:protected] => Array
(
)
[_new:BaseObject:private] =>
[_deleted:BaseObject:private] =>
[modifiedColumns:protected] => Array
(
)
)
[62] => Category Object
(
[languages:protected] =>
[bok_resources:protected] =>
[bok_topics:protected] =>
[bok_keywords:protected] =>
[id:protected] => 62
[type:protected] => category
[parent:protected] => 2
[label:protected] => Structural Ironworker
[alreadyInSave:protected] =>
[alreadyInValidation:protected] =>
[validationFailures:protected] => Array
(
)
[_new:BaseObject:private] =>
[_deleted:BaseObject:private] =>
[modifiedColumns:protected] => Array
(
)
)
[87] => Category Object
(
[languages:protected] =>
[bok_resources:protected] =>
[bok_topics:protected] =>
[bok_keywords:protected] =>
[id:protected] => 87
[type:protected] => category
[parent:protected] => 3
[label:protected] => Commercial & Institutional
[alreadyInSave:protected] =>
[alreadyInValidation:protected] =>
[validationFailures:protected] => Array
(
)
[_new:BaseObject:private] =>
[_deleted:BaseObject:private] =>
[modifiedColumns:protected] => Array
(
)
)
[88] => Category Object
(
[languages:protected] =>
[bok_resources:protected] =>
[bok_topics:protected] =>
[bok_keywords:protected] =>
[id:protected] => 88
[type:protected] => category
[parent:protected] => 3
[label:protected] => Demolition
[alreadyInSave:protected] =>
[alreadyInValidation:protected] =>
[validationFailures:protected] => Array
(
)
[_new:BaseObject:private] =>
[_deleted:BaseObject:private] =>
[modifiedColumns:protected] => Array
(
)
)
[91] => Category Object
(
[languages:protected] =>
[bok_resources:protected] =>
[bok_topics:protected] =>
[bok_keywords:protected] =>
[id:protected] => 91
[type:protected] => category
[parent:protected] => 3
[label:protected] => Heavy & Highway
[alreadyInSave:protected] =>
[alreadyInValidation:protected] =>
[validationFailures:protected] => Array
(
)
[_new:BaseObject:private] =>
[_deleted:BaseObject:private] =>
[modifiedColumns:protected] => Array
(
)
)
[90] => Category Object
(
[languages:protected] =>
[bok_resources:protected] =>
[bok_topics:protected] =>
[bok_keywords:protected] =>
[id:protected] => 90
[type:protected] => category
[parent:protected] => 3
[label:protected] => Industrial
[alreadyInSave:protected] =>
[alreadyInValidation:protected] =>
[validationFailures:protected] => Array
(
)
[_new:BaseObject:private] =>
[_deleted:BaseObject:private] =>
[modifiedColumns:protected] => Array
(
)
)
[93] => Category Object
(
[languages:protected] =>
[bok_resources:protected] =>
[bok_topics:protected] =>
[bok_keywords:protected] =>
[id:protected] => 93
[type:protected] => category
[parent:protected] => 3
[label:protected] => Renovations
[alreadyInSave:protected] =>
[alreadyInValidation:protected] =>
[validationFailures:protected] => Array
(
)
[_new:BaseObject:private] =>
[_deleted:BaseObject:private] =>
[modifiedColumns:protected] => Array
(
)
)
[94] => Category Object
(
[languages:protected] =>
[bok_resources:protected] =>
[bok_topics:protected] =>
[bok_keywords:protected] =>
[id:protected] => 94
[type:protected] => category
[parent:protected] => 3
[label:protected] => Residential
[alreadyInSave:protected] =>
[alreadyInValidation:protected] =>
[validationFailures:protected] => Array
(
)
[_new:BaseObject:private] =>
[_deleted:BaseObject:private] =>
[modifiedColumns:protected] => Array
(
)
)
[95] => Category Object
(
[languages:protected] =>
[bok_resources:protected] =>
[bok_topics:protected] =>
[bok_keywords:protected] =>
[id:protected] => 95
[type:protected] => category
[parent:protected] => 3
[label:protected] => Underground
[alreadyInSave:protected] =>
[alreadyInValidation:protected] =>
[validationFailures:protected] => Array
(
)
[_new:BaseObject:private] =>
[_deleted:BaseObject:private] =>
[modifiedColumns:protected] => Array
(
)
)
[97] => Category Object
(
[languages:protected] =>
[bok_resources:protected] =>
[bok_topics:protected] =>
[bok_keywords:protected] =>
[id:protected] => 97
[type:protected] => category
[parent:protected] => 5
[label:protected] => Images
[alreadyInSave:protected] =>
[alreadyInValidation:protected] =>
[validationFailures:protected] => Array
(
)
[_new:BaseObject:private] =>
[_deleted:BaseObject:private] =>
[modifiedColumns:protected] => Array
(
)
)
)
[categories_initialized:protected] => 1
[mapped_items:protected] =>
[content:protected] =>
[files:protected] =>
[language:protected] => Language Object
(
[id:protected] => 1
[code:protected] => en
[name:protected] => English
[alreadyInSave:protected] =>
[alreadyInValidation:protected] =>
[validationFailures:protected] => Array
(
)
[_new:BaseObject:private] =>
[_deleted:BaseObject:private] =>
[modifiedColumns:protected] => Array
(
)
)
[old_record:protected] =>
[id:protected] => 4006
[old_id:protected] =>
[elcosh_id:protected] => i002693
[type:protected] => image
[display_type:protected] => Image
[user_id:protected] => 0
[language_id:protected] => 1
[tagging_id:protected] => Bruce Lippy
[priority_id:protected] => 1
[title:protected] => Toolbox talk - long shot
[total_pages:protected] => 0
[billed_pages:protected] => 0
[publication_number:protected] =>
[part_of:protected] =>
[keywords:protected] => toolbox talk, tailgate talk, safety minute
[comments:protected] =>
[summary:protected] => This crew gathered every morning before starting work to discuss a new safety topic.
[transition_comments:protected] =>
[external_link:protected] =>
[consol_link:protected] => http://www.cpwrconstructionsolutions.org/electrical/solution/662/worker-training.html
[more_like_this:protected] => i002691,i002692,d001269,d000527
[permission_given_by:protected] =>
[published:protected] => T
[billable:protected] => F
[img_name:protected] =>
[img_ext:protected] => jpg
[img_width:protected] =>
[img_height:protected] =>
[img_credit:protected] => Morgan Zavertnik and Hoar Construction
[img_practice:protected] => good
[vid_source_id:protected] =>
[vid_running_time:protected] =>
[vid_intended_audience:protected] =>
[vid_acquisition_info:protected] =>
[vid_cost:protected] =>
[vid_producer:protected] =>
[vid_filename:protected] =>
[vid_filename_downloadable:protected] =>
[date_summary:protected] => November 2015
[date_permission_requested:protected] =>
[date_permission_received:protected] =>
[date_review_needed:protected] =>
[date_received:protected] => 03/02/16
[date_completed:protected] => 03/02/16
[date_billed:protected] =>
[date_modified:protected] => 03/02/16
[collBokExports:protected] =>
[lastBokExportCriteria:BaseElcoshItem:private] =>
[alreadyInSave:protected] =>
[alreadyInValidation:protected] =>
[validationFailures:protected] => Array
(
)
[_new:BaseObject:private] =>
[_deleted:BaseObject:private] =>
[modifiedColumns:protected] => Array
(
)
)
)
[3] => Search_Result Object
(
[title] => Safety officer discussing ongoing project with marketing coordinator
[image] => /record/images/4014-p.jpg
[blurb] => The safety officer (left) points out the good safety practices on this project that reflect well on the firm and may influence future clients....
[category] => Array
(
[0] => 97
[1] => 20
[2] => 46
[3] => 47
[4] => 49
[5] => 50
[6] => 51
[7] => 54
[8] => 55
[9] => 58
[10] => 60
[11] => 61
[12] => 64
[13] => 71
[14] => 75
[15] => 76
[16] => 63
[17] => 79
[18] => 80
[19] => 82
[20] => 62
[21] => 83
[22] => 87
[23] => 91
[24] => 90
[25] => 93
[26] => 94
)
[labels] => Array
(
[0] => Images
[1] => Media
[2] => Media & Documents
[3] => Safety Culture
[4] => Work Environment
[5] => Hazards
[6] => Boilermaker
[7] => Trades
[8] => Bricklayer
[10] => Carpenter
[12] => Carpet Layer
[14] => Cement Mason
[16] => Drywall Applicator Specialist
[18] => Electrical Worker
[20] => Glazier
[22] => HVAC
[24] => Interior Systems Carpenter
[26] => Laborer
[28] => Painter
[30] => Plasterer
[32] => Plumber/Pipefitter
[34] => Reinforcing Ironworker
[36] => Scaffold Erector
[38] => Sheetmetal Worker
[40] => Stonemason
[42] => Structural Ironworker
[44] => Terrazzo Worker
[46] => Commercial & Institutional
[47] => Jobsites
[48] => Heavy & Highway
[50] => Industrial
[52] => Renovations
[54] => Residential
)
[type] => Images
[sub_category] =>
[url] => /image/4014/i002700/Safety%2Bofficer%2Bdiscussing%2Bongoing%2Bproject%2Bwith%2Bmarketing%2Bcoordinator.html
[item:protected] => ImageRecord Object
(
[records:protected] => Array
(
)
[recordId:protected] =>
[searchWordClass:protected] =>
[searchWordPeerClass:protected] =>
[bok_record:protected] =>
[authors:protected] =>
[organizations:protected] =>
[collections:protected] =>
[categories:protected] => Array
(
[97] => Category Object
(
[languages:protected] =>
[bok_resources:protected] =>
[bok_topics:protected] =>
[bok_keywords:protected] =>
[id:protected] => 97
[type:protected] => category
[parent:protected] => 5
[label:protected] => Images
[alreadyInSave:protected] =>
[alreadyInValidation:protected] =>
[validationFailures:protected] => Array
(
)
[_new:BaseObject:private] =>
[_deleted:BaseObject:private] =>
[modifiedColumns:protected] => Array
(
)
)
[20] => Category Object
(
[languages:protected] =>
[bok_resources:protected] =>
[bok_topics:protected] =>
[bok_keywords:protected] =>
[id:protected] => 20
[type:protected] => category
[parent:protected] => 7
[label:protected] => Safety Culture
[alreadyInSave:protected] =>
[alreadyInValidation:protected] =>
[validationFailures:protected] => Array
(
)
[_new:BaseObject:private] =>
[_deleted:BaseObject:private] =>
[modifiedColumns:protected] => Array
(
)
)
[46] => Category Object
(
[languages:protected] =>
[bok_resources:protected] =>
[bok_topics:protected] =>
[bok_keywords:protected] =>
[id:protected] => 46
[type:protected] => category
[parent:protected] => 2
[label:protected] => Boilermaker
[alreadyInSave:protected] =>
[alreadyInValidation:protected] =>
[validationFailures:protected] => Array
(
)
[_new:BaseObject:private] =>
[_deleted:BaseObject:private] =>
[modifiedColumns:protected] => Array
(
)
)
[47] => Category Object
(
[languages:protected] =>
[bok_resources:protected] =>
[bok_topics:protected] =>
[bok_keywords:protected] =>
[id:protected] => 47
[type:protected] => category
[parent:protected] => 2
[label:protected] => Bricklayer
[alreadyInSave:protected] =>
[alreadyInValidation:protected] =>
[validationFailures:protected] => Array
(
)
[_new:BaseObject:private] =>
[_deleted:BaseObject:private] =>
[modifiedColumns:protected] => Array
(
)
)
[49] => Category Object
(
[languages:protected] =>
[bok_resources:protected] =>
[bok_topics:protected] =>
[bok_keywords:protected] =>
[id:protected] => 49
[type:protected] => category
[parent:protected] => 2
[label:protected] => Carpenter
[alreadyInSave:protected] =>
[alreadyInValidation:protected] =>
[validationFailures:protected] => Array
(
)
[_new:BaseObject:private] =>
[_deleted:BaseObject:private] =>
[modifiedColumns:protected] => Array
(
)
)
[50] => Category Object
(
[languages:protected] =>
[bok_resources:protected] =>
[bok_topics:protected] =>
[bok_keywords:protected] =>
[id:protected] => 50
[type:protected] => category
[parent:protected] => 2
[label:protected] => Carpet Layer
[alreadyInSave:protected] =>
[alreadyInValidation:protected] =>
[validationFailures:protected] => Array
(
)
[_new:BaseObject:private] =>
[_deleted:BaseObject:private] =>
[modifiedColumns:protected] => Array
(
)
)
[51] => Category Object
(
[languages:protected] =>
[bok_resources:protected] =>
[bok_topics:protected] =>
[bok_keywords:protected] =>
[id:protected] => 51
[type:protected] => category
[parent:protected] => 2
[label:protected] => Cement Mason
[alreadyInSave:protected] =>
[alreadyInValidation:protected] =>
[validationFailures:protected] => Array
(
)
[_new:BaseObject:private] =>
[_deleted:BaseObject:private] =>
[modifiedColumns:protected] => Array
(
)
)
[54] => Category Object
(
[languages:protected] =>
[bok_resources:protected] =>
[bok_topics:protected] =>
[bok_keywords:protected] =>
[id:protected] => 54
[type:protected] => category
[parent:protected] => 2
[label:protected] => Drywall Applicator Specialist
[alreadyInSave:protected] =>
[alreadyInValidation:protected] =>
[validationFailures:protected] => Array
(
)
[_new:BaseObject:private] =>
[_deleted:BaseObject:private] =>
[modifiedColumns:protected] => Array
(
)
)
[55] => Category Object
(
[languages:protected] =>
[bok_resources:protected] =>
[bok_topics:protected] =>
[bok_keywords:protected] =>
[id:protected] => 55
[type:protected] => category
[parent:protected] => 2
[label:protected] => Electrical Worker
[alreadyInSave:protected] =>
[alreadyInValidation:protected] =>
[validationFailures:protected] => Array
(
)
[_new:BaseObject:private] =>
[_deleted:BaseObject:private] =>
[modifiedColumns:protected] => Array
(
)
)
[58] => Category Object
(
[languages:protected] =>
[bok_resources:protected] =>
[bok_topics:protected] =>
[bok_keywords:protected] =>
[id:protected] => 58
[type:protected] => category
[parent:protected] => 2
[label:protected] => Glazier
[alreadyInSave:protected] =>
[alreadyInValidation:protected] =>
[validationFailures:protected] => Array
(
)
[_new:BaseObject:private] =>
[_deleted:BaseObject:private] =>
[modifiedColumns:protected] => Array
(
)
)
[60] => Category Object
(
[languages:protected] =>
[bok_resources:protected] =>
[bok_topics:protected] =>
[bok_keywords:protected] =>
[id:protected] => 60
[type:protected] => category
[parent:protected] => 2
[label:protected] => HVAC
[alreadyInSave:protected] =>
[alreadyInValidation:protected] =>
[validationFailures:protected] => Array
(
)
[_new:BaseObject:private] =>
[_deleted:BaseObject:private] =>
[modifiedColumns:protected] => Array
(
)
)
[61] => Category Object
(
[languages:protected] =>
[bok_resources:protected] =>
[bok_topics:protected] =>
[bok_keywords:protected] =>
[id:protected] => 61
[type:protected] => category
[parent:protected] => 2
[label:protected] => Interior Systems Carpenter
[alreadyInSave:protected] =>
[alreadyInValidation:protected] =>
[validationFailures:protected] => Array
(
)
[_new:BaseObject:private] =>
[_deleted:BaseObject:private] =>
[modifiedColumns:protected] => Array
(
)
)
[64] => Category Object
(
[languages:protected] =>
[bok_resources:protected] =>
[bok_topics:protected] =>
[bok_keywords:protected] =>
[id:protected] => 64
[type:protected] => category
[parent:protected] => 2
[label:protected] => Laborer
[alreadyInSave:protected] =>
[alreadyInValidation:protected] =>
[validationFailures:protected] => Array
(
)
[_new:BaseObject:private] =>
[_deleted:BaseObject:private] =>
[modifiedColumns:protected] => Array
(
)
)
[71] => Category Object
(
[languages:protected] =>
[bok_resources:protected] =>
[bok_topics:protected] =>
[bok_keywords:protected] =>
[id:protected] => 71
[type:protected] => category
[parent:protected] => 2
[label:protected] => Painter
[alreadyInSave:protected] =>
[alreadyInValidation:protected] =>
[validationFailures:protected] => Array
(
)
[_new:BaseObject:private] =>
[_deleted:BaseObject:private] =>
[modifiedColumns:protected] => Array
(
)
)
[75] => Category Object
(
[languages:protected] =>
[bok_resources:protected] =>
[bok_topics:protected] =>
[bok_keywords:protected] =>
[id:protected] => 75
[type:protected] => category
[parent:protected] => 2
[label:protected] => Plasterer
[alreadyInSave:protected] =>
[alreadyInValidation:protected] =>
[validationFailures:protected] => Array
(
)
[_new:BaseObject:private] =>
[_deleted:BaseObject:private] =>
[modifiedColumns:protected] => Array
(
)
)
[76] => Category Object
(
[languages:protected] =>
[bok_resources:protected] =>
[bok_topics:protected] =>
[bok_keywords:protected] =>
[id:protected] => 76
[type:protected] => category
[parent:protected] => 2
[label:protected] => Plumber/Pipefitter
[alreadyInSave:protected] =>
[alreadyInValidation:protected] =>
[validationFailures:protected] => Array
(
)
[_new:BaseObject:private] =>
[_deleted:BaseObject:private] =>
[modifiedColumns:protected] => Array
(
)
)
[63] => Category Object
(
[languages:protected] =>
[bok_resources:protected] =>
[bok_topics:protected] =>
[bok_keywords:protected] =>
[id:protected] => 63
[type:protected] => category
[parent:protected] => 2
[label:protected] => Reinforcing Ironworker
[alreadyInSave:protected] =>
[alreadyInValidation:protected] =>
[validationFailures:protected] => Array
(
)
[_new:BaseObject:private] =>
[_deleted:BaseObject:private] =>
[modifiedColumns:protected] => Array
(
)
)
[79] => Category Object
(
[languages:protected] =>
[bok_resources:protected] =>
[bok_topics:protected] =>
[bok_keywords:protected] =>
[id:protected] => 79
[type:protected] => category
[parent:protected] => 2
[label:protected] => Scaffold Erector
[alreadyInSave:protected] =>
[alreadyInValidation:protected] =>
[validationFailures:protected] => Array
(
)
[_new:BaseObject:private] =>
[_deleted:BaseObject:private] =>
[modifiedColumns:protected] => Array
(
)
)
[80] => Category Object
(
[languages:protected] =>
[bok_resources:protected] =>
[bok_topics:protected] =>
[bok_keywords:protected] =>
[id:protected] => 80
[type:protected] => category
[parent:protected] => 2
[label:protected] => Sheetmetal Worker
[alreadyInSave:protected] =>
[alreadyInValidation:protected] =>
[validationFailures:protected] => Array
(
)
[_new:BaseObject:private] =>
[_deleted:BaseObject:private] =>
[modifiedColumns:protected] => Array
(
)
)
[82] => Category Object
(
[languages:protected] =>
[bok_resources:protected] =>
[bok_topics:protected] =>
[bok_keywords:protected] =>
[id:protected] => 82
[type:protected] => category
[parent:protected] => 2
[label:protected] => Stonemason
[alreadyInSave:protected] =>
[alreadyInValidation:protected] =>
[validationFailures:protected] => Array
(
)
[_new:BaseObject:private] =>
[_deleted:BaseObject:private] =>
[modifiedColumns:protected] => Array
(
)
)
[62] => Category Object
(
[languages:protected] =>
[bok_resources:protected] =>
[bok_topics:protected] =>
[bok_keywords:protected] =>
[id:protected] => 62
[type:protected] => category
[parent:protected] => 2
[label:protected] => Structural Ironworker
[alreadyInSave:protected] =>
[alreadyInValidation:protected] =>
[validationFailures:protected] => Array
(
)
[_new:BaseObject:private] =>
[_deleted:BaseObject:private] =>
[modifiedColumns:protected] => Array
(
)
)
[83] => Category Object
(
[languages:protected] =>
[bok_resources:protected] =>
[bok_topics:protected] =>
[bok_keywords:protected] =>
[id:protected] => 83
[type:protected] => category
[parent:protected] => 2
[label:protected] => Terrazzo Worker
[alreadyInSave:protected] =>
[alreadyInValidation:protected] =>
[validationFailures:protected] => Array
(
)
[_new:BaseObject:private] =>
[_deleted:BaseObject:private] =>
[modifiedColumns:protected] => Array
(
)
)
[87] => Category Object
(
[languages:protected] =>
[bok_resources:protected] =>
[bok_topics:protected] =>
[bok_keywords:protected] =>
[id:protected] => 87
[type:protected] => category
[parent:protected] => 3
[label:protected] => Commercial & Institutional
[alreadyInSave:protected] =>
[alreadyInValidation:protected] =>
[validationFailures:protected] => Array
(
)
[_new:BaseObject:private] =>
[_deleted:BaseObject:private] =>
[modifiedColumns:protected] => Array
(
)
)
[91] => Category Object
(
[languages:protected] =>
[bok_resources:protected] =>
[bok_topics:protected] =>
[bok_keywords:protected] =>
[id:protected] => 91
[type:protected] => category
[parent:protected] => 3
[label:protected] => Heavy & Highway
[alreadyInSave:protected] =>
[alreadyInValidation:protected] =>
[validationFailures:protected] => Array
(
)
[_new:BaseObject:private] =>
[_deleted:BaseObject:private] =>
[modifiedColumns:protected] => Array
(
)
)
[90] => Category Object
(
[languages:protected] =>
[bok_resources:protected] =>
[bok_topics:protected] =>
[bok_keywords:protected] =>
[id:protected] => 90
[type:protected] => category
[parent:protected] => 3
[label:protected] => Industrial
[alreadyInSave:protected] =>
[alreadyInValidation:protected] =>
[validationFailures:protected] => Array
(
)
[_new:BaseObject:private] =>
[_deleted:BaseObject:private] =>
[modifiedColumns:protected] => Array
(
)
)
[93] => Category Object
(
[languages:protected] =>
[bok_resources:protected] =>
[bok_topics:protected] =>
[bok_keywords:protected] =>
[id:protected] => 93
[type:protected] => category
[parent:protected] => 3
[label:protected] => Renovations
[alreadyInSave:protected] =>
[alreadyInValidation:protected] =>
[validationFailures:protected] => Array
(
)
[_new:BaseObject:private] =>
[_deleted:BaseObject:private] =>
[modifiedColumns:protected] => Array
(
)
)
[94] => Category Object
(
[languages:protected] =>
[bok_resources:protected] =>
[bok_topics:protected] =>
[bok_keywords:protected] =>
[id:protected] => 94
[type:protected] => category
[parent:protected] => 3
[label:protected] => Residential
[alreadyInSave:protected] =>
[alreadyInValidation:protected] =>
[validationFailures:protected] => Array
(
)
[_new:BaseObject:private] =>
[_deleted:BaseObject:private] =>
[modifiedColumns:protected] => Array
(
)
)
)
[categories_initialized:protected] => 1
[mapped_items:protected] =>
[content:protected] =>
[files:protected] =>
[language:protected] => Language Object
(
[id:protected] => 1
[code:protected] => en
[name:protected] => English
[alreadyInSave:protected] =>
[alreadyInValidation:protected] =>
[validationFailures:protected] => Array
(
)
[_new:BaseObject:private] =>
[_deleted:BaseObject:private] =>
[modifiedColumns:protected] => Array
(
)
)
[old_record:protected] =>
[id:protected] => 4014
[old_id:protected] =>
[elcosh_id:protected] => i002700
[type:protected] => image
[display_type:protected] => Image
[user_id:protected] => 0
[language_id:protected] => 1
[tagging_id:protected] => Bruce Lippy
[priority_id:protected] => 1
[title:protected] => Safety officer discussing ongoing project with marketing coordinator
[total_pages:protected] => 0
[billed_pages:protected] => 0
[publication_number:protected] =>
[part_of:protected] =>
[keywords:protected] => Latino, safety officer, safety culture
[comments:protected] =>
[summary:protected] => The safety officer (left) points out the good safety practices on this project that reflect well on the firm and may influence future clients.
[transition_comments:protected] =>
[external_link:protected] =>
[consol_link:protected] => http://www.cpwrconstructionsolutions.org/index.php
[more_like_this:protected] => d000989,d001351,d001362,d000652, d001101, d000931, d001395
[permission_given_by:protected] =>
[published:protected] => T
[billable:protected] => F
[img_name:protected] =>
[img_ext:protected] => jpg
[img_width:protected] =>
[img_height:protected] =>
[img_credit:protected] => Hoar Construction, Photo by Neil Lippy
[img_practice:protected] => good
[vid_source_id:protected] =>
[vid_running_time:protected] =>
[vid_intended_audience:protected] =>
[vid_acquisition_info:protected] =>
[vid_cost:protected] =>
[vid_producer:protected] =>
[vid_filename:protected] =>
[vid_filename_downloadable:protected] =>
[date_summary:protected] => November 2015
[date_permission_requested:protected] =>
[date_permission_received:protected] =>
[date_review_needed:protected] =>
[date_received:protected] => 03/02/16
[date_completed:protected] => 03/02/16
[date_billed:protected] =>
[date_modified:protected] => 01/30/23
[collBokExports:protected] =>
[lastBokExportCriteria:BaseElcoshItem:private] =>
[alreadyInSave:protected] =>
[alreadyInValidation:protected] =>
[validationFailures:protected] => Array
(
)
[_new:BaseObject:private] =>
[_deleted:BaseObject:private] =>
[modifiedColumns:protected] => Array
(
)
)
)
[4] => Search_Result Object
(
[title] => Scaffolding at top of large column
[image] => /record/images/3994-p.jpg
[blurb] => This shot shows innovative guarding around the top of a large concrete column in the base of a high rise structure going up....
[category] => Array
(
[0] => 15
[1] => 21
[2] => 47
[3] => 51
[4] => 63
[5] => 78
[6] => 79
[7] => 80
[8] => 62
[9] => 87
[10] => 97
[11] => 56
[12] => 64
[13] => 74
)
[labels] => Array
(
[0] => Falls
[1] => Work Environment
[2] => Hazards
[3] => Scaffolds
[6] => Bricklayer
[7] => Trades
[8] => Cement Mason
[10] => Reinforcing Ironworker
[12] => Roofer/Waterproofer
[14] => Scaffold Erector
[16] => Sheetmetal Worker
[18] => Structural Ironworker
[20] => Commercial & Institutional
[21] => Jobsites
[22] => Images
[23] => Media
[24] => Media & Documents
[25] => Elevator Constructor
[27] => Laborer
[29] => Pile Driver
)
[type] => Images
[sub_category] =>
[url] => /image/3994/i002689/Scaffolding%2Bat%2Btop%2Bof%2Blarge%2Bcolumn.html
[item:protected] => ImageRecord Object
(
[records:protected] => Array
(
)
[recordId:protected] =>
[searchWordClass:protected] =>
[searchWordPeerClass:protected] =>
[bok_record:protected] =>
[authors:protected] =>
[organizations:protected] =>
[collections:protected] =>
[categories:protected] => Array
(
[15] => Category Object
(
[languages:protected] =>
[bok_resources:protected] =>
[bok_topics:protected] =>
[bok_keywords:protected] =>
[id:protected] => 15
[type:protected] => category
[parent:protected] => 7
[label:protected] => Falls
[alreadyInSave:protected] =>
[alreadyInValidation:protected] =>
[validationFailures:protected] => Array
(
)
[_new:BaseObject:private] =>
[_deleted:BaseObject:private] =>
[modifiedColumns:protected] => Array
(
)
)
[21] => Category Object
(
[languages:protected] =>
[bok_resources:protected] =>
[bok_topics:protected] =>
[bok_keywords:protected] =>
[id:protected] => 21
[type:protected] => category
[parent:protected] => 7
[label:protected] => Scaffolds
[alreadyInSave:protected] =>
[alreadyInValidation:protected] =>
[validationFailures:protected] => Array
(
)
[_new:BaseObject:private] =>
[_deleted:BaseObject:private] =>
[modifiedColumns:protected] => Array
(
)
)
[47] => Category Object
(
[languages:protected] =>
[bok_resources:protected] =>
[bok_topics:protected] =>
[bok_keywords:protected] =>
[id:protected] => 47
[type:protected] => category
[parent:protected] => 2
[label:protected] => Bricklayer
[alreadyInSave:protected] =>
[alreadyInValidation:protected] =>
[validationFailures:protected] => Array
(
)
[_new:BaseObject:private] =>
[_deleted:BaseObject:private] =>
[modifiedColumns:protected] => Array
(
)
)
[51] => Category Object
(
[languages:protected] =>
[bok_resources:protected] =>
[bok_topics:protected] =>
[bok_keywords:protected] =>
[id:protected] => 51
[type:protected] => category
[parent:protected] => 2
[label:protected] => Cement Mason
[alreadyInSave:protected] =>
[alreadyInValidation:protected] =>
[validationFailures:protected] => Array
(
)
[_new:BaseObject:private] =>
[_deleted:BaseObject:private] =>
[modifiedColumns:protected] => Array
(
)
)
[63] => Category Object
(
[languages:protected] =>
[bok_resources:protected] =>
[bok_topics:protected] =>
[bok_keywords:protected] =>
[id:protected] => 63
[type:protected] => category
[parent:protected] => 2
[label:protected] => Reinforcing Ironworker
[alreadyInSave:protected] =>
[alreadyInValidation:protected] =>
[validationFailures:protected] => Array
(
)
[_new:BaseObject:private] =>
[_deleted:BaseObject:private] =>
[modifiedColumns:protected] => Array
(
)
)
[78] => Category Object
(
[languages:protected] =>
[bok_resources:protected] =>
[bok_topics:protected] =>
[bok_keywords:protected] =>
[id:protected] => 78
[type:protected] => category
[parent:protected] => 2
[label:protected] => Roofer/Waterproofer
[alreadyInSave:protected] =>
[alreadyInValidation:protected] =>
[validationFailures:protected] => Array
(
)
[_new:BaseObject:private] =>
[_deleted:BaseObject:private] =>
[modifiedColumns:protected] => Array
(
)
)
[79] => Category Object
(
[languages:protected] =>
[bok_resources:protected] =>
[bok_topics:protected] =>
[bok_keywords:protected] =>
[id:protected] => 79
[type:protected] => category
[parent:protected] => 2
[label:protected] => Scaffold Erector
[alreadyInSave:protected] =>
[alreadyInValidation:protected] =>
[validationFailures:protected] => Array
(
)
[_new:BaseObject:private] =>
[_deleted:BaseObject:private] =>
[modifiedColumns:protected] => Array
(
)
)
[80] => Category Object
(
[languages:protected] =>
[bok_resources:protected] =>
[bok_topics:protected] =>
[bok_keywords:protected] =>
[id:protected] => 80
[type:protected] => category
[parent:protected] => 2
[label:protected] => Sheetmetal Worker
[alreadyInSave:protected] =>
[alreadyInValidation:protected] =>
[validationFailures:protected] => Array
(
)
[_new:BaseObject:private] =>
[_deleted:BaseObject:private] =>
[modifiedColumns:protected] => Array
(
)
)
[62] => Category Object
(
[languages:protected] =>
[bok_resources:protected] =>
[bok_topics:protected] =>
[bok_keywords:protected] =>
[id:protected] => 62
[type:protected] => category
[parent:protected] => 2
[label:protected] => Structural Ironworker
[alreadyInSave:protected] =>
[alreadyInValidation:protected] =>
[validationFailures:protected] => Array
(
)
[_new:BaseObject:private] =>
[_deleted:BaseObject:private] =>
[modifiedColumns:protected] => Array
(
)
)
[87] => Category Object
(
[languages:protected] =>
[bok_resources:protected] =>
[bok_topics:protected] =>
[bok_keywords:protected] =>
[id:protected] => 87
[type:protected] => category
[parent:protected] => 3
[label:protected] => Commercial & Institutional
[alreadyInSave:protected] =>
[alreadyInValidation:protected] =>
[validationFailures:protected] => Array
(
)
[_new:BaseObject:private] =>
[_deleted:BaseObject:private] =>
[modifiedColumns:protected] => Array
(
)
)
[97] => Category Object
(
[languages:protected] =>
[bok_resources:protected] =>
[bok_topics:protected] =>
[bok_keywords:protected] =>
[id:protected] => 97
[type:protected] => category
[parent:protected] => 5
[label:protected] => Images
[alreadyInSave:protected] =>
[alreadyInValidation:protected] =>
[validationFailures:protected] => Array
(
)
[_new:BaseObject:private] =>
[_deleted:BaseObject:private] =>
[modifiedColumns:protected] => Array
(
)
)
[56] => Category Object
(
[languages:protected] =>
[bok_resources:protected] =>
[bok_topics:protected] =>
[bok_keywords:protected] =>
[id:protected] => 56
[type:protected] => category
[parent:protected] => 2
[label:protected] => Elevator Constructor
[alreadyInSave:protected] =>
[alreadyInValidation:protected] =>
[validationFailures:protected] => Array
(
)
[_new:BaseObject:private] =>
[_deleted:BaseObject:private] =>
[modifiedColumns:protected] => Array
(
)
)
[64] => Category Object
(
[languages:protected] =>
[bok_resources:protected] =>
[bok_topics:protected] =>
[bok_keywords:protected] =>
[id:protected] => 64
[type:protected] => category
[parent:protected] => 2
[label:protected] => Laborer
[alreadyInSave:protected] =>
[alreadyInValidation:protected] =>
[validationFailures:protected] => Array
(
)
[_new:BaseObject:private] =>
[_deleted:BaseObject:private] =>
[modifiedColumns:protected] => Array
(
)
)
[74] => Category Object
(
[languages:protected] =>
[bok_resources:protected] =>
[bok_topics:protected] =>
[bok_keywords:protected] =>
[id:protected] => 74
[type:protected] => category
[parent:protected] => 2
[label:protected] => Pile Driver
[alreadyInSave:protected] =>
[alreadyInValidation:protected] =>
[validationFailures:protected] => Array
(
)
[_new:BaseObject:private] =>
[_deleted:BaseObject:private] =>
[modifiedColumns:protected] => Array
(
)
)
)
[categories_initialized:protected] => 1
[mapped_items:protected] =>
[content:protected] =>
[files:protected] =>
[language:protected] => Language Object
(
[id:protected] => 1
[code:protected] => en
[name:protected] => English
[alreadyInSave:protected] =>
[alreadyInValidation:protected] =>
[validationFailures:protected] => Array
(
)
[_new:BaseObject:private] =>
[_deleted:BaseObject:private] =>
[modifiedColumns:protected] => Array
(
)
)
[old_record:protected] =>
[id:protected] => 3994
[old_id:protected] =>
[elcosh_id:protected] => i002689
[type:protected] => image
[display_type:protected] => Image
[user_id:protected] => 0
[language_id:protected] => 1
[tagging_id:protected] => Bruce Lippy
[priority_id:protected] => 1
[title:protected] => Scaffolding at top of large column
[total_pages:protected] => 0
[billed_pages:protected] => 0
[publication_number:protected] =>
[part_of:protected] =>
[keywords:protected] => Guardrail, railing, fall prevention, falls
[comments:protected] =>
[summary:protected] => This shot shows innovative guarding around the top of a large concrete column in the base of a high rise structure going up.
[transition_comments:protected] =>
[external_link:protected] =>
[consol_link:protected] => http://www.cpwrconstructionsolutions.org/masonry/solution/8/adjustable-tower-scaffold.html
[more_like_this:protected] => c1002680,i002662,d000608,d001255
[permission_given_by:protected] =>
[published:protected] => T
[billable:protected] => F
[img_name:protected] =>
[img_ext:protected] => jpg
[img_width:protected] =>
[img_height:protected] =>
[img_credit:protected] => Photo by Pam Susi
[img_practice:protected] => good
[vid_source_id:protected] =>
[vid_running_time:protected] =>
[vid_intended_audience:protected] =>
[vid_acquisition_info:protected] =>
[vid_cost:protected] =>
[vid_producer:protected] =>
[vid_filename:protected] =>
[vid_filename_downloadable:protected] =>
[date_summary:protected] => January 2016
[date_permission_requested:protected] =>
[date_permission_received:protected] =>
[date_review_needed:protected] =>
[date_received:protected] => 02/01/16
[date_completed:protected] => 02/01/16
[date_billed:protected] =>
[date_modified:protected] => 02/01/16
[collBokExports:protected] =>
[lastBokExportCriteria:BaseElcoshItem:private] =>
[alreadyInSave:protected] =>
[alreadyInValidation:protected] =>
[validationFailures:protected] => Array
(
)
[_new:BaseObject:private] =>
[_deleted:BaseObject:private] =>
[modifiedColumns:protected] => Array
(
)
)
)
[5] => Search_Result Object
(
[title] => Construction bracing
[image] => /record/images/3995-p.jpg
[blurb] => This shows structural support that prevents collapses during construction....
[category] => Array
(
[0] => 12
[1] => 15
[2] => 21
[3] => 49
[4] => 51
[5] => 55
[6] => 56
[7] => 60
[8] => 64
[9] => 68
[10] => 74
[11] => 63
[12] => 78
[13] => 79
[14] => 80
[15] => 62
[16] => 87
[17] => 90
[18] => 97
)
[labels] => Array
(
[0] => Crushed/Struck By
[1] => Work Environment
[2] => Hazards
[3] => Falls
[6] => Scaffolds
[9] => Carpenter
[10] => Trades
[11] => Cement Mason
[13] => Electrical Worker
[15] => Elevator Constructor
[17] => HVAC
[19] => Laborer
[21] => Maintenance Worker
[23] => Pile Driver
[25] => Reinforcing Ironworker
[27] => Roofer/Waterproofer
[29] => Scaffold Erector
[31] => Sheetmetal Worker
[33] => Structural Ironworker
[35] => Commercial & Institutional
[36] => Jobsites
[37] => Industrial
[39] => Images
[40] => Media
[41] => Media & Documents
)
[type] => Images
[sub_category] =>
[url] => /image/3995/i002690/Construction%2Bbracing.html
[item:protected] => ImageRecord Object
(
[records:protected] => Array
(
)
[recordId:protected] =>
[searchWordClass:protected] =>
[searchWordPeerClass:protected] =>
[bok_record:protected] =>
[authors:protected] =>
[organizations:protected] =>
[collections:protected] =>
[categories:protected] => Array
(
[12] => Category Object
(
[languages:protected] =>
[bok_resources:protected] =>
[bok_topics:protected] =>
[bok_keywords:protected] =>
[id:protected] => 12
[type:protected] => category
[parent:protected] => 7
[label:protected] => Crushed/Struck By
[alreadyInSave:protected] =>
[alreadyInValidation:protected] =>
[validationFailures:protected] => Array
(
)
[_new:BaseObject:private] =>
[_deleted:BaseObject:private] =>
[modifiedColumns:protected] => Array
(
)
)
[15] => Category Object
(
[languages:protected] =>
[bok_resources:protected] =>
[bok_topics:protected] =>
[bok_keywords:protected] =>
[id:protected] => 15
[type:protected] => category
[parent:protected] => 7
[label:protected] => Falls
[alreadyInSave:protected] =>
[alreadyInValidation:protected] =>
[validationFailures:protected] => Array
(
)
[_new:BaseObject:private] =>
[_deleted:BaseObject:private] =>
[modifiedColumns:protected] => Array
(
)
)
[21] => Category Object
(
[languages:protected] =>
[bok_resources:protected] =>
[bok_topics:protected] =>
[bok_keywords:protected] =>
[id:protected] => 21
[type:protected] => category
[parent:protected] => 7
[label:protected] => Scaffolds
[alreadyInSave:protected] =>
[alreadyInValidation:protected] =>
[validationFailures:protected] => Array
(
)
[_new:BaseObject:private] =>
[_deleted:BaseObject:private] =>
[modifiedColumns:protected] => Array
(
)
)
[49] => Category Object
(
[languages:protected] =>
[bok_resources:protected] =>
[bok_topics:protected] =>
[bok_keywords:protected] =>
[id:protected] => 49
[type:protected] => category
[parent:protected] => 2
[label:protected] => Carpenter
[alreadyInSave:protected] =>
[alreadyInValidation:protected] =>
[validationFailures:protected] => Array
(
)
[_new:BaseObject:private] =>
[_deleted:BaseObject:private] =>
[modifiedColumns:protected] => Array
(
)
)
[51] => Category Object
(
[languages:protected] =>
[bok_resources:protected] =>
[bok_topics:protected] =>
[bok_keywords:protected] =>
[id:protected] => 51
[type:protected] => category
[parent:protected] => 2
[label:protected] => Cement Mason
[alreadyInSave:protected] =>
[alreadyInValidation:protected] =>
[validationFailures:protected] => Array
(
)
[_new:BaseObject:private] =>
[_deleted:BaseObject:private] =>
[modifiedColumns:protected] => Array
(
)
)
[55] => Category Object
(
[languages:protected] =>
[bok_resources:protected] =>
[bok_topics:protected] =>
[bok_keywords:protected] =>
[id:protected] => 55
[type:protected] => category
[parent:protected] => 2
[label:protected] => Electrical Worker
[alreadyInSave:protected] =>
[alreadyInValidation:protected] =>
[validationFailures:protected] => Array
(
)
[_new:BaseObject:private] =>
[_deleted:BaseObject:private] =>
[modifiedColumns:protected] => Array
(
)
)
[56] => Category Object
(
[languages:protected] =>
[bok_resources:protected] =>
[bok_topics:protected] =>
[bok_keywords:protected] =>
[id:protected] => 56
[type:protected] => category
[parent:protected] => 2
[label:protected] => Elevator Constructor
[alreadyInSave:protected] =>
[alreadyInValidation:protected] =>
[validationFailures:protected] => Array
(
)
[_new:BaseObject:private] =>
[_deleted:BaseObject:private] =>
[modifiedColumns:protected] => Array
(
)
)
[60] => Category Object
(
[languages:protected] =>
[bok_resources:protected] =>
[bok_topics:protected] =>
[bok_keywords:protected] =>
[id:protected] => 60
[type:protected] => category
[parent:protected] => 2
[label:protected] => HVAC
[alreadyInSave:protected] =>
[alreadyInValidation:protected] =>
[validationFailures:protected] => Array
(
)
[_new:BaseObject:private] =>
[_deleted:BaseObject:private] =>
[modifiedColumns:protected] => Array
(
)
)
[64] => Category Object
(
[languages:protected] =>
[bok_resources:protected] =>
[bok_topics:protected] =>
[bok_keywords:protected] =>
[id:protected] => 64
[type:protected] => category
[parent:protected] => 2
[label:protected] => Laborer
[alreadyInSave:protected] =>
[alreadyInValidation:protected] =>
[validationFailures:protected] => Array
(
)
[_new:BaseObject:private] =>
[_deleted:BaseObject:private] =>
[modifiedColumns:protected] => Array
(
)
)
[68] => Category Object
(
[languages:protected] =>
[bok_resources:protected] =>
[bok_topics:protected] =>
[bok_keywords:protected] =>
[id:protected] => 68
[type:protected] => category
[parent:protected] => 2
[label:protected] => Maintenance Worker
[alreadyInSave:protected] =>
[alreadyInValidation:protected] =>
[validationFailures:protected] => Array
(
)
[_new:BaseObject:private] =>
[_deleted:BaseObject:private] =>
[modifiedColumns:protected] => Array
(
)
)
[74] => Category Object
(
[languages:protected] =>
[bok_resources:protected] =>
[bok_topics:protected] =>
[bok_keywords:protected] =>
[id:protected] => 74
[type:protected] => category
[parent:protected] => 2
[label:protected] => Pile Driver
[alreadyInSave:protected] =>
[alreadyInValidation:protected] =>
[validationFailures:protected] => Array
(
)
[_new:BaseObject:private] =>
[_deleted:BaseObject:private] =>
[modifiedColumns:protected] => Array
(
)
)
[63] => Category Object
(
[languages:protected] =>
[bok_resources:protected] =>
[bok_topics:protected] =>
[bok_keywords:protected] =>
[id:protected] => 63
[type:protected] => category
[parent:protected] => 2
[label:protected] => Reinforcing Ironworker
[alreadyInSave:protected] =>
[alreadyInValidation:protected] =>
[validationFailures:protected] => Array
(
)
[_new:BaseObject:private] =>
[_deleted:BaseObject:private] =>
[modifiedColumns:protected] => Array
(
)
)
[78] => Category Object
(
[languages:protected] =>
[bok_resources:protected] =>
[bok_topics:protected] =>
[bok_keywords:protected] =>
[id:protected] => 78
[type:protected] => category
[parent:protected] => 2
[label:protected] => Roofer/Waterproofer
[alreadyInSave:protected] =>
[alreadyInValidation:protected] =>
[validationFailures:protected] => Array
(
)
[_new:BaseObject:private] =>
[_deleted:BaseObject:private] =>
[modifiedColumns:protected] => Array
(
)
)
[79] => Category Object
(
[languages:protected] =>
[bok_resources:protected] =>
[bok_topics:protected] =>
[bok_keywords:protected] =>
[id:protected] => 79
[type:protected] => category
[parent:protected] => 2
[label:protected] => Scaffold Erector
[alreadyInSave:protected] =>
[alreadyInValidation:protected] =>
[validationFailures:protected] => Array
(
)
[_new:BaseObject:private] =>
[_deleted:BaseObject:private] =>
[modifiedColumns:protected] => Array
(
)
)
[80] => Category Object
(
[languages:protected] =>
[bok_resources:protected] =>
[bok_topics:protected] =>
[bok_keywords:protected] =>
[id:protected] => 80
[type:protected] => category
[parent:protected] => 2
[label:protected] => Sheetmetal Worker
[alreadyInSave:protected] =>
[alreadyInValidation:protected] =>
[validationFailures:protected] => Array
(
)
[_new:BaseObject:private] =>
[_deleted:BaseObject:private] =>
[modifiedColumns:protected] => Array
(
)
)
[62] => Category Object
(
[languages:protected] =>
[bok_resources:protected] =>
[bok_topics:protected] =>
[bok_keywords:protected] =>
[id:protected] => 62
[type:protected] => category
[parent:protected] => 2
[label:protected] => Structural Ironworker
[alreadyInSave:protected] =>
[alreadyInValidation:protected] =>
[validationFailures:protected] => Array
(
)
[_new:BaseObject:private] =>
[_deleted:BaseObject:private] =>
[modifiedColumns:protected] => Array
(
)
)
[87] => Category Object
(
[languages:protected] =>
[bok_resources:protected] =>
[bok_topics:protected] =>
[bok_keywords:protected] =>
[id:protected] => 87
[type:protected] => category
[parent:protected] => 3
[label:protected] => Commercial & Institutional
[alreadyInSave:protected] =>
[alreadyInValidation:protected] =>
[validationFailures:protected] => Array
(
)
[_new:BaseObject:private] =>
[_deleted:BaseObject:private] =>
[modifiedColumns:protected] => Array
(
)
)
[90] => Category Object
(
[languages:protected] =>
[bok_resources:protected] =>
[bok_topics:protected] =>
[bok_keywords:protected] =>
[id:protected] => 90
[type:protected] => category
[parent:protected] => 3
[label:protected] => Industrial
[alreadyInSave:protected] =>
[alreadyInValidation:protected] =>
[validationFailures:protected] => Array
(
)
[_new:BaseObject:private] =>
[_deleted:BaseObject:private] =>
[modifiedColumns:protected] => Array
(
)
)
[97] => Category Object
(
[languages:protected] =>
[bok_resources:protected] =>
[bok_topics:protected] =>
[bok_keywords:protected] =>
[id:protected] => 97
[type:protected] => category
[parent:protected] => 5
[label:protected] => Images
[alreadyInSave:protected] =>
[alreadyInValidation:protected] =>
[validationFailures:protected] => Array
(
)
[_new:BaseObject:private] =>
[_deleted:BaseObject:private] =>
[modifiedColumns:protected] => Array
(
)
)
)
[categories_initialized:protected] => 1
[mapped_items:protected] =>
[content:protected] =>
[files:protected] =>
[language:protected] => Language Object
(
[id:protected] => 1
[code:protected] => en
[name:protected] => English
[alreadyInSave:protected] =>
[alreadyInValidation:protected] =>
[validationFailures:protected] => Array
(
)
[_new:BaseObject:private] =>
[_deleted:BaseObject:private] =>
[modifiedColumns:protected] => Array
(
)
)
[old_record:protected] =>
[id:protected] => 3995
[old_id:protected] =>
[elcosh_id:protected] => i002690
[type:protected] => image
[display_type:protected] => Image
[user_id:protected] => 0
[language_id:protected] => 1
[tagging_id:protected] => Bruce Lippy
[priority_id:protected] => 1
[title:protected] => Construction bracing
[total_pages:protected] => 0
[billed_pages:protected] => 0
[publication_number:protected] =>
[part_of:protected] =>
[keywords:protected] => Bracing, support, scaffold
[comments:protected] =>
[summary:protected] => This shows structural support that prevents collapses during construction.
[transition_comments:protected] =>
[external_link:protected] =>
[consol_link:protected] => http://www.cpwrconstructionsolutions.org/masonry/solution/8/adjustable-tower-scaffold.html
[more_like_this:protected] => i002660
[permission_given_by:protected] =>
[published:protected] => T
[billable:protected] => F
[img_name:protected] =>
[img_ext:protected] => jpg
[img_width:protected] =>
[img_height:protected] =>
[img_credit:protected] => Photo by Pam Susi
[img_practice:protected] => good
[vid_source_id:protected] =>
[vid_running_time:protected] =>
[vid_intended_audience:protected] =>
[vid_acquisition_info:protected] =>
[vid_cost:protected] =>
[vid_producer:protected] =>
[vid_filename:protected] =>
[vid_filename_downloadable:protected] =>
[date_summary:protected] => January 2016
[date_permission_requested:protected] =>
[date_permission_received:protected] =>
[date_review_needed:protected] =>
[date_received:protected] => 02/01/16
[date_completed:protected] => 02/01/16
[date_billed:protected] =>
[date_modified:protected] => 02/01/16
[collBokExports:protected] =>
[lastBokExportCriteria:BaseElcoshItem:private] =>
[alreadyInSave:protected] =>
[alreadyInValidation:protected] =>
[validationFailures:protected] => Array
(
)
[_new:BaseObject:private] =>
[_deleted:BaseObject:private] =>
[modifiedColumns:protected] => Array
(
)
)
)
)
[preview_mode] =>
[description] => Toolbox talks have been the main tool for communicating safety information on construction jobs for decades.
Unfortunately, there has been little research on what makes for effective toolbox talks. The IUOE National
Training Fund worked with OSHA and NIOSH to make sure their series of 24 Focus Four toolbox talks were based on the best recommendations for effective design. These toolbox talks accompany an entire package of training materials, but can be used alone. This guide points out the key features of these toolbox talks and how best to deliver them.
[keywords] => toolbox talks, tailgate talks
[related_items] => Array
(
[Toolbox Talks] => Array
(
[0] => DocumentRecord Object
(
[records:protected] => Array
(
)
[recordId:protected] =>
[searchWordClass:protected] =>
[searchWordPeerClass:protected] =>
[bok_record:protected] =>
[authors:protected] =>
[organizations:protected] =>
[collections:protected] =>
[categories:protected] =>
[categories_initialized:protected] =>
[mapped_items:protected] =>
[content:protected] =>
[files:protected] =>
[language:protected] => Language Object
(
[id:protected] => 1
[code:protected] => en
[name:protected] => English
[alreadyInSave:protected] =>
[alreadyInValidation:protected] =>
[validationFailures:protected] => Array
(
)
[_new:BaseObject:private] =>
[_deleted:BaseObject:private] =>
[modifiedColumns:protected] => Array
(
)
)
[old_record:protected] =>
[id:protected] => 1605
[old_id:protected] => 1262
[elcosh_id:protected] => d001137
[type:protected] => document
[display_type:protected] => HTML w/ PDF
[user_id:protected] =>
[language_id:protected] => 1
[tagging_id:protected] => Garber
[priority_id:protected] => 1
[title:protected] => Focus Four Toolbox Talks, Module 1 – Falls, Talk #2 – Falls from debris piles?
[total_pages:protected] => 1
[billed_pages:protected] => 1
[publication_number:protected] =>
[part_of:protected] =>
[keywords:protected] => disaster response, hazard clean-up, uneven surface, disaster site, disaster clean-up
[comments:protected] =>
[summary:protected] => A toolbox talk on preventing falls from debris piles. Includes questions to ask, an incident to discuss with images, and a place to record questions the trainer would like to ask about the incident. Part of a collection. Click on the 'collection' button to access the other items.
[transition_comments:protected] =>
[external_link:protected] =>
[consol_link:protected] => http://www.cpwrconstructionsolutions.org/roofing/hazard/1463/install-asphalt-roofs-fall-from-heights.html
[more_like_this:protected] => a000081,d000478,d000530
[permission_given_by:protected] =>
[published:protected] => T
[billable:protected] => F
[img_name:protected] =>
[img_ext:protected] =>
[img_width:protected] =>
[img_height:protected] =>
[img_credit:protected] =>
[img_practice:protected] =>
[vid_source_id:protected] =>
[vid_running_time:protected] =>
[vid_intended_audience:protected] =>
[vid_acquisition_info:protected] =>
[vid_cost:protected] =>
[vid_producer:protected] =>
[vid_filename:protected] =>
[vid_filename_downloadable:protected] =>
[date_summary:protected] =>
[date_permission_requested:protected] =>
[date_permission_received:protected] =>
[date_review_needed:protected] =>
[date_received:protected] => 02/15/12
[date_completed:protected] => 03/19/12
[date_billed:protected] =>
[date_modified:protected] => 07/10/12
[collBokExports:protected] =>
[lastBokExportCriteria:BaseElcoshItem:private] =>
[alreadyInSave:protected] =>
[alreadyInValidation:protected] =>
[validationFailures:protected] => Array
(
)
[_new:BaseObject:private] =>
[_deleted:BaseObject:private] =>
[modifiedColumns:protected] => Array
(
)
)
[1] => DocumentRecord Object
(
[records:protected] => Array
(
)
[recordId:protected] =>
[searchWordClass:protected] =>
[searchWordPeerClass:protected] =>
[bok_record:protected] =>
[authors:protected] =>
[organizations:protected] =>
[collections:protected] =>
[categories:protected] =>
[categories_initialized:protected] =>
[mapped_items:protected] =>
[content:protected] =>
[files:protected] =>
[language:protected] => Language Object
(
[id:protected] => 1
[code:protected] => en
[name:protected] => English
[alreadyInSave:protected] =>
[alreadyInValidation:protected] =>
[validationFailures:protected] => Array
(
)
[_new:BaseObject:private] =>
[_deleted:BaseObject:private] =>
[modifiedColumns:protected] => Array
(
)
)
[old_record:protected] =>
[id:protected] => 1610
[old_id:protected] => 1271
[elcosh_id:protected] => d001146
[type:protected] => document
[display_type:protected] => HTML w/ PDF
[user_id:protected] => 0
[language_id:protected] => 1
[tagging_id:protected] => Garber
[priority_id:protected] => 1
[title:protected] => Focus Four Toolbox Talks, Module 2 – Struck-by, Talk #5 – Rigging and Securing Loads
[total_pages:protected] => 1
[billed_pages:protected] => 1
[publication_number:protected] =>
[part_of:protected] =>
[keywords:protected] => rigging, lift loads, loading areas, chains
[comments:protected] =>
[summary:protected] => A toolbox talk on preventing struck-by incidents caused by not securing loads properly. Includes questions to ask, an incident to discuss with images, and a place to record questions the trainer would like to ask about the incident. Part of a collection. Click on the 'collection' button to access the other items.
[transition_comments:protected] =>
[external_link:protected] =>
[consol_link:protected] => http://www.cpwrconstructionsolutions.org/heavy_equipment/hazard/1591/move-equipment-to-from-and-between-sites-work-zone-struck-by-injuries-and-fatalities.html
[more_like_this:protected] => d000144,d000360,d000873
[permission_given_by:protected] =>
[published:protected] => T
[billable:protected] => F
[img_name:protected] =>
[img_ext:protected] =>
[img_width:protected] =>
[img_height:protected] =>
[img_credit:protected] =>
[img_practice:protected] =>
[vid_source_id:protected] =>
[vid_running_time:protected] =>
[vid_intended_audience:protected] =>
[vid_acquisition_info:protected] =>
[vid_cost:protected] =>
[vid_producer:protected] =>
[vid_filename:protected] =>
[vid_filename_downloadable:protected] =>
[date_summary:protected] =>
[date_permission_requested:protected] =>
[date_permission_received:protected] =>
[date_review_needed:protected] =>
[date_received:protected] => 02/15/12
[date_completed:protected] => 03/28/12
[date_billed:protected] =>
[date_modified:protected] => 05/12/14
[collBokExports:protected] =>
[lastBokExportCriteria:BaseElcoshItem:private] =>
[alreadyInSave:protected] =>
[alreadyInValidation:protected] =>
[validationFailures:protected] => Array
(
)
[_new:BaseObject:private] =>
[_deleted:BaseObject:private] =>
[modifiedColumns:protected] => Array
(
)
)
[2] => DocumentRecord Object
(
[records:protected] => Array
(
)
[recordId:protected] =>
[searchWordClass:protected] =>
[searchWordPeerClass:protected] =>
[bok_record:protected] =>
[authors:protected] =>
[organizations:protected] =>
[collections:protected] =>
[categories:protected] =>
[categories_initialized:protected] =>
[mapped_items:protected] =>
[content:protected] =>
[files:protected] =>
[language:protected] => Language Object
(
[id:protected] => 1
[code:protected] => en
[name:protected] => English
[alreadyInSave:protected] =>
[alreadyInValidation:protected] =>
[validationFailures:protected] => Array
(
)
[_new:BaseObject:private] =>
[_deleted:BaseObject:private] =>
[modifiedColumns:protected] => Array
(
)
)
[old_record:protected] =>
[id:protected] => 1645
[old_id:protected] => 1274
[elcosh_id:protected] => d001149
[type:protected] => document
[display_type:protected] => HTML w/ PDF
[user_id:protected] => 0
[language_id:protected] => 1
[tagging_id:protected] => Garber
[priority_id:protected] => 1
[title:protected] => Focus Four Toolbox Talks, Module 3 – Caught-in/between, Talk #2 – Trenches & Heavy Equipment
[total_pages:protected] => 1
[billed_pages:protected] => 1
[publication_number:protected] =>
[part_of:protected] =>
[keywords:protected] => back-up alarms, spotter, soil cave-in, spoil pikes, ROPs, trenching, rain
[comments:protected] =>
[summary:protected] => A toolbox talk on preventing incidents involving trenches such as trench collapse. Includes questions to ask, an incident to discuss with images, and a place to record questions the trainer would like to ask about the incident. Part of a collection. Click on the 'collection' button to access the other items.
[transition_comments:protected] =>
[external_link:protected] =>
[consol_link:protected] =>
[more_like_this:protected] => d000019,d000035,d000168
[permission_given_by:protected] =>
[published:protected] => T
[billable:protected] => F
[img_name:protected] =>
[img_ext:protected] =>
[img_width:protected] =>
[img_height:protected] =>
[img_credit:protected] =>
[img_practice:protected] =>
[vid_source_id:protected] =>
[vid_running_time:protected] =>
[vid_intended_audience:protected] =>
[vid_acquisition_info:protected] =>
[vid_cost:protected] =>
[vid_producer:protected] =>
[vid_filename:protected] =>
[vid_filename_downloadable:protected] =>
[date_summary:protected] =>
[date_permission_requested:protected] =>
[date_permission_received:protected] =>
[date_review_needed:protected] =>
[date_received:protected] => 02/15/12
[date_completed:protected] => 04/02/12
[date_billed:protected] =>
[date_modified:protected] => 05/23/23
[collBokExports:protected] =>
[lastBokExportCriteria:BaseElcoshItem:private] =>
[alreadyInSave:protected] =>
[alreadyInValidation:protected] =>
[validationFailures:protected] => Array
(
)
[_new:BaseObject:private] =>
[_deleted:BaseObject:private] =>
[modifiedColumns:protected] => Array
(
)
)
[3] => DocumentRecord Object
(
[records:protected] => Array
(
)
[recordId:protected] =>
[searchWordClass:protected] =>
[searchWordPeerClass:protected] =>
[bok_record:protected] =>
[authors:protected] =>
[organizations:protected] =>
[collections:protected] =>
[categories:protected] =>
[categories_initialized:protected] =>
[mapped_items:protected] =>
[content:protected] =>
[files:protected] =>
[language:protected] => Language Object
(
[id:protected] => 1
[code:protected] => en
[name:protected] => English
[alreadyInSave:protected] =>
[alreadyInValidation:protected] =>
[validationFailures:protected] => Array
(
)
[_new:BaseObject:private] =>
[_deleted:BaseObject:private] =>
[modifiedColumns:protected] => Array
(
)
)
[old_record:protected] =>
[id:protected] => 1654
[old_id:protected] => 1284
[elcosh_id:protected] => d001159
[type:protected] => document
[display_type:protected] => HTML w/ PDF
[user_id:protected] => 0
[language_id:protected] => 1
[tagging_id:protected] => Garber
[priority_id:protected] => 1
[title:protected] => Focus Four Toolbox Talks, Module 4 – Electrocutions, Talk #6 – Hazards on Disaster Sites
[total_pages:protected] => 1
[billed_pages:protected] => 1
[publication_number:protected] =>
[part_of:protected] =>
[keywords:protected] => powerlines, underground, utilities, generators, wet conditions, GFCIs, energized lines, disasters, emergency response
[comments:protected] =>
[summary:protected] => A toolbox talk on how to avoid electrocution on a disaster site. Includes questions to ask, an incident to discuss with images, and a place to record questions the trainer would like to ask about the incident. Part of a collection. Click on the 'collection' button to access the other items.
[transition_comments:protected] =>
[external_link:protected] =>
[consol_link:protected] => http://www.cpwrconstructionsolutions.org/electrical/hazard/1138/install-and-repair-high-voltage-lines-transformers-switches-electrical-shocks-burns-and-or-electrocution.html
[more_like_this:protected] => d000135,d000361,d000437
[permission_given_by:protected] =>
[published:protected] => T
[billable:protected] => F
[img_name:protected] =>
[img_ext:protected] =>
[img_width:protected] =>
[img_height:protected] =>
[img_credit:protected] =>
[img_practice:protected] =>
[vid_source_id:protected] =>
[vid_running_time:protected] =>
[vid_intended_audience:protected] =>
[vid_acquisition_info:protected] =>
[vid_cost:protected] =>
[vid_producer:protected] =>
[vid_filename:protected] =>
[vid_filename_downloadable:protected] =>
[date_summary:protected] =>
[date_permission_requested:protected] =>
[date_permission_received:protected] =>
[date_review_needed:protected] =>
[date_received:protected] => 02/15/12
[date_completed:protected] => 04/02/12
[date_billed:protected] =>
[date_modified:protected] => 05/23/23
[collBokExports:protected] =>
[lastBokExportCriteria:BaseElcoshItem:private] =>
[alreadyInSave:protected] =>
[alreadyInValidation:protected] =>
[validationFailures:protected] => Array
(
)
[_new:BaseObject:private] =>
[_deleted:BaseObject:private] =>
[modifiedColumns:protected] => Array
(
)
)
)
)
[collections] => Array
(
[1294] =>
[1295] =>
[1292] =>
[1293] => CollectionRecord Object
(
[collection_items:protected] =>
[records:protected] => Array
(
)
[recordId:protected] =>
[searchWordClass:protected] =>
[searchWordPeerClass:protected] =>
[bok_record:protected] =>
[authors:protected] =>
[organizations:protected] =>
[collections:protected] =>
[categories:protected] =>
[categories_initialized:protected] =>
[mapped_items:protected] =>
[content:protected] =>
[files:protected] =>
[language:protected] =>
[old_record:protected] =>
[id:protected] => 1293
[old_id:protected] =>
[elcosh_id:protected] => c000026
[type:protected] => collection
[display_type:protected] => Collection
[user_id:protected] =>
[language_id:protected] =>
[tagging_id:protected] =>
[priority_id:protected] =>
[title:protected] => Focus Four-Struck By
[total_pages:protected] =>
[billed_pages:protected] =>
[publication_number:protected] =>
[part_of:protected] =>
[keywords:protected] =>
[comments:protected] =>
[summary:protected] => The following are links to all of the items in this collection:
[transition_comments:protected] =>
[external_link:protected] =>
[consol_link:protected] =>
[more_like_this:protected] =>
[permission_given_by:protected] =>
[published:protected] => T
[billable:protected] => F
[img_name:protected] =>
[img_ext:protected] =>
[img_width:protected] =>
[img_height:protected] =>
[img_credit:protected] =>
[img_practice:protected] =>
[vid_source_id:protected] =>
[vid_running_time:protected] =>
[vid_intended_audience:protected] =>
[vid_acquisition_info:protected] =>
[vid_cost:protected] =>
[vid_producer:protected] =>
[vid_filename:protected] =>
[vid_filename_downloadable:protected] =>
[date_summary:protected] =>
[date_permission_requested:protected] =>
[date_permission_received:protected] =>
[date_review_needed:protected] =>
[date_received:protected] => 05/08/12
[date_completed:protected] => 05/08/12
[date_billed:protected] =>
[date_modified:protected] => 05/08/12
[collBokExports:protected] =>
[lastBokExportCriteria:BaseElcoshItem:private] =>
[alreadyInSave:protected] =>
[alreadyInValidation:protected] =>
[validationFailures:protected] => Array
(
)
[_new:BaseObject:private] =>
[_deleted:BaseObject:private] =>
[modifiedColumns:protected] => Array
(
)
)
)
[record] => DocumentRecord Object
(
[records:protected] => Array
(
)
[recordId:protected] =>
[searchWordClass:protected] =>
[searchWordPeerClass:protected] =>
[bok_record:protected] =>
[authors:protected] => Array
(
)
[organizations:protected] => Array
(
[256] => Organization Object
(
[id:protected] => 256
[elcosh_id:protected] => o000276
[user_id:protected] => 14
[province_id:protected] => 0
[country_id:protected] => 0
[title:protected] => IUOE National Training Fund
[address:protected] =>
[postal_code:protected] =>
[city:protected] =>
[department:protected] =>
[phone:protected] => 304-253-8674
[fax:protected] =>
[email:protected] =>
[website:protected] => http://www.iuoeiettc.org
[filename:protected] =>
[about:protected] =>
[comments:protected] =>
[logo_available:protected] => T
[no_details:protected] => F
[date_received:protected] => 2012-02-13
[date_completed:protected] => 2012-02-13
[date_billed:protected] =>
[alreadyInSave:protected] =>
[alreadyInValidation:protected] =>
[validationFailures:protected] => Array
(
)
[_new:BaseObject:private] =>
[_deleted:BaseObject:private] =>
[modifiedColumns:protected] => Array
(
)
)
)
[collections:protected] => Array
(
[1294] =>
[1295] =>
[1292] =>
[1293] => CollectionRecord Object
(
[collection_items:protected] =>
[records:protected] => Array
(
)
[recordId:protected] =>
[searchWordClass:protected] =>
[searchWordPeerClass:protected] =>
[bok_record:protected] =>
[authors:protected] =>
[organizations:protected] =>
[collections:protected] =>
[categories:protected] =>
[categories_initialized:protected] =>
[mapped_items:protected] =>
[content:protected] =>
[files:protected] =>
[language:protected] =>
[old_record:protected] =>
[id:protected] => 1293
[old_id:protected] =>
[elcosh_id:protected] => c000026
[type:protected] => collection
[display_type:protected] => Collection
[user_id:protected] =>
[language_id:protected] =>
[tagging_id:protected] =>
[priority_id:protected] =>
[title:protected] => Focus Four-Struck By
[total_pages:protected] =>
[billed_pages:protected] =>
[publication_number:protected] =>
[part_of:protected] =>
[keywords:protected] =>
[comments:protected] =>
[summary:protected] => The following are links to all of the items in this collection:
[transition_comments:protected] =>
[external_link:protected] =>
[consol_link:protected] =>
[more_like_this:protected] =>
[permission_given_by:protected] =>
[published:protected] => T
[billable:protected] => F
[img_name:protected] =>
[img_ext:protected] =>
[img_width:protected] =>
[img_height:protected] =>
[img_credit:protected] =>
[img_practice:protected] =>
[vid_source_id:protected] =>
[vid_running_time:protected] =>
[vid_intended_audience:protected] =>
[vid_acquisition_info:protected] =>
[vid_cost:protected] =>
[vid_producer:protected] =>
[vid_filename:protected] =>
[vid_filename_downloadable:protected] =>
[date_summary:protected] =>
[date_permission_requested:protected] =>
[date_permission_received:protected] =>
[date_review_needed:protected] =>
[date_received:protected] => 05/08/12
[date_completed:protected] => 05/08/12
[date_billed:protected] =>
[date_modified:protected] => 05/08/12
[collBokExports:protected] =>
[lastBokExportCriteria:BaseElcoshItem:private] =>
[alreadyInSave:protected] =>
[alreadyInValidation:protected] =>
[validationFailures:protected] => Array
(
)
[_new:BaseObject:private] =>
[_deleted:BaseObject:private] =>
[modifiedColumns:protected] => Array
(
)
)
)
[categories:protected] =>
[categories_initialized:protected] =>
[mapped_items:protected] => Array
(
[1605] => DocumentRecord Object
(
[records:protected] => Array
(
)
[recordId:protected] =>
[searchWordClass:protected] =>
[searchWordPeerClass:protected] =>
[bok_record:protected] =>
[authors:protected] =>
[organizations:protected] =>
[collections:protected] =>
[categories:protected] =>
[categories_initialized:protected] =>
[mapped_items:protected] =>
[content:protected] =>
[files:protected] =>
[language:protected] =>
[old_record:protected] =>
[id:protected] => 1605
[old_id:protected] => 1262
[elcosh_id:protected] => d001137
[type:protected] => document
[display_type:protected] => HTML w/ PDF
[user_id:protected] =>
[language_id:protected] => 1
[tagging_id:protected] => Garber
[priority_id:protected] => 1
[title:protected] => Focus Four Toolbox Talks, Module 1 – Falls, Talk #2 – Falls from debris piles?
[total_pages:protected] => 1
[billed_pages:protected] => 1
[publication_number:protected] =>
[part_of:protected] =>
[keywords:protected] => disaster response, hazard clean-up, uneven surface, disaster site, disaster clean-up
[comments:protected] =>
[summary:protected] => A toolbox talk on preventing falls from debris piles. Includes questions to ask, an incident to discuss with images, and a place to record questions the trainer would like to ask about the incident. Part of a collection. Click on the 'collection' button to access the other items.
[transition_comments:protected] =>
[external_link:protected] =>
[consol_link:protected] => http://www.cpwrconstructionsolutions.org/roofing/hazard/1463/install-asphalt-roofs-fall-from-heights.html
[more_like_this:protected] => a000081,d000478,d000530
[permission_given_by:protected] =>
[published:protected] => T
[billable:protected] => F
[img_name:protected] =>
[img_ext:protected] =>
[img_width:protected] =>
[img_height:protected] =>
[img_credit:protected] =>
[img_practice:protected] =>
[vid_source_id:protected] =>
[vid_running_time:protected] =>
[vid_intended_audience:protected] =>
[vid_acquisition_info:protected] =>
[vid_cost:protected] =>
[vid_producer:protected] =>
[vid_filename:protected] =>
[vid_filename_downloadable:protected] =>
[date_summary:protected] =>
[date_permission_requested:protected] =>
[date_permission_received:protected] =>
[date_review_needed:protected] =>
[date_received:protected] => 02/15/12
[date_completed:protected] => 03/19/12
[date_billed:protected] =>
[date_modified:protected] => 07/10/12
[collBokExports:protected] =>
[lastBokExportCriteria:BaseElcoshItem:private] =>
[alreadyInSave:protected] =>
[alreadyInValidation:protected] =>
[validationFailures:protected] => Array
(
)
[_new:BaseObject:private] =>
[_deleted:BaseObject:private] =>
[modifiedColumns:protected] => Array
(
)
)
[1610] => DocumentRecord Object
(
[records:protected] => Array
(
)
[recordId:protected] =>
[searchWordClass:protected] =>
[searchWordPeerClass:protected] =>
[bok_record:protected] =>
[authors:protected] =>
[organizations:protected] =>
[collections:protected] =>
[categories:protected] =>
[categories_initialized:protected] =>
[mapped_items:protected] =>
[content:protected] =>
[files:protected] =>
[language:protected] =>
[old_record:protected] =>
[id:protected] => 1610
[old_id:protected] => 1271
[elcosh_id:protected] => d001146
[type:protected] => document
[display_type:protected] => HTML w/ PDF
[user_id:protected] => 0
[language_id:protected] => 1
[tagging_id:protected] => Garber
[priority_id:protected] => 1
[title:protected] => Focus Four Toolbox Talks, Module 2 – Struck-by, Talk #5 – Rigging and Securing Loads
[total_pages:protected] => 1
[billed_pages:protected] => 1
[publication_number:protected] =>
[part_of:protected] =>
[keywords:protected] => rigging, lift loads, loading areas, chains
[comments:protected] =>
[summary:protected] => A toolbox talk on preventing struck-by incidents caused by not securing loads properly. Includes questions to ask, an incident to discuss with images, and a place to record questions the trainer would like to ask about the incident. Part of a collection. Click on the 'collection' button to access the other items.
[transition_comments:protected] =>
[external_link:protected] =>
[consol_link:protected] => http://www.cpwrconstructionsolutions.org/heavy_equipment/hazard/1591/move-equipment-to-from-and-between-sites-work-zone-struck-by-injuries-and-fatalities.html
[more_like_this:protected] => d000144,d000360,d000873
[permission_given_by:protected] =>
[published:protected] => T
[billable:protected] => F
[img_name:protected] =>
[img_ext:protected] =>
[img_width:protected] =>
[img_height:protected] =>
[img_credit:protected] =>
[img_practice:protected] =>
[vid_source_id:protected] =>
[vid_running_time:protected] =>
[vid_intended_audience:protected] =>
[vid_acquisition_info:protected] =>
[vid_cost:protected] =>
[vid_producer:protected] =>
[vid_filename:protected] =>
[vid_filename_downloadable:protected] =>
[date_summary:protected] =>
[date_permission_requested:protected] =>
[date_permission_received:protected] =>
[date_review_needed:protected] =>
[date_received:protected] => 02/15/12
[date_completed:protected] => 03/28/12
[date_billed:protected] =>
[date_modified:protected] => 05/12/14
[collBokExports:protected] =>
[lastBokExportCriteria:BaseElcoshItem:private] =>
[alreadyInSave:protected] =>
[alreadyInValidation:protected] =>
[validationFailures:protected] => Array
(
)
[_new:BaseObject:private] =>
[_deleted:BaseObject:private] =>
[modifiedColumns:protected] => Array
(
)
)
[1645] => DocumentRecord Object
(
[records:protected] => Array
(
)
[recordId:protected] =>
[searchWordClass:protected] =>
[searchWordPeerClass:protected] =>
[bok_record:protected] =>
[authors:protected] =>
[organizations:protected] =>
[collections:protected] =>
[categories:protected] =>
[categories_initialized:protected] =>
[mapped_items:protected] =>
[content:protected] =>
[files:protected] =>
[language:protected] =>
[old_record:protected] =>
[id:protected] => 1645
[old_id:protected] => 1274
[elcosh_id:protected] => d001149
[type:protected] => document
[display_type:protected] => HTML w/ PDF
[user_id:protected] => 0
[language_id:protected] => 1
[tagging_id:protected] => Garber
[priority_id:protected] => 1
[title:protected] => Focus Four Toolbox Talks, Module 3 – Caught-in/between, Talk #2 – Trenches & Heavy Equipment
[total_pages:protected] => 1
[billed_pages:protected] => 1
[publication_number:protected] =>
[part_of:protected] =>
[keywords:protected] => back-up alarms, spotter, soil cave-in, spoil pikes, ROPs, trenching, rain
[comments:protected] =>
[summary:protected] => A toolbox talk on preventing incidents involving trenches such as trench collapse. Includes questions to ask, an incident to discuss with images, and a place to record questions the trainer would like to ask about the incident. Part of a collection. Click on the 'collection' button to access the other items.
[transition_comments:protected] =>
[external_link:protected] =>
[consol_link:protected] =>
[more_like_this:protected] => d000019,d000035,d000168
[permission_given_by:protected] =>
[published:protected] => T
[billable:protected] => F
[img_name:protected] =>
[img_ext:protected] =>
[img_width:protected] =>
[img_height:protected] =>
[img_credit:protected] =>
[img_practice:protected] =>
[vid_source_id:protected] =>
[vid_running_time:protected] =>
[vid_intended_audience:protected] =>
[vid_acquisition_info:protected] =>
[vid_cost:protected] =>
[vid_producer:protected] =>
[vid_filename:protected] =>
[vid_filename_downloadable:protected] =>
[date_summary:protected] =>
[date_permission_requested:protected] =>
[date_permission_received:protected] =>
[date_review_needed:protected] =>
[date_received:protected] => 02/15/12
[date_completed:protected] => 04/02/12
[date_billed:protected] =>
[date_modified:protected] => 05/23/23
[collBokExports:protected] =>
[lastBokExportCriteria:BaseElcoshItem:private] =>
[alreadyInSave:protected] =>
[alreadyInValidation:protected] =>
[validationFailures:protected] => Array
(
)
[_new:BaseObject:private] =>
[_deleted:BaseObject:private] =>
[modifiedColumns:protected] => Array
(
)
)
[1654] => DocumentRecord Object
(
[records:protected] => Array
(
)
[recordId:protected] =>
[searchWordClass:protected] =>
[searchWordPeerClass:protected] =>
[bok_record:protected] =>
[authors:protected] =>
[organizations:protected] =>
[collections:protected] =>
[categories:protected] =>
[categories_initialized:protected] =>
[mapped_items:protected] =>
[content:protected] =>
[files:protected] =>
[language:protected] =>
[old_record:protected] =>
[id:protected] => 1654
[old_id:protected] => 1284
[elcosh_id:protected] => d001159
[type:protected] => document
[display_type:protected] => HTML w/ PDF
[user_id:protected] => 0
[language_id:protected] => 1
[tagging_id:protected] => Garber
[priority_id:protected] => 1
[title:protected] => Focus Four Toolbox Talks, Module 4 – Electrocutions, Talk #6 – Hazards on Disaster Sites
[total_pages:protected] => 1
[billed_pages:protected] => 1
[publication_number:protected] =>
[part_of:protected] =>
[keywords:protected] => powerlines, underground, utilities, generators, wet conditions, GFCIs, energized lines, disasters, emergency response
[comments:protected] =>
[summary:protected] => A toolbox talk on how to avoid electrocution on a disaster site. Includes questions to ask, an incident to discuss with images, and a place to record questions the trainer would like to ask about the incident. Part of a collection. Click on the 'collection' button to access the other items.
[transition_comments:protected] =>
[external_link:protected] =>
[consol_link:protected] => http://www.cpwrconstructionsolutions.org/electrical/hazard/1138/install-and-repair-high-voltage-lines-transformers-switches-electrical-shocks-burns-and-or-electrocution.html
[more_like_this:protected] => d000135,d000361,d000437
[permission_given_by:protected] =>
[published:protected] => T
[billable:protected] => F
[img_name:protected] =>
[img_ext:protected] =>
[img_width:protected] =>
[img_height:protected] =>
[img_credit:protected] =>
[img_practice:protected] =>
[vid_source_id:protected] =>
[vid_running_time:protected] =>
[vid_intended_audience:protected] =>
[vid_acquisition_info:protected] =>
[vid_cost:protected] =>
[vid_producer:protected] =>
[vid_filename:protected] =>
[vid_filename_downloadable:protected] =>
[date_summary:protected] =>
[date_permission_requested:protected] =>
[date_permission_received:protected] =>
[date_review_needed:protected] =>
[date_received:protected] => 02/15/12
[date_completed:protected] => 04/02/12
[date_billed:protected] =>
[date_modified:protected] => 05/23/23
[collBokExports:protected] =>
[lastBokExportCriteria:BaseElcoshItem:private] =>
[alreadyInSave:protected] =>
[alreadyInValidation:protected] =>
[validationFailures:protected] => Array
(
)
[_new:BaseObject:private] =>
[_deleted:BaseObject:private] =>
[modifiedColumns:protected] => Array
(
)
)
)
[content:protected] =>
[files:protected] => Array
(
[9400] => File Object
(
[id:protected] => 9400
[filename:protected] => 1.jpg
[downloadable:protected] => F
[timestamp:protected] => 2014-05-08 15:05:37
[alreadyInSave:protected] =>
[alreadyInValidation:protected] =>
[validationFailures:protected] => Array
(
)
[_new:BaseObject:private] =>
[_deleted:BaseObject:private] =>
[modifiedColumns:protected] => Array
(
)
)
[9401] => File Object
(
[id:protected] => 9401
[filename:protected] => d001298.pdf
[downloadable:protected] => T
[timestamp:protected] => 2014-05-08 15:05:37
[alreadyInSave:protected] =>
[alreadyInValidation:protected] =>
[validationFailures:protected] => Array
(
)
[_new:BaseObject:private] =>
[_deleted:BaseObject:private] =>
[modifiedColumns:protected] => Array
(
)
)
)
[language:protected] => Language Object
(
[id:protected] => 1
[code:protected] => en
[name:protected] => English
[alreadyInSave:protected] =>
[alreadyInValidation:protected] =>
[validationFailures:protected] => Array
(
)
[_new:BaseObject:private] =>
[_deleted:BaseObject:private] =>
[modifiedColumns:protected] => Array
(
)
)
[old_record:protected] =>
[id:protected] => 3827
[old_id:protected] =>
[elcosh_id:protected] => d001298
[type:protected] => document
[display_type:protected] => HTML w/ PDF
[user_id:protected] => 23
[language_id:protected] => 1
[tagging_id:protected] => Bruce Lippy
[priority_id:protected] => 1
[title:protected] => Getting the most out of the IUOE Toolbox Talks
[total_pages:protected] => 2
[billed_pages:protected] => 2
[publication_number:protected] =>
[part_of:protected] =>
[keywords:protected] => toolbox talks, tailgate talks
[comments:protected] =>
[summary:protected] => Toolbox talks have been the main tool for communicating safety information on construction jobs for decades.
Unfortunately, there has been little research on what makes for effective toolbox talks. The IUOE National
Training Fund worked with OSHA and NIOSH to make sure their series of 24 Focus Four toolbox talks were based on the best recommendations for effective design. These toolbox talks accompany an entire package of training materials, but can be used alone. This guide points out the key features of these toolbox talks and how best to deliver them.
[transition_comments:protected] =>
[external_link:protected] =>
[consol_link:protected] =>
[more_like_this:protected] => d001137,d001146,d001149,d001159
[permission_given_by:protected] => IUOE National Hazmat Program
[published:protected] => T
[billable:protected] => F
[img_name:protected] =>
[img_ext:protected] => png
[img_width:protected] =>
[img_height:protected] =>
[img_credit:protected] =>
[img_practice:protected] =>
[vid_source_id:protected] =>
[vid_running_time:protected] =>
[vid_intended_audience:protected] =>
[vid_acquisition_info:protected] =>
[vid_cost:protected] =>
[vid_producer:protected] =>
[vid_filename:protected] =>
[vid_filename_downloadable:protected] =>
[date_summary:protected] => 2007
[date_permission_requested:protected] =>
[date_permission_received:protected] =>
[date_review_needed:protected] =>
[date_received:protected] => 05/08/14
[date_completed:protected] => 05/08/14
[date_billed:protected] =>
[date_modified:protected] => 05/08/14
[collBokExports:protected] =>
[lastBokExportCriteria:BaseElcoshItem:private] =>
[alreadyInSave:protected] =>
[alreadyInValidation:protected] =>
[validationFailures:protected] => Array
(
)
[_new:BaseObject:private] =>
[_deleted:BaseObject:private] =>
[modifiedColumns:protected] => Array
(
)
)
[show_text] =>
[document_content] => ElcoshItemDocumentContent Object
(
[id:protected] => 2896
[item_id:protected] => 3827
[type:protected] => main
[title:protected] =>
[content:protected] =>
Why were these talks developed?
Toolbox talks have been the main tool for communicating safety information on construction jobs for decades. Unfortunately, there has been almost no research on what makes for effective toolbox talks. The IUOE National Training Fund has worked with OSHA, the National Institute for Occupational Safety and Health and the Lippy Group, LLC to make sure these Focus Four toolbox talks are based on the latest fi ndings on the most effective design and tailored to the hazards operating engineers face daily. These toolbox talks accompany an entire package of training materials, but can be used alone. The way these are delivered is as important as how well they are designed.
What did NIOSH find out?
- Just handing out factsheets and toolbox talks to workers doesn’t work. Providing copies after toolbox talks doesn’t make much of an impact either.
- Using case studies (real life stories of accidents that ended in fatality or injury) in toolbox talks is effective.
- When toolbox talks containing case studies were accompanied by discussion questions to encourage group participation, they were more effective. Consequently, getting the workers to participate in the discussion about the case study is important. It’s not enough to tell the story, it is better to have the workers engage in problem solving that analyzes why the accident occurred and how it could have been prevented. Active learning is always better than passive.
How should you deliver these toolbox talks?
- Choose a topic that is related to work going on at the site.
- Hold the meeting on the job, preferably where everyone can sit and relax.
- Hold the meeting at the beginning of a shift or after a break. Folks are too tired at the end of a shift to carefully listen and they want to get home.
- Read the toolbox talk sheet on the topic prior to conducting the talk.
- Start at the top of the form and work right through to the end, which should take around 10 to 15 minutes. Guidance is provided in blue print to help you with each section.
- Use the questions provided to generate discussions. Always allow time for the crew to respond to your questions before you provide an answer. Some suggested responses are written in italics.
- Review the case study and emphasize that this was a real incident. Ask the crew for a case study before you review the one provided, however.
- Always end with a discussion of the particular worksite where you are conducting the talk. Tie the talk as closely to hazards on the site as possible and encourage the crew to constantly look for and immediately correct hazards. They should also know how to report any problems that can’t be immediately corrected.
- Provide copies to each person, if you like, but NIOSH has not found that to be particularly effective.
- Encourage workers to do similar talks on their sites and provide them with the IUOE phone number for ordering in bulk.
- Have everyone sign the back of the form to indicate they attended this session and point out it is a pledge to look out for the health and safety of everyone on the site.
What are the key features of these toolbox talks?

[content_transformed:protected] =>
Why were these talks developed?
Toolbox talks have been the main tool for communicating safety information on construction jobs for decades. Unfortunately, there has been almost no research on what makes for effective toolbox talks. The IUOE National Training Fund has worked with OSHA, the National Institute for Occupational Safety and Health and the Lippy Group, LLC to make sure these Focus Four toolbox talks are based on the latest fi ndings on the most effective design and tailored to the hazards operating engineers face daily. These toolbox talks accompany an entire package of training materials, but can be used alone. The way these are delivered is as important as how well they are designed.
What did NIOSH find out?
- Just handing out factsheets and toolbox talks to workers doesn’t work. Providing copies after toolbox talks doesn’t make much of an impact either.
- Using case studies (real life stories of accidents that ended in fatality or injury) in toolbox talks is effective.
- When toolbox talks containing case studies were accompanied by discussion questions to encourage group participation, they were more effective. Consequently, getting the workers to participate in the discussion about the case study is important. It’s not enough to tell the story, it is better to have the workers engage in problem solving that analyzes why the accident occurred and how it could have been prevented. Active learning is always better than passive.
How should you deliver these toolbox talks?
- Choose a topic that is related to work going on at the site.
- Hold the meeting on the job, preferably where everyone can sit and relax.
- Hold the meeting at the beginning of a shift or after a break. Folks are too tired at the end of a shift to carefully listen and they want to get home.
- Read the toolbox talk sheet on the topic prior to conducting the talk.
- Start at the top of the form and work right through to the end, which should take around 10 to 15 minutes. Guidance is provided in blue print to help you with each section.
- Use the questions provided to generate discussions. Always allow time for the crew to respond to your questions before you provide an answer. Some suggested responses are written in italics.
- Review the case study and emphasize that this was a real incident. Ask the crew for a case study before you review the one provided, however.
- Always end with a discussion of the particular worksite where you are conducting the talk. Tie the talk as closely to hazards on the site as possible and encourage the crew to constantly look for and immediately correct hazards. They should also know how to report any problems that can’t be immediately corrected.
- Provide copies to each person, if you like, but NIOSH has not found that to be particularly effective.
- Encourage workers to do similar talks on their sites and provide them with the IUOE phone number for ordering in bulk.
- Have everyone sign the back of the form to indicate they attended this session and point out it is a pledge to look out for the health and safety of everyone on the site.
What are the key features of these toolbox talks?
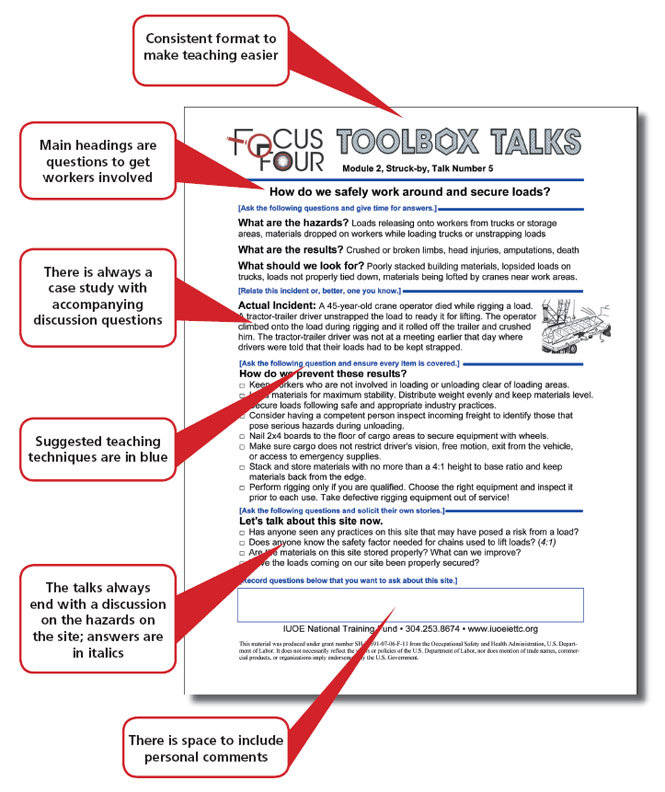
[disclaimer:protected] =>
[disclaimer_transformed:protected] =>
[alreadyInSave:protected] =>
[alreadyInValidation:protected] =>
[validationFailures:protected] => Array
(
)
[_new:BaseObject:private] =>
[_deleted:BaseObject:private] =>
[modifiedColumns:protected] => Array
(
)
)
[template] => record
)
[_globalContext:PHPTAL_Context:private] => stdClass Object
(
)
[_echoDeclarations:PHPTAL_Context:private] =>
[referer] => http://www.elcosh.org/document/3827/d001298/Getting%2Bthe%2Bmost%2Bout%2Bof%2Bthe%2BIUOE%2BToolbox%2BTalks.html
[curr_module] => Record
[styles] => Array
(
)
[javascript] => Array
(
[0] => jquery.min.js
)
[metas] => Array
(
[language] => en
[robots] => index, follow
)
[user] =>
[curr_url] => https://www.elcosh.org/index.php?module=Record&id=3827&type=document
[base_url] => https://www.elcosh.org/index.php?module=Record
[title] => eLCOSH : Getting the most out of the IUOE Toolbox Talks
[language] => en
[search_query] =>
[module] => Record
[new_records] => Array
(
[0] => Search_Result Object
(
[title] => Toolbox Talk: Fixed Ladder
[image] => /record/images/notavailable-p.png
[blurb] => The CPWR Toolbox Talk on Fixed Ladders addresses the potential risks associated with using fixed ladders. The resource includes a brief case example,...
[category] => Array
(
[0] => 15
[1] => 47
[2] => 49
[3] => 51
[4] => 53
[5] => 55
[6] => 60
[7] => 64
[8] => 73
[9] => 76
[10] => 78
[11] => 80
[12] => 86
[13] => 87
[14] => 90
[15] => 92
[16] => 93
[17] => 94
[18] => 100
)
[labels] => Array
(
[0] => Falls
[1] => Work Environment
[2] => Hazards
[3] => Bricklayer
[4] => Trades
[5] => Carpenter
[7] => Cement Mason
[9] => Concrete Polisher
[11] => Electrical Worker
[13] => HVAC
[15] => Laborer
[17] => PCC/Restoration
[19] => Plumber/Pipefitter
[21] => Roofer/Waterproofer
[23] => Sheetmetal Worker
[25] => Welder
[27] => Commercial & Institutional
[28] => Jobsites
[29] => Industrial
[31] => LEED/Green Construction
[33] => Renovations
[35] => Residential
[37] => Toolbox Talks
[38] => Documents
[39] => Media & Documents
)
[type] => Toolbox Talks
[sub_category] =>
[url] => /document/4430/d001660/Toolbox%2BTalk%253A%2BFixed%2BLadder.html
[item:protected] => DocumentRecord Object
(
[records:protected] => Array
(
)
[recordId:protected] =>
[searchWordClass:protected] =>
[searchWordPeerClass:protected] =>
[bok_record:protected] =>
[authors:protected] =>
[organizations:protected] =>
[collections:protected] =>
[categories:protected] => Array
(
[15] => Category Object
(
[languages:protected] =>
[bok_resources:protected] =>
[bok_topics:protected] =>
[bok_keywords:protected] =>
[id:protected] => 15
[type:protected] => category
[parent:protected] => 7
[label:protected] => Falls
[alreadyInSave:protected] =>
[alreadyInValidation:protected] =>
[validationFailures:protected] => Array
(
)
[_new:BaseObject:private] =>
[_deleted:BaseObject:private] =>
[modifiedColumns:protected] => Array
(
)
)
[47] => Category Object
(
[languages:protected] =>
[bok_resources:protected] =>
[bok_topics:protected] =>
[bok_keywords:protected] =>
[id:protected] => 47
[type:protected] => category
[parent:protected] => 2
[label:protected] => Bricklayer
[alreadyInSave:protected] =>
[alreadyInValidation:protected] =>
[validationFailures:protected] => Array
(
)
[_new:BaseObject:private] =>
[_deleted:BaseObject:private] =>
[modifiedColumns:protected] => Array
(
)
)
[49] => Category Object
(
[languages:protected] =>
[bok_resources:protected] =>
[bok_topics:protected] =>
[bok_keywords:protected] =>
[id:protected] => 49
[type:protected] => category
[parent:protected] => 2
[label:protected] => Carpenter
[alreadyInSave:protected] =>
[alreadyInValidation:protected] =>
[validationFailures:protected] => Array
(
)
[_new:BaseObject:private] =>
[_deleted:BaseObject:private] =>
[modifiedColumns:protected] => Array
(
)
)
[51] => Category Object
(
[languages:protected] =>
[bok_resources:protected] =>
[bok_topics:protected] =>
[bok_keywords:protected] =>
[id:protected] => 51
[type:protected] => category
[parent:protected] => 2
[label:protected] => Cement Mason
[alreadyInSave:protected] =>
[alreadyInValidation:protected] =>
[validationFailures:protected] => Array
(
)
[_new:BaseObject:private] =>
[_deleted:BaseObject:private] =>
[modifiedColumns:protected] => Array
(
)
)
[53] => Category Object
(
[languages:protected] =>
[bok_resources:protected] =>
[bok_topics:protected] =>
[bok_keywords:protected] =>
[id:protected] => 53
[type:protected] => category
[parent:protected] => 2
[label:protected] => Concrete Polisher
[alreadyInSave:protected] =>
[alreadyInValidation:protected] =>
[validationFailures:protected] => Array
(
)
[_new:BaseObject:private] =>
[_deleted:BaseObject:private] =>
[modifiedColumns:protected] => Array
(
)
)
[55] => Category Object
(
[languages:protected] =>
[bok_resources:protected] =>
[bok_topics:protected] =>
[bok_keywords:protected] =>
[id:protected] => 55
[type:protected] => category
[parent:protected] => 2
[label:protected] => Electrical Worker
[alreadyInSave:protected] =>
[alreadyInValidation:protected] =>
[validationFailures:protected] => Array
(
)
[_new:BaseObject:private] =>
[_deleted:BaseObject:private] =>
[modifiedColumns:protected] => Array
(
)
)
[60] => Category Object
(
[languages:protected] =>
[bok_resources:protected] =>
[bok_topics:protected] =>
[bok_keywords:protected] =>
[id:protected] => 60
[type:protected] => category
[parent:protected] => 2
[label:protected] => HVAC
[alreadyInSave:protected] =>
[alreadyInValidation:protected] =>
[validationFailures:protected] => Array
(
)
[_new:BaseObject:private] =>
[_deleted:BaseObject:private] =>
[modifiedColumns:protected] => Array
(
)
)
[64] => Category Object
(
[languages:protected] =>
[bok_resources:protected] =>
[bok_topics:protected] =>
[bok_keywords:protected] =>
[id:protected] => 64
[type:protected] => category
[parent:protected] => 2
[label:protected] => Laborer
[alreadyInSave:protected] =>
[alreadyInValidation:protected] =>
[validationFailures:protected] => Array
(
)
[_new:BaseObject:private] =>
[_deleted:BaseObject:private] =>
[modifiedColumns:protected] => Array
(
)
)
[73] => Category Object
(
[languages:protected] =>
[bok_resources:protected] =>
[bok_topics:protected] =>
[bok_keywords:protected] =>
[id:protected] => 73
[type:protected] => category
[parent:protected] => 2
[label:protected] => PCC/Restoration
[alreadyInSave:protected] =>
[alreadyInValidation:protected] =>
[validationFailures:protected] => Array
(
)
[_new:BaseObject:private] =>
[_deleted:BaseObject:private] =>
[modifiedColumns:protected] => Array
(
)
)
[76] => Category Object
(
[languages:protected] =>
[bok_resources:protected] =>
[bok_topics:protected] =>
[bok_keywords:protected] =>
[id:protected] => 76
[type:protected] => category
[parent:protected] => 2
[label:protected] => Plumber/Pipefitter
[alreadyInSave:protected] =>
[alreadyInValidation:protected] =>
[validationFailures:protected] => Array
(
)
[_new:BaseObject:private] =>
[_deleted:BaseObject:private] =>
[modifiedColumns:protected] => Array
(
)
)
[78] => Category Object
(
[languages:protected] =>
[bok_resources:protected] =>
[bok_topics:protected] =>
[bok_keywords:protected] =>
[id:protected] => 78
[type:protected] => category
[parent:protected] => 2
[label:protected] => Roofer/Waterproofer
[alreadyInSave:protected] =>
[alreadyInValidation:protected] =>
[validationFailures:protected] => Array
(
)
[_new:BaseObject:private] =>
[_deleted:BaseObject:private] =>
[modifiedColumns:protected] => Array
(
)
)
[80] => Category Object
(
[languages:protected] =>
[bok_resources:protected] =>
[bok_topics:protected] =>
[bok_keywords:protected] =>
[id:protected] => 80
[type:protected] => category
[parent:protected] => 2
[label:protected] => Sheetmetal Worker
[alreadyInSave:protected] =>
[alreadyInValidation:protected] =>
[validationFailures:protected] => Array
(
)
[_new:BaseObject:private] =>
[_deleted:BaseObject:private] =>
[modifiedColumns:protected] => Array
(
)
)
[86] => Category Object
(
[languages:protected] =>
[bok_resources:protected] =>
[bok_topics:protected] =>
[bok_keywords:protected] =>
[id:protected] => 86
[type:protected] => category
[parent:protected] => 2
[label:protected] => Welder
[alreadyInSave:protected] =>
[alreadyInValidation:protected] =>
[validationFailures:protected] => Array
(
)
[_new:BaseObject:private] =>
[_deleted:BaseObject:private] =>
[modifiedColumns:protected] => Array
(
)
)
[87] => Category Object
(
[languages:protected] =>
[bok_resources:protected] =>
[bok_topics:protected] =>
[bok_keywords:protected] =>
[id:protected] => 87
[type:protected] => category
[parent:protected] => 3
[label:protected] => Commercial & Institutional
[alreadyInSave:protected] =>
[alreadyInValidation:protected] =>
[validationFailures:protected] => Array
(
)
[_new:BaseObject:private] =>
[_deleted:BaseObject:private] =>
[modifiedColumns:protected] => Array
(
)
)
[90] => Category Object
(
[languages:protected] =>
[bok_resources:protected] =>
[bok_topics:protected] =>
[bok_keywords:protected] =>
[id:protected] => 90
[type:protected] => category
[parent:protected] => 3
[label:protected] => Industrial
[alreadyInSave:protected] =>
[alreadyInValidation:protected] =>
[validationFailures:protected] => Array
(
)
[_new:BaseObject:private] =>
[_deleted:BaseObject:private] =>
[modifiedColumns:protected] => Array
(
)
)
[92] => Category Object
(
[languages:protected] =>
[bok_resources:protected] =>
[bok_topics:protected] =>
[bok_keywords:protected] =>
[id:protected] => 92
[type:protected] => category
[parent:protected] => 3
[label:protected] => LEED/Green Construction
[alreadyInSave:protected] =>
[alreadyInValidation:protected] =>
[validationFailures:protected] => Array
(
)
[_new:BaseObject:private] =>
[_deleted:BaseObject:private] =>
[modifiedColumns:protected] => Array
(
)
)
[93] => Category Object
(
[languages:protected] =>
[bok_resources:protected] =>
[bok_topics:protected] =>
[bok_keywords:protected] =>
[id:protected] => 93
[type:protected] => category
[parent:protected] => 3
[label:protected] => Renovations
[alreadyInSave:protected] =>
[alreadyInValidation:protected] =>
[validationFailures:protected] => Array
(
)
[_new:BaseObject:private] =>
[_deleted:BaseObject:private] =>
[modifiedColumns:protected] => Array
(
)
)
[94] => Category Object
(
[languages:protected] =>
[bok_resources:protected] =>
[bok_topics:protected] =>
[bok_keywords:protected] =>
[id:protected] => 94
[type:protected] => category
[parent:protected] => 3
[label:protected] => Residential
[alreadyInSave:protected] =>
[alreadyInValidation:protected] =>
[validationFailures:protected] => Array
(
)
[_new:BaseObject:private] =>
[_deleted:BaseObject:private] =>
[modifiedColumns:protected] => Array
(
)
)
[100] => Category Object
(
[languages:protected] =>
[bok_resources:protected] =>
[bok_topics:protected] =>
[bok_keywords:protected] =>
[id:protected] => 100
[type:protected] => category
[parent:protected] => 6
[label:protected] => Toolbox Talks
[alreadyInSave:protected] =>
[alreadyInValidation:protected] =>
[validationFailures:protected] => Array
(
)
[_new:BaseObject:private] =>
[_deleted:BaseObject:private] =>
[modifiedColumns:protected] => Array
(
)
)
)
[categories_initialized:protected] => 1
[mapped_items:protected] =>
[content:protected] =>
[files:protected] =>
[language:protected] => Language Object
(
[id:protected] => 1
[code:protected] => en
[name:protected] => English
[alreadyInSave:protected] =>
[alreadyInValidation:protected] =>
[validationFailures:protected] => Array
(
)
[_new:BaseObject:private] =>
[_deleted:BaseObject:private] =>
[modifiedColumns:protected] => Array
(
)
)
[old_record:protected] =>
[id:protected] => 4430
[old_id:protected] =>
[elcosh_id:protected] => d001660
[type:protected] => document
[display_type:protected] => HTML only (and links)
[user_id:protected] => 0
[language_id:protected] => 1
[tagging_id:protected] => Mike Aguilar
[priority_id:protected] => 1
[title:protected] => Toolbox Talk: Fixed Ladder
[total_pages:protected] => 0
[billed_pages:protected] => 0
[publication_number:protected] =>
[part_of:protected] =>
[keywords:protected] => Fixed Ladders, Fall Prevention, Falls
[comments:protected] =>
[summary:protected] => The CPWR Toolbox Talk on Fixed Ladders addresses the potential risks associated with using fixed ladders. The resource includes a brief case example, steps to prevent a related injury and questions for discussion. It includes an image that illustrates the hazard, which can be posted in a central location as a reminder of steps to work safely.
Available in
English
and
Spanish.
[transition_comments:protected] =>
[external_link:protected] =>
[consol_link:protected] =>
[more_like_this:protected] => d001257,d001254,d001255,d001256,d001258,d001262,d001279
[permission_given_by:protected] =>
[published:protected] => T
[billable:protected] => F
[img_name:protected] =>
[img_ext:protected] =>
[img_width:protected] =>
[img_height:protected] =>
[img_credit:protected] =>
[img_practice:protected] =>
[vid_source_id:protected] =>
[vid_running_time:protected] =>
[vid_intended_audience:protected] =>
[vid_acquisition_info:protected] =>
[vid_cost:protected] =>
[vid_producer:protected] =>
[vid_filename:protected] =>
[vid_filename_downloadable:protected] =>
[date_summary:protected] =>
[date_permission_requested:protected] =>
[date_permission_received:protected] =>
[date_review_needed:protected] =>
[date_received:protected] => 06/10/22
[date_completed:protected] => 06/10/22
[date_billed:protected] =>
[date_modified:protected] => 05/22/23
[collBokExports:protected] =>
[lastBokExportCriteria:BaseElcoshItem:private] =>
[alreadyInSave:protected] =>
[alreadyInValidation:protected] =>
[validationFailures:protected] => Array
(
)
[_new:BaseObject:private] =>
[_deleted:BaseObject:private] =>
[modifiedColumns:protected] => Array
(
)
)
)
[1] => Search_Result Object
(
[title] => Toolbox Talk: Challenges Preventing Falling Objects
[image] => /record/images/notavailable-p.png
[blurb] => The CPWR Toolbox Talk on Challenges Preventing Falling Objects addresses the hazards of being struck by falling objects on the job site. The resource...
[category] => Array
(
[0] => 12
[1] => 47
[2] => 49
[3] => 51
[4] => 55
[5] => 64
[6] => 68
[7] => 71
[8] => 75
[9] => 78
[10] => 79
[11] => 82
[12] => 62
[13] => 86
[14] => 87
[15] => 88
[16] => 89
[17] => 91
[18] => 90
[19] => 92
[20] => 93
[21] => 94
[22] => 95
[23] => 100
)
[labels] => Array
(
[0] => Crushed/Struck By
[1] => Work Environment
[2] => Hazards
[3] => Bricklayer
[4] => Trades
[5] => Carpenter
[7] => Cement Mason
[9] => Electrical Worker
[11] => Laborer
[13] => Maintenance Worker
[15] => Painter
[17] => Plasterer
[19] => Roofer/Waterproofer
[21] => Scaffold Erector
[23] => Stonemason
[25] => Structural Ironworker
[27] => Welder
[29] => Commercial & Institutional
[30] => Jobsites
[31] => Demolition
[33] => Disasters
[35] => Heavy & Highway
[37] => Industrial
[39] => LEED/Green Construction
[41] => Renovations
[43] => Residential
[45] => Underground
[47] => Toolbox Talks
[48] => Documents
[49] => Media & Documents
)
[type] => Toolbox Talks
[sub_category] =>
[url] => /document/4431/d001661/Toolbox%2BTalk%253A%2BChallenges%2BPreventing%2BFalling%2BObjects.html
[item:protected] => DocumentRecord Object
(
[records:protected] => Array
(
)
[recordId:protected] =>
[searchWordClass:protected] =>
[searchWordPeerClass:protected] =>
[bok_record:protected] =>
[authors:protected] =>
[organizations:protected] =>
[collections:protected] =>
[categories:protected] => Array
(
[12] => Category Object
(
[languages:protected] =>
[bok_resources:protected] =>
[bok_topics:protected] =>
[bok_keywords:protected] =>
[id:protected] => 12
[type:protected] => category
[parent:protected] => 7
[label:protected] => Crushed/Struck By
[alreadyInSave:protected] =>
[alreadyInValidation:protected] =>
[validationFailures:protected] => Array
(
)
[_new:BaseObject:private] =>
[_deleted:BaseObject:private] =>
[modifiedColumns:protected] => Array
(
)
)
[47] => Category Object
(
[languages:protected] =>
[bok_resources:protected] =>
[bok_topics:protected] =>
[bok_keywords:protected] =>
[id:protected] => 47
[type:protected] => category
[parent:protected] => 2
[label:protected] => Bricklayer
[alreadyInSave:protected] =>
[alreadyInValidation:protected] =>
[validationFailures:protected] => Array
(
)
[_new:BaseObject:private] =>
[_deleted:BaseObject:private] =>
[modifiedColumns:protected] => Array
(
)
)
[49] => Category Object
(
[languages:protected] =>
[bok_resources:protected] =>
[bok_topics:protected] =>
[bok_keywords:protected] =>
[id:protected] => 49
[type:protected] => category
[parent:protected] => 2
[label:protected] => Carpenter
[alreadyInSave:protected] =>
[alreadyInValidation:protected] =>
[validationFailures:protected] => Array
(
)
[_new:BaseObject:private] =>
[_deleted:BaseObject:private] =>
[modifiedColumns:protected] => Array
(
)
)
[51] => Category Object
(
[languages:protected] =>
[bok_resources:protected] =>
[bok_topics:protected] =>
[bok_keywords:protected] =>
[id:protected] => 51
[type:protected] => category
[parent:protected] => 2
[label:protected] => Cement Mason
[alreadyInSave:protected] =>
[alreadyInValidation:protected] =>
[validationFailures:protected] => Array
(
)
[_new:BaseObject:private] =>
[_deleted:BaseObject:private] =>
[modifiedColumns:protected] => Array
(
)
)
[55] => Category Object
(
[languages:protected] =>
[bok_resources:protected] =>
[bok_topics:protected] =>
[bok_keywords:protected] =>
[id:protected] => 55
[type:protected] => category
[parent:protected] => 2
[label:protected] => Electrical Worker
[alreadyInSave:protected] =>
[alreadyInValidation:protected] =>
[validationFailures:protected] => Array
(
)
[_new:BaseObject:private] =>
[_deleted:BaseObject:private] =>
[modifiedColumns:protected] => Array
(
)
)
[64] => Category Object
(
[languages:protected] =>
[bok_resources:protected] =>
[bok_topics:protected] =>
[bok_keywords:protected] =>
[id:protected] => 64
[type:protected] => category
[parent:protected] => 2
[label:protected] => Laborer
[alreadyInSave:protected] =>
[alreadyInValidation:protected] =>
[validationFailures:protected] => Array
(
)
[_new:BaseObject:private] =>
[_deleted:BaseObject:private] =>
[modifiedColumns:protected] => Array
(
)
)
[68] => Category Object
(
[languages:protected] =>
[bok_resources:protected] =>
[bok_topics:protected] =>
[bok_keywords:protected] =>
[id:protected] => 68
[type:protected] => category
[parent:protected] => 2
[label:protected] => Maintenance Worker
[alreadyInSave:protected] =>
[alreadyInValidation:protected] =>
[validationFailures:protected] => Array
(
)
[_new:BaseObject:private] =>
[_deleted:BaseObject:private] =>
[modifiedColumns:protected] => Array
(
)
)
[71] => Category Object
(
[languages:protected] =>
[bok_resources:protected] =>
[bok_topics:protected] =>
[bok_keywords:protected] =>
[id:protected] => 71
[type:protected] => category
[parent:protected] => 2
[label:protected] => Painter
[alreadyInSave:protected] =>
[alreadyInValidation:protected] =>
[validationFailures:protected] => Array
(
)
[_new:BaseObject:private] =>
[_deleted:BaseObject:private] =>
[modifiedColumns:protected] => Array
(
)
)
[75] => Category Object
(
[languages:protected] =>
[bok_resources:protected] =>
[bok_topics:protected] =>
[bok_keywords:protected] =>
[id:protected] => 75
[type:protected] => category
[parent:protected] => 2
[label:protected] => Plasterer
[alreadyInSave:protected] =>
[alreadyInValidation:protected] =>
[validationFailures:protected] => Array
(
)
[_new:BaseObject:private] =>
[_deleted:BaseObject:private] =>
[modifiedColumns:protected] => Array
(
)
)
[78] => Category Object
(
[languages:protected] =>
[bok_resources:protected] =>
[bok_topics:protected] =>
[bok_keywords:protected] =>
[id:protected] => 78
[type:protected] => category
[parent:protected] => 2
[label:protected] => Roofer/Waterproofer
[alreadyInSave:protected] =>
[alreadyInValidation:protected] =>
[validationFailures:protected] => Array
(
)
[_new:BaseObject:private] =>
[_deleted:BaseObject:private] =>
[modifiedColumns:protected] => Array
(
)
)
[79] => Category Object
(
[languages:protected] =>
[bok_resources:protected] =>
[bok_topics:protected] =>
[bok_keywords:protected] =>
[id:protected] => 79
[type:protected] => category
[parent:protected] => 2
[label:protected] => Scaffold Erector
[alreadyInSave:protected] =>
[alreadyInValidation:protected] =>
[validationFailures:protected] => Array
(
)
[_new:BaseObject:private] =>
[_deleted:BaseObject:private] =>
[modifiedColumns:protected] => Array
(
)
)
[82] => Category Object
(
[languages:protected] =>
[bok_resources:protected] =>
[bok_topics:protected] =>
[bok_keywords:protected] =>
[id:protected] => 82
[type:protected] => category
[parent:protected] => 2
[label:protected] => Stonemason
[alreadyInSave:protected] =>
[alreadyInValidation:protected] =>
[validationFailures:protected] => Array
(
)
[_new:BaseObject:private] =>
[_deleted:BaseObject:private] =>
[modifiedColumns:protected] => Array
(
)
)
[62] => Category Object
(
[languages:protected] =>
[bok_resources:protected] =>
[bok_topics:protected] =>
[bok_keywords:protected] =>
[id:protected] => 62
[type:protected] => category
[parent:protected] => 2
[label:protected] => Structural Ironworker
[alreadyInSave:protected] =>
[alreadyInValidation:protected] =>
[validationFailures:protected] => Array
(
)
[_new:BaseObject:private] =>
[_deleted:BaseObject:private] =>
[modifiedColumns:protected] => Array
(
)
)
[86] => Category Object
(
[languages:protected] =>
[bok_resources:protected] =>
[bok_topics:protected] =>
[bok_keywords:protected] =>
[id:protected] => 86
[type:protected] => category
[parent:protected] => 2
[label:protected] => Welder
[alreadyInSave:protected] =>
[alreadyInValidation:protected] =>
[validationFailures:protected] => Array
(
)
[_new:BaseObject:private] =>
[_deleted:BaseObject:private] =>
[modifiedColumns:protected] => Array
(
)
)
[87] => Category Object
(
[languages:protected] =>
[bok_resources:protected] =>
[bok_topics:protected] =>
[bok_keywords:protected] =>
[id:protected] => 87
[type:protected] => category
[parent:protected] => 3
[label:protected] => Commercial & Institutional
[alreadyInSave:protected] =>
[alreadyInValidation:protected] =>
[validationFailures:protected] => Array
(
)
[_new:BaseObject:private] =>
[_deleted:BaseObject:private] =>
[modifiedColumns:protected] => Array
(
)
)
[88] => Category Object
(
[languages:protected] =>
[bok_resources:protected] =>
[bok_topics:protected] =>
[bok_keywords:protected] =>
[id:protected] => 88
[type:protected] => category
[parent:protected] => 3
[label:protected] => Demolition
[alreadyInSave:protected] =>
[alreadyInValidation:protected] =>
[validationFailures:protected] => Array
(
)
[_new:BaseObject:private] =>
[_deleted:BaseObject:private] =>
[modifiedColumns:protected] => Array
(
)
)
[89] => Category Object
(
[languages:protected] =>
[bok_resources:protected] =>
[bok_topics:protected] =>
[bok_keywords:protected] =>
[id:protected] => 89
[type:protected] => category
[parent:protected] => 3
[label:protected] => Disasters
[alreadyInSave:protected] =>
[alreadyInValidation:protected] =>
[validationFailures:protected] => Array
(
)
[_new:BaseObject:private] =>
[_deleted:BaseObject:private] =>
[modifiedColumns:protected] => Array
(
)
)
[91] => Category Object
(
[languages:protected] =>
[bok_resources:protected] =>
[bok_topics:protected] =>
[bok_keywords:protected] =>
[id:protected] => 91
[type:protected] => category
[parent:protected] => 3
[label:protected] => Heavy & Highway
[alreadyInSave:protected] =>
[alreadyInValidation:protected] =>
[validationFailures:protected] => Array
(
)
[_new:BaseObject:private] =>
[_deleted:BaseObject:private] =>
[modifiedColumns:protected] => Array
(
)
)
[90] => Category Object
(
[languages:protected] =>
[bok_resources:protected] =>
[bok_topics:protected] =>
[bok_keywords:protected] =>
[id:protected] => 90
[type:protected] => category
[parent:protected] => 3
[label:protected] => Industrial
[alreadyInSave:protected] =>
[alreadyInValidation:protected] =>
[validationFailures:protected] => Array
(
)
[_new:BaseObject:private] =>
[_deleted:BaseObject:private] =>
[modifiedColumns:protected] => Array
(
)
)
[92] => Category Object
(
[languages:protected] =>
[bok_resources:protected] =>
[bok_topics:protected] =>
[bok_keywords:protected] =>
[id:protected] => 92
[type:protected] => category
[parent:protected] => 3
[label:protected] => LEED/Green Construction
[alreadyInSave:protected] =>
[alreadyInValidation:protected] =>
[validationFailures:protected] => Array
(
)
[_new:BaseObject:private] =>
[_deleted:BaseObject:private] =>
[modifiedColumns:protected] => Array
(
)
)
[93] => Category Object
(
[languages:protected] =>
[bok_resources:protected] =>
[bok_topics:protected] =>
[bok_keywords:protected] =>
[id:protected] => 93
[type:protected] => category
[parent:protected] => 3
[label:protected] => Renovations
[alreadyInSave:protected] =>
[alreadyInValidation:protected] =>
[validationFailures:protected] => Array
(
)
[_new:BaseObject:private] =>
[_deleted:BaseObject:private] =>
[modifiedColumns:protected] => Array
(
)
)
[94] => Category Object
(
[languages:protected] =>
[bok_resources:protected] =>
[bok_topics:protected] =>
[bok_keywords:protected] =>
[id:protected] => 94
[type:protected] => category
[parent:protected] => 3
[label:protected] => Residential
[alreadyInSave:protected] =>
[alreadyInValidation:protected] =>
[validationFailures:protected] => Array
(
)
[_new:BaseObject:private] =>
[_deleted:BaseObject:private] =>
[modifiedColumns:protected] => Array
(
)
)
[95] => Category Object
(
[languages:protected] =>
[bok_resources:protected] =>
[bok_topics:protected] =>
[bok_keywords:protected] =>
[id:protected] => 95
[type:protected] => category
[parent:protected] => 3
[label:protected] => Underground
[alreadyInSave:protected] =>
[alreadyInValidation:protected] =>
[validationFailures:protected] => Array
(
)
[_new:BaseObject:private] =>
[_deleted:BaseObject:private] =>
[modifiedColumns:protected] => Array
(
)
)
[100] => Category Object
(
[languages:protected] =>
[bok_resources:protected] =>
[bok_topics:protected] =>
[bok_keywords:protected] =>
[id:protected] => 100
[type:protected] => category
[parent:protected] => 6
[label:protected] => Toolbox Talks
[alreadyInSave:protected] =>
[alreadyInValidation:protected] =>
[validationFailures:protected] => Array
(
)
[_new:BaseObject:private] =>
[_deleted:BaseObject:private] =>
[modifiedColumns:protected] => Array
(
)
)
)
[categories_initialized:protected] => 1
[mapped_items:protected] =>
[content:protected] =>
[files:protected] =>
[language:protected] => Language Object
(
[id:protected] => 1
[code:protected] => en
[name:protected] => English
[alreadyInSave:protected] =>
[alreadyInValidation:protected] =>
[validationFailures:protected] => Array
(
)
[_new:BaseObject:private] =>
[_deleted:BaseObject:private] =>
[modifiedColumns:protected] => Array
(
)
)
[old_record:protected] =>
[id:protected] => 4431
[old_id:protected] =>
[elcosh_id:protected] => d001661
[type:protected] => document
[display_type:protected] => HTML only (and links)
[user_id:protected] => 0
[language_id:protected] => 1
[tagging_id:protected] => Mike Aguilar
[priority_id:protected] => 1
[title:protected] => Toolbox Talk: Challenges Preventing Falling Objects
[total_pages:protected] => 0
[billed_pages:protected] => 0
[publication_number:protected] =>
[part_of:protected] =>
[keywords:protected] => dropped objects, falling objects, struck by incidents, struck by fatalities
[comments:protected] =>
[summary:protected] => The CPWR Toolbox Talk on Challenges Preventing Falling Objects addresses the hazards of being struck by falling objects on the job site. The resource includes a brief example, steps to prevent a related injury, and questions for discussion. It includes a graphic that illustrates a group workers observing a scaffold free of debris during high winds, which can be posted in a central location as a reminder of steps to work safely.
Available in
English and
Spanish.
[transition_comments:protected] =>
[external_link:protected] =>
[consol_link:protected] =>
[more_like_this:protected] => d001234,d001238,d001244,d001251,d001253,d001260,d001268,d001278
[permission_given_by:protected] =>
[published:protected] => T
[billable:protected] => F
[img_name:protected] =>
[img_ext:protected] =>
[img_width:protected] =>
[img_height:protected] =>
[img_credit:protected] =>
[img_practice:protected] =>
[vid_source_id:protected] =>
[vid_running_time:protected] =>
[vid_intended_audience:protected] =>
[vid_acquisition_info:protected] =>
[vid_cost:protected] =>
[vid_producer:protected] =>
[vid_filename:protected] =>
[vid_filename_downloadable:protected] =>
[date_summary:protected] =>
[date_permission_requested:protected] =>
[date_permission_received:protected] =>
[date_review_needed:protected] =>
[date_received:protected] => 06/10/22
[date_completed:protected] => 06/10/22
[date_billed:protected] =>
[date_modified:protected] => 05/22/23
[collBokExports:protected] =>
[lastBokExportCriteria:BaseElcoshItem:private] =>
[alreadyInSave:protected] =>
[alreadyInValidation:protected] =>
[validationFailures:protected] => Array
(
)
[_new:BaseObject:private] =>
[_deleted:BaseObject:private] =>
[modifiedColumns:protected] => Array
(
)
)
)
[2] => Search_Result Object
(
[title] => Toolbox Talk: Tower Crane Safety
[image] => /record/images/notavailable-p.png
[blurb] => The CPWR Toolbox Talk on Tower Crane Safety addresses the potential hazards of Tower Cranes and the importance of following procedure before and durin...
[category] => Array
(
[0] => 11
[1] => 12
[2] => 18
[3] => 70
[4] => 87
[5] => 88
[6] => 91
[7] => 90
[8] => 92
[9] => 100
)
[labels] => Array
(
[0] => Cranes & Hoists
[1] => Work Environment
[2] => Hazards
[3] => Crushed/Struck By
[6] => Motor Vehicles/Heavy Equipment
[9] => Operating Engineer
[10] => Trades
[11] => Commercial & Institutional
[12] => Jobsites
[13] => Demolition
[15] => Heavy & Highway
[17] => Industrial
[19] => LEED/Green Construction
[21] => Toolbox Talks
[22] => Documents
[23] => Media & Documents
)
[type] => Toolbox Talks
[sub_category] =>
[url] => /document/4427/d001657/Toolbox%2BTalk%253A%2BTower%2BCrane%2BSafety.html
[item:protected] => DocumentRecord Object
(
[records:protected] => Array
(
)
[recordId:protected] =>
[searchWordClass:protected] =>
[searchWordPeerClass:protected] =>
[bok_record:protected] =>
[authors:protected] =>
[organizations:protected] =>
[collections:protected] =>
[categories:protected] => Array
(
[11] => Category Object
(
[languages:protected] =>
[bok_resources:protected] =>
[bok_topics:protected] =>
[bok_keywords:protected] =>
[id:protected] => 11
[type:protected] => category
[parent:protected] => 7
[label:protected] => Cranes & Hoists
[alreadyInSave:protected] =>
[alreadyInValidation:protected] =>
[validationFailures:protected] => Array
(
)
[_new:BaseObject:private] =>
[_deleted:BaseObject:private] =>
[modifiedColumns:protected] => Array
(
)
)
[12] => Category Object
(
[languages:protected] =>
[bok_resources:protected] =>
[bok_topics:protected] =>
[bok_keywords:protected] =>
[id:protected] => 12
[type:protected] => category
[parent:protected] => 7
[label:protected] => Crushed/Struck By
[alreadyInSave:protected] =>
[alreadyInValidation:protected] =>
[validationFailures:protected] => Array
(
)
[_new:BaseObject:private] =>
[_deleted:BaseObject:private] =>
[modifiedColumns:protected] => Array
(
)
)
[18] => Category Object
(
[languages:protected] =>
[bok_resources:protected] =>
[bok_topics:protected] =>
[bok_keywords:protected] =>
[id:protected] => 18
[type:protected] => category
[parent:protected] => 7
[label:protected] => Motor Vehicles/Heavy Equipment
[alreadyInSave:protected] =>
[alreadyInValidation:protected] =>
[validationFailures:protected] => Array
(
)
[_new:BaseObject:private] =>
[_deleted:BaseObject:private] =>
[modifiedColumns:protected] => Array
(
)
)
[70] => Category Object
(
[languages:protected] =>
[bok_resources:protected] =>
[bok_topics:protected] =>
[bok_keywords:protected] =>
[id:protected] => 70
[type:protected] => category
[parent:protected] => 2
[label:protected] => Operating Engineer
[alreadyInSave:protected] =>
[alreadyInValidation:protected] =>
[validationFailures:protected] => Array
(
)
[_new:BaseObject:private] =>
[_deleted:BaseObject:private] =>
[modifiedColumns:protected] => Array
(
)
)
[87] => Category Object
(
[languages:protected] =>
[bok_resources:protected] =>
[bok_topics:protected] =>
[bok_keywords:protected] =>
[id:protected] => 87
[type:protected] => category
[parent:protected] => 3
[label:protected] => Commercial & Institutional
[alreadyInSave:protected] =>
[alreadyInValidation:protected] =>
[validationFailures:protected] => Array
(
)
[_new:BaseObject:private] =>
[_deleted:BaseObject:private] =>
[modifiedColumns:protected] => Array
(
)
)
[88] => Category Object
(
[languages:protected] =>
[bok_resources:protected] =>
[bok_topics:protected] =>
[bok_keywords:protected] =>
[id:protected] => 88
[type:protected] => category
[parent:protected] => 3
[label:protected] => Demolition
[alreadyInSave:protected] =>
[alreadyInValidation:protected] =>
[validationFailures:protected] => Array
(
)
[_new:BaseObject:private] =>
[_deleted:BaseObject:private] =>
[modifiedColumns:protected] => Array
(
)
)
[91] => Category Object
(
[languages:protected] =>
[bok_resources:protected] =>
[bok_topics:protected] =>
[bok_keywords:protected] =>
[id:protected] => 91
[type:protected] => category
[parent:protected] => 3
[label:protected] => Heavy & Highway
[alreadyInSave:protected] =>
[alreadyInValidation:protected] =>
[validationFailures:protected] => Array
(
)
[_new:BaseObject:private] =>
[_deleted:BaseObject:private] =>
[modifiedColumns:protected] => Array
(
)
)
[90] => Category Object
(
[languages:protected] =>
[bok_resources:protected] =>
[bok_topics:protected] =>
[bok_keywords:protected] =>
[id:protected] => 90
[type:protected] => category
[parent:protected] => 3
[label:protected] => Industrial
[alreadyInSave:protected] =>
[alreadyInValidation:protected] =>
[validationFailures:protected] => Array
(
)
[_new:BaseObject:private] =>
[_deleted:BaseObject:private] =>
[modifiedColumns:protected] => Array
(
)
)
[92] => Category Object
(
[languages:protected] =>
[bok_resources:protected] =>
[bok_topics:protected] =>
[bok_keywords:protected] =>
[id:protected] => 92
[type:protected] => category
[parent:protected] => 3
[label:protected] => LEED/Green Construction
[alreadyInSave:protected] =>
[alreadyInValidation:protected] =>
[validationFailures:protected] => Array
(
)
[_new:BaseObject:private] =>
[_deleted:BaseObject:private] =>
[modifiedColumns:protected] => Array
(
)
)
[100] => Category Object
(
[languages:protected] =>
[bok_resources:protected] =>
[bok_topics:protected] =>
[bok_keywords:protected] =>
[id:protected] => 100
[type:protected] => category
[parent:protected] => 6
[label:protected] => Toolbox Talks
[alreadyInSave:protected] =>
[alreadyInValidation:protected] =>
[validationFailures:protected] => Array
(
)
[_new:BaseObject:private] =>
[_deleted:BaseObject:private] =>
[modifiedColumns:protected] => Array
(
)
)
)
[categories_initialized:protected] => 1
[mapped_items:protected] =>
[content:protected] =>
[files:protected] =>
[language:protected] => Language Object
(
[id:protected] => 1
[code:protected] => en
[name:protected] => English
[alreadyInSave:protected] =>
[alreadyInValidation:protected] =>
[validationFailures:protected] => Array
(
)
[_new:BaseObject:private] =>
[_deleted:BaseObject:private] =>
[modifiedColumns:protected] => Array
(
)
)
[old_record:protected] =>
[id:protected] => 4427
[old_id:protected] =>
[elcosh_id:protected] => d001657
[type:protected] => document
[display_type:protected] => HTML only (and links)
[user_id:protected] => 0
[language_id:protected] => 1
[tagging_id:protected] => Mike Aguilar
[priority_id:protected] => 1
[title:protected] => Toolbox Talk: Tower Crane Safety
[total_pages:protected] => 0
[billed_pages:protected] => 0
[publication_number:protected] =>
[part_of:protected] =>
[keywords:protected] => Tower Crane, Crane, Stability, Tipping, Lift Zone Safety, Lift, Zone, Safety, Struck by
[comments:protected] =>
[summary:protected] => The CPWR Toolbox Talk on Tower Crane Safety addresses the potential hazards of Tower Cranes and the importance of following procedure before and during Tower Crane operation. The resource includes a brief example, steps to prevent a related injury, and questions for discussion. It includes a graphic that illustrates a worker inspecting a Tower Crane before operation, which can be posted in a central location as a reminder of steps to work safely.
Available in
English and
Spanish.
[transition_comments:protected] =>
[external_link:protected] =>
[consol_link:protected] =>
[more_like_this:protected] => d001234,d001238,d001250,d001251,d001253,d001258,d001262,d001273
[permission_given_by:protected] =>
[published:protected] => T
[billable:protected] => F
[img_name:protected] =>
[img_ext:protected] => jpg
[img_width:protected] =>
[img_height:protected] =>
[img_credit:protected] =>
[img_practice:protected] =>
[vid_source_id:protected] =>
[vid_running_time:protected] =>
[vid_intended_audience:protected] =>
[vid_acquisition_info:protected] =>
[vid_cost:protected] =>
[vid_producer:protected] =>
[vid_filename:protected] =>
[vid_filename_downloadable:protected] =>
[date_summary:protected] =>
[date_permission_requested:protected] =>
[date_permission_received:protected] =>
[date_review_needed:protected] =>
[date_received:protected] => 12/23/21
[date_completed:protected] => 12/23/21
[date_billed:protected] =>
[date_modified:protected] => 05/19/23
[collBokExports:protected] =>
[lastBokExportCriteria:BaseElcoshItem:private] =>
[alreadyInSave:protected] =>
[alreadyInValidation:protected] =>
[validationFailures:protected] => Array
(
)
[_new:BaseObject:private] =>
[_deleted:BaseObject:private] =>
[modifiedColumns:protected] => Array
(
)
)
)
[3] => Search_Result Object
(
[title] => Toolbox Talk: Work Zone Safety: Working Around Vehicles
[image] => /record/images/notavailable-p.png
[blurb] => The CPWR Toolbox Talk on Working Around Vehicles in the Work Zone addresses methods to avoid being struck-by a vehicle on a construction site. The res...
[category] => Array
(
[0] => 12
[1] => 18
[2] => 52
[3] => 57
[4] => 70
[5] => 85
[6] => 87
[7] => 88
[8] => 89
[9] => 91
[10] => 90
[11] => 92
[12] => 93
[13] => 94
[14] => 95
[15] => 100
)
[labels] => Array
(
[0] => Crushed/Struck By
[1] => Work Environment
[2] => Hazards
[3] => Motor Vehicles/Heavy Equipment
[6] => Commercial Diver
[7] => Trades
[8] => Flagger
[10] => Operating Engineer
[12] => Truck Driver
[14] => Commercial & Institutional
[15] => Jobsites
[16] => Demolition
[18] => Disasters
[20] => Heavy & Highway
[22] => Industrial
[24] => LEED/Green Construction
[26] => Renovations
[28] => Residential
[30] => Underground
[32] => Toolbox Talks
[33] => Documents
[34] => Media & Documents
)
[type] => Toolbox Talks
[sub_category] =>
[url] => /document/4428/d001658/Toolbox%2BTalk%253A%2BWork%2BZone%2BSafety%253A%2BWorking%2BAround%2BVehicles.html
[item:protected] => DocumentRecord Object
(
[records:protected] => Array
(
)
[recordId:protected] =>
[searchWordClass:protected] =>
[searchWordPeerClass:protected] =>
[bok_record:protected] =>
[authors:protected] =>
[organizations:protected] =>
[collections:protected] =>
[categories:protected] => Array
(
[12] => Category Object
(
[languages:protected] =>
[bok_resources:protected] =>
[bok_topics:protected] =>
[bok_keywords:protected] =>
[id:protected] => 12
[type:protected] => category
[parent:protected] => 7
[label:protected] => Crushed/Struck By
[alreadyInSave:protected] =>
[alreadyInValidation:protected] =>
[validationFailures:protected] => Array
(
)
[_new:BaseObject:private] =>
[_deleted:BaseObject:private] =>
[modifiedColumns:protected] => Array
(
)
)
[18] => Category Object
(
[languages:protected] =>
[bok_resources:protected] =>
[bok_topics:protected] =>
[bok_keywords:protected] =>
[id:protected] => 18
[type:protected] => category
[parent:protected] => 7
[label:protected] => Motor Vehicles/Heavy Equipment
[alreadyInSave:protected] =>
[alreadyInValidation:protected] =>
[validationFailures:protected] => Array
(
)
[_new:BaseObject:private] =>
[_deleted:BaseObject:private] =>
[modifiedColumns:protected] => Array
(
)
)
[52] => Category Object
(
[languages:protected] =>
[bok_resources:protected] =>
[bok_topics:protected] =>
[bok_keywords:protected] =>
[id:protected] => 52
[type:protected] => category
[parent:protected] => 2
[label:protected] => Commercial Diver
[alreadyInSave:protected] =>
[alreadyInValidation:protected] =>
[validationFailures:protected] => Array
(
)
[_new:BaseObject:private] =>
[_deleted:BaseObject:private] =>
[modifiedColumns:protected] => Array
(
)
)
[57] => Category Object
(
[languages:protected] =>
[bok_resources:protected] =>
[bok_topics:protected] =>
[bok_keywords:protected] =>
[id:protected] => 57
[type:protected] => category
[parent:protected] => 2
[label:protected] => Flagger
[alreadyInSave:protected] =>
[alreadyInValidation:protected] =>
[validationFailures:protected] => Array
(
)
[_new:BaseObject:private] =>
[_deleted:BaseObject:private] =>
[modifiedColumns:protected] => Array
(
)
)
[70] => Category Object
(
[languages:protected] =>
[bok_resources:protected] =>
[bok_topics:protected] =>
[bok_keywords:protected] =>
[id:protected] => 70
[type:protected] => category
[parent:protected] => 2
[label:protected] => Operating Engineer
[alreadyInSave:protected] =>
[alreadyInValidation:protected] =>
[validationFailures:protected] => Array
(
)
[_new:BaseObject:private] =>
[_deleted:BaseObject:private] =>
[modifiedColumns:protected] => Array
(
)
)
[85] => Category Object
(
[languages:protected] =>
[bok_resources:protected] =>
[bok_topics:protected] =>
[bok_keywords:protected] =>
[id:protected] => 85
[type:protected] => category
[parent:protected] => 2
[label:protected] => Truck Driver
[alreadyInSave:protected] =>
[alreadyInValidation:protected] =>
[validationFailures:protected] => Array
(
)
[_new:BaseObject:private] =>
[_deleted:BaseObject:private] =>
[modifiedColumns:protected] => Array
(
)
)
[87] => Category Object
(
[languages:protected] =>
[bok_resources:protected] =>
[bok_topics:protected] =>
[bok_keywords:protected] =>
[id:protected] => 87
[type:protected] => category
[parent:protected] => 3
[label:protected] => Commercial & Institutional
[alreadyInSave:protected] =>
[alreadyInValidation:protected] =>
[validationFailures:protected] => Array
(
)
[_new:BaseObject:private] =>
[_deleted:BaseObject:private] =>
[modifiedColumns:protected] => Array
(
)
)
[88] => Category Object
(
[languages:protected] =>
[bok_resources:protected] =>
[bok_topics:protected] =>
[bok_keywords:protected] =>
[id:protected] => 88
[type:protected] => category
[parent:protected] => 3
[label:protected] => Demolition
[alreadyInSave:protected] =>
[alreadyInValidation:protected] =>
[validationFailures:protected] => Array
(
)
[_new:BaseObject:private] =>
[_deleted:BaseObject:private] =>
[modifiedColumns:protected] => Array
(
)
)
[89] => Category Object
(
[languages:protected] =>
[bok_resources:protected] =>
[bok_topics:protected] =>
[bok_keywords:protected] =>
[id:protected] => 89
[type:protected] => category
[parent:protected] => 3
[label:protected] => Disasters
[alreadyInSave:protected] =>
[alreadyInValidation:protected] =>
[validationFailures:protected] => Array
(
)
[_new:BaseObject:private] =>
[_deleted:BaseObject:private] =>
[modifiedColumns:protected] => Array
(
)
)
[91] => Category Object
(
[languages:protected] =>
[bok_resources:protected] =>
[bok_topics:protected] =>
[bok_keywords:protected] =>
[id:protected] => 91
[type:protected] => category
[parent:protected] => 3
[label:protected] => Heavy & Highway
[alreadyInSave:protected] =>
[alreadyInValidation:protected] =>
[validationFailures:protected] => Array
(
)
[_new:BaseObject:private] =>
[_deleted:BaseObject:private] =>
[modifiedColumns:protected] => Array
(
)
)
[90] => Category Object
(
[languages:protected] =>
[bok_resources:protected] =>
[bok_topics:protected] =>
[bok_keywords:protected] =>
[id:protected] => 90
[type:protected] => category
[parent:protected] => 3
[label:protected] => Industrial
[alreadyInSave:protected] =>
[alreadyInValidation:protected] =>
[validationFailures:protected] => Array
(
)
[_new:BaseObject:private] =>
[_deleted:BaseObject:private] =>
[modifiedColumns:protected] => Array
(
)
)
[92] => Category Object
(
[languages:protected] =>
[bok_resources:protected] =>
[bok_topics:protected] =>
[bok_keywords:protected] =>
[id:protected] => 92
[type:protected] => category
[parent:protected] => 3
[label:protected] => LEED/Green Construction
[alreadyInSave:protected] =>
[alreadyInValidation:protected] =>
[validationFailures:protected] => Array
(
)
[_new:BaseObject:private] =>
[_deleted:BaseObject:private] =>
[modifiedColumns:protected] => Array
(
)
)
[93] => Category Object
(
[languages:protected] =>
[bok_resources:protected] =>
[bok_topics:protected] =>
[bok_keywords:protected] =>
[id:protected] => 93
[type:protected] => category
[parent:protected] => 3
[label:protected] => Renovations
[alreadyInSave:protected] =>
[alreadyInValidation:protected] =>
[validationFailures:protected] => Array
(
)
[_new:BaseObject:private] =>
[_deleted:BaseObject:private] =>
[modifiedColumns:protected] => Array
(
)
)
[94] => Category Object
(
[languages:protected] =>
[bok_resources:protected] =>
[bok_topics:protected] =>
[bok_keywords:protected] =>
[id:protected] => 94
[type:protected] => category
[parent:protected] => 3
[label:protected] => Residential
[alreadyInSave:protected] =>
[alreadyInValidation:protected] =>
[validationFailures:protected] => Array
(
)
[_new:BaseObject:private] =>
[_deleted:BaseObject:private] =>
[modifiedColumns:protected] => Array
(
)
)
[95] => Category Object
(
[languages:protected] =>
[bok_resources:protected] =>
[bok_topics:protected] =>
[bok_keywords:protected] =>
[id:protected] => 95
[type:protected] => category
[parent:protected] => 3
[label:protected] => Underground
[alreadyInSave:protected] =>
[alreadyInValidation:protected] =>
[validationFailures:protected] => Array
(
)
[_new:BaseObject:private] =>
[_deleted:BaseObject:private] =>
[modifiedColumns:protected] => Array
(
)
)
[100] => Category Object
(
[languages:protected] =>
[bok_resources:protected] =>
[bok_topics:protected] =>
[bok_keywords:protected] =>
[id:protected] => 100
[type:protected] => category
[parent:protected] => 6
[label:protected] => Toolbox Talks
[alreadyInSave:protected] =>
[alreadyInValidation:protected] =>
[validationFailures:protected] => Array
(
)
[_new:BaseObject:private] =>
[_deleted:BaseObject:private] =>
[modifiedColumns:protected] => Array
(
)
)
)
[categories_initialized:protected] => 1
[mapped_items:protected] =>
[content:protected] =>
[files:protected] =>
[language:protected] => Language Object
(
[id:protected] => 1
[code:protected] => en
[name:protected] => English
[alreadyInSave:protected] =>
[alreadyInValidation:protected] =>
[validationFailures:protected] => Array
(
)
[_new:BaseObject:private] =>
[_deleted:BaseObject:private] =>
[modifiedColumns:protected] => Array
(
)
)
[old_record:protected] =>
[id:protected] => 4428
[old_id:protected] =>
[elcosh_id:protected] => d001658
[type:protected] => document
[display_type:protected] => HTML only (and links)
[user_id:protected] => 0
[language_id:protected] => 1
[tagging_id:protected] => Daniela Caceres
[priority_id:protected] => 1
[title:protected] => Toolbox Talk: Work Zone Safety: Working Around Vehicles
[total_pages:protected] => 0
[billed_pages:protected] => 0
[publication_number:protected] =>
[part_of:protected] =>
[keywords:protected] => Struck, Struck by, Vehicle, Work Zone Safety, Truck, Operator, Driver, Mobile Equipment
[comments:protected] =>
[summary:protected] => The CPWR Toolbox Talk on Working Around Vehicles in the Work Zone addresses methods to avoid being struck-by a vehicle on a construction site. The resource includes a case example, steps to prevent a related injury, and questions for discussion. It includes a graphic that illustrates the hazard, which can be posted in a central location as a reminder of steps to work safely. Available in
English and
Spanish.
[transition_comments:protected] =>
[external_link:protected] =>
[consol_link:protected] =>
[more_like_this:protected] => d001640
[permission_given_by:protected] =>
[published:protected] => T
[billable:protected] => F
[img_name:protected] =>
[img_ext:protected] =>
[img_width:protected] =>
[img_height:protected] =>
[img_credit:protected] =>
[img_practice:protected] =>
[vid_source_id:protected] =>
[vid_running_time:protected] =>
[vid_intended_audience:protected] =>
[vid_acquisition_info:protected] =>
[vid_cost:protected] =>
[vid_producer:protected] =>
[vid_filename:protected] =>
[vid_filename_downloadable:protected] =>
[date_summary:protected] =>
[date_permission_requested:protected] =>
[date_permission_received:protected] =>
[date_review_needed:protected] =>
[date_received:protected] => 12/23/21
[date_completed:protected] => 12/23/21
[date_billed:protected] =>
[date_modified:protected] => 05/19/23
[collBokExports:protected] =>
[lastBokExportCriteria:BaseElcoshItem:private] =>
[alreadyInSave:protected] =>
[alreadyInValidation:protected] =>
[validationFailures:protected] => Array
(
)
[_new:BaseObject:private] =>
[_deleted:BaseObject:private] =>
[modifiedColumns:protected] => Array
(
)
)
)
[4] => Search_Result Object
(
[title] => Construction Dive -- DeWalt's Jobsite Pro headphones recalled for fire hazards
[image] => /record/images/notavailable-p.png
[blurb] => A recall notice by the United States Consumer Product Safety Commission affects over 300,000 DeWalt Jobsite Pro Headphones. The recall is a result of...
[category] => Array
(
[0] => 16
[1] => 44
[2] => 45
[3] => 46
[4] => 47
[5] => 48
[6] => 49
[7] => 50
[8] => 51
[9] => 52
[10] => 53
[11] => 54
[12] => 55
[13] => 56
[14] => 57
[15] => 58
[16] => 59
[17] => 60
[18] => 61
[19] => 64
[20] => 65
[21] => 66
[22] => 67
[23] => 68
[24] => 69
[25] => 70
[26] => 71
[27] => 72
[28] => 73
[29] => 74
[30] => 75
[31] => 76
[32] => 77
[33] => 63
[34] => 78
[35] => 79
[36] => 80
[37] => 81
[38] => 82
[39] => 62
[40] => 83
[41] => 84
[42] => 85
[43] => 86
[44] => 87
[45] => 88
[46] => 89
[47] => 91
[48] => 90
[49] => 92
[50] => 93
[51] => 94
[52] => 95
)
[labels] => Array
(
[0] => Fire & Explosions
[1] => Work Environment
[2] => Hazards
[3] => Acoustical Ceiling Carpenter
[4] => Trades
[5] => Asbestos/Insulator
[7] => Boilermaker
[9] => Bricklayer
[11] => Cabinetmaker
[13] => Carpenter
[15] => Carpet Layer
[17] => Cement Mason
[19] => Commercial Diver
[21] => Concrete Polisher
[23] => Drywall Applicator Specialist
[25] => Electrical Worker
[27] => Elevator Constructor
[29] => Flagger
[31] => Glazier
[33] => Hazardous Waste Cleanup
[35] => HVAC
[37] => Interior Systems Carpenter
[39] => Laborer
[41] => Landscaper
[43] => Lather
[45] => Lead Abatement Worker
[47] => Maintenance Worker
[49] => Millwright
[51] => Operating Engineer
[53] => Painter
[55] => Paper Hanger
[57] => PCC/Restoration
[59] => Pile Driver
[61] => Plasterer
[63] => Plumber/Pipefitter
[65] => Refractory Worker
[67] => Reinforcing Ironworker
[69] => Roofer/Waterproofer
[71] => Scaffold Erector
[73] => Sheetmetal Worker
[75] => Sprinkler Fitter
[77] => Stonemason
[79] => Structural Ironworker
[81] => Terrazzo Worker
[83] => Tile Setter
[85] => Truck Driver
[87] => Welder
[89] => Commercial & Institutional
[90] => Jobsites
[91] => Demolition
[93] => Disasters
[95] => Heavy & Highway
[97] => Industrial
[99] => LEED/Green Construction
[101] => Renovations
[103] => Residential
[105] => Underground
)
[type] =>
[sub_category] =>
[url] => /document/4426/d001656/Construction%2BDive%2B--%2BDeWalt%2527s%2BJobsite%2BPro%2Bheadphones%2Brecalled%2Bfor%2Bfire%2Bhazards.html
[item:protected] => DocumentRecord Object
(
[records:protected] => Array
(
)
[recordId:protected] =>
[searchWordClass:protected] =>
[searchWordPeerClass:protected] =>
[bok_record:protected] =>
[authors:protected] =>
[organizations:protected] =>
[collections:protected] =>
[categories:protected] => Array
(
[16] => Category Object
(
[languages:protected] =>
[bok_resources:protected] =>
[bok_topics:protected] =>
[bok_keywords:protected] =>
[id:protected] => 16
[type:protected] => category
[parent:protected] => 7
[label:protected] => Fire & Explosions
[alreadyInSave:protected] =>
[alreadyInValidation:protected] =>
[validationFailures:protected] => Array
(
)
[_new:BaseObject:private] =>
[_deleted:BaseObject:private] =>
[modifiedColumns:protected] => Array
(
)
)
[44] => Category Object
(
[languages:protected] =>
[bok_resources:protected] =>
[bok_topics:protected] =>
[bok_keywords:protected] =>
[id:protected] => 44
[type:protected] => category
[parent:protected] => 2
[label:protected] => Acoustical Ceiling Carpenter
[alreadyInSave:protected] =>
[alreadyInValidation:protected] =>
[validationFailures:protected] => Array
(
)
[_new:BaseObject:private] =>
[_deleted:BaseObject:private] =>
[modifiedColumns:protected] => Array
(
)
)
[45] => Category Object
(
[languages:protected] =>
[bok_resources:protected] =>
[bok_topics:protected] =>
[bok_keywords:protected] =>
[id:protected] => 45
[type:protected] => category
[parent:protected] => 2
[label:protected] => Asbestos/Insulator
[alreadyInSave:protected] =>
[alreadyInValidation:protected] =>
[validationFailures:protected] => Array
(
)
[_new:BaseObject:private] =>
[_deleted:BaseObject:private] =>
[modifiedColumns:protected] => Array
(
)
)
[46] => Category Object
(
[languages:protected] =>
[bok_resources:protected] =>
[bok_topics:protected] =>
[bok_keywords:protected] =>
[id:protected] => 46
[type:protected] => category
[parent:protected] => 2
[label:protected] => Boilermaker
[alreadyInSave:protected] =>
[alreadyInValidation:protected] =>
[validationFailures:protected] => Array
(
)
[_new:BaseObject:private] =>
[_deleted:BaseObject:private] =>
[modifiedColumns:protected] => Array
(
)
)
[47] => Category Object
(
[languages:protected] =>
[bok_resources:protected] =>
[bok_topics:protected] =>
[bok_keywords:protected] =>
[id:protected] => 47
[type:protected] => category
[parent:protected] => 2
[label:protected] => Bricklayer
[alreadyInSave:protected] =>
[alreadyInValidation:protected] =>
[validationFailures:protected] => Array
(
)
[_new:BaseObject:private] =>
[_deleted:BaseObject:private] =>
[modifiedColumns:protected] => Array
(
)
)
[48] => Category Object
(
[languages:protected] =>
[bok_resources:protected] =>
[bok_topics:protected] =>
[bok_keywords:protected] =>
[id:protected] => 48
[type:protected] => category
[parent:protected] => 2
[label:protected] => Cabinetmaker
[alreadyInSave:protected] =>
[alreadyInValidation:protected] =>
[validationFailures:protected] => Array
(
)
[_new:BaseObject:private] =>
[_deleted:BaseObject:private] =>
[modifiedColumns:protected] => Array
(
)
)
[49] => Category Object
(
[languages:protected] =>
[bok_resources:protected] =>
[bok_topics:protected] =>
[bok_keywords:protected] =>
[id:protected] => 49
[type:protected] => category
[parent:protected] => 2
[label:protected] => Carpenter
[alreadyInSave:protected] =>
[alreadyInValidation:protected] =>
[validationFailures:protected] => Array
(
)
[_new:BaseObject:private] =>
[_deleted:BaseObject:private] =>
[modifiedColumns:protected] => Array
(
)
)
[50] => Category Object
(
[languages:protected] =>
[bok_resources:protected] =>
[bok_topics:protected] =>
[bok_keywords:protected] =>
[id:protected] => 50
[type:protected] => category
[parent:protected] => 2
[label:protected] => Carpet Layer
[alreadyInSave:protected] =>
[alreadyInValidation:protected] =>
[validationFailures:protected] => Array
(
)
[_new:BaseObject:private] =>
[_deleted:BaseObject:private] =>
[modifiedColumns:protected] => Array
(
)
)
[51] => Category Object
(
[languages:protected] =>
[bok_resources:protected] =>
[bok_topics:protected] =>
[bok_keywords:protected] =>
[id:protected] => 51
[type:protected] => category
[parent:protected] => 2
[label:protected] => Cement Mason
[alreadyInSave:protected] =>
[alreadyInValidation:protected] =>
[validationFailures:protected] => Array
(
)
[_new:BaseObject:private] =>
[_deleted:BaseObject:private] =>
[modifiedColumns:protected] => Array
(
)
)
[52] => Category Object
(
[languages:protected] =>
[bok_resources:protected] =>
[bok_topics:protected] =>
[bok_keywords:protected] =>
[id:protected] => 52
[type:protected] => category
[parent:protected] => 2
[label:protected] => Commercial Diver
[alreadyInSave:protected] =>
[alreadyInValidation:protected] =>
[validationFailures:protected] => Array
(
)
[_new:BaseObject:private] =>
[_deleted:BaseObject:private] =>
[modifiedColumns:protected] => Array
(
)
)
[53] => Category Object
(
[languages:protected] =>
[bok_resources:protected] =>
[bok_topics:protected] =>
[bok_keywords:protected] =>
[id:protected] => 53
[type:protected] => category
[parent:protected] => 2
[label:protected] => Concrete Polisher
[alreadyInSave:protected] =>
[alreadyInValidation:protected] =>
[validationFailures:protected] => Array
(
)
[_new:BaseObject:private] =>
[_deleted:BaseObject:private] =>
[modifiedColumns:protected] => Array
(
)
)
[54] => Category Object
(
[languages:protected] =>
[bok_resources:protected] =>
[bok_topics:protected] =>
[bok_keywords:protected] =>
[id:protected] => 54
[type:protected] => category
[parent:protected] => 2
[label:protected] => Drywall Applicator Specialist
[alreadyInSave:protected] =>
[alreadyInValidation:protected] =>
[validationFailures:protected] => Array
(
)
[_new:BaseObject:private] =>
[_deleted:BaseObject:private] =>
[modifiedColumns:protected] => Array
(
)
)
[55] => Category Object
(
[languages:protected] =>
[bok_resources:protected] =>
[bok_topics:protected] =>
[bok_keywords:protected] =>
[id:protected] => 55
[type:protected] => category
[parent:protected] => 2
[label:protected] => Electrical Worker
[alreadyInSave:protected] =>
[alreadyInValidation:protected] =>
[validationFailures:protected] => Array
(
)
[_new:BaseObject:private] =>
[_deleted:BaseObject:private] =>
[modifiedColumns:protected] => Array
(
)
)
[56] => Category Object
(
[languages:protected] =>
[bok_resources:protected] =>
[bok_topics:protected] =>
[bok_keywords:protected] =>
[id:protected] => 56
[type:protected] => category
[parent:protected] => 2
[label:protected] => Elevator Constructor
[alreadyInSave:protected] =>
[alreadyInValidation:protected] =>
[validationFailures:protected] => Array
(
)
[_new:BaseObject:private] =>
[_deleted:BaseObject:private] =>
[modifiedColumns:protected] => Array
(
)
)
[57] => Category Object
(
[languages:protected] =>
[bok_resources:protected] =>
[bok_topics:protected] =>
[bok_keywords:protected] =>
[id:protected] => 57
[type:protected] => category
[parent:protected] => 2
[label:protected] => Flagger
[alreadyInSave:protected] =>
[alreadyInValidation:protected] =>
[validationFailures:protected] => Array
(
)
[_new:BaseObject:private] =>
[_deleted:BaseObject:private] =>
[modifiedColumns:protected] => Array
(
)
)
[58] => Category Object
(
[languages:protected] =>
[bok_resources:protected] =>
[bok_topics:protected] =>
[bok_keywords:protected] =>
[id:protected] => 58
[type:protected] => category
[parent:protected] => 2
[label:protected] => Glazier
[alreadyInSave:protected] =>
[alreadyInValidation:protected] =>
[validationFailures:protected] => Array
(
)
[_new:BaseObject:private] =>
[_deleted:BaseObject:private] =>
[modifiedColumns:protected] => Array
(
)
)
[59] => Category Object
(
[languages:protected] =>
[bok_resources:protected] =>
[bok_topics:protected] =>
[bok_keywords:protected] =>
[id:protected] => 59
[type:protected] => category
[parent:protected] => 2
[label:protected] => Hazardous Waste Cleanup
[alreadyInSave:protected] =>
[alreadyInValidation:protected] =>
[validationFailures:protected] => Array
(
)
[_new:BaseObject:private] =>
[_deleted:BaseObject:private] =>
[modifiedColumns:protected] => Array
(
)
)
[60] => Category Object
(
[languages:protected] =>
[bok_resources:protected] =>
[bok_topics:protected] =>
[bok_keywords:protected] =>
[id:protected] => 60
[type:protected] => category
[parent:protected] => 2
[label:protected] => HVAC
[alreadyInSave:protected] =>
[alreadyInValidation:protected] =>
[validationFailures:protected] => Array
(
)
[_new:BaseObject:private] =>
[_deleted:BaseObject:private] =>
[modifiedColumns:protected] => Array
(
)
)
[61] => Category Object
(
[languages:protected] =>
[bok_resources:protected] =>
[bok_topics:protected] =>
[bok_keywords:protected] =>
[id:protected] => 61
[type:protected] => category
[parent:protected] => 2
[label:protected] => Interior Systems Carpenter
[alreadyInSave:protected] =>
[alreadyInValidation:protected] =>
[validationFailures:protected] => Array
(
)
[_new:BaseObject:private] =>
[_deleted:BaseObject:private] =>
[modifiedColumns:protected] => Array
(
)
)
[64] => Category Object
(
[languages:protected] =>
[bok_resources:protected] =>
[bok_topics:protected] =>
[bok_keywords:protected] =>
[id:protected] => 64
[type:protected] => category
[parent:protected] => 2
[label:protected] => Laborer
[alreadyInSave:protected] =>
[alreadyInValidation:protected] =>
[validationFailures:protected] => Array
(
)
[_new:BaseObject:private] =>
[_deleted:BaseObject:private] =>
[modifiedColumns:protected] => Array
(
)
)
[65] => Category Object
(
[languages:protected] =>
[bok_resources:protected] =>
[bok_topics:protected] =>
[bok_keywords:protected] =>
[id:protected] => 65
[type:protected] => category
[parent:protected] => 2
[label:protected] => Landscaper
[alreadyInSave:protected] =>
[alreadyInValidation:protected] =>
[validationFailures:protected] => Array
(
)
[_new:BaseObject:private] =>
[_deleted:BaseObject:private] =>
[modifiedColumns:protected] => Array
(
)
)
[66] => Category Object
(
[languages:protected] =>
[bok_resources:protected] =>
[bok_topics:protected] =>
[bok_keywords:protected] =>
[id:protected] => 66
[type:protected] => category
[parent:protected] => 2
[label:protected] => Lather
[alreadyInSave:protected] =>
[alreadyInValidation:protected] =>
[validationFailures:protected] => Array
(
)
[_new:BaseObject:private] =>
[_deleted:BaseObject:private] =>
[modifiedColumns:protected] => Array
(
)
)
[67] => Category Object
(
[languages:protected] =>
[bok_resources:protected] =>
[bok_topics:protected] =>
[bok_keywords:protected] =>
[id:protected] => 67
[type:protected] => category
[parent:protected] => 2
[label:protected] => Lead Abatement Worker
[alreadyInSave:protected] =>
[alreadyInValidation:protected] =>
[validationFailures:protected] => Array
(
)
[_new:BaseObject:private] =>
[_deleted:BaseObject:private] =>
[modifiedColumns:protected] => Array
(
)
)
[68] => Category Object
(
[languages:protected] =>
[bok_resources:protected] =>
[bok_topics:protected] =>
[bok_keywords:protected] =>
[id:protected] => 68
[type:protected] => category
[parent:protected] => 2
[label:protected] => Maintenance Worker
[alreadyInSave:protected] =>
[alreadyInValidation:protected] =>
[validationFailures:protected] => Array
(
)
[_new:BaseObject:private] =>
[_deleted:BaseObject:private] =>
[modifiedColumns:protected] => Array
(
)
)
[69] => Category Object
(
[languages:protected] =>
[bok_resources:protected] =>
[bok_topics:protected] =>
[bok_keywords:protected] =>
[id:protected] => 69
[type:protected] => category
[parent:protected] => 2
[label:protected] => Millwright
[alreadyInSave:protected] =>
[alreadyInValidation:protected] =>
[validationFailures:protected] => Array
(
)
[_new:BaseObject:private] =>
[_deleted:BaseObject:private] =>
[modifiedColumns:protected] => Array
(
)
)
[70] => Category Object
(
[languages:protected] =>
[bok_resources:protected] =>
[bok_topics:protected] =>
[bok_keywords:protected] =>
[id:protected] => 70
[type:protected] => category
[parent:protected] => 2
[label:protected] => Operating Engineer
[alreadyInSave:protected] =>
[alreadyInValidation:protected] =>
[validationFailures:protected] => Array
(
)
[_new:BaseObject:private] =>
[_deleted:BaseObject:private] =>
[modifiedColumns:protected] => Array
(
)
)
[71] => Category Object
(
[languages:protected] =>
[bok_resources:protected] =>
[bok_topics:protected] =>
[bok_keywords:protected] =>
[id:protected] => 71
[type:protected] => category
[parent:protected] => 2
[label:protected] => Painter
[alreadyInSave:protected] =>
[alreadyInValidation:protected] =>
[validationFailures:protected] => Array
(
)
[_new:BaseObject:private] =>
[_deleted:BaseObject:private] =>
[modifiedColumns:protected] => Array
(
)
)
[72] => Category Object
(
[languages:protected] =>
[bok_resources:protected] =>
[bok_topics:protected] =>
[bok_keywords:protected] =>
[id:protected] => 72
[type:protected] => category
[parent:protected] => 2
[label:protected] => Paper Hanger
[alreadyInSave:protected] =>
[alreadyInValidation:protected] =>
[validationFailures:protected] => Array
(
)
[_new:BaseObject:private] =>
[_deleted:BaseObject:private] =>
[modifiedColumns:protected] => Array
(
)
)
[73] => Category Object
(
[languages:protected] =>
[bok_resources:protected] =>
[bok_topics:protected] =>
[bok_keywords:protected] =>
[id:protected] => 73
[type:protected] => category
[parent:protected] => 2
[label:protected] => PCC/Restoration
[alreadyInSave:protected] =>
[alreadyInValidation:protected] =>
[validationFailures:protected] => Array
(
)
[_new:BaseObject:private] =>
[_deleted:BaseObject:private] =>
[modifiedColumns:protected] => Array
(
)
)
[74] => Category Object
(
[languages:protected] =>
[bok_resources:protected] =>
[bok_topics:protected] =>
[bok_keywords:protected] =>
[id:protected] => 74
[type:protected] => category
[parent:protected] => 2
[label:protected] => Pile Driver
[alreadyInSave:protected] =>
[alreadyInValidation:protected] =>
[validationFailures:protected] => Array
(
)
[_new:BaseObject:private] =>
[_deleted:BaseObject:private] =>
[modifiedColumns:protected] => Array
(
)
)
[75] => Category Object
(
[languages:protected] =>
[bok_resources:protected] =>
[bok_topics:protected] =>
[bok_keywords:protected] =>
[id:protected] => 75
[type:protected] => category
[parent:protected] => 2
[label:protected] => Plasterer
[alreadyInSave:protected] =>
[alreadyInValidation:protected] =>
[validationFailures:protected] => Array
(
)
[_new:BaseObject:private] =>
[_deleted:BaseObject:private] =>
[modifiedColumns:protected] => Array
(
)
)
[76] => Category Object
(
[languages:protected] =>
[bok_resources:protected] =>
[bok_topics:protected] =>
[bok_keywords:protected] =>
[id:protected] => 76
[type:protected] => category
[parent:protected] => 2
[label:protected] => Plumber/Pipefitter
[alreadyInSave:protected] =>
[alreadyInValidation:protected] =>
[validationFailures:protected] => Array
(
)
[_new:BaseObject:private] =>
[_deleted:BaseObject:private] =>
[modifiedColumns:protected] => Array
(
)
)
[77] => Category Object
(
[languages:protected] =>
[bok_resources:protected] =>
[bok_topics:protected] =>
[bok_keywords:protected] =>
[id:protected] => 77
[type:protected] => category
[parent:protected] => 2
[label:protected] => Refractory Worker
[alreadyInSave:protected] =>
[alreadyInValidation:protected] =>
[validationFailures:protected] => Array
(
)
[_new:BaseObject:private] =>
[_deleted:BaseObject:private] =>
[modifiedColumns:protected] => Array
(
)
)
[63] => Category Object
(
[languages:protected] =>
[bok_resources:protected] =>
[bok_topics:protected] =>
[bok_keywords:protected] =>
[id:protected] => 63
[type:protected] => category
[parent:protected] => 2
[label:protected] => Reinforcing Ironworker
[alreadyInSave:protected] =>
[alreadyInValidation:protected] =>
[validationFailures:protected] => Array
(
)
[_new:BaseObject:private] =>
[_deleted:BaseObject:private] =>
[modifiedColumns:protected] => Array
(
)
)
[78] => Category Object
(
[languages:protected] =>
[bok_resources:protected] =>
[bok_topics:protected] =>
[bok_keywords:protected] =>
[id:protected] => 78
[type:protected] => category
[parent:protected] => 2
[label:protected] => Roofer/Waterproofer
[alreadyInSave:protected] =>
[alreadyInValidation:protected] =>
[validationFailures:protected] => Array
(
)
[_new:BaseObject:private] =>
[_deleted:BaseObject:private] =>
[modifiedColumns:protected] => Array
(
)
)
[79] => Category Object
(
[languages:protected] =>
[bok_resources:protected] =>
[bok_topics:protected] =>
[bok_keywords:protected] =>
[id:protected] => 79
[type:protected] => category
[parent:protected] => 2
[label:protected] => Scaffold Erector
[alreadyInSave:protected] =>
[alreadyInValidation:protected] =>
[validationFailures:protected] => Array
(
)
[_new:BaseObject:private] =>
[_deleted:BaseObject:private] =>
[modifiedColumns:protected] => Array
(
)
)
[80] => Category Object
(
[languages:protected] =>
[bok_resources:protected] =>
[bok_topics:protected] =>
[bok_keywords:protected] =>
[id:protected] => 80
[type:protected] => category
[parent:protected] => 2
[label:protected] => Sheetmetal Worker
[alreadyInSave:protected] =>
[alreadyInValidation:protected] =>
[validationFailures:protected] => Array
(
)
[_new:BaseObject:private] =>
[_deleted:BaseObject:private] =>
[modifiedColumns:protected] => Array
(
)
)
[81] => Category Object
(
[languages:protected] =>
[bok_resources:protected] =>
[bok_topics:protected] =>
[bok_keywords:protected] =>
[id:protected] => 81
[type:protected] => category
[parent:protected] => 2
[label:protected] => Sprinkler Fitter
[alreadyInSave:protected] =>
[alreadyInValidation:protected] =>
[validationFailures:protected] => Array
(
)
[_new:BaseObject:private] =>
[_deleted:BaseObject:private] =>
[modifiedColumns:protected] => Array
(
)
)
[82] => Category Object
(
[languages:protected] =>
[bok_resources:protected] =>
[bok_topics:protected] =>
[bok_keywords:protected] =>
[id:protected] => 82
[type:protected] => category
[parent:protected] => 2
[label:protected] => Stonemason
[alreadyInSave:protected] =>
[alreadyInValidation:protected] =>
[validationFailures:protected] => Array
(
)
[_new:BaseObject:private] =>
[_deleted:BaseObject:private] =>
[modifiedColumns:protected] => Array
(
)
)
[62] => Category Object
(
[languages:protected] =>
[bok_resources:protected] =>
[bok_topics:protected] =>
[bok_keywords:protected] =>
[id:protected] => 62
[type:protected] => category
[parent:protected] => 2
[label:protected] => Structural Ironworker
[alreadyInSave:protected] =>
[alreadyInValidation:protected] =>
[validationFailures:protected] => Array
(
)
[_new:BaseObject:private] =>
[_deleted:BaseObject:private] =>
[modifiedColumns:protected] => Array
(
)
)
[83] => Category Object
(
[languages:protected] =>
[bok_resources:protected] =>
[bok_topics:protected] =>
[bok_keywords:protected] =>
[id:protected] => 83
[type:protected] => category
[parent:protected] => 2
[label:protected] => Terrazzo Worker
[alreadyInSave:protected] =>
[alreadyInValidation:protected] =>
[validationFailures:protected] => Array
(
)
[_new:BaseObject:private] =>
[_deleted:BaseObject:private] =>
[modifiedColumns:protected] => Array
(
)
)
[84] => Category Object
(
[languages:protected] =>
[bok_resources:protected] =>
[bok_topics:protected] =>
[bok_keywords:protected] =>
[id:protected] => 84
[type:protected] => category
[parent:protected] => 2
[label:protected] => Tile Setter
[alreadyInSave:protected] =>
[alreadyInValidation:protected] =>
[validationFailures:protected] => Array
(
)
[_new:BaseObject:private] =>
[_deleted:BaseObject:private] =>
[modifiedColumns:protected] => Array
(
)
)
[85] => Category Object
(
[languages:protected] =>
[bok_resources:protected] =>
[bok_topics:protected] =>
[bok_keywords:protected] =>
[id:protected] => 85
[type:protected] => category
[parent:protected] => 2
[label:protected] => Truck Driver
[alreadyInSave:protected] =>
[alreadyInValidation:protected] =>
[validationFailures:protected] => Array
(
)
[_new:BaseObject:private] =>
[_deleted:BaseObject:private] =>
[modifiedColumns:protected] => Array
(
)
)
[86] => Category Object
(
[languages:protected] =>
[bok_resources:protected] =>
[bok_topics:protected] =>
[bok_keywords:protected] =>
[id:protected] => 86
[type:protected] => category
[parent:protected] => 2
[label:protected] => Welder
[alreadyInSave:protected] =>
[alreadyInValidation:protected] =>
[validationFailures:protected] => Array
(
)
[_new:BaseObject:private] =>
[_deleted:BaseObject:private] =>
[modifiedColumns:protected] => Array
(
)
)
[87] => Category Object
(
[languages:protected] =>
[bok_resources:protected] =>
[bok_topics:protected] =>
[bok_keywords:protected] =>
[id:protected] => 87
[type:protected] => category
[parent:protected] => 3
[label:protected] => Commercial & Institutional
[alreadyInSave:protected] =>
[alreadyInValidation:protected] =>
[validationFailures:protected] => Array
(
)
[_new:BaseObject:private] =>
[_deleted:BaseObject:private] =>
[modifiedColumns:protected] => Array
(
)
)
[88] => Category Object
(
[languages:protected] =>
[bok_resources:protected] =>
[bok_topics:protected] =>
[bok_keywords:protected] =>
[id:protected] => 88
[type:protected] => category
[parent:protected] => 3
[label:protected] => Demolition
[alreadyInSave:protected] =>
[alreadyInValidation:protected] =>
[validationFailures:protected] => Array
(
)
[_new:BaseObject:private] =>
[_deleted:BaseObject:private] =>
[modifiedColumns:protected] => Array
(
)
)
[89] => Category Object
(
[languages:protected] =>
[bok_resources:protected] =>
[bok_topics:protected] =>
[bok_keywords:protected] =>
[id:protected] => 89
[type:protected] => category
[parent:protected] => 3
[label:protected] => Disasters
[alreadyInSave:protected] =>
[alreadyInValidation:protected] =>
[validationFailures:protected] => Array
(
)
[_new:BaseObject:private] =>
[_deleted:BaseObject:private] =>
[modifiedColumns:protected] => Array
(
)
)
[91] => Category Object
(
[languages:protected] =>
[bok_resources:protected] =>
[bok_topics:protected] =>
[bok_keywords:protected] =>
[id:protected] => 91
[type:protected] => category
[parent:protected] => 3
[label:protected] => Heavy & Highway
[alreadyInSave:protected] =>
[alreadyInValidation:protected] =>
[validationFailures:protected] => Array
(
)
[_new:BaseObject:private] =>
[_deleted:BaseObject:private] =>
[modifiedColumns:protected] => Array
(
)
)
[90] => Category Object
(
[languages:protected] =>
[bok_resources:protected] =>
[bok_topics:protected] =>
[bok_keywords:protected] =>
[id:protected] => 90
[type:protected] => category
[parent:protected] => 3
[label:protected] => Industrial
[alreadyInSave:protected] =>
[alreadyInValidation:protected] =>
[validationFailures:protected] => Array
(
)
[_new:BaseObject:private] =>
[_deleted:BaseObject:private] =>
[modifiedColumns:protected] => Array
(
)
)
[92] => Category Object
(
[languages:protected] =>
[bok_resources:protected] =>
[bok_topics:protected] =>
[bok_keywords:protected] =>
[id:protected] => 92
[type:protected] => category
[parent:protected] => 3
[label:protected] => LEED/Green Construction
[alreadyInSave:protected] =>
[alreadyInValidation:protected] =>
[validationFailures:protected] => Array
(
)
[_new:BaseObject:private] =>
[_deleted:BaseObject:private] =>
[modifiedColumns:protected] => Array
(
)
)
[93] => Category Object
(
[languages:protected] =>
[bok_resources:protected] =>
[bok_topics:protected] =>
[bok_keywords:protected] =>
[id:protected] => 93
[type:protected] => category
[parent:protected] => 3
[label:protected] => Renovations
[alreadyInSave:protected] =>
[alreadyInValidation:protected] =>
[validationFailures:protected] => Array
(
)
[_new:BaseObject:private] =>
[_deleted:BaseObject:private] =>
[modifiedColumns:protected] => Array
(
)
)
[94] => Category Object
(
[languages:protected] =>
[bok_resources:protected] =>
[bok_topics:protected] =>
[bok_keywords:protected] =>
[id:protected] => 94
[type:protected] => category
[parent:protected] => 3
[label:protected] => Residential
[alreadyInSave:protected] =>
[alreadyInValidation:protected] =>
[validationFailures:protected] => Array
(
)
[_new:BaseObject:private] =>
[_deleted:BaseObject:private] =>
[modifiedColumns:protected] => Array
(
)
)
[95] => Category Object
(
[languages:protected] =>
[bok_resources:protected] =>
[bok_topics:protected] =>
[bok_keywords:protected] =>
[id:protected] => 95
[type:protected] => category
[parent:protected] => 3
[label:protected] => Underground
[alreadyInSave:protected] =>
[alreadyInValidation:protected] =>
[validationFailures:protected] => Array
(
)
[_new:BaseObject:private] =>
[_deleted:BaseObject:private] =>
[modifiedColumns:protected] => Array
(
)
)
)
[categories_initialized:protected] => 1
[mapped_items:protected] =>
[content:protected] =>
[files:protected] =>
[language:protected] => Language Object
(
[id:protected] => 1
[code:protected] => en
[name:protected] => English
[alreadyInSave:protected] =>
[alreadyInValidation:protected] =>
[validationFailures:protected] => Array
(
)
[_new:BaseObject:private] =>
[_deleted:BaseObject:private] =>
[modifiedColumns:protected] => Array
(
)
)
[old_record:protected] =>
[id:protected] => 4426
[old_id:protected] =>
[elcosh_id:protected] => d001656
[type:protected] => document
[display_type:protected] => HTML only (and links)
[user_id:protected] => 0
[language_id:protected] => 1
[tagging_id:protected] => Mike Aguilar
[priority_id:protected] => 1
[title:protected] => Construction Dive -- DeWalt's Jobsite Pro headphones recalled for fire hazards
[total_pages:protected] => 1
[billed_pages:protected] => 1
[publication_number:protected] =>
[part_of:protected] =>
[keywords:protected] => DeWalt, Fire Hazards, recall, headphones
[comments:protected] =>
[summary:protected] => A recall notice by the United States Consumer Product Safety Commission affects over 300,000 DeWalt Jobsite Pro Headphones. The recall is a result of a malfunction that can cause earbuds to overheat while charging or during use, leading to fire and burn hazards.
[transition_comments:protected] =>
[external_link:protected] => https://www.constructiondive.com/news/dewalts-jobsite-pro-headphones-recalled-for-fire-hazards/611248/?utm_source=Sailthru&utm_medium=email&utm_campaign=Issue:%202021-12-10%20Construction%20Dive%20Newsletter%20%5Bissue:38532%5D&utm_term=Construction%20Dive
[consol_link:protected] =>
[more_like_this:protected] =>
[permission_given_by:protected] =>
[published:protected] => T
[billable:protected] => F
[img_name:protected] =>
[img_ext:protected] =>
[img_width:protected] =>
[img_height:protected] =>
[img_credit:protected] =>
[img_practice:protected] =>
[vid_source_id:protected] =>
[vid_running_time:protected] =>
[vid_intended_audience:protected] =>
[vid_acquisition_info:protected] =>
[vid_cost:protected] =>
[vid_producer:protected] =>
[vid_filename:protected] =>
[vid_filename_downloadable:protected] =>
[date_summary:protected] =>
[date_permission_requested:protected] =>
[date_permission_received:protected] =>
[date_review_needed:protected] =>
[date_received:protected] => 12/13/21
[date_completed:protected] => 12/13/21
[date_billed:protected] =>
[date_modified:protected] => 12/13/21
[collBokExports:protected] =>
[lastBokExportCriteria:BaseElcoshItem:private] =>
[alreadyInSave:protected] =>
[alreadyInValidation:protected] =>
[validationFailures:protected] => Array
(
)
[_new:BaseObject:private] =>
[_deleted:BaseObject:private] =>
[modifiedColumns:protected] => Array
(
)
)
)
)
[new_images] => Array
(
[0] => Search_Result Object
(
[title] => Morning Toolbox Talk
[image] => /record/images/4003-p.jpg
[blurb] => This photo is from an early morning toolbox talk on a construction job in Mclean, Virginia. It is being delivered in English and Spanish....
[category] => Array
(
[0] => 20
[1] => 51
[2] => 57
[3] => 64
[4] => 70
[5] => 63
[6] => 78
[7] => 82
[8] => 62
[9] => 87
[10] => 88
[11] => 89
[12] => 91
[13] => 90
[14] => 93
[15] => 94
[16] => 97
)
[labels] => Array
(
[0] => Safety Culture
[1] => Work Environment
[2] => Hazards
[3] => Cement Mason
[4] => Trades
[5] => Flagger
[7] => Laborer
[9] => Operating Engineer
[11] => Reinforcing Ironworker
[13] => Roofer/Waterproofer
[15] => Stonemason
[17] => Structural Ironworker
[19] => Commercial & Institutional
[20] => Jobsites
[21] => Demolition
[23] => Disasters
[25] => Heavy & Highway
[27] => Industrial
[29] => Renovations
[31] => Residential
[33] => Images
[34] => Media
[35] => Media & Documents
)
[type] => Images
[sub_category] =>
[url] => /image/4003/i002691/Morning%2BToolbox%2BTalk.html
[item:protected] => ImageRecord Object
(
[records:protected] => Array
(
)
[recordId:protected] =>
[searchWordClass:protected] =>
[searchWordPeerClass:protected] =>
[bok_record:protected] =>
[authors:protected] =>
[organizations:protected] =>
[collections:protected] =>
[categories:protected] => Array
(
[20] => Category Object
(
[languages:protected] =>
[bok_resources:protected] =>
[bok_topics:protected] =>
[bok_keywords:protected] =>
[id:protected] => 20
[type:protected] => category
[parent:protected] => 7
[label:protected] => Safety Culture
[alreadyInSave:protected] =>
[alreadyInValidation:protected] =>
[validationFailures:protected] => Array
(
)
[_new:BaseObject:private] =>
[_deleted:BaseObject:private] =>
[modifiedColumns:protected] => Array
(
)
)
[51] => Category Object
(
[languages:protected] =>
[bok_resources:protected] =>
[bok_topics:protected] =>
[bok_keywords:protected] =>
[id:protected] => 51
[type:protected] => category
[parent:protected] => 2
[label:protected] => Cement Mason
[alreadyInSave:protected] =>
[alreadyInValidation:protected] =>
[validationFailures:protected] => Array
(
)
[_new:BaseObject:private] =>
[_deleted:BaseObject:private] =>
[modifiedColumns:protected] => Array
(
)
)
[57] => Category Object
(
[languages:protected] =>
[bok_resources:protected] =>
[bok_topics:protected] =>
[bok_keywords:protected] =>
[id:protected] => 57
[type:protected] => category
[parent:protected] => 2
[label:protected] => Flagger
[alreadyInSave:protected] =>
[alreadyInValidation:protected] =>
[validationFailures:protected] => Array
(
)
[_new:BaseObject:private] =>
[_deleted:BaseObject:private] =>
[modifiedColumns:protected] => Array
(
)
)
[64] => Category Object
(
[languages:protected] =>
[bok_resources:protected] =>
[bok_topics:protected] =>
[bok_keywords:protected] =>
[id:protected] => 64
[type:protected] => category
[parent:protected] => 2
[label:protected] => Laborer
[alreadyInSave:protected] =>
[alreadyInValidation:protected] =>
[validationFailures:protected] => Array
(
)
[_new:BaseObject:private] =>
[_deleted:BaseObject:private] =>
[modifiedColumns:protected] => Array
(
)
)
[70] => Category Object
(
[languages:protected] =>
[bok_resources:protected] =>
[bok_topics:protected] =>
[bok_keywords:protected] =>
[id:protected] => 70
[type:protected] => category
[parent:protected] => 2
[label:protected] => Operating Engineer
[alreadyInSave:protected] =>
[alreadyInValidation:protected] =>
[validationFailures:protected] => Array
(
)
[_new:BaseObject:private] =>
[_deleted:BaseObject:private] =>
[modifiedColumns:protected] => Array
(
)
)
[63] => Category Object
(
[languages:protected] =>
[bok_resources:protected] =>
[bok_topics:protected] =>
[bok_keywords:protected] =>
[id:protected] => 63
[type:protected] => category
[parent:protected] => 2
[label:protected] => Reinforcing Ironworker
[alreadyInSave:protected] =>
[alreadyInValidation:protected] =>
[validationFailures:protected] => Array
(
)
[_new:BaseObject:private] =>
[_deleted:BaseObject:private] =>
[modifiedColumns:protected] => Array
(
)
)
[78] => Category Object
(
[languages:protected] =>
[bok_resources:protected] =>
[bok_topics:protected] =>
[bok_keywords:protected] =>
[id:protected] => 78
[type:protected] => category
[parent:protected] => 2
[label:protected] => Roofer/Waterproofer
[alreadyInSave:protected] =>
[alreadyInValidation:protected] =>
[validationFailures:protected] => Array
(
)
[_new:BaseObject:private] =>
[_deleted:BaseObject:private] =>
[modifiedColumns:protected] => Array
(
)
)
[82] => Category Object
(
[languages:protected] =>
[bok_resources:protected] =>
[bok_topics:protected] =>
[bok_keywords:protected] =>
[id:protected] => 82
[type:protected] => category
[parent:protected] => 2
[label:protected] => Stonemason
[alreadyInSave:protected] =>
[alreadyInValidation:protected] =>
[validationFailures:protected] => Array
(
)
[_new:BaseObject:private] =>
[_deleted:BaseObject:private] =>
[modifiedColumns:protected] => Array
(
)
)
[62] => Category Object
(
[languages:protected] =>
[bok_resources:protected] =>
[bok_topics:protected] =>
[bok_keywords:protected] =>
[id:protected] => 62
[type:protected] => category
[parent:protected] => 2
[label:protected] => Structural Ironworker
[alreadyInSave:protected] =>
[alreadyInValidation:protected] =>
[validationFailures:protected] => Array
(
)
[_new:BaseObject:private] =>
[_deleted:BaseObject:private] =>
[modifiedColumns:protected] => Array
(
)
)
[87] => Category Object
(
[languages:protected] =>
[bok_resources:protected] =>
[bok_topics:protected] =>
[bok_keywords:protected] =>
[id:protected] => 87
[type:protected] => category
[parent:protected] => 3
[label:protected] => Commercial & Institutional
[alreadyInSave:protected] =>
[alreadyInValidation:protected] =>
[validationFailures:protected] => Array
(
)
[_new:BaseObject:private] =>
[_deleted:BaseObject:private] =>
[modifiedColumns:protected] => Array
(
)
)
[88] => Category Object
(
[languages:protected] =>
[bok_resources:protected] =>
[bok_topics:protected] =>
[bok_keywords:protected] =>
[id:protected] => 88
[type:protected] => category
[parent:protected] => 3
[label:protected] => Demolition
[alreadyInSave:protected] =>
[alreadyInValidation:protected] =>
[validationFailures:protected] => Array
(
)
[_new:BaseObject:private] =>
[_deleted:BaseObject:private] =>
[modifiedColumns:protected] => Array
(
)
)
[89] => Category Object
(
[languages:protected] =>
[bok_resources:protected] =>
[bok_topics:protected] =>
[bok_keywords:protected] =>
[id:protected] => 89
[type:protected] => category
[parent:protected] => 3
[label:protected] => Disasters
[alreadyInSave:protected] =>
[alreadyInValidation:protected] =>
[validationFailures:protected] => Array
(
)
[_new:BaseObject:private] =>
[_deleted:BaseObject:private] =>
[modifiedColumns:protected] => Array
(
)
)
[91] => Category Object
(
[languages:protected] =>
[bok_resources:protected] =>
[bok_topics:protected] =>
[bok_keywords:protected] =>
[id:protected] => 91
[type:protected] => category
[parent:protected] => 3
[label:protected] => Heavy & Highway
[alreadyInSave:protected] =>
[alreadyInValidation:protected] =>
[validationFailures:protected] => Array
(
)
[_new:BaseObject:private] =>
[_deleted:BaseObject:private] =>
[modifiedColumns:protected] => Array
(
)
)
[90] => Category Object
(
[languages:protected] =>
[bok_resources:protected] =>
[bok_topics:protected] =>
[bok_keywords:protected] =>
[id:protected] => 90
[type:protected] => category
[parent:protected] => 3
[label:protected] => Industrial
[alreadyInSave:protected] =>
[alreadyInValidation:protected] =>
[validationFailures:protected] => Array
(
)
[_new:BaseObject:private] =>
[_deleted:BaseObject:private] =>
[modifiedColumns:protected] => Array
(
)
)
[93] => Category Object
(
[languages:protected] =>
[bok_resources:protected] =>
[bok_topics:protected] =>
[bok_keywords:protected] =>
[id:protected] => 93
[type:protected] => category
[parent:protected] => 3
[label:protected] => Renovations
[alreadyInSave:protected] =>
[alreadyInValidation:protected] =>
[validationFailures:protected] => Array
(
)
[_new:BaseObject:private] =>
[_deleted:BaseObject:private] =>
[modifiedColumns:protected] => Array
(
)
)
[94] => Category Object
(
[languages:protected] =>
[bok_resources:protected] =>
[bok_topics:protected] =>
[bok_keywords:protected] =>
[id:protected] => 94
[type:protected] => category
[parent:protected] => 3
[label:protected] => Residential
[alreadyInSave:protected] =>
[alreadyInValidation:protected] =>
[validationFailures:protected] => Array
(
)
[_new:BaseObject:private] =>
[_deleted:BaseObject:private] =>
[modifiedColumns:protected] => Array
(
)
)
[97] => Category Object
(
[languages:protected] =>
[bok_resources:protected] =>
[bok_topics:protected] =>
[bok_keywords:protected] =>
[id:protected] => 97
[type:protected] => category
[parent:protected] => 5
[label:protected] => Images
[alreadyInSave:protected] =>
[alreadyInValidation:protected] =>
[validationFailures:protected] => Array
(
)
[_new:BaseObject:private] =>
[_deleted:BaseObject:private] =>
[modifiedColumns:protected] => Array
(
)
)
)
[categories_initialized:protected] => 1
[mapped_items:protected] =>
[content:protected] =>
[files:protected] =>
[language:protected] => Language Object
(
[id:protected] => 1
[code:protected] => en
[name:protected] => English
[alreadyInSave:protected] =>
[alreadyInValidation:protected] =>
[validationFailures:protected] => Array
(
)
[_new:BaseObject:private] =>
[_deleted:BaseObject:private] =>
[modifiedColumns:protected] => Array
(
)
)
[old_record:protected] =>
[id:protected] => 4003
[old_id:protected] =>
[elcosh_id:protected] => i002691
[type:protected] => image
[display_type:protected] => Image
[user_id:protected] => 0
[language_id:protected] => 1
[tagging_id:protected] => Bruce Lippy
[priority_id:protected] => 1
[title:protected] => Morning Toolbox Talk
[total_pages:protected] => 0
[billed_pages:protected] => 0
[publication_number:protected] =>
[part_of:protected] =>
[keywords:protected] => toolbox talk, tailgate talk, Spanish, bilingual
[comments:protected] =>
[summary:protected] => This photo is from an early morning toolbox talk on a construction job in Mclean, Virginia. It is being delivered in English and Spanish.
[transition_comments:protected] =>
[external_link:protected] =>
[consol_link:protected] => http://www.cpwrconstructionsolutions.org/electrical/solution/662/worker-training.html
[more_like_this:protected] => d001285,d001304,c000079
[permission_given_by:protected] =>
[published:protected] => T
[billable:protected] => F
[img_name:protected] =>
[img_ext:protected] => jpg
[img_width:protected] =>
[img_height:protected] =>
[img_credit:protected] => Morgan Zavertnik and Hoar Construction
[img_practice:protected] => good
[vid_source_id:protected] =>
[vid_running_time:protected] =>
[vid_intended_audience:protected] =>
[vid_acquisition_info:protected] =>
[vid_cost:protected] =>
[vid_producer:protected] =>
[vid_filename:protected] =>
[vid_filename_downloadable:protected] =>
[date_summary:protected] => November 2015
[date_permission_requested:protected] =>
[date_permission_received:protected] =>
[date_review_needed:protected] =>
[date_received:protected] => 03/02/16
[date_completed:protected] => 03/02/16
[date_billed:protected] =>
[date_modified:protected] => 03/02/16
[collBokExports:protected] =>
[lastBokExportCriteria:BaseElcoshItem:private] =>
[alreadyInSave:protected] =>
[alreadyInValidation:protected] =>
[validationFailures:protected] => Array
(
)
[_new:BaseObject:private] =>
[_deleted:BaseObject:private] =>
[modifiedColumns:protected] => Array
(
)
)
)
[1] => Search_Result Object
(
[title] => Toolbox talk - crew view
[image] => /record/images/4005-p.jpg
[blurb] => Photo of crew listening to a toolbox safety talk before starting work....
[category] => Array
(
[0] => 97
[1] => 20
[2] => 47
[3] => 49
[4] => 51
[5] => 55
[6] => 61
[7] => 64
[8] => 71
[9] => 75
[10] => 63
[11] => 79
[12] => 62
[13] => 87
[14] => 88
[15] => 91
[16] => 90
[17] => 93
[18] => 94
[19] => 95
)
[labels] => Array
(
[0] => Images
[1] => Media
[2] => Media & Documents
[3] => Safety Culture
[4] => Work Environment
[5] => Hazards
[6] => Bricklayer
[7] => Trades
[8] => Carpenter
[10] => Cement Mason
[12] => Electrical Worker
[14] => Interior Systems Carpenter
[16] => Laborer
[18] => Painter
[20] => Plasterer
[22] => Reinforcing Ironworker
[24] => Scaffold Erector
[26] => Structural Ironworker
[28] => Commercial & Institutional
[29] => Jobsites
[30] => Demolition
[32] => Heavy & Highway
[34] => Industrial
[36] => Renovations
[38] => Residential
[40] => Underground
)
[type] => Images
[sub_category] =>
[url] => /image/4005/i002692/Toolbox%2Btalk%2B-%2Bcrew%2Bview.html
[item:protected] => ImageRecord Object
(
[records:protected] => Array
(
)
[recordId:protected] =>
[searchWordClass:protected] =>
[searchWordPeerClass:protected] =>
[bok_record:protected] =>
[authors:protected] =>
[organizations:protected] =>
[collections:protected] =>
[categories:protected] => Array
(
[97] => Category Object
(
[languages:protected] =>
[bok_resources:protected] =>
[bok_topics:protected] =>
[bok_keywords:protected] =>
[id:protected] => 97
[type:protected] => category
[parent:protected] => 5
[label:protected] => Images
[alreadyInSave:protected] =>
[alreadyInValidation:protected] =>
[validationFailures:protected] => Array
(
)
[_new:BaseObject:private] =>
[_deleted:BaseObject:private] =>
[modifiedColumns:protected] => Array
(
)
)
[20] => Category Object
(
[languages:protected] =>
[bok_resources:protected] =>
[bok_topics:protected] =>
[bok_keywords:protected] =>
[id:protected] => 20
[type:protected] => category
[parent:protected] => 7
[label:protected] => Safety Culture
[alreadyInSave:protected] =>
[alreadyInValidation:protected] =>
[validationFailures:protected] => Array
(
)
[_new:BaseObject:private] =>
[_deleted:BaseObject:private] =>
[modifiedColumns:protected] => Array
(
)
)
[47] => Category Object
(
[languages:protected] =>
[bok_resources:protected] =>
[bok_topics:protected] =>
[bok_keywords:protected] =>
[id:protected] => 47
[type:protected] => category
[parent:protected] => 2
[label:protected] => Bricklayer
[alreadyInSave:protected] =>
[alreadyInValidation:protected] =>
[validationFailures:protected] => Array
(
)
[_new:BaseObject:private] =>
[_deleted:BaseObject:private] =>
[modifiedColumns:protected] => Array
(
)
)
[49] => Category Object
(
[languages:protected] =>
[bok_resources:protected] =>
[bok_topics:protected] =>
[bok_keywords:protected] =>
[id:protected] => 49
[type:protected] => category
[parent:protected] => 2
[label:protected] => Carpenter
[alreadyInSave:protected] =>
[alreadyInValidation:protected] =>
[validationFailures:protected] => Array
(
)
[_new:BaseObject:private] =>
[_deleted:BaseObject:private] =>
[modifiedColumns:protected] => Array
(
)
)
[51] => Category Object
(
[languages:protected] =>
[bok_resources:protected] =>
[bok_topics:protected] =>
[bok_keywords:protected] =>
[id:protected] => 51
[type:protected] => category
[parent:protected] => 2
[label:protected] => Cement Mason
[alreadyInSave:protected] =>
[alreadyInValidation:protected] =>
[validationFailures:protected] => Array
(
)
[_new:BaseObject:private] =>
[_deleted:BaseObject:private] =>
[modifiedColumns:protected] => Array
(
)
)
[55] => Category Object
(
[languages:protected] =>
[bok_resources:protected] =>
[bok_topics:protected] =>
[bok_keywords:protected] =>
[id:protected] => 55
[type:protected] => category
[parent:protected] => 2
[label:protected] => Electrical Worker
[alreadyInSave:protected] =>
[alreadyInValidation:protected] =>
[validationFailures:protected] => Array
(
)
[_new:BaseObject:private] =>
[_deleted:BaseObject:private] =>
[modifiedColumns:protected] => Array
(
)
)
[61] => Category Object
(
[languages:protected] =>
[bok_resources:protected] =>
[bok_topics:protected] =>
[bok_keywords:protected] =>
[id:protected] => 61
[type:protected] => category
[parent:protected] => 2
[label:protected] => Interior Systems Carpenter
[alreadyInSave:protected] =>
[alreadyInValidation:protected] =>
[validationFailures:protected] => Array
(
)
[_new:BaseObject:private] =>
[_deleted:BaseObject:private] =>
[modifiedColumns:protected] => Array
(
)
)
[64] => Category Object
(
[languages:protected] =>
[bok_resources:protected] =>
[bok_topics:protected] =>
[bok_keywords:protected] =>
[id:protected] => 64
[type:protected] => category
[parent:protected] => 2
[label:protected] => Laborer
[alreadyInSave:protected] =>
[alreadyInValidation:protected] =>
[validationFailures:protected] => Array
(
)
[_new:BaseObject:private] =>
[_deleted:BaseObject:private] =>
[modifiedColumns:protected] => Array
(
)
)
[71] => Category Object
(
[languages:protected] =>
[bok_resources:protected] =>
[bok_topics:protected] =>
[bok_keywords:protected] =>
[id:protected] => 71
[type:protected] => category
[parent:protected] => 2
[label:protected] => Painter
[alreadyInSave:protected] =>
[alreadyInValidation:protected] =>
[validationFailures:protected] => Array
(
)
[_new:BaseObject:private] =>
[_deleted:BaseObject:private] =>
[modifiedColumns:protected] => Array
(
)
)
[75] => Category Object
(
[languages:protected] =>
[bok_resources:protected] =>
[bok_topics:protected] =>
[bok_keywords:protected] =>
[id:protected] => 75
[type:protected] => category
[parent:protected] => 2
[label:protected] => Plasterer
[alreadyInSave:protected] =>
[alreadyInValidation:protected] =>
[validationFailures:protected] => Array
(
)
[_new:BaseObject:private] =>
[_deleted:BaseObject:private] =>
[modifiedColumns:protected] => Array
(
)
)
[63] => Category Object
(
[languages:protected] =>
[bok_resources:protected] =>
[bok_topics:protected] =>
[bok_keywords:protected] =>
[id:protected] => 63
[type:protected] => category
[parent:protected] => 2
[label:protected] => Reinforcing Ironworker
[alreadyInSave:protected] =>
[alreadyInValidation:protected] =>
[validationFailures:protected] => Array
(
)
[_new:BaseObject:private] =>
[_deleted:BaseObject:private] =>
[modifiedColumns:protected] => Array
(
)
)
[79] => Category Object
(
[languages:protected] =>
[bok_resources:protected] =>
[bok_topics:protected] =>
[bok_keywords:protected] =>
[id:protected] => 79
[type:protected] => category
[parent:protected] => 2
[label:protected] => Scaffold Erector
[alreadyInSave:protected] =>
[alreadyInValidation:protected] =>
[validationFailures:protected] => Array
(
)
[_new:BaseObject:private] =>
[_deleted:BaseObject:private] =>
[modifiedColumns:protected] => Array
(
)
)
[62] => Category Object
(
[languages:protected] =>
[bok_resources:protected] =>
[bok_topics:protected] =>
[bok_keywords:protected] =>
[id:protected] => 62
[type:protected] => category
[parent:protected] => 2
[label:protected] => Structural Ironworker
[alreadyInSave:protected] =>
[alreadyInValidation:protected] =>
[validationFailures:protected] => Array
(
)
[_new:BaseObject:private] =>
[_deleted:BaseObject:private] =>
[modifiedColumns:protected] => Array
(
)
)
[87] => Category Object
(
[languages:protected] =>
[bok_resources:protected] =>
[bok_topics:protected] =>
[bok_keywords:protected] =>
[id:protected] => 87
[type:protected] => category
[parent:protected] => 3
[label:protected] => Commercial & Institutional
[alreadyInSave:protected] =>
[alreadyInValidation:protected] =>
[validationFailures:protected] => Array
(
)
[_new:BaseObject:private] =>
[_deleted:BaseObject:private] =>
[modifiedColumns:protected] => Array
(
)
)
[88] => Category Object
(
[languages:protected] =>
[bok_resources:protected] =>
[bok_topics:protected] =>
[bok_keywords:protected] =>
[id:protected] => 88
[type:protected] => category
[parent:protected] => 3
[label:protected] => Demolition
[alreadyInSave:protected] =>
[alreadyInValidation:protected] =>
[validationFailures:protected] => Array
(
)
[_new:BaseObject:private] =>
[_deleted:BaseObject:private] =>
[modifiedColumns:protected] => Array
(
)
)
[91] => Category Object
(
[languages:protected] =>
[bok_resources:protected] =>
[bok_topics:protected] =>
[bok_keywords:protected] =>
[id:protected] => 91
[type:protected] => category
[parent:protected] => 3
[label:protected] => Heavy & Highway
[alreadyInSave:protected] =>
[alreadyInValidation:protected] =>
[validationFailures:protected] => Array
(
)
[_new:BaseObject:private] =>
[_deleted:BaseObject:private] =>
[modifiedColumns:protected] => Array
(
)
)
[90] => Category Object
(
[languages:protected] =>
[bok_resources:protected] =>
[bok_topics:protected] =>
[bok_keywords:protected] =>
[id:protected] => 90
[type:protected] => category
[parent:protected] => 3
[label:protected] => Industrial
[alreadyInSave:protected] =>
[alreadyInValidation:protected] =>
[validationFailures:protected] => Array
(
)
[_new:BaseObject:private] =>
[_deleted:BaseObject:private] =>
[modifiedColumns:protected] => Array
(
)
)
[93] => Category Object
(
[languages:protected] =>
[bok_resources:protected] =>
[bok_topics:protected] =>
[bok_keywords:protected] =>
[id:protected] => 93
[type:protected] => category
[parent:protected] => 3
[label:protected] => Renovations
[alreadyInSave:protected] =>
[alreadyInValidation:protected] =>
[validationFailures:protected] => Array
(
)
[_new:BaseObject:private] =>
[_deleted:BaseObject:private] =>
[modifiedColumns:protected] => Array
(
)
)
[94] => Category Object
(
[languages:protected] =>
[bok_resources:protected] =>
[bok_topics:protected] =>
[bok_keywords:protected] =>
[id:protected] => 94
[type:protected] => category
[parent:protected] => 3
[label:protected] => Residential
[alreadyInSave:protected] =>
[alreadyInValidation:protected] =>
[validationFailures:protected] => Array
(
)
[_new:BaseObject:private] =>
[_deleted:BaseObject:private] =>
[modifiedColumns:protected] => Array
(
)
)
[95] => Category Object
(
[languages:protected] =>
[bok_resources:protected] =>
[bok_topics:protected] =>
[bok_keywords:protected] =>
[id:protected] => 95
[type:protected] => category
[parent:protected] => 3
[label:protected] => Underground
[alreadyInSave:protected] =>
[alreadyInValidation:protected] =>
[validationFailures:protected] => Array
(
)
[_new:BaseObject:private] =>
[_deleted:BaseObject:private] =>
[modifiedColumns:protected] => Array
(
)
)
)
[categories_initialized:protected] => 1
[mapped_items:protected] =>
[content:protected] =>
[files:protected] =>
[language:protected] => Language Object
(
[id:protected] => 1
[code:protected] => en
[name:protected] => English
[alreadyInSave:protected] =>
[alreadyInValidation:protected] =>
[validationFailures:protected] => Array
(
)
[_new:BaseObject:private] =>
[_deleted:BaseObject:private] =>
[modifiedColumns:protected] => Array
(
)
)
[old_record:protected] =>
[id:protected] => 4005
[old_id:protected] =>
[elcosh_id:protected] => i002692
[type:protected] => image
[display_type:protected] => Image
[user_id:protected] => 0
[language_id:protected] => 1
[tagging_id:protected] => Bruce Lippy
[priority_id:protected] => 1
[title:protected] => Toolbox talk - crew view
[total_pages:protected] => 0
[billed_pages:protected] => 0
[publication_number:protected] =>
[part_of:protected] =>
[keywords:protected] => toolbox talk, tailgate talk, safety talk, Spanish
[comments:protected] =>
[summary:protected] => Photo of crew listening to a toolbox safety talk before starting work.
[transition_comments:protected] =>
[external_link:protected] =>
[consol_link:protected] => http://www.cpwrconstructionsolutions.org/electrical/solution/662/worker-training.html
[more_like_this:protected] => i002691,d001269, c000079, d001285
[permission_given_by:protected] =>
[published:protected] => T
[billable:protected] => F
[img_name:protected] =>
[img_ext:protected] => jpg
[img_width:protected] =>
[img_height:protected] =>
[img_credit:protected] => Morgan Zavertnik and Hoar Construction
[img_practice:protected] => good
[vid_source_id:protected] =>
[vid_running_time:protected] =>
[vid_intended_audience:protected] =>
[vid_acquisition_info:protected] =>
[vid_cost:protected] =>
[vid_producer:protected] =>
[vid_filename:protected] =>
[vid_filename_downloadable:protected] =>
[date_summary:protected] => November 2015
[date_permission_requested:protected] =>
[date_permission_received:protected] =>
[date_review_needed:protected] =>
[date_received:protected] => 03/02/16
[date_completed:protected] => 03/02/16
[date_billed:protected] =>
[date_modified:protected] => 03/02/16
[collBokExports:protected] =>
[lastBokExportCriteria:BaseElcoshItem:private] =>
[alreadyInSave:protected] =>
[alreadyInValidation:protected] =>
[validationFailures:protected] => Array
(
)
[_new:BaseObject:private] =>
[_deleted:BaseObject:private] =>
[modifiedColumns:protected] => Array
(
)
)
)
[2] => Search_Result Object
(
[title] => Toolbox talk - long shot
[image] => /record/images/4006-p.jpg
[blurb] => This crew gathered every morning before starting work to discuss a new safety topic....
[category] => Array
(
[0] => 20
[1] => 47
[2] => 49
[3] => 51
[4] => 55
[5] => 64
[6] => 68
[7] => 75
[8] => 76
[9] => 63
[10] => 78
[11] => 79
[12] => 82
[13] => 62
[14] => 87
[15] => 88
[16] => 91
[17] => 90
[18] => 93
[19] => 94
[20] => 95
[21] => 97
)
[labels] => Array
(
[0] => Safety Culture
[1] => Work Environment
[2] => Hazards
[3] => Bricklayer
[4] => Trades
[5] => Carpenter
[7] => Cement Mason
[9] => Electrical Worker
[11] => Laborer
[13] => Maintenance Worker
[15] => Plasterer
[17] => Plumber/Pipefitter
[19] => Reinforcing Ironworker
[21] => Roofer/Waterproofer
[23] => Scaffold Erector
[25] => Stonemason
[27] => Structural Ironworker
[29] => Commercial & Institutional
[30] => Jobsites
[31] => Demolition
[33] => Heavy & Highway
[35] => Industrial
[37] => Renovations
[39] => Residential
[41] => Underground
[43] => Images
[44] => Media
[45] => Media & Documents
)
[type] => Images
[sub_category] =>
[url] => /image/4006/i002693/Toolbox%2Btalk%2B-%2Blong%2Bshot.html
[item:protected] => ImageRecord Object
(
[records:protected] => Array
(
)
[recordId:protected] =>
[searchWordClass:protected] =>
[searchWordPeerClass:protected] =>
[bok_record:protected] =>
[authors:protected] =>
[organizations:protected] =>
[collections:protected] =>
[categories:protected] => Array
(
[20] => Category Object
(
[languages:protected] =>
[bok_resources:protected] =>
[bok_topics:protected] =>
[bok_keywords:protected] =>
[id:protected] => 20
[type:protected] => category
[parent:protected] => 7
[label:protected] => Safety Culture
[alreadyInSave:protected] =>
[alreadyInValidation:protected] =>
[validationFailures:protected] => Array
(
)
[_new:BaseObject:private] =>
[_deleted:BaseObject:private] =>
[modifiedColumns:protected] => Array
(
)
)
[47] => Category Object
(
[languages:protected] =>
[bok_resources:protected] =>
[bok_topics:protected] =>
[bok_keywords:protected] =>
[id:protected] => 47
[type:protected] => category
[parent:protected] => 2
[label:protected] => Bricklayer
[alreadyInSave:protected] =>
[alreadyInValidation:protected] =>
[validationFailures:protected] => Array
(
)
[_new:BaseObject:private] =>
[_deleted:BaseObject:private] =>
[modifiedColumns:protected] => Array
(
)
)
[49] => Category Object
(
[languages:protected] =>
[bok_resources:protected] =>
[bok_topics:protected] =>
[bok_keywords:protected] =>
[id:protected] => 49
[type:protected] => category
[parent:protected] => 2
[label:protected] => Carpenter
[alreadyInSave:protected] =>
[alreadyInValidation:protected] =>
[validationFailures:protected] => Array
(
)
[_new:BaseObject:private] =>
[_deleted:BaseObject:private] =>
[modifiedColumns:protected] => Array
(
)
)
[51] => Category Object
(
[languages:protected] =>
[bok_resources:protected] =>
[bok_topics:protected] =>
[bok_keywords:protected] =>
[id:protected] => 51
[type:protected] => category
[parent:protected] => 2
[label:protected] => Cement Mason
[alreadyInSave:protected] =>
[alreadyInValidation:protected] =>
[validationFailures:protected] => Array
(
)
[_new:BaseObject:private] =>
[_deleted:BaseObject:private] =>
[modifiedColumns:protected] => Array
(
)
)
[55] => Category Object
(
[languages:protected] =>
[bok_resources:protected] =>
[bok_topics:protected] =>
[bok_keywords:protected] =>
[id:protected] => 55
[type:protected] => category
[parent:protected] => 2
[label:protected] => Electrical Worker
[alreadyInSave:protected] =>
[alreadyInValidation:protected] =>
[validationFailures:protected] => Array
(
)
[_new:BaseObject:private] =>
[_deleted:BaseObject:private] =>
[modifiedColumns:protected] => Array
(
)
)
[64] => Category Object
(
[languages:protected] =>
[bok_resources:protected] =>
[bok_topics:protected] =>
[bok_keywords:protected] =>
[id:protected] => 64
[type:protected] => category
[parent:protected] => 2
[label:protected] => Laborer
[alreadyInSave:protected] =>
[alreadyInValidation:protected] =>
[validationFailures:protected] => Array
(
)
[_new:BaseObject:private] =>
[_deleted:BaseObject:private] =>
[modifiedColumns:protected] => Array
(
)
)
[68] => Category Object
(
[languages:protected] =>
[bok_resources:protected] =>
[bok_topics:protected] =>
[bok_keywords:protected] =>
[id:protected] => 68
[type:protected] => category
[parent:protected] => 2
[label:protected] => Maintenance Worker
[alreadyInSave:protected] =>
[alreadyInValidation:protected] =>
[validationFailures:protected] => Array
(
)
[_new:BaseObject:private] =>
[_deleted:BaseObject:private] =>
[modifiedColumns:protected] => Array
(
)
)
[75] => Category Object
(
[languages:protected] =>
[bok_resources:protected] =>
[bok_topics:protected] =>
[bok_keywords:protected] =>
[id:protected] => 75
[type:protected] => category
[parent:protected] => 2
[label:protected] => Plasterer
[alreadyInSave:protected] =>
[alreadyInValidation:protected] =>
[validationFailures:protected] => Array
(
)
[_new:BaseObject:private] =>
[_deleted:BaseObject:private] =>
[modifiedColumns:protected] => Array
(
)
)
[76] => Category Object
(
[languages:protected] =>
[bok_resources:protected] =>
[bok_topics:protected] =>
[bok_keywords:protected] =>
[id:protected] => 76
[type:protected] => category
[parent:protected] => 2
[label:protected] => Plumber/Pipefitter
[alreadyInSave:protected] =>
[alreadyInValidation:protected] =>
[validationFailures:protected] => Array
(
)
[_new:BaseObject:private] =>
[_deleted:BaseObject:private] =>
[modifiedColumns:protected] => Array
(
)
)
[63] => Category Object
(
[languages:protected] =>
[bok_resources:protected] =>
[bok_topics:protected] =>
[bok_keywords:protected] =>
[id:protected] => 63
[type:protected] => category
[parent:protected] => 2
[label:protected] => Reinforcing Ironworker
[alreadyInSave:protected] =>
[alreadyInValidation:protected] =>
[validationFailures:protected] => Array
(
)
[_new:BaseObject:private] =>
[_deleted:BaseObject:private] =>
[modifiedColumns:protected] => Array
(
)
)
[78] => Category Object
(
[languages:protected] =>
[bok_resources:protected] =>
[bok_topics:protected] =>
[bok_keywords:protected] =>
[id:protected] => 78
[type:protected] => category
[parent:protected] => 2
[label:protected] => Roofer/Waterproofer
[alreadyInSave:protected] =>
[alreadyInValidation:protected] =>
[validationFailures:protected] => Array
(
)
[_new:BaseObject:private] =>
[_deleted:BaseObject:private] =>
[modifiedColumns:protected] => Array
(
)
)
[79] => Category Object
(
[languages:protected] =>
[bok_resources:protected] =>
[bok_topics:protected] =>
[bok_keywords:protected] =>
[id:protected] => 79
[type:protected] => category
[parent:protected] => 2
[label:protected] => Scaffold Erector
[alreadyInSave:protected] =>
[alreadyInValidation:protected] =>
[validationFailures:protected] => Array
(
)
[_new:BaseObject:private] =>
[_deleted:BaseObject:private] =>
[modifiedColumns:protected] => Array
(
)
)
[82] => Category Object
(
[languages:protected] =>
[bok_resources:protected] =>
[bok_topics:protected] =>
[bok_keywords:protected] =>
[id:protected] => 82
[type:protected] => category
[parent:protected] => 2
[label:protected] => Stonemason
[alreadyInSave:protected] =>
[alreadyInValidation:protected] =>
[validationFailures:protected] => Array
(
)
[_new:BaseObject:private] =>
[_deleted:BaseObject:private] =>
[modifiedColumns:protected] => Array
(
)
)
[62] => Category Object
(
[languages:protected] =>
[bok_resources:protected] =>
[bok_topics:protected] =>
[bok_keywords:protected] =>
[id:protected] => 62
[type:protected] => category
[parent:protected] => 2
[label:protected] => Structural Ironworker
[alreadyInSave:protected] =>
[alreadyInValidation:protected] =>
[validationFailures:protected] => Array
(
)
[_new:BaseObject:private] =>
[_deleted:BaseObject:private] =>
[modifiedColumns:protected] => Array
(
)
)
[87] => Category Object
(
[languages:protected] =>
[bok_resources:protected] =>
[bok_topics:protected] =>
[bok_keywords:protected] =>
[id:protected] => 87
[type:protected] => category
[parent:protected] => 3
[label:protected] => Commercial & Institutional
[alreadyInSave:protected] =>
[alreadyInValidation:protected] =>
[validationFailures:protected] => Array
(
)
[_new:BaseObject:private] =>
[_deleted:BaseObject:private] =>
[modifiedColumns:protected] => Array
(
)
)
[88] => Category Object
(
[languages:protected] =>
[bok_resources:protected] =>
[bok_topics:protected] =>
[bok_keywords:protected] =>
[id:protected] => 88
[type:protected] => category
[parent:protected] => 3
[label:protected] => Demolition
[alreadyInSave:protected] =>
[alreadyInValidation:protected] =>
[validationFailures:protected] => Array
(
)
[_new:BaseObject:private] =>
[_deleted:BaseObject:private] =>
[modifiedColumns:protected] => Array
(
)
)
[91] => Category Object
(
[languages:protected] =>
[bok_resources:protected] =>
[bok_topics:protected] =>
[bok_keywords:protected] =>
[id:protected] => 91
[type:protected] => category
[parent:protected] => 3
[label:protected] => Heavy & Highway
[alreadyInSave:protected] =>
[alreadyInValidation:protected] =>
[validationFailures:protected] => Array
(
)
[_new:BaseObject:private] =>
[_deleted:BaseObject:private] =>
[modifiedColumns:protected] => Array
(
)
)
[90] => Category Object
(
[languages:protected] =>
[bok_resources:protected] =>
[bok_topics:protected] =>
[bok_keywords:protected] =>
[id:protected] => 90
[type:protected] => category
[parent:protected] => 3
[label:protected] => Industrial
[alreadyInSave:protected] =>
[alreadyInValidation:protected] =>
[validationFailures:protected] => Array
(
)
[_new:BaseObject:private] =>
[_deleted:BaseObject:private] =>
[modifiedColumns:protected] => Array
(
)
)
[93] => Category Object
(
[languages:protected] =>
[bok_resources:protected] =>
[bok_topics:protected] =>
[bok_keywords:protected] =>
[id:protected] => 93
[type:protected] => category
[parent:protected] => 3
[label:protected] => Renovations
[alreadyInSave:protected] =>
[alreadyInValidation:protected] =>
[validationFailures:protected] => Array
(
)
[_new:BaseObject:private] =>
[_deleted:BaseObject:private] =>
[modifiedColumns:protected] => Array
(
)
)
[94] => Category Object
(
[languages:protected] =>
[bok_resources:protected] =>
[bok_topics:protected] =>
[bok_keywords:protected] =>
[id:protected] => 94
[type:protected] => category
[parent:protected] => 3
[label:protected] => Residential
[alreadyInSave:protected] =>
[alreadyInValidation:protected] =>
[validationFailures:protected] => Array
(
)
[_new:BaseObject:private] =>
[_deleted:BaseObject:private] =>
[modifiedColumns:protected] => Array
(
)
)
[95] => Category Object
(
[languages:protected] =>
[bok_resources:protected] =>
[bok_topics:protected] =>
[bok_keywords:protected] =>
[id:protected] => 95
[type:protected] => category
[parent:protected] => 3
[label:protected] => Underground
[alreadyInSave:protected] =>
[alreadyInValidation:protected] =>
[validationFailures:protected] => Array
(
)
[_new:BaseObject:private] =>
[_deleted:BaseObject:private] =>
[modifiedColumns:protected] => Array
(
)
)
[97] => Category Object
(
[languages:protected] =>
[bok_resources:protected] =>
[bok_topics:protected] =>
[bok_keywords:protected] =>
[id:protected] => 97
[type:protected] => category
[parent:protected] => 5
[label:protected] => Images
[alreadyInSave:protected] =>
[alreadyInValidation:protected] =>
[validationFailures:protected] => Array
(
)
[_new:BaseObject:private] =>
[_deleted:BaseObject:private] =>
[modifiedColumns:protected] => Array
(
)
)
)
[categories_initialized:protected] => 1
[mapped_items:protected] =>
[content:protected] =>
[files:protected] =>
[language:protected] => Language Object
(
[id:protected] => 1
[code:protected] => en
[name:protected] => English
[alreadyInSave:protected] =>
[alreadyInValidation:protected] =>
[validationFailures:protected] => Array
(
)
[_new:BaseObject:private] =>
[_deleted:BaseObject:private] =>
[modifiedColumns:protected] => Array
(
)
)
[old_record:protected] =>
[id:protected] => 4006
[old_id:protected] =>
[elcosh_id:protected] => i002693
[type:protected] => image
[display_type:protected] => Image
[user_id:protected] => 0
[language_id:protected] => 1
[tagging_id:protected] => Bruce Lippy
[priority_id:protected] => 1
[title:protected] => Toolbox talk - long shot
[total_pages:protected] => 0
[billed_pages:protected] => 0
[publication_number:protected] =>
[part_of:protected] =>
[keywords:protected] => toolbox talk, tailgate talk, safety minute
[comments:protected] =>
[summary:protected] => This crew gathered every morning before starting work to discuss a new safety topic.
[transition_comments:protected] =>
[external_link:protected] =>
[consol_link:protected] => http://www.cpwrconstructionsolutions.org/electrical/solution/662/worker-training.html
[more_like_this:protected] => i002691,i002692,d001269,d000527
[permission_given_by:protected] =>
[published:protected] => T
[billable:protected] => F
[img_name:protected] =>
[img_ext:protected] => jpg
[img_width:protected] =>
[img_height:protected] =>
[img_credit:protected] => Morgan Zavertnik and Hoar Construction
[img_practice:protected] => good
[vid_source_id:protected] =>
[vid_running_time:protected] =>
[vid_intended_audience:protected] =>
[vid_acquisition_info:protected] =>
[vid_cost:protected] =>
[vid_producer:protected] =>
[vid_filename:protected] =>
[vid_filename_downloadable:protected] =>
[date_summary:protected] => November 2015
[date_permission_requested:protected] =>
[date_permission_received:protected] =>
[date_review_needed:protected] =>
[date_received:protected] => 03/02/16
[date_completed:protected] => 03/02/16
[date_billed:protected] =>
[date_modified:protected] => 03/02/16
[collBokExports:protected] =>
[lastBokExportCriteria:BaseElcoshItem:private] =>
[alreadyInSave:protected] =>
[alreadyInValidation:protected] =>
[validationFailures:protected] => Array
(
)
[_new:BaseObject:private] =>
[_deleted:BaseObject:private] =>
[modifiedColumns:protected] => Array
(
)
)
)
[3] => Search_Result Object
(
[title] => Safety officer discussing ongoing project with marketing coordinator
[image] => /record/images/4014-p.jpg
[blurb] => The safety officer (left) points out the good safety practices on this project that reflect well on the firm and may influence future clients....
[category] => Array
(
[0] => 97
[1] => 20
[2] => 46
[3] => 47
[4] => 49
[5] => 50
[6] => 51
[7] => 54
[8] => 55
[9] => 58
[10] => 60
[11] => 61
[12] => 64
[13] => 71
[14] => 75
[15] => 76
[16] => 63
[17] => 79
[18] => 80
[19] => 82
[20] => 62
[21] => 83
[22] => 87
[23] => 91
[24] => 90
[25] => 93
[26] => 94
)
[labels] => Array
(
[0] => Images
[1] => Media
[2] => Media & Documents
[3] => Safety Culture
[4] => Work Environment
[5] => Hazards
[6] => Boilermaker
[7] => Trades
[8] => Bricklayer
[10] => Carpenter
[12] => Carpet Layer
[14] => Cement Mason
[16] => Drywall Applicator Specialist
[18] => Electrical Worker
[20] => Glazier
[22] => HVAC
[24] => Interior Systems Carpenter
[26] => Laborer
[28] => Painter
[30] => Plasterer
[32] => Plumber/Pipefitter
[34] => Reinforcing Ironworker
[36] => Scaffold Erector
[38] => Sheetmetal Worker
[40] => Stonemason
[42] => Structural Ironworker
[44] => Terrazzo Worker
[46] => Commercial & Institutional
[47] => Jobsites
[48] => Heavy & Highway
[50] => Industrial
[52] => Renovations
[54] => Residential
)
[type] => Images
[sub_category] =>
[url] => /image/4014/i002700/Safety%2Bofficer%2Bdiscussing%2Bongoing%2Bproject%2Bwith%2Bmarketing%2Bcoordinator.html
[item:protected] => ImageRecord Object
(
[records:protected] => Array
(
)
[recordId:protected] =>
[searchWordClass:protected] =>
[searchWordPeerClass:protected] =>
[bok_record:protected] =>
[authors:protected] =>
[organizations:protected] =>
[collections:protected] =>
[categories:protected] => Array
(
[97] => Category Object
(
[languages:protected] =>
[bok_resources:protected] =>
[bok_topics:protected] =>
[bok_keywords:protected] =>
[id:protected] => 97
[type:protected] => category
[parent:protected] => 5
[label:protected] => Images
[alreadyInSave:protected] =>
[alreadyInValidation:protected] =>
[validationFailures:protected] => Array
(
)
[_new:BaseObject:private] =>
[_deleted:BaseObject:private] =>
[modifiedColumns:protected] => Array
(
)
)
[20] => Category Object
(
[languages:protected] =>
[bok_resources:protected] =>
[bok_topics:protected] =>
[bok_keywords:protected] =>
[id:protected] => 20
[type:protected] => category
[parent:protected] => 7
[label:protected] => Safety Culture
[alreadyInSave:protected] =>
[alreadyInValidation:protected] =>
[validationFailures:protected] => Array
(
)
[_new:BaseObject:private] =>
[_deleted:BaseObject:private] =>
[modifiedColumns:protected] => Array
(
)
)
[46] => Category Object
(
[languages:protected] =>
[bok_resources:protected] =>
[bok_topics:protected] =>
[bok_keywords:protected] =>
[id:protected] => 46
[type:protected] => category
[parent:protected] => 2
[label:protected] => Boilermaker
[alreadyInSave:protected] =>
[alreadyInValidation:protected] =>
[validationFailures:protected] => Array
(
)
[_new:BaseObject:private] =>
[_deleted:BaseObject:private] =>
[modifiedColumns:protected] => Array
(
)
)
[47] => Category Object
(
[languages:protected] =>
[bok_resources:protected] =>
[bok_topics:protected] =>
[bok_keywords:protected] =>
[id:protected] => 47
[type:protected] => category
[parent:protected] => 2
[label:protected] => Bricklayer
[alreadyInSave:protected] =>
[alreadyInValidation:protected] =>
[validationFailures:protected] => Array
(
)
[_new:BaseObject:private] =>
[_deleted:BaseObject:private] =>
[modifiedColumns:protected] => Array
(
)
)
[49] => Category Object
(
[languages:protected] =>
[bok_resources:protected] =>
[bok_topics:protected] =>
[bok_keywords:protected] =>
[id:protected] => 49
[type:protected] => category
[parent:protected] => 2
[label:protected] => Carpenter
[alreadyInSave:protected] =>
[alreadyInValidation:protected] =>
[validationFailures:protected] => Array
(
)
[_new:BaseObject:private] =>
[_deleted:BaseObject:private] =>
[modifiedColumns:protected] => Array
(
)
)
[50] => Category Object
(
[languages:protected] =>
[bok_resources:protected] =>
[bok_topics:protected] =>
[bok_keywords:protected] =>
[id:protected] => 50
[type:protected] => category
[parent:protected] => 2
[label:protected] => Carpet Layer
[alreadyInSave:protected] =>
[alreadyInValidation:protected] =>
[validationFailures:protected] => Array
(
)
[_new:BaseObject:private] =>
[_deleted:BaseObject:private] =>
[modifiedColumns:protected] => Array
(
)
)
[51] => Category Object
(
[languages:protected] =>
[bok_resources:protected] =>
[bok_topics:protected] =>
[bok_keywords:protected] =>
[id:protected] => 51
[type:protected] => category
[parent:protected] => 2
[label:protected] => Cement Mason
[alreadyInSave:protected] =>
[alreadyInValidation:protected] =>
[validationFailures:protected] => Array
(
)
[_new:BaseObject:private] =>
[_deleted:BaseObject:private] =>
[modifiedColumns:protected] => Array
(
)
)
[54] => Category Object
(
[languages:protected] =>
[bok_resources:protected] =>
[bok_topics:protected] =>
[bok_keywords:protected] =>
[id:protected] => 54
[type:protected] => category
[parent:protected] => 2
[label:protected] => Drywall Applicator Specialist
[alreadyInSave:protected] =>
[alreadyInValidation:protected] =>
[validationFailures:protected] => Array
(
)
[_new:BaseObject:private] =>
[_deleted:BaseObject:private] =>
[modifiedColumns:protected] => Array
(
)
)
[55] => Category Object
(
[languages:protected] =>
[bok_resources:protected] =>
[bok_topics:protected] =>
[bok_keywords:protected] =>
[id:protected] => 55
[type:protected] => category
[parent:protected] => 2
[label:protected] => Electrical Worker
[alreadyInSave:protected] =>
[alreadyInValidation:protected] =>
[validationFailures:protected] => Array
(
)
[_new:BaseObject:private] =>
[_deleted:BaseObject:private] =>
[modifiedColumns:protected] => Array
(
)
)
[58] => Category Object
(
[languages:protected] =>
[bok_resources:protected] =>
[bok_topics:protected] =>
[bok_keywords:protected] =>
[id:protected] => 58
[type:protected] => category
[parent:protected] => 2
[label:protected] => Glazier
[alreadyInSave:protected] =>
[alreadyInValidation:protected] =>
[validationFailures:protected] => Array
(
)
[_new:BaseObject:private] =>
[_deleted:BaseObject:private] =>
[modifiedColumns:protected] => Array
(
)
)
[60] => Category Object
(
[languages:protected] =>
[bok_resources:protected] =>
[bok_topics:protected] =>
[bok_keywords:protected] =>
[id:protected] => 60
[type:protected] => category
[parent:protected] => 2
[label:protected] => HVAC
[alreadyInSave:protected] =>
[alreadyInValidation:protected] =>
[validationFailures:protected] => Array
(
)
[_new:BaseObject:private] =>
[_deleted:BaseObject:private] =>
[modifiedColumns:protected] => Array
(
)
)
[61] => Category Object
(
[languages:protected] =>
[bok_resources:protected] =>
[bok_topics:protected] =>
[bok_keywords:protected] =>
[id:protected] => 61
[type:protected] => category
[parent:protected] => 2
[label:protected] => Interior Systems Carpenter
[alreadyInSave:protected] =>
[alreadyInValidation:protected] =>
[validationFailures:protected] => Array
(
)
[_new:BaseObject:private] =>
[_deleted:BaseObject:private] =>
[modifiedColumns:protected] => Array
(
)
)
[64] => Category Object
(
[languages:protected] =>
[bok_resources:protected] =>
[bok_topics:protected] =>
[bok_keywords:protected] =>
[id:protected] => 64
[type:protected] => category
[parent:protected] => 2
[label:protected] => Laborer
[alreadyInSave:protected] =>
[alreadyInValidation:protected] =>
[validationFailures:protected] => Array
(
)
[_new:BaseObject:private] =>
[_deleted:BaseObject:private] =>
[modifiedColumns:protected] => Array
(
)
)
[71] => Category Object
(
[languages:protected] =>
[bok_resources:protected] =>
[bok_topics:protected] =>
[bok_keywords:protected] =>
[id:protected] => 71
[type:protected] => category
[parent:protected] => 2
[label:protected] => Painter
[alreadyInSave:protected] =>
[alreadyInValidation:protected] =>
[validationFailures:protected] => Array
(
)
[_new:BaseObject:private] =>
[_deleted:BaseObject:private] =>
[modifiedColumns:protected] => Array
(
)
)
[75] => Category Object
(
[languages:protected] =>
[bok_resources:protected] =>
[bok_topics:protected] =>
[bok_keywords:protected] =>
[id:protected] => 75
[type:protected] => category
[parent:protected] => 2
[label:protected] => Plasterer
[alreadyInSave:protected] =>
[alreadyInValidation:protected] =>
[validationFailures:protected] => Array
(
)
[_new:BaseObject:private] =>
[_deleted:BaseObject:private] =>
[modifiedColumns:protected] => Array
(
)
)
[76] => Category Object
(
[languages:protected] =>
[bok_resources:protected] =>
[bok_topics:protected] =>
[bok_keywords:protected] =>
[id:protected] => 76
[type:protected] => category
[parent:protected] => 2
[label:protected] => Plumber/Pipefitter
[alreadyInSave:protected] =>
[alreadyInValidation:protected] =>
[validationFailures:protected] => Array
(
)
[_new:BaseObject:private] =>
[_deleted:BaseObject:private] =>
[modifiedColumns:protected] => Array
(
)
)
[63] => Category Object
(
[languages:protected] =>
[bok_resources:protected] =>
[bok_topics:protected] =>
[bok_keywords:protected] =>
[id:protected] => 63
[type:protected] => category
[parent:protected] => 2
[label:protected] => Reinforcing Ironworker
[alreadyInSave:protected] =>
[alreadyInValidation:protected] =>
[validationFailures:protected] => Array
(
)
[_new:BaseObject:private] =>
[_deleted:BaseObject:private] =>
[modifiedColumns:protected] => Array
(
)
)
[79] => Category Object
(
[languages:protected] =>
[bok_resources:protected] =>
[bok_topics:protected] =>
[bok_keywords:protected] =>
[id:protected] => 79
[type:protected] => category
[parent:protected] => 2
[label:protected] => Scaffold Erector
[alreadyInSave:protected] =>
[alreadyInValidation:protected] =>
[validationFailures:protected] => Array
(
)
[_new:BaseObject:private] =>
[_deleted:BaseObject:private] =>
[modifiedColumns:protected] => Array
(
)
)
[80] => Category Object
(
[languages:protected] =>
[bok_resources:protected] =>
[bok_topics:protected] =>
[bok_keywords:protected] =>
[id:protected] => 80
[type:protected] => category
[parent:protected] => 2
[label:protected] => Sheetmetal Worker
[alreadyInSave:protected] =>
[alreadyInValidation:protected] =>
[validationFailures:protected] => Array
(
)
[_new:BaseObject:private] =>
[_deleted:BaseObject:private] =>
[modifiedColumns:protected] => Array
(
)
)
[82] => Category Object
(
[languages:protected] =>
[bok_resources:protected] =>
[bok_topics:protected] =>
[bok_keywords:protected] =>
[id:protected] => 82
[type:protected] => category
[parent:protected] => 2
[label:protected] => Stonemason
[alreadyInSave:protected] =>
[alreadyInValidation:protected] =>
[validationFailures:protected] => Array
(
)
[_new:BaseObject:private] =>
[_deleted:BaseObject:private] =>
[modifiedColumns:protected] => Array
(
)
)
[62] => Category Object
(
[languages:protected] =>
[bok_resources:protected] =>
[bok_topics:protected] =>
[bok_keywords:protected] =>
[id:protected] => 62
[type:protected] => category
[parent:protected] => 2
[label:protected] => Structural Ironworker
[alreadyInSave:protected] =>
[alreadyInValidation:protected] =>
[validationFailures:protected] => Array
(
)
[_new:BaseObject:private] =>
[_deleted:BaseObject:private] =>
[modifiedColumns:protected] => Array
(
)
)
[83] => Category Object
(
[languages:protected] =>
[bok_resources:protected] =>
[bok_topics:protected] =>
[bok_keywords:protected] =>
[id:protected] => 83
[type:protected] => category
[parent:protected] => 2
[label:protected] => Terrazzo Worker
[alreadyInSave:protected] =>
[alreadyInValidation:protected] =>
[validationFailures:protected] => Array
(
)
[_new:BaseObject:private] =>
[_deleted:BaseObject:private] =>
[modifiedColumns:protected] => Array
(
)
)
[87] => Category Object
(
[languages:protected] =>
[bok_resources:protected] =>
[bok_topics:protected] =>
[bok_keywords:protected] =>
[id:protected] => 87
[type:protected] => category
[parent:protected] => 3
[label:protected] => Commercial & Institutional
[alreadyInSave:protected] =>
[alreadyInValidation:protected] =>
[validationFailures:protected] => Array
(
)
[_new:BaseObject:private] =>
[_deleted:BaseObject:private] =>
[modifiedColumns:protected] => Array
(
)
)
[91] => Category Object
(
[languages:protected] =>
[bok_resources:protected] =>
[bok_topics:protected] =>
[bok_keywords:protected] =>
[id:protected] => 91
[type:protected] => category
[parent:protected] => 3
[label:protected] => Heavy & Highway
[alreadyInSave:protected] =>
[alreadyInValidation:protected] =>
[validationFailures:protected] => Array
(
)
[_new:BaseObject:private] =>
[_deleted:BaseObject:private] =>
[modifiedColumns:protected] => Array
(
)
)
[90] => Category Object
(
[languages:protected] =>
[bok_resources:protected] =>
[bok_topics:protected] =>
[bok_keywords:protected] =>
[id:protected] => 90
[type:protected] => category
[parent:protected] => 3
[label:protected] => Industrial
[alreadyInSave:protected] =>
[alreadyInValidation:protected] =>
[validationFailures:protected] => Array
(
)
[_new:BaseObject:private] =>
[_deleted:BaseObject:private] =>
[modifiedColumns:protected] => Array
(
)
)
[93] => Category Object
(
[languages:protected] =>
[bok_resources:protected] =>
[bok_topics:protected] =>
[bok_keywords:protected] =>
[id:protected] => 93
[type:protected] => category
[parent:protected] => 3
[label:protected] => Renovations
[alreadyInSave:protected] =>
[alreadyInValidation:protected] =>
[validationFailures:protected] => Array
(
)
[_new:BaseObject:private] =>
[_deleted:BaseObject:private] =>
[modifiedColumns:protected] => Array
(
)
)
[94] => Category Object
(
[languages:protected] =>
[bok_resources:protected] =>
[bok_topics:protected] =>
[bok_keywords:protected] =>
[id:protected] => 94
[type:protected] => category
[parent:protected] => 3
[label:protected] => Residential
[alreadyInSave:protected] =>
[alreadyInValidation:protected] =>
[validationFailures:protected] => Array
(
)
[_new:BaseObject:private] =>
[_deleted:BaseObject:private] =>
[modifiedColumns:protected] => Array
(
)
)
)
[categories_initialized:protected] => 1
[mapped_items:protected] =>
[content:protected] =>
[files:protected] =>
[language:protected] => Language Object
(
[id:protected] => 1
[code:protected] => en
[name:protected] => English
[alreadyInSave:protected] =>
[alreadyInValidation:protected] =>
[validationFailures:protected] => Array
(
)
[_new:BaseObject:private] =>
[_deleted:BaseObject:private] =>
[modifiedColumns:protected] => Array
(
)
)
[old_record:protected] =>
[id:protected] => 4014
[old_id:protected] =>
[elcosh_id:protected] => i002700
[type:protected] => image
[display_type:protected] => Image
[user_id:protected] => 0
[language_id:protected] => 1
[tagging_id:protected] => Bruce Lippy
[priority_id:protected] => 1
[title:protected] => Safety officer discussing ongoing project with marketing coordinator
[total_pages:protected] => 0
[billed_pages:protected] => 0
[publication_number:protected] =>
[part_of:protected] =>
[keywords:protected] => Latino, safety officer, safety culture
[comments:protected] =>
[summary:protected] => The safety officer (left) points out the good safety practices on this project that reflect well on the firm and may influence future clients.
[transition_comments:protected] =>
[external_link:protected] =>
[consol_link:protected] => http://www.cpwrconstructionsolutions.org/index.php
[more_like_this:protected] => d000989,d001351,d001362,d000652, d001101, d000931, d001395
[permission_given_by:protected] =>
[published:protected] => T
[billable:protected] => F
[img_name:protected] =>
[img_ext:protected] => jpg
[img_width:protected] =>
[img_height:protected] =>
[img_credit:protected] => Hoar Construction, Photo by Neil Lippy
[img_practice:protected] => good
[vid_source_id:protected] =>
[vid_running_time:protected] =>
[vid_intended_audience:protected] =>
[vid_acquisition_info:protected] =>
[vid_cost:protected] =>
[vid_producer:protected] =>
[vid_filename:protected] =>
[vid_filename_downloadable:protected] =>
[date_summary:protected] => November 2015
[date_permission_requested:protected] =>
[date_permission_received:protected] =>
[date_review_needed:protected] =>
[date_received:protected] => 03/02/16
[date_completed:protected] => 03/02/16
[date_billed:protected] =>
[date_modified:protected] => 01/30/23
[collBokExports:protected] =>
[lastBokExportCriteria:BaseElcoshItem:private] =>
[alreadyInSave:protected] =>
[alreadyInValidation:protected] =>
[validationFailures:protected] => Array
(
)
[_new:BaseObject:private] =>
[_deleted:BaseObject:private] =>
[modifiedColumns:protected] => Array
(
)
)
)
[4] => Search_Result Object
(
[title] => Scaffolding at top of large column
[image] => /record/images/3994-p.jpg
[blurb] => This shot shows innovative guarding around the top of a large concrete column in the base of a high rise structure going up....
[category] => Array
(
[0] => 15
[1] => 21
[2] => 47
[3] => 51
[4] => 63
[5] => 78
[6] => 79
[7] => 80
[8] => 62
[9] => 87
[10] => 97
[11] => 56
[12] => 64
[13] => 74
)
[labels] => Array
(
[0] => Falls
[1] => Work Environment
[2] => Hazards
[3] => Scaffolds
[6] => Bricklayer
[7] => Trades
[8] => Cement Mason
[10] => Reinforcing Ironworker
[12] => Roofer/Waterproofer
[14] => Scaffold Erector
[16] => Sheetmetal Worker
[18] => Structural Ironworker
[20] => Commercial & Institutional
[21] => Jobsites
[22] => Images
[23] => Media
[24] => Media & Documents
[25] => Elevator Constructor
[27] => Laborer
[29] => Pile Driver
)
[type] => Images
[sub_category] =>
[url] => /image/3994/i002689/Scaffolding%2Bat%2Btop%2Bof%2Blarge%2Bcolumn.html
[item:protected] => ImageRecord Object
(
[records:protected] => Array
(
)
[recordId:protected] =>
[searchWordClass:protected] =>
[searchWordPeerClass:protected] =>
[bok_record:protected] =>
[authors:protected] =>
[organizations:protected] =>
[collections:protected] =>
[categories:protected] => Array
(
[15] => Category Object
(
[languages:protected] =>
[bok_resources:protected] =>
[bok_topics:protected] =>
[bok_keywords:protected] =>
[id:protected] => 15
[type:protected] => category
[parent:protected] => 7
[label:protected] => Falls
[alreadyInSave:protected] =>
[alreadyInValidation:protected] =>
[validationFailures:protected] => Array
(
)
[_new:BaseObject:private] =>
[_deleted:BaseObject:private] =>
[modifiedColumns:protected] => Array
(
)
)
[21] => Category Object
(
[languages:protected] =>
[bok_resources:protected] =>
[bok_topics:protected] =>
[bok_keywords:protected] =>
[id:protected] => 21
[type:protected] => category
[parent:protected] => 7
[label:protected] => Scaffolds
[alreadyInSave:protected] =>
[alreadyInValidation:protected] =>
[validationFailures:protected] => Array
(
)
[_new:BaseObject:private] =>
[_deleted:BaseObject:private] =>
[modifiedColumns:protected] => Array
(
)
)
[47] => Category Object
(
[languages:protected] =>
[bok_resources:protected] =>
[bok_topics:protected] =>
[bok_keywords:protected] =>
[id:protected] => 47
[type:protected] => category
[parent:protected] => 2
[label:protected] => Bricklayer
[alreadyInSave:protected] =>
[alreadyInValidation:protected] =>
[validationFailures:protected] => Array
(
)
[_new:BaseObject:private] =>
[_deleted:BaseObject:private] =>
[modifiedColumns:protected] => Array
(
)
)
[51] => Category Object
(
[languages:protected] =>
[bok_resources:protected] =>
[bok_topics:protected] =>
[bok_keywords:protected] =>
[id:protected] => 51
[type:protected] => category
[parent:protected] => 2
[label:protected] => Cement Mason
[alreadyInSave:protected] =>
[alreadyInValidation:protected] =>
[validationFailures:protected] => Array
(
)
[_new:BaseObject:private] =>
[_deleted:BaseObject:private] =>
[modifiedColumns:protected] => Array
(
)
)
[63] => Category Object
(
[languages:protected] =>
[bok_resources:protected] =>
[bok_topics:protected] =>
[bok_keywords:protected] =>
[id:protected] => 63
[type:protected] => category
[parent:protected] => 2
[label:protected] => Reinforcing Ironworker
[alreadyInSave:protected] =>
[alreadyInValidation:protected] =>
[validationFailures:protected] => Array
(
)
[_new:BaseObject:private] =>
[_deleted:BaseObject:private] =>
[modifiedColumns:protected] => Array
(
)
)
[78] => Category Object
(
[languages:protected] =>
[bok_resources:protected] =>
[bok_topics:protected] =>
[bok_keywords:protected] =>
[id:protected] => 78
[type:protected] => category
[parent:protected] => 2
[label:protected] => Roofer/Waterproofer
[alreadyInSave:protected] =>
[alreadyInValidation:protected] =>
[validationFailures:protected] => Array
(
)
[_new:BaseObject:private] =>
[_deleted:BaseObject:private] =>
[modifiedColumns:protected] => Array
(
)
)
[79] => Category Object
(
[languages:protected] =>
[bok_resources:protected] =>
[bok_topics:protected] =>
[bok_keywords:protected] =>
[id:protected] => 79
[type:protected] => category
[parent:protected] => 2
[label:protected] => Scaffold Erector
[alreadyInSave:protected] =>
[alreadyInValidation:protected] =>
[validationFailures:protected] => Array
(
)
[_new:BaseObject:private] =>
[_deleted:BaseObject:private] =>
[modifiedColumns:protected] => Array
(
)
)
[80] => Category Object
(
[languages:protected] =>
[bok_resources:protected] =>
[bok_topics:protected] =>
[bok_keywords:protected] =>
[id:protected] => 80
[type:protected] => category
[parent:protected] => 2
[label:protected] => Sheetmetal Worker
[alreadyInSave:protected] =>
[alreadyInValidation:protected] =>
[validationFailures:protected] => Array
(
)
[_new:BaseObject:private] =>
[_deleted:BaseObject:private] =>
[modifiedColumns:protected] => Array
(
)
)
[62] => Category Object
(
[languages:protected] =>
[bok_resources:protected] =>
[bok_topics:protected] =>
[bok_keywords:protected] =>
[id:protected] => 62
[type:protected] => category
[parent:protected] => 2
[label:protected] => Structural Ironworker
[alreadyInSave:protected] =>
[alreadyInValidation:protected] =>
[validationFailures:protected] => Array
(
)
[_new:BaseObject:private] =>
[_deleted:BaseObject:private] =>
[modifiedColumns:protected] => Array
(
)
)
[87] => Category Object
(
[languages:protected] =>
[bok_resources:protected] =>
[bok_topics:protected] =>
[bok_keywords:protected] =>
[id:protected] => 87
[type:protected] => category
[parent:protected] => 3
[label:protected] => Commercial & Institutional
[alreadyInSave:protected] =>
[alreadyInValidation:protected] =>
[validationFailures:protected] => Array
(
)
[_new:BaseObject:private] =>
[_deleted:BaseObject:private] =>
[modifiedColumns:protected] => Array
(
)
)
[97] => Category Object
(
[languages:protected] =>
[bok_resources:protected] =>
[bok_topics:protected] =>
[bok_keywords:protected] =>
[id:protected] => 97
[type:protected] => category
[parent:protected] => 5
[label:protected] => Images
[alreadyInSave:protected] =>
[alreadyInValidation:protected] =>
[validationFailures:protected] => Array
(
)
[_new:BaseObject:private] =>
[_deleted:BaseObject:private] =>
[modifiedColumns:protected] => Array
(
)
)
[56] => Category Object
(
[languages:protected] =>
[bok_resources:protected] =>
[bok_topics:protected] =>
[bok_keywords:protected] =>
[id:protected] => 56
[type:protected] => category
[parent:protected] => 2
[label:protected] => Elevator Constructor
[alreadyInSave:protected] =>
[alreadyInValidation:protected] =>
[validationFailures:protected] => Array
(
)
[_new:BaseObject:private] =>
[_deleted:BaseObject:private] =>
[modifiedColumns:protected] => Array
(
)
)
[64] => Category Object
(
[languages:protected] =>
[bok_resources:protected] =>
[bok_topics:protected] =>
[bok_keywords:protected] =>
[id:protected] => 64
[type:protected] => category
[parent:protected] => 2
[label:protected] => Laborer
[alreadyInSave:protected] =>
[alreadyInValidation:protected] =>
[validationFailures:protected] => Array
(
)
[_new:BaseObject:private] =>
[_deleted:BaseObject:private] =>
[modifiedColumns:protected] => Array
(
)
)
[74] => Category Object
(
[languages:protected] =>
[bok_resources:protected] =>
[bok_topics:protected] =>
[bok_keywords:protected] =>
[id:protected] => 74
[type:protected] => category
[parent:protected] => 2
[label:protected] => Pile Driver
[alreadyInSave:protected] =>
[alreadyInValidation:protected] =>
[validationFailures:protected] => Array
(
)
[_new:BaseObject:private] =>
[_deleted:BaseObject:private] =>
[modifiedColumns:protected] => Array
(
)
)
)
[categories_initialized:protected] => 1
[mapped_items:protected] =>
[content:protected] =>
[files:protected] =>
[language:protected] => Language Object
(
[id:protected] => 1
[code:protected] => en
[name:protected] => English
[alreadyInSave:protected] =>
[alreadyInValidation:protected] =>
[validationFailures:protected] => Array
(
)
[_new:BaseObject:private] =>
[_deleted:BaseObject:private] =>
[modifiedColumns:protected] => Array
(
)
)
[old_record:protected] =>
[id:protected] => 3994
[old_id:protected] =>
[elcosh_id:protected] => i002689
[type:protected] => image
[display_type:protected] => Image
[user_id:protected] => 0
[language_id:protected] => 1
[tagging_id:protected] => Bruce Lippy
[priority_id:protected] => 1
[title:protected] => Scaffolding at top of large column
[total_pages:protected] => 0
[billed_pages:protected] => 0
[publication_number:protected] =>
[part_of:protected] =>
[keywords:protected] => Guardrail, railing, fall prevention, falls
[comments:protected] =>
[summary:protected] => This shot shows innovative guarding around the top of a large concrete column in the base of a high rise structure going up.
[transition_comments:protected] =>
[external_link:protected] =>
[consol_link:protected] => http://www.cpwrconstructionsolutions.org/masonry/solution/8/adjustable-tower-scaffold.html
[more_like_this:protected] => c1002680,i002662,d000608,d001255
[permission_given_by:protected] =>
[published:protected] => T
[billable:protected] => F
[img_name:protected] =>
[img_ext:protected] => jpg
[img_width:protected] =>
[img_height:protected] =>
[img_credit:protected] => Photo by Pam Susi
[img_practice:protected] => good
[vid_source_id:protected] =>
[vid_running_time:protected] =>
[vid_intended_audience:protected] =>
[vid_acquisition_info:protected] =>
[vid_cost:protected] =>
[vid_producer:protected] =>
[vid_filename:protected] =>
[vid_filename_downloadable:protected] =>
[date_summary:protected] => January 2016
[date_permission_requested:protected] =>
[date_permission_received:protected] =>
[date_review_needed:protected] =>
[date_received:protected] => 02/01/16
[date_completed:protected] => 02/01/16
[date_billed:protected] =>
[date_modified:protected] => 02/01/16
[collBokExports:protected] =>
[lastBokExportCriteria:BaseElcoshItem:private] =>
[alreadyInSave:protected] =>
[alreadyInValidation:protected] =>
[validationFailures:protected] => Array
(
)
[_new:BaseObject:private] =>
[_deleted:BaseObject:private] =>
[modifiedColumns:protected] => Array
(
)
)
)
[5] => Search_Result Object
(
[title] => Construction bracing
[image] => /record/images/3995-p.jpg
[blurb] => This shows structural support that prevents collapses during construction....
[category] => Array
(
[0] => 12
[1] => 15
[2] => 21
[3] => 49
[4] => 51
[5] => 55
[6] => 56
[7] => 60
[8] => 64
[9] => 68
[10] => 74
[11] => 63
[12] => 78
[13] => 79
[14] => 80
[15] => 62
[16] => 87
[17] => 90
[18] => 97
)
[labels] => Array
(
[0] => Crushed/Struck By
[1] => Work Environment
[2] => Hazards
[3] => Falls
[6] => Scaffolds
[9] => Carpenter
[10] => Trades
[11] => Cement Mason
[13] => Electrical Worker
[15] => Elevator Constructor
[17] => HVAC
[19] => Laborer
[21] => Maintenance Worker
[23] => Pile Driver
[25] => Reinforcing Ironworker
[27] => Roofer/Waterproofer
[29] => Scaffold Erector
[31] => Sheetmetal Worker
[33] => Structural Ironworker
[35] => Commercial & Institutional
[36] => Jobsites
[37] => Industrial
[39] => Images
[40] => Media
[41] => Media & Documents
)
[type] => Images
[sub_category] =>
[url] => /image/3995/i002690/Construction%2Bbracing.html
[item:protected] => ImageRecord Object
(
[records:protected] => Array
(
)
[recordId:protected] =>
[searchWordClass:protected] =>
[searchWordPeerClass:protected] =>
[bok_record:protected] =>
[authors:protected] =>
[organizations:protected] =>
[collections:protected] =>
[categories:protected] => Array
(
[12] => Category Object
(
[languages:protected] =>
[bok_resources:protected] =>
[bok_topics:protected] =>
[bok_keywords:protected] =>
[id:protected] => 12
[type:protected] => category
[parent:protected] => 7
[label:protected] => Crushed/Struck By
[alreadyInSave:protected] =>
[alreadyInValidation:protected] =>
[validationFailures:protected] => Array
(
)
[_new:BaseObject:private] =>
[_deleted:BaseObject:private] =>
[modifiedColumns:protected] => Array
(
)
)
[15] => Category Object
(
[languages:protected] =>
[bok_resources:protected] =>
[bok_topics:protected] =>
[bok_keywords:protected] =>
[id:protected] => 15
[type:protected] => category
[parent:protected] => 7
[label:protected] => Falls
[alreadyInSave:protected] =>
[alreadyInValidation:protected] =>
[validationFailures:protected] => Array
(
)
[_new:BaseObject:private] =>
[_deleted:BaseObject:private] =>
[modifiedColumns:protected] => Array
(
)
)
[21] => Category Object
(
[languages:protected] =>
[bok_resources:protected] =>
[bok_topics:protected] =>
[bok_keywords:protected] =>
[id:protected] => 21
[type:protected] => category
[parent:protected] => 7
[label:protected] => Scaffolds
[alreadyInSave:protected] =>
[alreadyInValidation:protected] =>
[validationFailures:protected] => Array
(
)
[_new:BaseObject:private] =>
[_deleted:BaseObject:private] =>
[modifiedColumns:protected] => Array
(
)
)
[49] => Category Object
(
[languages:protected] =>
[bok_resources:protected] =>
[bok_topics:protected] =>
[bok_keywords:protected] =>
[id:protected] => 49
[type:protected] => category
[parent:protected] => 2
[label:protected] => Carpenter
[alreadyInSave:protected] =>
[alreadyInValidation:protected] =>
[validationFailures:protected] => Array
(
)
[_new:BaseObject:private] =>
[_deleted:BaseObject:private] =>
[modifiedColumns:protected] => Array
(
)
)
[51] => Category Object
(
[languages:protected] =>
[bok_resources:protected] =>
[bok_topics:protected] =>
[bok_keywords:protected] =>
[id:protected] => 51
[type:protected] => category
[parent:protected] => 2
[label:protected] => Cement Mason
[alreadyInSave:protected] =>
[alreadyInValidation:protected] =>
[validationFailures:protected] => Array
(
)
[_new:BaseObject:private] =>
[_deleted:BaseObject:private] =>
[modifiedColumns:protected] => Array
(
)
)
[55] => Category Object
(
[languages:protected] =>
[bok_resources:protected] =>
[bok_topics:protected] =>
[bok_keywords:protected] =>
[id:protected] => 55
[type:protected] => category
[parent:protected] => 2
[label:protected] => Electrical Worker
[alreadyInSave:protected] =>
[alreadyInValidation:protected] =>
[validationFailures:protected] => Array
(
)
[_new:BaseObject:private] =>
[_deleted:BaseObject:private] =>
[modifiedColumns:protected] => Array
(
)
)
[56] => Category Object
(
[languages:protected] =>
[bok_resources:protected] =>
[bok_topics:protected] =>
[bok_keywords:protected] =>
[id:protected] => 56
[type:protected] => category
[parent:protected] => 2
[label:protected] => Elevator Constructor
[alreadyInSave:protected] =>
[alreadyInValidation:protected] =>
[validationFailures:protected] => Array
(
)
[_new:BaseObject:private] =>
[_deleted:BaseObject:private] =>
[modifiedColumns:protected] => Array
(
)
)
[60] => Category Object
(
[languages:protected] =>
[bok_resources:protected] =>
[bok_topics:protected] =>
[bok_keywords:protected] =>
[id:protected] => 60
[type:protected] => category
[parent:protected] => 2
[label:protected] => HVAC
[alreadyInSave:protected] =>
[alreadyInValidation:protected] =>
[validationFailures:protected] => Array
(
)
[_new:BaseObject:private] =>
[_deleted:BaseObject:private] =>
[modifiedColumns:protected] => Array
(
)
)
[64] => Category Object
(
[languages:protected] =>
[bok_resources:protected] =>
[bok_topics:protected] =>
[bok_keywords:protected] =>
[id:protected] => 64
[type:protected] => category
[parent:protected] => 2
[label:protected] => Laborer
[alreadyInSave:protected] =>
[alreadyInValidation:protected] =>
[validationFailures:protected] => Array
(
)
[_new:BaseObject:private] =>
[_deleted:BaseObject:private] =>
[modifiedColumns:protected] => Array
(
)
)
[68] => Category Object
(
[languages:protected] =>
[bok_resources:protected] =>
[bok_topics:protected] =>
[bok_keywords:protected] =>
[id:protected] => 68
[type:protected] => category
[parent:protected] => 2
[label:protected] => Maintenance Worker
[alreadyInSave:protected] =>
[alreadyInValidation:protected] =>
[validationFailures:protected] => Array
(
)
[_new:BaseObject:private] =>
[_deleted:BaseObject:private] =>
[modifiedColumns:protected] => Array
(
)
)
[74] => Category Object
(
[languages:protected] =>
[bok_resources:protected] =>
[bok_topics:protected] =>
[bok_keywords:protected] =>
[id:protected] => 74
[type:protected] => category
[parent:protected] => 2
[label:protected] => Pile Driver
[alreadyInSave:protected] =>
[alreadyInValidation:protected] =>
[validationFailures:protected] => Array
(
)
[_new:BaseObject:private] =>
[_deleted:BaseObject:private] =>
[modifiedColumns:protected] => Array
(
)
)
[63] => Category Object
(
[languages:protected] =>
[bok_resources:protected] =>
[bok_topics:protected] =>
[bok_keywords:protected] =>
[id:protected] => 63
[type:protected] => category
[parent:protected] => 2
[label:protected] => Reinforcing Ironworker
[alreadyInSave:protected] =>
[alreadyInValidation:protected] =>
[validationFailures:protected] => Array
(
)
[_new:BaseObject:private] =>
[_deleted:BaseObject:private] =>
[modifiedColumns:protected] => Array
(
)
)
[78] => Category Object
(
[languages:protected] =>
[bok_resources:protected] =>
[bok_topics:protected] =>
[bok_keywords:protected] =>
[id:protected] => 78
[type:protected] => category
[parent:protected] => 2
[label:protected] => Roofer/Waterproofer
[alreadyInSave:protected] =>
[alreadyInValidation:protected] =>
[validationFailures:protected] => Array
(
)
[_new:BaseObject:private] =>
[_deleted:BaseObject:private] =>
[modifiedColumns:protected] => Array
(
)
)
[79] => Category Object
(
[languages:protected] =>
[bok_resources:protected] =>
[bok_topics:protected] =>
[bok_keywords:protected] =>
[id:protected] => 79
[type:protected] => category
[parent:protected] => 2
[label:protected] => Scaffold Erector
[alreadyInSave:protected] =>
[alreadyInValidation:protected] =>
[validationFailures:protected] => Array
(
)
[_new:BaseObject:private] =>
[_deleted:BaseObject:private] =>
[modifiedColumns:protected] => Array
(
)
)
[80] => Category Object
(
[languages:protected] =>
[bok_resources:protected] =>
[bok_topics:protected] =>
[bok_keywords:protected] =>
[id:protected] => 80
[type:protected] => category
[parent:protected] => 2
[label:protected] => Sheetmetal Worker
[alreadyInSave:protected] =>
[alreadyInValidation:protected] =>
[validationFailures:protected] => Array
(
)
[_new:BaseObject:private] =>
[_deleted:BaseObject:private] =>
[modifiedColumns:protected] => Array
(
)
)
[62] => Category Object
(
[languages:protected] =>
[bok_resources:protected] =>
[bok_topics:protected] =>
[bok_keywords:protected] =>
[id:protected] => 62
[type:protected] => category
[parent:protected] => 2
[label:protected] => Structural Ironworker
[alreadyInSave:protected] =>
[alreadyInValidation:protected] =>
[validationFailures:protected] => Array
(
)
[_new:BaseObject:private] =>
[_deleted:BaseObject:private] =>
[modifiedColumns:protected] => Array
(
)
)
[87] => Category Object
(
[languages:protected] =>
[bok_resources:protected] =>
[bok_topics:protected] =>
[bok_keywords:protected] =>
[id:protected] => 87
[type:protected] => category
[parent:protected] => 3
[label:protected] => Commercial & Institutional
[alreadyInSave:protected] =>
[alreadyInValidation:protected] =>
[validationFailures:protected] => Array
(
)
[_new:BaseObject:private] =>
[_deleted:BaseObject:private] =>
[modifiedColumns:protected] => Array
(
)
)
[90] => Category Object
(
[languages:protected] =>
[bok_resources:protected] =>
[bok_topics:protected] =>
[bok_keywords:protected] =>
[id:protected] => 90
[type:protected] => category
[parent:protected] => 3
[label:protected] => Industrial
[alreadyInSave:protected] =>
[alreadyInValidation:protected] =>
[validationFailures:protected] => Array
(
)
[_new:BaseObject:private] =>
[_deleted:BaseObject:private] =>
[modifiedColumns:protected] => Array
(
)
)
[97] => Category Object
(
[languages:protected] =>
[bok_resources:protected] =>
[bok_topics:protected] =>
[bok_keywords:protected] =>
[id:protected] => 97
[type:protected] => category
[parent:protected] => 5
[label:protected] => Images
[alreadyInSave:protected] =>
[alreadyInValidation:protected] =>
[validationFailures:protected] => Array
(
)
[_new:BaseObject:private] =>
[_deleted:BaseObject:private] =>
[modifiedColumns:protected] => Array
(
)
)
)
[categories_initialized:protected] => 1
[mapped_items:protected] =>
[content:protected] =>
[files:protected] =>
[language:protected] => Language Object
(
[id:protected] => 1
[code:protected] => en
[name:protected] => English
[alreadyInSave:protected] =>
[alreadyInValidation:protected] =>
[validationFailures:protected] => Array
(
)
[_new:BaseObject:private] =>
[_deleted:BaseObject:private] =>
[modifiedColumns:protected] => Array
(
)
)
[old_record:protected] =>
[id:protected] => 3995
[old_id:protected] =>
[elcosh_id:protected] => i002690
[type:protected] => image
[display_type:protected] => Image
[user_id:protected] => 0
[language_id:protected] => 1
[tagging_id:protected] => Bruce Lippy
[priority_id:protected] => 1
[title:protected] => Construction bracing
[total_pages:protected] => 0
[billed_pages:protected] => 0
[publication_number:protected] =>
[part_of:protected] =>
[keywords:protected] => Bracing, support, scaffold
[comments:protected] =>
[summary:protected] => This shows structural support that prevents collapses during construction.
[transition_comments:protected] =>
[external_link:protected] =>
[consol_link:protected] => http://www.cpwrconstructionsolutions.org/masonry/solution/8/adjustable-tower-scaffold.html
[more_like_this:protected] => i002660
[permission_given_by:protected] =>
[published:protected] => T
[billable:protected] => F
[img_name:protected] =>
[img_ext:protected] => jpg
[img_width:protected] =>
[img_height:protected] =>
[img_credit:protected] => Photo by Pam Susi
[img_practice:protected] => good
[vid_source_id:protected] =>
[vid_running_time:protected] =>
[vid_intended_audience:protected] =>
[vid_acquisition_info:protected] =>
[vid_cost:protected] =>
[vid_producer:protected] =>
[vid_filename:protected] =>
[vid_filename_downloadable:protected] =>
[date_summary:protected] => January 2016
[date_permission_requested:protected] =>
[date_permission_received:protected] =>
[date_review_needed:protected] =>
[date_received:protected] => 02/01/16
[date_completed:protected] => 02/01/16
[date_billed:protected] =>
[date_modified:protected] => 02/01/16
[collBokExports:protected] =>
[lastBokExportCriteria:BaseElcoshItem:private] =>
[alreadyInSave:protected] =>
[alreadyInValidation:protected] =>
[validationFailures:protected] => Array
(
)
[_new:BaseObject:private] =>
[_deleted:BaseObject:private] =>
[modifiedColumns:protected] => Array
(
)
)
)
)
[preview_mode] =>
[description] => Toolbox talks have been the main tool for communicating safety information on construction jobs for decades.
Unfortunately, there has been little research on what makes for effective toolbox talks. The IUOE National
Training Fund worked with OSHA and NIOSH to make sure their series of 24 Focus Four toolbox talks were based on the best recommendations for effective design. These toolbox talks accompany an entire package of training materials, but can be used alone. This guide points out the key features of these toolbox talks and how best to deliver them.
[keywords] => toolbox talks, tailgate talks
[related_items] => Array
(
[Toolbox Talks] => Array
(
[0] => DocumentRecord Object
(
[records:protected] => Array
(
)
[recordId:protected] =>
[searchWordClass:protected] =>
[searchWordPeerClass:protected] =>
[bok_record:protected] =>
[authors:protected] =>
[organizations:protected] =>
[collections:protected] =>
[categories:protected] =>
[categories_initialized:protected] =>
[mapped_items:protected] =>
[content:protected] =>
[files:protected] =>
[language:protected] => Language Object
(
[id:protected] => 1
[code:protected] => en
[name:protected] => English
[alreadyInSave:protected] =>
[alreadyInValidation:protected] =>
[validationFailures:protected] => Array
(
)
[_new:BaseObject:private] =>
[_deleted:BaseObject:private] =>
[modifiedColumns:protected] => Array
(
)
)
[old_record:protected] =>
[id:protected] => 1605
[old_id:protected] => 1262
[elcosh_id:protected] => d001137
[type:protected] => document
[display_type:protected] => HTML w/ PDF
[user_id:protected] =>
[language_id:protected] => 1
[tagging_id:protected] => Garber
[priority_id:protected] => 1
[title:protected] => Focus Four Toolbox Talks, Module 1 – Falls, Talk #2 – Falls from debris piles?
[total_pages:protected] => 1
[billed_pages:protected] => 1
[publication_number:protected] =>
[part_of:protected] =>
[keywords:protected] => disaster response, hazard clean-up, uneven surface, disaster site, disaster clean-up
[comments:protected] =>
[summary:protected] => A toolbox talk on preventing falls from debris piles. Includes questions to ask, an incident to discuss with images, and a place to record questions the trainer would like to ask about the incident. Part of a collection. Click on the 'collection' button to access the other items.
[transition_comments:protected] =>
[external_link:protected] =>
[consol_link:protected] => http://www.cpwrconstructionsolutions.org/roofing/hazard/1463/install-asphalt-roofs-fall-from-heights.html
[more_like_this:protected] => a000081,d000478,d000530
[permission_given_by:protected] =>
[published:protected] => T
[billable:protected] => F
[img_name:protected] =>
[img_ext:protected] =>
[img_width:protected] =>
[img_height:protected] =>
[img_credit:protected] =>
[img_practice:protected] =>
[vid_source_id:protected] =>
[vid_running_time:protected] =>
[vid_intended_audience:protected] =>
[vid_acquisition_info:protected] =>
[vid_cost:protected] =>
[vid_producer:protected] =>
[vid_filename:protected] =>
[vid_filename_downloadable:protected] =>
[date_summary:protected] =>
[date_permission_requested:protected] =>
[date_permission_received:protected] =>
[date_review_needed:protected] =>
[date_received:protected] => 02/15/12
[date_completed:protected] => 03/19/12
[date_billed:protected] =>
[date_modified:protected] => 07/10/12
[collBokExports:protected] =>
[lastBokExportCriteria:BaseElcoshItem:private] =>
[alreadyInSave:protected] =>
[alreadyInValidation:protected] =>
[validationFailures:protected] => Array
(
)
[_new:BaseObject:private] =>
[_deleted:BaseObject:private] =>
[modifiedColumns:protected] => Array
(
)
)
[1] => DocumentRecord Object
(
[records:protected] => Array
(
)
[recordId:protected] =>
[searchWordClass:protected] =>
[searchWordPeerClass:protected] =>
[bok_record:protected] =>
[authors:protected] =>
[organizations:protected] =>
[collections:protected] =>
[categories:protected] =>
[categories_initialized:protected] =>
[mapped_items:protected] =>
[content:protected] =>
[files:protected] =>
[language:protected] => Language Object
(
[id:protected] => 1
[code:protected] => en
[name:protected] => English
[alreadyInSave:protected] =>
[alreadyInValidation:protected] =>
[validationFailures:protected] => Array
(
)
[_new:BaseObject:private] =>
[_deleted:BaseObject:private] =>
[modifiedColumns:protected] => Array
(
)
)
[old_record:protected] =>
[id:protected] => 1610
[old_id:protected] => 1271
[elcosh_id:protected] => d001146
[type:protected] => document
[display_type:protected] => HTML w/ PDF
[user_id:protected] => 0
[language_id:protected] => 1
[tagging_id:protected] => Garber
[priority_id:protected] => 1
[title:protected] => Focus Four Toolbox Talks, Module 2 – Struck-by, Talk #5 – Rigging and Securing Loads
[total_pages:protected] => 1
[billed_pages:protected] => 1
[publication_number:protected] =>
[part_of:protected] =>
[keywords:protected] => rigging, lift loads, loading areas, chains
[comments:protected] =>
[summary:protected] => A toolbox talk on preventing struck-by incidents caused by not securing loads properly. Includes questions to ask, an incident to discuss with images, and a place to record questions the trainer would like to ask about the incident. Part of a collection. Click on the 'collection' button to access the other items.
[transition_comments:protected] =>
[external_link:protected] =>
[consol_link:protected] => http://www.cpwrconstructionsolutions.org/heavy_equipment/hazard/1591/move-equipment-to-from-and-between-sites-work-zone-struck-by-injuries-and-fatalities.html
[more_like_this:protected] => d000144,d000360,d000873
[permission_given_by:protected] =>
[published:protected] => T
[billable:protected] => F
[img_name:protected] =>
[img_ext:protected] =>
[img_width:protected] =>
[img_height:protected] =>
[img_credit:protected] =>
[img_practice:protected] =>
[vid_source_id:protected] =>
[vid_running_time:protected] =>
[vid_intended_audience:protected] =>
[vid_acquisition_info:protected] =>
[vid_cost:protected] =>
[vid_producer:protected] =>
[vid_filename:protected] =>
[vid_filename_downloadable:protected] =>
[date_summary:protected] =>
[date_permission_requested:protected] =>
[date_permission_received:protected] =>
[date_review_needed:protected] =>
[date_received:protected] => 02/15/12
[date_completed:protected] => 03/28/12
[date_billed:protected] =>
[date_modified:protected] => 05/12/14
[collBokExports:protected] =>
[lastBokExportCriteria:BaseElcoshItem:private] =>
[alreadyInSave:protected] =>
[alreadyInValidation:protected] =>
[validationFailures:protected] => Array
(
)
[_new:BaseObject:private] =>
[_deleted:BaseObject:private] =>
[modifiedColumns:protected] => Array
(
)
)
[2] => DocumentRecord Object
(
[records:protected] => Array
(
)
[recordId:protected] =>
[searchWordClass:protected] =>
[searchWordPeerClass:protected] =>
[bok_record:protected] =>
[authors:protected] =>
[organizations:protected] =>
[collections:protected] =>
[categories:protected] =>
[categories_initialized:protected] =>
[mapped_items:protected] =>
[content:protected] =>
[files:protected] =>
[language:protected] => Language Object
(
[id:protected] => 1
[code:protected] => en
[name:protected] => English
[alreadyInSave:protected] =>
[alreadyInValidation:protected] =>
[validationFailures:protected] => Array
(
)
[_new:BaseObject:private] =>
[_deleted:BaseObject:private] =>
[modifiedColumns:protected] => Array
(
)
)
[old_record:protected] =>
[id:protected] => 1645
[old_id:protected] => 1274
[elcosh_id:protected] => d001149
[type:protected] => document
[display_type:protected] => HTML w/ PDF
[user_id:protected] => 0
[language_id:protected] => 1
[tagging_id:protected] => Garber
[priority_id:protected] => 1
[title:protected] => Focus Four Toolbox Talks, Module 3 – Caught-in/between, Talk #2 – Trenches & Heavy Equipment
[total_pages:protected] => 1
[billed_pages:protected] => 1
[publication_number:protected] =>
[part_of:protected] =>
[keywords:protected] => back-up alarms, spotter, soil cave-in, spoil pikes, ROPs, trenching, rain
[comments:protected] =>
[summary:protected] => A toolbox talk on preventing incidents involving trenches such as trench collapse. Includes questions to ask, an incident to discuss with images, and a place to record questions the trainer would like to ask about the incident. Part of a collection. Click on the 'collection' button to access the other items.
[transition_comments:protected] =>
[external_link:protected] =>
[consol_link:protected] =>
[more_like_this:protected] => d000019,d000035,d000168
[permission_given_by:protected] =>
[published:protected] => T
[billable:protected] => F
[img_name:protected] =>
[img_ext:protected] =>
[img_width:protected] =>
[img_height:protected] =>
[img_credit:protected] =>
[img_practice:protected] =>
[vid_source_id:protected] =>
[vid_running_time:protected] =>
[vid_intended_audience:protected] =>
[vid_acquisition_info:protected] =>
[vid_cost:protected] =>
[vid_producer:protected] =>
[vid_filename:protected] =>
[vid_filename_downloadable:protected] =>
[date_summary:protected] =>
[date_permission_requested:protected] =>
[date_permission_received:protected] =>
[date_review_needed:protected] =>
[date_received:protected] => 02/15/12
[date_completed:protected] => 04/02/12
[date_billed:protected] =>
[date_modified:protected] => 05/23/23
[collBokExports:protected] =>
[lastBokExportCriteria:BaseElcoshItem:private] =>
[alreadyInSave:protected] =>
[alreadyInValidation:protected] =>
[validationFailures:protected] => Array
(
)
[_new:BaseObject:private] =>
[_deleted:BaseObject:private] =>
[modifiedColumns:protected] => Array
(
)
)
[3] => DocumentRecord Object
(
[records:protected] => Array
(
)
[recordId:protected] =>
[searchWordClass:protected] =>
[searchWordPeerClass:protected] =>
[bok_record:protected] =>
[authors:protected] =>
[organizations:protected] =>
[collections:protected] =>
[categories:protected] =>
[categories_initialized:protected] =>
[mapped_items:protected] =>
[content:protected] =>
[files:protected] =>
[language:protected] => Language Object
(
[id:protected] => 1
[code:protected] => en
[name:protected] => English
[alreadyInSave:protected] =>
[alreadyInValidation:protected] =>
[validationFailures:protected] => Array
(
)
[_new:BaseObject:private] =>
[_deleted:BaseObject:private] =>
[modifiedColumns:protected] => Array
(
)
)
[old_record:protected] =>
[id:protected] => 1654
[old_id:protected] => 1284
[elcosh_id:protected] => d001159
[type:protected] => document
[display_type:protected] => HTML w/ PDF
[user_id:protected] => 0
[language_id:protected] => 1
[tagging_id:protected] => Garber
[priority_id:protected] => 1
[title:protected] => Focus Four Toolbox Talks, Module 4 – Electrocutions, Talk #6 – Hazards on Disaster Sites
[total_pages:protected] => 1
[billed_pages:protected] => 1
[publication_number:protected] =>
[part_of:protected] =>
[keywords:protected] => powerlines, underground, utilities, generators, wet conditions, GFCIs, energized lines, disasters, emergency response
[comments:protected] =>
[summary:protected] => A toolbox talk on how to avoid electrocution on a disaster site. Includes questions to ask, an incident to discuss with images, and a place to record questions the trainer would like to ask about the incident. Part of a collection. Click on the 'collection' button to access the other items.
[transition_comments:protected] =>
[external_link:protected] =>
[consol_link:protected] => http://www.cpwrconstructionsolutions.org/electrical/hazard/1138/install-and-repair-high-voltage-lines-transformers-switches-electrical-shocks-burns-and-or-electrocution.html
[more_like_this:protected] => d000135,d000361,d000437
[permission_given_by:protected] =>
[published:protected] => T
[billable:protected] => F
[img_name:protected] =>
[img_ext:protected] =>
[img_width:protected] =>
[img_height:protected] =>
[img_credit:protected] =>
[img_practice:protected] =>
[vid_source_id:protected] =>
[vid_running_time:protected] =>
[vid_intended_audience:protected] =>
[vid_acquisition_info:protected] =>
[vid_cost:protected] =>
[vid_producer:protected] =>
[vid_filename:protected] =>
[vid_filename_downloadable:protected] =>
[date_summary:protected] =>
[date_permission_requested:protected] =>
[date_permission_received:protected] =>
[date_review_needed:protected] =>
[date_received:protected] => 02/15/12
[date_completed:protected] => 04/02/12
[date_billed:protected] =>
[date_modified:protected] => 05/23/23
[collBokExports:protected] =>
[lastBokExportCriteria:BaseElcoshItem:private] =>
[alreadyInSave:protected] =>
[alreadyInValidation:protected] =>
[validationFailures:protected] => Array
(
)
[_new:BaseObject:private] =>
[_deleted:BaseObject:private] =>
[modifiedColumns:protected] => Array
(
)
)
)
)
[collections] => Array
(
[1294] =>
[1295] =>
[1292] =>
[1293] => CollectionRecord Object
(
[collection_items:protected] =>
[records:protected] => Array
(
)
[recordId:protected] =>
[searchWordClass:protected] =>
[searchWordPeerClass:protected] =>
[bok_record:protected] =>
[authors:protected] =>
[organizations:protected] =>
[collections:protected] =>
[categories:protected] =>
[categories_initialized:protected] =>
[mapped_items:protected] =>
[content:protected] =>
[files:protected] =>
[language:protected] =>
[old_record:protected] =>
[id:protected] => 1293
[old_id:protected] =>
[elcosh_id:protected] => c000026
[type:protected] => collection
[display_type:protected] => Collection
[user_id:protected] =>
[language_id:protected] =>
[tagging_id:protected] =>
[priority_id:protected] =>
[title:protected] => Focus Four-Struck By
[total_pages:protected] =>
[billed_pages:protected] =>
[publication_number:protected] =>
[part_of:protected] =>
[keywords:protected] =>
[comments:protected] =>
[summary:protected] => The following are links to all of the items in this collection:
[transition_comments:protected] =>
[external_link:protected] =>
[consol_link:protected] =>
[more_like_this:protected] =>
[permission_given_by:protected] =>
[published:protected] => T
[billable:protected] => F
[img_name:protected] =>
[img_ext:protected] =>
[img_width:protected] =>
[img_height:protected] =>
[img_credit:protected] =>
[img_practice:protected] =>
[vid_source_id:protected] =>
[vid_running_time:protected] =>
[vid_intended_audience:protected] =>
[vid_acquisition_info:protected] =>
[vid_cost:protected] =>
[vid_producer:protected] =>
[vid_filename:protected] =>
[vid_filename_downloadable:protected] =>
[date_summary:protected] =>
[date_permission_requested:protected] =>
[date_permission_received:protected] =>
[date_review_needed:protected] =>
[date_received:protected] => 05/08/12
[date_completed:protected] => 05/08/12
[date_billed:protected] =>
[date_modified:protected] => 05/08/12
[collBokExports:protected] =>
[lastBokExportCriteria:BaseElcoshItem:private] =>
[alreadyInSave:protected] =>
[alreadyInValidation:protected] =>
[validationFailures:protected] => Array
(
)
[_new:BaseObject:private] =>
[_deleted:BaseObject:private] =>
[modifiedColumns:protected] => Array
(
)
)
)
[record] => DocumentRecord Object
(
[records:protected] => Array
(
)
[recordId:protected] =>
[searchWordClass:protected] =>
[searchWordPeerClass:protected] =>
[bok_record:protected] =>
[authors:protected] => Array
(
)
[organizations:protected] => Array
(
[256] => Organization Object
(
[id:protected] => 256
[elcosh_id:protected] => o000276
[user_id:protected] => 14
[province_id:protected] => 0
[country_id:protected] => 0
[title:protected] => IUOE National Training Fund
[address:protected] =>
[postal_code:protected] =>
[city:protected] =>
[department:protected] =>
[phone:protected] => 304-253-8674
[fax:protected] =>
[email:protected] =>
[website:protected] => http://www.iuoeiettc.org
[filename:protected] =>
[about:protected] =>
[comments:protected] =>
[logo_available:protected] => T
[no_details:protected] => F
[date_received:protected] => 2012-02-13
[date_completed:protected] => 2012-02-13
[date_billed:protected] =>
[alreadyInSave:protected] =>
[alreadyInValidation:protected] =>
[validationFailures:protected] => Array
(
)
[_new:BaseObject:private] =>
[_deleted:BaseObject:private] =>
[modifiedColumns:protected] => Array
(
)
)
)
[collections:protected] => Array
(
[1294] =>
[1295] =>
[1292] =>
[1293] => CollectionRecord Object
(
[collection_items:protected] =>
[records:protected] => Array
(
)
[recordId:protected] =>
[searchWordClass:protected] =>
[searchWordPeerClass:protected] =>
[bok_record:protected] =>
[authors:protected] =>
[organizations:protected] =>
[collections:protected] =>
[categories:protected] =>
[categories_initialized:protected] =>
[mapped_items:protected] =>
[content:protected] =>
[files:protected] =>
[language:protected] =>
[old_record:protected] =>
[id:protected] => 1293
[old_id:protected] =>
[elcosh_id:protected] => c000026
[type:protected] => collection
[display_type:protected] => Collection
[user_id:protected] =>
[language_id:protected] =>
[tagging_id:protected] =>
[priority_id:protected] =>
[title:protected] => Focus Four-Struck By
[total_pages:protected] =>
[billed_pages:protected] =>
[publication_number:protected] =>
[part_of:protected] =>
[keywords:protected] =>
[comments:protected] =>
[summary:protected] => The following are links to all of the items in this collection:
[transition_comments:protected] =>
[external_link:protected] =>
[consol_link:protected] =>
[more_like_this:protected] =>
[permission_given_by:protected] =>
[published:protected] => T
[billable:protected] => F
[img_name:protected] =>
[img_ext:protected] =>
[img_width:protected] =>
[img_height:protected] =>
[img_credit:protected] =>
[img_practice:protected] =>
[vid_source_id:protected] =>
[vid_running_time:protected] =>
[vid_intended_audience:protected] =>
[vid_acquisition_info:protected] =>
[vid_cost:protected] =>
[vid_producer:protected] =>
[vid_filename:protected] =>
[vid_filename_downloadable:protected] =>
[date_summary:protected] =>
[date_permission_requested:protected] =>
[date_permission_received:protected] =>
[date_review_needed:protected] =>
[date_received:protected] => 05/08/12
[date_completed:protected] => 05/08/12
[date_billed:protected] =>
[date_modified:protected] => 05/08/12
[collBokExports:protected] =>
[lastBokExportCriteria:BaseElcoshItem:private] =>
[alreadyInSave:protected] =>
[alreadyInValidation:protected] =>
[validationFailures:protected] => Array
(
)
[_new:BaseObject:private] =>
[_deleted:BaseObject:private] =>
[modifiedColumns:protected] => Array
(
)
)
)
[categories:protected] =>
[categories_initialized:protected] =>
[mapped_items:protected] => Array
(
[1605] => DocumentRecord Object
(
[records:protected] => Array
(
)
[recordId:protected] =>
[searchWordClass:protected] =>
[searchWordPeerClass:protected] =>
[bok_record:protected] =>
[authors:protected] =>
[organizations:protected] =>
[collections:protected] =>
[categories:protected] =>
[categories_initialized:protected] =>
[mapped_items:protected] =>
[content:protected] =>
[files:protected] =>
[language:protected] =>
[old_record:protected] =>
[id:protected] => 1605
[old_id:protected] => 1262
[elcosh_id:protected] => d001137
[type:protected] => document
[display_type:protected] => HTML w/ PDF
[user_id:protected] =>
[language_id:protected] => 1
[tagging_id:protected] => Garber
[priority_id:protected] => 1
[title:protected] => Focus Four Toolbox Talks, Module 1 – Falls, Talk #2 – Falls from debris piles?
[total_pages:protected] => 1
[billed_pages:protected] => 1
[publication_number:protected] =>
[part_of:protected] =>
[keywords:protected] => disaster response, hazard clean-up, uneven surface, disaster site, disaster clean-up
[comments:protected] =>
[summary:protected] => A toolbox talk on preventing falls from debris piles. Includes questions to ask, an incident to discuss with images, and a place to record questions the trainer would like to ask about the incident. Part of a collection. Click on the 'collection' button to access the other items.
[transition_comments:protected] =>
[external_link:protected] =>
[consol_link:protected] => http://www.cpwrconstructionsolutions.org/roofing/hazard/1463/install-asphalt-roofs-fall-from-heights.html
[more_like_this:protected] => a000081,d000478,d000530
[permission_given_by:protected] =>
[published:protected] => T
[billable:protected] => F
[img_name:protected] =>
[img_ext:protected] =>
[img_width:protected] =>
[img_height:protected] =>
[img_credit:protected] =>
[img_practice:protected] =>
[vid_source_id:protected] =>
[vid_running_time:protected] =>
[vid_intended_audience:protected] =>
[vid_acquisition_info:protected] =>
[vid_cost:protected] =>
[vid_producer:protected] =>
[vid_filename:protected] =>
[vid_filename_downloadable:protected] =>
[date_summary:protected] =>
[date_permission_requested:protected] =>
[date_permission_received:protected] =>
[date_review_needed:protected] =>
[date_received:protected] => 02/15/12
[date_completed:protected] => 03/19/12
[date_billed:protected] =>
[date_modified:protected] => 07/10/12
[collBokExports:protected] =>
[lastBokExportCriteria:BaseElcoshItem:private] =>
[alreadyInSave:protected] =>
[alreadyInValidation:protected] =>
[validationFailures:protected] => Array
(
)
[_new:BaseObject:private] =>
[_deleted:BaseObject:private] =>
[modifiedColumns:protected] => Array
(
)
)
[1610] => DocumentRecord Object
(
[records:protected] => Array
(
)
[recordId:protected] =>
[searchWordClass:protected] =>
[searchWordPeerClass:protected] =>
[bok_record:protected] =>
[authors:protected] =>
[organizations:protected] =>
[collections:protected] =>
[categories:protected] =>
[categories_initialized:protected] =>
[mapped_items:protected] =>
[content:protected] =>
[files:protected] =>
[language:protected] =>
[old_record:protected] =>
[id:protected] => 1610
[old_id:protected] => 1271
[elcosh_id:protected] => d001146
[type:protected] => document
[display_type:protected] => HTML w/ PDF
[user_id:protected] => 0
[language_id:protected] => 1
[tagging_id:protected] => Garber
[priority_id:protected] => 1
[title:protected] => Focus Four Toolbox Talks, Module 2 – Struck-by, Talk #5 – Rigging and Securing Loads
[total_pages:protected] => 1
[billed_pages:protected] => 1
[publication_number:protected] =>
[part_of:protected] =>
[keywords:protected] => rigging, lift loads, loading areas, chains
[comments:protected] =>
[summary:protected] => A toolbox talk on preventing struck-by incidents caused by not securing loads properly. Includes questions to ask, an incident to discuss with images, and a place to record questions the trainer would like to ask about the incident. Part of a collection. Click on the 'collection' button to access the other items.
[transition_comments:protected] =>
[external_link:protected] =>
[consol_link:protected] => http://www.cpwrconstructionsolutions.org/heavy_equipment/hazard/1591/move-equipment-to-from-and-between-sites-work-zone-struck-by-injuries-and-fatalities.html
[more_like_this:protected] => d000144,d000360,d000873
[permission_given_by:protected] =>
[published:protected] => T
[billable:protected] => F
[img_name:protected] =>
[img_ext:protected] =>
[img_width:protected] =>
[img_height:protected] =>
[img_credit:protected] =>
[img_practice:protected] =>
[vid_source_id:protected] =>
[vid_running_time:protected] =>
[vid_intended_audience:protected] =>
[vid_acquisition_info:protected] =>
[vid_cost:protected] =>
[vid_producer:protected] =>
[vid_filename:protected] =>
[vid_filename_downloadable:protected] =>
[date_summary:protected] =>
[date_permission_requested:protected] =>
[date_permission_received:protected] =>
[date_review_needed:protected] =>
[date_received:protected] => 02/15/12
[date_completed:protected] => 03/28/12
[date_billed:protected] =>
[date_modified:protected] => 05/12/14
[collBokExports:protected] =>
[lastBokExportCriteria:BaseElcoshItem:private] =>
[alreadyInSave:protected] =>
[alreadyInValidation:protected] =>
[validationFailures:protected] => Array
(
)
[_new:BaseObject:private] =>
[_deleted:BaseObject:private] =>
[modifiedColumns:protected] => Array
(
)
)
[1645] => DocumentRecord Object
(
[records:protected] => Array
(
)
[recordId:protected] =>
[searchWordClass:protected] =>
[searchWordPeerClass:protected] =>
[bok_record:protected] =>
[authors:protected] =>
[organizations:protected] =>
[collections:protected] =>
[categories:protected] =>
[categories_initialized:protected] =>
[mapped_items:protected] =>
[content:protected] =>
[files:protected] =>
[language:protected] =>
[old_record:protected] =>
[id:protected] => 1645
[old_id:protected] => 1274
[elcosh_id:protected] => d001149
[type:protected] => document
[display_type:protected] => HTML w/ PDF
[user_id:protected] => 0
[language_id:protected] => 1
[tagging_id:protected] => Garber
[priority_id:protected] => 1
[title:protected] => Focus Four Toolbox Talks, Module 3 – Caught-in/between, Talk #2 – Trenches & Heavy Equipment
[total_pages:protected] => 1
[billed_pages:protected] => 1
[publication_number:protected] =>
[part_of:protected] =>
[keywords:protected] => back-up alarms, spotter, soil cave-in, spoil pikes, ROPs, trenching, rain
[comments:protected] =>
[summary:protected] => A toolbox talk on preventing incidents involving trenches such as trench collapse. Includes questions to ask, an incident to discuss with images, and a place to record questions the trainer would like to ask about the incident. Part of a collection. Click on the 'collection' button to access the other items.
[transition_comments:protected] =>
[external_link:protected] =>
[consol_link:protected] =>
[more_like_this:protected] => d000019,d000035,d000168
[permission_given_by:protected] =>
[published:protected] => T
[billable:protected] => F
[img_name:protected] =>
[img_ext:protected] =>
[img_width:protected] =>
[img_height:protected] =>
[img_credit:protected] =>
[img_practice:protected] =>
[vid_source_id:protected] =>
[vid_running_time:protected] =>
[vid_intended_audience:protected] =>
[vid_acquisition_info:protected] =>
[vid_cost:protected] =>
[vid_producer:protected] =>
[vid_filename:protected] =>
[vid_filename_downloadable:protected] =>
[date_summary:protected] =>
[date_permission_requested:protected] =>
[date_permission_received:protected] =>
[date_review_needed:protected] =>
[date_received:protected] => 02/15/12
[date_completed:protected] => 04/02/12
[date_billed:protected] =>
[date_modified:protected] => 05/23/23
[collBokExports:protected] =>
[lastBokExportCriteria:BaseElcoshItem:private] =>
[alreadyInSave:protected] =>
[alreadyInValidation:protected] =>
[validationFailures:protected] => Array
(
)
[_new:BaseObject:private] =>
[_deleted:BaseObject:private] =>
[modifiedColumns:protected] => Array
(
)
)
[1654] => DocumentRecord Object
(
[records:protected] => Array
(
)
[recordId:protected] =>
[searchWordClass:protected] =>
[searchWordPeerClass:protected] =>
[bok_record:protected] =>
[authors:protected] =>
[organizations:protected] =>
[collections:protected] =>
[categories:protected] =>
[categories_initialized:protected] =>
[mapped_items:protected] =>
[content:protected] =>
[files:protected] =>
[language:protected] =>
[old_record:protected] =>
[id:protected] => 1654
[old_id:protected] => 1284
[elcosh_id:protected] => d001159
[type:protected] => document
[display_type:protected] => HTML w/ PDF
[user_id:protected] => 0
[language_id:protected] => 1
[tagging_id:protected] => Garber
[priority_id:protected] => 1
[title:protected] => Focus Four Toolbox Talks, Module 4 – Electrocutions, Talk #6 – Hazards on Disaster Sites
[total_pages:protected] => 1
[billed_pages:protected] => 1
[publication_number:protected] =>
[part_of:protected] =>
[keywords:protected] => powerlines, underground, utilities, generators, wet conditions, GFCIs, energized lines, disasters, emergency response
[comments:protected] =>
[summary:protected] => A toolbox talk on how to avoid electrocution on a disaster site. Includes questions to ask, an incident to discuss with images, and a place to record questions the trainer would like to ask about the incident. Part of a collection. Click on the 'collection' button to access the other items.
[transition_comments:protected] =>
[external_link:protected] =>
[consol_link:protected] => http://www.cpwrconstructionsolutions.org/electrical/hazard/1138/install-and-repair-high-voltage-lines-transformers-switches-electrical-shocks-burns-and-or-electrocution.html
[more_like_this:protected] => d000135,d000361,d000437
[permission_given_by:protected] =>
[published:protected] => T
[billable:protected] => F
[img_name:protected] =>
[img_ext:protected] =>
[img_width:protected] =>
[img_height:protected] =>
[img_credit:protected] =>
[img_practice:protected] =>
[vid_source_id:protected] =>
[vid_running_time:protected] =>
[vid_intended_audience:protected] =>
[vid_acquisition_info:protected] =>
[vid_cost:protected] =>
[vid_producer:protected] =>
[vid_filename:protected] =>
[vid_filename_downloadable:protected] =>
[date_summary:protected] =>
[date_permission_requested:protected] =>
[date_permission_received:protected] =>
[date_review_needed:protected] =>
[date_received:protected] => 02/15/12
[date_completed:protected] => 04/02/12
[date_billed:protected] =>
[date_modified:protected] => 05/23/23
[collBokExports:protected] =>
[lastBokExportCriteria:BaseElcoshItem:private] =>
[alreadyInSave:protected] =>
[alreadyInValidation:protected] =>
[validationFailures:protected] => Array
(
)
[_new:BaseObject:private] =>
[_deleted:BaseObject:private] =>
[modifiedColumns:protected] => Array
(
)
)
)
[content:protected] =>
[files:protected] => Array
(
[9400] => File Object
(
[id:protected] => 9400
[filename:protected] => 1.jpg
[downloadable:protected] => F
[timestamp:protected] => 2014-05-08 15:05:37
[alreadyInSave:protected] =>
[alreadyInValidation:protected] =>
[validationFailures:protected] => Array
(
)
[_new:BaseObject:private] =>
[_deleted:BaseObject:private] =>
[modifiedColumns:protected] => Array
(
)
)
[9401] => File Object
(
[id:protected] => 9401
[filename:protected] => d001298.pdf
[downloadable:protected] => T
[timestamp:protected] => 2014-05-08 15:05:37
[alreadyInSave:protected] =>
[alreadyInValidation:protected] =>
[validationFailures:protected] => Array
(
)
[_new:BaseObject:private] =>
[_deleted:BaseObject:private] =>
[modifiedColumns:protected] => Array
(
)
)
)
[language:protected] => Language Object
(
[id:protected] => 1
[code:protected] => en
[name:protected] => English
[alreadyInSave:protected] =>
[alreadyInValidation:protected] =>
[validationFailures:protected] => Array
(
)
[_new:BaseObject:private] =>
[_deleted:BaseObject:private] =>
[modifiedColumns:protected] => Array
(
)
)
[old_record:protected] =>
[id:protected] => 3827
[old_id:protected] =>
[elcosh_id:protected] => d001298
[type:protected] => document
[display_type:protected] => HTML w/ PDF
[user_id:protected] => 23
[language_id:protected] => 1
[tagging_id:protected] => Bruce Lippy
[priority_id:protected] => 1
[title:protected] => Getting the most out of the IUOE Toolbox Talks
[total_pages:protected] => 2
[billed_pages:protected] => 2
[publication_number:protected] =>
[part_of:protected] =>
[keywords:protected] => toolbox talks, tailgate talks
[comments:protected] =>
[summary:protected] => Toolbox talks have been the main tool for communicating safety information on construction jobs for decades.
Unfortunately, there has been little research on what makes for effective toolbox talks. The IUOE National
Training Fund worked with OSHA and NIOSH to make sure their series of 24 Focus Four toolbox talks were based on the best recommendations for effective design. These toolbox talks accompany an entire package of training materials, but can be used alone. This guide points out the key features of these toolbox talks and how best to deliver them.
[transition_comments:protected] =>
[external_link:protected] =>
[consol_link:protected] =>
[more_like_this:protected] => d001137,d001146,d001149,d001159
[permission_given_by:protected] => IUOE National Hazmat Program
[published:protected] => T
[billable:protected] => F
[img_name:protected] =>
[img_ext:protected] => png
[img_width:protected] =>
[img_height:protected] =>
[img_credit:protected] =>
[img_practice:protected] =>
[vid_source_id:protected] =>
[vid_running_time:protected] =>
[vid_intended_audience:protected] =>
[vid_acquisition_info:protected] =>
[vid_cost:protected] =>
[vid_producer:protected] =>
[vid_filename:protected] =>
[vid_filename_downloadable:protected] =>
[date_summary:protected] => 2007
[date_permission_requested:protected] =>
[date_permission_received:protected] =>
[date_review_needed:protected] =>
[date_received:protected] => 05/08/14
[date_completed:protected] => 05/08/14
[date_billed:protected] =>
[date_modified:protected] => 05/08/14
[collBokExports:protected] =>
[lastBokExportCriteria:BaseElcoshItem:private] =>
[alreadyInSave:protected] =>
[alreadyInValidation:protected] =>
[validationFailures:protected] => Array
(
)
[_new:BaseObject:private] =>
[_deleted:BaseObject:private] =>
[modifiedColumns:protected] => Array
(
)
)
[show_text] =>
[document_content] => ElcoshItemDocumentContent Object
(
[id:protected] => 2896
[item_id:protected] => 3827
[type:protected] => main
[title:protected] =>
[content:protected] =>
Why were these talks developed?
Toolbox talks have been the main tool for communicating safety information on construction jobs for decades. Unfortunately, there has been almost no research on what makes for effective toolbox talks. The IUOE National Training Fund has worked with OSHA, the National Institute for Occupational Safety and Health and the Lippy Group, LLC to make sure these Focus Four toolbox talks are based on the latest fi ndings on the most effective design and tailored to the hazards operating engineers face daily. These toolbox talks accompany an entire package of training materials, but can be used alone. The way these are delivered is as important as how well they are designed.
What did NIOSH find out?
- Just handing out factsheets and toolbox talks to workers doesn’t work. Providing copies after toolbox talks doesn’t make much of an impact either.
- Using case studies (real life stories of accidents that ended in fatality or injury) in toolbox talks is effective.
- When toolbox talks containing case studies were accompanied by discussion questions to encourage group participation, they were more effective. Consequently, getting the workers to participate in the discussion about the case study is important. It’s not enough to tell the story, it is better to have the workers engage in problem solving that analyzes why the accident occurred and how it could have been prevented. Active learning is always better than passive.
How should you deliver these toolbox talks?
- Choose a topic that is related to work going on at the site.
- Hold the meeting on the job, preferably where everyone can sit and relax.
- Hold the meeting at the beginning of a shift or after a break. Folks are too tired at the end of a shift to carefully listen and they want to get home.
- Read the toolbox talk sheet on the topic prior to conducting the talk.
- Start at the top of the form and work right through to the end, which should take around 10 to 15 minutes. Guidance is provided in blue print to help you with each section.
- Use the questions provided to generate discussions. Always allow time for the crew to respond to your questions before you provide an answer. Some suggested responses are written in italics.
- Review the case study and emphasize that this was a real incident. Ask the crew for a case study before you review the one provided, however.
- Always end with a discussion of the particular worksite where you are conducting the talk. Tie the talk as closely to hazards on the site as possible and encourage the crew to constantly look for and immediately correct hazards. They should also know how to report any problems that can’t be immediately corrected.
- Provide copies to each person, if you like, but NIOSH has not found that to be particularly effective.
- Encourage workers to do similar talks on their sites and provide them with the IUOE phone number for ordering in bulk.
- Have everyone sign the back of the form to indicate they attended this session and point out it is a pledge to look out for the health and safety of everyone on the site.
What are the key features of these toolbox talks?

[content_transformed:protected] =>
Why were these talks developed?
Toolbox talks have been the main tool for communicating safety information on construction jobs for decades. Unfortunately, there has been almost no research on what makes for effective toolbox talks. The IUOE National Training Fund has worked with OSHA, the National Institute for Occupational Safety and Health and the Lippy Group, LLC to make sure these Focus Four toolbox talks are based on the latest fi ndings on the most effective design and tailored to the hazards operating engineers face daily. These toolbox talks accompany an entire package of training materials, but can be used alone. The way these are delivered is as important as how well they are designed.
What did NIOSH find out?
- Just handing out factsheets and toolbox talks to workers doesn’t work. Providing copies after toolbox talks doesn’t make much of an impact either.
- Using case studies (real life stories of accidents that ended in fatality or injury) in toolbox talks is effective.
- When toolbox talks containing case studies were accompanied by discussion questions to encourage group participation, they were more effective. Consequently, getting the workers to participate in the discussion about the case study is important. It’s not enough to tell the story, it is better to have the workers engage in problem solving that analyzes why the accident occurred and how it could have been prevented. Active learning is always better than passive.
How should you deliver these toolbox talks?
- Choose a topic that is related to work going on at the site.
- Hold the meeting on the job, preferably where everyone can sit and relax.
- Hold the meeting at the beginning of a shift or after a break. Folks are too tired at the end of a shift to carefully listen and they want to get home.
- Read the toolbox talk sheet on the topic prior to conducting the talk.
- Start at the top of the form and work right through to the end, which should take around 10 to 15 minutes. Guidance is provided in blue print to help you with each section.
- Use the questions provided to generate discussions. Always allow time for the crew to respond to your questions before you provide an answer. Some suggested responses are written in italics.
- Review the case study and emphasize that this was a real incident. Ask the crew for a case study before you review the one provided, however.
- Always end with a discussion of the particular worksite where you are conducting the talk. Tie the talk as closely to hazards on the site as possible and encourage the crew to constantly look for and immediately correct hazards. They should also know how to report any problems that can’t be immediately corrected.
- Provide copies to each person, if you like, but NIOSH has not found that to be particularly effective.
- Encourage workers to do similar talks on their sites and provide them with the IUOE phone number for ordering in bulk.
- Have everyone sign the back of the form to indicate they attended this session and point out it is a pledge to look out for the health and safety of everyone on the site.
What are the key features of these toolbox talks?
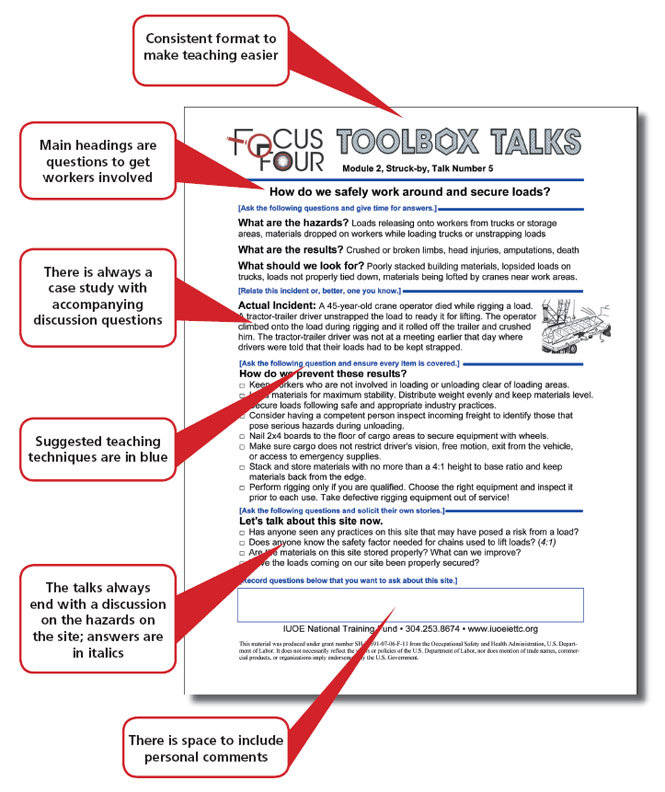
[disclaimer:protected] =>
[disclaimer_transformed:protected] =>
[alreadyInSave:protected] =>
[alreadyInValidation:protected] =>
[validationFailures:protected] => Array
(
)
[_new:BaseObject:private] =>
[_deleted:BaseObject:private] =>
[modifiedColumns:protected] => Array
(
)
)
[template] => record
)
[_file] => /home/agsafe5/repositories/elcosh/live/templates/elcosh/record_macros.html
[_errors:protected] => Array
(
)
[_encoding:protected] => UTF-8
[_outputMode:protected] => 11
[_forceReparse:protected] =>
[_phpCodeDestination:protected] => /tmp/
[_phpCodeExtension:protected] => php
[_cacheLifetime:protected] => 30
[_cachePurgeFrequency:protected] => 30
[externalMacroTemplatesCache:PHPTAL:private] => Array
(
)
)
)
)
[1] => PHPTAL_Context Object
(
[_line] =>
[_file] => /home/agsafe5/repositories/elcosh/live/templates/elcosh/record.html
[repeat] => stdClass Object
(
)
[_xmlDeclaration] =>
[_docType] =>
[_nothrow:PHPTAL_Context:private] =>
[_slots:PHPTAL_Context:private] => Array
(
)
[_slotsStack:PHPTAL_Context:private] => Array
(
[0] => Array
(
)
[1] => Array
(
)
)
[_parentContext:PHPTAL_Context:private] =>
[_globalContext:PHPTAL_Context:private] => stdClass Object
(
)
[_echoDeclarations:PHPTAL_Context:private] =>
[referer] => http://www.elcosh.org/document/3827/d001298/Getting%2Bthe%2Bmost%2Bout%2Bof%2Bthe%2BIUOE%2BToolbox%2BTalks.html
[curr_module] => Record
[styles] => Array
(
)
[javascript] => Array
(
[0] => jquery.min.js
)
[metas] => Array
(
[language] => en
[robots] => index, follow
)
[user] =>
[curr_url] => https://www.elcosh.org/index.php?module=Record&id=3827&type=document
[base_url] => https://www.elcosh.org/index.php?module=Record
[title] => eLCOSH : Getting the most out of the IUOE Toolbox Talks
[language] => en
[search_query] =>
[module] => Record
[new_records] => Array
(
[0] => Search_Result Object
(
[title] => Toolbox Talk: Fixed Ladder
[image] => /record/images/notavailable-p.png
[blurb] => The CPWR Toolbox Talk on Fixed Ladders addresses the potential risks associated with using fixed ladders. The resource includes a brief case example,...
[category] => Array
(
[0] => 15
[1] => 47
[2] => 49
[3] => 51
[4] => 53
[5] => 55
[6] => 60
[7] => 64
[8] => 73
[9] => 76
[10] => 78
[11] => 80
[12] => 86
[13] => 87
[14] => 90
[15] => 92
[16] => 93
[17] => 94
[18] => 100
)
[labels] => Array
(
[0] => Falls
[1] => Work Environment
[2] => Hazards
[3] => Bricklayer
[4] => Trades
[5] => Carpenter
[7] => Cement Mason
[9] => Concrete Polisher
[11] => Electrical Worker
[13] => HVAC
[15] => Laborer
[17] => PCC/Restoration
[19] => Plumber/Pipefitter
[21] => Roofer/Waterproofer
[23] => Sheetmetal Worker
[25] => Welder
[27] => Commercial & Institutional
[28] => Jobsites
[29] => Industrial
[31] => LEED/Green Construction
[33] => Renovations
[35] => Residential
[37] => Toolbox Talks
[38] => Documents
[39] => Media & Documents
)
[type] => Toolbox Talks
[sub_category] =>
[url] => /document/4430/d001660/Toolbox%2BTalk%253A%2BFixed%2BLadder.html
[item:protected] => DocumentRecord Object
(
[records:protected] => Array
(
)
[recordId:protected] =>
[searchWordClass:protected] =>
[searchWordPeerClass:protected] =>
[bok_record:protected] =>
[authors:protected] =>
[organizations:protected] =>
[collections:protected] =>
[categories:protected] => Array
(
[15] => Category Object
(
[languages:protected] =>
[bok_resources:protected] =>
[bok_topics:protected] =>
[bok_keywords:protected] =>
[id:protected] => 15
[type:protected] => category
[parent:protected] => 7
[label:protected] => Falls
[alreadyInSave:protected] =>
[alreadyInValidation:protected] =>
[validationFailures:protected] => Array
(
)
[_new:BaseObject:private] =>
[_deleted:BaseObject:private] =>
[modifiedColumns:protected] => Array
(
)
)
[47] => Category Object
(
[languages:protected] =>
[bok_resources:protected] =>
[bok_topics:protected] =>
[bok_keywords:protected] =>
[id:protected] => 47
[type:protected] => category
[parent:protected] => 2
[label:protected] => Bricklayer
[alreadyInSave:protected] =>
[alreadyInValidation:protected] =>
[validationFailures:protected] => Array
(
)
[_new:BaseObject:private] =>
[_deleted:BaseObject:private] =>
[modifiedColumns:protected] => Array
(
)
)
[49] => Category Object
(
[languages:protected] =>
[bok_resources:protected] =>
[bok_topics:protected] =>
[bok_keywords:protected] =>
[id:protected] => 49
[type:protected] => category
[parent:protected] => 2
[label:protected] => Carpenter
[alreadyInSave:protected] =>
[alreadyInValidation:protected] =>
[validationFailures:protected] => Array
(
)
[_new:BaseObject:private] =>
[_deleted:BaseObject:private] =>
[modifiedColumns:protected] => Array
(
)
)
[51] => Category Object
(
[languages:protected] =>
[bok_resources:protected] =>
[bok_topics:protected] =>
[bok_keywords:protected] =>
[id:protected] => 51
[type:protected] => category
[parent:protected] => 2
[label:protected] => Cement Mason
[alreadyInSave:protected] =>
[alreadyInValidation:protected] =>
[validationFailures:protected] => Array
(
)
[_new:BaseObject:private] =>
[_deleted:BaseObject:private] =>
[modifiedColumns:protected] => Array
(
)
)
[53] => Category Object
(
[languages:protected] =>
[bok_resources:protected] =>
[bok_topics:protected] =>
[bok_keywords:protected] =>
[id:protected] => 53
[type:protected] => category
[parent:protected] => 2
[label:protected] => Concrete Polisher
[alreadyInSave:protected] =>
[alreadyInValidation:protected] =>
[validationFailures:protected] => Array
(
)
[_new:BaseObject:private] =>
[_deleted:BaseObject:private] =>
[modifiedColumns:protected] => Array
(
)
)
[55] => Category Object
(
[languages:protected] =>
[bok_resources:protected] =>
[bok_topics:protected] =>
[bok_keywords:protected] =>
[id:protected] => 55
[type:protected] => category
[parent:protected] => 2
[label:protected] => Electrical Worker
[alreadyInSave:protected] =>
[alreadyInValidation:protected] =>
[validationFailures:protected] => Array
(
)
[_new:BaseObject:private] =>
[_deleted:BaseObject:private] =>
[modifiedColumns:protected] => Array
(
)
)
[60] => Category Object
(
[languages:protected] =>
[bok_resources:protected] =>
[bok_topics:protected] =>
[bok_keywords:protected] =>
[id:protected] => 60
[type:protected] => category
[parent:protected] => 2
[label:protected] => HVAC
[alreadyInSave:protected] =>
[alreadyInValidation:protected] =>
[validationFailures:protected] => Array
(
)
[_new:BaseObject:private] =>
[_deleted:BaseObject:private] =>
[modifiedColumns:protected] => Array
(
)
)
[64] => Category Object
(
[languages:protected] =>
[bok_resources:protected] =>
[bok_topics:protected] =>
[bok_keywords:protected] =>
[id:protected] => 64
[type:protected] => category
[parent:protected] => 2
[label:protected] => Laborer
[alreadyInSave:protected] =>
[alreadyInValidation:protected] =>
[validationFailures:protected] => Array
(
)
[_new:BaseObject:private] =>
[_deleted:BaseObject:private] =>
[modifiedColumns:protected] => Array
(
)
)
[73] => Category Object
(
[languages:protected] =>
[bok_resources:protected] =>
[bok_topics:protected] =>
[bok_keywords:protected] =>
[id:protected] => 73
[type:protected] => category
[parent:protected] => 2
[label:protected] => PCC/Restoration
[alreadyInSave:protected] =>
[alreadyInValidation:protected] =>
[validationFailures:protected] => Array
(
)
[_new:BaseObject:private] =>
[_deleted:BaseObject:private] =>
[modifiedColumns:protected] => Array
(
)
)
[76] => Category Object
(
[languages:protected] =>
[bok_resources:protected] =>
[bok_topics:protected] =>
[bok_keywords:protected] =>
[id:protected] => 76
[type:protected] => category
[parent:protected] => 2
[label:protected] => Plumber/Pipefitter
[alreadyInSave:protected] =>
[alreadyInValidation:protected] =>
[validationFailures:protected] => Array
(
)
[_new:BaseObject:private] =>
[_deleted:BaseObject:private] =>
[modifiedColumns:protected] => Array
(
)
)
[78] => Category Object
(
[languages:protected] =>
[bok_resources:protected] =>
[bok_topics:protected] =>
[bok_keywords:protected] =>
[id:protected] => 78
[type:protected] => category
[parent:protected] => 2
[label:protected] => Roofer/Waterproofer
[alreadyInSave:protected] =>
[alreadyInValidation:protected] =>
[validationFailures:protected] => Array
(
)
[_new:BaseObject:private] =>
[_deleted:BaseObject:private] =>
[modifiedColumns:protected] => Array
(
)
)
[80] => Category Object
(
[languages:protected] =>
[bok_resources:protected] =>
[bok_topics:protected] =>
[bok_keywords:protected] =>
[id:protected] => 80
[type:protected] => category
[parent:protected] => 2
[label:protected] => Sheetmetal Worker
[alreadyInSave:protected] =>
[alreadyInValidation:protected] =>
[validationFailures:protected] => Array
(
)
[_new:BaseObject:private] =>
[_deleted:BaseObject:private] =>
[modifiedColumns:protected] => Array
(
)
)
[86] => Category Object
(
[languages:protected] =>
[bok_resources:protected] =>
[bok_topics:protected] =>
[bok_keywords:protected] =>
[id:protected] => 86
[type:protected] => category
[parent:protected] => 2
[label:protected] => Welder
[alreadyInSave:protected] =>
[alreadyInValidation:protected] =>
[validationFailures:protected] => Array
(
)
[_new:BaseObject:private] =>
[_deleted:BaseObject:private] =>
[modifiedColumns:protected] => Array
(
)
)
[87] => Category Object
(
[languages:protected] =>
[bok_resources:protected] =>
[bok_topics:protected] =>
[bok_keywords:protected] =>
[id:protected] => 87
[type:protected] => category
[parent:protected] => 3
[label:protected] => Commercial & Institutional
[alreadyInSave:protected] =>
[alreadyInValidation:protected] =>
[validationFailures:protected] => Array
(
)
[_new:BaseObject:private] =>
[_deleted:BaseObject:private] =>
[modifiedColumns:protected] => Array
(
)
)
[90] => Category Object
(
[languages:protected] =>
[bok_resources:protected] =>
[bok_topics:protected] =>
[bok_keywords:protected] =>
[id:protected] => 90
[type:protected] => category
[parent:protected] => 3
[label:protected] => Industrial
[alreadyInSave:protected] =>
[alreadyInValidation:protected] =>
[validationFailures:protected] => Array
(
)
[_new:BaseObject:private] =>
[_deleted:BaseObject:private] =>
[modifiedColumns:protected] => Array
(
)
)
[92] => Category Object
(
[languages:protected] =>
[bok_resources:protected] =>
[bok_topics:protected] =>
[bok_keywords:protected] =>
[id:protected] => 92
[type:protected] => category
[parent:protected] => 3
[label:protected] => LEED/Green Construction
[alreadyInSave:protected] =>
[alreadyInValidation:protected] =>
[validationFailures:protected] => Array
(
)
[_new:BaseObject:private] =>
[_deleted:BaseObject:private] =>
[modifiedColumns:protected] => Array
(
)
)
[93] => Category Object
(
[languages:protected] =>
[bok_resources:protected] =>
[bok_topics:protected] =>
[bok_keywords:protected] =>
[id:protected] => 93
[type:protected] => category
[parent:protected] => 3
[label:protected] => Renovations
[alreadyInSave:protected] =>
[alreadyInValidation:protected] =>
[validationFailures:protected] => Array
(
)
[_new:BaseObject:private] =>
[_deleted:BaseObject:private] =>
[modifiedColumns:protected] => Array
(
)
)
[94] => Category Object
(
[languages:protected] =>
[bok_resources:protected] =>
[bok_topics:protected] =>
[bok_keywords:protected] =>
[id:protected] => 94
[type:protected] => category
[parent:protected] => 3
[label:protected] => Residential
[alreadyInSave:protected] =>
[alreadyInValidation:protected] =>
[validationFailures:protected] => Array
(
)
[_new:BaseObject:private] =>
[_deleted:BaseObject:private] =>
[modifiedColumns:protected] => Array
(
)
)
[100] => Category Object
(
[languages:protected] =>
[bok_resources:protected] =>
[bok_topics:protected] =>
[bok_keywords:protected] =>
[id:protected] => 100
[type:protected] => category
[parent:protected] => 6
[label:protected] => Toolbox Talks
[alreadyInSave:protected] =>
[alreadyInValidation:protected] =>
[validationFailures:protected] => Array
(
)
[_new:BaseObject:private] =>
[_deleted:BaseObject:private] =>
[modifiedColumns:protected] => Array
(
)
)
)
[categories_initialized:protected] => 1
[mapped_items:protected] =>
[content:protected] =>
[files:protected] =>
[language:protected] => Language Object
(
[id:protected] => 1
[code:protected] => en
[name:protected] => English
[alreadyInSave:protected] =>
[alreadyInValidation:protected] =>
[validationFailures:protected] => Array
(
)
[_new:BaseObject:private] =>
[_deleted:BaseObject:private] =>
[modifiedColumns:protected] => Array
(
)
)
[old_record:protected] =>
[id:protected] => 4430
[old_id:protected] =>
[elcosh_id:protected] => d001660
[type:protected] => document
[display_type:protected] => HTML only (and links)
[user_id:protected] => 0
[language_id:protected] => 1
[tagging_id:protected] => Mike Aguilar
[priority_id:protected] => 1
[title:protected] => Toolbox Talk: Fixed Ladder
[total_pages:protected] => 0
[billed_pages:protected] => 0
[publication_number:protected] =>
[part_of:protected] =>
[keywords:protected] => Fixed Ladders, Fall Prevention, Falls
[comments:protected] =>
[summary:protected] => The CPWR Toolbox Talk on Fixed Ladders addresses the potential risks associated with using fixed ladders. The resource includes a brief case example, steps to prevent a related injury and questions for discussion. It includes an image that illustrates the hazard, which can be posted in a central location as a reminder of steps to work safely.
Available in
English
and
Spanish.
[transition_comments:protected] =>
[external_link:protected] =>
[consol_link:protected] =>
[more_like_this:protected] => d001257,d001254,d001255,d001256,d001258,d001262,d001279
[permission_given_by:protected] =>
[published:protected] => T
[billable:protected] => F
[img_name:protected] =>
[img_ext:protected] =>
[img_width:protected] =>
[img_height:protected] =>
[img_credit:protected] =>
[img_practice:protected] =>
[vid_source_id:protected] =>
[vid_running_time:protected] =>
[vid_intended_audience:protected] =>
[vid_acquisition_info:protected] =>
[vid_cost:protected] =>
[vid_producer:protected] =>
[vid_filename:protected] =>
[vid_filename_downloadable:protected] =>
[date_summary:protected] =>
[date_permission_requested:protected] =>
[date_permission_received:protected] =>
[date_review_needed:protected] =>
[date_received:protected] => 06/10/22
[date_completed:protected] => 06/10/22
[date_billed:protected] =>
[date_modified:protected] => 05/22/23
[collBokExports:protected] =>
[lastBokExportCriteria:BaseElcoshItem:private] =>
[alreadyInSave:protected] =>
[alreadyInValidation:protected] =>
[validationFailures:protected] => Array
(
)
[_new:BaseObject:private] =>
[_deleted:BaseObject:private] =>
[modifiedColumns:protected] => Array
(
)
)
)
[1] => Search_Result Object
(
[title] => Toolbox Talk: Challenges Preventing Falling Objects
[image] => /record/images/notavailable-p.png
[blurb] => The CPWR Toolbox Talk on Challenges Preventing Falling Objects addresses the hazards of being struck by falling objects on the job site. The resource...
[category] => Array
(
[0] => 12
[1] => 47
[2] => 49
[3] => 51
[4] => 55
[5] => 64
[6] => 68
[7] => 71
[8] => 75
[9] => 78
[10] => 79
[11] => 82
[12] => 62
[13] => 86
[14] => 87
[15] => 88
[16] => 89
[17] => 91
[18] => 90
[19] => 92
[20] => 93
[21] => 94
[22] => 95
[23] => 100
)
[labels] => Array
(
[0] => Crushed/Struck By
[1] => Work Environment
[2] => Hazards
[3] => Bricklayer
[4] => Trades
[5] => Carpenter
[7] => Cement Mason
[9] => Electrical Worker
[11] => Laborer
[13] => Maintenance Worker
[15] => Painter
[17] => Plasterer
[19] => Roofer/Waterproofer
[21] => Scaffold Erector
[23] => Stonemason
[25] => Structural Ironworker
[27] => Welder
[29] => Commercial & Institutional
[30] => Jobsites
[31] => Demolition
[33] => Disasters
[35] => Heavy & Highway
[37] => Industrial
[39] => LEED/Green Construction
[41] => Renovations
[43] => Residential
[45] => Underground
[47] => Toolbox Talks
[48] => Documents
[49] => Media & Documents
)
[type] => Toolbox Talks
[sub_category] =>
[url] => /document/4431/d001661/Toolbox%2BTalk%253A%2BChallenges%2BPreventing%2BFalling%2BObjects.html
[item:protected] => DocumentRecord Object
(
[records:protected] => Array
(
)
[recordId:protected] =>
[searchWordClass:protected] =>
[searchWordPeerClass:protected] =>
[bok_record:protected] =>
[authors:protected] =>
[organizations:protected] =>
[collections:protected] =>
[categories:protected] => Array
(
[12] => Category Object
(
[languages:protected] =>
[bok_resources:protected] =>
[bok_topics:protected] =>
[bok_keywords:protected] =>
[id:protected] => 12
[type:protected] => category
[parent:protected] => 7
[label:protected] => Crushed/Struck By
[alreadyInSave:protected] =>
[alreadyInValidation:protected] =>
[validationFailures:protected] => Array
(
)
[_new:BaseObject:private] =>
[_deleted:BaseObject:private] =>
[modifiedColumns:protected] => Array
(
)
)
[47] => Category Object
(
[languages:protected] =>
[bok_resources:protected] =>
[bok_topics:protected] =>
[bok_keywords:protected] =>
[id:protected] => 47
[type:protected] => category
[parent:protected] => 2
[label:protected] => Bricklayer
[alreadyInSave:protected] =>
[alreadyInValidation:protected] =>
[validationFailures:protected] => Array
(
)
[_new:BaseObject:private] =>
[_deleted:BaseObject:private] =>
[modifiedColumns:protected] => Array
(
)
)
[49] => Category Object
(
[languages:protected] =>
[bok_resources:protected] =>
[bok_topics:protected] =>
[bok_keywords:protected] =>
[id:protected] => 49
[type:protected] => category
[parent:protected] => 2
[label:protected] => Carpenter
[alreadyInSave:protected] =>
[alreadyInValidation:protected] =>
[validationFailures:protected] => Array
(
)
[_new:BaseObject:private] =>
[_deleted:BaseObject:private] =>
[modifiedColumns:protected] => Array
(
)
)
[51] => Category Object
(
[languages:protected] =>
[bok_resources:protected] =>
[bok_topics:protected] =>
[bok_keywords:protected] =>
[id:protected] => 51
[type:protected] => category
[parent:protected] => 2
[label:protected] => Cement Mason
[alreadyInSave:protected] =>
[alreadyInValidation:protected] =>
[validationFailures:protected] => Array
(
)
[_new:BaseObject:private] =>
[_deleted:BaseObject:private] =>
[modifiedColumns:protected] => Array
(
)
)
[55] => Category Object
(
[languages:protected] =>
[bok_resources:protected] =>
[bok_topics:protected] =>
[bok_keywords:protected] =>
[id:protected] => 55
[type:protected] => category
[parent:protected] => 2
[label:protected] => Electrical Worker
[alreadyInSave:protected] =>
[alreadyInValidation:protected] =>
[validationFailures:protected] => Array
(
)
[_new:BaseObject:private] =>
[_deleted:BaseObject:private] =>
[modifiedColumns:protected] => Array
(
)
)
[64] => Category Object
(
[languages:protected] =>
[bok_resources:protected] =>
[bok_topics:protected] =>
[bok_keywords:protected] =>
[id:protected] => 64
[type:protected] => category
[parent:protected] => 2
[label:protected] => Laborer
[alreadyInSave:protected] =>
[alreadyInValidation:protected] =>
[validationFailures:protected] => Array
(
)
[_new:BaseObject:private] =>
[_deleted:BaseObject:private] =>
[modifiedColumns:protected] => Array
(
)
)
[68] => Category Object
(
[languages:protected] =>
[bok_resources:protected] =>
[bok_topics:protected] =>
[bok_keywords:protected] =>
[id:protected] => 68
[type:protected] => category
[parent:protected] => 2
[label:protected] => Maintenance Worker
[alreadyInSave:protected] =>
[alreadyInValidation:protected] =>
[validationFailures:protected] => Array
(
)
[_new:BaseObject:private] =>
[_deleted:BaseObject:private] =>
[modifiedColumns:protected] => Array
(
)
)
[71] => Category Object
(
[languages:protected] =>
[bok_resources:protected] =>
[bok_topics:protected] =>
[bok_keywords:protected] =>
[id:protected] => 71
[type:protected] => category
[parent:protected] => 2
[label:protected] => Painter
[alreadyInSave:protected] =>
[alreadyInValidation:protected] =>
[validationFailures:protected] => Array
(
)
[_new:BaseObject:private] =>
[_deleted:BaseObject:private] =>
[modifiedColumns:protected] => Array
(
)
)
[75] => Category Object
(
[languages:protected] =>
[bok_resources:protected] =>
[bok_topics:protected] =>
[bok_keywords:protected] =>
[id:protected] => 75
[type:protected] => category
[parent:protected] => 2
[label:protected] => Plasterer
[alreadyInSave:protected] =>
[alreadyInValidation:protected] =>
[validationFailures:protected] => Array
(
)
[_new:BaseObject:private] =>
[_deleted:BaseObject:private] =>
[modifiedColumns:protected] => Array
(
)
)
[78] => Category Object
(
[languages:protected] =>
[bok_resources:protected] =>
[bok_topics:protected] =>
[bok_keywords:protected] =>
[id:protected] => 78
[type:protected] => category
[parent:protected] => 2
[label:protected] => Roofer/Waterproofer
[alreadyInSave:protected] =>
[alreadyInValidation:protected] =>
[validationFailures:protected] => Array
(
)
[_new:BaseObject:private] =>
[_deleted:BaseObject:private] =>
[modifiedColumns:protected] => Array
(
)
)
[79] => Category Object
(
[languages:protected] =>
[bok_resources:protected] =>
[bok_topics:protected] =>
[bok_keywords:protected] =>
[id:protected] => 79
[type:protected] => category
[parent:protected] => 2
[label:protected] => Scaffold Erector
[alreadyInSave:protected] =>
[alreadyInValidation:protected] =>
[validationFailures:protected] => Array
(
)
[_new:BaseObject:private] =>
[_deleted:BaseObject:private] =>
[modifiedColumns:protected] => Array
(
)
)
[82] => Category Object
(
[languages:protected] =>
[bok_resources:protected] =>
[bok_topics:protected] =>
[bok_keywords:protected] =>
[id:protected] => 82
[type:protected] => category
[parent:protected] => 2
[label:protected] => Stonemason
[alreadyInSave:protected] =>
[alreadyInValidation:protected] =>
[validationFailures:protected] => Array
(
)
[_new:BaseObject:private] =>
[_deleted:BaseObject:private] =>
[modifiedColumns:protected] => Array
(
)
)
[62] => Category Object
(
[languages:protected] =>
[bok_resources:protected] =>
[bok_topics:protected] =>
[bok_keywords:protected] =>
[id:protected] => 62
[type:protected] => category
[parent:protected] => 2
[label:protected] => Structural Ironworker
[alreadyInSave:protected] =>
[alreadyInValidation:protected] =>
[validationFailures:protected] => Array
(
)
[_new:BaseObject:private] =>
[_deleted:BaseObject:private] =>
[modifiedColumns:protected] => Array
(
)
)
[86] => Category Object
(
[languages:protected] =>
[bok_resources:protected] =>
[bok_topics:protected] =>
[bok_keywords:protected] =>
[id:protected] => 86
[type:protected] => category
[parent:protected] => 2
[label:protected] => Welder
[alreadyInSave:protected] =>
[alreadyInValidation:protected] =>
[validationFailures:protected] => Array
(
)
[_new:BaseObject:private] =>
[_deleted:BaseObject:private] =>
[modifiedColumns:protected] => Array
(
)
)
[87] => Category Object
(
[languages:protected] =>
[bok_resources:protected] =>
[bok_topics:protected] =>
[bok_keywords:protected] =>
[id:protected] => 87
[type:protected] => category
[parent:protected] => 3
[label:protected] => Commercial & Institutional
[alreadyInSave:protected] =>
[alreadyInValidation:protected] =>
[validationFailures:protected] => Array
(
)
[_new:BaseObject:private] =>
[_deleted:BaseObject:private] =>
[modifiedColumns:protected] => Array
(
)
)
[88] => Category Object
(
[languages:protected] =>
[bok_resources:protected] =>
[bok_topics:protected] =>
[bok_keywords:protected] =>
[id:protected] => 88
[type:protected] => category
[parent:protected] => 3
[label:protected] => Demolition
[alreadyInSave:protected] =>
[alreadyInValidation:protected] =>
[validationFailures:protected] => Array
(
)
[_new:BaseObject:private] =>
[_deleted:BaseObject:private] =>
[modifiedColumns:protected] => Array
(
)
)
[89] => Category Object
(
[languages:protected] =>
[bok_resources:protected] =>
[bok_topics:protected] =>
[bok_keywords:protected] =>
[id:protected] => 89
[type:protected] => category
[parent:protected] => 3
[label:protected] => Disasters
[alreadyInSave:protected] =>
[alreadyInValidation:protected] =>
[validationFailures:protected] => Array
(
)
[_new:BaseObject:private] =>
[_deleted:BaseObject:private] =>
[modifiedColumns:protected] => Array
(
)
)
[91] => Category Object
(
[languages:protected] =>
[bok_resources:protected] =>
[bok_topics:protected] =>
[bok_keywords:protected] =>
[id:protected] => 91
[type:protected] => category
[parent:protected] => 3
[label:protected] => Heavy & Highway
[alreadyInSave:protected] =>
[alreadyInValidation:protected] =>
[validationFailures:protected] => Array
(
)
[_new:BaseObject:private] =>
[_deleted:BaseObject:private] =>
[modifiedColumns:protected] => Array
(
)
)
[90] => Category Object
(
[languages:protected] =>
[bok_resources:protected] =>
[bok_topics:protected] =>
[bok_keywords:protected] =>
[id:protected] => 90
[type:protected] => category
[parent:protected] => 3
[label:protected] => Industrial
[alreadyInSave:protected] =>
[alreadyInValidation:protected] =>
[validationFailures:protected] => Array
(
)
[_new:BaseObject:private] =>
[_deleted:BaseObject:private] =>
[modifiedColumns:protected] => Array
(
)
)
[92] => Category Object
(
[languages:protected] =>
[bok_resources:protected] =>
[bok_topics:protected] =>
[bok_keywords:protected] =>
[id:protected] => 92
[type:protected] => category
[parent:protected] => 3
[label:protected] => LEED/Green Construction
[alreadyInSave:protected] =>
[alreadyInValidation:protected] =>
[validationFailures:protected] => Array
(
)
[_new:BaseObject:private] =>
[_deleted:BaseObject:private] =>
[modifiedColumns:protected] => Array
(
)
)
[93] => Category Object
(
[languages:protected] =>
[bok_resources:protected] =>
[bok_topics:protected] =>
[bok_keywords:protected] =>
[id:protected] => 93
[type:protected] => category
[parent:protected] => 3
[label:protected] => Renovations
[alreadyInSave:protected] =>
[alreadyInValidation:protected] =>
[validationFailures:protected] => Array
(
)
[_new:BaseObject:private] =>
[_deleted:BaseObject:private] =>
[modifiedColumns:protected] => Array
(
)
)
[94] => Category Object
(
[languages:protected] =>
[bok_resources:protected] =>
[bok_topics:protected] =>
[bok_keywords:protected] =>
[id:protected] => 94
[type:protected] => category
[parent:protected] => 3
[label:protected] => Residential
[alreadyInSave:protected] =>
[alreadyInValidation:protected] =>
[validationFailures:protected] => Array
(
)
[_new:BaseObject:private] =>
[_deleted:BaseObject:private] =>
[modifiedColumns:protected] => Array
(
)
)
[95] => Category Object
(
[languages:protected] =>
[bok_resources:protected] =>
[bok_topics:protected] =>
[bok_keywords:protected] =>
[id:protected] => 95
[type:protected] => category
[parent:protected] => 3
[label:protected] => Underground
[alreadyInSave:protected] =>
[alreadyInValidation:protected] =>
[validationFailures:protected] => Array
(
)
[_new:BaseObject:private] =>
[_deleted:BaseObject:private] =>
[modifiedColumns:protected] => Array
(
)
)
[100] => Category Object
(
[languages:protected] =>
[bok_resources:protected] =>
[bok_topics:protected] =>
[bok_keywords:protected] =>
[id:protected] => 100
[type:protected] => category
[parent:protected] => 6
[label:protected] => Toolbox Talks
[alreadyInSave:protected] =>
[alreadyInValidation:protected] =>
[validationFailures:protected] => Array
(
)
[_new:BaseObject:private] =>
[_deleted:BaseObject:private] =>
[modifiedColumns:protected] => Array
(
)
)
)
[categories_initialized:protected] => 1
[mapped_items:protected] =>
[content:protected] =>
[files:protected] =>
[language:protected] => Language Object
(
[id:protected] => 1
[code:protected] => en
[name:protected] => English
[alreadyInSave:protected] =>
[alreadyInValidation:protected] =>
[validationFailures:protected] => Array
(
)
[_new:BaseObject:private] =>
[_deleted:BaseObject:private] =>
[modifiedColumns:protected] => Array
(
)
)
[old_record:protected] =>
[id:protected] => 4431
[old_id:protected] =>
[elcosh_id:protected] => d001661
[type:protected] => document
[display_type:protected] => HTML only (and links)
[user_id:protected] => 0
[language_id:protected] => 1
[tagging_id:protected] => Mike Aguilar
[priority_id:protected] => 1
[title:protected] => Toolbox Talk: Challenges Preventing Falling Objects
[total_pages:protected] => 0
[billed_pages:protected] => 0
[publication_number:protected] =>
[part_of:protected] =>
[keywords:protected] => dropped objects, falling objects, struck by incidents, struck by fatalities
[comments:protected] =>
[summary:protected] => The CPWR Toolbox Talk on Challenges Preventing Falling Objects addresses the hazards of being struck by falling objects on the job site. The resource includes a brief example, steps to prevent a related injury, and questions for discussion. It includes a graphic that illustrates a group workers observing a scaffold free of debris during high winds, which can be posted in a central location as a reminder of steps to work safely.
Available in
English and
Spanish.
[transition_comments:protected] =>
[external_link:protected] =>
[consol_link:protected] =>
[more_like_this:protected] => d001234,d001238,d001244,d001251,d001253,d001260,d001268,d001278
[permission_given_by:protected] =>
[published:protected] => T
[billable:protected] => F
[img_name:protected] =>
[img_ext:protected] =>
[img_width:protected] =>
[img_height:protected] =>
[img_credit:protected] =>
[img_practice:protected] =>
[vid_source_id:protected] =>
[vid_running_time:protected] =>
[vid_intended_audience:protected] =>
[vid_acquisition_info:protected] =>
[vid_cost:protected] =>
[vid_producer:protected] =>
[vid_filename:protected] =>
[vid_filename_downloadable:protected] =>
[date_summary:protected] =>
[date_permission_requested:protected] =>
[date_permission_received:protected] =>
[date_review_needed:protected] =>
[date_received:protected] => 06/10/22
[date_completed:protected] => 06/10/22
[date_billed:protected] =>
[date_modified:protected] => 05/22/23
[collBokExports:protected] =>
[lastBokExportCriteria:BaseElcoshItem:private] =>
[alreadyInSave:protected] =>
[alreadyInValidation:protected] =>
[validationFailures:protected] => Array
(
)
[_new:BaseObject:private] =>
[_deleted:BaseObject:private] =>
[modifiedColumns:protected] => Array
(
)
)
)
[2] => Search_Result Object
(
[title] => Toolbox Talk: Tower Crane Safety
[image] => /record/images/notavailable-p.png
[blurb] => The CPWR Toolbox Talk on Tower Crane Safety addresses the potential hazards of Tower Cranes and the importance of following procedure before and durin...
[category] => Array
(
[0] => 11
[1] => 12
[2] => 18
[3] => 70
[4] => 87
[5] => 88
[6] => 91
[7] => 90
[8] => 92
[9] => 100
)
[labels] => Array
(
[0] => Cranes & Hoists
[1] => Work Environment
[2] => Hazards
[3] => Crushed/Struck By
[6] => Motor Vehicles/Heavy Equipment
[9] => Operating Engineer
[10] => Trades
[11] => Commercial & Institutional
[12] => Jobsites
[13] => Demolition
[15] => Heavy & Highway
[17] => Industrial
[19] => LEED/Green Construction
[21] => Toolbox Talks
[22] => Documents
[23] => Media & Documents
)
[type] => Toolbox Talks
[sub_category] =>
[url] => /document/4427/d001657/Toolbox%2BTalk%253A%2BTower%2BCrane%2BSafety.html
[item:protected] => DocumentRecord Object
(
[records:protected] => Array
(
)
[recordId:protected] =>
[searchWordClass:protected] =>
[searchWordPeerClass:protected] =>
[bok_record:protected] =>
[authors:protected] =>
[organizations:protected] =>
[collections:protected] =>
[categories:protected] => Array
(
[11] => Category Object
(
[languages:protected] =>
[bok_resources:protected] =>
[bok_topics:protected] =>
[bok_keywords:protected] =>
[id:protected] => 11
[type:protected] => category
[parent:protected] => 7
[label:protected] => Cranes & Hoists
[alreadyInSave:protected] =>
[alreadyInValidation:protected] =>
[validationFailures:protected] => Array
(
)
[_new:BaseObject:private] =>
[_deleted:BaseObject:private] =>
[modifiedColumns:protected] => Array
(
)
)
[12] => Category Object
(
[languages:protected] =>
[bok_resources:protected] =>
[bok_topics:protected] =>
[bok_keywords:protected] =>
[id:protected] => 12
[type:protected] => category
[parent:protected] => 7
[label:protected] => Crushed/Struck By
[alreadyInSave:protected] =>
[alreadyInValidation:protected] =>
[validationFailures:protected] => Array
(
)
[_new:BaseObject:private] =>
[_deleted:BaseObject:private] =>
[modifiedColumns:protected] => Array
(
)
)
[18] => Category Object
(
[languages:protected] =>
[bok_resources:protected] =>
[bok_topics:protected] =>
[bok_keywords:protected] =>
[id:protected] => 18
[type:protected] => category
[parent:protected] => 7
[label:protected] => Motor Vehicles/Heavy Equipment
[alreadyInSave:protected] =>
[alreadyInValidation:protected] =>
[validationFailures:protected] => Array
(
)
[_new:BaseObject:private] =>
[_deleted:BaseObject:private] =>
[modifiedColumns:protected] => Array
(
)
)
[70] => Category Object
(
[languages:protected] =>
[bok_resources:protected] =>
[bok_topics:protected] =>
[bok_keywords:protected] =>
[id:protected] => 70
[type:protected] => category
[parent:protected] => 2
[label:protected] => Operating Engineer
[alreadyInSave:protected] =>
[alreadyInValidation:protected] =>
[validationFailures:protected] => Array
(
)
[_new:BaseObject:private] =>
[_deleted:BaseObject:private] =>
[modifiedColumns:protected] => Array
(
)
)
[87] => Category Object
(
[languages:protected] =>
[bok_resources:protected] =>
[bok_topics:protected] =>
[bok_keywords:protected] =>
[id:protected] => 87
[type:protected] => category
[parent:protected] => 3
[label:protected] => Commercial & Institutional
[alreadyInSave:protected] =>
[alreadyInValidation:protected] =>
[validationFailures:protected] => Array
(
)
[_new:BaseObject:private] =>
[_deleted:BaseObject:private] =>
[modifiedColumns:protected] => Array
(
)
)
[88] => Category Object
(
[languages:protected] =>
[bok_resources:protected] =>
[bok_topics:protected] =>
[bok_keywords:protected] =>
[id:protected] => 88
[type:protected] => category
[parent:protected] => 3
[label:protected] => Demolition
[alreadyInSave:protected] =>
[alreadyInValidation:protected] =>
[validationFailures:protected] => Array
(
)
[_new:BaseObject:private] =>
[_deleted:BaseObject:private] =>
[modifiedColumns:protected] => Array
(
)
)
[91] => Category Object
(
[languages:protected] =>
[bok_resources:protected] =>
[bok_topics:protected] =>
[bok_keywords:protected] =>
[id:protected] => 91
[type:protected] => category
[parent:protected] => 3
[label:protected] => Heavy & Highway
[alreadyInSave:protected] =>
[alreadyInValidation:protected] =>
[validationFailures:protected] => Array
(
)
[_new:BaseObject:private] =>
[_deleted:BaseObject:private] =>
[modifiedColumns:protected] => Array
(
)
)
[90] => Category Object
(
[languages:protected] =>
[bok_resources:protected] =>
[bok_topics:protected] =>
[bok_keywords:protected] =>
[id:protected] => 90
[type:protected] => category
[parent:protected] => 3
[label:protected] => Industrial
[alreadyInSave:protected] =>
[alreadyInValidation:protected] =>
[validationFailures:protected] => Array
(
)
[_new:BaseObject:private] =>
[_deleted:BaseObject:private] =>
[modifiedColumns:protected] => Array
(
)
)
[92] => Category Object
(
[languages:protected] =>
[bok_resources:protected] =>
[bok_topics:protected] =>
[bok_keywords:protected] =>
[id:protected] => 92
[type:protected] => category
[parent:protected] => 3
[label:protected] => LEED/Green Construction
[alreadyInSave:protected] =>
[alreadyInValidation:protected] =>
[validationFailures:protected] => Array
(
)
[_new:BaseObject:private] =>
[_deleted:BaseObject:private] =>
[modifiedColumns:protected] => Array
(
)
)
[100] => Category Object
(
[languages:protected] =>
[bok_resources:protected] =>
[bok_topics:protected] =>
[bok_keywords:protected] =>
[id:protected] => 100
[type:protected] => category
[parent:protected] => 6
[label:protected] => Toolbox Talks
[alreadyInSave:protected] =>
[alreadyInValidation:protected] =>
[validationFailures:protected] => Array
(
)
[_new:BaseObject:private] =>
[_deleted:BaseObject:private] =>
[modifiedColumns:protected] => Array
(
)
)
)
[categories_initialized:protected] => 1
[mapped_items:protected] =>
[content:protected] =>
[files:protected] =>
[language:protected] => Language Object
(
[id:protected] => 1
[code:protected] => en
[name:protected] => English
[alreadyInSave:protected] =>
[alreadyInValidation:protected] =>
[validationFailures:protected] => Array
(
)
[_new:BaseObject:private] =>
[_deleted:BaseObject:private] =>
[modifiedColumns:protected] => Array
(
)
)
[old_record:protected] =>
[id:protected] => 4427
[old_id:protected] =>
[elcosh_id:protected] => d001657
[type:protected] => document
[display_type:protected] => HTML only (and links)
[user_id:protected] => 0
[language_id:protected] => 1
[tagging_id:protected] => Mike Aguilar
[priority_id:protected] => 1
[title:protected] => Toolbox Talk: Tower Crane Safety
[total_pages:protected] => 0
[billed_pages:protected] => 0
[publication_number:protected] =>
[part_of:protected] =>
[keywords:protected] => Tower Crane, Crane, Stability, Tipping, Lift Zone Safety, Lift, Zone, Safety, Struck by
[comments:protected] =>
[summary:protected] => The CPWR Toolbox Talk on Tower Crane Safety addresses the potential hazards of Tower Cranes and the importance of following procedure before and during Tower Crane operation. The resource includes a brief example, steps to prevent a related injury, and questions for discussion. It includes a graphic that illustrates a worker inspecting a Tower Crane before operation, which can be posted in a central location as a reminder of steps to work safely.
Available in
English and
Spanish.
[transition_comments:protected] =>
[external_link:protected] =>
[consol_link:protected] =>
[more_like_this:protected] => d001234,d001238,d001250,d001251,d001253,d001258,d001262,d001273
[permission_given_by:protected] =>
[published:protected] => T
[billable:protected] => F
[img_name:protected] =>
[img_ext:protected] => jpg
[img_width:protected] =>
[img_height:protected] =>
[img_credit:protected] =>
[img_practice:protected] =>
[vid_source_id:protected] =>
[vid_running_time:protected] =>
[vid_intended_audience:protected] =>
[vid_acquisition_info:protected] =>
[vid_cost:protected] =>
[vid_producer:protected] =>
[vid_filename:protected] =>
[vid_filename_downloadable:protected] =>
[date_summary:protected] =>
[date_permission_requested:protected] =>
[date_permission_received:protected] =>
[date_review_needed:protected] =>
[date_received:protected] => 12/23/21
[date_completed:protected] => 12/23/21
[date_billed:protected] =>
[date_modified:protected] => 05/19/23
[collBokExports:protected] =>
[lastBokExportCriteria:BaseElcoshItem:private] =>
[alreadyInSave:protected] =>
[alreadyInValidation:protected] =>
[validationFailures:protected] => Array
(
)
[_new:BaseObject:private] =>
[_deleted:BaseObject:private] =>
[modifiedColumns:protected] => Array
(
)
)
)
[3] => Search_Result Object
(
[title] => Toolbox Talk: Work Zone Safety: Working Around Vehicles
[image] => /record/images/notavailable-p.png
[blurb] => The CPWR Toolbox Talk on Working Around Vehicles in the Work Zone addresses methods to avoid being struck-by a vehicle on a construction site. The res...
[category] => Array
(
[0] => 12
[1] => 18
[2] => 52
[3] => 57
[4] => 70
[5] => 85
[6] => 87
[7] => 88
[8] => 89
[9] => 91
[10] => 90
[11] => 92
[12] => 93
[13] => 94
[14] => 95
[15] => 100
)
[labels] => Array
(
[0] => Crushed/Struck By
[1] => Work Environment
[2] => Hazards
[3] => Motor Vehicles/Heavy Equipment
[6] => Commercial Diver
[7] => Trades
[8] => Flagger
[10] => Operating Engineer
[12] => Truck Driver
[14] => Commercial & Institutional
[15] => Jobsites
[16] => Demolition
[18] => Disasters
[20] => Heavy & Highway
[22] => Industrial
[24] => LEED/Green Construction
[26] => Renovations
[28] => Residential
[30] => Underground
[32] => Toolbox Talks
[33] => Documents
[34] => Media & Documents
)
[type] => Toolbox Talks
[sub_category] =>
[url] => /document/4428/d001658/Toolbox%2BTalk%253A%2BWork%2BZone%2BSafety%253A%2BWorking%2BAround%2BVehicles.html
[item:protected] => DocumentRecord Object
(
[records:protected] => Array
(
)
[recordId:protected] =>
[searchWordClass:protected] =>
[searchWordPeerClass:protected] =>
[bok_record:protected] =>
[authors:protected] =>
[organizations:protected] =>
[collections:protected] =>
[categories:protected] => Array
(
[12] => Category Object
(
[languages:protected] =>
[bok_resources:protected] =>
[bok_topics:protected] =>
[bok_keywords:protected] =>
[id:protected] => 12
[type:protected] => category
[parent:protected] => 7
[label:protected] => Crushed/Struck By
[alreadyInSave:protected] =>
[alreadyInValidation:protected] =>
[validationFailures:protected] => Array
(
)
[_new:BaseObject:private] =>
[_deleted:BaseObject:private] =>
[modifiedColumns:protected] => Array
(
)
)
[18] => Category Object
(
[languages:protected] =>
[bok_resources:protected] =>
[bok_topics:protected] =>
[bok_keywords:protected] =>
[id:protected] => 18
[type:protected] => category
[parent:protected] => 7
[label:protected] => Motor Vehicles/Heavy Equipment
[alreadyInSave:protected] =>
[alreadyInValidation:protected] =>
[validationFailures:protected] => Array
(
)
[_new:BaseObject:private] =>
[_deleted:BaseObject:private] =>
[modifiedColumns:protected] => Array
(
)
)
[52] => Category Object
(
[languages:protected] =>
[bok_resources:protected] =>
[bok_topics:protected] =>
[bok_keywords:protected] =>
[id:protected] => 52
[type:protected] => category
[parent:protected] => 2
[label:protected] => Commercial Diver
[alreadyInSave:protected] =>
[alreadyInValidation:protected] =>
[validationFailures:protected] => Array
(
)
[_new:BaseObject:private] =>
[_deleted:BaseObject:private] =>
[modifiedColumns:protected] => Array
(
)
)
[57] => Category Object
(
[languages:protected] =>
[bok_resources:protected] =>
[bok_topics:protected] =>
[bok_keywords:protected] =>
[id:protected] => 57
[type:protected] => category
[parent:protected] => 2
[label:protected] => Flagger
[alreadyInSave:protected] =>
[alreadyInValidation:protected] =>
[validationFailures:protected] => Array
(
)
[_new:BaseObject:private] =>
[_deleted:BaseObject:private] =>
[modifiedColumns:protected] => Array
(
)
)
[70] => Category Object
(
[languages:protected] =>
[bok_resources:protected] =>
[bok_topics:protected] =>
[bok_keywords:protected] =>
[id:protected] => 70
[type:protected] => category
[parent:protected] => 2
[label:protected] => Operating Engineer
[alreadyInSave:protected] =>
[alreadyInValidation:protected] =>
[validationFailures:protected] => Array
(
)
[_new:BaseObject:private] =>
[_deleted:BaseObject:private] =>
[modifiedColumns:protected] => Array
(
)
)
[85] => Category Object
(
[languages:protected] =>
[bok_resources:protected] =>
[bok_topics:protected] =>
[bok_keywords:protected] =>
[id:protected] => 85
[type:protected] => category
[parent:protected] => 2
[label:protected] => Truck Driver
[alreadyInSave:protected] =>
[alreadyInValidation:protected] =>
[validationFailures:protected] => Array
(
)
[_new:BaseObject:private] =>
[_deleted:BaseObject:private] =>
[modifiedColumns:protected] => Array
(
)
)
[87] => Category Object
(
[languages:protected] =>
[bok_resources:protected] =>
[bok_topics:protected] =>
[bok_keywords:protected] =>
[id:protected] => 87
[type:protected] => category
[parent:protected] => 3
[label:protected] => Commercial & Institutional
[alreadyInSave:protected] =>
[alreadyInValidation:protected] =>
[validationFailures:protected] => Array
(
)
[_new:BaseObject:private] =>
[_deleted:BaseObject:private] =>
[modifiedColumns:protected] => Array
(
)
)
[88] => Category Object
(
[languages:protected] =>
[bok_resources:protected] =>
[bok_topics:protected] =>
[bok_keywords:protected] =>
[id:protected] => 88
[type:protected] => category
[parent:protected] => 3
[label:protected] => Demolition
[alreadyInSave:protected] =>
[alreadyInValidation:protected] =>
[validationFailures:protected] => Array
(
)
[_new:BaseObject:private] =>
[_deleted:BaseObject:private] =>
[modifiedColumns:protected] => Array
(
)
)
[89] => Category Object
(
[languages:protected] =>
[bok_resources:protected] =>
[bok_topics:protected] =>
[bok_keywords:protected] =>
[id:protected] => 89
[type:protected] => category
[parent:protected] => 3
[label:protected] => Disasters
[alreadyInSave:protected] =>
[alreadyInValidation:protected] =>
[validationFailures:protected] => Array
(
)
[_new:BaseObject:private] =>
[_deleted:BaseObject:private] =>
[modifiedColumns:protected] => Array
(
)
)
[91] => Category Object
(
[languages:protected] =>
[bok_resources:protected] =>
[bok_topics:protected] =>
[bok_keywords:protected] =>
[id:protected] => 91
[type:protected] => category
[parent:protected] => 3
[label:protected] => Heavy & Highway
[alreadyInSave:protected] =>
[alreadyInValidation:protected] =>
[validationFailures:protected] => Array
(
)
[_new:BaseObject:private] =>
[_deleted:BaseObject:private] =>
[modifiedColumns:protected] => Array
(
)
)
[90] => Category Object
(
[languages:protected] =>
[bok_resources:protected] =>
[bok_topics:protected] =>
[bok_keywords:protected] =>
[id:protected] => 90
[type:protected] => category
[parent:protected] => 3
[label:protected] => Industrial
[alreadyInSave:protected] =>
[alreadyInValidation:protected] =>
[validationFailures:protected] => Array
(
)
[_new:BaseObject:private] =>
[_deleted:BaseObject:private] =>
[modifiedColumns:protected] => Array
(
)
)
[92] => Category Object
(
[languages:protected] =>
[bok_resources:protected] =>
[bok_topics:protected] =>
[bok_keywords:protected] =>
[id:protected] => 92
[type:protected] => category
[parent:protected] => 3
[label:protected] => LEED/Green Construction
[alreadyInSave:protected] =>
[alreadyInValidation:protected] =>
[validationFailures:protected] => Array
(
)
[_new:BaseObject:private] =>
[_deleted:BaseObject:private] =>
[modifiedColumns:protected] => Array
(
)
)
[93] => Category Object
(
[languages:protected] =>
[bok_resources:protected] =>
[bok_topics:protected] =>
[bok_keywords:protected] =>
[id:protected] => 93
[type:protected] => category
[parent:protected] => 3
[label:protected] => Renovations
[alreadyInSave:protected] =>
[alreadyInValidation:protected] =>
[validationFailures:protected] => Array
(
)
[_new:BaseObject:private] =>
[_deleted:BaseObject:private] =>
[modifiedColumns:protected] => Array
(
)
)
[94] => Category Object
(
[languages:protected] =>
[bok_resources:protected] =>
[bok_topics:protected] =>
[bok_keywords:protected] =>
[id:protected] => 94
[type:protected] => category
[parent:protected] => 3
[label:protected] => Residential
[alreadyInSave:protected] =>
[alreadyInValidation:protected] =>
[validationFailures:protected] => Array
(
)
[_new:BaseObject:private] =>
[_deleted:BaseObject:private] =>
[modifiedColumns:protected] => Array
(
)
)
[95] => Category Object
(
[languages:protected] =>
[bok_resources:protected] =>
[bok_topics:protected] =>
[bok_keywords:protected] =>
[id:protected] => 95
[type:protected] => category
[parent:protected] => 3
[label:protected] => Underground
[alreadyInSave:protected] =>
[alreadyInValidation:protected] =>
[validationFailures:protected] => Array
(
)
[_new:BaseObject:private] =>
[_deleted:BaseObject:private] =>
[modifiedColumns:protected] => Array
(
)
)
[100] => Category Object
(
[languages:protected] =>
[bok_resources:protected] =>
[bok_topics:protected] =>
[bok_keywords:protected] =>
[id:protected] => 100
[type:protected] => category
[parent:protected] => 6
[label:protected] => Toolbox Talks
[alreadyInSave:protected] =>
[alreadyInValidation:protected] =>
[validationFailures:protected] => Array
(
)
[_new:BaseObject:private] =>
[_deleted:BaseObject:private] =>
[modifiedColumns:protected] => Array
(
)
)
)
[categories_initialized:protected] => 1
[mapped_items:protected] =>
[content:protected] =>
[files:protected] =>
[language:protected] => Language Object
(
[id:protected] => 1
[code:protected] => en
[name:protected] => English
[alreadyInSave:protected] =>
[alreadyInValidation:protected] =>
[validationFailures:protected] => Array
(
)
[_new:BaseObject:private] =>
[_deleted:BaseObject:private] =>
[modifiedColumns:protected] => Array
(
)
)
[old_record:protected] =>
[id:protected] => 4428
[old_id:protected] =>
[elcosh_id:protected] => d001658
[type:protected] => document
[display_type:protected] => HTML only (and links)
[user_id:protected] => 0
[language_id:protected] => 1
[tagging_id:protected] => Daniela Caceres
[priority_id:protected] => 1
[title:protected] => Toolbox Talk: Work Zone Safety: Working Around Vehicles
[total_pages:protected] => 0
[billed_pages:protected] => 0
[publication_number:protected] =>
[part_of:protected] =>
[keywords:protected] => Struck, Struck by, Vehicle, Work Zone Safety, Truck, Operator, Driver, Mobile Equipment
[comments:protected] =>
[summary:protected] => The CPWR Toolbox Talk on Working Around Vehicles in the Work Zone addresses methods to avoid being struck-by a vehicle on a construction site. The resource includes a case example, steps to prevent a related injury, and questions for discussion. It includes a graphic that illustrates the hazard, which can be posted in a central location as a reminder of steps to work safely. Available in
English and
Spanish.
[transition_comments:protected] =>
[external_link:protected] =>
[consol_link:protected] =>
[more_like_this:protected] => d001640
[permission_given_by:protected] =>
[published:protected] => T
[billable:protected] => F
[img_name:protected] =>
[img_ext:protected] =>
[img_width:protected] =>
[img_height:protected] =>
[img_credit:protected] =>
[img_practice:protected] =>
[vid_source_id:protected] =>
[vid_running_time:protected] =>
[vid_intended_audience:protected] =>
[vid_acquisition_info:protected] =>
[vid_cost:protected] =>
[vid_producer:protected] =>
[vid_filename:protected] =>
[vid_filename_downloadable:protected] =>
[date_summary:protected] =>
[date_permission_requested:protected] =>
[date_permission_received:protected] =>
[date_review_needed:protected] =>
[date_received:protected] => 12/23/21
[date_completed:protected] => 12/23/21
[date_billed:protected] =>
[date_modified:protected] => 05/19/23
[collBokExports:protected] =>
[lastBokExportCriteria:BaseElcoshItem:private] =>
[alreadyInSave:protected] =>
[alreadyInValidation:protected] =>
[validationFailures:protected] => Array
(
)
[_new:BaseObject:private] =>
[_deleted:BaseObject:private] =>
[modifiedColumns:protected] => Array
(
)
)
)
[4] => Search_Result Object
(
[title] => Construction Dive -- DeWalt's Jobsite Pro headphones recalled for fire hazards
[image] => /record/images/notavailable-p.png
[blurb] => A recall notice by the United States Consumer Product Safety Commission affects over 300,000 DeWalt Jobsite Pro Headphones. The recall is a result of...
[category] => Array
(
[0] => 16
[1] => 44
[2] => 45
[3] => 46
[4] => 47
[5] => 48
[6] => 49
[7] => 50
[8] => 51
[9] => 52
[10] => 53
[11] => 54
[12] => 55
[13] => 56
[14] => 57
[15] => 58
[16] => 59
[17] => 60
[18] => 61
[19] => 64
[20] => 65
[21] => 66
[22] => 67
[23] => 68
[24] => 69
[25] => 70
[26] => 71
[27] => 72
[28] => 73
[29] => 74
[30] => 75
[31] => 76
[32] => 77
[33] => 63
[34] => 78
[35] => 79
[36] => 80
[37] => 81
[38] => 82
[39] => 62
[40] => 83
[41] => 84
[42] => 85
[43] => 86
[44] => 87
[45] => 88
[46] => 89
[47] => 91
[48] => 90
[49] => 92
[50] => 93
[51] => 94
[52] => 95
)
[labels] => Array
(
[0] => Fire & Explosions
[1] => Work Environment
[2] => Hazards
[3] => Acoustical Ceiling Carpenter
[4] => Trades
[5] => Asbestos/Insulator
[7] => Boilermaker
[9] => Bricklayer
[11] => Cabinetmaker
[13] => Carpenter
[15] => Carpet Layer
[17] => Cement Mason
[19] => Commercial Diver
[21] => Concrete Polisher
[23] => Drywall Applicator Specialist
[25] => Electrical Worker
[27] => Elevator Constructor
[29] => Flagger
[31] => Glazier
[33] => Hazardous Waste Cleanup
[35] => HVAC
[37] => Interior Systems Carpenter
[39] => Laborer
[41] => Landscaper
[43] => Lather
[45] => Lead Abatement Worker
[47] => Maintenance Worker
[49] => Millwright
[51] => Operating Engineer
[53] => Painter
[55] => Paper Hanger
[57] => PCC/Restoration
[59] => Pile Driver
[61] => Plasterer
[63] => Plumber/Pipefitter
[65] => Refractory Worker
[67] => Reinforcing Ironworker
[69] => Roofer/Waterproofer
[71] => Scaffold Erector
[73] => Sheetmetal Worker
[75] => Sprinkler Fitter
[77] => Stonemason
[79] => Structural Ironworker
[81] => Terrazzo Worker
[83] => Tile Setter
[85] => Truck Driver
[87] => Welder
[89] => Commercial & Institutional
[90] => Jobsites
[91] => Demolition
[93] => Disasters
[95] => Heavy & Highway
[97] => Industrial
[99] => LEED/Green Construction
[101] => Renovations
[103] => Residential
[105] => Underground
)
[type] =>
[sub_category] =>
[url] => /document/4426/d001656/Construction%2BDive%2B--%2BDeWalt%2527s%2BJobsite%2BPro%2Bheadphones%2Brecalled%2Bfor%2Bfire%2Bhazards.html
[item:protected] => DocumentRecord Object
(
[records:protected] => Array
(
)
[recordId:protected] =>
[searchWordClass:protected] =>
[searchWordPeerClass:protected] =>
[bok_record:protected] =>
[authors:protected] =>
[organizations:protected] =>
[collections:protected] =>
[categories:protected] => Array
(
[16] => Category Object
(
[languages:protected] =>
[bok_resources:protected] =>
[bok_topics:protected] =>
[bok_keywords:protected] =>
[id:protected] => 16
[type:protected] => category
[parent:protected] => 7
[label:protected] => Fire & Explosions
[alreadyInSave:protected] =>
[alreadyInValidation:protected] =>
[validationFailures:protected] => Array
(
)
[_new:BaseObject:private] =>
[_deleted:BaseObject:private] =>
[modifiedColumns:protected] => Array
(
)
)
[44] => Category Object
(
[languages:protected] =>
[bok_resources:protected] =>
[bok_topics:protected] =>
[bok_keywords:protected] =>
[id:protected] => 44
[type:protected] => category
[parent:protected] => 2
[label:protected] => Acoustical Ceiling Carpenter
[alreadyInSave:protected] =>
[alreadyInValidation:protected] =>
[validationFailures:protected] => Array
(
)
[_new:BaseObject:private] =>
[_deleted:BaseObject:private] =>
[modifiedColumns:protected] => Array
(
)
)
[45] => Category Object
(
[languages:protected] =>
[bok_resources:protected] =>
[bok_topics:protected] =>
[bok_keywords:protected] =>
[id:protected] => 45
[type:protected] => category
[parent:protected] => 2
[label:protected] => Asbestos/Insulator
[alreadyInSave:protected] =>
[alreadyInValidation:protected] =>
[validationFailures:protected] => Array
(
)
[_new:BaseObject:private] =>
[_deleted:BaseObject:private] =>
[modifiedColumns:protected] => Array
(
)
)
[46] => Category Object
(
[languages:protected] =>
[bok_resources:protected] =>
[bok_topics:protected] =>
[bok_keywords:protected] =>
[id:protected] => 46
[type:protected] => category
[parent:protected] => 2
[label:protected] => Boilermaker
[alreadyInSave:protected] =>
[alreadyInValidation:protected] =>
[validationFailures:protected] => Array
(
)
[_new:BaseObject:private] =>
[_deleted:BaseObject:private] =>
[modifiedColumns:protected] => Array
(
)
)
[47] => Category Object
(
[languages:protected] =>
[bok_resources:protected] =>
[bok_topics:protected] =>
[bok_keywords:protected] =>
[id:protected] => 47
[type:protected] => category
[parent:protected] => 2
[label:protected] => Bricklayer
[alreadyInSave:protected] =>
[alreadyInValidation:protected] =>
[validationFailures:protected] => Array
(
)
[_new:BaseObject:private] =>
[_deleted:BaseObject:private] =>
[modifiedColumns:protected] => Array
(
)
)
[48] => Category Object
(
[languages:protected] =>
[bok_resources:protected] =>
[bok_topics:protected] =>
[bok_keywords:protected] =>
[id:protected] => 48
[type:protected] => category
[parent:protected] => 2
[label:protected] => Cabinetmaker
[alreadyInSave:protected] =>
[alreadyInValidation:protected] =>
[validationFailures:protected] => Array
(
)
[_new:BaseObject:private] =>
[_deleted:BaseObject:private] =>
[modifiedColumns:protected] => Array
(
)
)
[49] => Category Object
(
[languages:protected] =>
[bok_resources:protected] =>
[bok_topics:protected] =>
[bok_keywords:protected] =>
[id:protected] => 49
[type:protected] => category
[parent:protected] => 2
[label:protected] => Carpenter
[alreadyInSave:protected] =>
[alreadyInValidation:protected] =>
[validationFailures:protected] => Array
(
)
[_new:BaseObject:private] =>
[_deleted:BaseObject:private] =>
[modifiedColumns:protected] => Array
(
)
)
[50] => Category Object
(
[languages:protected] =>
[bok_resources:protected] =>
[bok_topics:protected] =>
[bok_keywords:protected] =>
[id:protected] => 50
[type:protected] => category
[parent:protected] => 2
[label:protected] => Carpet Layer
[alreadyInSave:protected] =>
[alreadyInValidation:protected] =>
[validationFailures:protected] => Array
(
)
[_new:BaseObject:private] =>
[_deleted:BaseObject:private] =>
[modifiedColumns:protected] => Array
(
)
)
[51] => Category Object
(
[languages:protected] =>
[bok_resources:protected] =>
[bok_topics:protected] =>
[bok_keywords:protected] =>
[id:protected] => 51
[type:protected] => category
[parent:protected] => 2
[label:protected] => Cement Mason
[alreadyInSave:protected] =>
[alreadyInValidation:protected] =>
[validationFailures:protected] => Array
(
)
[_new:BaseObject:private] =>
[_deleted:BaseObject:private] =>
[modifiedColumns:protected] => Array
(
)
)
[52] => Category Object
(
[languages:protected] =>
[bok_resources:protected] =>
[bok_topics:protected] =>
[bok_keywords:protected] =>
[id:protected] => 52
[type:protected] => category
[parent:protected] => 2
[label:protected] => Commercial Diver
[alreadyInSave:protected] =>
[alreadyInValidation:protected] =>
[validationFailures:protected] => Array
(
)
[_new:BaseObject:private] =>
[_deleted:BaseObject:private] =>
[modifiedColumns:protected] => Array
(
)
)
[53] => Category Object
(
[languages:protected] =>
[bok_resources:protected] =>
[bok_topics:protected] =>
[bok_keywords:protected] =>
[id:protected] => 53
[type:protected] => category
[parent:protected] => 2
[label:protected] => Concrete Polisher
[alreadyInSave:protected] =>
[alreadyInValidation:protected] =>
[validationFailures:protected] => Array
(
)
[_new:BaseObject:private] =>
[_deleted:BaseObject:private] =>
[modifiedColumns:protected] => Array
(
)
)
[54] => Category Object
(
[languages:protected] =>
[bok_resources:protected] =>
[bok_topics:protected] =>
[bok_keywords:protected] =>
[id:protected] => 54
[type:protected] => category
[parent:protected] => 2
[label:protected] => Drywall Applicator Specialist
[alreadyInSave:protected] =>
[alreadyInValidation:protected] =>
[validationFailures:protected] => Array
(
)
[_new:BaseObject:private] =>
[_deleted:BaseObject:private] =>
[modifiedColumns:protected] => Array
(
)
)
[55] => Category Object
(
[languages:protected] =>
[bok_resources:protected] =>
[bok_topics:protected] =>
[bok_keywords:protected] =>
[id:protected] => 55
[type:protected] => category
[parent:protected] => 2
[label:protected] => Electrical Worker
[alreadyInSave:protected] =>
[alreadyInValidation:protected] =>
[validationFailures:protected] => Array
(
)
[_new:BaseObject:private] =>
[_deleted:BaseObject:private] =>
[modifiedColumns:protected] => Array
(
)
)
[56] => Category Object
(
[languages:protected] =>
[bok_resources:protected] =>
[bok_topics:protected] =>
[bok_keywords:protected] =>
[id:protected] => 56
[type:protected] => category
[parent:protected] => 2
[label:protected] => Elevator Constructor
[alreadyInSave:protected] =>
[alreadyInValidation:protected] =>
[validationFailures:protected] => Array
(
)
[_new:BaseObject:private] =>
[_deleted:BaseObject:private] =>
[modifiedColumns:protected] => Array
(
)
)
[57] => Category Object
(
[languages:protected] =>
[bok_resources:protected] =>
[bok_topics:protected] =>
[bok_keywords:protected] =>
[id:protected] => 57
[type:protected] => category
[parent:protected] => 2
[label:protected] => Flagger
[alreadyInSave:protected] =>
[alreadyInValidation:protected] =>
[validationFailures:protected] => Array
(
)
[_new:BaseObject:private] =>
[_deleted:BaseObject:private] =>
[modifiedColumns:protected] => Array
(
)
)
[58] => Category Object
(
[languages:protected] =>
[bok_resources:protected] =>
[bok_topics:protected] =>
[bok_keywords:protected] =>
[id:protected] => 58
[type:protected] => category
[parent:protected] => 2
[label:protected] => Glazier
[alreadyInSave:protected] =>
[alreadyInValidation:protected] =>
[validationFailures:protected] => Array
(
)
[_new:BaseObject:private] =>
[_deleted:BaseObject:private] =>
[modifiedColumns:protected] => Array
(
)
)
[59] => Category Object
(
[languages:protected] =>
[bok_resources:protected] =>
[bok_topics:protected] =>
[bok_keywords:protected] =>
[id:protected] => 59
[type:protected] => category
[parent:protected] => 2
[label:protected] => Hazardous Waste Cleanup
[alreadyInSave:protected] =>
[alreadyInValidation:protected] =>
[validationFailures:protected] => Array
(
)
[_new:BaseObject:private] =>
[_deleted:BaseObject:private] =>
[modifiedColumns:protected] => Array
(
)
)
[60] => Category Object
(
[languages:protected] =>
[bok_resources:protected] =>
[bok_topics:protected] =>
[bok_keywords:protected] =>
[id:protected] => 60
[type:protected] => category
[parent:protected] => 2
[label:protected] => HVAC
[alreadyInSave:protected] =>
[alreadyInValidation:protected] =>
[validationFailures:protected] => Array
(
)
[_new:BaseObject:private] =>
[_deleted:BaseObject:private] =>
[modifiedColumns:protected] => Array
(
)
)
[61] => Category Object
(
[languages:protected] =>
[bok_resources:protected] =>
[bok_topics:protected] =>
[bok_keywords:protected] =>
[id:protected] => 61
[type:protected] => category
[parent:protected] => 2
[label:protected] => Interior Systems Carpenter
[alreadyInSave:protected] =>
[alreadyInValidation:protected] =>
[validationFailures:protected] => Array
(
)
[_new:BaseObject:private] =>
[_deleted:BaseObject:private] =>
[modifiedColumns:protected] => Array
(
)
)
[64] => Category Object
(
[languages:protected] =>
[bok_resources:protected] =>
[bok_topics:protected] =>
[bok_keywords:protected] =>
[id:protected] => 64
[type:protected] => category
[parent:protected] => 2
[label:protected] => Laborer
[alreadyInSave:protected] =>
[alreadyInValidation:protected] =>
[validationFailures:protected] => Array
(
)
[_new:BaseObject:private] =>
[_deleted:BaseObject:private] =>
[modifiedColumns:protected] => Array
(
)
)
[65] => Category Object
(
[languages:protected] =>
[bok_resources:protected] =>
[bok_topics:protected] =>
[bok_keywords:protected] =>
[id:protected] => 65
[type:protected] => category
[parent:protected] => 2
[label:protected] => Landscaper
[alreadyInSave:protected] =>
[alreadyInValidation:protected] =>
[validationFailures:protected] => Array
(
)
[_new:BaseObject:private] =>
[_deleted:BaseObject:private] =>
[modifiedColumns:protected] => Array
(
)
)
[66] => Category Object
(
[languages:protected] =>
[bok_resources:protected] =>
[bok_topics:protected] =>
[bok_keywords:protected] =>
[id:protected] => 66
[type:protected] => category
[parent:protected] => 2
[label:protected] => Lather
[alreadyInSave:protected] =>
[alreadyInValidation:protected] =>
[validationFailures:protected] => Array
(
)
[_new:BaseObject:private] =>
[_deleted:BaseObject:private] =>
[modifiedColumns:protected] => Array
(
)
)
[67] => Category Object
(
[languages:protected] =>
[bok_resources:protected] =>
[bok_topics:protected] =>
[bok_keywords:protected] =>
[id:protected] => 67
[type:protected] => category
[parent:protected] => 2
[label:protected] => Lead Abatement Worker
[alreadyInSave:protected] =>
[alreadyInValidation:protected] =>
[validationFailures:protected] => Array
(
)
[_new:BaseObject:private] =>
[_deleted:BaseObject:private] =>
[modifiedColumns:protected] => Array
(
)
)
[68] => Category Object
(
[languages:protected] =>
[bok_resources:protected] =>
[bok_topics:protected] =>
[bok_keywords:protected] =>
[id:protected] => 68
[type:protected] => category
[parent:protected] => 2
[label:protected] => Maintenance Worker
[alreadyInSave:protected] =>
[alreadyInValidation:protected] =>
[validationFailures:protected] => Array
(
)
[_new:BaseObject:private] =>
[_deleted:BaseObject:private] =>
[modifiedColumns:protected] => Array
(
)
)
[69] => Category Object
(
[languages:protected] =>
[bok_resources:protected] =>
[bok_topics:protected] =>
[bok_keywords:protected] =>
[id:protected] => 69
[type:protected] => category
[parent:protected] => 2
[label:protected] => Millwright
[alreadyInSave:protected] =>
[alreadyInValidation:protected] =>
[validationFailures:protected] => Array
(
)
[_new:BaseObject:private] =>
[_deleted:BaseObject:private] =>
[modifiedColumns:protected] => Array
(
)
)
[70] => Category Object
(
[languages:protected] =>
[bok_resources:protected] =>
[bok_topics:protected] =>
[bok_keywords:protected] =>
[id:protected] => 70
[type:protected] => category
[parent:protected] => 2
[label:protected] => Operating Engineer
[alreadyInSave:protected] =>
[alreadyInValidation:protected] =>
[validationFailures:protected] => Array
(
)
[_new:BaseObject:private] =>
[_deleted:BaseObject:private] =>
[modifiedColumns:protected] => Array
(
)
)
[71] => Category Object
(
[languages:protected] =>
[bok_resources:protected] =>
[bok_topics:protected] =>
[bok_keywords:protected] =>
[id:protected] => 71
[type:protected] => category
[parent:protected] => 2
[label:protected] => Painter
[alreadyInSave:protected] =>
[alreadyInValidation:protected] =>
[validationFailures:protected] => Array
(
)
[_new:BaseObject:private] =>
[_deleted:BaseObject:private] =>
[modifiedColumns:protected] => Array
(
)
)
[72] => Category Object
(
[languages:protected] =>
[bok_resources:protected] =>
[bok_topics:protected] =>
[bok_keywords:protected] =>
[id:protected] => 72
[type:protected] => category
[parent:protected] => 2
[label:protected] => Paper Hanger
[alreadyInSave:protected] =>
[alreadyInValidation:protected] =>
[validationFailures:protected] => Array
(
)
[_new:BaseObject:private] =>
[_deleted:BaseObject:private] =>
[modifiedColumns:protected] => Array
(
)
)
[73] => Category Object
(
[languages:protected] =>
[bok_resources:protected] =>
[bok_topics:protected] =>
[bok_keywords:protected] =>
[id:protected] => 73
[type:protected] => category
[parent:protected] => 2
[label:protected] => PCC/Restoration
[alreadyInSave:protected] =>
[alreadyInValidation:protected] =>
[validationFailures:protected] => Array
(
)
[_new:BaseObject:private] =>
[_deleted:BaseObject:private] =>
[modifiedColumns:protected] => Array
(
)
)
[74] => Category Object
(
[languages:protected] =>
[bok_resources:protected] =>
[bok_topics:protected] =>
[bok_keywords:protected] =>
[id:protected] => 74
[type:protected] => category
[parent:protected] => 2
[label:protected] => Pile Driver
[alreadyInSave:protected] =>
[alreadyInValidation:protected] =>
[validationFailures:protected] => Array
(
)
[_new:BaseObject:private] =>
[_deleted:BaseObject:private] =>
[modifiedColumns:protected] => Array
(
)
)
[75] => Category Object
(
[languages:protected] =>
[bok_resources:protected] =>
[bok_topics:protected] =>
[bok_keywords:protected] =>
[id:protected] => 75
[type:protected] => category
[parent:protected] => 2
[label:protected] => Plasterer
[alreadyInSave:protected] =>
[alreadyInValidation:protected] =>
[validationFailures:protected] => Array
(
)
[_new:BaseObject:private] =>
[_deleted:BaseObject:private] =>
[modifiedColumns:protected] => Array
(
)
)
[76] => Category Object
(
[languages:protected] =>
[bok_resources:protected] =>
[bok_topics:protected] =>
[bok_keywords:protected] =>
[id:protected] => 76
[type:protected] => category
[parent:protected] => 2
[label:protected] => Plumber/Pipefitter
[alreadyInSave:protected] =>
[alreadyInValidation:protected] =>
[validationFailures:protected] => Array
(
)
[_new:BaseObject:private] =>
[_deleted:BaseObject:private] =>
[modifiedColumns:protected] => Array
(
)
)
[77] => Category Object
(
[languages:protected] =>
[bok_resources:protected] =>
[bok_topics:protected] =>
[bok_keywords:protected] =>
[id:protected] => 77
[type:protected] => category
[parent:protected] => 2
[label:protected] => Refractory Worker
[alreadyInSave:protected] =>
[alreadyInValidation:protected] =>
[validationFailures:protected] => Array
(
)
[_new:BaseObject:private] =>
[_deleted:BaseObject:private] =>
[modifiedColumns:protected] => Array
(
)
)
[63] => Category Object
(
[languages:protected] =>
[bok_resources:protected] =>
[bok_topics:protected] =>
[bok_keywords:protected] =>
[id:protected] => 63
[type:protected] => category
[parent:protected] => 2
[label:protected] => Reinforcing Ironworker
[alreadyInSave:protected] =>
[alreadyInValidation:protected] =>
[validationFailures:protected] => Array
(
)
[_new:BaseObject:private] =>
[_deleted:BaseObject:private] =>
[modifiedColumns:protected] => Array
(
)
)
[78] => Category Object
(
[languages:protected] =>
[bok_resources:protected] =>
[bok_topics:protected] =>
[bok_keywords:protected] =>
[id:protected] => 78
[type:protected] => category
[parent:protected] => 2
[label:protected] => Roofer/Waterproofer
[alreadyInSave:protected] =>
[alreadyInValidation:protected] =>
[validationFailures:protected] => Array
(
)
[_new:BaseObject:private] =>
[_deleted:BaseObject:private] =>
[modifiedColumns:protected] => Array
(
)
)
[79] => Category Object
(
[languages:protected] =>
[bok_resources:protected] =>
[bok_topics:protected] =>
[bok_keywords:protected] =>
[id:protected] => 79
[type:protected] => category
[parent:protected] => 2
[label:protected] => Scaffold Erector
[alreadyInSave:protected] =>
[alreadyInValidation:protected] =>
[validationFailures:protected] => Array
(
)
[_new:BaseObject:private] =>
[_deleted:BaseObject:private] =>
[modifiedColumns:protected] => Array
(
)
)
[80] => Category Object
(
[languages:protected] =>
[bok_resources:protected] =>
[bok_topics:protected] =>
[bok_keywords:protected] =>
[id:protected] => 80
[type:protected] => category
[parent:protected] => 2
[label:protected] => Sheetmetal Worker
[alreadyInSave:protected] =>
[alreadyInValidation:protected] =>
[validationFailures:protected] => Array
(
)
[_new:BaseObject:private] =>
[_deleted:BaseObject:private] =>
[modifiedColumns:protected] => Array
(
)
)
[81] => Category Object
(
[languages:protected] =>
[bok_resources:protected] =>
[bok_topics:protected] =>
[bok_keywords:protected] =>
[id:protected] => 81
[type:protected] => category
[parent:protected] => 2
[label:protected] => Sprinkler Fitter
[alreadyInSave:protected] =>
[alreadyInValidation:protected] =>
[validationFailures:protected] => Array
(
)
[_new:BaseObject:private] =>
[_deleted:BaseObject:private] =>
[modifiedColumns:protected] => Array
(
)
)
[82] => Category Object
(
[languages:protected] =>
[bok_resources:protected] =>
[bok_topics:protected] =>
[bok_keywords:protected] =>
[id:protected] => 82
[type:protected] => category
[parent:protected] => 2
[label:protected] => Stonemason
[alreadyInSave:protected] =>
[alreadyInValidation:protected] =>
[validationFailures:protected] => Array
(
)
[_new:BaseObject:private] =>
[_deleted:BaseObject:private] =>
[modifiedColumns:protected] => Array
(
)
)
[62] => Category Object
(
[languages:protected] =>
[bok_resources:protected] =>
[bok_topics:protected] =>
[bok_keywords:protected] =>
[id:protected] => 62
[type:protected] => category
[parent:protected] => 2
[label:protected] => Structural Ironworker
[alreadyInSave:protected] =>
[alreadyInValidation:protected] =>
[validationFailures:protected] => Array
(
)
[_new:BaseObject:private] =>
[_deleted:BaseObject:private] =>
[modifiedColumns:protected] => Array
(
)
)
[83] => Category Object
(
[languages:protected] =>
[bok_resources:protected] =>
[bok_topics:protected] =>
[bok_keywords:protected] =>
[id:protected] => 83
[type:protected] => category
[parent:protected] => 2
[label:protected] => Terrazzo Worker
[alreadyInSave:protected] =>
[alreadyInValidation:protected] =>
[validationFailures:protected] => Array
(
)
[_new:BaseObject:private] =>
[_deleted:BaseObject:private] =>
[modifiedColumns:protected] => Array
(
)
)
[84] => Category Object
(
[languages:protected] =>
[bok_resources:protected] =>
[bok_topics:protected] =>
[bok_keywords:protected] =>
[id:protected] => 84
[type:protected] => category
[parent:protected] => 2
[label:protected] => Tile Setter
[alreadyInSave:protected] =>
[alreadyInValidation:protected] =>
[validationFailures:protected] => Array
(
)
[_new:BaseObject:private] =>
[_deleted:BaseObject:private] =>
[modifiedColumns:protected] => Array
(
)
)
[85] => Category Object
(
[languages:protected] =>
[bok_resources:protected] =>
[bok_topics:protected] =>
[bok_keywords:protected] =>
[id:protected] => 85
[type:protected] => category
[parent:protected] => 2
[label:protected] => Truck Driver
[alreadyInSave:protected] =>
[alreadyInValidation:protected] =>
[validationFailures:protected] => Array
(
)
[_new:BaseObject:private] =>
[_deleted:BaseObject:private] =>
[modifiedColumns:protected] => Array
(
)
)
[86] => Category Object
(
[languages:protected] =>
[bok_resources:protected] =>
[bok_topics:protected] =>
[bok_keywords:protected] =>
[id:protected] => 86
[type:protected] => category
[parent:protected] => 2
[label:protected] => Welder
[alreadyInSave:protected] =>
[alreadyInValidation:protected] =>
[validationFailures:protected] => Array
(
)
[_new:BaseObject:private] =>
[_deleted:BaseObject:private] =>
[modifiedColumns:protected] => Array
(
)
)
[87] => Category Object
(
[languages:protected] =>
[bok_resources:protected] =>
[bok_topics:protected] =>
[bok_keywords:protected] =>
[id:protected] => 87
[type:protected] => category
[parent:protected] => 3
[label:protected] => Commercial & Institutional
[alreadyInSave:protected] =>
[alreadyInValidation:protected] =>
[validationFailures:protected] => Array
(
)
[_new:BaseObject:private] =>
[_deleted:BaseObject:private] =>
[modifiedColumns:protected] => Array
(
)
)
[88] => Category Object
(
[languages:protected] =>
[bok_resources:protected] =>
[bok_topics:protected] =>
[bok_keywords:protected] =>
[id:protected] => 88
[type:protected] => category
[parent:protected] => 3
[label:protected] => Demolition
[alreadyInSave:protected] =>
[alreadyInValidation:protected] =>
[validationFailures:protected] => Array
(
)
[_new:BaseObject:private] =>
[_deleted:BaseObject:private] =>
[modifiedColumns:protected] => Array
(
)
)
[89] => Category Object
(
[languages:protected] =>
[bok_resources:protected] =>
[bok_topics:protected] =>
[bok_keywords:protected] =>
[id:protected] => 89
[type:protected] => category
[parent:protected] => 3
[label:protected] => Disasters
[alreadyInSave:protected] =>
[alreadyInValidation:protected] =>
[validationFailures:protected] => Array
(
)
[_new:BaseObject:private] =>
[_deleted:BaseObject:private] =>
[modifiedColumns:protected] => Array
(
)
)
[91] => Category Object
(
[languages:protected] =>
[bok_resources:protected] =>
[bok_topics:protected] =>
[bok_keywords:protected] =>
[id:protected] => 91
[type:protected] => category
[parent:protected] => 3
[label:protected] => Heavy & Highway
[alreadyInSave:protected] =>
[alreadyInValidation:protected] =>
[validationFailures:protected] => Array
(
)
[_new:BaseObject:private] =>
[_deleted:BaseObject:private] =>
[modifiedColumns:protected] => Array
(
)
)
[90] => Category Object
(
[languages:protected] =>
[bok_resources:protected] =>
[bok_topics:protected] =>
[bok_keywords:protected] =>
[id:protected] => 90
[type:protected] => category
[parent:protected] => 3
[label:protected] => Industrial
[alreadyInSave:protected] =>
[alreadyInValidation:protected] =>
[validationFailures:protected] => Array
(
)
[_new:BaseObject:private] =>
[_deleted:BaseObject:private] =>
[modifiedColumns:protected] => Array
(
)
)
[92] => Category Object
(
[languages:protected] =>
[bok_resources:protected] =>
[bok_topics:protected] =>
[bok_keywords:protected] =>
[id:protected] => 92
[type:protected] => category
[parent:protected] => 3
[label:protected] => LEED/Green Construction
[alreadyInSave:protected] =>
[alreadyInValidation:protected] =>
[validationFailures:protected] => Array
(
)
[_new:BaseObject:private] =>
[_deleted:BaseObject:private] =>
[modifiedColumns:protected] => Array
(
)
)
[93] => Category Object
(
[languages:protected] =>
[bok_resources:protected] =>
[bok_topics:protected] =>
[bok_keywords:protected] =>
[id:protected] => 93
[type:protected] => category
[parent:protected] => 3
[label:protected] => Renovations
[alreadyInSave:protected] =>
[alreadyInValidation:protected] =>
[validationFailures:protected] => Array
(
)
[_new:BaseObject:private] =>
[_deleted:BaseObject:private] =>
[modifiedColumns:protected] => Array
(
)
)
[94] => Category Object
(
[languages:protected] =>
[bok_resources:protected] =>
[bok_topics:protected] =>
[bok_keywords:protected] =>
[id:protected] => 94
[type:protected] => category
[parent:protected] => 3
[label:protected] => Residential
[alreadyInSave:protected] =>
[alreadyInValidation:protected] =>
[validationFailures:protected] => Array
(
)
[_new:BaseObject:private] =>
[_deleted:BaseObject:private] =>
[modifiedColumns:protected] => Array
(
)
)
[95] => Category Object
(
[languages:protected] =>
[bok_resources:protected] =>
[bok_topics:protected] =>
[bok_keywords:protected] =>
[id:protected] => 95
[type:protected] => category
[parent:protected] => 3
[label:protected] => Underground
[alreadyInSave:protected] =>
[alreadyInValidation:protected] =>
[validationFailures:protected] => Array
(
)
[_new:BaseObject:private] =>
[_deleted:BaseObject:private] =>
[modifiedColumns:protected] => Array
(
)
)
)
[categories_initialized:protected] => 1
[mapped_items:protected] =>
[content:protected] =>
[files:protected] =>
[language:protected] => Language Object
(
[id:protected] => 1
[code:protected] => en
[name:protected] => English
[alreadyInSave:protected] =>
[alreadyInValidation:protected] =>
[validationFailures:protected] => Array
(
)
[_new:BaseObject:private] =>
[_deleted:BaseObject:private] =>
[modifiedColumns:protected] => Array
(
)
)
[old_record:protected] =>
[id:protected] => 4426
[old_id:protected] =>
[elcosh_id:protected] => d001656
[type:protected] => document
[display_type:protected] => HTML only (and links)
[user_id:protected] => 0
[language_id:protected] => 1
[tagging_id:protected] => Mike Aguilar
[priority_id:protected] => 1
[title:protected] => Construction Dive -- DeWalt's Jobsite Pro headphones recalled for fire hazards
[total_pages:protected] => 1
[billed_pages:protected] => 1
[publication_number:protected] =>
[part_of:protected] =>
[keywords:protected] => DeWalt, Fire Hazards, recall, headphones
[comments:protected] =>
[summary:protected] => A recall notice by the United States Consumer Product Safety Commission affects over 300,000 DeWalt Jobsite Pro Headphones. The recall is a result of a malfunction that can cause earbuds to overheat while charging or during use, leading to fire and burn hazards.
[transition_comments:protected] =>
[external_link:protected] => https://www.constructiondive.com/news/dewalts-jobsite-pro-headphones-recalled-for-fire-hazards/611248/?utm_source=Sailthru&utm_medium=email&utm_campaign=Issue:%202021-12-10%20Construction%20Dive%20Newsletter%20%5Bissue:38532%5D&utm_term=Construction%20Dive
[consol_link:protected] =>
[more_like_this:protected] =>
[permission_given_by:protected] =>
[published:protected] => T
[billable:protected] => F
[img_name:protected] =>
[img_ext:protected] =>
[img_width:protected] =>
[img_height:protected] =>
[img_credit:protected] =>
[img_practice:protected] =>
[vid_source_id:protected] =>
[vid_running_time:protected] =>
[vid_intended_audience:protected] =>
[vid_acquisition_info:protected] =>
[vid_cost:protected] =>
[vid_producer:protected] =>
[vid_filename:protected] =>
[vid_filename_downloadable:protected] =>
[date_summary:protected] =>
[date_permission_requested:protected] =>
[date_permission_received:protected] =>
[date_review_needed:protected] =>
[date_received:protected] => 12/13/21
[date_completed:protected] => 12/13/21
[date_billed:protected] =>
[date_modified:protected] => 12/13/21
[collBokExports:protected] =>
[lastBokExportCriteria:BaseElcoshItem:private] =>
[alreadyInSave:protected] =>
[alreadyInValidation:protected] =>
[validationFailures:protected] => Array
(
)
[_new:BaseObject:private] =>
[_deleted:BaseObject:private] =>
[modifiedColumns:protected] => Array
(
)
)
)
)
[new_images] => Array
(
[0] => Search_Result Object
(
[title] => Morning Toolbox Talk
[image] => /record/images/4003-p.jpg
[blurb] => This photo is from an early morning toolbox talk on a construction job in Mclean, Virginia. It is being delivered in English and Spanish....
[category] => Array
(
[0] => 20
[1] => 51
[2] => 57
[3] => 64
[4] => 70
[5] => 63
[6] => 78
[7] => 82
[8] => 62
[9] => 87
[10] => 88
[11] => 89
[12] => 91
[13] => 90
[14] => 93
[15] => 94
[16] => 97
)
[labels] => Array
(
[0] => Safety Culture
[1] => Work Environment
[2] => Hazards
[3] => Cement Mason
[4] => Trades
[5] => Flagger
[7] => Laborer
[9] => Operating Engineer
[11] => Reinforcing Ironworker
[13] => Roofer/Waterproofer
[15] => Stonemason
[17] => Structural Ironworker
[19] => Commercial & Institutional
[20] => Jobsites
[21] => Demolition
[23] => Disasters
[25] => Heavy & Highway
[27] => Industrial
[29] => Renovations
[31] => Residential
[33] => Images
[34] => Media
[35] => Media & Documents
)
[type] => Images
[sub_category] =>
[url] => /image/4003/i002691/Morning%2BToolbox%2BTalk.html
[item:protected] => ImageRecord Object
(
[records:protected] => Array
(
)
[recordId:protected] =>
[searchWordClass:protected] =>
[searchWordPeerClass:protected] =>
[bok_record:protected] =>
[authors:protected] =>
[organizations:protected] =>
[collections:protected] =>
[categories:protected] => Array
(
[20] => Category Object
(
[languages:protected] =>
[bok_resources:protected] =>
[bok_topics:protected] =>
[bok_keywords:protected] =>
[id:protected] => 20
[type:protected] => category
[parent:protected] => 7
[label:protected] => Safety Culture
[alreadyInSave:protected] =>
[alreadyInValidation:protected] =>
[validationFailures:protected] => Array
(
)
[_new:BaseObject:private] =>
[_deleted:BaseObject:private] =>
[modifiedColumns:protected] => Array
(
)
)
[51] => Category Object
(
[languages:protected] =>
[bok_resources:protected] =>
[bok_topics:protected] =>
[bok_keywords:protected] =>
[id:protected] => 51
[type:protected] => category
[parent:protected] => 2
[label:protected] => Cement Mason
[alreadyInSave:protected] =>
[alreadyInValidation:protected] =>
[validationFailures:protected] => Array
(
)
[_new:BaseObject:private] =>
[_deleted:BaseObject:private] =>
[modifiedColumns:protected] => Array
(
)
)
[57] => Category Object
(
[languages:protected] =>
[bok_resources:protected] =>
[bok_topics:protected] =>
[bok_keywords:protected] =>
[id:protected] => 57
[type:protected] => category
[parent:protected] => 2
[label:protected] => Flagger
[alreadyInSave:protected] =>
[alreadyInValidation:protected] =>
[validationFailures:protected] => Array
(
)
[_new:BaseObject:private] =>
[_deleted:BaseObject:private] =>
[modifiedColumns:protected] => Array
(
)
)
[64] => Category Object
(
[languages:protected] =>
[bok_resources:protected] =>
[bok_topics:protected] =>
[bok_keywords:protected] =>
[id:protected] => 64
[type:protected] => category
[parent:protected] => 2
[label:protected] => Laborer
[alreadyInSave:protected] =>
[alreadyInValidation:protected] =>
[validationFailures:protected] => Array
(
)
[_new:BaseObject:private] =>
[_deleted:BaseObject:private] =>
[modifiedColumns:protected] => Array
(
)
)
[70] => Category Object
(
[languages:protected] =>
[bok_resources:protected] =>
[bok_topics:protected] =>
[bok_keywords:protected] =>
[id:protected] => 70
[type:protected] => category
[parent:protected] => 2
[label:protected] => Operating Engineer
[alreadyInSave:protected] =>
[alreadyInValidation:protected] =>
[validationFailures:protected] => Array
(
)
[_new:BaseObject:private] =>
[_deleted:BaseObject:private] =>
[modifiedColumns:protected] => Array
(
)
)
[63] => Category Object
(
[languages:protected] =>
[bok_resources:protected] =>
[bok_topics:protected] =>
[bok_keywords:protected] =>
[id:protected] => 63
[type:protected] => category
[parent:protected] => 2
[label:protected] => Reinforcing Ironworker
[alreadyInSave:protected] =>
[alreadyInValidation:protected] =>
[validationFailures:protected] => Array
(
)
[_new:BaseObject:private] =>
[_deleted:BaseObject:private] =>
[modifiedColumns:protected] => Array
(
)
)
[78] => Category Object
(
[languages:protected] =>
[bok_resources:protected] =>
[bok_topics:protected] =>
[bok_keywords:protected] =>
[id:protected] => 78
[type:protected] => category
[parent:protected] => 2
[label:protected] => Roofer/Waterproofer
[alreadyInSave:protected] =>
[alreadyInValidation:protected] =>
[validationFailures:protected] => Array
(
)
[_new:BaseObject:private] =>
[_deleted:BaseObject:private] =>
[modifiedColumns:protected] => Array
(
)
)
[82] => Category Object
(
[languages:protected] =>
[bok_resources:protected] =>
[bok_topics:protected] =>
[bok_keywords:protected] =>
[id:protected] => 82
[type:protected] => category
[parent:protected] => 2
[label:protected] => Stonemason
[alreadyInSave:protected] =>
[alreadyInValidation:protected] =>
[validationFailures:protected] => Array
(
)
[_new:BaseObject:private] =>
[_deleted:BaseObject:private] =>
[modifiedColumns:protected] => Array
(
)
)
[62] => Category Object
(
[languages:protected] =>
[bok_resources:protected] =>
[bok_topics:protected] =>
[bok_keywords:protected] =>
[id:protected] => 62
[type:protected] => category
[parent:protected] => 2
[label:protected] => Structural Ironworker
[alreadyInSave:protected] =>
[alreadyInValidation:protected] =>
[validationFailures:protected] => Array
(
)
[_new:BaseObject:private] =>
[_deleted:BaseObject:private] =>
[modifiedColumns:protected] => Array
(
)
)
[87] => Category Object
(
[languages:protected] =>
[bok_resources:protected] =>
[bok_topics:protected] =>
[bok_keywords:protected] =>
[id:protected] => 87
[type:protected] => category
[parent:protected] => 3
[label:protected] => Commercial & Institutional
[alreadyInSave:protected] =>
[alreadyInValidation:protected] =>
[validationFailures:protected] => Array
(
)
[_new:BaseObject:private] =>
[_deleted:BaseObject:private] =>
[modifiedColumns:protected] => Array
(
)
)
[88] => Category Object
(
[languages:protected] =>
[bok_resources:protected] =>
[bok_topics:protected] =>
[bok_keywords:protected] =>
[id:protected] => 88
[type:protected] => category
[parent:protected] => 3
[label:protected] => Demolition
[alreadyInSave:protected] =>
[alreadyInValidation:protected] =>
[validationFailures:protected] => Array
(
)
[_new:BaseObject:private] =>
[_deleted:BaseObject:private] =>
[modifiedColumns:protected] => Array
(
)
)
[89] => Category Object
(
[languages:protected] =>
[bok_resources:protected] =>
[bok_topics:protected] =>
[bok_keywords:protected] =>
[id:protected] => 89
[type:protected] => category
[parent:protected] => 3
[label:protected] => Disasters
[alreadyInSave:protected] =>
[alreadyInValidation:protected] =>
[validationFailures:protected] => Array
(
)
[_new:BaseObject:private] =>
[_deleted:BaseObject:private] =>
[modifiedColumns:protected] => Array
(
)
)
[91] => Category Object
(
[languages:protected] =>
[bok_resources:protected] =>
[bok_topics:protected] =>
[bok_keywords:protected] =>
[id:protected] => 91
[type:protected] => category
[parent:protected] => 3
[label:protected] => Heavy & Highway
[alreadyInSave:protected] =>
[alreadyInValidation:protected] =>
[validationFailures:protected] => Array
(
)
[_new:BaseObject:private] =>
[_deleted:BaseObject:private] =>
[modifiedColumns:protected] => Array
(
)
)
[90] => Category Object
(
[languages:protected] =>
[bok_resources:protected] =>
[bok_topics:protected] =>
[bok_keywords:protected] =>
[id:protected] => 90
[type:protected] => category
[parent:protected] => 3
[label:protected] => Industrial
[alreadyInSave:protected] =>
[alreadyInValidation:protected] =>
[validationFailures:protected] => Array
(
)
[_new:BaseObject:private] =>
[_deleted:BaseObject:private] =>
[modifiedColumns:protected] => Array
(
)
)
[93] => Category Object
(
[languages:protected] =>
[bok_resources:protected] =>
[bok_topics:protected] =>
[bok_keywords:protected] =>
[id:protected] => 93
[type:protected] => category
[parent:protected] => 3
[label:protected] => Renovations
[alreadyInSave:protected] =>
[alreadyInValidation:protected] =>
[validationFailures:protected] => Array
(
)
[_new:BaseObject:private] =>
[_deleted:BaseObject:private] =>
[modifiedColumns:protected] => Array
(
)
)
[94] => Category Object
(
[languages:protected] =>
[bok_resources:protected] =>
[bok_topics:protected] =>
[bok_keywords:protected] =>
[id:protected] => 94
[type:protected] => category
[parent:protected] => 3
[label:protected] => Residential
[alreadyInSave:protected] =>
[alreadyInValidation:protected] =>
[validationFailures:protected] => Array
(
)
[_new:BaseObject:private] =>
[_deleted:BaseObject:private] =>
[modifiedColumns:protected] => Array
(
)
)
[97] => Category Object
(
[languages:protected] =>
[bok_resources:protected] =>
[bok_topics:protected] =>
[bok_keywords:protected] =>
[id:protected] => 97
[type:protected] => category
[parent:protected] => 5
[label:protected] => Images
[alreadyInSave:protected] =>
[alreadyInValidation:protected] =>
[validationFailures:protected] => Array
(
)
[_new:BaseObject:private] =>
[_deleted:BaseObject:private] =>
[modifiedColumns:protected] => Array
(
)
)
)
[categories_initialized:protected] => 1
[mapped_items:protected] =>
[content:protected] =>
[files:protected] =>
[language:protected] => Language Object
(
[id:protected] => 1
[code:protected] => en
[name:protected] => English
[alreadyInSave:protected] =>
[alreadyInValidation:protected] =>
[validationFailures:protected] => Array
(
)
[_new:BaseObject:private] =>
[_deleted:BaseObject:private] =>
[modifiedColumns:protected] => Array
(
)
)
[old_record:protected] =>
[id:protected] => 4003
[old_id:protected] =>
[elcosh_id:protected] => i002691
[type:protected] => image
[display_type:protected] => Image
[user_id:protected] => 0
[language_id:protected] => 1
[tagging_id:protected] => Bruce Lippy
[priority_id:protected] => 1
[title:protected] => Morning Toolbox Talk
[total_pages:protected] => 0
[billed_pages:protected] => 0
[publication_number:protected] =>
[part_of:protected] =>
[keywords:protected] => toolbox talk, tailgate talk, Spanish, bilingual
[comments:protected] =>
[summary:protected] => This photo is from an early morning toolbox talk on a construction job in Mclean, Virginia. It is being delivered in English and Spanish.
[transition_comments:protected] =>
[external_link:protected] =>
[consol_link:protected] => http://www.cpwrconstructionsolutions.org/electrical/solution/662/worker-training.html
[more_like_this:protected] => d001285,d001304,c000079
[permission_given_by:protected] =>
[published:protected] => T
[billable:protected] => F
[img_name:protected] =>
[img_ext:protected] => jpg
[img_width:protected] =>
[img_height:protected] =>
[img_credit:protected] => Morgan Zavertnik and Hoar Construction
[img_practice:protected] => good
[vid_source_id:protected] =>
[vid_running_time:protected] =>
[vid_intended_audience:protected] =>
[vid_acquisition_info:protected] =>
[vid_cost:protected] =>
[vid_producer:protected] =>
[vid_filename:protected] =>
[vid_filename_downloadable:protected] =>
[date_summary:protected] => November 2015
[date_permission_requested:protected] =>
[date_permission_received:protected] =>
[date_review_needed:protected] =>
[date_received:protected] => 03/02/16
[date_completed:protected] => 03/02/16
[date_billed:protected] =>
[date_modified:protected] => 03/02/16
[collBokExports:protected] =>
[lastBokExportCriteria:BaseElcoshItem:private] =>
[alreadyInSave:protected] =>
[alreadyInValidation:protected] =>
[validationFailures:protected] => Array
(
)
[_new:BaseObject:private] =>
[_deleted:BaseObject:private] =>
[modifiedColumns:protected] => Array
(
)
)
)
[1] => Search_Result Object
(
[title] => Toolbox talk - crew view
[image] => /record/images/4005-p.jpg
[blurb] => Photo of crew listening to a toolbox safety talk before starting work....
[category] => Array
(
[0] => 97
[1] => 20
[2] => 47
[3] => 49
[4] => 51
[5] => 55
[6] => 61
[7] => 64
[8] => 71
[9] => 75
[10] => 63
[11] => 79
[12] => 62
[13] => 87
[14] => 88
[15] => 91
[16] => 90
[17] => 93
[18] => 94
[19] => 95
)
[labels] => Array
(
[0] => Images
[1] => Media
[2] => Media & Documents
[3] => Safety Culture
[4] => Work Environment
[5] => Hazards
[6] => Bricklayer
[7] => Trades
[8] => Carpenter
[10] => Cement Mason
[12] => Electrical Worker
[14] => Interior Systems Carpenter
[16] => Laborer
[18] => Painter
[20] => Plasterer
[22] => Reinforcing Ironworker
[24] => Scaffold Erector
[26] => Structural Ironworker
[28] => Commercial & Institutional
[29] => Jobsites
[30] => Demolition
[32] => Heavy & Highway
[34] => Industrial
[36] => Renovations
[38] => Residential
[40] => Underground
)
[type] => Images
[sub_category] =>
[url] => /image/4005/i002692/Toolbox%2Btalk%2B-%2Bcrew%2Bview.html
[item:protected] => ImageRecord Object
(
[records:protected] => Array
(
)
[recordId:protected] =>
[searchWordClass:protected] =>
[searchWordPeerClass:protected] =>
[bok_record:protected] =>
[authors:protected] =>
[organizations:protected] =>
[collections:protected] =>
[categories:protected] => Array
(
[97] => Category Object
(
[languages:protected] =>
[bok_resources:protected] =>
[bok_topics:protected] =>
[bok_keywords:protected] =>
[id:protected] => 97
[type:protected] => category
[parent:protected] => 5
[label:protected] => Images
[alreadyInSave:protected] =>
[alreadyInValidation:protected] =>
[validationFailures:protected] => Array
(
)
[_new:BaseObject:private] =>
[_deleted:BaseObject:private] =>
[modifiedColumns:protected] => Array
(
)
)
[20] => Category Object
(
[languages:protected] =>
[bok_resources:protected] =>
[bok_topics:protected] =>
[bok_keywords:protected] =>
[id:protected] => 20
[type:protected] => category
[parent:protected] => 7
[label:protected] => Safety Culture
[alreadyInSave:protected] =>
[alreadyInValidation:protected] =>
[validationFailures:protected] => Array
(
)
[_new:BaseObject:private] =>
[_deleted:BaseObject:private] =>
[modifiedColumns:protected] => Array
(
)
)
[47] => Category Object
(
[languages:protected] =>
[bok_resources:protected] =>
[bok_topics:protected] =>
[bok_keywords:protected] =>
[id:protected] => 47
[type:protected] => category
[parent:protected] => 2
[label:protected] => Bricklayer
[alreadyInSave:protected] =>
[alreadyInValidation:protected] =>
[validationFailures:protected] => Array
(
)
[_new:BaseObject:private] =>
[_deleted:BaseObject:private] =>
[modifiedColumns:protected] => Array
(
)
)
[49] => Category Object
(
[languages:protected] =>
[bok_resources:protected] =>
[bok_topics:protected] =>
[bok_keywords:protected] =>
[id:protected] => 49
[type:protected] => category
[parent:protected] => 2
[label:protected] => Carpenter
[alreadyInSave:protected] =>
[alreadyInValidation:protected] =>
[validationFailures:protected] => Array
(
)
[_new:BaseObject:private] =>
[_deleted:BaseObject:private] =>
[modifiedColumns:protected] => Array
(
)
)
[51] => Category Object
(
[languages:protected] =>
[bok_resources:protected] =>
[bok_topics:protected] =>
[bok_keywords:protected] =>
[id:protected] => 51
[type:protected] => category
[parent:protected] => 2
[label:protected] => Cement Mason
[alreadyInSave:protected] =>
[alreadyInValidation:protected] =>
[validationFailures:protected] => Array
(
)
[_new:BaseObject:private] =>
[_deleted:BaseObject:private] =>
[modifiedColumns:protected] => Array
(
)
)
[55] => Category Object
(
[languages:protected] =>
[bok_resources:protected] =>
[bok_topics:protected] =>
[bok_keywords:protected] =>
[id:protected] => 55
[type:protected] => category
[parent:protected] => 2
[label:protected] => Electrical Worker
[alreadyInSave:protected] =>
[alreadyInValidation:protected] =>
[validationFailures:protected] => Array
(
)
[_new:BaseObject:private] =>
[_deleted:BaseObject:private] =>
[modifiedColumns:protected] => Array
(
)
)
[61] => Category Object
(
[languages:protected] =>
[bok_resources:protected] =>
[bok_topics:protected] =>
[bok_keywords:protected] =>
[id:protected] => 61
[type:protected] => category
[parent:protected] => 2
[label:protected] => Interior Systems Carpenter
[alreadyInSave:protected] =>
[alreadyInValidation:protected] =>
[validationFailures:protected] => Array
(
)
[_new:BaseObject:private] =>
[_deleted:BaseObject:private] =>
[modifiedColumns:protected] => Array
(
)
)
[64] => Category Object
(
[languages:protected] =>
[bok_resources:protected] =>
[bok_topics:protected] =>
[bok_keywords:protected] =>
[id:protected] => 64
[type:protected] => category
[parent:protected] => 2
[label:protected] => Laborer
[alreadyInSave:protected] =>
[alreadyInValidation:protected] =>
[validationFailures:protected] => Array
(
)
[_new:BaseObject:private] =>
[_deleted:BaseObject:private] =>
[modifiedColumns:protected] => Array
(
)
)
[71] => Category Object
(
[languages:protected] =>
[bok_resources:protected] =>
[bok_topics:protected] =>
[bok_keywords:protected] =>
[id:protected] => 71
[type:protected] => category
[parent:protected] => 2
[label:protected] => Painter
[alreadyInSave:protected] =>
[alreadyInValidation:protected] =>
[validationFailures:protected] => Array
(
)
[_new:BaseObject:private] =>
[_deleted:BaseObject:private] =>
[modifiedColumns:protected] => Array
(
)
)
[75] => Category Object
(
[languages:protected] =>
[bok_resources:protected] =>
[bok_topics:protected] =>
[bok_keywords:protected] =>
[id:protected] => 75
[type:protected] => category
[parent:protected] => 2
[label:protected] => Plasterer
[alreadyInSave:protected] =>
[alreadyInValidation:protected] =>
[validationFailures:protected] => Array
(
)
[_new:BaseObject:private] =>
[_deleted:BaseObject:private] =>
[modifiedColumns:protected] => Array
(
)
)
[63] => Category Object
(
[languages:protected] =>
[bok_resources:protected] =>
[bok_topics:protected] =>
[bok_keywords:protected] =>
[id:protected] => 63
[type:protected] => category
[parent:protected] => 2
[label:protected] => Reinforcing Ironworker
[alreadyInSave:protected] =>
[alreadyInValidation:protected] =>
[validationFailures:protected] => Array
(
)
[_new:BaseObject:private] =>
[_deleted:BaseObject:private] =>
[modifiedColumns:protected] => Array
(
)
)
[79] => Category Object
(
[languages:protected] =>
[bok_resources:protected] =>
[bok_topics:protected] =>
[bok_keywords:protected] =>
[id:protected] => 79
[type:protected] => category
[parent:protected] => 2
[label:protected] => Scaffold Erector
[alreadyInSave:protected] =>
[alreadyInValidation:protected] =>
[validationFailures:protected] => Array
(
)
[_new:BaseObject:private] =>
[_deleted:BaseObject:private] =>
[modifiedColumns:protected] => Array
(
)
)
[62] => Category Object
(
[languages:protected] =>
[bok_resources:protected] =>
[bok_topics:protected] =>
[bok_keywords:protected] =>
[id:protected] => 62
[type:protected] => category
[parent:protected] => 2
[label:protected] => Structural Ironworker
[alreadyInSave:protected] =>
[alreadyInValidation:protected] =>
[validationFailures:protected] => Array
(
)
[_new:BaseObject:private] =>
[_deleted:BaseObject:private] =>
[modifiedColumns:protected] => Array
(
)
)
[87] => Category Object
(
[languages:protected] =>
[bok_resources:protected] =>
[bok_topics:protected] =>
[bok_keywords:protected] =>
[id:protected] => 87
[type:protected] => category
[parent:protected] => 3
[label:protected] => Commercial & Institutional
[alreadyInSave:protected] =>
[alreadyInValidation:protected] =>
[validationFailures:protected] => Array
(
)
[_new:BaseObject:private] =>
[_deleted:BaseObject:private] =>
[modifiedColumns:protected] => Array
(
)
)
[88] => Category Object
(
[languages:protected] =>
[bok_resources:protected] =>
[bok_topics:protected] =>
[bok_keywords:protected] =>
[id:protected] => 88
[type:protected] => category
[parent:protected] => 3
[label:protected] => Demolition
[alreadyInSave:protected] =>
[alreadyInValidation:protected] =>
[validationFailures:protected] => Array
(
)
[_new:BaseObject:private] =>
[_deleted:BaseObject:private] =>
[modifiedColumns:protected] => Array
(
)
)
[91] => Category Object
(
[languages:protected] =>
[bok_resources:protected] =>
[bok_topics:protected] =>
[bok_keywords:protected] =>
[id:protected] => 91
[type:protected] => category
[parent:protected] => 3
[label:protected] => Heavy & Highway
[alreadyInSave:protected] =>
[alreadyInValidation:protected] =>
[validationFailures:protected] => Array
(
)
[_new:BaseObject:private] =>
[_deleted:BaseObject:private] =>
[modifiedColumns:protected] => Array
(
)
)
[90] => Category Object
(
[languages:protected] =>
[bok_resources:protected] =>
[bok_topics:protected] =>
[bok_keywords:protected] =>
[id:protected] => 90
[type:protected] => category
[parent:protected] => 3
[label:protected] => Industrial
[alreadyInSave:protected] =>
[alreadyInValidation:protected] =>
[validationFailures:protected] => Array
(
)
[_new:BaseObject:private] =>
[_deleted:BaseObject:private] =>
[modifiedColumns:protected] => Array
(
)
)
[93] => Category Object
(
[languages:protected] =>
[bok_resources:protected] =>
[bok_topics:protected] =>
[bok_keywords:protected] =>
[id:protected] => 93
[type:protected] => category
[parent:protected] => 3
[label:protected] => Renovations
[alreadyInSave:protected] =>
[alreadyInValidation:protected] =>
[validationFailures:protected] => Array
(
)
[_new:BaseObject:private] =>
[_deleted:BaseObject:private] =>
[modifiedColumns:protected] => Array
(
)
)
[94] => Category Object
(
[languages:protected] =>
[bok_resources:protected] =>
[bok_topics:protected] =>
[bok_keywords:protected] =>
[id:protected] => 94
[type:protected] => category
[parent:protected] => 3
[label:protected] => Residential
[alreadyInSave:protected] =>
[alreadyInValidation:protected] =>
[validationFailures:protected] => Array
(
)
[_new:BaseObject:private] =>
[_deleted:BaseObject:private] =>
[modifiedColumns:protected] => Array
(
)
)
[95] => Category Object
(
[languages:protected] =>
[bok_resources:protected] =>
[bok_topics:protected] =>
[bok_keywords:protected] =>
[id:protected] => 95
[type:protected] => category
[parent:protected] => 3
[label:protected] => Underground
[alreadyInSave:protected] =>
[alreadyInValidation:protected] =>
[validationFailures:protected] => Array
(
)
[_new:BaseObject:private] =>
[_deleted:BaseObject:private] =>
[modifiedColumns:protected] => Array
(
)
)
)
[categories_initialized:protected] => 1
[mapped_items:protected] =>
[content:protected] =>
[files:protected] =>
[language:protected] => Language Object
(
[id:protected] => 1
[code:protected] => en
[name:protected] => English
[alreadyInSave:protected] =>
[alreadyInValidation:protected] =>
[validationFailures:protected] => Array
(
)
[_new:BaseObject:private] =>
[_deleted:BaseObject:private] =>
[modifiedColumns:protected] => Array
(
)
)
[old_record:protected] =>
[id:protected] => 4005
[old_id:protected] =>
[elcosh_id:protected] => i002692
[type:protected] => image
[display_type:protected] => Image
[user_id:protected] => 0
[language_id:protected] => 1
[tagging_id:protected] => Bruce Lippy
[priority_id:protected] => 1
[title:protected] => Toolbox talk - crew view
[total_pages:protected] => 0
[billed_pages:protected] => 0
[publication_number:protected] =>
[part_of:protected] =>
[keywords:protected] => toolbox talk, tailgate talk, safety talk, Spanish
[comments:protected] =>
[summary:protected] => Photo of crew listening to a toolbox safety talk before starting work.
[transition_comments:protected] =>
[external_link:protected] =>
[consol_link:protected] => http://www.cpwrconstructionsolutions.org/electrical/solution/662/worker-training.html
[more_like_this:protected] => i002691,d001269, c000079, d001285
[permission_given_by:protected] =>
[published:protected] => T
[billable:protected] => F
[img_name:protected] =>
[img_ext:protected] => jpg
[img_width:protected] =>
[img_height:protected] =>
[img_credit:protected] => Morgan Zavertnik and Hoar Construction
[img_practice:protected] => good
[vid_source_id:protected] =>
[vid_running_time:protected] =>
[vid_intended_audience:protected] =>
[vid_acquisition_info:protected] =>
[vid_cost:protected] =>
[vid_producer:protected] =>
[vid_filename:protected] =>
[vid_filename_downloadable:protected] =>
[date_summary:protected] => November 2015
[date_permission_requested:protected] =>
[date_permission_received:protected] =>
[date_review_needed:protected] =>
[date_received:protected] => 03/02/16
[date_completed:protected] => 03/02/16
[date_billed:protected] =>
[date_modified:protected] => 03/02/16
[collBokExports:protected] =>
[lastBokExportCriteria:BaseElcoshItem:private] =>
[alreadyInSave:protected] =>
[alreadyInValidation:protected] =>
[validationFailures:protected] => Array
(
)
[_new:BaseObject:private] =>
[_deleted:BaseObject:private] =>
[modifiedColumns:protected] => Array
(
)
)
)
[2] => Search_Result Object
(
[title] => Toolbox talk - long shot
[image] => /record/images/4006-p.jpg
[blurb] => This crew gathered every morning before starting work to discuss a new safety topic....
[category] => Array
(
[0] => 20
[1] => 47
[2] => 49
[3] => 51
[4] => 55
[5] => 64
[6] => 68
[7] => 75
[8] => 76
[9] => 63
[10] => 78
[11] => 79
[12] => 82
[13] => 62
[14] => 87
[15] => 88
[16] => 91
[17] => 90
[18] => 93
[19] => 94
[20] => 95
[21] => 97
)
[labels] => Array
(
[0] => Safety Culture
[1] => Work Environment
[2] => Hazards
[3] => Bricklayer
[4] => Trades
[5] => Carpenter
[7] => Cement Mason
[9] => Electrical Worker
[11] => Laborer
[13] => Maintenance Worker
[15] => Plasterer
[17] => Plumber/Pipefitter
[19] => Reinforcing Ironworker
[21] => Roofer/Waterproofer
[23] => Scaffold Erector
[25] => Stonemason
[27] => Structural Ironworker
[29] => Commercial & Institutional
[30] => Jobsites
[31] => Demolition
[33] => Heavy & Highway
[35] => Industrial
[37] => Renovations
[39] => Residential
[41] => Underground
[43] => Images
[44] => Media
[45] => Media & Documents
)
[type] => Images
[sub_category] =>
[url] => /image/4006/i002693/Toolbox%2Btalk%2B-%2Blong%2Bshot.html
[item:protected] => ImageRecord Object
(
[records:protected] => Array
(
)
[recordId:protected] =>
[searchWordClass:protected] =>
[searchWordPeerClass:protected] =>
[bok_record:protected] =>
[authors:protected] =>
[organizations:protected] =>
[collections:protected] =>
[categories:protected] => Array
(
[20] => Category Object
(
[languages:protected] =>
[bok_resources:protected] =>
[bok_topics:protected] =>
[bok_keywords:protected] =>
[id:protected] => 20
[type:protected] => category
[parent:protected] => 7
[label:protected] => Safety Culture
[alreadyInSave:protected] =>
[alreadyInValidation:protected] =>
[validationFailures:protected] => Array
(
)
[_new:BaseObject:private] =>
[_deleted:BaseObject:private] =>
[modifiedColumns:protected] => Array
(
)
)
[47] => Category Object
(
[languages:protected] =>
[bok_resources:protected] =>
[bok_topics:protected] =>
[bok_keywords:protected] =>
[id:protected] => 47
[type:protected] => category
[parent:protected] => 2
[label:protected] => Bricklayer
[alreadyInSave:protected] =>
[alreadyInValidation:protected] =>
[validationFailures:protected] => Array
(
)
[_new:BaseObject:private] =>
[_deleted:BaseObject:private] =>
[modifiedColumns:protected] => Array
(
)
)
[49] => Category Object
(
[languages:protected] =>
[bok_resources:protected] =>
[bok_topics:protected] =>
[bok_keywords:protected] =>
[id:protected] => 49
[type:protected] => category
[parent:protected] => 2
[label:protected] => Carpenter
[alreadyInSave:protected] =>
[alreadyInValidation:protected] =>
[validationFailures:protected] => Array
(
)
[_new:BaseObject:private] =>
[_deleted:BaseObject:private] =>
[modifiedColumns:protected] => Array
(
)
)
[51] => Category Object
(
[languages:protected] =>
[bok_resources:protected] =>
[bok_topics:protected] =>
[bok_keywords:protected] =>
[id:protected] => 51
[type:protected] => category
[parent:protected] => 2
[label:protected] => Cement Mason
[alreadyInSave:protected] =>
[alreadyInValidation:protected] =>
[validationFailures:protected] => Array
(
)
[_new:BaseObject:private] =>
[_deleted:BaseObject:private] =>
[modifiedColumns:protected] => Array
(
)
)
[55] => Category Object
(
[languages:protected] =>
[bok_resources:protected] =>
[bok_topics:protected] =>
[bok_keywords:protected] =>
[id:protected] => 55
[type:protected] => category
[parent:protected] => 2
[label:protected] => Electrical Worker
[alreadyInSave:protected] =>
[alreadyInValidation:protected] =>
[validationFailures:protected] => Array
(
)
[_new:BaseObject:private] =>
[_deleted:BaseObject:private] =>
[modifiedColumns:protected] => Array
(
)
)
[64] => Category Object
(
[languages:protected] =>
[bok_resources:protected] =>
[bok_topics:protected] =>
[bok_keywords:protected] =>
[id:protected] => 64
[type:protected] => category
[parent:protected] => 2
[label:protected] => Laborer
[alreadyInSave:protected] =>
[alreadyInValidation:protected] =>
[validationFailures:protected] => Array
(
)
[_new:BaseObject:private] =>
[_deleted:BaseObject:private] =>
[modifiedColumns:protected] => Array
(
)
)
[68] => Category Object
(
[languages:protected] =>
[bok_resources:protected] =>
[bok_topics:protected] =>
[bok_keywords:protected] =>
[id:protected] => 68
[type:protected] => category
[parent:protected] => 2
[label:protected] => Maintenance Worker
[alreadyInSave:protected] =>
[alreadyInValidation:protected] =>
[validationFailures:protected] => Array
(
)
[_new:BaseObject:private] =>
[_deleted:BaseObject:private] =>
[modifiedColumns:protected] => Array
(
)
)
[75] => Category Object
(
[languages:protected] =>
[bok_resources:protected] =>
[bok_topics:protected] =>
[bok_keywords:protected] =>
[id:protected] => 75
[type:protected] => category
[parent:protected] => 2
[label:protected] => Plasterer
[alreadyInSave:protected] =>
[alreadyInValidation:protected] =>
[validationFailures:protected] => Array
(
)
[_new:BaseObject:private] =>
[_deleted:BaseObject:private] =>
[modifiedColumns:protected] => Array
(
)
)
[76] => Category Object
(
[languages:protected] =>
[bok_resources:protected] =>
[bok_topics:protected] =>
[bok_keywords:protected] =>
[id:protected] => 76
[type:protected] => category
[parent:protected] => 2
[label:protected] => Plumber/Pipefitter
[alreadyInSave:protected] =>
[alreadyInValidation:protected] =>
[validationFailures:protected] => Array
(
)
[_new:BaseObject:private] =>
[_deleted:BaseObject:private] =>
[modifiedColumns:protected] => Array
(
)
)
[63] => Category Object
(
[languages:protected] =>
[bok_resources:protected] =>
[bok_topics:protected] =>
[bok_keywords:protected] =>
[id:protected] => 63
[type:protected] => category
[parent:protected] => 2
[label:protected] => Reinforcing Ironworker
[alreadyInSave:protected] =>
[alreadyInValidation:protected] =>
[validationFailures:protected] => Array
(
)
[_new:BaseObject:private] =>
[_deleted:BaseObject:private] =>
[modifiedColumns:protected] => Array
(
)
)
[78] => Category Object
(
[languages:protected] =>
[bok_resources:protected] =>
[bok_topics:protected] =>
[bok_keywords:protected] =>
[id:protected] => 78
[type:protected] => category
[parent:protected] => 2
[label:protected] => Roofer/Waterproofer
[alreadyInSave:protected] =>
[alreadyInValidation:protected] =>
[validationFailures:protected] => Array
(
)
[_new:BaseObject:private] =>
[_deleted:BaseObject:private] =>
[modifiedColumns:protected] => Array
(
)
)
[79] => Category Object
(
[languages:protected] =>
[bok_resources:protected] =>
[bok_topics:protected] =>
[bok_keywords:protected] =>
[id:protected] => 79
[type:protected] => category
[parent:protected] => 2
[label:protected] => Scaffold Erector
[alreadyInSave:protected] =>
[alreadyInValidation:protected] =>
[validationFailures:protected] => Array
(
)
[_new:BaseObject:private] =>
[_deleted:BaseObject:private] =>
[modifiedColumns:protected] => Array
(
)
)
[82] => Category Object
(
[languages:protected] =>
[bok_resources:protected] =>
[bok_topics:protected] =>
[bok_keywords:protected] =>
[id:protected] => 82
[type:protected] => category
[parent:protected] => 2
[label:protected] => Stonemason
[alreadyInSave:protected] =>
[alreadyInValidation:protected] =>
[validationFailures:protected] => Array
(
)
[_new:BaseObject:private] =>
[_deleted:BaseObject:private] =>
[modifiedColumns:protected] => Array
(
)
)
[62] => Category Object
(
[languages:protected] =>
[bok_resources:protected] =>
[bok_topics:protected] =>
[bok_keywords:protected] =>
[id:protected] => 62
[type:protected] => category
[parent:protected] => 2
[label:protected] => Structural Ironworker
[alreadyInSave:protected] =>
[alreadyInValidation:protected] =>
[validationFailures:protected] => Array
(
)
[_new:BaseObject:private] =>
[_deleted:BaseObject:private] =>
[modifiedColumns:protected] => Array
(
)
)
[87] => Category Object
(
[languages:protected] =>
[bok_resources:protected] =>
[bok_topics:protected] =>
[bok_keywords:protected] =>
[id:protected] => 87
[type:protected] => category
[parent:protected] => 3
[label:protected] => Commercial & Institutional
[alreadyInSave:protected] =>
[alreadyInValidation:protected] =>
[validationFailures:protected] => Array
(
)
[_new:BaseObject:private] =>
[_deleted:BaseObject:private] =>
[modifiedColumns:protected] => Array
(
)
)
[88] => Category Object
(
[languages:protected] =>
[bok_resources:protected] =>
[bok_topics:protected] =>
[bok_keywords:protected] =>
[id:protected] => 88
[type:protected] => category
[parent:protected] => 3
[label:protected] => Demolition
[alreadyInSave:protected] =>
[alreadyInValidation:protected] =>
[validationFailures:protected] => Array
(
)
[_new:BaseObject:private] =>
[_deleted:BaseObject:private] =>
[modifiedColumns:protected] => Array
(
)
)
[91] => Category Object
(
[languages:protected] =>
[bok_resources:protected] =>
[bok_topics:protected] =>
[bok_keywords:protected] =>
[id:protected] => 91
[type:protected] => category
[parent:protected] => 3
[label:protected] => Heavy & Highway
[alreadyInSave:protected] =>
[alreadyInValidation:protected] =>
[validationFailures:protected] => Array
(
)
[_new:BaseObject:private] =>
[_deleted:BaseObject:private] =>
[modifiedColumns:protected] => Array
(
)
)
[90] => Category Object
(
[languages:protected] =>
[bok_resources:protected] =>
[bok_topics:protected] =>
[bok_keywords:protected] =>
[id:protected] => 90
[type:protected] => category
[parent:protected] => 3
[label:protected] => Industrial
[alreadyInSave:protected] =>
[alreadyInValidation:protected] =>
[validationFailures:protected] => Array
(
)
[_new:BaseObject:private] =>
[_deleted:BaseObject:private] =>
[modifiedColumns:protected] => Array
(
)
)
[93] => Category Object
(
[languages:protected] =>
[bok_resources:protected] =>
[bok_topics:protected] =>
[bok_keywords:protected] =>
[id:protected] => 93
[type:protected] => category
[parent:protected] => 3
[label:protected] => Renovations
[alreadyInSave:protected] =>
[alreadyInValidation:protected] =>
[validationFailures:protected] => Array
(
)
[_new:BaseObject:private] =>
[_deleted:BaseObject:private] =>
[modifiedColumns:protected] => Array
(
)
)
[94] => Category Object
(
[languages:protected] =>
[bok_resources:protected] =>
[bok_topics:protected] =>
[bok_keywords:protected] =>
[id:protected] => 94
[type:protected] => category
[parent:protected] => 3
[label:protected] => Residential
[alreadyInSave:protected] =>
[alreadyInValidation:protected] =>
[validationFailures:protected] => Array
(
)
[_new:BaseObject:private] =>
[_deleted:BaseObject:private] =>
[modifiedColumns:protected] => Array
(
)
)
[95] => Category Object
(
[languages:protected] =>
[bok_resources:protected] =>
[bok_topics:protected] =>
[bok_keywords:protected] =>
[id:protected] => 95
[type:protected] => category
[parent:protected] => 3
[label:protected] => Underground
[alreadyInSave:protected] =>
[alreadyInValidation:protected] =>
[validationFailures:protected] => Array
(
)
[_new:BaseObject:private] =>
[_deleted:BaseObject:private] =>
[modifiedColumns:protected] => Array
(
)
)
[97] => Category Object
(
[languages:protected] =>
[bok_resources:protected] =>
[bok_topics:protected] =>
[bok_keywords:protected] =>
[id:protected] => 97
[type:protected] => category
[parent:protected] => 5
[label:protected] => Images
[alreadyInSave:protected] =>
[alreadyInValidation:protected] =>
[validationFailures:protected] => Array
(
)
[_new:BaseObject:private] =>
[_deleted:BaseObject:private] =>
[modifiedColumns:protected] => Array
(
)
)
)
[categories_initialized:protected] => 1
[mapped_items:protected] =>
[content:protected] =>
[files:protected] =>
[language:protected] => Language Object
(
[id:protected] => 1
[code:protected] => en
[name:protected] => English
[alreadyInSave:protected] =>
[alreadyInValidation:protected] =>
[validationFailures:protected] => Array
(
)
[_new:BaseObject:private] =>
[_deleted:BaseObject:private] =>
[modifiedColumns:protected] => Array
(
)
)
[old_record:protected] =>
[id:protected] => 4006
[old_id:protected] =>
[elcosh_id:protected] => i002693
[type:protected] => image
[display_type:protected] => Image
[user_id:protected] => 0
[language_id:protected] => 1
[tagging_id:protected] => Bruce Lippy
[priority_id:protected] => 1
[title:protected] => Toolbox talk - long shot
[total_pages:protected] => 0
[billed_pages:protected] => 0
[publication_number:protected] =>
[part_of:protected] =>
[keywords:protected] => toolbox talk, tailgate talk, safety minute
[comments:protected] =>
[summary:protected] => This crew gathered every morning before starting work to discuss a new safety topic.
[transition_comments:protected] =>
[external_link:protected] =>
[consol_link:protected] => http://www.cpwrconstructionsolutions.org/electrical/solution/662/worker-training.html
[more_like_this:protected] => i002691,i002692,d001269,d000527
[permission_given_by:protected] =>
[published:protected] => T
[billable:protected] => F
[img_name:protected] =>
[img_ext:protected] => jpg
[img_width:protected] =>
[img_height:protected] =>
[img_credit:protected] => Morgan Zavertnik and Hoar Construction
[img_practice:protected] => good
[vid_source_id:protected] =>
[vid_running_time:protected] =>
[vid_intended_audience:protected] =>
[vid_acquisition_info:protected] =>
[vid_cost:protected] =>
[vid_producer:protected] =>
[vid_filename:protected] =>
[vid_filename_downloadable:protected] =>
[date_summary:protected] => November 2015
[date_permission_requested:protected] =>
[date_permission_received:protected] =>
[date_review_needed:protected] =>
[date_received:protected] => 03/02/16
[date_completed:protected] => 03/02/16
[date_billed:protected] =>
[date_modified:protected] => 03/02/16
[collBokExports:protected] =>
[lastBokExportCriteria:BaseElcoshItem:private] =>
[alreadyInSave:protected] =>
[alreadyInValidation:protected] =>
[validationFailures:protected] => Array
(
)
[_new:BaseObject:private] =>
[_deleted:BaseObject:private] =>
[modifiedColumns:protected] => Array
(
)
)
)
[3] => Search_Result Object
(
[title] => Safety officer discussing ongoing project with marketing coordinator
[image] => /record/images/4014-p.jpg
[blurb] => The safety officer (left) points out the good safety practices on this project that reflect well on the firm and may influence future clients....
[category] => Array
(
[0] => 97
[1] => 20
[2] => 46
[3] => 47
[4] => 49
[5] => 50
[6] => 51
[7] => 54
[8] => 55
[9] => 58
[10] => 60
[11] => 61
[12] => 64
[13] => 71
[14] => 75
[15] => 76
[16] => 63
[17] => 79
[18] => 80
[19] => 82
[20] => 62
[21] => 83
[22] => 87
[23] => 91
[24] => 90
[25] => 93
[26] => 94
)
[labels] => Array
(
[0] => Images
[1] => Media
[2] => Media & Documents
[3] => Safety Culture
[4] => Work Environment
[5] => Hazards
[6] => Boilermaker
[7] => Trades
[8] => Bricklayer
[10] => Carpenter
[12] => Carpet Layer
[14] => Cement Mason
[16] => Drywall Applicator Specialist
[18] => Electrical Worker
[20] => Glazier
[22] => HVAC
[24] => Interior Systems Carpenter
[26] => Laborer
[28] => Painter
[30] => Plasterer
[32] => Plumber/Pipefitter
[34] => Reinforcing Ironworker
[36] => Scaffold Erector
[38] => Sheetmetal Worker
[40] => Stonemason
[42] => Structural Ironworker
[44] => Terrazzo Worker
[46] => Commercial & Institutional
[47] => Jobsites
[48] => Heavy & Highway
[50] => Industrial
[52] => Renovations
[54] => Residential
)
[type] => Images
[sub_category] =>
[url] => /image/4014/i002700/Safety%2Bofficer%2Bdiscussing%2Bongoing%2Bproject%2Bwith%2Bmarketing%2Bcoordinator.html
[item:protected] => ImageRecord Object
(
[records:protected] => Array
(
)
[recordId:protected] =>
[searchWordClass:protected] =>
[searchWordPeerClass:protected] =>
[bok_record:protected] =>
[authors:protected] =>
[organizations:protected] =>
[collections:protected] =>
[categories:protected] => Array
(
[97] => Category Object
(
[languages:protected] =>
[bok_resources:protected] =>
[bok_topics:protected] =>
[bok_keywords:protected] =>
[id:protected] => 97
[type:protected] => category
[parent:protected] => 5
[label:protected] => Images
[alreadyInSave:protected] =>
[alreadyInValidation:protected] =>
[validationFailures:protected] => Array
(
)
[_new:BaseObject:private] =>
[_deleted:BaseObject:private] =>
[modifiedColumns:protected] => Array
(
)
)
[20] => Category Object
(
[languages:protected] =>
[bok_resources:protected] =>
[bok_topics:protected] =>
[bok_keywords:protected] =>
[id:protected] => 20
[type:protected] => category
[parent:protected] => 7
[label:protected] => Safety Culture
[alreadyInSave:protected] =>
[alreadyInValidation:protected] =>
[validationFailures:protected] => Array
(
)
[_new:BaseObject:private] =>
[_deleted:BaseObject:private] =>
[modifiedColumns:protected] => Array
(
)
)
[46] => Category Object
(
[languages:protected] =>
[bok_resources:protected] =>
[bok_topics:protected] =>
[bok_keywords:protected] =>
[id:protected] => 46
[type:protected] => category
[parent:protected] => 2
[label:protected] => Boilermaker
[alreadyInSave:protected] =>
[alreadyInValidation:protected] =>
[validationFailures:protected] => Array
(
)
[_new:BaseObject:private] =>
[_deleted:BaseObject:private] =>
[modifiedColumns:protected] => Array
(
)
)
[47] => Category Object
(
[languages:protected] =>
[bok_resources:protected] =>
[bok_topics:protected] =>
[bok_keywords:protected] =>
[id:protected] => 47
[type:protected] => category
[parent:protected] => 2
[label:protected] => Bricklayer
[alreadyInSave:protected] =>
[alreadyInValidation:protected] =>
[validationFailures:protected] => Array
(
)
[_new:BaseObject:private] =>
[_deleted:BaseObject:private] =>
[modifiedColumns:protected] => Array
(
)
)
[49] => Category Object
(
[languages:protected] =>
[bok_resources:protected] =>
[bok_topics:protected] =>
[bok_keywords:protected] =>
[id:protected] => 49
[type:protected] => category
[parent:protected] => 2
[label:protected] => Carpenter
[alreadyInSave:protected] =>
[alreadyInValidation:protected] =>
[validationFailures:protected] => Array
(
)
[_new:BaseObject:private] =>
[_deleted:BaseObject:private] =>
[modifiedColumns:protected] => Array
(
)
)
[50] => Category Object
(
[languages:protected] =>
[bok_resources:protected] =>
[bok_topics:protected] =>
[bok_keywords:protected] =>
[id:protected] => 50
[type:protected] => category
[parent:protected] => 2
[label:protected] => Carpet Layer
[alreadyInSave:protected] =>
[alreadyInValidation:protected] =>
[validationFailures:protected] => Array
(
)
[_new:BaseObject:private] =>
[_deleted:BaseObject:private] =>
[modifiedColumns:protected] => Array
(
)
)
[51] => Category Object
(
[languages:protected] =>
[bok_resources:protected] =>
[bok_topics:protected] =>
[bok_keywords:protected] =>
[id:protected] => 51
[type:protected] => category
[parent:protected] => 2
[label:protected] => Cement Mason
[alreadyInSave:protected] =>
[alreadyInValidation:protected] =>
[validationFailures:protected] => Array
(
)
[_new:BaseObject:private] =>
[_deleted:BaseObject:private] =>
[modifiedColumns:protected] => Array
(
)
)
[54] => Category Object
(
[languages:protected] =>
[bok_resources:protected] =>
[bok_topics:protected] =>
[bok_keywords:protected] =>
[id:protected] => 54
[type:protected] => category
[parent:protected] => 2
[label:protected] => Drywall Applicator Specialist
[alreadyInSave:protected] =>
[alreadyInValidation:protected] =>
[validationFailures:protected] => Array
(
)
[_new:BaseObject:private] =>
[_deleted:BaseObject:private] =>
[modifiedColumns:protected] => Array
(
)
)
[55] => Category Object
(
[languages:protected] =>
[bok_resources:protected] =>
[bok_topics:protected] =>
[bok_keywords:protected] =>
[id:protected] => 55
[type:protected] => category
[parent:protected] => 2
[label:protected] => Electrical Worker
[alreadyInSave:protected] =>
[alreadyInValidation:protected] =>
[validationFailures:protected] => Array
(
)
[_new:BaseObject:private] =>
[_deleted:BaseObject:private] =>
[modifiedColumns:protected] => Array
(
)
)
[58] => Category Object
(
[languages:protected] =>
[bok_resources:protected] =>
[bok_topics:protected] =>
[bok_keywords:protected] =>
[id:protected] => 58
[type:protected] => category
[parent:protected] => 2
[label:protected] => Glazier
[alreadyInSave:protected] =>
[alreadyInValidation:protected] =>
[validationFailures:protected] => Array
(
)
[_new:BaseObject:private] =>
[_deleted:BaseObject:private] =>
[modifiedColumns:protected] => Array
(
)
)
[60] => Category Object
(
[languages:protected] =>
[bok_resources:protected] =>
[bok_topics:protected] =>
[bok_keywords:protected] =>
[id:protected] => 60
[type:protected] => category
[parent:protected] => 2
[label:protected] => HVAC
[alreadyInSave:protected] =>
[alreadyInValidation:protected] =>
[validationFailures:protected] => Array
(
)
[_new:BaseObject:private] =>
[_deleted:BaseObject:private] =>
[modifiedColumns:protected] => Array
(
)
)
[61] => Category Object
(
[languages:protected] =>
[bok_resources:protected] =>
[bok_topics:protected] =>
[bok_keywords:protected] =>
[id:protected] => 61
[type:protected] => category
[parent:protected] => 2
[label:protected] => Interior Systems Carpenter
[alreadyInSave:protected] =>
[alreadyInValidation:protected] =>
[validationFailures:protected] => Array
(
)
[_new:BaseObject:private] =>
[_deleted:BaseObject:private] =>
[modifiedColumns:protected] => Array
(
)
)
[64] => Category Object
(
[languages:protected] =>
[bok_resources:protected] =>
[bok_topics:protected] =>
[bok_keywords:protected] =>
[id:protected] => 64
[type:protected] => category
[parent:protected] => 2
[label:protected] => Laborer
[alreadyInSave:protected] =>
[alreadyInValidation:protected] =>
[validationFailures:protected] => Array
(
)
[_new:BaseObject:private] =>
[_deleted:BaseObject:private] =>
[modifiedColumns:protected] => Array
(
)
)
[71] => Category Object
(
[languages:protected] =>
[bok_resources:protected] =>
[bok_topics:protected] =>
[bok_keywords:protected] =>
[id:protected] => 71
[type:protected] => category
[parent:protected] => 2
[label:protected] => Painter
[alreadyInSave:protected] =>
[alreadyInValidation:protected] =>
[validationFailures:protected] => Array
(
)
[_new:BaseObject:private] =>
[_deleted:BaseObject:private] =>
[modifiedColumns:protected] => Array
(
)
)
[75] => Category Object
(
[languages:protected] =>
[bok_resources:protected] =>
[bok_topics:protected] =>
[bok_keywords:protected] =>
[id:protected] => 75
[type:protected] => category
[parent:protected] => 2
[label:protected] => Plasterer
[alreadyInSave:protected] =>
[alreadyInValidation:protected] =>
[validationFailures:protected] => Array
(
)
[_new:BaseObject:private] =>
[_deleted:BaseObject:private] =>
[modifiedColumns:protected] => Array
(
)
)
[76] => Category Object
(
[languages:protected] =>
[bok_resources:protected] =>
[bok_topics:protected] =>
[bok_keywords:protected] =>
[id:protected] => 76
[type:protected] => category
[parent:protected] => 2
[label:protected] => Plumber/Pipefitter
[alreadyInSave:protected] =>
[alreadyInValidation:protected] =>
[validationFailures:protected] => Array
(
)
[_new:BaseObject:private] =>
[_deleted:BaseObject:private] =>
[modifiedColumns:protected] => Array
(
)
)
[63] => Category Object
(
[languages:protected] =>
[bok_resources:protected] =>
[bok_topics:protected] =>
[bok_keywords:protected] =>
[id:protected] => 63
[type:protected] => category
[parent:protected] => 2
[label:protected] => Reinforcing Ironworker
[alreadyInSave:protected] =>
[alreadyInValidation:protected] =>
[validationFailures:protected] => Array
(
)
[_new:BaseObject:private] =>
[_deleted:BaseObject:private] =>
[modifiedColumns:protected] => Array
(
)
)
[79] => Category Object
(
[languages:protected] =>
[bok_resources:protected] =>
[bok_topics:protected] =>
[bok_keywords:protected] =>
[id:protected] => 79
[type:protected] => category
[parent:protected] => 2
[label:protected] => Scaffold Erector
[alreadyInSave:protected] =>
[alreadyInValidation:protected] =>
[validationFailures:protected] => Array
(
)
[_new:BaseObject:private] =>
[_deleted:BaseObject:private] =>
[modifiedColumns:protected] => Array
(
)
)
[80] => Category Object
(
[languages:protected] =>
[bok_resources:protected] =>
[bok_topics:protected] =>
[bok_keywords:protected] =>
[id:protected] => 80
[type:protected] => category
[parent:protected] => 2
[label:protected] => Sheetmetal Worker
[alreadyInSave:protected] =>
[alreadyInValidation:protected] =>
[validationFailures:protected] => Array
(
)
[_new:BaseObject:private] =>
[_deleted:BaseObject:private] =>
[modifiedColumns:protected] => Array
(
)
)
[82] => Category Object
(
[languages:protected] =>
[bok_resources:protected] =>
[bok_topics:protected] =>
[bok_keywords:protected] =>
[id:protected] => 82
[type:protected] => category
[parent:protected] => 2
[label:protected] => Stonemason
[alreadyInSave:protected] =>
[alreadyInValidation:protected] =>
[validationFailures:protected] => Array
(
)
[_new:BaseObject:private] =>
[_deleted:BaseObject:private] =>
[modifiedColumns:protected] => Array
(
)
)
[62] => Category Object
(
[languages:protected] =>
[bok_resources:protected] =>
[bok_topics:protected] =>
[bok_keywords:protected] =>
[id:protected] => 62
[type:protected] => category
[parent:protected] => 2
[label:protected] => Structural Ironworker
[alreadyInSave:protected] =>
[alreadyInValidation:protected] =>
[validationFailures:protected] => Array
(
)
[_new:BaseObject:private] =>
[_deleted:BaseObject:private] =>
[modifiedColumns:protected] => Array
(
)
)
[83] => Category Object
(
[languages:protected] =>
[bok_resources:protected] =>
[bok_topics:protected] =>
[bok_keywords:protected] =>
[id:protected] => 83
[type:protected] => category
[parent:protected] => 2
[label:protected] => Terrazzo Worker
[alreadyInSave:protected] =>
[alreadyInValidation:protected] =>
[validationFailures:protected] => Array
(
)
[_new:BaseObject:private] =>
[_deleted:BaseObject:private] =>
[modifiedColumns:protected] => Array
(
)
)
[87] => Category Object
(
[languages:protected] =>
[bok_resources:protected] =>
[bok_topics:protected] =>
[bok_keywords:protected] =>
[id:protected] => 87
[type:protected] => category
[parent:protected] => 3
[label:protected] => Commercial & Institutional
[alreadyInSave:protected] =>
[alreadyInValidation:protected] =>
[validationFailures:protected] => Array
(
)
[_new:BaseObject:private] =>
[_deleted:BaseObject:private] =>
[modifiedColumns:protected] => Array
(
)
)
[91] => Category Object
(
[languages:protected] =>
[bok_resources:protected] =>
[bok_topics:protected] =>
[bok_keywords:protected] =>
[id:protected] => 91
[type:protected] => category
[parent:protected] => 3
[label:protected] => Heavy & Highway
[alreadyInSave:protected] =>
[alreadyInValidation:protected] =>
[validationFailures:protected] => Array
(
)
[_new:BaseObject:private] =>
[_deleted:BaseObject:private] =>
[modifiedColumns:protected] => Array
(
)
)
[90] => Category Object
(
[languages:protected] =>
[bok_resources:protected] =>
[bok_topics:protected] =>
[bok_keywords:protected] =>
[id:protected] => 90
[type:protected] => category
[parent:protected] => 3
[label:protected] => Industrial
[alreadyInSave:protected] =>
[alreadyInValidation:protected] =>
[validationFailures:protected] => Array
(
)
[_new:BaseObject:private] =>
[_deleted:BaseObject:private] =>
[modifiedColumns:protected] => Array
(
)
)
[93] => Category Object
(
[languages:protected] =>
[bok_resources:protected] =>
[bok_topics:protected] =>
[bok_keywords:protected] =>
[id:protected] => 93
[type:protected] => category
[parent:protected] => 3
[label:protected] => Renovations
[alreadyInSave:protected] =>
[alreadyInValidation:protected] =>
[validationFailures:protected] => Array
(
)
[_new:BaseObject:private] =>
[_deleted:BaseObject:private] =>
[modifiedColumns:protected] => Array
(
)
)
[94] => Category Object
(
[languages:protected] =>
[bok_resources:protected] =>
[bok_topics:protected] =>
[bok_keywords:protected] =>
[id:protected] => 94
[type:protected] => category
[parent:protected] => 3
[label:protected] => Residential
[alreadyInSave:protected] =>
[alreadyInValidation:protected] =>
[validationFailures:protected] => Array
(
)
[_new:BaseObject:private] =>
[_deleted:BaseObject:private] =>
[modifiedColumns:protected] => Array
(
)
)
)
[categories_initialized:protected] => 1
[mapped_items:protected] =>
[content:protected] =>
[files:protected] =>
[language:protected] => Language Object
(
[id:protected] => 1
[code:protected] => en
[name:protected] => English
[alreadyInSave:protected] =>
[alreadyInValidation:protected] =>
[validationFailures:protected] => Array
(
)
[_new:BaseObject:private] =>
[_deleted:BaseObject:private] =>
[modifiedColumns:protected] => Array
(
)
)
[old_record:protected] =>
[id:protected] => 4014
[old_id:protected] =>
[elcosh_id:protected] => i002700
[type:protected] => image
[display_type:protected] => Image
[user_id:protected] => 0
[language_id:protected] => 1
[tagging_id:protected] => Bruce Lippy
[priority_id:protected] => 1
[title:protected] => Safety officer discussing ongoing project with marketing coordinator
[total_pages:protected] => 0
[billed_pages:protected] => 0
[publication_number:protected] =>
[part_of:protected] =>
[keywords:protected] => Latino, safety officer, safety culture
[comments:protected] =>
[summary:protected] => The safety officer (left) points out the good safety practices on this project that reflect well on the firm and may influence future clients.
[transition_comments:protected] =>
[external_link:protected] =>
[consol_link:protected] => http://www.cpwrconstructionsolutions.org/index.php
[more_like_this:protected] => d000989,d001351,d001362,d000652, d001101, d000931, d001395
[permission_given_by:protected] =>
[published:protected] => T
[billable:protected] => F
[img_name:protected] =>
[img_ext:protected] => jpg
[img_width:protected] =>
[img_height:protected] =>
[img_credit:protected] => Hoar Construction, Photo by Neil Lippy
[img_practice:protected] => good
[vid_source_id:protected] =>
[vid_running_time:protected] =>
[vid_intended_audience:protected] =>
[vid_acquisition_info:protected] =>
[vid_cost:protected] =>
[vid_producer:protected] =>
[vid_filename:protected] =>
[vid_filename_downloadable:protected] =>
[date_summary:protected] => November 2015
[date_permission_requested:protected] =>
[date_permission_received:protected] =>
[date_review_needed:protected] =>
[date_received:protected] => 03/02/16
[date_completed:protected] => 03/02/16
[date_billed:protected] =>
[date_modified:protected] => 01/30/23
[collBokExports:protected] =>
[lastBokExportCriteria:BaseElcoshItem:private] =>
[alreadyInSave:protected] =>
[alreadyInValidation:protected] =>
[validationFailures:protected] => Array
(
)
[_new:BaseObject:private] =>
[_deleted:BaseObject:private] =>
[modifiedColumns:protected] => Array
(
)
)
)
[4] => Search_Result Object
(
[title] => Scaffolding at top of large column
[image] => /record/images/3994-p.jpg
[blurb] => This shot shows innovative guarding around the top of a large concrete column in the base of a high rise structure going up....
[category] => Array
(
[0] => 15
[1] => 21
[2] => 47
[3] => 51
[4] => 63
[5] => 78
[6] => 79
[7] => 80
[8] => 62
[9] => 87
[10] => 97
[11] => 56
[12] => 64
[13] => 74
)
[labels] => Array
(
[0] => Falls
[1] => Work Environment
[2] => Hazards
[3] => Scaffolds
[6] => Bricklayer
[7] => Trades
[8] => Cement Mason
[10] => Reinforcing Ironworker
[12] => Roofer/Waterproofer
[14] => Scaffold Erector
[16] => Sheetmetal Worker
[18] => Structural Ironworker
[20] => Commercial & Institutional
[21] => Jobsites
[22] => Images
[23] => Media
[24] => Media & Documents
[25] => Elevator Constructor
[27] => Laborer
[29] => Pile Driver
)
[type] => Images
[sub_category] =>
[url] => /image/3994/i002689/Scaffolding%2Bat%2Btop%2Bof%2Blarge%2Bcolumn.html
[item:protected] => ImageRecord Object
(
[records:protected] => Array
(
)
[recordId:protected] =>
[searchWordClass:protected] =>
[searchWordPeerClass:protected] =>
[bok_record:protected] =>
[authors:protected] =>
[organizations:protected] =>
[collections:protected] =>
[categories:protected] => Array
(
[15] => Category Object
(
[languages:protected] =>
[bok_resources:protected] =>
[bok_topics:protected] =>
[bok_keywords:protected] =>
[id:protected] => 15
[type:protected] => category
[parent:protected] => 7
[label:protected] => Falls
[alreadyInSave:protected] =>
[alreadyInValidation:protected] =>
[validationFailures:protected] => Array
(
)
[_new:BaseObject:private] =>
[_deleted:BaseObject:private] =>
[modifiedColumns:protected] => Array
(
)
)
[21] => Category Object
(
[languages:protected] =>
[bok_resources:protected] =>
[bok_topics:protected] =>
[bok_keywords:protected] =>
[id:protected] => 21
[type:protected] => category
[parent:protected] => 7
[label:protected] => Scaffolds
[alreadyInSave:protected] =>
[alreadyInValidation:protected] =>
[validationFailures:protected] => Array
(
)
[_new:BaseObject:private] =>
[_deleted:BaseObject:private] =>
[modifiedColumns:protected] => Array
(
)
)
[47] => Category Object
(
[languages:protected] =>
[bok_resources:protected] =>
[bok_topics:protected] =>
[bok_keywords:protected] =>
[id:protected] => 47
[type:protected] => category
[parent:protected] => 2
[label:protected] => Bricklayer
[alreadyInSave:protected] =>
[alreadyInValidation:protected] =>
[validationFailures:protected] => Array
(
)
[_new:BaseObject:private] =>
[_deleted:BaseObject:private] =>
[modifiedColumns:protected] => Array
(
)
)
[51] => Category Object
(
[languages:protected] =>
[bok_resources:protected] =>
[bok_topics:protected] =>
[bok_keywords:protected] =>
[id:protected] => 51
[type:protected] => category
[parent:protected] => 2
[label:protected] => Cement Mason
[alreadyInSave:protected] =>
[alreadyInValidation:protected] =>
[validationFailures:protected] => Array
(
)
[_new:BaseObject:private] =>
[_deleted:BaseObject:private] =>
[modifiedColumns:protected] => Array
(
)
)
[63] => Category Object
(
[languages:protected] =>
[bok_resources:protected] =>
[bok_topics:protected] =>
[bok_keywords:protected] =>
[id:protected] => 63
[type:protected] => category
[parent:protected] => 2
[label:protected] => Reinforcing Ironworker
[alreadyInSave:protected] =>
[alreadyInValidation:protected] =>
[validationFailures:protected] => Array
(
)
[_new:BaseObject:private] =>
[_deleted:BaseObject:private] =>
[modifiedColumns:protected] => Array
(
)
)
[78] => Category Object
(
[languages:protected] =>
[bok_resources:protected] =>
[bok_topics:protected] =>
[bok_keywords:protected] =>
[id:protected] => 78
[type:protected] => category
[parent:protected] => 2
[label:protected] => Roofer/Waterproofer
[alreadyInSave:protected] =>
[alreadyInValidation:protected] =>
[validationFailures:protected] => Array
(
)
[_new:BaseObject:private] =>
[_deleted:BaseObject:private] =>
[modifiedColumns:protected] => Array
(
)
)
[79] => Category Object
(
[languages:protected] =>
[bok_resources:protected] =>
[bok_topics:protected] =>
[bok_keywords:protected] =>
[id:protected] => 79
[type:protected] => category
[parent:protected] => 2
[label:protected] => Scaffold Erector
[alreadyInSave:protected] =>
[alreadyInValidation:protected] =>
[validationFailures:protected] => Array
(
)
[_new:BaseObject:private] =>
[_deleted:BaseObject:private] =>
[modifiedColumns:protected] => Array
(
)
)
[80] => Category Object
(
[languages:protected] =>
[bok_resources:protected] =>
[bok_topics:protected] =>
[bok_keywords:protected] =>
[id:protected] => 80
[type:protected] => category
[parent:protected] => 2
[label:protected] => Sheetmetal Worker
[alreadyInSave:protected] =>
[alreadyInValidation:protected] =>
[validationFailures:protected] => Array
(
)
[_new:BaseObject:private] =>
[_deleted:BaseObject:private] =>
[modifiedColumns:protected] => Array
(
)
)
[62] => Category Object
(
[languages:protected] =>
[bok_resources:protected] =>
[bok_topics:protected] =>
[bok_keywords:protected] =>
[id:protected] => 62
[type:protected] => category
[parent:protected] => 2
[label:protected] => Structural Ironworker
[alreadyInSave:protected] =>
[alreadyInValidation:protected] =>
[validationFailures:protected] => Array
(
)
[_new:BaseObject:private] =>
[_deleted:BaseObject:private] =>
[modifiedColumns:protected] => Array
(
)
)
[87] => Category Object
(
[languages:protected] =>
[bok_resources:protected] =>
[bok_topics:protected] =>
[bok_keywords:protected] =>
[id:protected] => 87
[type:protected] => category
[parent:protected] => 3
[label:protected] => Commercial & Institutional
[alreadyInSave:protected] =>
[alreadyInValidation:protected] =>
[validationFailures:protected] => Array
(
)
[_new:BaseObject:private] =>
[_deleted:BaseObject:private] =>
[modifiedColumns:protected] => Array
(
)
)
[97] => Category Object
(
[languages:protected] =>
[bok_resources:protected] =>
[bok_topics:protected] =>
[bok_keywords:protected] =>
[id:protected] => 97
[type:protected] => category
[parent:protected] => 5
[label:protected] => Images
[alreadyInSave:protected] =>
[alreadyInValidation:protected] =>
[validationFailures:protected] => Array
(
)
[_new:BaseObject:private] =>
[_deleted:BaseObject:private] =>
[modifiedColumns:protected] => Array
(
)
)
[56] => Category Object
(
[languages:protected] =>
[bok_resources:protected] =>
[bok_topics:protected] =>
[bok_keywords:protected] =>
[id:protected] => 56
[type:protected] => category
[parent:protected] => 2
[label:protected] => Elevator Constructor
[alreadyInSave:protected] =>
[alreadyInValidation:protected] =>
[validationFailures:protected] => Array
(
)
[_new:BaseObject:private] =>
[_deleted:BaseObject:private] =>
[modifiedColumns:protected] => Array
(
)
)
[64] => Category Object
(
[languages:protected] =>
[bok_resources:protected] =>
[bok_topics:protected] =>
[bok_keywords:protected] =>
[id:protected] => 64
[type:protected] => category
[parent:protected] => 2
[label:protected] => Laborer
[alreadyInSave:protected] =>
[alreadyInValidation:protected] =>
[validationFailures:protected] => Array
(
)
[_new:BaseObject:private] =>
[_deleted:BaseObject:private] =>
[modifiedColumns:protected] => Array
(
)
)
[74] => Category Object
(
[languages:protected] =>
[bok_resources:protected] =>
[bok_topics:protected] =>
[bok_keywords:protected] =>
[id:protected] => 74
[type:protected] => category
[parent:protected] => 2
[label:protected] => Pile Driver
[alreadyInSave:protected] =>
[alreadyInValidation:protected] =>
[validationFailures:protected] => Array
(
)
[_new:BaseObject:private] =>
[_deleted:BaseObject:private] =>
[modifiedColumns:protected] => Array
(
)
)
)
[categories_initialized:protected] => 1
[mapped_items:protected] =>
[content:protected] =>
[files:protected] =>
[language:protected] => Language Object
(
[id:protected] => 1
[code:protected] => en
[name:protected] => English
[alreadyInSave:protected] =>
[alreadyInValidation:protected] =>
[validationFailures:protected] => Array
(
)
[_new:BaseObject:private] =>
[_deleted:BaseObject:private] =>
[modifiedColumns:protected] => Array
(
)
)
[old_record:protected] =>
[id:protected] => 3994
[old_id:protected] =>
[elcosh_id:protected] => i002689
[type:protected] => image
[display_type:protected] => Image
[user_id:protected] => 0
[language_id:protected] => 1
[tagging_id:protected] => Bruce Lippy
[priority_id:protected] => 1
[title:protected] => Scaffolding at top of large column
[total_pages:protected] => 0
[billed_pages:protected] => 0
[publication_number:protected] =>
[part_of:protected] =>
[keywords:protected] => Guardrail, railing, fall prevention, falls
[comments:protected] =>
[summary:protected] => This shot shows innovative guarding around the top of a large concrete column in the base of a high rise structure going up.
[transition_comments:protected] =>
[external_link:protected] =>
[consol_link:protected] => http://www.cpwrconstructionsolutions.org/masonry/solution/8/adjustable-tower-scaffold.html
[more_like_this:protected] => c1002680,i002662,d000608,d001255
[permission_given_by:protected] =>
[published:protected] => T
[billable:protected] => F
[img_name:protected] =>
[img_ext:protected] => jpg
[img_width:protected] =>
[img_height:protected] =>
[img_credit:protected] => Photo by Pam Susi
[img_practice:protected] => good
[vid_source_id:protected] =>
[vid_running_time:protected] =>
[vid_intended_audience:protected] =>
[vid_acquisition_info:protected] =>
[vid_cost:protected] =>
[vid_producer:protected] =>
[vid_filename:protected] =>
[vid_filename_downloadable:protected] =>
[date_summary:protected] => January 2016
[date_permission_requested:protected] =>
[date_permission_received:protected] =>
[date_review_needed:protected] =>
[date_received:protected] => 02/01/16
[date_completed:protected] => 02/01/16
[date_billed:protected] =>
[date_modified:protected] => 02/01/16
[collBokExports:protected] =>
[lastBokExportCriteria:BaseElcoshItem:private] =>
[alreadyInSave:protected] =>
[alreadyInValidation:protected] =>
[validationFailures:protected] => Array
(
)
[_new:BaseObject:private] =>
[_deleted:BaseObject:private] =>
[modifiedColumns:protected] => Array
(
)
)
)
[5] => Search_Result Object
(
[title] => Construction bracing
[image] => /record/images/3995-p.jpg
[blurb] => This shows structural support that prevents collapses during construction....
[category] => Array
(
[0] => 12
[1] => 15
[2] => 21
[3] => 49
[4] => 51
[5] => 55
[6] => 56
[7] => 60
[8] => 64
[9] => 68
[10] => 74
[11] => 63
[12] => 78
[13] => 79
[14] => 80
[15] => 62
[16] => 87
[17] => 90
[18] => 97
)
[labels] => Array
(
[0] => Crushed/Struck By
[1] => Work Environment
[2] => Hazards
[3] => Falls
[6] => Scaffolds
[9] => Carpenter
[10] => Trades
[11] => Cement Mason
[13] => Electrical Worker
[15] => Elevator Constructor
[17] => HVAC
[19] => Laborer
[21] => Maintenance Worker
[23] => Pile Driver
[25] => Reinforcing Ironworker
[27] => Roofer/Waterproofer
[29] => Scaffold Erector
[31] => Sheetmetal Worker
[33] => Structural Ironworker
[35] => Commercial & Institutional
[36] => Jobsites
[37] => Industrial
[39] => Images
[40] => Media
[41] => Media & Documents
)
[type] => Images
[sub_category] =>
[url] => /image/3995/i002690/Construction%2Bbracing.html
[item:protected] => ImageRecord Object
(
[records:protected] => Array
(
)
[recordId:protected] =>
[searchWordClass:protected] =>
[searchWordPeerClass:protected] =>
[bok_record:protected] =>
[authors:protected] =>
[organizations:protected] =>
[collections:protected] =>
[categories:protected] => Array
(
[12] => Category Object
(
[languages:protected] =>
[bok_resources:protected] =>
[bok_topics:protected] =>
[bok_keywords:protected] =>
[id:protected] => 12
[type:protected] => category
[parent:protected] => 7
[label:protected] => Crushed/Struck By
[alreadyInSave:protected] =>
[alreadyInValidation:protected] =>
[validationFailures:protected] => Array
(
)
[_new:BaseObject:private] =>
[_deleted:BaseObject:private] =>
[modifiedColumns:protected] => Array
(
)
)
[15] => Category Object
(
[languages:protected] =>
[bok_resources:protected] =>
[bok_topics:protected] =>
[bok_keywords:protected] =>
[id:protected] => 15
[type:protected] => category
[parent:protected] => 7
[label:protected] => Falls
[alreadyInSave:protected] =>
[alreadyInValidation:protected] =>
[validationFailures:protected] => Array
(
)
[_new:BaseObject:private] =>
[_deleted:BaseObject:private] =>
[modifiedColumns:protected] => Array
(
)
)
[21] => Category Object
(
[languages:protected] =>
[bok_resources:protected] =>
[bok_topics:protected] =>
[bok_keywords:protected] =>
[id:protected] => 21
[type:protected] => category
[parent:protected] => 7
[label:protected] => Scaffolds
[alreadyInSave:protected] =>
[alreadyInValidation:protected] =>
[validationFailures:protected] => Array
(
)
[_new:BaseObject:private] =>
[_deleted:BaseObject:private] =>
[modifiedColumns:protected] => Array
(
)
)
[49] => Category Object
(
[languages:protected] =>
[bok_resources:protected] =>
[bok_topics:protected] =>
[bok_keywords:protected] =>
[id:protected] => 49
[type:protected] => category
[parent:protected] => 2
[label:protected] => Carpenter
[alreadyInSave:protected] =>
[alreadyInValidation:protected] =>
[validationFailures:protected] => Array
(
)
[_new:BaseObject:private] =>
[_deleted:BaseObject:private] =>
[modifiedColumns:protected] => Array
(
)
)
[51] => Category Object
(
[languages:protected] =>
[bok_resources:protected] =>
[bok_topics:protected] =>
[bok_keywords:protected] =>
[id:protected] => 51
[type:protected] => category
[parent:protected] => 2
[label:protected] => Cement Mason
[alreadyInSave:protected] =>
[alreadyInValidation:protected] =>
[validationFailures:protected] => Array
(
)
[_new:BaseObject:private] =>
[_deleted:BaseObject:private] =>
[modifiedColumns:protected] => Array
(
)
)
[55] => Category Object
(
[languages:protected] =>
[bok_resources:protected] =>
[bok_topics:protected] =>
[bok_keywords:protected] =>
[id:protected] => 55
[type:protected] => category
[parent:protected] => 2
[label:protected] => Electrical Worker
[alreadyInSave:protected] =>
[alreadyInValidation:protected] =>
[validationFailures:protected] => Array
(
)
[_new:BaseObject:private] =>
[_deleted:BaseObject:private] =>
[modifiedColumns:protected] => Array
(
)
)
[56] => Category Object
(
[languages:protected] =>
[bok_resources:protected] =>
[bok_topics:protected] =>
[bok_keywords:protected] =>
[id:protected] => 56
[type:protected] => category
[parent:protected] => 2
[label:protected] => Elevator Constructor
[alreadyInSave:protected] =>
[alreadyInValidation:protected] =>
[validationFailures:protected] => Array
(
)
[_new:BaseObject:private] =>
[_deleted:BaseObject:private] =>
[modifiedColumns:protected] => Array
(
)
)
[60] => Category Object
(
[languages:protected] =>
[bok_resources:protected] =>
[bok_topics:protected] =>
[bok_keywords:protected] =>
[id:protected] => 60
[type:protected] => category
[parent:protected] => 2
[label:protected] => HVAC
[alreadyInSave:protected] =>
[alreadyInValidation:protected] =>
[validationFailures:protected] => Array
(
)
[_new:BaseObject:private] =>
[_deleted:BaseObject:private] =>
[modifiedColumns:protected] => Array
(
)
)
[64] => Category Object
(
[languages:protected] =>
[bok_resources:protected] =>
[bok_topics:protected] =>
[bok_keywords:protected] =>
[id:protected] => 64
[type:protected] => category
[parent:protected] => 2
[label:protected] => Laborer
[alreadyInSave:protected] =>
[alreadyInValidation:protected] =>
[validationFailures:protected] => Array
(
)
[_new:BaseObject:private] =>
[_deleted:BaseObject:private] =>
[modifiedColumns:protected] => Array
(
)
)
[68] => Category Object
(
[languages:protected] =>
[bok_resources:protected] =>
[bok_topics:protected] =>
[bok_keywords:protected] =>
[id:protected] => 68
[type:protected] => category
[parent:protected] => 2
[label:protected] => Maintenance Worker
[alreadyInSave:protected] =>
[alreadyInValidation:protected] =>
[validationFailures:protected] => Array
(
)
[_new:BaseObject:private] =>
[_deleted:BaseObject:private] =>
[modifiedColumns:protected] => Array
(
)
)
[74] => Category Object
(
[languages:protected] =>
[bok_resources:protected] =>
[bok_topics:protected] =>
[bok_keywords:protected] =>
[id:protected] => 74
[type:protected] => category
[parent:protected] => 2
[label:protected] => Pile Driver
[alreadyInSave:protected] =>
[alreadyInValidation:protected] =>
[validationFailures:protected] => Array
(
)
[_new:BaseObject:private] =>
[_deleted:BaseObject:private] =>
[modifiedColumns:protected] => Array
(
)
)
[63] => Category Object
(
[languages:protected] =>
[bok_resources:protected] =>
[bok_topics:protected] =>
[bok_keywords:protected] =>
[id:protected] => 63
[type:protected] => category
[parent:protected] => 2
[label:protected] => Reinforcing Ironworker
[alreadyInSave:protected] =>
[alreadyInValidation:protected] =>
[validationFailures:protected] => Array
(
)
[_new:BaseObject:private] =>
[_deleted:BaseObject:private] =>
[modifiedColumns:protected] => Array
(
)
)
[78] => Category Object
(
[languages:protected] =>
[bok_resources:protected] =>
[bok_topics:protected] =>
[bok_keywords:protected] =>
[id:protected] => 78
[type:protected] => category
[parent:protected] => 2
[label:protected] => Roofer/Waterproofer
[alreadyInSave:protected] =>
[alreadyInValidation:protected] =>
[validationFailures:protected] => Array
(
)
[_new:BaseObject:private] =>
[_deleted:BaseObject:private] =>
[modifiedColumns:protected] => Array
(
)
)
[79] => Category Object
(
[languages:protected] =>
[bok_resources:protected] =>
[bok_topics:protected] =>
[bok_keywords:protected] =>
[id:protected] => 79
[type:protected] => category
[parent:protected] => 2
[label:protected] => Scaffold Erector
[alreadyInSave:protected] =>
[alreadyInValidation:protected] =>
[validationFailures:protected] => Array
(
)
[_new:BaseObject:private] =>
[_deleted:BaseObject:private] =>
[modifiedColumns:protected] => Array
(
)
)
[80] => Category Object
(
[languages:protected] =>
[bok_resources:protected] =>
[bok_topics:protected] =>
[bok_keywords:protected] =>
[id:protected] => 80
[type:protected] => category
[parent:protected] => 2
[label:protected] => Sheetmetal Worker
[alreadyInSave:protected] =>
[alreadyInValidation:protected] =>
[validationFailures:protected] => Array
(
)
[_new:BaseObject:private] =>
[_deleted:BaseObject:private] =>
[modifiedColumns:protected] => Array
(
)
)
[62] => Category Object
(
[languages:protected] =>
[bok_resources:protected] =>
[bok_topics:protected] =>
[bok_keywords:protected] =>
[id:protected] => 62
[type:protected] => category
[parent:protected] => 2
[label:protected] => Structural Ironworker
[alreadyInSave:protected] =>
[alreadyInValidation:protected] =>
[validationFailures:protected] => Array
(
)
[_new:BaseObject:private] =>
[_deleted:BaseObject:private] =>
[modifiedColumns:protected] => Array
(
)
)
[87] => Category Object
(
[languages:protected] =>
[bok_resources:protected] =>
[bok_topics:protected] =>
[bok_keywords:protected] =>
[id:protected] => 87
[type:protected] => category
[parent:protected] => 3
[label:protected] => Commercial & Institutional
[alreadyInSave:protected] =>
[alreadyInValidation:protected] =>
[validationFailures:protected] => Array
(
)
[_new:BaseObject:private] =>
[_deleted:BaseObject:private] =>
[modifiedColumns:protected] => Array
(
)
)
[90] => Category Object
(
[languages:protected] =>
[bok_resources:protected] =>
[bok_topics:protected] =>
[bok_keywords:protected] =>
[id:protected] => 90
[type:protected] => category
[parent:protected] => 3
[label:protected] => Industrial
[alreadyInSave:protected] =>
[alreadyInValidation:protected] =>
[validationFailures:protected] => Array
(
)
[_new:BaseObject:private] =>
[_deleted:BaseObject:private] =>
[modifiedColumns:protected] => Array
(
)
)
[97] => Category Object
(
[languages:protected] =>
[bok_resources:protected] =>
[bok_topics:protected] =>
[bok_keywords:protected] =>
[id:protected] => 97
[type:protected] => category
[parent:protected] => 5
[label:protected] => Images
[alreadyInSave:protected] =>
[alreadyInValidation:protected] =>
[validationFailures:protected] => Array
(
)
[_new:BaseObject:private] =>
[_deleted:BaseObject:private] =>
[modifiedColumns:protected] => Array
(
)
)
)
[categories_initialized:protected] => 1
[mapped_items:protected] =>
[content:protected] =>
[files:protected] =>
[language:protected] => Language Object
(
[id:protected] => 1
[code:protected] => en
[name:protected] => English
[alreadyInSave:protected] =>
[alreadyInValidation:protected] =>
[validationFailures:protected] => Array
(
)
[_new:BaseObject:private] =>
[_deleted:BaseObject:private] =>
[modifiedColumns:protected] => Array
(
)
)
[old_record:protected] =>
[id:protected] => 3995
[old_id:protected] =>
[elcosh_id:protected] => i002690
[type:protected] => image
[display_type:protected] => Image
[user_id:protected] => 0
[language_id:protected] => 1
[tagging_id:protected] => Bruce Lippy
[priority_id:protected] => 1
[title:protected] => Construction bracing
[total_pages:protected] => 0
[billed_pages:protected] => 0
[publication_number:protected] =>
[part_of:protected] =>
[keywords:protected] => Bracing, support, scaffold
[comments:protected] =>
[summary:protected] => This shows structural support that prevents collapses during construction.
[transition_comments:protected] =>
[external_link:protected] =>
[consol_link:protected] => http://www.cpwrconstructionsolutions.org/masonry/solution/8/adjustable-tower-scaffold.html
[more_like_this:protected] => i002660
[permission_given_by:protected] =>
[published:protected] => T
[billable:protected] => F
[img_name:protected] =>
[img_ext:protected] => jpg
[img_width:protected] =>
[img_height:protected] =>
[img_credit:protected] => Photo by Pam Susi
[img_practice:protected] => good
[vid_source_id:protected] =>
[vid_running_time:protected] =>
[vid_intended_audience:protected] =>
[vid_acquisition_info:protected] =>
[vid_cost:protected] =>
[vid_producer:protected] =>
[vid_filename:protected] =>
[vid_filename_downloadable:protected] =>
[date_summary:protected] => January 2016
[date_permission_requested:protected] =>
[date_permission_received:protected] =>
[date_review_needed:protected] =>
[date_received:protected] => 02/01/16
[date_completed:protected] => 02/01/16
[date_billed:protected] =>
[date_modified:protected] => 02/01/16
[collBokExports:protected] =>
[lastBokExportCriteria:BaseElcoshItem:private] =>
[alreadyInSave:protected] =>
[alreadyInValidation:protected] =>
[validationFailures:protected] => Array
(
)
[_new:BaseObject:private] =>
[_deleted:BaseObject:private] =>
[modifiedColumns:protected] => Array
(
)
)
)
)
[preview_mode] =>
[description] => Toolbox talks have been the main tool for communicating safety information on construction jobs for decades.
Unfortunately, there has been little research on what makes for effective toolbox talks. The IUOE National
Training Fund worked with OSHA and NIOSH to make sure their series of 24 Focus Four toolbox talks were based on the best recommendations for effective design. These toolbox talks accompany an entire package of training materials, but can be used alone. This guide points out the key features of these toolbox talks and how best to deliver them.
[keywords] => toolbox talks, tailgate talks
[related_items] => Array
(
[Toolbox Talks] => Array
(
[0] => DocumentRecord Object
(
[records:protected] => Array
(
)
[recordId:protected] =>
[searchWordClass:protected] =>
[searchWordPeerClass:protected] =>
[bok_record:protected] =>
[authors:protected] =>
[organizations:protected] =>
[collections:protected] =>
[categories:protected] =>
[categories_initialized:protected] =>
[mapped_items:protected] =>
[content:protected] =>
[files:protected] =>
[language:protected] => Language Object
(
[id:protected] => 1
[code:protected] => en
[name:protected] => English
[alreadyInSave:protected] =>
[alreadyInValidation:protected] =>
[validationFailures:protected] => Array
(
)
[_new:BaseObject:private] =>
[_deleted:BaseObject:private] =>
[modifiedColumns:protected] => Array
(
)
)
[old_record:protected] =>
[id:protected] => 1605
[old_id:protected] => 1262
[elcosh_id:protected] => d001137
[type:protected] => document
[display_type:protected] => HTML w/ PDF
[user_id:protected] =>
[language_id:protected] => 1
[tagging_id:protected] => Garber
[priority_id:protected] => 1
[title:protected] => Focus Four Toolbox Talks, Module 1 – Falls, Talk #2 – Falls from debris piles?
[total_pages:protected] => 1
[billed_pages:protected] => 1
[publication_number:protected] =>
[part_of:protected] =>
[keywords:protected] => disaster response, hazard clean-up, uneven surface, disaster site, disaster clean-up
[comments:protected] =>
[summary:protected] => A toolbox talk on preventing falls from debris piles. Includes questions to ask, an incident to discuss with images, and a place to record questions the trainer would like to ask about the incident. Part of a collection. Click on the 'collection' button to access the other items.
[transition_comments:protected] =>
[external_link:protected] =>
[consol_link:protected] => http://www.cpwrconstructionsolutions.org/roofing/hazard/1463/install-asphalt-roofs-fall-from-heights.html
[more_like_this:protected] => a000081,d000478,d000530
[permission_given_by:protected] =>
[published:protected] => T
[billable:protected] => F
[img_name:protected] =>
[img_ext:protected] =>
[img_width:protected] =>
[img_height:protected] =>
[img_credit:protected] =>
[img_practice:protected] =>
[vid_source_id:protected] =>
[vid_running_time:protected] =>
[vid_intended_audience:protected] =>
[vid_acquisition_info:protected] =>
[vid_cost:protected] =>
[vid_producer:protected] =>
[vid_filename:protected] =>
[vid_filename_downloadable:protected] =>
[date_summary:protected] =>
[date_permission_requested:protected] =>
[date_permission_received:protected] =>
[date_review_needed:protected] =>
[date_received:protected] => 02/15/12
[date_completed:protected] => 03/19/12
[date_billed:protected] =>
[date_modified:protected] => 07/10/12
[collBokExports:protected] =>
[lastBokExportCriteria:BaseElcoshItem:private] =>
[alreadyInSave:protected] =>
[alreadyInValidation:protected] =>
[validationFailures:protected] => Array
(
)
[_new:BaseObject:private] =>
[_deleted:BaseObject:private] =>
[modifiedColumns:protected] => Array
(
)
)
[1] => DocumentRecord Object
(
[records:protected] => Array
(
)
[recordId:protected] =>
[searchWordClass:protected] =>
[searchWordPeerClass:protected] =>
[bok_record:protected] =>
[authors:protected] =>
[organizations:protected] =>
[collections:protected] =>
[categories:protected] =>
[categories_initialized:protected] =>
[mapped_items:protected] =>
[content:protected] =>
[files:protected] =>
[language:protected] => Language Object
(
[id:protected] => 1
[code:protected] => en
[name:protected] => English
[alreadyInSave:protected] =>
[alreadyInValidation:protected] =>
[validationFailures:protected] => Array
(
)
[_new:BaseObject:private] =>
[_deleted:BaseObject:private] =>
[modifiedColumns:protected] => Array
(
)
)
[old_record:protected] =>
[id:protected] => 1610
[old_id:protected] => 1271
[elcosh_id:protected] => d001146
[type:protected] => document
[display_type:protected] => HTML w/ PDF
[user_id:protected] => 0
[language_id:protected] => 1
[tagging_id:protected] => Garber
[priority_id:protected] => 1
[title:protected] => Focus Four Toolbox Talks, Module 2 – Struck-by, Talk #5 – Rigging and Securing Loads
[total_pages:protected] => 1
[billed_pages:protected] => 1
[publication_number:protected] =>
[part_of:protected] =>
[keywords:protected] => rigging, lift loads, loading areas, chains
[comments:protected] =>
[summary:protected] => A toolbox talk on preventing struck-by incidents caused by not securing loads properly. Includes questions to ask, an incident to discuss with images, and a place to record questions the trainer would like to ask about the incident. Part of a collection. Click on the 'collection' button to access the other items.
[transition_comments:protected] =>
[external_link:protected] =>
[consol_link:protected] => http://www.cpwrconstructionsolutions.org/heavy_equipment/hazard/1591/move-equipment-to-from-and-between-sites-work-zone-struck-by-injuries-and-fatalities.html
[more_like_this:protected] => d000144,d000360,d000873
[permission_given_by:protected] =>
[published:protected] => T
[billable:protected] => F
[img_name:protected] =>
[img_ext:protected] =>
[img_width:protected] =>
[img_height:protected] =>
[img_credit:protected] =>
[img_practice:protected] =>
[vid_source_id:protected] =>
[vid_running_time:protected] =>
[vid_intended_audience:protected] =>
[vid_acquisition_info:protected] =>
[vid_cost:protected] =>
[vid_producer:protected] =>
[vid_filename:protected] =>
[vid_filename_downloadable:protected] =>
[date_summary:protected] =>
[date_permission_requested:protected] =>
[date_permission_received:protected] =>
[date_review_needed:protected] =>
[date_received:protected] => 02/15/12
[date_completed:protected] => 03/28/12
[date_billed:protected] =>
[date_modified:protected] => 05/12/14
[collBokExports:protected] =>
[lastBokExportCriteria:BaseElcoshItem:private] =>
[alreadyInSave:protected] =>
[alreadyInValidation:protected] =>
[validationFailures:protected] => Array
(
)
[_new:BaseObject:private] =>
[_deleted:BaseObject:private] =>
[modifiedColumns:protected] => Array
(
)
)
[2] => DocumentRecord Object
(
[records:protected] => Array
(
)
[recordId:protected] =>
[searchWordClass:protected] =>
[searchWordPeerClass:protected] =>
[bok_record:protected] =>
[authors:protected] =>
[organizations:protected] =>
[collections:protected] =>
[categories:protected] =>
[categories_initialized:protected] =>
[mapped_items:protected] =>
[content:protected] =>
[files:protected] =>
[language:protected] => Language Object
(
[id:protected] => 1
[code:protected] => en
[name:protected] => English
[alreadyInSave:protected] =>
[alreadyInValidation:protected] =>
[validationFailures:protected] => Array
(
)
[_new:BaseObject:private] =>
[_deleted:BaseObject:private] =>
[modifiedColumns:protected] => Array
(
)
)
[old_record:protected] =>
[id:protected] => 1645
[old_id:protected] => 1274
[elcosh_id:protected] => d001149
[type:protected] => document
[display_type:protected] => HTML w/ PDF
[user_id:protected] => 0
[language_id:protected] => 1
[tagging_id:protected] => Garber
[priority_id:protected] => 1
[title:protected] => Focus Four Toolbox Talks, Module 3 – Caught-in/between, Talk #2 – Trenches & Heavy Equipment
[total_pages:protected] => 1
[billed_pages:protected] => 1
[publication_number:protected] =>
[part_of:protected] =>
[keywords:protected] => back-up alarms, spotter, soil cave-in, spoil pikes, ROPs, trenching, rain
[comments:protected] =>
[summary:protected] => A toolbox talk on preventing incidents involving trenches such as trench collapse. Includes questions to ask, an incident to discuss with images, and a place to record questions the trainer would like to ask about the incident. Part of a collection. Click on the 'collection' button to access the other items.
[transition_comments:protected] =>
[external_link:protected] =>
[consol_link:protected] =>
[more_like_this:protected] => d000019,d000035,d000168
[permission_given_by:protected] =>
[published:protected] => T
[billable:protected] => F
[img_name:protected] =>
[img_ext:protected] =>
[img_width:protected] =>
[img_height:protected] =>
[img_credit:protected] =>
[img_practice:protected] =>
[vid_source_id:protected] =>
[vid_running_time:protected] =>
[vid_intended_audience:protected] =>
[vid_acquisition_info:protected] =>
[vid_cost:protected] =>
[vid_producer:protected] =>
[vid_filename:protected] =>
[vid_filename_downloadable:protected] =>
[date_summary:protected] =>
[date_permission_requested:protected] =>
[date_permission_received:protected] =>
[date_review_needed:protected] =>
[date_received:protected] => 02/15/12
[date_completed:protected] => 04/02/12
[date_billed:protected] =>
[date_modified:protected] => 05/23/23
[collBokExports:protected] =>
[lastBokExportCriteria:BaseElcoshItem:private] =>
[alreadyInSave:protected] =>
[alreadyInValidation:protected] =>
[validationFailures:protected] => Array
(
)
[_new:BaseObject:private] =>
[_deleted:BaseObject:private] =>
[modifiedColumns:protected] => Array
(
)
)
[3] => DocumentRecord Object
(
[records:protected] => Array
(
)
[recordId:protected] =>
[searchWordClass:protected] =>
[searchWordPeerClass:protected] =>
[bok_record:protected] =>
[authors:protected] =>
[organizations:protected] =>
[collections:protected] =>
[categories:protected] =>
[categories_initialized:protected] =>
[mapped_items:protected] =>
[content:protected] =>
[files:protected] =>
[language:protected] => Language Object
(
[id:protected] => 1
[code:protected] => en
[name:protected] => English
[alreadyInSave:protected] =>
[alreadyInValidation:protected] =>
[validationFailures:protected] => Array
(
)
[_new:BaseObject:private] =>
[_deleted:BaseObject:private] =>
[modifiedColumns:protected] => Array
(
)
)
[old_record:protected] =>
[id:protected] => 1654
[old_id:protected] => 1284
[elcosh_id:protected] => d001159
[type:protected] => document
[display_type:protected] => HTML w/ PDF
[user_id:protected] => 0
[language_id:protected] => 1
[tagging_id:protected] => Garber
[priority_id:protected] => 1
[title:protected] => Focus Four Toolbox Talks, Module 4 – Electrocutions, Talk #6 – Hazards on Disaster Sites
[total_pages:protected] => 1
[billed_pages:protected] => 1
[publication_number:protected] =>
[part_of:protected] =>
[keywords:protected] => powerlines, underground, utilities, generators, wet conditions, GFCIs, energized lines, disasters, emergency response
[comments:protected] =>
[summary:protected] => A toolbox talk on how to avoid electrocution on a disaster site. Includes questions to ask, an incident to discuss with images, and a place to record questions the trainer would like to ask about the incident. Part of a collection. Click on the 'collection' button to access the other items.
[transition_comments:protected] =>
[external_link:protected] =>
[consol_link:protected] => http://www.cpwrconstructionsolutions.org/electrical/hazard/1138/install-and-repair-high-voltage-lines-transformers-switches-electrical-shocks-burns-and-or-electrocution.html
[more_like_this:protected] => d000135,d000361,d000437
[permission_given_by:protected] =>
[published:protected] => T
[billable:protected] => F
[img_name:protected] =>
[img_ext:protected] =>
[img_width:protected] =>
[img_height:protected] =>
[img_credit:protected] =>
[img_practice:protected] =>
[vid_source_id:protected] =>
[vid_running_time:protected] =>
[vid_intended_audience:protected] =>
[vid_acquisition_info:protected] =>
[vid_cost:protected] =>
[vid_producer:protected] =>
[vid_filename:protected] =>
[vid_filename_downloadable:protected] =>
[date_summary:protected] =>
[date_permission_requested:protected] =>
[date_permission_received:protected] =>
[date_review_needed:protected] =>
[date_received:protected] => 02/15/12
[date_completed:protected] => 04/02/12
[date_billed:protected] =>
[date_modified:protected] => 05/23/23
[collBokExports:protected] =>
[lastBokExportCriteria:BaseElcoshItem:private] =>
[alreadyInSave:protected] =>
[alreadyInValidation:protected] =>
[validationFailures:protected] => Array
(
)
[_new:BaseObject:private] =>
[_deleted:BaseObject:private] =>
[modifiedColumns:protected] => Array
(
)
)
)
)
[collections] => Array
(
[1294] =>
[1295] =>
[1292] =>
[1293] => CollectionRecord Object
(
[collection_items:protected] =>
[records:protected] => Array
(
)
[recordId:protected] =>
[searchWordClass:protected] =>
[searchWordPeerClass:protected] =>
[bok_record:protected] =>
[authors:protected] =>
[organizations:protected] =>
[collections:protected] =>
[categories:protected] =>
[categories_initialized:protected] =>
[mapped_items:protected] =>
[content:protected] =>
[files:protected] =>
[language:protected] =>
[old_record:protected] =>
[id:protected] => 1293
[old_id:protected] =>
[elcosh_id:protected] => c000026
[type:protected] => collection
[display_type:protected] => Collection
[user_id:protected] =>
[language_id:protected] =>
[tagging_id:protected] =>
[priority_id:protected] =>
[title:protected] => Focus Four-Struck By
[total_pages:protected] =>
[billed_pages:protected] =>
[publication_number:protected] =>
[part_of:protected] =>
[keywords:protected] =>
[comments:protected] =>
[summary:protected] => The following are links to all of the items in this collection:
[transition_comments:protected] =>
[external_link:protected] =>
[consol_link:protected] =>
[more_like_this:protected] =>
[permission_given_by:protected] =>
[published:protected] => T
[billable:protected] => F
[img_name:protected] =>
[img_ext:protected] =>
[img_width:protected] =>
[img_height:protected] =>
[img_credit:protected] =>
[img_practice:protected] =>
[vid_source_id:protected] =>
[vid_running_time:protected] =>
[vid_intended_audience:protected] =>
[vid_acquisition_info:protected] =>
[vid_cost:protected] =>
[vid_producer:protected] =>
[vid_filename:protected] =>
[vid_filename_downloadable:protected] =>
[date_summary:protected] =>
[date_permission_requested:protected] =>
[date_permission_received:protected] =>
[date_review_needed:protected] =>
[date_received:protected] => 05/08/12
[date_completed:protected] => 05/08/12
[date_billed:protected] =>
[date_modified:protected] => 05/08/12
[collBokExports:protected] =>
[lastBokExportCriteria:BaseElcoshItem:private] =>
[alreadyInSave:protected] =>
[alreadyInValidation:protected] =>
[validationFailures:protected] => Array
(
)
[_new:BaseObject:private] =>
[_deleted:BaseObject:private] =>
[modifiedColumns:protected] => Array
(
)
)
)
[record] => DocumentRecord Object
(
[records:protected] => Array
(
)
[recordId:protected] =>
[searchWordClass:protected] =>
[searchWordPeerClass:protected] =>
[bok_record:protected] =>
[authors:protected] => Array
(
)
[organizations:protected] => Array
(
[256] => Organization Object
(
[id:protected] => 256
[elcosh_id:protected] => o000276
[user_id:protected] => 14
[province_id:protected] => 0
[country_id:protected] => 0
[title:protected] => IUOE National Training Fund
[address:protected] =>
[postal_code:protected] =>
[city:protected] =>
[department:protected] =>
[phone:protected] => 304-253-8674
[fax:protected] =>
[email:protected] =>
[website:protected] => http://www.iuoeiettc.org
[filename:protected] =>
[about:protected] =>
[comments:protected] =>
[logo_available:protected] => T
[no_details:protected] => F
[date_received:protected] => 2012-02-13
[date_completed:protected] => 2012-02-13
[date_billed:protected] =>
[alreadyInSave:protected] =>
[alreadyInValidation:protected] =>
[validationFailures:protected] => Array
(
)
[_new:BaseObject:private] =>
[_deleted:BaseObject:private] =>
[modifiedColumns:protected] => Array
(
)
)
)
[collections:protected] => Array
(
[1294] =>
[1295] =>
[1292] =>
[1293] => CollectionRecord Object
(
[collection_items:protected] =>
[records:protected] => Array
(
)
[recordId:protected] =>
[searchWordClass:protected] =>
[searchWordPeerClass:protected] =>
[bok_record:protected] =>
[authors:protected] =>
[organizations:protected] =>
[collections:protected] =>
[categories:protected] =>
[categories_initialized:protected] =>
[mapped_items:protected] =>
[content:protected] =>
[files:protected] =>
[language:protected] =>
[old_record:protected] =>
[id:protected] => 1293
[old_id:protected] =>
[elcosh_id:protected] => c000026
[type:protected] => collection
[display_type:protected] => Collection
[user_id:protected] =>
[language_id:protected] =>
[tagging_id:protected] =>
[priority_id:protected] =>
[title:protected] => Focus Four-Struck By
[total_pages:protected] =>
[billed_pages:protected] =>
[publication_number:protected] =>
[part_of:protected] =>
[keywords:protected] =>
[comments:protected] =>
[summary:protected] => The following are links to all of the items in this collection:
[transition_comments:protected] =>
[external_link:protected] =>
[consol_link:protected] =>
[more_like_this:protected] =>
[permission_given_by:protected] =>
[published:protected] => T
[billable:protected] => F
[img_name:protected] =>
[img_ext:protected] =>
[img_width:protected] =>
[img_height:protected] =>
[img_credit:protected] =>
[img_practice:protected] =>
[vid_source_id:protected] =>
[vid_running_time:protected] =>
[vid_intended_audience:protected] =>
[vid_acquisition_info:protected] =>
[vid_cost:protected] =>
[vid_producer:protected] =>
[vid_filename:protected] =>
[vid_filename_downloadable:protected] =>
[date_summary:protected] =>
[date_permission_requested:protected] =>
[date_permission_received:protected] =>
[date_review_needed:protected] =>
[date_received:protected] => 05/08/12
[date_completed:protected] => 05/08/12
[date_billed:protected] =>
[date_modified:protected] => 05/08/12
[collBokExports:protected] =>
[lastBokExportCriteria:BaseElcoshItem:private] =>
[alreadyInSave:protected] =>
[alreadyInValidation:protected] =>
[validationFailures:protected] => Array
(
)
[_new:BaseObject:private] =>
[_deleted:BaseObject:private] =>
[modifiedColumns:protected] => Array
(
)
)
)
[categories:protected] =>
[categories_initialized:protected] =>
[mapped_items:protected] => Array
(
[1605] => DocumentRecord Object
(
[records:protected] => Array
(
)
[recordId:protected] =>
[searchWordClass:protected] =>
[searchWordPeerClass:protected] =>
[bok_record:protected] =>
[authors:protected] =>
[organizations:protected] =>
[collections:protected] =>
[categories:protected] =>
[categories_initialized:protected] =>
[mapped_items:protected] =>
[content:protected] =>
[files:protected] =>
[language:protected] =>
[old_record:protected] =>
[id:protected] => 1605
[old_id:protected] => 1262
[elcosh_id:protected] => d001137
[type:protected] => document
[display_type:protected] => HTML w/ PDF
[user_id:protected] =>
[language_id:protected] => 1
[tagging_id:protected] => Garber
[priority_id:protected] => 1
[title:protected] => Focus Four Toolbox Talks, Module 1 – Falls, Talk #2 – Falls from debris piles?
[total_pages:protected] => 1
[billed_pages:protected] => 1
[publication_number:protected] =>
[part_of:protected] =>
[keywords:protected] => disaster response, hazard clean-up, uneven surface, disaster site, disaster clean-up
[comments:protected] =>
[summary:protected] => A toolbox talk on preventing falls from debris piles. Includes questions to ask, an incident to discuss with images, and a place to record questions the trainer would like to ask about the incident. Part of a collection. Click on the 'collection' button to access the other items.
[transition_comments:protected] =>
[external_link:protected] =>
[consol_link:protected] => http://www.cpwrconstructionsolutions.org/roofing/hazard/1463/install-asphalt-roofs-fall-from-heights.html
[more_like_this:protected] => a000081,d000478,d000530
[permission_given_by:protected] =>
[published:protected] => T
[billable:protected] => F
[img_name:protected] =>
[img_ext:protected] =>
[img_width:protected] =>
[img_height:protected] =>
[img_credit:protected] =>
[img_practice:protected] =>
[vid_source_id:protected] =>
[vid_running_time:protected] =>
[vid_intended_audience:protected] =>
[vid_acquisition_info:protected] =>
[vid_cost:protected] =>
[vid_producer:protected] =>
[vid_filename:protected] =>
[vid_filename_downloadable:protected] =>
[date_summary:protected] =>
[date_permission_requested:protected] =>
[date_permission_received:protected] =>
[date_review_needed:protected] =>
[date_received:protected] => 02/15/12
[date_completed:protected] => 03/19/12
[date_billed:protected] =>
[date_modified:protected] => 07/10/12
[collBokExports:protected] =>
[lastBokExportCriteria:BaseElcoshItem:private] =>
[alreadyInSave:protected] =>
[alreadyInValidation:protected] =>
[validationFailures:protected] => Array
(
)
[_new:BaseObject:private] =>
[_deleted:BaseObject:private] =>
[modifiedColumns:protected] => Array
(
)
)
[1610] => DocumentRecord Object
(
[records:protected] => Array
(
)
[recordId:protected] =>
[searchWordClass:protected] =>
[searchWordPeerClass:protected] =>
[bok_record:protected] =>
[authors:protected] =>
[organizations:protected] =>
[collections:protected] =>
[categories:protected] =>
[categories_initialized:protected] =>
[mapped_items:protected] =>
[content:protected] =>
[files:protected] =>
[language:protected] =>
[old_record:protected] =>
[id:protected] => 1610
[old_id:protected] => 1271
[elcosh_id:protected] => d001146
[type:protected] => document
[display_type:protected] => HTML w/ PDF
[user_id:protected] => 0
[language_id:protected] => 1
[tagging_id:protected] => Garber
[priority_id:protected] => 1
[title:protected] => Focus Four Toolbox Talks, Module 2 – Struck-by, Talk #5 – Rigging and Securing Loads
[total_pages:protected] => 1
[billed_pages:protected] => 1
[publication_number:protected] =>
[part_of:protected] =>
[keywords:protected] => rigging, lift loads, loading areas, chains
[comments:protected] =>
[summary:protected] => A toolbox talk on preventing struck-by incidents caused by not securing loads properly. Includes questions to ask, an incident to discuss with images, and a place to record questions the trainer would like to ask about the incident. Part of a collection. Click on the 'collection' button to access the other items.
[transition_comments:protected] =>
[external_link:protected] =>
[consol_link:protected] => http://www.cpwrconstructionsolutions.org/heavy_equipment/hazard/1591/move-equipment-to-from-and-between-sites-work-zone-struck-by-injuries-and-fatalities.html
[more_like_this:protected] => d000144,d000360,d000873
[permission_given_by:protected] =>
[published:protected] => T
[billable:protected] => F
[img_name:protected] =>
[img_ext:protected] =>
[img_width:protected] =>
[img_height:protected] =>
[img_credit:protected] =>
[img_practice:protected] =>
[vid_source_id:protected] =>
[vid_running_time:protected] =>
[vid_intended_audience:protected] =>
[vid_acquisition_info:protected] =>
[vid_cost:protected] =>
[vid_producer:protected] =>
[vid_filename:protected] =>
[vid_filename_downloadable:protected] =>
[date_summary:protected] =>
[date_permission_requested:protected] =>
[date_permission_received:protected] =>
[date_review_needed:protected] =>
[date_received:protected] => 02/15/12
[date_completed:protected] => 03/28/12
[date_billed:protected] =>
[date_modified:protected] => 05/12/14
[collBokExports:protected] =>
[lastBokExportCriteria:BaseElcoshItem:private] =>
[alreadyInSave:protected] =>
[alreadyInValidation:protected] =>
[validationFailures:protected] => Array
(
)
[_new:BaseObject:private] =>
[_deleted:BaseObject:private] =>
[modifiedColumns:protected] => Array
(
)
)
[1645] => DocumentRecord Object
(
[records:protected] => Array
(
)
[recordId:protected] =>
[searchWordClass:protected] =>
[searchWordPeerClass:protected] =>
[bok_record:protected] =>
[authors:protected] =>
[organizations:protected] =>
[collections:protected] =>
[categories:protected] =>
[categories_initialized:protected] =>
[mapped_items:protected] =>
[content:protected] =>
[files:protected] =>
[language:protected] =>
[old_record:protected] =>
[id:protected] => 1645
[old_id:protected] => 1274
[elcosh_id:protected] => d001149
[type:protected] => document
[display_type:protected] => HTML w/ PDF
[user_id:protected] => 0
[language_id:protected] => 1
[tagging_id:protected] => Garber
[priority_id:protected] => 1
[title:protected] => Focus Four Toolbox Talks, Module 3 – Caught-in/between, Talk #2 – Trenches & Heavy Equipment
[total_pages:protected] => 1
[billed_pages:protected] => 1
[publication_number:protected] =>
[part_of:protected] =>
[keywords:protected] => back-up alarms, spotter, soil cave-in, spoil pikes, ROPs, trenching, rain
[comments:protected] =>
[summary:protected] => A toolbox talk on preventing incidents involving trenches such as trench collapse. Includes questions to ask, an incident to discuss with images, and a place to record questions the trainer would like to ask about the incident. Part of a collection. Click on the 'collection' button to access the other items.
[transition_comments:protected] =>
[external_link:protected] =>
[consol_link:protected] =>
[more_like_this:protected] => d000019,d000035,d000168
[permission_given_by:protected] =>
[published:protected] => T
[billable:protected] => F
[img_name:protected] =>
[img_ext:protected] =>
[img_width:protected] =>
[img_height:protected] =>
[img_credit:protected] =>
[img_practice:protected] =>
[vid_source_id:protected] =>
[vid_running_time:protected] =>
[vid_intended_audience:protected] =>
[vid_acquisition_info:protected] =>
[vid_cost:protected] =>
[vid_producer:protected] =>
[vid_filename:protected] =>
[vid_filename_downloadable:protected] =>
[date_summary:protected] =>
[date_permission_requested:protected] =>
[date_permission_received:protected] =>
[date_review_needed:protected] =>
[date_received:protected] => 02/15/12
[date_completed:protected] => 04/02/12
[date_billed:protected] =>
[date_modified:protected] => 05/23/23
[collBokExports:protected] =>
[lastBokExportCriteria:BaseElcoshItem:private] =>
[alreadyInSave:protected] =>
[alreadyInValidation:protected] =>
[validationFailures:protected] => Array
(
)
[_new:BaseObject:private] =>
[_deleted:BaseObject:private] =>
[modifiedColumns:protected] => Array
(
)
)
[1654] => DocumentRecord Object
(
[records:protected] => Array
(
)
[recordId:protected] =>
[searchWordClass:protected] =>
[searchWordPeerClass:protected] =>
[bok_record:protected] =>
[authors:protected] =>
[organizations:protected] =>
[collections:protected] =>
[categories:protected] =>
[categories_initialized:protected] =>
[mapped_items:protected] =>
[content:protected] =>
[files:protected] =>
[language:protected] =>
[old_record:protected] =>
[id:protected] => 1654
[old_id:protected] => 1284
[elcosh_id:protected] => d001159
[type:protected] => document
[display_type:protected] => HTML w/ PDF
[user_id:protected] => 0
[language_id:protected] => 1
[tagging_id:protected] => Garber
[priority_id:protected] => 1
[title:protected] => Focus Four Toolbox Talks, Module 4 – Electrocutions, Talk #6 – Hazards on Disaster Sites
[total_pages:protected] => 1
[billed_pages:protected] => 1
[publication_number:protected] =>
[part_of:protected] =>
[keywords:protected] => powerlines, underground, utilities, generators, wet conditions, GFCIs, energized lines, disasters, emergency response
[comments:protected] =>
[summary:protected] => A toolbox talk on how to avoid electrocution on a disaster site. Includes questions to ask, an incident to discuss with images, and a place to record questions the trainer would like to ask about the incident. Part of a collection. Click on the 'collection' button to access the other items.
[transition_comments:protected] =>
[external_link:protected] =>
[consol_link:protected] => http://www.cpwrconstructionsolutions.org/electrical/hazard/1138/install-and-repair-high-voltage-lines-transformers-switches-electrical-shocks-burns-and-or-electrocution.html
[more_like_this:protected] => d000135,d000361,d000437
[permission_given_by:protected] =>
[published:protected] => T
[billable:protected] => F
[img_name:protected] =>
[img_ext:protected] =>
[img_width:protected] =>
[img_height:protected] =>
[img_credit:protected] =>
[img_practice:protected] =>
[vid_source_id:protected] =>
[vid_running_time:protected] =>
[vid_intended_audience:protected] =>
[vid_acquisition_info:protected] =>
[vid_cost:protected] =>
[vid_producer:protected] =>
[vid_filename:protected] =>
[vid_filename_downloadable:protected] =>
[date_summary:protected] =>
[date_permission_requested:protected] =>
[date_permission_received:protected] =>
[date_review_needed:protected] =>
[date_received:protected] => 02/15/12
[date_completed:protected] => 04/02/12
[date_billed:protected] =>
[date_modified:protected] => 05/23/23
[collBokExports:protected] =>
[lastBokExportCriteria:BaseElcoshItem:private] =>
[alreadyInSave:protected] =>
[alreadyInValidation:protected] =>
[validationFailures:protected] => Array
(
)
[_new:BaseObject:private] =>
[_deleted:BaseObject:private] =>
[modifiedColumns:protected] => Array
(
)
)
)
[content:protected] =>
[files:protected] => Array
(
[9400] => File Object
(
[id:protected] => 9400
[filename:protected] => 1.jpg
[downloadable:protected] => F
[timestamp:protected] => 2014-05-08 15:05:37
[alreadyInSave:protected] =>
[alreadyInValidation:protected] =>
[validationFailures:protected] => Array
(
)
[_new:BaseObject:private] =>
[_deleted:BaseObject:private] =>
[modifiedColumns:protected] => Array
(
)
)
[9401] => File Object
(
[id:protected] => 9401
[filename:protected] => d001298.pdf
[downloadable:protected] => T
[timestamp:protected] => 2014-05-08 15:05:37
[alreadyInSave:protected] =>
[alreadyInValidation:protected] =>
[validationFailures:protected] => Array
(
)
[_new:BaseObject:private] =>
[_deleted:BaseObject:private] =>
[modifiedColumns:protected] => Array
(
)
)
)
[language:protected] => Language Object
(
[id:protected] => 1
[code:protected] => en
[name:protected] => English
[alreadyInSave:protected] =>
[alreadyInValidation:protected] =>
[validationFailures:protected] => Array
(
)
[_new:BaseObject:private] =>
[_deleted:BaseObject:private] =>
[modifiedColumns:protected] => Array
(
)
)
[old_record:protected] =>
[id:protected] => 3827
[old_id:protected] =>
[elcosh_id:protected] => d001298
[type:protected] => document
[display_type:protected] => HTML w/ PDF
[user_id:protected] => 23
[language_id:protected] => 1
[tagging_id:protected] => Bruce Lippy
[priority_id:protected] => 1
[title:protected] => Getting the most out of the IUOE Toolbox Talks
[total_pages:protected] => 2
[billed_pages:protected] => 2
[publication_number:protected] =>
[part_of:protected] =>
[keywords:protected] => toolbox talks, tailgate talks
[comments:protected] =>
[summary:protected] => Toolbox talks have been the main tool for communicating safety information on construction jobs for decades.
Unfortunately, there has been little research on what makes for effective toolbox talks. The IUOE National
Training Fund worked with OSHA and NIOSH to make sure their series of 24 Focus Four toolbox talks were based on the best recommendations for effective design. These toolbox talks accompany an entire package of training materials, but can be used alone. This guide points out the key features of these toolbox talks and how best to deliver them.
[transition_comments:protected] =>
[external_link:protected] =>
[consol_link:protected] =>
[more_like_this:protected] => d001137,d001146,d001149,d001159
[permission_given_by:protected] => IUOE National Hazmat Program
[published:protected] => T
[billable:protected] => F
[img_name:protected] =>
[img_ext:protected] => png
[img_width:protected] =>
[img_height:protected] =>
[img_credit:protected] =>
[img_practice:protected] =>
[vid_source_id:protected] =>
[vid_running_time:protected] =>
[vid_intended_audience:protected] =>
[vid_acquisition_info:protected] =>
[vid_cost:protected] =>
[vid_producer:protected] =>
[vid_filename:protected] =>
[vid_filename_downloadable:protected] =>
[date_summary:protected] => 2007
[date_permission_requested:protected] =>
[date_permission_received:protected] =>
[date_review_needed:protected] =>
[date_received:protected] => 05/08/14
[date_completed:protected] => 05/08/14
[date_billed:protected] =>
[date_modified:protected] => 05/08/14
[collBokExports:protected] =>
[lastBokExportCriteria:BaseElcoshItem:private] =>
[alreadyInSave:protected] =>
[alreadyInValidation:protected] =>
[validationFailures:protected] => Array
(
)
[_new:BaseObject:private] =>
[_deleted:BaseObject:private] =>
[modifiedColumns:protected] => Array
(
)
)
[show_text] =>
[document_content] => ElcoshItemDocumentContent Object
(
[id:protected] => 2896
[item_id:protected] => 3827
[type:protected] => main
[title:protected] =>
[content:protected] =>
Why were these talks developed?
Toolbox talks have been the main tool for communicating safety information on construction jobs for decades. Unfortunately, there has been almost no research on what makes for effective toolbox talks. The IUOE National Training Fund has worked with OSHA, the National Institute for Occupational Safety and Health and the Lippy Group, LLC to make sure these Focus Four toolbox talks are based on the latest fi ndings on the most effective design and tailored to the hazards operating engineers face daily. These toolbox talks accompany an entire package of training materials, but can be used alone. The way these are delivered is as important as how well they are designed.
What did NIOSH find out?
- Just handing out factsheets and toolbox talks to workers doesn’t work. Providing copies after toolbox talks doesn’t make much of an impact either.
- Using case studies (real life stories of accidents that ended in fatality or injury) in toolbox talks is effective.
- When toolbox talks containing case studies were accompanied by discussion questions to encourage group participation, they were more effective. Consequently, getting the workers to participate in the discussion about the case study is important. It’s not enough to tell the story, it is better to have the workers engage in problem solving that analyzes why the accident occurred and how it could have been prevented. Active learning is always better than passive.
How should you deliver these toolbox talks?
- Choose a topic that is related to work going on at the site.
- Hold the meeting on the job, preferably where everyone can sit and relax.
- Hold the meeting at the beginning of a shift or after a break. Folks are too tired at the end of a shift to carefully listen and they want to get home.
- Read the toolbox talk sheet on the topic prior to conducting the talk.
- Start at the top of the form and work right through to the end, which should take around 10 to 15 minutes. Guidance is provided in blue print to help you with each section.
- Use the questions provided to generate discussions. Always allow time for the crew to respond to your questions before you provide an answer. Some suggested responses are written in italics.
- Review the case study and emphasize that this was a real incident. Ask the crew for a case study before you review the one provided, however.
- Always end with a discussion of the particular worksite where you are conducting the talk. Tie the talk as closely to hazards on the site as possible and encourage the crew to constantly look for and immediately correct hazards. They should also know how to report any problems that can’t be immediately corrected.
- Provide copies to each person, if you like, but NIOSH has not found that to be particularly effective.
- Encourage workers to do similar talks on their sites and provide them with the IUOE phone number for ordering in bulk.
- Have everyone sign the back of the form to indicate they attended this session and point out it is a pledge to look out for the health and safety of everyone on the site.
What are the key features of these toolbox talks?

[content_transformed:protected] =>
Why were these talks developed?
Toolbox talks have been the main tool for communicating safety information on construction jobs for decades. Unfortunately, there has been almost no research on what makes for effective toolbox talks. The IUOE National Training Fund has worked with OSHA, the National Institute for Occupational Safety and Health and the Lippy Group, LLC to make sure these Focus Four toolbox talks are based on the latest fi ndings on the most effective design and tailored to the hazards operating engineers face daily. These toolbox talks accompany an entire package of training materials, but can be used alone. The way these are delivered is as important as how well they are designed.
What did NIOSH find out?
- Just handing out factsheets and toolbox talks to workers doesn’t work. Providing copies after toolbox talks doesn’t make much of an impact either.
- Using case studies (real life stories of accidents that ended in fatality or injury) in toolbox talks is effective.
- When toolbox talks containing case studies were accompanied by discussion questions to encourage group participation, they were more effective. Consequently, getting the workers to participate in the discussion about the case study is important. It’s not enough to tell the story, it is better to have the workers engage in problem solving that analyzes why the accident occurred and how it could have been prevented. Active learning is always better than passive.
How should you deliver these toolbox talks?
- Choose a topic that is related to work going on at the site.
- Hold the meeting on the job, preferably where everyone can sit and relax.
- Hold the meeting at the beginning of a shift or after a break. Folks are too tired at the end of a shift to carefully listen and they want to get home.
- Read the toolbox talk sheet on the topic prior to conducting the talk.
- Start at the top of the form and work right through to the end, which should take around 10 to 15 minutes. Guidance is provided in blue print to help you with each section.
- Use the questions provided to generate discussions. Always allow time for the crew to respond to your questions before you provide an answer. Some suggested responses are written in italics.
- Review the case study and emphasize that this was a real incident. Ask the crew for a case study before you review the one provided, however.
- Always end with a discussion of the particular worksite where you are conducting the talk. Tie the talk as closely to hazards on the site as possible and encourage the crew to constantly look for and immediately correct hazards. They should also know how to report any problems that can’t be immediately corrected.
- Provide copies to each person, if you like, but NIOSH has not found that to be particularly effective.
- Encourage workers to do similar talks on their sites and provide them with the IUOE phone number for ordering in bulk.
- Have everyone sign the back of the form to indicate they attended this session and point out it is a pledge to look out for the health and safety of everyone on the site.
What are the key features of these toolbox talks?
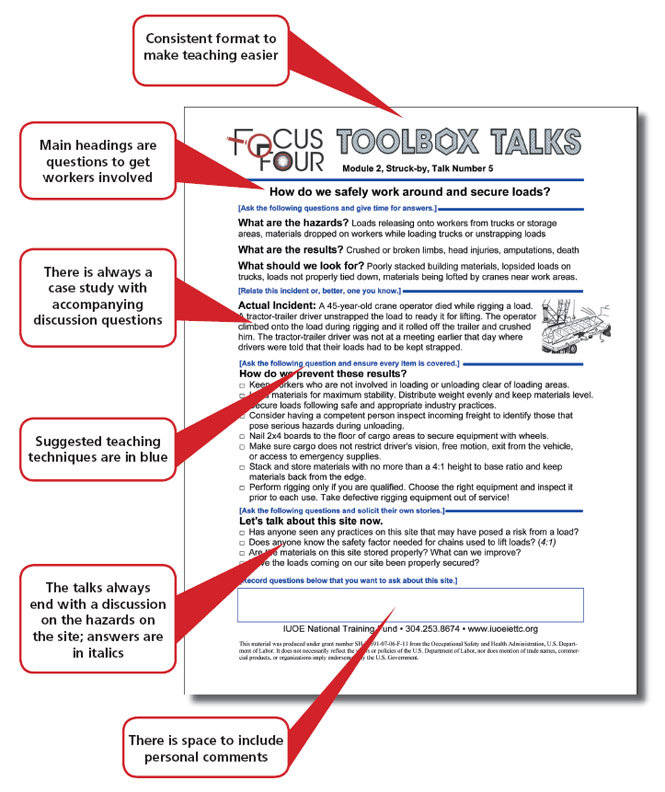
[disclaimer:protected] =>
[disclaimer_transformed:protected] =>
[alreadyInSave:protected] =>
[alreadyInValidation:protected] =>
[validationFailures:protected] => Array
(
)
[_new:BaseObject:private] =>
[_deleted:BaseObject:private] =>
[modifiedColumns:protected] => Array
(
)
)
[template] => record
)
)
)
[5] => Array
(
[file] => /home/agsafe5/repositories/elcosh/live/sblib/core/SB_Engine/page/PHPTAL_Page.php
[line] => 38
[function] => execute
[class] => PHPTAL
[type] => ->
[args] => Array
(
)
)
[6] => Array
(
[file] => /home/agsafe5/repositories/elcosh/live/sblib/core/SB_Engine/page/Decorator_Page.php
[line] => 34
[function] => render
[class] => SB_PHPTAL_Page
[type] => ->
[args] => Array
(
)
)
[7] => Array
(
[file] => /home/agsafe5/repositories/elcosh/live/sblib/core/SB_Engine/page/Decorator_Page.php
[line] => 23
[function] => render
[class] => SB_Decorator_Page
[type] => ->
[args] => Array
(
)
)
[8] => Array
(
[file] => /home/agsafe5/repositories/elcosh/live/sblib/core/SB_Engine/module/Module.php
[line] => 35
[function] => display
[class] => SB_Decorator_Page
[type] => ->
[args] => Array
(
)
)
[9] => Array
(
[file] => /home/agsafe5/repositories/elcosh/live/sblib/core/SB_Engine/Controller.php
[line] => 48
[function] => display
[class] => SB_Module
[type] => ->
[args] => Array
(
)
)
[10] => Array
(
[file] => /home/agsafe5/repositories/elcosh/live/sblib/core/SB_Engine/Controller.php
[line] => 36
[function] => main
[class] => SBE_Controller
[type] => ->
[args] => Array
(
[0] =>
[1] => Array
(
)
)
)
[11] => Array
(
[file] => /home/agsafe5/repositories/elcosh/live/web_root/elcosh/index.php
[line] => 14
[function] => run
[class] => SBE_Controller
[type] => ->
[args] => Array
(
)
)
)
[previous:Exception:private] =>
)